TABLE OF CONTENT:
Declaration..................................................................................i
Certification................................................................................................ii
Dedication..................................................................................................iii
Acknowledgement........................................................................................iv
TABLE OF CONTENT:
1
LIST OF TABLES
3
LIST OF FIGURES
4
ABSTRACT:
5
CHAPTER ONE:
6
INTRODUCTION
6
I. BACKGROUND
INFORMATION
6
II. STATEMENT OF
PROBLEM AND RESEARCH QUESTIONS
9
III. OBJECTIVES OF
THE STUDY
10
IV. RESEARCH
HYPOTHESES
10
V. SIGNIFICANCE OF
THE STUDY
10
CHAPTER TWO:
11
LITTERATURE REVIEW
11
I. DEFINITION OF
IMPORTANT CONCEPTS
12
A. COST TERMS, CONCEPTS AND
CLASSIFICATION.
12
1. Cost
12
2. Cost Objective or cost object.
13
3. Cost Centre
13
4. Cost allocation and apportionment
13
5. Cost drivers
14
6. Cost classifications
14
COSTS CLASSIFIED ACCORDING TO THEIR NATURE
15
b) COST CLASSIFICATIONS ACCORDING TO THEIR
FUNCTION
18
c) COSTS CLASSIFICATION ACCORDING TO THEIR
BEHAVIOUR
21
II. THEORY OF
COSTING: METHODS AND TECHNIQUES
25
A. COSTING METHODS
25
1. Specific order costing:
26
2. Continuous operation or process
costing:
26
a) Job costing
26
b) Batch costing.
26
c) Process costing.
26
B. COSTING TECHNIQUES
27
1. ABSORPTION COSTING
27
2. VARIABLE COSTING
28
III. PRICING
DECISIONS BASED ON COST INFORMATION
30
1. Pricing objectives
30
a) Survival:
30
b) Profit maximisation
30
c) Turn over maximisation
31
d) Growth maximisation
31
e) Goodwill and image preservation
31
2. Pricing techniques
31
a) Total cost-plus pricing
31
b) Manufacturing cost-plus method
31
c) Decision-relevant cost-plus method
32
Limitations of cost based pricing
32
IV. THE THEORY OF
JOB COSTING
33
V. EMPIRICAL STUDIES
ON JOB COSTING
34
VI. THE MECHANICS OF
JOB COSTING
34
1. Purchases of raw materials
35
2. Issue of raw materials
35
3. Labour costs
35
4. Manufacturing overheads
36
5. Non-manufacturing overhead costs.
37
6. Jobs completed.
37
CHAPTER THREE:
37
METHODOLOGY
37
I.
INTRODUCTION
37
II. BACKGROUND
INFORMATION ON THE STUDY AREA
38
OBJECTIVES OF SOPECAM AT ITS CREATION
39
THE SOURCES OF FUNDS OF SOPECAM
39
STRUCTURE OF SOPECAM
39
III. SAMPLING
PLAN
40
a) Sampling technique
40
b) Data collection
40
c) Variables of the study:
40
d) Data analysis
40
e) Model specification
40
CHAPTER FOUR:
42
PRESENTATION AND ANALYSIS OF THE RESULTS
42
I.
INTRODUCTION
42
II. SOPECAM'S COST
STRUCTURE
43
III. DETERMINATION
OF THE UNIT COST
48
A. ABSORPTION COSTING
48
B. MARGINAL COSTING
55
VII. ANALYSIS OF THE
DATA
63
CHAPTER FIVE:
66
SUMMARY OF FINDINGS, CONCLUSION AND
RECOMMENDATIONS
66
I. SUMMARY OF FINDINGS
66
II.
CONLUSIONS
66
III.
RECOMMENDATIONS
69
IV. LIMITATIONS OF
THE STUDY
70
V. PROPOSITIONS FOR
FURTHER STUDIES
70
BIBLIOGRAPHY
71
LIST OF TABLES
Table 4-1 Hourly rates for the various
departments
43
Table 4-2 Editorial staffs salaries
44
Table 4-3 Administrative and selling
expenses
46
Table 4-4 Materials used for the
production
46
Table 4-5 Balance sheet extract
47
Table 4-6 Overhead expenses
47
Table 4-7 Machine-hours used for the
production of the newspaper
48
Table 4-8 OAR for the various overhead
costs
48
Table 4-9 Unit cost determination using
absorption costing (income statement format)
50
Table 4-10 Marginal costing for the
determination of the unit cost of Cameroon Tribune (income statement
format)
57
Table 4-11 Recap of the information
63
LIST OF FIGURES
Figure 2-1Cost assignment methods
13
Figure 2-2: COST FLOW AND CLASSIFICATIONS IN
A MANUFACTURING COMPANY
16
Figure 2-3 The behaviour of total variable
cost
22
Figure 2-4 The behaviour of Unit variable
cost
22
Figure 2-5 Curvilinear concave variable
cost
22
Figure 2-6 Curvilinear convex variable
cost
23
Figure 2-7 The behaviour of Total Fixed
costs
23
Figure 2-8 The behaviour of unit fixed
cost
23
Figure 2-9 The behaviour of semi-variable
cost
24
Figure 2-10 The behaviour of semi-fixed
cost
24
Figure 2-11 Circular reasonning in cost
based-pricing
32
Figure 4-1 Unit cost determination
scheme
45
Figure 1-2 Evolution of the unit cost
(absorption costing)
55
Figure 4-3 Evolution of the unit cost
(variable costing)
63
Figure 5-1 Relative importance of the cost
components in SOPECAM's cost Structure (absorption costing).
67
Figure 5-2 Relative importance of the cost
components in SOPECAM's cost structure (marginal costing).
68
ABSTRACT:
One of the most important challenges to Cameroonian companies
today is the strong competition they face due to the free trade agreements and
other manifestations of the globalisation of the world's economies. They thus
need to adopt effective and efficient management techniques that may help them
to comply with the standards required in the world market place.
This study focuses on the application of job costing in the
printing industry in Cameroon and specifically at SOPECAM, a Nationalised
printing company. It is designed to determine the unit cost of their main
product, the newspaper Cameroon Tribune so as to propose a more reliable
basis for future pricing decisions in the company and also to analyse the cost
structure of the company for its management to take effective measures to
control those costs.
During the study, primary data were collected at SOPECAM
through the interview of the company executives and secondary data have been
gathered from the company accounting records. These data were analysed using
the absorption and variable costing techniques and the Student's
T-Distribution.
The unit cost of Cameroon Tribune was found to be FCFA 474 and
FCFA 325 using absorption and marginal costing respectively, and as such the
company should use absorption costing for its pricing decisions and marginal
costing for the cost control programmes.
Recommendations concerning the setting up of a managerial
accounting department, and for an increase in the selling price of the product
have been made.
CHAPTER ONE:
INTRODUCTION
I. BACKGROUND INFORMATION
As Cameroon progressively comes out of he deep economic
depression of the 1980's and 1990's, and as we are heading towards the
challenges set by the globalisation of the world's economies, there is a
pressing need for Cameroonian companies to adapt themselves to the world's
accounting and financial standards so that they will be able to compete with
their foreign opponents. One of the ways through which these companies could
become very competitive is by adopting recognised business practices as part of
their procedures for treating and processing data in order to obtain good
information that will improve the decisions made by their managers. In fact,
the afore-mentioned business practices are the accounting, finance, management
and economic tools, methods and techniques presently used in the business world
and that are of great importance to the success of any enterprise. These are
made up of quantitative as well as qualitative models that are used to analyse
business situations and help in the decision-making processes of the companies
concerned.
For this study, we will be dealing with the
Managerial and Cost
accounting standards and principles. Managerial and cost accounting are with
financial accounting the three parts of the broad science of Accountancy. While
financial accounting is concerned with «The classification and recording
of monetary transaction of an entity in accordance with established concepts,
principles, accounting standards, legal requirements and presentation of a view
of those of transactions during an accounting period.» Lucey1(*) (1993); Garrison &
Noreen2(*) (2003) defines
Managerial accounting as «the phase of accounting concerned with providing
information to managers for use in planning and controlling operations and in
decision making. Finally, cost accounting is defined by Lucey (1993) as «
the establishment of budgets, standard costs, and actual costs of operation,
processes, activities or products; and the analysis of variances, profitability
on the social use of funds.» Cost accounting is usually designed to help
managers control manufacturing and production costs and thus can be see as a
subset of managerial accounting. Some other differences can be established
between these three divisions of accounting; these differences are based on the
kind of information produced by those the accounting information system from
the data provided by the each of these accounting divisions.
Financial accounting generally provides:
· Figures in totals
· Information meant for external reporting
· The system itself is historic in nature.
Cost accounting on its own has the following characteristics
concerning the type of information provided:
· There is a breakdown of figures in the information
provided
· The information are usually meant for internal
reporting
· These are very current information necessary to
evaluate the present situations.
· The system itself is historic in nature.
Managerial or management accounting's features relating to the
information requirements could be summarised as providing information useful
for future strategic planning. Strategic planning being the process of
selecting an organisational goal, determining the policies and programmes
necessary to achieve en route the goals and establishing the methods necessary
to assure that the policies and strategic programmes are implemented. (Stoner
& Wankel3(*): 1986).
This is the reason why Horngren4(*) (1981) states that: «It emphasises the
preparation of reports of an organisation for its internal users such as
presidents, deans and head physicians.» It is by making use of the
information provided by the Management Accounting Information System (MAIS),
which is an information system that produces output information using inputs
and processes needed to satisfy specific management objectives, that the
preparation of reports can be achieved. The afore-mentioned processes are the
heart of the MAIS and are used to transform the inputs into outputs that
satisfy the firm's objectives. These processes are described by the activities
such as collecting, measuring, storing, analysing, reporting and managing
information. Outputs include special reports, product costs, customer's costs,
budgets, performance reports and even personal communication.
Hansen and Mowen5(*) (1997) have identified three main objectives of a
MAIS, these are:
1. To provide information for costing out services, products,
and other objects of interest to management.
2. To provide information for planning, control and
evaluation.
3. To provide information for decision-making.
From these definitions and characteristics, it appears that a
company, apart from taking care to the proper recording and classification of
its operations through financial accounting, it must give considerable
attention to the monitoring of its various costs of operations. There is
therefore a pressing need to devise and adopt objective and accurate costing
methods and systems that will provide the company with a reliable figure of its
products' unit cost. This is generally the job of the Managerial and
Cost accounting departments of the company.
Having spent three months last year at the Cameroon News and
publishing Corporation as an intern, we had the time to observe and analyse
that company accounting procedures and practices and we realised that the
managerial accounting department, though in existence, was not yet operational,
leaving the company without the required tools necessary for the company
management to appreciate the profitability of each of its products and
activities. The Cameroon News and Publishing Corporation, usually known under
its French acronym SOPECAM, is a State-owned enterprise specialised in printing
works and whose main product is the daily newspaper Cameroon Tribune. As
we are interested in the method of objectively costing a company's product and
since we are really preoccupied by the survival and growth of the SOPECAM, our
main focus will therefore be to determine which costing method or technique is
better applicable to this company.
From the literature available in the cost accounting, it has
been decided to analyse the possibility of using the Job-order costing
method in costing SOPECAM's products. This is because the printing industry is
among those that can easily use the job costing method as a mean for costing
their products Horngren & Foster6(*) (1991).
Horngren7(*) (1999) defines Job costing as a costing system in
which the cost of a product or service is obtained by assigning costs to a
distinct unit, batch or lot of a product or service. The above definition of
job costing makes little difference between job and batch costing; a more
concise and specific definition of it is given by the CIMA Terminology8(*), which considers job costing as
a costing method applicable where goods and services result from a sequence of
continuous or repetitive operations or processes. This is a product
costing method and in product costing we are generally interested in
determining the unit cost of a product or service. This unit cost can be
particularly helpful for various purposes such as the pricing decisions,
planning and control decisions or cost control programmes.
For this study, we will be interested in the usefulness of the
unit cost evaluation for the pricing decision, even though many other factors
are to be considered when setting the price of a product.
II. STATEMENT OF PROBLEM AND
RESEARCH QUESTIONS
The purpose of this study is to devise an objective basis for
costing SOPECAM's printing works such as the newspaper Cameroon Tribune
and also to set its selling price using the cost information obtained. The main
difficulty will concern the allocation and application of the company overheads
to the units of production. To perform this task in the right way, we need to
have adopted an objective and appropriate costing method such as the job
costing method that will help us in this task. The central problem of this
study will therefore be to provide the SOPECAM management with reliable and
accurate and scientific information about the unit cost of their main product
so that they will be able to evaluate the performance of that product and also
set a price that will reflect the real situation.
This study will be centred around three main research
questions:
Ø How to apply job costing to the company processes?
Ø What are the factors that should be taken into
account when costing the newspaper Cameroon Tribune?
Ø Finally, how could the results of job costing be used
in the pricing and cost control processes?
III. OBJECTIVES OF THE STUDY
This study has as a main objective, the determination of a
reliable and precise figure for the unit cost of the newspaper Cameroon
Tribune using job costing, so that the pricing process will be conducted on
an accurate and objective basis.
The figure will be determined from two approaches: the
Marginal and Absorption costing approaches to the job costing
method.
Apart from the afore mentioned main objective, there are also
objectives of smaller scope such as:
Ø Determining the right allocation bases for the
company overheads.
Ø Measuring with great accuracy the amounts of raw
materials, labour time and other costs to be used in the production of the
newspaper.
Ø Finally, show the importance of a managerial and cost
accounting department in a company.
IV. RESEARCH HYPOTHESES
The study being oriented towards the determination of a unit
cost using two approaches to the job costing method, that is the marginal and
absorption costing approaches, we will therefore be interested in the
usefulness of each of these approaches to the pricing process and the company
cost control programmes.
The first hypothesis of this study will then assume that any
of these approaches can be used for both the pricing process and the cost
control programmes without distinction; that is the mean unit cost will be the
same for the two methods. This will be the «No difference
hypothesis».
The second hypothesis, which is the «Alternative
Hypothesis» states that the marginal approach is better for the cost
control programmes while the absorption approach provides more accurate and
reliable data for the pricing process.
By the end, the results of this study will guide us for the
conclusion to adopt as far as these hypotheses are concerned and we will
therefore know which of these approaches to use in each situation.
