DEDICACE
Avec toute mon affection et l'intensité de mes
émotions, je dédie ce travail bienséant à mon
père,
M. Yossa Raphaël
Puisses-tu trouver ici la plus-value de l''abnégation
dont tu as fait preuve tout au long de mon apprentissage scolaire.
AVANT PROPOS
Dans le souci de valoriser l'enseignement supérieur au
Cameroun, le gouvernement Camerounais a apporté certaines
reformes ; telle que la réforme universitaire de 1993 qui fait
apparaître sur son territoire de multiples universités parmi
lesquelles l'université de DSCHANG qui comprend sept
(07) grandes écoles à l'instar de
l'Institut Universitaire de Technologie FOTSO Victor en
abrégé (IUT-FV) de Bandjoun.
Cette dernière a été construite en 1987 par le fondateur
donateur M. FOTSO Victor et l'a cédé à
l'Etat Camerounais le 12 Août 1992.Cette institut a pour but de donner
aux bacheliers une formation théorique et pratique, afin qu'ils soient
mieux préparés au marché de l'emploi.Elle leur offre
quatre (04) cycles de formations à savoir :
1. Le cursus du Diplôme Universitaire de
Technologie (DUT):
Ici, l'admission se fait uniquement sur concours avec comme
diplôme de base le Baccalauréat scientifique,
technique, le GCE-Al ou de tout autre diplôme équivalent.
La durée de la formation est de quatre (04) semestres
et suivant les mentions et parcours suivant :
Ø Mention: Génie
Mécanique et Productique (GMP)
· Parcours: Maintenance Industrielle et
Productique (MIP)
· Parcours: Mecatronik Automobile
(MKA)
Ø Mention: Génie des
Télécommunications et Réseaux (GTR)
· Parcours: Génie des
Télécommunications et Réseaux (GTR)
Ø Mention: Génie Informatique
(GI)
· Parcours: Informatique de Gestion
(IG)
· Parcours: Génie Logiciel
(GL)
· Parcours: Informatique et Services
Réseaux (ISR)
Ø Mention: Génie Civil (GC)
· Parcours: Génie Civil (GC)
Ø Mention: Génie Electrique
(GE)
· Parcours: Génie Electrique
(GE)
- Option: Electronique (EN)
- Option: Electrotechnique (EL)
2. Le cursus du Brevet de Technicien Supérieur
(BTS)
L'entrée se fait sur étude de dossier et
entretien des candidats avec un jury ; les diplômes de base sont
généralement le Baccalauréat scientifique,
Technique, le GCE-AL ou d'autre diplôme
équivalent.la durée da formation est également de quatre
(04) semestres et forme dans les filières suivantes:
Ø Génie Civil (GC)
Ø Electrotechnique (EL)
Ø Électronique (EN)
Ø Action Commerciale (Aco)
Ø Secrétariat de Direction (SD)
Ø Comptabilité et Gestion des Entreprises
(CGE)
Ø Banque (Bq)
3. Le cursus Licence Technologique (LT)
L'entrée se fait exclusivement par
étude de dossier et est ouverte au étudiants titulaires du
DUT, du BTS ou de tout autre diplôme
équivalent. Il a une durée de deux (02)
semestres suivant les parcours et mentions ci-dessous:
Ø Mention: Génie
Mécanique et Productique (GMP)
· Parcours: Maintenance Industrielle et
Productique (MIP)
· Parcours: Mecatronik
automobile-service après-vente (MKA-SAV)
· Parcours: Mecatronik
Automobile-recyclage/construction (MKA-R/C)
Ø Mention: Génie Informatique
(GI)
· Parcours: Informatique et
Réseaux (IR)
- Option: Concepteur Développeur
Réseaux et Internet (CDRI)
Ø Mention: Génie Civil (GC)
· Parcours: Bâtiment (BA)
· Parcours: Travaux Publics (TP)
· Parcours: Génie
Géomatique (GG)
Ø Mention: Génie des
Télécommunication et Réseaux (GTR)
· Parcours: Ingénierie des
Réseaux et Télécommunication (IRT)
Ø Mention: Génie Electrique
(GE)
· Parcours: Génie Electrique
(GE)
Ø Mention: Génie Thermique,
Energie et Environnement (GTEE)
· Parcours: Gestion et Maintenance des
Installations Energétique (GMIE)
· Parcours: Energie Renouvelables
(ER)
· Parcours: production
décentralisée (PDE)
4. Le cursusLicence Professionnelle
(LP)
Dont l'admission ce fait sur étude de dossier avec
à la base BTS ou d'autre diplôme équivalent selon les
mentions et parcours ci-après :
Ø Mention: Commerce et Marketing
(CM)
· Parcours : Marketing et Manager
Opérationnel (MMO)
Ø Mention: Gestion Administrative,
· Parcours: Gestion Administrative et
Management des Organisations (GAMO)
· Parcours: Gestion Comptable et
Financière (GCF)
Ø Mention: Banque (BQ)
· Parcours: Banque, Gestionnaire
relation Clientèle (BGRC)
NB: Par ailleurs, l'IUT
dispose d'une formation appelée CISCO et est offerte
à toute personne désirant se former sur les technologies de
l'information et de la communication en rapport direct avec le monde
professionnel. Elle a une durée moyenne d'un an selon l'option choisie,
à savoir:
· CITE 1 & 2
· CCNA 1 & 2
REMERCIEMENTS
c'est avec un grand plaisir que je réserve ces lignes
en gage d'obligeance et de gratitude envers tous ceux qui ont contribués
de près ou de loin à l'élaboration et la réussite
de ce travail.
· Je tiens à remercier le Pr. FOGUE
Médard, Directeur de L'IUT Fotso Victor de Bandjoun et mon
encadreur académique pour le cadre d'étude et la formation qu'il
met à notre disposition, transmise par des intervenants
compétents et qualifiés;
· Dr MTOPI FOTSO Blaise, chef de
département Génie Mécanique et Productique pour sa
disponibilité, son suivi et son encadrement tout au long de ce parcours
académique;
· Mes remerciements se dirigent aussi versM.
NGOUOTCHE NDJIYA Stéphane, enseignant à l'IUT Fotso
Victor de Bandjoun et mon encadreur académique pour sa formation de
qualité et ses conseils pertinents ;
· Mes vifs remerciements vont conjointement à
M. DIOGNE Jonas,chef de centre de CAMLAIT S.A
département plastique pour m'avoir accordé ce stage ;
· M. KENGNE Elvadas, responsable du
service maintenance et mon encadreur professionnel qui a su m'accompagner
durant cette expérience professionnelle avec beaucoup de patience et de
pédagogie
· M. KUIATA Ignace, responsable du
service qualité qui a accepté de me consacrer une partie de son
temps pour me guider dans mes travaux.
· M. KANIYONG Stève Verney, chef
d'équipe au service maintenancepour ses précieux conseils, le
partage de son expertise, sa franchise et sa participation à la
réalisation de ce travail ;
· Ma Tante MmeJACQUIN Léocadie,
pour son soutien et ses encouragements permanents.
· A mes camarades de promotion pour la largesse dont ils
ont fait preuve et les bons moments passés ensemble ;
Aux uns et aux autres, trouvez ici l'expression de ma profonde
gratitude.
LISTE DES ABREVIATIONS
AT : Administrateur Technique.
PP : Polypropylène.
PS : Polystyrène
PE : Polyéthylène.
PEHD : Polyéthylène haute
densité.
PEBD : Polyéthylène Basse
Densité.
S.A : Société Anonyme
AMDEC : Analyse des Modes de
Défaillance, de leurs Effets et de leur Criticité
Dr : Docteur
Pr : Professeur
CEMM : Chef d'Equipe Maintenance
Mécanique
CEME : Chef d'Equipe Maintenance
Electrique
LISTE DES FIGURES
Figure 1: Organigramme de CAMLAIT plastique
3
Figure 2: Phases de formation des Pots
17
Figure 3: Machine de fabrication des Pots: ADOLF
ILLIG
18
Figure 4: Diagramme d'Ishikawa du système de
production
28
Figure 5: Diagramme d'Ishikawa de la machine
29
Figure 6: Fabrication de feuille
31
Figure 7: Diagramme de PARETO des pannes de la
machine
35
Figure 8: Filtre Collecteur de boue Bas
débit
39
Figure
9: évolution des propriétés d'un polymère en
fonction du nombre de cycle de mise en oeuvre et du rapport matière
vierge/matière rebroyée.
40
Figure 10: Capteur thermocouple de type K
43
Figure 11: Régulateur de température
GEFRAN
43
Figure 12: Emetteur infrarouge ELSTEIN de type
T-FSR/2 avec une puissance dissipée de 750W
43
LISTE DES TABLEAUX
Tableau 1: fiche signalétique de Camlait
S.A
3
Tableau 2: Présentation de tous les produits
commercialisés par CAMLAIT plastique
8
Tableau 3: échelle de valeur permettant le
calcul de la criticité
25
Tableau 4: Durée des pannes machine
34
Tableau 5: Fiche AMDEC relative au système
de production
36
Tableau 6: tableau des procédures de
maintenance de routine des joints d'étanchéité.
42
RÉSUMÉ
Le travail que nous avons mené dans le cadre de notre
stage porte sur le contrôle qualité sur la chaine de fabrication
des pots de conditionnement de yaourts au sein de l'usine Camlait
département plastique. Le but de ce travail est de réduire au
maximum la quantité de mauvais pots fabriqués au sein de l'usine
car ceux-ci représentent non seulement une perte d'énergie mais
aussi un gaspillage de matière première, du temps de
fonctionnement et de l'argent. Cette étude devra ainsi garantir une
meilleure maitrise du processus de fabrication des pots de conditionnement de
yaourts, une réduction des interventions sur celui-ci et une
augmentation du rendement de la production.Pour mener à bien ce travail,
nous avons tout d'abord effectué une observation prononcée du
processus de fabrication des pots de yaourts, puis nous avons
procédé à une revue de littérature en ce qui
concerne le principe de fonctionnement de celui-ci et les
éléments qui le constituent. Puis nous avons
procédé à l'identification des différentes causes
pouvant engendrer une quantité anormale de mauvais pots, ensuite nous
avons étudié chaque cause individuellement dans le but
d'être le plus efficace possible et nous avons proposé des
solutions à ces causes. Pour cela, nous avons utilisé des outils
tels que le diagramme d'Ishikawa, le diagramme PARETO et l'AMDEC. Par la suite,
nous avons évalué le rendement de la machine à l'aide d'un
indicateur d'efficacité tel que le Taux de Rendement Synthétique
afin de connaitre sa rentabilité actuelle et de l'améliorer.
Enfin au terme de notre étude et après avoir posé des
actions correctives et préventives compte tenu des problèmes
identifiés plus haut, nous avons fait des propositions et des remarques
afin de palier à ces problèmes et d'assurer un suivi.
ABSTRACT
The work we have conducted in the framework of our training
focuses on the critical study of the quality of yoghurt packaging pots
manufactured in the factory plastic Camlait department. The purpose of this
work is to minimize the amount of bad pots manufactured in the factory because
they represent not only a loss of energy but also a waste of raw material, the
operating time and the money. This study should thus ensure better control of
the manufacturing process of packaging yoghurts pots, reduced interventions on
it and increased efficiency.To carry out this work we have first made an
observation of pronounced yoghurt pots manufacturing processes, and then we did
a review of the literature regarding the operating principle thereof and the
elements which constitute it. Then we proceeded to identify different causes
that can cause an abnormal amount of bad pots, then we studied each case
individually in order to be as efficient as possible and we proposed solutions
to these causes. Subsequently, we evaluated the performance of the machine in
order to know its current profitability and improvement. Finally at the end of
our study and after asking for corrective and preventive actions in view of the
problems identified above, we have made proposals and remarks to overcome these
problems and to monitor.
TABLE DES MATIERES
DEDICACE
Erreur ! Signet non
défini.
AVANT PROPOS
ii
REMERCIEMENTS
v
LISTE DES ABREVIATIONS
vi
LISTE DES FIGURES
vii
LISTE DES TABLEAUX
viii
RÉSUMÉ
ix
ABSTRACT
x
TABLE DES MATIERES
xi
INTRODUCTION GENERALE
1
Chapitre 1. PRESENTATION DE L'ENTREPRISE ET
DESCRIPTION DU PROJET
2
A. Présentation de CAMLAIT S.A
2
I. Camlait S.A en Général
2
1. Evolution du chiffre d'affaire
4
II.Présentation de CAMLAIT S.A
département plastique
4
1. Historique
4
2. Objectifs et Activités de
l'entreprise
4
2.1. Activités de l'entreprise
4
2.1.1. Activité de production
industrielle
5
2.1.1.1.Description et moyens matériels de
l'usine
5
a)Section « Emballage
alimentaire »
5
b)Section « Matériau de
construction »
5
c)Section
« Régénération » (recyclage des
déchets)
6
2.1.2. Activité commerciale
7
2.2. Objectifs de la structure
7
3. Les produits de CAMLAIT plastique
7
4. Organisation et fonctionnement de la
structure
9
B. Description du Projet
11
I.Présentation du service d'accueil :
Le service Maintenance
11
II.Compte rendu des activités
effectuées
12
III.Problématique
15
1. Etude du processus de production
actuel
15
2. Position du Problème
18
Chapitre 2. ANALYSE THEORIQUE DE LA SITUATION
20
A. Généralité sur la
Qualité et la Maintenance
20
I. Définition des concepts
20
1.La Qualité
20
1.1. Généralité sur la
qualité
20
a) Les Normes
21
1.2. Les outils d'analyse de la
qualité
22
1.2.1. Le Diagramme d'Ishikawa
22
1.2.2. Le Diagramme de PARETO
22
1.3. Concept de contrôle
qualité
22
2.La Maintenance
23
2.1. Généralité sur la
Maintenance
23
2.2. Les types de Maintenance
23
2.3. Les outils de maintenance
24
2.3.1. AMDEC
24
B. Indicateur d'efficacité dans un
système de production : le TRS
26
Chapitre 3. RESULTATS DU CONTROLE QUALITE :
PROPOSITIONS ET SUGGESTIONS
27
A. Résultat des analyses
27
I.Application des outils d'analyse de la
qualité au système de production actuel
27
1.Cahier des charges
27
2.Diagramme d'Ishikawa du système de
production
28
2.1. Matériel
29
2.2. Matière
30
2.3. Main d'oeuvre
32
2.4. Milieu
33
2.5. Méthode
33
3.Diagramme PARETO des pannes de la machine
33
II. Etude AMDEC relative au système
de production des pots de conditionnement de yaourts
35
III.Calcul du Taux de Rendement Synthétique
de la machine (TRS)
37
B. Mise en oeuvre des solutions
amélioratrices
38
I.Plan d'action
38
1.Actions correctives
38
2.Actions préventives
41
II.Amélioration éventuelles
43
1.Suggestions
43
2.Suivi de la production selon la méthode
des 5S
44
2.1. Définition
44
2.2. Concrétisation des 5S
46
III.Mise en place d'un système
qualité
47
1.Première étape : Le
contrôle
47
2.Deuxième étape : la maitrise
de la qualité
48
3.Troisième étape : l'assurance
qualité
49
4.Quatrième étape : la gestion
de la qualité
49
5.Cinquième étape : la
qualité totale
49
IV.Amélioration continue selon le principe
de la Roue de Deming
49
1.Démarche d'utilisation
50
1.1. L'étape Plan (en français
« prévoir »)
50
1.2. L'étape Do (en français
« faire »)
50
1.3. L'étape Check (en
français « vérifier »)
50
1.4. L'étape Act (en
français « action »)
50
V.REMARQUES
51
1.Remarques positives
51
2.Remarques négatives
51
CONCLUSION
52
BIBLIOGRAPHIE
53
ANNEXES
54
INTRODUCTION GENERALE
L'acquisition d'un avantage concurrentiel est
conditionnée par la réactivité de l'entreprise, sa
capacité à relever le défi de la
compétitivité en prenant les mesures nécessaires
d'économies. Par conséquent, elle ne peut se permettre ou
tolérer les gaspillages et doit bien gérer son budget et
optimiser ses dépenses afin de surmonter cette rude épreuve. Une
gestion efficace du système de production constitue donc un point
crucial pour toute entreprise industrielle car il permet d'optimiser ses
bénéfices et de garantir une meilleure qualité du produit
fabriqué. Cependant, cette politique gestion du système de
production et d'élimination des gaspillages n'est pas totalement
respectée dans notre entreprise d'accueil qu'est Camlait
département plastique puisque nous sommes
confrontés à de multiples problèmes qui engendrent une
quantité anormale de mauvais pots de conditionnement de yaourts lors de
leur fabrication et une production médiocre de ceux-ci. En tant que
entreprise industrielle cherchant à être leader dans son domaine,
elle doit s'efforcer de toujours veiller à augmenter sa
productivité et à mieux gérer ses couts dans
l'élimination des pertes de production (qui soit dit en passant
constituent le problème majeur à maitriser). En vue de
solutionner ces différents problèmes et surtout d'allier à
notre formation théorique une bonne formation pratique, il nous a
été demandé dans le cadre de notre stage d'effectuer un
CONTROLE QUALITE SUR LA CHAINE DE FABRICATIONDES POTS DE
CONDITIONNEMENTS DE YAOURTS AU SEIN DE L'USINE CAMLAIT
PLASTIQUE. Ainsi, dans le dessein de palier aux
problèmes qui occasionnent la quantité anormale de mauvais pots
de conditionnement de yaourts rencontrés à l'usine Camlait
plastique, nous allons tout d'abord effectuer une étude sur les
exigences de l'entreprise en ce qui concerne un bon pot et une bonne
production, puis nous allons étudier le processus de production des pots
et recenser les divers éléments susceptibles d'être
à l'origine de cette quantité anormale de mauvais pots. Ceci dit,
dans la visée de mener à bien le cahier de charges
précédemment défini, notre travail se fera selon les
articulations suivantes : Un premier chapitre axé sur la
présentation de l'entreprise et la description du projet; ensuite Un
deuxième chapitre destiné à effectuer une analyse
théorique de la situation; puis un troisième chapitre dont
l'objectif est d'exposer de façon précise les résultats
des différentes analyses effectuées et à proposer des
solutions en accord avec les problèmes définis aux chapitres
précédents.
