Dédicaces

A Vous,mes chers parents, pour votre soutien moral et
financier,
A vous, mes chères soeurs : Samira,
Chadia, Karima, Amina, Latifa et la petite Assiya pour votre sympathie et amour
inconditionné,
A toi, cher Oncle Mohammed pour tes conseils et ton
soutien,
A toi, ma famille pour ton souci et ta
disponibilité,
A toi, Imane, qui sait mieux que tout autre ce que le mot
« TFE » signifie, pour ta disponibilité et ton
soutien moral inconditionné,
A vous, mes amis pour votre entraide et
solidarité,
je dédie ce modeste travail, signe de
reconnaissance et de sentiments partagés.
Je vous dis, tous, merci de m'avoir donné le
courage d'aller jusqu'au bout.
Azddine
Avant propos
Étant donné l'ampleur de
l'alcali-réaction, comme phénomène attaquant les grandes
structures en béton, le comité de recherches scientifiques
n'épargne aucun effort pour y faire face. De ce fait, la tendance vers
l'exploitation et l'utilisation des ajouts minéraux, pour inhiber ces
réactions, s'est accentuée.
L'objectif de notre étude va de paire avec cette
tendance : l'ajout choisi est les cendres volantes, le but que l'on s'est
fixé est l'évaluation de l'impact de cet ajout sur l'inhibition
des réactions alcali-granulats.
Afin de remplir une telle finalité, un nombre optimal
de mélange, à différents dosages en cendres volantes, a
été réalisé à base des « plans
d'expériences ».Ces mélanges ont servi, par la suite,
à une série d'essais d'autoclavage. Les résultats, tout
processus expérimental réalisé minutieusement, ont
été satisfaisants : on est parvenu avec 50% de cendres
volantes (et 50% de Clinker broyé gypsé) à diminuer
l'expansion de 0.15% en absolu. Cependant, ces ajouts agissent
négativement sur la résistance du béton. Ainsi, faut-il
trouver un compromis entre les deux contraintes : résistance
normative et expansion moindre. La réalisation d'une formulation du
« ciment optimal » s'est avérée une solution
judicieuse.
Table des matières
CHAPITRE I: L'ALCALI-RÉACTION
10
I- 1: APERÇU HISTORIQUE
10
I- 2: DÉFINITION
10
I- 3: CONDITIONS D'APPARITION DE
L'ALCALI-GRANULAT
10
I-3-1: Alcalins
11
I-3-2: Silice
12
I-3-3: Environnement
12
I- 4: MÉCANISME DE
L'ALCALI-RÉACTION
13
I- 5: DÉSORDRES DUS À
L'ALCALI-RÉACTION
15
I- 6: PRÉVENTION DE L'ALCALI
RÉACTION
16
I-6-1: Démarche préventive
[10]
16
I-6-2: Bilan des alcalins
17
I-6-3: Utilisation des ajouts
minéraux
17
CHAPITRE II: CHOIX ET CARACTÉRISATION
DES MATÉRIAUX
19
II- 1: GRANULATS : BASALTE
19
II- 2: CENDRES VOLANTES
20
II-2-1: Définition
20
II-2-2: Aperçu historique
20
II-2-3: Composition
20
II-2-4: Production marocaine des cendres
volantes
21
II-2-5: Utilisation des cendres volantes
22
II- 3: CLINKER GYPSÉ BROYÉ(CBG)
23
II- 4: LES FILLERS CALCAIRES
24
II-4-1: Définition
24
II-4-2: Normalisation
24
II-4-3: Avantages
24
II-4-4: Inconvénients
24
II- 5: EAU DE GÂCHAGE
24
CHAPITRE III: PLANS
D'EXPÉRIENCES - PRÉPARATION DES MÉLANGES
25
III- 1: LES PLANS D'EXPÉRIENCES
[18]
25
III-1-1: Définition
25
III-1-2: Terminologie
25
III-1-3: Méthodologie des plans
d'expériences
26
III-1-4: Différents types de plans
d'expériences
28
III-1-5: Outils de calcul
30
III- 2: PRÉPARATION DES MÉLANGES
33
III-2-1: Essai d'expansion
33
III-2-2: Essais de résistance
36
CHAPITRE IV: ESSAIS ET RÉSULTATS
37
IV- 1: ESSAI ACCÉLÉRÉ SUR
MORTIER PAR AUTOCLAVAGE [5]
37
IV-1-1: Présentation
37
IV-1-2: Matériaux soumis à
l'essai
37
IV-1-3: Exécution de l'essai
38
IV-1-4: Expression des résultats
40
IV-1-5: Résultats
41
IV- 2: ESSAIS DE RÉSISTANCE [19]
42
IV-2-1: Présentation
42
IV-2-2: Exécution de l'essai
42
IV-2-3: Résultats
42
CHAPITRE V: MODÉLISATION ET
INTERPRÉTATION
44
V- 1: ANALYSE ET COMMENTAIRE DES
RÉSULTATS
44
V-1-1: Effet des cendres volantes sur
l'expansion
44
V-1-2: Effet des cendres volantes sur la
résistance
46
V- 2: MODÉLISATION :
48
V-2-1: Validité des
modèles :
49
V-2-2: Vérification et Exploitation des
trois modèles
49
V- 3: INTERPRÉTATION DES
RÉSULTATS
58
V- 4: OPTIMISATION
59
V-4-1: CPZ(A) 35
59
V-4-2: CPZ(A) 45
59
V-4-3: CPZ(B) 35
60
V-4-4: CPZ(B) 45
60
V-4-5: Ciment spécial pour
éliminer l'expansion
61
Conclusions et Recommandations
62
Annexe 1 : La soude ajoutée
64
Annexe 2 : Résultats d'expansion
65
Annexe 3 : La résistance à la
compression
68
Annexe 4 : La résistance à la
traction
69
Annexe 5 : Modélisation de la
résistance en traction et en compression
70
Références bibliographiques :
79
LISTE DES TABLEAUX :
TABLEAU 1 : COMPOSITION DES CENDRES VOLANTES
MAROCAINES ET SPÉCIFICATIONS DE LA NORME NF P18-505.
22
TABLEAU 2 : ANALYSE DE LA VARIANCE
32
TABLEAU 3 : MATRICE DES EXPÉRIENCES POUR
L'ESSAI D'AUTOCLAVAGE.
35
TABLEAU 4 : MÉLANGES
SUPPLÉMENTAIRES POUR L'ESSAI D'AUTOCLAVAGE
35
TABLEAU 5 : MATRICE DES EXPÉRIENCES POUR
L'ESSAI DE RÉSISTANCE
36
TABLEAU 6 : RÉPARTITION DES GRANULATS
UTILISÉS DANS L'ESSAI D'AUTOCLAVAGE
37
TABLEAU 7 : BILAN DES ALCALINS
38
TABLEAU 8: RÉSULTATS MOYENS DE L'EXPANSION
MOYENNE SUR TROIS ÉPROUVETTES 4*4*16
41
TABLEAU 9 : RÉSISTANCES MOYENNES À LA
COMPRESSION À 2, 7 ET À 28 JOURS
42
TABLEAU 10 : RÉSISTANCES MOYENNES À LA
TRACTION À 2, 7 ET À 28 JOURS
43
TABLEAU 11 : RECHERCHE DE BIAIS DES TROIS
MODÈLES
49
TABLEAU 12 : TEST DE FIABILITÉ DES TROIS
MODÈLES
49
TABLEAU 13 : TEST DE SIGNIFICATION POUR LE
MODÈLE LINÉAIRE
50
TABLEAU 14 : TEST DE SIGNIFICATION POUR LE
MODÈLE QUADRATIQUE
52
TABLEAU 15 : TEST DE SIGNIFICATION POUR LE
MODÈLE SPÉCIAL CUBIQUE
55
TABLEAU 16: LA SOLUTION OPTIMALE POUR UN CIMENT
CPZ(A)35
59
TABLEAU 17 : LA SOLUTION OPTIMALE POUR UN CIMENT
CPZ(A)45
60
TABLEAU 18 : LA SOLUTION OPTIMALE POUR UN CIMENT
CPZ(B)35
60
TABLEAU 19 : LA SOLUTION OPTIMALE POUR UN CIMENT
CPZ(B)45
61
TABLEAU 20: CIMENT SPÉCIAL POUR ANNULER
L'EXPANSION.
61
TABLEAU 21: RÉCAPITULATIF DES CIMENTS
SPÉCIAUX POUR FAIRE FACE À L'ALCALI-RÉACTION.
62
TABLEAU 22: LA QUANTITÉ DE LA SOUDE
AJOUTÉE À CHAQUE MÉLANGE
64
TABLEAU 23: RÉSULTATS DÉTAILLÉS
DE L'EXPANSION
66
TABLEAU 24: COMPARAISON DES VALEURS CALCULÉES
ET CELLES MESURÉES DE L'EXPANSION
67
TABLEAU 25 :
RÉSULTATS DÉTAILLÉS DE LA RÉSISTANCE À LA
COMPRESSION À 2, 7 ET À 28JOURS
68
TABLEAU 26 : RÉSULTATS
DÉTAILLÉS DE LA RÉSISTANCE À LA TRACTION À
2, 7 ET À 28 JOURS
69
TABLEAU 27: RECHERCHE DU BIAIS (RC2J)
70
TABLEAU 28: TEST DE FIABILITÉ (RC2J)
70
TABLEAU 29: TEST DE SIGNIFICATION
70
TABLEAU 30: COMPARAISON ENTRE LES VALEURS DE LA
RÉSISTANCE À LA COMPRESSION À 2 JOURS CALCULÉES PAR
LE MODÈLE LINÉAIRE ET LES VALEURS MESURÉES
71
TABLEAU 31: RECHERCHE DU BIAIS (RC7J)
71
TABLEAU 32: : TEST DE FIABILITÉ (RC7J)
71
TABLEAU 33: TEST DE SIGNIFICATION
72
TABLEAU 34: COMPARAISON ENTRE LES VALEURS DE LA
RÉSISTANCE À LA COMPRESSION À 7 JOURS CALCULÉES PAR
LE MODÈLE QUADRATIQUE ET LES VALEURS MESURÉES
72
TABLEAU 35: RECHERCHE DU BIAIS (RC28J)
73
TABLEAU 36 : TEST DE FIABILITÉ (RC28J)
73
TABLEAU 37: TEST DE SIGNIFICATION
73
TABLEAU 38 : COMPARAISON ENTRE LES VALEURS DE LA
RÉSISTANCE À LA COMPRESSION À 28 JOURS CALCULÉES
PAR LE MODÈLE LINÉAIRE ET LES VALEURS MESURÉES
74
TABLEAU 39 : RECHERCHE DU BIAIS (RT2J)
74
TABLEAU 40 : TEST DE FIABILITÉ (RT 2J)
74
TABLEAU 41: TEST DE SIGNIFICATION
75
TABLEAU 42 : COMPARAISON ENTRE LES VALEURS DE LA
RÉSISTANCE À LA TRACTION À 2 JOURS CALCULÉES PAR LE
MODÈLE QUADRATIQUE ET LES VALEURS MESURÉES
75
TABLEAU 43 : RECHERCHE DU BIAIS (RT7J)
76
TABLEAU 44 : TEST DE FIABILITÉ (RT 7J)
76
TABLEAU 45: TEST DE SIGNIFICATION
76
TABLEAU 46 : COMPARAISON ENTRE LES VALEURS DE LA
RÉSISTANCE À LA TRACTION À 7 JOURS CALCULÉES PAR LE
MODÈLE QUADRATIQUE ET LES VALEURS MESURÉES
77
TABLEAU 47 : RECHERCHE DU BIAIS (RT28J)
77
TABLEAU 48 : TEST DE FIABILITÉ (RT28J)
77
TABLEAU 49: TEST DE SIGNIFICATION
78
TABLEAU 50: COMPARAISON ENTRE LES VALEURS DE LA
RÉSISTANCE À LA TRACTION À 28 JOURS CALCULÉES PAR
LE MODÈLE CUBIQUE ET LES VALEURS MESURÉES.
78
LISTE DES FIGURES :
FIGURE 1 : SCHÉMA ILLUSTRANT LES
DIFFÉRENTES SOURCES DES ALCALINS PRÉSENTS DANS LE BÉTON
(D'APRÈS BÉRUBÉ ET AL. IN BARON ET OLLIVIER, 1992)
11
FIGURE 2: ILLUSTRATION DE LA PREMIÈRE
ÉTAPE DU MÉCANISE SELON A B POOLE [3]
14
FIGURE 3: ILLUSTRATION DE LA DEUXIÈME
ÉTAPE DU MÉCANISE SELON A B POOLE [3]
14
FIGURE 4: : EXEMPLE DE BÉTON
DÉGRADÉ PAR L'ALCALI-RÉACTION. [2]
16
FIGURE 5 : EFFET DE L'AJOUT DES CENDRES VOLANTES SUR
L'EXPANSION DU BÉTON [2]
18
FIGURE 6 : FACIÈS BASALTIQUE LPNA (PL,
PLAGIOCLASE ; M, MICROLITE ; PY, PYROXÈNE ; P, PÂTE ; O, OPAQUE).
[12]
19
FIGURE 7 : DOMAINE EXPÉRIMENTAL
34
FIGURE 8 : VARIATION DE L'EXPANSION EN FONCTION
DES DOSAGES EN CENDRES VOLANTES À CBG=50%.
44
FIGURE 9 : EFFET DES CENDRES VOLANTES SUR
L'EXPANSION À FC CONSTANT
45
FIGURE 10 : EFFET DES CENDRES VOLANTES SUR LA
RÉSISTANCE À LA TRACTION À 2, 7 ET À 28JOURS.
47
FIGURE 11 : EFFET DES CENDRES VOLANTES SUR LA
RÉSISTANCE À LA COMPRESSION À 2, 7 ET À
28JOURS.
48
FIGURE 12 : VALEURS CALCULÉES PAR LE
MODÈLE LINÉAIRE EN FONCTION DES VALEURS MESURÉES.
50
FIGURE 13 : COURBES ISO-EXPANSION DU MODÈLE
LINÉAIRE
51
FIGURE 14 : VALEURS CALCULÉES PAR LE
MODÈLE QUADRATIQUE EN FONCTION DES VALEURS MESURÉES.
53
FIGURE 15 : COURBES ISO-EXPANSION DU MODÈLE
QUADRATIQUE
54
FIGURE 16 : VALEURS CALCULÉES PAR LE
MODÈLE SPÉCIAL CUBIQUE EN FONCTION DES VALEURS
MESURÉES.
56
FIGURE 17 : ISO-EXPANSION DONNÉES PAR LE
MODÈLE SPÉCIAL CUBIQUE
57
Table des acronymes
CBG
|
Clinker Broyé Gypsé
|
CV
|
Cendres volantes
|
DL
|
Degré de liberté
|
FC
|
Fillers calcaire
|
RAG
|
Réaction Alcali-Granulat
|
Rc ij
|
Résistance à la compression à i jours
|
Rt ij
|
Résistance à la traction à i jours
|
Introduction
L'alcali-réaction est un
phénomène chimico-physique attaquant les masses de béton
dans les grands ouvrages (Barrages, Ponts,...). Le déclenchement d'une
telle réaction nécessite la coexistence d'un ensemble de facteurs
catalyseurs relatifs, d'une part, à la composition proprement dite du
béton utilisé dans ces édifices, et d'autre part à
l'environnement de ces derniers.
Les dites réactions sont à l'origine d'une
multitude de désordres se manifestant au niveau des structures
attaquées, et s'aggravant d'autant plus que les conditions sont
propices.
Étant responsable d'une anomalie structurale des les
grands ouvrages, l'alcali-réaction induit un surcoût excessivement
élevé, relatif au diagnostic et à la réparation de
ces désordres.
Vu la complexité due à la nature même des
réactions alcali-granulats, la mise en place d'une solution
définitive et unifiée s'avère peu commode. Cependant, une
démarche préventive, visant la qualification des granulats avant
leur utilisation, est actuellement adoptée. En parallèle, les
potentialités de recherche collaborent pour mieux contourner le
problème, en mettant en exergue l'utilisation des ajouts
minéraux, dont les cendres volantes font partie intégrante, dans
la formulation du ciment et/ou du béton.
Dans le cadre de notre travail de fin
d'études, nous avons cherché à évaluer
l'utilité de « l'utilisation des cendres volantes pour
la prévention des désordres dus à
l'alcali-réaction ». La réalisation de ce projet nous a
permis de mette en oeuvre une combinaison judicieuse entre les concepts
théoriques et les procédures expérimentales qui leurs sont
appropriées (essais de laboratoire, approche statistique,..).
