|
Yassir RAMDANI
Tuteur : Fabien BRUNESEAUX
|
Maîtrise des corrections en silicium dans la
fonte à graphite
sphéroïdale
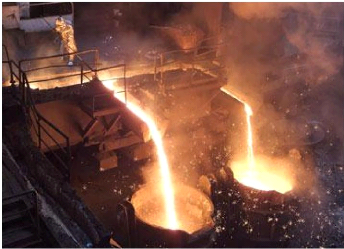
Stage de M2 SPM SIMM Effectué à Saint Gobain PAM 04
fev 2013 - 31 juil 2013

2
Remerciements
Je remercie Fabien BRUNESEAUX d'avoir été mon
maître de stage qui m'a proposé un stage intéressant, ainsi
que pour son aide tout au long de mon stage.
Je tiens à remercier aussi toutes les personnes des
services métallurgie et centrifugation du CRD pour leur accueil ainsi
que leur aide.
Je remercie aussi l'équipe du secteur métal de
l'usine et particulièrement Mathieu BRENIERE pour leur aide durant tous
mes essais en usine.
Je remercie aussi Pierre Gras-Yager et Antoine Vaugeois dont la
correspondance journalière m'a permis de rompre avec la monotonie de cet
été inespéré.
3
Table des Matières
I. Introduction 4
II. Analyse des FeSi utilisés 6
A. Analyse du produit actuellement utilisé 6
Granulométrie 6
Analyse élémentaire et analyse de phase 7
B. Analyse du FeSi 10 - 80mm 9
C. Déroulement des essais 10
Correction en four mi plein : 10
Correction en four plein 11
Correction en poche 11
Essais en usine 12
III. Essais CRD 13
A. Essais en four semi plein 13
B. Essais en poche 14
C. Essais en four plein 15
D. Récapitulatif 16
IV. Essais Usine 17
A. Essais en Four 18
Correction 0.05% 18
Corrections 0.15% 19
Correction 0.3% (en deux apports) 21
Correction 0.3% (en 1 apport) 22
B. Essai en poche 23
Essai 0.15% 24
Risque de fusion partiel du FeSi 26
V. Discussions 27
A. Meilleur rendement à 4min de brassage 27
B. Comparaison Four - Poche 27
C. Comparaison FeSi 2 - 10mm et 10 - 80mm 28
D. Influence du niveau de correction 29
VI. Conclusion 30
VII. Perspectives 31
4
I. Introduction
L'activité de l'usine Saint-Gobain PAM se positionne
principalement sur les canalisations et les plaques de voirie les canalisations
en Fonte à graphite sphéroïdal. Ces pièces doivent
faire preuve d'élasticité et de résilience, la
présence de précipités de cémentite est donc
à bannir.
Le silicium, principal élément d'alliage dans
les fontes après le carbone, a un comportement qui favorise la
précipitation du carbone en graphite et donc limite la formation de
carbures. Le chrome, au même titre que d'autres éléments
tels que le manganèse, le molybdène ou le vanadium, favorise la
combinaison du carbone et du fer en cémentite ou en carbures mixtes (Fe,
M)3 C entre autres.
Pour éviter la présence de cémentite, le
taux de silicium minimum requis devra mener
à un rapport > 16. Le taux de chrome
équivalent n'étant pas
modifiable, on joue sur le taux de Si pour atteindre le bon
indice de trempe. Pour atteindre la teneur en Si requise, du ferro-silicium est
régulièrement ajouté à différents stades du
circuit métal.
Ces corrections sont effectuées sous des
paramètres différents pouvant avoir des effets plus ou moins
néfastes sur le rendement de dissolution du ferro-silicium. Les ajouts
se font suivants les modes d'introduction cités :
· Ferro-Silicium en fond de poche avant remplissage
· Ferro-Silicium sur bain dans un four à
moitié plein, brassage puis remplissage du four
· Ferro-Silicium sur four plein puis brassage
Le ferro-silicium, utilisé pour toutes les corrections
présentées, a une plage de granulométrie de 2 à 10
mm à 75w% de Si, fourni par MICON®.
Le but de cette étude est de déterminer s'il y
a des différences de rendement en fonction de différents
paramètres tels que :
· Le mode d'introduction
· La granulométrie
· La chimie du FeSi
· Le taux de correction en Si
Dans un premier temps une série d'essais ont
été faits au centre de recherche sur des charges de 50kg en four
et 100 kg en poche. Ensuite les essais se feront à l'échelle de
l'usine sur les poches de transfert de 9T et les fours de maintien de 23 et
24T.
Suite à un entretien avec un employé chez
ELKEM®, il a été mis en évidence qu'en fonction de la
granulométrie et de la teneur en Si, les différents
ferro-alliages ne sont pas utilisés pour les mêmes fonctions.
5
Lors de correction en four, un ferro-silicium à 75w% de
Si est privilégié avec une granulométrie
élevée (10-80mm ou 50-150mm). Le point de fusion se situe aux
alentours de 1325°C et la réaction sera exothermique.
Pour une correction en poche, il est recommandé
d'utiliser du FeSi à 55 - 60 w% son point de fusion est plus bas
~1260°C et la réaction est endothermique.
