Modelisation du temps de reaction dun systeme industriel :
Application aux centrales thermiques d'OYOMABANG I et II
.
DEDICACE
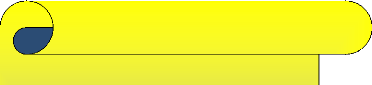
to travail-east cacri6 a ma &rand
mdre
..c/Can'e die qui m
a comik de ses
lien
I e,9c
enc
ent
accorcte fonjue vie.
|
~~~ ~~~~
~ ~~~~~ ~~~
|
~
|
|
|
|
|
|
|
|
|
|
|
|
|
|
|
|
|
|
|
|
|
|
|
|
|
|
|
|
|
|
|
|
|
|
|
|
|
|
|
|
diction
|
|
|
|
|
|
|
|
|
r~s
|
|
|
|
|
|
|
|
|
|
|
|
|
|
|
|
|
|
|
|
|
|
|
|
|
|
|
|
|
|
|
|
|
Sft
|
|
|
mess
|
trouve
|
|
|
|
id
|
|
|
|
touters
elle
|
|
|
|
|
|
|
|
|
|
|
|
|
|
|
|
|
|
|
|
|
|
|
|
|
|
|
|
|
|
|
|
|
|
|
|
|
|
|
|
|
|
|
|
|
|
|
|
|
|
|
|
|
|
|
|
|
|
|
|
|
|
|
|
|
|
|
|
|
|
|
|
|
|
|
|
|
|
|
|
|
|
|
|
|
|
|
|
|
|
|
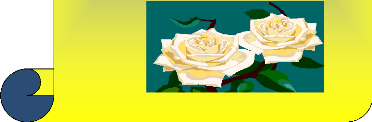
Modelisation du temps de reaction d'un systeme industriel :
Application aux centrales thermiques d'OYOMABANG I et II .
REMERCIEMENTS
Ce présent mémoire de fin d'étude est le
résultat de plusieurs efforts consentis dont seule la volonté du
Dieu tout puissant est à l'origine.
Je ne manquerai d'adresser ma profonde gratitude à toutes
ces personnes. Aussi, mes remerciements vont :
> Au Pr. JEAN NGANHOU, pour avoir accepté de
présider le jury de ma soutenance,
> Au Dr. MEVA'A Lucien, pour son encadrement,
> Au Dr. DANWE RAIDANDI, pour avoir accepté d'examiner
mon mémoire,
> Au Dr. NGUIMBIS, pour avoir accepté d'être
membre du jury de ma soutenance,
> Au Dr NSANGOU THEODORE, Directeur
Général d'EDC, qui nous a permis
d'effectuer ce stage dans son entreprise.
> A M .TCHOUTIO LEOPOLD, Chef des
Centrales Thermiques d'OYOMABANG I et II, qui nous a
ouvert les portes de sa centrale.
> A mes encadreurs industriels : M. BELL Constantin
Edouard et M. VENSA Mouhamadou qui m'ont permis de mener ce travail à
terme grâce à un appui remarquable,
> Au corps enseignant de L'ENSP, pour leur
disponibilité tout au long de mon cursus,
> A tout le personnel de la centrale thermique d'OYOMABANG
pour leur disponibilité et leur hospitalité,
Je remercie également :
> Tous les membres de ma famille, pour leur soutien
permanent
> Tous mes camarades de la promotion 2010
> Mlle NTENTIE Christelle, pour son soutien infaillible
durant mon cursus.
Finalement, je tiens à exprimer ma profonde
reconnaissance envers mes amis et collègues qui m'ont inlassablement
encouragé tout au long de ce travail.
Modelisation du temps de reaction d'un systeme industriel :
Application aux centrales thermiques d'OYOMABANG I et II .
GLOSSAIRE
SIGLES
|
DEFINITIONS
|
EDC
|
Electricity development corporation
|
ENS
|
Evènement Non Souhaité
|
Dn
|
Temps de réaction
|
RIS
|
Réseau interconnecté sud
|
Black- out
|
Coupure d'électricité dans tout le
réseau
|
SI
|
Système industriel
|
GRAI
|
Graphe à Résultats et Activités
Inter-reliés
|
LAP
|
Laboratoire d'automatique et de productique (université
de Bordeaux I)
|
CC
|
Chef de la centrale
|
DI
|
Demande d'intervention
|
OT
|
Ordre de travail
|
PT
|
Permit de travail
|
JSA
|
Job safety Analysis
|
FMD
|
Fiabilité - Disponibilité -
Maintenabilité
|
ENSP
|
Ecole Nationale Supérieure Polytechnique
|
|
Modelisation du temps de reaction d'un systeme industriel :
Application aux centrales thermiques d'OYOMABANG I et II .
RESUME
Le travail effectué porte sur la modélisation
du temps de réaction d'un système industriel. Il s'agit, de
mettre sur pied les meilleures techniques de réaction des
systèmes industriels suite à un évènement non
souhaité qui perturbe le fonctionnement normale du système.
Pour appliquer le modèle, nous avons choisit la
centrale thermique d'Oyomabang, qui est une centrale d'appoint et de secours ;
dont l'amélioration de la réactivité permettrait d'agir
rapidement, non seulement pour améliorer les paramètres du RIS
(tension, etc..), mais aussi pour alimenter les secteurs prioritaires de la
capitale en courant électrique, en cas de black- out total.
La démarche adoptée pour le conduire ce travail
est la suivante :
> Présenter les systèmes industriels de
façon générale,
> Faire une présentation de la
réactivité des systèmes industriels
> Présenter le fonctionnement de la centrale, pour
identifier sa hiérarchisation et les acteurs qui entrent en jeux dans le
processus de traitement des Evènements Non Souhaités et de prises
de décisions.
> Identifier le mode de traitement des
évènements non souhaités, qui perturbent la production
d'électricité,
> Définir les paramètres du modèle
> Evaluer le temps de réaction
> Réduire le temps de réaction par l'algorithme
proposé
> mettre sur pied un système de
réactivité qui doit mettre en oeuvre les techniques qui assurent
une meilleure réactivité et exploiter les retours
d'expériences dans le but d'une amélioration continue de la
réactivité.
Nos travaux nous permettent de gagner 5 (cinq)
minutes en traitement des Evènements Non Souhaités qui
n'interrompt pas la production et 30 (trente) minutes sur le
traitement des incidences (celles qui interrompt la production) ; Sur une
durée de traitement qui oscille entre 120 et 180
minutes en moyenne.
Mots clés : temps de
réaction, temps d'attentes, Evènement Non Souhaité,
Système
Industriel.
Modelisation du temps de reaction d'un systeme industriel :
Application aux centrales thermiques d'OYOMABANG I et II .
ABSTRACT
The work focuses on modeling the reaction time of an
industrial system. This is, to establish the best reaction techniques for
industrial systems as a result of unwanted event that disrupts the normal
functioning of the system.
To apply the model we chose the thermal power plant
Oyomabang, which is a standby and rescue, including improving the reactivity
would act quickly, not only to improve the RIS settings (voltage, etc. ..), but
also to feed the priority sectors of the capital in electricity, in case of
blackout.
The approach for conducting this work is as follows:
> Introduce the industry in general
> Making a presentation on the reactivity of industrial
systems
> Present the operation of the plant to identify its
hierarchical and actors that come into play in the process of undesirable event
and decision making.
> Identify the method of treatment for unwanted events that
disrupt the production of electricity,
> Define the model parameters
> Assess the reaction time
> Reduce response time by the algorithm
> Setting up a system of reactivity should implement
techniques that provide improved responsiveness and use the feedback with the
aim of continuous improvement in responsiveness.
Our work allows us to win 5 (five) minutes of
treatment undesirable event that does not interrupt production and 30
(thirty) minutes on the treatment effects (those that interrupt the
production), on the duration of treatment varies between 120 and 180
minutes on average.
Keywords: reaction time, waiting
time, undesirable event, Industrial Systems.
Modelisation du temps de reaction d'un systeme industriel :
Application aux centrales thermiques d'OYOMABANG I et II .
LISTE DES FIGURES
Figure 1 : organigramme d'EDC 13
Figure 2 : organigramme de la direction du projet Lom
Pangar. 15
Figure 3 : Structure centralisée 19
Figure 4 : structure hiérarchisée
20
Figure 5 : Structure coordonnée 21
Figure 6 : Structure distribuée 21
Figure 7 : Structure décentralisée
21
Figure 8 : Structure distribuée supervisée
22
Figure 9 : le système de pilotage et le
système piloté 24
Figure 10 : niveaux de planifications. 24
Figure 11 : Exemple de grille GRAI 25
Figure 12 : caractérisation temporelle d'un niveau
26
Figure 13 : Classifications des évènements
potentiels 29
Figure 14 : Le transfert `réfléchi-reflexe'
32
Figure 15 : Déploiement de la
réactivité industrielle 33
Figure 16 : Décomposition du temps de
réaction 35
Figure 17 : procédure de réaction sur trois
niveaux 36
Figure 18 : positions relatives possibles entre tO et Xm
(o) sur un niveau m 39
Figure 19 : objectif de la modélisation
39
Figure 20 : Grafcet de traitement des erreurs.
41
Figure 21 : les niveaux et leurs sous-processus.
42
Figure 22 : Exemple de circuit sur 3 niveaux (N=2)
43
Figure 23 : durée et changement d'état dans
un sous-processus Spi 45
Figure 24 : Représentation par un réseau de
pétri de la dynamique de traitement 45
Figure 25 : réduction empirique des temps
d'attente sur un niveau 50
Figure 26 : présentation schématique de la
salle des machines 54
Figure 27 : Organigramme de la centrale 56
Figure 28 : différentes formes de maintenance
58
Figure 29 : Les principales catégories d'ENS en
gestion de production et en
maintenance 64
Figure 30 : modélisation du processus de
traitement 69
Figure 31 : couple horizon/période par niveau de
prise de décision 73
Figure 32: diagramme d'Ishikawa 85
Modelisation du temps de reaction d'un systeme industriel :
Application aux centrales thermiques d'OYOMABANG I et II .
LISTE DES TABLEAUX
Tableau 1 : les états de traitement dans les
sous-processus i 41
Tableau 2 : répartition des taches au sein de l'entreprise
61
Tableau 3 : métiers de la maintenance 62
Tableau 4 : traitement des ENS sans interruption de production
70
Tableau 5 : traitement des incidences 71
Tableau 6 : activités dans les sous-processus en
traitement périodique. 75
Tableau 7 : temps d'activité dans les sous-processus en
traitement périodique. 76
Tableau 8 : Paramètres du système 77
Tableau 9 : Données initiales calculées 77
Tableau 10 : configuration initiale 79
Tableau 11 : réduction du temps niveau 0 80
Tableau 12 : réduction du temps niveau 1 80
Tableau 13 : réduction du temps niveau 2 81
Tableau 14 : récapitulatif. 81
Tableau 15 : activités dans les sous-processus en
traitement évènementiel. 83
Tableau 16 : temps d'activité dans les sous-processus en
traitement évènementiel. 84
Tableau 17 : identifications des indicateurs de
réactivités. 86
Tableau 18 : fiche d'identification et de traitements des ENS
87
Tableau 19 : analyse FMD de la centrale. 87
Modelisation du temps de reaction d'un systeme industriel :
Application aux centrales thermiques d'OYOMABANG I et II .
SOMMAIRE
DEDICACE 1
REMERCIEMENTS 2
GLOSSAIRE 3
RESUME 4
ABSTRACT 5
LISTE DES FIGURES 6
LISTE DES TABLEAUX 7
SOMMAIRE 8
INTRODUCTION GENERALE 11 CHAPITRE I : CONTEXTE ET
PROBLEMATIQUE
I.1. L'ENTREPRISE EDC 12
I.1.1. Historique. 12
I.1.2.structure et organisation d'EDC 12
I.1.3. organigramme d'EDC 12
I.1.4. fiche d'identification de l'entreprise. 14
I.1.5. Direction du projet Lom Pangar. 14
I.2.PROBLEMATIQUE 16
CHAPITRE II : PRESENTATION GENERALE DES SYSTEMES
INDUSTRIELS
II.1. ORGANISATION DES SYSTEMES INDUSTRIELS. 17
II.1.1. concepts et définitions
générales . 17
II.1.2. structure des systèmes industriels 19
II.1.3. Structure hiérarchisée 22
II.2 PRESENTATION D'UN MODELE DECISIONNEL : LE MODELE DE DECISION
GRAI (GRAPHE A RESULTATS ET ACTIVITES INTER-RELIES) 24
Modelisation du temps de reaction d'un systeme industriel :
Application aux centrales thermiques d'OYOMABANG I et II .
II.2.1.Généralités sur les niveaux de
planifications. 24
II.2.2. Rappel sur le concept de la méthode GRAI
25
II.2.3. Les niveaux de décision 26
CHAPITRE III : REACTIVITE DES SYSTEMES INDUSTRIELS
III.1. DEFINITIONS 27
III.2.DEFINITIONS ET CARACTERISTIQUES DES FONCTIONS DE DECISIONS
28
III.2.1.fonctions reflexes 28
III.2.2. fonctions réfléchies 28
III.3.PRISE EN COMPTE DES EVENEMENTS PAR LES FONCTIONS DE
DECISION 29
III.4.CLASSIFICATION DES EVENEMENTS POTENTIELS 29
III.5.LA PROBLEMATIQUE DE LA REACTIVITE DANS LES SYSTEMES
INDUSTRIELS 30
III.6.ELABORATION D'UN REFLEXE : LE TRANSFERT REFLECHI-REFLEXE
31
III.7.MISE EN OEUVRE DE LA REACTIVITE INDUSTRIELLE PAR UNE
DEMARCHE DE PILOTAGE 32
CHAPITRE IV : MODELISATION DU TEMPS DE REACTION D'UN
SYSTEME HIERARCHISE
IV.1 DEFINITION DU TEMPS DE REACTION. 34
IV.2 PRESENTATION DES MODELES DE TEMPS DE REACTION EXISTANT.
34
IV.2.1. Décomposition du temps de réaction.
35
IV.2.2. Modélisation du processus de traitement.
36
IV.2.3. Évaluation du temps de réaction d'un
Niveau : Dn 36
IV.2.4. Expressions des valeurs minimales
(Dnmin ) et maximales
(Dnmax) de Dn 37
IV. 3. EXPRESSION DU MODELE ADAPTE. 38
IV.3.1. procédure de traitement de l'ENS. 38
IV.3.2. hypothèses d'étude 38
IV.3.3. objectifs 39
IV.3.4.processus de traitement d'un ENS 40
IV.3.5.modélisation du processus. 44
IV.3.5.1. définition des paramètres 45
IV.3.5.1.1. Paramètres du processus 44
IV.3.6. Modélisation de la dynamique du traitement
dans un sous-processus. 45
IV.4. ÉVALUATION DU TEMPS DE REACTION. 47
IV.4.1. détermination de la date de sortie de
l'évènement du sous-processus 47
IV.4.2. Généralisation à l'ensemble du
processus. 48
Modelisation du temps de reaction d'un systeme industriel :
Application aux centrales thermiques d'OYOMABANG I et II .
IV.5. EXPRESSION DU TEMPS DE REACTION DU SYSTEME DN. 49
IV.6. ESSAI DE MINIMALISATION DU TEMPS DE REACTION 49
IV.6.1. Évaluation des temps d'attentes dans le
processus. 49
IV.6.2. Approche empirique de réduction des temps
d'attentes 50
IV.7. EXPRESSION DU TEMPS DE REACTION DU SYSTEME EN CONDUITE
EVENEMENTIELLE : Dn 52
CHAPITRE V : APPLICATIONS AUX CENTRALES THERMIQUES
D'OYOMABANG I ET II
V.1.PRISE EN MAIN DE LA CENTRALE. 53
V.1.1.fonctionnement, équipements et structure.
53
V.1.2.Maintenance 57
V.2.MODELISATION DES TEMPS D'ATTENTES SUITE A UN EVENEMENT NON
SOUHAITE (ENS). 63
V.2.1. définition et traitements des
évènements non souhaités (ENS). 63
v.2.2.modélisation du processus. 68
V.2.3. modélisation de la dynamique de traitement des
ENS. 69
V.2. 4.évaluation du temps de réaction.
74
V.2.5.expression du temps de réaction du
système. 79
V.3.OPTIMISATION DES TEMPS D'ATTENTE SUITE A UN EVENEMENT NON
SOUHAITE (ENS). 79
V.3.1.Evaluation des temps d'attentes dans le processus.
79
V.3.2 .Application de l'algorithme de réduction des
temps d'attente. 79
V.3.3. Interprétation des résultats. 81
V.4. TRAITEMENT EVENEMENTIEL. 82
V.4.1. Suppression des temps d'attentes. 82
V.4.2. Ajustement des temps des différentes
étapes. 82
V.5.IMPLEMENTATION DE LA REACTIVITE AUX CENTRALES THERMIQUES
D'OYOMABANG I ET II. 84
V.5.1. analyses des causes de non réactivité et
des leviers d'actions 84
V.5.2. amélioration de la réactivité
86
CONCLUSION GENERALE 89
BIBLIOGRAPHIE 90
ANNEXE : APPLICATION SOUS EXCEL 92
Modelisation du temps de reaction d'un systeme industriel :
Application aux centrales thermiques d'OYOMABANG I et II .
INTRODUCTION GENERALE
EDC, entreprise crée par décret du
président de la république le 29 Novembre 2006, pour la promotion
du secteur d'électricité au Cameroun, est engagé dans la
réalisation des centrales thermiques dans les zones à fortes
demande d'électricité du RIS (programme thermique
d'urgence) et la réalisation de l'usine de
pied de Lom Pangar ; doit s'assurer que ces dernières,
soient promptes à réagir à un évènement qui
viendrait perturber la production.
Les entreprises jusqu'à lors ne possédant
presque pas de méthodes de réactivité, ne pouvaient que
compter sur l'expérience, les méthodes heuristiques, le sens des
responsabilités et la conscience professionnelle de ses agents pour
garantir une réaction prompte suite aux évènements
perturbateurs. Il est donc important de leur proposer une méthode
élaborer (construite) d'évaluation, d'implémentation et
d'amélioration de la réactivité.
Ceci étant, le présent mémoire propose
une modélisation en vue de l'optimisation (diminution) du temps de
réaction des entreprises faces aux évènements
perturbateurs, et s'articule en 5 chapitres :
> Un premier chapitre est consacré au contexte et
à la problématique, où il sera question de situer le cadre
dans lequel l'étude est faite, mais aussi ressortir clairement les
préoccupations qui doivent trouver solutions dans la suite du
travail.
> Un deuxième chapitre qui portera sur la
présentation des systèmes industriels en général
> Un troisième chapitre qui présentera la
réactivité des systèmes industriels
> Un quatrième chapitre qui présentera la
modélisation proposée
> En fin un cinquième chapitre qui sera
consacré à l'application aux centrales thermiques d'OYOMABANG I
et II ; dont la finalité sera de faire des propositions pour
l'amélioration de la réactivité en tenant compte de la
modélisation faite.
Modelisation du temps de reaction d'un systeme industriel :
Application aux centrales thermiques d'OYOMABANG I et II .
CHAPITRE I : CONTEXTE ET PROBLEMATIQUE
I.1. L'entreprise EDC
I.1.1. Historique.
Créée par décret du président de
la République le 29 Novembre 2006 EDC (Electricity Development
Corporation), est une société chargée de la gestion du
patrimoine publique et de la promotion des investissements dans le secteur de
l'électricité au Cameroun. Cette structure, dont le capital est
détenu majoritairement par l'État, a la charge de construire et
de gérer toutes les infrastructures nécessaires au
développement du secteur de l'énergie au Cameroun. En outre, il
revient à EDC d'accroître l'offre d'énergie
électrique en direction des entreprises et des ménages
conformément aux engagements du chef de l'État. C'est aussi EDC
qui doit assurer la gestion et la régulation des fleuves du bassin; afin
de maintenir le nécessaire équilibre entre les divers
opérateurs intervenant dans le secteur de la production de
l'énergie électrique. Le premier grand défi d'EDC est la
mobilisation des financements nécessaires pour la construction du
barrage de retenu de Lom Pangar (projet hydroélectrique qui inclut un
barrage de 50 mètres de haut, une retenue de 610 km2 et une usine
hydroélectrique produisant environ 30 MW).
