TABLE OF CONTENT
DEDICATION
3
ACKNOWLEDGEMENTS
4
LIST OF FIGURES
5
LIST OF TABLES
6
LIST OF ABBREVIATIONS AND DEFINITIONS
7
ABSTRACT
8
RESUME
9
INTRODUCTION
10
CHAPTER I: PRESENTATION OF COMPANY
12
CHAPTER II: LITERATURE REVIEW
16
II.1- Scope of the literature review
16
II.2- Definitions regarding safety culture:
16
II.3- Reasons for assessing level of safety
culture:
19
II.4- Characteristics of identifiable good safety
culture in an organism:
20
II.5- Evolution of the concept of safety
culture
24
II.6- Indicators that are known to influence safety
culture
27
II.7- Some key attributes of a sound safety
culture:
30
II.8- Benefits of safety culture within
organisations
32
II.9- Health and safety policy:
33
II.10 Safety-culture-assessment / evaluation
34
CHAPTER III: SCIENTIFIC APPROACH
36
III.1- MATERIALS
36
III.2- METHODOLOGY
36
III.2.1- In situ observation
36
III.2.2- Interviews and
questionnaires:
36
CHAPTER IV: RESULTS, INTERPRETATIONS AND
RECOMMENDATIONS
38
IV.1- RESULTS AND INTERPRETATIONS
38
IV.1.1- Immediate
38
IV.1.2- Progressive
38
IV.2- RECOMMENDATIONS
42
CONCLUSION
44
REFERENCES
45
APPENDICES:
49
Appendix A - Codage questionnaire
d'évaluation niveau sécurité au sein des Laboratoires
BIOPHARMA S.A ayant pour objet d'améliorer la culture
sécurité.
49
Appendix B - Project of a Health and Safety Policy
statement
56
Appendix C - Installation of the health and safety
committee - BIOPHARMA
57
Appendix D - Trainings received by the health and
safety committee of BIOPHARMA
59
DEDICATION
This thesis is dedicated to my beloved family, friends and my
lecturers.
ACKNOWLEDGEMENTS
We are greatly indebted to all whose assistance helped in the
elaboration of the present memoire. Our acknowledgement goes to the
following:
The head of Chemistry Department in the Faculty of Sciences,
Pr Luc MBAZE MEVA'A who has always encouraged continual
improvement in this department.
The Coordinator of the Professional QSE Masters program,
Dr Achille B. NOUGA for his appreciable and continuous
coordinative spirit.
We want to seize this opportunity to thank very much
Pr. Guy Anatole Blaise AZEBAZE, lecturer in the Faculty of
Sciences, University of Douala, for his marvelous supervision of the present
work despite the numerous projects being handled by him.
The General Manager of LES LABORATOIRES BIOPHARMA S.A,
Mr Francis DJOMOU NANA, for his devotedness, understanding and
comprehensive spirit as well as the moral and financial support concerning the
realisation of this job within his firm.
Pr Ousmanou MOTAPON and Mr Franck
MENGUE for their various forms of supports (numerous documentations
and advices).
We also acknowledged the training provided to us by all our
QSE lecturers.
We wish to express our sincere gratitude to our colleagues of
Biopharma, friends, QSE network of the Faculty of Sciences, family members as
well as neighbours whose direct or indirect assistance have been of great help
to us for the achievement of this goal.
To my wife, Melanie Djomou Ngongang with all
my children: Rosine, Roland, Romain, Rogenia, Doris and Franck. We acknowledge
all the multiple forms of support from them as regards the tedious working and
studying times.
Special thanks go to all those who contributed in one way or
the other for the successful completion of this thesis but whose names could
not be listed.
Of course the Almighty is always around to guide us.
LIST OF FIGURES
Figure 1: Main entrance of
Biopharma....................................................... 12
Figure 2: GPS collecting datae in
Biopharma............................................... 12
Figure 3: Map for the localization of Biopharma S.A.
................................. ...13
Figure 4: Organigram of Biopharma
2012....................................................15
Figure 5: Key Elements of successful Health and Safety
Management.................. 26
Figure 6: Graph of Age
repartition.............................................................39
Figure 7: Graph of sex
repartition..............................................................39
Figure 8: Graph of socio-professional
status..................................................39
Figure 9: Current working
experience.........................................................40
LIST OF TABLES
Table 1: Presentation and activities of
Biopharma................................................. 13
Table 2: Sample High-Value
Questions..............................................................35
Table 3: Age
groups....................................................................................
39
Table 4: Sex
repartition................................................................................
39
Table 5: Socio-professional status of workers
interviewed...................................... 39
Table 6: Experience at current
post.................................................................. 40
Table 7: Major topics related to the three parts of our
questionnaires.......................... 41
LIST OF ABBREVIATIONS AND DEFINITIONS
The most important and commonly used abbreviations or short forms
are shown as follows:
BIOPHARMA
|
Les Laboratoires Biopharma S.A
|
COMAH
|
Control of Major Accident Hazards
|
COSHH
|
Control Of Substances Hazardous to Health regulations
|
GPS
|
Global Positioning System is a radio navigation system that
is used to determine the exact location, in all weather conditions, anywhere in
the world. (
http://www.gis2gps.com/GPS/GPSDEF/gpsdef.html).
|
HS&E
|
Health, Safety and Environment
|
HSC
|
Health and Safety Commission
|
HSE
|
Health and Safety Executive
|
HSG-65
|
Health & Safety Management» is a guidance (H&S
management model), developed by HSE UK
|
JSA
|
Job Safety Analysis
|
MTPS/IMT
|
Ministère de Travail et de la Prévoyance Sociale /
Inspection Médecine du Travail
|
OHSAS
|
Occupational Health and Safety Assessment Series (Britain
1999)
|
POPMAR
|
Policy, Organizing, Planning and Implementing, Measuring
performance, Auditing and Reviewing
|
PPE
|
Personal Protective Equipment
|
PRCS
|
Permit Required Confined Space
|
RSSB
|
Railway Safety and Standards Board
|
SMS
|
Safety Management Systems
|
UK
|
United Kingdom
|
ABSTRACT
We carried out our research in Douala for a period of six
months, from 02nd July to 31st December 2012 within LES
LABORATOIRES BIOPHARMA S.A situated in the MAGZI industrial zone of BASSA. Our
topic is titled «EVALUATION OF THE LEVEL OF SAFETY TO IMPROVE THE
CULTURE WITHIN BIOPHARMA». What motivated us to choose the above
topic was the fact that our company is financially growing very fast but safety
standards are not visibly following the same trend to allow for a sustainable
development of the firm.
To go about doing our job, we used inquiries and
questionnaires to analyze the initial situation of the company as regards
safety culture by striking on the commitment of the top management, the
personnel and the various means possessed by Biopharma. Literature reviews
helped us to carry out the research based on respect of laws and regulations be
it national or international.
The immediate results obtained are the creation, followed by
the installation of a health / safety committee, the establishment of a health
/ safety policy already being applied although its approval by managing
director is still pending.
Progressively, the elaboration of a datae base for owners of
vehicles and Moto bikes is going on, the amelioration of the working conditions
(ventilation) in the packaging service is under studies and the systematic
registration of accidents and near misses has started, with its big register
being controlled by the human resource service.
From all our findings, we can say that Biopharma via Order No
039/MTPS/IMT of 26 November 1984 is improving and will achieve much if each and
every one communicates sufficiently and efficiently.
Key words: safety, culture, quality,
behaviour, accident, incident, communication, commitment.
RESUME
Nous avons effectué nos travaux de recherche à
Douala pour une période de six mois, du 02 Juillet au 31 Décembre
2012 au sein des LABORATOIRES BIOPHARMA SA situé à la zone
industrielle MAGZI de Bassa. Notre sujet est intitulé "ÉVALUATION
DU NIVEAU DE LA SÉCURITÉ AFIN D'AMELIORER SA CULTURE AU SEIN DE
BIOPHARMA". Nous avons été motivé à choisir le
sujet ci-dessus à cause du fait que notre société est
financièrement en croissance très rapide, mais les normes de
sécurité apparemment ne se suivent pas avec la même
tendance afin de garantie son développement d'une manière
durable.
Pour réaliser notre travail, nous avons utilisé
des enquêtes et des questionnaires pour analyser la situation initiale de
la société en ce qui est de la culture de la
sécurité à travers l'engagement de la direction, le
personnel et les différents moyens possédés par Biopharma.
La revue de la littérature nous a permis de mener à bien la
recherche, fondés sur le respect des lois et règlements qu'ils
soient national ou international.
Les résultats obtenus immédiatement sont :
la création suivie de l'installation d'un comité
d'hygiène, de santé et sécurité au travail
(CHSST-BIOPHARMA), l'élaboration d'une politique de santé /
sécurité déjà appliquées, bien que son
approbation par le directeur général est toujours en suspens.
Progressivement, l'élaboration d'une base des
données pour les propriétaires des motocycles est en cours,
l'amélioration des conditions de travail (ventilation) dans la salle de
conditionnement est en études et l'enregistrement systématique
dans un registre des accidents ainsi que des incidents a commencé. Ledit
registre est tenu par le service des ressources humaines.
A partir de nos résultats, nous pouvons dire que
Biopharma a un niveau de culture sécurité appréciable au
vu de l'arrêté No 039/MTPS/IMT du 26 Novembre 1984, portant sur
les mesures d'hygiènes et de sécurité sur les lieux de
travail. Néanmoins ce niveau peut s'améliorer
considérablement si chacun communique suffisamment et efficacement.
Mots clés : Culture,
sécurité, qualité, comportement, accidents, incident,
communications, engagement.
INTRODUCTION
As recommended for our professional master's
degree program, we carried out studies in organizations which are aimed at
solving specific problems. It is for this reason that we carried out our
research in Douala for a period of six months starting from 02nd
July to 31st December 2012 within LES LABORATOIRES BIOPHARMA S.A.
I.Z MAGZI BASSA P.O BOX 1674 DOUALA. Our topic is titled
«EVALUATION OF THE LEVEL OF SAFETY TO IMPROVE ITS THE CULTURE WITHIN
BIOPHARMA». What motivated us to choose the above topic was the fact
that our company is growing very fast but safety standards are not visibly
following the same trend. The hypothesis «encouraging a safety culture by
putting in place a health and safety committee - HSE within Biopharma followed
by specialized trainings, could help us to ameliorate productivity.
What is the current situation of safety
culture; in other words, we verify whether our top management is committed
(inquiry) as well as the personnel (questionnaire), existence of a health and
safety committee and the available means of the firm.
To provide answers, we shall first of all give
some briefs on safety culture; assess the present situation in the company
followed by some examples of companies practicing this culture. Finally we
shall propose a health and safety policy for the company to its General Manager
for approval.
The true `health' of the safety of any
organisation is primarily defined by the frequency of key day-to-day behaviours
(frontline and management) and the extent to which these are encouraged and
supported by an effective and flexible safety management system. The shared
belief in the importance of safety, the extent to which an organisation
actively strives to ensure health and safety is done properly and always given
a high priority, is what defines a positive safety culture. Safety is for
everybody, thus visitors, clients, customers, contractors, friends and family
at any workplace have work health and safety (WHS) responsibilities and must
comply with any reasonable work health and safety instructions at the workplace
and take reasonable care not to put themselves or others at risk directly or
indirectly. There is a need for leaders to know how to manage safety on a day
to day basis throughout their areas of responsibility.
Today, it has generally become accepted that a high proportion
of accidents, incidents and near misses in companies are due to unsafe acts
(behaviours) by people. For example, improper equipment use, not following
procedures, positions / reactions of people, housekeeping. But, rather than
being the instigators, it is typically the case that unsafe (organisational)
conditions, that have been long developing and that have been inherited by
people, represent the root cause(s) of accidents and incidents. Examples of
systemic organisational weaknesses include lack of supervision, ill-defined
roles and responsibilities, inadequate training / assessment / procedures /
instructions, poor leadership and safety communications, competing job demands,
ineffective planning and safe systems of work. Such examples obviously
correspond to symptoms of a poor or negative safety culture.
In an organisation, the benefit in
consulting, sharing information and giving workers reasonable opportunity to
express their views and contribute towards decision making on health and safety
matters is that it can assist the employer in meeting its health and safety
obligations, thus more profit resulting from preventive measures of related
risks.
