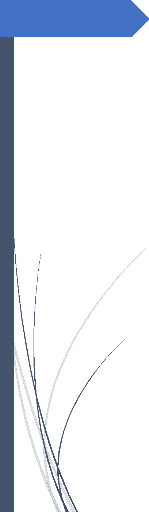
REPUBLIQUE DEMOCRATIQUE DU CONGO
UNIVERSITE DE LUBUMBASHI
FACULTE POLYTECHNIQUE
Possibilité de récupération du
cuivre par lixiviation acide des
boues anodiques des Usines de
Shituru
Présenté et défendu en vue de
l'obtention du grade de Bachelier en sciences de
l'Ingénieur
Par MUNUNG TAMBWE Guy
Directeur : Professeur ILUNGA NDALA Augustin Encadreur :
Ingénieur KABWE CIPAMA Fidèle
OCTOBRE 2021
Option : Chimie Industrielle
RESUME
Les boues anodiques d'électroaffinage de cuivre des
Usines de Shituru sont des produits qui titrent en moyenne 54,01% Cu ; 4,63% Pb
; 88ppm Au ; 0,91ppm Ag ; 0,14% Co ; 0,013% Ni ; 0,042% Zn et 0,558% Fe.
L'analyse chimique par spectrométrie d'absorption atomique renseigne une
forte teneur en cuivre (54,01%) et en plomb (4,63%) et l'analyse
minéralogique renseigne la présence du cuivre métallique
pulvérulent, des traces de malachite et du quartz.
Leur traitement pour la récupération du cuivre a
montré qu'en milieu acide sulfurique 2M, à la température
de 60°C et précédé d'un grillage oxydant de 3H, un
taux de dissolution du cuivre de 75,3%. Le résidu de lixiviation, qui
représente 44,7% du solide initial se retrouve avec 27,6% Cu et 11,62 %
Pb.
Ce travail n'a pas pris compte de l'influence de la structure
et des caractéristiques du milieu poreux granulaire formé par les
boues anodiques, c'est-à-dire la taille et la forme des grains, la
porosité et la surface spécifique, vis-à-vis des
réactions solide-gaz lors du grillage oxydant. Cela permettrait de
déterminer les meilleures conditions opératoires pour le grillage
oxydant. Cette perspective reste ouverte à d'autres chercheurs
désireux de poursuivre ce travail.
gtambwe934@gmail.com
Page | I
ABSTRACT
The copper electro-refining anodic sludge from the Shituru
Plants are products that average 54,01% Cu ; 4,63% Pb ; 88ppm Au ; 0,91ppm Ag ;
0,14% Co ; 0,013% Ni ; 0,042% Zn and 0,558% Fe. Chemical analysis by atomic
absorption spectrometry indicates a high copper (54,01%) and Lead (4,63%)
content and mineralogical analysis indicates the presence of metallic copper
powder, traces of malachite and quartz.
Their treatment for recovery of copper showed that in 2M
sulfuric acid environment, at a temperature of 60°C and preceded by an
oxidizing roasting of 3H, a copper dissolution rate of 75,3%. The leaching
residue, which represents 44,7% of the initial solid, is found with 27,6% Cu
and 11,62% Pb.
This work did not take into account the influence of the
structure and the characteristics of the granular porous environment formed by
the anodic sludge, the size and shape of the grains, the porosity and the
specific surface, concerning solid-gas reactions during oxidative roasting.
This would make it possible to determine the best operating conditions for the
oxidative roasting. This prospect remains open to other researchers wishing to
continue this work.
gtambwe934@gmail.com
Page | II
EPIGRAPHE
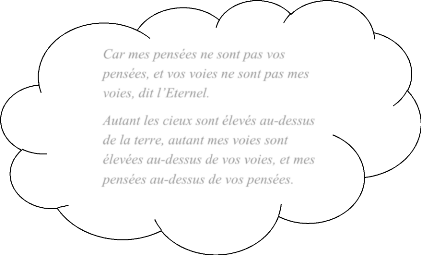
Car mes pensées ne sont pas vos pensées, et vos
voies ne sont pas mes voies, dit l'Eternel.
Autant les cieux sont élevés au-dessus de la
terre, autant mes voies sont élevées au-dessus de vos voies, et
mes pensées au-dessus de vos pensées.


Esaïe 55 : 8-9
Page | III
gtambwe934@gmail.com
Page | I
TABLE DES MATIERES
RESUME
ABSTRACT II
EPIGRAPHE III
TABLE DES MATIERES I
LISTE DES TABLEAUX III
LISTE DES FIGURES IV
LISTE DES ABREVIATIONS V
DEDICACE VI
AVANT-PROPOS VII
INTRODUCTION GENERALE 1
PARTIE BIBLIOGRAPHIQUE 3
CHAPITRE I GENERALITES 4
I.1 Introduction 4
I.2 Minerais de cuivre 4
I.1.1 Les minerais sulfurés 4
I.1.2 Les minerais oxydés et mixtes 4
I.3 Métallurgie du cuivre 5
I.3.1 Pyrométallurgie du cuivre 5
I.3.2 Hydrométallurgie du cuivre 8
I.4 Electroaffinage du cuivre 10
CHAPITRE II TRAITEMENT DES BOUES ANODIQUES 13
II.1 Introduction 13
II.2 Traitements classiques des boues anodiques 13
II.2.1 Grillage oxydant (Schloen et Elkin 1950, et 1954) 13
II.2.2 Grillage sulfatant (sulfatation) (Schloen et Elkin 1950,
1954; Pascal 1961; Hyvarinen et al,
1984; Bayraktar et Garner, 1985; Hoffmann, 1989) 13
II.2.3 Fusion alcaline (Schloen et Elkin, 1954; Pascal, 1961)
14
II.2.4 Grillage carbonaté (Schloen et Elkin 1954; Pascal
l961; Hoffmann 1989) 15
II.2.5 Electrolyse 16
II.3 Traitement des boues anodiques à la raffinerie
« Electrolytic Refining and Smelting Co.,
Australia (Schloen et Elkin 1954) » 16
PARTIE EXPERIMENTALE 18
CHAPITRE III MATERIEL ET PROCEDURE EXPERIMENTALE
19
III.1 Echantillonnage 19
Page | II
III.2 Caractérisation des boues anodiques des US 19
III.2.1 Caractérisation chimique 20
III.2.2 Caractérisation minéralogique 20
III.3 Tests de lixiviation 21
III.3.1 Grillage oxydant 21
III.3.2 Tests de lixiviation 22
CHAPITRE IV PRESENTATION ET ANALYSE DES RESULTATS
25
IV.1 Résultats de caractérisation chimique 25
IV.2 Résultats de caractérisation
minéralogique 26
IV.3 Résultats des tests de lixiviation 26
IV.3.1 Lixiviation des boues anodiques non grillées 26
IV.3.2 Lixiviation des boues anodiques grillées pendant 1H
29
IV.3.3 Lixiviation des boues anodiques grillées pendant 2H
et 3H 33
IV.3.4 Conclusion 37
CONCLUSION 38
REFERENCES 39
Page | III
LISTE DES TABLEAUX
Tableau 1 Teneurs moyennes des éléments dans les
cathodes commerciales des US 12
Tableau 2 Teneurs moyennes des éléments dans les
boues anodiques des US 25
Tableau 3 Résultats des tests de lixiviation des boues
anodiques non grillées en fonction du
temps 27
Tableau 4 Résultats des tests de
lixiviation des boues anodiques non grillées en fonction de la
concentration 28
Tableau 5 Dissolution du Cu et Pb contenus
dans les boues anodiques non grillées (H2SO4
1M; S/L 1/12; T° 60°C; Conditionnement 1H)
29
Tableau 6 Résultats des tests de lixiviation des boues anodiques
grillées durant 1H en fonction
du temps 30
Tableau 7 Résultats des tests de
lixiviation des boues anodiques grillées durant 1H en fonction
de la concentration 31
Tableau 8 Dissolution du Cu et Pb
contenus dans les boues anodiques grillées durant 1H
(H2SO4 1M; S/L 1/12; T° 60°C; Conditionnement 1H)
33
Tableau 9 Résultats des tests de lixiviation des boues anodiques
grillées durant 2H en fonction
de la concentration 33
Tableau 10 Résultats des
tests de lixiviation des boues anodiques grillées durant 3H en
fonction de la concentration 35
Tableau 11 Dissolution du
Cu et Pb contenus dans les boues anodiques grillées durant 3H
(H2SO4 2M; S/L 1/12; T° 60°C; Conditionnement 2H)
36
Page | IV
LISTE DES FIGURES
Figure 1 Les grandes voies de la métallurgie du cuivre
(Thiriart et al., 1988) 8
Figure 2 Microscope binoculaire stéréoscopique WILD
(Guy Munung) 21
Figure 3 Four à grillage (Guy Munung) 22
Figure 4 Dispositif pour la lixiviation (Guy Munung) 23
Figure 5 Filtrat obtenu au test de lixiviation aux conditions
opératoires : H2SO4 2M; S/L
1/12; Conditionnement 2H; T° 60°C; grillage oxydant 3H
(Guy Munung) 24
Figure 6 Evolution du taux de dissolution du Cu et Pb en
fonction du temps lors de la
lixiviation des boues anodiques non grillées. 27
Figure
7 Evolution du taux de dissolution du Cu et Pb en fonction de la concentration
lors de
la lixiviation des boues anodiques non grillées.
28
Figure 8 Evolution du taux de dissolution du Cu et Pb en fonction du
temps lors de la
lixiviation des boues anodiques grillées durant 1H.
30
Figure 9 Evolution du taux de dissolution du Cu et Pb en fonction de la
concentration lors de
la lixiviation des boues anodiques grillées durant 1H.
32
Figure 10 Evolution du taux de dissolution du Cu et Pb en fonction de la
concentration lors de
la lixiviation des boues anodiques grillées durant 2H.
34
Figure 11 Evolution du taux de dissolution du Cu et Pb en fonction de la
concentration lors de
la lixiviation des boues anodiques grillées durant 3H.
