Table des matières
INTRODUCTION
2
Partie1 :L'entreprise et le thème
3
Chapitre1:
Présentation du cadre de référence
4
1. Présentation du cadre
général de référence
4
2. Présentation du cadre de
référence spécifique
7
Chapitre2:
Présentation du sujet
10
1. Le thème et son importance
10
2. Présentation du cahier de charge
et objectif
12
Partie2 : Etude technique du projet
13
Chapitre1: Etude de
l'existant
14
1. Présentation de la ligne
14
2. Présentation de la maintenance
existante
25
3. Etude 5 M de l'existant.
30
Chapitre2: Etude des
défaillances des équipements
36
1. Données de base de
l'étude
36
2. Répartition des
défaillances de la ligne en fonction des équipements
37
3. Analyse des défaillances
43
Partie3 : Propositions de solutions et
étude de rentabilité
52
Chapitre 1: Propositions de
solutions.
53
1. Solutions aux problèmes
liés à la méthode de maintenance
53
2. Solutions aux problèmes
liés aux moyens matériels
56
3. Solutions liées aux
problèmes des matières
58
4. Solutions aux problèmes
liés à la main d'oeuvre
60
5. Solution aux problèmes du milieu
de travail
61
CHAPITRE2 :
Rentabilité du projet
62
Conclusion
63
Bibliographie
64
1 INTRODUCTION
Les entreprises se singularisentau niveau de leur performance
industrielle par la disponibilité, la productivité et la
flexibilité de leurs ressources ainsi que par l'obtention de faibles
coûts de revient.
Ainsi lorsqu'une entreprise envisage de travailler en Juste
à Temps et à stockZéro elle ne doit pas oublier qu'elle
pourra respecter les délaisqu'elle a annoncés à ses
clients si elle est certaine de la disponibilité des machines durant
tout le tempsprévu et que les quantités de produits lancés
seront obtenues en qualité dans les temps prévus.La
réalisation de ces objectifs passe nécessairement par la mise en
place d'activés de maintenance visant àéliminer tous les
arrêts de productions dus à des pannes.
C'est en se joignant à cette visionqu'Unilever CI a
décidé d'une amélioration de sa politique de maintenance
préventive. Et c'est dans le cadre de ses travaux qu'il nous a
été soumis pour projet d'étude de fin de cycle le
thème suivant :
« Activité zéro panne sur la
ligne de production de savon MAZZONI 1».
Il s'agit, à travers ceprojet d'étudier toutes
causes liées aux pannes sur la ligne et ensuite de faire ressortir un
plan d'actions en vue d'atteindre « le zéro
panne ».
Pour le présent travail nous suivrons le plan suivant :
De prime abord nous présenterons la structure d'accueil,
nous présenterons ensuite les instances fondamentales du projet à
travers une étude technique et nous terminerons par les
propositions de solutions et une étude de rentabilité du
projet.
Notre travail s'articulera autour de trois grandes parties :
-la première partie : L'entreprise et le thème
qui présentera de façon générale la structure
d'accueil et le sujet
-la seconde, l'étude technique sera consacrée
à l'étude de l'existant et l'étude des défaillances
des équipements
-La troisième partie : proposition de solution et
étude de rentabilités.
1
PARTIE
L'ENTREPRISE ET LE THEME
2 Partie1 :L'entrepriseet le thème
CHAPITRE 1 :Présentation du cadre
de référence
CHAPITRE 2 :Présentation du
sujet
3 Chapitre1: Présentation du cadre de
référence
Ce chapitre présente l'entreprise UNILEVER. Il fait son
historique, met l'accent sur son organisation et son fonctionnement. Aussi
décrit-il la mission, les objectifs et les activités de cette
structure.
1. Présentation du cadre
général de référence
1.1. Historique
L'an 1929, joseph BLOHORN joignait le rêve à la
réalité, le projet au concret, l'ambition au réel en
créant la première usine qui portait en son temps son nom dans la
commune de Cocody alors décrétée Zone industrielle. Son
entreprise avait pour matière première l'huile de palme locale,
l'eau et la soude importée et avait pour équipements,
essentiellement, de vieux moules en bois.
Sept (7) années plus tard, en 1936, l'entreprise de
joseph BLOHORN, dans un souci de spécialisation de l'activité ;
fut rebaptisée HUILERIE SAVONNERIE DES LAGUNES (H.S.L).Après la
disparition du `'père BLOHORN'', père fondateur de la
société `'mère'', c'était tout légitimement
qu'en 1939, le `'fils André BLOHORN'' assurait la continuation de la
mission, dans l'esprit et le principe.
De 1957 à 1971, plusieurs structures
complémentaires sont acquises .Il s'agit des Plantations et Huileries de
Cote d'Ivoire (PHCI), de la Société Africaine de Produits
Chimiques et de Synthèses (SAPROCSY), de Andrew John SEWARD (AJ SEWARD),
de la Société de Produits Chimiques du Niger (SPCN). A la vue de
ce développement, le besoin d'extension s'est fait ressentir ;
ainsi l'usine s'est vue déplacée sur le site de Vridi (Zone
Industrielle) en 1973.En 1982, les premiers contacts sont tissés avec
UNILEVER et l'entreprise passe sous la direction de la multinationale
Anglo-néerlandaise UNILEVER COMMONWEALPH HOLDING avec 90% du capital.
En 2001 BLOHORN prend la dénomination UNILEVER-CI ;
son capital actuel s'élève à 8,053 milliards de francs CFA
après avoir intégré les autres structures.
Notons par ailleurs que la Société a
réalisé, au cours de l'exercice 2009, un chiffre d'affaires hors
taxe de 85,772 milliards de Francs CFA contre 144,926 milliards de Francs CFA
en 2008, soit un recul de 40,82% dû essentiellement à la cession
l'activité huile à Sania (Groupe SIFCA).
1.2. Objectif
d'UNILEVER
Les objectifs visés par UNILEVER sont les
suivants :
Ø OEuvrer pour un avenir meilleur, jour après
jour.
Ø Aider les gens à se sentir bien, à avoir
bonne mine et à mieux profiter de la vie avec des marques et des
services qui sont bons pour eux et pour autrui.
Ø Inciter les gens à entreprendre de petites
actions quotidiennes qui, ensemble, peuvent faire une véritable
différence pour le monde.
Ø Développer de nouvelles manières de faire
des affaires qui doivent nous permettre de doubler l'ampleur de notre
entreprise et, dans le même temps, de réduire notre impact sur
l'environnement.
1.3. Les
activités d'UNILEVER-CI
UNILEVERCI intervient dansplusieurs domaines industriels. Au fil
du temps la diversification de ses activités lui a permis de devenir un
véritable groupe industriel.Ainsi, l'on relève les
sociétés ou départements suivants :
· SAPROCSY créée en 1964 pour
la fabrication des poudres à laver ;
· VRIDI qui est le siège où
sont centralisées toutes les activités.
Les activités de UNILEVER-CI couvrent une large gamme de
produits allant produits de soins corporels et de ménage et aux
denrées alimentaires. Les produits d'UNILEVER CI sont consignés
dans le tableau suivant
: Tableau 1:Produits UNILEVER-CI
HPC
|
AJ SEWARD
|
DENTIFRICES CLOSE UP ET SIGNAL FLUOR
|
SAVONNERIE
|
Savons de lessive BF, Maximousse, Fanico, et savons de toilette
Belivoir, Rexona et Lux.Liveboy
|
SAPROCSY
|
Poudre détergent OMO, Sunlight
|
FOOD
|
MARGARINNERIE
|
margarine Blue Band et beurre Rama
|
THE
|
Lipton
|
MAYONNAISERIE
|
Mayonnaise Calvé
|
1.4 La structure d'UNILEVER-CI
UNILEVER CI est sous la direction d'un comité
régional dirigé par un directeur général adjointqui
est sous le couvert d'une direction générale se trouvant au
Ghana.(En annexe 1 l'organigramme d'UNILEVER-CI.)Ledit comité
est composé de cinq directions à savoir :
· Finance
Sa tâche essentielle est de régler les
problèmes financiers d'UNILEVER. Elle s'occupe également des
moyens de paiement, de la politique bancaire, des crédits de
l'équipe financière du groupe UNILEV ER
· Market Development,
Elle s'occupe des études de marché et a le devoir
de promouvoir les produits à travers des actions publicitaires dans le
but d'informer les potentiels consommateur, de captiver leur attention puis les
amener à l'acte d'achat
· Humann Ressources,
Chargées de la gestion du personnel, elle règle
les litiges et les compromis au sein de l'entreprise. Elle veille au respect du
règlement intérieur au sein de l'entreprise et met en place une
politique de motivation du personnel, elle recrute, forme et retient les
salariés qui contribuent au succès de l'entreprise.
· Supply Chain,
Elle gère l'approvisionnement des ateliers en
matière premières, emballages de conditionnement commercial et
autres fournitures diverses. De l'entretien du matériel technique.
Aussi la Supply Chain s'occupe de la recherche des prestataires
de services pour le transport des produits finis.
· Vente
Elle est chargée de commercialiser et de promouvoir les
produits UNILEVER sur le marché.
La société compte à ce jour autour de 600
employés constitués d'ouvriers, d'agents de maîtrise et de
cadres. La politique de management d'Unilever intègre la
sécurité, la qualité et l'environnement. Ainsi de
manière fréquente tout le personnel suit des formations
SHE1(*). De
même chaque semaine est organisée une réunion
SHE afin de toujours rappeler aux travailleurs les risques
liés au non-respect des mesures de sécurité. Nous
soulignons par ailleurs que UNILEVER CI est certifié ISO
9001,ISO 14000 et OHASA 18001.
2. Présentation du cadre de
référence spécifique
3.1.1 2.1Présentation de la
Savonnerie/savonnetterie
La Savonnerie/ savonnetterie est chargée de la
fabrication et de la production du savon jusqu'à son produit fini. Elle
se compose deuxateliers à savoir l'atelier de Saponification et
l'atelier de savonnerie.
2.1.1 L'atelier de Saponification(Annexe
3)
Elle s'occupe de la fabrication préliminaire du savon
(état liquide sans parfum, ni colorant).
Cette préparation se fait par le mélange selon
des proportions et des étapes bien spécifiées de quatre
éléments qui sont : l'acide gras, l'eau salée, la
soude et le carbonate. Le produit obtenu après préparation est
stocké dans des cuves appelées chaudrons quipar la suite
alimentent les malaxeurs de la savonnerie pour l'étape finale.

Notons que les savons de bains et les savons de lessives ne
sont pas préparés avec les mêmes natures
d'ingrédients en les mêmes proportions.
La Sapo est constitué en trois unités à
savoir la Sapo 4 tonnes, la Sapo 12 tonnes et
la Sapo 14 tonnes.Qui signifie par exemple pour la Sapo 4
tonnes qu'elle produit 4 tonnes de savon l'heure.
Dans la suite nous nous intéresserons plus à la
savonnerie car c'est dans cet atelier qu'est implantée la ligne sujet de
notre étude.
