N° d' ordre:
République Algérienne Démocratique
et Populaire Ministère de l'Energie
Société Nationale pour la Recherche, la
Production, le Transport, la Transformation et la Commercialisation des
Hydrocarbures, SONATRACH-SPA
Institut Algérien du Pétrole
MÉMOIRE
Présenté pour l'obtention du diplôme
d'ingénieur spécialisé en :
MECANIQUE PETROLIERE
Spécialité : Maintenance
Par : Mr AIT RAHMANE Lotfi Thème
MODIFICATION DU SYSTEME
D'ETANCHEITE D'UN COMPRESSEUR
CENTRIFUGE PAR UN SYSTEME A
GARNITURE SECHE
Soutenue publiquement le ../../2017, devant le jury
composé de :
Mr. A. DJERRADI. Encadreur.
Mr. A. CHERAKA. Encadreur.
Mr. Examinateur.
Poste : MSP/ Ingénieur Mécanique
N1(ED). Affectation : Projets de développement/
Division EDV/ TRC.
Lieu des travaux de mémoire :
SONATRACH/ Activité transport par canalisation TRC/
Région de transport ouest RTO/ Station de compression de gaz naturel C
M'Seka/ Laghouat/ Algérie, année 2016.
DÉDICACE
Je dédie ce modeste travail à mes chers
parents qui tiennent une place immense dans mon coeur. Vous avez toujours
été là pour moi, et à aucun moment, vous n'avez
cessé de m'encourager.
REMERCIEMENTS
Avant tout, je remercie Dieu, le tout puissant de m'avoir
donné la force et le courage afin que je puisse accomplir ce
travail.
Je tiens à exprimer mes plus vifs remerciements
à Messieurs Ahmed DJERRADI et Abed CHERRAKA du service
maintenance mécanique S M'seka , pour la confiance qu'il m'a
témoignée, en acceptant l'encadrement de mon travail de
mémoire de fin de formation d 'induction.
Je leurs réitère ici mes remerciements les
plus sincères, pour le rythme éreintant qu'ils s'ont
imposé, et pour la constance dans l'effort et la
persévérance inflexible.
Je remercie aussi mes collègues de la formation
d'induction à SONATRACH, leurs soutiens inconditionnels et leurs
contributions effectives à la réalisation et la finalisation de
ce mémoire.
Enfin, Je voudrais rendre hommage à tous ceux qui nous
ont soutenus, et qui ont contribué à notre formation depuis notre
jeune âge jusqu'à ce jour, ainsi qu'à ceux qui nous ont
aidés de prés ou de loin, pour ce mémoire.
INTRODUCTION GENERALE
CHAPITRE I : Introduction à l'infrastructure
gazière SONATRACH
I.1.PRESENTATION DE LA COMPAGNIE 1
I.1.1.Histoire de la compagnie 1
I.1.2.Vue d'ensemble de la compagnie SONATRACH 2
I.2.ACTIVITES SONATRACH 3
I.2.1.Activité Amant 3
I.2.2.Le Transport par Canalisations 3
I.2.3.L'activité Aval 4
I.2.4.Commercialisation 5
I.3.INFRASTRUCTURE GAZIERE 5
I.3.1.Champs exploités par Sonatrach 5
I.3.2.Champs exploités en association 5
I.3.3.Le Centre National de Dispatching Gaz (le CNDG) 5
I.4.ORGANISATION DE LA TRC 7
I.5.REGION DE TRANSPORT OUEST RTO 9
I.5.1.Les missions de la Région Transport Ouest (RTO)
10
I.6.DESCRIPTION DU TRANSPORT PAR GAZODUCS ON-SHORE DE
10 LA REGION RTO
I.6.CONCLUSION 12
CHAPITRE II : Présentation du centre de
compression S m'seka.
II.1.INTRODUCTION 13
II.2.ORGANISATION DU PERSONNEL 14
II.2.a.Chef de Station 14
II.2.b.Service de Maintenance 14
II.2.c.Service Exploitation 14
II.2.d.Service des Moyens Généraux 15
II.2.e.Administration 15
II.2.f. Service de Sécurité 15
II.3.PRINCIPE DE FONCTIONNEMENT D'UNE STATION DE
16
COMPRESSION
II.3.a.Réseau principal 16
II.3.b.Tuyauterie d'entrée et de sortie station 17
II.3.c.Gare racleur 17
III.5.LES AUXILIAIRES DU COMPRESSEUR CENTRIFUGE
43
II.3.d. Les séparateurs 18
II.3.e. Collecteur d'aspiration et de refoulement des
compresseurs 18
II.3.f. Tuyauterie d'aspiration et de refoulement des
compresseurs 19
II.3.g.Circuit de gaz auxiliaire 20
II.4.DESCRIPTION GENERALE DES DIFFERENTES STATIONS
20
II.4.a. Station GZ1 40" 20
II.4.b.Station GZ2 40" 21
II.4.c.Station GZ3 42" 21
II.4.d. Bâtiments des turboalternateurs GZ 1/2 21
II.4.c. Bâtiment des turboalternateurs GZ 3 22
II.5.DESCRIPTION DES EQUIPEMENTS DE LA STATION
22
II.5.a. Les vannes 22
II.5.b. Les machines tournantes 24
II.5.LES PARAMETRES A SURVEILLER 29
II.5.a. Les Paramètres à surveiller en Salle de
contrôle 29
II.5.b. Les Différents Systèmes de Protection de
la machine 30
II.5.c.Les Différents systèmes de
sécurité et de protection de la station 31
II.5. CONCLUSION 32
CHAPITRE III : Les compresseurs centrifuges
III.I.INTRODUCTION 33
III.2.DESCRIPTION DES COMPRESSEURS INDUSTRIELS
33
III.2.1.Les catégories principales des compresseurs
33
III.2.1.LES DIFFERENTES APPLICATIONS 33
III.3. LES COMPRESSEURS CENTRIFUGES 35
III.3.1. Caractéristiques de construction des compresseurs
centrifuges 36
III.3.2. Utilisation des compresseurs centrifuges dans les
domaines industriels 36
III.3.3. Calcul des performances d'un compresseur 38
III.3.1.a.Taux de compression 39
III.3.1.b. Hauteur de compression 40
III.3.1.c. Rendement adiabatique 40
III.3.1.d. Puissance absorbée par le compresseur 40
41
41
42
III.4.REPRESENTATION ET DONNEES DES COMPRESSEURS
40
III.4.1.PLAN DE CIRCULATION DES FLUIDES (PCF / PFD)
III.4.1.a. Exemple d'un process de compression de gaz
III.4.2.PIPING & INSTRUMENTATION DIAGRAM (PID)
IV. CONCLUSION 65
Références bibliographiques
III.5.1. La fonction des auxiliaires 43
III.5.2. L'arrêt d'urgence 43
III.5.3.La lubrification 44
III.5.4.Anti pompage ou 'anti surge' 45
III.5.5.Protection contre les vibrations 46
III.5.CONCLUSION 47
CHAPITRE IV : Technologies des systèmes
d'étanchéité des machines tournantes
IV.1. INTRODUCTION 48
IV.2.LES PRINCIPALES CATEGORIES 48
IV.2.3.Les presse-étoupes (ou
étanchéité à contact) 49
IV.2.3.a. Les joints toriques 49
IV.2.3.b. Les joints tressés 49
IV.2.3.c.Les joints à lèvres 50
IV.2.3.d. Labyrinthe d'étanchéité 50
IV.3 CALCUL DES GARNITURES MECANIQUES 52
IV.3.1.Garniture mécanique hydraulique 'oil seal' (avec
contact) 52
IV.3.1.a. Description 52
IV.3.1.b. Analyse des forces agissant sur les faces de
frottement 53
IV.3.1.c. Consommation d'une garniture mécanique 56
IV.3.1.d. Coefficient de frottement/puissance absorbée
58
IV.3.2.Garniture mécanique sans contact 'dry gas seal'
58
IV.3.2.a. Description 58
IV.3.2.b. Analyse des forces agissant sur les faces sans
contact 60
IV.3.2.c. Consommation d'une garniture mécanique (sans
contact) 61
IV.3.3.Compensation des garnitures mécaniques 62
IV.3.3.a. Définition du coefficient de compensation k
62
IV.4.AVANTAGES ET INCONVENIENTS DES DIFFERENTS TYPES16
63
IV.4.1.Garniture mécanique avec contact 63
IV.4.1.a. Inconvénients 63
IV.4.1.b.Avantages 64
IV.4.2.Garniture à gaz sans contact 64
IV.4.1.a. Avantages 64
VI.3.PROPOSIONS DE MODIFICATION DE LA GARNITURE A 83
BAGUE FLOTTANTE
CHAPITRE V : Description du compresseur centrifuge
Cooper-Bessemer
V.1.INTRODUCTION 66
V.2. DISCRETION DU COMPRESSEUR 66
V.2.1. Donnée des paramètres de fonctionnement
66
V.2.2. Données de construction 67
V.2.2.a. Le carter 68
V.2.2.b. Le système à air (circuit du gaz) 68
V.2.2.c. Ensemble de rotor 69
V.2.2.d. Palier lisses et palier à butée 70
V.3. DESCRIPTION DU SYSTEM DE LUBRIFICATION ET
71 D'ETANCHEITE FILME D'HUILE
V.3.1. Description de la garniture à bagues flottante
embarquée (Flooting Oil 72 Seal)
V.3.2. Le circuit de d'huile de lubrification et
d'étanchéité (Console) 74
V.3.2.a. Pompes principales et pompes auxiliaires d'huile
d'étanchéité 75
V.3.2.b.Le réservoir d'étanchéité
75
V.3.2.c.Vanne de contrôle de la pression
différentielle d'huile d'étanchéité 75
V.3.2.d. Le système de piège d'huile 75
V.4. CONCLUSION 75
CHAPITRE VI : Opportunité de modification du
système d'étanchéité du compresseur
VI.I.INTRODUCTION 77
VI.2.ANALYSE DE LA MAINTENANCE ET ENTRETIEN DU
77
COMPRESSEUR COOPER-BESSEMER
VI.2.1.Maintenance préventive systématique du
compresseur 77
VI.2.2.Analyse d'historique des interventions 79
VI.2.3.Interprétations 79
VI.2.3.a. Première supposition 80
VI.2.3.b. Deuxième supposition 80
VI.2.4.Analyse de la consommation des huiles 82
VI.2.4.b. Analyse des débits d'huile de la machine
d'entrainement MS 3142 82
VI.3.1.Proposions de modification pour la réduction de
consommation 83
VI.3.1.a. Modification de la bague flottante
d'étanchéité interne par une bague à 83
rainure (Windback)
VI.3.1.b. Modification associée aux bagues
d'étanchéité flottante à rainure 84
VI.3.2.Faisabilité sur le compresseur Cooper-Bessemer
85
VI.3.3.Influence de rétrofit sur les perforante du
système d'étanchéité 86
VI.3.4.Exemple de rétrofit par la technologie par bague
d'étanchéité à rainures 88
Windback floating ring seal'
VI.4.PROPOSITION D'UNE GARNITURE SECHE SUR LE
89
COMPRESSEUR COOPER-BESSEMER
VI.4.1.Description de la technique
d'étanchéité sèche 90
VI.4.2.Faisabilité et Opportunité de
rénovation 92
VI.4.2.a. Espace de réception de la garniture 92
VI.4.2.b. Configuration du carter 93
VI.4.2.c. Comportement vibratoire 93
VI.4.2.c. Gaz d'étanchéité 94
VI.4.3.Paramètres industriel de fonctionnement 94
VI.4.3.a. Source d'alimentation de gaz
d'étanchéité 96
VI.4.3.b. Filtration et le système de conditionnement
de gaz d'étanchéité 97
VI.4.3.c. Régulation et Contrôle 97
VI.4.3.d. Event de la garniture primaire (Primary gas seal
vent) 98
VI.4.3.e. Gaz de séparation de la bague secondaire
(Secondary gaz seal vent) 99
VI.4.3.f. Bague secondaire (Barrier Seal) 99
VI.4.4.Aspect sécurité de fonctionnement du
compresseur 99
VI.4.5.Gain économique immédiat 100
VI.4.7.Exemples de rétrofit 103
CONCLUSION GENERALE
Liste des figures
Figure I.1 : Organigramme de la SONATRACH. 3
Figure I.2 : Production totale
commercialisée. 5
Figure I.3: Organigramme de la branche TRC. 8
Figure I.4: Organigramme de la région de
transport ouest RTO. 9
Figure I.5 : Schéma de principe des
stations du gazoduc GZ1 40". 11
Figure II.1: schémas d'implantation de la
station S M'seka. 13
Figure II.2 : Organigramme Station de
compression. 14
Figure II.3 : Schémas du gaz principal.
16
Figure II.4: Gare racleur arrivée. 17
Figure II.5: Filtres de trainement par
séparateurs du gaz naturel. 18
Figure II.6 : collecteurs d'aspiration et de
refoulement. 18
Figure II.7 : Schémas simplifié
Groupe compresseur. 19
Figure II.8 : Schématisation des Vannes
unité. 20
Figure II.9 : Compresseurs Cooper Bessemer &
Ingersoll Rand. 25
27
34
35
Figure II.10 : Schémas simplifié
des principaux organes d'une turbine à gaz.
Figure III.1 : Catégorie des compresseurs
volumétriques.
Figure III.2: Types des compresseurs
dynamiques.
Figure III.3: Domaines d'application des compresseurs (pression
en
36
fonction du débit). 35 Figure III.4 :
Compresseur centrifuge multi étage à joint
horizontal.4
Figure III.5 : Une roue à aubage tournant
sur son axe d'un compresseur
37
centrifuge. 36 Figure III.6: Un distributeur
dans l'axe de la roue.
Figure III.7: Un collecteur de section
croissante, en forme de spirale
38
(volute). 37 Figure III.8: Schéma de
circuit du gaz.
Figure III.9: Courbes de performance typique
d'un compresseur
centrifuge. 39
Figure III.10 : PFD du process de compression.
42
Figure III.11: PID du process de compression.
43
Figure III.12 : Schémas typique d'une
installation du système de control
de lubrification. 44 Figure III.13:
Illustration de la courbe de pompage d'un compresseur
centrifuge typique. 45 Figure III.14:
Illustration d'un schéma d'installation d'un système
anti
pompage. 46
Figure IV.1 : Catégorie du
différent système d'étanchéités. 48
Figure IV.2 : Figue d'un vérin et
emplacement des joints toriques. 49
Figure IV.3: Joint à tresse sur une
pompe. 49
Figure IV.4 : Joint à lèvre. 50
Figure IV.5 : Joint à labyrinthe. 50
Figure IV.6 : Etanchéité à
labyrinthe d'un compresseur embarqué sur 51
méthanier.
Figure IV.7 : Garniture mécanique
hydraulique. 52
Figure IV.8 : Montage type d'une garniture
mécanique en opposé. 53
Figure IV.9 : Schéma de principe d'une
garniture mécanique 53
Figure IV.10 : Schématisation du
diamètre hydraulique. 54
Figure IV.11 : Analyse des forces agissant
sur les faces de frottement. 55
Figure IV.12 : Distribution `x' des pressions
agissant en forces
d'ouvertures. 56 Figure IV.14 : Estimation
indicative de la consommation d'une garniture
mécanique. 57
Figure IV.13 : Macroscopie d'une interface
d'une garniture. 57
Figure IV.15 : Garniture mécanique
sèche. 59
Figure IV.16 : Rainure spiralés sur la
bague de matage d'une garniture
mécanique sèche. 59 Figure IV.17 :
Schémas des faces de frottement d'une garniture
mécanique sèche. 60
Figure IV.18: Principe de
l'établissement du filme à l'interface. 60
Figure IV.19: Elasticité du filme du
gaz vis-à-vis les perturbations. 61
Figure IV.20 : Caractéristiques de la
consommation des garnitures sans
contact. 62
Figure IV.21: Compensation des garnitures.
62
Figure V.1 : Coupe sur le compresseur
Cooper-Bessemer. 67
Figure V.2 : Carter du compresseur
Cooper-Bessemer. 68
Figure V.3 : Rotor du compresseur
Cooper-Bessemer. 69
Figure V.4 : palier lisse coté
accouplement du compresseur Cooper-
Bessemer. 70
Figure V.5 : Palier de butée du
compresseur Cooper-Bessemer. 71
Figure V.6 : Dessin d'ensemble des
éléments embarqués de la garniture
d'étanchéité. 72 Figure V.7 :
Identification des éléments
d'étanchéité du compresseur
Cooper-Bessemer. 73 Figure V.8 :
Schémas de principe du système
d'étanchéité à bagues
flottantes du compresseur 74 Figure V.9 :
Le système de contrôle et régulation (Console) du
système
d'huile 74 Figure VI.1: Champ de pression
et rupture du film dans l'interface d'une
garniture mécanique. 80 Figure VI.2:
Changement de phase en fonction de la pression et de
position radiale. 81 Figure VI.3:
Variation de l'épaisseur de film dans l'interface d'une
garniture en présence de changement de phase. 81
Figure VI.4: Bague flottante interne à
rainure Windback oil seal'. 84
Figure VI.5: Montage d'une garniture à
bague flottante d'étanchéité à
huile. 85
Figure VI.6: Garniture mécanique du
compresseur Cooper Bessemer. 86
Figure VI.7 : Le système de
contrôle et régulation (Console) du système
d'huile d'étanchéité (sans piège
d'huile). 87
Figure VI.8 : Diagramme de fiabilité
du système d'étanchéité à bague
flottante Windback (rétrofit). 87 Figure
VI.9: Diagramme de fiabilité du système
d'étanchéité à bague
flottante ordinaire 89 Figure VI.10 :
Liquides aperçu lors d'une opération de nettoyage par
piston racleur du gazoduc GZ2 (`S'). 90 Figure
VI.11: Évolution du nombre de brevets déposés sur
les garnitures
d'étanchéité. 90
Figure VI.12: composition d'une garniture
à gaz. 91
Figure VI.13: Montage en Tandem d'une
garniture d'étanchéité à gaz. 92
Figure VI.14: Espace de réception
d'une cartouche de garniture sèche sur
le compresseur Cooper-Bessemer. 93 Figure VI.15:
Diagramme typique de changeur de phase du gaz
d'étanchéité. 94 Figure VI.16:
Conditions aux limite de pression et de température d'un
filme d'étanchéité à gaz.
95 Figure VI.17 : Synoptique d'une console typique de
conditionnement et
contrôle du gaz d'étanchéité.20
96 Figure VI.20 : Synoptique d'un système de
tuyauterie typique d'évent de
la garniture primaire. 98 Figure VI.19 :
Synoptique d'un système typique de commande par
pression différentielle. 98 Figure VI.18:
Synoptique d'un système de filtration typique du gaz
d'alimentation. 97 Figure VI.21:
Synoptique d'un système typique de commande par
pression différentielle du gaz de séparation.
99 Figure VI.22 : Diagramme de fiabilité du
système d'étanchéité à bague
flottante Windback (rétrofit). 100 Figure
VI.23 : Diagramme de fiabilité du système
d'étanchéité à gaz
(rétrofit). 100 Figure VI.24 :
bague d'étanchéité qui remplace le labyrinthe,
qui a un
effet atténuateur de vibration. 102
Liste des tableaux
Tableau I.1 : Récapitulatif du parc
Turbine à gaz. 8
Tableau I.2 : Capacité de transport. 9
Tableau I.4 : Caractéristique d'une
station de compression du gaz. 11
Tableau II.1 : Caractéristiques des
pompes centrifuges. 24
Tableau II.2: Caractéristiques des pompes
volumétriques. 24
Tableau II.3 : Caractéristiques des
compresseurs axiaux. 25
Tableau II.4 : Caractéristiques des
compresseurs centrifuges. 26
Tableau II.5 : Caractéristiques des
turbines à gaz. 27
Tableau III.1 : L'utilisation des compresseurs
centrifuge dans le domaine 48 industriel.
Tableau VI.1 : Evaluation de la gestion de la
maintenance des 78 compresseurs Cooper-Bessemer sur S
Tableau VI.2: Consommation annuelle d'huile.
82
Tableau VI.3 : Les débits d'huile de
lubrification. 83
Tableau VI.4 : Comparaison de performances des
deux systèmes 104 d'étanchéité.
Introduction générale
INTRODUCTION
GENERALE
Introduction générale
INTRODUCTION GENERALE
Le gaz naturel est une source d'énergie de plus en plus
utilisée dans le monde. L'existence d'importantes réserves
mondiales et ses avantages environnementaux en ont favorisé l'essor,
notamment dans des secteurs à forte valeur ajoutée comme les
industries de précisions, la production d'électricité.
Son coût technique de production, de traitement et de
transport constitue cependant un fort frein au développement de son
utilisation. Les avancées technologiques futures seront
décisives pour en réduire le coût et
favoriser son développement.
Le gaz naturel se situe généralement dans des
zones géographiques éloignées de son lieu d'utilisation
comme le Sahara algérien, la Sibérie ou le désert du
Qatar. Il existe plusieurs modes d'acheminement vers son lieu d'utilisation.
A l'issus de la déclaration finale du 15e Forum
international de l'énergie d'Alger (IEF15) a relevé l'importance
du gaz naturel, tout en observant que l'industrie pétrolière
était devant des « défis structurels » en raison de la
baisse des prix. Dans cette déclaration finale distribuée
à la presse à l'issue des travaux de ce Forum, tenu à huis
clos, les participants ont mis en exergue le rôle important que joue le
gaz naturel dans l'approvisionnement en énergie face à une
demande croissante et l'importance de se tourner vers cette énergie qui
est « disponible » et «propre» (Demande nationale en hausse
et satisfaction des clients internationaux) [17].
Actuellement l'Algérie se trouve en face de grands
changements économique tributaire des aléas internationaux. Le
développement de différentes industries (lourde,
légère, de l'énergie, de la chimie et de la
pétrochimie, etc.) Exigent un système d'appareillage qui permet
d'améliorer le travail, accélérer les rythmes de
productivité, augmenter le volume des produits finis.
Parmi les machines ayant un rôle primordial dans les
domaines d'activité industrielle, on peut citer par exemple les
compresseurs centrifuges. Les compresseurs centrifuges constituent un
équipement de production très important dans le transport du gaz
naturel. Avec l'augmentation de la production une lecture sur les performances
des compresseurs s'impose dans ce contexte.
Pour être en mesure d'optimiser ces performances selon
les exigences technologiques et de les exploiter d'une façon
compétente, un spécialiste doit parfaitement connaître les
constructions de ces machines, leur principe de fonctionnement et la base
théorique qui sert à expliquer leurs caractéristiques.
Notre travail consiste à l'étude
d'opportunité de modification des garnitures à filme d'huile par
celle à garniture sèche des compresseurs Cooper-Besemer.
L'étude des données de maintenances et consommation
d'exploitation de ces équipements est impérative pour cerner ces
dépenses. Ce travail constitue une introduction à la technologie
des garnitures sèche appliquées sur les compresseurs
centrifuges.
Chapitre I
INTRODUCTION A
L'INFRASTRUCTURE
GAZIERS SONATRCH
1
Chapitre I : Introduction à l'infrastructure
gazière SONATRACH
I.1.PRESENTATION DE LA COMPAGNIE
I.1.1.Histoire de la compagnie
L'histoire des hydrocarbures en Algérie remonte au
19ème siècle avec la première découverte en 1877 de
Ain Zeft près de Relizane, et en 1948 celle Oued Gueterini à
caractère commerciale réalisée dans le bassin du Hodna,
région de Sidi Aissa.
Dans le Sahara, la première découverte a eu lieu
dans la région de In Salah (gisement de gaz de Djebel Berga) en 1953,
poursuivie par celles d'Edjelleh dans le bassin d'illizi à l'Est et les
géants gisements du pétrole de Hassi Messaoud et du gaz à
Hassi R'Mel en 1956 dans le Sahara central.
Sonatrach née le 31 décembre 1963 est
dénommée initialement Société pour le transport et
la commercialisation des hydrocarbures et réalisa et exploita
l'oléoduc OZ1.
Un élargissement des activités a était
effectué par la Sonatrach pour la prospection pétrolière,
la production et la transformation des hydrocarbures dès 1966 et
l'achèvement de la nationalisation des activités de raffinage en
1967.
La nationalisation des hydrocarbures le 24 février
1971, place Sonatrach dans une nouvelle dynamique avec l'extension de ses
activités à l'ensemble des installations
pétrolières et gazières et la maîtrise de toute la
chaîne pétrolière.
En 1980, une restructuration de l'entreprise a eu lieu par la
création des entreprises et filiales couvrant tous les services (Naftal,
Entp, Enafor, Ensp, Enageo, Engtp, Engcb, Naftec, Enep, Enip, Enpc, Enac,
Ceryd).
L'ouverture au partenariat en 1986, fut promulguée la
loi des hydrocarbures 86-14, et son amendement en 1991, autorisant le
partenariat et la contribution des sociétés
étrangères, en association avec Sonatrach, à
l'activité Recherche et Exploitation des amendements en
Algérie.
En 2005, le cadre juridique et réglementaire qui
régit l'industrie des hydrocarbures en Algérie a
été complètement refondu avec la création des
agences ALNAFT pour la gestion et la promotion du domaine minier et l'ARH
l'Agence de régulation des Hydrocarbures pour l'environnement, le
transport et la réglementation au nom de l'état.
Sonatrach devient ainsi la Société Nationale
pour la recherche, la production, le transport, la transformation et la
commercialisation des hydrocarbures et leurs dérivées [15].
Elle a pour missions de valoriser de façon optimale les
ressources nationales d'hydrocarbures et de créer des richesses au
service du développement économique et social du pays.
2
Chapitre I : Introduction à l'infrastructure
gazière SONATRACH
I.1.2.Vue d'ensemble de la compagnie Sonatrach
Sonatrach compagnie pétrolière
intégrée, est un acteur d'envergure majeur dans le domaine du
pétrole et du gaz. Ce qui la place, aujourd'hui, première
compagnie d'hydrocarbures en Afrique et en méditerranée. Elle
exerce ses activités dans quatre principaux domaines l'Amont, l'Aval, le
Transport par Canalisations et la Commercialisation.
Elle est présente dans plusieurs projets avec
différents partenaires en Afrique, en Amérique Latine et en
Europe.
La nouvelle macrostructure de l'Entreprise est
constituée de quatre (04) Activités Opérationnelles et
onze (11) Directions Fonctionnelles :
I.1.2.a. Activités Opérationnelles
Exploration -- Production (E&P), Liquéfaction,
Raffinage et Pétrochimie (LRP), Transport par Canalisations (TRC),
Commercialisation (COM).
I.1.2.b. Les Directions Fonctionnelles
Directions Coorporate : Stratégie,
Planification & Économie (SPE), Finances (FIN), Ressources Humaines
(RHU).
Directions Centrales : Filiales &
participations (FIP), Activités Centrales (ACT), Juridique (JUR),
Informatique & Système d'Information (ISI), Marchés et
Logistique (MLG), Santé sécurité & environnement
(HSE).
Business Développent (BSD) : nouvelle direction
chargée de détecter des opportunités de croissance,
d'évaluer et de lancer des nouveaux projets dans les activités de
base de l'entreprise.
Recherche & Développement (RDT) : nouvelle
direction chargée de promouvoir et de mettre en oeuvre la recherche
appliquée et de développer des technologies dans les
métiers de base de l'entreprise [9].
Chapitre I : Introduction à l'infrastructure
gazière SONATRACH
PRÉSIDENT DIRECTEUR GÉNÉRAL
COMITE D'ETHIC
DIRECTION AUDIT ET CONFORMITE
SERVICE SURETE INTERNE
COMITÉ EXÉCUTIF
COMITÉ D'EXAMEN ET D'OREINTATION
SECRÉTARIA GÉNÉRALE
CABINET
· DCP SPE
·
DCP FIN
DC NI
DC MLG
DC HSE
DC RDT
· ·
DC BSD
DCP DC DC DC
RHU FIP ACT JUR
EXPLORATION & PRODUCTION
|
|
LIQUEFACTION RAFINAGE ET PETROCHIMIE
|
|
|
|
COMMERCIALISATION
|
|
TRANSPORT PAR CANANLISATION
|
|
|
|
|
|
|
|
3
Figure I.1 : Organigramme de la SONATRACH.
I.2.ACTIVITES SONATRACH
I.2.1.Activité Amant
Sonatrach opère dans des gisements géants, dans
différentes régions du Sahara algérien, tels que Hassi
Messaoud, Hassi R'Mel, Hassi Berkine, Ourhoud, Tin Fouyé Tabankort,
Rhourde Nouss, In Salah et In Amenas, en effort propre ou en partenariat avec
des compagnies pétrolières étrangères. Les bassins
sédimentaires algériens couvrent plus de 1,5 million de
kilomètres carrés. avec une densité moyenne de forage
d'exploration de 15 puits/10000 km2. L'intensification de l'effort de recherche
ces dernières années a permis à Sonatrach de
dépasser le seuil de 100 puits terminés en 2014.
I.2.2.Le Transport par Canalisations
Le transport par canalisations assure l'acheminement des
hydrocarbures (pétrole brut, condensat, GNL, GPL). Les centres de
dispatching des hydrocarbures liquides et gaziers comptent parmi les
installations névralgiques de l'Activité.
Le Centre de Dispatching d'Hydrocarbures Liquides, le CDHL, se
trouve à Hassi Messaoud (Haoud El Hamra).
Le Centre National de Dispatching Gaz, le CNDG, se situe
à Hassi R'mel. Sonatrach dispose de 22 systèmes de transport par
canalisations (STC) : (21 en exploitation, 1 en cours de réalisation, le
GR5). Sonatrach dispose de 82 stations de pompage et de compression dont 39
stations de pompage destinées aux liquides. La longueur du réseau
de canalisation est passé de 19275 km en 2013 a 19644 en 2014, soit une
augmentation de 369km suite à
4
Chapitre I : Introduction à l'infrastructure
gazière SONATRACH
l'expansion du STC GPL/DLR1, Le réseau de canalisation
a transporté un volume de 360 millions de Tep à fin 2014.
I.2.3.L'activité Aval
-Sonatrach détient quartes (4) complexes de GNL d'une
capacité totale de production de 56 millions de m3/an, dont:
Un méga train a Skikda (GL1K) mis en service en 2013
d'une capacité de 10 millions m3/GNL/an
COMPLEXE GL1Z Localisation: Béthioua (à environ
40 km à l'Est d'Oran) 72 hectares GNL: 17,56 Millions m3/an Gazoline :
123 000 T/an Procédé de liquéfaction utilisé :
MCR-APCI Nombre de trains : Six (06) Date de mise en production : 1978. Postes
de chargement : 2 methaniers d'une capacité de 40 000 à 70
000m3.
COMPLEXE GL2Z Localisation: Béthioua (à environ
40 km à l'Est d'Oran) 72 hectares GNL : 17,820 Millions m3 /an Butane :
327 000 T/an Propane : 410 000 T/an Gazoline : 196 000 T/an
Procédé de liquéfaction utilisé : MCR-APCI Nombre
de trains : Trois (03) Date de mise en production : 1981. Postes de chargement
: 2 methaniers d'une capacité de 40 000 à 150 000 m3.
Un méga train à Arzew GL3Z, mis en service en
2014, d'une capacité de 10,5 millions m3/GNL/an. Sonatrach
détient également deux (02) complexes de GPL à Arzew,
d'une capacité totale de séparation de 10,4 millions de tonnes
/an.
-Cinq (05) raffineries de brut et une (1) raffinerie de condensat
:
La raffinerie d'Alger avec une capacité de traitement
de pétrole brut de 2,7 millions de tonnes /an.
La raffinerie de Skikda avec une capacité de traitement
de pétrole brut de 16,5 millions de tonnes/ an.
La raffinerie d'Arzew avec une capacité de traitement
de pétrole brut de 3,75 millions de tonnes/ an.
La raffinerie de Hassi Messaoud avec une capacité de
traitement de pétrole brut de 1,1 millions de tonnes/an.
La raffinerie d' Adrar avec une capacité de traitement
de pétrole brut de 600 000 Tonnes/an.
Une raffinerie de condensat à Skikda d'une
capacité de traitement de 5 millions de Tonnes/an. En partenariat,
Sonatrach détient deux (02) unités d'extraction d'hélium:
respectivement Helios (Arzew) et Helison (Skikda).
Chapitre I : Introduction à l'infrastructure
gazière SONATRACH
I.2.4.Commercialisation
Sonatrach a commercialisé 98,4 millions de TEP
d'hydrocarbures sur le marché international durant l'année 2014,
réparties par produit comme suit: Pétrole brut : 23,6 millions
Tonnes , Condensat : 4,8 millions Tonnes , GPL : 7,2 millions Tonnes, Produit
raffiné : 16,7 millions Tonnes, Gaz naturel : 27,4 milliard de m3, GNL :
28,5 millions m3.
Sonatrach possède (21) navires de transport (10 de
GPL), (09 de GNL) et (2 Pétroliers) et se positionne comme un acteur
majeur dans l'exportation du GPL et du GNL dans le bassin
euro-méditerranéen [10].
Production totale commercialisée