V. SIGNIFICANCE OF THE STUDY
This research work is primarily designed to contribute to the
evolution and the wide spreading of universally recognised accounting practices
in the Cameroon's business environment; as such we are interested in studying
the application and the use of the job costing method in a State-owned printing
company, this is because we wish to avoid the occurrence of bankruptcy in
another Parastatal printing enterprise as this has been the case with the
National Printing Press whose activities are now reduced to their mildest
level, because of many factors among which the lack of professionalism.
Concerning the scientific contribution of this research work,
this study is aimed at many goals. The first one is the achievement and
completion of a research work as the peak to three years of intense training at
the University of Buea department of Economics and Management.
Secondly, in conducting this research work, we were interested
in studying the public sector of the Cameroonian economy and therefore draw the
relevant conclusion as it concerns its chances to succeed in the extremely
competitive business environment.
Finally, this study can be particularly helpful as it provides
a case study to the use of an accounting principle and thus it can be regarded
as a valuable tool for tutorials or illustrations for cost and managerial
accounting classes.
CHAPTER TWO:
LITTERATURE REVIEW
The main objective of this chapter as its name suggests is an
explanation and a brief exposé of the concepts, studies and theories
related to the topic under study. Throughout this chapter we will try as much
as possible to give you an insight into the mechanics, processes, procedures
and theories related to job costing.
This chapter will be made up of three main parts:
· Some definitions of the important concepts
· The theory of job costing
· The results of studies conducted on job costing and the
use of other costing methods (Empirical literature).
I. DEFINITION OF IMPORTANT CONCEPTS
These are some of the terms, expressions and words that will
be used during the study and as such which need to be carefully analysed and
explained so that they will serve as a guide for the good understanding of the
topic. These explanations will be divided into two main parts: the first one
will focus on the cost terms and the various costs classifications, the second
one will be devoted to introducing the reader to the concepts of costing
methods and techniques.
A. COST TERMS, CONCEPTS AND
CLASSIFICATION.
From the accounting point of view, management main focus and
interest is on the costs of the company. For management to be able to plan that
is setting objectives and outlining how to attain these objectives, but also to
control activities and operations effectively, that is, taking steps to ensure
that objectives are realised (Garrison & Noreen, 2003), it must have
figures, data and information relating to the costs incurred by the company.
These costs are of various types; nature, use and they may be classified using
different parameters such as their nature, their function or their behaviour.
In order to determine what will be made of any cost data, we must therefore
have a good knowledge of its characteristics.
1. Cost
In everyday language, a cost may be defined as «the price
to be paid or amount of money to be incurred for something.» This
definition seems to be too simple for this study, in a more accounting sense, a
cost is defined by Needles, Anderson and Caldwell9(*) (1981) as the exchange price associated with a
business transaction at the point of recognition. This second definition is
quite more complete than the previous one but it is still not very accurate and
precise. Another expert, namely Lucey (1993) defines the cost, as the amount of
expenditure be it actual or notional, incurred on, or attributable to a
specified thing or activity.
All these definitions show that costs are measures of what it
takes a company or an entity to perform an activity, they measure and evaluate
the efforts directed towards the achievement of an objective; this implies
that, without information relating to costs we may not be able to evaluate the
success or failure of an entity or activity.
2. Cost Objective or
cost object.
A cost is used to achieve a certain objective; this objective
is termed cost object. It is defined by Garrison and Noreen (2003), as anything
for which cost data is desired. That is any activity that requires information
about the costs involved in performing that activity. Horngren and Foster
(1991) define a cost objective as any activity or item for which a separate
cost measurement is desired. It appears that a cost object is any activity on
which cost can be measured and it is of great importance in accounting because
it helps in assigning and allocating costs to various cost centres.
3. Cost Centre
Garrison and Noreen (2003) define a cost centre as a business
segment whose manager has control over costs but not revenue and investment
funds. This definition relates to those of revenue centre, profit centre and
investment centre.
A revenue centre is a segment of an organisation, mainly a
decentralised one whose manager is responsible of revenue generation.
A profit centre is defined as a business segment whose manager
has control over costs, revenues, but he does not have control over investment
funds.
Finally, an investment centre is the segment of an
organisation whose manager has control over costs, revenues and investment on
operating assets.
All these terms are grouped under the expression
Responsibility centres, and these centres are of great importance to
the cost accounting department of the an organisation because they are used in
the process of decentralising and delegating authority in an organisation and
as such they are a good yardstick for allocating and assigning costs.
4. Cost allocation and
apportionment
Lucey (1993) defines cost allocation as that part of cost
attribution which charges a specific cost to a cost centre or cost unit. The
purpose of allocating costs to cost units or cost centres is to determine with
accuracy the amount of costs used to perform a particular activity; this is
done with the goal of easing the unit cost determination. Cost allocation is
one of the methods used to assign costs to costs objects, the others are direct
tracing and driver tracing.
Direct tracing is quite the most accurate method of cost
assignment; it relies on physical observable causal relationships.
The next best method in terms of accuracy is diver tracing;
this method relies on causal factors called drivers to assign costs to costs
objects, the precision of the method depends on the casual relationship
described by the driver. But this method is very costly because it requires the
identification of drivers and the assessment of the quality of the causal
relationship.
Allocation has the advantage of being simple and of having a
low cost of implementation.
Graphically, the three methods could be summarised as such:
Figure 2-1Cost assignment methods
COST OF RESOURCES
Through physical observation
Convenience asumed linkage
Using activity drivers
Allocation
Driver Tracing
Direct tracing
COST OBJECTS
Source: Hansen, D.R., &Mowen, M.M.,(1997), Management
Accounting (4th edition), p 32, South-western College Publishing,
Cincinnati, Ohio
5. Cost drivers
Costs are always incurred when pursuing certain goals. These
goals must be subject to some factors that influence the level of cost
incurred. Such factors are called cost drivers. As such Drury10(*) (1992) defines a cost driver
as the events or forces that are the significant determinants of the cost of
the activities. This is an important aspect of Activity-based costing,
which is a generic term used to describe costing methods that assume that costs
are subject to changes in their level due to some forces or events as stated
above.
Cost drivers according to the nature of the cost being
studied, we may have costs that vary with the level of output or some that vary
with the level of inputs used such as the number of machine-hours or
labour-hours.
These variations in the level of costs lead us to the desire
to study their characteristics such that we may predict their behaviour with
reasonable certainty.
6. Cost
classifications
There are a variety of reasons why we need to classify costs.
Among the most important are the prediction of their behaviour, the tracing of
these costs to the various cost units or cost centres or the valuation of
inventories. Depending on the kind of company under study, we have different
types of costs in the picture; the costs identified in a manufacturing company
may not be the same as those of a service company, a retailer may not have the
same costs as his supplier dealing in the wholesale business.
In order to provide management with accurate information about
costs we therefore need to analyse them into logical sections that will be more
meaningful than the current bulk of data.
The three major ways of classifying costs use three
parameters, namely: the nature, function and behaviour.
COSTS CLASSIFIED ACCORDING TO THEIR
NATURE
The nature of a cost is related to its traceability,
relevance, and its sensitivity to management actions in the decision making
process. Here is a brief description of the different types of costs listed
according to their nature.
Direct cost:
This is an expression used to describe costs that can be
easily and conveniently traced to the particular cost object under
consideration. (Garrison & Noreen 2003). It is generally used along side
with the concept of indirect cost.
Indirect cost:
This is simply the contrary of the direct cost and Garrison
and Noreen (2003) refer to it as the cost that cannot be easily and
conveniently traced to the particular cost object under consideration.
Costs are generally classified as direct or indirect when we
need to devise a means for the assignment of costs to the cost objects. This is
very helpful as it gives the manager the opportunity to evaluate either the
profitability or implement cost control programmes for the cost object
concerned, as he will have valid information on the amount of resources
consumed by that cost object.
Product and period costs:
The nature of the cost here relate to the timing of their
liquidation as expenses on the income statement. This distinction between
product and period costs is mainly due to the Matching principle of
financial accounting, Drury (1992). This principle is based on the accrual
concepts and it states that: «Costs incurred to generate a particular
revenue should be recognised as expenses in the same period that the revenue is
recognised.» So the difference between product and period cost will be due
to the purpose for which the costs are incurred; if it is a cost used to
produce or acquire an item that may be sold then it will be considered as
product cost otherwise it is a period cost. We can therefore agree with the
definition of Garrison and Noreen (2003), that a product cost
includes all costs that are involved in the acquisition or making of a product.
Taking the example of a manufacturing company, product costs are the direct
materials, direct labour and manufacturing overhead costs that are used to
manufacture a particular item.
These costs have a double treatment according to the time and
financial account. Since these costs are incurred while acquiring or making a
product, they will be used in the valuation of the stocks of that product until
it is sold. This means that, before the sale, these costs are treated as assets
in the balance sheet of the company. Once the sale has been performed, the
revenue earned from their sales must be matched against the costs incurred for
during their production; these costs are then treated as expenses on the income
statement to match them to the sales revenues and obtain the margin or
contribution to the overall profits of the company. So these can be
called inventoriable costs as they are used for stock valuation
purposes.
Garrison and Noreen (2003) define a period cost as all the
costs that are not included in product costs. Since these costs are not used
for acquiring or making products, the company considers them as expenses in the
period in which they are incurred. Some examples of this type of costs include
selling and administrative costs, office rent or financial charges.
To better illustrate the concept of product and period cost,
let us draw a diagram that will show how costs may be classified and how they
flow into the various accounts of a company.
Figure 2-2: COST FLOW AND CLASSIFICATIONS IN A
MANUFACTURING COMPANY
Finished goods inventory
Raw materials inventory
Product costs
Work in progress inventory
Selling and administrative expenses
Goods completed (cost of goods manufactured)
Direct materials used in production
BALANCE SHEET
COSTS
Raw materials purchases
Direct labour
Manufacturing overhead
Period costs
Cost of goods sold
INCOME STATEMENT
Selling and administrative
Source: Garrison R. H., Noreen E. W., Managerial Accounting,
Mc-Graw Hill, New York, 2003, p 50
Relevant, irrelevant, differential, opportunity and
sunk costs:
In this situation, the nature of the cost will be tied to its
usefulness in the decision making process.
Differential or incremental cost
Incremental analysis is a valuable tool in accounting as in
finance and economics. Incremental simply means additional. Generally in the
business environment, we are faced with many alternatives ways of performing an
activity. A differential analysis is therefore essential to select which
alternative to take on. This differential analysis focuses on the costs and
revenues associated to each alternative. A differential cost is therefore the
difference in cost between any two alternatives, so it is not a constant
figure; it depends on the couple of alternatives selected. It refers to the
cost that may be avoided if the alternative is rejected so it can be called
avoidable cost.
Opportunity cost
As outlined by Garrison and Noreen (2003), it is a concept
that is not usually entered in accounting records; nevertheless, every manager
when making decisions must consider it. Samuelson and Nordhaus11(*) (2000) state that this concept
is much broader when defined in economic terms, but it refers to the potential
benefit that is given up when one alternative is selected over another. It is
the cost of the forgone alternative.
Sunk cost
Garrison and Noreen (2003) define it as a cost that has
already been incurred and that cannot be changed by any decision made now or in
the future. This can also be termed unavoidable cost. It is
not very relevant when making decisions as it cannot be changed or avoided
through a decision made by management; examples of this are the cost of
acquiring fixed assets.
Controllable and uncontrollable costs.
When decentralising an organisation and delegating the
authority to its various segment managers it becomes easier to evaluate and
judge their respective performances. In order to achieve this task, senior
management needs to identify the costs that can be monitored by those managers.
Such a situation leads to a new classification of costs as either controllable
or uncontrollable.
Controllable costs
Anthony & Reece 12(*)(1975) states that an item of cost is controllable if
the amount incurred in (or assigned to) a responsibility centre is
significantly influenced by the actions of the manager of the responsibility
centre. Controllable costs refer to all those cots that are under a manager's
authority, it means that this manager has the authority to modify them
depending on his plans. As an example a manager may have authority over
supervisors employed in his department, but he may not be able to fire or hire
them, so the supervisory costs of that department will not be classified as
controllable costs for the department's manager.
Uncontrollable cost
This is simply the contrary of the controllable cost. It is
one that is not under the regulation of a particular manager as the supervisory
cost of the previous example.
This classification of cost as either controllable or
uncontrollable must be used alongside with budgeted costs. These budgeted costs
will serve as standards for comparison against the actual performance. In order
to evaluate a manager's performance, we must have a yardstick or a measuring
rod that will ease the process and this measuring rod must be a Cost
Budget established at the beginning of the accounting period.
b) COST CLASSIFICATIONS ACCORDING TO THEIR
FUNCTION
The activities performed in a manufacturing company generally
encompass all the activities performed in all other forms of enterprises. In a
manufacturing company, for products to come out of the production lines a
number of processes must be completed. Each of these processes is performed in
a particular department or segment of the company; these are generally
described as functional departments controlled by specific
specialists; this division of the company into functional departments creates
the need to differentiate and classify costs according to the functional
department in which they are incurred.
Such a classification is made to come out with the various
departmental costs which will be used for stock valuation, control and decision
making purposes.
Manufacturing costs
This is generic term used to describe all the cost items that
enter into the production of a particular good. It usually consists of three
elements, namely: direct materials, direct labour and manufacturing
overheads.
Direct materials
Garrison and Noreen (2003) describe direct materials as those
materials that become an integral part of the finished product and that can be
physically and conveniently traced to it. The direct materials costs are an
integral part of the direct costs previously discussed under the nature of
costs. Direct materials refer to those costs that are incurred in the
assembling area of the production process, it consists of all those items that
are used to manufacture a product and that are specific to that product such as
the sheets of paper used to print a newspaper.
Direct labour
This is another element of the direct costs. Drury (1992)
defines it as the labour costs that can be specifically traced or identified
with a particular product; it is sometimes called Touch labour
since it generally requires direct labour workers to touch the product while it
is being made.
Direct expenses
It is very difficult to find this item in the cost structure
of many companies. Inman13(*) (2001) states that they refer to the services that
can be clearly and directly associated with a specific output or service.
Examples of this type of costs are copyright expenses, patent rights, royalties
or the cost of hiring a machine.
Manufacturing overheads
We have already defined the direct items of the cost incurred
to produce or make a particular product. There are also some costs that are
quite of the same origin as the direct costs but which are used for the whole
department or the company and cannot therefore be trace to specific units of
output; such costs are known as manufacturing overheads. Synonyms for these
cost items are factory overheads or factory burden. It
generally includes the lighting and heating costs, property taxes, insurance or
depreciation of the company assets. As it can be seen, it applies to the costs
incurred by the company to enable the processing of all its activities not only
a single one.
