REPUBLIQUE ALGERIENNE DEMOCRATIQUE ET POPULAIRE
MINISTERE DE L'ENSEIGNEMENT SUPERIEUR ET DE LA
RECHERCHE SCIENTIFIQUE UNIVERSITE MOHAMED KHIDER BISKRA
FACULTE DES SCIENCES ET DE LA TECHNOLOGIE
DÉPARTEMENT DE CHIMIE INDUSTRIELLE
Mémoire de fin d'Étude en Vue de
l'Obtention du Diplôme d'Ingénieur d'État
SPÉCIALITÉ: Chimie Industrielle
OPTION: Génie Chimique
THEME
L'effet du nombre du recyclage de PVC sur les
propriétés du polyéthylène réticulé
par le silane (PRS)
Présenté par:
Haddar Abderrahmene & Mimoune
Zoubeyr
Président: Mme. C. Bouremel
Examinateur: Melle. D. Smail
Encadreur: Melle. S. Kermiche
Promotion Juin 2009
Remerciements
Nous tenons en premier lieu à remercier
Dieu omnipotent omniprésent et omniscient,
qui nous a donné la santé, le courage et la volonté pour
arriver à bous de ce travail.
Nous tenons à remercier Melle. S.
KERMICHE qui a accepté de nous encadrer, ses commentaires et
réflexions nous ont permis de trouver des
applications intéressantes aux travaux que nous menons. Merci pour
l'aide et les conseils qu'elle nous a fournis durant la rédaction de ce
mémoire.
Nous voudrons également exprimer toutes nos
reconnaissances aux membres de jury pour l'intérêt qu'elles ont
porté à ce travail et pour l'honneur qu'elles nous ont fait pour
juger ce travail :
Melle. D. SMAIL et Mme. C.
BOUREMEL
Les travaux présentés dans ce manuscrit
ont été réalisés au laboratoire du
plastique de l''Entreprise National d'Industrie du Câble de Biskra
dirigé par monsieur ALOUANI, nous sommes très
reconnaissants de nous avoir accueilli.
Aussi un grand remerciement à RABOUH,
ABDELHALIME, SAOULI, BEN SASSI et AMINA pour leurs aides.
A tous, pour tous, merci.
En fin nous adressons de grands remerciements à
tous qui nous ont aidé de faire ce travail.
Résumé :
Les plastiques, en tant que matériaux de
commodité, sont utilisés dans diverses applications. Leur
consommation ne cesse d'augmenter et par conséquent leurs déchets
nécessitent une prise en considération vu l'impact
négative qu'ils peuvent avoir sur le plan économique et
environnemental.
Le recyclage des polymères est devenu de nos
jours un processus essentiel. Il est cependant important de déterminer
le comportement de ces matériaux dans le but d'optimiser la relation
polymère vierge-polymère recyclé et d'obtenir des
propriétés convenables du produit fini.
Dans notre travail nous avons essayé
d'étudier l'influence du nombre de recyclage du PVC et la concentration
de PRS sur le mélange (PRS/PVC) à savoir : Une étude
rhéologique, mécanique et thermique.
Pour l'étude rhéologique le
rhéomètre n'a pas donné une bonne lecture qui permit
de déduire le temps de
réticulation pour chaque mélange.
D'après l'étude mécanique et
d'une façon générale, on a constaté que le
mélange à base de PVC recyclé une fois
présente des propriétés mécaniques - avant et
après vieillissement (résistance à la rupture et
l'allongement à la rupture) - plus élevés que
les autres mélanges (PRS/PVC recyclé deux et trois fois). Pour
le même mélange les caractéristiques
mécaniques augmentent avec l'augmentation du taux de PRS.
La dureté Shore A possède une
légère augmentation. Elle est plus remarquable
à 90 % de PRS.
La stabilité thermique du mélange PRS /
PVC recyclé croit avec la croissance du nombre de
recyclage du PVC. En plus dans le même mélange cette
dernière diminue avec l'augmentation du taux de PVC recyclé.
Liste des figures
Figure I.1 :
|
Déchets d'emballages plastiques dans les ordures
ménagères.
|
Figure I.2 :
|
Collecte des déchets plastiques.
|
Figure I.3 :
|
Recyclage des déchets plastiques.
|
Figure II.1 :
|
Production mondiale du PVC en kt.
|
Figure II.2 :
|
Répartition mondiale de la consommation.
|
Figure II.3 :
|
Représentation schématique de différents
systèmes binaire.
|
Figure III.1 :
|
Organigramme de la partie expérimentale.
|
Figure IV.1 :
|
Variation du torque en fonction du temps pour le PRS pur.
|
Figure IV.2 :
|
Variation du torque en fonction du temps pour le
mélange PRS / PVC recyclé une fois.
|
Figure IV.3 :
|
Variation du torque en fonction du temps pour le
mélange PRS / PVC recyclé deux fois.
|
Figure IV.4 :
|
Variation du torque en fonction du temps pour le
mélange PRS / PVC recyclé trois fois.
|
Figure IV.5 :
|
Variation de la résistance à la rupture moyenne
avant vieillissement en fonction du taux de PRS.
|
Figure IV.6 :
|
Variation de la résistance à la rupture
médiane avant vieillissement en fonction du taux de PRS.
|
Figure IV.7 :
|
Variation de l'allongement à la rupture moyenne avant
vieillissement en fonction du taux de PRS
|
Figure IV.8 :
|
Variation de l'allongement à la rupture médiane
avant vieillissement en fonction du taux de PRS.
|
Figure IV.9 :
|
Variation de la résistance à la rupture moyenne
après vieillissement en fonction du taux de PRS.
|
Figure IV.10 :
|
Variation de la résistance à la rupture
médiane après vieillissement en fonction du taux de PRS.
|
Figure IV.11 :
|
Variation de l'allongement à la rupture moyenne
après vieillissement en fonction du taux de PRS.
|
Figure IV.12 :
|
Variation de l'allongement à la rupture médiane
après vieillissement en fonction du taux de PRS.
|
Figure IV.13 :
|
Variation de la dureté Shore A moyenne en fonction du
taux de PRS.
|
Figure IV.14 :
|
Variation de la dureté Shore A médiane en
fonction du taux de PRS.
|
Figure IV.15 :
|
Variation de la stabilité thermique en fonction du taux
de PRS.
|
Liste des tableaux
Tableau II.1 :
|
Propriétés mécaniques du PVC.
|
Tableau III.1 :
|
Quelques caractéristiques du DOP.
|
Tableau III.2 :
|
Les caractéristiques essentielles d'I2
E1CN.
|
Tableau III.3 :
|
Quelques caractéristiques du PRS.
|
SOMMAIRE
Introduction générale
|
Chapitre I : Recyclage des
polymères
|
I.1. Introduction
|
I.2. Définition de déchet
|
I.2.1. Déchets inertes
|
I.2.2. Déchets spéciaux
|
I.2.3. Déchets banals
|
I.3. Origine et répartition des déchets
plastiques
|
I.3.1. Déchets industriels
|
I.3.1.a. Les thermoplastiques
homogènes
|
I.3.1.b. Les thermoplastiques complexés,
imprimés ou collés
|
I.3.2. Déchets de distribution et
commerciaux (transport, suremballage)
|
I.3.3. Déchets des consommateurs
finaux
|
I.4. Recyclage des matières plastiques
|
I.4.1. Incinération
|
I.4.2. Recyclage direct
|
I.5. Processus de collecte
|
I.5.1. Collecte globale
|
I.5.2 Collecte sélective
|
I.5.3 Collecte spécifique des
bouteilles en plastique transparent
|
I.6. Méthodes de valorisation
|
I.6.1. Définitions
|
I.6.1.a. Valorisation
|
I.6.1.b. Valorisation matière
|
I.6.1.c. Valorisation
énergétique
|
I.6.1.d. Valorisation chimique
|
I .6.2. Facteur potentiel de valorisation
|
I.6.2.a. Facteurs tenant à l'utilisation
des produits et conditionnant la qualité du
déchet
|
I .6.2.b. Facteurs concernant la nature
même du déchet
|
I.6.3. Valorisation physico-mécanique
|
I.6.3.a. Cas des
thermoplastiques homogènes
|
I.6.3.b. Cas des thermorigides
|
I.6.3.c. Cas des plastiques
mélangés
|
I.6.4. Valorisation en matières
premières
|
I.6.5. Valorisation énergétique
|
Chapitre II : Les
mélanges polymériques
|
II.1. Le polychlorure de vinyle
|
II.1.1. Synthèse du monomère
|
II.1.2. Polymérisation
|
II.1.3. Propriétés
|
II.1.3. a. Propriétés
physiques
|
II.1.3.b. Propriétés
mécaniques
|
II.1.3.c. Propriétés chimiques
|
II.1.3.d. Propriétés
électriques
|
II.1.3.e. Propriétés
thermiques
|
II.1.3.f. Propriétés
dimensionnelles
|
II.1.3.g. Comportement au feu
|
II.1.4. Dégradation thermique du PVC
|
II.1.4. a. Amorçage
|
II.1.4. b. Propagation
|
II.1.4.c. terminaison
|
II.1.5. Application
|
II.1.6. Production mondiale
|
II.1.7. Consommation mondiale
|
II.1.8. Valorisation du PVC
|
II.1.5.a/ Incinération
|
II.1.5.b/ Recyclage de la
matière
|
II.2. Le polyéthylène
réticulé
|
II.2.1. Généralité sur la
réticulation
|
II.2.3. Type de réticulation
|
II.2.3.a) Par irradiation
|
II.2.3.b) Par peroxyde
|
II.2.3.c) Par addition de silane
|
II.2.4. Application de la réticulation par les
silanes
|
II.3.Les blends
|
II.3.1. Introduction
|
II.3.1.a. Les mélange de polymères
immiscibles
|
II.3.1.b. Les polymères
chargés
|
II.3.2. Définition des deux termes
miscibilité-compatibilité
|
II.3.2. a) miscibilité
|
II.3.2. b) compatible
|
II.3.3. Thermodynamiques des polymères
|
II.3.4. Techniques de mélangeage
|
II.3.5. Structure des mélanges
|
Chapitre III : Matériaux
et techniques
|
III.1. Matières utilisées
|
III.1.1. Le polychlorure de vinyle (PVC)
|
III.1.2. Le polyéthylène
réticulé par le silane (PRS)
|
III.2. Méthodologie
|
III.3. Préparation des mélanges
|
III.4. Préparation des
plaques
|
III.5. Préparation des
éprouvettes
|
III.6. Propriétés des
mélanges
|
III.6.1. Etude rhéologique
|
III.6.2. Etude mécanique
|
III.6.2.1. Comportement en traction
|
III.6.2.2. Essais de la dureté shore
A
|
III.6.3. La stabilité thermique
|
|
Chapitre IV : Résultats
et discussions.
|
IV.1. Etude rhéologique
|
IV.2. Etude mécanique
|
IV.2.1. Comportement en traction
|
IV.2.1.a. avant vieillissement
|
IV.2.1.b. Après vieillissement
|
IV.2.2. Dureté Shore A
|
IV.3. Etude thermique
|
IV.3.1. Stabilité thermique
|
Conclusion générale
|
Références
bibliographiques
|
Annexe
|
|
Introduction générale
Il est connu que le recyclage n'est pas un
procédé nouveau, en effet, les matériaux de
construction anciens ont été recyclés pendant plus d'un
millénaire, aussi la ferraille industrielle, pour sa part, a
été recyclée durant des décennies [1].