Chapitre 1. PRESENTATION DE
L'ENTREPRISE ET DESCRIPTION DU PROJET
Le but de ce chapitre est de présenter clairement le
problème que nous allons traiter. Pour cela nous commencerons par la
présentation de l'entreprise qui sera suivie par la description du
projet. La description des opérations effectuées au sein de
l'usine nous permettra de relever la pertinencedu problème qui se pose
et de définir les objectifs de notre travail.
A. Présentation de CAMLAIT S.A
I.
Camlait S.A en Général
Tableau 1: fiche
signalétique de Camlait S.A
RAISON SOCIALE
|
SOCIETE CAMEROUNAISE DE PRODUITS LAITIERS
|
DATE DE CREATION
|
Novembre 1972
|
STATUT JURIDIQUE
|
Société anonyme
|
ACTIVITES
|
Fabrication et commercialisation des produits
laitiers frais, boissons alimentaires infantiles
|
SIEGE SOCIAL
|
Douala Bassa Rue
TRATAFRIC(Cameroun)
|
CAPITAL SOCIAL
|
3.334.140.000 Francs CFA
|
NUMERO DU CONTRIBUABLE
|
NIU M 1172 0000 0887 N
|
NUMERO AU REGISTRE DU COMMERCE
|
RC/DLA/1972/B/4327
|
REGIME FISCAL
|
REEL
|
EFFECTIF
|
535 (2012)
|
TEL/FAX
|
Fax : +237 33 37 21 90 Télex :
5402KNTél. : +237 33 37 44 60/33 37 28 05
|
SITE WEB
|
www.camlait.com
|
La société camerounaise des produits laitiers
(CAMLAIT) est une entreprise camerounaise agroalimentaire
créé en novembre 1972 grâce à
l'initiative et au dynamisme de certains hommes d'affaires notamment :
M.ZUKO MICHEL, M. FODOUOP THOMAS, M. KAYO ELI.
Membre du Groupement Inter-patronal des entreprises du
Cameroun (GICAM), c'est un acteur majeur de la production et de la
commercialisation des produits laitiers frais et des boissons
rafraîchissantes dans la sous-région CEMAC. Elle a pour
activité la production et la distribution des produits laitiers et son
siège social est dans la zone industrielle de bassa-Douala entre PANZANI
et TRACTAFRIC.
Trois ans après sa création, la concurrence est
de plus en plus âpre et CAMLAIT a pour principal rival la
Société JEM. Ainsi pour s'imposer sur le marché et
occuper une position de leader dans le secteur de produits laitiers, elle
procédera à l'absorption de la société JEM en 1977.
La même année, CAMLAIT dans son élan expansionniste
s'enrichit d'un nouveau centre de production à Yaoundé.
En 1979, l'entreprise crée une autre unité de
production à GAROUA. Certes, cette dernière, suite au
foisonnement et au bon marché de substitution dans le septentrion, sera
fermée après une mévente persistante. En 1980 un centre de
distribution voit le jour à Bafoussam en vue de faciliter et de rendre
beaucoup plus efficace la distribution de leurs produits. En février
2008, elle crée à N'Gaoundéré une agence pour la
commercialisation des boissons nutritives RIVERR et des boissons
rafraichissantes JOVINO. La société CAMLAIT S.A met sur le
marché camerounais une variété de produit tel
que :
· Une gamme de Yaourt
· Une gamme de Nourris
· Une gamme de Riverr
· Une gamme de Crème
· Une gamme de Jus Naturel
· Une gamme de Beurre
· La Berger instant
Elle élargit également son assortiment en
mettant sur le marché du lait liquide et en changeant aussi sa forme
juridique pour devenir une société anonyme(SA).
1. Evolution du chiffre d'affaire
Elle a commencé sous la forme juridique de
société à responsabilité limité
(Sarl) avec un capital de base de 15 000 000 de
FCFA et ne produisait que du yaourt naturel. Cependant, la
fécondité du produit dans d'autres localités du pays
permettra une croissance vertigineuse du capital de la société
qui passera de 15.000.000Fcfa à
71.000.000Fcfa. Le capital de CAMLAIT s'accroît une fois
de plus pour se retrouver à 110.000.000 en 1988 ;
elle change alors son statut juridique pour devenir société
anonyme (S.A.) avec un chiffre d'affaire estimé
à plus de 1.122.760.000 FCFA. De nos jours, il est
estimé à 3.334.140.000 FCFA.
Dans l'optique de facilite la production et de satisfaire la
demande en qualité et en quantité de ses produits, elle s'est
subdivisée au fil des années en plusieurs département
parmi lesquels le département plastique.
II. Présentation de CAMLAIT S.A département
plastique
1. Historique
Situé dans la zone industrielle de Bonaberi à
Douala près de COMETAL, a cote de CIMENCAM, le département
plastique de Camlait S.A voit le jour en 1978 sous la dénomination de
SOFECAM (société de fabrication d'emballages du
Cameroun) avec pour activité principale la fabrication des emballages
pour le conditionnement des yaourts. Ayant pour souci d'étendre son
champ d'action, la SOFECAM achète
L'UNIPLAST en 1996, qui était une société
voisine spécialisée dans la fabrication des ustensiles plastiques
et dérivée, en plus des emballages alimentaires, les gaines
annelées, les tuyaux oranges pour canalisation électrique dans
les bâtiments, des coudes et tuyaux PVC pour plomberie. Dès
Janvier 2007 CAMLAIT SA absorbe SOFECAM et
devient le département Plastique.
2. Objectifs et Activités de
l'entreprise
2.1. Activités de l'entreprise
Depuis sa création, jusqu'à nos jours, la CAMLAIT
plastique a toujours menée deux types d'activités principales
:
2.1.1. Activité de production
industrielle
A tous points de vue, elle est considérée autant
que l'activité de distribution, comme principales activités de
l'Entreprise. Elle consiste à la prise en compte intégrale des
opérations inclues dans la fabrication physique. C'est à dire de
l'approvisionnement en passant par la transformation des matières
premières en produits fini, du conditionnement de ces produits
jusqu'à la distribution. Cette activité qui est la production des
produits plastiques est assurée par une usine située à
Douala (Bonaberi).
2.1.1.1. Description et
moyens matériels de l'usine
L'usine fait fonctionner les machines selon les commandes des
clients et le stock du magasin et est divisée en trois secteurs :
Matériaux construction, Emballage alimentaire,
régénération.
a) Section « Emballage
alimentaire »
Elle est constituée des équipements tel
que :
· La Ligne des feuilles : C'est une
ligne d'extrusion composée de 4 équipements (extrudeuse,
calandres, tireuse et enrouleur) destinés à la production des
bobines de feuilles en PS.
· L'Illig : C'est une machine de
thermoformage qui permet la fabrication des pots de conditionnement de yaourt
à partir des bobines de feuilles préalablement
fabriquées.
· Les SIDEL 1, 2 et 3 : Ce sont des
machines qui utilisent le principe de l'extrusion soufflage pour la fabrication
des bouteilles plastiques de conditionnement de vinaigre et autres liquides
alimentaires. Leur forme et leur contenance varient entre 1L, 1/2L, 30cL,
25cl.
· La presse 90 Tonnes : Elle est
une machine à injection capable de produire les bouchons de fermeture
des bouteilles fabriquées dans les différentes SIDEL. A chaque
injection de la matière dans le moule, on a 6 bouchons
fabriqués.
· L'OMSO et la
VANDAM: Ces équipements sont destinés à
l'impression en fonction d'un cliché préconçu pour les
pots de conditionnement de yaourts.
b) Section « Matériau de
construction »
Les produits de cette section sont en majorité des
gaines et des tuyaux de diamètre et de propriétés
différentes.
· Les lignes 104 et 105 :Ce sont
des équipements produisant des gaines annelées de diamètre
16mm, 20mm, 25mm, 32mm.
· Les lignes 103 et 101 : Ce sont
des machines conçues pour la fabrication des tuyaux noirs de
diamètre 25mm, 32mm, 40mm, 50mm, 63mm, 75mm, 90mm, 110mm.
· Les lignes 102 et 100 : Ces
équipements produisent les gaines orange de diamètre 9mm,
11mm ; 13mm, 16mm.
· La presse 200 tonnes : De
même que la presse 90 tonnes, elle produit aussi les bouchons de
fermeture des bouteilles mais en plus grandes quantités (16 bouchons par
injection).
· La presse 300 tonnes : C'est
aussi une machine à injection qui permet la fabrication des seaux de
10L.
c) Section
« Régénération » (recyclage des
déchets)
Cette division est consacrée à la transformation
des déchets en matériaux réutilisables. Les
équipements qui meublent cette section sont :
· Le Super Broyeur qui sert à
broyer des déchets très solides en grande quantité et plus
rapidement. Ce sont généralement les gaines orange, les seaux et
les tubes noirs en polyéthylène.
· Le Densifieur C'est une machine qui
permet de transformer les déchets plastiques acheté dans
certaines entreprises plastiques telles que (PLASTICAM, SUPERMONT...) pour
obtenir une matière homogène utilisée plus
précisément sur les lignes 100, 101, 102,103.
· Le Mélangeur C'est la machine
qui permet de mélanger la matière sortie du densifieur avec la
matière première selon un dosage bien précis.
· Le Broyeur PEBD pour le broyage des
carottes bouteilles plastiques.
· Le Broyeur PEHD : pour le
broyage des carottes bouchons plastiques.
· Le Broyeur de l'Illig qui permet de
broyer les pots vides de yaourts de 125cl et la feuille déjà
utilisée à l'Illig pour obtenir des granulés. Ces
granulés seront ensuite utilisés pour la fabrication des bobines
de feuilles.
La production ne saurait se faire sans le concours de deux
machines primordiales : le COMPRESSEUR qui produit de
l'air comprimé utilisé par les équipements de production,
la commande des vérins, des électrovannes et de deux
GROUPE FROID constitués d'un compresseur, d'un
condenseur, d'un détendeur, et d'un évaporateur dont le
rôle est de produire l'eau glacée pour le refroidissement des
équipements de production.
2.1.2. Activité
commerciale
Elles relèvent d'avantage de la distribution des
produits fabriqués sur le marché camerounais à travers
plusieurs dépôts à Douala, Yaoundé et
Bafoussam.
Mis à part la production et la distribution des
produits qu'elle fabrique, elle assure également le tri des
déchets qu'elle génère afin de réduire leur impact
au niveau de l'environnement interne et externe à l'usine et favoriser
le recyclage car de tels impactes peuvent comporter des implications pour la
santé et polluer l'environnement.
2.2. Objectifs de la structure
Tout comme le groupe CAMLAIT, les principaux objectifs de la
société CAMLAIT Département Plastique sont :
· Satisfaire sa clientèle par des produits de
bonne qualité.
· Avoir une main mise sur le procédé de
fabrication.
3. Les produits de CAMLAIT plastique
CAMLAIT plastique met à la disposition de ses clients
une large gamme de produits (les gaines annelées, les tuyaux oranges
pour canalisation électrique dans les bâtiments, des
« coudes et tuyaux pour plomberie, les pots de conditionnement de
yaourts....) qui ne limite pas au marché nationale mais s'ouvre
également aux marchés internationaux en exportant ses produits
dans plusieurs pays d'Afrique parmi lesquels : le BENIN, le CONGO, le
TOGO, le GABON, le BURKINA-FASO, le TCHAD et la RCA.
Tableau 2:
Présentation de tous les produits commercialisés par CAMLAIT
plastique
GAMME DE PRODUITS
|
ILLUSTRATION
|
Gaine annelée de
diamètre de 16, 20, 25, 32 mm pour des longueurs de 50 et 100m
|
|
Tuyau PE noir de diamètre de
25, 32, 40, 50, 63, 75, 90, 110mm pour des longueurs de 50 à 100m
|
|
Gaine Orange pour des
diamètres de 9, 11, 13, 16mm pour des longueurs de 50 à 100m
|
|
Bouteille plastique pour
conditionnement de denrée tel que le Vinaigre, l'acide des
bactéries, yaourts.... fabriqué en 1L, 1/2L, 30cl, 25cl
|
|
Seaux de 10Lpour usages
général
|
|
Pot de conditionnement de yaourt de 125cl
|
|
4. Organisation et fonctionnement de la
structure
La société CAMLAIT plastique semble afficher une
modularité, quant à ses fonctions sans que l'information ne
s'éloigne de la direction générale. C'est une
société organisée de façon hiérarchique et
dispose d'une structure administrative composée d'un conseil
d'administration ayant à sa tête un chef, un président
directeur, un administrateur et une administration constituée d'un chef
de centre, une secrétaire, un chef d'usine, un responsable administratif
et financier, un responsable qualité, un responsable commercial, un
responsable des services de maintenance, un responsable des magasins et enfin
un responsable de production. Il est composé de plusieurs services
chacun dirigés par un responsable. On distingue :
· Le service Qualité ;
· Le service administratif et financier ;
· Le service technique qui comporte en son sein le
service maintenance et le service fabrication ;
· La Direction du Générale ;
· Le service commercial ;
· Le service de gestion du personnel ;
Au sein de cette société de taille moyenne, il
est aisé de percevoir l'interaction constante entre les
différents services cités plus haut car possédant
plusieurs circuits de création de richesses, ceux-ci ne sauraient
être effectifs sans l'antagonisme de tous ces services.
L'organigramme suivant illustre de façon
détaillée les relations entre ces différents services
avec une extension de tous ceux-ci.

Figure 1: Organigramme de
CAMLAIT plastique
Toutefois, afin d'atteindre ses objectifs qui sont de
satisfaire ses clients par des produits de bonne qualité, elle dispose
d'une usine de fabrication sous la charge du service technique et
constituée de :
1er Centre de frais :
Emballages alimentaires
Il est caractérisée par la fabrication des
emballages alimentaires en matière plastique, plus
précisément en (PS) pour les pots de conditionnement des yaourts,
et du (PEHD) pour les Bouteilles de conditionnement du vinaigre et autres
produits chimiques.
2e Centre de frais :
Matériaux de construction.
Ici on fabrique les gaines orange, les gaines annelées
et les tuyaux de canalisations d'eau. La matière première
utilisée ici est le (PP) pour les gaines annelées, le plastique
densifié pour les gaines orange et le (PEHD) pour les tuyaux noir de
canalisations.
3e Centre de frais :
Régénération.
Dans cette partie de l'usine, on procède à la
récupération des déchets et leur transformation en
granulées réutilisables.
Nous avons présenté de façon global la
société CAMLAIT SA département plastique d'un point de vu
interne, il nous revient actuellement de compléter l'analyse en
présentant cette entreprise dans l'environnement technique de notre
travail d'où l'importance du chapitre suivant.
B. Description du Projet
Du 03 Aout au 03 Octobre 2015, nous avons effectué un
stage au sein de l'entreprise Camlait plastique ; en vue de rendre compte
de manière fidèle et analytique des deux Mois passés au
sein de cette entreprise, il apparait logique de présenter à
titre préalable le service dans lequel ce stage a été
effectué puis, il sera précisé les différentes
missions et tâches que nous avons pu effectuer au sein du service
maintenance. Enfin nous justifierons le choix de ce sujet d'étude et
enfin nous présenterons la problématique
générale.
I.
