RÉSUMÉ :
Culture emblématique au Cameroun, le cacao fait vivre
pas moins de trois millions de personnes au Cameroun. Il représente
58,7% des recettes d'exploitation agricoles et est le deuxième produit
d'exportation derrière les hydrocarbures. Depuis quelques années,
le cacao camerounais subit une décote au marché mondial. Le grief
qui lui est reproché c'est la présence de l'odeur de fumée
dans les fèves. Une situation qui dénote des insuffisances dans
le procédé de séchage artificiel. Une pratique
utilisée dans le bassin de production du Sud-ouest, une zone à
très forte pluviométrie où la saison de pluie
coïncide avec la période de récolte. Cette région
à elle seule représente environ 45% de la production nationale
(PRSC, 2014). Ce qui explique la perte de la notoriété de
« l'origine Cameroun ». Fort de ce constat, les pouvoirs
publics ont décidé de faire la promotion d'une économie
cacaoyère durable en initiant un plan de relance de la filière
dès 2014 avec la création de plusieurs projets. Le PRSC, sous la
tutelle du MINCOMMERCE a vu le jour avec pour objectif global, la
réduction des pertes post-récoltes et le relèvement du
prix de vente du cacao. Bien que le projet concerne tout le bassin de
production du Sud-ouest soit six départements, nous avons
travaillé sur la phase pilote du projet réalisé sur deux
départements à savoir MÉMÉ et FAKO.
Notre étude s'est reposée sur une enquête
étalée de manière exhaustive sur l'ensemble des
producteurs dont la liste est en annexe. Afin de démontrer l'influence
de l'amélioration du système de séchage artificielle sur
la qualité des fèves de cacao. Il s'est agi de prime à
bord de présenter les défauts des séchoirs SAMOA et de
démontrer les possibilités d'amélioration de ces
séchoirs, ensuite de démontrer les insuffisances dans
l'application du procédé de séchage artificiel des
fèves de cacao par les producteurs et la nécessité de les
accompagner.
Au terme de notre étude, nous avons pu démontrer
que l'amélioration du système de séchage des fèves
de cacao contribue à améliorer la qualité de celles-ci.
Ceci est possible si les défauts de fabrication des séchoirs
SAMOA sont corrigés d'une part et que l'accompagnement des producteurs
dans le procédé de séchage artificiel est effectif.
À la suite de ces résultats, nous recommandons
au PRSC de livrer les nouveaux séchoirs directement au lieu de
séchage plutôt que dans les coopératives afin de faciliter
la tâche aux producteurs et d'être sûr que les
séchoirs sont bien utilisés. Nous proposons également au
PRSC de substitué l'utilisation du bois de chauffage par le biogaz afin
de préserver la flore et participer à l'atteinte des ODD.
Mots-clés : Amélioration,
Système, séchage artificiel, fèves de Cacao,
pluviométrie
ABSTRACT:
An emblematic crop in Cameroon, cocoa provides a livelihood
for no less than three million people in Cameroon. It accounts for 58.7% of
farm revenues and is the second largest export product after hydrocarbons. For
several years now, Cameroonian cocoa has been undergoing a discount on the
world market. The complaint against it is the presence of the smell of smoke in
the beans. A situation that indicates inadequacies in the artificial drying
process. A practice used in the production basin of the Southwest, a zone with
very high rainfall where the rainy season coincides with the harvest period.
This region alone accounts for about 45% of national production. This explains
the loss of notoriety of the "Cameroon origin". On the strength of this
observation, the public authorities have decided to promote a sustainable cocoa
economy by initiating a plan to revive the sector from 2014 with the creation
of several projects. The PRSC, under the supervision of MINCOMMERCE was created
with the overall objective of reducing post-harvest losses and raising the
selling price of cocoa. Although the project concerns the entire production
basin of the South-West, i.e. six departments, we worked on the pilot phase of
the project carried out in two departments, namely MÉMÉ and FAKO.
Our study was spread out exhaustively over all the producers
listed in the appendix. In order to show the influence of the improvement of
the artificial drying system on the quality of cocoa beans. It was a question
of bonus on board to show the possibilities of improvement of the SAMOA dryers
and then to show the insufficiencies in the application of the process of
artificial drying of the cocoa beans by the producers.
At the end of our study, we were able to show that improving
the drying system for cocoa beans contributes to improving the quality of the
beans. This is possible if the manufacturing defects of the SAMOA dryers are
corrected on the one hand, and on the other hand if the producers are
effectively supported in the artificial drying process.
Following these results, we recommended to the PRSC to deliver
the new dryers directly to the drying site rather than to the cooperatives in
order to make the task easier for the producers and to be sure that the dryers
are well used. We also suggest that the CHRP replace the use of firewood with
biogas in order to preserve the flora and contribute to the achievement of
DOBs
Keywords: Improvement, system, artificial drying,
cocoa beans pluviometry
SOMMAIRE
INTRODUCTION GÉNÉRALE
1
PREMIÈRE PARTIE : EFFETS DES
DEFAILLANCES DES ÉQUIPEMENTS DE PRODUCTION EN MILIEU INDUSTRIEL
22
INTRODUCTION DE LA PREMIÈRE PARTIE
22
CHAPITRE 1 : CADRE CONCEPTUEL DES
DÉFAUTS DE FABRICATION DES ÉQUIPEMENTS
23
INTRODUCTION DU CHAPITRE 1
23
I. L'EVOLUTION DE L'INDUSTRIALISATION DES
ENTREPRISES
23
II. LES INFLUENCES DES DÉFAILLANCES
DES ÉQUIPEMENTS SUR LA PRODUCTION
30
CONCLUSION DU CHAPITRE 1
59
CHAPITRE 2 : ETAT DES LIEUX DE LA CONSTRUCTION ET DE
LA MAINTENANCE DU SÉCHOIR SAMOA
60
INTRODUCTION DU CHAPITRE 2
60
I. PRÉSENTATION DES MÉTHODES DE
SÉCHAGE THERMIQUES DE CACAO AU CAMEROUN
60
II. AMÉLIORATION DU SYSTÈME DE
SÉCHAGE SAMOA
69
CONCLUSION DU CHAPITRE 2
77
CONCLUSION DE LA PREMIÈRE PARTIE
78
SECONDE PARTIE : ACCOMPAGNEMENT DES
PRODUCTEURS COMME FACTEUR D'AMÉLIORATION DE LA QUALITÉ DES
FÈVES DE CACAO
79
INTRODUCTION DE LA SECONDE PARTIE
79
CHAPITRE 3 : ANALYSE THEORIQUE DE LA GRH EN VUE DE
L'OPTIMISATION DE LA QUALITE
80
INTRODUCTION DU CHAPITRE 3
80
I. L'ÉVOLUTION DE LA GESTION DES
RESSOURCES HUMAINES
80
II. LA CONTRIBUTION DE LA COMMUNICATION
INTERNE ET DE LA FORMATION DES RH
91
CONCLUSION DU CHAPITRE 3
98
CHAPITRE 4 : AMÉLIORATION DE LA
QUALITÉ DES FÈVES PAR L'ENCADREMENT DES CACAOCULTEURS
99
INTRODUCTION DU CHAPITRE 4
99
I. PRÉSENTATION DES PRINCIPAUX PARTIES
PRENANTES
100
II. LA DÉMARCHE DE LA MISE EN OEUVRE
DES ACTIONS SUR LE TERRAIN
109
CONCLUSION DU CHAPITRE 4
117
CONCLUSION DE LA SECONDE PARTIE
118
CONCLUSION GÉNÉRALE
119
LISTE DES ANNEXES :
121
BIBLIOGRAPHIE:
145
INTRODUCTION GÉNÉRALE
I. CONTEXTE ET JUSTIFICATION
De son nom botanique Théobroma cacao L1(*)., le cacaoyer est une plante de
la famille des sterculiacées des forêts tropicales humides
originaire d'Amérique Centrale et du Sud. Les Mayas2(*), les Aztèques3(*) et les Olmèques4(*) sont les premiers à
cultiver rationnellement cet arbre fragile dont les fèves servent
à payer le tribut à la cour, aussi à fabriquer une boisson
énergisante et aphrodisiaque. En 1519, à la suite du
débarquement des conquistadores conduit par Hernán Cortés
sur la côte du Tabasco au Mexique, ces derniers rencontrent l'empereur
Moctezuma II qui les reçoit avec une gigantesque coupe d'or remplie de
« xocoatl », l'ancêtre du chocolat. On
attribue à cette expédition, l'expansion de la culture et de la
consommation des produits issus des trois principales variétés de
cacaoyer existantes à ce jour (CIRAD, 1999 ; Solorzano, 2007). Ces
cépages sont désormais cultivés à travers le monde
à savoir le CRIOLLO originaire d'Amérique Centrale et du Mexique
qui représente 5% de la production mondiale, le FORASTERO Amazonien qui
représente 80% de la production mondiale et le TRINITARIO originaire de
Trinidad qui est un hybride des deux précédents cépages et
qui représente 15% de la production mondiale (Cassan, 2006 ;
Mounjouenpou, 2008). Ces variétés poussent dans toutes les zones
forestières où les températures sont comprises entre 18 et
32°C, notamment entre le tropique du Cancer et le tropique du capricorne
(C.C.I, 2001). Au Cameroun, le gouvernement encourage de plus en plus la
culture du TRINITARIO qui est une variété reconnue pour ses
références intrinsèques matérialisées par sa
robustesse qui lui permet de résister contre les maladies et son
meilleur rendement à l'hectare (CICC, 2016). Ce dernier est
également réputé pour la grosseur de ses fèves, son
grainage fort et stable, sa bonne homogénéité, sa couleur
rouge brique indispensable pour des confiseries. Ce cépage est
également doté d'une teneur en beurre envoisinant les 57%, d'une
bonne acidité, d'un arôme vif responsable de son goût
corsé et de ses notes fruitées (CCI, 2001 ; CICC, 2016). Les
produits issus de la transformation du cacao parviennent au Cameroun depuis le
Mexique via les Espagnols installés sur l'île de Fernando Pô
vers le XVe siècle dans le cadre du commerce triangulaire
(Badel, Belletti et Marescotti, 2013). Mais il faudra attendre seulement
à la fin du XIXe siècle pour que la culture du cacao
soit introduite au Cameroun par l'impulsion des colons Allemands (CICC, 2016).
Parmi les pays producteurs et exportateurs de cacao, le Cameroun occupe la
quatrième place sur le plan Africain et
la cinquième place mondiale derrière la Côte
d'Ivoire, le Ghana, l'Indonésie et le Nigéria (Badel, Belletti et
Marescotti, 2013).
Le Cameroun reconnu comme le berceau de la culture de
« l'or brun » agricole en Afrique, compte environ 4.000
km2 de surface exploitée repartie sur sept bassins de
production. Par ordre d'importance, nous pouvons citer le bassin de production
du Sud-ouest avec 45 % de la production nationale, le Bassin de production du
Centre 37%, le Bassin de production du Sud 7.8%, le bassin de production du
Littoral 6%, le bassin de production de l'Est 3%, le bassin de production de
l'Ouest 1% et le Bassin de production du Nord-ouest 0.2% (Alary, 1996 ;
ONCC, 2017 ; CICC, 2016). Le bassin du Sud-ouest est incontestablement le
plus important et c'est également l'un des bassins les plus anciens du
continent Africain qui s'étend depuis la côte passant par les
flancs du mont Cameroun dans le Fako, en direction de la Mémé, de
la Manyu, du Koupé-Manégouba, du Lébialem et de Ndian. Ces
départements abritent plus de 1 242 700 habitants (2011) pour
une superficie de 24.571 km2. Les plantations de cacao y occupent
une superficie estimée à 1.039 km2 et datent de
l'époque coloniale (Alary, 1996).
Michel, 1970 précise qu'en 1885, les
sociétés Allemandes, Woëermann et Jantzen-Thômaleen
sont les premières à acquérir des terres et à
créer des plantations à partir de la campagne 1886-1887 à
Victoria sur les flancs du Mont Cameroun à la suite de l'exploration de
Jesko von Puttkamer qui y deviendra gouverneur dix ans plus tard. À
l'aube de la première guerre mondiale en 1914, les
sociétés du Mont Cameroun contrôlent plus de 900
Km2 de superficie arable, des chiffres peu éloignés de
ceux d'aujourd'hui. Ces plantations passent en 1922 sous l'autorité
Anglaise à la suite de la défaite Allemande à la fin de la
grande guerre quatre ans plus tôt. Les Anglais prennent donc le
contrôle de l'économie cacaoyère et encourage par tous les
moyens la culture du cacao au sein des structures d'exploitation jusqu'au
début des années 1960. Depuis l'indépendance du Cameroun,
les mouvements migratoires en provenance du Nigeria et du Nord-Ouest du
Cameroun se poursuivent alimentant l'offre de travail salarial des petites
unités productrices de cette région. Ces migrations,
associées à une main d'oeuvre déterminée ont permis
l'apparition d'exploitations très importantes. Outre ces facteurs
déterminant pour sa position de leader, ce bassin jouit également
des conditions agro-écologiques adéquats
matérialisées par :
o L'existence d'un climat favorable (CICC, 2016) ;
o Le sol volcanique, noir et riche en humus, possède
une faible teneur en métaux lourds, apporte une très bonne
acidité, une amertume unique et renforce le goût corsé des
fèves, prisé par les consommateurs (ISF, 2017).
Malgré les facteurs propices sus cités, la
filière n'a pas échappé aux secousses de la crise
économique du début des années 1980 qui s'est traduite par
la chute drastique des prix des matières premières agricoles en
1986. Face à cette conjoncture, l'État du Cameroun s'est
montré impuissant via l'Office National de Commercialisation des
Produits de Base (ONCPB) à réguler davantage les prix de la
production (CCI, 2001). De ce fait, la filière cacao a été
plongée dans une longue période de léthargie qui a
duré plus d'une décennie. Une réforme a été
entreprise sous la houlette des bailleurs de fonds et l'État du Cameroun
mais cette dernière n'avait pas produit des résultats
escomptés une décennie après, poussant ainsi les
producteurs à s'orienter vers des cultures plus rentables (PRDFCC,
2014 ; Alary, 1996).
Dès la première moitié des années
2000, l'on note la reprise de la croissance de la production stimulée
par une augmentation de la demande mondiale, la bonne tenue des
coûts sur le marché international, la maîtrise de la
libéralisation et la réorganisation de la filière
notamment avec la loi 2004/025 du 30 décembre 2004,
complétant et modifiant la loi n° 95/11 du 27 juillet 1995 qui
stipule que l'achat aux producteurs s'effectue librement, sous
réserve du respect notamment des législations et des
règlementations sur les normes de la qualité des fèves en
général, le poids, les mesures en particulier, ainsi que sur les
normes de contrôle de la qualité des produits
phytosanitaires » (CICC,2017; Badel et al., 2013 ).
Le PRSC (2014), précise que l'État s'est ainsi
engagé à défendre « le label
Cameroun » en s'arrimant aux exigences qualitatives du marché
international et davantage dans le bassin leader où les pratiques post
récolte notamment le séchage pose des problèmes. Pour
cause, après la période de fermentation qui dure 6 à 8
jours, les producteurs ne peuvent pas procéder aux méthodes de
séchage solaire ordinaire connues jusqu'ici à savoir :
· Sur une dalle cimentée et lisse ;
· Sur le séchoir autobus qui comprend une case
fixe et des rails en bois sur lesquels coulissent des claies de
séchage ;
· Par le séchage à toit mobile,
composé d'une aire de séchage fixe avec un toit pouvant
être retiré selon les conditions climatiques ;
· Au moyen du séchoir à tente non plus qui
est couvert par un plastique transparent et l'aire de séchage est de
couleur noire afin de conserver l'énergie qui est progressivement
libérée pendant la nuit ;
· Le séchoir sous serre, quant à lui, est
plus onéreux, il permet de réduire les manipulations et de
sécher des grandes quantités de fèves.
Toutes ces méthodes de séchage sont
inadaptées dans cette région du fait que la grande période
de récolte coïncide avec la saison pluvieuse et des risques de
ré-humidification sont importants. Les producteurs sont contraints de
faire recours au séchage artificiel du cacao par les séchoirs
rustiques de type SAMOA afin de maitriser les écarts normatifs qui se
posent avec acuité (Mounjouenpou, 2008 ; Adabe et Ngo-Samnick, 2014 ;
PRSC, 2014). Ce type de séchage dit « artificiel »
présente beaucoup d'avantages entre autres l'économie de temps,
un séchage plus homogène, une teneur en eau dans les fèves
suffisamment basses après séchage (Jacquet, Vincent et Lotode,
1980). Ce procédé permet également de prémunir les
fèves de cacao contre le développement des ochratoxines5(*) A (OTA) dont l'apparition est
favorisée par les moisissures.
En 2014, Adabe et Ngo-Samnick décrivent le
séchoir SAMOA comme un dispositif composé de deux ensembles
à savoir une partie en structure métallique tubulaire
composé de deux buses. La première appelée buse de
combustion et la deuxième appelée buse de conduite située
en prolongement de la première. À l'extrémité de
cette dernière se trouve la cheminée d'évacuation de la
fumée. La deuxième partie en ouvrage maçonné
construite en agglos sous forme d'un enclos de 20 m2 avec une hauteur de 1,5
mètre dans laquelle les buses sont encastrées.
Les fèves de cacao sont épandues sur les claies
ou des étagères aménagées au-dessus des buses. La
combustion du bois dans la buse propage de l'air chaud compris entre 65 et 70
°C, ce qui provoque l'arrêt de la fermentation ;
l'élimination de 40% de l'acide acétique formé pendant la
fermentation et l'évaporation du liquide contenu dans les fèves
(Jacquet, Vincent et Lotode, 1980). Il est important de préciser
qu'au-delà de cette plage de température, il y a des risques de
destruction du polyphénol oxydase responsable du brunissement des
fèves (facteur de qualité). À la fin du séchage le
taux d'humidité obtenu après la fermentation devra diminuer de
55% à 7% afin de permettre une bonne conservation du produit contre les
réactions enzymatiques et la protection contre développement des
micro-organismes (Amani, 2014).
Pour accompagner des producteurs de cet important bassin de
production, l'État a lancé un projet financé par l'UE pour
la construction de 2500 séchoirs de type SAMOA durant les années
2000. Ces séchoirs ont été fabriqués dans le cadre
des projets nationaux notamment avec l'appui de la SOWEDA. Après
distribution, le nombre de séchoirs s'est avéré
insuffisant. Des reproductions locales ont vu le jour, construites par certains
producteurs délaissés. Moins d'une décennie après
leur installation tous ces séchoirs se sont retrouvés dans un
état de vétusté avancée altérant ainsi la
qualité des fèves.
Cette situation préoccupante a des effets directs sur
l'économie du Cameroun avec une régression de production de cacao
de 42 000 Tonnes environs en 2017 par rapport à 2016 (INS, 2017).
Les producteurs quant à eux, perdent 40% de leur revenu
(Jeuneafrique 2017). Cet état des choses a conduit
l'État du Cameroun et ses partenaires à se pencher
sérieusement sur cette question afin d'y remédier. D'où le
choix de notre thème dont la pertinence et l'actualité sont des
plus manifestes.
II. DÉFINITION
DES CONCEPTS CLÉS
Une bonne perception du sens des concepts clés
employés pour la formulation du thème en étude aiderait
à la bonne compréhension de la thématique.
Amélioration :
Selon le dictionnaire Larousse 2017, c'est une
rénovation ou une augmentation de la qualité, des
capacités de quelque chose ou toute autre entité. Pour l'ISO
9001, l'amélioration fait partie des Sept principes de management de la
qualité (PMQ).
Savas (tel que cité par Jasmin,2013) affirme que
l'amélioration d'un processus passe par sa transformation pour augmenter
son efficacité et/ou son efficience.
Le terme « Amélioration » ici fait
référence aux aspects qualitatifs donc normatifs. Il
définit une innovation, une augmentation des performances du
système de séchage des fèves de cacao, sur la base d'un
référentiel de sorte à obtenir un rendement meilleur.
Système :
Selon le dictionnaire Larousse 2017, un système est un
ensemble de procédés, de pratiques organisées et
destinées à assurer une fonction définie.
Le Biologiste américain Ludwig Von Bertalanffy (2012),
est le principal inventeur de la théorie des systèmes. Avant la
deuxième guerre mondiale, il a lancé sous l'expression de
« théorie du système général »,
l'idée d'une science qui devrait étudier les ensembles
constitués d'un certain nombre d'éléments en interaction
entre eux et avec leur environnement.
Dans le cadre de notre étude, le système ici est
constitué, du séchoir SAMOA, de la buse de foyer, la buse de
conduite, la cheminée, l'étagère en brique et l'abri
couvert.
Séchage artificiel :
Il convient de définir individuellement les deux mots
qui composent cette expression.
Selon le dictionnaire Larousse 2017, le séchage est le
traitement qui a pour but d'éliminer d'un corps, en totalité ou
en partie, l'eau qui s'y trouve incorporée. Le même dictionnaire
définit « artificiel » comme toute action de l'homme
à la place de la nature.
En 1980, Jacquet, Vincent et Lotode précisent que le
séchage permet de diminuer le taux d'humidité d'un objet
jusqu'à des proportions admissibles en adéquation avec son
environnement d'utilisation ou de séchage.
Nous pouvons reformuler la définition du
séchage artificiel comme étant l'accélération de
l'évaporation de l'eau ou tout autre liquide contenu dans les
fèves de cacao au moyen d'une source de chaleur autre que le soleil. La
source de chaleur est produite ici par le séchoir SAMOA.
Fève de Cacao :
La fève est une légumineuse dont la graine est
comestible selon le dictionnaire Larousse 2017.
Graine issue d'une plante ombrophile qui produit les cabosses
de cacao et se nomme le cacaoyer ou Théobroma cacao qui signifie en Grec
« nourriture des dieux », nom donné par le botaniste
Suédois Linnaeus qui avait une parfaite connaissance de la mythologie
Toltèque et Aztèque (Greet, 2002).
Il s'agit des graines contenues dans une cabosse nommée
cacao à la forme d'une balle de rugby. Ces graines sont destinées
à la fabrication du chocolat et des produits dérivés.
Pluviométrie :
Selon le dictionnaire Larousse 2017, la pluviométrie
est la branche de la climatologie qui étudie la répartition des
pluies dans l'espace et dans le temps.
D'après Kieny (2015) c'est également une
évaluation quantitative en millimètre (1 mm = 1 litre/m2) de
pluies ou autres précipitations tombées dans une région.
Les instruments les plus connus pour la calculer sont le pluviomètre et
le pluviographe. Généralement à partir de 8 mm par heures
la pluviométrie est considérée comme forte.
Bassin de production :
Sarrazin (2016) définit le bassin de production comme
une réalité physique, spatiale et agronomique marquant son
empreinte au sol du fait des pratiques culturales spécifiques à
une région.
Le bassin de producteur du Sud-ouest est une surface
cultivable délimitée par six départements (Fako,
Mémé, Manyu, Lébialem, Ndian et
Koupé-Manengoumba)
Le thème ainsi reformulé est le
suivant : Innovation de la méthode d'élimination
forcée de l'eau dans les graines de cacao dans les zones à
précipitations intenses au Cameroun.
III. PROBLÉMATIQUE
En dépit de tous les efforts menés par les
pouvoirs publics camerounais depuis quelques années, la filière
cacao connait une nouvelle crise, endogène cette fois, avec des effets
néfastes sur le plan national et international. Il se trouve qu'à
la fin du processus de séchage artificiel par des séchoirs SAMOA,
les fèves ne respectent pas les normes de qualité prescrites par
le marché international. Les griefs qui reviennent sont liés
à la dégradation des caractéristiques physiques et
organoleptiques des fèves de cacao reconnues sous le label
« l'origine Cameroun ». Cet état des choses est
à l'origine de la décote que subit le cacao du Cameroun sur le
plan international avec des conséquences immédiates sur la
dépréciation des prix de vente du cacao de 17 %, diminuant
ainsi les revenus des producteurs. Leur avenir économique devient ainsi
incertain si des mesures correctives efficaces et adaptées ne sont pas
envisagées dans l'immédiat. Ces derniers ne peuvent plus subvenir
à leurs besoins décemment, envoyer leurs enfants à
l'école, soigner leur famille entre autres (PRSC, 2014 ; ONCC,
2017).
Les raisons de cette décote proviennent de :
· La contamination des fèves de cacao durant le
processus de séchage, par des fumées issues de la combustion du
bois de chauffage altérant ainsi son aspect physique et son
goût (CAOBISCO/ECA/FCC, 2015) ;
· La contamination des fèves par des
Hydrocarbures Aromatiques Polycycliques6(*) (HAP) causés d'une part par l'installation
des séchoirs SAMOA près de la route bitumée et d'autres
parts l'utilisation du bois de chauffage (surtout l'hévéa
détenteur de résidus de latex). Il faut noter que les HAP sont
des molécules constituées d'atomes d'hydrogène et de
carbone par conséquent fortement cancérigènes (Badel,
Belletti, et Marescotti, 2013) ;
· Le Séchage non conforme des fèves
noté par une mauvaise acidité du fait d'une humidité
élevée et une température de séchage non
contrôlée (Kanmogne, Jannot et Nganhou, 2012).
Conscient des enjeux socio-économiques du fait de ces
écarts normatifs, les pouvoirs publics ont initié un plan de
relance et de développement des filières cacao et café
(PRDFCC) à travers la Cellule Technique de Suivi et de Coordination des
Filières Cacao et Café (CTSCCC) des services du Premier
Ministère. Ce plan de relance est à l'origine de
l'arrêté Ministériel N°0036/MINCOMMERCE/CAB/ DU 03
SEPTEMBRE 2014 qui a pour objectif de fixer les modalités de
commercialisation des fèves de cacao et de passer d'une production
nationale de 220 000 Tonnes de cacao pour la campagne 2014/2015 à
600 000 Tonnes à horizon 2020. Cette décision administrative
a contribué au lancement du projet de réhabilitation des
séchoirs à cacao (PRSC) dans les bassins de production du
Sud-Ouest et du Littoral (PRDFCC, 2014). La convention N°
003/MINCOMMERCE/FODECC/PJT a été signée entre le
MINCOMMERCE et le FODECC le 22 Octobre 2013 pour la relance de la fabrication
des nouveaux séchoirs SAMOA normalisés afin de prosséder
au remplacement des séchoirs vétustes de tous les producteurs
(PRDFCC, 2014).
Ce projet arrive à point nommé, car en attendant
la publication de la norme ISO 34101 qui spécifiera les exigences
applicables à un système de management pour la culture des
fèves de cacao et rendra plus durable la production de cacao, l'UE qui
est le principal client du cacao en provenance du Cameroun et qui
représente environ 84 % de la consommation de la production a mis en
vigueur dès le 1er avril 2013 ses règlements (confère
annexe 3 et annexe 4). À savoir :
· La norme UE n° 835/2011 du 19 août
2011 ;
· La norme UE n° 105/2010 qui ne
tolèrent aucun écart sur la qualité de cacao.
C'est dans le cadre de ce deuxième projet de
réhabilitation des séchoirs à cacao que nous orienterons
notre travail dont le but à terme est d'améliorer le processus de
séchage artificiel du cacao dans le bassin du Sud-ouest.
La question de recherche qui en découle et qui
orientera notre travail est la suivante :
« Comment améliorer le système
de séchage artificiel dans le bassin du Sud-ouest afin que les
fèves de cacao soient de qualité meilleure
? »
Cette interrogation engendre deux nouvelles questions
spécifiques (QS), et qui s'énoncent de la manière qui
suit :
QS1 : « L'état des
séchoirs SAMOA utilisés par les producteurs dans les
régions du Sud-ouest pour sécher les fèves de cacao
peut-il être améliorer ? »
QS2 : « L'accompagnement des
producteurs pendant le séchage du cacao est-il nécessaire pour
améliorer la qualité des
fèves » ?
IV. OBJECTIFS DE
L'ÉTUDE
L'objectif principal de cette recherche est de
démontrer l'influence de l'amélioration du système de
séchage artificiel sur la qualité des fèves de cacao.
De cet objectif principal, découlent deux objectifs
spécifiques (OS) à savoir :
OS1 : « Démontrer que
les séchoirs SAMOA sont défaillants et peuvent être
améliorés »
OS2 : « Démontrer
qu'il y a une nécessité d'accompagner les producteurs pendant le
séchage des fèves de cacao ».
V. HYPOTHÈSES DE RECHERCHE
L'hypothèse principale de recherche est :
« L'amélioration du système de séchage
artificiel des fèves de cacao contribue à améliorer la
qualité de celles-ci ».
De cette hypothèse principale se déclinent deux
hypothèses secondaires (H) qui sont les suivantes :
H1 : « Les séchoirs SAMOA
présentent des défauts de fabrication qui peuvent être
corrigés ».
H2 : « L'accompagnement des
producteurs dans le procédé de séchage artificiel est
nécécessaire pour améliorer la qualité des
fèves de cacao ».
VI. REVUE DE LA
LITTÉRATURE
Notre thème porte sur le domaine de recherche de la
qualité en général et particulièrement sur
l'optimisation des processus qui est un pan de l'amélioration continue.
C'est dans cette partie de la qualité que notre recherche va se
circonscrire.
Le monde vit de plus en plus de fortes mutations dans tous les
secteurs d'activités. Notre société devient de plus en
plus exigeante sur la qualité des produits et des services, gage de la
pérennisation et la fidélisation d'un partenariat. Cet
état de chose anime la concurrence et par ricochet la
compétitivité. Dans ce contexte concurrentiel, chaque entreprise
met tout en oeuvre pour sortir du lot en proposant des produits innovants et un
service additif, le tout à des prix attractifs.
En 2006, Margerand et Gillet-Goinard expliquent qu'en
période de forte concurrence et de forte compétitivité, la
qualité délivrée des produits et des services devient une
nécessité : vendre c'est bien ; vendre en ayant la garantie
que le client sera satisfait c'est mieux ! Une démarche qualité
doit apporter à l'entreprise une réelle valeur ajoutée.
Cette valeur ajoutée est la garantie de la satisfaction de ses clients
et un atout dans la recherche de la ?délisation. La démarche
qualité ne s'inscrit plus comme avant dans une simple relation client et
fournisseur. Aujourd'hui, à cause de la forte concurrence,
au-delà de la satisfaction des clients, on vise créer une
relation durable avec ces derniers, dits clients stratégiques. À
partir de cette analyse, la qualité donc serait l'aptitude d'un produit
ou d'un service à satisfaire les exigences du client.
Briol (2008) précise que la recherche
effrénée de la satisfaction du client à moindre effort
n'exclue pas la production de la valeur ajoutée pour les actionnaires et
les employés de l'organisation. Pour arriver à une satisfaction
globale de toutes les parties prenantes, il convient de passer d'une production
artisanale à une production industrielle.
Pour y parvenir, il convient de refondre l'organisation et
l'adapter à cette nouvelle migration de la production.
De par son ouvrage « Recherches sur la
nature et les causes de la richesse des nations », Adam
Smith7(*) (1776) qui est
considéré comme le pionnier de la division du travail
décompose les processus en tâches essentielles, celles-ci sont
affectées à un individu chargé de les exécuter de
manières répétitives. Les premières applications de
cette théorie ont trouvé un succès au début de la
révolution industrielle.
Plane, (2013) rappelle que la théorie de Adam Smith
est davantage exploitée et développée entre 1900 et 1930.
La révolution industrielle amorcée au XVIIIe
siècle et la concentration des moyens de production favorisent
l'émergence de nouvelles formes de production. Le secteur industriel
attire une main-d'oeuvre agricole nombreuse, peu adaptée à la
production technique qu'il va falloir intégrer. Dans ce contexte
l'école classique se développe à travers deux visions.
Celle de l'inspiration managériale dite approche scientifique avec
Frederick Winslow Taylor8(*)
et Henri Fayol9(*) et celle
des théories sur la bureaucratie avec le sociologue Max Weber10(*).
