Chapitre 2. - Les caractéristiques
mécaniques des granulats
L'aptitude des granulats à être utilisés
dans les assises de chaussée est appréciée par un certain
nombre d'essais. Ces essais ont été effectués au
laboratoire de géotechnique de Jean Lefebvre Sénégal dans
le cadre du projet de construction de l'autoroute Patte d'oie - Malick Sy.
1. - Essais caractéristiques de la
fabrication
1.1. - Analyse granulométrique
On appelle analyse granulométrique l'opération
permettant de déterminer :
o La granulométrie : c'est-à-dire la
détermination de la grosseur des grains et les pourcentages
pondéraux respectifs des différentes familles de grains
constituant les échantillons,
o La granularité : c'est-à-dire la
répartition dimensionnelle des grains dans un granulat.
L'analyse granulométrique consiste à
fractionner le matériau en différentes coupures à l'aide
de tamis à maille carrée. Elle s'applique à tous les
granulats de dimension nominale inférieure ou égale à 63
mm, à l'exclusion des fillers. Les masses des différents refus
sont rapportées à la masse initiale sèche du
matériau. Les pourcentages ainsi obtenus sont exploités sous
forme de graphique en portant les ouvertures des tamis en abscisse, sur une
échelle logarithmique, et les pourcentages en ordonnée, sur une
échelle arithmétique (Figures 22 à 25). La courbe
appelée courbe d'analyse granulométrique est tracée de
manière continue et peut ne pas passer rigoureusement par tous les
points.
Les tamis sont normalisés. Les ouvertures de mailles
carrées permettent un classement granulaire. Les dimensions
successives des mailles carrées suivent des progressions
géométriques de raison Normalisation).
|
|
= 1,25 pour la norme AFNOR (Association Française de
|
|
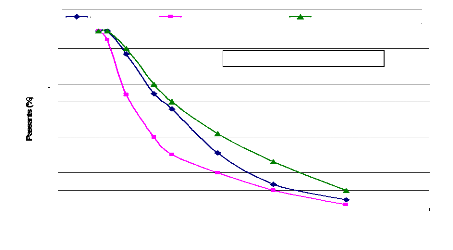
100
40
60
20
90
80
70
50
30
10
0
100
45/15/15/25 Branche inf fuseau Branche sup fuseau
10
Diamètre (mm)
Pourcentage de fines f = 4,6 %
1
0,1
0,01
Fig. 23. - Courbe granulométrique de la
fraction 0/31,5 mm du basalte dans le fuseau 0/31,5 mm - concassés
0/d (BCEOM-CEBTP, 1984)
36
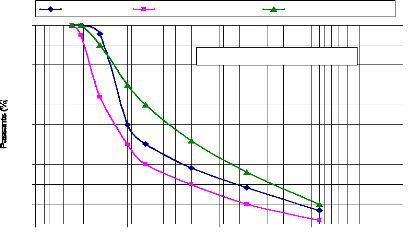
100
10
1
0,1
0,01
100
90
80
70
60
50
40
30
20
10
0
Pourcentage de fines f = 6,9 %
30/15/20/35 Branche inf fuseau Branche sup fuseau
Diamètre (mm)
Fig. 24. - Courbe granulométrique de
la fraction 0/31,5 mm du calcaire dans le fuseau 0/31,5 mm -
concassés 0/d (BCEOM-CEBTP, 1984)
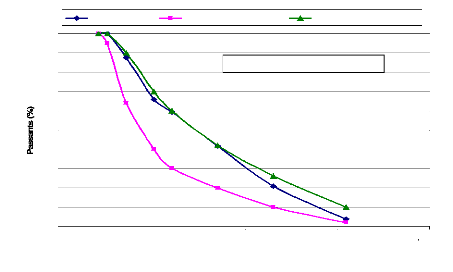
100
40
90
80
60
50
30
20
70
10
0
100
30/15/20/35 Branche inf fuseau Branche sup fuseau
10
Diamètre (mm)
Pourcentage de fines f = 3,6 %
1
0,1
0,01
Fig. 25. - Courbe granulométrique de la
fraction 0/31,5 mm du silexite dans le fuseau 0/31,5 mm - concassés
0/d (BCEOM-CEBTP, 1984)
37
Les différentes courbes granulométriques
indiquent une granularité continue et étalée. Seul le
calcaire n'entre pas dans le fuseau de spécification du CEBTP ; cela est
du à un pourcentage de refus faible au niveau du tamis de maille 20 mm.