From these items of manufacturing costs, we can derive two
important concepts: prime cost and conversion cost.
Prime cost refers to the combination of direct materials,
direct labour and direct expenses required to produce a particular item. It is
a very important concept when making the cost structure of an entity. It is the
primary cost of a product, it constitute the basic requirement for its
production.
Conversion cost is the combination of direct labour cost and
manufacturing overheads; it is called conversion cost because it refers to the
elements required to convert direct materials into finished goods. As we know,
direct materials constitute the heart of the product; direct labour and
manufacturing overheads just serve as facilities to ease the production of the
required item.
The company, as stated above may be divided into multiple
departments, the core one being the manufacturing department. Others could be
termed as non-manufacturing departments and this terminology will help us in
describing the costs incurred in these non-manufacturing departments.
Non-manufacturing costs
Administrative costs
Garrison & Noreen (2003) states that it includes all
executive, organisational and clerical costs associated with the general
management of an organisation rather than with the manufacturing, marketing or
selling activities of the company. It is another kind of overhead cost; they
are incurred by the administrative staff of the company and are not traceable
to any particular product, cost object or processing department.
Marketing and selling and distribution costs
These are the costs incurred to make sure that customers
receive their orders safely; that is they are the costs incurred by the company
during the promotion, advertising, sales and follow-up activities. They are
also called order getting and order-filling costs.
Research and development costs
These are the costs associated with the research and
development departments of the company. In that department, the aim is to
discover new products, devise new processes, improved means pf production. In
fact it is a matter of innovation. This is a very important department of the
company as it helps the company to differentiate its products and services form
those of competitors. So the costs of making such improvements should also be
taken into consideration when making certain decisions.
Quality cost
The image of a company is generally judged based on the
quality of its products and services. Companies would like to have defects-free
products in order to satisfy their customers and to reduce the after-service
and warranty costs. The need arises therefore to prevent, detect and reduce the
defects that may be found in the production. The costs associated with these
activities are known as quality costs; the quality costs can be divided into
four categories (Garrison and Noreen: 2003)
The first two categories are prevention and appraisal
costs which are incurred in an effort to avoid defective products from
being produced.
The last two categories are internal failure and
external failure costs which are incurred for the purpose of reducing
the effects of the production of defective items.
This description of costs from the functional point of view
has helped us in identifying various types of costs; but these costs can be
analysed from another point of view, namely their behaviour when related to
changes n the level of activity.
c) COSTS CLASSIFICATION ACCORDING TO THEIR
BEHAVIOUR
This classification of costs deals with the way costs react to
changes in some factors. The most important factors that cause some costs to
change are the level of activity and the time factor.
As it concerns the level of activity, generally costs are
incurred because of performing a particular activity, this activity may
consists of various processes among which a major one that is sometimes
regarded as the main cost driver. It is that one whose changes will result to
very significant changes in the level of costs. It becomes possible at that
point to relate the level of activity of that cost driver to the level of costs
and as such the behaviour of that cost will be linked to the cost driver.
Concerning the time factor, costs do not behave the same way
in the long run as in the short run. As time elapses, there may be changes in
the market conditions such as inputs costs, level of demand or production
procedures. Such changes in the market situation over time will lead to a need
to a new analysis of costs depending on the time span of the plans we are
making.
These two factors have led experts to classify costs as:
· Variable
· Fixed
· Semi-variable
· Semi-fixed
· Short-term variable
· Long-term variable
Variable costs
Lucey (1993) defines a variable cost as a cost that tends to
vary with the level of activity. Garrison and Noreen more precisely define it,
as a cost that varies in total in direct proportion to changes in the level of
activity. An important aspect of this definition is the fact that variable
costs vary in total, this is because on a per-unit basis the variable costs are
constant and it is only when the level of activity, which may be the output, or
the number of hours worked changes that the total variable cost also changes.
This explains why the variable cost is always expressed in relation to a
particular factor. The figure drawn below depicts that relationship between the
level of activity and the behaviour of variable cost.
Figure 2-3 The behaviour of total
variable cost
Total Cost
Level of activity
Figure 2-4 The behaviour of Unit variable
cost
Unit cost
Level of activity
Such descriptions of variable costs are only a linear
approximation of real-life situations. This is because, in real life, variable
costs are rarely completely linear; they may also be curvilinear. A
curvilinear variable cost is one which varies ion total in either «less
than» or « more than» proportionate variation with the level of
activity.
When an increase in the level of activity leads to a
«less than» proportionate increase in the level of costs, this cost
is referred to as concave curvilinear variable cost. The
opposite is a convex curvilinear variable cost. They are
illustrated in the graphics below.
Figure 2-5 Curvilinear concave variable cost
Level of activity
Figure 2-6 Curvilinear convex variable cost
Level of activity
Fixed cost
Garrison and Noreen (2003) define this, as a cost that remains
constant in total regardless of changes in the level of activity. On a per-unit
basis, fixed costs continuously decrease as the level of activity increases.
This is because there are constant amount of costs to be incurred by the
company whatever the level of activity is and as such, the greater the level of
activity, the greater the distribution of fixed costs over the units of
output.
Here is a graphical illustration of the behaviour of fixed
costs.
Figure 2-7 The behaviour of Total Fixed costs
Total costs
Level of activity
Figure 2-8 The behaviour of unit fixed cost
Unit cost
Level of activity
Semi-variable cost
This is a type of cost that has both fixed and variable
components. A semi-variable cost is one which remains constant up to a certain
level of activity and which becomes variable for any activity level above that
level.
Graphically, a semi-fixed cost looks the following way:
Figure 2-9 The behaviour of semi-variable cost
Level of activity
Total cost.
Fixed cost component
Semi-fixed cost
These are costs that remain constant during short time periods
but which vary in the long run. They are also described as step fixed costs.
This type of cost is subject to changes at various critical level of activity;
as long as the company remains in a certain range of activity, these costs are
fixed, but they change when the company shifts to a new critical level.
Graphically, it looks this way:
Figure 2-10 The behaviour of semi-fixed
cost
Total costs
Level of activity
Short and long term variable costs
These are two terms used to describe the behaviour of costs in
relation to the joint effects of the level of activity, the time factor and the
range of activity. Cooper and Kaplan14(*) (1987) defined a short-term variable cost as one that
varies with the production volume. These are the costs that are directly
affected by increases in the level of production. They are continuously
changing.
The long-term variable costs are those that are affected by
other factors than the level of activity and principally the range of items
produced. These costs are usually considered as fixed over short periods of
time but as the means and processes of producing various kinds of times change
in the long run, these costs obviously change and as such they will no more be
considered as simple fixed costs.
So, to conclude this discussion of cost behaviour, it is
important to note that the predominant aspect in analysing the behaviour of a
cost is the factor to which it is tied; the factor that really influence the
cost. There may not be only one factor, but as many as the number of cost
drivers.
II. THEORY OF
COSTING: METHODS AND TECHNIQUES
This study is concerned with the method of applying job
costing to the accounting procedures of SOPECAM. In the process of using job
costing, we shall take two approaches to the costing exercise, namely the
variable and absorption costing approaches. This simply means that we are
interested in studying a particular costing method and its use under two
costing techniques; we must therefore first of all understand what is meant by
costing methods and costing techniques and how they differ from each other.
A. COSTING METHODS
Lucey (1993) defines costing methods as the methods of costing
designed to suit the way goods are processed or manufactured or the way that
services are provided. It therefore refers to the various methods that can be
used to come out with the cost of an activity. It appears that the costing
method must suit the product or service to cost. This is the reason why we may
have two broad categories of costing methods, namely:
1. Specific order
costing:
This is a costing method applicable where the work consists of
separate jobs or batches. The main sub-divisions of specific order costing are:
job costing, contract costing and batch costing.
2. Continuous
operation or process costing:
This costing method applies where the goods or service
produced result from a sequence of conditions or repetitive operations or
processes to which costs are charged before being averaged over the units
produced during the period. Its main sub-divisions are: process costing
including joint product and by-product, and service/function costing.
a) Job costing
This is a traditional method of accounting for cost. This is a
method where the costs incurred are allocated, apportioned and absorbed by the
cost unit, which is the object to cost.
Here the company production is divided into jobs, which may be
of the same nature, but generally they are all different. The purpose here is
to determine the profit made on each job, as this will be helpful for future
planning.
b) Batch costing.
Being another type of specific order costing method, it is one
which applies when a quantity of identical items are manufactured as a batch.
It is very similar to job costing but the main feature of batch costing is that
the unit cost is the ratio of the total cost of the batch to the number of
units in the batch. This method is widely used in the footwear and clothing
industries where similar items are manufactured.
c) Process costing.
This is a costing method, which is used when the production
is essentially made of homogenous products, which are being produced on a
continuous basis. It is very close to job costing in that:
· They have the same basic purposes, the determination of
the unit cost.
· They use the same basic accounts
· The flow of costs through these accounts is quite the
same for the two methods.
The differences are due to two main factors:
· In process costing the flow of units is quite
continuous while job costing is concerned with separate and distinct
processes.
· Under process costing there is no need to try to
identify materials, labour or overhead costs with particular order since that
order is only part of the many that continuously flow.
Now that we know the different methods that can be used to
build a company costing system, we must now determine the techniques to be
employed depending on the destination of the output information.
B. COSTING TECHNIQUES
The costing techniques are the number of tools, processes and
procedures that may be used alongside with a costing method to come out with
the cost of an activity. There are several costing techniques among which:
absorption costing, marginal costing, standard costing or
activity-based costing.
For this study we will concentrate on the use of absorption
and variable costing used in conjunction with job costing to determine the unit
cost of the newspaper Cameroon Tribune. We therefore need to discuss each of
these methods to understand the mechanisms involved.
1. ABSORPTION
COSTING
Sometimes referred to as full costing, absorption
costing is a costing technique in which all costs are absorbed into the
production units and as such both fixed and variable costs are allocated to the
cost units. Drury (1992) states that in absorption costing, all manufacturing
costs are allocated to products, unsold stocks are valued at their total cost
of manufacture and non-manufacturing costs are not allocated to products but
are charged directly to the profit and loss account, so they should be excluded
from stock valuation.
The procedure to follow when preparing a profit statement
using absorption costing can be summarised as follows:
Sales ******
Less: costs
Opening stocks ***
Direct materials cost (fixed and variable) ***
Direct labour cost (fixed and variable) ***
Direct expenses cost (fixed and variable) ***
Indirect expenses (fixed and variable) ***
Less closing stocks ***
Cost of goods sold *******
Gross profit *******
Less:
Administrative costs ****
Selling and distribution costs ****
Finance expenses ****
Other non-manufacturing overhead costs**
*******
Net profit ********
Source: Coulthurst15(*) (2001)
The following are some of the arguments used by the proponents
for the use of absorption costing, Lucey, T (1992)16(*):
a) Fixed costs are a substantial and increasing proportion of
costs in modern industry. Production cannot be achieved without incurring fixed
costs, which thus form an inescapable part of production so they should be
included in stock valuations. Marginal costing may give the impression that
fixed costs are somehow divorced from production.
b) When production is constant, but sales fluctuate, net
profit fluctuations are less with absorption costing than with marginal
costing;
c) Where stock building is a necessary part of operations, the
inclusion of fixed costs in stock valuation is necessary and desirable.
Otherwise, a serious fictitious loss will be shown in earlier periods to be
offset eventually by excessive profits when the goods are sold.
d) The calculation of marginal cost and the concentration upon
contribution may lead to the firm setting prices which are below total cost
although producing some contribution. Absorption costing makes this less likely
to happen because of the automatic inclusion of fixed charges.
e) SSAP 9 which is about the stocks and Work in progress,
recommends the use of absorption costing for financial accounts because
revenues and costs much be matched in the period when revenues arise not when
the costs are incurred. Also, it recommends that stocks valuations must include
production overheads incurred in the normal cause of business even if such
overheads are time-related, that is fixed. The production overheads must be
based upon normal activity levels.
2. VARIABLE
COSTING
Also referred to as marginal costing, or in some other texts
as direct costing; variable costing as stated by Coulthurst (2001) is
a costing technique which places more emphasis on the behavioural
characteristics of the costs unlike absorption costing which focuses on the
functional nature of the those costs. The aim in variable costing is generally
to separate the costs into fixed and variable elements.
Copeland, Dasher et al (1995)17(*) defines variable costing as a form of cost
accumulation in which only the variable costs are accumulated with inventory as
it is being manufactured. Under variable costing, fixed overhead costs are not
accumulated with the inventory being manufactured; instead they are regarded as
period expenses. As shown in the above definition, unlike absorption costing
which assigns both fixed and variable costs to the cost units, variable costing
treats fixed costs as period costs and they are therefore not included in the
unit cost calculations.
The preparation of a profit statement using marginal costing
can be done using the following format:
Sales *******
Less: costs
Opening stocks ****
Variable Production costs
Direct materials costs ****
Direct labour costs ****
Direct expenses ****
Indirect expenses ****
Less closing stocks ****
Add Non-manufacturing variable costs *****
Cost of goods sold *****
Contribution ******
Fixed manufacturing costs *****
Fixed non-manufacturing costs ******
******
Net profit ********
Source : Drury (1992) p184
Marginal costing also has its proponents who claim that:
a) It is simple to operate
b) No apportionment, which are frequently on an arbitrary
basis of fixed costs to products or departments. Many fixed costs are invisible
by their nature.
c) Where sales are constant, but production fluctuates,
marginal costing shows a constant net profit whereas absorption costing shows
variable amounts of profits.
d) Under or over absorption of overheads is almost entirely
avoided; the usual reason fro under or over absorption is the inclusion of
fixed costs into overhead absorption rates and the level of activity being
different to that planned.
e) Fixed costs are incurred on a time-basis and do not relate
to activity, therefore, it is logical to write them off in the period they are
incurred; this is done using marginal costing.
f) Accounts prepared using marginal costing more nearly
approach the actual cash flow position.
Using a particular costing technique will mainly depend on the
use that will be made of the output information. This cost information may be
used for external reporting, internal decision-making or future planning.
Costing techniques do not replace the costing methods; they
are always used together in order to have a complete costing system.