Gareth, (1999) présente la contribution de
l'application de l'approche de F.W Taylor et de H. Fayol sur
l'amélioration de la productivité et l'efficacité en
usine, aussi la mise en place d'une rémunération des ouvriers en
fonction de leur rendement, facilitant l'analyse du travail scientifique en
soi. L'approche de la Max Weber quant à elle prône entre autres,
la formation appropriée du personnel, l'utilisation efficiente des
ouvriers et de la normalisation des comportements au travail.
Toutefois, il en ressort que l'approche scientifique
présente des limites telles que l'exploitation des ouvriers et le
mépris de leur épanouissement social. Il en est de même
pour l'approche de la bureaucratie où on constate également des
faiblesses. La structure organisationnelle est rigide avec une concentration de
pouvoir. Ce qui entraîne un mode de gestion autoritaire (
https://fr.scribd.com/doc/48690537/Les-limites-du-taylorisme;
https://fr.scribd.com/doc/7181495/Expose-Ecole-Classique).
Partant des principes de l'organisation scientifique du
travail (OST) et de leurs limites, Henry Ford11(*) élabore un modèle éponyme de
production appelé "Le Fordisme" ou travail à la
chaîne. Ford applique les OST tout en améliorant les revenus des
ouvriers. Nonobstant, le Fordisme renforce la déqualification
du salarié et standardise la production afin d'imposer une consommation
de masse. (Briol, 2008)
La rigidité de cette approche par rapport à
l'évolution de la demande conduit à une crise économique
et sociale de l'organisation scientifique du travail en particulier en raison
de la concurrence des entreprises nippones, fonctionnant selon le
Toyotisme qui offre une flexibilité en diversifiant l'offre et
en améliorant l'outil de production. (Mansencal et Michel, 2010 ;
http://www.jseco22.blog.lemonde.fr/files/2014/01/Il-y-a-100-ans-le-fordisme.pdf)
Développé à partir de 1961 par Eiji
Toyoda12(*) et Taiichi
Ohno13(*), le toyotisme
encore appelé lean management en occident est fondé sur
l'amélioration continue ou Kaizen. Cette méthode a deux
concepts, celui de la production en flux tendu (ou le « Juste
à temps ») dont le Kanban est l'un des
mécanismes et celui de la production par l'automatisation
(Jidoka).
Le cabinet XL Groupe (2003), dans son dossier
spécial « Lean Management » souligne que
ces principes poursuivent trois objectifs :
· Accroître la valeur créée pour le
client ;
· Améliorer les performances de
l'entreprise ;
· Prendre en compte les besoins des collaborateurs.
Pour atteindre ces objectifs, cette approche cherche à
éliminer les « 3M » :
· Muda ou les gaspillages (surproduction,
attentes, transport, étapes inutiles, stocks, mouvements inutiles,
corrections ou retouches) ;
· Muri (les excès) ;
· Mura (la variabilité).
En termes d'illustration de Muda, Kokou et
Ngo-Sammick (2014) recommandent de s'assurer en amont que les fèves de
cacao soient bien fermentées suivant les normes exigibles avant le
début du séchage. Ceci va permettre d'amoindrir la
variabilité ou Mura après le séchage. Amani
(2014) évoque un Mura manifeste dans le domaine du
séchage thermique du cacao, traduit par les fèves moisies ou
ardoisées du fait du non-respect des prescriptions du
procédé de séchage.
De façon synthétique, Chiarini (tel que
cité par Jasmin, 2013) explique que le Lean est une approche
qui se propose de réduire le temps de traitement des processus par
l'élimination des étapes sans valeur ajoutée pour le
client, ce qui permet par le fait même de réduire les coûts
de production.
Une dégradation des conditions de travail dans une
entreprise introduisant des méthodes Lean peut
être due à un mauvais choix des outils ou à une adaptation
insuffisante au modèle de l'organisation. Par exemple dans le secteur
public le Lean management a du mal à être appliqué
simplement parce que trop concentré sur l'efficience interne
plutôt que sur la satisfaction des bénéficiaires. Des
inconvénients de cette méthode sont soulignés
également par des
ergonomes, des
psychologues et
des spécialistes du travail, qui alertent sur le fait que la recherche
poussée du profit par la réduction des gaspillages peut aussi
être une source de stress excessif des travailleurs donc dangereux pour
leur santé. Un autre phénomène constaté est
l'apparition des
troubles
musculosquelettiques sur les ouvriers.
https://fr.wikipedia.org/wiki/Lean_(production).
Une autre limite du Lean est évoquée
par Marris (2010) qui estime que les résultats escomptés
après la mise en oeuvre du Lean management sont inscrits dans
le temps et la patience. Il arrive que les résultats obtenus se
transforment souvent en pure réduction des coûts souvent assortis
de licenciement du personnel.
Moen et Norman (2012), nous font la genèse du Lean
Management en affirmant que ce dernier tire ses origines des travaux de
Walter A. Shewhart14(*)
avec son triptyque Spécification-Production-Inspection
(Do-Study-Act en anglais). Sa théorie appliquée à
l'usine de Western Electric en 1930 permet d'éliminer les
défauts en cherchant les causes.
Chardonnet et Thibaudon (2003), soutiennent qu'en 1950,
William Edwards Deming15(*) modifie légèrement ce cycle. Les
japonais l'appellent « la Roue de Deming ». Le
cycle de Deming montre comment appliquer les principes de la démarche
qualité dans le but de respecter les exigences d'un produit ou d'un
service. Il concerne tous les domaines de l'entreprise (productifs et non
productifs).
La position de la roue sur une pente fait d'elle un outil
d'amélioration continue. Le cycle se compose de quatre
phases, chacun entraînant l'autre, et vise à établir
un
cercle vertueux:
· La phase « Plan » ou
planification: consiste à planifier la réalisation;
· La phase « Do » ou
réalisation: construction, le développement, la
réalisation de l'oeuvre;
· La phase « Check » ou
vérification : elle doit, se conformer aux processus définis
en amont;
· La phase « Act » ou
modifier ou encore ajuster est l'action correctrice et innovatrice.
Pour améliorer les performances des entreprises
industrielles plus rapidement en termes de production tout en maîtrisant
les coûts, les dirigent d'entreprises vont faire recours à une
méthode révolutionnaire appelée Six Sigma,
initiée aux États-Unis en 1986 chez Motorola. Cette
démarche a tout d'abord consisté en l'application des concepts de
la maîtrise statistique de processus et s'est ensuite largement
étoffée en intégrant tous les aspects de la maîtrise
des variabilités :
· Les variabilités sur les matériaux ;
· Les variabilités dans les procédures
;
· Les variabilités sur les conditions dans
lesquelles évolue le processus.
De manière empirique, les variabilités dans le
procédé de séchage artificielle du cacao se
caractérisent par une forte acidité, un goût fruité
des fèves et l'odeur de fumée dans les fèves (Jacquet et
al.,1980 ; PRSC, 2014).
Mikel
J. Harry16(*) et
William Bill Smith Jr.17(*), définissent les bases de Six Sigma chez
Motorola en s'appuyant sur la philosophie de
William Edwards
Deming. Il propose d'analyser les instabilités du processus de
fabrication à l'aide des
outils
statistiques et donne la priorité à l'
amélioration
continue. Dès lors, Motorola décide d'utiliser cette
méthode pour tous ses projets. Au fur et à mesure de sa diffusion
dans les autres entreprises notamment General Electric en 1990
où elle devient célèbre sous l'égide de son
président de l'époque de Jack Welsh. Le Six Sigma s'est
également structuré en associant davantage à sa
démarche les éléments managériaux et
stratégiques (Gabert et al., 2015).
La lettre grecque « Sigma »
représente à l'origine une unité de mesure statistique qui
définit la variabilité ou la dispersion de données. Par
extension, plus le « Sigma » d'un processus est
élevé, plus les éléments sortants du processus
(produits ou services) satisfont les besoins du client, et plus les
défauts de ce processus sont rares. Sigma est une philosophie
d'amélioration de la qualité fondée sur les faits et les
données, pour laquelle la prévention des défauts
prévaut sur leur détection. Le Six Sigma trouve une
application partout où la variation et les gaspillages existent, et tous
les employés doivent être impliqués. Une performance de
qualité Six Sigma représente seulement 3,4
défauts par million d'opportunités (Volck, 2009).
Briol (2008) argue comment l'approche Six Sigma
s'exécute suivant deux méthodes, chacune d'elle se
déclinant en cinq étapes. La première se contracte sous
l'acronyme en langue anglaise
« DMAIC » : Define, Measure,
Analyse, Improve. Elle s'applique sur l'amélioration des processus
existants. La seconde méthode qui se contracte en
« DMADV » pour « Définir,
Mesurer, Analyser, Développer et Vérifier », permet
d'élaborer des nouveaux processus. Chaque étape du DMAIC
possède des outils différents qui sont regroupés dans une
démarche cohérente. Lorsqu'un processus ne peut être
amélioré alors qu'il ne répond plus aux attentes du
client, Six Sigma se décline aussi en méthodes de
création de nouveaux processus ou de nouveaux produits sous le nom de
DFSS (Design For Six Sigma).
Outre le succès de cette approche chez
Motorola, Jasmin (2013) affirme que l'universalité des
principes de l'approche Six Sigma n'est pas effective ce qui constitue
une limite. Aussi une trop grande confiance envers les données peut
s'avérer une faiblesse puisque la mauvaise qualité peut
être retrouvée dans les données elles-mêmes. À
partir de ce qui précède, Pillet (2004) estime que la
méthode Six Sigma et la méthode Lean Management
sont complémentaires. Pendant que le Lean Management permet une
production massive avec une faible qualité, le Six Sigma va
produire avec une qualité élevée, mais avec beaucoup moins
de non-valeur ajoutée. Donc en combinant les deux méthodes dans
un processus, on obtient une autre approche hybride dite Lean Six
Sigma dont en fin de processus on apprécie une production de
qualité à faible coût.
Marris (2012) présente une autre approche de gestion de
la qualité dénommée la Théorie des contraintes ou
TOC (Theory of constraints). La TOC est applicable
à tous les processus métier et projets. Cette méthode est
développée par Eliyahu M. Goldratt18(*) au début des
années 1970 avec pour objectif de bâtir progressivement une
théorie du management induite par l'accumulation de faits issus
d'observations ou d'expériences. Partant du postulat que
désormais toutes les organisations sont
déséquilibrées. À tout moment, il y a des
ressources surchargées, les goulots ou contraintes et des non-goulots.
Les règles de gestion doivent être repensées en
conséquence.
Dans son ouvrage « Le But » sorti
en 1984, Goldratt présente la solution TOC dans une usine, en
montrant comment se focaliser sur la contrainte qui existe dans tout
système de ressources interdépendantes et en mesurant la
performance réalisée à partir de trois
indicateurs d'évaluation:
le « Throughput »: le rythme auquel le
système génère de l'argent par les ventes,
l' « Inventory »: tout l'argent que le
système a investi pour acheter des choses qu'il a l'intention de vendre
et les « Operating Expenses » : tout
l'argent que le système dépense pour transformer
l' « Inventory » en Ventes (Briol,
2008) .
En mode projet, Goldratt (1997) dans son ouvrage Critical
Chain souligne les dérives comportementales les plus
fréquentes. Il constate que la loi dite
de Cyril Northcote
Parkinson (1909-1993) se manifeste dans l'exécution des projets avec
acuité rendant impossible le respect du triptyque délais,
coût et qualité. Il s'agit de la surévaluation des marges
de sécurité temps attribuées à chaque tâche,
le démarrage des travaux au dernier moment, ou encore à
l'utilisation de toute la durée prévue d'une tâche
même si le temps effectif de réalisation en est bien
inférieur (Gaspoz, 2005 ; Jaeck , 2014).
Pour pallier ce fléau, Jaeck (2014) expose dans sa
thèse sur deux modifications à la méthode couramment
admise du chemin critique. En premier lieu, le délai pour
terminer un projet n'est plus seulement basé sur la longueur des
tâches séquentielles, mais sur la chaîne la plus longue de
tâches en tenant compte de la rareté des ressources
d'organisation, appelée chaîne critique. De plus la TOC
suggère une gestion des incertitudes au niveau global du projet
plutôt qu'au niveau local de chacune des tâches. Pour Marris
(2010), une bonne efficacité de la TOC dépend de sa
combinaison avec le Lean management. On aura d'un
côté l'approche Lean qui chasse les gaspillages et
l'approche TOC avec sa technique Tambour - Tampons - Corde (ou «
Drum - Buffer - Rope » en anglais) qui identifie les contraintes
sur lesquelles agir pour accroître le chiffre d'affaires. Ainsi la
conjugaison des deux approches permet d'atteindre un cercle vertueux par lequel
l'entreprise devient continuellement plus efficace. (Qualitique n°219,
2010).
Certaines organisations utilisent d'autres approches hybrides,
plus ressentes, toujours dans la recherche des complémentarités
plutôt que des différences, une méthode dite TLS (TOC +
Lean + Six Sigma) a vu le jour en mars 2006 grâce à la revue
de l'APICS (American Production and Inventory Society) sous
le titre :
- Continuous Improvement Trio: The top elements
of TOC, lean and six sigma make beautiful music together par Russ Pirasteh
& Kimberly Farah.
Il s'agit d'une juxtaposition des points forts de toutes les
méthodes sus-présentées créant ainsi un
système redoutable. (Marris, 2012) :
La course vers le développement de toutes ces
méthodes et la volonté de les combiner pour optimiser davantage
les processus fait suite à l'échec de la méthode
BPR (Business Process Reengineering) apparue au début
des années 1990. Bien que la méthode offre des effets
bénéfiques d'une part, elle engendre d'autre part un autre
registre de difficultés qui plongent les entreprises dans des gouffres
financiers. Initialement, elle préconisait une restructuration des
organisations en agissant surtout sur la technologie afin de les adapter aux
mutations exponentielles de l'époque (Jasmin, 2013). Hammer (tel que
cité dans Jasmin, 2013) estime que les améliorations
incrémentales proposées par les autres méthodes sont
néfastes parce que trop lentes et insuffisantes pour que les entreprises
demeurent performantes et compétitives. Le BPR va agir sur les
processus plutôt que sur les fonctions. Monard (2005) parle de
réorganisation fondamentale et de modernisation radicale des processus
organisationnels en vue de réaliser une amélioration
exceptionnelle des prestations. En bref BPR, est un terme technique
désignant un projet d'amélioration ou un projet de modernisation.
Son fondateur Hammer19(*) (1993) affirme: « Ce n'est pas un remède
minute pour les entreprises. Ce n'est pas un nouveau truc pour accroître
miraculeusement la qualité d'un produit ou service, ou pour
éliminer certains coûts. Le Reengineering n'est pas un
programme de motivation des travailleurs ou de stimulation de la force de
vente. Il ne fera pas travailler plus vite un vieux système
informatique. Il n'est pas un bricolage de quoi que ce soit. Le
Reengineering signifie tout reprendre, tout reprendre depuis le
début ».
Toutefois, le Reengineering est adapté aux
processus métiers à savoir les processus de management ou
pilotage, les processus de réalisation et les processus support. Une
autre catégorie de processus est ajoutée aux trois premiers, les
processus de mesure qui permettent de mesurer les résultats obtenus.
Ceci crée une restriction de l'applicabilité du BPR qui
reste inadapté dans une organisation fonctionnant en mode projet. (
Https://www.faq-logistique.com/BPR.htm).
La recension des écrits nous ont permis de partir de la
genèse de la qualité, de présenter son évolution
par des courants de pensées fiables et adaptés pour chaque
époque en fonction de la typologie de l'organisation. Désormais,
il ne s'agit plus de l'applicabilité de tel ou tel autre méthode,
mais il convient d'optimiser les processus afin de les adapter à des
organisations fussent-elles de production ou de service dans le secteur
privé ou public.
La présente revue de la littérature nous permet
de faire le tour d'horizon des méthodes de gestion de la qualité
les plus en vue. Elle nous a permis de cerner les forces et faibles de chaque
approche, de circonscrire le champ d'étude de chaque auteur et de frayer
un intervalle pour une contribution personnelle. Dans le cadre de notre travail
nous allons exploiter la méthode hybride Lean Six Sigma pour
guider notre recherche.
VII. METHODOLOGIE DE L'ETUDE
Morfaux et Lefranc (2007) définissent la méthode
comme étant l'ensemble de procédés raisonnées pour
parvenir à un but, que ce soit une argumentation quelconque, une
démonstration mathématique, une expérimentation
scientifique, ou encore l'enseignement d'une discipline. Procéder avec
méthode est respecté l'ordre des difficultés croissantes.
Méthodique est souvent synonyme de rationnel.
D'après le dictionnaire Larousse 2017, la
méthodologie est l'étude systématique, par observation de
la pratique scientifique, des principes qui la fondent et des méthodes
de recherche utilisées.
Pour analyser l'expérimentation de notre thème,
la rigueur de la démarche scientifique nous impose de définir une
méthodologie capable de guider notre recherche.
Dans cette rubrique nous allons aborder la méthode de
recherche, les techniques de collecte de données et la méthode
d'analyse de ces données.
VII.1. MÉTHODE DE RECHERCHE
La recherche est classifiée selon la méthode
employée. Cette dernière qui s'appuie sur des techniques
employées pour collecter et analyser les données. Cette
méthode peut être historique, descriptive,
corrélationnelle, ex-post facto et expérimentale. Pour cela nous
orientons notre choix vers la méthode
hypothético-déductive.
Nous apprenons de Verhagen (2010), que le terme «
hypothético-déductive » a supposément
été introduit par William Whewell20(*) dans le cadre de ses analyses des méthodes
scientifiques, publiés dans ses oeuvres « History of the
Inductive Sciences, from the Earliest to the Present Time » en 1837
et « Philosophy of the Inductive Sciences » en 1840. Selon
lui cette méthode de recherche communément reconnue comme
étant la base d'un travail robuste.
Si plusieurs validations de l'hypothèse ne
représentent pas une preuve absolue en faveur de la théorie (des
expériences plus sophistiquées pourraient invalider la
théorie ultérieurement), tout résultat négatif
obtenu par l'expérience invalide pour toujours l'hypothèse de
départ.
Pour expliquer plus simplement, l'approche
hypothético-déductive consiste à émettre des
hypothèses, à recueillir des données, puis à tester
les résultats obtenus pour réfuter ou appuyer les
hypothèses. (
Https://fr.wikipedia.org/wiki/M%C3%A9thode_hypoth%C3%A9tico-d%C3%A9ductive).
VII.2. TECHNIQUES DE COLLECTE DE
DONNÉES
Dans le cadre de notre travail nous avons fait recours deux
techniques de collectes de données à savoir la technique
qualitative et la technique quantitative. Pour chacune de ces techniques, nous
avons utilisé plusieurs méthodes de collecte de données
tant primaires que secondaires.
Les données primaires sont celles
spécialement collectées pour réaliser une étude
statistique afin de répondre à notre problématique. Dans
le cas de notre recherche, elles sont qualitatives.
La première technique dite
qualitative, utilisée pour la collecte de
données s'est effectué par des méthodes suivants :
· Les entretiens : ils ont
été menés de plusieurs manières. L'entretien
directif à partir d'un guide d'entretien (Annexe 6) définit au
préalable. Nous avons interviewé les producteurs avec qui nous
avons parlé des opérations de séchage, avec les
responsables des coopératives, nous avons abordé le stockage des
fèves une fois colisées dans les sacs en jute. Nous avons
utilisé un entretien libre avec l'équipe du PRSC et avec
l'administrateur du FODECC en la personne de Monsieur OND Dieudonné avec
eux, nous avons abordé la fermentation du cacao une fois
écabossé.
· La recherche documentaire : c'est la
collecte d'information à partir des documents et NTIC
sélectionnés en rapport avec le thème
étudié. La recherche documentaire a été possible
entre autres, grâce :
o Aux livres téléchargés sur internet,
concernant la production, le séchage, la fermentation et la
commercialisation du cacao;
o Aux mémoires concernant l'agriculture et la
santé obtenus auprès de la bibliothèque de l'Institut
Panafricain pour le Développement de Douala ;
o Aux thèses sur la cacao-culture
téléchargées sur Internet ;
o Aux articles de revues, publications, presses sur la
qualité en général et la qualité des fèves
en particuliers, obtenus via Internet;
o Aux termes de référence du PRSC ainsi que le
cahier des charges du projet.
· L'observation sur le terrain :
l'observation directe nous a permis de vérifier les informations
recueillies par le guide d'observation (Annexe 7) à partir des faits
observables. Elle concernait les installations, le processus complet de
séchage des fèves de cacao avec un accent sur l'étalage
des fèves, le remuage, l'attisement, la ventilation du séchoir
Samoa, l'évacuation des fumées et le contrôle des
températures. L'observation est un complément des techniques sus
évoquées et nous beaucoup aidé dans notre travail ;
Les données secondaires sont
recueillies pour d'autres raisons et sont rapidement accessibles et peu
dispendieux. Pour la deuxième technique dite
quantitative, nous avons utilisé :
· Le sondage : Nous avons
effectué le sondage exhaustif sur l'ensemble de la population cible.
Cette population a été circonscrit par l'équipe du
PRSC ;
o La population ici est représentée par les
producteurs ou cacaoculteurs. Il est à rappeler qu'un producteur est
celui qui fait de la cacaoculture une activité principale ;
o Le PRSC étant dans sa phase pilote, s'est
déployé sur deux départements (FAKO et
MÉMÉ). Nous avons donc enquêté sur l'ensemble de la
population suivant la liste des producteurs en annexe 8 ;
o Quelques données de l'enquête
ü La population de l'enquête c'est l'ensemble des
producteurs utilisant les séchoirs SAMOA soit 200
producteurs (Annexe 8);
TABLEAU 1 : REPARTITION DES PRODUCTEURS PAR DEPARTEMENT
|
Département
|
Fréquence
|
Pourcentage
|
Pourcentage valide
|
Pourcentage cumulé
|
Valide
|
Fako
|
65
|
32,5
|
32,5
|
32,5
|
|
Mémé
|
135
|
67,5
|
67,5
|
100,0
|
|
Total
|
200
|
100,0
|
100,0
|
|
Source: Travail étudiant. BAGNAKA (2016)
Le projet est sensé s'étendre sur les quatre
autres départements après l'évaluation de cette phase
pilote.
VII.3 MÉTHODE D'ANALYSE DE
DONNÉES
Les techniques de collecte nous révèlent la
nature à la fois quantitative et qualitative des données de
l'étude.
ü Les données quantitatives sont traitées
d'une part avec les logiciels tels que MS-Excel et SPSS
(Statistical Package For Social Science) ;
ü En raison de la nature qualitative des données
obtenues au cours de la recherche, une préférence est
accordée à l'analyse de contenu par laquelle sont
identifiées et retenues les informations déterminantes dans le
cadre de la présente thématique.
VIII. INTÉRÊT
Notre thématique permet de dégager des
intérêts pluriels à savoir :
· L'intérêt
académique
Il est important de souligner que le présent
mémoire est un préalable pour obtention du diplôme de
Master 2.
· L'intérêt personnel
À titre personnel ce mémoire nous a permis
d'aller puiser au-delà de notre zone de confort, dans des disciplines et
domaines que nous n'avions jamais explorés. Ceci a contribué
à acquérir des connaissances plurielles et
bénéfiques dans la cacao-culture en général et en
particulier dans le domaine du séchage des fèves de cacao.
· L'intérêt scientifique
L'intérêt scientifique de ce travail repose sur
le fait qu'il se veut une contribution à la problématique portant
sur les pratiques post récolte du cacao notamment le
séchage. La présente étude entend donc se focaliser sur la
qualité du cacao en s'appuyant sur les théories de
l'amélioration continue. Bien que partant sur des recherches
précédentes, elle reste une oeuvre soumise à la critique
et une base pour d'autres chercheurs à l'avenir.
· L'intérêt pratique
À l'issu de cette étude, les producteurs
pourront désormais bénéficier des modèles de
séchoirs SAMOA innovés et une procédure de
séchage adaptée.
· L'intérêt socio-économique
À travers cette recherche, nous voulons
améliorer la qualité des fèves après le processus
de séchage. Notre travail permettra aux producteurs de proposer un
produit de meilleure qualité sur le marché international,
d'accroitre leurs revenus et par conséquent leurs conditions de vie.
IX. PLAN DE L'ÉTUDE
Notre travail de recherche respecte le principe du plan
dichotomique. Nous mettrons en évidence deux parties, chacune
composée de deux chapitres.
Dans la première partie, nous allons nous
étendre sur les défaillances des équipements en milieu
industriel ainsi que leurs effets. Dans son premier chapitre, nous
étudierons le cadre théorique des défauts de fabrication
des équipements en général. Dans le deuxième
chapitre qui se voudra empirique, nous allons mettre en évidence notre
travail théorique dans le cas du séchage du cacao en nous
étalant sur l'état des lieux de la construction et la maintenance
du séchoir SAMOA.
Dans la seconde partie, nous allons nous appesantir sur
l'accompagnement des producteurs comme facteur d'amélioration de la
qualité des fèves de cacao. Cette partie est composée
également de deux chapitres. Le troisième chapitre traite de
l'analyse théorique de la GRH en vue de l'optimisation de la
qualité. Le quatrième chapitre abordera l'amélioration de
la qualité des fèves par l'encadrement des cacaoculteurs.
PREMIÈRE PARTIE : EFFETS DES DEFAILLANCES DES
ÉQUIPEMENTS DE PRODUCTION EN MILIEU INDUSTRIEL
INTRODUCTION DE LA PREMIÈRE
PARTIE
Les défis qui sont ceux des industries aujourd'hui sont
de nature à repousser les limites des équipements ou outillages
qui constituent le socle de la production. Il est donc indispensable de penser
à une politique de maintenance qui permettrait de garder la production
en phase avec les objectifs préalablement fixés. Cette politique
a aussi le rôle de rétablir un équipement dans un
état qui lui permettrait d'accomplir la fonction pour laquelle il est
dédié. Une entreprise qui ignore cette étape, condamne son
parc machine à une perte de fiabilité matérialisée
par des défaillances accrues des équipements impactant ainsi la
qualité des produits fabriqués.
La concurrence dans tous les domaines industriels bouscule les
habitudes et impose une démarche professionnelle et innovante aux
managers d'entreprise. Les contraintes de positionnement et de
pérennisation de l'activité en garantissant des produits de
qualité incitent les entreprises à s'inscrire dans la
durabilité. Pour le faire, un accent doit être mis sur la
maintenance de l'outil de production.
En ce qui concerne les équipements de production, les
préoccupations des managers dans le secteur de l'industrie tournent
autour de trois axes :
· La disponibilité
· La fiabilité
· La maintenabilité
Notre travail dans cette première partie consistera
à analyser ce triptyque. Cette démarche nous permettra
d'étudier le cadre conceptuel des défauts de fabrication des
équipements dans le premier chapitre. Dans le deuxième chapitre,
cette approche nous permettra d'optimiser les processus de fabrication des
séchoirs SAMOA utilisés dans le bassin de production du
Sud-ouest.
CHAPITRE 1 : CADRE CONCEPTUEL
DES DÉFAUTS DE FABRICATION DES ÉQUIPEMENTS
INTRODUCTION DU CHAPITRE 1
Il est clair ici que le terme défaut pour un
équipement désigne tout simplement sa défaillance dans
l'accomplissement des tâches tel qu'initialement prévu. Toutefois,
à la phase d'études d'une machine industrielle, le concepteur
peut contrecarrer les défauts éventuels si non de les
atténuer. Ceci passe par la prise en compte des sollicitations
auxquelles sont soumis les équipements durant leur exploitation,
à l'environnement d'utilisation, de leur maintenabilité et aussi
de leur simplicité à être utilisés par des
opérateurs. Dans ce chapitre, nous allons exposer de prime à bord
sur la conception des équipements, des machines de production et sur les
défaillances liées à l'exploitation de ces derniers. Par
la suite nous allons effectuer le tour d'horizon des méthodes
d'amélioration de la qualité en présentant quelques outils
qui les accompagnent.
I. L'EVOLUTION DE L'INDUSTRIALISATION DES
ENTREPRISES
La mise au point de la machine à vapeur en 1769 par
James Watt, transforme le travail et le transport. Des usines dans des secteurs
variés tels que la métallurgie, la mécanique, les textiles
naissent et emploient des ouvriers. Il s'en suit une course vers la recherche
de nouvelles sources d'énergie telle que le pétrole. Ceci va
permettre de mettre au point le moteur à explosion favorisant ainsi une
nouvelle étape d'industrialisation. L'accès à
l'électricité va permettre aux usines de concevoir des machines
et équipements industriels de plus en plus robustes et fiables capables
d'accroitre de temps de production et permettant par ricochet une augmentation
de la rentabilité. Toutefois afin de maintenir un niveau de
productivité acceptable et faire face à la
compétitivité, il va falloir concevoir des machines qui puissent
s'adapter à une production flexible. Toutefois la course
effrénée vers la production massive avec des délais
très compressés n'est pas sans risques sur la qualité du
produit en fin de fabrication.
I.1 LA CONCEPTION ET LA FABRICATION DES
ÉQUIPEMENTS DE PRODUCTION
La conception c'est l'art de créer soit à partir
de rien, soit à partir d'un modèle vétuste existant. On
parlera d'innovation. À partir des attentes du demandeur, il est
important de formaliser les solutions technologiques les plus adaptées.
Il s'agit de calculer, de dimensionner l'équipement. Pour le faire, les
industries mettent en place au sein de leur organisation un bureau
d'études. Ce dernier intervient dans les premières phases de la
vie d'un produit ou d'un système. Il est chargé des analyses
techniques et des activités d'ingénierie. Après les tests
des résultats obtenus et toutes les validations internes suivant les
protocoles de l'organisation, les « out put » du
bureau d'études que sont la notice de fabrication, la note de calcul,
les plans d'ensemble et les plans de définition sont
réceptionnés comme intrants par le bureau de méthodes qui
élabore les procédés de fabrication en prenant en compte
la disponibilité des ressources (machines, personnel, etc.). Le bureau
de méthode est la plaque tournante dans la méthodologie de
fabrication d'un équipement, car il est en relation avec la
qualité, la logistique, la production, les achats et le service
commercial. Il convertit le travail préalablement effectué par le
bureau d'études en phase de travail dans l'usine.
I.1.1 L'IMPORTANCE DU CAHIER DE CHARGES
La norme NF X50 151 de 1984 définit le cahier des
charges comme un document par lequel le demandeur exprime son besoin en termes
de fonctions de service ou contraintes. C'est un document qui reprend les
exigences et les attentes du donneur d'ordres. Il spécifie, explique,
délimite le travail à exécuter et permet aux parties
prenantes de se mettre d'accord prioritairement sur les conditions
technologiques du produit ou service. L'aspect technologique concerne non
seulement les propriétés intrinsèques de
l'équipement, mais aussi sa capacité à satisfaire son
utilisateur dans un environnement donné. Seront donc
évoqués, entre autres les plans, les matériaux
constitutifs de l'équipement, la robustesse et la maintenabilité.
Un inventaire de ressources est réalisé à partir de ce
document. Il en découlera toutes les ressources humaines,
matérielles et financières qui interviendront dans le processus
de réalisation de ce projet. Le fabricant peut ensuite donner un
délai de livraison à son client.
I.1.1.1 LE CADRE NORMATIF COMME GAGE DE LA
QUALITÉ DES ÉQUIPEMENTS
L'entrepreneur se doit de mettre en place une démarche
qualité. Celle-ci se définit comme son engagement envers son
client, lui garantissant la fiabilité de son produit, son service, ou
son équipement le cas échéant par la mise en oeuvre des
procédures validées. Ces procédures auront pour objectif
de donner une assurance au client que tous les moyens sont mis en oeuvre pour
obtenir des prestations de qualité. La norme AFNOR FD S99-132 d'Avril
2000, propose le schéma ci-après (Figure 1) comme une
illustration d'une démarche qualité.
Figure 1: Schématisation de la qualité dans
le domaine des services et adaptée à la santé.
