UNIVERSITE DE YAOUNDE I THE UNIVERSITY OF
YAOUNDE I
REPUBLIQUE DU CAMEROUN REPUBLIC OF
CAMEROON
DEPARTEMENT DE PHYSIQUE
DEPARTMENT OF PHYSICS
Mat : 93R943
FACULTE DES SCIENCES
FACULTY OF SCIENCES

LABORATOIRE DE THERMIQUE - ENERGETIQUE
ELECTRIFICATION RURALE ET MOTORISATION
VILLAGEOISE A PARTIR DE LA BIOMASSE DANS
LES CENTRES ISOLES SOUS FORET : CAS DE LA
PROVINCE DU CENTRE AU CAMEROUN
|
Mémoire présenté et soutenu en vue
de l'obtention du Diplôme d'Etudes Approfondies (DEA)
en PHYSIQUE Option :
ENERGETIQUE
Par
TAGUTCHOU Jean Philippe, Maître
ès Sciences Option Energétique
Sous
La Direction de : ET La Supervision de
:
Prof. Emile TANAWA, Prof-Dr-Ing. P.
OWONO ATEBA,
Maître de Conférences à l'ENSP Maître
de Conférences
Année Académique 2000 -
2001
Mémdre de DEA de physique, option Energétique /
Laboratdre de Thermique-Energëique 1
DEDICACES
Je dédie ce travail :
- Au Dieu tout puissant, père céleste
Jéhovah qui a toujours su me garder et qui n'a jamais
cessé de veiller sur moi ; ce travail est le fruit de sa
protection..
- A la mémoire de tous ceux là qui ont
oeuvré pour ma vie et ma scolarisation, mais qui malheureusement ne sont
plus là pour déguster le fruit de leur travail. Je pense à
ma feue grand-mère, à ma feue mère et à mon feu
père ; ce travail est le reflet de votre protection
d'au-delà.
- A la mémoire de maman DJOUMESSAP
Jeanne ; lorsqu'à la première page de mon mémoire
de Maîtrise, alors premier document de ma carrière de chercheur,
parlant de toi j'écrivais : « Ce premier document est le
début d'une carrière qui exige beaucoup de
bénédiction de ta part », c'était sans penser que tu
devrais me quitter seulement un mois plus tard. Mais je suis certain que cette
bénédiction, tu me l'as donnée avant de mourir à
travers ces larmes de joie que tu as sorties pendant la soutenance dudit
mémoire. Je sais pouvoir compter sur tes prières et ta
bénédiction d'au-delà.
- A mon frère aîné et tuteur,
TAMBA Edouard Berlin pour tout le soutien moral et
financier qu'il n'a cessé de me procurer jusqu'alors. Tu peux t'estimer
heureux de m'avoir propulsé jusqu'à ce niveau.
- A ma nourrice TAMBA Marianne qui,
plus qu'une maman n'a jamais cessé de me considérer comme un
fils. Oui tu as toujours été là à l'instant
souhaité pour m'encourager et me soutenir ; « C'est lorsque le
fruit mûrit qu'on le cueille».
- A mes frères aînés TAKAM Michel
, KAMADJOU Edouard, FOUE Happy Pierre,... pour tout le soutien qu'ils
m'ont toujours apporté. Trouvez ici l'aboutissement heureux de tous vos
efforts réunis.
- A mes soeurs aînées, MAPENKA Elise,
FEUKOUA Madeleine, TAWAMBA Jeannine, NGUELO Lucie, et toutes les
autres pour tous leurs soutiens et conseils. Vous avez toujours oeuvré
et prié pour ma réussite.
- A toutes mes belles soeurs, TAKAM Aissatou,
KAMADJOU Julienne, FOUE Marie Claire, ... pour leur soutien sans
relâche ; mention spéciale à Mami pour ses
différents conseils sans relâche : « l'arbre que vous
avez entretenu commence à porter des fruits » .
- A tous mes petits-neveux et
petites-nièces, que ce document constitue pour vous un
exemple de plus à suivre mais surtout à améliorer.
- A tous mes frères et soeurs
réunis, à tous mes parents, qu'ils reçoivent ici
l'expression de mes sentiments profonds.
- Enfin à tous ceux que j'ai oubliés, que personne
ne se sente lésé et qu'ils trouvent ici l'expression de mon
profond attachement.
REMERCIEMENTS
La réalisation de ce travail n'aurait pas vu le
jour sans l'apport de divers moyens et compétences humaines. Je tiens
donc à remercier vivement tous ceux qui ont mis à ma disposition
ces moyens et compétences. Je pense :
v' A l'ONG ERA-CAMEROUN
(Environnement Recherche Action au Cameroun) basée à
Yaoundé à travers son coordonnateur, Dr Emmanuel
NGNIKAM qui non seulement a mis à ma disposition toute une
bibliothèque bien fournie et un cadre logistique adéquat pour la
réalisation de ce travail, mais qui a su trouver tous les moyens
financiers pour la réalisation de ce travail.
v' Au CIRAD (Centre de
Coopération International en Recherche Agronomique pour le
Développement) basée à Montpellier, à travers
M. Philippe GIRARD du Laboratoire Energie / Environnement pour
le suivi de bout en bout de ces travaux malgré la distance.
v' Au LESEAU (Laboratoire Environnement et des
Sciences de L'Eau) de l'ENSP, qui m'a servi de cadre logistique
pour la réalisation de ce travail et où j'ai vécu une
grande expérience de travail rigoureux.
v' Au Département de Physique
de la Faculté des Sciences de l'Université de Yaoundé I
pour toute la formation qu'elle m'a procurée jusque là à
travers les riches enseignements que j'ai reçus.
1' AU Prof-Dr-Ing. Pierre OWONO
ATEBA, Vice Recteur en charge de l'Inspection à
l'Université de Yaoundé I et Chef du département de
Physique de la Faculté des sciences, qui a accepté malgré
ses multiples occupations de superviser mes travaux.
1' AU Dr Emile TANAWA, chef du
département de la Valorisation et de la Coordination de la Recherche et
Chef du Laboratoire Environnement et des Sciences de l'Eau à l'ENSP, qui
non seulement a accepté de diriger ce travail, mais n'a
ménagé aucun effort pour m'assurer un cadre de travail
adéquat et confortable. je vous suis particulièrement redevable
pour toute la patience dont vous avez fait preuve pour me faire
bénéficier de votre grande expérience dont la rigueur et
l'esprit de discernement m'ont permis de mener à bon port ce travail.
v' AU Dr Donatien NJOMO, responsable
du laboratoire de Thermique Energétique de et coordonnateur de la
filière Energétique, Faculté des Sciences pour toute la
confiance qu'il a mise en moi en m'acceptant dans son laboratoire.
v' AU Dr Henri Bosko DJEUDA TCHAPNGA
qui, par sa rigueur et l'amour d'un travail bien fait a su m'imprégner
petit à petit ses marques.
1' AU Dr Henri EKOBENA, Enseignant au
Département de Physique, Faculté des Sciences, pour ses
différentes orientations.
v' A Monsieur Charles TCHOUNGANG pour
le soutien moral et les conseils qu'il n'a cessé de me donner, mais
surtout l'ouverture d'esprit qui a été son oeuvre .
v' A tous mes camarades du LESEAU, en
occurrence François Xavier MPON, Thierry ELEMVA, YOMBI Tabué,
Marie Solange Mbang, Joseph EWODO, etc.
1' A tout ceux qui m'ont donné
un coup de main dans la phase expérimentale de ce travail, en occurrence
Calvin Noula WETHE, Edouard Michel NGNENGUIER, etc...
1' A tout le personnel de l'ONG
ERA-CAMEROUN pour tout le soutien moral dont j'ai
bénéficié. Je pense ici à , M. Elie TOLALE, Mme
SONKENG Florence née PEUMI, M. Joseph YIAH, M. Syriaque TALOM, M.
Honoré TAPOKO, etc.
1' Au Laboratoire d'Energétique (LAEN) de
l'ENSP pour le soutien matériel qu'il m'a
apporté.
v' A chacun de mes trois camarades
doctorants, qu'ils trouvent ici l'expression de
ma profonde gratitude. Je pense ici à, Benoit
Kameni, Annie Francie Kouedeu et Emmanuel Guemene.
Enfin, j'en oublie certainement beaucoup ; que tous ceux qui, de
près ou de loin ont contribué à la réussite de ce
travail trouvent ici l'expression de mes profonds remerciements.
RESUME
Le Cameroun est un pays situé dans une zone tropicale
humide et est de ce fait caractérisé par une
végétation forestière. Les zones rurales de ce pays
éprouvent beaucoup de problèmes d'approvisionnement en
énergie électrique. La biomasse constitue partout une ressource
disponible et facilement mobilisable et qui peut bien être
utilisée pour la production d'électricité. Ainsi la
technologie de gazéification du charbon de bois en vue de la production
thermique et électrique est mise en exergue dans ce travail. Il est fait
étalage ici des expériences de projet de gazéification en
cours dans le monde avant de passer à des tests expérimentaux sur
une unité pilote de gazogène de type indien. Ces tests ont
été précédés par la caractérisation
physico-chimique de la biomasse utilisée, qui n'est rien d'autre que du
charbon de bois commercialisé au marché Mokolo à
Yaoundé. Cette phase expérimentale nous a permis de mesurer les
températures au niveau de la paroi du réacteur au cours de la
gazéification et de constater leur évolution avec le temps. Ceci
nous a permis de poser les premières bases de la modélisation
mathématique des phénomènes de transfert thermiques qui
ont lieu dans le lit de charbon de bois pendant la gazéification.
Mots dles : Biomasse, ERD,
gazéification, charbon de bois, gazogènes, tests,
modélisation mathématique.
ABSTRACT
Cameroon as a country situated in the cold tropical area is
characterised by forest vegetation. But, the rural areas of the country can
hardly be supplied with electric power. Yet, biomass is everywhere an available
resource that can easily be taped
Thus in this work, after analysis of the problem of
Decentralised Rural Electrification (DRE) in Cameroon, the technology of
gasification of charcoal for thermal and electric production is put forward
with in particular the experimental tests being done on a pilot unit of gas
generator of the Indian type. These tests have been preceded by the
characterization of the biomass used, which here is charcoal that is
commercialised at the Mokolo market in Yaounde. This experimental phase enabled
us to measure the temperatures of the wall of gasifier reactor during the
gasification process and to note their evolution with time. This enabled us to
put forward the first bases of the mathematical modelling of the phenomena of
thermal transfer in the charcoal bed during the gasification process.
Key Words:: Biomass, DRE (Decentralised
Rural Electrification), gasification, wood charcoal, gasifiers, tests,
mathematical modelling
NOMENCLATURE
PED : Pays en voie de développement. ERD : Electrification
Rurale Décentralisée SONEL : Société Nationale
d'Electricité .
SOSUCAM : Société Sucrière du Cameroun. ONG
: Organisation Non Gouvernementale .
PCS : Pouvoir Calorifique Supérieur ; PCI : Pouvoir
Calorifique Inférieur.
HHV : Higher Heating Value ; LHV : Lower Heating Value.
MJ, kJ, kWh : Méga joule , kilojoule, kilowattheure ;
unités d'énergie.
tep : tonne équivalent pétrole ( ktep et Mtep...) ;
unité d'énergie.
kg : kilogramme, unité de masse.
W : Taux d'humidité.
m : masse de matière première.
MV : Taux de matière volatiles.
LV : Chaleur latente de vaporisation.
ÄH : Chaleur de réaction ou enthalpie de
réaction.
BT : Basse Tension ; MT : Moyenne Tension ; HT : Haute
Tension.
CF : taux de carbone fixe ;
T(r,t) : distribution de la température ; T :
température absolue
J0(ßr) et Y0(ßr) : fonctions de Bessel de
première te seconde espèce d'ordre zéro
? 1(t) , ? 2(t) : distribution de température
respectivement sur l'axe du réacteur
cylindrique et sur la paroi (condition aux limites) ;
a diffusivité thermique du lit de charbon de bois dans le
réacteur
: densité de matière (charbon de bois) ;
cp : capacité calorifique ou chaleur spécifique du
charbon de bois
k : conductivité thermique du charbon de bois ; k =
facteur pré-exponentiel d'Arrhenius
K : Constance de vitesse de la réaction de pyrolyse en s-1
E : énergie d'activation en kJ/kg
SOMMAIRE
Pages
Dedicaces i
Remerciements iii
Resume / Abstract v
Nomenclature ... vii
SOMMAIRE viii
INTRODUCTION GENERALE 1
CHAPITRE I : GENERALITES ET APERÇU
BIBLIOGRAPHIQUE......................................................................................................................
3
I/- PROBLEMATIQUE GENERALE DE
L'ELECTRIFICATION RURALE. 3
I.1- Analyse de la situation globale de
l'electrification
rurale decentralisee. .... 3
I.2/- Analyse du cas du Cameroun . 6
II/- BIOMASSE ET ELECTRIFICATION RURALE 8
III/- CHARBON DE BOIS DESCRIPTION
FABRICATION ET CARACTERISATION 10
III.1/- Caracteristiques generales du bois et de dechets de bois.
10
III.1.1/-Composition du bois 11
III 1.2/- Proprietes thermo-physiques du bois 12
III.2/- La carbonisation 12
III.2.1/- Description et theorie. . 12
III 2.2/- Caracteristiques principales du charbon de bois ..
16
III 2.3/- Technologie de carbonisation . 18
III.2.4/- Influence des conditions de carbonisation sur
les caracteristiques du charbon de bois. . 19
III.2.5/- Charbon de bois dans les Pays en
Developpement (PED) : Cas de Yaounde 19
IV/- ASPECT TECHNOLOGIQUE DE LA GAZEIFICATION.
22
IV.1/- Technologie de la gazeification de la biomasse .... 22
IV.1.1/- Principe de fonctionnement des gazogènes . 22
IV.1.2/- Differents types de gazogène 23
IV.1.3/- Utilisations et contraintes 24
IV.2/- paramètres influençant la qualite des gaz
de gazeification. 25
IV.3/- Charbon de bois à usage gazogène. 25
CHAPITRE II: LES EXPERIENCES DE GAZEIFICATION
DANSLE MONDE 28
INTRODUCTION 28
I/- ETAT ACTUEL DE LA TECHNOLOGIE DE GAZEIFICATION ..
28
I.1/ Bref historique de la gazéification . 28
I.2/- Gaz et gazéification de la Biomasse 29
I.3/- Etat actuel de la Technologie de gazéification
dans le monde 31
I.4/- Vision globale de la gazéification
dans le monde 34
II/- RESUME DE QUELQUES PROJETS DE GAZÉIFICATION
DANS LE MONDE 36
II.1/- Projet de gazéification à grande
échelle 36
II.2/- Projet de gazéification à petite
échelle 40
CHAPITRE III: CHOIX TECHNOLOGIQUE, PROCEDURES,
RESULTATS
DE L'ETUDE EXPERIMENTALE, ANALYSE, CONCLUSION
................... 44
INTRODUCTION .. 44
I/ MATÉRIEL 45
I.1/- description des équipements . 45
I.2/- Description des matériels de mesure . 49
II /- BIOMASSE UTILISÉE 50
III/- ASPECTS THÉORIQUE ET THERMODYNAMIQUE
DE LA GAZÉIFICATION . 55
III.1/- Théorie de la gazéification du charbon de
bois 55
III.2/- Caractérisation des échanges thermiques au
sein
de la charge et du réacteur 57
IV/- METHODOLOGIE DES TESTS DE GAZEIFICATION DU
CHARBON DE BOIS ET RESULTATS EXPERIMENTAUX
60
III.1/- Procédure expérimentale de la
gazéification 60
III.2/- Sécurité et Environnement 62
III.3/- Production des gaz, essai d'inflammation,
difficultés et quelques éléments
d'explication 63
III.4/- Mesure des températures, résultats et
analyse. 64
III.4/- Autre essai : durée de fonctionnement en fonction
du débit de charbon 67
CONCLUSION GENERALE 68
BIBLIOGRAPHIE 70
Annexes 1 I
Annexes 2 V
Annexes 3 VIII
INTRODUCTION GENERALE
Le problème d'électrification rurale dans le
monde est un problème qui focalise partout l'attention
particulière des gouvernements. Au Cameroun, les zones rurales souffrent
énormément du problème d'approvisionnement en
électricité. C'est ainsi que le problème
d'électrification rurale constitue une préoccupation
particulière aussi bien pour le monde scientifique que pour les pouvoirs
politiques. Pour l'électrification rurale, plusieurs options sont
possibles, mais ce sont les filières traditionnelles
d'électrification qui sont les plus sollicitées actuellement.
Compte tenu des contraintes d'approvisionnement des zones rurales, notamment
l'éloignement du réseau existant, le manque d'infrastructure
routière, l'habitat dispersé, la solution conventionnelle qui
consiste à électrifier par raccordement au réseau
interconnecté ne peut pas permettre à terme de satisfaire les
besoins qui selon les dernières statistiques du Ministère des
Mines, de l'Eau et de l'Energie sont énormes. En effet, seulement 5% des
villages du Cameroun étaient électrifiés en 1998. Le
Cameroun a pourtant beaucoup de potentialités en terme de biomasse
forestière. Il compte par exemple plus de 26 millions d'hectares de
forêt et 36 millions de m3 de déchets de bois sont
produits par an (MINEFI, 1997) c'est-à-dire environ, 18
millions de tonnes qui peuvent produire environ 1,5.104 GWh
d'électricité.
Techniquement, ces ressources peuvent être
valorisées pour la production d'électricité, moyennant
l'utilisation des technologies de conversion éprouvées. La
valorisation de ces déchets par gazéification et production
d'énergie nécessaire pour la force motrice et
l'électricité dans les zones rurales peut s'avérer
très intéressante et contribuer valablement à
résoudre le problème d'électrification rurale au Cameroun.
Après les études de faisabilité et d'applicabilité
des différentes techniques de valorisation énergétique de
la biomasse faites dans les différents villages de la province du Centre
dans le cadre des précédentes études, on est arrivé
à la conclusion selon laquelle l'électrification rurale
décentralisée de ces villages pouvait être assurée
en y intégrant la filière de gazéification de la biomasse
(TAGUTCHOU J. P., 2000).
C'est ainsi que parmi les 1321 villages que compte la province
du Centre, on est arrivé à partir d'une méthodologie
adéquate à présélectionner trois villages (Minlaba,
Nsem et Mekone II) qui devraient à l'avenir accueillir une installation
pilote de gazéification de la biomasse en vue d'approvisionner ces
localités en électricité.
Avant de transporter l'installation sur site pilote, il
fallait au cours des présents travaux faire une étude technique
du fonctionnement d'un dispositif de gazéification en provenance du
Burkina Faso. Il était question de faire des tests de
gazéification pour apprécier la qualité des gaz produits,
étudier les paramètres thermo-physiques influençant le
processus afin de faire des propositions pour l'optimisation du
phénomène. Il est clair qu'une pareille étude ne pouvait
se faire sans passer par une bonne caractérisation de la biomasse
utilisée : le charbon de bois dans notre cas.
La gazéification de la biomasse est un sujet qui
intéresse plusieurs structures de recherche dans le monde et beaucoup
d'auteurs innovent du jour au lendemain dans le domaine (SYRED N., 2001
; PLATIAU D., 1986) ; (P. GIRARD, 2000). Mais la diversité des
technologies dans le domaine impose la nécessité d'étudier
chaque type d'installation pour mieux appréhender certains aspects du
phénomène.
Dans l'élaboration de ce travail, nous avons
subdivisé le travail en trois chapitres :
v' Le chapitre 1 intitulé «
Généralités et aperçu bibliographique »
présente la question de l'électrification rurale
décentralisée dans le monde en générale et au
Cameroun en particulier ; c'est ici que nous abordons l'étude du charbon
de bois qui est la matière première que nous allons utiliser dans
la phase de tests.
v' Le chapitre 2 s'intitule «
Expériences de la gazéification dans le monde » ; ici,
nous
faisons le point sur les expériences de
gazéification en cours partout dans le monde en donnant un bref
résumé de quelques projets à grande et à petite
échelle de gazéification en cours dans le monde.
v' Le chapitre 3 est titré «
Choix technologiques, procédures, résultats de
l'étude
expérimentale, analyse et conclusion » et
présente l'essentiel des tests de gazéification que nous avons
conduits (inflammation des gaz sur brûleur, mesure des
températures des gaz à l'échappement d'une part et du
réacteur d'autre part au cours de la gazéification, ...). Le
problème de modélisation mathématique des
différents phénomènes qui ont lieu dans le réacteur
au cours de la gazéification est notamment posé avec la
détermination expérimentale des températures comme
premières bases des conditions aux limites du problème des
phénomènes de transfert thermique dans le lit de charbon pendant
la gazéification.
CHAPITRE I:
GENERALITES ET APERÇU BIBLIOGRAPHIQUE.
I/- PROBLEMATIQUE GENERALE DE L'ELECTRIFICATION
RURALE.
I.1- Analyse de la situation globale de
l'électrification rurale décentralisée.
Dans le monde entier, l'Electrification Rurale
Décentralisée (ERD), est une histoire dont l'origine est
récente. Bien entendu, l'utilisation des énergies
éoliennes et hydrauliques remonte à la nuit des temps mais ce
n'est que depuis le début du siècle dernier qu'elles produisent
l'électricité. Les groupes électrogènes ont depuis
leur conception, produit de l'électricité, même dans les
lieux les plus reculés, les plus difficiles d'accès et dans des
conditions extrêmes. C'est pourtant la technologie la plus
récente, le solaire photovoltaïque, qui semble avoir suscité
la dynamique de développement qui permet aujourd'hui de parler d'ERD et
suscite les multiples questions liées à sa banalisation
(Y. MAIGNE., 2000). Par ailleurs, dans les zones tropicales
humides sous forêt, l'idée de l'intégration de la biomasse
dans la production de l'électricité semble préoccuper de
plus en plus les chercheurs [(PLATIAU D., 1986), (P. GIRARD, 2000), (E.
TANAWA et al., 2000), (N. SYRED and al., 2001), (NGNIKAM et al., 2001),
...],, ce d'autant plus que cette filière
concourt à la protection de l'environnement par la diminution des
émissions à effet de serre. Le problème de l'ERD est
d'autant plus crucial que plus de 2 milliard d'êtres humains vivent sans
électricité sur la planète (Y. MAIGNE.,
2000). C'est ainsi que dans la plupart des pays concernés, tous
les nouveaux élus citent l'électrification des zones rurales
comme l'une de leurs priorités. La finalité de l'ERD est claire;
elle n'en recouvre pas moins une mosaïque d'acteurs et de domaines qui, si
l'un vient à manquer affecte sa crédibilité et
pénalise ses bénéficiaires (technologies de production, de
distribution et d'utilisation; développement socio-économique des
bénéficiaires par le service rendu; mécanismes
institutionnels, organisationnels et financiers; cohésion et synergie
entre les différents acteurs dans la conception, la réalisation
et l'exploitation). En matière de technologie par exemple, plusieurs
techniques sont en mesure de répondre, selon les situations locales, aux
besoins en énergie, mais aucune d'entre elles, considérée
seule, ne peut prétendre répondre globalement à l'ERD :
- Pour l'énergie éolienne, on ne peut pas
retrouver les grands vents dans toutes les régions; -
L'hydroélectricité est elle aussi limitée par la
fiabilité des équipements de petite taille, la rareté des
cours d'eau et la variation des débits;
- Le solaire photovoltaïque, même s'il
bénéficie des gisements souvent abondants, est handicapé
par son coût d'investissement et la nécessité des batteries
d'accumulateurs;
- Les groupes électrogènes dont la
fiabilité et la gamme de puissance disponible ne sont plus à
démontrer, se heurte à son coût de fonctionnement, dont
plus de 75% représentent celui du carburant, tendance qui s'aggrave avec
le temps, surtout en zone rurale; c'est le lieu de signaler l'importance de la
recherche sur les alternatives d'approvisionnement en carburant surtout compte
tenu des exigences des normes internationales en matière
d'environnement. C'est ici que la gazéification de la biomasse en vue de
la substitution des carburants pétroliers avec le gaz produit constitue
une solution de référence dans les zones tropicales humides sous
forêt.
Ce bref état des lieux montre combien la
complémentarité des technologies de production disponibles est,
au niveau technique, la solution susceptible de satisfaire le plus grand nombre
d'usagers avec une contrainte de disponibilité énergétique
minimale et dans des enveloppes budgétaires limitées.
Mais la tendance globale qui est observée aujourd'hui
est toute autre; en effet, rare sont les concepteurs, réalisateurs,
opérateurs, bailleurs de fonds, capables de jouer les atouts des
différentes options, au sein d'un même programme
d'électrification rurale décentralisée; la plupart d'entre
eux préférant se limiter à l'une d'entre elles quitte
à ignorer les demandes qu'elles ne peut satisfaire et à ne pas
valoriser d'autres sources locales d'énergie pourtant disponibles. Pour
une bonne réussite, cette tendance devrait être
renversée.
Par ailleurs, l'expression électrification rurale
même rappelle si besoin en était que la spécificité
des différents efforts est d'abord géographique. Il ne s'agit pas
d'objectifs et de difficultés associées à un secteur
d'activité (industrie, service, résidentiel,...) mais à
des zones dont les caractéristiques sont particulières. Quand on
parle d'électrification rurale, tout ou presque renvoie à une
dimension géographique et c'est encore plus vrai dès qu'il s'agit
de l'électrification rurale décentralisée : le choix des
techniques en fonction de la densité de peuplement et de la distance des
grands centres, la nature des besoins en fonction de la diffusion spatiale des
modes de consommation et du climat, le degré de monétarisation et
les capacités de paiement qui y sont associés, la localisation,
la disponibilité et les caractéristiques des ressources
renouvelables. Pour cette raison, la dimension géographique devrait
toujours être prise en compte quand on parle de projet d'ERD (Y.
MAIGNE., 2000).
Une parfaite connaissance des outils qui permettent
d'appréhender efficacement cette dimension est d'une importance
capitale. Sans rentrer dans les détails de ces outils, nous noterons
qu'il faut connaître :
v' Les différentes variables spatiales et les ordres de
grandeur qui caractérisent les peuplements ruraux, et qui sont
pertinentes pour sélectionner le type de solution technique le plus
approprié (densité de l'habitat, densité linéique
des villages à électrifier, accessibilité des sites,...)
(E. TANAWA et al., 2000).
v' S'orienter parmi les différentes sources de
données permettant d'obtenir les caractéristiques d'un potentiel
particulier d'énergies renouvelables (solaire, éolien, petite
hydraulique, biomasse ...) en un lieu particulier.
v' Les différents instruments de géomatique,
leur utilité pour la programmation d'ERD les différents logiciels
(ArcInfo, MapInfo, ArcView, Geoconcept, AutocadMap, ...) ainsi que les
différentes contraintes qui y sont associées; parlant de ces
instruments, nous citerons les SIG (systèmes d'Information
Géographique), les bases de données d'information
géographique physique, GPS (Global Positioning System) et images
satellitales (C. LAMACHE, 2000)..
> Intérêt des SIG pour l'ERD
Dans le cadre des projets d'ERD, le SIG peut être un outil
d'aide à la décision très utile. Il peut aider
à:
- localiser et identifier les foyers à
électrifier;
- effectuer un suivi et une meilleure gestion des
systèmes installés; Le SIG va permettre de localiser
précisément la position des foyers à électrifier et
des foyers déjà électrifiés. Par exemple, en
Tunisie, l'Agence Nationale des Energies Renouvelables s'est
équipée d'un logiciel SIG et de GPS; l'ensemble des installations
sont ainsi localisées grâce au GPS, puis intégrées
dans une base de données de SIG; les informations sur les installations
qu'on obtient ainsi automatiquement permettent de planifier leur gestion et
leur maintenance (C. LAMACHE, 2000).
- définir la solution d'électrification la plus
viable économiquement;
L'intégration des bases de données SIG dans les
projets d'électrification rurale décentralisée permet de
mieux planifier les actions à mener.
I.2/- Analyse du cas du Cameroun
Au Cameroun, le problème d'électrification
rurale se pose avec beaucoup de vigueur et nécessite une attention tout
à fait particulière dans le contexte de la mondialisation et de
lutte contre la pauvreté. Par exemple, dans la seule province du Centre,
sur les 1321 villages qu'elle compte, plus d'un millier ne sont pas
électrifiés (TAGUTCHOU, 2000). Pourtant, ici et
là, les besoins sont énormes ; les populations manifestent les
besoins d'éclairage, de confort, de motorisation, etc. Cette situation
se rencontre dans la plupart des zones du pays.
De façon globale, sur le plan de l'approvisionnement en
énergie, on peut faire la différence entre les zones urbaines et
les zones rurales.
Les grandes villes comme Douala et Yaoundé sont
entièrement couvertes par le réseau hydroélectrique (ici,
plus de 85% des ménages ont accès à
l'électricité).
En moyenne, dans les zones rurales moins de 10% des
ménages ont accès à l'électricité
(hydroélectricité), mais on peut distinguer 3 types de zones
rurales (TANAWA et al., 1998):
i) Les zones rurales pouvant être connectées au
réseau ; ce sont des zones non électrifiées mais qui
sont très proches (situées à moins de 7 km) du
réseau hydroélectrique, donc qui peuvent être
électrifiées à moindres coûts.
ii) Les zones rurales isolées situées entre 10
km et 50 km du réseau conventionnel ; elles sont à accès
difficile et le coût du transport de l'énergie
hydroélectrique pour y arriver est prohibitif. Pour ces zones, il est
plus réaliste d'envisager des solutions alternatives (groupes
électrogène, énergie solaire, éolienne,
biomasse,...).
iii) Les zones rurales spécifiques (ZRS) qui, quoique
étant isolées, sont situées à proximité des
grosses unités industrielles productrices de biomasse où il y a
suffisamment de déchets tels que la bagasse, ou à
proximité des industries forestières produisant de grosses
quantités de biomasse.
