DEDICACES
A ma mère
Et
A mon père
Pour votre soutien indéfectible, votre amour et
tous les efforts conjugués dans mon instruction et mon
épanouissement.
Sans oublier toute personne
Qui de près ou de loin a contribué à
l'aboutissement de ce travail.
REMERCIEMENTS
Mes premiers remerciements sont adressés à M.
N'TCHAYI MBOUROU Gaston, Directeur Général de l'Ecole
Polytechnique de Masuku, pour sa rigueur et son pragmatisme dans la gestion des
offres de formation de notre établissement dont il a la noble charge
d'être la première autorité.
Je tiens également à exprimer ma profonde
gratitude à M. ASSOUME BE Martial, Chef de département EIA de
l'Ecole Polytechnique, pour m'avoir proposé ce thème de travail
et pour toutes ces heures inestimables passées à ses
côtés afin de mener à bien ce travail. Je le remercie
également pour avoir coordonné ma formation et pour tous les
enseignements que j'ai pu recevoir par son entremise. Vous êtes un
exemple pour moi.
Je tiens aussi à remercier le Dr. NGANTCHA Jean Pierre
pour ses conseils techniques, ses remarques constructives et son aide
précieuse dans l'avancement et l'aboutissement de ce travail. Je vous
sais profondément gré.
J'adresse également mes remerciements au Pr. MOUTSINGA
Octave pour avoir présidé le jury de cette soutenance et pour
tous les conseils qu'il a pu me promulguer.
Je remercie le Pr. ALLOGHO Guy Germain, Pr. EKOGO Thierry
Blanchard, Pr. ANDAMI OVONO Armel, Dr. IPOPA Mohamed Ali, Dr. MOMBOBOUSSOUGOU
Yves Constant, Dr. OYOBE OKASSA Aimé Joseph,Dr. ROTIMBO MBOUROU Donald
Romarick, Dr. OBAME NDONG Elysée, Dr. ASSOUMOU ZUE Roland, Dr. MOUBAGOU
Deflandre et l'ensemble du corps professoral de l'Ecole Polytechnique de
Masuku. J'ai beaucoup appris à vos côtés.
Je remercie BOUTSOMBA Augustine, MOUKINDA Georges, MBOYI
Etienne, MOUKELI Pierre, MBINDZOUKOU Dieudonné, MBOYI Auguste, MIKOLO
Marie Jeanne, PAMBO MIKOLO Firmin, NZELA MIKOLO Florent, MOUKANDA MIKOLO
Clarisse, BOUNOUNOU Herline, MOUBOLI MIKOLO Serge, NZENGUE Fernand, VENGUE
MIKOLO Stany, AVOUODJA FoldyCarelle et MBOYI MASSALA Girel. Vous êtes la
famille que j'ai reçue de Dieu.
Je remercie le couple YENO, OKOUMBA Pauline (la mamie), NDAYI
Aïcha Chimène et tantine Ariane pour m'avoir accueilli et
encadré durant tout mon séjour à Franceville et
également pour les moments particuliers que nous avons
partagés.
Pour finir je dis merci à toute la quatrième
promotion des ingénieurs TELECOM de l'Ecole Polytechnique de Masuku.
J'ai également une pensée spéciale envers les
étudiants de la cinquième promotion ingénieur TELECOM qui
m'ont apporté un soutien indéfectible pendant la
présentation. Je termine en remerciant tous mes amis et connaissances
ainsi que tous ceux qui ont influencés positivement mon cursus scolaire.
RESUME
Ce travail présente un modèle théorique
d'estimation de la durée de vie résiduelle utiledes roulements
à billes en s'appuyant sur l'analyse vibratoire. Les vibrations sont des
phénomènes physiques utilisés pour mettre en
évidence les défauts de fonctionnement ou de dégradation
d'une machine tournante et donnent une meilleure mesure de son état. La
détection de la détérioration précoce d'un
roulement est mise en évidence par l'utilisation d'un indicateur de
défaut. Les roulements présentent plusieurs stades de
dégradation. Cette méthodologie sera basée sur deux
étapes clés. D'abord, il sera question de détecter les
défauts en procédant par l'analyse du spectre du signal. Puis
nous allons estimer la durée de vie utile restante en utilisant des
courbes d'ajustement exponentiel et les rapports des durées des phases
de dégradation du roulement.
Mots-clés : roulement à
billes, analyse vibratoire, vibration, machine tournante, indicateur de
défaut, spectre, courbe d'ajustement.
ABSTRACT
This workpresents a theoretical model for estimating the
usefulresidual life of ballbearingsbased on vibration analysis. Vibrations are
physicalphenomenaused to highlightmalfunctions or degradation of arotating
machine and give a bettermeasure of its condition. Detection of
earlybearingdeteriorationishighlighted by the use of a default indicator.
Bearings have several stages of degradation. This methodologywillbebasedon two
key steps. First, defaultwillbedetected by analyzing the signal spectrum. Then,
wewillestimate the remaininguseful life usingexponential fit curves and
bearingdegradation phase duration ratios.
Keywords : ballbearing, vibration
analysis, vibration, rotating machine, default indicator, spectrum, fit
curve.
TABLE DE MATIERE
INTRODUCTION GENERALE
2
CHAPITRE 1 : L'ECOLE POLYTECHNIQUE DE
MASUKU
12
1.1 Présentation de l'Ecole Polytechnique de
Masuku
12
1.2 Organigramme de l'EPM
13
CHAPITRE 2 : LA MAINTENANCE
14
2.1 Généralités sur la
maintenance
14
2.2 La maintenance curative (ou corrective)
14
2.3 La maintenance préventive
15
2.3.1 La maintenance préventive
systématique
15
2.3.2 La maintenance préventive
conditionnelle
15
2.4 Schémas synoptiques de la
maintenance
17
2.5 Les machines VIS
18
CHAPITRE 3 : L'ANALYSE VIBRATOIRE
20
3.1 Généralités sur l'analyse
vibratoire
20
3.2 Les vibrations
21
3.3 Notion d'indicateur
22
3.3.1 La valeur efficace ou RMS (Root
Mean Square)
23
3.3.2 La valeur crête et le facteur
crête
24
3.3.3 Le kurtosis
24
3.4 Les roulements à billes
25
3.4.1 Composition d'un roulement à
billes
26
3.4.2 Défaillances des machines
tournantes
27
3.4.3 Causes potentielles de dégradation
28
3.4.4 Fréquences caractéristiques de
défaut des éléments d'un roulement
29
CHAPITRE 4 : ACQUISITION DES DONNEES
30
4.1 Notion de spectre du signal
30
4.2 Principe de numérisation d'un signal
analogique
31
4.3 L'IEEE PHM 2012 Data Challenge
34
4.3.1 Aperçu global du Challenge
34
4.3.2 La plateforme PRONOSTIA
34
4.4 Conditions expérimentales d'acquisition
des données
38
CHAPITRE 5 : DETECTION D'ANOMALIES SUR LA
SIGNATURE FREQUENTIELLE ET ESTIMATION DU TEMPS DE SURVIE
44
5.1 La détection des premiers
défauts
44
5.2 Conception d'un modèle théorique
d'estimation du temps de survie
50
5.3 Application du modèle sur un roulement
d'essai
55
5.4 Estimation du RUL pour les cas particuliers
58
5.5 Perspective d'optimisation du modèle
théorique
60
CONCLUSION GENERALE ET PERSPECTIVE
62
ANNEXE A
63
ANNEXE B
66
ANNEXE C
69
BIBLIOGRAPHIE
71
LISTE DES TABLEAUX
Tableau 1: les différents types de
maintenances
2
Tableau 2 : techniques de surveillance des
roulements
21
Tableau 3: les types de roulements
26
Tableau 4: ensemble des données du
challenge
38
Tableau 5: valeurs des RUL fournis dans le
challenge
57
Tableau 6: résumé des erreurs
d'estimation du RUL
59
Tableau 7: évolution de l'erreur
d'estimation en fonction de N
60
LISTE DES FIGURES
Figure 0 : organigramme de
l'EPM....................................................................13
Figure 1: maintenance
corrective...........................................................................14
Figure 2: maintenance
systématique...................................................................15
Figure 3: maintenance
conditionnelle.....................................................................16
Figure 4: organigramme de la
maintenance...........................................................17
Figure 5: différents types de maintenances
conditionnelles........................................17
Figure 6 : masse suspendue à un
ressort...............................................................21
Figure 7: nature des
vibrations.............................................................................22
Figure 8: suivi de l'évolution d'un
indicateur.........................................................23
Figure 9:courbe d'évolution du facteur
crête.........................................................24
Figure 10 : éléments constitutifs d'un
roulement.....................................................27
Figure 11 : processus de dégradation d'un
roulement..................................................28
Figure 12 : fréquences caractéristiques des
défauts.....................................................29
Figure 13 : spectre d'un signal
sinusoïdal.............................................................30
Figure 14 : numérisation d'un signal
analogique.....................................................32
Figure 15 : propriétés temporelles et
fréquentielles du signal d'entrée...........................33
Figure 16 : propriétés temporelles et
fréquentielles du signal
échantillonné......................33
Figure 17 : échantillonnage provoquant un repliement
de spectre.................................33
Figure 18 : structure élémentaire d'un
convertisseur analogique/numérique.....................34
Figure 19 : dispositif
expérimental.....................................................................35
Figure 20 : schéma d'un
accéléromètre
piézo-électrique...........................................36
Figure 21 : accéléromètre de type
DYTRIAN 3035B...............................................36
Figure 22 : accéléromètres fixés
sur le roulement.......................................................37
Figure 23 : caractéristiques de
l'accéléromètre.......................................................37
Figure 24 : illustration des paramètres
d'acquisition...................................................39
Figure 25 : données du fichier acc_0001.csv du
roulement 1_1....................................39
Figure 26 : cas d'un roulement à contact
radial......................................................41
Figure 27 : cas d'un roulement à contact
angulaire..................................................41
Figure 28 : cas des roulements à double
rangées.......................................................42
Figure 29 : algorithme de calcul de la durée
nominale..............................................42
Figure 30 : vue globale des spectres des signaux
d'accélération horizontale.....................47
Figure 31 : vue globale des spectres des signaux
d'accélération verticale........................47
Figure 32 : vue de dessus du spectre du signal
d'accélération horizontale........................48
Figure 33 : vue de dessus du spectre du signal
d'accélération verticale...........................48
Figure 34 : détection d'anomalies dans le roulement
bearing1_3..................................49
Figure 35 : indicateur appliqué aux
accélérations
horizontales.....................................51
Figure 36 : indicateur appliqué aux
accélérations
verticales.......................................52
Figure 37 : courbe d'ajustement exponentiel appliquée
au roulement 1_1.......................54
Figure 38 : détection du premier défaut sur le
roulement bearing1_3.............................55
Figure 39 : courbe d'ajustement exponentiel du roulement
bearing1_3...........................56
Figure 40 : détection d'anomalie et évolution
de l'indicateur du roulement 2_2................58
LISTE DES ABREVIATIONS
AFNOR : Association Française de
Normalisation
ASCII : American Standard Code for
InformationsInterchange
AS2M : Automatique et Systèmes
Micro-Mécatroniques
CALCE : Center for Advanced Life Cycle
Engineering
ENSIL : Ecole Nationale Supérieure
des Ingénieurs de Libreville
Fc : Facteur crête
Fd : Facteur de défaut
FEMTO-ST : Franche-compté
Electronique Mécanique Thermique Optique - Sciences et
Technologies.
FFT : Fast Fourier Transform
IEEE : Institut of Electrical and
ElectronicsEngineers
Ku : Kurtosis
MPC : Maintenance Préventive
Conditionnelle
RMS : RootMean Square
RUL : RemainingUseful Life
TF : Transformée de Fourier
INTRODUCTION GENERALE
La production industrielle évolue dans un contexte de
plus en plus sévère en ce qui concerne la qualité, la
sécurité et les nuisances. Par conséquent, l'outil de
production doit faire l'objet d'une maintenance efficace. Des pannes
catastrophiques inattendues entraînent à la fois une perte de
production et des factures de réparation très
élevées.
Les roulements à billes sont certainement les
composants mécaniques les plus surveillés, car très
sollicités dans le cadre des machines tournantes. La défaillance
de ce système mécanique peut provoquer un arrêt de
production et engendrer des coûts de maintenance très
élevés.
Aujourd'hui, il existe de nombreux travaux sur la
détection de défaillance des roulements. On est capable
d'identifier l'élément défectueux et suivre
l'évolution de cette défaillance au cours du temps.
Néanmoins, on ne sait toujours pas estimer la durée de vie
résiduelle de cet élément défectueux à
partir des mesures vibratoires.
Le sujet soumis à cette étude a pour objectif
d'estimer la durée de vie utile restante d'un roulement à bille
à partir de la mesure de son signal vibratoire. L'idée
étant d'avoir un indicateur d'endommagement qui permettra de mieux
comprendre le mode de dégradation du roulement et de tenter de relier
cet indicateur à la durée de vie résiduelle.
Nous avons entrepris l'étude de l'estimation du temps
résiduel utile des roulements à billes en utilisant les
données expérimentales d'un challenge organisé par l'IEEE
Reliability Society en collaboration avec l'institut FEMTO-ST. Ce travail est
scindé en cinq chapitres.
Le premier chapitre présente l'Ecole Polytechnique de
Masuku et son organigramme.
Dans le second chapitre nous rappelons les grands types de
maintenances tout en signalant les avantages et les inconvénients de
chacune d'entre elles.
Le troisième chapitre présente la description de
l'analyse vibratoire, la théorie sur les différents indicateurs
de vibration et celles concernant la constitution des roulements et les types
de défaillances est également présenté.
Le quatrième chapitre présente la
procédure d'acquisition des données exploitées dans ce
travail. La théorie concernant la détermination de la
durée de vie d'un roulement est abordée.
Les résultats obtenus sur l'estimation de la
durée de vie résiduelle et l'estimation de leurs erreurs sont
présentés dans le dernier chapitre. Une comparaison sur
l'évolution de l'erreur d'estimation en fonction de la moyenne des
valeurs absolues du signal vibratoire temporel rangé dans l'ordre
décroissant est mentionnée.
Enfin, le bilan de ce travail sera résumé dans
une conclusion et perspective.
CHAPITRE 1 : L'ECOLE
POLYTECHNIQUE DE MASUKU
INTRODUCTION
Dans le cadre de la formation des ingénieurs à
l'Ecole Polytechnique de Masuku, il a été judicieusement
pensé de prévoir un stage ou un projet de fin cycle pour
l'obtention du diplôme. En effet, les enseignements théoriques et
pratiques auxquels les étudiants sont soumis, bien que riches par leur
contenu, ne peuvent pas à eux seuls leur garantir d'affronter
aisément la vie active. En outre, en plus d'être pour le futur
diplômé une occasion d'asseoir par la pratique les connaissances
acquises au cours de sa formation, ce stage ou projet est un moyen pour lui
d'accroitre ses compétences et de s'imprégner des
responsabilités qui seront siennes lorsqu'il sera amené à
exercer sa fonction d'ingénieur.
C'est dans ce contexte que ce projet nous a été
assigné au sein de l'Ecole Polytechnique de Masuku que nous allons
présenter dans ce premier chapitre.
1.1
Présentation de l'Ecole Polytechnique de Masuku
Créée le 30 décembre 1986 sur les bases
de l'ENSIL (Ecole Nationale Supérieure des Ingénieurs de
Libreville), l'Ecole Polytechnique de Masuku (EPM) est héritière
d'une culture d'excellence digne des grandes écoles d'ingénieurs.
Depuis sa création, l'EPM continue de former une élite
scientifique et technologique au service du développement du Gabon.
