INTRODUCTION GENERALE 1
CHAPITRE I RECHERCHES BIBLIOGRAPHIQUES
HYSTORIQUE 3
I. GENERALITES 4
I.1 DEFINITIONS 4
I.2 ORGANISATION ET CLASSIFICATION DES LAMINOIRS
6
I.3 LES CYLINDRES DE LAMINAGE À CHAUD
9
I.3.1 DEFENITION 9
I.3.2 MATERIAUX UTILISEES DANS LA FABRICATION
DES CYLINDRES DE TRAVAIL 9
I.3.3 PROCEDES DE FABRICATION DES CYLINDRES DE
12 TRAVAIL
· Processus CPC 14
· Processus HIP 15
· Processus ESR 16
I.3.4 USINAGE A L'OUTIL 17 I.3.5
SOLLICITATIONS EXERCEES SUR LES CYLINDRES DE
TRAVAIL 18
I.3.5.a FATIGUE THERMIQUE
19
I.3.5.b TENSIONS DE CONTACT
23
CHAPITRE II COMPORTEMENT EN FATIGUE THERMIQUE
DES CYLINDRES DE LAMINAGE
II.1 INTRODUCTION 27
II.2 CONTRAINTES ET FATIGUE THERMIQUE DES
CYLINDRES 27
II.2.1 CONTRAINTES THERMIQUES EN SURFACE DES
CYLINDRES 28 II.2.2 FATIGUE THERMIQUE DES
CYLINDRES DE LAMINAGE A
CHAUD 29 II.2.3 AUTRES PHENOMENES
CONDITIONNANT LA FATIGUE
THERMIQUE 30
II.2.4 DUREE DE VIE EN FATIGUE
30
II.2.5 RESISTANCE A LA FATIGUE THERMIQUE
31
II.3 ANALYSE NUMERIQUE DES CONTRAINTES THERMIQUES DANS
LES CYLINDRES DE TRAVAIL À CHAUD 31
II.3.1 INTRODUCTION 31
II.3.2 MODELISATION PAR LA METHODE DES ELEMENTS
FINIS
D'UN CYLINDRE DE TRAVAIL PAR LE LOGICIEL ANSYS10.0
31
II.3.3 METHODE DES ELEMENTS FINIS
32
II.3.4 CALCUL THERMOMECANIQUE DES CONTRAINTES
36
II.4 PROPRIETES DES MATERIAUX
II.4.1 PROPRIETES PHYSIQUES
37
II.4.2 PROPRIETES MECANIQUES
38
CHAPITRE III RESULTATS ET DISCUTIONS
III.1 INTRODUCTION 40
III.2 MODELESATION THERMIQUE PAR LA METHODE DES
ELEMENTS FINIS 41
III.2.1 DISTRIBUTION DE LA TEMPERATURE DANS LES
CYLINDRES DE TRAVAIL 41
III.2.2 EVALUATION DE LA TEMPERATURE SUR LA
PARTIE SUPERFICIELLE DU CYLINDRE DE TRAVAIL 43
III.2.3 GRADIENT THERMIQUE SUIVANT LE RAYON DU
CYLINDRE DE TRAVAIL 46 II.3 ANALYSE NUMERIQUE DES
CONTRAINTES THERMIQUES DANS
LES CYLINDRES DE TRAVAIL À CHAUD 49
III.3.1 CYLINDRE DE TRAVAIL: FONTE NODULAIRE/FONTE
RICHE EN CHROME 49
III.3.2 CYLINDRE DE TRAVAIL: FONTE
NODULAIRE/NI-HARD 56
III.3.3 CYLINDRE DE TRAVAIL: FONTE
NODULAIRE/ACIER RAPIDE 61
III.3.4 CYLINDRE DE TRAVAIL: FONTE NODULAIRE/ACIER
RICHE EN CHROME 65
III.4 RESULTATS 70
CONCLUSION GENERALE 74
Remerciement
Avant tous, je remercie le bon Dieu qui m a donné de
l'aide et de la patience pour atteindre mon objectif.
Je remercie bien sûr mes parents, sans qui je ne serais
pas ici.
Que monsieur AEK Ziadi (mon encadreur) trouve ici
l'expression de ma profonde reconnaissance pour m'avoir aidé à
réaliser ce travail. Sa grande disponibilité, les connaissances
qu'il m'a fait partager et son esprit d'entreprise m'ont été
très précieux.
Monsieur BACHIR BOUIADJRA B, BOUTABOUT B et BELHOUARI M, me font
l'honneur de participer à mon jury. Je les prie de croire à ma
respectueuse reconnaissance.
Je remercie vivement l'ensemble des étudiant de la 2 eme
année magistère pour m'avoir aidé du point de vie
informatique.
Enfin, je tien à exprimer toute mon amitié à
mes amis qui m'ont offert leurs soutien chaleureux tout le long de cette
période.
INTRODUCTION GENERALE
Le cycle de production d'un produit sidérurgique
comprend un passage à l'état solide. Autrefois ce passage se
situait à la coulée en lingots à l'aciérie,
aujourd'hui il se situe pour la grande majorité des produits à la
coulée continue. Les étapes ultérieures du cycle du
produit comprennent des mises en forme successives dans les ateliers de
laminage, à chaud en première étape, puis de laminage
à froid dans une seconde étape.
Comme pour la plupart des autres techniques
métallurgiques, on a su laminer bien avant que la moindre esquisse de
théorie ne vienne expliquer pourquoi on peut laminer. Il ne reste pas
moins que le laminage a fait et continue de faire l'objet d'un nombre
considérable de travaux. Certains visent à une
compréhension plus poussée des phénomènes
thermomécaniques du système ; d'autres s'attachent plus
prosaïquement à la solution de problèmes plus
immédiats qui se posent sur la machine.
En laminage à chaud, les points d'amélioration
du procédé résident dans l'allongement des compagnes de
laminage, la diminution des reprises des cylindres de travail par rectification
et donc dans l'allongement de la durée de vie des cylindres.
La durée de vie des cylindres est limitée par
les conditions de travail sévères en termes de sollicitations
thermomécaniques. Ces dernières résultent du contact
intime entre le cylindre de travail et la pièce. Outre l'usure, les
cylindres de travail sont généralement endommagés par de
la fissuration dite de fatigue thermique. Le mécanisme d'endommagement
par fatigue thermique provient principalement des contraintes d'origine
thermique alternées en compression et en traction à la surface
active des cylindres. Ces dernières résultent des
dilatations/contractions différentielles qui apparaissent lors des
variations brutales de température à la surface de travail des
outils lors du contact outil/pièce.
Ce travail a été réalisé dans le
but d'avoir une connaissance du comportement, de l'endommagement et de la
durée de vie des cylindres de travail à chaud sous sollicitations
thermomécaniques proches de celles subies par la surface active des
outils de travail à chaud.
Cette étude comporte trois chapitres. Le premier
chapitre porte sur des rappels théoriques sur le laminage, le rôle
des cylindres de travail dans le mécanisme de laminage et leur
comportement face aux conditions durs de fonctionnement. Le deuxième
chapitre est consacré à la description des contraintes thermiques
et leurs conséquences sur les cylindres de travail, l'application de la
méthode des éléments finis pour calculer ces contraintes
et le logiciel de calcul utilisé. Nous avons déterminé
numériquement par la méthode des éléments finis les
états, le niveau et la distribution des contraintes thermiques
présentes dans les cylindres de travail. Dans le troisième
chapitre, sont exposés les résultats obtenus tous le log de cette
étude. En fin nous finalisons notre étude par quelques
conclusions.
Historique :
Le laminage est apparu dans l'usine sidérurgique avec
d'autres techniques de mise en forme telles que le forgeage au martinet, au
marteau pilon ou à la presse. L'évolution des techniques de
forgeage et de laminage a historiquement suivi des voies complémentaires
dans la recherche de la productivité. Les premières forges
employaient l'énergie hydraulique et les premiers martinets furent
construits à partir du 12e siècle. Ils furent peu
à peu remplacés par un marteau-pilon entraîné par la
vapeur, dont on trouve le premier exemple à simple action en France en
1842. Le premier marteau à double action sera construit aux Etats-Unis
en 1888. La presse hydraulique est une invention anglaise datant de
l'année 1861.
Le premier laminoir fut employé en France en 1553 pour
travailler l'or et l'argent. Vers 1750 les premières applications des
laminoirs à la mise en forme de l'acier sont citées dans
plusieurs pays européens. Henry Cort en Angleterre introduira à
partir de 1783 les premières augmentations de tailles, de puissance et
de capacité ouvrant ainsi une période d'évolution rapide
des laminoirs. La force motrice sera en premier temps la vapeur
remplacée au 20e siècle par l'énergie
électrique [2].
I.GENERALITES I.1 DEFINITIONS
Le laminage est un des processus de fabrication les plus
importantes, d'une grande diversité, utilisé pour la mise en
forme par déformation plastique d'un volume de matériau plus
grand que ceux que traite n'importe quelle autre technique [1] il
consiste donc à faire passer un métal entre deux cylindres
tournant en sens inverses.
Le laminage commence à chaud quand on doit travailler
un produit de forte section (nécessaire à la rentabilité
des opérations de coulée), donc demandant de fortes puissances de
déformation.
Chauffer un métal, donc le ramollir, revient à
diminuer ces puissances et la taille des installations nécessaires, tout
en lui conférant la ductilité nécessaire aux très
grandes déformations à réaliser.
De nombreux produits (produits long, tôles fortes,
bande à chaud) ne subissent qu'un laminage à chaud, puis des
opérations de finition (traitement thermiques, dressage,
décapage, revêtement, usinage). Le passage à des
opérations à froid est, de manière générale,
nécessaire pour obtenir des tolérances serrées (de l'ordre
de quelques micromètres), des propriétés mécaniques
élevées par écrouissage, et un bon état de surface.
Ne sont laminées à froid pratiquement que les bandes minces.
Le laminage fournit surtout des demi produits, mais avec des
exceptions notables: tôles fortes, poutrelles et rails, certains
tubes...les autres produits long sont destinées à l'usinage
(barres), au tréfilage (fils machines), au forgeage ; quant au produits
plats, ils vont vers des opérations de mise en forme des métaux
en feuilles (emboutissage, découpage fin, repoussage et fluotournage).
[3]
Le laminage des tôles et des plats en acier est
assuré par des cylindres ; leur table cylindrique lisse est
légèrement concave ou convexe. La figure I.1.1 représente
le schéma de fabrication des plats.
Les profilés en acier courants et spéciaux sont
laminés dans des cylindres dont la table comporte des rainures
spéciales obtenues par tournage et qui correspondent à la forme
à donner au métal. Ces rainures circulaires s'appellent
cannelures. Les cannelures des deux cylindres forment l'empreinte
reproduisant le tracé du profilé à obtenir. La figure
I.1.2 représente le schéma de fabrication des rails.
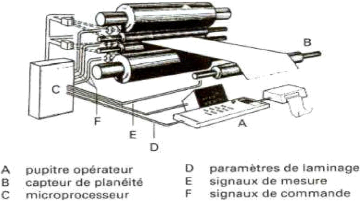
.Figure I.1.1 Fabrication des plats.
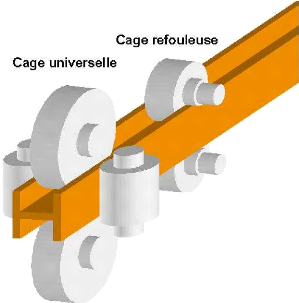
Figure I.1.2 Fabrication des rails.
I.2 ORGANISATION ET CLASSIFICATION DES LAMINOIRS
Une configuration typique d'un train de laminage à
chaud est exposée dans la figure (2) composé de 4 caisses
d'ébauche (R1, R4) et 6 caisses de finition (F1, F4), ou sont
indiquées les réductions typiques de caisses.