Il est aussi conseillé d'utiliser une
granulométrie plus fine de 2 - 10mm. Étant donné qu'il n'y
a pas de source de chaleur qui aide à faire fondre la charge, la plus
grande surface spécifique permet un échange de calories plus
rapide.
Il est préférable de choisir un ferro-alliage
ayant un point de fusion le plus bas possible afin de dissoudre toute la charge
de ferro-silicium avant de couler.
Ceci étant d'autant plus valable quand le silicium est
utilisé comme inoculant et donc mis dans la poche juste avant la
coulée ou directement injecté dans le jet de coulée.
6
II. Analyse des FeSi utilisés
Pour l'étude, différents FeSi ont été
utilisé :
? FeSi 75% Si 2 - 10 mm fourni par MICON® (actuellement
utilisé à l'usine).
? FeSi 75% Si 10 - 80mm fourni par MICON®.
Ces produits ont, dans un premier temps, été
analysé par :
? Granulométrie : pour vérifier l'étendue
et la distribution de taille dans les grains (seulement pour le 2 - 10mm).
? Florescence X : pour déterminer le taux de Si.
? Diffraction des rayons X : pour révéler la
présence de phases néfastes.
A. Analyse du produit actuellement
utilisé
Dans un premier temps, nous avons étudié le FeSi
utilisé à l'usine. C'est un FeSi75 d'une granulométrie de
2 - 10mm fourni par MICON®.
Granulométrie
Un échantillon de 80kg constitué de 3
prélèvements distincts a été tamisé, afin de
vérifier la répartition de la granulométrie dans le
produit.
Tranche
|
m (kg)
|
Pourcentage
|
Ø > 10
|
0,15
|
0,19%
|
6,3 < Ø < 10
|
6,23
|
7,82%
|
2 < Ø < 6,3
|
62,49
|
78,44%
|
Ø < 2
|
10,79
|
13,54%
|
Total
|
79,66
|
100,00%
|
Figure 1 : Analyse granulométrique FeSi
actuellement utilisé à Saint-Gobain Pa
Deux Tamis (mailles de 2 mm et 10mm) ont été
choisis afin de déterminer le taux de FeSi hors gabarit. Un autre tamis
de maillage 6.3mm sert à déterminer si la taille des grains tend
plutôt vers le haut ou le bas de la plage de granulométrie.
On remarque que les granulats de faible dimension (2 <
Ø < 6,3) sont majoritaires, de plus les fines (Ø < 2)
représentent plus de 13% de la masse étudiée.
Dans le but de vérifier
l'homogénéité des produits en fonction de la
granulométrie, une analyse par Fluorescence X et DRX a été
effectuée sur les tranches granulométriques suivantes :
? Ø < 2
? 2 < Ø < 6,3 ? 6,3 < Ø
< 10
Analyse élémentaire et analyse de phase

Figure 3 : Analyse fluorescence X du FeSi actuellement
utilisé à Saint-Gobain PAM
M % ?
Fines ? Si ?
Fines ? M 2 6 .3 % 2 6
.3
Si calculé ? MTotal
10.79x 0.66 ? 62.49x 0.72 ? 6.23x 0.69
Figure 2 : Analyse DRX du FeSi actuellement
utilisé à Saint-Gobain PAM
Si ? 6. 3 10 % 6 .3
10
M Si
? ? ? ?
7
Le pourcentage de Si des produits mesuré est compris
entre 66 et 72 %. De plus, les produits contiennent des éléments
résiduels (tels que Al, Ca, etc...). On remarque que le taux de Si de
l'échantillon non tamisé n'est pas celui annoncé par la
spécification. Le taux mesuré de 72% reste cohérent, par
rapport aux pourcentages de Si des différentes tranches
granulométriques, si l'on calcule le taux de Si du ferro-alliage
à l'aide d'une loi des mélanges.
Le résultat obtenu est en adéquation avec le
taux mesuré à 72 % de Si. La granulométrie 2-6.3mm
représente près de 80% de la masse totale il n'est donc pas
étonnant que l'analyse du produit non tamisé soit proche en terme
de Si.
8
Un rendement maximal théorique peut être
calculé d'après les informations précédentes:
= Rendement Théorique Calculé
= 94.7%
Le rendement maximal théorique serait donc de 94.7%
Les taux des autres échantillons analysés sont
encore plus bas, ce qui peut constituer un réel problème de
rendement car les différences de dimensions favorisent la
décantation des fines, lors du transport des BigBag de FeSi et du
remplissage des trémies de distribution, il est donc possible de
déplorer des chutes de rendement sur certaines corrections.
On remarque aussi des disparités dans les taux de fer
et d'éléments résiduels des différentes plages
granulométriques. Des suppositions peuvent être émises sur
l'origine diverses des produits, 6.3 - 10mm constitué de déchets
issus de la production d'un FeSi de granulométrie 10 - 80mm. Une analyse
des phases en présence des différents produits est donc faite
à la diffraction des rayons X.