L'EPM est située au sud-est du Gabon dans la province
du Haut-Ogooué et plus précisément dans la commune de
Franceville. Elle compte parmi les trois établissements de
l'Université des Sciences et Techniques de Masuku avec la Faculté
des Sciences (FS) et l'Institut National Supérieur d'Agronomie et de
Biotechnologies (INSAB).
Cet établissement d'enseignement supérieur est
membre de la CITEF (Conférence Internationale des Formations
d'Ingénieurs et des Techniciens d'Expression Française). L'EPM a
restructuré son offre de formation selon les dispositions du
système Licence-Master-Doctorat (LMD) en vigueur dans l'espace CEMAC
depuis l'année universitaire 2007-2008.
L'établissement offre les formations suivantes en cycle
court:
} Sciences Générales de
l'Ingénieur (SGI) :classes préparatoires
intégrées ayant un cursus très sélectif. Elle offre
en deux ans une formation en sciences fondamentales et sciences de
l'ingénieur. Les plus méritants accèdent directement au
cycle ingénieur.
} Diagnostics et Interventions sur Equipements et
Systèmes (DIES) : cette filière est destinée
aux bacs F et MI. Elle offre en deux ans une formation en alternance
école-entreprise.
} Diplôme Universitaire en Technologie
(DUT) : ces filières forment en deux ans des techniciens
de terrain compétents dans les domaines du Génie Civile (GC),
Génie Electrique et Informatique Industriel (GEII), Génie
Industriel et Maintenance (GIM) et Génie des Réseaux et
Télécommunications (GRT).
L'EPM forme également en trois ans des
ingénieurs dotés d'outils modernes de management dans les
domaines des Réseaux et Télécommunications, Génie
Civil et Génie Electromécanique.
1.2 Organigramme de
l'EPM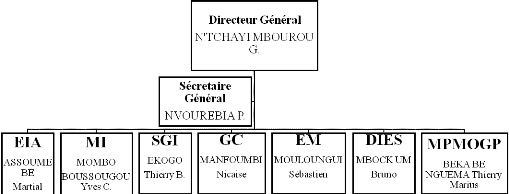
Figure 0: organigramme de l'EPM
EIA : Electronique - Informatique - Automatisme
MI : Maintenance Industrielle
SGI : Sciences Générales de
l'Ingénieur
GC : Génie Civil
EM : Electromécanique
DIES : Diagnostics et Intervention sur Equipement et
Systèmes
MPMOGP : Master Professionnel Maitrise d'Ouvrage et Grands
Projets
CONCLUSION
En somme, dans cette partie nous avons présenté
l'Ecole Polytechnique de Masuku aussi bien dans sa situation
géographique que dans son offre de formation et son organisation
hiérarchique.
CHAPITRE 2 : LA
MAINTENANCE
INTRODUCTION
Le travail soumis à cette étude s'inscrit dans
le cadre de la maintenance des machines tournantes. Il est alors important de
présenter les multiples facettes de la maintenance en procédant
par une étude comparative afin de faire un choix objectif sur le type de
maintenance qui sera utilisé dans la cadre de ce mémoire.
2.1
Généralités sur la maintenance
Selon la norme NF-X60-010, la maintenance est
définie comme étant un ensemble d'activités
destinées à maintenir ou rétablir un bien dans un
état ou dans les conditions données de sécurité de
fonctionnement pour accomplir la fonction requise [1]. Elle désigne
un ensemble d'actions administratives, techniques et managériales
apportées à un équipement durant son cycle de vie afin de
le préserver ou de le rétablir dans un état capable de
réaliser la ou les fonctions pour lesquelles il est utile.
L'intérêt suscité par la maintenance au
sein d'une entreprise est de garantir le fonctionnement des équipements
dans les meilleures conditions possibles afin d'en tirer un rendement optimal,
assurer la disponibilité maximale des équipements à un
prix minimal, augmenter la durée de vie de ces derniers ainsi qu'assurer
leur fonctionnement à tout moment de manière efficace [2].
On peut scinder la maintenance en deux grands champs
distincts, à savoir la maintenance dite curative et celle dite
préventive.
2.2 La maintenance curative (ou
corrective)
La maintenance curative vise à intervenir sur
l'équipement à la suite de la panne. Cela implique que la panne
n'a pas été détectée au préalable avant sa
manifestation effective. Ce type de maintenance requière des aptitudes
à rétablir un dispositif défaillant dans un état
lui permettant d'accomplir sa fonction de manière rentable pour
l'entreprise.Son principal avantage est le fait qu'elle ne nécessite pas
d'investissement en contrôle de l'état des équipements.
Toutefois, elle est également maculée de plusieurs
inconvénients, en l'occurrence des coûts de réparation
élevés, des dommages conséquents, absence de planification
et perte de production si la machine concernée occupe une place
prépondérante dans la chaîne de production de l'entreprise
[3].
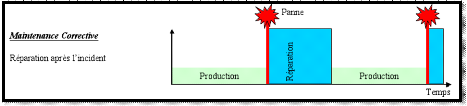
Figure 1: Maintenance
corrective
2.3 La maintenance
préventive
La maintenance préventive consiste à intervenir
sur les équipements avant que la panne ne survienne. Elle est
effectuée à des intervalles de temps déterminés
selon des critères prescrits et destinés à réduire
la probabilité de défaillance ou la dégradation du
fonctionnement d'une machine. La périodicité des visites
s'établit par l'étude des lois statistiques de la durée de
vie. Des gammes d'entretien sont élaborées de façon
à préciser le travail à exécuter et de garder la
traçabilité des entretiens. Cette politique de maintenance
s'applique aux éléments provoquant une perte de production ou des
coûts d'arrêts imprévisibles, mais importants. Les
équipements concernés par ce type de maintenance sont ceux dont
l'impact de la panne est désastreux pour la production. Il existe deux
types de maintenance préventive : la systématique et la
conditionnelle [1].
2.3.1 La maintenance
préventive systématique
La norme NF-X60-010 précise que la maintenance
préventive systématique est effectuée suivant un
échéancier établi selon le temps ou le nombre
d'unités d'usages [1]. Généralement la maintenance
préventive systématique s'adresse aux éléments dont
le coût de réparation en cas de panne est très
onéreux. Entre autre nous pouvons citer le changement
systématique d'huile, le changement de la courroie de synchronisation,
etc. Les avantages d'une telle maintenance sont la planification des
arrêts d'entretien, l'optimisation de l'intervention
(préparation), limitation des risques de pannes. Cependant, on note
quelques inconvénients : coût de maintenance
élevé, risque induit par une intervention parfois non
nécessaire [3].
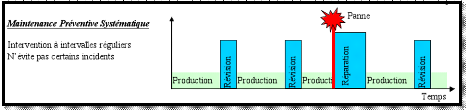
Figure 2: Maintenance
systématique
2.3.2 La maintenance
préventive conditionnelle
D'après la norme NF-X60-010, la maintenance
préventive conditionnelle est définie comme une maintenance
subordonnée à un type d'évènement
prédéterminé (auto diagnostic, information d'un capteur,
mesure d'une usure, révélateur de l'état de
dégradation d'un équipement) [1]. En termes d'avantages, cette
maintenance permet l'optimisation de la durée de fonctionnement,
l'optimisation de l'intervention (préparation), l'évaluation
réelle de l'état de la machine. Au titre des inconvénients
on peut souligner le coût de l'investissement et l'astreinte à un
programme de suivi [3].La surveillance d'un équipement est
assurée en relevant périodiquement un indicateur d'état de
dégradation ou de performance.
La Maintenance Préventive Conditionnelle (MPC) a pour
but :
} Surveiller le fonctionnement de la machine et prévoir
quand elle va défaillir
} Anticiper la maintenance et réduire les coûts
liés aux arrêts
} Réparer les machines que lorsque la
nécessité s'impose
} Optimiser les révisions que sur les seules
défaillances.
Par rapport à la maintenance corrective, la MPC
permet d'éviter les pannes et prévenir les
indisponibilités des machines qui peuvent représenter
jusqu'à 2/3 des coûts de production.
Par rapport à la maintenance préventive
systématique, la MPC permet d'éviter les interventions
coûteuses pas toujours nécessaires (ex : vidange d'un grand volume
d'huile sans qu'elle ne soit dégradée) et qui ne garantissent pas
de ne pas avoir une panne.
En MPC, le défaut est détecté avant que
ne survienne la panne. Le principe est donc de surveillerla machine
régulièrement et de noter son évolution Il existe
différentes techniques :
} La thermographie infrarouge : Cette
technique permet de mesurer la température des composants sans contact.
Les défauts se traduisant généralement par une
élévation de température anormale.
} L'analyse des huiles : Cette technique
permet à la fois de surveiller l'huile d'une machine afin de la changer
que lorsqu'elle est dégradée mais aussi, à l'instar de
l'analyse de sang pour l'être humain, de mesurer l'état de
santé de la machine. Elle est adaptée aux machines contenant des
fluides de lubrification.
} L'analyse vibratoire : Cette technique est
principalement utilisée pour la surveillance des machines tournantes.
Toute machine tournante vibre. Ces vibrations sont les conséquences de
défaut de machine. Plus la machine vibre, et plus le défaut est
important. Cette méthode est celle qui sera qui sera
développée dans le cadre de ce mémoire [4].
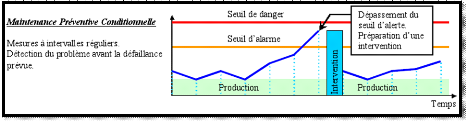
Figure 3: Maintenance
conditionnelle
2.4 Schémas
synoptiques de la maintenance
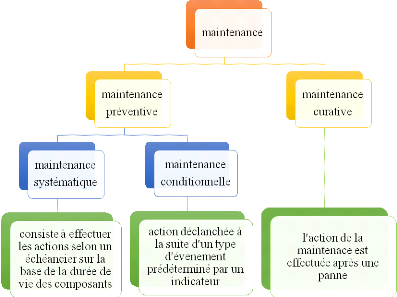
Figure 4: organigramme de la maintenance
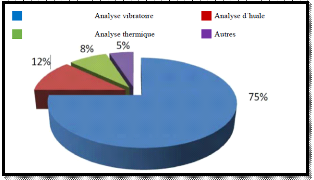
Figure 5: différents type de maintenances
conditionnelles
Tableau 1: les différents
types de maintenances
Type de maintenance
|
Description
|
Avantages
|
Inconvénients
|
Curative
|
intervention sur l'équipement défectueux
après que la panne soit survenue
|
Aucun investissement dans la surveillance de l'état des
équipements
|
Arrêt de la production pendant un temps
indéterminé, coût de réparations élevé
selon la gravité de la panne
|
Systématique
|
Maintenance régulière des machines suivant une
périodicité bien définie
|
Planification des interventions, maitrise de la dépense
liée aux actions à mener, intervention lorsque la production est
arrêtée
|
Remplacement des équipements ou des huiles qui ne sont pas
encore usés, dépenses ne garantissant pas la non manifestation
d'une panne
|
Conditionnelle
|
Des actions sont menées lorsque les indicateurs de
défaillance dépassent un seuil
|
Réduire les coûts liés aux arrêts de
production, réparer les machines lorsque la nécessité
s'impose, anticiper la maintenance
|
Coût élevé du matériel de surveillance
de l'état des équipements, risques liés aux erreurs de
mesure des capteurs utilisés
|
2.5 Les machines
VIS
La mise en place d'un dispositif de surveillance des
équipements par analyse vibratoire requière un investissement
financier important, c'est pourquoi il est judicieux de choisir les machines de
la chaine de production, qui sont d'une importance capitale, pour appliquer
cette méthode. Afin de ne pas surveiller des machines qui n'ont aucune
importance dans la chaine de production, les industriels établissement
le classement suivant :
} Machines Vitales : ce sont des
machines non doublées dont la panne entraîne l'arrêt de
production. Les frais et délais de remise en l'état sont
importants. Les pertes de production sont inestimables.
} Machines Importantes : Machines
doublées ou non, et dont la panne entraîne une baisse sensible de
production. Les frais et délais de remise en état sont
importants, les pertes de production aussi;
} Machines Secondaires : Machines
doublées et dont une panne ne remet pas en cause, les capacités
de production [4].
L'analyse vibratoire sera donc appliquéesur les
machines vitales.
CONCLUSION
Il existe deux grands types de maintenances : la
maintenance préventive et la maintenance curative. Chacune d'entre elles
comporte ses avantages et ses inconvénients. Parmi les
différentes techniques de maintenance préventive conditionnelle,
la plus utilisée dans le monde industriel est l'analyse vibratoire.
Il devient alors important de s'intéresser au contenu
technique de l'analyse vibratoire afin de mieux cerner son apport dans la
surveillance des machines tournantes.
CHAPITRE 3 : L'ANALYSE
VIBRATOIRE
INTRODUCTION
Les machines tournantes constituent la pierre angulaire des
systèmes industriels actuels et se révèlent comme
étant des éléments dont une panne est susceptible
d'affecter grièvement la chaine de production. C'est pourquoi il est
indispensable à l'entreprise d'accorder une attention
particulière à ce type de machine.
En partant du principe que toute machine tournante vibre,
l'analyse vibratoire se présente comme étant une solution
efficace pour surveiller en temps réel l'état de ces machines,
afin de détecter de manière précoce leurs
défaillances pour anticiper l'apparition d'une panne et ainsi assurer la
continuité de service de la chaine de production.
L'objectif de cette partie sera de présenter l'analyse
vibratoire et de montrer comment elle est utilisée pour la surveillance
des roulements à billes.
3.1
Généralités sur l'analyse vibratoire
Toutes les machines tournantes en fonctionnement produisent
des vibrations, images des efforts dynamiques engendrés par les
pièces en mouvement. Ainsi, une machine en excellent état de
fonctionnement produit très peu de vibrations. La
détérioration du fonctionnement conduit le plus souvent à
un accroissement du niveau des vibrations. En observant l'évolution de
ce niveau, il est par conséquent possible d'obtenir des informations
très utiles sur l'état de la machine.
L'analyse vibratoire est un type de maintenance
préventive conditionnelle qui consiste à surveiller une machine
tournante en relevant périodiquement un indicateur d`état de
dégradation ou de performance : la vibration.
Les vibrations produites par le fonctionnement d'une machine
occupent une place privilégiée parmi les paramètres
à prendre en considération pour effectuer un diagnostic. La
modification de la vibration d'une machine constitue souvent la première
manifestation physique d'une anomalie, cause potentielle de
dégradations, voire de pannes.
Elles fournissent desparamètres fondamentaux permettant
la détection précoce des défaillances et même la
désignation de l'organe défectueux sans démontage de la
machine. Par conséquent, la correction éventuelle et la
programmation des opérations de maintenance seront limitées aux
seuls maillons et organes défaillants. Toutes les machines vibrent et au
fur et à mesure que l'état de la machine se
détériore (balourd, usure de roulements, usure d'engrenages,
défaut d'alignement, défaut de graissage, desserrage, jeu,
fissures, etc.), la signature vibratoire change. C'est la première
manifestation physique d'une anomalie, cause potentielle de dégradation
et de panne [5].
Les techniques et les méthodes mises en oeuvre pour
caractériser et surveiller l'état des roulements dans une machine
tournante sont nombreuses et très diverses. Chacune de ces
méthodes correspond à des niveaux différents de
connaissances du phénomène et à l'utilisation de
matériels d'analyse. Ces techniques peuvent être regroupées
en trois familles selon le tableau suivant : [6]
Tableau 2 : techniques de
surveillance des roulements
Méthodes fréquentielles
|
Méthodes statistiques temporelles
|
Méthodes de filtrage
|
FFT, analyse d'enveloppe, analyse cepstrale, etc.
|
Valeur efficace (RMS), valeur crête, facteur crête,
kurtosis, etc.
|
Passe-haut et passe-bande
|
3.2 Les vibrations
D'après la norme NFE 90-001, une vibration est une
variation avec le temps d'une grandeur caractéristique du mouvement ou
de la position d'un système mécanique lorsque la grandeur est
alternativement plus grande et plus petite qu'une certaine valeur moyenne [4].