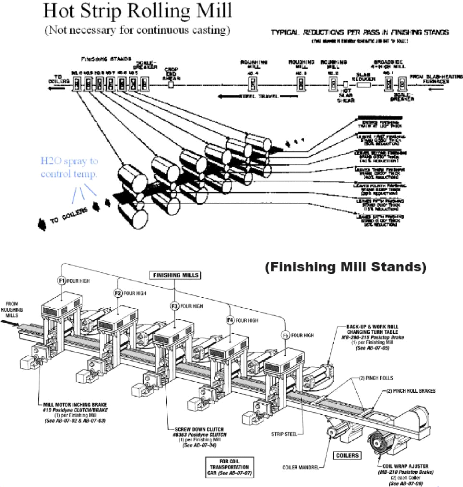
Figure I.2.1 Fabrication, formation et
traitement de l'acier.
Les ensembles fondamentaux d'un laminoir sont :
> Une ou plusieurs cages de laminage ; > Le moteur ;
> Le réducteur ;
> La cage à pignon ;
> Le volant ;
Toute l'installation est placée sur une fondation
commune.
Cage de laminage : bâti en fonte ou en
acier coulé comportant quatre colonne disposées de
façon à recevoir les cylindres de laminoirs dans un même
plan vertical. L'écartement
des cylindres est réglable grâce à des
dispositifs à vis (figure I.2.2) [5].
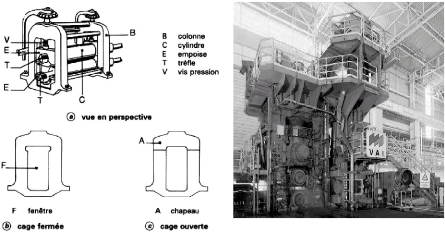
Figure I.2.2 Cage de laminage.
Les cages peuvent être réparties en cinq groupes
suivant le nombre et la disposition des cylindres (duos, trios, quarto,
à cylindres multiples et universelles). La figure I.2.3
représente les différents types de cages.
Les cages duos comptent deux cylindres à sens de rotation
constant, dont les axes sont placés horizontalement. (Figure
I.2.3.a).
Dans les cages trios (trois cylindres) chaque cylindre tourne
toujours dans le même sens ; les cylindres sont disposés dans le
plan vertical (figure I.2.3.b).
Les cages quarto comportent quatre cylindres placés
l'un au-dessus de l'autre dans le plan verticale. Les deux petits cylindres
sont les cylindres de travail, alors que les deux autre, plus grands, forment
l'appui ; ils reçoivent la pression développée pendant
l'opération et réduisent la flexion des cylindres de travail.
(Figure I.2.3.f).
Les cages universelles sont employées pour le laminage
des larges plats, des tôles et des brames. Dans ces cages, le
métal est réduit par les cylindres horizontaux et verticaux.
(Figure I.2.3.h).
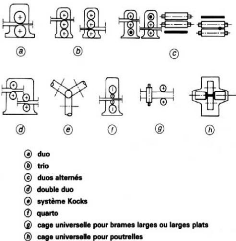
Figure I.2.3 Types de cages.
Les éléments de base du processus de laminage
sont les cylindres qui, à leur tour, sont utilisés dans des
opérations effectuées tant à chaud qu'à froid
fabriqués avec des matériaux ferreux (acier) et aussi avec des
alliages non ferreux [1] .ils représentent aussi un important
investissement dans le coût de la fabrication. Ainsi, prolonger la vie
utile des cylindres de travail à une importance immédiate tant
pour l'opérateur du train de laminage que pour le fabricant du
cylindre.
I.3 LES CYLINDRES DE LAMINAGE À CHAUD 1.3.1
DEFINITION
Les cylindres de laminage sont les outils essentiels de ce
procédé de mise en forme; ils sont soumis à de fortes
sollicitations cycliques tant mécaniques que thermiques. L'optimisation
de leur durée de vie est donc particulièrement cruciale car leur
détérioration influe de manière pénalisante sur la
qualité de surface des produits ainsi que sur les arrêts des
installations industrielles. Dans un souci multiple d'augmenter la
durabilité des outils, la qualité des produits et de
réduire les coûts, il est nécessaire de contribuer à
la maîtrise de ces dégradations et en particulier à celle
de l'usure.
I.3.2 MATERIAUX UTILISEES DANS LA FABRICATION DES
CYLINDRES DE TRAVAIL
Pour que ces cylindres réunissent les conditions de
qualité exigées en vue d'obtenir des tolérances
dimensionnelles du produit laminé très étroites et une
finition superficielle plus parfaite, et d'augmenter la productivité du
train de laminage, il est nécessaire d'améliorer la
résistance des cylindres dans les actions de service. Il s'agit alors
d'obtenir une plus grande qualité du produit laminé, uns plus
grande productivité, avec un plus petit nombre de changements des
cylindres dans le train pendant le service, ce qui permet d'obtenir finalement
un faible coût de production.
Les cylindres conventionnels ne peuvent pas satisfaire de nos
jours toutes ces exigences, particulièrement avec les conditions de
travail de plus en plus sévères. Les cylindres de travail doivent
être fabriqués avec un matériau dur et résistant,
capable de supporter la pression de contact due à la force de laminage,
les fortes gradients thermiques
cycliquement répétés et, en même
temps les cylindres doivent aussi posséder une haute résistance a
l'usure, dans le but de maintenir la qualité superficielle du produit
laminé et augmenter la productivité du train.
Les cylindres en fonte douce sont coulés dans des
moules de sable employés au dégrossissage a chaud de l'acier. Les
cylindres en fonte dure, coulés dans des coquilles, sont largement
employés dans des trains a tôles et dans et dans les cages de
finissage des trains profilés et a fils.
Les premiers essais des cylindres en acier rapide dans les
trains a bandes laminées a chaud sont très récents, ils
commencent a la fin des années 80 au Japon et au débit des
années 90 en Europe[1][15].
Dans la production des cylindres de laminage a chaud des
premières caisses finisseuses des trains a bande laminée a chaud,
les cylindres en acier rapide suscitent un intérêt en constante
croissance puisqu'ils permettent d'atteindre un meilleur rendement que les
cylindres en fonte a haute teneur en chrome [4].
La principale vertu des cylindres d'acier rapide est son
excellent comportement mécanique a des très hautes
températures, ajoutant a cela son supérieur résistance a
l'usure et a la fissuration thermique, favorisé par le haut pourcentage
de carbone (1.5 - 2.5 o/o) et des éléments
d'alliage, comme V, Nb, Cr, Mo et W, qui forment des carbures durs et
stables[4].
Le carbone est l'élément essentiel pour durcir
l'acier. Role des éléments d'alliage :
Les éléments carburigènes tels que le
chrome, le molybdène, le tungstène et le vanadium, ajouté
séparément ou conjointement a l'acier au carbone, ont des
influences communes sur le comportement de cet acier [16].
v' Vanadium;
Il est utilisé essentiellement comme
élément générateur de carbures. C'est un
élément d'alliage important dans les aciers rapides pour
l'obtention d'une bonne dureté a chaud et d'une bonne
résistance a l'usure en raison de la présence de particules
très durs de carbure
de vanadium. Le vanadium est rarement utilisé seul dans
les aciers à outils, mais la plupart du temps en association avec le
chrome, le molybdène et le tungstène [16].
v' Chrome;
Cet élément est utilisé dans la plupart
des aciers à outils (cylindre de laminage), en qualité allant de
0.5 à 17 o/o. cet élément joue un rôle
essentiel dans l'augmentation de la trempabilité. Il entraîne
également une très forte réduction de l'oxydation à
haute température, ainsi, l'addition de plus de 10
o/o de chrome entraîne une augmentation
substantielle de la résistance à la corrosion [16].
v' Tungstène ;
Il a été l'un des éléments
d'alliage les plus employés dans le domaine des aciers à outils
en raison de son pouvoir carburigène très important. Certains
aciers rapides contiennent jusqu'à 22 o/o de
tungstène. Plus la teneur en tungstène est élevée,
plus la température de fusion de l'alliage est augmentée. Les
aciers à outils au tungstène sont peu sensible à la
décarburation mais ont une résistance au choc thermique assez
faible [16].
v' Molybdène ;
Dans les cylindres de laminage, cet élément a
un comportement analogue à celui du tungstène. Les aciers au
molybdène présentent, par rapport aux aciers au tungstène,
un certain nombre d'avantages et d'inconvénients :
· Avantages ;
Meilleur ductilité et densité plus faible ;
Mise en solution plus facile des carbures de molybdènes
:
· Inconvénients ;
Plus grande sensibilité à la décarburation
et au phénomène d'oxydation catastrophique entre 1000 et 1100
°C [16].
D'une manière générale, les aciers pour
travail à chaud doivent avoir une résistance à la
déformation convenable, donc des caractéristiques
mécaniques à chaud et une résistance à l'usure
élevées sans que le ténacité, indispensable pour
limiter les risques de fissuration rapide, soit trop sacrifiée, ainsi
qu'une bonne tenue aux différences de température en cours de
travail, causes de chocs thermiques. Ces aciers doivent avoir également
une résistance à la déformation suffisante lors des
traitements thermiques. La plupart des aciers que nous étudions ici
étant assez alliés, et contenant du chrome en particulier, ont
une trempabilité élevée et répondent bien à
cette exigence. Une bonne usinabilité est également
recherchée.
Ces aciers sont répartis d'après la norme NF
A35-590 en cinq groupes :
> les aciers résistant aux chocs thermiques ;
> les aciers résistant à l'usure aux
températures élevées ; > les aciers résistant
aux très hautes températures;
> les aciers résistant à certaines corrosions
[16].
I.3.3 PROCEDES DE FABRICATION DES CYLINDRES DE TRAVAIL
Parmi les éléments constituant le train de
laminage à bandes, les cylindres de travail sont les plus importants
puisque ce sont eux qui contrôlent la réduction et la forme du
produit laminé. Ils diffèrent par leurs compositions chimiques,
par leurs processus de fabrication et le type de laminage ou ils sont
utilisés.
Les cylindres de travail sont généralement obtenus
à partir d'un processus de moulage:
> Un moulage statique, dans le cas d'un seul matériau.
> Moulage par centrifugation, avec deux coulées.
Les cylindres de travail à haute teneur en chrome et
les aciers rapides se substituent de plus en plus aux fontes nodulaires ou aux
fontes blanches pour des raisons se productivité. Ces cylindres sont
bimétallique avec une âme en acier (ou éventuellement,
quoique de moins en moins, pour des problèmes de rigidité, en
fonte nodulaire) et une périphérie en acier à outils. Ils
sont aussi fabriqués à une échelle commerciale en
recourant à de nouvelles méthodes, telles que les techniques CPC
(Continuos Pouring process for Cladding), ESR (Electroslag Remelting) et HIP
(Hot Isostatic Pressing).
|
coulée par centrifugation
|
|
Permet d'obtenir une bonne liaison sans mélange entre
les deux nuances des cylindres composites, ainsi qu'une structure de
solidification exempte de dendrites et de porosités dans le
matériau de l'enveloppe en acier à outils. Dans ce
procédé, les deux constituants du bimétal sont
élaborés successivement par centrifugation. Les épaisseurs
d'acier à outils sont voisines de 100mm.
C'est un processus utilisé habituellement en Europe et
en Amérique du nord pour la fabrication des cylindres en acier rapide,
alors qu'au Japon entre 30 o/o et 40
o/o des cylindres rapides sont réalisés par
cette méthode [6].
La figure (I.3.1) montre une esquisse du processus de la
coulée par centrifugation horizontale, bien qu'elle puisse aussi
être effectués en position vertical. De cette manière, il a
été obtenu des cylindres composés, constitués par
un noyau et des cols en fonte nodulaire et une couche extérieur,
appelée aussi table de travail du cylindre, en acier rapide, de telle
sorte que sa dureté et sa résistance à l'usure soient
élevées alors que le noyau et les cols sont relativement plus
ductiles et moins résistants. De toute manière, il s'agit d'un
processus de fabrication assez complexe, qui exige un contrôle strict de
ses paramètres.
La machine de coulée par centrifugation a une haute
productivité et peut atteindre la coulée d'un cylindre toute les
deux heures [7].
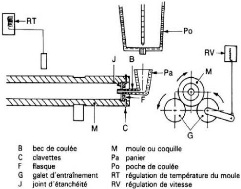
Figure I.3.1 Banc de centrifugation
horizontale.