Le traitement des déchets de matières
plastiques est devenu une préoccupation de tout premier plan, tant que
pour les industriels que pour les consommateurs qui se retrouvent
impliqués dans la gestion de leurs déchets par des
opérations de tri en amont. Le gisement global
de déchets de matières plastiques est particulièrement
complexe, compte tenu de la grande diversité des produits existant sur
le marché [2].
Il y a plus d'un demi-siècle que les
mélanges à base des polymères ont fait leur apparition
dans l'industrie des plastiques. En particulier, l'intérêt qu'ont
reçu les matériaux multicomposants, a entraîné
plusieurs tentatives d'études pour relier le comportement
mécanique à celui des phases constituantes adéquates. La
capacité d'un mélange d'exécuter une bonne performance
dans une application donnée dépend de la capacité des
composants à former une phase unique [1].
Le développement de nouveaux matériaux
plastiques à partir de polymère recyclé est une
possibilité intéressante du point de vue économique et
écologique [1].
L'objectif de notre travail consiste à
étudier le comportement du blend (polyéthylène
réticulé par le silane et le polychlorure de vinyle
recyclé) à savoir :
· Etude rhéologique
· Etude mécanique tel que le comportement en
traction (avant et après vieillissement) et l'essai de la dureté
Shore A
· Etude thermique (stabilité thermique).
Ce mémoire est subdivisé en :
Ø Introduction générale
Ø Quatre chapitres :
Le premier chapitre est consacré au recyclage des
polymères, le deuxième décrit les
mélanges polymériques, le troisième est consacré
à l'étude expérimentale ; il décrit les
matériaux utilisés et les techniques de mise en oeuvre et le
dernier chapitre expose les résultats expérimentaux ainsi que
leurs interprétations.
Ø Conclusion générale.
I.1. Introduction :
Comme tout producteur sensé et économe,
les transformateurs de matière plastique ont- dés le début
de leur fabrication- cherché à diminuer la quantité de
déchet produit dans leur usine. Ils ont donc les structures de
récupération de produit hors normes, de manière
à avoir des coûts de revient aussi faible que possible [3].
Dans de nombreuses fabrications il n'est pas rare que
les chutes obligées d'une production quelconque atteignent
30 à 50 % du poids de l'objet fini vendable. Ce sont par exemple
les chutes de fond et de goulots lors du soufflage de corps creux,
les lisières de calendre ou thermoformage, les chutes de découpe
lors de la fabrication de sac soufflage...etc. Cette quantité
obligé doit être récupérer pour éviter le
grever de manière insupportable le coût de revient
[3].
Dans de nombreux cas, ces chutes sont broyées
et envoyées immédiatement dans le processus de
fabrication ; elles ne sont pas souillés ou mélangées
à d'autre produit, elle se réincorpore facilement dans celui-ci,
et souvent facilite même la mise en oeuvre [3].
Dans d'autre cas, il n'est pas possible de
réincorporer les déchets directement dans la fabrication qui
en serait perturbé. Ils sont donc utilisés dans la fabrication de
différents produits [3].
I.2. Définition de déchet :
La notion de déchet semble relever du sens
commun et pourtant, il n'est pas toujours facile de la définir sans
ambiguïté [4].
On peut le définir comme tout matériau
produit involontairement, lors d'une fabrication ou d'une
utilisation [5].
On répartit les déchets en trois grandes
catégories qui sont les déchets inertes, les
déchets spéciaux et les déchets banals [4].
I.2.1. Déchets inertes :
Les déchets inertes sont des déchets
n'ayant pas d'action sur le milieu ambiant et non susceptibles
d'évolution physico-chimique ou biologique importante au cours du temps.
En particulier, ils ne se décomposent pas, il
ne sont pas biodégradables et ne brûlent pas [4].
I.2.2. Déchets spéciaux :
Les déchets spéciaux sont des
déchets dangereux. Leur nature nécessite des
protections particulières vis-à-vis de l'environnement lors de
leur collecte, de leur traitement et de leur éventuel stockage [4].
I.2.3. Déchets banals :
Les déchets banals sont des
déchets non inertes et non dangereux. On les retrouvera principalement
dans les ordures ménagères mais aussi dans les déchets des
entreprises. En général, les déchets plastiques se
retrouveront dans cette catégorie [4].
I.3. Origine et répartition des déchets
plastiques :
On est amené à classer les
déchets de matières plastique en :
I.3.1. Déchets industriels :
Ces déchets sont le plus souvent
homogènes, bien identifiés et peu souillés, ils sont
vendus à des récupérateurs ou recycleurs. Ces
déchets peuvent représenter des quantités notables mais
ils sont propres, bien identifiés. On distingue [5] :
I.3.1.a. Les thermoplastiques homogènes :
Les déchets sont produits lors des mises en
route et des arrêts des machines où sont inhérents aux
procédés eux-mêmes : chutes de découpage de films ou
de profilés, etc. Sauf en cas de produits souillés ou
oxydés, ils sont réintégrés dans le
procédé de transformation après broyage et granulation, ou
de séchage pour les plastiques sensibles à l'humidité [5].
I.3.1.b. Les thermoplastiques complexés, imprimés ou
collés :
Ces produits sont propres, bien identifiés
mais multicouches, donc hétérogènes. Il est souvent
malaisé de les recycler sur le site de fabrication et ils sont vendus
à l'extérieur pour une valorisation thermique ou pour fabriquer
une matière ultérieure [5].
I.3.2. Déchets de distribution et commerciaux
(transport, suremballage) :
Ces déchets concernent les emballages
industriels et commerciaux et ce présentent essentiellement sous la
forme de films de polyoléfine, dans une proportion très
importante de films étirables et rétractables qui
nécessitent des traitements appropriés, compte tenu de leur
comportement particulier, notamment lors des opérations de broyages.
La consommation de résines de ce secteur d'application
est très grande. Le taux de récupération et
de régénération de ces films est évalué
à 30% de la consommation totale. Ces derniers étant de bonne
qualité, ils trouvent facilement acquéreur [6] .
I.3.3. Déchets des consommateurs finaux :
Parmi ces déchets on trouve [5] :
· Déchets d'emballages plastiques dans les ordures
ménagères.
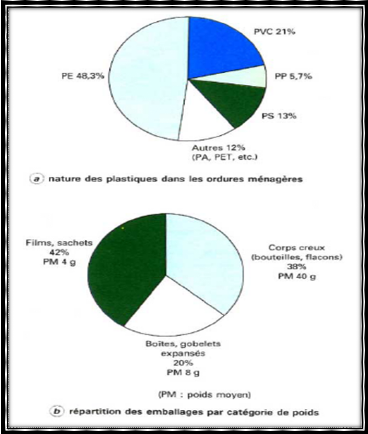
Figure I.1- Déchets d'emballages plastiques dans
les ordures ménagères [5].
· Déchets plastiques du bâtiment et travaux
publics.
· Déchets plastiques de l'automobile et du secteur
des pièces industrielles.
· Déchet dans le domaine de l'agriculture.
I.4. Recyclage des matières
plastiques :
Les principaux avantages des matières
plastiques (longue durée de vie, faible dégradation, faible
densité et grande diversité d'utilisation) deviennent des
inconvénients lorsque ces produits deviennent des déchets
légers. Ils sont facilement emportés par le vent ou les
rivières. Ils créent une pollution relativement durable ;
très divers et dispersés, ils sont difficiles à collecter
et à trier en vue d'un recyclage [7].
Les deux principaux modes d'élimination des
matières plastiques sont l'incinération et le recyclage [7].
I.4.a. Incinération :
La combustion totale des matières plastiques
ne produite, pour 80 % d'entre elles (PE, PS, PP....), que du dioxyde de
carbone et de la vapeur d'eau. Les polymères chlorés (PVC
principalement) produisent en plus du chlorure d'hydrogène. Certains
plastiques peuvent donner des gaz polluants, azotés ou soufrés
[7].
La plupart des usines d'incinération sont
équipées d'installations de lavage des
fumées destinées à capter l'essentiel de ces polluants.
Ainsi 90 % du chlorure d'hydrogène, les oxydes de soufre et le cyanure
d'hydrogène sont neutralisés par des lavages
basiques [7].
La combustion facile et très exothermique des
plastiques facilite en outre la combustion des autres
déchets auxquels ils sont mélangés, ce qui diminue la
quantité de combustibles nécessaire au fonctionnement des
usines d'incinération [7].
I.4.b. Recyclage direct :
Contrairement à ce que l'on imagine souvent,
la majorité des plastiques est recyclable [7].
Les thermoplastiques, une fois triés, peuvent
être fondus et à nouveau mis en forme pour une nouvelle
utilisation. Si le tri a été très strict, le nouveau
produit aura les mêmes qualités que le plastique initial et pourra
assurer les mêmes usages à 1a seule exception de l'emballage
alimentaire qui exige des matériaux neufs [7].
Les thermodurcissables ne peuvent bien sûr pas
être refondus, mais, après broyage, ils peuvent être
utilisés comme charge dans de nouveaux plastiques. Les
élastomères (essentiellement le caoutchouc des pneumatiques) sont
recyclables dans les revêtements routiers [7].
I.5. Processus de
collecte :
Le recyclage des déchets plastiques est
intimement lié aux opérations de
regroupement et de collecte. Ces dernières constituent la
véritable première étape de la chaîne
du recyclage [5].
I.5.1. Collecte globale :
C'est une opération consistant à
enlever les déchets présentés dans des récipients
prévus à cet effet pour les acheminer vers un lieu
d'élimination. C'est une collecte multi matériaux où la
phase organique des ordures ménagères est mélangée
avec les autres déchets des ménages (emballages, etc.) [5].
I.5.2. Collecte sélective :
Elle est pour objectif de sélectionner, au
départ des ménages, un ou plusieurs types de matériaux
afin de faciliter leur valorisation ou leur élimination
ultérieure. La participation du consommateur est
requise. Les méthodes de collecte et de ramassage sont extrêmement
variées et dépendent des choix faits par les collectivités
locales pour le ramassage, des conditions d'habitat ainsi que des
procédés et des unités de
traitement des déchets qui sont ou qui seront installés en aval
pour une valorisation ou une élimination optimale [5].
I.5.3. Collecte spécifique des bouteilles en
plastique transparent :
A l'issus de la tournée de collecte, les
bouteilles en plastique transparent sont acheminées vers un centre de
tri et de conditionnement [6].
I.6. Méthodes de valorisation :
I.6.1. Définitions :
I.6.1.a. Valorisation :
C'est toute opération
permettant de réintroduire un déchet dans un processus
de production ou de lui conférer une nouvelle valeur d'usage [5].
I.6.1. b. Valorisation
matière :
Elle est appelée également, recyclage
mécanique, il s'agit de l'opération globale consistant à
la production d'une nouvelle matière à partir d'un déchet.
Dans ce cas, il n'y a pas de destruction majeure de la structure chimique du
polymère [2].
I.6.1.c. Valorisation
énergétique :
Elle est appelée également, recyclage
énergétique, elle vise la production d'énergie calorifique
[2].
Plusieurs techniques permettent d'atteindre cet
objectif dont les plus connus sont l'incinération, la pyrolyse ou la
thermolyse. Cette énergie calorifique peut être utilisée
sur place ou transformée par la suite en énergie
électrique, en fonction des besoins du moment ou du lieu de traitement
[2].
