|
REPUBLIQUE ALGERIENNE DEMOCRATIQUE ET POPULAIRE
MINISTERE DE L'ENSEIGNEMENT SUPERIEUR
ET DE LA RECHERCHE SCIENTIFIQUE
|
|
UNIVERSITE CONSTANTINE 1
FACULTE DES SCIENCES EXACTES DEPARTEMENT DE
PHYSIQUE
MEMOIRE
PRESENTE POUR OBTENIR LE DIPLOME DE MASTER EN
SCIENCES EN PHYSIQUE
SPECIALITE
SCIENCES DES MATERIAUX
THEME
ETUDE STRUCTURALE ET EVOLUTION DE LA
TEXTURE
D'UN ACIER DOUX
PAR
MECHITOUA MOHAMED AMINE SOUS LA DIRECTION
DE Dr. AYAD ABDELHAK
Soutenue le :
Remerciement
Ce travail de thèse a été
effectué au Laboratoire de Microstructure et
Défauts
(LMDM) du département de Physique,
Université Constantine 1
Je tiens à exprimer toute ma profonde
gratitude à Monsieur AYAD ABDELHAK pour avoir accepté de me
diriger dans ce travail ce travail, de son soutien tout au long de ce travail,
pour son aide, ses conseils avisés.
Je voudrais remercier plus particulièrement
Madame N.ROUAG Professeur à l'université 1
Constantine. Je lui dis merci pour ses encouragements, ses remarques,
ses conseils et les nombreuses discussions fructueuses qui m'ont
toujours été très précieuses.
Mes sincères remerciements vont également
à l'ensemble de personnes du laboratoire
(LMDM) à Madame A.ROUSTILA, Madame
N.KEGHOUCHE, Monsieur L.CHEKOUR, Monsieur O.KHALFALLAH, pour le
dévouement et la disponibilité avec lesquels ils
m'a suivi tout au long de ce travail. Cette
disponibilité, en particulier pour ces derniers temps, m'a permis de
bénéficier pleinement de ses connaissances, de sa rigueur et de
sa gentillesse. Qu'elle
soit assurée de toute ma
reconnaissance.
Je remercie également tous mes camarades de
LMD, BOUABDALLAH ZINEB, DOUAS NIHAD, MOUATSI ISMAIL, RIAS BADIS, pour leur
aide, morale et leur amitié, et leur encouragement et les bons moments
passés ensemble.
J'adresse mes remerciements aussi aux Monsieur
LAMRI responsable des ressources humaines, et l'équipe
des traitements thermiques et analyse du SOMATEL pour leur
hospitalité et leur aide et collaboration avec notre
laboratoire.
Sommaire
Sommaire
Introduction générale 1
Chapitre I Etat de déformation
I.1. INTRODUCTION 3
I.2. MICROSTRUCTURES DE DEFORMATION 3
I.3. MODELES DE DEFORMATION 4
I.3.1. Modèle de Sachs 5
1.3.2. Modèle de Leffers 5
I.3.3. Modèle de Taylor 5
I.3.4. Modèle de Taylor relaxés
5
I.3.5. Modèles auto-cohérents
6
I.4. ENERGIE EMMAGASINEE 6
I.5. PHENOMENE DE RECRISTALLISATION 6
I.5.1. Restauration 7
I.5.3. Recristallisation primaire 7
I.5.4. Croissance normale 8
I.5.5. Croissance anormale (exagérée)
8
Chapitre II Textures de déformation et de
recristallisation
II.1. INTRODUCTION 10
II.2. ORIENTATION D'UN GRAIN 10
II.3. DESORIENTATION ENTRE DEUX GRAINS 12
II.4. REPRESENTATION DES TEXTURES 13
II.4.1. Figures de pôles directs 13
II.4.2. Figures de pôles inverses 14
II.4.3. La fonction de distribution des orientations
cristallographique (FDOC) 14
III.3. TECHNIQUES DE CARACTERISATION 15
II.3.1. Diffraction des rayons X 16
II.3.2. La diffraction des électrons
rétrodiffusés (EBSD) 16
II.4. TEXTURES DES ACIERS 17
II.4.1. Textures de déformation 18
II.4.2. Textures de recristallisation 19
Chapitre III Matériau et techniques
expérimentales
III.1. INTRODUCTION 21
III.2. MATERIAU 22
III.2.1. Aciers IF 22
II.2.2. Composition chimique 22
III.3. PROCEDURE EXPERIMENTALE ET PREPARATION DES
ECHANTILLONS 23
III.3.1. Laminage à froid 23
III.3.2. Préparation d'échantillons
24
III.4. MESURE DE LA DURETE 24 III.5. MESURE DES
TEXTURES PAR DIFFRACTION DES RAYONS X (DRX)
25
III.5.1. Principe 25
III.5.2. Conditions de mesure 28
Chapitre IV Résultats et discussions
IV.1. INTRODUCTION 31
IV.2. MICROSTRUCTURE ET TEXTURE DE LAMINAGE
31
IV.2.1. Mesures de Microdureté 32
IV.2.2. Analyse morphologique 33
IV.2.3. Analyse des textures cristallographiques
35
IV.2.3.1. Etat initial 35
IV.2.3.2. Evolution de la texture au cours du
laminage 38
Conclusions et perspectives 42
Annexe I 44
Annexe II 45
Annexe III 46
Introduction générale
1
Introduction générale
Introduction générale
La microstructure gouverne en grande partie
les propriétés d'usage des matériaux, entre autres
les pertes magnétiques, la résistance à la rupture, la
tenue à la fatigue et au fluage, l'aptitude à la mise en
forme et la recristallisation. La microstructure finale est fonction de
la chimie du matériau et de son histoire
métallurgique.
Le terme microstructure recouvre un grand nombre de
paramètres ; parmi les principaux, citons la répartition des
phases en présence, la taille et la forme des grains, la distribution
des joints de grains, les orientations préférentielles des grains
ou texture cristallographique. Nous somme intéressé par ce
dernier paramètre car toute propriété tensorielle
d'un matériau dépend de la direction de mesure, donc de
sa texture qui influe les propriétés moyennes du
polycristal.
Les tôles d'acier doux destinées à
l'industrie des automobiles sont fabriquées par
laminage à chaud, à des températures supérieures au
point de transformation de phases ferrite-austénite, ensuite par
laminage à froid et enfin des traitements thermique pour leur restaurer
un certain niveau de ductilité compatible avec toute mise en forme
ultérieure.
Les changements microstructuraux qui interviennent
tout au long de l'élaboration de ces tôles
affectent leur état de précipitation, leur microstructure (y
compris la distribution des précipités) et leur texture
cristallographique (par déformation, recristallisation et transformation
de phase). Il est essentiel de bien connaître les mécanismes par
lesquels sont modifiés ces paramètres, et en particulier les
textures cristallographiques, puisque les propriétés de mise en
forme, notamment en emboutissage, en dépendent fortement.
Notre travail constitue une contribution dans la
compréhension des mécanismes physiques gérant les
changements de texture cristallographique. Il s'agit notamment
de comprendre les changements microstructuraux qui ont lieu pendant la
déformation par le laminage à froid.
Notre objectif est le suivi de
l'évolution de la microstructure et de la texture de
déformation par laminage à froid, d'une tôle
d'acier IF, destinée à l'emboutissage.
Nous avons utilisé la Diffraction des rayons X (DRX) pour la
détermination de la texture, du fait de la difficulté
d'utiliser la diffraction des électrons
rétrodiffusés (EBSD : Electron Back
2
Introduction générale
Scattered Diffraction), notamment pour la
caractérisation des échantillons fortement
déformés.
Notre laboratoire a acquis récemment un
diffractomètre à rayons X équipé d'un
goniomètre de textures, qui permet, entre autres, la
détermination de la texture globale à partir des figures de
pôles expérimentales. Nous avons utilisé la DRX pour
:
· la caractérisation de l'état
recristallisé (laminé à chaud) de la tôle
étudiée, qui considéré comme notre état
initial ;
· le suivi de l'évolution de la
texture à différents taux de déformation par
laminage (25%, 50% et 75% de réduction).
Ce mémoire comporte cinq chapitres :
· Le premier chapitre est consacré
à la description de l'état du matériau
déformé et des différents modèles de
déformation généralement utilisés. Il comporte
aussi un rappel sur les phénomènes de recristallisation et de
croissance des grains.
· Le deuxième chapitre est
réservé à l'étude des textures :
définition, représentation et détermination. Il
comporte un rappel bibliographique sur l'évolution des
textures, au cours de la déformation et de la recristallisation,
des aciers doux et des aciers IF en particulier.
· Le troisième chapitre est
consacré à la présentation du matériau
considéré dans son état de réception et aux
différentes démarches et techniques expérimentales qui
permettent sa caractérisation morphologique et
cristallographique.
· Le quatrième chapitre présente
les résultats de l'état initial et ceux de
l'évolution de la microstructure et de la texture au cours du
laminage et leurs discussions.
Enfin, des conclusions et des perspectives terminent la
présentation de ce mémoire
Chapitre I
Etat de déformation
3
Chapitre I : Etat de déformation
I.1. INTRODUCTION
Plusieurs phénomènes peuvent se trouve
lorsqu'on déforme la matière, dans ce cas pour comprendre
mieux la déformation on doit savoir l'état
déformé de la matière et son indispensable
relation avec la microstructure. Le matériau peu se déformer par
certains mécanismes comme le laminage à chaud et
à froid, l'emboutissage et la traction. Les joins de grains
migrent pendant cette déformation avec la création des
dislocations et des défauts dans le matériau qui peuvent
s'accumulent pour former des nouveaux grains à
l'intérieur des premiers ce qui donne une nouvelle structure.
Lors de la déformation, l'énergie
importée dissipe presque complètement en chaleur et le
reste se transforme en énergie stocké dans les
dislocations. D'un autre côté, chaque grain tend
à s'orienter selon une direction différente de celle des
grains voisins ce qui donne une anisotropie ou une texture à
l'échelle microscopique.