I.1.2.Structure et organisation d'EDC
EDC dispose d'une organisation de type hiérarchique et
fonctionne grâce à un conseil d'administration, une direction
générale et trois (03) directions centrales, à savoir :
> Une Direction de développement des projets et
exploration
> Une Direction de projet Lom Pangar
> Une Direction Administrative et financière
A la tête de chaque direction, se trouve un directeur
aidé dans sa mission par une équipe constituée de sous-
directeurs, cadres, d'agents de maîtrise et employés.
La direction de projet Lom Pangar constitue notre cadre d'accueil
au sein de cette structure.
I.1.3. Organigramme d'EDC
L'organigramme de l'entreprise est représenté
ci-contre :
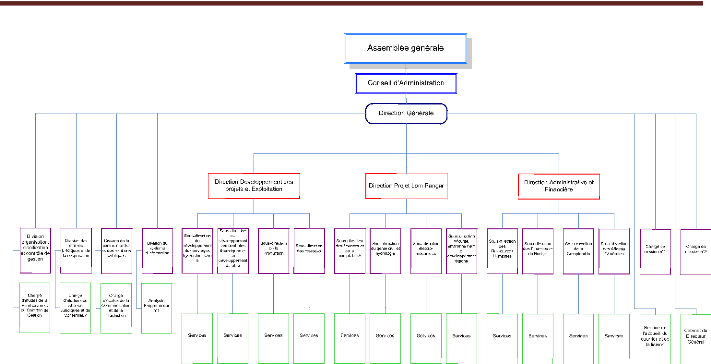
Figure 1 : organigramme d'EDC
Modelisation du temps de reaction d'un systeme industriel :
Application aux centrales thermiques d'OYOMABANG I et II .
I.1.4. fiche d'identification de l'entreprise.
Raison sociale
|
Electricity Development Corporation
|
Siège social
|
Yaoundé (Cameroun)
|
Capital
|
5 000 000 000 F CFA
|
Année de création
|
2006
|
Statut juridique
|
Société à capital public avec
Conseil d'Administration
|
Directeur général
|
Dr. Théodore NSANGOU
|
Adresse
|
BP : 15 111 Yaoundé-Cameroun
|
Téléphone
|
(237) 22 23 19 30 (237) 22 23 10 89
|
Fax
|
(237) 22 23 11 13
|
Site Internet
|
www.edc-cameroon.com
|
|
Adresse email
|
info@edc-cameroon.com
|
|
Secteurs d'activité
|
Électricité
|
Logo
|
|
|
I.1.5. Direction du projet Lom Pangar.
La direction du projet Lom Pangar, est en charge de
développer le projet d'aménagement hydroélectrique de Lom
Pangar sur le Lom dans la région de l'Est du Cameroun. Le projet
d'aménagement hydroélectrique de Lom Pangar a pour objectif la
création d'une retenue d'eau de 6 Milliards de m3 en amont du barrage
pour permettre :
· d'augmenter le débit garanti disponible en
période d'étiage aux usines hydroélectriques
situées en aval (Song loulou, Edéa, et conditionne la
construction de Nachtigal);
· de produire de l'énergie électrique par
l'usine de pied qui sera évacuée vers Bertoua par une ligne de 90
kV.
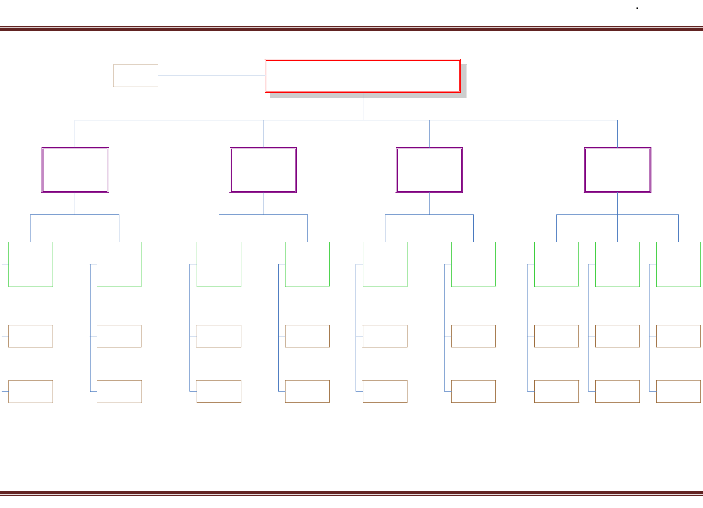
Modélisation du temps de reaction d'un systime industriel
: Application aux centrales thermiques d'OYOMABANG I et II
Secrétaire de Direction
Directeur Projet Lom Pangar
Chef Service Amenagement Genie Civil
Chef de bureau
n°1
Chef de bureau
n°2
Chef Service Hydrologie
Chef de bureau
n°1
Chef de bureau
n°2
Sous Directeur Sécurité, Environnement
et développement egional
Chef Service S~curit~
Chef de bureau
n°1
Chef de bureau
n°2
Chef Service Environnement
Chef de bureau
n°1
Chef de bureau
n°2
Chef Service Communication Communautaire
et Développement egional
Chef de bureau
n°1
Chef de bureau
n°2
Figure 2 : organigramme de la direction du projet Lom
Pangar.
Redige et soutenu par : BI55O NTYAM 5imon Alex Page 15
Chef Service Suivi des Financements
Chef Service Suivi des contrats et Assurances
Chef de bureau
n°1
Chef de bureau
n°1
Chef de bureau
n°2
Chef de bureau
n°2
Sous Directeur Financier
Sous Directeur Genie Civil et Hydrologie
Sous Directeur Electromecanique
Chef Service Amenagement Centrales
Chef Service Amenagement éseaux Electriques
Chef de bureau
n°1
Chef de bureau
n°1
Chef de bureau
n°2
Chef de bureau
n°2
Modelisation du temps de reaction d'un systeme industriel :
Application aux centrales thermiques d'OYOMABANG I et II .
I.2.problématique
L'électricité est devenu un élément
essentiel à notre bien être. Son indisponibilité peut avoir
des conséquences graves, surtout quand elle concerne des secteurs
prioritaires tels que :
> Les hôpitaux
> Les ministères
> Le quartier général des armés
> La présidence de la république.
> Etc....
En d'autres termes, le désarroi des consommateurs
d'électricité est d'autant plus grand quand
l'électricité tarde à venir. Il est donc un challenge pour
les entreprises qui produisent l'électricité de la
rétablir rapidement en cas de coupure provoquée par un ENS. EDC
dans le cadre du programme thermique d'urgence et du projet de la mise sur pied
de l'usine de production de 30 MW d'électricité à Lom
Pangar doit concevoir des systèmes qui soient capable de réagir
avec sérénité et dans un délai très court
face à un incident qui interrompt la production. Il y a donc une
question centrale à poser : Comment modéliser le temps de
réaction d'une centrale thermique ou hydraulique afin d'assurer une
meilleure réactivité ?
Pour s'assurer de l'efficacité de la
modélisation, nous avons choisi comme modèle d'étude, les
centrales thermiques d'Oyomabang I et II. Cette centrale thermique qui est
située à Yaoundé, joue un rôle très important
dans le système de production d'AES-SONEL ; car c'est une centrale
d'appoint et de secours. L'amélioration de la réactivité
de celle-ci permettrait de maintenir les secteurs prioritaires de la capitale
en éclairage permanent. Ce travail s'avère complexe compte tenu
des différents aspects à prendre en compte tels que les
ressources humaines, les ressources techniques, le système d'information
au sein de la structure. Il est donc primordial de bien définir le cadre
de l'étude, d'établir les objectifs visés ainsi que les
hypothèses qui les soustendent, l'intérêt de l'étude
et la méthodologie adoptée.
Modelisation du temps de reaction d'un systeme industriel :
Application aux centrales thermiques d'OYOMABANG I et II .
CHAPITRE II : PRESENTATION GENERALE DES
SYSTEMES INDUSTRIELS
|
|
II.1. organisation des systèmes industriels.
[002]
II.1.1. concepts et définitions
générales.
II.1.1.1. conduite des systèmes
industriels.
Conduire un système industriel revient à
prendre les décisions (mesures) nécessaires à
l'évolution du système pour atteindre les objectifs fixés,
à savoir développer et livrer un produit ou un service de
qualité, en maîtrisant les ressources et les délais.une
fois le processus lancé , il est question de :
> Corriger en permanence l'écart par rapport aux
objectifs ;
> Modifier éventuellement la trajectoire, lorsque
l'environnement extérieur change et montre que les objectifs
fixés au départ ne peuvent plus être maintenu.
Les décisions de modifications des objectifs sont prises
en fonctions des performances du système, de l'influence et de
l'état de l'environnement.
II.1.1.2. système décisionnels dans
les systèmes industriels.
La décision c'est la restriction d'un domaine de
valeur d'une variable, le tri sur plusieurs domaines ou valeurs, ou bien le
classement sur plusieurs valeurs ou domaines. En d'autres termes,
décider, c'est choisir entre plusieurs possibilités.
Le système décisionnel requis par le SCM
(supply Chain Management) s'appuie sur un système d'information. Le
système d'information est le support et la mémoire des
transactions des informations. La transaction de
l'information concerne l'acquisition, le transfert, le stockage et l'affichage
des données. Ainsi, des tableaux de bord permettent-ils simplement
d'alimenter un décideur en informations ? Par contre,
l'analyse de l'information est un
élément de l'activité de prise de décision.
Au-delà du système d'information, le système
décisionnel est l'organisation par laquelle le système tout
entier est conduit, définissant les décideurs à tous les
niveaux hiérarchiques et ce sur le court, moyen et long terme.
Modelisation du temps de reaction d'un systeme industriel :
Application aux centrales thermiques d'OYOMABANG I et II .
Les décideurs doivent aujourd'hui prendre en compte un
plus grand nombre de paramètres afin d'optimiser leur décision et
ainsi améliorer leur performance industrielle.
II.1.1.3. Agrégation de
données
Le concept d'agrégation (par opposition au
détail) est généralement défini comme une forme
d'idée par laquelle un ensemble de données présentant des
caractéristiques communes peut être remplacé par une
donnée ou une variable agrégée. La nécessité
d'agréer les données s'impose lorsqu'on a une multitude de
données hétérogènes et que le détail n'est
pas important pour la prise de décision.
II.1.1.4. Niveau
décisionnel
Le concept d'agrégation présenté
précédemment permet de proposer des structures basées sur
une décomposition en niveaux décisionnels. A chaque niveau de
décision correspond un degré d'agrégation des
données et des variables de décisions. Plus le niveau est
élevé, plus le degré d'agrégation est
élevé.
Les niveaux de décision permettent une
décomposition progressive du problème de gestion .Ce qui limite
le volume et la variété des données à chaque
niveau, diminuant ainsi la complexité du problème sur le
niveau.
II.1.1.5. Cohérence et Robustesse.
Une structure décisionnelle multi-niveau ne peut
fonctionner d'une façon satisfaisante que si d'une part, la
décision élaborée par le niveau supérieur assure
l'existence des solutions au niveau inférieur. D'autre part, toute
solution élaborée au niveau inférieure doit satisfaire la
décision du niveau supérieur. Cette analyse a permit la
définition des concepts de robustesse et de cohérence relatifs
respectivement aux décisions prises aux niveaux supérieure et
inférieur.
Cohérence et robustesse sont deux notions duales qui
sont associés à un niveau décisionnel relativement
à ses niveaux supérieur et inférieur. La cohérence
correspond à la capacité d'un niveau à prendre des
décisions respectant les contraintes imposées par le niveau
supérieur. La robustesse quant à elle représente la
capacité du niveau à produire des décisions compatibles
avec les contraintes du niveau inférieur.
Modelisation du temps de reaction d'un systeme industriel :
Application aux centrales thermiques d'OYOMABANG I et II .
II.1.2. structure des systèmes
industriels
Il existe différentes structures de systèmes
industriels. Le choix du type à implanter est fonction de la structure
du système opérant et des objectifs poursuivis. Nous avons entre
autres :
> La structure centralisée
> La structure hiérarchisée
> La structure coordonnée
> La structure distribuée
> La structure décentralisée
> La structure distribuée supervisée
II.1.2.1.Structure centralisée
C'est un type de structure très classique. Elle se
caractérise par un pilotage localisé au sein d'une ressource
unique qui supervise la production et gère seule, en temps réel,
les événements qui surviennent tout au long de la production
(fig.1). Elle est plus adaptée pour les petits et moyens
systèmes. L'avantage est que l'unité de décision a une vue
complète sur tout le système et il n'y a pas de conflits
décisionnels. Par contre, elle est vulnérable dans la mesure
où un dysfonctionnement de l'unité de décision peut
facilement entrainer la paralysie de tout le système.
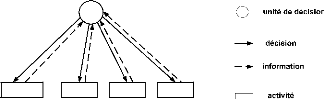
Figure 3 : Structure centralisée
II.1.2.2 Structure hiérarchisée
Chaque niveau coordonne les unités de pilotage du
niveau inférieur, et ce jusqu'au niveau le plus bas. La relation,
à un niveau donné, est donc de dépendance vis à vis
du niveau supérieur et de dominance vis à vis du niveau
inférieur. Chaque décision est élaborée au niveau
où un
Modelisation du temps de reaction d'un systeme industriel :
Application aux centrales thermiques d'OYOMABANG I et II
problème est détecté. Les niveaux
inférieurs traitent cette décision comme une contrainte et
transmettent en retour une information de suivi au niveau supérieur. La
gestion temps réel concerne les niveaux atelier, cellules, postes de
travail et automates.
Une telle structure a pour avantage la décomposition
des objectifs généraux en une succession de sous-objectifs de
dimension et de complexité acceptable. Par contre, on y note la
difficulté d'agréger les informations souvent
hétérogènes venant des branches différentes et
surtout le manque de communication entre les différentes unités
de décision, en particuliers entre celles d'un même niveau
dépendant d'une même unité de décision du niveau
supérieur. Par ailleurs, chaque unité de décision a une
vue partielle du système. Par conséquent, il est difficile
d'obtenir un optimum global d'un problème donné. Car, on ne
pourra optimiser que localement mais la somme des optimums locaux ne donnera
certainement pas l'optimum global recherché.
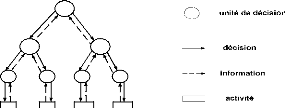
Figure 4 : structure
hiérarchisée
II.1.2.3 Structure coordonnée
Elle correspond à un ensemble de structures
hiérarchisées où une coopération est possible au
sein d'un même niveau. Ces structures accroissent la capacité de
décision au sein de chacun de ces niveaux. On accroit ainsi l'autonomie
et la capacité de décision au sein de chaque niveau. Ce qui aide
à la résolution locale des problèmes décisionnels
sans se référer systématiquement aux niveaux
supérieurs. On a donc un gain de réactivité. La
concrétisation de cette coopération peut se faire par exemple
à travers un simple échange d'informations entre acteurs d'un
même niveau.
Modelisation du temps de reaction d'un systeme industriel :
Application aux centrales thermiques d'OYOMABANG I et II .
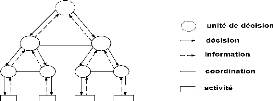
Figure 5 : Structure coordonnée
II.1.2.4 Structure distribuée
Elle est semblable aux deux précédentes et a
pour avantage de résoudre le problème de communication entre les
différentes unités de décision des différents
niveaux. Ainsi, tous les centres de décisions ont à leur
disposition des informations provenant des autres unités. Toutes les
unités de décisions ont une vision globale de l'état de
tout le système. Elles peuvent donc prendre leurs décisions avec
peu de risques de contradiction avec celles prises par d'autres unités
de décision.
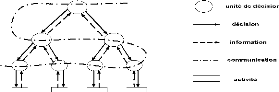
Figure 6 : Structure distribuée
II.1.2.5 Structure décentralisée
Ici, aucune unité de décision ne domine sur les
autres, car toutes sont au même niveau hiérarchique. Elles doivent
donc s'auto organiser pour assurer les taches globalement cohérentes.
Toute moindre défaillance dans la circulation de l'information peut
être fatale à tout le système. La communication a donc une
place très importante dans ce type de structure.
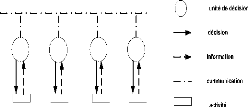
Figure 7 : Structure
décentralisée
Modelisation du temps de reaction d'un systeme industriel :
Application aux centrales thermiques d'OYOMABANG I et II .
II.1.2.6 Structure distribuée
supervisée
Ce type de structure est un compromis entre la structure
décentralisée et la structure distribuée. Elle se
caractérise par un ensemble d'unités de décision
coopérant entre elles sous le contrôle d'une même
unité de décision superviseur. Celle-ci possède ainsi une
vision plus globale du processus de production et à pour rôle
d'imposer, de conseiller ou de modifier une décision afin de respecter
un objectif global. Les unités supervisées se coordonnent pour
mettre en oeuvre les décisions fixées par le superviseur. Cette
étude présente une performance plus élevée en
termes de flexibilité et de réactivité. En effet, chaque
unité est à mesure de communiquer et coopérer en cas de
perturbation et est capable de remettre en cause la décision
initiale.
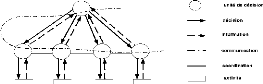
Figure 8 : Structure distribuée
supervisée
II.1.3. Structure hiérarchisée
Le plus souvent, l'architecture décisionnelle d'une
entreprise est divisée en trois niveaux : stratégique, tactique
et opérationnel, correspondant respectivement à des horizons
à long, moyen et court terme. La structure hiérarchisée
est organisée en niveau avec une certaine hiérarchie. Au sommet,
le niveau le plus élevé, qui définit les objectifs
généraux et la base constituée des activités
exécutoire de production. Quelques problématiques et travaux
rattachés à chacun des niveaux décisionnels sont
présentés ci-dessous :
II.1.3.1. Niveau stratégique
Ce niveau, regroupe toutes les décisions
stratégiques de l'entreprise. Ces décisions, prises par
la direction générale, sont des orientations sur le long terme
(de 6 mois à plusieurs années), comme, par exemple, la
recherche de nouveaux partenaires industriels, la sélection des
fournisseurs et sous-traitants, mais aussi les décisions d'ouverture
ou de fermeture de certains sites de production ou leur
délocalisation, l'affectation d'une nouvelle zone de marché
à un centre de distribution (entrepôt), le développement
d'un nouveau produit, la configuration de l'usine, son
Modelisation du temps de reaction d'un systeme industriel :
Application aux centrales thermiques d'OYOMABANG I et II
mode de fonctionnement, ainsi que les objectifs financiers
à atteindre (volume de production, nouveaux marchés, ...).
II.1.3.2. Niveau tactique
Le niveau décisionnel tactique s'intéresse aux
décisions à moyen et long terme (de quelques semaines à
quelques mois) qui devront être mises en application pour déployer
la stratégie décidée par l'entreprise. Les
décisions de ce niveau sont prises par les cadres de la production et
les chefs d'atelier. Elles portent sur les problèmes liés
à la gestion des ressources de l'entreprise, en particulier la
planification des activités sur ces
ressources.il est à noter que
ce niveau tactique a été très peu étudié par
les industriels et les scientifiques.
II.1.3.3 Niveau
opérationnel
En ce qui concerne le niveau opérationnel, les
décisions ont une portée plus limitée dans l'espace et
dans le temps (décisions sur la journée ou sur la semaine). Elles
sont prises par les chefs d'équipe et éventuellement les
opérateurs de production. A ce niveau, les décisions tactiques
génèrent un plan détaillé de production applicable
au niveau d'un atelier ou même d'un poste de travail.
Ces trois catégories de décisions
diffèrent non seulement par leur horizon, mais aussi par le niveau de
responsabilité des décideurs et par le niveau d'agrégation
des informations utilisées. On peut aussi différencier ces trois
catégories par l'incertitude régnant sur les données
manipulées et en particulier sur les commandes. A un niveau
stratégique, les commandes sont gérées essentiellement
sous forme de prévisions, obtenues par des calculs statistiques et des
études de marchés ; par nature, elles ne sont pas sûres et
peuvent être réévaluées à chaque remise en
cause des décisions à long terme. Les décisions tactiques
sont prises à partir de commandes fermes et de prévisions. Elles
sont entachées de moins d'incertitude, mais doivent aussi être
régulièrement remises en cause. A un niveau opérationnel,
on travaille sur des données fermes en grande majorité, mais
l'incertitude ne disparaît pas totalement (commandes urgentes,
annulées, etc.), même si elle est rarement prise en compte.