Il s'agit d'un processus développé au Japon
pour la fabrication des cylindres en acier rapide, ou entre 60 et 70
o/o de ces cylindres sont actuellement fabriqués
par cette technique. Un axe en acier dur, a été
préchauffé au moyen d'une bobine à induction et en suite
le bouillon d'acier rapide est versé, il occupe l'espace existant entre
le moule extérieur en cuivre (voir figure I.3.2) [8].
Une seconde bobine à induction agite le métal
et permet l'union, suite à quoi la région superficielle de l'axe
devrait fondre. Dans ce cas, l'obtention d'une bonne union entre le noyau et la
couche extérieure, nécessite de bien contrôler ce processus
[7] [9].
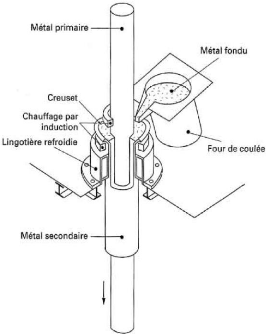
Figure I.3.2 Représentation
schématique du processus CPC [16].
Ce processus est utilisé pour fabriquer de petits
cylindres monoblocs. Un axe en acier résistant a été
utilisé ; il est introduit dans le moule, et rempli ensuite avec de
l'acier rapide en poudre (normalement une poussière
pulvérisée contre un gaz inerte ou l'eau) pour former la couche
extérieur. Celle-ci est consolidée en appliquant
simultanément une haute
pression (au-dessus de 100MPa) et une température
(1000oC) [9] (figure I.3.3). Ainsi, on obtient un cylindre avec une
bonne intégrité et une granulométrie (10-20um).
Le principal problème est la limitation dans la taille
maximale du cylindre obtenu par ce processus. Il n'existe actuellement dans le
monde aucune installation HIP qui pourrait avoir une capacité suffisante
pour produire des cylindres pour train à bandes laminées
à
chaud [8].
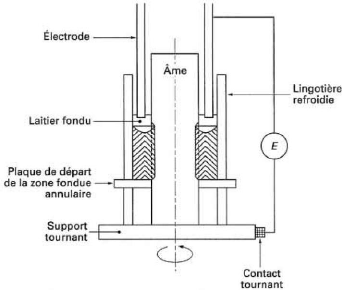
Figure I.3.3 Processus HIP [16].
Ce processus est semblable au CPC, mais le chauffage par
induction est remplacé par un processus ESR. L'électro-scorie
fondue préchauffe et nettoie l'axe solide. Le système agite le
métal ajouté qui se situe sous la scorie, en aidant à
effectuer l'union. La figure (I.3.4) montre la conception
générale du système de revêtement ESR.
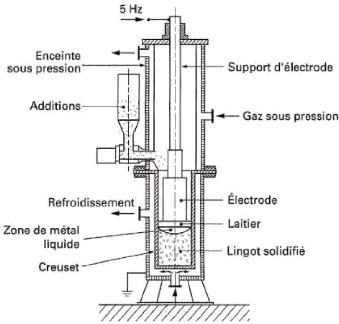
Figure I.3.4 Schéma du
procédé de refusions sous laitier et sous
pression (Système ESR)[16].
I.3.4 USINAGE A L'OUTIL
La fabrication d'un cylindre de laminage nécessite, le
plus souvent, des opérations d'usinage complexes et précises, et
le volume de copeaux enlevé par rapport au volume total de la
pièce peut être grand.
La réalisation des cannelures nécessite par
exemple l'emploi de nouvelles technologies. L'usinage par le laser et le
faisceau d'électrons et largement utilisé. La figure
(I.3.5) montre une des procèdes d'usinage d'un cylindre
de laminage.
Le traitement thermique constituant une étape essentielle
pour l'obtention des propriétés d'emploi des cylindres.

Figure I.3.5 Schéma du dispositif
Spark-Tec pour réaliser des textures par
électroérosion sur un cylindre de laminoir [16].
I.3.5. SOLLICITATIONS EXERCEES SUR LES CYLINDRES DE
TRAVAIL
En laminage à chaud, les points d'amélioration
du procédé résident dans l'allongement des compagnes de
laminage, la diminution des reprises des cylindres de travail par rectification
et donc dans l'allongement de la durée de vie des cylindres.
La durée de vie d'un cylindre est conditionnée par
la nature et l'amplitude des endommagements qu'il subit.
Ces endommagements sont induits par des sollicitations
d'ordre thermique, chimique et mécanique dépendantes des
caractéristiques de l'emprise et de fait, du laminoir (type de cage,
nuances laminées...). Ils sont globalement repris dans le terme d'usure
qui se quantifie à l'échelle industrielle par la quantité
de matière reprise par rectification à l'issue de chaque
montage.
La position des cylindres dans le train détermine la
prédominance d'une sollicitation par rapport aux autre. Les cylindres en
cage dégrossisseuses sont ainsi plus largement soumis à des chocs
thermiques (usure par fatigue), alors qu'en cages finisseuses, les
sollicitations mécaniques présentent une influence
prépondérante (usure abrasive).
Une voie d'innovation en laminage est alors
l'amélioration des propriétés physicochimiques et
mécaniques des nuances de cylindres de travail à chaud afin
d'optimiser la résistance aux sollicitations thermomécanique et
chimiques subies dans l'emprise.
Ces sollicitations sont :
> Les gradients thermiques supportés par le cylindre
lors du contact avec la bande à laminer et son refroidissement en sortie
d'emprise,
> La réduction appliquée conduisant à
une modification des forces de laminage, > Le cisaillement assurant
l'entraînement de la bande dans l'emprise,
> La température de laminage garantissant la
réduction et les propriétés de la bande, > La
lubrification assurant le refroidissement des cylindres et limitant les efforts
de laminage.
Autant de sollicitations qui vont être à
l'origine de la limitation de la durée de vie des cylindres et donc de
la quantité de rebut de bande laminée selon l'impact des
endommagements des cylindres sur la qualité de la bande.
Ces dégradations peuvent être assemblées en
deux groupes essentiels :
> Dégradations catastrophiques, telles que la rupture
des cols, fissures traversant le corps du cylindre ;
? Détérioration de la surface du cylindre due
à la fatigue thermique/mécanique ou à l'usure.
L'origine de la fatigue thermique est la variation de la
température superficielle dans le cylindre durant chaque rotation. La
fatigue mécanique est due aux tensions causées par la
déformation de la bande et le contact entre les cylindres de travail et
les cylindres d'appui. L'usure se justifie en vertu du glissement existant
entre le cylindre et la bande sous l'effet de la force de laminage, en
présence des particules oxydées dures au niveau du contact.
I.3.5.a FATIGUE THERMIQUE
La fatigue thermique réside dans la région
superficielle du cylindre par accumulation des déformations plastiques.
Suite à l'augmentation de la température de la surface du
cylindre de laminage en contact avec la bande, cette région du cylindre
augmente de volume; cependant, cette expansion est limitée par le corps
principal du cylindre relativement froid, induisant des tensions de compression
dans la direction circonférentielle et radiale du cylindre. Les tensions
de compression augmentent avec la température de la bande et du temps de
contact entre le cylindre et la bande (figure I.3.6).
Pendant le refroidissement (lubrification avec de l'eau), les
tensions de compressions se convertissent en tensions de traction. Cette
conversion est due à la diminution du volume du cylindre dans la zone de
contact. La tension thermique générée dans le cylindre est
exprimée par ; [8]
Ea AT
Ou ; E, a , v sont respectivement le module
élastique, le coefficient d'expansion linéaire et le coefficient
de Poisson.
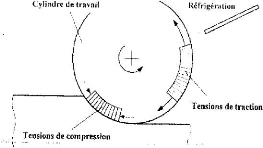
Figure I.3.6 Tensions thermiques sur la
surface du cylindre de travail au cours du laminage d'une bande en acier.
Quand la température à la surface du cylindre
dépasse les 370 oC, la limite élastique du
matériau du cylindre sera dépassée et cette zone se
déforme plastiquement tout au long de la ligne AB (figureI.3.7). Dans
cette région, l'augmentation de la température entraîne
celle de la déformation mais aussi une réduction de la tension
(diminution de la limite élastique avec la température). Quand la
température atteint 450 oC, au moment de la séparation
de la surface du cylindre et la bande, commence le refroidissement pendant
lequel les tensions de compression se réduisent élastiquement
tout le long de la ligne BC. Quand la température de la surface atteint
104 oC, au point C, en ce moment la limite élastique à
la traction sera dépassée et la déformation plastique aura
lieu sur toute la longueur de la ligne CD jusqu'à ce que la surface
atteigne les 20 oC, (température initiale).
Dans la seconde rotation du cylindre et au contact de la
bande, la température de la surface de celui-ci sera de nouveau
élevée et il se déforme élastiquement tout le long
de la ligne DE, continuant ainsi un nouveau cycle, EBCD, (figure I.3.7).
La variation de la température du cylindre dans le sens
radial, pour différentes profondeurs durant la première
rotation est représentée par la figure I.3.8 celle-ci montre
qu'il est possible d'atteindre ponctuellement des températures
superficielles très élevées (jusqu'à
600 oC dans des conditions de travail très
extrêmes), ces températures maximales descendent aussi très
rapidement en se déplaçant vers l'intérieur du
cylindre.
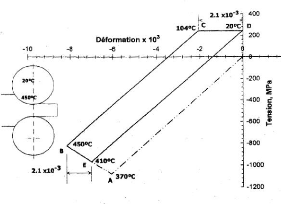
Figure I.3.7 Hystérésis
tesion-déformation au niveau de la surface du cylindre [10].
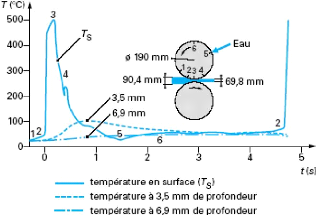
Figure I.3.8 Variation de la température
du cylindre durant les premières révolutions
actives [17].
Ces analyses nous indiquent que, inévitablement, au
cours de seulement quelques cycles de travail, se développe un
réseau de fissures thermiques superficielles, qui pourrait
s'accroître vers l'intérieur en vertu des mécanismes de
fatigue causée par l'existence des tensions
mécaniques.[8]
La température maximale atteinte sur la surface des
cylindres de travail des trains à bande laminée à chaud va
dépendre de la position de la caisse de laminage dans le train (voir
figure I.2.1). La variation de la température superficielle du cylindre
avec le temps durant son contact avec la bande chaude est illustrée sur
la figure (I.3.9). Le pic de température est atteint dans les
premières caisses finisseuses dans les quelles le contact bande/cylindre
est important et la vitesse de la bande est minime ; (sur ce point il est
à rappeler que la vitesse de la bande augmente avec la réduction
de son épaisseur). Alors que cette température se réduit
ostensiblement dans les dernières caisses finisseuses. Pour la
même raison, le pic thermique développé sur la surface des
cylindres de travail est élevé dans les caisses d'ébauche,
dans les quelles la température de la bande est maximale et sa vitesse
est minimale.

Figure I.3.9 Cycle thermique appliqué
sur la surface des cylindres dans les différentes caisses du train
à bandes laminées à chaud [8].
I.3.5.b TENSIONS DE CONTACT
Les tensions de laminage ou de travail, sont celles qui se
produisent en faisant passer la bande entre les cylindres de travail. Les
tensions de contact surgissent après compression du cylindre de travail
sur celui d'appui.
Dans l'objectif d'évaluer ces tensions de contact et
leurs distributions relatives, il a été utilisé la
théorie de Hertz. Les cylindres sont soumis à des tensions en
accord avec la figure (I.3.10). La zone de contact se déforme
élastiquement, en se transformant en une aire rectangulaire. La largeur,
b, de cette aire de contact et la valeur maximale de la pression de
compression, Pmax, sont données par les expressions
[11] :
E E
? 1 ?
b = 2. ( )
? 1
- ? ,
P
? 2
1 ? ? + ? 1
1 2
1 1
? ?? ? ? ??
2V L ?? R R
? ?
? ? ?
