Introduction Générale
Le troisième chapitre, fera l'objet du principe
d'équilibrage avec les différentes techniques de
réparation d'un cas du balourd et son application sur les moteurs
asynchrones. Afin de valider la théorie de l'équilibrage
étudié, nous allons effectuer un test par simulation sur le kit
simulateur.
Enfin, nous donnerons une conclusion générale
qui met en évidence les résultats de notre recherche et les
implications de nos résultats.
CHAPITRE I
Principaux Défauts de la Machine
Asynchrone, Causes et Conséquences
I.1. Chapitre I Principaux Défauts de la Machine
Asynchrone, Causes et Conséquences
Analyse Vibratoire des Machines sur un Banc d'Essai - Cas
d'un Disque Tournant - 4
Introduction
Selon le vocabulaire électrotechnique international,
`'Une machine asynchrone est une machine à courant alternatif dont la
vitesse en charge et la fréquence du réseau, auquel elle est
reliée, ne sont pas dans un rapport constant`' Ce vocable est le seul
utilisé en français, alors que les pays anglo-saxons
désignent par machine à induction (induction machine) `'une
machine asynchrone dont le circuit magnétique est associé
à deux ou plus de deux circuits électriques se
déplaçant l'un par rapport à l'autre et dans laquelle
l'énergie est transférée de la partie fixe à la
partie mobile, ou inversement par induction électromagnétique`'.
[1]
Le moteur à induction se caractérise par sa
simplicité, sa fiabilité et son faible coût,
associés à une capacité de surcharge raisonnable, des
exigences de service minimales et un bon rendement. Un moteur à
induction utilise directement le courant alternatif fourni au stator. Le rotor
reçoit la puissance par effet d'induction. [2]
Cependant, en raison de la durée de vie de ces
machines électriques, des défauts de fabrication, d'alignement,
mal fonctionnement ou d'autres problèmes d'origine électrique, de
nombreux types de défauts sont inévitables dans les machines
électriques et peuvent se produire dans leurs différents
composants.
I.2. Principe de fonctionnement
Les moteurs fonctionnent selon un principe commun qui est
celui de l'induction. Il y a une relation entre le stator, qui
génère le champ magnétique et le rotor, qui transmet la
force motrice, avec un isolement galvanique entre les deux
éléments. L'alimentation du bobinage du stator
génère une induction magnétique à laquelle est
associé un champ magnétique à partir duquel est
créée la force motrice. Pour produire un mouvement de rotation,
le rotor doit être soumis à deux flux alternatifs qui ne sont pas
synchronisés dans le temps et qui sont appliqués en deux endroits
distincts, décalés selon la direction du mouvement
souhaité. [3]
Le rotor. Celui-ci est constitué de conducteurs (des
bobinages ou carrément des barres métalliques) disposés le
long du rotor et court-circuités. Lorsque le champ tournant balaye ces
conducteurs, il induit des courants qui entrent en interaction avec le champ et
permettent à un couple moteur de se créer. Le rotor se met alors
à tourner et se stabilise à une vitesse toujours
légèrement inférieure à la vitesse de synchronisme.
Il est impossible pour le rotor de tourner à la vitesse de synchronisme
puisqu'il serait alors baigné dans un champ fixe, et donc parcouru par
un courant nul. En l'absence de courant, le couple serait nul, et la machine
décélèrerait. La légère différence de
vitesse justifie le terme de « glissement » du rotor par rapport au
champ tournant. [4]
Chapitre I Principaux Défauts de la Machine
Asynchrone, Causes et Conséquences
I.3. Construction de la machine asynchrone
La machine asynchrone (figure.I.1) comporte un stator muni
d'un enroulement triphasé et d'un rotor portant un enroulement
triphasé ou une cage. C'est un transformateur à champ tournant
dont le primaire est le stator et dont le secondaire, mis en court-circuit et
libre de tourner.
Deux composantes principales constituent le moteur asynchrone,
souvent appelé moteur d'induction. Elles sont faites de tôles
d'acier au silicium et comportent des encoches dans lesquelles on place les
enroulements. L'une des composants, appelée le stator, est fixe ; on y
trouve les enroulements reliés à la source. L'autre composante
nommée le rotor, est montée sur un axe et libre de tourner. Selon
que les enroulements du rotor sont accessibles de l'extérieur ou sont
fermés sur eux-mêmes en permanence, on reconnait deux types de
rotor : le rotor bobiné et le rotor à cage d'écureuil.
[5]
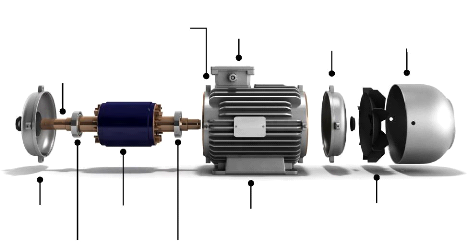
Ventilateur
Stator
Rotor à cage
Flasque palier
Roulement
Roulement
Boite de
raccordement Flasque
palier
Capot de ventilation
L'arbre du rotor
Enroulement statorique
Fig.I.1. Les composants d'un moteur asynchrone
[3].
