Carte de flux énergétiques et perspectives
d'efficacité dans une fonderie d'aluminium: cas particulier
d'alucam/socatral
UNIVERSITE DE YAOUNDE I UNIVERSITY OF YAOUNDE I
FACULTE DES SCIENCES FACULTY OF SCIENCE
DEPARTEMENT DE PHYSIQUE
LABORATOIRE D'ANALYSE DES TECHNOLOGIES DE L'ENERGIE ET DE
L'ENVIRONNEMENT (L.A.T.E.E)
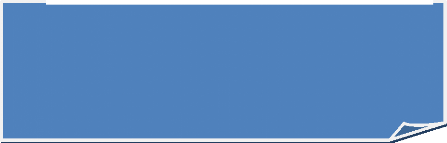
CARTE DES FLUX ENERGETIQUES ET PERSPECTIVES
D'EFFICACITE ENERGETIQUE DANS UNE FONDERIE D'ALUMINIUM : CAS PARTICULIER
DE LA FONDERIE D 'ALUCAM/SOCATRAL
Mémoire présenté et soutenu en vue de
l'obtention du Diplôme d'Etudes Approfondies (D.E.A) en
Physique Option : ENERGETIQUE Par NGOLLO MATEKE
Jean-aimé Maître ès Physique Sous
la Direction de : Prof. Dr.-Hab. NJOMO Donatien Maître
de Conférences Année académique : 2008/2009
Carte de flux énergétiques et perspectives
d'efficacité dans une fonderie d'aluminium: cas particulier
d'alucam/socatral
A mon feu père NGOLLO MOUANDJO Victor, tu
continues à vivre en moi. A ma tendre maman
Eboulè Matèkè Véronique pour ton amour et
soutien inconditionnel,
A mes frères et soeurs Aurore, Emmanuel, David,
Victorien NGOLLO, Pascal, Manfred, Grace, Flore, Urbain, Rebecca,
Emile, pour tous vos encouragements.
A Mlle Din Jeanne-léonie pour ton soutien.
Je vous aime profondément
Carte de flux énergétiques et perspectives
d'efficacité dans une fonderie d'aluminium: cas particulier
d'alucam/socatral
On dit souvent que le trajet est aussi important que la
destination. J'ai beaucoup appris de la vie tout au long de la rédaction
de ce mémoire. Ce parcours ne s'est pas fait sans défis, des
grands moments de doute. Je ne saurai me déroger à l'honneur qui
m'est offert aujourd'hui d'exprimer ma profonde gratitude à tous ceux et
celles qui m'ont encouragé.
Je rends grâce à JEHOVAH mon DIEU sans qui rien
n'est possible.
Je remercie le Pr. Dr. - Hab. Njomo Donatien mon directeur de
recherche pour son encadrement exemplaire, pour ses conseils précieux et
pour sa grande disponibilité.
Je remercie les responsables d'Alucam Messieurs : Alain Crapart
(directeur d'usine), Charles Ndjock (responsable des contrats maintenance) pour
leurs multiples conseils.
Je suis hautement reconnaissant à l'endroit de tous mes
enseignants de Physique, qui m'ont inculqué l'amour de la Physique ; Je
pense aux enseignants de la Faculté des Sciences de l'Université
de Douala au Dr Monkam David et au Dr O. Motapon en particulier. Et à
ceux de la Faculté des Sciences de l'Université de Yaoundé
I, Plus particulièrement à ceux du Laboratoire d'Analyse des
Technologies de l'Energie et de l'Environnement (L.A.T.E.E), Je pense au Dr.
Obounou Marcel et au Dr. Ekobena Henry.
Un grand merci à mon oncle le Pr. Mbonji Mbonji et sa
femme le Pr. Mouelle Mbonji pour leurs conseils.
Je remercie grandement mon grand frère Victorien Ngollo
depuis paris pour son soutien incontestable.
Un grand merci à Madame Mine (mère poule) et
à tous ses enfants ; j 'ai trouvé en toi une seconde maman,
à Tata Véro. Et au grand frère Colbert pour l'accueil
qu'ils m'ont réservé durant mon séjour à
Edéa.
Je tiens également à remercier mes grands
frères Massodi Lafont, Essembe Black, Martin Ebollo, Priso
léon.
Merci à mes neveux et nièces Nathalie, Rachel,
Donald, Willy, Alexandra, Brian, Abigaëlle, Ryan, Cohen, Priscilla et
Fritz pour toute la joie qu'ils m'apportent.
Merci à Michelle, Moukate Priso Corinne (mère DIN),
Freddy, Nadine, Emmanuelle, Andy, Boris et Willy pour leurs encouragements.
A mon amie Gaelle bobillot pour ses encouragements.
J'aimerais également remercier mes amis et camarades de
promotion pour l'ambiance conviviale qui a toujours régné au sein
du groupe, je pense ici à Kodji, Tamba, Fotseu, Noumi, Cyril, Castro,
Magloire, et Fossi.
A tous ceux et celles qui de près ou de loin ont
contribué à l'élaboration de ce travail, et que je n'ai
pas pu citer ici.
Carte de flux énergétiques et perspectives
d'efficacité dans une fonderie d'aluminium: cas particulier
d'alucam/socatral
DEDICACES i
REMERCIEMENTS ii
TABLE DES MATIERES~~~~~~~~~~~~~~~~~~~~~~~~~~~~~~~~~~~~~~~~ iii
TABLES DES PHOTOS ET FIGURES~~~~~~~~~~~~~~~~~~~~~~~~~~~~~~~~~
vii
TABLES DES GRAPHES~~~~~~~~~~~~~~~~~~~~~~~~~~~~~~~~~~~~~~~ viii
LISTE DES ABBREVIATIONS~~~~~~~~~~~~~~~~~~~~~~~~~~~~~~~~~~~~ ix
RESUME/ABSTRACT x
INTRODUCTION GENERALE 1
CHAPITRE I: PRESENTATION GENERALE
D'ALUCAM/SOCATRAL~~~~~~~~~~~~~~~ 3
INTRODUCTION~~~~~~~~~~~~~~~~~~~~~~~~~~~~~~~~~~~~~~~~~~~~ 4
I.1.1 Situation géographique 4
I.1.2 Bref historique~~~~~~~~~~~~~~~~~~~~~~~~~~~~~~~~~~~~~~~~~~
4
I.1.3 Organigramme activité Cameroun 5
I.1.4 Le groupe Alucam en
Afrique~~~~~~~~~~~~~~~~~~~~~~~~~~~~~~~~~~ 5
I.1.5 Histoire de
l'Aluminium~~~~~~~~~~~~~~~~~~~~~~~~~~~~~~~~~~~~~ 6
I.2 Process ALUCAM/SOCATRAL~~~~~~~~~~~~~~~~~~~~~~~~~~~~~~~~~~~
7
I.2.1 Process Alucam 8
I.2.1.1 Atelier d'électrodes 8
I.2.1.2 Atelier
d'électrolyse~~~~~~~~~~~~~~~~~~~~~~~~~~~~~~~~~~~~~~ 9
I.2.1.3 Atelier de fonderie~~~~~~~~~~~~~~~~~~~~~~~~~~~~~~~~~~~~~~
10
I.2.1.4 Laboratoire~~~~~~~~~~~~~~~~~~~~~~~~~~~~~~~~~~~~~~~~~~
10
I.2.1.5 Les services généraux 10
I.2.2 Process Socatral~~~~~~~~~~~~~~~~~~~~~~~~~~~~~~~~~~~~~~~~~
10
I.2.2.1 Le laminage~~~~~~~~~~~~~~~~~~~~~~~~~~~~~~~~~~~~~~~~~~
10
I.2.2.2 Le formage 11
I.2.2.3 Le
découpage~~~~~~~~~~~~~~~~~~~~~~~~~~~~~~~~~~~~~~~~~ 11
I.2.2.4 Production pour la grande
exportation~~~~~~~~~~~~~~~~~~~~~~~~~~~ 11
I.3 Fourniture
d'énergie~~~~~~~~~~~~~~~~~~~~~~~~~~~~~~~~~~~~~~~ 11
I.3.1 Configuration
d'exploitation~~~~~~~~~~~~~~~~~~~~~~~~~~~~~~~~~~ 12
Carte de flux énergétiques et perspectives
d'efficacité dans une fonderie d'aluminium: cas particulier
d'alucam/socatral
1.3.1.2 Alimentation 13
Conclusion 13
CHAPITRE II : CARACTERISTIQUES
ENERGETIQUES~~~~~~~~~~~~~~~~~~~~~~ 14
INTRODUCTION 15
II.1 Caractéristiques
électriques~~~~~~~~~~~~~~~~~~~~~~~~~~~~~~~~~~~ 15
II.1.1 Le réseau
électrique~~~~~~~~~~~~~~~~~~~~~~~~~~~~~~~~~~~~~~ 15
II.1.1.1 Jeu de barres~~~~~~~~~~~~~~~~~~~~~~~~~~~~~~~~~~~~~~~~~
15
11.1.1.2 Les transformateurs~~~~~~~~~~~~~~~~~~~~~~~~~~~~~~~~~~~~~
15
11.1.1.3 Les disjoncteurs~~~~~~~~~~~~~~~~~~~~~~~~~~~~~~~~~~~~~~~
16
11.1.2 Paramètres électriques 16
11.1.2.1 Energie active 16
11.1.2.2 Energie
réactive~~~~~~~~~~~~~~~~~~~~~~~~~~~~~~~~~~~~~~~ 16
II.1.2.3 Energie apparente~~~~~~~~~~~~~~~~~~~~~~~~~~~~~~~~~~~~~~
16
11.1.2.4 Facteur de Puissance 16
11.1.2.5 Inconvénients et compensation de l'énergie
réactive~~~~~~~~~~~~~~~~~~~ 17
II.1.2.6 La chute de tension 18
11.1.2.7 Les harmoniques~~~~~~~~~~~~~~~~~~~~~~~~~~~~~~~~~~~~~~~
19
II.1.2.8 Les courants de
court-circuit~~~~~~~~~~~~~~~~~~~~~~~~~~~~~~~~ 20
11.1.2.9 Effets d'anodes~~~~~~~~~~~~~~~~~~~~~~~~~~~~~~~~~~~~~~~~
20
11.2 Caractéristiques des
combustibles~~~~~~~~~~~~~~~~~~~~~~~~~~~~~~~ 21
11.2.1 Définition de la
combustion~~~~~~~~~~~~~~~~~~~~~~~~~~~~~~~~~~ 21
11.2.2 Energie dégagée et pouvoir calorifique 21
11.2.3 Combustion stoechiométrique 22
11.2.4 Combustion complète avec excès
d'air~~~~~~~~~~~~~~~~~~~~~~~~~~~~ 22
11.2.5 Combustion complète avec défaut d'air 23
11.2.6 La position du
brûleur~~~~~~~~~~~~~~~~~~~~~~~~~~~~~~~~~~~~~ 23
11.2.7 Contrôle de
combustion~~~~~~~~~~~~~~~~~~~~~~~~~~~~~~~~~~~~ 23
II.2.7.1 Interprétation de la teneur en CO2
~~~~~~~~~~~~~~~~~~~~~~~~~~~~~ 23
11.2.7.2 Mesures des
imbrûlés~~~~~~~~~~~~~~~~~~~~~~~~~~~~~~~~~~~~ 24
Carte de flux énergétiques et perspectives
d'efficacité dans une fonderie d'aluminium: cas particulier
d'alucam/socatral
II.2.7.3 Interprétation de la température des
fumées......................................................................24 Conclusion...........................................................................................................................................24 CHAPITRE
III : CARTES DE FLUX
ENERGETIQUES.......................................................................25
Introduction 26
III.1 Evolution de la consommation électrique 26
III.1.1 Consommation électrique atelier
électrolyse.........................................................................26
III.1.2 Consommation électrique des auxiliaires électrolyse 27
III.1.3 Consommation électrique atelier décharge
alumine.............................................................27
III.1.4 Consommation électrique des compresseurs 28
III.1.5 Consommation électrique atelier
d'électrodes.....................................................................
28
III.1.6 Consommation électrique auxiliaires scellement
29
III.1.7 Consommation four à cuire 29
III.1.8 Consommation électrique éclairage usine
30
III.1.9 Consommation électrique conditionnement des
bâtiments généraux 30
III.1.10 Consommation électrique atelier de
mécanique 31
III.1.11 Consommation électrique atelier électrique
31
III.1.12 Consommation électrique station de
pompage.................................................................. 32
III.1.13 Consommation électrique atelier de fonderie 32
III.1.14 Consommation électrique du four junker 33
III.1.15 Consommation électrique des hottes de
captation............................................................ 33
III.1.16 Consommation électrique du centre
médical.....................................................................
