
ÉÜíÑæÜÜåãÌáÇ
et Populaire
íÜãáÜÚáÇ
ÉÜíÈÚÜÜÔáÇ
ÉÜíØÇÑÜÞãíÏáÇ
ÉÜíÑÜÆÇÒÌáÇ
Algérienne Démocratique
ËÜÍÜÜÈáÇæ
íÜáÇÜÜÚáÇ
ÜãíÚáÜÜÊá
ÉÑÇÒæRépublique
Ministère de l'Enseignement Supérieure et
de la Recherche Scientifique
ÏãÍ äÈ
ÏãÍã 2 äÇÑåæ
ÉÚãÇÌ Université d'Oran 2 Mohamed Ben
Ahmed
Juillet 2019
íÚÇäÕáÇ
Institut de Maintenance et de Sécurité
Industrielle
Département de Sécurité
Industrielle et Environnement
MÉMOIRE
Pour l'obtention du diplôme de Master
Filière: Hygiène et
Sécurité Industrielle Spécialité :
Prévention/Intervention
Thème
ÉTUDE SÉQUENTIELLE DE DANGER DU
FOUR 11-F1 DE LA RAFFINERIE D'ARZEW
Présenté et soutenu publiquement par :
Nom : HAMZA Prénom : AYAT ALLAH ISMAHENE
Devant le jury composé de :
Nom et Prénom
|
Grade
|
Etablissement
|
Qualité
|
BENFEKIR Abderrahim
|
MCB
|
UNIV-ORAN 2
|
Président
|
LOUNIS Zoubida
|
Dr
|
UNIV-ORAN 2
|
Encadreur
|
TALHI Mama
|
MCB
|
UNIV-ORAN 2
|
Examinateur
|

REMERCIEMENTS
Au nom de dieu le tout miséricordieux, toute la louange
à Dieu qui m'aide, je le remercie beaucoup.
Je tiens à remercier en premier mon encadreur
Madame LOUNIS ZOUBIDA de m'avoir encouragée,
aidée avec ses précieux conseils durant mon cursus universitaire
et pendant tout le processus d'encadrement et de rédaction de mon
mémoire de master.
Je remercie aussi les membres du jury que j'ai eu la chance de
les avoir comme enseignants Monsieur BENFEKIR ABDERRAHIM et
Madame TALHI MAMA d'avoir acceptés d'examiner et juger
mon travail mais surtout de partager avec moi la clôture de tout mon
cursus universitaire.
Je remercie aussi tous les enseignants de l'institut de
maintenance et sécurité industrielle qui ont contribué
à ma formation.
Mes remerciements vont aussi à Madame ZITI,
Mademoiselle KHELF SIHAM, Monsieur MISSOUM, Monsieur HANSALI
NOUREDINE, Monsieur MAHREZ HBIB, Monsieur LABDI ABDEL JALIL
et Monsieur ZWAWI OMAR, cadres au
niveau de la raffinerie d'Arzew, pour m'avoir accueilli, expliqué et mis
à ma disposition toutes les informations nécessaires à la
réalisation de mon travail
J'adresse mes vifs remerciements à Monsieur
HAMZA ZRIGAT chef de service des ressources humaines pour le
suivi continu tout le long de la période du stage, je le remercie pour
son assistance.
Je remercie infiniment ma tante Madame MILOUDI
SCHAHRAZED avocate au niveau de la Daïra d'Arzew pour sa
gentillesse et son aimable accueil pendant toute la période de mon stage
afin d'être à proximité de la zone industrielle d'Arzew.
Merci à tous.
"L'homme et sa sécurité doivent constituer la
première préoccupation de toute aventure technologique"
II
Albert EINSTEIN
iii
TABLE DES MATIERES
LISTE DES FIGURES ix
LISTE DES TABLEAUX xii
INTRODUCTION GENERALE 1
CHAPITRE I :
GÉNÉRALITÉS
Présentation de la raffinerie d'Arzew. 2
Présentation des principales installations de RA1Z 4
Zone 03 et zone 19 (les Utilités de P1 et P2) 4
Zone 04 (production de carburants) 5
Zone 07(P1) / Zone 05(P2) (production de lubrifiants) 5
Zone 06 7 Zone 10 7 Zone 09 7
I.2.7 Zone 11, 12,13 7 Zone 16 7
Zone 17 7
Zone 18 7
Zone 24 7
Zone 25 7
Zone 26 7
Zone 27 (unité 1800) 8
Zone 28 8
I.2.16 Zone 29
iv
I.2.17 Zone 31 8
Composition du pétrole brut 10
CHAPITRE II :
DESCRIPTION DE L'UNITÉ TOPPING U11
Introduction 12
Description générale de l'unité Topping U11
12
Section de préchauffage 12
Section de distillation atmosphérique 13
Récupération du BRA 14
Récupération du HGO et LGO 14
Récupération du kérosène 14
Récupération du GPL, HSLN et LSRN. 15
Récupération des vapeurs de tète 15
Section de stabilisation 15
Itinéraire des sous produits 16
Description du four 11-F1. 16
Chauffage 16
Utilités 18 Fuel gaz 18
Electricité 19
Opérations 19
Procédures particulières 19
Procédure de démarrage 19
Procédure d'arrêt d'urgence 20
Conclusion 20
V
CHAPITRE III :
PRÉSENTATION DES POTENTIELS DE DANGERS LIÉS
AU
CHAUFFAGE DU FOUR 11-F1
Introduction 22
Potentiels de dangers liés aux produits mit en oeuvre
22
Potentiels de dangers liés au chauffage du four 11-F1
22
Conditions opératoires 22
Potentiels de dangers liés aux utilités 23
Alimentation en fuel gaz 23
Alimentation électrique 23
Alimentation en vapeur stripping 23
Historique du retour d'expérience 23
Accident passé survenu sur le four 11-F2 de l'unité
Topping U11, 2010 23
Accident passé survenu sur le four 100-F1 de la Raffinerie
de Skikda RA1/K, 3 Janvier 2013.
25
Description de la raffinerie de Skikda 25
Déroulement 25
Conclusion 26
CHAPITRE IV:
ANALYSE DES RISQUES LIÉS AU FOUR 11-F1
Introduction 28
Identification des risques liés au four 11-F1 par la
méthode HAZOP. 28
Scénarios retenus pour la modélisation 35
Modélisation des scénarios par le logiciel Arbre
Analyste 35
1er scenario : Explosion du tube de pétrole brut. 35
Résultats de la modélisation expérimentale
36
vi
Analyse de la courbe du manque de fiabilité du
système 37
Analyse du tableau IV.3. 38
Résultats de la modélisation réelle 39
: Analyse de la courbe du manque de fiabilité du
système 40
Analyse du tableau IV.6 41
Comparaison 41
La probabilité de défaillance du four 11-F1. 41
System unreliability (Manque de fiabilité) 41
Les coupes minimales 42
Le CIF (Facteurs d'Importance Critique) 42
Interprétation des résultats 42
2ème scénario : Explosion du nuage de fuel gaz
à l'intérieur de la chambre de
combustion 42
Résultats de la modélisation expérimentale
43
: Analyse de la courbe du manque de fiabilité du
système 44
Analyse du tableau IV.9 44
Résultats de la modélisation réelle 46
: Analyse de la courbe du manque de fiabilité du
système 47
Analyse du tableau IV.12. 47
Comparaison 48
La probabilité de défaillance du four 11-F1. 48
Les coupes minimales 48
Le CIF (Facteurs d'Importance Critique) 49
Interprétation des résultats 49
3ème scenario : Surpression du four 11-F1. 49
Résultats de la modélisation expérimentale
50
: Analyse de la courbe du manque de fiabilité du
système 51
vii
Analyse du tableau IV.15 51
Résultats de la modélisation réelle 53
: Analyse de la courbe du manque de fiabilité du
système 54
Analyse du tableau IV.18. 55
Comparaison 55
Probabilité de défaillance du four 11-F1. 55
System unreliability (Manque de fiabilité) 55
Les coupes minimales 56
Le CIF (Facteurs d'Importance Critique) 56
Interprétation des résultats 56
4ème scénario : Retour de flamme à
l'entrée des bruleurs 56
Résultats de la modélisation expérimentale
57
: Analyse de la courbe du manque de fiabilité du
système 58
Analyse du tableau IV.21. 59
Résultats de la modélisation réelle 61
: Analyse de la courbe du manque de fiabilité du
système 62
Analyse du tableau IV.24. 63
Comparaison 64
Probabilité de défaillance du four 11-F1. 64
System unreliability (Manque de fiabilité) 64
Les coupes minimales 64
Le CIF (Facteurs d'Importance Critique) 64
Interprétation des résultats 64
Simulation réelle des scénarios par le logiciel
AgenaRisk 65
Simulation des probabilités d'occurrence des
événements des sommets arbres 65
Simulation des Scénarios 65
Simulation de l'explosion du tube de pétrole brut 66
VIII
Simulation de l'explosion du nuage de fuel gaz 67
Simulation de la surpression du four 11-F1 68
Simulation du retour de flammes 69
Interprétation des résultats 70
Simulation des défiabilités totales des maillons
faibles du système 70
Simulation des scénarios 70
Simulation de l'explosion du tube de pétrole brut 71
Simulation de l'explosion du nuage de fuel gaz 72
Simulation de la surpression du four 11-F1 73
Simulation du retour de flammes 74
Interprétation des résultats 75
Matrice d'évaluation des risques 75
Synthèse et évaluation 76
CONCLUSION GENERALE 78
ANNEXES 79
REFERENCES BIBLIOGRAPHYQUES 88
ix
LISTE DES FIGURES
I.1: Vue de Google Earth de la raffinerie d'Arzew 2
I.2: Haoud El Hamra 3
I.3: Situation géographique de la Raffinerie d'Arzew
dans la zone industrielle 3
I.4: Plan de masse de la raffinerie d'Arzew RA1/Z 4
I.5: Pétroles bruts 10
I. 6: Molécule linéaire - Molécule
cyclique - Molécule raffinée 11
II. 1: Schéma présentatif de l'unité
TOPPING (U11) 13
II.2: Schéma présentatif de la colonne de
distillation atmosphérique (U11) 14
II.3: Schéma présentatif de la section de
stabilisation (U11) 16
II.4: Schéma présentatif du four 11-F1 (U11)
17
II.5: schéma présentatif d'un bruleur du four
11-F1 (U11) 17
II. 6: Schéma présentatif du ballon de
mélange (U35) 18
III. 1: Schéma présentatif du four rebouilleur
11-F2 (U11) 24
III.2: Situation géographique de la raffinerie de
Skikda RA1/K 25
III. 3: Explosion du four 100-F1, 3 Janvier 2013 26
IV. 4: Modélisation expérimentale de l'arbre
réduit 36
IV.5: Courbe du manque de fiabilité du système
37
IV.6: Modélisation réelle de l'arbre
réduit 39
IV.7: Courbe du manque de fiabilité du système
40
IV.10 : Modélisation expérimentale de l'arbre
réduit 43
IV.11: Courbe du manque de fiabilité du système
44
IV.12: Modélisation réelle de l'arbre
réduit 46
IV.13: Courbe du manque du manque de fiabilité du
système 47
IV.17: Modélisation expérimentale de l'arbre
réduit. 50
IV.18:
X
Courbe du manque de fiabilité du système 51
IV.19: Modélisation réelle de l'arbre
réduit 53
IV.20: Courbe du manque de fiabilité du système
54
IV.21: Modélisation expérimentale de l'arbre
réduit 57
IV.22: Courbe du manque de fiabilité du système
58
IV.23: Modélisation réelle de l'arbre
réduit 61
IV.24: Courbe du manque de fiabilité du système
62
IV.25: Simulation à priori de l'explosion d'un tube de
pétrole brut 66
IV.26: Simulation à priori de l'explosion d'un nuage
de fuel gaz 67
IV.27: Simulation à priori de la surpression du four
11-F1. 68
IV.28: Simulation à priori du retour de flammes 69
IV.29: Simulation à postériori de l'explosion
du tube de pétrole brut 71
IV.30: Simulation à postériori de l'explosion
d'un nuage de fuel gaz 72
IV.31: Simulation à postériori de la
surpression du four 11-F1. 73
IV.32: Simulation à postériori du retour de
flammes à l'entrée des bruleurs 74
IV.33: Matrice d'évaluation des risques 76
xi
LISTE DES TABLEAUX
II: Composition du fuel gaz 19
III: Caractéristiques physico-chimiques du fuel gaz et
du pétrole brut 22
IV.1: Tableau HAZOP 29
IV.3: Résumé exécutif 37
IV.4: CIF (Facteurs d'Importance Critique) 38
IV.5: Coupes minimales et leurs ordres 38
IV.6: Résumé exécutif 40
IV.7: Facteurs d'importance 41
IV.8: Coupes minimales et leurs ordres 41
IV.9: Résumé exécutif 44
IV.10: CIF (Facteur d'Importance Critique) 45
IV.11: Coupes minimales et leurs ordres 45
IV.12: Résumé exécutif 47
IV.13: CIF (Facteur d'Importance Critique) 48
IV.14: Coupes minimales et leurs ordres 48
IV.15: Résumé exécutif 51
IV.16: CIF (Facteurs d'Importance Critique) 52
IV.17: Coupes minimales et leurs ordres 52
IV.18: Résumé exécutif 54
IV.19: CIF (Facteurs d'Importance Critique) 55
IV.20: Coupes minimales et leurs ordres 55
IV.21: Résumé exécutif 58
IV.22: CIF (Facteurs d'Importance Critique) 59
IV.23: Coupes minimales et leurs ordres 59
IV.24:
XII
Résumé exécutif 62
IV.25: CIF (Facteur d'Importance Critique) 63
IV.26: Coupes minimales et leurs ordres 63
1
INTRODUCTION GÉNÉRALE
De nombreux accidents se sont produits récemment sur
des fours industriels qui ont des rendements énergétiques
élevés, surtout ceux liés au procédé de
raffinage du pétrole brut, comme c'est le cas de l'explosion du four
11-F2 de la raffinerie d'Arzew en 2010 ou encore celui de l'explosion du four
100-F1 de la raffinerie de Skikda le 3 Janvier 2013, générant
ainsi des phénomènes dangereux tels que l'effet de souffle
susceptible d'induire des effets de flexion et/ou cisaillement dans les
structures de l'entreprise, éventuellement de compression pour le corps
humain et de propulsion de projectiles associés à des effets
thermiques.
Malgré toutes les mesures prises, on n'arrive toujours
pas à éviter des accidents majeurs similaires, donc le but de ce
travail est de faire une étude d'analyse des risques relatifs au four de
l'unité de distillation atmosphérique du pétrole brut de
la raffinerie située dans la zone industrielle d'Arzew visant ainsi
à sélectionner toutes les défaillances à fin de les
prendre en charge à temps et ainsi améliorer la fiabilité
du four 11-F1.
Pour cela, nous allons d'abord décrire le
procédé de raffinage du pétrole brut avant de
décrire le four 11-F1, sujet de notre étude.
Une étude sur les retours d'expériences
vécues sera donnée pour en tirer les causes et prendre les
enseignements, suivi préalablement par la méthode inductive HAZOP
(analyse de risques et de sécurité de fonctionnement) afin
d'identifier les scénarios pouvant se produire sur le four 11-F1 et qui
méritent d'être retenus pour une analyse par l'ADD (Arbre de
Défaillances) en utilisant le logiciel Arbre Analyste.
Dans un second temps, nous allons faire la simulation de ces
scénarios par utilisation du logiciel AgenaRisk.
Enfin nous allons déterminer le niveau
d'acceptabilité ou non acceptabilité du risque associé
à chaque scénario en fonction de sa gravité et de sa
probabilité d'occurrence.
2
CHAPITRE I : GÉNÉRALITÉS
Présentation de la Raffinerie d'Arzew RA1/Z
:
Dans l'Aval pétrolier et gazier, le groupe Sonatrach
exploite un actif important de complexes industriels comme la raffinerie
d'Arzew RA1/Z.
La raffinerie d'Arzew RA1/Z a été construite dans
le cadre du 1er plan quadriennal durant la période 1970-1975,
par la compagnie pétrolière japonaise « JAPON GAZOLINE
CORPORATION ».
C'est la 3ème plus grande raffinerie en
Algérie après celles d'Alger et de Hassi Messaoud. Elle
s'étant sur une superficie de 170 hectares comme le montre la figure
ci-dessous :
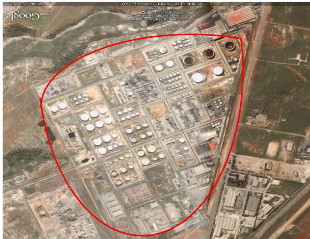
Figure I.1: Vue de Google Earth de la raffinerie d'Arzew
Elle traite 3,5 millions de tonnes de pétrole brut
Saharien par an et 280 000 tonnes de BAI (Brut Réduit
Importé).
Avec le pétrole brut Saharien, elle produit le propane,
le butane, l'essence Super et normale qui servent de carburants, le naphta, le
kérosène, le gasoil pour les moteurs diesel, le fuel BTS, le fuel
HTS, les lubrifiants, les graisses, les paraffines et avec les BRA (Brut
Réduit Atmosphérique) elle produit les bitumes routiers pour
faire les routes et les bitumes oxydés pour
l'étanchéité des plafonds.