I.3.1. Stator
Est une partie fixe, composé par trois enroulements
(bobines) régulièrement reparties et possédant deux
pôles`2p'. Ils peuvent être couplés en
étoile ou en triangle selon la règle suivante :
- Si la tension supportée par chaque enroulement est
égale á la tension simple du réseau, le Stator doit
être couplé en étoile.
Analyse Vibratoire des Machines sur un Banc d'Essai - Cas
d'un Disque Tournant - 5
Chapitre I Principaux Défauts de la Machine
Asynchrone, Causes et Conséquences
Analyse Vibratoire des Machines sur un Banc d'Essai - Cas
d'un Disque Tournant - 6
- Si la tension supportée par chaque enroulement est
égale á la tension composée du réseau, le stator
doit être couplé en triangle.
Les enroulements sont logés dans des encoches d'une
armature cylindrique constituée d'un matériau
ferromagnétique feuilleté afin de limiter les pertes par courant
de Foucault. Le stator est fixé au corps du moteur et se compose d'un
empilage de tôles très fines et de trois enroulements. En
réseau triphasé, chaque enroulement est bobiné autour d'un
noyau statorique et forme un électroaimant (une paire de pôles)
lorsqu'il est relié à une phase du réseau. Le moteur
asynchrone triphasé alternatif est le seul à fonctionner
grâce à l'alternance des phases du réseau
électrique.
L'explication physique est la suivante : La circulation d'un
courant dans une bobine crée un champ magnétique
H. Ce champ est dans l'axe de la bobine, sa direction et son
intensité sont fonction du courant Is. Si le
courant est alternatif, le champ magnétique varie en sens et en
direction à la même fréquence que le courant. Si deux
bobines sont placées à proximité l'une de l'autre, le
champ magnétique résultant est la somme vectorielle des deux
autres.
Dans le cas du moteur triphasé, les trois bobines sont
positionnées dans le stator à 120° les unes des autres, ce
qui crée trois champs magnétiques. Compte-tenu de la nature du
courant sur le réseau triphasé, les trois champs sont
déphasés. Ainsi alimenté, le stator génère
un champ magnétique, dit champ statorique tournant à une vitesse
qui est dite de synchronisme (Ns). La fréquence de
rotation de ce champ est liée à la fréquence du
réseau et au nombre de paires de pôles de l'enroulement.
Ns = 60f / p en nombre de tours par minute
(RPM). [3]
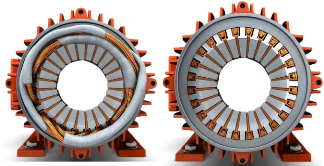
Fig.I.2. Le stator [6].
I.3.2. Rotor
Est un partie en mouvement, et en court-circuit, Il y a deux
types : bobine ou à cage d'écureuil. Il est composé d'un
empilage de fines tôles métalliques isolées entre elles
(afin d'éviter la circulation des courants de Foucault), d'enroulements
et de conducteurs qui sont en
Chapitre I Principaux Défauts de la Machine
Asynchrone, Causes et Conséquences
Analyse Vibratoire des Machines sur un Banc d'Essai - Cas
d'un Disque Tournant - 7
court-circuit. Sa particularité est de réagir au
champ magnétique généré par le stator, (le champ
statorique). Selon la loi de Lenz, le courant induit dans le rotor s'oppose,
par son champ magnétique aux effets du champ inducteur. Les variations
de flux entre les enroulements statoriques et rotoriques se traduisent par
l'apparition d'une force : le couple. Le rotor entre ainsi en rotation à
une vitesse nominale (N) qui se rapproche de la vitesse de
synchronisme (Ns) qui est la vitesse maximale de rotation
liée à la fréquence de l'alimentation.
La différence de vitesse entre Ns et N est
nommée vitesse de glissement, d'où l'emploi de l'appellation
« moteur asynchrone » qui traduit
cette différence de vitesse. Le glissement g est
exprimé en % de la vitesse de synchronisme et se calcule selon la
formule suivante :
Quand le moteur est en phase de démarrage, la vitesse
du rotor est nulle et la différence de vitesse de rotation du champ
magnétique et celle du rotor est maximale, ce qui génère
l'induction de forts courants rotoriques par l'absence de force contre
électromotrice (c'est l'origine du fort courant d'appel). Quand le rotor
accélère, la différence de vitesse se réduit et les
courants rotoriques diminuent. La vitesse du rotor se stabilise à sa
vitesse N. [3]
I.3.2.1. Rotor bobiné
Il n'est relié à aucune alimentation
électrique, il est muni d'un enroulement triphasé, composé
des bobines. L'enroulement généralement couplée en
étoile et connecté à trois bagues conductrices
isolées les unes des autres sur lesquelles frottent des balais en
graphite.