Présentation du service d'accueil : Le service Maintenance
Dès notre arrivée sur le site, nous avons
été accueillis et encadré par le service maintenance. Il
est responsable de l'installation et de la maintenance des machines et des
divers équipements de toute l'usine Fabrication. Il est également
chargé de la production du froid et de l'air comprimé. Ce service
analyse également les paramètres de maintenance de l'usine en
l'occurrence la fiabilité, la disponibilité des
équipements et les coûts de la maintenance. Le Service maintenance
comporte :
· Un service de maintenance mécanique ;
· Un service de maintenance électrique ;
· Un administrateur technique
· Le bureau méthode ;
· Les ateliers de fabrication mécanique, de
chaudronnerie et d'électricité ;
· Le magasin des pièces de rechange.
Cependant, ce dernier, opérant avec le service
fabrication qui s'occupe de la fabrication des gaines, pots, seaux et autres
sont sous la charge d'un chef d'usine chargé de coordonner et de
contrôler la réalisation des taches au sein l'usine de fabrication
qui représente l'environnement dans lequel nous avons effectué
notre stage.
II. Compte rendu des activités effectuées
Pendant ce stage, nous avons passé le plus clair de
notre temps à observer et a interagir avec les divers processus de
fabrication présent à l'usine. A mesure que nous nous
familiarisions avec ceux-ci, nos recherches se sont approfondies. Ce n'est donc
qu'à partir du deuxième mois de notre stage que nous
été véritablement opérationnel du fait de la
meilleure maîtrise de ces process en terme de production, des
différents problèmes auxquels ils sont constamment soumis et des
solutions associées à ces problèmes.
Toutefois, il parait nécessaire de développer de
façon détaillée et cursive toutes les activités
effectuées pendant notre stage à travers le journal de bord qui
suit. De ce fait, intégré quotidiennement dans équipe de
travail au sein du service maintenance, nous avons, sur une période
hebdomadaire de 05 jours (lundi à vendredi) effectué
principalement les taches suivantes :
· Semaine 1 : nous avons tout d'abord pris contact
avec l'environnement interne de l'entreprise et nous avons été
intégrés à un groupe de travail sur les chaines de
productions dans le but de se familiariser avec les machines et l'usine en
général.
· Semaine 2 : en début de cette semaine, nous
avons tout d'abord commencé par visiter d'autres services tels que le
service qualité ; ensuite, nous avons assisté les ouvriers
dans la production de gaine annelée sur les lignes 104 et 105. Puis, en
cours de semaine, nous avons assisté un employé dans la
maintenance d'une installation électrique où il a
été question de refaire le câblage du coffret de commande
d'un moteur. Notre rôle a été de changer le disjoncteur qui
commandait le moteur et d'assister le Maintenancier en dimensionnant et en
testant la continuité des câbles nécessaire pour refaire le
câblage.
· Semaine 3 : au cours de cette semaine, nous avons
assisté les ouvriers dans la fabrication des pots de conditionnement de
yaourt ; il a été question ici pour nous d'effectuer un
contrôle des pots dès leur sortie de la machine afin de s'assurer
de la conformité de ceux-ci. Cette même semaine, suite à un
signalement fait par les producteurs par rapport à un une fuite d'eau
sur la machine servant à produire ces pots, nous avons identifié
l'origine de cette fuite et conclu que un des tuyaux qui véhiculent
l'eau pour le refroidissement des pots était percé. Nous avons
donc procédé au changement de celui-ci sous la supervision d'un
Maintenancier
· Semaine 4 : au cours de cette semaine, nous avons
procédé au changement du moule de l'ILLIG dans le but de changer
le type de pots fabriqué. Pour ce faire, il était question dans
un premier temps de démonter la machine afin d'extraire le moule;
ensuite, l'extraction du moule s'est faite à l'aide d'un palan de 2,5
tonnes. Puis, le nouveau moule a été monté et la machine a
été remontée. Nous avons donc participé au
démontage et au remontage de la machine. Toujours durant cette
semaine, nous avons assisté un Maintenancier dans le changement d'un
collier chauffant sur la ligne de fabrication des gaines orange. Il
était question de changer l'ancien collier car celui-ci était
grillé et d'installer un nouveau. Et il fallait par la suite
vérifier que ce dernier était bien installé ; pour ce
faire nous avons utilisé un multimètre et il fallait
contrôler à partir du pupitre de commande que le collier
installé respectait les valeurs de consigne.
· Semaine 5 : pendant cette semaine, nous avons tout
d'abord assisté un Maintenancier lors du changement d'un joint
d'étanchéité d'un vérin sur la ligne de production
des feuilles PS suite à un constat fait par un producteur par rapport
à de l'huile qui s'échappait du vérin pendant son
fonctionnement. Nous avons d'abord mis la machine en fonctionnement afin
d'identifier l'origine du problème. Ensuite, nous avons
démonté le vérin, extrait le joint défectueux et
enfin nous avons remplacé celui-ci et remonté le vérin sur
la machine ; Cette même semaine, suite à un signalement fait
par les producteurs par rapport à un arrêt brusque du Densifieur,
nous avons constaté que des câbles étaient brulés
dans le coffret de commande de celui-ci. Nous avons donc procédé
au changement de ces câbles de grande section grâce à une
pince hydraulique ; après changement de ceux-ci, nous avons mis la
machine en fonctionnement constaté que le sens de rotation du moteur
était inversé. Nous avons donc inversé la polarité
du moteur sur le disjoncteur de commande de celui-ci.
· Semaine 6 : Suite à une observation faite
par rapport à l'apparition de givre sur le groupe froid, nous avons
effectué des tests à l'aide d'un multimètre et sous la
supervision d'un Maintenancier afin de s'assurer que le problème
n'était pas matériel. Ensuite, nous nous sommes rendu compte
qu'il fallait effectuer un bon calibrage du régulateur de
température du groupe froid. Ce calibrage a été
effectué par un Maintenancier. Toujours cette même semaine, nous
avons effectué un suivi suite à l'intervention faite sur le
Densifieur la semaine précédente. Il était question de
contrôler l'équilibrage des phases de celui-ci. Sous la
supervision d'un Maintenancier, nous avons fait ce test à l'aide d'une
pince ampèremetrique.
· Semaine 7 : inspection du compresseur suite
à un arrêt brusque de celui-ci. Il était question d'ouvrir
le boitier de commande de celui-ci afin d'effectuer des tests. Après
vérification, nous avons constaté qu'un connecteur était
mal fixé. Il a été par la suite refixé et le
compresseur a redémarré. Plus tard dans cette semaine, nous avons
participé au démontage de la tête de l'extrudeuse de la
SIDEL 1 pour nettoyage. On a utilisé de la graisse à haute
température lors du remontage des vis afin que ceux-ci ne grippent pas
à haute température.
· Semaine 8 : durant cette semaine, et dans le cadre
d'une maintenance préventive, nous avons effectué le soufflage de
toutes les armoires électriques présentes à l'usine. Nous
avons également effectué le serrage des vis de ces armoires.
Toujours au cours de cette semaine, l'on a effectué le Démontage
des matrices du moule de l'illig suite à un problème de
refroidissement du moule. Après le démontage de celui-ci, nous
avons constaté que les orifices destinés à faire circuler
l'eau pour le refroidissement du moule étaient bouchés par un
excès de saleté. Il était question de nettoyer ces
matrices de déboucher ses orifices à l'aide d'un tuyau à
air et de remonter les matrices et le moule.
Néanmoins, nous avons pu effectuer des tâches qui
se situent à la périphérie du service qualité.
Dès lors qu'elles nous ont permis d'apprendre divers aspects du
métier de qualiticien, il parait approprié de s'y attarder. Il
s'agit de :
· Le contrôle de la conformité des
extincteurs ;
· L'assistance à la gestion du tri des
déchets générés par l'usine afin de réduire
leur impact sur l'environnement ;
· Le pesage des différents produits
fabriqué à l'usine en vue d'effectuer un contrôle
qualité ;
Pendant l'exécution de toutes ces tâches, nous
avons surtout été confronté aux problèmes
d'adaptation car ne maitrisant pas les méthodes de travail et les
différents outils et appareillages utilisés. Malgré cette
difficulté, après de multiples interventions, nous avons pu
développer un savoir-faire nécessaire dans l'accomplissement de
nos diverses missions.
III. Problématique
Ce stage a été l'occasion de mieux assimiler les
divers enseignements reçu jusqu'ici et leur domaine d'application. Du
fait de la nécessité de contrôle et de
l'amélioration de la productivité des processus de production et
dans le but de favoriser notre insertion dans le monde professionnel, pendant
ce stage il nous a été affecté le thème :
CONTROLE QUALITE SUR LA CHAINE DE FABRICATION DES POTS DE CONDITIONNEMENT
DE YAOURTS AU SEIN DE L'USINE CAMLAIT PLASTIQUE. Le processus de
production actuel et les différents moyens employés dans la
fabrication des pots présentent certains défauts d'où
l'Object de notre étude.
1. Etude du processus de production
actuel
Au sein de l'usine CAMLAIT plastique, on retrouve plusieurs
processus de fabrication (extrusion, injection, extrusion soufflage,
calandrage, thermoformage....) chacun ayant son principe de fonctionnement. Un
Processus Est défini comme un «ensemble
d'activités corrélées ou interactives qui transforme des
éléments d'entrée en éléments de
sortie» et un Produit Est défini comme le
«résultat d'un processus ». Le processus de production que
nous allons étudier ici est le Thermoformage.
Le thermoformage est l'un des grands procédés de
mise en forme des Polymères utilisé en industrie plastique
permettant de réaliser, à partir de feuilles ou plaques PS
généralement extrudées ou calandrées, des objets
Concaves d'épaisseurs et de dimensions diverses (pots de conditionnement
de yaourt).
Principe : dans notre cas, Il consiste à
chauffer une portion du rouleau de feuille PS de façon progressive qui
est déroulé puis entrainé vers un moule a cinq pots en
traversant les résistances chauffantes qui, réglées
à près de 250 degrés ramollissent la feuille qui peut
être moulée afin d'obtenir des pots de yaourt sous le coup de la
pression de l'air et qui, refroidi immédiatement permet de faciliter la
formation et le démoulage des pots. La feuille est insérée
dans la machine à travers une glissière et déplacée
par une chaine picot entrainée par un moteur pas à pas. Le
chauffage de la feuille se fait en sandwich (le chauffage du bas
s'éclipsant au formage) à l'aide d'un four muni de
résistances chauffantes (annexe) de 625W chacune toutes
regroupées en 8 zones : 4 zones en bas de la feuille et 4 zones en
haut de la feuille, ceci dans le but de la ramollir de façon uniforme
afin d'obtenir des bon pots. Lorsque le ramollissement est suffisant, on pousse
la feuille à l'aide d'un poinçon afin de créer un
pré-étirement ; ce dernier facilite la déformation de
la feuille et permet de régulariser les épaisseurs finales par
apport d'une quantité de matière plus importante au fond du pot.
La course du poinçon est généralement proche de la hauteur
du moule, ce qui fait qu'une bonne partie de la déformation totale de la
feuille est réalisée à l'étape de
poinçonnage, d'où son importance. Ici, la matière
utilisée ici pour fabriquer le poinçon est le Téflon.
La déformation de la feuille est ensuite
complétée par l'action d'une pression d'air qui va plaquer la
feuille contre un moule froid (étape de soufflage). La pression de
soufflage est de l'ordre de 4 à 6 Bar. L'action de la pression se fait
généralement lorsque le poinçon arrive en fin de course,
pour que ce dernier agisse pleinement. Pour éviter l'augmentation de
pression dans le moule au cours du formage, celui-ci est muni d'évents
qui permettent l'évacuation de l'air emprisonné entre la feuille
et le moule. On cherche à obtenir une trempe rapide du pot lorsque
celui-ci entre en contact avec les parois du moule afin de figer sa forme. Les
moules utilisés ici fabriqué en aluminium en raison de leur
propriétés de bons conducteurs thermiques et ils sont
régulés par un circuit de refroidissement par eau glacée
pour être beaucoup plus froids que la feuille. L'ordre de grandeur de la
température du moule est de 10 à 40 °C.
Le moule est muni d'éjecteur et
lorsque celui-ci se ferme, il comprime des ressorts de compressions ;
après la formation des pots, le moule s'ouvre et relâche les
ressorts qui font sauter les éjecteurs sous le coup de la
décompression, libérant ainsi les pots qui seront soufflés
dans les goulottes. Le fonctionnement est alors semi continu (temps
d'arrêt au formage) et l'on récupère les chutes de
découpe pour les recycler.
En résumé, les pots sont formés en trois
phases :
· 1ère phase : arrivée de
la feuille chauffée sur le moule ;
· 2ème phase : descente du
poinçon sur la feuille ramollie;
· 3ème phase : fermeture du moule
et soufflage.
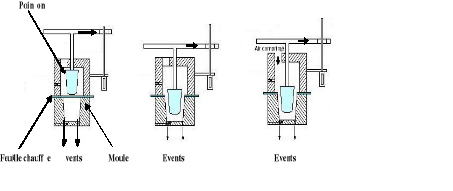
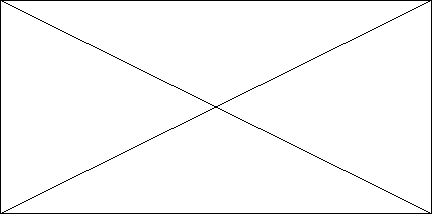
1ère phase
2ème phase
3ème phase
Figure 2: Phases de formation
des Pots
Remarque :
· Le moteur pas à pas est un moteur spécial
qui, au lieu de tourner sans arrêt comme un moteur normal, effectue une
rotation qui représente soit un ½ tour, ¼ tour : c'est
le Pas
La machine servant à produire ces pots est une ADOLF
ILLIG. La température étant une grandeur physique qui
évolue de façon exponentielle, il faudra environ 45 minutes pour
la mise en chauffe de la machine et pour atteindre la température de
consigne.
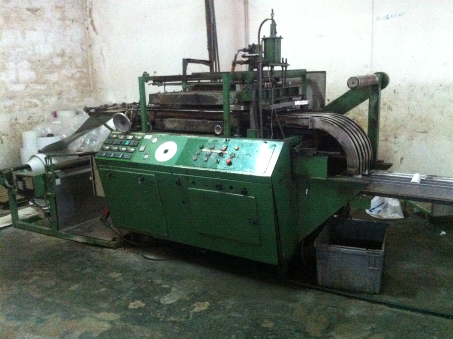
Rouleau de feuille PS
Zone d'insertion de la feuille (glissière)
Zone de chauffe de la feuille (four)
Zone de formage des pots (Moule)
Vérin de commande du poinçon
Figure 3: Machine de
fabrication des Pots: ADOLF ILLIG
2. Position du Problème
L'analyse du processus de fabrication des pots actuel par
thermoformage fait état d'un grand nombre de manquement au niveau
productique et technique.
Lors de la production des pots de conditionnement de yaourt,
il nous a été donné de consigner une quantité
flagrante de mauvais pots engendrant ainsi de grandes pertes. De prime abord,
notre observation des méthodes de travail et notre analyse des rapports
d'inspection des équipements servant à produire ces pots nous ont
permis de ressortir les insuffisances du système actuel et de conclure
que ce problème était beaucoup plus d'ordre matériel et
humain. Il vient donc la nécessité impérieuse de faire une
étude critique afin de recenser les diverses causes qui affectent la
qualité de ces pots ayant ainsi un impact sur l'efficacité et le
rendement de ce processus afin que l'on puisse concentrer les efforts
d'amélioration sur ces points.
Chapitre 2. ANALYSE
THEORIQUE DE LA SITUATION
Réussir à améliorer la qualité, la
productivité interne et à inscrire durablement son entreprise
dans une réelle dynamique d'amélioration continue, ne peut pas
être le fruit d'un hasard. Cela passe par l'utilisation des
méthodes et outils adaptés à la situation, à
l'objectif recherché et à la mobilisation des ressources de
l'entreprise. Pour chaque situation, il existe un ou plusieurs outils
facilitants l'atteinte des objectifs, car ils apportent des
méthodologies éprouvées, et permettent de canaliser les
efforts de tous afin d'éviter toute dispersion contre-productive. Pour
réussir à mettre en oeuvre des actions d'amélioration
pertinentes nous avons utilisé plusieurs outils que nous allons
présenter dans ce chapitre en commençant par la méthode
des 5M, ainsi que les outils tel que le diagramme Ishikawa, le diagramme Pareto
et l'AMDEC.
A. Généralité sur la
Qualité et la Maintenance
I.
Définition des concepts
1. La
Qualité
1.1.
Généralité sur la qualité
Chacun peut comprendre intuitivement ce qu'est la
qualité mais reste toutefois incapable d'en donner une définition
précise. Nous allons tenter à l'aide des définitions
suivantes d'aborder les différents aspects de la qualité afin de
mieux appréhender cette notion.