Dans notre travail, il est particulièrement question de
nous intéresser aux zones rurales isolées et aux ZRS. Les
premières ont un réel problème d'électrification et
les secondes ont d'énormes capacités d'auto - production
d'énergie électrique et peuvent même générer
des surplus d'énergie pour alimenter d'autres zones voisines.
Au Cameroun comme partout ailleurs, pour
l'électrification rurale, en dehors du problème de production de
l'électricité, un autre problème crucial réside au
niveau du transport, de la distribution et de la gestion de l'énergie
produite auprès des consommateurs. L'ERD se heurte ainsi plus ou moins
à certaines difficultés :
> Potentialités hydroélectriques non
exploitées.
Le potentiel hydroélectrique du Cameroun est
évalué à 55,2 GW pour un potentiel productible de 294
TWh/an. Mais dans ce potentiel, 19,6 GW soit 35.5% seulement, est techniquement
exploitable pour une capacité de 115 TWh/an1, ce qui place le
Cameroun 18eme rang mondial et en 2nd rang en Afrique
après le Congo Démocratique (MINEFI, 1998). En
plus des grands ouvrages de production, le pays dispose d'équipements de
production autonome d'une puissance installée estimée à 74
MW, appartenant à des particuliers et à des industries. La
production autonome est de 326 GWh par an, contre 2557 GWh par an pour la
Société Nationale d'Electricité (SONEL), concessionnaire
de distribution et de gestion de l'électricité du pays. Dans la
production totale de la SONEL, 61 GWh sont produits à partir des
centrales thermiques (centrale thermique de Bertoua) et 2496 GWh, soit 97,6%
à partir des centrales hydroélectriques pour une puissance
installée de 80 MW et 757 MW respectivement (MINEFI,
1998). Ces chiffres représentent moins de 2% des
potentialités hydrauliques du pays2. La production actuelle
ne parvient pas à satisfaire tous les besoins urbains. La demande
urbaine étant loin d'être satisfaite, les zones rurales se
trouvent délaissées. Ceci constitue un énorme
problème pour le Gouvernement Camerounais qui, durant les trois
dernières années a pris plusieurs mesures face à cette
situation, dont les suivantes:
- privatisation de la SONEL pour permettre une
amélioration de la production et optimiser la distribution et la
gestion.
- Création de l'Agence de l'Electrification Rurale
à travers la loi n°98/022/ du 24 décembre 1998 suivi du
décret n° 99/193 du 08 septembre 1999 portant organisation de cette
structure qui devra trouver des solutions alternatives pour
l'électrification des centres isolés.
- Institution de l'Agence de Régulation du Secteur de
l'Electricité par la loi n°98/022/ du 24 décembre 1998
régissant le secteur de l'électricité ; elle est
chargée d'assurer un contrôle systématique de la gestion et
la distribution de l'énergie électrique.
> Coût d'investissement élevé en
matière de transport de l'énergie
Le coût d'investissement des lignes haute tension (HT),
moyenne tension (MT) et basse tension (BT) est prohibitif en zone rurale et ce
d'autant plus que l'habitat y est très dispersé. Selon les
prévisions du Ministère Camerounais des Mines, de l'Eau et de
l'Energie en 2000, la répartition des coûts de transport des
différentes lignes est la suivante: 6 millions de FCFA/km pour les BT
monophasées, 8 millions de FCFA/km pour les BT triphasées et plus
de 45 millions de FCFA/km pour les HT. Avec ces coûts
élevés, le concessionnaire des
1 1 TWh = 1 milliard de kWh
2 Source: Atlas du potentiel
hydroélectrique du Cameroun
réseaux ne trouve pas d'intérêt
économique à investir. La solution décentralisée
d'électrification rurale reste donc la seule efficace et ce avec des
alternatives d'approvisionnement judicieuses pour les populations qui sont
restées en dehors des réseaux.. > Problème d'habitat
dispersé et d'accessibilité des zones isolées
Les zones rurales présentent généralement
une très faible densité de population (moins de 10 habitants au
km2 pour la province du Centre au Cameroun). Dans les villages, les
maisons sont alignées le long des axes routiers: la distribution de
l'énergie électrique nécessite donc de longues lignes, ce
qui appelle des linéaires de réseau encore plus importants.
De plus, dans la plupart des villages de la zone
d'étude, les infrastructures routières sont insuffisantes et
particulièrement en mauvais état notamment en saison de pluies.
Ceci constitue un problème car les installations doivent être
transportées, suivies et entretenues par des techniciens qui ne
résident pas forcement dans lesdites localités.
Toutes ces difficultés montrent comment il est
irréaliste de penser à une électrification rurale au
Cameroun par le seul réseau interconnecté. Les options faisables
sont donc celles qui favorisent la production locale de l'énergie
électrique, d'où le concept d'Electrification Rurale
Décentralisée. Il est donc judicieux de penser aux techniques de
production de l'énergie électrique par des sources locales en
fonction de leurs disponibilités respectives et des contraintes
environnementales. Dans le cas spécifique de la province du Centre au
Cameroun, la disponibilité de la biomasse fait beaucoup penser à
sa valorisation dans la production de l'électricité et la
motorisation pour satisfaire les besoins des ménages villageois.
II/- BIOMASSE ET ELECTRIFICATION RURALE
De manière générale, les zones tropicales
humides présentent une végétation florissante. Dans le
grand Sud du Cameroun, l'on est en zone forestière par essence. Le pays
regorge d'énormes potentialités en biomasse
végétale (bois, déchets de bois, déchets
agro-industriels). Au Cameroun entre 1997 et 1998, le potentiel
énergétique en biomasse était estimé à 36
millions de m3 sous forme de déchets laissés sur place
lors de l'exploitation de la forêt (MINMEE, 1990).
Cependant, malgré leur importante contribution à
l'économie nationale, les zones rurales souffrent
énormément du problème d'électrification. La
question difficile à laquelle il faut apporter des
éléments de réponse est donc celle de savoir comment
produire de l'électricité à partir de la biomasse,
à un coût aussi faible que possible, et ceci pour des puissances
installées pas très élevées. En effet, des
précédentes études effectuées dans ladite
zone (TAGUTCHOU J. P., 2000), il ressort que
ces zones pour leur besoins d'énergie électriques n'ont besoin
que de faibles puissances installées (inférieures à 50 kW
pour les plus grosses). Pour ce faire, des installations de
gazéification fiables, faciles d'entretien et respectant certaines
normes internationales en matière d'environnement seraient à
même de répondre à cette épineuse question. Mais ces
gammes de puissance restent trop faibles pour qu'on puisse envisager les
systèmes classiques (chaudières à turbo-alternateur).
Compte tenu de la disponibilité de la source d'énergie (biomasse)
(TANAWA et al., 1998), des petites centrales
électriques avec gazogènes et groupe moto-alternateur sont
capables de résoudre le problème dans ces zones. Cependant, au
regard de l'état d'avancement de la technologie de gazogène, en
ce qui concerne le système de traitement et d'épuration des gaz
notamment, il est encore prématuré de compter sur un
fonctionnement fiable et continu d'un ensemble générateur de
courant électrique par gazéification directe de la biomasse. Il
convient donc de penser à proposer un schéma innovant qui
intègre au niveau du process un combustible "propre" palliant les
imperfections momentanées du système. Le charbon de bois qui est
un produit transformé, de part sa composition ne contient
théoriquement pas de constituant susceptible de générer ni
des goudrons ni des pyroligneux lors de la gazéification
(PLATIAU D. et al, 1986). La gazéification du charbon
de bois pour la production électrique devrait donc de ce fait
éliminer une bonne partie de contraintes relatives à
l'épuration de gaz et ceci d'autant plus aisément que, comme nous
allons le voir plus loin, la production de ce combustible est
maîtrisée par des procédés de fabrication simples et
faciles à mettre en oeuvre (LIPS B. et al., 1999). Par
ailleurs comme nous allons le voir, le charbon de bois a plusieurs avantages
énergétiques dans la gazéification par rapport à
celle du bois pur ou des autres biomasses (Pouvoir calorifique doublé,
transport faciles, propriétés thermophysiques
intéressantes, ...) (BOIZI E., 1999), (P.
GIRARD, 1985).
III/- CHARBON DE BOIS DESCRIPTION FABRICATION ET
CARACTERISATION
Le charbon de bois est le résidu solide qui reste
lorsque le bois a été carbonisé ou pyrolysé dans
des conditions contrôlées dans les espaces fermés tel qu'un
four à charbon. Historiquement, le charbon de bois est ce produit qui a
permis à l'homme antique de traverser l'âge de la pierre.
Après plusieurs siècles d'utilisation en tant que combustible de
premier choix, le charbon de bois a connu depuis le siècle dernier un
déclin d'exploitation au profit des nouvelles sources d'énergies
fossiles (houille, pétrole)
Aujourd'hui encore, le contexte énergétique
européen et mondial reste très vulnérable compte tenu de
la prédominance du pétrole dans le bilan
énergétique et ses difficultés d'approvisionnement et de
la limitation des gisements en combustible fossiles exploitables. Cette
incertitude qui plane sur la demande et les approvisionnements
énergétiques vient se superposer aux contraintes
environnementales de plus en plus pressantes et limite ainsi en faveur d'une
diversification de ces approvisionnements notamment vers les sources locales.
Dès lors les potentialités forestières disponibles surtout
dans les pays du Sud offre une réelle opportunité de
diversification. Le développement de savoir-faire et de technologie
bioénergétiques devrait permettre l'utilisation rationnelle de
cette ressource à la fois dans les pays industrialisés, mais
aussi dans les PED au travers du transfert des technologies. De plus, le
charbon de bois est un produit convoité dans les industries chimiques,
métallurgiques, sidérurgiques et
électro-métallurgiques en particulier pour ses
propriétés adsorbantes et déshydratantes
recherchées.
En tant que combustible, le charbon de bois présente de
multiples avantages, il est facile à transporter et à poids
égal, il contient deux fois plus d'énergie que le bois brut.
Cependant, les contraintes environnementales liées à la
déforestation et la désertification limitent beaucoup sa
production dans les zones dépourvues de forêt. Cette production
est rendue économiquement rentable avec l'utilisation des déchets
de scieries installées dans les différentes régions
où celles-ci se trouvent. L'utilisation de ce produit comme source
d'alimentation de gazogène en vue de la productivité
d'électricité reste donc une option efficace pour la
gazéification.
III.1/- Caractéristiques générales du
bois et de déchets de bois.
Avant de rentrer dans la transformation du bois et
déchets de bois en charbon de bois, il convient d'abord d'exposer
quelques considérations générales sur les
propriétés physiques et chimiques du bois,
propriétés qui jouent un rôle important au cours de la
carbonisation
Il faut reconnaître que toutes les espèces de
bois peuvent être carbonisées, mais elles ne fournissent pas
toutes un charbon d'égale qualité. Voilà pourquoi il est
important de reconnaître certaines propriétés des bois
lorsqu'on veut obtenir des charbons dont les propriétés doivent
répondre à des spécifications plus précises.
Sans rentrer dans le détail de l'anatomie du bois, il
convient de noter que l'anatomie microscopique du bois distingue deux grandes
catégories de bois : les conifères ou bois résineux
(gymnospermes) et les feuillus (angiospermes) encore respectivement connus sous
les noms de "bois tendres" et "bois durs". La principale différence est
remarquée dans la structure, la compacité et les dimension des
fibres dont dépend la dureté relative du bois (P. GIRARD,
1985). Au cours de la carbonisation, la chaleur pénètre
dans le bois principalement dans la direction des fibres. La structure et les
propriétés de ces dernières auront donc une
répercussion directe sur les propriétés physiques des
charbons.
III.1.1/-Composition du bois
La composition élémentaire du bois varie
très peu quelle que soit l'espèce considérée. C'est
ainsi que l'analyse élémentaire du papyrus sec donne : 49,05% C,
40,9% O2, 5,24% H2, 0,52% N2 et 4,29% de cendres (PLATIAU D. et al,
1986). De façon générale, en moyenne on peut
estimer la composition élémentaire du bois comme étant la
suivante : 49,5 % de carbone, 6 %d'hydrogène, 43 %
d'Oxygène, 0,5 % d'azote, et 1% de cendres (TAGUTCHOU J. P.,
2000).
Il convient de noter ici que de nombreux
éléments font varier la teneur en cendre des bois et de ses
déchets (essence, nature du sol d'origine de l'arbre). On doit attacher
une certaine importance à la teneur en cendre du bois puisque la teneur
en cendre du charbon de bois en dépend directement; ainsi, pour la
gazéification, les charbons doivent avoir une teneur en cendre aussi
faible que possible, et surtout si le gaz produit est destiné à
un moteur. La teneur en cendre doit être faible et inférieure
à la teneur limite qui est de 5%, teneur à partir de laquelle
apparaissent généralement les premiers problèmes
d'agglutination de cendre en gazéification (PLATIAU D. et al,
1986). Il importe donc de faire un choix approprié des essences
à carboniser et de limiter au maximum la présence d'écorce
et les feuilles (sources de cendre) sur les bois de carbonisation.
La formule chimique globale approchée du bois est de la
forme CH1,5 O0,65 si on néglige l'azote et les cendres. Mais en tenant
rigoureusement compte de tous les éléments, la formule du bois
est de la forme C6H8,39O3,54N0,1 (KOBNOM O.,
1994)
La teneur en eau du bois vert est d'environ 50 % et plus, mais
cette teneur diminue avec l'évaporation progressive de l'eau pour tomber
au environ de 15 à 20 % après un séjour suffisamment
prolongé dans l'air ambiant et sans abri. L'humidité du bois est
probablement le facteur le plus important qui intervient dans la
carbonisation.
III 1.2/- Propriétés thermo-physiques du
bois
La masse volumique d'un bois à 12 % d'humidité
varie en général de 250 à environ 1200 kg/m3
sec. Elle dépend principalement de l'espèce et de l'âge de
la plante. Le pouvoir calorifique d'une matière solide est la
quantité de chaleur dégagée par la combustion
complète d'une unité de masse du combustible. Le PCI est une
fonction de l'analyse élémentaire en carbone et en
hydrogène. Le PCI de végétaux se situe entre 16500 et
19500 kJ/kg. On a par exemple 16,860 kJ/kg de PCI pour le papyrus rwandais
(PLATIAU D. et al, 1986).
La capacité thermique massique du bois ne varie que
très peu en fonction de l'espèce. Elle se situe en moyenne entre
1,0 et 3,0 kJ.kg-1.K-1 (pour un bois humide à
moins de 20 %).
La conductivité thermique du bois quant à elle
dépend du sens considéré pour le flux de transfert
thermique: 0,15 à 0,25 W.m-1K-1 dans le sens
transversal et 0,20 à 0,45 W.m-1.K-1 dans le sens
longitudinal du bois sec (BOIZI E., 1999). Globalement, les
pailles ont une conductivité inférieure à celle du bois :
environ 0,04 W.m-1.K-1. Cette différence a une
influence sur l'avancement de la réaction pour des conditions de
traitement données. Selon le procédé de traitement
utilisé, le rendement de carbonisation varie entre 15 et 32 % sur le
bois anhydre.
III.2/- La carbonisation
III.2.1/- Description et théorie.
La carbonisation est le processus de transformation
thermochimique de la biomasse en vue de la production du charbon de bois.
Celui-ci s'obtient par pyrolyse du bois c'est-à-dire la destruction,
sous l'action de la chaleur et en l'absence d'oxygène des
composés organiques ou minéraux du bois. Ici, c'est en
particulier la dégradation des deux polymères
végétales qui constituent le bois c'est-à-dire la
cellulose (C6H10O5)n et la lignine (C10H12O3)n. Cette
destruction donne naissance à trois types de produits :
- Le charbon de bois qui représente 25% à 30% du
poids du produit, contient 80% à 90% de carbone et regorge ainsi 45%
à 55% de l'énergie des produits.
- Les pyroligneux : représentant 40% à 45% de
l'énergie et est constituée essentiellement d'eau, d'acide
acétique, d'acétone, d'acide formique, de méthanol,
d'acide de méthyle, de phénol de crésol et plus quelques
goudrons épais.
- Les gaz quant à eux représentent 10% à
15% du poids, 10% à 15% de l'énergie du produit et sont
constitués essentiellement de l'oxyde de carbone (CO), du gaz carbonique
(CO2) du méthane (CH4) et de quelques traces d'hydrogène (H2)
(GIRARD P., 1985).
Les principaux paramètres qui influencent la pyrolyse sont
:
· la température dont l'augmentation fait
croître les proportions de gaz et de pyroligneux ;
· La vitesse de pyrolyse ;
· Taille, forme et qualité du bois ; Parlant de
la qualité, il est important de noter qu'un bois contenant plus de
lignine (Pin) donnera un résidu charbonneux plus important, car la
lignine est plus riche en carbone que la cellulose et l'hemicellulose ;
· L'humidité du bois : une partie de
l'énergie produite sert à évaporer l'humidité qu'il
contient.
Suivant la conduite de la réaction, on favorisera la
formation de gaz (on parle alors de gazéification) ou de charbon de
bois, (on parle de carbonisation). Bien entendu, le charbon produit peut
être à nouveau gazéifié.
Les travaux réalisé par Browne en
1958 lui ont permis de conclure que : "le rendement de production lors
de la pyrolyse complète du bois est quasiment similaire à celui
des principaux constituants traités séparément". On
retrouve dans une publication de Robert de 1970, que la pyrolyse des
matières végétales commence avec la dégradation des
hémicelluloses, constituants les moins actifs, entre 200°C et 260
°C, puis nous avons celle de la cellulose de 240°C à
350°C. La dégradation de la lignine commence à environ
280°C pour achever le processus à 500°C. De façon plus
détaillée, on retiendra que la pyrolyse suit l'évolution
suivante (GIRARD P., 1985) :
- Jusqu'à 100°C, le bois sous l'action de chaleur se
dessèche et perd son eau sans subir
de changement d'ordre chimique.
- Vers 150°C, le bois brunit et on peut déceler la
présence de l'acide acétique dans l'eau
condensée.
- Vers 280°C, le bois est en pleine décomposition par
condensation des vapeurs qui se
dégagent on obtient un liquide abondant qui se
sépare par dépôt en deux couches : les
14 CHAPITRE I: Généralités et Aperçu
Bibliographique
goudrons d'un noir intense à la couche
inférieure et les pyroligneux à la couche supérieure
aqueuse, de couleur rouge foncé. Les gaz incondensables qui s'y
échappent sont constitués d'anhydride carbonique, de monoxyde de
carbone de méthane et d'autres hydrocarbures.
- Vers 300°C la décomposition du bois augmente
encore, la température s'élève rapidement toute seule
sans chauffage à la suite du fort dégagement de chaleur qui
accompagne la réaction primaire. C'est la phase exothermique de la
carbonisation. La chaleur de réaction dégagée au cours de
cette phase est égale à 6% de la chaleur de combustion du
bois.
- Au-delà de 350°C, la distillation se ralentit et
elle devient pratiquement complète vers
450°C. Il ne se dégage plus alors que de faibles
quantités de gaz et de vapeur condensable. Après refroidissement
à l'abri de l'air, on trouve dans le four un résidu de charbon de
bois noir, brillant et sonore, si la carbonisation a été
suffisamment poussée et bien dirigée.
Dans le processus de carbonisation on peut donc distinguer les
quatre grandes phases suivantes :
Tableau n°1 : Les différentes
phases du processus de carbonisation.
Phases
|
Température approximative
|
Faits marquants
|
Produits
|
A- Combustion
|
Temp. Ambiante à 100°C
|
Séchage
|
Eau
|
B- Déshydratation
|
100°C à 270°C
|
De quelques heures à plusieurs jours
|
Eau, CO2
|
C- Phase exothermique
|
270°C à 450°C
|
- dégagement chaleur
- décomposition brutale du bois - dégagement des
matières (vapeurs condensables chargées de goudron, d'eau et
d'acide acétique)
|
Acide acétique, alcool methylitique, goudron,
CO2, CO, CH4, H2, N2
|
D- Refroidissement
|
De 450°C à la température ambiante
|
Vitesse de décroissement dépendant de la technique
de carbonisation
|
|
|
Si nous nous intéressons durant ces différentes
étapes aux proportions massiques d'évolution des produits obtenus
lors de la pyrolyse du bois ainsi que les proportions de carbone fixe, du
charbon correspondant, on peut avoir les différents valeurs en fonction
de la
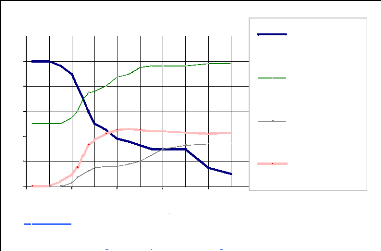
120
100
40
20
80
60
0
0 200 400 600 800 1000
TEMPERATURE (°C)
Figure n°1: Evolution de la proportion
massique des des produits obtenus lors de la pyrtolyse du bois et, du taux
de carbone fixe du charbon correspondant en fonction de la
température
Rendement n(%)
Taux de carbone fixe (%)
Taux de gaz (%)
Taux de matières condensables
(%)
température. Le rendement de la carbonisation peut
être considéré comme la proportion de matière solide
des produits par rapport à la masse de combustible anhydre de
départ.
En reconstituants les valeurs obtenues par E.M.Boizi en 1999
(BOIZI E., 1999) on peut avoir le tableau suivant :
Tableau n° 2: Evolution des
différents constituants du bois et de la température au cours de
la carbonisation
Température (°C)
|
Rendement
?(%)
|
Taux de carbone fixe (%)
|
Taux de matières condensables (%)
|
Taux de gaz (%)
|
T° ambiante
|
100
|
50
|
0
|
0
|
100
|
98
|
50
|
0
|
0
|
150
|
96
|
50
|
4
|
0
|
200
|
90
|
55
|
10
|
3
|
225
|
80
|
60
|
15
|
7
|
250
|
70
|
70
|
25
|
10
|
275
|
60
|
75
|
33
|
12
|
300
|
50
|
76
|
37
|
15
|
350
|
45
|
80
|
42
|
16
|
400
|
38
|
87
|
45
|
16
|
450
|
36
|
90
|
46
|
18
|
500
|
33
|
95
|
45
|
20
|
550
|
30
|
96
|
44
|
25
|
600
|
30
|
96
|
44
|
30
|
700
|
30
|
96
|
43
|
33
|
800
|
15
|
98
|
42
|
34
|
900
|
10
|
98
|
43
|
34
|
A partir du tableau n° 2, on peut avoir les courbes de la
figure n°1 qui donnent l'évolution des différentes
proportions des produits de pyrolyse en fonction de la température.
En ce qui concerne l'aspect cinétique de la
transformation, on admet que la dégradation thermique des
matières ligno-cellulosiques suit une loi cinétique qui est celle
de 1er ordre d'Arrhenius. Cette tendance fut observée par AKITA en 1929
puis vérifiée par TANG en 1967. On pose pour ce faire en pratique
l'équation suivante (ou une de ses variantes) (E. Boizi,
1999).
d E
( c ) .( c ) .exp( ).( )
- = - K - = - k - - c
dt RT
|
(1)
|
Cu :
? = densité de la matière à l'instant t en
kg/m3;
?c = la densité du charbon en fin de pyrolyse
kg/m3;
K = est la constante de vitesse de la
réaction de pyrolyse en s-1;
k = est le facteur
pré-exporentiel d'Arrhenius (s-1);
E= énergie d'activation en
kJ/kg
R = Constante universelle des gaz kJ.kg-1 K-1
T = température absolue (K)
k et E sont les données
cinétiques de la dégradation thermique d'une matière
carbonée. A titre indicatif, voici quelques valeurs du rapport E/R :
9500 K, 8810 K, 14700 K, 50946 K (BOIZI E., 1999).
Les valeurs de k varient avec des
rapports de plus de 1020. Cette variation des énergies
d'activation est liée aux conditions expérimentales (mode
d'évacuation des gaz, durée de traitement ...) et à
l'échantillon utilisé (taille, forme, distribution
spécifique de constituants).
III 2.2/- Caractéristiques principales du
charbon de bois
Du point de vue de la composition élémentaire,
un charbon végétal pur est principalement constitué de
carbone, d'hydrogène, d'azote et d'oxygène, avec des proportions
plus ou moins importantes selon les conditions de carbonisation. Notons que le
meilleur charbon à usage de gazéification est le charbon qui
contient le maximum de carbone. A titre indicatif, le tableau qui suit donne
quelques valeurs moyennes de a composition du charbon de bois en fonction de la
température de pyrolyse:
Tableau n°3: Composition du
charbon de bois en fonction de la température (GIRARD P.,
1985)
Température de carbonisation
(°C)
|
Rendement sur bois
|
Composition (%)
|
C
|
O2
|
H2
|
200
|
91.8
|
92.3
|
1.4
|
6.3
|
250
|
65.2
|
70.6
|
24.2
|
5.2
|
300
|
51.4
|
73.2
|
21.9
|
4.9
|
400
|
37.8
|
82.7
|
13.5
|
3.8
|
500
|
33.0
|
89.6
|
6.7
|
3.1
|
600
|
31.0
|
92.6
|
5.2
|
2.6
|
800
|
26.7
|
95.8
|
3.3
|
1.0
|
1000
|
26.5
|
96.6
|
2.9
|
0.5
|
L'analyse chimique révèle aussi des traces de
cendres qui sont des composés inorganiques initialement contenus dans la
matière première.
La masse volumique d'un charbon de bois massif peu varier de
0,14 à 0,60 t/m3. En comparant ces valeurs à celles du
bois de départ vues précédemment, (0,25 à
1,2t/m3, on se rend compte que la densité du charbon de bois
est fortement corrélée à celle du bois de départ,
un bois dense donnant un charbon dense et un bois léger donnant un
charbon léger, avec un coefficient massique de transformation de l'ordre
de 1/2 c'est-à-dire si ?b et ?c sont
respectivement les densités du bois de départ et du charbon,
produit alors on a ?c 1/2 ?b
Un des premiers tests réalisés sur du charbon de
bois est l'indice de matière volatile. En sortie de four, le charbon de
bois est totalement sec. La reprise d'humidité au cours du temps est
relativement faible (moins de 10% sur sec à l'équilibre) et
dépend de la structure du matériau : un charbon riche en
matière volatile aura un taux d'humidité moindre. On
définit également le taux de carbone fixe qui est la proportion
de matières autres que les matières volatiles.
Tout comme pour le bois, le pouvoir calorifique du charbon de
bois est une fonction de l'analyse élémentaire en carbone
hydrogène. En pratique il est fixé à une moyenne de 32
MJ/kg (contre environ 17 MJ/kg pour le bois initial).
La chaleur spécifique d'un charbon de bois varie entre
0,82 kJ.kg-1.K-1 et 1,25
kJ.kg-1.K-1. La conductivité thermique de la
particule de charbon se situe aux alentours de 0,06
W.m-1.K-1.
Pour ce qui est des propriétés
mécaniques, un charbon de bois est plus ou moins cher, plus ou moins
favorable et plus ou moins résistant. Ces qualités
mécaniques dépendent de la nature de l'espèce d'origine et
des paramètres thermiques de fabrications (BOIZI E.,
1999).
Dans tout état de cause pour la plupart des applications
(chaleur, gazéification, etc.) les tests préliminaires standards
nous intéressant sur le charbon de bois sont principalement :
- des tests physiques (densité, friabilité, reprise
d'humidité, pouvoir calorifique)
- des tests chimiques (taux de cendre, taux de matières
volatiles, taux de carbone fixe).
Notre objectif dans l'étude de la carbonisation est
donc de pouvoir être capable de caractériser le charbon de bois
pris sur le marché de Yaoundé, celui-là même qui
nous permettra de faire des tests de gazéification en vue de la
motorisation villageoise et de l'électrification rurale. Pour pouvoir
atteindre cet objectif, il est important de connaître la technologie de
fabrication de ce charbon de bois.
III 2.3/- Technologie de carbonisation
La carbonisation est un processus complexe de transformation
thermochimique nécessitant une source de chaleur pour son
déroulement. Cette transformation thermochimique nécessitant une
source de chaleur pour son déroulement, les technologies
employées aujourd'hui dans le monde pour la production du charbon de
bois peuvent être classées en trois procédés selon
le mode d'apport de l'énergie nécessaire au traitement : les
procédés à combustion partielle, les
procédés à contact de gaz chauds et les
procédés à chauffage externe.
a) Procédé de carbonisation à
combustion partielle.
La source thermique de ce procédé est la
combustion d'une partie de la charge. Tous les systèmes utilisant ce
mode sont de type artisanal et quelque fois semi-industriel. Pour ce
procédé, la charge du bois à carboniser est
disposée à l'intérieur d'une enceinte étanche
(terre, brique, métal). Des ouvertures judicieusement disposées
permettent l'admission de l'air nécessaire à la combustion de la
partie de la charge qui fournit la chaleur indispensable à la
carbonisation. Les différentes technologies utilisant ce
procédé sont :
* les fosses, principalement utilisées en Afrique et aux
Caraïbes;
* les meules utilisées dans les mêmes
régions mais qui sont plus volumineuses; * les fours
maçonnés;
* les fours métalliques qui présentent l'avantage
d'être mobiles.
b) Procédés de carbonisation à
chauffage externe
La carbonisation à chauffage externe a lieu en vase
clos (réacteur cornue) et l'énergie de traitement est fournie
à la charge par l'intermédiaire d'une surface d'échange.