L'ensemble du système de décision et du
système d'information constitue le système de pilotage ou
conduite des systèmes industriels. Le système de
production se réduit ainsi à deux systèmes : le
système de pilotage et le système piloté.
Modelisation du temps de reaction d'un systeme industriel :
Application aux centrales thermiques d'OYOMABANG I et II .
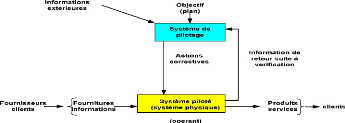
Figure 9 : le système de pilotage et le
système piloté
II.2 présentation d'un modèle
décisionnel : Le modèle de décision GRAI (Graphe
à Résultats et Activités Inter-reliés) [009].
II.2.1.Généralités sur les niveaux de
planifications.
En se référant à l'approche
systémique des organisations, il est possible de décomposer le
système de production (figure 10) en trois sous-systèmes : le
sous-système physique, le soussystème d'information, le
sous-système décisionnel. Il est possible de décrire les
décisions pour chaque niveau de décomposition temporel.
Au niveau opérationnel, le système de gestion de
production est représenté par la coordination entre le
sous-système de décision et le sous-système d'information.
Les différents types d'aléas présents au sein d'une
unité de production, notamment les perturbations liées à
la production et celles liées à l'ordonnancement, font que le
sous-système de décision doit réagir rapidement.
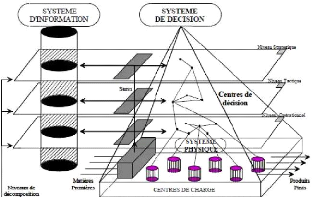
Figure 10 : niveaux de planifications.
[009]
Modelisation du temps de reaction d'un systeme industriel :
Application aux centrales thermiques d'OYOMABANG I et II .
II.2.2. Rappel sur le concept de la méthode GRAI
Cette méthode s'attache tout particulièrement
à mettre en évidence le système décisionnel de
l'entreprise. Elle définit un centre de décision comme
étant le croisement d'une fonction et d'un couple
horizon-périodicité de la prise de décision. Comme le
montre la figure 10, les centres de décision sont positionnés au
sein d'une grille GRAI. Chaque cadre de décision précise les
performances attendues de cette décision (les objectifs), les
éléments sur lesquels on peut agir (variables de
décision), les limites de ces variables (contraintes) et une aide au
choix parmi les actions possibles (critères). La grille GRAI permet de
différencier les liaisons dites décisionnelles (cadre de
décision) des liaisons dites informationnelles. Cette grille offre
finalement, par une syntaxe simple, une confrontation entre un point de vue
fonctionnel et informationnel (colonnes) et des niveaux de prise de
décision (lignes). Il existe deux types de grilles : la grille
fonctionnelle dans laquelle les fonctions indiquées représentent
les fonctions de l'entreprise et la grille de conduite dans laquelle les
fonctions indiquées représentent les fonctions
élémentaires de conduite (planifier, gérer les produits ou
les ressources). Pour compléter ce descriptif, le fonctionnement de
chaque centre de décision est détaillé par
l'intermédiaire d'un réseau. La principale caractéristique
de ce réseau réside dans la différenciation des
activités d'exécution de celles de décision. Le formalisme
du réseau GRAI insiste sur les éléments
déclencheurs, supports et résultats qui caractérisent les
activités d'exécution ou de décision.
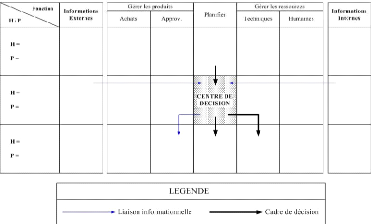
Figure 11 : Exemple de grille GRAI
Modelisation du temps de reaction d'un systeme industriel :
Application aux centrales thermiques d'OYOMABANG I et II .
Cette méthode nous permettra de modéliser le
processus de prise de décision dans l'application aux centrales
thermiques d'Oyomabang I et II.
II.2.3. Les niveaux de
décision
Le modèle décisionnel GRAI est un modèle
hiérarchique multi niveaux. Grâce au principe d'agrégation
d'informations, les niveaux les plus hauts vont pouvoir appréhender le
système dans sa globalité et veiller ainsi à ce qu'il
atteigne ses objectifs globaux. Les niveaux les plus bas quant à eux ont
besoin des informations détaillées pour que le système
soit opérationnel. Un niveau est caractérisé par deux
paramètres temporels qui sont : l'horizon et la
période. L'horizon d'une décision est
la durée sur laquelle le système est engagé par la
décision, c'est-à-dire le laps de temps sur lequel on veut
prévoir pour s'organiser. Néanmoins, étant donné
que d'inévitables perturbations vont éloigner les
résultats des objectifs recherchés, l'horizon est divisé
en périodes au terme desquelles la décision peut
être reconsidérée.
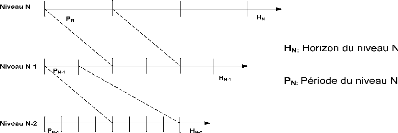
Figure 12 : caractérisation temporelle d'un
niveau
Modelisation du temps de reaction d'un systeme industriel :
Application aux centrales thermiques d'OYOMABANG I et II .
CHAPITRE III : REACTIVITE DES SYSTEMES
INDUSTRIELS
|
Une exigence importante du client est de recevoir sa livraison
dans les délais impartis et ce quel que soit le carnet de commande
(variable). Satisfaire une telle exigence impose au système industriel
d'être réactif, c'est-à-dire capable de répondre
rapidement, techniquement et économiquement à un changement
(fabrication multi-produit, introduction d'une commande urgente, modification
d'une norme, maintenance, etc.) ou à un aléa. Ces aléas
peuvent provenir soit du système de production (défauts
d'alimentation, défauts de réalisations d'une tâche, pannes
des machines, rebuts) soit de son environnement (approvisionnements des
matières premières).
III.1. définitions
La réactivité d'un système industriel est
définie comme l'aptitude à répondre (réagir) dans
un temps requis aux changements de son environnement interne ou externe
(aléa, situation nouvelle, perturbation, sollicitation, ...) par rapport
au régime (fonctionnement) permanent (stable) [004]. La
réactivité d'un système industriel impose une vision
dynamique des événements qui se passent dans le système.
Afin d'assurer cette propriété de réactivité du
système industriel, trois (03) fonctions annexes s'avèrent
nécessaires :
ü une fonction d'observation qui
collecte les variables nécessaires au suivi, afin de connaître
l'état courant du système (disponibilité et état
des produits, disponibilité et état des moyens de production)
;
ü une fonction de surveillance qui
détecte (suite au résultat d'une observation) et
interprète les écarts et les changements entre le plan
prévisionnel et le plan courant par anticipation;
ü une fonction de correction qui tente
à tout instant de corriger les écarts entre ces plans, ce qui
implique un ordonnancement dynamique.
Modelisation du temps de reaction d'un systeme industriel :
Application aux centrales thermiques d'OYOMABANG I et II .
III.2.définitions et caractéristiques des
fonctions de décisions
III.2.1.fonctions reflexes
On défini, le "réflexe" comme une
réponse préétablie immédiate à un
événement prévu qui survient dans un contexte parfaitement
déterminé [004].
La notion de réflexe appliquée à un
robot désigne un processus qui choisit la réponse
appropriée à un événement stimulus
identifié. Ce processus est de type algorithmique et est bâti sur
la connaissance du passé et du présent : les algorithmes
réflexes utilisent des informations sur les résultats de
l'application des consignes précédentes et sur la situation
courante.
Les fonctions réflexes de la décision
gèrent les réflexes du système commandé. Leur
rôle consiste à :
ü coordonner les mouvements du robot ;
ü exécuter les stratégies
élaborées par les fonctions réfléchies ;
ü réagir le plus rapidement possible à une
variation du robot ou de son environnement.
III.2.2. fonctions réfléchies
Les fonctions réfléchies de la décision
adaptent les modèles génériques disponibles aux objectifs
spécifiques que le système commandé doit
réaliser.
On défini, les fonctions réfléchies comme
des processus de projection de la connaissance du système sur des cas
particuliers soumis par le système de programmation
[004].
Les fonctions réfléchies utilisent des
traitements informatiques plus complexes que les traitements réflexes et
qui peuvent notamment relever des modes de raisonnements propres à
l'intelligence artificielle. Elle exploite la connaissance mise à sa
disposition ou acquise pendant son activité :
ü des modèles du système opérant, de
type mathématique (modèles cinématiques, équations
d'état ...) ou heuristique ;
ü des modèles de l'environnement, de type statique
ou dynamique (utilisant les capteurs du système) ;
ü des mécanismes d'élaboration de solutions :
règles de décision, processus d'apprentissage, raisonnements par
analogie ...
Les fonctions réfléchies ont deux rôles.
D'une part, elles sont chargées de répondre aux objectifs
assignés en préparant, organisant et lançant
l'exécution des tâches. D'autre part,
Modelisation du temps de reaction d'un systeme industriel :
Application aux centrales thermiques d'OYOMABANG I et II
elles doivent prendre en compte les informations provenant de
l'environnement pour réagir aux imprévus que les fonctions
réflexes ne savent pas gérer.
III.3.prise en compte des événements par les
fonctions de décision
En analysant la décision des systèmes de
commande du point de vue de la prise en compte des événements qui
surviennent au cours du fonctionnement du système, nous distinguons deux
sortes de décision :
ü au niveau proche du système opérant, la
décision qui a pour but de réagir rapidement aux
événements prévus pour lesquels une réponse est
préparée : le niveau " réflexe " ;
ü au niveau global, la décision qui a pour but de
réagir " intelligemment " aux événements imprévus :
le niveau " réfléchi ".
Il nous est donc apparu nécessaire d'approfondir
l'étude des événements dont le traitement constitue une
grande part des activités de la décision. Nous avons
engagé une réflexion portant sur l'analyse des
événements qui peuvent survenir pendant le fonctionnement d'un
système afin d'aboutir à l'élaboration d'une
classification. Notre objectif est de construire un outil qui permette
d'identifier les événements pour choisir rapidement une
réponse efficace, c'est-à-dire adéquate au problème
éventuellement généré par l'occurrence de l'un
d'eux.
III.4.classification des événements
potentiels
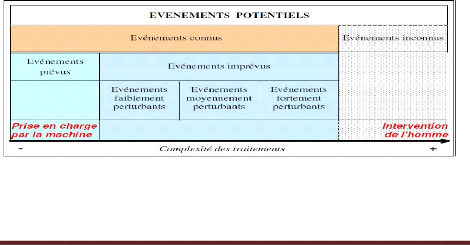
Figure 13 : Classifications des évènements
potentiels [004]
Les événements susceptibles de survenir pendant le
fonctionnement du système sont désignés sous le terme de "
potentiels ". Ils peuvent se classer comme le montre la figure 13.
Modelisation du temps de reaction d'un systeme industriel :
Application aux centrales thermiques d'OYOMABANG I et II .
Un premier niveau d'analyse nous permet de distinguer deux types
d'événements potentiels :
ü Les événements inconnus du
système. Ils sont non répertoriés dans l'ensemble des
connaissances du système. Ils provoquent l'intervention de l'homme qui
est seul capable de résoudre le problème
généré par l'occurrence d'un tel événement.
Les fonctions de décision ne sont donc pas concernées ;
ü Les événements connus du
système. Ils sont répertoriés dans l'ensemble des
connaissances du système. Les fonctions de décision sont
supposées capables de les prendre en charge, soit au niveau
réflexe, soit au niveau réfléchi. Ce sont ces
événements qui font l'objet d'une caractérisation plus
approfondie.
La classe d'événements connus doit être
précisée de manière à identifier quel niveau de
décision les prendra en charge.
Pour cela, nous utilisons la notion d'occurrence des
événements pour les caractériser:
ü si l'occurrence de l'événement est
prévue pendant l'exécution de la tâche, c'est le niveau
réflexe qui prend en charge le traitement de celui-ci en mettant en
oeuvre une réaction préprogrammée.
L'événement est appelé événement
prévu;
ü si l'occurrence de l'événement est
imprévue pendant l'exécution de la tâche, le niveau
réflexe n'est pas capable de prendre en charge le traitement. C'est le
niveau réfléchi qui prend le relais et construit la
réponse à cet événement. L'événement
est appelé événement imprévu.
III.5.la problématique de la
réactivité dans les systèmes industriels
Dans le contexte industriel actuel, les organisations ont
à faire face à la fois à :
1) un nombre croissant de perturbations et d'informations
perturbées qui obligent les systèmes de décision à
élaborer des solutions aux problèmes résultants en
exploitant des informations incertaines, incomplètes, voire
obsolètes au moment de leur utilisation ;
2) une complexification des produits et de leurs processus de
production, qui conduit à une complexification des systèmes
opérants : les moyens matériels (machines et outils) sont de plus
en plus sophistiqués, les moyens techniques (méthodes et
procédés de fabrication) sont de plus en plus compliqués.
Il devient essentiel de développer la conception des moyens
matériels et techniques en parfaite harmonie avec les besoins de la
production.
Face à ces contraintes, la réponse des
organisations se compose de deux axes qui contribuent à
l'amélioration de leur réactivité.
Modelisation du temps de reaction d'un systeme industriel :
Application aux centrales thermiques d'OYOMABANG I et II .
D'une part, pour répondre au point 1, elles s'attachent
à développer la capacité de leurs systèmes de
décision à répondre rapidement et efficacement aux
variations de l'environnement.
D'autre part, pour répondre au point 2, les
organisations tendent à favoriser l'intégration des fonctions de
production et de conception grâce à l'ingénierie
concourante. Leur but est de raccourcir le temps global de mise sur le
marché des produits en réduisant leur temps de
développement.
III.6.élaboration d'un reflexe : le transfert
réfléchi-reflexe
Nous nous intéresserons au fonctionnement de la
décision chez l'homme : il est capable de rendre réflexes des
actions qui nécessitent sa capacité d'attention et de
réflexion quand elles sont exécutées pour les
premières fois. Ce mécanisme lui permet d'alléger ses
activités cognitives au fur et à mesure de son apprentissage.
La génération de stratégie
effectuée par les fonctions réfléchies de la
décision permet de mettre en oeuvre un procédé semblable.
Dès qu'une stratégie est établie et validée par une
exécution satisfaisante, elle est intégrée dans l'ensemble
des connaissances du système de commande. Ce processus améliore
l'efficacité du système. Il s'enrichit d'éléments
de connaissance à chaque nouvelle intervention des fonctions
réfléchies de la décision. Par conséquent, le
niveau réfléchi ne sera plus sollicité pour les cas qu'il
aura déjà résolus. De plus, elle disposera de
connaissances évolutives pour mieux appliquer les différents
modes de raisonnement disponibles.
Supposons que ce processus puisse être exploité
complètement. Au bout d'un certain temps de fonctionnement du
système, la plupart des événements imprévus serait
apparu et aurait provoqué une réaction des fonctions
réfléchies de la décision, qui aurait été
mémorisée. Ces imprévus deviendraient des
événements prévus, c'est à dire reconnus comme
susceptibles de survenir pendant l'exécution de la tâche et pour
lesquels le système de décision disposerait d'une réponse
préétablie.
Ainsi, au cours de la vie du système de commande, le
travail des fonctions réfléchies sera progressivement
transféré vers les fonctions réflexes. Ce processus
accroît la capacité réflexe du système et donc son
efficacité à faire face aux événements. Il s'appuie
sur des mécanismes d'apprentissage tels que l'analogie ou
l'apprentissage par induction.
Modelisation du temps de reaction d'un systeme industriel :
Application aux centrales thermiques d'OYOMABANG I et II .
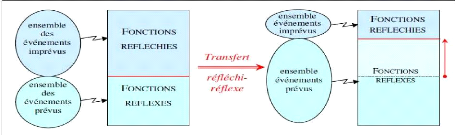
Figure 14 : Le transfert
`réfléchi-reflexe'
III.7.mise en oeuvre de la réactivité
industrielle par une démarche de pilotage Il s'agit des
sept étapes suivantes :
1. formulation d'un objectif global de référence
(ici, la réactivité industrielle) ;
2. déploiement de l'objectif global de
référence sur des processus (processus physiques,
informationnels, et de formation des opératrices) ;
3. analyse des causes de (non) réactivité et des
« leviers d'action » pour les pallier (un diagramme de type Ishikawa
est utilisé) ;
4. définition de plans d'action (ce que nous appelons la
« stabilisation » des processus, « l'amélioration
planifiée » ou « opportuniste ») ;
5. conception d'indicateurs de performance de
réactivité, de tableaux de bord à affichés;
6. conception d'un système d'information associé
;
7. mise en oeuvre d'un groupe de suivi et d'amélioration
de la réactivité.
Cette démarche procède à la fois d'une
logique de contrôle vertical (déploiement de l'objectif de
réactivité industrielle) et horizontal (implication des
différents processus et métiers concourant à l'objectif).
Elle a supposé une action simultanée sur différents
composants du système de production, à savoir :
ü le système de pilotage, avec l'optique
d'améliorer à terme son acuité ;
ü les ressources humaines, en élevant la polyvalence
des opérateurs, donc la flexibilité ;
ü les processus physiques et informationnels, en les
fluidifiants (réimplantation en cellules réactives,
informatisation de l'ordonnancement).
Modelisation du temps de reaction d'un systeme industriel :
Application aux centrales thermiques d'OYOMABANG I et II .
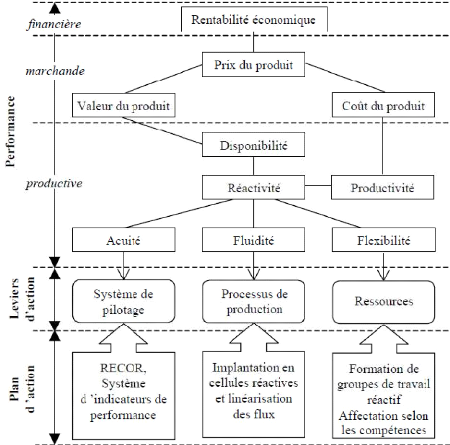
Figure 15 : Déploiement de la
réactivité industrielle [007]
Modelisation du temps de reaction d'un systeme industriel :
Application aux centrales thermiques d'OYOMABANG I et II .
CHAPITRE IV : MODELISATION DU TEMPS DE
REACTION D'UN SYSTEME HIERARCHISE
|
IV.1 définition du temps de
réaction.
Le temps de réaction d'un système industriel par
rapport à un Évènement Non Souhaité (ENS),
représente l'intervalle de temps qui s'écoule entre la date
d'occurrence de l'évènement sur un niveau et la date
d'application de la correction sur le même niveau. Ce temps doit
être le plus petit possible pour garantir une meilleure
réactivité. La réactivité d'un système
d'industriel est définie comme l'aptitude à répondre
(réagir) dans un temps requis aux changements de son environnement
interne ou externe (aléa, situation nouvelle, perturbation,
sollicitation, ...) par rapport au régime (fonctionnement) permanent
(stable).
IV.2 présentation des modèles de temps
de réaction existant. [003]
Cette modélisation qui est basée sur le
modèle GRAI du système industriel, repose sur un certain nombre
d'hypothèse :
> Propagation de l'événement :
l'événement apparait sur un niveau qui, n'arrivant pas à
le traiter localement après une tentative, le répercute au niveau
supérieur. Cette répercussion se répète ainsi de
niveau en niveau jusqu'à celui qui arrive à traiter
l'évènement. Cette phase ascendante (des niveaux bas vers les
niveaux hauts) est appelée phase amont. Elle a un dual : phase aval, qui
correspond à la répercussion de la réaction, du niveau
haut qui l'a élaborée vers le niveau bas qui doit la mettre en
oeuvre ;
> Fonctionnement périodique : la répercussion
d'un niveau à l'autre dans les deux phases amont (pour
l'évènement) et aval (pour la réaction) se fait en fin de
période.
> Existence d'un délai de transmission d'un niveau
à l'autre : la transmission d'un niveau à l'autre de
l'évènement ou de la réaction, selon la phase, n'est pas
instantanée. Il existe un délai de transmission amont et un
délai aval non nul entre deux niveaux consécutifs.
Modelisation du temps de reaction d'un systeme industriel :
Application aux centrales thermiques d'OYOMABANG I et II .
IV.2.1. Décomposition du temps de
réaction.