Selon l'ISO : « la
qualité est l'ensemble des propriétés et
caractéristiques d'un service ou d'un produit qui lui confère
l'aptitude à satisfaire des besoins exprimés ou implicites de
tous les utilisateurs. »
Selon le Petit Larousse :« la
Qualité c'est une manière d'être bonne ou mauvaise de
quelque chose : un produit de bonne ou de mauvaise
qualité. »
Cependant, la capacité d'un produit ou d'un service
à être bon ou mauvais est relative car la qualité des uns
n'est pas forcement celle des autres.
Ex : - La qualité n'est pas l'excellence :
une Ferrari peut représenter l'excellence, mais une voiture moins
prestigieuse peut être de bonne qualité.
Par conséquent, la qualité pour une entreprise
requiert une réponse à un objectif de conformité d'un
produit par rapport à des spécifications précisant
clairement les caractéristiques du produit.
On est donc confronté à un problème
d'évaluation ou de mesure de la qualité. Pour l'évaluer,
les entreprises ont très souvent recours à un étalon
universellement reconnu (norme) ou à des objectifs qu'elle s'est
fixée à travers l'audit qualité.
a) Les
Normes
Une Normeest un document officiel
réalisé par un organisme agrée. Ce terme
générique désigne un ensemble de caractéristiques
décrivant un Object, un être qui peut être virtuel ou non.
LaNormalisationest la rédaction de ces normes. Tout ce qui
entre dans une norme est considéré comme
« normal » alors que ce qui en sort est
« anormal » ; ces termes peuvent sous-entendre ou non
des jugements de valeur.
Les organismes qui rédigent les normes sont
appelés Organismes de Normalisation. Les plus connus sont : AFNOR,
CEN, OASIS et bien sûr ISO.
L'avantage des normes ISO est qu'elles garantissent des
produits et des services surs, fiable et de bonne qualité. Pour les
entreprises, elles sont des outils stratégiques permettant d'abaisser
les couts en augmentant la productivité et en réduisant les
déchets et les erreurs.
L'ISO à élaborer plus de 19500 norme
internationales couvrant presque tous les secteurs du monde économique,
de l'industrie et de la technologie. Toutefois, nous parlerons juste de l'ISO
9001 car c'est la famille de normes ISO la mieux adaptée à notre
étude.
- La norme ISO 9001 fait partie de la série de norme
ISO 9000, relatives aux systèmes de gestion de la qualité, elle
donne les exigences organisationnelles requises pour l'existence d'un
système de gestion de la qualité. Elle permet la reconnaissance
des aptitudes en qualité d'une organisation donnée par une tierce
partie indépendante.
Par ailleurs, pour analyser la qualité, on a très
souvent recours à plusieurs outils.
1.2. Les outils d'analyse
de la qualité
1.2.1. Le Diagramme
d'Ishikawa
C'est un outil permettant de visualiser de façon
ordonnée les causes conduisant à un effet constaté que
l'on cherche à analyser. Le diagramme « causes / effet » est
aussi appelé diagramme en arête de poisson, arbre des causes ou
diagramme d'Ishikawa, du nom de son inventeur : le japonais Kaoru Ishikawa.
C'est la représentation graphique d'une méthode d'analyse dite
méthode des « 5M » (abréviation de
Main d'oeuvre, Matériel,
Matière, Méthodes,
Milieu ou Maintenance ou Management ou Mercatique)
destinée à mettre en évidence les liens de
causalité entre les éléments conduisant à un
même effet.
1.2.2. Le Diagramme
de PARETO
Le diagramme de PARETO est un moyen simple pour classer les
phénomènes par ordre d'importance. Ce diagramme et son
utilisations ont aussi connus sous le nom de « Règle des 20/80
» Ou « Méthode de ABC ».
· Les objectifs sont :
ü Faire apparaître les causes essentielles d'un
phénomène.
ü Hiérarchiser les causes d'un
phénomène.
ü Evaluer les effets d'une solution.
ü Mieux cibler les actions à mettre en oeuvre.
· Méthodologie - Démarche
1. Etablir les listes des données.
2. Classer les valeurs du critère étudié
en ordre décroissantes.
3. Calculer le cumule de ces valeurs.
4. Calculer, pour chaque cumule le pourcentage.
5. Représenter le graphique des pourcentages
cumulés.
1.3. Concept de
contrôle qualité
Le contrôle qualité permet de savoir si les produits
ou les services vendus par l'entreprise sont conformes : aux exigences du
marché, à la demande du client, aux législations, au
cahier des charges de l'entreprise.
Le contrôle qualité analyse aussi les conditions de
retouche ou de rejet d'un produit.
Ce dernier a pour rôle de contrôler :
· Les composants d'un produit ou la matière
première dès la réception,
· La production en cours de réalisation,
· Les produits finis.
En outre, ilpermet de déterminer si les produits
fabriqués sont :conformes,non-conformes mais avec
possibilité de retouche,non-conformes et devant être
détruits.
2. La Maintenance
2.1.
Généralité sur la Maintenance
La Maintenanceest l'ensemble de toutes les actions techniques,
administratives et de management effectuées durant le cycle de vie d'un
bien et destinées à le maintenir ou à le rétablir
dans un état dans lequel il peut accomplir la fonction requise.
Dans la définition de la maintenance, nous trouvons
deux mots-clés : maintenir etrétablir. Le premier fait
référence à une action préventive. Le
deuxième fait référence à l'aspect correctif. Nous
présentons dans les paragraphes qui suivent les définitions de
chaque type de maintenance.
2.2. Les types de
Maintenance
On distingue deux types de maintenance : la maintenance
corrective et la maintenance préventive
- la maintenance corrective est une
maintenance effectuée après la détection d`une panne et
destinée à remettre une entité dans un état lui
permettant d'accomplir une fonction requise.
La maintenance corrective débouche sur 2 types
d'interventions. Le premier type est à caractère provisoire
(dépannage), ce qui caractérise la maintenance
palliative. Le deuxième type est à caractère
définitif (réparation), ce qui caractérise la
maintenance curative.
- La maintenance préventiveest une
maintenance effectuée dans l'intention de réduire la
probabilité de défaillance d'un bien ou la dégradation
d'un service rendu. Cette maintenance est subdivisée en deux à
savoir : la maintenance préventive systématique qui
est effectuée suivant un échéancier, la maintenance
préventive conditionnellequi est une maintenance subordonnée
à un type d'évènement prédéterminé
révélateur de l'état du bien.
2.3. Les outils de
maintenance
2.3.1. AMDEC
L'AMDEC (Analyse des Modes de Défaillance, de leurs
Effets et de leur Criticité) est une méthode d'analyse de la
fiabilité qui permet de recenser les défaillances dont les
Conséquences affectent le fonctionnement du système, dans le
cadre d'une application donnée. Ainsi dans le cas d'un système de
production, cette technique d'analyse peut être appliquée au
niveau : du produit, du processus, du procédé.
L'AMDEC est une méthode d'analyse préventive de
la fiabilité d'un produit, d'un processus, d'un moyen de production ou
d'un flux d'information. Elle permet de hiérarchiser les
défaillances redoutées qui sont caractérisées par
:
· F : fréquence d'apparition de la
défaillance : elle doit représenter la probabilité
d'apparition du mode de défaillance résultant d'une cause
donnée
· D : non-détectabilité de la
défaillance : elle doit représenter la probabilité de
ne pas détecter la cause ou le mode de défaillance avant que
l'effet survienne
· G : gravité des effets de la
défaillance : la gravité représente la
sévérité relative à l'effet de la
défaillance.
Le produit mathématique de ces trois
caractéristiques nous donne le niveau de priorité de risque
appelé Criticité pour exploiter les
systèmes ou sous-systèmes critiques et définir des actions
préventives et/ou correctives pertinentes et efficaces pour but de :
· minimiser les risques,
· minimiser le cout de non qualité,
· minimiser les pertes de production.
Criticité C=G x F x D.
Tableau 3: échelle de
valeur permettant le calcul de la criticité
Détection
|
Note
|
Critère
|
1
|
Détection automatisée (100%)
|
2
|
Détection humaine
|
3
|
Détection aléatoire
|
4
|
Aucun moyen de détection
|
Gravité
|
Note
|
Critère
|
1
|
Aucune incidence sur la conformité produit
|
2
|
Produit non-conforme mais fonctionnel
|
3
|
Produit non-conforme non fonctionnel
|
4
|
Produit non-conforme avec mise en danger du patient
|
Fréquence
|
Note
|
Critère
|
1
|
De une à deux fois par an
|
2
|
Au moins une fois par mois
|
3
|
Au moins une fois par semaine
|
4
|
Au moins une fois par jour
|
|
|
Il existe plusieurs types d'AMDEC, parmi les plus importants,
nous mentionnons :
· L'AMDEC organisation ;
· L'AMDEC processus ;
· L'AMDEC produit ;
· L'AMDEC moyen ;
· L'AMDEC service ;
· L'AMDEC sécurité ;
Nous ne nous intéresserons ici qu'a l'AMDEC processus
car c'est le type d'AMDEC le mieux adapté à notre
étude.
Dans notre cas celui-ci permettra de se focaliser sur le moyen
de production définit plus haut dans notre travail afin de :
· Diminuer le nombre de rebuts
· Diminuer le taux de pannes
· Augmenter la Capabilité (Capacité d'un
organisme, d'un système ou d'un processus à réaliser un
produit satisfaisant aux exigences relatives à ce produit.)
B. Indicateur d'efficacité dans
un système de production : le TRS
S'il est un secteur dans lequel toute usine peut progresser,
c'est dans la productivité. Un moyen efficace de mesurer la
productivité globale d'une usine est le TRS (taux de rendement
synthétique).
Le TRS est un indicateur utilisé en
production permettant de mesurer l'efficacité des procédés
de fabrication et riche en information. Le taux de rendement d'une production
dépend de plusieurs facteurs dont les performances se combinent pour
aboutir en sortie de production à un résultat plus ou moins
proche de l'objectif que l'on s'est fixé.
Ainsi, on retrouve trois taux dans le calcul théorique
du TRS :
Taux de Rendement Synthétique TRS =
Taux de disponibilité x Taux de performance x Taux de qualité
· Taux de disponibilité = Temps de production
réel / Temps de production théorique
· Taux de performance = Temps de cycle x Production
réelle/ Temps de production réel
· Taux de qualité = (Production réelle -
Production rejetée)/ Production réelle
Le TRS est le seul indicateur qui tient compte de tous les
paramètres qui affectent la productivité d'un système. Il
dépend des trois qui le composent, si l'un des trois se dégrade
le TRS chute.
Chapitre 3. RESULTATS DU
CONTROLE QUALITE : PROPOSITIONS ET SUGGESTIONS
« La solution définitive, n'existe
pas ». Les solutions les plus courantes consistent à
améliorer ou à supprimer les causes du ou des
problèmes.Dans ce chapitre, il est important d'apporter les bonnes
réponses aux vraies causes. Pour cela, nous avons fait appel à la
logique, aux qualités d'imagination et de créativité de
l'équipe au sein de laquelle nous avons évolué. L'objectif
ici ne consiste pas à rechercher LA solution, mais
des solutions à chaque cause du problème de
perte représenté par la quantité manifeste de mauvais
pots. Ce n'est pas toujours possible et il faut parfois faire des choix ou
trouver des compromis. Les solutions choisies ici conduisent alors à une
amélioration de la situation.
A. Résultat des analyses
I. Application des outils d'analyse de la qualité au
système de production actuel
1. Cahier des charges
Comme tout produit, un pot de conditionnement de yaourt doit
respecter un cahier des charges qui comporte les exigences par rapport à
son aspect physique et son poids. Le respect de ces exigences facilite les
conditions de remplissage et de transport de celui-ci car il nécessite
une tenue mécanique suffisante. Du fait des contraintes
économiques imposées à un produit de grande consommation,
il est important de s'assurer que ces contraintes sont respectées. Le
contrôle de la bonne qualité de ceux-ci apparaît donc
primordial. De nombreux paramètres peuvent contrôler la
qualité finale des pots, ce sont :
· L'aspect physique : Lisse, blanc,
flexible, uniforme et sans bavure, sans perforation
· Le Poids : Standard 1 pot =
6g ; 1 moulée = 30g ; acceptable à plus ou moins
0,5g
Ces exigences qui constituent les critères à
respecter afin de prétendre à la conformité du pot
représentent des référentiels qui permettront
d'évaluer la conformité de ce dernier.
2. Diagramme d'Ishikawa du
système de production
Pour déterminer les différentes causes
liées aux pertes engendrées par l'énorme quantité
de mauvais pots, nous avons synthétisé le résultat des
divers entretiens obtenus avec les membres des différents services de
l'entreprise et notre analyse personnelle. Ces causes sont ensuite
classées en selon la méthode des 5M et représentées
selon la figure suivante.

e
Figure
4: Diagramme d'Ishikawa du système de production
Par ailleurs, dans l'optique de résoudre le
problème posé, il convient d'étudier chaque cause
individuellement afin mener une action curative et améliorer
l'efficience (Rapport entre le résultat obtenu et les ressources
utilisées) du système de production actuel car lorsqu'on agit sur
l'effet d'un problème, on mène une action palliative et lorsqu'on
agit sur la cause de ce problème, on mène une action curative
empêchant ainsi la réapparition du problème.
2.1. Matériel
La machine utilisée dans ce processus est une ADOLF
ILLIG de type RDM 37/10 de 1971 regroupant en son sein plusieurs technologies
(pneumatique, mécanique...). Celle-ci dispose d'un Broyeur dont le
rôle est de recycler les déchets (carottes du moule)
générés lors de la production. Cette dernière, se
situe au coeur du processus de production car sans elle il n'y a pas de
production. Cependant, elle produit énormément de mauvais produit
dont les causes sont organisées selon le diagramme d'Ishikawa
suivant :

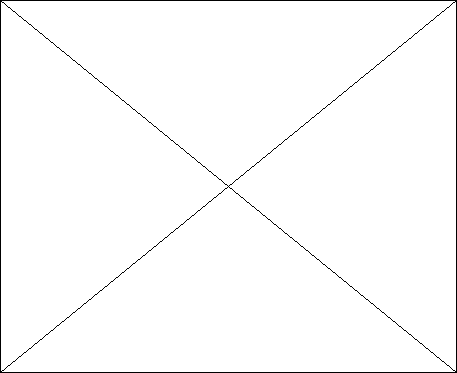
Figure 5: Diagramme d'Ishikawa
de la machine
Selon le diagramme ci-dessus, de nombreuses causes au niveau
de la machine peuvent engendrer la production de mauvais pots en
particulier la vétusté de celle-ci. Cependant, malgré son
état de vieillesse, elle fournit des produits de qualité lorsque
toutes les conditions sont remplies. D'autre part, cette mise au rebut peut
provenir du fait que les pièces de cette machine commandées
à un fournisseur de sous-ensembles ne lui sont pas totalement
compatibles dans son assemblage fini. Cette incompatibilité pourra donc
susciter des pertes. La dispersion géographique des équipes de
conception de la machine augmente ainsi les risques liés aux
inévitables modifications de dernière minute dans la conception
ou la fabrication.
2.2. Matière
La matière utilisée dans ce processus est un
semi-produit se présentant sous la forme de bobines de feuilles
résultant du mélange et du malaxage de PS et de divers additifs.
Il est ensuite obtenu une pate sèche qui est forcée entre deux
jeux de cylindre chauffés, dont l'écartement est de plus en plus
réduit jusqu'à obtenir l'épaisseur désirée
pour la feuille ainsi fabriquée.
Dans la fabrication de cette matière, on utilise le
polystyrène atactique, couramment nommé
polystyrène cristal car transparent et trop fragile. De
ce fait, il ne peut être travaillé à partir de bobines car
la feuille ne résiste pas au transport à froid sur les machines
de thermoformage. Pour pallier ce problème technologique et pour
améliorer les propriétés mécaniques du produit fini
(résistance aux chocs en particulier), on le mélange
fréquemment à du polystyrène choc. Le polystyrène
choc est un matériau opaque (qui ne laisse pas passer la
lumière), moins fragile que le polystyrène cristal. D'autres
additifs peuvent être ajoutés selon l'application, tel que des
colorants pour lesfeuilles blanches, le colorant est classiquement de l'oxyde
de titane (TiO2).
Les feuilles sont généralement obtenues par
extrusion dans une filière plate avec refroidissement en calandre avant
d'être enroulées en bobine. Ici La calandre comporte 3 cylindre de
travail, chacun est entrainé individuellement à une vitesse
très précise par un moteur électrique à vitesse
variable de façon à adapter la friction à la formulation
désirée et à la température de calandrage.