Le pétrole brut Saharien provient de la base de
Sonatrach à Haoud El Hamra qui est un village de la commune de Hassi
Messaoud, située dans la province de Ouargla, en Algérie comme le
montre les deux figures suivantes :
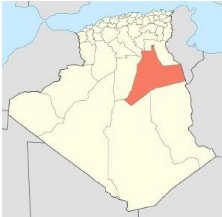
3
Figure I.2: Haoud El Hamra
La Raffinerie d'Arzew RA1/Z est située dans la zone
industrielle d'Arzew sur le plateau d'EL MOHGOUN à deux
kilomètres de la ville d'Arzew et à environ 40 kilomètres
de la ville d'Oran et au voisinage du port qui lui permet les
enlèvements par bateau comme le montre la figure ci-après :
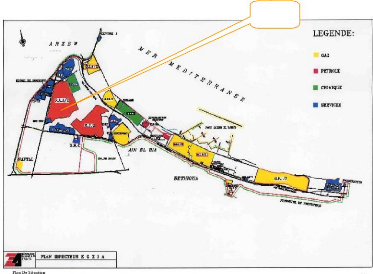
RA1/Z
Figure I.3: Situation géographique de la Raffinerie
d'Arzew dans la zone industrielle
Le complexe RA1/Z est divisé en 2 parties, presque la
totalité de la partie Nord/Ouest est réservée au stockage
des produits finis, intermédiaires et pétrole brut.
4
Quand à la partie Nord/Est, elle est
réservée principalement à la production des
utilités en zone 3, des bitumes routiers et oxydés en zone 10,
des lubrifiants en zone 6 et enfin des carburants en zone 4 comme le montre la
figure suivante :
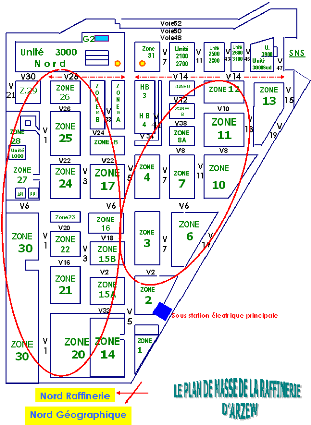
Figure I.4: Plan de masse de la raffinerie d'Arzew RA1/Z
La zone 4 est le poumon de la raffinerie d'Arzew car c'est
là où a lieu le procédé de raffinage du
pétrole brut dans l'unité Topping U11 mais avant de la
décrire il est important de définir la composition du
pétrole brut, par la suite nous allons savoir pourquoi.
Présentation des principales installations de
RA1/Z :
Zone 03 et zone 19 (les Utilités de P1 et P2)
:
Les utilités assurent les besoins du process de la
raffinerie (production et distribution) en :
Eau distillée (déminéralisée pour
zone 19), vapeur, électricité, air comprimé (de service et
d'instruments), eau de refroidissement (après traitement), gaz de
combustion (après
5
traitement), gaz inerte, eau potable, et assure le traitement des
eaux usées (Zone 19 unité 1800).
Zone 04 (production de carburants) :
C'est le point de départ du process de raffinage du
pétrole brut de HMD.
- Unité 11(distillation atmosphérique)
:
Elle a pour rôle la séparation par distillation
atmosphérique des différents composants
contenus dans le pétrole selon leurs densités, du
plus léger au plus lourd. Il s'agit ;
- Du gaz de pétrole
liquéfié (GPL).
- Du naphta léger LSRN (Light Straight
Run Naphta).
- Du naphta lourd HSRN (Heave Straight Run
Naphta).
- Du kérosène.
- Des gasoils légers (LGO).
- Des gasoils lourds (HGO).
- Du résidu atmosphérique(BRA).
- Unité 12(Reforming catalytique) :
Elle traite le naphta lourd (HSRN) provenant de la distillation
atmosphérique dans le but de produire une base à indice d'octane
élevé (reformat), du GPL, et un gaz riche en hydrogène.
- Unité 13(traitement du gaz) :
Elle traite le GPL obtenu de l'unité 11 , 12 et 17 en le
séparant en produits purs, tel que le propane et le butane (C3H8 ,
C4H10) .
- Unité 17 (Hydrotraitement et Penex
(Hydrotraitement et isomérisation du naphta léger)) :
Elle traite le naphta léger (LSRN) provenant de la
distillation atmosphérique, permettant l'amélioration de l'indice
d'octane d'essence légère contenant des hydrocarbures en C5et C6,
non traitables par le reformage catalytique.
- Unité 18 (l'unité du système de
l'huile chaude) :
Circuit est de fournir de la chaleur pour les unités
suivantes: Unité 11 et l'unité 17.
Zone 07(P1) / Zone 05(P2) (production de lubrifiants)
:
- Distillation sous vide (U 21 / U 100) :
Le brut réduit atmosphérique (BRA) est
fractionné dans cette unité sous vide, afin d'obtenir les coupes
nécessaires à la production des huiles de base (semi-finis). Ces
coupes sont : - Au sommet on obtient les gasoils (VGO).
- Latéralement on soutire les huiles
(SPO (spindle), l'huile mi-visqueusess (MVO) et l'huile visqueuse (VO).
- Au fond de colonne on aura le résidu
court sous vide, le Short Résidus (RSV).
6
- Unité 150 :
Cette unité fournie la chaleur (caloporteur) pour
réchauffer les unités 200, 300, 400 de P2. En
utilisant principalement le four H151.
? Desasphaltage au propane (U 22 / U 200) : le
short résidus venant de la distillation
sous vide, est traité avec un solvant sélectif qui
est le propane, afin d'éliminer l'asphalte
et obtenir l'huile DAO, qui alimentera l'unité 23 /
unité 300. elle inclut les étapes
suivantes :
- Mélange charge (RSV) et propane.
- extraction de l'huile
désasphalté DAO.
- Extraction de l'asphalte.
- Récupération du propane.
? Extraction au furfural (U 23 / U300) : Elle a
pour rôle l'élimination des aromatiques
et des naphtènes afin d'améliorer le VI (indice de
viscosité) des huiles (spindle, MVO,
VO, DAO). Elle comprend les étapes suivantes :
- La désaération (évite
l'oxydation du solvant en éliminant l'air dans la charge).
- L'extraction.
- La récupération du raffinat .
- La récupération de l'extrait
(solvant mélangé aux aromatiques).
- La récupération du solvant.
Quatre raffinats sont ainsi obtenus : spindle, mi-visqueux (SAE
10), visqueux
(SAE 30) et la Bright stock.
? Déparaffinage des huiles au Mectoluène,
et déshuilage (U24 / U400) : Le
mec-toluène (méthyle éthyle cétone
et toluène) est utilisé comme solvant sélectif pour les 4
coupes d'huiles à déparaffiner, afin d'éliminer les
paraffines, et pour améliorer le point d'écoulement (même
point d'écoulement à n'importe qu'elle période de
l'année, surtout en temps d'hiver).elle comprend les étapes
suivantes :
- mélange charge / solvant
- refroidissement du mélange à
-26 °C (batteries de réfrigération au propane (shilers)
).
- filtration entre paraffine
cristallisée et huile déparaffinée, en utilisant des
filtres rotatif sous vide créer par les compresseurs de gaz inerte.
- récupération du solvant par
filtration
En aura enfin l'huile déparaffinée (DO) d'un
coté et de la paraffine dure, et molle déshuilée
(amélioration de sa consistance et de son point de fusion ) d'un
autre.
La paraffine non déshuilée est aspirée par
pompage, tout en étant réchauffée par vapeur (3kg/cm2)
à 60°c, afin de faciliter le pompage.
? L'hydrofinishing (U25 / U500) : Les huiles
déparaffinées sont traitées alternativement à
l'hydrogène dans un réacteur contenant un catalyseur à
base de fer, de cobalt, et de
molybdène (enlever le soufre, l'azote,
oxygéné etc..) , Afin d'améliorer la couleur ,
7
l'odeur, la stabilité thermique et la résistance
à l'oxydation. En obtient l'huile de base BO.
? L'hydrofinishing des paraffines (U600) :
comme pour les huiles, dans cette unité on améliore la
paraffine cote couleur, odeur, stabilité thermique, et résistance
à l'oxydation par l'utilisation de l'hydrogène à travers
un catalyseur.
Zone 06 :
C'est la production (formulation) et le conditionnement des
huiles finis et de graisse à partir de la zone 7 en ajoutant des
additifs importés.
Zone 10 :
Production de bitumes routier et bitumes
d'étanchéité (bitumes oxydé).
? Unité 14 (flashe sous vide) : le BRI
et l'asphalte récupérer des unités de désasphaltage
au propane, sont fractionnés en gasoils sous vide ,et en un produit
visqueux obtenu en fond de colonne , lequel est traité dans la section
soufflage à l'air pur, pour obtenir du bitumes routier (avec
contrôle de sa dureté et son point de ramollissement).
? Unité 15 : on pousse l'oxydation de la
charge (bitume routier + gasoil) afin d'obtenir du bitume oxydé,
conditionné dans des sacs de 25 Kg
Zone 09 : stockage du résidu
atmosphérique dans 2 bacs. Zone 11, 12,13 : stockage du
brut de hassi-messaoud ; - 3 bacs de 60000 T.
- 2 bacs de 50000 T.
Zone 16 : - stockage eau brut pour incendie ; 1
bac de 30000 T
- stockage du naphta ; 2 bacs de 30000 T - stockage du naphta ; 2
bacs de 10000 T
Zone 17 : - stockage du kérosène ;
2 bacs de 10000 T, 2 bacs de 20000
- stockage d'essences de 1ere distillation ; 2 bacs.
Zone 18 : stockage du fuel pour mélange ;
5 bacs de 5000 T
Zone 24 : stockage de gasoils ; 7 bacs.
Zone 25 : stockage de fuel ; 6 bacs .
Zone 26 : stockage de GPL ;
8
- 1sphère de propane destinée aux
unités lubrifiants et au marché. - 3
sphères de butanes destinées au mélange de GPL.
- 2 sphères de butanes commerciales.
Zone 27 (unité 1800) :
récupération des eaux usées ; 2 bassins de
séparation et de décantation physique.
Zone 28 : zone d'expédition des produits
finis (ajouts d'additifs, couleurs, odeurs,...
Zone 29 : stockage du brut réduit
importé.
Zone 31 : contient deux torches (P1 et P2).
18- unité 3000 : elle comporte les
unités suivantes ;
? Unité 3100 production des huiles finis
:
a) but : elle est destinée à
fabriquer des huiles finis à partir des huiles de base fabriquées
dans les unités 100 à 500 et des additifs importés.
(Production de 132000 t/an pour une quantité de 10% d'additifs).
b) Grades d'huiles fabriquées :1)
huiles moteurs 81% de la production (essence, diesel, huiles pour
transmission). 2) huiles industrielles [hydraulique (tiska), turbines (torba),
engrenage (fodda), compresseur (torrada), et huiles divers].
L'unité utilise 2 méthodes de préparation
;
1) mélange en continu (mélangeuse en ligne).
2) mélange en discontinu (batch).
c) Mélange en continu : composé
de 3 mélangeuses associées à 3 groupes de bacs de
stockages des huiles finis, qui par la suite seront conditionnées en
fus, ou expédiés en vrac. Les 3 mélangeuses fabriquent les
3 catégories d'huiles moteurs avec 3 additifs (livrés en vrac, ou
conditionnés en fus et stockés dans 9 bacs. Une pré
dilution des additifs destinés aux mélangeuses en ligne dans le
ballon de pré mélange, en cas de forte viscosité des
additifs, stockage avant utilisation, additifs en faible proportion pour
être dosés directement.
Centrifugeuse ; l'huile finie présentant parfois des
traces d'eau (mauvais pour la commercialisation) doit être
déshydratée dans un ensemble composé de 3 centrifugeuses
disposées à la sortie de la mélangeuse en ligne.
d) Mélange en discontinu (batch) :
conçus pour la fabrication des huiles industrielles (2300 t/an).
9
On utilise pour ce mélange, 12 ballons divisés
en 4 groupes, selon le grade d'huile finie à produire (évite
problème de contamination).le remplissage d'huile est
contrôlé par le 31FQI 101, qui commande la fer/ouv de la vanne
auto, en amont du séparateur et la pompe P3105( la consigne de
prédétermination égale la valeur indiquée). L'ajout
des additifs est comptabilisé par le 31FQI 010. le remplissage des
additifs en fus se fait par le trous d'homme.
? Unité 3200 fabrication des graisses :
elle utilise 3 étapes.
a) saponification : un produit gras
(glycéride) en contact avec un alcali, forment un savon. Le linci est
utilisé pour épaissir l'huile (SAE30+Bride stocke), et donne au
produit la consistance de la graisse.
b) déshydratation : on soutire l'eau
du mélange savon huile sous vide.
c) finissage : on mélange dans le
savon déshydraté des additifs et du reste d'huile
minérale.
? Unité 3300 : elle est conçus
pour le démoulage de la paraffine provenant de l'U600. la paraffine est
introduite dans le skid (par P 2601/2) depuis TK2601/2 à 80°c, puis
pénètre dans la section de réfrigération à
temp° (-15 °c)au propane. Ensuite elle est démoulée en
pain de 5 kg, et conditionnés ensuite dans des cartons de 25 kg
Equipement ; - skid de maintient de temp° à
80°c
- chaîne pour véhiculer la
paraffine
- réfrigération afin de baisser la
temp° de la paraffine à 20 - 25 °c
? Unité 3400/3500/3600 : assure le
conditionnement des huiles finis
? Unité 3700 : structure implantée
à l'ISP, son rôle consiste :
- Au déchargement des additifs
importés des navires.
- Aux suivis des bacs de stockage
(contrôle de temp°, niveau, pression, etc.)
- Au transfert des additifs vers RA1z par
camions citerne.
- Au chargement d'huiles de base dans les
navires.
? Unité 3900 : réalisée
en 1997 elle assure le conditionnement et remplissage des huiles finis en
jerrycans de (2L/5L) et de la graisse dans des pots de 1 Kg Elle comporte :
a) Les utilités : incluant un
ensemble de transfos d'électricité, 2 compresseurs d'air
(atlas-copco), d'un système de refroidissement, et de silos de stockage
de matière première (PEHD).
b) Les machines : les machines à
soufflage, à injection, de remplissage, de
capsulage, d'étiquetage, de la mise en ballots, et de palettisation
(palettiseuse + filmeuse).ainsi que l'ensemble des éléments
nécessaires à la conversion d'une ligne de 2 l en 5 l, et les
bacs de stockage intermédiaires de bidons.
Fonctionnement : le chargement des silos en PEHD s'effectue
à partir de la station de crève sacs ( par un système de
pompes de vide). La matière 1ere est aspirée vers les
machines de soufflage pour la fabrication de bidon d'huiles et boite de
graisse, et vers les machines d'injection pour la fabrication des bouchons et
sous bouchons. Les carottes et rebuts sont entièrement
récupérables grâce aux broyeurs.
10
Les bidons passent après le soufflage, par le
système intégré pour le control
d'étanchéité, après être remplis , ils sont
capsulés, étiquetés, mis en ballots, palettisés, et
enfin stockés.
L'ensemble des machines et équipements étant
complètement automatisé, a permis d'amélioré la
qualité de l'emballage (bonne étanchéité, et un
résistance permettant le gerbage des ballots sur des palettes), et
permis aussi d'arriver à un taux de production jamais
égalé par les unités précédentes.
Composition du pétrole brut :
Le pétrole brut n'est pas nécessairement noir et
visqueux tout dépend de sa composition qui varie en fonction de
l'endroit où il provient (nature du gisement) comme le montre la figure
ci-après :
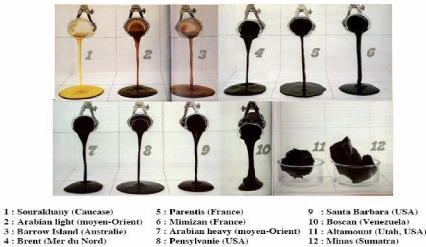
Figure I.5: Pétroles bruts
Ces pétroles sont tous constitués d'hydrocarbures,
de molécules, d'assemblages de carbone et d'hydrogène, pourtant
ces molécules ne sont pas toutes identiques, certaines sont
linéaires, d'autres sont cycliques, d'autres sont raffinées comme
le montre la figure ci-dessous :
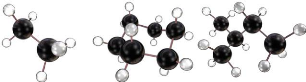
11
Figure I.6: Molécule linéaire - Molécule
cyclique - Molécule raffinée
Surtout elles n'ont pas le même poids, ce poids vari en
fonction de la quantité de carbone, plus il y'a de carbone, plus c'est
lourd et en fonction de la quantité de carbone les
propriétés ne sont pas les mêmes, donc il faut trier ces
hydrocarbures.
Et le tri commence dans la colonne de distillation
atmosphérique de l'unité Topping (U11).
12
CHAPITRE II :
DESCRIPTION DE L'UNITÉ TOPPING U11
Introduction :
Dans ce chapitre nous allons d'abord décrire la
localisation ainsi que l'environnement autour du four 11-F1, en outre nous
allons décrire l'unité Topping (U11) qui a pour but la
séparation des fractions d'hydrocarbures contenues dans le
pétrole brut les unes des autres selon leurs températures
moyennes d'ébullition, et nous citerons les produits soutirés,
puis nous attaquerons la description du four, c.à.d. l'installation sur
laquelle est basée notre étude, ainsi que les utilités
nécessaires à son bon fonctionnement, les procédures
particulières, les procédures de démarrage et les
procédures d'arrêt d'urgence liés au four 11-F1.
Description générale de l'unité
Topping (U11) :
Section de préchauffage :
A partir des bacs de stockage, le pétrole brut à
température ambiante et pression atmosphérique passe par un
filtre pour enlever toutes les impuretés, puis il est refoulé par
la pompe 11-G1 A/B, dans le train d'échangeurs de chaleur où il
se préchauffe dans le coté tube des échangeurs.
A la sortie des échangeurs, sa température est
à 120 °C et sa teneur en sel est toujours élevée il
entre alors dans le dessaleur afin de diminuer la teneur en sel susceptible de
corroder les tubes du four 11-F1.
Les sels les plus souvent trouvés sont les chlorures de
sodium, le calcium et le magnésium.
Selon les caractéristiques du brut à dessaler,
la température optimale de dessalage sera dans la gamme de 90
à150°C.
Après ça il traverse une deuxième
batterie d'échangeurs, la température augmente jusqu'à
216°C.
Puis il entre dans le ballon de détente 11-D1 (le
ballon de pré-flash ou le ballon séparateur) où la
pression de service est de 3,1 kg/cm2.