35
Figure 12 Résidu solide au test de lixiviation des boues
anodiques grillées durant 2H 36
Page | V
LISTE DES ABREVIATIONS
EMT : Etudes Métallurgiques
LIX/SX/EW : Lixiviation/Extraction par solvant/Electroextraction
SAA : Spectrométrie d'absorption atomique
US : Usines de Shituru
Page | VI
DEDICACE
A mes parents Gustave MUNUNG et Françoise KAMIN pour leur
confiance et leur amour ;
à mes frères : Patrick NTAMBWE,
Jérémie KABWIT, John KANYIMB, Tony MUTOMB, Guerschom MUNUNG, Ryan
NGWEJ pour leur amour et leur présence durant la réalisation de
ce travail ;
à mes soeurs : Noëlla KARUMB, Raïssa KAT, Nicia
KAVUND, Consola MUSENG pour leur
amour ;
à mes oncles et tantes, cousins et cousines, amis et amies
pour votre contribution à mon savoir et mon parcours ;
à tous ceux à qui je tiens et qui tiennent à
moi.
Je dédie ce travail !
GUY MUNUNG
Page | VII
AVANT-PROPOS
Au terme du premier cycle de notre parcours universitaire au
sein de la Faculté Polytechnique à l'Université de
Lubumbashi, un projet individuel doit être présenté et
défendu pour sanctionner la fin de ce long moment d'apprentissage. C'est
dans ce cadre que s'inscrit ce travail, ayant pour objet d'étudier la
possibilité de récupération du cuivre par lixiviation en
milieu acide sulfurique des boues anodiques des US.
Ce travail est le résultat d'une contribution de
plusieurs personnes que nous ne pouvons tous énumérer.
Je remercie premièrement l'Eternel au nom du Seigneur
Jésus-Christ, Lui qui a pourvu pour que nous arrivions à la fin
de ce travail. Son ouvrage est allé au-delà de mes
espérances.
J'exprime ma profonde gratitude et mes vifs remerciements au
Professeur ILUNGA NDALA qui, malgré ses innombrables occupations, a
accepté de diriger ce travail.
Je tiens à remercier sincèrement tous les
ingénieurs et responsables de la Gécamines/EMT,
particulièrement Monsieur Fidèle KABWE pour m'avoir
encadré durant la réalisation de ce travail.
Je remercie également le Professeur Jean-Marie KANDA,
Doyen de la Faculté, les professeurs Arthur KANIKI et Idriss KYONI,
vice-doyens pour la bonne gestion de notre faculté ainsi que tout le
corps professoral.
Je remercie du fond du coeur Monsieur Remy MAKONGA ainsi que
Monsieur Aimé KABONDE pour tous les efforts consentis.
Je suis très reconnaissant envers la famille MUKAZ, qui
a été pour moi comme une deuxième famille où j'ai
appris beaucoup de choses.
Je remercie mes amis et frères d'armes Emma MAKONGA,
Emile MAYOLA, Trobuch KASONGO et Serge KABULO pour leur présence et leur
amour. Sans eux non plus, nous n'y serons pas arrivés.
A tous mes amis : Steven NDALA, Gloire DJESE, Miriam ILUNGA,
Rapha ABEDI... pour vos encouragements et soutiens dans les moments difficiles,
je vous remercie.
Anticipativement, je remercie tous ceux qui porteront une
attention particulière à ce travail par leur lecture.
Page | 1
INTRODUCTION GENERALE
La métallurgie du cuivre génère, lors de
l'électroaffinage, des boues contenant une grande variété
d'éléments chimiques, Cu, Se, Te, As, Au, Ag et platinoïdes,
.... , dont les teneurs et les phases minérales qu'ils constituent
dépendent de la qualité des concentrés de cuivre
traité, de la composition chimique des anodes et des conditions
opératoires de l'électroaffinage. (K. Elamari, 1993)
Les boues anodiques provenant de l'électroaffinage sont
alors traitées en vue de récupérer les
éléments de valeur tels que Cu, Se, Te et les métaux
précieux. Les techniques utilisées pour traiter ces boues sont
pour la plupart des techniques pyrométallurgiques consistant
généralement en :
· Une sulfatation ou grillage en présence de l'acide
sulfurique,
· Un grillage carbonaté en présence de
Na2CO3,
· Une fusion alcaline en présence de NaOH
et de la silice.
Cependant, malgré l'efficacité de ces
techniques, elles présentent certains inconvénients, notamment
les effluents gazeux dans l'atmosphère contiennent du dioxyde de soufre
et d'autres impuretés.
Vers la fin du 20e siècle, certaines
recherches ont été axées sur le traitement par voie
hydrométallurgique qui s'avère être moins polluante et plus
économique, dont le but est l'élimination du cuivre, de l'arsenic
et du nickel, et celle du sélénium, du tellure et de
l'antimoine.
Parmi ces méthodes, on peut citer :
· L'oxydation sous pression d'oxygène en
présence d'acide sulfurique, pour la récupération du
cuivre et du nickel, (Jennings et al, (1968), Naboichenko et Gritchina,
(1981)), ou en présence de soude, pour extraire Se et Te, (Hoffmann,
1989),
· La lixiviation par l'acide nitrique en présence
de NaCI, (Sumiko Sanuki et al., 1989).
· La lixiviation par l'acide sulfurique en présence
d'un courant d'air, à 80-90°C, pour éliminer le cuivre, et
la lixiviation par NaOH pour éliminer le sélénium et le
tellure, (Yildrium, 1985),
Page | 2
? La lixiviation en milieu sulfurique à pression
atmosphérique et sous une pression d'oxygène, pour la
récupération du cuivre, de l'arsenic, du sélénium,
du tellure et de l'antimoine, (K. Elamari, 1993).
Les Usines de Shituru (US) produisent des quantités
importantes des boues anodiques lors de la préparation des feuilles
amorces pour l'électrolyse commerciale. Ces boues sont principalement
riches en Cu. Ils contiennent le Pb ainsi que d'autres variétés
d'éléments Co, Ni, Au, Ag, ...en teneurs très faibles.
Contrairement aux boues anodiques produites
généralement après solubilisation du cuivre blister, les
anodes solubles utilisées aux US sont des cathodes commerciales de
cuivre (99,98 %) produites toujours aux US.
La Gécamines ne disposant pas des unités de
traitement approprié, vend ces boues à des sociétés
étrangères. Leur valeur marchande dépend des teneurs des
éléments recherchés notamment le cuivre.
Ce travail a été réalisé aux
Etudes Métallurgiques (EMT), un département de la
Gécamines. Il comprend deux parties principales, outre l'introduction
générale et la conclusion :
? Une analyse bibliographique (chapitre I et II), visant à
donner une idée sur l'origine des boues anodiques et leur relation avec
les minerais et la métallurgie du cuivre. La fin de cette partie est
consacrée à une revue des procédés de traitement
des boues anodiques ;
? Une présentation du matériel et de la
procédure expérimentale (chapitre III), puis la
présentation et l'analyse des résultats (chapitre IV)
Page | 3
PARTIE BIBLIOGRAPHIQUE
Page | 4
CHAPITRE I GENERALITES
I.1 Introduction
Le raffinage du cuivre implique une génération
d'importantes quantités des boues anodiques. L'intérêt
économique que présentent ces boues réside en leur
richesse en métaux valorisables. Ces métaux (Cu, Ag, Au...) sont
plus concentrés dans ces résidus que dans le minerai
d'origine.
Afin de mieux connaître l'origine, la composition, la
production, etc, des boues anodiques, il est nécessaire de suivre le
cheminement de leurs constituants depuis le minerai de départ jusqu'au
produit fini. Les méthodes métallurgiques sont différentes
selon le type de minerai de cuivre (oxydé, sulfuré, ou mixte), et
selon la teneur en cuivre dans le minerai. Les minerais sulfurés sont
ainsi traités par voie pyrométallurgique, les minerais
oxydés ou pauvres en cuivre sont, par contre, traités par voie
hydrométallurgique. (K. Elamari, 1993)
I.2 Minerais de cuivre
La minéralogie des espèces cuprifères est
très variable et dépend de leur genèse et des associations
minérales. Les minerais peuvent toutefois être classés en
deux groupes : les minerais sulfurés et les minerais oxydés et
mixtes. (K. Elamari, 1993)
I.1.1 Les minerais sulfurés
Les minerais sulfurés constituent la principale source
économique de cuivre. Les minéraux les plus importants sont : la
chalcopyrite (CuFeS2), la bornite
(Cu5FeS4), la chalcosine (Cu2S), la covelline
(CuS). Il existe également des minéraux complexes de
cuivre et de fer associés à l'arsenic et l'antimoine, tels que la
tétraédrite (3Cu2S. Sb2S3) et l'énargite
(Cu3AsS4). Dans certains minerais on peut constater la présence
de molybdène, d'or, d'argent et de platinoïdes.
I.1.2 Les minerais oxydés et mixtes
Les minerais oxydés et mixtes se forment dans les zones
superficielles des gîtes par altération des minerais
sulfurés. Les principaux minéraux de ce groupe sont : la
malachite (CuCO3. Cu(OH)2), l'azurite
(2CuCO3. Cu(OH)2), la cuprite
(Cu2O), la ténorite (CuO), la chrysocolle
(CuO. SiO2. 2H2O).
Page | 5
I.3 Métallurgie du cuivre
Ce paragraphe concerne uniquement le traitement des
concentrés de cuivre et ne traite pas des techniques
minéralurgiques utilisées pour les obtenir.
L'obtention du cuivre relativement pur à partir des
concentrés peut être réalisée par deux voies
classiques : la pyrométallurgie et l'hydrométallurgie.
I.3.1 Pyrométallurgie du cuivre
La voie thermique classique a pour but d'extraire le cuivre
contenu dans les concentrés issus des opérations
minéralurgiques. Elle comprend plusieurs étapes qui conduisent
à l'obtention d'un cuivre non raffiné. (P. Blazy et El., 2001)
La première étape consiste à
opérer par grillage une désulfuration, partielle ou totale, ou
une production de sulfate de cuivre ou encore une élimination des
éléments indésirables.