I.6.1.d. Valorisation chimique :
Il s'agit de tout processus chimique permettant la
transformation d'un déchet en des produits chimiques
utilisables comme intermédiaires réactionnels dans l'industrie
chimique ou l'industrie de la transformation des matières plastiques
[2].
I .6.2. Facteur potentiel de
valorisation :
L'envergure du problème des déchets
solides, la diversité des matériaux et
des utilisations obligent à prendre en compte un certain nombre de
facteurs avant d'étudier les valorisations des déchets [2].
I.6.2.a. Facteurs tenant à l'utilisation des
produits et conditionnant la qualité du
déchet :
De multiples facteurs sont à considérer
: la localisation, la concentration et les tonnages, les
dimensions et les formes des objets, la nature et le degré
de contamination du déchet, le degré de dispersion
et l'hétérogénéité de l'ensemble auquel il
appartient [5].
I .6.2.b. Facteurs concernant la nature même du
déchet :
On distingue trois grandes familles de
matériaux dont les propriétés de base orientent vers des
voies de valorisation prioritaires [5] :
· Les déchets organiques :
Ils sont susceptibles de décomposer sans
résidus toxiques mais avec dégagements gazeux toxiques
(H2S ; etc.) ou explosifs (méthane) par les micro-organismes
[5].
· Les produits d'origines
minérales :
Ils résistent aux hautes températures.
La fusion des déchets permet d'éliminer les
molécules organiques plus fragiles. Bien que cette deuxième
fusion absorbe de l'énergie, le recyclage de
matière est la voie unique et prioritaire [5].
· Les macromolécules organiques d'origine
naturelle ou de synthèse :
Elles ont une résistance limitée
à la chaleur, à l'oxydation et au vieillissement. Elles perdent
une partie de leurs propriétés par des ruptures de chaîne
pour les plastiques [5].
I.6.3. Valorisation
physico-mécanique :
I.6.3.a. Cas des
thermoplastiques homogènes :
Les déchets, objets usagés, chutes de
fabrication, etc., sont triés, broyés, lavés (si
nécessaire), éventuellement micronisés,
séchés pour être ensuite fondus dans
une extrudeuse équipée le plus souvent d'un système
de filtrage manuel ou automatique. La matière est extrudée
puis découpée en granulés, ou encore granulée
directement par un système de coupe en tête. Le
produit obtenu est qualifié de régénérer. [5]
I.6.3.b. Cas des thermorigides :
Ile sont infusibles, souvent renforcés avec des
charges, les déchets sont broyés et
réincorporés dans de nouvelles formules. [5]
I.6.3.c. Cas des plastiques
mélangés :
Dans la mesure où l'ensemble des fractions
plastiques considérées garde après mélange une
bonne thermoplasticité et une bonne compatibilité, on peut
envisager des techniques dites de recyclage des plastiques
mélangés. La fraction plastique des ordures
ménagères composée essentiellement d'emballages
thermoplastiques (polyoléfines, polystyrènes, PVC) est donc une
source intéressante à considérer [5].
v Circuit des déchets
plastiques :
La collecte des déchets plastiques est
organisée selon le schéma de la figure I.2.
Une partie des déchets plastiques issus de
l'industrie, de la distribution, des collectes sélectives et des
déchetteries est directement prise en charge par la filière
d'origine (PVC, PET, etc.). Les autres plastiques ainsi que ceux contenus dans
les ordures ménagères constituent le gisement à traiter
par la filière du recyclage des plastiques mélangés. Il
existe aujourd'hui une dizaine d'entreprises qui ont développé
des procédés de recyclage des plastiques
mélangés [5].
Certains transformateurs utilisent ces technologies
avec les seuls déchets plastiques contenus dans les ordures
ménagères. D'autres, pour améliorer la qualité des
produits finis, incorporent des déchets plastiques moins
souillés, comme ceux provenant de l'industrie
[5].
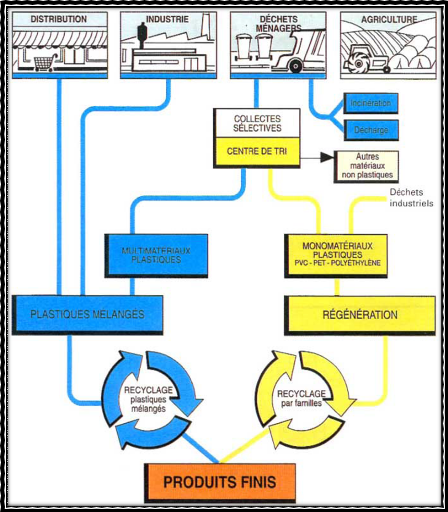
Figure I.2 - Collecte des déchets plastiques
[5].
v Techniques de recyclage des plastiques
mélangés :
Le traitement des déchets plastiques, avant
recyclage, nécessite une préparation selon le schéma de la
figureI.3. Une fois lavés, séchés,
déchiquetés et broyés, les déchets plastiques vont
subir un procédé de régénération
établi d'après les techniques utilisées pour la mise en
forme des produits finis. Il s'agit de [5] :
- L'extrusion.
- L'extrusion puis le moulage par intrusion basse pression.
- L'extrusion puis le moulage par compression.
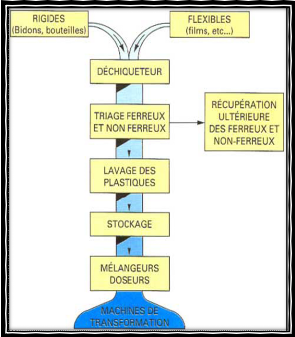
Figure I.3- Recyclage des déchets plastiques
[5].
I.6.4. Valorisation en matières
premières :
Le recyclage des matières pour la chimie vise
à décomposer les molécules constituantes des
résines en matières premières utilisables de nouveau dans
les raffineries, la pétrochimie et la chimie. Un certain nombre de
techniques sont actuellement à l'étude [5].
· Pyrolyse ;
· Hydrogénation ;
· Gazéification ;
· Décomposition chimique proprement dite par
l'application de procédés tels que l'hydrolyse, l'alcoolyse, la
glycolyse.
I.6.5. Valorisation
énergétique :
Les matières plastiques sont, parmi tous les
matériaux, capables de restituer la plus grande part de l'énergie
nécessaire à leur fabrication.
Dans une incinération avec
récupération de chaleur et production de vapeur, d'eau chaude ou
d'électricité, les matières plastiques sont d'autant plus
intéressantes à brûler que leur pouvoir calorifique est
élevé. C'est le cas particulièrement pour les plastiques
à PCI (pouvoir calorifique inférieur) élevé comme
les PE, PP et PS, qui représentent 70 % des déchets de
plastiques dans les ordures ménagères [6].
II. Les mélanges polymériques :
II.1. Le polychlorure de vinyle :
Les premiers développements industriels du
polychlorure de vinyle (PVC) ont été réalisés en
Allemagne vers 1930. Le PVC, qui a longtemps occupé le premier rang
des matières plastiques, atteint aujourd'hui l'âge
mûr : la consommation mondiale s'est hissée à 10 Mt en
1984 [8]. Le PVC est de formule générale :
Cl
CH2
CH
n
Le PVC est une matière thermoplastique de
synthèse obtenue par polymérisation du chlorure de vinyle
(CVM) ou monochloréthylène [9].
II.1.1. Synthèse du
monomère :
La synthèse du chlorure de vinyle
monomère (CVM) est réalisée suivant deux principaux
procédés [10] :
· L'addition du gaz chlorhydrique sur
l'acétylène :
C2H2+HCl CH2 =
CHCl
· La chloration de l'éthylène en
1,2-dichloroéthane, puis pyrolyse de se dernier :
CH2Cl - CH2Cl
CH2 = CHCl + HCl
II.1.2. Polymérisation:
La réaction de polymérisation du chlorure de
vinyle monomère par voie radicalaire donne naissance à des
macromolécules linéaires de masses moléculaires moyennes
déterminées dont la répartition présente une allure
gaussienne asymétrique. C'est une réaction
fortement exothermique [11].
Il existe plusieurs procédés industriels
de polymérisation du chlorure de vinyle monomère [11] :
- En suspension,
- En masse,
- En émulsion,
- En microsuspension.
II.1.3. Propriétés :
II.1.3.a. Propriétés
physiques :
Le PVC est un polymère atactique donc
essentiellement amorphe, mais il arrive que, localement sur de courts segments
de chaines, le PVC soit syndiotactique et puisse s'organiser en phase
cristalline, mais le taux de cristallinité ne dépasse
jamais 10 à 15% [12].
La masse volumique du PVC est de l'ordre de
1.38g/cm3. Le PVC amorphe est transparent et relativement
perméable à la vapeur d'eau. Sa masse moléculaire moyenne
du PVC est généralement donnée par la «valeur
K». Lorsque la valeur K augmente, la résilience, la
stabilité dimensionnelle à chaud et la résistance au
fluage augmentent alors que la transformation devient plus difficile [12].
II.1.3.b. Propriétés
mécaniques
Elles sont présentées dans le tableau
(II.1).
Tableaux (II.1) :
Propriétés mécaniques du PVC [12].
Propriétés
|
Unité
|
PVC rigide
|
PVC souple
|
Masse volumique
Contrainte à la rupture
Allongement à la rupture
Résistance à la flexion
Module de traction
Module de flexion
Résilience
Dureté shore D
|
g/cm3
MPa
%
MPa
MPa
MPa
J/m
__
|
1.38
50
10-50
70-80
2400
2000
50-200
70-84
|
1.3-1.7
10-20
200 à 500
__
__
__
__
20-40
|
II.1.3.c. Propriétés
chimiques :
· Résistance aux agents
chimiques :
Le PVC non plastifié possède une
résistance remarquable à bon nombre de produits chimique, une
gamme étendue d'application où cette qualité revêt
une importance primordiale [10].
Par contre, le PVC plastifié est sensible
à certains solvants organiques (aromatiques, cétoniques et
chlorés) [10].
· Tenue à la lumière :
(Résistance photochimique)
Compte tenu des précautions spéciales
prisent au stade de la formulation qu'à celui de la transformation, les
compositions à base de PVC présente une bonne tenue au
vieillissement naturel, qui peut être améliorée par
l'addition d'agents de protection anti-UV et le choix de colorants ou pigments
sélectionnés en vue d'utilisations particulières [10].
II.1.3.d. Propriétés
électriques :
Le PVC a de bonnes propriétés isolantes
mais les pertes électriques dans le matériau sont suffisamment
importantes pour permettre le soudage par haute fréquence [12].
II.1.3.e. Propriétés thermiques :
· Conductivité
thermique :
Elle est d'environ 0,2 W. m-1.K
-1.
· Capacité thermique
massique :
Elle est d'environ 1 046 J.kg-1.K
-1.
· Pouvoir calorifique :
Il est de 17 kJ/kg environ, pour les PVC non
plastifiés et de valeur supérieure mais variable suivant la
formulation pour les PVC plastifiés.
· Coefficient de dilatation
linéique :
Il est d'environ 5.10-5 à
8.10-5 K-1 pour les PVC non plastifiés et moins
significatif pour les PVC plastifiés.
· Température de ramollissement
Vicat :
La température de ramollissement Vicat pour les PVC
non plastifiés se situe entre 65 et 85 °C. Pour des
mélanges de PVC et de PVC chloré, elle peut atteindre des valeurs
supérieures à 100 °C.
· Température de fléchissement sous
charge :
Elle ne s'applique qu'aux PVC non plastifiés.
Elle varie de 55 à 70 °C selon les formulations et peut atteindre
90 °C pour celles contenant du PVC chloré.