Le présent rapport est constitué de
cinq grands chapitres :
La première partie est consacrée à une
recherche bibliographique sur l'alcali-réaction, ses mécanismes
et ses conditions d'apparition.
Le deuxième chapitre traite d'une
caractérisation des matériaux adoptés pour la
réalisation des essais en question, en particulier les cendres volantes
comme ajout minéral revêtant une importance
particulière.
La troisième partie de l'étude donne un
aperçu sur un outil statistique performant de traitement des
résultats : plans d'expériences.
Le mode opératoire et un éventuel
éventail des résultats sont présentés dans le
quatrième chapitre.
Un récapitulatif des différents
résultats, leurs modélisation, commentaires et
interprétation figurent dans le dernier chapitre. Une solution optimale,
donnant lieu à des ciments spéciaux résistants avec une
expansion moindre, est présentée dans le même chapitre.
L'alcali-réaction
I-
1: Aperçu Historique
En 1935, R.j Holden est le premier qui a observé
l'existence des réactions chimiques dans le béton, entre le
ciment et certains granulats. Ensuite Krammer et Carlson ont constaté
l'existence de désordres mais c'est l'américain Stanton qui a
précisé le premier, en 1940, la nature des réactions
causant les perturbations observées : ces réactions se
produisent entre les alcalins du ciment et certains types de granulats,
d'où le nom « Réaction Alcalis-Granulats »
(RAG).[1]
En France, l'alcali-réaction était
constatée, pour la première fois, vers la fin des années
70 au niveau de quelques ponts dans la région du nord.
Le Maroc n'a commencé à s'intéresser
à ce phénomène que dans les années 90, en adoptant
une démarche de qualification des granulats utilisés dans la
construction des barrages. [2]
I-
2: Définition
L'alcali-réaction est une réaction chimique entre
certaines formes de silice et de silicate pouvant être présentes
dans les granulats du béton, et les alcalins de la solution
interstitielle. Elle correspond à une attaque du granulat par la
solution basique du béton et provoque la formation d'un gel de
réaction (silicate alcalin), dont l'expansion engendre, sous certaines
conditions, un ensemble de désordres. [1][3]
Il existe trois grands types d'alcali-réaction : les
réactions alcali-carbonate (dolomitisation), alcali-silice et
alcali-silicate. La réaction alcali-silice est la plus
fréquente.
I-
3: Conditions d'apparition de l'alcali-granulat
Trois conditions doivent être simultanément
remplies pour que ces réactions puissent avoir lieu. Il faut que le
granulat soit potentiellement réactif, que l'humidité relative
excède 80 à 85% et que la concentration en alcalins
dépasse un seuil critique. [3]
I-3-1: Alcalins
L'établissement de la RAG nécessite la
présence d'un certain pourcentage d'alcalins dans le béton
(essentiellement K2O et Na2O). Ces alcalins proviennent
d'une part du ciment, et d'autre part, des autres constituants du béton
(granulats, eau de gâchage, adjuvants,..). Initialement, ils sont
présents à l'état diffus dans les phases anhydres, et ils
se dissolvent à l'état basique (K+OH-,
Na+OH-) lors de l'hydratation. [4]
Environnement
Eaux salines
Sels fondants
Alcalins
Béton
Additions minérales
Ciment
Granulats
Adjuvants
Eau de gâchage
Figure 1
: Schéma illustrant les différentes sources des alcalins
présents dans le béton (d'après Bérubé et
al. In Baron et Ollivier, 1992)
Lors de l'évaluation des risques de la RAG,
généralement, seuls les alcalins du ciment sont pris en compte.
Or, c'est la quantité totale des alcalins provenant du ciment et des
granulats qui est importante.
Pour l'évaluation de la teneur des alcalins d'un ciment,
on utilise généralement la notion d'alcalins équivalents
(Na2O équivalents) : % Alcalins
équivalents = % Na2O + 0.658 K2O
où 0.658 correspond au rapport des masses molaires Na2O/
K2O. [5]
I-3-2: Silice
La silice réactive, à laquelle on
s'intéresse, prend son origine des granulats. Toutes les
variétés de silice sont pratiquement insolubles dans l'eau pure.
Mais, en raison du caractère acide de SiO2, certaines peuvent
se dissoudre sous forme d'anions dans les solutions aqueuses fortement
basiques.[4]
La présence d'une silice solubilisable provenant des
minéraux sensibles pouvant réagir avec les alcalins, est
l'origine de la majorité des réactions alcali-granulats.
Le minéral le plus susceptible de réagir avec les
alcalins est l'opale ayant comme formule (SiO2, nH2O) ou
une silice amorphe. [1]
En général, la silice peut être
rencontrée dans les roches et alluvions siliceuses, dans les roches
carbonatées (sous forme d'inclusions) et dans les roches ou alluvions
silicatées polyphasées.
L'identification de ces roches n'est pas suffisante pour
permettre de caractériser un granulat comme réactif. Cette
première approche, absolument nécessaire, permet tout au plus
d'alerter sur l'existence ou non d'un risque. Dans l'affirmative, ce sont les
essais de stabilité dimensionnelle [6] qui permettent
la décision.
I-3-3: Environnement
L'expérience montre que les conditions d'exposition sont
à l'origine d'une évolution notable de la RAG :
l'humidité du sol sous l'ouvrage en contact, l'écoulement de
l'eau...A titre illustratif, on présente deux cas d'exposition:
L'exposition la plus favorisante de la RAG est lorsque les
constructions sont soumises à des cycles successifs d'atmosphère
humide puis sèche. Même si le béton est maintenu dans des
conditions d'humidité nulle, l'alcali-réaction reste potentielle,
mais dés la remise du matériau en contact avec l'eau, la
réaction se reproduit et les désordres auront lieu.
[7]
L'exposition des structures à des températures
élevées accélère aussi le processus de la RAG. En
effet, les sections massives et larges du béton dissipent lentement la
chaleur d'hydratation produite par la prise du ciment, ce qui favorise
l'apparition et le développement de la RAG. « Ainsi, une
atmosphère chaude et humide est un facteur aggravant
important ». [8]
I-
4: Mécanisme de l'alcali-réaction
Les mécanismes de l'alcali-réaction consistent,
généralement, en la dissolution de la silice par la solution
interstitielle alcaline du béton suivie de la formation d'un gel
gonflant.
L'alcali-réaction dépend de plusieurs facteurs
conditionnant les particularités de certains de ses mécanismes,
à savoir : [7] [8]
La structure : c'est-à-dire les facteurs
dépendant de la structure cristalline des minéraux
réactifs dont le réseau peut avoir des défauts. Ces
derniers sont en général dus à la destruction des liaisons
siloxanes . Ces anomalies constituent un site des réactions pour les ions
présents dans la solution (Na+, Ca2+,
K+, OH-).
La texture : les facteurs liés à cet aspect
concernent essentiellement la granularité, la microfissuration et la
microporosité. Ils conditionnent plus la cinétique des
réactions. Les surfaces d'échange des granulats en relation avec
l'état de microfissuration sont en croissance en fonction de leur classe
granulaire.
La composition chimique: on cite ici les facteurs : pH,
concentrations en K+, Na+, Ca2+, et la
quantité de la silice réactive.
La vitesse des réactions : dépend
essentiellement des facteurs structuraux, texturaux et des facteurs de
composition.
Le mécanisme général des réactions
alcali-silice est, généralement, présenté par un
processus en deux étapes fondamentales : [9]
Une première étape consistant à la
neutralisation des radicaux silanols Si-OH suivant une réaction du type
acide-base :
et 
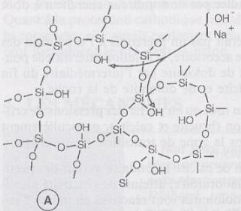
Figure 2: Illustration de la
première étape du mécanise selon A B Poole
[3]
Les charges terminales sont équilibrées par les
ions Na+, K+ diffusés. D'autres ions
OH- peuvent se présenter soit dans les trous de la structure
soit sur sa surface externe. L'accessibilité des OH- et de
Na+ est limitée par la dimension des trous et par leur
distance à la surface de la particule.
La deuxième phase, est une attaque des ponts siloxanes
Si-O-Si par les ions OH- :
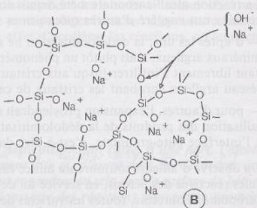

Figure 3: Illustration de la
deuxième étape du mécanise selon A B Poole
[3]
Lors de cette réaction, on remarque la destruction de la
structure du minéral et la formation d'un gel silico-alcalin
polymérisé.
I-
5: Désordres dus à
l'alcali-réaction
La dégradation du béton des ouvrages
résultant du phénomène d'alcali-réaction a
été répertoriée dans de nombreux pays. En
général les désordres apparaissent à des
échéances variables de deux à dix ans ou plus.
La pathologie et les manifestations externes de la RAG se
signalent par un ou plusieurs des symptômes suivants :
- Une fissuration,
- Un faïençage à mailles plus ou moins
larges ou en étoile ou une fissuration orientée suivant la
direction de distribution des armatures,
- Des exsudations blanches formées de calcite et
parfois de gels siliceux translucides,
- Des pustules ou cratères avec des
éclatements localisés en forme de petits cônes
résultant de la réaction de gros granulats superficiels qui sont
visibles au fond des cratères d'éclatement,
- Des déformations,
- Des colorations ou décolorations.....
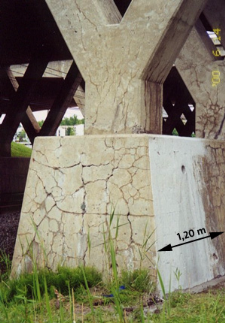
Figure 4: : Exemple de béton
dégradé par l'alcali-réaction. [2]
I-
6: Prévention de l'alcali réaction
I-6-1: Démarche préventive
[10]
En France, les premières études d'ouvrages
mettant en évidence l'alcali-réaction, comme source de
désordres, datent de la fin des années 70 et du début des
années 80. C'est à ce moment là que le gouvernement
français a pris conscience du grand risque que constitue ce
phénomène pour l'ensemble des ouvrages du pays.
Ainsi, un programme d'étude a été
lancé dans le but d'élaborer une démarche de
prévention contre l'alcali-réaction et d'assurer aux
différents maîtres d'oeuvres le pouvoir de construire sans risque
de dégradations ultérieures.
Cette démarche est représentée
actuellement par les différentes recommandations contre
l'alcali-réaction. Un premier document dit document provisoire, a
été publié par le LCPC en 1991. Sa version
définitive, toujours en vigueur, date de juillet 1994. Les ouvrages
intéressés par ces recommandations sont les ouvrages neufs
(à réaliser), alors que ceux existants sont exclus de son domaine
d'application.
La version de juillet 1994 propose une démarche
préventive, qui s'effectue en deux temps :
- Détermination d'un niveau de prévention
parmi trois cas possibles, selon la catégorie de l'ouvrage et sa classe
d'exposition.
- Orientation vers la (ou les) solution(s) possible(s),
en fonction du niveau de prévention retenu.
Au Maroc il n'existe pas encore une démarche nationale
pour la prévention contre l'Alcali réaction, l'ensemble des
mesures prises sont inspirées de la démarche française
actuelle.
Cette démarche recommande l'utilisation des ajouts
minéraux pour inhiber l'alcali-réaction. Parmi ces ajouts, elle a
mis le point sur les cendres volantes en encourageant leurs utilisations et les
études qui les valorisent.
I-6-2: Bilan des alcalins
Vu sa simplicité et son efficacité, cette
démarche est largement répondue dans le monde entier.
Son principe est de tenir compte des alcalins amenés
par tous les constituants du béton à savoir : le ciment, les
adjuvants, les granulats et l'eau de gâchage. Son but majeur est de faire
un bilan d'alcalins afin de limiter la teneur en Na2O
équivalent (= % Na2O + 0.658 K2O)
dans le béton à un seuil inférieur à 3.5
Kg/m3. [10] [11]
I-6-3: Utilisation des ajouts
minéraux
Des expériences ont montré que l'utilisation des
ajouts minéraux tels que : les cendres volantes, les laitiers de
haut fourneau et la fumée de silice ont un effet positif sur la
diminution de l'expansion du béton.
Le graphe suivant nous montre la variation de l'expansion en
fonction du temps, et ceci pour différents dosages de cendres volantes
et deux teneurs différentes en alcalins.
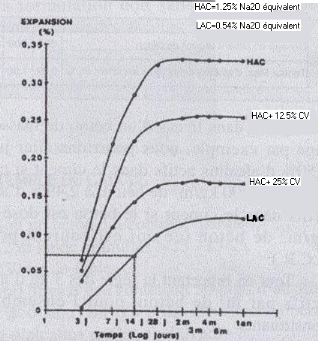
Figure 5 : Effet de l'ajout des
cendres volantes sur l'expansion du béton [2]
Des expériences similaires au niveau international ont
montré que les cendres volantes sont efficaces pour la diminution de
l'expansion et par suite, pour la prévention des désordres dus
à l'alcali réaction, d'où l'intérêt de
vérifier l'efficacité des cendres nationales.
Choix et caractérisation des matériaux
Le présent chapitre est une présentation
générale des différents matériaux utilisés
dans nos expériences, de leurs propriétés et de certaines
de leurs caractéristiques.
I-
7: Granulats : basalte
La roche mère du granulat testé est d'origine
volcanique, de type basalte andésitique porphyrique, à cristaux
de petite taille de feldspaths noyés dans une matrice fine de couleur
noire.
L'étude pétrographique [12][13]
de cette roche montre qu'elle contient du verre, phase jugée
d'une réactivité chimique importante. De plus ce faciès
est riche en minéraux alcalins (Microlites et phénocristaux de
plagioclase) susceptibles d`enrichir la solution interstitielle du béton
en alcalins (Na+ et K+) et par conséquent
favoriser l`attaque des phases siliceuses instables chimiquement.
Les phénocristaux sont composés de :
- Plagioclases
- Pyroxène,
- Minéraux opaques,
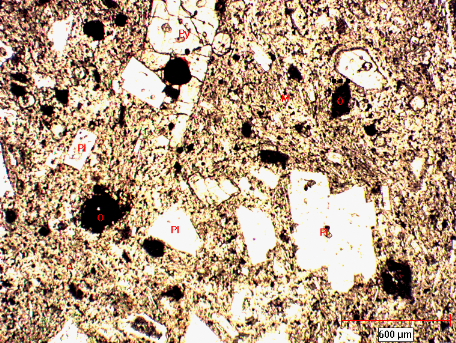
- Rares micas noirs (biotite).
Figure 6 : Faciès basaltique
LPNA (Pl, Plagioclase ; M, Microlite ; Py, Pyroxène ; P, Pâte ; O,
Opaque). [12]
I-
8: Cendres volantes
I-8-1: Définition
Les cendres volantes sont des fines particules recueillies
lors du dépoussiérage des gaz résultant de la combustion
du charbon pulvérisé, utilisé dans les centrales
thermiques. Leur composition est en relation avec les différents types
de matières incombustibles présentes dans le charbon. D'une
façon générale, les éléments présents
sont : le silicium, l'aluminium le fer, le calcium et le
magnésium.
L'intérêt des cendres volantes réside
dans la faculté qu'elles possèdent à réagir avec
l'hydroxyde de calcium pour former des silicates de calcium hydratés qui
ont des propriétés pouzzolaniques et hydrauliques (prise en
présence d'eau).
I-8-2: Aperçu historique
L'expression `'cendres volantes'' a été
crée par l'industrie de l'énergie électrique vers 1930
lorsque les quantités récupérées de ces
résidus de charbon deviennent de plus en plus importantes dans les
centrales thermiques. En 1937, Davis et ses collaborateurs de
l'université de Californie aux USA ont publié des
résultats de recherches sur un béton contenant des cendres
volantes. Ce travail a servi de base aux premières spécifications
contribuant à la valorisation des cendres volantes dans la construction
et l'industrie.
En Europe, l'utilisation des cendres volantes s'est beaucoup
développée après la seconde guerre mondiale lorsqu'il a
fallu faire face aux besoins grandissants de la construction. Il fallait
toutefois attendre les années soixante-dix pour noter une bonne
croissance de leur utilisation après la crise du pétrole et
l'augmentation de du coût de l'énergie. [14]
I-8-3: Composition
Selon leurs compositions, on distingue deux grandes familles de
cendres volantes : [15]
ü Cendres volantes dites
siliceuses, Ayant des propriétés pouzzolaniques.
