République Algérienne Démocratique
et Populaire
Ministère de l'Enseignement
Supérieur et de la Recherche Scientifique
Université Abou Bekr Belkaid -
Tlemcen
Faculté de Technologie
Département de Génie Electrique et
Electronique
Filière : Génie
industriel Génie Productique
Projet de Fin d'Etudes
Licence : Génie Productique
Intitulé :
Simulation d'une chaine de production au niveau de
l'unité de production Moulin Ouled Mimoun
Présenté par :
Jury :
Bouhenni Kaddour Issam
Président: HASSAM Ahmed
Toualbia Abderrahmane
Encadreur: MGHELLI Nihad
Chabani Rabah
Co encadreur: MKEDDER Amine
Tounsi Ramzi
Examinateur: BENSMAINE Nardjes
Boukhelef Somia
Examinateur: BESSENOUCI Hakim
Année
Universitaire : 2015/2016
Tables des matières
Listes des figures
3
Remerciement
6
Introduction générale
7
1. Chapitre 1
10
1.1. Introduction
10
1.2. L'entreprise d'Ouled
Mimoun (groupe ERIAD)
10
1.3. Ancien système
10
1.3.1. Procédée et techniques
appliques a la fabrication de farine
11
1.3.1.1. Réception des
matières premières
11
1.3.1.2. Nettoyage
12
1.3.1.3. Conditionnement
12
1.3.1.4. Mouture
12
1.3.1.5. L'ensachage
13
1.4. Nouveau système
14
1.4.1. Historique de MOLINO
15
1.4.2. Le parcours du grain de blé
dans le nouveau système
15
1.4.2.1 La Fosse de réception des
blés
15
1.4.2.2. Nettoyage
15
1.4.2.3. Pré mouture, Repos
16
1.4.2.4. Mouture
16
1.4.2.5. La mise en sacs
17
1.5. Conclusion
17
2. Chapitre 02
19
2.1. Introduction :
19
2.2. Définition de Arena et la
simulation
19
2.2.1. Définition de la simulation
19
2.2.2. Méthodologie
générale de simulation
20
2.2.3. Définition du logiciel ARENA et son
rôle
20
2.3. Modélisation du système par le
logiciel Arena
20
2.3.1. Les bibliothèque utilisés
20
2.3.1.1. La bibliothèque BasicProcess
20
2.3.1.2. La bibliothèque advanced
process
21
2.3.1.3. La bibliothèque Flow Process
21
2.3.2. Définition des modèle
23
2.3.2.1. Le modèle pour la partie
nettoyage
23
2.3.2.2. Le model pour la partie mouture
28
2.3.2.3. Le model pour la partie déchet
30
2.3.2.4. Le model pour la partie de la mise en
sacs
31
2.4. Conclusion
33
3. Chapitre 03
35
3.1. Introduction
35
3.2. Système automatisé de
production
35
3.2.1. Conception d'un système
automatisé
36
3.2.1.1. La partie opérative
36
3.2.1.2. La partie commande
37
3.2.2. Objectif de l'automatisation de
production
37
3.4. Instrumentation
38
3.4.1. Les captures utilisées dans
l'usine
38
3.4.1.1. Les capteurs de niveaux
38
3.4.1.2. Les capteurs mesurables
39
3.4.1.3. Les boutons poussoirs
40
3.4.1.4. Bouton d'arrêt urgence
40
3.4. Modélisation de l'usine par GRAFCET
40
3.4.1. Définition de logiciel step 7
41
3.4.1.1. Les avantages de ce logiciel sont
41
3.4.2. Définition de Grafcet
41
3.4.2.1. Histoires
41
3.4.2.2. L'outil Grafcet
41
3.4.2.3. Cahier de charge
42
3.4.3. Les entrées et les sorties
d'usine
42
3.4.4. Les différents GRAFCET de l'usine
44
Ø Cahier de charge Figure 3.7
44
Ø Cahier de charge de la figure
3.8
45
Ø Cahier de charge de la figure
3.9
47
3.5. Conclusion
60
4. Chapitre 04
62
4.1. Introduction
62
4.2. Comparaison
62
4.3. L'évolution des GRAFCET
64
4.4. Conclusion
69
Résumé
71
Abstract
71
??I?
71
Listes des figures
figure1. 1 le synoptique de production
3
figure1. 2 schéma représente la
fabrication de farine dans l'ancien système
11
figure1. 3 la représentation de la partie de
nettoyage sur logiciel utilisé
13
figure1. 4 la représentation de la partie du
mouture sur logiciel utilisé
14
figure1. 5 la partie de conditionnement
présenter sur logiciel utilisé
15
Remerciement
Nous remercions Allah, le tout puissant, le
miséricordieux, de nos avoir donné la santé et tout dont
nous nécessitassions pour l'accomplissement de cette thèse.
Au terme de ce modeste travail nous tenons à remercier
chaleureusement et respectivement tous ceux qu'ont contribués de
près ou de loin à la réalisation de ce modeste projet de
fin d'étude, à savoir nos encadreurs Mme
Meghelli Nihad et Mr Mkedder Amine, qu'ils trouvent
ici nos vifs remerciements particulièrement pour leurs écoute,
leurs disponibilité, leurs extrême bienveillance et aussi leurs
appréciables conseils.
Nous leurs exprimons tous très haute et respectueuse
gratitude.
Nous tiens à remercions tous les membres, les familles,
les amis et les camarades pour la patience, les encouragements, la gentillesse
et le soutien qu'ils m'ont prodigué tous au long de ce travail. Et
toutes les personnes qui ont contribué de près ou de loin
à l'accomplissement de ce travail.
Enfin, Nous tenons également à remercier les
membres du jury qui vont se pencher sur notre travail et vont lui prêter
toute l'attention qu'il mérite pour l'évaluer à sa juste
valeur.
Introduction
générale
Le milieu industriel s'est rapidement développé
durant le dernier siècle grâce à la science et la
technologie, c'est pour ça que la plupart des machines manuelles devient
automatisées cela modifie la nature même du travail.
L'automation industrielle est l'art d'utiliser les machines
afin de réduire la charge de travail tout en gardant la
productivité et la qualité.
Dans la phase de conception d'un système de production,
la simulation permet de tester puis de valider l'architecture de l'atelier et
d'expérimenter à moindre frais les différents
systèmes de conduite envisageables pour une production donnée.
Lors de l'apprentissage d'un pilote de conduite d'atelier, la simulation permet
à celui-ci d'acquérir une certaine expérience sans risque
d'accident ni de dégât matériel, toujours onéreux et
parfois catastrophiques. Enfin, dans les phases de développement ou de
réorganisation du système de production, les essais de validation
et de conception des commandes pourront être entrepris sans nuire
à l'installation actuelle ni à son fonctionnement.
Les moulins d'aujourd'hui sont entièrement
automatisés, une poignée d'hommes suffit à faire
fonctionner un moulin moderne. Un moulin, peut, selon les cas, tourner 24
heures sur 24, 365 jours par an ou sur un rythme plus traditionnel.
Pour obtenir la farine souhaitée, chaque meunier met au
point un diagramme de mouture « programme de réglage des machines
» qui permet la fabrication de la farine en fonction des
caractéristiques du blé reçu et de la farine
souhaitée.
L'ordonnancement et la planification sont très
importants pour l'amélioration de la production et pour gérer
l'entreprise bien comme il faut.
Nous nous intéressons dans ce projet à un
système de production du farine de l'usine de Ouled Mimoun,
d'après cet usine on a vu que toutes les phases du processus de
fabrication sont automatisées mais on a constaté qu'on peut faire
des améliorations dans le processus de la fabrication de farine en
utilisant des logiciels qu'on a déjà étudié
« step7 et Arena »
Notre mémoire est structuré comme
suite :
- Dans le premier chapitre, on va faire une étude sur
les différentes étapes de fabrication de la farine et la
différence entre l'ancien et le nouveau système
- Dans le deuxième chapitre on va donner une
idée générale sur le logiciel Arena et on va faire la
description du notre modèle
- Le troisième chapitre considéré
à citer les objectifs de l'automatisation de production et
décrire le fonctionnement de l'usine (cahier des charges) et faire la
modélisation de l'usine par Grafcet
- Le dernier chapitre contient le résultat final et la
différence qu'on a trouvée après notre étude
(simulation).
Chapitre 01 : présentation de l'usine
d'Oulad Mimoun (groupe ERIAD)
Chapitre 1
Introduction
Les céréales
et leurs dérivées constituent l'alimentation de base dans
beaucoup de pays en développement, particulièrement dans les pays
maghrébins. Parmi les plus importantes céréales dans le
monde et surtout dans l'Algérie les grains de blé.
Dans le cadre des stages pratiques des projets de fin
d'étude, nous avons fait notre stage au sein de l'unité d'Ouled
Mimoun. L'installation et ses annexes ont été
réalisées selon toutes les règles de l'art.
Néanmoins l'usine date maintenant de plus de 27 ans. Et sa
part de marché au niveau national devrait avoisiner les 1%.
1.1. L'entreprise d'Ouled
Mimoun (groupe ERIAD)
Les Moulins d'Ouled Mimoun est une filiale du groupe ERIAD,
entreprise publique économique (EPE) dénommée
entreprise des industries alimentaires, céréalières et
dérivés de Sidi Bel Abbés. Créée en
1979, elle avait le statut d'unité au sein de l'ancienne
société nationale des pâtes alimentaires et couscous
(SN SEMPAC).
La filière céréalière constitue une
des principales filières de la production agricole en Algérie, et
parmi les grands fabricants des céréales dans notre pays le
groupe ERIAD
Groupe ERIAD est l'entreprise publique économique (EPE)
dénommée Entreprise des industries alimentaires et
céréalières.
1.2. Ancien
système
La capacité du moulin est donnée pour 1000 t / 24h
mais le potentiel est vraisemblablement un peu supérieur. L'unité
de mouture et la section nettoyage ont été
conçues, dessinées et équipées par BUHLER, un
fabricant suisse mondialement réputé. Ces matériels
étaient à l'époque de l'installation
généralement classés parmi les meilleurs, BUHLER
étant le leader mondial en matière de matériels de
meunerie/semoulerie.
1.2.1 Procédée
et techniques appliques a la fabrication de farine
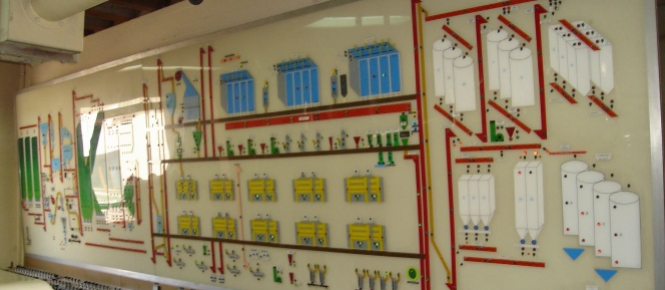
figure1. 1 le synoptique de
production
C'est le tableau de bord du moulin. Il permet de commander et de
visualiser le bon fonctionnement de tous les appareils du moulin.
1.1.1.1. Réception des matières
premières
Cette étape comprend le déchargement du blé
réceptionné au port dans des camions, selon deux modes
différents, à savoir le déchargement par grue et par
aspiration.
A l'arrivée du blé dur aux moulins, les camions
passent par le pont bascule où la quantité reçue sera
pesée puis versée dans une trémie. Cette dernière
est couverte d'une grille en acier de 25 mm d'ouverture pour retenir les
grosses impuretés telles que cailloux, bois, paille, etc...
Ensuite, le blé est transmis vers les silos de stockage
par le biais des transporteurs et des élévateurs à
godets.
La réception, on peut recenser 2 types de
blé ; le hard et le soft qui sont des variétés de
blé tendre génétiquement différentes.
Le « hard » ; plus sec, comprend
le blé Turc, Algérien, Ukrainien, Canadien et parfois Australien,
tandis que le « soft » regroupe les blés
Français et Américain
1.1.1.2. Nettoyage
Dans un premier temps, les grains de blé sont
nettoyés pour éliminer les impuretés et les particules
étrangères (grosses et petites). Cette phase permet aussi la
détermination de la qualité du blé et alors
sélectionner les sources d'approvisionnements en ce qui concerne
matière premier.
Les équipements de nettoyage es plus rencontrés
sont :
- Nettoyeur séparateur
- Trieur grain rond
- Trieur grain long
- Trieur hélicoïdal
- Epierreur à sec
- Aimant rotatif séparateur
- Tarare
1.1.1.3. Conditionnement
Le conditionnement de blé est une étape essentielle
pour le bon déroulement de la mouture, il vise à modifier
l'état physique des grains de manière à permettre la
meilleure séparation possible au cours de la mouture entre l'album en
amylase d'une part, les enveloppes, la couche à aleurone et le germe
d'autre part.