A ce moment là, l'effluent est flashé, les vapeurs
sont évacuées en tête du ballon et sont par la suite
intégrées directement dans la colonne de distillation
atmosphérique tandis que la phase liquide entre dans le four 11-F1 et ce
afin de lui fournir toute la chaleur nécessaire permettant de le
fractionner dans la colonne de distillation atmosphérique.
Le liquide est porté à une température de
l'ordre de 332°C, à cette température il aura tendance
à se vaporiser.
13
Au final, il quitte alors le four 11-F1 pour rejoindre la phase
vapeur dans la colonne de distillation atmosphérique comme il est
illustré dans la figure ci-dessous :
Vapeurs

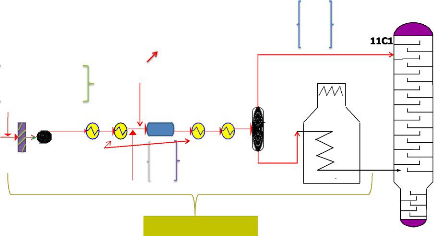
T = ambiante
P =1 atm =1. 013 * 10 -5
Coté tube
Brut
(sale)
Filtre
11 G1 A/B
Pompe Batterie d'échange
Injection de l'eau
% sel
T = 120 °C Ballon de pré-
flash (Ballon séparateur)
Dessaleur 11D1
Section de préchauffage
Agcl2 Cacl2 Nacl H20
Liquides
Four
C1
C3
C4
C5
11-F1
Colonne de distillation atmosphérique
Figure II.1: Schéma présentatif de l'unité
TOPPING (U11)
Section de distillation atmosphérique :
Dans n'importe quelle raffinerie du pétrole brut on
utilise une colonne de distillation atmosphérique à plateaux.
La colonne 11-C1 est la pièce principale de l'unité
de distillation atmosphérique. Elle comprend 49 plateaux à
clapets où le pétrole brut vient se détendre.
Au fur et à mesure que les vapeurs d'hydrocarbures montent
dans la tour, la température diminue, et en refroidissant elles se
condensent à des températures différentes en fonction de
leurs poids permettant ainsi de faire le tri.
Le BRA, l'hydrocarbure le plus lourd descend au fond de la
colonne tandis que les vapeurs plus légères montent naturellement
dans la tour.
Les vapeurs sont fractionnées en un produit
léger de tête et de plusieurs soutirages latéraux par ordre
de volatilité croissante.
On va donc récupérer le BRA au fond de la colonne,
au dessus le HGO (naphta lourd) au niveau du plateau n°37, entre les
plateaux n°30 et 31 le LGO (naphta léger), ensuite au plateau
n°14 le kérosène et enfin la coupe naphta en tête de
la colonne.
Le résidu flashé au fond de la colonne et les
produits soutirés latéralement contiennent des hydrocarbures
légers à l'état vapeur qui doivent être
renvoyés dans la colonne 11-C1 sous forme de reflux pour atteindre les
spécifications du point d'éclair pour cela on utilise de la
vapeur d'eau surchauffée sauf pour le kérosène comme le
montre la figure suivante :
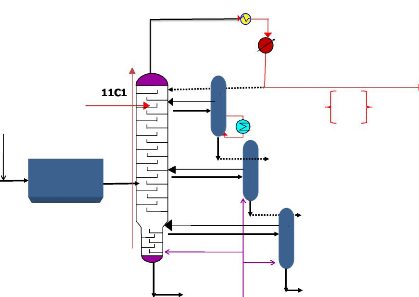
C4
HGO pure à 100 %
BRA
Echangeur
Condenseur 11-E17 A/D
Teb Reflux
Distillat liquide (coupe naphta)
P = 1 atm
Pétrole brut
Section de préchauffage et chauffage
Reflux
11C2
Kérosène
Reflux
11C3
Kérosène pure à 100 %
LGO
11
Reflux HGO pure à 100 %
Stripper
HGO
GPL HSRN LSRN
Rebouilleur
yap stripping
Figure II.2: Schéma présentatif de la colonne de
distillation atmosphérique (U11)
Récupération du BRA :
Le BRA surchauffé à 316 °C et recueilli au
fond du Topping est envoyé directement à la zone de stockage.
Récupération du HGO et LGO :
Le HGO est envoyé au stripper-sécheur 11-C4 tandis
que le LGO est envoyé au stripper-sécheur 11-C3.
14
Récupération du kérosène
:
15
Contrairement aux autres, le kérosène est
envoyé au stripper 11- où il est débarrassé des
vapeurs d'hydrocarbures légères à l'aide d'un
rebouillage.
En utilisant la vapeur d'eau surchauffée, la faible
tension de vapeur du kérosène ne permet pas de le
débarrasser de l'eau entraînée sans provoquer de grandes
pertes du produit. A fin que le produit soit dans les normes, on a
remplacé la vapeur stripping par le rebouilleur 11E10 qui assure
l'apport de chaleur.
Récupération du GPL, HSLN et LSRN :
Récupération des vapeurs de tète :
Les vapeurs obtenues en tête de la colonne 11-C1
constituent un mélange de GPL, HSRN et LSRN, après être
refroidies dans un échangeur, elles sont condensées partiellement
à travers les condenseurs 11-E17 A ou D avant d'être
envoyées à la section de stabilisation.
Section de stabilisation :
Dans cette section on va fractionner la coupe naphta et
récupérer les sous-produits GPL, naphta léger et naphta
lourd.
Le splitter 11-C5 fonctionne sous une pression de service de 8,1
kg/cm2, il permet de récupérer le HSRN.
Une partie du HSLN au fond du splitter est acheminée vers
le four de rebouillage 11-F2 afin d'y être portée à la
température de 226°C pour être ensuite renvoyée
à nouveau dans le splitter 11-C5.
Ce procédé permet ainsi de
récupérer un maximum de vapeurs en tête du splitter ainsi
qu'un HSLN correct.
Les vapeurs obtenues en tête du splitter 11-C5 sont
envoyées dans le stabiliseur 11-C6 et ce à fin de séparer
le GPL du LSRN comme le montre la figure suivante :
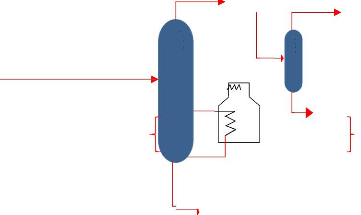
LPG + LSRN
GPL
11C5
11C6
Distillat liquide (coupe naphta)
GPL (mélange de C1 à C5) HSRN
LSLN
HSRN
11-F2
LSRN
16
Figure II.3: Schéma présentatif de la section de
stabilisation (U11)
Itinéraire des sous produits :
A la sortie des strippers, le BRA, le HGO, LGO et le
kérosène sont ensuite refroidis dans la série
d'échangeurs de la section de préchauffage avant d'être
envoyés vers la zone de stockage.
Le stockage du pétrole brut se fait en zone 11, 12 et 13,
quant à celui des produits dérivés il se fait
respectivement pour :
1. Le brut réduit atmosphérique en zone 9
2. Les gasoils lourds et léger en zone 24
3. Le H.R.S.N en zone 17
4. le L.R.S.N en zone 23
Description du four 11-F1 : Chauffage :
Le pétrole brut à 216°C entre dans la zone de
convection du four 11-F1 en quatre passes (4 tubes) comme le montre la figure
suivante :
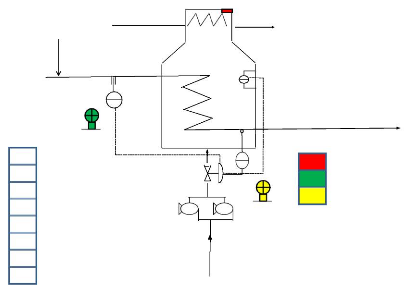
Vapeur stripping
Analyseur de fumées
Détecteur de fumées
Détecteur de gaz
Description du four 11-F1 :
11-F1
Tms = 332 °C
IDP
IF
Pms = 10 bar
Indicateur de débit IT
Vanne de contrôle
et régulation de débit
Indicateur de température de
la surface du pétrole brut
Indicateur de différence
de pression
Température maximale de service
Pression maximale de service
Pompe 1 Pompe 2
FRC
P2 P1
T = 216 C° Pétrole brut
Fuel gaz
IF
FRC
IT
IDP
Tms
Pms
P1
P2
8
17
Figure II.4: Schéma présentatif du four 11-F1
(U11)
Le chauffage du four est assuré par la combustion du fuel
gaz dans des brûleurs comme l'illustre la figure suivante :
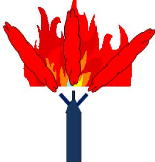
Figure II.5: schéma présentatif d'un bruleur du
four 11-F1 (U11)
Le fuel gaz alimentant le four 11-F1, il entre par
l'intermédiaire de 2 pompes P1 et P2 à fin d'être
chauffé dans des bruleurs.
Le four est équipé d'une boucle de
régulation de débit du fuel gaz et du pétrole brut, de
température, et de pression, puisque la vanne de contrôle et de
régulation de débit FRC, contrôle le débit du fuel
gaz entrant, en même temps elle est associée à :
1. l'indicateur de débit IF d'entrée du
pétrole brut
2. l'indicateur de température IT de température
de surface du pétrole brut
3. l'indicateur de différence de pression interne et
externe
Le four 11-F1 est aussi équipé de détecteurs
de gaz placés à l'entrée des bruleurs et de
détecteurs de fumées.
En haut des volets est placé l'analyseur de
fumées.
La température du pétrole brut monte jusqu'à
332°C et la pression de service est à 10 bar, Le four est
équipé d'une boucle de régulation du fuel gaz et du
pétrole brut entrant.
Utilités : Fuel gaz :
30 % de l'énergie gazière est assuré par
quelques unités de la raffinerie (Gaz Raffinerie), cependant le reste
est assuré par le Gaz Naturel de SONALGAZ.
C'est dans l'unité 35 de la zone 3 des utilités
précisément dans le ballon de mélange qu'a lieu le
mélange entre les deux, le gaz de la raffinerie et le gaz naturel, la
Pms étant à 3.5 bar comme le montre la figure suivante :
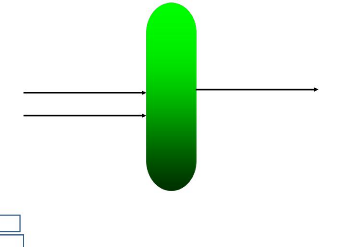
Pms = 3.5 bar
U11
30% GR
70% GN
Gaz Raffinerie Gaz Naturel
Pression maximale de service
GR
GN
Pms
18
Figure II.6: Schéma présentatif du ballon de
mélange (U35)
19
Le tableau suivant recense respectivement le volume molaire du
méthane, de l'éthane, du propane, du butane et du pentane en Gaz
Raffinerie et Gaz Naturel ainsi que la fraction volumique dans l'ensemble du
mélange fuel gaz.
Tableau II: Composition du fuel gaz
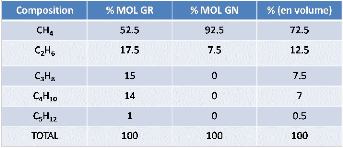
Electricité :
L'énergie électrique est assurée par
SONELGAZ.
Pour chaque pilote :
La puissance du courant : 200 A.
La tension : 1400 V.
Opérations :
Le four 11-F1 est surveillé depuis la salle de
contrôle située à proximité de l'unité
U11.
Cependant, certaines phases nécessitent des interventions
particulières des opérateurs, comme c'est le cas d'une mauvaise
transmission du signal en provenance d'un indicateur de flamme relatif à
chaque bruleur.
Procédures particulières :
Les procédures spéciales traitent des situations
précises qui nécessitent une vigilance particulière, cela
concerne particulièrement la protection contre la corrosion.
Procédure de démarrage :
A la suite d'un arrêt du four 11-F1,
SONATRACH/ACTIVITÉ AVAL/DIVISION RAFFINAGE prévoit qu'il sera
purgé à l'aide de la vapeur stripping.
Les précautions prises pour ces phases transitoires
d'arrêt et de démarrage permettent de minimiser les risques
d'accident et de garantir la sécurité du four 11-F1.
20
Procédure d'arrêt d'urgence :
En cas d'urgence SONATRACH/ACTIVITÉ AVAL/DIVISION
RAFFINAGE a mis en oeuvre une procédure d'arrêt complet du four
qui consigne étape par étape les actions à mener.
Lorsque le four 11-F1 est arrêté par le BMS (Burner
Management System) les brûleurs surveillés depuis la salle de
contrôle seront coupés (isolés), les vannes d'entrée
du fuel gaz (vannes de sectionnement ou vannes tout ou rien) et les vannes
d'entrée du pétrole brut se mettront en position fermé,
leurs positions sont définies par conception et sont adaptées,
ces FRC constituent une barrière passive efficace contre toute
dérive.
Ensuite les volets de la cheminée seront fermés et
cela pour minimiser le choc thermique sur la structure du four.
Et enfin, la vapeur stripping (vapeur d'eau) sera envoyée
dans le four.
La procédure d'arrêt d'urgence prévoit la
mise du four 11-F1 sous contrôle manuel le temps de revenir à la
normale.
Les cas d'arrêt du four 11-F1 sont les suivants :
1) manque de fuel gaz
2) manque de vapeur stripping
3) pannes électriques
4) Si le taux d'oxygène est inférieur ou
égale à 2 %.
Conclusion :
L'électricité, le combustible fuel-gaz et la vapeur
stripping sont des utilités nécessaires au bon fonctionnement du
four 11-F1.
Les produits soutirés de la colonne de distillation
atmosphérique sont le BRA, le HGO, le LGO, le kérosène, le
GPL, le HSRN, le LSRN.
Le four 11-F1 est équipé de moyens de
sécurité qui sont, les détecteurs de fumées, les
détecteurs de gaz, l'analyseur de fumées, une boucle de
régulation de débit d'entrée du fioul gaz, du
pétrole brut, et de température de surface du pétrole
brut, et de différence entre la pression interne et externe.
Il faut suivre régulièrement l'analyse des
fumées car si l'analyseur de fumées placé en haut des
volets détecte une mesure inférieur à 2 % du taux
d'oxygène dans les fumées sèches rejetés, cela
signifie qu'il y'a soit la présence d'un nuage de fuel gaz soit une
accumulation de fumées dans la chambre de combustion.
21
SONATRACH/ACTIVITÉ AVAL/DIVISION RAFFINAGE a mis des
procédures qui indiquent la marche à suivre lors pour le
démarrage et l'arrêt du four 11-F1, ou encore en cas de
phénomènes accidentels.
CHAPITRE III :
PRÉSENTATION DES POTENTIELS DE DANGERS
LIÉS AU CHAUFFAGE DU FOUR 11-F1
Introduction :
Le chapitre suivant traite les potentiels de dangers liés
aux produits mis en oeuvre, aux conditions opératoires et aux
utilités nécessaires au bon fonctionnement du four 11-F1.
Les potentiels de danger liés aux produits mis en oeuvre
concernent l'inflammabilité et seul le risque d'inflammabilité
sera traité dans la présente étude de danger.
Potentiels de dangers liés aux produits mis en
oeuvre :
Les propriétés physico-chimiques du pétrole
brut et du fuel gaz en termes d'inflammabilité sont les suivants :
Tableau III: Caractéristiques physico-chimiques du fuel
gaz et du pétrole brut
Inflammabilité
Température maximale atteinte dans le four
11-F1
Nom du produit
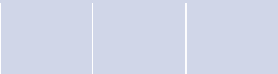
Point
Point
d'éclair
d'ébullition
Température
d'auto- inflammation
22
Fuel Gaz
|
-187°C
|
595°C
|
-161°C
|
40°C
|
Pétrole brut
|
<20°C
|
250°C
|
231,4°C
|
332°C
|
Potentiels de dangers liés au chauffage du four
11-F1 : Conditions opératoires :
Le choix des conditions de température et de pression est
déterminé à fin de limiter les besoins
énergétiques d'une part et d'autre part pour assurer une
réaction de combustion oxydante du fuel gaz pour séparer les
produits recherchés dans la colonne de distillation
atmosphérique, toute fois il est donc possible d'observer :
1) L'éventration rapide du foyer
(résistance mécanique insuffisante) en cas :
a)
23
D'accumulation du fuel gaz et la création d'une
atmosphère explosible (ATEX)
b) Rupture du tube transportant le pétrole brut à
l'intérieur du four.
c) Surpression du four.
2) Le retour de flamme en cas où la
flamme touche le bec du bruleur.
Potentiels de danger liés aux utilités :
Perte d'alimentation en fuel gaz :
La perte d'alimentation en fuel gaz n'engendre pas de
sérieuses conséquences car pas de gaz, pas d'explosion.
Perte d'alimentation électrique :
En cas de perte d'électricité, il y'aura extinction
des flammes des pilotes, par conséquent le fuel gaz entre dans la
chambre de combustion sans qu'il ne brule, et un nuage de fuel gaz se forme
à l'intérieur du four 11-F1 créant une ATEX
(Atmosphère Explosible) qui génère l'explosion interne du
four par inflammation du nuage.
Perte d'alimentation en vapeur stripping :
Dans le cas où le four n'a pas été
vaporisé avant son démarrage, des fumées peuvent
s'accumuler dans la chambre de combustion et ne seront pas
évacuées vers l'atmosphère en haut des volets, de ce fait
la pression interne augmente à l'intérieur du four et conduit son
explosion.
Afin de mieux illustrer les scénarios de danger que nous
avons cités ci-dessus nous allons présenter deux accidents
majeurs qui ont eu lieu récemment dans deux raffineries du pays, l'une
à l'est du pays à la raffinerie de Skikda et l'autre à
l'ouest du pays à la raffinerie d'Arzew
Historique du retour d'expérience :
Accident passé survenu sur le four 11-F2 de
l'unité Topping U11, 2010 :
Les catastrophes ne se produisent pas par hasard, elles sont
causées par un enchainement d'événements critiques dont la
chronologie est déterminante.