II.1.3.f. Propriétés
dimensionnelles :
Le PVC présente une bonne stabilité
dimensionnelle et un retrait limité dû à
sa structure amorphe [11].
II.1.3.g. Comportement au feu :
Le PVC se décompose dans une flamme en
libérant de l'acide chlorhydrique gazeux mais il est auto extinguible.
Les PVC plastifiés brulent plus facilement [12].
II.1.4. Dégradation thermique du PVC :
Sous l'influence de la chaleur, le PVC subit une
dégradation profonde, accompagnée d'une coloration
caractéristique. Plus cette dernière s'accentue, plus les
propriétés du PVC décroissent, et devient de plus en plus
fendillé et cassant et fini par se désagréger
complètement. Ce processus est déclenché selon deux
étapes principales [10]:
II.1.4.a. Amorçage :
La dégradation thermique du
PVC produit des atomes de chlore labiles, où un ion de chlore est
encore séparé pendant que le proton correspondant et sa charge
positive reste sur la chaîne [10].
~CH2 -- CHCl --
CH2 -- CHCl~ ~CH2
-- ÿCH -- CH2 --
CHCl~ + Clÿ
II.1.4.b. Propagation :
La réaction de dégradation thermique la
plus importante est la formation de l'acide chlorhydrique, laissant la place
à une double liaison. Cette déshydrochloruration obéit
à un mécanisme ionique, c'est-à-dire que le chlore est
séparé en tant qu'anion et l'hydrogène
en tant que proton à partir d'une unité structurale, il
déstabilise l'unité structurale voisine et facilite donc une
propagation en cascade, ce qu'on l'appelle en anglais
« unzipping » donnant ainsi naissance à des
séquences de double liaisons conjuguées, appelées un
polyéne conjugué, responsable des colorations parasites,
cette réaction est catalysée par l'acide chlorhydrique
formé [10].
Clÿ+ ~ CH2 -- CHCl
-- CH2 -- CHCl~ HCl
+ ~ÿCH -- CHCl -- CH2
-- CHCl~
~ÿCH -- CHCl
-- CH2 -- CHCl~
~CH = CH -- CH2 -- CHCl~ +
Clÿ
~CH = CH -- CH2
-- CHCl~ + Clÿ ~CH = CH
-- ÿCH -- CHCl~ + HCl
~CH = CH -- ÿCH --
CHCl~ ~CH = CH -- CH =
CH~ + Clÿ
Les atomes de chlore peuvent
s'échapper de cet environnement et attaquer une autre chaîne.
II.1.4.c. terminaison :
La réaction est terminée par :
Clÿ +
Clÿ Cl2
Certaines observations expérimentales ne
peuvent pas être expliquées par les
mécanismes radicalaires et il est particulièrement difficile
à expliquer l'effet de HCl.
Lorsque le nombre de doubles liaisons
conjuguées formées devient égal ou supérieur
à 5, le PVC commence à se colorer, il devient brun puis noirci,
avec augmentation du nombre de réticulation, si le
phénomène continue [10].
II.1.5. Application :
Grâce à ses propriétés
très diverses, le PVC est le polymère qui couvre tous
les secteurs de l'activité économique. C'est aussi un des plus
utilisés depuis 1996, avec une consommation mondiale de 20 millions de
tonnes dans le monde. Il se place au second rang après le
polyéthylène [11].
Cette diversité des propriétés et
son aptitude à répondre favorablement à plusieurs
exigences cumulées en font un matériau de choix pour les secteurs
du bâtiment, de l'emballage, de
l'électricité et de l'électronique, des transports et de
la santé [11].
II.1.6. Production mondiale:
La production mondiale du PVC en 2002 est 32 400
kt. [13]. La figure II.4 donne la production du PVC pour
quelques pays.
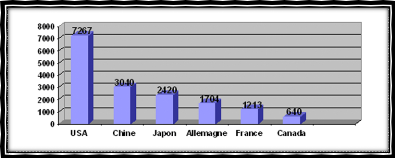
Figure II.1 : Production mondiale du PVC en
kt [13].
II.1.7. Consommation mondiale :
La consommation mondiale du PVC en 2003 est
27 400 kt [13]. La figure II.4 illustre la consommation du PVC pour
quelques pays.
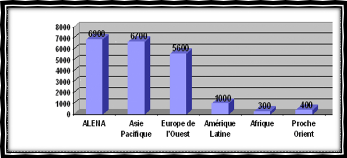
Figure II.2 Répartition mondiale de la
consommation [13]. [13].
II.1.8. Valorisation du PVC :
Le PVC est un matériau parfaitement
valorisable. Cette valorisation repose sur deux modes [11] :
· Incinération,
· Recyclage de la matière.
II.1.8.a. Incinération :
La composition vinylique à base de PVC a en moyenne
un pouvoir calorifique inférieur (PCI) voisin de 20 kJ/kg,
c'est-à-dire équivalent à celui du bois
ou du charbon. Le PVC peut donc être utilisé
comme combustible de substitution.
Dans les déchets ménagers, il facilite la combustion. La
combustion du PVC, comme celle de tous les composés
chlorés, peut donner naissance à des
dioxines [11].
La présence de carbone dans la molécule
de PVC conduit naturellement, par incinération, à la formation et
au dégagement d'oxyde de carbone CO et de gaz carbonique CO2.
Ce dernier est inférieur à celui libéré par les
autres matières plastiques [11].
II.1.8.b. Recyclage de la
matière :
Sous ce vocable, on peut englober deux approches de ce
type de valorisation [11]:
-- La régénération qui consiste à
réintroduire le PVC à un degré de pureté
élevé dans le circuit industriel de fabrication de
produits semi-finis (granulés par exemple) ou finis (tubes,
profilés...).
-- La production de matières premières qui
permet de récupérer le gaz chlorhydrique et sa
réintroduction dans la fabrication du chlorure de vinyle
monomère.
·
Régénération :
Quelle que soit l'origine du PVC collecté
(bouteilles, tubes, châssis de fenêtres...), un traitement
préalable de tri, nettoyage, purification, est nécessaire pour
assurer une valorisation judicieuse.
L'opération de tri vise à extraire les
polluants du type [11] :
-- Autres plastiques,
-- Verre,
-- Métaux,
-- Caoutchouc,
-- Papier.
Une opération de lavage et de traitement
préliminaire élimine les éléments
indésirables tels que terre, étiquettes...etc.
Par broyage, on obtient des copeaux de dimension
grossière (environ 30 mm de côté) qui suivent ensuite
différentes étapes de lavage et de séparation
basées sur la différence de densité (décantation,
hydrocyclonage) pour éliminer les résidus lourds (verre,
métaux...) ou légers (bouchons, papier d'étiquetage...)
[11].
Le PVC ainsi amené à une pureté
supérieure ou égale à 99,9 % est séché et
réduit en poudre de granulométrie adaptée aux
utilisations ultérieures (< 1mm). On utilise ensuite les mêmes
moyens de mise en oeuvre que pour les compositions vinyliques [11].
· Production de matières
premières :
Lorsque le PVC est soumis à des
températures élevées (supérieure à 200
°C), il se décompose en gaz chlorhydrique (HCl)
et en hydrocarbures, qui peuvent donner lieu à une valorisation
énergétique, selon les procédés de mis en oeuvre
[11].
Le gaz chlorhydrique provenant de cette
décomposition thermique est récupéré,
purifié et condensé. Il peut alimenter une unité
d'oxychloration.
L'élément chlore accomplit donc le cycle
[11]:
PVC HCl CVM
PVC
Il peut également être neutralisé
soit avec du bicarbonate de sodium (Na HCO3), soit avec de la soude
(NaOH) [11].
L'HCl est ainsi transformé en chlorure de
sodium (NaCl) qui, après purification, est électrolysé
pour donner du chlore, lequel est transformable en chlorure de vinyle puis
en PVC [11].
L'élément chlore accomplit donc le cycle
[11] :
PVC HCl NaCl
Cl2 CVM PVC
Si le PVC est présent à faible teneur,
par exemple dans le cas de plastiques mélangés, il peut faire
l'objet d'une valorisation matière. Si, au contraire, on traite une
fraction riche en PVC ou en produits chlorés en général,
il est préférable de procéder à
l'incinération avec valorisation énergétique [11].
Actuellement, il n'existe pas de réalisations
industrielles, mais des projets sont avancés [11].
II.2. Le polyéthylène
réticulé :
II.2.1. Généralité sur la
réticulation :
On appelle polyoléfines les polymères
dérivés de la polymérisation de l'éthylène
dans lesquels on peut substituer des hydrogènes par un groupement
hydrocarboné différent [12].
Lorsque les polyoléfines sont
réticulées, des liaisons covalentes sont formées liant
les différentes régions, un réseau tridimensionnel est
formé [14].
Le réseau tridimensionnel améliore les
propriétés électriques, mécaniques
et chimiques [15].
II.2.3. Type de réticulation :
Le polyéthylène basse densité
est réticulé par trois différentes techniques [15]
:
II.2.3.a. Par irradiation :
La réticulation par irradiation Bêta est
un processus chimique, où l'échantillon est simplement sujet
à une dose d'électrons de haute énergie pendant un temps
correspondant à une dose calculée pour le degré
nécessaire de réticulation. Celle-ci ce passe
à la température ambiante et à l'état solide [14].
II.2.3.b. Par peroxyde :
La réticulation par le peroxyde est la
technique la plus utilisée ces dernières années où
le polyéthylène basse densité réticulé par
le peroxyde est devenu le matériau isolant le plus dominant pour
les câbles électriques à moyen et haut voltage [15].
II.2.3.c. Par addition de silane :
La réticulation par les silanes est l'une des
plus importantes techniques de réticulation. Elle
a été introduite en 1968 à travers le processus de
Sioplas. Le PRS est généralement
utilisé pour l'isolation des câbles électriques à
bas voltage [15].
II.2.4. Application de la réticulation par les
silanes :
La réticulation par les silanes est une
méthode très économique. Les produits obtenus par cette
méthode sont largement utilisés dans le domaine de la plomberie.
[15]
L'utilisation du polyéthylène
réticulé par le silane se développe pour l'isolation
des câbles à haute tension [15].
II.3.Les blends :
II.3.1. Introduction :
La réalisation de mélanges de
polymères apparaît depuis quelques années comme un
moyen d'accéder à des matériaux offrant des
propriétés souvent inaccessibles par la synthèse
directe d'homopolymères ou de copolymères. Depuis le début
des années 1980, le nombre de mélanges de polymères
commercialisés n'a cessé de croître alors que pendant la
même période, très peu de nouveaux polymères de base
sont apparus. Cette croissance des mélanges repose essentiellement sur
des raisons économiques, la structure industrielle requise pour leur
production étant plus légère que celle requise pour la
production d'une nouvelle molécule. Dans son principe même,
la mise au point de mélanges permet souvent de mieux approcher le
rapport performance/coût nécessaire aux applications [16].
On rencontre sur le marché essentiellement deux types
de mélanges:
II.3.1.a. Les mélanges de polymères
immiscibles :
Les propriétés des
mélanges de polymères du produit fini sont des combinaisons plus
ou moins favorables des propriétés des polymères
constitutifs. Ces mélanges sont obtenus par mélange à
l'état fondu de deux polymères et souvent d'un troisième
composant jouant le rôle de compatibilisant nécessaire pour le
développement d'une morphologie contrôlée permanente. On
peut rencontrer des morphologies dispersées où l'un des deux
constituants, le plus souvent le composant minoritaire, forme des petites
gouttelettes noyées dans une phase continue de l'autre constituant ou
des morphologies co-continues où les deux phases apparaissent
continues et interpénétrées. Il existe également
quelques mélanges de polymères miscibles [16].