Qualité attendue
Qualité voulue
Qualité vécue
Qualité délivrée
Écart de vue des clients
Point de vue de l'entreprise
Écart de conception
Écart de perception
Écart de délivrance
Écart de satisfaction
Référentiels de bonne pratique
Source : AFNOR FD S 99-132-Avril 2000
· La qualité vécue par le client est celle
qu'il expérimente ; elle dépend de la qualité attendue et
de la qualité effectivement délivrée ;
· La qualité voulue est celle que l'entreprise
doit prendre en compte dans le cahier de charges. Elle est assimilée
à la qualité attendue par le client ;
· La qualité effectivement
délivrée : s'appuyant sur le référentiel de
bonne pratique, elle doit correspondre à la qualité voulue par
l'entreprise.
L'écart de délivrance est un exemple de
variabilité (Mura). L'écart de satisfaction aura un
impact sur la relation entre le client et son fournisseur.
I.1.1.2 LES DOCUMENTS DE
RÉFÉRENCE
Il s'agit de toute la documentation prescrite ou transmise par
le client dans son appel d'offres ou son cahier des charges. Celle-ci est
exigible pour :
· Mieux cerner le besoin du client ;
· L'utilisation des spécifications propres au
client ;
· La prescription des normes applicables.
Dans le cas où les normes sont insuffisantes,
l'entrepreneur qui est censé avoir une parfaite connaissance des travaux
à réaliser pour garantir un meilleur produit peut proposer des
documents de référence. Ceux-ci ne devront pas être en
contradiction avec ceux prévus par le MOA21(*).
I.1.1.3 LA GESTION DE LA DOCUMENTATION
Dans la phase d'études, le client peut être
amené à modifier la conception du produit à fabriquer.
Ceci peut naître des résultats des notes de calcul ou des essais
non concluants sur un prototype. Il en est de même pendant la production,
certaines opérations peuvent s'avérer irréalisables du
fait de l'environnement défavorable. Le client pour chacun de ces cas ou
encore pour d'autres raisons non évoquées, peut modifier la
conception du produit sans changer la fonction première de ce dernier.
Toute la documentation des échanges liés au changement du scope,
sera rigoureusement archivée et ces informations transmises à
l'ensemble de la chaîne de production.
I.1.2 LA QUALITÉ DANS LA CONCEPTION DES
ÉQUIPEMENTS DE PRODUCTION
Cette étape est indispensable en partie pour la
maîtrise de la sécurité des équipements. D'autres
parts, il s'agit d'atténuer des risques potentiels en matière de
défauts. La qualité dans la conception des équipements de
production sera de définir le taux de défauts acceptable et les
indices de capabilité requis. Il conviendra de mettre en place des
procédures régissant :
· Les approvisionnements des marchandises, des
matériaux, des consommables et autres intrants dans le processus de
production. Ces derniers doivent être traçables et
contrôlés à la réception. Les fournisseurs
eux-mêmes doivent être enregistrés et
évalués ;
· Les méthodes de production qui consistent
à lister les opérations, les machines de production et s'assurer
de la disponibilité de la main-d'oeuvre ;
· Le dévernissage après la production
(éventuellement), les points de contrôles et les tests pendant et
après la production. Ils permettent de se prémunir contre des
défaillances « de jeunesse », parlant des
défauts qui apparaissent une fois que l'équipement est
livré chez le client.
I.1.2.1 LA FIABILITE DES
ÉQUIPEMENTS
La fiabilité d'un équipement ou d'un
système est sa capacité à accomplir une fonction dans des
conditions données pendant un intervalle de donnée. C'est une
fonction de probabilité noté R(t) qui exprime la
probabilité que l'entité ne soit pas défaillante dans
l'intervalle de temps [0; t]. L'indice de fiabilité est la moyenne des
temps de bon fonctionnement (MTBF).
MTBF = Somme des temps de bon fonctionnement / nombre
de défaillances.
Les temps de bon fonctionnement incluent les temps
d'arrêt hors défaillance et les temps de micro-arrêt.
L'antonyme de la fiabilité est la défaillance
(non-fiabilité). Pour prévenir les défaillances et assurer
la fiabilité de son équipement, le recours à un
AMDEC22(*) est
décidé en règle générale pour tous nouveaux
processus, et aussi pour un processus existant afin de valider, modifier un
plan de contrôle. L'AMDEC est réalisé à titre
préventif pour :
· La recherche des défauts potentiels d'un produit
ou d'un service engendrés par un processus ;
· L'évaluation de leurs effets en clientèle
(client de l'opération suivante ou client de l'usine aval ou client
final) ;
· L'identification des causes possibles ;
· La recherche d'actions préventives et leur mise
en oeuvre.
Les trois courbes illustrées par Bellaouar et Beleulmi
(2014), permettent de mettre en évidence la particularité de
chaque défaillance selon d'elles sont de nature
électromécanique, électrique ou encore
mécanique.
Figure 2. Courbes caractéristiques du taux de
défaillance.
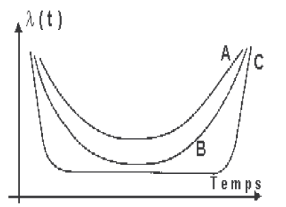
Source : BELLAOUAR et BELEULMI (2014)
Courbe A : Situation dans des systèmes
mécaniques
Courbe B : Situation dans des systèmes
électromécaniques
Courbe C : Situation dans des systèmes
électriques
ë (t) : Taux de
défaillance.
I.1.2.2 LA MAINTENABILITÉ DES
ÉQUIPEMENTS
Dans des conditions données, la maintenabilité
est l'aptitude d'un bien à être maintenu ou rétabli
rapidement dans un état où il peut accomplir une fonction
requise, lorsque la maintenance est accomplie dans des conditions
données, en utilisant des procédures et des moyens prescrits.
C'est aussi la probabilité de rétablir un système dans des
conditions de fonctionnement spécifiées, en des limites de temps
désirées, lorsque la maintenance est accomplie dans des
conditions données, en utilisant des procédures et des moyens
prescrits.
À partir de ces définitions, on distingue :
· La maintenabilité intrinsèque : elle est
construite dès la phase de conception à partir d'un cahier des
charges prenant en compte les critères de maintenabilité
(modularité, accessibilité, etc.) ;
· La maintenabilité prévisionnelle : elle
est également construite, mais à partir de l'objectif de
disponibilité ;
· La maintenabilité opérationnelle : elle
sera mesurée à partir des historiques d'interventions.
L'analyse de maintenabilité permettra d'estimer la MTTR
(Main time to repair ou Durée moyenne de réparation) qui
en est un indice. Elle permet également de déduire le taux de
réparation (u).
MTTR = Temps d'arrêt total / nombre
d'arrêts ì = 1 / MTTR
Il est à noter que la maintenabilité
dépend de plusieurs facteurs. Ils peuvent être liés
à la conception de l'équipement (études, facilité
d'utilisation, fiche technique, disponibilité des pièces de
rechange), à la qualité du service après-vente et à
la politique de maintenance applicable (formation du personnel, moyens).
I.1.2.3 LA DISPONIBILITÉ DES
ÉQUIPEMENTS
Toutes les actions en amont inhérentes à la
maintenance contribuent à la disponibilité des équipements
ou matériel impliqué dans un processus de production. Le concept
de disponibilité des équipements se manifeste par :
· La minimisation des arrêts pendant la
production ;
· La rapidité à remédier à
une panne lorsqu'elle survient.
La disponibilité des équipements est le reflet
de la fiabilité et de la maintenabilité, car ces derniers
permettent de maitriser réciproquement les MTBF (Moyenne des temps de
bon fonctionnement entre deux défaillances consécutives) et les
MTTR qui sont des indicateurs de maintenance.
Disponibilité = MTBF/ (MTTR-MTBF)
· La somme des temps de bon fonctionnement est
égale au temps total d'analyse (période de
référence) moins la somme des temps d'arrêts ;
· Le nombre de périodes de bon fonctionnement
(TBF) est normalement égal au nombre de défaillances
(arrêts) de la période si on considère le début et
la fin de la période comme un seul temps de bon fonctionnement (Cas
n°1) ou bien si on effectue l'analyse entre deux arrêts, sans
prendre en compte l'arrêt initial (Cas n°2).
Figure 3 : Cas numéro 1 de TBF

Source :
http://jackadit.com/index.php?page=indus3
Figure 4 : Cas numéro 2 de TBF

Source :
http://jackadit.com/index.php?page=indus3
Figure 5 : Schéma synoptique de la maintenance
des équipements
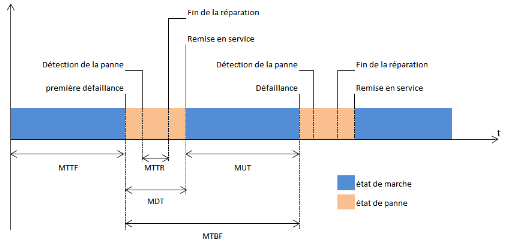
Source :
http://jackadit.com/index.php?page=indus3
MUT (Mean Up Time) : Durée moyenne de
fonctionnement après réparation
MDT (Mean Down Time) : Durée moyenne
d'indisponibilité (temps de détection de la panne + temps de
réparation + temps de remise en service)
MTBF = Ó Temps de bon fonctionnement / Nombre de
défaillances ou nombre de périodes de bon fonctionnement
MTTF (Mean Time To Failure) : Durée
moyenne de fonctionnement d'un équipement avant la première
défaillance MTTF = ? [0; +8[R(x).dx
II. LES INFLUENCES DES
DÉFAILLANCES DES ÉQUIPEMENTS SUR LA PRODUCTION
La fonction de défaillance c'est la fonction F
défini pour tout t = 0. t étant le temps. Le
nombre F(t) représente la probabilité qu'un dispositif
choisi au hasard ait une défaillance avant l'instant t. La
figure 3 donne l'allure de cette fonction. (Bellaouar et
Beleulmi ,2013).
Figure 6 : Fonction de défaillance
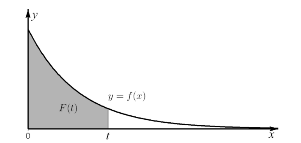
Source : BELLAOUAR et BELEULMI (2013)
Cette fonction nous amène naturellement une fonction
associée : la fonction de fiabilité vue dans le paragraphe
précédent est R définie pour tout t =0
par : R(t)= 1-F(t). Le nombre R(t)
représente la probabilité qu'un dispositif choisi au hasard
dans la population n'ait pas de défaillance avant l'instant t. La
figure 6 ci-dessous montre les deux fonctions associées.
(Bellaouar et Beleulmi ,2013).
Figure 7 : Fonction associée à la
fonction de défaillance.
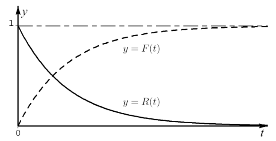
Source : BELLAOUAR et BELEULMI (2013).
Le taux d'avarie moyen dans l'intervalle de temps [t, t+?t]
est alors : [R(t)-R(t+?t) / R(t)] x 1/?t
II.1 LES DÉFAILLANCES DANS UN ÉQUIPEMENT
MULTI-TECHNOLOGIE
Un équipement multi-technologie est un
équipement qui est constitué de plusieurs sous-ensembles qu'il
convient de segmenter. Il peut s'agir entre autres du domaine de
l'électricité, l'électronique, la mécanique. Cette
segmentation permettra la mise en place d'une politique de maintenance ou
encore durant les phases d'intervention (diagnostic, entretien,
réparation). La figure 2 illustre les courbes
représentant les défaillances de trois types d'équipements
dans les domaines précédemment évoqués. Il en
ressort que pour chaque type d'équipement les défaillances
surviennent différemment dans le temps.
Lorsqu'un équipement est composé de plusieurs
sous-ensembles et que la défaillance d'une pièce inter agit sur
une autre on parle de système en série. Par ailleurs lorsque le
dysfonctionnement d'un composant n'empêche pas le système de
continuer à produire, on parle de système en parallèle.
Plus il y a des composants en parallèle plus l'équipement est
fiable. (Bellaouar et Beleulmi ,2013)
II.1.1 LES PHASES DE VIE D'UN
ÉQUIPEMENT
Une défaillance sur un équipement est un
dysfonctionnement aléatoire sur ce dernier et qui peut avoir pour
conséquence :
· Un arrêt de production ;
· Un incident ou un accident ;
· Une production non conforme.
Le nombre de défaillances d'un équipement sur
une période donnée permet d'en déterminer le taux de
défaillance. Cette donnée permet de mettre sur pied un plan de
maintenance sur son parc machine. Un équipement a une vie qui
s'étale sur trois phases. Elle peut être représentée
grâce à une courbe dite courbe en baignoire.
Figure 8: Phases de vie d'un équipement
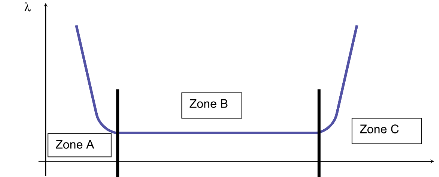
Source:
http://jackadit.com/index.php?page=indus3
Sur la courbe l'axe des ordonnées représente
l'évolution du taux de défaillance (ë) et l'axe des
abscisses représente l'évolution du temps.
Zone A : Elle représente la phase de jeunesse
Zone B : Elle représente la période de
maturité, fonctionnement normal, défaillance aléatoire
indépendante du temps.
Zone C : quant à elle, est une période de
vieillesse, de défaillances, d'usure qui laisse apparaître les
pannes de vieillesse.
II.1.1.1 LA PHASE DE JEUNESSE DES
ÉQUIPEMENTS
Dans cette phase, le taux de défaillance est en faible.
Les équipements sont prédisposés à tomber moins en
pannes. Ce résultat est l'oeuvre de tout processus de fabrication depuis
la conception. L'étape de conception est celle des études, du
choix des matériaux, des notes de calculs et de l'ordonnancement des
opérations de fabrication. Le fabricant quant à lui, va assurer
la mise en forme des pièces constitutives de l'équipement, de
l'assemblage et du conditionnement. L'objectif étant de fournir au
client une machine fiable dès le début de son exploitation.
Pendant et en fin de processus de fabrication, les machines sont soumises
à un dévernissage afin d'éliminer les
non-conformités éventuelles.
Généralement durant cette phase, en cas de
défaillance observée, l'équipement est retourné
chez le fabricant ou le concessionnaire pour le service après-vente. Les
clients sont obligés de subir une baisse de production du fait de
l'indisponibilité non planifiée de son équipement. Le
fabricant en plus de perdre de la crédibilité supporte des frais
qui viennent amoindrir le profit.
En cas d'usure anormale constatée des pièces de
rechange, il est recommandé aux utilisateurs des équipements de
retourner l'équipement au fabricant ou au concessionnaire.
En cas d'indisponibilité soudaine de
l'équipement, l'utilisateur peut se faire rembourser ou
l'équipement peut être remplacé suivant les conditions
d'acquisition.
II.1.1.2 LA PHASE DE MATURITÉ DES
ÉQUIPEMENTS
La phase de jeunesse terminée, l'équipement
entre dans la phase de maturité. Généralement dans cette
phase le taux de défaillance est constant ou sensiblement croissant.
Elle est également appelée la période utile pendant
laquelle le rythme de défaillance est considéré comme
aléatoire et par conséquent imprévisible. Toutes les
composantes des équipements ne présentent aucun signe de fatigue
ni d'usure. En cas de défaillance aléatoire, il ne peut y avoir
des causes systématiques.
Toutefois l'utilisateur veillera à respecter les
notices d'utilisation et à d'appliquer sa politique de maintenance avec
rigueur. Les mauvaises conditions d'utilisations telles que la surutilisation,
un environnement agressif peuvent générer une variation en hausse
du taux de défaillance.
La politique de maintenance dans une phase dite utile doit
être axée sur la prévention permanente des incidents. Les
opérateurs devront être sensibilisés sur les bonnes
pratiques en termes d'utilisation.
En cas d'indisponibilité de l'équipement dans
cette phase, l'utilisateur est contraint d'investir pour une nouvelle machine
avec des risques d'arrêt de production.
II.1.1.3 LA PHASE DE VIEILLISSEMENT DES
ÉQUIPEMENTS
Dans cette phase le taux de défaillance croît
sans cesse. Cette accélération annonce une usure normale des
composants de l'équipement à la suite d'une maintenance
approximative ou à un non-respect des conditions d'utilisations. Cette
défaillance peut entrainer la mise en place d'une maintenance
conditionnelle23(*) ou de
conduire à la mise au rebu des composants avariés ou encore de
conduire à un investissement sur un équipement neuf. Ces deux
dernières options sont envisagées à la suite de
l'évaluation du taux de défaillance d'un composant
réalisée dans des conditions données par observations
statistiques.
On peut noter deux formes de vieillissement des
équipements. Le vieillissement naturel qui le résultat de
l'exploitation de l'équipement dans le temps. Nous avons
également le vieillissement prématuré qui peut être
le résultat de déformations, rupture suite à une
sollicitation excessive, frottement (déficit de maintenance), corrosion
(environnement d'utilisation inapproprié).
II.1.2 AMÉLIORATION DE LA QUALITE DES
ÉQUIPEMENTS
L'enjeu des prochaines années sera la
généralisation et l'extension de garantie à deux ans
minimums des produits de grande consommation. Cette démarche rentre dans
l'harmonisation européenne et est favorisée par une directive de
la communauté européenne (Directive 1999/44/CE). Ainsi, pour
évaluer la qualité de leurs produits, les entreprises doivent
mettre en oeuvre des méthodes d'évaluation appropriées :
· À partir de banques de données de
fiabilité de composants connaissant l'architecture du système, et
éventuellement de la simulation de son fonctionnement. Cette
méthode donne de bons résultats dans le domaine de
l'électronique, mais de résultats moins satisfaisants dans le
domaine de la mécanique, d'autant que certains composants ne figurent
pas dans les recueils de données disponibles (Doyle, 1992 ; Leemis,
1994 ; BT-HRD, 1995 ; EIREDA, 1998 ; MIL-HDBK-217 F, 1995) ;
· À partir des retours garantis. Cette
méthode permet d'obtenir une bonne estimation de la fiabilité,
mais uniquement sur des produits déjà en vente (fiabilité
opérationnelle). On ne peut corriger les fautes qu'a posteriori, ce qui
peut donner une mauvaise image de l'entreprise. Ce retour d'expérience
riche en information participe au développement de futurs produits, non
seulement pour éliminer les défaillances constatées sur
les produits antérieurs, mais également dans l'évaluation
du niveau de fiabilité prévisionnelle. (Directive 1999/44/CE,
1999) ;
· À partir de l'avis d'experts quand on n'a aucune
connaissance sur la fiabilité d'un nouveau composant ou système.
En effet, à défaut d'autres informations utiles, ces experts
donnent par exemple un intervalle approximatif contenant le taux de
défaillance ou le temps moyen avant la première
défaillance du matériel, désigné par le MTTF ou
encore émettent un avis sur son fonctionnement ou pas au bout d'une
période donnée. (Lannoy et Procaccia, 2001);
· En réalisant des essais de qualification ou de
détermination sur le nouveau produit afin de vérifier ses
performances avant de lancer la production. Si le nombre d'essais est
suffisant, cette méthode permet d'obtenir une bonne estimation de la
fiabilité. Cependant, le contexte économique actuel ne permet pas
de tester suffisamment de produits et de consacrer suffisamment de temps pour
observer des défaillances de moins en moins probables. Les industriels
ne peuvent plus se permettre de tels coûts financiers. À
l'extrême, certains systèmes se fabriquent à
l'unité, ce qui rend les politiques d'essai difficiles. Ainsi, cette
problématique a été la source, pour la communauté
scientifique, de nombreuses voies de recherche (Afnor, 1981), (Afnor, 1988),
(Birolini, 1997), (Nelson, 1990), (Crowe and Feinberg, 2001), (ASTE, 1993).
Que le système soit simple ou complexe, qu'il s'agisse
d'une automobile ou d'une centrale nucléaire, la connaissance des
caractéristiques de fiabilité est essentielle : elle conditionne
la maintenance, les durées de vie et un niveau de sécurité
acceptable (Tebbi, 2005).
Toutes les démarches sus évoquées
concourent à la satisfaction du consommateur d'une part et aussi
à améliorer les processus de production. C'est donc le point de
départ de la mise en place des méthodes d'optimisation des
processus.
II.1.2.1 L'APPORT DES APPROCHES D'OPTIMISATION DES
PROCESSUS
Optimiser un processus pour une entreprise revient à
améliorer la manière d'exécuter chacun de ces processus.
Aujourd'hui, on compte presqu'autant d'approches que d'entreprises. Chacune se
façonne un nom accrocheur et des particularités tant sur le
découpage des étapes que sur les outils utilisés. Pour
comprendre les motivations de ces entreprises, une définition du
processus est indispensable.
Harrington (tel que cité dans Jasmin, 2013),
définit le processus comme toute activité ou ensemble
d'activités qui utilise un intrant, y ajoute une certaine valeur, et le
livre sous forme d'extrant à un client interne ou externe. Pour les
ordonner facilement, les entreprises déclinent les processus en trois
grandes catégories : opérationnel, de support et de gestion.
Les actions visant à optimiser les processus sont
plurielles :
· Mieux prendre en compte les attentes des
bénéficiaires pour améliorer les services fournis ;
· Permettre aux différents acteurs de s'impliquer
dans le fonctionnement du processus ;
· Clarifier les rôles et responsabilités des
acteurs, définir les marges de manoeuvre et les cohérences
nécessaires, simplifier les interfaces entre entités ;
· Transformer ou créer un nouveau processus pour
répondre à de nouvelles attentes ;
· Diminuer les coûts, les délais d'un
processus, augmenter sa performance au regard d'indicateurs définis ;
· Dieux réagir aux aléas ;
· Viser une certification via la mise en place d'un
système qualité ;
· Accompagner la mise en place d'un progiciel de
gestion.
Le succès de ces actions peut se faire soit par
benchmarking24(*), soit
par une analyse diagnostique de la performance des processus de l'organisation.
Toutefois le succès de l'optimisation des processus repose sur une
approche qui tient compte de la dimension humaine, qui assure la
continuité de la démarche et qui facilite le changement.
Parmi les approches d'optimisation formelles existantes
à ce jour, les plus répandues sont le Kaizen, la TOC, le
BPR, Lean et le Six Sigma. Il existe également des
approches hybrides qui résultent de la synthèse des points forts
de plusieurs approches tel que le LSS ou encore le TLS.
II.1.2.2 ETUDE DES APPROCHES D'AMELIORATION DE LA
QUALITE
Parmi la pléthore de méthodes
d'amélioration de la qualité, nous allons nous appesantir sur
celles qui ont écrites leurs lettres de noblesse au sein des grandes
organisations. Nous avons choisi de présenter celles qui nous
permettront de mener à bien notre travail.
v Le Six Sigma de Motorola
Azzabi (2010) affirme que le Six Sigma est le
système de management qui se développe le plus vite aujourd'hui
dans l'industrie. Centré sur une puissante méthodologie de
résolution de problème et d'optimisation des processus, le
Six Sigma a permis d'économiser de l'argent dans les
sociétés qui ont appliqué la démarche ces dix
dernières années. Sa puissance vient de l'application d'outils
statistiques dans le contexte d'une méthodologie structurée et
facile à mettre en oeuvre. Ces outils, utilisés le plus souvent
dans un environnement opérationnel de production, s'appliquent
également à tous les processus, y compris administratifs. Cette
démarche se décline de plusieurs façons, c'est :
ü Une certaine philosophie de la qualité
orientée vers la satisfaction totale du client ;
ü Un indicateur de performance permettant de savoir
où se situe l'entreprise en matière de qualité ;
ü Une méthode de résolution de
problèmes par l'implication totale des hommes permettant de
réduire la variabilité sur les produits et services ;
ü Une organisation des compétences et des
responsabilités des hommes de l'entreprise ;
ü Un mode de management par la qualité qui
s'appuie fortement sur une gestion par projet ;
En d'autres termes « Six Sigma » va
au-delà de la simple démarche de résolution de
problème et devient une véritable stratégie pour
l'entreprise en agissant sur :
ü Une amélioration de la disponibilité des
machines et des installations et par conséquent une optimisation dans
leur utilisation ;
ü Une réduction des dépenses suite à
une diminution des rebuts, retouches, des gaspillages et dysfonctionnements et
plus généralement des coûts de non-qualité ;
ü De meilleures parts de marché à la suite
à la réduction des coûts de l'amélioration de la
qualité des produits et des services ;
ü Une augmentation de la satisfaction des clients et une
plus grande fidélisation par l'amélioration de la qualité.
Azzabi et al (tel que cité Azzabi, 2010) soutient que
dans Tous les procédés, quel que soit leur degré de
précision, sont incapables de produire toujours exactement le même
produit. Il y aura toujours une petite variation entre les produits
réputés identiques, et ce sont ces variabilités qui
conduisent à la non-qualité. Quelles que soient la machine
étudiée et la caractéristique observée, on note
toujours une dispersion dans la répartition de la
caractéristique.
o Principe du Six Sigma
Prenons le cas d'une pièce mécanique dont la
longueur nominale est L. La pièce est utilisable si la longueur est
comprise entre L-ÄL et L+ÄL (ÄL est la tolérance). Le
processus de production, lui, produit des pièces dont la longueur varie,
la longueur moyenne est L, et avec un écart type ó (on suppose
que cette longueur suit une loi normale). En général, le
processus est réglé afin que l'on ait ó = ÄL/3 ; on
écrit en général plutôt ÄL = 3·ó,
mais c'est bien ÄL qui est une contrainte (la pièce est utilisable
ou pas), et ó qui est ajusté (les machines sont plus ou moins
bien réglées). Ceci conduit à un taux de rebut de 0,3 %,
soit 3 000 pièces au rebut pour une production d'un million de
pièces. Si l'on améliore le processus et que l'on diminue
ó jusqu'à avoir ÄL = 6·ó, on aura un taux de
rebut de 2·10-9, (0,000 000 2 %), soit deux pièces au rebut par
milliard produit (Azzabi, 2010).
Figure 9 : Illustration de la méthode Six
Sigma
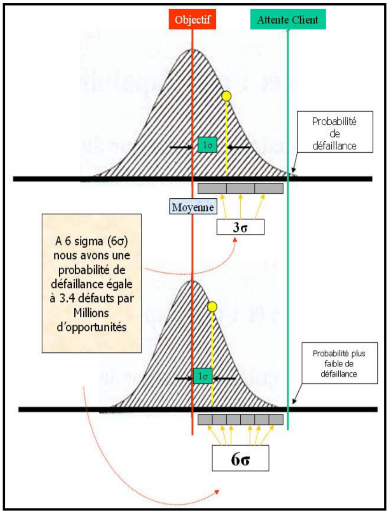
Source : AZZABI, 2010
Bien que structurante et très efficace, la
méthode Six Sigma présente toutefois quelques
manquements comme l'approche participative. Le manager est le seul à
déclencher ou pas le Six Sigma. Cet état de chose est
l'une des causes de l'échec de Motorola dans le domaine de la
téléphonie mobile. La culture d'ingénierie a fini par
étouffer le marketing au point de lasser les consommateurs qui se sont
orientés vers la concurrence.
o Les étapes de la méthode Six Sigma
La mise en oeuvre de cette méthode s'effectue au cours
de projets très encadrés et judicieusement choisis. Tous ces
projets sont menés à partir de la réalisation de cinq
étapes D-M-A-I-C : [ROGER G. et al 2008] s'obtenir que par
l'investissement dans un procédé nouveau.
Figure 10: Méthode
DMAIC
ï Définir clairement le problème de
l'entreprise
ï Clarifier les faits, fixer les objectifs et former
l'équipe du projet
Define
Définir
ï Collecter des données mesurables
ï Etablir une base de donnée
Mesure
Mesurer
ï Analyser les mesures du processus
ï Identifier les causes profondes du problème
Analyse
Analyser
ï Identifier, tester et mettre en oeuvre une solution pour
le problème
ï Eliminer les causes profondes
Improve
Améliorer
ï Créer un plan de surveillance de la solution mise
en place, mettre à jour les documents, former les ressources au nouveau
mode de travail
ï Standardiser la méthode et l'appliquer à
d'autre secteurs de l'entreprise selon le besoin
ï Féliciter l'équipe de travail ainsi que
toutes les personnes de l'entreprise ayant aidé à la
démarche
Check
Contrôler
Source : ROGER G. et al., 2008
v Le Lean Management
Nous rappelons que le Lean management est
système d'organisation industrielle initié dans les usines
japonaises de groupe Toyota.
L'objectif étant d'améliorer au mieux la
performance des processus en exploitant les méthodes, techniques et
pratiques déjà à la disposition des managers de la
production industrielle.
Le Juste à temps, la qualité à tous les
niveaux des processus et la réduction des coûts sont ainsi au
programme.
Vue sous un angle plus pratique, plus concret, la
démarche repose essentiellement sur la résolution active des
problèmes récurrents de la production industrielle quel que soit
le domaine d'activité.
Ainsi:
· La diminution des stocks ;
· La lutte contre les gaspillages et la réduction
des défauts ;
· Le juste à temps ;
· La production à flux tirés
(Kanban) et la maîtrise des délais ;
· La flexibilité et la gestion efficace des
compétences ;
· Tout comme la réduction des coûts, sont
parties intégrantes de la démarche.
Si le Six Sigma est utilisé pour
réduire drastiquement la variabilité' des processus, le
Lean, quant à lui, cherche non pas à réduire mais
bien à éliminer tout ce qui est inutile au sein du processus,
comme les temps d'attente qui nuisent à la fluidité, les
retouches qui n'engagent pas toujours à chercher à faire bien du
premier coup, les surproductions qui génèrent des stocks
inutiles, les déplacements superflus. Bref tout ce qui en théorie
peut être qualifié de gaspillage et pénalise les temps de
cycle.
Une ressente étude du cabinet XL Groupe
(2015), conclut que les entreprises s'intéressent principalement
à la boîte à outils du Lean qui est
constituée entre autres du « 5S », de
l'analyse de déroulement, de la TPM.
De nombreuses entreprises essaient les outils, puis au bout de
quelques mois l'engouement de départ fait place à du scepticisme
car les résultats attendus se font attendre et les changements
espérés ne se traduisent pas au quotidien. Dans d'autres cas, les
réactions du terrain se font virulentes car le sentiment de pression
prend le dessus sur l'amélioration réelle des activités,
espérée par la suppression des tâches sans valeur
ajoutée.
De nombreuses entreprises essaient les outils, puis au bout de
quelques mois l'engouement de départ fait place à du scepticisme
car les résultats attendus se font attendre et les changements
espérés ne se traduisent pas au quotidien. Dans certains cas, les
réactions du terrain se font virulentes car le sentiment de pression
prend le dessus sur l'amélioration réelle des activités,
espérée par la suppression des tâches sans valeur
ajoutée.
o Principe du Lean management
La méthode comporte quatre étapes, chacune
entraînant l'autre, et vise à établir un cercle
vertueux en capitalisant sur les connaissances acquises. Sa mise en place doit
permettre d'améliorer sans cesse la qualité d'un produit, d'un
service, d'une organisation. Il s'agit de :
· Trouver les causes racines des écarts
mesurés (par exemple à l'aide d'un diagramme de Pareto, d'un
diagramme d'Ishikawa ou de la méthode des « 5
pourquoi ») et appliquer les actions correctives ;
· Standardiser la meilleure pratique obtenue pour en
assurer la pérennité ;
· Définir les objectifs pour de nouvelles
améliorations.
o Les étapes du Lean management
Le Lean suit la méthodologie
mnémotechnique dite PDCA (Plan-Do-Check-Act) initiée par
Walter A. Shewart et améliorée par le statisticien William E.
Deming. Elle est représentée par une roue subdivisée en
quatre parties permettant de repérer et de simplifier les étapes
à suivre pour améliorer de manière sempiternelle la
qualité dans une organisation.
Figure 11 : Roue de Deming et méthode PDCA
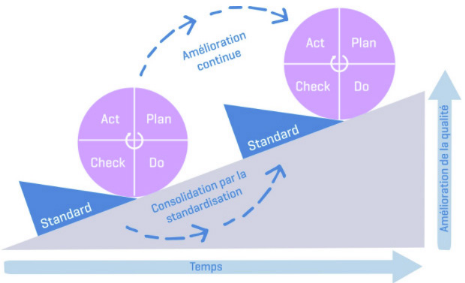
Source:
https://www.pyx4.com/blog/pdca-4-etapes-de-lamelioration-continue/
À chaque étape, la roue avance d'un quart de
tour. Cette avancée représente l'action de progresser.