La deuxième étape consiste à fondre dans
un four tous les composants de la charge à une température
suffisante pour atteindre l'état liquide. Il se dégage suivant le
procédé mis en oeuvre des gaz de combustion et des gaz de
réaction qui doivent être traités. Le type de fusion
opéré avec les minerais de cuivre est une fusion pour matte,
mélange de sulfures fondus, qui a pour but de rassembler le cuivre et
tous les éléments chalcophiles (Ni, Co, Pb, Zn, métaux
précieux, As, Sb, Se, Bi, Te...), en rejetant le fer et les
éléments de gangue sous forme d'une scorie et en abaissant la
teneur en soufre initiale par oxydation partielle en SO2.
La troisième étape consiste à convertir
la matte en cuivre métal, ou blister, par oxydation du soufre restant
par de l'air atmosphérique ou enrichi à l'oxygène. Le
soufre est oxydé en SO2, qui est
entraîné hors du convertisseur, et les métaux plus
oxydables que le cuivre passent dans la scorie. Le blister ainsi obtenu titre
98 à 99,5 % de cuivre, et contient un peu d'oxygène et les
éléments chalcophiles signalés précédemment.
Il est coulé dans un four à anodes sous forme de plaques d'anodes
ou de lingots devant être ensuite raffinés.
I.1.3.1 Grillage oxydant
Le grillage oxydant s'effectue à une température
de 500-550°C, afin d'éviter la formation de ferrites de cuivre dont
le point de fusion est très élevé. Il permet d'ajuster la
teneur en
Page | 6
cuivre du concentré, en oxydant partiellement le soufre
et le fer, et en éliminant certaines impuretés volatiles
notamment le dioxyde de soufre. Les principales réactions mises en jeu
lors du grillage oxydant, décrivant l'oxydation du cuivre et des
sulfures de fer en sulfates et oxydes, sont (Biswas et al. 1976) :
CuFeS2 + 4O2(9) = CuSO4 +
FeSO4 (1)
2CuFeS2 + 132 O2(9) = 2CuO
+ Fe2O3 + 4 SO2(9) (2)
2CuS + 7
2
|
O2(9) = CuO. CuSO4 + SO2(9) (3)
|
I.1.3.2 Fusion pour matte
La fusion pour matte s'effectue sur le produit grillé,
au-delà de 1100-1200°C. Elle permet de séparer deux phases
:
- une scorie constituée d'éléments de la
gangue ainsi que des oxydes. Elle se compose de 30-40% FeO +
Fe3O4, 35-40% SiO2, 10%
Al2O3, 10% CaO (Biswas et al. 1976),
- une matte contenant le cuivre combiné au soufre
résiduel sous forme de Cu2S, les sulfures de nickel, de cobalt,
de plomb et de zinc, les métaux précieux (or, argent,
platinoïdes), et enfin des impuretés telles que l'arsenic, le
bismuth, le sélénium, le tellure et l'antimoine.
Le premier objectif de la fusion pour matte est d'augmenter le
degré de sulfuration de tout le cuivre présent dans la charge qui
passe ensuite dans la matte et d'éliminer partiellement le fer. Ceci est
accéléré par la présence de FeS dans la
matte et qui tend à sulfurer tout le cuivre qui ne se trouve pas sous
forme de sulfure, suivant la réaction 4 (Biswas et al. 1976)
FeS(I) + Cu2O(I+scorie) = FeO(I+scorie)
+ Cu2S(I) (4)
Malheureusement, la fusion pour matte donne des gaz trop
dilués en SO2 (2%) pour permettre une production aisée
d'acide sulfurique. C'est la raison pour laquelle le procédé
Noranda opère une fusion pour matte avec injection d'air. Il permet
ainsi d'obtenir des gaz à 5% en volume de SO2.
Page | 7
I.1.3.3 Conversion
La conversion ou convertissage de la matte qui consiste en une
oxydation par insufflation d'air à 1150-1250°C, permet
d'éliminer le soufre et le fer restants, et d'assurer l'obtention du
cuivre métal non raffiné (cuivre blister, 99,8% Cu)
réactions 5, 6 et 7 (Blazy, 1979).
3FeS + 502 = Fe304 +
3S02 (5)
Cu2S + 2 02 = Cu20
+ S02 (6)
Cu20 + Cu2S = 6Cu + S02
(7)
Le fer est traditionnellement complexé par ajout de
Si02 lors de l'étape d'oxydation. La quantité de
Fei04 est soigneusement controlée pour éviter
d'avoir des scories trop visqueuses. Cette étape est le point sensible
du convertissage, ce qui explique que l'oxyde de cuivre n'est souvent pas
réduit.
Remarque : La métallurgie classique ayant
été la cible des lois antipollution, il existe des
procédés de fusion éclair (procédé
Outokumpu) combinant le grillage, la fusion pour matte et en partie le
convertissage en une seule opération. L'air peut être enrichi
à l'oxygène. Les gaz obtenus sont riches en
S02 (5-10% en volume).
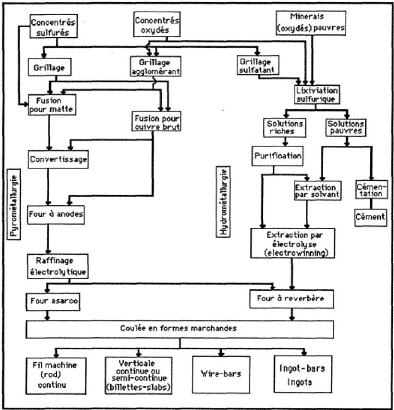
Page | 8
Figure 1 Les grandes voies de la métallurgie du cuivre
(Thiriart et al., 1988) I.3.2 Hydrométallurgie du cuivre
L'hydrométallurgie du cuivre consiste en une succession
d'opérations chimiques caractérisées par la mise en
solution du cuivre et son élaboration à partir de cette
solution.
Le procédé LIX/SX/EW est le plus utilisé et
les étapes essentielles de ce procédé sont
séparées par des opérations de séparation
solide/liquide
I.3.2.1 Lixiviation
La lixiviation est une opération qui consiste en une
mise solution sélective des minéraux valorisables contenus dans
un minerai à l'aide solvant approprié, notamment les
minéraux de cuivre mis en solution par l'acide sulfurique pour le cas
ci-présent.
Page | 9
Elle est l'opération la plus importante de
l'hydrométallurgie du cuivre. (N. Mukota, 2019)
Il existe plusieurs techniques de lixiviation dont celle qui
nous intéresse est la lixiviation en réacteur agité. Le
solide sous forme pulvérulente est mis en suspension dans la solution de
lixiviation.
Pour obtenir une liqueur claire après lixiviation, une
séparation solide/liquide est appliquée et c'est cette liqueur
qui sera soumise à l'extraction par solvant. (N. Mukota, 2019)
I.3.2.2 Extraction par solvant
Le terme « extraction par solvant » se rapporte
à la distribution d'un corps dissous entre deux phases liquides
non-miscibles en contact mutuel, c'est- à- dire une distribution
biphasée d'un corps dissous. L'extraction par solvant permet donc de
réaliser le transfert d'un soluté initialement contenu dans une
phase liquide, vers une autre phase non-miscible avec la première. Le
principe est fondé sur la distribution du soluté entre les deux
phases en fonction de son affinité pour chacune d'elles. (Rydberg,
2004)
La méthode est basée sur l'utilisation d'un
extractant dilué dans un solvant organique mis en solution avec la phase
aqueuse qui contient le métal à extraire, qui est le cuivre.
Lors de la lixiviation d'un minerai de cuivre par l'acide
sulfurique, le cuivre est mis en solution. La solution contient entre autres
les ions Cu2+ et
S042- : c'est la phase aqueuse. Elle sera
mise en contact avec une phase organique du type RH
et le cuivre va se complexer avec le radical R
selon l'équation ci-après :
Cu2+ +
S042- + RH
= R2Cu +
2H+ +
S042- (8)
Où RH est la molécule de
l'extractant dissoute dans la phase organique ; R2Cu
est le complexe métal/extractant dissout dans la phase
organique. Les deux phases sont ensuite séparées par
décantation.
Le métal est ensuite réextrait dans une nouvelle
phase aqueuse sous une forme raffinée et concentrée. Cette
deuxième opération est nommée stripage. L'extraction et le
stripage utilisent la même réaction chimique dont
l'équilibre est contrôlé principalement par le pH du
milieu. L'extraction est réalisée à pH un plus
élevé qu'au stripage. (M. Koji, 2010)
Les extractants les plus utilisés pour l'extraction du
cuivre sont pour la plupart des agents chélatants, notamment les oximes
dont les aldoximes et les cetoximes. (Cognis, 2009)
Page | 10
Les solvants les plus couramment employés sont
généralement les hydrocarbures aliphatiques aromatiques et les
solvants chlorés. (Ghebgoub, 2012)
L'extraction par solvant est utilisée en
hydrométallurgie pour la purification et/ou la concentration des
solutions. Combinée à l'électrolyse d'extraction, elle est
largement utilisée pour la production du cuivre cathodique de haute
pureté.
I.3.2.3 Electroextraction
L'électroextraction ou l'électrolyse
d'extraction du cuivre permet d'élaborer le cuivre de haute
pureté par décomposition de CuSO4 par passage du courant
continu dans le bain de telle sorte les anions SO42- se
dirigent vers l'électrode positive appelée anode tandis que les
cations Cu2+ vont vers l'électrode négative
appelée cathode.
A Shituru, les anodes sont constituées de plaques en
plomb antimonieux : elles sont donc insolubles. De sorte que dans ce cas, le
cuivre déposé provient de la solution de sulfate de cuivre
alimentée, et non d'une anode de cuivre brut, comme c'est le cas dans
l'opération du raffinage électrolytique. (E. Roger, 1946)
Les plaques de cathodes sur lesquelles se fait le
dépôt de cuivre sont de minces feuilles appelées feuilles
de départ ou feuilles mères.
Des bonnes feuilles mères ont été
couramment obtenues en employant, au lieu d'anodes coulées, les grosses
cathodes retirées des cuves de production commerciale. (E. Roger,
1946)
Aujourd'hui encore les feuilles mères sont produites de
cette même façon aux US.