Pour mieux appréhender les différents temps
composant le temps de réaction ; dans les hypothèses ci-dessus,
on se place dans un cas simple ou un évènement arrivant sur un
niveau k est traité au niveau k+1, soit une répercussion sur deux
niveaux : Les différents temps rencontrés sont :
> Le temps du rendez-vous : c'est-à-dire, le temps
s'écoulant entre la date d'arrivée de l'évènement
ou de la réaction, selon la phase amont ou aval, sur le niveau
considéré et la prochaine fin de période de ce niveau. A
cette fin de période, en phase amont, l'évènement est
traité, si le niveau en est capable, ou alors répercuté au
niveau supérieur, sinon. En phase aval, la réaction est
transmisse au niveau inférieur, si ce n'est pas le niveau d'occurrence
de l'évènement, ou mise en oeuvre, sinon ;
> Le temps (délai) amont : c'est-à-dire le
temps que dure le transfert de l'évènement en phase amont (entre
les niveaux k et k+1) ;
> Le temps (délai) d'élaboration de a
réaction : c'est le temps mis pour élaborer la réaction au
niveau apte à traiter l'évènement ;
> Le temps aval : c'est le temps que dure la transmission de
la réaction, en phase aval, (entre les niveaux k+1 et k).
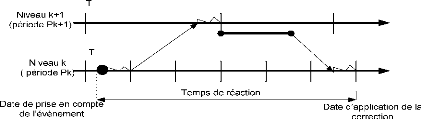

Figure 16 : Décomposition du temps de
réaction
Modelisation du temps de reaction d'un systeme industriel :
Application aux centrales thermiques d'OYOMABANG I et II .
IV.2.2. Modélisation du processus de
traitement.
Dans le cas ou le traitement de l'évènement
nécessite une succession de répercussion sur plusieurs niveaux,
la procédure étant la même entre deux niveaux
consécutifs, la schématisation du processus est obtenue en
superposant autant de fois qu'il le faut le modèle
précédent.
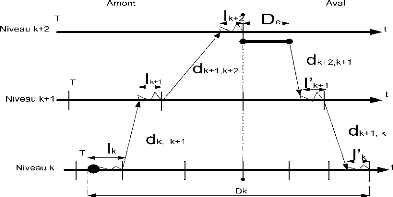
Figure 17 : procédure de réaction sur
trois niveaux
IV.2.3. Évaluation du temps de
réaction d'un Niveau : D.,
Considérons un ENS survenu au niveau n, quelconque, et
qui est finalement traité par un certain niveau m. La propagation dans
les deux phases amont et aval s'est donc déroulé entre ces deux
niveaux.
Pour un niveau quelconque k, entre les niveaux n et m, ayant
reçu l'évènement, on pose :
ü ~k: temps du au rendez vous au niveau k
en phase amont (pour l'évènement).
ü IIk: temps du au rendez vous
au niveau k en phase aval (pour la réaction).
· ( dk,k+i: temps
amont entre les niveaux k et k+1
· ( dk+i,k : temps
aval entre les niveaux k+1 et k
ü De: temps
d'élaboration de la réaction au niveau m, apte à traiter
l'évènement ;
ü Pk : temps limite de transmission ;
Modelisation du temps de reaction d'un systeme industriel :
Application aux centrales thermiques d'OYOMABANG I et II
.
Le temps de réaction s'écrit alors :
~~~
D ~ ? d, ~~~
~~~ ~ ? I
~~~ ~ D! ? I
~~~ ~ ? d, ~
~ ~~~ / (IV-1)
~~~ ~~~
IV.2.4. Expressions des valeurs minimales
(D,imin ) et maximales (Dnmax) de D.
Une expression du temps de réaction minimum, selon
cette modélisation, est proposée d'après l'auteur, elle
s'obtient lorsqu'il existe une parfaite synchronisation, à chaque
niveau, entre les instants de répercussion de la réaction et une
fin de période du niveau considéré. Ce qui se traduit par
:
4=0 et Pk=0, pour tout niveau k
du processus
Ainsi :
Diin -- ? d, ~~~
~~~ ~ D! ~ ? d, ~
~~~ (IV-2)
~~~ ~~~
De même, le temps de réaction serait maximum si l'on
a : 4=Pk et
rk=Pk, pour tout niveau k du processus.
On aura donc :
~~~
D#&' ~ ? d, ~~~
~~~ ~ ? P
~~~ ~ D! ? P
~~~ ~ ? d, ~
~ ~~~ / (IV-3)
~~~ ~~~
Dnmax = ? d, ~~~
~~~ ~~~ ~ P~~D! ~ ? d, ~
~~~
~ 2 ? P
~ (IV-4)
~~~ ~~~
Modelisation du temps de reaction d'un systeme industriel :
Application aux centrales thermiques d'OYOMABANG I et II .
IV. 3. Expression du modèle
adapté.
[002]. Cette étude se base sur une bonne structure
décisionnelle multi niveaux en fonctionnement périodique.
IV.3.1. procédure de traitement de
l'ENS.
Lorsqu'un ENS survient, la procédure de traitement est la
suivante :
Le niveau essaye d'abord de résorber
l'évènement localement : On parle de traitement «
sous contraintes ». S'il n'y arrive pas, il le
répercute ensuite au niveau supérieur : c'est le traitement
« sur contraintes ». Ce dernier à son tour
tente de le résorber, s'il n'y arrive pas aussi, il le répercute
au niveau au dessus. Ainsi de suite, jusqu'à ce qu'un niveau arrive
à résorber l'évènement. Cette procédure est
valable qu'on soit en conduite périodique ou
évènementielle. A la seule différence qu'en conduite
évènementiel, l'évènement est traité
aussitôt qu'il est détecté, sinon, répercuté
directement au niveau supérieur, alors qu'en conduite périodique,
le traitement de l'évènement a lieu en fin de période, sur
chaque niveau. Ce qui entraine des temps d'attente qui rallongent le temps de
réaction du système.
IV.3.2. hypothèses
d'étude
Pour l'étude nous faisons les hypothèses suivantes
:
> Le système fonctionne en régime
périodique, fonctionnement pour lequel les délais de
réaction sont plus long par rapport au fonctionnement
évènementiel ;
> Sur chaque niveau, il existe un décalage (pouvant
être nul) entre la date de référence, origine des temps
(to) et la date de début de la période de
référence, période suivant la
date de référence, Xin (o), du niveau m
considéré, ces décalages ne sont pas forcement
égaux pour tous les niveaux ;
> Nous supposons un classement en familles des
évènements Non Souhaités. Chaque famille étant
traitée, dans le cas le plus défavorable, par un niveau N ;
> Nous considérons, dans le cas la plus
défavorable d'une famille quelconque, un ENS qui apparait sur le niveau
0, et qui, n'arrivant pas à être traité, est
répercuté jusqu'au niveau
Modelisation du temps de reaction d'un systeme industriel :
Application aux centrales thermiques d'OYOMABANG I et II .
N ou il est finalement traité. Il va donc parcourir au
total N+1 niveaux. Ce cas particulier représente le temps de
réaction le plus long dans famille considérée.
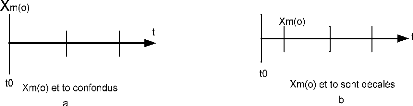
Figure 18 : positions relatives possibles entre to et
Xm (o) sur un niveau m
IV.3.3. objectifs
L'objectif est d'exprimer le temps de réaction du
système en fonction de la date d'occurrence de l'ENS et des
paramètres du système, notamment les dates de début de la
période de référence des différents niveaux
impliqués dans le traitement. Ce qui peut se représenter
schématiquement par la figure 14. Ensuite, nous cherchons à
réduire les temps d'attentes dans les différents niveaux afin de
minimiser le temps de réaction.
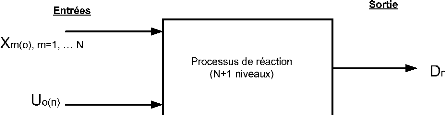
Figure 19 : objectif de la
modélisation
Xin (o) : date d'initialisation de
référence du niveau m ; U0(n) : Date
d'occurrence de l'ENS n ; Dn : Temps de
réaction du système.
Modelisation du temps de reaction d'un systeme industriel :
Application aux centrales thermiques d'OYOMABANG I et II .
Il est donc question d'exprimer :
Dn = f(u (1), 456/0089 = 0,1,...., N)
(IV.5)
IV.3.4.processus de traitement d'un ENS
Nous considérons un ENS détecté au niveau
0 et qui est répercuté jusqu'au niveau N ou il est enfin
traité. Le processus passe alors par N+1 niveaux hiérarchiques et
se décompose en deux phases.
> Une phase amont qui est montée vers les niveaux
supérieurs, à la recherche de la réaction adéquate
;
> Une phase aval qui est la descente de la réaction
vers le niveau d'origine de l'ENS pour son application.
Le processus traverse donc deux fois chaque niveau du circuit, le
niveau N, qui traite l'évènement. Ce dernier ne le reçoit
qu'une seule fois.
Nous désignerons par « sous processus, SP »
chaque passage de l'ENS dans un niveau. Ainsi,
tout niveau m, sauf le plus élevé (m=N),
comportent deux sous-processus (SPmet
SP2N_m) qui traitent l'évènement
respectivement en amont et en aval. Le niveau N qui traite
l'évènement n'a
qu'un seul sous-processus : SPN.
Le processus a donc au total 2N+1 sous-processus. Dans chaque
sous-processus i, SPi, sauf
(i=2N), l'ENS ou la réaction passe par quatre états
successifs : Le sous-processus 2N,SP2N, étant le
dernier, n'a que les trois premiers états.
Sans entrer dans le détail de ce qui se passe dans les
différents états, nous dirions simplement
que c'est l'état EL en phase amont, qui
détermine le mode de traitement (périodique ou
évènementiel) à adopter, en fonction de
l'appréciation de la gravité.
Il est à noter qu'en cas d'erreur de diagnostique, c'est
à l'étape E1 qu'elle est commise. Le constat est
fait, soit à l'Étape E3, soit à
l'étape E1 du niveau supérieur, et ainsi de
suite.
Modelisation du temps de reaction d'un systeme industriel :
Application aux centrales thermiques d'OYOMABANG I et II .
En cas d'erreur de diagnostique, nous proposons le Grafcet de
traitement ci-après :
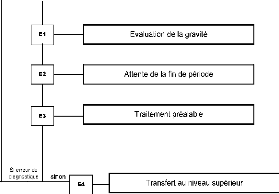
Figure 20 : Grafcet de traitement des
erreurs.
État
|
Désignation
|
Durée
|
Phase amont
|
Phase aval
|
E1
|
Évaluation de la gravité
|
Vérification de la cohérence
|
di, 1
|
E2
|
Attente de la fin de période
|
Attente de la fin de période
|
di, 2
|
E3
|
Traitement préalable
|
Élaboration du cadre de décision
|
di, 3
|
E4
|
Transfert au niveau supérieur
|
Transfert au niveau inférieur
|
di, 4
|
Tableau 1 : les états de traitement dans les
sous-processus i
Les duréesdi,i,
d1,3 et d1,4 des états
E1 , E3 et E4 sont des
valeurs moyennes, caractéristiques temporelles du processus de
traitement pour une famille d'évènements donnée. Elles
sont donc connues. Par contre, la durée d'attente
d1,2, de l'état, E2 est une
durée implicite qui est une
cause du rallongement du temps de réaction. Cette
étape est sanctionnée par une prise de décision.
Modelisation du temps de reaction d'un systeme industriel :
Application aux centrales thermiques d'OYOMABANG I et II .
Il est à noter que taches réalisées dans les
différentes étapes peuvent différées en fonction du
niveau de décision.
Par exemple : l'étape E1 du
sous-processus 0 peut être la constatation de l'ENS tant
dis que
l'étape E1 du sous-processus
Niveau N Niveau N-1
Niveau m
Niveau 1 Niveau 0
|
1 est l'évaluation de la gravité.
Phase amont
|
phase aval
|
|
Sous processus N
|
|
|
|
|
|
Sous-processus N-1
|
|
Sous -processus N+1
|
.
|
.
|
.
|
Sous-processus m
|
|
Sous processus 2N-m
|
.
|
.
|
.
|
Sous-processus 1
|
|
Sous processus 2N-1
|
|
|
|
Sous-processus 0
|
|
Sous processus 2N
|
Figure 21 : les niveaux et leurs sous-processus.
La succession des étapes est alors la suivante :
Modelisation du temps de reaction d'un systeme industriel :
Application aux centrales thermiques d'OYOMABANG I et II .
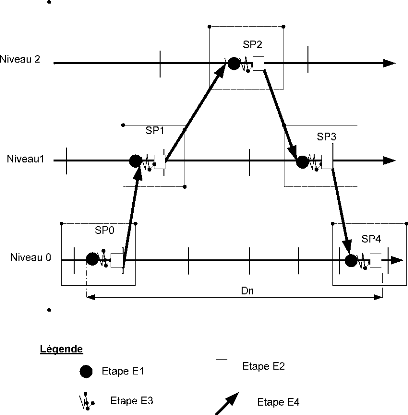
Figure 22 : Exemple de circuit sur 3 niveaux
(N=2)
Modelisation du temps de reaction d'un systeme industriel :
Application aux centrales thermiques d'OYOMABANG I et II .
IV.3.5.modélisation du processus.
IV.3.5.1.définition des paramètres
et variables. IV.3.5.1.1. Paramètres du processus
ü to : date de référence.
ü n : numéro d'ordre de
l'évènement.
ü m : niveau considéré.
ü i : indice du sous-processus considéré.
ü j : indice de l'État de
l'évènement.
ü k : numéro d'ordre de la période.
ü N : niveau qui traite l'évènement.
ü Spi : sous-processus i du système.
ü Ei: Etat i de traitement de
l'évènement.
ü Pin : durée d'une
période du niveau m.
ü kin : période de
synchronisation à laquelle est traité l'évènement n
dans Spi.
ü Xin (o) : date de
début de la période de référence du niveau m.
ü Xi : Date d'arrivée de
l'évènement n dans le sous-processus Spi.
ü di,j : durée de l'état
Ej de Spi.
ü S(n) : date de mise en oeuvre de la réaction.
ü Dn : temps de réaction
du système à l'évènement n.
IV.3.5.1.2. Variables du processus.
ü 11i(n) : date d'entrée, dans spi,
de l'évènement n ;
ü Xin(k) : date de fin de
période k du niveau m.
ü Xii(n) : date de fin de
l'étatEj, pour l'évènement n, de Spi.
ü Si(n) : date de sortie de
l'évènement n (fin de la dernière étape) de Spi
Modelisation du temps de reaction d'un systeme industriel :
Application aux centrales thermiques d'OYOMABANG I et II .
IV.3.5.2. modélisation d'un sous-processus Spi.
Dans tous les sous-processus, la procédure de traitement
est la même. La figure 23 représente les dates de changement
d'état de l'événement ou de la réaction dans le
sous-processus.
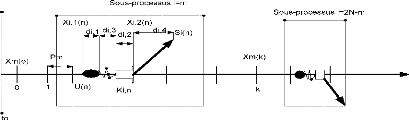
Figure 23 : durée et changement d'état
dans un sous-processus Spi.
IV.3.5.3. détermination du niveau auquel
appartient un sous-processus Spi.
Tout sous-processus i (i = O. 1, .., 2N), appartient à un
niveau m que l'on détermine comme suit: In --2N-
i
-- ti si i5N
sinon
IV.3.6. Modélisation de la dynamique du traitement
dans un sous-processus.
Il existe deux dynamiques distinctes dans le processus de
traitement, figure 24. D'une part, la dynamique de l'événement
(ses changements d'états) qui s'effectue à des instants
irréguliers en fonction des durées des différents
états qui sont des caractérisques intrinsèques du
système par rapport au traitement d'une famille
d'événements donnée. D'autre part, la dynamique de prise
de décision qui est régulière, car elle est
périodique sur chaque niveau.
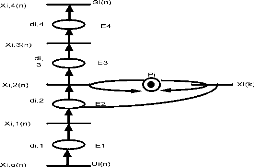
Figure 24 : Représentation par un réseau
de pétri de la dynamique de traitement
Modelisation du temps de reaction d'un systeme industriel :
Application aux centrales thermiques d'OYOMABANG I et II .
Mais, les deux dynamiques doivent se synchroniser pour que
l'événement puisse passer de l'état
E2 à l'étatE3,
afin qu'une décision relative il son traitement soit prise. L'une des
deux dynamiques doit s'adapter à l'autre· Et c'est ce qui va faire
la différence entre les conduites périodique et
événementielle.
En conduite événementielle, c'est la dynamique
de la prise de décision qui s'adapte à celle de
l'événement. Comme ce dernier est irrégulier, la conduite
événementielle l'est aussi forcement. Par contre, en conduite
périodique, c'est la dynamique de l'événement qui s'adapte
à celle de la prise de décision. Ce qui va entraîner des
temps d'attente avant le traitement de l'évènement en fin de
période.
Dans la réalité, les deux, modes de
fonctionnement coexistent sous la désignation de conduite mixte, En
fait, il s'agit d'une conduite périodique, mais, pour les
événements assez critiques, la décision est prise sans
attendre la fin de période.
IV.3.6.1 Dynamique de prise de décision : passage
d'une période à la suivante.
Le passage d'une période k à la suivante k+ 1, sur
un niveau quelconque m, s'effectue à la date de fin de la période
k, Xm(k) qui est donnée par :
Xin(k) = Pm + Xfli(k -- 1)
(IV-6)
===> Xrrl(k) = k x Prn +
41(0)
IV.3.6.2. Détermination de la
période de synchronisation : ki,~ En
conduite périodique, l"événement n est traité, dans
un sous-processusSPi, à une période
kO,~

du niveau m (auquel appartient le sous-processus
SPi), que l'on détermine de la manière suivante:
{jcin(0)=APm ki,n si 3 A. e IN tel que U i(n)+di,i_
(IV-7) ki,n'El /U1(n)+cli4 --Xm(0))Pm +1sinon Ou E(X)
représente la partie entière de X.
Modelisation du temps de reaction d'un systeme industriel :
Application aux centrales thermiques d'OYOMABANG I et II
.
IV.3.6.3.Dynamique de l'évènement
dans un sous-processus Spi Les dates de changement
d'état de l'événement n (passage de l'état
Ej à l'état Ej+i),
pour chacun
des quatre états, dans le sous processus
SPi , Xij(n) , sont données par :
f Xi,j (n)=Xi,j_i (n)+ di,j V
je[1,3,4}
(IV-8)
Xi,2(n)=Xm(ki,n) j=2
Pour j=2. L'équation que l'on a marque bien la
synchronisation entre les deux dynamiques, Elle permet de déterminer
la date à laquelle une décision est prise pour le traitement de
l'événement.
Cette date coïncide avec la fin de la période de
synchronisation, kO,~ du sous-processus Spi. IV.4.
Évaluation du temps de réaction.
IV.4.1. détermination de la date de sortie de
l'évènement du sous-processus
Les dates de changement d'état de
l'événement n (passage de l'état Ej
à l'état Ej+i). Pour chacun des
quatre états dans le sous processusSPi,
Xij(n) sont données par:
f Xi, (n)= Xij_ 1 (n)+ dij V je[1,3,4}
( Xi,2 (n)=Xm (ki,n) j=2
(IV-9)
L'entrée UL(n) et la sortie Si(n) de
SPi sont tels que:
i Ui(n)=X0(n)
1. Si (n)=Xi,4 (n) (IV-10)
Le système (IV-9) s'écrit alors :
/ Xi,t(n)= ui (n)+ di,1
X2 (n)=Xm (n)+ki,n xPm
Xi,3 (n)=Xi,2 (n)+di,3 (IV-11)
Si(n)=Xi,3(n)+di,4
Calcul de la date de sortie : Si(n)
Si(n) = Xm(0) + ki,n X Pm + ?
l=3dij (IV-12)
Modelisation du temps de reaction d'un systeme industriel :
Application aux centrales thermiques d'OYOMABANG I et II .
Le résultat précédent est valable pour tous
les sous-processus i, sauf le dernier, i=2N, Pour lequel l'état E4
n'existe pas, et donc d2N, 4 n'existe pas. Elle est égale il :
S2N(n) = XO(0) + k2N,1 X PO + d2N,3 (IV-13)
IV.4.2. Généralisation à
l'ensemble du processus.
Le processus comporte au total N+1 niveaux et 2N+ 1
sous-processus. L'événement passe par tous les Sous-processus.
La date d'entrée de l'évènement dans un
sous-processus est égale à sa date de sortie du sousprocessus
précédent.
