Ministère de l'Enseignement Supérieur, de
la Recherche Scientifique et de la Technologie
*** * ***
Université du 7 novembre à Carthage
*** * ***
Institut National des Sciences Appliquées et
de Technologie
|
|
Projet de Fin d'Études Pour
l'obtention du
Diplôme National d'Ingénieur en
Sciences Appliquées et en Technologie
Filière : Instrumentation et Maintenance
Industrielles Sujet :
Élaboration d'un système d'automatisme et
de
régulation d'une unité
d'aérocondenseur de vapeur
d'eau en replacement d'un condenseur de vapeur
à
eau de mer
Réalisé par : Chaker
ABDELJAOUED
Entreprise d'accueil : EPPM Soutenu le
14/01/2010
Responsables à
l'entreprise:
Messieurs:
Ridha ROMDHANE / Mohamed Lassaâd ISSAOUI Cachet &
Signature
|
Responsables à l'INSAT:
Messieurs:
Jawhar GHOMMAM / Slim KADDECHE Signature
|
|
|
Année Universitaire : 2009/2010
Fichier :
www.bh-automation.fr/Download/Automaticiens/automatisation-regulation-aerocondenseur-vapeur-rapport-projet-cad.pdf
Web :
www.bh-automation.fr/Ressources/Automaticiens/cv-chaker-abdeljaoued.html
DEDICACES
A celle qui a consacré sa vie à
l'éducation de ses enfants, A celle pour qui éducation rime avec
rigueur et travail, Aux sacrifices qu'elle a faits pour sa famille,
A celle qui m'a élevé avec amour et
tendresse,
A celle qui a toujours cru en moi,
A ma chère défunte mère,
A mon cher père qui n'a cessé de me
soutenir,
A mes frères,
A mes amis,
Je dédie ce modeste travail.
Remerciements
Je tiens à remercier dans un premier temps la direction
générale d'EPPM qui m'a bien accueilli au sein de son
établissement.
Je remercie vivement mes encadreurs d'entreprise ; Monsieur
Ridha ROMDHANE et Monsieur Mohamed Lassaâd ISSAOUI pour m'avoir permis
d'user de leurs précieux temps malgré les lourdes
responsabilités qu'ils endossent en tant que chefs de
départements, je leur suis reconnaissant pour les conseils utiles qu'ils
m'ont prodigué.
J'adresse également mes remerciements chaleureux
à mes encadreurs à l'INSAT ; Monsieur Jawhar GHOMMAM et Monsieur
Slim KADDECHE pour leurs soutien continuel et leurs encouragements tant
précieux.
Je tiens à témoigner toutes ma gratitude à
tous les membres d'EPPM, particulièrement : Mohamed, Sahbi, Hbib, Tayeb
et Sofiane.
Sommaire
Introduction Générale 13
Chapitre I : Problématique & Présentation de
l'aérocondenseur 15
Introduction 16
1 Présentation de l'entreprise d'accueil : EPPM 16
2 Présentation de l'entreprise cliente: GCT 18
3 Description de l'aérocondenseur 19
3.1 Définition 19
3.2 Principe de réalisation 20
3.3 Justification d'emploi 20
3.4 Réalisation 23
3.4.1 Condenseurs principaux 23
3.4.2 Tuyauteries de liaisons 24
3.4.3 Circulation de l'air 25
3.4.4 Charpente 28
3.4.5 Les auxiliaires 28
3.5 Perspectives et limites à l'utilisation des
aérocondenseurs 29
4 Les instruments de mesure 30
4.1 Les transmetteurs de pression 30
4.2 Les transmetteurs de température 30
4.3 Le transmetteur de niveau 31
4.4 Les interrupteurs de vibration (vibroswitch) 31
5 Systèmes de contrôle commande de
l'aérocondenseur 31
5.1 Le système de contrôle commande par PLC 32
5.2 Le système de contrôle, commande et supervision
SCADA 32
5.3 Le système de contrôle, commande et supervision
DCS 32
6 Cahier des charges et planning d'exécution 33
6.1 Cahier des charges 33
6.2 Planning d'exécution 34
Conclusion 35
Chapitre II : Etude thermodynamique & mise en oeuvre 36
Introduction 37
1 Principe de fonctionnement 37
2 Paliers de fonctionnement 40
3 Démarche 42
3.1 Courbe et équation de T = I?(P) 43
3.2 Courbe et équation de p = I?(P) . 45
3.3 Courbe et équation de chaleur massique de vapeur : Cp
= I?(P) 46
4 Etapes de fonctionnement 48
4.1 Etape 1 48
4.2 Etape 2 49
4.3 Etape 3 49
4.4 Etape 4 50
5 Etude thermodynamique 51
5.1 Expression du flux de chaleur échangé dans un
ventilateur 52
5.1.1 Détermination de la surface d'échange S
52
5.1.2 Détermination de la moyenne logarithmique des
différences de températures ?Tm 52
5.1.3 Détermination du coefficient d'échange global
h 53
5.1.4 Récapitulation 57
5.2 Etude du système moto-ventilateur 58
5.2.1 Relation entre débit d'air refoulé et vitesse
de rotation du ventilateur 58
5.2.2 Relation entre puissance reçue par le ventilateur et
puissance fournie par le moteur 59
5.2.3 Relation entre vitesse de rotation du ventilateur et
vitesse de rotation de l'arbre moteur 60
5.2.4 Relation entre vitesse de rotation de l'arbre moteur et
commande du variateur de vitesse 63
5.2.5 Récapitulation : ma = I? (fl) . 63
Conclusion 64
Chapitre III : Système de contrôle, commande et
supervision 65
Introduction 66
1 Système de contrôle, commande et supervision SCADA
66
2 Présentation de l'automate 68
2.1 Architecture des automates programmables 68
2.2 Structure interne des automates programmables 70
2.2.1 Le processeur 70
2.2.2 Les modules d'entrées/sorties 70
2.2.3 Les mémoires 71
2.2.4 L'alimentation 71
2.2.5 Liaisons de communication 71
3 Définition des documents utilisés 72
4 Identification des entrées/sorties 72
4.1 Les E/S PLC 72
4.2 Tableau d'échange MODBUS 74
5 Séquence de démarrage de l'unité
d'aérocondenseur 75
6 Séquence d'arrêt de l'aérocondenseur 76
7 Fonctionnement de l'ensemble ; vannes XV, vantelles et
ventilateurs 77
7.1 Diagrammes de fonctionnement des vannes XV 79
7.2 Diagramme de fonctionnement des vantelles 81
7.3 Fonctionnement des ventilateurs 82
8 Fonctionnement des pompes retour condensât 83
Conclusion 86
Chapitre IV : Programmation de l'automate 87
Introduction 88
1 Description du logiciel STEP7 88
1.1 Gestionnaire de projets SIMATIC Manager 88
1.2 Editeur de programme et les langages de programmation 88
1.3 Paramétrage de l'interface PG-PC 89
1.4 Le simulateur des programmes PLCSIM 89
1.5 Stratégie pour la conception d'une structure programme
complète et optimisée 90
2 Réalisation du programme de l'unité de
l'aérocondenseur 91
2.1 Création du projet dans SIMATIC Manager 91
2.2 Configuration matérielle (Partie Hardware) 92
2.3 Création de la table des mnémoniques (Partie
Software) 95
2.4 Elaboration du programme S7 (Partie Software) 97
2.4.1 Les blocs de code 97
2.4.1.1 Les blocs d'organisation (OB) 97
2.4.1.2 Les blocs fonctionnels (FB), (SFB) 97
2.4.1.3 Les fonctions (FC), (SFC) 97
2.4.1.4 Les blocs de données (DB) 98
2.4.2 Création du programme de l'unité
d'aérocondenseur 98
2.4.2.1 Architecture du programme réalisé 98
2.4.2.2 Programmation des blocs 100
Conclusion 106
Conclusion Générale 107
Bibliographie 108
Netographie 108
Liste des annexes 109
Nomenclature
Cm : couple de rotation de l'arbre moteur, N.m
Cp : chaleur massique, KJ/Kg
Cpv : chaleur massique de vapeur, KJ/Kg
Cr : couple de rotation du ventilateur, N.m
Da : diamètre de l'ailette, m
de : diamètre extérieur du tube, m
di : diamètre intérieur du tube, m
H : pertes de charges, bar
h : coefficient d'échange de chaleur global,
W/K.m2
he : coefficient d'échange par convection
à l'extérieur du tube, W/K.m2
hi : coefficient d'échange intérieur du
tube à ailettes, W/K.m2
I : courant de commande du variateur de vitesse, A
l : longueur des tubes, m
lac : longueur caractéristique de l'ailette, m
Lc : chaleur latente de condensation, KJ/Kg
Lv : chaleur latente de vaporisation, KJ/Kg
m : débit massique, Kg/s
ma : débit volumique d'air
refoulé par le ventilateur, m3/s mc :
débit massique de condensat, Kg/s
mv : débit massique de vapeur dans les
faisceaux, Kg/s nt : nombre moyen de tubes par rang
P : pression, bar
Pt : pas transversal du faisceau, m
Pm : puissance mécanique fournie par le
moteur, W Pr : puissance mécanique reçue par le
ventilateur, W Pt : puissance de condensation de vapeur, W
Q : débit massique de vapeur, Kg/s
Qm : débit massique de vapeur de maintien en
température, Kg/s Re : résistance
d'encrassement extérieure, m2.K/W
Ri : résistance d'encrassement
intérieure, m2.K/W
S : surface globale d'échange, m2
Sa: surface d'échange du tube avec ailettes
par mètre de tube, m Sas : surface d'échange des
ailettes seules par mètre de tube, m Se : surface
d'échange extérieure des tubes sans ailettes, m2
Si : surface d'échange intérieure, m2
T : température, K
T1e : Température de la vapeur à
l'entrée de l'échangeur, K T2s : Température de
l'air à la sortie de l'échangeur, K
T1s : Température de l'eau à la sortie
de l'échangeur, K T2e : Température de l'air à
l'entrée de l'échangeur, K V : vitesse de la vapeur
d'eau dans les tubes, m/s
Vm : vitesse de rotation de l'arbre moteur, tr/mn
Vr : vitesse de rotation du ventilateur, tr/mn
äa : épaisseur de l'ailette, m
?Tm : moyenne logarithmique des différences de
températures, K
~ : erreur acceptable
æ : coefficient d'anisothermie
çf : efficacité de l'ailette
çg: efficacité globale de la
surface à ailettes A : conductivité thermique, W/m.K
u : viscosité dynamique, Kg/m.s
õp : viscosité
cinématique de l'air, m2/s ñ : masse
volumique, Kg/m3
ñp : masse volumique de l'air,
Kg/m3 ö : flux de chaleur échangée, W
~ : fraction de vide
Abréviations
ABB : Asea Brown Boveri (multinationale Norvégienne,
leadeur dans les technologies d'automatisation)
API : Automate Programmable Industriel CEE : Cascade Energy
Engineering
CPG : Compagnie des Phosphates de Gafsa CPI : Controlleur
Permanant d'Isolement CPU : Central Processing Unit
DCS: Distributed Control System
EPPM : Engineering Procurement and Project Management
GCT : Groupe Chimique Tunisien
HMI: Human Interface Machine
MCC: Motor Control Center
P&ID: Piping and Instrumentation Diagram PLC : Programmable
Logic Controller PMP : Plan de Management Projet
RMF: Relais Multi Fonction
SCADA : Supervisory Control And Data Acquisition TEMA : Tubular
Exchanger Manufacturers Association
TOR: Tout Ou Rien
TSP : Triple Super Phosphate
VSD: Variable Speed Drive
Liste des figures
Figure 1 : Organigramme Projet EPPM 17
Figure 2 : Site du GCT à Skhira 18
Figure 3 : Vue en 3D de l'aérocondenseur (gauche) et
aérocondenseur sur site (droite) 20
Figure 4 : Ecart de température à
l'aérocondenseur et à l'aéroréfrigérant
22
Figure 5 : Faisceaux d'échange 24
Figure 6 : Coupe du tube à ailette 24
Figure 7 : Partie des canalisations de vapeur et de
condensât sur site 25
Figure 8 : Partie moto-ventilateur sur site 26
Figure 9 : Éléments composants d'un
aéroréfrigérant avec échangeurs en position
horizontale
et ventilateurs dans deux positions : tirage forcé ou
induit 27
Figure 10 : Pompes retour condensât sur site 29
Figure 11 : Transmetteur de pression ROSEMOUNT 2088 30
Figure 12 : Vibroswitch 31
Figure 13 : Etapes du projet 35
Figure 14 : Schéma représentatif de
l'aérocondenseur 38
Figure 15 : Interface de l'application de calcul de pertes de
charges 41
Figure 16 : Diagramme Température, Pression 42
Figure 17 : T = f(P) [0,02-0,1] 43
Figure 18 : T = f() [0,1-0,6] 44
Figure 19 : T = f() [0,6-2] 45
Figure 20 : p = f(P) [0,02-2] 45
Figure 21 : Cp = f(P) [0,02-0,1] 46
Figure 22 : Cp = f() [0,1-0,6] 47
Figure 23 : Cp = f() [0,6-2] 47
Figure 24 : Echangeur contre-courant 53
Figure 25 : Coupe longitudinale du tube sans ailettes 54
Figure 26 : Profil de l'ailette 55
Figure 27 : Types d'écoulement autour d'un faisceau de
tubes 56
Figure 28 : Système moto-ventilateur 58
Figure 29 : ma = f(r) 59
Figure 30 : Cr = f(r) . 61
Figure 31 : Pm = f(m) 62
Figure 32 : Vm = f(1) . 63
Figure 33 : Démarche pour le calcul de ma = I? (F) 64
Figure 34 : Architecture du système de commande,
contrôle et supervision 67
Figure 35 : Automate Programmable Industriel SIEMENS
69
Figure 36 : API S7300 69
Figure 37 : Structure interne d'un API 70
Figure 38 : Séquence de démarrage 75
Figure 39 : Séquence d'arrêt 76
Figure 40 : Diagramme de fonctionnement des batteries de
ventilateurs 78
Figure 41 : Diagrammes de fonctionnement des vannes XV 81
Figure 42 : Diagramme de fonctionnement des vantelles 82
Figure 43 : Diagramme de fonctionnement des ventilateurs de la
batterie 1 83
Figure 44 : Schéma du ballon à condensât
84
Figure 45 : Diagramme fonctionnel des pompes retour
condensât 85
Figure 46 : Diagramme de démarrage des pompes P10/A et
P10/B 86
Figure 47: Mode de représentation des langages basiques de
programmation STEP7 89
Figure 48 : Interface de simulation PLCSIM 90
Figure 49 : Page de démarrage de STEP7 92
Figure 50 : Choix du RACK 93
Figure 51 : Choix du CPU et de l'alimentation 94
Figure 52 : Choix des embases d'E/S 95
Figure 53 : Hiérarchie du programme STEP7 95
Figure 54 : Création des mnémoniques 96
Figure 55 : Table des mnémoniques du projet 96
Figure 56 : Blocs du projet 98
Figure 57 : Architecture des blocs du projet 99
Liste des tableaux
Tableau 1: Pertes de charges dans les conduites 42
Tableau 2 : Pertes de puissance pour différents modes
d'entrainement 59
Tableau 3 : Valeurs de Cr et Vr 60
Tableau 4 : Valeurs de Pm et Vm 61
Tableau 5 : Entrées PLC Analogiques 72
Tableau 6 : Sorties PLC Analogiques 73
Tableau 7 : Entrées PLC Numériques 73
Tableau 8 : Sorties PLC Numériques 74
Tableau 9 : Informations échangées depuis le Tiroir
A01 74
Tableau 10 : Informations échangées depuis le
tiroir A02 75
Tableau 11 : Informations échangées depuis la Boite
Jonction Instrumentation 75
Tableau 12 : Exemples d'interlock 77
Tableau 13 : Listes des E/S relatives au fonctionnement des
vannes XV 79
Tableau 14 : Listes des E/S relatives au fonctionnement des
vantelles 81
Tableau 15 : Listes des E/S relatives au fonctionnement des
ventilateurs de la batterie 1 82
Tableau 16 : Listes des E/S relatives au fonctionnement des
pompes 84
Introduction Générale
L'industrie minière en Tunisie ne cesse
d'évoluer et la demande croissante en engrais et produits chimique
contribue à la croissance de l'économie tunisienne ; cette
évolution a pour conséquences l'apparition de nouvelles
technologies de production et de transformation.
La Tunisie est le cinquième producteur mondial de
phosphate avec une production annuelle d'environ 8 millions de tonnes, cette
activité est plus que centenaire pour l'extraction du phosphate par la
Compagnie des Phosphates de Gafsa (CPG) et plus que cinquantenaire dans le
domaine de sa valorisation en divers engrais minéraux par le Groupe
Chimique Tunisien (GCT).
Le GCT, un des principaux groupes industriels en Tunisie,
compte quatre pôles industriels dont un des plus importants est
situé à Skhira ; ce pôle intègre une usine d'acide
phosphorique dont la fonction est de produire de l'acide phosphorique par un
procédé d'attaque par acide sulfurique.
La matière passe par plusieurs étapes de
transformation et nécessite des équipements fiables et
performants ; la modernisation et le remplacement de certains
équipements sont devenus une nécessité pour assurer des
cadences de production de plus en plus élevées.
C'est dans ce cadre que s'inscrit mon projet de fin
d'études qui consiste en l'élaboration d'un système
d'automatisme et de régulation d'une unité
d'aérocondenseur de vapeur d'eau en remplacement d'un condenseur de
vapeur à eau de mer.
Nous exposons dans le présent rapport quatre grands
chapitres décrivant les volets principaux de notre projet de fin
d'études :
Le premier chapitre englobera la présentation de
l'entreprise d'accueil où nous avons effectué l'étude, et
la présentation de l'entreprise cliente bénéficiaire du
projet.
Nous décrirons par la suite l'unité
d'aérocondenseur à implanter afin de pouvoir assimiler la suite
du travail. Un cahier des charges et un planning d'exécution feront le
guide d'enchainement des taches de ce projet.
Dans le deuxième chapitre, nous expliciterons le
principe de marche de l'équipement et les phénomènes
physiques régissant son fonctionnement ; une étude
thermodynamique soutiendra la démarche que nous avons adoptée.
Le troisième chapitre sera une description du
système de contrôle, commande et supervision ; nous y
présenterons son architecture et ses composants et nous traiterons les
blocs et diagrammes fonctionnels utiles lors de la phase de manipulation du
logiciel d'automatisme.
Le dernier chapitre de ce rapport (chapitre IV) traitera la
partie programmation de ce projet. Les étapes de la programmation de
l'unité d'aérocondenseur, qui fera l'objet de notre travail,
seront détaillées et expliquées et nous y décrirons
les ressources logicielles utilisées.
Chapitre I
PROBLEMATIQUE
&
PRESENTATION DE L'UNITE
D'AEROCONDENSEUR
Introduction
Dans ce premier chapitre, nous procéderons à une
présentation de l'entreprise d'accueil. Nous enchainerons par une
présentation des aérocondenseurs, puis une formulation du cahier
des charges.
En effet, nous commencerons par décrire
l'aérocondenseur en citant ses différents composants et en
décrivant son fonctionnement. Par la suite, nous présenterons les
différents systèmes de contrôle commande qui gèrent
le fonctionnement de l'aérocondenseur et nous ferons une description du
système choisi. Finalement, un cahier des charges suivi d'un planning
d'exécution détaillé sera exposé, tenant compte de
la problématique soulevée.
1 Présentation de l'entreprise d'accueil :
EPPM
EPPM, abréviation de Engineering Procurement &
Project Management, est une société anonyme fondée en
1993, elle offre des services d'Ingénierie, Approvisionnement, Gestion
de projet et opère pour réaliser des projets clés en main
dans le secteurs suivant :
· Traitement des eaux
- Traitement des eaux usées, - Traitement de l'eau
claire,
- Traitement des déchets solides, - Dessalement,
- Arrangement hydraulique.
· Pétrole & Gaz
- Centre de traitement de Pétrole - Centre de traitement
de Gaz
- Injection d'eau
- Injection de Gaz
- Pipelines
· Industrie
- Construction d'usines,
- Montage d'unités industrielles
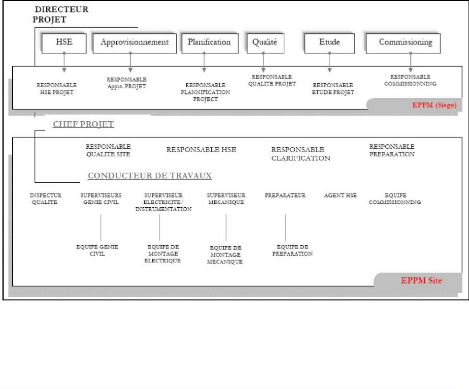
Figure 1 : Organigramme Projet EPPM
EPPM compte à son actif plusieurs
références en Tunisie et à l'étranger, notamment en
Nord Afrique. Ses prestations vont des études de bases et de
détails jusqu'aux projets clés en main. Elle offre plusieurs
services ; étude, approvisionnement, commissioning et pilotage de
projets.
EPPM regroupe plusieurs filiales répartis dans le
monde ; EPPM Algérie, EPPM Lybian branch, EPPM KSA branch, ENTRAC
international (management de projets), I2E (Ingénierie de
l'Environnement et de l'Energie) et EAM (étude d'impact sur
l'environnement et gestion des sites contaminés).
EPPM a mis en place des procédures de Management de
Projets conformément aux référentiels internationaux
incluant : ISO 9001 V2000, ISO 14001, OHSAS 18001.
A chaque Projet correspondent un PMP (Plan de Management Projet)
et des procédures spécifiques (lorsque nécessaire) sont
développées.
Chaque projet est organisé de la façon suivante
:
La société est considérée comme
un leader dans la réalisation de projets clés en main en Nord
Afrique et notamment en Algérie où elle est le principal
entrepreneur de la SONATRACH ; considérée comme le
12ème groupe pétrolier au niveau mondial et
3ème exportateur de gaz naturel. EPPM est une des principales
sociétés d'ingénierie et de réalisation en Tunisie,
elle a plusieurs projets en cours notamment pour le Groupe Chimique Tunisien
(GCT) ; pour lequel notre projet sera réalisé.
2 Présentation de l'entreprise ciente: GCT
Le Groupe Chimique Tunisien (GCT) est une entreprise publique
tunisienne dont l'objet est de produire et de transformer le phosphate extrait
en Tunisie en produits chimiques tels que l'acide phosphorique ou les
engrais.
Il résulte de la fusion d'entreprises opérant
dans les domaines de l'extraction du phosphate (Compagnie des Phosphates de
Gafsa) et de la transformation de celui ci (Société industrielle
d'acide phosphorique et d'engrais à Sfax, Industries chimiques
maghrébines à Gabès, Société arabe des
engrais phosphatés et azotés à Gabès, Engrais de
Gabès et Industrie chimique de Gafsa) entre 1992 et 1994. [1]