I.2. MICROSTRUCTURES DE DEFORMATION
Lors de la déformation d'un matériau les
grains changent leur forme pour mieux s'adapté à
la contrainte extérieur, donc chaque grain peu
s'orienter différemment des autres dans des cas spéciaux
on trouve des orientations dans des régions à
l'intérieur d'un grain lui-même. Dans ce dernier
processus, il apparait des bandes résultant de
l'inhomogénéité de déformation dite «
bandes de déformation » [1] (Fig.I.1). Ces bandes sont
utilisées pour décrire les volumes d'orientations
différentes dans le grain. Une bande est un changement
d'orientation dans le même grain.
Fig. I.1 : bandes de déformation [1].
4
Chapitre I : Etat de déformation
Barret [2] a observé ces
hétérogénéités et il l'a utilisé pour
prévoir le comportement de durcissement par déformation. Ces
bandes sont inévitables dans une structure d'un polycristal
déformée par un mode principal de déformation
(Glissement ou maclage).
Dans la figure (I.2), on peut visualiser les
différentes subdivisions qui se trouvent lors de la déformation
dans un grain initial A [3].
La région B a une orientation constant mais
différente de A est dite bande de déformation.
La région T est une bande de transition
[4] ou microbande car l'orientation qui passe de B à A n'est
pas un joint de grain.
La bande de déformation délimitée
par les faces parallèles créant une double orientation A-C et C-A
cette bande est dite bande de pliage [5].
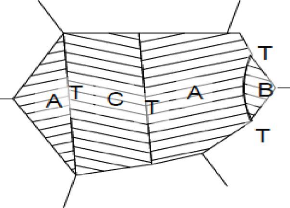
Fig. I.2 : Représentation schématique
d'un grain comportant plusieurs
hétérogénéités de déformation.
[6].
I.3. MODELES DE DEFORMATION
Les modèles de déformation
sont utilisés pour déduire la déformation d'un polycristal
à partir du comportement d'un monocristal. Le
modèle de Taylor [7], est le plus fameux et il est
considéré comme une base pour d'autres model
utilisés actuellement. Parmi ces modèles
5
Chapitre I : Etat de déformation
I.3.1. Modèle de Sachs
Dans ce modèle, les grains qui ont un
système de glissement, ayant le plus grand facteur de Schmidt, vont se
déformer les premiers. D'après Sachs [8], le
grain qui va se déformer est entouré par une matrice
élastique. L'inconvénient de ce modèle
est qu'après déformation, les grains laissent du
vide entre eux, avec un manque de matière, ce qui n'est pas
vrais dans le cas réel. Pour corriger ce modèle, les
dislocations sont misent en jeu pour compléter la
géométrie des grains. Donc ce modèle ne donne pas une
bonne prévision du comportement plastique lors de la
déformation.
1.3.2. Modèle de Leffers
Le modèle de Leffers est un bon modèle
pour prévoir le comportement plastique surtout dans le laminage des
métaux CFC [9]. Il a été utilisé
généralement pour les métaux CC par Wierzbanowski et
Jasienski [10]. Du fait qu'il est basé sur des
simulations, il nécessite des puissants moyens de calculs. Ce
modèle vient pour compléter le modèle de Sachs et donner
la continuité nécessaire au niveau des joins de grains.
Il suppose l'existence d'une zone étroite au voisinage des joins
qui assure la compatibilité de la déformation.
I.3.3. Modèle de Taylor
Pour conserver la continuité des joints,
Taylor suppose que chaque grain se déforme d'une manière
homogène et homothétique à l'éprouvette
[7]. La proposition de Taylor est d'introduire la
théorie macroscopique de la plasticité qui est la condition de
Von Mises (cinq composantes indépendantes pour définir un
tenseur de déformation). D'après cette
proposition, le matériau de Taylor est plus dur que celle de
Sachs et présente une limite élastique supérieure à
la scission maximale. En général, ce modèle donne des
bonnes prévisions des comportements des métaux cubiques et
hexagonales.
I.3.4. Modèle de Taylor relaxés
Ce modèle vient pour corriger les
incompatibilités du premier, en particulier, la forme des grains,
notamment dans le cas de laminage et les fortes déformations.
Ce qui n'est pas acceptable, les grains equiaxiaux du matériau
initial deviennent plats après la déformation. Honneff et Mecking
[11] ont montré qu'il n'est pas nécessaire d'introduire
tous les composantes de déformation car les faces des grains
deviennent plus petites pour assurer la continuité au niveau du
joint.
6
Chapitre I : Etat de déformation
I.3.5. Modèles auto-cohérents
Ces modèles donnent une approche
différente du comportement du polycristal, les plus fameux sont de
Kröner [12], Hill [13] et celui de Zaoui et Berveiller [14].
L'objectif de ces modèles est de
prévoir le comportement d'un grain vis-à-vis de
ses voisins. Ils s'intéressent au gain individuel et
considèrent le reste du matériau comme une matrice
élastique homogène, dans laquelle, le grain choisi est y
introduit.
I.4. ENERGIE EMMAGASINEE
Lorsqu'on déforme un matériau à
froid, la majorité de travail est perdue sous forme de chaleur.
La petite portion restée de l'énergie fournie est dite
énergie emmagasinée (~2 à 10%) [15, 16].
L'énergie stockée dans les défauts a une
importance énorme, car elle représente la force motrice de
plusieurs phénomènes. Cette énergie vienne de
l'accumulation des dislocations. Le piégeage continu
des dislocations mobiles, par les autres immobiles, forcent les uns, qui sont
mobiles, à s'accumuler pour former des structures
internes au niveau des grains ou d'augmenter la surface de grain. Elle
a une bonne relation avec la densité des dislocations, plus on
déforme plus cette densité augmente et plus
l'énergie augmente. [1].
I.5. PHENOMENE DE RECRISTALLISATION
La recristallisation est l'un des processus qui
gouvernent la formation des structures cristallines et le
contrôle des propriétés des matériaux.
Généralement, l'étude de la
recristallisation se fait par la simulation car elle est une technique
indispensable dans l'optimisation des paramètres
expérimentaux [17].
La recristallisation comporte les étapes
suivantes : restauration, recristallisation primaire, croissance normale ou
anormale des grains.
Au cours de la déformation plastique, le
glissement des dislocations change la forme des grains, en provoquant une
augmentation de la température du matériau déformé,
ce qui conduit à l'apparition des certains processus
thermique qui fait abaisser l'énergie libre par
plusieurs mécanismes tels que l'annihilation des
défauts ponctuels, annihilation de quelques dislocations et
l'arrangement des autres et la réduction de la surface totale
des joins de grains. [1].
7
Chapitre I : Etat de déformation
I.5.1. Restauration
La restauration est simplement le retour partiel des
propriétés mécaniques du matériau avant la
déformation. Dans cette étape, il n y a pas une formation de
nouveaux grains mais juste une diminution et un arrangement des défauts
existant dans le matériau, tels que : les dislocations et les lacunes.
Elle est mesurable expérimentalement par les changements
qu'elle produit sur des paramètres physiques telles que : la
limite d'élasticité [18], la
résistivité électrique [19].
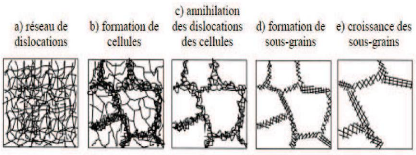
Fig. I.2 : Mécanismes de restauration des
métaux déformés plastiquement [20]. I.5.3.
Recristallisation primaire
La recristallisation primaire est
caractérisée par la formation des nouveaux grains aux
dépend de la matrice déformée. Elle s'appuie
à l'énergie emmagasinée dans les dislocations
comme force motrice et elle arrête lorsque la matrice
déformée est consommée complètement.
Ce phénomène est contrôlé par
des lois bien définies :
· Elle ne peut se déclencher
s'il y a une déformation suffisante dite
`écrouissage critique'.
· La température de
recristallisation est d'autant plus élevée lorsque la
déformation est faible.
· La taille de grains est
d'autant plus fine que la déformation est
importante.
· Les nouveaux grains vont croitre aux
dépends des grains déformés avec des orientations
différentes que celle des grains de la matrice initiale.
· Quand la pureté du métal est
élevée, la température de recristallisation est plus
basse.
8
Chapitre I : Etat de déformation
I.5.4. Croissance normale
La croissance normale vienne après la
recristallisation primaire. Elle est caractérisée par une
structure, pas encore stable, qui présente un excès
d'énergie sous forme de joints de grains courbés. La
croissance des grains peuvent être homogène et continue si le
matériau est maintenu en haute température, En recristallisation
primaire, les nouveaux grains changent d'orientation, en revanche, en
croissance normale, il n y a pas de changement total
d'orientations et la structure tend à se
homogénéiser.
I.5.5. Croissance anormale (exagérée)
Ce type de croissance démarre lorsque la
croissance normale est bloquée. Il est caractérisé par
l'apparition soudaine de quelques grains qui envahissent rapidement
toute la matrice recristallisée. Parmi les mécanismes qui
bloquent la croissance normale on cite :
· L'effet de ségrégation ; le joints
généraux (à grand angles) attirent les impuretés
[17].
· La présence des
précipités ou une seconde phase qui bloque les joints
généraux et pas les joints spéciaux.
· La présence de textures, qui gêne
le déplacement des joints de faible orientation.
· L'énergie de surface ;
les grains de surface tendent à se développer au dépend du
reste de la matrice.
9
Chapitre I : Etat de déformation
Références bibliographiques
[1] Humphreys. F.J, Hatherly. M; "Recrystallization and
related annealing phenomena"; Pergamon (1995).
[2] Barrett.C.S et Massalski.T. Structure of Metals, 3rd
ed Pergamon Press, Oxford (1980).
[3] Hansen. N; Metallurgical and Material Transactions;
Vol. 32A (2001); 2917.
[4] Walter.J.L, Koch. E.F; Acta Metallurgica; Vol. 11
(1963); 923.
[5] Orowan. E; Nature; Vol. 149 (1942); 643.
[6] Humphreys.F.J et Hatherly.M. Recrystallization and
related annealing phenomena. Pergamon Press, Oxford (1996).