Ø Premier mouillage :
Le blé issu du nettoyage à sec possède une
humidité initiale (Hi), passe par le premier mouilleur intensif
où il reçoit 2/3 de l'eau qu'il faut ajouter pendant 18 heures,
puis il est déchargé dans une cellule de repos.
Ø Deuxième mouillage :
Le blé extrait de la cellule du premier repos passe par le
deuxième mouilleur intensif, où on ajoute le dernier 1/3 de la
quantité d'eau qu'il faut incorporer au blé pendant 8 heures dans
une cellule de repos.
1.1.1.4. Mouture
Le blé passe dans la section mouture pour subir sa
transformation en farines et issues (son).alors la mouture va se passer par
plusieurs étapes en ordre : Le broyage, le convertissage, le blutage, le
plansichter et le sassage :
Ø Le broyage :
Le broyage mécanique a remplacé le travail des
meules de pierre, des gros cylindres métalliques tournent à sens
inverse, à vitesse différente, et vont écraser Les grains
qui passent entre leurs dents, les grains passent donc quatre fois dans des
cylindres de plus en plus rapprochés, aux cannelures de plus en plus
fines.
Ø Le convertissage :
Dans cette phase de la mouture, l'objectif est de réduire
progressivement le diamètre des particules d'amande pour produire de la
farine en préservant la qualité de celle-ci. Pour atteindre ce
but on utilise des cylindres lisses.
Ø Le blutage :
Cette opération permet la séparation des produits
de mouture selon leur grosseur après des passages successifs dans un
appareil à cylindre.
Ø Le plansichter :
L'utilisation du plansichter consiste à une
séparation de tamisage d'un produit granuleux sur surface blutée
en mouvement, dans le but de réaliser des séparations en fonction
de la taille des particules. La farine et stocker dans les grands silos, et le
refus va être recycler.
Ø Le sassage :
Les semoules sont faites de petites particules plus ou moins
fines et plus ou moins lourdes, qu'il faut classer selon leur grosseur et leur
densité.
Elles passent sur des tamis très fins animés d'un
mouvement rapide dans des appareils spéciaux appelés des
sasseurs. Les semoules les plus lourdes tombent ; les plus
légères sont aspirées vers le haut par un courant d'air
qui souffle continuellement et ils sont stocker dans les silos.
1.1.1.5. L'ensachage
Représente l'opération finale. Nos produits finis
passent dans d'autres appareils ou ils sont pesés et mis dans des
sachets, selon des techniques de pointe, prêts à être
stockés ou livrés directement à nos clients.
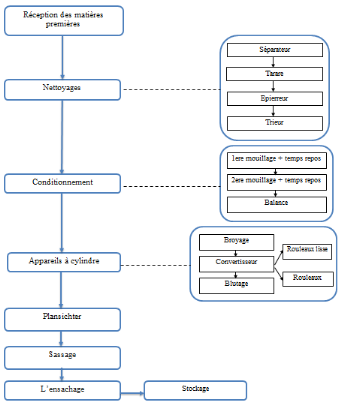
figure1. 2 schéma
représente la fabrication de farine dans l'ancien
système
1.3. Nouveau
système
Le nouveau système utilisé dans le moulin d'Ouled
Mimoun représente une chaine de production automatisé permet le
pilotage automatique d'un système de fabrication cohérents et
complet, en répondants aux impératifs et aux obligations de la
production d'aujourd'hui La minoterie utilise les équipements de la
société Turquie MOLINO ces installations sont pilotés par
un logiciel qui permet le contrôle de la chaine, et ils ont
réalisés cette rénovation dès 2015, avec une
capacité de 2000 tonne par jour.
1.3.1. Historique de
MOLINO
MOLINO est l'un des rares équipementiers mondiaux
(Original Equipement Manufacturer) en technologie industrielle de la Minoterie.
Il pourrait y avoir des centaines de sociétés dans le secteur,
mais le nombre de constructeurs ne dépasse pas une dizaine à
l'échelle mondiale.
MOLINO a été fondée en 1965. Nous avons
l'honneur d'être au service du secteur, depuis presque un
demi-siècle par la valeur ajoutée que nous avons
créée et par les installations sans problème, les machines
et équipements fiables que nous avons construits.
MOLINO possède une expérience et des ressources
nécessaires pour développer ses propres machines et fait
confiance en sa puissance technologique.
MOLINO est multilingue, capable de communiquer avec de divers
groupes et nationalités en anglais, français, italien, espagnol
ou arabe.
MOLINO, est une société qui croit en
amélioration d'une manière concentrée sur l'innovation et
une organisation qui travaille en esprit d'équipe. Ces
caractéristiques seront définitivement conservées et
améliorées.
1.3.2. Le parcours du grain de blé dans le nouveau
système
L'entreprise d'Ouled Mimoun a utilisé presque la
même procédure de fabrication dans l'ancien système avec
quelque petites modification. MOLINO ajoute quoi dans le nouveau
système ?
1.4.2.1 La Fosse de
réception des blés
Le blé est stocké dans des trois grands silos
puis transporté par des élévateurs. (Figure 1.3)
1.4.2.2. Nettoyage
Ensuite, il est déversé dans les nettoyeurs
lesquels éliminent les impuretés - terre, pierres, pailles,
grains vides, poussières, autres graines... Le système de
nettoyage est composé de : une balance, un séparateur, un
épierreur, un trieur et une brosse. Les trieurs permettent de ne
conserver que les grains de blé purs. (Figure 1.3)
1.4.2.3. Pré mouture,
Repos
Pour faciliter la séparation de l'amande de son
enveloppe, les grains de blé sains sont humidifiés et
stockés dans des grands silos pendant 18 heures. Ensuite, elles sont
humidifiées une deuxième fois et stockés dans des grands
silos pendant 8 heures. (Figure 1.3)
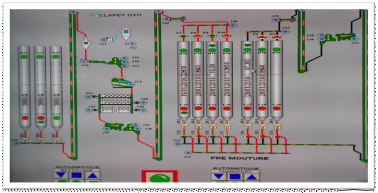
figure1. 3 la
représentation de la partie de nettoyage sur logiciel
utilisé
1.4.2.4. Mouture
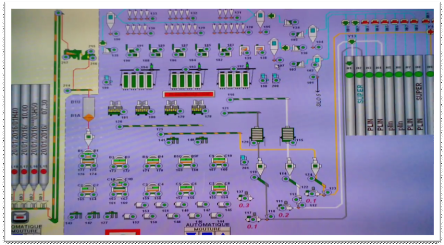
figure1. 4 la
représentation de la partie de la mouture sur logiciel
utilisé
Après le nettoyage et le repos, la transformation du
grain de blé s'opère en deux étapes : le broyage et
le convertissage.
Chacune de ces étapes représente plusieurs
passages de blé dans les machines. Le produit de chaque passage
successif est tamisé selon sa taille. Chaque opération
complémentaire permet d'extraire un peu plus de farine. Environ quatorze
opérations sont nécessaires pour obtenir la farine qu'attend le
boulanger.
1.4.2.5. La mise en sacs
La phase de conditionnement en sacs puis sur palettes est
entièrement automatisée.
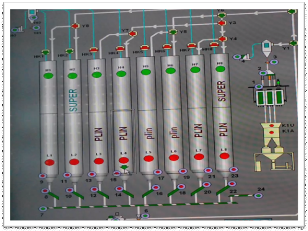
figure1. 5 la partie de
conditionnement présenter sur logiciel utilisé
Conclusion
Dans ce chapitre, nous avons présenté comment
fabriquer le farine et les différences étapes de la production
entre l'ancien système manuel et le nouveaux système
automatisé.
L'automatisation a permis à l'entreprise
d'améliorer sa compétitivité (coûts des produits,
qualité, adaptabilité à la demande, ...).
Elle a pour objet d'associer moyens de production et moyens de
commande automatique qui permettent d'assurer la reproductibilité du
résultat de la manière la plus autonome possible.
Chapitre 02 : la simulation du processus de
fabrication de la farine dans logiciel ARENA
2. Chapitre 02
2.1. Introduction :
Chaque système de production est
caractérisé par plusieurs facteurs agissant sur la performance de
système tels que : les règles de gestion des files
d'attente, le temps de changement d'outil sur une machine, la vitesse d'un
engin de manutention, la dextérité d'un opérateur et la
performance globale du système.
L'utilisation d'un modèle nous permet de mieux observer
et comprendre le fonctionnement du système réel sans avoir
à le réaliser physiquement, ce qui nous épargne le
coût et le temps à dépenser pour matérialiser ce
système qui nous sera moins facile à manipuler réellement
pour une bonne expérimentation.
Ensuite, par simulation, il est possible de mesurer l'impact
relatif de chacune de ces composantes sur la performance globale du
système de production.
2.2. Définition de Arena et la simulation
2.2.1. Définition de la simulation
La simulation est un processus qui consiste à concevoir
un modèle du système (réel) et mener des
expérimentations sur ce modèle, interpréter les
observations fournies par le déroulement du modèle et formuler
des décisions relatives au système.
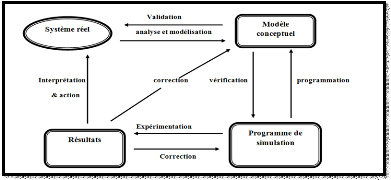
Figure 2. 1 Méthodologie générale
de simulation
2.2.2. Méthodologie générale de
simulation
On distingue classiquement quatre phases distinctes : La
modélisation (représenter le comportement du système), la
programmation, l'expérimentation et l'interprétation des
résultats (accompagnée d'actions). (Figure 2.1)
2.2.3. Définition du logiciel ARENA et son rôle
ARENA est le logiciel de simulation des flux à
évènements discrets, leader sur le marché. Edité
par Rockwell Automation, il compte plus de 370 000 utilisateurs formés
dans le monde. Distribué en France depuis 1987, ARENA a
accompagné de grands projets industriels pour Peugeot, Alstom,
Nestlé, Aéroport de Paris, Saint-Gobain ...etc.
ARENA représente à ce jour la version la plus
avancée dans la simulation des systèmes de production. Du premier
clic de souris jusqu'à la présentation des résultats. Il
est le premier outil de simulation permettant d'analyser les volumes
importants, la logique de commande complexe et l'équipement
spécialisé des systèmes de production.
La construction d'une simulation se fait au travers de deux
structures de données :
ï Le modèle, description des composantes statiques
et dynamiques du système
ï L'instance, spécification des conditions
expérimentales et paramètres propres à une
expérimentation
Il comporte plusieurs bibliothèques et des modules (des
blocs) qui rendent facile la tâche de modéliser une ressource, une
file d'attente, un convoyeur ainsi que tous les éléments d'un
système de production.
Par la suite, nous allons définir que les modules que
nous avons utilisés.
2.3. Modélisation du système par le logiciel
Arena
2.3.1. Les bibliothèque utilisés
2.3.1.1. La
bibliothèque BasicProcess
1. Create : Le bloc
« create » permet de modéliser une
arrivée de lots d'entités dans le modèle, il est
caractérisé par :
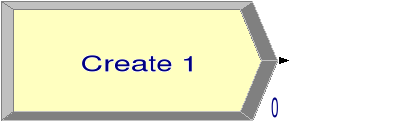
ï Le type des entités crée
« Entity type »
ï Temps entre deux création « Time
between arrivals »
ï Taille de lots « entities per
arrival »
ï Nombre maximum d'entités crées
« Max Arrivals »
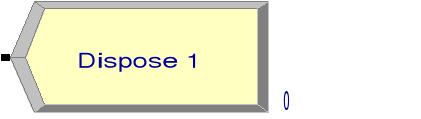
2. Dispose : Le bloc dispos permet de
modéliser la destruction des entités, il permet de
modéliser une sortie d'entité du modèle.
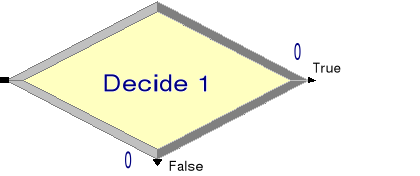
3. Decide : Le bloc decide
permet de diriger le flux d'entités parmi plusieurs destinations. Il
inclut l'option pour prendre une décision basée sur une ou
plusieurs conditions.
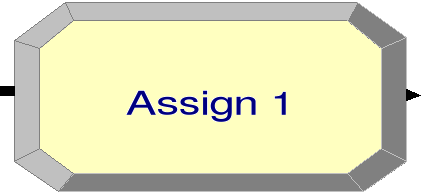
4. Assign : Ce bloc permet d'assigner
une valeur à un attribut, une variable, ...