II.3.1.b. Les polymères
chargés :
Ils sont obtenus par dispersion lors
de la phase de mélangeage d'agglomérats de particules
solides (fibres, noirs de carbone, silices, argiles...) dans une matrice
de polymère ou de mélange de polymères. Ces charges
sont utilisées principalement pour leurs propriétés
renforçantes, conductrices ou colorantes, mais elles peuvent
également être utilisées dans un but économique pour
réduire le coût d'un polymère. Selon les
propriétés attendues du produit fini, on cherchera à avoir
différents états de dispersion des charges (taille plus ou moins
grande des agglomérats, répartition homogène des charges
dans la matrice polymère ou encore formation de réseaux
localisés dans un des constituants ou à l'interface)
[16].
II.3.2. Définition des deux termes
miscibilité-compatibilité :
II.3.2.a. Miscibilité :
La miscibilité des
polymères est définie comme une solubilité mutuelle
des polymères au niveau macromoléculaire. Deux
polymères A et B sont miscible quand ils donnent un mélange
homogène. Ce phénomène peut avoir lieu dés que
l'énergie libre (ÄGm) est plus petite que
(ÄGi) des composants [17].
II.3.2.b. Compatibilité :
Ce terme est utilisé pour décrire les
mélanges de polymères présentant les
propriétés pratiques utiles et cela se soucier s'ils sont
théoriquement miscibles ou non [1].
On peut la définir comme la miscibilité
moléculaire qui est définie comme une
solubilité mutuelle des polymères au niveau
macromoléculaire [17].
II.3.3. Thermodynamiques des
polymères :
La comparaison des mélanges de polymères
avec des systèmes constitués de petites molécules permet
de comprendre la tendance des macromolécules à se séparer
en phases distinctes. Si l'on prend, pour ce faire, un réseau tel que
ceux représentés sur la figure II.1 dans lequel chaque case est
occupée soit par une molécule simple, soit par une unité
appartenant à une chaîne macromoléculaire, l'entropie de
mélange est, par définition, proportionnelle au logarithme du
nombre de complexions (c'est-à-dire d'arrangements possibles) des
différents composants du système [18] :
?S = k ln W
(II.1)
W : Etant le nombre de complexions
k : La constante de Boltzmann
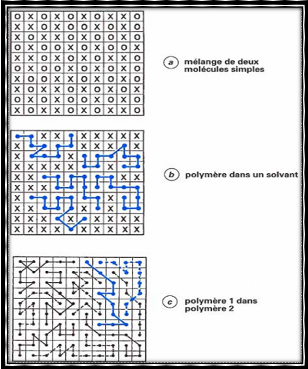
Figure II.1 : Représentation
schématique de différents systèmes binaire
[18].
Dans le cas d'un mélange de deux
molécules simples, le nombre de complexions s'élève
à 2100, tandis qu'il se réduit à 255
pour une solution de polymères et à 210 pour
un mélange de deux polymères différents. L'entropie de
mélange est donc d'autant plus faible que les chaînes
concernées sont longues et n'est généralement pas
suffisante pour compenser les interactions répulsives qui se manifestent
entre les unités de nature chimique différente. Ces interactions
répulsives reflètent la nature endothermique du processus
de mélange et se traduisent par une enthalpie de mélange
positive (?HM > 0). Dans ces conditions,
l'énergie libre de mélange est positive, ce qui est favorable
à la démixtion des polymères [18] :
?GM = ?HM - T?SM >
0
Toutefois, des mélanges miscibles peuvent
être obtenus lorsque les chaînes sont courtes [?SM est
alors plus important] ou lorsque l'enthalpie de mélange n'est que
faiblement positive. Dans certains cas favorables, il peut se produire que
l'énergie d'échange d'unités dissemblables, dont
l'intensité dépend des forces de Van der Waals qui s'exercent
dans le milieu, demeure faible [18].
En revanche, lorsque des interactions attractives du
type liaison hydrogène se forment entre entités de nature
chimique différente, l'enthalpie libre de mélange est
négative. Toutes les conditions sont alors réunies pour que le
mélange formé soit homogène. Il est possible de calculer
l'énergie libre de mélange grâce à la
théorie de Flory-Huggins, moyennant quelques hypothèses
simplificatrices. Ce modèle ne prend en compte que les interactions du
type London-Van der Waals et ignore des éléments comme la
polymolécularité [18].
L'énergie libre de mélange par site
s'écrit :
(II.2)
ÖA et ÖB : Les
fractions volumiques des constituants poly (A) et poly (B)
NA et NB : Degrés de
polymérisation des chaînes poly (A) et poly (B),
÷AB : Paramètre
d'interaction entre poly(A) et poly (B),
T : Température absolue,
k : Constante de Boltzmann.
La relation suivante représente, en fait, la
variation d'énergie ? åAB qu'impliquerait l'interaction
entre unités A et B, åAA et åBB
étant les énergies d'interaction respectives des unités A
et B entre elles.
(II.3)

÷AB prend des valeurs positives lorsque
l'interaction entre A et B nécessite un apport d'énergie
(?åAB > 0 et å AB supérieure
à la moyenne de åAA et åBB), c'est a
dire que cette interaction est répulsive ; le mélange est alors
endothermique. L'hypothèse des seules interactions du type London-Van
der Waals implique, par ailleurs, que l'énergie d'attraction entre les
unités dépend de la polarisation ái et du
potentiel d'ionisation I ij par l'expression å
ij= Iij ái áj et comme I est identique
quelle que soit l'unité considérée, le produit kT ÷
AB se réduit à [19] :
(II.4)

Cette expression, établie en ne prenant en
compte que les forces du type London-Van der Waals, montre bien que
l'interaction entre unités dissemblables est nécessairement
répulsive ou, au mieux, nulle. Les «
hétérocontacte» ne sont donc pas privilégiés.
Quand l'ensemble des N sites est pris en considération,
l'incompatibilité des deux polymères dépend alors du
produit ÷ ABN et est d'autant plus marquée que ÷
ABN est élevé. En pratique, et pour rendre compte de
la réalité des faits expérimentaux, on a
généralement recours à une expression plus
phénoménologique de la densité d'énergie libre du
mélange (par cm3) [18] :
(II.5)

VA, VB : Etant les volumes
molaires des unités constitutives A et B.
R : La constante molaire des gaz parfaits.
Dans cette expression, ËAB
représente un paramètre d'interaction empirique qui,
contrairement à ÷AB, peut dépendre de la
température, de la pression, de la composition du mélange ;
ËAB est considéré proportionnel au carré
de la différence des paramètres de solubilité
äA et äB des constituants poly (A) et poly (B)
[18].
II.3.4. Techniques de mélangeage :
La structure des mélanges de polymères
est très étroitement dépendante de la
technique utilisée pour les réaliser [18].
Dans le cas du mélangeage mécanique
(malaxage), la température doit être supérieure à la
température de transition vitreuse (et même à la
température de fusion si l'un des constituants est cristallin) pour que
la dispersion soit efficace. Le cisaillement lié au
malaxage peut provoquer une dégradation partielle qui aboutit parfois
à la formation de copolymères à blocs ou
greffés [18].
Le mélange peut être
réalisé à partir des solutions des deux polymères
dans un même solvant. Si les deux solutions sont
miscibles, le mélange se fait dans des conditions
idéales. Si ce n'est pas le cas, les viscosités des deux
solutions doivent être voisines [18].
Le mélange peut être
récupéré à partir de la solution, par
évaporation du solvant, par coprécipitation ou par
lyophilisation. Pour les mélanges issus de latex, la dispersion
des constituants est aisée à obtenir. Cependant, la forte
proportion des additifs introduits pour stabiliser les émulsions
amène ceux-ci à jouer un rôle de barrière et
empêche une bonne cohésion entre les phases
[18].
II.3.5. Structure des
mélanges :
Il faut signaler l'influence primordiale de la
cinétique de démixtion sur la structure des systèmes non
miscibles. En effet, au fur et à mesure de l'abaissement de la
température du système ou bien lors de l'évaporation du
solvant, la viscosité du milieu croît et s'oppose à la
diffusion des espèces macromoléculaires. Le paramètre
cinétique peut modifier fortement les morphologies de ces
systèmes par rapport à celles des systèmes qui sont en
équilibre thermodynamique [18].
Le degré d'interpénétration des
chaînes des systèmes miscibles dépend
de la valeur de ËAB. ËAB est inférieur
à 0, pour le mélange poly (nitrate de vinyle)-poly
(acétate de vinyle). Il en résulte une forte tendance à
l'interpénétration des chaînes. Lorsque Ë
AB est inférieur à 10-2, c'est le terme
entropique qui compense la valeur légèrement positive de
l'enthalpie et l'interpénétration des chaînes peut
n'être que partielle. La frontière entre phases est mal
délimitée mais, au niveau macroscopique, tout se passe comme si
le système était homogène [18].
Dans le cas des systèmes non miscibles
(ËAB élevé) leur morphologie dépend de
[18] :
- La valeur de ËAB;
- La technique de mélangeage ;
- La température de mélangeage ;
- Le rapport des viscosités des phases à
mélanger çA/çB;
- La présence éventuelle d'agents
compatibilisants.
Si la viscosité de la phase majoritaire est
nettement supérieure à celle de la phase dispersée et si
le refroidissement est rapide, on a une structure lenticulaire [18].
II.1. Matières
utilisées :
III.1.1. Le polychlorure de vinyle : (PVC)
Le mélange utilisé est
commercialisé sous la marque « I2
E1CN », il est présenté sous forme de
granulé sphérique de diamètre environ 3mm, d'une couleur
jaune. Il est utilisé pour la fabrication des câbles.
Il contient les composants suivants :
Ø Résine :
Le polychlorure de vinyle pur (poudre blanche).
Ø Charge CaCO3 :
La charge utilisée est le carbonate de calcium
(CaCO3), c'est une charge caractérisée par sa
blancheur éclatante.
a) Qualité physiques :
- Teneur en carbone de calcium = mini 97.80 %.
- Teneur en dioxyde de silicium = max 0.80 %.
- Teneur en oxyde de fer = max 0.20 %.
- Teneur en sulfate = max 0.25 %.
- Teneur en manganèse = max 0.01 %.
b) Qualité Constitutives :
- Teneur en humidité = max 0.20 %.
- Refus (tamis pour analyses 28 mm) = 0.
Ø Plastifiant :
Le plastifiant utilisé est le Phtalate de
dioctyle (DOP)
Quelques caractéristiques du DOP sont
résumées dans le tableau (III.1) :
Tableau (III.1) : Quelques
caractéristiques du DOP.
Caractéristiques
|
Spécification
|
Unité
|
- Masse volumique à 20°C
- Indice de réfraction nD
- Viscosité à 20°C
- Translucidité (échelle d'iode colorée)
- Perte d'évaporation (1 heure, 160°C)
- Point d'inflammation
- Point de congélation
- Indice d'acidité (mg KOH/g)
- Coefficient de saponification
|
0.982-0.986
1.436 - 1.483
76 - 80
Max 2
Environ 1
195
-45
Max 0.15
Min 0.80
|
g/cm3
-
mPa.S
-
%
°C
°C
mg KOH/g
mg KOH/g
|
Ø Stabilisant:
Le stabilisant utilisé est le Baeropan à
base de Ca/Zn sous forme de poudre blanche commercialisée sous la marque
MC8703 KA.
