ENP 2019
REPBLIQUE ALGERIENNE DEMOCRATIQUE ET
POPULAIRE Ministère de l'Enseignement Supérieur et de la
Recherche Scientifique École Nationale
Polytechnique Département Maitrise des Risques Industriels et
Environnementaux
Filière QHSE-GRI

Mémoire de projet de fin d'étude pour l'obtention
du diplôme d'Ingénieur d'état en QHSE-GRI
Sous le thème
Elaboration d'une nouvelle
méthodologie
d'étude des effets dominos et application:
cas
LINDE Gaz Algérie
Ghiles OUKACI
Mohamed Nadji BENFRIHA
Sous la direction de : M. Amine BENMOKHTAR
Maitre-Assistant
Mme.Chahrazed BOUTEKEDJIRET Professeur Présenté(e)
et soutenue publiquement le (30/06/2019)
Composition du jury :
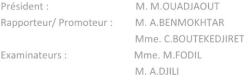

Président : M. M.OUADJAOUT Maitre-Assistant ENP
Rapporteur/ Promoteur : M. A.BENMOKHTAR Maitre-Assistant ENP
Mme. C.BOUTEKEDJIRET Professeur ENP
Examinateurs : Mme. M.FODIL Maitre-Assistant ENP
M. A.DJILI Maitre-Assistant ENP
ENP 2019
REPBLIQUE ALGERIENNE DEMOCRATIQUE ET POPULAIRE
+
Ministère de l'Enseignement Supérieur et de la
Recherche Scientifique École Nationale Polytechnique
Département Maitrise des Risques Industriels et
Environnementaux
Filière QHSE-GRI

Mémoire de projet de fin d'étude pour l'obtention
du diplôme d'ingénieur d'état en QHSE-GRI
Sous le thème
Elaboration d'une nouvelle
méthodologie
d'étude des effets dominos et application:
cas
LINDE Gaz Algérie
Ghiles OUKACI
Mohamed Nadji BENFRIHA
Sous la direction de : M. Amine BENMOKHTAR Maitre-assistant
Mme.Chahrazed BOUTEKEDJIRET Professeur Présenté(e)
et soutenue publiquement le (30/06/2019)
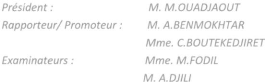

Composition du jury :
Président : M. M.OUADJAOUT Maitre-assistant
ENP
Rapporteur/ Promoteur : M. A.BENMOKHTAR Maitre-assistant
ENP
Mme. C.BOUTEKEDJIRET Professeur ENP
Examinateurs : Mme. M.FODIL Maitre-assistant ENP
M. A.DJILI Maitre-assistant ENP
j.21.1.4
LGA : ÉáÇÍ ìáÚ
ÇåÞíÈØÊæ
æäíãæÏáÇ
ÊÇÑíËÊ
ÉÓÇÑÏÈ ÉÕÇÎ
ÉÏíÏÌ
ÉíÌåäã
ÑíæØÊ æå
áãÚáÇ ÇÐå äã
ÖÑÛáÇ
. íÍíÖæÊ
ØØÎã áßÔ í
ÉíÌåäãáÇ
ãíÏÞÊ áæÇäÊ
áæáÇ ÁÒÌáÇ
ÇåÑÇËÂ
ÏíÏÍ Êæ
|
ÉíÌÑÇÎáÇ
æ
|
ÉíáÎÇÏáÇ
|
æäíãæÏáÇ
|
ËÇÏÍ
|
ÚæÞæá
|
íáÇãÊÍáÇÇ
ÏíÏÍÊáÇ
|
ÖÑÛá åíáÅ
|
ÇäáÕæÊ
Çã
|
ÞíÈØÊ ãÊ
|
ßáÐ ÏÚÈ
|
.
|
. íáÇãáÇ
|
åÑíËÊ
|
ßáÐßæ
|
áãÚáÇ
ÉíÑÇÑãÊÓÇ
ÉØÎ ÚÖæá
ÍÇÑÊÞÇ åíáí
ÉíÌÑÇÎáÇ
æäíãæÏáÇ
ËÇÏÍá äÇÞÊÅ
ãíÏÞÊ ãÊ
ÑíÎáÇ
ÁÒÌáÇ í
ÉØÎ
ÉÇßÇÍãáÇ
ËÏÇæÍáÇ
|
áíáÍÊ
ÏíÚÕÊáÇ
|
ÉíáÇãÊÍÇ
íÌÑÇÎáÇ
|
æäíãæÏáÇ
ÑíËÊ
|
íáÎÇÏáÇ
|
æäíãæÏáÇ
|
ÑíËÊ :
|
4,ÍL"+s,o11
û1.41511
|
áãÚáÇ
ÉíÑÇÑãÊÓÇ
Abstract
The purpose of this work is to develop a new specific methodology
to the study of domino effects and apply it to the case of LGA.
The methodology will be presented first in the form of an
explanatory diagram. It will then be applied for the purpose of
probabilistically identifying and estimating the occurrence of internal and
external domino events and determining their effects and their financial
impact. An external mastery of external domino events will then be presented,
followed by a proposal to put in place a business continuity plan.
Key words: Internal domino effect, external
domino effect, probability of escalation, accident analysis, simulation,
business continuity plan.
Résumé
Le but de ce travail est d'élaborer une nouvelle
méthodologie spécifique à l'étude des effets
dominos et l'appliquer au cas de LGA.
La méthodologie sera présenté en premier
lieu sous forme de schéma explicatif. Elle sera ensuite appliquée
dans le but d'identifier et d'estimer d'une manière probabiliste la
survenue d'événements dominos interne ou externe et de
déterminer leurs effets ainsi que leur impact financier. Un cadre de
maitrise des événements dominos externe serra ensuite
présenté, suivi d'une proposition de mise en place d'un plan de
continuité d'activité.
Mots clés : Effet domino interne, effet
domino externe, probabilité d'escalade, analyse accidentologie,
simulation, plan de continuité d'activité.
Remerciements
Nous voudrions remercier les membres du jury, Monsieur
OUADJAOUT, Enseignant Chercheur à l'ENP et Directeur du Cycle
Préparatoire -ENP qui nous a fait l'honneur de présider ce Jury,
madame M. FODIL et monsieur A. DJILI, Enseignants à l'Ecole Nationale
Polytechnique pour l'effort qu'ils ont prodigué pour examiner ce
travail.
Nous tenons également à remercier nos
promoteurs pour leur soutien, pour leur aide précieuse et pour leurs
précieux conseils tout au long de ce mémoire :
Monsieur BENMOKHTAR, A. Maître-Assistant à
l'ENP et Madame BOUTEKEDJIRET,C professeur à l'ENP .
Nos remerciements vont aussi à Monsieur KHELLAF
Farid ingénieur HSE au sein de LGA, pour de nous avoir
accompagné, donné de son temps et donné la chance
d'effectuer notre projet de fin d'étude au sein de LGA,
Dédicaces
À mes grands-parents, les plus adorables du monde, de
véritables modèles que dieu me les gardent,
À mes parents qui se sacrifient chaque jour pour
nous,
À mon frère Rayan la base comme j'aime
l'appelé et à ma petite soeur lina ma princesse., À toute
ma famille,
À mon meilleur ami, le sang Koceila,
À mes amis, Samy, Said, Abdou, Mounir, Lynda, Ines,
Yasmine et tous les autres qui m'ont aidé et soutenu,
Et enfin à la personne que j'ai la chance d'avoir
comme ami et binôme Nadji,
Ghiles
Je dédie ce travail est l'aboutissement
d'encouragements de la part de plusieurs personnes auprès desquelles je
tiens à exprimer ma gratitude.
À mes chers parents, sources de mes joies, secrets de
ma force, vous serez toujours modèle papa dans ta détermination,
ta force et ton honnêteté. Maman dans ta bonté ta patience
et tes Douaa. Merci pour tous vos sacrifices pour que vos enfants grandissent
et prospèrent, merci de trimer sans relâche, malgré les
péripéties de la vie au bien être de vos enfants. Merci
d'être tous simplement mes parents, c'est à vous que je dois cette
réussite et je suis fière de vous l'offrir.
À mes soeurs Amina et Nadjia en témoignage de
l'attachement, l'amour et l'affections que je porte pour vous.
À mon très cher oncle Tarik et sa famille, vous
avez toujours été présents pour le bon conseil,
À mes grands-parents et mes très chères
tantes maternelles et paternelles ainsi que tous mes cousins(es), votre
affection et votre soutien m'ont été d'un grand secours un
remerciement particulier à tous ceux qui ont partagé les bancs de
l'école avec moi et tous ceux qui ont partagés mon quotidien je
vous remercie du fond du coeur.
Mohamed Nadji
Nomenclature
Fed : Fréquence d'occurrence
annuelle de la séquence domino (installation j impactée
suite à
un accident dans i) (ans-').
Fep : Fréquence d'occurrence
annuelle de l'événement primaire (ans-').
Ferc : Fréquence d'occurrence
annuelle de l'événement redouté central
(ans-'). IR : Risque individuel
i : Equipement source de l'accident.
Ii,j : Intensité des radiations
thermique (kW.m-2).
J?? ?? : Vecteur dont les éléments sont les index
de la combinaison de k événements secondaires.
j : Equipement cible.
??d,i : Probabilité d'escalade pour le i-ème
événement secondaire
?Pi,j : Surpression statique (kPa).
P1 : Probabilité du scénario
primaire.
Pi,j : Probabilité que
l'équipement j soit endommagé suite à un accident
au sein de
l'équipement i.
V : Volume de l'équipement
(m3). í : Coefficient
stoechiométrique. Yi,j : Fonction Probit.
Liste des abréviations
ADD : Arbre De Défaillance
APR : Analyse Préliminaire de Risque
ASU : Air Separation Unit
BIA : Buisness Impact Analysis
DEA : Data Envelopment Analysis
DMIA : Durée Minimum d'Interruption
d'Activité
EDD : Etude De Danger
ENGI : Entreprise Nationale des Gaz
Industriels
EPI : Equipe de Première Intervention.
FREEDOM : FREquency Estimation of DOMino
accidents LGA : Linde Gas Algérie
MCAS : Maximum-Credible Accident Scenarios
PCA : Plan de Continuité d'Activité
SIS : Système Instrumenté de
Sécurité.
SMCA : Systéme de Management de
Continuité d'Activité SNS :
Société Nationale de Sidérurgie
UE : Union Européenne
VCE : Vapor Cloud Explosion.
Table des matière
Table des figures Liste des tableaux
Introduction générale 14
I. Chapitre 1 : CONTEXTE GENERAL DE L'ETUDE 17
I.1 Présentation de l'entreprise 17
I.1.1 : Présentation générale de Linde Gas
Algérie (LGA) 17
I.1.2 Vue globale 17
I.2 Généralités sur les effets dominos 24
I.2.1 Définition et caractéristiques des accidents
à effet domino 25
I.3 Problématique : 29
I.4 Méthodologie 30
I.4.1 Etude de l'existant 30
I.4.2 Réalisation d'une méthode d'étude des
effets dominos 31
II. Chapitre 2 : ETUDE DES EFFETS DOMINOS INTERNES 34
II.1 Compréhension du process existant à LGA 34
II.1.1 Présentation de l'Air Separation Unit (ASU) 34
II.1.2 Description du processus de séparation d'air 34
II.1.2.1 Récupération d'oxygène et d'azote
34
II.1.2.2 Récupération de l'argon brut et pur :
37
II.2 Critique de l'étude de danger 37
II.2.1 Contenue de l'étude de danger : 38
II.2.2 Cadre réglementaire algérien 38
II.2.3 Démarche de l'analyse critique des EDD 39
II.2.4 Application de l'analyse critique de l'EDD 42
II.3 Analyse de l'accidentologie 46
II.3.1 Présentation du logiciel R 46
II.3.2 Méthodologie 47
II.3.2.1 Acquisitions des données 47
II.3.2.2 Traitement des données 48
II.3.2.3 Visualisation : 48
II.4 Application de la méthode : 57
II.4.1 Les arbres de défaillances 58
II.4.2 Présentation du logiciel 59
|
|
II.4.2.1 Evaluation des effets
|
66
|
|
|
II.4.2.1.1 Evénement primaire 1 : VCE au niveau de
l'atelier CCAM
|
66
|
|
|
II.4.2.1.2 Evénement primaire 2 : Jet fire atelier CCAM
|
72
|
|
|
II.4.2.1.3 Evénement primaire 3 : VCE au niveau du parc
bouteilles
|
73
|
|
|
II.4.2.1.4 Evénement primaire 4 : Jet fire au niveau du
parc bouteilles
|
80
|
|
II.4.3 Calculs :
|
81
|
|
|
II.4.3.1 Méthodologie de calcul
|
81
|
|
|
II.4.3.2 . Identification des cibles et calcul des
probabilités d'escalade
|
86
|
|
|
II.4.3.2.1 Détermination des scénarios secondaires
|
87
|
|
|
II.4.3.2.2 Calculs :
|
87
|
|
|
II.4.3.2.3 Détermination des scénarios tertiaires :
|
88
|
|
II.4.4 Réalisation des réseaux bayésiens
|
91
|
|
|
II.4.4.1 Définition d'un réseau bayésien
|
91
|
|
|
II.4.4.2 Identification des séquences dominos
|
92
|
|
|
II.4.4.3 Présentation du logiciel AGENARISK
|
96
|
|
|
II.4.4.4 Réalisation des réseaux bayésien
|
98
|
|
|
II.4.4.4.1 Scénario 1
|
98
|
|
|
II.4.4.4.2 Scénario 2
|
99
|
|
|
II.4.4.4.3 Scénario 3
|
100
|
|
II.4.5 Calcul des probabilités de combinaison
|
101
|
|
II.4.6 Risque individuel
|
102
|
III.
|
|
Chapitre 3 : ETUDE DES EFFETS DOMINOS EXTERNES
|
105
|
|
III.1
|
Prévention des accidents dominos externes (EDAP)
Proposition de cadre Hazwim
|
106
|
|
III.1.1 La gestion multi-entreprise
|
106
|
|
III.1.2 Le cadre Hazwim EDAP
|
107
|
III.1.2.1 Étape 1: Définir la portée et la
zone de portée d'une étude de la zone industrielle
de sécurité domino externe 108
III.1.2.2 Étape 2: Etude initiale sur les effets dominos
108
III.1.2.3 Etape 3: le calendrier d'organisation 110
III.1.2.4 Étape 4: Composition de la Hazop et de la
What-If équipes dans chaque
entreprise 111
III.1.2.5 Étape 5: Explication visite du site 111
IV. Chapitre 4 : Impact financier, impact indirecte et
proposition d'implémentation d'un plan de
continuité d'activité 119
IV.1 Impact financier : 119
IV.2 Impact indirecte 120
IV.3 Plan de continuité d'activité (PCA) 123
IV.3.1 Compréhension de l'organisation et de son contexte
125
IV.3.2 Définition d'un périmètre 125
IV.3.3 Obtenir l'implication et l'engagement de la Direction
126
IV.3.4 Politique et objectifs du PCA 126
IV.3.5 Mise à disposition des ressources 127
IV.3.6 Compétences 127
IV.4 Business Impact Analysis (BIA) 129
Conclusion générale 133
Bibliographie 135
Annexes 137
Table des figures
Figure I-1 : Gamme de production des gaz par site en
Algérie 19
Figure I-2 : Schéma explicatif d'une chaine domino
25
Figure I-3 : Schéma explicatif d'une propagation
parallèle complexe 26
Figure II-1 : Etapes de la critique d'une EDD
40
Figure II-2 Démarche de détermination des
écarts 41
Figure II-3 Insuffisances de forme 42
Figure II-4 : Insuffisances de fond 43
Figure II-5 : Schéma représentant les types
d'écarts relevés 45
Figure II-6: Image de l'interface du logiciel R
47
Figure II-7 : Statistiques sur les types d'accidents
49
Figure II-8 : Statistiques sur les conséquences en
fonction des types d'accidents 50
Figure II-9 : Statistiques sur les types d'accident en
fonction des causes 51
Figure II-10 : Statistiques sur les types de produits mis
en cause 52
Figure II-11 : Types de substances dangereuses
impliquées dans les événements dominos 53
Figure II-12 : Types d'accidents primaires (initiateurs)
impliqués dans les cas enregistrés d'effets
dominos 54
Figure II-13 : Types d'incendies impliqués dans le
déclenchement de l'effet domino 54
Figure II-14 : Types d'explosions responsables du
déclenchement de l'effet domino. 55
Figure II-15 : Événements Dominos survenant
dans des installations fixes et pendant le
transport. 56 Figure II-16 : Probabilité
d'occurrence d'une explosion de bouteille d'acétylène
calculée par
Arbre Analyste 60
Figure II-17 : Arbre de défaillance d'une
explosion de bouteille d'acétylène 61
Figure II-18 : Probabilité d'occurrence d'une
fuite sur une bouteille calculée par Arbre Analyste
62
Figure II-19 : Arbre de défaillance d'une fuite de
bouteille 63
Figure II-20 : Effet de surpression en fonction de la
distance pour l'événement VCE au niveau
de l'atelier CCAM 70 Figure II-21 : Propagation de
l'effet de surpression pour l'événement VCE au niveau de
l'atelier
CCAM 71 Figure II-22 : Effet de radiation en fonction
de la distance pour l'événement Jet fire au niveau
de l'atelier CCAM 72
Les résultats de la propagation dans les deux cas sont
représentés dans les figures II-23 et II-24.
77
Figure II-24 : Effet de surpression en fonction de la
distance pour l'événement VCE au niveau
du parc bouteilles 78 Figure II-25 : Propagation des
effets de surpression pour l'événement VCE au niveau du
parc
bouteilles 79 Figure II-26 : Effet de radiation en
fonction de la distance pour l'événement jet fire au
niveau
du parc bouteilles 80
Figure II-27 Composantes d'un réseau
Bayésien 91
Figure II-28 : Modèle de propagation probable d'un
effet domino dans une usine à six unités 92
Figure II-29 : Réseau bayésien
modifié pour incorporer l'union des événements tertiaires
et
quaternaires en utilisant les noeuds auxiliaires L1 et L2
95 Figure II-30 Réseau bayésien
modifié pour incorporer les 3 niveaux d'effet domino et l'union
des
événements tertiaires et quaternaires
96
Figure II-31 : Réseau bayésien du
scénario 1 98
Figure II-32 : Réseau bayésien du
scénario 2 99
Figure II-33 : Réseau bayésien du
scénario 3 100
Figure II-34 : Illustration du risque individuel sur le
site de LGA 103
Figure III-1 Image satellite de l'emplacement de LGA et
AIR LIQUID 106
Figure IV-2 Comparaison des couts du PCA et des
conséquences d'une catastrophe 124
Figure IV-3 Déroulement du PCA après
l'événement domino au sein de LGA 132
Liste des tableaux
Tableau I-1 : Généralités sur LGA
17
Tableau I-2 : Production des gaz par site.
20
Tableau I-3 : Liste des abréviations
20
Tableau I-4 : Les différentes catégories
d'évènements dominos [4] 27
Tableau J-5 : Etude sur les méthodes
existantes et leurs limites 30
Tableau II-1 : Etat récapitulatif des dossiers
traités par les services de la protection civile 42
Tableau II-2 : Résumé de la critique de
l'EDD 43
Tableau II-3 : Appellation des données retenues
48
Tableau II-4 : Evénements primaires retenus
57
Tableau II-5 : Comparaison des températures d'auto
inflammation et d'énergie min
d'inflammation de différents gaz 57
Tableau II-6 : Vitesse de combustion laminaire des gaz
combustibles 58
Tableau II-7 : Seuils des effets de radiation thermique
sur l'homme 64
Tableau II-8 : Seuils des effets de radiation thermique
sur les structures 65
Tableau II-9 : Seuils des effets de surpression sur
l'homme 65
Tableau II-10 : Seuils des effets de surpression sur les
structures 65
Tableau II-11 : Seuils d'escalade, causés par la
surpression et la radiation thermique 66
Tableau II-12 : APR sur l'hydrogène au niveau de
l'atelier CCAM 68
Tableau II-13 : Données introduites dans le
logiciel PHAST® pour l'événement primaire «
VCE
au niveau de l'atelier CCAM »
69 Tableau II-14 : Données introduites dans le
logiciel PHAST® pour l'événement primaire « VCE
au
niveau du parc bouteilles 77
Tableau II-15 : Modèles de
vulnérabilité 86
Tableau II-16 : Scénarios secondaires et vecteurs
d'escalade 87
Tableau II-17 : Scénarios tertiaires et vecteurs
d'escalade 88
Tableau II-18 Scénario quaternaire et vecteurs
d'escalade 89
Tableau II-19 : Scénarios secondaires et vecteurs
d'escalade événements 2 et 4 90
Tableau II-20 : Table des probabilités
conditionnelles attribuées au noeud auxiliaire L1 montrant sa
dépendance conditionnelle à l'égard de ses parents par le
biais d'une porte logique
«OU» 95
Tableau II-21 : Probabilités des
événements 101
Tableau II-22 : Probabilités des combinaisons
d'évènements 101
Tableau III-1 : Matrice d'évaluation des risques
114
Tableau III-2 : HAZOP de l'atelier d'oxyde
d'éthylène 116
Tableau IV-1 BIA LGA 130
Introduction générale
14
Introduction générale
En Algérie, la production des Gaz Industriels fut
introduite pendant la période coloniale par l'entreprise Air Liquide. En
1972 l'État Algérien procède à la nationalisation
de la société et l'intègre à la
Société Nationale de Sidérurgie (SNS). En 1983, la
restructuration de la SNS, a donné naissance à L'Entreprise
Nationale de Gaz Industriels (ENGI) qui fut ensuite rachetée en 2008 par
Linde Gas.
A travers une gamme complète en Gaz industriels, LINDE
GAS ALGERIE, c'est donc implantée en Algérie et a eu pour
objectif principal la prise en charge des besoins générés
par la multiplication de l'utilisation de ces gaz dans divers secteurs
économiques.
Cependant, ce genre d'activité industrielle engendre
beaucoup de risques en termes de sécurité. Pour preuve, un
accident a attiré notre attention, celui d'une usine de gaz industriels
en France classé Seveso seuil haut selon la réglementation
européenne, ou une détonation suivie d'une boule de feu survient
à 12h28 le 10/04/2015 au niveau de la pompe de conditionnement de
l'oxygène située au pied d'un réservoir d'oxygène
liquide plein. La boule de feu se propage à 2 armoires
électriques voisines. L'incendie consécutif menace 2 autres
réservoirs proches d'argon et d'azote car il se propage dans les
caniveaux techniques. L'employé le plus proche donne l'alerte.
Le plan d'organisation interne (POI) est
déclenché à 12h35, 10 min avant l'arrivée des
services de secours. Le conditionnement des bouteilles de gaz est stoppé
ainsi que l'alimentation électrique de l'unité d'embouteillage.
Les 72 employés sont confinés pendant 2 h. L'incendie est
maîtrisé à 13h45.
Les tuyauteries du réseau de transfert des 3
réservoirs vers l'unité de conditionnement en bouteille sont
endommagées par les flux thermiques. Ces tuyauteries encore en charge
laissent s'échapper de l'azote et de l'argon. Craignant une propagation
de l'incendie pour la partie enterrée du réseau, les pompiers
l'arrosent et effectuent une vérification visuelle. Le site est
surveillé durant le week-end. 80 % des activités de
conditionnement des gaz industriels et spéciaux du site sont
arrêtées pendant 2 mois [1].
15
Ce type d'accidents qui aurait pu avoir des
conséquences beaucoup plus désastreuses, est nommé
accident à effet domino. L'effet domino étant la propagation
spatiale ou temporelle d'un événement primaire provoquant
d'autres événements secondaires.
L'objectif de notre travail est d'apporter une nouvelle
méthodologie pour l'étude de ces effets dominos et l'appliquer au
cas de LINDE GAS ALGERIE.
Le mémoire est structuré en trois chapitres comme
suit :
Le premier chapitre comporte une
présentation de l'entreprise suivie de quelques
généralités sur les effets dominos, qui nous aiderons
à mieux cerner la problématique qui sera posée. Une
étude sur quelques méthodologies existantes et leurs limites
serra ensuite développée pour enfin réaliser le
schéma explicatif de notre méthodologie.
Le second chapitre est la partie essentielle
de l'application de la méthode pour l'étude des effets dominos.
Il est constitué de plusieurs étapes où l'on
détaille et applique les différentes parties de la
méthodologie proposée. Cette méthodologie s'appuie sur
l'utilisation des logiciels R®, ARBRE ANALYSTE®, PHAST® et
AGENARISK® pour dans l'ordre une analyse de l'accidentologie, le calcul de
probabilités d'événements, la simulation de la propagation
des effets et la constitution de réseaux bayésiens.
Le troisième chapitre traite
l'étude des effets dominos externe en proposant l'application d'un cadre
nommé HAWZIM.
Le quatrième chapitre donne l'impact
financier du scénario majeur d'effet domino, il y est également
développé son impact indirect. On y retrouve une proposition
d'implémentation d'un plan de continuité d'activité.
Chapitre I
CONTEXTE GENERAL DE L'ETUDE
17
I. Chapitre 1 : CONTEXTE GENERAL DE L'ETUDE
Afin de bien connaitre l'environnement dans lequel nous
évoluerons, nous commencerons tout naturellement par une
présentation de l'entreprise. Etant le coeur de notre étude, des
généralités sur les effets domino seront ensuite
présentées. De ces deux éléments découlera
une problématique pour laquelle nous élaborerons finalement une
méthodologie de résolution.
I.1 Présentation de l'entreprise
I.1.1 : Présentation générale de Linde
Gas Algérie (LGA)
Installée en 2007 en Algérie, LGA est une
unité du groupe Allemand «The Linde Group»,
spécialisée dans la production, le conditionnement et la
distribution des gaz industriels et médicaux.
I.1.2 Vue globale
Nous allons commencer par la présentation
synthétique de l'entreprise à travers une fiche technique qui va
nous apporter d'avantage d'informations sur LGA et un tableau englobant les
différents produits offert.
Généralités sur LGA
Tableau I-1 : Généralités sur
LGA
Nom de l'entreprise
|
Linde Gas Algérie
|
Nature du capital/Forme juridique
|
Société Par Actions- SPA Linde Gas
Algérie.
|
Création et mise en service
|
Privatisation de l'ENGI devenue LINDE Gas Algérie,
signature officielle le 18 Juin 2007 avec la prise en charge dès le 1er
Juillet (66% parts Linde, 34% de Sonatrach).
|
Activité
|
Production, conditionnement, commercialisation et distribution
des Gas industriels alimentaires et Médicaux.
|
Marché où l'organisation
opère
avec répartition géographiques
|
LGA est présente sur l'ensemble du territoire national
par un réseau comprenant 09 sites de production : Réghaia,
Annaba,
Constantine, Ouargla, Oran, Bouira, S.B.Abbès, Arzew,
Skikda .répartis en trois régions : Centre/Sud, Ouest, Est.
|
Nombre de pays ou l'organisation est
implantée
|
L'entreprise est fondée par Carl Von Linde le 21 juin
1879, présente dans plus de 120 pays dans le monde entier avec plus
de
|
18
|
60000 Salariés.
|
Produits
|
- Gaz Médicaux : Oxygène Médical, Protoxyde
d'Azote, Oxyde d'éthylène.
- Gaz industriels : Azote, Oxygène industriel, Argon,
Acétylène, Hydrogène.
- Gaz à usage alimentaire : CO2 alimentaire
- Autres gaz : Fréons, Gaz purs, Mélanges
(Argon-CO2, ...).
|
Services
|
- Inertage à l'azote
- Installations pour fluides Médicaux.
- Dessalement de l'eau de Mer.
- Réfrigération, congélation et emballage
des aliments.
- Pisciculture.
|
Production
|
Capacités de production (site Reghaia)
- Gaz carbonique : 2 tonnes / heure.
- Oxygène : 4275 litres/heure.
- Azote : 1695 litres/heure.
- Protoxyde 100 kg/heure.
Capacité de Conditionnement (site
Reghaia)
- Oxygène : 400 m3 / heure.
- Azote : 400 m3 / heure.
Gaz carbonique : Bouteille : 400 kg/ heure.
Cadre : 100 kg/ heure
- Argon : 400 m3 / heure.
- Protoxyde d'azote : 200 kg/heure.
- Traitement de bouteilles : 200 b/jour
|
Taille de l'organisation
|
Effectifs : A la fin du mois de février
2015 le nombre d'employés
s'élèvait à 538 employés, dont :
- Site Reghaia : 132 employés.
- Siège : 78 employés.
Capital social : 1.500.000.000 de DA.
- La superficie du site de Reghaia : 35 000 m2
- La superficie du siège : 16840 m2 dont 6375
bâtie
|
Distinction
|
- Certification système de management qualité
ISO 9001 version 2015
- Certification système environnement ISO 14001 version
2015
- Certification Santé et sécurité au
travail, référentiel OHSAS 18001 version 2007
- Certification sécurité alimentaire FSSC 22000
version 2010
|
19
Adresse
|
Le siège est situé au : 23, Avenue
de l'ALN, Hussein Dey, Alger.
|
Tél/Fax
|
021 497 026 /
|
021 497 194
|
Site Web
|
www.linde.com
|
|
|
Logo de l'entreprise
|
|
|
Source : Documents de LGA
[2].
Gamme de production des gaz par site
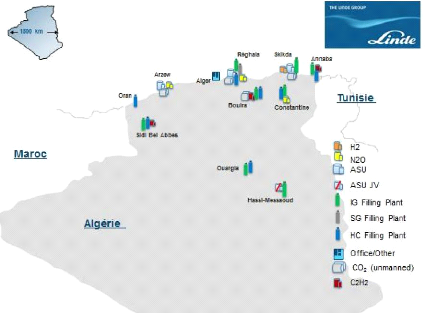
Figure I-1 : Gamme de production des gaz par site
en Algérie
20
Tableau I-2 : Production des gaz par
site.
REGIONS
|
SITES
|
PRODUCTION
|
CONDITIONNEMENT
|
LOX
|
LIN
|
LAR
|
LIC
|
LI N20
|
112
|
112
|
GOX
|
GAN
|
GAR
|
GC02
|
C02 Glace
|
GN20
|
MIX.
|
CENTRE/SUD
|
REGHAIA
|
*
|
*
|
|
*
|
*
|
|
|
*
|
*
|
*
|
*
|
*
|
*
|
*
|
BOUIRA
|
|
|
|
*
|
|
*
|
|
*
|
*
|
*
|
*
|
|
*
|
*
|
OUARGLA
|
|
|
|
|
|
|
|
*
|
|
|
*
|
|
|
|
EST
|
CONSTANTINE
|
|
|
|
|
*
|
|
|
*
|
*
|
|
*
|
|
*
|
|
ANNABA
|
|
|
|
|
|
*
|
|
*
|
*
|
|
*
|
|
|
|
SKIKDA
|
*
|
*
|
*
|
*
|
|
|
*
|
|
|
*
|
|
|
|
|
OUEST
|
SIDI BEL ABBES
|
|
|
|
|
|
*
|
|
*
|
*
|
*
|
*
|
|
*
|
*
|
ARZEW
|
*
|
*
|
|
*
|
|
|
|
|
|
|
|
|
|
|
ORAN
|
|
|
|
|
|
|
|
*
|
*
|
|
|
|
*
|
|
Tableau I-3 : Liste des
abréviations
Abréviations
|
Significations
|
- LOX
|
- Oxygène liquide
|
- LIN
|
- Azote liquide
|
- LAR
|
- Argon liquide
|
- LIC
|
- CO2 liquide
|
- C2H2
|
- Acétylène
|
- H2
|
- Hydrogène
|
- GOX
|
- Oxygène gazeux
|
- G AN
|
- Azote gazeux
|
- GAR
|
- Argon gazeux
|
- GCO2
|
- CO2 gaz
|
- GNO2
|
- Protoxyde d'Azote gaz
|
- LI NO2
|
- Protoxyde d'Azote liquide
|
- MIX
|
- Mélange de gaz exemple :
|
|
hydrogène/azote, azote /CO2...
|
21
Comme le montre ce tableau, LGA dispose d'une gamme de produit
très diversifiée, avec laquelle elle arrive à satisfaire
les besoins de ses clients en les approvisionnant en différents gaz
fabriqués, médicaux ou industriels à travers les neufs (9)
sites dispersés aux quatres coins de l'Algérie (Est, Ouest,
Centre-Sud), LGA assure une couverture nationale ce qui lui permet d'atteindre
et de cibler un plus grand segment de clients et couvrir toute la demande
nationale. Cette stratégie est aussi adoptée afin de
décentraliser les activités de LGA.