150
200
45,3
Réalisation 2013
44,2
Réalisation 2014

5
Marche National Exportations
Figure I.2 : Production totale
commercialisée.
I.3.INFRASTRUCTURE GAZIERE
La richesse du sous-sol algérien, le rythme des
investissements consentis, le travail des hommes et la place qu'elle occupe
dans l'approvisionnement des marchés gaziers internationaux, font
aujourd'hui de Sonatrach la première société
gazière en Méditerranée qui détient un
réseau de Transport par Canalisation de prés de 20 000 km, dont
10000 km de gazoduc.
I.3.1.Champs exploités par Sonatrach ;
Le champ de Hassi R'Mel, l'un des plus grands gisements de gaz au
monde, contribue à hauteur de 60% de la production primaire totale
algérienne, soit 90 milliards de m3.
6
Chapitre I : Introduction à l'infrastructure
gazière SONATRACH
I.3.2.Champs exploités en association ;
La production de gaz naturel en association participe à hauteur
de 20% du volume de gaz produit en Algérie, soit 34 milliards de m3. In
Salah est exploité en association avec BP et Statoil. In Amenas est
exploité en association avec BP et Statoil. Tin Fouyé Tabankort
est exploité en association Total et REPSOL. Menzel Ledjmet Est en
association avec ENI.
I.3.3.Le Centre National de Dispatching Gaz (le CNDG)
; Le CNDG se situe à Hassi R'Mel. C'est le point où se
font les collectes et le dispatching du gaz à travers les gazoducs vers
les clients nationaux, comme Sonelgaz, clients tiers et autoconsommations des
unités de Sonatrach notamment la livraison aux complexes de
liquéfaction, et en international à travers les gazoducs
transcontinentaux PEDRO DURAN FARELL, ENRICO MATTEI et MEDGAZ.
LE GAZODUC ENRICO MATTEI (GEM) : Gazoduc reliant
l'Algérie à l'Italie via la Tunisie, GO1 et GO2 sur le territoire
algérien.
Longueur 1647 Km
Capacité 33.15 Milliard de
m3/an
Mise en service 1982
LE GAZODUC PEDRO DURAN FARELL (GPDF): Le gazoduc reliant
l'Algérie à l'Espagne via le Maroc, (GME) sur le territoire
algérien.
Longueur 521 Km
Capacité 11.6 Milliard de
m3/an
Mise en service 1996
LE GAZODUC MEDGAZ : Gazoduc reliant directement
l'Algérie à l'Espagne. Partant de Beni Saf, (Ouest de
l'Algérie), la canalisation traverse la méditerranée, pour
aboutir près d'Almeria sur la côte espagnole, MEDGAZ Phase (I), et
Phase (III) sur le territoire algérien.
Longueur 210 Km
Capacité 8 Milliard de
m3/an
Mise en service 2011
Les gazoducs transcontinentaux en projet
LE GAZODUC GALSI : Projet de ligne directe reliant
l'Algérie à l'Italie via la Sardaigne. Le gazoduc pourra
desservir l'Italie, le Sud de la France et les pays européens au Nord
des Alpes avec une capacité de 8 millions m3/an.
7
Chapitre I : Introduction à l'infrastructure
gazière SONATRACH
Longueur
El Kala-Cagliari (Offshore) 285 Km
Olbia-C.d.Pescaia (Offshore) 275 Km
Cagliari-Olibia (On shore) 300 Km
Projet Gazoduc Nigeria --Algérie : Le Trans-Saharan Gas
Pipeline (TSGP) est une canalisation destinée à acheminer le Gaz
Naturel vers les marchés européens à partir de la
région de « Delta du Niger », au sud du Nigeria, via le Niger
et l'Algérie, puis par une conduite sous-marine qui traversera la
Méditerranée [10].
Longueur 4188 Km
Capacité 20 à 30 Milliard de
m3/ an
I.4.ORGANISATION DE LA TRC
L'activité Transport par Canalisation est
scindée en cinq régions de transport et deux directions :
· La RTO Région Transport Ouest.
· La RTE Région Transport Est.
· La RTC Région Transport Centre.
· La RTH Région Transport Hassi R'Mel.
· La RTI Région Transport In Amenas. Direction du
GPDF (Développement).
Direction du GEM (Exploitation et Maintenance).
Chapitre I : Introduction à l'infrastructure
gazière SONATRACH
1
Division Maintenance
Direction Approvisionnement
Direction Maintenance
Vice Président TRC
Division Exploitation
Division Régionale
Direction Controle des Opérations
I
Divition Etude et Développement
Techniques Nouvelle
8
Direction Technique
Direction Réparation des
Cananlisations
Figure I.3: Organigramme de la branche
TRC.
La TRC dispose de 116 turbines à gaz GE,
représentant 37% du parc turbines du réseau de Transport par
Canalisation (311 turbines).
Tous nos gazoducs sont équipés de turbines GE ou
sous licences GE (AEG KANIS)
Les gazoducs GZ 1, 2 et 3 sont équipés de turbines
à gaz GE MS 3002 & AEG KANIS MS 3142 totalisant 55 Turbocompresseurs
[11].
Tableau I.1 : Récapitulatif du parc
Turbine à gaz [11].
Ouvrage
|
Nombre de Type de machine Année de mise
en
machines service
|
|
GZ 1 20 MS 3002
1978 Ak 4
GZ 2 15 MS 3142 1982
GZ 3 20 M -1112
GK 1-2 20 MS 3002 1975 & 1978
GR 1-2 17 0/PGT25 illi 199
GEM 04 LM2500/PGT25 1996
OK 1 13 08 MS 3132+ 5 1976, 1980 & 1986
PGT 10
OH
2/MESDAR
|
02
|
11111M1172 2002
|
|
Chapitre I : Introduction à l'infrastructure
gazière SONATRACH
I.5.REGION DE TRANSPORT OUEST RTO
Elle a été crée le 19 Mars 1966 avec la
mise en exploitation de l'oléoduc (OZ1), première
réalisation de SONATRACH en Algérie.
La fonction principale de la direction régionale Ouest
d'Arzew de l'activité transport par canalisation est du transport et de
la livraison des hydrocarbures liquides et gazeux à savoir le
pétrole, le condensat le GPL et le gaz naturel, pour assurer le
transport entre les champs Hassi Messaoud, hassi Rmel vers différents
points de chargement du port. d'Arzew, RTO utilise son réseau
composé de 10 canalisations de 12" à 48" totalisant une longueur
de 5386 Km [12].

SOUS DIRECTION TECHNIQUE
SOUS DIRECTION ADMINISTRATION
SOUS DIRECTION FINANCE
CENTRE INFORMATIQUE
I I
I
SOUS DIRECTION OLEODUC
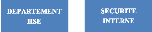
SOUS DIRECTION GAZODUC
9
Figure I.4: Organigramme de la région de
transport ouest RTO. Tableau I.2 : Capacité de
transport [12].
Ouvrage Produit transporté Nombre de
pipe
|
MTEP /an: Million
de Tonne Equivalent Pétrole/an.
|
|
OZ1-0Z2 Pétrole brut 02 oléoducs
45 MPET/an
NZ1 Condensat 01 oléoduc 18.39
MPET/an
LNZ1-LZ1 GPL pétrole
liquéfie 02 oléoducs 10.38 MPET/an
GZO-GZ1-GZ2-
Gaz naturel 04 gazoducs 39.60 MPET/an
GZ3
GZ4* Gaz naturel 01 gazoduc
* :En plus le nouveau gazoduc MEDGAZ (GZ4) avec une
capacité de transport de 8 Milliards de m3/an[10].
Chapitre I : Introduction à l'infrastructure
gazière SONATRACH
I.5.1.Les missions de la Région Transport Ouest
(RTO)
Sa mission essentielle est d'assurer le transport des
hydrocarbures à moindre coût et dans des conditions optimales de
sécurité, tout en respectant l'environnement.
· Le stockage et la livraison d'hydrocarbures liquides et
gazeux.
· L'exploitation, la maintenance et la protection du
patrimoine.
· L'élaboration et la réalisation des
programmes du budget annuel.
· Le suivi de la réalisation des projets
d'extension, de renouvellement de
valorisation du potentiel existant [12].
I.6.DESCRIPTION DU TRANSPORT PAR GAZODUCS ON-SHORE DE
LA REGION RTO
L'écoulement du gaz dans la canalisation d'un gazoduc
on-shore ne peut s'effectuer sans pertes de pression importante. Pour maintenir
le débit du gaz à la valeur spécifiée, il est
nécessaire de prévoir des stations de compression pour compenser
les chutes de pression le long de la canalisation. Dans le cas du gazoduc de
hassi R'Mel à Arzew, cinq stations de compression ont été
réalisées pour que le débit soit maintenu et de
compresseur les perte de charge du gaz transporté [12].
Tableau I.3 : Caractéristique des lignes
du transport.
Date mise en service
Par cours
Diamètre en pouce 111.
Nombre de station 4 5
GZO
|
GZ1
|
GZ2
|
GZ3
|
Avril1961
H.R'Mel- Arzew
|
Février1976
H.R'Mel-Arzew
|
Decembre 1982 H.R'Mel-Arzew
|
Février1989
H.R'Mel-Arzew
|
40 42
5 5
Nombre du
Turbocompresseurs 9 20
15 20
GZ4
(MEDGAZ) [10]
2011
H.R'Mel-Arzew
48
Postes coupures
Interconnect é
10
Poste de coupure :
Ils sont au nombre de 5 divisent la canalisation en 6 section
séparées, chaque poste est relié à une station de
compression d'appoint.
11
Chapitre I : Introduction à l'infrastructure
gazière SONATRACH
Poste de sectionnements :
Leur mise en fonction peut être la résultante d'un
accident tel l'éclatement d'un élément de la ligne, elles
peuvent être également actionnées par la présence
d'une basse pression de la ligne.
Poste de purge :
Ils sont implantés intervalles viables drainant ainsi le
condensât et purgeant la ligne. Station de compression
:
Le rôle d'une station de compression est d'assurer un
débit du gaz véhiculé par le gazoduc à une certaine
pression (compensation de perte de charge).
Tableau I.4 : caractéristique d'une
station de compression du gaz typique RTO.
Ouvrage Diamètre Nombre Turbine à
Compresseur Débit Année de
de gaz de charge Nm3/h mise en
machines service
G E MS ENGERSOLL
40" 04 3002 RAND 1,8
GZ1
1976
AEG COOPER
GZ2 40" 03 KANISBESSEMER
1,6 1982
MS3002
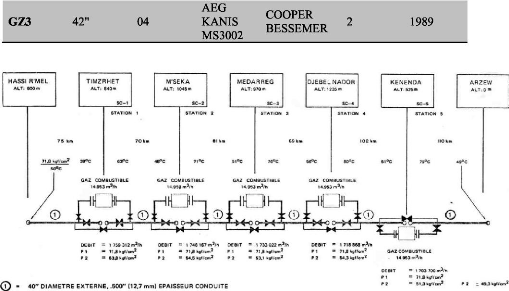
DEBIT - 1710505 m3M
r 1 = 71.1 4,4112
P2 = 54.3 4504142
DEBIT = I740 n377.3111 DENT =
173302247811,
P 1 = 71,B tplrrn ·P P I = 71 A
4504742
r 2 m E46.4114,7 P 2 m 531 .51m773
EEBIT = I 749 312401h
r1 -- 716 Ny7472
P 2 = 536 kgf 1m1.2
DA2 COM51t5T1 B4E 14E1E3 milk
P 7 = 49,3 p114742
DENT = 1 703 700 In
P 1 = 71.0 .161l4742
r z = 51a kk11cm2
1a - 40- DIAMETRE EXTERNE,
.500" (12,7 mm) EPAI $EUR CONDUITE
5 km
102 Y4
7C km
BI km
69 ks
HASS1 R'MEL ALT: 5D01.
TIMZRHET ALT: 840
STATION 1
M'SE K A
ALT. 1041.1
9C-2
STATION 2
ME DA RREG A LT. 970 m
SC-3
STATION 3
DJ E B E L NADOR ALT=123541
SC-4
STATION 4
/1.11, 39°C
SOOC
71^C 5IfC
76°C SE°C
00°C 6i°C
03°C
GAI COMBUSTIBLE
14.953 m261
6A2 COMBUSTIBLE 14.950 PA
GAZ COMBUSTIBLE 14.953 43ln
GAZ COMBUSTIBLE
14.%3 43l11
KENENDA ALT 425m
SC · 9
AEG COOPER
GZ3 42" 04 KANIS 2
BESSEMER
MS3002
1989
Figure I.5 : Schéma de principe des
stations du gazoduc GZ1 40".
12
Chapitre I : Introduction à l'infrastructure
gazière SONATRACH
I.6.CONCLUSION
Dans ce chapitre nous avons présenté un historique
de création et de développement de la société
SONATRACH. Un développement que ce soit au niveau infrastructure ou en
production. Une dimension internationale bien mérité a
été illustré.
Nous avons effectué un résumé de
différents activités, ouvrage et infrastructure exploité
par la société SONATRACH. Des infrastructures qui ne cessent
d'avoir de démenions en terme d'envergure ou de production.
Nous nous somme consacrer un temps pour illustrer les moyens
d'exploitation et du gaz naturel, depuis son extraction des gisements à
la commercialisation.
Chapitre II
PRESENTATION DU
CENTRE S M'SEKA
Chapitre II : Présentation du centre de compression S
m'seka
II.1.INTRODUCTION
Une station de compression a pour but principale d'assurer un
débit déterminé (supérieur au débit naturel)
du gaz véhiculé par le gazoduc et de compenser les pertes de
charge. Le processus consiste à aspirer le gaz dans la ligne amont du
gazoduc à une pression de l'ordre de 40 bars et à le refouler
à une pression de l'ordre de 71 bars dans la ligne aval.
CIATrSHtP
MUR Di CLOTURE
RPSE tif l'EUPHONIQUE ONDrnTR D'EAUC.~ LR D'ALDJB
IrkTED
E
CHAU GOIMAD I.EGFi4DE
N
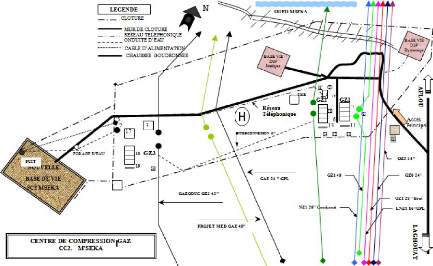
17
13 1
cir
· .wL IELLE
BASE DE \'IE .qC'2 SSSEKii
IL G
=U
43i 24.
erkZCODC IZ9 42.
FF,]] ET' ED CAI41.
CENTRE DE COMME S SION !GAZ C.
]rSEXÀ
rok.A D'EAU
Figure II.1: schémas d'implantation de la
station S M'seka.
1- Postedegarde
2- Bac d'eau anti-incendie
3- Salle de contrâle
4- Bâtiment technique
5- Salle des pompes incendie
6- Bâtiment basse tension
7- 04 Turbocompresseurs GZ1
8- 04 Turbocompresseurs GZ2
9- Gare racleur GZ1
10-Filtres séparateurs GZ1
11- Aéro réfrigérants GZ1/2
12-Bourbier GZ1/2
13- Aéra réfrigérant GZ2
14-Filtres séparateurs GZ2
15-Gare racleur GZ2
16-Transformateurs 250 KVA-5500V
17-02 Turboalternateurs
18-04 Turbocompresseurs GZ3
19- Aéroréfrigérant GZ3
20-Filtres séparateurs GZ3
21-Gare racleurs GZ3
22-Bourbier GZ3
Implantation : Le groupe de compression S M'SEKA
est implanté dans la wilaya de Laghouat à une distance de 55 km
au nord de celle-ci, à proximité de la route nationale 23
Laghouat.
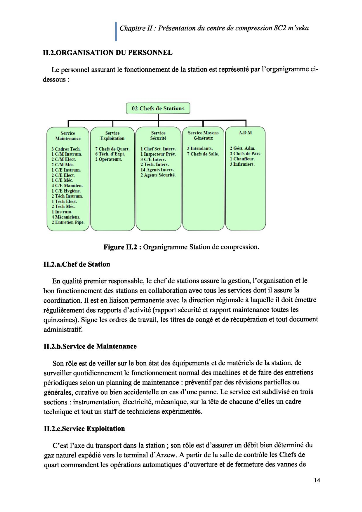
15
Chapitre II : Présentation du centre de compression S
m'seka
process et surveillent par DCS (Digital Control System) les
paramètres des turbocompresseurs et les turboalternateurs. Ainsi, pour
le relevé des paramètres sur site et les opérations qui
nécessitent un intervenant des techniciens et des opérateurs
d'exploitation sont à la disposition du service.
II.2.d.Service des Moyens Généraux
Il est chargé de l'hébergement et de la
restauration du personnel dans un centre de vie à 02 Km de la station ;
les intendants et les chefs de salles assurent la gestion de ce service.
II.2.e.Administration
Pour l'administration de la station elle est
représentée par des gestionnaires administratifs qui s'occupent
du pointage, les congés, les maladies, les missions,....des personnel.
Les chauffeurs du transport personnel et les infirmiers font partie
intégrante de ce service.
II.2.f. Service de Sécurité
Avec ses deux sections (Prévention et Intervention) le
service SHE veille d'une manière permanente sur la sûreté
des équipements et la sécurité du personnel travaillant
dans la station. Malgré l'absence d'un ingénieur SHE, le
personnel en place possède l'expérience requise dans ce
domaine.
Moyens matériels mobiles
- 01 Camion incendie (Eau : 7000 L, Emulsseur : 4000 L).
- 01 Land Rover (Poudre : 250 Kg, Eau/Emulseur : 250 L, 02
Bouteilles de chasses).
Moyens matériels fixes :
- Motopompe électrique : 120m3/h
- Motopompe Diesel : 120m3/h
- Pompe de pressurisation d'eau (Jockey) : 10m3/h
- Bac d'eau : 250m3
Protection des TC :
- Système détection de gaz.
- Système déluge (Eau)
- Explosimètre (Méthane)
- Extincteur CO2
- Extincteur poudre
Chapitre II : Présentation du centre de compression S
m'seka
II.3.PRINCIPE DE FONCTIONNEMENT D'UNE STATION DE
COMPRESSION4
II.3.a.Réseau principal
La tuyauterie du gaz principal a été
réalisée pour chaque ouvrage de gazoduc.
ByPass Statua MOV
a~.ve.oa,
p. 031
Racleur
W
rMOV
X84
MOV X41
Racleur
Entre SC
GZ1
MOV X81
MOV
028
w
MOV X83