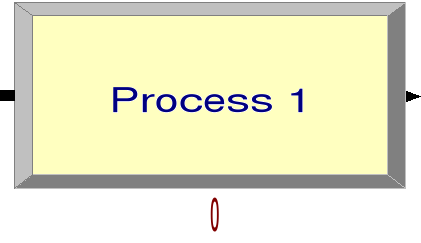
5. Process : Le module
« Process » représente le poste de travail. Il
permet de déclarer les ressources (machine ou homme), le temps de
traitement des entités et le stock.
2.3.1.2. La
bibliothèque advanced process
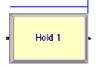
6. Hold : ce module va tenir une
entité dans une file d'attente pour attendre un signal, attendez une
condition spécifie pour devenir vrai (scan), ou être
infinité tenue(à retirer plus tard avec le module Romove).
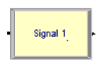
7. Signal : le module de signal à
chaque module de maintien dans le modèle mis à attendre le signal
et libère le nombre maximal spécifié d'entités.
2.3.1.3. La
bibliothèque Flow Process
Pour répondre aux exigences de la production, les
opérations de fabrication des produits emballés impliquent
généralement le traitement par lots semi-continu dans
l'industrie, et / ou les opérations d'emballage de haute vitesse. Bien
que certaines de ces opérations puissent être
modélisées en utilisant des approximations discrètes,
souvent une meilleure approche est nécessaire.
Le modèle de Flow process Aréna est l'un des
modèles de solution (RHS), construit sur ??le système de
simulation Aréna.
Les modèles de données organigramme et tableurs
dans le panneau de processus de flux ont été conçus
spécifiquement pour modèle combiné discret,
systèmes continus (par exemple, le traitement par lots et flux de
matières). Si un système contient semi processus de traitement
par lots en continu, ainsi que les opérations d'emballage ou de
remplissage à grande vitesse, il peut être souhaitable d'utiliser
des modèles à partir du modèle de processus de flux avec
ceux du modèle d'emballage.

1. Le bloc Tank
Le bloc de réservoir (Tank) définit un
emplacement où le produit est détenu ou stocké.
La capacité est la quantité maximale qui peut
être stocké dans le réservoir. Le niveau initial est la
quantité dans le réservoir au début de la simulation ou
lorsque le système est effacé.

2. le bloc Sensor
Le bloc capteur (Sensor) définit un dispositif de
détection qui surveille le niveau de matériau dans un
réservoir (bloc Tank). Un emplacement du capteur est
spécifié en utilisant le nom, l'emplacement du réservoir,
type, niveau, ou le pourcentage d'invites.

3. Le bloc Flow
Le bloc Flow est utilisé en conjonction avec le bloc
Tank au modèle semi-continu des opérations telles que l'ajout de
produit à un réservoir, de retirer du produit d'un
réservoir, ou le transfert du produit entre deux réservoirs.

4. Le bloc Regulate
Le bloc Regulate est un contrôle discret,
réglementé pour attribuer le taux maximal des régulateurs
définis dans le bloc Tank.
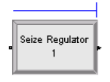
5. Seize Regulate : le module seize
régulateurs alloue un ou plusieurs régulateurs à une
entité. Lorsqu'une entité entre dans ce module, il attend dans
une file d'attente jusqu'à ce que tous les organismes de
réglementation spécifiques soient disponibles en même
temps. Un régulateur alloué est libéré par une
entité en utilisant la sortie module de régulateur.

6. Release Regulator : Le module de
sortie du régulateur est utilisé pour libérer les
régulateurs citernes qui ont été attribué à
une entité en utilisant le module de régulateur Seize. Cela rend
ces régulateurs disponibles à d'autres entités en attente
de saisir le régulateur (s).
Lorsque l'entité entre dans le module de sortie du
régulateur, il abandonne le contrôle du régulateur
spécifié (s). Toutes les entités en attente dans les files
d'attente pour les régulateurs gagneront le contrôle des
régulateurs immédiatement.
2.3.2. Définition des
modèle
2.3.2.1. Le modèle
pour la partie nettoyage
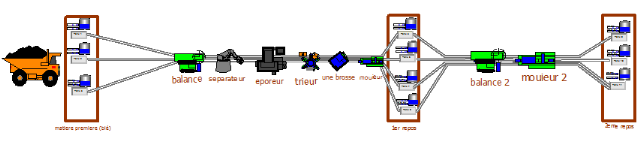
Figure 2 1 Model animation partie nettoyage
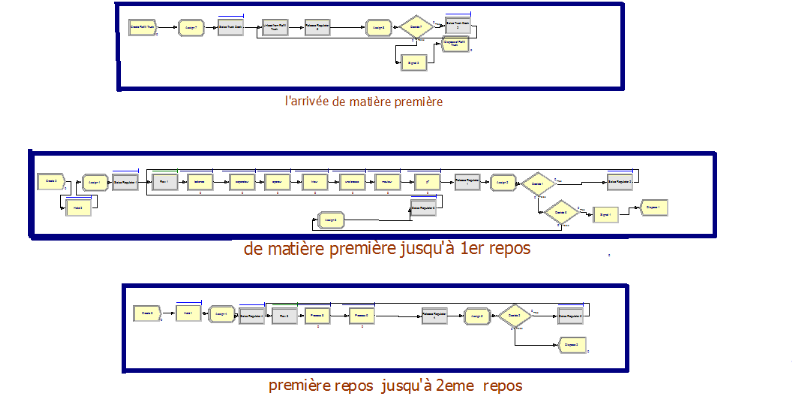
Figure 2 2 Model logique partie nettoyage
Ø Description du model :
Dans cette partie nous avons modélisé le
parcours du blé à partir des silos de la matière
première jusqu'aux silos des repos, en passant par les machines du
nettoyage.
Les silos sont représentés par des
réservoirs (le bloc tank) et les machines sont
représentées par des ressources dans le bloc process.
On a 7 réservoirs, 3 pour la matière
première, 4 pour le 1er repos et 3 pour le 2eme repos. Chaque
réservoir contient un régulateur (c'est le doseur dans notre
système).
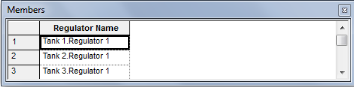
Figure 2 3 un tableau qui représenter les
réservoirs de la matière première
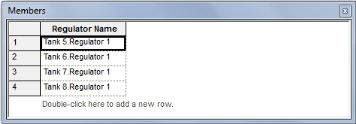
Figure 2 4 un tableau qui représenter les
réservoirs de 1er repos
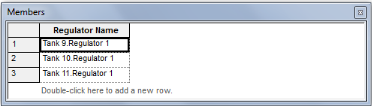
Figure 2 5 un tableau qui représenter les
réservoirs de 2eme repos
Le transfert du blé entre les silos se fait à
l'aide du bloc Flow.
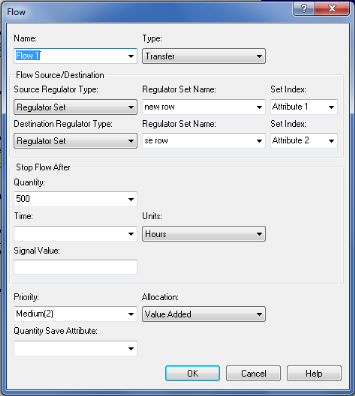
Figure 2 6 De la matière première
jusqu'à 1er repos
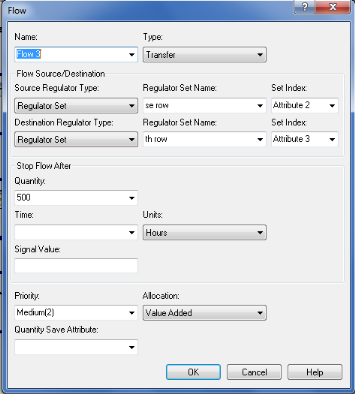
Figure 2 7 Du Première repos jusqu'à 2eme
repos
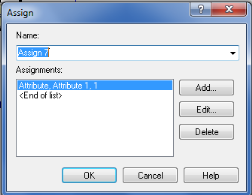
Figure 2 8 une fenêtre pour le bloc
assign
Nous avons utilisé le bloc Assign pour faire le passage
des réservoirs l'une après l'autre.
La condition pour finir le remplissage des silos (bloc Tank)
ce fait avec le bloc Decide.
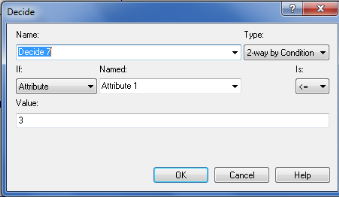
Figure 2 9 remplissage des silos de matière
1er
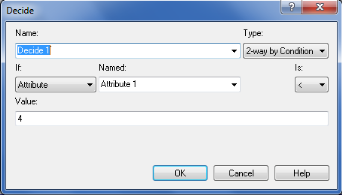
Figure 2 10 remplissage des silos de premier
repos
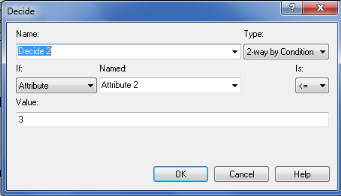
Figure 2 11 remplissage des silos de 2eme
repos

2.3.2.2. Le model pour la
partie mouture
Figure 2 12 Model logique
pour la partie mouture

Figure 2 13 Model animation
pour la partie mouture
Figure 2 14 un tableau qui
contient l'ensemble des ressources
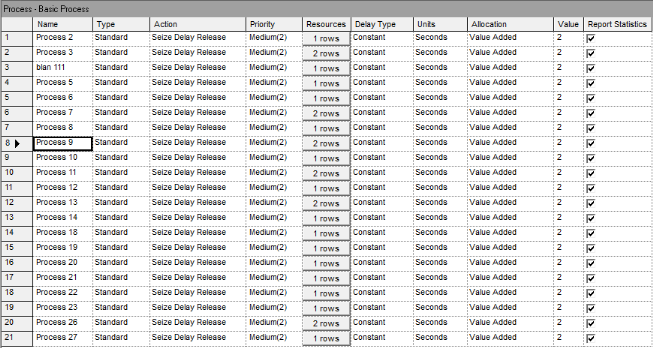
Ø Description du model :
Dans la partie de mouture on a représenté les
broyeurs et les convertisseurs par des ressources dans des `process'.
A l'aide du module `Decide', on a fait la répartition
du blé aux quatre machines valaques, trois machines plansichters et aux
trois machines broyeurs et cinq machine convertisseurs.
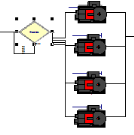
Figure 2 15 Machines Valaques
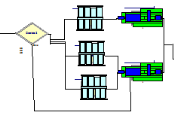
Figure 2 16 machines Plansichter
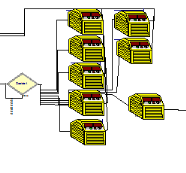
Figure 2 17 machines Broyeur et
convertisseurs
2.3.2.3. Le model pour la
partie déchet
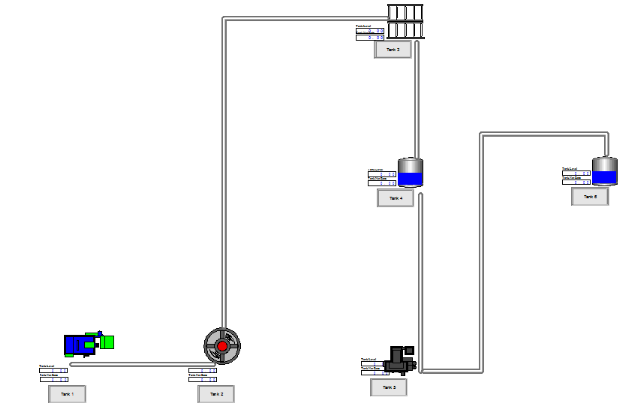
Figure 2 18 Model animation pour la partie
déchet
Figure 2 19 Model logique
pour la partie déchet
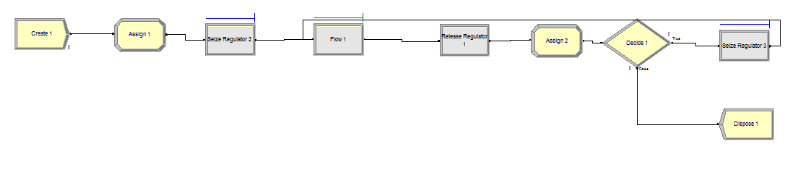
Ø Description du model :
Nous avons représenté la partie de
déchets avec une manière très simple. Just 6 tank l'une
passe le déches à l'autre. Chaque tank prendre le rôle
d'une machine mais le tank 4 et 6 sont vraiment des réservoirs.