L'organigramme de LGA
Linde Gas Algérie est organisée comme suit :
? Direction Plant Manager : Chaque site a un
Plant Manager (Directeur de site)
soit:
- Plant manager Canstantine, Annaba, Skikda, Bouira, Reghaia,
Ouergla, Sidi
Bel Abbes, Arzew et Oran.
? Direction réalisation : Elle est
composée de trois directions :
- Bulk
- Opération PGP
- Commerciale et marketing
? Direction support : Elle est composée
de six directions :
- Affaires juridiques
- Informatique et systèmes d'information
- Ressources humaines
- Achats
- Finance et comptabilité
- SHEQ
De la direction SHEQ découle des responsables nationnaux
des différentes composantes soit :
- Un responsable national de qualité et audit SMI au
niveau du Siège
- Responsable national de la sécurité au travail et
transport (Siège)
- Responsable environnement (Siège)
- Responsable national d'hygiènne et santé,
basé à Skikda
- Responsable national safety process MHRP au niveau de
canstantine.
22
- Responsable de sécurité alimentaire,
basé à Arzew
La direction SHEQ de LGA dispose de trois coordinateurs
régionnaux, soit :
- Un coordinateur centre-sud situé à Reghaia
- Un coordinateur Ouest situé à Arzew
- Un coordinateur Est situé au niveau de Skikda
Aussi au niveau de chaque region, on retrouve des responsables
SHEQ comme suit :
- SHEQ Site Bouira, Reghaia, Ouargla
- SHEQ Site Oran, Arzew et Sidi Bel Abbes
- SHEQ Site de Annaba, Constantine et Skikda.
Dans le but d'élaborer un diagnostic des pratiques et
comportements dits responsables et repondant aux exigences de la Norme ISO
26000 relative à la Responsabilité Sociétale de
l'Entreprise RSE, exploiter un outil de mesure de reporting nous parrait
nécessaire. De ce fait, avoir recours au Global Reporting Initiave dit
GRI nous semble approprié pour éclaircir les directives
annocées dans la Norme ISO 26000.
Gouvernance, engagement et implication de LGA
Nous allons maitenant élaborer un diagnostic des
pratiques dites responsables et existantes au sein de LGA, et cela en nous
basant sur un outil de reporting qui est le GRI. Avant de s'impliquer dans les
trois dimensions de la Responsabilité Sociétale de l'Entreprise
RSE, une identification de la gouvernance de l'organisation est primordiale.
Structure de gouvernance de l'organisation.
Le Conseil d'administration est composé de (05) cinq
personnes, dont le PDG de LGA qui est aussi Président du Conseil
d'Administration (PCA) ainsi que 2 membres de l'actionnaire à 34%
Sonatrach. Le PDG gouverne par délégation du Conseil
d'Administration (CA).
Le CA se réunit à fréquence de quatre (4)
fois par an afin de soulever des questions relatives à la
stratégie de l'entreprise ainsi que débattre des états
financiers.
Les politiques HSE et Qualité constituent des
éléments essenciels de la stratégie de LGA et du groupe
Linde. Elle est periodiquement revue et mise à jour par le comité
central du groupe. Le conseil d'administration s'engage dans la mise en oeuvre
de cette politique.
23
Mécanismes qui relient les actionnaires et les
salariés au conseil d'administration
? Mensuellement, une réunion est
organisée entre le PDG de Linde Gas et l'ensemble des directions (SHEQ,
Opérations, finances comptabilité, commerciale et marketing...)
qui porte sur la vision de l'entreprise et la stratégie à mettre
en place.
? Réunion de revue de direction : Elle
regroupe le PDG, les directeurs centraux, l'équipe SHEQ et les
directeurs des sites, qui se réunissent une fois par an afin de :
- Faire le point par rapport au bilan annuel du système de
management intégré (SMI), ainsi que les réalisations en
matière de production et de ventes.
- Mettre en place les plans d'action nécessaires pour
traiter les anomalies. - Fixer les objectifs à
atteindre lors du prochain exercice.
? Réunion CHSE ( Comité
d'Hygiènne et Sécurité de l'Entreprise) : C'est
une comission réglementaire qui se réunit trimestriellement au
niveau central et mensuellement au niveau de chaque site dans le but de traiter
les préoccupations des salariés en matière
d'hygiène, santé et sécurité. Cette commission
paritaire se compose de représentants de la direction et des
représentants des travailleurs.
Processus mis en place par le conseil d'administration
pour éviter les conflits
La politique de l'entreprise est axée sur la
participation des salariés et les partenaires dans la stratégie
ainsi que dans la prise de décision afin de gagner leur confiance. La
prise en compte de l'aspect social (Les Parties Prenantes) de l'entreprise est
l'une des valeurs fondamentale du Groupe Linde Gas.
Pour ce faire, chaque réunion du CA est
accompagnée d'une réunion avec le syndicat des travailleurs qui
est représentatif des attentes, réclamations et besoins des
salariés, afin de les intégrer dans le processus de prise de
décision et dans l'élaboration de la stratégie de
l'entreprise.
Tous les deux ans, le département ressource humaine
effectue un sondage auprès de chaque employé de Linde Group. Un
questionnaire leur est soumis, qui touche à tout les aspects relatifs
à la vie quotidienne de l'employé dans l'entreprise (Son
engagement, sa satisfaction, les conflits, la communication...). Le but de
cette
24
démarche est de récolter le feed-back des
employés relatif à leur perçeption de l'entreprise pour
pouvoir mener des actions permettant à chaque direction de conduire son
équipe dans une optique d'amélioration continue, tout en
atteingnant leurs satisfaction.
Référentiels internes déterminant de
la culture de Linde Gas Algérie
Le groupe Linde dispose d'un code d'éthique applicable
à tous ses employés y compris ceux de Linde Gas Algérie.
Ce code leur aient transmis, puis ils bénificient d'une formation qui se
solde par un test en ligne afin de leurs dicerner un diplôme s'ils
épousent et s'engagent à respecter ces instructions et
principes.
? Il existe un service d'éthique sur la platforme en
ligne de Linde Group, chargé du traitement des requètes
concernant toute anomalie, réclamation ou soupçon de
l'employé par rapport aux pratiques contraires à l'éthique
de Linde Group.
? Les valeurs ainsi que les principes de l'entreprise sont
communiqués aux salariés et affichés au niveau de
l'entreprise afin qu'ils soient integrés dans tous les processus de
Linde Gas et ancrés dans le comportement de chacun et surtout
respectés.
? L'année 2016 a été consacrée
à l'environnement, durant cette dernière, la mission des
responsables était de tracer des objectifs relatifs à la
protection de l'environnement. Des actions de sensibilisation, de communication
ont aussi été planifées [2].
Comme éxpliqué dans l'introduction , LGA est une
entreprise où le risque est omniprésent et la diversité
des produits se trouvant sur le site engendre une probabilité
d'occurence d'un phénoméme très délicat qui est les
effets dominos, pour preuve l'accident à effet domino
précédement cité. Nous allons donc maintenant nous
intérésser à définir les effets dominos.
I.2 Généralités sur les effets
dominos
Les accidents majeurs les plus destructeurs sont ceux
où il se produit un "effet domino", provoquant l'escalade d'un accident
et la propagation de cet événement primaire pouvant
éventuellement impliquer de multiples équipements et
unités de production.
Les installations ou équipements industriels sont dans
la majorité des cas regroupés dans un même espace, ce qui
implique une interaction entre eux et un danger encore plus grand pour les
infrastructures faisant partie de leur zone d'implantation et pour
eux-mêmes.
Du point de vue de la sécurité des installations
industrielles, l'étude des effets dominos est très complexe
à cause de la nécessité de prendre en considération
le fonctionnement de l'ensemble du système et non le fonctionnement de
ses parties individuellement. De ce fait, plusieurs paramètres et
données d'entrées doivent être pris en compte : la
quantité de substances présentes et leurs
propriétés physico-chimiques, les conditions spécifiques
du procédé, les distances entres les équipements ou les
installations, les conditions météorologiques, etc [3].
I.2.1 Définition et caractéristiques des
accidents à effet domino
L'effet domino tel que l'ont défini
Genserik Reniers et Valerio Cozzani dans leur ouvrage "Domino Effects in the
Process Industries-Modelling, Prevention and Managing" paru en 2013 est :
« la propagation spatiale ou temporelle d'un événement
primaire provoquant d'autres événements secondaires ». Par
conséquent, l'accident domino est l'accident dans
lequel un événement indésirable primaire se propage
temporellement (dans un équipement) ou/et spatialement (à
l'équipement voisin), séquentiellement ou simultanément,
déclenchant éventuellement d'autres événements
indésirables d'ordre supérieur et entraînant des
conséquences plus graves que celles de l'événement
primaire.
La propagation peut être simple, c'est-à-dire le
scénario primaire déclenche un scénario secondaire unique.
En général, une propagation simple à plusieurs niveaux
donne une chaîne domino ; un premier scénario
d'accident déclenche un deuxième scénario d'accident, le
deuxième scénario d'accident déclenche un troisième
scénario d'accident, et ainsi de suite.

25
Figure I-2 : Schéma explicatif d'une chaine
domino
26
Dans le cas où l'accident primaire est grave, la
propagation peut donner lieu à plusieurs scénarios secondaires
simultanés. Ces derniers vont déclencher à leur tour plus
d'un scénario ce qui va générer une propagation
parallèle complexe à plusieurs niveaux.
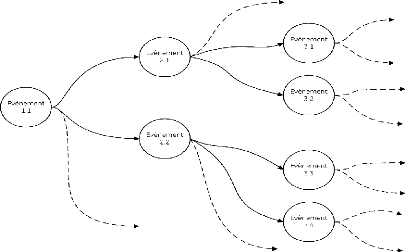
Figure I-3 : Schéma explicatif d'une
propagation parallèle complexe
L'identification de la cause de propagation de
l'évènement primaire est nécessaire pour mieux
décrire le scénario d'accident domino. Elle doit être
également identifiée pour tous les autres
évènements de la chaîne domino simple ou parallèle
complexe [3, 4].
Cependant, la propagation seule n'est pas suffisante pour
décrire le phénomène des accidents dominos et ne justifie
pas la prise en compte des accidents qui suivent le scénario primaire en
tant qu'accidents dominos.
Ceci permet de définir la notion de vecteur
d'escalade, qui est un élément fondamental dans
l'étude des accidents dominos. Il est indispensable afin de
considérer les scénarios d'accidents comme des scénarios
dominos. En effet, afin d'obtenir un accident à effet domino il est
impératif que les conséquences globales de cet accident soient
plus graves que celles du scénario primaire pris seul.
De ce fait, la propagation et l'escalade des scénarios
primaires sont obligatoirement associés pour définir l'accident
domino.
27
Il existe deux types d'escalade :
? L'escalade directe : causée par les dommages directs
des unités cibles par effet de rayonnement, surpression, ondes de choc
ou projection de fragments.
? L'escalade indirecte : causée
généralement par la perte de contrôle de l'installation
à cause de la destruction de la salle de contrôle ou
l'évacuation du personnel.
Les cibles dans les accidents dominos sont les installations
qui ont le potentiel, si elles sont endommagées, de déclencher un
scénario secondaire.
Afin de simplifier les évènements dominos et
faire lever l'ambiguïté par rapport aux caractéristiques de
ces accidents, ils ont été classés en 4 catégories
comme le montre le tableau I-4 [4].
Tableau I-4 : Les différentes
catégories d'évènements dominos [4]
Catégorie de l'évènement domino
|
Sous-catégorie
|
Définition
|
1
|
Interne
|
Le début et la fin du vecteur d'escalade
caractérisant l'événement domino sont
situés à l'intérieur de la même zone.
|
Externe
|
Le début et la fin du vecteur d'escalade
caractérisant l'événement domino ne sont
pas situés à l'intérieur de la même zone.
|
2
|
Direct
|
L'événement domino est la conséquence
directe de l'événement précédent.
|
Indirect
|
L'événement domino n'est pas une
conséquence directe de l'événement qui le
précède.
|
3
|
Temporel
|
L'événement domino se produit dans le même
équipement (ou installation) que l'événement
précédent, mais avec un retard.
|
Spatiale
|
L'événement domino se produit à
l'extérieur de l'équipement où l'événement
précédent a eu lieu
|
4
|
En série
|
L'événement domino se produit comme une seule
chaîne d'accidents.
|
En parallèle
|
L'événement domino se produit sous la forme de
plusieurs chaînes d'accidents.
|
Le danger dû aux effets dominos est bien connu et pris
en compte dans les normes de sécurité et de la
législation.
En effet, il est reconnu dans la législation
européenne depuis la première directive Seveso (directive
82/501/CEE), qui exigeait l'évaluation des risques à effet domino
dans toutes les
28
installations et l'obligation d'établir un rapport de
sécurité. Cette directive a été ensuite
remplacée en 2012 par l'article 9 de la directive Seveso-III (directive
2012/18/UE), consacrée aux effets dominos.
La directive Seveso-I exigeait une évaluation
complète de la sécurité sur les sites et la
nécessité d'évaluer la possibilité d'accidents
domino était déjà citée, bien qu'à
l'époque aucune approche technique ou outil spécifique n'existait
pour permettre l'identification et l'évaluation de tels
scénarios. Mais après la catastrophe de Mexico en 1984,
probablement l'un des accidents à effet dominos les plus connus, des
préoccupations spécifiques sur le risque d'escalade ont
été suscitées. Dès lors, la démonstration de
la gravité potentielle des accidents impliquant des effets dominos a
conduit à des efforts importants pour la prévention des
scénarios d'accidents dominos et les normes ainsi que la
législation relative à la maîtrise des risques d'accidents
majeurs comprennent désormais des mesures d'évaluation, de
contrôle et de prévention des effets dominos.
En effet, plusieurs normes introduisent des mesures
préventives, telles que les distances de sécurité ou
l'isolation thermique, afin de contrôler et de réduire la
probabilité d'événements dominos.
Cependant, les modèles d'évaluation des effets
dominos exigent un niveau élevé de détail en ce qui
concerne les données d'entrée. C'est cette raison, et la
combinaison des probabilités extrêmement faibles de tels
accidents, qui conduisent souvent à laisser de côté
l'évaluation de la sécurité des activités
industrielles, l'évaluation quantitative et la gestion des risques dus
aux scénarios dominos.
29
I.3 Problématique :
LINDE GAS est une entreprise spécifique ayant la
particularité d'avoir non seulement différents process avec un
niveau de risque assez élevé mais en plus la présence
permanente en quantités importantes de différents produits
présentant des caractéristiques pour le moins très
dangereuses. De plus l'entreprise se trouve dans une zone industrielle et est
mitoyenne d'une autre entreprise Air liquid qui est également une
entreprise à haut risque. Ces spécifications, font de LINDE GAS
l'environnement propice au déclenchement d'un accident majeur à
effet domino dont les conséquences en matière de vies humaines,
de dommages matériels et d'impacts financiers serraient
désastreuses.
Bien que le groupe LINDE ai une politique bien ficelée
en matière de sécurité, l'étude d'effet domino
étant un domaine assez récent et dont les méthodologies
restent assez peu nombreuses et peu maitrisés des ingénieurs, il
n y a pas d'étude dans ce sens au sein du groupe en Algérie,
d'où la nécessité d'un recensement de tous les
scénarios à effet domino crédibles, afin de juger si cette
politique est en mesure d'y faire face.
Cela nous amène donc aux questions suivantes :
? Quelles sont les séquences d'accidents à effet
domino qui pourraient toucher LINDE GAS ?
? Pouvons-nous élaborer une méthodologie
d'étude des effets domino présentant le moins
d'inconvénients et étant la plus complète possible ?
30
I.4 Méthodologie
I.4.1 Etude de l'existant
Afin de déterminer la méthodologie la plus
adéquate, nous avons réalisé une revue de
littérature sur le domaine des effets dominos.
Les résultats avec les limites de chaque méthode
sont résumés dans le tableau I-5, [5].
Tableau J-5 : Etude sur les méthodes
existantes et leurs limites
Méthodes
|
Domaine d'application
|
Objet /Principe
|
Limites
|
Méthodologie DEA
|
Industrie (chimique)
|
D'une unité à une autre si possible
|
- Reste assujettie à la pertinence du découpage du
système en unités, - Besoin de valeurs seuils plus
génériques,
- Ne considère pas le facteur humain.
|
Méthode MCAS
|
Industrie chimique matières toxiques
et inflammables
|
Local à
l'unité Classification des scénarios
|
- Ne considère pas la propagation d'effet domino
inter-unités,
- Se limite à la classification des scénarios
primaires sans étudier les scénarios de degré plus
élevés,
- Ne considère pas le facteur humain comme un
paramètre qui peut influencer le processus,
- N'explicite pas le processus de génération des
scénarios.
|
Procédure ORA
|
Industrie (pétrochimique)
|
Estimation de risques
|
- Spécifique à l'analyse des risques, - Ne
traite pas à proprement parler des effets dominos.
|
Méthodologie ARAMIS
|
Industrie chimique et stockage
|
Identification des risques (noeud papillon)
|
- Ne traite l'aspect d'effet domino que partiellement,
- Ne considère pas les risques d'origine
naturels,
- N'intègre pas le facteur humain.
|
Méthodologie HAZWIM
|
Industrie
|
Analyse des dangers
|
- Spécifique au traitement des
accidents dominos externes au site industriel,
- Dépendant d'autres approches (Hazop what-it,...)
|
Algorithme FREEDOM (FREquency Estimation of DOMino
accidents)
|
Industrie (système)
|
Comportement de système
multi- unités, défaillance d'un équipement
|
- Traite les effets domino qu'en interne par rapport au site,
- Ne considère pas les autres systèmes
environnant,
- Ne prend comme critère que la défaillance des
composants.
|
31
Sur les six méthodes étudiées, nous
remarquons que chaque méthode a certes ses avantages mais aussi des
limites spécifiques. Nous pouvons par exemple citer la non
considération du facteur humain, de la propagation d'effet dominos
inter-unité ou des effets dominos externes, n'explicite pas le processus
de génération des scénarios. Ces limites sont un obstacle
pour la réalisation d'une étude complète. Pour pallier
à ce problème, nous allons proposer une nouvelle méthode
qui prendrait en considération les points précédemment
cités
I.4.2 Réalisation d'une méthode
d'étude des effets dominos
Les observations précédentes nous amènent
à la proposition d'une nouvelle méthode de travail que nous
allons ensuite appliquer. Cette méthode est résumée dans
le schéma explicatif suivant, chaque partie sera ensuite
détaillée dans l'application de la méthode.
Compréhension des process existants au sein de
l'entreprise
Non-Conforme
Démarche d'analyse critique
Analyse comparative de l'étude de danger et de
la réglementation
Conforme
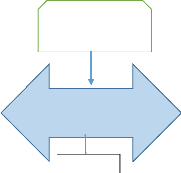
Output : maitrise des risques présents au sein de
l'entreprise
Analyse statistique de l'accidentologie
Output : Identification d'événements primaires
à effets dominos
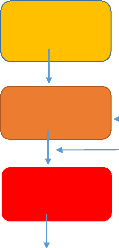
Identification des causes et des probabilités (par add)
Simulation des effets de l'événement
Identification de l'événement primaire
Output : Effets de surpression et de radiation
engendrés
Détermination des cibles et des conséquences
OUI
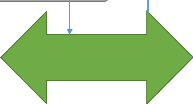
Les événements secondaires engendrent-ils
d'autres effets d'escalade ?
NON
32
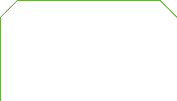
-Calcul des indices de risques et schématisation
réseau Bayésien -Etude des effets domino externe
-Calcul de l'impact financier -Impact continuité
d'activité
Calcul des probabilités d'escalade
Chapitre II
ETUDE DES EFFETS DOMINOS
INTERNES
34
II. ETUDE DES EFFETS DOMINOS INTERNES
Dans ce chapitre nous allons tout d'abord essayer de
détailler le process d'extraction des gaz de l'air qui se fait au sein
de LGA afin de comprendre les risques qui peuvent en découler. Nous
allons ensuite réaliser une critique de l'étude de danger pour
faire ressortir les manques qui peuvent exister en matière de
sécurité.
II.1 Compréhension du process existant à
LGA
II.1.1 Présentation de l'Air Separation Unit
(ASU)
Le site de LGA à Reghaïa est constitué des
ateliers pour la production des différents gaz industriels,
médicaux et mélanges, des ateliers de conditionnement, de la
ré-épreuve, un parc de distribution bouteille, un bloc
administration et de l'ASU. Cette dernière est le coeur de production du
site, en effet elle collecte l'air ambiant afin d'obtenir, grâce à
un procédé industriel, les différents gaz de l'air avec
une grande pureté. A l'issu de ce procédé, l'air est
décomposé en ses composants principaux ; Oxygène, azote et
argon. A partir de cette unité, les gaz liquéfiés seront
redistribués soit vers les ateliers de conditionnement bouteille ou bien
pour la distribution en vrac grâce à des camions citernes qui
pompent ces gaz à l'état liquide directement des
réservoirs de stockage
II.1.2 Description du processus de séparation
d'air
II.1.2.1 Récupération d'oxygène et
d'azote
La séparation de l'air est basée sur un
processus à basse température utilisant des adsorbeurs à
tamis moléculaires pour nettoyer l'air avant sa
pénétration dans la partie à basse température.
La poussière et d'autres particules contenues dans
l'air sont éliminées grâce à un système de
filtre d'air avant que l'air pénètre dans le compresseur
d'air.
Le compresseur d'air qui est entraîné par un
moteur électrique comprime l'air à environ 4,6 bar. Après
le 3ème étage, l'air est refroidi dans un refroidisseur de
sortie, puis refroidi encore à environ 20°C dans un refroidisseur
d'air par l'eau refroidie de l'unité de réfrigération.
L'eau condensée est éliminée de l'air par un
séparateur d'eau en aval de l'unité de
réfrigération. Un treillis en haut de la cuve du
séparateur élimine l'eau atomisée de l'air.
35
Après le séparateur d'eau, l'air traverse l'un
des adsorbeurs à tamis moléculaires où sont
éliminés le CO2, les hydrocarbures potentiellement dangereux et
la vapeur d'eau résiduelle. L'un des deux adsorbeurs fonctionne pendant
que l'autre est en cours de régénération. De l'azote impur
provenant de la boîte froide est utilisé pour la
régénération des adsorbeurs.
Ce gaz est chauffé dans le chauffage électrique
et traverse l'adsorbeur. Le cycle de chauffage est assisté par un
accumulateur de chaleur qui est chargé durant les étapes de
refroidissement, de pressurisation, de changement et de
dépressurisation. Durant le cycle de refroidissement, l'adsorbeur est
refroidi par l'azote résiduaire.
Une fois la séquence de
régénération terminée. L'adsorbeur est
pressurisé avant de passer au cycle d'adsorption.
Le changement de l'étape de
régénération à celle du fonctionnement et
vice-versa est contrôlé par un programme.
Après l'adsorbeur à tamis moléculaire,
une petite partie de l'air sec est nettoyé est prélevé en
tant qu'air instrument.
En aval de l'adsorbeur à tamis moléculaire, la
quantité totale de l'air du processus et l'air recyclé provenant
de la boîte froide sont ensuite comprimés à 33 bar par un
turbocompresseur d'air de recyclage à 3 étages avec
refroidissement. Après le dernier étage du compresseur de
recyclage, l'air est refroidi dans un refroidisseur de sortie, puis
comprimé encore à 49,6 bar par l'unité de
compresseur/surpresseur à turbine de détente. Le flux de
recyclage en aval du compresseur-surpresseur est ensuite refroidi dans un
refroidisseur de sortie par de l'eau de refroidissement, puis refroidi encore
par l'eau refroidie de l'unité de réfrigération dans le
refroidisseur.
La quantité totale d'air comprimé
pénètre dans la boite froide où elle est refroidie par les
flux de produit froids en tant qu'azote résiduaire, azote basse pression
et sous pression, oxygène et une partie d'air de recyclage dans le
principal échangeur de chaleur.
Une partie de l'air comprimé quitte le centre de
l'échangeur de chaleur avec une température de -70°C. Ce
flux est détendu dans la turbine de détente et
génère la réfrigération requise pour le processus
cryogénique. En aval de la turbine de détente, ce flux est
divisé. Une partie est dirigée vers la colonne de pression et
l'autre partie est recyclée vers le compresseur de recyclage.
36
L'autre partie de l'air comprimé est ensuite encore
refroidie jusqu'à sa température de liquéfaction et
directement détendu vers la colonne de pression.
Les produits traversant l'échangeur de chaleur
principal sont chauffés à environ 30°C par l'air du
processus à contre-courant.
Dans la colonne de pression, l'air du processus est
pré-séparé en liquide enrichi en oxygène au fond et
en azote pur en haut. Le reflux requis pour la rectification est
généré par la condensation de l'azote gazeux contre
l'oxygène bouillant dans le condenseur généré par
la condensation de l'azote gazeux contre l'oxygène bouillant dans le
condenseur. Une partie de l'azote liquide sert de reflux pour la colonne de
pression, la partie restante est sous-refroidie dans le sous-refroidisseur et
alimente la colonne basse pression dans laquelle elle sert de reflux.
L'azote liquide en excédent est dévié du
haut de la colonne basse pression et envoyé dans le réservoir de
stockage.
Une petite partie de l'azote gazeux sous pression est
prélevée en haut de la colonne de pression et sert de gaz de
purge et d'étanchéité pour l'unité de
séparation d'air (ASU).
Une partie d'air liquide est prélevée d'un
collecteur séparé dans la colonne de pression, puis
sous-refroidie. Elle à améliorer la rectification dans la colonne
basse pression.
Le liquide enrichi en oxygène du fond de la colonne de
pression est également sous-refroidi dans le sous-refroidisseur et
l'évaporateur d'argon puis est détendu dans le condenseur d'argon
brut. Le liquide enrichi en oxygène sert de réfrigérant
pour le condenseur d'argon brut et pour le condenseur d'argon pur. Le liquide
en excédent du condenseur d'argon brut s'écoule par le trop-plein
dans la colonne basse pression en tant qu'alimentation d'oxygène.
Dans la colonne basse pression, la séparation finale en
oxygène liquide pur a lieu, en tant que produit inférieur et
azote gazeux en haut de la colonne. Le produit d'oxygène liquide
prélevé au fond la colonne basse pression est pompé par
une pompe cryogénique et divisé en deux flux.
L'un des flux est directement dirigé via le
sous-refroidisseur vers le réservoir de stockage d'oxygène.
L'autre flux est introduit dans le condenseur. Une partie de l'oxygène
gazeux prélevé dans le condenseur devient du gaz
résiduaire d'oxygène et quant à l'autre alimente dans la
colonne basse pression.
37
Le gaz d'azote pur en haut de la colonne basse pression est
réchauffé dans le sous-refroidisseur et l'échangeur de
chaleur principal, puis quitte la boite froide en tant que produit LP-GAN, mais
la conduite de produit LP-GAN est aveugle et s'échappe via la conduite
d'évacuation de produit et le silencieux.
Le gaz résiduaire d'azote de la colonne basse pression
est réchauffé dans le sous refroidisseur et l'échangeur de
chaleur principal et sert à régénérer les
absorbeurs à tamis moléculaires. Ensuite le gaz résiduaire
est évacué dans l'atmosphère.
II.1.2.2 Récupération
de l'argon brut et pur :
Le gaz d'argon enrichi est dévié de la colonne
basse pression et alimente le bas de la colonne d'argon brut T4110 où le
gaz est séparé en liquide enrichi en oxygène en bas et en
gaz enrichi en argon en haut. Le liquide dans le fond retourne dans la colonne
basse pression.
Le gaz d'argon brut en haut va vers la colonne d'argon brut
T4111 et se liquéfie dans sa totalité dans le condenseur d'argon
brut contre l'air liquide enrichi en oxygène provenant de la colonne de
pression. Le liquide d'argon brut sert de reflux pour la colonne d'argon brut
T4111.
Le liquide du fond de T4111 est pompé vers la colonne
d'argon brut T4110 où il sert également de reflux. Environ 3,4%
du gaz d'argon brut en haut est dévié en tant que gaz et est
ensuite dirigé vers la colonne d'argon pur. La concentration
d'oxygène de l'argon brut répond déjà aux
spécifications pour le produit argon (<1 vppm de gaz
oxygène).
Dans la colonne d'argon pur, l'azote est séparé
de l'argon brut. L'argon gazeux contenant de l'azote se liquéfie dans le
condenseur d'argon pur contre l'air liquide enrichi du condenseur d'argon brut.
L'azote est évacué dans l'atmosphère, l'argon
liquéfié sert de reflux pour la colonne d'argon pur. En bas de la
colonne d'argon pur, l'argon pur liquide est rebouillit dans
l'évaporateur d'argon et sert de gaz ascendant dans la colonne d'argon
pur. Le liquide en excédent est dévié en tant qu'argon
liquide (LAR) vers le réservoir d'argon.
II.2 Critique de l'étude de danger
L'étude de dangers (EDD) est un principe de la
sécurité industrielle et surtout une exigence
réglementaire régit par le décret exécutif
numéro 06-198, dont un préalable est l'inventaire des
38
objets et activités avec leurs dangers
intrinsèques. C'est un bon moyen d'obtenir des informations sur les
activités de l'entreprise et les risques identifiés au sein de
cette dernière ainsi que les réponses apportées aux
exigences réglementaires. Nous commencerons donc le travail par une
critique de l'étude de danger. Cela nous permettra également
d'apporter notre contribution aux éventuels manques de
l'étude.
II.2.1 Contenue de l'étude de danger :
L'étude de danger a pour objet de préciser les
risques directs ou indirects par lesquels l'activité de
l'établissement classé met en danger les personnes, les biens et
l'environnement, que la cause soit interne ou externe.
L'étude de danger doit permettre de définir les
mesures d'ordre technique propre à réduire la probabilité
et les effets des accidents ainsi que les mesures d'organisation pour la
prévention et la gestion de ces accidents.
II.2.2 Cadre réglementaire
algérien
En Algérie c'est le décret exécutive
n°06-198 du 4 Joumada El oula 1427 correspondant au 31 mai 2006 qui
définit la réglementation applicable aux établissements
classés pour la protection de l'environnement (ICPE) [11].
Ce décret comporte deux articles, 14 et 28, portant sur
les EDD. Selon l'article 14 de ce décret, l'EDD doit comporter les
éléments suivants [6] :
- Présentation générale du projet ;
- Description de l'environnement immédiat du projet et
du voisinage potentiellement affecté en cas d'accident comprenant les
données physiques (géologie, hydrologie,
météorologie et les conditions naturelles) et les données
socio-économiques et culturelles (population, habitat, occupation des
sols, activités économiques, voies de communication ou de
transport et aires protégées) ;
- Description du projet et ses différentes
installations (implantation, taille et capacité, accès, choix du
procédé retenu, fonctionnement, produits et matières mises
en oeuvre...) en se servant au besoin de cartes (plan d'ensemble, plan de
situation, plan de masse, plan de mouvement ...) ;
39
- Identification de tous les facteurs de risque
générés par l'exploitation de chaque installation
considérée. Elle doit tenir compte non seulement des facteurs
intrinsèques propres aux installations mais également à
l'environnement auquel la zone est exposée ;
- Analyse des risques et des conséquences au niveau de
l'établissement classé afin d'identifier de façon
exhaustive les événements accidentels pouvant survenir. Leur
attribuer une cotation en terme de gravité et de probabilité
permettant de les hiérarchiser avec la méthode
d'évaluation des risques utilisée pour l'élaboration de
l'étude de danger ;
- Analyse des impacts potentiels en cas d'accidents sur les
populations (y compris les travailleurs au sein de l'établissement),
l'environnement ainsi que les impacts économiques et financiers
prévisibles;
- Modalité de prévention des accidents majeurs
et du système de gestion de la sécurité et des moyens de
secours.
Suivant l'article 28 du décret exécutif
n°06-198, l'EDD a pour objectif de [6]:
- Préciser les risques directs ou indirects par
lesquels l'activité de l'établissement classé met en
danger les personnes, les biens et l'environnement, que la cause soit interne
ou externe ;
- Définir les mesures d'ordre technique propres
à réduire la probabilité et les effets des accidents ainsi
que les mesures d'organisation pour la prévention et la gestion de ces
accidents ;
- Procéder à l'information préventive sur
les risques du public, du personnel et des exploitants des installations
voisines ;
- Favoriser l'émergence d'une culture du risque au
voisinage des établissements ; - Servir de base à
l'élaboration des règles d'urbanisation et des plans
d'urgence.
II.2.3 Démarche de l'analyse critique des
EDD
Dans cette partie nous allons exposer les différentes
étapes constituant notre démarche de l'analyse critique des
EDD.
Les différentes étapes d'une critique d'EDD sont
résumées dans la figure II-1.