[7] Taylor.G.I. J. Inst.Met. 62, (1938). 307
[8] Sachs.E. Z.Verein.Deut.Ing. V 72, (1928).
734
[9] Leffers.T. Proc. 2nd Inter. RisØ Symp.
RisØ, Denmark. Ed: Hansen et al , (1981). 55
[10] Wierzbanowski.K.et Jasienski.Z. Scripta Met. V15,
(1981). 585
[11] Honeff.H et Mecking.H. Proc.ICOTOM5, ed: Gottstein
et Lücke, Springer Verlag, Berlin, (1978). 265
[12] Kröner.E. Acta Met. V9, (1960).
155
[13] Hill.R.J, Mech Phys Solid. V13, (1965).
89
[14] Zaoui.A et Berveiller.M. J Mech Phys Solid. V26,
(1979). 325
[15] Benard.J, Michel.A, Philbert.J, Metal Gén,
Masson et Cie, édi (1969). A329, (1972). 405
[16] Martin.G, Levy.J, Oudar.J, Saada.G, Saintfort.G,
Interfaces et surfaces en metallurgie. trans tech Publications
(1973).
[17] Ballufi. R. W, `Interfacial segregation',
W. C. Jhonson and J. M. Blakely (Eds), American society for metals,
USA, (1977). 193.
[18] Michalak.J.Tet Paxton.H.W. Trans Met Soc of AIME.
V221, (1961). Pergamon (1995). 850
[19] Drew.R.A.L, Muir.W.B et Williams.W.M. Metals
Technology, V11, (1984). 550
[20] Humphreys.F.J. Materials Science Forum. V 467-470,
(2004). 107
Chapitre II
Textures de déformation et de
recristallisation
Chapitre II : Textures de déformation et de
recristallisation
INTRODUCTION
Les matériaux présentent une anisotropie
cristallographique ou texture lorsqu'un certain nombre de
leurs grains ne sont pas orientés au hasard, mais possèdent une
ou plusieurs orientations préférentielles [1]. Souvent on obtient
une texture par une déformation mécanique ou un traitement
thermique. Parmi les processus que l'on utilise pour obtenir une
texture nous motionnant : la solidification, la déformation, la
recristallisation et/ou les transformations des phases. La
présence d'une texture a une influence plus ou moins
marquée sur les propriétés physiques des
matériaux.
II.1. ORIENTATION D'UN GRAIN
La caractérisation d'un grain dans un
polycristal nécessite six paramètres : trois
paramètres de position (les coordonnées x, y, z) et trois
paramètres d'orientation.
Pour caractériser la texture
cristallographique, on ne considère que l'orientation des
grains. Si on définit :
· un référentiel lié à
l'échantillon décrit par la direction de laminage (DL), la
direction transverse (DT) et la direction normale au plan de laminage
(DN) (Fig. II.1).
· un référentiel lié au
cristal, caractérisé avec des vecteurs de base du réseau
cristallin de la maille cubique [100], [010], [001] (Fig. II.1).
Les trois paramètres d'orientation
définissent la rotation qui met le référentiel
échantillon parallèle au référentiel
cristal.
|
Fig. II.1 : Référentiel
échantillon (X, Y, Z) ou (Xs //DL, YS //DT, ZS //DN) et
référentiel cristal (XB //[100], YB //[010], ZB
//[001]).
|
|
10
Dans l'étude de texture, il existe plusieurs
méthodes pour représenter une orientation [2], parmi ces
méthodes il y a :
Chapitre II : Textures de déformation et de
recristallisation
· une direction cristallographique et un angle de
rotation autour de cette direction
· le doublet classique (hkl)[uvw], la normale au
plan de laminage et la direction de laminage respectivement.
· Les trois angles d'Euler Fig. II.2 :
ö1 : angle de rotation autour de l'axe OZ ö : angle
de rotation autour de l'axe OX'
ö2 : angle de rotation autour de l'axe
OZ'
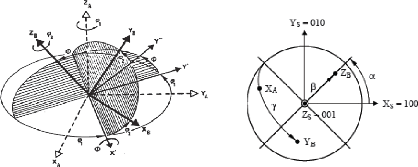
Fig. II.2 : Définition des trois angles d'Euler
d'après Bunge [2].
Dans ce formalisme de Bunge, chacune des rotations
précédentes est décrite par une matrice de rotation g
:
g = (p1, ö,
p2) = gzp2 *
gx'ö * gz (II.1)

cos(p2) sin(p2) 0
-sin(p2) cos(p2) 0
0 0 1
1 0 0
0 cos(ö)
sin(ö) 0 -sin(ö)
cos(ö)
cos(p1) sin(p1) 0
-sin(p1) cos(p1) 0
0 0 1
g =
(II.2)
11
Soit :
|
cos(p1)cos(p2) -
sin(p1)sin(p2)cos(ö)
|
sin(p1)cos(p2) +
cos(p1)sin(p2)cos(ö)
|
sin(p2)
cos(ö)
|
|
g =
|
-cos(p1) sin(p2) -
sin(p1)cos(p2)cos(ö)
|
-sin(p1)sin(p2) +
cos(p1)cos(p2)cos(ö)
|
cos(p2)
sin(ö)
|
(I.3)
|
|
sin(p1)sin(ö)
|
-cos(p1)sin(ö)
|
cos(ö)
|
|
|
12
Chapitre II : Textures de déformation et de
recristallisation
Les colonnes de cette matrice correspondent aux
directions DL, DT, DN, et les lignes correspondent aux normales des plans
(100), (010), (001).
D'après cette matrice nous pouvons déduire
:
· les angles d'Euler à partir les indices de Miller
avec les équations suivantes : tan
(()) cos ((p2) = k/l
tan ((p2) = h/k (II.4)
cos (()) tan ((p1)
=lw/ (ku-hv)
Les indices de Miller à partir des
angles d'Euler : h = sin (()) sin
((p2)
k = sin (())
cos((p2)
l = cos (()) (II.5) u = cos
((p1) cos ((p2) - sin ((p1)
sin ((p2) cos (()) u = - cos
(p1) sin ((p2) - sin
((p1) cos ((p2) cos (())
w = sin ((p1) sin (())
Dans l'espace d'Euler, deux notations sont possibles : ((p1,
4, (p2), utilisée par [2], et (ø, è, 4)
utilisée par [3]. Les angles ø, è et (p
sont les angles de rotation autour des axes OZ, OY et OZ,
respectivement. Le triplet de Roe (ø, è, (p) est obtenu
à partir du triplet de Bunge ((p1, 4, (p2), par :
ø = (p1 - ð /2, è = 4, 4 =
(p2 + ð /2 (II.6)
II.3. DESORIENTATION ENTRE DEUX GRAINS
La désorientation entre deux grains est une rotation
qui permet de passer d'un référentiel d'un grain à
un autre. Généralement, cette rotation est décrite par une
matrice de désorientation R :
R= g * g'-1
(II.7)
Ou g et g' sont les matrices d'orientation des deux grains dans
le repère de l'échantillon.
Chapitre II : Textures de déformation et de
recristallisation
L'angle et l'axe de rotation sont définit
à partir des éléments de Rij de la matrice R par
:
trace(R)
-1 )
O =Arcos ( (II.8)
2
u = R32 - R23 (II.10)
v = R13 - R31 (II.11)
w = R21 - R12 (II.12)
Selon les symétries existant dans les
matériaux, on trouve un nombre différent d'orientations
possibles. Dans le cas de la symétrie cubique il y a 24
orientations équivalentes. Parmi ces orientations, on choisit
celle qui a le plus petit angle et l'axe de rotation
correspondant [4].
II.4. REPRESENTATION DES TEXTURES
La représentation qualitative des textures se
fait par des figures de pôles expérimentales et quantitativement
par la fonction de distribution des orientations cristallines
(FDOC).
II.4.1. Figures de pôles directs
La représentation des textures avec les
figures de pôles directes est la plus directe. La figure de pôles
directe est une projection stéréographique de la densité
de pôles, d'une famille des plans {hkl}, sur un
plan de l'échantillon dans toutes les directions. Pour
caractériser une orientation cristalline dans un échantillon ou
une tôle mince, il faut au moins deux figures de pôles, dans le cas
des structures cubiques
|
Fig. II.3 : Construction d'une figure
de pôles directe.
|
|
13
.
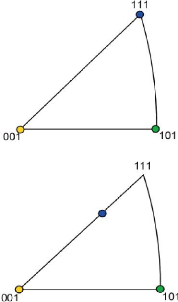
DL
DN
Chapitre II : Textures de déformation et de
recristallisation
II.4.2. Figures de pôles inverses
Une figure de pôles inverse est une projection
stéréographique, liée au cristal, de la distribution de la
densité des pôles, d'une famille des plans {hkl},
dans une direction donnée de l'échantillon (Fig.
II.4). La symétrie cubique nous permet de schématiser le triangle
standard de la projection stéréographique [001], [101], [001].
Elle est considérée comme une méthode excellente pour
représenter les textures de fibre.
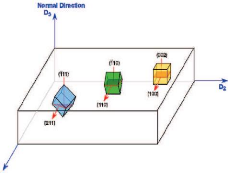
14
Fig. II.4 : Figures de pôles inverses selon DN et
DL de l'orientation idéal (111)[211]
II.4.3. La fonction de distribution des orientations
cristallographique (FDOC)
Cette méthode est la plus satisfaisante et la
plus complète pour décrire une texture. Pour un
échantillon de volume V, elle est proportionnelle à la
fraction volumique AV(g) des grains dont l'orientation est comprise
entre g et g +Ag. :
dV/V = F(g) dg.
(II.13)
1
Äg =
8
2
ð
sin(Ô) dqild'1dp2 (formalisme de Bunge)
(II.14)
Chapitre II : Textures de déformation et de
recristallisation
1
Ou Ag =
|
|
|
sin(0)dcIdO dW (formalisme de Roe) (II.15)
|
|
2
ð
|
|
15
La fonction f(g) peut être calculée par
la méthode harmonique ou les méthodes discrètes. La
méthode harmonique s'appuie sur un développement de
séries des bases harmoniques avec un ordre imposé par le
nombre de figures de pôles expérimentales. Elle a
été proposée par [5] et Roe [3]. La méthode
discrète qui est développée par Ruer et Baro [6] et par
Matthies [7] et Schaeben [8], elle consiste à associer un point
(ou ensembles des point) de l'espace des pôles à
un point de l'espace des orientations après avoir discrétiser ces
deux espaces.
