DEDICACES
I
REMERCIEMENTS
II
NOMENCLATURE
V
LISTE DES TABLEAUX ET FIGURES
VI
RESUMÉ
VII
ABSTRACT
VII
INTRODUCTION GENERALE ET
PROBLEMATIQUE
1
CHAPITRE I LA MIPROMALO ET LA
PRODUCTION DES CARREAUX
2
I-1. PRESENTATION DE L'ENTREPRISE
3
I-2. PRODUCTION DES CARREAUX
3
I-2-1. Le procédé de
fabrication
4
I-2-2. Le
ponçage
4
I-3. LES POUSSIERES
5
I-3-1.
Définition
5
I-3-2. Origine
5
I-3-3. Caractères physiques et
chimiques des poussières
5
I-3-4. Les risques de
poussières
6
I-3-5. Normes et
poussières
6
CHAPITRE II ANALYSE ET
ELABORATION DU CAHIER DES CHARGES FONCTIONNELLES
8
II-1. ANALYSE FONCTIONNELLE DU BESOIN
9
II-2. ANALYSE FONCTIONNELLE TECHNIQUE
10
II-2-1. Principe
10
II-2-2. FAST de
créativité du système
11
II-3. CAHIER DES CHARGES FONCTIONNELLES
12
CHAPITRE III GENERALITE SUR LES
CONVOYEURS PNEUMATIQUES
13
III-1. DEFINITION
14
III-2. PRINCIPE DE FONCTIONNEMENT
14
III-3. TYPES DE CONVOYEURS PNEUMATIQUES
14
III-4. CHOIX JUSTIFIE DU TYPE DE CONVOYAGE
14
III-5. LES VENTILATEURS
17
III-5-1.
Définition
17
III-5-2. Principe de
fonctionnement
17
III-5-3. Types de
ventilateurs
19
III-5-4. Choix justifié du type
de ventilateur
19
III-5-5. Description d'une machine
centrifuge
20
CHAPITRE IV CONCEPTION ET
DIMENSIONNEMENT DU SYSTEME D'ASPIRATION
24
IV-1. DESCRIPTION
25
IV-1-1. Schéma pneumatique du
système
25
IV-1-2. Vue en perspective du
système
26
IV-1-3. Fonctionnement du
système
27
IV-2. DIMENSIONNEMENT
29
IV-2-1. Dimensionnement du
réseau aéraulique
29
IV-2-1-1. Hypothèses
29
IV-2-1-1-1. Vitesse
d'écoulement
29
IV-2-1-1-2. Débit d'air à
prévoir
29
IV-2-1-2. Le capotage
30
IV-2-1-3. Calcul du réseau
32
IV-2-1-3-1. Choix de la méthode
33
IV-2-1-3-2. Diamètre des
conduites
33
IV-2-1-4. Calcul des pertes de charges
34
IV-2-1-4-1. Pertes de charges
linéaires
34
IV-2-1-4-2. Pertes de charges
singulières
36
IV-2-1-4-3. Pertes de charges à la
traversée du filtre
36
IV-2-1-4-4. Pertes du au capotage
(entrée du réseau de gaine)
36
IV-2-2. Calculs du
ventilateur
37
IV-2-2-1. Hauteur manométrique du
ventilateur
37
IV-2-2-2. Choix du ventilateur
37
IV-2-2-3. Puissance électrique
absorbée par le ventilateur :
38
V-2-2-4. Choix du moteur
39
IV-2-3. Dimensionnement de la
transmission de puissance
39
IV-2-3-1. Choix du Types de transmission de
puissance
39
IV-2-3-2. Dimensionnement des poulies et
courroies
40
VI-2-4.
Dimensionnement de la cabine
43
VI-2-5. Dimensionnement du
separateur
48
VI-3. SCHEMA ELECTRIQUE DU SYSTEME ET EVALUATION DU
COUT DE REALISATION
50
VI-3-1. Schéma de
puissance
51
VI-3-2. Schéma de
commande
52
VI-3-3. Description du
fonctionnement
53
VI-3-4. Coût de
réalisation du système
53
IV-4. PROCEDÉ D'OBTENTION DES COMPOSANTS DU
SYSTEME
54
CONCLUSION GENERALE
56
REFERENCES BIBLIOGRAPHIQUES
57
ANNEXES
58
ANNEXE 1. DESSINS DE DEFINITIONS
59
1-1. Cabine de
ponçage
59
1-2. Filtre à
poussière
60
ANNEXE 2. CHOIX DE LA VITESSE D'ASPIRATION
61
ANNEXE 3. COURBE DE FONCTIONNEMENT DU
VENTILLATEUR
62
ANNEXE 4. DIAGRAMME DE MODDY MOURINE (COEFFICIENT
DE PERTE DE CHARGE LINÉAIRE)
63
ANNEXE 5. COEFFICIENT DE PERTES DE CHARGES
SINGULIERES
64
ANNEXE 6. PERTES DE CHARGES DU AU CAPOTAGE
65
ANNEXE 7. ABAQUES POUR CYCLONES
66
NOMENCLATURE
|
Symbole
|
Définition
|
Unité
|
dP
|
Diamètre primitif petite poulie
|
m
|
DP
|
Diamètre primitif grande poulie
|
m
|
L
|
Longueur
|
m
|
LP
|
Longueur primitive de la courroie
|
m
|
Nd
|
Vitesse de rotation petite poulie
|
tr/min
|
ND
|
Vitesse de rotation grande poulie
|
tr/min
|
H
|
Hauteur monomérique
|
Pa
|
Ht
|
Hauteur manométrique totale
|
Pa
|
Q
|
Débit volumique
|
m3 /h
|
Re
|
Nombre de Reynolds
|
-
|
S
|
Section de la conduite
|
m2
|
V
|
Vitesse de l'écoulement
|
m/s
|
|
Variation de pression totale
|
Pa
|
|
Variation de pression statique
|
Pa
|
|
Variation de pression dynamique
|
Pa
|
|
Perte de charge d'un linéaire
|
Pa
|
|
Perte de charge d'un singulière
|
Pa
|
|
Rendement
|
-
|
|
Viscosité cinématique
|
m2 /s
|
|
Masse volumique
|
kg/m3
|
M
|
Masse
|
Kg
|
J
|
Moment d'inertie
|
Kg.m2
|
P
|
Pression
|
Bar
|
PD
|
Pression dynamique
|
Bar
|
Pt
|
Pression totale
|
Bar
|
PS
|
Pression statique
|
Bar
|
|
Hauteur des aspérités de surface
|
Mm
|
|
Coefficient de frottement
|
-
|
|
Coefficient de perte de charge singulière
|
-
|
I
|
Intensité de courant
|
A
|
cos
|
Facteur de puissance
|
-
|
LISTE DES TABLEAUX
ET FIGURES
|
TABLEAUX
|
Tableau
|
Titre
|
page
|
1
|
Comparaison des types de convoyage
|
16
|
2
|
Comparaison des types de ventilateurs
|
20
|
3
|
Nomenclature
|
35
|
4
|
Choix de la méthode de dimensionnement
|
38
|
5
|
Pertes de charges linéaires
|
39
|
6
|
Pertes de charges singulières
|
40
|
7
|
Récapitulatif des pertes de charges dans le
réseau
|
41
|
8
|
Caractéristiques du ventilateur
|
42
|
9
|
Caractéristiques du moteur
|
43
|
10
|
Choix de la transmission de puissance
|
45
|
11
|
Choix du séparateur
|
51
|
11
|
Caractéristiques du matériau
|
55
|
12
|
Coût d'acquisition
|
58
|
FIGURES
|
Figure
|
Titre
|
page
|
1
|
Présentation d'un carreau produit par la MIPROMALO
|
4
|
2
|
Process de fabrication des carreaux
|
4
|
3
|
Analyse externe du besoin
|
10
|
4
|
Principe du FAST
|
11
|
5
|
FAST multi niveau du système
|
12
|
6
|
Types de systèmes de convoyage
|
15
|
7
|
Dépression à travers un réseau
aéraulique
|
18
|
8
|
Hauteur manométrique totale d'un ventilateur
|
19
|
9
|
Mouvement d'air durant la compression
|
20
|
10
|
Vue éclaté d'un ventilateur centrifuge
|
21
|
11
|
Schéma d'un ventilateur centrifuge
|
22
|
12
|
Turbines de ventilateur centrifuge et leurs rendements
|
22
|
13
|
Schéma pneumatique du système d'aspiration
|
25
|
14
|
Forme des lignes d'égales vitesses à
l'entrée des conduites d'aspiration
|
33
|
15
|
Effets de la collerette sur les lignes d'égales
vitesses
|
34
|
16
|
Forme du capot choisi
|
34
|
17
|
Vue en perspective du réseau aéraulique
|
37
|
18
|
Transmission poulie courroie
|
44
|
19
|
Section de la courroie trapézoïdale
|
45
|
20
|
Cas de charge
|
48
|
21
|
Déplacement imposé
|
48
|
22
|
Répartition des contraintes de Von Mises
|
50
|
23
|
Déformé de la structure
|
51
|
24
|
Contrôle de conception
|
50
|
25
|
Fonctionnement du cyclone
|
52
|
26
|
Schéma électrique de puissance du système
|
55
|
27
|
Schéma électrique de commande du système
|
56
|
RESUMÉ
|
Le présent travail consiste à concevoir pour les
besoins de l'unité des carreaux de la Mission de Promotion des
Matériaux Locaux (MIPROMALO), un poste de ponçage muni d'un
système d'aspiration, de traitement et de collecte des poussières
issues du ponçage des carreaux. Pour mener à bien notre
étude, nous avons dans un premier temps redéfini les besoins et
étudié les solutions envisageables afin de justifier le choix de
la solution retenue. Ensuite, nous avons ressorti les dessins d'ensemble et de
définitions du système conçu et enfin, nous avons
dimensionné les différents éléments du
système afin d'obtenir les caractéristiques optimales et
d'ajuster les dessins de définition. Par ailleurs, nous avons ressorti
les schémas électriques illustratifs de puissance et de commande
du système. Cette étude nous a permise finalement
d'évaluer le coût de réalisation du dit système
à 1 216 150 F CFA. Montant largement
minimisé et à la portée de la MIPROMALO qui encourage
d'ailleurs le chargé de la recherche de MIPROMALO à passer au
plus vite à la phase de réalisation.