Figure 2 : Site du GCT à Skhira [1]
Ce groupe industriel, parmi les principaux du pays, exploite
le phosphate dont la Tunisie est le cinquième producteur mondial (huit
millions de tonnes en 2004). Ce phosphate est transformé dans quatre
pôles industriels du sud du pays. [1]
Si la production est concentrée dans le bassin minier
de Gafsa au niveau d'une dizaine de carrières à ciel ouvert
réparties sur cinq centres miniers (Gafsa, Métlaoui, Mdhila,
Redeyef et Moularès) , l'essentiel de sa transformation, à
l'exception d'une usine à Mdhila, est réalisée
dans des usines situées dans les zones
industrialo-portuaires de Sfax, Gabès et Skhira, sur le golfe de
Gabès.
Sfax possède la première usine de
transformation du phosphate, la SIAPE, inaugurée en 1952. Il s'agit
d'une usine produisant du TSP (Triple Super Phosphate) à partir de
l'acide phosphorique et ce par des procédés qui lui sont propres
sous la dénomination de « procédés SIAPE ». Elle
est située au sud de Sfax mais un programme de délocalisation est
lancé le 8 avril 2008, en raison de la pollution engendrée au
sein d'une zone urbaine. La NPK, autre usine implémentée juste
à côté du port commercial de Sfax a, quant à elle,
été fermée et son site fait l'objet d'un vaste projet de
dépollution (Projet Taparura). Sfax est également le port
d'exportation du phosphate brut du pays et le principal port pour l'exportation
des produits chimiques. Il possède un quai de 830 mètres pour un
bassin de 10 mètres de tirant d'eau, ce qui lui permet d'accueillir des
minéraliers de 35 000 tonneaux. La capacité journalière de
chargement peut atteindre 10 000 tonnes. [1]
Skhira possède une usine de production d'acide
phosphorique ainsi qu'un port en eaux profondes (tirant d'eau de 15
mètres).
3 Description de l'aérocondenseur
3.1 Définition
Certaines usines ou centrales de production
d'électricité sont équipées d'installations
utilisant de la vapeur d'eau et ont besoin de la condenser pour
réutiliser l'eau dans un circuit d'utilisation, la condensation de cette
vapeur se fait par différentes méthodes de refroidissement ; une
des méthodes les plus utilisées est le refroidissement dans un
appareil appelé aérocondenseur.
Les aérocondenseurs peuvent être employés
quand on veut utiliser l'air comme agent réfrigérant pour
condenser une vapeur qui doit rester contenue dans un circuit
étanche.
Ils se distinguent des aéroréfrigérants du
type sec indirect en ce sens que : [2]
· Dans les aéroréfrigérants,
l'eau (ou un autre fluide fonctionnellement équivalent), qui est
elle-même utilisée comme agent réfrigérant de la
vapeur à condenser dans un condenseur eau-vapeur est refroidit (le
système est dit « indirect » à cause du
circuit
d'eau intermédiaire entre l'atmosphère et le
condenseur) et il n'y a pas changement d'état du fluide à
refroidir;
· Dans les aérocondenseurs, la vapeur à
condenser est traitée sans agent intermédiaire (le système
est dit « direct ») et il y a changement d'état du
fluide à refroidir.
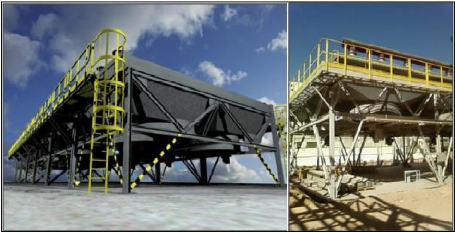
Figure 3 : Vue en 3D de l'aérocondenseur (gauche) et
aérocondenseur sur site (droite)
3.2 Principe de réalisation
Des tubes ailetés extérieurement, parcourus
intérieurement par la vapeur à condenser et extérieurement
par l'air atmosphérique, agent réfrigérant, sont
utilisés.
Le condensat est récolté en bas des tubes,
généralement repris par une pompe d'extraction et renvoyé
au circuit d'utilisation.
L'air qui circule à l'extérieur peut être
véhiculé soit par tirage mécanique, soit par tirage
naturel. La solution « tirage mécanique » (ventilateurs) a
toujours été celle utilisée jusqu'à ce jour, les
puissances thermiques évacuées s'étendant entre quelques
mégawatts et un maximum d'environ 1 000 MW. [3]
3.3 Justification d'emploi [2]
La raison fondamentale du choix d'un aérocondenseur,
tout comme d'un aéroréfrigérant, est l'absence
d'eau, d'où la demande du client de changer l'ancienne
installation fonctionnant à l'eau de mer.
Comparée à celle de
l'aéroréfrigérant (indirect), la mise en oeuvre de
l'aérocondenseur (direct) présente les autres avantages
suivants :
· Réduction de la surface d'échange et
réduction corrélative de la surface d'implantation. La figure 4
traduit le fait que, à égalité de températures air
et vapeur, l'écart moyen efficace est plus grand dans
l'aérocondenseur (figure 4a) que dans
l'aéroréfrigérant (figure 4b), cela résultant de ce
que le flux thermique est échangé une seule fois dans le
système direct, alors qu'il est échangé deux fois dans le
système indirect.
· Économie d'un circuit secondaire (condenseur,
canalisation, vannes et pompes de circulation).
· Facilités relatives d'exploitation :
v' Par sa conception (relativement faible inertie), le
système aérocondensation
permet une adaptation plus rapide de la charge aux conditions
atmosphériques ; v' Sécurité d'exploitation : le risque de
gel peut, facilement, être pratiquement
éliminé grâce à des dispositions
constructives, du fait que le condensat (fluide
froid) circule au contact direct du fluide chaud (vapeur).
Les inconvénients de
l'aérocondenseur restent de pure théorie car :
· La réalisation d'un appareil quasi
entièrement soudé permet de garantir une très haute
fiabilité en minimisant les risques d'entrée d'air pour les
appareils sous vide ;
· Les problèmes de corrosion interne
(consécutifs à des arrêts fréquents ou
prolongés) peuvent être résolus par des systèmes de
traitement d'eau, situés à la sortie des pompes d'extraction des
condensats.
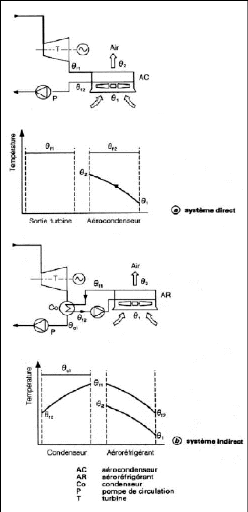
Figure 4 : Ecart de température à
l'aérocondenseur et à l'aéroréfrigérant
[2]
3.4 Réalisation
L'édification d'un aérocondenseur intègre
les éléments suivants :
· les éléments échangeurs de
chaleur : condenseurs
· les tuyauteries de liaisons (liaisons vapeur et
circuit de récupération des condensats) ;
· le dispositif de circulation d'air :
moto-ventilateur ;
· la charpente ;
· les auxiliaires (ballon condensats, pompes de
circulation) ;
· dispositif de mise sous vide, régulation et
contrôle, etc.
Le schéma de circulation des fluides est donné par
le P&ID dans l'annexe A pour l'aérocondenseur de vapeur d'eau.
3.4.1 Condenseurs principaux [2]
L'admission se fait en partie haute des tubes ailetés
et la vapeur circule dans le même sens que le condensat (de haut en bas),
ce dernier étant récupéré en partie basse des
éléments. Des faisceaux alignés contenants des tubes
à ailettes sont employés.
Les faisceaux tubulaires sont toujours inclinés,
disposition nécessaire pour assurer, à la fois,
l'écoulement des condensats et une bonne circulation de l'air à
travers les ailettes des tubes.
Les tubes à ailettes (figure 6) présents dans
les faisceaux d'échange ont pour fonction de favoriser le transfert de
chaleur par convection entre vapeur d'eau et air ; leurs principaux avantages
par rapport aux tubes nus sont leur importante surface d'échange et le
grand coefficient de conductivité des ailettes.
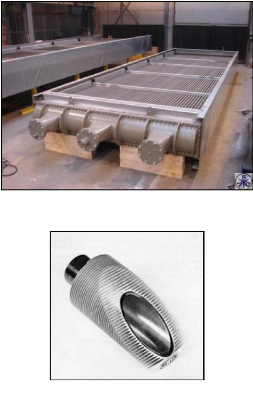
Figure 5 : Faisceaux d'échange
Figure 6 : Coupe du tube à ailette
3.4.2 Tuyauteries de liaisons [2]
· Liaison vapeur : Les performances de
l'aérocondenseur sont généralement garanties à la
liaison « générateur de vapeur » (bride
d'échappement de la turbine pour une centrale thermique, par exemple).
Le dessin de la liaison entre la bride d'échappement de la turbine et
l'entrée de l'aérocondenseur doit être étudié
avec beaucoup de soin afin de minimiser les pertes de charges : la distance
à l'aérocondenseur doit être la plus courte possible
(aérocondenseur placé sur le toit ou le long du bâtiment
turbine) ; la liaison doit comporter un minimum d'accidents (tels que coudes),
créant des pertes de charge singulières importantes ; les coudes
sont normalement équipés d'ailettes internes de guidage. Les
culottes de raccordement entre la canalisation principale et les lignes de
distribution de vapeur sur les éléments d'échange sont
exécutées avec un soin particulier.
Les canalisations vapeur sont réalisées en
tôles d'acier roulées et soudées. Elles sont
généralement soumises au vide et, de ce fait,
équipées de frettes pour éviter le flambage. Elles
sont, en outre, soumises à des efforts importants
d'origine thermique (dilatations) et mécanique (efforts sur les fonds) :
il y a lieu de minimiser les contraintes aux raccordements, notamment aux
brides d'échappement de la turbine. Le raccordement des liaisons vapeur
est généralement fait par soudure sur le site.
? Canalisation de condensât : Les canalisations de
condensats ne posent aucun problème particulier. Il y a lieu, cependant,
de respecter des conditions de vitesses d'écoulement faibles et
d'assurer des pentes permettant d'éviter l'engorgement de l'appareil.
Généralement, la structure de l'aérocondenseur n'est pas
prévue pour supporter l'installation pleine d'eau.
Le ballon est en principe réalisé à
partir de tôles roulées et soudées avec fonds
bombés. Le niveau d'eau est régulé en fonction du
débit de condensats, ce qui permet d'assurer un débit constant
sur les pompes d'extraction. De plus, tout danger de remplissage excessif ou de
vidange est évité par l'utilisation d'alarmes haute et basse
ramenées en salle de commande, permettant une intervention rapide.
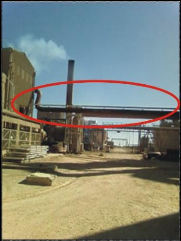
Figure 7 : Partie des canalisations de vapeur et de
condensât sur site 3.4.3 Circulation de l'air [2]
La circulation de l'air peut être assurée soit par
tirage naturel, soit par tirage mécanique. On note que la
quasi-totalité des aérocondenseurs construits à ce jour
sont à tirage mécanique, solution justifiée par le moindre
coût du dispositif. On utilise des ventilateurs axiaux, le plus souvent
à grands débits-volumes (hélices).
On peut noter les tendances suivantes :
Tirage forcé (figure 9a) :
· Avantages relatifs sur le tirage induit :
appareils plus compacts, simplicité de structure (réduction
de coût), accessibilité et mise en place/dépose des
ventilateurs plus facile ;
· Inconvénients relatifs : plus de
risques de recirculation d'air chaud, alimentation en air des faisceaux moins
régulière, et plus de risques d'avarie des faisceaux par
agressions verticales (par exemple, grêle) : protections souvent
nécessaires mais parfois aléatoires.
Tirage induit (figure 9b) :
· Avantages relatifs sur le tirage forcé :
très bonne répartition d'air sur les échangeurs,
influence de l'ensoleillement sur les échangeurs négligeable,
protection antigrêle inutile, et gain sur la puissance de ventilation
possible en ajoutant des diffuseurs (dont la mise en place est pratiquement
impossible en tirage forcé) ;
· Inconvénients relatifs : encombrement
plus important et structure du support plus lourde et plus chère.
La solution adoptée dans notre cas est le tirage
forcé.
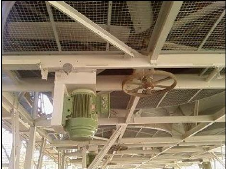
Figure 8 : Partie moto-ventilateur sur site
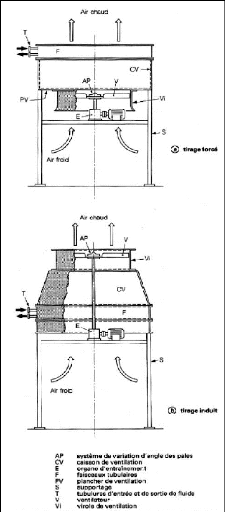
Figure 9 : Eléments composants d'un
aéroréfrigérant avec échangeurs en position
horizontale et ventilateurs dans deux positions : tirage forcé ou
induit [2]
3.4.4 Charpente
Son rôle essentiel est de supporter, en
surélévation, les éléments échangeurs et les
groupes moto-ventilateurs, et de permettre une alimentation correcte en air.
La charpente comprend les dispositifs suivants : [2]
· Support des échangeurs (condenseurs et
déphlegmateur) : cette charpente est constituée sur les
longs pans de l'installation par les cadres latéraux des faisceaux
condenseurs (éléments autoportants). L'ensemble des faisceaux et
des groupes motoréducteurs-ventilateurs est surélevé
au-dessus du plan de pose de l'appareil : la superstructure de
surélévation, comprenant une plate-forme horizontale au niveau
des ventilateurs, peut être réalisée soit
en béton, soit en charpente métallique ;
· Support des groupes moto-ventilateurs : les
supports sont réalisés en poutres en treillis, munies de
caillebotis et garde-corps. Un accès facile à l'ensemble des
groupes est ainsi réalisé. Chaque ventilateur tourne à
l'intérieur d'une virole généralement
réalisée en tôle d'acier (convenablement raidie) ou en
polyester. Cette virole comporte un convergent d'entrée (à
méridienne conique ou caliciforme) ;
· Accessoires : des échelles ou
escaliers d'accès sont prévus au niveau des groupes de
ventilation, des tôles d'étanchéité sur pignons,
entre cellules et au niveau du plancher supérieur de ventilation, et des
accessoires tels que serrurerie, rails de manutention, échelles
permettant le nettoyage des faisceaux, dispositifs antigrêle, murs de
protection périphérique, etc. La protection de la charpente peut
être faite par peinture après sablage ou par galvanisation
à chaud au bain.
3.4.5 Les auxiliaires
Il s'agit essentiellement des pompes de reprise des
condensats, de la régulation sur ballon, des éjecteurs, des
organes annexes d'extraction des purges sur la ligne de liaison turbine et des
organes de sécurité.
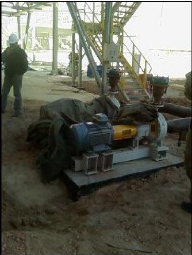
Figure 10 : Pompes retour condensât sur site
3.5 Perspectives et limites à l'utilisation des
aérocondenseurs
La grande majorité des aérocondenseurs
installés à ce jour sont de taille relativement modeste
(unités de l'ordre de 30 MW), mais leur mode de réalisation
(succession de cellules identiques équipées de groupes de
ventilation dont la conception est parfaitement maîtrisée du point
de vue mécanique et des performances) autorise actuellement une
extension vers des puissances électriques élevées de
l'ordre de 600 MW. [2]
Dans beaucoup de cas où le système sec est
nécessaire (absence d'eau totale ou coûts prohibitifs de pompage),
l'aérocondensation (système direct) peut s'imposer en raison de
ses coûts d'investissement et d'exploitation inférieurs à
ceux du système indirect et de sa souplesse de fonctionnement. Il faut
cependant être extrêmement prudent dans tous les cas, lors de la
conception de l'appareil, et, notamment, tenir compte très
sérieusement des problèmes de fonctionnement à basse
charge et à très basse température.
Les problèmes de corrosion atmosphérique sont
maîtrisés par utilisation de surfaces d'échange
judicieusement choisies. La taille des canalisations de liaison à la
turbine (tenue mécanique et tenue au vide) peut constituer une limite
à l'escalade de puissance actuellement constatée.
4 Les instruments de mesure
L'aérocondenseur contient plusieurs transmetteurs et
interrupteurs, ils sont présentés comme suit :
4.1 Les transmetteurs de pression
Deux transmetteurs de pression sont implémentés
dans l'unité de l'aérocondenseur ; en amont PT002 et relié
avec le PIC (Pressure Indicator Controller), en aval PT001 et relié avec
un PI (Pressure Indicator).