III.3. TECHNIQUES DE CARACTERISATION
Généralement les textures sont
caractérisées par plusieurs techniques, on peut les classer dans
deux catégories : des techniques globales qui
s'intéressent aux grandes plages (population des grains) et des
techniques locales qui s'intéressent aux grains individuels (grain par
grain).
Parmi les méthodes globales on trouve
:
· La diffraction des rayons X.
· La diffraction des neutrons. Parmi les
méthodes locales on trouve :
· Les diagrammes de la diffraction des
électrons rétrodiffusés (EBSD) lié au microscope
électronique à balayage.
· La diffraction des
électrons.
Couramment les techniques les plus utilisées
pour déterminer les textures dans les matériaux sont la
diffraction des rayons X et la diffraction des électrons
rétrodiffusées. Dans ce travail nous nous sommes
intéressés à la diffraction des rayons X, car cette
technique est plus statistique (surface analysée grande de
l'ordre de cm2). D'autre part, elle a un
profondeur de pénétration de l'ordre de
mm, elle facilite l'analyse contrairement à
l'EBSD qui ne donne pas une bonne indexation des
clichés de diffraction pour les fortes déformations orientations
[9].
|
Figure. III.3 : Cônes de
diffraction des électrons. Formation de lignes
de Kikuchi sur un écran de phosphore
|
|
16
Chapitre II : Textures de déformation et de
recristallisation
II.3.1. Diffraction des rayons X
Laue et ses collaborateurs, sont les premiers qui ont
obtenu Le premier diagramme de diffraction des RX en 1912. Cette technique a
été évoluée rapidement, surtout après le
développement des méthodes de mesures des intensités.
Plusieurs méthodes ont été proposées : Laue,
cristal tournant et Debye- Scherrer ; cette dernière a souvent
été utilisée pour mettre en évidence de
façon semi-quantitative la présence de textures, à partir
de la hauteur des raies de diffraction.
II.3.2. La diffraction des électrons
rétrodiffusés (EBSD)
L'EBSD (Electron Back Scattering Diffraction) est une
technique locale utilisée pour déterminer les
orientations cristallographiques, sur la surface des échantillons
massifs (profondeur d'interaction est de 20 à 30 nm). Elle est
couplée au Microscope Electronique à Balayage
(MEB).
Cette technique utilise un faisceau d'électrons
; les électrons rétrodiffusés, canalisés
par les plans cristallins forment une figure caractéristique
constituée de pseudo-lignes de Kikuchi (Fig.III.3). La figure obtenue
fournit des informations sur la symétrie, la qualité et
l'orientation du réseau cristallin. La canalisation est
souvent utilisée pour déterminer l'orientation
cristallographique d'une structure monocristalline ou la désorientation
entre les grains d'un polycristal et aussi déterminer la
fraction recristallisée d'un matériau [10,
11].
17
Chapitre II : Textures de déformation et de
recristallisation
Principe
L'EBSD utilise les électrons incidents
diffractés par les plans cristallins en position de Bragg. Les
électrons diffractés forment des cônes de diffraction,
chaque famille de plans formant deux cônes de diffraction
symétriques séparés d'un angle 20. L'intersection
de ces lignes avec un écran plan donne des hyperboles.
Considérant la taille de l'écran et des cônes de
diffraction, on observe des lignes parallèles, appelées lignes de
Kikuchi (Fig. III.3). Les angles entre ces lignes ainsi que leurs largeurs sont
caractéristiques d'une structure cristalline donnée. En
connaissant la structure cristalline du matériau étudié,
la mesure des angles entre les bandes permet de remontrer à
l'orientation de la zone cristallographique analysée.
II.4. TEXTURES DES ACIERS
Les textures des aciers à bas carbone
présentent l'existence de deux fibres : une fibre á et
une fibre y :
· La fibre á se trouve dans la section
iv2=45° avec p1=0 et p (de 0° à 55°),
elle a un axe de fibre <110> // DL qui contient les orientations
{hkl}<110> .
· La fibre y se trouve dans la section
q2=45° avec p=55° et p1 (de
0° à 90°), elle a un axe de fibre <111> perpendiculaire
à DN et elle contienne les orientations {111}<uvw> [12 , 13] (Fig.
II.5).
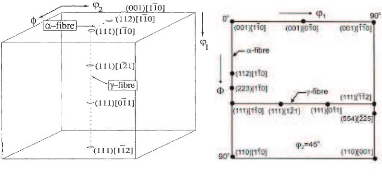
(a) (b)
Fig. II.5 : (a) fibres á et y dans l'espace
d'Euler [14], (b) orientations des deux fibres á et y dans la Section
p2=45°.
Chapitre II : Textures de déformation et de
recristallisation
II.4.1. Textures de déformation
Les textures de déformation des métaux et
alliages cubiques centrés (CC) sont généralement plus
complexes par rapport à celle des métaux cubiques à faces
centrées (CFC). Malgré l'importance de ces aciers dans
l'industrie, ils ont été relativement moins
étudiés, [15, 16].
L'évolution de la texture au cours du laminage
à froid peut peut être classée en deux parties [17]
:
· Taux de laminage inferieurs à 70% de
réduction :
Cette partie est caractérisée par une
augmentation uniforme des intensités des deux fibres á
et y pendant le laminage à froid, avec une fibre
á plus intense que la fibre y (Fig. II.7).
· Taux de laminage supérieurs à 70%
de réduction :
Cette partie est caractérisée par
un renforcement du maximum proche de l'orientation {112}<110>
sur la fibre á et une saturation de l'intensité de la fibre y
(Fig. II.7).
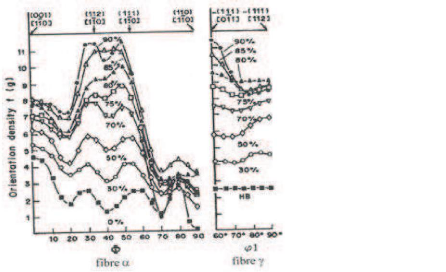
Fig. II.7: Evolution de l'intensité
de la FDOC (f(g)) le long des fibres á et y pour
différents taux de réduction par laminage à froid,
d'un acier à bas-carbone [13].
18
Pour les aciers IF les résultats disponibles
confirment cette tendance d'évolution de la texture au
cours de laminage [18] :
19
Chapitre II : Textures de déformation et de
recristallisation
Samajdar et al [19] ont montrés que
l'intensité de la fibre y sature dès 50% de réduction
tandis que l'intensité de la fibre á augmente de façon
continue sur tout l'intervalle de réduction d'un acier
IF déformé en compression plane entre 40% et 75% de
réduction.
A 70 % de réduction par laminage d'un
acier IF-Ti-Nb, Urabe et Jonas trouvent un maximum sur la
fibre á. Ensuite, entre 70% et 85 % de réduction, les deux fibres
á et y augmentent dans les mêmes proportions
[20].
De façon générale, après
des taux de laminage importants, les textures sont caractérisées
par une fibre á plus intense que la fibre y et par un maximum
situé sur la fibre á proche de l'orientation {112}<110>
[21].
II.4.2. Textures de recristallisation
Les tôles recristallisées d'acier
à bas carbone sont des produits de grande importance industrielle,
l'optimisation de leurs propriétés est d'un intérêt
continu. Leur texture de recristallisation est essentiellement semblable
à la texture de laminage. Elle peut encore être décrite par
référence aux fibres á et y, de
l'état laminé [12].
Après un recuit de recristallisation, les
textures des aciers à bas carbone sont caractérisées par
[22] :
· l'intensité des composantes {111}<110>,
{111}<112> et {111}<123> de la fibre y
diminuent au début, puis elle augmentent. Cette fibre reste
toujours la plus dominante.
· l'intensité de la composante {111}<110>
de la fibre á augmentent et la composante
{001}<110> diminue.
L'évolution des textures pendant un recuit
à 700° C, d'un acier doux, montre une accentuation
de la composante {111}<112> et une diminution de
l'intensité des composantes {112}<110> et
{001}<110>. L'orientation {111}<110> demeure stable
(Fig. II.8) [12].
20
Chapitre II : Textures de déformation et de
recristallisation
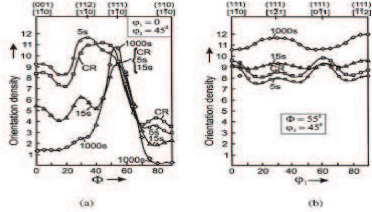
Fig. II.8 : Densités d'orientation
après 85% de réduction, d'un acier recuit à
700° C, le long de : (a) la fibre á, (b) la fibre
y [12].
La texture de recristallisation des aciers IF est
caractérisée par réduction de l'intensité
de la fibre á. La fibre y reste relativement stable. On
distingue deux évolutions : pour une fraction recristallisée
comprise entre 50% à 70%, la texture globale évolue peu.
Au-delà de 70% de fraction recristallisée,
l'évolution de la texture est caractérisée par
une décroissance de l'intensité de la fibre á et une
augmentation de l'intensité de la fibre y. Les travaux de Kiaei
[23], Hutchinson et Ryde [24] et Vanderschueren et al [25] sur des aciers IF,
ont montrés que les premiers germes qui apparaissent sont de la
fibre y.
21
Chapitre II : Textures de déformation et de
recristallisation
Références bibliographiques
[1] Guetaz. V, Thèse de Doctorat, Institut
National des Sciences Appliquées, Lyon, (2002).
[2] Bunge H. J., Texture analysis in material
science. Butterworth Publ. London.(1982)
[3] Roe R.J., J. Appl. Phys. 36 (1965)
2024-2031.
[4] Goux, Mem Scient Rev Met. LV III, 9(1961)
661.
[5] Bunge H.J., Z.Metallkunde.
56(1965)872-874
[6] Ruer D., Méthode vectorielle d'analyse de
la texture, Thèse de l'Université de Metz, (1976).
