République Islamique de Mauritanie
Honneur-Fraternité-justice Ministère de l'enseignement
supérieur
Et de la Recherche Scientifique
Université de Nouakchott
Faculté des sciences et techniques
Filière : Géologie Minière
.
Mémoire de Fin d'études
Sous
thème :
L'enrichissement du minerai ,
Oxydé
Usine des Guelbs
Préparé par : Sous
L'encadrement de :
Seyidna Ali O/ MED O/ HADJ WEISS
Mr.Dr. Ahmedou O/ MAHFODH (Université)
Mr: Ing. Mohamed El
Mokhtar O/ CHEIKH
.
Chef du service
process (SNIM)
Année Universitaire : 2007-2008
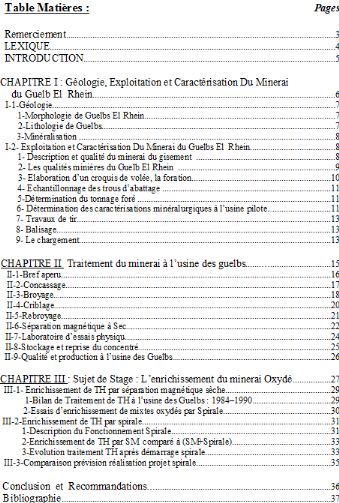
Remerciement
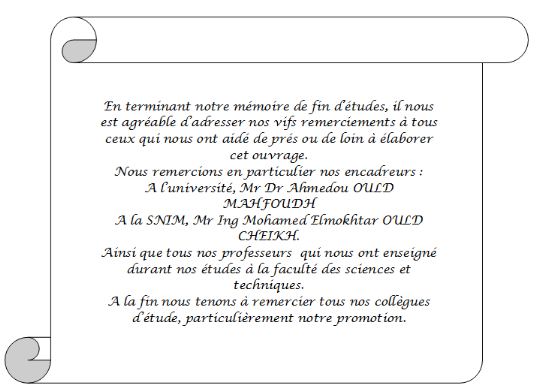
LEXIQUE
GMAB : (Guelb Magnétique:
types, A et B); c'est le nom commercial du concentré magnétique
de l'usine des Guelb ;
GFM : le concentré oxydé
de spirales
TS : Traitement à Sec: minerai
est apte pour le traitement en voie sèche.
TH : Traitement à Humide: le
minerai est apte pour le traitement en voie humide.
KM : particules fines du minerai
magnétique
KX : particules fines du minerai
oxydé
By pass : retour de la charge circulante
dans le broyeur (récirculés) ;
Broyage autogène : le broyage se
fait par les particules entre elles ;
Broyage semi-autogène : le
broyage se fait par les particules + boulets ;
Degré
d'oxydation : Pourcentage de Fe2+/Fe
total ;
Maille de libération : la finesse
à la quelle il faut broyer le minerai pour que le concentré
obtenu par séparation magnétique dépasse la teneur de
65%;
PIF : appareil de
Fluorescence X ;
Volée : une
partie d'un gradin ;
Plans d'abattages : sections
horizontales renseignées au regard des minerais mixtes et des
stérile au vu des teneurs en Fer des cuttings des trous d'abattage;
Balisage : détermination de la
ligne de contact minerai-stérile, pour éviter la confusion entre
le minerai et le stérile lors du chargement.
SM : séparation
magnétique
INTRODUCTION
Le procédé d'enrichissement du minerai de Fer de
Guelbs El Rhein est basé sur une
séparation magnétique à basse intensité par
aimants permanents en milieu sec.
Le choix de ce procédé unique dans le monde est
du à la rareté d'eau dans la région de Tiris à
l'époque ; les campagnes hydrogéologiques menées les
années précédentes ont mis en évidence un potentiel
d'eau important et pour cette raison la SNIM a introduit le
procédé humide dans le flowsheet de l'usine il s'agit de la
séparation gravimétrique par Spirale permettant d'enrichir le
minerai oxydé qui a été stocké en verses à
coté du concasseur de 1985 à 2000 à cause de
l'incompatibilité du procédé sec avec ce minerai
faiblement magnétique.
Les verses TH du gisement Guelbs renferment 32 millions de
tonnes de minerai oxydé et qui doivent être valorisées et
pour cela la SNIM a initié le projet spirale pour faire le meilleur
enrichissement de minerai oxydé en faisant une combinaison entre le
procédé sec (SM) et la séparation gravimétrique par
Spirale :
- La séparation magnétique du minerai
oxydé permet de fabriquer un concentré GMAB à 65,0% fe
avec un rendement poids de 15% et 42% de mixtes oxydés à
traiter par spirale.
- La spirale (séparation gravimétrique; milieu
humide) traite les mixtes oxydés pour en fabriquer un concentré
oxydé appelé « GFM » à 64 % en Fe avec
un rendement de 47%.
La contribution des Spirales dans la production de l'usine est
de 400 000 Tonnes de GFM par an ce qui correspond à 9% de la
production annuelle de l'usine des Guelbs.
L'unité de spirale a démarré en 2004 et
elle donne une grande souplesse pour la production de concentrés
malgré que l'atelier de spirale est fortement gêné par le
traitement de TS qui prend la quasi-totalité de la marche de l'usine.
La prévision de projet Guelbs est de 6 millions de
tonnes de concentrés et jusqu'à nos jours l'usine n'a pas pu
dépasser 4,4 millions de tonnes à cause de problèmes
techniques rencontrés lors du démarrage de l'usine en 1985 il
s'agit de : débit broyeur faible, mauvais traitement de TH par la
procédé à sec (SM).
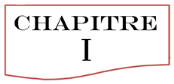
Géologie, Exploitation et de
Caractérisations de Minerai , du Guelb
Rhein
.
I-1-Géologie des Guelbs
I-1-1-Morphologie du Guelb El
Rhein :
· Le Guelb El Rhein est situé à 30km au
Nord de Zouerate (figure 1); se présente sous forme d'une masse noire
assez compacte, posée sur les Regs environnants, parfaitement
isolée de toute structure, ce Guelb de forme triangulaire
s'étend, pour la partie affleurante, sur 1600m de long selon la
direction Nord-Sud.
A l'intérieur du Guelb, la moitié Est est
traversée par une vallée de prés de 600m de long sur 300m
de large, fermée au Nord par verrou de quartzite à
magnétite.
Le point culminant de ce Guelb est de 540 mètres.
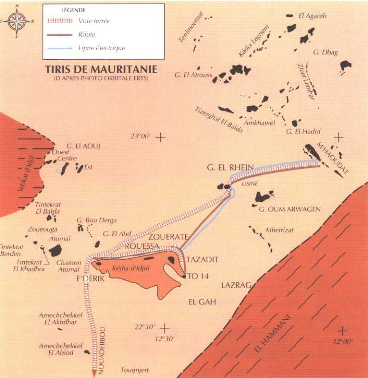
Figure 1. Distribution des formations et des gisements
de Fer dans la région de Zouérate
I-1-2-Lithologie du Guelbs El Rhein :
Le Guelb est l'un des plus beaux Guelbs du Tiris;
résultant des plissements multiples d'un simple banc d'une vingtaine de
mètres d'épaisseur de quartzites ferrugineux à 37% de Fer
en moyenne. Du point de vue lithologique, il est constitué
essentiellement de :
- Quartzites à magnétite: Elles sont de
trois types principaux selon les dimensions des grains:
i- Type A: aspect homogène généralement
à gros grains, taille 481 Microns ;
ii- Type B: hétérogène à grains
en général de petit dimension, 321 Microns;
iii- Type C: à grain moyen; peu magnétique, sa
position topographique indique qu'il est lié à des accidents
tectoniques, 395 microns.
- Les éboulis de quartzites à
magnétite: Ces éboulis recouvrent pratiquement tout le
Guelb ;
- Leptynites: selon leur position;
- Les pegmatites: ces roches constituées de
quartz et de feldspath ;
- Gneiss: sont plus fréquent sur flanc Ouest;
- Quartz blanc: à l'affleurement, ces roches
ont la même situation que les leptynites ;
- Les feldspaths ;
- Et Nontronite : qui est un
faciès argileux du groupe de smectites.
I-1-3-La minéralisation
Le minerai principal constitué de magnétite,
dure de couleur allant du gris au noir. Il reste cependant pauvre en Fer et
nécessite un enrichissement basé sur les propriétés
magnétiques du minerai. Par un procédé de
séparation à basse intensité en voie sèche ;
pour obtenir un concentré marchand appelé : GMAB ;
titrant : 66%Fe ,21%Fe++ et 7% SiO2.