En effet c'est la forme de la courbe qui est plus importante. Elle conditionne
l'aptitude au compactage, l'absence de ségrégation et la
compacité du matériau. Plus les contacts entre les grains sont
nombreux, plus la couche sera stable, plus le matériau sera compact,
moins on risquera de voir se produire des déplacements des grains et par
suite des tassements. A cet égard, ce sont donc les courbes
continues et bien graduées qui sont les plus
satisfaisantes.
Le pourcentage de fines est satisfaisant. Si ce pourcentage
est nul ou insuffisant pour combler les vides entre les gros grains, le
matériau est peu compact. S'il est excessif il y a formation de boue au
compactage et donc une augmentation ultérieure des déformations
permanentes. Cependant pour le calcaire le malaxage et le compactage
produisent des fines qui peuvent passer d'un pourcentage de 7 à 17,31 %
(Figure 25). C'est pourquoi la fourchette de 4 à 10 % de
fines proposée par le CEBTP semble ne pas être adaptée
à toutes les catégories de granulats. Si le pourcentage de fines
après compactage risque de dépasser un certain seuil, il faudrait
diminuer cette fourchette.

100
40
80
60
20
90
70
50
30
10
0
100 10 1 0,1
Diamètre (mm)
avant compactage après compactage fort
après compactage faible
0,01
Fig. 26. - Granulométrie après
compactage du calcaire
1.2. - Le coefficient d'aplatissement
La forme d'un granulat est définie par trois grandeurs
géométriques :
· La longueur L, distance maximale de deux plans
parallèles tangents aux extrémités du granulat,
· L'épaisseur E, distance minimale de deux plans
parallèles tangents au granulat ;
· La grosseur G, dimension de la maille carrée
minimale du tamis qui laisse passer le granulat.
Le coefficient d'aplatissement A d'un ensemble de granulats est
le pourcentage pondéral des
G
éléments qui vérifient la relation : >
1,58
E
On fait un tamisage classique sur une colonne de tamis
normalisés à mailles carrées afin de séparer les
granulats en une succession de classes granulaires d/D dont les dimensions
sont telles que D = 1 ,25d. Les différentes classes granulaires d/D
ainsi isolées sont tamisées une à
38
une sur une grille à fentes parallèles
d'écartement E = d/1,58 (ce qui correspond aussi à E = D/2).
L'échantillon est tamisé sur un tamis de 4 mm
d'ouverture et le refus de masse M0 est utilisé pour la
détermination de A.

Pour une classe granulaire d/D donnée, on peut
définir un coefficient d'aplatissement partiel. Ai = 100Mei
Mgi
Avec Mgi = masse de la classe granulaire d/D,
Mei = masse passant à travers le tamis à fentes
d'écartement E correspondant.
Le coefficient d'aplatissement global A du mélange
s'exprime en intégrant les valeurs partielles déterminées
sur chaque classe granulaire (Tableau 4) :

A =Mei M gi
Caractéristique
|
Basalte
|
Calcaire
|
Silexite
|
Coefficient d'aplatissement (%)
|
14,93
|
6,1
|
24,93
|
Tableau 4. - Coefficients d'aplatissement des
différents types de granulats
La forme des granulats calcaires est meilleure que
celle des granulats de basalte et de silexite. Ceci indique une
difficulté relative au concassage des basaltes et des silexites due
à leur aspect trop massif. Toujours est-il que les
granulats de silexite ont une forme plus plate que celle des granulats de
basalte.
Des matériaux très anguleux ne se mettent pas
toujours facilement en place et la compacité après compactage
peut ne pas être élevée. C'est ainsi que les graves
concassées, qui comportent une fraction importante de sable rond, sont
plus maniables et plus aisément compactables. Cependant la forme des
granulats a également une forte influence sur la résistance aux
déformations permanentes. En effet les matériaux alluvionnaires
roulés résistent mal à l'orniérage. Une
étude au triaxial de l'influence de la forme des granulats
(roulés ou concassés) sur le comportement des Graves Non
Traitées a montré que les matériaux concassés ont
la meilleure résistance aux déformations permanentes.