L'extrémité libre de chaque enroulement est
reliée à une bague tournant avec l'arbre. Ces bagues permettent,
par l'intermédiaire de trois balais, d'insérer une
résistance extérieure en série avec chacun des trois
enroulements lors du démarrage du moteur. En fonctionnement normal, les
trois balais sont court-circuités. [7]
Chapitre I Principaux Défauts de la Machine
Asynchrone, Causes et Conséquences
L'arbre du rotor
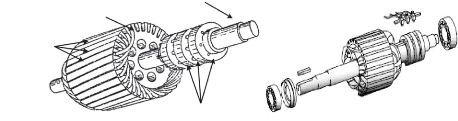
Enroulement de rotor
Encoches oblique de rotor
Brosses / Bagues
Fig.I.3. Structure d'un rotor bobiné
[3] [8].
I.3.2.2. Rotor cage d'écureuil
Dans le type le plus utilisé, connu sous le nom de
rotor à cage d'écureuil, des barres de cuivre ou d'aluminium sont
placées dans des fentes découpées dans le fer
laminé, les extrémités des barres étant
soudées ou brasées dans un lourd anneau conducteur (figure I.4).
Les conducteurs sont placés dans des fentes du noyau du rotor en fer
laminé. Si les fentes sont inclinées, on obtient un meilleur
démarrage et un fonctionnement plus silencieux. Ce type de rotor n'a pas
de connexion externe, ce qui signifie que les bagues collectrices et les balais
ne sont pas nécessaires. Le moteur à cage d'écureuil est
bon marché, fiable et efficace.[9]
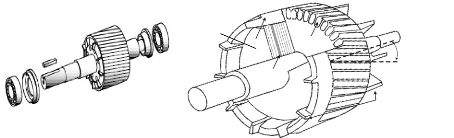
Bague d'extrémité
Tôles
Encoche Angle
d'inclinaison
Analyse Vibratoire des Machines sur un Banc d'Essai - Cas
d'un Disque Tournant - 8
Fig.I.4. Structure d'un rotor à cage
d'écureuil [3] [8]. I.3.3. Les organes
mécaniques
La carcasse sert de support, elle joue le rôle
d'enveloppe et assure la protection contre l'environnement extérieur.
L'arbre est un organe de transmission. Il comprend une partie
centrale qui sert de support au corps du rotor et un bout d'arbre sur lequel
est fixé un demi-accouplement. Il est généralement
constitué en acier moulé ou forgé. Son dimensionnement est
fonction des efforts de flexion (force centrifuge qui s'exerce sur lui,
attraction magnétique radial, etc....), des efforts radiaux et
tangentiels dus aux forces centrifuges, des efforts de torsion (couple
Chapitre I Principaux Défauts de la Machine
Asynchrone, Causes et Conséquences
Analyse Vibratoire des Machines sur un Banc d'Essai - Cas
d'un Disque Tournant - 9
électromagnétique transmis en régime
permanent, transitoire). Il est supporté par un ou plusieurs paliers.
Ces paliers soutiennent le rotor et assurent la libre rotation. Le second
palier est libre pour assurer les dilatations thermiques de l'arbre. Une
isolation électrique de l'un des paliers assure l'élimination des
courants dans l'arbre dû aux dissymétries des réluctances
du circuit magnétique. Ils sont généralement à
roulements pour les machines de petite et moyenne puissance.[10]
I.3.3.1. Les roulements
Éléments roulants ou antifriction Les roulements
à éléments roulants sont l'un des types les plus courants
utilisés dans les machines. Les roulements sont basés sur un
mouvement de roulement, par opposition au mouvement de glissement des paliers
lisses. L'utilisation d'éléments roulants entre les surfaces
tournantes et stationnaires réduit le frottement à une fraction
de celui résultant de l'utilisation de paliers lisses. L'utilisation de
roulements est déterminée par de nombreux facteurs, notamment la
charge, la vitesse, la sensibilité au désalignement, les
limitations d'espace et le désir de positionnement précis de
l'arbre. Ils supportent des charges radiales et axiales et sont
généralement utilisés dans des applications à
vitesse modérée à élever.
Contrairement aux paliers lisses à film fluide, les
roulements à éléments roulants ont la capacité
supplémentaire de supporter la charge totale de l'ensemble du rotor
à n'importe quelle vitesse. Alors que les paliers à film fluide
doivent avoir un engrenage tournant pour supporter le poids du rotor à
basse vitesse, les roulements à éléments roulants peuvent
maintenir l'axe central de l'arbre sur toute la plage de vitesse de la
machine.[11]
I.4. Maintenance
Dans le milieu industriel le maintien de la continuité
de service nécessite un effort de la part des exploitants de production.
Le maillon faible est principalement la machine électrique, car sa panne
paralyse immédiatement la production et entraîne une perte
financière très importante. Une maintenance dite «
prédictive » doit donc être assurée afin de
prévenir à temps les défauts susceptibles de se produire
dans les moteurs.
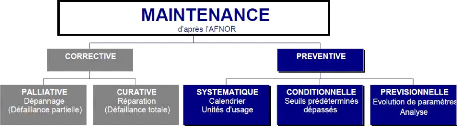
Chapitre I Principaux Défauts de la Machine
Asynchrone, Causes et Conséquences
Fig.I.5. Types de maintenance [12]
.