L'existence d'un conglomérat renfermant des galets de
magnétite permet d'avancer un âge antérieur à la
transgression infracambrienne de la mer. En outre les datations
effectuées sur roches totales de la série de Tiris, par G.
Bronner et J.J.Chauvel (1991), (méthode Rb/Sr) donnent un même
âge de 2700 #177; 61 Ma; c'est-à-dire Archéen. Ces auteurs
en concluent que ces formations issues d'un socle Archéen ou les
formations ferrifères sont intiment liées à des roches
volcaniques.
I-2-Exploitation et
Caractérisations de , Minerai des Guelbs
Rhein
I-2-1-Description et qualité du minerai du
gisement du Guelb :
Le gisement du Guelb El Rhein est constitué de
quartzite à magnétite encaissée dans les leptynites et
pégmatites.
Le complexe leptyno-amphibolique est d'âge
archéen (2.8 Ga); l'intensité variable des contraintes et du
métamorphisme a conduit à la formation de trois bancs de minerai
à magnétite de puissances différentes. La partie
supérieure de chaque banc est coiffée d'un minerai
oxydé.
Pour ne pas avoir un écart considérable entre
les prévisions des réserves et les réalisations : il
est indispensable de connaître le nombre exacte de bancs
minéralisés qui joue un rôle très important lors de
l'estimation des réserves.
Le tout venant du gisement titre 37% de Fe comme teneur
moyenne; donc on est devant un minerai naturellement pauvre et
nécessitant un enrichissement par séparation magnétique
à basse intensité vu l'importance de son caractère
magnétique.
Généralement l'exploitation minière passe
par les étapes suivantes:
v La répartition du gisement en plusieurs gradins,
chacun de 15m de hauteur
v L'implantation des trous d'abattage par le topographe selon
les coordonnées topographiques ;
v L'exécution de la foration des trous;
v L'échantillonnage des trous d'abattage;
v La détermination des caractéristiques
minéralurgiques du minerai foré (Laboratoire du suivi
industriel);
v Les travaux de tir à l'explosif par les nitrates;
v Le balisage du minerai;
v Le chargement;
v L'envoi du minerai vers le concasseur;
v Le traitement du minerai à l'usine.
La SNIM exploite trois mines à ciel ouvert à
Zouerate, qui sont reliées entre elles par une voie ferroviaire jusqu'au
port minéralier de Nouadhibou.
I-2-2-La qualité du minerai du Guelb El
Rhein:
Le tout-venant (quartzite à magnétite) ayant une
teneur en Fer > à 28% est considéré comme un minerai
(d'après teneur de coupure), celui à teneur inférieure
à 28 %Fe est rejeté en stérile. Le degré
d'oxydation
(Fe 2+/Fe) est le paramètre permettant de
séparer le minerai oxydé de celui magnétique :
- minerai magnétique : Fe2+/Fe > 84
% ;
- minerai oxydé : Fe 2+/Fe < 84%
- Les degrés d'oxydation: Fe2+ (le
pourcentage de susceptibilité magnétique)
- La maille de libération: C (taille des grains)
Suivant cette classification on distingue les qualités
suivantes (Figure 2) :
. Minerai magnétique type TS1 pour une
maille de libération C > 4OO u
. Minerai magnétique type TS2 pour une
maille de libération C < 4OO u
. Minerai magnétique Oxydé TH1
Fe2+/Fe < 84; C > 6OO u
. Minerai magnétique Oxydé TH2
Fe2+/Fe < 84; 4OO < C < 6OO u
. Minerai magnétique Oxydé KX
Fe2+ /Fe < 84; C < 4OO u
. Minerai magnétique Oxydé KM
Fe2+/Fe > 84; C < 1OO u
Les minerais oxydés TH1,TH2 sont mis en verse à
la mine sachant qu'ils nécessitent un traitement par séparation
gravimétrique humide. Les minerais KX et KM sont
considérés comme stériles à cause de leur
finesse.
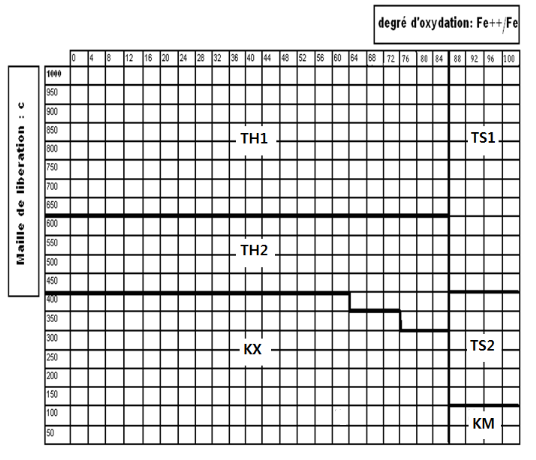
Figure 2: Détermination de la qualité
minière de Trous d'abattage, Guelbs Rhein
I-2-3-L'élaboration d'un croquis de
volée, la foration:
Le gradin destiné à l'exploitation fait l'objet
d'un découpage en plusieurs volées et chaque volée est
divisée en panneaux.
Juste après les travaux d'ouverture et de terrassement;
c'est le rôle du topographe qui vient pour implanter les trous d'abattage
selon la maille: 7m x 8m ou
8m x 9m ; il reporte la disposition des
rangées sur un plan en précisant: les limites du front, la
maille,
La sur-profondeur, et le numéro de la volée
précédé par celui du gradin, et les coordonnées.
La représentation de toutes ces informations sur un
plan constitue ce qu'on appelle: le croquis de la volée qui sera
utilisé ultérieurement par le géologue lors de
l'échantillonnage des trous d'abattage.
La foration est le premier maillon de la chaîne de
production minière. Elle s'effectue à l'aide des perforatrices
équipées d'outil en forme de trépan ayant des dents
armées d'alliages durs; lors de la rotation du trépan, les dents
détruisent les roches du fond du trou. les cuttings (débris) sont
évacués à la surface par l'air comprimé
soufflé au fond du trou.
I-2-4-Echantillonnage des trous d'abattage:
Pour avoir une idée sur la qualité du minerai
à abattre; on est obligé d'échantillonner les trous
d'abattage en vue de les analyser ce qui va nous permettre de déterminer
la qualité du minerai par l'intermédiaire de la teneur en Fer, de
la coupure granulométrique et du degré d'oxydation.
Une fois l'échantillon analysé on dessine le
plan d'abattage qui est utilisé souvent pour entamer les travaux de tir
permettant l'accès au minerai charge.
Sur le plan d'abattage; la coupure de teneurs est de
28% Fe:
- Les teneurs de trous inférieures à 28%Fe sont
considérées comme stérile;
- Les teneurs de trous supérieures à 28%Fe sont
considérées comme minerai.
Sur le même plan on mentionne le tonnage foré en
précisant la qualité du minerai et celle du stérile.
I-2-5-Détermination du tonnage
foré :
Le tonnage foré est déterminé par la
relation suivante:
Tonnage foré = M x M x D x P x N;
D'où :
- M: maille d'échantillonnage;
- D: densité du minerai ou du stérile si c'est
le stérile;
- P: profondeur du trous (au Guelb, elle est
généralement de 15m);
- N: nombre de trous résultant de la foration;
Dans le cas du minerai:
d=3,2
Maille: 7m x 8m;
Tonnage foré (minerai):7 x 8 x 15 x 3,2 x N = 2688t x
N.
Maille: 8m x 9m;
Tonnage foré (minerai):8 x 9 x 15 x 3,2 x N = 3456t x
N.
Dans le cas stérile: d=
2,7
Maille: 7m x 8m;
Tonnage foré (stérile): 8 x 7 x 15 x 2,7 x N =
2268t x N.
Maille: 8m x 9m;
Tonnage foré (stérile): 8 x 9 x 15 x 2,7 x N =
2916t x N.
I-2-6-Détermination des
caractéristiques minéralurgiques des ,
échantillons à l'usine pilote:
L'usine pilote est une unité d'enrichissement, à
l'échelle semi-industrielle, dont le rôle primordial est
d'effectuer les essais préliminaires sur les différents minerais
du fer de Tiris (y compris Guelb El Rhein), et la détermination du
dimensionnement d'une unité d'enrichissement à l'échelle
industrielle (l'actuelle usine des Guelb).
L'usine est doté d'un laboratoire physique qui
constitue une unité de traitement des échantillons des trous
d'abattage, de la recherche minière, des concentrés
chargés (Kédiat), et des échantillons de l'usine du Guelb.
Le traitement d'échantillon des trous d'abattage
à l'usine pilote permet de connaître les caractéristiques
minéralurgiques du minerai qui sera abattu et envoyé
ultérieurement à l'usine.