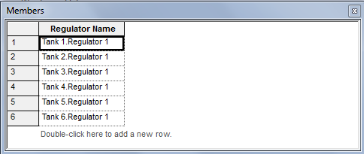
Figure 2 20 un tableau qui représenter les
réservoirs
2.3.2.4. Le model pour la
partie de la mise en sacs
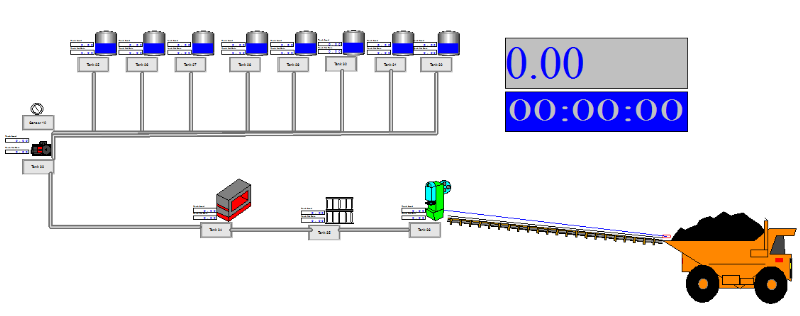
Figure 2 21 Model animation pour la partie de la mise
en sacs
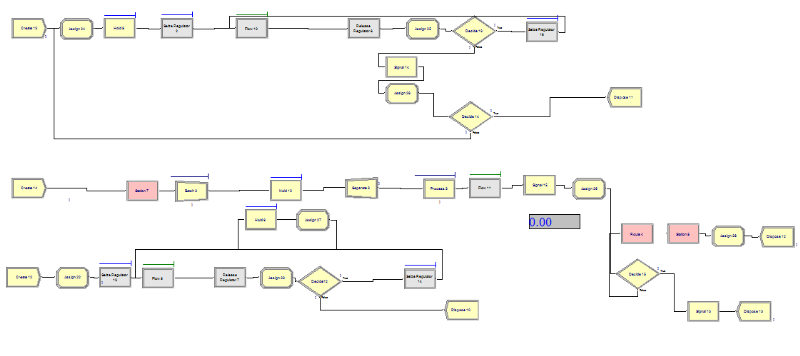
Figure 2 22 Model logique pour la partie de la mise en
sacs
Ø Description du model :
Dans ce model nous avons créé 8
réservoirs (bloc Tank) (les réservoirs de stockage pour le
produit fini), et pour chaque réservoir on a un régulateur.

Figure 2 23 un tableau qui représenter les
réservoirs produit fini
Et nous avons représenté chaque machine par un
le bloc tank parce que les machines utiliser sont comme des
réservoirs.
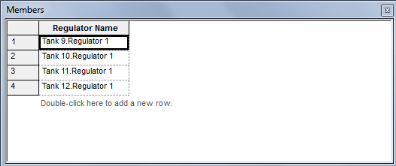
Figure 2 24 un tableau qui représenter les
réservoirs des machines
Et pour le transfert du sac entre la machine de remplissage et
le camion, nous avons utilisé les deux blocs `station` et `Route'.
Le bloc station :

Le module `station' définit une station (ou un ensemble
de stations) correspondant à un emplacement physique ou logique lorsque
la transformation a lieu. Si la station module définit un ensemble de
station, il est effectivement la définition de plusieurs emplacements de
traitement.

Le module Route transfère une entité d'un poste
spécifié ou la prochaine station dans la séquence de
visite définis pour l'entité. Un délai de transfert vers
la station suivante peut être défini.
2.4. Conclusion
Dans ce chapitre, nous avons modélisé le nouveau
système du moulin, pour cela nous avons utilisé le logiciel
Arena. Afin de représenter le flux, le parcours du blé entre les
différentes étapes de la production, nous avons utilisé la
bibliothèque FlowProcess.
Chapitre 03 : modélisation et simulation
de l'usine de la farine par GRAFCET
3. Chapitre 03
3.1. Introduction
L'accélération de la concurrence et des
échanges internationaux impose aux entreprises de toutes tailles une
évolution vers de nouveaux modes de production qui entraînent
obligatoirement la mise en place de systèmes de communication.
Dans les ateliers, les automatismes industriels de commande des
installations s'organisent en architectures hiérarchisées et
réparties intégrant des produits nouveaux
Les besoins des systèmes de production qu'ils soient
continus ou discontinus ont augmentés de façon
considérable d'où la nécessité d'introduire le
concept de système automatisé de production afin de piloter
les SAP on utilise les automates programmables industriels (API) qui permettent
une grande flexibilité dans les modifications de comportement à
apporter au système. Cet équipement doit être
configuré et programmé pour définir le comportement
souhaité du système automatisé .il apporte des atouts
importants pour les systèmes comportant une grande complexité et
fournit une facilité de mise en oeuvre et une évolutivité
lorsque des modifications des comportements à apporter à la
commande .Il permettent aussi la communication avec des
périphériques déportés notamment d'autres automates
programmables industriels .
Dans ce chapitre nous mettrons l'accent sur la description des
différents éléments constituant l'usine ainsi que de leurs
fonctionnement, nous présenterons aussi, un modèle du
procédé de commande de station nettoyage de l'usine, qui nous
permettra d'identifier les fonctions nécessaires au bon fonctionnement
de l'automatise de conduites de celles-ci ainsi que les variables des automates
(entrée/sortie), et nous avons posé des Problèmes qu'on a
trouvées à l'aide d'utilisation diagramme de GAND.
3.2. Système
automatisé de production
L'automatisation industriel a connu, au cours de ces
dernières décennies une évolution importante
consécutive à l'accroissement des exigences de qualité, de
flexibilité et de disponibilité dans les procédés
industriels. L'automatisation de ses dernière concerne tous les aspects
de l'activité industrielle :production , assemblage ,montage,
contrôle , conditionnement ,manutention ,stockage...son objectif est de
réaliser ,de manière automatique des fonction
particulières répondant à des besoins spécifiques
.un système automatisé de production (SAP) doit donc traiter une
matière d'oeuvre pour lui apporter une valeur ajoutée de
façon reproductible et rentable.
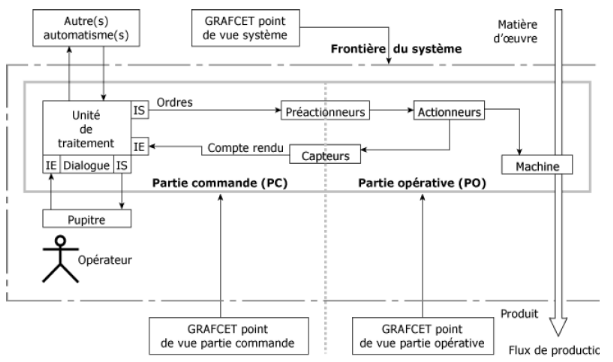
Figure 3 1 Schéma général de
communication entre la partie commande et la partie opérative d'un
système automatisé []
3.2.1. Conception d'un
système automatisé
Dans la conception d'un système automatisé
séquentiel, il faut tenir compte des deux composantes qui le forment
:
3.2.1.1. La partie
opérative
Cette partie se compose de trois ensembles qui sont :
1. L'unité de production, qui a pour fonction de
réaliser la fabrication ou la transformation dans le processus
industriel.
2. les actionneurs qui mettent en mouvement la partie
mécanique par l'intermédiaire des effecteurs et des capteurs. Les
actionneurs sont des éléments physiques qui apportent à
l'unité de production l'énergie nécessaire à son
fonctionnement à partir d'une source d'énergie extérieure.
Un moteur est considéré comme un actionneur.
3. Les capteurs sont aussi des éléments physiques
dont le rôle consiste à créer à partir
d'informations de natures diverses (températures, déplacement,
etc.) des informations utilisables par la partie "commande", par exemple,
l'ouverture ou la fermeture d'un circuit électrique.[]
3.2.1.2. La partie
commande
La partie "commande" élabore des ordres destinés au
processus à automatiser en fonction des informations (comptes rendus)
qui lui parviennent de la partie "opérative" et des consignes qu'elle
reçoit en entrée.
La partie "commande" d'un système automatisé peut
être réalisée par l'intermédiaire d'un automate,
d'un ordinateur ou par un circuit de logique câblée
(séquenceur).
Il faut remarquer qu'il y a un lien très étroit de
communication entre la partie "commande" et la partie "opérative" d'un
système automatisé.
La partie "commande" donne des ordres à la partie
"opérative" par l'intermédiaire des préactionneurs.
De l'autre côté, les capteurs de la partie
"opérative" communiquent des informations (comptes rendus) à la
partie "commande".[]
3.2.2. Objectif de
l'automatisation de production
les productions industrielles sont de plus en plus
automatisées .cette progression du degré de l'automatisation
concerne l'automatisation d'opérations autre fois manuelles comme les
assemblages ou les contrôles, mais aussi l'automatisation plus
poussée d'opérations déjà partiellement
automatisées .ceci se trouve, par exemple, dans le passage en
automatique de machines semi-automatiques ou le remplacement de machines
rigides (ne fabriquant qu'un seul type de produit) par des machines flexibles
susceptibles d'opérer sur plusieurs variantes de produits.
Recherche de diminution du coût pour le produit, par
réduction des frais de main-d'oeuvre, d'économie de
matière, d'économie d'énergie....
Suppression des travaux dangereux ou pénibles, et
amélioration de la condition de travail par l'ennoblissement des
tâches...
Recherche d'une meilleure qualité du produit, en limitant
le facteur humain, et en multipliant les contrôles
automatisés...
Réalisation d'opérations impossibles à
contrôler manuellement ou intellectuellement, par exemple des assemblages
miniatures, des opérations très rapides, des coordinations
complexes...
3.3. Description du fonctionnement de l'usine
Station de nettoyage : les sous
unités de production sont indépendantes les unes des autre, elles
entrent en production séparément. Chaque élément de
sous unité est commandé par son propre automate programmable. il
y a six automates programmables, dont un pour le remplissage des silos
réceptions, un pour passage de blé au premier vis, et deux pour
mise en marche des différents machines de ce atelier et deux autre
pour chaque repos des silos
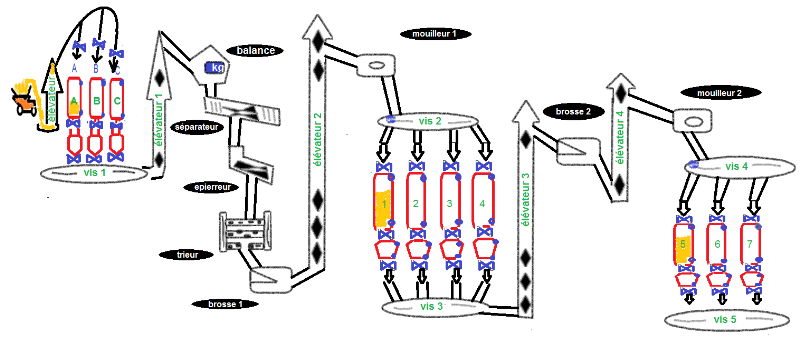
Figure 3 2 schéma de fonctionnement station de
nettoyage
3.4. Instrumentation
3.4.1. Les captures
utilisées dans l'usine
La nature de l'information délivrée par le capteur
peut être logique (deux états) ou analogique et dans ce dernier
cas, on introduira des convertisseurs analogiques/numérique et de
convertisseurs numérique /analogique. Dans l'usine d'OULAD MIMOUNE
plusieurs capteurs sont utilisés pour mesurer les différentes
grandeurs. Par exemple :
3.4.1.1. Les capteurs de
niveaux
Les détecteurs de niveau et de bourrage sont des
instruments simples et économiques pour le contrôle des niveaux de
produits en vrac dans des silos par mise en marche ou arrêt des
systèmes d'alimentation. Ils sont constitués d'un boîtier
en aluminium fondu, muni d'une membrane flexible en acier ou en
néoprène. Ils sont utilisés dans le contrôle des
niveaux minimum et maximum de produit en vrac, poussiéreux, granuleux ou
poudreux
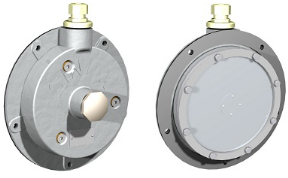 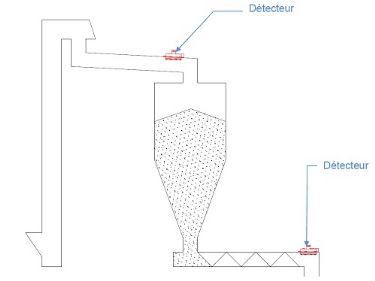
Figure 3 3 les capteurs de niveaux
3.4.1.2. Les capteurs
mesurables
Les transmetteurs de mesures de mesure de masses sont des
dispositifs électriques ou électroniques qui sont conçus
pour relier les appareils de mesure à un autre équipement comme
une machine de fabrication, une machine informatique...