Through the research it has been revealed that
questionnaires have a wide area of application. It can be used within an
organisation for diagnosing the organisation's safety culture level, and
bringing into focus how the organisation handles safety cultural issues. It can
be used as a personal assessment tool which can create motivation and awareness
for safety culture among organisational members (Camilla, 2003).
This research work is made up of four
chapters. Chapter I gives some brief presentation and activities of
LABORATOIRES BIOPHARMA S.A. Chapter II places our study in the context of the
literatures concerning OHSAS 18001:2007 with much emphasis on safety cultures
and the Cameroonian law on health and safety at workplace (Order No
039/MTPS/IMT of 26 November 1984). Chapter III outlines and spells out the
materials and methodology used, with explanations of why and how it was used to
yield our results, their interpretation, discussions and the recommendations
expressed in chapter IV. Finally the general conclusion will close up our
research.
CHAPTER I: PRESENTATION OF
COMPANY
In the paragraph below, we shall
write briefly on the presentation, activities and administrative structure of
BIOPHARMA S.A
«LES LABORATOIRES BIOPHARMA S.A» whose short form is
BIOPHARMA in our memoire, was created on the 04th of July 2001. It
is a private company with a current capital of 700,000,000 FCFA headed by a
General Manager named Mr DJOMOU NANA Francis. Biopharma employs over 180
permanent workers within its two production units. The first is the plastic
unit which produces most of our plastic bottles, caps and nylon films meanwhile
the second unit is meant for the manufacturing of cosmetic products. The main
activity of Biopharma is the production and distribution of cosmetic products.
More details are shown in table 1 and Figure 1 below.
LES LABORATOIRES BIOPHARMA S.A (Figure 1) found in Cameroon is
located in the Littoral region, Wouri division, Douala 3 subdivision at the
Magzi industrial zone Bassa. With the GPS (Figure 2), datae were collected and
used to indicate the precise position of our company as shown in the map below
(Figure 3).
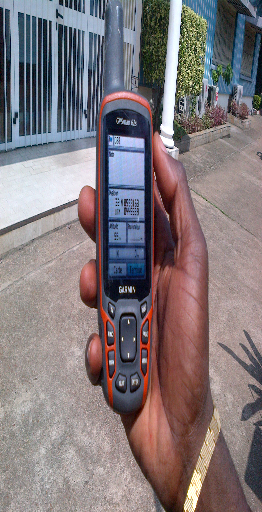
Figure 1: Main entrance of Biopharma. Figure
2: GPS collecting datae
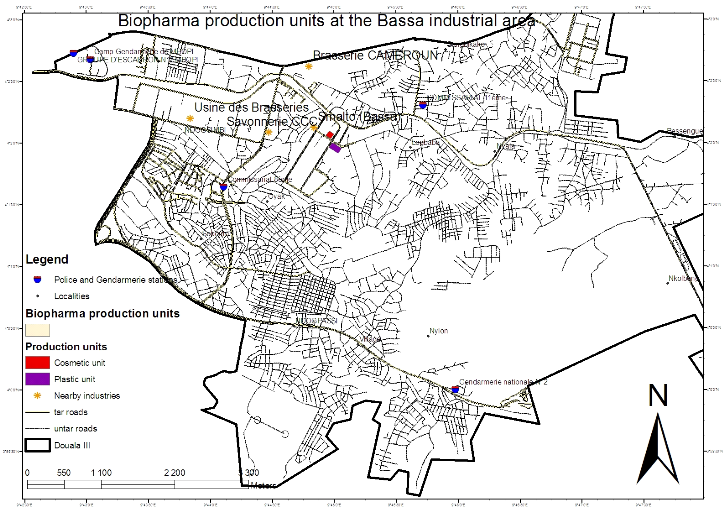
Figure 3: Map for the localisation of Biopharma S.A.
Table 1: Presentation and Activities of Biopharma
S.A
Identity of firm
|
|
Name of firm
|
LES LABORATOIRES BIOPHARMA S.A.
|
Address
|
P.O BOX 1674 Douala magzi industrial zone Bassa /
Cameroon
|
Contacts (IT)
|
Telephones
|
(00237) 33 37 56 16
(00237) 77 93 44 87
|
E-mail
|
biopharma@camnet.cm
|
General Manager
|
Mr Francis DJOMOU NANA
|
Created on
|
04 Juillet 2001 (1st production : 2002)
|
Activities
|
Principal
|
Production and distribution of cosmetic and OTC products.
|
Secondary
|
Plastic unit which produces our plastic bottles, caps and
films (shrink nylon)
|
Type of Company
|
PRIVATE PLC
|
Tax payer statistic No
|
M070100012311D
|
|
Business register No
|
026968
|
|
Financial situation
|
Turn-over
|
700 000 000 FCFA
|
Principal brands
|
Primo, Rapid'clair, Essentiel, Stay White, Talangai, Lumina,
Pluviherbal, Pluvicare, White Express Moby bébé, Nivys, Bettina,
Citro clair, Biosuccess, BLIGHT, Talcum powder, Parfumes, Nail polish (Celine
France, Lumina) etc.
|
Localisation of Customers
|
Cameroon, Gabon, Democratic Republic of Congo, Angola, RCA,
West Africa, Europe (Italy, Spain)
|
Competitors
|
SIPCA, GANDOUR, Products imitated in Nigeria
|
Suppliers of licenced products
|
Mirato - Italy, Evoluderm and Dark § Lovely - France
|
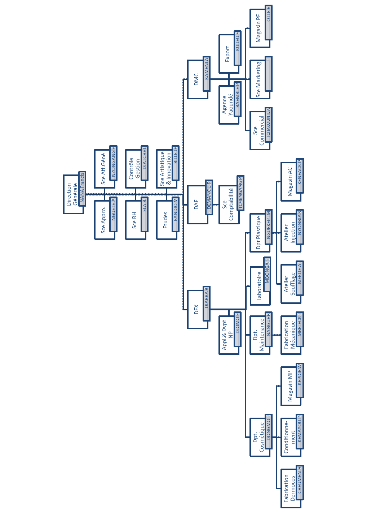
Figure 4:
Organigram of Biopharma 2012
CHAPTER II: LITERATURE
REVIEW
II.1- Scope of the
literature review
Our review has considered the literature surrounding safety
culture published since 1986. The focus is on discerning the characteristics of
positive and negative safety cultures which will help to evaluate the level of
safety culture of Biopharma. Documents for review were sourced from academic
and applied literature, and we also exploited standards and laws.
II.2- Definitions regarding safety culture:
II.2.1 Safety:
Safety can be defined as relative freedom from danger, risk,
or threat of harm, injury, or loss to personnel and/or property,
whether caused deliberately or by accident.
II.2.2 Culture:
Culture not only influences its members' decisions and
practices in the here and now; it impacts individual habits and the decisions
and practices of future members as well. It could be defined truly as "the way
we do things around here" and "what we do when no one is watching." These
common practices can be maintained through generations with little outside
management necessary. However, without an overall safety strategy that is well
understood by the culture and without process metrics to help the culture
continuously measure and improve, most safety cultures fail to reach, much less
sustain, excellent safety performance.
Many approaches to improving safety culture also focus on the
characteristics of the culture rather than the capabilities. Excellent safety
cultures are "can-do" cultures with the vision and tools to continuously
improve. They have a strategy and metrics to keep them on track. They develop
the characteristics of success as a by-product rather than a precursor of their
performance
If your organization desires to achieve safety excellence, you
must first develop a deep understanding of what excellence is. Deming called
such an understanding "profound knowledge". It not only is a performance goal,
but a definition of what excellence is and a process to achieve the goal. It
also must have process metrics that facilitate understanding of how excellence
is achieved. Excellence cannot be defined simply in terms of short-term
results. The definition of excellence cannot inadvertently include results
produced by luck and normal variation. Truly excellent safety organizations
don't just get to zero; they know exactly how to duplicate and improve their
success.
Terry L. Mathis, founder and CEO of ProAct Safety, an
international expert and safety culture practitioner, has worked with hundreds
of organizations, customizing innovative approaches to achieve and sustain
safety culture excellence. He considered a near miss as the result of a Poor
and/or a Bad attitude toward developing an excellent safety culture and Safety
Management System, due to lack of caring, concern, control monitoring and
training. With a great Safety Culture and Safety Management System,
Near misses would not or should not really occur. This is achieved by culture,
training, management planning, monitoring, identification, attitude changes,
commitment and enthusiasm. Thus a Near Miss is/or was merely an accident
looking for a place to happen. Hence we can differentiate between near
miss and accident as follows:
II.2.3 A Near Miss is an unplanned
event that did not result in injury, illness, or damage, but had the potential
to do so. Hence we can say a miss that was nonetheless very near.
II.2.4 An accident is an unforeseen
and unplanned event or circumstance, which did occur, often with lack of
intention or necessity. It usually implies a generally negative outcome
(Injury, Illness, Fatality, Damages, Unwarranted loss of income, expenditure,
production or profits...) which might have been avoided or prevented if the
circumstances leading up to it had been recognized, identified and acted upon,
before its occurrence. Consequently, safety activities should be
proactive and not reactive whenever profit is envisaged in an
organisation. Thus loses should be monitored.
With a proper safety culture and SMS, safety is drilled into
employees in an acceptable and presentable manner similar to the way soldiers
are drilled and trained in the military with the necessary discipline concern
and care for themselves and their colleagues.
No employee would work at height without ensuring that the
risk assessment (JSA) has been completed and is suitably acceptable and that
the required safety measures are in place. Fall prevention equipment is used
and where not suitable, fall arrest systems are used.
· Workers shall no more climb ladders without either
inspecting them or without support or being tied off. They would not over
extend or lean sideways on the ladder. Remember the «With the Aaargh!
It won't happen to me» attitude.
info@proactsafety.com (2012).
We hope to observe as from now, the following attitudes in our
company:
The term `safety culture' first made its appearance in the
International Atomic Energy Agency's initial report following the Chernobyl
disaster (IAEA, 1986). Since then, inquiries into major accidents such as the
King's Cross fire (Fennell, 1988), Piper Alpha (Cullen, 1990) and the Herald of
Free Enterprise (Justice Sheen, 1987) have found faults in the organisational
structures and safety management systems, throwing the importance of safety
culture into the spotlight. Safety culture has been defined in a variety of
ways but none is standard as will be read below.
The safety culture of an organisation is the product of
individual and group values, attitudes, perceptions, competencies and pattern
of behavior that determine the commitment to, and the style and proficiency of
an organisation's health and safety management (Phil. Hughes et al, 2007).
(Pidgeon, 1998) considers it as a constructed system of meaning through which
the hazards of the world are understood. Whereas the Confederation of British
Industry [(CBI), 1990)] defines safety culture as `The way we do things around
here. Meanwhile (Turner, 1989) thinks that it is a set of attitudes, beliefs or
norms. According to (Wert, 1986), it is equivalent to safety ethic. Finally, in
the layperson's terms, safety culture defines what people do when no one is
watching them. (
http://www2.dupont.com).
Meanwhile the UK Health and Safety Executive defines safety
culture as « . . . the product of the individual and group values,
attitudes, competencies and patterns of behavior that determine the
commitment to, and the style and proficiency of, an organization's
health and safety programs.» (Ref: HSL/2002/25, 2002). A more
succinct definition has been suggested: «Safety culture is how the
organization behaves when no one is watching».
Every organization has a safety culture, operating at one
level or another. The challenges to the leadership of an organization are
to: a) determine the level at which their safety culture is currently
functioning; b) decide where they wish to take the culture; and c)
chart and navigate a path from here to there.
Followings these proposed definitions of the term `safety
culture' we shall proceed with some of its benefits as well as its
characterization.
II.3- Reasons for assessing level of safety culture:
A safety culture assessment allows an organisation to better
understand how its people perceive safety and the company's approach to health
& safety management. It allows the organisation to identify both
strengths and weaknesses that then enable it to continuously monitor and
improve its approach to health and safety. The most important reason for
understanding a company's safety culture is because it has a direct impact on
the safety of its employees, contractors and the public. Several high
profile accidents in the rail and other industries have highlighted the
consequences of poor safety cultures. The benefits of an improved safety
culture, in other words, a positive safety culture; are improved safety
performance and reduced accidents. Still from this source, the improved
management processes and attitudes to work involved in developing a good safety
culture will also have other benefits which are external to safety namely
improved reliability and performance, as well as reduced costs due to the
reduction of errors. Erreur ! Référence de lien
hypertexte non valide. (Oct 212).