1 2 ? ?
|
1/ 2
|
|
1/ 2
Pmax = ( ) - 1
r 2 ? 1
_ ( ? ? R R
? 1
V
1 P ? ?
+ 1
1 2
I 1 1
?? ? ? ?
? ? L ??
1 2 ? ? ?
? ? E E
? ?
?
Où P' est la force par unité de
longueur qu'exerce un cylindre sur un autre, R1 et R2 les rayons des cylindres,
E1 et E2 leurs modules élastiques respectivement et v le
coefficient de Poisson.
En plus des tensions normales à l'aire de contact,
seront aussi engendrés des contraintes de cisaillement qui tendent
à cisailler le cylindre à travers ses sections rectilignes, et
qui atteignent une magnitude tant importante qu'ils provoquent la
plastification localisée du matériau.
La valeur maximale de la tension de cisaillement
apparaît dans la ligne qui unit les centres des deux cylindres et
orientée de 45o, prend des valeurs comprises entre
zéro, juste au point de contact, jusqu'un maximum donné à
une certaine distance au dessous de la surface déformée du
cylindre. En plus de celle-ci, existent autres tensions de cisaillement
parallèles aux axes X et Y [8].
Dans la figure (I.3.11), sont indiquées la magnitude
et la distribution des tensions normales, en plus des valeurs maximales et
points ou se produisent les tensions de cisaillement, sous des conditions
normales de laminage.
La tension effective de Von Misesa eff ,
que le cylindre doit être capable de supporter
durant le service, montre des valeurs maximales
légèrement inférieurs à 1 GPa, à une
profondeur de quelques millimètres (figure I.3.12).
La pression de contact entre le cylindre de travail et la
bande, suit une distribution hétérogène tous le long de la
longueur de contact en accord avec la théorie de Von Kermann qui a
développé la première équation
différentielle classique pour décrire la distribution depression
Pc tout le long de l'arc de contact l, (figure I.3.13) [8].
Le quotient entre la pression de contact (cylindre de
travail/bande) Pc et la limite élastique de la bande crYs
est montrée dans la figure (I.3.14), qui exprime aussi la grande
influence du coefficient de friction i sur ce paramètre.
Les tensions de laminage ont aussi une importance
spéciale dans la transition entre le cou et la table, qui est une zone
de grande concentration de tensions due au changement brusque du
diamètre, zone à partir de laquelle les cylindres peuvent
être rompu quand ils sont surchargés[8].
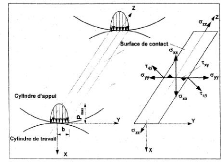
Figure I.3.10 Représentation des
tensions ce contact.
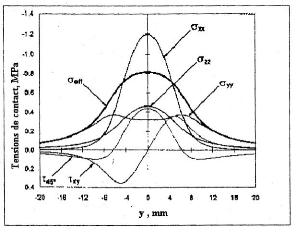
Figure 1.3.11 Tensions de contact cylindre de
travail/cylindre d'appui [11].
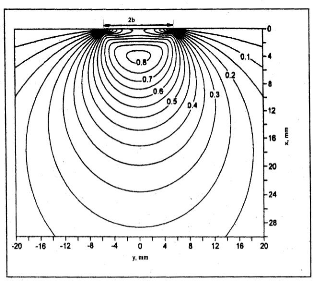
Figure 1.3.12 Contours de tension, montra les
variations de la tension eff(GPa) agissant au dessous de la
surface du cylindre de travail [11].
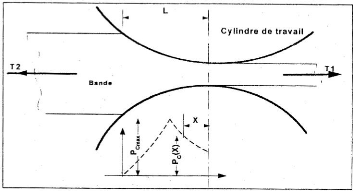
Figure 1.3.13 Contact cylindre de
travail/bande et répartition de la pression tout le long du cylindre
[8].
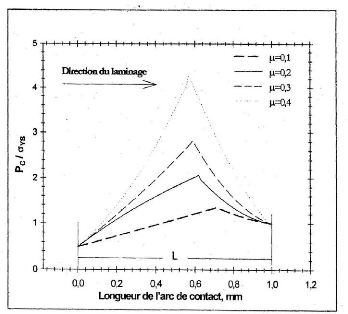
Figure 1.3.14 Distribution de la pression de
contact (cylindre/bande).
II.1 INTRODUCTION
Dans le domaine du laminage, parvenir à prédire
et à augmenter la durée de vie des cylindres de travail peut
permettre à l'entreprise de réaliser d'importantes
économies. Lorsqu'un cylindre est cassé ou trop usé, il
faut non seulement le changer, mais il faut aussi parfois changer son support.
En outre il faut arrêter la chaîne de production et mettre les
pièces au rebut.
Au cours du laminage, différents modes d'endommagement
peuvent entraîner un changement d'outillage. On distingue principalement
l'usure, la fatigue et la déformation plastique. Nous nous
intéresserons plus particulièrement ici au problème de
fatigue thermique.
II.2 CONTRAINTES ET FATIGUE THERMIQUE DES CYLINDRES
La figure II.1 présente un faciès typique de
faïençage, c'est-à-dire le fin réseau de
fissures induit par fatigue thermique qui se développe dans les
conditions de laminage sans glissement du métal sur le cylindre et
provoque, à terme, une dégradation de l'état de surface
des cylindres. Ce processus de fatigue thermique est induit par l'histoire
thermique de la couche extérieure du cylindre [17].
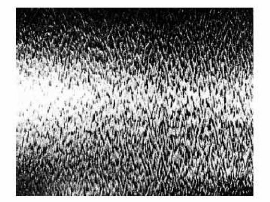
Figure II.1 Faïençage thermique
d'un cylindre de laminage à chaud [13].
II.2.1 CONTRAINTES THERMIQUES EN SURFACE DES CYLINDRES
Du fait des hétérogénéités
de la température induites par le contact et de leurs degrés de
liaison avec leur environnement, des contraintes élastiques voir
élastoplastiques vont se développer en surface des cylindres.
Considérons la surface d'un cylindre soumis à un chargement
thermique superficiel (figure II.2).
Pour des perturbations thermiques modérées, les
déformations induites sont élastiques et peuvent être
calculées par les équations de la
thermoélasticité [17] :
( 1 + v ) ( P
8 = a + 3 v +a · AT
) II. 1
E E
Oil ; E, a ,v , sont respectivement le
module élastique, le coefficient d'expansion linéaire et
le coefficient de Poisson, AT variation de
température et P représente la pression de contact.
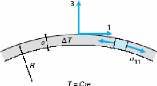
Figure II.2 Contrainte thermique dues à
une perturbation thermique superficielle [17].

La profondeur de pénétration thermique et de
l'ordre de 6 aAt 0 et, pour des temps de contact
brefs, petite devant les dimensions du cylindre. En première
approximation, le reste de la pièce frette donc la bande
perturbée thermiquement, lui imposant en tout point M des
déformations
8 11=8 22 = 0 : la bande perturbée
thermiquement ne subit qu'une déformation 8 33 et, la surface
étant libre, 8 33=0. On en déduit facilement que :
a EAT
II.2
a 11= a 22=
( 1-v)
( 1 + v)a AT
II.3
c ·33 (-v)
Les contraintes développées sont donc du signe
inverse de la perturbation thermique : compressives pour un
échauffement, de traction pour une refroidissement ; leur
intensité est proportionnelle au facteur qui caractérise la
réaction du matériau aux
hétérogénéités thermiques a E / ( 1
- v ) E17].
II.2.2 FATIGUE THERMIQUE DES CYLINDRES DE LAMINAGE A
CHAUD
Les contraintes de contact (contrainte normale) sont
typiquement de l'ordre de 0.1 GPa en laminage à chaud, et, comme nous
allons le voir, relativement faibles devant les contraintes
développées par les fluctuations thermiques superficielles. Ces
contraintes thermiques sont décrites sur la figure II.3 qui donne
l'évolution des contraintes d'un point de la surface d'un cylindre de
laminoir conventionnel effectuant des laminages à chaud dans les
conditions de la figure I.3.8 (Chapitre I).
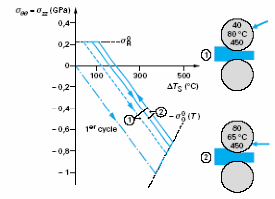
Figure II.3 Influence du mode de
refroidissement du cylindre de laminage à chaud sur le cycle de
contraintes E17].
Avec, 0
o R , 0
o 0 sont respectivement la contrainte de
rupture en traction du matériau du cylindre et la contrainte
d'écoulement plastique en compression du matériau du cylindre.
II.2.3 AUTRES PHENOMENES CONDITIONNANT LA FATIGUE THERMIQUE
La vitesse de faïençage thermique est la
conséquence d'interactions complexes entre divers
phénomènes. Leur description précise reste encore un
problème ouvert. Nous en évoquons ci-dessous deux aspects
importants.
> Sur le plan thermomécanique :
Le modèle précédent (figure II.2) est
une schématisation de la réalité. L'évaluation des
cycles de contrainte et de l'endommagement associé engendrés par
les variations de température nécessite la détermination
de la loi d'évolution, en sollicitation cyclique, des courbes
contraintes-déformation o (S ) des couches
superficielles du matériau à outil et la loi d'initiation et de
propagation des fissures [17].
> Sur le plan physico-chimique :
Des études ont montré que la vitesse de
fissuration thermique des matériaux peut fortement dépendre des
caractéristiques (épaisseur, porosité,
ductilité...) des couches d'oxydes qui se forment à leur surface
[17].
II.2.4 DUREE DE VIE EN FATIGUE
Lorsqu'un matériau est soumis à des
déformations cycliques on constate que les contraintes correspondantes
évoluent au cours du cycle. Lorsque la contrainte augmente au cours du
chargement cyclique, on parle de durcissement (ou consolidation) cyclique. Si
au contraire la contrainte diminue, on utilise le terme d'adoucissement (ou
déconsolidation) cyclique [19].
Pour les cylindres de travail des trains à bande
laminés à chaud, la durée de vie varie fortement en
fonction du niveau de l'amplitude contrainte appliqué.
II.2.5 RESISTANCE A LA FATIGUE THERMIQUE
Le facteur d'Eichelberg permet de faire une comparaison entre
les quatre matériaux employés dans la fabrication des cylindres
de travail. Le matériau qui possède un meilleur facteur
d'Eichelberg présente une meilleure résistance à la
fatigue thermique. Ce facteur est défini par:
E.cc
Où v : coefficient de Poisson, K :
conductivité thermique, a : coefficient d'expansion thermique,
E : module de Young et o u tension limite à
la traction à température ambiante[8].
II.3 ANALYSE NUMERIQUE DES CONTRAINTES THERMIQUES DANS
LES CYLINDRES DE TRAVAIL À CHAUD
II.3.1 INTRODUCTION
La fatigue thermique des cylindres de travail des trains
à bandes laminées à chaud est causée principalement
par les contraintes thermiques cycliquement répétées.
Dans ce travail nous analysons numériquement par la
méthode des éléments finis le niveau, l'intensité
et la distribution des contraintes thermiques dans les cylindres de travail en
fonction de leurs propriétés physique et mécanique.
II.3.2 MODELISATION PAR LA METHODE DES ELEMENTS FINIS
D'UN CYLINDRE DE TRAVAIL PAR LE LOGICIEL ANSYS10.0
Notre étude porte sur l'évaluation des
contraintes thermiques dans les cylindres de travail des trains laminés
à chaud. Pour ce faire, nous avons utilisé le logiciel «
Ansys10.0 ». Ce dernier, utilisant la méthode des
éléments finis, a été conçu par le groupe
« ANSYS.inc » à Canonsburg en Pennsylvanie.
? A propos d'ANSYS10.0
ANSYS10.0, la libération la plus récente du
soumissionnaire très spécialisé et comme auparavant
indépendant du logiciel de simulation ANSYS inc avec le siège
dans les Pittsburg/PA, est depuis juillet 2005 sur le marché.
ANSYS se consacre à l'élaboration de solutions
ouvertes et souples qui permettent aux utilisateurs d'analyser directement sur
ordinateur les modèles conçus, ce qui leur procure une
plate-forme commune pour assurer un développement rapide, efficace et
économique des produits, depuis l'étape de la conception
jusqu'à la vérification finale et à la
validation[12].