2.1.2 L'atelier de la savonnerie
La savonnerie est l'atelier chargé de la production de
tous les savons vendus par Unilever CI. L'atelier se divise en deux
compartiments quisont la savonnerie pour les savons de lessives et
la savonnetterie pour les savons de toilettes ou de bain. Chaque
compartiment comporte des lignes spécialisées dans la production
d'une gamme de savon selon la demande du marché.
La savonnerie comprend (8) huit lignes de production :
MAZZONI 1 pour la fabrication du BF 4
MAZZONI 2 MAXIMOUS / IDEAL PLUS
MAZZONI 3 BF 8
MAZZONI 4 pour la confection du BF 4 ou du BF 8
Ligne 5FANICO
Ligne 6 FANICO
Ligne 7 FANICO CITRON
Ligne 8 croco
La savonnetterie quant à elle ne comprend que deux lignes
de production: une pour la fabrication du savon BELIVOIR et l'autre pour les
savons REXONA ou LUX.
Dans son fonctionnement, cet atelier a en son sein plusieurs
services qui collaborent. Ces services sont principalement le service
Fourth Shiftdont le rôle est d'évaluer
le tonnage de la production journalier, le service PAMCO pour noter tout
dysfonctionnement sur les équipements de production et évaluer
leur influence sur la production, le service des ventes qui fixe les tonnages
de chaque gamme de savon suivant la demande et enfin le service qui nous a
accueilli le service maintenance HPC ( Home and Personal Care), chargé,
comme son nom l'indique de la maintenance de tous les équipements des
lignes de production
2.2 Présentation du service HPC
Le service HPC est chargé de la maintenance et
l'entretien des équipements de la savonnerie/savonnetterie, A.J.SEWARD
et le silicate.Elle organise et planifie les
différentesopérations de maintenance qui sont le contrôle
et les inspections des différentséquipements pour réduire
au maximum les temps d'arrêt.
Pour mener à bien les tâches qui lui sont
affectées la maintenance HPC doit travailler avec ces différentes
sections :
· La section
électricité : elle assure le suivi et l'entretien
des moteurs électriques, la maintenance, dépannage et la mise
à jour des installations électrique de l'usine. Travail en
collaboration avec des sociétés extérieures.
· L'atelier de mécanique
générale : il est chargé de l'usinage de
certaines pièces de rechanges. Doté d'équipements
performants tels que les tours et fraiseuses à commande
numérique, il est sollicité lorsqu'il y des modifications
à apporter sur des machines ou pour la reproductiondes pièces
abimées.
· L'atelier de régulation et
d'instrumentation : il est chargé des appareils de mesure
et de contrôle (débitmètre, vanne de régulation,
pressostat), cet ateliertravaillant également en étroite
collaboration avec les société extérieures, intervient
également sur les appareils électriques,(dépannage et
entretien)
· Le magasin de
piècesdétachées : Qui s'occupe de la gestion
des pièces de rechange des équipements.
Le personnel du service HPC est reparti en deux grands
groupes : les mécaniciens journaliers et les mécaniciens de
quart. Les hommes du quart se relaient à la tâche tous les jours
de la semaine suivant les horaires suivants :
7 H - 14 H
14 H - 21 H
21 H - 7 H
Et les journaliers travaillent tous les jours ouvrables de 8 h
à 17 h. Le week-end et les jours fériés une permanence est
assurée par les mécaniciens de jour.
Notons en plus que chaque mécanicien journalier a,
à sa charge une ou plusieurs lignes dont il doit assurer l'entretien.
v Organigramme du service en annexe 2
4 Chapitre2: Présentation du sujet
Ce chapitre traite la définition du thèmeet son
importance. Présente aussi le cahier de charge et de la démarche
adoptéepour la résolution du problème.
1. Le thème et son importance
1.1 Le thème.
Le thèmesoumis à notre étudeest le
suivant : « Activité zéro panne sur
la ligne Mazzoni 1 ».La panne se définie comme
étant une interruption ou détérioration du fonctionnement
(disponibilité, performance, qualité,sécurité) de
l'équipement. On assimile aux pannes les dépassementsdes temps
programmés de maintenance préventive : dépassementdes
temps alloués ou réalisation d'interventions urgentes non
plani?ées. Aussi selon les Japonais le mot panne peut se traduire
par« obstacle causé intentionnellement »
Les pannes ne sont pas donc une fatalité ; des hommes
créent des pannes enne respectant pas les conditions de conduite et
d'entretien des équipements.
L'activité Zéro panne consistera donc en une
éliminationcomplète des pannes de la ligne Mazzoni 1. D'aucun
trouverons que cette activité est irréalisable mais comme le
ditJean Bufferme dans son livre Le guide
de la TPM"Le zéro panne n'est pas une utopie
mais il nécessite un changement de comportement des hommes de production
et de maintenance [1]."
Nous abordons dans le paragraphe suivant de l'importance du
thème.
1.2 Importance du thème.
Dans le souci de satisfaire totalement ses clients coté
qualité et respect des temps de livraison, UNILEVER-CI s'est
imposé certains impératifs qui sont :
§ L'élimination des pertes machinesdû à
des pannes ou des marches à vide
§ La diminution dela non qualité
§ L'augmentation de la productivité
§ La maitrise des coûts de maintenance
L'atelier savonnerie ou est implanté la ligne Mazzoni
1fonctionne 24h sur 24.Cette ligne est chargée uniquement de la
production du BF 4 et la production exigée est de 6400 cartons par
jour.
Cet objectif est très souvent compromis et cela pour
plusieurs raisons dont les pannes des équipements qui constituent un
véritable problème.
L'analyse du rapport des arrêts par nature de l'atelier
durant l'année 2011 nous a permis sortir le diagramme
suivant (figure 2):
Figure 1: Diagramme des temps d'arrêt par
nature
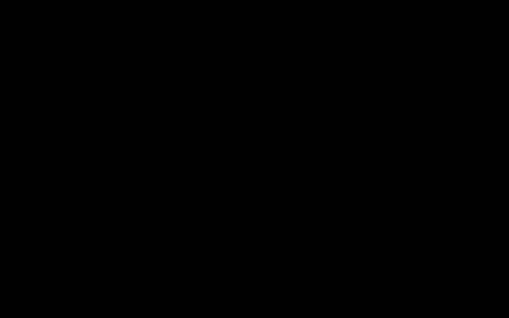
Le diagramme nous montre que la ligne Mazzoni 1 a
enregistré le plus d'arrêt tout au long de l'année 2011
avec 90% de temps d'arrêt dûà des pannes
mécaniques
Il s'en suit alors que le retard dans la production de la
ligneMazzoni 1 par rapport aux autres lignes est la conséquence
directede grands nombres d'arrêts occasionnés par cette ligne.
Tout ceci montre notre intérêt particulier pour cette ligne car
une plus grande disponibilité de cette ligne serait très
bénéfique pour UNILEVER-CI.
2. Présentation du cahier de charge
et objectif
4.1.1 2.1 Cahier de charge
La résolution de ce projet s'est fait selon le cahier de
charge suivant ;
Ø Obtenir l'efficacité maximale des
équipements de la ligne
Ø Prévoir une politique de Maintenance
préventive
Ø Faire un planning de maintenance préventive
des équipements de la ligne
2.2 Objectifs du thème
Ce thème a été proposé dans le but de
réduire les temps d'arrêt de la ligne MAZZONI 1. Ceci dans le
souci d'accroitre la disponibilité de cette ligne afin de pouvoir
atteindre les objectifs de la production et ainsi satisfaire aisément
à la demande des clients.
2.3. Démarche
adoptée
L'étude de ce projet c'est fait selon la démarche
suivante :
Ø L'étude du procédé de fabrication
de la ligne
Ø L'étude de la maintenance existante
Ø L'étude générale des 5 M pour faire
ressortirtoutes les causes de pannes liées à la méthode de
travail, aux matériels (machines), au milieu de travail , la
matière utilisée et la main d'oeuvre.
Ø L'étudedes défaillances des
équipements de la ligne par :
· récolte des données statistiques des pannes
(lignes-équipements-organes)
· Analyse des temps d'arrêt par la méthode
Pareto
· Analyse des modes de défaillances et leur
criticité (AMDEC)
Ø Propositions de solutions
Ø Implémentation des solutions proposées
Ø Mesures de gains.
2
PARTIE
ETUDE TECHNIQUE DU PROJET
CHAPITRE 1 : Etude de l'existant
CHAPITRE 2 : Etude des défaillances des
équipements
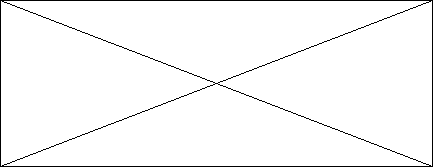
5 Partie2 : Etude technique du projet
6 Chapitre1: Etude de l'existant
. Dans ce chapitre nous présenterons d'abord la ligne et
ses équipements ensuite nous nous pencheront sur la maintenance mis en
place pour enfin terminé par une étude 5M ou nous ferons
ressortir toutes les causes primaires des pannes et long temps
d'arrêt.
1. Présentation de la ligne
1.1 Inventaire des
équipements
Dans l'exécution de notre travail, il a été
question pour nous de répertorier tous les équipements de la
ligne sur laquelle notre étude fera l'objet. Nous nous sommes
procuré des données existant de la ligne au bureau d'étude
que nous avons mis à jour. Nous soulignons que la codification
utilisée est celle de l'entreprise.
Le travail ainsi effectué nous a permis de sortir le
tableau suivant :
Tableau 2 Inventaire des
équipements
CODIFICATIIONS
|
Equipements
|
FABRIQUANT
|
10512020
|
Pompe alimentation savon
|
MAZZONI
|
10511072
|
Atomiseur cylindrique
|
MAZZONI
|
10512056
|
Pompe à vide -1
|
TRAVAINI EURL
|
10511074
|
Boudineuse primaire -
|
SPM
|
10511075
|
Boudineuse finale -
|
10512133
|
Pompe dosage parfum
|
OFFICINE GALLARATESSI
|
10511286
|
Coupeuse
|
MAZZONI
|
10511316
|
Convoyeur alimentation aligneur droit
|
BONFIGLIOLI
|
10511314
|
Déviateur cote droit aliment° mouleuse 1 et 2
|
PACKITAL
|
10511317
|
Convoyeur alimentation aligneur cote gauche
|
BONFIGLIOLI
|
10511315
|
Déviateur cote gauche alimentation° mouleuse 3 et
4
|
PACKITAL
|
10511319
|
Convoyeur alimentation mouleuse 1
|
BONFIGLIOLI
|
10511145
|
Mouleuse S.A.S. nø1 -mazzoni 1
|
SAS
|
10511320
|
Convoyeur alimentation mouleuse N° 1
|
BONFIGLIOLI
|
10511112
|
Mouleuse à savon S.A.S. nø2 -mazzoni 1
|
SAS
|
10511321
|
Convoyeur alimentation mouleuse
|
BONFIGLIOLI
|
10511111
|
Mouleuse a savons S.A.S. nø3 -mazzoni 1
|
SAS
|
|
Convoyeur alimentation mouleuse
|
BONFIGLIOLI
|
10511109
|
Mouleuse a savons S.A.S. nø4 -mazzoni 1
|
SAS
|
|
Convoyeurs alimentation emballeuse1
|
BONFIGLIOLI
|
10511180
|
Convoyeur. Alimentationemballeuse 2
|
BONFIGLIOLI
|
10511258
|
EmballeuseACMAN°1
|
ACMA
|
|
Convoyeurs alimentation emballeuse ACMA
|
BONFIGLIOLI
|
10511282
|
Emballeuse ACMA N°2 MAZZONI 1
|
ACMA
|
10511182
|
Convoyeur. Alimentation. Emballeuse 3 -
|
BONFIGLIOLI
|
10511284
|
Emballeuse ACMA n°3 mazzoni 1
|
ACMA
|
10511184
|
Convoyeur. Alimentation emballeuse 4
|
BONFIGLIOLI
|
12511284
|
Emballeuse ACMA n°4 mazzoni 1
|
ACMA
|
10511184
|
Convoyeur. Alimentation. Emballeuse 4
|
BONFIGLIOLI
|
|
Imprimante laser
|
MARKEM IMAJE
|
|
Encolleuse
|
LITTLE DAVID 3M
|
6.1.1 1.2. Description du procédé de
fabrication de la ligne
Le processus de fabrication du savon sur Mazzoni 1 commence tout
d'abord par l'envoi du savon du malaxeur à l'atomiseur par le biais
d'une pompe volumétrique.