En plus de contenir un taux en Si inférieur à la
spécification, les plages dimensionnelles < 2mm et 6.3 - 10 mm
contiennent des carbures de silicium ainsi que du quartz. Le carbure de
Silicium n'est pas réellement problématique car certaine
entreprises s'en servent pour leurs corrections en Si. Par contre, le quartz ne
réagit pas dans la fonte et finit tel quel dans les crasses qui
surnagent dans le bain.
En plus de contenir moins de Silicium que prévu, la
présence de quartz diminue encore le rendement du ferro-silicium. Le
taux de quartz reste tout de même très bas (inférieur
à 3%. Analyse semi quantitative en DRX).
9
B. Analyse du FeSi 10 - 80mm
|
|
Figure 4 : Analyse DRX du FeSi 10 - 80mm testé en
usine
|
Figure 5 : Analyse fluorescence X du FeSi 10 - 80mm
testé en usine
L'analyse fluorescence X du FeSi 10 - 80 mm fait apparaitre un
taux de Si de 71% au lieu des 75% annoncées
On peut d'attendre donc à un rendement maximal réel
calculé de : = 94.67%
En cas de réaction totale du Si contenu dans les FeSi
analysé, le rendement mesuré devrait être de 94.67%.
L'échantillon a aussi été soumis aux DRX
afin de mettre en évidence la présence ou l'absence de phases
néfaste, tel le quartz.
Dans ce FeSi, seules les phases qu'on serait en droit
d'attendre en lisant le diagramme de phases sont présentes.
Ce FeSi n'ayant pas de phases inertes, la totalité de
son Si devrait agir lors d'une correction.
10
C. Déroulement des essais
Comme mentionné précédemment, l'influence
du mode d'introduction a été étudiée suivant les
séries d'essais suivantes. Tous ces essais ont d'abord été
simulés au CRD avant d'être mis en place à l'usine.
Correction en four mi plein :

Figure 6 : Description Essai en four semi-plein
(CRD)
Pour ces essais des charges de 50kg sont mises en fusion.
Après mise en température, une poche de 20kg sera remplie. On
corrige alors la fonte (en prenant compte de la fonte qui sera ajoutée
pour remplir le four). Le four est brassé durant 2 minutes avant
remplissage du four par la fonte retirée au préalable.
11
Correction en four plein
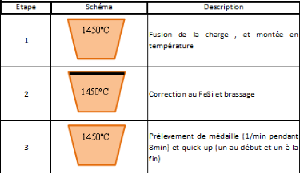
Figure 7 : Description Essai en four plein
(CRD)
Après fusion de la charge, le ferro-silicium sera mis
sur la surface du bain après décrassage. La charge sera ensuite
brassée dans le four pendant 2minutes.
Correction en poche
Le ferro-silicium est mis en fond de poche avant remplissage
de celle-ci par de la fonte liquide. L'agitation du remplissage sera le seul
"moteur" de brassage du ferro-silicium.
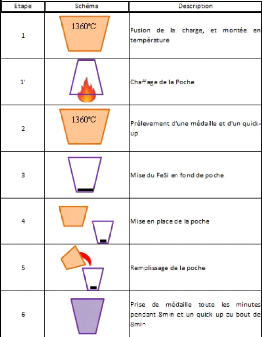
12
Figure 8 : Description Essai en poche (CRD)
Essais en usine
S'en suivront des essais en usine sur les fours CEM® et
Junker®. Les corrections seront apportées pour augmenter le taux de
Si d'un four plein de 0.15 et 0.3% (2 modes d'introduction : en une fois et en
deux fois). Avec différentes granulométries 2-10mm et 10-80mm.
III. Essais CRD
Des essais de correction ont été faits avec des
quantités identiques pour chaque plage granulométrique. Le taux
de silicium devra théoriquement monter de 0.31%.
A. Essais en four semi plein
La première série d'essais de fera dans un four de
50kg contenant une fonte à 1.8% de Si. Le taux final recherché
est donc de 2.11% de Si. Cet essai de laboratoire simulera les corrections
effectuées à l'usine sur les fours CEM.
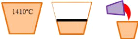
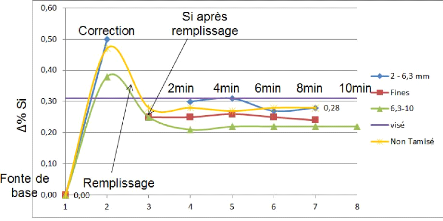
Prélèvements
13
Figure 9 : Résultat essai four semi-plein
CRD
Les résultats de rendements finaux sont
présentés dans le tableau ci-dessous :
Plage Granulométrique
|
fines
|
2 - 6,3 mm
|
6,3 - 10 mm
|
Non Tamisé
|
Rendement final
|
77,42
|
90,32
|
70,97
|
90,32
|
Comme attendu, le meilleur rendement est détenu par le
FeSi 2 - 6.3mm et de fait le non tamisé (composé à
près de 80% de 2 - 6.3mm). On remarque que le FeSi 6.3 - 10mm a un
rendement moins bon que les fines (< 2mm) malgré un taux de Si plus
important, d'après les mesures en Fluorescence X. Cette
différence en silicium peut être due à un taux de quartz
plus important dans le 6.3 - 10mm que dans les fines et donc un rendement
effectif plus faible malgré un taux de Si apparemment plus haut.