Ce traitement consiste à déterminer: Fe (tout
venant), degré d'oxydation(Fe+2/Fe) et la maille de
libération(c) de chaque trou. Les échantillons des trous
d'abattage sont acheminés dans des sacs de 5 kg après leur
séchage au soleil ou à l'étuve si l'échantillon est
très humide, chaque échantillon subit la préparation
suivante :
- quartage:
L'échantillon est divisé en 4 parties en le
passant sur un diviseur à riffles (DJ6).
- broyage (0-3mm) :
L'échantillon est broyé dans un broyeur à
mâchoires dit broyeur dragon.
Ce broyage est effectué dans un broyeur à
cylindres dit Moritz, si le pourcentage de la fraction est supérieur 1
mm dépasse 3%, on retourne ce refus pour être rebroyé.
Le produit broyé fait l'objet d'un quartage visant
à préparer un échantillon de 2 kg divisé en deux,1
kg pour l'archivage et l'autre kilo est divisé en 5 lots (chacun de 200
grammes) à analyser comme suit:
Lot n°1: Broyeur Humide
broyage humide suivi de la séparation
magnétique humide à basse intensité dans le tube Davis, si
le concentré de cette séparation titre entre 64,5 et 65,5 % Fe;
l'échantillon est libéré et on effectue son analyse
granulométrique afin de déterminer sa maille de
libération; dans le cas contraire, on applique un troisième temps
de broyage.
Lot n°2 : Tube Davis
Le tube Davis est un appareil de
séparation magnétique à basse intensité dans l'eau
(milieu humide).
Ce lot analysé, dans le tube Davis permet de
déterminer la teneur du concentré à 0 minutes (vient juste
après le broyage Moritz; pris comme référence).
Ce test permet la récupération de la
quantité de magnétite contenue dans un échantillon, il est
conçu pour une petite quantité; dans ce cas le poids de
l'échantillon à analyser est de 60 grammes.
Lot n°3 : Satmagan
Cette analyse consiste à broyer l'échantillon
à 80u, dans un vibro-broyeur à disques (porphyrisation),
l'échantillon qui va subir l'analyse du fer bivalent a la balance
satmagan et l'analyse du fer surtout un poids de 10 grammes.
Satmagan est une balance magnétique pour
déterminer la concentration Fe2+. Charger une capsule
coutenant l'échantillon à analyser est introduite dans
l'appareil. La valeur déterminée par l'appareil est
reportée sur la courbe d'étalonnage qui donne la concentration en
Fe2+ de l'échantillon.
Satmagan sert aussi à la détermination du
degré d'oxydation par l'intermédiaire d'une porphyrisation
à 80u suivi du passage sur la balance satmagam (Fe2+),
l'autre partie du lot est utilisée pour la teneur Fe (tout venant)
déterminée par le laboratoire de chimie.
Lot n°4 et 5 :
Ces deux lots sont considérés comme des
échantillons témoins à archiver pour parer aux
éventuelles contestations ou pertes.
La détermination de la maille de libération est
faite uniquement pour les échantillons libérés,
c'est-à-dire, ceux qui ont une teneur entre 64,5 et 65,5% Fe,
après leur séparation magnétique humide dans le tube
Davis.
Pour déterminer la maille de libération, on
passe l'échantillon sur une tamiseuse Rottalbe contenant une colonne de
tamis ( 800u, 630u, 500u,400u, 315u, 250u, 200u, 160u) durant 15 minutes pour
assurer des vibrations nécessaires au tamisage. On pèse par la
suite le poids obtenu sur chaque tamis et en faisant le cumul poids de cette
opération, on précise le tamis qui retient 10% du produit et
laisse passer 90%; cette dimension sera la maille de libération de
l'échantillon analysé.
I-2-7-Travaux de tir:
La préparation des roches à l'extraction est le
processus qui consiste à détruire le massif rocheux, par les
moyens techniques, en morceaux de dimensions nécessaires et admissibles
pour un travail efficace de l'usine d'enrichissement du minerai de Fer du Guelb
El Rhein.
Le tir par trou de mine consiste à placer du
Nitrate fuel dans une poche au fond du trou (booster); la
charge d'explosif occupe 83% de la profondeur du trou, le restant constitue le
bourrage qui est fait avec les cutting de foration. Ces charges continues
détruisent bien la partie inférieure du gradin mais dans sa
partie supérieure il se forme des blocs hors-gabarits nécessitant
un débitage secondaire. Dans le cas des trous humides; l'explosif est
mis dans une gaine de protection en contact avec le détonateur.
Le boute feu assure la surveillance et l'exécution des
travaux de tir ainsi que la sécurité du site minier.
I-2-8-Balisage:
Après l'abattage des roches, une opération de
balisage doit être faite pour éviter la confusion qu'elle pouvait
y avoir entre la minerai et le stérile lors du chargement.
Le balisage consiste à mettre des bornes
alignées et blanchies de la chaux (CaO) sur les points
de contact minerai-stérile, en prenant en considération le
pendage des tas qui influe fortement sur la ligne de disposition du contact,
car parfois on voit une ligne droite constituant le contact et lorsqu'on change
la position d'observation, on aura du stérile qui a été
couvert par le minerai tout au long de la ligne du pendage, dans d'autres cas
on constate cette situation avec l'avancement du chargement.
I-2-9-Le chargement:
Les travaux d'extraction et de chargement représentent
l'extraction des roches du massif vierge ou préalablement ameubli et
leur chargement dans les engins de transport (camions).
Pour le chargement ex-front des pelles électriques sont
employées à cette tache. Ces pelles travaillent en combinant le
cavage et le levage du godet dans les matériaux. Ensuite le godet
chargé est orienté en rotation jusqu'au dessus de la benne du
camion ou il est vidé.
Ainsi le cycle de chargement d'une pelle comprend les
étapes suivantes :
· Temps de remplissage du godet;
· Temps de rotation du godet en charge;
· Temps de vidage du godet dans la benne;
· Temps de rotation du godet à vide.
Ceci représente un cycle pur et qui ne comprend pas les
attentes des camions, il permet de déterminer le rendement de la pelle
lorsqu'elle est saturée (rendement maximal).
En général, pour des pelles puissantes, comme
les PH 2800, l'ensemble de ces temps est inférieur à une minute.
Rendement d'une pelle est égal a :
Capacité Godet
Rdt (t/h) = ---------------------
Cycle du Godet
Rendement d'un camion est égal a :
Charge en tonne x 60
Rdt (t/h) = ---------------------------
Durée du cycle (mn)
A l'aide d'une pelle électrique munie d'un excavateur
à godet; on grignote le produit (minerai ou stérile) en le
déversant dans le camions de transport (capacité: 120 à
170 tonnes).
Selon le produit chargé, on aura les
possibilités suivantes:
Si c'est le TS1 ou TS2 on l'envoie directement au concasseur
(dans le cas de l'indisponibilité de ce dernier, on décharge le
minerai dans les verses-minerais).
Si c'est du TH1 ou TH2: le minerai est déchargé
dans les verses-TH.
Et si c'est les roches encaissantes ou (KM, KX) qui sont des
stériles; les camions les acheminent vers les verses-stériles.
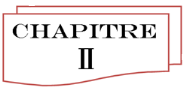
Traitement du Minerai à ,
L'usine des Guelbs
II-1-Bref aperçu de l'usine et de son
historique :
Le flowsheet de l'usine (figure 3) a
été extrapolé à partir des études
métallurgiques à l'échelle semi-industrielle ; et ces
dernières ont prévu une production annuelle de 6 millions de
tonnes de concentré de GMAB; si on observe l'historique de la production
de l'usine depuis son démarrage (1985) jusqu'à nos jours qui est
de 4,2 millions de tonnes; on voit clairement que ceci est loin des
premières estimations.
La cause de cet échec est du à plusieurs
facteurs qui ont été négligés :
Ø L'hétérogénéité de
la qualité minière traitée à l'usine des Guelbs;
Ø L'indisponibilité
électromécanique de l'usine; qui restant en dessous de 55%
jusqu'à 1995;
Ø Le faible débit des broyeurs resté
autour de 680 t/h jusqu'au démarrage de presses à rouleaux ;
à partir de cette date le débit a commencé à
frôler les 900 t/h car le rebroyage par presses permet au broyeur
d'être à l'abri de bridage généré dans le
passé par la charge circulante (les refus de criblage et des mixtes TS
de la séparation magnétique à sec).