MOV X01 Il
MOV' X82 ;I
MOV
Sortie SC
GZ1
030
MOV j
033
ro.a.rmo
MOV MOV ·
r_
X62 P,o.hmian xe

y MOV X60
LI X61
oeaem.
dl Sava w.r.irmn
Filtrage
Aspiration
TC TC
TC TC TC TC
SKID + FILTRE COMBUSTIBLE
16
Figure II.3 : Schémas du gaz
principal.
La ligne (c'est la canalisation de transport) qui comporte
gare de réception et de départ de pistons racleurs. Des vannes de
sectionnement des gares racleurs.
La fonction by-pass est assurée par un clapet
isolé et une vanne qui remplit le rôle de bypass pour les
stations.
L'aspiration et le refoulement de chaque compresseur sont
munis chacun d'une vanne d'isolement à servomoteur
télécommandé depuis le tableau de contrôle commande
du groupe.
Le piquage dans les deux cotes du by-pass est destiné
à l'alimentation en gaz carburant des groupes, il peut également
alimenter les actionneurs des vannes de groupes et la base de vie ainsi que les
turboalternateurs.
17
Chapitre II : Présentation du centre de compression S
m'seka
On décrit le trajet du gaz principal à travers la
station dans le système de tuyauterie de gaz principal. Ce
système commence à la vanne d'aspiration de la station et se
termine à la vanne de refoulement de la station. La tuyauterie est
divisée en plusieurs sections comme suit :
Tuyauterie d'entrée et sortie station
Gare racleur
Les séparateurs
Collecteur d'aspiration et de refoulement des compresseurs
Tuyauterie d'aspiration et de refoulement des compresseurs
By-pass station
Circuit du gaz auxiliaire.
II.3.b.Tuyauterie d'entrée et de sortie station
Est le système de tuyauterie de 36 pouces d'entrée
de la station, qui commence à partir de la vanne d'aspiration de la
station, jusqu'à la tuyauterie de 36 pouces des séparateurs.
Cette tuyauterie comprend :
- La vanne d'aspiration de la station
- Les raccords de la conduite de pressurisation de 4 pouces. - La
conduite de by-pass de la gare racleur de 10 pouces. - La conduite de recyclage
de 12 pouces
II.3.c.Gare racleur
La gare racleur est constituée essentiellement d'une
section de tube en cul-de-sac, d'un diamètre de 36" à 4"
supérieur à celui de la canalisation, dans laquelle on introduit
le racleur en l'engageant jusqu'à l'entrée de la canalisation
même, pour le départ laquelle, à l'arrivée, le
racleur vient s'arrêter n'étant plus propulsé. Le passage
des racleurs destinés à nettoyer les parois internes des
canalisations, est une pratique caractéristique des pipelines. Il est
donc nécessaire de prévoir des gares permettant l'envoi et la
réception des racleurs.
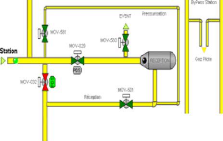
E..Pict Atm
Prti5sere
0+601
Rie
sawn
L. La
Figure II.4: Gare racleur arrivée.
Chapitre II : Présentation du centre de compression S
m'seka
II.3.d. Les séparateurs
L'emploi de compresseurs exige une filtration poussée
du gaz et une bonne élimination des produits liquides, tels qu'eau,
condensât, etc.
Le conduites d'entrée et de sorties des
séparateurs sont installées pour distribuer le gaz vers les six
séparateurs (36pouces), ces conduite comprend un évent de 4
pouces.
Le gaz combustible de la station est fourni par un raccord sur
le collecteur de sortie des séparateurs de 6 pouces.
La tuyauterie d'entrée et sortie sont munis des vannes
manuelles de 24 pouces normalement ouvertes qui sont utilisées pour
isoler les séparateurs, pour entretien.
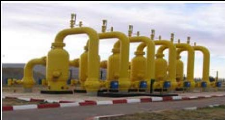
Figure II.5: Filtres de trainement par
séparateurs du gaz naturel. II.3.e. Collecteur d'aspiration et
de refoulement des compresseurs
Les collecteurs de raccordement du compresseur sont d'un
diamètre inférieur aux collecteurs généraux sur
lesquels ils sont raccordés.
Collecteur aspiration : Le collecteur
d'aspiration comporte entre les filtres et le raccordement du premier groupe,
dont le rôle est l'alimentation des compresseur avec le gaz pour le
comprime.
Collecteur refoulement : il collecte le gaz
comprime pour le conduire vers le conduit de refoulement.
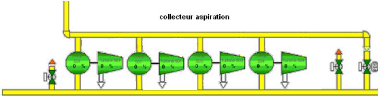
collecteur refoulement
18
Figure II.6 : collecteurs d'aspiration et de
refoulement.
19
Chapitre II : Présentation du centre de compression S
m'seka II.3.f. Tuyauterie d'aspiration et de refoulement des
compresseurs
Les compresseurs sont placés en parallèle : dans
ce cas, chaque compresseur fournit la hauteur manométrique totale de la
station. Les vannes principales sont définit pour chaque groupe de
compresseurs.
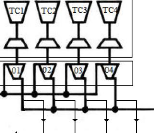
1
Recyclage
Refoulemet
<1
GR
Aspiration
GR dépar.
Groupe Turbines â gaz
Groupe compresseurs
Obi
By-pass
Figure II.7 : Schémas simplifié Groupe
compresseur.
-La vanne d'aspiration : est dotée d'un by-pass de
petit diamètre comportant une vanne avec servomoteur et une vanne amont
manuelle d'isolement pour entretien et d'un capteur de pression
différentielle. Ces éléments sont destinés à
la mise en gaz (évacuation de l'air pour un compresseur mis à
l'air à l'arrêt) et à la mise en pression de gaz du
compresseur avant démarrage.
Le capteur différentiel n'autorise l'ouverture de la
vanne d'aspiration que pour une différence de pression inférieure
à 2,5 bar.
-La vanne de refoulement : s'ouvre
après la vanne d'aspiration. En amont de cette vanne, un piquage de
petit diamètre muni d'une vanne à servomoteur et aboutissant
à un évent équipé d'un silencieux. Ce circuit est
destiné à mettre à l'air le compresseur.
-Vanne de recyclage: une vanne dite "de
recyclage" et une vanne de régulation étanche à la
fermeture dite "vanne anti pompage" sont montées sur un circuit
piqué en amont sur le circuit de refoulement et en aval sur le
collecteur général de recyclage de l'ensemble des groupes qui
revient sur le collecteur d'aspiration juste en aval des filtres (recyclage
long).
20
Chapitre II : Présentation du centre de compression S
m'seka
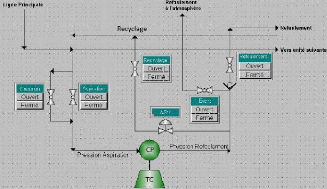
Ouvert I Fermé
Ouvert Fermé
YLI~ne Prin[ipale
Récyc age
lLefoul entent à · l'atmosphére
Refoulement
Vers unité suivante
Ouvert
..Fermé.
· Pression Refaulemen
Pression Aspiratian
Figure II.8 : Schématisation des Vannes
unité. II.3.g.Circuit de gaz auxiliaire
Sont appelés gaz auxiliaires les gaz
prélevés sur le gazoduc et conditionnés par un Skid de
traitement de gaz qui assure :
Leur filtration (détente et séparation)
La régulation de pression.
Le réchauffeur gaz combustible.
Le circuit de gaz auxiliaire comprend :
Skid de filtration et régulation de gaz.
Circuit de gaz combustible. Circuit de gaz de
démarrage.
Circuit de gaz secours.
Circuit gaz de motorisation des vannes.
II.4.DESCRIPTION GENERALE DES DIFFERENTES
STATIONS
II.4.a.Station GZ1 40"
Elle comprend :
04 Turbocompresseurs 02 Turbo alternateurs
01 Bâtiment pompe incendie
01 Réservoir d'eau anti-incendie 250m3.
01 Bâtiment technique administratif
02 Gares racleurs arrivée/ départ
21
Chapitre II : Présentation du centre de compression
S m'seka
06 Séparateurs à cyclone
01 Salle de contrôle
01 Bourbier
04 Aéroréfrigérant
01 Bâtiment MCC
01 Salle de batterie
01 Bâtiment des transformateurs
01 Réchauffeur gaz
II.4.b.Station GZ2 40"
Elle comprend :
03 Turbocompresseurs
- 01 Turbo alternateurs
- 02 Gares racleurs arrivée/ départ - 06
Séparateurs à cyclone
- 03 Aéroréfrigérant - 01 Réchauffeur
gaz - 01 Salle de batterie
II.4.c.Station GZ3 42"
Elle comprend :
04 Turbocompresseurs
01 Turbo alternateurs « RSTON » 01 Bâtiment pompe
incendie
01 Réservoir d'eau anti-incendie 250m3.
02 Gares racleurs arrivée/ départ
06 Séparateurs à cyclone
01 Salle de contrôle
01 Bourbier
04 Aéroréfrigérant
01 Bâtiment MCC
01 Salle de batterie
01 Réchauffeur gaz
II.4.d. Bâtiments des turboalternateurs GZ 1/2
L'énergie électrique est fournie par SONELGAZ (3
postes de Tr. De 30 KV) ou produite localement par des turboalternateurs, les
stations GZ 1/2 disposent de 03 groupes dont un en charge, les deux autres sont
en réserve, la puissance unitaire disponible est de l'ordre de 1000 KVA
.Chaque turboalternateur est constitué d'une turbine à gaz de
marque SOLAR de dimension réduite attelée à un
alternateur, le groupe fonctionne au gaz naturel.
22
Chapitre II : Présentation du centre de compression S
m'seka
Les trois turboalternateurs de marque SOLAR sont abrités
dans un local désigné (bâtiment TA) et servent à
l'alimentation des stations GZ 1/2 (éclairage bâtiment TC et TA),
du centre de commande des moteurs, la salle de contrôle, de la salle des
pompes, du bâtiment administratif et la base résidentielle.
II.4.c. Bâtiment des turboalternateurs GZ 3
La station GZ 3 est équipée de deux
turboalternateurs (Marque Ruston) délivrant individuellement une
puissance maximale de 1250 KVA, alimentés en GN, ces groupes fournissent
l'énergie électrique pour les besoins de la station, des
unités en phase d'arrêt et de démarrage, de la salle des
pompes et éclairage périphérique station. La station GZ 3
dispose d'une arrivée 30KV/380V.
II.5.DESCRIPTION DES EQUIPEMENTS DE LA STATION
II.5.a. Les vannes
Tous les sectionnements sur les lignes de gaz de
diamètre supérieur à 1" sont réalisés par
des vannes à boisseau sphérique. Toutes ces vannes à
boisseau sont à section de passage réduite à l'exception
les vannes à 2"de mise à l'évent des compresseurs.
Les deux positions Ouverte/Fermée sont en quadrature
(90°). Suivant les conditions de montage, les vannes sont à embout
soudé ou à brides ; montage de type joint annulaire à
l'exception de deux vannes sur lesquelles sont montées de part et
d'autre des brides à lunettes.
Pour la motorisation de ces vannes on distingue deux grands
types de vannes motorisées sur la station de différentes
dimensions:
Vannes GOV (Gas Operating Valve) tels que :
vannes mise à l'évent d'aspiration et de refoulement de
compresseur, vannes entrée / sortie des filtres,....etc.
Vannes MOV (Motor Operating Valve) tels que :
les vannes d'entrée et de sortie de la station de compression, vanne
by-pass de la station, vannes des gares arrivée et départ
racleurs, vannes de pressurisation.
1. Les Vannes GOV
Les vannes GOV fonctionnent par rotation d'un quart de tour
d'un boisseau sphérique à l'intérieur d'un corps d'acier
de forme cylindrique comportant des garnitures assurant
l'étanchéité de la vanne. La nature des sièges de
l'axe de rotation du boisseau permet de réduire les frottements
mécaniques d'où le couple de manoeuvre. Aucune lubrification de
vanne n'est nécessaire.
23
Chapitre II : Présentation du centre de compression S
m'seka
Motorisation : Les motorisations des vannes GOV
sont toutes de type hydropneumatique, de marque BIFFI :
- Fluide moteur : gaz.
- Fluide actionneur : huile.
- Fluide de contrôle local : gaz.
- Contrôle et signalisation à distance :
électrique.
Toutes les motorisations sont à commande pneumatique
locale, et avec renvoi électrique à
la salle de contrôle au moyen de contacts de fm de course,
sauf les vannes d'isolement des
filtres séparateurs.
2. Les Vannes MOV
Leurs motorisation est à commande locale et avec renvoi
électrique à la salle de contrôle. Ont les trouvent dans la
station représentés par les vannes d'entrée et de sortie
de la station de compression, vanne by-pass de la station, vannes des gares
arrivée et départ racleurs, vannes de pressurisation.
3. Les Vannes manuelles
Sur tous les circuits d'eau, les sectionnements sont
réalisés par des vannes à opercule. Les vannes
montées sur le circuit incendie sont des vannes à brides. Ces
vannes sont constituées d'un corps en fonte démontable avec joint
perpendiculaire à la tige de manoeuvre.
4. Les Vannes régulatrices
Pour les vannes régulatrices montées sur les
installations, la station possède les types :
- Vanne régulatrice de température type papillon
sur le Skid Combustible de GZ1.
- Vanne régulatrice de température à trois
voies sur les Skids Combustible de GZ2 et de
GZ3.
- Vannes autorégulatrices de pression sur les Skids
Combustible.
- Vanne régulatrice thermostatique d'huile lubrifiant au
niveau de la turbine.
- Vanne régulatrice de pression au distributeur des
paliers.
- Vanne compensateur de pression au niveau de la pompe
hydraulique principale.
- Vanne lubrifiant palier de la turbine de lancement.
- Vanne régulatrice pression/arrêt de gaz de la
turbine de lancement.
- Vanne de distributeur de paliers.
Chapitre II : Présentation du centre de compression S
m'seka
II.5.b. Les machines tournantes : 1. Les Pompes
Centrifuges
Tableau II.1 : Caractéristiques des
pompes centrifuges.
Type de pompe centrifuge
Caractéristiques
Pompe de lubrification auxiliaire TC
Type : entrainée par moteur
Debit :13501/min
Pression de refoulement : 6.3Kg/cm2
Pompe de lubrification de secours TC
Type : entrainée par moteur
Débit : 8001/min
Pompe a eau de refroidissemTC Pompe Jockey (réseau
anti-incendie)
Pression de refoulement : 1.4 kg/cm2
Caractéristique de moteur : 20CV,
3000tr/min, 50Hz triphasé.
Marque :KSB.
Débit : 120 m3/h
Puissance : 3.15 KW
Pompe principale électrique (réseau
anti-
· cendie)
Pompe diesel de secours (réseau
anti-incendie)
Marque : KSB.
Débit :120 m3/h
Puissance :46.2 KW
Marque : KSB.
Débit :120 m3/h
Puissance : 43.3KW
24
2. Les Pompes Volumétriques
Tableau II.2: Caractéristiques des pompes
volumétriques.
Type de pompe centrifuge
Caractéristiques
Pompe de lubrification principale TC
|
Type : entrainée par l'arbre solidaire de boite
d'engrenage.
Débit :13501/min
Pression de refoulement : 6.3Kg/cm 2~
|
imm
|
|
|
|
Pompe d'alimentation en huile hydraulique TC
Pompes principales d'huile
d'étanchéité Compresseurs.
|
Type : entrainée par l'arbre solidaire de boite
d'engrenage.
Débit : 0-62.51/min
Pression de refoulement : 80 k /cm2 Marque :
IMO
Débit : 105 1/h
Pression d'aspiration :1.75 Kg/cm3 Pression de
refoulement :74 Kg/cm3 Caractéristiques moteur :AEG DAM 180M,
2945 tr/min, 380V, 50Hz.
|
Chapitre II : Présentation du centre de compression S
m'seka
3.Les Compresseurs
Les Compresseurs axiaux
Tableau II.3 : Caractéristiques des
compresseurs axiaux.
Type de compresseurs axiaux
|
Caractéristiques
|
Compresseur d'air turbine GE
|
Nombre d'étage :15. Joint du corps :horizontal Ailettes de
guidage : fixe, grande capacité. Vitesse : 7100 tr/min.
|
Compresseurs d'air Solar
|
Nombre d'étage : 8.
|
Les Compresseurs centrifuges :
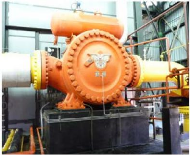
r
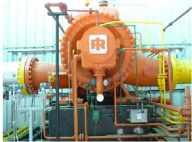
25
Figure II.9 : Compresseurs Cooper Bessemer
& Ingersoll Rand.
26
Chapitre II : Présentation du centre de compression S
m'seka Tableau II.4 : Caractéristiques des
compresseurs centrifuges.
Type de compresseurs centrifuge
|
Caractéristiques
|
Compresseur de gaz Cooper Bessemer
|
Nombre d'étage :01.
|
GZ2 et GZ3.
|
Rotation : sens horaire
|
|
Joint du corps :Vertical, O'Ring.
|
|
Utilisation : Trasport du gaz naturel.
|
|
Huile de lubrification : Torba 33 SH.
|
|
Puissance nominale :7.457 KW.
|
|
Volume d'entrée :12.20 m3/h
|
|
Vitesse nominale : 6500 tr/min.
ler vitesse critique : aucune dans la gamme de
service.
|
|
Régime continu maximal :6825 tr/min.
|
|
Pression de refoulement maximale théorique : 84.4
kg/cm2.
|
|
Pression d'entrée : 53.7Kg/cm2
|
|
Température d'entrée : 49°C
|
|
Pression d'aspiration de service :84.81
|
|
Kg/cm2
|
|
Température d'aspiration de service :45.62
|
|
°C.
|
|
Pression de refoulement de service : 69.3 bar.
|
|
Température de refoulement de service :
|
|
78.18 °C
|
|
Température de sortie permise : 87°C
|
|
Garniture d'étanchéité : Hydraulique,
Mécanique.
|
Compresseur de gaz Ingersoll-Rand GZ1
|
Nombre d'étage : 01.
|
|
Rotation sens horaire vers le flasque.
|
|
Joint de corps : Horizontal.
|
|
Utilisation : Transport de gaz.
|
|
Hiole de lubrification : Torba 33 SH.
|
|
Volume d'entrée :212.4m3/min.
|
|
Régime nominal · 6500tr/min.
|
|
Pression de refoulement maximale théorique :85.33
Kg/cm2.
|
|
Pression d'entrée : 53.1 Kg/cm2.
|
|
Température d'entrée : 50.9°C.
|
|
Pression d'aspiration de service : 48.81 bars.
|
|
Température d'aspiration de service :45.62°C.
|
|
Pression de refoulement de service : 69.3 bars
|
|
Température de refoulement de service :
|
|
78.18 °C.
|
|
Température de sortie permise :93.33 °C.
|
|
Garniture d'étanchéité : Hydraulique,
Mécanique.
|
Chapitre II : Présentation du centre de compression S
m'seka
3.Les Turbines à gaz15
Tableau II.5 : Caractéristiques des
turbines à gaz.
Type de turbine à gaz
|
Caractéristiques
|
Turbine de production (Heavy-Duty).
|
Caractéristiques de construction :
|
|
Série : MS-3002.
|
|
Type : entrainement mécanique.
|
|
Cycle : simple.
|
|
Nombre d'arbre :02.
|
|
Sens de rotation : sens trigonométrique.
|
|
Données nominales sur la plaque des turbines:
|
|
Puissance nominale · 11 700 CV.
|
|
Température d'admission : 35 °C.
|
|
Température d'échappement : 541°C.
|
|
Pression d'admission : 0.9645 Kg/cm2.
|
|
Pression d'échappement : 0.9786 Kg/cm2.
|
|
Caractéristiques maximales :
|
|
Puissance maxi : 15 200 CV.
|
|
Altitude : 526 m.
|
|
Température d'admission : -10 °C.
|
|
Turbine :
|
|
Nombre d'étage :02 séparé
mécaniquement.
|
|
Joint de corps :Horizontal.
|
|
Vitesse sous charge : 6500 tr/min.
|
|
Vitesse de d déclanchement électrique 2'
étage : 7150 tr/min.
|
|
Poids approximatif :
|
|
Turbine à gaz : 21 650 Kg.
|
|
Socle de turbine et tuyauterie : 22 250 Kg.
|
|
Appareillage de démarrage et accessoires :
|
|
7 580 Kg.
|
AIR COMPRIME
ECHAPPEMENT
SYSTEME DE COMBUSTION
GAZ CHAUDS