Généralement, les transmetteurs de mesure de masses permettent de
transformer un signal analogique en un signal électronique pour que
cette dernière soit exploitable par les machines et les
équipements électroniques et informatiques. Dans la
majorité des cas, les transmetteurs de mesure de masses sont
caractérisés par la résolution de la sortie des signaux
[http://www.hellopro.fr/]
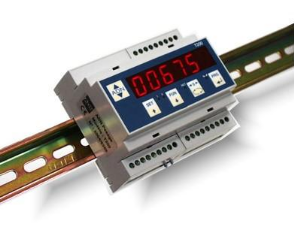
Figure 3 4 capteur mesurable
3.4.1.3. Les boutons
poussoirs
Les boutons poussoirs sont des interrupteurs particuliers
actionnables par pression. Ils sont généralement utilisés
dans le cadre de pilotage d'installation d'éclairage ou de
sécurité électrique.
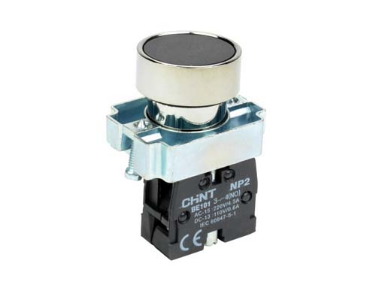
Figure 3 5 bouton poussoirs
3.4.1.4. Bouton
d'arrêt urgence
L'arrêt d'urgence provoque une mise hors énergie des
actionneurs, l'arrêt immédiat de tout processus en cours et
informe l'automate de cette situation. L'automate est programmé par une
séquence spéciale qui permet au retour du courant (lorsque le
bouton d'arrêt d'urgence est dés enclenché et les
actionneurs réenclenchés) de se trouver en mode non critique et
sécurisé pour les opérateurs. [WIKI]

Figure 3 6 bouton d'arrêt
urgence
3.4. Modélisation
de l'usine par GRAFCET
Le développement des ateliers flexibles et la robotisation
ont imposé un outil graphique simple qui permet à partir d'un
cahier de charges bien défini de résoudre un problème
d'automatisation de d'établir le cycle de fonctionnement du processus.
Cet outil est le GRAFCET le GRAFCET répond particulièrement
bien aux besoins de l'industrie dans les automatismes séquentiels dont
la décomposition en étapes est possible. Il nous permet non
seulement d'analyser le problème posé mais également de
concevoir une solution programmable quel que soit la technologie de l'automate.
Cet outil se base sur une représentation graphique très
détaillée du système et ceci avant de faire sa
synthèse.
Notre choix s'est porté sur cet outil car c'est un
langage clair, strict permettant de décrire un fonctionnement sans
ambiguïté
3.4.1. Définition de
logiciel step 7
Step 7 est le progiciel de base pour la configuration et la
programmation de système d'automatisation SIMATIC, le plus connu et le
plus utilisé dans le monde pour l'automatisation industrielle.[]
3.4.1.1. Les avantages de
ce logiciel sont
Programmation intuitive et rapide - avec des éditeurs de
programmation nouvellement développés :
SCL, CONT, LOG, LIST et GRAPH
Efficacité accrue grâce aux innovations
linguistiques de STEP 7 - programmation symbolique uniforme, Calculate Box,
ajout de blocs durant le fonctionnement, et bien plus encore.
Sécurité accrue avec Security Integrated -
Protection du savoir-faire, protection contre la copie, protection
d'accès et protection contre la falsification.
3.4.2. Définition de
Grafcet
3.4.2.1. Histoires
Depuis plusieurs années, il devenait urgent d'unifier et
de rationaliser les langages de description des systèmes logiques
séquentiels en général et des langages des automatismes
séquentiels industriels.
Ainsi, l'Association française pour la cybernétique
économique et technique (AFCET) déposait un rapport à ce
propos en octobre 1977 après deux ans d'études. Le grafcet
était né. La nécessité d'un langage clair conduisit
également au développement d'un outil de description du cahier
des charges qui soit normalisé et dépourvu
d'ambiguïtés tout en étant facile à comprendre et
à utiliser.[]
3.4.2.2. L'outil
Grafcet
Cet outil est un diagramme fonctionnel, constitue la
réalisation directe de l'automatisme par les séquenceurs et les
automates programmables. Il est désigné par Grafcet ou GRAphe
Fonctionnel de Commande Étape/Transition.
Le Grafcet permet la représentation graphique du cahier
des charges qui accompagnera le système automatisé, de sa
conception à son exploitation.[]
3.4.2.3. Cahier de
charge
Le cahier des charges d'un automatisme est un document qui
régit les rapports entre le concepteur de l'ensemble de la commande et
l'utilisateur de cet ensemble.[]
3.4.3. Les entrées
et les sorties d'usine
Tableau 1.1 : Les entrées (les
réceptivités) de l'usine
Réceptivité
|
Signification
|
Dcy
|
Bouton poussoir de démarrage du mode automatique
|
p. alarme
|
Pas d'alarme
|
Au
|
Arrêt d'urgence
|
N
|
Bouton de marché l'élévateur
|
S 1,2,3,4,5,6,7,A,B,C P
|
Silo plein 1,2,3,4,5,6,7,A,B,C
|
S 1,2,3,4,5,6,7,A,B,C V
|
Silo vide 1,2,3,4,5,6,7,A,B,C
|
dcp 1,2,3,4,5,6,7,A,B,C
|
Capteur de doseur plein 1,2,3,4,5,6,7,A,B,C
|
dcv 1,2,3,4,5,6,7,A,B,C
|
Capteur de doseur vide 1,2,3,4,5,6,7,A,B,C
|
B
|
Capteur d'existence le blé dans la vis 2
|
C
|
Capteur d'existence le blé dans la vis 4
|
M
|
Bouton poussoir de premier cycle
|
m1
|
Bouton poussoir de deuxième cycle
|
Tableau 1.2 : Les sorties (les actionneurs) de
l'usine :
Actions
|
Signification
|
OVS A,B,C 1,2,3,4,5,6,7
|
Ouverture de la vanne silo A,B,C 1,2,3,4,5,6,7
|
FVS A,B,C 1,2,3,4,5,6,7
|
Fermeture de la vanne silo A,B,C 1,2,3,4,5,6,7
|
OVD A,B,C 1,2,3,4,5,6,7
|
Ouverture de la vanne doseur A,B,C 1,2,3,4,5,6,7
|
FVD A,B,C 1,2,3,4,5,6,7
|
Fermeture de la vanne doseur A,B,C 1,2,3,4,5,6,7
|
vis sans fin ON 1,2,3,4,5
|
Démarrage du moteur de la vis 1,2,3
|
vis sans fin OFF 1,2,3,4,5
|
Arrêt du moteur de la vise sans fin 1,2,3
|
élévateur 1, 2, 3,4 ON
|
Elévateur 1,2, 3,4 marche
|
élévateur 1, 2
, 3,4 OFF
|
Elévateur 1, 2, 3,4 arrêt
|
séparateur ON
|
Séparateur marche
|
séparateur OFF
|
Séparateur arrêt
|
épierreur ON
|
Epierreur marche
|
épierreur OFF
|
Epierreur arrêt
|
trieur ON
|
Trieur marche
|
trieur OFF
|
Trieur arrêt
|
brosse 1,2 ON
|
Brosse 1,2 marche
|
brosse 1,2 OFF
|
Brosse 1,2 arrêt
|
mouilleur 1,2 ON
|
Mouilleur 1,2 marche
|
Mouilleur OFF
|
Mouilleur 1,2 arrêt
|
OVV 1,2,3,4
|
Ouverture de la vanne de la vis 1,2,3,4
|
FVV 1,2,3,4
|
Fermeture de la vanne de la vis 1,2,3,4
|
OV 5,6,7 V
|
Ouverture de la vanne de vis 5,6,7
|
FV 5,6,7 V
|
Fermeture de la vanne de vis 5,6,7
|
3.4.4. Les différents
GRAFCET de l'usine
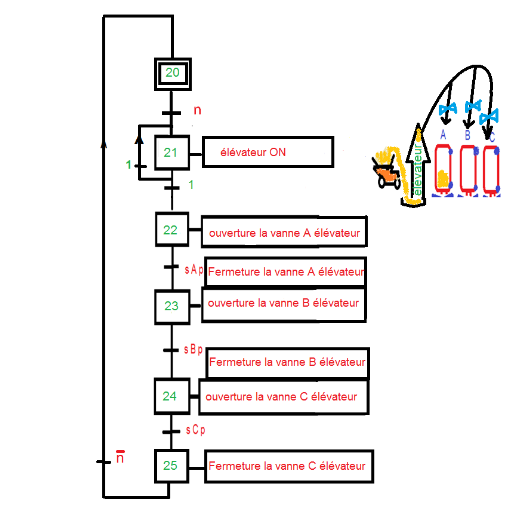
Figure 3 7 le GRAFCET qui exprime le remplissage des 3
silos
Ø Cahier de charge Figure 3.7
Premièrement noté que les 3 silos sont
vides à l'état initial juste appuyé sur le bouton n ,
l'élévateur marche et la vanne A de l'élévateur
ouverte va commencer remplit le premier silo A lorsque le silo A est plein le
capteur de niveau s A p détecté ca .On passé vers
l'étape suivante et la vanne B ouverte et la vanne A fermée et
commence remplisse de silo B lorsque le silo B est plein le
capteur de niveau s B p détecté ca .On passé vers la
dernière étape qui consiste le remplissage de silo C par l'action
de l'ouverture de la vanne C et ferme la vanne B lorsque le capteur s C p
détecté que le silo C est plein en revient à
l'étape initiale .
D'après l'analyse de ce GRAFCET nous ne trouvons pas de
problèmes dans le gaspillage du temps de ce systeme ,c'est la solution
optimal pour remplir les trois silos alors on ne doit faire aucun modification
pour cette partie d'usinage .
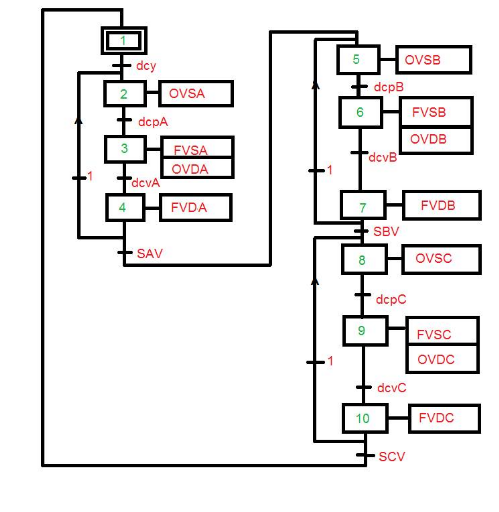
Figure 3 8 le GRAFCET qui exprime le passage de
blé à la première vis
Ø Cahier de charge de la figure 3.8
Voilà le deuxième GRAFCET qui exprime
le passage de blé réceptionné vers la vise 1 juste
appuyé sur le bouton dcy la vanne ouvert de silo A:OVS A est
vidé le blé dans le doseur A le capteur dcp A
détectés la fin de remplissage de doseur A. On passé vers
l' autre étape qui consiste la fermeture de vannes de silos A (FVS A)et
ouverture la vanne de doseur A (OVD A)Lorsque dcv A détecte que le
doseur A est vide la vanne de doseur A fermée (FVD A) si le capteur SAV
franchisée on passe vers l'étape 5 qui consiste l'ouverture de la
vanne silo B :OVS B est vidé le blé dans le doseur B
le capteur dcp B détectés la fin de remplissage de doseur B. On
passé vers l' autre étape qui consiste la fermeture de vannes de
silos B (FVS B)et ouverture la vanne de doseur B (OVD B)Lorsque dcv B
détecte que le doseur B est vide la vanne de doseur B fermée (FVD
B) si le capteur SBV franchisée on passe vers l'étape 8 qui
consiste l'ouverture de la vanne silo C :OVS C est vidé le blé
dans le doseur C
le capteur dcp C détectés la
fin de remplissage de doseur C. On passé vers l'autre étape qui
consiste la fermeture de vannes de silos C (FVS C) et ouverture la vanne de
doseur C (OVD C) Lorsque dcv C détecte que le doseur C est vide la vanne
de doseur C fermée (FVD C) si le capteur SBC franchisée
on passe vers l'étape 1(l'étape initiale)
Par contre , en analysant le GRAFCET qui concérne l'usine
de OULED MIMOUNE , on peut remarquer un probléme au niveau du
temps ; d'abord le silo A est vider petit a petit dans son doseur , qui
ensuite apres son remplissage complet , vide son contenu dans la vis . ensuite
la meme action est repétée jusqu'à la fin du blé
dans le silo A ( tandis que les autres silo ne fonctionnent pas jusqu'à
la fin du silo A) . ce faite constitue donc une perte de temps qui est
remarquée lors du remplissage du doseur a chaque fois (..min)
Afin de régler ce problème, nous proposons le
GRAFCET suivant qui constitue une solution à cette perte de
temps

Figure 3 9 le GRAFCET qui exprime la solution du
passage de blé à la première vis
Ø Cahier de charge de la figure 3.9
Voilà le GRAFCET qui exprime le passage de blé
réceptionné vers la vise 1 juste appuyé sur le bouton
dcy les 3 silos (les 3 vannes ouvert des silos A,B ,C :OVS A.OVS B.