According to the referential OHSAS 18001:2007,
a safe and healthy workplace through the provision of tools that allow
the organisation to consistently identify and control its health and safety
risks, minimizing the potential for accidents. As such this enhances safety
culture.
It is said that the British Standards Institute developed the
Occupational Health and Assessment Series version 2007, to provide guidance to
organizations desiring to improve their health and safety performance prior to
their certification. This document is then utilized as a risk assessment model
to determine the level of risk an organization has as regards its health and
safety hazards and risks, and to implement methods to continually improve the
health and safety performance of the given organization.
One will often hear the following statement from companies or
organisations «we have never had a serious employee injury, why do
we need OHSAS 18001:2007?»
In fact, OHSAS 18001:2007 is a proactive management system
designed to assist an organization in the developing of programs which will
actually improve their employee health and safety performance. The simple fact
of having not experienced a serious accident does not mean the organizations
are the best stewards of the health and safety of their workforce. It also
assists the organization in developing a holistic approach as to how it manages
its' activities which can have a serious risk to the health and safety of its
employees.
OHSAS 18001 demonstrates Legal and Regulatory Compliance and
commitment to improving the health and safety performance of the organization;
instills a culture of prevention through the systematic evaluation of the
health and safety risks of the organization. A real time analysis is performed
and controls implemented thus reducing the risk of an accident. Also by
establishing and certifying the organization's health and safety management
system to the above standard, it joins a unique group of companies who have
committed their organizations to health and safety excellence. A continuous
state of readiness is established. On the other hand, by implementing and
maintaining an OHSAS 18001:2007 based management system; the organization will
improve its profitability. As the organization reduces the safety risks, many
of the more expensive costs such as workers compensation claims in terms of
down time due to accidents, ill health and insurance premiums will be reduced
significantly. The nature of the management review, defined roles and
responsibilities and internal assessments will make the organization more
transparent, accountable and sustainable. Furthermore, through the management
review process, top management becomes more readily aware of resource
requirements.
In our research, notions on safety culture, Safety culture
assessment criteria and indicators as well as Safety culture measurement tools,
shall be provided.
II.4- Characteristics of identifiable good safety culture in
an organism:
In recent years, companies have begun to recognize the
important contribution that an effective safety culture can make to the control
of their ongoing operational costs and efficiency of their ongoing operations.
Many organizations have realized that this provides the perfect opportunity for
them to streamline their operational processes and optimize the associated
management and control systems. Hence, more than ever before, all levels of
line management need to possess a much greater knowledge of how to develop and
implement high quality safety management systems. There is also a need to know
how to manage safety on a day to day basis throughout their areas of
responsibility.
The safety practitioner's role is now that of a high-level
internal consultant who offers independent advice to senior management on
development of the organization's safety policies and their short, medium and
long term strategic objectives for creating and maintaining a positive safety
culture. Modern safety practitioners must be as familiar with all aspects of
managements as those practitioners from other disciplines (such as human
resources, production, finance, commercial, etc.) that comprise the senior
management team.
Some characteristics of identifiable good safety culture in an
organism can be understood according to Cooper, (2001) in the following
headings: immediate, intermediate and ultimate.
Ø Immediate
The first pointer to look for is the quality of safety
leadership demonstrated by the organisation's chief Executive officer (CEO) and
senior management team. The regular active monitoring and review of line
management's implementation of these strategic plans by the senior management
team demonstrates the most important aspect of good safety leadership. The
findings of these reviews should be communicated to every person in the
organization on regular basis. Hence informations about the ongoing progress
being made readily available to all employees.
The status accorded to the safety practitioner by the CEO of
an organisation indicates the level of safety culture. Thus, if the safety
practitioner has direct, independent and unimpeded access to the CEO, it can be
said that the organisation actively recognizes the important contribution that
the safety function offers to all aspects of its business.
The presence and quality of the organisation's risk control
systems also indicates its level of safety culture. If risk assessment have
been conducted and recorded, on all the organisation's activities and the
appropriate control measures fully implemented, it is probably that safety is
being actively controlled at the operational level.
Ø Intermediate:
The presence and quality of the organisation's safety
management information system is the next visible characteristic of a positive
safety culture. It provides the means by which the organisation can evaluate
its ongoing safety activities as well as providing the knowledge required to
facilitate error correction, problem-solving, decision-making and forward
planning.
Regular planning and conduction of safety management audits
throughout the whole organisation is another indicator of a positive safety
culture within an organisation.
Ø Ultimate level:
It is concerned with the wining of people's heart and minds to
the organisation's safety principles through:
ü the development of high quality safety training
programs,
ü seeking and acting upon employees' points of view
ü empowering them to become actively involved with safety
issues on a daily basis.
In fact, the extent to which an organisation actually changes
its systems and management practices to support the safety training provided
will also provide a useful indicator of a positive safety culture.
We can say that the most important indicator of a positive
safety culture is the extent to which employees are actively involved in safety
on a daily basis. Thus where safety issues are identified and acted upon by all
the employees as part of their normal working day, the organisation can be said
to have won over people's hearts and minds to the safety cause and therefore,
has a living, breathing, proactive and safety culture.
According to Phil. Hughes et al, (2007) some other important
indicators of a health and safety culture could be obtained by exploring the
numbers of accidents, near misses, the perception of a blame culture, frequency
of high staff turnover, cases of insufficient resources and the lack of
compliance with relevant health and safety law and the safety rules and
procedures of the organization, poor selection procedures and management of
contractors, poor level of communication, cooperation and control, absence or
presence of a weak health and safety management structure (SAFETY COMMITTEE),
poor levels of health and safety competence, high insurance premiums and
occupational ill-health cases occurring within the organisation.
Thus an organisation with a high accident incidence rate is
likely to have a negative or poor health and safety culture.
Furthermore, Reason (1997) has also identified four
characteristics that go to make up such a safety culture.
These are:
· a reporting culture in which people are
willing to report errors and near misses.
· a just culture; culture of `no blame' where an
atmosphere of trust is present and people are encouraged or even rewarded for
providing essential safety-related information - but also where it is a clear
line between acceptable and unacceptable behaviour.
· a flexible culture which can take different
forms but is characterized as shifting from the conventional hierarchical mode
to a flatter professional structure
· a learning culture, the willingness and the
competence to draw the right conclusions from its safety information system,
and the will to implement major reforms when the need is indicated.
A good safety culture, however, is believed to positively
impact upon an organisation's quality, reliability, competiveness and
profitability. In fact, reliability has been reported to improve by a factor of
three, and sometimes by as much as a factor of ten, when quality improvements
are initiated. These improvements are related to the use of better monitoring
and feedback systems. Safety culture may affect people's way of thinking and
lead to the development of safety features. It positively impacts on employees'
commitment and loyalty to the organisation, resulting in greater job
satisfaction, productivity and reduced absenteeism. Profitability is achieved
by minimizing loss and adding the capital value.
Research has highlighted some confusion and inconsistency in
the literature over the use of the terms `safety climate' and `safety culture'.
The review has provided a useful framework for approaching these terms, based
upon the work done by Cooper (2000). The term safety culture can be used to
refer to the behavioral aspects (i.e. `what people do'), and the situational
aspects of the company (i.e. `what the organisation has'). The term safety
climate should be used to refer to psychological characteristics of employees
(i.e. `how people feel'), corresponding to the values, attitudes, and
perceptions of employees with regard to safety within an organism. There have
been some evolutions in the concept of safety culture.
II.5- Evolution of the concept of safety culture
Traditionally, attempts to identify the most effective methods
for preventing accidents have typically addressed two fundamental issues:
whether or not employees should be provided with the maximum possible
protection and whether or not employees should be trained to recognize
potentially hazardous situations and take the most appropriate actions.
The first approach is based on the fundamental belief that
protecting an individual from the potential for harm, either by statutory means
or via physical barriers, is the best way to proceed. The second approach is
predicated on the fundamental belief that, if the individual possesses the
relevant knowledge and skills, accidents will be avoided.
The central idea was that the Health and Safety Commission
would promote proactive self-regulatory safety management practices by
influencing attitudes and creating an optimal framework for the organisation of
health and safety. It is clear that legislation can only be effective if it is
adequately resourced and policed. As a result of recent European directive, the
legislative focus has now firmly shifted to proactive management of safety
rather than an inspection of sites/premises approach. Thus employers are now
required to take steps to identify and manage hazards by undertaking formal
assessments of risk say Cooper, (2001 ).
One of the issues highlighted in the literature is the lack of
a universal consensus regarding the terms culture and climate. In many cases
the terms safety culture and safety climate are often used interchangeably. A
good framework based on some work, views safety culture as a product of three
interrelated aspects as stated below, according to Cooper , (2000).
· Psychological Aspects or `safety climate' (individual
and group attitudes, perceptions and values).
· Behavioural Aspects (safety-related actions and
behaviours).
· Situational Aspects (policies, procedures,
organisational structures and management systems).
Organizations with a positive safety culture are characterized
by communications founded on mutual trust, by shared perceptions of the
importance of safety and by confidence in efficacy of preventive measures.
There must be a joint commitment in terms of attitudes and values. The
workforce must believe that safety measures put in place will be effective and
followed even when financial and performance targets may be affected.
With time-tested methodologies in employee, contractor and
process safety, DuPont Sustainable Solutions experts help companies to reduce
lost-time incidents, build skills, and minimize risks, while improving your
efficiency, productivity and safety culture (http://www2.dupont.com).
According to the Royal Aeronautics Society (2004, slide 6) the
best way to measure safety culture is to observe individuals when they are
working. This allows the inspector to witness:
o Hands-on-behaviour - (the `behavioural' aspect of the
culture).
o Management practices and policies.
o The inclusion of human factors considerations in day-to-day
activities.
o Working relationships, communication styles and application
of revised processes.
The approach consists of a self-assessment questionnaire,
designed to help companies identify the strengths and weaknesses within their
HS&E systems, and identify opportunities for improvement. The assessment
covers health, safety and environment, product stewardship; internal
communications and community liaison; and distribution, and provides a
selection of indicators to measure performance and emergency responses
(Chemical Industries Association, 19982b, page 1)
Still continuing with the evolution of safety culture, the
HSE's model for successful health and safety management, namely POPMAR is shown
in Figure 3 below. This encourages organisations to manage health and safety
with the same degree of expertise and to the same standard as other core
business activities, in order to control risks effectively and prevent harm to
people (HSE, 2002b).
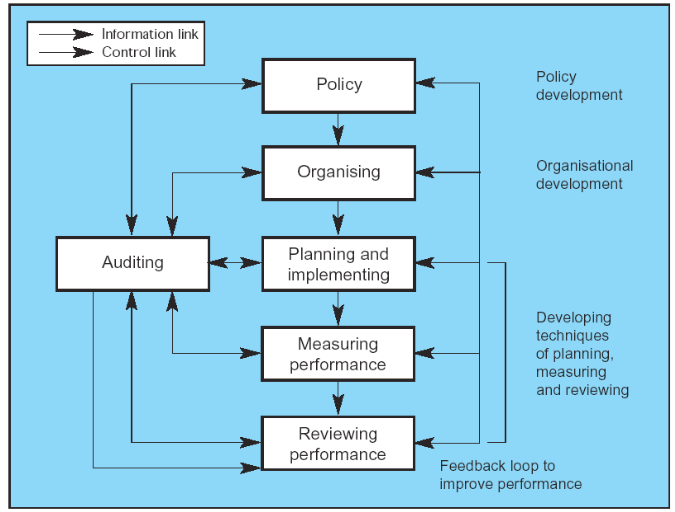
Figure 5 -Key Elements of Successful Health and Safety
Management (HSG65)
An explanation of what each stage of POPMAR requires for the
determining of the state of the health and safety management system has been
provided below:
ï Policy -Are there effective policies
in place that set a clear direction for the organisation to follow?
ï Organising -Is there an effective
management structure and are arrangements in place for delivering the policy?
ï Planning and Implementing - Is there a
planned and systematic approach for implementing the policy through an
effective health and safety management system?
ï Measuring Performance - Is performance
measured against agreed standards to reveal when and where improvement is
needed?