II.3.3 METHODE DES ELEMENTS FINIS ·
GENERALITES
Depuis ses premières applications en calcul des
structures vers le début des années 70, la méthode des
éléments finis est devenue un moyen incontournable pour la
résolution de problèmes très variés de la
mécanique des solides et des fluides, de transfert thermique,
d'électromagnétisme et de bien d'autres domaines
d'applications.
Dans la méthode des éléments finis les
calculs s'appuient sur un maillage (discrétisation spatiale) associe
à la géométrie du domaine dans lequel on désire
effectuer la simulation. Leur précision dépend de la taille des
éléments (le pas de discrétisation spatiale). Plus ces
derniers sont petits plus les calculs sont précis et plus la simulation
est fiable. En pratique, il n'est pas possible de raffiner uniformément
la taille des éléments autant que nécessaire, pour des
raisons évidentes de temps et de coûts de calculs. Toutefois, il
est possible de raffiner le maillage dans les zones critiques du cylindre de
laminage.
Dans notre étude, les zones les plus sensibles et qui
demandent par conséquent un raffinage sont la zone de contact bande
laminé/cylindre et l'interface (noyau/couche extérieure du
cylindre).
· REALISATION DU MODELE
Le logiciel ANSYS10.0 permet de modéliser les
structures à l'aide de différents types d'éléments
bidimensionnels et tridimensionnels (quadratique à quatre noeuds,
à huit noeuds, triangulaire à trois et à six noeuds)
[12].
La modélisation porte sur une section transversale d'un
cylindre de travail, où sont montré la couche extérieure,
l'interface et le noyau (voir figures II.4 et II.5).
· CHOIX DU MAILLAGE
Une étape cruciale dans la simulation numérique
de tout problème physique par la méthode des
éléments finis est la génération d'un maillage
associe à la géométrie du domaine considéré.
La construction du maillage est un processus d'autant plus délicat quant
il s'agit de simuler un problème industriel dans lequel les
géométries sont très arbitraires et très souvent
complexes. D'après le principe de la méthode des
éléments finis, la qualité de la solution dépend
fortement de celle du maillage. Par conséquent, dans un problème
donné, le maillage construit par l'une ou l'autre des techniques doit
satisfaire un ensemble de contraintes liées à la qualité
requise de la solution, on parle ainsi d'adaptation de maillage.
Pour notre cas, la construction du maillage a
été réalisée automatiquement par le logiciel de
calcul. A noter que les zones critiques (interface par exemple) ont
été raffinées manuellement (figures II.4 et II.5).
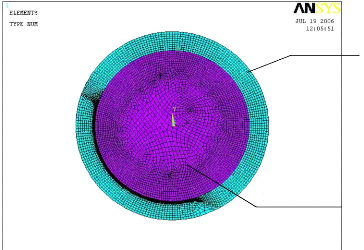
Noyau.
Matériau utilisé.
Figure II.4 Maillage.
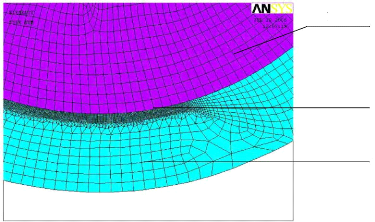
Noyau.
Interface.
Matériau utilisé.
Figure II.5 Maillage au niveau de
l'interface.
· CHOIX DE L'ELEMENT FINI
Le choix de l'élément fini est primordial
puisqu'il va conditionner tout le calcul numérique réalisé
par la machine. Il en existe différents types, chacun devant être
utilisé dans les conditions prévues à leur effet par le
code de calcul [13].
Dans le cas d'une étude thermique 2D, les
éléments (figure II.6) susceptibles d'être utilisés
sont :
+ PLANE 55 + PLANE 77
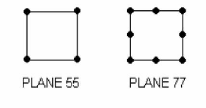
Figure II.6 Éléments de
thermique en 2D.
Pour le calcul des contraintes thermique en 2D, les
éléments (figure II.7) qui peuvent être utilisés
sont :
+ PLANE 42
+ PLANE82
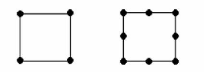
PLANE 42 PLANE 82
Figure II.7 Éléments de structure
en 2D.
L'élément PLANE 55 est un élément
quadrilatère à 4 noeuds et possèdent quatre degrés
de liberté (ddl), soit une température à chaque noeud. Le
code de calcul utilise une interpolation linéaire entre chaque noeud
pour calculer le ddl. Il est approprié pour des géométries
simples (ce qui est notre cas) et il ne nécessite pas un long temps de
calcul.
Le second est aussi un élément
quadrilatère mais à 8 noeuds. Cet élément offre une
meilleure précision des résultats car il effectue une
interpolation quadratique entre deux noeuds de la même ligne.
L'inconvénient à utiliser cet élément est le temps
de calcul qu'il va nécessiter, temps de calcul bien plus élever
que son homologue. Il serait peut-être judicieux de l'utiliser dans le
cas d'une prédiction ou une vérification [13].
Nous avons donc choisis pour mener cette étude 2D :
l'élément PLANE 55, car il permet un bon compromis entre la
précision et le temps de calcul.
II.3.4 CALCUL THERMOMECANIQUE DES CONTRAINTES
Il existe deux types de calcul thermomécanique
découplé, selon l'introduction des données
réalisée. On peut effectuer un calcul thermique complet et
déterminer des cartes de températures dans la structure. Le
calcul mécanique va alors relire à l'instant demandé la
carte de température, affecte à chaque noeud du maillage cette
donnée est récupérée en automatique. C'est le cas
de nôtre étude en 2D. Le logiciel de calcul converti
automatiquement l'élément de calcul thermique PLANE 55 en
élément de calcul de structures PLANE 42.
L'autre possibilité consiste à donner au
programme la température estimée en quelques noeuds et il
interpole (conduction pure, aucun échange par les parois) la
température en tout point. Les non linéarités dues
à des coefficients thermiques dépendant de la température,
et de l'influence des conditions aux limites, ne sont pas prises en compte.
A partir de là, le programme détermine la
température moyenne dans l'élément et modifie en
conséquence le module d'élasticité (si cette variation est
prise en compte). Connaissant la température de l'état
thermiquement non contrait (qui est une donnée), le programme calcule le
saut de température dans l'élément et génère
les charges nodales équivalentes. Le coefficient de dilatation thermique
ne doit pas être oublié dans les données mécaniques,
faute de quoi les charges thermiques sont identiquement nulles.
II.4 PROPRIETES DES MATERIAUX
Actuellement, il existe plusieurs types de cylindres de travail
dans le monde, dont le matériau de fabrication reste un secret pour des
raisons de concurrence.
Nous avons contacté l'entreprise espagnole Fundicion
Nodular spécialisée dans la fabrication des cylindres de
laminage, qui nous a transmet certaines données de base concernant
quatre nuances utilisées dans la fabrication des cylindres. Ces
cylindres sont tous obtenus par un processus de double coulée
(centrifugation verticale) qui permet d'obtenir des cylindres
bi-matériaux dont le noyau est en fonte nodulaire et la couche
superficielle est fabriquée par un des matériaux suivants:
1' Acier rapide ;
1' Acier à haute teneur en Chrome; 1' Fonte riche en
Chrome;
1' Ni-hard ;
II.4.1 PROPRIETES PHYSIQUES
Il s'agit essentiellement du module
d'élasticité à la température ambiante, du
coefficient de dilatation entre 20 et 100 °C, 20 et 400 °C ou 20 et
600 °C selon les conditions d'emploi et de la conductivité
thermique à la température ambiante. Le tableau II.1 illustre ces
propriétés physiques.
Matériaux
|
K [w/mk] entre
|
a [10-6 k-1]
|
E [GPa] entre
|
V
|
|
20 et 500 °C.
|
entre 20 et 600
|
20 et 500 °C.
|
|
|
|
°C.
|
|
|
Fonte nodulaire
|
36
|
13.5
|
170
|
0.275
|
Acier rapide (HSS)
|
20.2
|
12.2
|
226.7
|
0.3
|
|
Acier à haute teneur en Chrome
|
En fonction de (T) voir le tableau (II.2).
|
17.5
|
200
|
0.29
|
Fonte riche en
|
17
|
12.6
|
215
|
0.27
|
Chrome
|
|
|
|
|
Ni-hard
|
18
|
13.3
|
160
|
0.27
|
|
Tableau II.1 Propriétés physique
des matériaux de fabrication des cylindres de travail.
Température
|
|
|
|
|
|
en °C.
|
20
|
200
|
400
|
500
|
600
|
K (w/m k)
|
13,8
|
16,3
|
18,4
|
19,2
|
20
|
|
Tableau II.2 Variation de la
conductivité thermique de l'acier riche en Chrome en fonction de la
température.
II.4.2 PROPRIETES MECANIQUES
Les limites élastiques en traction et en compression
sont fonction de la température. L'entreprise Fundicion Nodular nous
nous a envoyé ces limites élastiques dans la plage de
température de travail des cylindres (entre 30 et 500 °C). Les
valeurs des limites élastiques des matériaux de fabrication des
cylindres de travail sont données sur le tableau III.3.
Matériau de cylindre.
|
Résistance à la traction. [MPa]
|
Résistance à la compression. [MPa]
|
|
500 °C
|
30 °C
|
500 °C
|
Acier rapide
|
940
|
748
|
3600
|
2546
|
Acier riche en Chrome
|
900
|
670
|
3500
|
2500
|
Fonte riche en Chrome
|
800
|
600
|
850
|
600
|
Ni-hard
|
600
|
400
|
700
|
500
|
|
Tableau II.3 Propriétés
mécaniques des matériaux de fabrication des cylindres
de laminage.
III.1 INTRODUCTION
Les travaux sur la fatigue thermique et le
faïençage des cylindres de travail des trains à bande
laminée à chaud occupent une place importante dans les projets
d'amélioration des performances de laminage car ces endommagements
limitent la durée de vie des outils et minimisent la qualité du
produit laminé. Le mécanisme d'endommagement par fatigue
thermique provient principalement des contraintes d'origine thermique
alternées en compression et en traction à la surface active des
cylindres.
Dans notre travail, nous analysons numériquement par
la méthode des éléments finis le niveau,
l'intensité et la distribution des contraintes thermique dans une coupe
transversale d'un cylindre de laminage à chaud.
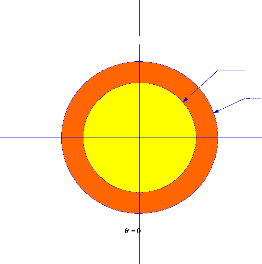
NOYAU
d=320mm
D=400mm
90
ENVELOPPE
180
Pour résoudre ce problème nous avons
procédé deux étapes. Dans un premier temps, le
problème thermique a été résolu en 2D (x, y)
à fin de déterminer des cartes de températures dans la
structure. Puis le calcul des contraintes thermiques est pris en compte dans
une seconde étape. La figure III.1 représente la
géométrie et les dimensions du domaine a étudie.
III.2 MODELESATION THERMIQUE PAR LA METHODE DES
ELEMENTS FINIS
Notre objectif est le calcul numérique du champ de
température T(x, y). Pour ce faire, nous appliquons la méthode
des éléments finis.
La méthode des éléments finis est une
résolution approchée de la reformulation intégrale exacte
de l'équation d'origine, c'est pourquoi elle est
considérée comme faisant des méthodes d'approximation de
solution. Cette méthode consiste à décrire le champ de
température par des fonctions d'interpolation sur chaque
élément.
III.2.1 DISTRIBUTION DE LA TEMPERATURE DANS LES
CYLINDRES DE TRAVAIL
Les figures III.2, III.3, III.4 et III.5 représentent
les cartes de températures dans une coupe transversale d'un cylindre de
travail dont la couche supérieure est réalisée
respectivement par la fonte riche en Chrome, le Ni hard, l'acier rapide et
l'acier riche en Chrome.