Une cale est représentée sous la roue de Deming
pour symboliser que les étapes PDCA s'enchaînent toujours dans cet
ordre. Si chaque étape est bien respectée et conduite, ce
déroulement empêche la roue de redescendre grâce au retour
d'expériences, à un système d'audits réguliers ou
à un système documentaire qui capitalise les bonnes pratiques et
les décisions.
Que l'organisation soit lourde ou non, le PDCA est toujours
applicable. La roue tourne simplement plus ou moins vite.
v Le Lean Six Sigma
Psychogios et al. (Tel que cité dans Jasmin,
2013) affirme qu'avec le temps, les deux approches qui étaient en
compétition ont été mises en collaboration par certains
auteurs, ce qui ferait suite à une expérience réussie chez
General Electric.
L'approche Lean vise la performance en termes de
productivité, qualité, délais et coûts grâce
à l'élimination des gaspillages et l'amélioration
continue. La méthodologie Six Sigma cherche à
éliminer les défauts et la variation des processus de production.
Le Lean Six Sigma25(*) est aujourd'hui reconnue comme la
synthèse des meilleures pratiques d'amélioration de la
performance opérationnelle et permet de résoudre un large
éventail de problèmes quotidiens rencontrés par les
différentes équipes dans leurs entreprises.
Ainsi, la méthode Lean Six Sigma amène
les entreprises à développer une véritable culture de
l'amélioration continue.
o Principe du lean Six Sigma (LSS)
La méthodologie LSS fonctionne pour les entreprises de
toutes les tailles et de tous les secteurs. Il s'agit d'une méthode
simple et efficace, basée sur la pratique du bon sens.
Déployée en mode projet, l'approche Lean Six
Sigma suit les cinq phases du DMAIC (Définir, Mesurer,
Analyser, Améliorer (improve en anglais), Contrôler)
et permet :
· D'améliorer la satisfaction du client et
des
parties
prenantes ;
· D'accroître la performance opérationnelle
et financière de l'entreprise ;
· De répondre aux objectifs
stratégiques.
Pour résumer, la méthode Lean Six Sigma
vous aide à identifier la cause d'un problème et à
mettre en oeuvre une solution efficace basée sur des observations et des
faits, et non sur de simples suppositions.
Les avantages de cette démarche sont pluriels :
· Augmentation des bénéfices : LSS
permet de rationaliser vos processus, c'est-à-dire de produire plus
rapidement et efficacement sans réduire la qualité et sans
augmenter les coûts. Pour simplifier, avec LSS, vous produisez des
produits de qualité avec un minimum d'argent, de ressources et de
temps.
· Réduction des coûts : Lean Six
Sigma permet à l'entreprise d'améliorer ses processus. Ainsi
vous réduisez vos dépenses en éliminant les tâches
qui ne produisent pas de valeur ajoutée (suppression des gaspillages) et
en traitant les différents problèmes pour chaque processus
(élimination des défauts sur un produit qui engendrent un retour
client).
· Amélioration de l'efficacité et du
rendement : grâce à LSS, vous créez des processus
plus efficaces et vous maximisez vos efforts pour délivrer un produit
satisfaisant du premier coup. Ainsi, vous produisez plus de produits et vous
pouvez satisfaire plus de clients.
· Création d'un sentiment d'appartenance et de
responsabilité : impliquer votre équipe dans
l'amélioration des processus la rend plus responsable, développe
la confiance et créé un sentiment d'appartenance. C'est aussi un
bon moyen de montrer que chaque personne au sein de l'entreprise est
importante. Votre équipe est alors plus motivée et plus
performante.
La méthode Lean Six Sigma affecte vos
employés de façon positive en les encourageant à
améliorer leurs conditions de travail. En effet, qui mieux qu'eux sait
ce qu'il faut améliorer au sein de l'entreprise. En participant avec
succès aux projets LSS, vos employés renforcent leur confiance en
eux et en l'entreprise et ils deviennent ainsi vos meilleurs atouts.
o Points forts des deux méthodes
Le tableau ci-après présente la recension des
points forts de deux approches.
TABLEAU 2 : POINTS FORTS DES METHODES LEAN
ET SIX SIGMA
Approche
|
Origine
|
Particularités
|
LEAN
|
Démarche d'amélioration continue
|
Objectif « Zéro gaspillage »
|
Suppression des non-valeurs ajoutées
|
Besoin des données opérationnelles
|
Amélioration de la productivité
|
Utilisation des outils tels que Kaizen, VSM, 5S, TPM
|
Création de standard
|
SIX SIGMA
|
Démarche d'amélioration par percée
|
Objectif « Zéro défaut »
|
Méthode statistique de maîtrise de la
variabilité
|
Besoin des données chiffrées
|
Augmentation de la qualité
|
Méthode DMAIC
|
Maîtrise de l'écart au standard
|
Source : Travail étudiant.
BAGNAKA (2017)
II.1.2.3 PRESENTATION DES OUTILS D'AMELIORATION DE LA
QUALITE
Réussir à améliorer la
qualité (interne et
externe) et à inscrire durablement son entreprise dans une
réelle dynamique d'amélioration continue, ne peut pas être
le fruit du hasard. Cela passe par :
· L'utilisation de méthodes et outils de la
qualité adaptés à la situation et à l'objectif
recherché ;
· La mobilisation des hommes et des femmes de
l'entreprise.
Pour chaque situation, il existe un ou plusieurs outils de la
qualité facilitant l'atteinte des objectifs car ils apportent des
méthodologies éprouvées, et permettent de "canaliser" les
efforts de tous afin d'éviter toute dispersion contre-productive. Cela
est d'autant plus important qu'il faut souvent travailler en équipe car
tous les processus et activités de l'entreprise sont
interdépendants.
v Les outils pour l'optimisation de la valeur dans les flux et
les processus
o Value Stream Mapping (VSM)
La Value Stream Mapping s'inscrit dans une
démarche de mise en oeuvre de l'amélioration continue et du
Lean. Véritable cartographie visuelle des flux (physiques et
d'informations) dans un processus étudié, c'est l'outil de
diagnostic par excellence qui permet d'identifier les dysfonctionnements et les
axes d'optimisation.
Réussir une VSM, se traduit par :
· La réduction des délais de
réalisation ;
· La réduction des gaspillages ;
· L'optimisation des ressources ;
· L'amélioration des performances de l'usine.
Figure 12 : Modèle VSM
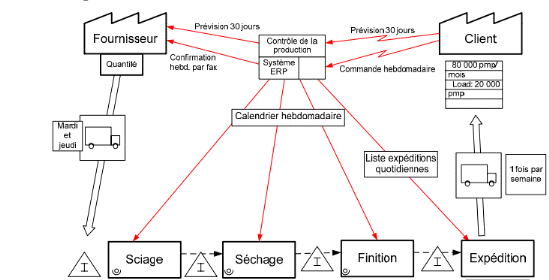
Source :
http://logistique-pour-tous.fr/la-trousse-a-outils-du-lean-110-la-vsm-value-stream-mapping/
o Analyse de déroulement (AD ou APP)
L'analyse de déroulement est une représentation
détaillée des activités d'un flux ou processus
localisé. On distingue celles à Valeur Ajoutée de celles
à Non-Valeur ajoutée en les valorisant en termes de :
· Temps passé ;
· Quantité transformée ;
· Distance parcourue ;
· Poids ;
L'objectif est de déterminer l'efficience du processus,
c'est à dire, le pourcentage de VA et de cibler tous les gaspillages,
afin d'identifier les actions prioritaires d'optimisation
«Lean».
Figure 13 : Modèle Analyse de
Déroulement
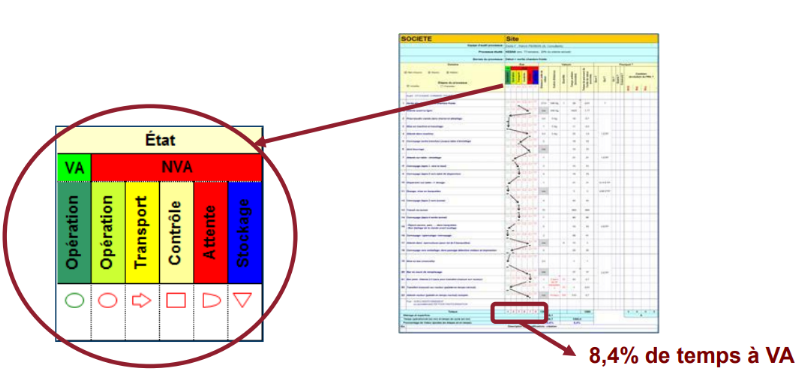
Source : XL Groupe
o Diagramme spaghetti
Le diagramme spaghetti est un outil qui sert à donner
une vision claire du flux physique des pièces ou des individus. Il tire
son nom de sa ressemblance avec un plat de spaghettis, car lors de son premier
tracé, en général, les flux s'entremêlent. Cette
visualisation sert à identifier les flux redondants, les croisements
récurrents et à mesurer le trajet parcouru par chaque produit ou
personne. Il aide à la réimplantation ou réorganisation
géographique des machines ou des services pour limiter les temps de
déplacements et leur non-valeur ajoutée.
Figure 14 : Modèle diagramme spaghetti
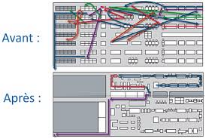
Source :
http://theos.fr/diagramme-spaghetti-une-solution-simple-et-efficace/
v Les outils pour garantir la qualité et la
productivité au poste de travail
o Les « 5S »
La méthode des « 5S » est
une technique de management japonaise visant à l'amélioration
continue des tâches effectuées dans les entreprises.
Élaborée dans le cadre du système de production de Toyota
(en anglais Toyota Production System ou TPS), elle doit son
appellation de la première lettre de chacune de cinq opérations
constituant autant de principes simples. Il est essentiel pour amorcer une
démarche de la Qualité Totale (TQC). Le terme
« 5S » vient des initiales des mots clés de
la méthode :
· Seiri signifie Débarrasser : le
poste de travail n'a que les objets nécessaires, propres et en bon
état ;
· Seiton signifie Ranger : les objets
nécessaires sont immédiatement disponibles au moment
voulu ;
· Seiso signifie Nettoyer : le poste de travail n'a
aucun déchet et le maintien de la propreté est facile et
naturel ;
· Seiketsu signifie Standardiser : toute
anomalie est facilement visible afin de systématiser l'ordre et la
propreté ;
· Shitsuke signifie Pérenniser : la
volonté et la dynamique d'amélioration continue est portée
par une démarche structurée dans le temps.
Dans une organisation où les
« 5S » sont appliqués, cette
dernière peut apprécier :
ü L'amélioration la productivité,
l'efficacité et la qualité ;
ü La diminution les pannes
(gravité/fréquence) ;
ü La réduction les pertes de temps (recherche d'un
outil par exemple) ;
ü La contribution à l'implication et à la
motivation du personnel ;
ü Le gain en confiance et en image de marque pour
l'entreprise ;
ü Le gain de l'espace inutilement
utilisé ;
ü L'amélioration de la sécurité au
travail, réduit les risques de pollution et permet au personnel d'avoir
une meilleure qualité de vie au travail.
o Standards du poste
Les standards de travail peuvent être assimilés
à des normes de travail et constituent, à ce titre, une sorte de
cadre dans lequel évoluent les opérateurs et leur évite de
dévier à un moment ou un autre dans l'exécution de leurs
tâches. Ainsi, lorsque de nouveaux collaborateurs arrivent, on peut se
baser sur le standard de travail pour les former, ce qui permet de ne pas faire
baisser la qualité des produits et même de l'améliorer.
Cela donne également la possibilité d'améliorer les
délais et la productivité.
Le standard de travail amène également les
équipes à réaliser des démarches de
résolution de problème, ce qui apporte aussi sa pierre à
l'édifice de l'
amélioration
continue.
o SMED
Le Single Minute Exchange of Die est une
méthode de changement rapide de série qui permet de
réduire les temps non productifs. Il rend le système de
production plus réactif et répond à la demande du client
en termes d'optimisation des stocks et des tournées
d'approvisionnement.
Figure 15 : Modèle SMED
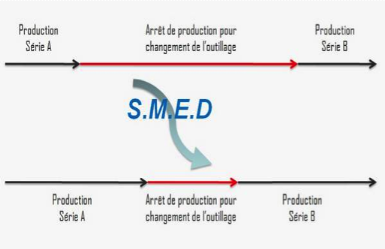
Source:
https://articles-agroalimentaires.blog4ever.com/standardisation-une-des-vocations-du-damaway-danone-manufacturing-way
o Capabilité du processus
Capabilité du processus est l'aptitude, la
capacité d'un process à respecter des spécifications,
à atteindre en permanence le niveau de qualité souhaité.
L'indice de Capabilité Processus (Cp) fournit une indication sur la
performance d'un processus par rapport aux limites admissibles, ce nombre sans
unité indique le rapport entre la dispersion (la variabilité du
processus) et la plage entre les tolérances. Plus grand ce nombre et
plus le processus est "capable". Moins l'indice est élevé est
plus la variabilité s'étend vers les limites, voire les
dépasse.
Un processus est réputé capable si la dispersion
de ses résultats est faible comparativement à la
tolérance.
On calcule la capabilité (notée Cp) par le
rapport : intervalle de tolérance / dispersion.
Avec Ts = tolérance
supérieure, Ti = tolérance
inférieure

· Pour Cp > 1.67 : Non préoccupant,
chercher à simplifier la gestion pour les coûts ;
· Pour 1.67 > Cp > 1.33 : Situation
idéale à maintenir ;
· Pour 1.33 > Cp > 1.00 : Situation trop
juste, nécessite de l'attention, Cp proche de 1 signifie qu'une
dérive peut créer des défauts ;
· Pour 1.00 > Cp > 0.67 : Existence de Non
conformes. Il faut contrôler à 100%, analyser le processus et si
possible l'améliorer ;
· Pour 0.67 > Cp : Analyse immédiate
des causes, urgence de mise en place de contre-mesures, révision des
tolérances.
v Les outils pour développer l'autonomie de la
responsabilisation et la réactivité des équipes
o Unités autonomes de production (UAP)
L'organisation d'une usine en Unités Autonomes de
Production permet de déléguer aux opérateurs le suivi des
indicateurs d'une zone de travail, l'analyse des problèmes et la mise en
place des mesures correctives. Cela permet de démultiplier les moteurs
de l'amélioration continue du Lean Manufacturing et de
permettre leur appropriation par les opérateurs.
v Les outils pour le pilotage et la gestion des
activités
o Management visuel
Le management visuel contribue à la communication et
à l'image de marque de la société. Son objectif est de
définir, à l'aide d'outils visuels, un environnement de travail
ayant les qualités suivantes :
ü Être le plus près possible de
l'opérateur ;
ü Faciliter la réactivité et donc
être une aide à la prise de décision ;
ü Faciliter et simplifier la définition des
objectifs.
La vue est certainement notre principal sens permettant
d'appréhender une situation, dans ce cas, comment traiter et
résoudre un problème s'il n'est pas visible. Le management visuel
tel qu'envisagé par le Lean est un révélateur de
la réalité qui demeure bien trop souvent cachée dans nos
entreprises.
o Supervision active
La supervision active est un système et un mode de
management fondée sur des relations de proximité entre le
responsable hiérarchique et ses collaborateurs. Lorsque l'on conduit le
changement, que ce soit dans le domaine marketing et commercial ou de
façon générale lorsqu'on touche à l'organisation
d'une entreprise, il est essentiel de disposer d'outils pour conduire ce
changement. La supervision active en est un qui vous permet, très
simplement de revoir et d'optimiser sa façon de gérer et
superviser ses équipes. Des bonnes habitudes que vous garderez ensuite
au quotidien.
o Animation globale à partir des indicateurs physiques
de performance (IPP)
Un Indicateur Physique de Performance en anglais Key
performance Indicator (KPI) est une mesure ou un ensemble de mesures
portant sur un aspect critique de la performance globale de l'organisation.
L'idée générale est de fixer des objectifs pour chacun de
ces indicateurs de performance et de mesurer ensuite leur valeur réelle
au fil du temps, à l'aide d'un tableau de bord. Lorsque les valeurs
réelles diffèrent des objectifs, le tableau de bord doit faire
ressortir ces écarts et les gestionnaires doivent alors agir en
conséquence.
o Démarche TPM
La Total Productive Maintenance vise à fiabiliser les
équipements de production tout en assurant la qualité du produit
et en réduisant les coûts de production et de maintenance. En
milieu industriel, elle permet d'améliorer le rendement des
équipements, diminuer les taux de pannes, développer la
maintenance préventive et la maintenance autonome, améliorer la
fiabilité et la maintenabilité des équipements.
v Les outils pour résoudre les problèmes et
s'améliorer en continu
o 5P
C'est un outil d'analyse causale tout comme l'arbre des
causes. La méthode de base de résolution de problèmes du
Lean insiste sur la nécessité de se poser cinq fois la
question « pourquoi ? » pour aller au-delà des causes
symptomatiques et trouver les causes fondamentales (sur lesquelles on pourra
alors agir pour éliminer le problème une fois pour toutes). Le
piège du «5 pourquoi ?» est la déduction en salle.
À chaque « pourquoi ?» il faut aller sur le terrain (Marche
Genba26(*)), et
s'adresser à la personne qui fait le travail et qui pourra donner une
réponse concrète plutôt qu'une réponse
imaginée par déduction.
o 5M
Le diagramme de causes et effets appelé
également diagramme d'Ishikawa, diagramme arêtes de poisson ou 5M
(Matière, Matériel, Méthode, Main d'oeuvre et Milieu) est
un outil développé par Kaoru Ishikawa utilisé dans la
gestion de la qualité. Ce diagramme représente de façon
graphique les causes aboutissant à un effet. Il peut être
utilisé comme outil de modération d'un brainstorming, comme outil
de visualisation synthétique et de communication des causes
identifiées. Il peut être utilisé dans le cadre de
recherche de cause d'un problème existant ou d'identification et gestion
des risques lors de la mise en place d'un projet. Ce diagramme se structure
habituellement autour des 5M.
Figure 16 : Diagramme d'Ishikawa
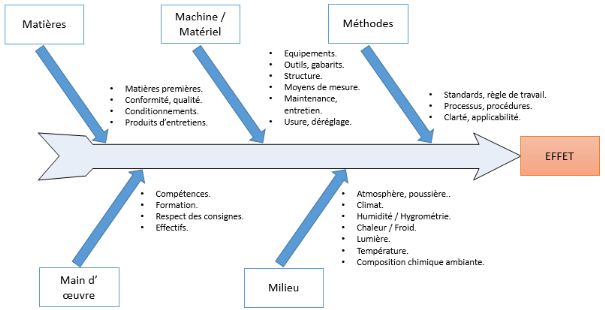
Source:
https://leanpourtous.wordpress.com/2016/11/02/diagramme-dishikawa/
o Arbre des causes
C'est un outil qui se présente sous la forme d'un
schéma arborescent, utilisé dans le domaine des risques
professionnels pour mieux identifier à posteriori tous les faits
nécessaires ayant abouti à un évènement
indésirable tel que l'accident de travail ou la défaillance d'un
processus.
De manière conventionnelle, on construit l'arbre
de droite à gauche, c'est-à-dire du pourquoi au comment,
afin que le sens de lecture (de gauche à droite) corresponde à
l'enchaînement logique des faits. À droite du tableau, on note
l'accident. C'est le point de départ.
On détermine les causes critiques primaires
en se posant la question "Qu'a-t-il fallu pour qu'advienne
l'accident ?". Ensuite, pour chaque cause trouvée, on
détermine les causes relatives (secondaires) en se posant les
deux questions suivantes :
ü « Est-ce que le fait X a été
nécessaire pour que le fait suivant Y apparaisse ? ».
Cette étape permet de supprimer toutes les informations inutiles.
ü « Est-ce que le fait X a été
suffisant pour que le fait suivant Y apparaisse ? ». Cette
étape permet d'assurer l'exhaustivité des informations utiles.
Maintenant que les faits sont organisés, l'arbre des
causes peut être construit. Les faits sont liés entre eux à
l'aide de trois types de liens logiques :
· Lorsqu'un fait X a été nécessaire
et suffisant pour que le fait Y se produise, on parle
d'enchaînement ;
Figure 17 : Symbolisation d'un Enchaînement
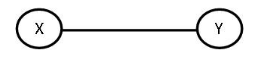
Source :
https://fr.wikipedia.org/wiki/Arbre_des_causes
· Lorsqu'un fait possède plusieurs
antécédents, il s'agit d'une conjonction ;
Figure 18: Symbolisation d'une Conjonction
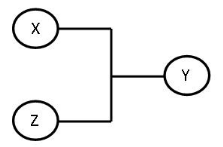
Source :
https://fr.wikipedia.org/wiki/Arbre_des_causes
· Un antécédent peut avoir plusieurs
conséquences différentes. C'est une disjonction.
Figure 19 : Symbolisation d'une Disjonction
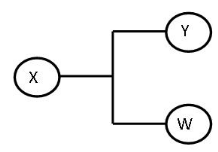
Source :
https://fr.wikipedia.org/wiki/Arbre_des_causes
Figure 20 : Modèle d'un arbre de causes
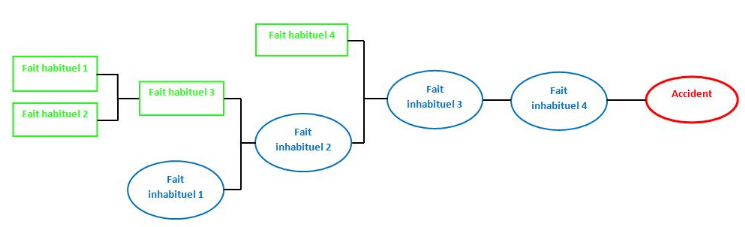
Source :
https://fr.wikipedia.org/wiki/Arbre_des_causes.
o QQOQCCP
Le sigle QQOQCCP également connu sous la variante
mnémotechnique CQQCOQP est un sigle résumant une méthode
empirique de questionnement. Outil qualité très efficace
pour cerner le plus complètement possible un problème, une
cause, une situation donnée. Très utile aussi dans le travail de
rédaction des procédures. Son nom vient des questions auxquelles
on doit répondre :
ü Quoi ? : De quoi s'agit-il ? (Objet,
opération, nature, ...)
ü Qui ? : Qui est concerné ?
(Exécutants, qualification)
ü Où ? : Où cela se produit-il
?
ü Quand ? : Quand cela survient-il ?
(Durée, fréquence...)
ü Comment ? : Comment procède-t-on ?
(Matériel, matières, méthode...)
ü Combien ? : Combien de fois cela se
produit-il ?
ü Pourquoi ? : Pourquoi cela se passe-t-il
ainsi ?
Toute démarche d'analyse implique en effet une phase
préalable de questionnement systématique et exhaustif dont la
qualité conditionne celle de l'analyse proprement dite. Ceci en vue de
collecter les données nécessaires et suffisantes pour dresser
l'état des lieux et rendre compte d'une situation, d'un problème,
d'un processus. Sa simplicité, son caractère logique et
systématique, font que beaucoup l'utilisent aussi pour structurer la
restitution des résultats de leurs analyses.
o Le diagramme de Pareto27(*)
Le diagramme de Pareto est un outil qualité
d'analyse, d'aide à la décision, mais aussi de communication. Il
permet de mettre en évidence la loi des « 80/20 »,
c'est-à-dire que 20% des causes provoquent 80% des effets, et donc
qu'une grande partie du problème peut être résolue en
traitant un nombre limité de causes. Le diagramme de Pareto permet de
déterminer les priorités d'actions.
o AMDEC (corrective / Préventive)
L'AMDEC est l'acronyme de l'Analyse des Modes de
Défaillance, de leurs Effets et de leurs Criticités. C'est une
méthode qui vise à répertorier pour un processus
donné l'ensemble des modes de défaillance qu'on peut lui associer
et d'évaluer la criticité de ces défaillances afin de
déterminer et de hiérarchiser ses points faibles. Il existe
plusieurs types d'AMDEC : l'AMDEC procédé, l'AMDEC produit,
l'AMDEC machine, l'AMDEC service et l'AMDEC processus. L'objectif de l'AMDEC
est d'évaluer les risques liés à un processus de
fabrication. Il pourra s'agir de risques liés à la
sécurité, à la qualité, à la performance de
production.
Le principe consiste à recenser toutes les causes
potentielles de chaque mode de défaillance et d'évaluer la
criticité. Cette dernière résulte d'une triple cotation
:
ü Note "G" : Gravité ou
sévérité de l'effet du défaut ou de la
défaillance ;
ü Note "O" : Occurrence ou fréquence
d'apparition de la cause ;
ü Note "D" : Détection : probabilité
de non détection de la cause.
L'indice de criticité (C) est obtenu par le produit des
trois notes : C = G x O x D
Plus la criticité est importante, plus la
défaillance considérée est préoccupante. Lorsque la
criticité dépasse la limite prédéfinie par le
groupe, ce dernier recherche les actions d'amélioration possibles pour
la ramener à un niveau acceptable en jouant sur :
ü La gravité (exemple : la gravité
d'une fuite de carburant sera diminuée par la mise en place d'un bassin
de rétention) ;
ü L'occurrence (exemple : en augmentant la
fiabilité d'un composant, en jouant sur la maintenance préventive
...) ;
ü La non détection (exemple : en mettant en
place des outils de contrôle et de surveillance, en formant les
contrôleurs ...).
o Global 8 Disciplines (8D)
Le G8D ou 8DO est une démarche issue de l'automobile
qui permet d'éradiquer un problème au sein d'une entreprise ou
organisation. La méthode a pour but de standardiser et formaliser les
procédures de gestion des problèmes au sein d'une organisation.
C'est une méthode de réaction rapide face à un
problème, qui s'applique dans le double objectif d'assurer la
continuité des flux et de trouver en même temps des solutions pour
éradiquer les causes racines du problème. Elle demande un travail
collaboratif entre différentes équipes. Les solutions
trouvées aux problèmes ponctuels sont continuellement
améliorées. Les huit étapes à entreprendre en
cas de problème ponctuel sont les suivantes :
ü 1D : Constitution d'un
groupe d'action corrective et nomination de l'animateur ;
ü 2D : Définition du
problème à traiter ;
ü 3D : Mise en place des
mesures de sauvegarde et/ou des actions curatives ;
ü 4D : Recherche des causes du
problème ;
ü 5D : Sélection des
actions correctives ;
ü 6D : Mise en place des
actions correctives retenues ;
ü 7D : Actions
préventives ;
ü 8D : Mesure de
l'efficacité des actions engagées, reconnaissance du travail de
l'équipe, clôture du dossier.
v Les outils pour une production sans défaut
o Poka-Yoke
Les systèmes anti-erreur permettent d'éradiquer
les erreurs et ainsi supprimer les contrôles afin de viser un niveau
d'excellence qualité.
o Maîtrise Statistique des Procédés
(MSP)
La Maîtrise Statistique des Procédés
repris en anglais Statistical Process Control (SPC) montre au travers
de représentations graphiques les écarts à une valeur
donnée de référence et sert à anticiper sur les
mesures à prendre pour améliorer n'importe quel processus de
fabrication industrielle (automobile, métallurgie, etc.).
Figure 21 : Carte de contrôle
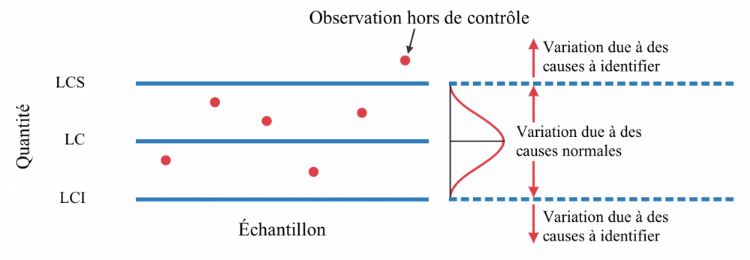
Source:
https://wikiagile.cesi.fr/index.php?title=Carte_de_contr%C3%B4le
o Plan d'expérience / Design Of Experiments
(DOE)
Dans la recherche maîtrisée de la
productivité et de la qualité, il est difficile d'identifier les
paramètres influents des processus, de savoir rendre les processus
robustes face aux variabilités, de quantifier les facteurs influents que
nous devons régler pour obtenir une production stable, économique
et à faible variabilité. Les plans d'expérience sont des
outils statistiques performants qui permettent d'atteindre ces objectifs. Bien
utilisés, ils aident à étayer par des faits, certaines
présomptions et à franchir une étape importante dans la
connaissance des processus afin de passer de la maîtrise des
caractéristiques des produits à une réelle maîtrise
des conditions de fabrication.
o La Méthodologie de résolution de
problème (MRP)
Outil qualité de travail en groupe destiné
à résoudre un problème, qui utilise une combinaison de
plusieurs outils tels que le Brainstorming, le diagramme de Pareto, le QQOQCCP,
les 5M...
II.1.2.4 LA STANDARDISATION DES PROCESSUS
Dans une démarche qualité, la standardisation
des processus est la phase qui vient après celle du diagnostic et du
plan d'action. Il est important également de noter que la
standardisation des processus précède deux phases toutes aussi
importante. Le pilotage de la performance d'une part, les audits et
l'amélioration d'autres parts. Il s'agit ici d'aboutir à la
modélisation des processus et d'obtenir une vision transversale de
l'organisation. Pour le faire, il revient de procéder par l'approche
processus.
Brandenburg et Wojtyna, (2003) affirment que l'approche
processus est une méthode d'analyse ou de modélisation. Elle
consiste à décrire de façon méthodique une
organisation ou une activité, généralement dans le but
d'agir dessus.
Standardiser les processus métier permet de
répondre aux exigences de la norme ISO 9001 (ou de tout autre
référentiel de démarche qualité) de manière
plus rapide tout en impliquant l'ensemble du personnel et en créant de
la cohérence et de la transparence pour l'organisation.
Selon la méthode développée par le
cabinet 8M Management, cinq étapes sont nécessaires
à la standardisation :
1. Identification et catégorisation des processus
stratégiques pour la performance, la qualité des produits et
services et la satisfaction client, définition de leur contenu :
processus de réalisation des produits et services de la demande client
au sens large à la livraison et retours client, processus supports qui
contribuent à la réalisation des produits et services et
processus de direction fournissant un cadre cohérent pour
déployer vos objectifs de performance et de qualité ;
2. Analyse et optimisation des processus : détail des
activités, ressources, éléments d'entrée et de
sortie, informations, recensement des erreurs, lourdeurs, redondances,
incohérences, risques, collecte des données sur les
résultats des activités ;
3. Définition des règles métier visant
l'amélioration, la baisse des risques et automatisation de certaines
tâches ;
4. Formalisation des processus selon la méthode de
modélisation adaptée à l'organisme, rédaction des
documents nécessaires à votre système qualité
(manuel qualité, fiches processus, procédures, instructions,
enregistrements, etc.) ;
5. Mise en application.
La standardisation permet d'analyser et d'organiser les
activités de manière optimale, de partager l'information et la
connaissance en interne et avec les parties prenantes (clients, fournisseurs,
etc.) tout en restant cohérent avec votre stratégie et vos
objectifs. L'organisation est plus lisible, le positionnement est
renforcé.
La norme ISO9001 : 2000 distingue trois grandes
catégories de processus :
· Les processus de réalisation : ils contribuent
directement à la réalisation du produit ou du service, depuis la
détection du besoin du client à sa satisfaction. Ils
correspondent au coeur de métier de l'organisation. Ces processus sont
souvent appelés « processus métier » ;
· Les processus de support : ils contribuent au bon
fonctionnement des processus de réalisation en leur apportant les
ressources nécessaires ;
· Les processus de gestion (pilotage) : ce sont les
processus qui permettent la maîtrise des autres processus et
l'amélioration continue en fournissant des indicateurs répondant
à des objectifs précis.
