IV-1-2 La plasticité
La rhéologie étudie l'écoulement et la
déformation de la matière [9]. Ainsi, l'étude de la
rhéologie des pâtes peut conduire à la connaissance de la
plasticité. Une masse semi-solide comme l'argile humide peut être
plus ou moins déformée par une force mécanique sans perdre
sa cohésion et sans que la masse montre une tendance à reprendre
sa forme initiale. C'est dans ce sens qu'on emploie le terme «
plasticité » en céramique [9].
Les résultats des limites de liquidité et de
plasticité sont donnés dans le tableau V.
Tableau V : Résultats du test de
plasticité des matériaux AE et AN comparés à
ceux
des terres argileuses pour brique de référence
[6].
Échantillon
|
Limite de liquidité (%)
|
Limite de plasticité (%)
|
Indice de plasticité (%)
|
AE
|
41
|
26
|
15
|
AN
|
29
|
19
|
10
|
Argile de référence pour terre cuite
|
30 - 35
|
12 - 22
|
7 - 18
|
30
De ces résultats, il en ressort que les
matériaux AE et AN peuvent contenir 41 et 19% d'eau respectivement sans
couler sous leur propre poids. Par contre, ils ne peuvent se déformer de
manière plastique quand ils ont moins de 26 et 19% d'eau respectivement.
Plus une argile est plastique, plus elle nécessitera d'eau pour former
une pâte de consistance dite « normale » (c'est-à-dire
ne collant pas aux doigts et pouvant supporter des corps inertes
(dégraissant) tout en conservant une aptitude au façonnage
appréciable et une résistance mécanique à sec
suffisante pour assurer la fabrication ) [8,9].
La teneur en fraction fine du matériau AE
supérieure à celle du matériau AN est l'une des raisons
pour laquelle AE est plus plastique que AN
Ces résultats montrent donc qu'il est nécessaire
d'envisager des ajouts de corps inertes dans le matériau AE pour
améliorer son aptitude au séchage.
IV.1.3- Le pH
La mesure du pH d'une solution saturée d'argile AE a
donné 5,70 . Ce résultat montre donc le caractère acide de
ce matériau et laisse entrevoir la possibilité d'améliorer
les propriétés rhéologiques de cette argile par le
carbonate de sodium (si l'on s'en tient au fait expérimental qu'une
argile acide convenablement traitée et dont les propriétés
sont améliorées au maximum a un pH compris entre 6 et 8,5)
[7].
IV.2- LE SÉCHAGE
Les études sur le séchage des formulations
élaborées montrent que l'aptitude au séchage du
matériau AE est améliorée par ajout d'argile AN ou du
sable (figure 4a et 5a ). Le sable étant un dégraissant à
faible porosité [8], pour une même teneur en eau d'imbibition,
l'ajout de dégraissant a pour effet de diminuer la consistance de la
pâte. Ce qui inhibe la tendance du sable à réduire le
retrait linéaire de séchage. Dans la pratique industrielle, c'est
plutôt la consistance de la pâte qui intervient au cours du
façonnage, de sorte que l'ajout du sable a pour rôle la diminution
de la quantité d'eau d'imbibition, la facilitation du séchage et
la réduction du retrait linéaire de séchage [7,8]. La
diminution des variations dimensionnelles entraînant alors la diminution
du risque d'apparition de fentes de séchage.
a) Le séchage naturel
Les résultats obtenus sur le séchage naturel
sont consignés dans le tableau VI. Les figures 4a et 4b montrent
l'évolution de la perte de masse et du retrait linéaire de
séchage des éprouvettes de matériau pendant le
séchage (air atmosphérique).
31
Au cours du premier jour, la surface des produits est assez
humide et la vitesse de séchage reste dans une large mesure fonction de
la vitesse d'évaporation d'eau à la surface des
éprouvettes de matériau, ce qui justifie les pertes de masse
assez voisines pour 24 heures de séchage (figure 4a). A partir du
2e jour, l'humidité de la surface commence à
être conditionnée par le phénomène de diffusion
capillaire : l'influence des dégraissants (qui améliore la
diffusion capillaire) commence à devenir perceptible. Au 5e
jour, on observe une perte de masse de 16,9% pour E0 contre 18,1 , 18,6 , 18,8
,et 19,4% pour E20,E30, AS9, et AS15 respectivement. A partir du 7e
jour, la diffusion d'eau dans les échantillons amaigris
(E20,E30,AS9,AS15) est limitée par le gradient d'humidité. La
différence de vitesse de séchage entre les éprouvettes de
matériau non amaigris (E0), et amaigris (E20,E30,AS9,AS15) devient de
plus en plus faible et il apparaît une perte de masse voisine de 22%
après 10 jours de séchage pour toutes les formulations
étudiées.