This paragraph ends our discussion on cost concepts. This
study is not only aimed at studying the cost structure of SOPECAM, it is also
designed to help management in the process of pricing their products. As such
we need to have an insight into the pricing theory based on cost information
and this will be the topic of the next paragraphs.
III. PRICING DECISIONS BASED ON COST INFORMATION
After having determined the unit cost of its products or
services, analysed other factors such as the expected demand or the market
structure, the company focuses on establishing a price that will lead the
maximisation of the profits. This is the essence of the pricing decision.
Pricing simply means setting a price for a product or service
as stated by Kotler and Dubois18(*) (1997). When setting a price for its products, a
company is surely seeking to achieve certain goals and for this to be done, the
company must follow some principles and techniques.
1. Pricing objectives
The objectives of the pricing policy which are also outlined
by the afore-mentioned book are as follows:
a) Survival:
Any company must set prices that will at least help it to
remain in the market even if the company is operating in a highly competitive
environment.
b) Profit
maximisation
The main objective of any business enterprise is to maximise
profits and as such any policy or method used by a company must first be aimed
at maximising these profits.
c) Turn over
maximisation
Since this is an indication of healthiness for companies where
it is difficult to evaluate costs, it must therefore be maximised to be sure
that the company is safely operating.
d) Growth
maximisation
This objective is mainly derived from the economies of scale
concept of the economists; this concept states that higher sales lead to long
term cost reductions and therefore greater profits.
e) Goodwill and
image preservation
This stems from the desire of the company to be regarded as
one maintaining a certain standard or policy in pricing; this standard or image
surely relate to the quality of the products or services offered by the
company.
2. Pricing techniques
Depending therefore on the objectives of the company, it can
adopt various pricing techniques. These techniques normally are based on a
great number of factors, but here we will be interested in studying those that
are based on the cost information provided to management. Pride, Hughes and
Kapoor 19(*)(1988) call
them cost-based or cost-plus pricing
techniques). We will focus on three of them namely:
Total cost-plus, manufacturing cost-plus, and decision-relevant
cost-plus method.
a) Total cost-plus
pricing
In this method, the future selling price is the result of the
addition of a desired set of mark up to the total unit cost of a product or
service. This method may be a good one, but the problem here is that it is
sometimes difficult in some industries to succeed in allocating overhead
expenses to the units of production.
b) Manufacturing
cost-plus method
It follows quite the same procedure as the previous one, but
here, the costs that are taken into account are the manufacturing costs and as
such overhead costs are left out of the calculations. A large mark up
percentage is therefore required to cover these overheads and allow for
reasonable profits for the firm.
Drury (1992) identified that this method has as main advantage
the fact that the cost figure used for pricing is the one used for stock
valuation. In this case, if the firm has been producing similar products in the
past, it may be easy to determine the estimate of the total manufacturing costs
by simply adjusting the old figures.
c)
Decision-relevant cost-plus method
It consists of basing the pricing policy the figures of the
incremental costs due to producing the new elements. Here what is required is a
perfect knowledge of the avoidable and unavoidable costs if the production of a
particular item is started. Since the fixed costs of the company will remain
constant for short period, then the mark up is added to the additional cost of
producing that new item.
The above three refer to the most popular methods of pricing,
there is another one based on activity-based cost, which just consists of
adding the mark up to the activity based-determined cost. That method is not
very different from the others, the main difference residing in the method of
determining the unit cost.
These costing methods as we have outlined at the beginning
ignore many factors and as such must be used alongside with other elements to
come out with a more reliable selling price. The following limitations of these
methods explain why they should not be solely used.
Limitations of cost based
pricing
Ø They ignore the market demand: these
methods do not take into account the price demand relationships characterised
by the economic concept of price-elasticity of demand.
Ø Circular reasoning: this is to say
that the selling price affects the volume of sales, which in turn affects the
unit fixed cost, which will also lead to further price changes. The figure
drawn below illustrates that situation.
Figure 2-11 Circular reasonning in cost
based-pricing
SALES ESTIMATES
PROPOSED SELLING PRICE
UNIT FIXED COST
Source: Drury C. Management Accounting (2000)20(*)
Ø Common fixed costs: this limitation
is in relation to the method used to apportion costs and depending on the
method used the cost obtained will be different and will therefore lead to a
different pricing decision.
Ø Pricing floor: generally, cost based
pricing is referred to as a method that gives the seller a little amount of
security against loses as the cost are always covered by the selling price. But
in real life situation, it is sometimes found that the sales of the product are
subject to fluctuations in demand and as such the total revenues may not be
able to cover the total costs at certain levels of sales other than the
budgeted ones.
Recalling again that these methods are used just as a guide
to final pricing decisions, we must not therefore pay too much attention to
their limitations, but understand that theses methods are helpful as initial
approximations of future selling prices.
IV. THE THEORY OF
JOB COSTING
Job costing is a costing method that has constituted the
central point of many studies conducted by various researchers.
Drury (1992) has described the procedures used in a job
costing system and the accounting entries necessary to record the transactions
taking place in a company using job costing. While analysing the various
costing methods, he stated that job costing should be used when the company
output is made of various jobs or orders from separate customers; he also
stated that there are two alternative ways of designing a job costing system:
either as an integrated cost accounting system or
as an interlocking cost accounting system. These
systems will be explained later in the chapter.
Drury (1992) advocated the use of an integrated cost
accounting system as this reduces or avoids the duplication of records as found
in an interlocking system.
Lucey (1993) also examined the mechanics of a costing system
where job costing is employed. He first stated that this system must be used
where the work to be performed is on customer's requirements. Secondly, this
system must be based on good records obtained from production, works
documentation, material and labour bookings. The documents used here are the
Material requisition forms, time tickets and the job cost sheet. Once prime
costs have been gathered, overheads must be charged to jobs and this can be
done using either the Traditional methods based on the labour
or machine hours overhead absorption rates or using
the cost drivers rates of an activity-based system. He finally pinpointed that,
for profits to be derived from a job costing system, it will depend on the
costing technique used.
Garrison and Noreen (2003) also contribute in the advancement
of the knowledge on job costing. They first identified the type of industries
where job costing can be used, namely: furniture, manufacturing, hospitals or
legal firms. These are industries where the companies offer a wide variety of
products or services.
From their point of view, material requisition forms, labour
time tickets must be used for the assignment of direct materials and labour to
the various jobs; then concerning the manufacturing overheads, they must be
assigned using he predetermined overhead rates. The predetermined overhead
rates generally use labour or machine time as the allocation bases.
They finally make a point in illustrating the flow of costs in
a job costing system, from the raw materials to the foods sold.
V. EMPIRICAL STUDIES ON JOB COSTING
As a product costing method, job costing has been mentioned in
various studies conducted by some researchers exploring the topic of product
cost determination.
One of them, Gorpinpaitoon21(*) (1982) made a study on the use of job costing in the
shipbuilding industry in Thailand.
His study was aimed at examining the costing method used by
shipbuilding firms in Thailand in order to ascertain the principle, the costing
method and its problems. This study was made through direct observation of the
actual operations and the interviews of the personnel involved in that
industry.
At the end of the study, it was realised that the costs of
direct materials and direct labour are charged to the job, but factory
overheads are accumulated and allocated to each job on the basis of direct
labour cost or as a percentage of work finished.
Ngu22(*)
(1997) conducted a study on the topic of product cost and in it, he identified
importance of a product cost to the decision making process of the company. The
data used were got from primary and secondary sources and had been analysed
using quantitative and qualitative means. In the study, he made the point to
differentiate the various costing methods that can be used to come out with the
product cost among which job costing. The study revealed that companies making
one of a kind or special order products use job costing.
The study finally showed that it is very important to
determine the cost of a product as this is of great importance to the decision
making process of the company.
VI. THE MECHANICS
OF JOB COSTING
Job costing is cost accounting method, and as such when using
it or adopting it in a company, we are required to follow a set of procedures
for the recording of the various transactions in the company.
This recording can be made using either an interlocking or an
integrated cost accounting system. An integrated cost accounting system is one
in which the financial and cost accounts are combined in one set of accounts.
In an interlocking cost accounting system, the financial and cost accounts are
maintained independently. As stated by Drury (1992), it is better to adopt an
integrated cost accounting system as this permits to avoid the duplication of
records.
In job costing, the basis for the recording of transactions is
a set of control accounts. A control account is a summary account where entries
are made from totals of a period's transactions; these totals come from the
individual accounts where the transactions are primarily recorded and these are
called subsidiary ledger accounts. In addition to posting these transactions in
the various accounts concerned, we will have to post them on a Job cost card or
job cost sheet.
The job cost sheet is a form prepared for each separate job
that records the materials, labour and overheads costs charged to the job.
The accounting procedures and mechanics of job costing will be
examined following the various steps involved in the manufacture of a product
by a manufacturing company, that is from the purchase of raw materials to the
selling of the finished goods, passing through the charging of labour and
overhead costs, Drury (1992) and Garrison & Noreen (2003).
1. Purchases of raw
materials
Following the double entry principle and the other rules of
financial accounting, if raw materials are acquired, this represents an
increase in current assets but also an increase in the level of current
liabilities until cash payment is made; this transaction will then be recorded
as such:
Dr stores ledger control
account......................******
Cr creditors control
account..................******
2. Issue of raw
materials
This transaction occurs when materials are needed in the
production department, the production department will request a particular
quantity of materials using a material requisition form on which the job number
will be specified. This form will be presented to the storekeeper, who in turn
will supply the materials requested.
Dr Work in progress
account.................*****
Cr stores ledger
account..............*****
The work in progress account represents the products that are
not yet completed and until a good is complete it is considered as part of the
work in progress stock and all the items entering in its production should be
posted on that account.
The above record concerned the issue of direct materials, if
some indirect material is issued, then the following record should be used:
Dr Factory overhead control
accounts...........*****
Cr stores ledger control
account.........*****
3. Labour costs
Once the payroll accounting has been done, that is the
determination of the gross pay for each employee and the calculation of
payments to be made to employees, government, pension funds and others. We can
now allocate labour costs to the various jobs, overhead accounts and capital
accounts.
The wages due to employees are computed from the records of
each employee time tickets. These tickets show the time periods spent on each
job and the various indirect labour hours. It is recorded as follows:
Dr works in progress
account...................................*****
Dr factory overhead
account...................................******
Cr salaries and wages payable
account..............******
4. Manufacturing
overheads
This concerns all the factory costs other than direct
materials, labour and expenses. They are entered into the factory overhead
account as they are incurred. This is done as follows:
Dr factory overhead account
...............******
Cr account payable.............
......****
Cr property tax payable account. ...****
Cr prepaid insurance
account...........****
Cr accumulated depreciation account...***
Now we must charge these costs to the various jobs, this needs
to be done following an objective measure. This measure is known as the
predetermined overhead absorption rate. The overhead
absorption rate is a kind of coefficient, which is used to allocate
manufacturing overhead costs to jobs. It is computed using an allocation base;
this allocation base refers to the most influential cost driver for that
particular cost. This means that there may be several overhead absorption rates
for various costs depending on the allocation base used. The overhead
absorption rate is determined at the beginning of the accounting period using
the formula:
Predetermined overhead absorption rate=estimated total
manufacturing overhead cost/ estimated total units in the allocation
base
Once we have obtained the overhead absorption rate (OAR),
assigning overheads to a job is done as such:
Overhead applied to a job= OAR*amount of the
allocation base incurred by the job
Given the OAR, we can then apply manufacturing overheads to
the jobs and this is reflected in the accounts as follows:
Dr Work in progress
account.........................*****
Cr factory overhead
account.................*****
Once all the entries have been posted into the factory
overhead control account, we can then reconcile the two sides of that account.
Normally if the two sides are equal, this will mean that the company charged
the same costs that it incurred. A larger debit side means that the company
charged less than what it actually incurred and the balance between the two
sides is referred to as the under absorbed overhead costs and
they must be posted to the debit side of the profit and loss account as a
period cost.
A larger credit side of the factory overhead account will mean
that the company charged more costs than what it actually incurred and the
balance between the two sides is called the over absorbed overhead
cost, and it must be posted to the credit side of the profit and loss
account in order to reconcile between the various accounts of the company.
5.
Non-manufacturing overhead costs.
These are not product costs and as such should not be charged
to the work in progress account. When incurred by the company in the process of
manufacturing the products, they should be recorded as follows:
Dr non-factory overhead
account...................******
Cr account
payable............................*******
At the end of the period, these costs will be transferred to
the profit and loss account, as they are period costs.
Dr profit and loss
account.......................*****
Cr non-factory overhead account...*******
6. Jobs
completed.
When a job is complete, the output is transferred from the
factory to the finished goods stores. The cost of this job is transferred from
the work in progress account to the finished goods account.
Dr finished goods
account.............*****
Cr work in progress account...****
This transaction ends the first part of the work, as the cost
of the goods manufactured is known. What is required is then to compute the
cost of goods sold and the various profits to be derived from each job; this
will require the use of particular costing techniques depending on the purpose
of the computation of the profits and this will constitute the core of the next
chapter.
CHAPTER THREE:
METHODOLOGY
I. INTRODUCTION
So far we have already tried to lay the bases for the
continuation of our study; much has been done to give the reader an insight
into the theory of job costing and the related costing techniques that can be
used in conjunction with that costing method. An overview of the pricing theory
has also been done and we have tried to relate the costing theory to that of
pricing and we can now assume that it is possible to draw or formulate a
pricing policy depending on our cost information.
In order to make these theories relevant, we need to apply
them to a particular or real-life case. It was mentioned at the beginning of
the study that SOPECAM and its product, the newspaper Cameroon tribune,
constituted our area of interest. We will therefore try to adapt the costing
and pricing theories to the case of SOPECAM. Before we reach that level, some
specifications have to be made about the way the study will be conducted and
this constitute the core of this chapter.
As such, this chapter will be aimed at first providing a
background information on the area of study, it will then concentrate on the
techniques that will be used to analyse the situation by specifying the
variables of the study, the model that will be used to analyse the data, which
may have been collected using particular techniques and finally, some
precisions will be made about the sampling plan.
II. BACKGROUND INFORMATION ON
THE STUDY AREA
The Cameroon News and Publishing Corporation (SOPECAM) is a
State-owned enterprise whose headquarters are located in Yaoundé, the
Nation's Capital. The principal activities of this enterprise consist in
publishing and printing the bilingual daily newspaper «Cameroon
Tribune», the collection and sale of news, and finally some printing and
publishing works. This commercial and industrial enterprise placed under the
administrative supervision of the Minister of communication, is today 25 years
old.