34
III.1.17 Consommation électrique poste Serem 34
III.1.18 Consommation électrique Socatral 35
III.2 Consommation de l'énergie calorifique 36
III.2.1 Consommation d'énergie calorifique du secteur
électrodes................................................ 36
Conclusion 36
CHAPITRE IV : ANALYSES ET
PERSPECTIVES...............................................................................37
Introduction..........................................................................................................................................38
Carte de flux énergétiques et perspectives
d'efficacité dans une fonderie d'aluminium: cas particulier
d'alucam/socatral
IV.1 Energie théorique
requise~~~~~~~~~~~~~~~~~~~~~~~~~~~~~~~~~~~ 38
IV.2 Evolution de la production mensuelle
d'aluminium~~~~~~~~~~~~~~~~~~~~~ 39
IV.3 Analyse et interprétation de
l'IPM~~~~~~~~~~~~~~~~~~~~~~~~~~~~~~~ 40
IV.4 Analyse de la consommation des compresseurs 41
IV.5 Analyse de la consommation électrique de
l'éclairage~~~~~~~~~~~~~~~~~~~~ 42
IV.6 Analyse de la consommation d'énergie
calorifique~~~~~~~~~~~~~~~~ 42
Conclusion 42
CONCLUSION
GENERALE~~~~~~~~~~~~~~~~~~~~~~~~~~~~~~~~~~~~~~ 43
ANNEXES~~~~~~~~~~~~~~~~~~~~~~~~~~~~~~~~~~~~~~~~~~~~~~~.46
ANNEXE I ~~~~~~~~~~~~~~~~~~~~~~~~~~~~~~~~~~~~~~~~~~~~~~~ 47
ANNEXE II ~~~~~~~~~~~~~~~~~~~~~~~~~~~~~~~~~~~~~~~~~~~~~~ 50
REFERENCES~~~~~~~~~~~~~~~~~~~~~~~~~~~~~~~~~~~~~~~~~~~~~
56
Carte de flux énergétiques et perspectives
d'efficacité dans une fonderie d'aluminium: cas particulier
d'alucam/socatral
TABLES DES GRAPHES
Graphe III.1 : Atelier d'électrolyse
Graphe III.2 : Aux. Electrolyse
Graphe III.3 : Atelier décharge alumine
Graphe III.4 : Compresseurs
Graphe III.5 : atelier d'électrodes
Graphe III.6 : Auxiliaires scellement
Graphe III.7 : Four à cuire
Graphe III.8 : Eclairage usine
Graphe III.9 : Conditionnement bâtiments
généraux
Graphe III.10 : Atelier de mécanique
Graphe III.11 Atelier électrique
Graphe III.12 : Station de pompage
Graphe III.13 Atelier fonderie
Graphe III.14 : Fours junker
Graphe III.15 : Hottes de captation
Graphe III.16 : Centre médical
Graphe III.17 : Poste Serem
Graphe III.18 : Socatral
Graphe III.19 : Secteur électrodes
Graphe IV. 1 : Production mensuelle d'aluminium
Graphe IV.2 : Proportion d'énergie électrique
consommée par secteur Graphe IV.3 : Indice de puissance maximale
Carte de flux énergétiques et perspectives
d'efficacité dans une fonderie d'aluminium: cas particulier
d'alucam/socatral
TABLES DES PHOTOS ET DES FIGURES
Photo 1 : Usine d'Edéa vue aérienne
Photo 2 : Une électrode
Photo 3 : Cuve d'électrolyse
Photo 4 : Lingots
Photo II.1 Explications sur les ICC
Figure I.1 : Etapes de fabrication de l'aluminium Figure 2.1
Composition vectorielle des puissances
Carte de flux énergétiques et perspectives
d'efficacité dans une fonderie d'aluminium: cas particulier
d'alucam/socatral
LISTE DES ABBREVIATIONS
AL2O3 : Alumine
cv : Cheval vapeur
GR : générateur
JDBD : jeu de barre droit
JDBG : jeu de barre gauche
ICC : courant de court-circuit
kVA : kilovolt Ampère
kVar : kilovolt Ampère réactif GWh : Gigawatt
heure
MWh : Mégawatt heure
PFC : Perfluorocarbures
IPM : Indice de puissance maximale
Carte de flux énergétiques et perspectives
d'efficacité dans une fonderie d'aluminium: cas particulier
d'alucam/socatral
RESUME
Ce mémoire présente l'usine ALUCAM/SOCATRAL,
analyse et interprète les résultats issus des mesures de la
consommation de l'énergie électrique, et calorifique de chaque
atelier du processus de production d'aluminium.
Il présente l'évolution électrique par
atelier sur une période de 24 mois (Janvier 2007/Décembre 2008),
et l'évolution de la consommation de l'énergie calorifique du
secteur électrodes pendant la même période. Puis on propose
après avoir ciblé les ateliers à fortes pertes
d'énergie, quelques solutions pour y répondre.
ABSTRACT
This thesis presents the plant ALUCAM/SOCATRAL. The
manufacturing process of aluminum analyzes and interprets the results of the
consumption of electric power and heat output of each workshop in the
manufacture of aluminum.
It present the evolution of electricity consumption by telier
over a period of 24 months (January 2007/ December 2008), and changes in the
consumption of heat energy sector electrodes during the same period. And
finally, after targeted workshops with high loss of energy can be addressed.
Carte de flux énergétiques et perspectives
d'efficacité dans une fonderie d'aluminium: cas particulier
d'alucam/socatral
INTRODUCTION GENERALE
Carte de flux énergétiques et perspectives
d'efficacité dans une fonderie d'aluminium: cas particulier
d'alucam/socatral
L'aluminium a connu en un peu plus de cent ans, une croissance
prodigieuse, le mettant au premier rang des métaux non ferreux et au
deuxième de tous les métaux, derrière le fer. On en a
consommé dans le monde, 13 tonnes en 1886 et 50 millions de tonne en
2007 [9]. Soit un taux de croissance de 13,23% qui est considérable.
C'est l'élément métallique le plus abondant sur la terre,
avec un pourcentage massique entre 8 et 10 %, alors que le fer ne
représente que 5 %. [1]
Nous n'avons qu'à regarder autour de nous, pour nous
rendre compte des nombreuses applications de l'aluminium. Nous citerons les
secteurs de l'automobile, l'aéronautique, le bâtiment,
l'électronique, etc... Au Cameroun, l'entreprise productrice de
l'aluminium est Alucam. C'est une filiale du géant minier Australien Rio
Tinto.
La crise économique et financière récente
a affecté l'industrie de l'aluminium. Celle-ci a eu d'autant plus
d'impacts sur le Groupe Rio Tinto car celui-ci est écrasé par sa
dette due au rachat d'Alcan en 2007.Une analyse statistique publiée dans
la revue « Ecomine », en 2008 montre que le cours de l'aluminium a
baissé entre 2007 et 2008 entre - 28% et - 43% [2]. Dans ces conditions
le Groupe a pris des mesures drastiques, entre-autres mettre en veille le
projet d'extension de l'usine d'Edéa, et l'application des solutions
internes aux entreprises dont l'une est la réduction des coûts en
accroissant la production. C'est dans cette optique que s'inscrit le programme
d'efficacité énergétique.
L'aluminerie est largement tributaire des ressources
énergétiques (eau, air, électricité et
hydrocarbures). L'électricité intervient à diverses phases
de la production. Elle représente un peu plus du tiers des coûts
d'exploitation, d'une aluminerie (35%) ; c'est pourquoi elles
s'établissent là où l'énergie est abondante.
L'électrolyse représente plus de 90% de
l'électricité consommée. Elle consomme entre 12,8 et 17
kWh/kg d'aluminium.
La flambée du prix de l'énergie, les
problèmes environnementaux astreignent les dirigeants à
rationaliser la consommation d'énergie en faisant la chasse aux
gaspillages dans les différents ateliers. Pour répondre à
ces préoccupations, nous avons élaboré notre travail
autour de quatre chapitres ; le premier présente l'aluminerie en faisant
ressortir le procédé de fabrication. Le deuxième chapitre
parle des caractéristiques énergétiques, le
troisième et le quatrième ressortent l'évolution de la
consommation électrique et calorifique par atelier. Puis nous faisons
une analyse de ces différents résultats et émettons des
perspectives d'efficacité.
Carte de flux énergétiques et perspectives
d'efficacité dans une fonderie d'aluminium: cas particulier
d'alucam/socatral
CHAPITRE I
PRE S ENTATI ON GENERALE
D 'ALUCAM/SOCATRAL
Carte de flux énergétiques et perspectives
d'efficacité dans une fonderie d'aluminium: cas particulier
d'alucam/socatral
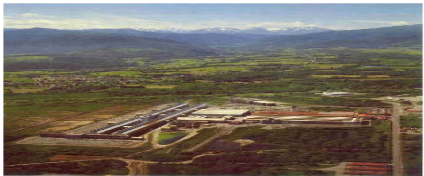
Photo 1 : Usine d'Edéa vue
aérienne
I.1.1 Situation géographique
L'usine d'Alucam/Socatral est située dans l'île
(ONG-NGOMEN), île de la ville d'Edéa chef lieu du
département de la Sanaga-maritime dans la province du littoral ;
situé à 60 km de Douala, 50 km de Mouanko, 120 km de Kribi et 180
km de Yaoundé. La ville d'Edéa est traversée par l'axe
lourd Yaoundé-Douala et par le chemin de fer camerounais.
I.1.2 Bref historique
La compagnie Camerounaise de l'Aluminium (Alucam) a
été constituée en Décembre 1954. En février
1957, l'usine entrait en production pour une capacité de 55.000
tonnes/an.
Depuis 1981, à la faveur de la mise en service de la
centrale de Song-Loulou, Alucam a procédé à une extension
de son usine. Dans le même temps, elle a effectué une
modernisation de ses installations d'électrolyse en remplaçant
les cuves à anodes Sderberg par les cuves à anodes
précuites à meilleur rendement. Grâce à ces
aménagements, la capacité de production est passée de
55.000 tonnes à 84.000 tonnes puis 87.000 tonnes/an.
Ancienne filiale du groupe français Pechiney, entre
1954 et 2000 Alucam est devenue filiale du groupe Canadien Alcan avant de
passer, il y'a trois ans, sous le contrôle du géant Australien Rio
Tinto.
Carte de flux énergétiques et perspectives
d'efficacité dans une fonderie d'aluminium: cas particulier
d'alucam/socatral
I.1.3. Organigramme activité Cameroun
Directeur Général
DRH Dir. Usine
Directeur P.CONTINU
DAF Resp. Socatral
Secrétaire
Chargé de mission


I.1.4 Le groupe Alucam en Afrique
Le développement d'Alucam est lié au volume du
tonnage exporté et au cours du métal sur le marché
international. Il dépend également des opportunités du
marché local et sous régional ; c'est pourquoi Alucam s'est
associé dès les années 60 à la création et
au développement en aval des structures de transformation de
l'Aluminium.
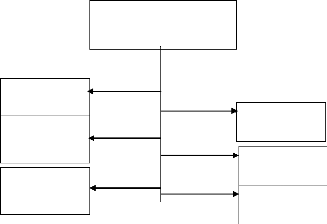
Hostellerie Sanaga
SOTRALGA GABON
COLALU R.C.A
56,48%
38,29
67,50%
Alucam
55,29%
52,55%
70,09%
Socatral Alubassa
Alu Congo
Ces pourcentages représentent les actions d'ALUCAM dans le
capital de l'entreprise en question.
Carte de flux énergétiques et perspectives
d'efficacité dans une fonderie d'aluminium: cas particulier
d'alucam/socatral
I.1.5. Histoire de l'Aluminium
L'aluminium est le métal industriel le plus
récemment découvert puisqu'il n'est utilisé que depuis la
fin du XIX° siècle. Pourtant l'alun, sulfate double d'aluminium et
de potassium, le composé d'aluminium le plus anciennement connu,
était déjà décrit par Pline, et
utilisé à Rome comme mordant pour les couleurs. Il a fallu
attendre 1825 pour que le chimiste Danois Hans Christian Oersted
obtienne l'aluminium à l'état de corps simple, sous
forme de poudre grise contenant encore une très grande quantité
d'impuretés. En 1827, Friedrich Wöhler obtint
cette même poudre grise d'aluminium contenant cependant moins
d'impuretés. [9]
Ce n'est qu'en 1854 qu'Henri Sainte-Claire
Deville présente le premier lingot d'aluminium obtenu,
à l'état fondu, par un procédé mis en application
en 1859 de façon industrielle par Henry Merle dans son usine de
Salindres (Gard), berceau de la société Pechiney. Mais ce
procédé était compliqué, ce qui donnait un
métal dont le prix était comparable à celui de l'or (1200
et 1500 F or/kg et l'argent 210 F/kg seulement). [5] Et qui le réservait
à des applications dans le luxe et l'orfèvrerie.
En 1886, Paul Louis Toussaint Héroult
en France et Charles Martin Hall aux Etats- Unis
déposent indépendamment leur brevet sur la production d'aluminium
par électrolyse à chaud de l'alumine (oxyde d'aluminium extrait
du minerai appelé « bauxite ») dissoute dans de la cryolithe
fondue (fluorure double d'aluminium et de sodium). L'invention par
Zénobe Gramme, en 1871, de la dynamo, qui
remplaça la pile de Volta comme source d'électricité, et
l'utilisation des chutes hydrauliques, la « houille blanche », rendit
possible la production économique du métal. P.L.T. Héroult
monte sa première usine en 1887 à Neuhausen en Suisse, sur une
chute du Rhin ; cette usine donnera naissance à la société
Alusuisse. Il monte en 1889 une usine à Froges (Isère), berceau
de l'hydroélectricité française développée
par Aristide Bergès, puis une autre à La Praz dans la
vallée de la Maurienne (Savoie). [9]
C.M. Hall monte de son côté en 1888 une usine
pour la Pittsburgh Reduction Company qui deviendra en 1907
l'Aluminum Company of America.
Le premier alliage d'aluminium fut inventé par
Alfred Wilm, chimiste allemand, en 1908. Cet alliage
d'aluminium contenant du cuivre et du magnésium fut exploité par
les usines de Düren et fut baptisé l'aluminium de Düren, le
« Duralumin ». C'est un alliage à « durcissement
structural » par traitement thermique, phénomène
découvert par Conrad Claessens en 1905. C'est
aujourd'hui le 2017 A, autrefois appelé en France l'A-U4G.