> Données :
I
Entrées : UO(0) V 9 = 0,1 ... . . =
Xin(0)
Pin(0) V 9 = 0,1 ..... N
Paramètre : fX , ,
171.0 )V jEf1, 3, 41 et i = 0,1 ... . .2N(sauf
d2N,4)
> Calcul :
r1(1)=Xm(O)+ki,n
xPm-F? 1=3 du
Pour i=0,1, .,2N-1 :
Ui+10
1
)=Si (
1
)
Pour i=2N : S2N(n) = XO(0) + k2N,1 X PO +
d2N,3
,
> Date de sortie du processus :
La date de sortie de l'évènement du processus de
traitement, S(n), qui représente aussi la date de mise en oeuvre de
La réaction, est égale à la date de sortie du même
événement du dernier sous-
processus, S2N (n).
S(n) = S2N(n) = XO(0) + k2N,1 X PO + d2N,3
(IV-14)
Modelisation du temps de reaction d'un systeme industriel :
Application aux centrales thermiques d'OYOMABANG I et II .
IV.5. expression du temps de réaction du
système D .
Le temps de réaction représente le temps qui
s'écoule entre l'occurrence de l'événement et la mise en
oeuvre de la réaction, Par rapport à notre modélisation,
il s'agit de la différence entre la date de sortie de
l'événement du processus de réaction (date de sortie du
dernier sous-processus Sp2N) et la date d'occurrence de
l'événement au premier niveau O. Ce qui se traduit par:
Dn = S2N(n) - Up(n) (IV-15)
Soit :
Dn = [X0(0) + k2N,n x PO +
d2N,3 ] -- (0(n) (IV-16)
On a bien une expression du temps de réaction en fonction
des paramètres du système. IV.6. Essai de
minimalisation du temps de réaction
IV.6.1. Évaluation des temps d'attentes dans
le processus.
IV.6.1.1. autre expression du temps de
réaction.
Une autre expression du temps de réaction est obtenue
en l'exprimant uniquement comme une somme, sur tout le processus, des
durées de l'événement dans tous les états de chaque
sousprocessus. Ce qui donne:
~1 ~ 3? ? ~A,G
B@ E B@
A+ p ~ ? ~A,B
B@
~ ~B@,D ~ ? A, A+ (IV-17)
A+ G~D
Ou
~1 ~ 3? ? Gs4~,D,Et ~A,G
B@ ~ ? Gs4~,D,t ~B@,G p ~ ? ~A,B
B@
A+ (IV-18)
A+
A B
L'expression ci-dessus montre que le temps de réaction est
composé de partie:
> une partie A, constituée de temps
caractéristiques du processus, et donc à priori incompressible,
et ;
> une partie B constituée des temps d'attente, qu'il
serait intéressant de réduire, voir de supprimer.
Modelisation du temps de reaction d'un systeme industriel :
Application aux centrales thermiques d'OYOMABANG I et II
.
IV.6.1.2. Expression des temps d'attentes dans le
processus. De l'équation (IV-18), on peut alors tirer
:
B@
? ~A,B
B@
A+ ~ ~1 ? 3? ? Gs4~,D,Et ~A,G ~ ? Gs4~,D,t
~B@,G p (IV-19)
A+
De l'équation (IV-16), on peur alors avoir :
? ~A,B
A+ ~ ,+/00 ~ FB@,1 L ~+ ? 3.+/0 ~ ? ? Gs4
D,Et ~A,G
B@
B@ ~ ? A,
B@
A+ p (IV-20)
A+
Ou encore :
? ~A,B
A+ ~ FB@,1 L ~+ ? 3,+/00 ~ .+/~0 ~ ? ? Gs4
D,Et ~A,G
B@
B@ ~ ? A,
B@
A+ p (IV-21)
A+
Dans l'équation précédente, seul
k2N,n est variable en fonction des dates de
début de la
période de référence des niveaux. Tous les
autres termes sont constants. Pour un système et un
événement donné.
IV.6.2. Approche empirique de réduction des
temps d'attentes
IV.6.2.1. principe Cette
approche consiste à réduire, sur un niveau m, les temps
d'attente, din,2 et
d2N_m,2 (durée
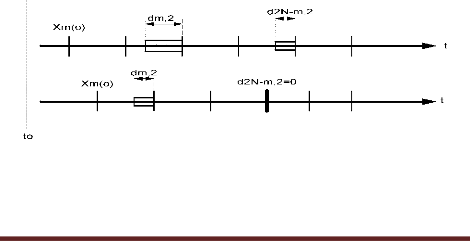
Figure 25 : réduction empirique des temps
d'attente sur un niveau
de l'étapeE 2) des deux sous-processus
amont et aval, appartenant au niveau m, en ajustant la date de début de
la période de référence du
niveau,X,n(0) de façon à annuler l'un
des deux temps d'attente. La figure 25 schématise cette approche.
Modelisation du temps de reaction d'un systeme industriel :
Application aux centrales thermiques d'OYOMABANG I et II
.
L'ajustement sur un niveau s'effectue de la manière
suivante :
Si min
(dm,2;d2N_m,2)
c Xm(0) alors
Xm(0)=4,(0) - min
(d-,2;d2N--m,2)
Sinon
Xm(0)=Pm, +
(Xm(0) - min
(dm,2;d2N-m,2))
Le résultat est l'annulation de la plus petite des
deux, temps d'attente. On obtient une nouvelle date de début de la
période de référence et un nouveau temps d'attente plus
faible. Pour l'ensemble du processus de traitement, on applique successivement
le même principe à tous les niveaux du processus, en
commençant par le plus bas de préférence. Un algorithme
présenté dans la suite permet d'effectuer ce calcul.
IV.6.2.2. Algorithme de réduction des temps
d'attentes. Xm(0) = 0 quelque soit m = 0, l, ...,
N
Pour m allant de 0 à N, faire :
Si min (dm,2;d2N_m,2) = 0,
alors
m =m-+l
Sinon, Si min
(dm,2;d2N_m,2)
=Xm(0))
Xm(0)=Xm(0)
- min (dm,2;d2N_m,2)
Sinon
Xm(0)=Pm, +
(Xm(0) - min
(Ci,2;d2N-m,2)) Fin si
m=m+1
Fin si
Fin.
Modelisation du temps de reaction d'un systeme industriel :
Application aux centrales thermiques d'OYOMABANG I et II .
IV.7. Expression du temps de réaction du
système en conduite évènementielle :
Dn
En conduite événementiel, le processus de
traitement est le même qu'en conduite périodique. La seule
différence est que les temps d'attente,di,2
durée de l'étatE 2 , sont nuls, pour tous les
sousprocessus.
Dans l'équation (IV-18), on obtient une expression de
Dn en supprimant le terme :
2N
B =Icli.,2
i=0
Qui est nul. On a alors l'expression du temps de réaction
suivant :
Dn = ? r0 --1? jet1,3,4} dij + ? .16{1,3,}
d2N,i (IV-22)
0n voit donc que, dans ce cas, le temps de réaction ne
dépend que des seules durées des états « actifs»
de l'évènement dans le processus de réaction. Ces
durées sont des caractéristiques du système, pour une
famille d'événements donnée.
La seule voie pour diminuer ce temps est l'amélioration
de ces caractéristiques, par exemple en améliorant la
procédure de traitement (moins de paperasse, moins de signature,
décentralisation de la prise de décision, etc.). .
Mais, comme nous l'avons déjà dit, dans la
réalité, la conduite est mixte. C'est la gravité de
l'événement qui déterminer le mode de réaction.
S'il est jugé peu critique on peut attendre la fin de période
avant de le traiter (conduite périodique). Sinon, on le traiter
directement sans attendre (conduite événementielle). Ce pendant,
un événement peu critique au départ, et donc traité
en fin de période, peut voir sa gravité augmenter si la
réaction se fait attendre à cause des temps d'attentes de fin de
période pour la prise de décision, ou une raison.
Modelisation du temps de reaction d'un systeme industriel :
Application aux centrales thermiques d'OYOMABANG I et II .
CHAPITRE V : APPLICATIONS AUX CENTRALES
THERMIQUES D'OYOMABANG I ET II
|
V.1.Prise en main de la centrale.
V.1.1.fonctionnement, équipements et structure.
La centrale thermique d'oyomabang I a été
construite en 2000 et celle d'oyomabang II en 2002. Les deux centrales
disposaient au départ d'une puissance installé de 35.7 MW. Elles
disposent actuellement d'une puissance installée de 32.5 MW.
La centrale thermique d'oyomabang est une centrale thermique
d'appoint au réseau inter connecté sud (RIS) et de secours :
ü Secours parce qu'elle est capable d'alimenter une partie
de la ville (principalement les zones prioritaires) en cas de « Black- out
» total.
ü Appoint parce qu'elle vient en complément des
sources d'énergie principales que sont la centrale de Song Loulou et
celle d'Edéa. Dans son rôle de centrale d'appoint, elle permet
d'améliorer les paramètres du RIS. Sa mise en production est
gérée par le centre de dispatching du RIS (Grid dispach)
basé à Edéa.
CENTRALE THERMIQUE D'OYOMABANG 1
Cette Centrale a une puissance installée de 19.66 MW,
mais la puissance de fonctionnement est de 18 MW. Elle est constituée de
trois groupes diesel de marque WARTSILA. Chaque groupe est constitué de
plusieurs éléments à savoir:
ü Un moteur diesel;
ü Un alternateur ;
ü Un disjoncteur ;
ü Des auxiliaires du groupe.
Ces trois groupes ont en commun un certain nombre
d'auxiliaires.
Le schéma ci-contre illustre la disposition
générale des groupes:
Modelisation du temps de reaction d'un systeme industriel :
Application aux centrales thermiques d'OYOMABANG I et II .
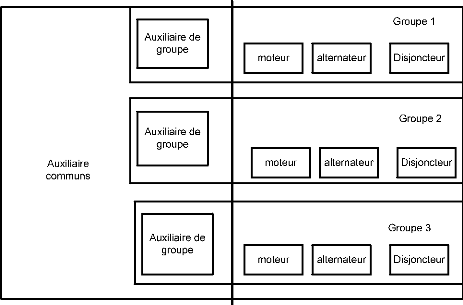
Figure 26 : présentation schématique de
la salle des machines
ü Le moteur diesel de chaque groupe est constitué de
18 cylindres.
Il démarre à air comprimé de 30 bars et
fonctionne avec du fuel LFO (Light Fuel Oïl) et du HFO (Heavy Fuel
Oïl), qui a une viscosité de 380. Il utilise de l'huile TBN 40 pour
sa lubrification.
ü L'arbre de moteur fournit une puissance maximum de 6.556
MW sous une tension de 15 KV. C'est un alternateur à auto-excitation.
ü Le disjoncteur du groupe fonctionne sous une tension de
15KV et protège le groupe contre les défauts électriques
pouvant survenir lors du fonctionnement.
ü Les auxiliaires du groupe constituent l'ensemble
d'organes utiles pour la mise en service et le fonctionnement du groupe; il
s'agit entre autres de : filtres à gas-oil, filtres à huile,
séparateurs d'huile, pompes multiples, résistance de
préchauffage, électrovannes et distributeurs, ventilateur,
armoire électriques de commande,
ü Les auxiliaires communs sont constitués de:
Booster (dispositif de traitement de fuel et de sélection avant
transfert dans les groupes), séparateurs HFO, pompes, modules de
traitement d'eau, aéroréfrigerants, cuve d'eau de maintenance,
les armoires électriques de commande, ...
ü Deux transformateurs abaisseurs de tension
15KV/400V.
Modelisation du temps de reaction d'un systeme industriel :
Application aux centrales thermiques d'OYOMABANG I et II .
Le site est doté en outre, d'un certain nombre de Cuves
pour le stockage et le traitement du fuel avant utilisation.
Chaque groupe dispose d'une armoire de contrôle
commande dans la salle de commande équipée d'un Automate
Programmable Industriel (API). Les groupes ont en communs une armoire de
contrôle commande dotée d'un automate qui assure le contrôle
et le suivi des groupes, communique avec l'homme via un Ordinateur.
Le système est assez moderne, avec l'utilisation de
nouvelle technologie de contrôle commande et de communication
Homme-Machine.
CENTRALE THERMIQUE D'OYOMABANG
II
Cette Centrale a une puissance installée actuelle de
12.8 MW, mais la puissance de fonctionnement est de 12 MW. Constituée de
10 groupes diesel de marque CATERPILLAR à la création, elle ne
dispose plus que de 8 groupes actuellement; les deux autres groupe ayant
été transférés dans d'autres unités de
production. Chaque groupe est constitué de plusieurs
éléments, à savoir:
ü Un moteur diesel;
ü Un alternateur ;
ü Un disjoncteur;
ü Des auxiliaires du groupe.
Ces trois groupes ont en commun un certain nombre
d'auxiliaires.
ü Le moteur diesel de chaque groupe est constitué
des cylindres.
Il démarre avec un démarreur électrique
grâce à une batterie de 24 V CC et fonctionne avec du gasoil LFO
(Light Fuel Oil) Il utilise de l'huile Delvac CF4 pour sa lubrification.
ü L'arbre du moteur, fournit une puissance maximum de
1.6 MW sous une tension de 400 V. C'est un alternateur à auto
excitation. La tension est élevée en sortie par un transformateur
élévateur de niveau de tension 400V /15KV.
ü Le disjoncteur du groupe fonctionne sous une tension de
400V et protège le groupe contre les défauts électriques
pouvant survenir lors du fonctionnement.
ü Les auxiliaires du groupe constituent l'ensemble
d'organes utiles pour la mise en service et le fonctionnement du groupe; il
s'agit entre autres de: résistance de préchauffage, Vases
d'expansion, ventilateurs, armoire électriques de commande, ...
Le site dispose de trois citernes identiques de 60 m3 pour le
stockage du fuel en provenance de Centrale d'Oyomabang 1.
Il existe également une salle de contrôle commande,
mais pas assez moderne.
Modelisation du temps de reaction d'un systeme industriel :
Application aux centrales thermiques d'OYOMABANG I et II .
STRUCTURE ET ORGANIGRAMME
La centrale est structurée ainsi qu'il est
présenté dans l'organigramme suivant :
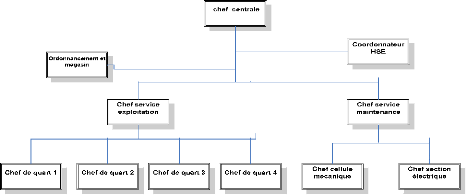
Figure 27 : Organigramme de la centrale La
centrale thermique d'Oyomabang c'est :
> Une production d'énergie d'environ 319425MW/H
(novembre 2009)
> Une consommation de gasoil et de fuel lourd d'environ 78
638 m3
> Plus de 3200 jours sans accident
> Près de 19.5 Milliard injecté dans
l'économie camerounaise.
Pour l'année 2009,
L'unité de production OYOMABANG 1 c'est :
> Une production d'énergie de 34258 MW/H
> Un taux de disponibilité de 93.64%
> Une moyenne d'heures de marches des groupes de 1995
heures
> Un taux d'incident de 3%
L'unité de production OYOMABANG 2 c'est :
> Une production d'énergie de 10219 MW/H
> Un taux de disponibilité de 73.28%
> Une moyenne d'heures de marches des groupes de 1075
heures
> Un taux d'incident de 1% et un taux de maintenance de
26%.
Modelisation du temps de reaction d'un systeme industriel :
Application aux centrales thermiques d'OYOMABANG I et II .
V.1.2.Maintenance
V.1.2.1.) Définition
générale de la maintenance.
La maintenance est définie comme étant «
l'ensemble des actions permettant de maintenir ou de rétablir un bien
dans un état spécifié ou en mesure d'assurer un service
déterminé au coût global optimum. »
[005]
Maintenir c'est donc effectuer des opérations qui
permettent de conserver le potentiel du matériel pour assurer la
continuité et la qualité de la production.
V.1.2.2) Les objectifs de la maintenance.
Ces objectifs sont doubles : réduire les dépenses
de maintenance et diminuer les capitaux immobilisés. Le premier objectif
se décline en :
Dépenses du personnel interne : salaires, charges
patronales, frais liés à la formation,... Elles dépendent
du métier et du niveau hiérarchique mais ces coûts doivent
être majorés de la perte de temps occasionnée par
l'opération de maintenance (préparation, coordination, ...). La
distinction entre les activités à valeur ajoutée et celles
à non-valeur ajoutée permet de définir des axes
d'amélioration au cours de réunion avec les différents
métiers concernés. L'analyse de Compression de Temps Cycle
concerne plus particulièrement les causes de non-valeur ajoutées
durant l'intervention: en effet, ces dernières empêchent le
redémarrage de la production sans améliorer l`installation.
L'organisation des tâches de maintenance en parallèle permet de
réduire la durée de l'intervention et la complexité des
corps de métiers impose une planification plus efficace pour ce qui ne
touche pas à la maintenance curative. Le déroulement d'une
journée doit être entièrement prévu. Seules les
actions urgentes de réparation peuvent l'affecter. En outre, les
activités menées doivent améliorer la fiabilité des
installations. Il faut prendre en compte les risques liés au non-respect
des programmes de maintenance préventive. Les entreprises recourent
à l'AMDEC (Analyse des Modes de Défaillance, de leurs Effets et
de leur Criticité). Cette méthodologie permet d'identifier les
modes de défaillances et leurs effets sur le fonctionnement global de
l'installation.
Consommation de fournitures industrielles : les pièces de
rechanges, ... Il faut :
définir et prendre les mesures nécessaires pour
réduire l'usure de ces pièces (type de fonctionnement, ...) ;
Modelisation du temps de reaction d'un systeme
industriel : Application aux centrales thermiques d'OYOMABANG I et
II .
ü vérifier le respect des conditions de
stockage ;
ü limiter le nombre de fournisseurs ;
ü recourir au service achat pour négocier
les prix. Le second objectif de la maintenance vise
à :
n Diminuer des stocks de fournitures
industrielles: l' entreprise vise à garder les
pièces nécessaires au bon fonctionnement de
l'outil industriel, tout en minimisant la valeur ainsi
immobilisée.
n Reporter des investissements: l'
entreprise qui souhaite augmenter sa production doit
d'abord
améliorer sa maintenance et la fiabilité de
son outil de production avant d'investir dans de nouvelles
installations.
V.1.2.3) Les différentes formes de maintenances et
leurs définitions
Les formes de maintenances se présentent comme
dans le diagramme à carreaux ci-dessous :
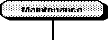
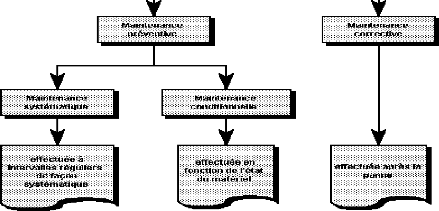
Figure 28 : différentes formes de
maintenance
Modelisation du temps de reaction d'un systeme industriel :
Application aux centrales thermiques d'OYOMABANG I et II .
V.1.2.3.1) La maintenance corrective
Il s'agit d'une "maintenance effectuée après
défaillance". C'est une politique de maintenance qui correspond à
une attitude de réaction à des évènements plus ou
moins aléatoires et qui s'applique après la panne.
V.1.2.3.2) La maintenance préventive
V.1.2.3.2.1) Maintenance systématique
"Maintenance préventive effectuée selon un
échéancier établi en fonction du temps ou du nombre
d'unités d'usage".
V.1.2.3.2.2) La maintenance conditionnelle
"Maintenance préventive subordonnée à un
type d'évènement prédéterminé
révélateur de l'état de dégradation d'un bien".
V.1.2.4) Les niveaux de la maintenance
Ils sont au nombre de cinq (05) et leur utilisation pratique
n'est concevable qu'entre des parties qui sont convenues de leur
définition précise, selon le type de bien à maintenir.
1° Niveau
> Réglages simples prévus par le constructeur
au moyen d'organes accessibles sans aucun démontage ou ouverture de
l'équipement,
> Échanges d'éléments consommables
accessibles en toute sécurité, tels que voyants, huiles, filtres,
...
> Type d'intervention effectuée par l'exploitant sans
outillage et à l'aide des instructions d'utilisation.
2° Niveau
> Dépannages par échange standard des
éléments prévus à cet effet,
> Opérations mineures de maintenance
préventive,
> Type d'intervention effectuée par un technicien
habilité de qualification moyenne,
> Outillage portable défini par les instructions de
maintenance,
> Pièces de rechange transportables sans délai
et à proximité du lieu d'exploitation.