On the 1st July 1974, date of the launching of the
daily newspaper «Cameroon Tribune», SOPECAM has not yet been given
birth; the publishing, printing and distribution of this newspaper was done
through three enterprises, namely:
Ø AGRACAM: The French acronym for «Ateliers
Graphiques du Cameroon»
Ø SCP S.A.: The French acronym for Societe Camerounaise
de Publication
Ø ACAP: The French acronym for «Agence
Camerounaise de Presse».
These three enterprises continue to assure the publishing of
«Cameroon Tribune» until the creation of SOPECAM by the presidential
decree N° 77/250 of the 18 July 1977 aimed at the creation and
organisation of SOPECAM. This corporation was the result of the vertical merger
of the three preceding enterprises. The capital of this enterprise amounted to
CFA 250,000,000. Concerning the legal side of the operation, this corporation
is a complete legal entity having its life distinct from that of its unique
owner (the State) and financially, this enterprise is also completely
autonomous; finally the enterprise is ranked at the second category of the
State-owned enterprises.
When creating this enterprise, the Cameroonian State was
trying to solve two mains problems:
Ø Firstly, there was a political wish to organise into
a unique entity the vast sector of the public written press, in order to ease
the collection and spreading of the news and the printing and publishing of
newspapers.
Ø Secondly, from an economic point of view, there was a
need to reduce the operating costs of AGRACAM, SCP and ACAP.
Later run, SOPECAM was reorganised through a second decree,
the decree N° 85/1716 of the 12 December 1985; this decree brought about
some changes in the structure of SOPEACM
As it is common with any human organisation, SOPECAM had some
major goals to be achieved when the enterprise was created, we will try to list
and explain these goals.
OBJECTIVES OF SOPECAM AT ITS CREATION
On the 18th July 1977, SOPECAM had as main goals
the following:
Ø To try by all the appropriate means to obtain the
components of complete news in and out of Cameroon.
Ø Through alliances and contracts with foreign news
agencies, make sure that international news will be constantly available to the
public.
Ø To make all the national and foreign news available
to all users, be them public or private users from within and without the
National territory, in the form of newspapers, periodicals, telegraphic means,
at some cost, with a view of providing the world with better information about
the life, political, economic, social and cultural activities.
Ø To provide public and private users with publishing
services.
Ø To provide public and private users with printing
services.
But, in order to achieve these objectives, SOPECAM needs to
have enough resources, especially financial resources.
THE
SOURCES OF FUNDS OF SOPECAM
These resources are made up of:
Ø State endowments
Ø The sale of its goods and services
Ø Its own resources
Ø State subsidies
Ø Donations and legacies
STRUCTURE OF SOPECAM
From the content of the decree N° 85/1716 of the 12
December 1985, the SOPECAM has three main components:
Ø The Board of Directors
Ø The General Management
Ø The Financial Commission
III. SAMPLING PLAN
a) Sampling
technique
Since we are mainly interested in studying the public sector
companies of the printing industry, we will take SOPECAM as our
convenient sample. This is because SOPECAM is very a
representative element of the population we wish to study.
b) Data collection
Data will be collected from primary and secondary sources.
i. The primary sources will be made of the results of the
interviews of the executives and employees of SOPECAM and the results of the
observations made by the researcher.
ii. Concerning the secondary sources of data, they constitute
the most important source of data for this study. They had been collected
through the company accounting, financial and managerial reports and
statements.
c) Variables of the study:
In this study we will pay a particular attention to the
evolution of the unit cost of the newspaper Cameroon Tribune and its effects on
the pricing and cost control policies.
d) Data analysis
Data will be analysed using both qualitative and quantitative
models. But much of the analysis will be done using quantitative tools.
e) Model specification
In this study, we will make use of the Student's-t
distribution in order to test our hypothesis.
The Student's-t-distribution is a probability distribution
used to test the research hypothesis for situations involving the comparison of
two means when the sample size is small or when the variances are not known.
As stated by Grais23(*) (2000), the model assumes that there are two
populations P1 and P2 from which two samples are collected:
· A sample X11,
X12...X1n of size N1 taken from
P1
· A sample X21...X2n of sizeN2
taken from P2
In our case, the populations will be represented by the
monthly production of the newspaper and we will draw a sample production week
from that month. Let us assume that ì1and
ì2 are the respective mean unit costs of the week obtained by
applying absorption and variable costing respectively and
ó²1 and ó²2 are the respective
unknown variances whose sample estimates suggest relatively equal variances
that is S²1=S²2.
The sample sizes, represented by the number of production days
per week, that is 5, being known and less than 30, there is a need to estimate
a pooled weighted variance denoted S²
(N1-1) S²1 +(N2-1)
S²2
N1+N2-2
S² = ........equation 3.1
? (X1i-A1) ²+? (X2i-A2) ²
N1+N2-2
= ...........equation 3.2
It appears that the difference in means
A1-A2 is normally distributed with mean and variance
expressed as follows:
(1/N1+1/N2)
(N1-1) S²1 + (N2-1)
S²2
N1+N2-2
A1-A2 ~N
[ì1-ì2, .eq.3.3
From this information, it is now possible to state our
hypothesis in mathematical terms such that it can be tested using the
afore-mentioned test.
Ho: (Null hypothesis)
A1-A2=0, there is no difference between the sample means
and both can be used for the same purposes.
H1: (Alternative Hypothesis)
A1-A2?0 the two sample means are different and cannot be
used for the same purposes.
It is now necessary to start with the analysis of the data
collected and the test of the research hypotheses; this will be done in the
next chapter, which is mainly about the presentation and the analysis of the
results of the study.
CHAPTER FOUR:
PRESENTATION AND ANALYSIS OF THE
RESULTS
I. INTRODUCTION
The purpose of this chapter is to present and analyse the
results of the studies conducted on the field. We will first give a rough
presentation of the cost structure of SOPECAM for the newspaper Cameroon
Tribune. Then, we will direct the study towards the determination of the weekly
unit cost for the newspaper. These unit costs will then be analysed using the
Student's -T-distribution.
II. SOPECAM'S COST
STRUCTURE
First of all, it seems worthy to mention at this point that
there are various processes necessary for the effective production of Cameroon
Tribune.
These processes are:
· Editorial work; this is mainly done by the journalistic
staff of the company.
· Pre-Printing works; it mainly consist in the
preparation of the photographic sheets that will be used to print the
newspaper.
· Factory or printing stage; this is the final stage in
the production of the newspaper, as its name implies it is at this stage that
the newspaper is printed and the pages are arranged following a certain
order.
The various materials used in the manufacture of the newspaper
are consumed at the various stages of the production process in addition to the
labour provided by each employee of SOPECAM, particularly those of the
editorial staff. Concerning the work of the other employees, the associated
costs are charged to the unit cost of the newspaper following an allocation
system based on the labour hours required for the production.
That system is the foundation of the determination of the unit
cost currently used by the company; it is determined from an adapted
«process costing» method in which various departments of the company
have been allocated hourly rates as measure of their contribution to the unit
cost of the newspaper. These rates are as follows:
Table 4-1 Hourly rates for
the various departments
DEPARTMENT
|
PRE-PRINTING
|
SOAKING
|
COPY
|
PRINTING
|
Rate
|
6000F/hour
|
6000F/Hour
|
2500F/hour
|
45000F/hour
|
Number of Hours used everyday
|
8
|
3
|
2
|
3
|
Source: SOPECAM technical department
As it can be observed from the table, there is no information
relating to the labour cost of the editorial staff, therefore, this will be one
of the weaknesses of our research work as it could not have been possible for
us to obtain data relating to that elements as a matter of confidentiality.
Therefore we will have to make an estimate of these costs.
The editorial board of SOPECAM is made up of 12 journalists
and secretaries whose work can be directly related to the newspaper. Their
salaries can be distributed as follows:
Table 4-2 Editorial staffs
salaries
TYPE OF EMPLOYEE
|
Number
|
Salary (monthly)
|
DAILY
|
Daily total
|
Secretaries
|
2
|
F 120 000
|
F 4000
|
F 8000
|
Journalists
|
5
|
F 240 000
|
F 8000
|
F 40 000
|
Senior journalists
|
3
|
F 300 000
|
F 10 000
|
F 30 000
|
Editor in chiefs
|
2
|
F 360 000
|
F 12 000
|
F 24 000
|
Source: the author
From the data obtained after the interview of the executives
of the company, particularly the inventory department manager (annex1), the
Manufacturing department manager and the head of the Accountancy and budget
service, we have been able to determine the various raw materials that enter
into the production of the newspaper, the hourly rates for the labour costs and
information about the overhead costs incurred by the company. Normally, this
study should be oriented towards the determination of the total unit cost of
the company, that is the unit cost after having sold the newspaper as shown on
the following diagram:
Figure 4-1 Unit cost determination scheme
Purchases
Determination of the purchase cost of raw materials
Stocks
Determination of the cost of materials used
Manufacturing
Determination of the Manufacturing cost
stocks
Determination of the cost of units sold
distribution
Total unit cost
Source24(*): Fayel, A. & Pernot, D.,(2001)
Comptabilité Génerale de l'Entreprise, 12th edition, Dunod,
Paris.
Unfortunately, since there is no managerial accounting office
in the company, it has not been possible to obtain figures relating to the
allocation bases of these overheads; this shortage of information led us to
estimate the expenses related to the selling and distribution and even
administrative costs of the company.
As such we have the following data:
Table 4-3 Administrative
and selling expenses
Type of expense
|
Monday
|
Tuesday
|
Wednesday
|
Thursday
|
Friday
|
Fixed selling
|
F 100 000
|
F 100 000
|
F 100 000
|
F 100 000
|
F 100 000
|
Variable selling
|
F 200 000
|
F 150 000
|
F 250 000
|
F 150 000
|
F 200 000
|
Fixed administrative
|
F 500 000
|
F 500 000
|
F 500 000
|
F 500 000
|
F 500 000
|
Variable administrative
|
F 250 000
|
F 300 000
|
F 350 000
|
F 250 000
|
F 200 000
|
Source: The author
We can then present the information relating to the materials
used to produce the newspaper, they are:
Table 4-4 Materials used
for the production
ITEMS
|
UNITS
|
UNIT COST
|
BEHAVIOUR
|
Direct materials
|
|
|
|
Paper
|
Spool
|
246 330 F
|
Variable
|
Black ink
|
Kg
|
10 000 F
|
Variable
|
Blue ink
|
Kg
|
10 000 F
|
Variable
|
Red ink
|
Kg
|
10 000 F
|
Variable
|
Yellow ink
|
Kg
|
10 000 F
|
Variable
|
Photographic sheet
|
Piece
|
25 000 F
|
Fixed
|
Photographic film
|
Roll
|
300 000 F
|
Fixed
|
Sheet Developer
|
Dose
|
198 000 F
|
Variable
|
Film developer
|
Dose
|
45 000 F
|
Variable
|
Film fixing liquid
|
Dose
|
45 000 F
|
Variable
|
Sheet proofreader
|
Bottle
|
10 800 F
|
Variable
|
Eraser
|
litre
|
8 000 F
|
Variable
|
Soaking solution
|
litre
|
6 000 F
|
variable
|
Sheet cleaner
|
Litre
|
15 600 F
|
Variable
|
Tracing paper
|
Ream
|
50 000 F
|
Variable
|
Photocopy paper A4
|
Ream
|
5 000 F
|
Variable
|
Photocopy paper A3
|
Ream
|
17 500 F
|
Variable
|
Transparent sellotape
|
Roll
|
350 F
|
Variable
|
Packaging sellotape
|
Roll
|
1 400 F
|
Variable
|
Packaging string
|
Roll
|
4 500 F
|
Variable
|
White glue
|
Kg
|
3 500 F
|
Variable
|
Industrial rag
|
Ballot
|
70 000 F
|
Variable
|
Soap paste
|
Kg
|
3 000 F
|
Variable
|
Toner cartridge HP1200
|
Cartridge
|
120 000 F
|
Variable
|
Toner cartridge HP5000
|
Cartridge
|
180 000 F
|
Variable
|
Toner cartridge HP8500-black
|
Cartridge
|
150 000 F
|
Variable
|
Toner cartridge HP8500-blue
|
Cartridge
|
150 000 F
|
Variable
|
Toner cartridge HP8500-Red
|
Cartridge
|
150 000 F
|
Variable
|
Toner cartridgeHP8500-yellow
|
Cartridge
|
150 000 F
|
Variable
|
Drummer KitC4153A
|
Cartridge
|
150 000 F
|
Variable
|
Source: SOPECAM inventory department
The following is an extract of the balance sheet of the
company of the period concerned which we cannot state here because of
confidentiality; it gives data relating to the annual expenses of the company
for the total labour costs, taxes, depreciation, water consumption and many
other overhead costs.
Table 4-5 Balance sheet
extract
ITEMS
|
AMOUNT (Frs.)
|
Department
|
Depreciation
|
349 199 867
|
Factory
|
Spare parts
|
32450941
|
Factory
|
Electricity
|
16382666
|
Factory
|
Water
|
5 272 398
|
Factory
|
Source: SOPECAM balance sheet
Now we are concerned with the determination of the allocation
basis for these costs. Because of the lack of precise information, we will use
labour as the basis for this allocation. From these data, will try to
approximate the weekly and daily figures relating to these expenses so as to be
able to arrive at a daily manufacturing unit cost.
We therefore have the following table:
Table 4-6 Overhead
expenses
OVERHEAD COSTS
|
|
|
ITEMS
|
Yearly
|
Weekly
|
Daily
|
Water
|
5 272 398 F
|
101 392 F
|
20 278 F
|
Electricity
|
16 382 666 F
|
315 051 F
|
63 010 F
|
Depreciation
|
349 199 867 F
|
6 715 382 F
|
1 343 076 F
|
Spare parts
|
32 540 941 F
|
625 787 F
|
125 157 F
|
Total
|
403 395 872 F
|
7 757 613 F
|
1 551 523 F
|
Source: the author
The information given above about those costs are just daily
means, and this means that for most of them we will have to estimate their real
daily amounts as they are not all fixed costs. The only fixed costs among them
is the one relaying to the depreciation of the factory machineries.