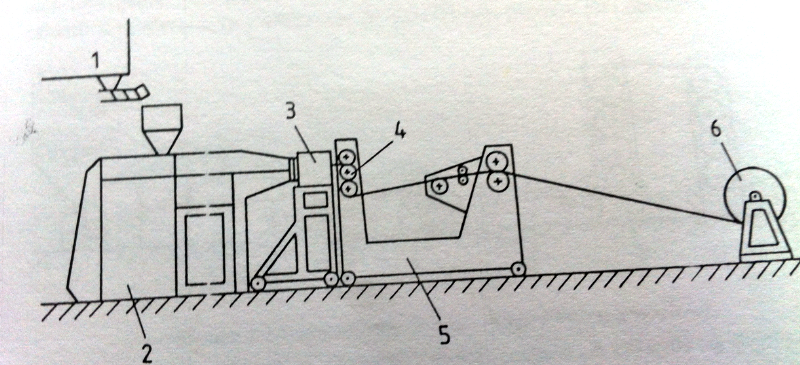
Figure 6: Fabrication de
feuille
1 : Granulé de PS ; 2 : extrudeur ;
3 : Filière plate ; 4 : Calandre ; 5 : Train de
tirage ; 6 : Bobine de feuille
Cependant, la qualité de la feuille conditionne pour
une bonne part la qualité finale du pot. Durant notre étude, et
surtout résultant des multiples remue-méninges que nous avons eu
à effectuer avec les Maintenanciers et les producteurs, nous avons pu
recenser les différentes causes pouvant engendrer la mauvaise
qualité de celle-ci ; ce sont :
· Les irrégularités de l'épaisseur
de la feuille. En effet, l'épaisseur de la feuille dépend
directement de la flexion des cylindres par rapport à leur profil
initial. Pour pallier à ce défaut, le service maintenance utilise
un dispositif permettant cambrer celui-ci, dans la direction du serrage, de
façon à corriger sa flexion par rapport à son profil
initial. Pour ce faire, on exerce une force sur les paliers secondaires
extérieurs du bâti, à l'aide de vérin hydrauliques.
La correction obtenue est de l'ordre de 0,05mm. Toutefois, ces
vérins présentent des défauts de joints
d'étanchéité qui créent des fuites d'huile et qui
ont ainsi un impact sur leur course ; cette fuite, va donc créer un
décalage entre les tiges des vérins et entrainant ainsi la
flexion des cylindre.
· Un mauvais réglage de la vitesse des cylindres
par rapport au débit d'écoulement de la matière sur
ceux-ci pourra causer une mauvaise qualité de la feuille. Nous avons
constaté que les afficheurs du pupitre de commande destiné
visualiser cette vitesse étaient non fonctionnel. De ce fait, les
producteurs règlent la vitesse des cylindre à l'aveuglette or
cette vitesse est très précise pour l'obtention de bonne
feuille.
· D'autre part, une inhomogénéité de
la température de chauffage de la matière à sa sortie de
la filière dû à la défectuosité de certaines
résistances de chauffage ou au mauvais réglage de celles-ci
pourra conduire à la mauvaise qualité de la feuille.
· L'utilisation excessive de matière
rebroyé pourra aussi causer la mauvaise qualité de la feuille car
le fait de recycler et de transformer plusieurs fois le PS conduira à un
affaiblissement ou une perte de ses caractéristiques se manifestant par
un étirage de celui-ci lors du chauffage ou une présence de
fissure.
· Le non-respect des conditions de stockage des bobines
de feuilles PS pourrai détériorer celles-ci et avoir un impact
négatif lors la production des pots.
Ainsi, la qualité de la matière (feuille PS)
dépend de plusieurs critère qu'il incombe de maitriser afin de
garantir une bonne production.
2.3. Main d'oeuvre
Il va sans dire qu'un processus de production aussi performant
soit-il ne saurait être effectif si le personnel qui le manipule n'est
pas qualifié. Il nous a été donné de constater que
la mauvaise qualité des pots pouvait être due en partie à
cause de la main d'oeuvre. Il est indéniable que la production est
d'autant plus meilleure lorsque les ouvriers sont motivés et satisfait
dans leur travail. Cependant, de nombreux critères de la part de la main
d'oeuvre handicapent la production de pots tel que :
· La non qualification des opérateurs de
ligne : ce dernier à un impact direct sur la productivité et
le process de production. De ce fait, un opérateur qualifié peut
identifier les problèmes qui peuvent avoir des effets néfastes
sur la productivité avant qu'ils ne surviennent, évitant ainsi
des pertes. N'étant pas qualifiés ce dernier laissera survenir
ces problèmes.
· La non motivation et le manque de rigueur des
opérateurs de lignes : La motivation étant le moteur de la
qualité, elle doit à tout prix exister chez les opérateurs
afin d'avoir une bonne productivité. Cependant, nous avons
constaté que ces derniers, mécontents des conditions de travail,
ne sont pas motivés et n'effectuent pas ainsi leurs tâches dans
les normes et font preuve d'un laxisme flagrant en ne reportant pas
correctement les évènements qui impactent sur l'abondance des
mauvais pots. Le suivi de la production n'est donc pas correctement
assuré.
Il est important de garder à l'esprit que ces
employés qui ont le potentiel de causer des problèmes qui
impactent sur la productivité constituent aussi la première ligne
de défense dans la bataille pour améliorer le rendement de la
machine.
2.4. Milieu
La qualité ne peut s'épanouir dans des espaces
de travail sales et encombrés d'objets. Le désordre laissé
sur les lieux de travail crée un environnement peu agréable et
peu propice au travail, il nuit au désir de bien faire et favorise le
laisser-aller de la part des opérateurs, ce qui nuit à la
productivité. Les petites négligences, les petits écarts
de conduite répétés, les accrocs aux règles en
usage, altèrent profondément le climat d'une unité.
2.5. Méthode
En ce qui concerne les méthodes de travail, on constate
que certains éléments ont une conséquence néfaste
sur la productivité tel que le non-respect des consignes d'utilisation
de la machine, le mauvais réglage de certains éléments
tels que la température, la mauvaise insertion de la feuille dans la
machine. D'autre part, la maintenance et l'entretien de cette machine jouent un
rôle prépondérant sur la baisse de la productivité
car mal exécutées et mal gérées, elles exposent le
système de production à de grand risques de mauvaise
qualité des produits. Ainsi, un excès de maintenance palliative
sur cette installation conduit la machine vers un risque de dégradation
accéléré, agissant ainsi sur la qualité des
pots.
Par ailleurs, cette machine est soumise à de nombreuses
pannes qu'il importe de maitriser car celles-ci ont un impact sur sa
productivité ; Il convient alors d'agir rapidement sur les pannes
principales afin de limiter au maximum les temps d'arrêt. Pour ce faire,
nous allons utiliser le Diagramme PARETO afin de
hiérarchiser ces pannes par ordre d'importance.
3. Diagramme PARETO des pannes de la
machine
Cet outil nous permettra de mettre en évidence les
20% de pannes sur lesquelles il faut agir pour réduire 80 % des temps
d'arrêt. Il sera utile pour déterminer sur quels leviers on doit
agir en priorité pour améliorer de façon significative la
situation.Cette étude PARETO est faite selon un historique de panne
allant de Janvier à Août 2015. On a donc classé les pannes
observées en se basant sur la durée de chacune d'elles et on a
obtenu les résultats suivants :
Tableau 4: Durée des
pannes machine
Equipement
|
Temps d'arrêt (min)
|
% des temps d'arrêt
|
% Cumulés
|
Moule
|
675
|
32,37%
|
32,37%
|
Moteur
|
405
|
19,42%
|
51,79%
|
Four bas
|
180
|
8,63%
|
60,42%
|
Circuit d'eau
|
160
|
7,67%
|
68,09%
|
Valve soufflette
|
155
|
7,43%
|
75,52%
|
Circuit pneumatique
|
120
|
5,76%
|
81,28%
|
Circuit d'air
|
110
|
5,28%
|
86,56%
|
Goulotte
|
90
|
4,32%
|
90,88%
|
Vérin poinçon
|
80
|
3,84%
|
94,72%
|
Ejecteur
|
60
|
2,88%
|
97,60%
|
Régulateur de température
|
40
|
1,92%
|
99,52%
|
Soufflette
|
10
|
0,48%
|
100%
|
TOTAL
|
2085
|
100%
|
|
Après le remplissage du tableau, vient la phase de la
représentation du diagramme Pareto afin d'en sortir les
équipements critiques. La Fig.5 Représente le diagramme Pareto
obtenu à partir du tableauci-dessus
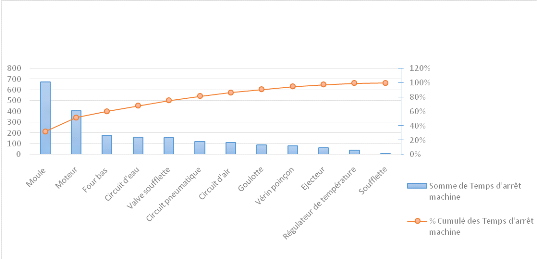
Figure 7: Diagramme de PARETO
des pannes de la machine
· Conclusion : D'après cette
courbe de PARETO et selon la loi des 20/80 on trouve que 6 sous-ensemble
(Moule, Moteur, Four bas, Circuit d'eau, Valve Soufflette, Circuit pneumatique)
parmi les 12 représentent plus de 80% de la durée cumulée
des pannes.
II. Etude AMDEC relative au
système de production des pots de conditionnement de yaourts
Afin de proposer des actions amélioratrices pour les
défauts qui engendrent les pertes et qu'on a analysés, nous avons
traité chaque défaut au cours d'un brainstorming avec le
responsable de maintenance, les producteurs et les Maintenanciers. L'ensemble
des données sont regroupées dans le tableau suivant :
Tableau 5: Fiche AMDEC
relative au système de production
Elément
|
Mode de défaillance
|
Cause
|
Effet
|
Moyens de détection
|
Criticité
|
Action de la maintenance
|
F
|
D
|
G
|
C
|
Bobine de feuille
|
Mauvaise qualité
|
Recyclage du PS
|
Etirage lors du chauffage de la feuille PS
|
Visuelle
|
4
|
2
|
2
|
16
|
Changement de la bobine de PS non conforme par
l'opérateur
|
Résistances chauffantes
|
T0de formage non adéquat
|
T0 basse
|
-mauvais formage du fond des pots
-perçage
|
visuelle
|
4
|
2
|
3
|
18
|
Régulation de la température des
résistances chauffantes à l'aide de régulateurs de
température
|
T0 élevée
|
-fissuration des pots
-perçage
|
Poinçon
|
Disfonctionnement du vérin des poinçons
|
Capteur de fin de course défectueux
|
Mauvais formage des pots
|
Visuelle
|
2
|
2
|
2
|
8
|
-remplacement du capteur de fin de course
|
Circuit de refroidissement
|
T0 du moule élevée
|
-tuyau percé
-tuyau bouché
|
-perçage des pots
-fissuration des pots
-mauvais formage des pots
|
Visuelle
|
2
|
2
|
2
|
8
|
-remplacement des tuyaux percés
-serrage des colliers d'assemblage
-débouchage du circuit d'eau
|
Moule
|
Disfonctionnement des éjecteurs
|
Ressort de compression cassé
|
Mauvaise éjection des pots du moule
|
Visuelle
|
2
|
2
|
3
|
12
|
-Remplacement du ressort de compression
-réparation de la valve simple effet
|
Valve simple effet défectueuse
|
Circuit pneumatique
|
Mauvais soufflage pour la formation des pots
|
interrupteur de position défectueux
|
Les pots ne se forment pas
|
Visuelle
|
2
|
2
|
3
|
12
|
Recâblage de l'interrupteur de position de soufflage
|
Insuffisance d'air de soufflage des pots
|
Soufflette
|
Mauvais soufflage des pots
|
Soufflette cassée
|
Production abondante de mauvais pots
|
Visuelle
|
2
|
2
|
3
|
12
|
Remplacement de la soufflette cassée
|
III. Calcul du Taux
de Rendement Synthétique de la machine (TRS)
· Calcul du taux de
disponibilité.
Le travail est planifié pour des équipes de 8h
par Quart avec une pause de 30min et une mise en chauffe de la machine de
45min. le temps planifié de production est alors de 8h-1h15 = 6h45min.
Au cours de la production nous avons rencontré un arrêt de 20min
pour le changement de la bobine de feuille, 10min de réglage, 30 d'un
arrêt du à la maintenance. Alors, le temps de production est de
6h45-1h = 5h15min.
Le Taux de disponibilité est alors de : Td =
5h15/6h45 = 77%
· Calcul du taux de performance
La cadence réelle de la machine est de 50pots/min.
Cependant, après 1 quart de travail, nous avons pu relever que la
machine n'a produit que 6048 pot, la production théorique étant
de 18750 pots pour 1 quart.
Le Taux de performance est alors de : 6048/18750 =
32%
Les pertes sont donc évaluées à
12702 pots par quart
· Calcul du taux de qualité
Sur les 6048 pots fabriqués, 1000 sont recalé
lors de l'inspection qualité ; on a alors : 6048 - 1000 =
5048
Le taux de qualité est alors de 5048/6048 =
83%
Le résultat final : TRS = Taux de
disponibilité * Taux de performance * Taux de qualité
TRS = 77% * 32% * 83% =
20%
NB : Un TRS de 85% est considéré comme une
excellente performance, mais cette valeur peut varier selon les industries.
Obtenir un tel TRS signifie que la disponibilité est de 90%, la
performance de 95% et la qualité de 99,9%. Si on considère que la
majorité des usines ont un TRS d'environ 60%, cela donne une idée
du potentiel incroyable de progression en productivité.
Le calcul du TRS nous montre à quel point le rendement
de la machine est assez bas. Le taux de rendement synthétique
dépend des trois taux calculés plus haut et l'on constate que le
taux de disponibilité et le taux de performance sont assez bas par
conséquent ils font chuter le rendement de la machine. Le taux de
performance dépend de la bonne qualité de la feuille et de
l'implication du personnel et le taux de disponibilité dépend de
la réduction des interruptions ; Il faudra donc mener des actions
destinées à agir de manière implicite sur ceux-ci afin de
les améliorer le rendement de la machine.
B. Mise en oeuvre des solutions
amélioratrices
I. Plan d'action
Pour remédier aux problèmes rencontrés,
nous avons effectué une synthèse des éléments
collectés au cours des Brainstorming exercé avec les
différents intervenants sur le processus de production
étudié et ainsi par la suite proposé des actions
correctives et préventives.
1. Actions correctives
Une action corrective est une action
entreprise pour éliminer une cause de non-conformité, d'un
défaut ou de tout autre événement indésirable
existant, pour empêcher leur renouvellement. Dans cette visée,
nous proposons un certain nombre d'action tel que :
· Installer un filtre collecteur de boue à
l'entrée du système de refroidissement par eau glacée pour
éviter les dépôts d'impureté (boue) dans les
évents du moule et obstruant ainsi ses orifices.
Nous proposons ainsi d'utiliser un filtre collecteur de boue
à bas débit. Le système est conçu sur la base d'un
ralentissement du flux qui provoque une décantation basse qui permet
d'évacuer les boues. Le fluide passe au travers d'un collecteur de
boues, qui définit un circuit de passage de l'eau (grâce à
sa géométrie) et réduit sa vitesse (par son volume). Le
traitement se compose de 3 phases successives :
- Décantation basse des boues
- Captation des oxydes métalliques sur barreaux
magnétiques
- Filtration sur tamis inox
Les eaux ainsi clarifiées en continu, assurent :
- La bonne marche des organes de régulation
(mécanismes des vannes, robinets thermostatiques, capteurs de
température...)
- La non obstruction des orifices du moule destiné
à faire circuler l'eau du refroidissement.
- La réduction des temps d'indisponibilité de la
machine.
Pour la maintenance de ce dernier, il faudra :
- Purger le fond du pot à boues.
- Nettoyer les barreaux magnétiques.
- Nettoyer le filtre 300 microns.
La fréquence de ces interventions dépend de
l'état initial du circuit et décroît rapidement
après la pose du collecteur de boues.
L'appareil peut être intégré au réseau
existant pour permettre la désincrustation et le désembouage du
système étudié et obstrués par le tartre ou les
produits issus de la corrosion.Il permettra de retenir les infines particules
de boues qui s'agglutinent dans les orifices du moule. La fiche technique de ce
dernier est disponible en Annexe2.
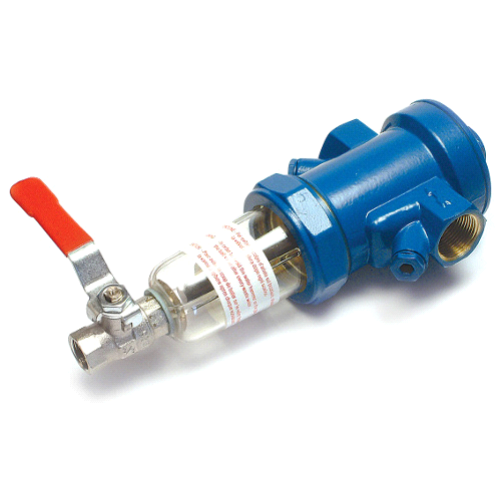
Figure 8: Filtre Collecteur de boue
Bas débit
· Stocker les bobines de feuille dans un environnement
sec, à l'abri de la chaleur et de l'exposition directe de la
lumière du soleil afin de ne pas détériorer celle-ci. En
effet, la photo-oxydation du polystyrène, se traduisant par un
jaunissement du matériau, est accentuée en présence
d'ultraviolets ce qui affecte la qualité de la feuille.