ï Auditing and Reviewing - Does the
organisation learn from all relevant experience and apply those lessons?
According to the HSE, the five steps will help to retain staff
within an organisation and help to reduce the cost of injuries, illness, and
property and equipment damage. It is likely that this would also encourage
fewer stoppages, higher output, and better quality. To be a `quality'
organization, sound management principles to health and safety should be
applied (HSE 1998a).
After briefing on the evolution of the issue of safety
culture, we shall look at some indicators which have an influence on it.
II.6- Indicators that are known to influence safety
culture
The five indicators are as follows: Leadership, Two-way
communication, Employee involvement, Learning culture and Attitude towards
blame. In the following paragraph, we shall see how these
indicators influences positively or negatively safety culture in
organisations.
II.6.1- Leadership
The literature has highlighted key criteria of successful
leadership, which are likely to promote a positive safety culture. These
criteria are: Performance versus Safety Priority, High Visibility of
Management's Commitment to Safety and Safety Management Systems.
From Performance versus Safety Priority,
senior management should give safety a high status within the
organisation's business objectives and safety should be prioritized in all
situations by providing:
ï Health and safety budget, Opportunities for safety
communication, Health and safety training, Support to personnel and Manpower
(including health and safety specialists).
Leadership can be measured by looking at how visible
management is to the workforce. Not only is visibility important, but so also
is the extent to which management provide the opportunity for two-way
communication.
Examples of a positive and negative evidence point for the
indicator «Leadership» includes:
· Positive- There should be clear
evidence that action lists or action plans are developed, signed and tracked by
management.
· Negative- Safety issues identified by
management are not dealt with but are just «filed». No action is
taken which could help to learn a lesson.
Concerning High Visibility of Management's Commitment
to Safety, Senior managers should visibly and repeatedly demonstrate
their commitment to safety throughout all areas of the organisation. This will
create a shared vision of the importance of safety. This can be achieved by the
use of verbal communication (e.g. scheduled safety tours and meetings) and
written safety communication (e.g. statements, newsletters). See paragraph
below for distribution.
Meanwhile for the Safety Management Systems,
organisations should have effective systems put in place for the management and
co-ordination of safety. This should be led by a strategic safety management
team.
II.6.2- Two-Way Communication: (notice board on safety
issues, intra-net/outlook, internet, telephone and verbal)
A positive safety culture requires effective channels for
top-down, bottom-up and horizontal communication on safety matters. The main
learning points from this review are listed below:
ü Top-down Communication: Effective
communication from management to staff is the key to providing successful
health and safety leadership. This can be achieved through a visible safety
policy statement, and newsletters describing safety news, safety issues, and
major accident risks.
ü Safety Reporting: Communicating a
problem or concern is only one step on the route towards a good safety culture.
Feedback mechanisms should be put in place to respond to the reporter (if
required) concerning any actions taken.
ü Horizontal Communication: The
organisation should provide a system for the effective transfer of information
between individuals, departments and teams. In practice, appropriate safety
information should be available when required.
II.6.3- Involvement of employee (Staff):
The literature has identified best practice approaches in
relation to the involvement and participation of staff or employee. The
consensus is that, active employee participation is a positive step towards
preventing and controlling hazards. The main points identified have been
summarised below:
· Ownership for safety can be increased by providing
effective training, and providing opportunities for employees to be responsible
personally for areas of safety.
· Safety specialists should play an advisory or
consultancy role.
· It should be easy for staff at all levels to report
concerns about decisions that are likely to affect them, particularly during an
organizational change.
· Feedback mechanisms should be put in place to inform
staff about any decisions that are likely to affect them be it direct or
indirect.
II.6.4- Learning Culture
It is widely recognized that a learning culture is vital to
the success of the safety culture within an organisation. The main findings
from the research revealed that:
· The existence of a learning culture enables
Organisations to identify, learn and change unsafe conditions. A system should
be put place that will allow all employees to proactively contribute ideas for
improvement.
· In-depth analysis of incidents, and good communications
with provisions for feedback and sharing of information enable a learning
culture to develop.
· All levels of the workforce should be included in
safety climate surveys. This helps to increase employees' involvement in the
company and it provides the opportunity for issues or concern to be raised.
Feedback regarding the outcomes of the survey, and any actions taken should be
disseminated throughout the company.
Learning culture can be measured by the extent to which safety
culture surveys are conducted. Thus, a positive evidence point for a successful
safety culture review is the involvement of all employees within the survey.
II.6.5- Attitude towards blame.
Companies or Organisations with a blame culture have been
described by Whittingham (2004) as those which: `over-emphasise individual
blame for the human error, at the expense of correcting defective systems'.
Blame allocates fault and responsibility to the individual making the error,
rather than to the system, organisation or management process. Below are
summarised the main findings.
ü Organisations should move from a blame culture to a
just culture or one of accountability.
ü Those investigating incidents/accidents should have a
good understanding of the mechanism of human error and a system should be put
in place that enables the degree of culpability to be well assessed.
ü Management should demonstrate care and concern towards
employees.
ü Employees should feel that they are able to report
issues or concerns without fear that they will be blamed or disciplined
personally.
ü Confidentiality should be maintained throughout the
course of the investigation.
II.7- Some key attributes of a sound safety culture:
From the findings of Fleming (2001) in the Offshore Technology
Report conducted by Robert Gorden University on behalf of the HSE, this author
states that four factors appeared to have a positive effect on the safety
perceptions: valuing subordinates, visiting the worksite frequently, work group
participation in decision-making and effective safety communication. Reason
(1997) also emphasized that an organisation needed a just culture to be able to
have a good safety culture. This author says a just culture is recognized by
the organisation's ability to create an atmosphere of trust and where people
are encouraged and rewarded for providing essential safety-related
informations.
Furthermore assuming an incident occurred because a
control room operator, leaving at the end of the shift, failed to alert the
oncoming operator of a serious, off-standard condition in the process.
This problem might be diagnosed generally as a communications problem,
with a specific root cause defined as «Communications between shifts
less than adequate.» In this circumstance, another root cause
related to supervisory practices, «Improper performance
not corrected,» might be identified. The only thing of real
importance that leaders do is to create and manage culture (Schein et al 2004).
The leadership of an organization has the primary responsibility for
identifying the need for safety, fostering cultural change and
for sustaining a sound safety culture once it is established. If
the organization feels strongly about a particular behavior, there will be
little tolerance for deviation, and there will be strong societal
pressures for conformance (Weick et al, 2001). Each individual in the
organization has a role in reinforcing the behavioral norms.
The values of the group (e.g., corporation, plant, shift team)
help shape the beliefs and attitudes of the individual, which in turn,
play a significant role in determining individual behaviors. A weak safety
culture likely will be evidenced by the actions and inactions of personnel
at all levels of the organization. For example, the failure of a critical
part in one of our machines might have been caused by the technician who failed
to do preventive maintenance of the instrument and falsified the maintenance
records. Alternatively, it might have been caused by the plant manager who
denied the fundings requested to address staffing shortages in the instrument
department.
In a sound safety culture, an individual would be
expected to intercede if they saw a coworker about to commit an unsafe
act. Also under same situation, leadership would be expected to monitor
the heath of the safety culture and reinforce and nurture it when required.
Finally, individuals and groups would be expected to speak out if they
perceived management acting in a fashion inconsistent with the
organization's safety values.
Case study:
The Basic Nestlé Management and Leadership Principles'
document describes the management style and the corporate values, specifically
in the area of interpersonal relations. We gathered the following major
elements: a prerequisite for dealing with people is respect and trust,
transparency and honesty in dealing with people are a sine qua non for
efficient communication complemented by open dialogue with the purpose of
sharing competencies and boosting creativity. To communicate is not only to
inform; it is also to listen and to engage in dialogue. The willingness to
cooperate, to help others and to learn is a required basis for advancement and
promotion within Nestlé. This is firmly stated in their human resources
policy, a totally new policy that encompasses the guidelines that constitute a
sound basis for efficient and effective human resource management. (
http://www.nestle.com/asset-library/Documents/Library/Documents/People/People-Development-Review-EN.pdf
retrieved 12th Dec 2012).
For an organization to be conformed to the OHSAS 18001:2007
requirements, it must:
1) determine the activities of the organization and how they
impact the health and safety,
2) determine its' workforce,
3) determine which of these risks are intolerable,
4) establish objectives, measurable targets and programs for
the reduction of these,
5) possess only unacceptable risks,
6) establish emergency preparedness programs in the event of
non-conformances,
7) identify the health and safety legal requirements of the
organization,
8) measure the level of compliance to legal requirements,
9) perform periodic assessments as to how well the
organization conforms to its' health and safety requirements,
II.8- Benefits of safety culture within organisations
Organisations will surely benefit the following situations below
if a positive safety culture is existing within it.
ï Reduction of the direct and indirect costs of
accidents. Fines, repair costs, damage claims, and increased insurance premiums
are a few of the potential economic consequences.
ï Improved employee morale and productivity. Promoting
communication between management and the rest of the organization prevents
disenfranchisement and lifts morale.
ï Establishing a marketable safety record. A record of
consistently safe operations can be used to attract new business and
investment.
ï Logical prioritization of safety needs. SMS emphasizes
risk mitigation actions that provide the biggest impact on both safety and the
bottom line.
ï More ef?cient maintenance scheduling and resource
utilization. Effective hazard reporting in SMS allows proactive scheduling of
maintenance tasks when resources are available; increasing the likelihood that
maintenance is performed on time and more efficiently.
ï Avoiding incident investigation costs and operational
disruptions. Improved communication and risk mitigation will prevent many
accidents from ever occurring.
ï Compliance with legal responsibilities for safety.
II.9- Health and safety policy:
The Health and Safety at work act (1974) requires all
companies employing five or more people to prepare a safety policy. According
to the ACSNI Study Group on Human Factors (HSC, 1993), a written corporate
statement on the safety policy and organisation should be a crucial element in
the promotion and maintenance of a positive safety culture within the firm. Its
objective should be to establish the corporate attitude to safety and the
organisational framework through which the safety objectives can be assured.
Thus we can say that a Safety Policy is a written document
developed by the top management of an organisation or proposed by its
representative, that is communicated to all employees as well as the other
affiliated entities with a stake in organizational safety. The content of such
a document should have vital topics like commitment to implementation of the
SMS, assurance that executives are monitoring safety performance just as keenly
as ?nancial performance, encouragement for all employees to report potential
safety issues without fear of reprisal, establishment of clear standards for
acceptable behavior related to safety, commitment to providing the necessary
resources and finally indication of possibilities to review the policy
statement so as to assure continual improvement. (see health and safety policy
proposed in annex).
Duane et al (2007) states that having a safety culture means
that all employees are responsible for safety. Such a culture is led by example
expressed by top management, especially in the manner with which they deal with
day-to-day activities. Employees must fully trust that they will have
management support for decisions made in the interest of safety, while also
recognizing that intentional breaches of safety will not be tolerated. The
result is a non-punitive environment that encourages the identi?cation,
reporting and correction of safety issues.
One of the primary workplace problems near miss incident
reporting attempts to solve directly or indirectly is to try to create an open
culture whereby everyone shares and contributes in a responsible manner.
Near-Miss reporting has been shown to increase employee relationships and
encourage teamwork in creating a safer work environment.
http://www.clmi-training.com/safetyblog/near-miss-incident-reporting-its-about-trust/
II.10
Safety-culture-assessment / evaluation
From our research, we got some literature on the methodology
of evaluating or assessing safety culture. It starts by indicating that the
measurement of such a culture seems to be the equivalent of the «holy
grail» for the safety world which has been made more difficult due to the
lack of an agreed definition and scope, (
http://www.safetyculturetoolkit.rssb.co.uk/safety-culture-information/safety-culture-assessment.aspx).
However, the assessment of safety culture is a vital process for measuring
key elements of safety culture and identifying an organisation's current level
of development in order to improve. There are a variety of different
assessment methods provided by the famous RSSB of the UK. Some of these methods
are safety attitude surveys (using questionnaires to elicit workforce
attitudes) and Safety management audits (using an audit process and trained
auditor to examine the presence and effectiveness of safety management
systems).