As demonstrated in the second chapter, the Overhead Absorption
Rate is got from the formula:
OAR=estimated total manufacturing overhead cost/
estimated total units in the allocation base
OAR=(depreciation+ spare parts+ Electricity+ water)/(total
number of labour hours used per day i.e.: 24)
We already have data relating to the daily overhead expenses,
what we need now is some information about the machine-hours used to
manufacture the newspaper so that we can charge some of the overhead costs its
unit cost. These machine-hours will also be used as the labour hours required
for the production of the newspaper in the absence of data relating to the
exact salaries the company workers.
Table 4-7 Machine-hours
used for the production of the newspaper
LABOUR RATES AND
AMOUNT
|
|
|
DEPARTMENT
|
Pre-printing
|
Soaking
|
Copy
|
Printing
|
Rate
|
6000
|
6000
|
2500
|
45000
|
Hours used
|
8
|
3
|
2
|
3
|
Total n° of hours used
|
16
|
|
|
|
Source: the author
The OARs and associated amounts to be charged for the various
expenses are therefore equal to:
Table 4-8 OAR for the
various overhead costs
|
|
|
|
|
|
OVERHEAD COSTSITEMSYearly
WeeklyDailyOARMean Amount chargedWater
5 272 398 F101 392 F20 278 F845 F13 519 F
Electricity
16 382 666 F315 051 F63 010 F2 625 F42 007 F
Depreciation
349 199 867 F6 715 382 F1 343 076 F55 962 F895 384 F
Spare parts
32 540 941 F625 787 F125 157 F5 215 F83 438 F
Total
403 395 872 F7 757 613 F1 551 523 F
|
|
|
|
|
|
|
|
|
|
|
|
|
|
|
|
|
|
|
|
|
|
|
|
|
|
|
|
|
|
|
|
|
|
|
|
|
|
|
|
|
|
|
|
|
|
|
|
|
|
|
|
|
|
Source: The author
|
|
|
|
|
|
|
Now that we have information relating to the materials,
labour, and factory overhead expenses, it is possible for us to determine the
daily unit costs using the absorption and variable costing techniques.
III. DETERMINATION OF THE UNIT COST
A. ABSORPTION COSTING
Using the computer software Microsoft EXCEL®, it has been
possible for us to come out with the following daily unit manufacturing cost
for the newspaper Cameroon Tribune. It can be roughly presented as follows
using the format of an income statement:
Table 4-9 Unit cost determination using absorption
costing (income statement format)
ABSORPTION COSTING METHOD FOR THE DETERMINATION OF THE
UNIT COST OF THE NEWSPAPER
|
|
Monday
|
TUESDAY
|
Wednesday
|
Thursday
|
Friday
|
Totals
|
|
|
|
|
|
|
|
COSTS
|
|
|
|
|
|
|
DIRECT MATERIALS
|
|
|
|
|
|
|
|
|
|
|
|
|
|
paper
|
985 320 F
|
1 231 650 F
|
985 320 F
|
1 231 650 F
|
1 724 310 F
|
6 158 250 F
|
black ink
|
150 000 F
|
140 000 F
|
110 000 F
|
150 000 F
|
150 000 F
|
700 000 F
|
blue ink
|
30 000 F
|
10 000 F
|
20 000 F
|
20 000 F
|
20 000 F
|
100 000 F
|
red ink
|
40 000 F
|
10 000 F
|
30 000 F
|
20 000 F
|
50 000 F
|
150 000 F
|
yellow ink
|
20 000 F
|
20 000 F
|
20 000 F
|
20 000 F
|
20 000 F
|
100 000 F
|
photographic sheet
|
500 000 F
|
500 000 F
|
500 000 F
|
500 000 F
|
500 000 F
|
2 500 000 F
|
photographic film
|
60 000 F
|
60 000 F
|
60 000 F
|
60 000 F
|
60 000 F
|
300 000 F
|
Sheet Developer
|
99 000 F
|
79 200 F
|
59 400 F
|
79 200 F
|
79 200 F
|
396 000 F
|
Film developer
|
4 500 F
|
9 000 F
|
9 000 F
|
9 000 F
|
13 500 F
|
45 000 F
|
Film fixing liquid
|
9 000 F
|
9 000 F
|
4 500 F
|
9 000 F
|
13 500 F
|
45 000 F
|
sheet proofreader
|
1 080 F
|
3 240 F
|
2 160 F
|
2 160 F
|
2 160 F
|
10 800 F
|
eraser
|
2 400 F
|
4 000 F
|
800 F
|
4 000 F
|
4 800 F
|
16 000 F
|
soaking solution
|
30 000 F
|
24 000 F
|
24 000 F
|
12 000 F
|
30 000 F
|
120 000 F
|
sheet cleaner
|
10 920 F
|
12 480 F
|
9 360 F
|
14 040 F
|
15 600 F
|
62 400 F
|
tracing paper
|
5 000 F
|
10 000 F
|
10 000 F
|
10 000 F
|
15 000 F
|
50 000 F
|
photocopy paper A4
|
15 000 F
|
20 000 F
|
25 000 F
|
20 000 F
|
10 000 F
|
90 000 F
|
photocopy paper A3
|
1 750 F
|
3 500 F
|
3 500 F
|
5 250 F
|
3 500 F
|
17 500 F
|
transparent sellotape
|
280 F
|
280 F
|
280 F
|
280 F
|
280 F
|
1 400 F
|
packaging sellotape
|
1 120 F
|
1 120 F
|
1 120 F
|
1 120 F
|
1 120 F
|
5 600 F
|
packaging string
|
2 700 F
|
2 700 F
|
2 700 F
|
2 700 F
|
2 700 F
|
13 500 F
|
white glue
|
700 F
|
700 F
|
700 F
|
700 F
|
700 F
|
3 500 F
|
industrial rag
|
14 000 F
|
14 000 F
|
14 000 F
|
14 000 F
|
14 000 F
|
70 000 F
|
soap paste
|
600 F
|
600 F
|
600 F
|
600 F
|
600 F
|
3 000 F
|
toner cartridge HP1200
|
90 000 F
|
90 000 F
|
120 000 F
|
180 000 F
|
240 000 F
|
720 000 F
|
toner cartridge HP5000
|
10 800 F
|
12 600 F
|
9 000 F
|
9 000 F
|
12 600 F
|
54 000 F
|
toner cartridge HP8500-black
|
1 200 F
|
1 200 F
|
1 200 F
|
1 200 F
|
1 200 F
|
6 000 F
|
toner cartridge HP8500-blue
|
1 200 F
|
1 200 F
|
1 200 F
|
1 200 F
|
1 200 F
|
6 000 F
|
toner cartridge HP8500-Red
|
1 200 F
|
1 200 F
|
1 200 F
|
1 200 F
|
1 200 F
|
6 000 F
|
toner cartridgeHP8500-yellow
|
1 200 F
|
1 200 F
|
1 200 F
|
1 200 F
|
1 200 F
|
6 000 F
|
drummer KitC4153A
|
1 200 F
|
1 200 F
|
1 200 F
|
1 200 F
|
1 200 F
|
6 000 F
|
|
|
|
|
|
|
|
|
|
|
|
|
|
|
total material cost
|
2 090 170 F
|
2 274 070 F
|
2 027 440 F
|
2 380 700 F
|
2 989 570 F
|
11 761 950 F
|
|
|
|
|
|
|
|
DIRECT LABOUR
|
|
|
|
|
|
|
direct labour for pre-printing
|
42 000 F
|
48 000 F
|
45 000 F
|
54 000 F
|
48 000 F
|
237 000 F
|
direct labour for copy
|
4 500 F
|
5 000 F
|
5 000 F
|
4 500 F
|
5 500 F
|
24 500 F
|
direct labour for soaking
|
15 000 F
|
18 000 F
|
15 000 F
|
18 000 F
|
18 000 F
|
84 000 F
|
direct labour for printing works
|
112 500 F
|
112 500 F
|
135 000 F
|
135 000 F
|
135 000 F
|
630 000 F
|
direct labour for edition
|
102 000 F
|
102 000 F
|
102 000 F
|
102 000 F
|
102 000 F
|
510 000 F
|
Total labour costs
|
276 000 F
|
285 500 F
|
302 000 F
|
313 500 F
|
308 500 F
|
1 485 500 F
|
total material and labour costs
|
2 366 170 F
|
2 559 570 F
|
2 329 440 F
|
2 694 200 F
|
3 298 070 F
|
13 247 450 F
|
|
|
|
|
|
|
|
FACTORY OVERHEADS
|
|
|
|
|
|
|
water bills (variable)
|
14 000 F
|
12 000 F
|
15 000 F
|
13 600 F
|
13 000 F
|
67 600 F
|
electricity bills (variable)
|
42 000 F
|
45 000 F
|
40 000 F
|
43 000 F
|
40 000 F
|
210 000 F
|
depreciation (fixed)
|
895 384 F
|
895 384 F
|
895 384 F
|
895 384 F
|
895 384 F
|
4 476 921 F
|
spare parts (variable)
|
85 000 F
|
100 000 F
|
110 000 F
|
60 000 F
|
63 000 F
|
418 000 F
|
Total factory overheads
|
1 036 384 F
|
1 052 384 F
|
1 060 384 F
|
1 011 984 F
|
1 011 384 F
|
5 172 521 F
|
|
|
|
|
|
|
|
|
|
|
|
|
|
|
SELLING AND ADMIN.
|
|
|
|
|
|
|
fixed admin. Exp.
|
500 000 F
|
500 000 F
|
500 000 F
|
500 000 F
|
500 000 F
|
2 500 000 F
|
variable admin. Exp.
|
250 000 F
|
300 000 F
|
350 000 F
|
250 000 F
|
200 000 F
|
1 350 000 F
|
variable selling exp.
|
200 000 F
|
150 000 F
|
250 000 F
|
150 000 F
|
200 000 F
|
950 000 F
|
fixed selling exp.
|
100 000 F
|
100 000 F
|
100 000 F
|
100 000 F
|
100 000 F
|
500 000 F
|
Total seling and Admin. Costs
|
1 050 000 F
|
1 050 000 F
|
1 200 000 F
|
1 000 000 F
|
1 000 000 F
|
5 300 000 F
|
|
|
|
|
|
|
|
total costs
|
4 452 554 F
|
4 661 954 F
|
4 589 824 F
|
4 706 184 F
|
5 309 454 F
|
23 719 971 F
|
Units produced
|
10 000
|
10 000
|
10 000
|
10 000
|
10 000
|
50 000 F
|
daily unit cost
|
445 F
|
466 F
|
459 F
|
471 F
|
531 F
|
474,3994274
|
Mean unit cost
|
474 F
|
|
|
|
|
|
Source: The author
From the figures above, it appears that the unit cost
is 474 F for the week under consideration using the absorption costing
technique. This figure represents one of the mean that will be compared during
the process of testing our hypotheses.
Since we are dealing with job costing, the best method of
determining that unit cost is through the use of a Job cost Sheet like the
following:
JOB COST SHEET: Absorption
costing
|
|
Job number: 1
|
|
Start date: 01st august 2002
|
|
|
|
|
Department: printing
|
|
Delivery date: 05th august 2002
|
|
|
|
|
Item: Five-day production of CT
|
|
Units completed: 50 000
|
|
|
|
|
|
|
|
|
|
|
|
|
|
|
|
|
Direct Materials
|
|
|
|
|
|
|
Requisition N°
|
Amount
|
type of labour
|
ticket
|
Hours
|
Amount
|
|
|
|
|
paper 100
|
6 158 250 F
|
direct labour for pre-printing
|
1
|
39,5
|
237 000 F
|
|
|
|
|
black ink 101
|
700 000 F
|
direct labour for copy
|
2
|
9,8
|
24 500 F
|
|
|
|
|
blue ink 102
|
100 000 F
|
direct labour for soaking
|
3
|
14
|
84 000 F
|
|
|
|
|
red ink 103
|
|
150 000 F
|
direct labour for printing works
|
4
|
14
|
630 000 F
|
|
|
|
|
yellow ink 104
|
100 000 F
|
direct labour for edition
|
5
|
35
|
510 000 F
|
|
|
|
|
photographic sheet 104
|
2 500 000 F
|
Total C/F
|
|
|
1 485 500 F
|
|
|
|
|
photographic film 105
|
300 000 F
|
|
|
|
|
|
|
|
|
Sheet Developer 106
|
396 000 F
|
EXPENSES
|
|
|
Manufacturing Overheads
|
|
Film developer 107
|
45 000 F
|
Description
|
Amount
|
|
Type
|
Hours
|
Rate
|
Amount
|
|
Film fixing liquid 108
|
45 000 F
|
fixed admin. Exp.
|
2 500 000 F
|
|
water
|
80
|
845 F
|
67 600 F
|
|
sheet proofreader 109
|
10 800 F
|
variable admin. Exp.
|
1 350 000 F
|
|
electricity
|
80
|
2 625 F
|
210 000 F
|
|
eraser 110
|
|
16 000 F
|
variable selling exp.
|
950 000 F
|
|
depreciation
|
80
|
55 962 F
|
4 476 921 F
|
|
soaking solution 111
|
120 000 F
|
fixed selling exp.
|
500 000 F
|
|
spare parts
|
80
|
5 162 F
|
418 000 F
|
|
sheet cleaner 112
|
62 400 F
|
Total C/F
|
5 300 000 F
|
|
Total C/F
|
|
|
5 172 521 F
|
|
tracing paper 113
|
50 000 F
|
|
|
|
|
|
|
|
|
|
photocopy paper A4 114
|
90 000 F
|
|
|
|
|
|
|
|
|
|
photocopy paper A3 115
|
17 500 F
|
Job cost Summary
|
|
|
|
|
|
transparent sellotape 116
|
1 400 F
|
Direct materials
|
11 761 950 F
|
|
|
|
|
|
|
packaging sellotape 117
|
5 600 F
|
Direct Labour
|
1 485 500 F
|
|
|
|
|
|
|
packaging string 118
|
13 500 F
|
Manufacturing Overheads
|
5 172 521 F
|
|
|
|
|
|
|
white glue 119
|
3 500 F
|
Selling and Admin. Exp.