B. Essais en poche
Cette série d'essais se fera sur des poches de 125kg.
La correction sera toujours faite de manière à augmenter le taux
de Si de 0.31%. Ici seront simulées les corrections dans les poches de
transfert qui cheminent la fonte des mélangeurs aux fours CEM.
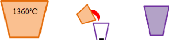
Ä% Si
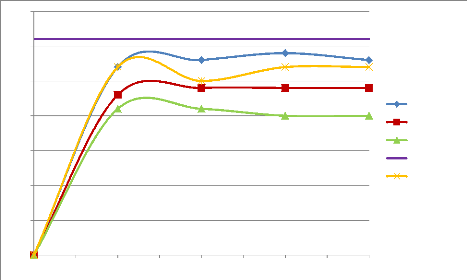
0 1 2 3 4 5 6 7 8
0,35
0,30
0,25
0,20
0,15
0,10
0,05
0,00
2 - 6,3 mm Fines
6,3 - 10 mm Visé
Non Tamisé
14
Temps (min)
Figure 10 : Résultat essai en poche
CRD
Les résultats de rendements finaux sont
présentés dans le tableau ci-dessous :
Plage Granulométrique
|
fines
|
2 - 6,3 mm
|
6,3 - 10 mm
|
Non tamisé
|
Rendement final
|
77,42%
|
90,32%
|
64,52%
|
90 %
|
Le rendement final des fines ainsi que du FeSi 2 - 6.3mm reste
identique à la correction en four. Par contre, le FeSi 6.3 - 10mm a un
rendement qui diminue par rapport à la correction en four.
L'agencement des rendements reste le même :
rendement 2 - 6.3mm > rendement non-tamisé >
rendement fines > rendement 6.3 - 10mm
15
C. Essais en four plein
Le mode opératoire veut que les corrections se fassent
en four semi plein, après l'envoi d'une poche à la coulée
et avant l'arrivée d'une poche provenant du mélangeur. Mais il
arrive que la correction soit trop peu efficace ou que le timing ne soit pas
optimisé et donc on se retrouve à devoir faire une correction sur
un four plein.
Les essais suivants ont été faits pour
déterminer s'il y a une différence de rendement ou non sur le
fait de corriger sur un four semi plein ou sur un four plein.

Ä% Si
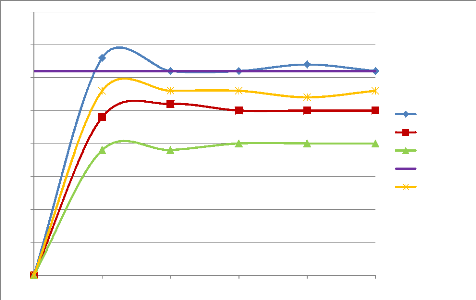
0 2 4 Temps (min)
6 8 10
0,40
0,35
0,30
0,25
0,20
0,15
0,10
0,05
0,00
2 - 6,3 mm Fines
6,3 - 10 mm visé
Non Tamisé
Figure 11 : Résultat essai four plein
CRD
Les résultats de rendements finaux sont
présentés dans le tableau ci-dessous :
Plage Granulométrique
|
fines
|
2 - 6,3 mm
|
6,3 - 10 mm
|
Non Tamisé
|
Rendement final
|
80,65%
|
100,00%
|
64,52%
|
90,32%
|
La tendance reste inchangée, les plus forts rendements
sont obtenus par les tranches 2 - 6.3mm et non tamisée alors que les
tranches fines et 6.3 - 10 mm sont à la traine
On observe un rendement amélioré pour les fines
et le FeSi 2 - 6.3 mm. Ce rendement amélioré peut être
dû à une plus faible oxydation du silicium grâce au fait que
l'on brasse moins longtemps, On a donc une durée de contact plus courte
entre le métal en fusion et l'air.
16
La différence en termes de pourcentage est de 0.03% de
Silicium pour le 2 - 6.3mm et de 0.01% pour les fines. Cette différence
pourrait tout simplement être due à la marge d'erreur de la
machine de mesure ceci étant d'autant plus plausible qu'un rendement de
100% est théoriquement impossible au vu des pourcentages en Si
réels mesuré par fluorescence X le rendement maximum
théorique serait de 94.7%.
Des conclusions pourront être tirées plus
précisément en répétant l'essai afin de
vérifier la répétabilité de l'essai ainsi que de
mettre en place une barre d'erreur sur la mesure des valeurs.
Le rendement du FeSi 6.3 - 10mm reste le plus faible. Il est
identique au rendement en poche et légèrement inférieur au
four semi plein.
Concernant le FeSi non tamisé, le rendement est
identique sur les 2 essais en four. Ces résultats tendent à
confirmer les suppositions précédentes qui veulent que la
différence de rendement entre les deux essais ne serait due qu'à
la marge d'erreur de la machine de mesure spectroscopique.
D. Récapitulatif
Suite à cette série d'essai il est observé
que :
? Le rendement en four, qu'il soit plein ou semi-plein, est
relativement identique et proche des résultats en poche.