Figure 11 : Transmetteur de pression ROSEMOUNT 2088
Leurs caractéristiques :
Mesure de pression: 0-30 psi (0-2,1 bar) 1,5 psi (103,0 mbar) 30
psi (2,1 bar)
Type: Piézo-électrique Type de pression: relative
Calibration: 0-1,6 barg
Sortie: 4-20 mA avec protocole HART
4.2 Les transmetteurs de température
Deux transmetteurs de température sont
implantés dans l'unité de l'aérocondenseur ; en amont
TT002 et relié avec le TI (Temperature Indicator), en aval TT001 et
relié avec un TIC (Temperature Indicator Controller).
Caractéristique :
Type: Sonde à résistance, Pt 100 Ohm
Calibration : 0-200°C
Sortie: 4-20 mA avec protocole HART
4.3 Le transmetteur de niveau
Un transmetteur de niveau LT001 est implanté dans le
ballon à condensât pour contrôler le niveau d'eau dans le
ballon et actionner les pompes retour condensât.
Caractéristique :
Type : Capteur de niveau à pression
différentielle
Mesure de niveau : 0-1,8 m
Sortie: 4-20 mA avec protocole HART
4.4 Les interrupteurs de vibration (vibroswitch)
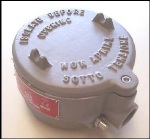
Figure 12 : Vibroswitch
Ils sont au nombre de 10 et servent à détecter
toute vibration excessive dues à un fonctionnement impropre de la
machine. Lors d'un déclenchement de l'interrupteur de vibration, le
moteur devra être automatiquement stoppé.
5 Systèmes de contrôle commande de
l'aérocondenseur
Les systèmes de contrôle commande sont divers et
différents dans l'industrie.
La modernisation remarquable de ces systèmes laisse
apparaître de nouvelles technologies de commande qui permettent de mieux
gérer les process industriels devenus de plus en plus complexes.
Parmi les systèmes de contrôle commande les plus
courants, et s'intégrant dans la logique programmée, on cite :
5.1 Le système de contrôle commande par
PLC
Ce type de système de contrôle commande est basique
et simple d'utilisation.
Le PLC (Programmable Logic Controller), qui représente
le cerveau de la commande, est programmé en tenant compte des
entrées logiques et analogiques qu'il reçoit via ses modules
d'entrées. Après exécution du programme
implémenté dedans, il reçoit les commandes
adéquates via les modules de sorties vers les différents
actionneurs et préactionneurs équipant les machines à
piloter.
Son inconvénient majeur est l'absence d'une interface de
supervision permettant un contrôle visuel par l'opérateur dans la
salle de contrôle du processus industriel.
5.2 Le système de contrôle, commande et
supervision SCADA
Ce type de logique programmée est basé sur des
PLCs, la supervision SCADA (Supervisory Control And Data Acquisition) est une
solution très performante pour la commande des systèmes
industriels complexes.
Le poste opérateur intègre une interface
utilisateur permettant à l'opérateur de superviser la machine
à partir d'un tableau de bord virtuel comportant des boutons, des
voyants, des alertes et toutes les données dont il a besoin pour la
prise de décision. L'ensemble PLC/HMI (Interface Homme Machine) forme ce
qu'on appelle le SCADA.
Bien entendu, le SCADA peut comporter plusieurs PLCs qui sont
extensibles en plusieurs modules d'entrées/sorties. Il présente
une souplesse et une adaptabilité dans son installation puisque les
fonctions logiques sont toutes rassemblées en un seul programme qui peut
être aisément modifié.
5.3 Le système de contrôle, commande et
supervision DCS
Le système de contrôle commande DCS
(Systèmes de Commande Distribuée), développé au
début des années 70, ressemble en grande partie au SCADA. Sauf
que ce dernier est destiné pour gérer des processus plus
étendus et plus complexes.
La principale différence entre un DCS et un SCADA
réside essentiellement dans la nature de l'architecture et la
criticité du process supervisé. En effet le DCS gère
beaucoup plus rapidement le transfert de données et se distingue par un
temps de réponse remarquable.
Le DCS présente une architecture très
organisée qui empêche toutes sortes de conflits et de collisions
de données.
Ses contrôleurs sont reliés entre eux via un
réseau Profinet pour échanger des données
partagées. Chaque contrôleur est doté de modules
d'entrées/sorties qui lui sont propres via lesquels il communique avec
le système.
Il est vrai que de nos jours, suite au développement
des PLCs, plusieurs caractéristiques qui étaient propres au DCS
deviennent disponibles sur le système SCADA, on ne distingue plus de
différences entre les deux technologies de commande.
6 Cahier des charges et planning
d'exécution
EPPM a été sollicitée pour la
conception, la fourniture, la réalisation, le montage et la mise en
service d'un aérocondenseur de vapeur en remplacement du condenseur de
vapeur à eau de mer des utilités chaudes de l'usine SKHIRA du
GCT.
Dans ce qui suit nous allons présenter le cahier des
charges et le planning d'exécution regroupant les tâches à
exécuter.
6.1 Cahier des charges
L'objet de ce projet est l'étude des paramètres
thermodynamiques de l'aérocondenseur, d'élaborer des
séquences de fonctionnement en fonction de ces paramètres, de
collecter et développer la documentation technique nécessaire
pour l'établissement du programme d'automatisme, développer ce
programme et le simuler.
Cette étude doit satisfaire à plusieurs exigences
qui ont été fixées par les cadres techniques du GCT.
Les spécifications suivantes doivent êtres prises
en considération lors de l'élaboration du projet :
· Sécurité et haut niveau de fiabilité
sont de prime lors des phases étude et conception.
· La solution doit être flexible, optimisées
de point de vue câblage et facilement maintenable.
· Un moyen de supervision performant, pratique et
instinctif doit être inclus.
· Le système doit être extensible et
aisément modifiable par les techniciens du GCT.
· En cas de panne du système de contrôle, les
organes pourront êtres commandés manuellement.
· En cas de défaillance de l'automate principal,
l'automate secondaire prendra le relais sans perturber le fonctionnement de
l'aérocondenseur.
· Un logiciel de collecte et de traitement de
données compatible MODBUS doit être fourni.
Le client exige :
· Un dossier technique complet comportant les
différentes spécifications techniques détaillées
des composants de l'aérocondenseur et de la tuyauterie, le dossier des
divers plans et schéma (plan d'ensemble, plans d'isométries...)
et nomenclatures et certificats des différents composants.
· La garantie des performances techniques de
l'installation.
6.2 Planning d'exécution
Les principales étapes du projet sont :
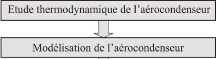
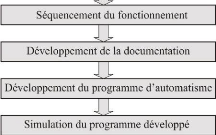
Figure 13 : Etapes du projet
· L'étude thermodynamique de l'unité
d'aérocondenseur : Comprendre et assimiler les phénomènes
physiques qui régissent le fonctionnement de l'équipement.
· La modélisation thermodynamique de
l'aérocondenseur : Elaborer une approche relationnelle des
paramètres de fonctionnement.
· L'établissement des séquences de
fonctionnement de l'aérocondenseur : Planifier des séquences pour
la mise en marche des différents composants de l'équipement de
manière optimale et efficace.
· La collecte et le développement de toute la
documentation technique nécessaire pour l'établissement du
programme d'automatisme.
· Le développement du programme d'automatisme :
Réaliser un programme d'automatisme à implanter dans
l'automate pour piloter l'unité d'aérocondenseur.
· La simulation des programmes développés
selon les procédures d'acceptation en usine préparées dans
le cadre de la documentation technique.
Conclusion
Après avoir décrit le contexte
général de ce projet et présenté les attentes du
client, nous allons adopter le planning d'exécution établi pour
procéder à la réalisation de ce projet et à remplir
toutes les exigences du cahier des charges.
Le chapitre qui va suivre aura pour objet l'étude
thermodynamique et la mise en oeuvre de l'aérocondenseur.
Chapitre II
ETUDE THERMODYNAMIQUE
&
MISE EN OEUVRE
Introduction
L'unité d'aérocondenseur de l'usine d'acide
phosphorique est actuellement en cours d'installation, l'élaboration du
système d'automatisme nécessite une étude approfondie et
la mise en place d'étapes de marche.
Dans ce chapitre, nous allons expliciter le principe de
fonctionnement de l'aérocondenseur, étudier l'équipement
de point de vu thermodynamique et nous allons définir les
séquences de fonctionnement.
1 Principe de fonctionnement
Fonction de l'aérocondenseur : Condenser de la vapeur
d'eau saturée et atteindre une capacité de condensation de 100
T/H.
La vapeur d'eau saturée à condenser provient de 3
points regroupés dans une seule conduite :
· Echappement de la turbine du groupe turbo-alternateur
:
Débit : 3 - 30 T/H
Pression : 1 - 1,4 bar
Température : 105 - 140 °C
· Circuit de détente 3/1,2 bar : Débit : 0 -
30 T/H
Pression : 1,2 bar
Température : 120 - 150 °C
· Unités de production :
Débit : 0 - 100 T/H
Pression : 1 - 1,2 bar
Température : 120 - 150 °C
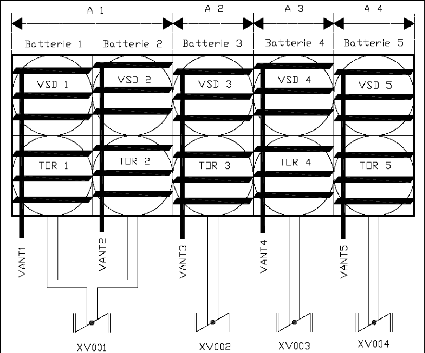
Figure 14 : Schéma représentatif de
l'aérocondenseur
VSD : Ventilateur avec variateur de vitesse TOR :
Ventilateur sans variateur de vitesse VANT : Vantelle (volet)
XV00.. : Vanne Tout Ou Rien
La vapeur d'eau est acheminée dans une conduite vers
l'aérocondenseur, ce dernier contient cinq batteries ; chaque batterie
contenant deux ventilateurs (un fonctionnant avec variateur de vitesse VSD
(Variable Speed Drive) et l'autre fonctionnant sans variateur de vitesse TOR
(Tout Ou Rien)).
Quatre vannes XV Tout Ou Rien laissent passer la vapeur dans les
faisceaux d'échange, ces vannes ont été placées
selon des paliers définis ultérieurement.
La vanne XV001 fait passer la vapeur dans deux batteries, les
autres vannes (XV002. XV003 et XV004) font passer la vapeur dans une batterie
chacune.
La vapeur passe dans les faisceaux d'échange contenant
les tubes à ailettes, les ventilateurs soufflent de l'air dans ces
faisceaux et la condensation se fait.
L'eau condensée est collectée dans le ballon
à condensât puis refoulée vers la bâche à
condensât grâce aux deux pompes situées en aval du
ballon.
Des vantelles (volets) situées au dessus des faisceaux
et commandées par des vérins pneumatiques assurent le maintien en
température des échangeurs ; elles sont refermées lorsque
le débit de vapeur est assez faible et ouverts pour permettre
l'extraction de chaleur.
Un débit de vapeur d'eau de maintien en
température des faisceaux est injecté pour éviter les
chocs thermiques (du fluide chaud ne peut pas être brusquement introduit
lorsque l'appareil est froid, ni du fluide froid lorsque l'appareil est chaud).
Cette vapeur ne passe pas par les vannes ; elle est acheminée à
travers des conduites de diamètre réduit (50-SLS-2133- 007-2A3
dans le P&ID annexe A)
Ce débit de vapeur qu'on va appeler débit de
maintien Qm est fixé comme suit :
Qm = 2% du débit nominal de vapeur Q si
la température ambiante est supérieure à 0°C ; soit
Qm = 2 T/H. (consigne constructeur)
Qm = 10% du débit nominal de vapeur Q
si la température ambiante est inférieure à 0°C
; soit Qm = 10 T/H, et cela pour assurer le non gel dans les tubes.
Dans ce cas les vantelles doivent êtres fermées.
Si le débit de vapeur Q I? ~m ; les persiennes sont
ouvertes progressivement, et, à 100%
d'ouverture, le refroidissement se fait par les ventilateurs.
2 Paliers de fonctionnement
L'aérocondenseur devra pouvoir fonctionner selon les
paliers suivants :
Paliers 1 : débit entre 0 et 50 T/II
La pression correspondante est entre 0 et 0,6 bar
Palier 2 : débit entre 50 et 75 T/II
La pression correspondante est entre 0,6 et 0,8 bar
Palier 3 : débit entre 75 et 100 T/II
La pression correspondante est entre 0,8 et 1 bar
Palier 4 : débit supérieur à 100 T/h
La pression correspondante est supérieure à 1
bar
Pour savoir les pertes de charges "II" correspondantes à
chaque palier, nous avons eu recourt à une application de calcul des
pertes de charges développée par
CARF-Engineering.com
(site spécialisé dans les calculs hydrauliques), il suffit
d'entrer le diamètre de la conduite, sa rugosité, sa longueur,
son élévation et les coudes présents.
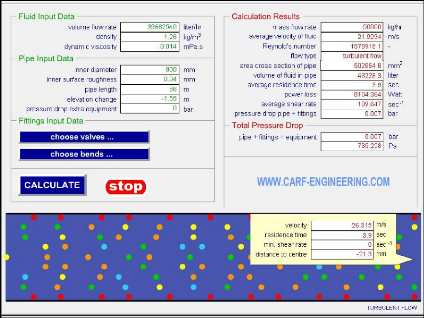
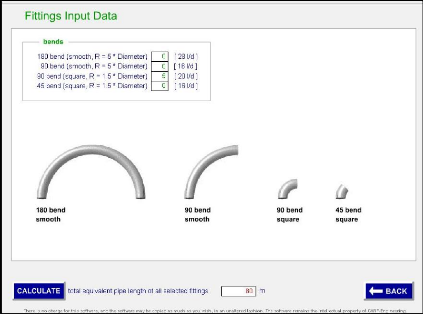
Figure 15 : Interface de l'application de calcul de pertes de
charges
Nous avons dégagé les pertes de charges comme
suit :
Débit (T/II)
|
50
|
75
|
100
|
120
|
Pertes de charge "II" (bar)
|
0,007
|
0,016
|
0,028
|
0,04
|
|
Tableau 1: Pertes de charges dans les conduites
3 Démarche
Le schéma suivant représente un diagramme
T, P contenant les trois courbes d'équilibre solide-gaz ou
courbe de sublimation, liquide-vapeur ou courbe de vaporisation, liquide-solide
ou courbe de fusion.
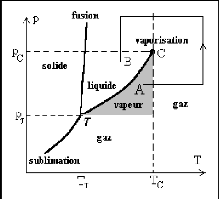
Figure 16 : Diagramme Température, Pression [4]
La frontière entre la zone A (vapeur) et la zone B
(liquide) est appelée courbe de rosée, c'est la limite
d'apparition des premières gouttes de liquide.
Pour savoir s'il y a condensation, nous allons mesurer la
pression et la température en sortie des faisceaux et la comparer
à des valeurs expérimentales de condensation de vapeur d'eau
saturée.
Notons que le prélèvement de température
et de pression doit se faire à la sortie des faisceaux; deux couples de
transmetteurs (Pression et Température) se trouvent en amont et en aval
de l'aérocondenseur.
Pour ce faire, nous allons utiliser le tableau dans l'annexe
B;
Il représente les caractéristiques de la vapeur
d'eau saturée ; ces valeurs ont été obtenus
expérimentalement et ne sont régis par aucune équation
;
Pour pouvoir facilement exploiter les données du
tableau, nous avons procéder comme suit :
· On trace les courbes de variation des différents
paramètres en fonction de la pression avec le logiciel MATLAB.
· On interpole avec la fonction "Basic Fitting".
· On détermine les équations correspondant
aux courbes tracées.
Ces équations nous permettrons de trouver, par exemple,
pour des pressions données, les températures, les masses
volumiques et les chaleurs massiques.
3.1 Courbe et équation de T = f(P)
Nous avons décomposé la plage de pression en 3
intervalles puisque l'interpolation n'est pas parfaite :
Pression entre 0,02 et 0,1 bar / Pression entre 0,1 et 0,6 bar /
Pression entre 0,6 et 2 bar
Coubre 1 ;
Pour une pression entre 0,02 et 0,1 bar Equation:
T = 2,4.104P3 -
7.103P2 + 8,9.102P + 2,9
|
(1)
|
|
|
|
Figure 17 : T = f(P) [0,02-0,1]
|
|
|
|
|
|
|
Courbe 2;
Pour une pression entre 0,1 et 0,6 bar Equation :
(2)
T = -2,1.102P4 +
5,2.102P3 - 4,9.102P2 +
2,5.102P + 25
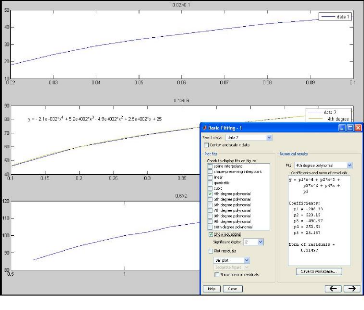
Figure 18 : T = f(l) [0,1-0,6]
Courbe 3 ;
Pour une pression entre 0,6 et 2 bar Equation:
(3)
~ = -9,8P5 + 55P' - 1,1.10 + 81P2 + 24P +
60
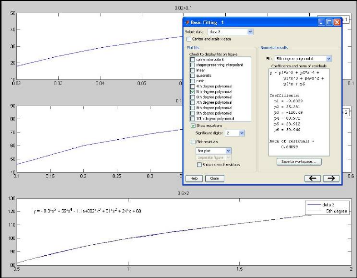
Figure 19 : T = f(P) [0,6-2]
3.2 Courbe et équation de p = f(P)
Equation:
ñ = 0,012P - 0,061P2 + 0,64P + 0,0042
|
(4)
|
|
|
|
Figure 20 : p = f(P) [0,02-2]
|
|
|
|
|
|
|
3.3 Courbe et équation de chaleur massique de
vapeur : ~~ = ~(~)
Nous avons décomposé la plage de pression en 3
intervalles puisque l'interpolation n'est pas parfaite :
Pression entre 0,02 et 0,1 bar / Pression entre 0,1 et 0,6 bar /
Pression entre 0,6 et 2 bar
(5)
(6)
Courbe 1 ;
Pour une pression entre 0,02 et 0,1 bar Equation :
~~ = 3,5. 106P5 -
1,2.106/4 + 1,8.105P3 -
1,4.10P2 + 9,4.102P + 1,847.10
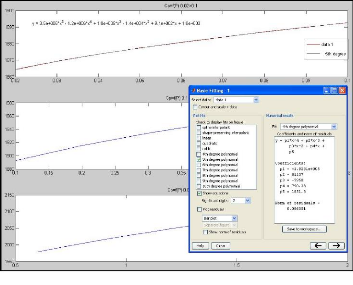
Figure 21 : Cp = f(P) [0,02-0,1]
Courbe 2;
Pour une pression entre 0,1 et 0,6 bar Equation:
~~ = -1,1. 10 + 2,5.102P + 1,87.103
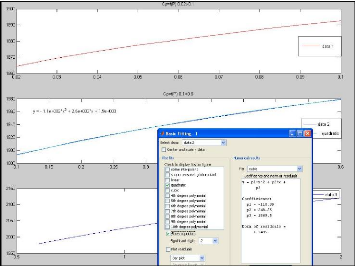
Figure 22 : Cp = f() [0,1-0,6]
Courbe 3;
Pour une pression entre 0,6 et 2 bar
Equation:
Cp = 6,1 p - 39p2 + 1,7. 102p + 1,89.
10
|
(7)
|
|
|
|
Figure 23 : Cp = f() [0,6-2]
|
|
|
|
|
|
|
4 Etapes de fonctionnement
Pour assurer un fonctionnement nominal de
l'aérocondenseur, on procède comme suit :
Une vanne XV est ouverte, on cherche l'intervalle
d'emplacement de T = ~ (~ - ~) (entre
0,02 et 0,1 bar / entre 0,1 et 0,6 bar / entre 0,6 et 2 bar).
La régulation se fait sur la température de sortie
de l'eau en fonction de la pression;
Pour chaque intervalle ; T = ~(~ - ~)
· Si T - ~ (~ - l) > 0 ; il n'y pas condensation de
vapeur d'eau donc on augmente la
capacité de refroidissement (définie dans le
paragraphe §II.5.1) jusqu'à ce que
T - Y (P - 1) = 0 .
· Si T - ~( I - 1) < 0 ; il y'a condensation de la
vapeur d'eau, on diminue la capacité
de refroidissement jusqu'à T - ~( r - l) = 0.
4.1 Etape 1
On fixe un débit Qm comme définit
ci-dessus, toutes les vantelles sont fermées, la Vanne XV001 est ouverte
et le fonctionnement se fait dans le 1er palier, la vapeur avec un
débit Q et une pression P (PT002) est injectée, on
relève la température T en sortie (TT001), on cherche
l'intervalle de T = ~(P - ~) et on compare si l'équation
T - Y( ~ - 1) avec 0 ;
· Si T - Y( - 1) < 0 ; on laisse les vantelles 1,2,3,4,5
fermées.
· Si T - Y( - 1) > 0 ; on ouvre les vantelles 1 et 2
(VANT 1 et VANT 2)
progressivement tout en contrôlant si T - ~( ~ + ~) =
0.
Le seuil est atteint ; si T - Y( P - 1) < 0 on ferme les
vantelles tout en continuant à
contrôler T = ~(P - l).
Lorsque les vantelles VANT 1 et 2 sont totalement ouvertes, et
T - ~( r - i) > 0,
on actionne simultanément les ventilateurs TOR 1 et 2 et
on continu à contrôler T = P( -
W) ; si T - ~( r - i) > 0, on actionne les ventilateurs VSD 1
et 2 à 40%, si la capacité
de refroidissement définit dans
§5.1 chapitre II doit être augmentée on
augmente la cadence de VSD 1 et 2 jusqu'à arriver à 100%.
Les 4 ventilateurs du 1er palier fonctionnement
à 100%, T - ~( ~ - l) < 0, on
diminue VSD 1 et 2 jusqu'à arriver à 40%, on coupe
les TOR 1 et 2. Arrivé à l'arrêt des ventilateurs on
referme progressivement les vantelles VANT 1 et 2.
4.2 Etape 2
Le 2ème palier est atteint, XV001 et XV002
sont ouvertes.
TOR 1 et 2, VSD 1 et 2 marchent à leur cadence nominale,
VANT 1 et 2 ouvertes à 100%.
On cherche l'intervalle de T = f(~ - l) et on compare
l'équation T - y( r - l) avec 0.
· Si T - ~( r - l) < 0 ; on laisse VANT 3
fermée.
· Si T - ~( r - l) > 0 ; on ouvre VANT 3 progressivement
tout en contrôlant si
T - ~( r - l) = 0.
Le seuil est atteint ; si T - y( p - i) < 0 on ferme VANT 3
tout en continuant à
contrôler T = f(~ - ~).
Lorsque VANT 3 est totalement ouverte, et T - ~( r - 1) > 0,
on actionne le
ventilateur TOR 3 et on continu à contrôler T =
f( - ~) ; si T - ~( r - l) < 0, on
augmente la capacité de refroidissement définie
dans §5.1 paragraphe II en augmentant la cadence de VSD 3
jusqu'à arriver à 100%.
Les 6 ventilateurs du 2er palier fonctionnement
à 100%, T - ~( ~ - l) < 0, on
diminue VSD 3 jusqu'à arriver à 40%, on coupe le
TOR 3. Arrivé à l'arrêt du VSD 3 on referme progressivement
VANT 3 et on passe au 1er palier.
4.3 Etape 3
Le 3ème palier est atteint, XV001, XV002 et
XV003 sont ouvertes.
TOR 1, 2 et 3, VSD 1,2 et 3 marchent à leur cadence
nominale, VANT 1, 2 et 3 ouvertes à 100%.
On cherche l'intervalle de T = f(~ - l) et on compare
l'équation T - y( r - l) avec 0.
· Si T - ~( r - l) < 0 ; on laisse VANT 4
fermée.
· Si T - ~( 2 - 1) > 0 ; on ouvre VANT 4
progressivement tout en contrôlant si
T - ~( 2 - l) = 0.
Le seuil est atteint ; si T - y( p - i) < 0 on ferme VANT 4
tout en continuant à
contrôler T = ~(P - ~).
Lorsque VANT 4 est totalement ouverte, et T - ~( r - 1f) >
0, on actionne TOR 4 et
on continu à contrôler T = ~(P - ~) ; si T - ~( r
- l) < 0, on augmente la capacité
de refroidissement définie dans
§5.1 paragraphe II en augmentant la cadence de VSD 4
jusqu'à arriver à 100%.
Les 8 ventilateurs du 3ème palier
fonctionnement à 100%, T - ~( ~ - l) < 0, on
diminue VSD 4 jusqu'à arriver à 40%, on coupe le
TOR 4. Arrivé à l'arrêt du VSD 4 on referme progressivement
VANT 4 et on passe au 2ème palier.
4.4 Etape 4
Le 4ème palier est atteint, XV001, XV002,
XV003 et XV004 sont ouvertes.
VSD 1, 2, 3 et 4, TOR 1, 2, 3 et 4 marchent à leur
cadence nominale, VANT 1, 2, 3 et 4 ouvertes à 100%.
On cherche l'intervalle de T = ~(P - 1) et on compare
l'équation T - y( r - 1) avec 0.
· Si T - ~( r - i) < 0 ; on laisse VANT 5
fermée.
· Si T - ~( r - l) > 0 ; on ouvre VANT 5 progressivement
tout en contrôlant si
T - ~( r - l) = 0.
Le seuil est atteint ; si T - y( p - i) < 0 on ferme VANT 5
tout en continuant à
contrôler T = ~(P - ~).
Lorsque la VANT 5 est totalement ouverte, et T - ~( r - 1f)
> 0, on actionne le
TOR 5 et on continu à contrôler T = ~(P - ~) ; si
T - ~( 2 - 1) < 0, on augmente la
capacité de refroidissement définie dans
§5.1 paragraphe II en augmentant la cadence de VSD 5
jusqu'à arriver à 100%.
Les 10 ventilateurs du 4ème palier
fonctionnement à 100%, T - ~( r - i) < 0, on
diminue VSD 5 jusqu'à arriver à 40%, on coupe TOR
5. Arrivé à l'arrêt du VSD 5 on referme progressivement
VANT 5 et on passe au 3ème palier.
5 Etude thermodynamique
L'aérocondenseur, appartient à la famille des
réfrigérants secs (refroidissement avec changement
d'état). Cet appareil est à tirage forcé. [5]
L'échange est réglé uniquement par les lois
du transfert de chaleur par convection.
(8)
(9)
(10)
(11)
(12)
La chaleur "Q" dans un fluide subissant un changement
d'état : [6]
Q = n . Lc
La puissance de condensation de vapeur d'eau :
Pt = ~sensib1e + ~1atente
Avec :
'sensib1e = Thp . CP~ .?T
?T = ~entré~ - ~sortie
'1atente = ~~ . ~~
Puissance sensible : C'est la puissance qui modifie la
température d'une matière.
Puissance latente de condensation : C'est la puissance
nécessaire pour passer de l'état gazeux à l'état
liquide.
Pour avoir condensation, on extrait la quantité de chaleur
de vaporisation présente dans la vapeur d'eau.
Pour un débit donné, pression donnée ; on
calcule la puissance totale Pt.
Exemple :
Pour un débit (m) de 50 T/h 13,88 Kg/s et une
pression de 0,6 bar
On a Cpv = 1,979.103 J/Kg et
Tsortie = Tcondensation = Tévaporation = 86°C Supposons que la
température d'entrée de vapeur = Tmax = 150 °C
Lc = Lv = 2293,64.103 J/Kg
Pnsibie = 13,88 × 1,979.103
× (150 - 86) = 1,757985 MW
Piatente = 13,88 ×
2293,64.103 = 31,835723 MW
Pour ce palier, il faut extraire environ 34 MW de quantité
de chaleur de la vapeur d'eau pour avoir condensation.
5.1 Expression du flux de chaleur échangé
dans un ventilateur
Les caractéristiques données par le constructeur
sont valables pour un point de fonctionnement donné (annexe C); par
conséquent, nous sommes dans l'obligation de faire une étude
thermodynamique sur notre échangeur (échangeur de chaleur
croisé à tubes à ailettes).
Notre échangeur présente 4 rangs de tubes, et ainsi
il est possible de le considérer comme un échangeur
contre-courant pur.
Loi de Newton :
(13)
(14)
cp = h .S .ATm
5.1.1 Détermination de la surface
d'échange S [7]
S totale (donnée constructeur) pour 10 faisceaux
= 45678 m2
Chaque ventilateur contient un seul faisceau donc S = ~
t°tale
to
5.1.2 Détermination de la moyenne logarithmique
des différences de températures ?Tm
ATm =
|
ATs -- ATe
|
(15)
|
Ln (ATs)1
ATe
|
Avec ?Te = T vapeur en entrée - T air en sortie ?Ts = T
eau en sortie - T air en entrée
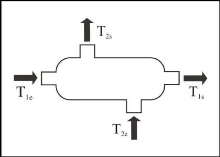
Figure 24 : Echangeur contre-courant
5.1.3 Détermination du coefficient
d'échange global h [7]
(16)
1-1
h= [( 1 + Ri) Se + Se de 1I
Ln + R+ e
hi ) Si 2T A I di Tighe
· hi : Coefficient d'échange
intérieur du tube à ailettes
Nus A
(17)
hi =
di
Avec :
(19)
Nus = 0,0243 Re°,9 Prn ; nombre de
Nusselt
Re = ñ W D ; nombre de Reynolds (19)
u
u Cp
Pr =
|
; nombre de Prandtl
|
(20)
|
V = 37.9 m/s
di = 23,29 .10-3 m
u = 0,000012 Kg/m.s
A = 60 W/m.K (voir annexe D)
n = 0,3 (dans le cas d'un refroidissement)
· Ri = 0,00017 m2.K/W
(donnée constructeur, voir annexe C)
· Se : surface d'échange extérieure
des tubes sans ailettes Se totale (donnée constructeur) = 1971
m2
Se =
· Si : surface d'échange
intérieure
|
1971
|
= 197,1 m2
|
|
|
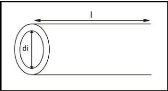
Figure 25 : Coupe longitudinale du tube sans ailettes
Chaque ventilateur contient un faisceau et chaque faisceau
contient 206 tubes.
(22)
(23)
(24)
di
Si = 206 × 2ir
lITI 206 × ir di li
2I
Si = 206 × ir × 23,29.10-3 × 12,192 =
183,77 m2
· l : longueur des tubes
l = 206 × 12,192 = 2511,552 m
· de : diamètre extérieur du tube
(de = 25,4.10-3 m)
· rig:
efficacité globale de la surface à ailettes 0 < ig
< 1
Sas
çg = 1 -- (1 -- çf Sa
çf =
|
Tanh(æ lac)
|
æ lac
|
æ = j2
|
he
2...a ~a
|
(25)
|
lac = 0,5 de (i9a* -- 1)[1 + 0,35 iiin
(i9a* )] (26)
(27)
Da
Da* 1= 1
1ie
/ac = 0,5 × 25,4.10-3 × (1,25 - 1)[1 + 0,35
× tn (1,25)] = 3,42.10-3 m
* 311175
Da = 25,4 = 1,25
(28)
æhe
=l 1\12
380 × 0,0004
Da : diamètre de l'ailette (Da =
31,75.10-3 m)
6a : épaisseur de
l'ailette (äa = 0,4.10-3 m)
Sas : surface d'échange des ailettes seules par
mètre de tube
(30)
11-
Sn = 11-.2 = 4 . 1i2 = 7,92.10-4 m2
On a 433 ailettes par mètre de tube ;
Sas = Sn × 433 = 0,343 m2
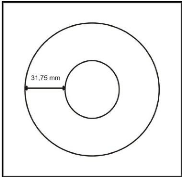
Figure 26 : Profil de l'ailette
Sa: surface d'échange du tube avec ailettes par
mètre de tube
Sa totale = 45678 m2
On a 10 faisceaux, chaque faisceau contient 206 tubes et chaque
tube mesure 12,192 m ;
donc ;
( 10 × 206 × 12,192) = 1,819 m2
Sa totale
Sa =
· he : coefficient d'échange par
convection à extérieur du tube à ailettes pour un faisceau
aligné
he = 0,67 ~e (30)
he : coefficient d'échange par
convection à extérieur du tube à ailettes pour un faisceau
en quinconce.