Le second alliage d'aluminium fut découvert en 1920 par
le hongrois Aladar Pacz, émigré aux Etats-Unis ;
c'est un alliage d'aluminium avec 13 % de silicium affiné au sodium,
baptisé l' « Alpax », alliage dévolu au moulage et
autrefois appelé en France l'A-S13.
Carte de flux énergétiques et perspectives
d'efficacité dans une fonderie d'aluminium: cas particulier
d'alucam/socatral
I.2. PROCESS ALUCAM/SOCATRAL
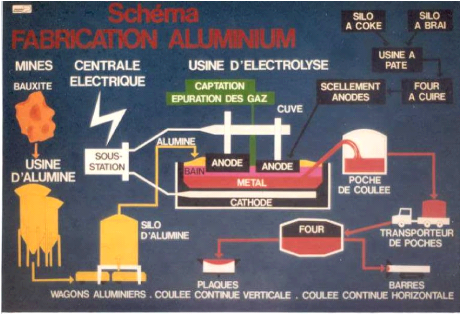
Figure I.1 : Etapes de fabrication de
l'Aluminium
Sur le site de l'usine Alucam/Socatral le processus de
fabrication de l'Aluminium va de la transformation de l'alumine en aluminium
sur le site d'Alucam puis la transformation de
cette Aluminium en produit finis par la Socatral.
La production d'aluminium primaire, se fait en
deux étapes :
1. Du minerai (bauxite), on extrait l'alumine
(Al2O3) à l'aide d'un procédé nommé
procédé de Bayer : le principe est basé
sur la dissolution de l'alumine par la soude caustique pour la transformer en
aluminate de soude soluble.
Carte de flux énergétiques et perspectives
d'efficacité dans une fonderie d'aluminium: cas particulier
d'alucam/socatral
2. Ensuite, on réduit cet oxyde en
métal par l'action d'un courant continu de forte intensité de
l'ordre des Méga Ampères. C'est le métallurgiste
français Paul Héroult et
l'américain Charles Martin Hall qui en 1886 eurent
l'idée d'appliquer l'électrolyse à la fabrication de
l'aluminium. L'astuce d'Héroult, fut de travailler avec un
mélange composé d'alumine (matériau isolant) et de
cryolithe (minerai naturel : fluorure double d'aluminium et de sodium). Ce
mélange avait en effet des caractéristiques électriques et
thermiques permettant une mise en oeuvre réaliste, c'est-à-dire
une faible résistance électrique et des caractéristiques
thermiques particulières avec une température de fusion du
mélange à 935 °C (température beaucoup plus basse que
celle de fusion de l'alumine à 2040 °C).
Cette opération a donc lieu à 960 °C dans
une cellule d'électrolyse appelée cuve où l'alumine est
dissoute dans un bain de cryolithe. Ce procédé donne lieu
à un dégagement d'oxygène qui vient brûler les
anodes qu'il faut donc renouveler régulièrement. Un service
spécialisé de l'usine fabrique le sous-ensemble anodique.
L'aluminium liquide se dépose au fond de la cuve
(cathode) d'où on l'extrait par aspiration dans une poche de
coulée étanche en acier garnie de briques réfractaires
dans laquelle on réalise le vide partiel.
Ce métal est ensuite stocké dans des fours en
fonderie. Il est ensuite solidifié sous forme de plaques ou de lingots
dans l'atelier de Fonderie.
L'aluminium secondaire ou aluminium
recyclé
L'aluminium a une excellente recyclabilité. Pour
recycler l'aluminium, on le fait simplement fondre. En plus des
bénéfices environnementaux, le recyclage de l'aluminium est
beaucoup moins coûteux que l'extraction à partir du minerai de
bauxite. Il nécessite 95 % d'énergie en moins et une tonne
d'aluminium recyclée permet d'économiser quatre tonnes de
bauxite. En sautant l'étape de l'électrolyse, qui réclame
beaucoup d'énergie, on évite les rejets polluants qui lui sont
associés.
L'aluminium est quasi recyclable à l'infini sans perdre
ses qualités, à condition de ne pas fondre dans un même
bain des alliages de composition différente. L'aluminium ménager
est récupéré avec les emballages dans le cadre du tri
sélectif. Dans les centres de tri, l'aluminium est trié
manuellement ou plus couramment grâce à des machines de tri par
courants de Foucault. Il est ensuite broyé avant d'être refondu
par des affineurs d'aluminium pour redonner du métal utilisable,
appelé aluminium de seconde fusion. L'aluminium de seconde fusion est
utilisé essentiellement pour la fabrication de pièces de fonderie
pour l'automobile (blocs moteur, culasses, pistons, etc.).
I.2.1 PROCESS ALUCAM
I.2.1.1 ATELIER D'ELECTRODES
C'est un ensemble d'ateliers pour la fabrication des
électrodes comprenant une usine à pâte d'anode, un
vibrotasseur pour la mise en forme des anodes, un four à cuisson
d'anodes (1.100°C) et un atelier de scellement des anodes et des blocs
cathodiques.
Carte de flux énergétiques et perspectives
d'efficacité dans une fonderie d'aluminium: cas particulier
d'alucam/socatral
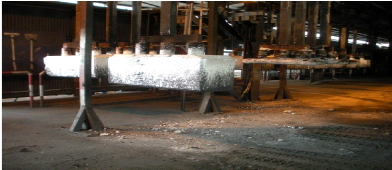
Photo 2 : une Electrode
Les blocs cathodiques sont en graphite, alors que les anodes sont
constituées par un mélange contrôlé de coke et de
brai. L'usine consomme 35.000 tonnes de coke et 8.000 tonnes de brai.
I.2.1.2 Atelier d'Electrolyse
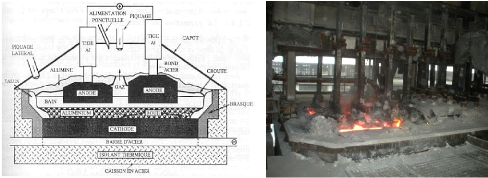
Photo 3 : cuve d'électrolyse
La cuve d'électrolyse se compose des
éléments suivants :
· Un caisson en acier,
· Un garnissage isolant thermique constitué de
briques réfractaires,
· Un creuset polarisé catholiquement
constitué d'un assemblage de blocs de carbone cuits à base
d'anthracite et liés par une pâte carbonée appelée
pâte de brasque,
· Des barres d'acier traversant le caisson et permettant
l'arrivée du courant à la cathode,
· Des tiges sur une superstructure en aluminium au dessus
du creuset maintenant les anodes carbonées,
· Un système d'aspiration des gaz vers la station de
traitement,
· Un système d'alimentation en alumine.
Carte de flux énergétiques et perspectives
d'efficacité dans une fonderie d'aluminium: cas particulier
d'alucam/socatral
L'Atelier d'électrolyse compte 274 cuves en
série reparties dans 6 salles disposées parallèlement. La
technologie 138.000 A est développée par Péchiney. Pour
protéger l'environnement, les cuves ont été
équipées des hottes de captation des gaz issus de la
réaction d'électrolyse. Ces gaz sont recyclés dans les
cuves après absorption sur l'alumine dans un centre de traitement des
gaz.
L'électrolyse consomme 170.000 tonnes/an d'alumine
importées de la République de Guinée et stockées
dans les silos. Pour son fonctionnement 1000 tonnes de cryolithe (sel double
sodium et d'aluminium) sont nécessaire pour constituer un bain
électrolytique dont la température est de 970°C.
L'atelier d'électrolyse est équipé d'un
système informatisé pour le contrôle des opérations
de production.
I.2.1.3 Atelier de Fonderie
La fonderie assure la mise en forme de l'aluminium en lingots
et en plaques ainsi que la refusion des déchets d'aluminium provenant de
Socatral. Elle dispose à cet effet de fours et d'installations de
coulée semi continue verticale pour produire des plaques et des lingots
« tés» et d'une chaine automatisée pour la production
des petits lingots
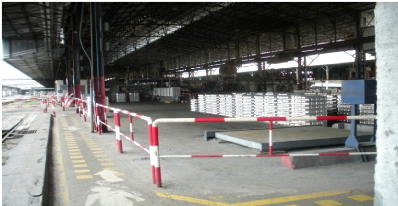
Photo 4 : lingots
I.2.1.4 Laboratoire
Le laboratoire procède aux analyses des matières
premières de même qu'à des analyses du métal pour en
déterminer la composition et la pureté. Il dispose
d'équipements perfectionnés.
I.2.1.5 Les Services Généraux
Carte de flux énergétiques et perspectives
d'efficacité dans une fonderie d'aluminium: cas particulier
d'alucam/socatral
Le fonctionnement continu des installations est assuré
grâce à la planification de la maintenance des équipements
assurés par les services d'entretien électrique et
mécanique.
Les services logistiques assurent le transport et le
déchargement des matières premières et l'expédition
des produits finis.
I.2.2 PROCESS SOCATRAL Nous distinguons quatre
étapes à savoir : I.2.2.1 Le laminage
La première étape de la transformation est le
laminage à chaud : il consiste à écraser en plusieurs
passages successifs sous les cylindres d'un laminoir une plaque d'aluminium
de forme parallépipédique préalablement
préchauffée dans un four pour améliorer la
malléabilité.
En fin de laminage à chaud, on obtient une
ébauche de 6 mm d'épaisseur. Cette dernière
préalablement refroidie, subit un laminage à froid dans un
premier laminoir à froid dit « quarto » en quelques passes de
préparation et est bobinée en rouleau.
La bobine ainsi préparée subit quelques passes
de finition dans un deuxième laminoir quarto à froid. Les
caractéristiques mécaniques demandées par le client sont
obtenues dans certaines conditions de travail lors du laminage et du traitement
thermique. L'installation du laminage se compose donc :
- De fours de réchauffage ;
- D'un laminoir à chaud à deux cylindres, d'une
puissance de 1000 CV;
- De deux laminoirs quarto à froid, équipés
d'un système de régulation automatique d'épaisseur et de
contrôle de planéité par un dispositif d'arrosage
piloté par un automate ;
- De fours de recuit ;
I.2.2.2 Le Formage
A partir des bobines Socatral fabrique des : -Bacs autoportants
;
-Tôles ondulées ;
-Tôles planes ;
I.2.2.3 Le découpage
Pour fabriquer les disques qui serviront de matières
premières pour les usines de fabrication d'articles ménagers,
Socatral part des bobines obtenues au laminage. Ces bobines sont refendues en
bobineaux dans les lignes de refendage.
Carte de flux énergétiques et perspectives
d'efficacité dans une fonderie d'aluminium: cas particulier
d'alucam/socatral
On découpe des disques dans les bobineaux obtenus
à l'aide des presses mécaniques. Lorsque le diamètre du
disque excède 530 mm le bobineau est préalablement
cisaillé en formats. Les formats passent ensuite dans une escargoteuse
pour la fabrication du disque.
I.2.2.4 Production pour la grande
exportation
Pour assurer le développement de la grande exportation,
Socatral dispose d'une ligne continue de rivage, planage, débitage et
conditionnement automatique.
I.3. Fourniture en Energie
La fourniture d'énergie est assurée par 2
centrales hydroélectriques Edéa et Song-Loulou sur le fleuve
Sanaga. Une sous-station électrique de conversion de l'énergie
équipée de 13 groupes de transformateurs-redresseurs, produit
138.000 A de courant continu.
La variabilité de l'hydraulicité de la Sanaga a
souvent rendu précaire, dans le passé, l'approvisionnement en
énergie de l'usine. Cette situation est cependant moins
préoccupante depuis la mise en service de la Mappé,
3ième barrage réservoir qui est venu s'ajouter
à Bamendjin et Mbakaou. Ces barrages réservoirs d'une
capacité totale de 7,6 milliards de m3 d'eau, servent d'appoint à
la Sanaga pendant la période d'étiage afin de satisfaire
l'établissement en besoin d'énergie.
Carte de flux énergétiques et perspectives
d'efficacité dans une fonderie d'aluminium: cas particulier
d'alucam/socatral
I.3.1 Configuration d'exploitation
GR4 et
GR5
|
GR1 à GR3
GR12à GR14
|
GR10 ou
|
|

JDBG


L2
L1

G GR6 à G G G
GR9

90k
GR11
JDBD
SOC
U2
U1

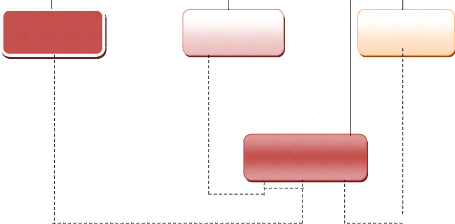


(1)
(2)
(11
SG
SOC
AL
(3) (4)
(5)
(10
EL
Nous avons 4 départs usine U1, U2, U3, SOC ;
Chaque usine est alimentée en antenne par sa propre
arrivée :
- Départ U1 pour les services généraux (SG)
;
- Départ U2 pour le poste Electrode (EL) ;
- Départ U3 pour le poste Aluminium (AL) ;
- Départ SOC pour le poste Socatral ;
Les câbles en pointillés sont les départs de
secours en cas de travaux ou de pannes.
I.3.1.2 Alimentation
Carte de flux énergétiques et perspectives
d'efficacité dans une fonderie d'aluminium: cas particulier
d'alucam/socatral
Il y'a 14 générateurs en tout GR1 à GR14
:
- Les générateurs uniquement affectés au
10kV sont GR4 à GR9 (24,5 MVA chacun) ;
- Les générateurs uniquement affectés au 90
kV sont GR1 et GR2 (11,8 MW chacun) et GR12 à GR14 (20,8 MW chacun) ;
Les configurations possibles d'alimentation sont :
- Configuration minimale (puissance minimale)
155 MW ;
Puissance minimale (contrat AES-SONEL) : 148,5 MW repartie entre
le 10 kV et le 90 kV. Il faut disposer d'au moins 100 à 110 MW sur les
10 kV et de 45 à 55 MW sur le 90kV.