Modelisation du temps de reaction d'un systeme industriel :
Application aux centrales thermiques d'OYOMABANG I et II .
3° Niveau
Identification et diagnostic des pannes.
> Échanges de constituants.
> Réparations mécaniques mineures.
> Réglage et réétalonnage des mesureurs.
4° Niveau
Travaux importants de maintenance corrective ou
préventive.
> Démontage, réparation, remontage,
réglage d'un système.
> Révision générale d'un
équipement (exemple: compresseur).
> Remplacement d'un coffret d'équipement
électrique
5°Niveau
Travaux de rénovation, de reconstruction ou de
réparation importante.
> Révision générale d'un
équipement (chaufferie d'une usine).
> Rénovation d'une ligne de production en vue d'une
amélioration.
> Réparation d'un équipement suite à un
accident grave (exemple: dégât des eaux).
V.1.2.5) Organisation de la
maintenance. V.1.2.5.1) Le rôle de l'opérateur de production
dans les activités de maintenance.
La maintenance préventive implique très souvent
l'opérateur de production. Il peut être chargé de
différentes activités de maintenance simples ou du signalement
des dysfonctionnements de l'outil de production. Cependant, ce rôle
apparaît aujourd'hui limité par :
> la diversité des appareils et leur accès
limité (éloignement et normes de sécurité) ;
> L'efficacité inférieure à celle d'un
service de maintenance ;
> le manque de motivation, de formation et d'habilitation.
Modelisation du temps de reaction d'un systeme industriel :
Application aux centrales thermiques d'OYOMABANG I et II .
V.1.2.5.2) : Répartition des tâches de
maintenance au sein de l'entreprise
la préparation des interventions de maintenance
planifiée
|
Arrêts programmés
|
Planification des travaux et Exécution
|
Réglementaire
|
Relations avec l'organisme de contrôle
|
Gestion
|
Gestion des pièces de rechanges Contractualisation de la
maintenance
|
Préventif
|
Évolution et suivi des plans de maintenance
|
Documentation
|
Mise à jour des plans
|
La fiabilité à long terme
|
Progrès
|
Proposition d'amélioration technique Chasse aux pertes
|
Expertise
|
Assistance des postés lors de dépannages
|
Formation
|
Formation des postes et des opérateurs techniciens
|
Travaux neufs
|
Participation aux études et aux mises en service
|
Documentation
|
Mise à jour des documents techniques
|
La maintenance / assistance
|
Curative
|
Dépannage et résolution des anomalies
|
Préventif
|
Réalisation lors du fonctionnement
|
Consignations
|
Réalisation des consignations
|
Formation
|
Formation des opérateurs techniciens et de fabrication
|
Tableau 2 : repartition des taches au sein de
l'entreprise
Modelisation du temps de reaction d'un systeme industriel :
Application aux centrales thermiques d'OYOMABANG I et II .
Cette répartition des tâches reflète la
diversité des métiers exposés ci-dessous: ces trois
services correspondent respectivement au technicien d'intervention, au
technicien méthode et à l'agent de maintenance. Cependant, leur
travail ne se limite pas exactement à leurs attributions.
V.1.2.5.3) Les métiers de la maintenance.
Les différents profils de métiers peuvent
être résumés ainsi :
DENOMINATION
L'agent de maintenance
RÔLE
Maintenance curative (problème de dysfonctionnement
imprévisible / identifier des défaillances) Préventive
(assurer le contrôle et le changement des pièces, actions
programmées) Consignation (suivi des méthodes)
FORMATION
doit acquérir des compétences dans tous les
domaines technologiques, relationnelles et organisationnelles.
Le technicien
d'intervention
|
Maintenance prédictive (mise en place de solutions
techniques visant à éliminer des problèmes et à
améliorer le rendement) Analyse de la fiabilité (ratios,
diagramme de Pareto) "gammes opératoires"
|
doit acquérir des performances de plus en plus pointues
participe à la formation des techniciens non qualifiés
|
|
Le technicien de
méthode
|
Améliorer les modalités d'intervention
(optimisation du coût)
|
|
Cahier des charges
|
Tableau 3 : métiers de la
maintenance
Modelisation du temps de reaction d'un systeme industriel :
Application aux centrales thermiques d'OYOMABANG I et II .
Les techniciens doivent assurer également la gestion des
pièces de rechange, et la définition des caractéristiques
techniques des matériels.
Les activités d'encadrement participent pleinement
à l'amélioration de la rentabilité de l'entreprise :
l'agent de maîtrise planifie et gère les actions quotidiennes. De
plus, il est responsable de la formation et il contrôle les actions
réalisées mais il peut être amené à effectuer
lui-même des actions de maintenance. Il doit privilégier la
préparation et l'organisation des activités ainsi que le suivi
des plans d'amélioration.
V.2.Modélisation des temps d'attentes suite à
un évènement non souhaité
(ENS).
V.2.1. définition et traitements des
évènements non souhaités (ENS).
Les systèmes de décision des entreprises sont
plongés dans un environnement qui génère de plus en plus
d'événements. Une des principales tâches des
systèmes de décision consiste donc à les prendre en charge
de façon efficace les « évènements non
souhaités », c'est à dire lorsqu'ils gênent le
fonctionnement normal du système industriel. C'est dans ce cas que
l'amélioration de la réactivité est primordiale. Les
Évènements Non Souhaités doivent donc
être caractérisés afin que le système de
décision puisse rapidement les identifier et mettre en oeuvre le
traitement adéquat.
V.2.1.1. Définition.
Un évènement non souhaité est
définie comme étant toute information qui contredit une
prévision faite aussi bien sur le système opérant que sur
l'évolution des objectifs élaborés à partir de la
prévision de l'évolution de l'environnement [004].
En d'autres termes les ENS sont des
événements dont l'occurrence n'est pas planifiée, qui sont
susceptibles de gêner le déroulement d'opérations de
production et dans certains cas, de remettre en cause l'objectif même de
production.
Modelisation du temps de reaction d'un systeme industriel :
Application aux centrales thermiques d'OYOMABANG I et II .
V.2.1.2. Catégories
d'Évènements Non Souhaités (ENS).
Les principales catégories d'ENS reconnues en
gestion de production sont recensées par la
figure 29.
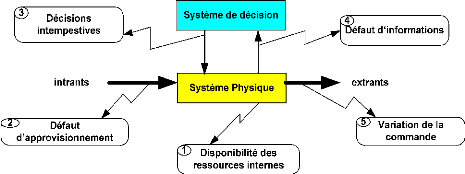
Figure 29 : Les principales catégories d'ENS en
gestion de production et en maintenance
1) Les ENS générées par le
système opérant sont parfois appelées "ENS internes".
Elles sont principalement engendrées par les aléas de
disponibilité et de fiabilité des ressources (hommes ou machines)
du système opérant. On trouve dans cette catégorie les
erreurs humaines, l'absentéisme, les pannes machines, les casses
d'outils, etc.
2) Les aléas liés aux fournisseurs et
sous-traitants se transforment en ENS sur les intrants qui se traduisent par
des défauts d'approvisionnement du système de production.
Généralement, ces ENS sont générées par des
retards de livraison ou la présence de non- conformités dans les
matières, pièces ou composants livrés.
3) Les aléas de fonctionnement du système de
décision créent des ENS que l'on peut qualifier de
décisions intempestives. Elles résultent
généralement de solutions élaborées à la
hâte ou sans prendre en compte certaines contraintes ou encore sans
considération pour les conséquences qu'elles entraînent sur
les autres activités de l'entreprise. C'est le cas, par exemple, de la
décision du service commercial de proposer des délais de
livraison excessivement courts pour enlever un marché au mépris
de la capacité réelle de production du système
opérant.
4) Les aléas de fonctionnement du système
d'information produisent des ENS dans les transmissions de données. En
découlent des défauts d'informations qui se traduisent soit par
un manque total (l'information ne parvient pas à son destinataire), soit
par une
Modelisation du temps de reaction d'un systeme industriel :
Application aux centrales thermiques d'OYOMABANG I et II .
insuffisance (l'information est incomplète ou
erronée). Concrètement, on trouve dans cette catégorie les
perturbations générées par des défaillances
humaines (oubli de transmission d'informations, erreurs de transcription de
données, etc.) ou techniques (panne du matériel support de la
communication, etc.).
5) Les aléas liés aux clients
génèrent des ENS sur les extrants. Leur origine est une variation
de la demande des clients qui porte principalement sur la quantité ou
les délais de livraison des produits. Dans cette catégorie d'ENS,
sont classées, par exemple, les augmentations ou baisses soudaines du
niveau des commandes dues à une variation de l'environnement ou à
un effet de mode (le succès imprévu d'un produit aboutit à
une incapacité du système à le produire dans les
délais annoncés, etc.).
Les ENS qui entrent dans les quatre dernières
catégories sont parfois appelées "ENS externes" parce qu'elles
sont générées par l'environnement du système
opérant.
V.2.1.3. Évènement Non
Souhaité flou
Qu'elles soient exogènes ou qu'elles soient
endogènes, les ENS peuvent avoir un caractère « flou ».
C'est le cas par exemple, de celles engendrées par les commandes clients
(annulation d'une commande, arrivée d'une commande urgente,
etc.)[004]. En effet, les prévisions de ventes au
début d'une année nécessite d'intégrer des
commandes en cours de négociation. Ce type de commande engendre des
bouleversements. De ce fait, ces commandes doivent pouvoir être
modélisées de façon à pouvoir en tirer le
caractère « sûre ». Il est cependant difficile de
répondre objectivement par « oui ou non » à la question
« La commande est elle sûre ? » et ceci tout simplement parce
que la commande d'un client est incertaine. Elle ne peut donc pas être
modélisée par la logique booléenne au risque de nous
écarter de la réalité. On fait appel pour ce type de
problème à la logique floue qui permet de définir une
fonction d'appartenance permettant de mieux le rapprocher de la
réalité.
En conclusion, qu'elles soient internes, externes et/ou floues,
les ENS ont toutes un impact sur le système opérant.
Modelisation du temps de reaction d'un systeme industriel :
Application aux centrales thermiques d'OYOMABANG I et II .
V.2.1.4. classification des
évènements non souhaités
Du point de vue de la réactivité du
système industriel, l'objectif est d'identifier rapidement les ENS et de
mettre en oeuvre le traitement adéquat. La complexité de ce
traitement est essentiellement fonction de l'importance de l'impact des ENS sur
le fonctionnement du système opérant.
En conduite de système industriel, les ENS se classent en
trois catégories :
> ENS faiblement perturbantes si elles ne
contraignent pas le système de décision à remettre en
cause le plan de production ; les objectifs assignés au système
opérant peuvent être remplis grâce à un traitement
des ENS qui ne prend en compte que le groupe d'opérations
perturbées et les ressources associées ;
> ENS moyennement perturbantes si elles
impliquent le calcul d'un nouveau plan de production sans générer
de conséquences sur les extrants ; ces ENS peuvent être
absorbées par le système opérant sans effet
détectable sur les sorties du système de production ; les
objectifs de coût, qualité et délais sont respectés
;
> ENS fortement perturbantes si,
malgré l'élaboration d'un nouveau plan de production, elles ont
des conséquences sur les extrants du système opérant ; les
objectifs de coût, de qualité et particulièrement de
délais ne peuvent plus être respectés.
V.2.1.5. Traitement des
évènements non souhaités
La survie des entreprises dépend de leur
faculté à faire face aux fluctuations de leur contexte
économique, technologique, social voire politique. C'est pourquoi, dans
un premier temps, il est indispensable de réduire le nombre d'ENS
qu'elles auront à affronter. Ce sont des actions stratégiques
à long terme, de nature préventive, qui permettent de mettre en
place des moyens susceptibles d'éviter l'occurrence de certains ENS. Par
exemple, pour le cas des fournisseurs et sous-traitants, il peut être
bénéfique pour l'entreprise de mettre en place des relations
étroites de partenariat. Elle peut ainsi obtenir la garantie de la
régularité et de la qualité de la fourniture
nécessaire à l'entreprise. En ce qui concerne les clients, elle
peut disposer d'un organe de veille qui lui permet de surveiller les signes
d'évolution de la demande. Les moyens déployés pour
limiter les ENS liés aux systèmes de production peuvent consister
en la formation des hommes, le développement d'une maintenance
préventive, etc.
Modelisation du temps de reaction d'un systeme industriel :
Application aux centrales thermiques d'OYOMABANG I et II .
Toutes les mesures ainsi mises en place ne peuvent
empêcher l'apparition de certains ENS tels que: ceux qui sont liés
à des informations manquantes, erronées ou mal exploitées,
ceux qui surviennent au cours de la réalisation des tâches comme
la casse d'un outil ou la panne inopinée d'une machine, etc.
Il est donc indispensable de mettre en place des moyens
palliatifs qui permettent d'assurer l'efficacité de la
réactivité du système pour prendre en charge ces ENS. Une
grande partie de celle-ci est détectée au niveau du
système opérant et peuvent donc être rapidement prises en
charge par le niveau de décision le plus proche de celui-ci.
En général, les travaux effectués sur le
traitement des ENS se concentrent uniquement sur les ENS internes ayant pour
origine les machines de productions. En fonction du plus haut niveau d'impact
de la perturbation, le traitement visera alors à trouver une nouvelle
planification et/ou un nouvel ordonnancement qui soit aussi proche que possible
de ce qui était initialement prévu et appliqué jusque
là, pour atteindre les mêmes objectifs initiaux. Dans ce contexte
plusieurs résolutions sont proposées. Nous citerons quelques unes
:
> Une approche par modification de la planification qui
consiste en des ajustements successifs du planning initial, à partir de
modifications locales et limités des plans de charge des ressources
impliquées ;
> La méthode AHP (Analytic Hierarchy process), qui
est une approche multicritères permettant, lorsqu'on est face à
l'impossibilité de réaliser une tache sur une machine
initialement prévue, de déterminer la « meilleure
»machine pouvant la remplacer. Cette approche intègre
différente indicatrice propre à chaque machine candidate, selon
les critères temps, cout et fiabilité.
> Une approche par séquence de groupe de taches
permutables qui consiste à rechercher un ensemble d'ordonnancement
admissible prédictif.
Lorsque l'ENS est d'origine externe le plus souvent, les
objectifs de production sont remis en cause, et par ricochet la planification
initiale. Le traitement va donc consister à définir de nouveaux
objectifs et donc une nouvelle planification.
Modelisation du temps de reaction d'un systeme industriel :
Application aux centrales thermiques d'OYOMABANG I et II
v.2.2.modélisation du processus.
V.2.2.1) Traitement périodique (ENS sans
arrêt de production).
Lorsqu'un problème technique se pose (appareil
défectueux, panne de machine, incident d'exploitation, etc.),
constaté soit par l'exploitant de la salle de commande, soit lors de la
ronde des exploitants, une demande d'intervention (D.I) est remplie par le chef
de quart et transmise à son supérieur, le chef de service
exploitation, pour validation. Si celui-ci valide la D.I, il la transmet au
chef service maintenance. Ce dernier évalue la gravité du
problème et planifie l'intervention en fonction du degré de
gravité de l'ENS (immédiatement si l'ENS peut interrompre la
production, quelques jours après, ou une semaine après si ce
n'est pas le cas). Ce dernier émet alors le l'ordre de travail, (OT)
correspondant, et la transmet à la section correspondante
(mécanique ou électrique) pour la formation d'une équipe
de travail et l'intervention. L'équipe formée, doit
élaborer une JSA (Job safety Analysis), qui décrit les
étapes de travail, les risques courus, et les précautions
à prendre. Le chef d'équipe présente donc tous les
documents relatif à l'intervention (DI, OT, JSA) au chef de quart qui
les vérifie et initie le permet de travail pour le faire valider par le
chef de la centrale. Ensuite, le chef de la centrale vérifie tous les
documents et signe le permit de travail (PT). Ce n'est qu'après cette
signature que l'équipe de maintenance peut intervenir sur un
équipement. Apres le travail, les maintenanciers signalent le chef de
quart qui clôture le Permet de travail.
N.B: il est à noter pour les
raison de célérité, la signature du permit de travail
à été délégué par le CC. Les chefs
services et le coordonnateur HSE peuvent alors signer le permit de travail.
V.2.2.2) traitement évènementiel
(incident : ENS avec arrêt de production). Lorsqu'un
problème technique se pose lors de la production
d'électricité (lorsque les groupes sont en marchent),
constaté par l'exploitant de la salle de commande, une demande
d'intervention (D.I) est remplie par le chef de quart après avoir mis
hors service l'équipement concerné (consignation). Ce dernier
informe immédiatement : le chef service d'exploitation, le chef de la
centrale, le chef service maintenance, le Grid dispach et essaye de
repérer l'origine du problème. Fait appel aux personnes en
astreintes, pour intervention immédiate tout en respectant toutes les
mesures de sécurités au travail. Le chef de quart est tenu de
rédiger un rapport d'incident qu'il va transmettre à la
hiérarchie.
Modelisation du temps de reaction d'un systeme industriel :
Application aux centrales thermiques d'OYOMABANG I et II .
Après chaque incident, il est prévu une
root causes Analysis: qui est une réunion qui regroupe
tous les acteurs qui entrent en jeu dans le processus de traitement pour faire
une évaluation profonde des causes de l'incident afin d'en tirer les
résolutions pouvant ainsi permettre de prévenir ce genre
d'incident dans le futur.
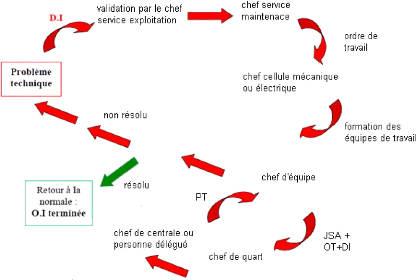
Figure 30 : modélisation du processus de
traitement
V.2.3. modélisation de la dynamique de
traitement des ENS.