Une fois dans l'atomiseur le savon est séché par un
système de vide composé d'une pompe à vide et d'un thermo
compresseur qui en envoyant la vapeur par sa buse à haute pression
créeune dépression dans la chambre de l'atomiseur. Le savon ainsi
séché passe par une boudineuse ou il sort sous forme de boudons
par une filière ensuite le savon est découpé en morceau,
moulé, emballé et enfinencartonné. (Voir figure de la page
suivante.)
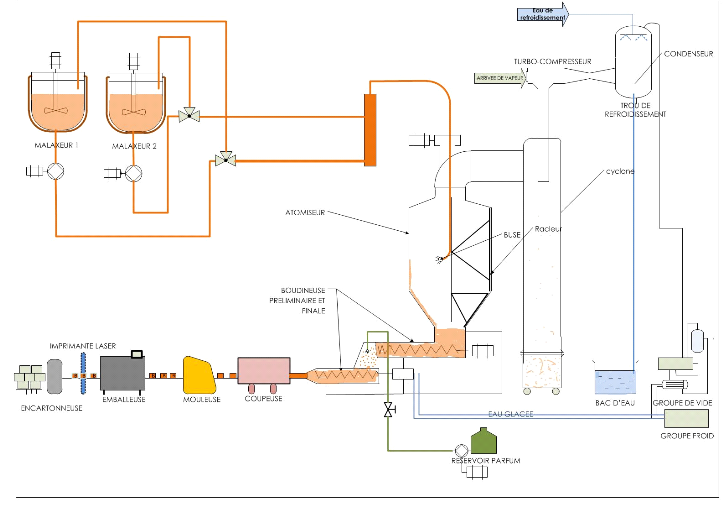
Figure 2: Processus de fabrication de la
ligne
v Schéma d'implantation de la ligne
Figure 3: Schéma d'implantation
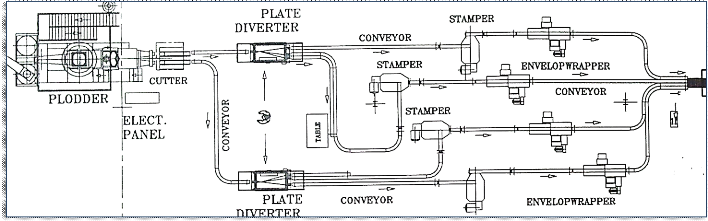
1.3 Fonctionnement des différents
équipements de la ligne.
· L'Atomiseur (figure 4)
L'atomiseur est une enceinte hermétique dans laquelle le
savon liquideapprovisionné par lapompe alimentation de savon, est soumis
à un vide. Ce vide appliqué au savon qui gicle dans l'atomiseur
via une buse va permettre de le sécher en y extrayant
l'humidité.
L'atomiseur est composé de racleur qui étant
fixé àun arbre moteur, racle les parois de celui-ci pour
éviter tout dépôt de savon. Cet arbre est entrainé
en rotation par un moteur électrique.
L'atomiseur reçoit, pour une bonne atomisation, un vide de
5 à 15 mbar produit par une pompe à vide en
premier lieu et un thermo compresseur. Le vide ainsi transmis
va servir à absorber l'humidité se trouvant dans le savon. Pa
ailleurs lespoudres de savon qui pourraientêtreaspiré par le vide
sont stockées dans deux cyclones placés en aval et relié
à l'atomiseur par une gaine de liaison.
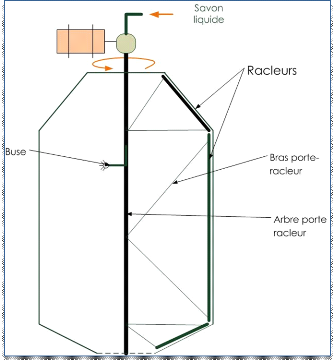
Figure4 Atomiseur
· La boudineuse(figure5)
La boudineuse permet de compacter et d'homogénéiser
le savon rendu sous forme de patte sèche par l'atomisation. Elle est
alimentée en savon directement par l'atomiseur. La boudineuse est
constituée de deux niveaux ce sont :
Le niveau 1 : Boudineuse primaire
Elle se situe en aval de l'atomiseur. Cette boudineuse recueille
directement le savon séché en provenance de l'atomiseur. Ce savon
tombe sur ses vis sans fin qui vont le compacter et le convoyer au travers
d'une plaque perforée vers la chambre intermédiaire de la
boudineuse ou l'on ajoute le parfum au savon. Cette chambre est sous vide
produit cette fois par la pompe à vide uniquement.
Le niveau 2 : boudineuse finale
Figure 5: Boudineuse
La chambre intermédiaire débouche sur la boudineuse
finale. C'est en son sein que le savon sera mélangé au parfum par
le biais de vis sans fin qui vont le compacter, homogénéiser pour
le faire sortir enfin par une tète conique en bout duquel se trouve une
filière.
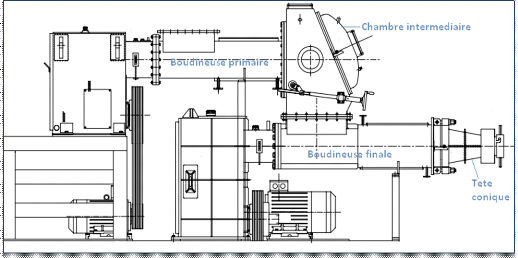
· La coupeuse (figure 6)
La coupeuse est placée en aval de la boudineuse permet de
découper le cordon de savon produit par la boudineuse en morceaux
suivant les dimensions désirées.
Figure 6: Coupeuse
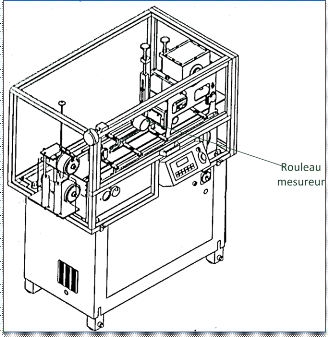
La barre de savon produite par la filière entre dans la
coupeuse électronique et une fois entrée en contact avec le
rouleau mesureur, envoie un signal à l'unité de coupe.
L'unité de coupe fait déplacer la lame à la fois
horizontalement avec un mouvement égal à l'avancement de la barre
et verticalement pour obtenir la coupe. On obtient ainsi des morceaux de
savons
· Le déviateur (2) (figure7)
De la coupeuse sort deux files de savons qui doiventêtre
distribuées entre 4 mouleuses. Pour réaliser cette distribution
l'on dispose de 2 déviateursplacés après la coupeuse. Il
permet de diviser une ligne de savon en l'entré en trois lignes de
sortie avec une servant à éviter l'accumulation de savons.
Les morceaux de savons sont alorsrepartissur les convoyeursdes
mouleuses pour la prochaine étape.
La répartition se fait à l'aide d'un
déviateur pneumatique qui modifie la direction des profilés de
guide des plaquettes après le passage de 6 savons devant le capteur. Un
deuxième capteur placé à la sorte permet de confirmer le
signal envoyé par le premier capteur.En annexe 6 le dessin d'ensemble du
déviateur.
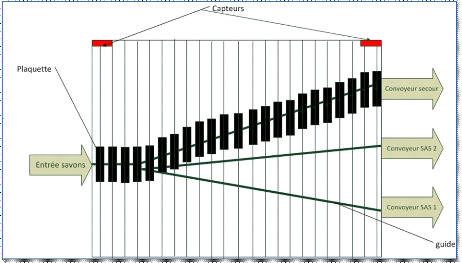
Figure7: Déviateur
· La mouleuse SAS (4)(figure 8)
A leur sortie du déviateurles savons sont
transportés aux mouleuses par des convoyeurs. Chacun des convoyeurs
placés en aval des mouleuses est entrainé par un
motoréducteurcommandé par une photocellule. Ces photocellules
sont placées au niveau des tapis entrés savons permettant ainsi
de réguler l'alimentation de savons des mouleuses. En effet lorsqu'il y
aprésence de savons devant son réflecteurla photocellule commande
l'arrêt du convoyeur qui alimente son tapis d'entré évitant
ainsi les encombrements des mouleuses.
La mouleuse fonctionne selon le principe suivant : Un moteur
à vitesse variable transmet son mouvement de rotation à un
embrayage. Un pignon arbré reçoit une fois la friction
insérée et la communique à la grande roue dentée
montée sur l'arbre central avec plusieurs cames. Ce mouvement de
rotation est ensuite transformé en un mouvement rectiligne grâce
à une bielle et des leviers. C'est le système bielle manivelle.
Ce sont les cames qui commandent les mouvements du poussoir de l'extracteur des
timbres inférieurs- supérieurs et latéraux dans un
moule.Figure 8: Mouleuse SAS
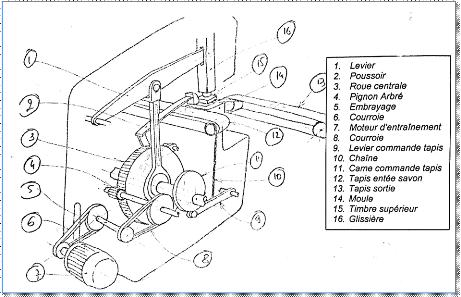
· Emballeuse ACMA 381(4)
Pour l'emballage du savon l'on dispose de quatre emballeuses ACMA
381 ls
Les emballeuses ACMA sont des machines automatisées dont
tous les mouvements des organes sont gérés par un automate. Elle
se compose de quatre moteurs qui sont : le moteur principal pour la
commande des cames, le moteur d'alimentation savon, le moteur culbuteur et un
moteur pas à pas pour le positionnement du film avant la coupe.