Figure 3: Flowsheet de l'Usine des
Guelb
II-2-Concassage
L'installation dans laquelle est effectuée le
concassage primaire est l'une des parties vitales de l'usine
du Guelb du fait qu'elle se trouve en tête du circuit et qu'elle
reçoit parfois d'énormes blocs (hors gabarits).
Les concassés ont une granulométrie
composé entre 0-250mm. En conséquence ; la taille et la
structure de cet atelier tiennent compte :
- De la capacité des camions : de 170 à 200
tonnes ;
- De la l'impérieuse nécessite d'avoir un
grizzly en tête du concasseur pour éliminer les fragmentations de
ferrailles et les blocs non admissibles (blocs hors gabaries);
- De la topographie nécessitant implantation du
concasseur en souterrain.
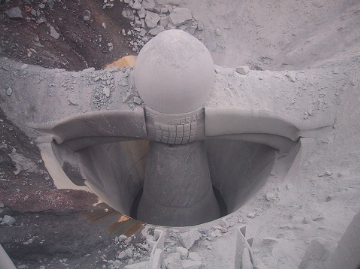
Photo N°1 : la noix du concasseur
usine du Guelb
Le concassage est effectué par un concasseur
giratoire de (60" x 89"); son alimentation est
inférieure à 1500 mm.
Le choix de ce concasseur ne vient pas du hasard; mais d'une
comparaison très logique entre les différents types de
concasseurs primaires (giratoire et mâchoire); ce qui a donné les
résultats suivants :
- A pleine charge; le concasseur giratoire à un
débit 3,5 fois plus qu'un concasseur à mâchoires.
- La tonne par unité d'énergie et par heure est
plus forte pour le giratoire que pour le concasseur à mâchoire;
- La lubrification (la lubrification comprend une cuve
d'huile d'une capacité de 2800 litres assurant le mouvement de
l'ensemble) est meilleure sur le giratoire.
Ce concasseur comprend une noix (Photo N°1)
composée de quatre rangées de concaves, une
supérieure, deux médianes et la dernière inférieure
qui reposent sur une nappe d'huile.
La marche du concasseur est commandée par un ordinateur
installé dans la cabine du concasseur; le démarrage du concasseur
nécessite une temporisation d'une minute ; c'est-à-dire que
le concasseur démarre après une minute de l'ordre de
démarrage donne par l'opérateur.
Le concasseur peut en moyenne recevoir 17 camions/ heure comme
valeur moyenne, avec une rotation de deux camions toutes les trois minutes.
Le réglage du concasseur :
- Dimension concasseur: (60"x 89");
- Dimension maximale des produits à l'entrée du
concasseur : 1500 mm;
- Dimension maximale des produits à la sortie du
concasseur : 250 mm;
- Source d'énergie : 5500 volts;
- Vitesse de rotation : 370 tr/mn;
- Débit de concasseur : entre 2800 et 3200 t/h;
- Puissance installée est de 315 kw;
- Consommation énergétique : 0,25
kwh/t ;
- Rapport de réduction : 6.
Le stockage en parc du concassé:
Ce stockage permet l'homogénéisation des
concassés devant alimenter l'usine afin d'éviter toute
difficulté lors au broyage dûe à
l'hétérogénéité des produits
d'alimentation.
Les produits concassés sont stockés dans les
aires de stockage de 480kt
La reprise du concassé:
La reprise du concassé est réalisée par
deux roues-pelles:
. Parc Nord: La roue-pelle
du parc Nord; déverse le concassé sur le convoyeur à bande
qui alimente la goulotte
. Parc Sud: la roue-pelle se déplace
sur le parc Sud pour verser le produit sur le convoyeur relié au
convoyeur à bande qui alimente directement la trémie principale
de l'usine d'une capacité de 2000 tonnes.
La roue-pelle a un godet de dents en alliages durs, qui
fonctionnent d'une façon continue; elle est mise en mouvement
électrique par un moteur de 5000 volts; le débit nominal de la
roue-pelle est de 2500-3000t/h.
L'alimentation directe de l'usine
Dans ce cas; on utilise le stocker qui alimente l'usine
directement en envoyant les concassés vers la goulotte assurant
l'alimentation de la trémie principale de l'usine.
II-3-Le Broyage
Le minerai repris par les roues-pelles arrive à une
grande trémie principale à deux compartiments d'une
capacité totale de 2000 tonnes et ensuite par 2 extracteurs;
l'extracteur verse le produit sur le convoyeur à bande dont le
débit normal est de 900 t/h pour le TS1 et 650 t/h pour le TS2 et 1300
t/h pour le TH.
Le broyage autogène ou semi-autogène
assuré par deux broyeurs à boulets, type Aerofall (photo2) ligne
A et B, chacun permettant de broyer les concassés jusqu'à une
granulométrie de 0 à 12,5mm.
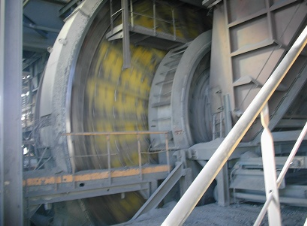
Photo N°2 : Broyage Aerofall
à l'usine du Guelb
Pour aboutir à un débit optimum de ces broyeurs;
il a été recommandé de les faire tourner dans les
conditions suivantes:
- Broyeur Aerofall: (34,5"x 8,5")
- Diamètre: 10,24 m
- Longueur: 4 m
- Vitesse de rotation: 11tr/mn;
- Charge en boulets de 66 tonnes;
- Taux de remplissage de 33%;
- Une ouverture de ventelles de 75% permettant de balayer
toutes les particules broyées;
- Puissance consommée: 4000 à 4500kw;
- Puissance installée: 5220kw.
Le débit du broyeur dépend de :
· La régulation (puissance, ouverture vantelle,
dépression sortie.......);
· La recharge de boulets;
· Usure blindage (il existe a l'intérieure du
broyeur des blindages de viroles, des flasques, et des tourillons);
· Qualité minerai;
· Mode de fonctionnement du broyeur;
· Intervention de l'opérateur.
La décharge du broyeur est répartie entre le
classificateur vertical et l'alimentation du criblage.
Au niveau du classificateur se déroule une
séparation gravimétrique. La sous-verse se dirige vers le
criblage; tandis que la sur-verse (0-500um) non retenus par le
classificateur verticale sont entraînés par le courant
d'air vers une batterie de 6 cyclones de
chaque ligne pour qu'elle fasse l'objet d'une deuxième
séparation gravimétrique. La sous-verse (100 à 500um) est
envoyée par le convoyeur vers la séparation magnétique;
par contre la sur verse (0-100um) des cyclones prend le chemin des
filtres électrostatiques. Après filtration la
sous verse (exhaure) est acheminée vers le stérile, en attendant
le projet de séparation magnétique humide, et la sur verse est
rejetée dans l'air par la cheminée du ventilateur.
II-4-Le Criblage
Après le broyage (0-12,5mm), le crible est
alimenté par les sorties de broyeurs Aerofall (A, B) et la sortie
de presses à rouleaux.
Le minerai est envoyé vers le criblage pour subir un
classement dimensionnel selon la maille du crible (1,6 mm). Les grains d'une
dimension inférieure à la maille du crible constituent le
passant, tandis que ceux qui ont une dimension supérieure
représentant le refus.
Pour être compatible avec le broyage, le criblage
comporte deux lignes: A et B. chaque ligne est constituée de 24 cribles
vibrants; type DERRICK et l'agencement de ces cribles est
représenté par 12 sections, chacune formée de 2
cribles.
Le crible est constitué de haut en bas des
éléments suivants :
- Un chariot verseur : transitant sur un
accumulateur pour le remplir de minerai à cribler, qui sera
divisé entre les cribles. Dans le cas de remplissage de l'accumulateur,
le vérin hydraulique s'avance pour ouvrir la goulotte du chariot pour
qu'il puisse se déplacer vers les deux cribles de by pass (23 et 24)
utilisés souvent dans le cas d'indisponibilité de l'accumulateur.
- L'accumulateur : c'est la caisse qui
assure l'alimentation des cribles en stockant les produits à
cribler,
- L'alimentateur : alimente directement
les cribles,
- Caisson hydraulique : assure
l'énergie,
- Registre denté : il permet le
réglage de l'ouverture d'alimentation du crible qui joue un rôle
déterminant dans l'efficacité de criblage ; cette ouverture
est graduée de 0 a 100 %.
- Crible : chaque crible comprend :
un moteur vibrant et trois toiles, chacune de 1,6 mm
- La goulotte : permet
l'évacuation des passants du criblage.