This work consists in designing a pumicing workstation
equipped with a dust sucking and processing system for the tile production unit
of MIPROMALO. Initially, after having redefined the needs and studied the
possible solutions, we have justified the one retained for our system. Then,
we brought out the full drawings as well as definitions drawings of the
designed system and finally, we sized the various elements of the system in
order to obtain the optimal characteristics and to adjust the design drawings.
In addition, we made the illustrative electric diagrams of the system. This
study helped us finally to evaluate the realization cost of the system as
1 216 150 F CFA, this sum been within the reach of MIPROMALO which
besides, encourages the research department of MIPROMALO to realize the system
as fast as possible.
.
INTRODUCTION GENERALE ET PROBLEMATIQUE
|
La Mission de Promotion des Matériaux Locaux
(MIPROMALO) est un organisme parapublic spécialisé dans la
recherche et la valorisation des matériaux de construction locaux. Elle
a pour objectif premier de réduire le coût de l'habitat au
Cameroun. C'est dans cette optique qu'elle produit des briques de terre
stabilisées, des carreaux et tuiles à des coûts très
accessibles. Or, lors des multiples phases de ponçage qui sanctionnent
la production des carreaux à micro béton, l'atelier de production
des carreaux et même celle de cuisson et de séchage des briques
avoisinant, se trouvent quasiment obligé d'interrompre les travaux vu la
quantité importante de poussières issues de l'opération de
ponçage.
En considérant les dommages causés en perte de
production, vu le fait que les poussières sont causes de maladies
professionnelles telles que le cancer de l'ethmoïde et sachant que les
règlementations internationales limitent le taux
d'empoussièrement des postes de travail à d'air pour les poussières alvéolaires, la MIPROMALO a
donc décidé de se doter d'un poste de ponçage muni d'un
système d'aspiration, de traitement et de collecte des poussières
issues de l'opération de ponçage.
Le dit système devra être d'utilisation facile,
de longévité élevé et de coût de
réalisation et de maintenance faible. Pour ce faire, nous allons tour
à tour :
· faire une analyse fonctionnelle externe et interne du
besoin question de repréciser le cahier des charges.
· présenter les différentes techniques
d'aspiration et de dépoussiérage afin d'en justifier celle
retenue pour notre système.
· présenter le système conçu
à travers les différents dessins d'ensemble et de
définitions.
· dimensionner tous les éléments du
système pour un fonctionnement optimal.
· proposer les modèles de fabrication et
d'obtention des différents éléments.
· ressortir les schémas électriques du
système et évaluer le coût d'acquisition de ce dernier.
CHAPITRE I LA MIPROMALO ET LA PRODUCTION DES
CARREAUX
|
Contenu du chapitre
|
I-1. PRESENTATION DE L'ENTREPRISE
I-2. PRODUCTION DES CARREAUX
I-2-1. Le procédé de
fabrication
I-2-2. Le ponçage
I-3. LES POUSSIERES
I-3-1. Définition
I-3-2. Origine
I-3-3. Caractères physiques et chimiques des
poussières
I-3-4. Les risques de poussières
I-3-5. Normes et poussières
L'étude de tout système de
dépoussiérage commence par la connaissance du matériel
à capter. Dans ce chapitre, après avoir présenté
brièvement la MIPROMALO, nous nous attarderons sur le
procédé de fabrication des carreaux et à la fin du
chapitre, nous donnerons les caractéristiques principales des
poussières à capter.
I-1. PRESENTATION DE
L'ENTREPRISE
La mission de promotion des matériaux locaux
(MIPROMALO) a été crée en 1990 par décret No
90/ 1253 et a démarré ses activités trois ans plus
tard. Elle a pour principale mission de valoriser l'emploi des matériaux
localement fabriqué en vue de réduire les coûts de
l'habitat au cameroun.
Depuis 2000 et conformément à la loi
No 99/016 du 22 décembre 1999 portant statut
général des établissements publics et des entreprises du
secteur public et parapublic, la MIPROMALO a un statut d'établissement
public doté de l'autonomie financière et de la
personnalité juridique.
La MIPROMALO est placé sous la tutelle technique du
ministère de la recherche scientifique et technique.
Les principaux produits proposés par la MIPROMALO
sont :
- Les blocs de terre comprimée.
- Les tuiles en micro-béton.
- Les carreaux.
- Les briques réfractaires et les briques
stabilisées au ciment.
- Les pavés.
- Les produits de la poterie.
Il parait nécessaire de s'attarder sur l'unité
de production des carreaux étant donne que notre travail y est
consacré.
I-2. PRODUCTION DES
CARREAUX
La MIPROMAALO fabrique des carreaux en micro béton
standard double (figure 1) couche. La `'couche de marche'' est faite de roche
et de ciment blanc (CPA 35). La `'couche de pose'' est faite de mortier
classique c'est à dire sable Sanaga, plus du ciment gris (CPJ35) La
roche utilisée est soit le marbre soit le granite, soit le gneiss. La
figure 1 nous donne la présentation du carreau produit par la
MIPROMALO.
Caractéristiques des carreaux obtenus [1]
- dimensions : longueur 30 cm, largeur : 30 cm
- épaisseur : 10 mm
- densité : 2
- résistance mécanique : 600 N
- porosité : 10,5%
- Durée de vie 100 ans
00000000000000000000000000000000000000000000000000000000000000000000000000000
I-2-1. Le procédé
de fabrication
Le procédé simplifié de production des
carreaux est décrit par la figure 2 ci-dessous et fait bien ressortir
les deux phases de ponçage qui interviennent dans la fabrication des
carreaux.
00000000000000000000000000000000000000
I-2-2. Le ponçage
Le ponçage est un procédé de
rectification qui permet d'obtenir des états de surface très
précis question de tendre vers l'objectif de planéité de
50 ìm [1] fixé pour les carreaux de la MIPROMALO. Il est
fait à l'aide d'un outil meule de type classique (BOSCH) tournant
à 33 m/s. La meule est munie d'un disque de marque NORTON DOMOLO de
caractéristiques produisant des copeaux de taille moyenne 0,07 mm [1]. Le ponçage
intervient plusieurs fois dans le processus de fabrication des carreaux comme
l'indique la figure 2 ci-dessus. Il est une source incroyable de production de
poussière qui à la fois met en péril la santé des
employés et l'environnement. Il est donc nécessaire de purifier
l'environnement de travail en captant cette poussière et en la traitant
au fur et à mesure de sa production.
I-3. LES POUSSIERES
L'étude d'une installation de
dépoussiérage, nécessite une connaissance préalable
de la nature et des caractéristiques des poussières à
capter et à séparer, notamment pour les plus fines qui sont les
plus nocives.
I-3-1. Définition
La poussière est une substance en poudre très
fine, avec des particules comprises entre 0 ,01 et 100 voire même 250 , qui est susceptible de se trouver en suspension dans l'air sous
certaines circonstances et pendant un temps plus ou moins long. [6]
I-3-2. Origine
Les poussières peuvent être de source diverses
tels que : Naturelle (minérale ou végétale),
mécanique, chimique, thermique ... celle qui nous intéresse
ici est de source mécanique et est particulièrement issue du
processus de ponçage des carreaux. La première
particularité des poussières d'origine mécanique est
qu'elles sont généralement de dimension supérieure
à 5 et que la proportion de celles qui sont de dimensions inférieure
au micron est extrêmement faible. [6]
I-3-3. Caractères
physiques et chimiques des poussières
Plusieurs paramètres sont à prendre en
compte : taille, concentration, toxicité, abrasivité,
densité.
Les particules à capter sont de forme ronde, de taille
moyenne 5 ìm, de densité apparente 0,3 (masse de poussière
dans un mètre cube d'air) et de concentration 30 g/m3. Par
ailleurs, elles sont de nature minérale, sèche et non toxique.
I-3-4. Les risques de
poussières
La nécessité d'extraction des dites
poussières vient du fait qu'elles font plus de mal que nous ne pouvons
l'imaginer. En plus du fait qu'elles causent salissures et
détérioration du matériel lors de leur déposition,
les poussières contiennent des agents nocifs qui affectent l'organisme
par contact cutané ou par inhalation.
Le contact cutané
Les affections se caractérisent par la survenue
d'allergies de contact, notamment sur le cou, le visage, les mains, les
avant-bras et parfois les yeux (conjonctivite). Elles se manifestent par des
vésicules suintantes accompagnées de démangeaisons et
souvent de fissures.
L'inhalation
L'inhalation de poussières se traduit par une
irritation des voies respiratoires. Elle se manifeste par des
éternuements répétés, des rhinites aiguës
(rhumes), des saignements de nez, de l'asthme. Les plus fines (dimensions
comprises entre 0,3 et 5 ) sont encore plus dangereuses car elles peuvent par inhalation,
à travers les poumons et la circulation sanguine, atteindre les autres
organes. Cette inhalation, peut aussi provoquer le cancer de
l'ethmoïde, os constituant la partie supérieure des fosses
nasales. Les premiers signes surviennent parfois des années après
la fin de l'exposition. Il s'agit d'écoulements purulents et sanglants
par le nez accompagnés de douleurs de la face. C'est une maladie
très grave dont le traitement est difficile.
En définitive, les particules de tailles
inférieure à sont inhalées mais on considère qu'elles sont
rejetées lors de l'expiration tandis que les particules de tailles
comprises entre sont les plus dangereuses et ceci même lorsque la matière
qui les composent n'est pas toxique. Les particules de tailles
supérieure à sont généralement arrêtées au niveau des
voies respiratoires et par suite expulsées par les voies naturelles.
Elles ne sont pas dangereuses mais peuvent devenir gênantes.