Gillot (tel que cité dans Gaibor, 2011) propose de
répondre aux trois questions suivantes pour identifier correctement les
processus :
ü Le processus est-il transverse à de multiples
départements/services ?
ü Le processus génère-t-il du revenu ?
ü Le processus est-il orienté client ?
Apporte-t-il de la valeur ajoutée au client ?
La norme ISO 900128(*) :2000 n'exige pas une classification des processus,
mais elle préconise de bien distinguer et identifier les processus
suivant leur type. Cette identification reste toujours individuelle et
dépend du contexte, et de l'activité de l'organisation.
Figure 22 : Exemple de fiche synthétique du
processus commercial
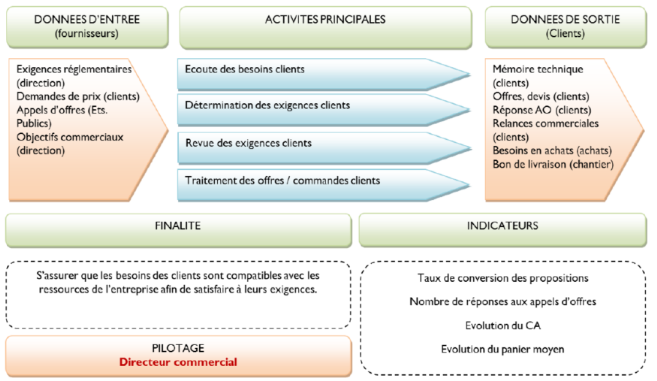
Source : Jérémy CICERO -
www.qualiblog.fr
CONCLUSION DU CHAPITRE 1
Nos écrits nous ont permis de mettre en évidence
l'importance d'un cahier des charges qui permettrait aux différentes
parties prenantes de s'accorder sur les exigences d'un livrable. Cette
démarche préalable doit s'accompagner d'une démarche
qualité afin d'anticiper sur les écarts pendant la production.
Il en ressort également l'importance de prendre en
compte en plus des contraintes environnementales mais aussi le triptyque
fiabilité, maintenabilité et disponibilité des
équipements afin d'assurer une production optimale et en anticipant sur
les défaillances éventuelles des machines.
Par ailleurs, il est important de standardiser les processus
de production non seulement des équipements mais aussi des produits.
L'amélioration continue s'impose à toutes les entreprises qui
souhaitent s'inscrire durablement comme acteur incontournable dans leur secteur
d'activités.
CHAPITRE 2 : ETAT DES LIEUX DE LA
CONSTRUCTION ET DE LA MAINTENANCE DU SÉCHOIR SAMOA
INTRODUCTION DU CHAPITRE 2
Le cacao camerounais connu sous le label « origine
Cameroun » souffre du fait de la dégradation des
caractéristiques organoleptiques (odeurs de fumée, goût)
pourtant jadis prisé sur le marché international. Cette
détérioration de son image de marque est due à des
mauvaises pratiques post récolte.
Les producteurs qui sont les principaux acteurs du processus
de séchage utilisent des séchoirs défectueux avec pour
résultat des fèves imprégnées d'odeur de
fumées, des fèves qui moisissent et des risques de
ré-humidification.
Partant de ce constat, le gouvernement a initié un
projet dans le Sud-ouest du Cameroun afin de réhabiliter les
séchoirs SAMOA vétustes. Il s'agit du PRSC dont la mission est
d'accompagner les producteurs durant la phase de séchage artificiel des
fèves de cacao afin d'améliorer leur qualité et
reconquérir les parts de marché.
A moyen terme, l'objectif poursuivi est l'amélioration
des revenus des producteurs de la filière cacao, le rehaussement de
l'« origine Cameroun » sur le marché international
et la réduction du coût environnemental des opérations de
séchage.
I. PRÉSENTATION DES MÉTHODES
DE SÉCHAGE THERMIQUES DE CACAO AU CAMEROUN
Parmi les bassins de production du cacao que regorgent le
Cameroun, certains bénéficient d'un climat tempéré
et favorable pour le séchage naturel des fèves de cacao
après la fermentation.
Dans deux régions, la période de récolte
coïncide avec la saison de récolte des cabosses de cacao. Sont
concernées, une partie du département du Moungo dans la
région du Littoral et toute la région du Sud-ouest. Dans ces
zones, les producteurs sont contraints de pratiquer le séchage
artificiel.
Le challenge des pouvoirs publics camerounais dans ces zones
est d'accompagner les producteurs dans le mieux des cas afin de leur
éviter un investissement supplémentaire lors des
opérations post-récolte et de maintenir l'engouement de ces
acteurs à l'égard de la filière cacao.
I.1 ÉTUDE DES DIFFÉRENTES
MÉTHODES DE SÉCHAGE THERMIQUES
Après fermentation des fèves, il convient
d'éliminer les restes de pulpe en lavant les fèves ou en les
mélangeant à de la sciure de bois et à des feuilles
sèches de bananier. Les fèves sont ensuite séchées
de façon naturelle ou artificielle en fonction de la zone
agro-écologique afin de ramener la teneur en eau de 55% à 7%. Le
but du séchage des fèves de cacao est d'assurer leur bonne
conservation et éliminer une partie de l'acide acétique
formé pendant la fermentation soit environ 40% (Amani, 2014).
Facile à conduire, le séchage naturel ou solaire
est la méthode la plus utilisée dans les bassins de production
à climat favorable et dure huit à quinze jours. Dans les petites
exploitations, les fèves sont souvent étalées sur des
nattes en bambou ou en pailles posées sur le sol, sur des bâches
en plastique noir, etc. Remuer fréquemment pendant environ cinq jours.
Trier pour éliminer les fèves défectueuses et plates.
Le séchage artificiel quant à lui, est
pratiqué dans les bassins de production à fortes
pluviométries et nécessite un investissement
supplémentaire en termes d'équipement. Toutefois le
séchage est rapide avec une durée moyenne d'une
journée.
Dans les deux cas, une fois les fèves
séchées, leur poids moyen est d'un gramme avec une teneur en
humidité d'environ 7 %. Mettre à l'abri dans un endroit sec et
bien aéré pour les protéger de l'humidité (pluie,
humidité nocturne) et éviter les risques de développement
de moisissures et l'action des insectes.
Dans certaines zones agro-écologiques, les producteurs
pratiques dans un premier temps un pré-séchage naturel au soleil
et ensuite applique un séchage artificiel.
Quel que soit le type de séchage :
· S'assurer que le produit à sécher est
bien fermenté ;
· Procéder au tri des fèves pour enlever
les saletés, les impuretés, ainsi que les fèves qui sont
plates ou germées ;
· Respecter l'épaisseur de la couche à
sécher : 4 à 6 cm pour le séchage naturel et 5 à 10
cm pour le séchage artificiel ;
· Surveiller régulièrement le cacao en
prélevant quelques fèves vers la fin du séchage. Les faire
craquer sous la main et en fendre quelques-unes pour s'assurer que le cacao est
tout à fait sec aussi bien à l'intérieur qu'à
l'extérieur.
I.1.1 ÉTUDE DES DIFFÉRENTES
MÉTHODES DE SÉCHAGE THERMIQUES
La méthode de séchage solaire ou naturel est
pratiquée dans les plantations de petite taille et demande une forte
mobilisation de main d'oeuvre.
Tout au long de la période de séchage, les
fèves sont remuées afin de favoriser un séchage
homogène. Cette méthode offre des fèves de bonne
qualité avec notamment :
· Une acidité acceptable ;
· Un goût fruité, caractéristique
dû à une teneur forte en acide acétique.
Au Cameroun, pour sécher le cacao, plusieurs types de
séchoirs sont utilisés. En fonction des zones de production, nous
pouvons les classer comme suit :
ü Séchage sur une aire cimentée dans la
zone du Centre ;
ü Le séchoir « autobus » au
Sud ;
ü Le sol nu sur des nattes ou des bâches dans
toutes les zones ;
ü Le séchage sous serre.
Il est à noter que les autres méthodes de
séchage pratiquées au Cameroun tel que le séchage à
même le sol, le séchage sur des routes bitumées sont
considérées comme des mauvaises pratiques à ne pas
promouvoir.
I.1.1.1 LE SÉCHAGE DE CACAO SUR UNE AIRE
CIMENTÉE
Le séchage solaire sur aire cimentée,
généralement pratiqué dans la région du Centre a
l'avantage que le cacao est exempt des corps étrangers tels que les
cailloux et les morceaux de bois. L'inconvénient est que le produit
n'est pas protégé contre les pluies et les intempéries.
Les dalles de ciment surchauffent la coque et la font éclater. Ceci
constitue un inconvénient pour la qualité du produit obtenu, car
c'est cette coque qui protège la masse du cacao (Kamogne et
al.,2012).
Photo 1: Séchage sur aire cimentée
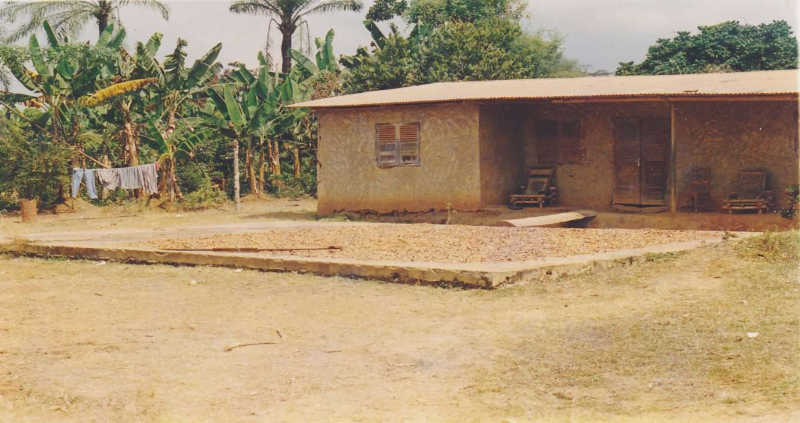
Source: KAMOGNE et al., 2012
I.1.1.2 LE SÉCHOIR « AUTOBUS
»
C'est une plateforme de séchage construite en
matériaux locaux (bambou de raphia, natte tissée). La toiture en
natte est fixe. Les claies en natte de bambou coulissent sur des rails
constitués de bambou de raphia fixés de chaque côté
sous la toiture. Quand il pleut, on pousse les claies sous la toiture fixe. Les
dimensions des nattes tressées en bambou sont généralement
de 3 m x 4 m. La densité du cacao frais au mètre carré
varie de 10 à 25 kg ; la densité recommandée étant
de 10 kg/m². La photo ci-dessous illustre le séchoir autobus en
deux variantes. Ce type de séchoir est le plus utilisé par les
planteurs du sud Cameroun. Son avantage est la protection des produits contre
la pluie et son inconvénient est que le produit n'est pas
protégé contre les insectes. (Kamogne et al.,2012).
Photo 2: Séchage
« Autobus »
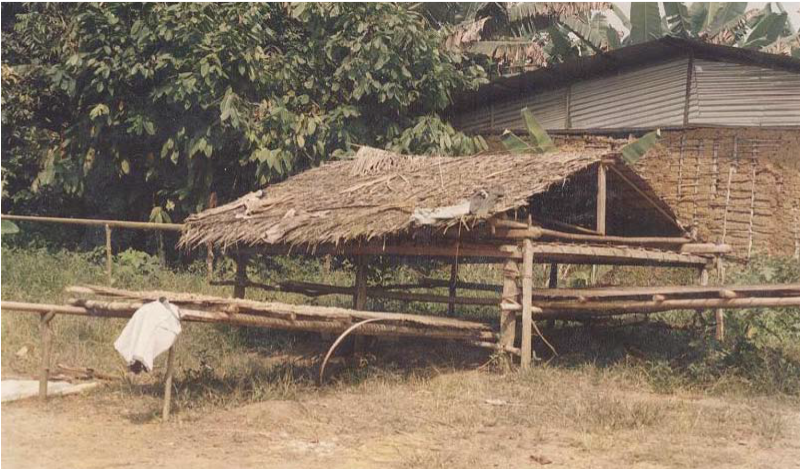
Source: KAMOGNE et al., 2012
I.1.1.3 LE SÉCHOIR SOUS TENTE À TOIT
MOBILE
Le séchoir à toit mobile comprend une aire de
séchage fixe avec un toit pouvant être retiré selon les
conditions climatiques. C'est une plateforme de séchage construite en
matériaux locaux (bambou de raphia, natte tissée). La claie en
natte de bambou est fixe et soutient le toit. (Kamogne et al.,
2012).
Photo 3 : Séchage sous tente (Toiture
mobile)
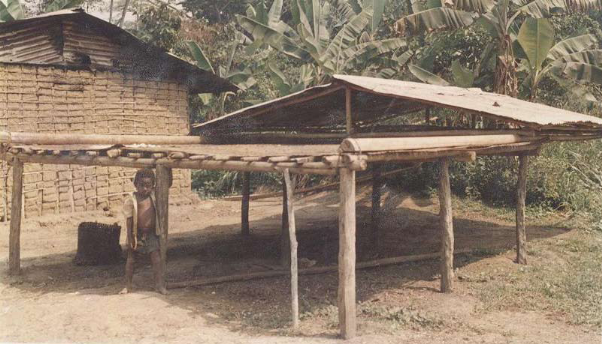
Source : KAMOGNE et al., 2012
I.1.1.4 LE SÉCHOIR PAR EFFET DE
SERRE
Le séchoir sous serre permet de réduire les
manipulations et de sécher de grandes quantités de fèves.
Il nécessite toutefois un investissement important et il est
nécessaire de prévoir un système de ventilation
(basé sur le principe de la convection) et un système de
contrôle des paramètres de séchage.
Photo 4 : Séchage sous serre
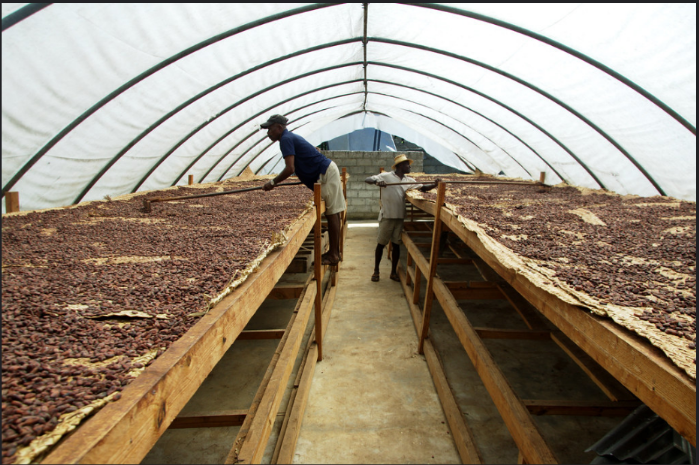
Source :
https://www.flickr.com/photos/reforestaction/31200731586
I.2.1 ÉTUDE DE LA MÉTHODE DE
SÉCHAGE ARTIFICIEL
Le séchage artificiel est généralement
utilisé pour les exploitations importantes et dans d'autres cas dans des
zones à forte pluviométrie. Dans d'autres cas le séchage
artificiel intervient après un pré-séchage ou
séchage solaire. Dans chacun des cas le type d'équipement est
différent.
Lors de ce type de séchage, il est important de
maitriser la température de chauffe et éviter de traverser la
barre de 55°C. Au-delà de cette température, il y a des
risques de destruction de la polyphénol-oxydase responsable du
brunissement des fèves considérées comme facteur de
qualité (Amani, 2014).
I.2.1.1 PRÉSENTATION DU SÉCHOIR
ROTATIF
Le séchage complet en séchoir rotatif dure
environ 30 heures, cependant il est conseillé de procéder
à un pré-séchage solaire des fèves pendant 24
heures pour éviter de colmater les perforations des grilles. Le
séchage final en séchoir rotatif sera alors achevé en 20
heures.
Les séchoirs de types GUARDIOLA ou OKRASSA,
déjà fort anciens, sont encore utilisés. Ils se composent
d'un cylindre (en aluminium) perforé et compartimenté,
monté sur un châssis, et animé d'un mouvement de
rotation.
La distribution d'air chaud est assurée par un tube
central perforé ou par des tubes perforés radiaux fixés
sur l'arbre creux. On leur reproche :
· Un investissement élevé pour la
capacité de séchage ;
· Un rendement calorifique faible ;
· Une puissance installée élevée/kg de
cacao traité ;
· Un remplissage et une vidange malaisés.
Figure 23 : Séchoir rotatif
« Guardiola »
Source : AMANI, 2014
I.2.1.2 PRÉSENTATION DU SÉCHOIR
MÉCANIQUE STATIQUE
Les séchoirs statiques sont souvent utilisés en
plantation. Il s'agit d'une plate-forme constituée par un treillis
métallique ou une tôle perforée sous laquelle est
pulsé de l'air chaud provenant d'un générateur à
échangeur, alimenté soit au fuel, soit au bois. Le fuel est de
plus en plus utilisé pour des raisons de commodités d'emploi et
de réglage de température.
Un système plus perfectionné consiste à
faire circuler un remueur-déblayeur (arbre muni de palettes ou de
doigts) animé d'un mouvement de rotation ou non. Ce système
évite la prise en masse du cacao, surtout dans la phase humide du
séchage (60 à 30 % d'eau), permet d'homogénéiser la
masse, et ne nécessite plus de manutention, le produit étant
évacué à l'extrémité du séchoir
(Amani, 2014).
Figure 24: Séchoir Statique
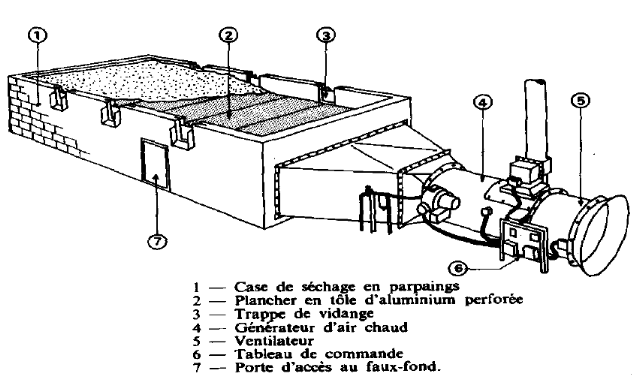
Source : AMANI, 2014
Ces séchoirs statiques sont généralement
d'un coût peu élevé à l'achat, mais sont peu
économiques à l'usage, car l'air n'est pas recyclé et, en
fin de séchage, sort après avoir traversé la couche de
cacao avec une humidité relative trop basse (faible rendement
thermique). Il est important de travailler sur une épaisseur de couche
aussi élevée que possible pour sécher
économiquement le produit. (En général la couche est de 30
à 40 cm). Néanmoins ce type de séchoir est surtout utile
lorsque le produit à sécher sort de fermentation, en
complément au séchage solaire. La température d'attaque de
l'air ne doit pas dépasser 60° C à 65° C pour que
l'acidité des fèves reste faible. En pratique, on cherche
à se rapprocher du séchage solaire. Les vitesses d'air doivent
être lentes (0,4 m/s à 0,5 m/s), et le séchage de 55 %
à 7 % doit durer au moins 20 heures, c'est-à-dire que la vitesse
de séchage ne doit pas dépasser 2,5 % par heure.
I.2.1.3 SÉCHOIR SAMOA À CACAO
UTILISÉ DANS LE BASSIN DU SUD-OUEST
Les séchoirs "SAMOA" ont été
installés, pour la plupart, en 2002 et 2003 dans la région du
Sud-ouest au Cameroun. Près de 2500 séchoirs SAMOA ont
été construits et distribués aux producteurs de cacao. Le
présent projet d'innovation du modèle de séchoir "SAMOA"
entre dans le cadre de la volonté du gouvernement camerounais
d'améliorer de la qualité du cacao.
Ce type de séchoirs présente de nombreux
avantages :
ü Une capacité importante : 400 Kg de fèves
peuvent être séchés en même temps ;
ü Le séchage ne nécessite pas la
présence du soleil : le séchage peut se faire de jour comme de
nuit ;
ü Le séchage peut se faire même en
période de pluies ;
ü Le séchoir est facile à mettre en
oeuvre dans la mesure où il est de fabrication facile et il est
fait avec les matériaux locaux et facilement disponibles (hormis la buse
en acier) ;
ü Le séchoir utilise comme source d'énergie
le bois disponible dans la zone ;
ü Il permet d'avoir le taux d'humidité voulu
pendant un temps plus court qu'avec le séchage solaire.
Ces séchoirs posent malheureusement aussi de nombreux
problèmes à l'usage dans les zones où ils sont
exploités :
ü Le séchage se fait pendant un temps plus ou
moins long ; la fin du séchage est le plus souvent jugée au
goûté ou manuellement en frottant les fèves sèches
entre elles. C'est le son produit qui permet de juger si le séchage peut
être arrêté;
ü Le phénomène de retour de la
fumée (l'une des causes des Mura) : celui s'explique par
le fait que la fumée produite n'est pas totalement évacuée
à travers la cheminée, une partie est refoulée et sort par
l'orifice d'alimentation du bois. Une partie de cette fumée entre en
contact avec les fèves ;
ü Les perforations observées au niveau des
buses du séchoir (Mura en fin de fabrication des
séchoirs SAMOA) : elles entraînent un passage de la fumée
à travers les orifices avec pour conséquence un
dépôt de fumées sur les fèves ;
ü La source d'énergie : les opérateurs
utilisent le plus souvent des troncs morts d'hévéa qui est un
bois qui consume en produisant assez de fumées avec des substances
cancérigènes et dangereuses ;
ü Les pertes de chaleur au niveau du
séchoir : le séchoir n'est pas thermiquement isolé, par
conséquent une partie de la chaleur produite arrive à la paroi et
se dissipe à travers le mur ;
ü Les chutes de brisures de cacao
(gaspillages) : les brisures passent le plus souvent à travers les
nattes de séchage et par percussion avec la buse créent des
étincelles qui peuvent aboutir à leur combustion et,
éventuellement, à un incendie (des cas d'incendies ont
été observés d'après les cacaoculteurs).
De ces différentes dérives se dégagent
des constats qui peuvent être orientés suivant trois axes :
ü La qualité du produit : risque de
teneur élevée en HAP, humidité résiduelle des
fèves plus ou moins élevée ;
ü La performance du séchoir : perte de
chaleur, consommation excessive de bois ;
ü Sécurité : risque d'incendie.
Photo 5 : Séchoir SAMOA
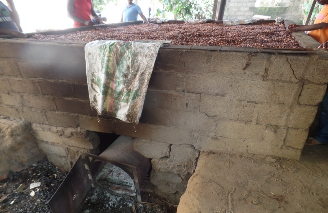
Source: Observation BAGNAKA (2017)
Adabe et Ngo-Samnick (2014) illustrent en détails ce
dispositif de séchage dans le schéma ci-après.
Figure 25: Détails du Séchoir SAMOA
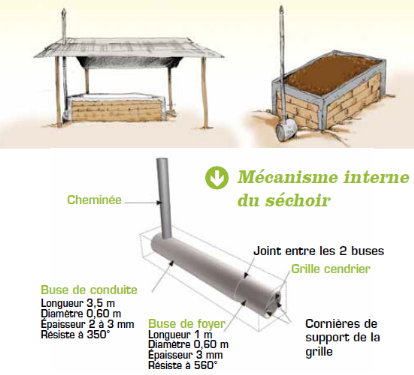
Source : ADABE et NGO-SAMNICK (2014)
II.
AMÉLIORATION DU SYSTÈME DE SÉCHAGE SAMOA
L'observation de la pratique de séchage artificiel dans
le bassin a permis de déceler des failles dans le fonctionnement de
l'équipement même si le facteurs humains est aussi
incriminés. Ces défaillances sont plurielles. Depuis la
conception jusqu'à l'utilisation en passant par la fabrication. Pour
corriger ces défauts, il est important de comprendre leurs origines afin
de réviser le cahier de charges en conséquence. La mise en place
d'une démarche qualité hybride telle que le Lean Six
Sigma pendant la phase de fabrication de ces séchoirs est possible.
Pendant que le Lean Management s'articule autour de
trois principaux axes dont :
ü La fabrication des séchoirs à moindre
coûts ;
ü L'optimisation des délais de
fabrication ;
ü La recherche de la qualité.
Le Six Sigma va permettre :
ü D'améliorer le processus de fabrication des
séchoirs ;
ü D'éliminer des défauts sur les
séchoirs ;
ü De réduire le risque de rejet par
l'utilisateur.
Le succès de cette approche d'amélioration est
possible si la connaissance de la démarche et la maitrise des outils
présentés dans le chapitre 1 sont maitrisés.
II.1 LES DÉFAUTS DE CONCEPTION DES
SÉCHOIRS SAMOA
Le séchoir SAMOA a été conçu par
des bureaux d'études basés en métropole. Les
ingénieurs n'ont pas pris suffisamment connaissance des contraintes
d'utilisation et des contraintes environnementaux.
· Les producteurs se plaignent d'un séchoir
très lourd et difficile à transporter et à mettre en
oeuvre (installation) ;
· Le système d'évacuation des fumées
doit être amélioré en combinant :
o La création d'une pente sur le long de la conduite
(mise en place des berceaux)
o L'installation d'un soufflet pour accélérer
l'évacuation des fumées d'une part et pour attiser le feu
également.
II.1.1 LES FACTEURS ENVIRONNEMENTAUX À PRENDRE
EN COMPTE
La plupart des plantations des producteurs sont
enclavées et les voies d'accès sont exiguës. Les producteurs
sont donc obligés d'installer leur séchoir à
proximité de leurs plantations.
Les séchoirs sont livrés et
réceptionnés dans les coopératives. Chaque producteur
s'occupe de transporter son séchoir jusqu'à sa destination
finale.
II.1.2 LES CONTRAINTES D'UTILISATION
Les insuffisances sur le contrôle de température
ont été constatées. Les séchoirs
« nouvelles générations » devront
être équipés des thermomètres afin de
contrôler la température de chauffe. La température de
séchage doit être maintenue dans seuil compris entre 55°C et
65°C.
Afin d'éviter de maintenir la porte du foyer ouverte
pendant le séchage, un soufflet sera préconisé afin
d'attiser le feu en cas de besoin.
Une note de calcul doit être effectuée
également en amont afin de trouver une épaisseur optimale des
tôles afin d'alléger au mieux le séchoir.
II.1.3 LE CAHIER DES CLAUSES TECHNIQUES
PARTICULIÈRES
Ce document est indispensable pour l'exécution des
travaux publics et fait partie du cahier des charges. Ce sont les stipulations
qui donnent une description précise des prestations à
réaliser et permettent au sous-traitant d'avoir un canevas pour la
réalisation des travaux et au maître d'oeuvre de suivre le
déroulement du marché et la bonne exécution de ces
prestations.
II.2 LES DEFAUTS DE FABRICATION SUR LES SECHOIRS
SAMOA
L'organisation au sein du PRSC, ne permet pas au chef de
mission d'être à la fois sur le terrain pour l'accompagnement, la
sensibilisation des producteurs et de suivre la fabrication des séchoirs
auprès des entreprises adjudicataires. Ces chefs de mission ne
possèdent pas des connaissances pointues dans le domaine de la
chaudronnerie et du soudage.
Beaucoup de défauts de fabrication ont
été constaté sur les séchoirs au moment de la
livraison. Pour déceler les erreurs de fabrication pendant
l'exécution des travaux, il convient de confier cette tâche
à un expert du domaine de la métallurgie qui va jouer le
rôle de maître d'oeuvre.
Photo 6 : Défaut de soudage et défaut
d'étanchéité
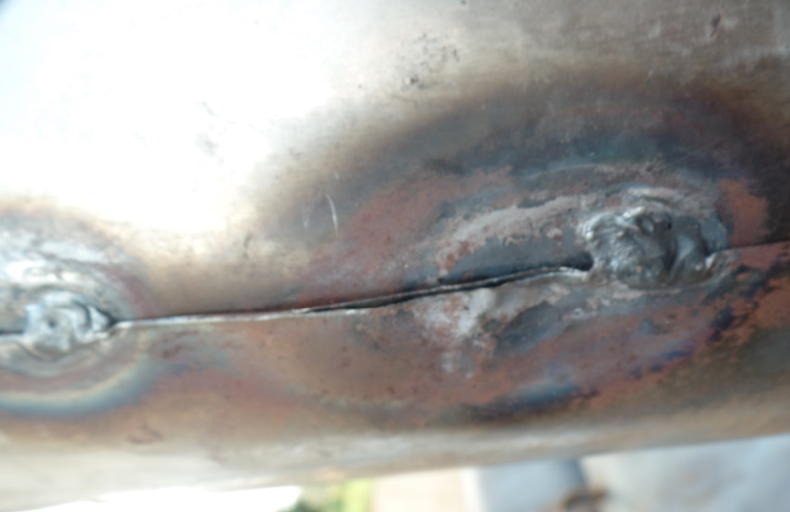
Source : Observation BAGNAKA (2017)
II.2.1 LA NATURE DES MATERIAUX À
UTILISER
Depuis novembre 1992, la norme européenne NF EN 10027
« Système de désignation des aciers »
définit deux systèmes de désignation des aciers : une
désignation symbolique qui se substitue à l'ancienne
désignation française (NF 35-501) et un système
numérique qui constitue une désignation simplifiée.
La désignation symbolique, la plus répandue,
classe les aciers en fonction de leur emploi, leurs caractéristiques
physiques ou mécaniques ou leur composition chimique. (
http://www.aciersspeciaux.fr/aciers-de-construction/)
Certains séchoirs sont fabriqués avec des aciers
présentant un niveau de corrosion avancé avec des pertes
d'épaisseur manifeste. La maîtrise d'oeuvre doit s'assurer que les
aciers utilisés sont neufs et possèdent des certificats
matières afin d'assurer toute traçabilité. Pour le cas
échéant, le matériau requis est un acier ordinaire sans
alliage codifié sous l'appellation S235. La lettre
« S » (Structure) désigne la nature de l'acier et le
domaine d'utilisation. Le chiffre « 235 » est la limite
élasticité minimale de ce métal en MPa
(Méga-Pascal). Toutes ces informations sont consignées dans le
certificat matière qui est remis à l'entreprise au moment de
l'achat de ces matériaux.
Il en est de même pour les électrodes à
souder qui doivent être vérifiées avant utilisation. Le
choix de l'électrode à souder tient compte de la nature du
métal à souder et de son épaisseur.
II.2.2 LES CONTRÔLES ET TESTS APRES
FABRICATION
Les contrôles doivent être faits au fur et
à mesure que l'exécution des travaux se déroule. Les
points de contrôle sont définis en amont dans le cahier des
charges.
Les contrôles requis sont non destructifs. Après
le traçage des tôles planes un contrôle dimensionnel est
effectué et un contrôle visuel.
Après les travaux de soudage, il convient d'effectuer
des contrôles surfaciques appelé ressuage. Cette examen permet de
se rassurer que la soudure est parfaite et continue.
Sur certains séchoirs il a été
constaté des percements au niveau des cordons de soudage. Ce type de
défauts est de nature à laisser passer les fumées pendant
le séchage.
Ajouter à ce défaut, nous avons constaté
des défauts d'étanchéité entre le foyer et le reste
de la conduite. Un joint réfractaire est à préconiser afin
d'éviter la propagation des fumées hors de la conduite.
Photo 7 : Défaut de fabrication sur Séchoir
SAMOA (Tôle perforée)
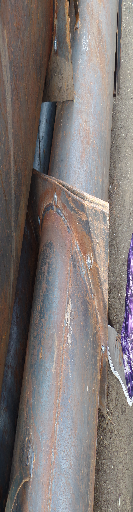
Source : Observation BAGNAKA (2017)
II.2.3 LA LIVRAISON DES SECHOIRS
Les entrepreneurs chargés de l'exécution des
travaux de fabrication des s'séchoirs sont installés en
majorité à Douala. Il faut dont transporter les séchoirs
jusqu'à Kumba. Le séchoir sont empilés les uns sur les
autres dans des camions de fortunes. Les points de levage
aménagés pour la manutention ne sont pas équidistants et
ne permettent pas un levage des séchoirs à l'horizontal. Des
réserves ont également été émise pour
améliorer ces points de levages et sélectionner des transporteurs
professionnels afin d'éviter également la déformation des
séchoirs pendant le transport et la manutention.