L'avantage majeur de l'électroextraction est que le
cuivre est libéré sous forme métallique à la
cathode, tandis que les ions SO42- provenant de la
dissociation du sulfate de cuivre régénèrent à
l'anode une quantité d'acide équivalente.
I.4 Electroaffinage du cuivre
C'est le procédé de base de production du cuivre
raffiné. Il consiste à dissoudre électrochimiquement le
« blister » coulé sous forme d'anodes, par le
procédé d'anode soluble. Le cuivre se dépose sur les
cathodes alors que la plupart des impuretés Zn, Fe, Ni, Co, Sn, Pb
restent dans le bain sans se déposer. Au, Ag et Pt, insolubles dans
l'électrolyte CuSO4, s'accumulent dans les boues
appelées boues anodiques.
Page | 11
Kitamura et al., (1976), Palacios et al. (1976), Blazy (1979);
Fouletier (1980) et Chen et Dutrizac (1987) donnent des valeurs,
légèrement différentes les unes des autres, concernant les
caractéristiques de chaque paramètre agissant sur
l'électroaffinage du cuivre, (composition de l'électrolyte,
conditions opératoires, densité de courant, etc.). Ces variations
s'expliquent par les différences entre les raffineries
considérées. Toutefois, d'une manière
générale, le cuivre blister est fondu puis coulé dans des
moules pour former des anodes solubles, sous forme de plaques d'environ 13
à 50 mm d'épaisseur, 1m2 de surface et pesant 300 à 350
kg. (K. Elamari, 1993)
Les cathodes utilisées pour le dépôt du
cuivre, appelées feuilles de départ, sont préparées
dans un circuit annexe. Ce sont des feuilles de titane ou de cuivre, d'environ
1 m2 de surface et 0,6 mm d'épaisseur. (K. Elamari, 1993)
L'électrolyte CuSO4 maintenu
à une température de 50 à 60°C contient environ 40
g/1 de cuivre et 100 à 200 g/1 d'acide sulfurique. L'ajout de certains
additifs dans l'électrolyte est nécessaire pour produire un
dépôt à la cathode relativement lisse et
régulièrement épais. Parmi ces additifs, certaines
raffineries ajoutent HCI ou NaCI pour maintenir la
concentration d'ions chlorure, entre 0,02 et 0,035 g/1. Le rôle des ions
chlorures dans l'électrolyte permettent la précipitation de
l'argent en solution. D'autres additifs tels que la colle animale (animal
glue), qui est une protéine complexe, permet d'inhiber le
dépôt nodulaire et dendritique du cuivre. Chaque raffinerie
détermine par l'expérience la quantité optimale de glue.
Habituellement, on utilise 45 g de glue par tonne de cuivre
déposé, (Bertocci et Turner, 1974).
La consommation des anodes dure 21 à 28 jours, alors
que les cathodes atteignent leur masse normale deux fois durant cette
période. La dissolution des anodes est interrompue avant que celles-ci
ne soient complètement consommées pour ne pas affecter la
qualité de la cathode. A Inco's Copper Cliff Copper Refinery par
exemple, (Chen et Dutrizac 1987), l'électrolyse est stoppée quand
le taux de dissolution des anodes atteint 80%. En effet, si l'on poursuivait
l'électrolyse au-delà, Sb, Bi, etc ... viendraient polluer les
cathodes. (K. Elamari, 1993)
L'électroaffinage aboutit alors à des cathodes
de cuivre très pures (99,99% Cu) ; à un électrolyte
contenant certains éléments en solution tels que Ni, Sb, As, et
à des boues anodiques de cuivre composées
d'éléments aux potentiels normaux supérieurs à
celui du cuivre, donc théoriquement non réduits au niveau de la
cathode.
Aux US, ce sont les cathodes commerciales qui sont
utilisées comme anodes solubles. La solubilisation des anodes dure 40
jours avec un taux de dissolution de 80%.
L'électroraffinage a pour rôle la fabrication des
feuilles de départ.
D'après un rapport de la Gécamines intitulé
« Qualité cathodes commerciales mois de Janvier-Février-Mars
2021 », les analyses effectuées sur 82 cathodes ont donné
les teneurs moyennes des éléments ci-après.
Tableau 1 Teneurs moyennes des éléments dans
les cathodes commerciales des US
|
|
Co
|
Fe
|
Ni
|
Zn
|
Se
|
S
|
Mn
|
Ag
|
As
|
Sn
|
Sb
|
Pb
|
ELEMENTS
|
Cu %
|
ppm
|
ppm
|
ppm
|
ppm
|
ppm
|
ppm
|
ppm
|
ppm
|
ppm
|
ppm
|
ppm
|
ppm
|
TENEURS
|
99.98
|
|
|
0.25
|
<0.3
|
<0.40
|
21.1
|
<0.10
|
0.90
|
<0.3
|
<0.60
|
|
97.9
|
|
|
2.21
|
7.81
|
|
|
|
|
|
|
|
|
7.88
|
|
MOYENNES
|
4
|
|
|
1
|
00
|
0
|
9
|
00
|
8
|
00
|
0
|
|
9
|
Page | 12
Page | 13
CHAPITRE II TRAITEMENT DES BOUES ANODIQUES
II.1 Introduction
Les études réalisées sur le traitement
des boues anodiques de cuivre évoquent surtout leur intérêt
économique. Hormis la récupération du cuivre constituant
l'élément majeur, les métaux précieux (Ag, Au,
Pt...) en teneurs assez importantes sont aussi
récupérés.
Les méthodes classiques de traitement des boues
anodiques, appliquées à l'échelle industrielle, sont pour
leur majorité des méthodes pyrométallurgiques.
II.2 Traitements classiques des boues anodiques
Les procédés de traitement des boues anodiques
de cuivre se basent essentiellement sur trois techniques principales : le
grillage, la fusion et l'électrolyse. Ces étapes se
succèdent, dans cet ordre dans la majorité des
procédés, afin d'éliminer sélectivement le cuivre,
ensuite le sélénium et le tellure et enfin les métaux
précieux à partir du produit final enrichi, appelé
communément Bullion ou métal doré. (K. Elamari, 1993)
II.2.1 Grillage oxydant (Schloen et Elkin 1950, et 1954)
Le grillage oxydant consiste à oxyder principalement le
cuivre afin de l'éliminer. Il est réalisé à des
températures qui varient entre 250° et 425°C sous un courant
d'air. Dans une seconde étape, le produit de grillage est traité
par l'acide sulfurique, puis la solution obtenue subit l'électrolyse
pour récupérer le cuivre.
II.2.2 Grillage sulfatant (sulfatation) (Schloen et Elkin
1950, 1954; Pascal 1961; Hyvarinen et al, 1984; Bayraktar et Garner, 1985;
Hoffmann, 1989)
Le grillage sulfatant regroupe les deux étapes du
grillage oxydant. L'acide sulfurique concentré, mélangé
aux boues anodiques dans le four, agit à la fois en tant qu'oxydant et
sulfatant du cuivre et du nickel selon les réactions suivantes :
????(??) + 2 H2SO4(t) = ????SO4(t) +
2 H2O(t) + SO2(??) (9)
????O(??) + H2SO4(t) = ????SO4(t) +
H2O(t) (10)
Le sélénium, le tellure et l'argent peuvent
également réagir avec l'acide sulfurique selon les
réactions :
Page | 14
S??(s) + 2 H2SO4(????) = S??O2(??) +
2 SO2(??) + 2 H2O(??)
|
(11)
|
????2S??(s) + 4 H2SO4(????) = ????2SO4(s)
+ S??O2(??) + 4 H2O(??) + 2 SO2(??)
|
(12)
|
Cu2????(s) + 6 H2SO4(????) = 2
CuSO4(s) + ????O2(s) + 4 SO2(??) + 4
SO2(??)
|
(13)
|
|
Le grillage à haute température permet donc la
volatilisation du sélénium sous forme de
S??O2. Cette température ne doit pas dépasser
650°C afin d'éviter la décomposition du sulfate de cuivre.
Le produit de grillage est ensuite lavé à l'eau pour
éliminer les sulfates de cuivre et de nickel et une partie de Se, Te et
Ag. L'argent peut être cémenté sélectivement sur le
cuivre ; le sélénium et le tellure ont une cinétique de
cémentation très lente et nécessitent un milieu
très acide pour être précipités. Le
sélénium métal est obtenu à partir de l'anhydride
séléneux par oxydation par le dioxyde de soufre gazeux. Cette
oxydation permet également de régénérer l'acide
sulfurique :
S??O2(??) + 2 SO2(??) + 2 H2O =
S??(s) + 2 H2SO4(????) (14)
Le tellure est ensuite récupéré à
partir du résidu d'oxydation soit :
- par fusion du résidu en présence de soude ou
de carbonate de sodium mélangé ou non au nitrate de sodium. Ceci
conduit à la formation d'une solution de tellurite de sodium qui est
ensuite neutralisée avec l'acide sulfurique dilué, à pH=6
pour précipiter l'anhydride tellureux:
????2????O3(????) + H2SO4(????) = ????O2(s)
+ H2O + ????2SO4(????) (15)
- ou par lixiviation avec HCI. Cette opération
posera toutefois des problèmes à l'aval du procédé
de traitement car, d'une part HCI convertit l'argent en chlorure
très peu soluble et difficile à récupérer. D'autre
part, si le tellure hexavalent est présent, il peut oxyder HCI,
et le chlore libéré solubilise l'or. La séparation de l'or
et du tellure devient alors difficile.
II.2.3 Fusion alcaline (Schloen et Elkin, 1954; Pascal, 1961)
Les boues décuivrées sont fondues en
présence d'un mélange de soude et de silice. Les premières
scories sont principalement silicatées, et contiennent des
impuretés comme le fer, l'arsenic et l'antimoine. La masse fondue est
ensuite oxydée par un courant d'air pour
Page | 15
volatiliser Se et Te sous forme d'anhydrides
séléneux et tellureux. Le sélénium et le tellure
restants dans les scories résiduelles se trouvent sous forme de
sélénite et de tellurite de sodium, solubles dans l'eau. Ils sont
alors lessivés par l'eau, filtrés, puis la solution est
neutralisée par l'acide sulfurique à pH 6,2 pour
précipiter l'acide tellureux, (réaction 16). Le filtrat est
soumis à un courant de S02 pour précipiter le
sélénium (réaction 17).