I.4.1. Maintenance curative
Après un arrêt par défauts ou bien malle
fonctionnement :
- Nécessite une équipe d'entretien
surdimensionnée
- Ne permet pas de maîtriser la disponibilité des
équipements
I.4.2. Maintenance systématique Selon un
échéancier préétabli :
- Engendre le remplacement prématuré de
composants
- Ne permet pas de prendre en compte l'évolution
réelle de leur état I.4.3. Maintenance
prévisionnelle
Maintenance préventive subordonnée à
l'analyse de l'évolution surveillée de paramètres
significatifs de la dégradation du bien, permettant de retarder et
planifier les interventions.
I.4.4. Maintenance préventive
Maintenance exécutée à intervalles
prédétermines ou selon des critères prescrits et
destinée à réduire la probabilité de
défaillance ou la dégradation du fonctionnement d'un bien.
I.4.5. Maintenance conditionnelle
Maintenance préventive qui comprend une combinaison de
surveillance en fonctionnement et/ou d'essais, d'analyse et les actions qui en
découlent.
La maintenance conditionnelle est basée sur l'analyse de
l'évolution dans le temps de paramètres significatifs.
Note : Les définitions des types de
maintenance selon les normes EN NF 13306 , AFNOR X60-010) .
Analyse Vibratoire des Machines sur un Banc d'Essai - Cas
d'un Disque Tournant - 10
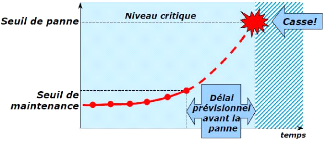
Chapitre I Principaux Défauts de la Machine
Asynchrone, Causes et Conséquences
Analyse Vibratoire des Machines sur un Banc d'Essai - Cas
d'un Disque Tournant - 11
Fig.I.6. Seuil de maintenance [13]
I.4.6. L'importance de la maintenance
Les enjeux économiques liés à la
maintenance des systèmes industriels, dont ceux entrainés par des
moteurs asynchrones, sont très importants pour les entreprises. Cette
remarque est d'autant plus vraie aujourd'hui en raison de l'automatisation, de
la complexification et de l'interdépendance des machines et des lignes
de production. Cependant, ce poste de dépense a longtemps
été considéré comme inéluctable et faisant
partie des frais généraux de fonctionnement.
La maintenance industrielle constitue pourtant un gisement de
compétitivité élevé pour beaucoup d'entreprises.
Les coûts directement ou indirectement associés à la
maintenance représentent en effet un pourcentage élevé
dans l'analyse du coût du cycle de vie (CCV) des systèmes
industriels et peuvent être diminués en optimisant la
stratégie de maintenance adoptée. [14]
Les coûts de maintenance, tels qu'ils sont
définis par les procédures comptables normales des usines,
représentent normalement une part importante des coûts
d'exploitation totaux dans la plupart des usines. Aux États-Unis, les
coûts d'entretien traditionnels (c'est-à-dire la main-d'oeuvre et
les matériaux) ont augmenté à un rythme
effréné au cours des dix dernières années. En 1981,
les usines nationales ont dépensé plus de 600 milliards de
dollars pour entretenir leurs systèmes critiques. En 1991, les
coûts avaient augmenté à plus de 800 milliards de dollars,
et on prévoyait qu'ils atteindraient 1,2 billion de dollars en l'an
2000. Ces évaluations indiquent qu'en moyenne, un tiers, soit 250
milliards de dollars, de tous les dollars consacrés à la
maintenance sont gaspillés en raison de méthodes de gestion de la
maintenance inefficaces. L'industrie américaine ne peut absorber ce
niveau incroyable d'inefficacité et espérer être
compétitive sur le marché mondial.
Chapitre I Principaux Défauts de la Machine
Asynchrone, Causes et Conséquences
Analyse Vibratoire des Machines sur un Banc d'Essai - Cas
d'un Disque Tournant - 12
Chapitre I Principaux Défauts de la Machine
Asynchrone, Causes et Conséquences
En raison de la nature exorbitante des coûts de
maintenance, ils représentent le plus grand potentiel
d'amélioration à court terme. Les retards, les rejets de
produits, les temps d'arrêt prévus pour la maintenance et les
coûts de maintenance traditionnels (tels que la main-d'oeuvre, les heures
supplémentaires et les pièces de rechange) sont
généralement les principaux facteurs contribuant aux coûts
de maintenance anormaux dans une usine.
Jusqu'à récemment, les cadres moyens et
supérieurs n'ont pas tenu compte de l'impact des opérations de
maintenance sur la qualité des produits, les coûts de production
et, surtout, les bénéfices nets. L'opinion générale
était que "la maintenance est un mal nécessaire" ou que "rien ne
peut être fait pour améliorer les coûts de maintenance". Ces
affirmations étaient peut-être vraies il y a 10 ou 20 ans.