Le tableau (III.2) définit les
caractéristiques essentielles de I2E1CN.
Tableau (III.2) : Les
caractéristiques essentielles de I2 E1CN.
Caractéristiques
|
Spécification
|
Unité
|
- Résistance à la traction (avant le
vieillissement)
- Allongement (avant vieillissement)
- Résistance à la traction (après
vieillissement)
- Allongement (après vieillissement)
- Variation dans la résistance
- Variation dans l'allongement
- Densité théorique
- Densité à l'éthanol
- Densité de déchargement
- Perte de masse
- Stabilité thermique
- Résistivité
- Résistance d'isolement
|
14.43
300
14.30
285
0.9
5
1.412
1.42
0.74
0.29
62
0.01688
2.97x1016
|
MPa
%
MPa
%
%
%
g/cm3
g/cm3
g/cm3
-
-
.mm
M.cm
|
III.1.2. Le polyéthylène
réticulé par le silane (PRS) :
Le PRS est présenté sous forme de
granulé sphérique de diamètre environ 3mm
à une odeur spécifique non toxique. Son nom commercial est
« POLIDAN® EC/MD ».
Il est utilisé pour les câbles
électriques et l'isolation. Ces caractéristiques sont
indiquées dans le tableau (III.3).
Tableau (III.3) : Quelques
caractéristiques du PRS.
Caractéristiques
|
Spécification
|
Unité
|
- Densité à 23°C (ASTM D 792)
- Résistance à la traction (IEC 60811)
- Allongement (IEC 60811)
|
0.934
21.5
420
|
g/cm3
N/mm2
%
|
- Les propriétés après vieillissement
à 150°C pendant 168heurs
- Variation dans la résistance
- Variation dans l'allongement
|
16
0
|
%
%
|
- Absorption d'eau à 100°C, 24h
- Absorption d'eau à 85°C, 336h
|
0.3
0.3
|
mg/cm2
mg/cm2
|
- Résistivité à 20°C
|
à 20°C
|
4.1 1015
|
.cm
|
- à 90°C
|
1.4 1015
|
- L'isolation
|
à 20°C
|
15000
|
M.km
|
à 90°C
|
5000
|
PRS
PRS
PRS
Mélange
(1)
Mélange
(2)
Extrusion à T = 175 °C
Cuisson : T=95 °C
t =3 h
Compression: T=130°C
P= 300 bar
Réticulation
Etude rhéologique
Etude mécanique
Dureté shore A
Essais de traction avant et après vieillissement
Résultats et interprétations
1er recyclage du PVC
2ème recyclage du PVC
3ème recyclage du PVC
III.2. Méthodologie :
Mélange
(3)
Etude thermique
Stabilité thermique
Figure III.1 : Organigramme de la partie
expérimentale.
III.3. Préparation des mélanges :
En premier lieu, une première extrusion a
été effectuée pour une quantité bien
déterminé du PVC sous forme de granulé dans une
extrudeuse monovis de marque «BRABENDER » de type «PLE
330». Le PVC obtenue est un PVC recyclé une fois.
Selon le nombre d'extrusion on obtient un PVC
recyclé deux ou trois fois.
v Conditions de travails :
- La température des trois zones : 165°C.
- La vitesse de rotation de la vis : 25 tr/min.
Une fois le PVC est recyclé, il est
incorporé dans le PRS où le taux de ce dernier varie de 50 %
à 100 % avec un pas de 10.
v Conditions de travail :
- La température des trois zones : 175°C.
- La vitesse de rotation de la vis : 40 tr/min.
III.4. Préparation des
plaques :
La bande obtenue par l'extrusion est
découpée et compressées dans une presse de marque
«SCHVABENTHAN» de type «POLUSTATE 300S» pour obtenir des
plaques d'épaisseur environ 2mm.
v Condition de travail :
- La température des deux plateaux : 130
°C ;
- Le temps de compression :
A 0 bar pendant 5min.
A 100 bar pendant 2min.
A 200 bar pendant 2min.
A 300 bar pendant 4min.
- Refroidissement par l'eau froid.
III.5. Préparation des
éprouvettes :
Les plaques obtenues ont été
découpées par une découpeuse spéciale pour obtenir
des éprouvettes selon la norme ISO 527-2 destinées aux
différents tests.
III.6. Propriétés des
mélanges :
III.6.1. Etude rhéologique :
Cette étude a été
effectuée sur le rhéomètre de marque « RHEOMETRE
100 Monsato ». C'est l'un des appareils qui permet d'étudier
le comportement rhéologique des polymères et le
phénomène de réticulation pour les polymères
modifiés.
Avant de commencer cette étude, une partie des
bandes extrudées est amenée à la
cuisson.
v Conditions de travail :
- La température de cuisson : 95 °C.
- Le temps de cuisson : 3heures.
Après cuisson, les bandes ont été
découpées en petits fragments et déposées dans
la chambre du rhéomètre
v Conditions de travail :
- La masse introduite dans la chambre de
rhéomètre : 4.5g.
- La température : 180 °C.
- L'angle d'oscillation du disque : 5°.
III.6.2. Etude mécanique :
Avant d'entamer cette étude, les
éprouvettes préparées sont soumises
au vieillissement dans un four de type WSU 100, à une
température de 90 °C, pendant sept jours. Elles sont placées
verticalement et librement dans le four. Le but de ce travail est
d'étudier l'influence de température sur le comportement
mécanique du mélange.
III.6.2.1. Comportement en traction :
Les propriétés ultimes (contrainte et
allongement à la rupture) sont déterminées en utilisant
une machine spéciale pour les essais de traction de type
« ZWICK ROELL Z100 » où
l'éprouvette de géométrie bien définie est
encastrée à ces deux extrémités dans deux
mâchoires. L'un de ces mâchoires est fixe, l'autre est mobile.
v Conditions de travail :
- La vitesse de déplacement des mâchoires :
80mm/min ;
- Conditions normales de température et de pression.
La contrainte à la rupture a été
calculée en accord avec la relation suivante :
ó = F/S
F : La force appliquée (N)
S : Section de l'éprouvette
(mm2)
L'allongement à la rupture a été
calculé à partir de la relation :
å % = [(I-I0)/I0] x
100
å : Allongement à la rupture
en %.
I : Allongement final mesuré en mm.
I0 : Allongement initial
mesuré en mm.
III.6.2.2. Essais de la dureté shore
A :
La dureté d'un matériau est la
résistance de celui-ci à l'enfoncement de
pénétrateur de forme et de dimension donnée.
On appelle indice de dureté de
pénétration Shore ou plus couramment dureté Shore A ou
Shore D, le résultat de la mesure effectuée selon un mode
opératoire bien déterminé et réalisé
à l'aide d'un duromètre Shore A ou d'un duromètre Shore
D.
Les mesures sont effectuées sur le
duromètre Shore A de type « ZWICH ROELL HPE », sous
la norme ISO 868.
III.6.3. La stabilité
thermique :
Cette étude a été
effectuée dans un thermoplaste spécial pour l'essai de
stabilité thermique statistique équipé d'un
thermomètre et relié à un régulateur de
température exacte.
La température a été fixée
à 200°C, ce thermoplaste contient des orifices qui sont remplis
avec de l'huile de silicone ou les tubes sont émergés.
Pour chaque mélange, une petite quantité
de la bande extrudée a été découpée
en petits fragments. Ces derniers ont été introduits dans des
tubes spéciaux pour l'essai de stabilité, en ajoutant un
papier pH et en mettant ces tubes dans le thermoplaste.
La coloration du papier pH indique le
dégagement d'HCl et la mesure du temps à ce moment et
celui de la stabilité thermique.
IV.1. Etude rhéologique :
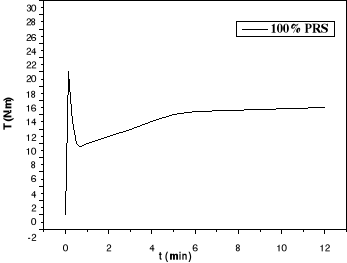
Figure IV.1: Variation du torque en fonction du
temps pour le PRS pur.

Figure IV.2: Variation du torque en fonction du temps
pour le mélange PRS / PVC recyclé une
fois.
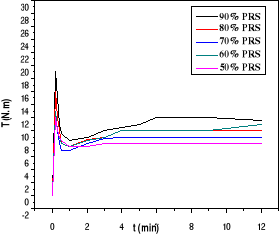
Figure IV.3: Variation du torque en fonction du temps
pour le mélange PRS / PVC recyclé deux
fois.
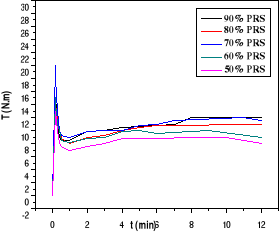
Figure IV.4: Variation du torque en fonction du temps
pour le mélange PRS / PVC recyclé trois
fois.
D'après les figures (VI.1, IV.2, IV.3, IV.4),
il a été observé que les plastogrammes obtenus ont la
même allure que le PRS pur et la variation du torque est presque
constante après les deux minutes de transformation car la
température est insuffisante pour déclanché la
réaction de réticulation. Dans le cas général, la
réticulation présente une augmentation du torque indiquant la
croissance de la résistance du polymère sur le disque
oscillatoire.
IV.2. Etude mécanique :
IV.2.1. Comportement en traction :
IV.2.1.a. Avant vieillissement :
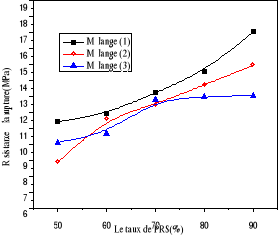
Figure IV.5: Variation de la résistance à
la rupture moyenne avant vieillissement en fonction du taux de PRS.
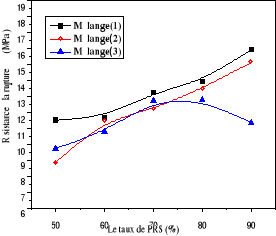
Figure IV.6 : Variation de la résistance
à la rupture médiane avant vieillissement en fonction du taux de
PRS.
Les figures (IV.5 et IV.6) présentent la
variation de la résistante à la rupture des
différents mélanges en fonction du taux de PRS. Il a
été remarqué que la contrainte à la rupture
augmente avec l'augmentation de la concentration du PRS. Ceci est dû
probablement à l'interpénétration des chaînes
macromoléculaires les unes dans les autres.
Les mêmes figures montrent que
généralement la contrainte à la rupture
décroît en fonction du nombre de recyclage. Ceci est
expliqué par le fait que le mélange possède moins de
molécules d'attache et de liaisons inter-cristallines.
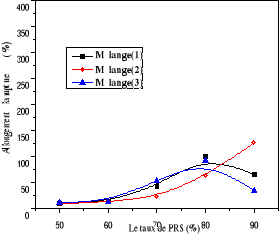
Figure IV.7 : Variation de l'allongement à
la rupture moyenne avant vieillissement en
fonction du taux de PRS.

Figure IV.8 : Variation de l'allongement à
la rupture médiane avant vieillissement en fonction du taux de
PRS.
Les figures (IV.7 et IV 8) montrent la variation de
l'allongement à la rupture en fonction du taux de PRS et aux
différentes formulations de PVC recyclé. Il est noté que
l'allongement à la rupture augmente jusqu'une concentration de 80% de
PRS, au-delà de cette valeur on observe une
décroissance pour les mélanges à base de PVC
recyclé une et trois fois.