· Effectuer les mélanges de matière PS en
fonction du nombre de mise en oeuvre de celle-ci ; lors de chaque mise en
oeuvre, la matière plastique subit des altérations physiques et
chimiques, elle perd de ses propriétés. Comme on le voit à
la figure suivante, on observe une diminution linéaire de ses
propriétés en fonction du nombre de cycle de mise en oeuvre. Dans
le but de renforcer les caractéristiques de celle-ci et de garantir
ainsi la bonne qualité de la feuilleil faudra effectuer un
mélange avec des pourcentages définis de matière vierge et
de rebroyé en fonction du nombre de fois où la feuille a
été recyclée. La figure suivante illustre les
mélanges à effectuer en fonction du nombre de cycle de mise en
oeuvre
K = 0,6

K = 0,2

K = 0,1

K = 0
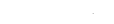
100
Propriété
0
0 5 10 15 20 25
Figure 9: évolution des
propriétés d'un polymère en fonction du nombre de cycle de
mise en oeuvre et du rapport matière vierge/matière
rebroyée.
En effet, sur la figure ci-dessus, on constate que la valeur
de la propriété se stabilise pour k> 0,6 (k étant le
rapport matière vierge/matière rebroyée). Cependant, afin
d'effectuer les mélanges appropriés, il est nécessaire de
connaitre le nombre de fois où la matière a été
recyclée. Pour cela, nous avons établi une fiche de suivi de la
matière disponible en annexe 5.
· Effectuer une étude du marché des
fabricants de pièces détachées afin de se procurer des
pièces de qualité qui doivent correspondre à l'assemblage
fini de la machinetel que : les résistances chauffantes, les joints
d'étanchéité, les vis + écrou (CHC, HM), les tuyaux
tressés multicolore destiné à assurer le bon
fonctionnement du process ;
2. Actions préventives
Une action préventive est une action
entreprise pour éliminer une cause de non-conformité, d'un
défaut ou de tout autre événement indésirable
potentiel, pour empêcher qu'il ne se produise.
Vu l'apparition des défaillances sur les
éléments critiques de la ligne de production des pots, nous avons
proposé des actions préventives de façon à
intervenir avant que les défaillances surviennent.
· effectuer l'étalonnage des sondes de
façon périodique afin de s'assurer que celle-ci fonctionnement
correctement et fournissent les vraies valeurs lors du fonctionnement de la
machine permettant ainsi de suivre rigoureusement les pertes. Cet
étalonnage est exécuté selon le planning de maintenance
disponible en annexe 4.
· La machine servant à produire les pots
étant vétuste, le service maintenance devrait contrôler son
état en continu afin de prévoir ses arrêts. De ce fait, les
travaux de maintenance ne seront effectués que dans le cadre de la
prochaine révision du prochain arrêt prévu au lieu
d'intervenir à tout moment sur la machine. Ainsi, l'exécution
à temps des divers travaux de maintenance protègera la machine et
les outils qui la constituent de dommage consécutifs, réduisant
ainsi les temps d'arrêt et par conséquent, augmentant la
productivité. Ces travaux seront effectués suivant le planning de
maintenance disponible en annexe 4.
· Vérifier aussi l'état de fonctionnement
des sous-ensembles les plus critiques établi selon l'AMDEC processus
précédent, qui sont : les résistances chauffantes, la
bobine de feuille, la soufflette, le circuit pneumatique, le moule ceci suivant
une démarche de maintenance préventive systématique et
conditionnelle.
· Lors de la maintenance, Agir en priorité sur le
Moule, le Moteur, le Four bas, le Circuit d'eau, la Valve Soufflette, le
Circuit pneumatique qui sont les éléments qui
génèrent 80% des temps d'arrêt selon le diagramme PARETO
précédent.
· Effectuer un contrôle périodique des
joints d'étanchéité et du niveau d'huile des vérins
hydraulique des calandres utilisé dans la fabrication des bobines PS
afin d'éviter la flexion de ceux-ci causant dès lors une
irrégularité de l'épaisseur de la feuille. Pour cela, le
tableau suivant décrit de façon ordonnée les actions de
maintenance à effectuer sur ces vérins.
Tableau 6: tableau des
procédures de maintenance de routine des joints
d'étanchéité.
Quoi faire
|
Quand le faire
|
Comment le faire
|
Inspections journalières
|
Avant le démarrage de l'essai du jour
|
Vérifier si le vérin a des fuites de fluide
hydraulique
|
Nettoyage du vérin
|
Toutes les 40 heures de fonctionnement continu ou une fois par
semaine
|
Nettoyez les surfaces exposées de la tige
du piston du vérin à l`aide d`un chiffon
propre, sec et non-pelucheux.
|
Vérification des traces
d'usure
|
Une fois par mois
|
Vérifiez si la tige du piston du vérin et les
joints d`étanchéité montrent des signes
d`usure excessifs et/ou de fuite.
|
Renouvellement des joints
d`étanchéité du vérin
|
Une fois par an ou plus tôt si
une fuite excessive du vérin est
décelée pendant son inspection
|
Démonter le vérin et changer le joint
|
· Prévoir des pièces de rechanges pour les
éléments qui tombent constamment en panne.
· Harmoniser le choix des résistances chauffantes,
des capteurs de température et des régulateurs de
température. Pour ce faire, utiliser des Emetteurs infra rouge de type
FSR T-FSR/2 d'une tension d'alimentation de 220V, une puissance de 325W pour
une température de 750°C avec un Régulateur de
température configurable GEFRAN 450 dont la fiche technique est
disponible en annexe et un Capteur de température thermocouple de Type
NiCr-Ni (type K) afin de maitriser et d'uniformiser la température de
chauffage. Actuellement, l'on utilise un capteur thermocouple de type J ;
cependant selon la fiche technique fournie lors de la livraison des
émetteurs infrarouge, les capteurs les plus adéquats sont des
capteurs thermocouple de type K en raison de leur bonne tenue aux hautes
températures.
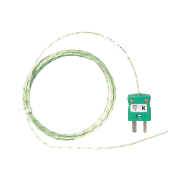 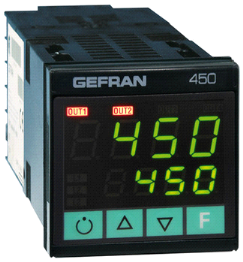
Figure 10: Capteur thermocouple de
type KFigure 11: Régulateur de
température GEFRAN
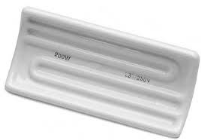
Figure 12: Emetteur infrarouge
ELSTEIN de type T-FSR/2 avec une puissance dissipée de 750W
II. Amélioration
éventuelles
1. Suggestions
Afin d'améliorer la performance de notre processus de
production, nous avons émis un certain nombre de suggestions entre
autre :
· L'éducation du personnel aux respects des
conditions de sécurité
· Prévoir des plaques signalétiques dans le
langage approprié afin de protéger toute personne à
proximité de la machine contre des contacts accidentels.
· Etiqueter les sacs de matière rebroyé
afin de faciliter le suivi de celles-ci
· Effectuer des formations et des actions de
sensibilisation auprès des employés dans le but de les initier
à optimiser les pertes et corriger leur démarche de travail toute
fois aléatoire.
· Mettre en place une boîte à idées
afin de collecter les idées intéressantes qui peuvent se trouver
au sein des équipes du conditionnement et qui peuvent être source
d'économies ou d'un renforcement de la compétitivité de
l'unité.
· Respecter le planning de la maintenance
préventive afin qu'il soit efficace.
· Faire preuve de rigueur dans lors du recrutement du
personnel et mettre un accent sur la formation et la qualification du personnel
car comme nous l'avons identifié au Chap3, un personnel non
qualifié pourrai être à l'origine des pertes
rencontrées.
· Faire également preuve de rigueur lors du
réglage des températures car l'importance de l'exactitude du
calibrage et de la mesure de température réalisée à
non seulement un impact sur l'énergie utilisée mais aussi sur la
durée de vie de l'équipement.
· Privilégier l'éco-conception en
réduisant les carottes de moules.
· Nous recommandons également à l'usine
d'effectuer un Audit Qualité
· Réparer le pupitre de commande des cylindres
afin de visualiser la vitesse de ceux-ci et ainsi garantir la bonne
qualité des feuilles fabriquées.
Les améliorations sont maintenant mises en oeuvre et
des outils sont mis en place pour faire en sorte que les variables clés
restent dans les limites acceptables au fil du temps afin de maintenir les
performances de notre processus à long terme.
Un suivi doit se faire pour s'assurer de l'application de ces
solutions par les opérateurs afin d'augmenter le rendement de la
machine.
2. Suivi de la production selon la
méthode des 5S
2.1. Définition
La méthode des 5S est une technique qui, mise en
oeuvre, consiste à améliorer la qualité interne, la
production et les conditions de travail d'une entreprise et dans notre cas, de
son rendement.
L'acronyme 5S tire son origine de la première lettre de
chacune des cinq opérations à conduire dans le cadre de cette
technique : Seiri, Seiton, Seiso, Seiketsu, Shitsuke.
La première opération
: Seiri ou Débarras, vise à trier
sur le poste de travail ce qui est strictement nécessaire et qui doit
être gardé en se débarrassant du reste. Elle touche
à la fois les objets matériels et immatériels qui
environnent les méthodes de travail (normes, règles,
documentations...). Cette opération lutte contre le penchant bien
naturel de l'homme à accumuler. Il s'agit d'établir un
système de classification des objets en fonction de leur
nécessité.
La deuxième opération
: Seiton ou Rangement, consiste à
aménager au mieux les moyens nécessaires en réduisant les
gestes inutiles et les pertes de temps : une place pour chaque chose, chaque
chose à sa place. Il s'agit de marquer les emplacements et identifier
visuellement les objets afin de créer un milieu de travail bien
rangé.
La troisième opération
: Seiso ou Nettoyage, assure la propreté
du poste de travail en luttant contre la poussière, la saleté,
les chutes de matériaux, les fuites d'huile. L'entretien des sols et des
machines y prend une importance toute particulière. Le nettoyage devient
l'occasion et le moyen d'inspection des machines pour détecter les
anomalies et les usures prématurées. Il s'agira par la suite de
définir les modalités précises du nettoyage afin de
conserver les locaux et les équipements en parfait état de
propreté.
La quatrième opération :
Seiketsu ou Ordre, définit les règles par
lesquelles le poste de travail restera débarrassé des objets
inutiles, rangé, nettoyé. Elle consolide les trois
opérations précédentes mais demeure plus
particulièrement associée à la troisième
opération, le nettoyage ; elle précise notamment les moyens
d'élimination des causes de salissures ou de désordre. Il s'agit
de rendre visible et améliorer l'information relative aux règles
et aux tâches à effectuer, de créer des documentations et
de mettre en place des contrôles visuels afin de gagner du temps et de
faciliter la formation et la polyvalence.
La cinquième opération
: Shitsuke ou Rigueur, est pleinement du ressort
hiérarchique. Elle se fixe pour but le maintien des bonnes habitudes, en
soutenant et en encourageant le personnel à adhérer aux
règles et aux standards, et de les améliorer. Le choix du terme
de Rigueur dans le sens du respect de ce qui est exigé ou imposé
par les règles en tire toute sa justification. Il s'agit de
développer une discipline collective, d'établir des règles
afin de rendre durable les résultats précédents.
C'est, en bref, un outil qui s'applique dans tous les secteurs
de l'entreprise et qui permet d'améliorer la productivité, la
qualité, l'implication du personnel (donc sa motivation). Il trouve sa
place dans une stratégie d'amélioration de la productivité
et du rendement de production. Cette méthode permettra de
concrétiser et d'assurer le suivi de toutes les actions et suggestions
faites plus haut.
2.2. Concrétisation des 5S
Suite à cette analyse théorique portée
sur les 5S au moyen des documents techniques qui ont été
récoltés, on peut dire que le rôle des 5S est
d'éliminer le gaspillage. Cependant, il est important de définir
clairement en quoi consistent les 5S, où ils sont censés nous
mener et comment les activités qui s'y rattachent doivent être
structurées pour nous permettre d'atteindre ce but.
· Dans un premier temps, l'opérateur devra
hiérarchiser les éléments utilisés dans son espace
de travail afin d'éviter toutes dispersion contre-productive.
· Eliminer les déchets, les saletés, les
corps étrangers, afin de garder le poste de travail propre. Le nettoyage
devient ainsi un mode de contrôle. En effet, compte tenu de la
précision et des techniques de production, le plus petit détail
peut avoir des répercussions importantes.
· Il faudra aussi fournir à l'opérateur les
procédures de maintenance qui seront une occasion pour lui de
contrôler sa machine. Il ne faut pas oublier que la propreté peut
avoir des répercussions considérables sur le temps
d'indisponibilité des machines, la qualité, la
sécurité, le moral des employés.
· Il faudra apprendre aux opérateurs ce qu'ils
doivent faire et comment le faire pour perdre les mauvaises habitudes et
s'habituer à travailler selon les règles.
· Utiliser le marquage au sol. Celui-ci aidera à
organiser le milieu de travail. Il consiste à entourer d'un trait bien
visible chaque ensemble de production. Il permet de créer une
appropriation sans ambigüité de chacun sur sa zone. Pour se faire,
nous proposons d'utiliser un ruban vert de 50mm.
· Dans le but d'éviter d'encombrer l'espace de
travail, nous proposons de parquer les bobines de mauvaise qualité dans
leur zone où elles seront prêtes à être
recycléesà côté de la machine prévue à
cet effetde la machine. Dans la même lancée, parquer aussi les
sacs de matière rebroyé et étiqueté dans leur zone
près de la machine destinée à fabriquer les bobines
feuilles
En outre, l'application de la méthode des 5S permettra
de diminuer les différents gaspillages :
· Les gaspillages des temps d'attentes
· Les gaspillages propres aux pièces
défectueuses
· Les gaspillages dans le processus de fabrication
Il est primordial de réaliser toutes les actions
proposées plus haut dans le cadre des 5S car la mise en pratique de
celles-ci permettront d'assurer le suivi de toutes les actions correctives et
préventives proposées.
Il est cependant difficile de quantifier les 5S, le
scepticisme de certains pourrait s'expliquer par le fait que l'application
d'une telle méthode ne peut se justifier que par l'expérience.
C'est pour cela qu'il est nécessaire d'engager moralement et
physiquement les opérateurs à la réalisation de tels
changements sur leur poste à travers la mise sur pied d'un
système qualité.
III. Mise en place d'un système qualité
Grâce au concours de toutes les actions posées
précédemment, nous proposons la mise en place d'un
système qualité. Celle-ci se déroulera en 5 étapes
qui sont :
1. Première
étape : Le contrôle
La première étape dans une démarche
traditionnelle de mise en place d'un système qualité est
l'instauration de contrôles. On définit pour cela un objectif et
des limites d'acceptation. Le Contrôle est la comparaison entre ce qui
est réellement et l'état idéal, c'est-à-dire
l'objectif à atteindre.Mais la qualité a son coût :
contrôles, tests, mesures, analyses ne confèrent aucune valeur
ajoutée au produit, mais fournissent une assurance quant à sa
qualité.
Pour réduire ce coût, des méthodes
statistiques ont été développées : plutôt que
de tester chaque pièce, on n'en contrôle que quelques-unes par
échantillonnage. Un barème indique que le lot entier est
acceptable ou refusé en fonction des résultats des tests sur les
échantillons. C'est le NQA ou Niveau de Qualité
Acceptable.
Niveau de qualité acceptable (NQA) : c'est le
pourcentage maximum d'individus défectueux d'un lot qui peut être
considéré comme satisfaisant en tant que moyenne d'un processus.
Il est déterminé par un accord commun entre le fournisseur et le
client.
Lorsque la taille des lots et le NQA sont définis, on
peut déterminer à l'aide de tables (disponible en annexe 6) la
taille des échantillons et le nombre de pièces
défectueuses dans l'échantillon au-delà duquel on va
refuser le lot.
Dans notre cas, le lot est constitué de 3024 pots et
par accord entre le client et le fournisseur, le NAQ est fixé à
6,5%. Selon la première table disponible en annexe, la lettre code nous
permettant de déterminer l'effectif de l'échantillon est K et la
taille de l'échantillon est de 125 pots. La deuxième table nous
permet de déterminer à partir de la lettre code et du NAQ (6,5%)
les critères d'acceptation A et de rejet R.