En d'autres termes,un système mécanique est dit en vibration
lorsqu'il est animé d'un mouvement de va-et-vient autour d'une position
moyenne, dite position d'équilibre. Si l'on observe le mouvement d'une
masse suspendue à un ressort on constate qu'il se traduit par :
} Un déplacement : La position de la
masselotte varie de part et d'autre du point d'équilibre, de la limite
supérieure à la limite inférieure du mouvement ;
} Une vitesse : variation du
déplacement par rapport au temps. Cette vitesse sera nulle au point haut
et au point bas du mouvement de la masselotte et sera maximale autour du point
d'équilibre ;
} Une accélération : variation
de la vitesse par rapport au temps. Celle-ci permet à la masselotte de
passer de sa vitesse minimale à sa vitesse maximale [7].
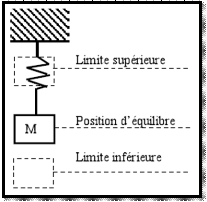
Figure 6: Masse suspendue à un ressort
Une vibration se caractérise principalement par sa
fréquence, son amplitude et sa phase.
La fréquence (notée f) est le nombre de
fois qu'un phénomène se répète en un temps
donné. Lorsque l'unité de temps choisie est la seconde, la
fréquence s'exprime en hertz [Hz]. Une vibration qui se produira 20 fois
par seconde aura donc une fréquence de 20 hertz. [7]
1 Hertz= 1 cycle/seconde. La durée
d'un cycle est appelée période (notée T).
La relation liant la période à la fréquence est :

On appelle amplitude d'une onde vibratoire la valeur de ses
écarts par rapport au point d'équilibre. On peut définir
l'amplitude maximale par rapport au point d'équilibre appelée
amplitude crête ou niveau crête, l'amplitude double, aussi
appelée l'amplitude crête a crête ou niveau
crête-crête, et enfin l'amplitude efficace aussi connue sous
l'acronyme RMS (RootMean Square en Anglais) qui s'obtient en faisant
la racine carrée de la moyenne du carré du signal [7].
Une machine tournante quelconque en fonctionnement
génère des vibrations que l'on peut classer de la façon
suivante:
Les vibrations périodiques de type sinusoïdal
simple [figure 7 a] ou sinusoïdal complexe [figure 7 b]
représentatives du fonctionnement normal ou anormal d'un certain nombre
d'organes mécaniques (rotation de lignes d'arbres,
engrènements,...) ou d'un certain nombre d'anomalies
(déséquilibre, désalignement, déformations,
instabilité de paliers fluides, déversement de bagues sur
roulements, ...).
Les vibrations périodiques de type impulsionnel [figure
7 c] sont appelées ainsi par Référence aux forces qui les
génèrent et à leur caractère brutal, bref et
périodique. Ces chocs peuvent être roduits par des
évènements normaux (presses automatiques, broyeurs a marteaux,
compresseurs à pistons, ...) ou par des évènements
anormaux comme l'écaillage de roulements ou un défaut sur des
engrenages, un jeu excessif, ...
Les vibrations aléatoires de type impulsionnel [figure
7 d] peuvent, par exemple, être générées par un
défaut de lubrification sur un roulement, la cavitation d'une pompe
[7].
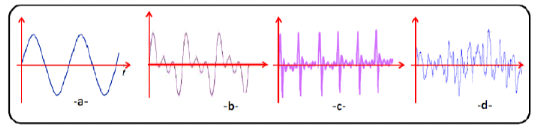
Figure 7: Nature des vibrations
3.3 Notion d'indicateur
La vibration dépend des conditions de fonctionnement de
l'équipement. Le signal vibratoire contient des informations sur les
efforts engendrés par le fonctionnement de la machine, mais aussi sur
l'état mécanique des structures. Il permet par conséquent
d'avoir une image des contraintes internes et de diagnostiquer un certain
nombre de défauts de fonctionnement. Mais en raison même de la
richesse qu'il peut apporter, il n'est en général pas directement
utilisable. Il contient trop d'informations qu'il faut trier puis traiter [4].
Afin de détecter un défaut de la machine, il
convient de définir un ou plusieurs indicateurs d'états de la
machine qui pourront être suivis selon la figure 8 :
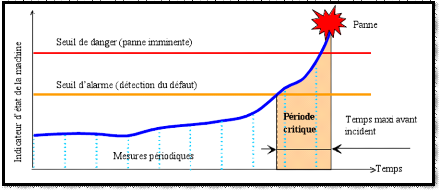
Figure 8: suivi de l'évolution d'un
indicateur
L'indicateur d'état évolue dans le temps. On
définit alors au moins deux seuils :
} Un seuil d'alarme : il nous
prévient que l'état de la machine se dégrade et qu'il va
falloir prévoir une intervention de maintenance. On a le temps de
programmer l'arrêt de la machine afin de pénaliser le moins
possible la production.
} Un seuil de danger : il nous
prévient de l'imminence d'une panne. Il nous faut rapidement intervenir.
On peut également définir des seuils intermédiaires afin
d'être plus précis dans notre analyse [6].
Les indicateurs sont utilisés en analyse vibratoire
selon deux niveaux différents à savoir la surveillance et le
diagnostic des machines :
} La surveillance : Le but de la
surveillance d'une machine est de suivre l'évolution, par comparaison de
relevés successifs de ses vibrations. Une tendance à la hausse ou
à la baisse de certains indicateurs par rapports aux valeurs de
référence constituant la signature alerte
généralement d'un dysfonctionnement probable. Cette valeur de
référence est établie lors de la première campagne
de mesure sur une machine neuve ou révisée.
} le diagnostic : Le diagnostic met en
oeuvre des outils mathématiques élaborés. Il permet de
désigner l'élément défectueux suite à une
évolution anormale découlant de la surveillance. Le diagnostic
n'est réalisé que lorsque la surveillance a permis de
détecter une anomalie ou une évolution dangereuse du signal
vibratoire.
3.3.1 La valeur
efficace ou RMS (RootMean Square)
La valeur efficace permet de contrôler rapidement
l'état de la machine et d'indiquer si les conditions de fonctionnement
ont évolué de manière inquiétante depuis la
dernière mesure. Ce critère n'évolue pas de manière
significative au cours de la 1ère phase de dégradation, il ne
commence à croître que pendant la deuxième phase de
dégradation [8]. Ceci est un point faible pour la maintenance
conditionnelle et rend la détection précoce impossible. De plus
le signal vibratoire recueilli par le capteur contient toujours des bruits non
seulement de la machine mais aussi de l'environnement, ce qui peut
entraîner une mauvaise interprétation de la valeur RMS, surtout
dans un espace industriel où les machines ne sont pas isolées,
sans toutefois oublier l'effet de masque. Elle désigne la racine
carrée de la moyenne du carrée du signal et se calcule à
l'aide de la formule suivante :

3.3.2La valeur crête et
le facteur crête
La valeur crête, donnée par la formule: ,où Amax désigne
l'amplitude maximale et ó l'écart type. C'est un indicateur qui
caractérise l'amplitude maximale des chocs. Il se manifeste dès
l'apparition de la première écaillure et donne une information
très précoce de la prédiction. Malheureusement, c'est un
mauvais indicateur une fois que la dégradation s'accentue. Il faut
remarquer aussi, que ces deux indicateurs (VRMS, Vc)
dépendent de la vitesse de rotation, des charges de la machine et des
dimensions des roulements. Ceci est un inconvénient pour la surveillance
des roulements (seuil de la surveillance). Pour pallier à cela, des
méthodes équivalentes ont étéintroduites, telles
que :
- le facteur de crête : ;
- le facteur de défaut : .
Le défaut majeur du facteur crête est de
présenter environ les mêmes valeurs à l'état neuf et
en fin de vie du roulement. Seule l'évolution dans le temps de cet
indicateur est utilisable. Si Fc augmente, la situation n'est pas alarmante,
par contre s'il diminue, le roulement est en fin de vie (figure 9).
Malheureusement, il est impossible de déterminer si le
roulement est en début ou en fin de dégradation, au moins pendant
les premières mesures. Un autre indicateur permettant de
caractériser le caractère impulsif d'un signal vibratoire, en
particulier pour les roulements, fondés sur l'examen de la distribution
d'amplitude d'un signalvibratoire, est le kurtosis [6].
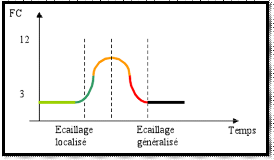
Figure 9: courbe d'évolution du facteur
crête.
3.3.3Le kurtosis
Le kurtosis, donnée par : , est un indicateur adimensionnel permettant de caractériser le
degré d'aplatissement d'une distribution d'un signal vibratoire [8]. Il
a l'avantage d'être indépendant des variations des vitesses de
rotation et des charges de la machine. Prenons l'exemple d'un roulement dont
nous avons suivi l'évolution du kurtosis, en faisant varier la gamme de
fréquence et celle de l'amplitude. Cette étude permet
d'introduire le kurtosis, comme l'un des paramètres de la loi de
dégradation d'un roulement. En effet, le signal vibratoire d'un
roulement en bon état génère un signal de distribution
gaussienne avec un kurtosis voisin de 3 compris entre (2.75 - 3.25) [9]. Par
contre, la détection d'un défaut précoce produit un signal
transitoire et périodique avec une allure de distribution
modifiée et un kurtosis plus grand. Pour quantifier ce changement de
distribution, le kurtosis est le facteur le plus sensible.
3.4 Les roulements à
billes
Les roulements sont des dispositifs mécaniques qui
permettent de réaliser une liaison pivot entre deux classes
d'équivalences, une classe fixe appelée palier
et une autre rotative appelée arbre. Ces
éléments constituent les pièces maitresses des machines
tournantes. Pour optimiser les performances des roulements, un lubrifiant
adapté et en quantité correcte doit être présent
afin de réduire le frottement dans le roulement et le protéger
contre la corrosion. En général, les roulements sont
classés en fonction du type d'éléments roulants et de la
forme des pistes de roulement. Il existe alors plusieurs types de roulement
[Tableau 3]. Les roulements radiaux supportent des charges principalement
perpendiculaires par rapport à l'arbre pendant que les butées
supportent des charges axiales, c'est-à-dire agissant principalement
dans le sens de l'arbre [10].
À l'exception des roulements à
éléments roulants jointifs, tous les roulements sont
équipés d'une cage. Le nombre de cages dépend du nombre de
rangées de billes ou de rouleaux à l'intérieur du
roulement et de la conception des cages. Les cages sont soumises à des
contraintes mécaniques dues aux frottements, déformations et
forces d'inertie. Elles peuvent également subir des contraintes
chimiques causées par certains lubrifiants, additifs et sous-produits et
leur vieillissement, les solvants organiques ou les agents de refroidissement.
Par conséquent, la conception et le matériau d'une cage ont une
influence importante sur la capacité d'un roulement pour une application
donnée.Les principales fonctions d'une cage sont de :
} Séparer les éléments roulants pour
réduire le moment de frottement et la chaleur due au frottement dans le
roulement.
} Maintenir les éléments roulants à
intervalles égaux de manière à optimiser la
répartition de la charge et à permettre un fonctionnement
silencieux et uniforme.
} Guider les éléments roulants dans la zone non
chargée pour améliorer les conditions de roulement et
empêcher les dommages dus aux mouvements de glissement.
} Retenir les éléments roulants des roulements
séparables lorsqu'une bague de roulement est retirée lors du
montage ou du démontage. [10]
Tableau 3: les types de
roulements
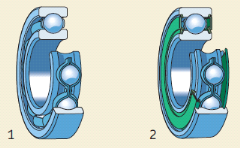
roulements rigides à billes
|
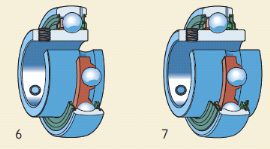
roulements Y
|
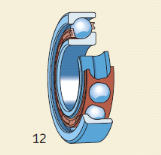
roulements à contact oblique
|
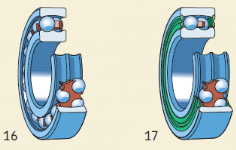
roulements à rotule sur bille
|
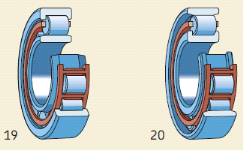
roulements à rouleaux cylindriques
|
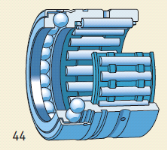
roulements à aiguilles
|
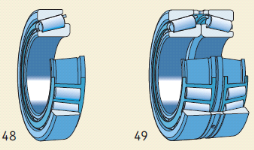
roulements à rouleaux coniques
|
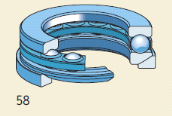
butées à billes
|
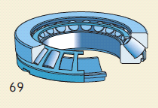
butées à rotules sur rouleaux
|
3.4.1 Composition d'un
roulement à billes
Le roulement est constitué généralement
de deux bagues dans lesquelles sont pratiquées des gorges de roulement,
où se meuvent les parties roulantes. C'est un organe qui assure à
lui seul plusieurs fonctions principales. Il permet le positionnement d'un
arbre par rapport à son logement, tout en assurant une rotation
précise avec le minimum de frottement et transmet les efforts radiaux
et/ou axiaux, ainsi que le guidage en rotation. C'est un organe de
précision (précision de rotation et précision de
position), difficile d'accès et dont l'entretien et/ou le remplacement
peuvent engendrer des arrêts de maintenance longs et coûteux
[11].
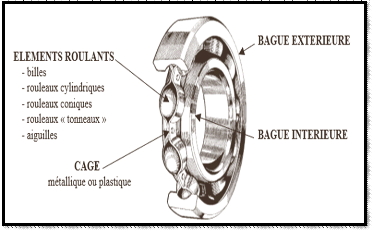
Figure 10: éléments constitutifs d'un
roulement
3.4.2 Défaillances des
machines tournantes
Une défaillance est l'altération ou la cessation
de l'aptitude d'un équipement à accomplir ses fonctions requises
avec les performances définies dans les spécifications
techniques.Plusieurs types de défauts peuvent affecter les roulements
à bille, on peut citer les défauts suivants :
} L'usure: est un phénomène
local caractérisé par un enlèvement de matière
dû au glissement de deux surfaces l'une contre l'autre. Le
développement de l'usure est lié à la charge et à
la vitesse de glissement en chaque point des surfaces de contact, ainsi
qu'à la présence plus ou moins grande d'éléments
abrasifs dans le lubrifiant. L'usure normale, progresse lentement, elle est
inversement proportionnelle à la dureté superficielle de la
denture. L'usure anormale se produit lorsque le lubrifiant est souillé
de particules abrasives ou lorsque le lubrifiant est corrosif, elle conduit
à un mauvais fonctionnement du roulement, voire à sa mise hors
service [10].
} La piqûre : il s'agit de trous peu
profonds, qui affectent toutes les éléments roulants. La
piqûre est une avarie qui se produit surtout sur des roulements en acier
de construction relativement peu dur. Il est moins à craindre si la
viscosité du lubrifiant est élevée. L'apparition des
piqûres est associée aussi à un rapport épaisseur de
film lubrifiant sur rugosité composite [10].
} La fissuration : généralement
par fatigue, elle progresse à chaque mise en charge, à partir
d'un point initial, elle apparaît surtout sur des aciers fins, durcie par
traitement thermique, qui sont très sensibles aux concentrations de
contraintes, l'apparition de ces fissures est la conséquence d'une
contrainte qui dépasse la limite de fatigue du matériau [10].
} L'écaillage : il se manifeste par
une perte de fragments de métal sur la partie de la machine qui
présente cette défaillance [10].