IV.2.1.b. Après vieillissement
D'après le test de traction et d'une
manière générale, il a été remarqué
que la résistance à la rupture augmente avec le
taux de PRS. Ceci est lie probablement à la formation des
pontages durant le temps de vieillissement (figures IV.9 et IV.10).
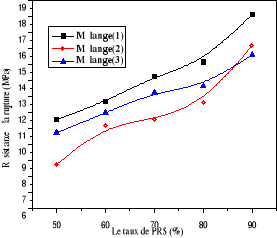
Figure IV.9: Variation de la résistance à
la rupture moyenne après vieillissement en fonction du taux de
PRS.
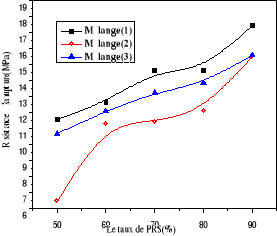
Figure IV.10 : Variation de la résistance
à la rupture médiane après vieillissement en fonction du
taux de PRS.
Selon les mêmes figures, il a été
constaté que le mélange (1) présente des valeurs de la
contrainte à la rupture les plus élevées et les petites
valeurs pour le mélange (2).
Les figues (IV.11 et IV.12) donnent la variation de
l'allongement à la rupture. Il a été observé que
cette propriété reste pratiquement constante jusqu'à 80 %
de PRS.
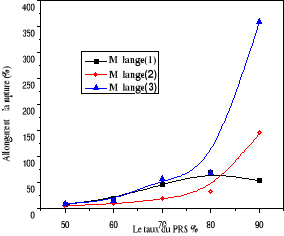
Figure IV.11 : Variation de l'allongement à
la rupture moyenne après vieillissement en fonction du taux de
PRS.
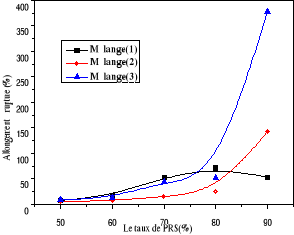
Figure IV.12 : Variation de l'allongement à
la rupture médiane après vieillissement en fonction du taux de
PRS.
Ceci met en évidence que le PRS n'affecte pas
l'allongement, mais au-delà de 80 % une augmente brusque est
notée ce qui est expliqué par la substitution graduelle
des glissements des chaînes linière par
l'étirement du réseau tridimensionnel
à des concentrations élevées.
Pour une même concentration du PRS, une
croissance remarquable de l'allongement à la rupture est donnée
à 90 % de PRS est 10 % de PVC recyclé trois fois.
IV.2.2. Dureté Shore A :
Figure IV.13 : Variation de la dureté Shore A
moyenne en fonction du taux de PRS.

Figure IV.14 : Variation de la dureté Shore
A médiane en fonction du taux de PRS.
D'après les valeurs de la dureté Shore A
illustrées sur les figures (IV.13, IV.14).
Les mélanges présentent des duretés plus
ou moins constantes pour le même taux de PRS, c'est-à-dire que le
nombre de recyclage de PVC n'affecte pas la rigidité superficielle du
matériau.
Pour le même mélange on constate une
légère augmentation. Elle est plus remarquable à 90 % de
PRS, ce ci est dû à la rigidité de ce dernier.
IV.3. Etude thermique :
IV.3.1. Stabilité thermique :
Les résultats du test
thermique sont représentés sur la figure (IV.15) où on
remarque que la stabilité thermique augmente en fonction du taux de PRS,
donc le blend (PRS/PVC recyclé) est plus stable dans le cas ou la
concentration du PVC recyclé est minoritaire.
Cette dernière a un effet direct sur la
réaction de dishydrochloruration, plus le taux de PVC est
élevé, le dégagement de l'acide chlorhydrique est grand,
ce qui implique une instabilité thermique du blend.
On constate aussi que la stabilité thermique augmente
avec le nombre de recyclage du PVC où le mélange à base de
PVC recyclé trois fois est le plus stable. Ceci est expliqué par
le nombre d'atomes de chlore dégagé lors du
chauffage.
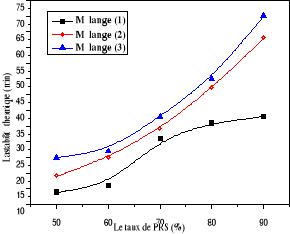
Figure IV.15 : Variation de la stabilité
thermique en fonction du taux de PRS.
Conclusion générale
Les résultats présentés dans ce
travail concernant l'étude rhéologique, mécanique
(résistance à la rupture, allongement à la rupture et la
dureté Shore A) et thermique nous a permis de conclure que :
Ø D'après l'étude rhéologique on
constate qu'il faut atteindre une certaine température afin de
déclencher la réaction de réticulation et pour que
le rhéomètre donne des plastogrammes
qui permettent de déduire le temps de
réticulation.
Ø Les résultats de la caractérisation
mécaniques avant et après vieillissement montrent que le
mélange à base de PVC recyclé une fois présente des
propriétés mécaniques (résistance à la
rupture et l'allongement à la rupture) plus élevés que
les autres mélanges (PRS/PVC recyclé deux et trois fois).
Généralement, l'allongement à la rupture
et la résistance à la rupture croient avec la croissance du taux
de PRS.
On outre, la dureté Shore A reste presque constante en
fonction du nombre de recyclage de PVC et elle augmente
légèrement en fonction du taux de PRS.
Ø En fin, la stabilité thermique du
mélange augmente avec l'augmentation du taux de PRS et le nombre de
recyclage de PVC.
Références bibliographiques
[1] :
|
K.Berdjane, "Optimisation des propriétés des
mélanges de polyoléfines provenant de l'emballage alimentaire
recyclé", Mémoire de magister, Université Ferhat Abbas,
Sétif, (2003).
|
[2] :
|
J. J. Robin, "Technique de l'ingénieur", A 3 832,
Paris,(1985).
|
[3] :
|
N. Heymans, H. K. V. Schmeling, H. Kausch, C.J. Plummer,
"Matériaux polymères : propriétés
mécaniques et physiques", Disponible sur le site :
http://books.google.com/books?id=QAPpepjfZEsC&pg=PR1&dq=mat%C3%A9riaux+polym%C3%A8res&hl=fr#PPR1,M,
Consulté en Mai 2009.
|
[4] :
|
C. Auval, " Matières plastiques et environnement,
recyclage, valorisation, biodégradabilité, Eco-conception",
France, (2004).
|
[5] :
|
P. Gautron, "Technique de l'ingénieur", A 3 830,
Paris, (1985).
|
[6] :
|
H. Arrar et K. Baiti, "Effet de cycle de transformation sur
les propriétés du PET ½déchet½", Mémoire
d'ingéniorat, Université Ferhat Abbas, Sétif, (2004).
|
[7] :
|
F.
Niquet,
V.
Beurotte,
C.
Darrigan et
B.
Bouyssiere, "Identification et recyclage de plastiques", Disponible
sur :
http://ocp.asso.fr/wiki/index.php?title=Identification_et_recyclage_des_plastiqes
Consulté en Mars 2009.
|
[8] :
|
J. P. Arlie "Les thermoplastiques de grand tonnage
½caractéristiques techniques et économiques" ,2ème
édition, Technip, Paris, (1987).
|
[9] :
|
C. Kunststoff et Tabellen, "Technique de l'ingénieur",
Paris, (1985)
|
[10] :
|
L. Djoudi, " Etude de la stabilisation du polychlorure de
vinyle et les phénomènes de
dégradation", Mémoire de magister, Université Med Khider,
Biskra, (2007).
|
[11] :
|
D. Ausseur, " Technique de l'ingénieur", AM 3 325,
Paris, (2005).
|
[12] :
|
J.P. Trotignon, M .Piperaud, J. Verdu et A. Dobraczynski,
"Précis de matières plastiques, structures,
propriété, mise en oeuvre et normalisation", 4ème
édition, Nathen, France, (1987)
|
[13] :
|
Société Française de Chimie,
Disponible sur le site :
www.sfr.fr/donées/mater/pvc%5B1%5D.htm,
consulté en Avril 2009
|
[14] :
|
C. Khaloua, "Etude de l'influence de la réticulation
par le peroxyde dicumyl sur les propriétés rhéologique,
mécanique, thermique et spectrale du polyéthylène haute
densité", Mémoire de magister, Université Ferhat Abbas,
Sétif, (2003).
|
[15] :
|
S. Behlouli, "l'effet de l'incorporation du peroxyde comme
agent de réticulation sur les propriétés d'un blend
PEbd/PEhd ", Mémoire d'ingéniorat, Université Ferhat
Abbas, Sétif, (2001).
|
[16] :
|
M. Astruc, "Étude rhéo-optique des
mécanismes de dispersion de mélange sous cisaillement simple :
1. mélanges concernant les polymères immiscibles
2. mélanges polymères-charges poreuses ",
Mémoire de doctorat, l'École des Mines, Paris, (2001).
|
[17] :
|
I. Ameur et W. Khodeir, "Etude rhéologique,
mécanique et thermique du blend PRS/PVC", Mémoire
d'ingéniorat, Université Med Khider, Biskra, (2008).
|
[18] :
|
M. Fontalinne et Y. Gnanou, "Technique de
l'ingénieur", A 3 042, Paris, (1985).
|
A.I. Tableaux des compositions des
mélanges :
A.I.1. Mélanges (1) (PVC recyclé une
fois) :
Matériaux
|
Quantité en gramme
|
PRS (Polidan EC/MD)
|
400
|
PVC (I2 E1 CN)
|
0
|
Matériaux
|
Quantité en gramme
|
PRS (Polidan EC/MD)
|
360
|
PVC (I2 E1 CN)
|
40
|
Matériaux
|
Quantité en gramme
|
PRS (Polidan EC/MD)
|
320
|
PVC (I2 E1 CN)
|
80
|
Matériaux
|
Quantité en gramme
|
PRS (Polidan EC/MD)
|
280
|
PVC (I2 E1 CN)
|
120
|
Matériaux
|
Quantité en gramme
|
PRS (Polidan EC/MD)
|
240
|
PVC (I2 E1 CN)
|
160
|
Matériaux
|
Quantité en gramme
|
PRS (Polidan EC/MD)
|
200
|
PVC (I2 E1 CN)
|
200
|
A.I.2. Mélanges (2) (PVC recyclé deux
fois) :
Matériaux
|
Quantité en gramme
|
PRS (Polidan EC/MD)
|
360
|
PVC (I2 E1 CN)
|
40
|
Matériaux
|
Quantité en gramme
|
PRS (Polidan EC/MD)
|
320
|
PVC (I2 E1 CN)
|
80
|
Matériaux
|
Quantité en gramme
|
PRS (Polidan EC/MD)
|
280
|
PVC (I2 E1 CN)
|
120
|
Matériaux
|
Quantité en gramme
|
PRS (Polidan EC/MD)
|
240
|
PVC (I2 E1 CN)
|
160
|
Matériaux
|
Quantité en gramme
|
PRS (Polidan EC/MD)
|
200
|
PVC (I2 E1 CN)
|
200
|
A.I.3. Mélanges (3) (PVC recyclé trois
fois) :
Matériaux
|
Quantité en gramme
|
PRS (Polidan EC/MD)
|
360
|
PVC (I2 E1 CN)
|
40
|
Matériaux
|
Quantité en gramme
|
PRS (Polidan EC/MD)
|
320
|
PVC (I2 E1 CN)
|
80
|
Matériaux
|
Quantité en gramme
|
PRS (Polidan EC/MD)
|
280
|
PVC (I2 E1 CN)
|
120
|
Matériaux
|
Quantité en gramme
|
PRS (Polidan EC/MD)
|
240
|
PVC (I2 E1 CN)
|
160
|
Matériaux
|
Quantité en gramme
|
PRS (Polidan EC/MD)
|
200
|
PVC (I2 E1 CN)
|
200
|
A.II. Essais de traction :
A.II.1. Mélange (1) :
Tableau (A.II.1.1.) : Essai de traction
avant vieillissement du blend PRS/ PVC recyclé une fois.