I-3-5. Normes et
poussières
Il est important de noter que le respect des normes est une
démarche volontaire. Son élaboration consensuelle permet à
l'entreprise y adhérant de bénéficier d'une "veille techno
normative" lui permettant de rester à jour de toutes évolutions,
d'assurer l'interchangeabilité et la maintenance facile de ses
équipements. La mission normative pour le matériel de
dépoussiérage aborde les sujets suivants.
§ l'émission admissible des poussières
à l'intérieur et à l'extérieur des locaux ;
§ la conception des réseaux ;
§ les risques d'incendie et le matériel de
prévention ;
§ le niveau sonore ;
§ les appareils de contrôle et de
sécurité ;
§ etc.
Nous présentons ci-dessous quelques
éléments importants provenant de la réglementation
Française [6] à retenir pour la conception de notre
système.
1. En cas de panne du système d'épuration ou de
filtration, le système doit être arrêté.
2. Dans les locaux à pollution spécifique, les
concentrations moyennes en poussières totales et alvéolaires de
l'atmosphère inhalée par une personne, évaluées sur
une période de huit heures, ne doivent pas dépasser
respectivement 10 et 5 milligrammes par mètre cube d'air.
3. le taux maximal d'empoussièrement au poste de
travail est de 5 mg/m3 pour les poussières alvéolaires.
4. Les diamètres, les formes des éléments
de tuyauterie pour un réseau d'aspiration des polluants
atmosphériques sont normalisés. Elles ont été
établies dans le but d'avoie des conduites standard ayant un minimum de
perte de charge et donnant la possibilité à l'utilisateur
d'assurer le renouvellement ou le remplacement indépendamment du
fabricant.
5. interdiction de prévoir des filtres
(dépoussiéreur) à l'intérieur des locaux pour des
débits supérieurs à 6000 m3/h, au
delà de ce débit, le filtre à poussière devra
être installé à l'extérieur du bâtiment ou
dans un local qui lui est propre.
CHAPITRE II ANALYSE ET ELABORATION DU
CAHIER DES CHARGES FONCTIONNELLES
|
Contenu du chapitre
|
II-1. ANALYSE FONCTIONNELLE DU BESOIN
II-2. ANALYSE FONCTIONNELLE TECHNIQUE
II-2-1. Principe
II-2-2. FAST de créativité du
système
II-3. CAHIER DES CHARGES FONCTIONNELLES
Le but de ce chapitre est d'établir le cahier des
charges fonctionnelles, c'est-à-dire : définir et
préciser les objectifs du projet, les services attendus du
système, les conditions d'utilisation, de performances, les
critères d'appréciation et enfin la constitution technique
globale du système par l'analyse fonctionnelle technique.
II-1. ANALYSE FONCTIONNELLE
DU BESOIN
Ici, nous énoncerons les fonctions de service du
système ; c'est-à-dire les actions attendues du produit pour
répondre aux besoins d'un utilisateur donné. Nous effectuons une
observation extérieure du système afin d'y dégager les
relations qu'il entretient avec l'environnement.
Nous analyserons les dits besoins en utilisant la
méthode apte ou pieuvre matérialisée par la figure 3 sur
laquelle
désigne la fonction principale c'est à dire la raison
d'être du système
désigne la ième fonction contrainte c'est
à dire la contrainte à respecter pour que le système
s'adapte aux exigences de l'environnement.
000000000000000000000000000000000000000000000
Formulation littérale de chaque relation
· Fonction principale 
: extraire la poussière du poste de ponçage
· Fonctions contraintes 
: évacuer la poussière extraite (ne pas la laisser
s'épandre sur d'autres postes)
: exempter l'environnement de poussière
: être insensible au vent
: utiliser la source d'énergie électrique
: être de commande facile pour l'opérateur
: être agréable à voir
: résister à la corrosion (rouille)
II-2. ANALYSE FONCTIONNELLE
TECHNIQUE
Il s'agit de dire dans cette partie comment sont
réalisées les fonctions de services énoncées
ci-dessus. Il faut donc observer le système du point de vue interne
question de la disséquer, de voir sa composition et mettre en
évidence les relations entre les différentes parties du
système. Celles-ci constituent les fonctions techniques
nécessaires pour assurer les fonctions de service. L'outil que nous
utiliserons à cet effet est le FAST (Fonctional Analysis System
Technic)
II-2-1. Principe
Le FAST [3] est d'origine américaine et peut se
traduire comme : Technique d'Analyse Fonctionnelle Systématique. Il
constitue un mode de visualisation permettant de relier et d'ordonner toutes
les fonctions techniques. Sa construction répond aux questions de la
figure 4.
000000000000000000000000
Figure 4 : Principe du
FAST
|
Selon les cas ; on distingue le FAST de
créativité et le FAST de description. Les opérateurs ET et
OU permettent d'établir des relations logiques entre les
différentes fonctions techniques
ET
II-2-2. FAST de créativité du
système
00000000000000000000000000000000000000
II-3. CAHIER DES CHARGES
FONCTIONNELLES
C'est l'occasion de donner toutes les spécifications
importantes pour la conception du système. Les critères
d'appréciation du système seront ; la propreté de
l'unité de production, l'esthétique, l'invariabilité de la
vitesse d'aspiration, le faible effet sonore, la résistance à la
corrosion, l'étanchéité, la résistance et la
stabilité mécanique de la structure. La meule utilisée est
celle existante de marque BOSH muni d'un disque de diamètre 230 mm La
source d'énergie disponible à utiliser est
l'électricité (triphasé 220/380V-50 Hz). L'encombrement de
la structure sera minimisé vu les dimensions de l'unité des
carreaux qui devra la contenir mais aussi, l'air épuré sera
rejeté à l'extérieur du bâtiment et à une
hauteur d'au moins 3 m question de pas nuire aux voisins
CHAPITRE III GENERALITE SUR LES
CONVOYEURS PNEUMATIQUES
|
Contenu du chapitre
|
III-1. DEFINITION
III-2. PRINCIPE DE FONCTIONNEMENT
III-3. CHOIX JUSTIFIE DU TYPE DE CONVOYAGE
III-4. LES VENTILATEURS
III-4-1. Définition
III-4-2. Principe de fonctionnement
III-4-3. Types de ventilateurs
III-4-4. Choix justifié du type de
ventilateur
III-4-5. Description d'une machine centrifuge
III-1. DEFINITION
Un convoyeur pneumatique est un système de ventilation
qui en plus de déplacer l'air, transporte une quantité
significative de particules en suspension. [5] Il est donc
utilisé soit pour acheminer un produit d'un point A à un point B,
soit pour assurer le dépoussiérage.
III-2. PRINCIPE DE
FONCTIONNEMENT
Le matériel à transporter (ici, la
poussière) est introduit dans un tuyau qui transporte de l'air ; le
matériel en suspension suit le courant d'air jusqu'au point de
décharge ou alors jusqu'au point de traitement lorsqu'il s'agit du
dépoussiérage.
III-3. TYPES DE CONVOYEURS
PNEUMATIQUES
Les convoyeurs pneumatiques peuvent être classées
selon les niveaux de pressions d'utilisation (basse, moyenne, grande pression)
ou alors selon les types d'agencement des différents constituants. Nous
nous focalisons ici sur cette dernière classification [5] en sachant que
nous fonctionnons en basse pression.
La figure 6 montre trois agencements possible à
savoir : l'agencement pression, l'agencement dépression et
l'agencement mixte. Dans l'agencement pression, le ventilateur est situé
à l'entrée du circuit et donc tout le circuit fonctionne sous une
pression supérieure à la pression atmosphérique. Dans
l'agencement dépression, le ventilateur est situé à la
sortie du circuit et fait donc fonctionner ce dernier sous une pression
inférieure à la pression atmosphérique. L'agencement mixte
comporte un circuit aspirant en dépression et un circuit refoulant en
pression ; le ventilateur ici fait partie intégrante du circuit.
III-4. CHOIX JUSTIFIE DU
TYPE DE CONVOYAGE
Pour ce faire, nous avons fait, dans le tableau 1 une
étude comparative des trois types de convoyages présentés
à la figure 6 en faisant ressortir les avantages et les
inconvénients de chaque type de convoyage
00000000000000000000000000000000000000000000000
Pour ces trois types d'associations, le ventilateur est
l'élément moteur du circuit. C'est lui qui crée la
dépression de débit suffisant dans le circuit. le
dépoussiéreur est l'élément filtrant, encore
appelé séparateur,il pour rôle de séparer la
poussière de l'air dans lequel il est en suspension. La vanne rotative a
pour rôle de réguler l'entrée et la sortie du
matériel du circuit tout en empêchant d'éventuelles fuites
d'air. Les conduites sont représentées en trait fort et les
interrompus indiquent les possibilités d'extension.
Tableau 1 : Comparaison des types de
convoyage
|
Types
|
Avantages
|
Inconvénients
|
Agencement
pression
|
- Peut facilement être dirigé vers plusieurs
dépoussiéreurs (point de réception)
- Plusieurs convoyeurs peuvent aller au même
dépoussiéreur
|
- Requiert une vanne rotative et une alimentation à
chaque point d'alimentation en matériel
|
Agencement
Dépression
|
- Peut facilement ramasser plusieurs points en même
temps
- Pas besoin de vannes rotatives aux points d'aspiration
|
- Impossibilité de diriger le matériel vers
plusieurs points de réception.
|
Agencement
mixte
|
- Peut facilement ramasser plusieurs points en même
temps
- Pas besoin de vannes rotatives aux points
d'aspiration
- Peut facilement être dirigé vers plusieurs
dépoussiéreurs (point de réception)
- Plusieurs convoyeurs peuvent aller au même
dépoussiéreur
|
- Usure et vibrations excessives du ventilateur car le
matériel doit y passer
- Consommation d'énergie du ventilateur
augmenté jusqu'à 100 % car
o On utilise une roue ouverte moins efficace
o On doit partiellement ré accélérer le
matériel qui y passe
|
Après avoir examiné le tableau 1 et étant
donné que notre système présente un seul point
d'aspiration et un seul point de (dépôt), nous optons pour un
convoyeur agencé en dépression car il limite l'usure du
ventilateur et donc le coût de fonctionnement du système. En plus
il ne nécessite pas de vannes rotatives aux points d'aspiration. C'est
l'agencement le plus adapté pour les systèmes de
dépoussiérage.