} Grippage : conséquence directe d'une
destruction brutale du film d'huile, ou d'un frottement sous charge provoquant
des hausses de températures, le grippage est favorisé
essentiellement par des vitesses élevées de gros modules [10].
3.4.3 Causes potentielles de
dégradation
La norme AFNOR NF X60010, définit la cause de
défaillance par « les circonstances liées à la
conception, la fabrication ou l'emploi et qui ont entraîné la
défaillance ».Comme tous les organes mécaniques, les causes
dedysfonctionnement des roulements sont très nombreuses. Le plus
souvent, ce sont l'écaillage, le grippage et la corrosion. Tous ces
défauts ont en commun le fait qu'ils se traduisent tôt ou tard par
une perte de fragments de métal, qu'on appelle l'écaillage [12,
13]. L'écaillage s'accentue par des chocs répétés
des billes sur la cage ou les pistes du roulement. Ces chocs provoquentune
vibration de type impulsionnel qui se propage sur labague, puis sur la cage
externe du roulement : impulsion [9] (Fig. 3). Ces impulsions deviennent la
source de modulation d'amplitude du signal aléatoire de vibrations.
Elles sont caractérisées par une montée très raide
et par une durée très courte et par conséquent, il se
produira une augmentation de la valeur efficace du signal vibratoire et de son
facteur crête [13, 14]. La reconnaissance de la nature des vibrations est
un élément précieux pour la détermination de
l'origine d'une anomalie. En mettant en évidence la
répétition de cette impulsion, nous définissons ainsi les
fréquences caractéristiques des défauts de chaque
élément du roulement.
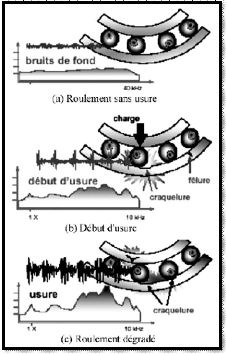
Figure 11: Processus de dégradation d'un
roulement
3.4.4Fréquences
caractéristiques de défaut des éléments d'un
roulement
Lorsqu'on met en relief l'apparition répétitive
des impulsions des signes de dégradation, nous définissons ainsi
les fréquences caractéristiques des défauts de chaque
élément du roulement sur la figure suivante :
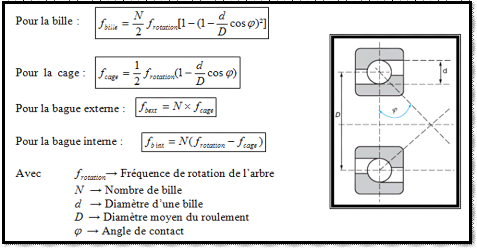
Figure 12: Fréquences caractéristiques des
défauts
CONCLUSION
Nous avons montré que l'analyse vibratoire utilise des
outils mathématiques qui permettent de surveiller l'état des
machines tournantes en prélevant périodiquement le signal
vibratoire. Ce signal contient une grande quantité d'informations, c'est
pourquoi en pratique il est impossible de l'utiliser directement. Dès
lors, on utilise des méthodes de filtrage pour extraire le signal utile.
De même on peut concevoir des indicateurs d'endommagement des roulements
à partir du signal vibratoire afin d'évaluer en temps réel
l'état de la machine. En sus, l'analyse vibratoire a aussi l'avantage
d'élaborer un diagnostic de l'équipement une fois la panne
détectée afin de désigner l'élément
défectueux sans démonter la machine, juste à l'aides des
fréquences caractéristiques des défauts.
CHAPITRE 4 :
ACQUISITION DES DONNEES
INTRODUCTION
Ce chapitre s'intéresse aux moyens mis en oeuvre pour
obtenir les données auxquelles nous allons appliquer les techniques de
l'analyse vibratoire. De prime abord, nous allons revenir sur les concepts
fondamentaux de la numérisation d'un signal analogique et la notion de
spectre d'un signal en posant quelques bases mathématiques sur les
concepts de produit de convolution et de peigne de Dirac.
4.1 Notion de spectre du
signal
La rotation de l'arbre d'une machine tournante est le
phénomène donnant naissance aux vibrations. Cette rotation
étant par nature périodique, les vibrations enregistrées
le sont aussi. Le mathématicien français Joseph Fourier
(1768-1830) a montré que tout signal périodique de forme
quelconque pouvait être décomposé en une somme de signaux
élémentaires sinusoïdaux (fondamental et harmoniques, les
harmoniques étant les multiples du fondamental) autour d'une valeur
moyenne (composante continue) qui pouvait être nulle. L'ensemble de ces
composantes forme le spectre du signal ou bande de fréquence
occupée par le signal (largeur de bande). La somme de ces
sinusoïdes est connue sous le terme de série de
Fourier. Si S (S peut désigner l'accélération, la
vitesse ou le déplacement) est une fonction du temps, on peut
écrire :
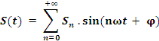
La représentation graphique du signal vibratoire en
fonction du temps reste assez « illisible ». Elle ne
favorise pas l'analyse car tous les termes sont superposés. On a besoin
d'un outil mathématique supplémentaire. La
transformée de Fourier, lorsqu'elle s'applique à
une fonction du temps comme l'accélération, la vitesse ou le
déplacement, donne pour résultat une autre fonction dont la
variable est la fréquence. Cette nouvelle fonction est appelée
spectre. Le spectre est la représentation de
l'amplitude d'une grandeur en fonction de la fréquence. On le
détermine par la relation suivante :
s(f) = TF(S(t)) = .
Par exemple, le spectre d'un signal sinusoïdal est un pic
à la fréquence du signal comme on peut le voir sur la figure
suivante :
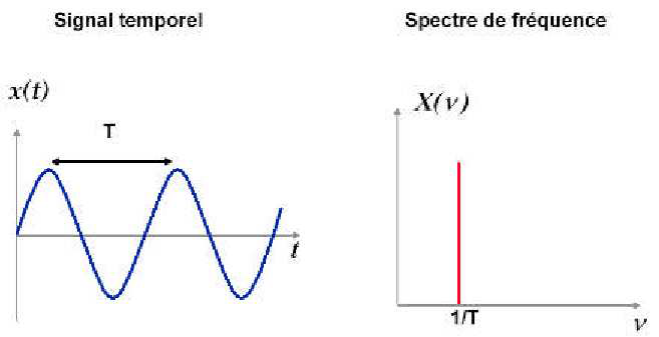
Figure 13 : spectre d'un signal
sinusoïdal
Un signal vibratoire étant la somme de plusieurs sinus,
son spectre sera par conséquent une succession de fréquences
caractéristiques du signal de départ.Il y a complète
dualité entre l'espace temporel et l'espace fréquentiel qui est
représenté par la transformée de Fourier. Cela implique
l'existence de la transformée de Fourier inverse :
e(t) = TF-1(E(f)) = 
La transformée de Fourier introduit la notion de spectre
d'un signal qui est la caractéristique fréquentielle d'un signal.
Un signal peut être ainsi défini dans deux espaces, soit temporel
soit fréquentiel.
Introduisons deux concepts mathématiques importants du
traitement de signal que sont le produit de convolution et le peigne de
Dirac.On définit le produit de convolution entre deux signaux en
décalant de l'un des deux signaux et en intégrant leur produit
sur le temps :
s(t) = e(t)*h(t) = .
On peut montrer aisément la commutativité du
produit de convolution en procédant par un changement de variable de la
forme u = . On notera que la transformée de s(t) traversant un filtre de
réponse impulsionnelle h(t) vaut :
S(f )= E(f ).H(f )
Inversement, si S(f )= E(f )*H(f ) alors s(t) = e(t).h(t)
C'est une propriété très importante. Une
multiplication temporelle devient un produit de convolution fréquentiel.
De même un produit de convolution temporel devient une multiplication
fréquentielle.
L'impulsion de Dirac, notée (t), est une impulsion de
durée to, d'amplitude Ato, avec to très petit. C'est une
impulsion d'énergie constante. Mathématiquement on la
défini de la manière qui suit : t ? 0 (t) = 0, .
De plus e(t0) = . L'impulsion de Dirac est le neutre de la convolution : s(t) =
s(t)*(t).
On en déduit donc que :
TF((t)) = 1 
Le peigne de Dirac est un train d'impulsions espacés de
Te. On le note PTe(t) et :
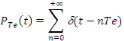
De plus :
TF(PTe(t)) = P1/Te(t).
Pour un système linéaire qui, à une
d'entrée e(t), fait correspondre la fonction de sortie s(t) par une
fonction de transfert h(t), si e(t) = (t) alors S(f) = E(f).H(f) = H(f). Donc
s(t) = h(t). On appelle ainsi h, la réponse impulsionnelle.
4.2 Principe de
numérisation d'un signal analogique
Numériser une grandeur analogique consiste à
transformer la suite continue de valeurs en une suite discrète et finie.
À cet effet, on prélève, à des instants
significatifs, un échantillon du signal et on exprime son amplitude par
rapport à une échelle finie (quantification).
Le récepteur, à partir des valeurs transmises,
reconstitue le signal d'origine. Une restitution fidèle du signal
nécessite que soient définis :
- l'intervalle d'échantillonnage qui doit être
une constante du système (fréquence d'échantillonnage);
- l'amplitude de l'échelle de quantification :
celle-ci doit être suffisante pour reproduire la dynamique du signal
(différence d'amplitude entre la valeur la plus faible et la valeur la
plus forte) ;
- que chaque valeur obtenue soit codée.
La figure 13 représente les différentes
étapes de la numérisation du signal.Le capteur est l'interface
entre le monde physique et le monde électrique. Il va délivrer un
signal électrique image du phénomène physique que l'on
souhaite numériser.L'étape de l'amplification du signal permet
d'adapter le niveau du signal issu du capteur à la chaîne globale
d'acquisition, car en général le courant fourni par le capteur
est de très faible amplitude. Le filtre d'entrée est
communément appelé filtre anti-repliement. Son
rôle est de limiter le contenu spectral du signal aux fréquences
qui nous intéressent. Ainsi il élimine les parasites. C'est un
filtre passe bas que l'on caractérise par sa fréquence de coupure
et son ordre. À intervalle régulier (période
d'échantillonnage Te), l'échantillonneur prélève
une fraction du signal (échantillon). On l'associe de manière
quasi-systématique à un bloqueur. Le bloqueur va figer
l'échantillon pendant le temps nécessaire à la conversion.
Ainsi durant la phase de numérisation, la valeur de la tension de
l'échantillon reste constante.On parle d'échantillonneur
bloqueur. Puis, on fait correspondre à l'amplitude de chaque
échantillon une valeur (quantification), cette valeur est ensuite
transformée en valeur binaire (codification).
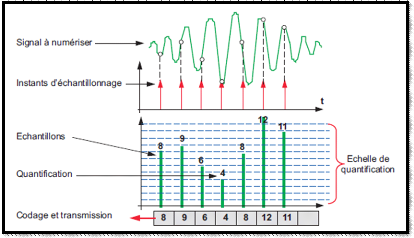
Figure 14:Numérisation d'un signal
analogique
La quantification définit des valeurs en escalier (par
bond) alors que le phénomène à quantifier varie de
façon continue. Aussi, quel que soit le nombre de niveaux
utilisés, une approximation est nécessaire, celle-ci introduit
une erreur dite de quantification ou bruit de quantification qui est la
différence entre la valeur réelle de l'échantillon et la
valeur quantifiée.
Pour reproduire correctement le signal à
l'arrivée, le récepteur doit disposer d'un minimum
d'échantillons. Il existe donc une relation étroite entre la
fréquence maximale des variations du signal à discrétiser
et le nombre d'échantillons à prélever.
L'opération mathématique associée
à la discrétisation d'un signal revient à multiplier ce
signal e(t) par un peigne de Dirac Te(t) :
e(t) = e(t).Te(t) = e(t).Ó(t - nTe)
On peut ainsi calculer la transformée de Fourier du
signal échantillonné en utilisant les propriétés
liant une multiplication temporelle qui dans l'espace fréquentiel
devient un produit de convolution :
E*(f) = TF(e(t).Te(t)) ? E*(f)
= E(f) * Fe=1/Te(f)
Soit : E*(f) = E(f - k.Fe)
Echantillonner le signal e(t) dans le domaine temporel,
revient donc à recopier dans le domaine fréquentiel son spectre
E(f) sur tous les multiples de Fe.
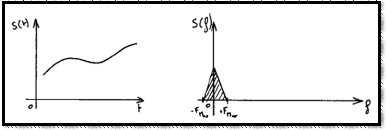
Figure 15: Propriétés temporelles et
fréquentielles du signal d'entrée

Figure 16: Propriétés temporelles et
fréquentielles du signal échantillonné
On remarquera que si le spectre du signal d'origine à
une largeur supérieur à 2Fe on a ce qu'on appelle un
repliement de spectre. Dans le cas d'un spectre de largeur
infinie (la réalité), il y a donc toujours repliement de spectre.
Il est donc nécessaire de filtrer le signal d'origine afin de limiter
cet effet de repliement.
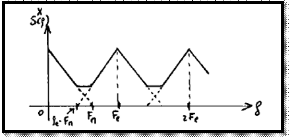
Figure 14: Echantillonnage
provoquant un repliement de spectre
S'il y a repliement de spectre, il n'est plus possible de
retrouver le spectre du signal d'origine. Dans ce cas, l'opération
d'échantillonnage modifie les caractéristiques du signal
d'entrée.
Soit un signal dont le spectre est limité et dont la
borne supérieure vaut Fmax, Shannon a montré
que si Fe est la fréquence d'échantillonnage, le spectre du
signal échantillonné est le double de Fmax et est
centré autour de Fe, 2Fe... nFe. Par conséquent, pour
éviter tout recouvrement de spectre, le signal à
échantillonner doit être borné à une
fréquence supérieure telle que Fmax soit
inférieure à la moitié de l'intervalle d'écartement
des spectres (Fe). On en déduit que la fréquence minimale
d'échantillonnage (fréquence de Nyquist) d'un signal doit
être le double de la fréquence maximale du signal à
échantillonner. Au final, si l'on ne veut pas perdre d'informations par
rapport au signal que l'on échantillonne, on devra toujours respecter la
condition :
Féchantillon= 2 ·
Fmax du signal(relation de Shannon)
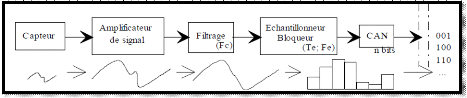
Figure 18: Structure élémentaire d'un
convertisseur analogique/numérique
4.3 L'IEEE PHM 2012 Data
Challenge
4.3.1 Aperçu global du
Challenge
L'IEEE Reliability Society et
l'Institut FEMTO-STont conjointement organisé un
concours intitulé l'IEEE PHM 2012 Data Challenge. Le
défi était axé sur l'estimation de la durée de vie
utile restante (RUL en anglais pour RemainingUseful Life) des
roulements à billes à gorge profonde en rotation, un
problème critique car la plupart des défaillances des machines
tournantes sont liées à ces composants, affectant fortement la
disponibilité, la sécurité et la rentabilité des
systèmes et équipements mécaniques dans les secteurs tels
que l'énergie et le transport. L'ensemble des données du
PHM challenge ont été fournis par l'institut
FEMTO-ST de Besançon en France. Des expériences ont
été réalisées sur la plateforme
expérimentale PRONOSTIA, qui permet une dégradation
accélérée des roulements sous certaines conditions de
fonctionnement, tout en recueillant des données de surveillance en temps
réel. Des essais ont été effectués sous trois
conditions de chargement différentes allant de de 1500 à 1800
tr/min et une charge portante de 4000 à 5000 N dans une configuration
d'essai expérimentale permettant une dégradation
accélérée des paliers. 6 ensembles de données
d'entrainement pour développer les algorithmes d'estimation du RUL et 11
ensembles de donnéesde test contenant des signaux de vibration et de
température ont été fournis. L'objectif du défi
était d'estimer la durée de vie utile restante des roulements
dans les 11 ensembles de données de test.
