CHAPITRE I
PRE S ENTATI ON GENERALE
D 'ALUCAM/SOCATRAL
Carte de flux énergétiques et perspectives
d'efficacité dans une fonderie d'aluminium: cas particulier
d'alucam/socatral
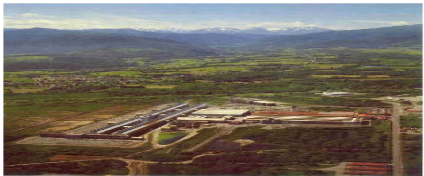
Photo 1 : Usine d'Edéa vue
aérienne
I.1.1 Situation géographique
L'usine d'Alucam/Socatral est située dans l'île
(ONG-NGOMEN), île de la ville d'Edéa chef lieu du
département de la Sanaga-maritime dans la province du littoral ;
situé à 60 km de Douala, 50 km de Mouanko, 120 km de Kribi et 180
km de Yaoundé. La ville d'Edéa est traversée par l'axe
lourd Yaoundé-Douala et par le chemin de fer camerounais.
I.1.2 Bref historique
La compagnie Camerounaise de l'Aluminium (Alucam) a
été constituée en Décembre 1954. En février
1957, l'usine entrait en production pour une capacité de 55.000
tonnes/an.
Depuis 1981, à la faveur de la mise en service de la
centrale de Song-Loulou, Alucam a procédé à une extension
de son usine. Dans le même temps, elle a effectué une
modernisation de ses installations d'électrolyse en remplaçant
les cuves à anodes Sderberg par les cuves à anodes
précuites à meilleur rendement. Grâce à ces
aménagements, la capacité de production est passée de
55.000 tonnes à 84.000 tonnes puis 87.000 tonnes/an.
Ancienne filiale du groupe français Pechiney, entre
1954 et 2000 Alucam est devenue filiale du groupe Canadien Alcan avant de
passer, il y'a trois ans, sous le contrôle du géant Australien Rio
Tinto.
Carte de flux énergétiques et perspectives
d'efficacité dans une fonderie d'aluminium: cas particulier
d'alucam/socatral
I.1.3. Organigramme activité Cameroun
Directeur Général
DRH Dir. Usine
Directeur P.CONTINU
DAF Resp. Socatral
Secrétaire
Chargé de mission


I.1.4 Le groupe Alucam en Afrique
Le développement d'Alucam est lié au volume du
tonnage exporté et au cours du métal sur le marché
international. Il dépend également des opportunités du
marché local et sous régional ; c'est pourquoi Alucam s'est
associé dès les années 60 à la création et
au développement en aval des structures de transformation de
l'Aluminium.
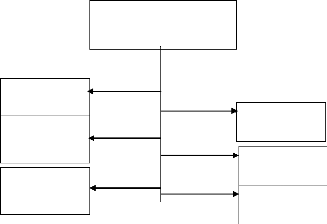
Hostellerie Sanaga
SOTRALGA GABON
COLALU R.C.A
56,48%
38,29
67,50%
Alucam
55,29%
52,55%
70,09%
Socatral Alubassa
Alu Congo
Ces pourcentages représentent les actions d'ALUCAM dans le
capital de l'entreprise en question.
Carte de flux énergétiques et perspectives
d'efficacité dans une fonderie d'aluminium: cas particulier
d'alucam/socatral
I.1.5. Histoire de l'Aluminium
L'aluminium est le métal industriel le plus
récemment découvert puisqu'il n'est utilisé que depuis la
fin du XIX° siècle. Pourtant l'alun, sulfate double d'aluminium et
de potassium, le composé d'aluminium le plus anciennement connu,
était déjà décrit par Pline, et
utilisé à Rome comme mordant pour les couleurs. Il a fallu
attendre 1825 pour que le chimiste Danois Hans Christian Oersted
obtienne l'aluminium à l'état de corps simple, sous
forme de poudre grise contenant encore une très grande quantité
d'impuretés. En 1827, Friedrich Wöhler obtint
cette même poudre grise d'aluminium contenant cependant moins
d'impuretés. [9]
Ce n'est qu'en 1854 qu'Henri Sainte-Claire
Deville présente le premier lingot d'aluminium obtenu,
à l'état fondu, par un procédé mis en application
en 1859 de façon industrielle par Henry Merle dans son usine de
Salindres (Gard), berceau de la société Pechiney. Mais ce
procédé était compliqué, ce qui donnait un
métal dont le prix était comparable à celui de l'or (1200
et 1500 F or/kg et l'argent 210 F/kg seulement). [5] Et qui le réservait
à des applications dans le luxe et l'orfèvrerie.