Outre la possibilité de carboniser sans un conditionnement important de
la matière première végétale, les
procédés à chauffage externe sont coûteux,
facilement mécanisables et peuvent permettre
un bon contrôle des rejets gazeux vers l'atmosphère.
Les capacités de production sont assez élevées (5000
à 6000 t/an et les rendements avoisinent les 30 % (sur sec).
c) Procédés de carbonisation par contact de
gaz chauds
Ici, l'énergie utilisée est fournie par un gaz
chaud provenant d'un foyer externe (possibilité de valorisation des gaz
résiduaires) et mis en contact avec la charge. Ce procédé
est plus exigeant en terme de conditionnement préliminaire de la
matière première.
III.2.4/- Influence des conditions de carbonisation sur
les caractéristiques du charbon de bois.
Outre les éléments déjà
abordés, il est important de signaler que :
* la qualité du charbon de bois ne dépend pas de la
capacité du four;
* les fours doivent être bien étanches pour
éviter les entrées d'air (le refroidissement ne se fait pas bien
parce qu'une combustion lente continue à consommer le charbon de bois,
d'où les rendements désastreux avec une qualité
médiocre).
* les fours doivent être bien remplis pour plusieurs
raisons, d'une part la carbonisation par cycle d'une grande quantité de
bois anhydre augmente le rendement technologique du dispositif, ensuite, il
diminue les charges en main d'oeuvre et enfin, minimise la qualité d'air
dans le four, permettant une meilleure conduite du cycle ce qui par
conséquent augmente le rendement pondéral.
En conclusion, les principaux facteurs qui règlent le
rendement et la qualité du charbon de bois sont la qualité des
bois à carboniser et la température finale de la carbonisation.
La vigueur de la réaction dépend surtout de la teneur en
humidité du bois enfourné, tandis que la teneur en carbone du
charbon de bois dépend de la température finale de la
carbonisation. D'autre part, toutes les techniques de carbonisation permettent
d'obtenir un charbon de bois de qualité, pour autant que le personnel et
les matières premières s'y prêtent. Les
éléments de choix de matériel doivent donc plutôt
tenir compte du prix de ce matériel, de la facilité de mise en
oeuvre et de sa productivité.
III.2.5/- Charbon de bois dans les Pays en
Développement (PED) : Cas de Yaoundé au Cameroun
Commencé par le bois de chauffe, le charbon de bois est
utilisé de manière marginale à Yaoundé, capitale du
Cameroun; mais il reste une source d'énergie importante pour la
population. A Yaoundé, on retrouve l'usage exclusif du charbon de bois
dans un certain
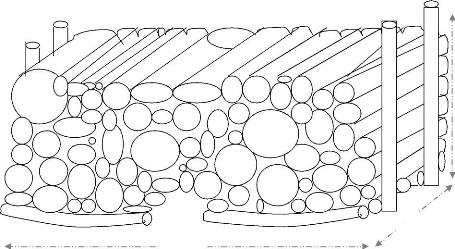
nombre de cuisson : grillade de poulets, poissons, viandes dans
les plus grands restaurants de la ville.
Le charbon de bois consommé à Yaoundé
provient de deux filières différentes :
- des charbonniers des environs de Yaoundé qui exploitent
la forêt. Ce charbon est de qualité variable mais en
général assez léger.
- des différentes scieries situées entre 50 et
200 km de la ville où on retrouve des équipes de charbonniers
souvent d'origine malienne ou ivoirienne qui fabriquent du charbon à
partir des déchets de bois de scierie. Ici l'utilisation de bois lourds
permet d'obtenir un charbon dense de très bonne qualité
(LIPS B. et al., 1999).
Les deux filières de production sont de type
traditionnel, mais la matière première et les techniques sont
très variables. Le procédé de fabrication le plus usuel
est le procédé de carbonisation à combustion partielle
dans des meules et fosses. La figure n°2 présente le schéma
d'une meule à charbon dans la localité de Baba, située
dans l'arrondissement de Soa, à une quinzaine de km de Yaoundé
(LIPS B. et al., 1999).
1.5
1 à 1.5
Ouverture
3 à 4
Figure n°2: ..Schéma d'une meule artisanale dans la
localité de Baba, près de Yaoundé m
Les meules ont généralement un volume variant
entre 4,5 m3 et 8 m3 et ont généralement un taux de
remplissage d'à peu près 70 % pendant la carbonisation. Le taux
de carbonisation est généralement élevé (73,8 % par
exemple). Le rendement pondéral ou rendement de production sur
matière anhydre est donné par le rapport masse de charbon produit
sur masse initiale anhydre de bois enfournée et vaut 11,5 % tandis que
le rendement énergétique est de 19 % (LIPS B. et al.,
1999). Le charbon de bois produit est commercialisé
dans les principaux marché de Yaoundé (Mokolo,
Madagascar, Elig Edzoa ...). La production du charbon de bois issu de la
forêt autour de Yaoundé est estimée à 1000 sacs de
40 kg environ par semaine, soit une production annuelle évaluée
à 2000 tonnes. Ceci représente une consommation d'environ 2 kg
par habitant de Yaoundé et par an. Ce chiffre est très faible
comparé à celui d'autres villes africaines du Sahel (Nouakchott,
Dakar, ...) où on a 100 à 200 kg/habitant/an (LIPS B. et
al., 1999). Ceci s'explique par le fait que les habitants de
Yaoundé utilisent très peu le charbon de bois pour la cuisson
chez eux (le bois brut leur semblant meilleur marché) et l'essentiel de
la consommation est dû aux ventes de grillades dans la rue (maïs,
plantain, prune, poissons, viande,...).
A Yaoundé, le charbon de bois peut se retrouver
commercialisé à un prix moyen de 75 Frs/kg. Soit environ 3000
FCFA par sac de 40 kg. Mais généralement on retrouve ces sacs
chez des grossistes à un prix allant de 2500 Frs à 3000 Frs. Le
charbon provenant des scieries est plus dense et les sacs peuvent avoir un
poids de 50 kg. Le prix de vente de ces sacs est très homogène
à 2500 Frs/sac et reste moins cher que le charbon artisanal provenant
des charbonniers des villages voisins de Yaoundé (localité de
Baba près de Soa). 3
Les possibilités de production sont nombreuses
notamment avec la multitude de scieries qu'on retrouve à l'Est du pays.
La valorisation de leurs déchets dans la carbonisation est une
excellente idée, mais il faut faire face aux contraintes de transport si
l'utilisation ne doit pas être faite sur place. C'est donc ici que se
justifie l'excellente idée de gazéification du charbon de bois
produit pour la production d'électricité et la force motrice dans
ces localités qui ne sont pas électrifiées.
3 Ces informations ont été vérifiées
au "marché charbon " du marché Mokolo à Yaoundé en
Octobre 2001.
IV!- ASPECT TECHNOLOGIQUE DE LA GAZEIFICATION.
La gazéification d'un combustible solide est son
oxydation partielle par l'air, l'oxygène, la vapeur d'eau, le gaz
carbonique, seuls ou en mélange, conduisant à un produit gazeux
combustible composé principalement d'hydrogène et de monoxyde de
carbone. C'est une technique bien connue, la gazéification du charbon de
bois ayant longtemps fourni le gaz de ville. Par rapport à l'historique,
il faut noter que depuis le début du 20e siècle, est
apparu le premier gazogène sur véhicule en Europe ; cette
époque constitue un véritable tournant pour la technologie de
gazéification. Les gazogènes à bois et à charbon de
bois sont alors développés partout en Europe et aux Etats Unis.
C'est ainsi que suite aux problèmes d'approvisionnement en carburants
pétroliers pendant la seconde guerre mondiale, on va compter en 1942
près de 300 000 unités de gazogènes installés sur
véhicules en Allemagne et une centaine de mille chacun pour la France,
le Japon et l'Union Soviétique. Après 1945, avec le retour des
carburants pétroliers, on va assister à une chute de la
gazéification qui va être redécouverte pendant la
décennie 1974 - 1984 à l'occasion du choc pétrolier
(TAGUTCHOU, 2000). D'après l'histoire, la
gazéification est une technique éprouvée qui a fait ses
preuves en situation difficile, jouant le rôle d'alternative
d'approvisionnement en carburant. Avec un champ d'application vaste, c'est une
technique qui devrait constituer une solution au problème difficile
d'électrification rurale en centre isolé, surtout en zone
forestière humide où la matière première est
disponible et bon marché.
Notre préoccupation ici est donc d'analyser la
gazéification du charbon de bois en vue de la production de
l'électricité et de la force motrice en zone forestière
humide. C'est ainsi que nous nous convenons de présenter la
théorie de gazéification de la biomasse en générale
et celle du charbon de bois ; nous essayerons de voir aussi les avantages et
inconvénients de la gazéification du charbon de bois par rapport
à celle du bois brut; il sera aussi succinctement présenté
la technologie fondamentale de gazéification.
IV.1!- Technologie de la gazéification de la
biomasse
IV.1.1!- Principe de fonctionnement des
gazogènes
Le principe de fonctionnement des gazogènes part du
principe fondamental du gazogène à lit fixe et à tirage
inversé qui fut développé par l'Ingénieur
IMBERT en 1921 et qui constitue la base des
gazogènes aujourd'hui commercialisés (figure n° 3):
Alimentation en combustible
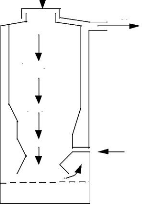
Air
Gaz
Séchage
Pyrolyse
Gaz
Oxydation
Réduction
Cendrier
Figure nO 3:
schéma du générateur IMBERT
C'est un gazogène à bois comprenant deux axes
concentriques : une cuve centrale cylindroconique constituant le
réacteur et une cuve extérieure jouant le rôle
d'échangeur de chaleur:
Dans la cuve centrale, cylindro-conique, le combustible traverse
4 zones successives : 1' Une zone de séchage entre 100°C et
200°C.
1' Une zone de pyrolyse entre 200°C et 800°C où
la biomasse est transformée en charbon, gaz (CO, CO2, CH4, H2) et des
goudrons.
1' Une zone d'oxydation entre 800°C et 1200°C
où le carbone du charbon de bois et les produits volatiles
dégagés dans la zone de pyrolyse sont craqués totalement
ou partiellement en présence de l'air distribué par des
tuyères.
1' Une zone de réduction où les molécules de
carbones de CO2 et de H2O sont transformées en monoxyde de carbone, H2
et CH4.
Le gaz quitte ensuite la zone de réduction et entre
dans la cuve extérieure; il remonte cette double enveloppe en se
refroidissant par transfert de chaleur (conduction et convection) vers la cuve
centrale et vers l'extérieur.
IV.1.2/- Différents types de gazogène
Suivant le mode de circulation dans le
générateur du gaz produit (c'est-à-dire selon que le
combustible et le gaz produit se déplacent dans le même sens ou
dans le sens inverse), selon la granulométrie des particules à
gazéifier, on distingue trois variétés de gazogènes
dits à lit fixe, à lit mobile, et à lit
fluidifié.
Si le principe de gazéification n'est pas nouveau, la
technologie peut être améliorée en ce qui concerne la
taille des appareils (et donc le coût d'investissement), leur rendement
(absence de carbone dans les cendres, absence de goudrons dans le gaz) et leur
facilité de conduite. Les gazogènes de petites puissances pour
des besoins des petits groupements ont fait l'objet de travaux en Inde
où des sociétés spécialisées commercialisent
des gazogènes de petite et moyenne puissance. En fonction de leur taille
on distingue :
> Des gazogènes de petite puissance allant
jusqu'à quelques dizaines de kW. Ces gazogènes sont
adaptés pour l'électrification rurale et la production de la
force motrice dans les centres isolés.
> Des gazogènes de moyenne puissance pour des besoins
plus importants.
> Des gazogènes de grande puissance environ 200kW
à 500kW pour des besoins importants des industries.
Il faut noter que la gamme de puissances varie avec le
coût d'investissement, les grandes puissances nécessitant de plus
gros investissements. A titre d'exemple, le coût d'acquisition d'un
gazogène de 5 kW peut être évalué à environ
2,5 millions de FCFA tandis qu'un groupe gazo-électrogène de
grande unité d'environ 300 kW peut nécessiter un peu plus de 115
millions de FCFA (TAGUTCHOU J. P., 2000).
IV.1.3/- Utilisations et Contraintes
Les utilisations des gazogènes sont variées et vont
de la production thermique à la production électrique en passant
par la synthèse des produits chimiques.
Pour la production électrique, il nécessite la
connexion d'un moteur pouvant fonctionner au gaz pauvre comme le moteur Diesel.
Ici on peut avoir 2 options :
- Option tout-gaz où le moteur est un moteur à
allumage commandé dérivé du moteur à essence ou
à gaz et où on introduit un mélange carburé air-gaz
de gazogène et dont l'ignition est effectuée par
l'étincelle d'une bougie d'allumage.
- Option dual-fuel où le moteur est de type Diesel-gaz
qui est un moteur Diesel standard dans lequel on introduit un mélange
carburé air-gaz de gazogène et dont l'ignition du mélange
est effectuée par une injection pilote de diesel représentant 10
à 20% de l'énergie totale.
Après la production de l'énergie mécanique
par le moteur Diesel, les besoins de force motrice peuvent être
satisfaits (motopompes, presse à huile, moulin, ...).
Pour la production thermique, un brûleur doit être
connecté à la sortie et alimenté de gaz de
gazogène.
La pratique des gazogènes ne va pas sans contraintes
remarquables:
- Contraintes liées au coût d'investissement.
- Contraintes liées au combustible (conditionnement).
Ici le combustible (bois) utilisé doit respecter certaines normes de
granulométrie, de taux d'humidité en fonction des usages qu'on
fera du gaz. Par exemple, pour le bois, le taux d'humidité doit
être inférieur à 20% et la granulométrie de l'ordre
de 5%; de plus, le gaz produit ici doit être destiné aux
brûleurs et moins conseillés pour les moteurs à moins
qu'une bonne épuration soit faite car ce gaz contient beaucoup, de
goudrons. Si le combustible est le charbon de bois, celui-ci doit être
bien sec et le gaz produit pourra alors être adapté pour les
moteurs pour la production électrique car le taux de goudrons dans le
gaz est bien réduit.
IV.2/- paramètres influençant la
qualité des gaz de gazéification.
Etant donné que nous nous préparons à
gazéifier le charbon de bois, il est primordial de connaître les
paramètres de gazéification sur lesquels on pourrait
éventuellement jouer pour optimiser la production d'un gaz de bonne
qualité pour la combustion dans les moteurs à combustion interne.
Sans entrer en détail, les principaux facteurs qui influencent la
composition des gaz sont :
- la température de gazéification ainsi que la
cinétique de montée en température ; - la nature physique
et chimique du produit à gazéifier ;
- la conception du gazogène, notamment pour ce qui
concerne le système de cracking des goudrons ;
- la composition de l'atmosphère de réaction (la
présence de vapeur d'eau enrichit le gaz produit en
hydrogène).
IV.3/- Charbon de bois à usage gazogène.
Les propriétés les plus importantes d'un charbon de
bois concernant son emploi dans les gazogènes sont:
- Le PCI (pouvoir calorifique inférieur);
- La dureté;
- La friabilité; - La grosseur; - La
propreté;
- L'activité chimique;
- Le comportement au cours de la carbonisation en fonction du
temps, de la température ainsi que du degré d'humidité et
de la forme des diverses essences.
Dans le numéro 23 hors série de la revue
"combustible et carburants forestier", il est recommandé pour
la fabrication de charbon de bois à l'alimentation des gazogènes
que ces caractéristiques principales se rapprochent des suivantes
(GIRARD P., 1985):
· Résistance à l'écrasement : 15
à 18 kg;
· Dureté et friabilité : très dur et
peu friable;
· Densité minimale : 0,180;
· Humidité maximale: 8%;
· Teneur en carbone fixe minimale: 80%;
· Teneur en cendre maximale: 3%;
· PCI minimum: 30 kJ/kg;
· Température d'inflammabilité
:200°C.
Les résultats obtenus pour les essais faits sur les
charbons de la ville de Yaoundé se trouvent dans le § III du
chapitre 3 suivant.
Connaissant toutes ces propriétés, la question
qu'on devrait logiquement se poser est celle de savoir comment peut-on faire
pour obtenir un charbon de bois de toutes ces qualités. Sans revenir sur
les parties précédentes concernant la carbonisation, rappelons
simplement que pour obtenir un charbon de bois ayant toutes les
caractéristiques énumérées ci-dessus, il faut:
i. Utiliser les essences de bois dur, si possible
dépourvues d'écorce;
ii. Effectuer la carbonisation de manière à
obtenir une température finale de carbonisation élevée,
mais compatible avec les réalités économiques (rendement
pondéral acceptable);
iii. carboniser des bois aussi secs que possible;
iv. favoriser des réactions de carbonisation lentes.
Enfin, pour être employé dans le gazogène,
le charbon de bois doit être exempt de morceaux trop gros et trop petits
(le poussier est particulièrement nuisible); Avant son chargement dans
le générateur du gazogène, le charbon de bois doit subir
les opérations suivantes: concassage, criblage et
dépoussiérage.
Avantages et inconvénients de la gazéification du
charbon de bois par rapport à celle de la biomasse brute.
Il est important de noter ici les avantages et les
inconvénients que l'on a en gazéifiant le charbon de bois
plutôt que le bois brut.
1' En terme d'avantage on retiendra que :
? le charbon de bois est plus concentré en énergie
que le bois brut;
? il a déjà perdu la quasi-totalité des
matières volatiles du bois de départ;
? La combustion du charbon de bois comparée à celle
du bois produit très peu de goudron, source de corrosion des chambres de
combustion;
? Le charbon de bois est essentiellement constitué de
carbone (plus de 80%) contrairement à la biomasse brute qui n'en
contient que moins de 50%;
? Lors de son utilisation dans les gazogènes, le temps
d'allumage est plus réduit.
? La gazéification du charbon de bois fournit des gaz
propres et plus riches en énergie (ce gaz contient de moins en moins du
CO2 et du N2);
? Le charbon de bois est facilement transportable ;
? Le gaz produit par gazéification du charbon de bois
contient moins de goudrons et est ainsi adapté pour les moteurs à
combustion interne.
1' Pour ce qui est des inconvénients, on
n'en note pas beaucoup, mais on peut quand même signaler:
? Le charbon de bois a perdu une bonne partie de son
énergie au cours de la carbonisation;
? Par rapport au bois brut, le charbon de bois
nécessite une transformation supplémentaire de la matière
première, ce qui contribue à augmenter le coût de
production finale de l'électricité;
? Le charbon de bois nécessite une contrainte
supplémentaire de conservation, car il
reprend facilement l'humidité (à cause de la
structure poreuse qui le constitue);
Les différentes réactions de
gazéification sont encore mal maîtrisées et de nombreux
travaux sont encore en cours pour mieux connaître les différentes
réactions de gazéifications afin de pouvoir les orienter dans le
sens d'une plus grande production de gaz à PCI élevé.
Cependant il existe sur le marché du matériel ayant atteint un
niveau de technologie qui peut être suffisant pour assurer
l'approvisionnement en énergie de quelques sites très
isolés non raccordés au réseau national
d'électricité, surtout en zone forestière humide.
Après avoir fait le point sur la revue bibliographique
concernant la biomasse et l'électrification rurale en
générale et la technologie de gazéification en
particulier, nous allons essayer de faire le points sur les expériences
que nous retrouvons de part le monde à propos de la gazéification
de la biomasse. C'est ce qui va faire l'objet du prochain chapitre.
CHAPITRE II EXPÉRIENCES DE
GAZÉIFICATION DANS LE MONDE
INTRODUCTION
Pendant que la combustion de la biomasse produit de la chaleur
directement utilisable, la gazéification produit un gaz qui peut
être utilisé pour des procédés thermiques plus
contrôlés, pour faire fonctionner des moteurs à combustion
interne ou des turbines à gaz et pour la synthèse des produits
chimiques combustibles liquides (méthanol, ammoniac....). La biomasse
reste le seul combustible renouvelable pour la gazéification.
En 1979 un des auteurs dans le domaine avait publié
alors un article sur "Enquête sur la gazéification de la Biomasse"
pour le compte de la SERI (Solar Energy Renewable Institute) aujourd'hui NREL
(National Renewable Energy Laboratory). En ce moment les seules connaissances
sur la gazéification restaient celles des archives de la 2e
guerre mondiale. Aujourd'hui une impulsion est donnée dans le domaine de
la gazéification de la biomasse et plusieurs gazogènes ont
été construits, mis en opération avant d'être
abandonnés. Dans cette partie, nous nous proposons de présenter
l'état actuel de la technologie de gazéification dans le monde,
dans l'optique de donner quelques perspectives dans ce domaine très
vaste car il y a plusieurs milliers de systèmes de gazéification
de part le monde avec très peu de différence de conception les
uns des autres. Ensuite nous essayerons de présenter un
résumé de quelques projets de gazéification en cours dans
ce domaine ainsi que l'état des recherches y afférant.
I/- ETAT ACTUEL DE LA TECHNOLOGIE DE GAZEIFICATION
I.1/ Bref historique de la gazéification
Le destin de la gazéification de la biomasse et du
charbon s'est beaucoup contrarié dans un monde riche en pétrole,
houille et autres réserves en combustibles fossiles. L'âge
classique de la gazéification peut être considéré
comme s'étendant entre les années 1800 et 1940. Jusqu'en 1920,
plusieurs pays du monde avaient des "gasworks" où les producteurs de gaz
(mélange primaire de CO, CO2, 112 C114 et N2) délivraient,
stockaient dans des bonbonnes à gaz et fournissaient aux ménages
et les industries. Avec le développement du transport du gaz naturel
à travers des pipelines, ces industries et leur connaissances ont
disparu. Aujourd'hui avec les menaces qui pèsent sur les gisements
fossiles et les contraintes environnementales y afférant, nous avons
encore besoin de ces connaissances. La 2e guerre mondiale
était l'âge d'or pour la gazéification de la biomasse avec
plusieurs milliers de gazogènes utilisés en Europe. Avec
l'embargo énergétique de 1970, plusieurs projets de
gazéification étaient mal conçus
basés sur des technologies inappropriées de charbon.
C'était alors l'âge noir de la gazéification de la
biomasse. Certains de ces projets sont passés de la phase de conception
à la phase de test pilot jusque totalement à l'échelle
commerciale. C'est ainsi qu'en 1979, on retrouve plus de 81 projets et
constructeurs de gazogènes reportés dans la première revue
"Survey of Biomass Gazéifification " publiée en 1979
(REED T. B. and al, 1999).
La crise de l'énergie de 1974 - 1984 a
été tempérée par la conception selon laquelle la
crise était largement artificielle et politique et ne
représentait pas la chute imminente du pétrole. La chute du prix
du pétrole au milieu des années 1980 a causé le
déclin de tous les projets de gazéification en cours qui avaient
vu le jour avec la hausse du prix du pétrole. Depuis ce temps, avec
l'entrée en jeu de plusieurs autres paramètres liés
à la protection de l'environnement, des ressources naturelles et la peur
de provoquer de brusques changements climatiques, on a assisté à
la renaissance de l'intérêt de la gazéification comme la
meilleure manière d'utiliser la source renouvelable que constitue la
biomasse.
Durant la 2e guerre mondiale, la
gazéification de la biomasse était utilisée pour le
transport civil des cars, autobus, locomotives, etc. Mais, aujourd'hui, cette
gazéification est vue premièrement comme une source potentielle
de production d'électricité. Cette vision est plus
réaliste encore quand il s'agit de la production
décentralisée de l'énergie électrique.
I.2/- Gaz et gazéification de la Biomasse
Depuis l'existence de l'homme, le bois et ses
dérivés ont été brûlés pour la
production de la chaleur. Depuis l'apparition de la gazéification dans
les années 1800, il est apparu que le gaz était meilleur comme
combustible pour plusieurs usages. Le gaz produit est un mélange de H2,
CH4 et CO comme source d'énergie et CO2 et N2 comme composés
inertes. Dans tous les cas, la gazéification a de nombreux avantages par
rapport à la combustion directe du bois ou charbon :
v' le gaz est plus facile à distribuer dans les tuyaux
pour une ville, dans des brûleurs ou lampes ou encore à injecter
dans les cylindres des moteurs à combustion interne ;
v' la combustion du gaz est plus facile à contrôler
;
v' le gaz peut opérer en continue ;
v' la combustion des gaz est claire puisque les impuretés
ont disparu au cours de la gazéification ;
v' le rendement de la combustion des gaz est élevé
puisqu'on peut mélanger le gaz avec la proportion réelle d'air
pour une combustion optimale ;
1' la température de combustion est élevée
pour des usages industrielles ;
1' la combustion est intense et il y a croissance de transferts
thermiques ;
1' bon rendement pour la production de la force motrice : pour
la production de la vapeur pour les turbines à vapeur avec le bois ou la
houille, le rendement est faible et demande un espace plus large pour la
condensation ; par contre, le gaz peut être utilisé dans des
turbines à gaz et les moteurs à combustion interne avec un bon
rendement et ce dans un espace plus réduit ;
1' de plus beaucoup de produits chimiques sont
synthétisés à partir des gaz.
Donc le gaz est utile pour la cuisson, la
réfrigération (réfrigérateur à gaz) et
l'éclairage, production de chaleur, les moteurs pour la production du
travail et la force motrice, et pour la synthèse des produits chimiques.
La révolution industrielle dépend de la logique d'avoir des
combustibles contrôlables et efficacement utilisés.
Par ailleurs, le terme "biomasse" a été
amené à usage courant par la première crise de
l'énergie pour le bois et autres formes de matières organiques
lorsque ceux-ci peuvent subvenir aux besoins énergétiques. La
biomasse est une forme d'énergie renouvelable et peut potentiellement
subvenir aux besoins énergétiques de l'humanité. Les
récentes pressions environnementales sur la croissance des proportions
du CO2 et autres gaz à effet de serre dans l'atmosphère appellent
à l'usage de la biomasse renouvelable comme source d'énergie non
polluante étant donné que le CO2 produit est immédiatement
recyclé (ou capté) pour la génération de nouvelles
plantes. En effet, le cycle du carbone dans ce cas se présente comme
indiqué sur la figure n° 4 ci-dessous.
Ainsi, il est possible de fabriquer des gazogènes de
biomasse plus petits que ceux utilisant la houille pour des usages à
petites échelles pour les PED (Pays en voie de développement) et
les Communautés villageoises isolées.
Nous ne reviendrons plus sur le principe même de la
gazéification étant donné que nous avons amplement
exposé la théorie y afférant dans le chapitre
précédant. Nous allons nous préoccuper dans la suite
à faire néanmoins un état des lieux sur la technologie
existante aujourd'hui dans le monde.
Cycle du CO2
Figure n°4: Cycle du gaz carbonique
par rapport à la valorisation de la biomasse dans la production
électrique
|
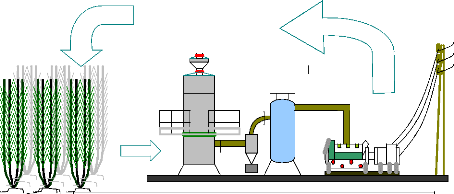
Photosynthèse
CO2
Emission
I.3/- Etat actuel de la Technologie de gazéification
dans le monde
Les gazogènes les plus usuels aujourd'hui dans le monde
sont des gazogènes dit à lit fixe. Ce nom commun donné aux
gazogènes se rapporte à la manière dont le combustible
circule et la manière dont il est supporté d'une part, et
simultanément le mode de circulation du flux gazeux. Ainsi on distingue
des gazogènes à tirage inversé ou descendant, à
tirage direct ou ascendant, ou encore à contre-courant, à tirage
transversal ou horizontal, à lit fluidisé. L'utilisation de ces
noms aide dans la lecture ou la littérature sur les gazogènes,
mais dérange (ou gêne) en même temps aujourd'hui dans la
compréhension des opérations des nouveaux gazogènes. C'est
donc des noms qu'il faudrait utiliser avec beaucoup de réservation. Dans
le processus de gazéification, la chaleur nécessaire au
procédé peut provenir de la combustion directe du gaz de pyrolyse
(tirage descendant et co-courant) ou de la combustion du charbon de bois
séparément (tirage ascendant) ou encore de la combinaison des
deux combustions (lit fluidisé).
Chaque gazogène et dispositif de combustion utilise une
forme de recyclage de la chaleur pour générer les 5 à 15 %
de la chaleur nécessaire pour la pyrolyse comme le montre le tableau
n°4 ci-dessous. Dans la conception des gazogènes, le principal
problème est celui de s'arranger à fournir cette quantité
de chaleur au combustible entrant, et est déterminant dans la grande
variété des gazogènes.
Tableau n°4 : Répartition des
différents types de gazogènes en fonction de la source
de chaleur nécessaire pour le procédé.
Type de gazogène
|
source de chaleur pour le
procédé
|
tirage ascendant
|
combustion du charbon
|
tirage descendant
|
combustion partielle des volatiles
|
lit fluidisé
|
combustion partielle des volatiles et du charbon
|
lit mobile
|
combustion partielle des volatiles et du charbon
|
> Quelques paramètres important de l'aspect
scientifique de la gazéification :
Nous allons essayer d'énumérer sans rentrer dans
les détails quelques paramètres importants pour une étude
minutieusement détaillée du fonctionnement d'un gazogène
:
1' Rapport air combustible, le pouvoir comburivore et/ou
le taux d'équivalence.