Qu'est qui a déclenché l'enchainement fatale des
événements et comment un four qui a fonctionné pendant des
années s'est il soudain transformé en brasier ?
Après interview avec les différents experts du
site, nous avons recensé les causes de cette tragédie,
voici la chronologie des faits qui ont précédé
l'accident :
En 2010, en plaine journée, la FRC (vanne d'entrée
du combustible) du HSRN non stabilisé bi-phasique (liquide-gaz) à
l'entrée du four rebouilleur 11-F2 de l'unité de distillation
atmosphérique est tombée en panne.
Dans ce cas les mesures de sécurité dictent qu'il
faut isoler la vanne en panne puis de purger sa conduite par le service
production, mais en cas de pépin il faut appeler le service
instrumentation qui va s'en en charger.
Mais malheureusement ce n'est pas ce qui s'était vraiment
passé, voici pourquoi :
Le chef de quart isole la FRC en fermant les vannes manuelles de
garde en attendant de la réparer, et pendant ce temps le HSRN passe
à travers son bipasse (vanne de roue de secoure) placé en
parallèle comme le montre la figure suivante :
11-F2
bipasse
HSLN non stabilisé
Vapeur stripping
IF
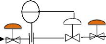
FRC

Tms = 223 °C

Pms = 21 Kg
Indicateur de débit
Vanne de contrôle et régulation de
débit Température maximale de service Pression maximale de
service
Vanne de contrôle manuelle

Tms
Pms
IF FRC
24
Figure III.1: Schéma présentatif du four
rebouilleur 11-F2 (U11)
Mais quand la vanne était bouchée au lieu d'appeler
le service instrumentation pour la déboucher, la démonter et
faire sa maintenance, il a insisté à purger la conduite de la
vanne, soudain la vanne est débouchée et un grand débit
massique de naphta lourd envahi son corps de la tète au pied, puis le
vent l'amène rapidement au four, au lieu que l'air pénètre
dans la conduite d'entrée d'air d'un bruleur, c'est le naphta lourd qui
est entré.
Le naphta lourd se propage dans la chambre de combustion du four
11-F2 en générant un retour de flamme instantané qui brule
le chef de quart et le tue.
25
Un autre homme par angoisse s'est jeté du haut d'une
échelle et s'est blessé puis réintégré dans
un autre poste, et un troisième avait été atteint du
cancer du sang suite aux troubles psychiques qu'il a vécu.
Accident passé survenu sur le four 100-F1 de la
Raffinerie de Skikda RA1/K, 3 Janvier 2013 :
Description de la raffinerie de Skikda RA1/K:
La raffinerie de Skikda, dénommée RA1/K a
été construite en 1979 à Skikda au bord de la mer.
Elle a pour mission de transformer le pétrole brut
provenant de Hassi-Messaoud et le pétrole brut réduit
importé.
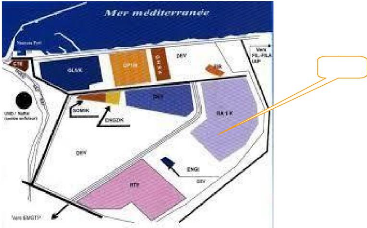
RA1/K
Figure III.2: Situation géographique de la raffinerie de
Skikda RA1/K
Déroulement :
Voici le cheminement des failles qui ont conduit à cette
tragédie :
Peu de temps avant l'accident, le four de l'unité 100-F1
de l'unité de raffinage du pétrole brut a fait l'objet d'une
rénovation par Samsung dans le cadre du projet de réhabilitation
et d'extension des capacités de raffinage.
En raison du manque d'effectifs, les quaristes (le personnel du
service quart) ont été retenus par le chef de production et ont
doublé leurs quarts 3 journées consécutives avant
l'accident, ils étaient donc à bout de force, et l'accident
survenu dans la nuit du 3 Janvier 2013, quant à 21h la direction de la
raffinerie de Skikda RA1/K a décidé d'augmenter le débit
d'entrée du combustible.
26
Par surplus de pression et chaleur, la tuyauterie transportant le
brut à l'intérieur du four s'est fragmentée et des vapeurs
d'hydrocarbures s'échappent à l'intérieur du four,
conséquences, à 21h45 explosion du four 100-F1 des flammes
à plus de 20 mètres et d'épaisses couches de fumées
s'élevaient de loin sur la raffinerie de Skikda.
L'explosion a carrément détruit le four 100-F1,
touchant ainsi le réacteur, un autre four, des ballons, des
équipements et installations sophistiquées d'instruments de
mesure installés récemment par Samsung. Au titre de ces
dégâts 3 hommes ont été blessés.
Par conséquent l'unité complète devant
produire des carburants et des matières premières avait
été soumise à l'arrêt, quelques minutes plus tard se
fut l'arrêt de la production, en effet les autres unités l'ont
suivi et ont été arrêtées par manque de charge,
conséquences ruineuses sur le plan économique de l'entreprise et
sur le marché national des hydrocarbures.
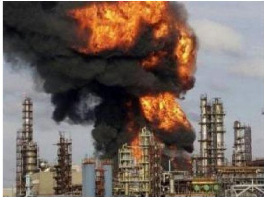
Figure III.3: Explosion du four 100-F1, 3 Janvier 2013
Conclusion :
Le four 11-F1 est une installation très sensible de
l'unité Topping U11 car :
1. Le pétrole brut entrant dans la chambre de combustion
du four 11-F1 peut être explosible car il se trouve à une
température supérieure à son point d'éclair. Le
fuel gaz alimentant le four 11-F1 est quant à lui très
inflammable.
2. La perte d'alimentation électrique ou vapeur stripping
ne constitue pas directement un potentiel de dangers significatif mais peut
intervenir en tant qu'un événement initiateur conduisant à
un accident (des conditions opératoires particulières).
D'après l'histoire de l'accident qui s'est produit sur le
four 11-F2 de l'unité Topping U11, 2010on constate que le respect des
mesures de sécurité est indispensable pour la
sécurité et la santé des travailleurs et devant chaque
incident survenu sur le four 11-F1 il faut immédiatement l'arrêter
même en cas de panne de vannes comme dans le cas ici présent et
qu'il faut anticiper les événements en faisant de la maintenance
périodique préventive et non
27
pas attendre jusqu'à ce que l'équipement tombe en
panne soudainement comme cette vanne d'entrée du naphta lourd.
L'accident de la Raffinerie de Skikda RA1/K qui a fait 3
blessés et des dommages matériels et économiques
irréversibles en 1 heure, aurait pu être prévenu et par
conséquent évité!
Car malgré que le four 100-F1 a été
récemment rénové, il fallait le maintenir et éviter
de le surcharger et ne pas réduire l'encadrement (sous effectifs) sous
n'importe quel contrainte.
Le retour de flamme et l'explosion d'un tube de pétrole
sont parmi les scénarios pouvant se produire sur un four, conduisent
à des accidents industriels majeurs avec des dégâts
immenses pour l'entreprise et sur la vie humaine et la santé des
travailleurs.
CHAPITRE IV:
ANALYSE DES RISQUES LIES AU FOUR 11-F1
Introduction :
Dans ce chapitre nous allons d'abord procéder à
l'analyse des risques liés au four 11-F1 par la méthode HAZOP, et
ce à fin d'identifier les déviations possibles et les causes de
défaillance prévisibles des composants du système
conduisant à des événements centrales redoutés.
Dans un deuxième temps, à l'aide du logiciel «
Arbre Analyste » nous allons construire deux ADD (Arbres De
Défaillances) pour chaque événement redouté pour
déterminer l'enchainement des défaillances possibles des
équipements propres au four 11-F1 et leurs probabilités
d'occurrence en introduisant dans l'un, des données théoriques et
dans l'autre des données pratiques.
L'attribution des données théoriques
expérimentales des évènements de base provient de la base
de données Ourida et le site de l'IFP training pour une
modélisation théorique expérimentale, cependant,
après interview, les données pratiques proviennent des jugements
des experts du site pour une modélisation pratique réelle, tout
en retenant que certains événements élémentaires
correspondent à des éléments dont la probabilité de
défaillance est constante d'une part, d'autre part les
équipements électroniques ne sont pas réparables
contrairement aux équipements mécaniques.
Les taux théoriques de défaillance, de
réparation et de défaillance par sollicitation ainsi que les taux
pratiques de défaillance, de réparation et de défaillance
par sollicitation sont présentés dans l'annexe IV.
Après nous allons interpréter les résultats
obtenus en identifiant l'état du système par comparaison entre
les deux types de données, les données expérimentales et
les données réelles.
Dans un deuxième temps, nous allons faire l'application
des réseaux bayésiens à l'aide du logiciel AgenaRisk sur
le cas de figure des données réelles.
L'étude est faite pour un temps de mission allant
jusqu'à un an soit 8760 heures.
Au final nous allons déterminer le niveau de risque
associé à chaque événement indésirable
après l'avoir caractérisé par évaluation de ses
dommages potentiels et estimation de sa probabilité d'occurrence.
28
Identification des risques liés au four 11-F1 par
la méthode HAZOP :
29
Tableau IV.1: Tableau HAZOP
Paramètre
|
Mot clés
|
Déviation
|
Causes
|
Conséquences
|
Mode de détection
|
Sécurité existante
|
Recommandation
|
Pression
|
Plus de
|
Haute pression (Augmentation
|
1. accumulation de fumées dans la
|
1. Signale de montée de pression dans la salle de
|
1. DIP.
|
1. Le damper.
|
1. Maintenance périodique des
|
|
|
de la pression
|
chambre de
|
contrôle provenant du DIP.
|
2. L'alarme
|
2. L'arrêt
|
instruments et
|
|
|
à l'intérieur du
|
combustion en cas
|
|
sonore et
|
automatique
|
entretien préventif
|
|
|
four 11-F1 ou
|
d'absence de
|
2. augmentation du débit de
|
visuelle dans
|
du four soit
|
des équipements.
|
|
|
surpression du
|
vapeur stripping ou
|
la charge (pétrole brut)
|
la salle de
|
par le potto
|
|
|
|
four).
|
en cas où le débit du fuel gaz à
l'entrée est élevé.
2. Défaillance de la boucle automatique de
régulation de pression (DIP- BMS- FRC bloqué ouverte).
|
entrant dans le four 11-F1 par l'opérateur humain dans la
salle de contrôle.
3. Si pression interne du four > 1.7 bar et débit fuel
gaz > 6120 m3/h explosion du four avec des
phénomènes dangereux tel qu'une onde de surpression et effets
missiles
|
contrôle.
3. Visuel sur site ou en salle de contrôle.
4.
L'analyseur de fumées.
|
d'arrêt d'urgence soit par le BMS.
3. L'analyseur de
fumées.si (?O2 >
2%).
|
2. Programme de suivi.
|
|
|
|
|
+ perte du pétrole brut + perte du fuel gaz + atteintes
aux opérateurs humains et à l'environnement + pertes
matérielles.
|
|
4. Le contrôle manuel.
|
|
30
Tableau IV.1: Tableau HAZOP
Débit
|
Plus de
|
Haut débit (augmentation du débit du fuel gaz
entrant dans le four 11-F1).
|
1. Défaillance de la boucle automatique de
régulation de débit (IF-BMS- FRC bloqué ouverte).
2. Rendements de P1 et P2 élevés.
|
1. augmentation de la pression interne du four.
2. ouverture du damper et diminution de la pression sinon la
pression explosion du four.
3. augmentation de la
|
1. Visuel sur site ou en salle de contrôle.
2. Alarmes (sonore et visuelle).
|
1. L'arrêt automatique du four soit par le potto
d'arrêt d'urgence soit par le le BMS.
|
1. Maintenance périodique des instruments et entretien
préventif des équipements.
2. Programme de suivi.
|
|
|
|
|
température interne du four et
|
3. IF
|
2. Le contrôle
|
|
|
|
|
|
|
des dépôts de coke dans les
|
|
manuel.
|
|
|
|
|
|
bruleurs.
|
|
|
|
|
|
|
|
4. Si débit fuel gaz > 6120
|
|
|
|
|
|
|
|
m3/h explosion du four avec
|
|
|
|
|
|
|
|
des phénomènes dangereux
|
|
|
|
|
|
|
|
tel qu'une onde de
|
|
|
|
|
|
|
|
surpression et effets missiles
|
|
|
|
|
|
|
|
+ perte du pétrole brut + perte
|
|
|
|
|
|
|
|
du fuel gaz + atteintes aux
|
|
|
|
|
|
|
|
opérateurs humains et à
|
|
|
|
|
|
|
|
l'environnement + pertes
|
|
|
|
|
|
|
|
matérielles.
|
|
|
|
31
Tableau IV.1: Tableau HAZOP
|
Moins
|
Moins de débit
|
1. Débit fuel gaz à
|
1. Réaction de combustion
|
1. Visuel sur
|
1. L'arrêt
|
1. Maintenance
|
|
|
(débit
|
l'entrée insuffisant
|
incomplète.
|
site ou en
|
automatique
|
périodique des
|
|
|
insuffisant du
|
(en amont FRC).
|
|
salle de
|
du four soit
|
instruments et
|
|
|
fuel gaz
|
|
2. Si débit fuel gaz < 6120
|
contrôle.
|
par le potto
|
entretien préventif
|
|
|
entrant dans le
|
2. Défaillance de la
|
m3/h les flammes des bruleurs
|
|
d'arrêt
|
des équipements.
|
|
|
four 11-F1l).
|
boucle automatique
|
de températures entre 900 et
|
2. Alarmes
|
d'urgence ou
|
|
|
|
|
de régulation de
|
1500 °C touchent le bec du
|
(sonore et 1.
|
par le BMS.
|
2. Programme de
|
|
|
|
débit (IF-BMS- FRC).
|
bruleur, déforment le métal et retournent par les
conduites
|
visuelle).
|
2. Le contrôle
|
suivi.
|
|
|
|
3. Fuites des
|
du fuel gaz (retour de
flamme) + perte du fuel gaz +
|
3. IF
|
manuel.
|
3. Protection des conduites contre la
|
|
|
|
conduites du fuel gaz.
|
atteintes aux opérateurs humains et à
l'environnement
|
4. Détecteurs de gaz.
|
|
corrosion.
|
|
|
|
|
+ perte matériel.
|
|
|
|
|
|
|
5. P1 ou P2 est défaillante.
|
|
5. Détecteurs de fumées.
|
|
|
32
Tableau IV.1: Tableau HAZOP
|
Pas de
|
Pas de débit.
|
1. Défaillance de la
|
1. Pas de réaction de
|
1. Visuel sur
|
1. L'arrêt
|
1. Maintenance
|
|
|
|
boucle automatique
|
combustion.
|
site ou en
|
automatique
|
périodique des
|
|
|
|
de régulation de
|
|
salle de
|
du four soit
|
instruments et
|
|
|
|
débit (IF-BMS-
|
2. Diminution de la
|
contrôle.
|
par le potto
|
entretien préventif
|
|
|
|
FRC).
|
température interne du four
|
2. Alarmes
|
d'arrêt
d'urgence ou
|
des équipements.
|
|
|
|
2. P1 et P2
|
2. Si débit fuel gaz < 6120
|
(sonore et
|
par le BMS.
|
2. Programme de
|
|
|
|
défaillante.
|
m3/h pas d'échauffement du pétrole brut
donc pas de
|
visuelle).
|
2. Le contrôle
|
suivi.
|
|
|
|
3. bouchage de toutes les conduites du fuel gaz.
|
reflux pour le soutirage des produits latéraux.
|
3. IF.
|
manuel.
|
3. Prévoir une autre source d'alimentation en fuel gaz.
|
|
|
|
4. Tous les bruleurs sont en panne.
|
|
|
|
|
|
|
|
5. Absence du fuel gaz à l'entrée du four.
|
|
|
|
|
33
Tableau IV.1: Tableau HAZOP
Température
|
Plus de
|
Augmentation
|
1. Défaillance de la
|
1. L'ouverture des tubes fuel
|
1. Indicateur
|
1. L'arrêt
|
1. Maintenance
|
|
|
de la
|
boucle automatique
|
gaz dans la zone des brûleurs
|
de
|
automatique
|
périodique des
|
|
|
température à
|
de régulation de
|
suite à une surchauffe.
|
température
|
du four soit
|
instruments et
|
|
|
l'intérieur du
|
température (IT-
|
|
du tube de
|
par le potto
|
entretien
|
|
|
four 11-F1.
|
BMS- FRC).
2. Débit du fuel gaz à l'entrée
élevé.
|
2. Si température de surface du pétrole brut >
480 °C explosion du four par rupture longitudinale du tube de
pétrole brut suite à une surchauffe avec inflammation
instantané par les flammes des brûleurs et explosion avec des
phénomènes dangereux tel qu'une onde de surpression, effets
missiles et feu de nappe + perte du pétrole brut + perte du fuel gaz +
atteintes aux opérateurs humains et à l'environnement
|
pétrole brut.
2. Indicateur de température du pétrole brut.
3. Indicateur de température des parois du four.
4. Alarmes
|
d'arrêt
d'urgence ou par le BMS.
2. Le contrôle manuel.
|
préventive des équipements.
2. Programme de suivi.
|
|
|
|
|
+ pertes matériels.
|
(sonore et visuelle).
|
|
|
|
|
|
|
3. Dépôts de coke dans les bruleurs.
4. L'ouverture des tubes de chauffe du fuel gaz dans la zone
des brûleurs suite à la corrosion.
|
5. Visuel sur site ou en sale de contrôle.
|
|
|
34
Tableau IV.1: Tableau HAZOP
|
bas
|
Baisse de la
|
1. Débit du fuel gaz
|
Si température de surface
|
1. IT.
|
1. L'arrêt
|
1. Maintenance
|
|
|
température à
|
à l'entrée
|
pétrole brut < 360 °C pas
|
|
automatique
|
périodique des
|
|
|
l'intérieur de
|
insuffisant.
|
d'échauffement du pétrole
|
2. Indicateur
|
du four soit
|
instruments et
|
|
|
four.
|
|
brut et pas de reflux suffisant
|
de
|
par le potto
|
entretien préventif
|
|
|
|
2. Panne des
|
pour le soutirage des produits
|
température
|
d'arrêt
|
des équipements.
|
|
|
|
bruleurs.