? La chimie du produit a une importance
o Présence ou non de quartz
o Différents taux de Si dans les diverses tranches
granulométriques
17
IV. Essais Usine
Faisant suite aux essais de laboratoire, des séries
d'essais en usine ont été lancés. Seront comparés
:
? Le mode d'introduction
· En four
· En Poche de transfert
? La granulométrie du FeSi utilisé
· 2 - 10 mm
· 10 - 80 mm
? Le taux de correction
· + 0.05%
· + 1.15%
· + 0.03% (introduit en 1 fois 0.30% ou 2 fois 0.15%)
Voici le plan d'expérience prévu à
l'usine.
|
Granulométrie
|
2 - 10 mm
|
10 - 80 mm
|
Mode d'introduction
|
|
0,05%
|
0,05%
|
Four
|
0,15%
|
0,15%
|
|
0,30%
|
0,30%
|
|
0,15
|
Essais non
|
Poche
|
0,3
|
validés
|
Figure 12 : Mode opératoire des essais
effectués en usine
Les essais ont été fait suivants les plans
d'essais spécifié dans les Figure 6 à Figure 8
portés à l'échelle de l'usine.
18
A. Essais en Four
Correction 0.05%
Les essais se font sur des fours de 22T auxquels sont
ajoutés 14.67kg de FeSi 75. La correction se fait sur le bain
après le chargement de la première poche. Un premier brassage de
5min a servi à dissoudre et homogénéiser le Si dans la
fonte. Une poche de métal en fusion non traitée a ensuite
été versée dans le four afin de remplir le four.
Ä% Si
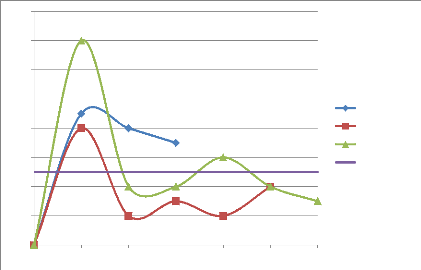
0,16
0,14
0,12
0,10
0,08
0,06
0,04
0,02
0,00
1 2 3 4 5 6 7
2 - 10 mm
10 - 80 mm A 10 - 80 mm B Visé
Prélèvements
Figure 13 : Résultats essais en four semi-plein
pour un ajout de 0.05% de Si (Usine)
Essai
|
2 - 10 mm
|
10 - 80 mm A
|
10 - 80 mm B
|
Rendement final
|
140 %
|
80 %
|
60 %
|
Cet essai a rapidement été abandonné, car
les valeurs mesurées étaient trop proches de la marge d'erreur de
l'installation de mesure et donc les rendements mesurés sont aberrants
et donc non exploitables.
19
Corrections 0.15%
Ä% Si
Ont été ajoutés, pour 22T de fonte, 44kg de
FeSi 75 afin de corriger le four à hauteur de 0.15% de Si.
0,35 0,30 0,25 0,20 0,15 0,10 0,05 0,00
|
|
|
|
|
10-80 mm 2 - 10 mm A 2 - 10 mm B Visé
|
1 2 3 4 5 6
Prélèvements
Figure 14 : Résultats essais en four semi-plein
pour un ajout de 0.15% de Si (Usine)
Essai
|
2 - 10 mm A
|
2 - 10 mm B
|
10 - 80 mm
|
Rendement final
|
60 %
|
66.67 %
|
86.67 %
|
On remarque une nette amélioration du rendement de
correction avec l'augmentation de la granulométrie.
Le rendement plus efficace, malgré un taux de Si
apparent identique, est vraisemblablement dû au taux de fines beaucoup
plus faible dans le 10 - 80mm que dans le 2 - 10mm. Donc moins de pertes au feu
directes sont à déplorer.
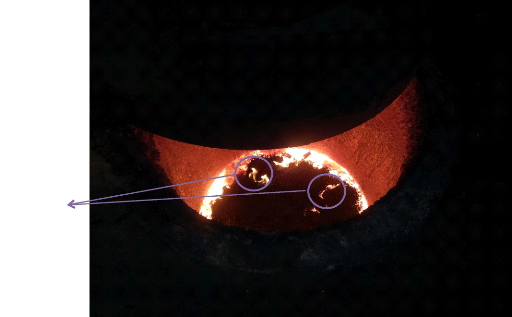
Fines brûlant à La surface du bain
20
Figure 15 : Charge de FeSi (2 -10 mm) flottant sur le
bain de fonte avant brassage
Les fines ont tendance à bruler en surface de bain ou se
trouvent, pour les plus fines, portées par le courant d'air chaud
au-dessus du bain hors du four et ne prennent par conséquent pas part
à la correction.
De plus, aucune phases néfastes n'ont été
détectée dans le FeSi 10 - 80mm suite à l'analyse DRX. Le
taux silicium n'étant pas entamé par la présence de
quartz, il peut réagir en totalité lors de la correction. S'en
suit donc un meilleur rendement.
21
Correction 0.3% (en deux apports)
Deux méthodes ont été utilisées
pour cet essai. L'introduction du FeSi en une fois, en versant la
totalité de la masse de ferro-alliage sur le bain dans un four mi plein.
Et en deux fois, en versant la moitié de la charge de ferro-alliage sur
le bain dans un four mi plein et l'autre moitié sur le bain après
remplissage du four.