La figure 4b montre l'évolution du retrait
linéaire en fonction du temps pour le séchage à l'air
atmosphérique. De cette figure, il en ressort que les
dégraissants diminuent le retrait linéaire de séchage.
Cependant, la teneur en eau étant la même pour toutes les
formulations élaborées, au-delà d'une certaine valeur de
dégraissant incorporé, la pâte devient si molle que le
retrait de séchage s'en trouve augmenté. Ce qui justifie le fait
que AS9 présente un retrait linéaire de séchage
inférieur à E0 , contrairement à E30 et AS15.
b) Le séchage par étuvage
Les résultats sur le séchage à
l'étuve sont regroupés dans le tableau VII. Les figures 5a et 5b
présentent les variations de la perte de masse et du retrait
linéaire de séchage en fonction du temps. Ces résultats
montrent que les variations observées pour le séchage à
l'étuve restent semblables à celles du séchage dans l'air
atmosphérique.
Toute fois, en industrie, le coût
énergétique du séchage artificiel nous amène
à ressortir l'influence des dégraissants. La figure 5a
présente l'évolution de la perte de masse en fonction du temps de
séchage. D'après cette figure, après un jour
d'étuvage, il apparaît une perte de masse de 12,6% pour E0 contre
14,4 , 15,1 , 14,4 , 15,2% respectivement pour E20,E30 , AS9 , AS15. En
considérant un séchoir industriel qui contient 10 tonnes de
produit à sécher, si l'apport de dégraissant
entraîne le départ supplémentaire de 2% d'eau par rapport
au matériau non dégraissé, pendant un même temps de
séchage, cela revient à économiser une énergie
nécessaire pour le départ de 200 kg d'eau des produits, ce qui
n'est pas négligeable.
Pour toutes les formulations élaborées, les
éprouvettes séchées aussi bien à l'air
atmosphérique qu'à l'étuve n'ont présenté
aucune fissuration. Les résultats obtenus montrent que la plus grande
partie des fentes de séchage observées à la PROMOBAT
seraient due à une préparation inadéquate de la
matière première. En effet, beaucoup d'impuretés
grossières se retrouvent dans la pâte suite au manque de broyeur
en début de chaîne de production.
32
|
1er jour
|
2e jour
|
3e jour
|
4e jour
|
5e jour
|
6e jour
|
7e jour
|
8e jour
|
9e jour
|
10e jour
|
AM
(%)
|
R
(%)
|
AM
(%)
|
R
(%)
|
AM
(%)
|
R
(%)
|
AM
(%)
|
R
(%)
|
AM
(%)
|
R
(%)
|
AM
(%)
|
R
(%)
|
AM
(%)
|
R
(%)
|
AM
(%)
|
R
(%)
|
AM
(%)
|
R
(%)
|
AM
(%)
|
R(%)
|
E1
|
4,9
|
4,28
|
8,95
|
6,9
|
11,97
|
7,14
|
14,45
|
7,14
|
16,92