A l'usine des Guelb, l'efficacité du criblage varie
entre 75% et 90% et pour la fraction critique. Cette efficacité exprime
la qualité de l'épuration du produit passant, autrement dit, le
pourcentage des grains de dimension supérieure à la maille de
crible contenus dans le passant, dans notre cas le pourcentage de refus dans le
passant est de l'ordre de 10 à 15%.
L'efficacité du criblage dépend
de :
- Débit d'alimentation de crible,
- L'état des toiles du crible qui doivent être en
bon état et ne présentent pas des défauts tels que :
usure, tension et colmatage,
- L'inclinaison du crible, elle doit être constante,
- Sens de marche des moteurs du crible.
Le débit moyen d'un crible est de 105 tonnes par heure,
les facteurs suivants affectent la
capacité du crible dépend:
- pourcentage passant,
- % de la fraction critique,
- % en eau,
- Et la forme de grains,
Après le criblage; le passant est envoyé
directement vers la séparation magnétique; tandis que le refus
prend l'itinéraire des presses a rouleaux pour être
rebroyé.
II-5-Rebroyage par presses à rouleaux :
Le rebroyage a été introduit dans le flowsheet
de l'usine pour augmenter la production de l'usine de 10 à 15%, en
évitant le retour de la charge circulante (les refus de criblage et des
mixtes TS de la séparation magnétique) vers le broyeur Aerofall,
afin d'améliorer son débit. Le circuit de rebroyage est
alimenté par un convoyeur à bande assurant une alimentation
horaire de 1425 t/h pour chaque ligne.
Cette mesure permet au broyeur de ne recevoir que
l'alimentation fraîche, son débit sera alors meilleur. Le
rebroyage est assuré par les presses à rouleaux; qui sont des
broyeurs à cylindres. Les presses à rouleaux sont des broyeurs
à cylindres forcés en rotation inverse; ces broyeurs sont
composés de 2 rouleaux (un mobile et l'autre statique).
L'écartement entre deux rouleaux (gap) agit sur la pression de rebroyage
en fonction de la granulométrie et la dureté du minerai.
Les avantages de ces broyeurs :
- capacité de broyage fin;
- consommation énergétique faible par rapport
aux autres broyeurs;
- débit réglable.
Le bon fonctionnement dépend de:
- l'écartement entre les rouleaux;
- la pression de rebroyage; elle oscille entre 90 et 110
bars;
- Le réglage des déflecteurs: écoulement
de matière.
Les caractérisations des presses à rouleaux
utilisés sont:
- Diamètre: 1,7 mètres;
- Largeur: 1,8 mètres;
- Vitesse périphérique: 1,6 m/s;
- Vitesse de rotation: 18,06 Tr/mn;
- Puissance installé: 900 Kw;
- Tension moteur: 5500 V;
- Fréquence: 50 Hz.
Le débit d'un rouleau est déterminé par
la formule suivante: Q (Débit): D x L x G x V.
D: diamètre du rouleau;
L: longueur du rouleau;
V: vitesse périphérique;
G: le gap : c'est la distance entre les deux rouleux.
Si les presses ne sont pas disponibles, on revient à la
situation primaire (retour des mixtes de séparation magnétique et
du refus de criblage vers le broyeur par le convoyeur à bande) ; et
dans ce cas c'est le phénomène du by pass qui se reproduit, Le
débit du broyeur est inversement proportionnel au by pass.
II-6- La Séparation magnétique à
Sec :
II-6-1- Minerai magnétique :
Le minerai magnétique est appelé
TS (traitement sec) comme se prête au traitement à sec .
Ce type de minerai a été classé en 3
types, comme suit:
- TS1: minerai grossier présentant les
caractéristiques suivantes: maille de libération
supérieure à 400u,
- TS2: minerai magnétique moyen; avec
une maille de libération composé entre 400
et 150u, - KM: maille de libération
inférieure à 150u. Cette qualité est très fine et
elle ne peut pas être traité par le procédé actuel
de l'usine à cause de sa finesse.
Comme ce minerai présente une forte
susceptibilité magnétique ; il s'est avéré que
la séparation magnétique à basse intensité en voie
sèche est la méthode la plus appropriée pour l'enrichir.
Le procédé donne trois produits : un concentré
magnétique à 66%Fe ; un mixte à 50% et un
stérile définitif à 9%Fe.
II-6-2- Atelier de séparation magnétique
a sec
C'est le coeur du procédé; il
comporte deux lignes (A, B) de séparation magnétique; chaque
ligne est alimentée par le passant de son criblage et sous-verse de
cyclones.
Chaque ligne de séparation magnétique est
composée de 14 groupes séparateurs à aimants permanents;
et 2 groupes qui constituent une section. Chaque ligne comporte 7 sections; et
qui sont munies de viroles (diamètre de 900 mm et une longueur de 2000
mm) créant des champs magnétiques suffisants pour extraire les
particules fortement ferrifères de ce minerai ; ce qui a conduit
à l'application d'une séparation magnétique à basse
intensité.
Un groupe séparateur est composé de haut en bas
des éléments suivants:
- Un registre: qui sert à isoler le
groupe de l'accumulation en charge, contenant le produit à traité
(commande manuelle)
- Un dispositif d'alimentation: permet le
réglage du débit en agissant sur le trappe à casque
- Un module de traitement: autonome,
équipe d'un séparateur de premier passage;
- Un socle/châssis : comprenant une
goulotte qui prolonge l'évacuation des produits concentrés
magnétiques obtenus par le premier passage et deux goulottes assurant
l'alimentation des deux séparateurs du deuxième passage;
- Deux modules de traitement;
- Une enveloppe: tournante
non magnétique;
- Un socle chariot: il supporte la
totalité des éléments qui composent le groupe
séparateur; ce socle/chariot conçu pour évacuer les
produits séparés est équipé de deux volets de
coupures équilibres et orientables manuellement.
Selon la qualité de minerai traité (TS1, TS2)
les viroles de séparateurs sont orientées à des vitesses
variables et les volets de coupure sont aussi orientables.
Le débit du minerai arrivant sur chaque groupe de
séparateur dépend de deux facteurs:
- L'ouverture de la trappe à casque qui varie de 0
à 100 mm;
- La vitesse de rotation de l'alimentation (0,25-1,65 m/s).
Le groupe séparateur comprend 3 séparateurs :
Un séparateur de 1er passage et deux
séparateurs de 2éme passage (fig4) .
v Premier passage:
La vitesse du séparateur du 1er passage (2
à 10 m/s) et la position du volet de coupure
dépend de la qualité traitée.
La virole du premier passage est en fibre de verre de 4,5 mm
d'épaisseur et revêtue d'un revêtement en caoutchouc
anti-abrasion de 3 mm d'épaisseur.
Ce passage permet d'avoir deux produits: un concentré
définitif et un préconcentré (mixtes).
v Deuxième passage:
C'est le lieu ou s'effectue la séparation du
préconcentré en mixtes et stérile définitif, la
vitesse du séparateur du 2éme passage est de 1 à 5 m/s.
La virole du deuxième passage est en
acier inoxydable magnétique de 2 mm d'épaisseur revêtu par
un caoutchouc anti-abrasion. Les mixtes (50% Fe) retournent vers le rebroyage,
par contre le stérile (9% Fe) est envoyé directement vers la
digue à stérile.
Le concentré de l'usine de Guelb est dit GMAB, et a les
caractéristiques suivantes:
- 66% Fe
- 7% S iO2
- 0,015% P
- 35 à 40% inférieur à 160u.
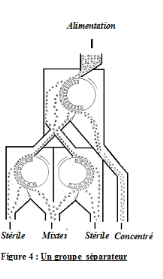
II-7-Laboratoire d'essais physiques usine des
Guelbs :
Ce laboratoire a pour principal objectif le suivi de la
qualité du traitement de minerai à l'usine par
l'intermédiaire d'une analyse physique des échantillons
prélevés aux différents points de l'usine, et surtout du
concentré qui est analysé toutes les heures pour savoir la teneur
du concentré obtenu.
L'échantillonnage et la préparation
mécanique des échantillons prélevés à
l'usine se fait en plusieurs étapes:
A/ L'échantillonnage:
Le prélèvement des échantillons se fait
à l'aide d'une pelle verseuse sur l'axe parallèle du convoyeur
c'est-à-dire au centre et sur les deux droites toutes les heures ;
ces échantillons sont mis dans des sachets. En ce qui concerne le
chargement, on prélève sur le convoyeur du chargement toutes les
5 minutes et le cumul des prises sera le poids de wagons chargés divise
par dix.
NB : si l'échantillon est humide; on le passe
à l'étuve pour le séchage.