III-5. LES VENTILATEURS
Le ventilateur constitue le moteur du réseau et doit
donc être adaptés le plus précisément possible au
réseau, de façon à satisfaire le cahier des charges
(débit correct) tout en gardant un comportement
énergétique optimum.
III-5-1. Définition
Le ventilateur est une turbomachine, comportant une ou
plusieurs roues autour d'un axe, entraînée par une puissance
mécanique primaire qui lui est transmise. Il entretient
l'écoulement d'un fluide gazeux qui reçoit ainsi, en le
traversant, une puissance mécanique utilisable (puissance utile)
correspondant à un travail réel.
III-5-2. Principe de
fonctionnement
Les installations aérauliques sont classées en
fonction de leurs pressions totales les classements généralement admis sont :
· Basse pression : 
· Moyenne pression : 
· Haute pression : 
Le ventilateur fournit la différence de pression totale
entre ses ouies entrée et sortie de l'air. Comme indiqué
à la figure 7, [9] cette pression totale obtenue
à la sortie du ventilateur, se dissipe progressivement dans le
réseau aéraulique.
La pression produite par le ventilateur, appelé
pression TOTALE est la somme de deux pressions distinctes : STATIQUE +
DYNAMIQUE

Ou est la pression statique qui correspond aux frottements que l'air doit
vaincre pour s'écouler dans le circuit et est la pression dynamique ou encore la surpression nécessaire
pour générer la vitesse de l'air dans la conduite. Elle vaut avec V=vitesse de refoulement et =masse volumique du fluide
00000000000000000000000000000000000000
La somme de la pression totale à l'ouïe
d'aspiration et de la pression totale au refoulement représente la
hauteur manométrique totale du ventilateur (figure 8). Il s'ensuit
l'établissement d'un débit de fluide continu.
000000000000000000000000000000000000000
III-5-3. Types de ventilateurs
Deux types de ventilateurs sont principalement utilisés
en aéraulique :
· Les ventilateurs axiaux (ou hélicoïde),
· Les ventilateurs centrifuges.
Ces deux types font partie des turbomachines. Leurs noms
proviennent du mouvement de l'air durant la compression comme
présenté à la figure 9. [8]
000000000000000000000000000000000000000000000000000000000000000000000000000
Tableau 2 :
Comparaison des types de ventilateurs
|
TYPES de ventilateur
|
Ventilateurs axiaux (ou
hélicoïde),
|
ventilateurs centrifuge
|
PRINCIPE DE FONCTIONNEMENT
|
l'air a un mouvement hélicoïdal
la distance entre la veine fluide et l'axe de la roue reste
constante
|
l'air s'éloigne de cet axe au fur et à mesure
de la traversée du ventilateur
Il résulte de cet éloignement de l'axe une
augmentation de la vitesse de l'air, et donc de la pression dynamique qui va
s'ajouter à la pression statique créée par les
pales
|
DIFFERENCE DE PRESSION
|
Faible différence de pression totale entre l'amont et
l'aval
|
Forte différence de pression totale entre l'amont et
l'aval
|
DEBIT VOLUMIQUE
|
section d'entrée grande et donc forte capacité
de débit volumique
|
section d'entrée faible et donc faible capacité
de débit volumique
|
III-5-4. Choix justifié
du type de ventilateur
Pour un choix méthodique, nous avons fait une
étude comparative des deux types de ventilateurs cités
ci-dessus.
Vu le tableau comparatif 2 ci-dessus et en tenant compte du
débit voulu qui est assez modeste, nous optons pour un ventilateur centrifuge avec
turbine à roue fermée incliné.
III-5-5. Description d'une
machine centrifuge
Vue éclatée [8]
0000000000000000000000000000000000000000000000
· Le pavillon d'entrée : de sa conception
dépend une bonne partie du rendement du ventilateur ;
· La turbine qui sera choisie pour une classe
d'application selon un rendement (type de matière à transporter,
hauteur manométrique)
· La volute ou enveloppe, de forme spiraloïde c'est
d'elle que dépendront souvent les problèmes de bruit ; la volute
participe aussi au rendement et à la hauteur manométrique du
ventilateur ;
· le socle support comportant les éléments
de transmissions de la vitesse de rotation et permettant de poser le
ventilateur au sol.
Schéma d'un ventilateur centrifuge
000000000000000000000000000000000
La roue
Elle comporte des canalisations formées par le disque,
les flasques de recouvrement et les aubages.
Les différentes turbines sont
représentées à la figure 12 avec leurs utilisations.
0000000000000000000000
Le distributeur
Le rôle du distributeur, situé en amont de la
roue (non représenté sur la figure 11) est de permettre une
orientation correcte des filets fluides à leur entrée dans la
roue. Il n'existe en fait que dans les pompes à plusieurs étages
de compression. Il permet alors d'effectuer la liaison entre l'étage
amont (au niveau de la volute) et l'étage aval (au niveau des
ouïes).
Le diffuseur
Avec ou sans aubages, cet organe permet de transformer en
partie l'énergie cinétique (pression dynamique) en énergie
potentielle (pression statique) et d'orienter correctement le fluide à
la sortie de la roue pour son entrée dans la volute ou dans le
distributeur de l'étage suivant.
La volute
Son rôle consiste essentiellement à transformer
le mouvement de rotation du fluide en mouvement de translation.
Le divergent
Comme le diffuseur, il permet de transformer une fraction de
l'énergie cinétique du fluide en énergie potentielle, ceci
afin de limiter les pertes de charge dans les canalisations de transport du
fluide
CHAPITRE IV CONCEPTION ET DIMENSIONNEMENT
DU SYSTEME D'ASPIRATION
|
Contenu du chapitre
|
IV-1. DESCRIPTION
IV-1-1. Schéma pneumatique du système
IV-1-2. Vue en perspective du système
IV-1-3. Description du fonctionnement
IV-2. DIMENSIONNEMENT
IV-2-1. Dimensionnement du réseau aéraulique
IV-2-1-1. Hypothèses
IV-2-1-1-1.
Vitesse
d' écoulement
IV-2-1-1-2.
Débit
d'air à prévoir
IV-2-1-2. Le capotage
IV-2-1-3. Calcul du réseau
IV-2-1-3-1. Choix de la méthode
IV-2-1-3-2. Sections (diamètre) des
conduites
IV-2-1-4. Calcul des pertes de charges
IV-2-1-4-1. Pertes de charges
linéaires
IV-2-1-4-2. Pertes de charges
singulières
IV-2-1-4-3. Pertes de charges à la
traversée du filtre
IV-2-1-4-4. Pertes du au capotage
(entrée du réseau de gaine)
IV-2-2. Calculs du ventilateur
IV-2-2-1. Hauteur manométrique du
ventilateur
IV-2-2-2. Choix du ventilateur
IV-2-2-3. Puissance électrique absorbée par
le ventilateur :
IV-2-3. Dimensionnement de la transmission de puissance
IV-2-3. Dimensionnement de la cabine
IV-2-4. Choix du filtre à poussières
IV-3. SCHEMA ELECTRIQUE DU SYSTEME ET EVALUATION DU COUT
DE REALISATION
VI-3-1. Schéma de puissance
VI-3-2. Schéma de commande
VI-3-3. Description du fonctionnement
VI-3-4. Coût de réalisation du système
IV-1. DESCRIPTION
Il est question dans cette section de présenter les
différentes illustrations du système conçu à
savoir : le schéma pneumatique et le dessin d'ensemble. Nous
décrirons à la fin de la section le fonctionnement du
système et le rôle de chaque composant sera
spécifié.
IV-1-1. Schéma
pneumatique du système
00000000000000000000000000000000
Sur le plan pneumatique, le système est
constitué d'un ventilateur, d'un filtre à poussière, et
d'un réseau de tuyauterie. Les autres accessoires nécessaires au
fonctionnement du système ne sont pas visibles sur ce schéma.
Mais, ils sont explicités sur le dessin d'ensemble.
IV-1-2. Vue en perspective du
système
00000000000000000000000000000000000000
000000000000000000000000000000000
IV-1-3. Fonctionnement du
système
Le ventilateur centrifuge (5), mis en mouvement par un moteur
électrique (6), à travers un système poulie courroie (7 -
10), crée le flux d'air de vitesse suffisante dans le réseau de
gaine mis en place (3) et permet ainsi le transport des poussières
produites dans la cabine de ponçage (1). Les dites poussières,
à la traversée du dépoussiéreur (4) sont retenues
et permets ainsi d'épurer l'air rejeté dans la nature par le
circuit refoulant.
ROLE DE CHAQUE ELEMENT
· Cabine de ponçage
La cabine de ponçage est constituée
essentiellement d'une table de ponçage adaptée et d'un pupitre de
commande simple d'utilisation, elle sert de poste de travail et est
conçue de façon à limiter l'effet du vent extérieur
qui rendrait le système inefficace en acheminant la poussière
hors du circuit réservé
· Capot d'aspiration
Il a pour rôle de confiner la source de poussière
de façon à ce que la vitesse de l'air résultant de cette
restriction soit suffisante pour entraîner les particules
libérées car l'ampleur et le coût d'un système de
dépoussiérage sont intimement liés au volume d'air
extrait. Par conséquent, le dit capot sera le plus proche possible de la
source de poussière et il sera au mieux orienté dans la direction
d'écoulement des copeaux.
· Conduites
Les conduites servent essentiellement à canaliser le
flux d'air créé par le ventilateur. Elles sont conçues de
façon à minimiser les pertes de charges lors de
l'écoulement tout en assurant l'étanchéité des
liaisons.
· Filtre séparateur
Son rôle est de séparer la poussière de
l'air dans lequel elle est en suspension.