L'emballage du savon se fait en quatre grandes phases
La phase d'alimentation savon
Au cours de cette phase le savon provenant des mouleuses sont
soumis à une rotation de 90°par un culbuteur commandé par un
détecteur de proximité qui s'enclenche en présence de
savon
La phase d'alimentation film
Figure 9: Schéma cinématique ACMA
381, vue de dessus
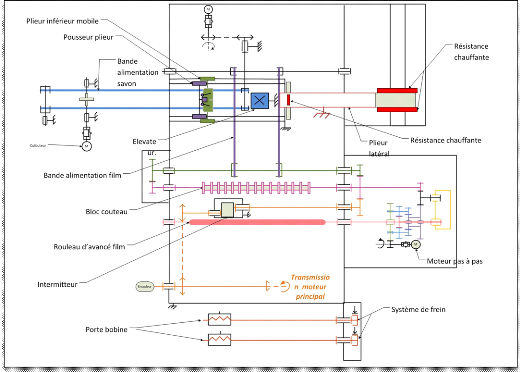
A ce stade, la bobine de film est déroulée à
l'aide de galet en gomme. Ces galet sont entrainé en rotation par le
moteur principal via l'arbre àcame, unsystème pignon chaine et un
itermitteur. Le positionnement du film est assuré par un moteur pas
à pas avant la coupe réalisé par un couteau tournant et un
couteau fixe.
Phase de pliage (annexe 7)
Le savon se positionne en dessous du film d'emballage et est
ensuite emmené vers le haut par l'élévateur qui entame le
pliage. Arrivé au point haut le pousseur plieur achève le pliage
du savon avec le plieur inférieur mobile, la trémie .et l'envoi
dans la rampede pliage pour le pli des cornes. Les cames commandent le
mouvement de l'élévateur, du pousseur, du plieur inférieur
et la trémie.
Phase de scellage (annexe 7)
Le scellage de l'emballage se fait grâce à deux
plaques chauffantes pour le scellage transversal et une plaque chauffante pour
le scellage longitudinal. Le mouvement des plaques est assuré par un
vérin et des cames.
· Imprimante Laser
Après sa sortie de l'emballeuse, le savon est
marqué par une imprimante laser. Cette imprimante est dotée d'un
capteur de proximité qui commande à l'imprimante d'envoyer un jet
d'encre dès qu'il y a présence de savon. Le savon est ainsi
codifier avec toute ses caractéristiques de production.
L'imprimante est composée :
- D'un microcontrôleur
- De de l'imprimante laser
- D'un capteur
· L'encolleuse LITTLE DAVID 3M +imprimante (figure
11)
L'encolleuse LITTLE DAVID 3M permet d'appliquer du ruban
adhésif sur les cartons. En effet quand le carton arrive sur le banc
d'entrée de l'encolleuse, il est plié et poussée sous
l'encolleuse qui applique du ruban adhésif sur la partie
supérieur et inférieur du carton. L'encolleuse réalise le
scellage définitif du carton de savons avant qu'il soit
déporté sur des palettes.
Elle est composée :
- D'un tapis d'entrainement supérieur et
inférieur
- De guides pour la translation des cartons afin d'en assurer le
bon scellage
- De bras pivotant servant de support pour le rouleau de bande
adhésif
- De ressort de rappel permettant de coordonner les mouvements
des différents bras pivotant de la machine lors du scellage
- D'un couteau denté permettant de couper la bande
après le scellage d'un carton
- D'une imprimante laser pour lcodification des cartons
Figure 10: encolleuse
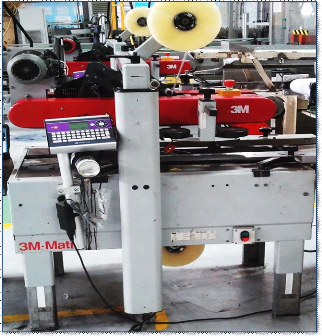
La rotation des tambours du tapis lui est transmise par un
motoréducteur.
2. Présentation de la maintenance
existante
2.1 Documents du service maintenance
HPC
2.1.1 Cahier de rapport journalier
Ce cahier sert à enregistrer les différentes
opérations effectuées par le personnel duservice de la
maintenance HPC. Le mécanicien ou l'électricien de la maintenance
yrédige des notes et informations concernant les interventions qu'il a
menéesaucours de la journée. (Un exemplaire en
annexe4)
2.1.2 Demande d'intervention
La demande d'intervention se compose de deux parties à
savoir :
La demande d'intervention
Le compte rendu d'intervention
Dans ce document est mentionné, le type de la panne, le
temps d'intervention, la pièce de rechange, le nom du demandeur et des
intervenants. Ces fiches sont fournies que pour les interventions qui ne sont
pas du ressort des agents du service maintenance HPC. On les adresse alors aux
autres services compétents de l'usine (sociétés
extérieures). Ces fiches sont établies par le logiciel MP2 et
sont archivé dans la base de données dudit logiciel.
2.1.3 Les OT (Ordre de travail)
Ces documents sont établis pour des opérations de
dépannage nécessitant des pièces de rechange ou des
travaux d'usinage. L'OT est émise par le logiciel MP2 et
précise :
§ L'heure de la demande
§ La nature de l'intervention
§ La cause de la défaillance
§ La pièce à remplacer
§ Le coût de l'intervention
§ L'heure de fin d'intervention
Toutes les OT sont codifiées et permettent ainsi
d'archiver toutes les opérations en cas d'audit. Ces informations sont
stockées dans la base de données du logiciel comme historique.
2.1.4Logiciel de GMAO (MP2)
MP22(*) est un
logiciel de Gestion Productive des actifs qui applique la GMAO
auxopérations de maintenance. MP2 facilite le développement
à long terme de toutes opérations de maintenance, quelles qu'en
soit l'ampleur. Les mécaniciens s'en serventplus pour lancer des ordres
de travaux (OT) et des demandes d'intervention. Nous ajoutons qu'UNILEVERa
opté pour le système SAP3(*) en remplacement de MP2 et donc des mesures sont prises
à cet effet.
2.1.5 Cahier de rapport PAMCO pour les
opérateurs
Ce cahier est suivi par le service PAMCO4(*)et est rempli par les
opérateurs de la ligne et sert d'historique de toutes les
activités effectuées sur la ligne. Dans ce cahier est
précisé les différents arrêtsde la production, leur
durée, la nature (panne mécanique, électrique,..) ainsi
que desobservations concernant l'arrêt.
Ces information sontrecueillies et entrées dans la base de
données du logiciel PAMCO afin de sortir les différents temps de
bon fonctionnements et autres informations pouvant servir à
l'amélioration de la productivité de la ligne.(Une fiche du
cahier en annexe4)
2.1.6 Cahiers de lubrification et inspection
Le service de maintenance est doté de cahiers
d'inspection qui enregistre les contrôles hebdomadaires de certains
sous-ensembles des équipements de productions. Il existe des cahiers de
lubrification qui définissent un planning des organes à lubrifier
de certains organes des équipements
6.1.2 2.2. Interventions sur les équipements
v Les interventions curatives
Les interventions curatives se font selon le
procédé défini dans le tableau de la page suivante.
Tableau 3:procédés des interventions
curatives
Agent de production
|
Service de maintenance
|
magasinier
|
Atelier de mécanique générale
|
Constat de panne
Demande d'intervention très souvent verbale
Fin
Réception de la demande d'intervention
Agent de dépannage
Constat de la panne
Demande d'opération d'usinage
Demande de pièces de rechange
Dépannage
Réception de l'ordre de Travail
Sortie de pièces de rechange
Réception de la Demande d'Intervention
Usinage de pièces
Sortie de pièces usinées
Remplissage des cahiers de rapport
Repérage des anomalies et émission de demande
d'intervention
v Les interventions préventives
· Les visites annuelles
Les visites annuelles s'effectuent selon le
procédé défini dans le tableau ci-dessous :
Tableau 4:procédés des visites
annuelles
Chefs de la maintenance
|
Service de maintenance
|
magasinier
|
Atelier de mécanique générale
|
Archivage
Réception de l'exécution des travaux
Demande d'opération d'usinage
Demande de pièces de rechange
Finition des travaux
Réception de l'Ordre de Travail
Sortie de pièces de rechange
Réception de la Demande d'Intervention
Usinage de pièces
Sortie de pièces usinées
Remarques et commentaires
Programme d'entretien annuel
Exécution des travaux
Contrôle de l'exécution des travaux
Analyse des remarques et commentaires
Dossier fermé
3. Etude 5 M de l'existant.
La résolution de problème obéit à une
méthodologie rigoureuse. L'étape de recherche des causes du
problème se solde souvent par une liste impressionnante de causes. Il
est alors nécessaire de les classer, afin de déterminer les plus
importantes, celles qui seront traitées en priorité. Pour ce
faire nous utiliserons la méthode 5 M qui consistera à passer en
revue toutes les causes possibles de panne.
3.1 Présentation de la
méthode 5M
v Préalable à la construction du
diagramme
La construction du diagramme des 5 M est basée sur un
travail de groupe. Il est important de former une équipe de travail
pluridisciplinaire et de faire participer chaque membre. Pour ce faire nous
avons
· pratiqué un brainstorming5(*) pour trouver toutes les causes
possibles au problème des pannes.
· Sélectionné les causes principalement
responsables du défaut ou du problème ;
· Classé les causes liées au problème
posé.
v Construction du diagramme
Le diagramme 5 M se présente sous la forme d'un graphe en
arêtes de poisson. Dans ce dernier sont classées par
catégorie les causes selon la loi des 5 M (Matière, Main
d'oeuvre, Matériel, Méthode, Milieu).
· M1 - Matières : matière
utilisée par les équipements pour la fabrication du produit.
· M2 - Matériel : Machine, les
supports techniques des machine, pièces de rechange
· M3 - Main d'oeuvre : agent de la
maintenance, opérateurs
· M4 - Milieu : environnement physique,
éclairage, bruit, aménagement, température.
· M5 - Méthodes : système de
maintenance en place
3.2 Application de la méthode
Le problème qui fera pour nous l'objet d'étude
est : Pannesélevées sur MAZZONI 1.
Pour ce fait nous avons mis en place une équipe de travail
constitué de :
Ø Mr Fofana Sehena chef d'atelier
Ø Mr Sako Mamadou : chef des
mécaniciens
Ø Mr Koffi Edward opérateur de la ligne
Mazzoni
Ø Mr Tra Bernard : Mécanicien
Ø Niamké Tanoh Abel F. Stagiaire
Résultats
Le travail effectué nous apermis de sortir le tableau
suivant :
Tableau 5: Tableau étude 5 M
PROBLEM LIÉ À :
|
CAUSES
|
INCIDENCES
|
Matière
Ø Savon collant ou mou
Ø Film corrosif
|
Ø Mauvais qualité matière première,
top de parfum
Ø Qualité du film
|
Ø Savon reste collé au lieu de se détacher
de la parties de l'équipement ou il est en contact cela occasionne des
encombrements qui sont les causes d'usures ou de cassures de pièces
Ø les parties en contact avec le film se corrode ce qui
cause pour l'usure fréquent du couteau voir (Photo 1 pour
illustration)
|
Matériel
Ø indisponibilitéfréquente des pièces
de rechange
Ø Mauvaise gestion de la documentation machine
Ø Absence d'indicateur de vitesse sur certain
équipements
Ø Suppression de la pompe de lubrification
|
Ø Pas de prévision
Ø Absence de local approprié.