- Configuration maximale (puissance maximale)
210 MW ;
Puissance maximale en 10 kV= 130 MW.
NB : La puissance max est prise égale à 130 MW
(7x18, 5 MW) au lieu de 146 MW. Puissance maximale en 90 kV= 80 MW.
Pour tenir compte des conditions d'exploitation de la
centrale hydroélectrique, une période des hautes eaux a
été définie : pendant cette période, la hauteur de
chute est telle que la puissance mécanique transmise à l'arbre de
la turbine se trouve réduite.
Il faut aussi préciser que c'est en fonction de la
disponibilité côté centrale et du besoin côté
Alucam ou besoin « secteur public » que l'on alimente soit le
réseau 10 kV, soit le réseau 90 kV avec les groupes GR1 0 et GR1
1.
Conclusion
Ce premier chapitre nous a permis dans un premier temps de
comprendre l'historique et le fonctionnement d'ALUCAM/SOCATRAL, son statut en
tant que grande entreprise dans la sous-région Afrique Centrale. Au
second de comprendre le procédé de fabrication de l'aluminium,
métal très important a plusieurs usages.
Carte de flux énergétiques et perspectives
d'efficacité dans une fonderie d'aluminium: cas particulier
d'alucam/socatral
CHAPITRE II
Carte de flux énergétiques et perspectives
d'efficacité dans une fonderie d'aluminium: cas particulier
d'alucam/socatral
CARACTERI S TIQUE S
ENERGETI QUE S
Carte de flux énergétiques et perspectives
d'efficacité dans une fonderie d'aluminium: cas particulier
d'alucam/socatral
Les efforts pour économiser l'énergie dans une
fonderie peuvent commencer par l'examen du détail des
caractéristiques électriques et combustibles. Les ressources
énergétiques doivent être traitées au même
titre que la matière première. Dans ce chapitre nous exposerons
les différents leviers sur lesquels l'on pourrait agir pour une
production optimale.
II.1- CARACTERISTIQUES ELECTRIQUES II.1.1- Le
réseau Electrique
Le réseau Electrique d'ALUCAM/SOCATRAL a pour point de
départ la centrale électrique d'AES-SONEL du barrage
hydroélectrique d'Edéa. Son contrat avec AES-SONEL lui permet en
raison de ses besoins en usine d'être soit alimentée par une
puissance de 155 MW ou par une puissance de 210MW.
Nous avons 8 lignes d'arrivée sur le JDB 10 kV parmi
lesquelles 7 lignes sont alimentées en 10kV par 5
générateurs d'environ 20MW et une ligne est alimentée en
90kV par 6 générateurs qui atteignent 5 5MW.
II.1.1.1- Jeu de Barre
Pour la distribution des grands courants, dans les
installations industrielles et les armoires de distribution électrique,
on utilise le cuivre en barres plates. Ces barres sont utilisées
à la place des câbles pour une raison de coût, mais aussi de
facilité de connexion et de rigidité.
II.1.1.2- Les Transformateurs
La tension livrée par AES-SONEL n'est pas
utilisée telle quelle par Alucam, elle est réduite par des
transformateurs en des tensions appropriées avant d'alimenter les
ateliers. Les transformateurs à Alucam sont tous à type de flux
libre et diélectrique d'isolation liquide.
Nous avons :
- Un transformateur de 2000 kVA, - 17 transformateurs de 1250
kVA, - 13 transformateurs de 1000 kVA,
- 3 transformateurs de 630 kVA,
- 4 transformateurs de 500 kVA, - 2 transformateurs de 460
kVA,
II.1.1.3- Disjoncteurs
Puissance active (kW)
Puissance apparente (kVA)
P S

=
FP =
Carte de flux énergétiques et perspectives
d'efficacité dans une fonderie d'aluminium: cas particulier
d'alucam/socatral
C'est un appareil de protection essentiel d'un réseau
à haute tension. Car il est le seul capable d'interrompre un courant de
court-circuit et donc d'éviter que le matériel connecté
sur le réseau ne soit endommagé par ce court-circuit.
La performance principale qui caractérise un
disjoncteur est son « pouvoir de coupure en court-circuit »
c'est-à-dire le courant maximal qu'il est capable d'interrompre sous sa
tension assignée (tension maximale du réseau où il est
utilisé).
II.1.2- Paramètres Electriques [11]
L'énergie électrique est essentiellement
distribuée aux utilisateurs sous forme de courant alternatif par des
réseaux en haute, moyenne et basse tension. L'énergie
consommée est composée d'une partie « active »
transformée en chaleur ou en mouvement, et d'une partie «
réactive » transformée par les actionneurs
électriques pour créer leurs propres champs
magnétiques.
II.1.2.1- Energie active
L'énergie active consommée (kWh) résulte
de la puissance active P (kW) des récepteurs. Elle se transforme
intégralement en puissance mécanique (travail) et en chaleur
(pertes).
II.1.2.2- Energie réactive
L'énergie réactive consommée (kVarh)
correspond à la puissance réactive Q (kVar) des
récepteurs. L'utilisateur ne bénéficie que de l'apport
énergétique de la partie « active ». Il convient de
préciser que la partie réactive ne peut être
éliminée, mais doit être compensée. Les
économies d'énergie se chiffrent par dizaines de pour cent de la
consommation globale, situant les procédés de compensation
d'énergie réactive en première ligne du combat pour la
réduction de l'impact des activités humaines sur
l'écosystème de notre planète.
II.1 .2.3-Energie apparente
L'énergie apparente (kVAh) est la somme vectorielle
des deux énergies précédentes. Elle correspond à la
puissance apparente S (kVA) des récepteurs, somme vectorielle de P (kW)
et Q (kVar). C'est une énergie fictive car elle ne produit pas de
travail ou de chaleur mais sert au dimensionnement des sections des conducteurs
de la ligne de distribution ainsi que celle du circuit magnétique et des
bobinages des différentes machines.
II.1 .2.4-Facteur de Puissance
Le facteur de puissance est égal par définition
à :
Carte de flux énergétiques et perspectives
d'efficacité dans une fonderie d'aluminium: cas particulier
d'alucam/socatral
Si les courants et tension sont des signaux parfaitement
sinusoïdaux, le facteur de puissance est égal à cos ??.
On définit ainsi :
-la puissance apparente : S= UI (kVA), -la puissance active : P=
UI cos ?? (kW),
-la puissance réactive ; Q= UI sin ?? (kVar).
P (kW)
Q (kVar)
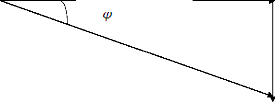
S (kVA)
Figure 2.1: composition vectorielle des puissances
II.1.2.5- Inconvénients et compensation de
l'énergie réactive
Du fait d'un courant appelé plus important, la
circulation de l'énergie réactive sur les réseaux de
distribution entraîne :
- Des surcharges au niveau des transformateurs ; - Des pertes
supplémentaires ;
- L'augmentation de la facture électrique ; - Des chutes
de tension importantes ;
Compensation : [6]
Pour les raisons évoquées ci-dessus, il est
nécessaire de produire l'énergie réactive au plus
près possible des charges, pour éviter qu'elle ne soit
appelée sur le réseau. C'est ce qu'on appelle «compensation
de l'énergie réactive».
V' Compensation globale : la batterie est
raccordée en tête d'installation et assure la compensation pour
l'ensemble des charges. Elle convient lorsqu'on cherche essentiellement
à supprimer les pénalités et soulager le poste de
transformation.
V' Compensation locale ou par secteurs : la batterie
est installée en tête du secteur d'installation à
compenser. Elle convient lorsque l'installation est étendue et comporte
des ateliers dont les régimes de charge sont différents.
Carte de flux énergétiques et perspectives
d'efficacité dans une fonderie d'aluminium: cas particulier
d'alucam/socatral
V' Compensation individuelle : la batterie est
raccordée directement aux bornes de
chaque récepteur inductif (moteur en particulier). Elle
est à envisager lorsque la
puissance du moteur est importante par rapport à la
puissance souscrite. Cette
compensation est techniquement idéale puisqu'elle
produit l'énergie réactive à
l'endroit même où elle est consommée, et en
quantité ajustée à la demande.
En présence des harmoniques, Ces harmoniques
perturbent le fonctionnement de nombreux dispositifs. En particulier, les
condensateurs y sont extrêmement sensibles du fait que leur
impédance décroît proportionnellement au rang des
harmoniques présents. Dans certaines circonstances, des
phénomènes de résonance peuvent se produire
entraînant une forte distorsion de tension et la surcharge des
condensateurs. Selon la puissance des générateurs d'harmoniques
présents, différents types de condensateurs doivent être
choisis, associés éventuellement à des inductances. Pour
les valeurs élevées de puissance des générateurs
d'harmoniques, le traitement des harmoniques est en général
nécessaire. Le dispositif approprié (filtre d'harmonique) remplit
à la fois les fonctions de compensation d'énergie réactive
et de filtrage des harmoniques.
II.1.2.6- La chute de tension
Les chutes de tension sont calculées par la formule :
U= b (P1
COS ço + jiL SiflÇo)IB
L S

U: étant la chute de tension en volts
b : étant un coefficient égal à 1 pour les
circuits triphasés et égal à 2 pour les circuits
monophasés.
p 1 : étant la résistivité des conducteurs
en service normal.
L : étant la longueur simple de la canalisation, en
mètres.
S : étant la section des conducteurs en mm2.
Cos p : étant le facteur de puissance, en absence
d'indication précises prendre cos p= 0,8 et sin q9 = 0,6.
ji : étant la réactance linéique d'emploi
en ampères.
La chute de tension relative (en %) est égale à
:
U

U0
L\U= 100
U0 : étant la tension entre phase et neutre en volts.
Les chutes de tension sont néfastes pour les appareils
connectés sur le réseau.
Carte de flux énergétiques et perspectives
d'efficacité dans une fonderie d'aluminium: cas particulier
d'alucam/socatral
Lorsque l'installation alimente des moteurs, il peut
être nécessaire de vérifier que la chute de tension due aux
courants de démarrage de ces moteurs est compatible avec les conditions
de démarrage.
La chute de tension est alors calculée en
remplaçant dans le calcul du courant IB , le courant déduit de la
puissance des moteurs par le courant de démarrage. Il y'a lieu de
s'assurer que la puissance appelée pendant le démarrage des
moteurs n'est pas supérieure à la puissance de la ou les sources
; sinon il y'a lieu de tenir compte de la chute de tension interne de la
source.
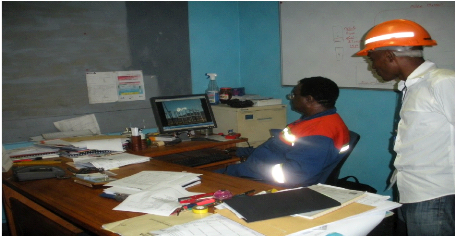
Photo II. 1 : Explications sur les
ICC
II.1.2.7- Les harmoniques
Les courants ou tension harmoniques sont des courants ou
tension « parasites » du réseau électrique. Ils sont
dus aux transformateurs d'intensité, aux arcs électriques et
surtout aux redresseurs et convertisseurs statistiques (électronique de
puissance). Ces charges sont appelées charges déformantes. Ils
déforment l'onde de courant ou de tension et provoquent :
- Une augmentation de la valeur efficace du courant ;
- La circulation d'un courant dans le neutre pouvant être
supérieure au courant de phase ;
- La saturation des transformateurs ;
- Des perturbations dans les réseaux à faibles
courants ; - Le déclenchement intempestif des disjoncteurs ;
- Des mesures faussées (courant, tension,
énergie,...)
Solutions :
y' Il faut alimenter les charges perturbantes par des ASI
(Alimentations Statistiques sans Interruption) ;
Carte de flux énergétiques et perspectives
d'efficacité dans une fonderie d'aluminium: cas particulier
d'alucam/socatral
V' Utilisation des filtres anti-harmoniques ;
V' Augmentation des sections des conducteurs ;
surdimensionnement de l'appareillage ; II.1.2.8- Les courants de
court-circuit
Un courant de court-circuit est un courant provoqué par
un défaut d'impédance négligeable entre des points
d'installation présentant normalement une ddp.
On distingue trois niveaux de courant de court-circuit :
- Le courant de court-circuit crête (Icc
crête) correspondant à la valeur extrême de l'onde,
générant des forces électromagnétiques
élevées notamment au niveau des JDB et des courants ou connexion
d'appareillage.
- Le courant de court-circuit efficace (Icc eff)
valeur efficace du courant de défaut qui provoque des
échauffements dans les appareils et les conducteurs et peut porter les
masses des matériels électriques à un potentiel
dangereux.
- Icc minimum : valeur efficace du courant de
défaut s'établissant dans des circuits d'impédance
élevée. Il est nécessaire d'éliminer rapidement ce
type de défaut dit impédant par des moyens appropriés.
II.1.2.9- Effets d'anodes
L'aluminium de première fusion est produit dans des
usines d'électrolyse par un courant électrique traversant un bain
électrolytique et un mélange d'alumine situés dans des
contenants électrochimiques, les «cuves», reliés en
série dans une «salle de cuves»
Pour assurer une bonne performance d'électrolyse, la
teneur en alumine du bain électrolytique d'une cuve doit être
optimisée et demeurer stable dans le temps. Ce facteur est difficile
à contrôler et un «effet anodique» se produit
périodiquement lorsque la teneur en alumine du bain
électrolytique est trop faible.