Le rapport air combustible est la masse d'air
nécessaire pour la combustion complète d'une unité de
masse de combustible tandis que le pouvoir comburivore est cette
quantité en terme de volume
D'après la relation suivante, (TAGUTCHOU J. P.,
2000), il ressort qu'on a besoin de 6,26 kg d'air pour brûler
1kg de bois sec.
2,66C 7,94H 0,998S - O
+ +
2 2
(A/F) = (kg air/kg comb) (2).
TGS 0,232
Le taux d'équivalence quant à lui est le rapport
entre la quantité d'air effectivement utilisée dans le
procédé et la quantité d'air stoïchiométrique
requise pour la combustion complète.
Les calculs thermodynamiques montrent que pour être
converti en gaz, cette quantité d'1kg de bois sec a besoin de 1,56 kg
d'air.
Dans tous les cas, l'apport en air est une donnée
importante dont dépend la température de la réaction.
L'apport en air doit donc être bien contrôler pour avoir une
certaine gamme de température pour les différentes
réactions comme le montrent les courbes de la figure n°5 cidessous
(REED T. B., 1981).
Température de réaction en fonction du
taux d'équivalence
2200
2000
1800
1600
1400
Temperature
1200
1000
800
600
400
200
0
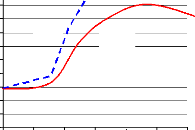
O2 Air
0 0,2 0,4 0,6 0,8 1 1,2
Taux d'équivalence
Figure n° 5: Dépendance de la température de
réaction avec l'apport en air
v' Aspects thermodynamiques des
réactions
Ici plusieurs calculs doivent être faits et les mesures
prises sur les taux d'humidité, la pression, les températures et
la composition des gaz et des imbrûlés à la sortie du
gazogène.
v' Aspect cinétique des
réactions
Ici on doit avoir :
* La vitesse superficielle des gaz (VSG) qui est le rapport
entre le débit de gaz produit (m3/s) et la section interne du
réacteurs (m2). Le terme superficiel réfère au
fait que le VSG n'est pas encore une vitesse en soit, mais a juste la dimension
d'une vitesse. La VSG est basée sur des mesures faites sur le gaz dans
les CNTP4 et non à la Température du réacteur.
La VSG est un paramètre de performance qui a longtemps permis de faire
la différence sur les gammes de gazogènes longtemps
commercialisés. De ce nombre peuvent en dériver un bon nombre de
caractéristiques de gazogènes ;
*Puissance thermique P(th) = VSG x PCI
(3).
où PCI est le pouvoir calorifique du gaz produit
* Puissance électrique P(e) = VSG x E(P)
x PC (4).
où E désigne le rendement de production
électrique.
* Vitesse de combustible VC = ? x e(g) x VSG x
( )
PC g (5).
( )
PC c
4 Conditions Normales de Température et de Pression
e(g) = rendement gazéification
PC(g) et PC(c) = PC du gaz et du combustible
? = densité du combustible
* la production superficielle de gaz qui mesure
le taux de production du gaz par
unité de volume de gazogène. On a aussi : PSG =
VSG/hxA (6).
avec (h = hauteur du réacteur, A = section du
réacteur ) hA= volume réacteur PSG (m3
gaz/s)/(m3 réacteur).
1' Energie contenue dans le gaz
En fonction de leur composition et de leur pouvoir calorifique
(énergie contenue dans le gaz), on distingue les gaz pauvres (4<PCI
< 7 MJ/m3), les gaz à moyen PC (9 <
PCI<15MJ/m3 et les gaz riches PCI>20MJ/m3.
> Problèmes de gazogènes
De la conception à la mise en fonctionnement des
gazogènes beaucoup de problèmes existent :
- contrainte de charge de la matière première ;
- production des goudrons ;
- production des imbrûlés et cendres ;
- problèmes d'utilisation de biomasse à taux de
matière minérale élevé (balles de riz, coques
d'arachides, ...).
I.4/- Vision globale de la gazéification dans le
monde
On peut écrire tout un livre sur les gazogènes
en se referant simplement aux récentes publications sur le sujet et des
pareils livres sont publiés ou en cours de publication. Nous essayons de
présenter ici l'état de quelques projets de gazéification
tel qu'on a dans le monde.
> Gazéification à grande
échelle
Les pays comme les USA, le Canada, les Pays Scandinaves, la
Finlande ont de grandes ressources forestières et des grosses
installations industrielles dépendant de celles-ci. C'est évident
qu'ils ont fondé leur intérêt pour la gazéification
à grande échelle et étant donné que les
gazogènes à lits fluidisés sont les plus appropriés
pour les grandes productions (> 10
MW, 10 tonnes/heure), ce type de gazogène est partout
le plus prisé. On retrouve dans ces pays et dans d'autres encore des
installations qui peuvent être considérées comme ayant
atteint un stade commercial et plusieurs d'autres approches comme objectifs.
> Gazogène à petite échelle (10
kW à 5 MW)
Comme mentionné précédemment, il est
perçu que depuis 1980, les gazogènes pour les utilisations
thermiques et la production de la force motrice avaient déjà fait
leur preuve en petite échelle. Mais jusqu'aujourd'hui les pays comme les
Pays Bas, la Suisse, linde, la Chine et le Danemark ont encore un
intérêt accru pour les petites installations, qui sont les plus
appropriées pour l'utilisation de la biomasse dont les ressources sont
dans la plupart des cas dispersées. Par tout dans le monde, beaucoup de
travaux sont conduits sur les petites installations. La USDE (United States
Development of Energy) a montré récemment son
intérêt pour la distribution des gazogènes de petite
puissance.
> Cuisinière à gaz de
gazogène
Il est possible maintenant de concevoir des petits
gazogènes pour les besoins de cuisson domestique. Ceci se fonde sur le
principe de gazogène à tirage inversé ou descendant,
où l'ignition se fait au dessus d'une cuve cylindrique contenant la
biomasse (pellets, briquettes, brindilles, ...) et l'air entrant par le bas et
traversant la cuve de bas en haut par convection naturelle ou forcée.
Les cuisinières à convection naturelle sont les plus simples
à mettre en oeuvre et à opérer. Une excellente
cuisinière peut être conçue à partir d'une cuve
cylindrique nécessitant une cheminée-brûleur au-dessus du
lit du combustible dans laquelle le gaz provenant de la pyrolyse brûle
naturellement par inspiration d'air. Pour ce qui est des unités à
convection forcée, elles nécessitent un petit ventilateur
électrique (2W) et génèrent environ 3 à 5 kW de
puissance thermique (REED, 1999). Tous ces deux types peuvent
être chargés, brûlés et éteints à
l'intérieur d'une maison sans qu'on soit exposé au
problème d'odeur.
> Gazogène pour la production thermique de
la force motrice et des carburants de synthèse.
Les gazogènes peuvent produire du gaz pour des
applications thermiques (séchage, briqueterie et cimenterie, verrerie,
cuisson opération dans les turbines à gaz pour l'énergie
électrique, chaudières, ...).
Pour ces utilisations, la production de gaz est relativement
simple nécessitant un minimum de réduction du taux de goudron, en
s'assurant de maintenir le gaz assez chaud pour
empêcher la condensation des goudrons dans la tuyauterie
et le brûleur. Malgré le peu de support qui a jalonné leur
développement depuis 1970, ces gazogènes ont été
lentement développés et représentent aujourd'hui la
majorité des gazogènes en opération dans le monde.
Les gaz peuvent être aussi utilisés pour la
production de la force motrice dans le moteur diesel, les moteurs à
étincelle et gaz, les turbines à gaz, etc.
Dans cette seconde grande utilisation, il faut redouter les
proportions importantes de goudrons dans les gaz produits, impuretés qui
peuvent provoquer des corrosions dans les moteurs. Ainsi plusieurs
succès commerciaux des gazogènes concernent aujourd'hui des
productions thermiques. Un excellent effort est aujourd'hui fait en direction
de la diminution des impuretés comme les goudrons dans le gaz produit
par filtration ou catalyse.
Finalement, les gazogènes peuvent être
utilisés pour la synthèse des produits chimiques à travers
la voie de production des gaz de synthèse.
Il est donc clair que la technologie de gazéification
est en plein essor partout dans le monde comme dans les années
d'après seconde guerre mondiale. Malgré le fait qu'il est
démontré que c'est une technologie de développement, on
constate que c'est encore les pays du Nord qui pour la grande majorité
se lancent dans le développement de celle-ci. Par souci d'utilisation
des énergies vertes renouvelables pour ainsi contribuer à la
réduction des émissions à effet de serre, et la
maîtrise des changements climatiques, les pays du Sud devraient
déjà embrasser cette dynamique globale, surtout avec la crainte
d'épuisement des gisements pétroliers. Pour mieux
appréhender les expériences de la technologie de
gazéification dans le monde, nous nous proposons de présenter
succinctement dans la suite les résumés de quelques projets de
production des gaz en cours dans le monde.
II/- RESUME DE QUELQUES PROJETS DE GAZÉIFICATION
DANS LE MONDE
Dans cette partie dans le souci de mieux cerner les contours
de la gazéification de la biomasse dans le monde, nous essayons de
présenter ici un petit résumé de quelques projets qui sont
en cours. Nous ne pouvons pas faire le tour de toutes les activités,
mais quelquesunes prises au hasard devraient apporter une clarté
d'esprit sur la vision globale à propos du sujet. Il est fait aussi
allusion ici aux fabricants de gazogènes.
II.1/- Projet de gazéification à grande
échelle
II.1.1/- Burlington Electric (FERCO, Battelle) :
Gazogène intégré à double lits fluidisés.
Durant les 15 dernières années, Battelle
(Columbus) a développé une unité à double lit
fluidisé qui produit un gaz à 18 - 22 MJ/m3 sans
utilisation d'oxygène. La biomasse est
pyrolysée dans un lit de fluide sans oxygène,
produisant du gaz, du charbon et des composés organiques. Le charbon et
le sable sont séparés dans le cyclone et introduits dans l'autre
lit qui brûle le charbon, réchauffant le sable à
1000°C et 1050 °C. Ensuite le sable chauffé est introduit dans
le premier lit apportant ainsi la chaleur nécessaire pour la
pyrolyse.
En 1984, "Burlington Electric" a été la plus
large installation de bois dans le monde utilisant 85 tonnes/heure pour
générer 50 MWe de puissance électrique. Politiquement,
l'équipement et le nouveau projet sont supportés officiellement
par l'Etat et le Sénateur local. (T. B. REED, 1999)
II.1.2/- Forster Wheeler - Pyroflow (Formerly
Ahlestrom) Corporation : Gazogène à lit fluidisé
mobile
Forster Wheeler est un fabricant en Finlande qui commercialise
à la fois des gazogènes atmosphériques et à lit
fluidisé. La biomasse utilisée pour la gazéification
atmosphérique est constituée de bois, déchets de bois,
charbon, etc.... Les Charges approximatives minimales et maximales pour les
systèmes atmosphériques étaient 2000 kg/h et 27000 kg/h
respectivement. Une unité pilote existe mais n'est plus utilisée
depuis avril 1992.
Les recherches sont en cours sur l'unité à lit
fluidisé. Forster Wheeler est une Compagnie Commerciale Multinationale
spécialisée dans les chaudières et les gazogènes
avec environ 12 années d'expériences dans la
gazéification. En 1990, les ventes du groupe s'élevaient à
plus 2300 millions de dollars avec environ 12000 employés.
II.1.3/- Institut Technologique du gaz :
Gazéification à lit fluidisé
L'institut technologique du gaz est une institution
basée au Sud de Chicago, conduisant des tests de gazéification
sur le procédé "Renugas" depuis 1979. c'est une structure
d'éducation et de développement qui conduit des recherches
à but non lucratif dans l'intérêt du gaz naturel et de la
force motrice des industries. Il a déjà 18 années
d'expériences sur les technologies de gazéification de la
biomasse.
Le but du procédé qu'il développe est
d'arriver à la gazéification de 11 tonnes /jour de biomasse
à l'échelle pilote pour produire un gaz à moyen PCI
pouvant être utilisé comme combustible gazeux dans les industries
ou pour substituer le gaz naturel ou de synthèse. Le gazogène
peut opérer avec de l'air ou l'oxygène à la pression de
plus de 32,7 bars et à la température de 850°C à
900°C.
Les caractéristiques des gaz produits sont les
suivantes.
Tableau n°5 : composition du gaz produit
par l'Institut Technologique du gaz
Gaz
|
H2
|
CO
|
CO2
|
CH4
|
C2+
|
O2, H2, H20
|
% volume
|
25,3
|
16,0
|
39,4
|
17,8
|
1,5
|
0
|
- Débit de gaz à la sortie : 335 Nm3/h
- Température d'échappement des gaz : 816
°C
- Pouvoir calorifique : 12,97 MJ/Nm3
- Proportion de goudron : 0,0200,03 kg/kg de combustible.
II.1.4/- "Lurgi Energie" Und Umweltlechnik" :
gazogène à lit mobile pour la production de la force motrice.
L'objectif principal de ce projet mis en oeuvre à
Francfort en Allemagne est la gazéification du bois, RDF et charbon de
bois pour la production d'un gaz à moyen PCI dans un gazogène
à lit fluidisé circulant. La charge de l'installation commerciale
est approximativement 8030 kg/h à 15 % d'humidité et 5 % de taux
de cendre ; il y a une installation pilote fonctionnant à la pression
atmosphérique avec l'air ou l'oxygène. Un système
modifié opérant avec l'oxygène et la vapeur peut produire
un gaz de synthèse pour la conversion en méthanol et les autres
produits chimiques.
"Lurgi" a une installation pilote de gazéification
à Frankfort. Celle-ci utilise comme matière première le
RDF (Refuse Derived Fuel) et produit un gaz d'environ 3,1 kg/kg de combustion.
Les données de composition des gaz de gazéification du RDF de
cette installation sont :
8,27 % H2, 9,76 %CO, 9,30 % CO2, 1,55 %CH4, 0,64 %
C2+, 0 %,O2, 43,06 % N2, 0,07 %, H2S, 27,35 %.H20 (REED T.
B., 1999).
`Les autres données sont : PCI : 3,2 MJ/Nm3,
HCl : 18 mg/Nm3
Cette installation fait habituellement des contrôles de
pollution sur la base des taux d'émission officiels admis par la norme
allemande en la matière.
Le coût d'un système de gazéification
comme celui de Lurgi CFB, dépend d'un certain nombre de facteurs
incluant le type de biomasse utilisée et le procédé
utilisé. En excluant la charge de site d'installation, une installation
comme celle de Frankfort en design et en taille peut avoir un coût de
l'ordre de 21 millions de Deutschemark allemand (environ 7,5 millions de
£, 5soit environ 7.1milliards de FCFA).
5 £ est la livre sterling anglaise qui vaut environ 950
FCFA
Les installations de gazéification de Pols et
l'équipement de gazéification à l'échelle pilote de
Frankfort sont encore opérationnels. Les deux équipements ont
été vendus pour un montant total de 90,1 millions de Deutschemark
allemand (environ 30,2 milliards de FCFA) et seront les plus grandes centrales
électriques utilisant la biomasse d'Europe.
II.1.5/- Thermochem Inc. (Manufacturing and Technology
Conversion International (MTCI)
Avec la coopération du département de l'Energie
des Etats Unis, la commission d'Energie de Californie, l'Agence de production
de l'environnement et les compagnies privées, la MTCI et sa filiale
Thermochem, Inc, ont développé une technologie de transformation
de la vapeur qui est uniquement capable de transformer la matière
organique pour produire un gaz à moyen PCI, riche en hydrogène.
La « MTCI/Thermochem Steam Reformer » peut utiliser pour la
conversion de l'énergie des matières premières telles que
RDF (Refuse Derived Fuel), déchets de céréale,
déchets ménagers, charbon et toute autre matière contenant
des substances organiques. MTCI est une compagnie américaine de
développement des technologies basée à Baltimore, Maryland
qui a plusieurs références dans la conversion de
l'énergie, le traitement des déchets et les
procédés de contrôle de pollution de l'air. Thermochem Inc,
est aussi situé à Baltimore et assure les marchés et les
commissions des systèmes développés par MTCI.
Les premières installations de démonstration de
MTCI/Thermochem ont été construites en 1992 à la "Inland
Container Corporation", usine de recyclage de papier à Ontario en
Californie et opérait avec des excrétas contenant des petites
fibres et des plastiques. Cette installation de démonstration avait une
capacité de 12 tonnes par jour. En 1995, MTCI a conduit une excellente
démonstration de capacité de 50 tonnes/jour ("Pulse Enhance Black
Lipror Steam Reformer) à New Bern en Caroline du Nord. Thermochem et
MTCI ont aussi excellemment conduit plusieurs campagnes de
démonstrations avec les mélanges de déchets à
bas-niveau (MDBN) autour du procédé de développement des
unités de transformation de vapeur, ceci avec 750 heures de tests
continus. Les résultats de ces tests ont indiqué essentiellement
la destruction totale des halogénures organiques, et la rétention
des radio nucléides dans les résidus solides du volume
réduit.
Le système global est peu coûteux et offre une
sécurité environnementale non incinérable, et est
facilement acceptable par le public comme méthode pour les
mélanges de déchets à bas niveaux. Une évaluation
commandée par la zone "Mixe Waste Focus Area" du département de
l'Energie des Etats Unis, a quotté cette technologie comme la
première des 23
technologies en liste pour l'alternative d'incinération
pour la destruction des déchets organiques (SCHWINKENDORF,
1997).
Les résultats des compositions de gaz provenant des
différents types de biomasse sont dans le tableau n°6 suivant : le
méthane apparaît comme étant relativement constant (5
à 12%).
Tableau n°6: Composition des
gaz produits pour différents types de biomasse par la MTCI
Composition (Vol. %)
|
Plaquette de bois
|
Balles de riz
|
Déchets de fibre de mil
|
Déchet de papier
|
RDF
|
Déchets ménagers
|
112
|
48.11
|
42.83
|
38.86
|
50.50
|
45.54
|
55.21
|
CO
|
22.91
|
19.67
|
23.34
|
19.26
|
25.26
|
28.10
|
CO2
|
20.18
|
24.4
|
23.27
|
20.10
|
14.51
|
5.95
|
C114
|
8.32
|
11.56
|
8.31
|
8.42
|
8.30
|
5.00
|
C2+
|
0.48
|
1.54
|
6.40
|
1.72
|
6.38
|
5.74
|
PCI (MJ/Nm3)
|
13.16
|
14.68
|
16.48
|
14.56
|
16.72
|
14.96
|
Température (°C)
|
697
|
719
|
677
|
719
|
788
|
765
|
II.1.6/- Wellman process Engineering LTD:
Gazogène à tirage ascendant avec craquage catalytique pour la
génération de la force motrice
La compagnie Anglaise Wellman conçoit des
gazogènes pour le charbon et le bois depuis 75 ans. Elle manufacture
aussi des chauffe-eau et autres équipements thermiques. Ils ont
conçu une centaine de gazogènes qui produisaient du gaz pour les
villes du monde pendant la période 1923-1950. En 1990 ils ont conclu
à la suite d'une étude de marché qu'il y avait des
possibilités de génération de l'énergie
électrique à base du bois dans la gamme 2,5 à 20 MW c'est
à dire (2,5 à 10 tonnes par jour) en utilisant des
gazogènes à tirage ascendant. Le gaz qui à la sortie du
gazogène a un PCI d'environ 5,53 MJ/Nm3 et à la
composition suivante : 6,9 % de 112 , 22,2 % de composés
hydrocarbonés, 29,5 % de CO, 55,3 % de N2 et 6,1 % de CO2.
II.2/- Projets de gazéification à petite
échelle
Le monde des gazogènes à petite échelle
est en perpétuel bouleversement avec des hommes, des compagnies et des
installations qui viennent et disparaissent à tout moment. Certains
gazogènes sont développés pour des petites
échelles, d'autres sont largement vendus
et certains disparaissent tout simplement. Les petites
unités peuvent être utilisées pour approvisionner des
procédés ou des besoins thermiques domestiques.
La production du gaz pour les besoins électriques et de
la force motrice sont encore plus difficiles. Mais les petits gazogènes
seront dans tous les cas la clé pour le développement et
l'industrialisation des PED. Les pays développés dépendent
des infrastructures établies sous forme de réseaux
(réseaux de communication, de télécommunication,
d'assainissement, d'eau, d'électricité, de gaz,...)
installés durant les 100 dernières années. Mais pour avoir
accès à ces réseaux, il faut se rapprocher des grandes
villes. Les zones reculées se trouvent négligées et ont
donc besoin des installations localisées pour atteindre les
consommateurs. L'exemple qui frappe aux yeux dans ce sens est celui des
téléphones cellulaires qui rend possible la communication sans
ligne téléphonique naturelle. Dans le même sens, les
gazogènes de faible puissance (10 - 100 KW) peu coûteux pour la
génération de l'énergie mécanique et
électrique pourraient contribuer à rendre disponible partout
où besoin sera l'énergie électrique, l'eau et le gaz
ménager.
Dans les paragraphes suivant, il est question de
présenter quelques petits projets de gazéification à
petite échelle qui ont été réalisés ou sont
en cours de réalisation dans le monde.
II.2.1/- AEW Associated Engineering Works
C'est une compagnie indienne qui est en service depuis 1986 et
qui fabrique les gazogènes pour l'énergie thermiques (0,1-1 CW/h)
et les applications électriques. Ces gazogènes utilisent les
bois, les plaquettes de bois, copeaux, charbon de bois, balle de riz,... et
peut être facilement adapté aux autres combustibles biomasse.
Ces gazogènes sont disséminés un peu partout
dans le monde et sont spécialisés dans des applications
localisées comme l'électrification rurale à petite
puissance.
A propos, il faut noter que c'est cette compagnie qui est le
fabricant de l'unité qui nous permet de faire des tests pour sou tendre
l'étude objet de notre travail ici. C'est donc sur un gazogène
AEW que nous avons focalisé notre étude et dont les
résultats des premiers tests sont présentés dans le
chapitre suivant.
II.2.2/- The Biomass Energy Foundation
Biomass Energy Foundation (BEF) est une organisation qui
travaille sur le terrain depuis 1983 sur la gazéification de la
biomasse. Depuis 1989, avec l'arrivée dans cette structure de nouveau
spécialistes du domaine, (Thomas REED par exemple), plusieurs livres et
articles scientifiques ont été publiés dans la presse de
la BEF sur l'énergie, la biomasse et la
gazéification. Actuellement, T.B. REED a
développé une cuisinière turbo fonctionnant au gaz du bois
et qui brûle le plus de biomasse avec un bon rendement sans
émission. Elle utilise un ventilateur électrique de 3 W pour
produire environ 3 KWth d'énergie thermique pour la
cuisson.
Thomas B; REED travaille aussi dans le développement
des micro-utilisations à travers de petits programmes du
département américain de l'Energie (DOE). A ce propos, un
gazogène automatique de 12 KW est actuellement en cours de
développement (REED T. B., 1999).
II.2.3/- HTV Energy
HTV Energy est une structure de recherche suisse qui oeuvre
dans la valorisation énergétique de la biomasse. Depuis 1985
pratiquement, ce développement a été lancé par Mr
Helmut Juch, qui démontrait quelques 6 années plus tard que leur
système pouvait produire un gaz pouvant être utilisé dans
les engins sans les problèmes usuels, de corrosion par le goudrons et
phénol. En octobre 1996, date d'une visite effectuée sur le site
basé à Mittelgaustrasse en Suisse, leur installation était
encore en opération. Le gazogène à tirage descendant
utilisé opérait avec un générateur
électrique de 750 kW. Au jour d'aujourd'hui, le gazogène a
déjà opéré pendant 3500 heures et le moteur 250
heures environ sur le site de Kestenholz. Le gaz produit ici avec un rendement
de 75 - 95 % a un PCI de 5 à 6,5 MJ/Nm3. Toutes les
émissions sont dans les limites des normes allemandes pour ce qui est de
l'impact environnemental.
II.2.4/- Université de Cardfiff aux Pays de
Gales
Le Département de Mécanique et des Etudes
Energétiques de l'Université de Cardiff travaille depuis
longtemps dans le domaine de la gazéification sous la houlette du Prof.
N.Syred. C'est ainsi que sous sa direction plusieurs recherches sont conduites
dans le domaine
de la caractérisation et du contrôle et de la
modélisation de la gazéification de la biomasse.
Iiconduit maintenant une recherche sur l'analyse et
l'amélioration des opérations de charge
manuelle de la biomasse dans des unités de chauffage
à l'air. Un gazogène à lit fixe de 200 kW thermique
intégré d'un échangeur gaz-air a été
conçu et construit par un projet monté conjointement entre
l'Université de Cardiff et l'Université Technologique de
Malaisie. Ce système utilise les déchets agricoles et les
résultats des différents tests ont fait l'objet de la
thèse du Dr David BEEDIE de la Division d'Electronique de l'Ecole
d'Ingénierie de l'Université de Cardiff basée aux Pays de
Galles (United Kingdom) .
Parallèlement des recherches sont menées ici sur
la valorisation de la biomasse en vue de la production de
l'électricité. Le contexte de ces recherches est la
nécessité de développer efficacement la production
d'électricité a partir de la biomasse et ceci, a coût
réduit et a petite échelle. Ces études sont fondées
sur les directives de l'Union européenne de mai 2000 qui invite les
Etats membres a adopter des priorités pour l'énergie renouvelable
pour que la commission puisse atteindre ses objectifs de 12 % d'énergie
et 22,1 % d'électricité a partir des sources renouvelables a
l'horizon 2010.
Pour les Royaumes Unis, ceci signifie atteindre les 10 %
d'électricité a partir des sources renouvelables a cette date.
Les récents résultats d'études dans le domaine ont
été atteints avec le soutien financier de l'Union
Européenne.
II.2.5/- Institut National des Industries Extractives
(INIEX)
Depuis une vingtaine d'années, l'INIEX basée a
Liège en Belgique, conduit une étude expérimentale sur la
valorisation énergétique de la biomasse par gazéification
au Rwanda. C'est ainsi qu'en 1985 il a publié un rapport sur le
thème "Intégration de générateurs de gaz dans un
système de valorisation énergétique du papyrus au Rwanda
(PLATIAU D. et al, 1986). Le projet avait pour objet de
démontrer le bon fonctionnement du gazogène de la firme W. EVRARD
dans une unité de compactage de Papyrus des marais au Rwanda.
L'intérêt principal du recours a la technique de
gazéification dans ce cas étant de rendre autonome sur le plan
énergétique, l'unité de compactage grâce a
l'intégration d'un ensemble gazogènegroupe
électrogène utilisant comme combustible une partie de Papyrus
récoltée.
Le Papyrus est une plante a grande tige nue, haute de 2 a 4
mètres, a section triangulaire se terminant par des ombrelles. A sec le
papyrus a un PCI égale a 16,86 MJ/kg contre 17,87 MJ/kg et 14,42 MJ/kg
pour le bois de chêne et les parches de café respectivement
(Platiau D. et al, 1986). Par ses propriétés physiques et
chimiques le papyrus mérite une place de choix dans la liste des
biomasses valorisables a des fins énergétiques. L'unité de
compactage de Kigali permet la production de 1,5 tonne/jour de briquette de
papyrus en moyenne. Avec le groupe électrogène correctement
chargé, la production de 1 tonne de briquettes de papyrus
nécessite la consommation énergétique de 105 kg de papyrus
a 20 % d'humidité et 8,5 litres de gasoil.
Après ce point sur ces expériences, nous allons
dans le chapitre suivant présenter les résultats de la phase
expérimentale que nous avons effectuée sur un gazogène
indien de type AEW.
CHAPITRE III: CHOIX TECHNOLOGIQUES, PROCEDURES,
RESULTATS DE L'ETUDE EXPERIMENTALE, ANALYSE ET CONCLUSION
INTRODUCTION
En vue d'envisager une contribution exemplaire de la biomasse
dans le processus d'électrification rurale décentralisée
en cours dans notre pays, nous avons opté pour la gazéification
du charbon de bois en vue de l'approvisionnement des groupes
électrogènes pour la production d'électricité dans
les centres isolés. L'installation utilisée à cet effet se
trouve actuellement à Yaoundé en provenance de l'IRSAT (Institut
de Recherche en Sciences Appliquées et Technologies) de Ouagadougou au
Burkina-Faso d'où elle a été transférée
après des tests de faisabilité non concluant (à cause
semble-t-il de la qualité et de la disponibilité de la biomasse
utilisée à cet effet). Ce n'est donc qu'après les
présentes études que l'installation devra être
transférée sur site pilote dans un village de la province du
Centre.
Pour bien mener ces tests de gazéification du charbon
de bois, nous avons commencé par rechercher au cours des
expériences pratiques les différentes caractéristiques du
charbon de bois provenant d'un des marchés de Yaoundé, en
occurrence le marché Mokolo. Nous nous sommes limités aux
caractéristiques qui sont les plus importantes et qui sont à
notre portée compte tenu du matériel que nous disposons (taux de
carbone fixe, PCI, taux d'humidité, taux de matières volatiles
taux de cendre).