Photo 8 : Point de levage non conforme
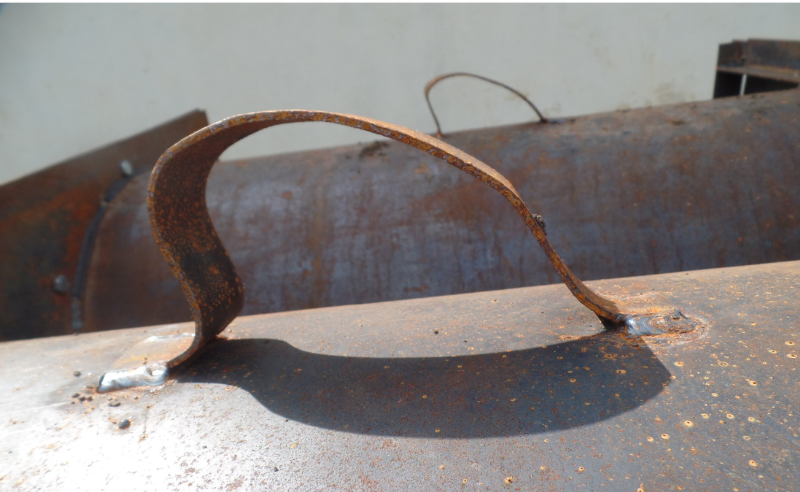
Source : Observation BAGNAKA (2017)
II.3 L'EXPLOITATION DES SECHOIRS SAMOA
Nous avons observé et interrogé les producteurs
durant la phase d'exploitation des séchoirs. Le premier constat
effectué est le fait que les séchoirs SAMOA ne sont pas toujours
livrés avec un guide d'utilisation encore moins avec un guide
d'installation.
Le tableau ci-dessous justifie que 69,5 % de producteurs n'ont
pas de manuel d'utilisation de séchoirs.
En cas de défauts apparus sur les séchoirs
pendant l'exploitation, les producteurs continuent quand même de les
utiliser. Par exemple la récurrence de l'absence
d'étanchéité qui conduit directement à la
contamination des fèves par l'odeur des fumées.
TABLEAU 3: UTILISATION DES SECHOIRS SAMOA
|
Fréquence
|
Fréquence
|
%
|
% valide
|
% cumulé
|
Valide
|
Producteurs ayant un manuel d'utilisation des séchoirs
SAMOA
|
61
|
30,5
|
30,5
|
30,5
|
|
Producteurs n'ayant pas un manuel d'utilisation des
séchoirs SAMOA
|
139
|
69,5
|
69,5
|
100,0
|
|
Total
|
200
|
100,0
|
100,0
|
|
Source : Travail étudiant.
Enquête BAGNAKA (2017)
II.3.1 LA MATRICE DES DÉFAUTS DES
SÉCHOIRS SAMOA
Le tableau ci-dessous présente le récapitulatif
des défauts majeurs sur les séchoirs SAMOA susceptibles
d'être corrigés pour l'obtention d'un équipement fiable.
TABLEAU 4: RÉCAPITULATIF DES DÉFAUTS DES
SÉCHOIRS SAMOA
Item
|
Type de défauts
|
Origine du défaut
|
Impact
|
Mesure correctives
|
1
|
Absence d'un joint d'étanchéité entre le
foyer et la conduite de fumée
|
Défaut de conception
|
Contamination des fèves par des fumées
|
Mettre en place un joint d'étanchéité
adapté
|
2
|
Discontinuité des cordons de soudures
|
Défaut de fabrication
|
Contamination des fèves par des fumées
|
- Choix approprié des électrodes à souder
- Bon réglage du poste à souder
- Maitrise d'oeuvre
|
3
|
Percement sur le séchoir
|
Défaut de fabrication
|
Contamination des fèves par des fumées
|
- Bon réglage du poste à souder
- Contrôle qualité pendant la fabrication
- Maitrise d'oeuvre
|
4
|
Déformation de la conduite de fumée
|
Mauvais conditionnement
|
Contamination des fèves par des fumées
|
Sélection des transporteurs professionnels
|
5
|
Déformation de la cheminée
|
Mauvais conditionnement
|
Contamination des fèves par des fumées
|
Sélection des transporteurs professionnels
|
6
|
Forte épaisseurs de la conduite
|
Défaut de conception
|
Difficulté à installer le Séchoirs
|
Optimisation de l'épaisseur des aciers par une note de
calcul
|
7
|
Point de levage inadapté
|
Défaut de conception
|
Chute des séchoirs pendant la manutention
|
- Mise à jour du cahier de charges
- Maitrise d'oeuvre
|
Source : Travail étudiant.
Enquête BAGNAKA (2017)
II.3.2 LES ACTIONS DE MAINTENANCE
Le séchoir SAMOA une fois installé, ne peut plus
être amovible. D'où l'importante de l'installer avec soin
après s'être rassuré qu'il est bien conforme.
Toutefois il convient de noter à chaque
opération de séchage, le foyer doit être nettoyé et
débarrassé des cendres et autres résidus de bois avant sa
prochaine exploitation.
II.3.3 LES INNOVATIONS À APPORTER SUR LES
SÉCHOIRS SAMOA
Le séchoir SAMOA a été conçu pour
être directement utilisable par les producteurs sans investissement
supplémentaire.
Nos propositions vont à l'endroit des pouvoirs publics
à travers le MINCOMMERCE qui est garant de cette partie de la
filière cacao.
Il est important d'intégrer un dispositif
(thermomètre industriel) pour palper la température de
séchage pendant le procédé de séchage.
Un système de ventilation est également à
concevoir afin de maintenir la porte du foyer fermée.
La combustion dans le foyer est faite par du bois de
chauffage. Nous avons proposé au PRSC d'envisager une autre source de
combustion telle que le biogaz qui peut être mis en place avec des moyens
modestes. Il peut être obtenu par fermentation des matières
organiques à l'absence de l'oxygène.
CONCLUSION DU CHAPITRE 2
Ce chapitre nous a permis d'établir l'efficacité
de l'action des pouvoirs publics sur le terrain à travers le PRSC qui
s'attèle à distribuer les séchoirs à tous les
producteurs.
Au demeurant, des actions fortes doivent être mises en
place pour améliorer ces équipements. Outre les limites
constatées durant les phases de conception et de fabrication, il
convient de systématiser la mise à disposition d'un manuel
d'utilisation et de maintenance des séchoirs.
Nous avons également relevé la
possibilité de corriger les défauts des séchoirs. La
fabrication et la distribution des séchoirs se faisant en vague, nos
propositions seront prises en compte dans le sens d'améliorer les
performances de cet outil.
A titre de rappel, l'hypothèse à laquelle
répond ce chapitre est la première des deux hypothèses
spécifiques à savoir « Les séchoirs SAMOA
présentent des défauts de fabrication qui peuvent être
corrigés »
A la fin de ce chapitre, cette hypothèse s'avère
vérifier par de nombreux indicateurs et arguments. La mise à jour
du cahier des charges, la mise en place d'un plan d'assurance qualité et
de contrôle qualité partant de la fabrication des séchoirs
jusqu'à leur installation sur le terrain.
CONCLUSION DE LA PREMIÈRE
PARTIE
Les enjeux du séchage des fèves de cacao sont
d'ordre économique et social. Autant pour les producteurs que pour
l'Etat du Cameroun.
Pour les producteurs, il s'agit d'améliorer leur bien
être à travers leur revenu. L'amélioration du
séchage des fèves permettrait d'obtenir des fèves de
meilleure qualité.
Le cacao est la deuxième source de recette
d'exportation du Cameroun après les hydrocarbures. L'État a un
grand intérêt à mettre en oeuvre toutes les actions qui
contribueraient à améliorer la filière cacao.
Le projet de réhabilitation des séchoirs va
s'étendre dans les autres départements de bassin de production du
Sud-ouest en dépit du conteste sécuritaire particulier.
SECONDE PARTIE :
ACCOMPAGNEMENT DES PRODUCTEURS COMME FACTEUR D'AMÉLIORATION DE LA
QUALITÉ DES FÈVES DE CACAO
INTRODUCTION DE LA SECONDE
PARTIE
La majeure partie du cacao mondial est commercialisée
au moyen des contrats FCC (Federation of Cocoa Commerce). La FCC
prévoit trois grades pour attester de la qualité des fèves
: Good Fermented (bien fermenté), qui correspond pour
le Grade 1 ; Fair Fermented (moyennement
fermenté), pour celui du Grade 2 et hors standard, pour le
cacao Grade 3. Malgré une qualité jadis reconnue de la
fève camerounaise, le procédé de séchage de cette
dernière peine encore à être pleinement maitrisée.
De ce fait, plus de 95 % de la production nationale est constituée de
cacao de Grade 2 et exportée en Fair Fermented, ce qui est
à l'origine d'une décote significative de l'un des poumons de
l'économie camerounaise. Cette situation impacte non seulement les
caisses de l'État et aussi dégrade les conditions de vie des
cacaoculteurs.
Les raisons de cet état des choses sont
étroitement liées aux mauvaises pratiques post récoltes.
Des études sur le terrain ont permis de déceler des insuffisances
sur la maitrise des techniques de séchage. Il convient d'agir sur la
main d'oeuvre incarnée par les producteurs en vue de booster la
qualité de la fève.
Dans cette partie de notre travail, nous allons traiter au
troisième chapitre du concept de la gestion des ressources humaines en
insistant sur la formation et la communication afin de montrer la
corrélation avec optimisation sur la qualité. Ensuite au
quatrième chapitre nous allons expérimenter l'apport de
l'encadrement des cacaoculteurs sur la qualité des fèves de
cacao.
CHAPITRE 3 : ANALYSE THEORIQUE DE
LA GRH EN VUE DE L'OPTIMISATION DE LA QUALITE
INTRODUCTION DU CHAPITRE 3
Face à la mondialisation, chaque organisation veut
affirmer son immersion dans cette mouvance et faire face aux nouveaux
défis qu'impose le marché. Les entreprises sont soucieuses de
devenir incontournable dans leur secteur d'activité respectif.
La nécessité à être à
l'écoute des clients, la rapidité des innovations, la
difficulté grandissante à prévoir, à gérer
les risques sont quelques préoccupations qui conduisent les entreprises
à prendre conscience de l'importance du facteur humain.
En effet les chefs d'entreprises se sont rendus compte qu'il
n'est de richesse que des hommes et qu'il faut savoir gérer, dynamiser,
et promouvoir cette richesse afin d'accroitre leurs performances et leur
rentabilité.
Les entreprises doivent en permanence booster les
compétences disponibles afin d'en tirer le maximum de profit. La
formation des ressources humaines et la communication deviennent des
activités névralgiques, des atouts concurrentiels à la
firme.
I. L'ÉVOLUTION DE LA GESTION DES
RESSOURCES HUMAINES
Le début du XX ème siècle est
marqué par plusieurs courants de pensées au sein des
organisations. La première est l'école classique
caractérisée par l'organisation scientifique du travail.
Le premier auteur à amorcer une tentative de
définition est Fréderic Taylor en 1911 avec sa théorie sur
l'organisation du travail. Son approche se fonde sur la motivation
financière et la recherche du gain. II explique la motivation de l'homme
au travail par la volonté de maximiser le profit individuel. Cette
conception économique de la motivation inspire les différents
systèmes reposant sur l'intéressement et le
bénéfice des primes au rendement. Ainsi à partir de
l'approche mécaniste qui vise à développer les gains de
productivité, Fréderic Taylor invente l'Organisation Scientifique
du Travail.
Peu après, l'ingénieur français Henry
Fayol va énoncer un ensemble de principe d'action sur l'art de diriger
avec sa doctrine appelé le fayolisme. Fayol définit
cette fonction par des injonctions telles qu'organiser, prévoir,
coordonner, commander et contrôler. Dans le même courant de
pensées, au début du XXème siècle Henry
Ford développe le travail à la chaine qu'il va appeler le
fordisme. C'est la rationalisation poussée du travail avec une
parcellisation des tâches et une séparation du travail de
conception et d'exécution.
L'allemand Max Weber va développer le processus de
rationalisation des organisations sociales. Il créé le concept de
la bureaucratie qu'il définit comme une forme d'organisation qui repose
sur une sorte de domination légale - rationnelle.
Partant des insuffisances majeures des OST et les limites de
la simple motivation économique des salariés, l'école des
relations humaines et la sociologie du travail voient le jour. Elton Mayo en
est l'un des précurseurs. Il explique que le travail répond
à un besoin de relations humaines et résulte de l'appartenance
à un groupe social. Il montre que l'argent n'est pas la seule motivation
de l'homme au travail et développe une approche sociale de la
motivation. L'expérience réalisée par Elton Mayo entre
1927-1932 dans les ateliers de Hawthorne à Chicago a permis de
démontrer que le rendement du groupe peut augmenter en lien avec la
considération et la valorisation portée aux travailleurs.
Abraham Maslow de son côté travaille sur la
hiérarchie des besoins. Celle-ci explique le phénomène de
la motivation par des sources intrinsèques de l'individu. Selon lui les
besoins fondamentaux des individus peuvent se classer en cinq grandes
catégories hiérarchisées.
Figure 26 : Pyramide de Maslow
Source:
https://my-psychologie.com/2018/06/20/faut-il-oublier-la-pyramide-de-maslow/
Mc Gregor élabore la théorie X/Y. Il estime que
sous toute décision, ou tout acte d'un individu se cachent deux
suppositions ou impulsions qui nous amènent à agir de telle
façon. Ces hypothèses, qui sont le processus de base de nos
motivations, Mc Gregor les appelle de manière tout à fait
impersonnelle, théorie X et théorie Y.
La notion psychologique du travail reprise par Frederick I.
Herzberg. Il est connu comme le père de l'enrichissement des
tâches, une approche visant à améliorer la
réactivité et le bonheur de l'être humain en milieu de
travail.
La société industrielle est née de ces
découvertes techniques, de créations de richesses mais aussi d'un
mouvement d'idées nouvelles qui se sont propagées progressivement
dans les organisations. Au XIXème siècle, le lieu de
création de richesses est symbolisé par l'usine
considérée comme la principale source de valeur ajoutée.
Le fonctionnement de l'usine et ses ateliers reposent sur une discipline
particulière, une organisation rationnelle du travail, une
manière spécifique de voir les relations sociales. Aujourd'hui,
les organisations de notre société sont héritières
de ces changements (Plane, 2013).
I.1 LE CONTEXTE À L'ORIGINE DE LA
GRH
Autrefois appelé la gestion du personnel, la gestion
des ressources humaines ne s'est pas forgé ex-nihilo. Il a fallu
qu'apparaissent des dysfonctionnements au sein des organisations pour que germe
ce nouveau concept. Son apport immédiat est de maîtriser
l'explosion sociale de plus en plus manifeste. La GRH aura donc pour missions
de s'adapter au nouveau contexte social.
I.1.1 LES CHANGEMENTS TECHNOLOGIQUES
La notion de ressources humaines a évolué en
raison d'un certain contexte. À partir des années 1960, les
changements technologiques provoquent une évolution dans la gestion des
ressources humaines. Ces mutations technologiques ont été
constantes : il a fallu changer les méthodes de gestion des
ressources humaines pour améliorer l'adaptabilité. Les
changements technologiques ont permis une amélioration des
conditions de travail. Dans la mesure où les machines remplacent
les individus dans les tâches physiquement ardues, ces derniers n'ont
plus à faire le travail le plus pénible.
Le temps de travail est aussi modifié : on
parle d'aménagement du temps de travail. Grâce à
cela, la productivité augmente et les qualifications changent. Les
machines-outils ont une durée de vie plus courte et sont
également plus chères. Pour les rentabiliser, il faut donc
augmenter leur rendement. Pour obtenir un rendement maximal, on les utilise
presque tout au long de l'année sans interruption. On introduit les
équipes de semaine, de week-end, de jour et de nuit d'où
découle toute une gestion du personnel.
I.1.2 LA MONDIALISATION
La mondialisation a également changé
l'optique des ressources humaines dans la mesure où elle oblige
l'organisation à tenir compte des
spécificités de chaque culture locale. La mobilité
des facteurs de production s'améliore. La mondialisation exerce une
certaine pression sur l'entreprise. Cette pression se répercute
largement sur la gestion des ressources humaines dans la mesure où le
monde devient très compétitif. La mondialisation va de pair avec
la concurrence, la flexibilité et la rentabilité. Ces trois
exigences se répercutent sur la gestion des ressources humaines. Si le
personnel d'une usine n'est plus utile pour cause de délocalisation,
cela peut entrainer des licenciements, des mises à la retraite
anticipée.
I.1.2.1 LA CONCURRENCE
La concurrence peut se définir comme étant
l'aptitude à soutenir durablement la compétitivité,
celle-ci peut se fonder sur un ensemble élargi de facteurs : les prix et
les coûts certes, mais aussi la qualité, les délais,
l'innovation, les relations avec les fournisseurs, les compétences et
les capacités d'apprentissage internes.
Dyer, Schafer et Barney (tel que cité par
Nwahanye,2015) affirment que pour répondre à la
nécessité de disposer d'outils originaux qui permettraient aux
entreprises de se démarquer de la concurrence, en développant un
avantage compétitif durable qui contribuerait à la performance
de l'entreprise, au renforcement de sa compétitivité et
sa rentabilité, les ressources humaines ont été
évoquées par la théorie des ressources stratégiques
comme une ressource à la fois précieuse, rare, difficilement
imitable et non substituable par tout autre facteur de production,
contrairement aux autres actifs organisationnels
La littérature scientifique atteste d'ailleurs que le
capital humain représente un avantage compétitif indubitable. En
effet, plusieurs auteurs s'accordent ces dernières années, pour
dire que la principale source d'avantages concurrentiels est sans contredit les
RH (Persais, Guérin et Wils, tel que cité par Nwahanye, 2015).
I.1.2.2 LA FLEXIBILITÉ DU TRAVAIL
La flexibilité du travail est l'un des moyens
permettant à une
entreprise de
s'adapter aux évolutions de sa
demande et de
son environnement. Cette flexibilité est une des composantes de sa
réactivité
industrielle. Elle implique toutes les ressources de l'entreprise et en
particulier son personnel, par ses modes de
gestion
des ressources humaines.
La flexibilité du travail implique donc la remise en
cause de l'organisation du travail au sein de l'entreprise ou de la
société, afin de s'adapter aux contraintes du marché.
Le responsable des ressources humaines fonde sa gestion
sur l'adaptation de l'entreprise et de l'individu. Les aléas
commerciaux peuvent amener une flexibilité, au niveau des
rémunérations, on reste payé annuellement, mais le salaire
mensuel est flexibilisé. La flexibilité s'impose également
dans l'organisation du travail, par exemple le télétravail. Le
salarié accepte de prendre sur lui lorsque l'entreprise est en
difficulté.
Cependant, s'il est possible de flexibiliser un processus de
production, il est plus difficile de demander à des travailleurs
d'arrêter de travailler pendant une période car ils ne
toucheraient plus de salaires. De nombreuses entreprises concentrent donc leurs
efforts sur un noyau dur de collaborateurs très performants. Pour faire
face aux fluctuations de l'activité, elles font appel à des
travailleurs intérimaires ou en CDD. Pour autant, ce type de
fonctionnement n'est pas sans limite puisqu'il a pour effet de
développer le phénomène des travailleurs
précaires.
L'anticipation fait partie des nouvelles approches de
l'entreprise. Toutefois, les emplois du temps peuvent être
érigés sur le court terme. La reconnaissance de la
pénibilité, du stress, des conditions de travail et de la
sécurité améliore la vie de l'individu dans
l'organisation.
I.1.2.2 LA RENTABILITÉ
La rentabilité s'impose aujourd'hui comme un
critère dominant d'évaluation des performances au sein des
organisations et conditionne fortement stratégies industrielles et
pratiques sociales.
Une entreprise cherche à être la plus rentable
possible, c'est-à-dire faire le
plus de bénéfices possibles en cherchant par
exemple à être plus productive.
La productivité par salarié est trouvée
par le rapport entre la production et ne nombre de salariés.
La rentabilité étant étroitement
liée au capital humain, il est important que les managers s'assurent du
bien-être de leurs salariés afin que les résultats obtenus
soient à la hauteur des attentes.
I.1.3 L'INCERTITUDE ÉCONOMIQUE ET LE CONTEXTE
SOCIALE
L'incertitude économique provoque de l'attentisme
chez les entreprises car elles ne savent pas comment gérer le personnel.
Le contexte social devient de plus en plus important pour les entreprises en
raison des revendications sociales, source importante de tension pour les
organisations.
I.1.3.1 L'INCERTITUDE ÉCONOMIQUE
Reconnaître l'importance de l'incertitude met
profondément en question l'analyse économique. Les premiers
économistes à s'emparer de ce thème, Knight et Keynes, ont
lancé le débat. Dans certaines situations, l'incertitude peut
être traitée par les probabilités : on parle alors de
risque. Dans d'autres cas, les probabilités ne sont d'aucun recours.
Cette distinction permet de caractériser deux démarches. La
première, majoritaire, retient les probabilités pour
représenter l'incertitude, la seconde, qui regroupe des courants
hétérogènes, postule que l'incertitude n'est pas
probabilisable et refuse toute vision mécanique de l'économie. Le
message de Knight29(*) et
Keynes30(*) est clair.
L'incertitude est souveraine, son existence impose au théoricien une
règle : toute simplification est dangereuse. Il n'existe pas d'outil
magique permettant de saisir toute la complexité d'un mode incertain, le
raisonnement probabiliste n'a qu'une capacité limitée à
rendre compte de phénomènes incertains et de la façon dont
les êtres humains font des prévisions. Ne faites pas une confiance
aveugle aux probabilités. Ne prêtez pas aux agents
économiques qui les utiliseraient une clairvoyance divine (Moureau et
Rivaud-Danset, 2004).
En économie grâce aux travaux de F.H Knight, il
est traditionnel de distinguer les situations de risques des situations
d'incertitude. Les premières sont caractérisées par
l'existence de diverses alternatives probabilistes, les derniers par
l'incapacité d'assigner des probabilités aux états de la
nature.La distinction de Knight est suffisamment précise car
l'incertitude peut avoir des causes très différentes. Depuis le
développement de la théorie subjective des probabilités et
de la théorie bayésienne, l'inexistence de probabilités
objectives n'est plus un obstacle au calcul économique, en l'absence
totale d'informations l'individu peut toujours considérer les
différents états de la nature comme équiprobables. C'est
le ce que Keynes appelle le principe de la raison insuffisante, si l'agent n'a
aucune connaissance sur le problème, il n'a aucune raison de
pondérer différemment les états de la nature (Vivani,
1994).
I.1.3.2 LE CONTEXTE SOCIALE
Les préoccupations telles que les questions du genre
apparaissent et imposent aux managers de reconsidérer les
méthodes de gestion. Les femmes montent en compétences et
revendiquent une parité dans les postes à pouvoir. Ceci conduit
des entreprises à aménager des postes de travail pour les femmes
et aussi pour les handicapés.
Les syndicats des travailleurs travaillent de plus en plus
pour défendre la condition du salarié et tentent
d'équilibrer les relations entre ce dernier et l'employeur.
Du fait de la compétitive, le niveau de turn-over
dans les entreprises explose. Ceci pousse les entreprises à
améliorer les traitements du salarié avec la mise en place des
politiques de rétention des talents.
I.2 LA PERFORMANCE ORGANISATIONNELLE COMME ENJEUX DE LA
GRH
L'importance de la fonction Ressources humaines peut
s'appréhender à plusieurs niveaux :
· Sur le plan de la production, la fonction ressources
humaines permet à l'entreprise de disposer d'un personnel
compétent qui améliore la productivité de
l'entreprise ;
· Sur le plan commercial, la gestion des ressources
humaines contribue au recrutement de personnel de vente (vendeurs, directeurs
de magasin) efficaces et motivés. Grâce à eux, les ventes
doivent donc être améliorées ;
· Sur le plan financier, une gestion pertinente du
personnel limite les dépenses liées aux salaires. Le salaire
n'est plus seulement un coût pour l'entreprise, mais un
investissement ;
· Sur le plan stratégique, la fonction ressources
humaines permet à l'entreprise de se différencier de la
concurrence grâce à l'excellence de son personnel. Ses
salariés vont permettre à l'entreprise de créer une valeur
supplémentaire pour les clients.
Dans un contexte organisationnel, la performance se
définit comme étant le résultat obtenu par rapport aux
objectifs, à la stratégie de l'entreprise et aux attentes des
parties prenantes. Elle porte sur la qualité, la quantité,
les coûts et le temps.
Pour atteindre les objectifs fixés, l'
entreprise doit
faire les bonnes choses qui témoignent de son
efficacité.
Elle doit bien faire les choses pour que ses actions soient
efficientes
et le tout au bon moment à des coûts optimaux.
Pour atteindre un haut niveau de performance dans une
entreprise, il est nécessaire d'utiliser les bonnes
stratégies,
les bons
outils
de gestion, compter sur des
conditions favorables,
utiliser les bonnes
compétences
de gestion, s'assurer que les
parties
prenantes sont satisfaites,
gérer
la performance,
gérer
les risques,
gérer
les opportunités,
gérer
le stress.
La
recherche
de l'équilibre, de la
performance
durable et de la
performance
optimale devrait être une préoccupation constante.
I.2.1 IMPACT DE CERTAINES PRATIQUES DE GRH SUR LA
PERFORMANCE ORGANISATIONNELLE ET FINANCIÈRE DES PME
Suivant les perspectives économique et
stratégique, par exemple, les entreprises doivent effectuer le passage
à une économie du savoir et développer des
compétences uniques [Barney et al tel que cité par
Lacoursière, Fabi, St-Pierre (2000)], fondées sur l'innovation et
la création de la valeur [Moran et Ghoshal (tel que cité par
Lacoursière et al, 2000)]. Pour y arriver, l'entreprise devra
s'assurer un bassin de main-d'oeuvre compétente, qualifiée et
capable de créer de la valeur ; elle doit aussi mettre en place des
processus difficiles à imiter. Or, les gestionnaires sont sujets au
risque de sélection adverse lorsqu'ils procèdent à
l'embauche du personnel [Coff (Tel que cité par Lacoursière et
al., 2000)] dont ils espèrent mettre à profit la
capacité d'innovation et de création. Ce personnel, une fois
embauché, peut fort bien décider d'aller travailler pour une
entreprise concurrente, ce qui augmenterait les risques éventuels
d'imitation. Le risque de roulement de la main-d'oeuvre s'applique
particulièrement aux PME, non seulement parce que leurs processus de
recrutement et sélection sont moins sophistiqués que dans les
grandes entreprises, mais aussi parce que ces dernières sont en mesure
d'offrir de meilleurs salaires. D'autre part, des pratiques tel le travail en
équipe, le partage de l'information et la participation aux
décisions y facilite le développement de processus difficiles
à imiter et à reproduire [Reed et DeFilippi, (Tel que cité
par Lacoursière et al., 2000)]. Selon une perspective
psychosociologique, par ailleurs, les entreprises doivent de plus en plus
considérer les ressources humaines comme des partenaires et chercher
à obtenir leur coopération dans la mise en oeuvre des
stratégies poursuivies [(Ghoshal et al., Rousseau et Arthur,
(tel que cité par Lacoursière et al., 2000)]. Les
stratégies envisagées et, s'il y a lieu, les changements à
opérer, peuvent toutefois se heurter aux intérêts
divergents et à un manque de coopération des individus
chargés de les appliquer. La tendance à la réduction de
l'effort [Kidwell et Bennett (tel que cité par Lacoursière et
al., 2000)] et la résistance au changement figurent parmi les
facteurs à prendre en considération. La mise en place de
pratiques telles que la communication et le partage des informations, la
participation aux décisions et différentes formes de
reconnaissance, dont la rémunération, contribueront à
l'établissement d'un climat de confiance et faciliteront le changement
[Fabi et al. (Tel que cité par Lacoursière et
al., 2000)].
L'état de l'art révèle l'existence de
plusieurs courants théoriques qui semblent montrer l'existence d'un
effet plausible de la mise en oeuvre des pratiques GRH (entre autre, le
recrutement, la formation, la gestion des compétences, des emplois et
des carrières, la mise en oeuvre d'une politique globale et individuelle
d'évaluation, l'aménagement des temps de travail,
l'amélioration des conditions de travail, la communication, la
négociation) sur l'accroissement de la performance ainsi que sur la
capacité des entreprises à développer de nouveaux
procédés ou produits et à réussir leurs changements
organisationnels [Allani-Soltan (tel que cité par Dorra, 2008)]. A
partir de ces courants théoriques se dessinent trois approches
empiriques reliant les pratiques GRH et la performance à
savoir l'approche universaliste, contingente et configurationnelle.
I.2.1.1 L'APPROCHE UNIVERSALISTE
L'approche universaliste veut que les pratiques les plus
reconnues de GRH aient un effet positif partout où on les applique.
Suivant ce modèle, l'application d'une ou de plusieurs pratiques de GRH
pourrait influencer directement la performance d'une entreprise. Cette approche
est également désignée sous l'appellation de
« best practices » et de « one best
way » [McMahan et al., (tel que repris par Dorra,
2008)]. C'est ainsi que certaines études ont trouvé une relation
positive entre les programmes de partage des profits et la performance
organisationnelle et financière des entreprises (Saint-onge,Commeiras et
Balkin, 2007). D'autres ont identifié une relation positive entre la
présence de pratiques de formation et une augmentation de la
productivité (Bartel, 1994 ; Russell, Terborg et Powers, 1985). Une
étude de Terpstra et Rozell (1993), a établi l'existence d'une
relation positive entre l'application de pratiques de sélection et
recrutement d'une part, et la performance financière des entreprises de
services d'autre part. L'approche universelle a également donné
lieu à des études cherchant à mesurer l'impact de
plusieurs pratiques sur la performance. L'une des études les plus
percutantes à cet égard est celle de Patterson et al.
(1998). Selon cette étude longitudinale, les pratiques de GRH
expliqueraient 18% de la variance observée en ce qui a trait à
l'amélioration de la productivité et 19% de la variance
observée en ce qui a trait à l'augmentation de la
rentabilité des entreprises étudiées. Les pratiques de GRH
expliquant la plus grande part de ces variances seraient celles de :
sélection et recrutement, accueil, formation, évaluation du
rendement, polyvalence (tâches), rotation de tâches,
responsabilités (décisions) et travail en équipe. Delery
et Doty (tel que cité par Liouville et Bayad, 2001) ont également
trouvé une relation positive entre la présence des pratiques
d'évaluation du rendement (avec fixation d'objectifs), de
sécurité d'emploi et de partage des profits et la performance
financière des entreprises dans l'industrie des services bancaires.
Soltan, Bayad et Arcand (tel que cité par
Adraoui,2015)
reprennent l'idée des tenants de l'approche universaliste pour
considérer, indéniablement le recours au paradigme universaliste
comme déterminant dans la recherche des pratiques qui maximisent
l'efficacité de la firme. Ils affirment que dans la conception
universaliste, dominante en littérature nord-américaine, la
recherche, de nature hypothético-déductive, consiste à
partir d'évidences et de constats et procède par la suite
à leur généralisation ou « universalisation ».
En effet, comme dans le cas de la plupart des sciences sociales, le contexte
importe peu par rapport aux caractéristiques intrinsèques de
l'organisation.
Ainsi, l'approche universaliste suppose que,
indépendamment du contexte d'affaires, certaines pratiques de GRH
permettent d'améliorer la manière dont les ressources humaines
sont stratégiquement gérées au sein des organisations et,
par voie de conséquence, d'accroître la performance de la firme
[Pfeffer, 1994, 1998a, 1998b ; Pfeffer et Viega, (tel que cité par
Lishou, 2009)].