Cependant, le développement de microprocesseurs ou d'instruments
informatiques pouvant être utilisés pour surveiller l'état
de fonctionnement des équipements, des machines et des systèmes
de l'usine a fourni les moyens de gérer les opérations de
maintenance. Ils ont permis de réduire ou d'éliminer les
réparations inutiles, de prévenir les pannes catastrophiques des
machines et de réduire l'impact négatif des opérations de
maintenance sur la rentabilité des usines de fabrication et de
production.[11]
I.5. Terminologie dédiée au
diagnostic
Le tableau ci-dessous défier les étapes de la
terminologie dédiée au diagnostic. Tab.I.1.
Terminologie & définitions [15].
Terminologie
|
Définitions
|
Défaut
|
Déviation non permise d'au moins d'une
propriété ou d'un paramètre caractéristique du
système par rapport aux conditions normales de fonctionnement.
|
Panne ou
défaillance
|
Interruption permanente de la capacité du
système à remplir une fonction requise dans des conditions
d'opérations spécifiées.
|
Dysfonctionnement
|
Exécution d'une fonction du système au cours de
laquelle le service rendu n'est pas délivré ou est
délivré de manière incomplète.
|
Symptôme
|
Changement d'une quantité observable par rapport à
un
comportement normal.
|
Perturbation
|
Signal d'entrée non contrôlé dont la
présence est non souhaitable mais considérée comme
normale.
|
Suivi
|
Fonction maintenant en permanence un historique des
traitements effectués par le système de commande/supervision et
une trace des événements que perçoit le système.
|
Détection de
défauts
|
Détermination de la présence de défauts
et de l'instant d'occurrence de ces défauts.
|
Localisation de
défauts
|
Détermination du type, de la localisation et de la date
d'un défaut détecté. Elle consiste à remonter d'un
ensemble de symptômes à un
|
Analyse Vibratoire des Machines sur un Banc d'Essai - Cas
d'un Disque Tournant - 13
|
ensemble de composants défaillants.
|
Identification de
défauts
|
Détermination de la taille et du comportement temporel
d'un défaut. C'est une fonction qui suit la localisation.
|
Diagnostic
|
Détermination du type, de la taille, de la localisation et
de l'instant d'occurrence d'un défaut. C'est une fonction qui suit la
détection et inclut les fonctions de localisation et
d'identification.
|
Surveillance
|
Ensemble de fonctions s'exécutant en temps réel
ayant pour but de reconstituer l'état réel du
procédé au sein des modèles utilisés par le
système de conduite du procédé. Elle consiste à
l'enregistrement de
l'information ainsi qu'à la reconnaissance et
l'indication des comportements anormaux.
|
Supervision
|
Représente la surveillance d'un système physique
et la prise de décisions appropriées en vue de maintenir son
opération face à des défaillances.
|
I.6. Généralités sur les
défauts des machines électrique
Il existe deux types de défauts principaux : internes
et externes. Nous pouvons ainsi remarquer que les défauts internes de la
machine sont causés par les constituants de la machine (circuit
magnétique rotorique et statorique, bobinage statorique, entrefer
mécanique, cage rotorique, ...) alors que les défauts externes
sont provoqués, soit par les tensions d'alimentation et la charge
mécanique, soit par l'environnement de l'utilisation de la machine.
[16]
Nous citerons à titre indicatif des origines de type :
- Mécaniques: mauvaise fabrication, vibrations de la
machine, force électromagnétiques
déséquilibrées, force centrifuge,
fluctuations de la charge.
- Electriques: dégradations d'isolement, décharges
partielles, étincelles.
- Thermiques: pertes dans le cuivre, manque de refroidissement
général ou localisé.
- Environnementales: humidité, température,
poussière.
Afin d'orienter notre étude vers la détection
d'une ou plusieurs catégories de défaillances, il est
nécessaire de connaitre les défauts se produisant le plus
régulièrement dans les systèmes d'entrainement asynchrones
et également ceux dont les conséquences sont les plus graves.
Dans la littérature, plusieurs études ont été
menées à grande échelle sur des moteurs asynchrones aux
caractéristiques fortement différentes afin de connaitre la
répartition des défaillances survenant dans ces systèmes
[17], [18], [19] . Les résultats obtenus à l'issue de ces
différentes études sont représentés sur la figure
I.7 en classant les défauts selon 4 catégories : roulements,
stator, rotor et autres.
Chapitre I Principaux Défauts de la Machine
Asynchrone, Causes et Conséquences
Analyse Vibratoire des Machines sur un Banc d'Essai - Cas
d'un Disque Tournant - 14
Fig.I.7. Répartition des défauts
rencontrés dans les entrainements asynchrones [14] selon les
études [17], [18] et [19].
Ces études statistiques nous informent que la
majorité des défaillances rencontrées concernent les
roulements à billes. Les défaillances au stator (majoritairement
liées à l'isolation des bobinages) constituent également
un pourcentage important des dégradations observées. Enfin, les
défauts au rotor (arbre, accouplement, etc.) semblent se produire moins
fréquemment.