ilp 011633 1
he = I 029 Rep - Prp3If
de s
(31)
Sa
S
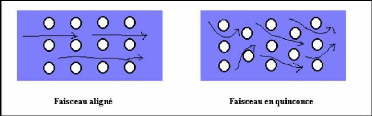
Figure 27 : Types d'écoulement autour d'un faisceau de
tubes
Rep = I _ ; nombre de Reynolds coté air
uF.ginax
IMF. (32)
n = 2 0l04 m ; longueur caractéristique de
l'écoulement
2 (33)
U13111nax ILI ; vitesse de l'air dans le faisceau
F3-1 ma
l ptntPP (34)
a air ×Cp airi
Pr =
= 0,708 ; nombre de Prandtl pour l'air
A air
l-o1r
(35)
ëp = 380 W/m.K (voir annexe D) de = 25,4
.10-3 m
Pt = 55.10-3 m
nt = 51,5
pp = 1,2 Kg/m3
Up = 15,6 .10-6 m2/s
u air = 1,8.10-5 Kg/m.s Cp air =
1000 J/Kg Aair = 0,0262 W/m.K
Détermination de A : Dans notre caste
Pt* =I 1/ =I
23513: =1 2,5 > 1
Donc
|
A = 1
|
n-
|
(36)
|
Avec ;
|
|
|
Pt 55
Pt* =M = = 2I16
Ode 25E4
|
(37)
|
Donc
|
A = 1 --
|
n-
|
0,64
|
|
× 2,16
|
· Re = 0,0002
m2.K/W (selon le standard TEMA)
5.1.4 Recapitulation
L'étude effectuée nous permet d'élaborer un
algorithme de calcul de chaleur dissipée (extraite) en fonction des
variables suivantes :
T1e : Température de la vapeur d'eau en
entrée
T1s : Température de l'eau en sortie
p : masse volumique de la vapeur d'eau
Cp : Capacité calorifique ou chaleur massique de
la vapeur d'eau ma : débit massique de l'air
V = 41 (~te ,~ts ,b , rP , ina (38)
5.2 Etude du système moto-ventilateur
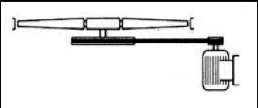
Figure 28 : Système moto-ventilateur
La figure représente le système d'entrainement
des pales du ventilateur ; une liaison par courroie assure la transmission du
mouvement de rotation de l'arbre moteur vers le ventilateur.
Le moteur de type triphasé asynchrone est commandé
par un variateur de vitesse à commande par flux constant.
Le but de cette étude est de chercher une relation entre
le débit d'air refoulé par le ventilateur et la commande du
variateur de vitesse.
Nous allons procéder comme suit :
5.2.1 Relation entre débit d'air refoulé
et vitesse de rotation du ventilateur
D'après CEE ; le débit d'air refoulé est
approximativement proportionnel à la vitesse de rotation du ventilateur
; 50% de vitesse de rotation correspond à 50% de débit
refoulé. [8]
D'après le fournisseur du ventilateur ;
ma = 150 m3/s pour Vr = 190 tr/mn En
utilisant la règle de trois ;
150 m3/s 190 tr/mn
100 m3/s 126,6 tr/mn
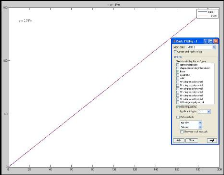
Figure 29 : ma = f(~r)
Donc ma = 0,79 Yr
Il est à rappeler que le débit volumique d'air
refoulé sera converti en débit massique ; soit en multipliant par
la masse volumique de l'air (ñair = 1,2 Kg/m3)
5.2.2 Relation entre puissance reçue par le
ventilateur et puissance fournie par le moteur
La puissance transmise par courroie subit des pertes du fait du
glissement de cette dernière sur les poulies ; ces pertes sont
données dans le tableau suivant :
Mode d'entraînement
|
Pertes
|
|
Moteur à entraînement direct (roue du
ventilateur directement calée sur l'arbre du moteur)
|
2 à 5 %
|
|
Entraînement par accouplement
|
3 à 8 %
|
|
Transmission par courroies
|
P moteur < 7,5 kW : 10 %
|
|
Transmission par courroies
|
7,5 kW < P. mot < 11 kW : 8
|
%
|
Transmission par courroies
|
11 kW < P. mot < 22 kW : 6
|
%
|
Transmission par courroies
|
22 kW < P. mot < 30 kW : 5
|
%
|
Transmission par courroies
|
30 kW < P. mot < 55 kW : 4
|
%
|
Transmission par courroies
|
55 kW < P. mot < 75 kW : 3
|
%
|
Transmission par courroies
|
75 kW < P. mot < 100 kW : 2,5 %
|
Tableau 2 : Pertes de puissance pour différents modes
d'entrainement [9]
Dans notre cas les pertes sont de l'ordre de 5%, donc :
Pr = 0,95 ~m
Cr ~~ Yr = 0,95 ~m ~~
60 60
5.2.3 Relation entre vitesse de rotation du ventilateur
et vitesse de rotation de l'arbre moteur
En se basant sur les documents fournis par le constructeur
(courbe de variation du couple ventilateur en fonction de la vitesse de
rotation du ventilateur et courbe de variation du couple mécanique en
fonction de la vitesse de rotation du moteur en annexe E), nous allons extraire
une relation entre Vr et Pm.
Démarche :
. Relation entre Cr et Vr :
En utilisant MATLAB, nous déterminons l'équation Cr
= ~(~r)
Cr (N.m)
|
Vr (tr/mn)
|
0
|
0
|
0
|
10
|
14.715
|
20
|
29.43
|
30
|
68.67
|
40
|
107.91
|
50
|
147.15
|
60
|
196.2
|
70
|
255.06
|
80
|
318.82
|
90
|
407.11
|
100
|
500.31
|
110
|
593.5
|
120
|
696.51
|
130
|
799.51
|
140
|
931.95
|
150
|
1059.48
|
160
|
1187.01
|
170
|
1343.97
|
180
|
1485.23
|
190
|
1653.97
|
200
|
Tableau 3 : Valeurs de Cr et Vr
Nous saisissons ces valeurs sous MATLAB ;
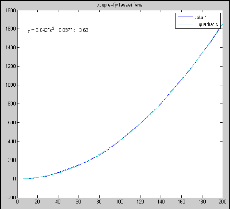
Figure 30 : Cr = f(~r)
(41)

|
Cr = 0,042 1Yr2 - 0,087 1Yr - 0,63
|
. Relation entre Pm et Vm :
Nous faisons de même pour Pm et Vm :
Pm (W)
|
Vm (tr/mn)
|
0
|
0
|
51
|
49
|
123
|
98
|
277
|
147
|
431
|
196
|
641
|
245
|
985
|
294
|
1724
|
343
|
2545
|
392
|
3417
|
441
|
4310
|
490
|
6491
|
539
|
7666
|
588
|
9873
|
637
|
12356
|
686
|
15010
|
735
|
18144
|
784
|
21764
|
833
|
25954
|
882
|
31442
|
931
|
35882
|
980
|
Tableau 4 : Valeurs de Pm et Vm
Nous saisissons ces valeurs sous MATLAB;
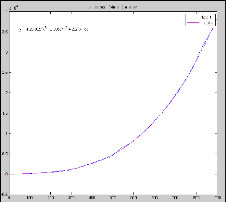
Figure 31 : Pm = f(Vm)


rm = 4,2. 10-5 rm3 - 0,0058 rm2
+ 2,2 rm - 55 (41)
· Relation entre Vr et Pm :
ir = 0,042 rr2 - 0,087 rr - 0,63
0,95 rm = rr × ir