Tout d'abord intéressons-nous à l'introduction par
moitié.

Ä% Si
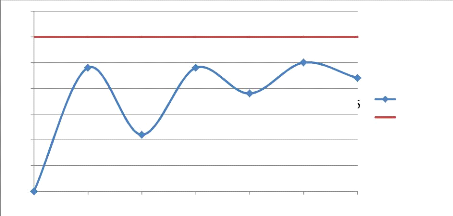
0,00
Fonte de base
1 2 3 4 5 6 7
Fonte après
|
Fonte après
|
|
|
|
1ere correction
|
2e correction
|
|
|
|
|
|
|
|
|
|
|
2min
|
4min
|
6
|
|
|
|
|
|
Fonte après
|
|
|
|
|
remplissage
|
|
|
|
|
0,35
0,30
0,25
0,20
0,15
0,10
0,05
10 - 80mm Visé
min
Prélèvements
Figure 16 : Résultats essais en four semi-plein
pour un ajout de 0.3% de Si en 2 ajouts (Usine)
Les résultats de rendements finaux sont
présentés dans le tableau ci-dessous :
Essai
|
10 - 80 mm (2fois)
|
Rendement final
|
73.33 %
|
Le rendement est relativement bas par rapport aux essais
à suivre. De plus les corrections se font
préférentiellement en une seule fois afin de diminuer les pertes
par oxydation du Si et l'agglomération du FeSi dans les crasses qui
surnagent sur le bain.
Cette série d'essai sera donc abandonnée
après les premiers résultats.
22
Correction 0.3% (en 1 apport)
Ä% Si
Pour l'essai en un seul apport il faut ajouter 88kg de FeSi 75
pour augmenter de 0.3% les 22T de fonte du four.
0,60 0,50 0,40 0,30 0,20 0,10 0,00
|
|
|
|
|
10 - 80 mm 2 - 10 mm A 2 - 10 mm B Visé
|
1 2 3 4 5 6 7
Prélèvements
Figure 17 : Résultats essais en four semi-plein
pour un ajout de 0.3% de Si (Usine)
Les résultats de rendements finaux sont
présentés dans le tableau ci-dessous :
Essai
|
2 - 10 mm A
|
2 - 10 mm B
|
10 - 80 mm
|
Rendement final
|
83.33 %
|
73.33 %
|
90 %
|
Comme pour la correction à 0.15% le FeSi 10 - 80mm a un
rendement meilleur que le 2 - 10mm. Cette amélioration de rendement est
due au taux de fines présent dans le 2 - 10mm qui n'est pas
présent dans le 10 - 80mm et ne fait donc pas chuter le rendement.
On remarque que de manière générale, le
meilleur rendement se trouve après 4min de brassage après le
remplissage du four. Au-delà le Si commence à diminuer à
cause des pertes au feu.
Pour un rendement optimal, il faut brasser seulement 4 min
après remplissage du four, pour une correction faite en four
semi-plein.
23
B. Essai en poche
En plus de corriger dans les fours, il est possible de
corriger la fonte directement dans les poches de transfert au moyen d'une
trémie automatisée.
La dissolution et la diffusion sont gouvernées par le
brassage induit par le remplissage de la poche
Si la dissolution du FeSi ne se fait pas totalement lors du
remplissage, les crasses qui remontent sur le bain vont emprisonner le FeSi non
dissout. Lors du décrassage de la poche, le FeSi emprisonné dans
les crasses est éliminé en même temps que ces
dernières.
La température de la fonte dans les poches de transfert
est en général entre 1300 et 1350°C et le FeSi 75 a une
température de liquidus à 1325°C. Dans certains cas, la
fusion du FeSi n'est que partiel car la température n'est pas assez
élevée.
Après les premiers tests effectués avec le FeSi
10 - 80mm, la majorité de la charge surnageait car les granulats
étaient trop gros pour fondre lors du remplissage et finissaient par se
retrouvés pris dans les crasses sur le bain.
Seul le rendement du FeSi 2 - 10mm a été
analysé lors de cette série d'essais.
Essai 0.15%
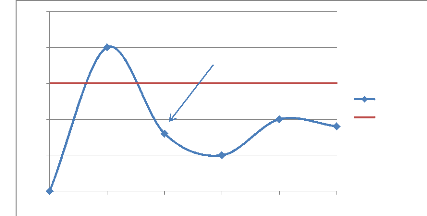
Ä% Si
0,25
Poche corrigée
Fonte après complément
0,2
0,15
2 - 10 mm Visé
0,1
2min 4min 6min
0,05
0
Fonte de base
1 2 3 4 5 6
24
Prélèvements
Figure 18 : Résultats essais en poche pour un
ajout de 0.15% de Si (Usine)
Les résultats de rendements finaux sont
présentés dans le tableau ci-dessous :
Essai
|
2 - 10 mm
|
Rendement final
|
60 %
|
Ici aussi on remarque que le rendement optimal se trouve à
4 min après le complément de fonte non traitée.