En 1886, Paul Louis Toussaint Héroult
en France et Charles Martin Hall aux Etats- Unis
déposent indépendamment leur brevet sur la production d'aluminium
par électrolyse à chaud de l'alumine (oxyde d'aluminium extrait
du minerai appelé « bauxite ») dissoute dans de la cryolithe
fondue (fluorure double d'aluminium et de sodium). L'invention par
Zénobe Gramme, en 1871, de la dynamo, qui
remplaça la pile de Volta comme source d'électricité, et
l'utilisation des chutes hydrauliques, la « houille blanche », rendit
possible la production économique du métal. P.L.T. Héroult
monte sa première usine en 1887 à Neuhausen en Suisse, sur une
chute du Rhin ; cette usine donnera naissance à la société
Alusuisse. Il monte en 1889 une usine à Froges (Isère), berceau
de l'hydroélectricité française développée
par Aristide Bergès, puis une autre à La Praz dans la
vallée de la Maurienne (Savoie). [9]
C.M. Hall monte de son côté en 1888 une usine
pour la Pittsburgh Reduction Company qui deviendra en 1907
l'Aluminum Company of America.
Le premier alliage d'aluminium fut inventé par
Alfred Wilm, chimiste allemand, en 1908. Cet alliage
d'aluminium contenant du cuivre et du magnésium fut exploité par
les usines de Düren et fut baptisé l'aluminium de Düren, le
« Duralumin ». C'est un alliage à « durcissement
structural » par traitement thermique, phénomène
découvert par Conrad Claessens en 1905. C'est
aujourd'hui le 2017 A, autrefois appelé en France l'A-U4G.
Le second alliage d'aluminium fut découvert en 1920 par
le hongrois Aladar Pacz, émigré aux Etats-Unis ;
c'est un alliage d'aluminium avec 13 % de silicium affiné au sodium,
baptisé l' « Alpax », alliage dévolu au moulage et
autrefois appelé en France l'A-S13.
Carte de flux énergétiques et perspectives
d'efficacité dans une fonderie d'aluminium: cas particulier
d'alucam/socatral
I.2. PROCESS ALUCAM/SOCATRAL
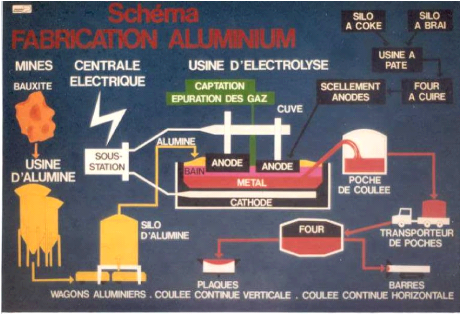
Figure I.1 : Etapes de fabrication de
l'Aluminium
Sur le site de l'usine Alucam/Socatral le processus de
fabrication de l'Aluminium va de la transformation de l'alumine en aluminium
sur le site d'Alucam puis la transformation de
cette Aluminium en produit finis par la Socatral.
La production d'aluminium primaire, se fait en
deux étapes :
1. Du minerai (bauxite), on extrait l'alumine
(Al2O3) à l'aide d'un procédé nommé
procédé de Bayer : le principe est basé
sur la dissolution de l'alumine par la soude caustique pour la transformer en
aluminate de soude soluble.