[7] Matthies S., Phys. Status Solidi (b) 92(1979)
135.
[8] Schaeben H., Phys. Status Solidi (b) 123 (1984)
425.Université Paris 13 (1996).
[9] Haldar. A, Suwas. S, and Bhattacharjee. D (eds.),
Microstructure and Texture in Steels, Springer 2009
[10] Black M.P. and Higginson R.L., Scripta
Materialia, 41 (2)(1999) 125-129.
[11] Ayad A., Allain-Bonasso N., Rouag N., Wagner F.,
Mater. Sci. For. 702-703 (2012) 269-272.
[12] Emren. F, Von Schlippenbach. U et Lücke. K,
Acta Metall. 34 (1986) 2105.
[13] Von Schlippenbach U., Emren F. et Lücke K.,
Acta Metall. 34(1986) 1289.
[14] Raabe D., Acta Metall Mater. 43(1995)
1531-1540.
[15] Hutchinson B. et Ryde L., Proc. 16th Riso inter.
Symp. Of Mat. Sci., éd. Par N.
[16] Hutchinson B. ET Ryde L., Proc. Thermomechanical
processing and theory, Modelling and practice (TMP 2) (1997)
145-161
[17] Von Schlippenbach U., Emren F. et Lücke K.,
Acta Metall. 34(1986) 1289.
[18] Miroux A., Thèse de PhD . France:
Université Paris 13, (1999).
[19] Samajdar I., Verlinden B., Van Houtte P., ISIJ
inter. 38 (7) (1998) 759-765.
[20] Urabe T. et Jonas J.J., ISIJ inter. 34 (5)
(1994) 435-442.
[21]Samajdar I., Verlinden B., Van Houtte P. et
Vanderschueren D., Scripta Mater. 37 (6)(1997a) 869-874.
[22] Lücke K. et Engler O., Proc 3rd
Int Conf on Aluminium Alloys. Trondheim (1992) 439.
[23] Kiaei M., Etude des mécanismes de
recristallisation des aciers à bas carbone. Thèse
[24] Hutchinson B. et Ryde L., Proc. 16th Riso inter.
Symp. Of Mat. Sci., éd. Par N. Hansen, D. JuulJensen, Y. L. Yui and B.
Ralph, Riso National Lab, Roskilde, Denmark (1995)105 117.
[25] Vanderschueren D., Yoshinaga N., Koyama K., ISIJ
inter. 36 (8) (1996)1046-1054.
Chapitre III
Matériau et techniques expérimentales
22
Chapitre III : Matériau et techniques
expérimentales
III.1. INTRODUCTION
Ce chapitre présente le matériau
utilisé et la procédure expérimentale suivie dans cette
étude. Les techniques utilisées pour la caractérisation
morphologique de la microstructure sont la microscopie optique et la
microdureté Vickers. Pour le suivi de l'évolution des
textures cristallographiques, nous avons utilisé la diffraction
des rayons X. Un rappel sur le principe de base de ces techniques, notamment la
diffraction des RX, est nécessaire pour mieux lire les résultats
et les figures qui en sont issues dans le prochain chapitre.
III.2. MATERIAU
III.2.1. Aciers IF
Les aciers IF `Interstitiel Free' ou sans interstitiels sont
des aciers ou les interstitiels sont piégés par
des éléments d'alliage substitutionnels, ayant une forte
affinité pour le carbone ou l'azote (titane, niobium et
vanadium). Ces aciers sont à la base, des aciers calmés
à l'aluminium (Al-K) ayant subi un traitement
poussé de décarburation et dénitruration lors de leurs
élaborations. [1]
Rappelons que les aciers calmés
à l'aluminium (Al-K) ou `Aluminium Killed' sons
des aciers où l'aluminium est ajouté dans leurs
bains liquides pour piéger l'oxygène. Tellement,
l'aluminium est moins dense que l'acier, il remonte
à la surface. Le reste d'aluminium, en solution solide,
est utilisé pour piéger l'azote et former le
nitrure d'aluminium (AlN) qui peut se formé dans le
recuit.
II.2.2. Composition chimique
La composition chimique de l'acier IF utilisé dans
cette étude est présentée dans dans le tableau
(III.1).
Element
|
C
|
Mn
|
P
|
S
|
N
|
Si
|
Cu
|
Ni
|
Cr
|
Al
|
Ti
|
%pds 10-3
|
8
|
196
|
4
|
10
|
3.1
|
4
|
7
|
18
|
14
|
41
|
97
|
Tableau III.1: Composition chimique de l'acier
étudié.
Le matériau initial est une tôle
d'acier IF, laminée à chaud,
d'épaisseur 2.8 mm.
|
Fig. III.2 : laminoir de l'atelier
CHAABAT ERSSAS.
|
23
Chapitre III : Matériau et techniques
expérimentales
III.3. PROCEDURE EXPERIMENTALE ET PREPARATION DES
ECHANTILLONS
III.3.1. Laminage à froid
Pour l'étude de l'évolution de la
microstructure et de la texture au cours de la déformation de notre
acier IF, un laminage à froid a été réalisé
à plusieurs taux de réduction : 25%, 50% et 75%.
Le laminoir utilisé pour la procédure de
formation est de type `REDEX' de l'unité de recherche
du département de physique (située à CHAABAT ERSSAS) (Fig.
III.2). Le tableau (III.2) montre les différentes épaisseurs
obtenues pour chaque taux de laminage.
Taux de réduction
|
Epaisseur obtenue
|
25% de réduction
|
2.1 mm
|
50% de réduction
|
1.4 mm
|
75% de reduction
|
0.7 mm
|
Tableau III.2: les differentes taux de laminage
à froid avec les epaisseurs finales dans chaque etape.
24
Chapitre III : Matériau et techniques
expérimentales
III.3.2. Préparation d'échantillons
- Diffraction des RX : pour
l'analyse des textures par la diffraction des RX la
préparation des échantillons consiste en un polissage
mécanique jusqu'à la granulométrie 4000
suivi d'un polissage de finition avec la patte
diamantée de 3 micron.
- Microscopie Optique : pour les observations
métallographiques, en plus du polissage mécanique, les
échantillons ont été attaqués par une solution du
Nital 2%, pour révéler leurs microstructures.
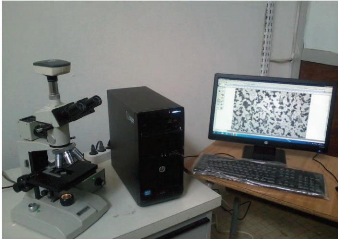
Fig. III.1 : microscope optique de département de
physique.
- Microdureté : pour les essaies de la
microdueté, les échantillons ont subit la même
préparation que celle pour la DRX, c.à.d. un polissage
mécanique avec la patte diamentée de 3um.
III.4. MESURE DE LA DURETE
La mesure de dureté Vickers se fait avec une
pointe pyramidale normalisée en diamant de base carrée et d'angle
au sommet entre faces égal à 136°. L'empreinte a donc la
forme d'un carré ; on mesure les deux diagonales d1 et d2 de ce
carré à l'aide d'un appareil optique. On obtient la valeur d en
effectuant la moyenne de d1 et d2. C'est d qui sera utilisé pour le
calcul de la dureté. La force et la durée de l'appui sont
également normalisées.
Chapitre III : Matériau et techniques
expérimentales
La relation (III-5) décrit le principe de la
dureté Vickers :
HV= 1.8 P /d 2 (III.1) Avec d est la longueur de la
diagonale moyenne de l'empreinte, P est la charge utilisée.
Les mesures de la dureté Vickers ont
été effectuées sur une surface polie de
l'échantillon, en utilisant un
microduromètre de modèle `HMV2T' de
`SHIMADZU' du laboratoire LMDM (Fig. III.6).
La charge utilisée est 9.08 N. Dans chaque état laminé,
dix essais ont été fait pour remonter à la dureté
moyenne.
|
Fig. III.6 : microduromètre de laboratoire
LMDM.
|
25
III.5. MESURE DES TEXTURES PAR DIFFRACTION DES RAYONS X
(DRX)
III.5.1. Principe
La diffraction des rayons X est basée sur la
loi de Bragg. Cette loi donne la relation pour qu'il y ait
diffraction entre l'angle d'incidence O du faisceau (angle de
Bragg) par rapport aux plans considérés et sa longueur
d'onde (X), pour une famille donnée de plans cristallographiques
de distance interréticulaire (d) :
2.d.sinO=n.X (III.2)
Avec n un nombre entier signifie l'ordre de
diffraction.
La détermination de la texture par diffraction
des RX se fait par la mesure des figures de pôles, par
l'utilisation d'un goniomètre de textures. Ces
figures de pôles expérimentales permettent de calculer la
densité des pôles Phi(y) qui correspond à la fraction
volumique de
26
Chapitre III : Matériau et techniques
expérimentales
cristallites dans la normale hi au plan (hkl) est
parallèle à une direction y du repère de
l'échantillon selon l'équation
(III.2).
dV 1
= P (y)
V 4 ð hi (III.3)
La méthode utilisée pour mesurer les
textures cristallographiques est celle de Schulz [2]. Le principe est
d'envoyer des RX contenu dans le plan horizontal vers le centre commun
de rotations du goniomètre (Fig.III.4). Le détecteur des photons
X est placé dans ce même plan horizontal et il fait un
angle 2O, par rapport au faisceau incident. La valeur de
l'angle O est liée à la distance des plans
réticulaires, sur lesquels on mène l'expérience de
diffraction, par la relation de Bragg (Eq. III.1).
Pendant les mouvements du goniomètre, une
intensité proportionnelle à la densité des pôles
(hkl) est collectée dans la direction y.
Les rotations nécessaires pour ramener tous les
plans en position de diffraction sont deux : une rotation autour la normale de
l'échantillon ( (l'angle d'azimut) et une rotation de
déclinaison x (l'angle polaire). Cette
déclinaison est généralement limitée à
80° car le faisceau diffracté s'élargit et
le compteur ne peut pas collecter qu'une partie de l'intensité
(défocalisation).