4.3.2 La plateforme
PRONOSTIA
La plateforme PRONOSTIA permet de faire tourner le roulement
jusqu'à sa rupture en seulement quelques heures. Elle a
été conçue et réalisée au département
AS2M (Automatique et Systèmes Micro-Mécatroniques) de l'institut
FEMTO-ST. Cette plateforme est composée de 3 parties, une composantede
rotation, une composante de charge et une composante de mesure.
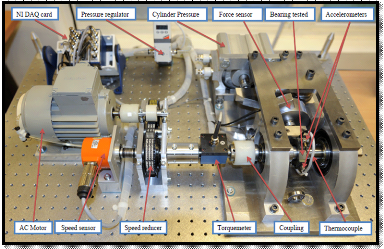
Figure 19: dispositif expérimental
} La composante de rotation contient un
moteur capable de communiquer une vitesse de rotation au roulement. Il s'agit
d'un moteur asynchrone avec une boîte de vitesses et deux arbres. Le
moteur a une puissance égale à 250W et transmet le mouvement de
rotation à travers une boîte de vitesses, ce qui permet au moteur
d'atteindre sa vitesse nominale de 2830 tr/min, de telle sorte qu'il puisse
délivrer son couple nominal tout en maintenant la vitesse de l'arbre
secondaire inférieure à 2000 tr/min. L'accouplement d'arbre
rigide est utilisé pour créer des connexions pour la transmission
du mouvement de rotation produit par le moteur au palier support du roulement.
L'arbre de support du roulement guide le roulement à travers sa bague
intérieure. Une interface homme-machine permet à
l'opérateur de régler la vitesse, de sélectionner la
direction de rotation du moteur et de définir les paramètres de
surveillance tels que la température instantanée du moteur
exprimée en pourcentage de la température maximale
d'utilisation.
} La composante de charge permet d'appliquer
une force radiale sur le roulement afin de réduire sa durée de
vie.Les éléments de ce module sont tous groupé dans une
seule et même cage en aluminium partiellement isolée du module
d'instrumentation par une couche en polymère. La cage en aluminium
comporte un vérin pneumatique, un axe vertical et ses bras de levier, un
capteur de force, une bague de serrage du roulement testé, un arbre de
support d'essai et deux paliers. La force issue du vérin pneumatique est
d'abord amplifiée par un bras de levier, et est ensuite appliquée
indirectement sur la bague extérieure du roulement à bille
à travers sa bague de serrage. Ce module de charge constitue le coeur du
système global. En effet, la force radiale produite permet de
réduire la durée de vie du roulement en paramétrant sa
valeur au-dessus de la charge dynamique maximale supportée par un
roulement qui vaut 4000 N. cette charge est générée par un
actionneur. Il s'agit d'un vérin pneumatique dont la pression
d'alimentation est fournie par un régulateur électropneumatique
numérique.
} La composante de mesure permet d'obtenir
des informations sur le roulement tout au long de l'expérience à
l'aide de capteurs de vibrations et de températures. Les conditions
expérimentales sont déterminées par des mesures
instantanées de la force radiale appliquée sur le roulement, de
la vitesse de rotation de l'arbre du roulement, et le couple infligé au
roulement. Chacune de ces trois mesures analogiques sont
prélevées à une fréquence égale à 100
Hz. La caractérisation de la dégradation du roulement sur deux
types de données : la vibration et la
température.
Le signal thermique obtenu serait très
intéressant pour une étude axée sur la thermographie
infrarouge, mais rappelons que ce mémoire est focalisé sur
l'analyse vibratoire, par conséquent c'est le signal vibratoire qui doit
retenir notre attention.
Les capteurs de vibration sont deux
accéléromètres miniatures, de type DYTRAN 3035B
positionnés à 90° l'un de l'autre. Le premier est
placé sur l'axe vertical et le second sur l'axe horizontal. Les deux
accéléromètres ont une position radiale par rapport
à la bague extérieure du roulement.
Un accéléromètre
piézoélectrique est composé d'un disque en matériau
piézoélectrique (quartz), qui joue le rôle d'un ressort sur
lequel repose une masse sismique précontrainte. Les
accéléromètres piézoélectriques tendent
à devenir les capteurs de vibration absolue les plus utilisés
pour la surveillance. Ils possèdent les avantages suivants :
} le signal d'accélération peut être
intégré électroniquement pour donner le déplacement
et la vitesse ;
} Extrêmement durable ;
} Facilité d'installation ;
} Petit et léger ;
} Supporte les hautes températures.
Toutefois, ils ne sont pas exempts des quelques
inconvénients qui suivent :
} Nécessite une double intégration pour le
déplacement ;
} Nécessite une source extérieure (capteur
passif);
} Fournit des informations limitées sur la dynamique
d'arbre ;
} Médiocre pour les faibles vitesses.
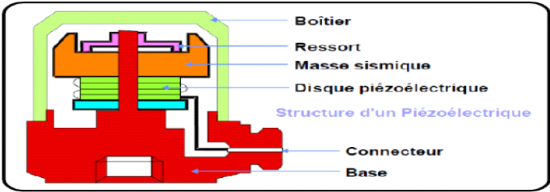
Figure 20: schéma d'un
accéléromètre piézoélectrique
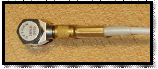
Figure 21: accéléromètre de type
DYTRIAN 3035B
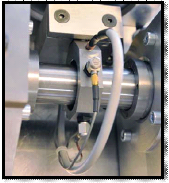
Figure 22: accéléromètres fixés
sur le roulement
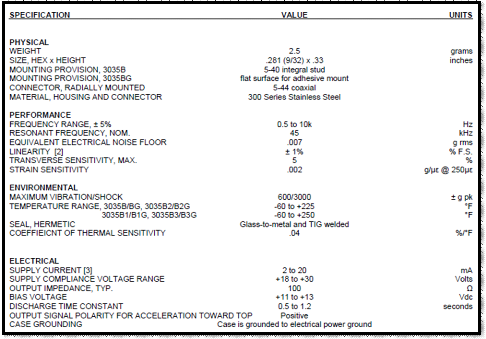
Figure 23: caractéristiques de
l'accéléromètre
4.4 Conditions
expérimentales d'acquisition des données
Les roulements ont été utilisés selon les
trois conditions expérimentales suivantes :
} Condition 1 : la vitesse de rotation
de l'arbre vaut 1800 tr/min et la charge radiale appliquée au roulement
est de 4000 N.
} Condition 2 : la vitesse de rotation
de l'arbre vaut 1650 tr/min et la charge radiale appliquée au roulement
est de 4200 N.
} Condition 3 : la vitesse de rotation
de l'arbre vaut 1500 tr/min et la charge radiale appliquée au roulement
est de 5000 N.
Six expériences ont été menées sur
trois couples de roulements.Les conditions expérimentales changeaient
d'un coupleà un autre. Ces six roulements, appartenant au groupement
learning set,ont été utilisés
jusqu'à l'usure. Leurs signaux vibratoires vont permettre de concevoir
le modèle théorique d'estimation du temps de survie des
roulements. Le modèle ainsi obtenu sera appliqué sur les onze
autres roulements de la famille test set,
afin de prédire leurs temps de survie, car ces roulements n'ont pas
été utilisés jusqu'à la fin de vie. En
réalité, les données de surveillances des onze roulements
test ont été expressément tronquées afin que les
participants puissent prédire la durée restante, et ainsi
effectuer des estimations du RUL. De plus, aucune hypothèse sur la
défaillance à prévoir n'a été
formulée, rien n'est connu sur la nature et l'origine de la
dégradation.
Tableau 4: ensemble des
données du challenge
conditions expérimentales
|
condition 1
|
condition 2
|
condition 3
|
Learning set
|
bearing1_1
bearing1_2
|
bearing2_1
bearing2_2
|
bearing3_1
bearing3_2
|
Test set
|
bearing1_3
bearing1_4
bearing1_5
bearing1_6
bearing1_7
|
bearing2_3
bearing2_4
bearing2_5
bearing2_6
bearing2_7
|
bearing3_3
|
Le capteur situé dans le plan vertical mesure
l'accélération verticale et l'autre situé dans le plan
horizontal mesure l'accélération horizontale. Le signal
vibratoire est échantillonné à la fréquence
Fe = 25,6 kHz, à chaque instant de
prélèvement qui dure de seconde on récolte 2560 valeurs (échantillons). La
durée entre deux instants de prélèvement successifs est de
10 secondes.
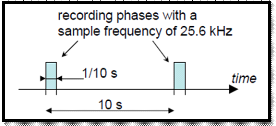
Figure 24: illustration des paramètres d'acquisition
des données
Les données recueillies à chaque instant de
prélèvement sont enregistrées dans des fichiers ASCII
nommées acc_XXXXX.csv. Sur chaque ligne de
chacun de ces fichiers on retrouve un certain nombre d'informations
rangées dans l'ordre suivant : heure,
minute, seconde,
microseconde, accélération
horizontale, accélération verticale. Le
séparateur utilisé dans ces fichiers est la virgule.
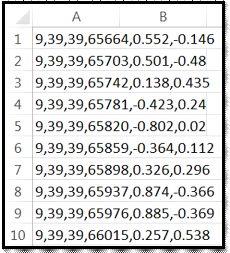
Figure 25: données du fichier acc_00001.csv du
roulement1_1
Il faut toutefois notifierque les modèles
théoriques basés sur la signature fréquentielle pour
détecter les défauts de roulements ne fonctionnent pas. En effet,
les signatures de fréquence sont difficiles à obtenir du fait que
la dégradation peut concerner tous les composants du roulement à
la fois.
D'autre part, les lois de fiabilité existantes pour
l'estimation de la durée de vie des roulements, telles que la
durée nominale L10, ne donnent pas les mêmes
résultats que ceux obtenus par les expériences
réalisées (la durée de vie théorique estimée
est différente de celle donnée par les expériences).
Rappelons le contenu théorique de la loi
L10.La durée de vie d'un roulement est définie par le
nombre de tours qu'il peut effectuer sous une charge donnée avant
qu'apparaisse le premier signe d'écaillage. Selon la norme ISO 281, la
durée nominale vaut :
L10 = [en millions de tours]
C désigne la charge dynamique de base,
P désigne la charge dynamique équivalente et
k vaut 3 pour les roulements à billes et pour les roulements à rouleaux. Lorsque la vitesse est
constante, il est généralement préférable
d'exprimer la durée nominale en heures de fonctionnements avec :
L10h = L10
Où n désigne la vitesse de
rotation de l'arbre.
La charge statique C0, d'une série de
roulements identiques, est la charge radiale (axiale pour les butées),
constante en intensité et en direction, que peut endurer 90
0/0 de roulements du groupe, avant que n'apparaissent les
signes de détérioration.
La charge dynamique de base C, est la charge radiale (axiale
pour les butées), constante en intensité et en direction, que
peut endurer 90 0/0 de roulements du groupe, avant que
n'apparaissent les premiers signes de fatigue.
La charge équivalente P est la Charge radiale Pure,
donnant exactement la même durée de vie que la combinaison des
charges axiale Fa et radiale Fr réellement exercée sur le
roulement. P est différent de la charge combinée F. En principe
les composantes de F qui sont Fa et Fr sont déterminées par
une étude mécanique.
Remarque :
Si on porte sur un système d'axe (Fa, Fr) l'ensemble
des pointeurs (O, F) correspondant aux charges combinées Fa et Fr
donnant la même durée de vie à un roulement, on obtient la
courbe d'équidurée (lieu de F) du roulement.
Pour des raisons pratiques, on remplace la courbe par deux
droites limitées par un angle â tel que .
La charge équivalente P se calcule différemment
selon le type de roulement utilisé comme nous allons le voir dans les
figures suivantes :
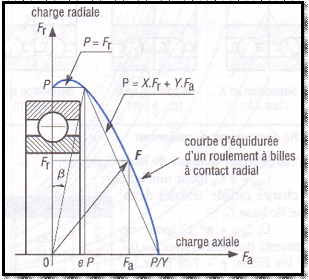
Figure 26: cas d'un roulement à contact
radial
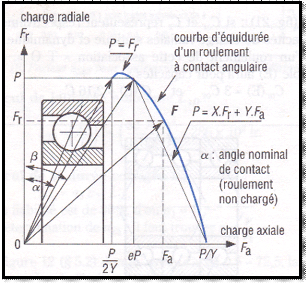
Figure 27: cas d'un roulement à contact
angulaire
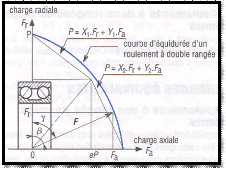
Figure 28: cas des roulements à double
rangée
La durée nominale se calcule en exécutant
l'algorithme suivant :
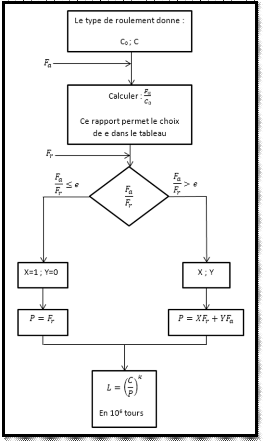
Figure 29: algorithme de calcul de la durée
nominale
CONCLUSION
Au terme de ce chapitre on peut retenir que les données
exploitées dans ce travail émanent d'un challenge intitulé
IEEE PHM 2012 Data Challenge, organisé par l'IEEE Reliability Society en
collaboration avec l'institut FEMTO-ST. Les expériences ont
été menées sur la plateforme PRONOSTIA qui permet
d'accélérer le processus de dégradation des roulements.
Parmi les roulements testés, six d'entre eux ont été
utilisés jusqu'à l'usure afin de permettre la conception du
modèle théorique d'estimation du temps de survie. Les onze autres
roulements qui n'ont pas été utilisés jusqu'à
l'usure permettent de tester le modèle afin de prédire leurs
temps de vie restant.
Le signal vibratoire a été prélevé
à l'aide de deux accéléromètres placés dans
le plan horizontal et vertical du roulement. La fréquence
d'échantillonnage a été fixée à 25,6 kHz et
les données ont été enregistrées dans des fichiers
ASCIInommées acc_XXXXX.csv. Un fichier
correspond à instant de prélèvement.
Pour finir, nous avons souligné le fait que les
méthodes conventionnelles d'estimation du temps de survie des
roulements, à l'instar de la durée nominale L10,
étaient inefficaces dans notre cas. Ce constat nous conduit au chapitre
suivant qui sera axé sur la conception des algorithmes d'estimation du
temps résiduel utiles des roulements à billes.
CHAPITRE 5 : DETECTION
D'ANOMALIES SUR LA SIGNATURE FREQUENTIELLE ET ESTIMATION DU TEMPS DE
SURVIE
INTRODUCTION
Les résultats expérimentaux obtenus ont
clairement montré les limites des méthodes classiques de calcul
du temps de vie des roulements, à l'instar de la durée nominale
L10. C'est dans l'optique d'apporter une solution palliative
à ce problème que cettesection décrira une
méthodologie d'estimation du temps résiduel utile des roulements
testés en deux étapes majeures. De prime abord il sera question
de la détection des premiers défauts par analyse spectrale du
signal vibratoire, puis l'approximation du temps de survie. Le modèle
théorique présenté ici a été proposé
par une équipe d'étudiants du département génie
mécanique du centre d'ingénierie du cycle de vie avancé
(CALCE en anglais pour Center for Advanced Life Cycle Engineering). Cette
équipe a remporté la première place du PHM 2012 Data
Challenge dans la catégorie académique.
L'ensemble des scripts utilisés dans cette partie ont
été implémentés dans l'environnement
développement intégré dans MATLAB, logiciel
optimisé pour les traitements des signaux.