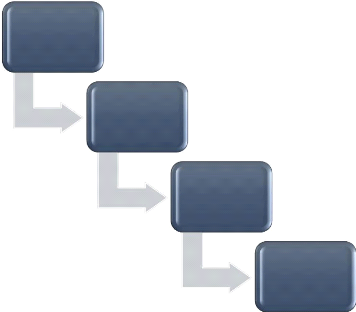
Etude des insuffisances relevées par les
services de la protection civile
Identification des principales insuffisances des EDD
Formulation des insuffisances sous forme
d'écarts
Réduction/Elimination des écarts
40
Figure II-1 : Etapes de la critique d'une EDD
Les étapes de la démarche sont
développées ci-dessous [7] :
Étape 1 : Etude des insuffisances relevées par
les services de la protection civile
Afin de mieux cibler notre critique nous allons nous baser sur
des statistiques réalisées par les services de la protection
civile au sujet des non conformités récurrentes dans les EDD
déposées.
Étape 2 : Identification des principales insuffisances
des EDD
Dans cette étape, nous avons caractérisé
toutes les insuffisances du contenu de l'EDD, par rapport à ce qui a
été mentionné dans l'article 14 du décret
exécutif 06-198. Les insuffisances sont classées dans un tableau
en fonction des chapitres développés dans l'EDD.
Étape 3 : Formulation des insuffisances sous forme
d'écarts
La classification des écarts s'est faite en fonction des
sous-écarts et des responsables de la mise en oeuvre. Tous les
écarts identifiés ont été classés par
catégorie. Le schéma de la figure 3-2 explique la
répartition de l'écart résultat.
Les types de sous écarts expliqués
précédemment sont :
41
Écart mise en oeuvre : c'est l'écart entre ce
qui a été tracé comme objectif et ce qui a
été fait dans l'étude de danger (le résultat).
Écart contenu : ce sont des chapitres qui n'ont pas
été traités dans l'EDD et qui ont été
essentiellement décrits dans le cadre réglementaire.
Écart réalisation : l'absence de toute
évaluation des risques en utilisant des méthodes d'analyse (APR,
AMDEC, ADD, Noeud papillon...) permettant de faire ressortir des
scénarios plausibles susceptibles de se produire dans une installation
bien déterminée. Cet écart peut être dû suite
au mauvais déploiement d'une méthode d'analyse (la
méthodologie suivit ne correspond pas à celle décrite dans
la bibliographie).
Écart examen et approbation : c'est l'écart qui
correspond aux critères d'examen qui n'ont pas été pris en
considération lors de l'approbation de l'étude de danger.
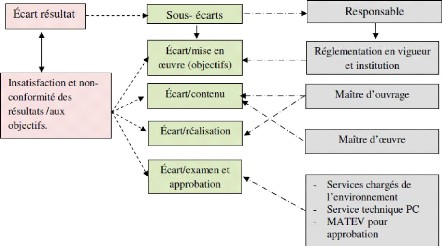
Figure II-2 Démarche de détermination
des écarts
Étape 4 : Réduction/élimination des
écarts
Cette dernière étape de la critique permet de
nous renseigner sur les mesures à prendre en considération pour
avoir une étude de danger conforme à la réglementation en
vigueur.
42
II.2.4 Application de l'analyse critique de
l'EDD
Étape 1 : Etude des insuffisances relevées par
les services de la protection civile Les résultats obtenus pour
cette étape sont résumés dans le tableau II-1.
Tableau II-1 : Etat récapitulatif des
dossiers traités par les services de la protection
civile
pour les ICPE
Nombre de dossiers
Année traités
|
|
Nombre de Taux de conformité
conformités
|
2011
|
3687
|
486
|
13%
|
2012
|
3896
|
623
|
16%
|
2013
|
5918
|
758
|
13%
|
|
Total : 13501
|
Total : 1867
|
Total : 14%
|
Observation : la conformité est délivrée
suite à la visite effectuée par les services de la
|
protection civile à la demande du propriétaire
une fois que le projet, objet de l'EIE/EDD, est achevé
|
Statistique de non conformités :
Sur un panel de 35 études de danger
étudiées, les statistiques suivantes ont été
calculées :
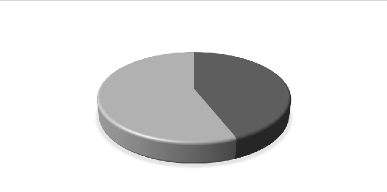
Non-conformes;
56%
Conformes; 44%
Figure II-3 Insuffisances de forme
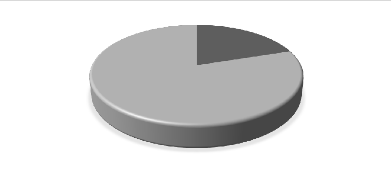
Non-conformes;
80%
Conformes; 20%
43
Figure II-4 : Insuffisances de
fond
Les insuffisances les plus fréquentes relevées de
cette étude sont l'omission des références de grilles,
l'absence d'outils pertinents d'analyse de risque, le passage d'analyse
qualitative à l'analyse quantitative ou encore l'absence de
critère d'acceptabilité
Étape 2 : Identification des principales insuffisances de
l'étude de danger LINDE GAS Reghaia. Les insuffisances relatives
à chaque chapitre de l'EDD sont relevées dans le tableau II-2.
Tableau II-2 : Résumé de la critique
de l'EDD
Contenu requis
|
Contenue de l'EDD
|
Ecart
|
Résumé non technique
|
Pas de résumé non
technique
|
Absence du résumé non
technique dans l'étude de danger
|
Description générale du
projet
|
Description du projet
|
/
|
Description du projet et de ses installations
|
Activités, capacités,
utilités, plan de masse,
description des locaux,
plan de situation, processus de production
|
Absence de l'accidentologie de ce type d'entreprise et de la
politique HSE de LGA
|
Description de
l'environnement
|
Géographie, géologie,
pédologie, population,
climat, faune et flore
|
-La répartition de la
population dans le projet
et dans la commune n'est pas mentionnée.
-La description des industries avoisinante est inexistante or
LGA est à proximité très réduite d'autres
entreprises à
|
44
|
|
haut risque
|
Identifications des facteurs de risque
|
Risque général des
produits contenus dans l'entreprise
|
Absence de facteurs de
risques intrinsèques propres
aux installations mais également à
l'environnement auquel la zone est exposée. L'origine des risques
majeurs
identifiés n'est pas mentionnée.
Les conditions d'occurrence des risques majeurs ne sont pas
citées.
|
Analyse du risque
|
Le document contient un
historique d'accident d'entreprises utilisant un des
produits que LINDE produit
|
-L'étude ne contient aucune analyse des risques ni
même
d'analyse préliminaire des risques (APR)
- Aucun scénario d'accident n'a été
réalisé
-Absence de cotation du risque (probabilité,
gravité)
-Absence de méthode d'analyse des risques qu'elle
soit qualitative ou quantitative.
|
Évaluation des risques
majeurs
|
X
|
Aucune analyse des risques majeurs n'a été
effectuée
|
Modalité de prévention des
accidents majeurs et du système de gestion de
la sécurité
|
Description de moyens de
lutte anti incendie et
quelques mesures préventives
|
-Aucune mesure de réduction de risques adéquate
proposée.
|
45
Étape 3 : Formulation des insuffisances sous forme
d'écarts
Les écarts soulevés sont essentiellement des
écarts de contenus et des écarts de réalisation
(Figure II-5).
Type d'écart Chapitre concerné
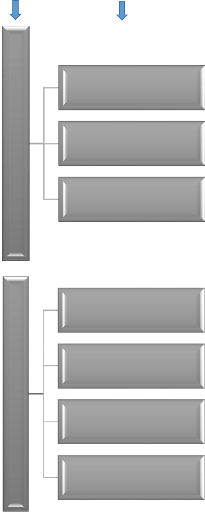
Écart contenu
Écart réalisation
Description du projet et de ses installations
Modalité de prévention des accidents
majeurs et du système de gestion de la
sécurité
Identifications des facteurs de risque
Analyse du risque
Évaluation des risques majeurs
Résumé non technique
Description de l'environnement
Figure II-5 : Schéma représentant les
types d'écarts relevés
46
Étape 4 : Réduction/élimination des
écarts
Cette étape serra partiellement réalisée
car l'objectif global de notre étude n'est pas l'amélioration de
l'étude de danger, mais la réalisation d'une méthode pour
l'étude des effets dominos. Une grande partie de sa réalisation
sera néanmoins acquise grâce aux résultats de
l'étude qui sera effectuée.
A travers les deux étapes précédentes
nous avons pu mieux cerner les caractéristiques de LGA, ce qui nous a
permis de faire ressortir entre autre les zones critiques. Toutefois afin de
pouvoir identifier les événements les plus susceptibles de
créer des accidents dominos, nous allons nous référer
à une analyse de l'accidentologie.
II.3 Analyse de l'accidentologie
Contrairement à la plupart des autres branches de la
science et de la technologie, dans laquelle des expériences
reproductibles fournissent la base pour la construction d'un cadre
théorique, il est très difficile de réaliser de telles
expériences dans le domaine de la prévision et la
prévention des accidents.
Cette situation donne une grande importance à l'analyse
des accidents passés dans l'industrie. Elle se fait par la
reconstruction minutieuse des événements et l'identification de
leurs évènements déclencheurs, la séquence, et
leurs conséquences. Ce qui peut donner lieu à des études
comme la nôtre très utiles à l'élaboration de
stratégies de prévention des accidents.
Comme la majorité des accidents majeurs dans le
passé ayant causé un préjudice important pour les vies
humaines et d'autres ressources ont impliqué un effet domino, nous nous
sommes basés dans cette étude sur les exemples de plus de
224 accidents.
II.3.1 Présentation du logiciel R
RStudio est un environnement de développement gratuit,
libre et multiplateforme pour R, il utilisé pour le traitement de
données et l'analyse statistique. Il est disponible sous la licence
libre AGPLv3, ou bien sous une licence commerciale, soumise à un
abonnement annuel.
47
RStudio est disponible en deux versions : RStudio Desktop,
pour une exécution locale du logiciel comme toute autre application, et
RStudio Server qui, lancé sur un serveur Linux, permet d'accéder
à RStudio par un navigateur web. Des distributions de RStudio Desktop
sont disponibles pour Microsoft Windows, OS X et GNU/Linux.
RStudio a été écrit en langage C++, et
son interface graphique utilise l'interface de programmation Qt.
RStudio intègre la possibilité d'écrire
des notebooks combinant de manière interactive du code R, du texte mis
en forme en markdown et des appels à du code Python ou Bash [8].
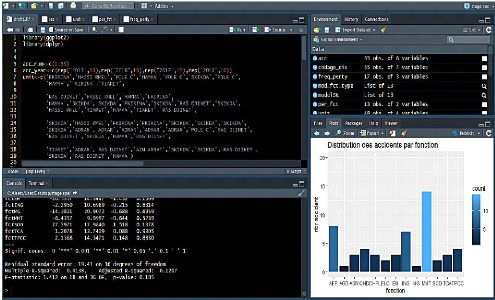
Figure II-6: Image de l'interface du logiciel
R
II.3.2 Méthodologie
II.3.2.1 Acquisitions des données
Les accidents recueillis proviennent de la base de données
ARIA et sont classés dans des tableaux dont le contenu des colonnes est
comme suit :
48
Numéro ARIA
|
Code NAF
|
Pays
|
Département
|
Commune
|
Type Accident
|
Type
évènement
|
Matières
|
Equipements
|
Classe de
danger
|
Causes profondes
|
Causes premières
|
Conséquences
|
Echelle
|
URL
|
Contenu
|
|
CLP
|
|
|
|
|
|
|
II.3.2.2 Traitement des données
Les données qui ont été jugées utiles
et prises en considération sont :
Numéro ARIA
Type accident
Matières
Causes
Conséquences humaines
Conséquences économiques
Conséquences environnementales
Rejets
Les données retenues sont nommées comme suit :
Tableau II-3 : Appellation des données
retenues
Numéro ARIA
|
acc_num_year
|
Type accident
|
type_acc
|
Matières
|
source_produit
|
Causes
|
cause
|
Conséquences humaines
|
cons_hum_ARIA
|
Conséquences économiques
|
cons_eco_ARIA
|
Conséquences environnementales
|
cons_envi_ARIA
|
Rejets
|
rejet_matière_ARIA
|
A noté que le code écrit pour la visualisation de
toutes les données comporte plus de 273 lignes.
II.3.2.3 Visualisation :
Les figures II-7 à II-11, représentent les
statistiques relatives aux types d'accidents, aux conséquences en
fonction des types d'accidents, aux types d'accident en fonction des causes,
aux types de produits mis en cause, et aux types de substances dangereuses
impliquées dans les événements dominos.
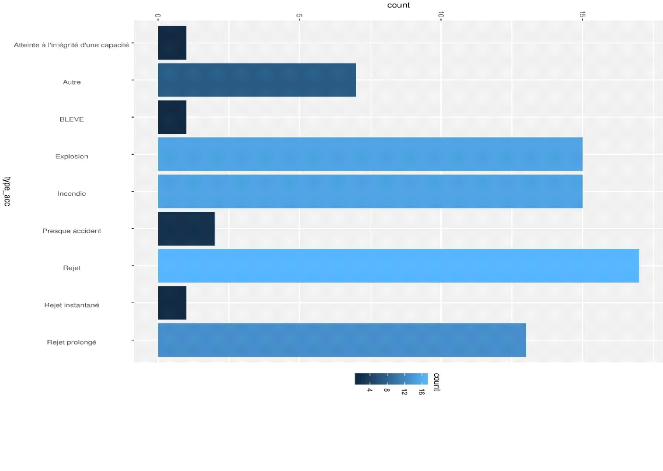
Figure II-7 : Statistiques sur les types
d'accidents
49
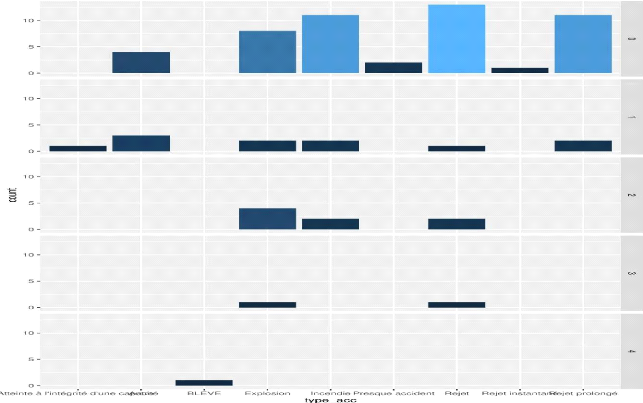
1 0 -
a s-
0-
10-
5 -
0 -
kttsi nte à i ·i ntégrité
d'u ne Ga atr+
6LEVE ExplGsion Incendie Presque accident ejet insta
ntarf jet proIong$
tyrreaLCG
1 0
s
o
1 0 -
s -
O
1 0 -
s-
0-
count
I 1 2.5 -I 0.0 7.5 5.0
2.5
50
Figure II-8 : Statistiques sur les
conséquences en fonction des types d'accidents
Ss
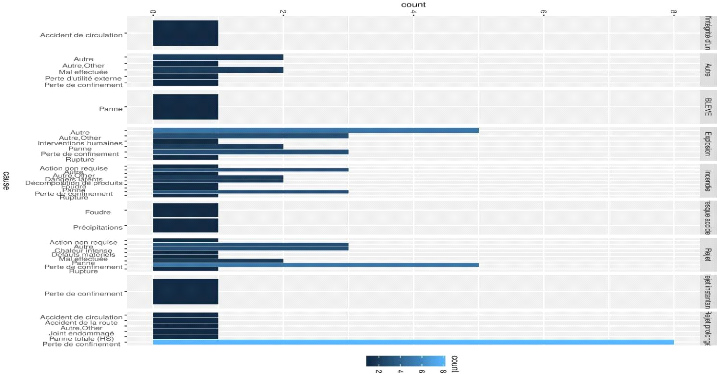
Figure II-9 : Statistiques sur les types d'accident
en fonction des causes
51
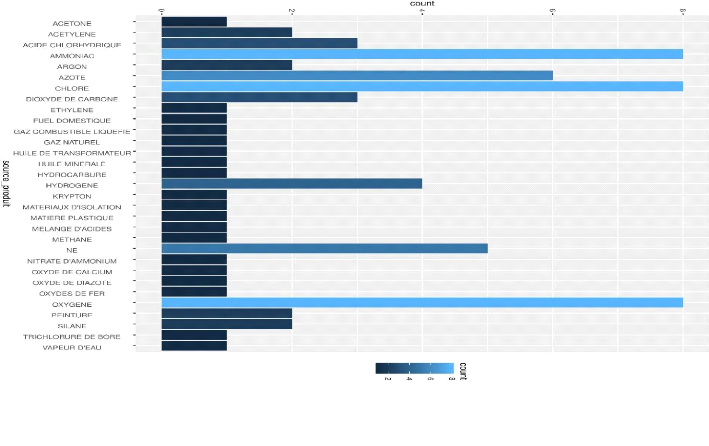
Figure II-10 : Statistiques sur les types de produits
mis en cause
52
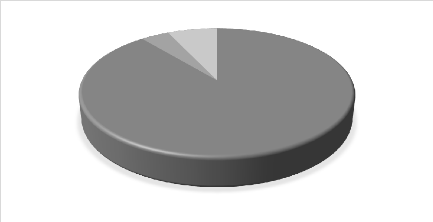
Toxique
4%
Autres
7%
Inflammable
89%
53
Figure II-11 : Types de substances dangereuses
impliquées dans les événements dominos
Commentaire : Les substances
inflammables sont associées à une très grande fraction
(89%) de tous les événements dominos (Fig.
II-11). Les produits pétroliers, hydrocarbures en aval et
explosifs en phase condensée sont les substances les plus couramment
impliquées. Les produits non-inflammables ont également
provoqué des événements à effets dominos majeurs,
comme ce fut le cas à Milligan, États-Unis en 1979 et à
Chogging (Chine) en 2004; les deux impliquant le chlore. Même un produit
extincteur comme le CO2 a été associé à des effets
dominos, comme ce fut le cas à Repcelak, en Hongrie, en 1969. Une des
explosions majeures ayant eu lieu lors de la catastrophe de la raffinerie de
Skikda, en Algérie en 2004 a été, selon tous les comptes
rendus, causée par l'eau (surchauffe; explosion de chaudière).
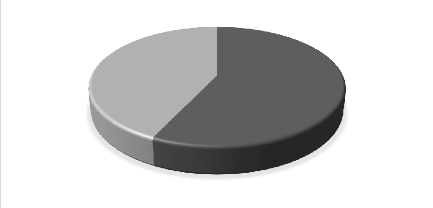
Feu
43%
Explosion
57%
54
Figure II-12 : Types d'accidents primaires
(initiateurs) impliqués dans les cas enregistrés
d'effets
dominos
Commentaire : Types d'accidents les plus
susceptibles de précipiter un effet domino
Les événements enregistrés dans cette
étude révèlent que l'explosion est la cause la plus
fréquente d'effet domino, suivie du feu (Fig. II-12).
C'est une statistique intéressante car, parmi les accidents
isolés, la fraction la plus importante est celle du feu [9] [10]. Une
explication de cette curieuse déviation dans les
événements de dominos provient des données sur des types
spécifiques d'explosions et d'incendies impliqués.
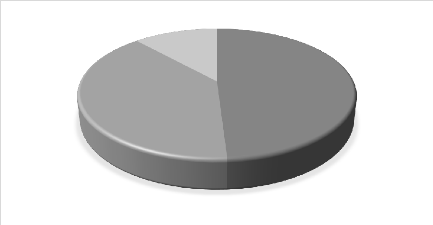
Jet Fire
39%
VCF
12%
Pool Fire
49%
Figure II-13 : Types d'incendies impliqués
dans le déclenchement de l'effet domino
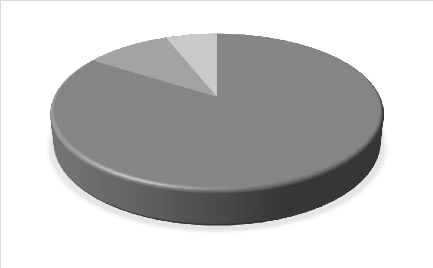
Explosion physique
10%
Explosion de poussiére
6%
VCE
84%
55
Figure II-14 : Types d'explosions responsables du
déclenchement de l'effet domino.
Commentaire : Dans un grand nombre de
références le type d'explosion ou de feu n'a pas
été précisé, mais parmi les
références où il l'a été, la distribution
est comme celle représentée dans les figures II-13 et II-14.
Parmi les dominos événements déclenchés par un
incendie (Fig. II-13), la cause la plus fréquente a
été le pool fire (feu de nappe 80%), suivi de VCF (feu de nuage
de vapeur 12%). Parmi les événements dominos initiés par
une explosion, le VCE (explosion de nuage de vapeur) a été la
cause la plus fréquente (Fig. II-14). Ainsi, il peut
être dit que, dans l'ensemble, les fuites de substances inflammables
générant des VCF / VCE sont la cause la plus fréquemment
responsable de l'effet domino dans l'industrie de transformation. Une
enquête sur l'historique des accidents révèle
également que même si le BLEVE est rarement l'initiateur
d'accident dans une séquence de dominos, il est très souvent le
résultat d'un VCF / VCE, et il devient un puissant propagateur de la
chaîne des accidents comme cela s'est produit, par exemple, à Port
Newark, aux États-Unis, en 1951; Feyzin, en France, en 1966; et Mexico,
Mexique, en 1984.
56
Etant dans une entreprise où il y a des installations
fixes dangereuses et également énormément de transport de
produits par des camions, il est intéressant d'étudier les
pourcentages d'accidents pouvant être initiés par ces types
d'installations, et lors du transport.
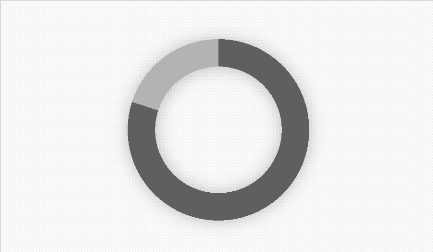
Transport
20%
Instalation fixe
80%
Figure II-15 : Événements Dominos
survenant dans des installations fixes et pendant le
transport.
Les quatre cinquièmes de tous les
événements impliquant des effets dominos passés ont eu
lieu sur des installations fixes (Fig. II-15). Parmi les 20%
d'accidents survenus pendant le transport, la plus grande partie est survenue
sur les routes suivies de près par les événements
ferroviaires; et pipelines.
Conclusion :
Les trois étapes précédentes ont fait
ressortir deux événements qui sont l'incendie et le VCE ainsi que
2 unités critiques concernés : le parc bouteilles
d'acétylène et l'atelier CCAM . Nous allons donc nous pencher sur
la partie calcul de ces événements redoutés.
57
II.4 Application de la méthode :
L'analyse de l'accidentologie ainsi que de l'étude de
danger et donc des spécificités de Linde Gas Algérie nous
permettent de faire ressortir les événements primaires suivants
:
Tableau II-d : Evénements primaires
retenus
Evénement primaire
|
Unité concernée
|
VCE
|
Parc bouteilles acétylène
|
Atelier CCAM (112)
|
Incendie
|
Parc bouteilles acétylène
|
Atelier CCAM (112)
|
Le choix de ces événements c'est fait
également au vu des caractéristiques très dangereuses de
ces deux gaz (Tableaux II-5 et II-6).
Tableau II-5 : Comparaison des températures d'auto
inflammation et d'énergie min d'inflammation
de différents gaz
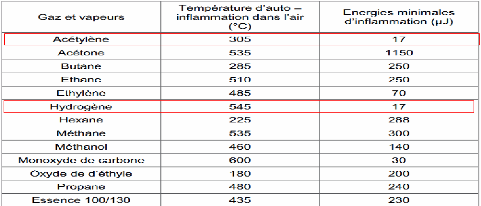
58
Tableau II-6 : Vitesse de combustion laminaire des gaz
combustibles
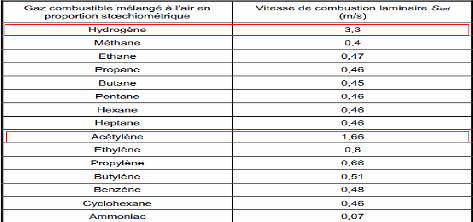
Afin de déterminer les causes et les
probabilités d'occurrences des événements primaires
retenus, nous allons réaliser des arbres de causes.
II.4.1 Les arbres de défaillances
L'arbre de défaillances est une technique
d'ingénierie très utilisée dans les études de
sécurité et de fiabilité des systèmes. Cette
méthode, aussi appelée arbre de pannes ou arbre de fautes,
consiste à représenter graphiquement les combinaisons possibles
d'événements qui permettent la réalisation d'un
événement indésirable prédéfini. L'arbre de
défaillances est ainsi formé de niveaux successifs
d'événements qui s'articulent par l'intermédiaire de
portes logiques. En adoptant cette représentation et la logique
déductive (allant des effets vers les causes) ainsi que la logique
booléenne qui lui est propre, il est possible de remonter d'effets en
causes de l'événement indésirable à des
événements de base, indépendants entre eux et
probabilisables.
59
II.4.2 Présentation du logiciel
Arbre Analyste est conçu par des ingénieurs
spécialistes du domaine de la sûreté de fonctionnement dans
le but de proposer un outil qui réponde aux mieux aux besoins des
études.
L'interopérabilité est primordiale si on souhaite
capitaliser les études de Sûreté de fonctionnement. Arbre
Analyste respecte le standard Open-PSA permettant ainsi de s'assurer d'une
parfaite interopérabilité.
Les algorithmes de calculs s'améliorent et
entraînent donc des évolutions dans les moteurs de calculs. Arbre
Analyste utilise le moteur XFTA permettant ainsi de profiter des
dernières évolutions en la matière.
Arbre Analyste est libre d'utilisation. Il peut être
téléchargé, distribué et utilisé sans aucune
limite.
Comment fonctionne Arbre-Analyste ?
Arbre-Analyste est construit autour de deux piliers : ?
Open-PSA
Le format d'enregistrement utilisé respecte le standard
Open-PSA. Open-PSA définit un formalisme XML permettant de
décrire un arbre de défaillance. Il a pour but une
interopérabilité complète.
? XFTA
Le moteur de calcul utilisé pour effectuer les analyses
probabilistes des arbres de défaillances est XFTA. Il est
développé par M. Rauzy [11].
Les arbres construits ont donné les résultats
représentés sur les figures II-16 à II-19.
* Moteur de calculs XFTA
|
Temps de missio-n: 111 Porte de tète: P6 J Lime:
|
|
Calculer
|
|
|
|
|
Résumé
|
Importance
|
l Coupes pes minimales
|
Probabilités
|
I Sensibilité
|
|
Po-rte de tète emps de missio-n Probabilité
|
P6
0.1
7.9e-05
7.86e-0.5 0,0e+00
|
|
|
|
|
|
|
|
|
|
|
Défiabilitésystème Lambda système
MTTFsystème
Du rée dindispan ibilité
réparable: No-mbre de pannes MTTRsystème MTBF
système
7.857e-136
|
no-ne 0,0e+00
no-ne no-ne
no-ne no-ne no-ne
d 0e+00
|
|
|
|
|
|
|
|
|
|
Indis
onibilit Défiabilit Fréquene
|
|
0,0e+00
0
|
0 0.03
|
0.04
|
|
0.06
:xm 0.09
|
l
0.1
|
Figure II-16 : Probabilité d'occurrence d'une
explosion de bouteille d'acétylène calculée par Arbre
Analyste

'bhhh.opsa - Arbre Analyst - Logiciel d'analyse de
Sùreté de fonctionnement Fichier Edition Pages Zoom
Données Calculs Modules Aide
aldlâcAlialhr}I3IGtG0ÿl.l ·01Q 9 a
P6
Explosion dune bouteille dacêthylène
T4I.1
7.9e05 F.1.OeOoe
P4
Surpression
P5
Combustion intern e
E183
|
F2
Echauffement de la bouteille
Déclaration dun feu
·
P1
El
Défaillance du système d'arrosage
E691
Manque d'acéton e dans la bouteille
·
15.23e-05
E685
Matière poreuse utilisée
détériorée
·
E172
Pompe défectueuse
·
y=.6oee.03
Retour de flamme â rintérieur de la bouteille
·
}2.30=--05
E173
Plus d'eau dans le bassin
·
E671 r1 .60e-03
Pulvérisateur Beau bouché
·
1=1.oee03
Page
A- Last of water pumpir B - Lost of electrical distributic C
- Failure of componen
61
Figure II-17 : Arbre de défaillance d'une
explosion de bouteille d'acétylène
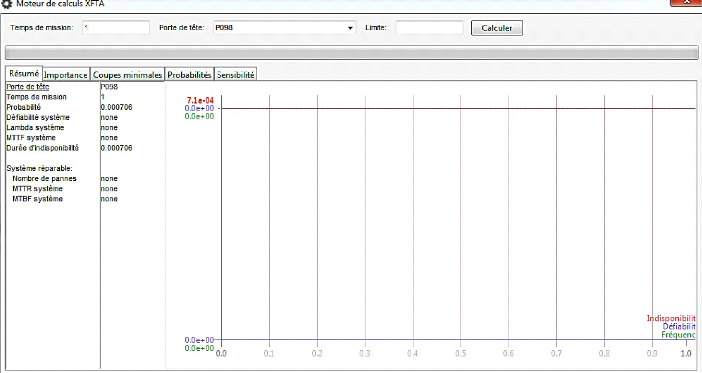
Limite:
Calculer
Porte de tète: P093
Temps de mission: 1
Moteur de calculs XFTA
u
Résumé (Importance Coupes minimales
Probabilités Sensibilité
Porte de tète
|
P493
1 7.1e-04
4.{}44746 0.Oe+00
none 0.Oe+00
none none
4.44746
none none none
0.0e+ 00
|
|
|
|
|
|
|
|
|
|
|
Temps de mission Probabilité
Défiabilitésystème Lambda système
MTTEsystème
Durée d'indisponibilité
Système réparable: Nombre de pannes
MTTRsystème MTBFsystème
|
|
|
|
|
|
|
|
|
In
|
d isp uni b il it Défie b il it Fréquenc
|
0.0e+000~y0~y
00
|
/ry
01 )3 0
|
/y
4 05
|
_ .Ix
|
'}}9'}
V1
|
y ~y
1.V
|
62
Figure II-18 : Probabilité d'occurrence
d'une fuite sur une bouteille calculée par Arbre
Analyste
|
|
|
|
|
|
|
|
|
|
|
|
|
|
'bhhh.opsa - Arbre Analyst - Logiciel d'analyse de
SLreté de fanctionnemen Fichier Edition Pages Zoom Données
Calculs Modules Aide
|
|
|
|
|
|
|
|
|
|
|
|
|
|
|
|
|
|
|
|
|
|
|
|
|
|
|
|
|
|
|
|
|
|
|
|
|
|
|
|
|
|
|
|
|
|
|
|
|
q lâlârAlielgPl1] C ,rÿlefF1' 1g4;A
E
|
q
|
q
|
q
|
q
|
q
|
q
|
q
|
q
|
q
|
q
|
P098
Fuite dune bouteille (H2 où H2 )
T=1r)
q =7.1 e04
F=0.0e+00
|
|
|
|
|
|
|
E097
|
|
|
|
|
|
E095
|
|
Bouteille deféctueuse
|
|
|
E096
|
|
Robinet défaillant
|
|
·
|
|
|
|
|
|
y=1.00e-45
|
Erreur humaine où sabotage
|
|
·
y=3.00e-45
|
|
E094
|
Impacte du â un choc sur la bouteille
|
· y=6 56e-04
|
|
y=1 00e-05

63
|
|
|
|
|
|
Pagel Page a I-
|
|
|
|
|
|
|
|
|
|
|
|
|
A - Lost of water pumpi
|
|
0 - Lost of efectricaf distributi
|
|
C- Failure of compone
|
|
|
|
|
|
|
|
|
|
|
|
|
|
|
|
|
|
|
Figure II-19 : Arbre de défaillance d'une
fuite de bouteille
64
Les arbres de défaillance ont permis de faire ressortir
deux probabilités qui sont celle de l'explosion d'une bouteille
d'acétylène qui est de 7.9*10-5 et celle d'une fuite
d'une bouteille qui est de 7 .1*10-4 que nous utiliseront plus tard
dans nos calculs.
L'étape suivante est donc la simulation des effets
engendrés par les événements primaires
identifiés.
Les simulations permettront entre autres, l'élaboration
d'une carte des effets physiques mais également, grâce à la
comparaison des valeurs obtenues par rapport aux seuils d'escalade, à
évaluer les vecteurs d'escalade et déduire s'il y aura
propagation des effets ou non.