????2????O3(????) + H2??O4(????) =
H2????O2(??) + H2O + ????2??O4(????)
(16)
????2????O3(????) + ??O2(??) = ????O(??)
????2??O4(????) (17)
II.2.4 Grillage carbonaté (Schloen et Elkin 1954; Pascal
l961; Hoffmann 1989)
Le grillage carbonaté est utilisé quand la
teneur en tellure dans les boues n'est pas trop élevée. Il a lieu
à des températures de 530 à 650°C, et consiste en une
conversion du sélénium et du tellure en leurs formes hexavalentes
non volatiles selon les réactions suivantes :
??????(??)
|
+ ????2CO3
|
+ 2O2(??)
|
= ??O + ????2????O4(??)
|
+ CO2(??)
|
(18)
|
??????(??)
|
+ ????2CO3
|
+ 2O2(??)
|
= ??O + ????2????O4(??)
|
+ CO2(??)
|
(19)
|
|
Le produit de grillage est lessivé par l'eau. Le Se
(VI) passe en solution sous forme de sélénate de sodium
(????2????O4). Le tellurate de sodium
(????2????O4), étant insoluble dans
l'eau, reste dans le résidu. La séparation du
sélénate et tellurate de sodium se fait alors par une simple
filtration. Le sélénium est récupéré
à partir de la solution par deux méthodes :
- soit par cristallisation des sélénate et
sélénite de sodium (????2????O3),
qui consiste en une évaporation et un mélange avec du charbon de
bois le réduisant en séléniure de sodium
(????2????) selon les réactions 20 et 21:
????2????O4(??)+ 2 C = ????2????(??) +
2 CO2(??) (20)
????2????O3(??)+ 3 C = ????2????(??) +
Na2Se(s) + 3 CO(??) (21)
Le séléniure de sodium est ensuite
lessivé par l'eau et oxydé par passage d'un courant d'air
à travers la solution, pour précipiter le sélénium
élémentaire et générer la soude :
????2????(??) + H2O + 21 O2(??) =
????(??) + 2 ????OH(????) (22)
- soit par réduction avec HCl de l'acide
sélénique obtenu par conversion du sélénate de
sodium par H2??O4 :
Page | 16
????2S????4(??) +
H2S??4(????) = H2S????4(????)
+ ????2S??4(????) (23)
H2S????4(????) +
2HC??(????) =
H2S????3(????) + H2?? +
C??2(9) (24)
Le sélénium est précipité sous
forme métal à partir de H2S????3
par un courant de gaz sulfureux:
H2S????3(????) + 2 S??2(9)
+ H2?? = S??(??)
+ 2 H2S??4(????) (25)
II.2.5 Electrolyse
L'électrolyse est utilisée, pour
récupérer les métaux précieux contenus dans les
boues anodiques de cuivre, dans l'ultime étape de traitement à
partir du bullion. (K. Elamari, 1993)
- La récupération de l'argent se fait
classiquement de la manière suivante : le métal doré est
coulé en anodes puis électrolysé pour le
dépôt d'argent dans des cellules à électrodes
verticales (procédé Moebius, Yanagida et Hosoda 1975), ou
horizontales (procédé Thum-Balbach, Scloen et Elkin 1954). Dans
ces deux procédés l'électrolyte support est l'acide
nitrique.
- L'or est raffiné électrolytiquement par le
procédé Wohlwill (Schloen et Elkin 1954 ; Yanagida et Hosoda
1975) où l'électrolyte support est l'acide chlorhydrique.
II.3 Traitement des boues anodiques à la raffinerie «
Electrolytic Refining and Smelting Co., Australia (Schloen et Elkin 1954)
»
Des boues anodiques d'origines diverses sont traités
dans cette raffinerie. Elles sont soumises à :
? un grillage oxydant pendant un temps plus ou moins long
selon leur composition et appliqué principalement pour éliminer
le cuivre. Il est réalisé à des températures qui
varient entre 250° et 425°C sous un courant d'air. Le cuivre passe
sous forme d'oxyde, le sélénium et le tellure sont
transformés en sélénite et tellurite. Une faible
quantité de sélénium et d'arsenic est
volatilisée.
? une lixiviation du produit de grillage par l'acide
sulfurique pour éliminer le cuivre, puis la solution obtenue est
renvoyée dans le cycle de l'électroaffinage. Les
sélénites et tellurites, insolubles à l'attaque
sulfurique, restent dans le résidu solide.
? une fusion du résidu de lixiviation qui engendre :
Page | 17
- des gaz qui seront traités pour récupérer
leur contenu en Se et Te, - des boues cuprifères qui seront
renvoyées à la fusion,
- et enfin un métal doré qui sera traité par
électrolyse pour la récupération des métaux
précieux.
Page | 18
PARTIE EXPERIMENTALE
Page | 19
CHAPITRE III MATERIEL ET PROCEDURE EXPERIMENTALE
Dans ce chapitre, nous allons présenter la
procédure expérimentale ainsi que le matériel qui nous a
permis de réaliser ce travail.
III.1 Echantillonnage
Les boues anodiques de cuivre qui font l'étude de notre
travail, proviennent de la section Strippage des US. C'est une section
d'électroaffinage pour la fabrication des feuilles amorces qui seront
utilisées comme cathodes à la salle d'électrolyse du
Cu.
Le prélèvement de l'échantillon à
la section Strippage se fait de manière aléatoire.
L'échantillon recueilli a subi un mélange manuel pour
l'homogénéisation après le séchage à
l'étuve à 60°C et la pulvérisation.
L'échantillonnage a été effectué
par la méthode de quartage et cela pour soumettre des
échantillons aux analyses chimique et minéralogique. Les
étapes de la méthode de quartage sont :
? Etaler l'échantillon sur une toile de plastique
? A l'aide d'une spatule, faire un tas de forme
régulière et diviser le tas en quatre
? Enlever les deux quarts opposés
? Combiner les deux quarts restants et répéter
le procédé 3 fois jusqu' à l'obtention d'un
échantillon de volume souhaité.
III.2 Caractérisation des boues anodiques des US
Avant d'entamer les tests de grillage et de lixiviation des
boues anodiques des US, une étude préliminaire a
été effectuée sur les échantillons pour
déterminer leurs caractéristiques chimiques et
minéralogiques. La connaissance de ces informations est
nécessaire pour le choix des conditions de grillage et de lixiviation et
doit permettre d'appréhender les mécanismes réactionnels
de dissolution des éléments métalliques.
Les boues anodiques des US sont des produits granuleux ayant
un taux d'humidité de 19%. L'échantillon prélevé
aux US a été séché à l'étuve à
60°C, puis pulvérisé et enfin
homogénéisé avant la caractérisation et les
essais.
Page | 20
III.2.1 Caractérisation chimique
Les analyses chimiques ont été effectuées
au Laboratoire Central de Panda (LCP) de la Gécamines/US par SAA pour
les éléments Cu, Pb, Co, Ag, Au, Zn, Ni, Fe. Mais les
éléments étudiés sont le cuivre et le plomb.
La spectrométrie d'absorption atomique (SAA) ne peut
être dissociée de l'émission de flamme (EF) appelée
aussi photométrie de flamme. La SAA et l'EF permettent de doser dans
pratiquement toute sorte d'échantillon, un ou plusieurs
éléments prédéfinis (métaux ou non
métaux).
Dans les deux méthodes, les mesures sont
effectuées sur des éléments à l'état
d'atomes libres. Pour ce faire l'échantillon, est porté à
une température de plusieurs milliers de degrés dans une flamme ;
on obtient ainsi un gaz d'atomes libres.
- En absorption atomique, la concentration est déduite
de la mesure de l'absorption de la lumière par les atomes de
l'élément restés à l'état fondamental
lorsqu'ils sont éclairés par une source lumineuse convenable
(lampe a cathode creuse)
- En émission de flamme, au contraire, on mesure
l'intensité des radiations émises par la fraction des atomes
passées à l'état excité par simple effet
thermique
III.2.2 Caractérisation minéralogique
L'analyse minéralogique a été
effectuée au microscope binoculaire stéréoscopique de la
marque Wild à EMT. Avec deux oculaires optiquement indépendants,
cet appareil permet la perception stéréoscopique de
l'échantillon par grossissement des images afin d'identifier les
éléments et minéraux.
L'échantillon a subi un lavage à l'eau avant
l'observation au microscope afin de permettre une bonne perception.
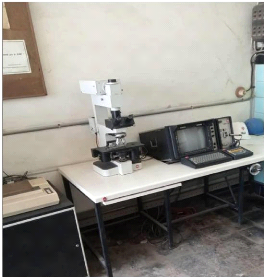
Page | 21
Figure 2 Microscope binoculaire
stéréoscopique WILD (Guy Munung)
III.3 Tests de lixiviation
III.3.1 Grillage oxydant
III.3.1.1 Matériel et procédure
expérimentale
Le grillage oxydant a été étudié
à pression atmosphérique en réacteur ouvert dans un four
électrique à grillage. Les tests ont été
menés sur un échantillon de boues anodiques séchées
l'étuve à 60°C, pulvérisées et
homogénéisées.
L'enceinte est amenée à la température de
travail, puis on y introduit l'échantillon où il se produira la
réaction d'oxydation.
Le paramètre qui a fait l'objet de l'étude est le
temps de grillage.
L'influence de la durée du grillage oxydant sur les boues
anodiques des U.S, a été étudiée dans les
conditions opératoires suivantes : Température = 400°C ;
Pression atmosphérique ; Temps de grillage = 1H ; 2H et 3H.
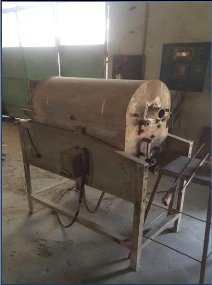
Page | 22
Figure 3 Four à grillage (Guy Munung) III.3.1.2
Mécanisme réactionnel probable (Mansour, 2013).