Comme nous l'avons mentionné au paragraphe ci-dessus,
le processus de traitement comporte 3 niveaux dans le cas le plus
défavorable et 5 sous-processus. Pour définir les
paramètres de notre modèle, nous avons fait un recensement des
ENS qui ne nécessite pas un arrêt de production et des incidences
pendant la période allant de janvier à juin 2010. Ces
résultats sont consignés dans les tableaux qui suivent :
Modelisation du temps de reaction d'un systeme industriel :
Application aux centrales thermiques d'OYOMABANG I et II .
date
|
installation
|
Description de la tache
|
Début
|
fin
|
Temps
|
05/01/10
|
GRP 203
|
Nettoyage de radiateur
|
08/01/10 à
|
08/01/10 à
|
06H00
|
|
|
|
8H00
|
14H00
|
|
08/01/10
|
GRP 102
|
Étanchéité des Fuites d'eau pipe circuit
|
08/01/10 à
|
08/01/10 à
|
06H50
|
|
|
préchauffé
|
8H00
|
14H50
|
|
18/01/10
|
GRP 102
|
Etanchéité fuite de fuel et resserrage de
|
18/01/10 à
|
13/01/10 à
|
05H30
|
|
|
canalisation fuel
|
8H00
|
13H30
|
|
19/01/10
|
GRP 101
|
Remplacement des pipes hautes pressions
|
19/01/10 à
|
19/01/10 à
|
03H30
|
|
|
cylindre B7
|
8H00
|
11H30
|
|
20/01/10
|
GRP 102
|
Inspection et recherche fuite d'eau et vapeur,
|
20/01/10 à
|
20/01/10 à
|
03H00
|
|
|
poste de visite arbres à cames, resserrages
visserie canalisation retour fuel cylindriques
|
8H00
|
11H00
|
|
25/01/10
|
GRP 102 et
|
Révision des équipements des culasses
|
25/01/10 à
|
25/01/10 à
|
05H00
|
|
GRP 208
|
|
8H00
|
13H00
|
|
23/02/10
|
Pompe HFO
|
nettoyage des filtres pompe dépotage HFO
|
23/02/10
|
24/0/10
|
06H00
|
|
dépotage
|
colmate.
|
8H00-
|
08H00-
|
|
|
|
|
11H00
|
11H00
|
|
01/03/10
|
Porterelle
|
refixer porte local dépotage cassé
|
01/03/10
|
01/03/10
|
06H00
|
|
dépotage
|
|
09H00
|
15H00
|
|
11/03/10
|
Pompe effluent
|
Révision de la pompe effluente.
|
16/03/10
|
16/03/10
|
06H00
|
|
|
|
9H00
|
15H00
|
|
17/03/10
|
Vanne
|
Traitement de la Vanne d'appoint d'eau
|
17/03/10
|
17/03/10
|
02H00
|
|
d'appoint d'eau
|
|
8H00
|
10H00
|
|
24/03/10
|
Pompe
|
Dépose et entretient de la pompe
|
24/03/10
|
24/03/10
|
02H00
|
|
d'appoint
|
|
8H00
|
10H00
|
|
31/03/10
|
Bac de rétention
|
Déboucher la canalisation permettant
|
31/03/10
|
31/03/10
|
03H10
|
|
|
l'écoulement
|
8H00
|
11H10
|
|
08/04/10
|
SEPHF (2)
|
Remplacement des masselottes
|
08/04/10
|
08/04/10
|
02H00
|
|
|
|
8H00
|
10H00
|
|
|
Tableau 4 : traitement des ENS sans interruption de
production
Sources : cahier de programmation et consignations des
travaux mécaniques
date
|
installation
|
Description et causes probables de l'incident
|
Actions menées
|
Début
|
fin
|
Temps
|
18//01/10
|
GRP101
|
Raccord de fixation pipe d'alimentation pompe d'injection
N° B7 dévissé, provoqué probablement suite aux
multiples vibrations.
|
Information de la hiérarchie, établissement
d'une DI, ronde autour du groupe et fixation des raccords de fixation pipe
d'alimentation.
|
20H26min
|
20H48min
|
22min
|
01/02/2010
|
GRP103
|
Importante fuite de combustible au niveau du pipe principal
combustible banc A cylindre A9.les vis de fixation du distributeur de fioul se
seraient desserrées suite probablement aux vibrations.
|
Balisage et consignation du groupe, Information de la
hiérarchie, appel du chef cellule mécanique pour intervention,
intervention effective dans 30min,
|
17H43min
|
20H30
|
2H47 min
|
25/02/10
|
GRP 101
|
Fumée abondante et la présence des flammes au
niveau des turbos compresseurs du groupe. Les causes probables sont, la
projection de combustible sur le turbo et les parties chaudes du groupe
provoquant ainsi des flammes suite à une rupture des vis de fixation du
pipe d'alimentation en combustible du banc B
|
Arrêt d'urgence du groupe, prompte réaction dans
l salle des machines des exploitants et des main tenanciers extincteurs en
mains pour éteindre le feu, arrêt des modules du groupe,
information de la hiérarchie, balisage de la zone et début de
nettoyage du groupe et du sol au provalent, interventions immédiate de
la maintenance mécanique et électrique.
|
16H01min
|
19H01
|
03H00
|
01/03/10
|
GRP 101
|
Arrêt automatique du groupe par déviation d'un
cylindre, causes probables, disfonctionnement du connecteur de sonde du
cylindre B1 qui transmettait de mauvaises valeurs au superviseur.
|
Information de la hiérarchie, appel de du chef cellule
mécanique pou intervention, intervention des exploitant et des
mécaniciens.
|
19H00
|
20H01
|
1H01
|
|
Tableau 5 : traitement des
incidences
Sources : rapports d'incidences.
Modelisation du temps de reaction d'un systeme industriel :
Application aux centrales thermiques d'OYOMABANG I et II .
A partir des tableaux précédant, nous constatons
que :
Les ENS détectés lors du fonctionnement sans
interruption de la production sont traité le lendemain. Et quand il y a
pas d'ENS ce sont les travaux de maintenance planifiés tels que les
visite après un certains nombres d'heures de marche, le nettoyage et
l'entretient de certains équipements. Nous pouvons alors définir
les paramètres de notre modélisation comme suit :
> Unité de temps : minutes
> Date de référence : nous allons prendre
06H00 qui est l'heure de prise de service du 1er quart de la journée qui
travaillera pour préparer la période de pointe. Cette date sera
considérée comme origine de temps : to
> Nous supposons que la date d'occurrence de l'ENS est la
6ème heure après l'heure de référence,
soit 360 minutes : U0.0= 360. Donc à 12 heures. (c'est
une variable qui dépend des ENS, cette valeur est arbitraire et
n'influence aucunement le résultat).
> Les périodes des niveaux sont les suivantes :
ü Après constatation de l'ENS, l'exploitant (chef
de quart) a 5 minutes pour remplir la DI, la transmettre au chef service
exploitation et informer le Grid dispach et le chef de la centrale.
Parallèlement, les équipes d'interventions disposent du
même temps pour remplir la fiche d'évaluation des risques et
transmettre les documents du chantier au chef de quart pour validation du
permit de travail. P0 = 5.
ü Le chef de service exploitation quant à lui a
10 minutes pour vérifier l'effectivité de l'ENS, mesure la
gravité, la valide et la transmet au chef service maintenance.
Parallèlement, les chefs de cellules mécaniques et
électricités ont également le même temps pour former
les équipes de travail quand ils ont reçu l'ordre d'intervention
du chef service de maintenance : P1= 10.
ü Le chef service maintenance lui a 15 minutes pour
valider les suggestions de solutions proposées, planifier
l'intervention, donner l'ordre d'intervention (permis de travail), et
désigner les cellules impliquées pour la résolution du
problème : P2= 15.
> Nous allons initialiser la période de
référence de toutes les périodes à la date de
référence to ainsi, on a :
X0=X1=X2=0.
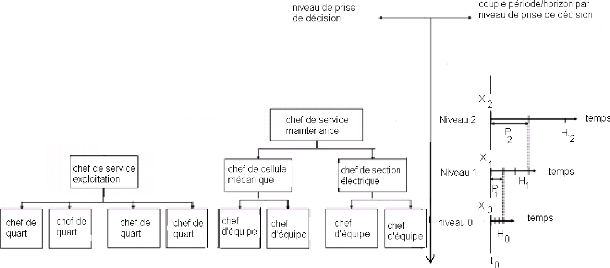
Figure 31 : couple horizon/période par niveau de
prise de décision.
Modelisation du temps de reaction d'un systeme industriel :
Application aux centrales thermiques d'OYOMABANG I et II .
V.2. 4.évaluation du temps de
réaction.
D'après la classification des ENS par ordre de
gravité, il est important de signaler que, compte tenu de notre
processus de traitement, certains ENS trouverons d'embler leur solution
après leur examens par les exploitants et d'autres ayant une
gravité un peu plus grande trouverons leur solutions après
l'examen du chef de service maintenance et/ou avec l'apport du chef de la
centrale. Dans la suite nous allons présenter le temps mis pour le
traitement dans chaque étape et par niveau de prise de décision.
Nous avons la modélisation suivante :
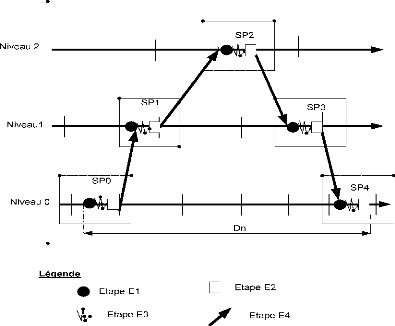
Il est à noter que :
Ce sont les exploitants qui interviennent dans le
sous-processus 0, le chef service exploitation dans le sous-processus 1, le
chef service maintenance dans le sous-processus 2, les chefs de cellules dans
le sous-processus 3 et les équipes de maintenances dans le
sous-processus 4.
|
: Etape E1
|
|
: Etape E3
|
: Etape E4
|
|
: Etape E2
|
Sous-processus 0 (SPo)
|
constatation de l'ENS. Cette étape peut
prendre 1 minute
|
c'est le temps qui s'écoule entre la fin de la
rédaction et le la transmission de la DI ; c'est le temps d'attente.
|
rédaction de la DI par le chef de quart cela peut prendre
3 minutes
|
c'est la transmission de la DI chez le chef d'exploitation cela
peut prendre 2 minutes.
|
Sous-processus1 (SP1)
|
prise en compte de la DI par le chef service exploitation.
Cette étape peut prendre 2 minutes
|
C'est le temps qui s'écoule entre la fin de
l'examination de l'ENS par le chef service exploitation et sa transmission chez
le chef service maintenance : c'est le temps d'attente
|
c'est l'étape ou le chef d'exploitation examine la
gravité de l'ENS et son impact sur la production. Cela peut 5
minutes.
|
c'est la transmission de la DI chez le chef service maintenance
cela peut prendre 2 minutes.
|
Sous-processus2(SP2)
|
prise en compte de la DI par le chef service maintenance, cela
peut prendre 2 minutes
|
c'est le temps qui s'écoule entre la fin de traitement
de la DI et la transmission du PT et de la DI correspondante aux chefs de
cellules : c'est le temps d'attente
|
validation des propositions de solutions proposées pour
la résolution de la DI, planification de l'intervention, et choix des
cellules qui doivent intervenir. cela peut prendre 10 minutes.
|
c'est la rédaction de l'ordre de travail et la
transmission aux chefs de cellules concernées. Cela peut prendre 4
minutes.
|
Sous-processus3(SP3)
|
réception des DI et PT validé par le chef
service maintenance par les chefs de cellules. Cela peut prendre 1 minute
|
temps qui s'écoule entre la formation des
équipes de travail et la mise en leur possession des DI et PT : c'est le
temps d'attentes.
|
Formations des équipes de travail pour l'intervention par
les chefs de cellules. Cela peut prendre 5 minutes
|
transmission des DI et PT aux équipes d'intervention. Cela
peut prendre 3 minutes.
|
Sous-processus4(SP4)
|
réception DI et des PT par les chefs
d'équipes et remplissage de la fiche d'analyse des
risques. Cela peut prendre 2 minutes.
|
temps d'observation du comportement de la
structure réhabilitée : c'est le temps
d'attente.
|
Validation des documents d'intervention par le chef de quart
et intervention. La durée de cette étape dépend de la
gravité de l'ENS. Ici nous allons prendre 3 heures soit 180 minutes.
|
|
Tableau 6 : acti vités dans les sous-processus
en traitement périodique.
Modelisation du temps de reaction d'un systeme industriel :
Application aux centrales thermiques d'OYOMABANG I et II .
Nous pouvons donc résumer les temps des différentes
étapes dans le tableau qui suit :
Sous-processus(i)
|
Durée E1 (di, 1)
|
Durée E3 (di, 3)
|
Durée E4 (di, 4)
|
0
|
1
|
3
|
2
|
1
|
2
|
5
|
2
|
2
|
2
|
10
|
4
|
3
|
1
|
5
|
3
|
4
|
2
|
180
|
|
Tableau 7 : temps d'activite dans les sous-processus
en traitement
periodique.
Comme le temps de réaction du système est la
différence du temps de sortie et du temps d'entrée que nous
connaissons déjà, nous allons donc déterminer le temps de
sortie du système Sn.
U0=360
système
|
paramètre définissant le système
|
sous-processus
|
Xm (0)
|
période Pm
|
Durée di, 1
|
Durée di, 3
|
Durée di, 4
|
SPO
|
0
|
5
|
1
|
3
|
2
|
SP1
|
0
|
10
|
2
|
5
|
2
|
SP2
|
0
|
15
|
2
|
10
|
4
|
SP3
|
0
|
10
|
1
|
5
|
3
|
SP4
|
0
|
5
|
2
|
180
|
|
Tableau 8 : Paramètres du
système
sous-processus i
|
Entrée Ui
|
|
attente di, 2
|
|
synchronisation Ki, n
|
sortie SPI
|
|
SPO
|
|
360
|
|
4
|
73
|
|
370
|
SP1
|
|
370
|
|
8
|
38
|
|
387
|
SP2
|
|
387
|
|
1
|
26
|
|
404
|
SP3
|
|
404
|
|
5
|
41
|
|
418
|
SP4
|
|
418
|
|
0
|
84
|
|
600
|
Tableau 9 : Données initiales
calculées
Modelisation du temps de reaction d'un systeme industriel :
Application aux centrales thermiques d'OYOMABANG I et II .
Pour le calcul des données, nous procédons de la
manière suivante :
Les périodes de synchronisation Ki, n en appliquant la
formule suivante : iki,n=A. si 3 A. e IN
Ut(n)+di,i_xm(o)=APin
/U1 (n)+clio. --Xm(0))
(V-1)
ki,n=E1 +1 sinon
Pm
Après avoir calculé
ki,1 nous calculons alors la sortie du
sous-processus Si(n) de la manière suivante :
Si(n) = Xm(0) + ki,1 X
Pm + ? l=3clij (V-2)C'est à partir de la
que nous pouvons alors calculer les temps d'attente du sous processus ainsi
qu'il suit :
c11,2 = Si(n) -- (Ui(n) + ? jEti,3,41 di,i)
(V-3)
Nous pouvons donc calculer toutes les données du tableau
précédent quant on sait que la sortie du sous-processus n est
l'entrée du sous-processus n+1.
Modelisation du temps de reaction d'un systeme industriel :
Application aux centrales thermiques d'OYOMABANG I et II .
V.2.5.expression du temps de réaction du
système.
Nous avons établi plus haut que :
Dn = S2N(n) -- U0(n) (V-4)
D'après le tableau 9, nous avons : S2N(n)
= 600 et U0 ( n)= 360 Nous pouvons donc déduire que
:
Dn=240
V.3.Optimisation des temps d'attente suite à un
évènement non souhaité (ENS).
V.3.1.Evaluation des temps d'attentes dans le processus.
D'après le tableau 4, nous avons évalué
les temps d'attentes dans tous les sous-processus. Nous allons donc faire une
somme de ses temps d'attentes pour avoir le temps d'attente du processus qui
fera l'objet de réduction, voir de suppression dans le meilleur des
cas.
Nous avons alors dans le cas précédent :
E di,2= 18.
V.3.2 .Application de l'algorithme de réduction des
temps d'attente.
Dans cette partie nous allons réduire les temps d'attentes
dans le processus de traitement de l'ENS.
Le processus initial nous présente la configuration
suivante :
RESULTATS
|
VARIABLES
|
do, 2
|
di, 2
|
d2, 2
|
d3, 2
|
d4, 2
|
S(n)
|
Dn
|
Tat
|
Xo(o)
|
Xi(o)
|
X2(o)
|
4
|
8
|
1
|
5
|
0
|
600
|
240
|
18
|
0
|
0
|
0
|
Tableau 10 : configuration initiate
Modelisation du temps de reaction d'un systeme industriel :
Application aux centrales thermiques d'OYOMABANG I et II .
Niveau 0 : sous-processus i=0 et i=4 (SP0 et SP4).
Nous avons min ( 4,2;E,2) = min
(4 ; 0) = 0
Donc pas besoin d'ajuster la date de début de
période de référence de ce niveau. Nous conservons alors
la configuration de départ :
RtSULTATS
|
VARIABLES
|
do, 2
|
di, 2
|
d2, 2
|
d3, 2
|
d4, 2
|
S(n)
|
Dn
|
Tat
|
Xo(o)
|
Xi(o)
|
X2(o)
|
4
|
8
|
1
|
5
|
0
|
600
|
240
|
18
|
0
|
0
|
0
|
Tableau 11 : reduction du temps ni veau 0 Niveau 1 :
sous-processus i=1 et i=3 (SP1 et SP3).
Nous avons min ( d1,2;d3,2) =
min (8 ; 5) = 5
De plus X1(n) = 0 ; on a bien 520 donc min
( d1,2;d3,2) 2
X1(n) D'où X1(n) = P1 +
(X1(n)- min
(d1,2;d3,2)) = 10 + (0
- 5) = 5.
Donc X1(n)= 5 Nous allons faire un nouveau
calcul des données qui sont résumés dans le tableau
suivant :
RtSULTATS
|
VARIABLES
|
do, 2
|
di, 2
|
d2, 2
|
d3, 2
|
d4, 2
|
S(n)
|
Dn
|
Tat
|
Xo(o)
|
Xi(o)
|
X2(o)
|
4
|
3
|
6
|
0
|
0
|
595
|
235
|
13
|
0
|
5
|
0
|
Tableau 12 : reduction du temps ni veau 1 Niveau 2 :
sous-processus i=2(SP2).
Nous avons d2,2= 6 ? 0
De plus X2(n) = 0 ; on a bien 6 20 donc
d2,2? X2(n)
D'où X2(n) = P2 +
(X2(n) -d2,2) = 15 + (0 - 6) =
9
Donc X2(n) = 9. Nous allons alors faire un
nouveau calcul des données qui sont résumés dans le
tableau suivant :
Modelisation du temps de reaction d'un systeme industriel :
Application aux centrales thermiques d'OYOMABANG I et II .
RtSULTATS
|
VARIABLES
|
do, 2
|
di, 2
|
d2, 2
|
d3, 2
|
d4, 2
|
S(n)
|
Dn
|
Tat
|
Xo(o)
|
Xi(o)
|
X2(o)
|
4
|
3
|
0
|
6
|
0
|
595
|
235
|
13
|
0
|
5
|
9
|
Tableau 13 : réduction du temps ni veau
2
RECAPITULATIF
niveau m
|
|
RtSULTATS
|
VARIABLES
|
|
|
do, 2
|
di, 2
|
d2, 2
|
d3, 2
|
d4, 2
|
S(n)
|
Dn
|
Tat
|
Xo(o)
|
Xi(o)
|
X2(o)
|
initiale
|
|
4
|
8
|
1
|
5
|
0
|
600
|
240
|
18
|
0
|
0
|
0
|
|
0
|
4
|
8
|
1
|
5
|
0
|
600
|
240
|
18
|
0
|
0
|
0
|
|
1
|
4
|
3
|
6
|
0
|
0
|
595
|
235
|
13
|
0
|
5
|
0
|
|
2
|
4
|
3
|
0
|
6
|
0
|
595
|
235
|
13
|
0
|
5
|
9
|
Tableau 14 : récapitulatif.
Finalement, nous avons alors :
V.3.3. Interprétation des résultats.
Ces résultats nous permettent de reconfigurer le
processus de traitement périodique des ENS. Nous pouvons déduire
que : Quand l'incident survient, pour atteindre cette réactivité,
les exploitants commencent leur intervention directement au début de
l'origine des temps considéré. Donc à 6 heures dès
leur prise de service. Ils doivent systématiquement faire l'inventaire
des équipements. Le chef service exploitation quant à lui doit
commencer son travail 5 minutes après que les exploitants aient
commencés. Le chef service maintenance lui doit faire son intervention 9
minutes après celui des exploitants et 4 minutes après celui du
chef service exploitation.
Il est à noter que cette modélisation nous
permet d'effectuer un gain de 5 minutes sur le temps de réaction. Et que
ce temps est le même pour les évènements de la même
classes. Ces classes sont donc déterminées en fonction du temps
mis pour implémenter la solution : c'est en fonction de la
gravité de l'ENS.
Modelisation du temps de reaction d'un systeme industriel :
Application aux centrales thermiques d'OYOMABANG I et II .
V.4. Traitement évènementiel.
Comme nous l'avons présenté plus haut dans le
traitement évènementiel, il n'est pas question de perdre de
temps, il faut agir immédiatement. Pour cela, nous allons utiliser la
modélisation précédente, mais en supprimant tous les temps
d'attentes. Pour l'optimisation du temps de réaction dans ce cas, nous
allons ajuster les di,G en supprimant également les
étapes qui ne sont pas nécessaires.
V.4.1. Suppression des temps
d'attentes.
Nous avons :
Dn = (? LN0-1? je{1,3,4} dij + ?
je{1,3,} d2N ,j) + ? .-Ivo 42 (V -5)
En évènementiel, ?
i_No dc2=0. On peut donc avoir dans notre cas
:
Dn = 222
V.4.2. Ajustement des temps des différentes
étapes.
Dans la suite nous allons présenter les
différentes étapes et leurs ajustements en traitement
évènementiels. Ainsi à partir du tableau 5 qui fait un
inventaire de la manière de traiter des incidences qui sont en fait des
ENS qui nécessite un traitement évènementiel, nous
pouvons, recenser les différentes actions menées par les agents
de la centrale lorsqu'un ENS survient et interrompt la production :
ü Arrêt d'urgence de l'installation (consignation et
balisage pour les groupes) : cette action se fait de façon
immédiate après constation de la défaillance.
ü Information de la hiérarchie et du Grid dispach :
cette action se fait par les moyens de communication qui sont disponibles dans
la salle de commande.