|
5 300 000 F
|
|
|
|
|
|
|
industrial rag 120
|
70 000 F
|
Total Cost
|
23 719 971 F
|
|
|
|
|
|
|
soap paste 121
|
3 000 F
|
Unit product cost
|
474 F
|
|
|
|
|
|
|
toner cartridge HP1200 122
|
720 000 F
|
|
|
|
|
|
|
|
|
|
toner cartridge HP5000 123
|
54 000 F
|
|
|
|
|
|
|
|
|
|
toner cartridge HP8500-black124
|
6 000 F
|
|
|
|
|
|
|
|
|
|
toner cartridge HP8500-blue 125
|
6 000 F
|
|
|
|
|
|
|
|
|
|
toner cartridge HP8500-Red 126
|
6 000 F
|
|
|
|
|
|
|
|
|
|
toner cartridgeHP8500-yellow 127
|
6 000 F
|
|
|
|
|
|
|
|
|
|
drummer KitC4153A 128
|
6 000 F
|
|
|
|
|
|
|
|
|
|
Total C/F
|
|
11 761 950 F
|
|
|
|
|
|
|
|
|
|
Graphically, the data on the daily unit costs could be presented
as such:
Figure 1-2 Evolution of the unit cost (absorption
costing)
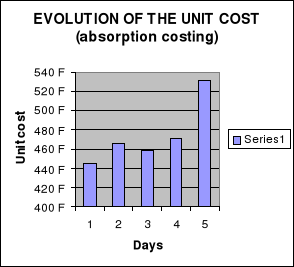
Source: the author
We also need the standard deviation of the daily unit cost and
this can be obtained from the formula:
SD=(?Xi-A1)/N1
Xi: daily unit cost
A1: Mean unit cost
N1: number of production days
Again, using the spreadsheet,
B. MARGINAL COSTING
The following results have been obtained using Microsoft
EXCEL® spreadsheets:
Table 4-10 Marginal costing
for the determination of the unit cost of Cameroon Tribune (income statement
format)
VARIABLE COSTING FOR THE DETERMINATION OF THE UNIT COST
OF THE NEWSPAPER
|
|
MONDAY1
|
TUESDAY 1
|
WEDNESDAY1
|
THUSRDAY1
|
FRIDAY1
|
Totals
|
COST
|
|
|
|
|
|
|
DIRECT MATERIALS
|
|
|
|
|
|
|
paper
|
1 231 650 F
|
985 320 F
|
1 231 650 F
|
1 231 650 F
|
1 477 980 F
|
6 158 250 F
|
black ink
|
150 000 F
|
140 000 F
|
120 000 F
|
140 000 F
|
150 000 F
|
700 000 F
|
blue ink
|
20 000 F
|
20 000 F
|
20 000 F
|
20 000 F
|
20 000 F
|
100 000 F
|
red ink
|
30 000 F
|
20 000 F
|
40 000 F
|
30 000 F
|
30 000 F
|
150 000 F
|
yellow ink
|
20 000 F
|
10 000 F
|
10 000 F
|
30 000 F
|
30 000 F
|
100 000 F
|
photographic sheet
|
500 000 F
|
500 000 F
|
500 000 F
|
500 000 F
|
500 000 F
|
2 500 000 F
|
photographic film
|
60 000 F
|
60 000 F
|
60 000 F
|
60 000 F
|
60 000 F
|
300 000 F
|
Sheet Developer
|
79 200 F
|
99 000 F
|
59 400 F
|
59 400 F
|
99 000 F
|
396 000 F
|
Film developer
|
9 000 F
|
4 500 F
|
13 500 F
|
4 500 F
|
13 500 F
|
45 000 F
|
Film fixing liquid
|
4 500 F
|
4 500 F
|
13 500 F
|
9 000 F
|
13 500 F
|
45 000 F
|
sheet proofreader
|
1 080 F
|
3 240 F
|
2 160 F
|
2 160 F
|
2 160 F
|
10 800 F
|
eraser
|
3 200 F
|
3 200 F
|
3 200 F
|
3 200 F
|
3 200 F
|
16 000 F
|
soaking solution
|
30 000 F
|
18 000 F
|
24 000 F
|
24 000 F
|
24 000 F
|
120 000 F
|
sheet cleaner
|
12 480 F
|
9 360 F
|
10 920 F
|
10 920 F
|
18 720 F
|
62 400 F
|
tracing paper
|
10 000 F
|
5 000 F
|
15 000 F
|
5 000 F
|
15 000 F
|
50 000 F
|
photocopy paper A4
|
20 000 F
|
15 000 F
|
25 000 F
|
15 000 F
|
15 000 F
|
90 000 F
|
photocopy paper A3
|
3 500 F
|
1 750 F
|
1 750 F
|
5 250 F
|
5 250 F
|
17 500 F
|
transparent sellotape
|
280 F
|
280 F
|
280 F
|
280 F
|
280 F
|
1 400 F
|
packaging sellotape
|
1 120 F
|
1 120 F
|
1 120 F
|
1 120 F
|
1 120 F
|
5 600 F
|
packaging string
|
2 700 F
|
2 700 F
|
2 700 F
|
2 700 F
|
2 700 F
|
13 500 F
|
white glue
|
700 F
|
700 F
|
700 F
|
700 F
|
700 F
|
3 500 F
|
industrial rag
|
14 000 F
|
14 000 F
|
14 000 F
|
14 000 F
|
14 000 F
|
70 000 F
|
soap paste
|
600 F
|
600 F
|
600 F
|
600 F
|
600 F
|
3 000 F
|
toner cartridge HP1200
|
120 000 F
|
120 000 F
|
180 000 F
|
60 000 F
|
240 000 F
|
720 000 F
|
toner cartridge HP5000
|
10 800 F
|
9 000 F
|
7 200 F
|
12 600 F
|
14 400 F
|
54 000 F
|
toner cartridge HP8500-black
|
1 200 F
|
1 200 F
|
1 200 F
|
1 200 F
|
1 200 F
|
6 000 F
|
toner cartridge HP8500-blue
|
1 200 F
|
1 200 F
|
1 200 F
|
1 200 F
|
1 200 F
|
6 000 F
|
toner cartridge HP8500-Red
|
1 200 F
|
1 200 F
|
1 200 F
|
1 200 F
|
1 200 F
|
6 000 F
|
toner cartridgeHP8500-yellow
|
1 200 F
|
1 200 F
|
1 200 F
|
1 200 F
|
1 200 F
|
6 000 F
|
drummer KitC4153A
|
1 200 F
|
1 200 F
|
1 200 F
|
1 200 F
|
1 200 F
|
6 000 F
|
Total cost of direct materials
|
2 340 810 F
|
2 053 270 F
|
2 362 680 F
|
2 248 080 F
|
2 757 110 F
|
11 761 950 F
|
|
|
|
|
|
|
|
|
|
Direct labour
|
|
|
|
|
|
|
direct labour for pre-printing
|
48 000 F
|
42 000 F
|
48 000 F
|
42 000 F
|
48 000 F
|
228 000 F
|
direct labour for copy
|
5 000 F
|
4 500 F
|
4 500 F
|
5 000 F
|
5 000 F
|
24 000 F
|
direct labour for imposition
|
18 000 F
|
15 000 F
|
18 000 F
|
15 000 F
|
18 000 F
|
84 000 F
|
direct labour for printing works
|
135 000 F
|
112 500 F
|
135 000 F
|
112 500 F
|
135 000 F
|
630 000 F
|
direct labour for edition
|
102 000 F
|
102 000 F
|
102 000 F
|
102 000 F
|
102 000 F
|
510 000 F
|
Total labour costs
|
308 000 F
|
276 000 F
|
307 500 F
|
276 500 F
|
308 000 F
|
1 476 000 F
|
|
|
|
|
|
|
|
Variable factory overhead costs
|
|
|
|
|
|
|
water bills (variable)
|
14 000 F
|
12 000 F
|
15 000 F
|
13 600 F
|
13 000 F
|
67 600 F
|
electricity bills (variable)
|
42 000 F
|
45 000 F
|
40 000 F
|
43 000 F
|
40 000 F
|
210 000 F
|
spare parts (variable)
|
85 000 F
|
100 000 F
|
110 000 F
|
60 000 F
|
63 000 F
|
418 000 F
|
Total Variable factory exp.
|
141 000 F
|
157 000 F
|
165 000 F
|
116 600 F
|
116 000 F
|
695 600 F
|
|
|
|
|
|
|
|
Variable cost of goods to be sold
|
2 789 810 F
|
2 486 270 F
|
2 835 180 F
|
2 641 180 F
|
3 181 110 F
|
13 933 550 F
|
|
|
|
|
|
|
|
|
|
Variable selling and admin. Costs
|
|
|
|
|
|
|
variable admin. Exp.
|
250 000 F
|
300 000 F
|
350 000 F
|
250 000 F
|
200 000 F
|
1 350 000 F
|
variable selling exp.
|
200 000 F
|
150 000 F
|
250 000 F
|
150 000 F
|
200 000 F
|
950 000 F
|
Total variable selling and admin. Exp.
|
450 000 F
|
450 000 F
|
600 000 F
|
400 000 F
|
400 000 F
|
2 300 000 F
|
|
|
|
|
|
|
|
Total cost of goods sold
|
3 239 810 F
|
2 936 270 F
|
3 435 180 F
|
3 041 180 F
|
3 581 110 F
|
16 233 550 F
|
Units produced
|
10 000
|
10 000
|
10 000
|
10 000
|
10 000
|
50 000 F
|
|
|
|
|
|
|
|
|
|
Daily unit cost
|
324 F
|
294 F
|
344 F
|
304 F
|
358 F
|
325 F
|
Unit cost 325 F
Source: The author
JOB COST SHEET: Marginal costing
|
|
Job number: 1
|
|
Start date: 01st august 2002
|
|
|
|
|
Department: printing
|
|
Delivery date: 05th august 2002
|
|
|
|
|
Item: Five-day production of CT
|
|
Units completed: 50 000
|
|
|
|
|
|
|
|
|
|
|
|
|
|
|
|
|
Direct Materials
|
Direct Labour
|
|
|
|
|
|
Requisition N°
|
Amount
|
Type of labour
|
Ticket
|
Hours
|
Amount
|
|
|
|
|
paper 100
|
6 158 250 F
|
Direct labour for pre-printing
|
1
|
39,5
|
228 000 F
|
|
|
|
|
black ink 101
|
700 000 F
|
Direct labour for copy
|
2
|
9,8
|
24 000 F
|
|
|
|
|
blue ink 102
|
100 000 F
|
Direct labour for soaking
|
3
|
14
|
84 000 F
|
|
|
|
|
red ink 103
|
|
150 000 F
|
Direct labour for printing works
|
4
|
14
|
630 000 F
|
|
|
|
|
yellow ink 104
|
100 000 F
|
Direct labour for edition
|
5
|
35
|
510 000 F
|
|
|
|
|
photographic sheet 104
|
2 500 000 F
|
Total C/F
|
|
|
1 476 000 F
|
|
|
|
|
photographic film 105
|
300 000 F
|
|
|
|
|
|
|
|
|
Sheet Developer 106
|
396 000 F
|
EXPENSES
|
|
|
Manufacturing Overheads
|
|
Film developer 107
|
45 000 F
|
Description
|
Amount
|
|
Type
|
Hours
|
Rate
|
Amount
|
|
Film fixing liquid 108
|
45 000 F
|
|
|
|
Water
|
80
|
845 F
|
67 600 F
|
|
sheet proofreader 109
|
10 800 F
|
Variable admin. Exp.
|
1 350 000 F
|
|
Electricity
|
80
|
2 625 F
|
210 000 F
|
|
eraser 110
|
|
16 000 F
|
Variable selling exp.
|
950 000 F
|
|
Spare parts
|
80
|
5 162 F
|
418 000 F
|
|
soaking solution 111
|
120 000 F
|
|
|
|
|
|
|
|
|
sheet cleaner 112
|
62 400 F
|
Total C/F
|
2 300 000 F
|
|
Total C/F
|
|
|
695 600 F
|
|
tracing paper 113
|
50 000 F
|
|
|
|
|
|
|
|
|
|
photocopy paper A4 114
|
90 000 F
|
|
|
|
|
|
|
|
|
|
photocopy paper A3 115
|
17 500 F
|
Job cost Summary
|
|
|
|
|
|
transparent sellotape 116
|
1 400 F
|
Direct materials
|
11 761 950 F
|
|
|
|
|
|
|
packaging sellotape 117
|
5 600 F
|
Direct Labour
|
1 476 000 F
|
|
|
|
|
|
|
packaging string 118
|
13 500 F
|
Manufacturing Overheads
|
695 600 F
|
|
|
|
|
|
|
white glue 119
|
3 500 F
|
Selling and Admin. Exp.
|
2 300 000 F
|
|
|
|
|
|
|
industrial rag 120
|
70 000 F
|
Total Cost
|
16 233 550 F
|
|
|
|
|
|
|
soap paste 121
|
3 000 F
|
Unit product cost
|
325 F
|
|
|
|
|
|
|
toner cartridge HP1200 122
|
720 000 F
|
|
|
|
|
|
|
|
|
|
toner cartridge HP5000 123
|
54 000 F
|
|
|
|
|
|
|
|
|
|
toner cartridge HP8500-black124
|
6 000 F
|
|
|
|
|
|
|
|
|
|
toner cartridge HP8500-blue 125
|
6 000 F
|
|
|
|
|
|
|
|
|
|
toner cartridge HP8500-Red 126
|
6 000 F
|
|
|
|
|
|
|
|
|
|
toner cartridgeHP8500-yellow 127
|
6 000 F
|
|
|
|
|
|
|
|
|
|
drummer KitC4153A 128
|
6 000 F
|
|
|
|
|
|
|
|
|
|
Total C/F
|
|
11 761 950 F
|
|
|
|
|
|
|
|
|
|
Source: the author
Graphically, the situation can be represented as follows:
Figure 4-3 Evolution of the unit cost (variable
costing)
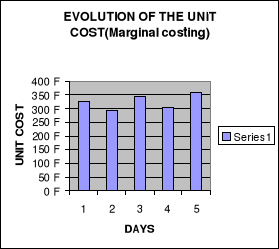
Source: The author
Using variable costing, the mean unit cost is therefore 325F
The standard deviation is
Given all these information that can be summarised in the
following table, we can now start with the analysis part of this chapter.
Table 4-11 Recap of the
information
|
ABSORPTION COSTING
|
VARIABLE COSTING
|
MEAN UNIT COST
|
474 F
|
325 F
|
STANDARD DEVIATION
|
33.04 F
|
26.74F
|
Source: the author
VII. ANALYSIS OF THE DATA
In this part, our work will be focused on testing the hypotheses
outlined in the first chapter; for this, we will use the student's T-test. This
test is concerned with analysing the difference in means; in our case, the two
means are the weekly unit cost obtained using absorption and marginal
costing.