3. bouchage des conduites du fuel gaz.
|
latéraux.
|
du tube de pétrole brut.
3. Indicateur de température des parois du four
placé à l'intérieur.
|
d'urgence ou par le BMS.
2. Le contrôle manuel.
|
2. Programme de suivi.
|
|
|
|
|
|
4. Alarmes
|
|
|
|
|
|
|
|
(sonore et visuelle).
|
|
|
|
|
|
|
|
5. Visuel sur site ou en salle de contrôle.
|
|
|
35
Scénarios retenus pour la modélisation
:
La gravité des dommages ont conduit à choisir
l'explosion d'un tube de pétrole brut et l'explosion d'un nuage de fuel
gaz à l'intérieur de la chambre de combustion, la surpression du
four 11-F1 ainsi que le retour de flamme à l'entrée des bruleurs
comme événements centraux redoutés.
Modélisation des scénarios par le logiciel
Arbre Analyste :
1er scenario : Explosion du tube de pétrole brut
:
L'explosion du tube de pétrole brut est dut à au
tube de pétrole brut qui est en charge et à la défaillance
des installations qui sont soit la vanne de contrôle et de
régulation de débit qui est bloqué ouverte ou le BMS (le
Burner Management System) ou les instruments de mesure (instrument de mesure de
la température ou de débit).
Résultats de la modélisation
expérimentale
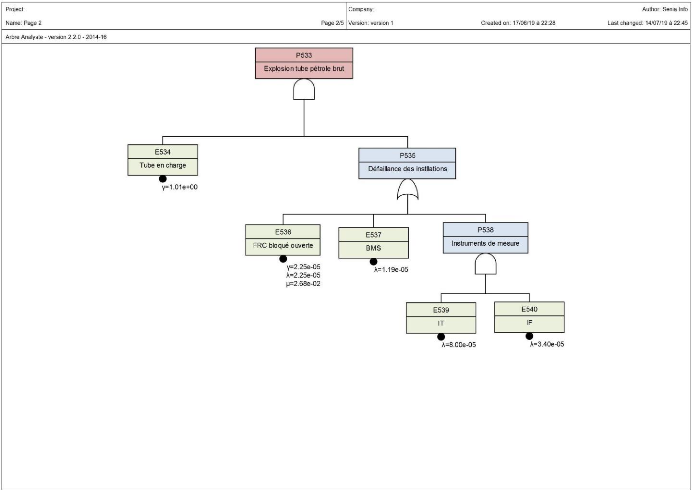
36
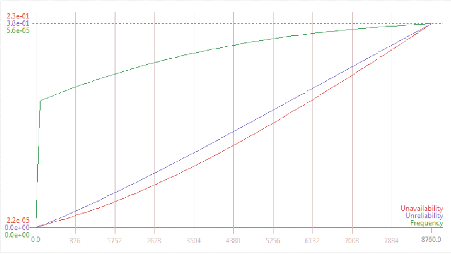
37
Figure IV.5: Courbe du manque de fiabilité du
système
|
Unreliability (manque de fiabilité) Unvailability
(indisponibilité) Frequency (fréquence)
|
Analyse de la courbe du manque de fiabilité du
système :
Sur l'intervalle [0h - 8760 h], le manque de fiabilité du
four augmente dans le temps pour atteindre une valeur maximale de 2.3 *
10-1, en parallèle l'indisponibilité du four augmente
pour atteindre une valeur de 3.8 * 10-1, quand à la
fréquence de l'événement redouté « explosion
du tube de pétrole brut » est augment subitement sur l'intervalle
{0h-876h] puis progressivement jusqu'à atteindre 3.6*
10-5.
Tableau IV.3: Résumé exécutif
Results
|
Probability:
|
0.217
|
System unreliability:
|
0.38
|
System MTTR
|
4746
|
38
Analyse du tableau IV.3 :
Le taux de défaillance du four par apport au
scénario « explosion du tube de pétrole brut » est
0.217.
Le manque de fiabilité du système sur une
année augmente jusqu'à atteindre 0.38.
Le MTTR (« Mean Time de Reaper » ou « temps moyen
de réparation ») est égale à 4746 h.
Tableau IV.4: CIF (Facteurs d'Importance Critique)
Le tableau ci-dessous contient les grandeurs du CIF (Facteur
d'Importance Critique) de chacun des événements de base
contribuant à l'événement redouté et qui sont :
Event
|
Description
|
CIF
|
E534
|
Tube en charge
|
1
|
E536
|
FRC bloqué ouverte
|
0.0036
|
E537
|
BMS
|
0.43
|
E540
|
IF
|
0.57
|
E539
|
IT
|
0.57
|
Tableau IV.5: Coupes minimales et leurs ordres
N°
|
Order
|
Probability
|
Event
|
Description
|
1
|
3
|
0.13
|
E534
|
Tube en charge
|
|
|
|
E539
|
IT
|
|
|
|
E540
|
IF
|
2
|
2
|
0.099
|
E534
|
Tube en charge
|
|
|
|
E537
|
BMS
|
3
|
2
|
0.000837
|
E534
|
Tube en charge
|
|
|
|
E536
|
FRC bloqué ouverte
|
Résultats de la modélisation
réelle
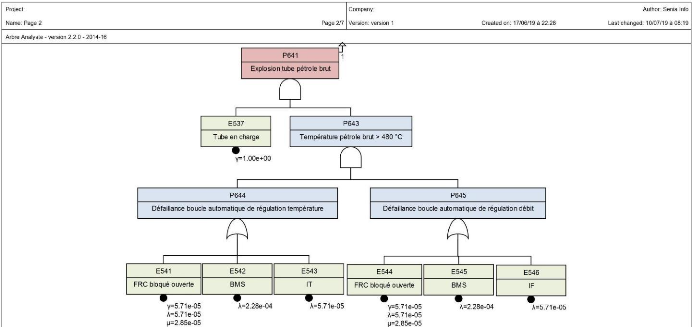
39
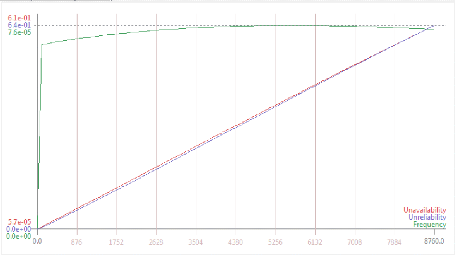
40
Figure IV.7: Courbe du manque de fiabilité du
système
|
Unreliability (manque de fiabilité) Unvailability
(indisponibilité) Frequency (fréquence)
|
: Analyse de la courbe du manque de fiabilité du
système :
Sur l'intervalle [0h - 8760 h], le manque de fiabilité du
four augmente dans le temps pour atteindre une valeur maximale de 6.4 *
10-1, en parallèle l'indisponibité du four augmente
pour atteindre une valeur de 6.1 * 10-1, quand à la
fréquence de l'événement redouté « explosion
du tube de pétrole brut » est augment subitement sur l'intervalle
{0h-876h] puis progressivement jusqu'à atteindre 7.6*
10-5.
Tableau IV.6: Résumé exécutif
Results
|
Probability:
|
0.926
|
System unreliability:
|
6.4e-09
|
System MTTR
|
8630
|
41
Analyse du tableau IV.6 :
Le taux de défaillance du four par apport au
scénario « explosion du tube de pétrole brut » est
0.926.
Le manque de fiabilité du système sur une
année augmente jusqu'à atteindre une valeur maximale de 6.4 *
10-9.
Le MTTR (« Mean Time de Reaper » ou « temps moyen
de réparation ») est égale à 8630 h. Tableau IV.7:
Facteurs d'importance
Event
|
Description
|
CIF
|
E537
|
Tube en charge
|
1.4
|
E754
|
BMS
|
0.86
|
E752
|
FRC bloqué ouverte
|
0.35
|
E757
|
IT
|
0.15
|
E756
|
IF
|
0.15
|
Tableau IV.8: Coupes minimales et leurs ordres
N°
|
Order
|
Probability
|
Event
|
Description
|
1
|
2
|
0.864
|
E537
|
Tube en charge
|
|
|
|
E754
|
BMS
|
2
|
2
|
0.352
|
E537
|
Tube en charge
|
|
|
|
E752
|
FRC bloqué ouverte
|
3
|
3
|
0.155
|
E537
|
Tube en charge
|
|
|
|
E756
|
IF
|
|
|
|
E757
|
IT
|
Comparaison :
La probabilité de défaillance du four 11-F1
:
La probabilité de défaillance du four 11-F1
à partir des données théoriques est inférieure au
taux de défaillance par apport aux données pratiques (0.217 <
0.926).
System unreliability (Manque de fiabilité)
:
Le manque de fiabilité du système à
partir du modèle théorique est inférieur à celui du
modèle pratique (0.38 < 1).
42
Les coupes minimales :
Les probabilités des coupes minimales à partir des
données théoriques sont faibles par apport à celles des
données pratiques.
A partir des données théoriques, la
probabilité de la coupe minimale (E534.E539.E540) pour provoquer
l'explosion du tube de pétrole brut est la plus élevée,
contrairement aux données pratiques, la probabilité de la coupe
minimale (E537.E754) est la plus élevée.
Le CIF (Facteurs d'Importance Critique):
A partir des données théoriques et pratiques, la
probabilité pour que le tube de pétrole brut qui était en
charge ait provoqué l'explosion du tube de pétrole brut est la
plus élevée et elle est égale à 1 donc
forcément au moment de l'explosion les tubes de pétrole brut
étaient en charge et c'est l'événement le plus
critique.
Interprétation des résultats :
Le taux de défaillance et le manque de fiabilité,
ainsi que les probabilités des coupes minimales plus
élevées par apport à la normale indiquent qu'il est en
état dégradé.
La coupe minimale (E537.E754) à partir des données
pratiques est la combinaison des événements sur les quelles il
est le plus intéressant de faire de la maintenance préventive et
correctives pour atteindre la probabilité de la coupe minimale
(E534.E539.E540) à partir des données théoriques.
A partir des données pratiques, le facteur d'importance
critique nous indique que l'événement « tube de
pétrole brut en charge» est le meilleur candidat pour les efforts
visant à améliorer la fiabilité du système et
éviter son explosion.
2ème scénario : Explosion du nuage de fuel
gaz à l'intérieur de la chambre de combustion :
L'explosion d'un nuage de fuel gaz est dût à
l'accumulation du fuel gaz dans la chambre de combustion et à
l'inflammation de ce nuage de gaz.
L'accumulation du nuage de fuel gaz dans la chambre de combustion
est dût soit à la perte d'alimentation électrique soit
à l'extinction de la flamme du bruleur en cas où il tombe en
panne.
L'étincelle peut être provoquée soit par un
incendie à proximité du four, soit par des travaux de soudage.
Résultats de la modélisation
expérimentale
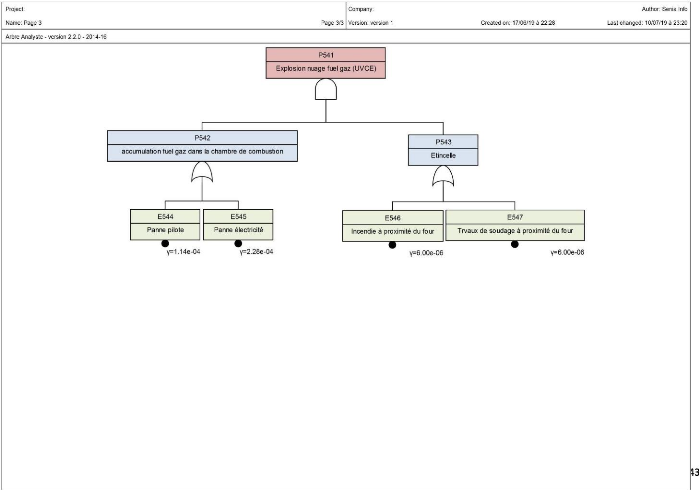
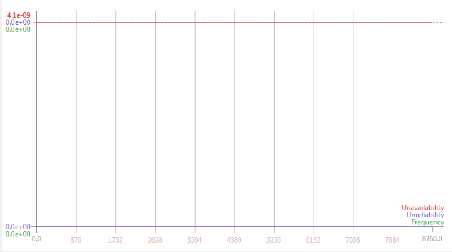
44
Figure IV.11: Courbe du manque de fiabilité du
système
|
Unreliability (manque de fiabilité) Unvailability
(indisponibilité) Frequency (fréquence)
|
: Analyse de la courbe du manque de fiabilité du
système :
Sur l'intervalle [0h - 8760 h], le manque de fiabilité du
four ainsi que la fréquence du scénario « explosion d'un
nuage de fuel gaz » n'apparaissent pas puisque nous avons entré des
valeurs constantes des événements de base, de même pour
l'indisponibilité du four elle est constante sur l'intervalle [0h - 8760
h] et est égale à 4.1 * 10-9.
Tableau IV.9: Résumé exécutif
Results
|
Probability:
|
4.1e-09
|
System unreliability:
|
none
|
System MTTR
|
none
|
Analyse du tableau IV.9 :
Le taux de défaillance du four par apport au
scénario « explosion d'un nuage de fuel gaz » est 4.1 *
10-9.
45
System unreliability (le manque de fiabilité du
système et le MTTR (« Mean Time de Reaper » ou « temps
moyen de réparation ») sur 8760 h sont indéterminés
parce que les probabilités des événements de base suivent
une loi constante.
Tableau IV.10: CIF (Facteur d'Importance Critique)
Event
|
Description
|
CIF
|
E545
|
Panne électricité
|
0.67
|
E544
|
Panne pilote
|
0.33
|
E547
|
Travaux de soudage à proximité du four
|
0.5
|
E546
|
Incendie à proximité du four
|
0.5
|
Tableau IV.11: Coupes minimales et leurs ordres
N°
|
Order
|
Probability
|
Event
|
Description
|
1
|
2
|
1.37e-09
|
E545
|
Panne électricité
|
|
|
|
E547
|
Travaux de soudage à proximité du four
|
2
|
2
|
1.37e-09
|
E545
|
Panne électricité
|
|
|
|
E546
|
Incendie à proximité du four
|
3
|
2
|
6.84e-10
|
E544
|
Panne pilote
|
|
|
|
E547
|
Travaux de soudage à proximité du four
|
4
|
2
|
6.84e-10
|
E544
|
Panne pilote
|
|
|
|
E546
|
Incendie à proximité du four
|
Résultats de la modélisation
réelle
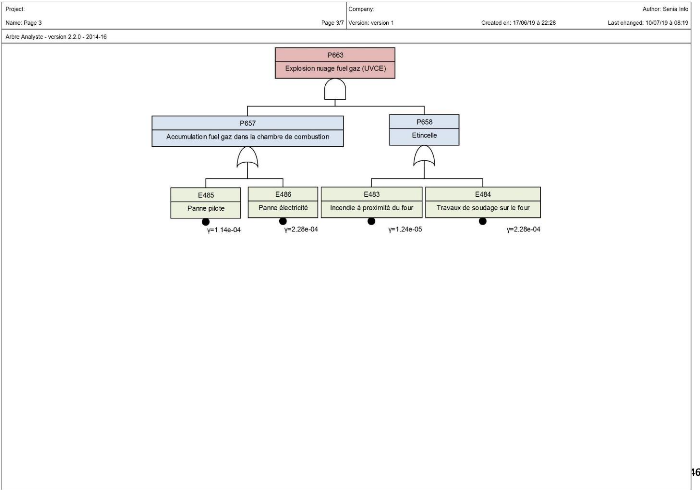
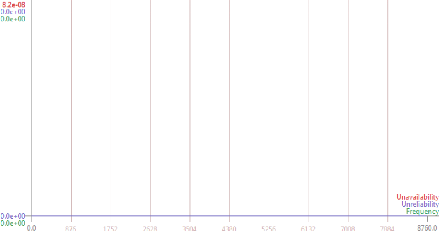
47
Figure IV.13: Courbe du manque du manque de fiabilité du
système
|
Unreliability (manque de fiabilité) Unvailability
(indisponibilité) Frequency (fréquence)
|
: Analyse de la courbe du manque de fiabilité du
système :
Sur l'intervalle [0h - 8760 h], le manque de fiabilité du
four ainsi que la fréquence du scénario « explosion d'un
nuage de fuel gaz » n'apparaissent pas puisque nous avons entré des
valeurs constantes des événements de base, de même pour
l'indisponibilité du four elle est constante sur l'intervalle [0h - 8760
h] et est égale à 8.2 * 10-8.
Tableau IV.12: Résumé exécutif
Results
|
Probability:
|
8.24e-08
|
System unreliability:
|
none
|
System MTTR
|
none
|
Analyse du tableau IV.12 :
Le taux de défaillance du four par apport au
scénario « explosion d'un nuage de fuel » est 8.24*
10-8.
48
System unreliability (le manque de fiabilité du
système et le MTTR (« Mean Time de Reaper » ou « temps
moyen de réparation ») sur 8760 h sont indéterminés
parce que les probabilités des événements de base suivent
une loi constante.
Tableau IV.13: CIF (Facteur d'Importance Critique)
Event
|
Description
|
CIF
|
E484
|
Travaux de soudage sur le four
|
0.95
|
E483
|
Incendie à proximité du four
|
0.052
|
E486
|
Panne électricité
|
0.67
|
E485
|
Panne pilote
|
0.33
|
Tableau IV.14: Coupes minimales et leurs ordres
N°
|
Order
|
Probability
|
Event
|
Description
|
1
|
2
|
5.21e-08
|
E484
|
Travaux de soudage sur le four
|
|
|
|
E486
|
Panne électricité
|
2
|
2
|
2.6e-08
|
E484
|
Travaux de soudage sur le four
|
|
|
|
E485
|
Panne pilote
|
3
|
2
|
2.83e-09
|
E483
|
Incendie à proximité du four
|
|
|
|
E486
|
Panne électricité
|
4
|
2
|
1.41e-09
|
E483
|
Incendie à proximité du four
|
|
|
|
E485
|
Panne pilote
|
Comparaison :
La probabilité de défaillance du four 11-F1
:
La probabilité de défaillance du four 11-F1
à partir des données théoriques est dix fois moins
inférieure que le taux de défaillance par apport aux
données pratiques (4.1*10-9 < 8.24*10-8).