From the research conducted by another author, Weigman et al
(2002), safety culture assessments should be conducted using a variety of
methods, including both qualitative techniques (e.g. observations, focus groups
discussions and historical information reviews) and quantitative methods such
as interviews, surveys and questionnaires. The use of a combination of
methods is commonly referred to as triangulation. Table 2 below contains
samples of high-value questions that were assembled from referenced sources
based on generally accepted interviewing principles. In the interview guide,
the questions were organized into seven important areas for safety culture.
Table 2: Sample High-Value Questions
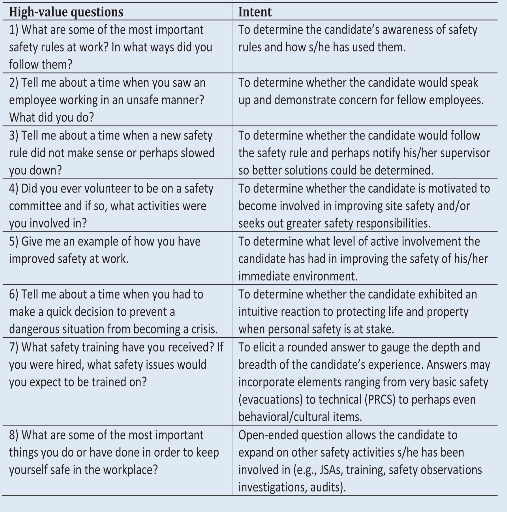
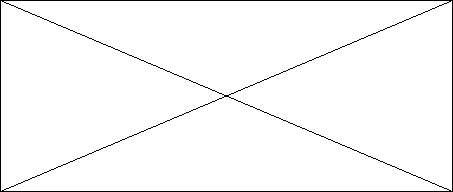
Source : Hartshorn, (1999).
CHAPTER III: SCIENTIFIC APPROACH
III.1- MATERIALS
We used the workers of Biopharma, company's documentations
related to HSE, Camera, Telephone and Computer (Internet, Printer, Word and
Excel) as well as stationaries (pens, papers).
III.2- METHODOLOGY
From the literature on the various methodologies of evaluating
safety culture, we chosed one from the famous RSSB of the UK - safety attitude
surveys (using questionnaires to elicit workforce attitudes) including the
qualitative techniques (e.g. observations, focus groups discussions and
historical information reviews) stated by Weigman et al (2002). This method is
commonly referred to as triangulation.
III.2.1- In situ observation
Given that we have been working in Biopharma since its
creation, we noticed that in addition to the General Manager who actively
encourages safety at a certain level, the other employees try to do the same.
Never-the-less, somethimes what is done concerning HSE is not written correctly
and what is written is not correctly done.
III.2.2- Interviews and questionnaires:
Not all the employees were selected for our preliminary test,
the criteria was based either on the worker's age, gender, working experience,
socio-professional category or proneness to HSE issues. Hence we discussed with
the following managers (Managing Director, human resource, finance,
purchase/logistics...), accountants, lines supervisors, quality controllers,
personnel representatives, day/night watchers, gardeners, store keepers as well
as some housekeepers. We started by performing a pre-test through an overall
interviews of this group of workers on health and safety issues. Their
responses guided the setting of the questionnaire. Given that more than 90% of
the workforce of Biopharma speak and understand principally the French language
our questionnaire was written in French (see appendix A page 49).
We then went onwards, sharing these questionnaires to the
various leaders of our newly formed and installed HSE-committee, who in their
turn distributed them to the workers. This method was chosen so as to minimize
as much as possible the loosing of copies.
For workers out of Douala, we forwarded PDF files to them and
their responses returned to us through the same internet system.
Out of the 150 copies distributed, we received only 120 and
proceeded by coding them, analyzing and interpreting the results.
To facilitate the search of solutions, we enumerated some
temporal hypothesis which was to be verified from the results of the analysis
of the questionnaires composed of three parts with the last part subdivided
into five sections. (Appendix-A).
1. Part one is concerned with informations related to the
employee's profile and socio-professional status.
2. Part two highlights on organisational issues.
3. Part three is intended to demonstrate how the front and bottom
line in Biopharma manages risk and the questions are grouped in the following
sections:
· Section A is based on training, supervision and learning
culture.
· Second B talks about safe work procedures.
· Section C focuses consultation and communication
(reporting safety).
· Section D is related to management commitment.
· While the last section E, gives responses to injury management.
CHAPTER IV: RESULTS,
INTERPRETATIONS AND RECOMMENDATIONS
IV.1- RESULTS AND
INTERPRETATIONS
Immediate and progressive results were obtained as could be seen
below.
IV.1.1- Immediate
We immediately achieved the following results:
a) Health and safety policy statement with copy in page 55 in
annex, has been established and proposed to the managing board but not yet
approved though it is already being executed since September 2012,
b) Creation and installation of a well-structured health and
safety committee of which Mr Fandio Moise is the coordinator, appendix C page
57,
c) Training of members in the management of a safety committee
(see photos page 59 appendix D),
d) Trainings received by some members in the domain of field of
fire-fighting, (see photos page 59 appendix D),
IV.1.2- Progressive
· The elaboration of a datae base for owners of vehicles
and Moto bikes is going on.
· Amelioration of the working conditions (ventilation) in
the packaging service is under studies.
· The systematic registration of accidents and near
misses has started, with a register at the human resource service.
Proceeding with further verifications based on the datae of
120 workers using the spread sheet and analyzing, we observed the following:
In part one concerning informations related to the employee's
profile and socio-professional status, 54% of those who responded were born
between 1975 - 1985 with 74% being men while 15% are women and 11% did not
chosed their sex. See tables 3 and 4 as well as figures 6 and 7 below.
Table 3: Age groups
|
AGE range
|
Number of workers
|
[1955-1965[
|
16
|
[1965-1975[
|
11
|
[1975-1985[
|
64
|
[1985-1995
|
18
|
Omission
|
11
|
|
|
Figure 6: Graph of Age repartition
As regards the organisational issues in Biopharma, it is
noticed that 61% of the work force is found at the bottom line and 29% being
supervisors. See table 5 as well as figure 8. Amongst these workers, 82% as
deduced in table 6 and figure 9 have an appreciable experience of one to five
years, within a company of only 11 years old.
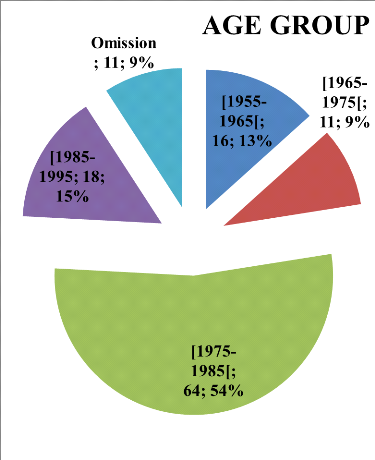
Table 4: Sex repartition
|
GENDER
|
NUMBER
|
MALE
|
89
|
FEMALE
|
18
|
OMITTED
|
13
|
Figure 7: Graph of sex repartition
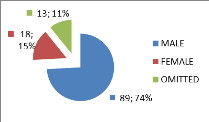
|
|
|
|
|
Table 5: Socio-professional status of workers
interviewed
|
|
|
|
|
Senior managers
|
3
|
|
|
|
|
Managers
|
9
|
|
|
|
|
leaders/supervisors
|
35
|
|
|
|
|
bottom line
|
73
|
|
|
|
|
|
|
Figure 8: Graph of socio-professional status
|
|
|
|
|
|
|
|
|
|
|
|
|
|
|
|
Table 6: Experience at current post
|
|
|
|
|
|
|
|
|
|
YEARS
|
NUMBER OF WORKERS
|
|
|
|
|
[0 - 1 [ANS
|
13
|
|
|
|
|
[1 - 5[ans
|
99
|
|
|
|
|
[5-10[ans
|
6
|
|
|
|
|
[10 - 11]ANS
|
2
|
|
|
|
|
Figure 9: Current working experience
Furthermore, we have presented in table 7 below a summary of
the major topics of our questionnaires which was exploited in parts A
(training and supervision or learning culture), B (safe work
procedures), C (reporting safety), D (management
commitment) and E (injury management) which are in accordance
with the various authors quoted in our literature review. Thus:
Ø The issue of safety culture is supported by the
General Manager and the other leaders as indicated by 71% employees, with 69%
mastering the essence of a health/safety policy although only 68% confirmed
that safety procedures, rules and regulations are respected. This idea goes in
line with Duane et al (2007).
Ø Just like Fleming (2001), 89% of the workers
interviewed agree that hazard and their associated risks will be detected
faster when frequent inspections of the various sites are made and reported.
For 82% of the employees, safety is primordial for each and every one in such a
way that lessons are learned for past experiences in this domain as supported
by 78%. Thus 68% agree that sensitization is helpful to enhance safety culture.
This same point is highlighted by Weick et al (2001), the Royal Aeronautics
society (2004) as well as Phil. Hughes and Ed Ferrett (2007).
Ø Cleanliness is well considered by 81% whereas 84% are
aware that collaboration is necessary for the implementation of safety culture
hence considers the various attitudes within the company. Safety management,
thus safety culture is enhanced as earlier sated in HSE, 2002b.
Ø As regards injury management, 75% confirms that it is
appreciable and risky situations according to 66% of the employees will be
minimized if they are proactive.
Ø For 64% of those interviewed, leaders look for
solutions to eventual safety tempers reported such that workers are not blamed
when an accident occurs; instead the managers look for its origin and justice
made. This could also be justified by 65% workers who declare that the discuss
safety issues freely during work with everybody and take part in several
decision making regarding the above mentioned domain. By so doing, a just
culture as also stated by the following authors: Reason (1997), Whittingham,
R.B (2004) and Schein et al (2004) exists.
Table 7: Major topics related to the three parts of our
questionnaires.