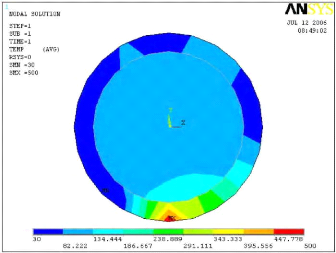
Figure III.2 Distribution de la
température dans un cylindre de travail fonte nodulaire/ fonte riche
en chrome.
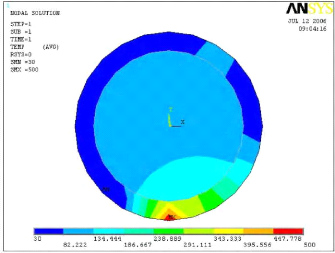
Figure III.3 Distribution de la
température dans un cylindre de travail fonte nodulaire/Ni hard.
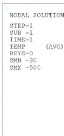
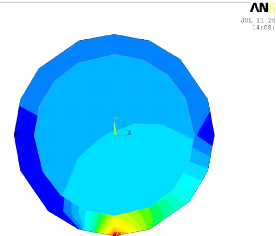

Figure III.4 Distribution de la
température dans un cylindre de travail fonte nodulaire/acier
rapide.
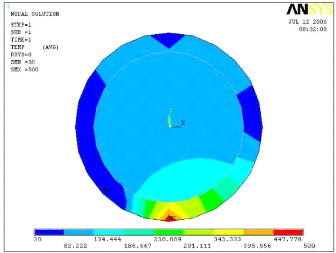
Figure III.5 Distribution de la
température dans un cylindre de travail fonte nodulaire/acier haute
teneur en Chrome.
On remarque que la température atteint une valeur
maximale au niveau du contact entre le cylindre et la bande chaude (pour un
angle 0 =0, voir figure III.1). Pour les quatre nuances
utilisées, cette température est de 500 °C. Au niveau de
contact entre le fluide de refroidissement et le cylindre de travail, la
température présente une valeur minimale proche de 30 °C, et
cela pour les quatre matériaux utilisés( pour 0 =40 ).
Le transfert thermique par conduction provoque un gradient thermique important
sur la partie superficielle (présence des deux valeurs extrêmes de
température). La température du noyau reste presque constante
estimée aux alentours de 120°C.
III.2.2 EVALUATION DE LA TEMPERATURE SUR LA PARTIE
SUPERFICIELLE DU CYLINDRE DE TRAVAIL
Les figure III.6, III.7, III.8 et III.9 représentent
le chargement thermique de la partie superficielle du cylindre. La
température est estimée en fonction du périmètre
extérieur (DIST).
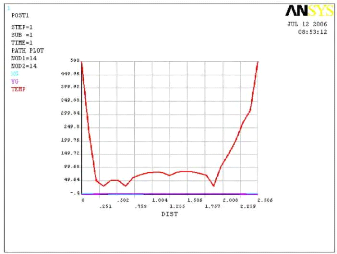
Figure III.6 Variation de la
température sur la partie superficielle d'un cylindre de travail :
fonte nodulaire/fonte haute teneur en Chrome.
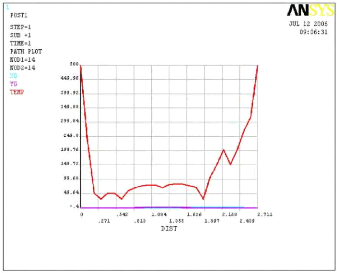
Figure III.7 Variation de la
température sur la partie superficielle (de travail) d'un cylindre de
travail: fonte nodulaire/Ni-hard.
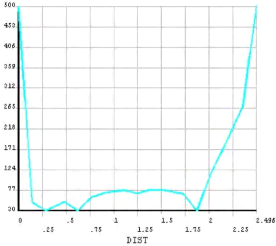
Figure III.8 Variation de la
température sur la partie superficielle d'un cylindre de
travail: fonte nodulaire/acier rapide.
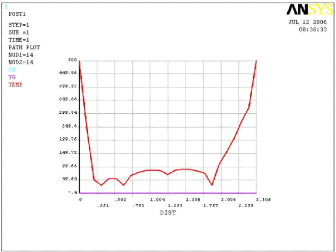
Figure III.9 Variation de la
température sur la partie superficielle d'un cylindre de
travail: fonte nodulaire/acier haute teneur en Chrome.
On remarque qu'il y a une analogie entre les quatre courbes.
La température maximale au niveau du contact entre la bande chaude et le
cylindre de travail est de 500 °C. Au moment du refroidissement du
cylindre, et pour les matériaux du cylindre utilisés tels que la
fonte haute teneur en Chrome, le Ni-hard et l'acier riche en chrome, la
température décroît pour atteindre une valeur minimale de
30 °C et elle se stabilise aux alentours de 50 °C. Pour l'acier
rapide, la température se stabilise aux alentours de 40 °C. Au
niveau du contact entre le cylindre de travail et le cylindre d'appui, la
température est de 100°C. Cette augmentation est due à la
chaleur générée par le frottement entre les deux
cylindres. La température décroît de nouveau et elle se
stabilise pour atteindre des valeurs comprises entre 35 °C et 48 °C
selon le type de matériau utilisé. Cette stabilité de
température est due essentiellement au fluide de lubrification qui
maintien la température presque constante (30°<0 <
150° et 200° <0 < 320° ).Un accroissement de la
température est observé au voisinage de la zone de contact entre
le cylindre de travail et la bande chaude (c'est-à-dire pour des valeurs
de 0 comprises entre 320° et 360°) pour atteindre de nouveau
les 500 °C.
III.2.3 GRADIENT THERMIQUE SUIVANT LE RAYON DU CYLINDRE
DE TRAVAIL
La température varie également suivant le
rayon, cette variation est moins importante par rapport au gradient thermique
appliqué sur la partie superficielle. Les figures III.10, III.11, III.12
et III.13 représentent la variation de température suivant le
rayon du cylindre. Cette fois-ci, DIST représente la distance suivant
l'axe y (perpendiculaire à la bande chaude).
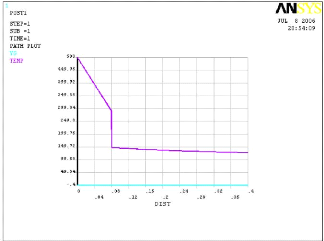
Interface.
Figure III.10 Gradient thermique suivant le
rayon d'un cylindre de travail : fonte nodulaire/fonte haute teneure en
Chrome.
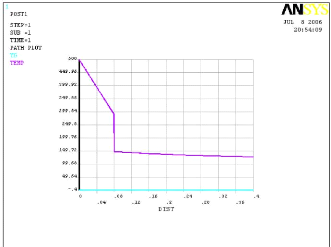
Interface.
Figure III.11 Gradient thermique suivant le
rayon d'un cylindre de travail : fonte nodulaire/Ni-hard.
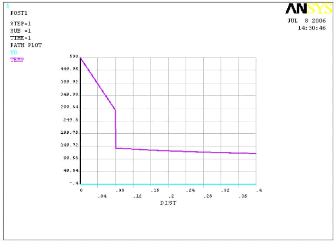
Interface.
Figure III.12 Gradient thermique suivant le
rayon dans un cylindre de travail: fonte nodulaire/acier rapide.
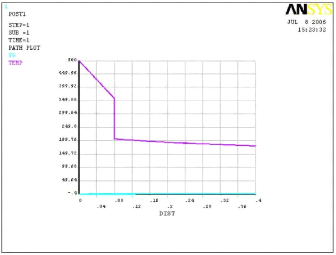
Interface.
Figure III.13 Gradient thermique suivant le
rayon d'un cylindre de travail : fonte nodulaire/acier riche en Chrome.
La température extérieure au niveau du contact
cylindre /bande chaude (pour y=-0.4m) est de 500 °C pour les quatre
cylindres. Cette température décroît linéairement
jusqu'au voisinage de l'interface ou sa valeur sera proche de 300 °C pour
la fonte haute teneur en Chrome, la Ni-hard et l'acier rapide. Ces trois
matériaux ont des valeurs de conductivité thermique très
proches. Par contre, l'acier haute teneur en Chrome présente une chute
de température jusqu à une valeur de 250 °C.
L'interface présente une importante résistance
thermique due non seulement à la différence entre la
conductivité thermique de l'enveloppe et celle du noyau mai aussi aux
conditions d'élaboration de ce type de cylindres appelés
cylindres composés. Cette résistance thermique provoque une chute
brusque de température où elle passe pour les trois premiers
matériaux d'une valeur de 300 °C pour un point de l'interface
appartenant à l'enveloppe, à une température de 150
°C pour un point de l'interface appartenant au noyau. L'acier haute teneur
en Chrome présente une chute de température d'une valeur de
250°C vers une valeur de 200 °C.
La température se stabilise au niveau du noyau autour
de 130 °C pour les trois premiers matériaux (fonte haute teneur en
Chrome, Ni-hard et l'acier rapide) et autour de 170 °C pour l'acier riche
en Chrome.
III.3 MODELESATION THERMOMECANIQUE PAR LA METHODE DES
ELEMENTS FINIS
L'objectif de notre étude est la détermination par
l'analyse numérique du champ de contraintes thermiques, en utilisant la
méthode des éléments finis.
Le calcul des contraintes thermiques, défini comme
étant problème structural, est basée sur les
résultats du champ de température déterminé
ultérieurement dans le problème thermique.
III.3.1 CYLINDRE DE TRAVAIL: FONTE NODULAIRE/FONTE RICHE
EN CHROME
Les résultats ainsi obtenus sont
représentés sur la figure III.14. Cette figure montre la
répartition et le niveau des contraintes thermiques dans une coupe
transversale d'un cylindre de travail en fonte nodulaire/fonte riche en
Chrome.
La figure III.14.a montre la répartition des
contraintes thermiques suivant l'axe x (cr xx). Nous remarquons que la
partie superficielle du cylindre est sollicitée par des contraintes de
traction et de compression. Le terme MIN au niveau du contact entre le cylindre
et la bande chaude (pour 0 =0) représente la valeur maximal du
contrainte de compression (-139 MPa). Le terme MAX se trouve également
sur cette partie superficielle du cylindre, proche de la zone de contact
bande/cylindre, représente la contrainte maximale en traction (86
MPa).
La figure III.14.b représente la distribution des
contraintes thermiques suivant l'axe y (cr yy). On remarque
également que les contraintes thermiques ont des valeurs extrêmes
sur la partie superficielle du cylindre, plus précisément, au
niveau de la zone de contact bande/cylindre.
La figure III.14.c montre le niveau des contraintes
thermiques de cisaillement suivant le plan xy (r xy), les
contraintes les plus importantes sont localisées au niveau du bord de
l'interface.
La figure III.14.d donne un aperçu global de
l'état des contraintes de traction et de compression dans le
cylindre.
On remarque qu'il existe deux zones critiques dans le cylindre
:
- La couche superficielle du cylindre en contact avec la bande
laminée, dont les contraintes thermiques présentent des valeurs
importantes.
- L'interface qui présentes des contraintes thermiques
relativement faibles par rapport à la couche superficielle.
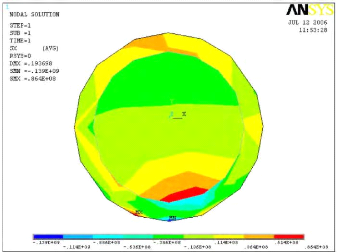
a) Evaluation des contraintes thermiques
normaleso xx
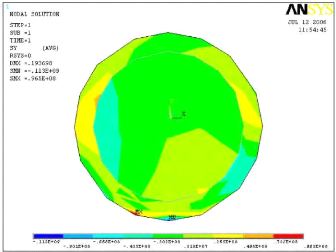
b) Evaluation des contraintes thermiques
normales o yy
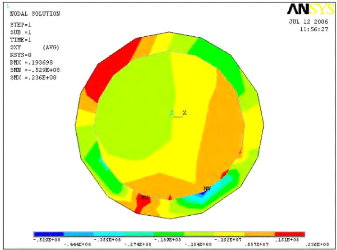
c) Evaluation des contraintes thermiques de
cisaillement? xy
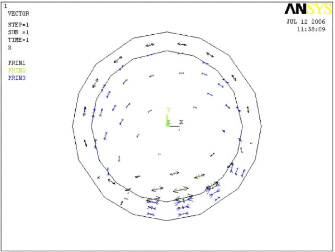
d) Etat des contraintes
thermiques Figure III.14 Contour des contraintes
thermiques.