Ces mêmes valeurs seront ensuite comparées aux
seuils limites pour les personnes et les structures afin d'estimer la
gravité de l'accident à effet domino à travers le calcul
des indices de risques développés plus tard.
Les seuils des effets de radiation thermique sur l'homme et
les structures, référencés dans la littérature sont
donnés dans les tableaux II-7 et II-8.[12]
Tableau II-7 : Seuils des effets de radiation
thermique sur l'homme
Types d'effets constatés Flux
radiatifs
(kw/m2)
|
Durée du phénomène > 2min
|
Létaux
|
|
|
5
|
Irréversibles
|
|
|
3
|
Durée du phénomène < 2min
|
Létaux (100 %)
|
|
|
6000-7000
|
Brûlures du 3ème degré superficielles
|
|
|
2600
|
Létaux (50 %)
|
|
|
2000 - 2200
|
Brûlures du 2éme degré
sévères
|
|
|
1200
|
Létaux (1 %)
|
|
|
1000
|
Irréversibles
|
|
|
600
|
Brûlures superficielles
degré
|
du
|
2éme
|
700
|
Brûlures du 1er degré
|
|
|
200
|
|
|
|
|
Seuil de douleur
|
|
|
85
|
65
Tableau II-8 : Seuils des effets de radiation
thermique sur les structures
Dégâts constatés Flux de
radiation thermique (Kw/m2)
|
Bris de vitres
|
5
|
Apparitions d'un risque d'inflammation pour les
matériaux
combustibles en présence d'une source d'ignition
|
10
|
Limite de tenue des structures pour une exposition
prolongée, hors structure béton
|
16
|
Tenue du béton pendant plusieurs heures
|
20
|
Auto-inflammation du bois
|
35
|
Propagation du feu à des réservoirs de stockage
d'hydrocarbures, même refroidis
|
36-100
|
Rupture ou destruction des éléments en acier
|
100
|
Ruine du béton en quelques dizaines de minutes
|
200
|
Les seuils des effets de surpression sur l'homme et sur les
structures, référencés dans la littérature, sont
donnés dans les tableaux II-9 et II-10.
Tableau II-9 : Seuils des effets de surpression sur
l'homme
Types d'effets constatés Surpression (mbar)
Effets irréversibles indirects
|
20
|
Effets Irréversibles directs
|
50
|
Effets létaux indirects
|
150
|
Détérioration des tympans
|
340
|
Effets létaux directs
|
1000
|
Tableau II-10 : Seuils des effets de surpression
sur les structures
Dégâts constatés Surpression
(mbar)
|
Destruction de 10% des vitres
|
20
|
Dégâts légers aux structures et
destruction de 75% des vitres
|
50
|
Destruction totale des vitres et démolition partielle
des structures
|
70
|
Dommages mineurs aux structures métalliques
|
100
|
Effondrement partiel des murs
|
140
|
Limite inférieure des dégâts graves aux
structures
|
160
|
Destruction de 50% des murs en brique ou parpaing
|
170
|
Destruction des bâtiments légers en charpente
métallique, rupture des réservoirs de stockage, rupture des
structures autoporteuses industrielles (seuil d'effet dominos)
|
200
|
66
Rupture de canalisation, destruction des poteaux
|
350
|
Renversement des wagons chargés, destructions des murs
en brique d'une épaisseur de 20 à 30 cm
|
500
|
Destruction des murs en béton armé, dommage
graves des machines situées dans les bâtiments industriels.
|
700
|
Destructions totale des structures
|
830
|
Les seuils d'escalade, causés par la surpression et la
radiation thermique, sont donnés dans le tableau II-11.
Tableau II-11 : Seuils d'escalade, causés
par la surpression et la radiation thermique
Vecteur d'escalade
|
Equipement cible
|
Seuil d'escalade
|
Radiation thermique
|
Atmosphérique
|
15 kW.m-2 durant 10 min
|
Pressurisé
|
50 kW.m-2 durant 10 min
|
Surpression
|
Atmosphérique
|
22 kPa
|
Pressurisé
|
17 kPa
|
Allongé (toxique)
|
16 kPa
|
Allongé (inflammable)
|
31 kPa
|
Auxiliaire (toxique)
|
37 kPa
|
Auxiliaire (inflammable)
|
Non disponible dans la littérature
|
II.4.2.1 Evaluation des effets
II.4.2.1.1 Evénement primaire 1 : VCE au niveau de
l'atelier CCAM
L'événement prit en considération est la
fuite d'une bouteille d'hydrogène. Pour faire ressortir les causes
pouvant mener à cet événement, nous allons rassembler les
informations de base sur l'hydrogène afin de les étudier et faire
ressortir une APR.
Caractéristiques de l'hydrogène :
Dangers physiques : Gaz inflammable -Catégorie 1 -Danger
(H220) ; Gaz sous pression -Gaz comprimé.
Mention de danger : H220 : Gaz extrêmement inflammable ;
H280 : Contient un gaz sous pression; peut exploser sous l'effet de la
chaleur.
Mentions de mise en garde-Prévention :
67
P210 : Tenir à l'écart de la chaleur/des
étincelles/des flammes nues/des surfaces chaudes. Ne pas fumer
-Intervention :
P377 : Fuite de gaz enflammé : Ne pas éteindre si
la fuite ne peut être arrêtée sans risque ; P381 :
Éliminer toutes les sources d'ignition si cela est faisable sans
danger.
Risques spécifiques : L'exposition prolongée au
feu peut entraîner la rupture et l'explosion des récipients.
Manipulation : Prendre des mesures de précaution contre
les décharges électrostatiques. Empêcher l'aspiration d'eau
dans le récipient. Purger l'air de l'installation avant d'introduire le
gaz. Interdire les remontées de produits dans le récipient.
Utiliser seulement l'équipement spécifié approprié
à ce produit et à sa pression et température
d'utilisation. Contacter le fournisseur de gaz en cas de doute. Maintenir
à l'écart de toute source d'inflammation (y compris de charges
électrostatiques). Se reporter aux instructions du fournisseur pour la
manipulation du récipient.
Stockage : Stocker le récipient dans un endroit bien
ventilé, à température inférieure à
50°C. Entreposer à l'écart des gaz oxydants et d'autres
oxydants.
Matières incompatibles : Peut former un mélange
explosif avec l'air. Peut réagir violemment avec les oxydants. Air,
Oxydant.
Ces informations ont été utilisées pour
construire l'APR suivante :
68
Tableau II-12 : APR sur l'hydrogène au
niveau de l'atelier CCAM
Evénements redoutés Conséquences
Barrières de prévention
existantes
|
|
Phénomènes dangereux Barrières de
protection
existantes
|
Défaillance d'un
robinet
|
-Perte de confinement
-Emission d'un produit inflammable à
l'atmosphère
|
Remplacement des robinets des bouteilles tous les 10 ans en
même temps que l'épreuve
|
-Feu de jet
-Explosion UVCE
|
Pas de détection possible
|
Défaillance d'un
flexible de
branchement (usure)
|
-Perte de confinement du flexible
-Emission d'un produit inflammable à
l'atmosphère
|
Changement des flexibles tous les 5 ans
|
-Feu de jet
-Explosion UVCE
|
Pas de détection possible
|
Agressions externes
liées au transport : Enlèvement d'un
cadre non débranché par un chariot
|
-Perte de confinement du flexible
-Emission d'un produit inflammable à
l'atmosphère
|
-
|
-Feu de jet
-Explosion UVCE
|
Pas de détection possible
|
69
Suite à la construction de l'APR, nous avons
procédé à la simulation des effets. Le modèle
utilisé pour la modélisation PHAST® est le modèle
TNT.
Les données introduites dans le logiciel sont
répertoriées dans le tableau II.13.
Tableau II-13 : Données introduites dans le
logiciel PHAST® pour l'événement primaire « VCE au
niveau de l'atelier CCAM »
Combustible
|
Hydrogène
|
Quantité
|
10 kg
|
Condition météorologique
|
1.5/F,1.5/D,5D
|
Rendement de l'explosion
|
50 %
|
Distance minimale
|
0
|
Distance maximale
|
50 m
|
Pas
|
0.2 m
|
Les résultats de la propagation dans les deux cas sont
représentés dans les figures II-20 et II-21.
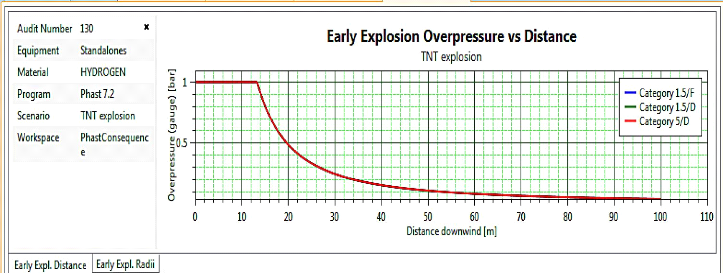
70
Figure II-20 : Effet de surpression en fonction de
la distance pour l'événement VCE au niveau de l'atelier
CCAM
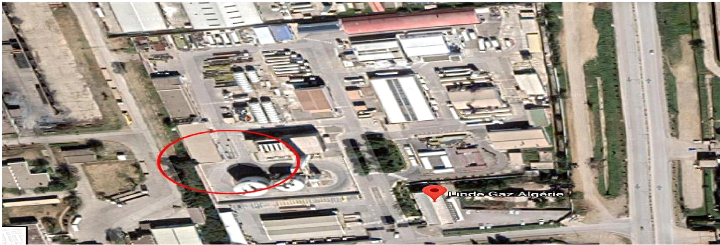
71
Figure II-21 : Propagation de l'effet de
surpression pour l'événement VCE au niveau de l'atelier
CCAM
Interprétation :
La simulation montre que l'explosion engendrera de graves
effets de surpression. Ainsi nous aurons un ?P = 1 bar qui est l'effet maximal
à environs 14 m tout autour de la zone de l'atelier. Nous aurons
également un ?P = 0.2 bar dans un rayon de 33 m autour de l'atelier.
Cette dernière est la valeur seuil des effets dominos qui engendrent la
rupture des réservoirs de stockage, et la rupture des structures
autoporteuses industrielles. Cet effet touchera aussi les deux
réservoirs d'oxygène liquide et d'azote liquide comme le montre
la figure II-21.
72
II.4.2.1.2 Evénement primaire 2 : Jet fire atelier
CCAM
La même méthodologie a été suivie pour
l'événement primaire 2 : Jet fire dans l'atelier CCAM.
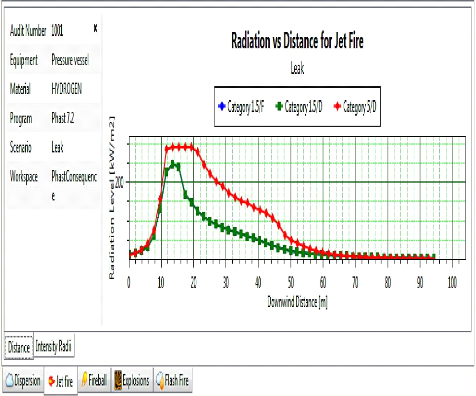
Figure II-22 : Effet de radiation en fonction de la
distance pour l'événement Jet fire au niveau de
l'atelier CCAM
Interprétation :
La simulation montre que la configuration de vent 5/D est la
plus susceptible d'engendrer de forts effets. Les effets de radiation thermique
sont maximaux de 10 à 20 m du lieu du déclenchement du jet fire,
ils atteignent ainsi la valeur de 300 kw /m2 qui est un niveau de
destruction de toutes les structures.
73
On remarque également que le niveau de radiation de 100
kw/m2 qui équivaut à une rupture ou destruction des
éléments en acier est atteint jusqu'à une distance de 45
m.
II.4.2.1.3 Evénement primaire 3 : VCE au niveau du
parc bouteilles
L'évènement qui va maintenant être
étudié est un VCE au niveau du parc bouteilles causé par
la fuite d'une bouteille d'acétylène. Cet événement
a été sélectionné compte tenue de l'analyse de
l'acétylène :
Les bouteilles d'acétylène
La particularité d'une bouteille
d'acétylène est qu'elle continue à rester dangereuse
même si la cause principale du sinistre est traitée (cas d'un
incendie d'atelier mécanique dans lequel ont été
exposées une ou plusieurs bouteilles. Il faudra prendre le plus grand
soin des bouteilles non explosées, une explosion ultérieure
n'étant pas à écarter totalement).
Dans les lignes qui suivent, nous présenteront de
quelle façon l'acétylène est conditionné et la
description de situations accidentelles en tentant d'expliquer les
différents mécanismes mis en jeu.
Au-delà des fiches reflexes existantes, il convient de
bien comprendre ces phénomènes et les paramètres qui les
influencent.
Utilisation de l'acétylène
En dehors de l'industrie chimique, l'acétylène
est très utilisé pour réaliser des soudures ou de la
découpe de métaux. Ainsi, on en trouve dans beaucoup de secteurs.
L'utilisation la plus connue est celle associée à
l'oxygène en plomberie: postes oxy-acétylénique,
constitués d'un ensemble de deux bouteilles en acier, une
d'acétylène et une d'oxygène.
L'acétylène est utilisé, car
associé à l'oxygène, il permet d'obtenir des
températures très élevées permettant la
réalisation de soudure ou de brasure sur tout type de métaux. Les
températures atteintes dépassent les 2500 °C pour les
combustions stoechiométriques dans l'air et peuvent atteindre plus de
3000 °C en association avec de l'oxygène pur. C'est ce qui
constitue également sa dangerosité.
74
Conditionnement
L'acétylène est un composé très
instable, qui ne demande qu'à se décomposer à la moindre
sollicitation (température, pression). Ainsi, son mode de stockage est
différent de celui des autres gaz. On le retrouvera dans des bouteilles
en acier, dissout dans un solvant (comme pour l'eau gazeuse, le CO2 est dissout
dans l'eau). Ce moyen de stockage permet de maintenir une faible pression dans
les bouteilles, comparativement aux autres gaz et à stabiliser le
produit. Le solvant utilisé est très souvent l'acétone,
solvant oxygéné, très inflammable. C'est le solvant
utilisé chez LINDE GAS ALGERIE.
Afin de stabiliser encore le produit et de parer à un
éventuel début de décomposition dans la bouteille, cette
dernière est en plus remplie d'une matière poreuse afin de
limiter les mouvements de liquide et de gaz à l'intérieur. Cette
matière poreuse a notamment pour rôle de contenir un
éventuel début de décomposition à
l'intérieur de la bouteille.
Nous avons donc affaire à une bouteille en acier
similaire à celui utilisé pour d'autres gaz, mais rempli d'un
solide poreux, lui-même imbibé d'acétone et dans laquelle
on aura injecté de l'acétylène qui sera dissout dans le
solvant. Les "trois" états de la matière sont donc
présents à l'intérieur de la bouteille.
La pression de stockage dans la bouteille est de 15 bars
environ à la livraison. Le fait d'ouvrir le robinet de la bouteille va
libérer le gaz, un peu à l'image de ce qui se passe lorsqu'on
ouvre une bouteille d'eau pétillante.
Pour des utilisations plus importantes, les bouteilles peuvent
être contenues dans ce que l'on appelle un "cadre" et reliées
entre elle. Cette technique permet de pouvoir disposer d'un débit plus
important en sortie pour des utilisations industrielles.
Propriétés physico-chimiques
A température ambiante et pression normale,
l'acétylène est un gaz. Ce gaz possède la
particularité d'être instable et tend à se
décomposer en carbone et hydrogène, ce qui le rend très
dangereux et extrêmement inflammable.
Risques
Les risques de l'acétylène sont liés
essentiellement à son inflammabilité et à son
instabilité. Son mode de conditionnement engendre également un
risque qui peut être immédiat ou différé dans le
temps, ce qui complique fortement le mode d'intervention dans pareils cas.
75
Explosion dans un incendie
Lorsqu'une bouteille d'acétylène est prise dans
un incendie, elle risque fort de libérer le gaz qu'elle contient. La
pression d'épreuve des bouteilles d'acétylène est de 60
bars, soit à peu près 4 fois la pression de service. En
règle générale, les bouteilles d'acétylène
sont équipées d'un ou plusieurs bouchons fusibles qui fondent
à environ 100 °C ce qui peut limiter le risque d'explosion dans un
incendie, mais toutes les bouteilles ne sont pas équipées et on a
déjà vu des bouteilles exploser avec leur bouchon fusible intact.
Cela peut se produire par exemple lorsque la bouteille est soumise à une
flamme sur une petite partie de sa surface, loin du bouchon fusible. Si
localement la température dépasse les 400 °C, la
décomposition du gaz s'amorce et la bouteille monte en pression et se
déchire à proximité de la partie chauffée. La
présence de matière poreuse dans la bouteille va empêcher
la propagation de la chaleur au travers de celle-ci et donc limiter
l'efficacité du bouchon fusible.
Fuite enflammée
Comme pour toute fuite de gaz, il n'est pas recommandé
d'éteindre la flamme sans arrêter la fuite simultanément.
Toutefois, cette extinction peut être réalisée si on est
certain qu'il n'y a pas de point chaud à proximité et que
l'environnement est largement ventilé.
Après avoir contrôlé que la bouteille est
froide (avec une caméra thermique par exemple ou par un court jet
diffusé sur la bouteille), il peut être envisagé de
s'approcher pour fermer le robinet si ce dernier est manoeuvrable facilement.
Il faut faire attention, si une autre bouteille est impactée par la
flamme ou que la bouteille apparait chaude à la caméra thermique
(ou que l'eau de refroidissement semble s'évaporer à la surface
de la bouteille), toute approche est à proscrire et il convient alors de
protéger ce que l'on peut et de s'abriter derrière des obstacles
en attendant l'explosion ou la vidange de la bouteille. Une bouteille qui a
chauffé reste dangereuse tant qu'elle est chaude et jusqu'à 24
heures après avoir été "refroidie". Il convient donc de
poursuivre le refroidissement de la bouteille même si le sinistre semble
terminé. En pratique, la bouteille froide est fermée et
plongée dans un récipient d'eau ou mieux dans une rivière
ou un étang pendant 24 heures avant d'être transportée vers
un centre de retraitement de déchets ou récupérée
par le propriétaire de l'emballage. A noter qu'une bouteille qui reste
fuyarde aura plus de chance de s'échauffer qu'une bouteille correctement
fermée.
76
Combustion interne
L'acétylène est très instable et reste
combustible ou dégradable même à l'intérieur de la
bouteille, sans nécessairement d'apport d'oxygène (la LSE est de
100%). C'est le cas lorsqu'il se produit un retour de flamme dans la bouteille
et qu'une combustion interne s'amorce et se propage dans la bouteille si rien
n'est fait. Une bouteille exposée à la chaleur peut réagir
dans les mêmes conditions et se mettre à "brûler" à
l'intérieur.
Cette réaction de combustion interne est heureusement
fortement ralentie par la présence de matière poreuse à
l'intérieur de la bouteille.
En cas de retour de flamme, le soudeur a pour consigne de
fermer immédiatement la bouteille afin de limiter l'accident et de
permettre à la masse poreuse de jouer tout son rôle pour
stabiliser la dégradation du produit.
Si le robinet n'est pas fermé et que la fuite perdure,
il s'échappe de la bouteille une fumée noire,
caractéristique d'une combustion incomplète de produit à
l'intérieur (combustion en manque d'oxygène). L'appel de produit
provoqué par ce robinet ouvert va avoir tendance à faire migrer
le gaz dissous depuis le bas de la bouteille vers la sortie, et donc va
contribuer à alimenter en combustible la zone fragilisée (zone
qui commence à chauffer et donc à dégrader
l'acétylène). La réaction va donc s'amplifier
jusqu'à devenir dangereuse pour l'intégrité de la
bouteille et donc des intervenants où témoins de l'accident.
Une erreur souvent faite par les intervenants est de laisser
fuir la bouteille afin d'éviter une surpression et se préserver
de l'explosion. C'est une erreur grave, qui va à l'encontre de
l'objectif recherché. Un robinet de bouteille de gaz n'est en aucune
façon une soupape de surpression, il n'est absolument pas
dimensionné pour jouer ce rôle. D'autre part, la fuite va
entrainer la migration du gaz au travers des zones chaudes de la bouteille et
empêcher la masse poreuse de jouer son rôle de stabilisateur.
L'explosion de la bouteille est alors plus probable que dans le cas où
celle-ci serait fermée.
77
Simulation des effets :
Le modèle utilisé pour la modélisation
PHAST® est le modèle TNT.
Les données introduites dans le logiciel sont
répertoriées dans le tableau II-14.
Tableau II-14 : Données introduites dans le
logiciel PHAST® pour l'événement primaire « VCE
au niveau du parc bouteilles
Combustible
|
Hydrogène
|
Quantité
|
6.66 kg
|
Condition météorologique
|
1.5/F,1.5/D,5D
|
Rendement de l'explosion
|
50 %
|
Distance minimale
|
0
|
Distance maximale
|
50 m
|
Pas
|
0.2 m
|
Les résultats de la propagation dans les deux cas sont
représentés dans les figures II-23 et II-24.
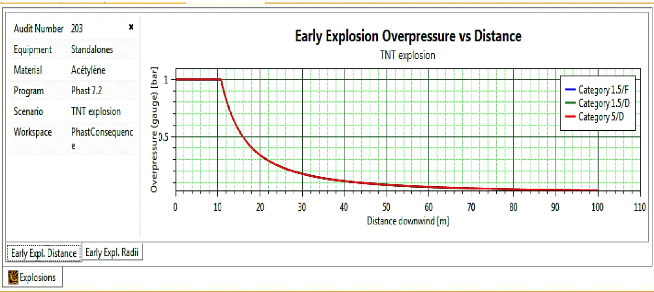
78
Figure II-243 : Effet de surpression en fonction de
la distance pour l'événement VCE au niveau du parc
bouteilles
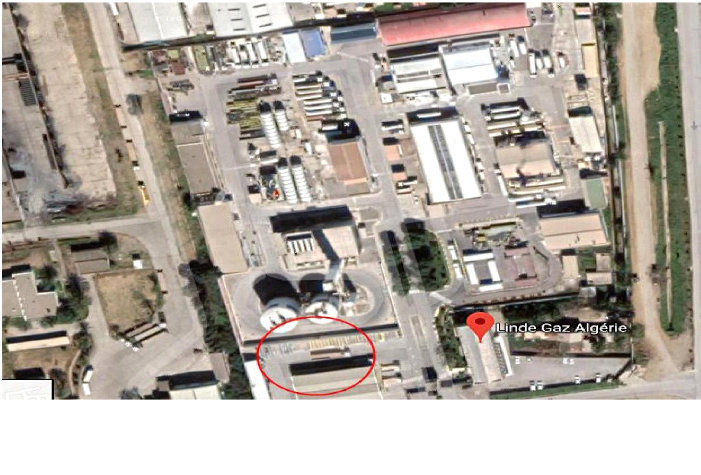
Figure II-254 : Propagation des effets de surpression
pour l'événement VCE au niveau du parc
bouteilles
79
80
Interprétation :
La simulation montre que l'explosion engendrera de graves
effets de surpression. Ainsi nous aurons un ?P = 1 bar qui est l'effet maximal
à environs 12 m tout autour de la zone de l'atelier. Nous aurons
également un ?P = 0.2 bar dans un rayon de 28 m autour de l'atelier et
qui est la valeur seuil des effets dominos qui engendrent la rupture des
réservoirs de stockage, et la rupture des structures autoporteuses
industrielles.
Cet effet touchera ainsi les deux réservoirs
d'oxygène liquide et d'azote liquide comme le montre la figure II-24.
II.4.2.1.4 Evénement primaire 4 : Jet fire au
niveau du parc bouteilles
Evénement : fuite d'une bouteille
d'acétylène Simulation des effets :
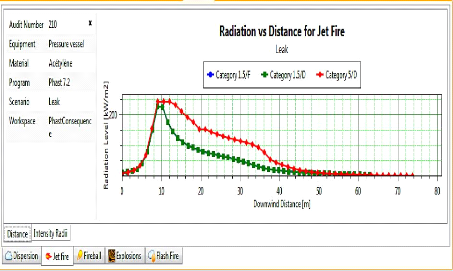
Figure II-265 : Effet de radiation en fonction de la
distance pour l'événement jet fire au niveau du
parc bouteilles
81
Interprétation :
La simulation montre que la configuration de vent 5/D est la
plus susceptible d'engendrer de forts effets. Les effets de radiation thermique
sont maximaux à 10 m du lieu de déclenchement du jet fire, ils
atteindront ainsi la valeur de 250 kw /m2 qui est un niveau de
destruction de toute les structures.
On remarque également que le niveau de radiation de 100
kw/m2 qui équivaut à une rupture ou destruction des
éléments en acier est atteint jusqu'à une distance de 35
m.
II.4.3 Calculs :
La méthode de calcul qui va être adoptée
dans ce travail n'est pas une méthode conventionnelle
préétablie. C'est une méthode que nous avons
développé en nous inspirons de différents travaux
d'articles et de références scientifiques des quelles sont
tirés les relations mathématiques utilisées.
II.4.3.1 Méthodologie de calcul
Il convient de noter que, dans ce qui suit, les
scénarios secondaires seront définis de manière à
considérer qu'ils se produisent de façon simultanée avec
l'événement principal, même si en réalité,
ils se déroulent en séquence (uniquement quelques secondes
à quelques minutes après l'événement primaire, en
fonction du vecteur d'escalade primaire et de l'intensité des pertes au
niveau de l'unité secondaire endommagée par
l'événement primaire).
Dans une présentation complexe, un seul
événement primaire peut généralement
déclencher simultanément plusieurs événements
secondaires. Cela a été documenté dans plusieurs accidents
passés (on peut facilement le constater dans la base de données
utilisée pour notre analyse d'accidentologie). Dans ce cadre,
l'équation proposée est toujours valide, donnant la
probabilité globale qu'un événement secondaire
donné soit initié par l'événement principal
considéré. Toutefois, les fréquences des scénarios
de dominos doivent être calculées en tenant compte de la
possibilité que plusieurs scénarios secondaires soient
déclenchés par le même événement
principal.
Il faut noter que si nous ne considérons pas la
possibilité d'une nouvelle escalade simultanée
d'événements secondaires, cela veut dire que nous
considérons que ces événements ne sont pas liés
à l'événement primaire et donc indépendant d'un
point de vu probabiliste. Par conséquent, il faut considérer
cette possibilité et donc si N événements secondaires
sont
82
probabilité d'un scénario secondaire
donnée par une combinaison générique m de k
événements secondaires (k N) est la suivante :
??
????(??,??) = ?[1 - ????,?? +
??(??,??????)(2 * ????,?? - 1)] (??. ??) ??=1
Où ????,?? est la probabilité d'escalade pour le
i-ème événement secondaire. ?????? est un vecteur dont les
éléments sont les index de la même combinaison de k
événements secondaires. La fonction ??(??,??????) est
définie comme suit :
??
??(??,?????? {1
) = ?? ? ?????? (2.2)
0 ?? ? ????
Calcul de la probabilité d'escalade pour chaque
cible
Pour l'estimation de la probabilité d'escalade,
l'équation suivante sera utilisée :
1.005
Pi,j = ????,??-5.004 (2.3)
1+??( 0.6120 )
Avec :
Pi,j : Probabilité que l'équipement
j soit endommagé suite à un accident au sein de
l'équipement i
Yi,j : Fonction Probit.
Définition d'une fonction probit
La fonction Probit Yi,j est définie comme
étant la réciproque de la fonction de répartition de la
loi normale centrée réduite.
Afin de démontrer d'où l'expression des
fonctions Probit a été déduite, l'hypothèse
suivante a été établie :
Yi,j est une variable aléatoire avec une moyenne
de 5 et une variance de 1. (Eisenberg et al., 1975). Pour un facteur
d'endommagement ou de blessure X qui correspond à la distribution
log-normale : X ? log N (ì , ?2)
La fonction Probit s'écrit plus communément sous la
forme :
Yi,j = k1+ k2 ln(x) (2.4)
Il existe une relation qui relie la probabilité P à
la fonction Probit Y et qui est donnée par l'Eq. Suivante :
??2
2 ???? (2.5)
P = 1
?v2?? ? ??-
??-5
-8
La détermination d'une équation du type
général donné par l'Eq. (2.6) est facilement
démontrée en considérant d'abord une distribution
normale.
Soit X une variable aléatoire qui suit la loi normale de
paramètre ì et ?2 X ?N (ì , ?2)
Définie par sa fonction densité f
f = 1??
?v2??
|
(??-??)2
2?2
|
(2.6)
|
83
Et sa fonction de répartition F
F = ? ??(??)????
?? -8 (2.7)
En sachant que la fonction de répartition dans le cas
continu est égale à la probabilité,
??
c'est-a-dire : F(x) = P(X= x) = ? ??(??)????
-8
(??-??)2
??
? P = 1
?v2?? ? ?? -2?2 ???? (2.8)
-8
L'égalité entre les équations (2.5) et (2.8)
nous donne :
84
{Y??, ?? - 5 = x = u ?? + 5 = (5 - ??
??-??
?? = ?? Yi,j = ??-?? ?? ) + 1 ?? x
Yi,j = k1' + k2' ln(x) (2.9)
Avec
k1' = 5 - ??
??
{ k2' = 1
??
Même chose pour la distribution log-normale:
Yi,j = k1 + k2 ln(x) (2.10)
Avec
k1 = 5 - ??'
??
{ k2 = 1
??
L'équation (2.10) est la forme la plus
généralement utilisée pour la fonction Probit.
L'approche Probit est utilisée pour l'évaluation
quantitative des risques à effet dominos dus à la surpression et
à la radiation thermique. Les modèles Probit ne dépendant
pas des valeurs seuils de dommage, ils peuvent donc facilement être
modifiés pour tenir compte des catégories spécifiques
d'équipements. Par conséquent, l'analyse des probits a
été appliquée à la fois pour réviser les
modèles existants et pour développer davantage les modèles
probabilistes pour les dommages causés à des catégories
spécifiques d'équipements.
? Application des fonctions Probit dans
l'évaluation de l'impact des effets physiques
En 1975, Eisenberg et ses collaborateurs ont d'abord
utilisé un modèle simplifié pour évaluer la
probabilité de blessures pour l'être humain et les dommages
causés aux équipements par les effets de surpression et de
radiation.
Les auteurs ont ensuite défini des fonctions Probit
pour relier les dommages causés à l'équipement par la
surpression statique de pointe AP°.
85
Y = k1 + k2 ln (ÄP°) (2.11)
Le modèle d'Eisenberg et ses collaborateurs
était basé sur l'évaluation expérimentale du
déplacement de l'équipement avec la déformation et la
rupture subséquente des connexions, ne tenant pas compte de la
défaillance catastrophique directe de l'équipement.
Les résultats obtenus sont:
{
k1 = -23.8 k2 = 2.92
L'approche Probit a ensuite été suivie par
d'autres auteurs comme Khan et Abbasi, 1998 [13], qui ont proposé une
fonction Probit similaire à l'équation d'Eisenberg, mais
substituant la surpression statique à la pression totale (la somme de la
pression statique et dynamique). Khan et Abbasi donnent les mêmes
coefficients de Probit d'Eisenberg, ce qui est compréhensible car, la
pression dynamique est négligeable pour la plupart des explosions
industrielles.
Plus récemment, Cozzani et Salzano (2005) ont
élaboré un ensemble étendu de données concernant
l'explosion dans le milieu de l'industrie que Zhang et Jiang ont affiné
en 2008 pour faire ressortir des fonctions Probit pour les effets de radiation
thermique et de surpression au niveau de différents types
d'équipements.
Ainsi, des fonctions différentes sont utilisées
selon l'effet physique et le type d'équipement étudiés.
Une étude récente (Sun et al. 2013) montre la validité et
la rationalité des modèles Probit pour l'étude des effets
dominos causés par des ondes de surpression dans l'industrie chimique.
Concernant l'effet des radiations thermiques, la fiabilité des
modèles de calcul de probabilité d'escalade
présentés, a été démontrée lors de
leur application à plusieurs cas d'études, notamment celle
réalisée par Landucci (Landucci et al. 2012).
Les modèles proposés par Zhang et Jiang reconnus
comme étant les plus fiables, ils seront donc utilisés pour la
suite de notre étude. En effet, ce qui importe dans l'étude des
effets dominos, c'est l'évaluation de la propagation au niveau des
équipements et donc la vulnérabilité de ces derniers et
non la vulnérabilité de l'Homme par rapport aux effets
physiques.