Lorsque cela se produit, la conductivité
électrique de l'électrolyte diminue énormément et
celui-ci réagit avec l'anode, produisant ainsi des émissions
gazeuses de perfluorocarbures (PFC), dont les effets sont très nocifs
pour l'environnement. Par exemple, 1 kilo de PFC (composé à
environ 90 % de CF4 et à 10 % de C2F6) a le même effet
sur la couche d'ozone que 6 500 kilos de CO2 (CF4) et 9 200 kilos de CO2
(C2F6). Il détériore également l'anode.
Solutions :
Carte de flux énergétiques et perspectives
d'efficacité dans une fonderie d'aluminium: cas particulier
d'alucam/socatral
Il faut donc réduire au maximum les effets d'anode en
surveillant automatiquement la teneur en alumine dans le bain
électrolytique.
II.2- Caractéristiques des combustibles
Dans les alumineries pour atteindre des fortes
températures on a recourt à la combustion. Après
l'obtention de l'aluminium liquide provenant de l'atelier d'électrolyse,
on achemine cet aluminium dans l'atelier de fonderie pour la mise en forme de
l'aluminium en lingots, pour ce fait on dispose des fours dans lesquels on
brûle les combustibles qui ici sont des hydrocarbures le fuel lourd.
II.2.1 Définition de la combustion
La combustion est une réaction chimique dans laquelle
un oxydant réagit avec un combustible pour libérer son
énergie thermique emmagasinée sous forme de gaz à haute
température. Cette réaction, lorsqu'elle est théoriquement
optimale est appelée combustion stoechiométrique. Elle survient
lorsque la quantité d'agent oxydent théoriquement
nécessaire, sous forme d'oxygène dans l'air ou d'un
mélange à base d'oxygène, est ajouté à un
combustible.
II.2.2- Énergie dégagée et pouvoir
calorifique
La quantité d'énergie produite par la
combustion est exprimée en joules (J) ; il s'agit de l'enthalpie de
réaction. Dans les domaines d'application (fours, brûleurs,
moteurs à combustion interne, lutte contre incendie), on utilise souvent
la notion de pouvoir calorifique, qui est l'enthalpie de réaction par
unité de masse de combustible ou l'énergie obtenue par la
combustion d'un kilogramme de combustible, exprimée en
général en kilojoule par kilogramme (noté kJ/kg ou
kJ·kg-1).
Les combustions d'hydrocarbures dégagent de l'eau sous
forme de vapeur. Cette vapeur d'eau contient une grande quantité
d'énergie. Ce paramètre est donc pris en compte de manière
spécifique pour l'évaluation du pouvoir calorifique, et l'on
définit :
· le pouvoir calorifique supérieur
(PCS) : « Quantité d'énergie dégagée
par la combustion complète d'une unité de combustible, la vapeur
d'eau étant supposée condensée et la chaleur
récupérée »
· le pouvoir calorifique inférieur
(PCI) : « Quantité de chaleur dégagée par la
combustion complète d'une unité de combustible, la vapeur d'eau
étant supposée non condensée et la chaleur non
récupérée »
La différence entre le PCI et le PCS est la chaleur
latente de vaporisation de l'eau (Lv) multipliée par
la quantité de vapeur produite (m), qui vaut à
peu-près 2 250 kJ·kg-1 (cette dernière valeur
dépend de la pression et de la température).
Carte de flux énergétiques et perspectives
d'efficacité dans une fonderie d'aluminium: cas particulier
d'alucam/socatral
On a la relation PCS = PCI +
m·Lv.
II.2.3 - combustion stoechiométrique
Une combustion est dite stoechiométrique lorsqu'elle
se déroule sans excès d'air et sans imbrûlés. Lors
d'une combustion stoechiométrique, le réactif brûlera en
présence de dioxygène (comburant), ce qui limite les produits de
la réaction. Quand un hydrocarbure brûle dans le dioxygène,
les produits sont ainsi uniquement du dioxyde de carbone et de l'eau. Quand des
éléments comme le carbone, l'azote, le soufre, et le fer sont
brûlés, on remarque la production des oxydes les plus communs.
Réactifs
|
produits
|
Chaleur dégagée
|
Carbone
|
Dioxyde de carbone
|
81133 kcal//kg
|
Dihydrogène
|
De l'eau
|
34500 kcal/kg
|
Soufre
|
Dioxyde de soufre
|
2224 kcal/kg
|
|
Cette combustion théorique est cependant impossible
à atteindre dans un appareil de combustion de type commercial où
le mélange air/combustible n'est jamais parfaitement distribué.
C'est pourquoi, en pratique, on ajoute toujours une quantité
additionnelle d'air appelée « excès d'air ».
II.2.4 - combustion complète avec excès
d'air
On s'assure ainsi que tous les éléments
combustibles rencontrent l'oxygène excédentaire. Ce
supplément d'air varie selon plusieurs facteurs et se situe
généralement autour de 10 %. L'excès d'air peut varier
également selon la modulation de production de chaleur demandée
au brûleur du four. En général, un brûleur
opérant à charge partielle a plus de difficultés à
obtenir un mélange air/combustible adéquat. C'est pourquoi on
ajuste souvent l'excès d'air à la hausse pour une faible charge.
Par exemple, un brûleur ayant 10 % d'excès d'air à pleine
capacité pourra en utiliser jusqu'à 30 % lorsqu'il fonctionnera
à 25 % de sa capacité. Ce surplus de consommation
énergétique, utilisé principalement comme
sécurité, doit être optimisé et être
vérifié sur une base régulière, afin d'assurer une
saine gestion de la consommation énergétique du
procédé de combustion.
Carte de flux énergétiques et perspectives
d'efficacité dans une fonderie d'aluminium: cas particulier
d'alucam/socatral
II.2.5- Combustion complète avec défaut
d'air
Lorsqu'il y'a manque d'air, ou un mauvais mélange
combustible/comburant il se produit une combustion dite réductrice.
Celle-ci a pour conséquence qu'on ne récupère pas
complètement l'énergie disponible dans le combustible D'autres
types de combustions réductrices peuvent se produire :
- Le carbone ne brûle pas entièrement (fumée
noire) donc ne produit aucune énergie ;
- L'hydrogène peut ne pas brûler entièrement
ou peut même s'associer à d'autres molécules de carbone
pour former des imbrûlés gazeux de type CmHn
combinaison endothermique ;
A tous les coups c'est une perte d'énergie qu'il faut
éviter.
II.2.6- La position du brûleur
Il existe peu de données disponibles sur la position
idéale du brûleur à l'intérieur d'un four. Cette
localisation est déterminée pour chaque installation et
dépend de divers paramètres comme la localisation des portes du
four et à l'entrée de la cheminée. Cependant pour qu'une
combustion puisse s'amorcer et se maintenir, il faut qu'il règne dans le
foyer une température appropriée. Cette température
dépend de plusieurs paramètres tels que le degré
d'humidité du combustible, sa nature et son degré de division.
II.2.7- Contrôle de Combustion
II.2.7.1- Interprétation de la teneur en CO2
Les pertes de la cheminée dépendent
essentiellement des conditions de conduite de la combustion et de l'entretien
du matériel. Pour chaque combustible, il résulte du
mélange idéal combustible/air. La teneur en CO2 des fumées
est en relation direct avec l'excès d'air. Plus le CO2 mesuré est
inférieur au CO2 neutre, plus l'excès d'air est important et plus
les pertes par la cheminée sont élevées car la
quantité d'air introduite en trop représente une masse gaz qu'il
faut chauffer inutilement. La mesure de la teneur en CO2 se fait par un
analyseur de gaz. Le cas d'une combustion incomplète ne peut être
décelé que par la mesure du taux du CO ou d'O2. Dans ce cas la
flamme devient moins brillante et prend des couleurs orangées.
II.2.2.7.2- Mesure des imbrûlés
Nous avons vu qu'un mauvais mélange air/combustible se
traduit par une combustion incomplète. Il s'ensuit donc des
éléments imbrûlés qui s'envolent à travers la
cheminée, ceci représente une perte d'énergie importante.
Le principe des appareils de contrôle des imbrûlés est
basé sur la recherche du CO, car une combustion incomplète
entraine forcement la présence du CO.
II.2.2.7.3- interprétation de la température
des fumées
Carte de flux énergétiques et perspectives
d'efficacité dans une fonderie d'aluminium: cas particulier
d'alucam/socatral
Les pertes à la cheminée par chaleur sensible
des fumées sont fonction de la température de sortie à la
cheminée. Plus cette température est élevée, plus
la chaleur emportée est importante. Pour une charge donnée du
four, cette température est en principe fixée. La mesure de cette
température présente donc un grand intérêt. La
mesure des températures des fumées se fait par la canne
pyrométrique dont l'extrémité devra être
placée bien au centre du flux gazeux.
CONCLUSION
Dans ce chapitre nous avons définit quelques grandeurs
et paramètres énergétiques et l'intérêt que
revêt leur gestion. La bonne intervention sur ceux-ci déterminera
la réussite de toute politique d'efficacité
énergétique.
Carte de flux énergétiques et perspectives
d'efficacité dans une fonderie d'aluminium: cas particulier
d'alucam/socatral
CHAPITRE III
CARTE DES FLUX
ENERGETIQUE S
Carte de flux énergétiques et perspectives
d'efficacité dans une fonderie d'aluminium: cas particulier
d'alucam/socatral
Introduction
La mise en place en 1999, sur tous les départs usines
à la centrale de nouveaux compteurs électroniques a permis de
fiabiliser pour AES-SONEL, l'exactitude de son comptage de facturation.
Conjointement Alucam/Socatral a installé au niveau de chaque atelier des
compteurs pour une meilleure visibilité de la consommation
électrique. La base de tout programme d'efficacité
énergétique, étant la comptabilisation de la consommation
électrique et calorifique au niveau de chaque atelier, c'est avec grand
intérêt que nous avons analysé les données
récoltées sur ces compteurs. Dans ce chapitre nous tracerons les
courbes d'évolution de la consommation énergétique sur
chaque atelier sur une période de 24 mois, allant de Janvier 2007
à Décembre 2008.
III.1- Evolution de la consommation électrique
III.1.1- Consommation électrique atelier électrolyse
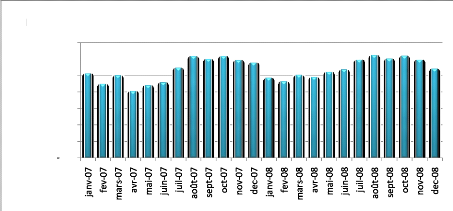
140 000 000
120 000 000
100 000 000
80 000 000
40 000 000
60 000 000
20 000 000
kWh
graphe III.1: Atelier d'Electrolyse
III.1.2- Consommation électrique des auxiliaires
électrolyse
Carte de flux énergétiques et perspectives
d'efficacité dans une fonderie d'aluminium: cas particulier
d'alucam/socatral

1 000 000
400 000
900 000
800 000
700 000
500 000
300 000
600 000
200 000
100 000
kWh
-
graphe III.2: Auxiliaire électrolyse
C'est le secteur qui consomme le plus dans une fonderie
d'aluminium, la valeur plus basse 80,6 GWh est prise au quatrième mois
et la plus haute 122,8 GWh est prise au dixième mois ce qui nous fait
une moyenne mensuelle de 107 GWh. Ce qui est bien entendu énorme. C'est
pour cette raison qu'il est conseillé d'utiliser une ligne
particulière pour l'électrolyse.
III.1.3- Consommation électrique atelier
décharge Alumine
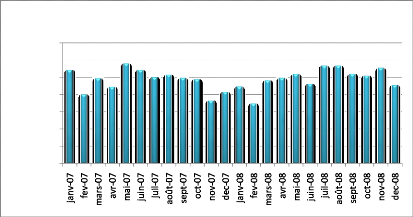
350 000
300 000
250 000
200 000
150 000
100 000
50 000
kWh
-
graphe III.3: atelier Décharge
Alumine
L'atelier de la décharge d'alumine a une consommation
qui est bien fluctuante ceci est dû d'une part à la
disponibilité de l'alumine et à la vitesse de disparition de
l'alumine dans la cuve d'électrolyse. La plus grande valeur est 288,6
MWh et elle est prise au cinquième mois et la plus petite est 172,9 MWh
prise au quatorzième mois.
III.1.4- Consommation électrique des
compresseurs
Carte de flux énergétiques et perspectives
d'efficacité dans une fonderie d'aluminium: cas particulier
d'alucam/socatral
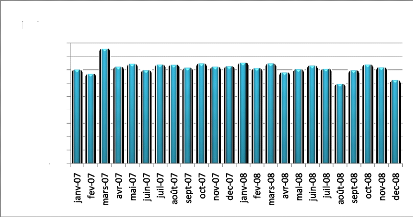
1 800 000
1 600 000
1 400 000
1 200 000
1 000 000
400 000
800 000
600 000
200 000
kWh
-
graphe III.4: Compresseurs
Après l'atelier d'électrolyse on remarque que
c'est l'atelier des compresseurs qui consomme le plus ceci se justifie par le
fait que c'est à travers les compresseurs qu'on fabrique l'air
comprimé qui a plusieurs fonctionnalités dans une fonderie. L'air
comprimé est la source la plus dispendieuse dans une fonderie. Cette
industrie utilise énormément d'air comprimé à des
fins de production. La consommation la plus basse est de 1,18 GWh et la plus
élévée est 1,70 GWh ce qui nous donne une moyenne
mensuelle de 1,43 GWh.