Ø Négligence
|
Ø Cause de long temps d'arrêt inutile
Ø Perte de document machine
Ø Mauvaise appréciation de la vitesse, la machine
marche souvent à une cadence excessive ce qui cause l'usure des
pièces mécaniques (photo 2 pour illustration)
Ø Mauvaise lubrification de l'équipement.
|
Main d'oeuvre
Ø Négligence des défauts
Ø dépanneur
Ø Pas motivé
|
Ø Débordé, plusieurs tache pour un seul
opérateur ou mécanicien
|
Ø Pas de bon entretien des équipements, long temps
d'arrêt
|
Milieu
Ø Difficulté d'accès aux
équipements
Ø Taux de salinité élevé
|
Ø Encombrement des machines
Ø Présence de la mer
|
Ø Long temps de dépannage
Ø Corrosion des équipements risque de grippage
pendant les temps d'arrêt
|
Méthode
Ø Pas de planification réelle des taches
Ø Mauvaise application des opérations d'entretien
et contrôle
Ø Production privilégié au détriment
de la maintenance préventive
Ø Pas de réunion de pannes
|
Ø Négligence
Ø Pas de suivi et négligence
|
Ø pannes, et de long temps d'arrêt
|
Photo 1:Corrosion par le film sur ACMA
381
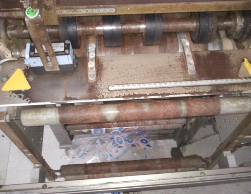
Photo 2:Absence d'afficheur de vitesse sur les
Mouleuse SAS
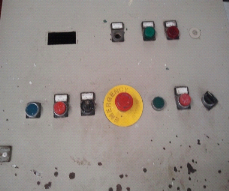
En résumé nous avons le diagramme de Poisson de la
page suivante
Figure 11: Poisson
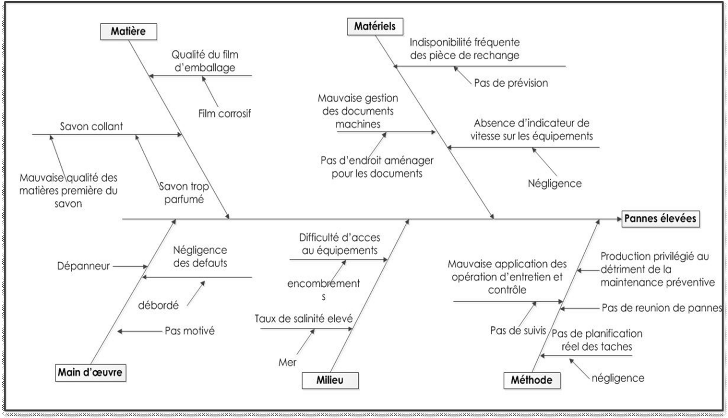
Il conviendra pour la suite d'agir sur ces causes pour corriger
les défauts en mettant en place des actions correctives et
préventive appropriées pour éradiquer les pannes.
Dans ce qui suis nous ferons une étude approfondie sur les
causes dedéfaillances liées auxéquipements eux même
pour en ressortir leurs points faibles. Notons par ailleursque les autres
problèmesévoqués dans l'étude 5 M ne feront pas
l'objet d'une étudeapprofondie car ceux-ci peuvent
êtrerésolus par un plan d'action bien défini que nous
exposerons dans la prochaine partie de notre rapport.
7 Chapitre2:Etude des défaillances des
équipements
L'étude de tous les équipements de la ligne serait
exhaustif nous utiliserons donc le critère de choix Pareto pour une
étude optimal et plus approfondi des équipements qui pose le plus
de problème.Ces équipements ainsi identifié feront l'objet
d'une étude AMDEC.
1. Données de base de
l'étude
v Engagement de la ligne : compte tenu de la forte demande du
produit ligne de production fonctionne 24heures/24.
v Période d'étude : notre période
d'étude s'étend du 15 janvier 2011 au 1Juiellet 2012 environs
18 mois
v Sources des données :
Ø Cahiers PAMCO : cecahier enregistre toutes les
défaillances quisurviennent sur les lignes de productions tout en
précisant leur durée.
Ø Expériences professionnelles : avis des
mécaniciens et desopérateurs car chacun d'eux à une
connaissance des équipements.
Ø Documentation des équipements
L'exploitation des sources des données nous permet
d'établir l'historique suivant :
:
Tableau 6:Historique des pannes
MACHINES
|
temps d'arrêt en heure
|
fréquence d'arrêt
|
atomiseur cylindrique
|
20
|
9
|
boudineuse primaire
|
12,2
|
3
|
boudineuse final
|
24,5
|
16
|
coupeuse de savon
|
61,5
|
27
|
convoyeur alimentationSAS 3
|
38,3
|
8
|
convoyeur alimentationSAS 2
|
48,1
|
12
|
mouleuse SAS1
|
140,7
|
59
|
convoyeur alimentationSAS 1
|
23
|
12
|
mouleuse SAS2
|
414,7
|
124
|
mouleuse SAS3
|
583,8
|
116
|
mouleuse SAS4
|
138,5
|
65
|
emballeuse acma1
|
551,3
|
171
|
convoyeur alimentationACMA 1
|
9,4
|
1
|
convoyeur alimentation sas4
|
9,8
|
5
|
emballeuseACMA 4
|
387,1
|
147
|
emballeuse ACMA 2
|
524,8
|
167
|
emballeuse ACAMA3
|
554,8
|
179
|
pompe dosage parfum
|
8
|
5
|
pompe à vide
|
8,8
|
5
|
Enveloppeuse de carton
|
0,3
|
1
|

Notons que les équipements absents de cette liste non pas
enregistrés de pannes durant la période d'étude comme par
exemple les déviateurs qui sont de nouveaux équipements en
fonction sur la ligne.
2. Répartition des
défaillances de la ligne en fonction deséquipements
L'étude des différentes défaillances de la
ligne a été réaliséegrâce aux
cahiersPAMCO6(*). Nous
rappelons que lors de la production les opérateurs et agents de la
maintenance utilisent ce cahier pour le recensement de toutes les
activités de la ligne dont les pannes. Dans ces cahiers sont
marqués la date, le type d'intervention, la durée de
l'intervention et des observations
Ainsi pour notre étude nous avons procédé au
recensement des défaillances de la ligne de la période du 15
janvier 2011 au 1 juillet 2012 soit 18 mois environ.
Ensuite nous avons utilisé le critère de choix
Pareto pour nous orienter vers les équipements les plus
pénalisants de la ligne selon les deux critères
suivants :
Ø Les temps
d'arrêtsqu'occasionnent les défaillances : ce
critère nous permettra de déterminer les équipements dont
les défaillances causentle plus grands temps d'arrêts de la
ligne.
Ø La fréquence
d'apparitiondes défaillances (c'est-à-dire le
nombre defoisqu'un équipement tombe en défaillance) : ce
critère nous permettra dedéterminer les équipements de la
ligne qui tombent le plus endéfaillance.
Notons que :

Le diagramme de Pareto est un outil statistique qui permet
d'identifier l'importance relative de chaque catégorie dans une liste
d'enregistrements, en comparant leur fréquence d'apparition. Un
diagramme de Pareto est mis en évidence lorsque 20 % des
catégories produisent 80 % du nombre total d'effets. Cette
méthode permet donc de déterminer rapidement quelles sont les
priorités d'actions. Si on considère que 20 % des causes
représentent 80% des occurrences, agir sur ces 20 % aide à
solutionner un problème avec un maximum d'efficacité.
2.1 Répartition de Pareto des
temps d'arrêts qu'occasionnent lesdéfaillances des
équipements
Nous avons effectué une première analyse de Pareto
en prenant comme critèred'analyse les temps d'arrêts. Les
résultats de l'analyse sont consignés dans tableau suivant.
Tableau 7:Temps d'arrêts
Equipements
|
Temps d'arrêt en heure
|
Pourcentage.
|
Cumul des temps d'arrêt
|
Pourcentage du cumul
|
Mouleuse SAS3
|
583,8
|
16%
|
583,8
|
16%
|
Emballeuse acama3
|
554,8
|
16%
|
1138,6
|
32%
|
EmballeuseACMA1
|
551,3
|
15%
|
1689,9
|
47%
|
Emballeuse ACMA 2
|
524,8
|
15%
|
2214,7
|
62%
|
Mouleuse sas2
|
414,7
|
12%
|
2629,4
|
74%
|
Emballeuse ACMA 4
|
387,1
|
11%
|
3016,5
|
85%
|
Mouleuse SAS1
|
140,7
|
4%
|
3157,2
|
89%
|
Mouleuse SAS4
|
138,5
|
4%
|
3295,7
|
93%
|
Coupeuse
|
61,5
|
2%
|
3357,2
|
94%
|
Convoyeur alimentation SAS 2
|
48,1
|
1%
|
3405,3
|
96%
|
Convoyeur alimentationSAS 3
|
38,3
|
1%
|
3443,6
|
97%
|
Boudineuse final
|
24,5
|
1%
|
3468,1
|
97%
|
Convoyeur alimentationSAS 1
|
23
|
1%
|
3491,1
|
98%
|
Atomiseur cylindrique
|
20
|
1%
|
3511,1
|
99%
|
Boudineuse primaire
|
12,2
|
0%
|
3523,3
|
99%
|
Convoyeuralimentation Sas4
|
9,8
|
0%
|
3533,1
|
99%
|
Convoyeur alimentationACMA 1
|
9,4
|
0%
|
3542,5
|
99%
|
Pompe à vide
|
8,8
|
0%
|
3551,3
|
100%
|
Pompe dosage parfum
|
8
|
0%
|
3559,3
|
100%
|
Encolleuse
|
0,3
|
0%
|
3561,9
|
100%
|
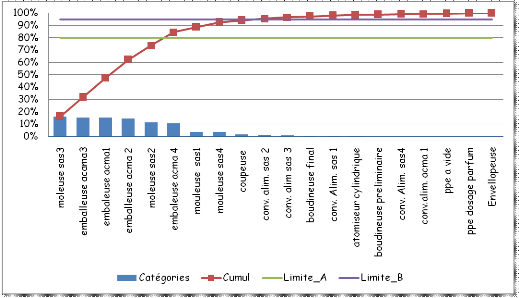
On obtient le diagramme de Pareto suivant :
Ø Figure 12: Courbe Pareto des temps
d'arrêts
Interprétation des
résultats
L'étude Pareto nous montre que 80% des longs temps
d'arrêtde la ligne sont dusaux équipements suivant :
· Mouleuse SAS 3
· Emballeuse ACMA 3
· Emballeuse ACMA 1
· Mouleuse SAS 2
· Emballeuse ACMA 4
Les mouleuses et les emballeusessontles équipements les
plus pénalisants selon les temps d'arrêts.