De même Arcand et al. (Tel que cité par
Jamoussi, 2008), stipulent que la perspective universaliste représente
le raisonnement le plus simple en gestion stratégique des ressources
humaines (GSRH). Selon cette approche, il existerait des pratiques de GRH qui,
indépendamment du contexte d'affaires, pourraient aider les firmes
à accroître de manière significative leur niveau de
performance organisationnelle. Bien que ces dernières varient d'un
auteur à l'autre, le rôle clé de certaines pratiques RH est
tout de même reconnu dans l'accroissement de la performance de la
firme.
Parmi les principales pratiques RH qualifiées de «
performantes » par la littérature scientifique, les auteurs citent
celles liées aux activités de rémunération
incitative, à la participation des employés, à la
formation et au développement de la main d'oeuvre, ainsi qu'à
l'aspect sécurité d'emploi (Fortier, 2011). S'il peut encore
exister une certaine divergence en ce qui concerne l'identification des
pratiques « performantes » de GRH, il semble, tout de même, se
dégager un consensus lorsque vient le moment de justifier les assises
théoriques sur lesquelles repose l'hypothèse universaliste des RH
(Becker et Gerhart, 1996 ; Boxall et Steeneveld, 1999 ; McMahan, Virick et
Wright, 1999). En fait, deux arguments théoriques servent de pierre
d'assise aux tenants de l'approche universaliste des RH.
I.2.1.2 L'APPROCHE CONTINGENTE
L'approche de contingence suggère quant à elle
que les pratiques de GRH, pour être efficaces, doivent être
contingentes aux autres aspects de l'organisation (Lengnick Hall et Lengnick
Hall, 1988 ; Schuler et Jackson, 1987) et particulièrement à la
stratégie, qui est le principal aspect considéré par la
GSRH. Suivant ce modèle, une pratique de GRH ne pourra influencer la
performance d'une entreprise que dans la mesure où elle est
alignée avec la stratégie, qui agit alors comme variable
modératrice. Les études empiriques menées sur la base de
cette approche cherchent donc à établir comment les pratiques
individuelles de GRH interagissent avec la stratégie d'entreprise pour
permettre d'améliorer la performance. On parle d'un alignement externe
des pratiques de GRH, par opposition à un alignement interne, qui est
également pris en considération dans l'approche de configuration.
Delery et Doty (tel que cité par Liouville et Bayad,2001)
suggèrent de retenir l'innovation comme variable centrale de contingence
lorsque vient le temps de distinguer entre les différentes
stratégies adoptées par les entreprises. On obtient de cette
façon une variable unique qui permet d'utiliser la théorie de
Miles et Snow (1978) comme cadre d'analyse, les entreprises fortement
innovatrices étant associées aux prospecteurs, les entreprises
moyennement innovatrices constituant les analystes et les entreprises
faiblement innovatrices représentant les défenseurs. Suivant
Miles et Snow (1978), en effet, les caractéristiques des prospecteurs
incluent notamment une ligne de produits diversifiée et le recours
à plusieurs technologies; les caractéristiques des
défenseurs incluent plutôt une ligne de produits limitée et
le recours à une seule technologie; les caractéristiques des
analystes, enfin, incluent une ligne limitée de produits de base, la
recherche d'un nombre restreint de nouveaux produits/marchés
apparentés, une technologie efficiente pour le créneau stable et
des technologies de pointe pour les nouveaux produits. Les études ayant
cherché à établir une relation entre des pratiques
individuelles de GRH, leur alignement avec la stratégie d'entreprise et
la performance de celles-ci, sont plutôt rares.
La théorie de la contingence appliquée à
la GRH a permis de mettre en exergue principalement deux formes d'alignement :
l'alignement vertical et l'alignement horizontal [Delery et Doty (tel que
cité par Liouville et Bayad, 2001)]. L'alignement vertical, par
l'entremise de la perspective comportementale, suggère que chaque
stratégie externe (stratégie d'affaires) requiert des
comportements spécifiques et que le rôle de la GRH est justement
de stimuler ces comportements (Schuler et Jackson 1987). De l'autre
côté, l'alignement horizontal appuie l'idée que ce sont les
stratégies internes à l'entreprise qui sont la source d'un
avantage concurrentiel et que la cohérence entre les politiques de
rémunération et les systèmes de ressources humaines
(organisation du travail, gestion de la qualité, culture
organisationnelle) serait plus déterminante que la cohérence
entre les pratiques de rémunération et les stratégies
d'affaires [Baird et Meshoulam (tel que cité par Ingrassia, 2017)]
I.2.1.3 L'APPROCHE CONFIGURATIONNELLE
Parmi ces principales approches de la gestion
stratégique des ressources humaines, l'approche configurationnelle des
ressources humaines retient l'intérêt d'une grande partie de la
communauté scientifique la GRH n'a de réel effet sur
l'efficacité de l'organisation que dans la mesure où elle
parvient à constituer un regroupement cohérent de pratiques
capables de s'harmoniser avec les principales caractéristiques de
l'organisation. [Baird et Meshoulam (tel que cité par Ingrassia,
2017)]
L'approche configurationnelle implique l'idée d'un
processus de décision holistique et incrémental. Les
configurations, qui ne sont que des idéaux-types, peuvent être
vues comme une architecture de liens multiples (non linéaires) et
interactifs entre les éléments de la stratégie et les
grappes de pratiques de GRH ; une architecture susceptible d'évoluer au
cours du temps (Miller, 1989) pour atteindre un niveau maximal
d'efficacité. La perspective configurationnelle dépasse ainsi le
cadre de l'ajustement vertical introduit par l'approche de contingence, qui
fait référence à la cohérence externe pouvant
exister entre un groupe de pratiques de GRH et une caractéristique
organisationnelle (la stratégie d'affaires par exemple), et
intègre parallèlement à celui-ci un principe d'ajustement
horizontal portant sur la cohérence interne entre les pratiques de
GRH. [N.Allani, M.Bayad, M.Arcand, (tel que cité par Jamoussi,
2008)]
Les configurations issues des idéaux-sont obtenues soit
par construction théorique soit par observation empirique. Toutefois et
comme le soulignent Doty et Glick (1994), la plupart des chercheurs en GRH
préfèrent les configurations basées sur des construits
théoriques.
La complexité théorique de l'approche
configurationnelle par rapport à celle de l'approche de contingence
réside également dans le fait que les configurations
résultent d'effets de synergies et d'interactions non linéaires
ne pouvant être obtenus par des analyses bivariées comme dans le
cas de l'approche contingente Contrairement au principe de
supériorité de l'approche universaliste, l'approche
configurationnelle postule, à travers le principe
d'équifinalité, que plusieurs configurations peuvent conduire
à un niveau de performance maximal. Ces configurations ne doivent pas
être vues comme étant des catégories immuables dans
lesquelles doivent venir s'inscrire les organisations, mais comme des profils
idéaux dont les organisations se rapprochent plus ou moins. [Allani
et al. (Tel que cité par Jamoussi, 2008)]
Le fait de regrouper des pratiques de GRH en un système
cohérent remonte aux années 1960 et plus
précisément aux travaux de Woodward, de Burns et Stalker qui ont
montré l'importance, pour une organisation, de l'alignement de la
technologie ou de la structure organisationnelle sur des éléments
de la GRH. Les écrits de Lawrence et Lorsch ont de leur
côté montré l'importance de créer une certaine forme
d'arrimage interne entre la structure organisationnelle, les tâches, les
processus administratifs et les individus, et ont servi de base à des
validations empiriques intéressantes [Burns et Stalker ;
Woodward ; Lawrence et Lorsch ;Allani et al. (Tel que
cité par jamoussi, 2008)]
II. LA CONTRIBUTION DE
LA COMMUNICATION INTERNE ET DE LA FORMATION DES RH
La communication interne et la formation sont actuellement
deux services de l'entreprise qui doivent travailler et s'allier ensemble pour
un résultat optimal. En effet, ces derniers visent le même
objectif, celui d'orienter les ressources humaines par la diffusion d'un
message et par l'adaptation des compétences par le biais de la
formation. Néanmoins, de quelle manière la communication interne
peut inciter les salariés à se former et surtout de justifier de
sa pertinence.
L'outil pour susciter l'intérêt de la formation
c'est la communication. Il est important de démontrer à
l'employer que la formation est un levier du développement social. La
démarche est toute simple :
· La détection des besoins en formation ;
· L'élaboration d'un plan de formation ;
· La mise en oeuvre des actions de formation ;
· L'évaluation des résultats.
II.1. LA MOTIVATION DES SALARIÉS À LA
FORMATION
Il est plus facile de motiver les salariés à
aller en formation quand celle-ci fait partie intégrante de
la culture de l'entreprise, c'est-à-dire quand le personnel de
direction communique régulièrement sur la place de la formation,
quand les managers s'impliquent dans la réalisation de la formation et
enfin quand le lien est clair entre les objectifs de la formation et les
décisions stratégiques de l'entreprise.
La motivation des salariés passe aussi par la mise en
place de processus internes qui permettent de baliser le chemin jusqu'à
la formation. L'objectif est de tout mettre en oeuvre pour éviter que
certains salariés considèrent qu'il n'y pas de formation pour
eux.
Trois facteurs clés sont susceptibles de motiver de
salarié à suivre la formation ;
· L'implication du salarié dans la
préparation de la formation ;
· Les gains de la formation (capacité à
être autonome à son poste) ;
· Les retombés de la formation (l'avancement, la
promotion, avantages pécuniaires)
II.1.1 LE RÔLE DE LA COMMUNICATION
INTERNE
Le défi pour le responsable formation d'une entreprise
est de pouvoir motiver les salariés à suivre une
formation. En effet, communication interne et formation vont de pair. Avant de
mettre en place une formation, il est primordial de communiquer sur
les décisions prises aux différentes personnes que vous
avez consultées tout au long de la construction du plan de formation. En
effet, ce retour sur investissement sera considéré comme une
marque de considération.
La communication permet de donner du sens à
la formation. Il s'agit dans un premier temps de donner l'envie
d'apprendre, de démontrer l'intérêt, ainsi que de
développer la motivation par le biais de la formation.
Il convient par la suite de prolonger les effets, en
précisant que cela se poursuit à l'issue de la formation. En
effet, l'important est de pouvoir dire aux apprenants qu'il est possible
d'appliquer ce qui a été appris en formation.
En dernier lieu, la formation suivie par un salarié ne
doit pas rester aux oubliettes. De ce fait, il est impératif de
communiquer sur les résultats de la formation.
II.1.2 L'ÉTABLISSEMENT D'UNE STRATÉGIE
DE COMMUNICATION POUR INCITER À SE FORMER
La communication doit être effectuée
à grande échelle. Elle doit s'adresser à l'ensemble
des salariés de l'entreprise.
Une bonne communication permet de vendre de nombreuses actions
de formation. Il suffit pour cela de trouver les mots et surtout expliquer aux
salariés ce qu'apporte en plus la formation à court ou à
moyen terme. C'est la raison pour laquelle il est primordial de travailler en
étroite collaboration avec le service communication. La communication
interne est un atout pour faire passer un message dont le responsable formation
est l'initiateur.
Les étapes à suivre pour mettre en
place une stratégie de communication sont les suivantes :
· L'établissement d'un diagnostic ;
· La fixation d'objectifs ;
· La détermination de la cible et le message
à faire passer ;
· La définition des outils ;
· L'établissement d'un planning et d'un budget.
Sans communication forte autour de la formation, le risque
principal est d'engendrer de l'amertume et de la démotivation. Dans la
mise en place de la stratégie, le rôle du responsable
formation sera de valoriser la formation. Dans un premier temps, il reviendra
à ce dernier de cibler les sources de motivation des salariés. On
peut y trouver :
· La promotion ;
· L'augmentation de salaire s'il y a un changement
de poste ;
· L'épanouissement professionnel et donc
personnel.
Par ailleurs, en mobilisant les managers dans cette
stratégie de communication, l'entreprise s'assure des engagements sur
les objectifs opérationnels et sur la mise en place du suivi. En effet,
ils constituent un relais pertinent pour une direction qui ne
peut pas être toujours présente sur le terrain.
De plus, la communication doit s'inscrire dans
une politique de communication RH en valorisant les aspects positifs
et en démontrant aux collaborateurs que la direction prend soin
d'eux.
Du côté du responsable formation, son travail
sera de :
· Définir les priorités de formation par
service ;
· Intégrer et impliquer les managers dans chaque
projet de formation ;
· Identifier le programme de formation correspondant aux
besoins de l'apprenant ;
· Trouver l'organisme de formation adéquat.
Il est à noter que si les processus de
communication interne sont clairement définis et respectés, la
communication en est facilitée et le résultat assuré. Par
ailleurs, pour donner envie à un salarié d'être
motivé lors du suivi d'une formation, il faut varier les outils, les
moyens pédagogiques et également les supports de
communication.
II.1.3 LES FORMES DE
COMMUNICATION
Le défi premier pour le responsable formation
est de
motiver les
salariés à se former. Pour cela, la communication
collective peut être utilisée pour inciter les
salariés à se former. Dans ce cas bien précis, ce sont des
réunions organisées au sein de l'entreprise. Il est
également conseillé d'envoyer des mails à l'ensemble des
salariés.
La communication personnalisée peut
également être utilisée lorsque des salariés
souhaitent avoir des informations plus précises. Ces dernières
peuvent donc être données lors de l'entretien annuel,
professionnel ou lors d'une réunion classique individuelle.
Il est à préciser que les outils de
communication doivent être maitrisés pour motiver
le personnel en interne.
II.2 LA NOTION D'ACCOMPAGNEMENT DES RH
Il y a bien effectivement une structure identique et
constitutive de toutes les formes d'accompagnement inscrite dans la
sémantique même du verbe
accompagner, ac-cum-pagnis, ac (vers), cum (avec), pagnis (pain),
dotant l'accompagnement d'une double dimension de relation et de cheminement.
Ainsi la définition minimale de toute forme
d'accompagnement est : Etre avec et aller vers, sur la base
d'une valeur symbolique, celle du partage. Mais on ne chassera pas aussi
facilement l'idée qui se profile : celle d'appartenance, question
incontestablement nostalgique renvoyant à l'idée d'un sens
partagé et de communauté. (Paul, 2009)
Le partage ne dit-il pas aussi une redistribution des
places ? Signification qui prend un sens dans la conception de
l'accompagnement comme entretien où s'exerce une « parole
partagée », autrement dit un dialogue, lequel renvoie de
nouveau à l'instauration d'un type de relation qui le permette. Cette
valeur de partage se constituerait en visée éthique guidant
l'action.
Le terme accompagnement renvoie ainsi à quatre
idées. Tout d'abord, il renvoie à celle de
secondarité : celui qui accompagne est second, c'est-à-dire
« suivant » (et non « suiveur »). S'il
n'a pas la primauté, il n'est pour autant pas accessoire puisqu'il n'y
aurait accompagnement sans ce binôme initial. Sa fonction est de soutenir
au sens de valoriser celui qui est accompagné. (Paul, 2009)
Le terme d'accompagnement renvoie ensuite à
l'idée de cheminement incluant un temps d'élaboration et des
étapes qui composent la « mise en chemin ».
En trois, vient l'idée d'un effet d'ensemble :
quelle que soit la dissymétrie relationnelle, l'action vise à
impliquer les deux éléments à tous les stades de ce
cheminement.
Enfin, c'est l'idée de transition, liée à
une circonstance, une actualité, un événement, une
situation qui vient dire que tout accompagnement est temporaire avec un
début, un développement et une fin.
II.2.1 LES FORMES D'ACCOMPAGNEMENT
Dans des travaux menés précédemment
(Paul, 2004), on a inventorié les pratiques se déclarant relever
de
l'accompagnement: counselling, coaching, sponsoring, mentoring coexistent
avec tutorat, conseil ou consultance, parrainage ou
encore compagnonnage. Bien que toutes tendent à se déclarer
spécifiques, elles le sont au regard de leurs contextes. Toutes ces
pratiques sont des formes d'accompagnement, d'où leur « air de
famille ». Il semble qu'à fonctionner sans reconnaître
comment toutes ces formes font système, on ne perçoive plus la
complexité dont elles témoignent : l'idée
d'accompagnement s'émiette, le sens de l'acte d'accompagner se dilue. Il
est donc important de bien distinguer en quoi tutorat et coaching, par exemple,
sont des formes d'accompagnement et quelles réalités
spécifiques chacune recouvre en tant que telle.
II.2.1.1 LE SPONSORING ET LE PARRAINAGE
Le terme sponsoring, aujourd'hui
équivalent de parrainage, provient à la fois du latin
classique sponsor signifiant répondant, caution et
du latin religieux avec le sens de parrain d'un néophyte. Selon le
premier, il a le sens de promesse verbale entre deux parties et
d'engagement réciproque. Du second, il désigne celui qui
veille à l'éducation religieuse, garant s'engageant sur la
moralité et la fidélité du baptisé. Comme un
père promet sa fille au sponsus (époux), le
parrain promet l'enfant à l'église. Être sponsor,
c'est donc parier sur l'avenir d'un enfant et son sens de la communauté.
Par analogie, le parrain est celui qui préside à
l'introduction dans le monde ou dans un cercle. On ne résistera pas
à rappeler que la marraine joue dans les contes de fées la
fonction du « souffleur de dons » (Houde, 1996). Ici se
joue une dimension relationnelle d'engagement réciproque et de
projection sur l'avenir avec un gage d'appartenance.
II.2.1.2 LE COACHING
Si coach provient effectivement du
hongrois kocsi, il aurait une même origine que le
mot cocher désignant le conducteur de voitures
hippomobiles transportant des personnes. Chargé donc d'opérer un
déplacement, un changement, le coach est d'abord défini
comme entraîneur, répétiteur ou professeur particulier.
Issu du milieu sportif, le coaching est lié au domaine de
l'action en termes de performance ou d'efficacité. Le dictionnaire
Robert (2015) définit le coach comme une
personne chargée de l'entraînement d'une équipe ou d'un
sportif quand le dictionnaire Larousse (2017) tient
le coaching pour une action de conseil individuel ou
d'accompagnement de collaborateur. Quant à Délivré (2002),
il le définit comme une série d'entretiens individuels entre
une personne (le coaché) et un professionnel (le
coach) qui ont pour but d'aider la personne à atteindre un
objectif et réussir sa vie personnelle ou professionnelle. L'idée
principale est celle d'un entraînement justifié par un défi
de changement.
II.2.1.3 LE MENTORING
On sait que le mentoring introduit en
anglais début XVIIIe siècle n'a pas d'autre
origine que Mentor, guide et conseiller d'Ulysse31(*) auprès de son fils
Télémaque. Mentor désignait une
personne sage et expérimentée servant de conseiller, terme qui a
eu tendance à être par la suite confondu avec celui de
précepteur : qui prend soin de l'éducation d'un jeune
homme (Saint-Simon), celui qui enseigne, qui est chargé de
l'éducation d'un enfant (1460), personne qui instruit les
hommes, leur apprend à mieux vivre. Le mentor aujourd'hui est
en général chargé d'accompagner un apprenant à
accomplir le passage vers la vie professionnelle et à comprendre les
valeurs de l'entreprise à laquelle il va appartenir.
II.2.1.4 LE TUTORAT
Le terme tutorat, récent en
français (1980), est issu du vocabulaire juridique et familial :
utilisé métaphoriquement dans le registre horticole, il tend
à se dégager de la connotation de tutelle qu'il détient de
ses origines latines, désignant un défenseur, un protecteur, un
gardien (tueri : protéger). Le titre de tuteur tend
à remplacer d'anciennes appellations telles que maître formateur
ou d'application dans le domaine de la formation, maître d'apprentissage
ou de stage. Le déploiement de la fonction de tuteur, comme encadrant du
stagiaire dans son parcours au sein de l'entreprise, correspond à
l'important développement des formations en alternance, puis des
formations à distance. Il hérite également, comme toute
pratique d'accompagnement, d'une visée d'insertion dans la vie
professionnelle. Le tutorat se trouve alors à la croisée de deux
logiques, productive et éducative, et défini comme dispositif de
formation en situation de travail. Par conséquent, c'est moins la
relation entre un professionnel expérimenté et un novice en
apprentissage qui permettra de saisir sa spécificité que le
dispositif auquel il appartient.
II.2.1.5 L'ACCOMPAGNONNAGE
Quant à la parenté
entre accompagnement et compagnonnage, on ne saurait
l'éviter car elle délivre une information sur ce qui lie tout ce
matériel sémantique. La philosophie du compagnonnage
réside dans cette veille constante à ne pas dissocier les trois
composantes de sa mission : apprendre, pratiquer et transmettre. Ainsi
peut-on concevoir que l'apprentissage des vertus d'un métier
s'acquière « en les pratiquant chaque jour sous le conseil
fraternel d'un ancien ». Dans cette relation d'ancien à
apprenti, celui-ci est « accompagné » techniquement
et moralement. On est bien ici non dans une intervention sur mais dans une
relation avec. Les compagnons entre eux sont des pairs tandis que
l'accompagnement concerne deux personnes de statut inégal mais qui,
néanmoins, vont devoir fonctionner au sein d'une relation conjuguant
disparité des places et parité relationnelle. [De Castera ;
Ibid (tel que cité par Paul, 2009)]
II.2.1.6 LE COUNSELLING
Développé aux États Unis par Carl Roger,
le counselling est une approche à la relation
psychothérapeutique visant à aider les personnes
à mieux vivre leur quotidien. Il s'agit d'un accompagnement
relationnel favorisant la confrontation avec les problèmes
rencontrés dans la vie courante (problèmes relationnels, de
santé, économiques, émotionnels, physiques...) et la
recherche de ressources internes et externes pour faire face à ces
problèmes (Schneider-Harris, 2007).
CONCLUSION DU CHAPITRE 3
Ce chapitre a permis de mettre en lumière l'apport de
la GRH dans une organisation quel que soit la taille et la nature de cette
dernière. Née de la grogne sociale, elle permet de maintenir un
climat viable au sein de l'entreprise et d'anticiper sur d'éventuelles
fuites de compétences vers la concurrence.
L'aspect de la formation en entreprise a été
abordé et présenté comme l'un des facteurs clés de
succès pour les organisations. La formation s'impose avec pour objectifs
de pousser les limites des salariés tout en développant leur
autonomie à leur poste.
La communication interne quant à elle, est un moyen
d'écoute active et d'information pour l'employé d'une part. Elle
permet également de sensibiliser les concernés sur le
bien-fondé de cette initiative, sur les objectifs, les attentes et dans
une certaine mesure l'impact sur leur carrière. C'est à travers
donc l'implication des managers, des formateurs que ce succès est
possible.
Le concept d'accompagnement des ressources humaines vient
étayer la logique selon laquelle les formations sporadiques sont
insuffisantes dans le cadre du PRSC. Un déploiement réel et
efficace sur le terrain va permettre une réelle immersion des
productions dans le procédé de séchages des fèves
de cacao.
CHAPITRE 4 : AMÉLIORATION DE
LA QUALITÉ DES FÈVES PAR L'ENCADREMENT DES CACAOCULTEURS
INTRODUCTION DU CHAPITRE 4
L'UE est le principal client de la production national des
fèves de cacao en provenance des sept bassins de production parmi
lesquels le bassin du Sud-ouest à lui tout seul représente
à peu près 45% de la production national (PRSC, 2014). Les normes
sur la qualité des fèves de cacao deviennent de plus exigibles
sur le marché international (CCIC, 2014).
D'après les statistiques officielles, le cacao
représente environ 25% des exportations nationales. A peine 5% de la
production du cacao est réalisée en local (INS, 2016).
Outre la couleur rouge qui constitue l'un des atouts des
fèves de cacao reconnues sous le label « Origine
Cameroun » souffre de la décote du fait des mauvaises
pratiques post récolte. On peut citer le défaut du respect des
prescriptions de la fermentation (délais conditionnement), le
séchage inapproprié des fèves (utilisation des aires
bitumées, sécheurs SAMOA vétustes). Toutes ces mauvaises
pratiques sont à l'origine entre autre des fèves moisies, l'odeur
de fumée dans les fèves.
Il subsiste une méconnaissance du fonctionnement du
marché du cacao autant par les producteurs que par les opérateurs
intermédiaires. Ceci constitue un frein pour l'émergence des
bonnes pratiques. En effet, les producteurs ignorent ce que devient leur cacao
après qu'ils l'aient vendu. Certains ne sont pas convaincus qu'en
faisant plus d'effort pour la qualité, leurs revenus s'en trouveraient
améliorés (CICC, 2013).
L'initiative de mettre en place le PRSC vient à point
nommé avec pour objectifs d'encadrer et d'accompagner les producteurs
dans la prise de conscience de l'impact de leurs activités.
Dans le développement qui suit il sera question de
présenter l'organisation des producteurs, les actions du PRSC et les
résultats attendus des différentes parties prenantes. Les
fèves de cacao quant à elles doivent retrouver ses
caractéristiques organoleptiques (amertume, astringence, acidité,
arôme).
I. PRÉSENTATION DES PRINCIPAUX
PARTIES PRENANTES
Les différents acteurs qui influencent la
filière cacao est étendue et va au-delà des
frontières. Il est important de les évoquer dans le cadre de
notre étude et préciser leur niveau de responsabilité. Il
s'agit entre autre des producteurs qui sont au début de la chaine, les
importateurs, l'UE qui est l'un des plus gros acheteurs, les
coopératives, les mutuelles, les ministères (MINADER,
MINCOMMERCE, MINRESI et MINEPAT), les cellules d'accompagnement et de
régulation (ONCC, SODECAO, SOWEDA, UCCAO, FODECC, CICC, IRAD, PRSC), les
agro-industries (SIC CACAOS, CHOCOCAM, FAPAM) et les transformateurs
artisanaux.
I.1 LE RÔLE ET ATTENTES DES PARTIES
PRENANTES
Il est important pour toutes les parties prenantes que la
filière se porte bien et que chacun trouve son compte.
L'Etat et toutes ses organes concernés souhaitent
accroître les recettes, améliorés le label Cameroun, et
réduire la pauvreté des populations cibles.
Les producteurs souhaitent une rémunération
équitable, assoir des sources de revenus durable et améliorer
leur bien-être.
Au niveau des autres opérateurs, il s'agit de
créer des conditions de concurrence saines et loyale, de disposer un
cadre de concertation permanent et de rentabiliser les investissements.
L'UE souhaite acquérir un produit de qualité,
qui respecte les exigences du consommateur.
I.1.1 LES BENEFICIAIRES DIRECTS DU PROJET
Les premiers bénéficiaires du projet sont les
producteurs de cacao sur l'étendue du bassin. La plupart est
organisée en mutuelles ou en coopératives afin avoir un vrai
pourvoir de négociation avec les acheteurs. Les coopératives
octroient des crédits et des avances sur des paiements.
Ils plantent et assurent l'évolution de la
cacaoyère jusqu'à sa maturité. Ils récoltent,
fermentent, sèchent et assurent le conditionnement. L'organisation en
coopératives leur facilite les tâches telles que la collecte du
produit, le transport et les tracasseries avec les acheteurs bord champ. Il
joue également le relais en termes d'assistance pour les producteurs
dans l'acquisition des produits phytosanitaires.
Dans le cadre du PRSC, les producteurs participent au
processus de collecte des données, ils construisent leurs hangars
eux-mêmes pour abriter leur séchoir SAMOA et ils installent ces
derniers.
I.1.1.1 LA LOCALISATION DES ZONES ARABLES
Le plus important bassin de production des fèves de
cacao se trouve dans la région éponyme du Sud-ouest du Cameroun
entre la latitude 10°23'06,00? Nord et la longitude
3°18'14,40? Ouest. Il pèse environs 40% de la production
nationale.
Bénéficiant d'énormes surfaces arables,
un climat favorable et un sol volcanique riche en humus c'est également
le berceau du cacao culture dans le pays.
Le nombre de producteurs dans cette région est
estimé à 6 000 personnes. La main d'oeuvre est artisanale et
familiale (PRSC, 2014).
Carte 1 : Départements de la région du
Sud-ouest
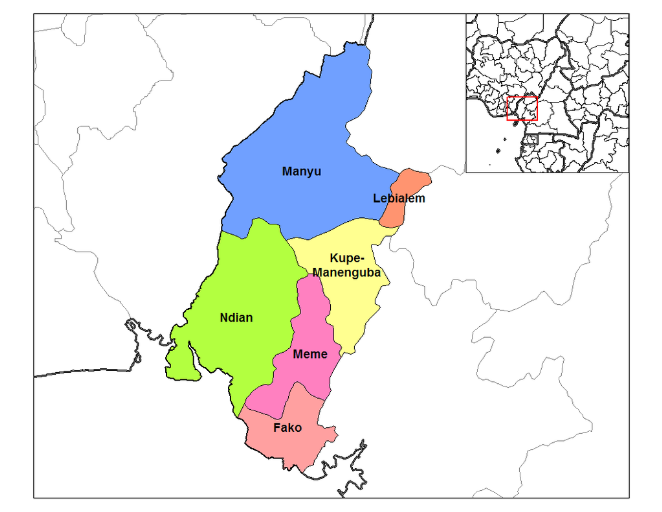
Source:
https://fr.wikipedia.org/wiki/R%C3%A9gion_du_Sud-Ouest_(Cameroun)
Ce bassin de production a un relief très agressif. Les
zones cultivables sont enclavées. On retrouve des chaines de montagnes
et des cours d'eau, ce qui rend des conditions difficiles de transport du cacao
vers les villages.
I.1.1.2 LES CATÉGORIES SOCIALES
Les données recueillies après le sondage sont
classifiées dans le tableau ci-dessous en quatre catégories et
présentent le niveau de scolarisation des producteurs. La
première catégorie renferme 45% de la population cible
(producteurs) sans aucune scolarisation. La deuxième catégorie de
personne représente des personnes ayant arrêté les classes
au niveau primaire à hauteur de 24,5 %. Ces deux groupes de personnes
représentent à eux seuls environs les trois quarts des
producteurs des deux départements où le sondage a
été effectué.
Ces données confirment la nécessité
d'accompagner les producteurs sur le terrain afin qu'ils s'approprient des
prescriptions du procédé de séchage des fèves.
TABLEAU 5 : CATÉGORIE SOCIALE
|
Catégorie de producteurs
|
Fréquence
|
%
|
%
valide
|
%
cumulé
|
Valide
|
N'est Pas allé à l'école
|
90
|
45,0
|
45,0
|
45,0
|
|
A été au primaire
|
49
|
24,5
|
24,5
|
69,5
|
|
A été au secondaire
|
19
|
9,5
|
9,5
|
79,0
|
|
A été au supérieur
|
42
|
21,0
|
21,0
|
100,0
|
|
Total
|
200
|
100,0
|
100,0
|
|
Source : Travail étudiant.
Enquête BAGNAKA (2017)
I.1.1.3 LA RÉPARTITION GÉOGRAPHIQUE DES
PRODUCTEURS
L'enquête nous a conduits auprès des populations
de tous les arrondissements ou communes des départements du FAKO et de
la MÉMÉ. Il nous a permis d'échanger avec les
cacaoculteurs dans ces communes. Tous partagent les mêmes
difficultés. Difficultés du fait de l'enclavement des
plantations. Le besoin en terme de séchoirs SAMOA
« nouvelle génération ».
Au vu de l'importance du sous bassin de KUMBA (chef-lieu du
département de la MÉMÉ), le PRSC y a établi ses
bureaux afin que le déploiement de ses équipes soit retentissant
le plus rapidement possible.
TABLEAU 6 : REPARTITION DES PRODUCTEURS PAR COMMUNE
|
Commune / Arrondissements
|
Fréquence
|
Pourcentage
|
Pourcentage valide
|
Pourcentage cumulé
|
Valide
|
Buéa
|
13
|
6,5
|
6,5
|
6,5
|
|
Limbé 1er
|
9
|
4,5
|
4,5
|
11,0
|
|
Limbé IIe
|
8
|
4,0
|
4,0
|
15,0
|
|
Limbé IIIe
|
9
|
4,5
|
4,5
|
19,5
|
|
Muyuka
|
10
|
5,0
|
5,0
|
24,5
|
|
Tiko
|
8
|
4,0
|
4,0
|
28,5
|
|
West Coast
|
7
|
3,5
|
3,5
|
32,0
|
|
Konye
|
27
|
13,5
|
13,5
|
45,5
|
|
Kumba Ier
|
27
|
13,5
|
13,5
|
59,0
|
|
Kumba IIe
|
41
|
20,5
|
20,5
|
79,5
|
|
Kumba IIIe
|
22
|
11,0
|
11,0
|
90,5
|
|
Mbonge
|
19
|
9,5
|
9,5
|
100,0
|
|
Total
|
200
|
100,0
|
100,0
|
|
Source : Travail étudiant.