5.1 La détection des
premiers défauts
Un défaut est détecté lorsqu'on observe
un changement dans le spectre du signal, soit par l'apparition des pics
très élevés ou par la disparition d'une gamme
fréquentielle. Le spectre de fréquences est
généré via l'algorithme de la transformée de
Fourier rapide noté FFT (Fast Fourier Transform) déjà
implémenté dans MATLAB.
Le spectre doit être déterminé pour tous
les signaux prélevés pendant le test du roulement et
l'observation de tous les spectres doit se faire sur un seul graphe afin de
bien voir comment évolue les magnitudes des fréquences d'un
spectre à l'autre.
Pour obtenir ce résultat, nous avons
implémenté une fonction que nous avons
baptiséevue_3d.m. Les grandes lignes de son
algorithme sont les suivantes :
Début algorithme
Récupération du nombre de fichiers (instants de
prélèvement) du roulement traité
Fixation de la fréquence d'échantillonnage Fe =
25600 Hz
Pour i allant de 1 au nombre de fichiers
traités
Construction du nom du fichier à exploiter
Extraction des données contenues dans le fichier
traité
Récupération de la colonne
d'accélération horizontale
Récupération de la colonne
d'accélération verticale
Calcul des spectres des signaux extraits
Construction de la matrice de maillage de
l'accélération horizontale
Construction de la matrice de maillage de
l'accélération verticale
Fin Pour
Sauvegarde des spectres des signaux dans des fichiers
EXCEL
Construction de l'axe des abscisses
Construction de l'axe des fréquences
Troncature des matrices de maillage
Construction des graphes 3d des spectres des
signaux
Finalgorithme
Le code source complet de cette fonction sera fourni dans
l'annexe A. Toutefois, nous allons décortiquer ligne par ligne
l'algorithme ci-dessus.
De prime abord, nous avons récupéré le
nombre de fichiers contenu dans le roulement traité. En effet chaque
fichier correspond à un instant de prélèvement, tous les
fichiers sont contenus dans un répertoire comportant le nom du roulement
correspondant. Ces fichiers ASCII contiennent toutes les informations
prélevées par les capteurs comme nous l'avons susmentionné
dans le chapitre précédant. Pour rendre effective cette
récupération de données, nous avons compté
l'ensemble des fichiers contenus dans le répertoire du roulement
à étudier, ensuite nous avons inscrit ce nombre dans un fichier
nommé nbr_files.csv. A l'aide de la fonction
loadqui prend en paramètre le nom du fichier,
nous avons réussi à importer le contenu de ce dernier dans le
logiciel MATLAB et nous avons affecté cette valeur à la variable
nbr_files.
La fixation de la fréquence d'échantillonnage a
consisté à affecter la valeur de la fréquence
d'échantillonnage du signal (elle vaut 25,6 kHz) à la variable
Fe.
Ensuite nous avons utilisé une boucle for
qui va nous permettre de parcourir tous les fichiers du roulement
à traiter. La variable d'incrémentation est notée
i.
Pour exploiter les données contenues dans un fichier il
faut passer en paramètre le nom de ce dernier à une fonction
d'extraction de données, comme les fonctions load, xlsread,
csvread, etc. Voilà pourquoi il est important de
construire le nom du fichier à exploiter à l'aide de la variable
d'incrémentation de la structure itérative
for car chaque roulement possède plusieurs
fichiers. En effet la structure générale du nom des fichiers est
de la forme acc_XXXXX.csvoù la suite
XXXXXcorrespond au numéro du fichier qu'on
traite. Pour construire le nom du fichier, on converti le nombre contenu dans
la variable d'incrémentation i en
chaîne de caractère à l'aide de la fonction
int2str, puis on fait une concaténation avec
la chaîne de caractère acc_ et
l'extension .csv à l'aide de la fonction
strcat. Le nom du fichier obtenu est affecté
à la variable file_name.
Une fois le nom du fichier obtenu, on importe ses
données avec la fonction loadet on
insère ces informations dans une variable appelée
data. Cette variable devient une matrice à
2560 lignes (le nombre d'échantillons
récoltés par instant de prélèvement) et 6
colonnes. Chaque colonne correspond respectivement aux données
relatives à l'heure, la minute, la seconde, la microseconde,
l'accélération horizontale et l'accélération
verticale.
Dans MATLAB, pour récupérer la n-ième
colonne d'une matrice X, on se sert de la commande X( : ,
n). Par conséquent, pour récupérer les
données de l'accélération horizontale nous avons
utilisé la commande data( : , 5) et pour
l'accélération verticale nous avons utilisé la commande
data( : , 6).
Les signaux temporels d'accélérations sont
acquis, maintenant il faut déterminer leurs spectres. Pour se faire, on
utilise l'algorithme de la transformée de Fourier rapide FFT. Cette
fonction renvoie des valeurs complexes. On calcule ensuite leurs modules
respectifs avec la fonction abs. Par exemple, la
commande complète pour calculer le spectre de
l'accélération horizontale est : abs(fft(
data( : , 5))).
Après avoir calculé les spectres des signaux, on
les enregistre dans une matrice de maillage dans laquelle chaque colonne
correspond au spectre d'un fichier. On déduit aisément que le
nombre de colonnes de la matrice de maillage correspond au nombre de fichiers
(instants de prélèvements) contenu dans le roulement
considéré. Cette matrice de maillage va permettre d'obtenir une
représentation en trois dimensions de tous les spectres des signaux
prélevés. Si on a un vecteur X de
longueurmet un deuxième vecteur Y de
longueurn, leur matrice de maillage Z sera de
dimension n×m et Z(i ; j) =
f(Xj ; Yi). Dans notre cas d'usage, le
vecteur X correspond aux numéros des fichiers traités, Y
correspond à l'axe des fréquences et la fonction f corresponds au
spectre. Par conséquent Z(i ; j) correspond à la magnitude
de la fréquences j du fichier numéro i.
A la fin de la boucle for, nous avons deux matrices
de maillages contenant chacune les spectres des accélérations
horizontales et verticales. Nous sauvegardons toutes ces données dans
des fichiers EXCEL à l'aide de la fonction
xlswrite. Cette fonction prend en paramètre le
nom du fichier dans lequel on souhaite enregistrer les données et la
matrice qui contient les données. D'autres fonctions permettent de
réaliser cette tâche sur MATLAB, à l'instar de
csvwrite et save.
Pour générer le graphe à trois dimensions
il nous faut définir l'axe des abscisses, l'axe des ordonnées et
l'axe des côtes. L'axe des côtes correspond à la matrice de
maillage que nous avons déterminé dans la boucle for.
L'axe des abscisses correspond aux numéros des fichiers
(instants de prélèvement). Pour le construire, on
génère un vecteur dont les valeurs vont de 1 au nombre de
fichiers contenus dans la variable nbr_files qu'on avait
créée au début de l'algorithme. Le pas vaut 1.
L'axe des ordonnées correspond aux fréquences du
spectre. Un signal numérique est défini par un nombre
d'échantillons N relevés à une
fréquence d'échantillonnage Fe. Afin de rester
cohérent avec les mesures, il est important de respecter les grandeurs
physiques impliquées dans le signal. L'axe des fréquences est un
vecteur de N points compris entre 0 et Fe. On le génère avec la
syntaxe suivante : axe_freq = (0 : N-1)×Fe/N.
Pour finir, on génère le graphe à trois
dimensions à l'aide de la fonction mesh. Cette
fonction prend en paramètre l'axe des abscisses X qui correspond au
vecteur contenant les numéros des fichiers, l'axe des ordonnées Y
qui correspond au vecteur des fréquences et Z la matrice de maillage.
Aux points X(j) etY(i) elle fait correspondre Z(i ; j).
Nous avons exécuté cet algorithme sur le roulement
bearing1_3, et nous avons obtenu les graphes suivants :
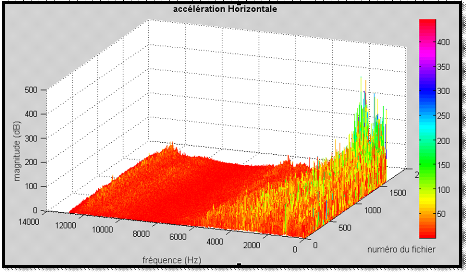
Figure 30: vue globale des spectres des signaux
d'accélération horizontale
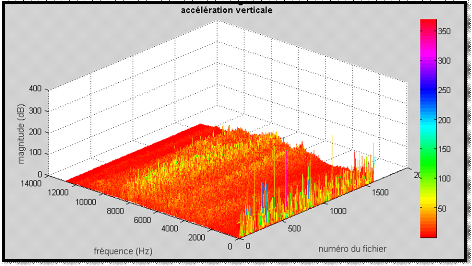
Figure 31: vue globale des spectres des signaux
d'accélération verticale
Pour mieux observer l'évolution des pics nous nous
sommes proposés d'effectuer une vue de dessus de ces graphes en faisant
une rotation autour de l'axe des fréquences. Nous avons obtenu les
résultats suivants :
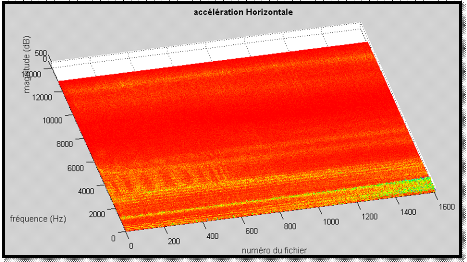
Figure 32: vue de dessus du spectre de
l'accélération horizontale
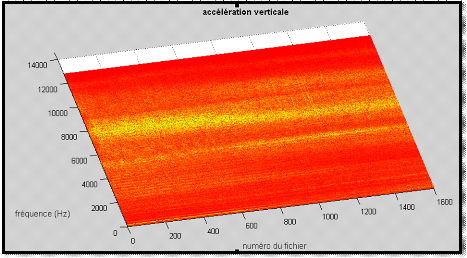
Figure 33: vue de dessus du spectre de
l'accélération verticale
Les résultats obtenus ne sont pas très lisibles,
cela est dû au fait que tous les pics apparaissent sur le graphe. Pour
remédier à ce problème, il faut supprimer les pics sans
importance et ne garder que ce qui ont des valeurs élevées. Les
données relatives aux deux types d'accélérations sont
affichées simultanément sur le même graphe. On obtient
dès lors la figure suivante :
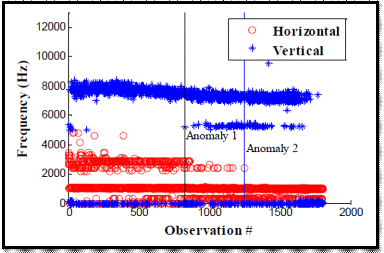
Figure 34: détection d'anomalies dans le roulement
bearing1_3
On remarque que dans le spectre du signal
d'accélération verticale, à l'instant de
prélèvement #822 il y'a l'apparition d'une nouvelle gamme de pics
de fréquences autour de 5300 Hz. En plus de cela, on remarque
également un changement dans le spectre du signal
d'accélération horizontale, de l'observation #822 à #1247
une gamme de fréquence qui existait autour de 2500 Hz disparait
progressivement.
A toutes fins utiles, il est important de rappeler que chaque
numéro d'observation (instant de prélèvement) est
équivalent à une durée de 10 secondes.
Une explication physique possible des changements
observés dans les spectres des signaux est l'apparition des fissures ou
d'autres défauts de surface dans le roulement. Ces
phénomènes peuvent justifier le fait que la structure vibre avec
de nouvelles gammes de fréquences. Cependant, cette hypothèse ne
peut pas être confirmée car aucune information sur l'analyse des
défauts n'a été fournie dans le challenge.
En nous appuyant sur les résultats obtenus sur les
graphes précédents, nous émettons l'assertion selon
laquelle le roulement comporte plusieurs stades de dégradation
avant d'atteindre l'usure totale. Certains roulements
présentent des stades de dégradations ayant une manifestation
graduelle, pendant que d'autres ne montrent aucune tendance puis subitement
montrent une croissance brusque de la magnitude des fréquences et
s'affaiblit lentement.
5.2 Conception d'un
modèle théorique d'estimation du temps de survie
Dans le chapitre sur l'analyse vibratoire nous avons vu que pour
surveiller une machine il fallait suivre l'évolution des indicateurs de
défauts de cette dernière. L'indicateur que nous avons
utilisé pour détecter l'apparition des premiers défauts du
roulement est la moyenne des cinq plus grandes valeurs absolues des
accélérations mesurées dans chaque fichier d'observation.
La moyenne a été utilisée pour réduire
l'effet du bruit. La formule qui définit cet indicateur est la
suivante :

Où accdésigne
l'accélération et i est le rang de la
donnée après avoir trié dans l'ordre décroissant
les valeurs absolues de l'accélération.
Cet indicateur doit être évalué dans
chaque instant de prélèvement, puis on doit générer
un graphe pour suivre son évolution. Pour atteindre cet objectif, nous
avons implémenté une fonction que nous avons baptisée
moyenne5.m dont l'algorithme est le suivant :
Début algorithme
Récupération du nombre de fichiers (instants
de prélèvement) du roulement traité
Pour i allant de 1 au nombre de fichiers
traités
Construction du nom du fichier à exploiter
Extraction des données contenues dans le fichier
traité
Récupération de la colonne
d'accélération horizontale
Récupération de la colonne
d'accélération verticale
Calcul des valeurs absolues des signaux temporels
Tri des valeurs absolues dans l'ordre
décroissant
Récupération des cinq premières valeurs
des tableaux
Calcul de la moyenne de ces valeurs
Insertion du résultat dans un tableau
Fin Pour
Sauvegarde des spectres des signaux dans des fichiers
EXCEL
Construction de l'axe des abscisses
Construction de la courbe d'évolution de
l'indicateur des deux signaux
Finalgorithme
Le code source complet de cette fonction sera fourni dans
l'annexe B. Nous allons revenir sur certaines spécificités de cet
algorithme vu qu'on retrouve quelques instructions qui apparaissent
déjà dans l'algorithme précédent.
Le calcul de la valeur absolue se fait à l'aide de la
fonction abs déjà contenue dans la
bibliothèque mathématique de MATLAB. Pour l'utiliser, il suffit
de lui passer en paramètre le vecteur contenant les nombres dont on
souhaite obtenir les valeurs absolues.
Le tri d'un tableau est réalisé à l'aide
de la fonction sort de MATLAB. On lui envoie un
vecteur en paramètre (dans notre cas le vecteur comporte les valeurs
absolues des signaux temporels d'accélération) et en sortie elle
nous renvoie le vecteur trié dans l'ordre croissant. Pour qu'elle puisse
trier le tableau dans l'ordre décroissant comme nous souhaitons le
faire, il faut lui ajouter un second paramètre, notamment la chaine de
caractères « descend ».
Lorsqu'on a un vecteur X dans MATLAB et qu'on
veut obtenir les n premières valeurs de ce
dernier, on utilise la syntaxe : X(1 : n). Dans
notre cas d'usage n = 5, car on souhaite
récupérer les cinq premières valeurs du vecteur
trié dans l'ordre décroissant. Ces cinq valeurs sont en effet les
plus grandes du vecteur. Pour finir, on calcul la moyenne de ces cinq valeurs
en utilisant la fonction
meanimplémentée dans MATLAB.
Pour générer le graphe d'évolution de
l'indicateur, nous avons utilisé la fonction plot
de MATLAB. Cette fonction permet de construire un graphe à
deux dimensions lorsqu'on lui fournit en paramètre l'axe des abscisses
dans un premier vecteur et l'axe des ordonnées dans un second vecteur.
Dans notre cas, en abscisse nous avions les numéros de chaque fichier
(instants de prélèvement) et en ordonnées nous avions les
valeurs de l'indicateur correspondant à chaque fichier d'observation.