COMBUSTIBLE
TURBINE HAUTE PRESSION
TURBINE BASSE PRESSION
|
|
J CHARGE
|
|
|
|
|
|
COMPRESSEUR
4
ADMISSION D'AIR
27
Figure II.10 : Schémas simplifié
des principaux organes d'une turbine à gaz.
28
Chapitre II : Présentation du centre de compression S
m'seka
Système de lancement
Comme toute machine à combustion interne, une turbine
à gaz ne peut pas produire de couple à vitesse nulle, un
dispositif de lancement doit être employé pour lancer la turbine
pour ça mise en route.
Un dispositif de lancement doit remplir trois fonctions :
Fournir un couple élevé à vitesse nulle pour
effectuer le décollage de la turbine. Entrainer la turbine pas encore
allumée jusqu'à une vitesse acceptable pour effectuer
l'allumage.
Aider la turbine déjà allumée à
atteindre la vitesse autonome, apres quoi la dispositif de lancement est
débrayé de la turbine à gaz.
Le système de démarrage pneumatique utilise gaz
naturel et pour fournir la puissance de démarrage à la
turbine.
Système de gaz combustible
Le système de gaz combustible, avec le système
de commande électrique et le système d'huile de commande de la
turbine programment automatiquement le carburant pendant
l'accélération, et modulent le débit du carburant pendant
le fonctionnement. Le système assure également l'arrêt
automatique en cas de défaillance d'un composant de carburant.
Le système de gaz combustible requiert une alimentation
constante en débit de gaz, et dans une plage de pressions
spécifiées sur le schéma d'installation mécanique.
Une partie de l'alimentation du gaz carburant est utilisée pour activer
les vannes pilotes du système.
Système de lubrification
Le système d'huile de lubrification utilise une pompe
à huile de pré-/post-lubrification pour la lubrification avant et
pendant le cycle de démarrage et après la séquence
d'arrêt. Le système utilise une pompe principale
entraînée par turbine pour la lubrification après que la
turbine ait atteint sa vitesse adéquate.
La vanne régulatrice de température achemine
l'huile à travers le réfrigérant d'huile ou autour du
réfrigérant d'huile selon la température de l'huile. Le
manifold d'huile achemine l'huile au carter de la prise d'entraînement
des accessoires, aux paliers de la turbine et à l'équipement
entraîné.
29
Chapitre II : Présentation du centre de compression S
m'seka
Aero-réfrigérants
Le système d'eau de refroidissement est un système
de distribution au circuit fermé conçu pour satisfaire à
l'exigence de transfert de chaleur du système de lubrification.
Les aéro-réfrigérants consistent chacun en
un échangeur de chaleur eau-air avec faisceau tubulaire, pour maintenir
la température d'huile à un niveau n'excédant pas le seuil
de dégradation.
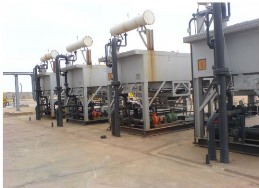
Figure II.11: Les
aéro-réfrigérants d'huile de lubrification.
Unité réductrice de vitesse
Un engrenage réducteur de vitesse est installé
pour réduire la vitesse de sortie de la turbine à niveau
acceptable pour entraîner la pompe de lubrification principale.
Le système électrique
Pour une station équipée de groupes
turbocompresseurs, l'ensemble de l'appareillage est installé dans le
local contrôle&commande MCC (Motor Command Centre).
II.5.LES PARAMETRES A SURVEILLER
II.5.a. Les Paramètres à surveiller en Salle
de contrôle
Le prélèvement des paramètres à
contrôler des machines se fait chaque heure.
Paramètres Station :
Pression d'aspiration.
Pression de refoulement.
T° d'aspiration.
T° de refoulement.
30
Chapitre II : Présentation du centre de compression S
m'seka
Paramètres Turbine
% HP.
% BP.
Angle de directrice.
Pression de Ref. compresseur.
T° Ref. compresseur.
AT° turbine avant ler étage.
AT° turbine arrière ler étage.
AT° turbine avant 2ème étage.
AT° turbine arrière 2ème étage.
T° Moyenne d'échappement.
Vibrations HP.
Vibrations BP.
Pression Gaz combustible.
Paramètres Compresseur
T° Palier N° 1.
T° Palier N° 2.
T° Palier Butée.
% Recyclage.
II.5.b. Les Différents Systèmes de Protection
de la machine
- Protection des arbres tournants et engrenages par des
caches.
- Protection contre haute température 90°C.
- Protection contre la haute température chambre de
combustion par limitation de vitesse.
- Protection contre les vibrations seuils alarme critique.
- Protection contre les pressions d'air d'admission.
- Protection de survitesse de turbine de lancement 4600tr/min.
- Protection de survitesse de turbine 7950tr/min.
- Protection contre la haute T° échappement.
- Détection gaz de la machine seuil préalarme 25%
LIE, 40% LSE.
- Détection incendie de la machine.
Joint d'étanchéité sur l'arbre du
compresseur : le point où l'arbre passe à travers le
corps du compresseur, un joint d'étanchéité est
prévu pour empêcher les fuites du gaz haute pression contenu dans
le corps. Ce joint est du type hydraulique -- mécanique,
c'est-à-dire que l'écoulement de gaz à travers un espace
annulaire étroit autour de l'arbre est empêché par le
débit d'huile à une pression plus élevée. Le joint
d'étanchéité comprend trois parties :
- L'arbre.
- La bague d'étanchéité
intérieure.
- Les bagues d'étanchéité
extérieures.
31
Chapitre II : Présentation du centre de compression S
m'seka II.5.c.Les Différents systèmes de
sécurité et de protection de la station
- Collecteur d'évent pour la mise hors gaz de la
station.
- Dispositif de fin de course de fermeture ou d'ouverture des
vannes.
- Arrêt d'urgence station USD : automatique ou manuel.
- Protection contre la T° sortie (Refoulement 80°C).
- Protection contre la haute pression sortie 71,5 bar (soupapes
de décharge).
- Protection contre la foudre des installations suivantes :
Bâtiment turbocompresseur.
Bâtiment turboalternateur.
Bâtiment technico-administratif.
Bâtiment motopompes anti-incendie.
Bâtiment contrôle.
Bac de réserve d'eau.
- Protection cathodique de la tuyauterie.
- Protection de mise à la terre de toutes les
installations.
1.Le Système d'arrêt d'urgence "Emergency
Shoot Down
La mise en condition de sécurité s'effectue au
moyen de vannes dont les motorisations des vannes sont munies d'un dispositif
« Line Beark » (rupture de conduite). Le système d'arrêt
d'urgence se compose de deux sous systèmes :
-Sous-système d'arrêt pneumatique (circuit gaz
sécurité).
-Sous système d'arrêt électropneumatique
(circuit électrique aboutissant sur le solénoïde d'une
électrovanne dans le circuit gaz sécurité).
L'ESD de la station est prévu pour fermer rapidement la
station et pour éventer toute la tuyauterie en cas d'urgence, pour
éviter une explosion, ou un incendie majeur.
Causes de déclenchement : le
système ne peut être déclenché automatiquement que
dans les cas suivant :
-un opérateur qui déclenche le système si il
`y a lieu (vannes d'évent pilote). -perte de pression du gaz de
commende, ou gazoduc.
-les systèmes de détection d'incendie des
bâtiments basse tension, compresseurs. -perte de l'alimentation de
commande 125 Vcc.
2. La protection cathodique :
La protection cathodique de la station contente de la
protection passive des collecteurs bien protégés par leur
enrobage. Si le sol est peu résistif, on met tous les collecteurs sous
protection cathodique. Cette protection est dite "globale". Tous les
éléments enterrés de la station sont mis sous tension.
32
Chapitre II : Présentation du centre de compression S
m'seka
II.5. Conclusion
Dans ce chapitre nous avons défini une station de
compression parmi les cinq stations installés sur la région du
transport Ouest de l'activité TRC (Transport par canalisation Ouest).
Nous avons montré les deux aspects structurel et
fonctionnel de la station de compression S M'seka. La station S M'seka a
été le siège de notre stage d'induction 24 mois.
Une collecte bibliographique riche a été
analysée pour résumer ce chapitre.
Chapitre III
LES COMPRESSEURS
CENTRIFUGES
33
Chapitre III : Les compresseurs centrifuges
III.1.INTRODUCTION
Les compresseurs sont des machines réceptrices, qui
transforment l'énergie mécanique fournie par le moteur
d'entraînement en énergie de pression. Ils sont
considérés les plus répondus dans l'industrie
pétrolière et pétrochimique, et sont largement
utilisés dans les systèmes : automatique; pneumatique et surtout
dans les stations de compression (expédition
et injection des gaz), etc
Le rôle des compresseurs est primordial dans le domaine
d'activité industrielle, ils accélèrent les cycles de
production.
Dans toutes les branches de l'industrie
pétrolière, on utilise les compresseurs grâce à la
simplicité de leur construction et à la facilité de leur
exploitation [14].
III.2.DESCRIPTION DES COMPRESSEURS INDUSTRIELS
Les compresseurs sont des équipements mécaniques
permettant d'élever la pression d'un gaz. Les applications des
compresseurs sont très diversifiées.
III.2.1.Les catégories principales des
compresseurs
On peut diviser les compresseurs en quatre catégories
principales, qui seront détaillées dans les chapitres suivants: [
14]
· Alternatif (volumétrique)
· Rotatif (volumétrique)
· Centrifuge
· Axial
Il s'agit de : compresseur volumétriques, dans cette
famille de machine on distingue ; Les compresseur volumétriques
alternatif à piston, à membranes. Les compresseurs
volumétriques rotatifs à palettes, à vis, à lobes,
et spirales.
34
Chapitre III : Les compresseurs centrifuges
Compresseurs volumétriques
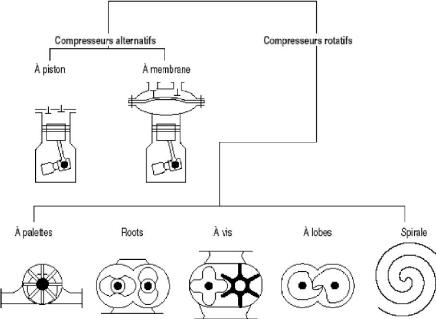
Avis
Roots
Spirale
A lobes
 palettes
Compresseurs alternatifs Compresseurs rotatifs.
A membrane
C
A piston
Figure III.1 : Catégorie des
compresseurs volumétriques.
Et de compresseurs dynamiques, dans cette famille de machine on
distingue ;
· Les compresseur centrifuge, un seul étage, et
multi étages
· Les compresseurs axiaux à ailettes.
Chapitre III : Les compresseurs centrifuges
Compresseurs dynamiques
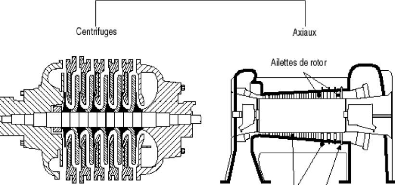
Axiaux
Ailettes de rotor
WIN
nuu11111111n.1111ia
Centrifuges
""r
11111111111111MMM,
A,i lettes Ailettes
siatoriques staioriques
orientables
Figure III.2: Types des compresseurs
dynamiques.3
III.2.1.LES DIFFERENTES APPLICATIONS
Le choix d'un compresseur alternatif ou centrifuge sera
tributaire des débits et pressions que l'on souhaite obtenir. D'autres
paramètres seront à prendre en compte pour le choix final
(taille, poids, prix, etc...).
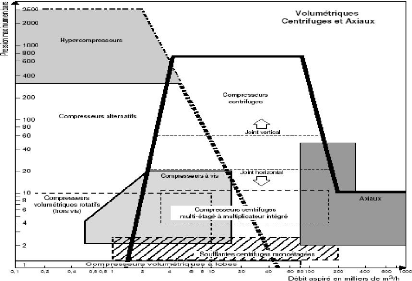
- 100
- 90
- 60
- 40
Compresseurs alternatifs
o o r irO
2CO
x
É - 2000 1
_ i
, HypFrcxnpreaa aura
- 1000 ;
r_ - 900 1
- COO
- 400
- 200
Valu métrique s Centrifuges et Axiaux
Corrprcaaeur3 centrifugea
rt
Joint
Yr
orlaonlaI
4an $ presseurs vis
10 - -
- 9 Compresseurs
- .+olurnéüigJes rotalils
s (hors vis)
r ~
À
JJ Sorllllanles rzclihrfil s
11101104aCi f
FJ~ L L L~CiGJJ~ l
le l L L LJ~fJ~
Csaillyisa z=z=saurea vola.rirrdkriy uee âbeu r
i
, 1 2 9 9 a 10 20 90 d0 an1W
Clbbit aspiré en millie:rs de m.R1
- 20
Ami aux
Figure III.3: Domaines d'application des
compresseurs (pression en fonction du débit).
1i
R
I r +
I C ·arnprc- aura centrifugea
I
i rnul ti-61sgé ·è mulhplira6eur
n6égrQ
L r- i
35
Chapitre III : Les compresseurs centrifuges
III.3. LES COMPRESSEURS CENTRIFUGES
Ce sont des machines dans lesquelles l'échange
d'énergie a lieu entre un rotor muni d'aubages tournant autour d'un axe
et un fluide en écoulement permanent [2].
Un compresseur centrifuge est un dispositif de compression
dynamique qui utilise la force centrifuge pour augmenter la pression du gaz
d'un point à un autre.
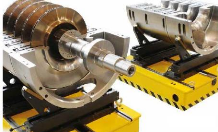
Figure III.4 : Compresseur centrifuge multi
étage à joint horizontal. III.3.1.
Caractéristiques de construction des compresseurs
centrifuges
Examinons maintenant les diverses composants du compresseur
centrifuge constitué par [2]:
somme I Compression centrifuge
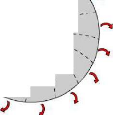

k
941
·

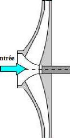
36
Ecoulement perpendiculaire du fluide
Figure III.5 : Une roue à aubage
tournant sur son axe d'un compresseur centrifuge.
37
Chapitre III : Les compresseurs centrifuges
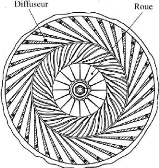
Figure III.6: Un distributeur dans l'axe de la
roue.
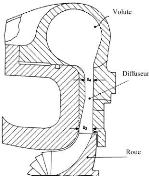
Figure III.7: Un collecteur de section
croissante, en forme de spirale (volute).
Le gaz arrive dans l'axe de l'appareil par le distributeur et
ensuite la force centrifuge, générée par la rotation de la
roue à aubes, le projette vers l'extérieur de la roue. Il
acquiert une grande énergie cinétique qui se transforme en
énergie de pression dans la volute où la section est
croissante.
A l'entrée et la sortie de chaque roue le gaz est
guidé par des pièces du stator qui sont constitué de
[2]:
Le canal d'entrée du gaz de la bride d'aspiration
à l'entrée de la première roue ; Le diffuseur à la
sortie dans le diffuseur se produit une augmentation de pression de gaz par
ralentissement ; due à l'augmentation de section.
Le canal de retour qui guide le fluide a la sortie du
diffuseur et l'amène à l'entrée de la roue suivante La
volute d'évacuation du gaz vers la bride de refoulement.
38
Chapitre III : Les compresseurs centrifuges
refoulement
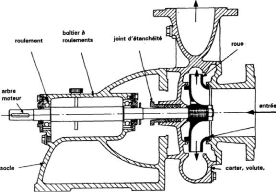
baitier roulements
joint d'éteneMité
Figure III.8: Schéma de circuit du
gaz.
III.3.2. Utilisation des compresseurs centrifuges dans les
domaines industriels6
Le compresseur centrifuge trouve beaucoup d'applications dans de
nombreux secteurs de l'industrie, où les procédés
demandent des gammes de travail très larges [2].
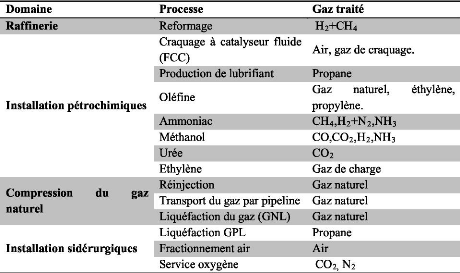
Processe
Domaine
Gaz traité
u
Raffinerie
H2+CH4
Reformage
Air, gaz de craquage.
Craquage à catalyseur fluide (FCC)
Propane
Production de lubrifiant
Gaz naturel, éthylène,
propylène.
Oléfine
Installation pétrochimiques
cll4,llim
Ammoniac
Méthanol
CO,CO2,H2,NH3
CO
Urée
Compression du gaz
naturel
Installation sidérurgiques
Ethylène
Réinjection
Transport du gaz par pipeline
Liquéfaction GPL
Service oxygène
Gaz de charge Gaz naturel Gaz naturel Gaz naturel Propane
CO2, N2
Fractionnement air
Air
Tableau III.1 : L'utilisation des compresseurs
centrifuge dans le domaine industriel.
39
Chapitre III : Les compresseurs centrifuges
III.3.3. Calcul des performances d'un compresseur
Le fonctionnement des compresseurs est accompagné de
certaines pertes de l'énergie fournie par la machine motrice [13].
Ces pertes changent considérablement les
caractéristiques théoriques, elles ne peuvent pas être
calculées avec précision suffisante pour tracer les
caractéristiques réelles.
C'est pourquoi les caractéristiques sont obtenues
expérimentalement à la suite des essaies du compresseur.
Les caractéristiques principales sont :
· La hauteur en fonction du débit : H=F (Q).
· La puissance en fonction du débit : N=F (Q).
· Le rendement en fonction du débit : 1=F (Q).
Les caractéristiques du compresseur ont une
particularité qui les différent des caractéristiques des
pompes. Cette particularité est une zone instable appelée zone de
pompage limitée par un point critique dit limite de pompage.
H(m)_ N(K',1i.
·
Limite. de
Pompage



e
Figure III.9: Courbes de performance typique
d'un compresseur centrifuge.
40
Chapitre III : Les compresseurs centrifuges
III.3.1.a.Taux de compression
Le taux de compression est le rapport entre les pressions
absolues du gaz au refoulement et à l'aspiration. = pression absolue de
refoulement / pression absolue d'aspiration.
III.3.1.b. Hauteur de compression
L'énergie transmise par le compresseur à chaque
kg de gaz qui le traverse est appelée hauteur effective (mesurée
en kg.m/kg ou bien en mètre).
Supposons qu'il n'y pas d'échange de chaleur
considérable entre le compresseur et l'extérieur, la hauteur
minimale nécessaire pour atteindre le taux de compression adiabatique
s'appelle hauteur adiabatique (dit également isentropique) est une
compression idéale sans échange de chaleur entre le gaz et
l'extérieur.
En générale il est impossible d'obtenir une
compression adiabatique, par conséquent il faut fournir au gaz une
hauteur effective supérieure à la hauteur adiabatique.
III.3.1.c. Rendement adiabatique
C'est le rapport entre la hauteur adiabatique et la hauteur
effective fournie au gaz. read = Had / Heff
La valeur du rendement adiabatique est en fonction du type de
roues et des conditions du gaz.
La hauteur adiabatique nécessaire pour fournir un taux
de compression donné dépend du gaz utilisé ainsi que des
conditions de pression et de température à l'aspiration de
celui-ci. En particulier, en ce qui concerne les gaz parfait, la hauteur
adiabatique dépend uniquement de la température absolue et du
poids moléculaire du gaz, et plus précisément elle est
d'autant plus élevée quand la température augmente et
diminue en fonction de l'accroissement du poids moléculaire
(évidemment elle est plus élevée quand le taux de
compression est important).
III.3.1.d. Puissance absorbée par le
compresseur
La disponibilité des diagrammes fournis par le
constructeur indique pour un nombre déterminé de valeurs du
régime de rotation N, la hauteur H (polytropique ou adiabatique) et nous
permet de déterminer le travail réel spécifique W1-2 .
Le travail réel ou hauteur réelle Heff est
donné par la relation : W1-2 --
Hpol ipol '
|
wp ipoil et Heff
|
|
Une fois le travail est connu, W1-2 est possible de
déterminer la puissance totale requise par la compression, par la
relation suivante:
41
Chapitre III : Les compresseurs centrifuges
Pa = Qm W1-2 + Pertes.
Pa = Qm (Wpol / ipol) + Pertes.
Pa = Qm (Wpol / ipol) + Pfd + Pig .
Où : Qm: est le débit massique
Pfd : la puissance perdue en raison des fuites.
Pig : la puissance des pertes mécaniques.
III.4.REPRESENTATION ET DONNEES DES COMPRESSEURS
Nous décrirons dans ce chapitre comment est
représentée un processe, sur les principaux
documents mis À la disposition de l'exploitant [2]:
· Plan de circulation des fluides (PCF / PFD)
· Piping and Instrumentation Diagram (P&ID)
III.4.1.PLAN DE CIRCULATION DES FLUIDES (PCF / PFD)
Plan de circulation des Fluides (PCF/PFD) : ce document,
édité lors de la phase projet, présenté sous format
simplifié, les principales lignes et capacités process ainsi que
leurs paramètres de fonctionnement principaux.
Chapitre III : Les compresseurs centrifuges
III.4.1.a. Exemple d'un process de compression de
gaz: deux compresseurs en série avec deux séparateurs de
condensat.
EC 501 OS 501 GX 501 A/B KX 501 EC 502 OS 502 KX
502
15T STACE 1ST STACE IST STACE SCROBSER 1ST STAGE 2N0 STAGE 21(1
STAGE 2ND STAGE
CONDENSER GAS SCRUBBER CDNDENSATE PBNPS GAS COMPRESSER CONDENSER
GAS SCRUBBER CAS COMPRESSOR 2 . IBBY
s ·
f: 0o N AI
NOTE 1

1B
w · ' T7
2zzzZEZZ21
3
7.6 w1
~B'ôô o7centsI)
r NEDraE
A T1-SWGE '..
NOTE 1
B ·
Ir RECYCLE
Axil-SMGE
RECYCLE
ANTI-SURCE SYSTEMe..
TCYCLE ANT1-SLNCE SYSTEM
PF1) LIA MM
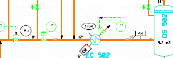
6
---
Mn 2

KX 502
KX 501
Gx 501 A/B
42
T
Figure III.10 : PFD du process de
compression.
Chapitre III : Les compresseurs centrifuges
III.4.2.PIPING & INSTRUMENTATION DIAGRAM (PID)
Ce document édité lors de la phase projet,
présente sous format beaucoup plus complexe que le PFD, toutes les
lignes conduites et capacités process ainsi que tous leurs
paramètres de fonctionnement et instrumentation.
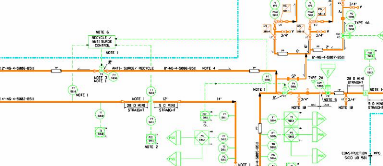
MIE
*KITE I
I4-410-5-58/24511
NOIE 1 4J ]2
NOIE 6
ECxSLE E-- i
-- -- LONTIOL , 1
1~ I
17-NG- -58~6-8511 i ` t, ri- ROSE/ RECYCLE
8.-N0--5841E-8511 rg,E
1.a
8'-FS-1-SM2S511
PIO~~P~éé 55
~~p'S°e asn
/'-1G-45///-E511
5ONN1 STRAIGHT
CONSTRJCTION NNE
SKID s 501
NOTE 1
SOMINI SIRAIEMI
2B8MNI
971.1"G.::
l J

IONT.V110, J 1--IR-5.833/4"
Ce3
SEPA11, IOx NITROGEN MEAL .5 SECON.RY VENT.
A.- Av-A-5081-6511
3,c-Av-s-500A-0511
NOTE I1
IA
NOTE ]
6W 6... 3/B. 1 e
M. /4 EL.1225/1 IP-AY-4-5//3$511
EL:122400
I
I LLYE OIL SEAL GS
~iô â e9icentsLR 7'"ON-/-9IN-9061 10
51dbIL-E [[L ENS I LUEliox OI
I OIL
IcaaENS KX 5I
KA é°cISKâ2 P°18
3-CN-/-941E-SI
I
I
2-E5-4-5093.9511
FPI
1.-AV-4-51312.135U
3210 ~2° C+5
·
RF
(13
SEAL LAS L.E SEAL ENS
IV T1' OIL wax VE il VExT NIIRD[EN
FOR CONTINUATION SEE PID-AA-0504
|
|
|
|
|
|
|
|
|
|
2-DE-4-5082.S511
|
|
|
|
|
|
|
|
|
|
|
|
|
UNIE BAN
|
|
|
|
|
|
|
|
|
|
|
|
|
1_651
|
|
ô0/°
150 · ® \
1 1 2-F5-4-0U12-0511I w/ AA ae5 L FLm€ kp DA.
|
|
|
€L. 109000 I ~ ·~~~
|
|
|
|
|
|
|
|
|
|
|
|
|
|
|
|
|
|
43
Figure III.11: PID du process de
compression.
III.5.LES AUXILIAIRES DU COMPRESSEUR CENTRIFUGE
III.5.1. La fonction des auxiliaires : est
d'assurer le fonctionnement correct du compresseur dans toute la plage de
caractéristiques exigée par le procédé.
L'appareillage avertira l'opérateur de l'approche des zones de pompage
et de surcharge de la machine et, le cas échéant, mettra en
service les auxiliaires d'anti-pompage ou de limitation de vitesse
correspondant, le démarrage du groupe sans incidence néfaste sur
l'état mécanique de ses composants : compresseur, machine
d'entraînement, accouplement, multiplicateur..., [2]
III.5.2. L'arrêt d'urgence :
signalisation, ralentissement et isolement du compresseur. La fonction
principale des alarmes est de réaliser à temps les
opérations de correction d'anomalies de fonctionnement, de
réglage et d'entretien courant sans arrêter la machine.
44
Chapitre III : Les compresseurs centrifuges
Parmi ces diverses fonctions, le système d'anti-pompage
est une sécurité importante pour la protection du compresseur.
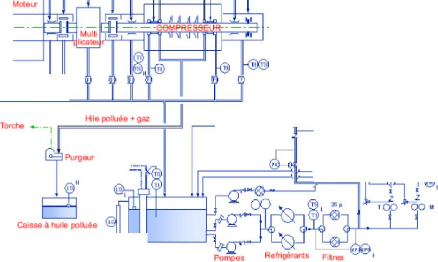
Nine L1-ril.5i14.;11

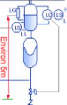
'1I t)ri fic.a non
1'?
i
Pompes
V
Ligne de feférence loref,siari gato
7 cg1I TZ
'Anne secours r
LL
ai
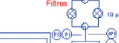
111
GAK@H huiI
Figure III.12 : Schémas typique d'une installation du
système de control de lubrification
et d'étanchéité à huile.12
III.5.3.La lubrification
Le fonctionnement des paliers et butées est
subordonné au caractère "hydrodynamique" c'est-à-dire
à l'établissement et à la stabilité du « coin
» d'huile.
Coin d'huile : C'est la très fine couche d'huile qui se
trouve entre deux pièces, qui lorsqu'elles sont mises en mouvement
permet d'éviter un frottement direct entre les pièces
La pression de lubrification n'aide en rien à la
formation de ce coin d'huile, elle n'intervient qu'au niveau du remplissage et
du débit qui lui-même conditionne la température du palier
et par là même la viscosité de l'huile dans le palier et la
butée.
Le maintien d'une température convenable de l'huile est
assuré par le réchauffeur de caisse à huile (trop froide
l'huile est trop visqueuse) et par les réfrigérants (huile trop
chaude inutilisable) installés sur le circuit. Ils assurent
l'enlèvement des calories apportées: par les
Chapitre III : Les compresseurs centrifuges
1x
Zone de fonctionnement interdite
sections pleines de l'arbre (en particulier côté
refoulement), par le fonctionnement propre des paliers et butées.
La viscosité de l'huile nécessaire au bon
fonctionnement du palier déterminera la qualité du lubrifiant
choisi en fonction des paramètres de la machine : vitesse de rotation,
poids du rotor, charge spécifique, type du palier, température de
fonctionnement en charge de la machine, matériau constitutif du rotor,
etc.
III.5.4.Anti pompage ou 'anti surge'
Le pompage est un phénomène très violent
qui met en jeu toute la masse de gaz présente dans la machine [2].
Le gaz ne traverse plus la machine
régulièrement mais subit des mouvements alternatifs dans une
partie ou dans la totalité du compresseur
Il s'accompagne :
· De vibrations des aubages des roues.
· D'inversion des poussées axiales du rotor.
· De vibrations de très basse fréquence de
l'ensemble du compresseur (Grondements sourds) qui sont bien sûr
extrêmement préjudiciables à la bonne tenue
mécanique de la machine.
Le phénomène de pompage apparaît dans des
zones de fonctionnement aux bas débits. Il est donc possible de mettre
en évidence dans un diagramme taux de compression-débit une zone
de fonctionnement interdite limité par une courbe appelée courbe
limite de pompage.
Courbe limite de &- pom page
|
N ' Vitesse ce rotation
N2
|
|
45
Ni
Debit masse
Figure III.13: Illustration de la courbe de
pompage d'un compresseur centrifuge typique.
En pratique si le débit nécessité par le
procédé devient inférieur au débit limite de
pompage, une régulation anti-pompage semblable à celle
présentée dans la courbe ci-dessus permet d'assurer un
débit dans le compresseur suffisant pour qu'il fonctionne dans une
zone
Chapitre III : Les compresseurs centrifuges
stable : l'excédent de gaz qui traverse la machine
étant réfrigéré et recyclé à
l'aspiration ou mis à l'atmosphère dans le cas de compresseur
d'air.
FLOW PRESSURE
TRANSMITTER TRANSMITTER