B/ La préparation mécanique:
Elle permet la réduction de l'échantillon
prélevé en vue d'en prendre une partie représentative.
ü Le quartage :
Il permet l'homogénéisation et la
réduction en poids de l'échantillon; cette opération
consiste à passer un échantillon à travers des diviseurs
de dimensions décroissantes (DJ30, DJ15, DJ6) à l'issue du
quartage, on prend un échantillon de 80 à 120 grammes pour le
broyage.
ü Le broyage :
On procède par un broyage à 80u dans un
vibro-broyeur à disques.
Pour l'analyse physique on prend 30 grammes de
l'échantillon broyé pour déterminer sa teneur en fer sur
le PIF d'analyse.
C/ L'analyse physique:
Cette analyse comprend:
ü Le PIF analyser :
Avant la détermination de la teneur, on entasse
l'échantillon convenablement pour le rendre homogène. La teneur
en fer de l'échantillon est déterminée en projetant la
valeur enregistrée par l'appareil sur la courbe d'étalonnage.
Si la teneur obtenue est supérieure à 65,5% Fe,
le concentré est dit conforme.
Si la teneur est inférieure à 65,5% Fe; le
concentré est non-conforme.
ü L'analyse
granulométrique :
Il est recommandé d'effectuer l'analyse
granulométrique et voir sa situation avec les valeurs contractuelles. On
utilise généralement la colonne de tamis de 3,15mm jusqu'au
0,160mm.
ü Séparation magnétique dans le
laboratoire:
Le laboratoire d'essais physiques (usine du Guelb) dispose
d'appareils de séparation magnétique à basse
intensité à aimants permanents pour permettre d'établir
d'une façon continue la comparaison; en cas de problème sur l'une
des lignes du procédé de séparation magnétique de
l'usine.
La séparation magnétique se déroule en
deux épisodes :
-Premier passage :
Sur un séparateur test de 46 pôles de
diamètre de 0,917m, le résultant de ce passage (à basse
intensité) est un concentré du premier passage (c1) et des
mixtes.
- Deuxième passage :
C'est une séparation magnétique à
intensité plus élevée que celle du premier passage, cette
séparation consiste à passer les mixtes du premier passage dans
un séparateur test de 24 pôles pour obtenir un concentré de
deuxième passage (c2) et un stérile définitif (s).
Ces deux appareils doivent être réglés en
faisant la conversion de la vitesse virole de l'usine du m/s en tr/mn au moment
du prélèvement de l'échantillon.
Premier passage : 1m/s correspond à 42 tr/mn.
Deuxième passage : 1 m/s donne 46 tr/mn.
II-8-Stockage et reprise du concentré :
II-8-1- Mise à stock
Après l'obtention du concentré GMAB,
résultant du procédé de concentration par
séparation magnétique à basse intensité, les
concentrés des deux lignes de séparation magnétique sont
acheminés par le convoyeur à bande pour être stocké
dans les parcs de concentrés (en attente du chargement).
La qualité du concentré: conforme ou non
conforme; ceci nous pousse à définir la notion de la
conformité.
Pour le stockage du concentré; deux possibilités
se présentent:
- Parcs Nord
Cette aire de stockage a une capacité de 120 kt, qui
est subdivisée en deux partie; une réservée aux
concentré du TS1: SiO2 = 6,5 à 7,5% et l'autre à ceux du
TS2: SiO2 = 8 à 9%.
Le concentré est déversé sur le convoyeur
à bande, permettant de stocker le concentré dans l'un de points
du parc Nord: NA ou NB.
- Parcs Sud
Cette aire de stockage a une capacité de 120 kt, le
concentré est déversé sur le convoyeur à bande,
d'un débit anormal de 2500 t/h; qui stocke le concentré dans l'un
des points du parc Sud (SA ou SB).
Chaque stocker est muni d'une sonde, déterminant le
niveau de concentré dans le cônes.
Les aires de stockage sont réparties selon la
qualité du concentré de la manière suivante:
- 2/3 des aires sont destinées au stockage du
concentré conforme; avec une capacité de 160 kt.
- 1/3 des aires de stockage pour le concentré
non-conforme; capacité de 80 kt.
II-8-2- Chargement
La reprise du concentré GMAB est effectuée
à l'aide d'une roue-pelle , placée au milieu des parcs pour
faciliter la reprise sur les deux côtés. La roue pelle prend le
concentré pour le déverser sur un convoyeur à bande, qui
l'achemine vers les grandes trémies de chargement.
Ce chargement comprend une trémie tampon d'une
capacité de 400 tonnes placée en dessous d'une trémie
peseuse de 85 tonnes. Quand un wagon est en bonne position les portes s'ouvrent
et l'une des trémies de 85 t est déchargée dans le wagon,
pendant le mouvement du train, la trémie suivante est remplit afin de
charger le wagon suivant dés qu'il sera en position.
Au cours de ces opérations, on mouille les
concentrés chargés à raison de 1% d'eau, afin de limiter
la perte de produit par le vent pendant son transport et pour faciliter la
manutention au port minéralier de Nouadhibou.
Selon les spécifications commerciales, la teneur du
concentré GMAB doit être de 66 #177; 0,8% Fe lors de
l'expédition en train (wagons minéraliers) et de 66 #177; 0,5%
Fe lors de l'expédition en navires à partir du port
minéralier de Nouadhibou.
II-9-Qualité et production à l'usine des
Guelbs
Comme l'usine des Guelbs traite des minerais de
qualités différentes (TS, TH) ; les concentrés qui en
résultent sont différents par leur magnétisme.
Le minerai magnétique produit un concentré
magnétique dit GMAB tandis que le minerai oxydé donne deux
concentrés : le premier passage de la séparation
magnétique fournit un GMAB et le concentré oxydé des
spirales est dit GFM.
Le concentré magnétique (GMAB)
a les caractéristiques suivantes :
- 66% Fe
- 7% S iO2
- 0,015% P
- 35 à 40% inférieur à 160u.
Le concentré oxydé de spirale
(GFM) a les caractéristiques suivantes:
- 64.3% Fe
- 7% S iO2
- 0,015% P.
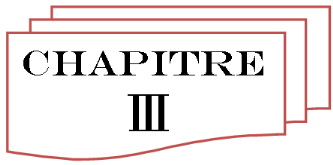
Sujet de stage :
L'enrichissement du minerai
Oxydé
Au vu de la rareté d'eau dans la région de Tiris
, le procédé sec a été adopté pour enrichir
le minerai oxydé pour en fabriquer un concentré GMAB à
65,0%Fe mais comme le rendement poids de ce concentré est très
faible ; l'usine a abandonné le traitement de TH et pour faciliter
les travaux de découverture, le minerai TH a été mis en
verse en attendant de trouver un procédé adéquat pour
l'enrichir ; ce qui a été finalisé
ultérieurement par le démarrage du projet Spirale.
Comme le comportement de TH diffère de celui de TS au
niveau de la séparation magnétique à basse
intensité qui est prévue pour l'enrichissement de minerai
magnétique (fortement magnétique : TS) ; nous avons
voulu présenter la comparaison du traitement de TH par rapport au TS
dans le cas du procédé à sec en essayant de montrer les
grandes lignes de différence du comportement TS et TH à l'usine
du broyage jusqu'à l'obtention du concentré GMAB :
|
Traitement TS par SMBI, Usine Guelbs
|
Traitement TH par SMBI
Usine des Guelbs
|
Débit Broyeur (T/H )
|
900
|
1300
|
% poids GMAB
|
42,0
|
15,0
|
% Fe concentré
|
66,0
|
65,0
|
%Fe ++
|
21,4
|
15,0
|
Réglage volets de coupure premier passage ( C1 )
|
35°AR
|
0°
|
Réglage volets de coupure deuxième passage
|
0°
|
25°AV
|
Vitesse C1
|
8 m/s
|
7m/s
|
Vitesse
|
5 m/s
|
1,75 m/s
|
%Fe stérile
|
9
|
17
|
A partir du tableau ci-dessus on peut dire que :
§ Le débit du broyeur en cas de TH est
supérieur au celui du TS à cause de la friabilité du
minerai oxydé ce qui incite un temps de séjour de particules
oxydées dans le broyeur très réduit ; par contre le
minerai magnétique est dur d'où la nécessité d'un
séjour plus important pour garantir le broyage ;
§ Comme la séparation magnétique est une
basse intensité et les deux minerais ont différence
d'équivalence magnétique ; il est très logique qu'on
récupère plus dans le cas du minerai magnétique et le
pourcentage de particules fortement magnétiques est très faible
dans le cas du minerai résultant de l'oxydation (TH ) ;
§ La différence du réglage SM en cas de TS
et TH , est du à la nature de deux qualités minières et
l'objectif visé du traitement de TH ( production de maximum possible de
mixtes pour alimenter spirale) ;
§ Le fer bivalent de concentré GMAB du TS et celui
du TH montre clairement la différence du degré de
magnétisme de ces qualités.