OVS C) sont vidés le blé dans les 3 doseurs au même
temps . les capteurs dcp A , dcp B , dcp B
détectés la fin de remplissage des 3 doseurs. On passé
vers les autres étapes qui consiste la fermeture des vannes des 3 silos
A,B et C(FVS A.FVS B.FVS C) mais l'étape 3 consiste 2 actions au
même temps la fermeture de la vanne silo A( FVS A) et l'ouverture de la
vanne doseur A(OVD A)
Lorsque dcv A détecte que le doseur A est vide
l'étape 7 qui consiste l'ouverture de la vanne doseur B (OVD B) et passe
directement sur l'étape 4 qui consiste la fermeture de la vanne de
doseur A (FVD A) Lorsque dcv A détecte que le doseur A est
vide et dcv B détecte que le doseur B est vide l'étape 11 qui
consiste l'ouverture de la vanne doseur C (OVD C) et passe directement sur
l'étape 8 qui consiste la fermeture de la vanne de doseur B (FVD
B)
Lorsque dcv C détecte que le doseur C est vide
l'étape 12 qui consiste la fermeture de la vanne de doseur
C(FVDC).lorsque appuyé sur dcy en revient à
l'étape initiale.
pour eviter cette perte de temps , on a effectuer ce GRAFCET ,
qui nous donnent une solution optimale pour ce probléme : c'est a
dir : dabord les 3 doseurs sont remplies en meme temps par les
silos ; puis le doseur A vide son contenu dans la vis ; mais au lieu
d'attendre qui ce méme doseur se remplisse a nouveau , le doseur B se
vide tandis que le A est entrin de se remplir , et ainsi pour le doseur C .
les resultats ce sont representer dans le diagramme du gantt
suivant :
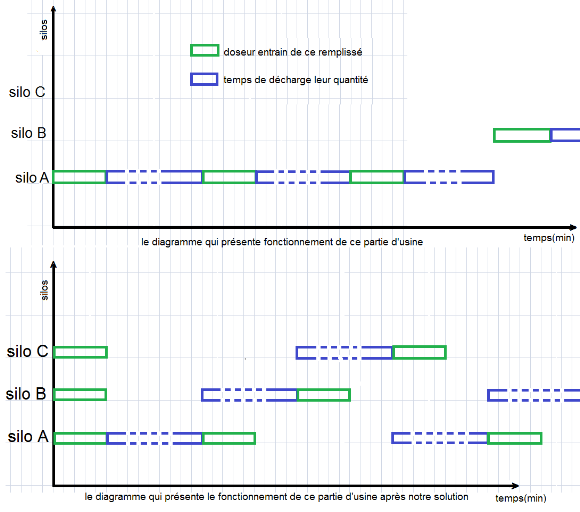
Figure 3 10 le diagramme le fonctionnement de cette
partie d'usine avant et après la solution proposé
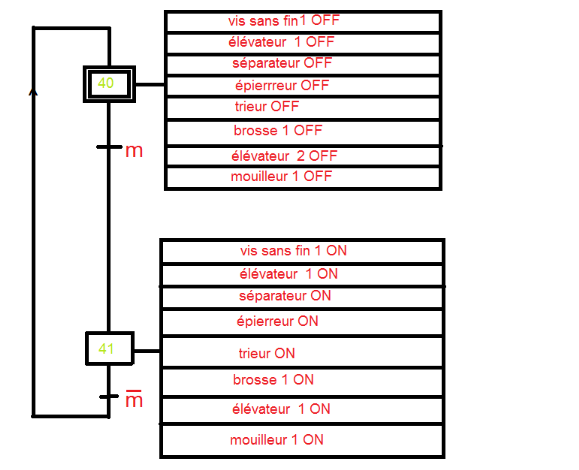
Figure 3 11 : le GRAFCET de démarrage des
machines qui sont trouvent avant les silos de premier repos
Ø Cahier de charge Figure 3.11 :
le GRAFCET qui exprime le démarrage des machines
qui sont trouvent avant les silos de premier repos (la vise sans fin 1,
élévateur 1, séparateur, épierreur, trieur, brosse
1, élévateur 2, mouilleur 1).On l'état initiale toutes les
machines interrompre (arrêtés) juste appuyé sur le bouton m
toutes les machines marches au même temps. Lorsque appuyé sur
m en revient à l'étape initiale
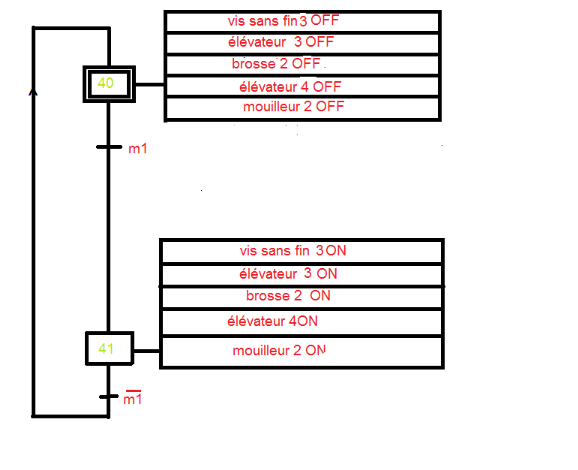
Figure 3 12 : le GRAFCET de démarrage des
machines qui sont trouvé après les silos de premier
repos
Ø Cahier de charge Figure 3.12 :
le GRAFCET qui exprime le démarrage des machines qui
sont trouvent après les silos de premier repos (la vise sans fin 3,
élévateur 3, brosse 2, élévateur 4,mouilleur 2).On
l'état initiale toutes les machines interrompre(arrêtés)
Juste appuyé sur le bouton m1 toutes les machines marches
au même temps. lorsque appuyé sur m1 en revient à
l'étape initiale
Ces GRAFCETS conçu par l'usine, représente le
fonctionnement des machines de l'usine.
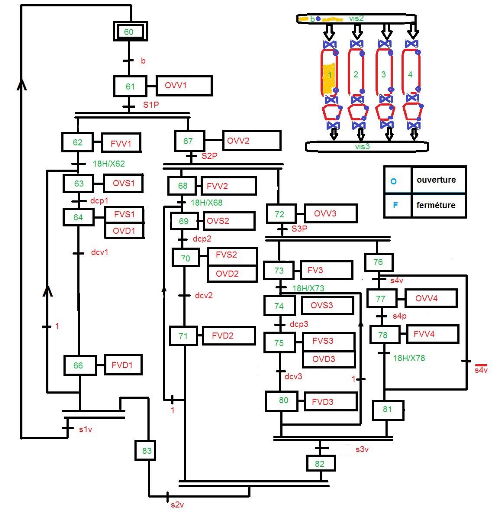
Figure 3 13 GRAFCET qui expriment le passage de
blé dans la vis 2 vers la vis 3
Ø Cahier de charge Figure 3.13 :
Voilà le GRAFCET qui exprime le passage de
blé dans la vis 2 vers la vis 3 juste le capteur b détecté
les grains de blé, la vanne de la vise de silo1 ouverte OVV1.Lorsque le
silo 1 est plein on a deux choses : la vanne de la vise de silo 1
fermée(FVV1) et la vanne de la vise de silo 2 ouvrée (OVV 2)
Lorsque le silo 2 est plein on a deux choses : la vanne
de la vise de silo 2 fermée(FVV2) et la vanne de la vise de silo 3
ouvrée (OVV 3)
Lorsque le silo 3 est plein on a deux choses : la vanne
de la vise de silo 3 fermée(FVV3) et la vanne de la vise de silo 4
ouvrée (OVV 4)
Lorsque le silo 4 est plein on a la vanne de la vise de silo 4
fermée(FVV4)
Après la fermeture de chaque vanne de vise (FVV1,
FVV2 ,FVV3 ,FVV4) le système attendre une durée de
premier repos (18h)
Après cette durée les vannes des 4 silos
ouvertes (OVS 1, OVS 2 , OVS 3 , OVS 4 ) quand les 4silos sont pleins :
les vannes des silos fermées (FVS 1,FVS 2,FVS 3,FVS 4)et les vannes des
doseurs ouvrées (OVD 1,OVD 2,OVD3,OVD 4)
Quand les 4 doseurs vides ont fermé chaque vannes des 4
doseurs (FVD 1, FVD 2,FVD 3,FVD 4)et le blé commence leur enchainement
vers la vise 3
D'après l'analyse de ce GRAFCET, on a pu constater une
perte temps :
Lors du passage du blé de la vis 2 vers la vis 3, d'abord
le silo 1 est rempli, ensuite il passe a la phase de repos tandis que le silo 2
est entrain de ce remplir et de même pour les 2 autres silos (et les
silos sont vider juste âpres leur repos). Mais le problème est que
le remplissage du silo 1 pour la deuxième fois de ce fait qu'une fois
que le dernier silo soit vide.
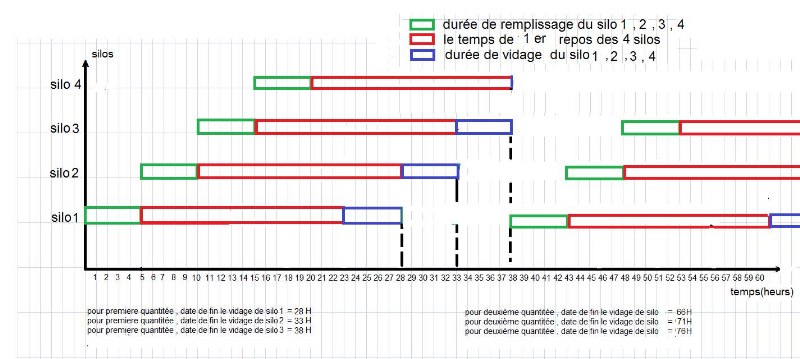
Ces résultats sont simulés dans
le diagramme de GANTT ci-dessous :
Figure 3 14 diagramme de GANTT qui exprime le
gaspillage du temps dans le premier repos
Les conséquences de cette perte de temps
sont :
-la production n'est pas à son maximum
-le bénéfice de l'usine n'est pas à son
maximum aussi.