86
Tableau II-15 : Modèles de
vulnérabilité
Effets physiques
|
Equipements cibles
|
Modèles de vulnérabilité
|
Radiation thermique
|
Atmosphérique
|
Yi,j = 12.54 - 1.847 x ln (ttf)
ln (ttf) = - 1.13 ln (Ii,j) - 2.67 x 10-5 V + 9.9
|
Pressurisé
|
Yi,j = 12.54 - 1.847 x ln (ttf) ln (ttf) = - 0.95 ln (Ii,j) +
8.845 V 0.032
|
Surpression
|
Atmosphérique
|
Yi,j = - 9.36 + 1.43 x ln (?Pi,j)
|
Pressurisé
|
Yi,j = - 14.44 + 1.82 x ln (?Pi,j)
|
Allongé (tour de
distillation...)
|
Yi,j = - 28.07 + 3.16 x ln (?Pi,j)
|
Tels que :
i : équipement source de l'accident.
j : équipement cible.
Yi,j : fonction Probit.
ttf : temps-avant-défaillance (s).
V : volume de l'équipement (m3).
Ii,j : intensité des radiations thermique
(kW.m-2).
?Pi,j : surpression statique maximale en kPa
Concernant les effets de projection de fragments, du fait
qu'aucun modèle de vulnérabilité précis n'existe
pour l'estimation des dommages causés sur la cible, seule une estimation
qualitative de la propagation peut être obtenue [15].
II.4.3.2 . Identification des cibles et calcul des
probabilités d'escalade
Pour le calcul de la probabilité d'escalade de chaque
cible, la fonction Probit appropriée à chaque cible est
utilisée afin d'appliquer la relation (2.3).
Pour rappel :
87
Pi,j = 1.005
-(????,??-5.004
0.6120 ) (2.3)
1+e
Pi,j : Probabilité que l'équipement j
soit endommagé suite à un accident au sein de
l'équipement i,
Yi,j : Fonction Probit.
II.4.3.2.1 Détermination des scénarios
secondaires
Les Scénarios secondaires et vecteurs d'escalade sont
résumés dans le tableau II-16.
Tableau II-16 : Scénarios secondaires et
vecteurs d'escalade
Source
|
Vecteurs d'escalade
|
Cibles
|
Equipements
|
Type
|
VCE hydrogène
atelier CCAM
|
Surpression
|
Réservoir d'oxygène liquide
|
Pressurisé
|
Réservoir d'azote liquide
|
Pressurisé
|
VCE d'acétylène
parc bouteilles
|
Surpression
|
Réservoir d'oxygène liquide
|
Pressurisé
|
Réservoir d'azote liquide
|
Pressurisé
|
II.4.3.2.2 Calculs :
1) Bouteille hydrogène atelier CCAM Réservoir
d'oxygène liquide par VCE H2
Yi,j = - 14.44 + 1.82 ln (?Pi,j) avec ?P =27.8
Yi,j = -8.39
Pi,j = 3.14 * 10-10
2) Bouteille hydrogène atelier CCAM Réservoir
d'azote liquide par VCE H2 Yi,j = - 14.44 + 1.82 ln (?Pi,j) avec ?P
= 24.6
Yi,j = -8.61
Pi,j = 2.19 * 10-10
3) Bouteille d'acétylène parc
bouteilles Réservoir d'oxygène liquide par VCE C2H2
88
Yi,j = - 14.44 + 1.82 ln (?Pi,j) avec ?P = 25.3
Yi,j = -8.56
Pi,j = 2.38 * 10-10
4) Bouteille d'acétylène parc
bouteilles Réservoir d'azote liquide par VCE C2H2 Yi,j = - 14.44 +
1.82 ln (?Pi,j) avec ?P = 23.6
Yi,j = -8.69
Pi,j = 1.93 * 10-10
II.4.3.2.3 Détermination des scénarios
tertiaires :
Les Scénarios tertiaires et vecteurs d'escalade sont
résumés dans le tableau II-17.
Tableau II-17 : Scénarios tertiaires et
vecteurs d'escalade
Source
|
Vecteurs d'escalade
|
Cibles
|
Equipements
|
Type
|
Synergie VCE +
incendie réservoir d'oxygène
liquide
|
Radiation thermique
|
Incendie au niveau de la tour ASU
|
Pressurisé
|
Pressurisé
|
Synergie VCE +
incendie réservoir d'azote liquide
|
Radiation thermique
|
Incendie au niveau de la tour ASU
|
Pressurisé
|
Pressurisé
|
1) Bouteille hydrogène atelier CCAM Réservoir
d'oxygène liquide par VCE 112 Incendie au niveau de la tour ASU.
Yi,j = 12.54 - 1.847 ln (ttf)
ln (ttf) = - 0.95 ln (Ii,j) + 8.845V 0.032 =
5.65
Yi,j = 2.10
Pi,j = 8.66 * 10-3
2) Bouteille hydrogène atelier CCAM Réservoir
d'azote liquide par VCE 112 Incendie au niveau de la tour ASU.
Yi,j = 12.54 - 1.847 ln (ttf)
89
ln (ttf) = - 0.95 ln (Ii,j) + 8.845V 0.032 =
5.41
Yi,j = 2.55
Pi,j = 0.018
3) Bouteille d'acétylène parc bouteilles
Réservoir d'oxygène liquide par VCE 112 Incendie au niveau de
la tour ASU.
Yi,j = 12.54 - 1.847 ln (ttf)
ln (ttf) = - 0.95 ln (Ii,j) + 8.845V 0.032 = 6.04 Yi,j =
1.38
Pi,j = 2.69 * 10-3
4) Bouteille d'acétylène parc bouteilles
Réservoir d'azote liquide par VCE 112
Incendie au niveau de la tour ASU.
Yi,j = 12.54 - 1.847 ln (ttf)
ln (ttf) = - 0.95 ln (Ii,j) + 8.845V 0.032 = 6.27 Yi,j =
0.96
Pi,j =1.35 * 10-3
II.4.3.2.4. Détermination des scénarios
quaternaires :
Les Scénarios quaternaires et vecteurs d'escalade sont
résumés dans le tableau II-18.
Tableau II-18 Scénario quaternaire et
vecteurs d'escalade
Source
|
Vecteurs d'escalade
|
Cibles
|
Equipements
|
Type
|
Synergie des scénarios
|
Projection et radiation thermique
|
Bloc administratif
|
atmosphérique
|
Yi,j = 1.05
Pi,j =2.12 * 10-3
90
Evénements primaires 2 et 4
Détermination des scénarios secondaires
Tableau II-19 : Scénarios secondaires et
vecteurs d'escalade événements 2 et 4
Source
|
Vecteurs d'escalade
|
Cibles
|
Equipements
|
Type
|
Jet fire hydrogène atelier CCAM
|
Radiation thermique
|
Réservoir d'oxygène liquide
|
Pressurisé
|
Réservoir d'azote liquide
|
Pressurisé
|
Jet fire d'acétylène parc
bouteilles
|
Radiation thermique
|
Réservoir d'oxygène liquide
|
Pressurisé
|
Réservoir d'azote liquide
|
Pressurisé
|
1) Jet fire hydrogène atelier CCAM Réservoir
d'oxygène liquide Yi,j = 12.54 - 1.847 ln (ttf)
ln (ttf) = - 0.95 ln (Ii,j) + 8.845V 0.032 = 6.41 Yi,j =
0.70
Pi,j = 8.86 * 10-4
2) Jet fire hydrogène atelier CCAM Réservoir
d'azote liquide Yi,j = 12.54 - 1.847 ln (ttf)
ln (ttf) = - 0.95 ln (Ii,j) + 8.845V 0.032 = 6.20 Yi,j =
1.09
Pi,j =1.67 * 10-3
3) Jet fire d'acétylène parc bouteilles
Réservoir d'oxygène liquide Yi,j = 12.54 - 1.847 ln (ttf)
ln (ttf) = - 0.95 ln (Ii,j) + 8.845V 0.032 = 6.53 Yi,j =
0.48
Pi,j =6.19 * 10-4
4) Jet fire d'acétylène parc bouteilles
Réservoir d'azote liquide Yi,j = 12.54 - 1.847 ln (ttf)
91
ln (ttf) = - 0.95 ln (Ii,j) + 8.845V 0.032 =
6.28
Yi,j = 0.95
Pi,j = 1.33 * 10-3
D'après les conditions de l'événement
primaire, cet événement secondaire pourra être
géré et n'engendre pas d'événement tertiaire.
Les calculs de probabilités étant fait, nous
allons nous intéresser à la réalisation des réseaux
bayésiens des événements cités.
II.4.4 Réalisation des réseaux
bayésiens
II.4.4.1 Définition d'un réseau
bayésien
Un réseau bayésien est un modèle
graphique dans lequel les noeuds représentent des variables
reliés par des arcs dirigés (causaux). Les arcs dénotent
des dépendances ou des relations de cause à effet entre les
noeuds liés, tandis que les probabilités conditionnelles
assignées aux noeuds déterminent le type et la force de ces
dépendances.
Les noeuds à partir desquels les arcs sont
dirigés sont appelés noeuds parents, alors que les noeuds vers
lesquels les arcs sont dirigés sont appelés noeuds enfants. Tel
que, un noeud peut être simultanément l'enfant d'un noeud et le
parent d'un autre noeud.
Les noeuds sans parent et les noeuds sans enfant sont
appelés respectivement noeuds racines et noeuds feuilles (Jensen et
Nielsen, 2007).
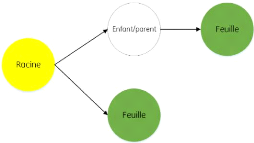
Figure II-27 Composantes d'un réseau
Bayésien
Dans le cas de l'étude des effets dominos au niveau de
LGA la disposition des différentes unités des process seront
considérées comme un ensemble de variables ; c'est-à-dire
que
92
chaque variable représente une unité ou un
élément de l'équipement, selon le niveau de détail
de l'analyse.
Un réseau bayésien peut donc être
utilisé pour modéliser qualitativement et quantitativement
l'influence des unités les unes sur les autres via les arcs causaux et
les probabilités conditionnelles, pour estimer la probabilité
d'un effet domino à différents niveaux.
Il étend la distribution de probabilité commune
d'un ensemble de noeuds liés, par exemple :
U = {X1, X2,..., Xn}
En d'autres termes, en ne considérant que les
dépendances locales, en factorisant la distribution des
probabilités communes comme la multiplication des probabilités
des noeuds compte tenu de leurs parents immédiats (Khakzad et al.,
2013).
II.4.4.2 Identification des séquences dominos
Afin de modéliser la propagation probable d'un effet
domino, les étapes suivantes sont suivies :
Étape 1: Un noeud sera
affecté à chaque unité du process.
Avant d'appliquer la méthode à notre cas
d'étude, l'exemple d'une usine de 6 unités (les colonnes de
distillation, les réservoirs de stockage atmosphérique, les
réservoirs de stockage sous pression, etc.) sera présenté
dans ce qui suit (Fig. II-27).
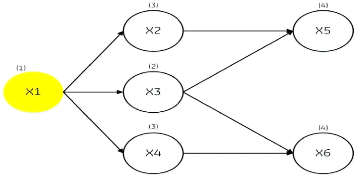
Figure II-287 : Modèle de propagation probable
d'un effet domino dans une usine à six unités
93
Étape 2: Identification de
l'unité primaire où l'accident primaire a lieu. Elle est
schématisée en jaune (noeud racine) dans la figure
II-27.
Étape 3: Une fois les vecteurs
d'escalade et les cibles identifiés à l'aide des valeurs seuil
d'escalade (comme expliqué dans la section I.2.2.1.4.), les
probabilités d'escalade des unités secondaires vont être
calculées compte tenu de l'événement primaire,
c'est-à-dire P(X2/X1), P(X3/X1) et P(X4/X1). Telles que, les
unités ayant la probabilité d'escalade la plus
élevée sont choisies comme unités secondaires (par
exemple, X3 dans la figure II-27).
Puisque les événements secondaires sont
causés par l'événement primaire, un arc causal doit
être dirigé de X1 à X3, montrant que l'occurrence de X3 est
conditionnelle à l'occurrence de X1. En rappelant que pour le cas de LGA
la probabilité d'escalade se calcule à l'aide des fonctions
Probit.
Étape 4: En remplaçant
l'unité primaire par les unités secondaires, l'étape 3 est
répétée pour déterminer les unités
tertiaires potentielles (par exemple : X2 et X4), les unités
quaternaires potentielles (par exemple : X5 et X6) et ainsi de suite.
Dans cet exemple, X2 et X4 (X5 et X6) ont les mêmes
probabilités d'escalade et sont tous deux sélectionnés
comme unités tertiaires (quaternaires).
Il convient de noter que lorsqu'on répète la
même procédure pour les unités secondaires ou les
unités d'ordre supérieur, il faut tenir compte des effets
synergiques.
On entend par effet de synergie que les vecteurs d'escalade
des unités nouvellement engagées (d'ordre i) coopèrent
avec ceux des unités déjà engagées (d'ordre i-1)
pour avoir un impact sur les unités d'ordre supérieur (d'ordre i
+ 1) qui n'avaient pas dépassé les critères de seuil dans
les niveaux précédents.
Par exemple, dans la figure II-27, X2 et X3 coopèrent
entre eux (c'est-à-dire que leurs vecteurs d'escalade sont
superposés) pour déclencher un accident dans X5.
Ainsi, les arcs causaux doivent être dirigés de
X2 et X3 vers X5, montrant la dépendance conditionnelle de ces derniers
par rapport aux premières unités. Par conséquent, lors de
l'attribution de la probabilité conditionnelle d'escalade de X5 due
à l'effet synergique, P(X5/X2,X3) est également calculée
à l'aide des fonctions Probit mais en sommant les vecteurs
d'escalade.
94
Une fois le modèle de propagation probable de l'effet
domino développé sous la forme d'un réseau
bayésien, la probabilité de l'événement primaire et
les probabilités conditionnelles des autres événements
calculées, la distribution conjointe des probabilités des
événements contribuant à l'effet domino peut être
calculé.
Pour l'exemple de la figure II-27, la distribution de
probabilité conjointe des événements qui contribuent
à l'effet domino U = {X1,.,., X6} est calculée comme suit :
P(U) = P(X1)P(X3/X1)P(X2/X1,X3)P(X4/X1,X3)P(X5/X2,X3)P(X6/X3,X4)
(2.12)
Il est à noter qu'en choisissant un autre point de
départ plutôt que X1, on obtiendrait un réseau
bayésien différent et, par conséquent, une distribution de
probabilité commune différente de celle montrée dans
l'équation (2.12)
En supposant que X1 est l'unité primaire et selon la
figure II-27, la chronologie ou l'ordre séquentiel probable des
événements serait X1-)X3-)X2(ou X4)-)X5(ou X6).
En connaissant le modèle de propagation d'un effet
domino, sa probabilité d'occurrence à différents niveaux
peut être estimée. Généralement, la
probabilité de l'effet domino est calculée comme la
multiplication de la probabilité de l'événement primaire
et de la probabilité d'escalade. Pour qu'il y ait un effet domino au
premier niveau, il est nécessaire que l'accident dans l'unité
primaire se propage dans au moins une des unités secondaires voisines.
Par exemple, sur la figure II-27, en considérant X3 comme unité
secondaire, la probabilité de l'effet domino de premier niveau peut
être calculée comme suit :
PNiveau1= P(X1)P(X3/X1) (2.13)
De même, l'effet domino ne pourrait passer au
deuxième niveau que si au moins l'une des unités tertiaires X2 ou
X4 est touchée par l'accident de premier niveau. Par conséquent,
la probabilité de l'effet domino de deuxième niveau est
calculée comme suit :
PNiveau2 = P(X1)P(X3/X1)P(X2?X4/X1,X3) (2.14)
Pour tenir compte de l'union de X2 et X4
représentée dans Eq. (2.14), la figure II-28
peut être modifiée en ajoutant le noeud auxiliaire L1 de
telle sorte que L1 = X2?X4 (Fig. II-29).
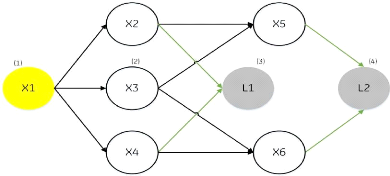
95
Figure II-29 : Réseau bayésien
modifié pour incorporer l'union des événements tertiaires
et quaternaires en utilisant les noeuds auxiliaires L1 et
L2
Ainsi, X2 et X4 sont reliés à L1 à l'aide
d'arcs causaux de porte logique « OU », ce qui donne la table de
probabilité conditionnelle présentée dans le tableau
II-20 pour le noeud L1.
Tableau II-20 : Table des probabilités
conditionnelles attribuées au noeud auxiliaire L1 montrant sa
dépendance conditionnelle à l'égard de ses parents par le
biais d'une porte logique «OU»
Unités
|
P(L1/X2,X4)
|
X2
|
X4
|
Accident
|
Absence d'accident
|
Accident
|
Accident
|
1
|
0
|
Accident
|
Absence d'accident
|
1
|
0
|
Absence d'accident
|
Accident
|
1
|
0
|
Absence d'accident
|
Absence d'accident
|
0
|
1
|
La probabilité de L1 est égale à la
probabilité de propagation de l'effet domino au deuxième niveau,
c'est-à-dire la probabilité qu'au moins une des unités
tertiaires X2 ou X4 soit impliquée dans l'accident. De même, pour
que l'effet domino passe au troisième niveau, il est nécessaire
que l'accident dans les unités tertiaires se propage dans au moins une
des unités quaternaires. [14]
La probabilité de l'effet domino de premier niveau peut
être estimée comme le produit de P(X1) et P(X3/X1). Ainsi, si DL1
(Domino Level 1) est connecté à X1 et X3 par des arcs causaux de
porte logique « ET », P(DL1) serait égal à la
probabilité de l'effet domino de
96
premier niveau. Cela implique que pour que l'effet domino de
premier niveau se produise, non seulement l'événement primaire X1
mais aussi l'événement secondaire X3 sont nécessaires.
De même, si DL2 est connecté aux noeuds DL1 et L1
par des arcs causaux de porte logique « ET », P(DL2) serait
égal à la probabilité de l'effet domino de deuxième
niveau. Cela indique que pour que l'effet domino de deuxième niveau se
produise, l'effet domino de premier niveau (c.-à-d. DL1) et au moins un
des événements tertiaires, c.-à-d. L1 se produisent.
Même chose pour le niveau 3. (Voir figure
II-30)
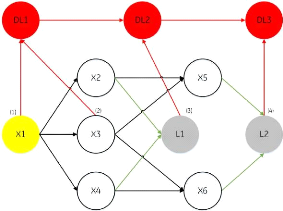
Figure II-31 Réseau bayésien
modifié pour incorporer les 3 niveaux d'effet domino et l'union des
événements tertiaires et quaternaires
II.4.4.3 Présentation du
logiciel AGENARISK
AGENARISK utilise les derniers développements du
domaine de l'intelligence artificielle bayésienne et du raisonnement
probabiliste pour modéliser des problèmes complexes et
risqués et améliorer la manière dont les décisions
sont prises.
Il est utilisé pour établir des
prévisions, effectuer des diagnostics et prendre des décisions en
combinant des données et des connaissances sur les dépendances
causales complexes et autres dans le monde réel.
97
AgenaRisk est aussi utilisé pour modéliser
divers problèmes comportant des risques et des incertitudes, notamment
les risques opérationnels, l'analyse actuarielle, l'analyse des
informations, la sécurité et la fiabilité des
systèmes, les risques pour la santé, les risques liés
à la cyber sécurité et la planification financière
stratégique.
II.4.4.4 Réalisation des réseaux
bayésien
II.4.4.4.1 Scénario 1
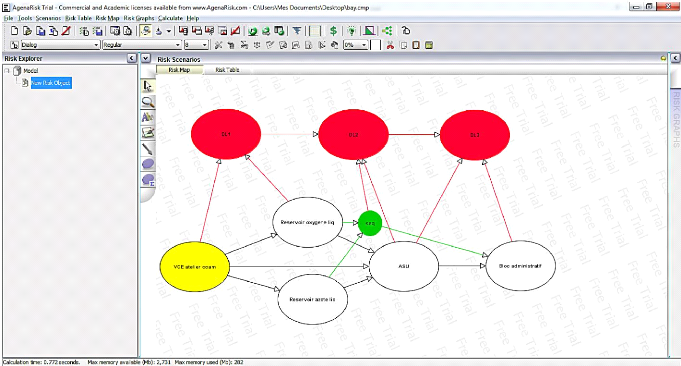
Figure II-32 : Réseau bayésien du
scénario 1
98
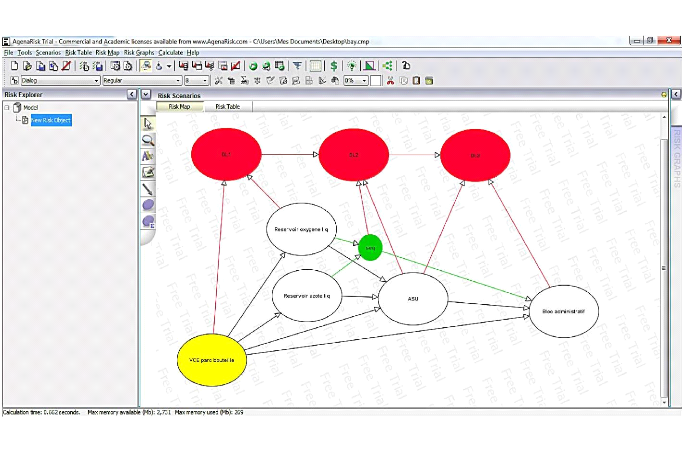
II.4.4.4.2 Scénario 2
Figure II-33 : Réseau bayésien du
scénario 2
99
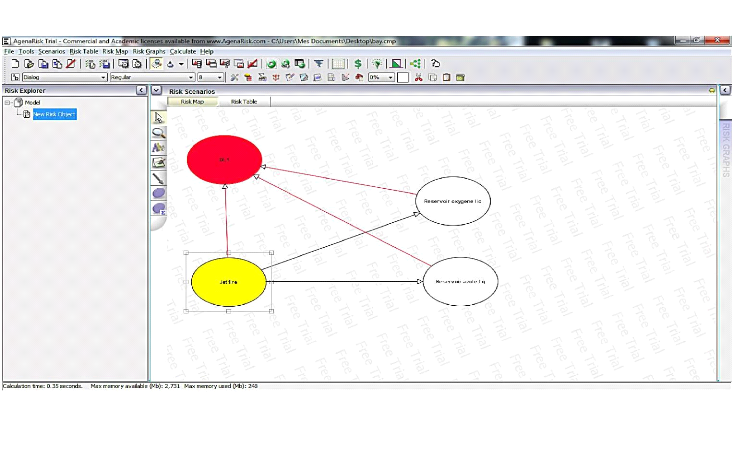
II.4.4.4.3 Scénario 3
Figure II-34 : Réseau bayésien du
scénario 3
100
101
II.4.5 Calcul des probabilités de
combinaison
Evènement primaire de risque :
VCE au niveau du parc bouteilles 7.1 *10-4
Evénements engendrés :
Tableau II-21 : Probabilités des
événements
Evénement
|
Numéro de
|
Probabilité
|
l'événementDe??truction ??u ré??ervoir
??'oxy??ène ??iqui??e
|
1
|
3.14 * 10-10
|
De??truction ??u ré??ervoir ??'azote liquide
|
2
|
2.19 * 10-10
|
Incendie au niveau de la tour ASU
|
3
|
18 * 10-3
|
Destruction du bloc administratif
|
4
|
2.12 * 10-3
|
Pour rappel
Y
???? (??,??) = ? [1 - ????,?? + ??(i,???? ?? )(2 * ????,?? -
1)] (2.1)
??=1
Où ????,?? est la probabilité d'escalade
pour le i-ème événement secondaire. ?????? est un
vecteur
dont les éléments sont les index d'une même
combinaison de k événements secondaires. La
fonction ??(i,??????) est
définie comme suit :
1 i ? ??m
22
??(i,??????) =
0 i? ??im,, ( )
Tableau II-22 : Probabilités des combinaisons
d'évènements
1
|
2
|
3
|
4
|
Probabilité de la combinaison
|
*
|
|
|
|
2.05 * 10-14
|
*
|
*
|
|
|
4.48 * 10-23
|
*
|
|
*
|
|
4 * 10-15
|
|
*
|
*
|
|
1.42* 10-14
|
*
|
*
|
*
|
|
8.8* 10-25
|
*
|
|
|
*
|
3.2* 10-16
|
|
*
|
|
*
|
3 * 10-17
|
*
|
*
|
|
*
|
1.02 * 10-25
|
*
|
*
|
*
|
*
|
1.84* 10-27
|
102
D'un point de vue quantitatif, les probabilités
obtenues sont relativement acceptables. Elles nous renseignent également
sur les combinaisons d'accidents les plus probables.
L'étape suivante serra le calcul du risque individuel
à l'aide des probabilités obtenues
II.4.6 Risque individuel
Le risque individuel exprime le risque encouru par une
personne simple exposée à un danger dans la zone d'effet
potentiel d'un incident ou d'un ensemble d'incidents. Il faut signaler que
l'ampleur de tout incident, en termes de nombre de personnes impactées
par un seul événement, n'affecte pas le risque individuel.
Les mesures du risque individuel peuvent être des
nombres simples, des tableaux de nombres ou divers graphiques.
Les mesures de risque individuel couramment utilisées
comprennent les contours de risques individuels et montrent la
répartition géographique du risque individuel. Les courbes de
risque sont calculées à partir des prévisions
fréquence d'un événement susceptible de causer le niveau
de préjudice spécifié à un endroit
spécifié, que quelqu'un soit ou non présent à cet
endroit pour subir ce préjudice. Ainsi, le risque individuel des cartes
de contour sont générés en calculant le risque individuel
à chaque emplacement géographique en supposant que quelqu'un sera
présent, sans protection (par exemple, en plein air), et soumis au
risque 100 % du temps (exposition annuelle de 8760 heures par an).
C'est dans cette configuration ci que nous avons
travaillé. II.4.6.1. Calcul du risque individuel
La relation utilisée est inspirée de la relation
donnée par Albdelhamid 2010 FrEEDOM [3] et adaptée à des
installations au lieu d'équipements pour la relation initiale.
L'avantage de cette relation est qu'elle prend en compte les effets dominos.
n n
IR = ? ?
|
Fi * Pi,?? * P??
|
(2.17)
|
??=1
|
??=1
|
Le calcul donne une fréquence de risque individuelle de
5.63 * ??O-??
Cette valeur peut être interprétée comme
assez élevée d'où l'importance du système de
sécurité au sein de LGA.
103
Les contours du risque individuel ont été
fixés sur la base des seuils des effets de suppression et de radiation
thermique donnés précédemment et des simulations
effectuées.
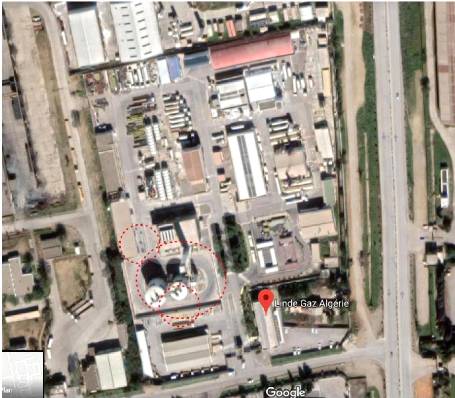
Figure II-35 : Illustration du risque individuel
sur le site de LGA
Chapitre III
ETUDE DES EFFETS DOMINOS
EXTERNES
105
III. ETUDE DES EFFETS DOMINOS EXTERNES
Beaucoup d'industries sont sujettes à la production,
stockage et traitement de quantités importantes de substances
dangereuses et parmi elles : LINDE GAS Algérie. Ainsi, elles
maintiennent le risque d'accidents déclenchant une réaction en
chaîne d'incidents majeurs dans les centrales adjacentes. Ces
chaînes d'accidents sont appelées effets dominos. Du point de vue
d'une entreprise, les risques d'accidents dominos peuvent être internes
ou externes dans la nature. Les effets dominos internes proviennent dans les
locaux de l'entreprise, alors que les accidents externes sont induits par les
entreprises voisines. Ainsi les effets dominos internes sont
généralement comptabilisés par la conception d'un
système de gestion de la sécurité de l'entreprise, les
effets dominos externes ne le sont pas.
Des études empiriques récentes
réalisées par Reniers, Dullaert, Soudan, et al. (2005) illustre
le fait que les responsables de la sécurité reconnaissent
l'importance de la coopération transfrontalière entre les
entreprises pour la réduction des risques dominos. L'absence d'un cadre
général pour la prévention des accidents extérieurs
communs, la crainte des coûts élevés d'inspection des
risques communs et l'analyse des risques, sont présentés comme
les principales objections contre la coopération de
sécurité inter-entreprises.
LINDE GAS Reghaia étant une entreprise se trouvant dans
une zone industrielle, elle est directement impliquée dans ce genre de
risques. En effet, il se trouve qu'elle est voisine direct avec une autre
entreprise opérant dans le même secteur et concurrente AIR
LIQUIDE. Un mur seulement sépare les deux géants de l'industrie
de gaz de l'air comme le montre la figure III-1.
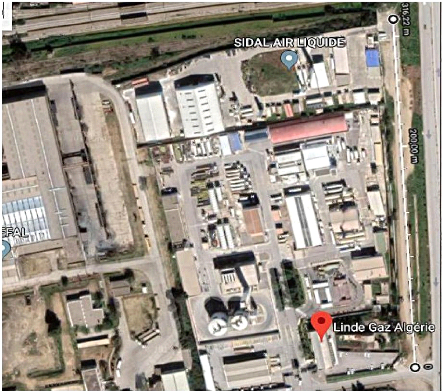
106
Figure III-1 Image satellite de l'emplacement de
LGA et AIR LIQUID
C'est pour cela que nous allons nous pencher sur
l'étude des effets dominos externes que pourrait causer une entreprise
sur l'autre. Pour ce faire, nous proposons l'application de la méthode
HAZWIM.
III.1 Prévention des accidents dominos externes
(EDAP) Proposition de cadre Hazwim
III.1.1 La gestion multi-entreprise
La gestion multi-entreprise diffère essentiellement de
la gestion unique de l'entreprise par le montant qu'ont à leur
disposition les gestionnaires d'information. Un autre problème est que
les différentes perspectives organisationnelles doivent être
combinées. Comme l'explique Hovden (refe1998) chaque cadre ou
perspective fournit une façon d'interpréter les
événements et les actions, et chacun implique une orientation
différente avec des conséquences pour le
107
choix des stratégies et approche de la gestion
efficace. Par conséquent, ce qui porte ces points de vue ensemble n'est
pas une tâche facile. Il devrait n'y avoir aucun problème de
communication ou de malentendus entre les parties concernées. Par
conséquent, une stratégie de gestion des risques doit être
élaborée pour être sûr que le personnel responsable
des différentes parties communique avec le même savoir-faire, au
même niveau, et sur les mêmes problèmes de
sécurité.
A cet effet, un aperçu de la gestion des risques
inter-entreprises basé sur un modèle unique de
société de la Australie / Nouvelle-Zélande standard (1999)
peut être développé.
Cet aperçu peut être utilisé pour
l'élaboration d'un cadre qui favorise l'échange d'informations
inter-entreprises sur les effets de dominos externes. Fournir une situation
où communication et conflits sont réduits au minimum, les
procédures d'analyse des risques et de leurs résultats doivent
être compris par les différents experts concernés par
l'étude. Dans la section suivante, un cadre est élaboré
basé sur la vue d'ensemble de la gestion des risques
inter-sociétés et selon des procédures bien connues.
III.1.2 Le cadre Hazwim EDAP
L'objectif d'un cadre de prévention des accidents
dominos externes est de faciliter la structuration hors site d'une
coopération de prévention d'effets dominos entre les entreprises
de manipulation ou stockage de substances dangereuses. Le cadre devrait inclure
une analyse des risques dominos externes solide consistant en deux
étapes fournissant des informations clés pour la gestion externe
des risques dominos : identification et évaluation externe des risques
d'effets.
La combinaison de Haz (analyse hazop), W chapeau- I (l'analyse
des risques) et de la f M Atrix dans un cadre Hazwim permet de constituer un
outil de méta-technique pour optimiser l'organisation de discuter des
performances d'analyse des risques de processus par les employés des
entreprises voisines dans une zone industrielle.