0,95 rm = 0,042 rr3 - 0,087 rr2 - 0,63 rr
(42)
· Relation entre Vr et Vm :
rm = 0,042 rr3 - 0,087 rr2 - 0,63 rr
(43)
Nous obtenons une équation de 3ème
degré, cette équation sera résolue par la méthode
de Newton :
" La méthode de Newton, ou méthode de
Newton-Raphson, est un algorithme efficace pour trouver des
approximations d'un zéro (ou racine) d'une fonction d'une variable
réelle à valeurs réelles. L'algorithme consiste à
linéariser une fonction f en un point et de prendre le point
d'annulation de cette linéarisation comme approximation du zéro
recherché." [4]
kk-Ft = kk
|
f(kk)
f'(kk)
|
(44)
|
5.2.4 Relation entre vitesse de rotation de l'arbre
moteur et commande du variateur de vitesse
La vitesse de l'arbre moteur est comprise entre 40 et 100% soit ;
392 et 980 tr/mn. Le variateur de vitesse est commandé en courant (4 -
20 mA)
Plage : 40 % 100 %
Vitesse : 392 tr/mn 980 tr/mn

Commande : 4 mA 20 mA
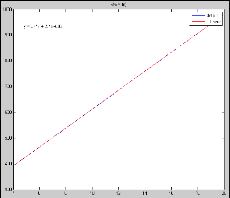
(45)
Figure 32 : Vm = /(r)
5.2.5 Récapitulation : ma = / (r)
· Les équations à utiliser :
1- Vm = 37 2 + 240
2- Pm = 4,2.10-5 Vm3 - 0,0058
Vm2 + 2,2 Vm - 55
3- Pm = 0,042 Vr3 - 0,087 Vr2 - 0,63 Vr
4- ma = 0,79 Vr
· Démarche :
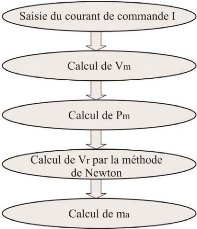
Figure 33 : Démarche pour le calcul de ma = I
(~)
(46)
(47)
Pour le calcul de Vr par la méthode de Newton
;
f(k) = 0,042 ~3 - 0,087 ~2 + 2,2 ~ - rm
f'(k) = 0,126 ~2 - 0,174 k - 0,63
Racine (valeur de départ): 140
Condition d'arrêt : lf(Ik + 1) - y(k)i < t
£ = 1% du couple maximal ; soit approximativement 3 N.m
Conclusion
L'étude thermodynamique nous a permis de créer un
modèle relationnel pouvant régir le fonctionnement de
l'aérocondenseur.
Dans la suite du projet, nous allons nous baser sur ce
modèle pour préparer les diagrammes et séquences de
fonctionnement de l'équipement et élaborer le système
d'automatisme.
Chapitre III
SYSTEME DE CONTROLE,
COMMANDE ET SUPERVISION
Introduction
Après la description du fonctionnement de
l'équipement, nous allons procéder à son automatisation,
le système que nous allons installer démarrera avec la mise en
service de l'unité.
Dans ce chapitre, nous allons présenter l'architecture du
système que nous avons choisi pour le contrôle, la commande et la
supervision de l'unité d'aérocondenseur.
Par la suite, nous allons définir les documents utiles
à cette étape et nous allons réaliser des diagrammes
logiques de fonctionnements des différentes parties de
l'équipement.
1 Système de contrôle, commande et
supervision SCADA
Nous allons utiliser le système SCADA pour le
contrôle, la commande et la supervision de l'unité
aérocondenseur ;
L'architecture du système est la suivante :
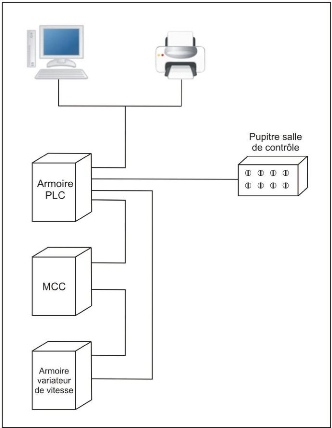
Figure 34 : Architecture du système de commande,
contrôle et supervision
Armoire PLC : elle regroupe deux automates A et B, les
cartes des entrées/sorties analogiques et numériques, les cartes
de communication ainsi que les borniers de connexion.
MCC (Motor Control Center) : regroupe les
départs moteurs, les protections contre les surcharges et
défauts, les RMF (Relais Multi Fonction), les CPI (Contrôleur
Permanant d'Isolement) et les relais auxiliaires.
Armoire variateur de vitesse : contient les variateurs
de vitesse des moteurs électriques. Pupitre : contient les
sélecteurs AUTO/MANU et le bouton AU et se trouve dans la salle de
commande.
2 Présentation de l'automate
2.1 Architecture des automates programmables
De forme compacte ou modulaire, les automates sont
organisés suivant l'architecture suivante :
· Un module d'unité centrale ou CPU, qui assure
le traitement de l'information et la gestion de l'ensemble des unités.
Ce module comporte un microprocesseur, des circuits périphériques
de gestion des entrées/sorties, des mémoires RAM et EEPROM
nécessaires pour stocker les programmes, les données, et les
paramètres de configuration du système.
· Un module d'alimentation qui, à partir d'une
tension 220V/50Hz ou dans certains cas de 24V fournit les tensions continues +
/- 5V, +/-12V ou +/-15V.
· Un ou plusieurs modules d'entrées `Tout Ou Rien'
(TOR) ou analogiques pour l'acquisition des informations provenant de la partie
opérative (procédé à conduire).
· Un ou plusieurs modules de sorties `Tout Ou Rien'
(TOR) ou analogiques pour transmettre à la partie opérative les
signaux de commande. Il y a des modules qui intègrent en même
temps des entrées et des sorties. [10]
· Un ou plusieurs modules de communication comprenant
:
-Interfaces série utilisant dans la plupart des cas comme
support de communication, les liaisons RS-232 ou RS422/RS485 ;
-Interfaces pour assurer l'accès à un bus de
terrain ;
-Interface d'accès à un réseau Ethernet.
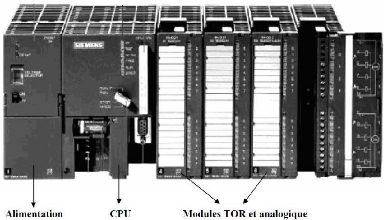
Figure 35 : Automate Programmable Industriel SIEMENS
[11]
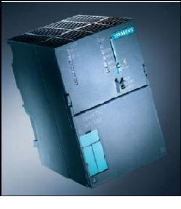
Figure 36 : API S7300 [11]
L'automate utilisé dans notre projet appartient
à la gamme SIMATIC S7 de SIEMENS ; le S7300
est un mini-automate modulaire pour les applications d'entrée et de
milieu de gamme, avec possibilité d'extensions jusqu'à 32
modules, et une mise en réseau par l'interface multipoint (MPI),
PROFIBUS et Industrial Ethernet.
2.2 Structure interne des automates programmables
La structure matérielle interne d'un API obéit au
schéma donné sur les figures 35 et 37.
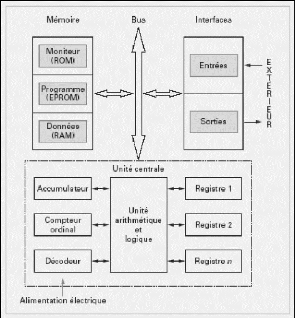
Figure 37 : Structure interne d'un API [12]
Détaillons successivement chacun des composants qui
apparaissent sur ces schémas. 2.2.1 Le processeur
Il Constitue le coeur de l'appareil dans l'unité
centrale ; En fait, un processeur devant être automatisé, se
subdivise en une multitude de domaine et processeur partiels plus petits, lies
les uns aux autres.
2.2.2 Les modules d'entrées/sorties
Ils assurent le rôle d'interface entre la CPU et le
processus, en récupérant les informations sur l'état de ce
dernier et en coordonnant les actions.
Plusieurs types de modules sont disponibles sur le
marché selon l'utilisation souhaitée :
· Modules TOR (Tout Ou Rien): l'information traitée
ne peut prendre que deux états (vrai/faux, 0 ou 1 ...)
C'est le type d'information délivrée par une
cellule photoélectrique, un bouton poussoir ...etc.
· Modules analogiques : l'information traitée est
continue et prend une valeur qui évolue dans une plage bien
déterminée. C'est le type d'information délivrée
par un capteur (débitmètre, capteur de niveau,
thermomètre...etc.).
· Modules spécialisés : l'information
traitée est contenue dans des mots codes sous forme binaire ou bien
hexadécimale. C'est le type d'information délivrée par un
ordinateur ou un module intelligent.
2.2.3 Les mémoires
Un système de processeur est accompagné par un ou
plusieurs types de mémoires. Elles permettent :
· De stocker le système d'exploitation dans des ROM
ou PROM,
· Le programme dans des EEPROM,
· Les données système lors du fonctionnement
dans des RAM. Cette dernière est généralement secourue par
pile ou batterie. On peut, en règle générale, augmenter la
capacité mémoire par adjonction de barrettes mémoires type
PCMCIA.
2.2.4 L'alimentation
Elle assure la distribution d'énergie aux
différents modules. L'automate est alimenté
généralement par le réseau monophasé 230V-50 Hz
mais d'autres alimentations sont possibles (110V ...etc.).
2.2.5 Liaisons de communication
Elles Permettent la communication de l'ensemble des blocs de
l'automate et des éventuelles extensions.
Les liaisons s'effectuent :
· Avec l'extérieur par des borniers sur lesquels
arrivent des câbles transportant le signal électrique ;
· Avec l'intérieur par des bus reliant divers
éléments, afin d'échanger des données, des
états et des adresses.
3 Définition des documents utilisés
· P&ID : "Piping and Instrumentation Diagram";
diagramme schématique illustrant la tuyauterie, l'équipement et
les connexions de l'instrumentation dans l'unité de
l'aérocondenseur, ce document est réalisé par le
département Process.
· Spécification du système de
contrôle : document élaboré par le département
Instrumentation dans lequel sont définis les exigences minimales et les
spécifications de l'ingénierie de détail pour le
système de contrôle pour le projet.
· Schémas électriques : Schéma
unifilaire, Tableau MCC ; documents représentant, à l'aide de
symboles graphiques, les différentes parties d'un réseau, d'une
installation ou d'un équipement qui sont reliées et
connectées fonctionnellement, ils ont pour but d'expliquer le
fonctionnement des équipements.
· Schémas des armoires automates, variateurs de
fréquence : documents représentant la configuration des
automates, les E/S du PLC et les connexions fonctionnelles.
· Documentation technique du fournisseur :
représente les caractéristiques et les spécifications
techniques des composants et des équipements présents dans
l'unité de l'aérocondenseur.
4 Identification des entrées/sorties
4.1 Les E/S PLC
Les Entrées/Sorties du PLC se décomposent en :
Entrées PLC analogiques :
TAG
|
Description
|
2133TT002
|
Transmetteur de Température Entrée Condenseur
|
2133PT002
|
Transmetteur de Pression Entrée Condenseur
|
2133PT001
|
Transmetteur de Pression Manifold 6
|
2133TT001
|
Transmetteur de Température Manifold 6
|
2133LT001
|
Transmetteur De Niveau Ballon Condensât
|
|
Tableau 5 : Entrées PLC Analogiques
Sorties PLC analogiques :
TAG
|
Description
|
2130-SVAR-VF10-1
|
Sortie Variation de Fréquence 1
|
2130-SVAR-VF10-3
|
Sortie Variation de Fréquence 2
|
2130-SVAR-VF10-5
|
Sortie Variation de Fréquence 3
|
2130-SVAR-VF10-7
|
Sortie Variation de Fréquence 4
|
2130-SVAR-VF10-9
|
Sortie Variation de Fréquence 5
|
K-EV-F101
|
Sortie commande VANT 1 (volets 1+2)
|
K-EV-F102
|
Sortie commande VANT 2 (volets 3+4)
|
K-EV-F103
|
Sortie commande VANT 3 (volets 5+6)
|
K-EV-F104
|
Sortie commande VANT 4 (volets 7+8)
|
K-EV-F105
|
Sortie commande VANT 5 (volets 9+10)
|
|
Tableau 6 : Sorties PLC Analogiques
Entrées PLC numériques :
TAG
|
Description
|
P-220VAC
|
Présence tension 220 VAC
|
SA-F10-1-1
|
Sélecteur en mode Automatique B1-1
|
SA-F10-1-2
|
Sélecteur en mode Automatique B1-2
|
SA-F10-2-1
|
Sélecteur en mode Automatique B2-1
|
SA-F10-2-2
|
Sélecteur en mode Automatique B2-2
|
SA-F10-3-1
|
Sélecteur en mode Automatique B3-1
|
SA-F10-3-2
|
Sélecteur en mode Automatique B3-2
|
SA-F10-4-1
|
Sélecteur en mode Automatique B4-1
|
SA-F10-4-2
|
Sélecteur en mode Automatique B4-2
|
SA-F10-5-1
|
Sélecteur en mode Automatique B5-1
|
SA-F10-5-2
|
Sélecteur en mode Automatique B5-2
|
SA-P10-A
|
Sélecteur en mode Automatique P-A
|
SA-P10-B
|
Sélecteur en mode Automatique P-B
|
USD-L-1
|
Unit Schut Down local -1
|
USD-L-2
|
Unit Schut Down local -2
|
USD-SC
|
Unit Schut Down Salle de Contrôle
|
PSD-RC
|
Process Shut Down Pompes Retour Condensat
|
ZSH-XV001
|
Fin de Course Fermeture vanne XV001
|
ZSH-XV002
|
Fin de Course Fermeture vanne XV002
|
ZSH-XV003
|
Fin de Course Fermeture vanne XV003
|
ZSH-XV004
|
Fin de Course Fermeture vanne XV004
|
2133LSL001
|
Contacteur de Niveau Bas
|
|
Tableau 7 : Entrées PLC Numériques
Sorties PLC numériques :
TAG
|
Description
|
CK
|
Commande Klaxon
|
2133-ED-10A
|
Sortie commande contacteur (pompe A)
|
2133-ED-10B
|
Sortie commande contacteur (pompe B)
|
2133-RUN-VF10-1
|
Variateur de Fréquence en Mode Marche (batterie 1)
|
2133-ED- F10-2
|
Sortie Commande Contacteur (batterie 1)
|
2133-RUN-VF10-3
|
Variateur de Fréquence en Mode Marche (batterie 2)
|
2133-ED- F10-4
|
Sortie Commande Contacteur (batterie 2)
|
2133-RUN-VF10-5
|
Variateur de Fréquence en Mode Marche (batterie 3)
|
2133-ED- F10-6
|
Sortie Commande Contacteur (batterie 3)
|
2133-RUN-VF10-7
|
Variateur de Fréquence en Mode Marche (batterie 4)
|
2133-ED- F10-8
|
Sortie Commande Contacteur (batterie 4)
|
2133-RUN-VF10-9
|
Variateur de Fréquence en Mode Marche (batterie 5)
|
2133-ED- F10-10
|
Sortie Commande Contacteur (batterie 5)
|
KF-XV-001
|
Sortie Commande Fermeture Vanne XV001
|
KF-XV-002
|
Sortie Commande Fermeture Vanne XV002
|
KF-XV-003
|
Sortie Commande Fermeture Vanne XV003
|
KF-XV-004
|
Sortie Commande Fermeture Vanne XV004
|
|
Tableau 8 : Sorties PLC Numériques
4.2 Tableau d'échange MODBUS
Des informations sont transmises par MODBUS (annexe F) à
partir du MCC dans le RMF et de l'armoire variateur, (voir annexe G)
Un exemple de ces informations sont regroupées dans les
tableaux suivants et le reste en annexe H:
Tiroir A01 (Batterie 1-1)
Description
|
Type
|
Défaut sonde PTC
|
Numérique
|
Arrêt urgence
|
Numérique
|
Défaut disjoncteur
|
Numérique
|
Etat disjoncteur
|
Numérique
|
Défaut variateur
|
Numérique
|
Marche variateur
|
Numérique
|
|
Tableau 9 : Informations échangées depuis le
Tiroir A01
Tiroir A02 (Batterie 1-2)
Description
|
Type
|
Défaut PTC
|
Numérique
|
Arrêt urgence
|
Numérique
|
Etat contacteur
|
Numérique
|
Fusion fusible
|
Numérique
|
Etat sectionneur
|
Numérique
|
|
Tableau 10 : Informations échangées depuis le
tiroir A02 Boite Jonction Instrumentation
Description
|
Type
|
VibroSwitch 1
|
Numérique
|
VibroSwitch 2
|
Numérique
|
VibroSwitch 3
|
Numérique
|
VibroSwitch 4
|
Numérique
|
VibroSwitch 5
|
Numérique
|
VibroSwitch 6
|
Numérique
|
VibroSwitch 7
|
Numérique
|
VibroSwitch 8
|
Numérique
|
VibroSwitch 9
|
Numérique
|
VibroSwitch 10
|
Numérique
|
|
Tableau 11 : Informations échangées depuis la
Boite Jonction Instrumentation
5 Séquence de démarrage de
l'unité d'aérocondenseur (selon le standard ABB)
Pour démarrer, l'unité d'aérocondenseur
doit se soumettre aux étapes suivantes :
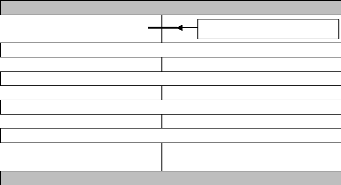
Démarrer aérocondenseur
Voir verrouillage équipement Ouvrir vannes XV
Démarrer vantelles Démarrer
ventilateurs Démarrer pompes retour
condensat Aérocondenseur démarré
Figure 38 : Séquence de démarrage
6 Séquence d'arrêt de
l'aérocondenseur (selon le standard ABB)
Pour arrêter les équipements de
l'aérocondenseur, nous devons passer par les étapes suivantes
:
Arrêter aérocondenseur
|
Voir verrouillage équipement
|
|
|
Arrêter pompes retour condensat
Arrêter ventilateurs
Arrêter vantelles
Fermer vannes XV
Aérocondenseur arrêté
Figure 39 : Séquence d'arrêt
Verrouillage équipement :
Parfois, certaines conditions peuvent empêcher le
démarrage d'un actionneur. Ces conditions sont appelées des
verrouillages.
Nous définissons dans ce paragraphe les verrouillages
relatifs à l'équipement. Les verrouillages sont classés en
5 catégories différentes :
· Verrouillages de démarrage : le PLC teste
cette condition au moment de son démarrage. Si cette dernière est
satisfaite, l'équipement démarre.
· Verrouillage de process : un actionneur ne
peut fonctionner correctement que lorsque cette condition est satisfaite. Un
verrouillage process permet donc un fonctionnement normal de
l'équipement en question.
· Verrouillage électrique : cette condition
permet d'identifier un défaut électrique dans un
sous-équipement.
· Verrouillage de sécurité USD:
cette condition est nécessaire pour que l'actionneur puisse
fonctionner en toute sécurité. Si elle n'est pas satisfaite,
l'actionneur n'est pas en mesure de fonctionner.
· Verrouillage de feedback : l'actionneur ne teste
pas cette action au moment de son démarrage mais plutôt
après un certain temps de son démarrage.
Le tableau suivant représente des exemples de
verrouillages (interlock), le reste est en annexe I:
Aérocondenseur
|
Tag capteur / Description
|
Actions
|
|
Interlock Démarrage
|
Interlock Process
|
Interlock Electrique
|
Interlock Sécurité USD
|
Functional Feedback
|
USD-L-1
|
Unit Schut Down local -1
|
|
|
|
X
|
|
BAU-Batterie 1
|
Bouton Arrêt D'urgence Batterie 1
|
|
|
|
X
|
|
2130-DJD-10A
|
Etat disjoncteur (pompe A)
|
X
|
|
|
|
|
2130-KM-10A
|
Confirmation contacteur (pompe A)
|
X
|
|
|
|
|
2130-KA2-10A
|
Défaut électrique (pompe A)
|
|
|
X
|
|
|
2130-DJ-F10-1
|
Etat disjoncteur (Batterie 1-1)
|
X
|
|
|
|
|
2130-KA2-VF10-1
|
Variateur de Fréquence en Défaut (Batterie1)
|
|
|
X
|
|
|
2130-DJ-F10-2
|
Etat disjoncteur (Batterie 1-2)
|
X
|
|
|
|
|
2130-KM-F10-2
|
Confirmation Contacteur (Batterie 1)
|
X
|
|
|
|
|
2130-KA2-F10-2
|
Défaut Electrique (Batterie 1)
|
|
|
X
|
|
|
ZSH-XV001
|
Fin de Course Fermeture vanne XV001
|
|
X
|
|
|
|
2130LSL001
|
Contacteur de Niveau Bas
|
|
X
|
|
|
|
SA-F10-1-1
|
Sélecteur en mode Automatique B1-1
|
|
X
|
|
|
|
SA-F10-1-2
|
Sélecteur en mode Automatique B1-2
|
|
X
|
|
|
|
SA-F10-2-1
|
Sélecteur en mode Automatique B2-1
|
|
X
|
|
|
|
|
Tableau 12 : Exemples d'interlock
7 Fonctionnement de l'ensemble ; vannes XV, vantelles
et ventilateurs
Le fonctionnement des ventilateurs se fait par paliers ;
A1 : regroupe les batteries 1 et 2
A2 : représente la batterie 2 A3: représente la
batterie 3 A4 : représente la batterie 4
P1 : premier palier de fonctionnement
P2 : second palier de fonctionnement
P3 : troisième palier de fonctionnement
P4 : quatrième palier de fonctionnement USD : Unit Shut
Down (Arrêt d'urgence)
PSD : Process Shut Down (Arrêt d'un équipement)
Chaque batterie contient un ventilateur TOR, un ventilateur VSD,
une vanne XV et deux vantelles.
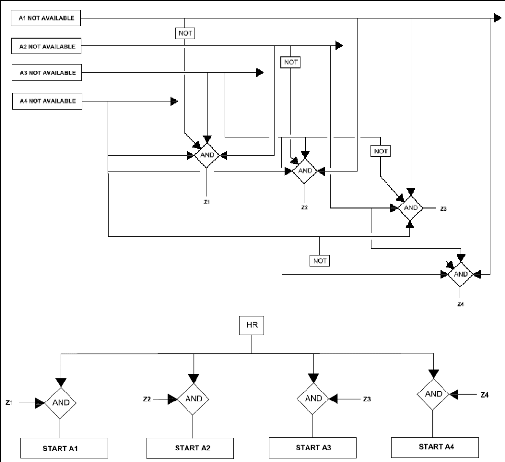
Les ventilateurs, dans leur fonctionnement, doivent tenir
compte des critères de disponibilité et de volume horaire ; si
une batterie est HS (Hors Service), une autre prendra la relève.
Un comparateur de volume horaire de fonctionnement HR ;
compare le volume horaire de travail de chaque batterie de ventilateurs et
sélectionne en conséquence la batterie la moins
utilisée.
Le diagramme fonctionnel est le suivant :
Figure 40 : Diagramme de fonctionnement des batteries de
ventilateurs
7.1 Diagrammes de fonctionnement des vannes XV
TAG
|
Description
|
Type
|
2133TT001
|
Transmetteur de Température Manifold 6
|
AI
|
2133PT001
|
Transmetteur de Pression Manifold 6
|
AI
|
USD-L-1
|
Unit Shut Down local-1
|
DI
|
USD-L-2
|
Unit Shut Down local-2
|
DI
|
USD-SC
|
Unit Shut Down Salle de Contrôle
|
DI
|
KF-XV-001
|
Sortie Commande Fermeture Vanne XV001
|
DO
|
KF-XV-002
|
Sortie Commande Fermeture Vanne XV002
|
DO
|
KF-XV-003
|
Sortie Commande Fermeture Vanne XV003
|
DO
|
KF-XV-004
|
Sortie Commande Fermeture Vanne XV004
|
DO
|
|
Tableau 13 : Listes des E/S relatives au fonctionnement des
vannes XV
Avec ;
AI (Analogic Input) : Entrée Analogique DI (Digital
Input) : Entrée Numérique
AO (Analogic Output) : Sortie Analogique DO (Digital Output) :
Sortie Numérique
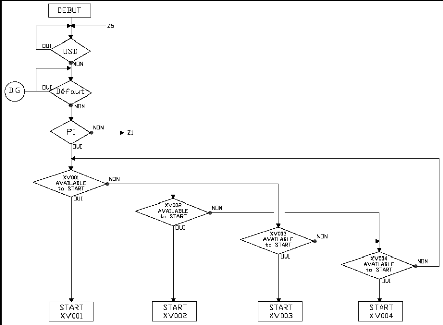
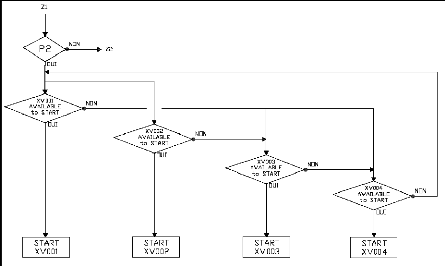
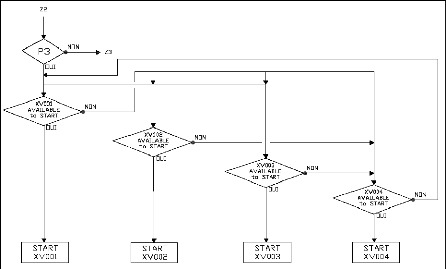
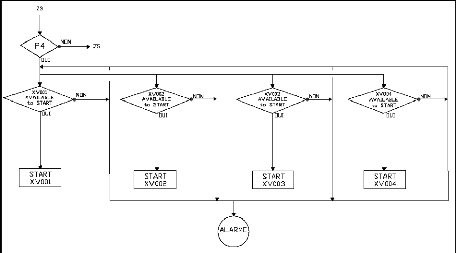
Figure 41 : Diagrammes de fonctionnement des vannes XV
7.2 Diagramme de fonctionnement des vantelles
TAG
|
Description
|
Type
|
2133TT001
|
Transmetteur de Température Manifold 6
|
AI
|
2133PT001
|
Transmetteur de Pression Manifold 6
|
AI
|
ZSH-XV001
|
Fin de Course Fermeture vanne XV001
|
DI
|
ZSH-XV002
|
Fin de Course Fermeture vanne XV002
|
DI
|
ZSH-XV003
|
Fin de Course Fermeture vanne XV003
|
DI
|
ZSH-XV004
|
Fin de Course Fermeture vanne XV004
|
DI
|
K-EV-F101
|
Sortie Commande Volets (1+2)
|
AO
|
K-EV-F102
|
Sortie Commande Volets (3+4)
|
AO
|
K-EV-F103
|
Sortie Commande Volets (5+6)
|
AO
|
K-EV-F104
|
Sortie Commande Volets (7+8)
|
AO
|
K-EV-F105
|
Sortie Commande Volets (9+10)
|
AO
|
|
Tableau 14 : Listes des E/S relatives au fonctionnement des
vantelles
Avec ;
AI (Analogic Input) : Entrée Analogique DI (Digital
Input) : Entrée Numérique
AO (Analogic Output) : Sortie Analogique DO (Digital Output) :
Sortie Numérique
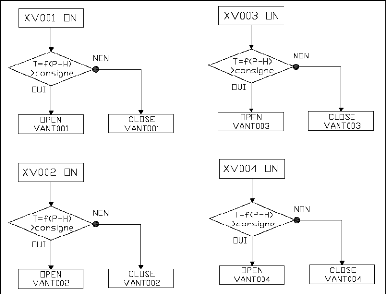
Figure 42 : Diagramme de fonctionnement des vantelles
7.3 Fonctionnement des ventilateurs
En se basant sur l'étude thermodynamique (§5
chapitre II), nous allons définir le fonctionnement des
ventilateurs ;
Après calcul de la chaleur à extraire de la vapeur
d'eau en entrée (§5.1.4 chapitre II), nous
déterminons le nombre de ventilateurs à faire fonctionner.
Pour savoir la cadence à imposer à un ventilateur
VSD, nous nous basons sur l'équation (38):
Xf = ~ (~~~ , ~~~ , ~ , ~~ , ~~ )
Nous allons élaborer le diagramme de fonctionnement des
ventilateurs de la batterie 1, les ventilateurs des autres batteries auront le
même diagramme de fonctionnement.
TAG
|
Description
|
Type
|
2133TT001
|
Transmetteur de Température Manifold 6
|
AI
|
2133PT001
|
Transmetteur de Pression Manifold 6
|
AI
|
2130-SVAR-VF10-1
|
Sortie Variation de Fréquence 1
|
AO
|
2133-RUN-VF10-1
|
Variateur de Fréquence en Mode Marche (batterie 1)
|
DO
|
2133-ED- F10-2
|
Sortie Commande Contacteur (batterie 1)
|
DO
|
|
Tableau 15 : Listes des E/S relatives au fonctionnement des
ventilateurs de la batterie 1
Avec ;
AI (Analogic Input) : Entrée Analogique DI (Digital
Input) : Entrée Numérique
AO (Analogic Output) : Sortie Analogique DO (Digital Output) :
Sortie Numérique
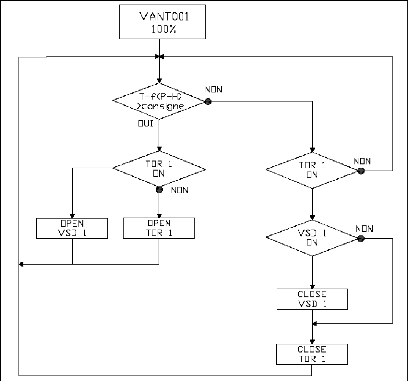
Figure 43 : Diagramme de fonctionnement des ventilateurs de la
batterie 1
8 Fonctionnement des pompes retour condensât
Les Pompes Retour Condensât P10/A et P10/B doivent
fonctionner en 1+1 ; L'une des pompes est en fonctionnement et l'autre en
½stand by½,
En cas d'activation du niveau haut du ballon à
condensât, les deux pompes seront sollicitées
simultanément.
LIT (Level Indicator Transmetter) : Transmetteur d'indication de
niveau LSL (Level Switch Low) : représente le niveau bas critique du
condensât
LSH (Level Switch High) : représente le niveau de
condensât en dessous duquel une seule pompe est sollicitées et
dessus duquel les deux pompes sont sollicités.
LSHH (Level Switch High High) : représente le niveau haut
critique de condensât à ne pas atteindre.
D.G : Défaut Général
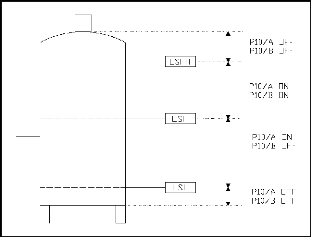
Figure 44 : Schéma du ballon à
condensât
TAG
|
Description
|
Type
|
2133LT001
|
Transmetteur de Niveau Ballon Condensat
|
AI
|
SA-P10-A
|
Sélecteur en Mode Automatique P-A
|
DI
|
SA-P10-B
|
Sélecteur en Mode Automatique P-B
|
DI
|
2133-ED-10A
|
Sortie Contacteur Pompe A
|
DO
|
2133-ED-10B
|
Sortie Contacteur Pompe B
|
DO
|
PSD-P
|
Process Shut Down Pompes
|
DI
|
2133LSL001
|
Contacteur de Niveau Bas
|
DI
|
|
Tableau 16 : Listes des E/S relatives au fonctionnement des
pompes
Avec ;
AI (Analogic Input) : Entrée Analogique DI (Digital
Input) : Entrée Numérique
AO (Analogic Output) : Sortie Analogique DO (Digital Output) :
Sortie Numérique
Le schéma de principe de fonctionnement des pompes
retour condensât pour assurer la disponibilité du système
est le suivant :