Les coupes minimales :
Les probabilités des coupes minimales à partir des
données théoriques sont dix fois plus faibles par apport à
celle des données pratiques.
A partir des données théoriques, les
probabilités des coupes minimales (E545.E547) et (E545.E546) pour
provoquer l'explosion du nuage de gaz sont les plus élevées,
contrairement aux coupes minimales à partir des données
pratiques, la coupe minimale (E484.E486) est la plus probable.
49
Le CIF (Facteurs d'Importance Critique):
A partir des données théoriques, la
probabilité pour que la panne d'électricité ait
provoqué l'explosion du nuage de fuel gaz est la plus
élevée, contrairement aux données pratiques, les travaux
de soudage ont la plus grande part d'importance.
Dans le cas de figure des données pratiques,
l'événement « travaux de soudage à proximité
du four 11-F1 » est l'événement le plus critique.
Interprétation des résultats :
Le taux de défaillance et le manque de fiabilité,
ainsi que les probabilités des coupes minimales plus
élevées par apport à la normale indiquent qu'il est en
état très dégradé.
Les coupes minimales (E484.E486) à partir des
données pratiques est la combinaison des événements sur
lesquelles il est le plus intéressant de faire de la maintenance
préventive et corrective pour atteindre la probabilité de la
coupe minimale (E545.E547) à partir des données
théoriques.
A partir des données pratiques, le facteur d'importance
critique nous indique que l'événement «Travaux de soudage
à proximité du four 11-F1 » est le meilleur candidat pour
les efforts visant à améliorer la fiabilité du
système et éviter son explosion.
3ème scenario : Surpression du four 11-F1
:
La surpression du four 11-F1 est dût soit à la
b=vanne de con trole et de régulation de débit FRC qui est
bloqué ouverte ou bien à la défaillance du BMS (Burner
management system) qui déclenche le four ou bien à la
défaillance des équipements qui sont l'indicateur de
différence de pression IDP et soit à une fuite du réseau
de distribution de vapeur soit à la défaillance de l'indicateur
de débit IF.
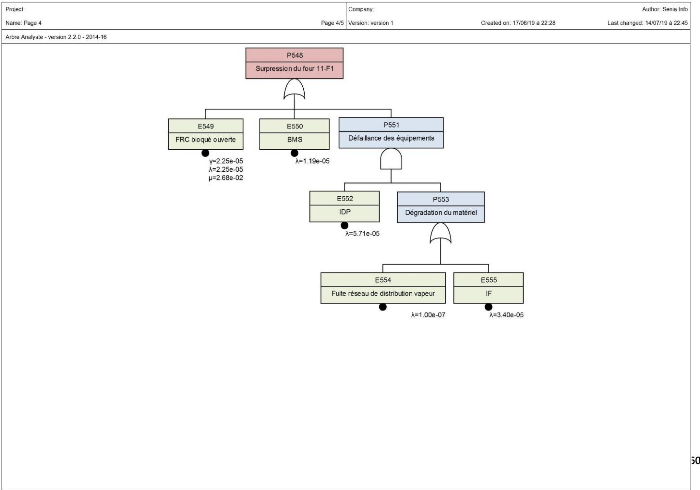
Résultats de la modélisation
expérimentale
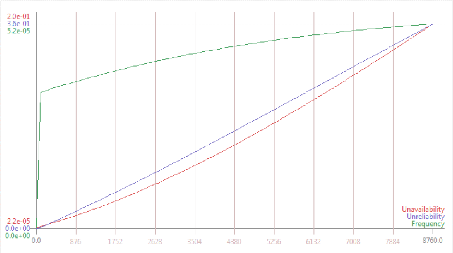
51
Figure IV.18: Courbe du manque de fiabilité du
système

Unreliability (manque de fiabilité) Unvailability
(indisponibilité) Frequency (fréquence)
: Analyse de la courbe du manque de fiabilité du
système :
Sur l'intervalle [0h - 8760 h], le manque de fiabilité du
four augmente dans le temps pour atteindre une valeur maximale de 3.6 *
10-1, en parallèle l'indisponibité du four augmente
pour atteindre une valeur de 2 * 10-1, quand à la
fréquence de l'événement redouté
« surpression du four » elle augmente subitement sur
l'intervalle {0h-876h] puis progressivement jusqu'à atteindre 5.2*
10-5.
Tableau IV.15: Résumé exécutif
Probability:
0.191
System unreliability:
0.355
System MTTR 4462
Results
Analyse du tableau IV.15 :
Le taux de défaillance du four par apport au
scénario « surpression du four » est 0.191.
52
Le manque de fiabilité du système sur une
année augmente jusqu'à atteindre une valeur maximale de 0.355.
Le MTTR (« Mean Time de Reaper » ou « temps
moyen de réparation ») est égale à 4462 heures.
Tableau IV.16: CIF (Facteurs d'Importance Critique)
Event
|
Description
|
CIF
|
E549
|
FRC bloqué ouverte
|
0.0042
|
E550
|
BMS
|
0.49
|
E552
|
IDP
|
0.5
|
E554
|
Fuite réseau de distribution vapeur
|
0.0017
|
E555
|
IF
|
0.5
|
Tableau IV.17: Coupes minimales et leurs ordres
N°
|
Order
|
Probability
|
Event
|
Description
|
1
|
2
|
0.101
|
E552
|
IDP
|
|
|
|
E555
|
IF
|
2
|
1
|
0.099
|
E550
|
BMS
|
3
|
1
|
0.000837
|
E549
|
FRC bloqué ouverte
|
4
|
2
|
0.000345
|
E552
|
IDP
|
|
|
|
E554
|
Fuite réseau de distribution vapeur
|

Résultats de la modélisation
réelle

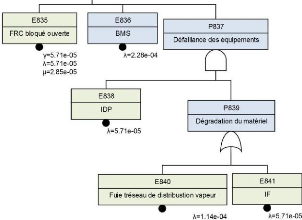
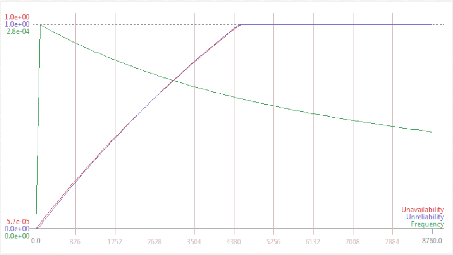
54
Figure IV.20: Courbe du manque de fiabilité du
système
|
Unreliability (manque de fiabilité) Unvailability
(indisponibilité) Frequency (fréquence)
|
: Analyse de la courbe du manque de fiabilité du
système :
Sur l'intervalle [0h - 4380 h], l'indisponibité du
système augmente en même temps que le manque de fiabilité
du four pour atteindre une valeur maximale de 1 et restent constants à
cette valeur, donc il ne sera plus fiable et disponible après 4380
heures de travail, quand à la fréquence de
l'événement redouté « surpression du four » elle
augmente subitement sur l'intervalle {0h-876h] puis progressivement
jusqu'à atteindre 2.8* 10-4.
Tableau IV.18: Résumé exécutif
Results
Probability: 0.944
System unreliability: 0.998
System MTTR 8633
55
Analyse du tableau IV.18 :
Le taux de défaillance du four par apport au
scénario « surpression du four » est 0.944, donc c'est certain
qu'il se produit sur une année.
Le manque de fiabilité du système sur une
année augmente jusqu'à atteindre une valeur maximale de 0.998,
donc au bout d'une année le four 11-F1 ne sera plus en état
fiable pour accomplir sa mission de chauffage du pétrole brut.
Le MTTR (« Mean Time de Reaper » ou « temps moyen
de réparation ») est égale à 8633 heures.
Tableau IV.19: CIF (Facteurs d'Importance Critique)
Event
|
Description
|
CIF
|
E836
|
BMS
|
0.86
|
E835
|
FRC bloqué ouverte
|
0.35
|
E838
|
IDP
|
0.4
|
E841
|
IF
|
0.15
|
E840
|
Fuie réseau de distribution vapeur
|
0.25
|
Tableau IV.20: Coupes minimales et leurs ordres
N°
|
Order
|
Probability
|
Event
|
Description
|
1
|
1
|
0.864
|
E836
|
BMS
|
2
|
1
|
0.352
|
E835
|
FRC bloqué ouverte
|
3
|
2
|
0.249
|
E838
|
IDP
|
|
|
|
E840
|
Fuie tréseau de distribustion vapeur
|
4
|
2
|
0.155
|
E838
|
IDP
|
|
|
|
E841
|
IF
|
Comparaison :
Probabilité de défaillance du four 11-F1
:
La probabilité de défaillance du four 11-F1
à partir des données théoriques est moins
inférieure que le taux de défaillance par apport aux
données pratiques (0.191 < 0.944).
System unreliability (Manque de fiabilité)
:
Le manque de fiabilité du système à
partir du modèle théorique est inférieur à celui du
modèle pratique (0.355 < 0.998).
56
Les coupes minimales :
Les probabilités des coupes minimales à partir des
données théoriques sont dix fois plus faibles par apport à
celles des données pratiques.
A partir des données théoriques, la
probabilité de la coupe minimale (E552.E555) pour provoquer la
surpression du four 11-F1 est la plus élevée, contrairement aux
coupes minimales à partir des données pratiques, la coupe
minimale E836 est la plus probable.
Le CIF (Facteurs d'Importance Critique):
A partir des données théoriques, la
probabilité pour que l'IDP ait provoqué la surpression du four
11-F1 conduisant à son explosion est la plus élevée,
contrairement aux données pratiques, la défaillance du BMS a la
plus grande part.
Dans le cas de figure des données pratiques,
l'événement « défaillance du BMS » est
l'événement le plus critique.
Interprétation des résultats :
Le taux de défaillance et le manque de fiabilité,
ainsi que les probabilités des coupes minimales plus
élevées que la normale du four par apport à la normale
indiquent qu'il est en état dégradé.
Les coupes minimales (E836) à partir des données
pratiques est la combinaison des événements sur lesquels il est
le plus intéressant de faire de la maintenance préventive et
corrective pour atteindre la probabilité de la coupe minimale
(E552.E555) à partir des données théoriques.
A partir des données pratiques, le facteur d'importance
critique nous indique que l'événement « défaillance
du BMS » » est le meilleur candidat pour les efforts visant à
améliorer la fiabilité du système et éviter son
explosion.
4ème scénario : Retour de flamme à
l'entrée des bruleurs :
Le retour de flammes à l'entrée des bruleurs est
dût à la réalisation de tout les événements
qui sont : la FRC est resté bloquée partiellement ouverte, la
défaillance du BLS (Burner Management System), la défaillance du
IF, et que la flamme d'un ilote est restée allumée, et soit une
fuite d'un conduite de fuel gaz qui s'est produite soit à la
défaillance d'une pompe P1 ou P2.
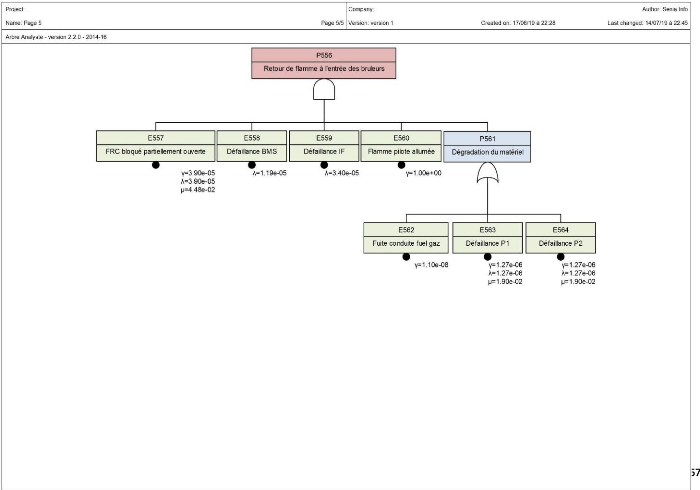
Résultats de la modélisation
expérimentale
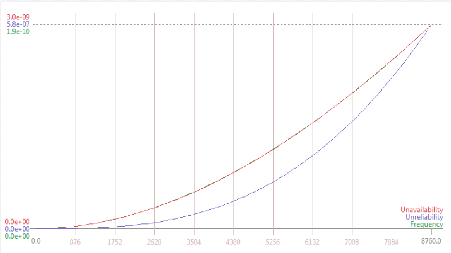
58
Figure IV.22: Courbe du manque de fiabilité du
système
|
Unreliability (manque de fiabilité) Unvailability
(indisponibilité) Frequency (fréquence)
|
: Analyse de la courbe du manque de fiabilité du
système :
Sur l'intervalle [0h - 8760 h], le manque de fiabilité du
système augmente en fur et à mesure jusqu'à atteindre une
valeur de 5.8 * 10-7.
L'indisponibilité du four augmente quand à elle
pour atteindre une valeur maximale de
3*10-9.
La fréquence de l'événement redouté
« retour de flamme à l'entrée des bruleurs » elle
augmente dans le temps pour atteindre une valeur de 1.9* 10-10.
Tableau IV.21: Résumé exécutif
Results
|
Probability:
|
2.95e-09
|
System unreliability:
|
5.82e-07
|
System MTTR
|
44.47
|
59
Analyse du tableau IV.21 :
Le taux de défaillance du four par apport au
scénario « retour de flammes à l'entrée des bruleurs
» est 2.95*10-9.
Le manque de fiabilité du système sur une
année augmente jusqu'à atteindre une valeur maximale de 5.95 *
10-7.
Le MTTR (« Mean Time de Reaper » ou « temps moyen
de réparation ») est égale à 44.47 heures.
Tableau IV.22: CIF (Facteurs d'Importance Critique)
Event
|
Description
|
CIF
|
E557
|
FRC bloqué partiellement ouverte
|
1
|
E560
|
Flamme pilote allumée
|
1
|
E559
|
Défaillance IF
|
1
|
E558
|
Défaillance BMS
|
1
|
E564
|
Défaillance P2
|
0.5
|
E563
|
Défaillance P1
|
0.5
|
E562
|
Fuite conduite fuel gaz
|
8.2e-05
|
Tableau IV.23: Coupes minimales et leurs ordres
N°
|
Order
|
Probability
|
Event
|
Description
|
1
|
5
|
1.48e-09
|
E557
|
FRC bloqué partiellement ouverte
|
|
|
|
E558
|
Défaillance BMS
|
|
|
|
E559
|
Défaillance IF
|
|
|
|
E560
|
Flamme pilote allumée
|
|
|
|
E564
|
Défaillance P2
|
2
|
5
|
1.48e-09
|
E557
|
FRC bloqué partiellement ouverte
|
|
|
|
E558
|
Défaillance BMS
|
|
|
|
E559
|
Défaillance IF
|
|
|
|
E560
|
Flamme pilote allumée
|
|
|
|
E563
|
Défaillance P1
|
3
|
5
|
2.44e-13
|
E557
|
FRC bloqué partiellement ouverte
|
|
|
|
E558
|
Défaillance BMS
|
|
|
|
E559
|
Défaillance IF
|
Flamme pilote allumée Fuite conduite fuel gaz
E560 E562
60

Résultats de la modélisation
réelle

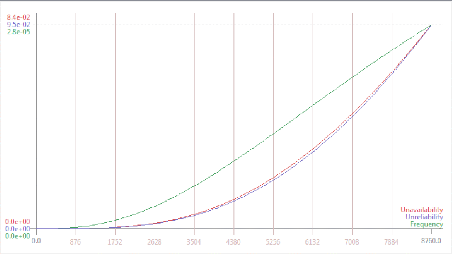
62
Figure IV.24: Courbe du manque de fiabilité du
système
|
Unreliability (manque de fiabilité) Unvailability
(indisponibilité) Frequency (fréquence)
|
: Analyse de la courbe du manque de fiabilité du
système :
Sur l'intervalle [0h - 8760 h], le manque de fiabilité du
système augmente en fur et à mesure jusqu'à atteindre une
valeur de 9.5 * 10-2
L'indisponibité du four augmente quand à elle pour
atteindre une valeur maximale de 8.4 * 10-2.
La fréquence de l'événement redouté
« retour de flamme à l'entrée des bruleurs » elle
augmente dans le temps pour atteindre une valeur de 2.8* 10-5.
Tableau IV.24: Résumé exécutif
Results
Probability:
|
0.0825
|
|
|
System unreliability:
|
|
0.0952
|
System MTTR 7717
63
Analyse du tableau IV.24 :
Le taux de défaillance du four par apport au
scénario « retour de flammes à l'entrée des bruleurs
» est 8.25 *10-2.
Le manque de fiabilité du système sur une
année augmente jusqu'à atteindre une valeur maximale de 9.52 *
10-2.
Le MTTR (« Mean Time de Reaper » ou « temps moyen
de réparation ») est égale à 7717 heures.