Avant la première étape du cadre EDAP, les
animateurs Hazwim et chefs de projet expérimentés doivent
être nommés dans chaque entreprise. Dans la première
étape du cadre, ces animateurs et les responsables du projet dans chaque
entreprise doivent définir la portée de l'étude des effets
dominos externes. Dans la deuxième étape, une étude
technique initiale est effectuée par chaque entreprise pour identifier
le potentiel par installation (faisant partie de
108
la zone de portée) pour les effets dominos et leurs
conséquences. Par conséquent, une hiérarchisation est
faite et les installations sont classées par ordre de danger
décroissant. Dans l'étape suivante, l'ingénieur de projet
de l'entreprise met en place le calendrier d'organisation de la zone de
portée de sa propre entreprise en utilisant les données de
classification et. Si elle ce n'est pas la première fois que
l'installation est à l'étude, le régime Hazwim
utilisé précédemment pour l'installation permet de
décider si une Hazop ou une analyse par simulation est
nécessaire. Une fois que les équipes sont
sélectionnées, une visite dans la zone de portée des
entreprises voisines est organisée. Les participants au projet Hazwim
exécutent ensuite la sixième étape du cadre Hazwim. Cette
étape finale du cycle cadre est terminée lorsque chaque
installation qui a été retenue pour enquête sur la
prévention des effets dominos a été analysé [17]
III.1.2.1 Étape 1: Définir la portée et
la zone de portée d'une étude de la zone industrielle de
sécurité domino externe
Le succès de la mise en oeuvre du cadre domino
d'analyse des risques dépend des accords mutuels des deux entreprises.
Le niveau des détails de l'Hazop et de What-Si des analyses à
effectuer doit rester dans des limites raisonnables défini par le niveau
de contrôle formel que la gestion de la sécurité doit
exercer. L'objectif de l'étude de sécurité domino externe
par installation, comme la vérification de la conception de la
sécurité d'une installation, de décider où
construire de nouveaux éléments d'installation ou de faire des
adaptations, améliorer la sécurité d'une installation
existante, etc, joue un rôle clé pour établir la zone
à mettre au point. La portée de l'étude devrait donc
décrire les types de risques et de contrôles des risques dans les
différentes installations concernées par l'équipe Hazop /
What-If. Par exemple, si le cadre Hazwim est utilisé pour
déterminer la zone pour construire une nouvelle installation ayant un
minimum d'impact sur la sécurité publique, il devrait être
centré sur les écarts des paramètres du processus qui
entraînent des risques hors site mettant en danger un espace public. Les
limites physiques du cadre EDAP devraient être explicites pour faire en
sorte que l'exercice reste concentré. Cependant, être trop
spécifiques peut également être dangereux car cela peut
conduire à négliger d'importantes séquences d'accidents. A
la fin de cette étape, la zone d'identification portée
concrétisées peut s'étendre
III.1.2.2 Étape 2: Etude initiale sur les effets
dominos
Chaque installation dans une zone industrielle est un fil
potentiel de ses environs. Par conséquent, la zone d'installation
entière doit être prise en compte dans l'analyse. La mise en
109
oeuvre de chaque régime Hazwim est influencée
par des corrélations dangereuses entre le processus d'installations des
risques d'une part et une autre installation, une unité de traitement
où un ensemble d'unités de traitement. Les interactions
potentielles entre les parties d'unités ou des installations, qui ne
peuvent être dangereuses en soi, peuvent causer d'autres risques qui
s'enchainent et se traduisent par une séquence d'accidents.
Notre étude ultérieure a permis de faire
ressortir l'unité critique pour les effets dominos. Il s'agit de
l'atelier d'oxyde d'éthylène se trouvant en contact direct avec
le mur séparant les deux entreprises. Une simulation des effets de
surpression et effets thermiques d'une explosion de cette unité a
été effectuée avec le logiciel PHAST. Les résultats
sont représentés dans les figures III-2 et III-3:
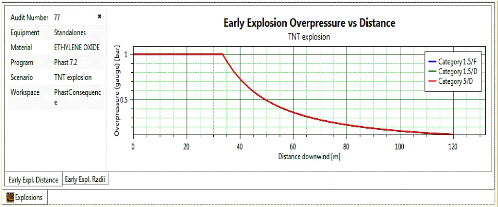
Figure III-2 : Effet de surpression en fonction de la
distance pour l'événement VCE au niveau de l'atelier d'oxyde
d'éthylène
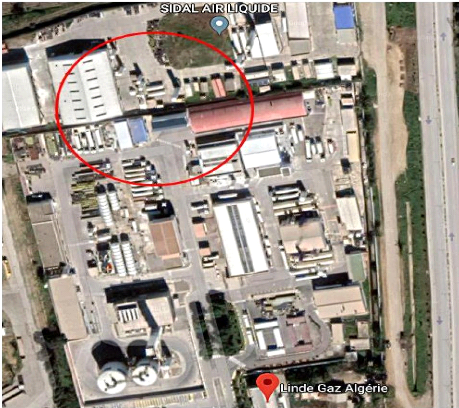
110
Figure III-3 : Propagation des effets de
surpression pour l'événement VCE au niveau de
l'atelier
d'oxyde d'éthylène
III.1.2.3 Etape 3: le calendrier d'organisation
La nécessité d'une flexibilité dans
l'application des régimes Hazwim sur diverses installations et
l'implication des différentes parties conduisent à une situation
complexe dans laquelle les conditions de temps, les responsabilités et
les compétences doivent être bien définies. Le chef de
projet Hazwim de chaque usine prévoit chronologiquement les
différentes étapes du régime Hazwim pour les installations
de l'usine située dans la zone considérée.
Les installations dans la zone à vérifier sont
répertoriées et pour chaque installation un tableau
récapitulatif est fait. Ce tableau récapitulatif contient au
moins les données estimées suivantes : le niveau de danger
relatif de chaque installation, le temps nécessaire pour effectuer une
Hazop ou une What-If procédure sur l'installation et la distance
à toutes les autres installations de l'entreprise. Le niveau de danger
relatif est calculé en fonction des contours de risque d'information
rédigé comme expliqué dans le paragraphe
précédent.
111
Il est évident que la distance entre les installations
respectives doit être un facteur contribuant au potentiel d'occurrence
d'un événement domino, car l'ampleur des effets de
conséquence se réduit selon une certaine fonction de la distance
de la source.
Sur la base de ces données d'installation, un
calendrier d'optimisation pour enquêter sur le danger domino externe dans
la zone de portée peut être tiré.
III.1.2.4 Étape 4: Composition de la Hazop et de la
What-If équipes dans chaque entreprise La clé du
succès et l'efficacité dans l'exécution d'un cadre de
prévention domino externe solide est la compétence
appropriée des membres de l'équipe. Les animateurs de Hazwim
doivent se familiariser avec les méthodes Hazop et What-If analyse ainsi
qu'avec la méthode d'évaluation de la matrice des risques.
Ils devraient également avoir une connaissance des
processus et de la maintenance des installations situées dans les locaux
de leur entreprise. Membres à temps partiel comme les ingénieurs
de processus et les ingénieurs de maintenance des installations à
examiner, ils devraient être disponibles pour tout appel à l'aide
et d'informations. Différentes situations doivent être prises en
considération lors de la composition d'une Hazop adaptée /
What-If équipe. Par entreprise deux procédures d'identification
des risques doivent être effectués, donc théoriquement deux
équipes sont nécessaires. Étant donné que les
procédures sont effectuées à des moments différents
dans le temps et les deux équipes possèdent également
à peu près les mêmes caractéristiques et fonctions,
la même équipe peut agir comme une équipe de Hazop et
réduite en équipe What-If. De cette façon, les deux types
d'études sont menées principalement par le même personnel
expérimenté.
III.1.2.5 Étape 5: Explication visite du site
Un examen élémentaire des
caractéristiques techniques des installations voisines est
nécessaire. L'accent sera mis sur les risques qui peuvent conduire
à des accidents dominos hors site. L'examen permettra aux membres de
l'équipe d'imaginer d'éventuels écarts, des
hypothèses et des questions sur le fonctionnement de l'installation
examinée et les installations adjacentes. Par conséquent, une
visite explicative des installations adjacentes du site est indispensable.
Cette visite guidée est organisée une fois que tous les membres
de l'équipe sont choisis.[17] Elle permettra la collecte d'informations
spécifiques sur les contours des risques et des substances
dangereuses.
Partie B : inter compagnie (LINDE-AIR LIQUIDE)
Étape 6: Schéma de la procédure Hazwim
Partie A : intra compagnie (LINDE GAS)
Evaluation des risques
Indentification des risques
Interprétation commune de l'évaluation des
risques
Optimisation commune des mesures de
sécurité
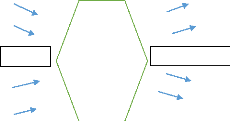
Causes
Conséquences
Risques liés à l'industrie
112
|
|
|
|
|
Analyse HAZOP approfondie à
travers l'identification de risque
|
Matrice de risque, évaluation de risque, mesures
recommandées
|
Discussion des résultats de la matrice de risque
|
Mesures de protection
|
|
|
T= [1....n]
113
Le schéma de la procédure Hazwim combine les
risques techniques identification de Hazop et analyse par simulation avec la
technique d'évaluation des risques de la matrice des risques, comme le
montre la figure ci-dessus. Il y est décrit comment les
caractéristiques complémentaires des trois techniques peuvent
être utilisées pour les intégrer dans une combinaison
optimale et de décider des actions qui peuvent être prises pour
arrêter le développement des incidents majeurs externes.
La partie A de la figure se compose d'une identification de
risques. Dans notre cas, il s'agit de l'atelier d'oxyde
d'éthylène de LIND GAS et une unité qui reste à
déterminer pour AIR LIQUIDE.
L'analyse se fait exclusivement par le personnel de chaque
entreprise. L'exercice d'identification est caractérisé par une
structure de noeud papillon. La partie centrale dans le noeud papillon est le
danger, le côté gauche du noeud papillon décrit comment les
événements et les circonstances, soit de façon
isolée où en combinaison, peuvent libérer un danger avec
le potentiel de dommages aux biens, aux personnes ou à l'environnement.
Le côté droit représente les différents
scénarios qui pourraient se développer de
l'événement indésirable.
La première étape du processus Hazwim, consiste
à déterminer toutes les causes possibles de danger et les
conséquences de danger, elle est effectuée en utilisant la
procédure Hazop étendue avec domino. Les résultats de
l'Hazop comprennent généralement une liste de recommandations qui
répondent aux problèmes potentiels identifiés.
Malheureusement, les résultats ne fournissent aucune orientation aux
décideurs quand les problèmes potentiels sont plus importants.
L'étape suivante du processus est une évaluation des risques
liés aux actions recommandées. Cette partie a été
effectuée et la HAZOP suivante en est ressortis ;
La maille choisis est l'atelier d'oxyde
d'éthylène car c'est le système plus le apte a
générer des effets dominos externes.
Les paramètres sélectionnés sont la
pression, la température, la concentration de CO2.
Nous n'avons pas l'habitude de déterminer la
criticité dans la HAZOP mais dans ce travail nous avons suivi le model
de LGA qui eux ajoute l'analyse quantitative de la criticité.
Dans cette HAZOP la criticité va être
calculée en s'appuyant sur la matrice suivante :
Tableau III-1 : Matrice d'évaluation des
risques

MATRICE
D'EVALUATION DES RISQUES
FREQUENT
|
0 à 1 par semaine
|
probabilité
|
OCCASIONNEL
POSSIBLE
|
1 par semaine à 1 par mois 1
par mois à 1 par an
|
RARE
|
dans 1 à 10 par ans
|
IMPROBABLE
|
plus de 10 ans
|
Gravité
114
MINEUR
|
MODERE
|
SERIEUX
|
MAJEUR
|
CATASTROPHIQUE
|
Blessure légère - simple
inconfort premiers soins peuvent être donnés
|
Traitement médical (sans
effets)
|
Arrêt
de travail avec rémission complète.
|
Arrêt de travail
avec lésion permanente, invalidité
ou maladie
|
Incident extrêmement grave pouvant
être mortel ou décès
Extrêmement élevé
Extrêmement élevé
Elevé
|
Moyen
|
Moyen
|
Elevé
|
Elevé
|
Faible
|
Moyen
|
Moyen
|
Elevé
|
Faible
|
Moyen
|
Moyen
|
Elevé
|
Faible
|
Faible
|
Moyen
|
Moyen
|
Elevé
|
Extrêmement faible
|
Faible
|
Faible
|
Moyen
|
Moyen
|
115
Item
|
Déviation
|
Causes
|
Conséquences
|
F
|
G
|
C
|
Barrières de sécurité
|
Recommandations/Actions Correctives F
|
G
|
C
|
1.1
|
Plus de pression dans le fût ETO
|
Ouverture simultanée des vannes V14 (CO2) et V12
|
Rupture du fût
|
2
|
5
|
10 H
|
Indicateur de pression à
l'entrée et à la sortie du fût
|
REC. Contrôle réglementaire des IEM
|
1
|
5
|
5 M
|
|
|
(ETO)
|
|
|
|
|
|
|
|
|
|
|
|
Pression d'azote élevée à l'entrée du
fût
|
Explosion
|
|
|
|
REC. Check-list de contrôle
Inspection visuelle
|
|
|
|
|
|
Défaillance de la vanne
|
Fatalité
|
|
|
|
Réseau anti incendie
|
REC. Formation des opérateurs
|
|
|
|
|
|
Source de chaleur externe
|
|
|
|
|
Fût à l'intérieur du local
|
|
|
|
|
|
|
|
|
|
|
|
Manodétendeur à la sortie du cadre
|
|
|
|
|
1.2
|
Plus de pression d'azote à l'entrée du fût
|
Défaillance du manomètre PCV 53
|
Surpression du fût
Explosion
|
2
|
5
|
10 H
|
Manodétendeur à la sortie du cadre
|
REC. Explorer la possibilité d'installer un
compresseur ATEX pour stabiliser la pression
d'entrée
REC. Contrôle réglementaire des IEM
|
1
|
5
|
5 M
|
|
|
|
Fatalité
|
|
|
|
|
REC. Check-list de contrôle
|
|
|
|
1.3
|
Plus de T° dans le
laveur (Scrabber)
|
Ouverture simultanée des vannes V13 (Purge) et V12
|
Le fût ETO se vide dans le laveur
|
2
|
4
|
8 M
|
Thermomètre
|
REC. Contrôle réglementaire des IEM
|
1
|
4
|
4 L
|
|
|
(ETO)
|
|
|
|
|
|
|
|
|
|
|
|
|
Surchauffe et débordement du laveur
|
|
|
|
Indicateur de niveau avec
alarme sonore/lumineuse
|
REC. Check-list de contrôle
|
|
|
|
|
|
|
Blessures et effets sur la santé
|
|
|
|
Arrêt automatique de la pompe
|
REC. Formation des opérateurs
|
|
|
|
|
|
|
|
|
|
|
Arrêt d'urgence
|
|
|
|
|
|
|
|
|
|
|
|
Electrovannes à fermeture
automatique
|
|
|
|
|
1.4
|
Plus de concentration
de CO2 dans le laveur
|
Vannes défaillante
|
Surpression dans le laveur
|
2
|
5
|
10 H
|
Electrovannes à fermeture
automatique
|
REC. Check-list de contrôle
|
1
|
5
|
5 M
|
|
|
Erreur humaine
|
Rupture du laveur
|
|
|
|
Transmetteur de pression
|
REC. Formation des opérateurs
|
|
|
|
|
|
|
Déversement d'acide ou
d'éthylène Glycol
|
|
|
|
|
|
|
|
|
|
|
|
Fatalité
|
|
|
|
|
|
|
|
|
1.5
1.6
Plus de concentration d'ETO dans l'atelier
Ajout d'acide plutôt que l'eau dans le Scrabber
Fuite dans le panel de remplissage
Fuite dans le Scrabber lors du traitement
Défaillance du flexible ou du robinet de la bouteille
Erreur humaine Manque de formation
Non-respect de la
procédure
Lésions sur la peau/yeux Inhalation d'un produit
toxique
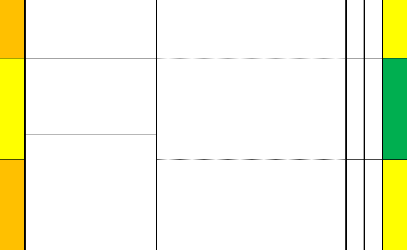
REC. Check-list de contrôle
REC. Formation des opérateurs
REC. EPI adéquats
8 M
1
4
REC. Etablir une instruction/procédure 'vidange du
Scrabber'
REC. Formation des opérateurs
10 H
1
5
Vérification des flexibles
Alarme sonore
Arrêt d'urgence
Extracteurs
Instructions
4 L
5 M
2
2
4
5
Réaction exothermique
Dégagement de chaleur explosion du laveur
116
Tableau III-2 : HAZOP de l'atelier d'oxyde
d'éthylène
117
Dans la partie B du processus Hazwim, les résultats de
la partie A sont discutés par les responsables de la
sécurité des deux usines afin de décider des mesures de
prévention à prendre. La partie B est donc une question de
gestion inter-compagnie.
Après n analyses enquêtant sur
les risques de l'installation, il est nécessaire d''effectuer une
analyse par simulation. L'identification de risques plus approfondie par
analyse Hazop est exécutée pour assurer ensuite une
sécurité domino externe optimale.
Le processus Hazwim est donc un schéma
standardisé mais flexible. Le temps durant lequel le personnel des
frontières doit être adapté dépend de
différents facteurs et diverses circonstances.
Dans cette proposition d'installation du cadre HAWZIM nous
avons expliqué le cheminement de la méthodologie et
réalisé uniquement la partie liée à LGA . Afin de
pouvoir appliquer toute la méthodologie, une collaboration avec
l'entreprise voisine AIR LIQUID est impérative et devra se faire
ultérieurement.
Chapitre IV
Impact financier, impact indirecte et
proposition d'implémentation d'un plan
de
continuité d'activité
119
Impact financier, impact indirecte et proposition
d'implémentation d'un plan de continuité
d'activité
III.2 Impact financier :
Cout de l'occurrence de la séquence domino : En termes
d'installations
Type d'installation en cause
|
Couts des dégâts
|
Destruction bac d'oxygène liquide
|
945.000.000 DA
|
Destruction bac d'azote liquide
|
630.000.000 DA
|
Endommagement de l'ASU
|
1.155.000.000 DA
|
Endommagement du bloc administratif
|
13.000.000 DA
|
Autres couts divers liées aux effets
|
210.000.000 DA
|
En termes de produit :
Quantité stockés en moyenne sur site :
Oxygène : 1.000.000 litres
Azote : 500.000 litres
Oxyde d'éthylène : 6* 700 kg
Produit
|
Couts
|
Oxygène
|
25.000.000 DA
|
Azote
|
7.500.000 DA
|
Oxyde d'éthylène
|
480.000 DA
|
En termes de jour d'arrêt de production Capacité de
production :
Oxygène : 4275 L/h marchant 24h/24 Azote 1695 L/h marchant
24h/24 Argon 70 L/h marchant 24h/24
Durée d'arrêt \ produits
|
Oxygène
|
Azote
|
Argon
|
1 journée
|
2.565.000 DA
|
610.200 DA
|
554.400 DA
|
1 semaine
|
17.955.000 DA
|
4.271.400 DA
|
3.880.800 DA
|
2 semaines
|
38.475.000 DA
|
9.153.000 DA
|
8.316.000 DA
|
1 mois
|
76.950.000 DA
|
18.306.000 DA
|
16.632.000 DA
|
3 mois
|
230.850.000 DA
|
54.918.000 DA
|
49.896.000 DA
|
120
III.3 Impact indirecte
Dans la majorité des cas nous nous intéressons
uniquement à l'impact direct de la catastrophe. Or ces accidents majeurs
peuvent avoir de lourdes conséquences sur d'autres industries et
secteurs. C'est le cas pour LGA car comme nous l'avons montré
l'entreprise est mitoyenne de AIR LIQUID et ce sont les deux seuls fournisseurs
des produits de gaz de l'air pour la région d'Alger et ses environs. Un
événement domino qui toucherait les deux entreprises et
engendrerai un arrêt de production serrait très dangereux pour
plusieurs secteurs qui eux-mêmes pourrait engendrer une séquence
domino sur d'autres secteurs. Pour mieux voir l'effet sur les industries voici
la liste de certains clients que LGA fournit en produit :
Tableau 0-1 Client LGA par produit
Oxygène
|
Azote
|
C02
|
Algesco
|
Algesco
|
Baticim
|
BATICIC
|
Cdta Centre Developpement Des Technologies
|
EMB BAG
|
Cdta Centre Developpement Des Technologies
|
Comena Crna Centre De Recherche Nucleaire D.alger
|
Eurl Algad
|
Cosider Travaux Public Utps Rouiba
|
Enap Upl Lakhdaria
|
SIMAF
|
Ecm Sidi Moussa
|
Eniem
|
Snc Lavalin Intern Hadjret Ennous
|
Engtp Reghaia
|
Hcr Udts
|
Snvi Cir
|
Eniem
|
Mdn Base Aerienne Ain Oussera
|
Snvi Cvi Complexe De Vehicule Industriel
|
Epe Electro Industrie
|
Mdn Ctsa
|
Snvi Epe Spa For
|
Mdn Base Aerienne Ain Oussera
|
Sarl Stic
|
SPA EMB BAG
|
Mdn Bcl Beni Mered
|
Snvi Cvi Complexe De Vehicule Industriel
|
Spa Fruital Il
|
Sarl Groupe Mokabli Pour Les Grands Travaux
|
Sonatrach Activite Aval
|
ABC PEPSI
|
Snvi Cir
|
Spa El Sewedy Cables
|
Hamoud Boualem
|
Snvi Cvi Complexe De Vehicule Industriel
|
Spa Emb Fbf
|
Sarl MGB Royal
|
Snvi Epe Spa For
|
Spa Mediterranean Float Glass Mfg
|
SPA TENES LILMIYAH
|
Somabe Filaile Enmtp
|
|
UTE DESSALADORA TENES CONSTRUCTION
|
Spa Alieco
|
|
Tala Boghni
|
Spa Alrim
|
|
Taiba Food
|
Spa Erc Ex (erwa Urd)
|
|
Eurl Boisson Bouchra
|
|
|
Liberta
|
La liste des hôpitaux que LGA fournit sont dans le
tableau 0-2 Tableau 0-3 Liste des hôpitaux clients de
LGA
EPE/SPA Saidal Medea
EPH Aflou
EPH Ain Defla
EPH BIRTRARIA
EPH BORDJ MENAEL
EPH BOUFARIK
EPH DJELFA
EPH EL ATTAF
EPH HASSI BAH BAH
EPH HASSI BAH BAH
EPH Kouba
EPH LAGHOUAT
EPH LAGHOUAT
EPH LAGHOUAT
EPH MEFTAH
EPH MESSAD
EPH MILIANA
EPH ROUIBA
EPH ROUIBA
EPH Sidi Ghiles
EPH THENIA
EPH THENIA
EPH ZERALDA
HUMC Salim Zemirli
HUMC Salim Zemirli
Institut du Rein Blida
121
HOPITAUX
|
Centre National de toxicologie
|
Centre Piere Marie Curie
|
CHU Bab El Oued
|
CHU Béni Messous
|
CHU Douera
|
CHU Hopital Mustapha
|
CHU Nafissa Hamoud, Parnet
|
CHU Nedir Mohamed
|
Clinique Chahrazad
|
CMCI Bousmail
|
CNIAAG
|
EHS Ben Aknoune
|
EHS CAC Blida
|
EHS Dr Maouche Mohand Amokrane
|
EHS Draa Ben Khedda
|
EHS Kettar
|
EHS Laghouat
|
EHS Laghouat
|
EHS Mohamed Abderrahmani
|
Ehs Mere et enfant de Djelfa
|
EHS Sbihi Tassadit
|
EPE/SPA Saidal Medea
|
|
|
|
|
122
Comme nous pouvons le voir par les tableaux 0-1 et 0-4
les secteurs touchés sont diverses : bâtiment,
construction et travaux publics, chimie, automobile, compagnies
pétrolières, agroalimentaire et surtout santé. Un
arrêt de production pourrait donc avoir de très grosses
conséquences.
C'est pour ceci qu'il est primordial de mettre en place un plan
de continuité d'activité.
123
III.4 Plan de continuité d'activité
(PCA)
La nature, la fréquence et le coût des crises ont
sensiblement évolué au cours des vingt dernières
années. On comprend sans doute mieux aujourd'hui à quel point
sont étroitement imbriquées les différentes dimensions de
ces événements qui perturbent très fortement le
fonctionnement de nombreuses organisations, publiques et privées, avec
des conséquences allant jusqu'à la cessation définitive
d'activité. Les retours d'expérience des grandes crises
récentes montrent que les organisations ayant entrepris une
démarche préalable visant à garantir la continuité
de leur activité sont les plus résilientes face aux
événements déstabilisants.
Bien qu'il soit utopique de chercher à tout
prévoir et maîtriser, le responsable d'une organisation - publique
ou privée - se doit de concevoir et mettre en oeuvre des
stratégies de protection permettant d'éviter certains
événements, ou tout du moins d'en limiter les effets directs sur
les objectifs de l'organisation, et d'assurer la continuité de
l'activité malgré la perte de ressources critiques. C'est dans ce
sillage que nous proposons la mise en place d'un PCA au sein de LGA.
Les contraintes économiques imposent de devoir
justifier les dépenses, y compris celles qui concernent les actions
à entreprendre dans le domaine de la sécurité, et de
pouvoir prioriser ces dépenses dans le cadre d'une stratégie
globale. Il faut par conséquent disposer d'outils méthodologiques
permettant d'optimiser l'efficience de ces actions, en cohérence avec
les objectifs de l'organisation. Des outils existent déjà pour
couvrir séparément plusieurs domaines indissociables : la gestion
de risque, la gestion de crise, l'intervention, le maintien et la reprise
d'activité. La démarche de continuité de l'activité
est le moyen d'associer de manière globale et cohérente tous ces
domaines
L'ISO 22301:2012 spécifie les exigences pour planifier,
établir, mettre en place et en oeuvre, contrôler, réviser,
maintenir et améliorer de manière continue un système de
management documenté afin de se protéger des incidents
perturbateurs, réduire leur probabilité de survenance, s'y
préparer, y répondre et de s'en rétablir lorsqu'ils
surviennent.
124
Les exigences spécifiées dans l'ISO 22301:2012
sont génériques et prévues pour être applicables
à toutes les organisations, ou parties de celles-ci,
indépendamment du type, de la taille et de la nature de l'organisation.
Le champ d'application de ces exigences dépend de l'environnement et de
la complexité de fonctionnement de l'organisation.
Cette norme appartient à une catégorie bien
particulière : les "management systems" ou "systèmes de
management". Cela signifie qu'elle se concentre sur la manière de se
rapprocher volontairement d'un état cible décidé.
Autrement dit, elle présente des dispositifs à mettre en place
pour permettre d'améliorer la situation en matière de
continuité de l'activité. Ce type de norme s'appesantit beaucoup
plus sur le fait de se rapprocher d'une cible de bonnes pratiques que sur les
bonnes pratiques elles même. Ceux qui y recherchent des "recettes" en
auront pour leurs frais.
Pour montrer l'avantage financier que peut présenter le
PCA nous proposons la figure 0-1 ( la notion de durée maximale
d'interruption de service acceptable (DMIA) serra définis dans le point
0.3.6 )
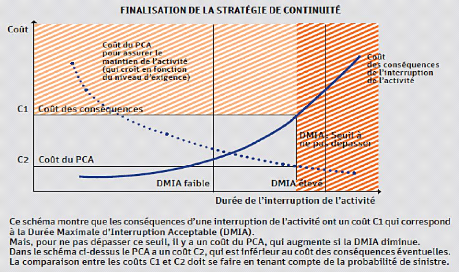
Figure 0-2 Comparaison des couts du PCA et des
conséquences d'une catastrophe
125
III.4.1 Compréhension de l'organisation et de son
contexte
Avant de commencer un projet PCA il est indispensable de
comprendre l'organisation : son activité, ses objectifs, ses valeurs, sa
stratégie, son environnement interne et externe.
Cette première action est essentielle et
conditionne l'efficacité d'ensemble de la démarche. Elle
vise à préciser le périmètre géographique et
fonctionnel de l'organisation qui doit être pris en compte, puis à
identifier tout ce qui peut orienter les choix en rapport avec la
spécificité de l'organisation. Notamment, il convient de prendre
en compte aussi bien le contexte externe (demande des actionnaires, des
autorités chargées de la réglementation et du
contrôle, contrats existants et niveaux d'exigence associés,
environnement politique, social, culturel, juridique, économique et
financier, dépendances, etc.), que le contexte interne (histoire et
culture de l'organisation, style de gouvernance et de pilotage, politique
interne de gestion des ressources humaines, informatiques, matérielles
et immatérielles, stratégie et objectifs internes, organisation,
processus, système d'information, flux, etc).
Cette première étape doit permettre :
- de définir un PCA cohérent avec la
stratégie de l'organisation,
- d'identifier les relations avec les parties prenantes
(clients, fournisseurs, autorités administratives...),
- de lister les besoins et attentes de ces parties prenantes,
- de lister les exigences légales,
réglementaires et contractuelles ayant un lien avec la continuité
d'activités,
- de définir les facteurs internes et externes qui peuvent
influencer le PCA.
III.4.2 Définition d'un
périmètre
Définir le périmètre est un
préalable indispensable à la mise en oeuvre d'un SMCA (
systéme de management de continuité d'activité. Avec un
périmètre organisationnel, fonctionnel et physique clair il est
plus facile d'obtenir l'appui de la Direction et de commencer à
mobiliser les parties concernées.
Toutes exclusions du périmètre doit être
justifiée.
Le périmètre organisationnel représente les
directions, services, filiales pris en compte.
Le périmètre fonctionnel concerne les produits
et/ou services concernés (souvent liés au périmètre
organisationnel).
126
Le périmètre physique regroupe tous les
emplacements physiques, à la fois internes et externes, qui sont inclus
dans le SMCA.
Une fois le périmètre identifié et
clairement délimité il convient de le communiquer dans
l'organisation.
III.4.3 Obtenir l'implication et l'engagement de la
Direction
Toute réussite d'un projet SMCA est assujettie à
une forte implication de la Direction.
L'engagement de la Direction peut s'obtenir de différentes
façon (liste non exhaustive) :
- participation de la Direction au Comité de Pilotage
SMCA,
- signature de la politique SMCA par le top management,
- allocation des ressources pour le projet,
- le PCA est directement rattaché à la Direction
Générale,
- le « sponsor » du projet SMCA est un membre de la
Direction.
III.4.4 Politique et objectifs du PCA
La Direction de l'organisation doit établir et
démontrer son adhésion à la politique de
continuité des activités.
Cette politique doit inclure ou faire référence
:
- aux objectifs de continuité des activités de
l'organisation,
- au périmètre du plan de continuité des
activités, en précisant les exclusions.
En plus de recevoir l'adhésion de la Direction de
l'organisation, cette politique de continuité
des activités doit :
- être communiquée à toute personne
travaillant pour, ou en lien étroit avec l'organisation,
- être révisée à intervalles
réguliers ou lorsqu'un changement significatif intervient dans
l'organisation.
La définition du périmètre et des objectifs
doit intégrer les points suivants :
- exigences pour la continuité des activités,
- objectifs organisationnels et obligations,
- niveaux de risques acceptables,
- devoirs statutaires, réglementaires et contractuels,
- intérêts des parties prenantes.
127
III.4.5 Mise à disposition des
ressources
L'organisation doit déterminer et mettre à
disposition les ressources nécessaires pour établir, mettre en
oeuvre et maintenir le SMCA.
L'organisation des acteurs du PCA et leur rôle au sein du
plan doivent être définis et documentés.
La Direction de l'organisation doit désigner un
responsable en charge de la politique PCA et de sa diffusion. D'autres
personnes doivent être désignées pour gérer le suivi
et la maintenance du SMCA.
III.4.6 Compétences
L'organisation doit s'assurer que l'ensemble des acteurs
désignés du PCA dispose des
compétences nécessaires pour assumer le rôle
qui leur est assigné.
Cela implique de :
- déterminer les compétences de ces personnels,
- assurer leur formation spécifique au PCA,
- s'assurer des résultats de ces formations,
- d'assurer des mises à jour régulières des
niveaux de compétences dans le cadre du PCA.
7. Contrôle et gestion documentaire
Concernant la documentation, des contrôles doivent
être établis pour s'assurer : - qu'elle reste lisible,
aisément identifiable et traçable,
- qu'elle est stockée, protégée et
disponible.
Ces contrôles doivent également permettre de
s'assurer que :
- les documents ont été approuvés et
validés,
- les documents ont été révisés, mis
à jour et revalidés,
- les mises à jour et modifications apportées sont
identifiables,
- les documents d'origine externe sont identifiés et leur
diffusion contrôlée,
- les documents devenus obsolètes sont retirés ou
clairement identifiés par rapport aux
documents maintenus.
Pour maintenir l'activité au niveau exigé par les
objectifs et obligations identifiés, les
processus doivent répondre à des objectifs de
sécurité, que l'on appelle « attentes » ou «
besoins » et qui doivent être identifiés.