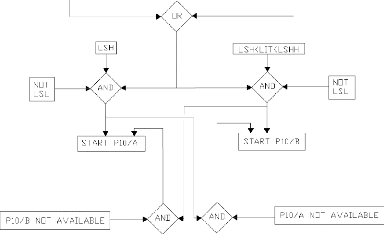
Figure 45 : Diagramme fonctionnel des pompes retour
condensât
Le diagramme de démarrage des pompes est le suivant :
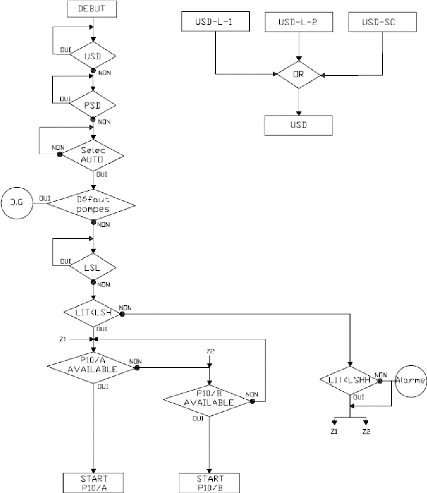
Figure 46 : Diagramme de démarrage des pompes P10/A et
P10/B
Conclusion
Le choix de l'architecture du système de
contrôle, commande et supervision et l'élaboration de la
documentation technique est une étape cruciale pour l'élaboration
du programme d'automatisme de l'unité d'aérocondenseur.
Dans ce qui va suivre, nous allons détailler les
principaux volets de la programmation de l'automate.
Chapitre IV
PROGRAMMATION DE
L'AUTOMATE
Introduction
Pour piloter l'unité de l'aérocondenseur, nous
allons réaliser un programme que nous allons implanter dans l'automate
grâce au logiciel de conception de programmes de systèmes
d'automatisation SIMATIC STEP7.
Dans ce chapitre, nous allons présenter le logiciel
STEP7 et nous allons décrire l'implantation du programme
d'automatisation.
1 Description du logiciel STEP7
STEP7 est le progiciel de base pour la configuration
et la programmation de systèmes d'automatisation SIMATIC S300
et S400. Il fait partie de l'industrie logicielle SIMATIC. Le
logiciel de base assiste dans toutes les phases du processus de création
de la solution d'automatisation, La conception de l'interface utilisateur du
logiciel STEP7 répond aux connaissances ergonomiques modernes.
[13]
STEP7 comporte les quatre sous logiciels de base
suivants :
1.1 Gestionnaire de projets SIMATIC Manager