2.2 Répartition de Pareto des
fréquences de défaillance des équipements
Nous avons effectué une seconde analysePareto en prenant
en compte cette fois les fréquences d'arrêts des
équipements.Les résultats de ladite analyse sont consignés
dans le tableau suivant :
Tableau 8: fréquence
d'arrêt
Equipements
|
Fréquence d'arrêt
|
Pourcentage d'arrêt
|
Cumuldes fréquences d'arrêt
|
Pourcentage
|
Emballeuse acama3
|
179
|
16%
|
179
|
16%
|
Emballeuse acma1
|
171
|
15%
|
350
|
31%
|
Emballeuse acma 2
|
167
|
15%
|
517
|
46%
|
Emballeuse acma 4
|
147
|
13%
|
664
|
59%
|
Mouleuse sas2
|
124
|
11%
|
788
|
70%
|
Mouleuse sas3
|
116
|
10%
|
904
|
80%
|
Mouleuse sas4
|
65
|
6%
|
969
|
86%
|
Mouleuse sas1
|
59
|
5%
|
1028
|
91%
|
Coupeuse
|
27
|
2%
|
1055
|
93%
|
Boudineuse final
|
16
|
1%
|
1071
|
95%
|
Convoyeur alimentation sas 2
|
12
|
1%
|
1083
|
96%
|
Convoyeur alimentation sas 1
|
12
|
1%
|
1095
|
97%
|
Atomiseur cylindrique
|
9
|
1%
|
1104
|
97%
|
Convoyeur alimentation sas 3
|
8
|
1%
|
1112
|
98%
|
Convoyeur alimentation sas4
|
5
|
0%
|
1117
|
99%
|
Pompe dosage parfum
|
5
|
0%
|
1122
|
99%
|
Pompe à vide
|
5
|
0%
|
1127
|
99%
|
Boudineuse primaire
|
3
|
0%
|
1130
|
100%
|
Convoyeur alim. acma 1
|
1
|
0%
|
1131
|
100%
|
Enveloppeuse
|
1
|
0%
|
1132
|
100%
|
Figure 13: Courbe Pareto des fréquences
d'arrêts
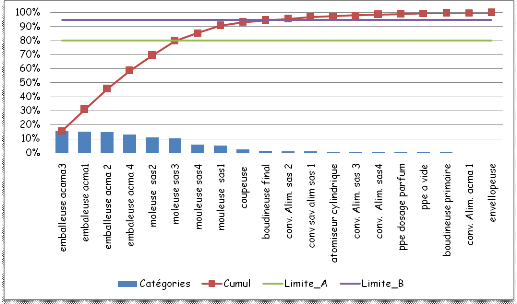
On obtient le diagramme de Pareto suivant :
Ø Interprétation des
résultats
Cette fois les résultats nous montre que les plus grands
contributeursen termes de fréquences d'arrêtsont les ACMA et
ensuite les mouleuses selon l'ordre suivant :
Ø Emballeuse ACMA 3
Ø Emballeuse ACMA 1
Ø Emballeuse ACMA 2
Ø Emballeuse ACMA 4
Ø Mouleuse SAS2
v Conclusion partielle de
l'étude
Il en ressort que les équipements qui feront l'objet de
l'étude sont les emballeuses et les mouleuses. Les
autreséquipements seront soumis uniquementà des maintenances
correctives.
Dans ce qui suit nous utiliserons la méthode A.M.D.E.C
pour l'étude des défaillances des équipements sujets de
notre étude couplée à un arbre de défaillance de
l'évènement redouté.
3. Analyse des défaillances
Cette analyse consistera dans un premier temps en une
étude A.M.D.E.C des équipements et ensuite une analyse selon
l'arbre de défaillance des évènements redoutés
ressortipar l'étude A.M.D.E.C7(*)
3.1 Etude A.M.D.EC
3.1.1 Présentation de la méthode
3.1.1.1Définition et objectifs de la
méthode
A.M.D.E.C qui signifie Analyse des
Modes de Défaillance de leurs
Effets et leurs Criticité est une
méthode prédictive qui permetd'identifier les causes et les
effets de la défaillance des fonctions d'un système pour
maintenir un taux de service de la finalité
« acceptable ».
Cette méthode regroupe deux aspects que sont les aspects
quantitatifs et qualitatifs.
· Qualitatif
® détermination des Causes de défaillances
® détermination des Modes de défaillances
® détermination des Effets de ces
défaillances
· Quantitatif :
® évaluation fréquence d'apparition de ces
défaillances
® évaluation de la maintenabilité
® calcul de la criticité
L'A.M.D.E.C permet donc de faire ressortir les points critique
afin de les éliminer, deprévoir un mode de prévention et
peut aussi servir de fiche de diagnostic.
3.1.1.2 Les étapes de la réalisation
(annexe8)
3.1.2 Application
3.1.2.1 Mis en place du groupe de travail
Pour l'exercice de notre projet, afin d'atteindre nos objectifs,
nous avons constitué une équipe de travail constitué
de :
Ø Mr Fofana Sehena chef d'atelier de production de la
savonnerie
Ø Mr Sako Mamadou chef des mécaniciens
Ø Mr Begue Nicolas mécanicien
Ø Mr Agbalessi Stanislas mécanicien de la ligne
Mazzoni 1
Ø Mr Kpodjahon Anani électricien de l'atelier de la
savonnerie
Ø Mr Koffi Edward, opérateur de la ligne
Ø Niamké Tanoh Abel F. ,stagiaire
3.1.2.2 Décomposition fonctionnelle des
équipements
La réalisation de cette étude s'est faite
grâce aux documentations existantes des équipements et avec le
concours des agents de maintenance.
Les équipements faisant l'objet de notre étude sont
les emballeuses ACMA 381ls et les mouleuses de savons. Les
décompositions de ces équipements sontprésentées
enannexe 9.
3.1.2.3 Analyse qualitative
A ce stade de l'étude nous avons procédé
d'abord au recensement des modes de défaillancesdu système. Par
mode de défaillance nous attendons la façon par laquelle le
système peut échouer dans l'accomplissement de sa fonction de
base. Nous nous somme posé la question suivante :
« Que peut-il arriver à notre
système ».
Ensuite nous avons recherché les causes
c'est-à-dire les anomalies susceptibles de conduire à un mode de
défaillance en nous posant la question « Pourquoi cette
défaillance est-elle arrivée ? ». Pour
nous aider nous avons utilisé la méthode 5M que nous avons
utilisé plus haut. En voici un exemple celle de la défaillance
photocellule.
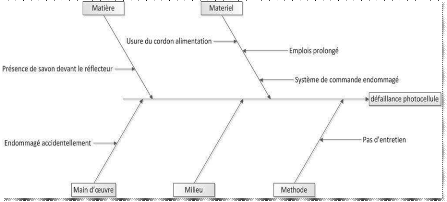
Figure 14: 5M photocellule
Enfin nous avons indiqué les conséquences de cette
défaillance sur le système en nous posant la question
suivante « Quelles peuvent être les
conséquences de cette défaillance ? ».
3.1.2.4Analyse quantitative
Dans cette partie, nous avons cherché à quantifier
l'impact de ces défaillances sur le système.
Ø La maintenabilité
On l'estime à l'aide des MTTR (mean time to repair :
Moyenne des temps de réparation). Avec des techniciens du service
entretien de l'équipe nous avons procédé à la
segmentation suivante :
Tableau 9:Classe de maintenabilité
coefficients
|
Caractéristiques
|
Temps de réparations(TR)
|
1
|
Intervention très difficile
|
4 H = TR.
|
2
|
Intervention difficile
|
2.5 H < TR= 4 H
|
3
|
Intervention délicate
|
1 H < TR. = 2.5 H
|
4
|
Intervention sans difficulté
|
0 H < TR. = 1 H
|
Ø La criticité
Plusieurs méthodes existent pour la détermination
de la criticité. Pour notre part nous utiliserons
laméthodeP.I.E.U bien connu et fiable.Nous
présentons en annexe 10 le tableau PIEU et sa grille de
d'appréciation.
Nous procédons ainsi pour la déterminationde la
criticité.
Ø La fréquence des pannes
Nous avons grâce à l'étude des cahiers PAMCO
et surtout de l'expérience des mécaniciens déterminer les
classes de fréquence des pannes ces résultats sont dans le
tableau suivant :
Tableau 10: classe de fréquence
CLASSES
|
NOMBRE DE DEFAILLANCES (D)
|
OBSERVATIONS
|
A
|
0 = D = 4
|
Très improbable
|
B
|
5 = D = 9
|
Improbable
|
C
|
10 = D = 14
|
Possible
|
D
|
D = 15
|
Fréquent
|
3.1.2.5 Présentation des résultats
Avant cela nous soulignons que pour chaque mode
étudié nous avons proposé une série d'action
préventive ou curative le concernant.
Nous vous présentons une fiche AMDEC de l'emballeuse ACMA
381 ls.,l'étude complète se trouvant en annexe 8
Equipement : ACMA 381 LS
|
REF
|
Désignation
|
fonction
|
|
Ø C
|
F
|
M
|
D
|
Mesures
|
Ø Modes
|
Ø causes
|
Ø conséquences
|
Prévention
|
corrections
|
AC15
|
Bande d'alimentation savon
|
Entraine le savon
|
Ø usure
Ø déchirure
|
Ø utilisation prolongée
Ø mauvais positionnement ou mauvais centrage
|
Ø Mauvais guidage
Ø Bourrage de savon
|
2
|
A
|
3
|
V
|
Nettoyage périodique tout en respectant les
précautions consigné et remplacement périodique des
bandes
|
remplacer
|
AC16
|
bandes d'alimentation film
|
Entraine le film
|
Ø Usure
Ø déchirure
|
Ø utilisation prolongée
Ø mauvais positionnement ou mauvais centrage
|
Ø mauvais guidage du film
Ø Pas d'avancé du film d'emballage
|
3
|
A
|
3
|
V
|
Nettoyage périodique tout en respectant les
précautions consigné et remplacement périodique des
bandes
|
remplacer
|
AC17
|
roulement des rouleaux d'avance du film
|
Entraine et guide le film vers l'élévateur
|
Ø Usure
Ø grippage
|
Ø milieu corrosif
Ø Emploi prolongé
Ø présence de copeaux de savon
Ø Mauvais entretien
Ø Pas de lubrification
|
Ø Mauvais emballage
Ø Risque de patinage
Ø perte d'emballage
|
3
|
A
|
4
|
V
|
Nettoyage périodique et contrôle des
ressorts et roulements
|
Nettoyer avec une solution légèrement
détergente
|
3.1.2.6 Interprétation des résultats
Ø Matrice de criticité
|
|
A
|
B
|
C
|
D
|
|
Echelle
D'occurrences
Classe
de gravité
|
Très improbable
|
Improbable
|
Possible
|
Fréquent
|
4
|
Sans influence
|
AC10. A8. A9.SA19.SA20
|
|
|
|
3
|
Peu critique
|
AC5. AC12. AC13. AC16. AC17. A5. A7. AC30. SA2. SA3.SA4. SA9.