Afin de régler ce problème, nous proposons le
GRAFCET suivant qui constitue une
solution à cette perte de temps :
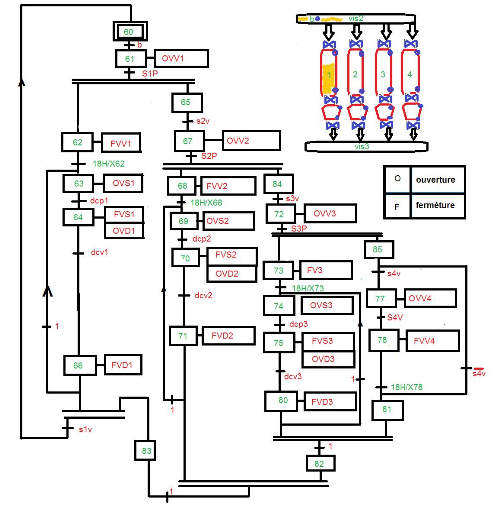
Figure 3 15 GRAFCET qui expriment la solution pour le
passage de blé dans la vis 2 vers la vis 3
Ø Cahier de charge Figure 3.15 :
Voilà le GRAFCET qui exprime le passage de blé
dans la vis 2 vers la vis 3 juste le capteur b détecté les grains
de blé, la vanne de la vise de silo1 ouverte OVV1 .Lorsque le silo
1 est plein on a deux choses :la vanne de la vise de silo 1
fermée(FVV1) et si le silo 2 vide S2V la vanne de la vise de silo 2
ouvrée(OVV 2)
Lorsque le silo 2 est plein on a deux choses : la vanne
de la vise de silo 2 fermée(FVV2) et si le silo3 vide S3V la vanne de la
vise de silo 3 ouvrée (OVV 3)
Lorsque le silo 3 est plein on a deux choses :la vanne
de la vise de silo 3 fermée(FVV3) et si le silo 4 vide S4V la vanne de
la vise de silo 4 ouvrée (OVV 4)
Lorsque le silo 4 est plein on a la vanne de la vise de
silo 4 fermée(FVV4)
Après la fermeture de chaque vanne de vise (FVV1,
FVV2 ,FVV3 ,FVV4) le système attendre une durée de
premier repos (18h)
Après cette durée les vannes des 4 silos
ouvertes (OVS 1, OVS 2 , OVS 3 , OVS 4 ) quand les 4silos sont pleins :
les vannes des silos fermées (FVS 1,FVS 2,FVS 3,FVS 4)et les vannes des
doseurs ouvrées (OVD 1,OVD 2,OVD3,OVD 4)
Quand les 4 doseurs vides ont fermé chaque vannes des
4 doseurs (FVD 1, FVD 2,FVD 3,FVD 4)et le blé commence leur enchainement
vers la vis 3
D'abord le silo 1 est rempli, ensuite il passe à la phase
de repos tandis que le silo 2 est entrain de ce remplir et de même pour
les 2 autres silos (et les silos sont vider juste âpres leur repos). Sauf
que pour cette solution : le remplissage du silo 1 pour la deuxième
fois se fait directement après qu'il soit vider (on n'attend pas que le
4eme silo soit vide), et de même pour les 3 autres. Voilà le
résultat représenté par le diagramme de GANTT.
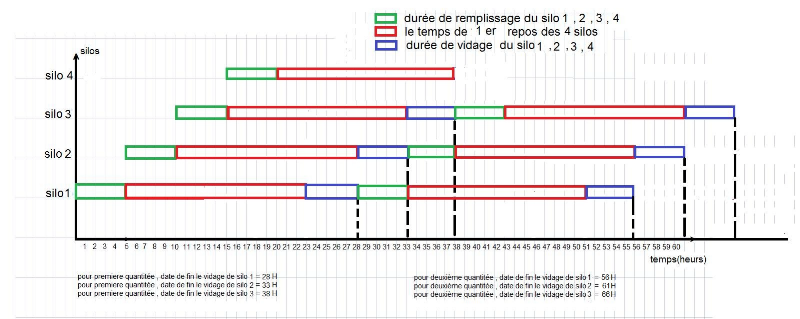
Figure 3 16 diagramme de GANTT qui exprime la solution
pour le gaspillage du temps dans le premier repos
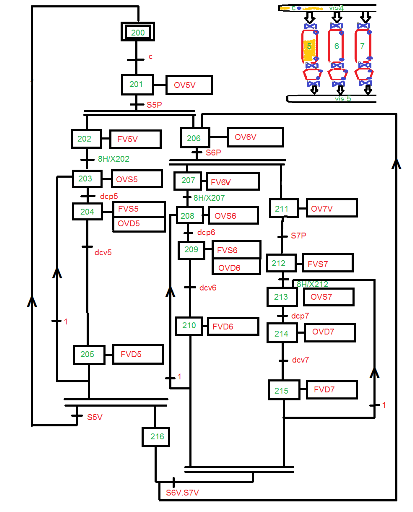
Figure 3 17 GRAFCET qui expriment le passage de
blé dans la vis 4 vers la vis 5
Ø Cahier de charge Figure 3.17 :
Voilà le GRAFCET qui exprime le passage de
blé dans la vis 4vers la vis 5 juste le capteur c détecté
les grains de blé, la vanne de la vise 1 ouverte OVV5 .Lorsque le
silo 5 est plein on a deux choses : la vanne de la vise de silo 5
fermée (FVV5) et la vanne de la vise de silo 6 ouvrée (OVV 6)
Lorsque le silo 6 est plein on a deux choses :la vanne
de la vise de silo 6 fermée(FVV6) et la vanne de la vise de silo
7ouvrée(OVV 7)
Lorsque le silo 7 est plein on a la vanne de la vise de silo
7fermée(FVV7)
Après la fermeture de chaque vanne de vise (FVV5,
FVV6 ,FVV7 ) le système attendre une durée de premier
repos (08h)
Après cette durée les vannes des 3 silos
ouvertes (OVS 5, OVS 6 , OVS 7) quand les 3silos sont pleins : les vannes
des silos fermées (FVS 5,FVS 6,FVS 7)et les vannes des doseurs
ouvrées (OVD 5,OVD 6,OVD7)
Quand les 3 doseurs vides ont fermé chaque vannes des
3doseurs (FVD 5, FVD 6,FVD 7) et le blé commence leur enchainement vers
la vis 5
Apres l'analyse de ce GRAFCET, on conclue que le problème
pour cette partie de l'usinage est le même que pour le passage de la vis
2 a la vis 3 et les résultats sont sur le diagramme de GANTT
suivant :
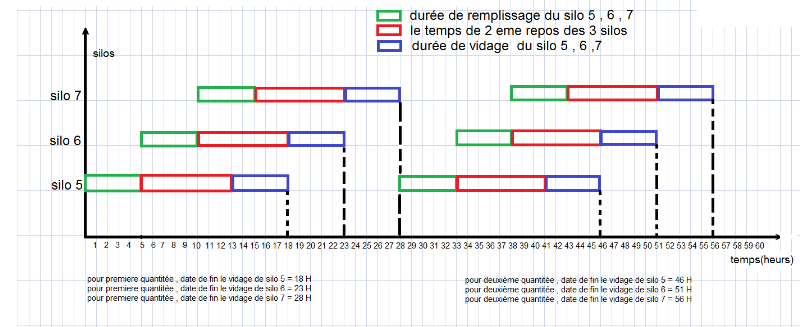
Figure 3 18 diagramme de GANTT qui exprime pour le
gaspillage du temps dans le deuxième repos
Pour la solution : on a d'abord proposé une
première solution qui consiste au remplissage des 3 silos en même
temps (les résultats sont sur le diagramme de GANTT en dessous),
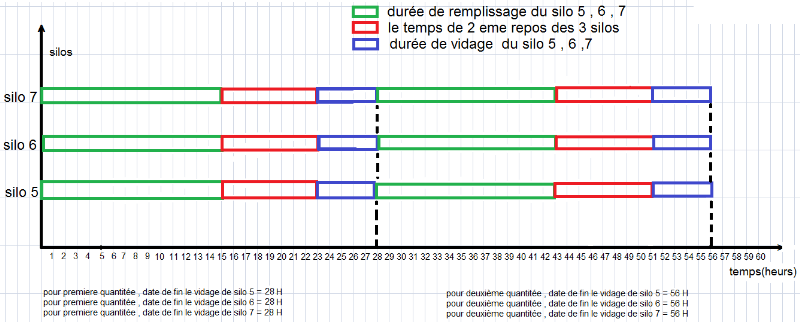
Figure 3 19 diagramme de GANTT qui exprime la
première solution pour le gaspillage du temps dans le deuxième
repos
Pour cette solution on a remarqué un problème,
c'est que le temps de remplissage du silo augmente parce que les 3 sont en
train de se remplir en même temps, et il n y a donc pas de
bénéfice de temps pour cette solution
On a donc proposé une autre solution optimale qui est la
même que pour le premier repos :
Le GRAFCET est :
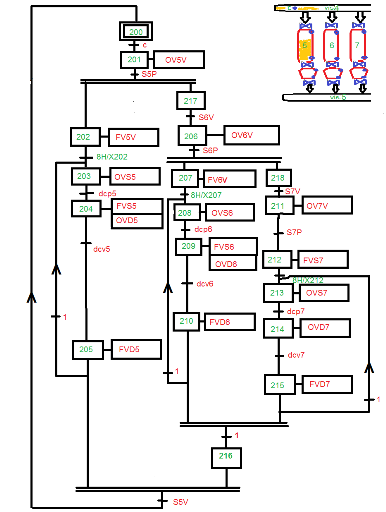
Figure 3 20 : GRAFCET qui exprime la solution pour le
passage de blé dans la vis 4 vers la vis 5
Ø Cahier de charge Figure 3.2 :
Voilà le GRAFCET qui exprime le passage de
blé dans la vis 4vers la vis 5 juste le capteur c détecté
les grains de blé, la vanne de la vise 1 ouverte OVV5 .Lorsque le
silo 5 est plein on a deux choses : la vanne de la vise de silo 5
fermée (FVV5) et si le silo 6 est vide S6V la vanne de la vise de silo 6
ouvrée (OVV 6)
Lorsque le silo 6 est plein on a deux choses : la vanne
de la vise de silo 6 fermée(FVV6) et si le silo 7 est vide S7V la vanne
de la vise de silo 7 ouvrée (OVV 7)
Lorsque le silo 7 est plein on a la vanne de la vise de silo
7fermée(FVV7)
Après la fermeture de chaque vanne de vise (FVV5,
FVV6 ,FVV7 ) le système attendre une durée de premier
repos (08h)
Après cette durée les vannes des 3 silos
ouvertes (OVS 5, OVS 6 , OVS 7) quand les 3silos sont pleins : les vannes
des silos fermées (FVS 5,FVS 6,FVS 7)et les vannes des doseurs
ouvrées (OVD 5,OVD 6,OVD7)
Quand les 3 doseurs vides ont fermé chaque vannes
des 3doseurs (FVD 5, FVD 6,FVD 7) et le blé commence leur enchainement
vers la vis 5
Le diagramme de GANTT est représenté
ci-dessous :
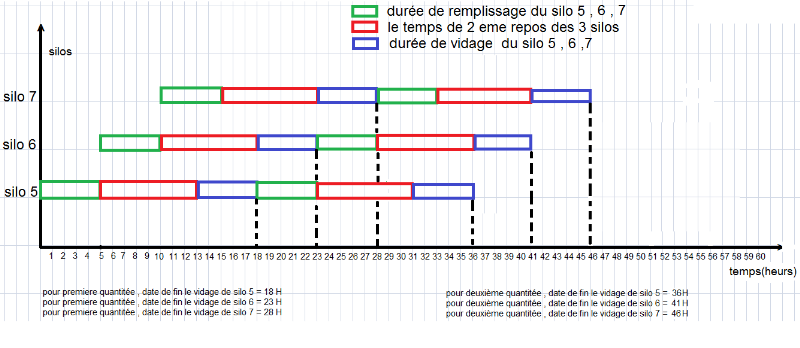
Figure 3 21 diagramme de GANTT qui exprime la solution
pour le gaspillage du temps dans le deuxième repos
3.5. Conclusion
L'usine d'OULAD MIMOUNE incite les responsables de
l'entreprise à chercher une solution de supervision qui centralise
l'ensemble des ateliers de production pour une meilleure gestion de
l'usine. Le GRAFCET est l'outil adéquat pour la modélisation
des systèmes industriel séquentiel pour sa souplesse et sa
facilité d'utilisation.
Ce chapitre nous a servi à décrire et à
modéliser nos procédés de commande et à identifier
les fonctions nécessaires au bon fonctionnement de l'automatisme de
conduite de nos systèmes ainsi que les variables des différents
automates (entrées/sorties), Il nous à servis aussi à
trouver la configuration adéquat pour la communication des
automates.
Chapitre 04 : analyse les résultats
trouvés
4. Chapitre 04
4.1. Introduction
Comme notre objectif est d'optimiser les temps de remplissages
des silos de première repos et deuxième repos nous avons
utilisé deux modélisation ARENA et STEP 7. Dans ce chapitre
nous allons présenter une comparaison entre la simulation ancienne sur
ARENA et la nouvelle simulation de l'amélioration proposée et
définir les solutions trouvées. On peut ainsi suivre
l'évolution des GRAFCET par rapport aux anciennes GRAFCET et formuler
des solutions relatives au système à partir des nouveaux GRAFCET
proposée.
Dans le cadre de ce chapitre nous avions réalisé
une conclusion générale sur la modélisation et simulation
de l'usine de la farine par ARENA et GRAFCET
4.2. Comparaison
Comparaison entre la simulation ancienne sur ARENA et la
nouvelle simulation de l'amélioration
proposée :
Apres qu'on a réalisé la simulation sur
aréna de tous les processus, on a trouvé un problème au
niveau de la partie nettoyage, exactement au niveau du remplissage des silos du
1er repos, on ne pouvait pas refaire le remplissage du
1er silo sauf si le vidage du 3eme silo aura lieu. Ce qui rend le
processus plus long.