1.3. - L'Equivalent de Sables
L'Equivalent de sables est un rapport conventionnel
volumétrique entre les grains fins et les autres. Il permet donc de
caractériser l'importance des fines par une valeur numérique
(Tableau 5).
Cet essai s'applique assez bien aux sols faiblement plastiques et
peut s'appliquer à tous les matériaux grenus.
L'essai est effectué sur la fraction 0/5 mm du
matériau à étudier. On lave l'échantillon, selon un
processus normalisé, et on laisse reposer le tout. Au bout de 20
minutes, on mesure les éléments suivants :
- hauteur H1 : sable propre + éléments fins, -
hauteur H2 : sable propre seulement.
Il existe deux types de mesures en fonction du degré
d'argilosité du matériau. En effet pour les sols par exemple, la
mesure de la hauteur H2 peut être délicate, on substitue à
l'essai visuel, l'essai au piston.

ES=100H2 H1
39
Caractéristique
|
Basalte
|
Calcaire
|
Silexite
|
Equivalent de Sables (%)
|
50,82
|
45,22
|
52
|
Tableau 5. - Equivalent de sables des
différents types de granulats
L'Equivalent de sables satisfait à tous les niveaux de
trafic. Il indique le degré de pollution des éléments
sableux des granulats. Plus l'Equivalent de sables est élevé,
moins le matériau contient d'éléments fins nuisibles. A
cet égard les calcaires sont moins propres que les basaltes et
les silexites. Cet essai rend compte globalement de la quantité des
éléments les plus fins mais est moins fiable en ce qui concerne
l'aspect qualitatif c'est-à-dire donne peu d'informations sur la nature
minéralogique de ces fines. En effet, il faut savoir si
ces particules fines sont « inertes » c'est-à-dire sont un
simple filler minéral provenant du broyage de la roche par concassage
comme les fines siliceuses ou calcaires, ou s'il s'agit de particules «
actives » c'est-à-dire des particules argileuses qui vont se
gonfler en présence d'eau faisant chuter le frottement interne
jusqu'à l'annuler presque totalement entraînant l'orniérage
de la couche incriminée.
2. - Les essais caractéristiques des
propriétés intrinsèques 2.1. - Masses
volumiques
2.1.1. - Définitions
o La masse volumique absolue
La masse volumique absolue d'un matériau est la masse
de l'unité de volume de ce matériau, déduction faite de
tous les vides, aussi bien des vides entre les grains que des vides à
l'intérieur des grains.
La densité absolue est le rapport de la masse absolue
d'une unité de volume du matériau à température
donnée à la masse du même volume d'eau distillée
à la même température.
o La masse volumique réelle
La masse volumique réelle d'un matériau est la
masse de l'unité de volume de ce matériau déduction faite
des vides entre particules. La déduction ne concerne pas les vides
compris dans le matériau mais seulement ceux entre les particules
(Tableau 6).
La densité réelle est le rapport de la masse
réelle d'une unité de volume du matériau sec dans l'air
à température donnée à la masse d'un égal
volume d'eau distillée à la même température.
o La masse volumique apparente
La masse volumique apparente d'un matériau est la masse
de l'unité de volume du matériau pris en tas, comprenant à
la fois des vides perméables et imperméables de la particule
ainsi que les vides entre particules.
La densité apparente est le rapport de la masse apparente
d'une unité de volume du matériau à la masse d'un
égal volume d'eau distillée à la même
température.
Caractéristique
|
Basalte
|
Calcaire
|
Silexite
|
Poids spécifique ãs
(kN/m3)
|
27,25
|
24,44
|
24
|
Tableau 6. - Poids spécifiques des
différents types de granulats 40
2.2. - Résistance à l'usure et aux
chocs
2.2.1. - Essai Los Angeles
Cet essai permet de mesurer les résistances
combinées à la fragmentation par choc et à l'usure par
frottements réciproques des éléments d'un granulat
(Tableau 7). Il consiste à mesurer la quantité
d'éléments inférieurs à 1,6 mm produite en
soumettant le matériau à une série de chocs et de
frottements dans la machine Los Angeles. A un coefficient Los Angeles faible
correspond un excellent matériau. Dans la machine Los Angeles,
introduire la prise d'essai M = 5000 g et la charge de boulets de la classe
granulaire choisie. Après 500 rotations de la machine, à une
vitesse régulière comprise entre 30 et 33 tr/min, recueillir le
granulat et le tamiser à 1,6 mm, peser le passant m.
m
Par définition le coefficient Los Angeles est le rapport :
=
LA
× 100
M
2.2.2. - Essai Micro-Deval
L'essai permet de mesurer la résistance à
l'usure par frottements entre les granulats et une charge abrasive (Tableau 7).