SIMATIC Manager constitue l'interface d'accès
à la configuration et à la programmation.
Ce gestionnaire de projets présente le programme
principal du logiciel STEP7 il gère toutes les données
relatives à un projet d'automatisation, quelque soit le système
cible sur lequel elles ont été créées. Le
gestionnaire de projets SIMATIC démarre automatiquement les
applications requises pour le traitement des données
sélectionnées.
1.2 Editeur de programme et les langages de
programmation
Les langages de programmation CONT, LIST et LOG, font partie
intégrante du logiciel de base.
· Le schéma à contacts (CONT) est un
langage de programmation graphique. La syntaxe des instructions fait penser aux
schémas de circuits électriques. Le langage
CONT permet de suivre facilement le trajet du courant entre les
barres d'alimentation en passant par les contacts, les éléments
complexes et les bobines. [14]
· La liste d'instructions (LIST) est un langage de
programmation textuel proche de la machine. Dans un programme LIST, les
différentes instructions correspondent, dans une large mesure, aux
étapes par lesquelles la CPU traite le programme. [14]
· Le logigramme (LOG) est un langage de programmation
graphique qui utilise les boites de l'algèbre de Boole pour
représenter les opérations logiques. Les fonctions complexes,
comme par exemple les fonctions mathématiques, peuvent être
représentées directement combinées avec les boites
logiques. [14]
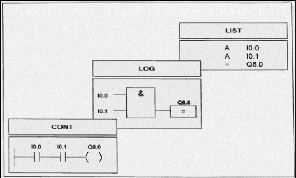
Figure 47: Mode de représentation des langages basiques
de programmation STEP7 [15] 1.3 Paramétrage de
l'interface PG-PC
Cet outil sert à paramétrer l'adresse locale
des PG/PC, la vitesse de transmission dans le réseau MPI (Multi-Point
Interface ; protocole de réseau propre à SIEMENS) ou
PROFIBUS en vue d'une communication avec l'automate et le transfert du
projet.
1.4 Le simulateur des programmes PLCSIM
L'application de simulation de modules S7-PLCSIM
permet d'exécuter et de tester le programme dans un Automate
Programmable (AP) qu'on simule dans un ordinateur ou dans une console de
programmation. La simulation étant complètement
réalisée au sein du logiciel STEP7, il n'est pas
nécessaire qu'une liaison soit établie avec un matériel S7
quelconque (CPU
ou module de signaux). L'AP S7 de simulation permet
de tester des programmes destinés aux CPU S7-300 et aux CPU
S7-400, et de remédier à d'éventuelles erreurs.
[16]
S7-PLCSIM dispose d'une interface simple permettant
de visualiser et de forcer les différents paramètres
utilisés par le programme (comme, par exemple, d'activer ou de
désactiver des entrées). Tout en exécutant le programme
dans l'AP de simulation, on a également la possibilité de mettre
en oeuvre les diverses applications du logiciel STEP7 comme, par
exemple, la table des variables (VAT) afin d'y visualiser et d'y forcer des
variables.
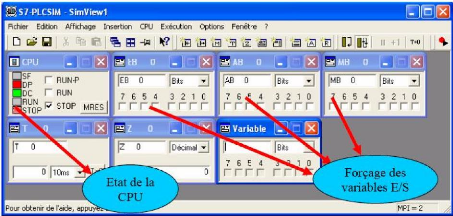
Figure 48 : Interface de simulation PLCSIM
1.5 Stratégie pour la conception d'une structure
programme complète et optimisée
La mise en place d'une solution d'automatisation avec
STEP7 nécessite la réalisation des taches fondamentales
suivantes :
· Création du projet SIMATIC STEP7
· Configuration matérielle HW Config
Dans une table de configuration, on définit les
modules mis en oeuvre dans la solution d'automatisation ainsi que les adresses
permettant d'y accéder depuis le programme utilisateur, pouvant en
outre, y paramétrer les caractéristiques des modules.
· Définition des mnémoniques
Dans une table des mnémoniques, on remplace des adresses
par des mnémoniques locales ou globales de désignation plus
évocatrice afin de les utiliser dans le programme.
· Création du programme utilisateur
En utilisant l'un des langages de programmation mis à
disposition, on crée un programme affecté ou non à un
module, qu'on enregistre sous forme de blocs, de sources ou de diagrammes.
· Exploitation des données:
Création des données de
références : Utiliser ces données de
référence afin de faciliter le test et la modification du
programme utilisateur et la configuration des variables pour le
"controlecommande"
· Test du programme et détection d'erreurs
Pour effectuer un test, on a la possibilité d'afficher
les valeurs de variables depuis le programme utilisateur ou depuis une CPU,
d'affecter des valeurs à ces variables et de créer une table des
variables qu'on souhaite afficher ou forcer.
· Chargement du programme dans le système cible
Une fois la configuration, le paramétrage et la
création du programme terminés, on peut transférer le
programme utilisateur complet ou des blocs individuels dans le système
cible (module programmable de la solution matérielle). La CPU contient
déjà le système d'exploitation.
· Surveillance du fonctionnement et diagnostic du
matériel
La détermination des causes d'un défaut dans le
déroulement d'un programme utilisateur se fait à l'aide de la
« Mémoire tampon de diagnostic », accessible depuis le
SIMATIC Manager.
2 Réalisation du programme de l'unité
de l'aérocondenseur
2.1 Création du projet dans SIMATIC Manager
Afin de créer un nouveau projet STEP7, il
nous est possible d'utiliser « l'assistant de création de projet
», ou bien créer le projet soi même et le configurer
directement, cette dernière est un peu plus complexe, mais nous permet
aisément de gérer notre projet.
En sélectionnant l'icone SIMATIC Manager, on
affiche la fenêtre principale, pour sélectionner un nouveau projet
et le valider.
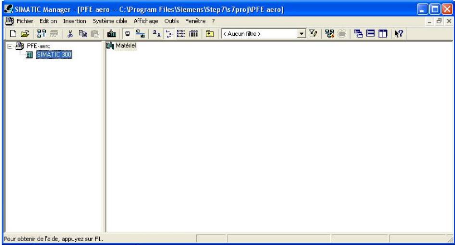
Figure 49 : Page de démarrage de STEP7
Comme le projet est vide il nous faut insérer une station
SIMATC 300.
Deux approches sont possibles. Soit on commence par la
création du programme puis la configuration matérielle ou bien
l'inverse.
2.2 Configuration matérielle (Partie Hardware)
C'est une étape importante, qui correspond à
l'agencement des châssis, des modules et de la périphérie
décentralisée.
Les modules sont fournis avec des paramètres
définis par défaut en usine. Une configuration matérielle
est nécessaire pour :
· Modifier les paramètres ou les adresses
prérègles d'un module,
· Configurer les liaisons de communication.
Le choix du matériel SIMATIC S300 avec une
CPU314 nous conduit à introduire la hiérarchie suivante :
On commence par le choix du châssis selon la station
choisie auparavant, Pour la station SIMATIC S300, on aura le
châssis « RACK-300 » qui comprend un rail profilé.
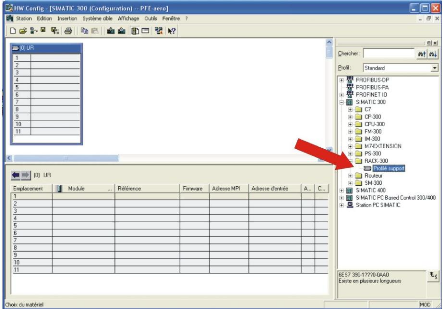
Figure 50 : Choix du RACK
Sur ce profile, l'alimentation préalablement
sélectionnée se trouve dans l'emplacement
n°1.
Parmi celles proposées notre choix s'est porte sur la
<< PS-307 5A ».
La << CPU 314 » est impérativement mise
à l'emplacement n°2.
L'emplacement n°3 est réservé comme adresse
logique pour un coupleur dans une configuration multi-châssis.
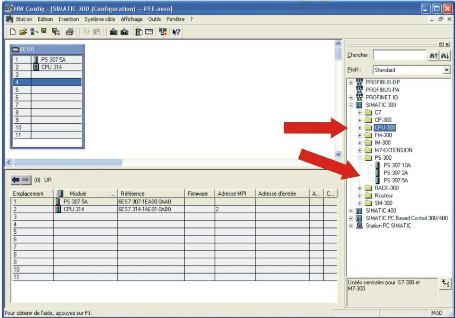
Figure 51 : Choix du CPU et de l'alimentation
A partir de l'emplacement 4, il est possible de monter au choix
jusqu'a 8 modules de signaux (SM), processeurs de communication (CP) ou modules
fonctionnels (FM).
Nous allons y mettre les modules d'entrées et de sorties
analogiques et numériques ; D'après l'identification des E/S du
PLC dans le chapitre III il y a :
· 4 entrées analogiques (AI)
· 10 sorties analogiques (AO)
· 21 entrées numériques (DI)
· 17 sorties numérique (DO)
Pour assurer la flexibilité du système, 20% de
réserves des E/S sont à pourvoir lors de l'implantation du PLC,
donc les cartes des E/S sont comme suit :
· 2 embases de 4 entrées analogiques (2 × 4
AI)
· 3 embases de 4 sorties analogiques (3 × 4 AO)
· Une embase de 32 entrées numériques (32
DI)
· Une embase de 32 sorties numériques (32 DO)
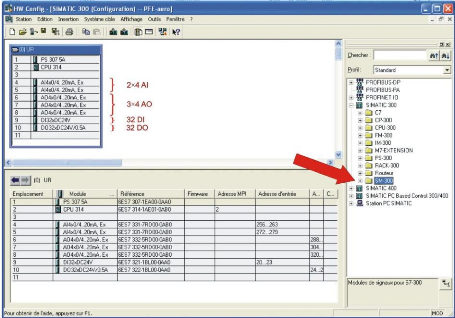
Figure 52 : Choix des embases d'E/S
Apres cela il ne nous reste qu'à enregistrer et
compiler.
La configuration matérielle étant terminée,
un dossier << Programme S7 >> est automatiquement
inséré dans le projet, comme indique dans la figure suivante :
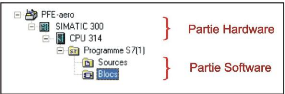
Figure 53 : Hiérarchie du programme STEP7
2.3 Création de la table des mnémoniques
(Partie Software)
Dans tout programme il faut définir la liste des
variables qui vont être utilisées lors de la programmation. Pour
cela la table des mnémoniques est crée. L'utilisation des noms
appropriés rend le programme plus compréhensible est plus facile
à manipuler. Ce type d'adressage est appelé << relatif
>>.
Pour créer cette table, on suit le cheminement suivant
:
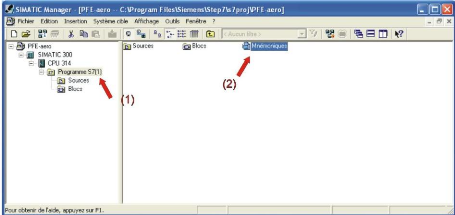
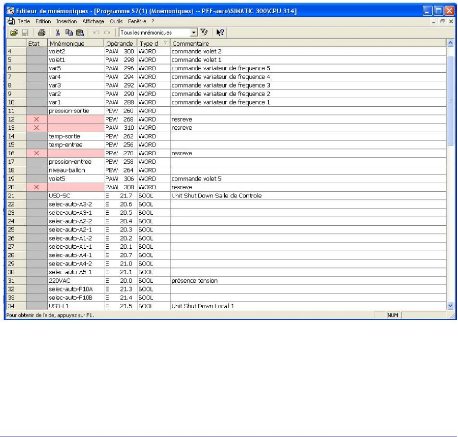
Figure 55 : Table des mnémoniques du projet
Figure 54 : Création des mnémoniques
On édite la table des mnémoniques en respectant
notre cahier de charges, pour les entrées et les sorties.
2.4 Elaboration du programme S7 (Partie Software)
2.4.1 Les blocs de code
Le dossier bloc, contient les blocs que l'on doit charger dans
la CPU pour réaliser la tache d'automatisation, il englobe :
· Les blocs de code (OB, FB, SFB, FC, SFC) qui contiennent
les programmes,
· Les blocs de données DB d'instance et DB globaux
qui contiennent les paramètres du programme.
2.4.1.1 Les blocs d'organisation (OB)
Les OB sont appelés par le système d'exploitation,
on distingue plusieurs types :
· ceux qui gèrent le traitement de programmes
cycliques
· ceux qui sont déclenchés par un
événement,
· ceux qui gèrent le comportement à la mise
en route de l'automate programmable
· et en fin, ceux qui traitent les erreurs. [15]
Le bloc OB1 est généré automatiquement lors
de la création d'un projet. C'est le programme cyclique appelé
par le système d'exploitation.
2.4.1.2 Les blocs fonctionnels (FB), (SFB)
Le FB est un sous programme écrit par l'utilisateur et
exécuté par des blocs de code. On lui associe un bloc de
données d'instance relatif à sa mémoire et contenant ses
paramètres.
Les SFB système sont utilisés pour des fonctions
spéciales intégrées dans la CPU. [15]
2.4.1.3 Les fonctions (FC), (SFC)
La FC contient des routines pour les fonctions
fréquemment utilisées. Elle est sans mémoire et sauvegarde
ses variables temporaires dans la pile de données locales. Cependant
elle peut faire appel à des blocs de données globaux pour la
sauvegarde de ses données. [15]
Les SFC sont utilisées pour des fonctions
spéciales, intégrées dans la CPU S7, elle est
appelée à partir du programme.
2.4.1.4 Les blocs de données (DB)
Ces blocs de données servent uniquement à
stocker des informations et des données mais pas d'instructions comme
les blocs de code. Les données utilisateurs stockés seront
utilisées par la suite par d'autres blocs.
2.4.2 Création du programme de l'unité
d'aérocondenseur
2.4.2.1 Architecture du programme
réalisé
Le programme réalisé contient les blocs suivants
:

Figure 56 : Blocs du projet
Nous allons représenter les liaisons qui existent entre
quelques blocs, cette architecture est donnée par la figure 57.
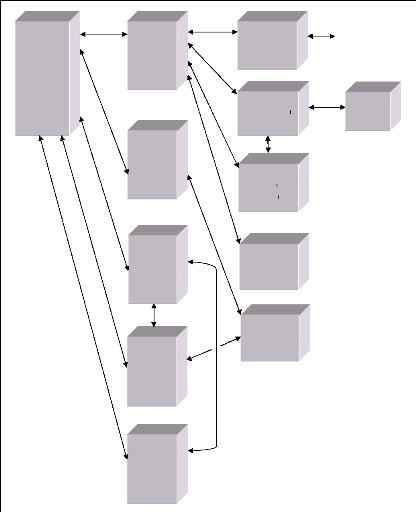
OB1
Bloc Objet
Call FB1, FB2, FB3, FB4, FB5,
FB6
FB4
Traitement des Entrées.Analogiques
Call FB3, FB21
FB5
Traitement des Sorties.Analogiques
Call FB3
Call DB11, FB11, FB12, DB12, FB21
FB1
Bloc Commande
FB2 Démarrage/Arrêt
Call FB21
FB3 Traitement Défauts
Call FB4, FB5
FB11
~ =
~(~~~ , ~~~ ,~ , ~~ , ~~)
Call FC121
FB12 Fonctions
DB11
Echange MODBUS
Call FB3, FB4, FB5
DB12
Volume horaire de fonctionnement
FB21 Interlock
Cp = '(~)
T = '(~)
p = ~(~)
Vers
FB3, FB4 et FB5
FB121
m, = f (1)
Figure 57 : Architecture des blocs du projet
2.4.2.2 Programmation des blocs
La programmation des blocs se fait du plus profond sous-bloc
vers le bloc principal ; nous avons choisi le langage de programmation à
contact (CONT), nous allons commencer par programmer le bloc FC121 et
rebrousser chemin vers le bloc OB1.
· FB121 :
Ce bloc est programmé selon la démarche faite dans
§5.2.5 chapitre II et a pour but de
trouver ma = ~ (T) ,
Les équations et paramètres à utiliser
sont:
Vm = 37 2 + 240
Pm = 4,2. 10-5 'm3 - 0,0058 'm2
+ 2,2 rm - 55
Pm = 0,042 rr3 - 0,087 rr2 - 0,63 rr
ma = 0,79 ~r
f(k) = 0,042 ~3 - 0,087 k2 + 2,2 t - rm
f'(k) = 0,126 k2 - 0,174 t - 0,63
Racine (valeur de départ): 140
Condition d'arrêt : lf(Ik + 1) - y(k)i < t
La programmation se fait par réseaux ; le FB121 contient 9
réseaux ; dont voici un aperçu :







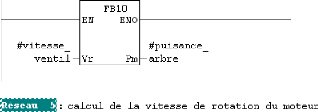

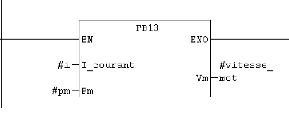
? DB11 :
Le bloc de données DB11 contient les informations
échangées par MODBUS, il est programmé en insérant
les informations dans un tableau dont voici un aperçu:
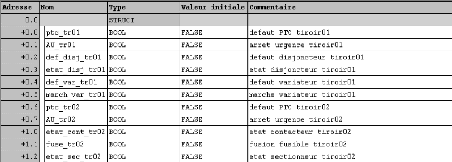
? FB11 :
Le bloc fonctionnel FB11 est programmé pour calculer le
flux de chaleur échangé par un ventilateur explicité dans
§5.1 chapitre II, voici un aperçu des
réseaux programmés :




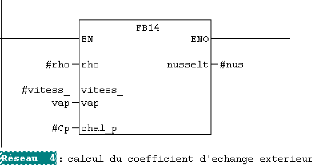

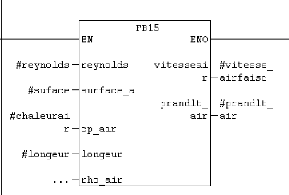
. FB1 :
Le bloc fonctionnel FB1 sert à commander l'unité
d'aérocondenseur, il fait appel à différents blocs et il
est composé de 34 réseaux de programmation dont voici un
aperçu :




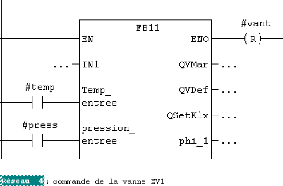

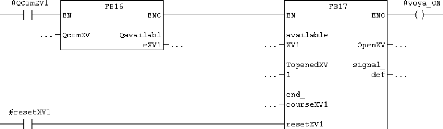
? FB3 :
FB3 est un bloc de traitement des défauts, en dessous un
aperçu des réseaux qu'il contient :



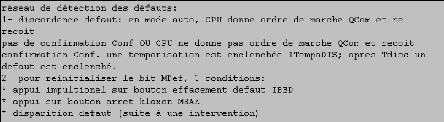
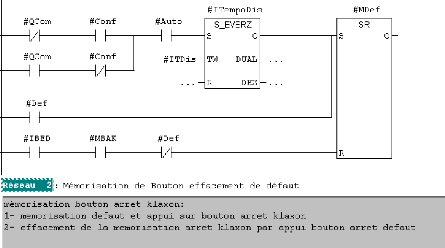
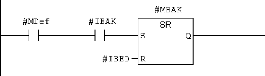

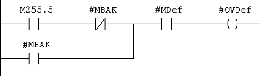
? OB1 :
OB1 regroupe les instructions que le programme va exécuter
d'une manière cyclique, parmi ces blocs on a :