La première phase des tests sur l'installation a
porté sur la maîtrise même du phénomène de
gazéification. Il s'agit donc de savoir comment le gaz pouvait
être produit et sous quelles conditions on pouvait avoir un gaz de
meilleure qualité ; c'est-à-dire dans le cas précis, un
gaz dépourvu de composés inertes (N2, CO2, ...) et riche en
éléments combustibles (H2, CO, CH4, ...). Ainsi il a
été question pour nous de faire une étude thermodynamique
théorique du phénomène même de gazéification
de l'installation, le gaz produit devant être testé sur un
brûleur. Ceci devrait permettre de voir les différents
problèmes de l'installation en général et du
gazogène en particulier afin de proposer des solutions pour
l'amélioration de la qualité des gaz produits. Pour ce faire nous
avons opté pour le suivi d'un paramètre important du
phénomène. Pour arriver à notre dessein, il est important
d'appréhender les différents phénomènes qui ont
lieu dans le réacteur lors de la production des gaz. Ceci ne peut se
faire que par une modélisation mathématique des réactions
chimiques et des transferts thermiques dans le lit de charbon de bois. La
température apparaît donc ainsi comme un paramètre
important qu'il faut suivre en des points particuliers pour
avoir une idée des conditions au limites en vue d'une
modélisation complète et le dimensionnement des appareils dans la
suite des études. C'est pourquoi nous avons opté pour la prise
des températures au niveau de la paroi du réacteur. Ainsi, les
mesures ont été prises au cours du temps en continu sur une
durée d'à peu près 2 heures avec des valeurs
décalées de quelques secondes seulement.
It MATERIEL.
L'installation que nous avons utilisée pour notre
étude est une installation de gazéification de la biomasse en vue
de la production thermique et électrique, installation située
à ERA-Cameroun, une ONG camerounaise basée à
Yaoundé. Ce matériel est une oeuvre indienne de la
société AEW (Associated Engeneering Works) basée dans la
localité indienne de TANUKU et qui est spécialisée depuis
plusieurs années dans la conception et la fabrication des
gazogènes à petite échelle pour des applications
thermiques et électriques. Quelques photos de l'installation se trouvent
en annexe n°2.
Des thermocouples d'une précision, ?T = #177;1°C ont
été utilisés pour la prise des températures.
I.1/- description des équipements
L'installation d'expérimentation est un ensemble de
matériels soudés sur une plate-forme de superficie 12
m2 (3m x 4m) environ. Pour que cette plate-forme puisse supporter
tout cet ensemble de matériel sans problème, elle a
été constituée de poutres et de poteaux en béton
armé. L'installation comporte un gazogène
(générateur à gaz), un dispositif d'épuration et de
filtrage, un moteur diesel, un alternateur, des accessoires de motorisation
(pilon, moulin, pompe à eau...) et un ventilateur électrique pour
l'alimentation en air (voir photo n°1).
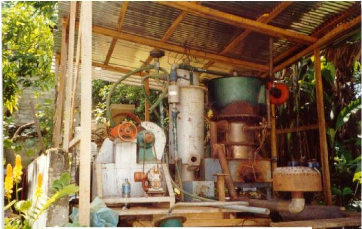
Photo n°1 : Une vue de
l'installation
Les composantes de l'installation comprennent entre
autres :
> Le gazogène Indien AEW (Associated
Engineering Works)
C'est un gazogène indien à tirage inversé
(co-courant) de puissance électrique d'environ 158 kW et dont les
caractéristiques théoriques sont les suivantes:
- débit de gaz: 20 m3/h ;
- taille des bois : 100mm x 80mm;
- consommation de biomasse 6kg/h;
- pouvoir calorifique des gaz: 1000 kcal/m3 (4190
kJ/m3);
- Alimentation en air: l'air est injecté au coeur du
réacteur par le haut;
- Rendement de la gazéification: 70%.
Ce gazogène est constitué d'un réacteur
à double enveloppe, avec à l'intérieur un cône
rétréci à la base et qui comporte une grille au travers
duquel transitent les cendres et les fines particules de charbon avant de se
retrouver dans le cendrier. Ce dernier est un
parallélépipède de 0,1 m3 (0,5m x 0,5m x 0,4m)
qui sert à la fois à recueillir les cendres et de dispositif
tampon qui empêche la fuite des gaz à la sortie du réacteur
; raison pour laquelle on le remplit entièrement d'eau.
A l'intérieur du cendrier est fixé un agitateur qui
débouche directement dans la zone de réduction; il supporte la
grille fixée immédiatement en dessous de la zone de
réduction .
Sur le réacteur est fixé un ventilateur manuel
centripète qui assure l'allumage du gazogène. Le
générateur a 2 ouvertures de chargement, l'une au dessus et
l'autre sur sa partie latérale.
Un brûleur de grande puissance est associé au
gazogène est nécessite d'être déconnecté de
l'installation si on veut utiliser le gaz produit dans un moteur.
L'alimentation en air du gazogène et du brûleur
se fait à travers un ventilateur électrique de 0,75 kW. Pour ce
faire, deux vannes sont utilisées, l'une débouchant au coeur du
réacteur et apportant l'air par le sommet et l'autre sur le
brûleur pour apporter l'air nécessaire à l'inflammation des
gaz.
Pour l'utilisation de l'installation en vue de la production
électrique et de la force motrice, dispositif plus ou moins complexe est
mis en place :
> Dispositif d'épuration et de
refroidissement:
Il est constitué d'un filtre et d'un refroidisseur. Le
gaz qui sort du réacteur à haute température entre d'abord
dans un refroidisseur à eau, puis dans un filtre fait de granulats et
d'eau avant de ressortir refroidi et épuré pour le moteur
Diesel.
> Le moteur Diesel
Il est de marque Kirloskar de 7,4 kW de type DM10 sur lequel on
peut lire les caractéristiques suivantes: rpm =1500; bhp =10.
> Un alternateur (générateur de courant
alternatif)
Il est de marque Kirloskar, type 4DL 2/4, de 6,0 kVA
délivrant un courant alternatif de 240 V, 25A, 50 Hz.
> Le ventilateur d'alimentation du
gazogène
C'est un appareil électrique de 0,75 kW fonctionnant au
courant alternatif (220/230 V, 6,1A, 50 Hz).
> Les courroies de transmission
Deux courroies assurent la transmission du mouvement de
rotation du moteur à un arbre qui lui, transmet son mouvement à
travers d'autres courroies pour les autres besoins de motorisation (Moulin
à écraser, presse à huile, décortiqueuse à
café, pilon pour les produits agricoles durs, pompe à eau).
Pour l'utilisation électrique, l'arbre est relié
à l'alternateur par deux courroies.
La figure n° 6 ci-dessous représente le schéma
de l'installation telle qu'elle se trouve sur place à ERA-Cameroun.
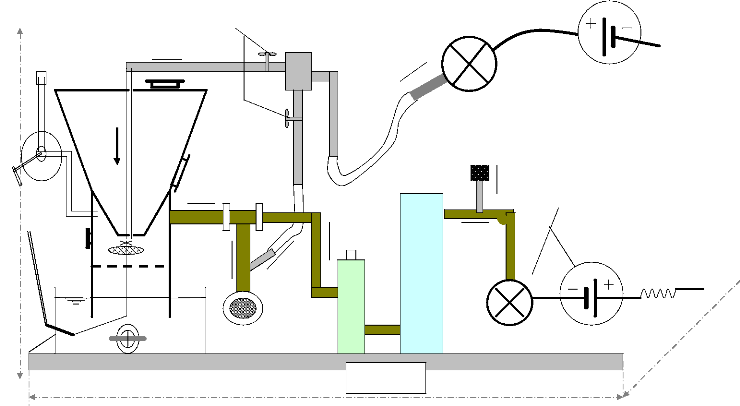
2 m
Air
H2O
Gaz
Vannes
Brûleur
4 m
Laveur
Air
Gaz
Ventilateur électrique
Air
Moteur + alternateur
(utilisations)
charge
Secteur (220V)
3m

48 CHAPITRE 3 : Choix Technologiques, Procedures , Resultats
De L'etude Experimentale, Analyse et conclusion
Figure n° 6: Schéma de
l'installation de Gazéification avec le gazogène Indien AEW
I.3/ Description des matériels de mesure
v' La balance
Nous avons eu à notre disposition une balance de 20
kilogrammes de portée avec une précision de 50 grammes.
v' Matériel de mesure des
températures
- Un thermomètre à affichage digital
(modèle 305 thermometer) que nous avons acquis du Laboratoire
d'Energétique (LAEN) de l'ENSP de Yaoundé ; il effectue des
mesures rapides des hautes températures (pouvant atteindre 2000°C)
à lui envoyer par un thermocouple avec une précision ? T =
#177;1°C.
- Deux thermocouples de type K (chromel-alumel), acquis du
même laboratoire.
- Deux autres thermomètres appartenant l'un à
ERA-Cameroun et l'autre au Laboratoire Environnement et Science de l'Eau
(LESEAU) de l'ENSP ont été utilisés pour la
circonstance.
v' Un chronomètre pour les prises de temps
;
Notons que les températures sont prises au même
moment que le temps en vue de répliquer l'évolution de la
température en fonction du temps.
v' Autres matériels de mesures
nécessaires
Pour assurer le bon fonctionnement du gazogène,
plusieurs paramètres (débit d'air, pression de l'air et des gaz,
excès d'air, température du réacteur et des gaz ...),
doivent être suivis ; ceci nécessite alors un appareillage tout
à fait diversifié. D'après l'INIEX (Institut National des
Industries Extractives) de Liège en Belgique, une installation de
gazéification peut être dotée :
d'un ventilateur-extracteur de vitesse de
rotation contrôlée par un onduleur qui assure le tirage
(l'extraction) des gaz en régime statique ou dynamique de manière
à reproduire sur le banc d'essais le régime réel de
fonctionnement du gazogène (PLATIAU D., 1986) ;
d'un manomètre en U pour la mesure
des pressions dans le circuit des gaz ;
des analyseurs infrarouges (CO, CH4, CO2),
paramagnétiques (O2) et à
conductibilité thermique (H2) pour l'enregistrement de
la composition des gaz durant toute la période de l'essai ; des analyses
complémentaires peuvent être faites au laboratoire par
chromatographie en phase gazeuse ;
d'un tube de Pitot ou un
diaphragme selon la norme NF X 10-102 pour la mesure des
débits des gaz produits .
La connaissance du débit et de la composition des gaz
permet de déduire la puissance thermique du générateur de
gaz et le pouvoir calorifique des gaz produits.
En récapitulatif, le tableau n°5 suivant donne la
composition du petit matériel nécessaire pour une bonne
étude de fonctionnement d'une installation de gazéification
destinée à la production électrique et thermique
(PLATIAU D., 1986).
Tableau n°7 : composition du petit
matériel de suivi d'une installation de gazéification .
Nature de la mesure
|
Appareillage
|
Température ambiante
|
Thermomètre
|
Pression atmosphérique
|
Baromètre
|
Humidité relative
|
Température sèche et humide
|
Températures - Parois
- Fluide
|
Thermocouples
- sondes de contact
- sonde de veine fluide
|
Débit de gaz
|
Tube de Pitot pour gaz chargés en aérosol
|
Puissance électrique
|
-Wattmètre
-Ampèremètre et voltmètre
-Fréquencemètre
-Cosf -mètre
|
Pression dans le circuit des gaz
|
Manomètre en U
|
Débit de combustible
|
Balance pour pesée des chargements
|
Composition des gaz
|
-Analyseurs de gaz
-Chromatographes équipés de détecteurs
à conductibilité thermique
|
Débit de gasoil
|
Jauge graduée
|
II/- BIOMASSE UTILISÉE
Cette étude a été
précédée par une identification des possibilités
qu'offre la biomasse
pour l'approvisionnement en énergie. C'est ce qui a
fait l'objet des études antérieures faites dans le cadre du
mémoire de maîtrise. Dans cette étude, il
a été question de faire un inventaire de toutes les ressources en
biomasse qui pouvaient être utilisées à des fins
énergétiques. Il en ressort que le charbon de bois est une
matière première qui peut avoir beaucoup d'avantages dans la
gazéification en vue de la production de la force motrice à
travers des moteurs à combustion internes (§ IV.3/- du chapitre
I), notre choix a porté pour les présents tests sur le
charbon de bois que nous nous sommes procurés au
marché Mokolo à Yaoundé. Nous y avons trouvé deux
types de charbons, un de type artisanal et l'autre de type industriel.
F Caractérisation du charbon de bois
utilisé
La matière première utilisée ici est le
charbon de bois qui provient du marché Mokolo à Yaoundé.
Nous avons opté pour deux types de charbon de bois:
· un charbon de bois traditionnel ou artisanal, provenant
des charbonniers de Baba, un village de la localité de Soa à 15
km de Yaoundé.
· Un charbon de bois industriel provenant des scieries de
la ville de Mbalmayo située à 40 km environ de Yaoundé.
Avant de passer à l'utilisation de ces deux types de
charbon, nous avons procédé à l'estimation des
caractéristiques les plus importantes de ce combustible. Les essais
préliminaires ont tour à tour porté sur:
> Densité du charbon utilisé
;
Nous avons fait un test de densité de ces
échantillons et nous avons eu comme densité pour le charbon
industriel, 280 #177;11 kg/m3. Le charbon artisanal quant à
lui reste moins dense et sa densité est d'environ 260 #177;11
kg/m3. ceci nous donne une incertitude de l'ordre de 4% sur ces
mesures.
> Rapport Air/combustible
Par définition ce rapport est défini par la
formule suivante et détermine la quantité d'air nécessaire
pour la combustion complète stoechiométrique d'une unité
de masse de combustible:
C
= 2 , 66 7 , 94 2 0 , 994
+ H -
+ S O 2
( / )
A F m (kg air/kg) (7)
, 232
0
La composition du charbon de bois étant: 95,8%C, 1,0%H2,
3,2%O2, on trouve donc A/F=2,77 kg air/kg.
> Taux de cendre
Le taux de cendre correspond à la quantité de
résidus obtenus après la combustion du charbon. Pour avoir une
idée de la valeur de ce paramètre, nous avons fait le test
suivant:
Le résidu que nous avons eu après
gazéification a été séché et pesé; la
masse obtenue après cette opération est considérée
comme étant constituée des cendres et des imbrûlés.
Nous avons constaté que les imbrûlés représentaient
environ 40% de ce résidu en poids (cette valeur élevée
s'explique par le fait que la grille destinée à filtrer les
cendres dans le générateur laisse passer beaucoup de petits
morceaux de charbon non brûlés, mais qui auraient pu être
brûlés
s'ils n'étaient pas entraînés par
gravité dans le cendrier); ceci signifie que les 60 % de ce
résidu comme est constitué des cendres de notre matière
première. Partant de ce principe, sur 80 #177;0,5 kg de charbon
gazéifié, on a eu 3.8 #177;0,5 kg de cendres +
"imbrûlé". On a alors:.
mt = 80 kg = masse totale de la matière première;
mc + mi = 3.8 = masse de cendre et d'imbrûlés. On a
lors mc = (mc + mi) x 60% = 2.48 #177;0,3 kg;
le taux de cendre est C = mc x
100 = 4.56 #177;0,39 % (8)
mt
Comme on peut le constater, cette mesure est faite avec une
incertitude relative de 8,6% qui paraît assez élevé pour ce
genre de mesure. Ceci s'explique par le mode opératoire et le
défaut de matériel adéquat. Dans tous les cas, elle nous
donne une idée assez claire de ce que pourrait être la valeur
exacte. Pour ce qui est de la procédure expérimentale pour la
détermination du taux de cendre du charbon de bois, selon la norme AFNOR
NF B 55 - 101 il faut se référer à l'annexe n°3.
> Taux d'humidité
Le taux d'humidité a été mesuré au
département de Génie Civil de l'ENSP par dessiccation dans des
fours. En effet en pesant un échantillon avant et après
dessiccation dans le four, on peut déduire la quantité d'eau
contenue dans l'échantillon initial par calcul de la perte de masse.
Ainsi on peut exprimer l'humidité du charbon de bois en pourcentage
massique par la formule:
W =
|
m m
2 3
-
|
x 100 (9)
|
m m
2 1
-
|
m1= masse de la tare (récipient d'étuvage vide et
sec)
m2 = masse de la tare + masse d'échantillons avant
étuvage
m3 = masse de la tare + masse d'échantillons après
étuvage et refroidissement.
Les mesures ont été faites au Laboratoire de
Géotechnique et de Matériaux (LGM) de l'ENSP ; après les
différents calculs, les résultats obtenus sont : W1 =
9.8 #177;0,2% de taux d'humidité pour le
charbon artisanal et W2 = 12.1
#177;0,6% de taux d'humidité pour le
charbon industriel. La procédure de
détermination du taux d'humidité selon la norme AFNOR NF B 55 -
101 se trouve à l'annexe n°3 du présent document. Au regard
de ce résultat sur le taux d'humidité des deux types de charbon
commercialisé au marché Mokolo, on remarque que le charbon
artisanal a un faible taux d'humidité par rapport au charbon industriel.
Ceci peut s'expliquer par plusieurs raisons:
- il faut tout d'abord noter que ce paramètre
dépend fortement de l'espèce de bois qui a
été carbonisé et du mode de croissance de
celui-ci;
- le charbon de bois artisanal est obtenu à partir de
plusieurs échantillons de bois, (car les
charbonniers utilisent pour la circonstance tous les types de
bois qu'ils trouvent à leur disponibilité) alors que le charbon
industriel provenant des déchets des scieries peut provenir des
échantillons plus réduits. Et puis par souci de commercialisation
rapide toutes les conditions de carbonisation ne sont pas toujours
respectées (voir §III.2.4/- du chapitre 1) . C'est
pourquoi on retrouve très souvent dans les sacs de charbon industriel
des morceaux de bois non carbonisés.
Dans tous les cas, il faut noter que ces valeurs sont
susceptibles de varier d'un échantillon à un autre et des essais
sur des échantillons variés étalés dans le temps
sont les bienvenus pour arriver à des résultats rigoureux afin de
généraliser les conclusions.
> L'indice de matières volatiles
C'est la perte de masse exprimée en pourcentage,
obtenue dans des conditions normalisées, après pyrolyse du
charbon chauffé à l'abri de l'air, abstraction faite de la perte
de masse due à l'humidité. Le principe de mesure part du fait
qu'un échantillon de charbon anhydre est constitué de carbone
fixe, de matières minérales (cendres) et de matières
volatiles. Nous n'avons pas pu faire des essais de détermination faute
de matériel adéquat, mais dans tous les cas pour le charbon de
bois, le taux de matières volatiles peut être
considéré comme étant d'environ 5.5%. (PLATIAU D.,
1986) La procédure de détermination de ce
paramètre pour un échantillon donné se trouve en annexe
n°3.
> Taux de carbone fixe
Le taux de carbone fixe est la proportion de matières
carbonées autre que les matières volatiles contenues dans
l'échantillon de charbon. Selon la norme NF B551010, il se calcule
après la détermination du taux d'humidité, du taux de
cendre et de l'indice de matières volatiles. Ainsi le taux de carbone
fixe exprimé en pourcentage massique par rapport à
l'échantillon brut est donné par la formule :
CF = 100 - (W + MV + C) (10)
H, W et C désignant respectivement le taux
d'humidité, de matières volatiles et de cendres. Avec nos
échantillons et les mesures précédentes, on a:
- pour le charbon artisanal, W = 9.8%, MV = 5.5%, C = 4.56%,
on a : CF = 80.2 #177;0,3% - pour le charbon industriel, W =
12.1%, MV= 5.5%, C= 3.05%, on a: CF = 79.4 #177;0,7% >
Pouvoir calorifique:
Par définition, on retiendra que le pouvoir calorifique
est la quantité de chaleur dégagée par la combustion
complète d'une unité de masse du combustible; il est
supérieur lorsque l'eau produite est entièrement condensée
et les autres produits de la combustion sont
ramenés à la température initiale; il est
inférieur lorsque l'eau produite demeure à l'état vapeur
et les autres produits de la combustion sont ramenés à la
température initiale.
Le principe de sa détermination réside sur le
principe selon lequel la combustion d'une quantité
déterminée de combustible en présence d'oxygène
dans une bombe calorimétrique plongée dans un volume connu d'eau
élève la température de celle-ci; le PCS se
détermine dans ces conditions à partir de
l'élévation constatée de la température du volume
constant d'eau. Le PCI se détermine à partir du PCS par calcul
selon la formule:
PCI = PCS - 2,508 x (W + 9H2). (kJ/kg)
(11)
Où W représente le taux d'humidité, 2,508 la
valeur de la chaleur latente de vaporisation de l'eau à 0°C et H2
la teneur massique en Hydrogène du combustible.
La procédure complète de détermination de ce
paramètre selon la norme AFNOR NF B 55-101 se trouve en annexe
n°3.
Nous n'avons pas pu effectuer cette mesure sur bombe
calorimétrique, mais le PCS de notre combustible a pu être
déduit des autres paramètres qui ont été
déterminés. Si nous considérons la composition suivante
pour le charbon anhydre, 95.7%C, 1.1% H2, 3.2% O2, alors on a d'après la
formule de Dulong .
PCS = 32.83C + 143.50 (H2 - 1/8O2) + 9.28S (MJ/kg)
(12)
On remarque donc qu'en tenant compte de l'effet cumulé de
la teneur en humidité (W) et de la teneur en cendre ou en
matières minérales (Mm), d'après la formule
suivante:
PCIW = PCIs (1-Mm)/(1+W) - 2.508.W/(1+W) (MJ/kg)
(13)
On a donc pour le charbon artisanal un PCS de 28.4
#177;2,9MJ/kg et pour le charbon industriel un PCS de 27,8
#177;2,9MJ/kg. La légère différence qu'on a sur
ces deux valeurs provient évidemment de la teneur en humidité et
de la teneur en matières minérales.
Tableau n°8 : récapitulatif
des caractéristiques des deux échantillons de charbon de bois:
Caractéristiques
|
Type de charbon
|
Charbon artisanal
|
Charbon industriel
|
C (%)
|
95.7
|
95.7
|
O2 (%)
|
32
|
32
|
H2 (%)
|
11
|
11
|
W (%)
|
9
|
12
|
Mm (%)
|
4
|
3
|
PCS(sec) (MJ/kg)
|
32,4
|
32,4
|
PCI(sec) (MJ/kg)
|
32,2
|
32,2
|
PCSW (MJ/kg)
|
28,4
|
27,8
|
PCIW (MJ/kg)
|
28,1
|
27,6
|
III/- ASPECTS THEORIQUE ET THERMODYNAMIQUE DE LA
GAZEIFICATION
III.1/- Théorie de la gazéification du
charbon de bois
La gazéification d'un combustible de type
CxHyOz est assez complexe et mal connue. De nombreux composés
intermédiaires peuvent en effet se former au cours des réactions.
On peut néanmoins considérer les réactions fondamentales
suivantes :
C + O2
|
CO2
|
ÄH298 = - 394 KJ/mole
|
(14).
|
|
|
|
2CO
|
ÄH298 = + 172 KJ/mole
|
(15).
|
|
|
|
CH4
|
ÄH298 = - 75 KJ/mole
|
(16).
|
|
|
|
CO2 + H2
|
ÄH298 = - 42 KJ/mole
|
(17).
|
|
|
|
On admet que le bois type a pour formule brute C3H5O2 ; sa
gazéification théorique suit alors la réaction suivante
:
C3H5O2 + 1/2 O2 3CO + 2,5 H2
(18).
En calculant l'enthalpie de cette réaction, on se rend
compte que c'est une réaction légèrement endothermique
(ÄH = 2 MJ / kg).
Pour ce qui est de la gazéification du charbon de bois,
il faut noter que l'oxydation de celui-ci par l'oxygène de l'air
commence à des températures plus basses que l'on ne pense
généralement. Le charbon de bois subit une combustion lente
déjà à température ordinaire. A 100°C, la
vitesse de cette combustion croît rapidement, mais, ce qui est
déjà particulièrement important, l'oxydation se passe
déjà à basse température. Par ailleurs,
après défournement du charbon de bois, celui-ci absorbe les gaz
de l'atmosphère (O2 et N2) et ceci se fait avec dégagement de
chaleur. Donc le seul contact du charbon de bois avec l'oxygène et
même avec l'azote de l'air échauffe le charbon fraîchement
carbonisé. C'est ainsi que vers 100°C et même au-dessous de
cette température, l'oxygène absorbé commence son
rôle d'agent d'oxydation, phénomène qui, lente au
début dégage encore de la chaleur. On assiste donc à un
double phénomène exothermique d'absorption et d'oxydation qui
peut alors se répéter
indéfiniment au point d'élever
considérablement la température de la masse de charbon
jusqu'à son inflammation spontanée.
En fait, le mécanisme de la combustion du charbon de
bois dépend de la quantité d'oxygène disponible. En
présence d'une quantité insuffisante d'oxygène, le charbon
de bois se transforme en monoxyde de carbone. C'est le principe même de
la gazéification. La gazéification du charbon de bois n'est donc
autre que la combustion de celui-ci dans un milieu pauvre en oxygène. On
a donc la réaction principale suivante :
2C + O2 2CO Äll = - 221 KJ/mole (19).
Mais en présence d'un excès d'oxygène, on a
une combustion complète suivant la réaction :
C + O2 CO2 Äll = - 394 KJ/mole (20).
Les deux réactions sont donc fortement exothermiques.
Lorsqu'un foyer de charbon de bois est incandescent, il peut y
avoir dissociation des deux produits de combustion précédents :
le monoxyde de carbone se dissocie en carbone et en CO2.
2CO C + CO2 Äll = - 172 KJ/mole (21).
tandis que l'anhydride carbonique se dissocie en monoxyde de
carbone et en oxygène :
2CO2 2 CO + O2 Äll = + 570 KJ/mole
(22).
La réaction la plus intéressante du CO2
formé est sa réduction en présence d'un excès de
charbon incandescent :
C + CO2 2CO Äll = + 172 KJ/mole (23).
Même si cette réaction absorbe une grande
quantité de la chaleur du foyer, elle fournit du CO dont la production
est recherchée pour l'utilisation dans les moteurs.
Enfin en présence d'eau, il peut aussi y avoir
dissociation de l'eau par le carbone porté à haute
température :
C + 112O CO + 112 Ä11 = + 180 KJ/mole
(24).
Cette réaction a pour effet d'enrichir le gaz pauvre en
hydrogène dont le pouvoir calorifique est très
élevé ; cette opération nécessite également
de grosses quantités d'énergie.
Il est important de noter que plus la teneur en carbone fixe
du charbon végétal est élevé, plus simples sont les
réactions de gazéification. En effet, la gazéification du
charbon de bois se rapprochant de celle du carbone pur, limite ainsi les
réactions intermédiaires qui se produisent avec un composé
complexe comme le bois brut.
III.2/- Caractérisation des échanges
thermiques au sein de la charge et du réacteur.
Le mécanisme de transfert dans un lit fixe de
particules portées à haute température comme dans le cas
du réacteur pendant la gazéification sont complexes et font
appels à la fois à des phénomènes de transfert de
chaleur et de masse et à des réactions cinétiques. Dans le
dispositif qui fait l'objet de notre étude, ces phénomènes
sont d'autant plus complexes qu'il serait important de penser à les
modéliser. Une modélisation fine de ces problèmes
imposerait un travail important qui n'est pas l'objet de cette étude.
Néanmoins, la connaissance des températures exactes de certains
endroits précis du réacteur nous donne une idée assez
claire des conditions limites qui devront à l'avenir aider à la
modélisation de ces phénomènes ou même le
dimensionnement des pareils réacteurs. Dans le même ordre
d'idées, ces mesures expérimentales devraient nous permettre de
vérifier les éventuels modèles mis au point à ce
sujet. Si nous nous intéressons uniquement aux échanges
thermiques qui ont lieu dans le réacteur, nous pouvons mettre d'ores et
déjà les bases d'une modélisation des transferts
thermiques en vue du dimensionnement d'un réacteur de
gazéification du charbon de bois. Pour envisager un tel modèle,
nous pouvons considérer les hypothèses suivante :
v' Le réacteur est cylindrique et le lit de charbon est
supposé être chauffé à partir de l'axe du
cylindre ;
v' Les échanges de chaleur sont supposés
globalement conductifs et l'ensemble et
l'ensemble des transferts thermiques dans le lit de charbon
sont exprimés au moyen d'une conductivité thermique effective
englobant à la fois la conduction, la convection et le rayonnement ;
ü L'échantillon de charbon est homogène avec
des propriétés thermophysiques constantes ;
ü A cause de la symétrie cylindrique, la
distribution spatio-temporelle de la température dans le lit se
réduit à une fonction du temps et du rayon ;
T(r, ?, z, t) = T(r, t) (25).
ü Conditions aux limites spatiales : A partir de
l'instant initial, les températures de l'axe du cylindre et de la paroi
interne de celui-ci suivent une évolution dépendante du temps en
fonction des différentes réactions chimiques
présentées dans le § III.1/- précédent ; on
admet donc que les conditions au frontières suivantes :
r = 0, ===> T(0, t) = ? 1(t), et r = R, ===> T(R, t) = ?
2(t), (26).
ü Le lit de charbon est initialement à la
température T(r, 0) = F(r) = T0. (27). Il est
important de noter qu'un des résultats de notre phase
expérimentale est de pouvoir déterminer les valeurs
discrètes de la fonction ? 2(t) et donner son allure.