-III
PRESSURE TRANSMITTER
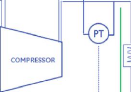
L_______
|
|
ANTI$uRGe CO NTROL
|
|
|
|
|
|
|
|
|
æ
46
ANTISURGEVALhVE
Figure III.14: Illustration d'un schéma
d'installation d'un système anti pompage. III.5.5.Protection
contre les vibrations
La Protection contre les vibrations est
généralement assurée par les capteurs de vibration :
radial et axial qui transmettent les signaux au système de protection de
la machine réglé par les points de consigne indiqués dans
le manuel d'instruction du fournisseur.
Dans le cas d'une bonne conception, le compresseur va
très peu vibrer et le rendement sera maximal. Et durant l'exploitation,
des perturbations vont apparaître dues principalement aux
[8]:
· Fondations
· Déformations des pièces
· Désalignement
· Usure des paliers
· Jeux entre éléments
47
Chapitre III : Les compresseurs centrifuges
III.5.Conclusion
Ce chapitre a été consacré à
l'introduction et définition des différentes catégories de
compresseurs à application industriel ainsi leurs calcul de
performance.
Nous avons donné un aperçu sur les
systèmes de protections, régulation et d'exploitation des
compresseurs centrifuges.
Chapitre IV
LA TECHNOLOGIE
DES SYSTEMES
D'ETANCHEITE
Chapitre IV : Technologies des systèmes
d'étanchéité des machines tournantes
IV.1. INTRODUCTION
Le rôle d'une étanchéité c'est
d'empêcher une fuite de fluide de l'intérieur vers
l'extérieure ou d'empêcher un contaminant extérieur
d'entrer à l'intérieure d'un équipement.
Nous aborderons dans ce chapitre principalement les
étanchéités dynamiques avec les garnitures
mécaniques et les presses étoupes.
Et puis, nous présentons une méthode de calcul des
garnitures mécaniques.
IV.2.LES PRINCIPALES CATEGORIES
ETANCHEITE GENERALE
STATIQUE
DYNAMIQUE
48
|
LINEAIRE ALTERNATIF ROTATIF OU OSCILLANTE
|
|
|
|
|
Joint talque
Joints â section carré ou
pièces moulées
Joint métallique
Joint fibres
Joints plats Joints spiralés
Pièces d'étanchéité otiques
|
Garniture chevron muid levres
Joint composites Joints racleurs
Tresse de bourrage presse étoupe
Segments de compresseurs
Joint
d'amortissement
|
Bagues à lèvres
Joint à contact axial
Joints rotatif
Garniture mécanique
Tresses de presse étoupe
|
Figure IV.1 : Catégorie du
différent système d'étanchéités.
49
Chapitre IV : Technologies des systèmes
d'étanchéité des machines tournantes
IV.2.3.Les presse-étoupes (ou
étanchéité à contact)
IV.2.3.a. Les joints toriques
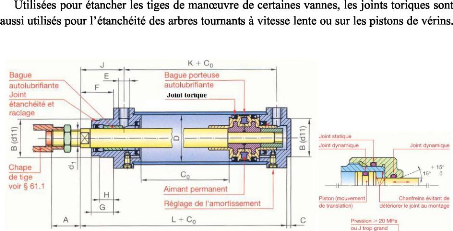
autolubrifiante Joint étanchéité et
raclage
E
Bague
Joint dynamique
Utilisées pour étancher les tiges de manoeuvre
de certaines vannes, les joints toriques sont aussi utilisés pour
l'étanchéité des arbres tournants à vitesse lente
ou sur les pistons de vérins.
K + Co
Joint torique
Joint statique Joint dynamique
Co Aimant permanent
Réglage de l'amortissement
L + Co
Chanfreins évitant de
détériorer le joint au montage
Pression - 2G MPa
ou J trop grand 1
Chape de tige voir § 61.1
A
Piston (mouvemen de translation)
Bague porteuse autolubrifiante
Figure IV.2 : Figue d'un vérin et
emplacement des joints toriques. IV.2.3.b. Les joints
tressés
Ils ont une grande résistance, durabilité et
imperméabilité dans tous milieux de fluide dur, vapeurs, eau
chaude jusqu'à 500° C, acide organique, sels et huiles
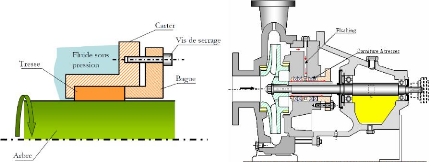
Carter
lus
Fluide sous --
pression
-n ·-
Arbre
Garniture à tresses
Figure IV.3: Joint à tresse sur une
pompe.
50
Chapitre IV : Technologies des systèmes
d'étanchéité des machines tournantes
IV.2.3.c.Les joints à lèvres
Appelé aussi joint Spi, on les trouve
dans les secteurs d'activités divers. Utilisé principalement pour
l'étanchéité des arbres, ils sont aussi utilisés
pour l'étanchéité des arbres tournants.
|
|
|
|
|
|
|
|
L - 0.2
|
|
|
|
|
|
|
|
|
|
|
|
|
|
|
|
|
|
|
|
|
|
|
|
|
|
|
|
|
|
|
|
|
|
|
|
|
13
|
|
|
|
|
|
|
|
|
V max. 10 m/s HRC == 60
|
|
|
|
|
|
|
|
|
|
|
Figure IV.4 : Joint à lèvre.
IV.2.3.d. Labyrinthe
d'étanchéité
Un labyrinthe d'étanchéité est
une forme d'étanchéité utilisé dans les
compresseurs. Les labyrinthes n'arrêtent pas les fuites
complètement mais ils les réduisent beaucoup, il faut cependant
les contrôler si la fuite acceptable n'augmente pas, car, dans ce cas il
y aura une influence sur le rendement du compresseur .I1 faut a ce moment
réaliser une remise en état des labyrinthe.
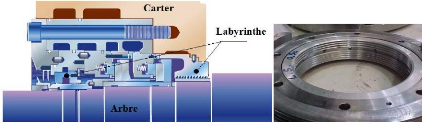
Carter
'211111111111111111111111111111110
Figure IV.5 : Joint à labyrinthe.
51
Chapitre IV : Technologies des systèmes
d'étanchéité des machines tournantes Exemple
d'étanchéité d'un compresseur embarqué sur un
méthanier :
Le système d'étanchéité consiste
à injecter de l'azote dans un labyrinthe en carbone pour empêcher
l'entrée de brouillard d'huile dans le corps du compresseur et
éviter des flux de gaz froid dans la boite à vitesse
(multiplicateur de vitesse). Ainsi, le gaz d'étanchéité
est appliqué entre le palier d'arbre de transmission et la roue du
compresseur L'azote est utilisé comme gaz
d'étanchéité pour ses propriétés de gaz
inerte et son état gazeux à très basse température.
Il est fourni par une installation de production d'azote à bord [6].
La régulation de pression de gaz
d'étanchéité est effectuée en fonction de la
pression de refoulement du compresseur en gardant toujours une
légère hausse de pression par rapport à la pression du
gaz.
Le gaz d'étanchéité entrant dans la boite
de vitesse est envoyé vers le carter pour être
séparé de l'huile par le Demister et ventilé vers
l'atmosphère.
~ol+rr
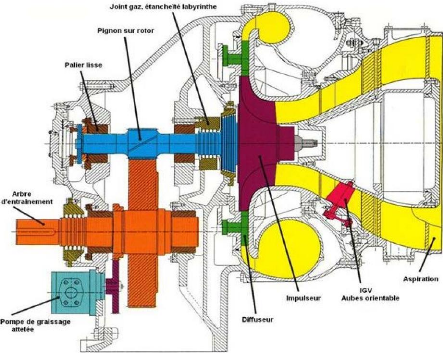
gin, e+ancIrerré iainrin#he
Pignon Gur rMror
Pailler lisse
d'en[rair3emcn[
Aepirstlun
IGV
Aubes orientable
irepuleeur
Pompe de graissage
.frgl
puha*..rt lr
Figure IV.6 : Etanchéité
à labyrinthe d'un compresseur embarqué sur un
méthanier.
52
Chapitre IV : Technologies des systèmes
d'étanchéité des machines tournantes
IV.3 CALCUL DES GARNITURES MECANIQUES
IV.3.1.Garniture mécanique hydraulique `oil seal'
(avec contact)
IV.3.1.a. Description
Lorsque le niveau d'étanchéité doit
être parfait comme c'est le cas pour les hydrocarbures, les labyrinthes
ne sont plus suffisants et l'on installe en plus des garnitures
mécaniques
d'étanchéité hydraulique nécessitant
un circuit d'huile.
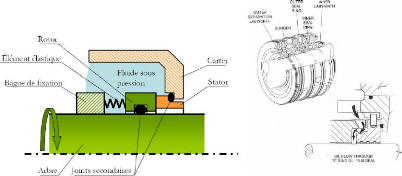
(JUTES SEPARATION LnSYRINTH
Rotor
Carte
Bague de fixation Stator
7 Arbre joints secondaires
OUTER INNER
SEAL LaarR NTN
RING
71W1
Q. FLQ9v11-11.pVGN .S. RING OIL FILM SPA&
Figure IV.7 : Garniture mécanique
hydraulique.
Très utilisées dans
l'étanchéité des pompes ou des machines tournantes en
générale les garnitures mécaniques sont de type et de
caractéristiques très différentes en fonction des
paramètres du fluide à étancher.
Pour fonctionner correctement, une garniture
d'étanchéité doit être refroidie et alimentée
en permanence par un liquide appelé "flushing" ou "arrosage" ou encore
"circulation".
Chapitre IV : Technologies des systèmes
d'étanchéité des machines tournantes
L H GAS INERT SEAL SEPARATION
SUPPLY GAS SUPPLY L=1T GAS SUPPLY
1T
PROCESS ~,~' 3EARING
SIDE &IDE
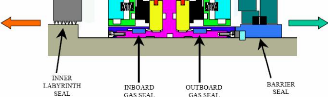
INNER LABYRINTH SEAL
BARRIER SEAL
INBOARD GAS SEAL
OUTBOARD GAS SEAL
Figure IV.8 : Montage type d'une garniture
mécanique en opposé.
Le principe de base consiste à assurer
l'étanchéité entre deux faces en mouvement relatif
(rotation) lubrifiées par un film liquide[3].
IV.3.1.b. Analyse des forces agissant sur les faces de
frottement
Élément élastique (ressort) Entraîneur
axial
Vis d'entraînement
Joint de chapeau*
Joint coulissant*
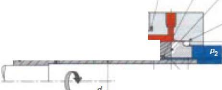
Joint de chemise* · w-
\
Faces de frottement*

Grain de fond Chemise
Joint de partie fixe*
P7 Ijs
SF SN
Côté -- pompe
FRS
tie h d.
- Côté atmosphére
53
Figure IV.9 : Schéma de principe d'une
garniture mécanique Les éléments principaux sont :
- les faces de frottement, une par sous-ensemble ;
- les étanchéités secondaires (joints,
soufflet métallique, membrane synthétique), au moins une par
sous-ensemble ;
- un élément élastique (ressort(s),
soufflet métallique, membrane synthétique), dans l'un des
sous-ensembles ;
54
Chapitre IV : Technologies des systèmes
d'étanchéité des machines tournantes
- des éléments de liaison des deux
sous-ensembles à la machine (chemise, couvercle, vis, support, etc.).
En statique, ces deux sous-ensembles sont maintenus en
contact par l'action de l'élément élastique.
Cet élément élastique peut être :
incorporé dans le sous-ensemble statique ou tournant, ou immergé
dans le fluide à étancher ou protégé de
celui-ci.
Quels que soient les sollicitations et les petits
défauts de rotation, le sous-ensemble contenant l'élément
élastique (ressort) doit être mobile dans toutes les directions de
manière à assurer un contact permanent des faces. Il est
appelé semi-dynamique. L'étanchéité secondaire de
ce sous-ensemble subit les mouvements axiaux alternatifs de faible, voire
très faible amplitude et, de ce fait, est appelé
étanchéité secondaire semi-dynamique. Le diamètre
du cylindre sur lequel celle-ci coulisse est appelé diamètre
hydraulique dh: il délimite le piston annulaire de surface SH
sur laquelle s'applique la pression du fluide à étancher :
SH = -2, _ ·
4 Gt - G,
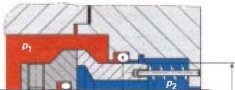
Figure IV.10 : Schématisation du
diamètre hydraulique. Les forces ont deux origines [3]:
- l'une mécanique, transmise par l'élément
élastique ;
- l'autre hydraulique, communiquée par la pression du
fluide appliquée sur les surfaces annulaires normales à l'axe.
Chapitre IV : Technologies des systèmes
d'étanchéité des machines tournantes
55
dft d,
349=P,-P2
gradient de pression du film dans une interface a faces
parallèles et planes
Figure IV.11 : Analyse des forces agissant
sur les faces de frottement.
L'élément à considérer dans
l'analyse est le sous-ensemble semi dynamique car lui seul possède la
liberté axiale de déplacement pouvant rapprocher ou
écarter les faces de frottement.
Les forces sont au nombre de trois :
L'élément élastique développe un
effort FR car il rapproche les faces la pression du fluide agissant sur la face
de frottement semi dynamique développe une force hydraulique de
fermeture
EH = SH \p
Le gradient du champ de pression du film dans l'interface
agissant sur la surface de frottement
SF développe une force d'ouverture : FO = x .p
SF
X : est un coefficient compris entre 0 et 1 ; il est fonction
de la loi de décroissance du champ de pression du film lubrifiant.
Il dépend de nombreux paramètres tels que la
géométrie des faces, l'état de surface, la pression, la
température, les caractéristiques physiques du fluide à
étancher. Dans la pratique, on utilise x = 0,5.
Chapitre IV : Technologies des systèmes
d'étanchéité des machines tournantes
h
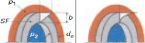
d'-
rim
x = 0,5
Interface parallèle Surfaces de frottement
planes
X ,- 0,5
Interface divergente Surfaces de frottement concaves
Interface convergente Surfaces de frottement convexes
56
Figure IV.12 : Distribution 'x' des pressions
agissant en forces d'ouvertures. SF : désigne la surface de frottement
(comprise entre di et de).
71 = -
4
..
Les forces conduisent aux résultantes suivantes :
- force de fermeture totale : FE = FR + EH
- force résiduelle de fermeture :
FRF = F - f-
FRF : doit être positif pour maintenir le contact des deux
faces de frottement. IV.3.1.c. Consommation d'une garniture
mécanique
La partie du film liquide entretenue par la rotation qui
s'échappe hors des faces constitue la consommation de la garniture
mécanique.
Celle-ci varie avec la distance qui sépare les deux
faces (h hauteur d'interface = épaisseur de film) [3].
Les surfaces glissent l'une contre l'autre, avec localement
des points de contact, c'est pourquoi le degré de finition des surfaces
a une très grande importance : la rugosité la plus faible est
recherchée.
Chapitre IV : Technologies des systèmes
d'étanchéité des machines tournantes
Relation entre rugosité Ra et le taux
de surface en contact suivant son mode d'élaboration
Ra
|
|
|
|
L1
=
Ra=0,01 Rn
|
MM.
|
Mn
|
WIN
|
|
|
|
VII
|
|
1iOii!'
|
|
|
1111
|
|
|
|
|
IIIIIIII
|
|
|
Ra-0,5}rm
|
Ra=10jam
|
Ra- 0,1 um
|
Mode d'iWxratian
|
Tournage fin
|
Rectification
|
Rodage
|
Polissage
|
95 %
|
Tallith
surface M mrelfnf
|
4%
|
12 %
|
40%
|
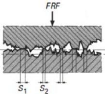
Ra
S-51+32+S3+54+S5
1_t
S3 S4 S5
5 _ FRF(charge normal&
p (pression de fluage)