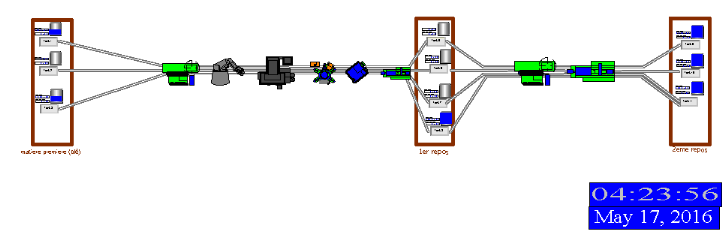
Figure 4 1le temps nécessaire pour remplir le
dernier silo dans le 2eme repos pour un 2eme cycle.
On a modélisé le système sous le logiciel
de simulation Aréna qui a comme objectif de faire une analyse pour ne
pas perdre du temps. La simulation a commencé le 14 mai
2016 : le temps nécessaire pour remplir le dernier silo dans le
2eme repos pour un 2eme cycle est 3jours et
4heures.23minutes 56 secondes (76 heures 23minutes 56 secondes) selon la
façon similaire (procédure d'usine).
Le 1er
silo doit attendre le vidage du 2eme silo pour qu'il se remplisse pour la 2eme
fois.
Pour la nouvelle simulation de l'amélioration
proposée .Nous avions pu réaliser la structure du modèle
sous contrainte d'une façon optimale (solution) le remplissage du
1er silo se fait directement après son vidage et sans qu'il
attend le vidage du 3eme. 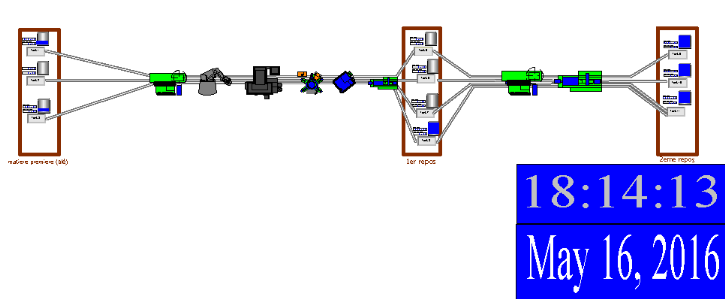
Figure 4 2 le temps nécessaire pour remplir le
dernier silo dans le 2eme repos pour un 2eme cycle après la
Apres la modification le temps nécessaire pour remplir le
dernier silo dans le 2eme repos pour un 2eme cycle est
de 2jours et 18heures.14minutes 13 secondes (66 heures 14 minutes 13 secondes)
selon la façon optimale (solution).
Donc on a pu réduire le temps du travail jusqu'à
10h.
Comme notre objectif est d'optimiser les temps de
remplissages des silos du premier repos et deuxième repos. On propose
ajouter un 4eme silo supplémentaire comme une réserve à la
partie nettoyage (1ére repos) on l'utilise lorsqu'on ne peut pas
utiliser la matière des trois silos (qu'ils soient vides ou durant la
période de leurs repos) afin d'éviter le manque de la
matière.
4.3. L'évolution
des GRAFCET
Les besoins des systèmes de
production qu'ils soient continus ou discontinus ont augmentés de
façon considérable d'où la nécessité
d'introduire le concept de système automatisé de production.
On utilise le diagramme de gant, pour vérifier les dates de
fin de remplissage les silos(les silos de premier repos :1 ,2,3 et
les silos de deuxième repos :5,6,7).La procédure de
remplissage suppose en façon similaire (procédure
d'usine) : on a pu constater une perte de temps presque 10heures pour
faire un deuxième cycle (deuxième remplissage) et la date de fin
2éme remplissage pour les silos de 1ére repos 76 heures et la
date de fin 2éme remplissage pour les silos de 2éme repos 56
heures

Figure 4 3 diagramme de GAND qui représente le
temps perdu
76
10 heures
10 heures
10 heures
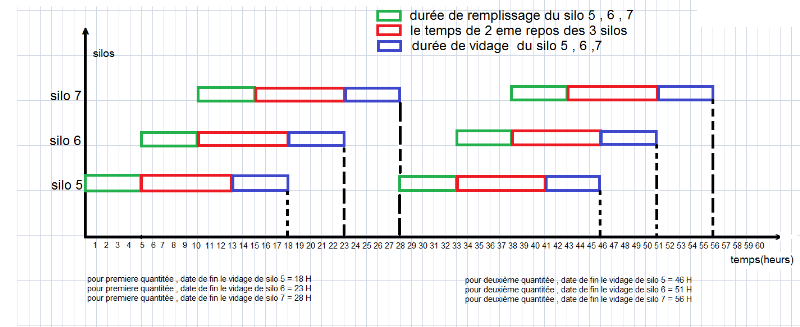
Façon optimale (solution) : Cette façon
proposée, permet de diminuer la durée jusqu'aux 10 heures par
rapport la méthode précédente (66heures pour les silos de
première repos et 46 heures pour les silos de deuxième
repos) 66
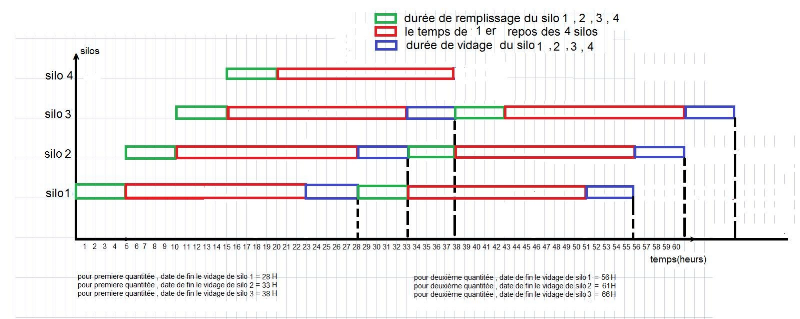
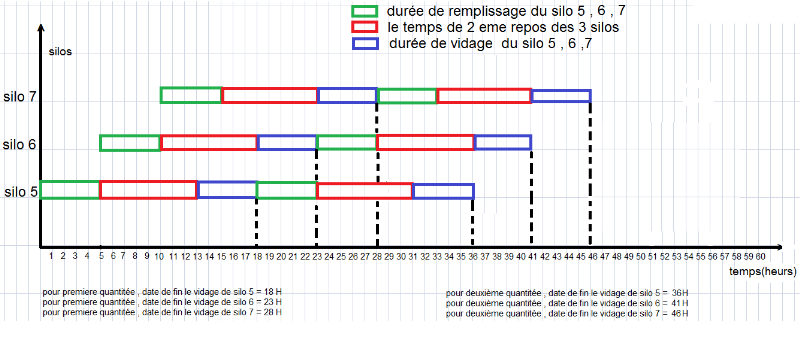
Formuler des solutions relatives au système
à partir des nouveaux GRAFCET proposés :
Et
comme résultats obtenue, on propose non seulement d'analyser le
problème posé mais également de concevoir une solution
programmable quel que soit la technologie de l'automate et de gérer
d'une façon optimale le programme GRAFCET pour commander et
résoudre un problème d'automatisation et d'établir le
cycle de fonctionnement du processus.
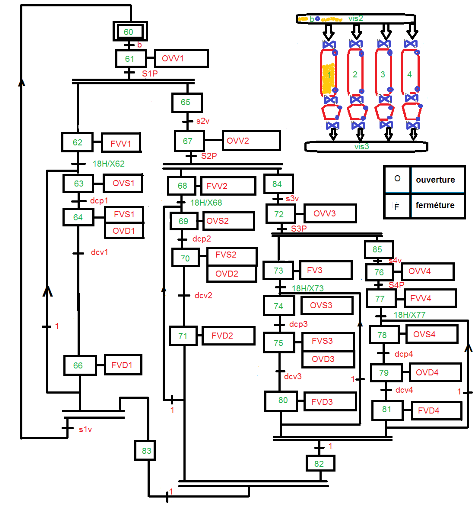
Figure 4 4 GRAFCET qui exprime la solution du premier
repos
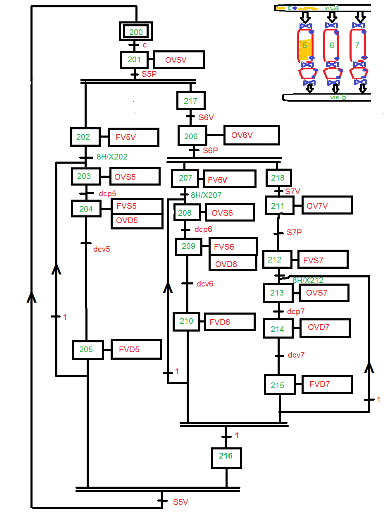
Figure 4 5 GRAFCET qui exprime la solution de
deuxième repos
GRAFCET qui exprime le passage de blé à la
première vise: pour éviter la perte de temps
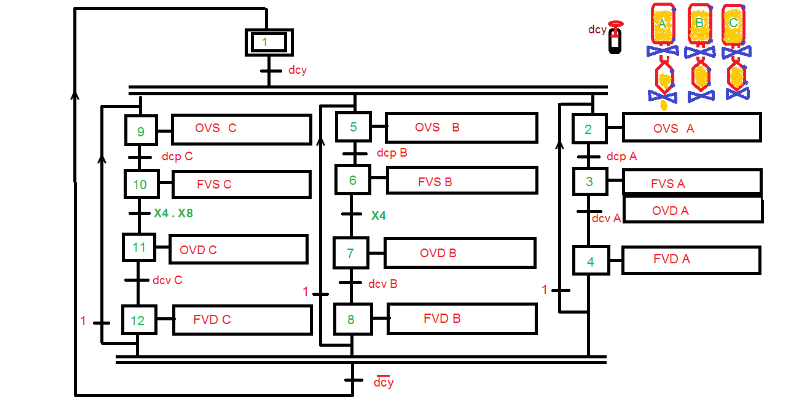
Figure 4 6 GRAFCET qui exprime le passage de blé
à la première vise: pour éviter la perte de
temps
4.4.
Conclusion
Ce chapitre représente notre réalisation
qui avait comme but d'améliorer le système de l'entreprise
(gagner du temps et éviter le manque de la matière). En
appliquant la modélisation sur Aréna et la simulation sur
Graphcet.
Conclusion Générale
Durant les trois années passées nous avions appris
beaucoup d'informations dans le domaine de l'amélioration de production
dans le coté gestion (planification. Ordonnancement ...) ainsi que dans
le côté technique (informatique et automates programmables....).
De plus nous avions eu la possibilité de faire des sorties et des stages
à travers de nombreuses usines, la raison pour laquelle qu'on a
pensé à faire notre projet de soutenance dans l'une de ces
entreprises qui englobe la majorité de connaissances acquises pour
atteindre un travail de valeur.
Lors de notre visite à l'entreprise d'Oulad Mimoun (groupe
ERIAD) qui travaille dans le domaine de fabrication de la farine nous avons
remarqué qu'il y avait un problème de perte de temps au niveau de
la partie nettoyage, exactement au niveau du remplissage des silos du
1er repos.
On a proposé une solution qui nous permettra de gagner 10h
dans deux cycles, sachant que 1cycle représente la durée de
l'entrée de la matière première jusqu'au 2eme
repos.
On a aussi proposé d'ajouter un 4eme silo au
niveau de l'opération du 1er repos, son rôle est de
combler le manque de la matière.
On utilise le Grafcet pour que la partie opérative
fonctionne de la façon qu'il applique nos commandes.
Finalement, on a réalisé l'amélioration dans
le processus de la fabrication de la Farine.
Résumé
Le but de ce mémoire est l'amélioration dans le
processus de la fabrication de la Farine au sein de l'entreprise d'Oulad
Mimoun.
Après cette étude et de recherche, nous avons
proposé une solution qui consiste à gagner du temps et
éviter le manque de la matière. On a trouvé ces solutions
on utilisant Arena, et on applique nos commandes on utilisant le Grafcet.
Abstract
The purpose of this memory is to améliorate the process of
flowr production in the factory of Oulad Mimoun.
After our studies and research,we proposed a solution which is to
save time and avoid lack of material.
We applied our orders by using Grafcet.
ãáÎÕ
C??I? ?? ??C C??O??? ?? E???? ????E C?EC? C????? ??? ??E?? ????E
C??CI ?????.
E?I ??? C?I?C?E ? C?E?E, C?E???C ??C ?? C?? ?E? C???E ? E?CI?
??? C???CI. ? E????C C?? ??? C????? EC?E??C? E??C?? ARENA, ? ?? C?? E?E???C
C?EII??C GRAFCET
|