Dans ces conditions, le système qu'il convient de
résoudre dans ce cas là s'établit comme suit :
? T _a1
? ( r?T)
?t r? r ?r
|
|
équation générale de transfert
(28).
|
|
|

T(r, t) = T0 0< r <R et pour t = 0;
T(r, t) = ? 1(t) r = 0 et ? t
T(r, t) = ? 2(t) r = R et ? t
Pour résoudre ce système, on procède la
méthode de superposition en posant,
T(r, t) =G(t).R(r) ; (29).
La résolution de l'équation ci-dessus se
réduit donc à (oil ß est une constante):
d dt G(t) = - aß2
(30).
d R(r) + ß2R(r) = 0
(31).
dr
2
d
2
R(r) +
dr
La solution de l'équation (18) est donnée par
G(t) = A exp [-aß2t] (32).
tandis que l'équation (19) représente
l'équation de Bessel d'ordre zéro dont les solutions sont
données par : R(r) = C1J0(ßr) + C2Y0(ßr)
(33).
Oil J0 et Y0 sont respectivement les fonctions de Bessel de
première et de seconde espèce d'ordre zéro. La solution
complète du problème s'obtient à partir des
méthodes de Green ou du théorème de Duhamel (DE
VRIENDT A. B. 1982). Mais, comme dans tout problème physique,
la plus grande difficulté ici consiste à bien définir les
conditions limites, notamment
les valeurs des fonctions ? 1(t) et ? 2(t). Nous ne
nous préoccupons pas ici de la solution de ce problème, mais nous
allons nous atteler dans le paragraphe suivant à procéder
à la détermination expérimentales des valeurs
discrètes d'une de ces fonction, la fonction ? 2(t). C'est ce
qui va faire l'objet de la phase expérimentale de cette étude.
Par ailleurs, le paramètre le plus important qu'il faut
pour la modélisation de ce problème est la diffusivité
thermique a du lit de charbon. En supposant que les particules de charbon ont
un faible diamètre, on peut estimer cette diffusivité de la
manière suivante :
Nous avons vu au § III.2.2 du chapitre 1 que la chaleur
spécifique Cp d'un charbon de bois était d'environ 0,82
#177;0.01kJ.kg-1.K-1 et que la conductivité
thermique de celui-ci se situait aux alentours de 0,06.10-3
#177;0.01.10-3 kW.m-1.K-1. par ailleurs, le
charbon de bois du
marché Mokolo que nous utilisons dans cette étude
a pour masse volumique 280 #177;11kg/m3 ; sachant que la
diffusivité thermique a est définie par la relation, a = Cp
k , on peut estimer
que pour le charbon de bois de Yaoundé, a=
2,61.10-7 #177;0,57.10-7
m-2.s-1.
Avec toutes ces données, il est possible de trouver un
modèle mathématique pour les phénomènes très
complexes qui ont lieu dans le réacteur au cours de la
gazéification du charbon de bois.
VI!- METHODOLOGIE DES TESTS DE GAZEIFICATION DU CHARBON
DE BOIS ET RESULTATS EXPERIMENTAUX
III.1!- Procédure expérimentale de la
gazéification
Avant de lancer la phase d'expérimentation, un test
d'étanchéité a été fait sur toutes les
jointures du gazogène et de la tuyauterie. Ce test consistait à
imbiber du savon sur toutes ces jointures, fermer toutes les vannes, mettre
l'intérieur du gazogène sous pression (avec le ventilateur
électrique) et voir si on a des bulles de savon au niveau des jointures.
Ceci nous permettait de savoir s'il peut avoir fuite de gaz. Ce test a donc
été négatif, ce qui nous a assuré que tous les
joints étaient en bon état.
La biomasse utilisée est comme nous l'avons
annoncée du charbon de bois acquis au marché Mokolo à
Yaoundé. Celui-ci avait une granulométrie faible adaptée
aux gazogènes.
Avant de commencer on prépare les appareils de mesures et
les blocs notes préalablement tracés pour le relevé des
mesures.
Au début de chaque essai, il faut commencer par
vérifier que toutes les vannes sont fermées, que la cuve qui sert
en même temps de cendrier est entièrement pleine d'eau.
Après ces vérifications préliminaires, le charbon est
pesé et on procède au chargement du générateur par
une des ouvertures prévues au-dessus ou sur le côté du
générateur. Ce dernier est chargé jusqu'au niveau de
l'orifice d'allumage ; la mise en flamme de cette quantité de charbon
est facilitée par l'utilisation du pétrole lampant ; on utilise
le souffleur manuel pour ventiler jusqu'à ce que les braises aient pris
le charbon de bois ; le gazogène est alors allumé ; A ce moment
on fait le plein du générateur puis on met le ventilateur
électrique en marche en ouvrant en même temps la vanne qui
débouche au réacteur. Le générateur étant
hermétiquement fermé, après à peu près 10
à 15 minutes, le gaz commence à sortir au niveau du
brûleur. On peut alors y approcher une torche en coton pour l'allumage.
Pendant la mise à feu on ouvre lentement la deuxième vanne d'air
destiné à alimenter le brûleur. Il faut noter que
l'inflammation ne se fait que lorsque le mélange air/gaz est optimal
(rapport air/combustible optimal).
Pour ce qui est des prises de températures les
thermocouples sont placés aux différents endroits (parois du
réacteur, brûleur, etc.) et les relevés se font avec l'aide
d'au moins trois opérateurs dont l'un est chargé de la lecture et
les deux autres chargés de l'enregistrement des différentes
valeurs avec les temps correspondants. C'est ainsi que les valeurs sont prises
à intervalle de 10 secondes au plus. Certaines valeurs brutes
enregistrées se trouvent en annexe n°1. La figure n°7
présente l'organigramme de la procédure générale
d'expérimentation.
DEBUT
61
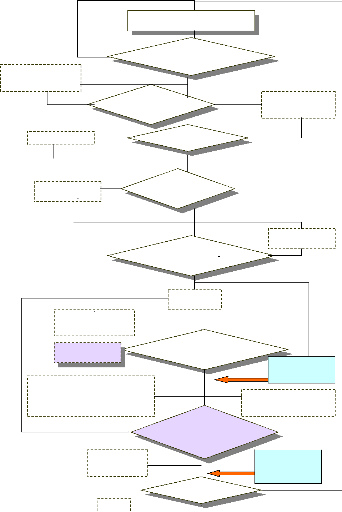
Conditionnement de la matière première
Fermer les
ü Faire le plein du générateur ;
ü Actionner le ventilateur électrique
enouvrant la vanne d'alimentation du
Remplir la
d'
Actionner le ventilateur manuel
Gazogène ll é
non Matière
première oui
Ouverture vanne
non
FIN
non
non
non
adaptée ?
Vérifications préliminaires
Tests d'étanchéité (jointures
étanches ?)
Orifice d'allumage
Cuve (cendrier)
oui
Prise du charbon par les braises ?
atteint par le non
oui
10 à 15 min. après, sortie du gaz au brûleur
?
Allumer
Vannes
oui
oui
Tests
oui
oui
oui
ü Fermer le générateur ;
Précautions de sécurité
Préparation des appareils de
Chargement du générateur
Précautions de sécurité
non
III.2/- Sécurité et Environnement
Pour pouvoir travailler dans des conditions saines et
sûres avec un gazogène, il faut avoir reconnu les sources de
danger et leur nature. Les différentes sources de danger sont
récapitulées dans le tableau n°9.
Tableau n°9: Sources et
dangers de la gazéification ;
Sources
|
Dangers
|
Gaz de gazogène
|
- Toxique (contient du monoxyde de carbone) - Inflammable
|
Goudrons
|
- Inflammables secs,
- Peuvent être cancérigènes
|
Eaux de lavage
|
Peuvent contenir certains composés
cancérigènes
|
Charbon de bois
|
- Combustible
- Peut couver un feu longtemps sans flamme
|
Paroi du gazogène
|
Température très élevée (plus de
450°C)
|
Tuyères
|
Retour de flammes ou de gaz
|
Au cours de la période de chauffage du gazogène,
il y a rejet de gaz vers l'atmosphère. On veillera toujours à
disperser ce gaz vers l'atmosphère, hors de portée du personnel
et de l'enflammer si possible.
Les gaz d'échappement du moteur doivent également
être rejetés hors de portée du personnel.
Au moment de l'ouverture de la fenêtre de chargement, il
peut y avoir inflammation spontanée des gaz qui se trouvent à
l'intérieur (voir photo n°3 en annexe n°2).
Ce danger peut être prévenu en jetant, en se tenant hors de
portée, une torche enflammée dans le gazogène.
Les goudrons et les eaux de lavage doivent être
traités comme des polluants. On évitera tout contact avec les
eaux à usage domestique. Les parois du foyer sont très chaudes en
fonctionnement. Le port des gants est indispensable pour limiter les risques de
brûlure.
Même après un arrêt prolongé, le
foyer du gazogène et le circuit de refroidissement peuvent contenir un
gaz encore inflammable. On évitera la présence de toute flamme ou
arc électrique avant d'avoir vérifié que toutes les
conduites et les volumes ont été correctement ventilés.
Toutes ces précautions doivent être prises
même quand le gazogène sera déporté en site
pilote.
L'expérience montre que les accidents surviennent
généralement avec les gazogènes lorsque des actes
dangereux ont été commis. Une prévention efficace des
accidents passe donc par une bonne formation du personnel d'exploitation.
III.3/- Production des gaz, essai d'inflammation,
difficultés et quelques éléments d'explication.
v' Production
Une dizaine de minutes après le démarrage du
gazogène, on voit le gaz sortir à un débit plus ou moins
important. Malheureusement nous n'avons pas eu de matériel
adéquat pour avoir une idée de ce que vaut ce débit. Ce
gaz sort de manière continue pendant toute la durée de
fonctionnement du gazogène. Il faut noter que la durée de
fonctionnement dépend de la quantité de charbon
chargée.
Durant tous les tests, le gaz a effectivement
été produit sans problème ; nous avons remarqué que
ce gaz était très toxique, raison pour laquelle les
opérateurs étaient obligés de porter des masques nasaux au
cours de la manipulation et essayaient de prendre une cure de lait à la
fin des travaux.
v' Essai d'inflammation
Nous avons été confrontés au
problème d'inflammation du gaz produit en continu. En effet, les flammes
que nous essayions d'avoir pendant les tests ne se maintenaient que pendant
quelques secondes. Mais pendant cette courte durée, nous pouvions
apprécier la qualité du gaz par la couleur de la flamme
éphémère. Celle-ci avait néanmoins une couleur
tirant au bleu, preuve qu'on avait un gaz de bonne qualité. Mais de
prime abord, plusieurs raisons peuvent être à l'origine de ce
problème de l'ininflammabilité des gaz produits.
v' Quelques éléments d'explication
:
Pour essayer d'apporter des éléments
d'explication sur les difficultés rencontrées au niveau de
l'inflammation du gaz produit, plusieurs hypothèses peuvent être
émises. Il faut noter que comme dans tout travail scientifique, une
hypothèse est une éventualité qu'il faut vérifier
avant de confirmer ; c'est ainsi que dans notre cas précis, au regard de
certaines observations, nous pouvons déjà dire un mot sur ce
qu'il pourra être nécessaire de regarder avec plus d'attention
pendant les autres essais :
- Les vannes d'alimentation en air provenant du ventilateur
électrique ne fonctionnent pas et il est impossible de contrôler
la quantité d'air entrant au réacteur ; ce qui fait que la
quantité d'air peut être insuffisante tout comme elle peut
être en excès, ce qui n'est pas bon pour les différentes
réactions de gazéification qui ont besoin d'une quantité
d'air bien contrôlée.
Mémoire de DEA de physique, option Energétique
/ Laboratoire de Thermique 63
- Dans le générateur, l'air n'est pas
uniformément reparti, car la seule tuyère qui conduit l'air
débouche au coeur du réacteur ; il serait judicieux qu'au moins
une tuyère soit installée dans le générateur pour
assurer l'apport d'air suffisant pour les différentes
réactions.
- Il est possible qu'une partie de gaz se brûle avant la
sortie du réacteur de façon qu'on retrouve au niveau du
brûleur un gaz qui est trop dilué pour s'enflammer.
- Une autre raison et celle qui nous paraît plus
réaliste est que le brûleur tel qu'il est conçu
actuellement soit très gros pour pouvoir délivrer un gaz assez
concentré pour s'enflammer. Toutes ces raisons ne sont que des
hypothèses qu'il faudrait vérifier. Dans tous les cas, une
analyse des gaz produits est nécessaire pour pouvoir arriver à
des conclusions plus formelles.
III.4/- Mesure des températures, résultats et
analyse.
Le fonctionnement d'un petit gazogène est toujours
très difficile. Pour obtenir des données exploitables sur ce
fonctionnement, il faut soit enregistrer des mesures horaires,
journalières et hebdomadaires et les intégrer sur des
périodes de plusieurs mois, soit chercher à s'approcher le plus
près possible d'une analyse en continu en augmentant au maximum la
fréquence des mesures. Compte tenu des contraintes de temps, nous avons
adopté cette seconde procédure pour l'enregistrement des
températures.
A l'aide de thermocouples et de chronomètres, nous
avons mesuré les températures de certaines parties du
gazogène au cours de son fonctionnement et ce dans le temps. Des
résultats bruts de l'expérimentation figurent en annexe n°1
où nous pouvons voir l'évolution dans le temps de ces
températures. Les photos n°2 et 3 présentent quelques
opérations d'enregistrement des températures.
Les résultats obtenus pour ce qui est par exemple des
températures du réacteur et des gaz d'échappement sont
consignés sur la figure N°8. Sur la figure
N°9 nous avons reporté les courbes de tendance
correspondant à ces valeurs.
On remarque sur ces courbes que durant les 15 premières
minutes, on assiste à une croissance considérable des deux
températures qui partent de la température ambiante pour
atteindre 450°C pour le réacteur et un peu plus de 300°C pour
les gaz d'échappement. C'est cette période qui est la
période d'échauffement préliminaire au début de la
gazéification. Après cette période c'est le début
de la gazéification et c'est à ce moment qu'on remarque
l'arrivée des gaz au brûleur.
Par ailleurs, la courbe de tendance nous permet de noter que
la différence de température entre le réacteur et le
brûleur varie très peu, c'est-à- dire entre 150°C et
200°C, ce
qui nous permet d'avoir une idée des pertes de chaleur qui
ont lieu dans les tuyères qui conduisent au brûleur.
Cependant il faut noter que les températures obtenues
restent inférieures à celles auxquelles on se serait attendu
d'après la littérature. Ceci pourrait être dû aux
différentes raisons citées précédemment ; il s'agit
des paramètres influençant le phénomène même
de gazéification comme l'apport en air, du taux d'humidité du
gaz, de la taille du brûleur que nous jugeons assez costaud, de la
possibilité de combustion des gaz dans le réacteur, de
l'extrême pauvreté du gaz d'échappement. Ceci est d'autant
plus vrai que pendant notre manipulation, nous avons remarqué la
température grimper considérablement pendant les courts moment de
passage de vent (apport supplémentaire d'air). Dans tous les cas, il est
clair que même si ces températures sont encore un peu basses, leur
tendance d'évolution est quasiment la même que celle obtenue en
2001 sur un gazogène à lit fixe à tirage descendant par
l'équipe de recherche conduite par le Prof N. SYRED du
Département de Mécanique et des Etudes Energétiques de
l'Université de Cardiff en Grande Bretagne (SYRED N., 2001)
(voir figure n°10 suivant).
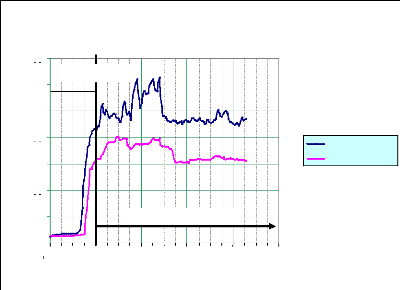
Temperature en °C
400
200
700
600
500
300
100
0
0,0 20,0 40,0 60,0 80,0 100,0
temps t en min
Échauffement
Evolution des températures du réacteur et
des gaz d'échappement au cours de la gazéification
Début de la gazéification
T1 normalisée (°C)
T2 normalisée (°C)
Figure n°8 : évolution de la
température du réacteur et des gaz d'échappement avec le
temps6
6Les températures ont
été normalisées en prenant la valeur maximale d'une
série de valeurs enregistrées pendant une période de 30
secondes.
Mémoire de DEA de physique, option Energétique
/ Laboratoire de Thermique 65
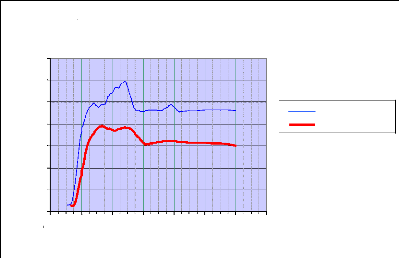
Temperature en °C
400
200
700
600
500
300
100
0
0,0 20,0 40,0 60,0 80,0 100,0 120,0 140,0
temps t en min
Evolution des températures du réacteur et
des gaz d'échappement au cours de la gazéification
TempératureT1
TempératureT2
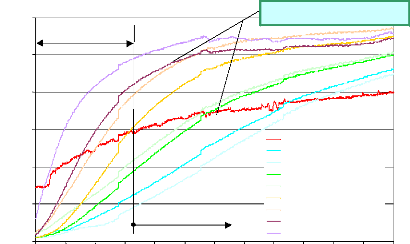
Temperature [°C]
600
400
200
1200
1000
800
0
Courbes concernées
warm-up
start of gasification
Exhaust Gas Temperature z/De=3 (IN)
z/De=3 (OUT)
z/De=1.83 (IN) z/De=1.83 (OUT) z/De=0.83 (IN) z/De=0.83 (OUT)
z/De=-0.33 (IN) z/De=-0.33 (OUT)
Figure n°9 : courbe de tendance de
l'évolution de la température du réacteur et des gaz
d'échappement avec le temps
0 3 6 9 12 15 18 21 24 27 30 33 36
Elapsed Time [minutes]
Figure n°10 : évolution dans
le temps des températures au cours de la gazéification
(SYRED N., 2001)
III.4/- Autre essai : autonomie de fonctionnement en
fonction du débit de charbon
Pendant les différentes séries de tests que nous
avons faits, nous avons essayé de mesurer parallèlement la
durée de fonctionnement du gazogène avec différents
chargements. La durée de fonctionnement ici est en fait le temps
nécessaire pour que la biomasse soit consommée
complètement. C'est ainsi que les résultats obtenus sont
récapitulés dans le tableau n°10 et la courbe obtenue est
représentée sur la figure n°
Tableau n°10 : Durée de
fonctionnement en fonction de la quantité de charbon chargée.
Chargement (kg)
|
5
|
10
|
15
|
20
|
30
|
40
|
60
|
Temps de fonctionnement (min)
|
25
|
65
|
90
|
125
|
160
|
253
|
350
|
durée de fonctionnement en fonction du
chargement
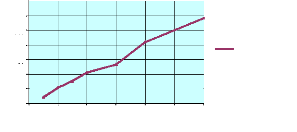
420
360
Temps de fonctionnement (min)
300
0 10 20 30 40 50 60
0
60
120
180
240
quantité de charbon chargée (kg)
Temps de fonctionnement (min)
Figure n°10 : Autonomie de
fonctionnement du gazogène
Nous constatons que cette courbe est presque linéaire
avec une pente d'à peu près 60 min / 10kg. Ceci nous permet de
déduire la capacité du gazogène qui est d'environ 10 kg /
heure.
Beaucoup d'autres tests pour la mesure de certains
paramètres sont encore nécessaires pour mieux comprendre le
fonctionnement du gazogène indien AEW. Dans tous les cas, les tests vont
se poursuivre pour apprécier toutes les difficultés. Une analyse
des gaz produits reste incontournable pour mieux cerner le fonctionnement de
cette installation.
Mémoire de DEA de physique, option Energétique
/ Laboratoire de Thermique 67
68 CONCLUSION
CONCLUSION GENERALE
Il ressort de ce travail que la décentralisation de la
production d'électricité semble s'être imposée avec
des techniques nouvelles et modernes de conversion des sources renouvellables.
Au Cameroun, cette conviction semble traîner encore les pas alors qu'on
est en zone forestière par essence où les ressources en biomasse
sont abondantes. Parmi les techniques de production, la production du gaz de
substitution des carburants fossiles dans les moteurs à combustion
interne par gazéification du charbon de bois a focalisé notre
attention. C'est ainsi qu'après avoir fait le tour sur la technique et
la technologie de production de ce gaz, sur la caractérisation de la
matière première (charbon de bois), ainsi que sur les
différentes expériences dans le monde, nous avons
procédé au lancement d'une phase de tests de production sur une
installation grandeur nature. Au cours de ces tests sur un gazogène
indien de type AEW (Associated Engineering Works), notre préoccupation a
porté sur la production, des tests d'inflammation du gaz produit sur un
brûleur et la mesure des températures du réacteur et des
gaz à l'échappement pendant le processus de gazéification
du charbon de bois commercialisé dans la ville de Yaoundé. Il est
apparu notamment que pour une modélisation mathématique des
phénomènes physico-chimiques qui ont lieu au cours de la
gazéification, la connaissances de l'évolution de ces
températures dans le temps reste incontournable car fait partie
intégrante des conditions aux limites du problème pour ce qui est
des transferts thermiques dans le lit du charbon. Ces tests ont eu un
résultat assez concluant dans la mesure où les gaz ont
effectivement été produits, malgré le fait que les flammes
au niveau du brûleur ne se sont pas maintenues assez longtemps. Par
ailleurs, nous avons enregistré les maximums de température de
l'ordre de 650°C alors qu'on s'attendait à avoir une gamme de
800°C à 1000°C. Plusieurs raisons ont expliqué ce
phénomène, notamment l'apport en air qui doit être
suffisamment contrôlé et dont il faudrait suivre à
l'avenir. C'est le lieu ici de noter que malgré les valeurs un peu
basses de la température du réacteur, les courbes
d'évolution au cours du temps que nous avons obtenues sont semblables
à celles obtenues cette année même par l'équipe de
recherche du Prof. N. SYRED du Département de Mécanique et des
Etudes Energétiques de l'Université de Cardiff en Grande Bretagne
(N. SYRED, 2001). D'autres tests d'autonomie de fonctionnement ont
été faits et les résultats obtenus pour notre installation
et pour le charbon de bois de Yaoundé ont donné 10 kg/heure comme
autonomie de fonctionnement.
Pour ce qui est des perspectives pour ce travail, on devrait
à l'avenir faire une analyse technico-économique de
l'installation et envisager la possibilité d'installation en site
pilote
69 CONCLUSION
dans les villages pré-sélectionnés dans
le cadre des études précédentes (TAGUTCHOU J. P., 2000).
Dans le contexte de l'approvisionnement en électricité des zones
rurales, nous avons remarqué que notre installation avait besoin d'une
source d'énergie (ventilateur électrique) ne serait-ce que pour
le démarrage, énergie pas du tout disponible en zone rurale,
raison pour laquelle il serait important d'envisager une autre source
d'énergie pour le démarrage de l'installation (cellule
photovoltaïque par exemple). Ceci devrait être pris en compte pour
l'optimisation de la filière. Par ailleurs l'allure de
l'évolution des températures de paroi telles que nous avons
obtenues constitue une base pour des simulations numériques et la
modélisation mathématique de la complexité des
phénomènes qui ont lieu dans les réacteur des
gazogènes au cours de la gazéification, travail qui devra
constituer notre cheval de bataille dans les prochaines recherches.
Mémoire de DEA de physique, option Energétique
/ Laboratoire de Thermique 69
70 BIBLIOGRAPHIE
REFERENCES BIBLIOGRAPHIQUES
1- BOIZI E. M. (1999), `Co-valorisation de
déchets lignocellulosiques en tant qu'adsorbants appliqués en
dépollution aqueuse et production de chaleur par combustion' ;
Thèse de doctorat en science de l'ingénieur, Université de
Technologie de Compiegne - France, décembre 1999, 162 pp + annexes.
2- DE VRIENDT A. B. (1982); `La transmission de
la chaleur' Volume I, tome 1 et tome 2 `La conduction' ; edition Gaëtan
Morin, Quebec - Canada, 3e trimestre 1982, 720 p.
3- GIRARD P., 1985; Rapport de
l'étude réalisée pour EDF DER par le cabinet LOUIS
MOULHERAT sur le thème "Etude de la faisabilité de la
gazéification du charbon de bois pour la production de
l'électricité"; Monpellier-France, 1985; 127 Pp.
4- GIRARD P., and CHALON J., (2000) ; `Acte
de l'atelier sur la faisabilité de projets d'électrification
rurale décentralisée à partir de la biomasse'
Yaoundé, 25-30 septembre 2000 CIRAD-Forêt, Monpellier-France,
2000.
5- KOBNOM O. (1994) ; `La fabrication et
l'utilisation du charbon de bois à Yaoundé (étude
technique et économique)', mémoire de fin d'étude
d'ingénieur de conception, option mécanique, ENSP de
Yaoundé, juin 1994.
6- LAMACHE C. et VANDENBERGH M., 2000 : Les
outils modernes de la géomatique au service de l'ERD in :
L'Electrification Rurale Décentralisée, Une chance pour les
Hommes, des techniques pour la planète Systèmes Solaires, Paris,
décembre 2000, Pp 119 - 138.
7- LIPS B., NGANHOU J., KOBNOM O. et WAFO L. (1999);
`Production et Consommation du Charbon de Bois à Yaoundé
(Cameroun)' In Bulletin Africain `'Bioressources -
Energie Développement Environnement», N°11, Dakar,
juillet 1999, Pp 32 - 41.
8- MAIGNE Y., 2000; L'ERD à l'aube de
la maturité in: L'Electrification Rurale
Décentralisée, Une chance pour les Hommes, des techniques pour la
planète. Systèmes Solaires, Paris, décembre 2000, Pp
11-19.
71 BIBLIOGRAPHIE
9- MINEFI (1998) 'Annuaire statistique du
Cameroun, 1997' MINEFI / Direction de la Statistique et de la
Comptabilité Nationale; Yaoundé-Cameroun, Août 1998.
211p.
10- MINMEE (1990), 'Etude du plan
énergétique national, phase 1 : projet de politique et de plan
énergétique pour le Cameroun' Rapport final, Ministère des
Mines, de l'Eau et de l'Energie / Direction de l'Energie; étude
réalisée par LAVELIN International avec le financement de l'ACDI;
203 pp.
11- NGNIKAM E., TANAWA E et SACLIER P,
(2000) `Identification d'un projet d'électrification
villageoise en zone forestière au Cameroun' In: Girard, P, and
Chalon, J, `acte de l'atelier sur la faisabilité de projets
d'électrification rurale décentralisée à partir de
la biomasse' Yaoundé, 25-30 septembre 2000 CIRAD-Forêt,
Monpellier, p 115 - 135.
12- PLATIAU D., LIEGEOIS R, TARTE P, PIRARD N,
(1986) 'Intégration de générateurs de gaz dans un
système de valorisation énergétique de Papyrus au Rwanda'
Rapport publié, Liège, mars 1986, 40 pages + annexes.
13- REED T. B. and GAUR S., (1999) `A survey
of biomass gasification 2000; gasifiers project and manufacturers around the
world'; The National Renewable Energy Laboratory, 1617 Cole blvd., Golden, CO
and The Biomass Energy Foundation, Inc., 1810 Smith Rd., Golden, CO. 80401,
September 1999, 180 pp.
14- REED T. B. and WALT R. (1999) `The
«Turbo» Wood-Gas Stove', to be presented at 4th Biomass of Americas
Conference, Oakland, CO, August 29, 1999.
15- REED T. B., (1981) `Biomass to methanol
specialists' Workshop», Ed. T. B. Reed and M. Graboski, SERI Conference,
1981, BEF Press, 1997.
16- SCHWINKENDORF W. E., MUSGRAVE B. C., DRAKE R. N.
(1997) ; `Evaluation of Alternative Nonflame Technologies for
Destruction of Hazardous Organic Waste' prepared for the U.S. Department of
Energy / Assistant Secretary for Environmental Management, DOE Idaho Operation
Office, by Idaho National Engineering Laboratory, Mixed Waste Focus Area,
Lockheed Martin Idaho Technologies Company, Idaho Falls, Idaho, April 1997.
Mémoire de DEA de physique, option Energétique
/ Laboratoire de Thermique 71
72 BIBLIOGRAPHIE
17- SYRED N., FICK W., FRASER T., and GRIFFITHS A. J.
(2001); `Biomass Gasification for Small Gas Turbines' University of
Wales, Cardiff, BP 925, The Parade, Newport Road, Cardiff, CF 24 OYF, Wales,
U.K., 2001, 29 pp.
18- TAGUTCHOU J. P., (2000)
'Possibilités d'utilisation de la biomasse comme alternative
d'approvisionnement en électricité dans les centres
isolés'. Mémoire de Maîtrise de Physique, option
Energétique, Faculté des Sciences, Université de
Yaoundé I, juillet 2000, 67 pages + annexes.
19- TANAWA E., NGNIKAM E.. et SACLIER P.
(2000) 'Rapport d'Identification d'un projet d'électrification
villageoise en zone forestière au Cameroun' Rapport conjoint ERACAMEROUN
et IED (Innovation Energie pour le Développement). 115 p.
20- TANAWA E., NGNIKAM E., NKAMWOUO N. J., WETHE J.
and TCHOUNGANG C., (1998) 'Essais de motorisation villageoise et
électrification à partir de la biomasse en zone de forêt'
Communication au séminaire d'orientation scientifique des CRESA, non
publié 7 p.