Figure IV.13 : Macroscopie d'une interface
d'une garniture.
Dans le cadre d'une théorie simplifiée, le
débit d'écoulement peut être estimé à l'aide
de l'abaque (figure) de l'écoulement laminaire, à travers une
interface radiale circulaire.
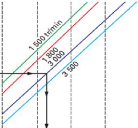
Diamètre (mml
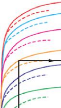
100
80
50
10
30
20
57
I I I I I I I I I I I I I'I'rI
I I'I'"1
0 2 4 6 8
"'3" 10121416182D 1
0,01 0,1 1 10 100
Pression effective (bar) Fuite iml_ih)
Figure IV.14 : Estimation indicative de la
consommation d'une garniture mécanique.
58
Chapitre IV : Technologies des systèmes
d'étanchéité des machines tournantes
IV.3.1.d. Coefficient de frottement/puissance
absorbée
La puissance absorbée Pa par une garniture
mécanique en fonctionnement est [3]:
Pa = Pt + Pf
Avec :
Pt puissance dissipée en turbulence, en
général négligeable ; elle n'est à
considérer que dans les cas de vitesse périphérique
importante (> 20 m/s), Pf puissance de frottement dissipée en
chaleur, calculée par :
DNfFRF
Où f est le coefficient de frottement et N la vitesse de
rotation.
En régime établi et stable, le coefficient f
dépend du film (nature, viscosité et température), de la
pression à étancher, des matériaux utilisés et de
leur état de surface.
Les expériences et essais effectués en
laboratoire ou sur banc tribologique ont confirmé une valeur moyenne f =
0,08.
La puissance absorbée Pa doit être
comparée à la puissance disponible pour la fonction
étanchéité prévue pour la machine. Elle est
généralement négligeable par rapport à la puissance
de la machine à étancher. Lorsque ce n'est pas le cas, il faut
veiller à en tenir compte pour la machine motrice. Lors des
démarrages, cette puissance et peut être doublée,
triplée, etc., par manque de lubrification et collage des faces.
IV.3.2.Garniture mécanique sans contact 'dry gas
seal'
IV.3.2.a. Description
Dite `sèche' Contrairement aux garnitures
mécaniques avec contact lubrifiées par un liquide[3], les
garnitures sèches fonctionnent avec un contact réel (on pourrait
dire avec un film solide pour se rapprocher de la classification liquide et
gaz).
Il en résulte, par conséquent, une usure et un
échauffement plus importants.
Pour minimiser ces phénomènes, des
matériaux particuliers sont utilisés afin de combiner leurs
propriétés tribologiques (frottement), leur résistance
mécanique et leur résistance chimique.
Généralement, on utilise des faces carbones
contre des sièges céramiques (oxyde d'alumine) ou carbure de
silicium.
59
Chapitre IV : Technologies des systèmes
d'étanchéité des machines tournantes
Le principe de base consiste à assurer
l'étanchéité entre deux faces en mouvement relatif
(rotation) par un film gazeux[3]
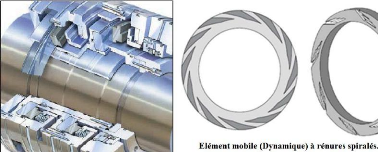
Elément mobile (Dynamique) à rénures
spiralés.
Figure IV.15 : Garniture mécanique
sèche.
Les garnitures mécaniques à gaz se trouvent
principalement dans les compresseurs ou machines similaires. D'où 80%
des compresseurs sont maintenant équipés de ce type de
garnitures.
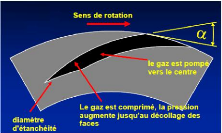
le gaz est pomp"
vers le centre
Sens de rotation
r Le gaz est comprimé, la
preséion
diamètre augmente jusqu'au décollage
des
faces
d'étanchéité
Figure IV.16 : Rainure spiralés sur la
bague de matage d'une garniture mécanique sèche.
Le principe de fonctionnement de la garniture à gaz
à rainures spiralées est basé sur un équilibre des
forces aérostatiques et des forces aérodynamiques qui fournit un
jeu interfaces minimum et stable.
Chapitre IV : Technologies des systèmes
d'étanchéité des machines tournantes
Element mobile Element free
(Dvnamgiue) (Semi-dynamgiue)
|
Carter
Element élastique (Resort)
Chemise
|
Rainures spirales Faces de frottement
Figure IV.17 : Schémas des faces de
frottement d'une garniture mécanique sèche.
Les forces aérodynamiques sont produites seulement en
rotation. Pendant la rotation, les rainures spiralées jouent un
rôle primordial en générant une force d'ouverture qui
permet d'obtenir un jeu interfaces acceptable.
IV.3.2.b. Analyse des forces agissant sur les faces
sans contact
En fonctionnement, le point d'équilibre est atteint
lorsque FF = FO avec le jeu interface défini[3].
FF FG
FF O
Force de fermeture Force d'ouverture
FR p
60
Ressort Distribution de
+ hydrostatique pression du film gazeux
Figure IV.18: Principe de
l'établissement du filme à l'interface.
La force de fermeture FF correspond à la pression
exercée axialement sur l'arrière de la face et la force FR
à celle exercée par les ressorts.
La force d'ouverture FO est le résultat du
système de pression aérostatique auquel s'ajoutent les forces
aérodynamiques générées par les rainures lors de la
rotation de la face.
61
Chapitre IV : Technologies des systèmes
d'étanchéité des machines tournantes
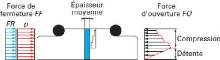
Épaisseur moyenne
Force de fermeture FF
FR p
Force d'ouverture FO
Compression Détente
Pression + charge ressort
C fonctionnement normal
Force de fermeture FF
|
Épaisseur du film
'
|
|
Farce
d'ouverture FO
|
|
FR p
|
|
|
|
|
|
|
|
|
|
|
|
|
|
|
|
|
\ _ Compression
|
|
|
|
|
|
|
|
|
|
|
|
|
|
|
|
|
|
|
|
|
|
|
|
Détente
|
|
|
|
|
|
|
|
|
|
Pression + charge ressort
0 diminution de l'épaisseur du film
Force de Épaisseur Force
fermeture FF du film d'ouverture FO
Pression+ charge ressort
Ci augmentation de l'épaisseur du filin
Figure IV.19: Elasticité du filme du
gaz vis-à-vis les perturbations.
S'il y avait des perturbations ayant pour effet de diminuer
le jeu interface, la pression produite par les rainures augmenterait
considérablement (figure).
De la même façon, si les perturbations avaient
pour effet d'augmenter le jeu interface, il y aurait une réduction de la
pression générée par les rainures (figure).
Dans chaque cas, la force de fermeture FF reste constante et
de la sorte, quelle que soit la situation, le point d'équilibre est
rapidement atteint et le jeu interface restitué.
Ce mécanisme de restitution de l'équilibre est dit
à film élastique. IV.3.2.c. Consommation d'une garniture
mécanique (sans contact)
Le principe de décollement des faces par le film
gazeux génère un débit de consommation. L'abaque (figure
13) indique un ordre de grandeur de la consommation[3]. Toutefois, cet abaque
repose sur des hypothèses de base théoriques.
En raison de l'association non quantifiable de
paramètres divers (vibrations, nature des matériaux, états
de surface, environnement, etc.), les résultats industriels peuvent
différer.
Chapitre IV : Technologies des systèmes
d'étanchéité des machines tournantes
16
14
12
10
8
E 6
g 4
8 2
0 2 4 6 8 10 12 14 16 18 20
Pression de gaz utilise bar
Ces courbes sont données a titre indicatif.
Les valeurs de consommation sont obtenues pour une
garniture en montage simple fonctionnant dans des conditions
standards d'essais de laboratoire {patrnosphsriquo' T. 25 'Ch
Figure IV.20 : Caractéristiques de la
consommation des garnitures sans contact. Puissance
absorbée
La consommation de puissance d'une garniture mécanique
sans contact est liée au cisaillement du film gazeux du fait de
l'absence de contact entre les faces. La puissance absorbée est
d'environ 10 fois moins que dans le cas d'une garniture lubrifiée[3].
IV.3.3.Compensation des garnitures
mécaniques
IV.3.3.a. Définition du coefficient de
compensation k
Lorsque la pression du fluide à étancher
augmente, la force FI-1 maintenant les deux faces en contact augmente
également, d'où une étanchéité
supposée meilleure[3].
Ca] gamiture non compensée
{U}
62
:b) garniture compensée f6~
Figure IV.21: Compensation des garnitures.
63
Chapitre IV : Technologies des systèmes
d'étanchéité des machines tournantes
Cependant, plus de pression sur les faces de frottement
signifie aussi plus grande friction, couple plus élevé et usure
plus rapide, voire même destruction des faces de frottement en cas d'une
pression à étancher pl importante.
En faisant varier le diamètre hydraulique dh (qui agit
directement sur FIT ), on peut atténuer (ou au contraire accentuer)
l'influence de la pression sur la valeur de la résultante FF qui
s'applique aux faces de frottement. On définit ainsi un coefficient k,
appelé coefficient de compensation, tel que :
H cI - d
- -
SF af -c!?
Si , k > 1 la garniture est dite non compensée
(figure 6 a). Elle est désignée par la lettre U (unbalanced) -
norme EN 12756 (NF EN 12756 et DIN EN 12756) [3].
Si k < 1, la garniture est dite compensée (figure 6
b). Elle est désignée par la lettre B (balanced) - norme EN 12756
(NF EN 12756 et DIN EN 12756) [3].
Grâce à l'utilisation d'une garniture
compensée, on limitera l'influence de la pression sur les faces de
frottement [3].
IV.4.AVANTAGES ET INCONVENIENTS DES DIFFERENTS
TYPES
IV.4.1.Garniture mécanique avec contact
IV.4.1.a. Inconvénients
Maintenance très contraignante, nécessitant
l'arrêt de la machine.
Détérioration progressive de l'arbre.
Contamination du produit par des particules de tresse.
Couple résistant élevé.
Brûlure ou caramélisation de la matière
traitée.
Dégradation rapide de l'étanchéité
en cas de défaut d'alignement ou d'efforts radiaux.
64
Chapitre IV : Technologies des systèmes
d'étanchéité des machines tournantes
IV.4.1.b.Avantages
Remplacement aisé des tresses.
Faible coût de la maintenance (hors mis l'arrêt).
IV.4.2.Garniture à gaz sans contact.
IV.4.1.a. Avantages
Les garnitures mécaniques à rainures
spiralées offrent des avantages considérables par rapport aux
solutions conventionnelles :
· Faible absorption de puissance
· Pas d'usure de fonctionnement
· Pas de centrale d'huile
· Pas de limite pression-vitesse
· Pas de contamination de l'huile ou du gaz
· Faible absorption de puissance
La consommation parasitaire de puissance d'un système
d'étanchéité représente très souvent un
coût latent qui n'est pas entièrement pris en compte.
Pour établir une comparaison entre une garniture
ordinaire et une garniture à rainures pialées.
Pas d'usure de fonctionnement, Aucune
pièce n'est en contact lorsque la garniture à gaz à
rainures spiralées est en rotation. De ce fait, aucune pièce
n'est soumise à l'usure.
Fiabilité, Une durée de vie de
plusieurs années peut être envisagée.
Pas de centrale d'huile, Le fonctionnement
d'une garniture mécanique à film d'huile est dépendant de
la centrale de lubrification. La conception de celle-ci est complexe et
comprend, en général, un réservoir, des pompes, des
réfrigérants, des filtres, un réseau de tuyauterie, des
séparateurs et une instrumentation de réglage et de
contrôle dont certains éléments doivent être
doublés pour améliorer la sécurité de
l'ensemble.
Pas de limite pression-vitesse, Bien qu'une
limitation de vitesse à 150 m/s ait été imposée
pour la garniture à gaz, la vitesse la plus grande susceptible
d'être atteinte se voit limitée par la capacité de
résistance de matériau. Dans le cas de garnitures
mécaniques lubrifiées par liquide et dont l'absorption de
puissance est plus grande; ce qui entraîne des températures
interfaces supérieures, la limite n'est pas seulement une question de
résistance mécanique mais aussi un problème de
capacité de dissipation de chaleur. La garniture mécanique
à gaz à rainures spiralées n'est pas limitée par le
rapport pression/vitesse.
65
Chapitre IV : Technologies des systèmes
d'étanchéité des machines tournantes
Pas de contamination de l'huile ou du gaz,
comme les garnitures mécaniques à gaz à rainures
spiralées ne requièrent pas d'huile de lubrification ou de
refroidissement, toute contamination du produit est exclue.
IV. Conclusion
L'emploi des systèmes d'étanchéité
dépond principalement au type d'équipements (dimension,
régime, performances...), et des caractéristiques de fluide
à étancher.
En premier lieur nous avons défini les
différentes catégories des systèmes
d'étanchéités, et puis nous avons présenté
une méthode de calcule de la technique d'étanchéité
par analyse des forces agissant sur les surfaces en mouvement relatif (Avec
contact et sans contact).
Chapitre V
DESCRIPTION DU
COMPRESSEUR
COOPER-BESSEMER
66
Chapitre V : Description du compresseur centrifuge
Cooper-Bessemer
V.1.INTRODUCTION
Le compresseur centrifuge COOPER BESSEMER de type RF2/1B-30
à un seul étage (impulseur) est attelé à une
turbine à gaz AEG-KANIS. Il est conçu pour une pression de
service maximale de 84,5 Kg/cm2. Il est raccordé à des
brides d'aspiration et de refoulement de 75 cm de diamètre. Il est
destiné à augmenter la pression du gaz naturel dans les gazoducs
GZ2 etGZ3 par le biais de 5 stations de compression réparties entre
Hassi R'mel et Arzew. Les stations de GZ2, GZ3 comprennent respectivement, 03
et 04 turbocompresseurs chacune. La totalité des turbocompresseurs dans
les deux ouvrages est de 55 unités [1].
V.2. DISCRETION DU COMPRESSEUR
V.2.1. Donnée des paramètres de
fonctionnement
Huile de lubrification : Torba 33 SH.
Puissance nominale :7.457 KW.
Volume d'entrée :12.20 m3/h
Vitesse nominale : 6500 tr/min.
1 el. vitesse critique : aucune dans la gamme de
service.
Régime continu maximal : 6 825 tr/min.
Pression de refoulement maximale théorique : 84.4
kg/cm2.
Pression d'entrée : 53.7Kg/cm2
Température d'entrée : 49°C
Pression d'aspiration de service :84.81 Kg/cm2
Température d'aspiration de service :45.62 °C.
Pression de refoulement de service : 69.3 bar.
Température de refoulement de service : 78.18 °C
Température de sortie permise : 87°C
Taille des brides d'aspiration et de refoulement : 750 mm.
Poids de compresseur et de réservoir d'huile
d'étanchéité : 31 750 Kg.
Poids du flasque d'extrémité de compresseur : 5 896
Kg.
Garniture d'étanchéité : Hydraulique,
Mécanique.
V.2.2. Données de construction
Nombre d'étage :01.
Rotation : sens horaire
Joint du corps :Vertical, O'Ring.
Utilisation : Transport du gaz naturel.
67
Chapitre V : Description du compresseur centrifuge
Cooper-Bessemer
Le compresseur se compose des éléments
principaux suivants : Le carter, le système à air
(circuit du gaz) et l'ensemble d'arbre creux.
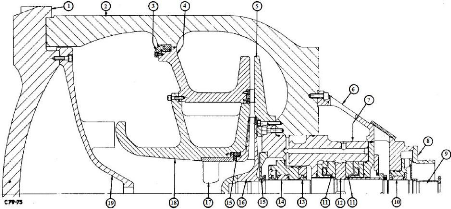
A ® o
roek.
=el
Figure V.1 : Coupe sur le compresseur
Cooper-Bessemer.
1. Flasque d'extrémité.
2. Carter.
3. Bague de retenue de diaphragme.
4. Diaphragme.
5. Galerie de refoulement.
6. Logement --support de palier lisse.
7. Logement de palier.
8. Adaptateur de protecteur d'accouplement.
9. Arbre d'impulseur.
10. Palier lisse coté accouplement.
11. Palier de butée.
12. Collier de butée.
13. Joints
14. Palier lisse coté Impulseur.
15. Joint à labyrinthe.
16. Impulseur (rouet) et dispositif de retenue.
17. Palette guide d'aspiration.
18. Support de palette guide d'aspiration.
19. Manche d'aspiration.
68
Chapitre V : Description du compresseur centrifuge
Cooper-Bessemer
V.2.2.a. Le carter
Le carter du compresseur est en acier
coulé, il est conçu pour résister aux vitesses et aux
pressions élevées. Un flasque d'extrémité amovible
(1) avec manche d'aspiration rattaché (19) permet d'accéder au
système à air (circuit de gaz) et
l'ensemble d'arbre creux[1].
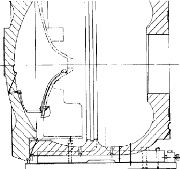
Figure V.2 : Carter du compresseur
Cooper-Bessemer.
Les supports du carter reposent sur une plaque d'assise et
comporte des vis de remise à niveau et des vérins à vis
pour l'alignement. Au fond du carter, deux drains permettent la vidange de
l'huile ou des liquides accumulée.
Pour permettre de connecter les contrôles de surpression
(instrumentations) au compresseur, on dispose d'un tube interne qui traverse
l'oeil de la manche d'air (guide de gaz) (19), jusqu'un trou percé dans
le flasque.
V.2.2.b. Le système à air (circuit du
gaz)
Manche d'aspiration (19) est rattachée au dessous du
flasque d'extrémité, elle receuille les gaz d'aspiration et les
dirige sur palette-guides.
Palettes-guides d'aspiration (17) sont fixes et montées
sur le support (18) du coté aspiration de l'impulseur, elles
réduisent la turbulence d'écoulement du gaz et dirige le courant
vers l'impulseur.des joints à labyrinthe (15) empêche le gaz
comprimé de retourner de l'impulseur vers les palettes-guides ou le
joints à huile.
Diaphragme (volute) (4) dirige le gaz d'aspiration sur
l'impulseur puis vers le coté refoulement du carter. Un diffuseur
hautement poli est rattaché à la gallerie de refoulement de
diaphragme [1].
Chapitre V : Description du compresseur centrifuge
Cooper-Bessemer
V.2.2.c. Ensemble de rotor
L'ensemble de rotor est composé de l'impulseur, du
collier de butée (8), du moyeu d'accouplement (17), d'intercalaires (7),
clavettes(6,14), contre-écrou (12,16), rondelles frein, et de l'arbre
d'impulseur (5). L'impulseur est mis en place et démonté
hydrauliquement, il est maintenu par une bague intercalaire, en acier et un
dispositif de retenue. L'impulseur et l'arbre sont équilibrés
séparément. L'impulseur a subi les essais de rotation à
115% de la vitesse maximale de fonctionnement continu, puis il a
été monté sur l'arbre et l'ensemble a été
équilibré [1].
69
Figure V.3 : Rotor du compresseur
Cooper-Bessemer.
70
Chapitre V : Description du compresseur centrifuge
Cooper-Bessemer V.2.2.d. Palier lisses et palier à
butée
Le rotor (arbre et impulseur) est supporté par deux
paliers lisses auto-alignant, avec des segments inclinables.
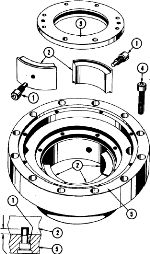
T6
Figure V.4 : palier lisse coté
accouplement du compresseur Cooper-Bessemer.
2. Segments de palier (Qt5).
3. Dispositif de retenu de palier lisse. 5. Logement de palier
lisse.
Le palier de butée se compose de deux coussinets
inclinables à six segments séparé par un collier de
butée en acier à polissage de précision.
Les segments de palier sont auto-nivelant et se partagent
également la charge. La poussée de fonctionnent est
absorbée par le palier de butée extérieur du coté
accouplement de l'arbre.
71
Chapitre V : Description du compresseur centrifuge
Cooper-Bessemer
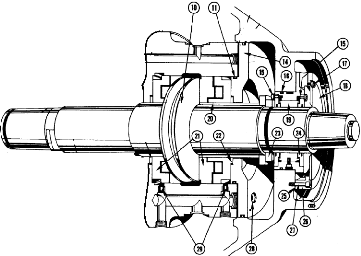
Figure V.5 : Palier de butée du
compresseur Cooper-Bessemer. 10. Collier de butée.
20. Intercalaire.
21. Palier de butée et segments de palier (Qt 6).
22. Bague d'étanchéité.
V.3. DESCRIPTION DU SYSTEM DE LUBRIFICATION ET
D'ETANCHEITE FILME D'HUILE
Le système sert à éliminer les fuites de
gaz vers l'air libre, ils se composent de deux bagues flottantes (joints
d'étanchéité) et un labyrinthe. L'huile
d'étanchéité haute pression est amenée vers le
joint d'extrémité de l'impulseur et s'écoule à
travers les bagues hautes et basse pression, ce qui empêche le gaz de
s'écouler le long de l'arbre et de s'échapper par les
joints[1].
L'huile chargée contaminée par le gaz (le gaz
qui passerait le labyrinthe) est emporté vers un système de
piège d'huile de vidange. Une vanne à pression
différentielle maintient la pression voulue de l'huile
d'étanchéité. La pression du gaz au niveau de la vanne de
contrôle à pression différentielle et du réservoir
supérieur d'huile est appelée la pression du gaz de
référence[1].
72
Chapitre V : Description du compresseur centrifuge
Cooper-Bessemer V.3.1. Description de la garniture à bagues
flottante embarquée (Flooting Oil Seal)
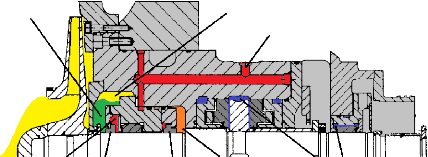
Huile chargée du gaz 1 ers
le piège d'huile
Chambre du gaz de référence
Huile d'étanchéité haute
pression
Huile d'étanchéité vers la vanne de
pression différentielle
|
Bague d'étanchéité Interne
|
Bague
d'étanchéité Externe
|
Vapeur d'huile vers le reniflard
|
Huile de lubrification basse pression
|
Circuit du gaz
Elements fixes
Elêment en mouvement (Rotor)
pDément en frottement {joints
d'étanchéités Br segments des paliers
|
Huile d'étanchéité haute
pression 74 Kg/cm'
Huile chrgée du gaz
Huile de lubrification 1.4 Kg'cm"
Vapeur d'huile
|
Figure V.6 : Dessin d'ensemble des
éléments embarqués de la garniture
d'étanchéité et de lubrification Cooper-Bessemer.
73
Chapitre V : Description du compresseur centrifuge
Cooper-Bessemer
Chambre
d'huile charaee du .2 sa
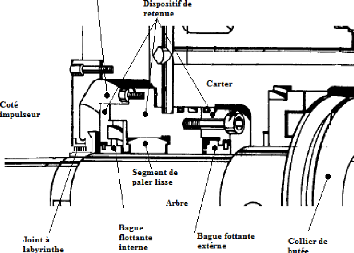
Jo-int labyriodse
Dispo-sitifde retenue
Carter
C ate impulseur
Segment de paler lisse
Arbre
Saque flotEarae io(eroe
Bague fo-moite extero e
Collier de butée
Figure V.7 : Identification des
éléments d'étanchéité du compresseur
Cooper-Bessemer.
La bague flottante interne (bague
d'étanchéité interne) a deux surfaces
d'étanchéité, la surface formée par du
diamètre interne avec l'arbre, et la surface de matage formée par
le montage de la bague avec le dispositif de retenue.
74
Chapitre V : Description du compresseur centrifuge
Cooper-Bessemer
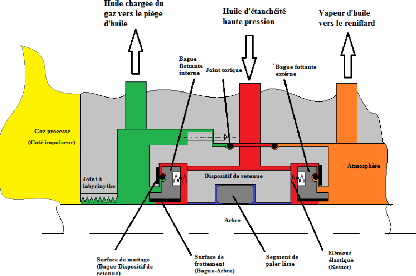
Huile chargée du gar E ers le piège d'huile
Huile d'étanchéité haute pression
Vapeur d'huile
n ers le reniflard
Bague
flattante
interne Saint torique
Gaz promesse (Cotê imputseur)
Surface de maltage (B a gu e-Dispositif de
retenue)
Bague fo ttan te estérne
Elements fixes Circuit du gaz
Element en mouvement (Rotor) Huile
d'étanchéité haute
pression 74 Kg cm
Elément en frottement (joints
d'étanchéités & segments des paliers
IIHuile chrgée du gaz
Huile de lubrification 1.4 Kglcm2
Vapeur d'huile
Figure V.8 : Schémas de principe du
système d'étanchéité à bagues flottantes du
compresseur
Cooper-Bessemer.
V.3.2. Le circuit de d'huile de lubrification et
d'étanchéité (Console) Le système d'huile de
lubrification et d'étanchéité a deux fonctions :
· Il fournit de l'huile de lubrification basse pression au
palier lisse (coté accouplement) et au palier de butée, à
raison de 413 1/min et sous 1.4Kg/cm2.
· Et du l'huile d'étanchéité haute
pression aux joints, (le palier lisse coté impulseur est lubrifié
par cet huile).
Le système d'huile d'étanchéité
se compose de deux pompes motorisée haute pression, d'un
réservoir d'huile d'étanchéité monté
au-dessus du compresseur, d'interrupteurs, de vanne et de tuyauteries .l'huile
de l'entrainement passe aux pompes à raison de
7.05m3/h[1].
Chapitre V : Description du compresseur centrifuge
Cooper-Bessemer
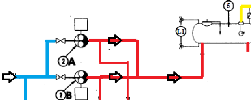
Huile de lubrification 1.4 Kgltinn
Pompes
Réservoir

Vanne de commande

Vapeurs d'huile
}
Gaz de référence
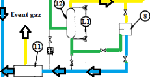
0 I

9 d

40
Soupape de décharge S4 Kgicot
Drain d'huile principal
prr 7Ers
Gaz sers L'aspiration
t
Systême de maintien de
pression et dégazage
75
Figure V.9 : Le système de contrôle
et régulation (Console) du système d'huile
d'étanchéité.
V.3.2.a. Pompes principales et pompes auxiliaires
d'huile d'étanchéité
Les deux pompes 2A et 2B, sont identiques et ont une
capacité de refoulement de 105 1/h sous 74 Kg/ cm2, refoulent
vers le réservoir d'étanchéité.
Une vanne de détente (21) dirige une partie de l'huile
refoulé par la pompe vers le drain du collecteur d'huile de
lubrification au cas où la pression d'huile dépasse 84.4 Kg/
cm2.
V.3.2.b.Le réservoir
d'étanchéité
Ce réservoir placé au-dessus du compresseur,
fournit de l'huile d'étanchéité aux joints
d'étanchéité et palier et le palier lisse coté
impulseur pendant environ 8 minutes en cas de panne de pompes ou d'arrêt
du compresseur.
La pression de gaz de référence de la chambre
de joint à labyrinthe est appliquée directement au sommet du
réservoir d'huile d'étanchéité, et sur la surface
d'huile pour maintenir une pression d'huile adéquate. Un niveau d'huile
à regard (L1) permet de contrôler le niveau d'huile dans le
réservoir (5).
76
Chapitre V : Description du compresseur centrifuge
Cooper-Bessemer V.3.2.c.Vanne de contrôle de la pression
différentielle d'huile d'étanchéité
La vanne de contrôle commande la pression d'huile (7)
au niveau des joints du compresseur à environ 0.7 Kg/ cm2 au
dessus de la pression du gaz de référence, afin d'empêcher
le gaz de pénétrer dans la chambre de palier.
V.3.2.d. Le système de piège
d'huile
Le piège d'huile permet de vidanger l'huile
d'étanchéité chargée du gaz de la chambre de joint
à labyrinthe sans perte de pression.
D'où la pression du gaz est maintenue par un
désembueur et un piège haut pression (8) installé sur la
ligne de vidange.
Le désembueur (12) et le piège d'huile haute
pression (8) élimine la plus grande partie du gaz entrainé par
l'huile d'étanchéité et évacué vers
l'aspiration du compresseur. L'huile retourne ensuite à la ligne de
vidange principale à travers un dégazeur (11) où le gaz
entrainé restant est évacué vers l'air libre.
V.4. Conclusion
Dans ce chapitre nous avons décrit l'aspect de
construction le compresseur centrifuge Cooper-Bessemer, et définir les
différents organes principal (Carter, Rotor, diaphragme...).
La deuxième partie de ce chapitre, nous avons
entamé la description des éléments de construction de la
garniture d'étanchéité embarquée (Bague
d'étanchéité interne, bague
d'étanchéité externe, paliers lisses, palier de
butée...), et le éléments constitutifs du circuit de
système de lubrification et étanchéité (Pompes,
soupapes, réservoir, vanne de commande différentielle...).
Chapitre VI
OPPORTLTNITES DE
MODIFICATION DU
SYSTEME
D'ETANCHEITE PAR
GARNITURE SECHE
77
Chapitre VI : Opportunité de modification du
système d'étanchéité du compresseur
Cooper-Bessemer
VI.I.INTRODUCTION
Un projet de rénovation d'un compresseur exige
l'étude de ces performances, et le cout associé à sont
exploitation.
Nous allons commencer par l'analyse d'historique
d'intervention de la maintenance préventive et accidentelle de ce
compresseur. Donner des interprétations sur des défaillances
fréquentes. Et puis nous analysons les dépenses
éventuelles sur sa consommation des huiles de lubrification et
d'étanchéité.
Nous allons essayer d'estimer la faisabilité d'un
rétrofit sur la garniture mécanique à bague flottante
embarqué sur le compresseur Cooper-Bessemer, et puis étudier son
influence sur les aspects de maintenances consommations et
sécurité.
VI.2.ANALYSE DE LA MAINTENANCE ET ENTRETIEN DU
COMPRESSEUR COOPER-BESSEMER
VI.2.1.Maintenance préventive systématique
du compresseur
La maintenance adoptée par la DML est la maintenance
préventive systématique, de niveau 3 et 4 [7].
Le cycle d'intervention du compresseur CB est défini
comme suit : -Enceins cycle avant 2004 :
RP (Révision partielle) : 10 000 Heurs RG
(Révision générale) :30 000 Heurs
-Nouveau cycle de révision :
RP (Révision partielle) : 30 000 Heurs RG
(Révision générale) :60 000 Heurs
Gamme de maintenance RP 30 000 Heurs [7].
· Désacouplage turbine-compresseur
· Contrôle d'alignement entre la turbine et le
compresseur
· Démontage de la tuyauterie
· Démontage de moyeu d'accouplement
· Démontage du palier (coté accouplement)
· Jeux de palier :
· Diamètre de palier lisse coté impulseur :
0,254 à 0,305 mm
· Diamètre de palier lisse coté accouplement
: 0,164 à 0,215 mm
· Diamètre de palier de butée : 0,279
à 0,432 mm
78
Chapitre VI : Opportunité de modification du
système d'étanchéité du compresseur
Cooper-Bessemer
· Jeux de joint : Bague flottante externe : 0,165 à
0,178 mm
Bague flottante interne coté impulseur : 0,114 à
0,140 mm Joint à labyrinthe coté impulseur : 0,457 à
0,508mm
Inspecter la surface rodée entre les bauges
d'étanchéité flottante et les dispositif de retenu de
joints.
· Seuils de vibration :
Alarme : 2 mm/s
Déclenchement : 2,5 mm/s
Tableau VI.1 : Evaluation de la gestion de
la maintenance des compresseurs Cooper-Bessemer sur S [7] :
Compresseur
|
Révision
|
Année
|
Heurs de fonctionnement
|
Prix Moyen
|
OBS
|
T05
|
RA
|
2007
|
60
|
847
|
2
|
000
|
000.00
|
VIBRATION PHENOMENE D'ECOULEMENT
|
T05
|
RG
|
2010
|
|
000
|
000.00
|
BON
|
T06
|
RP
|
-
|
59
|
980
|
2
|
000
|
000.00
|
BON
|
T06
|
RG
|
2000
|
|
000
|
000.00
|
BON
|
T07
|
RP
|
1997
|
51
|
521
|
2
|
000
|
000.00
|
BON
|
T07
|
RG
|
-
|
|
000
|
000.00
|
BON
|
T08
|
RP
|
1998
|
63
|
558
|
2
|
000
|
000.00
|
BON
|
T08
|
RG
|
-
|
|
000
|
000.00
|
BON
|
T08
|
RA
|
2012
|
|
000
|
000.00
|
VIBRATION PHENOMENE D'ECOULEMENT
|
T08
|
RP
|
2015
|
|
000
|
000.00
|
BON
|
T09
|
RP
|
1997
|
61
|
441
|
2
|
000
|
000.00
|
BON
|
T09
|
RG
|
-
|
|
000
|
000.00
|
BON
|
T09
|
RP
|
2015
|
|
000
|
000.00
|
BON
|
T10
|
RP
|
1998
|
50
|
974
|
2
|
000
|
000.00
|
BON
|
T10
|
RG
|
2004
|
|
000
|
000.00
|
BON
|
T10
|
RP
|
-
|
|
000
|
000.00
|
BON
|
T11
|
RP
|
-
|
60
|
895
|
2
|
000
|
000.00
|
BON
|
T11
|
RG
|
2003
|
|
000
|
000.00
|
BON
|
T11
|
RP
|
2016
|
|
000
|
000.00
|
BON
|
|
79
Chapitre VI : Opportunité de modification du
système d'étanchéité du compresseur
Cooper-Bessemer
Résultats
· Nombre de machine :7 compresseurs Cooper-Bessemer.
· Nombre d'intervenions : 17 opération
périodique + 1 accidentelle.
· Période d'évaluation :19 ans.
· Heurs de fonctionnement total :409 216 heurs.
· Prix moyen estimé par opération : 2 000
000.00 DA.
· Prix total : 36 000 000.00 DA.
D'après l'analyse des rapports d'entretient fournit
soit par la DML ou la RTO chargé des opérations RP, nous avons
constaté que la garniture d'étanchéité ne constitue
aucun malaise lors du démontage et contrôle des
jeux fonctionnels.
VI.2.2.Analyse d'historique des interventions
La majorité des RP (Révision partielle)
on tire l'observation suivante :
· Contrôle de l'alignement.
· Contrôle les jeux.
· Test concluant, RAS.
La majorité des RG (Révision
général) on tire l'observation suivante:
· Démontage le compresseur, contrôle des jeux
et de l'état des pièces.
· Contrôle de l'alignement.
· Contrôle les garnitures mécaniques.
· Changement tous les joints
· Teste concluant.
VI.2.3.Interprétations
A l'exception de l'intervention corrective sur le compresseur
TC 205 et TC 208 de la machine qui présente des vibrations excessives
dues aux phénomènes d'écoulements, et
pour ce cas aucun remède n'a été apporté sauf la
limitation de la vitesse d'exploitation de 65% et partage des charges des
machines (même phénomène existe sur TC 410 SC4). Cependant
ce phénomène ne cesse de ce généralisé sur
d'autres compresseurs de la ligne.
On peut anticiper l'incrimination du système du joints
d'étanchéité installés dans ce compresseur de type
; garniture avec contact [3], puisque ce genre de dispositifs peut
présenter des phénomènes d'écoulement cycliques.
80
Chapitre VI : Opportunité de modification du
système d'étanchéité du compresseur
Cooper-Bessemer
VI.2.3.a. Première supposition
Rupture du filme d'huile [16] :Il a
été montré que la lubrification hydrodynamique peut
générer des zones de dépression. Si les pressions sont
suffisamment basses, le film fluide peut se rompre selon trois processus:
de l'air ou du gaz en provenance de l'atmosphère peut
s'introduire dans le contact ;
les gaz dissous dans le lubrifiant sont expulsés ;
le fluide peut se vaporiser (si c'est initialement un
liquide).
En 1969, Nau et al est probablement un des premiers auteurs
à mettre en évidence expérimentalement le
développement de cavitation entre les faces d'une garniture (figure ).
Pour cela, il utilise un stator plan en verre et un rotor en carbone dont la
face est ondulée.
En cas de rupture du film, la pression atteint une limite
physique qui est soit la pression de vapeur saturante soit la pression
atmosphérique, suivant la localisation de la zone de cavitation.
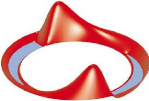
Figure VI.1: Champ de pression et rupture du
film dans l'interface d'une garniture
mécanique.
Dès 1961, Denny et al. [16] avait montré que le
film fluide pouvait générer une pression moyenne bien
supérieure à la pression d'alimentation ce qui n'est possible
qu'avec une composante hydrodynamique et des zones de rupture de film.
VI.2.3.b. Deuxième supposition
Changement de phase [16]: Lorsque le fluide
traversant l'interface d'une garniture mécanique change de phase, les
variations importantes de masse volumique qui apparaissent peuvent conduire
à des comportements instables.
Chapitre VI : Opportunité de modification du
système d'étanchéité du compresseur
Cooper-Bessemer
Ce thème a donc intéressé un certain
nombre scientifiques, l'aspect expérimental ayant toutefois
été moins abordé.
Liquide Vapeur
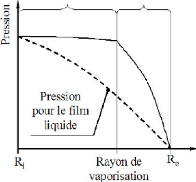
Rayon de vaporisation
Figure VI.2: Changement de phase en fonction
de la pression et de position radiale.
La viscosité cinématique de la vapeur
étant très supérieure à celle de l'eau, on observe
un discontinuité dans le gradient radial de pression qui se traduit par
une augmentation de la portance générée par le fluide.
Celle-ci dépend bien sûr de la position de la frontière
dans l'interface.
S T
E G
5-
4
Q 5
tÎ
1, 15 20 25 Tirne (ms)
i
30 35 40
81
Figure VI.3: Variation de l'épaisseur
de film dans l'interface d'une garniture en présence de changement de
phase[16].
82
Chapitre VI : Opportunité de modification du
système d'étanchéité du compresseur
Cooper-Bessemer
VI.2.4.Analyse de la consommation des huiles
Nous avons établi la consommation des huiles TORBA 32
(Naftal), pour trois ans 2014,2015 et 2016, des compresseurs Cooper-Bessemer,
résumée dans le tableau suivant :
Tableau VI.2: Consommation annuelle d'huile.
2014
|
|
2015
|
2016
|
|
|
Consommati
|
Consommati
|
|
Consommati
|
|
on d'Huile
|
N° on d'Huile
|
N° s
|
on d'Huile
|
|
[L] [L]
|
|
[L]
|
|
AMAL
|
|
|
T05
|
200 T05 830
|
T05
|
400
|
|
|
030
|
T06
|
|
T07
|
0
|
T07 100
|
T07
|
0
|
T08
|
316
|
T08 Mil
|
T08
|
min
|
T09
|
500
|
T09 120
|
T09
|
433
|
|
|
T10
|
|
|
T11
|
716
|
T11 650
|
T11
|
733
|
3 499
Total général 9 517
Résultats : La consommation moyenne
annuelle (jours ouvrable) est de 3172 L. VI.2.4.b. Analyse des
débits d'huile de la machine d'entrainement MS 3142 Le
système de lubrification Turbine d'entrainement MS 3142 est
composé de :
· Pompes
· Carter de 6400 L
· Réfrigérant
· Filtres
· Vannes et dispositifs de commande et de
sécurité.
· Collecteur principal de lubrification des paliers 1.76
Kg/cm2.
83
Chapitre VI : Opportunité de modification du
système d'étanchéité du compresseur
Cooper-Bessemer
NB. Une partie d'huile de ce système
est consacrée comme source d'huile pour le système d'huile de
lubrification et d'étanchéité de la charge (compresseur)
:
Tableau VI.3 : Les débits d'huile de
lubrification.
Dispositif consommateur Débit d'huile
[L/min]
Equipement de charge (Compresseur) 380
Palier N°1 158.5
Plaier N°4 1111
Engrenage accessoires 57