Elles se présentent sous forme d'une poudre allant du gris au noir
suivant les teneurs en imbrûlés et en oxyde de fer (plus
foncée que le ciment) ; douces au toucher. Elles doivent contenir
essentiellement de la silice SiO2 réactive et de l'alumine
Al2O3. Le restant contient de l'oxyde de fer
Fe2O3 et d'autres oxydes. La proportion de la chaux
réactive CaO doit être inférieure à 5% en masse et
celle de la silice réactive ne doit pas être inférieure
à 25% en masse.
ü Cendres calciques :
à forte teneur en chaux (CaO). Se présentent sous forme d'une
poudre fine de couleur grise ayant des propriétés physiques et/ou
pouzzolaniques. Elles contiennent essentiellement de la chaux réactive,
de la silice réactive et de l'alumine. La quantité de la chaux
(CaO) dans ce type de cendres est élevée, c'est pourquoi elles
sont susceptibles de faire prise sans liant. Elles font prise seulement avec de
l'eau (d'où leur nom : Cendres hydrauliques) et dégagent de
la chaleur en s'hydratant. La teneur en chaux réactive ne doit pas
être inférieure à 5% en masse. La cendre volante contenant
entre 5 et 15% de chaux réactive doit contenir plus de 25% en masse de
silice réactive.
I-8-4: Production marocaine des cendres
volantes
Au Maroc, plus de 467.000 tonnes de cendres volantes sont
produites annuellement, par les centrales thermiques suivantes :
[14]
I-8-4-1 Centrale
thermique de Jerrada
Cette centrale est mise en service en 1970, sa puissance
électrique est de 3*55 MW. Sa production annuelle en cendres volantes
est 147 000 tonnes. Ces cendres sont évacuées
simultanément avec les mâchefers par voie hydraulique vers un
bassin à cendres situé à 2 km environ de la centrale.
Étant donné que ces cendres sont
évacuées par voie humide, elles ne peuvent être
réutilisées ni dans le béton ni dans le ciment.
I-8-4-2 Centrale
thermique de Mohammedia
Cette centrale est mise en service en 1981, sa puissance
électrique est de 2*150 MW. Sa production annuelle en cendres volantes
est de 80 000 tonnes. Ces cendres sont envoyées dans un silo à
cendres avant d'être évacuées par voie hydraulique à
la mer. Elles sont aussi stockées à l'état humide,
inutilisables dans l'industrie du ciment et comme ajout dans les
bétons.
I-8-4-3 Centrale
thermique de JORF Lasfar
Cette centrale est mise en service en 1994, sa puissance
électrique est de 4*330 MW. Sa production annuelle en cendres volantes
est de 240 000 tonnes. Elles sont évacuées par voie sèche,
et sont les seules au Maroc susceptibles d'être utilisées dans le
ciment et le béton.
La composition chimique des trois cendres est donnée
dans le tableau suivant :
|
CV
Jorf Lasfar
|
CV
Mohammedia
|
CV
Jerrada
|
NF
P18-505
|
SiO2
|
56.7
|
47
|
50
|
25
|
Al2O3
|
28.4
|
25.1
|
24.2
|
|
Fe2O3
|
8.58
|
8.54
|
9.49
|
|
SiO2+Al2O3+
Fe2O3
|
93.7
|
80.6
|
83.7
|
|
MgO
|
0.99
|
0.87
|
1.44
|
|
CaO
|
2.48
|
1.83
|
0.92
|
10
|
Na2O
|
0.38
|
0.3
|
0.73
|
|
K2O
|
2.63
|
2.33
|
3.3
|
|
SO3
|
1.78
|
0.53
|
0.41
|
3
|
Tableau
1 : Composition des cendres volantes marocaines et spécifications
de la norme NF P18-505.
I-8-5: Utilisation des cendres volantes
I-8-5-1 Utilisation
dans les ciments
Les cendres volantes sont utilisées en
cimenterie :
ü Soit pour la préparation de la matière
première (le cru), en remplaçant de l'argile puisqu'elles
apportent la silice, l'alumine et le fer. Le cimentier n'a plus à broyer
et à sécher l'argile, les cendres sont faciles à doser,
à transporter et les imbrûlés qu'elles contiennent
constituent un apport de combustible suffisant.
ü Soit lors du broyage final (avec le clinker, le gypse
et les éventuels autres constituants secondaires). Le passage dans le
broyeur permet d'augmenter leur réactivité et d'obtenir un
mélange homogène. De plus, les cendres volantes favorisent le
broyage et augmentent le rendement des broyeurs (grâce aux
imbrûlés).
D'une manière générale les ciments
contenant des cendres volantes présentent les caractéristiques
suivantes :
Ø Les temps de prise sont légèrement plus
longs que dans le cas des ciments sans ajouts
minéraux, de même les résistances
mécaniques sont un peu plus faibles les premiers jours, mais elles
deviennent plus importantes à long terme (effet de la
pouzzolanicité des cendres). Cependant, par temps froid ou pour
décoffrer plus rapidement, on peut ajouter des
accélérateurs chimiques (aluminate de soude par exemple).
Ø Les chaleurs d'hydratation ont diminué,
d'où l'utilisation des ciments aux cendres pour le bétonnage en
grande masse par temps chaud.
Ø Le retrait hydraulique après prise a souvent
diminué à terme.
I-8-5-2 Utilisation
dans les bétons
Les cendres volantes peuvent être ajoutées au
béton à raison de 40 à 100 kg par de béton, soit à l'état sec, soit à
l'état humide. Il convient de bien les mélanger au béton
pour obtenir une teinte uniforme.
L'action des cendres volantes permet une amélioration
de l'ouvrabilité, de la plasticité et de la compacité des
bétons. Elles remplissent plus facilement les coffrages et l'aspect du
béton au démoulage est amélioré (cela est dû
en partie à la forme arrondie des cendres brutes jouant un peu le
rôle de petits roulements à billes).
Les cendres permettent de réduire la teneur en eau
à ouvrabilité égale et dans ce cas de diminuer le
ressuage, d'augmenter l'imperméabilité et par conséquent
la durabilité. L'amélioration est d'autant plus marquée
que les cendres sont plus fines.
I-
9: Clinker gypsé broyé(CBG)
La cuisson à haute température (vers
1450°C) d'un mélange minéral composé essentiellement
du calcaire et de l'argile donne lieu au Clinker sous forme de poudres
constituées de minéraux anhydres et instables. Ces poudres
forment avec l'eau une pâte capable, par hydratation, de faire prise et
de durcir progressivement. Au moment du broyage, on ajoute au Clinker une
faible quantité de sulfate de gypse pour régulariser sa prise et
des ajouts de mouture.
Le clinker doit être constitué d'au moins deux
tiers en masse de silicates de calcium [(CaO)3.SiO2] et
[(CaO)2.SiO2], la partie restante contenant de l'oxyde
d'aluminium (Al2O3), de l'oxyde de fer
(Fe2O3) et d'autres oxydes. Le rapport en masse
(CaO)/(SiO2) ne doit pas être inférieur à 2.0.
la teneur en oxyde de magnésium (MgO) ne doit pas dépasser 5% en
masse.[15]
La quantité du clinker présente dans le ciment
varie, selon le type de ciment, de 20% à 100% en masse. Par exemple dans
un ciment Composé, la norme tolère une teneur en clinker variant
de 20% à 39% en masse du ciment, et dans un ciment Portland la teneur en
clinker peut varier de 95% à 100% en masse du ciment.
[16]
I-
10: Les fillers calcaires
I-10-1: Définition
Il s'agit d'un matériau sec et fin obtenu par broyage
et/ou sélection des gisements de roches calcaires ; parfois
dolomitiques, massives ou meubles. Les fillers doivent être
préparés correctement et ce en tenant compte de leurs conditions
de production ou de livraison.
I-10-2: Normalisation
L'utilisation des fillers calcaire dans la préparation
des ciments est réglementée par la norme (NF P15-301) .
Lorsqu'ils sont employés dans une proportion excédant 5% en
masse, ils doivent répondre aux caractéristiques
suivantes :
ü La teneur en calcaire : CaCO3 > 70%
en masse.
ü La teneur en argile : absorption de bleu de
méthylène < 2g/100g.
ü La teneur en matières organiques : TOC <
0.5% en masse.
I-10-3: Avantages
Le principal avantage des fillers calcaire est de
réduire le coût final unitaire du ciment en réduisant son
contenu énergétique. De plus, l'addition de fillers calcaire au
clinker permet d'augmenter significativement la capacité de mouture des
broyeurs, et d'améliorer les propriétés physiques du
béton, à savoir l'ouvrabilité du béton frais, tout
en permettant de densifier la matrice de mortier en retenant de l'eau.
I-10-4: Inconvénients
Les fillers calcaire présentent deux
inconvénients majeurs : d'une part la diminution
légère des résistances en compression à court terme
des bétons, et d'autre part, la vulnérabilité du
béton frais contenant des fillers calcaire au retrait plastique.
I-
11: Eau de gâchage
Une eau de gâchage est essentiellement destinée
à :
- Eau d'hydratation du ciment : cette eau (0.25 à
0.6 du poids de ciment) reste chimiquement liée à la
microstructure du béton durci.
- Eau libre : Elle joue un rôle rhéologique
en permettant une bonne ouvrabilité du mélange à
l'état frais. Cette eau, ainsi que celle absorbée par les
granulats poreux, est destinée à s'évaporer. Le temps de
séchage peut être long suivant les dimensions de
l'élément, la qualité du béton et
l'hygrométrie environnante. [17]
Plans d'expériences - Préparation des
mélanges
Dans le but d'optimiser le nombre des essais, et par suite le
nombre de mélanges à préparer, qui répondent
correctement à nos attentes, nous avons utilisé une approche
statistique pratique et informatisée dite « plans
d'expériences ». L'utilisation de cet outil demande une
connaissance préalable de son principe et de son mode de fonctionnement.
Pour cela et avant d'entamer la procédure de la détermination de
nos mélanges, nous rappelons ci-après les différents types
de plans d'expériences, leurs domaines d'utilisation ainsi que
leur démarche.
I-
12: Les plans d'expériences [18]
I-12-1: Définition
Un plan d'expérience est une approche statistique
permettant de maîtriser un problème à plusieurs
paramètres tout en suivant un programme préconçu des
différentes expériences qu'on se doit effectuer. Il a pour but
de minimiser le nombre d'essais pour obtenir des résultats fiables qui
reflètent la variation réelle du phénomène
étudié en fonction de ses diverses caractéristiques.
Dans les années trente, les premiers plans
d'expériences structurés ont vu le jour en agronomie. Ces plans
se sont développés au cours des dernières années et
leur utilisation s'est étendue pour intéresser, finalement, tous
les secteurs de production et de compétitivité.
I-12-2: Terminologie
Avant d'entamer l'élaboration du plan
d'expérience, la connaissance d'une certaine terminologie qui lui est
associée revêt une importance primordiale.
ü Facteurs
Un facteur est un paramètre que l'on peut varier d'une
expérience à une autre, et qui influence le résultat final
(réponse). Le nombre de facteurs entrant en jeu est, couramment,
supérieur à celui des réponses. Deux types de facteurs
sont distingués :
- Facteur quantitatif : tout facteur mesurable. Sa
variation est soit continue, à savoir le dosage en cendres volantes, en
CBG ou en fillers de calcaire, soit discontinue dans le cas de classes de
ciment par exemple.
- Facteur qualitatif : tout facteur non mesurable tel que
la nature de granulats ou leur type.
ü Niveau des facteurs
C'est la délimitation du domaine de variation d'un
facteur donné. En général, la variation de chaque facteur
est délimitée par deux niveaux : supérieur et
inférieur.
ü Domaine expérimental
Le domaine expérimental est schématisé
par un polyèdre à k dimensions, où k est le nombre de
facteurs considérés. Chaque côté de ce
polyèdre, est défini par les deux niveaux extrêmes
caractérisant le facteur correspondant à ce côté.
ü Réponses
Les réponses sont les propriétés à
mesurer pour la variation d'un facteur.
ü Effet
L'effet d'un facteur X sur une réponse Y est obtenu en
étudiant les variations des valeurs de Y en fonction de celles de X. Si
le facteur X a une interaction avec lui-même, on parle d'un effet
quadratique. Un effet peut être positif, nul ou négatif. Il est
exprimé par le coefficient multiplicatif de X dans un modèle
mathématique de la réponse. La signification de l'effet de X sur
Y est donnée par des tests statistiques.
ü Interaction
On dit qu'il y a interaction entre deux facteurs X et X' si
l'effet de X dépend du niveau de X' et inversement. Cette interaction
est notée interaction XX' ou interaction X'X.
I-12-3: Méthodologie des plans
d'expériences
Pour l'élaboration d'un plan d'expériences, on
passe généralement par les trois étapes
suivantes :
I-12-3-1 La recherche
des facteurs influents
Cette étape consiste à répondre à
un ensemble de questions concernant l'influence des facteurs
considérés sur le phénomène
étudié : parmi tous les facteurs susceptibles d'influer sur
la réponse, lesquels ont une influence significative ? Que vaut
cette influence ? et y a t il des interactions entre ces
facteurs ?
Une fois les facteurs influents sont bien
déterminés et leurs influences est quantifiées, on passe
au second stade :
I-12-3-2 La
modélisation
Dans cette phase, on cherche quelle est la forme de
l'influence définie dans la première étape :
linéaire, courbe.... et quelle est l'équation mathématique
régissant, avec une précision donnée, la variation du
phénomène en fonction des facteurs influents.
La modélisation d'une réponse se fait en
choisissant des points expérimentaux dont le nombre est au moins
égal à la somme des effets, des interactions et des effets
quadratiques. Ainsi on définit une matrice de n lignes et k colonnes,
où n est le nombre d'expériences et k est le nombre des
effets.
I-12-3-3
L'optimisation
Après la détermination de la forme graphique et
analytique de notre réponse, il est primordial d'aller chercher les
conditions expérimentales donnant le meilleur résultat. Cette
étape nécessite préalablement une connaissance assez
profonde du phénomène étudié.
Un plan d'expériences est dit optimal, s'il satisfait,
au moins, l'un des critères d'optimalité suivants :
· Matrice d'HADAMARD :
pour atteindre en n expériences la variance minimale, la matrice X
associée au plan doit vérifier la condition d'Hadamard :
tX*X= n*I.
· Déterminant
maximal : le plan choisi est optimal si et seulement si
dét(tX*X) est maximal.
· Trace : le plan optimal
est celui ayant trace((tX*X-1)) minimale.
· Diagonale : le plan
optimal est celui ayant la valeur maximale sur la diagonale de
(tX*X-1) la plus faible possible.
I-12-4: Différents types de plans
d'expériences
Trois grandes familles de plans d'expériences sont
présentes :
I-12-4-1 Plans
factoriels complets à deux niveaux
Ces plans permettent l'étude de k facteurs à
raison de deux niveaux (-1, +1) par facteur. Ils renferment toutes les
combinaisons possibles des k facteurs à leurs deux niveaux.
Pour étudier k facteurs, sur la base des plans
factoriels à deux niveaux, il faut réaliser 2k essais,
d'où le nom de plans 2k donné à cette famille
de plans.
La matrice des essais comporte k colonnes et 2k
lignes. Elle se construit de la façon suivante :
- Colonne du 1er facteur : alternance de -1 et
+1.
- Colonne du 2éme facteur : alternance de -1 et +1
de 2 en 2
- Colonne du 3éme facteur : alternance de -1 et +1
de 4 en 4
- ....
Le domaine expérimental est présenté dans
l'espace des facteurs à k dimensions. Les points expérimentaux
sont situés aux sommets du polyèdre.
I-12-4-2 Plans
fractionnaires à deux niveaux
Les plans fractionnaires à deux niveaux sont des plans
optimaux, permettant de réduire la charge expérimentale,
proposée par un plan factoriel complet, en focalisant sur les effets
les plus intéressants.
Un plan factoriel complet comporte 2k essais et
permet d'estimer, non seulement les effets des facteurs, mais aussi toutes
leurs interactions possibles. De ce fait, on est toujours amené
à faire plus d'essais pour collecter moins d'informations car les
interactions d'ordre supérieur ou égal à 2 sont
négligeables et ne peuvent rien nous apporter.
La solution proposée par les plans fractionnaires
consiste à utiliser pour l'étude de k facteurs les matrices des
effets des plans complets 2k-p. L'avantage de ces plans est
évident : la charge expérimentale est divisée par
2p par rapport aux premiers plans, p est le nombre de facteurs
aliasés « confondus »
délibérément, c'est-à-dire qui ont des niveaux de
même alternance dans la matrice des expériences.