This test requires us to compute some elements of analysis such
as:
· The pooled weighted variance S²
· The various standard deviations
· The difference in means
In the previous chapter, explanations have been given on the
above concepts; we therefore do not need to dwell on it again. As such, we have
the following:
(N1-1) S²1 +(N2-1)
S²2
N1+N2-2
S² = .......equation 4.1
? (X1i-A1) ²+? (X2i-A2) ²
N1+N2-2
= ....equation 4.2
Numerically, we have:
S²=[(5-1)*33.04²
+(5-1)*26.74²]/(5+5-1)............equation 4.3
S²=802.96
The difference in the two means is expressed as follows:
ì1-ì2 =474-325
ì1-ì2 =149F
The difference in the two means is therefore normally distributed
with the following parameters:
A1-A2~N [149, 802.96]
At this level, it is now possible to test the hypotheses, which
were stated as follows:
Ho: (Null hypothesis)
A1-A2=0, there is no difference between the sample means
and both can be used for the same purposes.
H1: (Alternative Hypothesis)
A1-A2?0 the two sample means are different and cannot be
used for the same purposes.
These hypotheses will be tested using the following rules:
Given the test statistic Tc and the critical value
Tá/2,n1+n2-2 to be calculated,
The decision will be thus depending on the results
obtained:
Reject Ho if, Tc>Tá/2, n1+n2-2 or
Tc<- Tá/2, n1+n2-2
In this case, we have a Two-tailed test,
The level
of significance á=0.05
First sample size N1=5
Second sample size N2=5
The Degree of freedom F=N1+N2-2
F=5+5-2=8
From the statistical tables, we therefore have: tá/2
,8 =2.306 or : tá/2 ,8= -2.306 A1=474
A2=314
The test statistic is therefore equal to:
A1-A2
Tc= ..........equation4.4
S (1/N1 +1/N2)1/2
But S is the square root of S², S=802.961/2
474-325
Tc= ..............equation 4.5
28.34 (1/5 +1/5)1/2
Tc=8.312
The critical value previously obtained was 2.306, which is less
than the test statistic obtained: Tc>Tá/2, n1+n2-2. This
leads us to reject the null hypothesis stating that: there is no difference
between the sample means and both can be used for the same purposes. And we
accept the alternative hypothesis stating that: the two sample means
are different and cannot be used for the same purposes.
This conclusion ends our presentation and analysis of the data
collected at SOPECAM, and helps us to directly enter into the problem of the
lessons and conclusion to draw from this study, which is the main concern of
the next chapter.
CHAPTER FIVE:
SUMMARY OF FINDINGS, CONCLUSION
AND RECOMMENDATIONS
I. SUMMARY OF FINDINGS
As we are heading towards the end of the study entitled
«The use of Job costing as a tool for the pricing process», it seems
necessary to recall its objectives. This study was conducted for the sake of
coming out with a reliable unit cost figure for the newspaper «Cameroon
Tribune»; it was also designed to help in the determination of a good
allocation basis for the company overhead costs and finally, while engaging in
this research work, we wanted to improve the pricing and cost control processes
at SOPECAM.
The research, as mentioned above was conducted at SOPECAM, a
State-owned enterprise, responsible of the publishing of the newspaper Cameroon
Tribune. Data have been collected from primary and secondary sources
constituted by the results of interviews conducted at the company premises with
its executives and data gathered from the financial and accounting statements
of the company. These data were analysed using job costing associated to the
absorption and marginal costing techniques. The results of this analysis were
interpreted using the Student's -T- test. It was found that under absorption
costing, the unit cost of the newspaper is FCFA 474, while under marginal
costing, it was estimated at FCFA 325.
After having tested the hypotheses of the study, we came to
the conclusion that the two costing techniques used namely marginal and
absorption costing, cannot be used for the same purposes.
In Marginal costing, the company is only concerned with the
costs directly related to the product, the fixed production and
non-manufacturing costs are not taken into account, it is therefore preferable
to use this technique when trying to control the costs associated with a
particular product. It must as such be used for the cost control programmes
instead of the pricing decisions.
Concerning Absorption costing, with this technique, all the
costs incurred when manufacturing a product are taken into account, this
costing technique enables the company to ascertain with accuracy what it cost
the entire organisation to make a particular product. It relates to the overall
profitability of the company and for this reason, we must use this technique
for the pricing decision.
II. CONLUSIONS
After having reviewed the results of the study, we must
normally derive a conclusion from the information obtained. This conclusion
will stem from some remarks we have made throughout the study.
The first point to mention at this level is that the newspaper
under study is currently being sold at FCFA 300, which means from our findings,
that the company is under-pricing its product.
The second point to mention is that, although the production
of the newspaper is divided into three stages as explained in the previous
chapter, the method of allocating the manufacturing costs of the product using
hourly rates as done by the company seems not to be very adequate for this
product.
The third point of interest concerns the overhead allocation
bases. In the company, labour hours are used to assign and allocate overhead
costs to the various products, but from the observation of the researcher, it
seems as if the labour hours rarely change and can be treated as fixed costs;
This is mainly due to the fact that the company workers are all salaried worker
and none of them is employed on an hourly basis, thus the labour hours are not
a good yardstick as far as the spreading of overhead costs over production
units is concerned.
Another element of consideration in the analysis concerns the
cost structure of the company. When we decided to determine the unit cost of
this product it was not just for the sake of having a unit cost figure, but it
was also to examine the various components of that unit cost and their relative
importance as this may help us in determining the real cost centres of the
enterprise. From the analysis performed in the previous chapter, the following
results have been obtained:
Figure 5-1 Relative importance of the cost components
in SOPECAM's cost Structure (absorption costing).
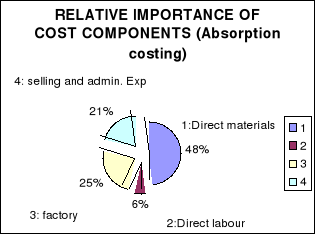
Source: the author
Figure 5-2 Relative importance of the cost components
in SOPECAM's cost structure (marginal costing).
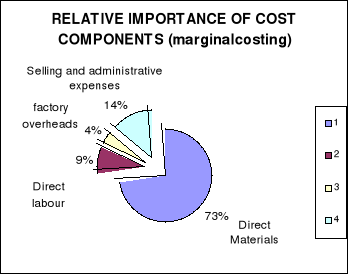
Source: the author
Having outlined our points of interest, we can now draw some
conclusions as far as our study is concerned.
One of the initial goal of this study was the determination a
reliable unit cost figure for the newspaper Cameroon tribune, it has appeared
using absorption costing that the unit cost could be estimated at FCFA 474
which as mentioned above is greater than the selling price of the product. As
such, it appears that the company is not following a profit-maximisation goal
when producing Cameroon Tribune, its main focus appears to be the provision of
daily, reliable and accurate information to the Cameroonian population; and for
this to be done, instead of maximising their profit, or taking advantage of
their position of leader of the market because they are the only daily
newspaper in Cameroon with the exception of the newspaper
«Mutations», they prefer to achieve a Goodwill preservation objective
by making sure that they remain at the level of the mean-income earner in
Cameroon. This goal of goodwill and image preservation is identified by Harper
(1989)25(*) as
strategy Pricing; the firm goal here is not so much profit
maximisation but the achievement of the long-term goal of the firm from the
marketing point of view, that is the satisfaction of the customer. This
situation may lead us to question ourselves about the survival of the company,
but since Cameroon Tribune is not the only product manufactured at SOPECAM, and
since SOPECAM is benefiting from the Sate endowments and subsidies, we can say
that the company is not supposed to face a situation of jeopardy because of the
production of Cameroon tribune.
Another objective of the study was the determination of the
right allocation basis for the overhead costs of the company. As previously
mentioned, the company currently uses the labour hours as allocation rates for
the company costs, and also it is important to mention the absence of a
managerial accounting department in the company which should have taken care of
such a problem; from our study, we realised that most of the processes depend a
lot on the effective functioning of specific machines and most of the labour
costs incurred by the company are quite fixed since all the employees of the
company are salaried workers and not wage earners. As such, it seems advisable
to make use of the machine-hours instead of the labour-hours as the basis for
the allocation of the overhead costs in the company.
Concerning the cost structure of SOPECAM, it appears from the
results of our study that the company should continuously monitor the materials
costs as they appear to be the most important component of the unit cost, they
represent 48%and 73% of the total cost when using absorption and marginal
costing respectively. The company management should also take into
consideration the relatively small share of the labour cost (6% and 9%) in the
cost structure. This quite small share may be a good indicator of the declining
importance of that cost in the company, which may lead the management to make
decisions about the overhead allocation bases.
These appreciations the current functioning of SOPECAM
directly introduce into the next heading, which is about the recommendations
that we could make in order to improve the processes at SOPECAM.
III. RECOMMENDATIONS
The recommendations to be made from the results of this study
are centred around one main point: the Managerial accounting department.
v The sketch-determination of the unit cost of
Cameroon-tribune that has been achieved by this study, is normally part of the
work to be achieved in a managerial accounting department, the determination of
the allocation bases for the overhead costs of the company are also the concern
of such a department; we therefore recommend the management of SOPECAM to
establish and make operational a managerial accounting department in order for
them to have accurate indicators of their profitability.
v This managerial accounting department will be encouraged to
use the job costing method when trying to cost the printing works of SOPECAM,
as it is an important tool for pricing and cost control (Maher & Deakin,
199426(*)). This is
because customers always ask fro estimates in advance and they award jobs on a
competitive basis, consequently, SOPECAM must be able to estimate costs
accurately if they are to compete and make a profit.
v Concerning the selling price of Cameroon Tribune, unless it
is part of the governmental policy, we wish to propose an increase in its
selling price. This will enable the company to prepare itself to the possible
shortage of funds from the government.
v As one could have mentioned, we have just made estimates of
the editorial labour costs, selling and distribution expenses of the newspaper.
The company must therefore endeavour to keep accurate data about all these
expenses, for they are all part of the unit cost of the product.
v Another recommendation to be added is at the level of the
cost structure of the company; since the labour costs are not that much
important as the management of the company tend to believe, we recommend the
company to look for another allocation basis for its overhead costs. Because of
the relative importance of the material costs, it may be possible to
investigate their composition in order to have a deeper insight into the cost
structure of the company and therefore the into the real causes of the
incurrence of costs by the company.
IV. LIMITATIONS OF
THE STUDY
The scope of this study has been continuously narrowed down
because of many factors, namely:
The
limited access to the confidential data of the company
The
time constraint; such a study normally requires enough time to analyse in
detail all the processes involved in the production and distribution of the
product, but here we have been obliged to limit our research because of the
shortage of the time resource.
By
far the most limiting factor to the effective conduct of the research work, the
financial resources did not enable us to make a thorough collection and
analysis of data as we wished.
Finally, the scarcity of empirical studies on job costing did not help us in
the process of making this research work an improvement of former studies.
V. PROPOSITIONS FOR FURTHER STUDIES
For this research work to be complete, other studies need to
be conducted on the following topics or areas:
Ø An analysis of SOPECAM's cost structure.
Ø The Marketing and distribution of the products of
Nationalised companies.
Ø Costing methods for routine Works: Job or Process
costing?
BIBLIOGRAPHY
* 1 Lucey, T. (1993), Costing,
(4th edition), D.P. Publications, London
* 2 Garrison, R. H. &
Noreen, W. E., (2003), Managerial Accounting,(10th edition) Mc
Graw-Hill, New York
* 3 Stoner, J.A., & Wankel,
C.,(1986), Management (3rd edition), Prentice Hall, Englewood
Cliffs, New Jersey.
* 4 Horngren, C.T., (1981),
Introduction to Management Accounting (5th edition), Prentice-Hall
Inc., Englewood Cliffs.
* 5 Hansen, D.R., &Mowen,
M.M.,(1997), Management Accounting (4th edition), South-western
College Publishing, Cincinnati, Ohio.
* 6 Horngren, C.T. & Foster,
G. (1991), Cost Accounting: A Marginal Emphasis (7th edition),
prentice-Hall, Englewood Cliffs.
* 7 Horngren, C., Bhimani, A. et
al (1999), Management and cost Accounting, European edition, Hemel
Hempstead.
* 8 CIMA, (1996), Management
Accounting official Terminology, London.
* 9
* 10 Drury, C. (1992)
Management and Cost Accounting (1992), London.
* 11 Samuelson, P.A., &
Nordhaus, W.D., (2000), Economics (16th edition), McGraw-Hill, New
York.
* 12 Anthony, R.N., &
Reece,J.S. (1975), Management Accounting, Text and Cases (5th
edition), Irwin, Homewood.
* 13 Inman, M.L., Costing
Basics for the 21st Century. Students' Newsletter, January 2001.
* 14 Kaplan and Cooper, Harvard
Business review
* 15 Coulthurst, N., Process
Costing, Students' Newsletter, January 2000.
* 16 Lucey, T. (1992):
Management Accounting (2nd edition), DP Publications, London.
* 17 Copeland, R.M., Dascher,
P.E., Strawser, J.R., Strawser, R.H., (1995): Managerial Accounting
(5th edition), Dame Publications Inc., Houston
* 18 Kotler, P. & Dubois,
B. (1997), Marketing Management (9th edition), Publi-Union Editions, Paris.
* 19 Pride, W.M., Hughes,
R.J.,& Kapoor, J.R. (1988): Business (2nd edition), Houghton
Miflin, Boston
* 20 Drury, C. (2000)
Management and Cost Accounting, London.
* 21 Gorpinpaitoon, S., (1982),
Job Order Cost System for Ship Building Industry in Thailand, Master thesis.
* 22 Ngu, S.D. (1997), Product
Costing : An aid to Management decision Making, the case of CDC, Research
Project, university of Buea
* 23 Grais, B.(2000),
Méthodes Statistiques (3rd edition), Dunod, Paris.
* 24 : Fayel, A. &
Pernot, D.,(2001) Comptabilité Générale de l'Entreprise,
12th édition, Dunod, Paris.
* 25 Harper, W.M. (1989):
Management Accounting (3rd edition), Pitman Publishing, London
* 26 Maher, M.W. & Deakin,
E.B. (1994), Cost Accounting (4th edition), Irwin, Homewood,
Illinois
|