Le mécanisme réactionnel décrivant le
comportement des boues anodiques lors du grillage oxydant est décrit de
la manière ci-après. L'élément concerné est
surtout le cuivre.
Les réactions chimiques qui ont lieu lors du grillage
oxydant sont :
?? ??(??) +1 4
|
?? 2 =
|
1 2?? ??2??(??)
|
(1)
|
????2??(??)
|
+ 1 2??2
|
= 2??????(??)
|
(2)
|
|
Les réactions (1) et (2) sont données selon
Mansour (2013). Le cuivre n'est jamais en équilibre avec l'oxyde
cuivrique(??????). Ainsi, cette dernière ne se forme que par conversion
de l'oxyde cuivreux (????2??).
III.3.2 Tests de lixiviation
III.3.2.1 Matériel et procédure
expérimentale
Les tests de lixiviation se sont déroulés en
réacteur ouvert à pression atmosphérique, à
température constante de 60°C et avec un rapport solide : liquide
de 1/12. (La masse de l'échantillon pour les tests est de 150g)
Page | 23
L'échantillon, initialement
homogénéisé, est mis en contact avec la solution d'acide
sulfurique sous une agitation suffisamment intense pour mettre tout le solide
en suspension. La température de lixiviation (60°C) est obtenue par
chauffage dans un bain-marie.
Les paramètres qui ont fait l'objet de l'étude
sont : la concentration en acide sulfurique H2????4
(1M, 2M et 3M) et le temps de conditionnement (1H, 2H et 3H) et le
temps du grillage oxydant dans le cas des boues anodiques grillées (1H,
2H et 3H).
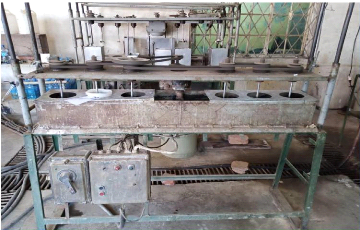
Figure 4 Dispositif pour la lixiviation (Guy
Munung)
La séparation liquide-solide est réalisée
par filtration classique sur papier filtre. L'échantillon initial, final
et le filtrat sont analysés pour déterminer leurs teneurs en Cu,
Pb dans les solides et leurs teneurs en ????2+,
????2+ et H2????4 résiduel pour
l'établissement des bilans matières.
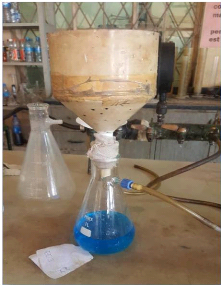
Page | 24
Figure 5 Filtrat obtenu au test de lixiviation aux
conditions opératoires : H2SO4 2M; S/L
1/12; Conditionnement 2H;
T° 60°C; grillage oxydant 3H (Guy Munung)
III.3.2.2 Proposition du mécanisme réactionnel
La caractérisation des échantillons solides avant
et après attaque par l'acide sulfurique et des solutions de lixiviation
permet d'établir les mécanismes probables de dissolution des
phases minérales. L'élément concerné est surtout le
cuivre.
Les réactions chimiques qui peuvent avoir lieu lors de la
lixiviation par l'acide sulfurique sont
:
CuSO4(??) + ??H2O = CuSO4(????) (3)
CuO(??) + H2SO4(????) = CuSO4(????) +
H2O (4) Les réactions (3) et (4) sont données
selon Elamari (1993).
Page | 25
CHAPITRE IV PRESENTATION ET ANALYSE DES RESULTATS
Les tests ont été réalisés pour
récupérer le cuivre des boues anodiques des US par mise en
solution après une caractérisation chimique et une
caractérisation minéralogique de ces boues.
Les paramètres suivis sont : la concentration en acide
sulfurique, le temps de conditionnement de la lixiviation et la durée du
grillage oxydant.
IV.1 Résultats de caractérisation chimique
La composition chimique des boues anodiques des US a
été déterminée par le dosage des
éléments les plus fréquemment rencontrés dans ce
type de produits. Le tableau 2 en présente une composition chimique
moyenne. Il met en évidence la forte teneur en cuivre, ce qui est normal
vu l'origine de l'échantillon, et des teneurs très faibles en
métaux précieux (Au et Ag) toujours dû à l'origine
de l'échantillon. La teneur en plomb est aussi importante alors que le
cobalt, le nickel, le zinc et les autres éléments constituent les
éléments mineurs.
La particularité des boues anodiques des US est que les
anodes solubles ne proviennent pas de la pyrométallurgie du cuivre
(où on obtient le cuivre blister) mais plutôt de
l'hydrométallurgie du cuivre. Ce sont les cathodes commerciales (d'une
teneur en Cu de 99,98%) produites toujours aux US qui sont utilisés
comme anodes solubles.
Les teneurs moyennes des éléments dans les boues
anodiques des U.S
Tableau 2 Teneurs moyennes des éléments dans
les boues anodiques des US
Elément
|
Teneur
|
Cu
|
54,01%
|
Pb
|
4,63%
|
Au
|
88ppm
|
Ag
|
0,91ppm
|
Co
|
0,14%
|
Ni
|
0,013%
|
Zn
|
0,042%
|
Fe
|
0,558%
|
Page | 26
IV.2 Résultats de caractérisation
minéralogique
L'analyse minéralogique a pour objectif de
déterminer la façon dont sont associés les
éléments contenus dans les boues anodiques. Ceci pourra servir
dans la suite du travail à établir les relations entre les
éléments et les phases minérales qui sont affectées
ou non lors des opérations de grillage et de lixiviation. Ainsi, les
éléments et minéraux présents dans
l'échantillon des boues anodiques ont été
identifiés par observation au microscope binoculaire
stéréoscopique.
Les éléments et minéraux observés au
microscope sont :
· Cuivre métallique Cu°
· Quartz SiO2
· Traces de malachite CuCO3.
Cu(OH)2
IV.3 Résultats des tests de lixiviation
IV.3.1 Lixiviation des boues anodiques non grillées
IV.3.1.1 Effet du temps de conditionnement
Conditions opératoires
- Concentration en H2SO4 : 2M
- Ratio S/L : 1/12
- Température : 60°C
- Temps : 1H, 2H et 3H.
Les résultats des tests sont consignés dans le
tableau 3 et illustrés à la figure 6.
Page | 27
Tableau 3 Résultats des tests de lixiviation des
boues anodiques non grillées en fonction du
temps
Temps (Heure)
|
Taux de dissolution (%)
|
Acidité libre
|
|
Cu
|
Pb
|
?????????? (g/l)
|
1
|
8,02
|
28,79
|
176,4
|
2
|
8,66
|
27,50
|
174,44
|
3
|
8,98
|
23,61
|
151,9
|
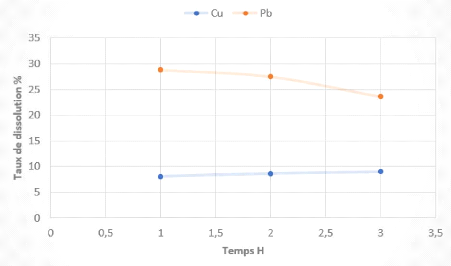
Figure 6 Evolution du taux de dissolution du Cu et Pb en
fonction du temps lors de la
lixiviation des boues anodiques non
grillées.
L'analyse des résultats obtenus montrent qu'une variation
du temps de conditionnement entre 1 heure et 3 heures n'affecte que très
peu le taux de dissolution du cuivre.
Une durée de 1H est alors suffisante pour dissoudre le
maximum de cuivre soluble et le plomb, notamment 8% Cu et 29% Pb.
On remarque que le taux de dissolution du Pb diminue avec le
temps dans l'intervalle de temps considéré.
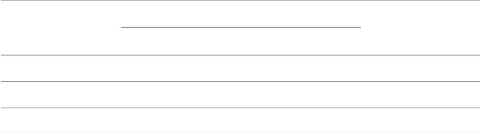
H2SO4 g/l
Cu Pb
1
|
8,24
|
18,14
|
85,26
|
2
|
8,66
|
27,50
|
174,44
|
3
|
9,11
|
20,59
|
281,42
|
Concentration en
H2SO4 (Molaire
M)
Taux de dissolution % Acidité libre
IV.3.1.2 Effet de la concentration en H2SO4
Conditions opératoires
- Temps de conditionnement : 2H
- Ratio S/L : 1/12
- Température : 60°C
- Concentration en H2SO4 : 1M, 2M et 3M.
Les résultats des tests sont consignés dans le
tableau 4 et illustrés à la figure 7.
Tableau 4 Résultats des tests de lixiviation des boues
anodiques non grillées en fonction de la
concentration
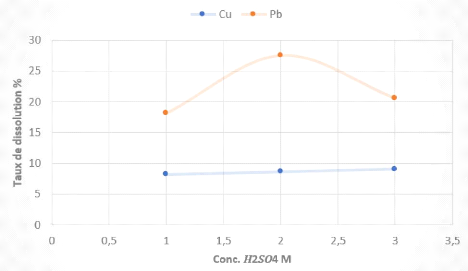
Figure 7 Evolution du taux de dissolution du Cu et Pb en
fonction de la concentration lors de
la lixiviation des boues anodiques non
grillées.
Page | 28
Page | 29
Les résultats obtenus montrent que la variation de la
concentration de ??2????4 entre 1 et 3 M affecte
très peu le taux de dissolution du cuivre, qui est en moyenne de
8,5%.
On remarque aussi que le taux de dissolution du Pb augmente
à la concentration de 2 M (27,5 %) puis diminue à la
concentration de 3 M (20,59 %).
IV.3.1.3 Analyse des résultats
L'examen de l'ensemble des résultats obtenus au cours
de cette phase de l'étude montre que le taux de dissolution du cuivre
dans les boues anodiques non grillées est très faible (8 à
9%). D'après les résultats, presque tout le cuivre soluble
présent dans les boues anodiques a été mis en solution
dans les conditions suivantes : Concentration de ??2????4 = 1 M ;
Rapport S : L = 1/12 ; Température = 60°C ; Durée de
l'attaque = 1H.