· Ventilateur
Le ventilateur crée et entretient l'écoulement
du flux d'air qui reçoit ainsi, en le traversant, une puissance
mécanique utilisable et suffisante pour déplacer les particules
dans les conduites. Il devra minimiser la consommation
énergétique du moteur et maintenir un niveau sonore acceptable.
· Moteur
Le moteur assure le mouvement de rotation de la turbine du
ventilateur à travers le système poulie courroie. Il transforme
alors l'énergie électrique qu'il reçoit en énergie
mécanique utile.
· Ensemble poulie courroie
Le système poulie courroie permet de transmettre le
mouvement de rotation de l'arbre du moteur à celui du ventilateur tout
en respectant les vitesses nécessaires pour le fonctionnement de chaque
élément.
IV-2. DIMENSIONNEMENT
En vue d'obtenir les caractéristiques idéales pour
chaque élément du système, nous allons les dimensionner au
fur et à mesure en gardant toujours è l'esprit l'exigence
économique sur le coût de réalisation
IV-2-1. Dimensionnement du
réseau aéraulique
Le réseau aéraulique doit permettre d'assurer
les différents flux d'air. Une fois les débits connus, il faut
alors déterminer les caractéristiques des ses différents
éléments (ventilateur, filtre, sections des conduites, bouches de
soufflage et d'aspiration ...) et la manière de les connecter (formes et
longueurs des gaines et des coudes, dérivations).
IV-2-1-1.
Hypothèses
IV-2-1-1-1. Vitesse
d'écoulement
Cette
vitesse de transport est un facteur essentiel pour les réseaux
d'évacuation d'air poussiéreux : elle doit d'une part avoir une
valeur suffisante pour éviter une sédimentation des
poussières et un bouchage des canalisations. D'autre part, nous
évitons d'utiliser des vitesses trop élevées de
façon à limiter les pertes d'énergie, le bruit
aéraulique et l'abrasion des tuyauteries. Enfin, le choix résulte
d'un compromis entre le coût de l'installation et celui de son
exploitation :
· Les grandes sections, qui correspondent aux petites
vitesses, sont limitées par les contraintes architecturales et la
sédimentation. Ceci entraînant un coût d'installation
élevé.
· Les petites sections, qui correspondent aux grandes
vitesses, sont limitées par le bruit engendré et la corrosion des
conduites qui réduit leurs durées de vie Ceci entraîne un
Coût d'exploitation élevé.
La figure de l'annexe 2 donne, en fonction du débit
volumique, les vitesses recommandées par la norme pour les installations
aérauliques, ainsi que les pertes de charge linéaires qu'elles
créent suivant le diamètre de la conduite.
La vitesse choisie à cet effet est de
20 m/s
IV-2-1-1-2. Débit
d'air à prévoir
Pour déterminer le débit d'air dans les
conduites, nous tiendrons compte des deux paramètres suivants :
- La vitesse de rotation de l'outil et sa dimension qui
engendrent, comme un ventilateur, un déplacement d'air qu'il sera
nécessaire de capter ;
- Le volume de copeaux ou de déchets produit par
l'outil meule.
Données
Surface du carreau à poncer : ; a =300 mm (surface carrée de coté a)
Épaisseur moyenne à enlever du
carreau : 
Masse Volumique du carreau : 
Taux de transport admissible :
Nombre de carreaux poncés par heure : 
Production Totale de déchets en kg à
l'heure : 
Débit
Étant donné que la réglementation
interdit d'utiliser des réseaux d'aspiration au delà de 0,2
kg/m3 /h, ou encore 5 m3/h par kg, nous
prévoyons avec un coefficient de sécurité de 1,25 un
débit de :

AN : 
Nous considérons donc un débit de 2700
m3/h
IV-2-1-2. Le capotage
Le capot désigne l'entrée du réseau de
gaine et la bouche d'aspiration. Il est déterminé de façon
à profiter de la trajectoire naturelle des poussières (et
notamment de leurs force ascensionnelle), pour mieux les canaliser et surtout
éviter toute conception de capotage, fondée sur un
entraînement à contre-courant qui se révèle toujours
d'une moindre efficacité pour une dépense
énergétique supérieure.
Un bon capot doit répondre aux exigences suivantes.
§ Ne pas gêner le fonctionnement de l'outil meule
;
§ Être dans la trajectoire de projection des
copeaux ;
§ Être suffisamment enveloppant, mais non
complètement fermé, pour capter le maximum de
poussières.
Variation des vitesses d'air au voisinage d'une
entrée d'aspiration
La vitesse de l'air varie très rapidement d'un point
à un autre tout autour de la bouche du capot. La figure 14 [6] montre
d'après les résultats de DALLA-VALLE, la forme des surfaces
d'égale vitesse devant une bouche d'aspiration circulaire sans
collerette et avec collerette. Les vitesses sont indiquées en
pourcentage de la vitesse moyenne dans la section d'entrée (V). Cette
figure montre que la vitesse décroît très rapidement avec
la distance au dispositif de captage. Par exemple, à une distance
égale au diamètre de l'ouverture, la vitesse de l'air n'est plus
dans l'axe que d'environ 7% de V sans collerette et d'environ 10% de V avec une
collerette.
0000000000000000000000000000000000
La forme des courbes d'égales vitesses dépend
d'autres facteurs directement liés à la géométrie
du capot, par exemple :
§ la proportion entre le grand et le petit
côté, si l'entrée est de section rectangulaire ;
§ la présence d'un flasque ou collerette sur le
pourtour de l'entrée qui repousse vers l'extérieur les courbes
d'égales vitesses et par conséquent accroît
l'efficacité du capot ; (figure 15)
Nous adoptons finalement le capot schématisé
à la figure 16 (comportant un convergent et une collerette) qui
enveloppe bien le poste de travail. La collerette permettra de repousser les
lignes d'égales vitesses vers l'extérieur et permettra ainsi de
maintenir la vitesse d'aspiration à une bonne distance de
l'entrée des gaines.
000000000000000000000000000000000000
000000000000000000000000000000000000000000
IV-2-1-3. Calcul du
réseau
Ici, nous devons déterminer les caractéristiques
des conduites à prévoir dans les différentes branches du
réseau, trouver les pertes de charges totales dans le réseau et
la hauteur manométrique du ventilateur à installer. De nombreuses
méthodes existent dont les plus connues sont :
· Le dimensionnement à perte de charge
linéaire constante,
· Le dimensionnement à vitesse constante,
· Le dimensionnement à regain de pression
statique,
· L'optimisation technico-économique.
IV-2-1-3-1. Choix de la
méthode
Une rapide étude comparative (tableau 3) des
différentes méthodes évoquées ci-dessus nous permet
de choisir rigoureusement celle qui répond le mieux au cahier des
charges de notre système.
Tableau 3 :
Choix de la méthode de dimensionnement
|
Méthode
|
dimensionnement à perte de charge
linéaire constante
|
dimensionnement à vitesse constante
|
dimensionnement à regain de pression
statique
|
L'optimisation
technico-économique
|
Objectif
|
déterminer le diamètre des différents
tronçons de façon à avoir une perte de charge
linéaire constante dans tout le réseau
|
dimensionner les différentes sections de passage de
façon à avoir une vitesse constante dans toute l'installation
|
L'objectif de cette méthode est d'obtenir une pression
statique quasi-constante à chaque noeud du réseau.
|
minimisation du coût énergétique de
fonctionnement de l'installation, d'investissement initial,
|
Avantage
|
méthode simple et rapide
appointé pour des réseaux à une branche
|
méthode simple et rapide
appointé pour des réseaux à une branche
|
méthode prenant en compte dès le départ
l'équilibrage du réseau.
l'utilisation optimale de la pression totale
délivrée par le ventilateur.
|
Optimisation de l'ensemble de l'installation, ventilateur
compris, d'un point de vue énergétique mais aussi
économique
|
Inconvénients
|
ne correspondent à aucun optimum puisque
l'équilibrage du réseau est « artificiel » :
|
ne correspondent à aucun optimum puisque
l'équilibrage du réseau est « artificiel » :
|
calculs itératifs sur chaque branche du réseau
pouvant rapidement devenir fastidieux
|
Calculs fastidieux
Programmation informatique obligatoire
|
En examinant le tableau 3 et en tenant compte des exigences du
cahier des charges qui demande une vitesse d'aspiration de 20 m/s à la
bouche d'aspiration et compte tenu du fait que notre réseau
présente une seule branche, nous avons opté pour la
méthode de dimensionnement à vitesse constante
IV-2-1-3-2. Diamètre
des conduites
Ayant choisi la méthode de dimensionnement à
vitesse constante, nous calculons le diamètre des conduites de
façon à maintenir une vitesse constance dans toute
l'installation. , soit :
(1)
AN : D = 0,195 m = 195 mm Nous utiliserons le
diamètre normalisé le plus proche D= 200 mm
IV-2-1-4. Calcul des pertes
de charges
Très simplement, la différence des pressions
statiques entre deux points A et B d'un circuit de fluide est appelée
perte de charge entre A et B. Ainsi pour l'étude de la pression
nécessaire, sous laquelle devra fonctionner le ventilateur à
installer pour fournir le débit d'air requis, il sera nécessaire
de décomposer l'installation en tronçons
élémentaires pour lesquels la perte de charge est facile à
calculer connaissant l'emplacement des différents accessoires (bouches
d'air, filtres, coude, etc...) et les flux d'air à mettre en oeuvre.
Nous avons à cet effet, dessiné le réseau
aéraulique, en utilisant une représentation en perspective
dimétriques (figure 17). Ce schéma comporte tous les accidents
(coudes, branchements...) auxquels nous avons attribué des
repères. Il est indiqué le débit qui traverse les
conduites, et, sur chaque partie rectiligne, la longueur séparant deux
accidents.