|
7,14
|
19,05
|
7,14
|
20,84
|
7,14
|
21,13
|
7,14
|
21,65
|
7,14
|
21,94
|
7,14
|
E3
|
5,48
|
3,09
|
9,22
|
5,71
|
12,98
|
6,9
|
15,32
|
7,14
|
18,10
|
7,14
|
20,30
|
7,14
|
21,5
|
7,14
|
21,79
|
7,14
|
22,23
|
7,14
|
22,41
|
7,14
|
E4
|
5,55
|
4,04
|
10,24
|
6,9
|
14,25
|
7,38
|
16,28
|
7,38
|
18,68
|
7,38
|
20,71
|
7,38
|
21,60
|
7,38
|
21,96
|
7,38
|
22,34
|
7,38
|
22,52
|
7,38
|
E9
|
5,67
|
3,09
|
9,51
|
5,23
|
12,43
|
5,95
|
15,68
|
6,66
|
18,8
|
6,66
|
21,00
|
6,66
|
21,68
|
6,66
|
21,99
|
6,66
|
22,67
|
6,66
|
22,82
|
6,66
|
E11
|
5,93
|
4,93
|
9,86
|
6,9
|
12,95
|
7,61
|
16,34
|
7,85
|
19,46
|
7,85
|
21,21
|
7,85
|
21,88
|
7,85
|
22,42
|
7,85
|
22,67
|
7,85
|
22,76
|
7,85
|
Tableau VII : Résultats sur le
séchage isotherme à l'étuve (t° = 50°C, Eau de
façonnage : 25% )
33
|
1er jour (air libre)
|
2e jour
|
3e jour
|
4e jour
|
AM (%)
|
R (%)
|
AM (%)
|
R (%)
|
AM (%)
|
R (%)
|
AM (%)
|
R (%)
|
E1
|
6,44
|
3,80
|
12,67
|
7,14
|
24,34
|
7,14
|
24,66
|
7,14
|
E3
|
6,46
|
3,09
|
14,43
|
7,14
|
24,56
|
7,14
|
24,72
|
7,14
|
E4
|
6,30
|
4,04
|
15,06
|
7,38
|
24,54
|
7,38
|
24,69
|
7,38
|
E9
|
6,66
|
3,09
|
14,38
|
6,66
|
24,48
|
6,66
|
24,75
|
6,66
|
E11
|
7,05
|
4,93
|
15,15
|
7,85
|
24,52
|
7,85
|
24,76
|
7,85
|
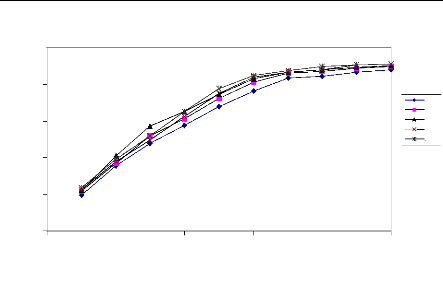
Perte de masse (%)
25
20
15
10
5
0
0 2 4 6 8 10
Jours
E0 E20 E30 E1 AS9
E3 AS15
E4
Figure 4a : Perte de masse des
éprouvettes de matériau
en fonction du temps de séchage (séchage
naturel)
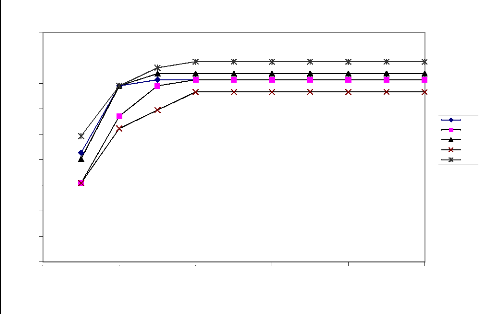
Retrait lineaire (%)
4
6
2
9
8
7
5
3
0
1
0 2 4 6 8 10
Jours
E0 E20 E30 AS9 AS15
Figure 4b : Retrait linéaire de
séchage des éprouvettes de matériau en fonction du temps
(séchage naturel )
34
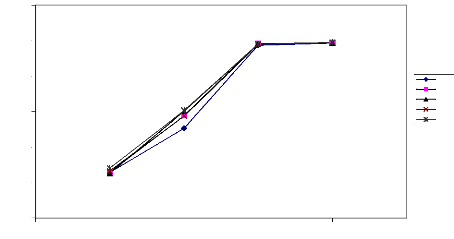
0 1 2 3 4 5
Perte de masse (%)
25
20
30
15
10
5
0
E0 E20 E30 AS9 AS15
Jours
Figure 5a : Perte de masse des
éprouvettes de matériau en fonction du temps (séchage
à l'étuve)
Jours
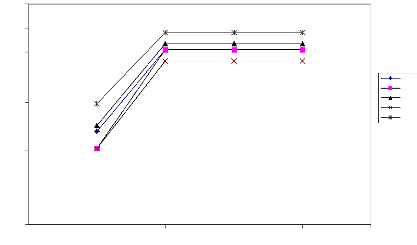
Retrait lineaire (%)
4
9
8
6
5
3
2
0
7
1
0 1 2 3 4 5
E0 E20 E30 AS9 AS15
Figure 5b : Retrait linéaire de
séchage des éprouvettes de matériau
en fonction du temps (séchage à l'étuve)
35
IV.3- PROPRIÉTÉS PHYSIQUES ET
MÉCANIQUES DES PRODUITS DE CUISSON
L'étude des propriétés physiques et
mécaniques a porté sur la couleur, le retrait linéaire de
cuisson, la perte au feu, le pourcentage d'absorption d'eau, la masse volumique
apparente et la résistance à flexion.
|
|