Il consiste à mesurer la quantité d'éléments
inférieurs à 1,6 mm produite dans un broyeur, dans des conditions
bien définies, à sec ou en présence d'eau. Plus le
coefficient Micro-Deval est faible, meilleur est le matériau.
Dans les cylindres de la machine, introduire chaque prise d'essai
M = 500 g et la charge abrasive (billes en acier de 10 mm de diamètre)
correspondant à la classe granulaire choisie. Les essais peuvent
s'effectuer à sec ou en présence d'eau. Dans ce dernier cas, on
ajoutera 2,5 litres d'eau par essai. Après rotation des cylindres
à une vitesse de 100 tr/min pendant 2 heures, tamiser le matériau
sur le tamis de 1,6 mm et peser passant m.
m
Par définition le coefficient Micro-Deval est le rapport :
=
M D
× 100
M
Les valeurs de LA et MDE ont été fournis par des
rapports de IK Consultance et du CEREEQ.
Caractéristiques mécaniques
|
Basalte
|
Calcaire
|
Silexite
|
Los Angeles (%)
|
12,54
|
32,65
|
21
|
Micro-Deval (%)
|
16
|
54,7
|
17
|
Tableau 7. - Coefficients Los Angeles et
Micro-Deval des différents types de granulats
Les coefficients Los Angeles et Micro-Deval du basalte et du
silexite sont conformes aux spécifications. Les granulats de
basalte et de silexite montrent une grande résistance à l'usure
et à la fragmentation due à leur aspect trop massif. Cependant le
silexite est moins résistant que le basalte. Les calcaires ont une
faible résistance à l'usure et au frottement.
3. - Essai Proctor - Essai CBR
3.1. - Essai Proctor modifié
Cet essai simule l'évolution du sol au cours du
compactage et permet de déterminer pour une énergie de compactage
donnée, la teneur en eau optimale pour obtenir la densité
sèche maximale (Figure 26).
L'essai consiste à compacter l'échantillon dans
un moule standard, à l'aide d'une dame normalisée, à
raison de 55 coups par couche (5 couches). Le compactage s'effectue avec des
teneurs en eau croissantes rapportées au poids du matériau sec.
Après chaque opération on mesure la masse apparente
(ãh) du matériau et la teneur en eau
(w) puis on calcule la masse volumique sèche
(ãd).
41
On trace ensuite la courbe Proctor du matériau avec en
abscisse les teneurs en eau et en ordonnée les masses volumiques
sèches. On détermine ensuite la teneur en eau optimale (w
opt) qui correspond à la masse volumique sèche maximale
(ãd max).
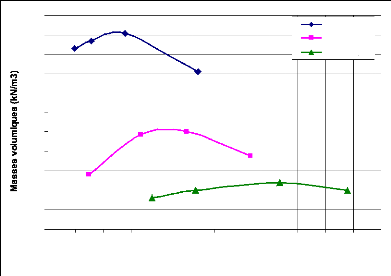
24,5
23,5
22,5
21,5
20,5
19,5
24
23
22
21
20
19
5,5 6 6,5 7 7,5 8 8,5 9 9,5 10 10,5 11 11,5
Teneur en eau (%)
Basalte 0/31,5 Calcaire 0/31,5 Silexite 0/31,5
Fig. 27. - Courbes Proctor des différents
types de granulats
Caractéristiques physiques
|
Basalte
|
Calcaire
|
Silexite
|
ãd max (kN/m3)
|
24,04
|
21,6
|
20,21
|
W opt (%)
|
6,8
|
7,65
|
9,5
|
ãs (kN/m3)
|
27,25
|
24,44
|
24
|
Porosité n (%)
|
11,84
|
12
|
15,64
|
Tableau 8. - Caractéristiques physiques
des différents types de granulats
3.2. - Essai CBR
Il sert à caractériser la portance du
matériau c'est à dire la charge qu'il peut supporter sans se
rompre, mais également à mesurer l'aptitude d'une chaussée
à une perméabilité amenée par une forte immersion
en cas de fortes pluies. Le CBR est un nombre sans dimension exprimant en
pourcentage le rapport entre les pressions produisant dans le même temps
un enfoncement donné dans le matériau étudié d'une
part et dans un matériau de référence (13,6 kN) d'autre
part.