0000000000000000000000000000000000000
IV-2-1-4-1. Pertes de
charges linéaires
Données
; 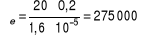
|
= 0,03 mm pour les conduites PVC rigide utilisées
|
= 0,00014 : rugosité relative
|
= 0,021 du diagramme de Moody Mourine en annexe
|
= 1,2 Kg/m3
|
= 20 m/s
|
= 220 mm
|
= longueur de chaque tronçon considéré
|
Longueur d'un coude 
|
La perte de charge linéaire est donnée par la
formule :
(2)
Avec :
|
:
|
Nombre de Reynolds (vaut )
|
|
:
|
Viscosité cinématique de l'air
|
|
:
|
Hauteur des aspérités de surface en mm
|
|
:
|
Coefficient de frottement ; fonction de et de 
|
|
:
|
Masse volumique du fluide (air)
|
|
:
|
Vitesse de l'air dans la conduite
|
|
:
|
Diamètre intérieur de la conduite (circulaire)
|
|
:
|
Longueur totale du tronçon considéré en
incluant les longueurs engendrées par les coudes.
|
En utilisant les données ci-dessus et la formule
(2), nous avons pour chaque tronçon, regroupé
les résultats dans le tableau 4 suivant :
Tableau 4 :
Pertes de charges linéaires
|
Tronçon
|
Longueur en m
|
Perte de charge en Pascal
|
A - E
|
5,642
|
129,25
|
F - G
|
0,6
|
13,75
|
H - J
|
4,314
|
98,83
|
IV-2-1-4-2. Pertes de
charges singulières
Données
= 1,2 Kg/m3
|
= 20 m/s
|
1 pour tous les coudes. Soit un coefficient de pertes de charges
singulières 1(*)
|
La perte de charge singulière pour chaque accident est
donnée par la formule :
(3)
Avec :
|
:
|
coefficient de perte de charge singulière de l'accident
considéré
|
|
:
|
Masse volumique du fluide (air)
|
|
:
|
Vitesse de l'air dans la conduite
|
En utilisant les données ci-dessus et la formule
(3), nous avons pour chaque tronçon, regroupé
les résultats dans le tableau 5 suivant :
Tableau 5 :
Pertes de charges singulières
|
Tronçon
|
Nombre de coudes
|
Coef 
|
Perte de charge en Pascal
|
A - E
|
3
|
0,30
|
216
|
F - G
|
0
|
-
|
0
|
H - J
|
1
|
0,30
|
72
|
Sortie J
|
-
|
1
|
240
|
IV-2-1-4-3. Pertes de
charges à la traversée du filtre
Les documents constructeurs des filtres nous donnent les valeurs
moyennes des pertes de charges à travers un filtre propre et
encrassé. Nous nous plaçons dans le pire en supposant le filtre
encrassé. On a alors : [9]

IV-2-1-4-4. Pertes du au
capotage (entrée du réseau de gaine)
En examinant l'abaque présentée en annexe 6 ;
nous trouvons pour le capot de forme conique avec collerette proposé
à la figure 16 un coefficient de perte de charge singulière de
et donc une perte de charge :
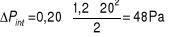
Tableau récapitulatif
Tableau 6 :
Récapitulatif des pertes de charges dans le
réseau
|
Branche
|
|
|
|
|
|
|
|
|
|
|
Entrée
|
-
|
-
|
-
|
-
|
-
|
-
|
0.20
|
-
|
48
|
48
|
A - E
|
220
|
5,642
|
0,03
|
20
|
275000
|
0,021
|
0,30
|
129,25
|
216
|
345,25
|
Filtre
|
-
|
-
|
-
|
-
|
-
|
-
|
-
|
-
|
300
|
300
|
F - G
|
220
|
0,6
|
0,03
|
20
|
275000
|
0,021
|
-
|
13,75
|
0
|
13,75
|
H - J
|
220
|
4,314
|
0,03
|
20
|
275000
|
0,021
|
0,30
|
98,83
|
72
|
170,83
|
Sortie
|
-
|
-
|
-
|
-
|
-
|
-
|
1
|
-
|
240
|
240
|
|
IV-2-2. Calculs du ventilateur
Il s'agit dans cette partie de trouver le ventilateur qu'il
faut pour vaincre les charges calculées ci-dessus et créer le
débit nécessaire. Nous allons donc déterminer ses
caractéristiques à l'aide des courbes de fonctionnement fournies par les constructeurs de ventilateurs.
IV-2-2-1. Hauteur
manométrique du ventilateur
Le ventilateur à installer doit donc pouvoir
débiter Q = 2700 m3/h et une hauteur
manométrique de car le circuit est formé d'une seule branche.
IV-2-2-2. Choix du
ventilateur
Tout le réseau étant défini, nous
pouvons maintenant déterminer la courbe caractéristique du
réseau (appelée aussi ouverture) avec : débit volumique dans la branche racine (ou débit
principal): en supposant que la perte de charge induite par le réseau
peut se mettre sous la forme: Cette caractéristique a une allure parabolique, avec toutefois
une partie linéaire pour les petits débits, correspondant au
régime laminaire. Cette zone n'étant jamais atteinte en
fonctionnement, nous pouvons l'ignorer car c'est le point de fonctionnement qui
nous intéresse. [4]
Connaissant le point de fonctionnement souhaité, . Nous trouvons le coefficient K :

Pour trouver le point de fonctionnement de l'installation,
nous reportons cette courbe de charge sur les caractéristiques [11] des
ventilateurs fournies par le constructeur (EUROPLAST). Le point de
fonctionnement est défini par l'intersection des deux courbes 2(*)
Point de fonctionnement : 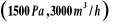
Avec ce point de fonctionnement, le ventilateur choisi est bien
adapté au circuit et vaincra les pertes de charges dans ce
dernier ; en effet :
La hauteur manométrique de fonctionnement (1500 Pa) est
largement supérieure à la perte de charge totale à travers
le réseau qui est de 1118 Pa et le débit de fonctionnement du
ventilateur (3000 m3/h) est supérieur au débit
souhaité (2700 m3/h)
Caractéristiques du ventilateur : VCPL 315
de EUROPLAST [11]
Tableau 7 :
Caractéristiques du ventilateur
|
caractéristique
|
Valeur
|
unité
|
Débit
|
3000
|
m3/h
|
Hauteur manométrique
|
1500
|
Pa
|
Vitesse de rotation
|
1850
|
tr/min
|
rendement
|
53
|
%
|
IV-2-2-3. Puissance
électrique absorbée par le ventilateur :
Connaissant le point de fonctionnement , nous pouvons calculer la puissance absorbée par le
ventilateur :
(4)
Avec = 0,53 = rendement global du ventilateur
AN. 
V-2-2-4. Choix du
moteur
Vu la puissance calculée ci-dessus ; et en consultant
les catalogues du fabricant [7] de moteur allemand
Germanischer Lloyd Det Nrske Veritas, nous prenons le moteur
asynchrone de type K21R 100 L2 de caractéristiques standard
suivantes :
Tableau 8 :
Caractéristiques du Moteur
|
caractéristique
|
Valeur
|
unité
|
P
|
3
|
KW
|
N
|
2865
|
tr/min
|
Puissance
|
100%
|
|
83,4
|
%
|
75%
|
|
84,2
|
%
|
100%
|
Cos
|
0,84
|
-
|
I
|
6,15
|
A
|
J
|
0,00275
|
Kg.m2
|
M
|
25
|
Kg
|
Avec :
: Puissance du moteur
: Vitesse de rotation du moteur
: Moment d'inertie
: Rendement
: Facteur de puissance
: Intensité du courant nominal
: Masse du moteur
IV-2-3. Dimensionnement de la
transmission de puissance
En considérant les caractéristiques du moteur
obtenu ci-dessus (2865 tr/min), et étant donné que le ventilateur
doit tourner à 1850 tr/min, mous devons donc trouver un accouplement
permettant d'assurer les vitesses voulues.
IV-2-3-1. Choix du Types de
transmission de puissance
Tableau 9 : Choix de la
transmission de puissance
|
|
Autres types de transmissions
|
Transmission poulies courroies
|
Caractéris-tiques
|
Par engrenage
|
Par roue et chaîne
|
Courroies crantées (synchrones)
|
Courroies trapézoïdales (en v)
|
Courroies plates
|
Couples admissibles
|
Très élevés
|
élevés
|
Assez élevés
|
Moyens
|
Faibles
|
Puissances admissibles
|
Très élevés
|
élevés
|
Assez élevés
|
élevés
|
Faibles
|
Rapport limite de transmission
|
|
|
|
|
|
Position des arbres
|
Tous cas possibles3(*)
|
Parallèles
|
Parallèles
|
Parallèles
|
Parallèles et autres
|
Vitesses limites ( )
|
à 
|
13 à 20
|
60
|
40
|
80 à 100
|
Rendements ( )
|
98
|
|
|
70 à 96
|
98
|
Durée de vie
|
Élevé
|
Assez élevé
|
limitée
|
limitée
|
Limitée
|
Lubrification
|
Nécessaire
|
Nécessaire
|
inutile
|
inutile
|
Inutile
|
Inconvénients
|
- Entraxe précis
- Lubrification
- encombrement
|
- Bruyantes
- lubrification
|
- Synchronisme non parfait
|
- rendement
|
- Faibles couples
|
Avantages
|
- Synchronisme
- Précision
- Grands couples
- Grandes puissances
|
- Assez bon synchronisme
- Supportent des tensions élevées
|
- Entretien réduit
- Vitesses angulaires constantes
|
- Économiques
- Encombrements réduits
- Permet un groupement en parallèle
|
- Grandes vitesses
- Rendements élevés
- Silencieuses
|
A la lecture du tableau 9, nous prendrons une transmission poulie
courroies trapézoïdales qui a l'avantage d'être
économique et qui permet des transmissions de puissances
élevés.
IV-2-3-2. Dimensionnement
des poulies et courroies
Il s'agit ici de trouver les caractéristiques (dimensions,
matière, ...) des différents éléments entrant dans
la transmission du mouvement de rotation de l'arbre du moteur à celui du
ventilateur.