Le compteur détecte une intensité Ihi
(y) (nombre de coups par unité de temps) proportionnelle à la
densité de pôles Phi(y), à chaque position (x,
p). Les intensités diffractées correspondant aux
pôles (hkl) peuvent être représentées, par des lignes
d'isointensité, sur la sphère des pôles ou sur le cercle
équatorial, par la projection stéréographique. Le calcul
de la fonction de la distribution des orientations cristallines
à partir de l'intensité diffractée requiert la
correction des données brutes, entachées d'erreurs [3].
Parmi les sources d'erreurs il y a la défocalisation et
le bruit de fond :
- La défocalisation : La
défocalisation est la conséquence de
l'élargissement de la surface irradiée sur
l'échantillon lorsqu'on fait une inclinaison en x. Elle conduit à
un élargissement des pics de diffraction [4] (Fig. III.3). Ce
phénomène ne permet pas d'exploiter directement la
périphérie des figures de pôles, car les intensités
diffractées caractérisant cette région sont
très fortement atténuées. On obtient alors, sur les
figures de pôles une zone dite `aveugle` [5], qui
débute typiquement vers x=60°. la zone
Chapitre III : Matériau et techniques
expérimentales
aveugle est la zone de détection qui ne peut
être vue par le détecteur. Elle est due à la
géométrie instrumentale et concerne les petits
angles.
|
Fig. III. 3 : Représentation d'un
échantillon pour deux positions de x
différentes.
|
27
- Bruit de fond : est le freinage des
électrons, de différentes vitesses, après ses interactions
avec la cible. Il en résulte une émission radiative qui constitue
un rayonnement de freinage ou fond continu.
La densité de pôles est proportionnelle
à l'intensité corrigée des effets de défocalisation
et de bruit de fond par le coefficient de normalisation Ni :
Phi(y)=NiIhi(y) (III.4)
Après le calcul des figures des pôles, il
y a la détermination de la fonction de distribution des orientations
f(g) par la méthode de Harmonique, avec un développement
en séries jusqu'à l'ordre 34
généralement et un calcul des parties paires et impaires.
La fonction f(g) nécessite la solution de
l'équation fondamentale :
P h (y) = ? f(g)dg (III.5)
i h i//y
Avec (hi//y) qui indique que
l'intégrale est calculé pour tous les cristallites dont
les normales <hi> aux plan {hkl} sont parallèles à une
direction <y> dans le repère de l'échantillon
[6].
Chapitre III : Matériau et techniques
expérimentales
|
Fig. III.4 : Un diffractomètre
cercles.
|
28
III.5.2. Conditions de mesure
Les figures de pôles sont
réalisées sur le goniomètre de texture d'un
diffractomètre de type `EMPYREAN' de
`PANALYTICAL' du laboratoire LMDM (Fig. III.5). Le
faisceau monochromatique utilisé est de type cuivre, avec une tension de
40 kV et un courant de 40 mA. L'échantillon subit deux
rotations : rotation en azimut (ö) de 0 à
360° avec un pas de 5° et rotation polaire (÷)
de 0 à 70°, avec un pas de 2.5°.
Le calcul de la FDOC nécessite un traitement de
données par le logiciel MTEX [7] installé sous MATLAB. Ce
logiciel permet de tracer les figures de pôles incomplètes et
recalculer et tracer les figures de pôles complètes après
le calcul de la FDOC.
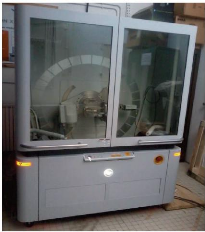
(a)
29
Chapitre III : Matériau et techniques
expérimentales
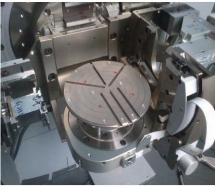
(b)
Figure. III.5 : (a) Diffractomètre du laboratoire
LMDM. (b) goniomètre texture
30
Chapitre III : Matériau et techniques
expérimentales
Références
[1] Réglé. H, recristallisation et genèse
des textures dans les tôles d'aciers à basse teneur en
carbone, Université Paris 13, 2006.
[2] Schulz L.G., Journal of Applied Physics 20 (1949)
1030-1033
[3] Gey N., Thèse de Doctorat, Université
de Metz (1997).
[4] Couterne, J-C, et G Cizeron. Journal of Applied
Crystallography 4, (1971) 461.
[5] Heizmann, J-J, et Laruelle. C, «Simultaneous
measurement of several x-ray pole figures» Journal of Applied
Crystallography 19, (1986) 467-472.
[6] Bunge H.J and Esling C, Quantitative Texture
analysis, DGM, SFM, (1982).
[7] Bachmann. F, Hielscher. R Schaeben. H, Texture
Analysis with MTEX - Free and open Source Software Toolbox,
Solid State Phenomena Vol. 160 (2010) pp 63-68.
Chapitre IV
Résultats et discussions
31
Chapitre IV : Résultats et discussions
INTRODUCTION
Ce chapitre regroupe les résultats de
l'étude expérimentale de l'évolution de
la microstructure et de la texture cristallographique au cours de la
déformation par laminage, de notre acier IF. Le laminage à froid
conduit à une modification de la structure et de la texture du
matériau. Il a une influence directe sur les propriétés
structurales comme la morphologie des grains et leurs orientations
cristallographiques. Nous avons donc été conduits à
effectuer de multiples taux de déformation par laminage (25%, 50% et 75%
de réduction) et à caractériser les états
métallurgiques ainsi produits. Le suivi expérimental de
l'évolution microstructurale permet d'avoir un suivi du
comportement des grains, notamment leur morphologie, en utilisant la
microscopie optique et leur texture globale par la diffraction des
RX.
Les techniques utilisées dans cette
étude sont : la microdureté Vickers, la microscopie optique pour
la caractérisation morphologique et la diffraction des RX pour
l'analyse des textures cristallographiques.
IV.1. MICROSTRUCTURE ET TEXTURE DE LAMINAGE
Suivant la composition chimique et les divers
paramètres du cycle de fabrication d'une tôle,
L'influence des modifications de formes de grains sur les
caractéristiques mécaniques est on peut avoir des grains
parfaitement équiaxes et réguliers ou des grains allongés
complexe ; ces modifications s'accompagnent généralement
d'une évolution importante de la texture cristallographique
[1].
En effet, la déformation par laminage à
froid provoque des modifications de la structure et de la texture du
matériau. Le laminage à froid influe directement sur les
propriétés structurales du matériau, comme la distribution
des précipités, les changements morphologiques de
l'ensemble des grains et les évolutions des orientations
cristallographiques. Au cours du laminage à froid, on observe un
durcissement et une perte de ductilité du métal. Les mesures
de la microdureté d'un matériau permettent
d'avoir une première estimation de son durcissement ou de son
état métallurgique.
Chapitre IV : Résultats et discussions
IV.2.1. Mesures de Microdureté
La microdureté Vickers a été
mesurée avec dix essaies pour remonter à la valeur moyenne de
la microdureté d'un état métallurgique
donné. La charge utilisée est de 9.08 N. ces mesures
ont été faites avec un microduromètre de
modèle `HMV2T' de `SHIMADZU' du laboratoire LMDM.
|
220
200
180
|
|
HV
|
160 140 120 100
|
32
-10 0 10 20 30 40 50 60 70 80
Taux de réduction
Fig. IV.1 : Evolution de la microdureté Vickers
avec le laminage à froid.
La courbe de la figure (IV.1)
représente l'évolution de la microdureté Vickers avec le
taux de réduction. Nous constatons que la microdureté de
notre acier augmente au cours du laminage. Elle
s'élève de 108.8 de l'état
laminé à chaud (recristallisé)
jusqu'à 211.7, de l'état laminé à
75%.
Cette évolution est logique et attendue car au
cours de la déformation par laminage à froid, la
déformation plastique est assurée par le glissement et la
multiplication des dislocations ce qui conduit au durcissement des
matériaux. En plus, dans les aciers IF, les déformations moyennes
et élevées conduisent à la fragmentation des gros grains
en plusieurs petits grains.
Chapitre IV : Résultats et discussions
Cette fragmentation provoque une augmentation de la
surface totale des joints de grains, qui font augmenter l'état
de contrainte du matériau et par conséquent sa
microdureté.
IV.2.2. Analyse morphologique
Les micrographies optiques de la figure (IV.2) montrent
l'évolution de la microstructure au cours du laminage,
de l'état recristallisé (laminé à
chaud), considéré comme état initial dans notre
étude, jusqu'à l'état laminé à
75%.
L'état initial est un état homogène
et bien recristallisé. Il est marqué par la présence
d'agglomération de petits ou de gros grains (Fig.
IV.2a). Il existe donc deux populations de grains, qui peuvent répondre
différemment à une même sollicitation du
matériau.
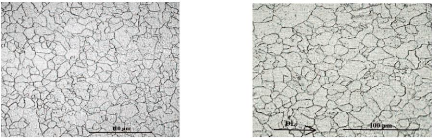
(b) Etat initial (a) Etat laminé à
25%
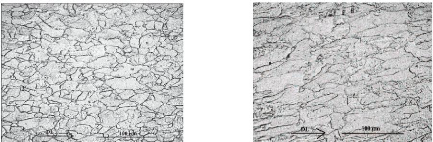
33
(c) Etat laminé à 50% (d) Etat
laminé à 75%
Fig. IV.2 : Evolution des microstructures au cours du
laminage.
34
Chapitre IV : Résultats et discussions
La distribution des contraintes dans une telle matrice
est certainement hétérogène. En effet,
l'existence d'une distribution hétérogène de
tailles de grains peut conduire à des amincissements locaux ou
des micro-fissures. Il peut exister localement des états de contraintes
élevés, les zônes correspondantes peuvent alors atteindre
la striction avant leur voisinage. Ce qui augmente la
probabilité d'apparition de fissuration ou d'amincissements
locaux, rendant ainsi le taux de rupture important, lors de la
déformation, surtout par emboutissage. La mise en forme des
pièces ou leur usinage devient difficile en présence d'une
telle répartition.