Une étude a été menée
auprès d'une filiale de service de Leroy Somer spécialisée
dans la maintenance des systèmes d'entrainement. Cette étude
n'est pas quantitative comme celles présentées dans [17], [18] et
[19] mais se base sur l'expérience acquise au cours des phases de
maintenance réalisées. Les chiffres fournis par la suite ne sont
donc probablement pas strictement fidèles à la
réalité mais fournissent une vision globale de la
répartition des défaillances observées dans les
systèmes entrainés par les moteurs asynchrones ciblés par
notre étude. Les résultats obtenus sont illustrés par la
figure I.8.
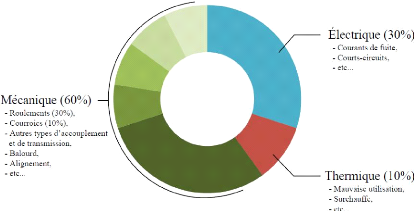
Fig.I.8. Répartition des défauts
rencontrés dans les applications entrainées par les moteurs
asynchrones de la gamme Leroy Somer selon l'enquête menée
auprès d'une filiale de maintenance. [14]
Chapitre I Principaux Défauts de la Machine
Asynchrone, Causes et Conséquences
Analyse Vibratoire des Machines sur un Banc d'Essai - Cas
d'un Disque Tournant - 15
I.6.1. Défaut des roulements
Les roulements sont des composants typiques des moteurs qui
sont utilisés pour permettre la rotation de l'arbre. La majorité
des pannes de moteur sont dues à un mauvais fonctionnement des
roulements. Les roulements sont constitués de billes, d'une cage et de
bagues intérieure et extérieure. Plusieurs éléments
roulants (billes) sont placés entre ces deux bagues. La cage est
utilisée pour maintenir les billes à égale distance les
unes des autres. Les contraintes développées dans le moteur
provoquent une fatigue des bagues des roulements, qui entraîne des
défauts localisés (défauts uniques tels que
l'écaillage, les piqûres, les bosses ou les trous) et des
défauts répartis (rugosité de surface
généralisée) dans les roulements du moteur.
Les défauts localisés sont induits
principalement par l'usure opérationnelle (fatigue de contact) des
roulements. Si les roulements sont correctement installés, exempts de
contamination et bien lubrifiés pendant le fonctionnement, la
défaillance des roulements ne se produira qu'après la
durée de vie prédéterminée (millions de cycles) des
roulements.
Ce type de défaillance commence initialement dans un
sous-sol à un niveau microscopique en un seul point, puis, en raison des
cycles de contrainte continus, elles peuvent finir par provoquer une rupture du
matériau. Ces défauts ponctuels sont caractérisés
comme des écaillages ou des piqûres, ou des défauts
localisés. La défaillance des roulements peut également se
produire en raison de leur température élevée.
La température des roulements ne doit pas augmenter
au-delà de certains degrés dans des conditions nominales.
Degrés spécifiques dans les conditions
nominales. Par exemple, dans les industries pétrolières et
chimiques, la norme IEEE 841 spécifie que l'augmentation de la
température des roulements, sous une charge nominale, ne doit pas
dépasser 45°. L'augmentation de la température du bobinage,
une mauvaise lubrification, la répartition de la température dans
le moteur et la vitesse de fonctionnement du moteur sont les principaux
facteurs d'augmentation de la température des roulements.[20]
Par conséquent, les mesures de la température
des roulements peuvent fournir des données utiles pour estimer
l'état de santé des roulements ainsi que celui du moteur.
Chapitre I Principaux Défauts de la Machine
Asynchrone, Causes et Conséquences
|
(a) Défaut localisé sur extérieur
du roulement
|
|
(b) Défauts distribués sur la bague
intérieure
|
Analyse Vibratoire des Machines sur un Banc d'Essai - Cas
d'un Disque Tournant - 16
Fig.I.9. Exemple de roulement. (a) Défauts
localisés. (b) Défauts distribués. [20]
I.6.1.1. Fréquences caractéristiques des défauts
du roulement
Nous pouvons distinguer quatre types de défauts de
roulement, en fonction de leur localisation :
· Défaut de bague externe,
· Défaut de bague interne,
· Défaut de billes,
· Défaut de cage.
Chaque type de défaut cité ci-dessus est
caractérisé par une fréquence fondamentale calculée
à partir des dimensions du roulement et de la fréquence de
rotation de l'arbre (????). Les expressions de ces fréquences pour les
défauts de bague externe, de bague interne, de billes et de cage sont
données respectivement, où ???? et ???? sont les diamètres
d'une bille et de la cage, ?? est l'angle de contact de la bille avec les
bagues et ???? est le nombre de billes.[21]
y' Défaut de bague externe
?? ?? ??
?? ?? ??
?? ??
??
y' Défaut de bague interne
?? ??
??
y' Défaut de billes
y' Défaut de cage
|
??
?? ??
??
?? ??
|
??