CODES
|
YES=1/3
|
NO=2/4
|
% YES
|
|
Q23
|
81
|
39
|
68
|
Nous qui travaillons à Biopharma aidons chacun à
travailler en sécurité par des multiples sensibilisations:
1-Très d'accord, 2-Pas d'accord, 3-Je suis d'accord, 4-Pas du tout
d'accord
|
Q28
|
79
|
41
|
66
|
Si nous sommes proactives, les risques sont minimisés:
1-Très d'accord, 2-Pas d'accord, 3-Je suis d'accord, 4-Pas du tout
d'accord
|
Q29
|
107
|
13
|
89
|
En multipliant les rondes sur un site, nous détectons
rapidement les dangers majeurs et les risques liés aux dits
dangers : 1-Très d'accord, 2-Pas d'accord, 3-Je suis d'accord,
4-Pas du tout d'accord
|
Q30
|
81
|
39
|
68
|
Les directeurs encouragent le personnel de Biopharma à
travailler conformément aux exigences de la règlementation en
vigueur portant sur l'hygiène, la sécurité et la
santé, même lorsque le programme est très surchargé
: 1-Très d'accord, 2-Pas d'accord, 3-Je suis d'accord, 4-Pas du
tout d'accord
|
Q42
|
94
|
26
|
78
|
Nous qui travaillons ici tirons des leçons à partir
de nos expériences dans la prévention des accidents :
1-Très d'accord, 2-Pas d'accord, 3-Je suis d'accord, 4-Pas du tout
d'accord
|
Q45
|
101
|
19
|
84
|
Notre attitude par rapport à la sécurité
peut influencer le comportement des autres membres de l'équipe :
1-Très d'accord, 2-Pas d'accord, 3-Je suis d'accord, 4-Pas du tout
d'accord
|
Q48
|
71
|
49
|
59
|
Les directeurs et/ou les chefs s'assurent que les
problèmes de sécurité sont toujours pris en compte et
résolus rapidement lorsque ceux-ci sont signales : 1-Très
d'accord, 2-Pas d'accord, 3-Je suis d'accord, 4-Pas du tout d'accord
|
Q50
|
77
|
43
|
64
|
Les directeurs et/ou les chefs encouragent les employés
à participer activement dans la prise de décision portant sur la
santé et la sécurité: 1-Très d'accord, 2-Pas
d'accord, 3-Je suis d'accord, 4-Pas du tout d'accord
|
Q53
|
97
|
23
|
81
|
Pour nous qui travaillons ici, nous prenons une double
responsabilité pour s'assurer que le lieu de service demeure toujours
propre: 1-Très d'accord, 2-Pas d'accord, 3-Je suis d'accord, 4-Pas
du tout d'accord
|
Q55
|
72
|
48
|
60
|
Nous qui travaillons ici nous nous sentons en
sécurité pour un travail d'ensemble : 1-Très
d'accord, 2-Pas d'accord, 3-Je suis d'accord, 4-Pas du tout d'accord
|
Q57
|
98
|
22
|
82
|
Nous qui travaillons ici savons que la sécurité est
l'affaire de tous et de chacun: 1-Très d'accord, 2-Pas d'accord, 3-Je
suis d'accord, 4-Pas du tout d'accord
|
Q59
|
78
|
42
|
65
|
Nous qui travaillons ici parlons toujours librement et
ouvertement des choses concernant notre sécurité au lieu de
travail : 1-Très d'accord, 2-Pas d'accord, 3-Je suis d'accord,
4-Pas du tout d'accord
|
Q66
|
83
|
37
|
69
|
Les directeurs et/ou les chefs connaissent parfaitement
l'importance d'une politique sécurité au sein de Biopharma:
1-Très d'accord, 2-Pas d'accord, 3-Je suis d'accord, 4-Pas du tout
d'accord
|
Q73
|
85
|
35
|
71
|
Dans notre entreprise, la locomotive de la sécurité
est le Directeur Général: 1-Très d'accord, 2-Pas
d'accord, 3-Je suis d'accord, 4-Pas du tout d'accord
|
Q76
|
90
|
30
|
75
|
Les directeurs et/ou les chefs prêtent grande attention
à tous ceux qui sont victimes d'accidents: 1-Très d'accord,
2-Pas d'accord, 3-Je suis d'accord, 4-Pas du tout d'accord
|
Q77
|
69
|
51
|
58
|
Les directeurs et/ou les chefs recherchent les causes et non les
coupables lorsqu'un accident se produit: 1-Très d'accord, 2-Pas
d'accord, 3-Je suis d'accord, 4-Pas du tout d'accord
|
Q82
|
77
|
43
|
64
|
Nous qui travaillons ici essayons de trouver la solution quand
quelqu'un identifie une menace de la sécurité dans le lieu de
travail : 1-Très d'accord, 2-Pas d'accord, 3-Je suis d'accord,
4-Pas du tout d'accord
|
Q83
|
70
|
50
|
58
|
Les directeurs et/ou les chefs s'assurent que les
problèmes de sécurité détectés pendant
l'évaluation de la sécurité de l'entreprise soient
traités immédiatement : 1-Très d'accord, 2-Pas
d'accord, 3-Je suis d'accord, 4-Pas du tout d'accord
|
IV.2- RECOMMENDATIONS
In general, from what we have observed in Biopharma, there are
some basic steps that one should consider to address the safety culture
issues for a rapid amelioration. Below are the recommendations which we
proposed.
§ Create Awareness: Corporate and/or
site leadership need an awareness of the importance of safety culture to
safety performance through exercises, seminars or workshops related to
safety issues.
§ Identify a Champion: While every
member of the organization should be a supporter of a sound safety
culture, Biopharma may require a Champion/leader. Whoever fulfils this role
must understand the dynamics of safety cultures and the process for, and
obstacles to, implementing cultural change.
§ Perform a gap
analysis: Learn/evaluate how the culture is performing. Identify
where the gaps are and prioritize a risk-based response to closing this
gaps. It should not only simply be stated but must be implemented. Elders say
«a melon cannot get rotten in one day» it is a gradual process. We
wish to develop a health and safety policy followed by the implementation of
100% of its content before December 2013.
§ Steward cultural change: Acceptable
behaviors must be modeled at all levels of the organization
through leadership by example. Values must be communicated and reinforced
frequently. By consistently reinforcing positive behaviors, linking
them to the benefits they bring, and relating these benefits to our
beliefs of why they are important, we should be able to gradually shift
the values of the organization in a positive direction.
§ Keep the organization focused: Many
organizations have already established sound safety cultures. Not
uncommonly, these cultures have been developed in response to, and are
reinforced by frequent reference to, significant loss events in the company's
past. Those organizations who are fortunate enough not to have experienced such
a similar event may find it helpful to draw the experience of others in their
industries.
CONCLUSION
We conclude that our company, Les Laboratoires Biopharma S.A
from what is observed within the two production units complies to the local
laws related to safety. The assessment also indicates that Biopharma's top
management and its personnel are committed to a certain degree above average
this can be seen an appreciable level of safety culture.
In very near future things will be finalized with the approval
of the proposed health and safety policy which we established during our
research period. The company's management is gradually putting resources at the
disposal of the newly created health and safety committee to help implement the
health and safety policy indicated above and to attain the goal which is that
of achieving the OHSAS 18001 distinction by 2014. The various datae bases being put in place will
enhance the above certification.
Given that no human act can be perfect and also considering
the short time allocated for this research, we shall appreciate that more
studies in this same domain be done with emphases on the behaviours and
perceptions of the workers outside Biopharma so as to evaluate well that safety
matters are considered by them not because of the fear to loose their job but
that of minimizing direct or indirect damages.
We should also have this saying in our minds:
«If you think safety is expensive then try an
accident»
REFERENCES
To carry out our research, we have gone through so many books
which deal with the issue of safety culture. We also supervised a student
engineer from ENSAI - NGAOUNDERE:
1. Arrête n° 039/MTPS/IMT du 26 novembre 1984,
fixant les mesures générales d'hygiènes et de
sécurité sur les lieux de travail.
2. Bergersen, C.,: Endring av sikkerhetskultur i
fragmenterte organisasjoner - utfordringer og erfaringer [Changing safety
culture in fragmented organisations - challenges and experiences]. In-depth
study spring. Department of Industrial Economics and Technology Management,
NTNU, Norway; (2003).
3. BS 8800 (1996) Guide des systèmes de management de la
santé et de la sécurité au travail - Norme britannique
très complète - 90 pages (version 2004).
4. BS OHSAS 18001:2007 Systèmes de management de la
santé et de la sécurité au travail - Norme britannique
très inspirée de l'ISO 14001 - 13 pages - Cette nouvelle version
s'est sensiblement rapprochée du référentiel international
l'ILO-OSH 2001.
5. Camilla Elén Bjørneide Bergersen: Diploma
Thesis in Safety, Health and Environment Autumn. Tools to be used to survey
and improve safety culture in the European railway industry, (2003).
6. Chemical Industries Association, 1998b. Responsible Care
Management Systems Self-Assessment.
7. Confederation of British Industry (CBI) Report, 1990.
Developing a Safety Culture-Business for Safety.
8. Cooper, M.D, Towards a Model of Safety Culture. Safety
Science, 36, 111-136. (2000).
9. Cullen, Lord. The Public Inquiry into the Piper Alpha
Disaster, HMSO. London, (1990)
10. Dominic Cooper: Improving safety Culture: A Practical
Guide, pages 3-5. ISBN 1 901128 02 4, (2001).
11. Duane A. et al, (2007). Safety Management Systems for
Airports; Volume 1: Overview; 26 pages. ISBN: 978-0-309-09896-0
12. Fennell, D., (1988). Investigation into the King's Cross
Underground Fire, Department of Transport, HMSO. London
13. Fleming, M. Effective Supervisory Safety Leadership
Behaviors in the Offshore Oil and Gas Industry. Offshore Technology Report
1999/065. ISBN 0 7176 1974 5 (2001).
14. Hartshorn, D. The safety interview. Occupational Hazards,
Vol.61 No 10. Page 107-110 (1999).
15. Health and Safety Commission (HSC). ACSNI Study Group on
Human Factors. 3rd Report: Organizing for Safety, London: HMSO, (1993).
16. Health and Safety Commission (HSC). Successful Health and
Safety Management. HS (G) 65. HSE Books. ISBN 0 7176 1276 7, (1997).
17. Health and Safety Executive (HSE), 1998a. Managing Health
and Safety: Five steps to Success. IND (G) 275. HSE Books Free leaflet.
18. Health and Safety Executive (HSE), 2002b. Framework for
Assessing Human Factors Capability. Offshore Technology Report. 2002/016.
Prepared by Nickleby HFE Ltd.
19. http://en.wikipedia.org/wiki/Safety (2012).
20.
http://www.latribune.fr/dossiers-la-tribune/entreprises/securite-industrielle/20110628trib000632874/l-oreal-dans-la-course-a-l-excellence.html
21. http://www.nestle.com/asset-library/Documents/Library/
Documents/People/People-Development-Review-EN.pdf retrieved 12th Dec 2012
22.
http://www.safetyculturetoolkit.rssb.co.uk/safety-culture-information/safety-culture-assessment/what-are-the-benefits.aspx
23.
http://www2.dupont.com/sustainable-solutions/en-us/dss/sustainable-solutions.html
, (2012 Oct).
24. IAEA. (International Atomic Energy Agency. Summary Report
on the Post-Accident Review Meeting on the Chernobyl Accident. International
Safety Advisory Group, Safety Series 75-INSAG-1-Vienna: IAEA, (1986).
25. info@proactsafety.com
(2012).
26. International Nuclear Safety Advisory Group (INSAG), Key
Practical Issues in Strengthening Safety Culture. INSAG-15. Vienna (2002).
27. JobBank USA. Safety skills--Interview questions. Retrieved
April 9, 2010, from
http://www.jobbankusa.com/interview_questions_answers/free_samples_examples/safety_skills.html.
28. McKinnon, Ron C. Safety Management: Near Miss
Identification, Recognition, and Investigation.
29.
Near-Miss Incident Reporting - It's About Trust. CLMI Safety
Training, (2011).
http://www.clmi-training.com/safetyblog/near-miss-incident-reporting-its-about-trust/
Retrieved December 2012.
30. NESTLE'S POLICY:
http://www.nestle.com/asset-library/Documents/Library/
Documents/People/People-Development-Review-EN.pdf retrieved
12th Dec 2012
31. Paul, M. Moving from Blame to Accountability. The Systems
Thinker Newsletter, Pegasus Communications, Inc., Waltham, Massachusetts,
(1997).
32. Phil. Hughes and Ed Ferrett. Published by Elsevier
Limited, pages 49 - 64, NEBOSH (National Examination Board in Occupational
Safety and Health), Third edition. ISBN 978-0-7506-8503-0, (2007).
33. Pidgeon, N.F, Safety Culture and Risk Management in
Organisations. Journal of Cross Cultural Psychology, 22, 129-140., (1991).
34. Rapport « développement
durable » Sanofi-Synthélabo-Aventis, (2001).
35. Reason, J: Managing the Risks of Organisational
Accidents. Ashgate, Kent (1997).
36. Royal Aeronautical Society; Measuring Cultural Change.
Conference of 26th April
www.raes-hfg.com/safetyculture260404.htm
(2004).
37. Schein, E.H., Organizational Culture and Leadership, 3rd Ed.,
San Francisco: Jossey-Bass, (2004).
38. Schein, Edgar H., (1992): Organisational Culture and
Leadership, 2nd Edition, Jossey-Bass, San Francisco.
39. TCHAKOUNTE Bob Patersson, in his report entitled:
«Initiation à la gestion des risques au sein de Biopharma
(Cosmetique)» (2012).
40. The Institution of Electrical Engineers (IEE), Health and
Safety Briefing, Blame Free Reporting, No 37 (2003).
41. Turner, B.A., Pidgeon, N.F., Blockley, D.I., Toft, B., Safety
Culture: its Position in Future Risk Management. Paper presented at the Second
World Back Workshop on Safety Control and Risk Management, Karlstad, Sweden
(1989).
42. UK Health and Safety Executive, Safety Culture: A Review of
the Literature, HSL/2002/25, (2002).
43. Weick, Karl E. and Sutcliffe, Kathleen M., Managing the
Unexpected, Jossey-Bass, (2001).
44. Wert, J., (1986) `Safety Culture at Nuclear Plants'. An
Unpublished Essay, as cited in O'Hara, P. (2003). `Nuclear Safety Culture: An
Organisational Development Model'.
http://www.ucelarsafetyculture.freeyellow.com
45. Whittingham, R.B., The Blame Machine. Why Human Error Causes
accidents. Elsevier (2004).
APPENDICES:
Appendix A - Codage questionnaire d'évaluation niveau
sécurité au sein des Laboratoires BIOPHARMA S.A ayant pour objet
d'améliorer la culture sécurité.