Et voici la réaction de l'altération de la
magnétite :
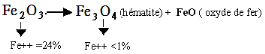
Comme le TH est un stade intermédiaire entre la
magnétite et l'hématite (stade martite) ;
le pourcentage de Fe ++ reste entre celui de la magnétite et
l'hématite.
III-1-Enrichissement de TH par Séparation
magnétique à sec :
Le minerai oxydé est dit TH (traitement humide), car il
nécessite l'eau pour être enrichi à cause de l'oxydation
et la finesse de particules à séparer. Il se distingue du celui
magnétique par le degré d'oxydation (Fe2+/Fe) ;
tout le minerai ayant Fe2+/Fe < 84% est déclaré
TH.
Le minerai oxydé comprend les trois qualités
suivantes:
TH1: minerai grossier présentant les
caractéristiques suivantes: Degré d'oxydation inférieur et
maille de libération supérieure à 600u,
TH2: minerai moyen; avec une maille de
libération comprise entre 600 et 400u.
KX: maille de libération
inférieure à 400u, celui-ci n'est pas enrichissable à
cause de sa finesse.
III-1-1-Bilan de Traitement de TH à l'usine des
Guelbs :
1984 -
1990 :
L'enrichissement de minerai oxydé par la
séparation magnétique permet de produire trois produits :
concentré, mixtes et stérile.
Le traitement de TH durant cette période a
été essentiellement limité aux jours de manque de TS ce
qui oblige l'usine à tourner avec le TH.
Le bilan de traitement de TH par la séparation
magnétique est comme suit :
|
% poids
|
%Fe
|
Récupération métallique
|
Concentré
|
17 ,4
|
64,3
|
32,2
|
Mixtes
|
26,7
|
51,5
|
39,6
|
Stérile
|
55,9
|
17,5
|
28,2
|
Reconstitué
|
100,0
|
34,7
|
100,0
|
D'après le tableau ci-dessus, on voit clairement que le
rendement poids du GMAB issu de minerai oxydé (TH ) est très
faible comparativement au celui de TS (42% ).
Ce bilan de traitement a permis à l'usine de prendre la
décision de ne pas tourner avec le TH en attendant de trouver une
solution pour l'enrichissement de cette qualité minière connue
par l'ampleur de son empoussièrement.
III-1-2-Essais d'enrichissement de mixtes oxydés
par Spirale
(Echelle
semi-industrielle):
Les années 90 ont été marquées par
le début de travaux de recherche de procédé adéquat
pour enrichir le TH : mixtes TH à valoriser ?
Comme le minerai oxydé présente un écart
de densité entre le concentré et le stérile ; le
procédé de séparation gravimétrique par spirale
s'est avéré comme le procédé le plus
adéquat.
Plusieurs essais à l'échelle laboratoire ont
été menés et après l'étude à l'usine
pilote, le bilan métallurgique suivant a été
retenu :
Traitement TH par séparation
magnétique (SM) :
|
% poids
|
%Fe
|
Récupération métallique
|
Concentré(GMAB)
|
12,0
|
65,0
|
21,2
|
Mixtes
|
45,0
|
50,0
|
61,3
|
Stérile
|
43,0
|
15,0
|
17,5
|
Reconstitué
|
100,0
|
36,7
|
100,0
|
Les mixtes oxydés sont traités par
spirale :
|
% poids
|
%Fe
|
Récupération métallique
|
Concentré (GFM)
|
61,2
|
65,0
|
79,6
|
Stérile
|
38,8
|
27,0
|
20,4
|
Reconstitué
|
100,0
|
50
|
100,0
|
La combinaison de deux procédés (SM+Spirale)
donne le bilan suivant :
(Prévisions Projet Spirale)
|
% poids
|
%Fe
|
Récupération métallique
|
Concentrés
(GMAB+GFM)
|
39,0
|
65,0
|
66,4
|
Stérile
|
61,0
|
21,0
|
33,6
|
Reconstitué
|
100,0
|
38,2
|
100,0
|
III -2- Enrichissement de TH par Spirale :
Le traitement du minerai oxydé à l'usine des
Guelbs passe par les mêmes étapes que celles du TS
(magnétique) sauf que pour le TH les mixtes sont envoyées vers
l'unité spirale, à une teneur de 50% Fe, pour subir une
séparation gravimétrique et produire un GFM à 65%Fe.
L'enrichissement du minerai oxydé comprend deux
procédés : séparation magnétique à sec
suivie par spirales ce qui permet d'avoir un bilan global de TH (Selon
prévisions projet spirale) :
|
% poids
|
%Fe
|
Récupération métallique
|
Concentrés
(GMAB+GFM)
|
39,0
|
65,0
|
66,4
|
Stérile
|
61,0
|
21,0
|
33,6
|
Reconstitué
|
100,0
|
38,2
|
100,0
|
III -2-1-Description du Fonctionnement
Spirale :
Principe :
Le fonctionnement de spirale est basé sur une
séparation gravimétrique qui tient compte de la différence
de densité entre les eux produits à séparer.
Les particules sont soumises à une force centrifuge et
dans ce cas ; les grains les plus lourds et fins se trouvent dans l'axe
central pour être récupérer dans les opercules tandis que
les grains légers et les plus gros débordent sur la paroi
externe de spirale.
Pour garantir les performances du procédé
spirale, il est recommandé de tourner dans les conditions
suivantes :
§ teneur d'alimentation ( mixtes ) de 45% Fe au
minimum ;
§ une granulométrie de mixtes inférieure
à 1,6mm ( maxi=5% de grossiers ) ;
§ le réglage des opercules de manière
à maximiser la récupération de toutes les particules
riches ;
§ % de solide de 33% de la pulpe ;
§ débit d'eau de lavage suffisant pour une
meilleure séparation.
Flowsheet Spirale :
La Spirale est connue par une grande consommation d'eau
(séparation gravimétrique, milieu humide). Elle est conçu
pour produire un concentré GFM ayant une teneur en fer d'au moins 64%
à partir des mixtes TH de la séparation magnétique
à sec. L'enrichissement par voie humide se fait grâce à une
seule ligne ayant une capacité de 400t /h. les mixtes oxydés sont
véhiculés vers un crible vibrant de contrôle à
maille 5mm (pour éviter toute pièce grossière dans le
circuit de traitement )
L'eau nécessaire pour la mise en pulpe des mixtes
oxydés TH est apportée en tête du crible et sur sa toile
grâce au système d'arrosage.
Le refus du crible constitué de pièces
grossières est évacué au sol.
Le passant du crible est dirigé gravitairement vers la
bâche à pulpe qui alimente l'atelier de spirales.
Après la mise en pulpe le produit passe par les
étapes suivantes :
- Spirales de dégrossissage
La pulpe est pompée vers le premier étage de la
séparation gravimétrique constituée de 7 bancs de 12
spirales doubles de dégrossissage de type WW6E ( MD Mineral Technologie)
(Photo3) .
La distribution de la pulpe à l'entrée de chaque
tour de spirales est assurée successivement par un distributeur
primaire, 8 voies (dont une obturée) distributeurs secondaires, 24 voies
7 alimentées par le haut depuis le distributeur primaire.
-Spirales de lavage
La pulpe ainsi diluée est pompée vers le
deuxième étage de la séparation gravimétrique
constituée de 6 bancs de 12 spirales de lavage de types WW6E.
La distribution homogène de la pulpe à
l'entrée est assurée successivement par :
Un distributeur primaire, 6 voies alimentées par sa
base
-Filtration de Concentré :
A l'aide de couloirs sous spirales, la pulpe du
concentré est conduite par gravité sur un filtre à bande,
le concentré est alors retenu par la bande.
- Humidité du
concentré :
Le concentré déshydraté, à une
ayant humidité maximale de 8%, tombe du filtre sur la bande
Du concentré.
-Les hydrocyclones :
Les stériles issus des spirales de dégrossissage
et de lavage sont collectés dans une même bâche qui alimente
la batterie d'hydrocyclones. de cette batterie , la pulpe épaisse est
conduite par gravité sur le filtre à bande et la sur-verse
contenant quelque particules fines est évacuée vers le
décanteur .
- Filtration du Stérile :
Le stérile à filtrer est collecté dans
une boîte de répartition qui permet par gravité
l'alimentation du filtre de façon régulière. La suspension
épaissie est déversée sur la toile filtrante. Le vide est
réalisé à l'aide d'une pompe à vide à anneau
.