Par définition cet indice est pris égal à la
plus grande des deux valeurs suivantes :
- ICBR2 , 5 = 100F2 , 5 13,6 -
ICBR5 =100F 5 20,5

ICBR = max(ICBR2 , 5 ;
ICBR5)
F2, 5 = Force à 2,5 mm d'enfoncement, F5 = Force à
5 mm d'enfoncement.
42
Le matériau est compacté à la teneur en
eau optimale suivant les procédures de l'essai Proctor modifié :
3 moules CBR qui seront compactés respectivement à raison de 55,
25, et 10 coups par couche (5 couches par moule). Après immersion des
moules pendant 4 jours, on détermine son poids, sa densité et sa
compacité. On poinçonne ensuite le moule avec un piston de 4,9cm
de diamètre à une vitesse de 1,27 mm/min. On trace la courbe
indices CBR/Compacités.
On peut alors déterminer les Indices CBR à 25, 95
ou 98 % de compacité (Figure 27 à 32).
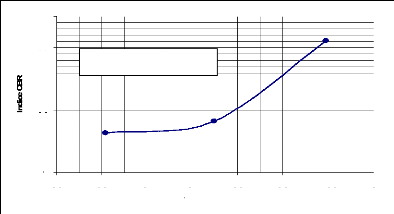
250
200
150
100
50
0
88 90 92 94 96 98 100 102
CBR (95%OMP) = 82 CBR (98%OPM) = 160
Com pacité(%)
Fig. 28. - Etude CBR après 96 heures
d'imbibition du basalte 0/31,5 mm
250
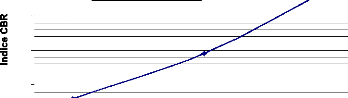
150
100
50
0

200
CBR (95% OPM) = 105 CBR (98% OPM) = 162
88 90 92 9496 98 100
Compacité (%)
Fig. 29. - Etude CBR après 96 heures
d'imbibition du silexite 0/31,5 mm 43
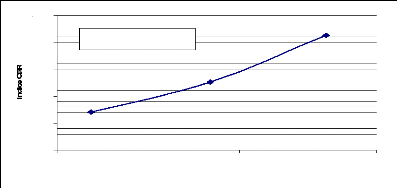
350
300
250
CBR (95% OPM) = 230 CBR (98% OPM) = 280
200
88 90 92 94 96 98 100 102
Com pacité(%)
150
100
Fig. 30. - Etude CBR après
poinçonnement immédiat du calcaire 0/31,5 mm
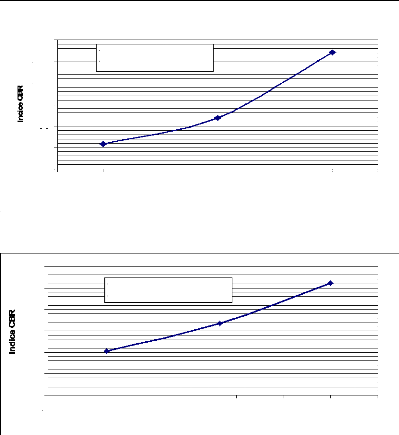
300
250
200
150
100
Fig. 31. - Etude CBR après 96 heures
d'imbibition du calcaire 0/3 1,5 mm
50
400
250
200
350
300
150
100
0
88 90 92 94 96 98 100 102
Compacité (%)
88 90 92 94 96 98 100 102
CBR (95%OPM) = 219 CBR (98% OPM) = 305
CBR (95 P) = 165
CBR (95% OPM) = 165
CBR (98 )
CBR (98% OPM) = 220
Com pacité(%)
Fig. 32. - Etude CBR après 8 jours
d'imbibition du calcaire 0/31,5 mm 44
250
50
0
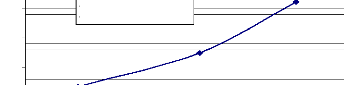
200
150
100
CBR (95%OPM) = 116 CBR (98%OPM) = 170
88 90 92 94 96 98 100 102
Com pacité(%)

Fig. 33. - Etude CBR après 16 jours
d'imbibition du calcaire 0/31,5 mm
Indice CBR
|
Basalte
|
Calcaire
|
Silexite
|
95 %OPM
|
82
|
219
|
105
|
98 %OPM
|
160
|
305
|
162
|
Tableau 9. - Les Indices Portant CBR
après 96 heures d'imbibition des différents types
de granulats
L'Indice Portant CBR à 95 % de l 'OPM
(Tableau 9) du calcaire (219) est largement supérieur