I-12-4-3 Plans de
mélange
La démarche générale des plans de
mélange consiste à traduire la variation d'une réponse en
fonction des constituants du mélange par la relation Y= f(Xi)
avec Xi =1 et i varie entre 1 et k (le nombre total de facteurs).
a- Modèles représentatifs d'un
mélange
Pour traduire les variations d'une réponse en fonction
de la composition du mélange, il existe plusieurs modèles,
à savoir le modèle linéaire, le modèle quadratique,
le modèle spécial cubique... Pour élaborer un tel
modèle de degré n avec k constituants, le réseau
Scheffé (k,n) propose de choisir les teneurs en Xi du mélange
suivant la série 0,1/n, 2/n,..., n/n ; ainsi on aura autant de
mélanges différents que de coefficients à
déterminer dans le modèle polynomial.
- Modèle linéaire
Dans le cas des mélanges, on a toujours la relation
suivante : Xi =1 qui exprime la notion d'un mélange. De
ce fait, le modèle linéaire prend sa forme : Y = ak
Xk . Ce modèle n'a pas de constante. Pour k=3, on
aura : Y = a1 X1 + a2 X2 +
a3 X3. La résolution de cette équation
nécessite alors trois mélanges chacun est situé au sommet
du triangle représentatif du domaine expérimental. Et pour tester
la validité du modèle, on effectue un autre essai au barycentre
du triangle.
- Modèle quadratique
C'est un modèle de degré 2. Sa forme
générale est : Y = aiXi +
aij XiXj (j>i).
Dans le cas du mélange ternaire on a :
Y= a1X1 + a2X2 +
a3 X3 + a12 X1 X2 +
a13 X1 X3 + a23 X2
X3
Ce modèle est dicté par un réseau
Scheffé (3,2) constitué par six points aux sommets et aux milieux
des arrêts du triangle. Pour tester la validité de ce
modèle, on a recours à faire quatre essais situés dans les
barycentres des sous triangles ainsi formés.
- Modèle spécial cubique
Il s'agit cette fois d'un modèle de degré 3,
ayant la forme générale suivante :
Y= amXm + aij
XiXj + aijh XiXjXh
(i<j<h) et m varie librement entre 1 et k.
Dans notre cas k=3, on a :
Y = a1X1 + a2X2 +
a3 X3 + a12 X1 X2 +
a13 X1 X3 + a23 X2
X3+ a123 X1X2X3
Dans ce cas, on a sept facteurs à déterminer
donc il nous faut sept mélanges qui seront pris aux sommets, aux milieux
des arrêts et au barycentre du domaine expérimental.
Pour tester la validité de ce modèle on effectue
les six mélanges correspondant aux 1/3 et 2/3 de chaque arrêt.
Ainsi, on aura au total 13 mélanges de ciments à
réaliser.
b- Différents types de
mélanges
Les plans de mélanges permettent le choix des
mélanges à tester de façon à pouvoir mieux estimer
les coefficients ai, aij et aijh. Ce sont des
plans optimaux.
Ces plans sont distingués selon les contraintes
auxquelles sont soumises leurs différentes composantes
xi :
- Plan de mélange type I : dans
ce plan, on note qu'il n'y a pas de contrainte particulière.
- Plan de mélange de type II :
est tel que Xi li. ses contraintes sont
fréquemment rencontrées. Si aucune contrainte n'est
signalée sur une composition, il y a toujours la contrainte naturelle
Xi0.
- Plan de mélange de type III :
est tel que li Xi ui. ce sont les plus
fréquents et les plus difficiles à utiliser.
- Plan de mélange type IV :
où Xi (i=2...k) <<X1 où X1
est le solvant. C'est un cas très particulier de solutions.
I-12-5: Outils de calcul
Parmi les outils mathématiques et statistiques
utilisés pour l'estimation des coefficients des modèles ainsi que
leur test, on trouve la régression linéaire. Pour étudier
cet outil on s'intéresse aux modèles linéaires, et on
réalise n essais. Si le modèle est polynomial, les
résultats de la régression sont applicables en posant :
X3 = X1², X4= X2²,
X5= X1X2 ....
Il est à noter que les différents types de plans
d'expériences ainsi que toutes les méthodes et tous les tests,
ci-après, sont informatisés et présentés dans un
logiciel « Design Expert » qu'on a utilisé pour
faire le traitement statistique de nos résultats.
I-12-5-1 Estimation des
coefficients du modèle
Soient :
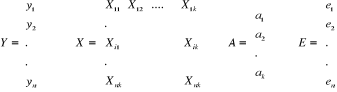
Y est le vecteur réponse.
X est la matrice des essais
A est le vecteur inconnu des coefficients.
E est le vecteur des écarts.
Ces vecteurs sont reliés par la relation matricielle
suivante : Y= XA + E
La contrainte des moindres carrés
« tE*E soit minimale » nous conduit à
trouver le vecteur inconnu A permettant de minimiser tE*E, en effet,
le vecteur recherché est donné par la formule suivante :
A'= (tX*X)-1* tX *Y
I-12-5-2 Analyse de la
variance
Le but des différentes méthodes de l'analyse des
variances est le test de la signification de la régression :
recherche de biais et le test de signification globale.
- L'équation de l'analyse de la variance :
En reprenant l'équation matricielle Y= XA+E, on peut
écrire donc tY*Y = tA'*tX*X+
tE*E
Dans cette équation :
· tY*Y représente yi²,
ayant un degré de liberté n.
· tE*E représente ei²,
ayant un degré de liberté n-(k+1)
· et tA'*tX*X représente la
somme des carrés dus à la régression, ayant un
degré de liberté k+1.
- Recherche du biais :
Pour ce faire, on doit disposer d'une estimation s² de la
variance aléatoire ou bien la variance des mesures ².
En faisant une comparaison, avec le test de Snedecor, de la
variance aléatoire et de la variance résiduelle définie
par : , on peut déboucher sur l'égalité (ou non) des ces
deux variances.
Le test de Snedecor, ou test F, consiste en la comparaison de
la valeur de F= sR²/s² à la valeur théorique
F1-,n-k,n-1 où est le risque choisi.
Si sR² n'est pas significativement
différente de s² on dit que le test F est non significatif,
alors :
· La variance résiduelle pourra être
considérée aussi comme estimation de ².
· La part des variations de y non expliquée par le
modèle est aléatoire et de variance ², le modèle est
sans biais.
Si le test F est significatif, alors le modèle
testé a un biais et il faut chercher un autre modèle en
introduisant d'autres variables ou en choisissant une autre fonction...
- Tests de signification :
Ces tests ne pourront être faits que dans le cas d'un
modèle sans biais. Pour savoir si la part des variations de y
expliquée par la régression est significativement plus grande que
celle due aux variations aléatoires, on calcule le rapport suivant
dit : loi de Snedecor: , si la valeur de F est significative (inégalité des deux
variances), on peut conclure que les variables retenues pour la
modélisation ont un effet significatif sur la réponse Y.
Test de signification
|
Sources de variation
|
Somme des carrés
|
Degrés de liberté
|
Carré moyen
|
F (Snedecor)
|
partielle
|
a0
a1
.
.
ak
|
na0²
.
.
.
nak²
|
1
.
.
.
1
|
na0²/1
.
.
.
nak²/1
|

.

|
Globale
|
Régression
|
tA'*tX*Y
|
K
|
tA'*tX*Y/k
|
|
Variance résiduelle
|
tE*E
|
n-k
|
tE*E/(n-k)
|
|
Dispersion totale
|
tY*Y
|
n
|
|
|
Tableau
2 : Analyse de la variance
Le test de signification globale n'est significatif que si
F> F1-, k,n-k. Une fois ce test est fait, on passe à un
autre test, mais cette fois ci pour chaque facteur : test de signification
partielle. Ce test ne sera lui même significatif que si F>
F1-,1,n-k.
En dernier lieu, et pour tester la fiabilité d'un
modèle on calcule le coefficient de corrélation multiple ou
« le pouvoir explicatif », donné par la
formule :
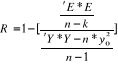
Où y0 est la moyenne des y.
Le modèle n'est fiable que si la valeur de R² est
proche de 1.
I-
13: Préparation des mélanges
I-13-1: Essai d'expansion
L'expansion d'un mortier est étroitement liée
à sa composition. Etant ceci, nous sommes amenés à
préparer un ensemble de mélanges (de ciments) sur la base des
plans d'expériences et ceci dans le but de montrer et d'analyser
l'influence de chaque constituant sur l'expansion du béton.
Dans cette étude, nous nous sommes limités
à un ciment ternaire composé du Clincker broyé
gypsé, des cendres volantes et des fillers calcaire.
Afin de répondre à des exigences commerciales
et techniques, on a choisi un pourcentage minimal de CBG de 50% dans nos
mélanges. Par contre, les autres constituants sont laissés
libres. On se retrouve donc dans le cas d'un plan de mélange de type
II de caractéristiques suivantes :
ü Facteurs
Les facteurs à considérer dans ce plan de
mélange sont les pourcentages des différents constituants du
ciment à savoir :
% en CBG.
% en fillers calcaire.
% en cendres volantes.
ü Réponse
Dans cette étude, la réponse choisie est
l'expansion du mortier du béton, exprimée en %.
ü Contraintes
Les contraintes à considérer dans cet essai sont
les suivantes :
Ø % CBG + % Cendres volantes + % filliers de calcaire =
100%
Ø 50% % CBG 100 %
Ø 0% % Cendres volantes 100 %
Ø 0% % filliers de calcaire 100 %
ü Plan expérimental
Conformément à la théorie des plans de
mélange type II, on obtient donc 13 mélanges qui doivent faire
l'objet d'une étude expérimentale.
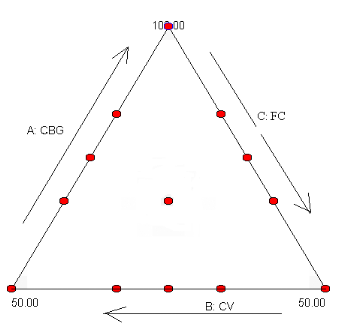
Figure 7 : Domaine
expérimental
Le tableau ci-après présente les
différents mélanges choisis avec leurs compositions.
Mélange(*)
|
% CBG
|
% CV
|
% filliers de calcaire
|
1
|
100
|
0
|
0
|
2
|
50
|
50
|
0
|
3
|
50
|
0
|
50
|
4
|
75
|
25
|
0
|
5
|
75
|
0
|
25
|
6
|
50
|
25
|
25
|
7
|
83.33
|
16.67
|
0
|
8
|
83.33
|
0
|
16.67
|
9
|
66.67
|
0
|
33.33
|
10
|
50
|
16.67
|
33.33
|
11
|
50
|
33.33
|
16.67
|
12
|
66.67
|
33.33
|
0
|
13
|
66.66
|
16.67
|
16.67
|
Tableau
3 : Matrice des expériences pour l'essai d'autoclavage.
Afin de valider ce modèle scientifique et juger de son
efficacité et de sa véracité, nous avons
préféré ajouter ces cinq mélanges
supplémentaires :
Mélange
|
% CBG
|
%CV
|
% fillers calcaire
|
14
|
58.33
|
25
|
16.67
|
15
|
33.33
|
50
|
16.67
|
16
|
58.33
|
16.67
|
25
|
17
|
41.67
|
33.33
|
25
|
18
|
25
|
50
|
25
|
Tableau
4 : Mélanges supplémentaires pour l'essai d'autoclavage
I-13-2: Essais de
résistance
Ces essais ont pour objectif la détermination de
l'influence des cendres volantes sur la résistance du béton
à jeune et moyen âge.
Dans cette étude nous nous sommes limités
à cinq ciments binaires composés du clinker broyé
gypsé et de cendres volantes. Un ciment ternaire supplémentaire
est ajouté pour la comparaison et l'analyse des résultas.
L'ensemble des ciments à tester sont
présentés dans le tableau suivant :
Mélange
|
Composition
|
CBG(%)
|
CV(%)
|
FC(%)
|
1
|
100
|
0
|
0
|
7
|
83.33
|
16.67
|
0
|
4
|
75
|
25
|
0
|
12
|
66.67
|
33.33
|
0
|
2
|
50
|
50
|
0
|
6
|
50
|
25
|
25
|
Tableau
5 : Matrice des expériences pour l'essai de résistance
Chapitre II: Essais et Résultats
Ce paragraphe est une présentation
générale de la démarche expérimentale
adoptée afin de réaliser les différents essais
prévus, ainsi qu'un résumé des résultats
obtenus.
II-
1: Essai accéléré sur mortier par autoclavage
[5]
II-1-1: Présentation
Cet essai est destiné à juger de l'influence des
cendres volantes sur l'expansion des éprouvettes de mortier 4*4*16
enrichies en alcalins, autoclavées pendant 5h à une
température de 127°C et à une pression de 0.15 MPa.
II-1-2: Matériaux soumis à l'essai
ü Basalte
La norme régissant cet essai nous impose un sable de
granularité entre 0.16 et 5 mm réparti, pour chaque
gâché, de la manière suivante :
Classe granulaire
|
Pourcentage en masse
|
0.16-0.315
|
10
|
0.315-0.63
|
10
|
0.63-1.25
|
25
|
1.25-2.5
|
25
|
2.5-5
|
30
|
Tableau 6
: Répartition des granulats utilisés dans l'essai
d'autoclavage
La préparation de ces quantités est faite
par tamisage et lavage. Les fractions obtenues sont ensuite
séchées dans le four à 80°C et conservées dans
des sacs plastiques en attendant la préparation du mortier.
ü Ciment
Comme nous l'avons déjà mentionné dans
les chapitres précédents, nous avons préparé des
ciments spéciaux pour notre étude afin d'inhiber l'effet de
l'alcali-réaction. Il s'agit de 18 ciments composés de trois
constituants principaux à savoir : Le CBG, Les fillers calcaire et
les cendres volantes.
Chaque ciment doit être enrichi par ajout de NaOH dans
l'eau de gâchage pour obtenir 4% d'équivalent de
Na20 par rapport à la masse totale du ciment.
Afin de déterminer la quantité de cet ajout, il
est primordial de faire un bilan d'alcalins.
|
% Na2O
|
% K2O
|
% Na2O équivalent
=% Na2O + 0.658
K2O
|
Cendres Volantes
|
0.42
|
0.9
|
1.01
|
Fillers Calcaire
|
0.12
|
0.12
|
0.2
|
CBG
|
0.26
|
1.02
|
0.93
|
Tableau
7 : Bilan des alcalins
La quantité totale de Na2O équivalent, dans
chaque mélange, est déduite en additionnant celle présente
dans le CBG, les fillers calcaire et les cendres volantes. Les quantités
de la soude à ajouter sont présentées en annexe1 (tableau
22).
II-1-3: Exécution de l'essai
II-1-3-1
Préparation du mortier
Pour chaque ciment préparé, on a prévu
une gâchée. Chaque gâchée est l'équivalente de
trois éprouvettes d'essai, elle est composée de :
ü 600 g de ciment.
ü 1200 g de granulats secs (Basalte).
ü 300 ml d'eau déminéralisée avec
ajout de NaOH correspondant.
Afin de préparer notre mortier on a passé par
les étapes suivantes :
ü On verse l'eau contenant l'ajout NaOH, dans le malaxeur
et on introduit le ciment.
ü On met le malaxeur en marche à vitesse lente et
après 30 s on introduit
régulièrement et successivement les
quantités spécifiées de chaque fraction du basalte en
commençant par la fraction la plus grosse. On met le malaxeur à
sa vitesse maximale et on continue à mélanger pendant 30 s
supplémentaires.
ü On arrête le malaxeur pendant 1min 30 s en
raclant pendant 15 s.
ü On reprend ensuite le malaxage à grande vitesse
pendant 60 s.
II-1-3-2
Préparation des éprouvettes
Pour préparer les éprouvettes, on a
utilisé des moules pour trois éprouvettes prismatiques de 40 mm *
40 mm * 160 mm munis à chaque extrémité des plots en acier
inoxydable, destinés à la mesure des variations dimensionnelles.
La longueur de base L0 entre les plots est de 160 mm.
Le moulage des éprouvettes est effectué selon la
procédure suivante :
D'abord on remplit le moule jusqu'à la moitié,
on l'égalise et on le met sur la table à choc. Ensuite, on met la
table à choc en marche en exécutant 60 chocs. Après, on
laisse le moule fixe sur la table à choc, on remplit l'autre
moitié et on remet la table en marche. Finalement on enlève le
moule, on l'arase et puis on le couvre par une lame de verre.