Accouplement 18.9
Turbine de démarrage 13.24
La consommation moyenne normalisée ne doit pas
dépasser 10 Galons/ J=37.85 L/J.
VI.3.PROPOSIONS DE MODIFICATION DE LA GARNITURE A
BAGUE FLOTTANTE
VI.3.1.Proposions de modification pour la
réduction de consommation
VI.3.1.a. Modification de la bague flottante
d'étanchéité interne par une bague à rainure
(Windback)
Aujourd'hui les systèmes
d'étanchéité à bagues flottantes, incluent beaucoup
d'améliorations et rénovations par rapport aux anciens
systèmes, en termes de performances,
maintenabilité et fiabilité.
La bague d'étanchéité flottante interne
représente l'élément critique et principal
d'étanchéité.
En effet, l'huile d'étanchéité et le gaz
processe trouve leur contact au niveau de cette bague flottante interne,
étant donné que la pression de l'huile est supérieure
à la pression du gaz, une quantité d'huile chargée de gaz
s'enfuie dans le gaz processe (Compresseur), et une quantité doit
être traité et récupérée dans le
réservoir d'huile [4].
84
Chapitre VI : Opportunité de modification du
système d'étanchéité du compresseur
Cooper-Bessemer
Parmi les améliorations les plus fréquentes,
apportées sur la bague flottante interne, est le remplacement par une
bague flottante interne à rainures (windback floating
ring seal),
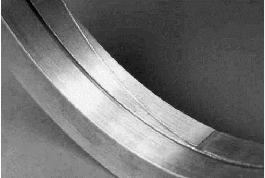
Figure VI.4: Bague flottante interne à
rainure Windback oil seal'.
Ces rainures sur la surface formée par du
diamètre interne avec l'arbre, consiste en un usinage partiel en spiral
qui créer une petite contre pression par la rotation relative de la
bague sur l'arbre et pompe de l'huile d'étanchéité vers le
palier lisse coté impulseur[4].
Cette modification diminue la quantité d'huile
d'étanchéité envoyée vers la chambre à gaz
de labyrinthe, ce qui va réduire la migration d'huile vers le
compresseur à travers le labyrinthe.
VI.3.1.b. Modification associée aux bagues
d'étanchéité flottante à rainure :
Une quantité d'huile aigre ou chargée du gaz
est généralement drainer vers un piège d'huile et puis
traitée par un dégazeur. Apres avoir modifié la bague
flottante interne, par celle à rainure (Windback seal), une
quantité importante de cette huile est diminuer en conséquence de
ce rétrofit, ce qui a permis à certaine utilisateurs
d'éliminer ce piège d'huile, puis l'huile est simplement
envoyée au dégazeur pour éventer ou torcher le gaz [4].
Cependant, pour répondre aux exigences
environnementale, certain utilisateur préfère d'installer un
système de production d'azote (Nitrogen Buffer) pour l'injecter dans la
chambre d'huile chargée du gaz (huile aigre entre la bague
d'étanchéité et le labyrinthe) qui sert comme un gaz
séparateur huile-gaz processe, donc le gaz à torcher est
éliminer
85
Chapitre VI : Opportunité de modification du
système d'étanchéité du compresseur
Cooper-Bessemer
Or, cette modification nécessite une installation d'un
équipement de production d'azote, et des couts d'énergie
supplémentaire sont ajouté, en plus ce type de garniture consomme
beaucoup d'azote de séparation de 40 à 70 scfm, qui est
équivalent à 68 à 119 m3/h.
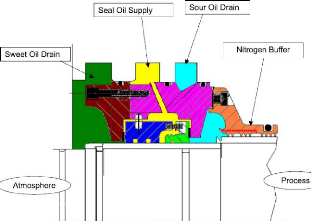
Seal Oil Supply
Sour Oil Drain
Process
Nitrogen Buffer
Sweat Oil Drain
Figure VI.5: Montage d'une garniture à
bague flottante d'étanchéité à huile.9
VI.3.2.Faisabilité sur le compresseur
Cooper-Bessemer
I ya deux aspects techniques qui doive être
examiné, pour achever à l'amélioration du système
d'étanchéité à bagues flottante :
Existence d'une dimension d'installation d'une bague Windback
: en effet les dimensions requises sur le compresseur Cooper-Bessemer sont
donnés par l'emplacement original de la bague
d'étanchéité flottante interne. Et ce la n'exclu pas la
connaissance approfondi des dimensions et de la bague et du dispositif de
retenue [4].
86
Chapitre VI : Opportunité de modification du
système d'étanchéité du compresseur
Cooper-Bessemer
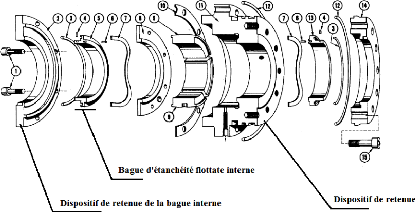
Dispositif de retentie
Bague d'étanchéité flottate interne
Dispositif de retenue de la bague interne
Figure VI.6: Garniture mécanique du
compresseur Cooper Bessemer.
Existence d'un système du support du circuit d'huile
d'étanchéité : pour le cas du compresseur Cooper-Bessemer,
le système d'huile d'étanchéité doit être
révisé pour réglage et control après installation
d'une bague d'étanchéité Windback.
VI.3.3.Influence de rétrofit sur les perforante du
système d'étanchéité
Diminution de consommation d'huile jusqu'à environ 90%
( 1" Exemple de rétrofit de la référence [4]).
Diminution systématique d'émission des gaz
éventés et séparés des huiles aigres.
Elimination du système de piège d'huile et le
maintien du système de vanne de commande et dégazeur.
Chapitre VI : Opportunité de modification du
système d'étanchéité du compresseur
Cooper-Bessemer
c>
Gaa h rifireeer
C.4 Tem ra.spiraliea
a 4 .4.-JI
Û
Soupape d*
dichorge &l $piem=
t
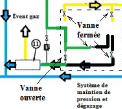
nram priecipal


Vanna de Eammaod!
Huile de 1cents1:Krihiesti n
1.4 Sp ltd

i apiYn d ·k il ·
d
I}ésembueur et piege d'huile enlevés
87
Figure VI.7 : Le système de
contrôle et régulation (Console) du système d'huile
d'étanchéité (sans piège d'huile).
Avec l'élimination du système de piège
d'huile, l'intervention accidentelle sur ces organes est
éliminée, et le risque de fuite d'huile est réduit. Par
contre le risque de perte d'huile par défaillance de la vanne de
commande différentielle est émanent.
Diagramme de fiabilité :
5veréme
1 erancltéiré
|
|
|
|
|
|
|
|
|
|
Pompes
|
|
Soupapes deRésettioit d'huile y BaEue
decltar_e d'éranchéiré
Gaz de référence
|
|
|
|
|
Présion de sen ice Kg2cnt
|
|
|
|
Vanne de commande
LFon:donneniens fiable

Gaz de référence
Figure VI.8 : Diagramme de fiabilité
du système d'étanchéité à bague flottante
Windback
(rétrofit).
88
Chapitre VI : Opportunité de modification du
système d'étanchéité du compresseur
Cooper-Bessemer
VI.3.4.Exemple de rétrofit par la
technologie par bague d'étanchéité à rainures
Windback floating ring seal'.
ter exemple :
La plus grande raffinerie aux USA de la Californie,
fonctionne avec une large gamme de compresseurs à garniture conique.
Ces compresseurs centrifuges sont entrainés par des
turbines à vapeur pour recycler l'hydrogène à un
régime de 500 tr/min en mode standby, cette vitesse est inférieur
à la vitesse nominal de fonctionnement des compresseurs (Speed
design).
Avec la réduction du régime de fonctionnement
et la diminution de vitesse des compresseurs, de 500 tr/min, ces garnitures
d'étanchéités ont eu de très faible performances,
et développe moins de contre pression
d'étanchéité.
Les huiles de récupération ont
dépassée la barre de 870 L/jour de fonctionnement.
Cette consommation d'huile excessive faisait appel à
l'amélioration de la bague d'étanchéité flottante
interne par une bague d'étanchéité flottante à
rainures spirale (Windback flotting seal). La consommation d'huile est
arrivée à 37 L/jour de fonctionnement.
Et le retour d'investissement a été estimé
approximativement (06) six mois [4]. 2ème exemple :
Une centrale de traitement de gaz à l'ouest des USA,
constituée de trois types différents de compresseurs centrifuges
implantés dans le processe, avec un système
d'étanchéité à bague flottante installé dans
les années 1980.
L'huile d'étanchéité
récupérée est traités dans le système de
séparation et de dégazage et puis retournée aux
réservoirs d'huile des trois compresseurs, et les gaz extrait est
notamment éventé ou torché, estimé 200 000 à
300 000 SCFD qui est équivalent à 248 Nm3/heure
à 372 Nm3/heure.
L'opérateur de la centrale souhaite de réduire
l'émission des gaz, pour satisfaire des réglementations
environnementales en vigueur, et la diminution des couts engendrés par
la perte du gaz processe.
Pour arriver à ces objectifs, les compresseurs
centrifuges subissent un rétrofit en 2003, qui remplace l'ancienne bague
d'étanchéité flottante par une bague
d'étanchéité flottante à rainures spirale (Windback
flotting seal).
En résultats les, les huiles de
récupération chargées de gaz ont été
dramaticalement réduit, ce qui fait diminuer l'huile recyclée et
le gaz torché.
Chapitre VI : Opportunité de modification du
système d'étanchéité du compresseur
Cooper-Bessemer
Ce la a permis à l'opérateur de la centrale,
d'isoler le système de piège d'huile et de dégazage
d'huiles d'étanchéité.
Et le retour d'investissement a été estimé
approximativement (02) ans [4].
VI.4.PROPOSITION D'INSTALLATION D'UNE GARNITURE
D'ETANCHEITE SECHE SUR LE COMPRESSEUR COOPER-BESSEMER
Analysant les interventions de la maintenance
systématique (RI' et RG) des compresseurs Cooper-Bessemer, nous avons
constaté qu'à chaque intervention, les bagues
d'étanchéité et de labyrinthe rejoignent bien les
tolérances prescrites par le constructeur.
Or, un volume horaire considérable
d'indisponibilité est engendré par la défaillance des
auxiliaires du système d'étanchéité (pompes,
piège d'huile, vanne de commande différentielle...), sans autant
d'évoquer la consommation des huiles par le système
d'étanchéité qui fait d'environ 3172 L/an sur la
population des compresseurs étudiés.
.[odificarion de bague ilorranre interne
|
|
|
|
|
|
|
L_
|
|
Sye renie
d'érancheite
|
Huile de Lubrification
|
|
|
|
|
Présiao de service 1.1 kgicm
|
|
|
|
|
|
Piége d'huile
|
Vanne de commande
|
|
|
|
Désembueur Gaz de référence
L_DégazeurI
ELévementdu svstéme de pii_e d'huile
L
Faoctiaonemeot fiable
89
Figure VI.9: Diagramme de fiabilité du
système d'étanchéité à bague flottante
ordinaire.
Une défaillance de piège d'huile, ou la vanne
de commande différentielle, peut engendrer une consommation d'huile
excessive, qui entraine cette huile vers le gaz processe, et puis au gazoduc
(huile constatée lors des opérations de nettoyage par piston
racleur).
Chapitre VI : Opportunité de modification du
système d'étanchéité du compresseur
Cooper-Bessemer
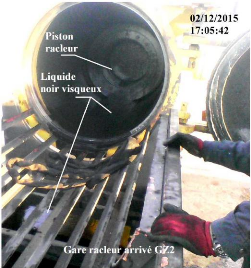
02/12/2015
17:05:42
Figure VI.10 : Liquides aperçu lors
d'une opération de nettoyage par piston racleur du gazoduc GZ2
(`S').
VI.4.1.Description de la technique
d'étanchéité sèche
Plus de 20 ans d'existence, les garnitures sèches
à gaz trouvent leurs applications sur des compresseurs centrifuges
opérants dans différents processus industriel (Raffinage,
transport du gaz, réinjection des gisements...) [5].
u
60
t.
50 -cu a 1D i
3026-- 20
E a z
10
0
0 0 o a a a a 9 0 0
o ) b a
90
Figure VI.11: Évolution du nombre de
brevets déposés sur les garnitures
d'étanchéité.
91
Chapitre VI : Opportunité de modification du
système d'étanchéité du compresseur
Cooper-Bessemer
Durant ces années d'application intensive de cette
technologie, aucune norme industrielle n'existait. L'API (American Petrolium
Institut) a récemment dressé les recommandations et standards API
614 de conception des systèmes d'étanchéité
à gaz et les garnitures sèches en 1999[5].
Aujourd'hui, plus de 80% des compresseurs centrifuges dans le
mandes, sont originalement fabriqués avec des garnitures
mécanique sèche[5].
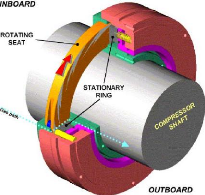
INBOARD
ROTATING
SEAT ------------y
Figure VI.12: composition d'une garniture
à gaz.
Une tendance de cette solution alternative, qui fait que, les
utilisateurs remplacent les enceins système
d'étanchéité à garniture à huile par celle
de la garniture sèche[4].
Cette modification engendre le déclassement de la
garniture à filme d'huile (bague d'étanchéité
flottante), et l'installation d'une nouvelle cartouche
d'étanchéité sèche, et le système de
conditionnement du gaz d'étanchéité.
Chapitre VI : Opportunité de modification du
système d'étanchéité du compresseur
Cooper-Bessemer
PRIMARY SECONDARY
VENT VENT
Î 4f
SEPARATION GAS SUPPLY
SEAL GAS SUPPLY
41i
T
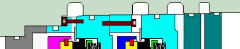
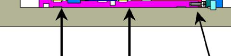
92
PROCESS ~~ BESIARING
INNER
LABYRINTH PRIMARY SECONDARY BARRIER
SEAL GAS SEAL GAS SEAL SEAL
Figure VI.13: Montage en Tandem d'une
garniture d'étanchéité à gaz.
Les garnitures mécaniques sèches consistent
d'une bague rotative fixée à l'arbre qui représente la
surface de matage, et une bague primaire stationnaire fixé dans le
carter.
Durant le fonctionnement, des rainures spirales
façonnées sur la bague de matage génèrent des
forces aérodynamiques et aérostatiques.
Ces forces engendrées par la rotation séparent
les deux bagues d'environ 3 à 10 microns sans liquide de lubrification,
et un filme fin de gaz s'installe entre les deux surfaces. Ce filme de gaz
sépare le gaz processe de l'atmosphère.
Ces garnitures existent sur plusieurs configurations. Pour
les applications générales en utilise la configuration
Tandem[4].
VI.4.2.Faisabilité et Opportunité de
rénovation
Il ya beaucoup de considérations techniques pour
effectuer un rétrofit par garniture sèches : VI.4.2.a.
Espace de réception de la garniture
Existence d'une cavité d'emplacement
sur le carter du compresseur. Si les dimensions de l'alésage ne
suffisent pas il ya lieu de d'effectuer un usinage au carter pour recevoir la
nouvelle garniture. Généralement une entretoise est
ajoutée à l'arbre pour installer les éléments de la
garniture[4].
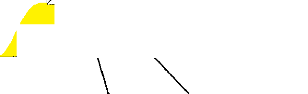
Chapitre VI : Opportunité de modification du
système d'étanchéité du compresseur
Cooper-Bessemer
Espace de réception de la cartouche de garniture
séche â gaz

i ;11.1111V1
Aill
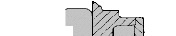
g `1E6
0 14
41 liiSP
. 'IL All k r'
re
:11111r
iiiMMIIIIIIIIIMIIIMIlmi

"1,`
Huile de
Consércation de la bague Labyrinthe
Consérvation de lubrification
la posistion du basse pression
palier lisse
93
ELéments fixes
Elément en mouz-ement (Rotor)
Elémeut en frottement
Circuit du gaz
Huile de Lubrification 1.4 Kgicm2
Figure VI.14: Espace de réception
d'une cartouche de garniture sèche sur le
compresseur Cooper-Bessemer.
VI.4.2.b. Configuration du carter
La garniture de configuration Tandem
nécessite au moins (04) quatre lumières[4] :
· Alimentation du gaz d'étanchéité
(Seal gaz supply).
· Event de la garniture primaire (Primary vent).
· Event de la garniture secondaire (Secondary vent).
· Et l'alimentation du gaz de séparation (Barrier
gas).
Si le carter contient des lumières inadéquates, ce
dernier doit subir un usinage.
VI.4.2.c. Comportement vibratoire
L'étude du comportement vibratoire doit être
effectuée avant le rétrofit. Néanmoins l'enlèvement
de la garniture à bague flottante affecte systématiquement le
comportement
vibratoire.si l'atténuation
des vibrations est affecté, le compresseur nécessite des
éléments d'atténuation supplémentaire [4].
94
Chapitre VI : Opportunité de modification du
système d'étanchéité du compresseur
Cooper-Bessemer
VI.4.2.c. Gaz d'étanchéité
Il est très important de connaitre le comportement
thermodynamique du gaz d'étanchéité (Gaz naturel). Or ce
gaz peut changer de nature thermodynamique opérant sur la garniture
mécanique de rétrofit. Ce la peut être évalué
par un diagramme de phase du gaz d'étanchéité [4].
1601) mie i2oo moi
aao 500 406 206
|
~
|
|
Cou
|
be de
|
|
|
|
|
|
|
|
|
can
|
.ensatiun
|
|
|
|
|
|
|
|
|
|
|
|
|
|
|
|
|
|
|
|
|
|
|
Ga.
|
non chauffé
|
|
|
|
Gaz€hauffë
|
|
Mixed
|
(Gas1 L,quidj
|
Phase
|
|
|
Gas Phase
|
|
|
|
|
|
|
|
|
|
|
|
|
|
|
|
|
|
Détente
|
|
|
|
|
|
|
Détente
|
|
|
|
|
|
|
|
|
|
|
|
|
|
|
|
|
|
|
|
|
|
|
|
|
20 -00 60 80 '00 12) 140 160 180 A6
2M,
tMipaveum (AFc F)
Seal Cm Dew Une mOmIleal t3®e'Ah 20 aes F Sapat
t9eal c .::..ti n 100 deg. F supeneal
Figure VI.15: Diagramme typique de
changeur de phase du gaz d'étanchéité.
Le champ de température calculé dans un film de
gaz d'étanchéité est présenté sur la figure.
Celui-ci présente des variations similaires à la courbe de
pression. Toutefois, la température varie très peu dans la
section d'entrée pour atteindre des gradients très importants
près de la sortie où le fluide se détend [16].
Chapitre VI : Opportunité de modification du
système d'étanchéité du compresseur
Cooper-Bessemer
i
|
|
|
Rétrécissement brusque
p(Re)
|
Écoulement isentropique
Pe Te
|
290 280 270 260
a m 250
~ 240
|
|
|
|
(Ri)
|
|
|
|
Filin fluide
|
T(Re)
|
|
t - I

ohimoi
r/
~~
~
0175
0.08
~~
0,005ik
S

0 09
75E 06 `+~~ s~u
5E-06
F -06
0 07
0°111%%111% _..id111011101P.
4411
95
Figure VI.16: Conditions aux limite de
pression et de température d'un filme d'étanchéité
à
gaz.
La détente du gaz conduit à une baisse
très significative de la température d'environ 60K. D'autre part,
on peut noter que les variations suivant l'épaisseur du film,
très faibles en entrée atteignent une vingtaine de Kelvins
près du rayon intérieur. Toutefois, il faut garder à
l'esprit que l'amplitude des variations est accrue en raison des parois
adiabatiques qui ne participent pas aux transferts de la chaleur qui est
entièrement transportée par l'écoulement [16].
L'API 614 (1999) recommande un système de chauffage du
gaz d'alimentation d'étanchéité maintenue à
20°F supérieur au point de condensation du gaz [5].
Chapitre VI : Opportunité de modification du
système d'étanchéité du compresseur
Cooper-Bessemer
VI.4.3.Paramètres industriel de fonctionnement
:
Separation gas filters
- lie Separtitien