Enquête BAGNAKA(2017)
I.1.2 LES POUVOIRS PUBLICS
Le gouvernement du Cameroun a prescrit une relance et de
développement de la filière cacao et café (PRDFCC) pour la
période 2015-2020. Ce plan prévoit un accroissement de la
production à travers l'extension de son verger et l'exploitation
efficiente des réserves de productivité en vue d'une promotion
d'une économie cacaoyère et caféière durable.
Cet engouement des pouvoirs publics est stimulé du fait
que cette filière a généré une progression de 47
000 Tonnes de production de fèves entre 2005 et 2010. Soit une
augmentation en valeur FOB de 195,8 milliards de FCFA. Ajouté à
ceci la stabilité du prix du kilogramme au marché mondial.
(PRDFCC, 2014)
Le PRDFCC a été élaboré de
manière participative, sous la responsabilité de la Cellule
Technique de Suivi et de Coordination de Filières Cacao et Café
(CTSCCC).
I.1.2.1 LES MINISTERES
· Le MINADER
Le MINADER interviendra à travers l'encadrement des
producteurs et la vulgarisation des itinéraires techniques de
production. Il détient des champs semenciers tout comme l'IRAD et la
SODECAO. Ces activités sont également perceptibles à
travers les actions de la CICC.
· Le MINCOMMERCE
Au titre de sa mission organique de promotion et de
défense du label de qualité des produits à l'exportation,
le MINCOMMERCE agit en tant que Maître d'Ouvrage du PRSC.
· Le MINRESI
Le MINRESI est un support à la recherche et au
développement à travers l'IRAD qui détient des champs
semenciers.
I.1.2.2 LES AUTRES ORGANES ETATIQUES
Les organes étatiques ci-dessous sont concernés
directement par ce projet et bénéficient chacune d'une
redevance.
· Le FODECC
C'est le fond de développement des filières
cacao et café, créé par le décret n°20062/085
du 09 Mars 2006, il apporte son appui financier à la relance de la
filière au nom du gouvernement.
· L'ONCC et le CCIC
A la dissolution de l'ONCPB en 1991, s'en est suivie en
substitution la création de l'Office National du Cacao et du Café
(ONCC) et du Conseil Interprofessionnel du Cacao et du Café (CICC).
Créé par le décret N°91/271 du 12
Juin 1991, puis modifié et complétée par le décret
N°97/141 du 25 Août 10097, l'ONCC supervise entre autre, le
contrôle de la qualité, en mettant en exergue les actions
menées dans le cadre de l'amélioration des pratiques
post-récoltes et notamment celles liées à la
réhabilitation des séchoirs de cacao.
En tant qu'organe consultatif regroupant l'ensemble des
intervenants des filières cacao et café, le CICC met à
disposition son expertise pour ce qui est de la facilitation de la tenue
des réunions de concertation avec les producteurs, et du suivi des
travaux de réfection des séchoirs le cas échant.
· LA SODECAO
Les missions de la SODECAO (Société de
développement du cacao) sont plurielles. Sous la tutelle du MINADER,
elle intervient dans :
ü La production et diffusion des plants de cacaoyers
performants ;
ü La production des plants d'accompagnement (bananiers
plantains, arbres fruitiers, légumineuses, etc.) ;
ü L'encadrement technique des producteurs, leur formation
et leur structuration ;
ü L'approvisionnement en intrants ;
ü La protection du verger ;
ü L'appui conseil sur les opérations
post-récoltes ;
ü La promotion de la transformation et à la
consommation locales des produits cacao ;
ü L'appui à la commercialisation ;
ü L'aménagement des espaces agricoles.
· LE PRSC
Il a pour rôle d'implémenter le plan de relance
de la filière sur le terrain. Ces principales missions
sont d'améliorer la productivité, la qualité des
fèves de cacao après le séchage suivant la norme
ISO2291-1972. Ceci nécessite l'accompagnement des producteurs par la
formation sur les procédés de séchage, la mise à
disposition des outils et équipements adaptés (bâches,
séchoirs SAMOA, manuel d'installation et d'utilisation des
séchoirs).
I.2. ORGANISATION DU PRSC
Sous la tutelle du MINCOMMERCE, le chef de projet assure le
pilotage des activités et rend également compte au comité
de suivi.
Les chargés de mission servent d'interface entre le
PRSC et les bénéficiaires. C'est à eux qu'incombe les
activités de terrain telles que les études, la sensibilisation,
le suivi et la formation des producteurs, les enquêtes et la
remontée des informations pour exploitation.
La gestion du projet est assurée par une équipe
structurée comme indiqué par l'organigramme
ci-après :
Figure 27: Organigramme du PRSC
Coordonnateur du Projet
Chargé de mission N°1
Chargé de mission N°2
Responsable approvisionne-ment
Agents de Suivi
Agents de Suivi
- Secrétaire
- Comptable
- Assistant
Responsable Qualité
- Logisticien
- Chauffeurs
Acheteurs
Qualiticiens
- Experts
- Sous-traitants
- Stagiaires
S
Source : PRSC(2014)
I.2.1 LA MÉTHODOLOGIE DE TRAVAIL
Après les enquêtes menées sur le terrain
grâce aux entretiens, à l'observation par les agents de suivi sous
la supervision des chargés de missions, leurs informations sont
traitées et des solutions palliatives sont envisagées.
L'accompagnement peut commencer avec un cahier de charges précis.
Le responsable qualité et ses assistants sont mis
à contribution afin de vérifier la conformité des
fèves après la fermentation. Ces fèves représentent
les données d'entrées dans le processus de séchage.
Le procédé de séchage dure environ une
journée pour environ 400 kg de fèves par claie. Des
prélèvements sont effectués pour analyse toutes les deux
heures. A la fin du séchage les qualiticiens valident ou invalident le
procédé de séchage et la qualité des fèves.
Ces étapes permettent de mettre à jour la procédure de
séchage. Les résultats obtenus sont des retours
d'expérience.
Pour stimuler les producteurs, le ministère du commerce
a promis une prime de séchage pour ceux qui se démarques et dont
les fèves obtiennent une reconnaissance.
Des encouragements sont également apportés par
la SOWEDA et la SODECAO par la distribution gratuite des plants aux
producteurs.
Dans des zones où les séchoirs sont
vétustes, des nouveaux séchoirs sont distribués
gratuitement. Toutes ces mesurent sont mises en oeuvre pour rendre la
filière attractive et stimuler l'effort.
I.2.1.1 LA VÉRIFICATION DES « IN
PUT »
Cette étape consiste à se rassurer que le
procédé de fermentation s'est déroulé suivant les
prescriptions et suivant les règles de l'art.
Beaucoup d'écarts ont en effet été
constatés à travers les résultats des enquêtes. Ceci
nous a permis de confirmer que dans certains cas les fèves de cacao ne
sont pas bien fermentées. Notamment :
· L'utilisation inappropriée des contenants pour
le la fermentation ;
· Le non-respect des durées de
fermentation ;
· L'absence de brassage des fèves à des
périodes indiquées ;
· Le stockage inapproprié des fèves
après fermentation.
La sensibilisation à l'endroit des producteurs sur les
conséquences de cet état des choses est obligatoire.
Il est à souligner que la mauvaise fermentation des
fèves empêche le développement des caractéristiques
organoleptiques de ces derniers. A savoir :
· L'amertume ;
· L'astringence ;
· L'acidité ;
· L'arôme.
Outre ces facteurs essentiels, la fermentation empêche
la germination et l'aspect ardoisé des fèves. Il est important de
rappeler que les défauts de fermentation ne sont pas corrigibles par le
séchage.
Notre enquête nous a permis de confirmer 78,5 % de
producteurs ne respectent pas la durée requise pour la fermentation.
TABLEAU 7 : RESPECT DE LA FERMENTATION
|
Durée de fermentation
|
Fréquence
|
Pourcentage
|
Pourcentage valide
|
Pourcentage cumulé
|
Valide
|
= 3 jours
|
42
|
21,0
|
21,0
|
21,0
|
|
= 5 jours
|
115
|
57,5
|
57,5
|
78,5
|
|
= 7jours
|
43
|
21,5
|
21,5
|
100,0
|
|
Total
|
200
|
100,0
|
100,0
|
|
Source : Travail étudiant.
Enquête BAGNAKA (2017)
I.2.1.2 LE CONTRÔLE DU STOCKAGE DES FÈVES
AVANT LE SÉCHAGE
Une vérification du stockage du cacao fermenté
et en attente du séchage a permis de constater les écarts et de
sensibiliser également les producteurs sur la nécessité
d'aménager un espace tampon propre. Les producteurs doivent se rassurer
qu'une fois la fermentation achevée, le cacao doit être
étalé pour séchage. La photo ci-dessous a
été prise in-situ avant le début du séchage
artificiel.
Photo 9 : Stockage des fèves
fermentées
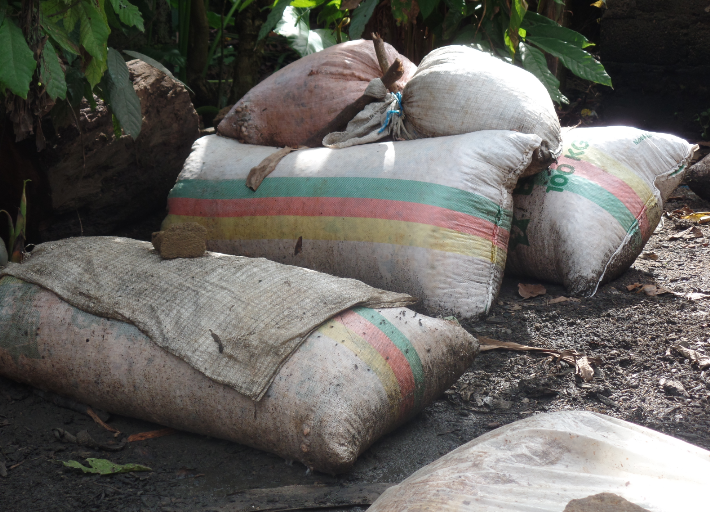
Source : Observation BAGNAKA (2017)
I.2.1.3 LE PROCÉDÉ DE SÉCHAGE
ARTIFICIEL DES FÈVES DE CACAO
Les fèves de cacao sont étalées sur les
étagères au-dessus de la conduite en acier. La chaleur issue de
la combustion du bois de chauffage dans le foyer se répand dans tout le
séchoir.
Un brassage est effectué toutes les deux heures pendant
vingt-quatre heures. Les producteurs n'ont pas la possibilité de
contrôler la température de séchage tout au long du
procédé.
Il a été constaté également que la
porte du foyer reste ouverte à cause de l'absence du système de
ventilation pour entretenir la combustion. Nous avons pu constater
également que des fumées qui se dégagent de ce foyer
reviennent vers les fèves et sont sources de contagion.
Le test de séchage se fait au gouter et au toucher
suivant la dextérité et l'expérience de chaque producteur
qui décide de la fin du séchage.
Photo 10 : Porte du foyer du séchoir ouvert
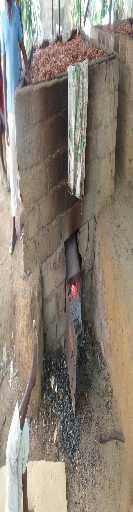
Source : Observation BAGNAKA
(2017)
II. LA DÉMARCHE DE LA MISE EN OEUVRE DES ACTIONS SUR LE
TERRAIN
Les actions à mettre en place sur le terrain doivent
permettre de classifier la graduation des fèves produites.
Seules certaines caractéristiques des fèves de
cacao peuvent donner lieu à une appréciation par des
méthodes objectives: évaluation de la teneur en eau, mesure de la
richesse en beurre de cacao, recherche de résidus de pesticides par
exemple.
Mais, à l'exception de l'évaluation de la teneur
en eau, l'appréciation d'un cacao, au niveau du marché
lui-même, ne fait appel qu'à des méthodes subjectives
limitées le plus souvent à ce que l'on désigne sous le
terme d'« épreuve à la coupe» («cut
test»), c'est-à-dire un examen visuel de la surface de coupe
des cotylédons, complétée parfois par une épreuve
de dégustation.
Le prélèvement des échantillons est
effectué au hasard sur au moins un sac sur trois. La sonde de
prélèvement doit être enfoncée successivement
à la partie supérieure, au milieu et à la partie
inférieure du sac. L'analyse doit porter au moins sur 300 fèves
par tonne ou fraction de tonne de cacao marchand (Maisonneuve et Larose,
1990).
Les résultats obtenus permettent de classifier le cacao
en trois grades (CNUCED, 2016) :
· Qualité I (Grade I)
o Fèves moisies, maximum 3% par test ;
o Fèves ardoisées maximum 3% par test ;
o Fèves plates, germées ou attaquées par
les insectes, maximum total de 3% par test.
· Qualité II (Grade II)
o Fèves moisies, maximum 4% par test;
o Fèves ardoisées maximum 8% par test ;
o Fèves plates, germées ou attaquées par
les insectes, maximum total de 6% par test.
· Qualité III (Grade III)
o Considéré comme hors grade ;
o Fèves moisies > 4% par test ;
o Fèves ardoisées > 8 % par test ;
o Fèves plates, germées ou attaquées par
les insectes, > 6% par test.
II.1 LES ACTIVITÉS DES ÉQUIPES PRSC SUR
LE TERRAIN
Les actions sur le terrain par les équipes du PRSC
consistent à :
· Identifier les séchoirs
vétustes ;
· Réhabiliter les séchoirs
identifiés comme défectueux ;
· Renforcer les capacités des producteurs par la
formation sur le procédé de séchage.
Le troisième point est crucial parce qu'il permet de
rendre les producteurs autonomes et professionnels.
L'objectif des activités à terme ont pour but
d'améliorer la qualité du cacao Cameroun qui est actuellement
relégué au grade II suivant le classement de le FCC
(Federation of Cocoa Commerce).
Le tableau ci-après montre sur la population
enquêtée, 52 % de producteurs produisent un cacao de grade II et
22% de producteurs produisent un cacao hors standard, ce qui constitue une
forte perte de production.
TABLEAU 8 : QUALITÉ DES FÈVES
SECHÉES
|
Niveau de qualité
|
Fréquence
|
Pourcentage
|
Pourcentage valide
|
Pourcentage cumulé
|
Valide
|
Grade I
|
52
|
26,0
|
26,0
|
26,0
|
|
Grade II
|
104
|
52,0
|
52,0
|
52,0
|
|
Grade III (Hors standard)
|
44
|
22,0
|
22,0
|
74,0
|
|
Total
|
200
|
100,0
|
100,0
|
|
Source : Travail étudiant.
Enquête BAGNAKA (2017)
II.1.1. LES DIFFICULTÉS DES PRODUCTEURS PENDANT
LE SÉCHAGE
Nous avons effectué la recension des difficultés
des producteurs après observation des opérations de
séchage et à travers notre questionnaire.
Les résultats de cette enquête permettent
d'affirmer que le système de séchage est responsable de la
contamination de la fumée dans les fèves.
Pour chaque difficulté décelée, les
producteurs doivent être capables d'y faire face ou alors de se
référer à la coopérative dans laquelle il est
affilié.
Le tableau ci-après ressort la récurrence des
problèmes rencontrés par les producteurs tout au long du
processus de séchage. La quasi-totalité des préoccupations
sont liées à la combustion et à l'évacuation des
fumées source de contamination
TABLEAU 9 : REPERTOIRE DES DIFFICULTES RENCONTREES PAR LES
PRODUCTEURS PENDANT LE SECHAGE
|
Difficultés des producteurs
|
Fréquence
|
Pourcentage
|
Pourcentage valide
|
Pourcentage cumulé
|
Valide
|
Utilisation exagéré du bois de chauffage
|
51
|
25,5
|
25,5
|
25,5
|
|
Evacuation des fumées
|
31
|
15,5
|
15,5
|
41,0
|
|
Ventilation du foyer
|
28
|
14,0
|
14,0
|
55,0
|
|
Répartition inégale de la chaleur
|
25
|
12,5
|
12,5
|
67,5
|
|
Absence de l'étanchéité sur la
cheminée
|
30
|
15,0
|
15,0
|
82,5
|
|
Contrôle de température
|
35
|
17,5
|
17,5
|
100,0
|
|
Total
|
200
|
100,0
|
100,0
|
|
Source : Travail étudiant.
Enquête BAGNAKA (2017)
II.1.2 LA NÉCESSITÉ DE FORMATION DES
PRODUCTEURS
L'enquête sur le terrain a permis de confirmer que la
plupart des producteurs ne sont pas formés. La majorité
n'étant pas scolarisé et incapable d'être autodidacte.
Le tableau ci-dessous indique que 76,5% de producteurs n'ont
aucune formation sur le procédé de séchage artificiel.
Tous sont formés sur le tas.
Dans le lot de 23,5% restant, il existe une partie de
producteurs illettrés qui ne comprend pas la nécessité de
se former.
TABLEAU 10 : ESTIMATION DU BESOIN EN FORMATION
|
Besoin en formation sur le processus de séchage
artificiel
|
Fréquence
|
%
|
%
valide
|
% cumulé
|
Valide
|
Oui
|
47
|
23,5
|
23,5
|
23,5
|
|
Non
|
153
|
76,5
|
76,5
|
100,0
|
|
Total
|
200
|
100,0
|
100,0
|
|
Source : Travail étudiant.
Enquête BAGNAKA (2017)
II.2. LE DIAGNOSTIC SUR LE TERRAIN
Le diagnostic est schématisé par l'arbre
à problèmes ci-après afin d'analyser les causes et les
conséquences. L'objectif est d'identifier le problème central,
ses effets et les causes premières. Il clarifie les objectifs essentiels
d'une intervention voulant s'attaquer à ce problème central et
à parvenir à un accord sur les activités requises pour les
atteindre.
Figure 28 : Arbre des problèmes
Les fèves de cacao sont de qualité
médiocre après séchage
(Fève de Grade II)
Les séchoirs SAMOA ont des défauts
Les producteurs ne maitrisent pas le procédé de
séchage des fèves
Le label Cameroun se dégrade sur le marché
international
Les pertes post récoltes élevées
Les prix de vente sont dépréciés
La production nationale de cacao diminue
La rentabilité de la filière cacao diminue
Le cacao Camerounais est boudé sur le marché
international
La filière cacao est moins attractive
Source: BAGNAKA (2017)
II.3. LES OBJECTIFS À ATTEINDRE
L'élaboration d'un arbre à problèmes oblige
une représentation des objectifs sur un arbre à objectifs. Ce
dernier permet :
· De mieux appréhender l'objectif principal en le
décomposant en sous-objectifs ;
· D'établir une hiérarchie des objectifs
;
· De mettre en évidence les relations entre les
objectifs ;
· De montrer comment les sous-objectifs vont permettre
d'atteindre l'objectif principal.
Figure 29 : Arbre des objectifs
Les pertes post récoltes sont diminuées
Les fèves de cacao sont de qualité meilleure
après séchage (Fève de Grade
I)
Les défauts des séchoirs SAMOA sont
corrigés
Les producteurs sont formés et motivés
Le label Cameroun est rehaussé sur le marché
international
Les prix de vente sont relevés
La production nationale de cacao augmente
La rentabilité de la filière cacao est
améliorée
Le cacao Camerounais est plus demandé sur le
marché international
La filière cacao est plus attractive
Source: BAGNAKA (2017)
CONCLUSION DU CHAPITRE 4
Dans ce chapitre, il a été
démontré que la dégradation des fèves de cacao est
liée aux insuffisances dans l'application du procédé du
procédé de séchage.
Le PRSC sait dorénavant qu'au-delà de la
distribution des séchoirs qui reste une initiative louable, un
accompagnement auprès des producteurs est indispensable. Il doit se
matérialiser par la formation sur les techniques de séchage, la
sensibilisation sur l'impact des mauvaises pratiques post récolte.
Ce chapitre répond à la deuxième
hypothèse à savoir « L'accompagnement des producteurs
dans le procédé de séchage artificiel est
nécessaire pour améliorer la qualité des fèves de
cacao ». La vérification de cette hypothèse est
justifiée par le résultat constaté en 2018. Les
fèves exportées en Grade I sont passées de 1099 à
8933 Tonnes entre les deux dernières campagnes.
Ces résultats sont possibles grâce à des
centres d'excellence de traitement post-récolte du cacao dans certains
sous-bassins de production qui sont progressivement mis en place par le CICC au
profit des coopératives formées à de meilleures pratiques
culturales et post-récoltes.
CONCLUSION DE LA SECONDE PARTIE
Des espoirs sont actuellement placés dans la
filière cacao pour réduire la dépendance de
l'économie camerounaise au secteur extractif. Le Document de
Stratégie pour la Croissance et l'Emploi (DSCE) adopté en 2009
fait de la dynamisation de cette filière une de ses priorités
(aux côtés des cultures de café, de la banane et du coton),
avec pour double objectif d'augmenter le niveau de production et de renforcer
la transformation locale.
Le PRSC a une mission de cinq ans pour contribuer à
l'atteinte des objectifs du plan de relance de la filière cacao. Le
gouvernement camerounais annonçait en 2014 sa volonté de porter
à 600 000 tonnes la production annuelle de cacao à l'horizon
2020. Bien que la CCIC estime ces objectifs très ambitieux, les
résultats de ces deux dernières années sont encourageants.
Les évaluations du projet à mi-parcours vont
permettre de recadrer les actions et relever ces défis.
Au sortir de nos enquêtes beaucoup d'écarts ont
été constaté du point de vue du respect de l'environnement
avec le déboisement des forêts afin de générer de la
combustion dans les séchoirs.
Les producteurs également estiment que l'État
doit contribuer en totalité pour l'installation des séchoirs
à leur position finale. Le PRSC gagnerait à remonter ces
préoccupations qui ont pour seul but de motiver les producteurs et de
s'assurer que les séchoirs sont conformes et remplissent leur
fonction
.
CONCLUSION
GÉNÉRALE
Le séchage de cacao est l'une des dernières
étapes post récolte la plus importante. Il a fait l'objet de la
thématique en analyse tout au long de notre étude. Afin
d'apporter notre pierre à l'édifice, nous avons intitulé
notre thème de mémoire de la manière suivante :
« Amélioration du système de séchage artificiel
des fèves de Cacao dans les régions à forte
pluviométrie: Cas du bassin de production du Sud-ouest ».
L'interrogation principale qui a orienté notre
recherche a consisté à se demander comment améliorer le
système de séchage artificiel dans le bassin du Sud-Ouest afin
que les fèves de cacao soient de qualité meilleure. Cette
question a engendré deux nouvelles questions spécifiques, la
première étant de savoir si les séchoirs SAMOA sont-ils
susceptibles d'amélioration et la seconde de savoir si les producteurs
se sont-ils appropriés du procédé de séchage
artificiel des fèves de cacao.
Des hypothèses ont été posées pour
répondre par anticipation à cet ensemble de préoccupation,
atteindre nos objectifs et déterminer notre travail. L'hypothèse
principale a été que : l'amélioration du
système de séchage des fèves de cacao contribue à
améliorer la qualité de celles-ci. L'hypothèse
spécifique n° 1 pour sa part a été libellée de
la manière suivante : les séchoirs SAMOA présentent des
défauts de fabrication qui peuvent être corrigés ;
tandis que l'hypothèse n°2 se présente ainsi :
l'accompagnement des producteurs dans le procédé de
séchage artificiel est nécessaire pour améliorer la
qualité des fèves de cacao.
Deux grandes parties nous ont servi de support. Elles ont
été structurées de sorte à exposer chacune un
chapitre théorique portant respectivement sur le cadre conceptuel des
défauts de fabrication des équipements et l'analyse
théorique de la GRH en vue de l'optimisation de la qualité. Pour
chaque partie de notre travail, nous avons contextualisé nos
théories par deux chapitres, l'état des lieux de la construction
et de la maintenance des équipements pour le premier chapitre et
l'amélioration de la qualité des fèves par l'encadrement
des cacaoculteurs pour le deuxième chapitre.
Les deux réponses prédites ont pu être
confrontées par l'expérience et confirmées par les deux
chapitres empiriques. La première l'a été par l'existence
d'indicateurs que nous notons : la nécessité de
réviser le cahier des charges des séchoirs SAMOA, la mise en
place d'un plan de contrôle qualité pendant la fabrication des
séchoirs, le recrutement de la maitrise d'oeuvre et l'élaboration
d'une notice d'utilisation du séchoir. La deuxième est
confirmée par la nécessité d'encadrer les cacaoculteurs
par la formation, la communication et accompagnement permanent sur le
terrain.
Au terme de notre étude, nous avons pu formuler des
recommandations au PRSC, parmi lesquelles, à court terme, la
révision du cahier des charges, le recrutement d'un expert en
construction métallique ; l'assistance à l'installation des
séchoirs à leur position finale. A moyen terme le PRSC doit faire
recours à la cartographie par géolocalisation des séchoirs
livrés ; la substitution de la combustion au bois par du biogaz
afin de limiter le déboisement ; l'installation d'un dispositif de
contrôle de température pendant le séchage.
* 1 L., abréviation de
Linnaeus : Accompagne généralement l'espèce du
cacaotier qui fait l'objet de notre étude (Theobroma cacao L.). Carl
Linnæus, puis Carl Von Linné après son
anoblissement,
né le
23 mai
1707 à
Råshult et mort
le
10
janvier
1778 à
Uppsala, est un
naturaliste
suédois qui a
fondé les bases du système moderne de la
nomenclature
binominale.
* 2 Les Mayas (
2600 av.
J.-C. à
1520 apr. J.-C.), formaient
l'une des grandes
civilisations de
Mésoamérique
principalement connue pour ses avancées dans les domaines de l'
écriture, de
l'art, de l'architecture, de l'
agriculture, des
mathématiques et de l'astronomie.
* 3 Les Aztèques (
1200 apr. J.-C. jusqu'à
1521 apr. J.-C.)
Ou Mexicas (du nom de leur capitale,
Mexico-Tenochtitlan),
étaient un peuple
amérindien.
* 4
Les Olmèques sont un ancien peuple précolombien de
Mésoamérique s'étant épanoui de 1200 av. J.-C.
jusqu'à 500 av. J.-C. sur la côte du golfe du Mexique, dans le
bassin de Mexico, et le long de la côte Pacifique (États du
Guerrero, Oaxaca et Chiapas)
* 5 Les ochratoxines A (OTA)
sont des mycotoxines produites par plusieurs
champignons microscopiques
(genres
Penicillium et
Aspergillus) et
naturellement présentes dans de nombreux produits végétaux
du monde entier, tels que les
céréales, les
grains de
café, le
cacao et les
fruits séchés.
C'est un poison naturel fortement toxique pour les reins et pouvant être
cancérogène, qui est produit par une moisissure que l'on trouve
parfois sur les fèves de café et de cacao.
* 6 Hydrocarbures Aromatiques
Polycycliques sont des constituants naturels du charbon et du
pétrole, ou qui proviennent de la combustion incomplète de
matières organiques telles que les carburants, le bois, le tabac.
Ils sont présents dans l'air, l'eau ou l'alimentation.
* 7 Adam Smith, (
1723 -
1790) est un
philosophe et
économiste écossais
considéré comme le père des
sciences
économiques modernes.
* 8 Frederick Winslow Taylor,
(
1856-
1915) est un ingénieur
américain, promoteur le plus connu de l'
organisation
scientifique du travail
* 9 Henri Fayol, (1841-1925) est un
ingénieur
civil des mines
français,
un des pionniers de la gestion d'entreprise
* 10 Max Weber (1864-1920)
est un
économiste et
sociologue
allemand originellement
formé en droit
* 11 Henry Ford, (1863-1947)
est un industriel de la première moitié
du 20e siècle et le fondateur du constructeur
automobile
Ford.
* 12 Eiji Toyoda (1913-1993)
est un industriel japonais, cousin et collaborateur de
Kiichiro Toyoda (
1894-1952) lui même
fils de
Sakichi Toyoda (
1867-1930), fondateur du
groupe japonais
Toyota.
* 13 Taiichi Ohno
(1912-1990) est un
ingénieur
industriel japonais. Il est considéré comme le
père du système de production de
Toyota
* 14 Walter A. Shewhart
(1891-1967) est un physicien et statisticien américain,
considéré comme le père de l'assurance qualité.
* 15 William Edwards Deming
(1900-1993) est un
statisticien,
professeur d'université, auteur et consultant américain.
* 16 Mikel J. Harry
(1951-2017) Ingénieur chez Motorola
* 17 William Bill Smith Jr,
(1929-1993) Ingénieur chez Motorola
* 18 Eliyahu M. Goldratt,
(1947-2011) est un
consultant
israélien,
physicien de formation
* 19 Michael Martin Hammer
(1948-2008) était un ingénieur américain, auteur de
gestion et ancien professeur d'informatique au
Massachusetts
Institute of Technology (MIT), connu comme l'un des fondateurs avec
James
A. Champy (né en 1942) de la théorie de la
gestion des
processus
d'affaires. La réingénierie (BPR)
* 20 William Whewell, est
un
polymathe anglais,
scientifique,
philosophe et
historien des
sciences, né à
Lancaster le
24 mai
1794 et mort
à
Cambridge le 6
mars
1866.
* 21 MOA : Maître
d'ouvrage
* 22 AMDEC : Analyse
des Modes de Défaillances, de leurs Effets et de leur Criticité.
Est un outil de sûreté de fonctionnement et de gestion de la
qualité développé par l'armée américaine
dans les années 1940.
* 23 Ce type de maintenance
est de loin le plus intéressant Il permet de décider du
changement de la pièce en fonction de l'évolution de l'usure. De
plus, la mesure régulière de l'état de l'usure permet de
mieux appréhender le fonctionnement de la machine et ainsi, mieux cerner
les problèmes et les solutions à y apporter.
* 24 Benchmarking :
c'est une technique marketing ou de gestion de la qualité qui consiste
à étudier et analyser les techniques de gestion, les modes
d'organisation des autres entreprises afin de s'en inspirer et d'en tirer le
meilleur
* 25 Lean Six Sigma :
concept apparut pour la première fois en 2001, dans un livre
intitulé Leaning into Six Sigma: The Path to integration of
Lean Enterprise and Six Sigma, écrit par Barbara Wheat, Chuck Mills
et Mike Carnell
* 26 La marche
Genba ou Gemba est mot d'origine japonaise et qui désigne
une activité des managers qui consiste à aller sur le terrain
pour rechercher les gaspillages et les opportunités
d'amélioration
* 27 Pareto était un
économiste italien du 17ème siècle qui avait
remarqué que 80% des sommes payées au titre des impôts
étaient données par 20% des contribuables. Cette proportion de
relation entre causes et effets se rencontre fréquemment dans de
nombreuses autres observations.
* 28 ISO 9001 est une norme
internationale qui spécifie les exigences relatives au système de
management de la qualité lorsqu'un organisme doit démontrer son
aptitude à fournir régulièrement un produit conforme aux
exigences des clients et aux exigences réglementaires applicables. Elle
vise à accroître la satisfaction de ses clients par l'application
efficace du système, y compris les processus pour l'amélioration
continue du système et l'assurance de la conformité aux exigences
des clients et aux exigences réglementaires applicables.
* 29 Frank Knight
(1885-1972) est un économiste américain fondateur de la
première école de Chicago. Membre de l'académie des
américaine des arts et des sciences
* 30 John Maynard Keynes
(1883-1946) est
économiste,
haut
fonctionnaire et
essayiste
britannique. Il est le
fondateur de la
macroéconomie
keynésienne.
* 31 Ulysse ou Odysseus est
l'un des héros les plus célèbres de la mythologie grecque
du temps de la guerre de Troie et dont le fils s'appelait
Télémaque
|