Nous avons exécuté cet algorithme sur le
roulement bearing1_1 et nous avons obtenu le graphe de la figure
suivante :
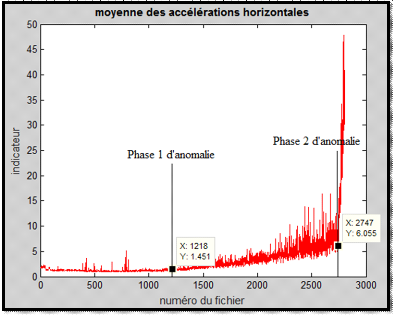
Figure 35: indicateur appliqué aux
accélérations horizontales
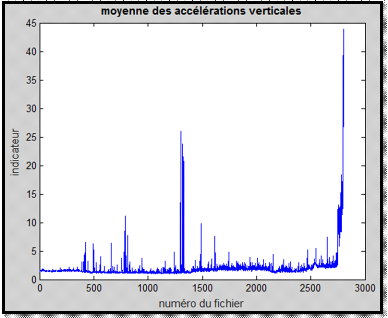
Figure 36: indicateur appliqué aux
accélérations verticales
Le résultat obtenu sur le signal
d'accélération verticale n'est pas facile à exploiter. Par
contre celui obtenu sur le signal d'accélération horizontale
montre d'abord une évolution quasi constante de l'indicateur, et
à partir de l'observation #1218 on remarque une croissance graduelle. A
cet instant, le roulement entre dans la première phase (ou stade) de
dégradation.
A l'observation #2747 on observe une croissance brusque de
l'indicateur. Le roulement entre dans la deuxième de
dégradation.
La tendance de dégradation du roulement bearing1_1
est la même que celle observée dans le roulement
bearing1_3. Ce sont les deux seuls cas dans lesquels nous avons
observéune croissance progressive de l'indicateur après
l'apparition du premier défaut. Dans les autres roulements, l'indicateur
présente des successions de croissances et de décroissances
après l'apparition du premier défaut.
Nous allons donc concevoir le modèle d'estimation du
temps de survie à l'aide du roulement bearing1_1 et nous allons
l'appliquer sur le roulement bearing1_3.
Pour mettre en place le modèle de prédiction,
une approche à deux étapes a été adoptée.
La première étape consiste à estimer le
temps au bout duquel le roulement entre dans la deuxième phase
d'anomalie et la deuxième étape est d'estimer la durée
entre le début de la deuxième phase d'anomalie et l'instant
où le roulement est hors d'usage.
A partir du résultat obtenu à la figure 35,
l'idée est de générer une courbe d'ajustement
exponentielle à partir de l'instant de détection du
premier défaut (phase 1 d'anomalie) jusqu'au début de la phase 2
d'anomalie. Pour atteindre cet objectif, nous avons développé une
fonction dans MATLAB que nous avons
baptiséeexp_fit.m. Cette fonction obéit
à l'algorithme suivant :
Début algorithme
Récupération du nombre de fichiers (instants
de prélèvement) du roulement traité
Pour i allant de 1 au nombre de fichiers
traités
Construction du nom du fichier à exploiter
Extraction des données contenues dans le fichier
traité
Récupération de la colonne
d'accélération horizontale
Calcul des valeurs absolues des signaux temporels
Trie des valeurs absolues dans l'ordre
décroissant
Récupération des cinq premières valeurs
du tableau
Calcul de la moyenne de ces valeurs
Insertion du résultat dans un tableau
Fin Pour
Sauvegarde des spectres des signaux dans des fichiers
EXCEL
Troncature du tableau des valeurs de l'indicateur
Génération de la courbe d'ajustement
exponentiel
Construction de la courbe d'évolution de
l'indicateur et la courbe d'ajustement
Finalgorithme
Le code source complet de ce script sera fourni dans l'annexe
C de ce document. Revenons toutefois sur les étapes clés de cet
algorithme.
La troncature permet de récupérer les valeurs de
l'indicateur qui sont comprises entre la phase 1 et la phase 2 d'anomalie. Dans
MATLAB, lorsqu'on a un vecteur X et qu'on souhaite
récupérer les valeurs comprises entre les positions n
et m du vecteur, on utilise la syntaxe
suivante : X(n : m). Dans notre cas, X correspond au
tableau d'évolution des valeurs de l'indicateur appliqué à
l'accélération horizontale, n vaut 1218 et m vaut 2747.
Pour générer la courbe d'ajustement exponentiel
des données, on utilise la fonction fit
contenue dans MATLAB. Cette fonction prend trois
paramètres, à savoirl'axe des abscisses et des ordonnées
ainsi que la chaine de caractère
« exp1 » qui spécifie le
type d'ajustement qu'on applique aux données. Dans la dernière
version de MATLAB, un outil spécial a été
développé spécifiquement pour résoudre les
problèmes d'ajustement linéaire, logarithmique, exponentiel, etc.
Cet outil permet une manipulation beaucoup plus souple des courbes
d'ajustement.
Après l'exécution de ce script, nous avons
obtenu le graphe suivant :
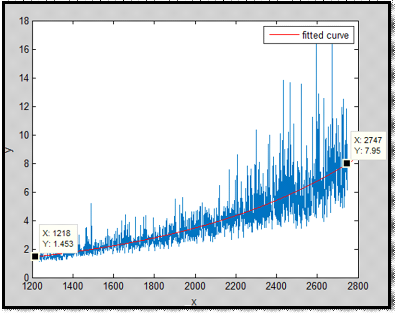
Figure 37: courbe d'ajustement exponentiel appliquée
au roulement bearing1_1
Cette fonction renvoie également l'expression
littérale de la courbe d'ajustement exponentiel. Son équation est
de la forme :
f(x) = aebx
Le logiciel MATLAB nous indique que les coefficients
a et b sont estimés
dans un intervalle de confiance à 95% et valent respectivement
0,3757 et 0,00111. Au
final, l'expression littérale de l'équation de la courbe
d'ajustement exponentiel est :
f(x) = 0,3757e 0,00111x
L'image du début de la phase 1 d'anomalie par la
fonction d'ajustement est 1,453 comme on peut si bien
le lire sur le graphe de la figure 37, et celle du début de la phase 2
d'anomalie est 7,95. Leur rapport vaut :
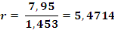
On détermine ensuite le temps au bout duquel le
roulement s'abîme complètement après être
entré dans la phase 2 d'anomalie. Sachant que chaque instant de
prélèvement est équivalent à une durée de 10
secondes, ce temps vaut :
?t1 = tf - ti =
28030s - 27470s = 560s
On évalue également la durée entre les
phases 1 et 2 d'anomalie :
?t2 = tf - ti =
27470s - 12180s = 15290s
Les durées que nous venons de calculer correspondent
respectivement à celle de la première et de la deuxième
anomalie. Pour finir, on évalue leur rapport qu'on va appeler le
ratio d'anomalies :

5.3 Application du
modèle sur un roulement d'essai
Le modèle théorique sera testé sur le
roulement bearing1_3. Rappelons que ce roulement n'a pas
été utilisé jusqu'à l'usure. Le but du travail sera
donc dans un premier temps de détecter l'instant d'apparition du premier
défaut, c'est-à-dire le début de la phase 1, ensuite
trouver l'instant du début de la phase 2 et du temps au bout duquel le
roulement est hors d'usage à partir des coefficients calculés
dans le modèle théorique, et enfin calculer le temps de vie
restant, car ce roulement d'essai n'a pas encore atteint sa fin de vie.
Pour détecter le premier défaut nous allons
appliquer l'algorithme moyenne5.m. Voici le
résultat obtenu :
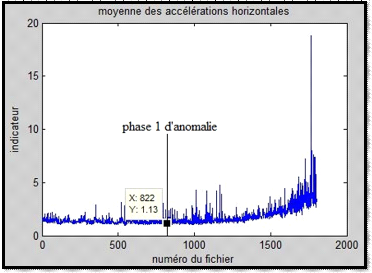
Figure 38: détection du premier défaut sur le
roulement bearing1_3
On remarque que l'indicateur commence à croître
progressivement à partir de l'observation #822. C'est donc à
partir de cet instant de prélèvement que nous supposons qu'il y'a
apparition du premier défaut. Nous allons maintenant tronquer les
données à partir de cette valeur et générer la
courbe d'ajustement exponentiel puis déduire l'instant du début
de la phase 2 d'anomalie.
Pour cela, nous allons exécuter la fonction
exp_fit.m. On obtient le graphe suivant :
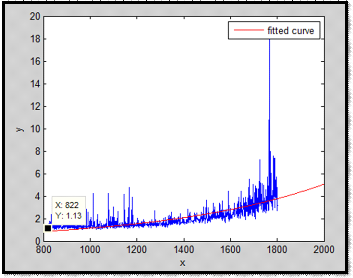
Figure 39: courbe d'ajustement exponentiel du roulement
bearing1_3
L'équation de la courbe d'ajustement exponentiel
générée par cette fonction est :
f(x) = 0,2595e0, 001485
Pour obtenir l'image de l'instant correspondant au
début de la phase 2 d'anomalie, on multiplie l'image de l'observation
#822 par le coefficient r. soit :

Maintenant il faut trouver l'instant d'observation qui admet
6 comme image. Ce problème revient à
déterminer la réciproque de la fonction d'ajustement afin de
calculer l'antécédent du nombre 6. Pour se faire, nous allons
résoudre l'équation y = f(x) avec
f(x) = aebx.
On a :

En appliquant le logarithme :

Au final : 
Le numéro de l'observation où commence la phase 2
d'anomalie se calcule comme suit :

En soustrayant 822 dans 2115, on obtient le nombre
d'observations qui constituent la première phase d'anomalie, soit 1293
observations. Par ailleurs, une observation correspond à une
durée de 10 secondes, donc le temps que dure la phase 1 est :
1stAno.Duration = 1293 ×10 =
12930s
La durée de la deuxième phase d'anomalie est
estimée en multipliant la durée de la première anomalie
par le facteur AnomalyRatio obtenu
précédemment. Soit :
2ndAno.Duration = 0,0366 ×
1stAno.Duration = 478s
Le temps de dégradation à partir de l'instant de
détection de la première anomalie (jusqu'à la fin de vie)
se déduit en sommant les durées des deux phases
d'anomalie :
T = 1stAno.Duration +
2ndAno.Duration = 12960s + 478s = 13404s
Dès l'entame de ce point, nous avons
précisé que le roulement bearing1_3n'avait pas
été utilisé jusqu'à l'usure. Ce roulement contient
1802 fichiers de prélèvement. Or nous avons détecté
le premier défaut à l'observation #822. On déduit donc que
le roulement a déjà survécu pendant :
Ts = (1802 - 822)×10 =
9800s
Nous connaissons maintenant la durée T
des deux anomalies et le temps Tsmis par
le roulement depuis l'apparition du premier défaut. On peut dès
lors déduire aisément le temps de vie utile restant
RUL (RemainingUseful Life) :
RUL = T - Ts = 13404s - 9800s =
3604s.
Les organisateurs du challenge ont fourni les temps de vie
utiles restant (RUL) des onze roulements d'essai. Ces valeurs ont
été obtenues de manière expérimentale, il s'agit
donc des RUL réels. On peut les voir sur la figure suivante :
Tableau 5: valeurs des RUL
fournis dans le challenge
Test set
|
Actual RUL
|
Bearing1_3
|
5730s
|
Bearing1_4
|
339s
|
Bearing1_5
|
1610s
|
Bearing1_6
|
1460s
|
Bearing1_7
|
7570s
|
Bearing2_3
|
7530s
|
Bearing2_4
|
1390s
|
Bearing2_5
|
3090s
|
Bearing2_6
|
1260s
|
Bearing2_7
|
580s
|
Bearing3_3
|
820s
|
On peut alors calculer le pourcentage d'erreur de
prédiction de la manière suivante :

Le pourcentage d'erreur de prédiction du RUL du
roulement bearing1_3 en appliquant le modèle théorique
que nous avons décrit est de 37,1%.
5.4 Estimation du RUL pour les
cas particuliers
Le roulement bearing1_3 était l'unique
roulement d'essai dans lequel on pouvait appliquer la courbe d'ajustement
exponentiel sur le graphe d'évolution de l'indicateur. Dans les autres
cas, la courbe d'évolution de l'indicateur ne présentait pas
toujours une tendance croissante après l'apparition du premier
défaut.
Prenons par exemple le cas du roulement bearing2_2.
C'est un roulement d'étude, donc il a été utilisé
jusqu'à l'usure total. La figure 40 présente le graphe de la
détection d'anomalies et ceux de l'évolution de l'indicateur des
signaux d'accélération horizontale et verticale.
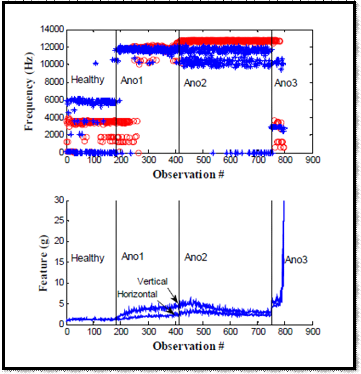
Figure 40: détection d'anomalie et évolution
de l'indicateur du roulement bearing2_2
La courbe de l'indicateur du signal
d'accélération verticale divise le graphe en une phase normale
suivie de trois phases anormales. Dans le cas des roulements d'essai où
l'évolution de la courbe de l'indicateur ne présentait pas une
tendance croissante après la détection du premier défaut,
l'estimation du RUL a été faite en calculant les rapports de
durées des différentes phases d'anomalie
Pour revenir sur le cas du roulement bearing2_2, la
première phase anormale va de l'observation #181 à #415, soit
2340s. La deuxième phase anormale va de l'observation #416 à
#752, soit une durée totale de 3360s. Et enfin la troisième phase
anormale va de l'observation #753 jusqu'à l'usure totale, cette phase
dure 440s.
Dans la majorité des roulements d'essai, les phases 2
et 3 d'anomalie ne sont pas connues. Cependant, la durée des anomalies 2
et 3 ont été estimées en s'aidant de la durée que
met l'anomalie 1.
En prenant les rapports des durées d'anomalies pour le cas
du roulement bearing2_2, nous obtenons les relations
suivantes :


Pour chaque roulement test, deux RUL ont été
calculés à partir des coefficients issus des roulements
d'études de chaque condition d'expérience, puis on évalue
les pourcentagesd'erreur de prédiction de chacun de ces RUL. On effectue
ensuite la moyenne des erreurs d'estimation si et seulement si le produit des
deux valeurs est positif. Dans le cas où l'une des valeurs est
négative ont omet sciemment le calcul de la moyenne et cette valeur est
considérée comme le taux d'erreur d'estimation du RUL du
roulement concerné. Un résumé des pourcentages d'erreur
d'estimation des RUL en utilisant la méthode décrite
précédemment est présenté dans le tableau
suivant :
Tableau 6: résumé
des erreurs d'estimation du RUL
Test set
|
%Err
|
Bearing1_3
|
37
|
Bearing1_4
|
80
|
Bearing1_5
|
9
|
Bearing1_6
|
-5
|
Bearing1_7
|
-2
|
Bearing2_3
|
64
|
Bearing2_4
|
10
|
Bearing2_5
|
-440
|
Bearing2_6
|
49
|
Bearing2_7
|
-317
|
Bearing3_3
|
90
|
Pour chaque roulement d'essai, deux valeurs du RUL sont
générées en utilisant les deux roulements d'études
(Learning set) fournies pour chaque condition d'utilisation. La
moyenne des deux valeurs des RUL a été effectuée.
Une exception a été faite pour le cas du
roulement bearing1_3, car c'est le seul cas dont la tendance
d'évolution de l'indicateur était semblable à celle du
roulement bearing1_1. Une autre exception a été faite
lorsque l'un des RUL était un nombre négatif. Dans ce cas, le
calcul de la moyenne a été délibérément
omis.