L'hétérogénéité
morphologique est généralement due aux conditions du
cycle de fabrication. En effet, c'est le contrôle de
celui-ci, essentiellement la dernière étape (recuit de
recristallisation) qui donne au matériau les caractéristiques
structurales adéquates pour une mise en forme ultérieure
[2].
Au cours du laminage, les grains deviennent de plus en
plus allongés vers la direction de laminage. L'évolution
de la microstructure n'est pas évidente pour l'échantillon
déformé à 25% (Fig.IV.2b). Le changement
microstructural devient plus notable à partir de 50 % de
réduction (Fig.IV.2c). Cependant, les grains de l'état
laminé à 75% sont fortement allongés suivant la
direction de laminage (Fig. IV.2d).
L'existence d'une telle texture
morphologique peut entraîner une variation des propriétés
plastiques avec la direction ; en effet, la déformation a lieu par
glissement sur des plans cristallographiques bien déterminés, ce
glissement est limité par les joints de grains ; si la forme des grains
est très allongée, le glissement ne se produit pas de la
même façon dans des directions différentes.
Les propriétés liées aux joints
de grains, comme le glissement aux joints au cours du fluage, la diffusion
intergranulaire ou la résistance électrique due aux joints,
seront également anisotropes, si la forme des grains n'est pas
équiaxe, et si donc le nombre de joints par unité de
longueur varie suivant la direction [3].
35
Chapitre IV : Résultats et discussions
IV.2.3. Analyse des textures cristallographiques
La texture globale des échantillons
déformés a été déterminée à
partir des figures de pôles expérimentales, obtenues par la
diffraction des rayons X. Avant de réaliser les figures de pôles
des différentes familles de plans {hkl}, nous avons
procédé à l'identification des positions
29, de ces familles de plans de diffraction, pour notre acier
IF, par un scan 9-29.
La figure (IV.3) présente le spectre de la
diffraction de notre acier IF. Les positions 29 des trois
premiers pics de diffraction sont : 44.69°, 64.98° et 82.28°.
Ces angles correspondent à ceux des des plans {111}, {200} et {220}
respectivement (Fig. IV.3).
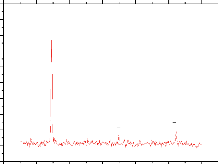
(110)
(200)
(211)
1000 900 800 700
intensity(c)
600
500
400
300
200
100
0
30 40 50 60 70 80 90
2teta(°)
Fig. IV.3 : Spectre expérimental de
diffraction de l'acier IF.
En tenant compte des données du spectre de
diffraction de la figure (IV.3), trois figures de pôles
expérimentales (FDP) ont été mesurées : {110},
{200} et {211}, avec un goniomètre de texture. Le rayonnement
utilisé est celui du Ká du cuivre. La
tension d'accélération utilisée est de 40 kV avec
un courant de 40 mA.
IV.2.3.1. Etat initial
La figure (IV.4) montre les figures de pôles brutes
{110}, {200} et {211} de l'état initial, avec une
inclinaison maximale de 70° (figures de pôles
incomplètes).
36
Chapitre IV : Résultats et discussions
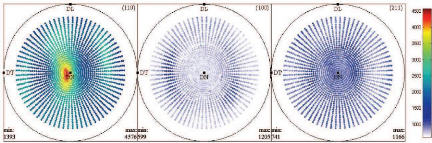
Fig.IV.4 : Figures de pôles brutes
(incomplètes) de l'état initial.
La FDOC est ensuite calculée et les FDP
complètes sont recalculées, par le logiciel MTEX, installé
sous MATLAB [4] avec accès libre.
Les figures (IV.5 et IV-6) montrent la
texture de l'état initial présentée sous
différentes formes : figures de pôles directes et inverses (IV.5a
et IV.5b respectivement) et fonction de distribution des orientations
cristallines (FDOC) dans l'espace d'Euler (IV.6).
D'après ces figures, l'échantillon laminé
à chaud est caractérisé par une très faible
texture, car la distribution des orientations est presque aléatoire. La
figure (IV.6b) montre qu'il possède un léger
maximum, étalé, autour de l'orientation de Goss
{110}<001>, caractérisée par le triplet
d'Euler (q1= 90°, q= 90°, q2= 45°) et
une valeur de la fonction de texture f(g)=1.9. Cette texture est une
caractéristique des tôles laminées à chaud et en
particulier la présence de la composante de Goss qui résulte de
la recristallisation dynamique lors du laminage à chaud des tôles
d'aciers.
37
Chapitre IV : Résultats et discussions
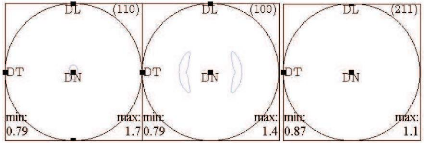
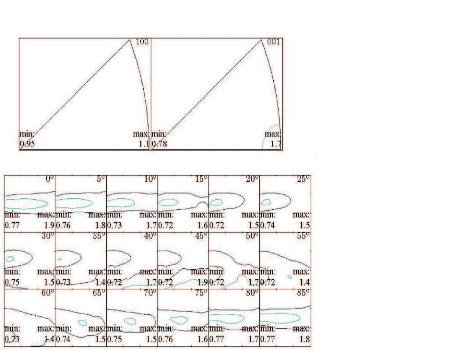
Fig. IV.5 : Texture de l'état
initial : (a) figures de pôles complètes
(recalculée), (b) figures de pôles inverses.
DL
DN
(b)
Lignes de niveau de 1, 1.4
(a)
(a) Fig. IV. 6 : La FDOC de l'état
initial : (a) Espace
d'Euler (18 sections), (b) section
q2=45°.
38
Chapitre IV : Résultats et discussions
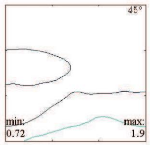
(b)
IV.2.3.2. Evolution de la texture au cours du
laminage
La figure (PV.7) montre l'évolution de
la texture au cours de la déformation. Elle présente les sections
ö2= 45° de la FDOC des échantillons laminés à
25%, 50% et 75% de réduction.
Jusqu'à un laminage de 25% de réduction
(Fig.IV.7a), la texture évolue peu et reste toujours similaire de celle
de l'état initial. Elle est caractérisée par une
légère augmentation de l'intensité de la FDOC notamment
pour la composante {110}<011> qui présente une valeur de
la FDOC égale à 2.6.
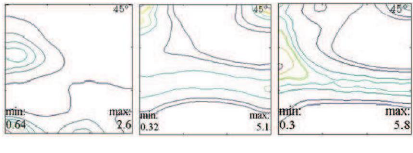
Lignes de niveau : 0.7, 1.1, 1.8, 2.5, 3.2, 3.9, 4.6,
5.3
(a) Etat laminé à 25% (b) Etat
laminé à 50% (b) Etat laminé à 75%
Fig.IV.7 : Sections p2= 45° de la FDOC
des états laminés à froid.
L'échantillon laminé à 50% de
réduction montre un changement considérable de la
texture avec l'apparition des fibres á
et y au dépend des composantes {110}<011>
et {110}<001>
39
Chapitre IV : Résultats et discussions
(Goss), qui disparaissent complètement
(Fig.IV.7b). Cette évolution est caractérisée par une
augmentation uniforme des intensités des deux fibres, á
et y, avec une fibre á plus intense que la fibre y. La
composante {100}<011> de la fibre á présente le maximum de
la FDOC avec une valeur de la fonction de textures égale à
4.6.
La texture de l'échantillon laminé
à 75% est caractérisée toujours par la présence des
deux fibres á et y, avec une fibre á plus intense que la fibre y
(Fig.IV.7c). le maximum de la FDOC est sur la fibre á autour de
l'orientation {223}<110> , f(g) = 5.7.
L'évolution de la texture globale, obtenue par
DRX, au cours du laminage de notre acier IF est en concordance avec la
littérature, notamment les travaux de Schlippenbach [5], Urabe et Jonas
[6] et Samajdar et al. [7]. Ce comportement peut être justifié par
:
- D'une part : les grains aléatoires de la
tôle laminée à chaud tendent à s'orienter vers des
orientations plus stables, selon les schémas suivants [8-11]
:
·
{001}<100>--*{001}<110>--*{112}<110>--*{223}<110>
.
·
{110}<001>--*{554}<225>--*{111}<112>--*{111}<110>--*{223}<110>.
Par conséquent, l'orientation {223}<110>
a été identifiée comme l'orientation stable finale de la
texture de laminage des matériaux (CC) polycristallins. Les grains des
deux fibres á et y tendent donc à s'orienter vers l'orientations
la plus stable, typiquement, vers la composante {223}<110>.
- D'autre part : pendant le laminage, les grains de la
fibre á sont plus stables contre la rotation, par rapport à ceux
de la fibre y. Cette stabilité dépend de l'accumulation
l'énergie stockée, c.à.d. de la désorientation
intergranulaire [12].
La présence de la composante de Goss et de la
fibre y facilite l'écoulement plastique au cours du laminage à
froid. L'aptitude à la déformation peut donc être
reliée à leur présence dans la tôle non
déformé.
40
Chapitre IV : Résultats et discussions
Conclusion
Dans ce chapitre, une étude
expérimentale détaillée de l'évolution de
la microstructure et de la texture, d'un acier IF a
été faite. Nous avons fait la caractérisation de la
tôle initiale, c.à.d. la tôle laminée à chaud,
du point de vue morphologique et cristallographique :
- La tôle présente une
hétérogénéité de distribution de tailles de
grains, elle possède une distribution bimodale de tailles de
grains.
- La texture est presque aléatoire, ayant un
léger maximum sur la composante de Goss au cours du laminage
à froid, l'évolution est résumée comme suit
:
- La microdureté augmente avec la
déformation, ce que signifie le durcissement de l'acier et la
perte de son ductilité.
- En morphologie : les grains deviennent de plus en
plus allongés vers la direction de laminage.
- En ce qui concerne la texture, le laminage conduit
au renforcement des fibres á et y qui apparaissent à
partir de 50% de réduction, avec une fibre á plus intense
que y. Le maximum de la FDOC est sur la fibre á pour la
composante {223}<110>.