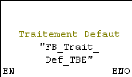



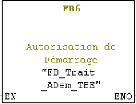
Conclusion
Dans ce chapitre, nous avons présenté le
logiciel de programmation des automates SIEMENS et donné un
aperçu des blocs utilisés lors de la programmation de
l'unité d'aérocondenseur avec STEP7.
Conclusion Générale
La réalisation de ce projet au sein de la
société EPPM, nous a permis de connaitre de près la
démarche de résolution des problèmes, surtout dans un
projet aussi complexe que la mise en oeuvre d'une unité industrielle.
En effet, tout au long de cette période, nous avons
fait face à de nombreux problèmes ; les difficultés
majeures étant la compréhension du système et
l'établissement des séquences de son fonctionnement.
Il a fallu assurer un fonctionnement nominal tout en tenant
compte des critères de fiabilité et de disponibilité,
être précis et efficace lors de chaque étape du projet et
éviter les erreurs en vérifiant les documents et les
séquences élaborées.
Un travail minutieux a été fait, ce qui nous a
permis d'apprendre une certaine méthodologie d'analyse, une
réactivité plus accrue et un sens de déduction plus
affuté.
Ce travail nous a permis d'enrichir nos connaissances
grâce à un projet pluridisciplinaire et de gagner une certaine
polyvalence. Nous avons appris à maitriser un outil d'automatisation et
nous avons concrétisé nos connaissances en thermodynamique et
instrumentation que nous avons acquis durant nos études
académiques au sein de la filière Instrumentation et Maintenance
Industrielles à l'INSAT.
La période passée au sein d'EPPM nous a aussi
permis d'apprendre les rudiments d'une communication hiérarchique et
d'une transmission d'informations efficace et selon les procédures.
Le déplacement sur site nous a nettement aider à
mieux assimiler l'envergure du projet et nous a permis d'avoir un avant-gout
des responsabilités qui incombent aux ingénieurs.
Bibliographie
[2] Manas B. (2006). Aéroréfrigérants
Secs.Techniques de l'Ingénieur. B 2 482.
[3] Serth R. (2007). Process Heat Transfer. Elsevier
Science & Technology Books, Missouri.
[5] Bejan A & Krauss A. (2003). Heat Transfer
Handbook. John Wiley & Sons, Inc, New Jersey.
[6] Zaghdoudi M.C. (2005). Cours de Thermodynamique.
INSAT
[7] Bougriou C. (2005). Etude du Récupérateur de
Chaleur Croisé à Tubes à Ailette. Revue Energies
Renouvelables, vol 5, 59-74.
[10] Michel G. (1987). Les API, Architecture et Application
des Automates Programmables Industriels. DUNOD, Paris.
[12] Manuel SIEMENS. (2005). Appareils de Terrain pour
l'Automatisation des Processus.
[13] Manuel SIEMENS. (2000). STEP7, Régulation
PID.
[14] Jargot P. (2006). Langages de Programmation pour API.
Norme IEC 1131-3. Techniques de l'Ingénieur. S 8 030.
[15] Manuel SIEMENS. (2000). Programmation avec
STEP7.
[16] Manuel SIEMENS. (2002). STEP7 PLCSIM, Testez vos
Programmes.
Netographie
[1]
www.gct.com.tn, Novembre
2009.
[4]
www.wikipédia.com,
Octobre 2009.
[8]
www.cascadeenergy.com,
Octobre 2009.
[9]
www.thermexcel.com,
Août 2009.
[11]
www.siemens.com,
Décembre 2009.
[17]
www.aluminium.matter.org.uk,
Octobre 2009.
LISTE DES ANNEXES
Annexe B
Caractéristiques de la vapeur d'eau saturée
: [9]
Pression absolue
|
Températ. évaporation
|
Volume massique vapeur
|
Masse volumique vapeur
|
Enthalpie spécifique de l'eau (Chaleur
sensible)
|
Enthalpie spécifique de la vapeur (chaleur
totale)
|
Chaleur latente de vaporisation
|
Chaleur spécifique vapeur
|
Viscosité dynamique vapeur
|
bar
|
°C
|
m3/kg
|
kg/m3
|
kj/kg
|
Kcal/kg
|
kj/kg
|
Kcal/kg
|
kj/kg
|
Kcal/kg
|
kj/kg
|
kg/m.s
|
0.02
|
17.51
|
67.006
|
0.015
|
73.45
|
17.54
|
2533.64
|
605.15
|
2460.19
|
587.61
|
1.8644
|
0.000010
|
0.03
|
24.10
|
45.667
|
0.022
|
101.00
|
24.12
|
2545.64
|
608.02
|
2444.65
|
583.89
|
1.8694
|
0.000010
|
0.04
|
28.98
|
34.802
|
0.029
|
121.41
|
29.00
|
2554.51
|
610.13
|
2433.10
|
581.14
|
1.8736
|
0.000010
|
0.05
|
32.90
|
28.194
|
0.035
|
137.77
|
32.91
|
2561.59
|
611.83
|
2423.82
|
578.92
|
1.8774
|
0.000010
|
0.06
|
36.18
|
23.741
|
0.042
|
151.50
|
36.19
|
2567.51
|
613.24
|
2416.01
|
577.05
|
1.8808
|
0.000010
|
0.07
|
39.02
|
20.531
|
0.049
|
163.38
|
39.02
|
2572.62
|
614.46
|
2409.24
|
575.44
|
1.8840
|
0.000010
|
0.08
|
41.53
|
18.105
|
0.055
|
173.87
|
41.53
|
2577.11
|
615.53
|
2403.25
|
574.01
|
1.8871
|
0.000010
|
0.09
|
43.79
|
16.204
|
0.062
|
183.28
|
43.78
|
2581.14
|
616.49
|
2397.85
|
572.72
|
1.8899
|
0.000010
|
0.1
|
45.83
|
14.675
|
0.068
|
191.84
|
45.82
|
2584.78
|
617.36
|
2392.94
|
571.54
|
1.8927
|
0.000010
|
0.2
|
60.09
|
7.650
|
0.131
|
251.46
|
60.06
|
2609.86
|
623.35
|
2358.40
|
563.30
|
1.9156
|
0.000011
|
0.3
|
69.13
|
5.229
|
0.191
|
289.31
|
69.10
|
2625.43
|
627.07
|
2336.13
|
557.97
|
1.9343
|
0.000011
|
0.4
|
75.89
|
3.993
|
0.250
|
317.65
|
75.87
|
2636.88
|
629.81
|
2319.23
|
553.94
|
1.9506
|
0.000011
|
0.5
|
81.35
|
3.240
|
0.309
|
340.57
|
81.34
|
2645.99
|
631.98
|
2305.42
|
550.64
|
1.9654
|
0.000012
|
0.6
|
85.95
|
2.732
|
0.366
|
359.93
|
85.97
|
2653.57
|
633.79
|
2293.64
|
547.83
|
1.9790
|
0.000012
|
0.7
|
89.96
|
2.365
|
0.423
|
376.77
|
89.99
|
2660.07
|
635.35
|
2283.30
|
545.36
|
1.9919
|
0.000012
|
0.8
|
93.51
|
2.087
|
0.479
|
391.73
|
93.56
|
2665.77
|
636.71
|
2274.05
|
543.15
|
2.0040
|
0.000012
|
0.9
|
96.71
|
1.869
|
0.535
|
405.21
|
96.78
|
2670.85
|
637.92
|
2265.65
|
541.14
|
2.0156
|
0.000012
|
1
|
99.63
|
1.694
|
0.590
|
417.51
|
99.72
|
2675.43
|
639.02
|
2257.92
|
539.30
|
2.0267
|
0.000012
|
1.1
|
102.32
|
1.549
|
0.645
|
428.84
|
102.43
|
2679.61
|
640.01
|
2250.76
|
537.59
|
2.0373
|
0.000012
|
1.2
|
104.81
|
1.428
|
0.700
|
439.36
|
104.94
|
2683.44
|
640.93
|
2244.08
|
535.99
|
2.0476
|
0.000012
|
1.3
|
107.13
|
1.325
|
0.755
|
449.19
|
107.29
|
2686.98
|
641.77
|
2237.79
|
534.49
|
2.0576
|
0.000013
|
1.4
|
109.32
|
1.236
|
0.809
|
458.42
|
109.49
|
2690.28
|
642.56
|
2231.86
|
533.07
|
2.0673
|
0.000013
|
1.5
|
111.37
|
1.159
|
0.863
|
467.13
|
111.57
|
2693.36
|
643.30
|
2226.23
|
531.73
|
2.0768
|
0.000013
|
1.5
|
111.37
|
1.159
|
0.863
|
467.13
|
111.57
|
2693.36
|
643.30
|
2226.23
|
531.73
|
2.0768
|
0.000013
|
1.6
|
113.32
|
1.091
|
0.916
|
475.38
|
113.54
|
2696.25
|
643.99
|
2220.87
|
530.45
|
2.0860
|
0.000013
|
1.7
|
115.17
|
1.031
|
0.970
|
483.22
|
115.42
|
2698.97
|
644.64
|
2215.75
|
529.22
|
2.0950
|
0.000013
|
1.8
|
116.93
|
0.977
|
1.023
|
490.70
|
117.20
|
2701.54
|
645.25
|
2210.84
|
528.05
|
2.1037
|
0.000013
|
1.9
|
118.62
|
0.929
|
1.076
|
497.85
|
118.91
|
2703.98
|
645.83
|
2206.13
|
526.92
|
2.1124
|
0.000013
|
2
|
120.23
|
0.885
|
1.129
|
504.71
|
120.55
|
2706.29
|
646.39
|
2201.59
|
525.84
|
2.1208
|
0.000013
|
Annexe C
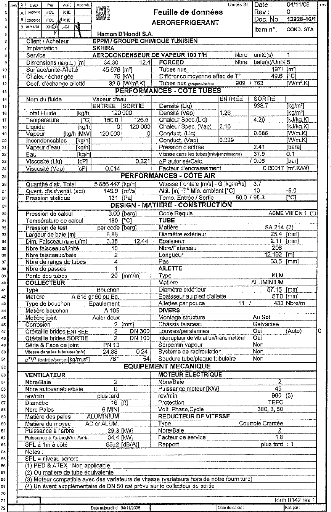
Annexe D
Diagramme des propriétés de
matériaux : [17]
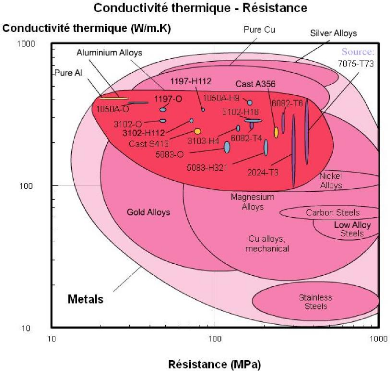
Figure D : Propriétés des matériaux
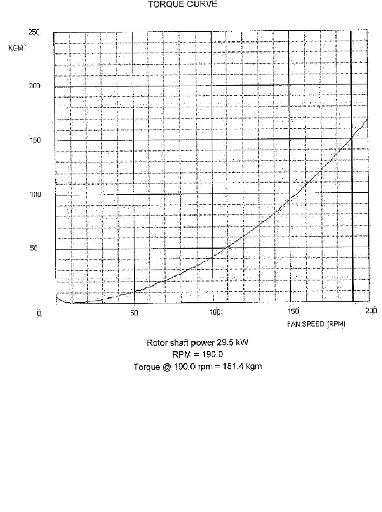
Figure E : Cr = f(r) pour le ventilateur
Annexe E
Annexe F
Le protocole MODBUS
Le protocole MODBUS (marque déposée par MODICON)
est un protocole de dialogue basé sur une structure
hiérarchisée entre un maitre et plusieurs esclaves.
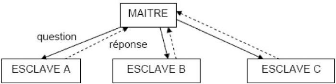
Figure E.1 : Le principe mono maitre du protocole MODBUS
Le protocole MODBUS consiste en la définition de trames
d'échange. Le maitre envoie un message constitué de la
façon suivante:
· Adresse de l'esclave concerné, pour établir
la liaison avec lui,
· Instruction,
· Donnée,
· Contrôle, calculé sur l'ensemble du message
et destiné à assurer l'intégrité de
l'échange. Un contrat d'échange doit être crée, et
ceci pour définir la table de réception, dédie à
l'écriture du maitre dans l'esclave, et une table d'émission pour
la lecture du maitre dans l'esclave.
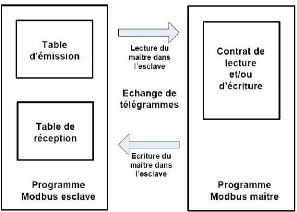
Figure E.2 : Principe des échanges MODBUS
Il existe deux types de dialogue possible en MODBUS :
· Echange maître vers 1'esclave,
· Echange Maître vers tous les esclaves (Message
Broadcast).
Annexe G
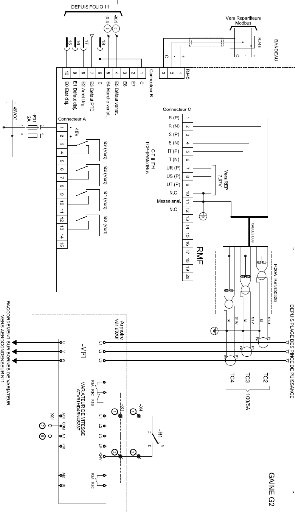
Annexe H
Tableaux d'échange MODBUS Tiroir A01
(Batterie 1-1)
Description
|
Type
|
Défaut sonde PTC
|
Numérique
|
Arrêt urgence
|
Numérique
|
Défaut disjoncteur
|
Numérique
|
Etat disjoncteur
|
Numérique
|
Défaut variateur
|
Numérique
|
Marche variateur
|
Numérique
|
Tiroir A02 (Batterie 1-2)
Description
|
Type
|
Défaut PTC
|
Numérique
|
Arrêt urgence
|
Numérique
|
Etat contacteur
|
Numérique
|
Fusion fusible
|
Numérique
|
Etat sectionneur
|
Numérique
|
Tiroir A03 (Batterie 2-1)
Description
|
Type
|
Défaut sonde PTC
|
Numérique
|
Arrêt urgence
|
Numérique
|
Défaut disjoncteur
|
Numérique
|
Etat disjoncteur
|
Numérique
|
Défaut variateur
|
Numérique
|
Marche variateur
|
Numérique
|
Tiroir A04 (Batterie 2-2)
Description
|
Type
|
Défaut PTC
|
Numérique
|
Arrêt urgence
|
Numérique
|
Etat contacteur
|
Numérique
|
Fusion fusible
|
Numérique
|
Etat sectionneur
|
Numérique
|
Tiroir A05 (Batterie 3-1)
Description
|
Type
|
Défaut sonde PTC
|
Numérique
|
Arrêt urgence
|
Numérique
|
Défaut disjoncteur
|
Numérique
|
Etat disjoncteur
|
Numérique
|
Défaut variateur
|
Numérique
|
Marche variateur
|
Numérique
|
Tiroir A06 (Batterie 3-2)
Description
|
Type
|
Défaut PTC
|
Numérique
|
Arrêt urgence
|
Numérique
|
Etat contacteur
|
Numérique
|
Fusion fusible
|
Numérique
|
Etat sectionneur
|
Numérique
|
Tiroir A07 (Batterie 4-1)
Description
|
Type
|
Défaut sonde PTC
|
Numérique
|
Arrêt urgence
|
Numérique
|
Défaut disjoncteur
|
Numérique
|
Etat disjoncteur
|
Numérique
|
Défaut variateur
|
Numérique
|
Marche variateur
|
Numérique
|
Tiroir A08 (Batterie 4-2)
Description
|
Type
|
Défaut PTC
|
Numérique
|
Arrêt urgence
|
Numérique
|
Etat contacteur
|
Numérique
|
Fusion fusible
|
Numérique
|
Etat sectionneur
|
Numérique
|
Tiroir A09 (Batterie 5-1)
Description
|
Type
|
Défaut sonde PTC
|
Numérique
|
Arrêt urgence
|
Numérique
|
Défaut disjoncteur
|
Numérique
|
Etat disjoncteur
|
Numérique
|
Défaut variateur
|
Numérique
|
Marche variateur
|
Numérique
|
Tiroir A10 (Batterie 5-2)
Description
|
Type
|
Défaut PTC
|
Numérique
|
Arrêt urgence
|
Numérique
|
Etat contacteur
|
Numérique
|
Fusion fusible
|
Numérique
|
Etat sectionneur
|
Numérique
|
Tiroir B03 (Pompe Retour Condensât P10/A)
Description
|
Type
|
Défaut PTC
|
Numérique
|
Arrêt urgence
|
Numérique
|
Etat contacteur
|
Numérique
|
Fusion fusible
|
Numérique
|
Etat sectionneur
|
Numérique
|
Tiroir B04 (Pompe Retour Condensât P10/B)
Description
|
Type
|
Défaut PTC
|
Numérique
|
Arrêt urgence
|
Numérique
|
Etat contacteur
|
Numérique
|
Fusion fusible
|
Numérique
|
Etat sectionneur
|
Numérique
|
Boite Jonction Instrumentation
Description
|
Type
|
VibroSwitch 1
|
Numérique
|
VibroSwitch 2
|
Numérique
|
VibroSwitch 3
|
Numérique
|
VibroSwitch 4
|
Numérique
|
VibroSwitch 5
|
Numérique
|
VibroSwitch 6
|
Numérique
|
VibroSwitch 7
|
Numérique
|
VibroSwitch 8
|
Numérique
|
VibroSwitch 9
|
Numérique
|
VibroSwitch 10
|
Numérique
|
Annexe I
Tableaux des Interlock
Aérocondenseur
|
Tag capteur / Description
|
Actions
|
|
Interlock Démarrage
|
Interlock Process
|
Interlock Electrique
|
Interlock Sécurité USD
|
Functional Feedback
|
USD-L-1
|
Unit Schut Down local -1
|
|
|
|
X
|
|
USD-L-2
|
Unit Schut Down local -2
|
|
|
|
X
|
|
USD-SC
|
Unit Schut Down Salle de Contrôle
|
|
|
|
X
|
|
BAU-Batterie 1
|
Bouton Arrêt D'urgence Batterie 1
|
|
|
|
X
|
|
BAU-Batterie 2
|
Bouton Arrêt D'urgence Batterie 2
|
|
|
|
X
|
|
BAU-Batterie 3
|
Bouton Arrêt D'urgence Batterie 3
|
|
|
|
X
|
|
BAU-Batterie 4
|
Bouton Arrêt D'urgence Batterie 4
|
|
|
|
X
|
|
BAU-Batterie 5
|
Bouton Arrêt D'urgence Batterie 5
|
|
|
|
X
|
|
BAU-RC
|
Bouton Arrêt D'urgence pompe retour condensat
|
|
|
|
X
|
|
2130-DJD-10A
|
Etat disjoncteur (pompe A)
|
X
|
|
|
|
|
2130-KM-10A
|
Confirmation contacteur (pompe A)
|
X
|
|
|
|
|
2130-KA2-10A
|
Défaut électrique (pompe A)
|
|
|
X
|
|
|
2130-DJD-10B
|
Etat disjoncteur (pompe B)
|
X
|
|
|
|
|
2130-KM-10B
|
Confirmation contacteur (pompe B)
|
X
|
|
|
|
|
2130-KA2-10B
|
Défaut électrique (pompe B)
|
|
|
X
|
|
|
2130-DJ-F10-1
|
Etat disjoncteur (Batterie 1-1)
|
X
|
|
|
|
|
2130-KA2-VF10-1
|
Variateur de Fréquence en Défaut (Batterie1)
|
|
|
X
|
|
|
2130-DJ-F10-2
|
Etat disjoncteur (Batterie 1-2)
|
X
|
|
|
|
|
2130-KM-F10-2
|
Confirmation Contacteur (Batterie 1)
|
X
|
|
|
|
|
2130-KA2-F10-2
|
Défaut Electrique (Batterie 1)
|
|
|
X
|
|
|
2130-DJ-F10-3
|
Etat disjoncteur (Batterie 2-1)
|
X
|
|
|
|
|
2130-KA2-VF10-3
|
Variateur de Fréquence en Défaut (Batterie2)
|
|
|
X
|
|
|
2130-DJ-F10-4
|
Etat disjoncteur (Batterie 2-2)
|
X
|
|
|
|
|
2130-KM-F10-4
|
Confirmation Contacteur (Batterie 2)
|
X
|
|
|
|
|
2130-KA2-F10-4
|
Défaut Electrique (Batterie 2)
|
|
|
X
|
|
|
2130-DJ-F10-5
|
Etat disjoncteur (Batterie 3-1)
|
X
|
|
|
|
|
2130-KA2-VF10-5
|
Variateur de Fréquence en Défaut (Batterie3)
|
|
|
X
|
|
|
2130-DJ-F10-6
|
Etat disjoncteur (Batterie 3-2)
|
X
|
|
|
|
|
2130-KM-F10-6
|
Confirmation Contacteur (Batterie 3)
|
X
|
|
|
|
|
2130-KA2-F10-6
|
Défaut Electrique (Batterie 3)
|
|
|
X
|
|
|
2130-DJ-F10-7
|
Etat disjoncteur (Batterie 4-1)
|
X
|
|
|
|
|
2130-KA2-VF10-7
|
Variateur de Fréquence en Défaut (Batterie4)
|
|
|
X
|
|
|
2130-DJ-F10-8
|
Etat disjoncteur (Batterie 4-2)
|
X
|
|
|
|
|
2130-KM-F10-8
|
Confirmation Contacteur (Batterie 4)
|
X
|
|
|
|
|
2130-KA2-F10-8
|
Défaut Electrique (Batterie 4)
|
|
|
X
|
|
|
2130-DJ-F10-9
|
Etat disjoncteur (Batterie 5-1)
|
X
|
|
|
|
|
2130-KA2-VF10-9
|
Variateur de Fréquence en Défaut (Batterie5)
|
|
|
X
|
|
|
2130-DJ-F10-10
|
Etat disjoncteur (Batterie 5-2)
|
X
|
|
|
|
|
2130-KM-F10-10
|
Confirmation Contacteur (Batterie 5)
|
X
|
|
|
|
|
2130-KA2-F10-10
|
Défaut Electrique (Batterie 5)
|
|
|
X
|
|
|
ZSH-XV001
|
Fin de Course Fermeture vanne XV001
|
|
X
|
|
|
|
ZSH-XV002
|
Fin de Course Fermeture vanne XV002
|
|
X
|
|
|
|
ZSH-XV003
|
Fin de Course Fermeture vanne XV003
|
|
X
|
|
|
|
ZSH-XV004
|
Fin de Course Fermeture vanne XV004
|
|
X
|
|
|
|
2130LSL001
|
Contacteur de Niveau Bas
|
|
X
|
|
|
|
SA-F10-1-1
|
Sélecteur en mode Automatique B1-1
|
|
X
|
|
|
|
SA-F10-1-2
|
Sélecteur en mode Automatique B1-2
|
|
X
|
|
|
|
SA-F10-2-1
|
Sélecteur en mode Automatique B2-1
|
|
X
|
|
|
|
Aérocondenseur
|
Tag capteur / Description
|
Actions
|
|
Interlock Démarrage
|
Interlock Process
|
Interlock Electrique
|
Interlock Sécurité USD
|
Functional Feedback
|
SA-F10-2-2
|
Sélecteur en mode Automatique B2-2
|
|
X
|
|
|
|
SA-F10-3-1
|
Sélecteur en mode Automatique B3-1
|
|
X
|
|
|
|
SA-F10-3-2
|
Sélecteur en mode Automatique B3-2
|
|
X
|
|
|
|
SA-F10-4-1
|
Sélecteur en mode Automatique B4-1
|
|
X
|
|
|
|
SA-F10-4-2
|
Sélecteur en mode Automatique B4-2
|
|
X
|
|
|
|
SA-F10-5-1
|
Sélecteur en mode Automatique B5-1
|
|
X
|
|
|
|
SA-F10-5-2
|
Sélecteur en mode Automatique B5-2
|
|
X
|
|
|
|
SA-P10-A
|
Sélecteur en mode Automatique P-A
|
|
X
|
|
|
|
SA-P10-B
|
Sélecteur en mode Automatique P-B
|
|
X
|
|
|
|
|