Primary gas seal vents { ty caI.
bath 'dents)
|
|
Y
Secondary gas seal vents
|
|
96
Figure VI.17 : Synoptique d'une console typique
de conditionnement et contrôle du gaz
d'étanchéité.
VI.4.3.a. Source d'alimentation de gaz
d'étanchéité
En industrie, généralement on alimente le gaz
d'étanchéité depuis la décharge du compresseur
lui-même, ou un générateur d'azote.
Une source de gaz d'étanchéité doit
être disponible en quantité et en préssion sufisante durant
le fonctionnement d'un compresseur (Demarage, régime pemanet,
arrets).
Généralement la pression du gaz
d'étanchéité doit être supérieure à la
pression requise de 50 psi, (3.44bar) [5].
Le gaz d'étanchéité ne doit pas contenir
des particules solides de dimension supérieurs à 10 microns et
99.97% sèche.
Pour éviter la condensation du gaz
d'étanchéité durant le fonctionnement, l'API 614
recommande la température du gaz employé qui doit au minimum
avoir une température supérieur à 20 °F (11°C)
du point de condensation du ce gaz [5].
97
Chapitre VI : Opportunité de modification du
système d'étanchéité du compresseur
Cooper-Bessemer
VI.4.3.b. Filtration et le système de
conditionnement de gaz d'étanchéité
L'utilisation des garnitures sèche nécessite un
système de conditionnement du gaz d'alimentation de la garniture,
à savoir :
· Filtration et séchage du gaz d'alimentation (Clean
and Dry supply gas seal).
· Filtration et séchage du gaz barrière
(Clean and Dry barrier gas seal) [5].
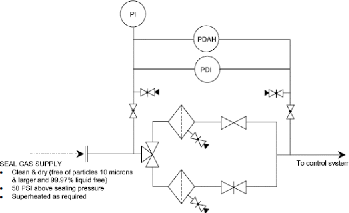
PDAH
ppI
SEAL GAS SUPPLY
· Clean 8 dry (irae of pari cies 10 microns $ larger
ond 99.97% liq.aid free)
· 60 PSI above reeling pressure
· Superheated as required
To control system
Figure VI.18: Synoptique d'un système de
filtration typique du gaz d'alimentation. VI.4.3.c. Régulation
et Contrôle
Il ya deux méthodes de control d'alimentation en gaz
d'étanchéité. Contrôle par pression
différentielle par régulation de la pression du gaz
d'étanchéité envoyé à labyrinthe
d'étanchéité, qui est maintenu d'environ 10 psis (0.6 bar)
supérieur à la pression du gaz de référence [5].
Chapitre VI : Opportunité de modification du
système d'étanchéité du compresseur
Cooper-Bessemer
Suai gas from filters
98
To compressor seal Y gas supply, low pressure or
intake end
|
To compressor seal gas
· supply, high pressure or
Seal gas reference from discharge end compressor ("process
side)
|
|
Figure VI.19 : Synoptique d'un système
typique de commande par pression différentielle. VI.4.3.d. Event
de la garniture primaire (Primary gas seal vent)
Le gaz d'étanchéité est injecté
entre le labyrinthe et la bague d'étanchéité primaire.
La majorité du gaz injecté passe à
travers le labyrinthe, et une petite quantité passe à travers la
garniture primaire. Cette quantité perdue à travers la bague
d'étanchéité primaire représente de 5 à 15
scfm, équivalent à 8.5 m3/h à 25.5
m3/h[5].
To lare
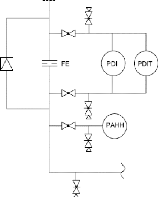
PSE
From compressor prImary seal vent area
Low point drain
Figure VI.20 : Synoptique d'un système
de tuyauterie typique d'évent de la garniture
primaire.
Chapitre VI : Opportunité de modification du
système d'étanchéité du compresseur
Cooper-Bessemer
VI.4.3.e. Gaz de séparation de la bague
secondaire (Secondary gaz seal vent)
VI.4.3.f. Bague secondaire (Barrier Seal) :
sépare le gaz d'étanchéité de la garniture
de système de paliers lisse. Cette séparation est
effectuée par l'injection d'un gaz barrière
généralement l'Azote ou l'air.
La première fonction de la bague de barrière est
d'empêcher l'huile de lubrification des paliers de pénétrer
à la garniture d'étanchéité.
La deuxième fonction est d'assurer
l'étanchéité dégradée en cas ou la
détérioration des bagues d'étanchéité
primaire et secondaire (Primary and secondary gaz seal) [5].
Delayed shutdown
----~ P~ALL}r--- ·
f
|
|
|
|
|
|
|
|
|
Secondary vent reference from pipe
|
|
|
|
Separation gas from filters
PDAL Low pressure alarm & permissive
to shirt lube oil pumps

99
Secnndary vent
from compressor 'n co-irrcsInr harrier
|
V
To compressor bnr-c.
|
|
se,: I ro e_'6_. e or seal, high pressure
Figure VI.21: Synoptique d'un système
typique de commande par pression différentielle du
gaz de séparation.
VI.4.4.Aspect sécurité de fonctionnement du
compresseur
La pression et le débit de l'évent primaire de
la garniture doit être contrôlé pour veiller à aux
signes de détérioration de la garniture primaire (augmentation du
débit et de pression au niveau de l'évent primaire). Pendant le
démarrage et l'arrêt du compresseur, les paramètres de
lecture doivent être soigneusement contrôlés.
La garniture secondaire doit mécaniquement remplir la
fonction d'étanchéité en cas ou la garniture primaire
cède de fonctionner, jusqu'à l'arrêt total du
compresseur.
Chapitre VI : Opportunité de modification du
système d'étanchéité du compresseur
Cooper-Bessemer
Il est très recommandé d'utiliser l'azote comme
un gaz de séparation au niveau d'alimentation de gaz de
séparation, pour éviter les complications engendrées par
l'utilisation de l'air. Cependant l'utilisation du l'air comme un gaz
séparateur dans des compresseurs à gaz naturel créer un
mélange qui peut être explosif [5].
Dans le cas ou l'air est utilisé, l'ai d'alimentation
est injecté dans la tuyauterie de l'évent de gaz de
séparation et l'évent de secondaire pour garantir un niveau
inférieur de mélange air-gaz LEL inférieur à
50%[5].
VI.4.5.Gain économique immédiat
Apres une rétrofit par garniture sèche bien
conçu, l'intérêt économique peut se présenter
dans les cas suivant :
VI.4.5.a.Consommation des huiles (les pertes
des huiles au compresseur) est éliminée, à cause de
déclassement du système de contrôle et du traitement
d'huile d'étanchéité (piège d'huile).
syetime
d'étanchi té
Huile de lubrification
Pompes
Soupapes. de Réservoir d'huile y Balte
Présion de sersice
1,414cm2
Vanne de
commande
Fonctionnement fiable

décharge
d'étanchéité
41=1 1 Gaz de
référence
100
Gaz de référence
Figure VI.22 : Diagramme de fiabilité du
système d'étanchéité à bague flottante
Windback
(rétrofit)

Svstéme
d'êtanchéitê â gar

Gaz d' eta ncheité Seal gaz supply
Gaz processe
Gaz séparateur
Air ou Azote
Filtration N21
0.3 micron
Filtration Nc2
>20 °F de point de condensation (API
614)
Vanne de Nat commande

commande
de Etanchéitê ti°1
commande primaire
Réchauffeur
Fonctionnement fiable
Etanchéité secondaire

Figure VI.23 : Diagramme de fiabilité du
système d'étanchéité à gaz
(rétrofit)
VI.4.5.b.Complexité de maintenance :
le système de conditionnement du gaz
d'étanchéité est beaucoup plus simple que celui du support
d'huile d'étanchéité de la garniture à filme
d'huile [5].
101
Chapitre VI : Opportunité de modification du
système d'étanchéité du compresseur
Cooper-Bessemer
VI.4.5.c.Cout d'exploitation: Réduire
les pertes mécaniques d'entrainement du compresseur absorbées par
le système d'étanchéité à bagues flottantes
de 10 fois par rapport au système d'étanchéité gaz
[6]. Le cout estimé de perte de gaz est très réduit
à savoir :
Pertes de gaz du système à garniture
sèche de 0.5 à 3 scfm, qui est équivalent à 0.85
à 5.1 m3/h, contre la perte engendrée par le
système à filme d'huile de 40 à 200 scfm, qui est
équivalent à 68 à 340 m3/h[5].
VI.4.5.d.Maintenabilité :
après une défaillance diagnostiquée sur des
garnitures à gaz, l'opérateur peut remettre à niveau cette
garniture sans autant de les changer, au contraire de celle des garnitures
à bague flottante qui se consomme [5].
Augmenter la fiabilité du système
d'étanchée du compresseur. Ce système présente un
taux de défaillance de 0.175 pannes/an sans entretien, ce qui vaut une
panne par (06) ans ou plus [5].
VI.4.5.e.Sécurité : Augmenter
le niveau de sécurité par l'élimination des huiles
chargée du gaz, et de quantité de perte du gaz processe (Gaz
naturel) qui peuvent engendrée un mélange combustion dans le
système de torche [5].
VI.4.6.Inconvénients
En revanche, les solutions de rénovation
technologiques ne peut vent être des solutions parfaites, une
modification par garniture sèche présente des
inconvénients :
VI.4.6.a. Nécessité d'usinage
et reworking du compresseur pour adaptation dimensionnelle de la
cartouche de garniture sèche à installer.
VI.4.6.b. Changement de comportement vibratoire
du compresseur, changement de la vitesse critique, amplification de
facteur logarithmique vibratoire, donc il est nécessaire d'examiner le
comportement dynamique du compresseur. Si cet examen ne sera pas satisfaisant,
il est nécessaire d'ajouter des pièces d'atténuation
vibratoire (Damping equipment) comme des bague à nie d'abeilles
(Honeycomb ring) [4].
102
Chapitre VI : Opportunité de modification du
système d'étanchéité du compresseur
Cooper-Bessemer
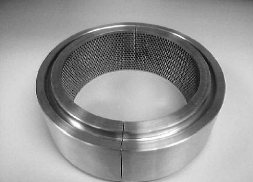
Figure VI.24 : bague
d'étanchéité qui remplace le labyrinthe, qui a un effet
atténuateur de
vibration.
VI.4.6.c. Influence de la filtration 26:
Très grand risque de défaillance lors de l'existence de
particules ou liquide de gaz t'étanchéité. Ces particules
affectent fatalement les surfaces fonctionnelles de la
garniture. Or cette condition est décisive en ce qui
concerne la fiabilité du système. Le gaz
d'étanchéité doit être sec et filtré.
VI.4.6.d. Fiabilité 26: La
fiabilité du système peut être affectée par les
arrêts les démarrages et le fonctionnement à bas
régime. Cette situation nécessite un système de
pressurisation supplémentaire.
VI.4.6.e. Prix d'achat d'une cartouche26:
Des couts élevés. Une cartouche d'une
étanchéité sèche coute de US$ 50 000.00 à
US$ 60 000.00, or l'ensemble des pièces à bague
d'étanchéité flottante cout d'environ US$ 20 000.00
à US$ 30 000.00[4].
VI.4.6.f. Maintenabilité modulaire 26:
Un système complexe, le système de conditionnement de la
garniture sèche est moins complexe que celui à bague
d'étanchéité flottante, par contre la cartouche de la
garniture sèche est plus complexe en construction. Lors d'intervention
du service maintenance, la cartouche est enlevé et envoyer au
constructeur pour la réparation, puisque le diagnostique ce fait sur un
banc d'essai.
Nécessité d'un gaz barrage (azote ou l'air),
pour éviter le passage des huiles de lubrification des paliers aux
surfaces d'étanchéité de la cartouche.
103
Chapitre VI : Opportunité de modification du
système d'étanchéité du compresseur
Cooper-Bessemer
VI.4.7.Exemples de rétrofit ler
exemple
Une raffinerie en Angleterre UK, opérant avec un
compresseur model 2M8-6 implanté dans le processe de convertisseur
catalytique des fluides.
Ce compresseur fonctionne avec une garniture
d'étanchéité à bagues flottante avec injection
d'azote, pour prévenir de la contamination par les sulfures
(H2 S).
Dans un but de réduction de consommation d'huile et
d'azote baffer, l'opérateur de la raffinerie adopte un projet de
rétrofit d'une garniture sèche de configuration
opposée.
La consommation d'azote baffer, a été
réduite de 137 scfm à 6 scfm, qui est équivalent à
une réduction de 232 m3/h à 10 m3/h.
Depuis ce temps, et après conversion
d'étanchéité, le compresseur fonction avec zéro
émission, et le système d'étanchéité
à filme d'huile a été éliminé [4].
2ème exemple
Un complexe de pétrochimie de production d'ammoniac et
d'urée Petrobas' situé à Camaçari, Brésil,
réaménagé pour produire 1500 ton/jour.
Comme effort de rénovation de différents
équipements, l'un de ces rénovations, le remplacement des
garnitures à bagues flottante d'huile des compresseurs de
synthèses.
La consommation des huiles a été excessive
durant les années d'exploitation de l'usine.
Le train de procédé de synthèse, est
constitué de deux compresseurs, entrainés par des turbines
à vapeur d'une puissance totale de 22 670 kW.
Le compresseur basse pression aspire du gaz à 25.5 bar
et refoule à 65.2 bar.
Le compresseur haute pression aspire du gaz à 65.2 bar
et refoule à 156 bars.
De jeux de cartouches en tandem
d'étanchéité à gaz ont été
installées sur les compresseurs
[5].
104
Chapitre VI : Opportunité de modification du
système d'étanchéité du compresseur
Cooper-Bessemer
Tableau VI.4 : Comparaison de performances des
deux systèmes d'étanchéité [4] :
Etanchéité à filme d'huile
Etanchéité à gaz
Cout d'entretien Pompes, vannes, filtres, Sans
frais d'entretient
i piége d'huile, consoles..
|
Consommation
|
3.7 à 378 L/jour
|
Pas du système à huile
|
de Remplaccém nt sur la durée
Tres négligeable du vie du compresseur
|
|
Consommation de Bagues : De 10 à 30
HP < 1 à 2 HP
puissance du système Pompes : 20
à 100 HP d'étanchéité.
Fuites du gaz
|
>25 scfm (42 m3/h)
|
< 2 scfm (3.4 m3/h)
|
Contamination
|
Cout de nettoyage du pipe Pas de contamination
Contamination du gaz processe
|
Gaz de séparation (N2) ir à 70
scfm (68 à 119 m3/h) De 2 à 4 scfm (3.4 à
6.8
m3/h)
|
|
Indisponibilité Très haut cout
indirect Très fiable
(accidentelle) d'indisponibilité
Démarrages ratés
Avec l'élimination du système de
piège d'huile, l'intervention accidentelle sur ces organes est
éliminée, et le risque de fuite d'huile est réduit. Par
contre le risque de perte d'huile par
Conclusion générale
CONCLUSION GENERALE
Un projet de rénovation d'un compresseur exige
l'étude de ces performances, et le cout associé à sont
exploitation.
D'après l'analyse des rapports d'entretient
fournit soit par la DML Laghouat chargé des opérations
RP et RG, nous avons constaté que la garniture
d'étanchéité ne constitue aucun malaise lors du
démontage et contrôle des jeux fonctionnels, et la plupart des
interventions corrective sont dues aux phénomènes
d'écoulements.
On peut anticiper l'incrimination du système du joint
d'étanchéité installée dans ce compresseur, puisque
ce genre de dispositifs peut présenter des
phénomènes d'écoulement cycliques.
Ces phénomènes ont été
interprétés par deux suppositions,
référencées à des travaux scientifiques [16],
à savoir : Rupture du filme d'huile, et changement de phase du liquides
d'étanchéité.
L'examen de la consommation des huiles sur
les compresseurs Cooper-Bessemer, nous a donné les valeurs de la
consommation moyenne annuelle (jours ouvrable) de 31721.
En premier lieu, pour palier à ce
problème de consommation nous avons proposé une
modification sur la bague d'étanchéité flottante interne
(l'élément critique et principal
d'étanchéité) par celle d'une bague flottante à
rainure (windback floating ring seal),
Cette modification a donné des bon résultats
(Exemples de rétrofit dans le mande) constaté sur la diminution
de quantité d'huile d'étanchéité envoyée
vers la chambre à gaz de labyrinthe, ce qui va réduire la
migration d'huile vers le compresseur à travers le labyrinthe.
Apres étude de faisabilité.les résultats
de rétrofit ont un gain positif sur l'aspect maintenance du
système d'étanchéité et la consommation des huiles
à savoir :
· Diminution de consommation d'huile jusqu'à
environ 90% ( ler exemple de rétrofit de la
référence [4]).
· Diminution systématique d'émission des
gaz éventés et séparés des huiles aigres.
· Elimination du système de piège d'huile
et le maintien du système de vanne de commande et dégazeur.
· Prolonger la durée de vie et les couts de
nettoyage du pipeline, après avoir réduire la quantité
d'huile entrainée vers cet ouvrage.
· Le retour d'investissement de rétrofit, a
été estimé approximativement de 06 six mois
à (02) ans [4].
Conclusion générale
défaillance de la vanne de commande
différentielle et le bagues d'étanchéité
usée est émanent.
Un volume horaire considérable
d'indisponibilité (constatés par les opérateurs de la
station de compression) est engendré par la défaillance des
auxiliaires du système d'étanchéité à bague
flottante (pompes, piège d'huile, vanne de commande
différentielle...).
D'abords, pour palier à ce problème
d'intervention accidentelle, nous avons proposé une modification sur le
system d'étanchéité embarqué à bague
flottantes par celui de la garniture à gaz
sèche. Apres étude de faisabilité,
argumentés par des exemples de rétrofit effectués dans le
monde, nous constatant ce qui suit :
Gain économique immédiat
· Consommation des huiles (les pertes des huiles au
compresseur) est éliminée, à cause de déclassement
du système de contrôle et du traitement d'huile
d'étanchéité (piège d'huile).
· Complexité de maintenance : le système
de conditionnement du gaz d'étanchéité est
beaucoup plus simple que celui du support d'huile
d'étanchéité de la garniture à filme d'huile
[5].
· Réduire les pertes mécaniques
d'entrainement du compresseur absorbées par le système
d'étanchéité à bagues flottantes de 10 fois par
rapport au système d'étanchéité gaz.
· Pertes de gaz du système à garniture
sèche de 0.5 à 3 scfm, qui est équivalent à 0.85
à
5.1 m3/h, contre la perte engendrée par le
système à filme d'huile de 40 à 200 scfm, qui est
équivalent à 68 à 340 m3/h[5].
· Maintenabilité : après une
défaillance diagnostiquée sur des garnitures à gaz,
l'opérateur peut remettre à niveau cette garniture sans autant de
les changer, au contraire de celle des garnitures à bague flottante qui
se consomme [5].
· Augmenter la fiabilité du système
d'étanchée du compresseur. Ce système présente un
taux de défaillance de 0.175 pannes/an sans entretien, ce qui vaut une
panne par (06) ans ou plus [5].
· Sécurité : augmenter le niveau de
sécurité par l'élimination des huiles chargée du
gaz, et de quantité de perte du gaz processe (gaz naturel) qui peuvent
engendrée un mélange combustion dans le système de torche
[5].
En revanche, les solutions de rénovation
technologiques ne peut vent être des solutions parfaites, une
modification par garniture sèche présente des
inconvénients :
Inconvénients
Conclusion générale
· Nécessité d'usinage et reworking du
compresseur pour adaptation dimensionnelle de la cartouche de garniture
sèche à installer.
· Changement de comportement vibratoire du compresseur,
changement de la vitesse
critique, amplification de facteur logarithmique vibratoire.
Si cet examen ne sera pas satisfaisant, il est nécessaire d'ajouter des
pièces d'atténuation vibratoire (damping equipment) comme des
bague à nie d'abeilles (honeycomb ring) [4].
· Figure : bague d'étanchéité qui
remplace le labyrinthe, qui a un effet atténuateur de vibration.
· Influence de la filtration : très grand risque
de défaillance lors de l'existence de particules ou liquide de gaz
t'étanchéité. Or cette condition est décisive en ce
qui concerne la fiabilité du système. Le gaz
d'étanchéité doit être sec et filtré.
· Fiabilité : la fiabilité du
système peut être affectée par les arrêts les
démarrages et le fonctionnement à bas régime. Cette
situation nécessite un système de pressurisation
supplémentaire.
· Prix d'achat d'une cartouche : des couts
élevés. Une cartouche d'une étanchéité
sèche
coute de US$ 50 000.00 à US$ 60 000.00, or l'ensemble
des pièces à bague d'étanchéité flottante
cout d'environ US$ 20 000.00 à US$ 30 000.00[4].
· Maintenabilité modulaire : un système
complexe, le système de conditionnement de la garniture sèche est
moins complexe que celui à bague d'étanchéité
flottante, par contre la cartouche de la garniture sèche est plus
complexe en construction. Lors d'intervention du service maintenance, la
cartouche est enlevé et envoyer au constructeur (Réparation &
Retour) pour la réparation, puisque le diagnostique ce fait sur un banc
d'essai.
· Nécessité d'un gaz barrage (azote ou
l'air), pour éviter le passage des huiles de lubrification des paliers
aux surfaces d'étanchéité de la cartouche.
Aspect sécurité de fonctionnement du
compresseur :
Pour un système d'étanchéité
à garnitures sèches très sécurisé, il faut
garantir les aspects suivants :
· La pression et le débit de l'évent
primaire de la garniture doit être contrôlé, pour veiller
à aux signes de détérioration de la garniture primaire,
pendant le démarrage et l'arrêt du compresseur, les
paramètres de lecture doivent être soigneusement
contrôlés.
· Il est très recommandé d'utiliser
l'azote comme un gaz de séparation au niveau
d'alimentation de gaz de séparation, pour
éviter les complications engendrées par l'utilisation de l'air.
Cependant l'utilisation du l'air comme un gaz séparateur dans des
compresseurs à gaz naturel créer un mélange qui peut
être explosif [5].
Conclusion générale
· Dans le cas ou l'air est utilisé, l'ai
d'alimentation est injecté dans la tuyauterie de l'évent de gaz
de séparation et l'évent de secondaire pour garantir un niveau
inférieur de mélange air-gaz LEL inférieur à
50%[5].
Références bibliographique
[1]Manuel instruction N° 92275 , Manuel d'exploitation et
d'entretien, Compresseur centrifuge, RF2/1B-30, COOPER-BESSEMER.
[2] TOTAL/ Manuel de formation/ Cours EXP-PR-EQ130,
révision 0.3/ Exploration et Production/ Les équipements/ Les
compresseurs.
[3] Technique de l'ingénieur, BM 5 425, Garnitures
mécaniques, Technologie.
[4] John S.Staley, Manager Tutbo Product Upgrades,Mecanical
upgrades to improve centrifugal compressor operation and reliability.
Dresser-Rand Company.Olean, NexYork.
[5] John S.Staley, Manager Tutbo Product Upgrades, Dry gaz
seal system design satandards for centrifugal compressor apllications.
Dresser-Rand Company.Olean, NexYork.
[6] Site web www.institut-numerique.org/ les compresseurs
à gaz à bord des navires méthaniers, consulté le
21/01/2017.
[7] Donnée méthode de maintenance, Direction
Maintenance Laghouat, Département Méthode, année 2016.
[8] M. BOUMAIEL, Cours de Gestion de la Maintenance, IAP
Boumerdes, Unité de Formation et de Recherche, Promotion Février
2016.
[9]Site web officiel
www.sonatrach.com,
consulté le mois de Décembre 2016.
[10] Site web officiel
www.sonatrach.com,
Présentation : Sonatrach une dimension gazière internationale,
consulté le mois de Décembre 2016.
[11] BELALA Nacer, Présentation portant sur
l'opportunité du rétrofit du système de démarrage
`turbine de lancement' des turbines GE MS3002, TRC,MNT-TECH, 12/09/2012.
[12] Document informatique d'un rapport de stage, auteurs
CMT/RTO, dernière impression le 22/05/2011.
[13] Maamoune saad et al, Adaptation d'un nouveau
système d'étanchéité `Garniture sèche' au
compresseur K201B, L'Université KASDI MERBAH-Ouargla, 2010/2011.
[14] M. BOULAHDID, Séminaire sur les compresseurs, du
17 /05 au 21/ 05/ 08, IAP Skikda.
[15] IAP Boumerdes, Unité de Formation et de Recherche
en HSE/IAP, Rapport de Stage N° 01 d'Ingénieur
Spécialisé TRC, Heath, Safety & Environment, Promotion
2007/2008.
[16] Noel Brunetière. Les garnitures mécaniques
: Etude théorique et expérimentale.
Mécanique,[physics.med-ph]. Université de Poitiers, France, 2010,
HAL Id.
[17] Presse nationale le 30 Novembre 2016, Déclaration
finale du 15e FIE Forum international de l'énergie d'Alger,
Le gaz naturel et les défis de l'industrie pétrolière mis
en exergue, Publié le 29 septembre 2016.
|