Tableau IV.25: CIF (Facteur d'Importance Critique)
Event
|
Description
|
CIF
|
E867
|
Flamme pilote allumé
|
1
|
E866
|
Défaillance IF
|
1
|
E865
|
Défaillance BMS
|
1
|
E864
|
FRC bloquée partiellement ouverte
|
1
|
E871
|
Défaillance P2
|
0.5
|
E870
|
Défaillance P1
|
0.5
|
E869
|
Fuite conduite fuel gaz
|
1.6e-05
|
Tableau IV.26: Coupes minimales et leurs ordres
N°
|
Order
|
Probability
|
Event
|
Description
|
1
|
5
|
0.0421
|
E864
|
FRC bloquée partiellement ouverte
|
|
|
|
E865
|
Défaillance BMS
|
|
|
|
E866
|
Défaillance IF
|
|
|
|
E867
|
Flamme pilote allumé
|
|
|
|
E871
|
Défaillance P2
|
2
|
5
|
0.0421
|
E864
|
FRC bloquée partiellement ouverte
|
|
|
|
E865
|
Défaillance BMS
|
|
|
|
E866
|
Défaillance IF
|
|
|
|
E867
|
Flamme pilote allumé
|
|
|
|
E870
|
Défaillance P1
|
3
|
5
|
1.36e-06
|
E864
|
FRC bloquée partiellement ouverte
|
|
|
|
E865
|
Défaillance BMS
|
|
|
|
E866
|
Défaillance IF
|
|
|
|
E867
|
Flamme pilote allumé
|
|
|
|
E869
|
Fuite conduite fuel gaz
|
64
Comparaison :
Probabilité de défaillance du four 11-F1
:
La probabilité de défaillance du four 11-F1
à partir des données théoriques est 10000000 moins
inférieure que le taux de défaillance par apport aux
données pratiques (2.95*10-9 < 0.0825).
System unreliability (Manque de fiabilité)
:
Le manque de fiabilité du système à partir
du modèle théorique 100000000 est inférieur à celui
du modèle pratique (2.82*10-7 < 0.0952).
Les coupes minimales :
Les probabilités des coupes minimales à partir des
données théoriques sont 100000000 plus faibles par apport
à celles des données pratiques.
A partir des données théoriques et pratiques, la
combinaison des événements « FRC bloqué partiellement
ouverte » et la « défaillance du BMS » et la «
défaillance de l'IF » et la « flamme du pilote allumé
» et la défaillance de soit « pompe P1 » ou la «
pompe P2 » est la plus probable pour provoquer le retour de flamme.
Le CIF (Facteurs d'Importance Critique):
A partir des données théoriques et pratiques, les
probabilités de la « FRC bloqué partiellement ouverte »
et la « défaillance du BMS » et la « défaillance
du IF » et la « flamme du pilote allumé » sont les plus
élevés et sont certains puisque qu'elles sont égales
à 1, ceux sont les événements les plus critiques.
Interprétation des résultats :
Le taux de défaillance et le manque de fiabilité,
ainsi que les probabilités des coupes minimales plus
élevées par apport à la normale indiquent qu'il est en
état très dangereux.
Les deux coupes minimales citées
précédemment par apport aux données pratiques, sont les
combinaisons des événements sur lesquels il est le plus
intéressant de faire de la maintenance préventive et corrective
pour atteindre la probabilité des coupes minimales qui sont à
partir des données théoriques.
A partir des données pratiques, les facteurs d'importance
critique nous indiquent que les événements « FRC
bloqué partiellement ouverte » et « défaillance BMS
» et « défaillance IF » et « flamme du pilote
allumé » sont les meilleurs candidats pour les efforts visant
à améliorer la fiabilité du système et
éviter son explosion.
65
Simulation réelle des scénarios par le
logiciel AgenaRisk :
Simulation des probabilités d'occurrence des
événements des sommets arbres : Simulation des Scénarios
:
Après avoir identifié les causes les plus probables
de ces quatre scénarios à partir des CIF par utilisation des taux
de défaillance réels, nous allons maintenant voir les
probabilités d'occurrence réelles de ces événements
dangereux.
La quantification réelle des événements de
base prise de l'avis des experts du site est donnée dans l'annexe V.
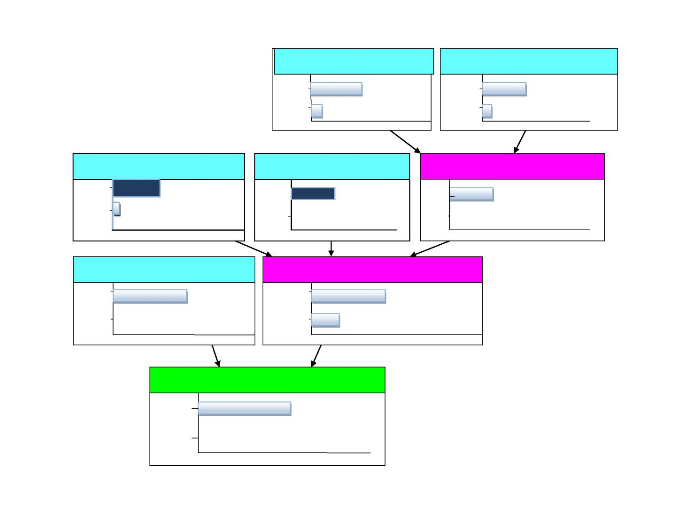
Figure IV.25: Simulation à priori de l'explosion
d'un tube de pétrole brut
IT
IF
Simulation de l'explosion du tube de pétrole
brut
Explosion tube petrole brut
True
False
99.312 %
True
True
False
False
FRC bloquee ouverte
Tube en charge
4 %
15 %
85 %
96 %
False True
True
False
True 6 %
False
2 %
Defaillance des installations
BMS
98 %
17.2 %
94 %
82 %
False
True
True 10 %
False
Instruments de mesures
99.4 %
90 %
66
Simulation de l'explosion du nuage de fuel
gaz
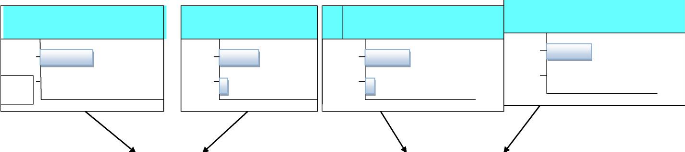
Panne pilote
Panne electricite
Incendie a proximite du four
Travaux de soudage
False
False
99 %
95 %
True
True
5 %
False
90 %
True
10 %
20 %
True
False
80 %
Etincelle
Accumulation fuel gaz
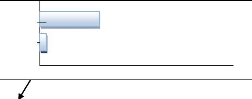
5.95 %
True
False 94.05 %
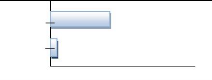
72 %
False
28 %
True
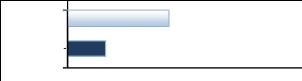
False
True
1.666 %
98.334 %
67
Figure IV.26: Simulation à priori de l'explosion
d'un nuage de fuel gaz
Explosion nuage fuel gaz (UVCE)
Simulation de la surpression du four 11-F1
Fuite reseau de distribution vapeur
False
|
IF
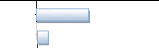
True
4%
False
96 %
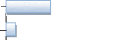
False 90 %
True 10 %
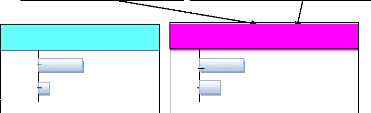
False
86.4 %
True
13.6 %
Degradation du materiel
IDP
False
True 20 %
80 %
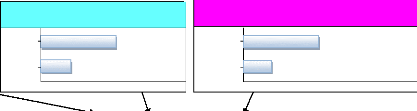
Defaillance des installations
False
97 97.28 %
2.72 %
True
BMS
False
98
True
2 %
98 %
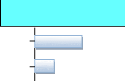
False
85 %
FRC bloquee ouverte
15 %
True
Figure IV.27: Simulation à priori de la
surpression du four 11-F1
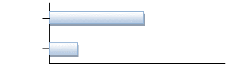
81.034 %
False
True 18.966 %
68
Surpression du four 11F1
Figure IV.28: Simulation à priori du retour de
flammes
Simulation du retour de flammes
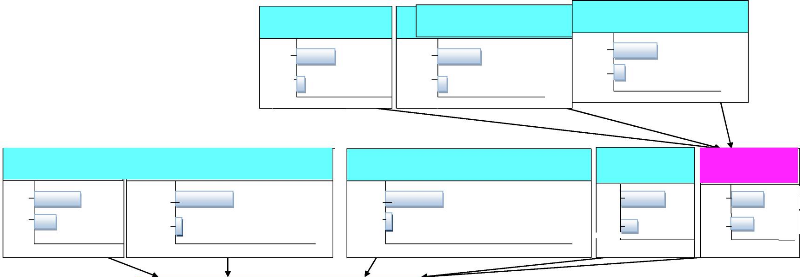
FRC bloquee partiellement ouverte
Accumulation fuel gaz
Panne electricite
Incendie a proximite du four
Travaux de soudage
False
False
97 %
False
80 %
80 %
True 20 %
True
3 %
True
20 %
Etincelle
False
10 %
True
Flamme pilote allume
10 %
90 %
Degradation du materiel
False
True
37.92 %
62.08 %
90 %
True
False
True
False
85 %
15 %
False
True
2 %
98 %
69
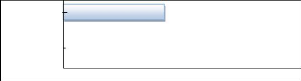
False
True
99.99 %
Explosion nuage fuel gaz (UVCE)
Interprétation des résultats : La
probabilité d'avoir :
1) l'explosion d'un des tubes de pétrole brut est
égale à 0.688 %.
2) l'explosion d'un nuage de fuel gaz à
l'intérieur de la chambre de combustion est égale à 1.666
%.
3) la surpression du four 11-F1 est égale à 18.966
%.
4) le retour de flamme à l'entrée des bruleurs est
à égale à 0.01 %.
Simulation des défiabilités totales des
maillons faibles du système :
Dans cette partie, nous allons voir l'influence des principales
causes des quatre types d'accident étudiés et montrer dans
quelles proportions augmentent ces risques d'explosion et retour de flamme
quand les défiabilités de ces événements de base
sont portés à 1.
70
Simulation des scénarios :
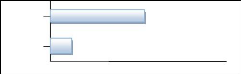
True
False
17.2 %
82.8 %
Figure IV.29: Simulation à postériori de
l'explosion du tube de pétrole brut
Simulation de l'explosion du tube de pétrole
brut
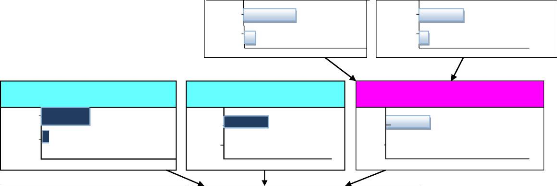
False 94 %
False 90 %
True 6 %
True 10 %
FRC bloquee ouverte
BMS
Instruments de mesures
True
False
15 %
85 %
False True
2 %
98 %
False
True
99.4 %
Tube en charge
|
|
Defaillance des installations
|
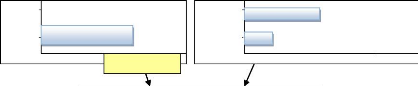
True
False
Scenario 1 : true
100 %
True
False
17.2 %
82.8 %
71
Explosion tube petrole brut
Figure IV.30: Simulation à postériori de
l'explosion d'un nuage de fuel gaz
Simulation de l'explosion du nuage de fuel
gaz
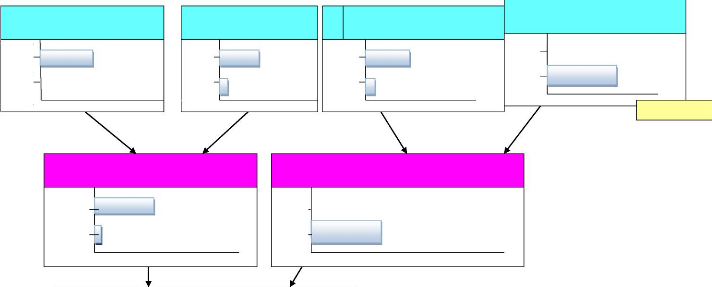
Etincelle
False
28 %
True
72 %
100 %
True
False
10 %
90 %
False
True
Panne electricite
False
20 %
True
Incendie a proximite du four
False
95 %
True
Travaux de soudage
False
100 %
Scenario 1 : true
80 %
5 %
True
Panne pilote
Accumulation fuel gaz
72
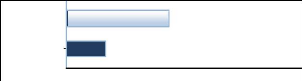
False
True
28 %
72 %
Explosion nuage fuel gaz (UVCE)
Simulation de la surpression du four 11-F1
Fuite reseau de distribution vapeur
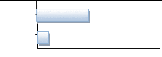
False
96 %
4%
True
IF
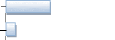
False 90 %
True 10 %
BMS
IDP
80 %
True 20 %

Degradation du materiel
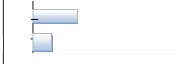
False
86.4 %
True
13.6 %
Defaillance des installations
False
True
2.72 %
97 .28 %
FRC bloquee ouverte
False
85 %
15 %
True
Scenario 1 : true
Figure IV.31: Simulation à postériori de la
surpression du four 11-F1
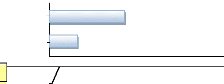
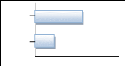
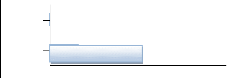
18966 %
False
True
100 %
73
Surpression du four 11F1
Figure IV.32: Simulation à postériori du
retour de flammes à l'entrée des bruleurs
Simulation du retour de flammes
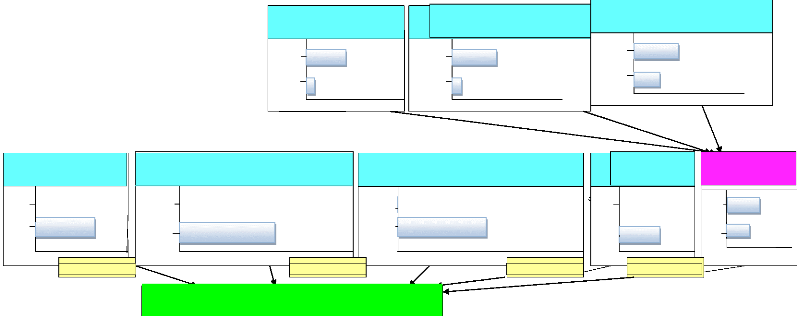
True
False
FRC bloquee partiellement ouverte
Scenario 1 : true
100 %
False
True
Defaillance BMS
Explosion nuage fuel gaz (UVCE)
False
True
100 %
Scenario 1 : true
Panne electricite
3 %
97 %
True
False
True
False
Incendie a proximite du four
Etincelle
20 %
100 %
80 %
Scenario 1 : true
F
True
lse
80 %
True 20 %
False
Flamme pilote allume
Scenario 1 : true
Travaux de soudage
100 % T rue
Fa
lse
Degradation du materiel
37.92 %
62.08 %
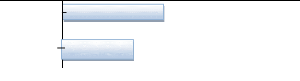
False
True
62.08 %
37.92 %
74
75
Interprétation des résultats : La
probabilité pour que :
1) le tube de pétrole brut qui en charge cause son
explosion est de 17.2 %.
2) les travaux dangereux causent l'explosion d'un nuage de fuel
gaz à l'intérieur du four 11F1 est de 28 %.
3) La défaillance du BMS cause la surpression du four
11-F1 est de 100 %.
4) La combinaison des événements « FRC
bloqué ouverte », « défaillance du BMS », «
défaillance de IF » et « flamme du pilote allumé »
cause le retour de flamme à l'entrée des bruleurs est de 37.92
%.
1
Matrice d'évaluation des risques :
Après analyse des scénarios « le retour de
flamme » et « l'explosion du tube de pétrole brut »
mentionnée dans la partie de l'analyse des accidents et retour
d'expérience nous plaçons les quatre scénarios
étudiés précédemment dans la grille de
criticité-probabilité-gravité conformément aux
critères d'évaluation des niveaux de probabilité -
gravité utilisés au quotidien dans l'industrie
présentés dans l'annexe VI.
76
|
Probabilité d'occurrence (sens croissant de E
vers A)
|
E
|
D
|
C
|
B
|
A
|
Gravité des conséquences sur
les personnes exposées aux risques
à l'intérieur de l'établissement
|
Désastreux (G5)
|
|
|
|
|
|
Catastrophique (G4)
|
|
|
|
Retour de flamme
|
|
Important (G3)
|
|
Explosion du nuage fuel gaz (UVCE)
|
Explosion du tube de pétrole
brut
|
|
|
Sérieux (G2)
|
|
|
|
|
|
Modéré (G1)
|
|
|
|
|
Surpression du four 11-F1
|
Figure IV.33: Matrice d'évaluation des risques
Synthèse et évaluation :
Après diagnostic des résultats obtenus à
l'aide du logiciel Arbre Analyste et à fin d'éviter :
1) L'explosion des tubes de pétrole brut à
l'intérieur de la chambre de combustion du four 11-F1, il faut
prévoir deux vannes de sectionnement en parallèle pour couper la
charge en cas d'anomalie.
2) L'explosion d'un nuage de fuel gaz, il faut limiter les
travaux de soudage sur le four 11-F1 et sensibiliser le personnel de
façon a ce que lorsqu'ils sont fait, il est tenu en compte de la
présence ou non d'une atmosphère explosible, car ils restent les
causes non marginales d'accidents.
3) La surpression du four 11-F1, il est important de maintenir
le niveau de fiabilité du BMS car c'est le composant le plus
intéressant sur lequel il faut faire la maintenance préventive en
plus de la maintenance corrective, car la maintenance corrective en elle
même ne suffit pas puisque son poids influe énormément sur
la défaillance du système et contribue à varier le risque
de surpression associé au four 11-F1 dans d'importantes proportions.
77
4) Le retour de flamme, nous recommandons vivement l'installation
de deux « coupes feux », reliés chacun à un
débitmètre à l'entrée des bruleurs, en cas
où l'un sera en panne l'autre prendra la relève.
Après simulation par utilisation du logiciel AgenaRisk,
nous pouvant déduire que :
1) il y'a plus de chances d'avoir le scénario «
surpression du four 11-F1 » que les autres scénarios.
2) malgré que la probabilité de
l'événement de base « Défaillance du BMS » est
très faible, lorsqu'il apparait, son apparition se traduit par une forte
augmentation du risque et rend impossible l'ensemble des barrières, car
il est sûre qu'il entrainera la surpression du four 11F1
(probabilité de la surpression du four 11-F1 = 100 %).
La matrice de criticité nous révèle que le
scénario « retour de flamme » situés dans la zone rouge
de risque élevé inacceptable nécessitent la prise de
mesures urgentes pour réduire ces risques à un niveau acceptable.