5.5 Perspective d'optimisation
du modèle théorique
L'observation majeure qui découle
inéluctablement des résultats obtenus dans le tableau synoptique
des erreurs de prédiction du RUL est que seuls quatre roulements parmi
les onze roulements d'essai présentent un pourcentage d'erreur
d'estimation dont la valeur absolue est inférieure à 10%.
Ce constat en particulier nous entraine à penser que le
modèle théorique présenté ci-dessus peut être
sujet à une optimisation afin d'améliorer ces pourcentages
d'erreurs en les réduisant considérablement.
Pour cela, on se propose de généraliser le terme
de calcul de l'indicateur utilisé dans ce modèle théorique
de la manière qui suit :

On calcule la moyenne des N premiers termes du tableau des
valeurs absolues du signal vibratoire temporel rangé l'ordre
décroissants. On fait varier N dans l'ensemble des valeurs
suivantes :

En appliquant ce principe sur tous les roulementstest, on
obtient les résultats suivants :
Tableau 7: évolution de
l'erreur d'estimation en fonction de N
valeur de N
|
2
|
3
|
5
|
7
|
10
|
bearing1_3
|
42,37
|
38,97
|
37,1
|
15,85
|
13,33
|
bearing1_4
|
85,84
|
84,96
|
80
|
79,06
|
75,81
|
bearing1_5
|
25,04
|
25,04
|
9
|
8,26
|
7,35
|
bearing1_6
|
12,6
|
12,6
|
-5
|
11,3
|
9,79
|
bearing1_7
|
28,8
|
28,8
|
-2
|
-8,6
|
-6,48
|
bearing2_3
|
62,03
|
59,08
|
64
|
58,98
|
58,41
|
bearing2_4
|
16,43
|
14,62
|
10
|
-8,74
|
-9,15
|
bearing2_5
|
-399,54
|
-339,57
|
-440
|
-421,06
|
-412,39
|
bearing2_6
|
-67,03
|
-78,28
|
49
|
40,72
|
39,11
|
bearing2_7
|
412,01
|
412,01
|
-317
|
-305,23
|
-290,42
|
bearing3_3
|
103,47
|
112,25
|
90
|
83,63
|
77,59
|
Lorsqu'on diminue la valeur de N on remarque une augmentation
considérable du taux d'erreur d'estimation du RUL. Ce constat est
général à tous les roulements test. Cette approche est par
conséquent à rejeter car elle ne cadre pas avec notre objectif
d'amélioration du taux d'erreur.
Par contre en augmentant la valeur de N on diminue le
pourcentage d'erreur d'estimation du RUL. Pour le cas par du roulement
bearing1_3 nous sommes passés de 37,1% à
13,33%, soit une réduction de plus
de20% du taux d'erreur. On déduit qu'il est
nettement mieux d'augmenter le nombre de valeurs au niveau du calcul de
l'indicateur afin d'améliorer le pourcentage d'erreur d'estimation du
RUL.
CONCLUSION
Nous venons de décrire une méthode d'estimation
du RUL basée sur les comparaisons des durées des phases de
dégradation entre les roulements d'étude et les roulements
d'essai. A partir de roulements d'étude nous avons été
capables, à partir du modèle théorique proposé par
les lauréats de l'IEEE PHM 2012 Data Challenge, d'estimer la
durée de vie résiduelle utile des roulements d'essai. Pour le cas
du roulement bearing1_3, grâce à l'évolution de la
courbe de son indicateur qui était semblable à celle du roulement
bearing1_1, nous avons utilisé une courbe d'ajustement
exponentiel et les rapports des durées des phases d'anomalie pour
estimer son RUL. Dans les cas particuliers où la courbe d'ajustement
exponentiel ne s'appliquait pas, nous avons uniquement travaillé avec
les rapports de durées des différentes phases d'anomalie. Parmi
les onze roulements test, seuls quatre avaient un taux d'erreur d'estimation du
RUL acceptable. Pour améliorer ces pourcentages nous avons
proposé d'augmenter le nombre de valeurs dans le calcul de l'indicateur
du modèle théorique utilisé.
CONCLUSION GENERALE ET
PERSPECTIVE
Au terme de ce travail nous pouvons retenir que l'analyse
vibratoire s'inscrit dans le panel des techniques de maintenance
préventive conditionnelle appliquée aux machines tournantes.
Cette technique à l'avantage de prévenir les pannes afin de mieux
planifier les interventions sur les équipements. Elle permet
également, en cas de panne, de détecter l'élément
défaillant sans démonter la machine, mais juste en analysant le
spectre de son signal vibratoire. Le seul bémol, c'est que la mise en
place de cette technique requiert d'énormes investissements financiers,
c'est pourquoi on applique cette méthode que sur les machines dont une
panne pourrait affecter grièvement la chaine de production.
Cette méthode repose sur le traitement du signal
vibratoire de l'équipement surveillé. Une vibration est la
variation périodique d'un objet entre une position minimale et une
position maximale, autour d'une position d'équilibre. Elle est
caractérisée par sa fréquence, son amplitude et sa phase.
Un signal est une grandeur physique porteuse d'information. Or la
quasi-totalité des équipements de mesure fonctionnent avec un
signal électrique. Voilà pourquoi on utilise un
accéléromètre afin de convertir le signal vibratoire (le
mesurande) en signal électrique, puis en suivant la chaine d'acquisition
du capteur, on numérise ce signal afin de l'enregistrer dans un support
de stockage ou de le traiter à l'aide d'un microprocesseur (DSP).
Les données que nous avons exploitées
proviennent d'une plateforme expérimentale baptisée PRONOSTIA.
Cette plateforme permet de dégrader un roulement en quelques heures en
lui appliquant une charge supérieure à la charge maximale qu'il
peut supporter. Les données du signal vibratoire sont
prélevées à l'aide de deux
accéléromètres : l'un sur le plan horizontal et
l'autre sur le plan vertical. Ces signaux sont numérisés à
une fréquence d'échantillonnage de 25,6 kHz et sont
enregistrées dans des fichiers ASCII. Un fichier correspond à un
instant de prélèvement.
Les résultats des méthodes conventionnelles
d'estimations du temps de vie d'un roulement, telle que la durée
nominale L10, n'étaient pas conformes aux observations
expérimentales. Ce constat fait tout l'objet de ce travail qui est donc
de concevoir un modèle théorique d'estimation du temps de vie
résiduel utile des roulements à billes. Nous avons donc
présenté la méthode proposée par les
lauréats de l'IEEE PHM 2012 Data Challenge. Cette méthode
comporte deux parties. La première consiste à détecter les
défauts par analyse spectrale du signal. La deuxième permet
d'estimer le temps de vie utile restant (RUL) en utilisant les courbes
d'ajustement exponentiel et les rapports des durées des
différentes phases d'anomalie. En appliquant cette méthode sur le
roulement bearing1_3, le résultat obtenu présentait une erreur
d'estimation de 37,1%. Ce résultat ouvre des perspectives d'optimisation
de cette méthode. En effet, en augmentant le nombre de points dans le
calcul de l'indicateur utilisé, nous sommes parvenus à
réduire le taux d'erreur d'estimation du RUL de tous les roulements
d'essai.
Cette étude nous a permis d'estimer les durées
de vie résiduelle et leurs erreurs dans les roulements à billes
à partir de la méthode de détection des fréquences
d'anomalie dans les différents stades de dégradations et le
rapport des durées des phases d'anomalies. Elle pourra être
complétée par la méthode de la moyenne d'une série
deKurtosis en fonction du temps sur les spectres obtenus après filtrage
du signal (Méthode de Monte Carlo).
ANNEXE A
******************** code source de la fonction
vue_3d.m********************
function vue_3d(nbr_files)
% nbr_files passé en paramètre dans la fonction
désigne le nombre de% fichiers contenu le repertoire
Fe = 25600; % fréquence
d'échantillonage
data = load('acc_00001.csv');
z1 = data(:,5);
z2 = data(:,6);
% calcul de la transformée de Fourier
Z_horiz = abs(fft(z1));
Z_vert = abs(fft(z2));
N = length(z1);
for i = 2 : nbr_files %boucle principale qui permet de
parcourir tous les fichiers
% l'étape qui suit va nous permettre de construire
le nom de chaque fichier
if i < 10
indice = int2str(i);
file_name = strcat('acc_0000',indice,'.csv');
elseif i < 100
indice = int2str(i);
file_name = strcat('acc_000',indice,'.csv');
elseif i < 1000
indice = int2str(i);
file_name = strcat('acc_00',indice,'.csv');
else
indice = int2str(i);
file_name = strcat('acc_0',indice,'.csv');
end
% fin de la construction du nom du fichier
%maintenant nous passons à l'étape de la
récupération des données
data = load(file_name);
z1 = data(:,5);
z2 = data(:,6);
% calcul de la transformée de Fourier
z1 = abs(fft(z1));
z2 = abs(fft(z2));
% construcion des matrices de maillage
Z_horiz = [Z_horiz z1];
Z_vert = [Z_vert z2];
end
%sauvegarde des données
xlswrite('spectre_horiz_roulement1.xlsx' , Z_horiz);
xlswrite('spectre_vert_roulement1.xlsx' , Z_vert);
%axes des abscices et des ordonnées
x = 1 : nbr_files ;
y = (0 : N-1)*Fe/N ;
%axe des fréquences
freq = y(1,1:N/2);
% Matrices de maillage
Zh = Z_horiz(1:N/2,:);
Zv = Z_vert(1:N/2,:);
% représentation graphique
accélération horizontale
figure(1)
mesh(x,freq,Zh)
xlabel('numéro du fichier')
ylabel('fréquence (Hz)')
zlabel('magnitude (dB)')
title('accélération Horizontale')
% représentation graphique
accélération verticale
figure(2)
mesh(x,freq,Zv)
xlabel('numéro du fichier')
ylabel('fréquence (Hz)')
zlabel('magnitude (dB)')
title('accélération verticale')
ANNEXE B
****************** code source de la fonction
moyenne5.m******************
functionmoyenne5(nbr_files)
% nbr_files passé en paramètre dans la fonction
désigne le nombre de % fichiers contenu le repertoire
for i = 1 : nbr_files %boucle principale qui permet de
parcourir tous les fichiers
% l'étape qui suit va nous permettre de construire
le nom de chaque fichier
if i < 10
indice = int2str(i);
file_name = strcat('acc_0000',indice,'.csv');
elseif i < 100
indice = int2str(i);
file_name = strcat('acc_000',indice,'.csv');
elseif i < 1000
indice = int2str(i);
file_name = strcat('acc_00',indice,'.csv');
else
indice = int2str(i);
file_name = strcat('acc_0',indice,'.csv');
end
% fin de la construction du nom du fichier
% maintenant nous passons à l'étape de la
recupération des données
data = load(file_name);
acc_horiz = data(:,5);
acc_vert = data(:,6);
% étape du trie décroissant des valeurs
absolues des accélérations
acc_horiz = sort(abs(acc_horiz),'descend');
acc_vert = sort(abs(acc_vert),'descend');
% calcul de l'indicateur f
f_horiz(i) = mean(acc_horiz(1:5));
f_vert(i) = mean(acc_vert(1:5));
end
%sauvegarde des données
xlswrite('indicateur_horiz_roulement1.xlsx' ,
f_horiz);
xlswrite('indicateur_vert_roulement1.xlsx' , f_vert);
% axe des abscices
x = 1 : nbr_files ;
% représentation graphique
figure(1)
plot(x ,f_horiz , 'r')
xlabel('numéro du fichier')
ylabel('indicateur')
title('moyenne des accélérations
horizontales')
figure(2)
plot(x ,f_vert , 'b')
xlabel('numéro du fichier')
ylabel('indicateur')
title('moyenne des accélérations
verticales')
ANNEXE C
****************** code source de la fonction
exp_fit.m******************
functionexp_fit(nbr_files)
% nbr_files passé en paramètre dans la fonction
désigne le nombre de % fichiers contenu le repertoire
for i = 1 : nbr_files %boucle principale qui permet de
parcourir tous les fichiers
% l'étape qui suit va nous permettre de construire
le nom de chaque fichier
if i < 10
indice = int2str(i);
file_name = strcat('acc_0000',indice,'.csv');
elseif i < 100
indice = int2str(i);
file_name = strcat('acc_000',indice,'.csv');
elseif i < 1000
indice = int2str(i);
file_name = strcat('acc_00',indice,'.csv');
else
indice = int2str(i);
file_name = strcat('acc_0',indice,'.csv');
end
% fin de la construction du nom du fichier
% maintenant nous passons à l'étape de la
recupération des données
data = load(file_name);
acc_horiz = data(:,5);
% étape du trie décroissant des valeurs
absolues des accélérations
acc_horiz = sort(abs(acc_horiz),'descend');
% calcul de l'indicateur f
f_horiz(i) = mean(acc_horiz(1:5));
end
%sauvegarde des données
xlswrite('indicateur_horiz_roulement1.xlsx' ,
f_horiz);
xlswrite('indicateur_vert_roulement1.xlsx' , f_vert);
% axe des abscices
x = (822 : 2115)' ;
y = f_horiz(822 : 2115)';
% représentation graphique
f = fit(x,y, 'exp1')
plot(x,y)
hold on
plot(f)
BIBLIOGRAPHIE
[1] Jean Héng, « Pratique de La Maintenance
Préventive -Mécanique » Pneumatique - Hydraulique-
Electrique- Froid Édition Afnor (2002) Dunod
[2] M .T. Nabti, « Etude de l'évolution des
indicateurs spectraux et cepstraux dans la détection des défauts
mécaniques ».Mémoire de Magister. Université Ferhat
Abbas Setif (2011)
[3] ABA. A, « Diagnostic vibratoire sur des pompes rotatives
EP2 & P112 ». Rapport de Fin de Mise en Situation Professionnelle du
Technicien Supérieur en Mécanique Industrielle, DIRECTION
REGIONALE HAOUD BERKAOUI (2015)
[4] Huber FAIGNER, « Analyse vibratoire des machines
tournantes », Stratégies de Maintenance BTS MI (2003)
[5] Rasolofondraire L., "Mise en oeuvre des méthodes
paramétriques adaptatives pour la surveillance d'une machine de
production par analyse vibratoire", Thèse de doctorat de
l'université de Reims Champagne-Ardenne, Déc. (1995).
[6] R. CHAIB, S. MEZIANI, I. VERZEA, « surveillance des
roulements par analyse vibratoire », Sciences & Technologie B -
N°21, juin (2004)
[7] LandolsiFoued, «Cours De Techniques de Surveillance,
Partie I Surveillance Des Machines Par Analyse Vibratoire».
[8] Boulenger A., Pachaud C., "Surveillance des machines par
analyse des vibrations. Du dépistage au diagnostic", AFNOR, 2ème
Tirage, (1998).
[9] Arques P., "Diagnostic prédictif de l'état des
machines", Masson (1996).
[10] Groupe SKF, « Notions de base sur les
roulements », Roulements SKF, mai (2014)
[11] SKF, assistance technique. Les lubrifiants et les outils
SKF. Pour un fonctionnement sans problème, avril (1999).
[12] des Forges X., « Méthodologies de
surveillance en fabrication mécanique. Application de capteur
intelligent à la surveillance d'axe de machine-outil », Janv.
(1999).
[13] Morel J., "Vibration des machines et diagnostic de leur
état mécanique", Eyrolles (1992).
[14] Boulenger A., Pachaud C., "Surveillance des machines par
analyse des vibrations. Du dépistage au diagnostic", AFNOR, 2ème
Tirage, (1998).
[15] IEEE PHM 2012 Data Challenge, Outline, Experiments, Scoring
of results, Winners.
|