?? ??
?? ??
??
|
I.6.2. Défauts au stator
Les défauts qui sont les plus récurrents,
localisés au niveau du stator, peuvent être définis comme
suit : défaut d'isolant, court-circuit entre spires, court-circuit entre
phases, court-
Chapitre I Principaux Défauts de la Machine
Asynchrone, Causes et Conséquences
circuit entre phase et bâti, déséquilibre
d'alimentation, défaut de circuit magnétique. Ces défauts
sont habituellement liés à une dégradation de
l'isolement.
Le court-circuit entre spires de la même phase est l'un
des défauts les plus fréquents, qui peut être
modélisé par une résistance connectant deux points de la
bobine, sa valeur dépend de la gravité du défaut. La
figure I.10 montre le bobinage du stator de la machine avec défaut entre
spires. Le défaut est survenu sur l'enroulement de la phase
as avec une résistance de
défaut rf. Lorsque le défaut
évolue vers un court-circuit franc, la résistance diminue vers
zéro. A un stade avancé, un défaut de court-circuit entre
spires peut s'aggraver et évoluer vers un court-circuit phase-phase ou
phase-terre. L'augmentation de la température engendrée
entraîne par la suite la destruction progressive des isolants et par
effet cumulatif, la destruction complète de la machine. En
général, un défaut de court-circuit engendre des
vibrations et des oscillations de couple synonymes de présence de
nouvelles composantes dans le couple électromagnétique. En effet,
la résistance de court-circuit forme un nouveau bobinage qui induit un
champ magnétique additionnel dans la machine.[22]
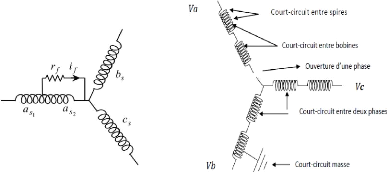
Analyse Vibratoire des Machines sur un Banc d'Essai - Cas
d'un Disque Tournant - 17
Fig.I.10. Différents types de défauts
statorique [22] [23] I.6.3. Défauts au
rotor
Dans une machine asynchrone avec un rotor à cage
d'écureuil, les défauts se résument à la rupture de
barres ou à la rupture d'anneaux de court-circuit. Ils sont souvent
causés par les mauvaises conditions d'opérations essentiellement
par des hautes températures ou les fortes charges surtout aux
démarrages. En effet, une rupture partielle ou totale d'une de ces
composantes peut être considérée comme un défaut. En
conséquence, l'évolution du défaut réduit la valeur
moyenne du couple électromagnétique, provoque des oscillations de
la vitesse de rotation et engendre des vibrations mécaniques.
L'augmentation de ces phénomènes accélère la
dégradation de la cage rotorique. Les barres cassées peuvent
alors s'ouvrir à l'extérieur en raison des forces centrifuges et
endommager de façon catastrophique les enroulements statoriques.[22]
Chapitre I Principaux Défauts de la Machine
Asynchrone, Causes et Conséquences
Une portion d'anneau Deux portion d'anneaux
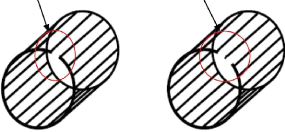
Analyse Vibratoire des Machines sur un Banc d'Essai - Cas
d'un Disque Tournant - 18
Fig.I.11. Rupture d'un anneau. [24]
I.6.4. Défaut d'excentricité
Dans une machine idéale, le centre du rotor est
aligné sur celui du stator et l'axe de rotation du rotor est le
même que l'axe du stator, comme illustré dans la figure I.12.
Toutefois, les conséquences des défauts mécaniques peuvent
se manifester au niveau de l'entrefer par un décentrement du rotor, se
traduisant par des oscillations de couple . Ce phénomène est
appelé excentricité défini comme une asymétrie dans
l'entrefer entre le stator et le rotor. Ce défaut existe en
général dans la machine, mais avec un faible niveau, dès
sa fabrication et évolue avec le temps. Certains utilisateurs et
fabricants spécifient un niveau d'excentricité maximal admissible
de 5% alors que d'autres permettent un niveau maximal de 10% de la largeur de
l'entrefer .Tout niveau d'excentricité supérieur à 60%
nécessite une intervention immédiate afin d'éviter un
frottement entre le rotor et le stator [21], ce qui peut mener à une
panne très grave de la machine.
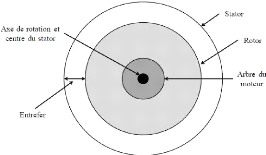
Fig.I.12. Positions du rotor et du stator dans une
machine parfaite. [21]
Trois catégories d'excentricité peuvent
être identifiées dans la littérature et sont
illustrées dans la figure I.13 :
- Excentricité statique (figure I.13 (a)) : le rotor
est déplacé du centre de l'alésage du stator mais il
tourne toujours autour de son axe. Elle est due généralement soit
à une imperfection de
Chapitre I Principaux Défauts de la Machine
Asynchrone, Causes et Conséquences
l'alésage du stator, soit à un mauvais
positionnement du rotor ou du stator à l'étape de mise en
service.