128
À partir des discussions avec les responsables des
métiers, il est possible de dégager des attentes, qui peuvent
être sériées par critères, sous la forme D.I.C.T.E.S
:
Disponibilité, continuité de
service, régularité, résistance aux dysfonctionnements et
aux ruptures, robustesse. Ceci doit pouvoir être mesurable, par exemple
en termes de fiabilité des prestations.
Intégrité, c'est-à-dire
que le service/produit livré est bien celui attendu, dans l'état
prescrit. Si ce n'est pas le cas, le service n'est pas rendu, conduisant
à un arrêt (plus ou moins long) du service.
Confidentialité, protection des
informations sensibles. Une perte de confidentialité peut conduire
à l'arrêt de certaines activités très sensibles,
voire à la faillite de certaines organisations (cf. les cas
présentés en annexe).
Traçabilité, visibilité,
connaissance des événements. La traçabilité peut
être indispensable pour permettre d'assurer des prestations (par exemple
le transport de matières dangereuses).
Évolutivité, capacité à s'adapter
aux changements et à l'environnement et donc à assurer la
robustesse. L'absence d'évolutivité peut conduire à
l'arrêt dans des contextes changeants. Sûreté,
capacité à limiter les effets d'actes malveillants.
Lors de cette étape, il est souhaitable de
quantifier le niveau du besoin de continuité, en utilisant trois
indicateurs :
1. Le niveau de service minimum (une perte
de service qui maintient le fonctionnement au-dessus de ce seuil affecte peu le
service final. A contrario une perte de niveau de service en dessous de ce
seuil est considérée comme une indisponibilité). Ce seuil
peut être défini comme un pourcentage de conformité minimum
ou un pourcentage de produits/services commandés livrés à
la date/heure convenue. Durant la phase de reprise d'activité
après un sinistre, il est possible de définir des seuils plus
faibles, en mode dégradé.
2. Le niveau d'indisponibilité minimum.
Tout arrêt de durée inférieure à ce niveau
est tolérable. Pour des indisponibilités de courtes durées
et relativement fréquentes l'exigence est exprimée en
durée maximale d'interruption et en fréquence maximale, ce qui se
combine en pourcentage de temps d'indisponibilité pendant une
durée significative. Pour ce qui concerne un sinistre, rare par
définition, la mesure se fait par la durée maximale
d'interruption de service acceptable (DMIA).
129
3. Les ressources qui restent indispensables
pour permettre la reprise de l'activité. Elles peuvent
s'exprimer en quantité de stock à préserver, de locaux de
repli, ou de niveau de mise à jour des données
sauvegardées (ce qui revient à définir la perte de
données maximale admissible, depuis la dernière sauvegarde).
Pour illustrer la notion de DMIA, on peut citer l'exemple du
processus de livraison ou de fourniture de certains produits ou services
sensibles qui ne peut accepter un délai de retard (DMIA)
supérieur à 12 heures (ce peut être le cas d'une livraison
de médicaments), ou supérieur à 30 minutes (une
intervention de service d'urgence par exemple). Dans un autre domaine, on peut
citer l'exemple d'un processus de paye qui ne peut pas accepter un retard
(DMIA) supérieur à trois jours, en mode dégradé
(avec un versement de provisions sur salaires). Cette possibilité de
pouvoir fonctionner en mode dégradé permet une interruption
maximale (DMIA) du fonctionnement normal de plusieurs mois. Une autre
formulation consiste à dire que la durée maximale de
fonctionnement en mode dégradé est de plusieurs mois.
Le mode dégradé est souvent
présenté comme un palliatif sans qu'il y ait une analyse
précise de son contenu. Cependant, pour tout mode dégradé
il convient de :
- Définir les circonstances de sa mise en place.
Intégrer les aspects réglementaires spécifiques au mode
dégradé, et notamment les modifications envisageables des textes
réglementaires dans des circonstances exceptionnelles.
- Définir des procédures spécifiques et
des mesures d'ordre juridique. Pouvoir transférer le personnel sur des
postes nouveaux.
- Faire éventuellement appel à l'intérim.
- Respecter les textes réglementaires
spécifiques (comme dans le domaine du transport de voyageurs ferroviaire
ou aérien, avec des dispositifs permettant d'adapter les moyens de
transport aux ressources humaines disponibles, dans le cadre d'un dialogue
social).
- Disposer de solutions de dernier secours, connues et rapidement
mises en oeuvre
III.5 Business Impact Analysis (BIA)
Cette phase de la mise en oeuvre du SMCA doit permettre
d'identifier les activités critiques de l'organisation et les ressources
minima nécessaires pour fonctionner en mode dégradé, de
comprendre les menaces qui pèsent sur ses activités et de
déterminer des actions appropriées pour minimiser voire annuler
les risques identifiés.
a)
130
Les objectifs d'un BIA
Le BIA doit permettre :
- d'obtenir une compréhension des produits et services
clés de l'organisation ainsi que des
processus dont ils dépendent,
- de déterminer les activités prioritaires pour
l'organisation et leur délai maximum
d'interruption,
- d'identifier les ressources clés nécessaires
à la continuité et à la relève des
activités,
- d'identifier les dépendances (internes et
externes).
b) Les étapes du BIA
Les principales étapes pour réaliser une
étude d'impact sur les activités sont les suivantes :
- identifier les activités et processus critiques de
l'organisation,
- analyser les impacts qui résulteraient d'un
arrêt de ces activités et processus critiques (sur
une échelle de 1 à 4) et déterminer
comment ces impacts évolueraient dans le temps en cas
d'arrêt prolongé,
- établir le temps d'arrêt ou
d'indisponibilité maximum supportable (Tams/Tims) - Maximum
tolerable period of disruption - des processus et
activités critiques,
- identifier et considérer toute autre activité
critique dépendant des fournisseurs et autres
parties prenantes,
- estimer le délai cible de rétablissement (RTO
: Return Time Objective) des activités après
un sinistre (délai toujours inférieur à
la période maximum tolérable d'arrêt),
Réalisation d'un BIA pour LGA :
Tableau 0-5 BIA LGA
1 journée
|
1 à 3
jours
|
3 à 7
jours
|
1 à 2
semaines
|
1 mois
|
3 mois
|
Produits
|
1
|
2
|
2
|
2
|
3
|
4
|
Oxygène
|
1
|
1
|
2
|
2
|
3
|
3
|
Azote
|
1
|
1
|
2
|
2
|
3
|
|
Argon
|
1
|
1
|
1
|
2
|
3
|
3
|
Oxyde éthylène
|
1
|
1
|
1
|
1
|
3
|
3
|
CO2
|
131
Démarche de réalisation
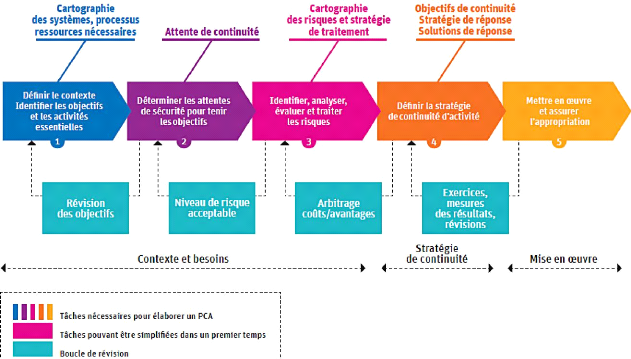
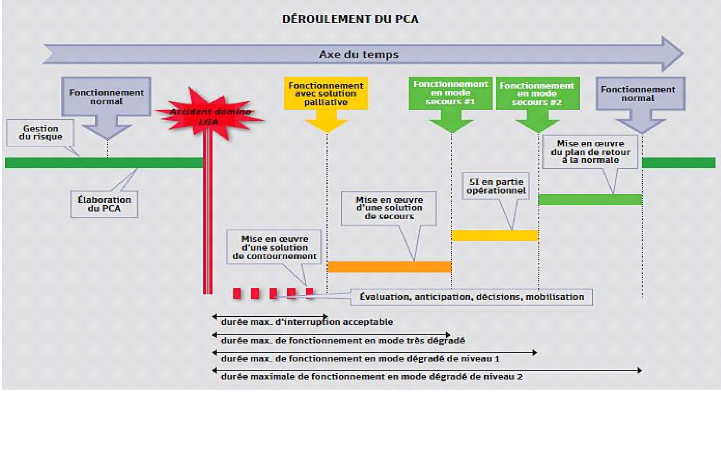
Figure 0-3 Déroulement du PCA après
l'événement domino au sein de LGA
132
133
Conclusion générale
Ce travail a été effectué dans le cadre
de l'élaboration d'une méthodologie d'étude des effets
dominos et son application au niveau de LGA, situé à
Réghaia. Pour ce faire, nous avons procédé comme suit :
La première partie du travail c'est faite en analysant
plusieurs méthodes existantes d'étude des effets dominos et de
leurs limites. Nous nous sommes basés sur cela afin de réaliser
une méthode qui regroupe le moins de limites possibles. Une fois la
méthode posée, nous somme ensuite passé à son
application. Nous avons effectué une étude critique de
l'étude de danger existante puis nous avons enchainé avec une
analyse de l'accidentologie liée aux entreprises ayant des produits de
même type que LGA et des accidents à effets dominos, l'analyse
s'est faite sur la base de 224 accidents. De ces étapes nous avons pu
déterminer les événements primaires les plus susceptibles
d'engendrer des effets dominos au sein de LGA et qui sont :
- VCE au niveau de l'atelier CCAM (cause hydrogène). - VCE
au niveau du parc bouteilles d'acétylène.
- Incendie au niveau de l'atelier CCAM (cause hydrogène).
- Incendie au niveau du parc bouteilles d'acétylène.
Grace aux simulations à l'aide des logiciels nous avons
pu déterminer les effets de ces événements et la chaine
d'événements qu'ils engendreront ainsi que le niveau de celle-ci.
Nous avons ainsi construit 3 réseaux bayésiens.
Des calculs sur les probabilités d'occurrences des
événements ont étaient fait et suivi de calculs de
probabilités de combinaisons d'événements. Enfin nous
avons pu déterminer l'indice de risque individuel qui permet de
délimiter les zones où toute personne présente est
touchée par l'effet. Ces données permettront ainsi une
évaluation très concrète du risque.
Une autre partie a été consacrée aux
effets dominos externes, nous y avons appliqué un cadre nommé
HAZWIM qui permet d'apporter des solutions solides aux accidents dominos
externes. Nous avons appliqué la partie qui concerne LGA et
détaillé la partie que doit effectuer l'entreprise en
collaboration avec AIR LIQUID.
Nous avons achevé cette étude par la
présentation de l'impact financier des événements dominos
présentés qui s'élèverait à plus de
2.000.000.000 DA en terme d'installation et plus
134
de 2.700.000 DA journalière en pertes brutes en terme
de production à l'arrêt. Nous avons également montré
l'impact indirect de ces événements dominos sur d'autres
entreprises et enfin nous avons proposé l'implémentation d'un
plan de continuité d'activité.
Nous tirons beaucoup d'enseignements de ce travail, notamment
la complexité de détermination de manière précise
le flux du risque du fait que c'est une fonction multiparamétrique
extrêmement complexe de tous les facteurs circonstanciels entourant la
source de l'événement. Nous avons également pu constater
que le domaine de l'étude des effets dominos est assez récent et
qu'il reste beaucoup de travail à y effectuer.
135
Bibliographie
[1] ARIA : Analyse, Recherche et Information
sur les Accidents ; Retour d'expériences sur les accidents
technologiques.
[2] Documents internes LGA
[3] Abdolhamidzadeh, B., Abbasi, T., Rashtchian, D., Abbasi,
S.A., 2010. A new method for assessing domino effect in chemical process
industry. Journal of Hazardous Materials 182, 416-426.
[4] Cozzani, V., Gubinelli, G., Antonioni, G., Spadoni, G.,
Zanelli, S., 2005. The assessment of risk caused by domino effect in
quantitative area risk analysis. Journal of Hazardous Materials 127, 14-30.
[5] Farid Kadri, Eric Chatelet, Babiga Birregah 2011. Analyse
d'Effet Domino : Méthodes et Outils. Workshop interdisciplinaire sur la
sécurité globale, 1-15.
[6] Journal officiel de la république Algérienne
N°37, Dimanche 8 Joumada El Oula 1427 Correspondant au 4 juin,
Décret exécutif n° 06-198 définissant la
réglementation applicable aux établissements classés pour
la protection de l'environnement, Edition original, p.8.
[7] SAADI.S, 18 Décembre 2015. Développement et
validation d'une approche globale, dynamique et participative
d'évaluation environnementale stratégique.
Doctorat de l'Université El Hadj Lakhdar BATNA, Institut
d'Hygiène et de Sécurité Industrielle, p.44.
[8]
http://www.biostatisticien.eu/springeR/livreR_presentation.pdf
, consulté le 25/05/2019 à 15h00.
[9] Khan, F. I., & Abbasi, S. A. (1999a). Major accidents
in process industries and ananalysis of causes and consequences.Journal of Loss
Prevention in the ProcessIndustries, 12,361 178.
[10] Khan, F. I., & Abbasi, S. A. (1999b). Assessment of
risks posed by chemical indus-triesdapplication of a new computer automated
tool MAXCRED-III.Journal ofLoss Prevention in the Process Industries, 12(6),
455 469
[11]
www.arbre-analyste.fr
, consulté le 28/05/2019 à 13h00.
[12] INERIS, 2004, Guide technique relatif aux valeurs seuils
des effets des phénomènes accidentels des installations
classées
[13 ] Khan F.I., and Abbasi S.A., 1998,
Models for domino effect analysis in chemical process industries. Process
Safety Progress-AIChE, 17(2):107-113.
[14]
136
Khakzad, N., Khan, F., Amyotte, P., 2011. Safety analysis in
process facilities: comparison of fault tree and Bayesian network approaches.
Journal of Reliability Engineering and System Safety. 96, 925-932.
[15] Hind Bouchra MENAI & Tiziri AIT MESSAOUD, Juin
2018.. Etude des effets dominos et optimisation de la surveillance des
paramètres critiques des Process à haut risque - cas du centre de
maintenance BHGE-ALGESCO. Mémoire de fin d'études.
Département de Maîtrise des Risques Industriels et
Environnementaux, Ecole Nationale Polytechnique, Alger.
[16] Bahman Abdolhamidzadeh a, Tasneem Abbasi b, D.
Rashtchian a, S.A. Abbasi, 2010, Domino effect in process-industry accidents an
inventory of past events and identification of some patterns.20p.
[17] G.L.L. Reniersa, W. Dullaertb, B.J.M. Alec,, K. Soudana,
2005, Developing an external domino accident prevention framework: Hazwim
137
Annexes
138
Annexe 1 : Base de données accidents liés
au gaz de l'air (Aria)
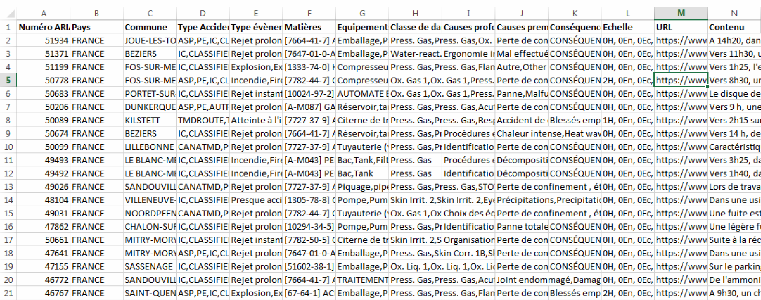
139
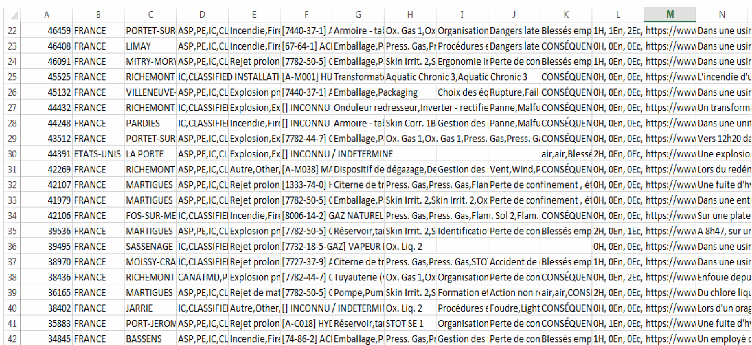
|
A B
|
C D
|
E F
|
G H I J K
|
L
|
M
|
N I
|
|
34835 FRANCE
|
RICHEMONT
|
IC,CLASSIFIE
|
Explosion,Ex [A-M025] FU
|
Onduleur redresseur,Inv
|
Gestion des risques,Risk rCONSÉQUENOH,
|
OEn, OEc,
|
https://wwn
|
Une explosior
|
|
34478
3672.5
33963
|
FRANCE
|
SASSENAGE MOISSY-CRA PORCHEVILLI SANDOUVILl
|
IC,CLASSIFIE
|
Autre,Other [] INCONNU / INDETERMII
|
Ox. Lig. 2
|
Gestion des Gestion des Formation el Formation el
|
Mal effectué Blessés emp
|
1H, QEn, OEc,
|
https://wwn
|
Dans une entr
|
FRANCE
|
IC,CLASSIFIEI
|
Incendie,Fin [7439-90-9] KRYPTON,[742
|
Press. Gas,P1
|
risques,Risk IjCONSÉQUENOH,
|
QEn, OEc,
|
https:/fwwvi
|
Un départ dei
|
FRANCE
|
ASP,PE,IC,CL
|
Explosion,Ex Incendie,Firi
|
[7803-62-5] ç
|
Emballage,P
|
Press. Gas,Pr
|
Autre,Other, Blessés emp
|
1H, QEn, OEc,
|
https://ww{n Dans une usin
|
32695 FRANCE
|
IC,CLASSIFIEI
|
[A-0021] MA
|
Echangeurd
|
MOT SE 1
|
Action non nCONSÉQUENOH,
|
QEn, OEc,
|
https://wwn
|
Un feu se décl
|
30887 FRANCE
|
ROGNAC
|
SALAISE-SURASP,PE,IC,CLAutre [ASP,PE,IC,CIi[Rejet prolon
p héna
|
[7727-37-9] /
|
Emballage,P
|
Press. Gas,Press. Gas,Flam. Sol 2,Acut BI FSSES TOT
|
2H, QEn, OEc,
|
https://wwn
|
Dans une usin
|
i
|
30375 FRANCE
|
7727-37-9 AZOTE
[ ]
|
Press. as r
P Gas,Pi
|
d es
|
Perte erte
I
|
0En OEc,htt
r r
|
s: wwn
p !f
|
Dans une usin
|
i
|
30325
|
FRANCE
|
DENAIN
|
IC,CLASSIFIEI
|
!noeud ie,Fii[74-85-1]
|
ETE Réservoir,ta
|
Press. Gas,Press. Gas,Acu
|
Foudre,LightCONSÉQUENOH,
|
OEn, OEc,
|
https://wwn
|
Un feu se décl
|
|
30157
|
FRANCE
|
JARRIE
|
ASP,PE,IC,CL
|
Autre,Other
|
[A-0O28] OXYDES DE FER,[
|
Ox. Iiq. 2
|
Gestion des
|
Mal effectuée,Yet poorly
|
OH, OEn, OEc,
|
https://wwn Dans une usin
|
|
26146
|
FRANCE
|
JARRIE
|
ASP,PE,IC,CL
|
Rejet prolon
|
[7664-41-7] /
|
Clapet,Chec
|
Press. Gas,Pi
|
Procédures
|
Perte de con
|
Blessés emp
|
1H, OEn, OEc,
|
https://wwn Une fuite de 1
|
|
25494
|
FRANCE
|
SALAISE-SU
|
IC,CLASSIFIEI
|
!noeud ie,Fir
|
[1333-74-0] I-
|
Emballage,P
|
Press. Gas,Pi Ergonomie i
|
Rupture,Fail
|
CONSÉQUENOH,
|
OEn, OEc,
|
https://wwn Dans une usin
|
|
24872
|
FRANCE
|
JOUE-LES-T ASP,PE,IC,CL
|
Rejet prolon [124-38-9] Dl
|
Dispositif d
|
Ox. Gas 1,Ox. Gas 1,Press.
|
Chaleur inte
|
CONSÉQUEN
|
OH, OEn, OEc,
|
https://wwn Alertés par un
|
|
25587
|
FRANCE
|
SAINT-YRIEI
|
ASP,PE,IC,CL
|
Rejet de mal [124-38-9] DI
|
Emballage,Packaging
|
Gestion des
|
Chaleur inte
|
CONSÉQUEN3H,
|
OEn, OEc,
|
https://wwv`Dans la courd
|
|
29220
|
ALLEMAGNE
|
LAICHINGEN
|
IC,CLASSIFIE
|
!noeud ie,Fin [7782-44-7] (Vanne
|
robin
|
Ox. Gas 1,Ox
|
Ergonomie i
|
Froid intens
|
CONSÉQUEN
|
2H, 0En, 1Ec,
|
https://wwvi
|
Une fuite d'or
|
|
21868 FRANCE
|
DOUAI
|
IC,CLASSIFIE
|
Rejet prolon [6484-52-2-E
|
Bac,Tank,Vai
|
Ox. Lig. 3,Ox
|
Organisatio
|
Défauts mat CONSÉQUENOH,
|
OEn, OEc,
|
https://wwv
|
Dans un établ
|
|
21119 FRANCE
|
GRAND-COU
|
IC,CLASSIFIE
|
Rejet de mal
|
[7564-41-7] AMMONIAC
[68476-30-2]
7782~Ca
[ ]
[7803-62-5] S
[7782-44-7] C
|
|
Press. Gas,PiGestion des risques,Risk r CONSÉQUEN
|
OH, 1En, OEc,
|
https://wwv
|
Un rejet d'ami
|
i i
|
20156 FRANCE
|
VITRY-SUR-S
|
IC,CLASSIFIE
|
Rejet prolon
|
|
Réservoir,taiCarc.2,Carc.2,Press.Gas
|
Perte de con lCONSÉQUEN
|
OH, 1En,OEc,
|
https://wwn
|
Des hydrocart un site en un site coi un site pH
|
16632
15206
|
FRANCE
|
CHALON-SUF
|
ASP PE IC CLASSIFIED INS
r r r
Incendie,Firi
CHALON-SUFASP,PE,IC,CL
|
teur Sen
P r
Emballage,P Actionneur a
|
Skin Irrit. 2 Skin
r
Press. Gas,Pi Ox. Gas 1,Ox.
|
Irrit. 2,0x. Gas 10x. Gt BLESSES TOT
r ~
|
1H,0En,OEc,htt
|
s: wwviSur
p ~~
https://wwviSur
|
FRANCE
|
|
Procédures
|
Autre,Other, CONSÉQUENOH,
|
OEn, 2Ec,
|
|
16072 FRANCE
|
PIERRELATTE IC,CLASSIFIE
|
Rejet de mal
|
Gas 1,Press.
|
Panne,Malfunction,Perte
|
OH, OEn, OEc,
|
https://wwnSur
|
|
10316IALLEMAGNE
|
HÜRTH
|
IC,CLASSIFIEI
|
Explosion,Ex [7782-50-5] C Capte ur,Sen]Skin Irrit.2,S,Choixdes
='
|
Panne,MalfL BI FS.SESTOT
|
1H, 0En, 1Ec,
|
https://wwv
|
Dans une unit
|
141
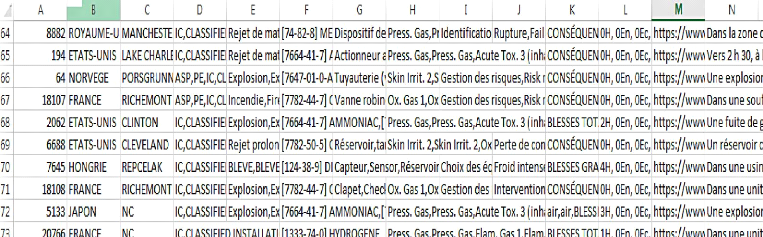
|
|
|
Annexe 2 : Base de données accidents à
effet dominos [16]
|
|
|
|
|
|
Aoeldenis7riwoC t1g ni 19171 6{]5 R re
MdE! nlaJarex; Lsi4i M.E! min4rex iürtl
DeaLhs Injurirts
lt5 evcral hi,intired-
53 t5p
Sî 439
138 W0-- 490
552 >3000
N. Year Location
1_ 1917 ,4sirton, Lilo
L 1917 NovoSccaia,
Canada
PEanLruni LrchernicaI
Explosives factoryI nitratOr
Ammunition ship
5egtlenCe 4f accide.:,
Spillage of hcéHM-3 F - laE--.F Collision with
another ship, F--MaE
°filer reparied impacts- Rekrrencr
Simnel DO} No uses derswlished
500 Tutal6yr blinded_ massive
property. damage
§
Severe darnage ro the plant and property. 1,iore than
33C0
dlrxel Ilin~s
and ]30 business bulldhkg
d amaged. GOO au-W.-mobile
and
350 box car damaged, several soorage ranks
dlescroyed
73 BULIe[ ranks were
d estroyed, misslles dsernahslcd a fillrns
:ear ion and ruptured underground water main
ô5 Million f}rrsOerl· (Larrlige.
3 storage [aDks damaged
Gasholder/Pawns gas TNT prnivctinn nitr7N7 BASF
uvorlts,rrali tank car Liquefaction plan ti
Shi prlammoniurri nitrate
mi -- rupture of pipeline - F.-MaF F ,
h6aE
Leak -- VC --. MaE
Tank ruptureleak F-- sertes of VIaU
F -- hlaE --MaE
LUILII n$9 Las Copland_ ] Ass:hewn_ ]930
Icier La mill1er, 11%53
h41-I lnhS, 20c19
kfarshall, 1987;
N ash, 197,0 Marsha3l. 1987; Nash.
1416
Marshall, 1987;
Nash, 197ffic
Natwn.] 1Suard urrirr Underwriters, 19415;
w hcaton. 1.9,48
Lenoir S Davenport, 4986
Lewis, 1993
Lenoir S Davenipar L, 1993
MH IUAS. 2009 hfH !nos, 21):19
Lenoir F. D. veltpo L
1993: Lewis_
1993: Mahoney, 1990; wpapwcurh. 1955 her <§
Muller, 19169
P Ul I! A.S, 21309 A91IFA5, 2009
142
1933 Neunkirchen, Germany
4, Saint Charrras.
France
5- 19.43 lrfdusi snaren,
Germany
§ 1E44 C1eueland. 4.1501,
7_ 1947 Texas, USA
Lewis, 1993; Marshall, 1987
M]ilüti5, 2009
Lewis, 199a
9.
|
19413
1949
|
Ludwiesharcn. cennany
Perth Amboy, L
|
Tank carJdimcthvi ether Asphalt tank
|
Tank rupture R dispersion of Torments -. Yi
MaE ·F
|
211w
9
|
3818
|
l
|
1951
|
rein: Newark, US
|
LPG sroragefpinpaitie
|
BEEVES
several BEEVES
|
|
14
|
11_
|
1951
|
Baton Poou2e, 4~A
|
ReRneryr naphtha
|
V€E -- nrultixple iexPlokirmt
|
2
|
|
12,
|
1952
|
Bound B*4ok. USA
|
Pheresllc resin ptarstj
phenollr resin powder
|
Powder
smouldering dere to overheawig
|
5
|
21
|
|
|
|
|
MaE--Ma6--M;aE
|
|
|
13_
|
1953
|
Caalvana. Argen[Ina
|
Renneryr recovery i nitrlasoLlne
|
VCE -- three expiosions
|
z
|
|
14_
|
1P-53
|
Warm_ USA
|
5[orarçe unitJLPG
|
F
|
|
|
|
ls
1Frra4
|
Lake Port, LISA
|
Storage arca,ILPÇ
|
MiE MaE
|
4
|
|
Lex
|
1955
|
Vulri[ir3, USA
|
IEe Finery+
liydr41îuriner
unit;naphfha
|
MaL r
|
|
dD
|
17.
|
] 957
|
Montreal,
Canada
|
5rorage tanksrhutane
|
VC ~ F --. 3 6LEVES
|
|
|
t8
|
1957
|
hSeraru,
USA
|
Storage lAnkjkliescl oil
|
Tank cotlapsr srvrre Bre
|
1
|
|
19_
|
195E1
|
|
Tank [rue kg_PG
|
F MULES
|
1
|
|
|
|
USA
|
|
|
|
|
Na.
|
Year
|
location
|
Plantiunil;rhemical
|
Sequence ofaccidcnts
|
Deaths
|
Injuries
|
20.
|
1958
|
Signal Hill.1.6A
|
Rcfineryfwisbrcakcr plan illull
|
Tank eruption F
|
2
|
11
|
21.
|
1959
|
Deer Lake, USA
|
Road rankerJLPG
|
LPG leak and ignition`;
|
t I
|
10
|
|
|
|
|
-.F - BLEW
|
|
|
22.
|
1959
|
Mac KitLrkt, USA
|
Storage areaJIPC
|
Mi E - EVE.
|
|
2
|
23.
|
196+0
|
Bakersfield, USA
|
Storage tankleaustic
|
MO E - F
|
|
-
|
24.
|
106L
|
Perey, USA
|
Tank tru€kfLPG
|
F - MaEs
|
|
|
25.
|
1062
|
Pampa, USA
|
Refineryjisopentane
|
/VILE - F
|
|
1
|
26.
|
1962
|
floe Run. USA
|
Ethanolarnine plantf ethylene oxide
|
Internal exptasion due Lu runaway - VC
|
1
|
2]
|
27.
|
1962
|
Marietta, USA
|
Phenol production plantfbPenzene
|
Discharge of benzene through relief valve
|
t
|
3
|
|
|
|
|
--0 VC damage
|
|
|
|
|
|
|
Overwork - F
|
|
|
28.
|
1962
|
Ibbenburen, Germany
|
Pipeline/hydrogen.
|
MIE - · Fand toxic release
|
|
1
|
29.
|
1963
|
Evanston. USA
|
Warehouse' methanol
|
F -. TaxLe release
|
-
|
1
|
34.
|
1964
|
Attleboro, LISA
|
Vinyl rhloritlr polymerization plant+vinyl
chloride
|
Leak - E - MaE
|
7
|
40
|
31,
|
1964
|
Niigata, Japan
|
RefineryjQil
|
Oil spillage F - L - F
|
2
|
|
32.
|
1.964
|
Liberal, USP,
|
Compressor sta/iourjpropane
|
VCE - multiple explosions
|
|
|
33.
|
1964
|
Louisville. USA
|
Neoprene plantimono veiny] acetylene
|
Deçgmposirinn nFmnno vinyl acetylene due ru
overheating - MaEs
|
12
|
g
|
|
31.
|
1965
|
Carxhage.
|
Process plan cïol I
|
p -. Ma E a nd F
|
-
|
-
|
|
|
USA
|
|
|
|
|
35.
|
1966
|
Feyzin, France
|
Refinery storage tanks/propane
|
Propane leak - F -. hTa E
|
113
|
El
|
36.
|
1967
|
lake
|
Refineryjisa butane
|
Mae major F
|
7
|
13
|
|
|
Charles, LISP
|
|
|
|
|
37.
|
1963
|
Romfoo,d, LfK
|
Naphtha
|
[jet)F -# F
|
-
|
-
|
38.
|
196E
|
Millard
|
RefineryJlyttrocarbans
|
MIE - F
|
-
|
-
|
|
|
Haven. LFIC
|
|
|
|
|
39.
|
196g
|
Port Arthur, USA
|
Storage tank/petrol
|
MIE -, F
|
3
|
5
|
40.
|
1968
|
Pernis, Netherlands
|
Refineryflrydrocarbon vapour
|
Overflow lead
ta VC MaE ·-- F
|
2
|
95
|
91.
|
1968
|
Lievcrkozcn. Germany
|
Fvrmarnidines LIpttinic acid plantturea
|
F -1 1aE
|
t
|
14
|
4L
|
19159
|
Dormagelk Germany
|
Ethylene oxide plantl ethylene oxide
|
MaE -b hfal
|
1
|
413
|
43_
|
19614
|
Glendora, USA
|
Rail tank carfvinyl chloride
|
Tank derailment and Irak -+ series
|
|
1
|
Other reported
impacts--'"ftelerence
L vis, 1993: WWtiwui L]. ] 9ii Kier Er Muller,
1983
MHIDAS, 2009 MHI1AS, 2409
MHFD!S, 2009 MEILDAS, 2009 Lewis, L993: Mahoney, 1990
Mahoney. 1990
MHLDAS, 2009 MT- RDAS. 2009
Lewis, 1993; Mahoney, 1990
97 Storage Mahoney, 1990
tanks destroyed
0.5 Million Lenoir. 1993 property damage
Lewis, 1993; Mahoney, 1990
M HFDAS, 2009
Five spheres Lewis, 1993;
destructed Mahoney, 1990
Health and Safely Executive, 1978; Marshall, 1977
MI4[DAS, 2409 MMIDAS, 2009
MHFDAS, 2009
Pamela 1969; Lewis, 1993; MSAPH report, 1968
MHFRAS., 2009
MI-IFL7AS. 2009
Icier & Muller, 1993; Slater, 1979
Nn
|
Vaar
|
Inc Firn
|
FtantinnirfrhFmiral
|
ÇuPrrvnFarri1pnrç
|
rlAarhç
|
injuries
|
49_
|
1955
|
Lauic.1,135.41.
|
LFG rankcarsjLPG
|
Tank derdiC[[LL'iIL lead ta seri al Tank expbasiDns and
fireballs
|
2
|
)33
|
45.
|
I0G9
|
R6poelalç Hungary
|
Carbonic acidJstorageJ purified CO2
|
MaE -- hlais
|
9-
|
15
|
41
|
1959
|
Round
|
React orfnitn hcna]
|
MiE --, MaE
|
1
|
1
|
|
|
Brook, USA
|
|
|
|
|
47.
|
1959
|
Geary, U5A
|
Rail tank earJbutane
|
F -- 9LEVE
|
--
|
--
|
48.
|
1969
|
Lang Beach.
|
Tank? petrel
|
F --. MaE
|
1
|
B3
|
|
|
USA
|
|
|
|
|
49.
|
1969
|
Texas City, USA
|
Petrochemical) butadiene
|
Detonation -- WE,
|
3
|
|
|
SD.
|
1970
|
6eaumon[, USA
|
OIL slnpe rank;oi]
|
Tank failure and oil spillage --
|
|
|
|
|
|
|
F--.Fin other
|
|
|
|
|
|
|
16 tanks nearby
|
|
|
St
|
1070
|
Crescent. LISA
|
Rai] tank cary propane
|
Propane teak --, V -- serial Mais
|
|
66
|
52_
|
19770
|
Ludwigshafen, Germany
|
Transportationf propylene
|
VOE ,-F Fand MaE
|
5
|
3
|
53_
|
1970
|
Big springs, USA
|
RellneryJalkyLttlon/ hydrocarbon vapors
|
Ya -- · MaE
|
--
|
|
59_
|
1970
|
Linden, USA
|
Refinery/
hydrorrackingtaail
|
Physical explosion --0/CE and Fire
|
--
|
|
55.
|
1971
|
Baton Rouge_
|
road tanker,lethylene
|
Physical B '. F
|
--
|
21
|
|
|
USA
|
|
|
|
|
51
|
1971
|
Houston, USA
|
Rai] rank car/vinyl chloride monomer
|
Tank derailment and punctured serial tank
explosions and Cires
|
1
|
5
|
57.
|
1971
|
Longview, USA
|
Polyethylene plant/ethylene
|
Gas pipe broke --. VC --, rupltkrre qF other ethylene
pipelines -- VCs
|
4
|
60
|
58.
|
1972
|
Yokkaichi,Japan
|
Rubber plantfwiste
water treatment unit/ waste water
|
MIE --. F and reactor rupture
|
--
|
--
|
59.
|
1972
|
Rio de
Janeiro, Brazil
|
Refineryts[orage areaJLPG
|
MIE --. BLEW
|
37
|
53
|
|
00.
|
1072
|
Duque de
|
Storage tarlkl[PC
|
VOE -- BLEVE
|
39
|
51
|
|
|
Caxias. Brazil
|
|
-- series of explosions
|
|
|
I.
|
1973
|
Kingman, LISA
|
Rail tank carJprppane
|
(Jet) P --i BLEUE and fireball
|
]3
|
more than 90
|
02,
|
1971
|
CUrnax. iJ A
|
Rail tank carpdinyt chloride monomer
|
Tank derailment and Vial leak -- VC --. F --
13LEVE
|
|
|
61
|
1974
|
Beaumont, USA
|
ltydroca] erns
|
via --I, F and MaE
|
2
|
10
|
64_
|
1974
|
FetaL USA
|
TerminaI1salt dome storaQerbutane
|
1wliE --P Mae
|
--
|
|
(ehar r19111111.11 imports Rafaren e
5[ruclural danlage Piseriberg,I oth,
within 400 It, hlmost lia Breeding, 1975;
all glasses were Lenoir I Dawenport,
shattered within 3993
hall a mile
Chiles. 2001
MHIDAS, 2009
MH IDAS, 2009 MU IRAS, 2009
30 Million property Lenoir&
I3awenport,
damage 1993
Mahoney, 1990
Lewis, 1993;Strehlow, 19733; W
itrous.15?0,
2 Barge caught MHIDAS. 2009 fire and
sunk
Property damage LeniEr & Dawenporr
worth 59.7 million 1593
Property damage Lenoir & Dawenpark
worth 5 87.6 million 1993
MHIDAS, 2609
Eisenberg et a]4 1975; Lewis.