II-1-3-3 Conservation
des éprouvettes
Les moules sont placés sans retard sur un support
horizontal, dans l'armoire de la salle de conservation à une
température de 20 °C et ceci jusqu'au démoulage.
Après 24 h du gâchage, on démoule les éprouvettes,
on les immerge dans l'eau potable à 20°C, convenablement
identifiées et espacées, jusqu'à l'essai d'autoclavage.
II-1-3-4
Procédure d'autoclavage
Après 48h du gâchage, on retire les
éprouvettes de l'eau et on mesure leurs longueurs initiales. La mesure
est faite dans la salle de conservation, régulée à
20°C, et ceci à l'aide d'un appareil spécial de
précision 0.001 mm. Ensuite, on place les éprouvettes dans
l'autoclave, en position verticale, espacées d'au moins 10 mm. On
remplit l'autoclave d'eau potable, de façon à ce que les
éprouvettes puissent être recouvertes de 30 mm d'eau. On ferme
l'autoclave et on règle la puissance de chauffage, de façon
à ce que le seuil de 0.15 MPa de pression relative et de 127°C de
température soit atteinte 1h après la mise en marche.
Après 5h d'autoclavage maintenu à la
température et à la pression relative spécifiées,
on arrête le chauffage et on règle l'ouverture de la soupape de
détente de façon à faire revenir la pression
atmosphérique en 15 min environ. On laisse refroidir les
éprouvettes dans l'autoclave ou dans un récipient
approprié, en les gardant constamment en immersion dans l'eau qui a
servi pour l'autoclavage, dans la salle de conservation. Les longueurs finales
des éprouvettes sont mesurées 18 h après cet essai
d'autoclavage dans la même salle.
II-1-4: Expression des
résultats
La déformation relative sur chaque éprouvette en prenant comme longueur de base L0
= 160 mm est donnée par la formule suivante :



: La déformation relative de l'éprouvette N° i (i =
1, 2,3).
: La longueur initiale de l'éprouvette N° i ( i =
1,2,3 ).
: La longueur finale de l'éprouvette N° i ( i = 1,2,3
).
Le résultat, exprimé en pourcentage, est la moyenne
arithmétique des .
La déformation relative de chaque éprouvette ne
doit pas s'écarter de 15% de la moyenne.
II-1-5: Résultats
Mélange
|
Composition
|
Expansion moyenne (%)
|
% CBG
|
% CV
|
% FC
|
1
|
100
|
0
|
0
|
0,154
|
2
|
50
|
50
|
0
|
0,032
|
3
|
50
|
0
|
50
|
0,184
|
4
|
75
|
25
|
0
|
0,090
|
5
|
75
|
0
|
25
|
0,208
|
6
|
50
|
25
|
25
|
0,086
|
7
|
83,33
|
16.67
|
0
|
0,121
|
8
|
83,33
|
0
|
16.67
|
0,183
|
9
|
66,67
|
0
|
33.33
|
0,233
|
10
|
50
|
16.67
|
33.33
|
0,109
|
11
|
50
|
33.33
|
16.67
|
0,058
|
12
|
66,67
|
33
|
0
|
0,054
|
13
|
66,67
|
16.67
|
16.66
|
0,097
|
14
|
58,33
|
25
|
16.67
|
0,088
|
15
|
33,33
|
50
|
16.67
|
0,019
|
16
|
58,33
|
16.67
|
25
|
0,110
|
17
|
41,67
|
33.33
|
25
|
0,051
|
18
|
25
|
50
|
25
|
0,008
|
Tableau 8: Résultats moyens
de l'expansion moyenne sur trois éprouvettes 4*4*16
Les résultats détaillés de l'expansion sont
présentés dans l'annexe2 (tableau23 ).
II-
2: Essais de résistance [19]
II-2-1: Présentation
Dans ce projet de fin d'étude, nous avons adopté
ce mode opératoire dans le but de déterminer l'influence des
cendres volantes sur la résistance mécanique des ciments.
En effet, nous avons réalisé cet essai avec six
ciments ayant des teneurs différentes de cendres volantes. Ces ciments
sont choisis des 18 mélanges déjà établis pour
l'essai d'autoclavage. Pour chaque ciment, on a prévu un
écrasement à 2,7 et 28 jours.
II-2-2: Exécution de l'essai
Pour chaque ciment choisi, on a prévu trois
gâchés. Chaque gâché est destinée à un
écrasement. Equivalente de trois éprouvettes d'essai, elle est
composée de :
ü 225 ml d'eau
ü 450g de ciment.
ü 1350 g de sable normalisé.
Le malaxage du mortier ainsi que la préparation des
éprouvettes sont identiques à l'essai d'autoclavage.
Après démoulage, les éprouvettes sont
introduites dans l'eau dans la salle de conservation jusqu'au moment
d'écrasement (2,7 et 28 jours).
II-2-3: Résultats
II-2-3-1
Résistance à la compression
Mélange
|
Composition
|
Résistances moyennes
|
% CBG
|
% CV
|
% FC
|
Rc2j MPa
|
Rc7j MPa
|
Rc28j MPa
|
1
|
100
|
0
|
0
|
30.1
|
36.1
|
52.5
|
7
|
83.33
|
16.67
|
0
|
24
|
31.6
|
48.6
|
4
|
75
|
25
|
0
|
22.2
|
29.4
|
40.2
|
12
|
66.67
|
33.33
|
0
|
17.9
|
27.4
|
39.1
|
2
|
50
|
50
|
0
|
13.4
|
18.6
|
27.4
|
6
|
50
|
25
|
25
|
14.3
|
20.1
|
28.2
|
Tableau 9 : Résistances
moyennes à la compression à 2, 7 et à 28 jours
Les résultats détaillés de la
résistance à la compression sont présentés dans
l'annexe3 (tableau25 )
II-2-3-2
Résistance de traction
Mélange
|
Composition
|
Résistances moyennes
|
% CBG
|
% CV
|
% FC
|
Rt2j MPa
|
Rc7j MPa
|
Rc28j MPa
|
1
|
100
|
0
|
0
|
5.2
|
6.7
|
8.8
|
7
|
83.33
|
16.67
|
0
|
4.7
|
6.4
|
8.4
|
4
|
75
|
25
|
0
|
4.7
|
6.2
|
8.3
|
12
|
66.67
|
33.33
|
0
|
4.2
|
5.6
|
8.1
|
2
|
50
|
50
|
0
|
3.2
|
4.3
|
5.2
|
6
|
50
|
25
|
25
|
3.3
|
4.5
|
6.4
|
Tableau 10 : Résistances
moyennes à la traction à 2, 7 et à 28 jours
Les résultats détaillés de la
résistance à la traction sont présentés dans
l'annexe4 (tableau26 )
Modélisation et interprétation
Le chapitre suivant est destiné à la
modélisation des différents résultas. Cette
modélisation est obtenue en utilisant le logiciel Design Expert.
Des représentations graphiques simples sont aussi
présentées, expliquées et interprétées de
façon à déduire l'influence de chaque constituant du
ciment sur le phénomène étudié (l'expansion du
béton).
II- 3: Analyse et commentaire des
résultats
II-3-1: Effet des cendres volantes sur
l'expansion
Effet des cendres volantes à CBG
constant

Le CBG est un élément fondamental qui assure la
compacité du béton et qui reflète ses
caractéristiques physiques et ses propriétés
mécaniques. Étant ceci, nous avons maintenu le CBG à une
teneur de 50% et nous avons varié le pourcentage des autres constituants
et ceci dans un objectif de repérer le degré d'influence des
cendres volantes sur la diminution de l'expansion.
Figure
8 : Variation de l'expansion en fonction des dosages en cendres volantes
à CBG=50%.
Il est clair que l'expansion baisse au fur et à mesure
qu'on augmente le dosage en cendres volantes. Ainsi, on peut dire que pour un
ciment ternaire, la substitution des fillers calcaire aux cendres volantes
contribuent énormément à la diminution de
l'expansion.
Avec un ciment de 50% de CBG et 50% de fillers calcaire,
l'expansion est de 0.18%, par contre avec 50% de CBG et 50% de cendres volantes
l'expansion est de 0.03%. Ainsi l'expansion chute de 0.15% en absolu et de 90%
en relatif.
Effet des cendres volantes à FC
constant
Dans un objectif d'avoir plus d'informations sur l'influence
de chaque constituant du ciment sur l'évolution de l'expansion, nous
avons choisi de maintenir les fillers calcaire à des teneurs fixes (0%,
16.67% et 25%) et de faire varier les deux autres constituants( le CBG et les
cendres volantes ).
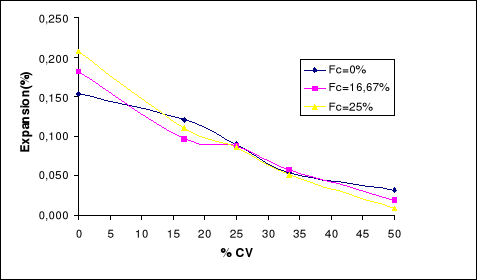
Ce qui nous permet d'avoir les représentations
graphiques suivantes :
Figure 9
: Effet des cendres volantes sur l'expansion à FC constant
D'après le graphe ci-dessus, on constate que :
ü Pour les trois courbes, l'expansion baisse au fur et
mesure qu'on augmente le dosage en cendres volantes.
ü En absence de cendres volantes, l'expansion augmente
avec la proportion des fillers calcaire présents dans le
mélange : avec 0% de FC et 100% de CBG l'expansion est de 0.154%,
avec 16.67% de FC et 83.33% de CBG l'expansion est de 0.18% et avec 25% de FC
et 75% de CBG l'expansion est de 0.21%.
ü Pour un pourcentage de cendres volantes entre 0% et
25%, l'expansion chute d'une manière significative.
ü A 25% de cendres volantes, les trois courbes
deviennent presque superposées : un point d'inflexion qui
caractérise un changement de comportement.
ü Au-delà de 25% de cendres volantes, les courbes
s'inversent, continuent à décroître et restent proches
l'une de l'autre.
ü Avec 25% de cendres volantes l'expansion baisse
d'environ 0.1% en absolu, et 60% en relatif.
ü Avec 50% de cendres volantes l'expansion baisse
d'environ 0.16% en absolu, et 90% en relatif.
De ces remarques, on peut tirer les conclusions
suivantes :
Ø Pour les trois dosages en fillers calcaire, les
cendres volantes ont un effet positif sur la diminution de l'expansion.
Ø Avec moins de 25% de cendres volantes, les fillers
calcaire jouent un rôle nuisible pour l'expansion : augmentation
très sensible de l'expansion.
Ø 25% de cendres volantes peut être
considéré comme un optimum qui décrit et
caractérise un phénomène physique ou chimique.
II-3-2: Effet des cendres volantes sur la
résistance
A la traction
Le graphe suivant représente l'effet de l'ajout des
cendres volantes sur l'évolution de la résistance à la
traction à 2, 7 et à 28jours.
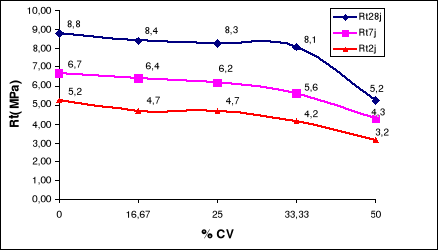
Figure 10 : Effet des cendres
volantes sur la résistance à la traction à 2, 7 et
à 28jours.
D'après ce graphe on remarque que :
- Les cendres volantes diminuent la résistance à
la traction du béton à 2j, 7j et à 28 jours.
- Lorsqu'on dépasse 33% de cendres volantes, la
diminution de la résistance devienne plus significative : une chute
de résistance à la traction à 28 jours de 8.07MPa pour
33.33% de cendres à 5.23MPa pour 50% de cendres.
La substitution des fillers calcaire par les cendres volantes
(mélange 2 et 6) diminue légèrement la résistance
à la traction à 2, 7 et à 28 jours.
A la compression
Le graphe suivant représente l'effet de l'ajout des
cendres volantes sur l'évolution de la résistance à la
compression à 2, 7 et à 28jours.
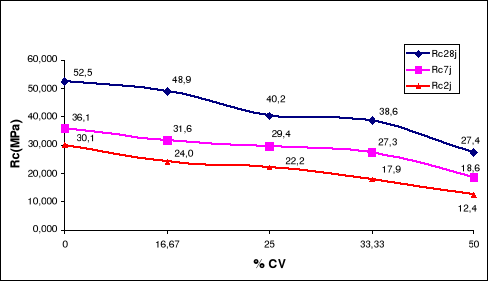
Figure 11 : Effet des cendres
volantes sur la résistance à la compression à 2, 7 et
à 28jours.
D'après ce graphe on constate que :
- Les cendres volantes diminuent la résistance à
la compression du béton à 2j, 7j et à 28 jours.
- Avec 50% de cendres volantes, la résistance à
la compression chute énormément : de 50% par rapport
à un CPA55.
La substitution des fillers calcaire par les cendres volantes
(mélange 2 et 6) diminue légèrement la résistance
à la compression à 2, 7 et à 28 jours.
II-
4: Modélisation :
Il s'agit d'une modélisation des résultats de
l'expansion à l'aide du logiciel Design Expert. Elle vise à
décrire et à refléter la variation de l'expansion en
fonction des trois constituants préparés. Plusieurs
modèles sont testés par cet outil informatique, un modèle
est jugé fiable s'il vérifie tous les tests statistiques.
II-4-1: Validité des
modèles :
Source
|
somme des carrés
|
DL
|
Carré moyen
|
F
|
Prob>F
|
Linéaire
|
0.13
|
2
|
0.064
|
135.11
|
< 0.0001
|
Quadratique
|
0.01
|
3
|
3.491 10-3
|
17.5
|
< 0.0001
|
Spécial cubique
|
2.303 10-3
|
1
|
2.303 10-3
|
17.21
|
0.0002
|
Résiduelle
|
1.026 10-3
|
29
|
3.536 10-5
|
|
|
Tableau
11 : Recherche de biais des trois modèles
Source
|
Std,Dev
|
R²
|
R² ajusté
|
R² prédit
|
Linéaire
|
0.022
|
0.8824
|
0.8759
|
0.8611
|
Quadratique
|
0.014
|
0.9546
|
0.9477
|
0.9415
|
Spécial cubique
|
0.012
|
0.9705
|
0.9650
|
0.9597
|
Tableau
12 : Test de fiabilité des trois modèles
Le logiciel sélectionne le modèle du plus
grand degré où les termes additionnels sont significatifs. Pour
notre étude, le modèle choisi pour représenter la
variation de l'expansion en fonction des constituants du ciment est le
modèle spécial cubique.
Cependant les autres modèles
mathématiques satisfont les tests statistiques et ont l'air de
présenter une modélisation significative.( R2 proche de 1).
Etant ceci, nous allons analyser les différents
résultats trouvés sous la base des trois modèles
mathématiques mentionnés par le logiciel et ceci pour avoir plus
d'explication, d'interprétation et de compréhension du rôle
joué par chaque constituant dans la variation de l'expansion. Ainsi, une
comparaison numérique entre les valeurs mesurées et celles
obtenues par ces modèles, est présentée en annexe 2
(tableau 24)
II-4-2: Vérification et Exploitation des trois
modèles
II-4-2-1 Modèle
linéaire
Le modèle linéaire propose la fonction
suivante :
Expansion(%)= +0.17424*CBG - 0.16945 *CV + 0.21453*
FC
CBG,CV et FC sont en 10-2%.
Source
|
Somme des carrés
|
DL
|
Carré moyen
|
F
|
Prob>F
|
Modéle
|
0.13
|
2
|
0.064
|
135.11
|
< 0.0001
|
CBG,CV,FC
|
0.13
|
2
|
0.064
|
135.11
|
< 0.0001
|
Résiduelle
|
0.017
|
36
|
4.738E-004
|
|
|
Tableau
13 : Test de signification pour le modèle linéaire
La valeur de probabilité prob>F est
inférieure à 0.05 indique que les termes du modèles sont
significatifs et que le modèle est significatif à 99.99%.
ü Vérification du
modèle :
Le graphe suivant exprime la variation des valeurs
prédites en fonction des valeurs mesurées. Le modèle
s'avère fiable : il n'y a pas de dispersion de points par rapport
à la bissectrice.