% PRS
|
N° d'épr
|
Epais
(mm)
|
ó (MPa)
|
å (%)
|
Résistance
(MPa)
|
Allongement
(%)
|
moyenne
|
médiane
|
moyenne
|
médiane
|
90
|
1
2
3
|
2.58
2.64
2.48
|
15.36
15.93
19.79
|
52.13
69.08
74.41
|
17.03
|
15.93
|
65.21
|
69.08
|
80
|
1
2
3
|
2.48
2.40
2.66
|
13.93
13.93
15.72
|
88.14
112.01
100.17
|
14.52
|
13.93
|
100.11
|
100.17
|
70
|
1
2
3
|
2.46
2.37
2.45
|
14.11
13.21
12.30
|
18.06
41.93
66.43
|
13.21
|
13.21
|
42.14
|
41.93
|
60
|
1
2
3
|
2.34
2.29
2.17
|
11.56
11.69
12.41
|
19.33
6.07
11.59
|
11.89
|
11.69
|
12.33
|
11.59
|
50
|
1
2
3
|
2.22
2.21
2.23
|
10.99
11.51
11.71
|
7.31
11.16
10.56
|
11.40
|
11.51
|
9.68
|
10.56
|
Tableau (A.II.1.2.) : Essai de traction
après vieillissement du blend PRS/ PVC recyclé une
fois.
% PRS
|
N° d'épr
|
Epais
(mm)
|
ó (MPa)
|
å (%)
|
Résistance
(MPa)
|
Allongement
(%)
|
moyenne
|
médiane
|
moyenne
|
médiane
|
90
|
1
2
3
|
2.56
2.72
2.66
|
17.45
20.21
16.74
|
92.43
53.55
13.46
|
18.13
|
17.45
|
53.15
|
53.55
|
80
|
1
2
3
|
2.74
2.45
2.60
|
16.84
14.63
13.99
|
111.36
71.65
26.67
|
15.15
|
14.63
|
69.89
|
71.65
|
70
|
1
2
3
|
2.51
2.53
2.60
|
13.68
14.60
14.48
|
75.29
52.97
10.84
|
14.25
|
14.60
|
46.36
|
52.97
|
60
|
1
2
3
|
2.29
2.19
2.20
|
12.93
12.40
12.64
|
18.23
28.85
11.91
|
12.66
|
12.64
|
19.66
|
18.23
|
50
|
1
2
3
|
2.30
2.29
2.29
|
11.40
11.57
11.68
|
7.49
8.49
6.72
|
11.55
|
11.57
|
7.57
|
7.49
|
A.II.2. Mélanges (2) :
Tableau (A.II.2.1.) : Essai de traction
avant vieillissement du blend PRS/ PVC recyclé deux
fois.
% PRS
|
N° d'épr
|
Epais
(mm)
|
ó (MPa)
|
å (%)
|
Résistance
(MPa)
|
Allongement
(%)
|
moyenne
|
médiane
|
moyenne
|
médiane
|
90
|
1
2
3
|
2.63
2.53
2.53
|
15.13
14.43
15.25
|
70.72
160.92
145.44
|
14.94
|
15.13
|
125.69
|
145.44
|
80
|
1
2
3
|
2.57
2.83
2.53
|
14.20
13.48
13.41
|
32.34
55.19
97.71
|
13.70
|
13.48
|
61.75
|
55.19
|
70
|
1
2
3
|
2.63
2.65
2.52
|
11.90
12.18
13.39
|
06.23
14.16
42.28
|
12.49
|
12.18
|
20.89
|
14.16
|
60
|
1
2
3
|
2.35
2.49
2.53
|
11.47
11.91
11.43
|
14.48
14.45
8.64
|
11.60
|
11.47
|
12.52
|
14.45
|
50
|
1
2
3
|
2.38
2.42
2.57
|
8.96
8.85
8.78
|
06.94
11.31
06.65
|
8.86
|
8.85
|
8.3
|
6.94
|
Tableau (A.II.2.2.) : Essai de traction
après vieillissement du blend PRS/ PVC recyclé deux
fois.
% PRS
|
N° d'épr
|
Epais
(mm)
|
ó (MPa)
|
å (%)
|
Résistance
(MPa)
|
Allongement
(%)
|
moyenne
|
médiane
|
moyenne
|
médiane
|
90
|
1
2
3
|
2.55
2.67
2.52
|
15.44
16.87
15.56
|
190.56
99.28
142.36.
|
15.96
|
15.56
|
143.88
|
142.36
|
80
|
1
2
3
|
2.60
2.57
2.55
|
13.98
11.66
12.10
|
58.98
11.20
25.52
|
12.58
|
12.10
|
31.9
|
25.52
|
70
|
1
2
3
|
2.57
2.46
2.75
|
11.41
15.60
7.65
|
15.22
33.00
05.61
|
11.55
|
11.41
|
17.94
|
15.22
|
60
|
1
2
3
|
2.48
2.59
2.49
|
11.28
10.73
11.51
|
6.88
7.77
10.22
|
11.17
|
11.28
|
8.29
|
7.77
|
50
|
1
2
3
|
2.49
2.16
2.63
|
6.47
12.54
7.23
|
3.70
8.40
5.13
|
8.75
|
6.47
|
5.74
|
5.15
|
A.II.3. Mélange (3) :
Tableau (A.II.3.1.) : Essai de traction
avant vieillissement du blend PRS/ PVC recyclé trois
fois.
% PRS
|
N° d'épr
|
Epais
(mm)
|
ó (MPa)
|
å (%)
|
Résistance
(MPa)
|
Allongement
(%)
|
moyenne
|
médiane
|
moyenne
|
médiane
|
90
|
1
2
3
|
2.63
2.72
2.72
|
16.92
10.90
11.33
|
68.33
13.16
19.80
|
13.05
|
11.33
|
33.76
|
19.80
|
80
|
1
2
3
|
2.31
2.33
2.53
|
12.78
12.71
13.38
|
98.21
61.57
115.15
|
12.96
|
12.78
|
91.64
|
98.21
|
70
|
1
2
3
|
2.45
2.49
2.55
|
12.69
12.73
12.93
|
57.75
47.00
52.86
|
12.78
|
12.73
|
52.53
|
52.86
|
60
|
1
2
3
|
2.55
2.42
2.37
|
9.49
10.77
11.73
|
8.87
12.78
17.31
|
10.66
|
10.77
|
12.99
|
12.78
|
50
|
1
2
3
|
2.59
2.40
2.42
|
11.06
9.72
9.53
|
14.14
08.42
10.08
|
10.10
|
9.72
|
10.88
|
10.08
|
Tableau (A.II.3.2.) : Essai de traction
après vieillissement du blend PRS/ PVC recyclé trois
fois.
% PRS
|
N° d'épr
|
Epais
(mm)
|
ó (MPa)
|
å (%)
|
Résistance
(MPa)
|
Allongement
(%)
|
moyenne
|
médiane
|
moyenne
|
médiane
|
90
|
1
2
3
|
2.54
2.57
2.43
|
16.09
15.15
15.58
|
405.84
291.70
378.39
|
15.61
|
15.58
|
358.64
|
378.39
|
80
|
1
2
3
|
2.43
2.65
2.41
|
13.13
13.93
13.82
|
50.12
100.70
52.99
|
13.63
|
13.82
|
67.94
|
52.99
|
70
|
1
2
3
|
2.57
2.67
2.51
|
13.08
13.46
13.22
|
89.91
37.51
44.38
|
13.25
|
13.22
|
57.26
|
44.38
|
60
|
1
2
3
|
2.34
2.39
2.44
|
12.08
11.69
12.15
|
13.44
12.66
16.55
|
11.97
|
12.08
|
14.22
|
13.44
|
50
|
1
2
3
|
2.53
2.68
2.47
|
11.78
9.75
10.68
|
12.90
07.21
9.00
|
10.74
|
10.68
|
9.70
|
9.00
|
A.III. Essai de la dureté shore A :
Tableau (A.III.1.) : La dureté Shore A pour le blend
PRS / PVC recyclé une fois.
PRS %
|
PVC %
|
Dureté shore A
|
moyenne
|
médiane
|
100
|
0
|
95.8
94.9
96.8
|
95.83
|
95.8
|
90
|
10
|
97.6
97.2
97.5
|
97.43
|
97.5
|
80
|
20
|
97.6
97.4
97.2
|
97.4
|
97.4
|
70
|
30
|
95.7
91.6
96.3
|
94.53
|
95.7
|
60
|
40
|
97.0
96.7
97.4
|
97.03
|
97
|
50
|
50
|
95.9
96.7
95.1
|
95.9
|
95.9
|
Tableau (A.III.2) : La
dureté Shore A pour le blend PRS / PVC recyclé deux fois.
PRS %
|
PVC %
|
Dureté shore A
|
moyenne
|
médiane
|
100
|
0
|
95.80
94.90
96.80
|
95.83
|
95.8
|
90
|
10
|
96.10
97.10
97.20
|
96.8
|
97.1
|
80
|
20
|
96.00
95.70
97.20
|
96.3
|
96
|
70
|
30
|
97.10
97.70
97.60
|
97.47
|
97.7
|
60
|
40
|
96.00
97.00
97.20
|
96.73
|
97
|
50
|
50
|
95.10
97.00
95.40
|
95.83
|
95.4
|
Tableau (A.III.3.) : La
dureté Shore A pour le blend PRS / PVC recyclé trois fois.
PRS %
|
PVC %
|
Dureté shore A
|
moyenne
|
médiane
|
100
|
0
|
95.80
94.90
96.80
|
95.83
|
95.8
|
90
|
10
|
97.50
97.40
96.70
|
97.2
|
97.5
|
80
|
20
|
95.50
93.90
95.50
|
94.97
|
95.5
|
70
|
30
|
96.80
95.30
95.50
|
95.87
|
95.5
|
60
|
40
|
96.80
95.70
96.50
|
96.33
|
96.5
|
50
|
50
|
96.50
95.20
96.10
|
95.93
|
96.1
|
A.IV. Stabilité
thermique :
Tableau (A.IV.1.) : La stabilité
thermique pour le blend PRS / PVC recyclé une fois.
PRS %/PVC %
|
Différence (min)
|
100/0
90/10
80/20
70/30
60/40
50/50
|
-
38
36
31
16
14
|
Tableau (A.IV.2.) : La stabilité
thermique pour le blend PRS / PVC recyclé deux fois.
PRS % /PVC %
|
Différence (min)
|
100/0
90/10
80/20
70/30
60/40
50/50
|
-
63
47
34
25
19
|
Tableau (A.IV.3.) : La stabilité
thermique pour le blend PRS / PVC recyclé trois fois.
PRS %/PVC %
|
Différence (min)
|
100/0
90/10
80/20
70/30
60/40
50/50
|
-
70
50
38
27
25
|
|