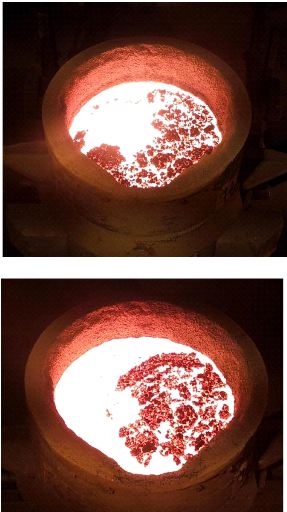
Figure 19 : Poche corrigée
25
Figure 20 : Poche non-Corrigée
On peut voir l'effet de l'ajout de FeSi sur la présence
de crasses en dessus de bain. Ici sont présentés deux poches
issues du même four remplies l'une derrière l'autre. La
première a été corrigée et pas la suivante. On peut
voir qu'il y a plus de crasses sur la poche corrigée que sur la fonte
non corrigée.
Risque de fusion partiel du FeSi
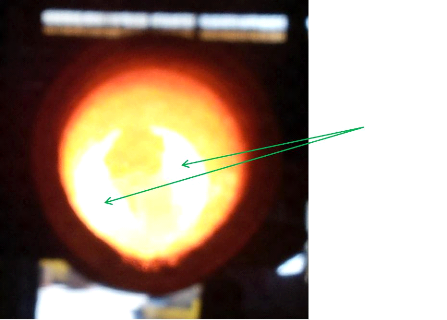
FeSi non dissout
26
Figure 21 : Poche corrigée après
vidange
Après vidange de la poche traitée, on peut
observer au fond des restes de FeSi n'ayant pas été dissous. Ils
restent en fond de poche dans un état pâteux.
Cet agrégat pâteux de FeSi peut être source
de dérives dans le taux de Si. Le FeSi non dissout continu à
diffuser à longueur que l'on remplit et vide la poche. Si le type de
tuyau produit vient à changer on risque d'avoir de la fonte trop riche
en Si par rapport à ce qui est requis. Ou tout simplement on risque
aussi de sur-corriger la fonte en cours de production.
27
V. Discussions
A. Meilleur rendement à 4min de
brassage
Pour tous les essais effectués à l'usine
confondus, on observe que le rendement maximal a été atteint au
bout de 4 min de brassage après remplissage du four. Au-delà des
4 min de brassage, il apparait que le %Si de la fonte diminue. Cette diminution
s'apparente à une désiliciation de la fonte.
B. Comparaison Four - Poche
Les résultats obtenus montrent que les rendements en Si
sont plus faibles pour les corrections réalisés en poche en
comparaison avec ceux obtenus en four. Cette différence de rendement
peut avoir pour origine la température du bain. Au sein des
mélangeurs, la fonte est maintenue aux alentours de 1380°C.
Après remplissage de la poche, la fonte perd entre 50 et 100°C, en
fonction de la température de la fonte dans le mélangeur, de la
poche et aussi de la vitesse à laquelle la fonte est versée dans
la poche.
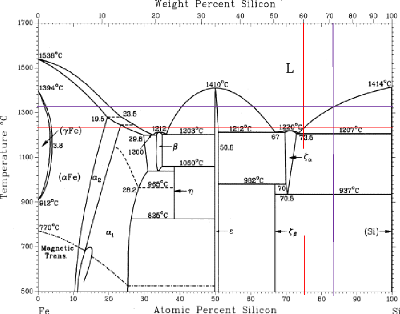
1320°C
1230°C
60 w%
71 w%
Figure 22 : Diagramme de phase binaire Fe
Si
Comme on peut le voir ci-dessus, le FeSi (granulométrie
2 a une température de liquidus à ~1320°C. La
température de liquidus du Ferro alliage est donc proche de la
température du bain de fonte liquide. Dans le cas de corrections Si
réalisées en poche, la
28
dissolution du FeSi peut être incomplète ce qui
pourrait être les faibles rendements obtenu en comparaison avec ceux
obtenus en four.
Prenons par exemple une correction effectuée, en
début de production, dans une poche pas suffisamment chauffée.
Après remplissage la fonte est à 1300°C. Or comme on le voit
ci-dessus dans le diagramme Fe-Si à 71% Si à 1300°C nous
sommes dans un domaine biphasé liquide + (Si).
-
= 7.93%
La solution solide de Si représente 7.93% de la masse
de FeSi. S'il n'y avait pas de diffusion de Si dans le métal en fusion,
nous aurions près de 8% de perte en Si presque pur.
Grace à la diffusion les pertes sont moindres mais il
arrive que le FeSi reste amalgamé au fond de la poche (cf. Figure 21) et
n'est pas suffisamment dispersé pour permettre une diffusion du silicium
qui permettrait d'amener le ferro-alliage à un taux de Si plus proche de
l'eutectique et de ce fait à une fusion.
Pour une correction en poche optimale, un FeSi 60% serait
sûrement une meilleure option. Avec un point de fusion à
1230°C, la fonte devrait rester à une température plus
élevée que son point de fusion même dans une poche
froide.
En four, une source d'énergie extérieure est
disponible afin de faire fondre le FeSi au cas où la fonte soit
livrée trop froide. De plus l'induction entraîne un brassage
mécanique du bain, ce qui favorise la dissolution du Si.