ü Appel des personnes astreintes pour intervention : les
personnes en astreintes ont une marge de 15 minutes avant de s'y rendre, pour
l'intervention, car la majorité des agents habitent dans le quartier ou
se trouve la centrale.
|
: Etape E1
|
|
: Etape E3
|
: Etape E4
|
|
|
|
constatation de l'ENS. Cette étape peut prendre 1
minute
|
Le temps d'attente est nul
|
rédaction de la DI par le chef de quart cela peut prendre
3 minutes
|
Information des différents responsables et des
personnes astreintes cela peut se faire en 5 minutes.
|
Sous-processus1 (SP1)
|
|
Le temps d'attente est nul
|
|
|
Sous-processus2(SP2)
|
|
Le temps d'attente est nul
|
|
C'est le temps ou le chef service de la maintenance donne des
instructions aux personnes astreintes. 2 minutes
|
Sous-processus3(SP3)
|
Le temps ou l'on attend l'arrivée des personnes
astreints environ 15 minutes
|
Le temps d'attente est nul
|
Elaboration de la fiche d'analyse de risque. Environ 3
minutes
|
|
Sous-processus4(SP4)
|
Validation du permit de travail
provisoire par le chef de quart 1 minutes.
|
Le temps d'attente est nul.
|
Traitement de la défaillance par les équipes
techniques. Cette action dépend aussi de la gravité de la
défaillance. Nous prendrons 180 minutes.
|
|
|
Tableau 15 : activités dans les
sous-processus en traitement événementiel.
Modelisation du temps de reaction d'un systeme industriel :
Application aux centrales thermiques d'OYOMABANG I et II .
Après nous avons alors la nouvelle configuration suivante
:
Sous-processus(i)
|
Durée E1 (di, 1)
|
Durée E3 (di, 3)
|
Durée E4 (di, 4)
|
0
|
1
|
3
|
5
|
1
|
/
|
/
|
/
|
2
|
/
|
/
|
2
|
3
|
15
|
3
|
/
|
4
|
1
|
180
|
/
|
|
Tableau 16 : temps d'activite dans les
sous-processus en traitement
evenementiel.
Nous avons alors le nouveau temps de réaction :
Dn = 210
V.5.Implémentation de la réactivité
aux centrales thermiques d'Oyomabang I et II.
V.5.1. analyses des causes de non
réactivité et des leviers d'actions
Cette analyse a été faite à partir des
analyses des rapports d'incidences, et des cahiers de programmation des travaux
mécaniques. Nous avons également pris en compte les
réponses des questions que les chefs de quart, ont bien voulu nous
accordé relatif aux traitements des incidences. Nous allons utiliser un
diagramme d'ISHIKAWA, qui est un diagramme causes-effets. Ce dernier nous
permettra de déceler les causes de retards d'intervention suite à
un ENS qui survient. Nous avons donc le diagramme d'Ishikawa ci-après
:
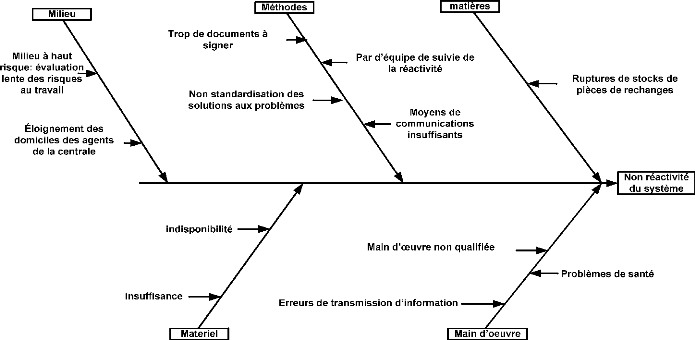
Figure 32: diagramme d'Ishikawa
Modelisation du temps de reaction d'un systeme industriel :
Application aux centrales thermiques d'OYOMABANG I et II .
V.5.2. amélioration de la
réactivité
La centrale pourrait mettre sur pied un groupe (constitué
de 2 membres de chaque services) de suivi et d'amélioration de la
réactivité qui aura pour mission de :
ü Mettre sur pied les indicateurs de performances de
réactivité
ü Mettre sur pied un système d'information fiable,
notamment concevoir des tableaux de bord et les mettre à la disposition
des agents.
ü Classer les différents incidents et travaux en
fonction de leur gravité et des solutions proposés pour faciliter
le passage du réfléchi au reflexe.
V.5.2.1. Indicateurs de performances de
réactivités
A partir de l'objectif principal qui est de diminuer au
maximum le temps de réaction du système suite à un
évènement non souhaité pouvant ainsi perturber, production
à la demande du Grid dispach des 18MW pour la centrale d'Oyomabang I et
des 13MW pour la centrale d'Oyomabang II. Ainsi le tableau qui suit
présente, l'identification des objectifs, des variables de
décision et des indicateurs de performance : c'est un tableau GRAI.
Contrôle de réactivité
|
Objectifs
|
· Assurer le respect des instructions assurant une
meilleure réactivité
|
Variables de décision
|
· La Disponibilité des tableaux de bord
d'informations affichés dans l'entreprise,
· Le niveau de formation et de professionnalisme des
ressources humaines,
· Une bonne stratégie de transfert du
réfléchi au reflexe
|
Indicateurs
|
· Délai de réaction en fonction de la
gravité des évènements.
|
Evaluer la fiabilité des ressources
|
Objectifs
|
· S'assurer du bon état des équipements de la
centrale
|
Variables de décision
|
· Contrôle des équipements
|
Indicateurs
|
· Indice de fiabilité des équipements
· Taux de visites techniques en cours de validité
|
Opérations de maintenance
|
Objectifs
|
· Assurer la maintenance des équipements
|
Variables de décision
|
· Ampleur des activités de maintenance
|
Indicateurs
|
· Taux d'opération de maintenance ;
· Temps de maintenance.
· Taux de défaillance des équipements
|
|
Tableau 17 : identifications des indicateurs de
réactivités.
Modelisation du temps de reaction d'un systeme industriel :
Application aux centrales thermiques d'OYOMABANG I et II .
V.5.2.2. descriptions des indicateurs de
performances.
> Délai de réaction en fonction
de la gravité des évènements. :
présente les différents incidents que l'on peut rencontrer par
équipement et leur temps de réaction, estimé tel que
présenté plus haut. Ainsi, l'on pourra avoir des tableaux tels
que ci-dessous correspondant à Chaque classe d'évènement
non souhaité:
équipement
|
Description
|
Causes de la
|
Solution à cette panne
|
Ressources
|
Temps de
|
Nombre de
|
|
de la panne
|
panne
|
|
humaines qualifiées
|
réaction (min)
|
fois survenu
jusqu'à lors.
|
GRP 101
|
Déviation base
moyenne température cylindre B7
|
Raccord de
fixation pipe
d'alimentation dévissé
|
Imbibition de provalent au niveau des cylindres
concernés
|
exploitants
|
15
|
5
|
GRP 103
|
Fuite de
combustible au niveau du pipe
principale
|
Vis du
distributeur de
fioul desserrées
|
Imprégnation de
provalent au niveau du hot box
|
mécaniciens
|
165
|
2
|
Tableau 18 : fiche d'identification et de traitements
des ENS
> Les indicateurs de performances concernant la
fiabilité des équipements et de la maintenance, permettent de
mettre sur pied des réactions prédictives. Pour y parvenir l'on
peut faire une analyse FMD qui a pour objectif d'identifier les
équipements vitaux, importants et secondaire. Nous pouvons alors
définir un tableau tel que ci-dessous, qui montre un aperçu des
arrêts machine et la durée associée d'une part ; d'autre
part les pertes en termes de production. Elles peuvent être
évaluées à partir des heures de non production et de la
production horaire moyenne.
Equipement
|
Nombre de défaillances (BM)
|
Durée totale (heures)
|
Durée Moyenne (hrs/panne)
|
Perte en terme s production de
(MWH)
|
GRP 101
|
35
|
109
|
3,12
|
16 218,7
|
GRP 103
|
57
|
64
|
1,12
|
9 476,8
|
|
|
|
|
|
TOTAL
|
|
|
|
25695,5
|
Tableau 19 : analyse FMD de la
centrale.
Modelisation du temps de reaction d'un systeme industriel :
Application aux centrales thermiques d'OYOMABANG I et II .
V.5.2.3. contributions. Il
est important de noter que, d'après notre étude, la centrale se
comporte plutôt bien en
traitement périodique car le gain en temps de
réaction n'est que de 5 minutes sur une durée de traitement de
120 à 180 minutes. Par contre il y a beaucoup à faire en
traitement évènementiel. Hors mis la modélisation faite
qui nous permet de gagner près de 30 minutes sur le traitement de 120
à 180 minutes, nous allons proposer dans la suite un ensemble de mesure
qui permettront d'améliorer de façons continuelle la
réactivité de la centrale.
Dans le paragraphe précédent, nous avons
définit les causes de non réactivités du système.
Dans la suite, nous allons proposer quelques solutions pour palier à
ces difficultés. Nous avons ainsi :
Les fiches que nous proposons précédemment, nous
permettent de résoudre simultanément les problèmes de
méthodes et une partie des problèmes de ressources humaines.
Cette actions permet de réduire de prime abord au moins 4 minutes du aux
rédactions des différents documents et surtout de réduire
le temps de diagnostique de la panne que nous ne pouvons pas estimer avec
précision, mais on peu évaluer ses gain à plus de 10
minutes.
Les indicateurs de performances qui permettent de mettre sur
pied des réactions prédictives, résolvent le
problème d'indisponible, d'insuffisance et de rupture de stocks du
matériel de rechange.
Par contre les personnes en astreintes peuvent rester dans la
centrale et travailler dans les périodes de pointe (18H-22H30) pour
réduire le temps d'attentes du départ de chez eux jusqu'à
la centrale. Pour assurer leur sécurité un véhicule peut
les raccompagner dans leurs domiciles respectifs. Cette action peut nous
permettre de réduire 15 minutes dans le traitement
évènementiel.
On se rend bien compte qu'en mettant sur pied ses mesures l'on
peut encore gagner au moins 29 minutes dans le traitement
évènementiel de 120 à 180 minutes.
Modelisation du temps de reaction d'un systeme industriel :
Application aux centrales thermiques d'OYOMABANG I et II .
CONCLUSION GENERALE
Le travail qui s'achève portait sur la modélisation
du temps de réaction d'un système industriel appliqué aux
centrales d'oyomabang I et II.
Pour y parvenir, nous avons :
> Défini les systèmes industriels.
> Défini un model décisionnel : le model
décisionnel GRAI,
> Modéliser le système décisionnel d'un
système hiérarchisé,
> Définir le mode de traitement périodique,
> Définir le mode de traitement
évènementiel
> Evaluer le temps de réaction dans les
différents modes de traitement,
> Optimiser ce temps de réaction en minimisant les
temps d'attentes,
> Optimiser ce temps d'attentes en supprimant certaines
étapes de traitement jugé pas nécessaires,
> Proposer la mise sur pied d'une équipe de suivie
de la réactivité et la mise sur pied d'indicateurs de
réactivités qui vont contribuer à construire un
système intelligent de gestion des ENS.
Comme amélioration continue de la
réactivité, ces indicateurs de réactivités nous
permettront de gérer et contrôler la réactivité, de
prévoir et d'analyser les effets des défaillances sur le long
terme. Pouvant ainsi permettre une planification prédictive de la
maintenance.
A partir de cette modélisation nous gagnons au moins
cinq (05) minutes en traitement périodique, et plus de
trente (30) minutes en traitement évènementiel
des ENS, sur une durée de traitement qui oscille entre 120 et 180
minutes.
Aussi, nous avons évoqué les gains potentiels
qu'aurait la centrale en terme de temps de traitement des ENS dans ce type de
traitement, dont le résultat le plus attendu est l'augmentation de la
disponibilité des équipements et la réaction prompte et
sereine face aux ENS.
Modelisation du temps de reaction d'un systeme industriel :
Application aux centrales thermiques d'OYOMABANG I et II .
BIBLIOGRAPHIE
[1] Lucien MEVA'A, cours de gestion de la
maintenance, ENSP-Yaoundé3GIM, 2007
[2] Jean Baptiste MENYE, Etude de la
promptitude d'un système de pilotage de production travaillant en
régime périodique, Mémoire de D.E.A, Université
Bordeaux 1/LAP, 2002/2003.
[3] P. REGNIER, conduite réactive des
systèmes de production : intégration des régimes
périodique et évènementiel, thèse,
Université de bordeaux1, 1998.
[4] Aline CAUVIN, Analyse,
modélisation et amélioration de la réactivité des
systèmes de décision dans les organisations industrielles : Vers
une aide à la conduite des processus d'entreprise dans un contexte
perturbé, Thèse, Université Paul
Cézanne Aix-Marseille III, 13 Juillet 2005.
[5] Jean NGANHOU, cours de gestion de la
maintenance industrielle, ENSPYaoundé-4GM, 2008.
[6] Eric DUVIELLA, Conduite réactive
des systèmes dynamiques étendus à retards variables. Cas
des réseaux hydrographiques, thèse, Institut national
polytechnique de Toulouse, 17 juin 2005.
[7] I. FILIPAS, G. DRAGHICI, A. EL MOUDNI, N. ZERHOUNI,
Démarche de pilotage pour améliorer la
réactivité industrielle, publication scientifique
[8] JULIEN FRANCOIS, Planification des
chaînes logistiques : Modélisation du système
décisionnel et performance, thèse, Université de
Bordeaux1, 17 décembre 2007.
[9] Thierry LATTANZIO, caractérisation
des entreprises organisées en «gestion par affaire»,
thèse, École Nationale Supérieure d'Arts et
Métiers, 26 octobre 2006.
[10] Assistance au Ministère de l'Energie et
de l'Eau dans l'élaboration du Plan de Développement à
long terme du Secteur de l'Électricité Horizon 2030 (PDSE
2030), rapport final, volume 3 : offre de production, mars 2006.
Modelisation du temps de reaction d'un systeme industriel :
Application aux centrales thermiques d'OYOMABANG I et II .
[11] JL CERVETTI, APD de l'Aménagement
Hydroélectrique de LOM PANGAR Etudes économiques et
financières, COYNE et BELLIER, janvier 2008.
[12] Philippe LAVACHERY, étude
environnementale du barrage de LOM PANGAR, ISL - OREADE-BRECHE - SOGREAH, juin
2005.
[13] T. TAMO TATIETSE, A. KEMAJOU, B.S.
DIBOMA, offre d'électricité et
développement des entreprises industrielles au CAMEROUN, publication
scientifique,
[14] VALERIE ZILLE, Modélisation et
évaluation des stratégies de maintenance complexes sur des
systèmes multi-composants, Université de Technologie de Troyes,
Institut Charles Delaunay, 28 janvier 2009.
[15] AES-SONEL : CENTRALE THERMIQUE
D'OYOMABANG, cahier de programmation des taches mécaniques,
2010.
Modelisation du temps de reaction d'un systeme industriel :
Application aux centrales thermiques d'OYOMABANG I et II .
ANNEXE : APPLICATION SOUS EXCEL
Dans cette annexe, nous allons présenter une
application que nous avons conçue et réalisée sous Excel
(VBA), nous permettant d'effectuer rapidement le calcul après avoir
modéliser notre système.
Ainsi, après ouverture du fichier Excel voici l'interface
de l'application :
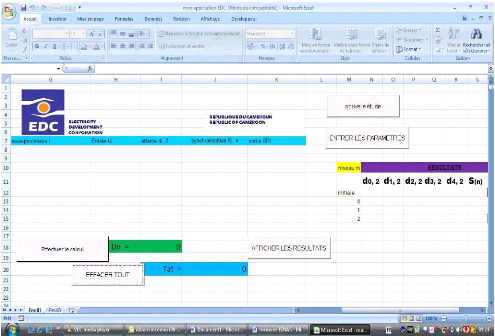
Nous allons présenter les différentes étapes
nous permettant ainsi d'effectuer le calcul.
Modelisation du temps de reaction d'un systeme industriel :
Application aux centrales thermiques d'OYOMABANG I et II .
La commande ci-après nous permet de tout initialiser. Donc
mettre à zéro toutes les cases.
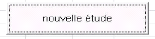
La commande ci-après nous permet d'entrer les
paramètres définissant le système à travers
l'ouverture d'une boite de dialogue.


Voici donc comment se présente la boite de dialogue qui
nous permettra d'entrer les paramètres du système.
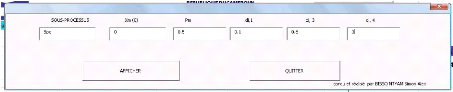
Voici comment se présente la boite de dialogue
après avoir remplit les paramètres du système.
Les paramètres sont stockés et classés au
fur et à mesure qu'ils sont remplit dans la boite de dialogue, comme
l'indique la figure ci-dessous.
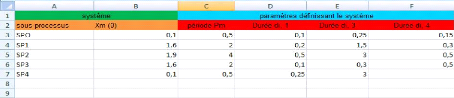
Modelisation du temps de reaction d'un systeme industriel :
Application aux centrales thermiques d'OYOMABANG I et II .
Après avoir remplit les paramètres du
système, on peut alors effectuer le calcul. La commande ci-dessous nous
permet d'ouvrir une boite de dialogue qui va nous permettre d'effectuer le
calcul.
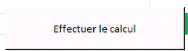
La boite de dialogue se présente donc ainsi qu'il suit
:
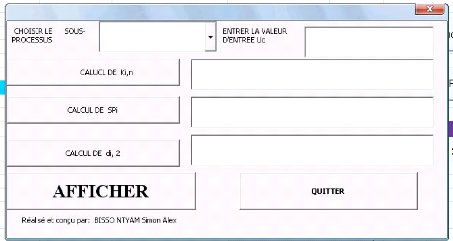
Nous effectuons le calcul en entrant une seule valeur ; qui est
celle de U0( n) .Nous calculons
alors tour à tourki,1 ,
Spi,di,2 tout en s'assurant au préalable que
ki,n est une valeur entière tel que
défini par la méthode. En fait l'application, nous calcule la
valeur suivante :
Ui (n) + di,i -- Xm(0)
Pm
C'est donc à nous de l'ajuster comme le stipule dans la
formule de calcul.
Modelisation du temps de reaction d'un systeme industriel :
Application aux centrales thermiques d'OYOMABANG I et II .
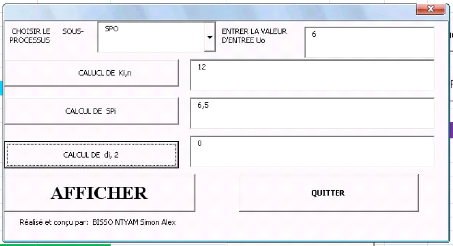
Après avoir parcouru tous les sous-processus, les
résultats s'affichent ainsi qu'il suit :
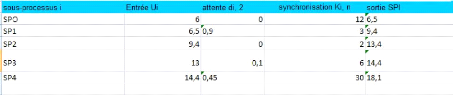
Nous pouvons donc lire, directement les valeurs de Dn et la somme
des temps d'attentes du système.
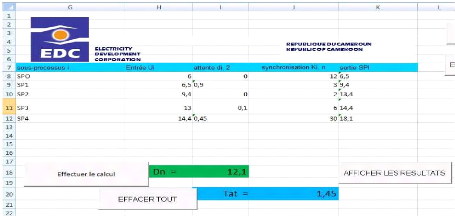
Modelisation du temps de reaction d'un systeme industriel :
Application aux centrales thermiques d'OYOMABANG I et II .
Comme le but de notre calcul est l'évaluation des temps
d'attentes dans le système, nous allons alors utiliser la commande
suivante pour les afficher.

Les résultats vont donc s'afficher au fur et à
mesure que nous allons appliquer l'algorithme de réduction des temps
d'attentes.
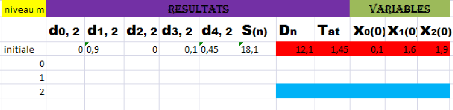
En définitive, nous pourrons donc avoir les
résultats consignés dans un tableau tel que
présenté ci-dessous. Nous avons alors la configuration initiale
en rouge et la configuration finale en bleue. C'est cette dernière que
nous devons considérer pour améliorer la réactivité
du système en fonctionnement périodique.
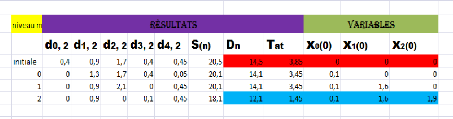
|