III.1.5- Consommation électrique atelier
d'électrodes
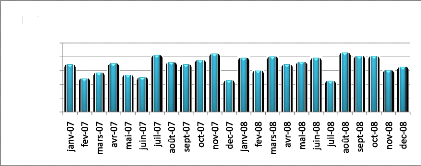
400 000
500 000
300 000
200 000
100 000
kWh
-
graphe III.5 atelier d'Electrodes
III.1.6- Consommation électrique auxiliaire
Scellement
Carte de flux énergétiques et perspectives
d'efficacité dans une fonderie d'aluminium: cas particulier
d'alucam/socatral
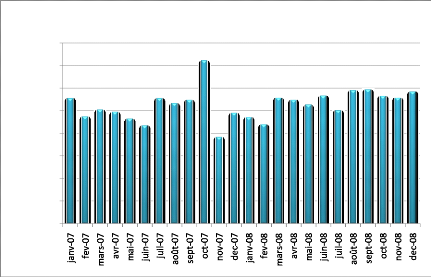
160 000
140 000
120 000
100 000
kWh
80 000
40 000
60 000
20 000
-
graphe III.6:Aux.Scellement
Ici la consommation est assez variable avec la valeur la plus
élevée prise au mois d'Octobre 2007 et la plus petite prise le
mois suivant c'est-à-dire Novembre 2007.
III.1.7- Consommation électrique four à
cuire
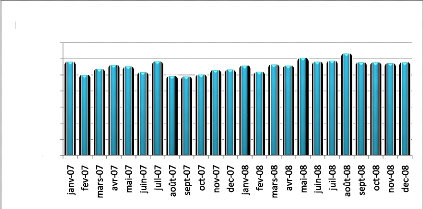
350 000
300 000
250 000
200 000
150 000
100 000
kWh
50 000
-
graphe III.7: Four à cuire

C'est un ensemble d'ateliers pour la fabrication
d'électrodes comprenant : Un four à cuisson d'anodes, ;
Une usine à pâte d'anode ;
Carte de flux énergétiques et perspectives
d'efficacité dans une fonderie d'aluminium: cas particulier
d'alucam/socatral

un vibrotasseur ;
Un atelier de scellement des anodes et des blocs cathodiques.
On remarque que que la consommation de l'atelier
d'élctrode est trop variable ceci s'explique par le fait que la
fabrication d'électrodes se fait en fonction des besoins.
III.1.8- Consommation électrique Eclairage
Usine
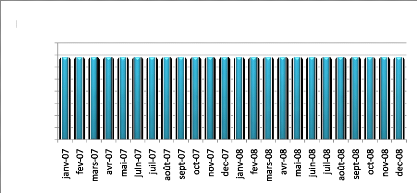
40 000
35 000
30 000
25 000
20 000
15 000
10 000
kWh
5 000
-
graphe III.8: Eclairage Usine
III.1.9- Consommation électrique Conditionnement
des bâtiments Généraux
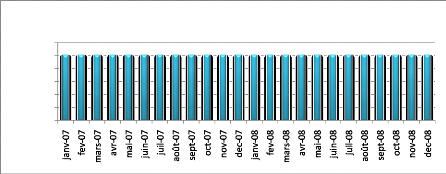
30 000
25 000
20 000
15 000
10 000
kWh
5 000
-
graphe III.9:
Cond.Bât.Généraux
On remarque que la consommation au niveau de
l'éclairage usine et le conditionnement des bâtiments
généraux est constante. Nous avons 34 MWh pour l'éclairage
usine et 25,25 MWh pour le conditionenement.
III.1.10- Consommation atelier de Mécanique
Carte de flux énergétiques et perspectives
d'efficacité dans une fonderie d'aluminium: cas particulier
d'alucam/socatral
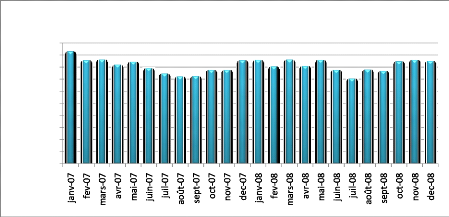
200 000
180 000
160 000
140 000
120 000
100 000
kWh
40 000
80 000
60 000
20 000
-
graphe III.10: Atelier Mécanique
L'atelier de mécanique a pour rôle principal le
dépannage des moteurs et la fabrication des pièces
mécaniques, et sa consommation dépend des facteurs
précedemment cités. Elle varie entre 140,4 MWh et 185,2 MWh.
III.1.11- Consommation électrique atelier
Electrique
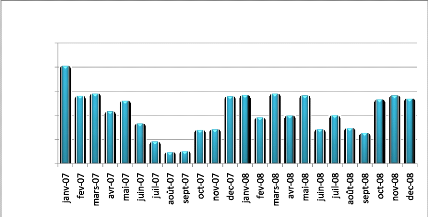
25 000
20 000
15 000
10 000
kWh
5 000
-
graphe III.11: Atelier Electrique
L'atelier électrique a pour rôle l'entretien du
réseau électrique, le rebobinage des machines. Ce qui justifie la
consommation ci-dessus.elle varie de 2,2 MWh à 20,15 MWh.
III.1.12- Consommation électrique station de
pompage
Carte de flux énergétiques et perspectives
d'efficacité dans une fonderie d'aluminium: cas particulier
d'alucam/socatral
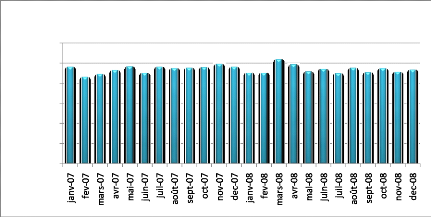
300 000
250 000
200 000
150 000
100 000
50 000
kWh
-
graphe III.12: Station Pompage
La consommation de la station de pompage n'est pas très
variable, elle varie de 223230 kWh à 258389 kWh. Elle est chargée
d'alimenter l'usine en eau.
III.1.13- Consommation électrique atelier de
fonderie
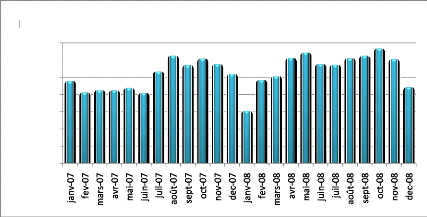
140 000
120 000
100 000
40 000
80 000
60 000
20 000
kWh
-
graphe III.13: Atelier Fonderie
La consommation de fonderie est constituée de fours et
d'installations de coulée. La consommation varie entre 60, 6 MWh et
128,2 MWh.
III.1.14- Consommation électrique des Fours
Junker
Carte de flux énergétiques et perspectives
d'efficacité dans une fonderie d'aluminium: cas particulier
d'alucam/socatral
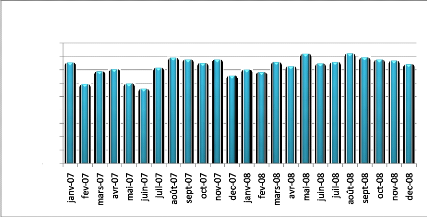
180 000
160 000
140 000
120 000
100 000
kWh
40 000
80 000
60 000
20 000
-
graphe III.14: Fours Junker
Les fours junker quant à eux, s'occupent de la refonte des
déchets provenant de la Socatral et le consommation varie entre 110,9
MWh et 163,5 MWh.
III.1.15- Consommation électrique des hottes de
captation
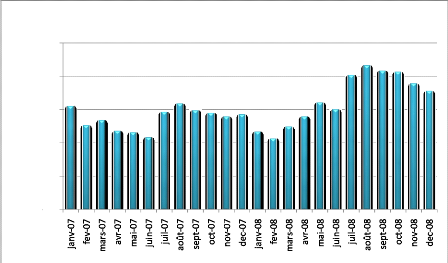
250 000
200 000
150 000
100 000
kWh
50 000
-
graphe III.15: Hottes de Captation
La consommation des hottes de captation est assez variable on
remarque cependant une hausse significative pour les 5 derniers mois ceci est
dû à la forte production des gaz issus du procédé
d'électrolyse. Elle varie entre 106 MWh et 216 MWh.
III.1.16- Consommation électrique du centre
Médical
Carte de flux énergétiques et perspectives
d'efficacité dans une fonderie d'aluminium: cas particulier
d'alucam/socatral
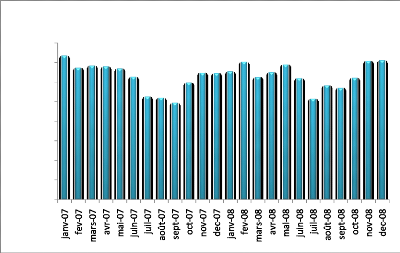
16 000
14 000
12 000
10 000
8 000
4 000
6 000
2 000
kWh
-
graphe III.16: Centre Médical
C'est le centre hospitalier de l'usine on y trouve 46 lits
d'hospitalisation, un laboratoire et un bloc opératoire. La consommation
varie entre 9,83 MWh et 14,65 MWh.
II.1.17- Consommation électrique poste Serem
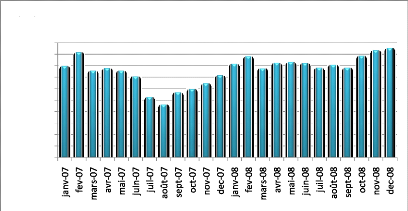
45 000
40 000
50 000
35 000
30 000
25 000
20 000
15 000
10 000
kWh
5 000
-
graphe III.17: poste Serem
III.1.18- Consommation électrique Socatral
Carte de flux énergétiques et perspectives
d'efficacité dans une fonderie d'aluminium: cas particulier
d'alucam/socatral
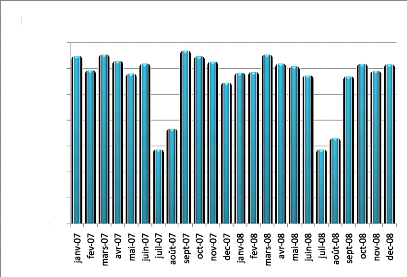
1 400 000
1 200 000
1 000 000
kWh
400 000
800 000
600 000
200 000
-
graphe III.18: Socatral
La consommation de Socatral est importante car elle regroupe
tout le processus de transformation de l'aluminium. elle varie entre 569 MWh et
1333 MWh, cette grosse différence est dû au fait que cette
consommation dépend de la disponibilité de l'aluminium, du nombre
et du type de commande. Les mois de juillet et août sont
généralement les mois de faible activité.
On recommande ici de mettre un dispositif de comptage au
niveau de chaque procédé pour avoir une meilleur
visibilité au niveau de la consommation. C'est à partir de cela
qu'on peut voir les pistes d'amélioration. Ne dit-on pas souvent «
diviser pour mieux règner ? »
III..2- Consommation de l'énergie calorifique
Carte de flux énergétiques et perspectives
d'efficacité dans une fonderie d'aluminium: cas particulier
d'alucam/socatral
III.2.1- Consommation d'énergie calorifique du
secteur électrodes
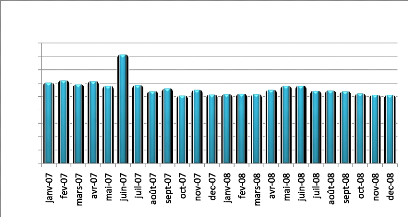
4500
4000
3500
3000
2500
2000
1500
1000
500
MJ/t
0
graphe III.19: secteur électrode
A travers ce graphe, on constate un pic de consommation au
sixième mois 4050 Mj/t pourtant le reste du temps, la consommation varie
entre 2520 Mj/t et 3056 Mj/t. Ce pic de consommation peut avoir trois
explications ; la première serait à cause de la qualité du
fuel, la deuxième serait la qualité de la combustion qui est
exprimée par le taux de combustion, qui varie selon le taux de
réaction chimique entre les composantes du combustible et
l'oxygène, le taux auquel l'oxygène est fourni au combustible,
c'est-à-dire le mélange air/combustible, et la température
maintenue dans la région de la combustion et enfin la troisième,
l'encrassement au niveau des parois des conduites.
CONCLUSION
L'observation de ces graphes nous a permis de mieux
appréhender l'évolution de la consommation électrique au
niveau de chaque atelier et l'évolution de la consommation
d'énergie calorifique au niveau du secteur électrodes pour ce qui
est de la production d'aluminium. Et pour la transformation de cet aluminium
nous avons également l'évolution de la consommation
électrique. L'analyse de ces graphes nous permettra de voir s'il y'a des
possibilités d'amélioration et nous donnerons des mésures
d'efficacité énergétique.
Carte de flux énergétiques et perspectives
d'efficacité dans une fonderie d'aluminium: cas particulier
d'alucam/socatral
Carte de flux énergétiques et perspectives
d'efficacité dans une fonderie d'aluminium: cas particulier
d'alucam/socatral
CHAPITRE IV
ANALYSES ET PERSPECTIVES
Carte de flux énergétiques et perspectives
d'efficacité dans une fonderie d'aluminium: cas particulier
d'alucam/socatral
INTRODUCTION
Dans ce chapitre il est question de regarder de près,
les consommations des ateliers gros consommateurs, les situer par rapport
à celles des usines les plus efficaces. Proposer les solutions pouvant
être implantées afin de réaliser des économies.