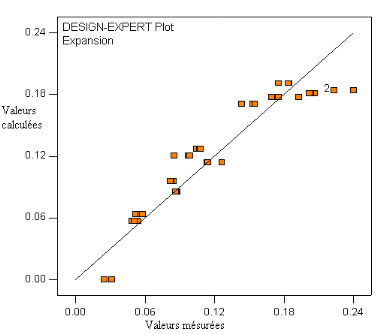
Figure 12 :
Valeurs calculées par le modèle linéaire en fonction des
valeurs mesurées.
ü Exploitation du modèle
Le graphe suivant représente des courbes iso-Expansion,
ces iso-valeurs sont obtenues par le modèle linéaire
précédemment calculé.
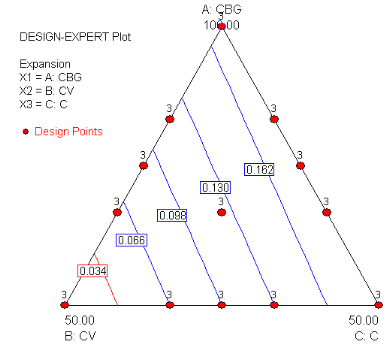
Figure 13 :
Courbes iso-Expansion du modèle linéaire
D'après ce modèle linéaire, on peut tirer
les conclusions suivantes :
Ø Les cendres volantes ont un effet positivement
significatif sur la diminution de l'expansion du béton :
L'expansion démunie au fur et à mesure que l'on augmente le
dosage en cendres volantes.
Ø Les fillers calcaire ainsi que Le CBG contribuent
à l'augmentation de l'expansion.
Le modèle présenté néglige les
interactions entre les différents constituants. Ce sont les
modèles suivants ( modèle quadratique et spécial cubique )
qui prennent en considération ces interactions ainsi que leurs
influences sur les résultats obtenus.
II-4-2-2 Modèle
quadratique
Le modèle quadratique propose la fonction suivante :
Expansion(%)= +0.15545*CBG - 0.018007 *CV - 0.018648*
FC - 0.15034*CBG*CV +0.50093*CBG * FC - 0.54858* CV * FC
CBG,CV et FC sont en 10-2%.
Source
|
Somme des carrés
|
DL
|
Carré moyen
|
F
|
Prob>F
|
Modèle
|
0.14
|
5
|
0.028
|
138.84
|
< 0.0001
|
CBG,CV,FC
|
0.13
|
2
|
0.064
|
320.85
|
<0.0001
|
CBG*CV
|
3.106E-004
|
1
|
3.106E-004
|
1.56
|
0.2209
|
CBG*FC
|
3.449E-003
|
1
|
3.449E-003
|
17.28
|
0.0002
|
CV*FC
|
4.136E-003
|
1
|
4.136E-003
|
20.73
|
< 0.0001
|
Résiduel le
|
6.584E-003
|
33
|
1.995E-004
|
|
|
Tableau
14 : Test de signification pour le modèle quadratique
La valeur de probabilité prob>F est
inférieure à 0.05 indique que les termes du modèle :
CV , FC , CBG , CBG * FC et CV * FC sont significatifs, cependant le terme du
CBG*CV est à rejeter ( probabilité supérieure à
0.05 ).
La modélisation devienne :
Expansion(%)= +0.15545*CBG - 0.018007 *CV - 0.018648* FC
+ 0.50093*CBG* FC - 0.54858* CV * FC.
CBG,CV et FC sont en 10-2%.
ü Vérification du
modèle
Le graphe suivant exprime la variation des valeurs
prédites en fonction des valeurs mesurées. Le modèle
s'avère fiable : il n'y a pas de dispersion de points par rapport
à la bissectrice.
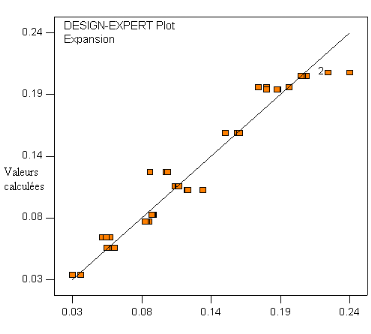
ü Exploitation du modèle
Le graphe suivant représente des courbes iso-Expansion,
ces iso-valeurs sont obtenues par le modèle quadratique
précédemment calculé.
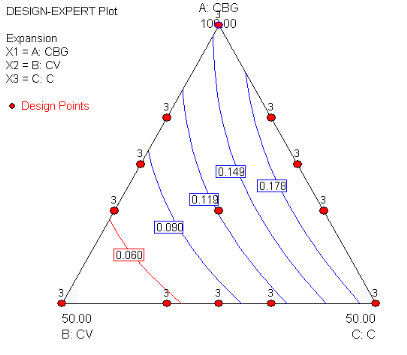
Figure 15 : Courbes iso-Expansion du
modèle quadratique
D'après ce modèle quadratique, on peut tirer les
conclusions suivantes :
Ø Les cendres volantes ont un effet positif et
significatif sur la diminution de l'expansion du béton :
L'expansion démunie au fur et à mesure qu'on augmente le dosage
en cendres volantes.
Ø L'interaction cendre volantes fillers calcaire
contribue à la diminution de l'expansion.
Ø L'interaction CBG fillers calcaire augmente
l'expansion.
Ø Le coefficient positif attribué à
l'interaction CBG fillers calcaire est plus important que le coefficient
négatif attribué au fillers calcaire : ces derniers jouent
toujours un rôle nuisible pour la diminution de l'expansion, ce qui
prouve les résultats du modèle précédent.
II-4-2-3 Modèle
spécial-cubique
Le modèle spécial-cubique propose la formulation
suivante :
Expansion(%) = +0.15194*CBG - 0.085272 *CV - 0.085913*
FC + 0.62845*CBG * FC + 2.98049 * CV * FC - 6.80308 * FC * CBG * CV
CBG,CV et FC sont en 10-2%.
Source
|
Somme des carrés
|
D.L
|
Carré moyen
|
F
|
Prob > F
|
Modèle
|
0.14
|
6
|
0.023
|
175.41
|
< 0.0001
|
CBG , CV ,FC
|
0.13
|
2
|
0.064
|
478.49
|
< 0.0001
|
CBG*FC
|
4.948 10-3
|
1
|
4.948 10-3
|
36.98
|
< 0.0001
|
CBG*CV
|
6.52 10-6
|
1
|
6.52 10-6
|
0.049
|
0.8267
|
FC*CV
|
2.221 10-3
|
1
|
2.221 10-3
|
16.60
|
0.0003
|
CBG*FC*CV
|
2.303 10-3
|
1
|
2.303 10-3
|
17.21
|
0.0002
|
résiduelle
|
4.281 10-3
|
32
|
1.338 10-4
|
|
|
Tableau
15 : Test de signification pour le modèle spécial cubique
La valeur de probabilité prob>F est
inférieure à 0.05 indique que les termes du modèles :
CV , FC , CBG , CBG * FC , CV * FC et CV*CBG*FC sont significatives, cependant
le terme du CBG*CV est à rejeter ( probabilité supérieure
à 0.05 ). La modélisation devient donc :
Expansion(%) = +0.15194*CBG - 0.085272 *CV - 0.085913*
FC + 0.62845*CBG * FC + 2.98049 * CV * FC- 6.80308 * FC * CBG * CV
CBG,CV et FC sont en 10-2%.
ü Vérification du
modèle
Le graphe suivant exprime la variation des valeurs
prédites en fonction des valeurs mesurées. Le modèle
s'avère fiable : il n'y a pas de dispersion de points par rapport
à la bissectrice.
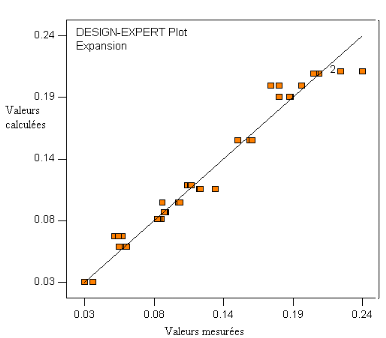
Figure 16 : Valeurs calculées
par le modèle spécial cubique en fonction des valeurs
mesurées.
ü Exploitation du modèle
Le graphe suivant des courbes iso-Expansion, ces iso-valeurs
sont obtenues par le modèle spécial cubique
précédemment calculé.
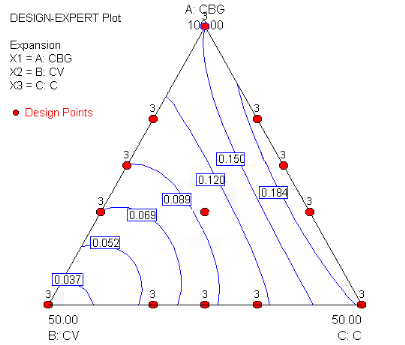
Figure 17 : Iso-Expansion
données par le modèle spécial cubique
Le modèle spécial cubique prouve et valorise les
résultats obtenus par le modèle quadratique. Il est à
souligner que l'interaction CBG, cendres volantes et fillers calcaire
s'avère importante et significative: En présence de CBG,
l'utilisation des cendres volantes avec les fillers calcaire favorise la
diminution de l'expansion.
II-
5: Interprétation des résultats
D'après la modélisation mathématique
obtenue ainsi que les différents graphes tracés on peut tirer les
interprétations et conclusions suivantes :
- Les fillers calcaire sont des ajouts minéraux qui
contribuent à l'augmentation de l'expansion. Cela peut être
expliqué par deux hypothèses :
Hypothèse1 :
Les fillers calcaire utilisés contient de la silice
réactive.
Hypothèse 2
Les fillers calcaire améliorent la courbe
granulométrique du ciment et par conséquent, ils jouent un
rôle favorable dans l'augmentation de la compacité du mortier et
la diminution des vides. Étant ceci les gels trouveront moins d'espace
pour se placer, ce qui provoque plus d'expansion et plus de fissuration.
- Les cendres volantes sont des ajouts minéraux qui
contribuent significativement à la diminution de l'expansion. Ceci peut
être justifié par :
Hypothèse 1
Grâce à leur forme granulaire sphérique et
creuse qui facilite leur déformation, les cendres volantes absorbent
l'expansion due à la formation du gel dans la masse squelettique du
béton.
Hypothèse 2
Les cendres volantes fixent les alcalins présents dans
le béton et empêchent par la suite la formation du gel.
Les cendres volantes ne manifestent d'effet pouzzolanique
qu'à moyen et à long terme( selon des expériences au
delà de 90 jours).
L'utilisation des cendres volantes avec des dosages compris
entre 25% et 30% revêt une importance particulière :d'une
part elles éliminent l'effet des éléments nuisibles
(fillers calcaire par exemple) et d'autre part elles permettent d'avoir des
caractéristiques mécaniques acceptables (résistance
à 28jours).
- Le CBG est un élément fondamental qui assure
la compacité et augmente la résistance du mortier. Un
béton compact est moins poreux et par conséquent plus sensible
à l'expansion.
II-
6: Optimisation
A l'aide de l'outil d'optimisation `' Solveur'' du tableau
Excel, on se propose de déterminer les compositions du ciment binaire (
CBG+Cendres volantes ) , lesquelles doivent minimiser l'expansion tout en
satisfaisant aux exigences normatives.
Afin d'annuler définitivement l'expansion, un ciment
spécial est proposé à la fin de ce paragraphe.
II-6-1: CPZ(A) 35
Les contraintes exigées par la norme sont :
ü
ü Étant donné que le CBG contient 7% du gypse,
donc : 
ü 


ü ü La résistance à la compression
à 7 jours et à 28 jours ainsi que l'expansion sont
déduites des modèles mathématiques proposés par le
logiciel Design Expert. La modélisation détaillée de la
résistance est présentée en annexe 5.
La solution optimale correspondant à ces exigences est la
suivante :
% CBG
|
69.9%
|
% Cendres volantes
|
30.1%
|
Expansion minimale en %
|
0.081
|
Rc (7jours) en MPa
|
27.64
|
Rc (28jours) en MPa
|
38.61
|
Tableau 16: La solution
optimale pour un ciment CPZ(A)35
II-6-2: CPZ(A) 45
Les contraintes exigées par la norme sont :
ü
ü Étant donné que le CBG contient 7% du gypse,
donc .




ü ü ü ü La résistance à la
compression à 7 jours et à 28 jours ainsi que l'expansion sont
déduites des modèles mathématiques proposés par le
logiciel Design Expert. La modélisation détaillée de la
résistance est présentée en annexe 5.
La solution optimale correspondante à ces exigences est la
suivante :
% CBG
|
76.6
|
% Cendres volantes
|
23.4
|
Expansion minimale en %
|
0.096
|
%Rc (7jours) en MPa
|
30.05
|
Rc (28jours) en MPa
|
42
|
Tableau 17 : La solution optimale
pour un ciment CPZ(A)45
II-6-3: CPZ(B) 35
Les contraintes exigées par la norme sont :
ü
ü Étant donné que le CBG contient 7% du
gypse, donc : 



ü ü ü La résistance à la compression
à 7 jours et à 28 jours ainsi que l'expansion sont
déduites des modèles mathématiques proposés par le
logiciel Design Expert. La modélisation détaillée de la
résistance est présentée en annexe 5.
La solution optimale correspondante à ces exigences est la
suivante :
% CBG
|
56.8%
|
% Cendres volantes
|
43.2%
|
Expansion minimale en %
|
0.05
|
Rc (7jours) en MPa
|
21.98
|
Rc (28jours) en MPa
|
32
|
Tableau 18 : La solution optimale
pour un ciment CPZ(B)35
II-6-4: CPZ(B) 45
Les contraintes exigées par la norme sont :
ü
ü Étant donné que le CBG contient 7% du
gypse, donc : 




ü ü ü ü La résistance à la
compression à 7 jours et à 28 jours ainsi que l'expansion sont
déduites des modèles mathématiques proposés par le
logiciel Design Expert. La modélisation détaillée de la
résistance est présentée en annexe 5.
La solution optimale correspondante à ces exigences est la
suivante :
% CBG
|
68.8%
|
% Cendres volantes
|
31.2%
|
Expansion minimale en %
|
0.078
|
Rc (7jours) en MPa
|
27.21
|
Rc (28jours) en MPa
|
38.06
|
Tableau 19 : La solution optimale
pour un ciment CPZ(B)45
II-6-5: Ciment spécial pour éliminer
l'expansion
Le but est d'avoir une formulation du ciment CPZ qui annule
l'expansion. Les contraintes sur la résistances ne sont pas prises en
comptes.
% CBG
|
35.9
|
% Cendres volantes
|
64.1
|
Expansion minimale en %
|
0.0001
|
Rc (7jours) en MPa
|
10.28
|
Rc (28jours) en MPa
|
21.42
|
Tableau 20: Ciment
spécial pour annuler l'expansion.
Ainsi avec 64.1% de cendres volantes et 35.9 % de CBG, on
arrive carrément à éliminer l'expansion du béton
tout en gardant une résistance à la compression à 28 jours
acceptable.
La résistance à la compression à 7 jours
et à 28 jours ainsi que l'expansion sont déduites des
modèles mathématiques proposés par le logiciel Design
Expert. La modélisation détaillée de la résistance
est présentée en annexe 5.
Conclusions et Recommandations
Les désordres dus à
l'alcali-réaction, attaquant les grands ouvrages, ont suscité un
grand intérêt dans les milieux de recherches scientifiques. La
majorité des études allant dans ce sens relèvent une
tendance vers l'utilisation des ajouts minéraux comme
éléments inhibiteurs pour de telles réactions. C'est dans
ce cadre que s'inscrit notre sujet de travail de fin d'études qui
présentait comme objectif, l'utilisation des cendres volantes dans la
formulation du ciment afin de faire face aux réactions
alcali-granulats.
Pour atteindre une telle finalité on a
procédé à la préparation d'un nombre optimal,
déterminé sur la base des plans d'expériences, de
mélanges suralcanisés à différents dosages en
cendres volantes. Cette phase préparatrice a été
succédée par le lancement d'une série d'essais
d'autoclavage sur des mortiers utilisant le basalte comme granulat, et ceci
afin de déterminer l'expansion et son évolution en fonctions des
proportions des cendres volantes dans les dits mélanges.
Étant conscient de l'impact de l'ajout des cendres
volantes sur la résistance du béton, une deuxième
série d'essais a été réalisée en
parallèle avec la première.
La phase expérimentale a débauché sur des
résultats satisfaisants et répondant aux objectifs fixés.
En effet, l'utilisation des cendres volantes a donné lieu à une
diminution considérable de l'expansion du béton ; avec 50%
de cendres volantes et 50% de CBG, on est parvenu à diminuer l'expansion
de 0.15% en absolu. Cependant, l'analyse des résultats a mis en
évidence l'effet négatif, inattendu, des fillers calcaire sur
l'expansion.