C. Comparaison FeSi 2 - 10mm et 10 - 80mm
Pour une correction en four, Il est assez flagrant que le FeSi
10 - 80mm a un rendement nettement supérieur au 2 -10mm. Ce se peut
s'expliquer par :
La chimie du produit 10 - 80 mm est exempte de quartz
contrairement au 2 -10mm. Le rendement est donc meilleur pour un taux de
silicium apparent identique. Le 2 -10 mm est constitué de sous-produits
de 10 - 80mm dont les fines qui sont issues du concassage de ce dernier.
De plus les fines dans le 10 - 80 mm (impossibles à
éviter car principalement issues de l'abrasion des granulats suite au
frottement des uns contre les autres lors du transport) qui ont tendance
à bruler avant même d'être en contact avec le bain,
constituent une fraction beaucoup plus faible que pour le 2 - 10 mm.
Pour une correction dans le four, le FeSi 10 - 80mm est alors
préférable. Malgré un prix à l'achat plus
élevé, le rendement étant meilleur, moins de
matière est utilisée et donc les coûts devraient
s'équilibrer et les corrections seront plus précises.
Dans la poche la tendance s'inverse, le FeSi 10-80 à
75% est trop gros pour bien fondre et comme il n'y a pas de source
d'énergie supplémentaire. De par son volume plus
élevé, la poussée d'Archimède qui lui est
imposée est d'autant plus élevée, il remonte en surface
beaucoup plus rapidement que le FeSi 2-10. Il surnage, donc, et se retrouve
emprisonné dans les crasses. Pour une correction en poche, un FeSi 2 -
10mm est requis car la
29
surface spécifique est suffisante pour permettre un
échange calorifique suffisamment rapide pour faire fondre la charge de
FeSi avant qu'elle ne remonte en dessus de bain et se retrouve engluée
dans les crasses présentes.
Pour la poche, seul le 2 - 10mm est utilisable. Dans le cas de
la granulométrie 10 - 80mm les grains de FeSi décantent à
la surface du bain et se mélange aux crasses initialement
présentes avant la diffusion du silicium dans le liquide.
D. Influence du niveau de
correction
Le rendement est meilleur pour les corrections à 0.3%
par rapport à celle à 0.15%. Cette amélioration de
rendement peut être supposée liée au fait que la perte de
Si lors d'une correction est identique quelle que soit le taux de
correction.
La perte étant fixe, elle représentera une chute
de rendement d'autant plus élevée que la correction est
faible.
30
VI. Conclusion
L'objectif de ce projet était d'étudier
l'influence de la nature du FeSi et de son mode d'introduction sur le rendement
des corrections en Si effectuées dans la fonte liquide.
Les principaux points mis en évidence lors de cette
étude sont les suivants :
Granulométrie : Tous les essais
réalisés montrent que la granulométrie 10 - 80mm est celle
qui a permis d'obtenir les meilleurs rendements.
Mode d'introduction : Ce paramètre a
été étudié avec la granulométrie 2 - 10mm
(en poche et en four), les rendements sont similaires et compris entre 60 et
66.7% pour les essais en usine et sont de 90% pour les essais au CRD. Cette
différence de rendement pourrait être attribuée à la
température de la fonte au moment de la correction. Celle-ci
était plus élevée pour les essais réalisés
au CRD.
Le mode d'introduction n'a donc pas d'influence significative
sur les corrections effectuées avec le FeSi 2 - 10mm.
Taux de correction : Les rendements de
correction s'améliorent avec l'augmentation du taux de correction, pour
les deux granulométries testées.
31
VII. Perspectives
Suite à divers impondérables, tels que des
pannes où des taux de Si trop élevés ne permettant pas
d'effectuer les essais en temps voulu. Certains essais seront faits
après la rédaction de ce rapport.
? Essais Usine
o Essais en poche à 0.3% en une fois
o Essais en poche à 0.3% en deux fois
? Essais CRD
o Essais sur l'influence de la chimie du FeSi pour une
correction en poche
? Essai en poche avec le FeSi usine 75% Si 2 - 10mm
MICON®
? Essai en poche avec un FeSi 60% Si 2 - 10mm disponible au
CRD
De plus, Certains résultats d'analyses chimiques sont
toujours manquants :
? Echantillons de fonte
o Certains échantillons ont été
envoyés pour être analysés en Fluorescence X et en DRX afin
de vérifier les résultats obtenus par spectroscopie. Mais les
délais de retour des résultats n'ont pas permis cette
comparaison.
Concernant le mode d'introduction du FeSi, voici les directions
possible :
? Dans le cas où il est choisi d'utiliser la
trémie automatisée actuellement en place sur le circuit des
poches de transfert. Il est possible de changer de produit utilisé pour
prendre du FeSi 60%. Après validation suite à des essais
en laboratoire et en usine.
? Au cas où l'introduction en four est
préférée, mettre en place des trémies
automatisées sur la plateforme des fours afin de diminuer au maximum le
transport de charge pour les opérateurs ainsi que l'erreur de mesure
lors du remplissage des sceaux. Cette trémie pourrait être
calibrée pour accueillir du 10 - 80mm dont le rendement, en four, est
meilleur.
|