Quand aux scénarios « explosion du tube de pétrole brut
», « explosion du nuage de fuel gaz » et « surpression du
four 11-F1 » situés dans la zone ALARP (niveau le plus faible qu'il
soit raisonnablement pratique d'atteindre), ils nécessitent la mise en
place de mesures réduisant le niveau de probabilité ou de
gravité, sinon des mesures de prévention doivent être mises
en place à fin de maintenir ces risques à ce niveau.
Par ailleurs, les interventions de maintenance corrective et
préventive sur le BMS, la FRC, le IF et le pilote sont prioritaires par
apport à ceux qui sont sur le tube de pétrole brut et les travaux
de soudage, puisque les risques de retour de flamme et de surpression du four
sont plus élevés que les risques d'explosion du tube de
pétrole brut et d'explosion d'un nuage de fuel gaz.
78
CONCLUSION GENERALE
Selon les résultats sur la fiabilité du four 11-F1
par comparaison entre le graphe obtenu suite aux données
théoriques expérimentales et le graphe obtenu suite aux
données pratiques réelles sur terrain (avis des experts du site),
notre cas d'étude ne rentre pas dans le modèle théorique
expérimentale proposé puisqu'il y'a un écart entre le
modèle étudié et le modèle théorique suite
à plusieurs facteurs d'où la manière d'utilisation des
équipements du four 11-F1, l'environnement où on trouve ces
équipements et la politique de maintenance de l'entreprise influent
énormément sur la décroissance de la fiabilité.
Il faut prendre en considération que le four 11-F1 a
été construit en 1973, par conséquent il n'est pas neuf,
et depuis, il n'a ni été rénové, ni des tests
réguliers et une maintenance préventive systématique sur
ses équipements et instruments de mesures ont été
établis, sauf dans le cas de l'accident du retour de flamme en 2010
où la vanne automatique d'entrée du naphta lourd FRC a
été remplacée par une autre par la suite. En plus, les
maintenances correctives ne sont pas mentionnées dans l'historique des
archives.
Et si nous voulons que la fiabilité du four 11-F1 soit
normale et soit vraiment ce que nous attendons, il faut appliquer les normes
API, les normes européennes et les normes ISO, établir des tests
périodiques et une maintenance préventive systématique sur
les équipements et les instruments les plus sensibles cités
précédemment à fin d'éviter la survenue des quatre
types de scénarios possibles de cinétique rapide et suite
à cette action nous allons remarquer que les nouveaux taux de
défaillance et de probabilités pratiques réelles sont
inférieurs aux initiaux.
Cependant la mise à jour des données
théoriques et expérimentales de la base de données Ourida
et du site de l'IFP training nécessite une mise à jour des
résultats des taux de défaillance, de MTTR selon ces
recommandations, mais pour en sortir avec des nouvelles données
théoriques il faut établir beaucoup d'essais sur un ensemble
d'équipements.
79
ANNEXE I
DEFINITIONS PRINCIPALES :
Accident majeur :
C'est un événement tel qu'une émission, un
incendie ou une explosion d'importance majeure résultant de
développements incontrôlés survenus au cours de
l'exploitation, entraînant pour la santé humaine ou pour
l'environnement, à l'intérieur ou à l'extérieur de
l'établissement, un danger grave immédiat ou
différé, et faisant intervenir une ou plusieurs substances ou des
préparations dangereuses.
Point éclair :
C'est la température la plus basse à laquelle un
corps combustible émet suffisamment de vapeurs pour former, avec l'air
ambiant, un mélange gazeux qui s'enflamme sous l'effet d'une source
d'inflammation.
Température d'Auto-inflammation :
C'est la température à partir de laquelle une
substance s'enflamme spontanément en l'absence de source
d'inflammation.
UVCE :
Explosion confiné d'un nuage de gaz, c'est l'explosion
d'un nuage de gaz ou de vapeurs combustibles.
Coupe minimale :
Coupe minimale ou chemin critique, c'est la plus petite
combinaison d'événements entrainant à
l'événement indésirable, c'est-à-dire, si un des
événements d'une coupe minimale ne se produit pas,
l'événement indésirable ne se réalise pas.
Les coupes minimales d'ordre minimal représentent en effet
les maillons faibles du système
80
ANNEXE II
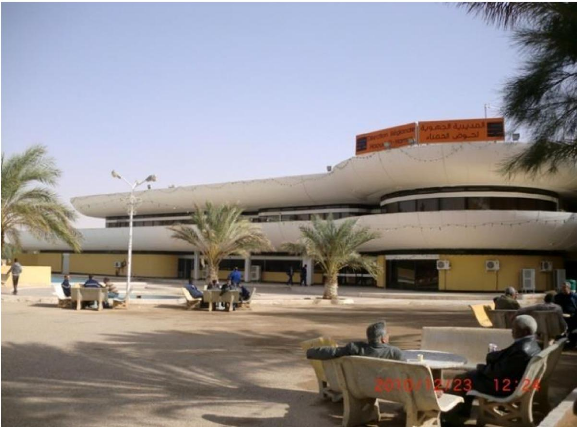
PHOTO BASE DE SONATRACH A HAOUD EL HAMRA, 23 DECEMBRE
2010
ANNEXE III
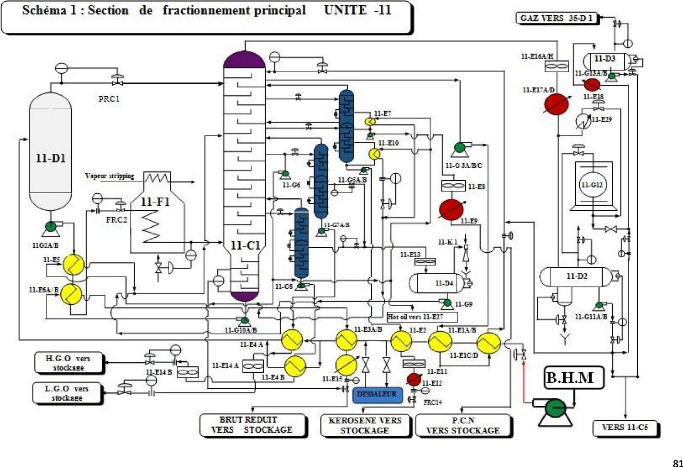
LUG21E
i~-
S4E6-1 E
Schéma 1 : Section de fractionnement principal
UNITE -lI
11-Di
PRC 1
V"ipe, -.rripn
l4G 33.1E C
-r
14E?
11-K 1
11.09
fi
ELG.0 vacs
stockaep li S
stoma a
11-ES4 A
E'RL r REMIT VERS STOCK4GE
H-E L _
k.EROSENE VERB I STCCIKAGE
li-EE
31-E11 11-Ell
RC~Iti
VERS STOCKAGE
9-GLQ313 ir_ts)
11-!1A E
ll-E4 A
11-E4
FRC]4
i~ 4
9cr cal rers 11-E17
81
ILH.I I
82
ANNEXE III
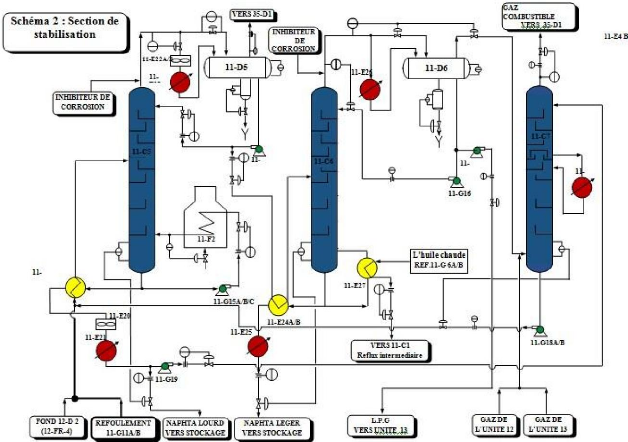
83
ANNEXE IV
Paramètres
|
|
|
|
|
|
|
|
|
|
|
|
|
|
|
|
|
|
|
|
|
|
|
|
|
|
|
Fuite
|
|
|
|
|
|
|
|
Tube
|
BMS
|
IT
|
IF
|
Panne
|
Panne
|
Incend-
|
Trava-
|
IDP
|
réseaux
|
Fuite
|
Pompes
|
Pompe
|
FRC bloqué
|
FRC
|
Flamme
|
Evenement
|
en charge
|
|
|
|
pilote
|
électric -ité
|
ie à proximi -té du four
|
ux de soudag-
e
|
|
de distributi -on vapeur
|
condu- ites fuel gaz
|
P1
|
P2
|
ouverte
|
bloqué partiell- ement ouverte
|
pilote allumé
|
-s
|
|
|
|
|
|
|
|
|
|
|
|
|
|
|
|
|
ã (taux de
|
1.1/h
|
.
|
.
|
.
|
1.14*
|
2.28*
|
6*
|
6*
|
.
|
1*
|
1*
|
1.27*
|
1.14*
|
22.45*
|
39*
|
9.99 *10
|
défaillance à la sollicitation)
|
|
|
|
|
10-4
|
10-4/h
|
10-6/h
|
10-6/h
|
|
10-7/h
|
10-8/h
|
10-6/h
|
10-5/h
|
10-6/h
|
10-6/h
|
-2/h
|
ë (taux de
|
.
|
1.19*
|
8*
|
3.4*
|
.
|
.
|
.
|
.
|
5.71*
|
.
|
.
|
1.27*
|
1.14*
|
22.45*
|
39*
|
.
|
défaillance)
|
|
10-5/h
|
10-5/h
|
10-5/h
|
|
|
|
|
10-5/h
|
|
|
10-6/h
|
10-5/h
|
10-6/h
|
10-6/h
|
|
ì (taux de
|
.
|
.
|
.
|
.
|
.
|
.
|
.
|
.
|
.
|
.
|
.
|
1.9*
|
1.9*
|
2.68* 10-2/h
|
4.48*
|
.
|
réparation)
|
|
|
|
|
|
|
|
|
|
|
|
10-2/h
|
10-2/h
|
|
10-2/h
|
|
TAUX DE DÉFAILLANCE THÉORIQUES DES
ÉQUIPEMENTS
84
ANNEXE IV
Paramètres
|
|
|
|
|
|
|
|
|
|
|
|
|
|
|
|
|
|
|
|
|
|
|
|
|
|
|
Fuite
|
|
|
|
|
|
|
|
Tube
|
BMS
|
IT
|
IF
|
Panne
|
Panne
|
Incend-
|
Trava-
|
IDP
|
réseaux
|
Fuite
|
Pompes
|
Pompe
|
FRC bloqué
|
FRC
|
Flamme
|
Evenement
-s
|
en charge
|
|
|
|
pilote
|
électric -ité
|
ie à proximi -té du four
|
ux de soudag-
e
|
|
de distributi -on vapeur
|
condu- ites fuel gaz
|
P1
|
P2
|
ouvert-e
|
bloqué partiell- ement ouverte
|
pilote allumé
|
ã (taux de défaillance à
|
9.99 *10 -2/h
|
.
|
.
|
.
|
1.14*
10-4
|
2.28* 10-4/h
|
1.24* 10-5/h
|
2.28* 10-4/h
|
.
|
1.14* 10-4/h
|
1.14* 10-5/h
|
1.14* 10-5/h
|
1.14* 10-5/h
|
5.71* 10-5/h
|
5.71* 10-5/h
|
9.99 *10 -2/h
|
la sollicitation)ë
(taux de
|
.
|
2.28*
|
5.71*
|
5.71*
|
.
|
.
|
.
|
.
|
5.71*
|
.
|
.
|
1.14*
|
1.14*
|
5.71*
|
5.71*
|
.
|
défaillance)
|
|
10-4/h
|
10-5/h
|
10-5/h
|
|
|
|
|
10-5/h
|
|
|
10-5/h
|
10-5/h
|
10-5/h
|
10-5/h
|
|
N (taux de réparation)
|
.
|
.
|
.
|
.
|
.
|
.
|
.
|
.
|
.
|
.
|
.
|
2.28*
|
2.28*
|
2.28* 10-4/h
|
2.85*
|
.
|
|
|
|
|
|
|
|
|
|
|
|
|
10-4/h
|
10-4/h
|
|
10-5 /h
|
|
TAUX DE DÉFAILLANCE PRATIQUES DES
ÉQUIPEMENTS
ANNEXE V
85
Probabilité
|
|
|
|
|
|
|
|
|
|
|
|
|
|
|
|
|
|
|
|
|
|
|
|
|
|
|
Fuite
|
|
|
|
|
|
|
|
Tube
|
BMS
|
IT
|
IF
|
Panne
|
Panne
|
Incend-
|
Trava-
|
IDP
|
réseaux
|
Fuite
|
Pompes
|
Pompe
|
FRC bloqué
|
FRC
|
Flamme
|
Evenement
-s
|
en charge
|
|
|
|
pilote
|
électric -ité
|
ie à proximi -té du four
|
ux de soudag-
e
|
|
de distributi -on vapeur
|
condu- ites fuel gaz
|
P1
|
P2
|
ouverte
|
bloqué partiell- ement ouverte
|
pilote allumé
|
P (probabilité d'occurrence)
|
96 %
|
2 %
|
6 %
|
10 %
|
10 %
|
20 %
|
5 %
|
1 %
|
20 %
|
4 %
|
3 %
|
20 %
|
20 %
|
15 %
|
15 %
|
90 %
|
PROBABILITÉ DE DÉFAILLANCE DES
ÉQUIPEMENTS
ANNEXE VI
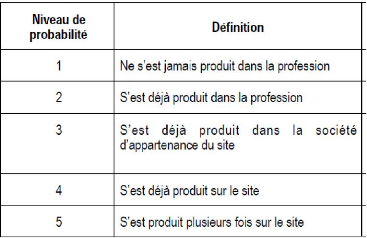
86
NIVEAUX DE PROBABILITÉS UTILISÉS AU
QUOTIDIEN DANS L'INDUSTRIE
ANNEXE VI
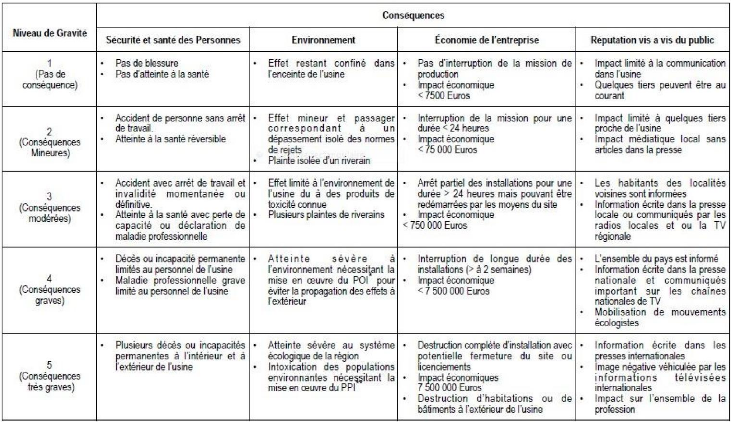
EXEMPLE DE CRITERES D'EVALUATION DU NIVEAU DE GRAVITE
UTILISE AU QUOTIDIEN DANS L'INDUSTRIE
87
88
REFERENCES BIBLIOGRAPHIQUES
[1] : TOUAHAR Bachir. Modélisation et Simulation
Numérique Pour La Dispersion Atmosphérique De Polluants.
Mémoire en Hygiène Et Sécurité Industrielle,
Institut de et Sécurité Industrielle, Université de BATNA
- HADJ LAKHDAR, 2013. Disponible sur :
<file:///C:/Users/Senia%20Info/Downloads/hyg%20TOUAHAR%20BACHIR%20(1).pdf>
(consulté en Juin 2019).
[2] : BENAMAR Ahmed et DIOUANI Otmane. Etude de la performance
de la colonne sous vide C101 de la zone 5 de la raffinerie d'ARZEW,
Mémoire en Industries pétrochimiques, Institut de Maintenance et
Sécurité Industrielle. Université d'Oran 2 - MOHAMED BEN
AHMED, 2017.
[3] : Jérôme DAUBECH, Emmanuel LEPRETTE, Christophe
PROUST. RAPPORT D'ÉTUDE, Formalisation du savoir et des outils dans le
domaine des risques majeurs, Les explosions non confinées de gaz et de
vapeurs - Ù UVCE. Disponible sur : <
https://www.ineris.fr/sites/ineris.fr/files/contribution/Documents/omega-uvce-final-2-avec-couv-sign-1468920253.pdf>
(consulté en Juillet 2019).
[4] : Laure HEUDIER. RAPPORT D'ÉTUDE, Formalisation du
savoir et des outils dans le domaine des risques majeurs, Les
éclatements de capacités, phénoménologie et
modélisation des effets - Ù 15. Disponible sur : <
https://www.ineris.fr/sites/ineris.fr/files/contribution/Documents/omega15-eclatement-reservoir-125630-04945b-2-1389868766.pdf>
(consulté en Juillet 2019).
[5] : Briqueterie LAMOUR. ETUDES DE DANGERS. Disponible sur :
<
http://www.nord.gouv.fr/content/download/5884/35705/file/3%20ETUDE%20DANGERS%20Briqu
eterie%20Lamour%20Roucourt.pdf> (consulté en Juin 2019).
[6] : NOURI Abdelfattah. Extraction des aromatiques,
étude d'un échangeur 200-E2. Mémoire en Génie des
procédés, Université d'EL-OUED, 2014. Disponible sur :
<
https://docplayer.fr/34126820-Memoire-de-fin-d-etudes-master.html>
(consulté en Juin 2019).
[7] : Kribi Souhila, Ledrux Yann. Chapitre B1-P1 : Topping.
Etude de dangers de la raffinerie d'Arzew, Sonatrach/Activité
Aval/Division raffinage EDD et AE. Bertin TECHNOLOGIES.
[8] : SINTEF Industrial Management. OREDA Offshore Reliability
Data Handbook 4th Edition. Base de données 2002.
|