Données :
P = 3 kW
= 2865 tr/min
= 1850 tr/min
Puissance de service Ps
Il est donné par la formule : ou KS est le facteur de service dépendant du taux
d'utilisation journalier et du type de fonctionnement du système. Ainsi,
pour un système fonctionnant en moyenne 07 heures par jour et sans
à coups, nous trouvons [3] : KS= 1,2 et par suite, 
Choix des sections (types de courroies)
Les sections normalisées des courroies
trapézoïdales sont classées en séries et
consignés dans un graphique [3]. Ces sections sont fonctions de la
puissance de service et de la vitesse de rotation de la petite poulie 
Ainsi, nous prenons en fin de compte une courroie de type A de la
série classique dont la section est représentée à
la figure 19.
0000000000000000000
Matériaux de la courroie : caoutchouc (usuel) de
caractéristiques suivantes :
Caractéristique de courroies usuelles en
caoutchouc.
Avec :
: Résistance à la rupture
: Masse volumique
E : Module d'élasticité
Diamètres primitifs des poulies 
Le rapport de transmission vaut 
Nous choisissons donc un diamètre normalisé
[3] pour la grande poulie et par suite nous trouvons celui de la petite poulie 
DP = 180 mm et dP = 118 mm
Vitesse linéaire des courroies

La vitesse linéaire de la courroie est bien
inférieure à la vitesse limite qui vaut 
Choix de l'entraxe a
On a : donc [3] soit encore : 
Calcul de la longueur primitive de la
courroie
(5)
La valeur trouvée ci-dessus n'étant pas
normalisée [3], nous prendrons celle qui l'est et qui est la plus
proche :
L'écart relatif entre est bien inférieur à l'écart maximal admis. En
effet : 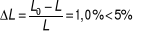
Puissance de base de la courroie
La puissance de base est fonction de la vitesse de la courroie
VC et du type de courroie (A), à la lecture des tables [3] y
afférentes nous trouvons : 
Angle d'enroulement des poulies
Pour la petite poulie, on a : 
Pour la grande poulie, on a : 
Donc les conditions de fonctionnement sont respectées
Puissance admissible

Avec :
: Puissance de base
: Coefficient de correction lié à la longueur de la
courroie car plus une courroie est longue, plus la durée de vie est
élevé. Sont donné par les abaques [3] et sont fonctions tous les deux
du type de courroie et respectivement fonction du diamètre de la poulie
et de la longueur de la courroie.



VI-2-4. Dimensionnement de la
cabine
OBJECTIF
L'étude de la cabine permet de répondre à
des questions comme :
· La cabine va-t-elle casser ?
· Va-t-elle beaucoup se déformer ?
· Puis-je utiliser moins de matière sans pour autant
diminuer les performances désirées ?
On peut donc à travers cette étude
réduire les coûts et le temps de conception en testant la cabine
sur ordinateur plutôt que lors de tests réels qui sont toujours
longs et chers.
MODELISATION
Nous utilisons dans cette section le logiciel de CAO
SolidWorks. Et les calculs sont effectués à l'aide du module
CosmosWorks entièrement intégré dans SolidWorks. Nous
avons identifié un seul cas de charge constitué par le poids
propre de la structure plus l'effort exercé par l'opérateur
à travers la meule au cours du ponçage. La figure 20 nous montre
la modélisation des ces efforts.
Au cours de la modélisation, nous avons
immobilisé les quatre supports en les assimilant à des liaisons
d'encastrement comme indiqué à la figure 21. Ceci impose lors du
calcul, des déplacements nuls à toutes les surfaces ainsi
désignées.
000000000000000000000000000000000000000000
Le matériau utilisé pour le calcul est l'acier
allié dont les caractéristiques principales sont
consignées dans le tableau 10
Tableau 10 :
caractéristiques du matériau
|
Nom de propriété
|
Symbole
|
Valeur
|
Module d'élasticité
|
E
|
2,0681e+011 N/m2
|
Coefficient de Poisson
|
|
0,28
|
Limite d'élasticité
|
|
6,2042e+008 N/m2
|
Masse volumique
|
|
7800.1 kg/m3
|
HYPOTHESES
Hypothèse de Linéarité
La relation entre le chargement et la réponse induite
est linéaire. Cette hypothèse est vérifiée
si : 1) La contrainte la plus élevée se situe dans la
portion linéaire de la courbe contrainte déformation,
caractérisée par un segment rectiligne partant de l'origine. 2)
Le déplacement maximum calculé est considérablement plus
petit que la dimension caractéristique de la pièce.
Hypothèse d'élasticité
La pièce doit retrouver sa forme d'origine si les
chargements sont supprimés (pas de déformation permanente).
Hypothèse de staticité
Les chargements sont appliqués lentement et
graduellement jusqu'à leur intensité maximale. Les chargements
appliqués brutalement sont source de déplacements,
déformations et contraintes additionnelles.
CALCUL
L'analyse statique, calcule les déplacements, les
déformations, et les contraintes dans la cabine, sous l'action de
chargements et de blocages imposés ci-dessus. COSMOSXpress utilise
l'analyse statique linéaire, basée sur la méthode des
éléments finis (Finite Element Method = FEM en anglais) pour
calculer les contraintes. L'analyse statique linéaire fait suppose les
hypothèses ci-dessus réunies pour calculer les contraintes dans
la pièce.
Nombre d'éléments :
|
34763
|
Nombre de noeuds :
|
69463
|
RESULTATS
La répartition des contraintes de Von Mises dans la
structure est donnée par la figure 22. La contrainte maximale vaut
1,6204 e+003 N/m2 et est bien inférieur à la
contrainte admissible dans le matériau qui est de 6,2042e+008
N/m2.
00000000000000000000000000000000000
La déformé de la structure est donné par
la figure 23. La déformation maximale est de 2 mm ce qui est bien
acceptable. Précisons que pour être visible à la
représentation de la figure 23, les déformations sont
amplifiées par un facteur d'échelle de 4.106.
La figure 24 nous permet de faire une comparaison rapide entre
la contrainte en tout point de la structure et la contrainte admissible de Von
Mises. Les zones critiques sont représentées en rouge sur la
figure 24 et les zones non critiques en bleu.
Nous nous réjouissons de voir que toute la structure
est bleue sur la figure 24.
000000000000000000000000
00000000000000000000000000000
VI-2-5. Dimensionnement du
separateur
Nous trouverons dans cette partie le type de séparateur
approprié pour le système et ensuite nous déterminerons
ses caractéristiques notamment ses dimensions et la perte de charge
qu'il induit dans le circuit.
CHOIX DU SEPARATEUR APPROPRIE
Un dépoussiéreur est un appareil qui permet la
séparation des particules polluantes solides ou gazeuses du courant
gazeux dans lequel elles sont en suspension. Dans tous les cas, il faudra
choisir l'appareil en considérant le problème des déchets,
de leur stockage intermédiaire et de leur évacuation. Dans le
choix du dépoussiéreur, on devra toujours examiner la
possibilité du recyclage de l'air. Les appareils de dépollution
des gaz sont habituellement classés en trois grandes familles
principales qui sont explicités dans le tableau 11 suivant :
Tableau 11 : choix du
séparateur
|
Types de
dépoussiéreurs
|
Fonctionnement
|
Avantages
|
Inconvénients
|
les séparateurs mécaniques, notamment
cyclones
|
Les séparateurs de cette famille mettent en jeu une force
mécanique pour assurer la séparation des polluants : pesanteur,
inertie ou force centrifuge
|
· Entretien facile
· Faible coût de mise en oeuvre
|
· Inutilisable pour les particules très fines
|
les séparateurs à couche filtrante (filtre
à manches, à lit de gravier)
|
Ces séparateurs utilisent les poches filtrantes faites en
polystyrènes, en coton, en laine ou en fibre métallique
|
· Adapté aux particules très fines
|
· Entretien non évident
· Coût de mise en oeuvre élevé
|
les séparateurs par voie humide
(dépoussiéreurs humides et laveurs de gaz)
|
Ici, on utilise un courant d'eau généralement sous
forme vapeur pour piéger les particules en suspension dans le gaz, ceci
permet aussi d'abaisser la température de l'air
|
· Adapté aux particules très fines
· Adapté pour les systèmes de recyclage
d'air
|
· Entretien difficile
· Coût de mise en oeuvre élevé
|
A la lecture du tableau 11 et étant donné que
nous ne recyclons pas l'air à la sortie du séparateur, nous
optons pour un cyclone à entrée tangentielle haute
efficacité (type HC) qui a l'avantage d'être économique et
d'entretien facile.
FONCTIONNEMENT
00000000000000000000
Le mélange air déchets arrivant par la bouche
d'entrée est mis en rotation immédiatement, du fait de la
courbure de la paroi. Le tourbillon créé transmet aux particules
solides une énergie cinétique qui tend à plaquer les
déchets les plus grossiers contre la paroi du cylindre C2
(figure 25) quant aux filets d'air ils se dirigent vers le tourbillon
ascensionnel qui s'est formé à l'intérieur de
C1, à cause de la différence de pression existant
entre celle du cyclone et celle de l'atmosphère. Le prolongement conique
à la partie basse du cyclone a pour effet de repousser progressivement
vers le tourbillon ascendant les filets d'air descendant et de les
intégrer à celui-ci, en même temps qu'il canalise les
déchets vers l'orifice d'évacuation inférieure. Une
particule débouche en A dans le cyclone et, par l'action de la
force centrifuge, tend à se rapprocher de la périphérie ;
elle prend contact avec la paroi en B et se trouve, à partir de
ce moment, dans le filet d'air tournant contre la paroi et contenant en
suspension une forte concentration de particules.
DIMENTIONNEMENT
Il faut maintenant déterminer les
caractéristiques du cyclone pour répondre aux exigences du
circuit.