Cela signifie que pour valider le lot nous allons contrôler
un échantillon de 125 pots.
Si l'échantillon comporte A (14) ou moins de 14 pots
défectueux, le lot sera accepté et si l'échantillon
comporte R (15) ou plus de 15 pots défectueux, le lot sera
refusé.
2. Deuxième
étape : la maitrise de la qualité
Dans notre cas, la maîtrise de la qualité suppose
la maîtrise des 5M, à savoir :
· Main d'oeuvre : formation et
qualification adéquate des intervenants
· Machines ou Moyens : qualité
des équipements de production et de contrôle
· Méthodes ou Modes
Opératoires : standardisation et répétabilité,
respect des spécifications...
· Milieu : environnement de travail
adapté, propre, ordonné (5S)...
· Matière : s'assurer de la
qualité de la matière première.
De ce fait, toutes les actions correctives, préventives
et de suivis proposés plus haut dans notre travail contribuerons
à l'atteinte de cet objectif. Cependant, le service qualité devra
s'assurer de la pérennité de cette maîtrise au sein de
l'usine.
D'autre part, filtrer la production et retenir les mauvaises
pièces pour prétendre maîtriser la qualité ne suffit
pas, car la Qualité ne naît pas au contrôle, mais au moment
de la fabrication. Le contrôle idéal serait un contrôle
à 100% peu coûteux. Nous proposons donc :
· Un contrôle successif, où
chaque opérateur contrôle le travail effectué par celui qui
précède.
· Un Autocontrôle où
l'opérateur contrôle lui-même le travail qu'il effectue.
Ceci lui permettra de repérer les erreurs qui pourraient affecter le
processus de fabrication de façon négative et d'y
remédier. Cette condition doit être réalisée pour
garantir l'élimination des rebuts.
3. Troisième
étape : l'assurance qualité
L'assurance qualité doit donner confiance aux clients.
Elle démontre la maîtrise des 5M et en apporte
les preuves à travers un produit (pot de conditionnement de yaourt) de
qualité. En gros on écrit ce que l'on fait, on fait ce
qui est écrit et l'on vérifie que ce qui est écrit est
fait.
4. Quatrième
étape : la gestion de la qualité
Englobant les étapes précédentes, la gestion
de la qualité introduit la dimension économique. On y gère
les coûts de la non-qualité et on optimise ces coûts afin de
poursuivre les objectifs financiers à travers le recyclage du produit
non conforme.
5. Cinquième
étape : la qualité totale
Toujours en englobant les étapes
précédentes, la qualité totale établit les
relations client/fournisseur et les partenariats internes et externes.
IV. Amélioration
continue selon le principe de la Roue de Deming
Le concept d'amélioration continue est une exigence
essentielle dans le référentiel ISO 9001.Le processus
d'amélioration continue suppose qu'il n'y a pas d'état stable
satisfaisant pour un système qualité. Cette démarche est
basée sur le cycle « Plan Do Check Act » de
Deming. En français Prévoir
Réaliser Vérifier Réagir.
La roue de Deming est un moyen
mnémotechnique permettant de repérer avec simplicité
les étapes à suivre pour améliorer la qualitédans
une organisation.
Il ne faut pas faire comme ce vice-président d'une
société d'ingénierie qui pensait que le sigle PDCA
signifiait Please Don't Change
Anything (« Prière de ne rien
changer »).
1. Démarche
d'utilisation
1.1. L'étape
Plan(en français « prévoir »)
Il s'agit ici de planifier les activités qualité de
la société pour satisfaire aux exigences de l'organisme
(qualité voulu). Elle se déroulera en trois phases :
· Identification du processus à
améliorer ;
· Recherche des causes racines à l'aide du
diagramme PARETO, du diagramme d'Ishikawa établit plus haut dans notre
travail.
· Recherche de solutions selon le planning et les actions
préétablies.
1.2. L'étape Do
(en français« faire »)
Il s'agit ici de mettre en oeuvre les activités
prévues lors de la planification pour atteindre le niveau de
qualité voulue.
1.3. L'étape Check
(en français « vérifier »)
Elle consiste à contrôler l'aptitude de la
solution mise en place pour résoudre le problème ou pour
améliorer le processus. Sont employés à cet effet des
moyens de contrôle, tels que le Taux de Rendement Synthétique.
1.4. L'étape Act
(en français « action »)
Il s'agit ici de reprendre le cycle à la
première étape en utilisant la connaissance acquise au cours des
cycles précédents.
De plus, pour éviter de revenir en arrière, on
représente une cale sous la roue, qui empêche celle-ci de
redescendre et qui symbolise le système qualité proposé
précédemment.
Ce cycle en boucle permet à l'organisme de
s'améliorer de façon permanente en comparant sans cesse la
qualité réalisée à la qualité voulue, et en
redéfinissant au vu des résultats obtenus, les plans d'actions
nécessaires pour atteindre la qualité voulue (n) ou le nouveau
degré de qualité attendue (n+1).
Le processus générique d'amélioration
continue doit s'appliquer à la satisfaction des produits, aux processus
de fabrication et au système qualité
V. REMARQUES
1. Remarques positives
Tout au long de notre stage, nous avons eu à faire
quelques observations qui ont attiré notre attention de manière
positive :
· Lors de notre assistance des Maintenanciers dans leurs
diverses tâches, nous avons eu à apprécier l'implication de
certain dans leur travail.
· D'autre part, les relations humaines entre les
différents employés de la société,
indépendamment de l'activité exercée par chacun d'eux,
maintien une ambiance conviviale au travers de laquelle nous avons pu
comprendre que l'activité d'une société est plus
performante dans une atmosphère chaleureuse et bienveillante.
· Nous avons également constaté que
l'entreprise réduit l'impact de son activité sur l'environnement
dans la gestion et le tri des déchets.
2. Remarques négatives
· Une indiscipline notoire de la part des
employés dans certains service de l'entreprise ce qui crée par
moment un désordre hiérarchique et ralenti les temps
d'interventions.
· Le non-respect des consignes de sécurité
et port des EPI de la part de certains producteurs.
· Un manque de rigueur toujours de la part de certains
producteurs dans l'exécution de leurs tâches et le remplissage des
fiche de production ce qui crée une entrave au suivi de la
production.
CONCLUSION
Le travail qui s'achève porte sur l'étude
critique de la qualité des pots de conditionnement de yaourts
fabriqués au sein de l'usine CAMLAIT plastique. Il a pour nous
été question d'étudier le processus de production des
pots, d'exposer ses manquements puis de proposer des solutions à ces
manquements-là.
Après avoir identifié les différentes
causes qui engendraient cette grande quantité de mauvais pots et
déterminé le rendement de la machine, nous avons proposé
des solutions devant permettre d'améliorer celui-ci en optimisant les
coûts de production à travers la diminution de la
non-qualité et d'assurer son suivi. Au cours de ce travail, nous avons
eu un certain nombre de problèmes notamment l'inexactitude des
données de fiches de production faisant ainsi entrave à notre
analyse.
Par ailleurs, l'analyse des diverses solutions
proposées montre que l'application de celles-ci permettront de garantir
une utilisation rationnelle des ressources (énergie, matière
première) et limiter au maximum les gaspillages ce qui permettra de
rehausser le rendement de la machine. Ceci permettra à l'entreprise
d'économiser et d'allonger la durée de vie de ses
équipements.
Au-delà d'enrichir nos connaissance techniques, ce
stage nous a permis de comprendre dans quelle mesure les enseignements
reçu tout au long de notre cursus pourront intervenir dans notre futur
parcours professionnel.
En perspective, nous proposons aux responsables Maintenance,
Qualité et production de l'usine CAMLAIT plastique d'adopter les
solutions et suggestions proposées plus haut dans ce travail.
BIBLIOGRAPHIE
Ouvrages
[1] Maurice Reyne. Technologie des Plastiques.
3e édition revue et augmentée. Editions HERMES
Documents électroniques
[2]GEFRAN 450 REGULATEUR CONFIGURABLE.
[En ligne]. Disponible sur :
www.autelec-distribution.
(Page consultée le 20 aout 2015)
[3]« Fiche technique du capteur
thermocouple » [En ligne]. Disponiblesur :
https://www.google.cm/webhp?sourceid=chrome-instant&ion=1&espv=2&ie=UTF-8#q=autre+regulateur+pour+capteurs+thermocouple+NiCr-Ni(Page
consultée le 11 aout 2015).
[4]« Technique
statistiques »[En ligne]. Disponiblesur :
http://www.lomag-man.org/gestion%20stock_wms/controle_techniques_statistiques.pdf.(Page
consultée le 28 Novembre 2015)
[5]« Niveau de qualité
acceptable »[En ligne]. Disponiblesur :
https://www.google.cm/url?sa=t&rct=j&q=&esrc=s&source=web&cd=4&cad=rja&uact=8&ved=0ahUKEwjTnoKd4bPJAhVF1hQKHYl9DZAQFggtMAM&url=http%3A%2F%2Fsupport.minitab.com%2Ffr-fr%2Fminitab%2F17%2Ftopic-library%2Fquality-tools%2Facceptance-sampling%2Fplan-details%2Facceptable-quality-level-aql%2F&usg=AFQjCNG8hff3ZJ6LnZA0pV-nq15MsqzQ4g&sig2=NOClmR8z0Qxtql3lxQWqCA&bvm=bv.108194040,d.ZWU.
(Page consultée le 28 Novembre 2015)
[6]« Plan
d'échantillonnage »[En
ligne]. Disponiblesur :
https://www.google.cm/webhp?sourceid=chrome-instant&ion=1&espv=2&ie=UTF-8#q=plan+d%27%C3%A9chantillonnage+controle+qualit%C3%A9+en+production.
(Page consultée le 28 Novembre 2015)
ANNEXES
ANNEXE 1 : Fiche technique Régulateur
GEFRAN 450.
Caractéristiques principales :
· Entrée universelle configurable par la face
avant
· Précision meilleure que 0,2% PE aux conditions
de référence
· Sortie régulation : relais ou logique avec
fonction chaud ou froid
· Une alarme à fonction configurable
· Autoréglage, auto-adaptation, rampe au
démarrage, fonction Auto/Manu
· Possibilité de configuration par liaison
numérique
Généralités :
Le régulateur de température série 450,
qui mesure 48x48mm (1/16 DIN), allie facilité d'utilisation et haute
qualité de régulation. L'entrée depuis les sondes de
température est « universelle » et configurable pour des
thermocouples des types J,K,R,S,T,B,E,N et des thermistances Pt100 à
trois fils. L'interface utilisateur se compose d'un double afficheur
très complet, comprenant des diodes vertes, 4 touches et deux diodes
rouges de signalisation des sorties actives.
Caractéristiques techniques:
· Entrées
Précision 0,2% f.s. +/- 1 digit
Acquisition de la mesure 120 ms
· TC - Thermocouples
J(Fe-CuNi) 0... 1000°C / 32 ... 1832°F
K(NiCr-Ni) 0...1300°C / 32...2372°F
R(Pt13Rh-Pt) 0...1750°C / 32...3182°F
S(Pt10Rh-Pt) 0...1750°C / 32...3182°F
T(Cu-CuNi) -200...400°C / -328...752°F
B(Pt30Rh-Pt6Rh) 44...1800°C / 111...3272°F
E(NiCr-CuNi) -100...750°C / -148...1382°F
N(NiCrSi-NiSi) 0...1300°C / 32...2372°F
· RTD 3 fils Pt100
-200...600°C / -328...1112°F
· Sorties
Sorties entièrement configurables pour la
régulation ou alarme
· Relais
Pouvoir de coupure : 5A/250Va.c., cos?=1
(Référence de commande R)
· Logique
12V (6V min 20mA) (Référence de commande D)
· Alimentation
-(Standard) 100...240 V a.c. +/- 10%
- (Optionnel) 11...27 V a.c./d.c. +/-10%
- 50/60Hz, max. 10VA
· Conditions Ambiantes
- Température de fonctionnement : 0...50°C
- Température de stockage : -20...70°C
- Humidité : 20...85% HR sans condensation
· Régulation
- On/Off, P, PD, PID pour chauffage ou refroidissement,
paramètres configurables depuis la face avant.
- Consigne « froid » asservie à la consigne
« chaud ».
- Reset manuel -999...999 digits
- reset puissance -100,0...100,0%
- Cycle 0...200sec
- Rampe au démarrage 0,0...500,0 min
· Alarme
- Une alarme avec seuil d'intervention programmable en valeur
absolue, relative ou relative symétrique par rapport au setpoint avec
fonction directe ou inverse.
- Alarme réglable sur toute l'étendue
d'échelle configurée.
- Alarme rupture de la boucle (LBA) -
Hystérésis d'alarme configurable
· Poids
- 210g pour la version complète
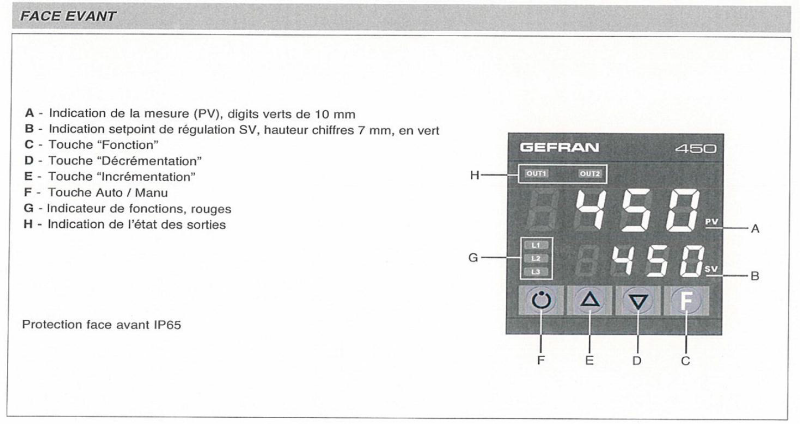
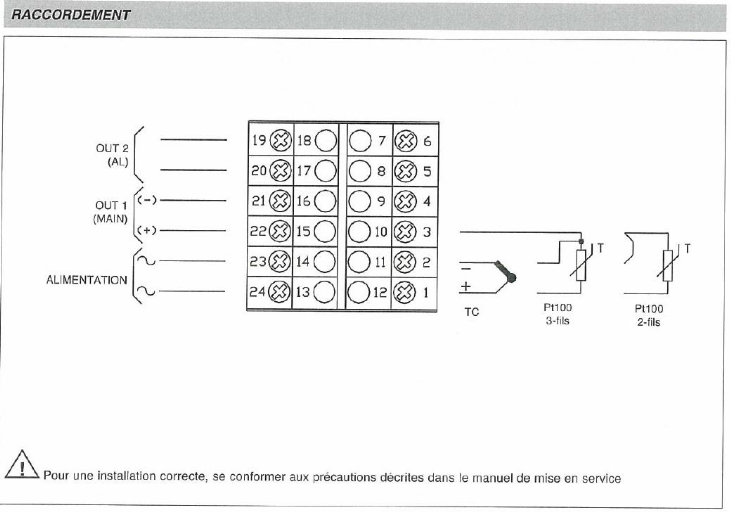
ANNEXE 2 : Fiche technique du Filtre Collecteur
de
Boue.
Caractéristiques techniques
- Pression de service = 5 bars maxi (à 60 °C).
- Captation magnétique par barreau magnétique
Alnico 600 positionné verticalement sur support facilement
démontable.
- Filtration 300 microns sur tamis inox (filtre vertical
entraînant la chute des boues).
- Réduction de vitesse 0,1 m/s dans le corps du
collecteur de boues mini-CDB.