Pour mieux illustrer la répartition des contraintes
représentées sur la figure III.14, nous
avons étudie la distribution des contraintes thermiques
o xx, yy et ? xy en fonction du périmètre du
cylindre.
La figure III.15 représente la distribution des
contraintes thermiques o xx, yy et ? xy sur la partie
superficielle du cylindre de travail.
La figure III.16 représente la distribution des
contraintes thermiques o xx, yy et ? xy au voisinage de
l'interface appartenant à l'enveloppe.
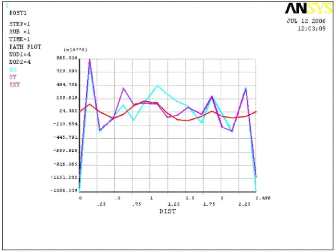
Figure III.15 Distribution des contraintes
thermiques sur la partie superficielle.
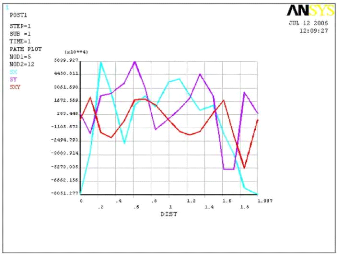
Figure III.16 Distribution des contraintes
thermiques au voisinage de l'interface.
Dans les deux graphes, SX, SY et SXY représentent
respectivement les contraintes normales o · xx,
o · yy et les contraintes de cisaillement ?
xy.
A partire de la figure III.15, les contraintes de cisaillement
xy sont relativement faibles
comparativement aux contraintes normales o ·
xx et o · yy , et se stabilisent
autour de 2.5MPa. L'évolution des contraintes normales 0
xx et 0 yy sur la surface extérieure
du cylindre est quasi-identique. Elle s'effectue en trois temps. Initialement,
les contraintes normales croient de façon linéaire dans la zone
de contact où 0 varie d'un ange de 0° à 36°.
Au cours de cette période, et au moment du contact, les contraintes
0 xx et 0 yy sont des contraintes de
compression et se transforment en contraintes de traction. Les contraintes
normales en compression à 0 =0 présentent un maximum (
o xx = -138.86 MPa et 0 yy = -115.12 MPa ) . Leurs valeurs
maximales en traction sont observés à 0 =36°( o
xx = 96.5 MPa et 0 yy = 80 MPa). Au-delà de cette zone,
nous remarquons une stabilité des valeurs de ces contraintes
jusqu'à 0 =324°( zone de refroidissement), à partir
de laquelle; les contraintes diminuent pour atteindre de nouveau les valeurs
précédemment trouvés, c'est-à-dire o xx =
-138.86 MPa et 0 yy = -115.12 MPa .
A partir des valeurs de contraintes trouvés ci-dessus,
nous concluons que les contraintes normales o · xx
présentent un grand risque de dégradation par fatigue thermique
de la surface extérieure du cylindre. Cette fatigue favorise
l'apparition de microfissures sur la surface du cylindre ce qui affectera
l'état de surface des produits laminés.
La figure III.16 montre l'évolution des contraintes au
niveau de l'interface (enveloppe/noyau) en fonction du
périmètre de l'interface. Les contraintes normales
o · xx sont beaucoup plus importantes que les contraintes
o · yy et les contraintes de cisaillement
? xy. L'évolution des ces contraintes
s'effectue aussi en trois temps. A O=0, les contraintes
o · xx atteignent une valeur maximal en compression
de-80.51 MPa, pour
atteindre la valeur en traction de 58.39 MPa pour
0=40° . La deuxième période de temps,
où U varie entre 40° et 280°, les
contraintes o xx varient cycliquement entre -25 MPa et
38 MPa. Dans la troisième période de temps, les contraintes
o xx diminuent linéairement à
partir d'une valeur de 15 MPa (0=278°) pour
atteindre de nouveau la valeur de -80MPa.
A partir des résultats trouvés ci-dessus, nous
pouvons conclure que les contraintes thermiques au niveau de la partie
superficielle du cylindre sont plus élevées que celles de
l'interface. Cette différence est due au chargement thermique
appliqué représenté par la figure III.6.
Dans la figure III.17, nous avons aussi déterminé
la variation de ces contraintes thermiques tous le long du rayon du cylindre,
perpendiculairement au laminage.
On constate que les contraintes thermiques au niveau de la
surface de travail sont plus importantes que celles proche de l'interface. La
partie intérieure du cylindre (noyau) présente des contraintes
plus au moins faible. Ceci est du à la stabilité de la
température dans cette zone.
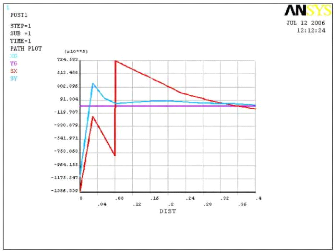
Interface.
Figure III.17 Evolution des contraintes
thermiques en fonction du rayon du cylindre de travail.
III.3.2 CYLINDRE DE TRAVAIL : FONTE NODULAIRE/NI-HARD
Les répartitions et les niveaux des contraintes normales
et de cisaillement dans une coupe transversale d'un cylindre de travail sont
indiquées sur la figure III.18-a, b, c et d.
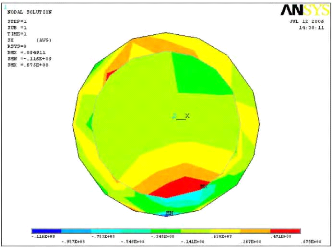
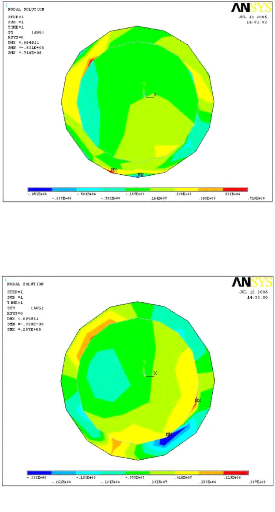
b) Evaluation des contraintes thermiques normaleso
yy
d) Evaluation des contraintes thermiques de cisaillement?
xy
a) Evaluation des contraintes thermiques
normaleso xx
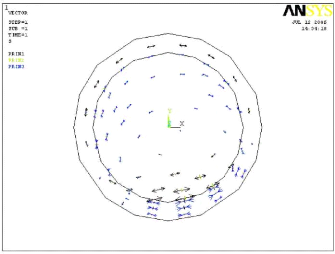
d) État des contraintes thermiques
(traction/compression). Figure III.18 Contour des
contraintes thermiques.
Les contraintes normales o xx
présentent une valeur maximale au niveau de l'interface et une valeur
minimale au niveau de la surface de travail (figure III.18.a) ; alors que les
contraintes normales suivant l'axe (y) o yy
présentent des valeurs extrêmes (max/min) sur la partie active du
cylindre de travail (figure III.18.b).
Les contraintes de cisaillement r xy ont des
valeurs critiques au niveau de l'interface (voir la figure III.18.c).
Pour une meilleure comparaison, nous ne tracerons que
l'évolution des contraintes thermiques en fonction du
périmètre du cylindre à l'interface et à la surface
extérieure, où ces contraintes sont maximales.
La figure III.19 montre la variation des contraintes thermiques
sur la surface extérieure.
La figure III.20 illustre la variation des contraintes thermiques
au voisinage de l'interface en fonction du périmètre.
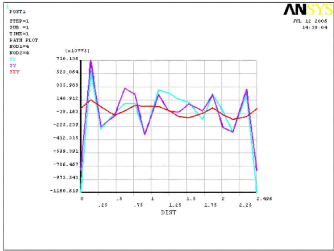
Figure III.19 Distribution des contraintes
thermiques en fonction du périmètre du cylindre.
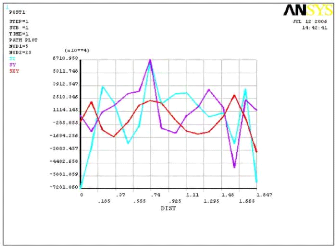
Figure III.20 Distribution des contraintes
thermiques en fonction du périmètre de l'interface.
A partir de la figure III.19, Les valeurs des contraintes de
cisaillement T xy sont faibles comparativement aux contraintes
normales.
Les contraintes de compression maximales sont atteintes au
moment du contact cylindre/bande pour 0 =0°( a
xx= -116.06MPa et o · yy =-90MPa),
alors que les valeurs des contraintes de traction maximales(cr
xx= 65MPa et o · yy =-71.013MPa)
sont atteintes quand 0 =25°. Au cours de la seconde
période, c'est-à-dire pour 25°< 0 < 340°
les contraintes normales varient entre -30MPa et 33.5 MPa. Au-delà de
340°, les contraintes diminuent pour atteindre de nouveau les valeurs
a xx= -116.06MPa et o · yy =-90MPa.
A l'interface, les contraintes normales suivant l'axe (x)
atteignent un minimum à 0 =0°( a xx= -72.81MPa)
et un maximum à 0 =144°( a
xx=67.1MPa).
Pour mieux comprendre l'évolution des contraintes au
niveau d'un cylindre de travail en Ni-hard, nous avons tracé la
variation des contraintes thermiques normales o xx, yy et de
cisaillement T xy en fonction du rayon (direction perpendiculaire au
laminage) (figure III.21).
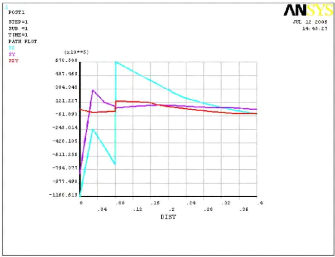
Interface
Figure III.21 Variation des contraintes
thermiques en fonction du rayon d'un cylindre de travail en Ni-hard.
On remarque que les contraintes les plus importantes sont les
contraintes normales. Le maximum des contraintes thermiques normales de
traction est atteint au niveau de l'interface (67 MPa); alors que le maximum
des contraintes thermiques normales de compression est obtenu cette fois ci au
niveau de la surface active du cylindre (-116.061 MPa). Les contraintes
thermiques au niveau du noyau sont presque nulles.
III.3.3 CYLINDRE DE TRAVAIL : FONTE NODULAIRE/ACIER
RAPIDE
Afin d'améliorer les performances des laminoirs, une
des solutions préconisées est l'utilisation de cylindres en acier
rapide (HSS). Se sont des cylindres de travail en bimatériaux, le noyau
est réalisé par la fonte nodulaire et la partie active en acier
rapide. Ce type de cylindres offre un meilleur module de Young et une meilleure
résistance à l'usure et des rendements hors incidents plus
importants que les cylindres classiques en fonte à haute teneur en
chrome.
La distribution des contraintes thermiques normales et de
cisaillement sur une coupe transversale d'un cylindre de travail dont la partie
active est en acier rapide, est montrée dans les figures III.22 (a,b,c
et d).
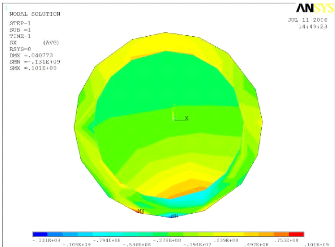
a) Evaluation des contraintes thermiques
normales o xx.
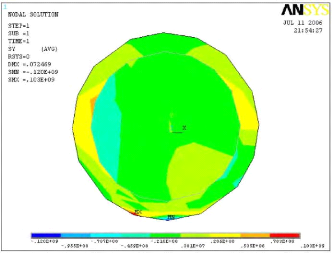
.b) Evaluation des contraintes thermiques
normales a yy.
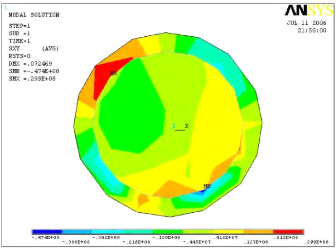
c) Evaluation des contraintes thermiques de
cisaillementT xy.