PARAMETRES CONNUS
Débit d'air : 2700 m3/h
Densité du solide : 2500 kg /m3
Diamètre moyen des particules 5 micron
Vitesse d'entrée du cyclone : 20 m/s
PARAMETRES A DETERMINER
Dimensions du cyclone
La Courbe des cyclones haute efficacité (HC) fournie en
annexe 7 nous permet de déterminer les dimensions principales du cyclone
connaissant la vitesse à l'entrée et le débit d'air
nécessaire nous obtenons le résultat suivant :
Diamètre extérieur :
150 mm
Perte de charge dans le cyclone
La deuxième courbe en annexe 7 nous donne la perte de
charge moyenne à la traversé d'un cyclone de dimensions connue
pour un débit donné. Avec le diamètre de 150 mm
trouvé précédemment et un débit de 2700
m3/s
Perte de charge à la traversé :
300 Pa
VI-3. SCHEMA ELECTRIQUE DU
SYSTEME ET EVALUATION DU COUT DE REALISATION
Cette section nous permettra de décrire tous les
éléments de protection à prévoir dans le circuit
électrique d'alimentation et de commande du moteur. Nous
évaluerons à la fin de la section le coût de
réalisation du système question de savoir si la
réalisation de ce dernier est économiquement rentable pour
l'entreprise.
VI-3-1. Schéma de
puissance
000000000000000000000000000
M : moteur asynchrone triphasé
|
|
F2 : relais magnétothermique
|
|
F1 : sectionneur à fusible
|
|
VI-3-2. Schéma de
commande
00000000000000000000000000000000000000000000000
H1 : voyant sous tension
|
S3 : bouton poussoir marche
|
H2 : voyant surcharge
|
S1 : bouton poussoir arrêt
|
H3 : Voyant marche
|
F2 : contact auxiliaire du relais
|
VI-3-3. Description du
fonctionnement
Le système comporte au niveau du pupitre de commande,
deux boutons poussoirs à retour automatique matérialisé
dans le circuit de commande par :
S2 pour le bouton poussoir marche
S1 pour le bouton poussoir arrêt systématique du
moteur
Le pupitre, situé au niveau de la cabine de
ponçage, comprend trois voyants lumineux indiquant l'état du
système à l'opérateur.
H1 : Allumé, indique que l'installation est sous
tension.
H2 : Allumé, indique une surcharge du moteur
H3 : Allumé, indique le fonctionnement normal du
système.
Au départ du cycle, nous supposons le moteur en
arrêt.
§ Si on actionne le bouton Poussoir S2, le contacteur KM1
est excité, le contact auxiliaire KM11 se ferme et maintient la bobine
de KM1 excité après le relâchement de S2. au même
instant, les contacts principaux de KM1 se ferment et le moteur M se met en
marche entraînant du même coup le ventilateur et par suite le
système d'aspiration. Le voyant lumineux H3 s'allume indiquant
l'état de fonctionnement du système.
§ Une action sur le Bouton Poussoir S1 provoque le
déxcitation immédiate de KM1 et l'arrêt du moteur. Le
voyant H3 s'éteint
§ Le voyant S1 reste allumé tant que le
système est sous tension (alimenté par le secteur) il ne
s'interrompt que lorsque le courant du secteur n'est plus disponible.
§ En cas de surcharge, le voyant H2 s'allume et permets
donc à l'opérateur d'arrêter le système question
d'aller décolmater le filtre étant donné que ce dernier
sera la principale cause de surcharge du moteur.
VI-3-4. Coût de
réalisation du système
Dans cette partie, nous donnons un devis estimatif des
différents équipements à mettre en oeuvre pour obtenir le
système d'aspiration étudié ci-dessus. Les
différents prix évoqués sont ceux du marché courant
et peuvent éventuellement suivre les fluctuations de ce dernier.
Tableau 14 : coût
d'acquisition
|
Désignation
|
Nombre
|
Prix unitaire (Fcfa)
|
Prix Total (Fcfa)
|
Ventilateur
|
01
|
|
125 000
|
Cabine
|
01
|
|
45 000
|
Conduites
|
|
|
78 000
|
Moteur
|
01
|
300 000
|
300 000
|
Courroies
|
01
|
4 000
|
4 000
|
Filtre
|
01
|
70 000
|
70 000
|
Prise
|
02
|
1 000
|
2 000
|
Accessoires
|
|
|
95 000
|
Lampes
|
03
|
500
|
1500
|
Poulies
|
02
|
10 000
|
20 000
|
Câble
|
30 m
|
250
|
15 000
|
Paliers
|
04
|
15 000
|
60 000
|
Boutons poussoirs
|
03
|
2 500
|
75 000
|
contacteur
|
01
|
8 000
|
30 000
|
Relais thermique
|
01
|
8 000
|
7000
|
Sectionneur à fusible
|
01
|
8 000
|
8 000
|
Total brut (Fcfa)
|
935 500
|
Main d'oeuvre
|
(20 %)
|
187 100
|
Marge de sécurité
|
(10 %)
|
93 550
|
Total (Fcfa)
|
1 216 150
|
Le coût brut de réalisation du projet
(1 216 150 F CFA) est bien à la portée
de la MIPROMALO (direction de la recherche et du développement des
équipements) et même, le dit coût peut être encore
minimisé dans la mesure ou l'on envisagerai une
récupération du ventilateur disponible à la MIPROMALO
IV-4. PROCEDÉ
D'OBTENTION DES COMPOSANTS DU SYSTEME
Le système devant être fabriqué en un
exemplaire, il est indélicat de penser aux techniques de production
comme le moulage qui coûterai très cher. Cela dit, pour obtenir
les différents composants, nous proposons ;
o Pour la cabine.
La cabine est un assemblage soudé des
différentes poutres et tôles de caractéristiques
indiqués au chapitre IV.
o Pour le ventilateur
Nous avons utilisé pour le dimensionnement du
réseau aéraulique la courbe de fonctionnement d'un ventilateur
particulier ; donc il sera plus commode d'e se procurer le dit
ventilateur. Mais à défaut, on pourra bien prendre un ventilateur
de caractéristiques équivalentes sur le marché. Dans une
certaine mesure, on peut envisager la récupération n du
ventilateur disponible à la MIPROMALO.
o Pour le cyclone
Il devra être assemblé par soudage.
o Pour le moteur
Il sera acheté dans le marché courant et on
devra tout simplement s'assurer de la correspondance des
caractéristiques.
o Pour les conduites
Il s'agit du PVC rigide standard de diamètre
normalisé connu (Chapitre IV)
o Pour la poulie, les courroies et les accessoires
électriques.
Ils sont trouvés sur le marché avec des
caractéristiques calculées au chapitre IV.
Notre travail a consisté à concevoir un
système de dépoussiérage du poste de ponçage de
carreau de la MIPROMALO. Nous avons fait une étude fonctionnelle
technique et économique du système. Après avoir
circonscrit le système et étudié les différentes
solutions possibles, nous avons ressorti les dessins d'ensemble et de
définitions du système d'aspiration. Un dimensionnement
adéquat de chaque élément du système nous a permis
de trouver les caractéristiques appropriées pour chacun d'eux.
Par ailleurs, nous avons réalisé un schéma
électrique illustratif de puissance et de commande du système
question de présenter les différents éléments de
protection à prévoir. Enfin, une évaluation du coût
de réalisation du système nous a permit de trouver que à
1 216 150 F CFA, la MIPROMALO peut réaliser
ce système qui lui apporterai un gain substantiel par suppression des
temps morts qui sanctionnent les créneaux de ponçage.
Bien que nous soyons arrivé au terme de notre
étude, il n'en demeure pas moins que nous avons rencontré
beaucoup de difficultés et par conséquent, nos proposons à
la MIPROMALO d'offrir d'avantages de moyens logistique aux stagiaires pour
mener à bien leurs travaux. Enfin, une pareille étude ne s'aurai
suffire pour la réalisation du système mais elle est tout de
même une phase indispensable et incontournable à cette fin. Il
faudra donc, avant la phase de mise en oeuvre du projet, dimensionner les
différents éléments de protection suggérés
dans le circuit électrique.
.
REFERENCES BIBLIOGRAPHIQUES
|
[ 1 ] TCHANDE TIAKO Yves Stéphane.
(2004)
Conception d'une ponceuse a eau pour le ponçage des
carreaux. Mémoire de fin d'études d'ingénieurs, ENSP,
Yaoundé Cameroun.
[ 2 ] Marcel SEDILLE. (1973)
Ventilateurs et compresseurs centrifuges et axiaux
aérodynamique générale calcul et dimensionnement, Tome 1,
édition EYROLLES, France.
[ 3 ] Jean Louis FANCHON. (1978)
Guide des sciences et technologies industrielles - Dessin
industriel et graphes. Matériaux. Éléments de
construction. Économie et organisation d'entreprise. Automatisme,
édition AFNOR, France.
[ 4 ] Michel A. Morel. (1993)
Exercices de mécanique des fluides - turbomachines,
construction graphique, phénomènes transitoires, Tome 2,
édition EYROLLES, France.
[ 5 ] Gaétan BEAULIEU (1998)
Guide de conception et calcul des convoyeurs pneumatiques
à basse et moyenne pression, édition Beaulier INC, Canada.
[ 6 ]
http://neveu.pierre.free.fr/index.htm
[ 7 ]
http://depollunet.free.fr/AspSom.html
[ 8 ]
http://www.aeib-ventilators.com/helicoides.html
[ 9 ]
http://www.thermexcel.com/french/index.htm
[ 10 ]
http://www.airliquide.com/fr_index.asp
[ 11 ]
http://www.europlast-paris.com/
ANNEXE 1. DESSINS DE DEFINITIONS
1-1. cabine de ponçage
1-2. filtre à poussière
ANNEXE 2. CHOIX DE LA VITESSE DE L'AIR
ANNEXE 3. COURBE DE FONCTIONNEMENT DU VENTILATEUR
ANNEXE 4. CHOIX DE LA VITESSE D'ECOULEMENT
ANNEXE 5. DIAGRAMME DE MODDY MOURINE (COEFFICIENT DE PERTE
DE CHARGE LINEAIRE)
ANNEXE 6. COEFFICIENT DE PERTES DE CHARGES SINGULIERES
ANNEXE 7. PERTES DE CHARGES DU AU CAPOTAGE
  
* 1 Voir le tableau en
Annexe
* 2 Voir ANNEXE 3
* 3 Arbres parallèles,
orthogonaux, et même de position quelconque
|