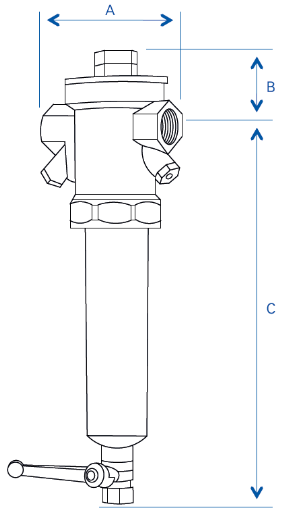
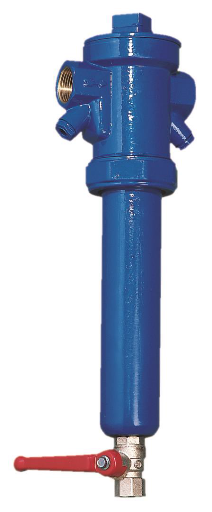
Matériau cuve
|
Température d'utilisation
|
Ø Entrée/ Sortie
|
Référence
|
A*
|
B*
|
C*
|
Plastique
|
5 à 60°C
|
3/4'
|
521006
|
96
|
65
|
190
|
1''
|
521008
|
123
|
93
|
190
|
1''1/4
|
521010
|
123
|
93
|
195
|
1'1/2
|
521012
|
145
|
110
|
230
|
2''
|
RI970047
|
145
|
110
|
230
|
Métallique
|
5 à 90°C
|
3/4'
|
521086
|
96
|
65
|
290
|
1''
|
521088
|
123
|
93
|
290
|
1''1/4
|
521090
|
123
|
93
|
295
|
1'1/2
|
521092
|
145
|
110
|
330
|
2''
|
RI970018
|
145
|
110
|
330
|
ANNEXE 3 :Fiche d'historique des pannes de
L'ILLIG
Date
|
Organe
|
Effet de la défaillance
|
Diagnostic
|
Travail à faire
|
activité
|
Temps mis
|
Matériaux utilisés
|
Priorité
|
Causes probables
|
|
Moule
|
La tige d'éjection est cassée
|
Tige cassée
|
Changer la tige
|
Démontage de l'esseuil ; Fixation de la tige ;
remontage
|
|
|
|
Accident imprévu
|
27-08-15
|
Vérin des poinçons
|
Le vérin des poinçons ne fonctionne pas
|
Fin de course défectueuse (30min)
|
Remplacer le fin de course
|
remplacement du fin de course ; réglage ;
essai
|
1h20min
|
Interrupteur de position
|
Très urgent
|
|
29-07-15
|
Valve
|
|
|
- - Remplacer les valves de commande des soufflettes
|
Remplacement des valves défectueuses : fixation du
support des valves par soudure
|
2h35min
|
valves simple effet ; écrou de diamètre
06
|
|
|
27-08-15
|
Circuit pneumatique
|
Impossible de produire (les pots ne se forment pas)
|
Disfonctionnement de l'interrupteur de position (30min)
|
Contrôler le circuit électrique et le circuit
pneumatique du soufflage des pots-
|
contrôle du circuit électrique (anormal) ;
Contrôle ; Circuit
Pneumatique
(anormal) ; fixation et Recâblage de
l'interrupteur de
position ; soufflage
essai et mise en service
|
2h
|
|
- Très urgent
|
Accident imprévu
|
24-08-15
|
Moule
|
Echange du produit
|
Changer le moule (30min)
|
Remplacer le moule 121-46 parle le moule 125-42
|
Démontage du moule 121-42 et ses accessoires
|
09h30min
|
|
- Très urgent
|
normal
|
04-08-15
|
Moteur
|
Trop de déchet (il faut tendre la chaine)
|
Chaine détendue (15min)
|
Tendre la chaine motrice
|
Chaine du moteur tendue ; serrage des vis de la
découpe pour remédier à la fuite d'eau sur le moule
|
1H15min
|
|
- Très urgent
|
Accident imprévu
|
30-07-15
|
Goulotte
|
La goulotte ne coulisse pas bien
|
Vis de fixation de bras cassée (15min)
|
Changer la vis et remonter le bras de commande de la
goulotte
|
Changement et montage du bras de commande de la goulotte ;
essai et mise en service
|
1h15min
|
Vis CHC, écrou, rondelle plate
|
Très urgent
|
fatigue
|
28-07-15
|
Ventilo
|
Présence de masse sur la machine
|
Ventilo broyeur illig à la masse (30min)
|
Rechercher la masse isolée ; sinon faire une mise
à la terre
|
Recherche de la masse, mise à la terre de la carcasse de
la machine ; essai et mise en service
|
45min
|
-
|
Très urgent
|
|
21-07-15
|
Ejecteur
|
Mauvaise injection des pots
|
Valve simple effet défectueuse (10min)
|
Réparation de la valve
|
Remplacement de la valve
|
1h
|
-
|
urgent
|
Usure
|
20-07-15
|
Moteur
|
Vibration du moteur
|
Vis de blocage cassée ; chaine principale
détendue (25min)
|
Remplacer les vis du moteur cassées ; tendre la
chaine principale
|
Remplacement des vis du moteur cassé ; tension de
la chaine du moteur principale
|
2h
|
- Vis CHC
- écrou
|
Très urgent
|
Mauvaise manipulation
|
16-07-15
|
Moule
|
Impossible de produire, présence d'eau sur les pots
|
Fuite d'eau sur le moule mobile (15min)
|
Corriger la fuite d'eau
|
Serrage des vis d'assemblage, essai et mise en service
|
45min
|
|
Très urgent
|
Accident imprévu
|
29-06-15
|
Graisseurs
|
|
|
Faire le graissage
|
Graissage des colonnes de guidage, des paliers de guidage, de
la canne, purger la graisse usée
|
30min
|
|
|
|
18-06-15
|
Moule
|
Mauvaise qualité des pots (l'eau entre dans le moule)
|
Fuite d'eau sur le raccord retour du moule mobile (15min)
|
Corriger les fuites d'eau
|
Correction des fuites d'eau ; essai et mise en service
|
45min
|
|
Très urgent
|
Accident imprévu
|
17-06-15
|
Moteur
|
Le moteur vibre
|
Vis de fixation cassée (30min)
|
Remplacer la vis de fixation cassée
|
Démontage de la chaine, démontage des trois vis
support moteur, remplacement des vis et fixation du moteur, remontage de la
chaine, essai et mise en service
|
2h30min
|
Vis CHC, écrou, rondelle
|
Très urgent
|
fatigue
|
15-06-15
|
Four bas
|
La zone 2 du bas ne chauffe pas
|
Alimentation contacteur zone 2 débranché
|
Fixer l'alimentation du contacteur
|
Alimentation fixée, essai et mise en service
|
15min
|
|
Très urgent
|
|
11-06-15
|
Chauffe
|
Le régulateur de température de la zone 1 ne
fonctionne pas bien
|
Régulateur de température grillé
(20min)
|
Remplacer le régulateur grillé
|
Remplacement régulateur, essai et mise en service
|
40min
|
Régulateur XMTE
|
Très urgent
|
|
22-05-15
|
Moteur
|
Difficulté de produire les pots
|
Vis de fixation du moteur principal coupée (10min)
|
Remplacer la vis coupée
|
Remplacement de la vis coupée
|
1h
|
Vis CHC ; écrou
|
Très urgent
|
|
29-04-15
|
Four bas
|
Le four ne chauffe pas
|
Résistance infrarouge cassées (10min)
|
Remplacer les résistances cassées
|
Démontage des résistances endommagées,
nettoyage du four, montage des nouvelles résistances, mise en chauffe et
observation
|
02h45min
|
Ecrou HC, émetteur infrarouge sans sonde 200W
|
Très urgent
|
Fatigue, matière qui se déverse sur les
résistances des
|
22-04-15
|
Circuit d'eau
|
Mauvais refroidissement des pots
|
Circuit d'eau bouché (30min)
|
Déboucher le circuit d'eau
|
Débouchage du circuit d'eau sur le moule
|
2h
|
|
Urgent
|
impureté
|
09-04-15
|
Moule
|
Mauvaise qualité des pots
|
Ressort de compression cassé, écrou de
réglage découpe défectueux (30min)
|
Remplacer le ressort cassé
|
Vis changée
|
08h30min
|
Vis épaulée, collier de serrage, ressort de
compression
|
Urgent
|
fatigue
|
26-03-15
|
Moule
|
Fuite d'eau sur le moule
|
Vis de serrage desserrée, tuyau percé (10min)
|
Serrer la vis de fixation du moule, remplacer le tuyau
percé
|
Serrage de la vis de fixation, remplacement du tuyau
percé, mise en service et essai
|
15min
|
Tuyau tressé tricolore
|
Très urgent
|
|
12-02-15
|
Goulotte
|
La goulotte ne fonctionne pas
|
Pas de vis du côté droit au bras de la goulotte
(15min)
|
Remplacer la vis cassée
|
Remplacement des vis cassées
|
15min
|
Vis HM, écrou HM, rondelle plate
|
Très urgent
|
Cassée
|
19-01-15
|
Circuit d'air
|
Impossible de produire
|
Filetage soufflette défectueux (10min)
|
Refaire le filetage de la soufflette
|
Filetage par Fillon, serrage de la vis support moteur
|
50min
|
Tube colle super glue
|
Très urgent
|
usure
|
17-02-15
|
Refroidissement
|
Fuite d'eau
|
Fissure de la conduite (15min)
|
Soudure de la fissure de la conduite
|
Soudure des fuites d'eau
|
40min
|
Baguette en cuivre
|
Urgent
|
|
17-02-15
|
Vanne d'air
|
Insuffisance d'air de soufflage des pots
|
Joints d'étanchéité défectueux dans
la vanne simple effet (30min)
|
Remplacer la vanne simple effet de commande
|
Adaptation d'un joint d'étanchéité, essai
et mise en service
|
1h
|
Super glue
|
Très urgent
|
fatigue
|
07-01-15
|
Soufflette
|
Impossible de produire
|
Soufflette cassée (5min)
|
Remplacer la soufflette cassée
|
Remplacement soufflette cassée, essai et mise en
service
|
10min
|
soufflette
|
Très urgent
|
|
ANNEXE 4 : Planning de maintenance
préventive
ILLIG RDM 37/10
|
Conducteur de la Machine
|
Equipe de Maintenance
|
Désignation de l'opération
|
Périodicité de l'intervention
|
20h
|
100h
|
200h
|
300h
|
500h
|
1500h
|
2500h
|
5000h
|
8760h
|
10200h
|
|
|
Vérification de l'état des émetteurs
infrarouge (Résistance chauffante)
|
|
|
|
|
|
|
|
|
|
|
|
|
Vérification des températures :
température affichée - température de consigne
(étalonnage)
|
|
|
|
|
|
|
|
|
|
|
|
|
Nettoyage des Capteurs
|
|
|
|
|
|
|
|
|
|
|
|
|
Vérification de l'état des tuyaux d'alimentation
en air du vérin des poinçons
|
|
|
|
|
|
|
|
|
|
|
|
|
Vérification de l'état du vérin des
poinçons
|
|
|
|
|
|
|
|
|
|
|
|
|
Vérification du circuit d'alimentation en air (circuit
pneumatique)
|
|
|
|
|
|
|
|
|
|
|
|
|
Vérification des lubrificateurs d'air
|
|
|
|
|
|
|
|
|
|
|
|
|
Vérification si la sonde de température est bien
fixée
|
|
|
|
|
|
|
|
|
|
|
|
|
Vérification de l'état des tuyaux d'alimentation
en eau pour le refroidissement dans le moule
|
|
|
|
|
|
|
|
|
|
|
|
|
Vérifier les colliers de serrages des tuyaux
d'alimentation en eau
|
|
|
|
|
|
|
|
|
|
|
|
|
Vérification de l'état et du serrage des vis de
différents organes (découpe, goulotte ; moteur)
|
|
|
|
|
|
|
|
|
|
|
|
|
Graissage des chaines picot
|
|
|
|
|
|
|
|
|
|
|
|
|
Vérifier si la chaine picot est tendue
|
|
|
|
|
|
|
|
|
|
|
|
|
Vérification du circuit d'éjection des pots
|
|
|
|
|
|
|
|
|
|
|
|
|
Vérification et serrage de la connectique dans l'armoire
électrique
|
|
|
|
|
|
|
|
|
|
|
|
|
Graissage des colonnes
|
|
|
|
|
|
|
|
|
|
|
|
|
Contrôle du degré d'usure des glissières
|
|
|
|
|
|
|
|
|
|
|
|
|
Serrage des cosses
|
|
|
|
|
|
|
|
|
|
|
|
|
Nettoyage du filtre à eau
|
|
|
|
|
|
|
|
|
|
|
|
|
Lubrification du vérin des poinçons
|
|
|
|
|
|
|
|
|
|
|
|
|
Changement des joints du vérin des poinçons
|
|
|
|
|
|
|
|
|
|
|
|
|
Contrôle des éléments roulant qui servent
au guidage des goulottes
|
|
|
|
|
|
|
|
|
|
|
|
|
Purger la graisse usée
|
|
|
|
|
|
|
|
|
|
|
|
|
Vérification de l'état des électrodes des
émetteurs infrarouge et des sondes de température
|
|
|
|
|
|
|
|
|
|
|
|
|
Nettoyage des émetteurs infrarouge
|
|
|
|
|
|
|
|
|
|
|
ANNEXE 5 : Fiche de suivi du recyclage
Centre : bonaberi Folio
n°1a
Atelier : Emballages Alimentaires
FICHE DE SUIVI DU RECYCLAGE DE MATIERE PS
Recyclage des feuilles et carottes
PROCESS
|
|
Production
|
Gros
Broyeur
|
Début broyage
|
|
|
Fin broyage
|
|
|
Temps réel de
broyage
|
|
|
Temps d'interruption
|
|
Heure
début
|
|
Heure
fin
|
|
Temps
mis
|
|
Motif de
L'arrêt
|
Date : _ _ _ _ _ Quart de : _ _ _ _ h
à _ _ _ _ h fiche n° : _ _ _ _
étiquette n° : _ _ _ _
observation
|
|
INTRANTS
|
|
Produits fabriqués
|
Article
|
unité
|
|
|
Bobine de feuille
|
Kg
|
|
|
Carotte de moule
|
Kg
|
|
|
Pots non conforme
|
Kg
|
|
|
Nombre de fois où la matière a été
rebroyé :
|
EXTRANT
|
|
Produits fabriqués
|
Article
|
unité
|
|
|
Matière rebroyé
|
Kg
|
|
|
Etat de recyclage actuel :
|
MAIN D'OEUVRE
|
|
Chef d'équipe
|
Producteur
|
|
Nom
|
|
|
Visa Kg
|
|
|
Observations : Nom et Visa du chef de quart
ANNEXE 6 :Table de niveau de contrôle II et
table de critère d'acceptation et de rejet
Effectif des lots
|
Lettre code
|
Effectif des échantillonnages
|
2 à 8
9 à 15
16 à 25
26 à 50
51 à 90
91 à 150
151 à 280
281 à 500
501 à 1200
1201 à 3200
3201 à 10000
10001 à 35000
35001 à 150000
150001 à 500000
Supérieur à 500001
|
A
B
C
D
E
F
G
H
J
K
L
M
N
P
Q
|
2
3
5
8
13
20
32
50
80
125
200
315
500
800
1250
|
Table de niveau de contrôle II
Lettre code
|
n
|
A = 0
R = 1
|
A = 1
R = 2
|
A = 2
R = 3
|
A = 3
R = 4
|
A = 5
R = 6
|
A = 7
R = 8
|
A = 10
R = 11
|
A = 14
R = 15
|
A = 21
R = 22
|
A
B
C
D
E
F
G
H
J
K
L
M
N
P
Q
|
2
3
5
8
13
20
32
50
80
125
200
315
500
800
1250
|
6,5
4
2,5
1,5
1
0,65
0,4
0,25
0,15
0,1
0,065
0,04
0,025
0,015
|
10
6,5
4
2,5
1,5
1
0,65
0,4
0,25
0,15
0,1
0,065
0,025
|
10
6,5
4
2,5
1,5
1
0,65
0,4
0,25
0,15
0,1
0,04
|
10
6,5
4
2,5
1,5
1
0,65
0,4
0,25
0,15
0,065
|
10
6,5
4
2,5
1,5
1
0,65
0,4
0,25
0,1
|
10
6,5
4
2,5
1,5
1
0,65
0,4
0,15
|
10
6,5
4
2,5
1,5
1
0,65
0,25
|
10
6,5
4
2,5
1,5
1
0,4
|
10
6,5
4
2,5
1,5
0,65
|
Table de critère d'acceptation et de rejet
Taille de l'échantillon : n
ANNEXE 7 :Plan de localisation de CAMLAIT S.A
département plastique
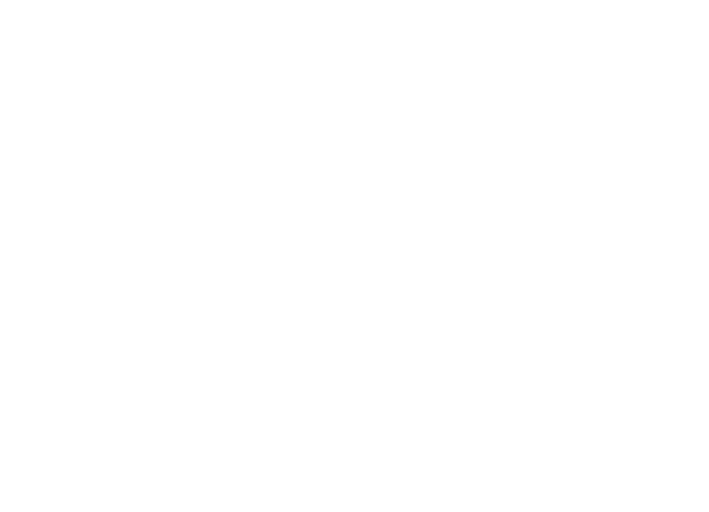
   
|