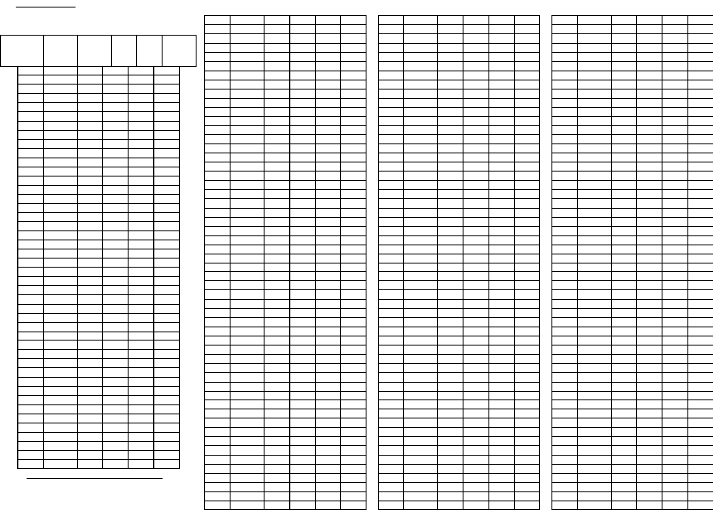
27
34
28
34
32
219
ANNEXE N° 1 : Quelques mesures
enregistrées
Manip du 13 Nov 2001
1.
|
13h06'00"
|
0,00
|
24
|
2.
|
|
|
26
|
3.
|
|
1,00
|
28
|
4.
|
|
|
29
|
5.
|
|
2,00
|
29
|
6.
|
|
|
30
|
7.
|
|
3,00
|
31
|
8.
|
|
|
30
|
9.
|
|
4,00
|
31
|
10.
|
|
|
32
|
11.
|
|
5,00
|
33
|
12.
|
|
|
33
|
13.
|
|
6,00
|
34
|
14.
|
|
|
34
|
15.
|
|
7,00
|
34
|
16.
|
|
|
33
|
17.
|
|
8,00
|
34
|
18.
|
|
|
33
|
19.
|
|
9,00
|
34
|
20.
|
|
|
32
|
21.
|
|
10,00
|
34
|
22.
|
|
11,00
|
33
|
23.
|
|
|
33
|
24.
|
|
12,00
|
34
|
25.
|
|
|
37
|
26.
|
13h19'20"
|
13,00
|
47
|
27.
|
|
|
52
|
28.
|
|
|
67
|
29.
|
|
|
68
|
30.
|
13h19'30"
|
13,50
|
69
|
31.
|
|
|
73
|
32.
|
|
|
85
|
33.
|
|
|
94
|
34.
|
|
|
102
|
35.
|
|
|
112
|
36.
|
13h19'50"
|
|
117
|
37.
|
|
|
120
|
38.
|
13h20'00"
|
14,00
|
130
|
39.
|
|
|
200
|
40.
|
|
|
205
|
41.
|
|
|
212
|
42.
|
|
14,50
|
219
|
43.
|
13h20'35"
|
|
220
|
44.
|
|
|
230
|
7 Température normalisée en prenant
la valeur max. des valeurs enregistrées pendant 30 secondes
45.
|
|
|
253
|
|
|
46.
|
|
|
240
|
|
|
47.
|
|
|
242
|
|
|
48.
|
13h21'00"
|
15,00
|
250
|
253
|
34
|
49.
|
|
|
265
|
|
38
|
50.
|
|
|
275
|
|
88
|
51.
|
|
|
285
|
|
89
|
52.
|
13h21'25"
|
|
293
|
|
90
|
53.
|
|
15,50
|
297
|
297
|
95
|
54.
|
|
|
303
|
|
|
55.
|
|
|
307
|
|
|
56.
|
|
|
310
|
|
|
57.
|
|
|
315
|
|
|
58.
|
|
|
325
|
|
|
59.
|
|
16,00
|
330
|
330
|
125
|
60.
|
|
|
333
|
|
|
61.
|
|
|
340
|
|
|
62.
|
|
|
345
|
|
|
63.
|
|
|
349
|
|
|
64.
|
|
|
350
|
|
|
65.
|
|
|
355
|
|
|
66.
|
|
|
362
|
|
|
67.
|
13h22'25"
|
|
363
|
|
|
68.
|
|
16,50
|
363
|
363
|
168
|
69.
|
|
|
365
|
|
|
70.
|
13h22'35"
|
|
369
|
|
|
71.
|
|
|
367
|
|
|
72.
|
|
|
368
|
|
|
73.
|
13h22'45"
|
|
365
|
|
|
74.
|
|
|
362
|
|
|
75.
|
13h22'50"
|
|
360
|
|
|
76.
|
|
17,00
|
355
|
369
|
220
|
77.
|
|
|
350
|
|
|
78.
|
13h23'05"
|
|
362
|
|
269
|
79.
|
|
|
375
|
|
270
|
80.
|
|
|
382
|
|
275
|
81.
|
13h23'20"
|
|
390
|
|
280
|
82.
|
|
|
395
|
|
|
83.
|
|
17,50
|
400
|
400
|
280
|
84.
|
|
|
402
|
|
|
85.
|
|
|
405
|
|
|
86.
|
13h23'50"
|
|
407
|
|
|
87.
|
|
|
410
|
|
|
88.
|
|
|
412
|
|
|
89.
|
13h24'00"
|
18,00
|
413
|
413
|
280
|
90.
|
|
|
415
|
|
|
91.
|
13h24'15"
|
|
420
|
|
|
92.
|
|
18,50
|
425
|
425
|
290
|
93.
|
13h25'15"
|
|
426
|
|
|
94.
|
|
|
427
|
|
|
95.
|
|
|
429
|
|
|
96.
|
|
19,00
|
431
|
431
|
302
|
97.
|
|
|
431
|
|
|
98.
|
|
|
432
|
|
|
99.
|
13h25'30"
|
19,50
|
430
|
432
|
308
|
100.
|
|
|
429
|
|
|
101.
|
|
|
430
|
|
|
102.
|
13h25'40"
|
|
431
|
|
|
103.
|
|
20,00
|
430
|
431
|
310
|
104.
|
13h26'05"
|
|
430
|
|
|
105.
|
|
|
428
|
|
312
|
106.
|
|
|
425
|
|
315
|
107.
|
|
|
420
|
|
317
|
108.
|
|
|
415
|
|
318
|
109.
|
|
|
412
|
|
|
110.
|
|
|
415
|
|
|
111.
|
13h26'30"
|
20,50
|
417
|
430
|
318
|
112.
|
|
|
436
|
|
|
113.
|
|
|
444
|
|
|
114.
|
|
|
433
|
|
|
115.
|
|
|
428
|
|
|
116.
|
13h27'00"
|
21,00
|
430
|
444
|
320
|
117.
|
|
|
428
|
|
|
118.
|
|
|
431
|
|
|
119.
|
|
|
432
|
|
|
120.
|
|
|
434
|
|
|
121.
|
|
|
431
|
|
|
122.
|
|
|
435
|
|
|
123.
|
13h27'30"
|
21,50
|
440
|
440
|
320
|
124.
|
|
|
445
|
|
|
125.
|
|
|
446
|
|
|
126.
|
|
|
446
|
|
|
127.
|
|
|
445
|
|
|
128.
|
|
|
448
|
|
|
129.
|
|
|
449
|
|
|
130.
|
|
|
458
|
|
|
131.
|
|
|
470
|
|
|
132.
|
13h28'00"
|
22,00
|
475
|
475
|
320
|
133.
|
|
|
485
|
|
|
134.
|
|
|
490
|
|
|
135.
|
|
|
495
|
|
|
136.
|
|
|
500
|
|
|
137.
|
|
|
502
|
|
|
138.
|
|
|
505
|
|
|
139.
|
|
|
513
|
|
|
140.
|
13h28'30"
|
22,50
|
515
|
515
|
330
|
141.
|
|
|
520
|
|
|
142.
|
|
|
520
|
|
|
143.
|
|
|
518
|
|
|
144.
|
|
|
527
|
|
|
145.
|
|
|
516
|
|
|
146.
|
|
|
509
|
|
|
147.
|
|
|
505
|
|
|
148.
|
|
|
505
|
|
|
149.
|
|
|
499
|
|
|
150.
|
|
|
502
|
|
|
151.
|
13h29'00"
|
23,00
|
502
|
527
|
335
|
152.
|
|
|
494
|
|
|
153.
|
|
|
490
|
|
|
154.
|
|
|
477
|
|
|
155.
|
|
|
475
|
|
|
156.
|
|
|
473
|
|
|
157.
|
|
|
473
|
|
|
158.
|
13h29'30"
|
23,50
|
477
|
494
|
342
|
159.
|
|
|
476
|
|
|
160.
|
|
|
474
|
|
|
161.
|
|
|
477
|
|
|
162.
|
|
|
475
|
|
|
163.
|
|
|
475
|
|
|
164.
|
13h30'00"
|
24,00
|
488
|
488
|
355
|
165.
|
|
|
495
|
|
|
166.
|
|
|
498
|
|
|
167.
|
|
|
498
|
|
|
168.
|
|
|
501
|
|
|
169.
|
13h30'30"
|
24,50
|
503
|
503
|
362
|
170.
|
|
|
498
|
|
|
171.
|
|
|
490
|
|
|
172.
|
|
|
485
|
|
|
173.
|
|
|
484
|
|
|
174.
|
|
|
480
|
|
|
175.
|
|
|
477
|
|
|
176.
|
13h31'00"
|
25,00
|
475
|
498
|
377
|
177.
|
|
|
470
|
|
378
|
178.
|
|
|
468
|
|
375
|
179.
|
|
|
478
|
|
378
|
180.
|
|
|
479
|
|
382
|
181.
|
|
|
470
|
|
382
|
182.
|
|
|
468
|
|
|
183.
|
|
|
469
|
|
|
184.
|
13h31'30"
|
25,50
|
469
|
479
|
382
|
185.
|
|
|
470
|
|
|
186.
|
|
|
471
|
|
|
187.
|
|
|
471
|
|
|
188.
|
|
|
470
|
|
|
189.
|
|
|
470
|
|
|
190.
|
13h32'00"
|
26,00
|
470
|
471
|
380
|
191.
|
|
|
469
|
|
|
192.
|
|
|
468
|
|
|
193.
|
|
|
473
|
|
|
194.
|
|
|
479
|
|
|
195.
|
|
|
480
|
|
|
196.
|
|
|
481
|
|
|
197.
|
13h32'30"
|
26,50
|
482
|
482
|
380
|
198.
|
|
|
480
|
|
|
199.
|
|
|
479
|
|
|
200.
|
|
|
476
|
|
|
201.
|
|
|
475
|
|
|
202.
|
|
|
477
|
|
|
203.
|
|
|
480
|
|
|
204.
|
13h33'00"
|
27,00
|
482
|
482
|
380
|
205.
|
|
|
484
|
|
|
206.
|
|
|
487
|
|
|
N° de
|
|
temps t
|
T1
|
n T1orm7.
|
T2 (°C)
|
mesure
|
Heure
|
(min)
|
(°C)
|
(°C)
|
|
27
27
28
29
29
29
29
29
30
32
37
47
69
130
II
207.
|
|
|
488
|
|
|
208.
|
|
|
490
|
|
|
209.
|
|
|
490
|
|
|
210.
|
13h33'30"
|
27,50
|
485
|
490
|
380
|
211.
|
|
|
487
|
|
|
212.
|
|
|
489
|
|
|
213.
|
|
|
490
|
|
|
214.
|
|
|
490
|
|
|
215.
|
13h34'00"
|
28,00
|
489
|
490
|
382
|
216.
|
|
|
487
|
|
|
217.
|
|
|
485
|
|
|
218.
|
|
|
482
|
|
|
219.
|
|
|
479
|
|
|
220.
|
13h34'30"
|
28,50
|
477
|
487
|
388
|
221.
|
|
|
476
|
|
|
222.
|
|
|
472
|
|
|
223.
|
|
|
470
|
|
|
224.
|
|
|
469
|
|
399
|
225.
|
13h35'00"
|
29,00
|
465
|
476
|
400
|
226.
|
|
|
465
|
|
400
|
227.
|
|
|
465
|
|
400
|
228.
|
|
|
465
|
|
|
229.
|
|
|
466
|
|
|
230.
|
|
|
470
|
|
|
231.
|
13h35'30"
|
29,50
|
471
|
471
|
400
|
232.
|
|
|
470
|
|
|
233.
|
|
|
468
|
|
|
234.
|
|
|
466
|
|
|
235.
|
|
|
464
|
|
|
236.
|
|
|
462
|
|
|
237.
|
|
|
460
|
|
|
238.
|
|
|
459
|
|
|
239.
|
13h36'00"
|
30,00
|
458
|
470
|
398
|
240.
|
|
|
457
|
|
|
241.
|
|
|
456
|
|
|
242.
|
|
|
455
|
|
|
243.
|
|
|
456
|
|
|
244.
|
|
|
456
|
|
|
245.
|
|
|
456
|
|
|
246.
|
|
|
456
|
|
|
247.
|
13h36'30"
|
30,50
|
456
|
457
|
390
|
248.
|
|
|
454
|
|
|
249.
|
|
|
455
|
|
|
250.
|
|
|
458
|
|
|
251.
|
|
|
455
|
|
|
252.
|
|
|
458
|
|
|
253.
|
|
|
455
|
|
|
254.
|
13h37'00"
|
31,00
|
459
|
459
|
390
|
255.
|
|
|
462
|
|
|
256.
|
|
|
472
|
|
|
257.
|
|
|
479
|
|
|
258.
|
13h37'30"
|
31,50
|
481
|
481
|
392
|
259.
|
|
|
474
|
|
|
260.
|
|
|
472
|
|
|
261.
|
|
|
471
|
|
|
262.
|
|
|
485
|
|
|
263.
|
13h37'45"
|
|
495
|
|
|
264.
|
|
|
505
|
|
|
265.
|
13h38'00"
|
32,00
|
515
|
515
|
395
|
266.
|
|
|
525
|
|
|
267.
|
|
|
536
|
|
|
268.
|
|
|
533
|
|
|
269.
|
|
|
530
|
|
|
270.
|
13h38'30"
|
32,50
|
530
|
536
|
396
|
271.
|
|
|
530
|
|
|
272.
|
|
|
515
|
|
|
273.
|
|
|
505
|
|
|
274.
|
|
|
505
|
|
|
275.
|
|
|
495
|
|
|
276.
|
13h39'00"
|
33,00
|
490
|
530
|
396
|
277.
|
|
|
487
|
|
|
278.
|
|
|
485
|
|
|
279.
|
|
|
478
|
|
|
280.
|
|
|
475
|
|
|
281.
|
|
|
470
|
|
|
282.
|
13h39'30"
|
33,50
|
470
|
487
|
394
|
283.
|
|
|
486
|
|
|
284.
|
|
|
485
|
|
|
285.
|
|
|
480
|
|
|
286.
|
|
|
479
|
|
|
287.
|
|
|
475
|
|
|
288.
|
13h40'00"
|
34,00
|
476
|
486
|
370
|
289.
|
|
|
482
|
|
|
290.
|
|
|
490
|
|
|
291.
|
|
|
485
|
|
|
292.
|
|
|
489
|
|
|
293.
|
|
|
495
|
|
|
294.
|
|
|
498
|
|
|
295.
|
13h40'30"
|
34,50
|
495
|
|
|
296.
|
|
|
490
|
|
|
297.
|
|
|
486
|
|
|
298.
|
|
|
478
|
|
|
299.
|
|
|
476
|
|
|
300.
|
|
|
478
|
|
|
301.
|
13h41'00"
|
35,00
|
479
|
490
|
360
|
302.
|
13h41'30"
|
35,50
|
463
|
463
|
357
|
303.
|
|
|
465
|
|
|
304.
|
|
|
464
|
|
|
305.
|
|
|
470
|
|
|
306.
|
|
|
467
|
|
|
307.
|
|
|
480
|
|
|
308.
|
|
|
478
|
|
|
309.
|
|
|
476
|
|
|
310.
|
|
|
480
|
|
|
311.
|
|
|
486
|
|
|
312.
|
|
|
485
|
|
|
313.
|
|
|
482
|
|
|
314.
|
|
|
477
|
|
|
315.
|
|
|
470
|
|
|
316.
|
|
|
480
|
|
|
317.
|
13h42'00"
|
36,00
|
522
|
522
|
358
|
318.
|
|
|
536
|
|
|
319.
|
|
|
541
|
|
|
320.
|
|
|
546
|
|
|
321.
|
|
|
551
|
|
|
322.
|
|
|
555
|
|
|
323.
|
|
|
558
|
|
|
324.
|
|
|
560
|
|
|
325.
|
|
|
562
|
|
|
326.
|
|
|
562
|
|
|
327.
|
|
|
567
|
|
|
328.
|
|
|
563
|
|
|
329.
|
|
|
560
|
|
|
330.
|
|
|
559
|
|
|
331.
|
|
|
561
|
|
|
332.
|
|
|
570
|
|
|
333.
|
|
|
572
|
|
|
334.
|
|
36,50
|
573
|
573
|
365
|
335.
|
|
|
572
|
|
|
336.
|
|
|
573
|
|
|
337.
|
|
|
572
|
|
|
338.
|
|
|
573
|
|
|
339.
|
|
|
574
|
|
|
340.
|
|
|
579
|
|
|
341.
|
|
|
581
|
|
|
342.
|
|
|
579
|
|
|
343.
|
|
|
580
|
|
|
344.
|
|
|
578
|
|
|
345.
|
|
|
574
|
|
|
346.
|
|
|
572
|
|
|
347.
|
|
37,00
|
572
|
581
|
370
|
348.
|
|
|
575
|
|
|
349.
|
|
|
578
|
|
|
350.
|
|
|
580
|
|
|
351.
|
|
|
584
|
|
|
352.
|
|
|
583
|
|
|
353.
|
|
|
587
|
|
|
354.
|
|
|
593
|
|
|
355.
|
|
|
597
|
|
|
356.
|
|
|
596
|
|
|
357.
|
|
37,50
|
595
|
597
|
375
|
358.
|
|
|
594
|
|
|
359.
|
|
|
592
|
|
|
360.
|
|
|
591
|
|
|
361.
|
|
|
591
|
|
|
362.
|
|
|
590
|
|
|
363.
|
|
|
589
|
|
|
364.
|
|
|
588
|
|
|
365.
|
|
|
585
|
|
|
366.
|
|
|
583
|
|
|
367.
|
|
|
582
|
|
|
368.
|
|
38,00
|
578
|
594
|
375
|
369.
|
|
|
575
|
|
|
370.
|
|
|
573
|
|
|
371.
|
|
|
572
|
|
|
372.
|
|
|
573
|
|
|
373.
|
|
|
578
|
|
|
374.
|
|
|
579
|
|
|
375.
|
|
|
577
|
|
|
376.
|
|
|
573
|
|
|
377.
|
|
|
572
|
|
|
378.
|
|
|
569
|
|
|
379.
|
|
38,50
|
552
|
579
|
375
|
380.
|
|
|
544
|
|
|
381.
|
|
|
539
|
|
|
382.
|
|
|
534
|
|
|
383.
|
|
|
530
|
|
|
384.
|
|
|
532
|
|
|
385.
|
|
|
526
|
|
|
386.
|
|
|
520
|
|
|
387.
|
|
|
514
|
|
|
388.
|
|
39,00
|
511
|
544
|
374
|
389.
|
|
|
510
|
|
|
390.
|
|
|
507
|
|
|
391.
|
|
|
506
|
|
|
392.
|
|
|
508
|
|
|
393.
|
|
|
513
|
|
|
394.
|
|
|
512
|
|
|
395.
|
|
|
510
|
|
|
396.
|
|
|
509
|
|
|
397.
|
|
|
509
|
|
|
398.
|
|
|
507
|
|
|
399.
|
|
39,50
|
508
|
513
|
372
|
400.
|
|
|
510
|
|
|
401.
|
|
|
506
|
|
|
402.
|
|
|
508
|
|
|
403.
|
|
|
512
|
|
|
404.
|
|
|
515
|
|
|
405.
|
|
|
521
|
|
|
406.
|
|
|
522
|
|
|
407.
|
|
|
523
|
|
|
408.
|
|
|
524
|
|
|
409.
|
|
40,00
|
528
|
528
|
373
|
410.
|
|
|
535
|
|
|
411.
|
|
|
532
|
|
|
412.
|
|
|
531
|
|
|
413.
|
|
|
533
|
|
|
414.
|
|
|
536
|
|
|
415.
|
|
|
536
|
|
|
416.
|
|
|
541
|
|
|
417.
|
|
|
544
|
|
|
418.
|
|
|
546
|
|
|
III
419.
|
13h46'30"
|
40,50
|
556
|
556
|
374
|
420.
|
|
|
572
|
|
|
421.
|
|
|
575
|
|
|
422.
|
|
|
575
|
|
|
423.
|
|
|
575
|
|
|
424.
|
|
41,00
|
575
|
575
|
375
|
425.
|
|
|
575
|
|
|
426.
|
|
|
569
|
|
|
427.
|
|
|
570
|
|
|
428.
|
|
|
566
|
|
|
429.
|
|
|
568
|
|
|
430.
|
|
41,50
|
565
|
575
|
375
|
431.
|
|
|
563
|
|
|
432.
|
|
|
561
|
|
|
433.
|
|
|
562
|
|
|
434.
|
|
|
557
|
|
|
435.
|
|
42,00
|
560
|
563
|
375
|
436.
|
|
|
563
|
|
|
437.
|
|
|
565
|
|
|
438.
|
|
|
563
|
|
|
439.
|
|
|
564
|
|
|
440.
|
|
42,50
|
561
|
565
|
376
|
441.
|
|
|
461
|
|
|
442.
|
|
|
563
|
|
|
443.
|
|
|
564
|
|
|
444.
|
|
|
562
|
|
|
445.
|
|
|
564
|
|
|
446.
|
|
43,00
|
566
|
566
|
375
|
447.
|
|
|
565
|
|
|
448.
|
|
|
570
|
|
|
449.
|
|
|
575
|
|
|
450.
|
|
|
580
|
|
|
451.
|
|
|
585
|
|
|
452.
|
|
|
580
|
|
|
453.
|
|
43,50
|
575
|
585
|
378
|
454.
|
|
|
580
|
|
|
455.
|
|
|
585
|
|
|
456.
|
|
|
585
|
|
|
457.
|
|
|
585
|
|
|
458.
|
|
|
584
|
|
|
459.
|
|
44,00
|
585
|
585
|
380
|
460.
|
|
|
582
|
|
|
461.
|
|
|
591
|
|
|
462.
|
|
|
583
|
|
|
463.
|
|
|
584
|
|
|
464.
|
|
|
591
|
|
|
465.
|
|
44,50
|
600
|
600
|
390
|
466.
|
|
|
600
|
|
|
467.
|
|
|
598
|
|
|
468.
|
|
|
602
|
|
|
469.
|
|
|
604
|
|
|
470.
|
|
45,00
|
605
|
605
|
395
|
471.
|
|
|
603
|
|
|
472.
|
|
|
599
|
|
|
473.
|
|
|
585
|
|
|
474.
|
|
|
590
|
|
|
475.
|
|
|
585
|
|
|
476.
|
|
45,50
|
580
|
603
|
395
|
477.
|
|
|
576
|
|
|
478.
|
|
|
570
|
|
|
479.
|
|
|
574
|
|
|
480.
|
|
|
575
|
|
|
481.
|
|
|
50
|
|
|
482.
|
|
|
578
|
|
|
483.
|
|
46,00
|
580
|
580
|
390
|
484.
|
|
|
577
|
|
|
485.
|
|
|
574
|
|
|
486.
|
|
|
575
|
|
|
487.
|
|
|
572
|
|
|
488.
|
|
|
572
|
|
|
489.
|
|
|
568
|
|
|
490.
|
|
46,50
|
567
|
577
|
390
|
491.
|
|
|
565
|
|
|
492.
|
|
|
560
|
|
|
493.
|
|
|
555
|
|
|
494.
|
|
|
560
|
|
|
495.
|
|
|
565
|
|
|
496.
|
|
|
573
|
|
|
497.
|
13h53'00"
|
47,00
|
575
|
575
|
390
|
498.
|
|
|
572
|
|
|
499.
|
|
|
574
|
|
|
500.
|
|
|
575
|
|
|
501.
|
|
|
574
|
|
|
502.
|
|
|
584
|
|
|
503.
|
13h53'30"
|
47,50
|
586
|
586
|
390
|
504.
|
|
|
594
|
|
|
505.
|
|
|
597
|
|
|
506.
|
|
|
600
|
|
|
507.
|
13h53'45"
|
|
603
|
|
|
508.
|
|
|
604
|
|
|
509.
|
|
|
595
|
|
|
510.
|
13h54'00"
|
48,00
|
575
|
604
|
395
|
511.
|
|
|
558
|
|
|
512.
|
|
|
559
|
|
|
513.
|
13h54'30"
|
48,50
|
550
|
559
|
370
|
514.
|
|
|
517
|
|
|
515.
|
|
|
510
|
|
|
516.
|
|
|
481
|
|
|
517.
|
13h55'00"
|
49,00
|
481
|
517
|
368
|
518.
|
|
|
481
|
|
|
519.
|
|
|
480
|
|
|
520.
|
|
|
479
|
|
|
521.
|
13h55'30"
|
49,50
|
480
|
481
|
365
|
522.
|
|
|
480
|
|
|
523.
|
|
|
480
|
|
|
524.
|
13h56'00"
|
50,00
|
480
|
480
|
368
|
525.
|
|
|
477
|
|
|
526.
|
|
|
477
|
|
|
527.
|
|
|
477
|
|
|
528.
|
13h56'30"
|
50,50
|
477
|
477
|
365
|
529.
|
|
|
470
|
|
|
530.
|
|
|
466
|
|
|
531.
|
|
|
463
|
|
|
532.
|
|
|
461
|
|
|
533.
|
13h57'00"
|
51,00
|
460
|
470
|
365
|
534.
|
|
|
459
|
|
|
535.
|
|
|
460
|
|
|
536.
|
13h57'30"
|
51,50
|
461
|
461
|
365
|
537.
|
|
|
460
|
|
|
538.
|
|
|
460
|
|
|
539.
|
|
|
459
|
|
|
540.
|
|
|
461
|
|
|
541.
|
13h58'00"
|
52,00
|
460
|
461
|
360
|
542.
|
|
|
459
|
|
|
543.
|
|
|
458
|
|
|
544.
|
|
|
457
|
|
|
545.
|
13h58'30"
|
52,50
|
452
|
459
|
355
|
546.
|
|
|
455
|
|
|
547.
|
|
|
456
|
|
|
548.
|
|
|
456
|
|
|
549.
|
|
|
458
|
|
|
550.
|
13h59'00"
|
53,00
|
459
|
459
|
355
|
551.
|
|
|
460
|
|
|
552.
|
|
|
463
|
|
|
553.
|
|
|
464
|
|
|
554.
|
|
|
465
|
|
|
555.
|
|
|
465
|
|
|
556.
|
|
|
465
|
|
|
557.
|
|
|
465
|
|
|
558.
|
13h59'30"
|
53,50
|
465
|
465
|
350
|
559.
|
|
|
464
|
|
|
560.
|
|
|
463
|
|
|
561.
|
|
|
462
|
|
|
562.
|
|
|
462
|
|
|
563.
|
|
|
461
|
|
|
564.
|
14h00'00"
|
54,00
|
461
|
464
|
335
|
565.
|
|
|
461
|
|
|
566.
|
|
|
461
|
|
|
567.
|
|
|
461
|
|
|
568.
|
|
|
460
|
|
|
569.
|
|
|
460
|
|
|
570.
|
|
|
460
|
|
|
571.
|
14h00'30"
|
54,50
|
461
|
461
|
310
|
572.
|
|
|
460
|
|
305
|
573.
|
|
|
458
|
|
304
|
574.
|
14h01'00"
|
55,00
|
456
|
460
|
304
|
575.
|
|
|
453
|
|
304
|
576.
|
|
|
454
|
|
304
|
577.
|
|
|
451
|
|
|
578.
|
14h01'30"
|
55,50
|
452
|
454
|
305
|
579.
|
|
|
450
|
|
|
580.
|
|
|
449
|
|
|
581.
|
|
|
450
|
|
|
582.
|
|
|
451
|
|
|
583.
|
14h02'00"
|
56,00
|
452
|
452
|
305
|
584.
|
|
|
452
|
|
|
585.
|
|
|
452
|
|
|
586.
|
|
|
452
|
|
|
587.
|
|
|
453
|
|
|
588.
|
|
|
454
|
|
305
|
589.
|
14h02'30"
|
56,50
|
455
|
455
|
306
|
590.
|
|
|
456
|
|
|
591.
|
|
|
455
|
|
|
592.
|
|
|
457
|
|
|
593.
|
|
|
458
|
|
|
594.
|
|
|
458
|
|
|
595.
|
14h03'00"
|
57,00
|
458
|
458
|
308
|
596.
|
|
|
460
|
|
|
597.
|
|
|
460
|
|
|
598.
|
|
|
460
|
|
|
599.
|
|
|
450
|
|
|
600.
|
|
|
457
|
|
|
601.
|
14h03'30"
|
57,50
|
455
|
460
|
306
|
602.
|
|
|
450
|
|
|
603.
|
|
|
448
|
|
|
604.
|
|
|
447
|
|
|
605.
|
|
|
447
|
|
|
606.
|
|
|
444
|
|
|
607.