En effet, l'essai réalisé dans ces conditions a
donné les résultats consignés dans le tableau
ci-après, avec une perte en poids de l'échantillon initial de 15
%. On déduit de ces résultats que le résidu solide de
lixiviation est devenu encore plus riche en Cu.
Tableau 5 Dissolution du Cu et Pb contenus dans les boues
anodiques non grillées (H2SO4
1M; S/L 1/12; T° 60°C;
Conditionnement 1H)
Elément
|
Cu
|
Pb
|
Taux de dissolution, %
|
8,36
|
12,38
|
Teneur en solide résiduel, %
|
57,67
|
4,72
|
Teneur solution lixiviation, g/l
|
6,68
|
0,86
|
IV.3.2 Lixiviation des boues anodiques grillées pendant 1H
IV.3.2.1 Effet du temps de conditionnement
Conditions opératoires
- Concentration en ??2????4 : 2M
- Ratio S/L : 1/12
- Température : 60°C
- Temps : 1H, 2H et 3H.
Les résultats des tests sont consignés dans le
tableau 6 et illustrés à la figure 8.
Tableau 6 Résultats des tests de lixiviation des
boues anodiques grillées durant 1H en
fonction du temps
Temps (Heure) Taux de dissolution % Acidité
libre
|
|
|
?????????? g/l
|
Cu
|
Pb
|
|
1
|
25,33
|
13,96
|
157,78
|
2
|
25,38
|
20,01
|
156,8
|
3
|
25,43
|
18,28
|
151,9
|
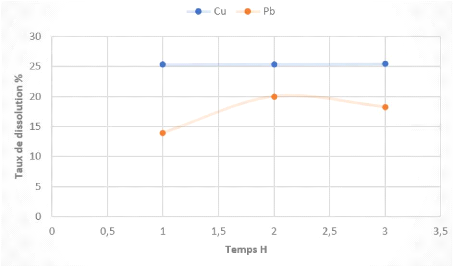
Figure 8 Evolution du taux de dissolution du Cu et Pb en
fonction du temps lors de la
lixiviation des boues anodiques grillées
durant 1H.
L'examen des résultats obtenus montrent qu'une variation
du temps de conditionnement entre 1 heure et 3 heures n'affecte que très
peu le taux de dissolution du cuivre comme dans le cas
précèdent.
Une durée de 1H est alors suffisante pour dissoudre le
maximum de cuivre soluble et le plomb, notamment 25% Cu et 13% Pb.
Page | 30
On remarque que le taux de dissolution du Pb augmente avec le
temps dans l'intervalle de temps considéré puis diminue vers les
3H de conditionnement.
IV.3.2.2 Effet de la concentration en H2SO4
Conditions opératoires
- Temps de conditionnement : 2H
- Ratio S/L : 1/12
- Température : 60°C
- Concentration en H2SO4 : 1M, 2M et 3M.
Les résultats des tests sont consignés dans le
tableau 7 et illustrés à la figure 9.
Tableau 7 Résultats des tests de lixiviation des boues
anodiques grillées durant 1H en fonction de la concentration
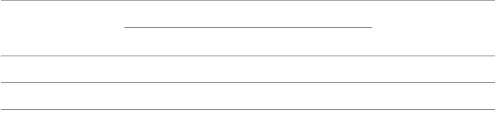
H2SO4 g/l
Cu Pb
1
|
23,23
|
6,76
|
59,78
|
2
|
25,38
|
20,01
|
156,8
|
3
|
24,96
|
13,86
|
258,72
|
Concentration en
H2SO4 (Molaire
M)
Taux de dissolution % Acidité libre
Page | 31
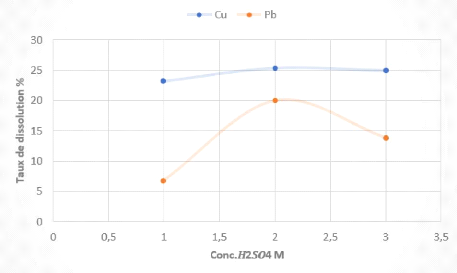
Page | 32
Figure 9 Evolution du taux de dissolution du Cu et Pb en
fonction de la concentration lors de la lixiviation des boues anodiques
grillées durant 1H.
L'examen des résultats obtenus montrent que la
variation de la concentration de ??2????4 entre
1 et 3 M affecte très peu le taux de dissolution du cuivre, qui est en
moyenne de 24,5%.
On remarque aussi que le taux de dissolution du Pb augmente
à la concentration de 2 M (20,01 %) puis diminue à la
concentration de 3 M (13,86 %).
IV.3.2.3 Analyse des résultats
D'après les résultats obtenus au cours de cette
phase de l'étude, le taux de dissolution du cuivre des boues anodiques
grillées durant 1H a augmenté par rapport aux boues anodiques non
grillées. Presque tout le cuivre soluble présent dans les boues
anodiques grillées durant 1H a été mis en solution dans
les conditions suivantes : Concentration de ??2????4 = 1 M ; Rapport S
: L = 1/12 ; Température = 60°C ; Durée de l'attaque =
1H.
En effet, l'essai réalisé dans ces conditions a
donné les résultats consignés dans le tableau
ci-après, avec une perte en poids de l'échantillon initial de 23
%. On déduit de ce tableau que le résidu solide de lixiviation
est toujours riche en Cu.
Tableau 8 Dissolution du Cu et Pb contenus dans les boues
anodiques grillées durant 1H (H2SO4 1M; S/L 1/12; T° 60°C;
Conditionnement 1H)
Elément
|
Cu
|
Pb
|
Taux de dissolution, %
|
23,41
|
5,32
|
Teneur en solide résiduel, %
|
53,31
|
5,79
|
Teneur solution lixiviation, g/l
|
18,7
|
0,37
|
IV.3.3 Lixiviation des boues anodiques grillées pendant 2H
et 3H
Ces tests ont porté sur l'étude de l'influence
de l'acidité du milieu uniquement. D'après les tests
précédents notamment sur la cinétique de lixiviation. Ils
montrent qu'une variation du temps de conditionnement entre 1 heure et 3 heures
n'affecte pas considérablement le taux de dissolution du cuivre.
IV.3.3.1 Lixiviation des boues anodiques grillées durant
2H Effet de la concentration en H2SO4
Conditions opératoires
- Temps de conditionnement : 2H
- Ratio S/L : 1/12
- Température : 60°C
- Concentration en H2SO4 : 1M, 2M et 3M.
Les résultats des tests sont consignés dans le
tableau 9 et illustrés à la figure 10.
Tableau 9 Résultats des tests de lixiviation des boues
anodiques grillées durant 2H en fonction de la concentration
Concentration en H2SO4 (Molaire M)
Taux de dissolution % Acidité libre
|
H2SO4 g/l
|
Cu Pb
|
1
|
68,32
|
0,86
|
2,94
|
2
|
65,8
|
1,15
|
58,8
|
3
|
54,94
|
1,15
|
108,23
|
Page | 33
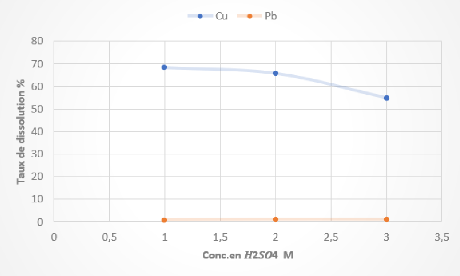
Page | 34
Figure 10 Evolution du taux de dissolution du Cu et Pb en
fonction de la concentration lors de la lixiviation des boues anodiques
grillées durant 2H.
IV.3.3.2 Lixiviation des boues anodiques grillées durant
3H Effet de la concentration en H2SO4
Conditions opératoires
- Temps de conditionnement : 2H
- Ratio S/L : 1/12
- Température : 60°C
- Concentration en ??2????4 : 1M, 2M et
3M.
Les résultats des tests sont consignés dans le
tableau 10 et illustrés à la figure 11.
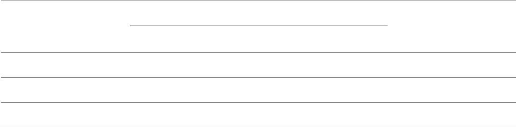
H2SO4 g/l
Cu Pb
1
|
66,19
|
1,44
|
3,92
|
2
|
75,3
|
1,74
|
46
|
3
|
70,04
|
1,44
|
120,5
|
Concentration en H2SO4 (Molaire M)
Taux de dissolution % Acidité libre
Tableau 10 Résultats des tests de lixiviation des
boues anodiques grillées durant 3H en fonction de la
concentration
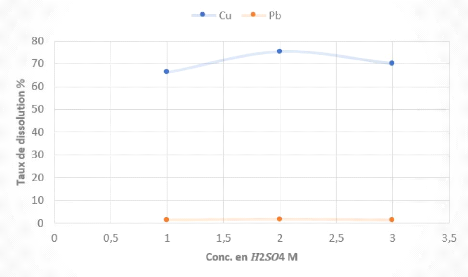
Figure 11 Evolution du taux de dissolution du Cu et Pb en
fonction de la concentration lors de la lixiviation des boues anodiques
grillées durant 3H.
IV.3.3.3 Résultats des tests sur les résidus
solides de lixiviation des boues anodiques grillées durant 2H et 3H
Nous avons remarqué, lors de ces tests, la formation d'un
précipité brun ainsi des cristaux bleus de sulfate de cuivre
CuSO4. Nous pensons du précipité qu'il s'agit du sulfate
de plomb PbSO4.
Page | 35
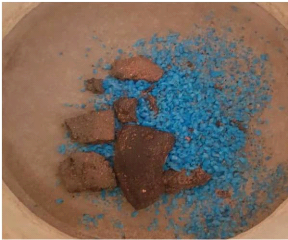
Page | 36
Figure 12 Résidu solide au test de lixiviation des
boues anodiques grillées durant 2H IV.3.3.4 Analyse des
résultats
L'examen des résultats obtenus au cours de cette phase de
l'étude, le taux de dissolution du cuivre est meilleur dans les
conditions opératoires suivantes : Concentration de H2SO4 = 2 M
; Rapport S : L = 1/12 ; Température = 60°C ; Durée de
l'attaque = 2H.