1960
Eisenberg er al.. 3975; Lewis, t 9E0
MHIDAS. 2009
Mal uney_ 1990 MH1DF5, 2009
Marshal I. 1981 Eisenberg et a]_ ] 915
MI!]DAS, 2009
Glass breakage Lenoir 15 Daeeoparr,
no to Ti km 1993
Other reported imgactt Reference
Damage in a Lewis, 1980, WARE,
radius 01-4,5.kin, 197E: Van E
jnatten,
6 tan burned, 1977
conrml room
demolished
M1-JD i.S, 2009
Mahoney, 1.990
Mii]DAS, 2049
MH]DA5, 2009 MI411DAS. 2009
Lewis, 1 g491,
Lewis, 1433. Erarc Wilier, 1983; Marshal 1987 Mli]DAS,
2009
Mahoney. 1990
Mahoney, l990
M1-I3DAS, 2009
Amyut, 1960; Lewis, 1993 Mississauga,
1979
MH]DAS. 2003
MH]DAS, 2009
MH]DAS, 2009
4540 People 1.11-01:1A -5,.
2009 evacuated;
damage worth
1 1.26 million
MIi]DPS, 2009 istnULdÇ ann4
|
Year
|
Location
|
PlantfunitrchemicaI
|
Sequence of accidents
|
Deaths
|
Inkuries
|
6.7,
|
1975
|
Reek.
hielher]ands
|
EthyFene plant? propylene
|
VC -i F(numerous Ares)
|
14
|
104 €inside the factory); 3 (our4ide}
|
58,
|
1975
|
MOIL 115A
|
Coking untqdrun crude vi]
|
F-rt F
|
-
|
-
|
69.
|
1976
|
Geisttlar, USA
|
Petrochemical plantboIy Iyrooi ether reactor/ethylene
oxide and propylene oxide
|
MaE -1. major F
|
-
|
-
|
'?fl.
|
1976
|
Baton
|
Chemical pLantjnaturai gas
|
MaE -4 toxic release
|
-
|
-
|
|
|
Rouge. USA
|
|
|
|
|
71.
|
1974
|
fiddyston, USA
|
Starasie arealmethanol
|
Ma G · -437
|
-
|
-
|
72.
|
1976
|
Gaiayaquit, Ecuador
|
'fankergl+hC
|
VCE -s cedes of explosions
|
-
|
.50
|
73.
|
1977
|
Puebla. Mexico
|
9tarage bullets/vinyl chloride monomer
|
VOA leakage
~* VCF -- 4 BLEVEs
|
1
|
3
|
74.
|
1377
|
West ego, USA
|
Crain silafgrain dust
|
hlaf -.Ala@ -. MaE
|
3E
|
10
|
75,
|
1977
|
Galveston, USA
|
Grain silojgrain dust
|
M1aE - MaE 4--. MaE
|
15
|
|
Ni,
|
1977
|
Romeoville, USA
|
ReFinery$stolaRe amt./diesel fuel
|
F -. F
|
-
|
-
|
77,
|
1978
|
?,Ixyliq, Sandi Arabia
|
Cas processing unIqmethane
|
Gas leak due to Internal corrosion
|
|
|
|
|
|
|
-* VC -0 la pipe section snuck a
|
|
|
|
|
|
|
LPG spheri[a1 tank -* release
|
|
|
|
|
|
|
82 L'CE)
|
|
|
78_
|
1978
|
Texas, USA
|
LPG storage tanks/LPG
|
Crack dine to internal overp ressurgi
|
7
|
10
|
|
|
|
|
Led to LPG Teak
|
|
|
|
|
|
|
- ·F-.]sLEVE
|
|
|
79.
|
1979
|
f5ttsheld
Towershlp, uSA
|
Road tanker!prupane
|
Leakage -.
series of explosion
|
-
|
-
|
8Q.
|
1979
|
Mississauga, Canada
|
Rail tank
catIprapane, ere
|
Tanks derailment and F - ELEVE.$ and toxic
release
|
|
|
Si.
|
1973
|
Tacoma, USA
|
Hydrogen compression system/hydrogen
|
MaE -. toxic release
|
-
|
3
|
82.
|
1973
|
Ras Tanura, Saudi Arabia
|
Re 9nery fstorage tankipetrol
|
MaE -. F
|
2
|
G
|
81
|
1974
|
Phials, Italy
|
Plastic plantfcumene
|
F -0 F
|
1
|
-
|
84,
|
1979
|
MI]lIgai1 U5A
|
Train of tank tars containing ammonia, acetone.
chlorine, etc
|
Derailment
- Ma.Es - F1fox
|
0
|
14
|
85,
|
I980
|
Deer Parr USA
|
Ship/Vacuum distillate
|
MaE -- F
|
3
|
12
|
|
Q
|
14Rf1
|
Rion,1,1Po F"rsnr6
|
TF,ernirsF c+ planed,'
|
11.1iF --.. F
|
--
|
--
|
wrier repartemmrat Kelv.r1144-
glas[ destroyed Lewis, 1993;
the a[kyiation Mahoney, 1994
unit, whale
refinery shutdown
MHIDAS. 2009
MHIDAS, 2009
500 people NIHIDI15, 2009 evacuated
Marshall, 1987
h1HIDA5,2009
NI'$9 annual repart, 1983 MHIDAS, 2009
MHIDAS, 20179
LewEs, 199;1; Mahoney, 1990 'Lewis,
1993; Mahoney, 1994
2 Blocks were 19HI1)A5, 2009 evacuated
MHIDAS, 2009
Hundreds of MHIDAS, 2009
people evacuated
1500 People MHIDAS,
2009 evacuated
MHIDAS, 20479 MHIDAS, 2009
PresslY, 2009
'Mahoney. 1940
Severe damage Lewis. 1993;
to nearby houses, Mahoney, 1990
3 31 million damage
Damage r0 electrical Lewis, 1953;
power supply system Mahoney, 1994
and fire extinguishing systen
entire storage complex MIU1 SS, 2009 devastated, a
barge Caught rire due #4 flying missiles
20 People evacuated M111DhS, 2009
Mahoney. 1990
|
|
..re 7117011
|
|
|
|
|
rra,
|
rta
|
am.rumerrnem ar
|
5equrnce orac€raenîs
|
ma s
|
injuries
|
87.
|
1980
|
ElaNger, Texas, USA
|
Refiaery+aikylarioot uni I./Light [-ICs
|
Vessel rupture
and HC release · VC
|
|
41
|
88.
|
1980
|
Salina
|
Sitirage tank+oil
|
Lightening '.- F -i · F
|
|
|
|
|
|
Out, Mexico
|
|
|
|
|
85_
|
1980
|
Deer Park, USA
|
Phenol planticurnene
|
F - F
|
-
|
-
|
90.
|
1981
|
South
|
Rai Icarfammpnia
|
F - Ma F
|
|
-
|
|
|
Hutchinson, USA
|
|
|
|
|
91.
|
1981
|
Montana, Mexico.
|
Rail tank car,l0lorine
|
Tanks derailment
|
17
|
1000
|
|
|
LISA
|
|
--P Maës
|
|
|
92.
|
19731
|
West Glamorgan, UK
|
Reiineryfpropane
|
MiE- ·MaE
|
-
|
-
|
93.
|
1982
|
Livingston, USA
|
Freight train/
petrochemical pradttcrs
|
Tank derailment
-, several explosions
|
-
|
-
|
94.
|
1982
|
Philadelphia, USA
|
Storage tankIcam,ene
|
MaE -- F
|
-
|
-
|
95.
|
1982
|
Houston, USA
|
Tank wck/propanc
|
F F
|
-
|
3
|
|
N.
|
11420
|
Caracas, Venezuela
|
Elea city 49mpany/
staraielloil
|
F - F -. boi lover
|
150
|
>$04
|
97.
|
1983
|
Milford Haven. UK
|
Refirtieryf storage tank? crude oil
|
F - 2 baallavers
|
-
|
2U
|
98.
|
1983
|
Hatr ton,115A
|
Chemical plant/ merhyt bvomFde
|
Ph+,aSica1 E - toxic release
|
2
|
Scveral
|
|
N.
|
1983
|
Part
|
Shi plcliesel foel
|
F - MaFs
|
-
|
-
|
|
|
Neches, USA
|
|
|
|
|
100.
|
1983
|
Dursley, UK
|
Diesel engine production plant
|
F -* toxic release
|
-
|
5
|
101,
|
1983
|
Baron Rouge, USA
|
Plastic plantflnyl chloride monomer
|
MaE -, F
|
-
|
2
|
102,
|
1983
|
Swindon. UK
|
Process plan[fresin
|
F - MaE
|
|
|
103,
|
1983
|
Dalhousie, Canada
|
Electrolysis plan[
|
M[E --* [mdc release
|
-
|
-
|
|
104.
|
1983
|
Newark, USA
|
Storage area,' unleaded gasoline
|
Tank overfilling - MiEs - MaE
|
|
|
105.
|
1924
|
Las Piedras. Venezuela
|
Refirter37hydrogers plantjoil
|
011 une Fractured -, F -, F (jet lire
ore gas pipe)
|
|
|
106.
|
1984
|
Mexico city, Mexico
|
Storage tenksjLF;G
|
Line rupture and LPG leak
|
650
|
6400
|
|
|
|
|
- VC - · F
|
|
|
|
|
|
|
13LFVEs
|
|
|
107.
|
1984
|
RumewwiIle, USA
|
Refinery/absorption column/propane, butane
|
Column crack -, VC - MaE
|
17
|
31
|
108.
|
19X1
|
Rumb ly, India
|
Port warthousel chemicals
|
Chain of
explosions - major F
|
-
|
-
|
|
109,
|
1985
|
Sits Antonio. nio. USA
|
Storage tankJamITNania
|
MaE - toxic release
|
4
|
23
|
110.
|
1935
|
Pii0k>. Italy
|
Ethylene plant'
|
Kel lei system
|
|
|
CltNrr repined imp4itt5 Fietereilte
Residemta in 2 mile radiun evacuated
â4 Families and local school puaxrared
3004 Residents evacuated
Praperry damage worth S 210 million
32.00 Person evacuated
MIDAS, 2E619 MIDAS, 2019 h1HlDA5,
2049
IAHIDArh 2000
Browning Searsnan, 1989 Lenoir
~5,5V 71purL, 1933
Mamsot, 1989
hiHIDASw 2009
MHIDAS, 2009
Lenoir Si Davenport, 1993
hIHIDAS. 2009
MHIDA.S. 2009 h111I1305, 2009 MHIDA5.
2009
10et4 l990:: Mahoney, 1990
Lewis, 3993: Mahoney, 1990
Anderssoal,
1991: Metz, 1990
MHID 2009 Mahoney, 1940 Lewis. ]993
MHIDA5, 2009 MAWS. 20134 Mahoney, 1990
|
|
|
|
|
Deaths
|
Imjuties
|
-7d157--Tar
|
cahDii
|
PlantAvant rchemial
|
Stirierireof-accidents
|
11.1_
|
1985
|
!Wks, Italy
|
TransportationNil
|
MOE -* F
|
|
170
|
112.
|
198S
|
Algeciras, Spain
|
Ship+naphtha
|
htaE MaE
|
|
|
113.
|
1935
|
centsripiez, Italy
|
Pelrleum trmmimal/oil
|
Tank ouerï1 Ill ng
VC major
|
4
|
1713
|
114.
|
1986
|
Petal, USA
|
Pipeline/LPG
|
MiE -- MaE and
rineL II
|
|
12
|
115.
|
193B
|
Thessaloniki, Greece
|
01] termLnal'al]s
|
411 spillage and
|
|
|
|
|
|
|
F - · several Fa
|
|
|
116.
|
1987
|
Antwerp, Belgium
|
Ethylene oxide p1#nt/diStilIJtiDf1
column/ethylene oa<idr
|
EO decomposition and iritsrnil explçxcentsuu --
F
|
|
14
|
|
11?.
|
]987
|
lvrt Herriot. France
|
Storage tanks/ail
|
Oil spray and flash
|
2
|
|
|
|
|
|
F WES
|
|
|
118.
|
1987
|
Genoa, Italy
|
Storage facdsty/ methanol and hexane
|
F klaEs
|
4
|
|
119.
|
1987
|
Ciudad
|
Refinery/gasoline
|
MiE F
|
|
|
|
|
Madero, Mexico
|
|
|
|
|
120.
|
1987
|
Pampa, USA
|
TeQ.€hemicaf/ acetic arid plant/
|
Damnation VCE
|
3
|
|
|
|
|
Ketone
|
|
|
|
121.
|
1988
|
Perth Amboy. USA
|
Road tanker/ bexaire
|
F ·F
|
|
|
122.
|
1936
|
Bombay, India
|
5roaage tank/ benzene
|
MIE-.F
|
35
|
15
|
123.
|
19134
|
RIMS
|
S14[aOfLPG
|
F SLEYE
|
|
|
|
|
IUpton, UK
|
|
|
|
|
124.
|
1988
|
Brisbane, Australia
|
Chemical Factory/ deier'genr
|
MiE -- · toxic release
|
|
30
|
125.
|
1989
|
Antwerp, Belgium
|
Ethylene oxide plain/ d istiIlatlxn {4]urnn eariltrie
ORide
|
Internal expiation pipemtrrk [rapt bred and
|
|
5
|
|
|
|
|
/lame flashed bask ro anjL1.er columns - ·
internal explosion
|
|
|
126.
|
193'9
|
Pasadena, USA
|
Polyethylene plant/FICs
|
Hydrocarbon vapour release -- VC -.
MaEs
|
24
|
i30
|
|
|
|
|
[a storage tank and a
|
|
|
127.
|
1989
|
ionova, Lithuania
|
Ammonia sttrragef ammonia
|
Ammonia tank rupnnre - Fs and ton(
drsperslon
|
7
|
57
|
128.
|
1989
|
AI ifi]lah, Iraq
|
Transportation/ explosives
|
MaE -.F
|
14]
|
|
|
139.
|
1989
|
Baran Rau,»/, USA
|
Brimes/ethane and propane
|
MiE - ·F
|
|
|
130.
|
1990
|
5tarilow, UK
|
Farah reactor/ chemical mixture
|
[Jet] F --. MaE and fireball
|
|
5
|
131.
|
19570
|
Sydney, Australia
|
LPG rerminalrrrG
|
Gas Leak -- F -. 6LEVEs
|
|
|
132.
|
1990
|
54. Peters AuStrdli,l
|
G,1s slepp10PC
|
MOE -- Mrstiall
|
|
|
133.
|
1991
|
Caatzaroa]ros, Mexico
|
PetrechQmical complex/vinyl drIontlr plant
|
htiE -- MaE
|
|
|
|
i,Pp; Tra<r 14Cdncin
rllrrrrlrrn[rl,.çrr+i4A arournre firm-norms
vratns' ri uurie5 vrT,['rrçp[rftra lm
134, 3992 La Melle, France Re1knetyrhyrdfocratker MaE -
Fand MiEs USS 364,4091000 The 100 LargesE
unitfhydracar1Xan and Losses,
2443 hydrogen
1354 1092 GrAd1Prd, 111{ Çht ·Tri al
wdrehouSt1 P17011 ormfainers 33 5ignifica n1 tir HC:3!I h Arid.
$,[rely
a2odi lsoburymnIerile rectured - MIE - Fs and waxer
po1luLi0is aeCL.Illitie, 1993
13e. 1992 Casiieford, UR Chrrniiails Jet -. Fs - -
Extensive Health and Safety
Ora0tti3+ 4arna8r EN4LcutiwE.1994
137. 1993 Ririgaskiddy. 3reland Pharmaceutical facility
MaE - · Iarze F 32 TyvuIxinational
Monitor, 2009
13& 1943 Shenzher. thLna Warehouse/ SaE - MaE 15
14] Gua€hurr 2000 ammonium nitrate
139. 1993 Jacksonville. USA Petroleum terminal/
F- · tank overflow 1 Erra 2009
unleaded gasoline - · several pool
fires
140. 1994 Se] Pre. HSA Petroaeu rr Walla? MIF -. F -
1.1.tE Two. buildirç s llealTh arid Safety
thermoplastic and a tank Farm Executive,
1993
lubber produce caught flee
141. 1994 Milford Trk..icC rrRnrtyrl-f[g Pipe failure -
26 L48 f.{i!Eion dames H$F 2î1043
Haven, LEA hydrocarbon release - · MaE
-Fs_.flue relief elamaer · · F
nitrocellulose
,53banla crude oil
HG. 11995 Voljtortad, Rail tanker] F -. Mal - - MHIDAS.
2009
Russia propane
117_ 1945 Savannah Chemical F -. · toxic
release Nearby ulwn EPA, 199B
USA s[afaRe a eti+.lcuaoed.
transfer facility environmental
Impace(flsh! kill)
|
|
|
|
|
|
|
|
|
|
|
|
14a_ 1996 Fae2e. ].PG Irr.mLling F1as1, fire -.
explosion - - zenvier, Anronelin,
|
Italy eernsinall PG and pool Lire -. BLFVEs
Dattilo, & Rasai 200]
|
|
|
|
|
|
|
|
-. fireballs
|
|
|
|
|
|
|
USA plantl'hydroxrn
|
|
149. 1996 Martinez Hydrogen VVE - F - 2
TMHIDAS, 2009
|
|
|
|
|
|
|
USA
|
|
150. 1997 [Surrulde, Grain dryer1LPG F - ·
6LEVE 2 2 Abbas! and A,bbasi, 2477,a
|
|
|
|
|
|
|
|
|
151. 1997 Viisakhapa tnam_ HPCL refinery/LPG Tank F --
Mat GO 5 ·20 Million Ulan A Abbas%,
India -. MaE and Fs damage 1999a, 199n b
|
|
|
|
|
|
|
|
ethykr c chloride and sulphur
|
152. 1947 roLogdalls · rmdrr.
TrAnaaprkrla,irurf F- · rrrajprlT - - hMHIDAtiS,
2009
|
|
|
|
|
|
|
Phlippinea hydrocarbons
|
|
153. /997 Zamboanga, T7anSpprl3#ipnf F - · MIE
-. 1 1 6 MF1IIMS, 2U09
|
|
|
|
|
|
|
|
|
154. 1998 Mbert City. EISA Turkey Farrr[lpropane
Vehicle struck pipeline 2 7 Wolf, 2006
|
|
|
|
|
|
|
|
|
- F -*BLEVE
|
|
|
|
|
|
|
|
hyd rix:arl7pn
|
155. 1993 Lori 1t rd Gas process! n2 plan11 VCE --
maloi F 2 8 The 100 Larges[
Victoria. Australia heat exchanger!' Lasses,
24103
|
|
|
|
|
|
|
|
|
|
155. 1949 Laem Refl,seryf[ank Tank over1t11uyg 7 ie
4600 Residents Pres4TV, 2009
Chabang, Thailand farmlgasoline -. VOE - F had to
be
|
|
|
|
|
F -- series of expledions 22
Inclepélldelt, 2009 Enwlronment-Agency.
2009 l.ir .wcr{d. 20(151.
Açus. 1e, 2009 Acusafe, 20139
Acusafe, 2009
Acusafe, 2009
Acusafr, 2009 The 100 Larges t DafieS. 2901
AcU$4*, 2009 Acusafe, 2009
Acusalè, 2009 Acusafe, 2009
NYtirrres. 2009 Acusafe, 2009
1JriEY. 2009
J LS E, 2009
No.
|
Year
|
location
|
157.
|
2000
|
Meidea
|
|
|
City, Mexico
|
155,
|
2000
|
C]oticestef. UK
|
159,
|
2E100
|
Douglas. USA
|
160.
|
2000
|
TrxaS, USA
|
161.
|
2000
|
Ontario. USA
|
|
16
|
20O1
|
Ohio, USA
|
163.
|
2001
|
Pennsylvania, USA
|
164,
|
2001
|
Louisiana. U5A
|
165.
|
2001
|
Roncador. Stazii
|
16e,
|
2001
|
Nev.P1 . U$A
|
167.
|
2001
|
Michigan. USA
|
16S.
|
2001
|
Castonla, USA
|
169.
|
2001
|
Delaware_
|
|
|
USA
|
170.
|
2001
|
Perrrt5ylvania, USA
|
171.
|
2001
|
Dayton, USA
|
|
t71
|
2001
|
Toulouse, rraade
|
173.
|
2071
|
ConacophIlltps, dumber Refinery. UK
|
1741.
|
2001
|
Tho de Janeiro offshore, maaI!
|
173.
|
2001
|
Mexico City, hlrxiaxr
|
17e.
|
2002
|
Mississippi, LISA
|
Plant1un ttfcheniiçal
Gad plan[+
natural gas
wasce Ranger station
Oil Held service company/propane
Tanker fnitkJ propane-
Water treatment plant/corrosive gases
ChetYliCal plar}t
Dynamite plant/
dynamite and fireworks RrFmryfLurUine fuel Offshore
platform/
d rain l nikJmixIwe of wader and
hydrocarbons
Ç hemicsi plsnr
Pressed hoard lnanuracturinx plant/wood chips
Electroplating complex
Refinery/sulfuric acid
DynArnire acrd flyeworlts platy Chemical 32 polymer
company
Petrochemical plant/ammonium
nitratr Warehouse RefIneryrfdeerhan12er overhead
pipeirn,xnrre of ethane, prapanc, butane
Oil platform /Firs
Dyc factoryfalcohni .i]iaf rie I laanol
Rv bl cr plant/dryer/
gurnce or accidents
F -- MaES
Propane leak - series of cisplosiona (a tank 9LE5#Es) MiE
MAE
F -. series of explosions
Chemicals awerheaIrd metes
of e9I451003 MaE--. MaEs
Leak -di enplmitt" --. F
E --. E and platform C600difg
F -- .eries or explosions F MaE
F series of expinsroris F -- acid spill
-- relleasIng a cloud of toxic gas
MaE aeries
o f eviovOh$
Refrigeration
system failed
-- overheating
of chemicals
-'- Series of explosions
MaE--liaE
P ipe ruprure and hydrocarbon
release
VC - other pipe ruptures -- Ireba 11
Tank rupture due toowerpreggure --. damage to srariaus
egülpinem gas dispersion -- F -- MaE F , MAEs
F--.Maé
J eat6-- [njurie Other reported impacts
Reference
2 EValtiaaied 200
residents
Several nearby companies were
evacuated
17
1 3 200 Residents
evacuated
2
10 USES S1 SA04,0OE
ilJellase
5
9
1 Million damages
a
1 3 200 People cvacualyd
3CI Mare than 5044 € 2,3 Billion
a
L2 The platform Perrul,rss,
sank Inox the waver 200 L; EPA,
2001
- t F More than 5000 Acusafc, 2009 mph.
evat'uattd
4 6 Atusafe.2009
N. Year Location flantjunitcchernical
1.77. 2002 ICuuirit OiI ProduCI Ille plc-nt/
crude oil
17$, 2002 Alhstin. USA Food procellirg palm
17g. 2003 perm Region. liai] tank can'
Ri.illia pr pone--buTaYleblend
i$ü, 2004 Skikda, LL,'C
planr1lsoiler Algeria
181. 2004 Cliors$gins, ChrmâCa1
plant!
China chlorine
182. !00A Vadadra, o I refinery"
andia slurry /eat Er
183. 2004 zaheda n. Trucir+gasollne Iran
181. 2001 Çcyshabur, Iran Rai] tank
rartuariety
of thrmicall; sulphur, gasoline, Fertilizers. caftan
woo]
185. 2005 Texas City, USA BP refmcry+
isamerizaIion unirlhydracarbons
1.843. 2005 Buncefirld, Uli Oil storage
terminal!'
Motor furl
187, 2005 Sr, Louis. LISA Cas repacking
&
distribution lac-ifityt propylene
L. 2005 FOr1 W4rSh. 415A SOimer1S A
other chemicals
Tés, 2007 Valero Refineryrf propane
41 cKee Refinery. deasplhalting
1TS.0, , niclPropar.e
190. 2009 Sharancl. Iran
Chemical plantj2-erhyle
heuan4l
191. am ;.larleapa, Grain
sllloygralis USA
192. 2009 r,7,agathane, Polymer
india plarn/L]DPElink'
cyclone filter
193. 2008 Yi1h 'U CO, PÙIp. irlyl ac [e
a
China other chemicals
194. 2006 lalbagh, Polymer Bangladesh
195. 2001 San Pwltto1114. Atlas
pallet USA
196 2008 Tar/Maim, Oil tankers
Sequence of accidents
|
Deaths
|
injuries
|
Leak --. Mak -- F MiEs --. MaE
|
4
|
--
5
|
MaE --. series nieNplasions
|
1
|
|
VC --. MiE -- MaE
|
27
|
74
|
|
|
|
Chlorine gas rrak --
|
9
|
3
|
MaEs --. chlorine dispersion
|
|
|
MaE --. F
|
2
|
]6
|
|
|
|
Truck IOU control
hit bus --. P-- arket lorry
lire
|
90
|
1 ] 4
|
Tank derailment
|
328
|
460
|
., F -- MaE
|
|
|
VC --. M.sE --. Es
|
15
|
180
|
|
|
|
|
|
|
Tank overfilling
|
0
|
60
|
, VC , MaE , F
|
|
|
F -- MaES.And f s
|
1
|
|
|
|
|
F -- MiE
|
0
|
4
|
--, other fires
|
|
|
Propane leak -- F -- pipe rack collapse --.
orner pipe rupcore .h.sd chlorine release
|
|
|
MaE -s McEs -- F
|
30
|
38
|
|
|
|
|
|
|
MaE -- MaE
|
--
|
3
|
|
|
|
MiE --, MaE
|
1
|
46
|
|
|
|
F -- Es -- Fs
|
16
|
57
|
|
|
|
I -- P5
|
6
|
6
|
F -- Mi E -- F
|
--
|
--
|
MaE w MaE --.
|
--
|
60
|
Other reported impacts Reference
rxusafe, 2009
Firrw rld, 2Ox13
Pravda, 2000
7 People missing gape, 20114
nearby elm-lividly generation plant & oil
refinery
shutdown
150004 people Chinadafy.
evacuated 2009
Thehindu-businessline. 200g
UNEP, 8009
BBC. 2000: LINF.P. 21)129
More than' billion Chemical Safety
dollar damage and Hazard
tnveatigati.aro Board, 2007 HSE, 2009
Chcrnsafety, 2046
[niowar . 20.09 CS1L. 2009
9111 Plant destroyeil, BBC, 2009
up to 301) m glasses
were flhahrered
Marktopa350. 204.3 Hindustannmac, 2009
11,5100 people Topneirus, 20(19
evacuated
Pity housesgutoed Meta q, 2009
-- Ksat. 2009
Forty oil tankers labri,
2009
No- rear 10E7E1011 ---reanqumrl Ell emtea1
ztiequence Orartiffenrs
umerreparrea Carpacrs rtenererrce
clean up costs $ 13 million
property damage
India
industrial and textile
chemicals
nearby buildings catalog heavy
damage
was a highly
ILammable mixture
0f C1Ierr F .r1S WO
for making #]ices
and tuhber
Pradesh, India manufacturing
company
to the accident is estimated to be between R3 LO and 14L1
minion
eyaruated, over 100 rendered homeless
by the incident needled psychiatric support.
211. 2009 liyderabad.1ndia Chemical solvent E -- F --,
leak 2 2 Hindu, 2005 extraction factory
212. 2009 Molo. Kenya Gasoline tinker Tanker overturned
111 >200 Firegeezer, 2009 -- Lzak -- fireball
u-arns
152
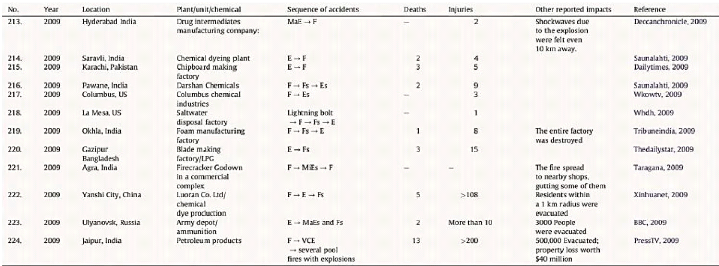
|