|
14h04'00"
|
58,00
|
444
|
450
|
304
|
608.
|
|
|
444
|
|
|
609.
|
|
|
446
|
|
|
610.
|
|
|
447
|
|
|
611.
|
|
|
450
|
|
|
612.
|
|
|
452
|
|
|
613.
|
|
|
455
|
|
|
614.
|
|
|
456
|
|
|
615.
|
|
|
458
|
|
|
616.
|
14h04'30"
|
58,50
|
459
|
459
|
304
|
617.
|
|
|
462
|
|
|
618.
|
|
|
464
|
|
|
619.
|
|
|
465
|
|
|
620.
|
|
|
465
|
|
|
621.
|
|
|
465
|
|
|
622.
|
|
|
465
|
|
|
623.
|
|
|
465
|
|
|
624.
|
|
|
465
|
|
|
625.
|
14h05'00"
|
59,00
|
465
|
465
|
304
|
626.
|
|
|
465
|
|
|
627.
|
|
|
465
|
|
|
628.
|
|
|
465
|
|
|
629.
|
|
|
466
|
|
|
630.
|
|
|
466
|
|
|
IV
631.
|
|
|
466
|
|
|
632.
|
|
|
467
|
|
|
633.
|
|
|
466
|
|
|
634.
|
14h05'30"
|
59,50
|
465
|
467
|
305
|
635.
|
|
|
461
|
|
|
636.
|
|
|
460
|
|
|
637.
|
|
|
459
|
|
|
638.
|
|
|
459
|
|
|
639.
|
|
|
458
|
|
|
640.
|
14h06'00"
|
60,00
|
458
|
461
|
308
|
641.
|
|
|
457
|
|
|
642.
|
|
|
455
|
|
|
643.
|
|
|
456
|
|
|
644.
|
|
|
457
|
|
|
645.
|
14h06'30"
|
60,50
|
456
|
457
|
301
|
646.
|
|
|
457
|
|
|
647.
|
|
|
456
|
|
|
648.
|
|
|
457
|
|
|
649.
|
|
|
456
|
|
|
650.
|
|
|
455
|
|
|
651.
|
|
|
454
|
|
314
|
652.
|
14h07'00"
|
61,00
|
455
|
457
|
313
|
653.
|
|
|
456
|
|
313
|
654.
|
|
|
454
|
|
313
|
655.
|
|
|
462
|
|
312
|
656.
|
14h07'30"
|
61,50
|
465
|
465
|
312
|
657.
|
|
|
470
|
|
|
658.
|
|
|
470
|
|
|
659.
|
|
|
468
|
|
|
660.
|
|
|
471
|
|
|
661.
|
|
|
462
|
|
|
662.
|
|
|
471
|
|
|
663.
|
14h08'00"
|
62,00
|
462
|
471
|
313
|
664.
|
|
|
471
|
|
|
665.
|
|
|
469
|
|
|
666.
|
|
|
470
|
|
|
667.
|
|
|
468
|
|
|
668.
|
14h08'30"
|
62,50
|
467
|
471
|
314
|
669.
|
|
|
466
|
|
|
670.
|
|
|
465
|
|
|
671.
|
|
|
464
|
|
|
672.
|
|
|
463
|
|
|
673.
|
|
|
463
|
|
|
674.
|
|
|
464
|
|
|
675.
|
|
|
464
|
|
|
676.
|
14h09'00"
|
63,00
|
463
|
466
|
315
|
677.
|
|
|
462
|
|
|
678.
|
|
|
463
|
|
|
679.
|
|
|
465
|
|
|
680.
|
|
|
464
|
|
|
681.
|
|
|
464
|
|
|
682.
|
14h09'30"
|
63,50
|
464
|
465
|
315
|
683.
|
|
|
461
|
|
|
684.
|
|
|
461
|
|
|
685.
|
|
|
461
|
|
|
686.
|
|
|
460
|
|
|
687.
|
|
|
461
|
|
|
688.
|
14h10'00"
|
64,00
|
462
|
462
|
316
|
689.
|
|
|
463
|
|
|
690.
|
|
|
464
|
|
|
691.
|
|
|
464
|
|
|
692.
|
|
|
464
|
|
|
693.
|
|
|
464
|
|
|
694.
|
14h10'30"
|
64,50
|
464
|
464
|
320
|
695.
|
|
|
465
|
|
|
696.
|
|
|
465
|
|
|
697.
|
|
|
470
|
|
|
698.
|
|
|
473
|
|
|
699.
|
14h11'00"
|
65,00
|
472
|
473
|
318
|
700.
|
|
|
469
|
|
|
701.
|
|
|
469
|
|
|
702.
|
|
|
467
|
|
|
703.
|
|
|
463
|
|
|
704.
|
|
|
469
|
|
|
705.
|
14h11'30"
|
65,50
|
459
|
469
|
318
|
706.
|
|
|
457
|
|
|
707.
|
|
|
457
|
|
|
708.
|
|
|
460
|
|
|
709.
|
|
|
460
|
|
|
710.
|
|
|
461
|
|
|
711.
|
14h12'00"
|
66,00
|
462
|
462
|
316
|
712.
|
|
|
462
|
|
|
713.
|
|
|
462
|
|
|
714.
|
|
|
461
|
|
|
715.
|
|
|
460
|
|
|
716.
|
14h12'30"
|
66,50
|
459
|
462
|
315
|
717.
|
|
|
458
|
|
|
718.
|
|
|
457
|
|
|
719.
|
|
|
454
|
|
|
720.
|
|
|
453
|
|
|
721.
|
|
|
453
|
|
|
722.
|
14h13'00"
|
67,00
|
451
|
458
|
315
|
723.
|
|
|
450
|
|
|
724.
|
|
|
451
|
|
|
725.
|
|
|
451
|
|
|
726.
|
|
|
451
|
|
|
727.
|
|
|
449
|
|
|
728.
|
14h13'30"
|
67,50
|
448
|
451
|
316
|
729.
|
|
|
450
|
|
|
730.
|
|
|
450
|
|
|
731.
|
|
|
451
|
|
|
732.
|
|
|
451
|
|
|
733.
|
14h14'00"
|
68,00
|
453
|
453
|
317
|
734.
|
|
|
460
|
|
|
735.
|
|
|
464
|
|
|
736.
|
|
|
466
|
|
|
737.
|
|
|
465
|
|
|
738.
|
14h14'30"
|
68,50
|
465
|
466
|
317
|
739.
|
|
|
464
|
|
317
|
740.
|
|
|
468
|
|
316
|
741.
|
|
|
465
|
|
315
|
742.
|
14h15'00"
|
69,00
|
456
|
468
|
316
|
743.
|
|
|
455
|
|
|
744.
|
|
|
457
|
|
|
745.
|
|
|
457
|
|
|
746.
|
|
|
453
|
|
|
747.
|
|
|
455
|
|
|
748.
|
14h15'30"
|
69,50
|
451
|
457
|
315
|
749.
|
|
|
451
|
|
|
750.
|
|
|
451
|
|
|
751.
|
|
|
453
|
|
|
752.
|
|
|
454
|
|
|
753.
|
|
|
453
|
|
|
754.
|
14h16'00"
|
70,00
|
454
|
454
|
315
|
755.
|
|
|
453
|
|
|
756.
|
|
|
454
|
|
|
757.
|
|
|
455
|
|
|
758.
|
|
|
453
|
|
|
759.
|
14h16'30"
|
70,50
|
454
|
455
|
318
|
760.
|
|
|
455
|
|
|
761.
|
|
|
454
|
|
|
762.
|
|
|
455
|
|
|
763.
|
|
|
455
|
|
|
764.
|
14h17'00"
|
71,00
|
458
|
458
|
322
|
765.
|
|
|
459
|
|
|
766.
|
14h17'30"
|
71,50
|
465
|
465
|
324
|
767.
|
|
|
458
|
|
|
768.
|
14h18'00"
|
72,00
|
463
|
463
|
327
|
769.
|
|
|
462
|
|
|
770.
|
14h18'30"
|
72,50
|
470
|
470
|
330
|
771.
|
|
|
498
|
|
|
772.
|
14h19'00"
|
73,00
|
498
|
498
|
328
|
773.
|
|
|
500
|
|
|
774.
|
14h19'30"
|
73,50
|
505
|
505
|
327
|
775.
|
14h20'00"
|
74,00
|
490
|
490
|
326
|
776.
|
|
|
480
|
|
|
777.
|
14h20'30"
|
74,50
|
475
|
480
|
323
|
778.
|
|
|
473
|
|
|
779.
|
|
|
471
|
|
321
|
780.
|
|
|
475
|
|
|
781.
|
14h21'00"
|
75,00
|
478
|
478
|
322
|
782.
|
|
|
485
|
|
322
|
783.
|
14h21'30"
|
75,50
|
490
|
490
|
323
|
784.
|
|
|
495
|
|
321
|
785.
|
14h22'00"
|
76,00
|
494
|
495
|
319
|
786.
|
|
|
498
|
|
|
787.
|
|
|
502
|
|
317
|
788.
|
14h22'30"
|
76,50
|
498
|
502
|
315
|
789.
|
|
|
496
|
|
316
|
790.
|
14h23'00"
|
77,00
|
494
|
496
|
318
|
791.
|
|
|
490
|
|
|
792.
|
|
|
485
|
|
|
793.
|
14h23'30"
|
77,50
|
476
|
490
|
320
|
794.
|
|
|
470
|
|
324
|
795.
|
14h24'00"
|
78,00
|
465
|
470
|
319
|
796.
|
14h24'30"
|
78,50
|
457
|
457
|
321
|
797.
|
14h25'00"
|
79,00
|
458
|
458
|
320
|
798.
|
|
|
455
|
|
|
799.
|
|
|
454
|
|
|
800.
|
14h25'30"
|
79,50
|
454
|
455
|
320
|
801.
|
14h26'00"
|
|
452
|
|
320
|
802.
|
|
|
452
|
|
|
803.
|
14h26'30"
|
80,00
|
450
|
452
|
318
|
804.
|
|
|
448
|
|
|
805.
|
|
|
446
|
|
316
|
806.
|
14h27'00"
|
80,50
|
445
|
448
|
316
|
807.
|
14h27'30"
|
81,00
|
450
|
450
|
317
|
808.
|
|
|
452
|
|
318
|
809.
|
14h28'00"
|
81,50
|
456
|
456
|
320
|
810.
|
|
|
450
|
|
318
|
811.
|
14h28'30"
|
82,00
|
442
|
450
|
315
|
812.
|
14h29'00"
|
82,50
|
445
|
445
|
313
|
813.
|
|
|
448
|
|
314
|
814.
|
14h29'30"
|
83,00
|
453
|
453
|
315
|
815.
|
|
|
462
|
|
316
|
816.
|
|
|
465
|
|
314
|
817.
|
14h30'00"
|
83,50
|
470
|
470
|
314
|
818.
|
|
|
474
|
|
314
|
819.
|
|
|
474
|
|
317
|
820.
|
14h30'30"
|
84,00
|
470
|
474
|
317
|
821.
|
|
|
463
|
|
318
|
822.
|
14h31'00"
|
84,50
|
465
|
465
|
316
|
823.
|
|
|
468
|
|
316
|
824.
|
14h31'30"
|
85,00
|
467
|
468
|
312
|
825.
|
14h32'00"
|
85,50
|
470
|
470
|
310
|
T1 = Température de paroi interne du
réacteur
T2 = température des gaz à
l'échappement
Photo n°2 : Opération d'allumage
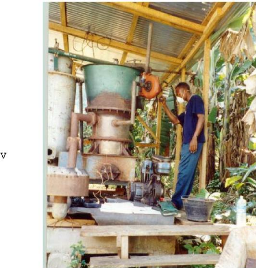
ANNEXES n°2 : Quelques photos
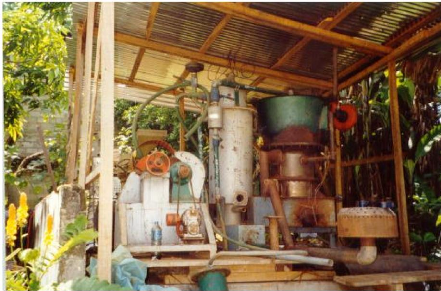
Photo n°1 : Une vue de l'installation
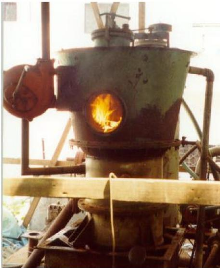
Photo n°3 : vue intérieure du
générateur pendant la gazéification
VI
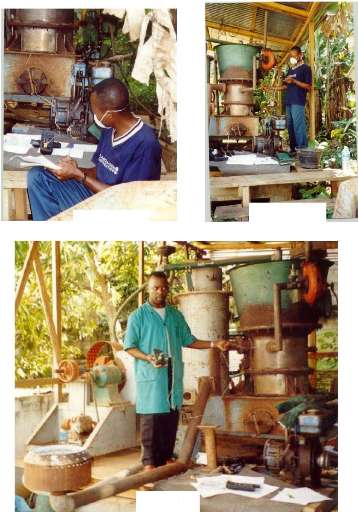
Photo n°4
Photo n°6
Photo n°5
Photos n°s 4, 5 et 6 :
Quelques opérations de mesure
ANNEXES n°3 : PROTOCOLES DE CARACTERISATION
PHYSICO-CHIMIQUE DU CHARBON DE BOIS.
(ces procédures sont les adaptations des
normes AFNOR NF B 55-101)
I- DETERMINATION DU TAUX DE CENDRES DANS LE BOIS 1/
Principe
Les cendres sont très fortement liées chimiquement
et mécaniquement au bois. Dans un même arbre, les régions
les plus tendres et les plus jeunes sont souvent les plus
minéralisées.
Le but de la détermination du taux de cendres est
d'obtenir par incinération, à 950 °C, un résidu
exempt de matières organiques et renfermant la plus grande part possible
d'éléments minéraux contenus dans l'échantillon Ca,
Na, Mn Fe, Si ... ainsi que certains sels (SO42-, NO3-,
CO3-)
2/ Mode opératoire
? Peser dans un creuset en Pyrex préalablement
taré au 1/10 mg près, 10 à 40g de matière finement
broyée (broyeur à couteaux) séchée à
l'étuve à 150 °C.
? Mettre ce creuset au four à moufle froid et
élever progressivement la température jusqu'à 450 °C
#177; 15 °C. Laisser une nuit à cette température.
? Les cendres obtenues sont généralement
claires, si elles sont sombres, les laisser encore quelques heures au four,
puis sortir le creuset et le laisser refroidir, recouvert d'un verre de montre,
dans un dessiccateur.
? Peser le creuset plein, au 1/10 mg près.
3/ Calculs
on exprime le taux de cendres en pourcentage de matière
sèche :
C = (m cendres / m échantillon) x 100
m centres = masse des cendres anhydres m échantillon =
masse de l'échantillon sec
Nota :
Les essais doivent concorder à moins de 5%. Cette limite
est portée à 100 % dans le cas de faibles taux de cendres.
II-
VII
DETERMINATION DE L'HUMIDITÉ D'UN
CHARBON
1/- But :
Connaître la teneur en eau d'un échantillon de
bois. Cette analyse accompagne toute détermination de PCS, taux de
cendre et indice de matières volatiles à effectuer sur le charbon
de bois.
2/- Principe:
Séchage à 105°C #177; 1°C d'une prise
d'essai pendant 1 à 1 heures 30 dans une étuve à air chaud
(1) calcul de l'humidité à partir de la perte de masse par
rapport à la masse initiale.
3/- Echantillonnage
Particules d charbon de diamètre inférieur à
0,20 mm.
4/- Mode opératoire :
? 2 à 3g (pesés à 0,1mg près) de
charbon (ml) sont introduits dans une boîte à tare
préalablement séchée à 105°C, refroidie et
pesée.
? Répandre uniformément le charbon dans le
récipient, et le placer dans l'étuve chauffée à
105°C pendant 1 à 1 heure 30. Sortir et placer l'ensemble dans le
dessiccateur pendant 30 minutes puis peser à 0,1mg près (m2).
Effectuer 2 déterminations sur chaque
échantillon.
5/- Expression des Resultats
L'humidité du charbon exprimée en pourcentage
massique est donnée par la formule :
M = (m2-m3) / (m2-m1) x 100
m1= masse du récipient vide et sec
m2 = masse du récipient = masse d'échantillon avant
étuvage
m3 = masse du récipient = masse d'échantillon
après étuvage et refroidissement
Dans le cas d'un charbon défourné peu de temps
avant son analyse (quelques heures) le temps de séjour de
l'échantillon dans l'étuvage peut être raccourci. (30
minutes)
III- POUVOIR CALORIFIQUE
1/- Définition
- Pouvoir calorifique supérieur :
C'est la quantité de chaleur, exprimée en joules
par unité de masse, dégagée par la combustion
complète de l'unité de masse combustible ramenée à
la température initiale fixée à 25°C.
- Pourvoir calorifique inférieur :
C'est la quantité de chaleur exprimée en joules
par unité de masse, dégagée par la combustion
complète de l'unité de masse du combustible, l'eau demeurant
à l'état de vapeur et les autres produits de la combustion
étant ramenés à la température initiale
fixée à 25°C, il est plus directement utilisable dans les
conditions normales de combustion.
2/- Principe
Combustion d'une prise d'essai de masse déterminée
en présence d'oxygène dans une bombe calorimétrique
plongée dans un volume d'eau connu.
VIII
Le pouvoir calorifique supérieur déterminé
dans ces conditions, c'est-à-dire à volume constant, se calcule
à partir de l'élévation de température
constatée, de l'eau.
Le pouvoir calorifique inférieur est
déterminé par calcul.
La valeur en eau du calorimètre aura été
préalablement déterminée à l'aide d'un
étalon. Parallèlement, on doit procéder à une
détermination de l'humidité de l'échantillon.
3/- Réactifs
- L'eau utilisée doit être de l'eau
distillée ou déminéralisée.` - Oxygène
sous pression et exempt de matière combustible.
4/- Appareillages Calorimètre
adiabatique
4.1/- le Calorimètre
Vase calorimètre en métal poli destiné
à recevoir la bombe et muni d'un couvercle. Sa section doit être
telle que la bombe soit juste immergée avec 21 d'eau environ.
- Jaquette : récipient métallique
calorifugé, et comportant une double paroi remplie d'eau; -
Agitateur.
4.2/- Bombe calorimétrique
Sa surface intérieure doit être inattaquable par
les produits de combustion. Elle est destinée à recevoir la
coupelle (6.4) et le dispositif d'allumage électrique (6.6). Elle doit
pouvoir résister à une pression de 210 bars.
4.3/- Thermomètre gradué en
0,01°C et muni d'un dispositif permettant les lectures à
0,0002°C près.
4.4 Coupelles.
4.5 Fil d'allumage en platine ou en
nickel-chrome de 0,10 mm de diamètre et fil à coudre de coton
blanc non mercerisé.
4.6 Vibreur mécanique destiné
à frapper doucement le thermomètre pendant 10 s. Toutes les
minutes est souhaitable, afin d'éviter l'adhérence de la colonne
de mercure.
5/- Echantillonnage
Bois : petits morceaux ( <1 cm3) ou poudre si
présence d'écorce.
Charbon : fines de diamètre inférieur à 0,20
mm. Echantillons non étuvés au préalable.
6/- Mode Opératoire
* Peser à 0,1mg près dans la coupelle. Une masse de
combustible permettant d'obtenir une élévation de
température de 2,5 à 3,5 °C (1g pour le bois, 0,8g pour le
charbon).
* Relier les 2 bornes de la bombe par un fil d'allumage de
longueur et de pouvoir calorifique connus. Ce fils devra être en contact
avec l'échantillon.
* Introduire la coupelle dans la bombe. Ajuster le couvercle et
le visser sur le corps de la bombe.
* Charger avec précaution la bombe en oxygène
jusqu'à une pression de 25 à 30 bars.
* Introduire dans le vase calorimétrique une
quantité d'eau suffisante pour immerger la face supérieure du
couvercle de la bombe. Cette quantité vérifiée par
pesée, doit être la même à 1g près que celle
utilisée au cours de l'étalonnage pour détermination de la
capacité calorifique effective. Elle sera de 200 ml.
* placer la bombe dans le vase calorimétrique et
celui-ci dans la jaquette, ajuster le thermomètre, établir les
connexions et mettre l'agitateur en marche. La température de l'eau du
calorimètre à jaquette adiabatique doit être
inférieure à la température ambiante de 1°C à
1,5°C.
Ix
* Régler la température de la jaquette afin
qu'elle soit égale ou légèrement inférieure
à celle du vase calorimétrique et attendre 5 minutes pour obtenir
l'équilibre. Ajuster la température de la jaquette de
manière qu'elle soit égale à #177;0,01°C près
à celle du vase calorimétrique et attendre 3 minutes.
*Noter la température initiale et fermer le circuit
électrique pour provoquer l'inflammation.
* Observer la température du vase calorimétrique
toutes les minutes jusqu'à ce que 3 lectures successives soient
identiques. Noter cette température comme température maximale,
les observations thermométriques seront lues à 0,002°C au
moyen d'un dispositif donnant cette précision.
* Retirer la bombe du calorimètre, la laisser reposer
pendant 10 minutes, réduire lentement la pression, ouvrir la bombe.
* Vérifier si la combustion est complète,
c'est-à-dire s'il n'y a pas de dépôt de suie à
l'intérieur de la bombe ou des traces de carbone résiduel sur les
parois de la coupelle.
* Mesurer la longueur du fil d'allumage métallique qui n'a
pas brûlé.
* Rincer soigneusement l'intérieur de la bombe et du
couvercle avec un peu d'eau distillée et verser cette eau de
rinçage en même temps que celle qui avait été mise
primitivement au fond de la bombe, dans une fiole de 400ml en vue du dosage des
acides qui se sont formés au cours de la combustion.
* Expression des résultats :
Le pouvoir calorifique, supérieur à volume constant
Pv de l'échantillon non étuvé est donné par la
formule suivante en joule par gramme.
Pv
(4,1855 x E) (t m - t i) - (a +b)
=
M
Le pouvoir calorifique supérieur à volume constant
sur un échantillon anhydre est égal à :
Pv x (100-Hi) / 100
Avec : E = équivalent en eau du calorimètre, de la
bombe, de leurs accessoires et de l'eau Introduire dans la bombe (E est
calculé en faisant au moins 5 déterminations concordantes du
pouvoir calorifique supérieur de l'acide benzoïque de
qualité "étalon pour calorimétrie" (26450kJ/kg).
ti = température initiale en °C
tm = température maximale en °C
a= correction nécessitée par la formation
d'acides (la totalité des acides est dosée avec une solution de
carbonate de sodium. Indicateur rouge de méthyle). Compter 12,56 joules
par millilitre de solution de carbonate de sodium 0,1N.
b = correction nécessitée par la chaleur de
combustion du fil d'allumage (en joule/cm). M = masse de la prise d'essai en
grammes.
Hi = humidité de l'échantillon sec à l'air
en pourcentage en masse.
Le PCI se déduit par le calcul du PCS en connaissant le
nombre de molécules d'eau formées et la chaleur
dégagée par le passage de l'état de vapeur d'eau à
l'état liquide à la température initiale.
On admet généralement pour un produit anhydre la
formule moyenne approchée suivante : PCI anhydre = PCS anhydre -
(2508 x 9H.) en J/g
H étant le % pondéral d'hydrogène dans le
bois, 250kJ/kg étant la valeur de la chaleur latente de condensation de
l'eau à 0°C
Pour 6 % d'hydrogène (teneur moyenne du bois), nous avons
donc :
PCI anhydre = PCS anhydre - 1354 en j/g
X
Dans la pratique, le PCI d'un corps varie dans de fortes
proportions suivant son degré d'humidité. La quantité de
chaleur fournie diminue quand la teneur en eau du bois augmente Les formules
suivantes peuvent être utilisées pour le calcul du PCI du bois en
fonction de son humidité.
* Si E = humidité du bois en % du bois brut :
100 -
- E
Pe P ox
= 25,08 xE en J/g
100
Avec Pe = PCI à l'humidité E (J/g)
Po = PCI sur bois anhydre (J/g)
7/- Etalonnage du Calorimètre
Procédé régulièrement à
l'étalonnage du calorimètre, notamment lorsque :
- la température ambiante varie beaucoup - un
élément de l'appareil a été remplacé - la
bombe calorimétrique est changée
Mode opératoire : '(Cf Celui des
échantillons)
Pour l'étalonnage utiliser de l'acide benzoïque
étalon pour PCS, il ne devra pas être étuvé (donc
pas d'humidité a calculer ).
5 mesures seront nécessaires pour la détermination
de l'équivalent en eau. Les résultats devront être
très proches.
Pour chaque mesure peser dans la capsule 1g d'acide
benzoïque en pastille soit M. Equivalant en eau:
(M
x PCS ) (a b)
acide benzoïque étalon + +
E = en cal/°C
(t m - t i )
IV- DETERMINATION DU TAUX DE CENDRES DANS LE CHARBON DE
BOIS
1/- But :
Déterminer le taux de résidu obtenu après
combustion du charbon
2/- Principe :
Combustion d'une prise d'essai dans un four a moufle a 950
°C. Le taux de cendre correspond a la quantité de résidu,
rapporté a la masse de la prise d'essai.
Parallèlement, on doit procéder a la
détermination de l'humidité de l'échantillon
3/- Echantillonnage
Granulométrie de l'échantillon inférieur a
0,20 mm
4/- Mode opératoire
* Calciner une nacelle de silice au four a 950°C pendant 20
minutes. Refroidir 30 minutes dans un dessiccateur et peser a 0,1 mg (ml).
* Peser dans la nacelle 1 a 2 de l'échantillon a 0,1 mg
près (soit m2) Répandre le charbon uniformément dans la
nacelle.
* Placer la nacelle dans le four a moufle (la température
initiale du four ne doit pas dépasser 300°C) et chauffer le four a
une vitesse de 250 a 300°C pour atteindre 950°C #177;
20°C.
* Maintenir la nacelle pendant 3 heures a cette
température puis sortir et refroidir dans le dessiccateur.
XI
*Peser a 0,1 mg près (m3). Effectuer 2
déterminations sur chaque échantillon.
5/- Expression des résultats
La teneur en cendres, esprimée en pourcentage en masse du
combustible brut est donné par la formule :
C = (m3-ml) / (m2-m1) x 100
ml = masse en gramme de la nacelle`
m2 = masse en gramme de la nacelle et du charbon
m3 = masse en gramme de la nacelle et des cendres
V- DETERMINATION DE L'INDICE DE MATIERES VOLATILES DANS
LE CHARBON DE BOIS
1/- Définition:
L'indice des matières volatiles est la perte de masse
exprimée en pourcentage, obtenue dans des conditions normalisées,
après pyrolyse du charbon chauffé a l'abri de l'air, abstraction
faite de la perte de masse due a l'évaporation de l'eau
d'humidité.
2/- Principe
* chauffage d'un échantillon a l'abri de l'air, a 950
°C pendant 1 heure.
* Protection du charbon contre l'oxydation, lors de la pyrolyse,
réalisé a l'aide de charbon de bois recouvrant le creuset
contenant l'échantillon (méthode de double creuset).
* Une détermination de l'humidité de
l'échantillon devra être réalisée en
parallèle.
3/- Echantillonnage
Particules de charbon de diamètre inférieur a 0,20
mm
4/- Mode opératoire
* Chauffer au préalable dans un four a moufle pendant
30 minutes a 950°C #177;20°C un creuset en silice muni de son
couvercle, le refroidir au dessiccateur et le peser a 0,1 mg près (ml).
Introduire dans le creuset 2 a 3g de l'échantillon, peser a 0,1 mg
près (m2). Recouvrir le fond d'un 2eme creuset de silice de taille
supérieure par une couche de 1 cm de charbon de bois8.
* introduire le creuset contenant l'échantillon a
analyser, muni de son couvercle dans le grand creuset de silice et remplir
totalement de charbon de bois. (*) Couvrir par le couvercle et placer
l'ensemble dans le four a moufle a 950°C #177; 20°C
* laisser séjourner pendant 1 heure a cette
température, refroidir le tout dans un dessiccateur puis sortir le
creuset contenant l'échantillon, nettoyer l'extérieur avec un
pinceau et peser a 0,1 mg près (m3).
Effectuer 2 déterminations sur chaque
échantillon.
4/- Expression des résultats
L'indice de matières volatiles en pourcentage en masse
de l'échantillon est égal a : V = 100 x (m2-m3) /
(m2-ml) - H
ml = masse en gramme du creuset vide et de son couvercle
m2 = masse en gramme du creuset, du couvercle et de
l'échantillon avant chauffage.
m3 = masse en gramme du creuset, de son couvercle et de son
contenu après chauffage H = Humidité exprimée en
pourcentage massique de l'échantillon analysé.
XII
VI- Taux de CARBONE FIXE D'UN CHARBON DE BOIS
Selon la norme NF B551010, le taux de carbone
fixe se calcule après la détermination des paramètres
suivant : humidité, indice de matières volatiles, taux de
cendres
Le taux de carbone fixe exprimé en pourcentage massique
par rapport a l'échantillon brut est donné par la formule :
CF = 100 - (H + MV - C)
où H= humidité en %
MV = Indice de matières volatiles %
C = taux de cendres %
8 Le charbon utilisé pour créer une
atmosphère inerte aura une granulation comprise entre 2 mm et 4 mm et
aura été débarrassé de ses matières
volatiles a 950°C pendant 1 heure.
|