Aussi efficaces qu'elles soient pour l'inhibition de
l'alcali-réaction, les cendres volantes peuvent être à
l'origine d'une baisse de la résistance du béton. Ainsi le ciment
« optimal » à préparer doit satisfaire d'une
part, aux exigences normatives en matière de résistance et
d'autre part, il doit avoir un taux minimal d'expansion (0.15%) .une
optimisation de la composition de ce ciment a été faite sur la
base de l'algorithme de simplex (solveur) :
Type du ciment
|
% CBG
|
% CV
|
Rc7j (Mpa)
|
Rc28j (Mpa)
|
Expansion (%)
|
CPZ(A) 35
|
69.9
|
30.1
|
27.64
|
38.61
|
0.081
|
CPZ(A)45
|
76.6
|
23.4
|
30.05
|
42
|
0.096
|
CPZ(B) 35
|
56.8
|
43.2
|
21.8
|
32
|
0.05
|
CPZ(B) 45
|
68.8
|
31.2
|
27.21
|
38.06
|
0.078
|
Spécial
|
35.9
|
64.1
|
10.28
|
21.42
|
0.0001
|
Tableau 21:
Récapitulatif des ciments spéciaux pour faire face à
l'alcali-réaction.
Vu la grande sensibilité des essais de notre
étude, la précision dans leur réalisation s'est
avérée primordiale et elle est toujours recommandée.
Certes, l'utilisation d'un seul granulat (basalte) nous a permis de faire
ressortir des résultats pertinents, cependant la réalisation d'un
modèle général nécessite l'utilisation de plusieurs
granulats dans des cycles d'essais de laboratoire afin de disposer d'une base
de données et un modèle beaucoup plus représentatif.
Il est aussi vivement souhaitable de mieux quantifier l'effet
des cendres volantes sur la résistance à moyen et à long
terme , par le biais d'une série d'essais appropriés servant
d'outil pour la modélisation du phénomène. Étant
donné le caractère chimico-physique de l'alcali-réaction,
la réalisation des analyses chimiques concises et poussées est
une tâche potentiellement significative pour des explications et des
interprétations plus élaborées. Notons ainsi que ces
analyses doivent être complémentées par d'autres portant
sur les caractères intrinsèques des matériaux (
densité, absorption, finesse Blaine,...) afin d'être en mesure
d'identifier, de caractériser ces matériaux et de quantifier les
interactions qui leur sont associées. Dans la même optique, il
serait souhaitable de réaliser une carte de classification des granulats
par carrière, à l'échelle nationale, en fonction de leur
réactivité.
Annexe 1 : La soude
ajoutée
Mélange
|
Composition
|
Na2O équivalent
|
Masse de NaOH nécessaire (g)
|
%CBG
|
% CV
|
% FC
|
Pourcentage
|
Masse en g
|
1
|
100
|
0
|
0
|
0.93
|
5.58
|
11.88
|
2
|
50
|
50
|
0
|
0.97
|
5.82
|
11.73
|
3
|
50
|
0
|
50
|
0.57
|
3.39
|
13.3
|
4
|
75
|
25
|
0
|
0.95
|
5.7
|
11.81
|
5
|
75
|
0
|
25
|
0.75
|
4.49
|
12.59
|
6
|
50
|
25
|
25
|
0.77
|
4.61
|
12.51
|
7
|
83.33
|
16.67
|
0
|
0.94
|
5.66
|
11.83
|
8
|
83.33
|
0
|
16.67
|
0.81
|
4.85
|
12.35
|
9
|
66.67
|
0
|
33.33
|
0.69
|
4.12
|
12.83
|
10
|
50
|
16.67
|
33.33
|
0.7
|
4.2
|
12.77
|
11
|
50
|
33.33
|
16.67
|
0.83
|
5.01
|
12.25
|
12
|
66.67
|
33.33
|
0
|
0.96
|
5.74
|
11.78
|
13
|
66.67
|
16.67
|
16.66
|
0.82
|
4.93
|
12.3
|
14
|
58.33
|
25
|
16.67
|
0.83
|
4.97
|
12.28
|
15
|
33.33
|
50
|
16.67
|
0.85
|
5.09
|
12.20
|
16
|
58.33
|
16.67
|
25
|
0.76
|
4.57
|
12.54
|
17
|
41.67
|
33.33
|
25
|
0.77
|
4.64
|
12.49
|
18
|
25
|
50
|
25
|
0.79
|
4.73
|
12.44
|
Tableau 22: La
quantité de la soude ajoutée à chaque mélange
Annexe 2 :
Résultats d'expansion
Mélange
|
Composition
|
Éprouvette
|
Expansion (%)
|
Ecart/moyenne (%)
|
% CBG
|
% CV
|
% FC
|
1
|
100
|
0
|
0
|
1
|
0,156
|
1,6260
|
2
|
0,158
|
2,8455
|
3
|
0,147
|
-4,4715
|
Moyenne
|
0,154
|
|
2
|
50
|
50
|
0
|
1
|
0,034
|
7,1148
|
2
|
0,034
|
6,1321
|
3
|
0,028
|
-13,5220
|
Moyenne
|
0,032
|
|
3
|
50
|
0
|
50
|
1
|
0,188
|
1,6811
|
2
|
0,187
|
1,3422
|
3
|
0,179
|
-3,0640
|
Moyenne
|
0,184
|
|
4
|
75
|
25
|
0
|
1
|
0,091
|
0,6944
|
2
|
0,090
|
0,0000
|
3
|
0,089
|
-0,6944
|
Moyenne
|
0,090
|
|
5
|
75
|
0
|
25
|
1
|
0,210
|
1,2048
|
2
|
0,207
|
-0,3012
|
3
|
0,206
|
-0,9036
|
Moyenne
|
0,208
|
|
6
|
50
|
25
|
25
|
1
|
0,088
|
1,9417
|
2
|
0,086
|
-0,2427
|
3
|
0,084
|
-1,6990
|
Moyenne
|
0,086
|
|
7
|
83,33
|
16.67
|
0
|
1
|
0,117
|
-3,6082
|
2
|
0,118
|
-3,0928
|
3
|
0,129
|
6,7010
|
Moyenne
|
0,121
|
|
8
|
83,33
|
0
|
16.67
|
1
|
0,196
|
7,5342
|
2
|
0,173
|
-5,4795
|
3
|
0,179
|
-2,0548
|
Moyenne
|
0,183
|
|
9
|
66,67
|
0
|
33.33
|
1
|
0,227
|
-2,4194
|
2
|
0,244
|
4,8387
|
3
|
0,227
|
-2,4194
|
Moyenne
|
0,233
|
|
10
|
50
|
16.67
|
33.33
|
1
|
0,108
|
-1,7143
|
2
|
0,110
|
0,5714
|
3
|
0,111
|
1,1429
|
Moyenne
|
0,109
|
|
11
|
50
|
33.33
|
16.67
|
1
|
0,061
|
4,7064
|
2
|
0,054
|
-6,0881
|
3
|
0,059
|
1,4680
|
Moyenne
|
0,058
|
|
Mélange
|
Composition
|
Éprouvette
|
Expansion (%)
|
Écart/moyenne (%)
|
12
|
66,67
|
33
|
0
|
1
|
0,057
|
5,3241
|
2
|
0,051
|
-5,0926
|
3
|
0,054
|
-0,4630
|
Moyenne
|
0,054
|
|
13
|
66,67
|
16.67
|
16.66
|
1
|
0,101
|
3,8442
|
2
|
0,102
|
5,1342
|
3
|
0,088
|
-9,0557
|
Moyenne
|
0,097
|
|
14
|
58,33
|
25
|
16.67
|
1
|
0,096
|
9,4787
|
2
|
0,084
|
-4,0284
|
3
|
0,083
|
-5,4502
|
Moyenne
|
0,088
|
|
15
|
33,33
|
50
|
16.67
|
1
|
0,020
|
2,5641
|
2
|
0,018
|
-10,2564
|
3
|
0,021
|
7,3718
|
Moyenne
|
0,019
|
|
16
|
58,33
|
16.67
|
25
|
1
|
0,116
|
5,2830
|
2
|
0,118
|
6,9811
|
3
|
0,097
|
-12,2642
|
Moyenne
|
0,110
|
|
17
|
41,67
|
33.33
|
25
|
1
|
0,051
|
0,4902
|
2
|
0,050
|
-1,9608
|
3
|
0,052
|
1,7157
|
moyenne
|
0,051
|
|
18
|
25
|
50
|
25
|
1
|
0,008
|
-9,6386
|
2
|
0,009
|
12,9518
|
3
|
0,008
|
-2,1084
|
moyenne
|
0,008
|
|
Tableau 23:
Résultats détaillés de l'Expansion
Mélange
|
CBG
|
CV
|
FC
|
Expansion mesurée
|
Linéaire
|
Quadratique
|
Spécial cubique
|
1
|
100
|
0
|
0
|
0,154
|
0,174
|
0,155
|
0,152
|
2
|
50
|
50
|
0
|
0,032
|
0,002
|
0,069
|
0,033
|
3
|
50
|
0
|
50
|
0,184
|
0,194
|
0,194
|
0,190
|
4
|
75
|
25
|
0
|
0,09
|
0,088
|
0,112
|
0,093
|
5
|
75
|
0
|
25
|
0,208
|
0,184
|
0,206
|
0,210
|
6
|
50
|
25
|
25
|
0,086
|
0,098
|
0,097
|
0,085
|
7
|
83,33
|
16,67
|
0
|
0,121
|
0,117
|
0,127
|
0,112
|
8
|
83,33
|
0
|
16,67
|
0,183
|
0,181
|
0,196
|
0,200
|
9
|
66,67
|
0
|
33,33
|
0,233
|
0,188
|
0,209
|
0,212
|
10
|
50
|
16,67
|
33,33
|
0,109
|
0,130
|
0,122
|
0,114
|
11
|
50
|
33,33
|
16,67
|
0,058
|
0,066
|
0,080
|
0,062
|
12
|
66,67
|
33
|
0
|
0,054
|
0,060
|
0,098
|
0,073
|
13
|
66,67
|
16,67
|
16,66
|
0,097
|
0,124
|
0,138
|
0,099
|
14
|
58,33
|
25
|
16,67
|
0,088
|
0,095
|
0,109
|
0,073
|
15
|
33,33
|
50
|
16,67
|
0,019
|
0,009
|
0,022
|
0,088
|
16
|
58,33
|
16,67
|
25
|
0,11
|
0,127
|
0,133
|
0,103
|
17
|
41,67
|
33,33
|
25
|
0,051
|
0,070
|
0,061
|
0,091
|
18
|
25
|
50
|
25
|
0,008
|
0,012
|
0.0001
|
0,173
|
Tableau 24:
Comparaison des valeurs calculées et celles mesurées de
l'expansion
Annexe 3 : La
résistance à la compression
Mélange
|
Composition
|
Rc2j (Mpa)
|
Rc7j(Mpa)
|
Rc28j(Mpa)
|
1
|
100%CBG
|
30,19
|
35,88
|
51,56
|
30,06
|
33,19
|
52,00
|
30,06
|
37,13
|
51,50
|
30,63
|
38,50
|
53,63
|
29,75
|
36,31
|
55,06
|
29,75
|
35,31
|
51,38
|
Moyenne
|
30,07
|
36,05
|
52,52
|
7
|
83,33CBG+16,67CV
|
23,44
|
31,19
|
43,56
|
25,00
|
31,44
|
50,69
|
24,19
|
32,31
|
51,38
|
22,81
|
32,25
|
47,44
|
24,31
|
29,75
|
37,44*
|
24,06
|
32,63
|
49,81
|
Moyenne
|
23,97
|
31,59
|
48,58
|
4
|
75CBG+25CV
|
23,63
|
28,19
|
38,19
|
21,56
|
29,56
|
39,38
|
21,50
|
30,19
|
41,31
|
22,44
|
29,00
|
41,25
|
21,06
|
29,38
|
40,81
|
23,06
|
30,19
|
40,13
|
Moyenne
|
22,21
|
29,42
|
40,18
|
12
|
66,67CBG+33,33CV
|
18,63
|
26,69
|
38,44
|
16,81
|
26,69
|
33,69*
|
17,50
|
26,94
|
39,75
|
18,19
|
28,63
|
40,31
|
17,56
|
28,06
|
36,44
|
18,50
|
25,00*
|
40,31
|
Moyenne
|
17,86
|
27,40
|
39,05
|
2
|
50%CBG+50%CV
|
13,00
|
18,88
|
26,69
|
12,63
|
18,50
|
28,56
|
11,94
|
18,88
|
28,00
|
14,44
|
18,69
|
26,75
|
13,94
|
18,19
|
26,63
|
14,63
|
18,69
|
27,75
|
Moyenne
|
13,43
|
18,64
|
27,40
|
6
|
50CBG+25CV+25FC
|
15,13
|
20,69
|
28,44
|
14,25
|
18,88
|
28,75
|
13,63
|
20,50
|
26,81
|
14,44
|
19,31
|
29,19
|
13,94
|
20,50
|
27,56
|
14,63
|
20,69
|
28,56
|
Moyenne
|
14,33
|
20,09
|
28,22
|
Tableau 25 :
Résultats détaillés de la résistance à la
compression à 2, 7 et à 28jours
(*) : Ces valeurs sont rejetées car elles
s'éloignent de la réalité.
Annexe 4 : La
résistance à la traction
Mélange
|
Composition
|
Rt2j (Mpa)
|
Rt7j(Mpa)
|
Rt28j(Mpa)
|
1
|
100%CBG
|
5,15
|
6,90
|
9,01
|
5,03
|
6,90
|
8,78
|
5,50
|
6,20
|
8,54
|
Moyenne
|
5,23
|
6,67
|
8,78
|
7
|
83,33CBG+16,67CV
|
4,68
|
6,08
|
8,19
|
4,80
|
5,85
|
9,01
|
4,56
|
7,25
|
7,96
|
Moyenne
|
4,68
|
6,40
|
8,39
|
4
|
75CBG+25CV
|
4,68
|
6,08
|
7,96
|
4,80
|
6,44
|
8,78
|
4,56
|
5,97
|
8,07
|
Moyenne
|
4,68
|
6,16
|
8,27
|
12
|
66,67CBG+33,33CV
|
4,10
|
5,73
|
8,31
|
4,33
|
5,50
|
7,96
|
4,10
|
5,62
|
7,96
|
Moyenne
|
4,17
|
5,62
|
8,07
|
2
|
50%CBG+50%CV
|
3,51
|
4,21
|
5,15
|
2,93
|
3,98
|
5,03
|
3,04
|
4,68
|
5,50
|
Moyenne
|
3,16
|
4,29
|
5,23
|
6
|
50CBG+25CV+25FC
|
3,16
|
4,33
|
6,44
|
3,39
|
4,56
|
7,25
|
3,28
|
4,68
|
5,62
|
Moyenne
|
3,28
|
4,52
|
6,44
|
Tableau 26 :
Résultats détaillés de la résistance à la
traction à 2, 7 et à 28 jours
Annexe 5 :
Modélisation de la résistance en traction et en
compression
I/ Résistance à la compression à 2
jours :
1/ Validité des modèles :
Source
|
somme des carrés
|
DL
|
Carré moyen
|
F
|
Prob>F
|
Linéaire
|
1045.79
|
1
|
1045.79
|
1549.53
|
< 0.0001
|
Quadratique
|
0.24
|
1
|
0.24
|
0.35
|
0.5605
|
cubique
|
0.13
|
1
|
0.13
|
0.19
|
0.6692
|
Résiduelle
|
18.52
|
26
|
0.71
|
|
|
Tableau 27:
Recherche du biais (Rc2j)
Source
|
Std,Dev
|
R²
|
R² ajusté
|
R² prédit
|
Linéaire
|
0.82
|
0.9823
|
0.9816
|
0.9806
|
Quadratique
|
0.83
|
0.9825
|
0.9812
|
0.9806
|
Cubique
|
0.84
|
0.9826
|
0.9806
|
0.9782
|
Tableau 28: Test de
fiabilité (Rc2j)
2/ Modélisation
Le modèle aisi choisi est le modèle
linéaire ayant comme expression :
Rc 2j = 30.16477*CBG -5.260432*CV
ü Analyse
de la variance
Source
|
Somme des carrés
|
DL
|
Carré moyen
|
F
|
Prob>F
|
Modèle
|
1045.79
|
1
|
1045.79
|
1549.53
|
< 0.0001
|
CBG,CV
|
1045.79
|
1
|
1045.79
|
1549.53
|
< 0.0001
|
Résiduelle
|
18.90
|
28
|
0.67
|
|
|
Tableau 29: test de
signification
Les deux facteurs sont significatifs car leur Prob>F est
inférieur à 0.05.