Carte de flux énergétiques et perspectives
d'efficacité dans une fonderie d'aluminium: cas particulier
d'alucam/socatral
2. Ensuite, on réduit cet oxyde en
métal par l'action d'un courant continu de forte intensité de
l'ordre des Méga Ampères. C'est le métallurgiste
français Paul Héroult et
l'américain Charles Martin Hall qui en 1886 eurent
l'idée d'appliquer l'électrolyse à la fabrication de
l'aluminium. L'astuce d'Héroult, fut de travailler avec un
mélange composé d'alumine (matériau isolant) et de
cryolithe (minerai naturel : fluorure double d'aluminium et de sodium). Ce
mélange avait en effet des caractéristiques électriques et
thermiques permettant une mise en oeuvre réaliste, c'est-à-dire
une faible résistance électrique et des caractéristiques
thermiques particulières avec une température de fusion du
mélange à 935 °C (température beaucoup plus basse que
celle de fusion de l'alumine à 2040 °C).
Cette opération a donc lieu à 960 °C dans
une cellule d'électrolyse appelée cuve où l'alumine est
dissoute dans un bain de cryolithe. Ce procédé donne lieu
à un dégagement d'oxygène qui vient brûler les
anodes qu'il faut donc renouveler régulièrement. Un service
spécialisé de l'usine fabrique le sous-ensemble anodique.
L'aluminium liquide se dépose au fond de la cuve
(cathode) d'où on l'extrait par aspiration dans une poche de
coulée étanche en acier garnie de briques réfractaires
dans laquelle on réalise le vide partiel.
Ce métal est ensuite stocké dans des fours en
fonderie. Il est ensuite solidifié sous forme de plaques ou de lingots
dans l'atelier de Fonderie.
L'aluminium secondaire ou aluminium
recyclé
L'aluminium a une excellente recyclabilité. Pour
recycler l'aluminium, on le fait simplement fondre. En plus des
bénéfices environnementaux, le recyclage de l'aluminium est
beaucoup moins coûteux que l'extraction à partir du minerai de
bauxite. Il nécessite 95 % d'énergie en moins et une tonne
d'aluminium recyclée permet d'économiser quatre tonnes de
bauxite. En sautant l'étape de l'électrolyse, qui réclame
beaucoup d'énergie, on évite les rejets polluants qui lui sont
associés.
L'aluminium est quasi recyclable à l'infini sans perdre
ses qualités, à condition de ne pas fondre dans un même
bain des alliages de composition différente. L'aluminium ménager
est récupéré avec les emballages dans le cadre du tri
sélectif. Dans les centres de tri, l'aluminium est trié
manuellement ou plus couramment grâce à des machines de tri par
courants de Foucault. Il est ensuite broyé avant d'être refondu
par des affineurs d'aluminium pour redonner du métal utilisable,
appelé aluminium de seconde fusion. L'aluminium de seconde fusion est
utilisé essentiellement pour la fabrication de pièces de fonderie
pour l'automobile (blocs moteur, culasses, pistons, etc.).
I.2.1 PROCESS ALUCAM
I.2.1.1 ATELIER D'ELECTRODES
C'est un ensemble d'ateliers pour la fabrication des
électrodes comprenant une usine à pâte d'anode, un
vibrotasseur pour la mise en forme des anodes, un four à cuisson
d'anodes (1.100°C) et un atelier de scellement des anodes et des blocs
cathodiques.
Carte de flux énergétiques et perspectives
d'efficacité dans une fonderie d'aluminium: cas particulier
d'alucam/socatral
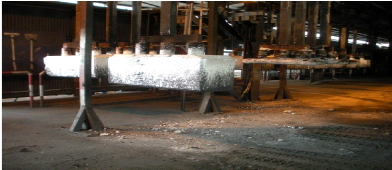
Photo 2 : une Electrode
Les blocs cathodiques sont en graphite, alors que les anodes sont
constituées par un mélange contrôlé de coke et de
brai. L'usine consomme 35.000 tonnes de coke et 8.000 tonnes de brai.