N°
|
Questions
|
CHOIX (Chiffre)
|
|
I-PROFIL DE L'ENQUETE (WORKER)
|
|
Q1
|
AGE : 1- [1955-1965[ 2- [1965-1975[ 3- [1975-1985[
4- [1985-1995[ 5-Omission
|
|
Q2
|
Sexe : 1-M 2-F 3- omission
|
|
Q3
|
Votre rang dans Les Laboratoires BIOPHARMA S.A. :1- Cadre
supérieur,
2-Cadre, 3- Agent de maitrise, 4-Ouvrier, 5- Autres
|
|
Q4
|
Vous travaillez principalement dans quelle section : 1-
Cosmétiques, 2- Plastiques,
3- Administration, 4- Commercial, 5- Autres
|
|
|
II- EXPERIENCES PROFESSIONNEL / Working
experience
|
|
Q5
|
Avez-vous déjà travaillé ailleurs avant
d'arrivée à Biopharma? 1-oui 2- non
|
|
Q6
|
Votre poste dans l'entreprise : 1- USINE
(Cosmétiques- Plastiques), 2- Administration, 3- Commercial, 4-
LABORATOIRE 6- AUTRES
|
|
Q7
|
Qui est votre chef HIERARCHIQUE DIRECT : 1-DG, 2-CE 3- DAF
4-DEX 5-DMC 6-CDM 7-CDC 8- CDP 9-CASO 10- CASE 11- AT INJ 12-ATFAB MECA
13-CQ 14- CAT COND 15- CAG 16- MP/AC 17- PF 18- AHAT 19- COMPTA 20- RH
21- VENTE 22- CGESTION 23- GARDIEN 24- CHEF EQUIP 25- AUTRES
|
|
Q8
|
Travaillez-vous en service de quart : 1- OUI 2- Non
|
|
Q9
|
Votre ancienneté dans Biopharma S.A: 1- [0 - 1 [ANS
2- [1 - 5[ans 3- [5-10[ans 4- [10 - 11] ANS
|
|
Q10
|
Votre ancienneté à votre poste actuel: 1-
[0 - 1 [ANS 2- [1 - 5[ans 3- [5-10[ans 4- [10 - 11] ANS
|
|
|
III-GESTION DES RISQUES PAR LA HIERARCHIE /
RISK MANAGEMENT BY THE HIERARCHY OF BIOPHARMA
|
|
|
A - FORMATION et SURVI / TRAINING and
SUPERVISION (Learning culture)
|
|
Q11
|
Connaissez-vous la différence entre Equipement pour la
Protection Collective (EPC) et Equipement pour la Protection Individuelle (EPI)
? 1-oui 2-non
|
|
Q12
|
Citez 2 exemples des EPC : 1-deux justes 2-un juste
3-zero
|
|
Q13
|
Citez 2 exemples des EPI : 1-deux justes 2-un juste
3-zero
|
|
Q14
|
Connaissez-vous tous les membres de notre comité
d'hygiène, sécurité et santé - CHSST? 1-oui
2-non
|
|
Q15
|
Connaissez-vous la différence entre actes dangereux et
conditions dangereuses ? 1-oui 2- non
|
|
Q16
|
Citez deux (2) exemples des conditions dangereuses :
1-deux justes 2-un juste 3-zero
|
|
Q17
|
Donnez trois exemples des actes dangereux : 1-Trois
justes 2-deux justes 3-un juste 4-zero
|
|
Q18
|
Avez-vous déjà entendu parler de » culture
sécurité» ? 1 - oui 2-non
|
|
Q19
|
Avez-vous une idée sur la notion »culture
sécurité» dans une entreprise? 1- oui 2- non
|
|
Q20
|
Si OUI, exprimez-en brièvement:
|
|
Q21
|
Les directeurs et/ou les chefs à travers des formations
s'assurent que tout un chacun influence positivement sur la santé et
sécurité pendant l'exercice de leur fonction : 1-Très
d'accord, 2-Pas d'accord, 3-Je suis d'accord, 4-Pas du tout d'accord
|
|
Q22
|
Nous qui travaillons ici constatons que chaque personnel
nouvellement arrivée reçoit la formation en
sécurité: 1-Très d'accord, 2-Pas d'accord, 3-Je suis
d'accord, 4-Pas du tout d'accord
|
|
Q23
|
Nous qui travaillons à Biopharma aidons chacun à
travailler en sécurité par des multiples sensibilisations:
1-Très d'accord, 2-Pas d'accord, 3-Je suis d'accord, 4-Pas du tout
d'accord
|
|
Q24
|
Nous qui travaillons ici savons que les dangers sont
présent partout et estimons que le risque est inévitable:
1-Très d'accord, 2-Pas d'accord, 3-Je suis d'accord, 4-Pas du tout
d'accord
|
|
Q25
|
Nous qui travaillons ici estimons que seule une
catégorie du personnel est expose aux dangers: 1-Très d'accord,
2-Pas d'accord, 3-Je suis d'accord, 4-Pas du tout d'accord
|
|
Q26
|
Nous qui travaillons ici avons confiance entre nous en ce qui
concerne la maitrise de la sécurité au travail :
1-Très d'accord, 2-Pas d'accord, 3-Je suis d'accord, 4-Pas du tout
d'accord
|
|
Q27
|
Faire la ronde du site régulièrement n'a pas
d'effet sur la sécurité: 1-Très d'accord, 2-Pas
d'accord, 3-Je suis d'accord, 4-Pas du tout d'accord
|
|
Q28
|
Si nous sommes proactives, les risques sont minimisés:
1-Très d'accord, 2-Pas d'accord, 3-Je suis d'accord, 4-Pas du tout
d'accord
|
|
Q29
|
En multipliant les rondes sur un site, nous détectons
rapidement les dangers majeurs et les risques liés aux dits
dangers : 1-Très d'accord, 2-Pas d'accord, 3-Je suis d'accord,
4-Pas du tout d'accord
|
|
|
B - RESPECT DES PROCEDURE EN SECURITE /
SAFE WORK PROCEDURES
|
|
Q30
|
Les directeurs encouragent le personnel de Biopharma à
travailler conformément aux exigences de la règlementation en
vigueur portant sur l'hygiène, la sécurité et la
santé, même lorsque le programme est très surchargé
: 1-Très d'accord, 2-Pas d'accord, 3-Je suis d'accord, 4-Pas du
tout d'accord
|
|
Q31
|
Les directeurs et/ou les chefs se rassurent que chacun
reçoit les informations nécessaire concernant la
sécurité : 1-Très d'accord, 2-Pas d'accord, 3-Je
suis d'accord, 4-Pas du tout d'accord
|
|
Q32
|
Les directeurs et/ou les chefs s'assurent que tous nos
sous-traitants travaillent selon les règles de la
sécurité : 1-Très d'accord, 2-Pas d'accord, 3-Je
suis d'accord, 4-Pas du tout d'accord
|
|
Q33
|
Nous qui travaillons ici ne faisons plus d'effort en
sécurité parce que nous sommes tous assures: 1-Très
d'accord, 2-Pas d'accord, 3-Je suis d'accord, 4-Pas du tout d'accord
|
|
Q34
|
Nous qui travaillons ici ne prenons aucune
responsabilité pour la sécurité de chacun: 1-Très
d'accord, 2-Pas d'accord, 3-Je suis d'accord, 4-Pas du tout d'accord
|
|
Q35
|
Tant qu'un accident ne se produit pas, nous qui travaillons
ici ne s'intéressons pas aux comportements dangereux :
1-Très d'accord, 2-Pas d'accord, 3-Je suis d'accord, 4-Pas du tout
d'accord
|
|
Q36
|
Nous qui travaillons ici ne respectons pas les mesures de
sécurité: 1-Très d'accord, 2-Pas d'accord, 3-Je suis
d'accord, 4-Pas du tout d'accord
|
|
Q37
|
Nous qui travaillons ici pensons que nos fournisseurs et
visiteurs ne doivent pas s'intéresser à la sécurité
au sein de la société: 1-Très d'accord, 2-Pas d'accord,
3-Je suis d'accord, 4-Pas du tout d'accord
|
|
Q38
|
Nous qui travaillons ici acceptons de nous exposer à
tout genre de danger surtout quand le volume du travail est grand:
1-Très d'accord, 2-Pas d'accord, 3-Je suis d'accord, 4-Pas du tout
d'accord
|
|
Q39
|
Nous de Biopharma pensons que seuls les employés
doivent avoir les informations concernant la sécurité au travail:
1-Très d'accord, 2-Pas d'accord, 3-Je suis d'accord, 4-Pas du tout
d'accord
|
|
Q40
|
Nous qui travaillons ici n'acceptons jamais de prendre des
risques surtout quand le volume du travail est grand: 1-Très d'accord,
2-Pas d'accord, 3-Je suis d'accord, 4-Pas du tout d'accord
|
|
Q41
|
Nous qui travaillons ici parlons de la sécurité
constamment durant l'exercice d'une tache surtout quand il n'y a pas eu
accident: 1-Très d'accord, 2-Pas d'accord, 3-Je suis d'accord,
4-Pas du tout d'accord
|
|
Q42
|
Nous qui travaillons ici tirons des leçons à
partir de nos expériences dans la prévention des accidents :
1-Très d'accord, 2-Pas d'accord, 3-Je suis d'accord, 4-Pas du tout
d'accord
|
|
Q43
|
L'achat et le port des équipements de protection
individuel est nécessaire et suffisant pour être à l' abri
des accidents : 1-Très d'accord, 2-Pas d'accord, 3-Je suis
d'accord, 4-Pas du tout d'accord
|
|
Q44
|
Nous savons que conduire les engins dans les
périmètres de l'usine par n'importe qui est mieux (moins
risquant) que sur la voie publique: 1-Très d'accord, 2-Pas d'accord,
3-Je suis d'accord, 4-Pas du tout d'accord
|
|
Q45
|
Notre attitude par rapport à la sécurité
peut influencer le comportement des autres membres de l'équipe :
1-Très d'accord, 2-Pas d'accord, 3-Je suis d'accord, 4-Pas du tout
d'accord
|
|
Q46
|
Lors que nous n'avons pas assez de temps pour faire un
travail, il est préférable de ne pas analyser les risques
éventuels lies à ce boulot : 1-Très d'accord, 2-Pas
d'accord, 3-Je suis d'accord, 4-Pas du tout d'accord
|
|
Q47
|
Dans notre entreprise, il y a très peu des couloirs
pour circuler parce que les magasiniers occupent pratiquement toutes les
espaces disponibles: 1-Très d'accord, 2-Pas d'accord, 3-Je suis
d'accord, 4-Pas du tout d'accord
|
|
|
C - CONSULTATIONS - COMMUNICATION /
REPORTING SAFETY
|
|
Q48
|
Les directeurs et/ou les chefs s'assurent que les
problèmes de sécurité sont toujours pris en compte et
résolus rapidement lorsque ceux-ci sont signales : 1-Très
d'accord, 2-Pas d'accord, 3-Je suis d'accord, 4-Pas du tout d'accord
|
|
Q49
|
Lorsque le personnel détecte un risque et le soumet
à la hiérarchie, les directeurs et/ou les chefs l'ignorent et ne
mènent aucune action : 1-Très d'accord, 2-Pas d'accord,
3-Je suis d'accord, 4-Pas du tout d'accord
|
|
Q50
|
Les directeurs et/ou les chefs encouragent les employés
à participer activement dans la prise de décision portant sur la
santé et la sécurité: 1-Très d'accord, 2-Pas
d'accord, 3-Je suis d'accord, 4-Pas du tout d'accord
|
|
Q51
|
Les directeurs et/ou les chefs ne demandent jamais l'opinion
du personnel avant de prendre des décisions concernant la
sécurité : 1-Très d'accord, 2-Pas d'accord, 3-Je
suis d'accord, 4-Pas du tout d'accord : 1-Très d'accord, 2-Pas
d'accord, 3-Je suis d'accord, 4-Pas du tout d'accord
|
|
Q52
|
Les directeurs et/ou les chefs ne prennent jamais en compte
les suggestions du personnel portant sur la santé et
sécurité lors des achats des nouvelles machines:1-Très