41
Chapitre IV : Résultats et discussions
Références bibliographiques
[1] Yala. F. Thèse de docteur en sci phys.
Université Paris-Sud, Centre d'Orsay (1991)
[2] Pomy.G. Tôles pour l'emboutissage, Techniques de
L'ingénieur 1, (1978). 669
[3] Parniere.P. Thèse de Docteur ES-Sciences
Physiques, Université de Paris-Sud, Centre
d'Orsay (1978).
[4] Hielscher R., and Schaebena H., J. Appl. Cryst. 41
(2008) 1024-1037.
[5] Von Schlippenbach. U, Emren. F et Lucke. K, Acta
Metall., 34 (1986), 1289.
[6] Samajdar I., Verlinden B., Van Houtte P. et
Vanderschueren D., Scrip Mater. 37(6) (1997) 869-874.
[7] Urabe T. et Jonas J.J., ISIJ inter. Vol 34 n°5
(1994) 435-442.
[8] Hutchinson. W. B, Nilsson. K.-I et Hirsch. J, Proc.
Metallurgy of vacuum-degassed steel products, ed Pradhan. R., Warrendale, PA,
Metallurgical Society of AIME, 1990, 109.
[9] Heckler. A.J et Granzow. W. G, Metall. Trans., 1
(1970), 2089
[10] Rabbe. D, Mater. Sci. Eng. A, A197 (1995),
31.
[11] Inagaki. H, ISIJ Inter., 34 (1994),
313.
[12] Inagaki. H et Suda. T, Texture, 1 (1972),
129.
[13] Inagaki. H, Trans. Iron Steel Inst. Jpn. 24 (1984),
266.
[14]. Kang. J.-K, Bacroix. B, Regle. H, Oh K.-H et. Lee.
H.-C, Acta Mater. 53 (2007), 4935.
Conclusions et perspectives
Conclusions et perspectives
Conclusions et perspectives
Dans ce travail, nous nous sommes
intéressés à l'étude de
l'évolution de la microstructure et de la texture
cristallographique, au cours de la déformation, d'un acier IF
destiné à l'industrie d'automobiles. Pour ce faire, nous
avons été conduits à effectuer de multiples taux de
déformation par laminage (25%, 50% et 75% de réduction) et
à caractériser les états métallurgiques
résultants. Le suivi expérimental de l'évolution
microstructurale permet d'avoir un suivi du comportement des grains, du
point de vu morphologique et cristallographique.
Les techniques utilisées dans cette
étude sont : la microdureté Vickers, la microscopie optique pour
la caractérisation morphologique et la diffraction des RX pour
l'analyse des textures cristallographiques.
Nous avons fait en premier lieu la
caractérisation de la morphologie et de la texture cristallographique,
de la tôle laminée à chaud, considérée comme
état initial recristallisé :
· Cette tôle présente une
distribution bimodale de tailles de grains. Cette
hétérogénéité de distribution de tailles de
grains peut être à l'origine de la fissuration du
matériau ou d'amincissements locaux, néfastes pour une mise en
forme ultérieure.
· La distribution d'orientations est presque
aléatoire. La FDOC possède un léger maximum
étalé autour de la composante de Goss avec une valeur de
f(g)=1.9. Cette texture est caractéristique des tôles
d'acier laminée à chaud.
Au cours du laminage, la microdureté de notre
acier augmente pour atteindre son maximum pour l'échantillon
laminé à 75% de réduction. Ce comportement résulte
du durcissement provoqué, d'une part, par le
glissement et la multiplication de dislocation (source de Frank et Read) en
présence des précipités AlN et les carbure de
titane et d'autre part, par la fragmentation de grains, pour
les déformations importantes.
L'évolution de la microstructure n'est pas
évidente pour l'échantillon déformé à 25%.
Cependant, les grains deviennent de plus en plus allongés vers
la direction de laminage, à partir de l'état
laminé à 50%. Les grains de l'état laminé à
75% sont fortement allongés suivant la direction de
laminage.
42
.
43
Conclusions et perspectives
L'évolution de la texture au cours de laminage
est très faible pour les faibles déformations ;
l'échantillon laminé à 25% de réduction
présente une texture semblable à celle de l'état initial
avec un basculement du maximum de la FDOC vers la composante
{110}<011> avec un f(g)=2.6. En revanche, cette évolution devient
plus importante à partir de 50% de réduction,
d'où l'appariation et l'intensification des fibres á
et ã. L'échantillon laminé à 50 %
présente une fibre á plus intense que la
fibre ã et un maximum de la FDOC sur la composante
{100}<011>, de la fibre á, avec une valeur de la
fonction de texture égale à 4.6. La texture de
l'échantillon laminé à 75%
présente également une fibre á
plus intense que ã, avec un déplacement
du maximum de la FDOC vers la composante {223}<011> et une valeur de
f(g)=5.3. Les grains de la fibre á sont plus stables contre
la rotation, par rapport à ceux de la fibre
ã. L'aptitude à la déformation peut donc
être reliée à l'évolution de cette
dernière. Du fait de sa présence dans la
tôle, l'écoulement plastique est facilité.
Cette évolution de la texture, au cours du laminage à
froid, de notre acier IF, est en parfaite concordance avec la
littérature.
L'analyse de ces résultats ouvre la voie à
plusieurs perspectives, parmi lesquelles :
· Le suivi de l'évolution de la
microstructure et de la texture de laminage par EBSD, pour une bonne
corrélation de l'hétérogénéité
microstructurale et la texture (corrélation entre taille de
grains et texture).
· Le suivi expérimental de l'évolution de
la microstructure et de la texture au cours de la recristallisation
primaire par EBSD et DRX. Le contrôle de l'état
recristallisé permet d'obtenir les composantes de
texture souhaitables pour une mise en forme ultérieure.
· Le suivi de l'évolution de la population des
joints de grains, au cours de la déformation et de la recristallisation,
dans le cadre d'une étude sur la migration des joints de
grains.
· La modélisation de
l'évolution des textures de laminage des aciers
IF.
· la modélisation de l'étape de
recristallisation primaire de l'acier IF.
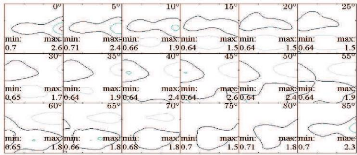
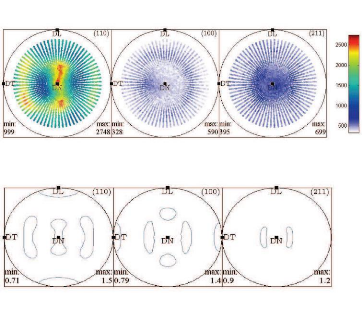
Annexe I: Texture de l'état laminé à
25%
Figure de pôles incomplets
Figure de pôles recalculés
44
Sections de la FDOC
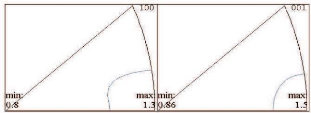
Figures de pôles inverses
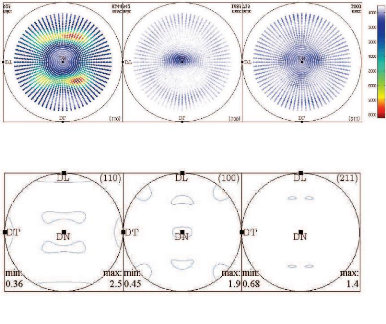
Figures de pôles incomplètes
Figures de pôles recalculés
Annexe II : Texture de l'état laminé
à 50%
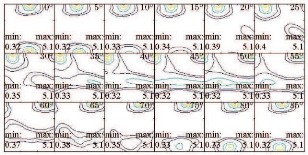
Sections de la FDOC
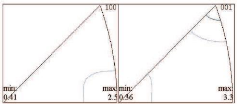
45
Figures de pôles inverses
Annexe III Texture de l'état laminé
à 75%
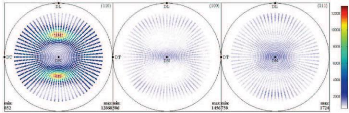
Figures de pôles incomplètes
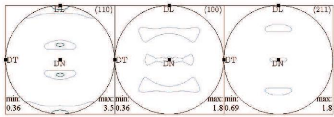
Figures de pôles recalculés
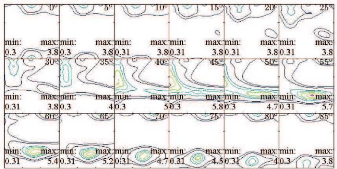
Sections de la FDOC
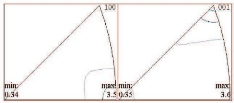
46
Figures de pôles inverses
Résumé
Dans ce travail, nous nous sommes
intéressés aux textures de déformation par laminage
d'un acier IF, destiné à
l'emboutissage. Nous avons suivi l'évolution de la
texture globale, à partir de figures de pôles
expérimentales, obtenues par la technique de diffraction des RX. Dans
cette étude, le matériau initial, laminé à chaud,
présente une hétérogénéité de
distribution de tailles de grains et une distribution aléatoire
d'orientations avec un léger maximum de la FDOC autour de la
composante de GOSS, f(g)=1.9. Pour suivre l'évolution des
textures de déformation, nous avons fait plusieurs taux de
réduction par laminage à froid, de 25%
jusqu'à 75%. L'échantillon
laminé à 25% présente une très faible
évolution de la texture. Cependant, les taux de laminage plus
élevée, 50% et 75%, conduisent à l'appariation et
l'intensification des fibres á et y. La fibre á est plus intense
que la fibre y et le maximum de la FDOC se déplace le long de la fibre
á, de la composante {100}<011> de
l'échantillon laminé à 50%, à la
composante {223}<110> de l'échantillon laminé
à 75%, avec des valeurs de la fonction de texture allant de 4.6
à 5.3, respectivement. Les grains de la fibre á sont
plus stables contre la déformation par rapport à ceux de
la fibre y. L'aptitude à la déformation peut être
donc reliée à la fibre y et à la
composante de GOSS ; leur présence dans la tôle facilite
l'écoulement plastique.
Mots clés : Déformation, laminage,
texture, DRX, acier IF
|