L'essai réalisé dans ces conditions a donné
les résultats consignés dans le tableau ci-après, avec une
perte en poids de l'échantillon initial de 55,3 %. On déduit de
ce tableau que la teneur du cuivre dans le résidu solide de lixiviation
a baissé.
Tableau 11 Dissolution du Cu et Pb contenus dans les boues
anodiques grillées durant 3H
(H2SO4 2M; S/L 1/12; T° 60°C;
Conditionnement 2H)
Elément
|
Cu
|
Pb
|
Taux de dissolution, %
|
75,30
|
1,74
|
Teneur en solide résiduel, %
|
27,66
|
11,62
|
Teneur solution lixiviation, g/l
|
61
|
0,12
|
La formation du précipité de sulfate de plomb
PbSO4 ainsi que des cristaux bleus de sulfate de cuivre
CuSO4 expliquerait la baisse exponentielle de
l'acidité des solutions de lixiviation comme le démontrent les
tableaux 9 et 10.
Page | 37
Remarque : dans les solutions de lixiviation des essais
(lixiviation des boues anodiques grillées durant 2H à 2M et 3M)
qui ont vieilli, plus de 16h après l'essai avant de subir la filtration,
on a observé une forte présence des cristaux de sulfate de cuivre
CuSO4 et du précipité de sulfate de plomb
PbSO4.
IV.3.4 Conclusion
La lixiviation des boues anodiques des U.S en milieu acide
sulfurique dilué dépend énormément des conditions
opératoires et des phases minérales présentes.
La lixiviation des boues anodiques non grillées
présente un résidu final de lixiviation représentant
environ 85% du produit initial et se compose de 57,67% Cu et 4,72% Pb. Il se
retrouve donc encore plus enrichi en cuivre. Le taux de dissolution de Cu ne
dépasse pas 9% et celui du Pb ne dépasse pas 29%, le cuivre
métallique est difficilement soluble dans ces conditions de lixiviation.
La dissolution de l'élément cuivre contenu dans les boues
anodiques des U.S nécessiterait un grillage oxydant pour transformer le
cuivre métallique Cu° en oxyde cuivrique
CuO qui, lui est soluble en milieu acide sulfurique.
En effet, la lixiviation des boues anodiques des U.S ayant
subi un grillage oxydant a permis de dissoudre une quantité assez
importante de cuivre et cela en fonction du temps de grillage. Cependant le
taux de dissolution du plomb a drastiquement chuté. Pour les boues
anodiques ayant subi un grillage oxydant d'1H, le taux de dissolution est en
moyenne de 24 % pour le cuivre et celui du plomb est très variable
allant de 6 à 20% ; pour les boues anodiques ayant subi un grillage
oxydant de 2H, le taux de dissolution ne dépasse pas 69 % pour le cuivre
et celui du plomb est de 1,15% et pour les boues anodiques ayant subi un
grillage oxydant de 3H, le taux de dissolution du cuivre a atteint 75 % et
celui du plomb 1,74 %.
Page | 38
CONCLUSION
La caractérisation des boues anodiques des US, montre
que ces produits, qui contiennent en moyenne 54,01% Cu ; 4,63% Pb ; 88ppm Au ;
0,91ppm Ag ; 0,14% Co ; 0,013% Ni ; 0,042% Zn et 0,558% Fe, ont une forte
teneur en Cu (54,01%). Le cuivre contenu dans ces boues se présente sous
forme métallique, d'où sa récupération par
lixiviation dépend énormément des conditions
opératoires, notamment l'oxydation du cuivre.
Le traitement de ces boues a montré qu'en milieu acide
sulfurique 2M, à la température de 60°C et
précédé d'un grillage oxydant de 3H, un taux de
dissolution du cuivre de 75,3%. Le résidu solide de lixiviation
représentant 44,7% du solide initial, titre 27,6% Cu et 11,62% Pb.
Au terme de cette étude, il apparaît donc que la
voie proposée (la lixiviation par l'acide sulfurique des boues anodiques
ayant subi un grillage oxydant) pour le traitement des boues anodiques, permet
bien de recycler le cuivre.
Il reste alors à déterminer les conditions
opératoires optimales pour le grillage oxydant afin d'améliorer
le taux de dissolution du cuivre lors de la lixiviation.
Page | 39
REFERENCES
1. Bayraktar 1. and Garner F. A.,l985. "Hydrometallurgical
processing of secondary copper anode slimes for metals recovery", "Recycle and
Secondary Recovery of Metals", International Symposium, Fort Landerdale,
Floride, U.S.A., pp.547-562.
2. Bertocci Ugo and Denis R. Turner, 1974. "Copper" pp.
384-481, from "Encyclopedia of electrochemistry of the elements" Volume II,
Editor J. Bard.
3. Biswas A.K. and Davenport W.G., 1976. «Extractive
metallurgy of copper", International series on Materials science and
technology, vol. 20, Editor, D. W. Hopkins, M.Sc.
4. Blazy P., 1979 "La métallurgie extractive des
métaux non ferreux " Société de l'industrie
minérale.
5. Blazy P. et JDID El-Aid, 2001. "Pyrométallurgie et
électroaffinage du cuivre", Techniques de l'ingénieur,
M-2241-2
6. Chen T.T. and Dutrizac J, E., 1987." Mineralogical
caracterization of anode slimes from the Kidd Creek Copper Refinery". From
Electrorefining and winning of copper". Ed. by Hoffmann J. E. et al, pp.
499-525.
7. Cognis, 2009. Extraction par solvent du cuivre, 2009.
8. Elamari K., 1993. Traitement hydrométallurgique en
milieux acides des boues anodiques d'électroaffinage de cuivre.
Thèse de doctorat.
9. Fouletier M., Mathieu J, B. et Nouai P., 1980. "Les
applications de l'électrochimie à l'hydrométallurgie" Ed.
Pluralis.
10. Ghebgoub F., 2012. Effet du diluant sur l'extraction par
solvant du cuivre(II), cobalt (II) et nickel (II) par l'acide di-(2-ethyhexyl)
phosphorique. Thèse de doctorat. p.171.
11. Hoffmann J, E., 1989 "Recovering selenium and tellurium
from copper refinery slimes"; J.O.M, pp.33-38.
12. Hyvarinen O.; E. Rosenberg; L. Lindroos; E. Yllo, 1984.
"Selenium and precious metals recovery from copper anode slimes at Outokumpu
Pori Refinery", "Meeting: Precious Metals; Mining, Extraction and Processing,
Los Angeles, Calif. U.S.A., pp 537-548.
13. Jennings P. H., Mcandrew R. T.and Stratigakos E. S., 1968
"A hydrometallurgical method for recovering selenium and tellurium from copper
refinery slimes" TMS paper selection, A 68-9.
14.
Page | 40
Kitamura T. Kawakita T. Sako Y. Sasaki K., 1976. "Design,
construction, and operation of periodic reverse current process at Tamano",
"Extractive metallurgy of copper" Yannoupoulos J. C.; International symposium
on copper extraction and refining, pp. 525-537.
15. Koji M., 2010. Approche d'un paramétrage des
conditions optimales d'un circuit lixiviation-extraction par solvent du cuivre
à l'usine à cuivre de Kolwezi sur base du minerai oxydé de
cuivre du gisement de Kilamusembu. Travail de fin d'études, Institut
Supérieur des Techniques Appliquées, Inédit.
16. Mansour M., 2013. Etude expérimentale et
modélisation de l'oxydation sèche de la poudre de nanoparticules
de cuivre. Thèse de doctorat. pp.37-38.
17. Mukota N., 2019. Approche d'un paramétrage des
conditions opératoires optimales des floculant Rhéomax et
Superfloc n100 dans un circuit de décantation : cas de Ruashi Mining.
Travail de recherche, Université de Lubumbashi, Inédit.
18. Naboichenko S. S. and Gritchina E. N., 1981. "Autoclave
leaching of copper electrolyte sludges" Tsvetn. Met., pp. 35-36.
19. Palacios and M. G8 de Pesquera, 1976.;" Expansion of the
Rio Tinto Patino tankhouse at Huelva" pp., 569-587, from" Extractive metallurgy
of copper" Yannoupoulos J. C. and Agarwal J. C. ; International Symposium on
Copper Extraction and Refining.
20. Pascal P., 1961."Nouveau traité de chimie
minérale", Tome XIII, Deuxième fascicule; Ed. Masson et Cie.
21. Roger E., 1946. La pratique du traitement
électrochimique des minerais de cuivre du Katanga. Mémoire,
Institut Royal Coloniale Belge. pp.41-42.
22. Schloen J, H. and Elkin E. M., 1950. "Treatment of
electrolytic copper refinery slimes" J. of Metals, 188 (5) pp. 764-777.
23. Schloen J. H. and Elkin E. M., 1954. "Treatment of
electrolytic copper refinery slimes", From, Copper, The Science and Technology
of the metal, its alloys and compounds; New York, pp. 265-289.
24. Sumiko Sanuki, Norio Minami, Koichi Arai, Toshio Izaki
and Hiroshi Majima, 1989. "Oxidative leaching treatment of copper anode slime
in a nitric acid solution containing sodium chloride" Metal transactions, JIM.,
Vol. 30, NO. 10, pp. 781-788.
25. Thiriart J., Guébels A. et Troch P., 1988.
"Métallurgie du cuivre", Techniques de l'ingénieur,
M-2240-1-11.
26. Yanagida T. and N. Hosoda, 1975. "Treatment of copper
electrolysis slimes at Osaka refinery" TMS paper selection, paper NO. A
75-42.
27.
Page | 41
Yildrium G., Fuat Y. B., 1985. "Hydrometallurgical treatment
of a copper refinery slime rich in both selenium and tellurium". Erzmetal138
Nr.4, pp. 196-199.
28. Rydberg J. et al., 2004. Solvent extraction: principles
and practice, 2e. New York: Taylor & Francis Group, LLC, 2004.
pp.11-35. ISBN 0-8247-5063-2.