IV.1- Energie théorique requise
Pour déterminer l'énergie requise pour le
procédé de fabrication de l'aluminium, on se base sur
l'évaluation de trois facteurs :
y' L'énergie pour conduire la réaction de
réduction LG (Energie libre de Gibbs) ;
y' L'énergie pour maintenir le système des
conditions de température et de pression LH (Enthalpie libre) ;
y' L'énergie pour changer la température des
réactifs et/ou les produits TLS (Entropie) ; Donc l'équilibre
thermodynamique et chimique de la réaction est décrite par
l'équation : LG=LH--TLS (4.1)

Réactifs Produits
2Al
Anode précuite

960°C
1/2 O2

25°C
Al2 O3

25°C
Ici l'énergie théorique requise est de 9,03
kWh/kg. Le procédé présente l'avantage d'une extrême
simplicité de principe ; il nécessite toutefois de surmonter un
certain nombre de handicaps essentiellement d'ordre technologique.
Bien qu'inchangé dans ses principes de base depuis
l'origine, le procédé de Hall-Héroult a connu des
progrès technologiques majeurs qui ont permis simultanément :
> D'abaisser très notablement la consommation
d'énergie électrique de 16000kWh/t en 1950 à 13000kWh/t en
1990,
> D'augmenter l'intensité du courant
d'électrolyse de 100 000 A en 1950 à 300 000 A en 1990,
d'où un gain de productivité,
> De réduire considérablement le taux de
pollution.
Chronologiquement les principaux progrès technologiques
ont été les suivants :
> Nouvelle conception de l'amenée de courant
cathodique par scellement de barres d'acier dans les blocs carbonés,
> Elimination de chutes ohmiques parasites,
Carte de flux énergétiques et perspectives
d'efficacité dans une fonderie d'aluminium: cas particulier
d'alucam/socatral
> Utilisation de cuves à haute intensité
à anode à auto-cuisson de type Söderberg
progressivement abandonnées pour des raisons de pollution
au profit des cuves à anodes précuites,
> Mise au point du captage et du recyclage des gaz
polluants,
> Maîtrise des phénomènes liés aux
forces de Laplace provoquées par les énormes intensités de
courant mis en jeu,
> Automatisation de la conduite du procédé et
en particulier contrôle de l'alimentation en alumine en fonction de sa
cinétique de dissolution. [2]
IV.2- Evolution de la production mensuelle d'aluminium
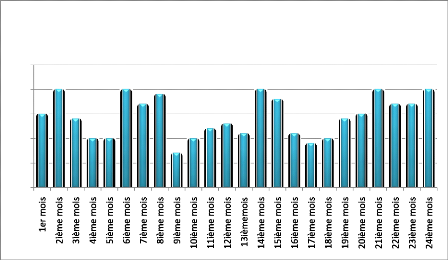
8,5
7,5
6,5
milles tonnes
8
7
6
graphe IV.1: produstion mensuelle
d'aluminium
On constate que la production varie entre 6,7 et 8 milles
tonnes d'aluminium par mois. Au vue de cette production, nous
établissons que le procédé d'électrolyse au sein de
l'entreprise consomme 14176 kWh/tonnes en moyenne les 12 premiers mois et 14513
kWh/tonnes en moyenne entre le 13ième et le
24ième mois. Ce qui nous fait une moyenne de 14344 kWh/tonnes
d'aluminium. La fonderie d'aluminium la plus efficace utilisant le même
procédé et le même type de cuve consomme 12800 kWh/tonnes
d'aluminium. On a donc un surplus de 1544 kWh par tonnes. Cette valeur
représente une perte considérable pour l'entreprise, pour y
pallier on devrait réduire au maximum le temps des effets d'anode en
surveillant automatiquement la quantité d'alumine dans la cuve.
Carte de flux énergétiques et perspectives
d'efficacité dans une fonderie d'aluminium: cas particulier
d'alucam/socatral
Graphe IV.2: proportion
d'énérgie
électrique consommée par
secteur
électrolyse autres transformation
3%0%

97%

Ceci vient une fois de plus nous signifier l'importance
d'appliquer une politique d'économie d'énergie à l'atelier
d'électrolyse.
IV.3- Analyse et interprétation de l'IPM (Indice de
Puissance Maximale)
Graphe IV.3: IPM
MW
250
100
50
0
0 5 10 15 20 25 30
Mois
Le niveau maximal de courant utilisé par la fonderie,
en kW ou en kVA, également appelé appel de puissance crête.
L'appel de puissance varie durant toute la journée en fonction du
fonctionnement des appareils électriques en concurrence. Le service
d'électricité mesure l'appel de puissance à l'intervalle
de 15 minutes.
A travers ce graphe, nous constatons que l'IPM varie de 140
MW à 230 MW. La moyenne sur les 24 mois donne 163 MW. Nous avons
cependant 11 mois pendant lesquels l'IPM est supérieur à la
moyenne mais inférieur à 185 MW. Donc même si l'entreprise
souscrit une puissance de 185 MW elle atteindra ses objectifs en se passant de
25 MW qui représentent 219 GWh/an. D'après le contrat avec
AES-SONEL cette énergie représente des économies
de 1.752.000.000 FCFA par an.
On peut aussi économiser en réduisant l'appel de
puissance par :
Carte de flux énergétiques et perspectives
d'efficacité dans une fonderie d'aluminium: cas particulier
d'alucam/socatral
y' Le délestage ;
y' Le déplacement de la charge, c.-à-d. le
ré ordonnancement des activités pour que d'autres s'effectuent
durant la période hors pointe ;
y' Les améliorations des procédés, qui
réduisent les besoins en courant électrique ;
IV.4- Analyse de la consommation des compresseurs
L'air comprimé est à tort, souvent
considéré comme « gratuit » par ceux qui l'utilisent du
fait que l'air libre utilisé vient de l'atmosphère. Le coût
électrique de l'air comprimé peut s'élever jusqu'à
70 % et plus des coûts d'exploitation annuels de tout un système,
tandis que l'entretien et l'amortissement peuvent engouffrer de 15 à 20
% chacun. Donc, il est clair que l'air comprimé est une technologie
où les améliorations du rendement énergétique sont
directement liées aux économies financières. En moyenne,
les économies proviennent généralement des solutions
apportées aux :
y' Fuites 25 % ;
y' Mauvaises applications 20 % ;
y' L'air perdu dans les réseaux d'évacuation 5 %
;
y' La demande artificielle 15 % ;
Le reste est constitué de l'utilisation d'air
comprimé utile nette, soit 35 %. La répartition des pertes
ci-dessus varie selon l'entreprise. Dans certains systèmes, les fuites
à elles seules peuvent représenter 60 %.
On peut calculer les pertes d'air comprimé par les fuites
durant une période autre que celle de consommation par la formule :
??L= [VC t]/T où
· VL= le volume de la perte par fuite ;
· VC= la capacité du compresseur à pleine
charge en m3/min ;
· t= le temps en secondes de fonctionnement du compresseur
à pleine charge (c.-à-d., le total du temps de mesure à
pleine charge) ;
· T= le total mesuré, le temps écoulé
;
Mais de façon générale les pertes ne
devraient pas dépasser 5 %.
IV.5- Analyse de la consommation électrique de
l'éclairage
La consommation de l'éclairage au sein de l'usine est
constante 34.000 kWh/mois. Etant sur place nous avons fait un constat 10 lampes
de 250W par atelier restent allumées de jour comme de nuit. Nous avons
10 ateliers en limitant le temps de fonctionnement à 14 heures par jour
on réalisera des économies de 91.250 kWh/an, qui
représentent l'énergie nécessaire pour produire 7,3 tonnes
d'aluminium.
L'amélioration de l'efficacité de
l'éclairage constitue l'un des projets à haute visibilité
dans toute industrie, car chacun peut en constater les résultats.
Carte de flux énergétiques et perspectives
d'efficacité dans une fonderie d'aluminium: cas particulier
d'alucam/socatral
IV.6- Analyse de la consommation calorifique
Pour réduire la consommation calorifique on doit
optimiser la fusion. Ce qui revient alors à rechercher la meilleure
position des brûleurs dans le four et à modifier leur angle de
flamme afin d'obtenir le meilleur rendement des brûleurs à
convection. En second lieu l'amélioration de
l'étanchéité des fours qui implique la connaissance de
plusieurs paramètres comme la pression optimale à
l'intérieur du four, le tirage du four et les phénomènes
reliés aux différences de pressions de l'air, du combustible et
des gaz de combustion lors de leur passage dans le four et au travers des
équipements.
CONCLUSION
La recherche des mesures d'économie exige une vision de
l'ensemble des composantes du procédé de fabrication et des
équipements utilisés. Notre étude nous a permis de
ressortir quelques points sur lesquels on peut s'appuyer pour réduire de
façon significative la consommation électrique au sein de
l'usine. L'atelier d'électrolyse et celui des compresseurs sont en
pôle position. Il ne faut non plus négliger les
opportunités qu'offrent les secteurs de l'éclairage, du
conditionnement, et de la ligne de fusion. Des mesures précises devront
être réalisées afin de quantifier de manière
complète les économies d'énergie à
réaliser.
Carte de flux énergétiques et perspectives
d'efficacité dans une fonderie d'aluminium: cas particulier
d'alucam/socatral
CONCLUSION GENERALE
Carte de flux énergétiques et perspectives
d'efficacité dans une fonderie d'aluminium: cas particulier
d'alucam/socatral
L'énergie est le moteur de l'économie moderne.
Extraction et transformation des matières premières, transport et
utilisation des produits. Pour toutes nos activités, nous
dépendons d'un approvisionnement continu et garanti en énergie.
La moindre menace de pénurie pouvant mettre en péril, la
prospérité de notre activité. Ainsi instituer une
réelle politique de gestion de l'énergie est
nécessaire.
La question d'approvisionnement et de consommation
d'énergie est une question très importante pour une entreprise
comme Alucam/Socatral, qui occupe une grande place dans le paysage industriel
Camerounais.
L'objectif de ce mémoire visait à
élaborer la carte des flux énergétiques au sein de la
fonderie d'Alucam afin d'identifier dans l'usine les secteurs pour lesquels
elle connaît des pertes d'énergie. Les résultats de notre
étude nous ont permis de tirer plusieurs conclusions à savoir
:
V' Le procédé d'électrolyse est gros
consommateur d'énergie électrique, il est donc prioritaire d'y
appliquer une politique d'économie d'énergie afin d'optimiser
cette application ;
V' La réduction de la puissance souscrite permettrait
d'importantes économies ;
V' Optimiser le système d'air comprimé en y
instituant une réelle politique de gestion dont les détails sont
faits au chapitre IV ;
V' Le temps de fonctionnement de l'éclairage des ateliers
doit être optimisé ; V' Compenser l'énergie réactive
;
V' Lutter contre les chutes de tension ;
V' Installer les filtres des harmoniques ;
Cette analyse bien qu'elle soit non exhaustive, nous a permis
d'identifier le potentiel d'économie d'énergie lié
à l'optimisation des opérations des composantes importantes de la
chaîne de production. Au vue de tout ceci, nous pouvons donc faire des
suggestions suivantes aux dirigeants d'Alucam/Socatral :
V' Faire des mesures ponctuelles et en continu pouvant aller
au delà de deux ans et augmenter le nombre de points de mesures pour
permettre une quantification plus précise des économies
potentielles afin d'éviter le rejet de projets basé sur des
estimations trop approximatives ;
V' Prévoir les ressources nécessaires pour
l'implantation des mesures ;
Notre ambition pour les deux années à venir est
d'aider le groupe Alucam/Socatral à mettre en place un programme
rigoureux d'efficacité énergétique pour exploiter
Carte de flux énergétiques et perspectives
d'efficacité dans une fonderie d'aluminium: cas particulier
d'alucam/socatral
l'énorme gisement d'économies d'énergie que
nous avons identifié au cours de notre stage.