ü Comparaison entre valeurs calculées et
valeurs mesurées :
Composition
|
valeur mesurée
|
Valeur calculée
|
CBG
|
CV
|
FC
|
RC 2j
|
RC 2j
|
100
|
0
|
0
|
30,073
|
30,165
|
83,33
|
16,67
|
0
|
23,969
|
24,259
|
75
|
25
|
0
|
22,208
|
21,308
|
66,67
|
33,33
|
0
|
17,865
|
18,358
|
50
|
50
|
0
|
12,427
|
12,452
|
Tableau 30:
Comparaison entre les valeurs de la résistance à la compression
à 2 jours calculées par le modèle linéaire et les
valeurs mesurées
II/ Résistance à la compression à 7
jours :
1/ Validité des modèles :
Source
|
somme des carrés
|
DL
|
Carré moyen
|
F
|
Prob>F
|
Linéaire
|
1003.73
|
1
|
1003.73
|
378.29
|
< 0.0001
|
Quadratique
|
33.57
|
1
|
33.57
|
22.6
|
<0.0001
|
cubique
|
4.73
|
1
|
4.73
|
3.41
|
0.0761
|
Résiduelle
|
36
|
26
|
1.38
|
|
|
Tableau 31:
Recherche du biais (Rc7j)
Source
|
Std,Dev
|
R²
|
R² ajusté
|
R² prédit
|
Linéaire
|
1.63
|
0.9311
|
0.9286
|
0.9188
|
Quadratique
|
1.23
|
0.9622
|
0.954
|
0.9521
|
Cubique
|
1.18
|
0.9666
|
0.9628
|
0.9541
|
Tableau 32: : Test
de fiabilité (Rc7j)
2/ Modélisation
Le modèle ainsi choisi est le modèle
quadratique ayant comme expression :
Rc 7j = 35.85910*CBG -17.4287*CV +37.16457*CBG*CV
ü Analyse
de la variance
Source
|
Somme des carrés
|
DL
|
Carré moyen
|
F
|
Prob>F
|
Modèle
|
1037.30
|
2
|
518.65
|
343.87
|
< 0.0001
|
CBG,CV
|
1003.73
|
1
|
1003.73
|
656.49
|
< 0.0001
|
CBG*CV
|
33.57
|
1
|
33.57
|
22.26
|
< 0.0001
|
Résiduelle
|
40.72
|
27
|
1.51
|
|
|
Tableau 33: Test de
signification
Les trois facteurs sont significatifs car leur Prob>F est
inférieur à 0.05.
ü Comparaison entre valeurs calculées et
valeurs mesurées :
Composition
|
valeur mesurée
|
Valeur calculée
|
CBG
|
CV
|
FC
|
RC 7j
|
RC 7j
|
100
|
0
|
0
|
36,052
|
35,859
|
83,33
|
16,67
|
0
|
31,594
|
32,139
|
75
|
25
|
0
|
29,417
|
29,506
|
66,67
|
33,33
|
0
|
27,323
|
26,357
|
50
|
50
|
0
|
18,635
|
18,506
|
Tableau 34:
Comparaison entre les valeurs de la résistance à la compression
à 7 jours calculées par le modèle quadratique et les
valeurs mesurées
III/ Résistance à la compression à
28 jours :
1/ Validité des modèles :
Source
|
somme des carrés
|
DL
|
Carré moyen
|
F
|
Prob>F
|
Linéaire
|
2113.65
|
1
|
2113.65
|
244.09
|
< 0.0001
|
Quadratique
|
17.72
|
1
|
17.72
|
2.13
|
0.1561
|
cubique
|
0.095
|
1
|
0.095
|
0.011
|
0.9172
|
Résiduelle
|
224.64
|
26
|
8.64
|
|
|
Tableau 35:
Recherche du biais (Rc28j)
Source
|
Std,Dev
|
R²
|
R² ajusté
|
R² prédit
|
Linéaire
|
2.94
|
0.8971
|
0.8934
|
0.8861
|
Quadratique
|
2.89
|
0.9046
|
0.8975
|
0.8903
|
Cubique
|
2.94
|
0.9047
|
0.8937
|
0.8739
|
Tableau 36 : Test
de fiabilité (Rc28j)
2/ Modélisation
Le modèle ainsi choisi est le modèle
linéaire ayant comme expression :
Rc 28j = 53.58450*CBG +3.22205*CV
ü Analyse
de la variance
Source
|
Somme des carrés
|
DL
|
Carré moyen
|
F
|
Prob>F
|
Modèle
|
1037.30
|
2
|
518.65
|
343.87
|
< 0.0001
|
CBG,CV
|
1003.73
|
1
|
1003.73
|
656.49
|
< 0.0001
|
Résiduelle
|
40.72
|
27
|
1.51
|
|
|
Tableau 37: Test de
signification
Les deux facteurs sont significatifs car leur Prob>F est
inférieur à 0.05.
ü Comparaison entre valeurs calculées et
valeurs mesurées :
Composition
|
valeur mesurée
|
Valeur calculée
|
CBG
|
CV
|
FC
|
RC 28j
|
RC 28j
|
100
|
0
|
0
|
52,521
|
53,585
|
83,33
|
16,67
|
0
|
48,927
|
45,189
|
75
|
25
|
0
|
40,177
|
40,994
|
66,67
|
33,33
|
0
|
38,615
|
36,799
|
50
|
50
|
0
|
27,396
|
28,403
|
Tableau 38 :
Comparaison entre les valeurs de la résistance à la compression
à 28 jours calculées par le modèle linéaire et les
valeurs mesurées
IV/ Résistance à la traction à 2
jours :
1/ Validité des modèles :
Source
|
somme des carrés
|
DL
|
Carré moyen
|
F
|
Prob>F
|
Linéaire
|
6.75
|
1
|
6.75
|
93.35
|
< 0.0001
|
Quadratique
|
0.40
|
1
|
0.4
|
8.96
|
0.0112
|
cubique
|
0.045
|
1
|
0.045
|
1
|
0.3396
|
Résiduelle
|
0.49
|
11
|
0.045
|
|
|
Tableau 39 :
Recherche du biais (Rt2j)
Source
|
Std,Dev
|
R²
|
R² ajusté
|
R² prédit
|
Linéaire
|
0.27
|
0.878
|
0.8684
|
0.8256
|
Quadratique
|
0.21
|
0.93
|
0.9183
|
0.8747
|
Cubique
|
0.21
|
0.9358
|
0.9183
|
0.8708
|
Tableau 40 : Test
de fiabilité (Rt 2j)
2/ Modélisation
Le modèle ainsi choisi est le modèle
quadratique ayant comme expression :
Rt 2j = 5.19016*CBG -1.70950*CV +5.74971*CBG*CV
ü Analyse
de la variance
Source
|
Somme des carrés
|
DL
|
Carré moyen
|
F
|
Prob>F
|
Modèle
|
7.15
|
2
|
3.58
|
79.72
|
< 0.0001
|
CBG,CV
|
6.75
|
1
|
6.75
|
150.49
|
< 0.0001
|
CBG*CV
|
0.40
|
1
|
0.40
|
8.96
|
0.0112
|
Résiduelle
|
0.54
|
12
|
0.045
|
|
|
Tableau 41: Test de
signification
Les trois facteurs sont significatifs car leur Prob>F est
inférieur à 0.05.
ü Comparaison entre valeurs calculées et
valeurs mesurées :
Composition
|
valeur mesurée
|
Valeur calculée
|
CBG
|
CV
|
FC
|
Rt 2j
|
Rt 2j
|
100
|
0
|
0
|
5,23
|
5,190
|
83,33
|
16,67
|
0
|
4,68
|
4,839
|
75
|
25
|
0
|
4,68
|
4,543
|
66,67
|
33,33
|
0
|
4,17
|
4,168
|
50
|
50
|
0
|
3,16
|
3,178
|
Tableau 42 :
Comparaison entre les valeurs de la résistance à la traction
à 2 jours calculées par le modèle quadratique et les
valeurs mesurées
V/ Résistance à la traction à 7
jours :
1/ Validité des modèles :
Source
|
somme des carrés
|
DL
|
Carré moyen
|
F
|
Prob>F
|
Linéaire
|
9.40
|
1
|
9.40
|
39.23
|
< 0.0001
|
Quadratique
|
1.24
|
1
|
1.24
|
7.92
|
0.0156
|
Cubique
|
2.281 10-4
|
1
|
2.281 10-4
|
1.337 10-3
|
0.9715
|
Résiduelle
|
1.88
|
11
|
0.17
|
|
|
Tableau 43 :
Recherche du biais (Rt7j)
Source
|
Std,Dev
|
R²
|
R² ajusté
|
R² prédit
|
Linéaire
|
0.49
|
0.7511
|
0.7320
|
0.6594
|
Quadratique
|
0.40
|
0.8501
|
0.8251
|
0.7669
|
Cubique
|
0.41
|
0.8501
|
0.8092
|
0.7076
|
Tableau 44 : Test
de fiabilité (Rt 7j)
2/ Modélisation
Le modèle ainsi choisi est le modèle
quadratique ayant comme expression :
Rt 7j =+6.66361 * CBG - 3.13430 * CV + 10.09543
* CBG * CV
ü Analyse
de la variance
Source
|
Somme des carrés
|
DL
|
Carré moyen
|
F
|
Prob>F
|
Modèle
|
10.64
|
2
|
5.32
|
34.02
|
< 0.0001
|
CBG,CV
|
9.40
|
1
|
9.40
|
60.11
|
< 0.0001
|
CBG*CV
|
1.24
|
1
|
1.24
|
7.92
|
0.0156
|
Résiduelle
|
1.88
|
12
|
0.16
|
|
|
Tableau 45: Test de
signification
Les trois facteurs sont significatifs car leur Prob>F est
inférieur à 0.05.
ü Comparaison entre valeurs calculées et
valeurs mesurées :
Composition
|
valeur mesurée
|
Valeur calculée
|
CBG
|
CV
|
FC
|
Rt 7j
|
Rt 7j
|
100
|
0
|
0
|
6,67
|
6,664
|
83,33
|
16,67
|
0
|
6,4
|
6,433
|
75
|
25
|
0
|
6,16
|
6,107
|
66,67
|
33,33
|
0
|
5,62
|
5,641
|
50
|
50
|
0
|
4,29
|
4,289
|
Tableau 46 :
Comparaison entre les valeurs de la résistance à la traction
à 7 jours calculées par le modèle quadratique et les
valeurs mesurées
V/ Résistance à la traction à 28
jours :
1/ Validité des modèles :
Source
|
somme des carrés
|
DL
|
Carré moyen
|
F
|
Prob>F
|
Linéaire
|
18.01
|
1
|
18.01
|
29.68
|
0.0001
|
Quadratique
|
5.53
|
1
|
5.53
|
28.08
|
0.0002
|
Cubique
|
1.02
|
1
|
1.02
|
8.42
|
0.0144
|
Résiduelle
|
1.34
|
11
|
0.12
|
|
|
Tableau 47 :
Recherche du biais (Rt28j)
Source
|
Std,Dev
|
R²
|
R² ajusté
|
R² prédit
|
Linéaire
|
0.78
|
0.6954
|
0.672
|
0.5774
|
Quadratique
|
0.44
|
0.9088
|
0.8936
|
0.8712
|
Cubique
|
0.35
|
0.9483
|
0.9343
|
0.9087
|
Tableau 48 : Test
de fiabilité (Rt28j)
2/ Modélisation
Le modèle ainsi choisi est le modèle
cubique ayant comme expression :
Rt 28j =+8.77936* CBG- 44.25785 * CV+91.87843*
CBG * CV-47.03400* CBG * CV * (CBG-CV)
ü Analyse
de la variance
Source
|
Somme des carrés
|
DL
|
Carré moyen
|
F
|
Prob>F
|
Modèle
|
24.57
|
3
|
8.19
|
67.32
|
< 0.0001
|
CBG,CV
|
18.01
|
1
|
18.01
|
148.09
|
< 0.0001
|
CBG*CV
|
5.53
|
1
|
5.53
|
45.44
|
<0.0001
|
CBG*CV*(CBG-CV)
|
1.02
|
1
|
1.02
|
8.42
|
<0.0001
|
Résiduelle
|
1.34
|
11
|
0.12
|
|
|
Tableau 49: Test de
signification
Les quatre facteurs sont significatifs car leur Prob>F est
inférieur à 0.05.
ü Comparaison entre valeurs calculées et
valeurs mesurées :
Composition
|
valeur mesurée
|
Valeur calculée
|
CBG
|
CV
|
FC
|
Rt 28j
|
Rt 28j
|
100
|
0
|
0
|
8,78
|
8,649
|
83,33
|
16,67
|
0
|
8,39
|
8,738
|
75
|
25
|
0
|
8,27
|
8,338
|
66,67
|
33,33
|
0
|
8,07
|
7,642
|
50
|
50
|
0
|
5,23
|
5,361
|
Tableau 50:
Comparaison entre les valeurs de la résistance à la traction
à 28 jours calculées par le modèle cubique et les valeurs
mesurées.
Références
bibliographiques :
[1]
|
A.Le roux (Novembre 92) ; Alcali-réaction,
État des connaissances en 1982
|
[2]
|
Revue Marocaine de génie civil, N° 100-
4ème trimestre 2002.
|
[3]
|
M.A. Bérubé et A.Carles-Gibergues ; la
durabilité des bétons face à l'alcali-réaction.
-la durabilité des bétons. Presses ENPC 1992
|
[4]
|
Françoise BRIVOT, Roger DRON, Thierry CHAUSSADENT ;
Mécanisme de la réaction alcali-silice, Extrait du
bulletin des LPC, N°214- Mars-Avril 1998. REF 4175 pp 61-68.
|
[5]
|
AFNOR : Stabilité dimensionnelle en milieu
alcalin, la norme P18-590, Avril 93.
|
[6]
|
AFNOR : Stabilité dimensionnelle en milieu
alcalin, la norme P18-587, Décembre 90.
|
[7]
|
Hugues HORNAN ; Mécanismes physico-chimiques
d'alcalis-réactions- Annales de l'institut technique du
bâtiment et des t
ravaux publics- Octobre 93. N°517- pp 97-113.
|
[8]
|
A. Le roux ; Origine, mécanismes et techniques
d'études de l'alcali-réaction : Journées de
Nantes 29-30 Mars 1994.
|
[9]
|
Jean-Armand Calgaro et Roger Lacroix ; Maintenance et
réparation des ponts ; Presses de l'ENPC 1991.
|
[10]
|
LCPC, La démarche préventive- Juillet
1994.
|
[11]
|
Philipe TOUZE et Bruno GODART ; les méthodes de
calcul pour le bilan des alcalins actifs dans les ciments ; Extrait
du bulletin des LPC, N°217- septembre-Octobre 1998. REF 4197 pp 90-95.
|
[12]
|
A.Le roux, J.THIEBAUT, J.-S. GUEDON, C.WACKENHEIM ;
Pétrographie appliquée à
l'alcali-réaction, LCPC- Mars 1999.
|
[13]
|
A.Le roux, Abdellah OUALI, Jeanne-Sylvine GUEDON-DUBIED ;
Importance de la connaissance pétrographique dans la démarche
préventive, Extrait du bulletin des LPC, N°211- septembre-Octobre
1997. REF 4128pp 133-139..
|
[14]
|
K.LAHLOU, M.ARJOUANE, A.FARAH, K.ZAGHWAGH et M.MAAZOUZ ;
Valorisation des cendres volantes Marocaines dans les bétons de
barrages : Séminaire organisé par LPEE- Rabat 12-13
Février 98.
|
[15]
|
AFNOR ; Liants Hydrauliques, Ciments
courants ; NFP 15-301 Juillet 1994.
|
[16]
|
AFNOR ; Liants Hydrauliques, Guide d'utilisation des
ciments ; P15-010 Octobre 97.
|
[17]
|
K.LAHLOU ; Cours de Matériaux, EHTP.
|
[18]
|
Gilles Sado, Marrie Christine Sado : Les plans
d'expériences. AFNOR 1991.
|
[19]
|
AFNOR ; Méthodes d'essais des ciments ;
partie1 : Détermination des résistances
mécaniques, NF EN 196-1, Août 1995.
|
|