SA12.SA14.SA16.SA17. SA18. SA22. SA23.SA25. SA28
|
A0. AC19. SA10. SA13.
|
|
A2. A4
|
2
|
Critique
|
AC1. A. AC3. AC4. AC6. AC7. AC10. AC14. AC19. SA1. SA2. SA5. SA7.
SA8. SA11. SA15. SA21. SA26. SA27
|
AC9. AC12. A6
|
A3
|
AC18.
|
1
|
Très critique
|
SA6. SA7.SA21. SA23. SA24.
|
|
|
|
1
|
Très difficile
|
AC7. AC10. AC14. SA5. SA11
|
|
|
|
2
|
Difficile
|
|
AC8. AC11
|
A2
|
|
3
|
Délicate
|
AC1. A. AC3. AC4. AC12. AC16. AC19. A8.A9.AC30.SA1. SA2. SA6.
SA9. SA16. SA24. SA28
|
SA10
|
|
AC18 A4
|
4
|
Sans difficulté
|
AC5. AC6. AC9. AC13. AC17. A5. A7.SA3. SA4. SA8. SA12. SA14.
SA15. SA17.SA18.SA19.SA20. SA22. SA25. SA26. SA27
|
A0 .A1. A6. SA13
|
A2.
|
|
|
Maintenabilité
|
|
|
|
|
Ø Interprétation
La matrice de criticité des deux équipements ayant
étéétablie. Les éléments
considérés comme les plus critique sont ceux qui apparaissent
dans la zone ombré à; savoir le couteau fixe et mobile(AC18).Des
défaillances à leur niveau sont des évènements
redoutés dont une prise en charge particulière serait
bénéfique pour la production.Ils (couteau fixe et mobile)devront
doncêtre soumis à une politique de maintenancepréventive
conditionnelle, être prédisposé à des mesures de
secours, être tenu en stock et enfin recevoir une amélioration de
leurs maintenabilité.
3.2 Arbre de défaillance
Cette méthode déductive (de l'effet vers ses
causes) a pour objet la recherche de toutes les combinaisons de
défaillances élémentaires pouvant aboutir à
l'évènement redouté, identifié par l'AMDEC. A
partir de cet « évènement sommet », nous avons
construit une arborescence (schéma graphique en forme d'arbre
inversé) représentant l'enchaînement logique des «
évènements intermédiaires » jusqu'à la
mise en cause des « évènements
élémentaires » (défaillance d'un composant
Ce type d'analyse permet, dans le domaine de la maintenance :
Ø d'améliorer la conception ;
Ø de faire un diagnostic rapide ;
Ø de prévoir une meilleure logistique.
On obtient ainsi l'arbre de défaillance suivant avec
évènement redouté : défaillance du couteau
fixe ou mobile.
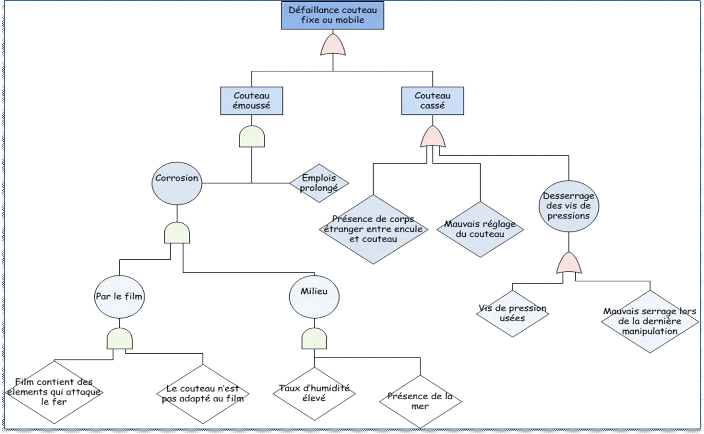
Figure15: Arbre de défaillance du couteau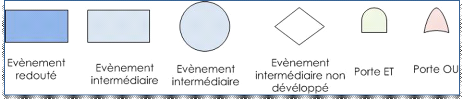
Figure 16:Symboles arbre de
défaillance
Ø Conclusion arbre de défaillance
Il en ressort de cette étude que les causes majeures des
défaillances du couteau sont dues :
Ø Au couple film-couteau
Ø A la négligence des opérations de la
maintenance
Les causes dues au milieu de travail ont desrépercussions
négligeablessur les défaillances du couteau. .
Dans la prochaine partie nous aborderons des solutions qui
doivent être prise dans l'objectif d'atteindre le
« zéro panne ».
3
PARTIE
PROPOSITIONS DE SOLUTIONS ET RENTABILTE DU
PROJET
8 Partie3 : Propositions de solutions etétude de
rentabilité
CHAPITRE 1 : Proposition de solutions
CHAPITRE 2 : Etude de rentabilité
9 Chapitre 1: Propositions de solutions.
Ce chapitre présente les solutions aux problèmes
ressortis par la méthode des 5 M et aussi de l'étude des
défaillances de la ligne MAZZONI 1. Aussi présente-t-il les
mesures selon le guide TPM à mettre en place pour l'obtention du
« zéro panne. »
Nous proposons en annexe 13des mesures tirées du
livreLe guide de la TPMdeJean
Buffermedans le cadre de la mise ne place d'une activité
zéro panne. Mesures qui constituent un plan d'action à appliquer
aux 5 M pour éradiquertous les problèmes liés aux pannes.
Dans ce qui suit nous proposeront des solutions pratiques
à mettre en place dans les 5M.
1. Solutions aux problèmes
liés à la méthode de maintenance
La mise en place de standard de Nettoyage, de lubrification et
d'inspection bien définiset selon un plan contribuerait en une meilleur
organisation des activités de la maintenance et aussi à son
suivit.
A cet effet nous proposons les différentes gammes de
nettoyage, lubrification et inspections des équipements
pénalisant de la ligne qui sont les mouleuses et les emballeuses les
autres équipements seront quant à eux soumis t à des
opérations de nettoyages simples et à une maintenance corrective.
1.1 Gamme de nettoyage
® Importance du nettoyage
Le nettoyage de l'équipement et de son environnement est
une mesure essentielleà la prévention des défaillances et
à la sécurité du personnel en présence
dansl'atelier. Il concoure fortement à la prolongation de la
durée de vie deséquipements. En plus, cette opération
est le garant de l'absence des corpsétrangers pouvant
entraîner des pannes imprévues et des dysfonctionnements
del'équipement.
Aussi nous oblige-t-ilà nous approcher de la machine,
à la toucher,à la regarder de près. Ce qui permet de :
Ø faire apparaître les anomalies (boulons
desserrés ou manquants,jeu, conducteurs non fixés ou inutiles,
etc.),
Ø détecter d'où proviennent les fuites
(c'est lorsque la machine estpropre que l'on voit où se crée la
fuite),
Ø évaluer la vitesse d'encrassement,
Ø suivre l'avancement de l'inspection et de
visualiser les zonesoubliées.
® Proposition de gamme de nettoyage (annexe 14)
1.2 Gamme lubrification
® Importance de la lubrification
C'est un outil fondamental pour l'entretien voir même pour
la durée de vie d'un équipement, elle doit être
rigoureusement suivie. Si par contre elle n'est pas soigneusement
appliquée elle occasionne des cassures et des
détériorations au niveau des éléments qui composent
l'équipement. Ces opérations doivent êtrerigoureuses et
convenablement gérées :
Ø en quantité (volume de graisse ou d'huile),
Ø en qualité (types et catégories de
lubrifications),
Ø en délais (fréquences calendaires)
® Proposition de gamme. (Annexe 12)
® Gestion de la lubrification
Comme le préconise la TPM dans le cadre de la maintenance
autonome, les agents responsables de la lubrification des équipements
sont les opérateurs de la ligne. Pour ce faire ceux-ci ont besoin d'une
formation dans ce domaine par les agents de la maintenance et aussi d'un suivi
des différentes opérations de lubrification à cet effet
nous proposons en annexe 16un diagramme sur la manière de
gestion de cette activité (diagramme inspiré par d'une
étude de la maintenance UNILEVER-Brésil).
1.3 Fiche d'inspection
® Importance de l'inspection
Les opérations d'inspections permettent de détecter
toute non-conformité par rapportaux conditions de base (fixations
boulons, bruits anormaux, état d'usure...) et auxconditions
opératoires de l'équipement de production. Ce sont ces anomalies
quiconstituent les défauts latents et qui par synergie sont à
l'origine desdéfaillancesdes équipements.
® Proposition de fichesd'inspection (Annexe 17)
1.4 Moyens de la bonne application
Pour la bonne application de ces travaux, la maintenance doit
disposer d'un certain nombre de moyens. Moyens que nous proposons dans le cadre
du bon nettoyage des équipements et de la bonne application des
opérations d'entretien selon le constructeur des machines.
Ø Nettoyage et d'entretien
Pour la bonne conduite des opérations de nettoyage et
d'entretien, il est indispensable que les agents d'entretiens :
soient munis des outils nécessaires au nettoyage
Aient un temps de nettoyage acceptable
Soient en nombre suffisant.
Nous proposons donc :
§ l'installation d'une armoire à outils sur la ligne
Mazzoni 1(Spatules, clés, cure moule)
§ L'achat d'un aspirateur pour le nettoyage des machines
§ Qu'une concordance soit faite entre les activités
de maintenance et celle de la production
§ L'insertion d'agents supplémentaires dans le
nettoyage en plus des opérateurs de la ligne (au moins trois en plus des
deux).
Ø Contrôle visuel
Le meilleur suivi des opérations d'entretien se fera
correctement si des indicateurs sont placés sur les équipements.
Ces indicateurs afficheront par exemple pour la lubrification :
Ø la date de lubrification
Ø la date de la prochaine lubrification
Ø le type de lubrifiant utilisé (EP2, DTE 26..).
En annexe 16un exemple d'indicateur mise en place.
1.5 Organisation de réunion de
panne
L'objectif « zéro panne » est une
activité qui passe nécessairement par une
améliorationcontinue des activités de la maintenance. En effet
toutes les pannes et problèmes qui subviennent sur la ligne
doiventêtre après dépannagetraités en réunion
afin de trouver des voies et moyens pour les éradiquer
définitivement. Nous proposons donc l'organisation de réunions de
pannes que nous appellerons « breakdown meeting »
toutes les semaines où les agents de la maintenanceviendront discuter
des problèmes subvenus ou qui pourraientsubvenir sur la ligne et par la
même occasion faire le point des différentes
inspectionsmenées sur la ligne.
Photo 3: Agent HPC UNILEVR-Brésil en
réunion de panne
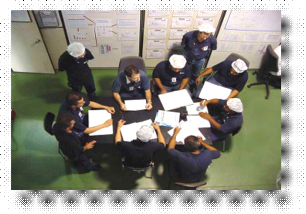
2. Solutions aux problèmes
liés aux moyens matériels
2.1 Restauration des conditions de base
des équipements
Certains équipementstravaillent dans demauvaises
conditions de base sur la ligne ce sont en particulier les mouleuses
d'où leur place dans le rang des équipements les plus
pénalisants. Cette activité est très importante car
malgré une bonne maintenance préventiveen place il y aura des
échecs si les équipements ne fonctionnent pas dans leurs
conditions de base.