Carte de flux énergétiques et perspectives
d'efficacité dans une fonderie d'aluminium: cas particulier
d'alucam/socatral
Tableau I.1 :
LES GENERATEURS GR1, GR2 (TURBINES SFAC, ALTERNATEUR SW) :
Vitesse
|
N
|
Trs/mn
|
214
|
Tension assignée
|
Ur
|
kV
|
5,5
|
Puissance assignée
|
Sr
|
kVA
|
14200
|
Puissance active
|
P
|
kW
|
11800
|
Réactances substransitoires ; direct et en quadrature
|
X ''d
|
%
|
25
|
X ''q
|
%
|
25
|
Tension d'excitation max/Tension nominale
|
|
|
220V
|
Réactance synchrone saturée
|
Xdsat max
|
? ou Pu
|
0,8
|
Tableau I.2 :
LES GENERATEURS GR3 (TURBINE VEVEY, ALTERNATEUR SECHERON) :
Vitesse
|
N
|
Trs/mn
|
187
|
Tension assignée
|
Ur
|
kV
|
5,5
|
Puissance assignée
|
Sr
|
kVA
|
14300
|
Puissance active
|
P
|
kW
|
12200
|
Réactances substransitoires ; direct et en quadrature
|
X ''d
|
%
|
25
|
X ''q
|
%
|
25
|
Tension d'excitation max/Tension nominale
|
|
|
220V
|
Réactance synchrone saturée
|
Xdsat max
|
? ou Pu
|
0,8
|
Carte de flux énergétiques et perspectives
d'efficacité dans une fonderie d'aluminium: cas particulier
d'alucam/socatral
Tableau I.3 :
LES GENERATEURS GR4 à GR9 (TURBINE VEVEY, ALTERNATEUR
SECHERON) ;
Vitesse
|
N
|
Trs/mn
|
167
|
Tension assignée
|
Ur
|
kV
|
10 ?3
|
Puissance assignée
|
Sr
|
kVA
|
24500
|
Facteur de puissance nominale
|
cos??
|
|
0,85
|
Réactances substransitoires ; direct et en quadrature
|
X»d
|
%
|
25
|
X ''q
|
%
|
25
|
Tension d'excitation max/Tension nominale
|
|
|
400/250V
|
Réactance synchrone saturée
|
Xdsat max
|
? ou Pu
|
0,8
|
Tableau I.4 :
LES GENERATEURS GR10 à GR14 (Turbine VEVY, Alternateur
BREDA) :
Vitesse
|
N
|
Trs/mn
|
167
|
Tension assignée
|
Ur
|
kV
|
10,3
|
Puissance assignée
|
Sr
|
kVA
|
29400
|
Puissance active
|
P
|
kW
|
20800
|
Réactances substransitoires ; direct et en quadrature
|
X»d
|
%
|
21
|
X ''q
|
%
|
25
|
Tension d'excitation max/Tension nominale
|
|
|
400V
|
Carte de flux énergétiques et perspectives
d'efficacité dans une fonderie d'aluminium: cas particulier
d'alucam/socatral
Réactance synchrone saturée
Xdsat max
Pu 0,8
La formule qui nous a permis de calculer le taux de croissance
puisque le temps est ici une grandeur discrète nous avons utilisé
la formule :
Yt= (1 +á)t+1Y0
V' Avec Yt étant la consommation après t
années et Y0 la consommation au départ ; V' á le taux de
croissance ;
Carte de flux énergétiques et perspectives
d'efficacité dans une fonderie d'aluminium: cas particulier
d'alucam/socatral
Tableau II.1 : CONSOMMATION ELECTRIQUE PAR ATELIER
(kWh)
|
janv-07
|
fev-07
|
mars- 07
|
avr-07
|
mai-07
|
juin-07
|
juil-07
|
août- 07
|
sept- 07
|
Electro lyse
|
102
023 465
|
89
287 591
|
99 573
949
|
80
595 284
|
87
603 636
|
91
029 027
|
108
773 159
|
122
781 096
|
11
343 925
|
Aux. électro lyse
|
911 370
|
793 861
|
812 832
|
852 632
|
880 532
|
822 880
|
810 202
|
810 220
|
767 261
|
Déchar ge
Alumin e
|
270 417
|
199 013
|
246 116
|
221 232
|
288 626
|
269 728
|
248 780
|
256 331
|
246 650
|
Compr esseurs
|
1
395 144
|
1
332 186
|
1
709 974
|
1
438 228
|
1
482 625
|
1
385 550
|
1
468 779
|
1
467 956
|
422 232
|
Electro des
|
343 204
|
241 218
|
283 226
|
348 734
|
266 148
|
248 722
|
409 183
|
356 649
|
343 132
|
Ecla ira ge
Usine
|
34 000
|
34 000
|
34 000
|
34 000
|
34 000
|
34 000
|
34 000
|
34 000
|
34 000
|
Cond. Bât. Généra ux
|
25 250
|
25 250
|
25 250
|
25 250
|
25 250
|
25 250
|
25 250
|
25 250
|
25 250
|
Atelier Mécani que
|
185 277
|
170 750
|
171 927
|
163 260
|
168 441
|
157 413
|
148 654
|
143 549
|
144 077
|
Carte de flux énergétiques et perspectives
d'efficacité dans une fonderie d'aluminium: cas particulier
d'alucam/socatral
Atelier Electri que
|
20 155
|
13 929
|
14 433
|
10 718
|
12 939
|
8 213
|
4 459
|
2 271
|
2 497
|
Stat. Pompa ge
|
239 383
|
214 423
|
221 929
|
231 595
|
240 587
|
224 835
|
239 666
|
236 399
|
237 387
|
Fonder ie
|
95 286
|
81 921
|
84 533
|
84 268
|
87 087
|
81 385
|
106 273
|
124 657
|
113 754
|
Fours Junker
|
150 284
|
118 023
|
136 780
|
140 352
|
118 719
|
110 946
|
142 032
|
157 285
|
154 789
|
Aux. scelle ment
|
110 946
|
94 474
|
100 610
|
98 570
|
92 625
|
86 561
|
110 692
|
106 238
|
109 133
|
Four à cuire
|
290 047
|
248 902
|
267 654
|
279 757
|
275 053
|
257 044
|
290 538
|
245 477
|
243 790
|
Captati on
|
154 839
|
125 966
|
133 473
|
117 051
|
115 320
|
107 770
|
145 821
|
158 425
|
147 968
|
Poste Serem
|
39 741
|
45 660
|
37 611
|
38 806
|
37 691
|
35 223
|
26 215
|
22 949
|
28 244
|
Socatr al
|
1
291 000
|
1
182 000
|
1
303 000
|
1
253 000
|
1
155 000
|
1
233 000
|
569 000
|
732 000
|
333 000
|
Carte de flux énergétiques et perspectives
d'efficacité dans une fonderie d'aluminium: cas particulier
d'alucam/socatral
Tableau II.2 : CONSOMMATION ELECTRIQUE PAR ATELEIR
(kWh)
|
jan v-
08
|
fev -08
|
mar s-
08
|
avr-
08
|
mai
-08
|
juin
-08
|
juil-
08
|
aoû t-08
|
sep t-08
|
oct-
08
|
nov
-08
|
dec
-08
|
Electro lyse
|
96
504 603
|
92
529 793
|
99
997 361
|
97
479 380
|
103 817 447
|
106 588 597
|
118 764 842
|
124 180 844
|
119 745 469
|
123 303 804
|
118 612 914
|
107 484 956
|
Aux. électro lyse
|
789 634
|
744 476
|
845 969
|
852 612
|
864 920
|
777 360
|
825 778
|
907 642
|
882 943
|
905 882
|
837 999
|
822 309
|
Déchar .
Alumin e
|
221 465
|
172 944
|
239 210
|
246 410
|
258 212
|
229 595
|
282 938
|
282 001
|
258 009
|
253 555
|
275 664
|
226 400
|
Compr esseur s
|
1
500 184
|
1
417 565
|
1
487 119
|
1
353 835
|
1
402 218
|
1
455 854
|
1
408 130
|
1
183 251
|
1
385 358
|
1
472 479
|
1
429 267
|
1
240 129
|
Electro des
|
389 846
|
298 782
|
398 795
|
341 415
|
360 755
|
390 300
|
223 177
|
428 374
|
403 146
|
401 988
|
299 111
|
324 612
|
Ecla ira ge
Usine
|
34
000
|
34
000
|
34
000
|
34
000
|
34
000
|
34
000
|
34
000
|
34
000
|
34
000
|
34
000
|
34
000
|
34
000
|
Cond.B ât.
Génér aux
|
25
250
|
25
250
|
25
250
|
25
250
|
25
250
|
25
250
|
25
250
|
25
250
|
25
250
|
25
250
|
25
250
|
25
250
|
Atelier
|
171
|
160
|
171
|
161
|
170
|
154
|
140
|
155
|
152
|
169
|
171
|
169
|
Carte de flux énergétiques et perspectives
d'efficacité dans une fonderie d'aluminium: cas particulier
d'alucam/socatral
Mécan ique
|
116
|
285
|
843
|
262
|
995
|
610
|
404
|
220
|
843
|
037
|
072
|
509
|
Atelier
|
|
|
|
|
|
|
|
|
|
|
|
|
Electri
|
14
|
9
|
14
|
9
|
14
|
7
|
9
|
7
|
6
|
13
|
14
|
13
|
que
|
085
|
443
|
397
|
862
|
034
|
012
|
904
|
273
|
254
|
194
|
067
|
397
|
Stat.
|
|
|
|
|
|
|
|
|
|
|
|
|
Pompa
|
224
|
224
|
258
|
245
|
227
|
234
|
223
|
236
|
226
|
235
|
227
|
232
|
ge
|
914
|
740
|
389
|
765
|
830
|
840
|
230
|
686
|
402
|
942
|
357
|
733
|
Fonder
|
|
|
|
|
|
|
|
|
|
|
|
|
ie
|
60
|
96
|
100
|
121
|
128
|
114
|
114
|
121
|
124
|
132
|
120
|
88
|
|
635
|
410
|
761
|
815
|
263
|
853
|
233
|
714
|
371
|
814
|
521
|
184
|
Fours
|
|
|
|
|
|
|
|
|
|
|
|
|
Junker
|
139
|
135
|
150
|
144
|
163
|
148
|
151
|
163
|
157
|
154
|
153
|
147
|
|
326
|
863
|
784
|
553
|
339
|
549
|
041
|
556
|
942
|
636
|
007
|
688
|
Aux.
|
|
|
|
|
|
|
|
|
|
|
|
|
Scelle
|
93
|
87
|
111
|
109
|
104
|
113
|
99
|
117
|
118
|
112
|
111
|
116
|
ment
|
883
|
405
|
162
|
244
|
902
|
064
|
954
|
755
|
454
|
765
|
208
|
633
|
Four à
|
|
|
|
|
|
|
|
|
|
|
|
|
cuire
|
277
|
258
|
281
|
278
|
301
|
289
|
292
|
315
|
288
|
287
|
285
|
288
|
|
930
|
812
|
371
|
004
|
902
|
650
|
774
|
370
|
153
|
894
|
196
|
204
|
Captati
|
|
|
|
|
|
|
|
|
|
|
|
|
on
|
115
|
106
|
123
|
138
|
160
|
149
|
200
|
216
|
207
|
206
|
188
|
177
|
|
973
|
072
|
799
|
947
|
161
|
746
|
965
|
054
|
546
|
034
|
560
|
239
|
Centre
|
|
|
|
|
|
|
|
|
|
|
|
|
Médic
|
13
|
14
|
12
|
12
|
13
|
12
|
10
|
11
|
11
|
12
|
14
|
14
|
al
|
034
|
033
|
464
|
966
|
764
|
346
|
265
|
606
|
371
|
395
|
117
|
176
|
Poste
|
|
|
|
|
|
|
|
|
|
|
|
|
Serem
|
40
|
43
|
38
|
41
|
41
|
40
|
38
|
40
|
38
|
44
|
46
|
47
|
|
725
|
920
|
688
|
060
|
454
|
970
|
957
|
247
|
958
|
133
|
605
|
536
|
Socatr
|
|
|
|
|
|
|
|
|
|
|
|
|
al
|
1
|
1
|
1
|
1
|
1
|
1
|
570
|
658
|
1
|
1
|
1
|
1
|
|
163
|
167
|
303
|
233
|
213
|
143
|
000
|
000
|
134
|
232
|
177
|
229
|
Carte de flux énergétiques et perspectives
d'efficacité dans une fonderie d'aluminium: cas particulier
d'alucam/socatral
|
000
|
000
|
000
|
000
|
000
|
000
|
|
|
000
|
000
|
000
|
000
|
Tableau II.3 : CONSOMMATION DE FUEL LOURD DES
SECTEURS ELECTRODES (Mj/t)
|
janv-
|
fev-
|
mars-
|
avr-
|
mai-
|
juin-
|
juil-
|
août-
|
sept-
|
oct-
|
nov-
|
dec-
|
janv-
|
fev-
|
mars-
|
a
|
|
07
|
07
|
07
|
07
|
07
|
07
|
07
|
07
|
07
|
07
|
07
|
07
|
08
|
08
|
08
|
0
|
Secteur
|
3006
|
3087
|
2939
|
3056
|
2882
|
4050
|
2907
|
2677
|
2783
|
2520
|
2727
|
2563
|
2572
|
2586
|
2566
|
2
|
Electrodes
|
|
|
|
|
|
|
|
|
|
|
|
|
|
|
|
|
CARACTERISTIQUES DU FUEL LOURD
Densité moyenne
PCI moyen 0,887
10003,15 Kcal/kg
Carte de flux énergétiques et perspectives
d'efficacité dans une fonderie d'aluminium: cas particulier
d'alucam/socatral
[1] Jacques Régnier, »la bauxite: de la
méditerranée à l'Afrique et au-delà», Cahiers
d'histoire de l'aluminium, n°24 été 1999, p15.
[2] Extrait de la revue Ecomine, Décembre 2008
[2] William T. Chouate, John A. S. Green U.S. Energy
Requirements for Aluminum Production: Historical perspective, Theoretical
Limits and New Opportunities 115p Febuary 2003.
[3] Guide sur l'efficacité Energétique dans les
alumineries, Association de l'aluminium du Canada Rncan, PEEIC 54p Avril
1998.
[4] Les possibilités d'amélioration du rendement
énergétique dans les fonderies Canadiennes, PEEIC 143p 2003.
[5] Suzanne Savey, les transformations récentes de
l'industrie française de l'aluminium Revue géographique alpine,
année 1968 volume 56 Numéro 3 p.569-591.
[6] Njomo Donatien, efficacité énergétique
(PH430) cours de maîtrise énergétique Université de
Yaoundé I, 2006/2007.
[7] Solaz Philippe Contribution à l'étude des
perturbations électromagnétiques conduites : Usine
d'électrolyse Aluminium Pechiney de Lannemezan.
[8] Aluminium et électricité : Une combinaison
gagnante Association de l'aluminium du Canada 12p 2004.
[9] « L'âge de l'aluminium » CCSTI (Centre de
culture scientifique Technique et industrielle 28p. Juin 2006.
[10] Analyse de la valeur et de l'efficacité
énergétique (Aluminerie de BaieComeau).
[11] Intersections (La compensation de l'énergie
réactive) 9p. nov 2006.
[12] Rapport d'activité d'ALUCAM
[13] Véronique Ferlay-FERRAND, Claude Picard, Claude Prin
CEREN Approche toxicologique des fumées.
|