I.2.1.2 Atelier d'Electrolyse
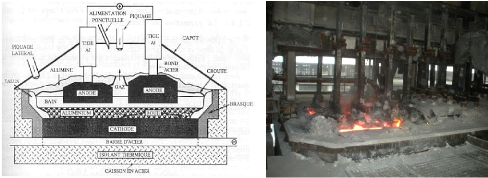
Photo 3 : cuve d'électrolyse
La cuve d'électrolyse se compose des
éléments suivants :
· Un caisson en acier,
· Un garnissage isolant thermique constitué de
briques réfractaires,
· Un creuset polarisé catholiquement
constitué d'un assemblage de blocs de carbone cuits à base
d'anthracite et liés par une pâte carbonée appelée
pâte de brasque,
· Des barres d'acier traversant le caisson et permettant
l'arrivée du courant à la cathode,
· Des tiges sur une superstructure en aluminium au dessus
du creuset maintenant les anodes carbonées,
· Un système d'aspiration des gaz vers la station de
traitement,
· Un système d'alimentation en alumine.
Carte de flux énergétiques et perspectives
d'efficacité dans une fonderie d'aluminium: cas particulier
d'alucam/socatral
L'Atelier d'électrolyse compte 274 cuves en
série reparties dans 6 salles disposées parallèlement. La
technologie 138.000 A est développée par Péchiney. Pour
protéger l'environnement, les cuves ont été
équipées des hottes de captation des gaz issus de la
réaction d'électrolyse. Ces gaz sont recyclés dans les
cuves après absorption sur l'alumine dans un centre de traitement des
gaz.
L'électrolyse consomme 170.000 tonnes/an d'alumine
importées de la République de Guinée et stockées
dans les silos. Pour son fonctionnement 1000 tonnes de cryolithe (sel double
sodium et d'aluminium) sont nécessaire pour constituer un bain
électrolytique dont la température est de 970°C.
L'atelier d'électrolyse est équipé d'un
système informatisé pour le contrôle des opérations
de production.
I.2.1.3 Atelier de Fonderie
La fonderie assure la mise en forme de l'aluminium en lingots
et en plaques ainsi que la refusion des déchets d'aluminium provenant de
Socatral. Elle dispose à cet effet de fours et d'installations de
coulée semi continue verticale pour produire des plaques et des lingots
« tés» et d'une chaine automatisée pour la production
des petits lingots
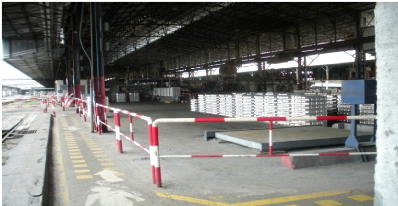
Photo 4 : lingots
I.2.1.4 Laboratoire
Le laboratoire procède aux analyses des matières
premières de même qu'à des analyses du métal pour en
déterminer la composition et la pureté. Il dispose
d'équipements perfectionnés.
I.2.1.5 Les Services Généraux
Carte de flux énergétiques et perspectives
d'efficacité dans une fonderie d'aluminium: cas particulier
d'alucam/socatral
Le fonctionnement continu des installations est assuré
grâce à la planification de la maintenance des équipements
assurés par les services d'entretien électrique et
mécanique.
Les services logistiques assurent le transport et le
déchargement des matières premières et l'expédition
des produits finis.
I.2.2 PROCESS SOCATRAL Nous distinguons quatre
étapes à savoir : I.2.2.1 Le laminage
La première étape de la transformation est le
laminage à chaud : il consiste à écraser en plusieurs
passages successifs sous les cylindres d'un laminoir une plaque d'aluminium
de forme parallépipédique préalablement
préchauffée dans un four pour améliorer la
malléabilité.
En fin de laminage à chaud, on obtient une
ébauche de 6 mm d'épaisseur. Cette dernière
préalablement refroidie, subit un laminage à froid dans un
premier laminoir à froid dit « quarto » en quelques passes de
préparation et est bobinée en rouleau.
La bobine ainsi préparée subit quelques passes
de finition dans un deuxième laminoir quarto à froid. Les
caractéristiques mécaniques demandées par le client sont
obtenues dans certaines conditions de travail lors du laminage et du traitement
thermique. L'installation du laminage se compose donc :
- De fours de réchauffage ;
- D'un laminoir à chaud à deux cylindres, d'une
puissance de 1000 CV;
- De deux laminoirs quarto à froid, équipés
d'un système de régulation automatique d'épaisseur et de
contrôle de planéité par un dispositif d'arrosage
piloté par un automate ;
- De fours de recuit ;
|