à celui du silexite (105) et du basalte (82). En se basant sur cet essai
on a tendance à penser, à tort, que le calcaire a les meilleures
performances mécaniques que le basalte. Ceci est du au fait que
malgré la dureté du squelette, le basalte est un matériau
moins cohésif, tirant sa stabilité du seul frottement interne,
donc sujet à l'attrition. C'est ainsi que le CBR à 98 %
de l'OPM peut atteindre 160 chez le basalte, 162 chez le silexite, et plus de
300 chez le calcaire, ce qui démontre clairement les exigences de
compacité des matériaux non liés. On doit avoir au moins
98 % de compacité in situ (BCEOM-CEBTP, 1984).
Indice CBR
|
Immédiat
|
4 jours
|
8 jours
|
16 jours
|
95 %OPM
|
230
|
219
|
165
|
116
|
98 %OPM
|
280
|
305
|
220
|
170
|
Tableau 10. - Tableau de variation de l'Indice
CBR du calcaire en fonction de la durée d'imbibition
45
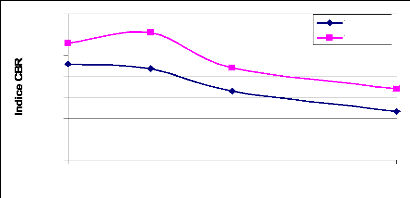
250
200
350
300
150
100
50
0
0 4 8 12 16
Jour
95%OPM 98%OPM
Fig. 34. - Evolution du CBR du calcaire en
fonction de la durée d'imbibition
Il a été observé à 98 % de
compacité que l'Indice Portant CBR du calcaire après 96 heures
d'immersion (305) est supérieur à l'Indice Portant après
poinçonnement immédiat (280) (Tableau 10). Ce
comportement peut laisser penser que la présence de l'eau a
contribué à l'hydratation de la chaux entraînant une
cimentation plus forte. C'est pourquoi il a été
effectué des essais sur des échantillons immergés pour des
durées de 8 à 16 jours pour mieux comprendre l'effet de l'eau
(Figure 33). Le constat est que l'accroissement de la portance n'est pas
un phénomène continu. Au-delà de 96 heures d'imbibition,
la portance du matériau diminue.
Le Tableau 11 donne les spécifications et les
résultats des différentes caractéristiques des
granulats.
Caractéristiques
|
Spécifications
|
Basalte
|
Calcaire
|
Silexite
|
Fuseau
|
|
0/3 1,5 mm
|
Conforme
|
Non conforme
|
Conforme
|
% fines
|
|
4 < f < 10
|
4,6
|
6,9
|
3,6
|
ES
|
T1-T2
|
~ 30
|
50,82
|
45,22
|
52
|
T3-T4
|
~ 40
|
CBR
|
95 %OPM
|
~ 80
|
82
|
219
|
105
|
98 %OPM
|
|
160
|
305
|
162
|
Porosité
|
|
< 15
|
11,84
|
12
|
15,64
|
LA
|
T1-T3
|
S 45
|
12,54
|
32,65
|
21
|
T4-T5
|
S 30
|
MDE
|
T1-T3
|
S 15
|
16
|
54,7
|
17
|
T4-T5
|
S 10
|
A
|
|
< 30
|
14,93
|
6,1
|
24,93
|
Tableau 11. - Tableau récapitulatif des
caractéristiques des différents types de granulats 46
|