Nous proposons comme restauration :
Ø La remise en état des indicateurs de vitesse sur
les mouleusespour la gestion optimale de la cadence.
Ø La remise en état de la pompe de lubrification
des leviers des mouleuses pour diminuer le taux d'usure des leviers.
Ø La remise en état des FRL des emballeuses pour
augmenter la durée de vie des vérins
Ø La révision complète des emballeuses et
des mouleuses selon un plan bien défini.
La restauration ainsi réalisé doit s'accompagner de
l'application des différentes gammes d'entretien.
2.2 Contribution à lagestion des
pièces de rechange
Gérer les stocks, c'est répondre à deux
questions :
Ø Quand acheter ?
Ø Quelle quantité acheter ?
Et cela tout en minimisant les risques de rupture de stock et les
couts de stockage des biens.
La politique de d'approvisionnement du magasin en pièce
détaché est celle la quantité variable et de la date
fixe.Ici le calcul de la quantité théorique à
commander est égal à la somme des consommations entre la
livraison à venir et la livraison suivante.
Mais fort estde constater des ruptures de stock dues
à la mauvaise détermination de la quantité
théorique à commander. Soulignons que cette quantité
théorique est déterminée par les agents de la
maintenance.
Pour éviter toute rupture de stock nous
proposons :
Ø En annexe 18 la liste des pièces de
rechange des équipements pénalisant avec leur stock mini
déterminé à partir des statistiques de consommation de
pièces des années antérieures.
Ø la mise en place d'indicateurs pour montrer à
quel niveau se trouve le stock et s'il ya nécessité d'encommander
pour une meilleuregestion (exemple photo4).
Ø Formation à la méthode KANBAN8(*) de gestion de stock.
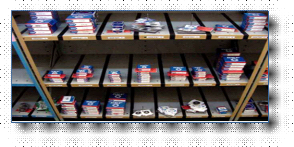
Ø Photo 4:Rangement des roulements au
magasin UNILEVER-Brésil
2.3 Gestion de la documentation
Le manque de connaissances d'un équipement est l'une des
causes de pannes. Car c'est à partir de la documentation du constructeur
que peut sortir les différentesrecommandations d'entretiens et des
précautions d'utilisation. Une connaissance et une disponibilité
de cet outil seront bénéfiques pour la maintenance. Nous
proposons à cet effet la mise en place d'un endroit où tous
les documents machine seront rangés et disposés selon des
règles bien spécifique pour éviter toutes disparitions ou
pertes.
3. Solutions liées aux
problèmes des matières
Les matièresutilisées par les équipements de
la production sont le savon et le film d'emballage. Ceux-ci ont des incidences
sur le fonctionnement des équipements en fonction de leurs
qualités
3.1 Influence savon sur les
équipements.
Le savon est cause de défaillance au niveau des
équipements lorsqu'il est collant et mous. Ces états occasionnent
des bourrages et des efforts importants dans les mécanismes du
système qui par la suite causent des pannes.
Ces états sont dus aux causes suivantes :
Ø Mauvaise qualité des matières
premières
Ø Taux de parfum élevé dans le savon
Ø Mauvais vide dans l'atomiseur
Nous proposons donc :
· Le contrôle de la composition du savon
Pour ce faire un test visant à déterminer la
qualité du savon doit être faitavant la finition (tout juste
après la saponification).Si la composition ou les proportions des
composants ne sont pas conformes aux normes, alors il faudra corriger la
qualité de ce savon avant de le conduire sur la ligne en y ajoutant des
réactifs. Les valeurs à respecter sont les suivantes :
Ø 61,3 = %Acide Gras = 65,7
Ø 1,3 = %Carbonate = 1,7
Ø 0,04 = Alcali = 0,14
Ø 0,4 = %Sel = 0,6
· L'amélioration du système de dosage de
parfum
Ici nous proposons la mise en place d'un robinet de dosage de
parfum plus adapté pour régulation du débit de parfum.
· Le respect des procédés
d'établissement de vide dans l'atomiseur.
3.2 Film
Le film utilisé pour le l'emballage du savon est un
matériau plastique : le polypropylène. Nous avons
constaté que celui-ci a une incidence sur la machine et cela se voit
à travers la Photo 5.
Parties en contact avec le film
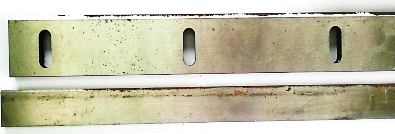
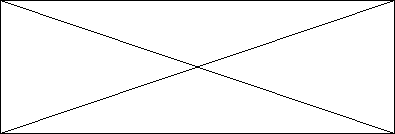
Photo 5:La partie en contact avec le film est
corrodée (couteau plus enclume)
Nous remarquons sur la photo ci-dessus que la corrosion est
accentuée sur la partie en contact avec le film. De plusnotons le taux
d'usure du couteau a augmenté depuis l'utilisation de l'emballage pp
(polypropylène) en remplacement de l'emballage en PVC (polychlorure de
vinyle).
Pour résoudre ce problème nous avons
travaillé avec le service R and D (recherche et
développement) qui s'occupe de laréalisation de projet
d'innovation (nouvelle emballage, carton, produit...) dans le but de connaitre
la constitution de l'emballage. A cet effet nous avons contacté les
fournisseurs de l'emballage et en prélude à leurs propositions,
nous suggérons :
Ø L'utilisation pour le couteau d'un matériau
résistant à la corrosion par le film.
Ø Le remplacement systématique descouteauxpour
affutage toutes les 700 heures de travail. Aussi envisager la mise en place
d'un système d'affutage automatique du couteau.
Ø L'utilisation d'un emballage moins corrosif
proposé par les fournisseurs.
4. Solutions aux problèmes
liés à la main d'oeuvre
Le problème majeur à ce niveau est le manque de
motivation des agents de maintenance et opérateur de la ligne.Sans la
participation et l'implication des hommes, les plus belles démarches
mêmeJaponaises restent sans effet. Les opérateurs de la production
et les techniciens dela maintenance doivent trouver un avantage dans la
politique « zéro panne » quenous menons. La motivation est un
véritable catalyseur de l'action ; c'est donc unecomposante
déterminante du changement de culture dans l'entreprise.
Cela doit se traduire par :
· Le soutien permanent et la reconnaissance des efforts de
chacun,
· L'amélioration des conditions de travail à
tous points de vue,
· Le développement d'un système de
communication écrit, visuel et oralefficace. La communication doit
être professionnelle et productrice de valeurajoutée.
5. Solution aux problèmes du
milieu de travail
La situation géographique d'UNILEVER Vridi par rapport
à la mer lui impose d'adopter un certain comportement pour limiter les
risques de corrosion au niveau des équipements.
Nous proposons à cet effet :
Ø Le contrôle de l'état des couches
antirouille sur les équipements .Dans le cas échéant un
renouvèlement de cette couche
Ø L'utilisation d'outilsmoins agressifspour le nettoyage
des équipements car certains outils ont tendance à enlever la
couche antirouille sur les équipements
Ø Le contrôle de la lubrification des
équipements
10 CHAPITRE2 : Rentabilité
du projet
L'activité « zéro panne » que nous avons
menée permettra de réduire les tempsd'arrêts
occasionnés par les défaillances des équipements. Cette
réduction des temps d'arrêts aura unimpact positif sur le volume
de production.
Considérons l'une des emballeuses de la ligne la ACMA 1.La
cadence nominale de cetteemballeuses : 70 savons / minute.
Les temps d'arrêt de l'emballeuse dû aux pannes est
de 551.3 heures or la production de savon de cette ligne s'élève
à 2.78tonnes/h
D'où la mise en place de cette activité
zéro, pourrais faire gagner à la production plus de 1534.614
tonnes en considérant uniquement cette seule emballeuse.
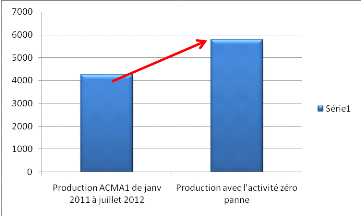
Figure 17: Gain de production
Cette activité est donc bénéfique pour
l'entreprise
11 CONCLUSION
Notre thème consistait à réduire les temps
d'arrêt sur la ligne MAZZONI1 en réduisant au maximum les temps
d'arrêts dus aux équipements les plus pénalisants.
D'abord nous avons, consulté l'historique des
équipements de la savonnerie. L'analyse de ces données nous a
permis de savoir que la ligne MAZZONI 1 enregistrait le nombre de temps
d'arrêt le plus élevé. Et sur cette ligne, les
équipements ayant à leur compte les temps d'arrêt les plus
grands sont les emballeuses ACMA 381 LS et les mouleuses SAS.
Ensuite nous avons étudié les causes de
défaillances des équipements par la méthodeAMDEC. Cette
Méthode nous apermis de faire ressortir les éléments
critiques des équipements ainsi que l'évènement
redouté associé. A l'aide d'un arbre de défaillance nous
avons montré les causes qui pourraient entrainer
cetévènement redouté.
En fin à partir de la méthode 5 M
réalisé en étude de l'existant et l'étude AMDEC
nous avons terminé nos travaux par la proposition d'un plan
préventif adapté aux conditions d'exploitations actuelles.
Pour notre part les contraintes critiques qui peuvent
empêcher l'implémentation de notre projet est principalement le
manque de motivation du personnel. Le service maintenance gagnerait à
favoriser la mise en place d'un management motivationnel.
Au terme de notre étude, nous avons la conviction d'avoir
appris énormément dans la mesure où nous avons
amélioré nos connaissances en maintenance, nos connaissances
de l'entreprise et aussi nos connaissances en matière de
relationshumaines.
12 Bibliographie
[1] JEAN Bufferne, 2006. Le guide de la TPM
Total Productive Maintenance, EYROLLES Editions d'organisation.
[2] JEAN Héng, 2002.Pratique de la
maintenance préventive, DUNOD Edition
[3] AKPO Bessekon Paul, Organisation et Gestion
de la maintenance, Ingénierie pédagogique, 4eme édition
Septembre 2000.
 
* 1Safety Health Environment
* 2Maintenance Productive 2
* 3 System application
production
* 4PAMCO : plaints And
Machines Controls
* 5 - Le BRAINSTORMING est une
technique de créativité en groupe permettant de produire le plus
d'idées possibles, dans un minimum de temps sur un thème
donné.
* 6PAMCO: Plaints And Machines
Controls
* 7 Crée aux Etats-Unis
en 1966 par la société Mc Donnell Douglas, l'AMDEC est selon
l'AFNOR une méthode inductive qui permet de réaliser une analyse
qualitative et quantitative de la fiabilité d'un système.
* 8Méthode Japonaise de
gestion de stock mise en application en année 50 par Toyota
|