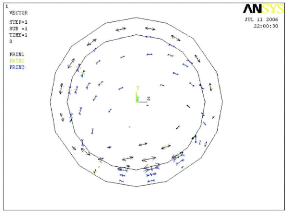
d) État des contraintes thermiques
(traction/compression). Figure III 22 Contour des contraintes
thermiques.
Pour les cylindres en acier rapide, les valeurs maximales des
contraintes thermiques normales sont situées sur la superficie du
cylindre alors que les contraintes thermiques de cisaillement sont maximales au
niveau de l'interface.
Les figures III.23 et III.24 analysent les contraintes thermiques
au niveau des zones critiques citées précédemment est.
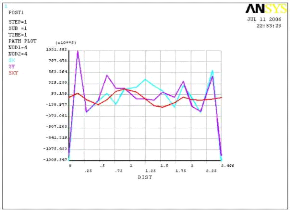
Figure III.23 Variation des contraintes
thermiques normales et de cisaillement sur la partie superficielle en
fonction du périmètre.
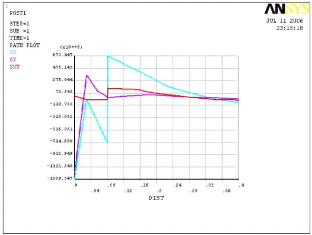
Interface.
La figure III.23 montre que les contraintes de cisaillement
sont relativement faible para rapport aux contraintes normales, et varient
entre -13 MPa +15 MPa. On constate par ailleurs, que les variations des
contraintes a xx et a yy en fonction du
périmètre du cylindre sont presque identiques.
Les contraintes thermiques maximales de compression o xx
= -130MPa et 0 yy = -125MPa, sont obtenues au niveau du contact
cylindre/bande.
Les valeurs maximales des contraintes thermiques normales sont
celles par rapport à l'axe (x), obtenues respectivement au point de
contact cylindre /bande à 0 = 0° et à 0 = 20° (figure
III.24).
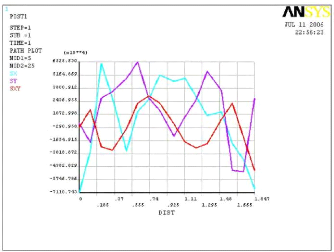
Figure III.24 Variation des contraintes
thermiques normales et de cisaillement au niveau de voisinage proche de
l'interface en fonction du périmètre.
Nous représentons aussi dans la figure III 25, la
variation des contraintes thermiques en fonction du rayon du cylindre.
Figure III.25 Variation des contraintes
thermiques en fonction du rayon du cylindre.
Dans le cas des cylindre en acier rapide, les contraintes
thermiques normales présentent un maximum au niveau de la superficie
extérieure (-130.9 MPa). Par contre les contraintes de traction sont
maximales au niveau de l'interface(67.34 MPa). Lorsqu'on s'éloigne de
l'interface vers le noyau, ces contraintes deviennent de plus en plus faibles
pour atteindre des valeurs proches de 11MPa. Les valeurs des contraintes de
cisaillement sont négligeables comparativement aux contraintes
thermiques normales.
III.3.4 CYLINDRE DE TRAVAIL: FONTE NODULAIRE/ACIER RICHE
EN CHROME
Nous avons analysé par la méthode des
éléments finis, la répartition des contraintes thermiques
et leurs intensité dans un cylindre de travail en fonte nodulaire/acier
à haute teneur en Chrome.
Les figures III.26 (a, b, c et d) montrent la répartition
des contraintes thermiques normales et tangentielles dans une coupe
transversale d'un cylindre de travail.
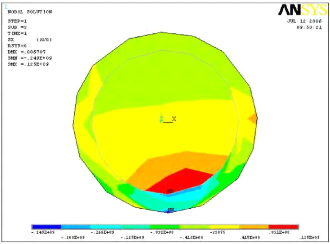
a) Variation des contraintes thermiques
normales o xx.
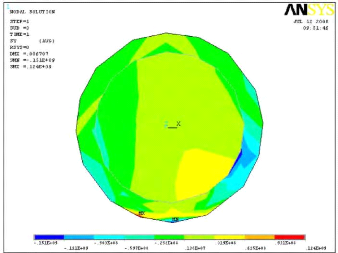
b) Variation des contraintes thermiques
normales o yy.
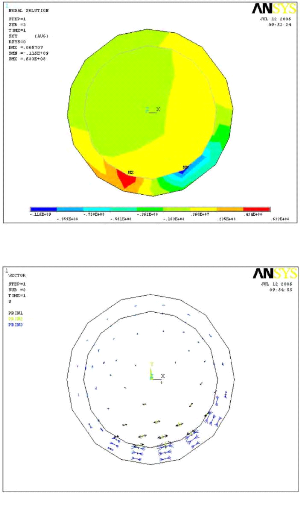
c) Variation des contraintes thermiques de
cisaillement T xy.
d) État des contraintes thermiques
(traction/compression).
Figure III.26 Contour des contraintes
thermiques.
Dans ce type de cylindre de travail, les contraintes
thermiques normales de compression ? xx sont maximales au niveau de la
superficie extérieure du cylindre et celles de traction
présentent un maximum au voisinage de l'interface en direction du
noyau.
Pour les contraintes thermiques normales suivant l'axe (y),
les valeurs maximales en traction et en compression se trouvent sur la partie
active du cylindre. Les valeurs extrêmes des contraintes thermiques de
cisaillement résident au niveau de la partie l'interface appartenant
à l'enveloppe.
La variation des contraintes thermiques sur la partie
superficielle du cylindre de travail est représentée par la
figure III.27.
L'évolution des contraintes thermiques au niveau de la
partie de l'interface la plus proche de l'enveloppe est donnée par la
figure III.28.
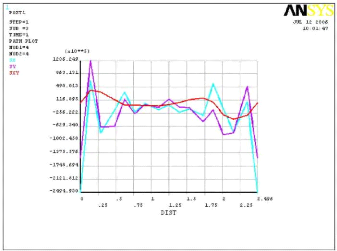
Figure III.27 Variation des contraintes
thermiques sur la partie superficielle.
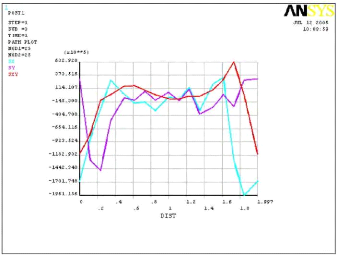
Figure III.28 Variation des contraintes thermiques normales et
tangentielles au voisinage de l'interface.
On peut conclure donc que c'est au niveau de la partie
superficielle que le risque de détérioration par fatigue
thermique est important.
La figure III.27 montre la variation des contraintes thermiques
normales et de compression en fonction du rayon du cylindre de travail.
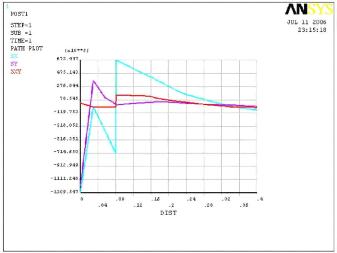
Figure III.29 Variation des contraintes
thermiques en fonction du rayon du cylindre.
D'après la figure III.29, les contraintes tangentielles
sont faibles par rapport aux contraintes normales. Les valeurs maximales des
contraintes thermiques obtenues sont celles dirigées suivant l'axe
(x).
III.4 RESULTATS
Pour les quatre types de matériaux utilisés pour
la fabrication des cylindres de laminage à chaud, les zones où
les contraintes thermiques normales présentent un extremum sont la
superficie extérieure et l'interface, alors que les contraintes
tangentielles sont négligeables.
Dans la plus part des cas étudiés, les contraintes
thermiques normales suivant l'axe (x) sont beaucoup plus importantes que les
contraintes par rapport à l'axe (y).
Nous en déduisant que le comportement en fatigue thermique
de ces cylindres dépend des contraintes (x).
Nous comparons dans ce qui suit, la répartition des
contraintes thermiques normales axx, dans les deux zones critiques du
cylindres, des quatre matériaux étudiés (figures III.30 et
III.31).
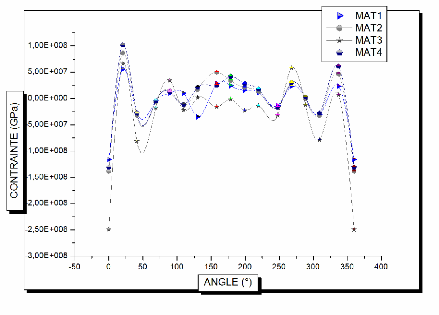
Figure III.30 Variation des contraintes
thermique sur la superficie des cylindres de travail.
A partir de la figure III.30 on peut conclure que les
contraintes thermiques suivant l'axe (x) des quatre matériaux
utilisés varient de la même manière en fonction du
périmètre du cylindre. Les cylindres en acier riche en chrome
génèrent des contraintes thermiques maximales de compression.
Pour les trois autres matériaux, on constate une légère
différence de la variation des contraintes thermiques.
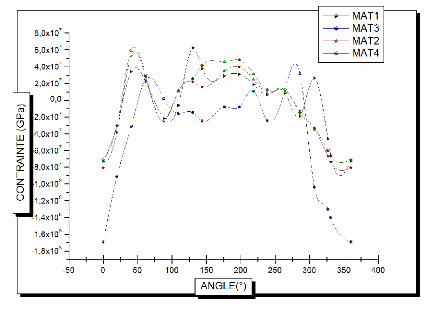
Figure III.31 Variation des contraintes
thermiques des quatre cylindres sur la partie voisine de l'interface.
Avec :
MAT 1 : Ni-hard.
MAT 2 : Fonte à haute teneur en Chrome.
MAT 3 : Acier riche en Chrome.
MAT 4 : Acier rapide.
Au niveau de l'interface, les contraintes thermiques induites
dans l'acier riche en chrome présentent des valeurs maximales en
compression, alors que les contraintes thermiques maximales de traction sont
générées par les cylindres en Ni-hard et ceux en acier
rapide.
Les valeurs extrêmes des contraintes thermiques sur la
partie proche de l'interface sont faibles devant celles mesurées sur la
partie superficielle.
Pour faire un choix entre les quatre nuances, nous avons
établi à partir du tableau III.1 les différentes
valeurs maximales des contraintes thermiques en traction et en compression
mesurées sur chaque matériau ainsi que leurs
valeurs normalisées par rapport aux contraintes maximales à la
rupture en traction. Nous avons défini aussi le facteur d'Eichelberg qui
déterminera les limites de fissurations des cylindres de laminage.
Matériaux
|
Valeurs maximales.
|
Facteur d'Eichelberg.
|
Traction
|
Compression
|
[MPa]
|
%
|
[MPa]
|
%
|
Acier rapide.
|
100
|
13.36
|
130
|
5
|
4.8 .106
|
Acier ++ Cr
|
123.6
|
18.44
|
249.4
|
10
|
1.87 .106
|
Fonte ++ Cr
|
96.5
|
16
|
138.86
|
23.14
|
2.74 .106
|
Ni-hard.
|
71.013
|
17.75
|
116.06
|
23.21
|
2.46 .106
|
Tableau III.1 Valeurs maximales des contraintes
thermiques.
CONCLUSION
CONCLUSIONS
A partir de l'analyse numérique des contraintes thermiques
dans les cylindres de laminage à chaud, nous pouvons conclure ce qui
suit:
· :. Pour les quatre matériaux utilisés ;
la concentration des contraintes thermiques est observée dans deux zones
du cylindre qui sont la superficie extérieure du cylindre et l'interface
entre le noyau et l'enveloppe.
· :. Les valeurs les plus critiques des contraintes
thermiques sont suivant l'axe x-x.
· :. ·Parmi les quatre matériaux
utilisés; seuls les cylindres en acier rapide engendrent de faibles
contraintes thermiques normales normalisées.
· :. En comparant les facteurs d'Eichelberg des quatre
matériaux utilisés, seuls les cylindres en acier rapide
présentent une meilleure résistance à la fissuration
thermique.
· :. En fin cette étude nous a permis de nous
familiariser avec l'outil de calcul numérique ANSYS.
|