- Humidité Stérile :
Le stérile déshydraté, ayant une
humidité maximale de 25%.
-Le décanteur:
Le coeur de cet atelier est constitué par un
décanteur de 40m de diamètre qui reçoit principalement la
surverse de la batterie d'hydrocyclones , du stérile et les filtrats de
filtration du stérile .
Le décanteur comprend essentiellement une cuve
recevant la suspension à traiter, un dispositif pour extraire sous forme
de boue les matières solides décantées dans le fond et un
autre dispositif pour recueillir l'eau clarifiée débordant
à la périphérie de la cuve.
Le soutirage de la sous-verse est effectué à
l'aide des pompes centrifuges alimentent la filtration du stériles.
-Station de floculation et
Coagulation :
Deux stations, de préparation du floculant et de
coagulant, apportent les polymères dilués au décanteur ,
afin d'accélérer et faciliter la sédimentation des
particules en suspension et améliorer la clarification de l'eau de
sur-verse. Ces stations sont gérées automatiquement par des
pompes.
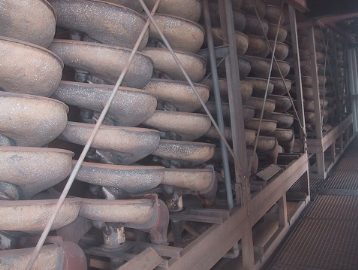
Photo N°3 : Banc de spirales
de dégrossissage
III-2-2- Enrichissement de TH par SM comparé
à (SM+Spirale)
Voici d'une façon succinte ; la comparaison de
flowsheet d'enrichissement de TH à l'usine des Guelbs :
Première phase : Séparation
magnétique de 1984 à 1990
Deuxième phase : (Séparation
magnétique + Spirale ) de 2004 à 2007
|
Enrichissement TH par SM
seulement
|
Enrichissement TH par
(SM+Spirale)
|
% poids Concentré
|
17,4
|
35,0
|
% Fe
|
64,3
|
64,4
|
Récupération métallique
|
44,2
|
64,2
|
|
|
|
La comparaison ci-dessus montre l'apport important de spirale
pour l'enrichissement de TH ; qui assure la rentabilité du
traitement de ce type de minerai.
III-2-3-Evolution Traitement TH après
démarrage Spirale :
La mise en marche de l'unité spirale est une
étape cruciale pour l'enrichissement du minerai oxydé comme elle
permet :
L'amélioration de rendement de poids de
concentrés issus du TH et la valorisation de ressources existantes de ce
minerai (32 millions de tonnes en verse ).
Et voici l'évolution de la production Usine des Guelbs
en concentrés (GMAB et GFM) :
Année 2006
Mois
|
GMAB TH
|
GFM
|
janv-06
|
10000
|
5000
|
févr-06
|
26000
|
22000
|
mars-06
|
19000
|
25000
|
avr-06
|
12000
|
25000
|
mai-06
|
24000
|
22000
|
juin-06
|
12000
|
29000
|
août-06
|
29000
|
26000
|
sept-06
|
12000
|
24000
|
oct-06
|
37000
|
37000
|
nov-06
|
21000
|
23000
|
déc-06
|
21000
|
23000
|
TOTAL
|
223000
|
261000
|
moyenne mensuelle
|
20273
|
23727
|
Le tableau ci-dessus montre que la production du GFM
(concentré spirale) est supérieure à celle du GMAB
(concentré SM) ce qui confirme l'apport important de spirale dans la
production de l'usine.
Courbe montrant l'évolution de la production
du TH après concentrés issus
démarrage Spirale
Le démarrage de l'unité spirale a permis
d'améliorer la qualité et quantité de concentrés
obtenus lors du traitement de minerai oxydé (TH).
III-3-Comparaison Prévision et
Réalisation Projet spirale:
Malgré que l'apport de l'unité spirale dans la
production d'Usine des Guelbs n'est pas négligeable ; mais la
réalisation de performances process de cette unité reste en
dessous de l'objectif du projet spirale et voici le tableau
récapitulatif de ce constat :
|
Prévision Projet Spirale
|
Réalisation Projet Spirale
|
% poids Concentré
|
39,0
|
35,0
|
% Fe
|
65,0
|
64,4
|
Récupération
métallique
|
66,4
|
64,2
|
|
|
|
L'usine des Guelbs n'a pas pu réaliser les
objectifs du projet Spirale à cause de paramètres
suivants :
§ le minerai utilisé pour l'essai spirale provient
directement du front (minerai propre) contrairement au minerai traité
actuellement qui provenait d'une ancienne verse TH connue par son
hétérogénéité ;
§ le rendement poids de mixtes TH de 45% poids à
50%Fe ; l'usine n'a pas pu l'obtenir quelque soit le réglage de la
séparation magnétique (question de minerai) ;
§ comme les jours de traitement de TH sont
limités ; et pour produire un tonnage important de mixtes
oxydés, l'usine visait une teneur de 45%Fe ce qui incitera la diminution
du rendement poids de spirale.
Nous pouvons établir une simulation permettent de
préciser l'apport de spirale dans le traitement de minerai
oxydé : programme de production Usine des Guelbs en 2008
prévoit le traitement de 2 millions de tonnes de TH qui doivent
donner :
Alimentation Usine
|
2000000 Tonnes
|
GMAB
|
300000 T
|
GFM
|
400000 T
|
Concentrés (GMAB+GFM)
|
700000T
|
% poids Concentrés
|
35%
|
%Fe Concentrés
|
65,0
|
Récupération
métallique
|
65,0
|
A partir de la prévision production usine des
Guelbs ; nous pouvons dire que l'unité spirale assure 57% de
concentrés issus du traitement TH.
Conclusion et Recommandations
Ce stage de fin d'études nous a permis de voir
tous les aspects du procédé de l'usine des Guelbs et de
concrétiser nos connaissances dans le domaine d'enrichissement ; le
sujet de notre stage a été très intéressant comme
il aborde le procédé de la séparation gravimétrique
par spirale ; à l'issue de ce stage nous avons pu sortir avec la
conclusion suivante :
v en dépit de la valorisation de ressources en
minerai oxydé, l'unité spirale permet d'améliorer
l'enrichissement TH par l'augmentation du tonnage de concentré issu de
minerai oxydé de 50% ;
v le concentré de spirale est d'une bonne
qualité 65,0%Fe et 7,0%SiO2 ;
v l'enrichissement de TH par spirale permet
d'améliorer le rendement poids de concentrés issus de TH en
passant de 15% seulement (cas SM) à 39% ;
v le traitement de TH à l'usine des Guelbs a des
impacts environnementaux liés à l'empoussièrement
dégagé de cette qualité minière et la consommation
d'eau qui est de 0,3 m3/ Tonne de GFM ; et pour résoudre ces
problèmes, l'usine doit améliorer le système d'arrosage et
la filtration au niveau de spirale afin de limiter les pertes d'eau
malgré que l'eau recyclé au niveau de spirale est à un
taux acceptable (85%) ;
v la forte
hétérogénéité de la verse TH ne permet pas
de réaliser les objectifs du projet spirale d'où la
nécessité d'une caractérisation de cette verse
(échantillonnage verse TH pour déterminer les
caractéristiques minéralurgiques).
v Pour la réussite du traitement de TH à
l'usine ; il est impératif d'avoir une usine spirale
indépendante (concasseur, SM...) de l'usine de Traitement à sec
pour pouvoir faire le programme du TH directement à partir des
réserves dormantes dans la verse TH à proximité du
concasseur Rhein sans perturber le traitement du minerai
magnétique(TS).
Bibliographie :
1- G. Bronner et J.J.Chauvel « méthode
Rb/Sr », Les datations sur les roches totales de la série de
Tiris, (1991), CHAPITRE I ;
2- Lebas Ph. « Géologie des Guelbs
El Rhein »; Miferma-Zouerate, Mauritanie 1979, CHAPITRE
I ;
3- Med-El Mokhtar OULD CHEIKH « Rapport de fin
de stage » Usine des Guelbs; Zouerate, Mauritanie (juin
2003) CHAPITRE II ;
4- Note Annuel de la direction générale
SNIM (année : 2008), CHAPITRE III ;
5- Rapport annuel du service process de l'usine des
Guelbs de 1984 à 2007 CHAPITRE III ;
6- Rapport annuel usine des Guelbs (année :
2006) CHAPITRE III ;
7- Site de la SNIM :
www.SNIM.com, CHAPITRE I.
|