d'accord, 2-Pas d'accord, 3-Je suis d'accord, 4-Pas du tout d'accord
|
|
Q53
|
Pour nous qui travaillons ici, nous prenons une double
responsabilité pour s'assurer que le lieu de service demeure toujours
propre: 1-Très d'accord, 2-Pas d'accord, 3-Je suis d'accord, 4-Pas
du tout d'accord
|
|
Q54
|
Nous qui travaillons ici évitons d'analyser les
risques que nous détectons pendant l'exercice de notre travail:
1-Très d'accord, 2-Pas d'accord, 3-Je suis d'accord, 4-Pas du tout
d'accord
|
|
Q55
|
Nous qui travaillons ici nous nous sentons en
sécurité pour un travail d'ensemble : 1-Très
d'accord, 2-Pas d'accord, 3-Je suis d'accord, 4-Pas du tout d'accord
|
|
Q56
|
La sécurité doit être assurée
uniquement par le patron de l'entreprise: 1-Très d'accord, 2-Pas
d'accord, 3-Je suis d'accord, 4-Pas du tout d'accord
|
|
Q57
|
Nous qui travaillons ici savons que la sécurité
est l'affaire de tous et de chacun: 1-Très d'accord, 2-Pas d'accord,
3-Je suis d'accord, 4-Pas du tout d'accord
|
|
Q58
|
Nous qui travaillons ici prenons très au sérieux
les opinions et suggestions de chacun lors des débats portant sur la
sécurité : 1-Très d'accord, 2-Pas d'accord, 3-Je
suis d'accord, 4-Pas du tout d'accord
|
|
Q59
|
Nous qui travaillons ici parlons toujours librement et
ouvertement des choses concernant notre sécurité au lieu de
travail : 1-Très d'accord, 2-Pas d'accord, 3-Je suis d'accord,
4-Pas du tout d'accord
|
|
Q60
|
Grace au grand nombre d'Ordinateurs avec accès
à l'internet plus les BlackBerry au sein de notre entreprise tous le
personnel est rapidement informe des problèmes de
sécurité: 1-Très d'accord, 2-Pas d'accord, 3-Je suis
d'accord, 4-Pas du tout d'accord
|
|
Q61
|
La peur des sanctions à infliger par les directeurs
et/ou les chefs empêchent le personnel de Biopharma de déclarer
les incidences ou presque-accident : 1-Très d'accord, 2-Pas
d'accord, 3-Je suis d'accord, 4-Pas du tout d'accord
|
|
Q62
|
Nous qui travaillons ici pensons que la formation en
sécurité au travail réduit les bénéfices de
notre société : 1-Très d'accord, 2-Pas d'accord,
3-Je suis d'accord, 4-Pas du tout d'accord
|
|
Q63
|
Nous qui travaillons ici pensons que la sensibilisation et la
formation en sécurité au travail aident très peu dans la
prévention des accidents dans notre société :
1-Très d'accord, 2-Pas d'accord, 3-Je suis d'accord, 4-Pas du tout
d'accord
|
|
|
D - ENGAGAEMENT DE L'ENCADREMANT /
MANAGEMENT COMMITMENT
|
|
Q64
|
Les directeurs et/ou les chefs sont laxistes lorsqu'un
employé ignore les notions de sécurité lors de l'exercice
d'un travail : 1-Très d'accord, 2-Pas d'accord, 3-Je suis
d'accord, 4-Pas du tout d'accord
|
|
Q65
|
Les directeurs et/ou les chefs donnent plus de
considération à la sécurité plus que la production:
1-Très d'accord, 2-Pas d'accord, 3-Je suis d'accord, 4-Pas du tout
d'accord
|
|
Q66
|
Les directeurs et/ou les chefs connaissent parfaitement
l'importance d'une politique sécurité au sein de Biopharma:
1-Très d'accord, 2-Pas d'accord, 3-Je suis d'accord, 4-Pas du tout
d'accord
|
|
Q67
|
Les directeurs et/ou les chefs acceptent que les
employés de Biopharma prennent des risques quand le travail est
intense : 1-Très d'accord, 2-Pas d'accord, 3-Je suis d'accord,
4-Pas du tout d'accord
|
|
Q68
|
Les directeurs et/ou les chefs n'ont pas la volonté
pour gérer la sécurité au sein de Biopharma:1-T
rès d'accord, 2-Pas d'accord, 3-Je suis d'accord, 4-Pas du tout
d'accord
|
|
Q69
|
Les directeurs et/ou les chefs apprécient le coût
de la sécurité seulement après un accident:1-Très
d'accord, 2-Pas d'accord, 3-Je suis d'accord, 4-Pas du tout d'accord
|
|
Q70
|
Les directeurs et/ou les chefs déploient tous les
moyens aux personnels pour que chacun puisse acquérir suffisamment de
notion et de pratique en matière de la sécurité :
1-Très d'accord, 2-Pas d'accord, 3-Je suis d'accord, 4-Pas du tout
d'accord
|
|
Q71
|
Nous qui travaillons ici pensons que la production a plus de
valeur que la sécurité: 1-Très d'accord, 2-Pas d'accord,
3-Je suis d'accord, 4-Pas du tout d'accord
|
|
Q72
|
Nous qui travaillons ici refusons de respecter les mesures de
sécurité surtout quand il faut terminer le travail à
temps: 1-Très d'accord, 2-Pas d'accord, 3-Je suis d'accord, 4-Pas du
tout d'accord
|
|
Q73
|
Dans notre entreprise, la locomotive de la
sécurité est le Directeur Général: 1-Très
d'accord, 2-Pas d'accord, 3-Je suis d'accord, 4-Pas du tout d'accord
|
|
Q74
|
Nous qui travaillons ici estimons que l'augmentation de
bénéfice dans notre entreprise signifie que la
sécurité sur nos lieux de travail augment : 1-Très
d'accord, 2-Pas d'accord, 3-Je suis d'accord, 4-Pas du tout d'accord
|
|
|
E - GESTION DES ACCIDENTS/INCIDENTS /
INJURY MANAGEMENT
|
|
Q75
|
Connaissez-vous tous les membres de notre comité
d'hygiène, sécurité et santé - CHSST? 1-oui
2-non
|
|
Q76
|
Les directeurs et/ou les chefs prêtent grande attention
à tous ceux qui sont victimes d'accidents: 1-Très d'accord,
2-Pas d'accord, 3-Je suis d'accord, 4-Pas du tout d'accord
|
|
Q77
|
Les directeurs et/ou les chefs recherchent les causes et non
les coupables lorsqu'un accident se produit: 1-Très d'accord, 2-Pas
d'accord, 3-Je suis d'accord, 4-Pas du tout d'accord
|
|
Q78
|
Les directeurs et/ou les chefs font toujours des reprochent
à tous ceux qui sont victimes d'un accident: 1-Très d'accord,
2-Pas d'accord, 3-Je suis d'accord, 4-Pas du tout d'accord
|
|
Q79
|
Nous qui travaillons ici enregistrons systématiquement
dans un registre tous les incidents majeurs et accidents: 1-Très
d'accord, 2-Pas d'accord, 3-Je suis d'accord, 4-Pas du tout d'accord
|
|
Q80
|
Nous qui travaillons ici considérons les accidents
mineurs comme un évènement normal dans l'exercice de notre
travail quotidien: 1-Très d'accord, 2-Pas d'accord, 3-Je suis
d'accord, 4-Pas du tout d'accord
|
|
Q81
|
Il faut absolument punir les coupables lorsqu'un accident se
produit dans notre entreprise afin que cela ne se répète plus:
1-Très d'accord, 2-Pas d'accord, 3-Je suis d'accord, 4-Pas du tout
d'accord
|
|
Q82
|
Nous qui travaillons ici essayons de trouver la solution quand
quelqu'un identifie une menace de la sécurité dans le lieu de
travail : 1-Très d'accord, 2-Pas d'accord, 3-Je suis d'accord,
4-Pas du tout d'accord
|
|
Q83
|
Les directeurs et/ou les chefs s'assurent que les
problèmes de sécurité détectés pendant
l'évaluation de la sécurité de l'entreprise soient
traités immédiatement : 1-Très d'accord, 2-Pas
d'accord, 3-Je suis d'accord, 4-Pas du tout d'accord
|
|
Appendix B - Project of a Health and Safety Policy
statement
Les Laboratoires Biopharma S.A is committed to providing and
maintaining a safe and healthy workplace for all staff, and to providing the
information, training and supervision needed to achieve this aim.
Our objectives for this period will be the following:
1. Put in place a health and safety committee.
2. Identification of dangers within Biopharma I and store the
informations inside a register.
3. Have in each service two well-trained fire fighters.
4. A person trained in each of our units who will crosscheck
the whole sections and make sure the level of risk minimized (with respect to
the dangers identified).
5. Ameliorate the working conditions in the packaging service
of Biopharma I by increasing ventilation and reducing noise.
Les Laboratoires Biopharma S.A will take responsibility for
health and safety procedures, however, employees need to be aware of their
responsibilities and comply with the business' health and safety policy.
Each employee is encouraged to play a vital and responsible
role in maintaining a safe and healthy workplace through:
§ Being involved in the workplace health and safety
system.
§ Sticking to correct procedures and equipment.
§ Wearing protective clothing and equipment as and when
required.
§ Reporting any painful situation or discomfort in the
working environment as soon as possible.
§ Ensuring all accidents and incidents are reported.
§ Helping new employees, trainees, contractors and
visitors to the workplace understand the right safety procedures and why they
exist.
§ Telling your manager immediately of any health and
safety concerns.
§ Keeping the work place to minimize the risk of any
trips and falls.
This health and safety policy will only be effective and
efficient if all of us follow it.
We shall review our health and safety policy once each year
and/or whenever there is need.
Thanks for your participation within our company to enhance
the achievement of our goal, the safety culture.
Done in DOUALA on the 13th of August 2012
THE MANAGING DIRECTOR
DJOMOU NANA Francis
Appendix C - Installation of the health and safety committee -
BIOPHARMA
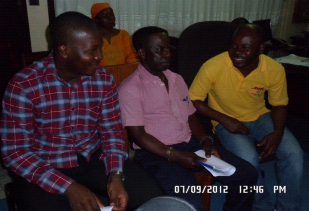
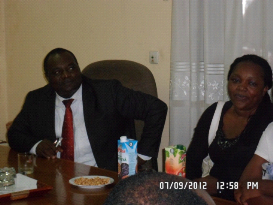
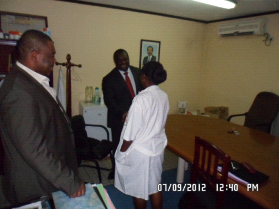
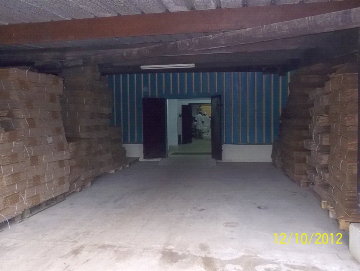
COMPARE THE TWO IMAGES AND APPRECIATE THE NOTION OF CONTINUOUS
AMELIORATION AUGUST / OCTOBER 2012
Appendix D - Trainings
received by the health and safety committee of BIOPHARMA
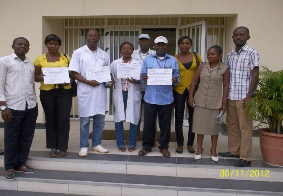
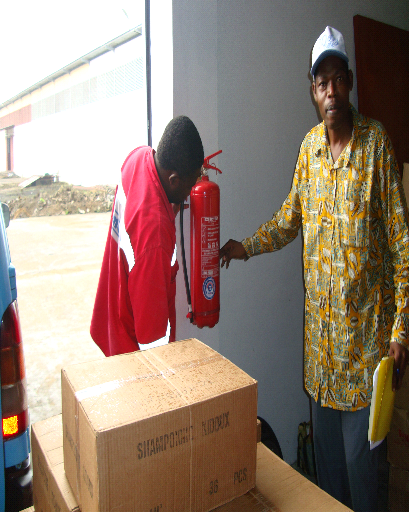
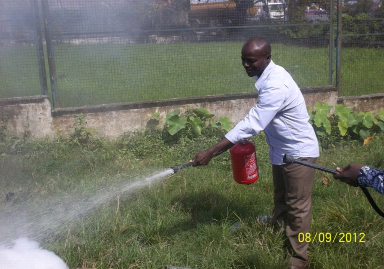 
|