- Excentricité dynamique (figure I.13 (b)) : le rotor
est positionné au centre de l'alésage du stator mais il ne tourne
plus autour de son axe. Ce type peut être provoqué par divers
facteurs tels que l'usure des roulements, les résonnances
mécaniques à la vitesse critique et le désalignement.
- Excentricité mixte (figure II.13 (c)) : la combinaison
des deux cas cités précédemment.
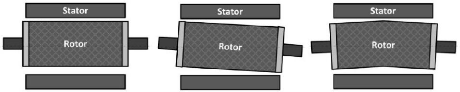
(a) (b) (c)
Fig.I.13. Types d'excentricités statiques (a),
dynamique (b) et mixte (c) [21] I.6.5. Alignement
d'arbres
L'alignement des arbres est le positionnement correct des axes
des arbres des composants d'entraînement et des composants
entraînés (c'est-à-dire les pompes, les boîtes de
vitesses, etc.) qui constituent la chaîne cinématique de la
machine. L'alignement est réalisé soit en calant, soit en
déplaçant un composant de la machine, soit les deux. Son objectif
est d'obtenir un axe de rotation commun à l'équilibre de
fonctionnement pour deux arbres couplés ou un train d'arbres
couplés. [11]
I.6.5.1. Alignement parfait
Deux arbres parfaitement alignés sont
colinéaires et fonctionnent comme un arbre solide lorsqu'ils sont
couplés. Cette condition est illustrée à la figure I.14
Cependant, il est extrêmement rare que deux arbres soient parfaitement
alignés sans qu'une procédure d'alignement ne soit
effectuée sur eux. En outre, l'état de l'alignement doit
être contrôlé régulièrement pour maintenir la
condition d'alignement parfait.
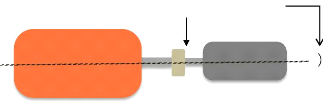
D = 0 mm et Äö = 0 °
Charge
Moteur
Fig.I.14. Alignement parfait. [S. Kouidri et
K. Ghris]
Analyse Vibratoire des Machines sur un Banc d'Essai - Cas
d'un Disque Tournant - 19
Chapitre I Principaux Défauts de la Machine
Asynchrone, Causes et Conséquences
Analyse Vibratoire des Machines sur un Banc d'Essai - Cas
d'un Disque Tournant - 20
I.6.5.2. Désalignement angulaire ou frontal (le
délignage ou défaut de lignage)
Une bonne connaissance de l'alignement angulaire,
également appelé désalignement frontal, est
nécessaire pour comprendre les conditions d'alignement et effectuer les
tâches associées à l'alignement des machines et des trains,
telles que le dessin des graphiques d'alignement, le calcul des corrections de
pied, la spécification de la croissance thermique, l'obtention des
spécifications cibles et la détermination de l'alignement des
arbres d'espacement. Le désalignement angulaire fait
référence à la condition dans laquelle les arbres ne sont
pas parallèles mais se trouvent dans le même plan sans
décalage. Ce cas est illustré à la figure I.15 Notez qu'en
cas de désalignement angulaire, il est possible que les arbres
correspondants soient dans le même plan à l'intersection de la
face de l'accouplement mais qu'ils aient une relation angulaire telle qu'ils ne
sont pas colinéaires.[11]
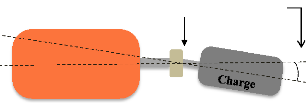
D = 0 mm et Äö > 0 °
Moteur
Fig.I.15. Désalignement angulaire (pas de
décalage) [S. Kouidri et K. Ghris] I.6.5.3.
Désalignement décalé ou parallèle
Le désalignement décalé, également
appelé désalignement parallèle, fait
référence à la distance entre deux axes d'arbres et se
mesure généralement en millièmes de pouce. Le
décalage peut être présent dans le plan vertical ou
horizontal. La figure I.16 illustre le décalage, montrant deux arbres
appariés qui sont parallèles l'un à l'autre mais non
colinéaires. Théoriquement, le décalage est mesuré
au niveau de l'axe de l'accouplement.
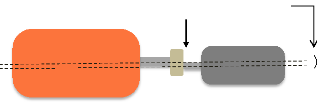
D > 0 mm et Äö = 0 °
Moteur
Charge
Fig.I.16. Désalignement parallèle.
[S. Kouidri et K. Ghris] I.6.5.4. Désalignement
combiné ou oblique
Un désalignement combiné ou oblique se produit
lorsque les arbres ne sont pas parallèles (c'est-à-dire
angulaires) et ne se croisent pas au niveau de l'accouplement
(c'est-à-dire
Chapitre I Principaux Défauts de la Machine
Asynchrone, Causes et Conséquences
décalés). La figure I.17 montre deux arbres
obliques, ce qui est le type de problème de désalignement le plus
courant. Ce type de désalignement peut se produire dans le plan
horizontal ou vertical, ou dans les deux plans (horizontal et vertical).
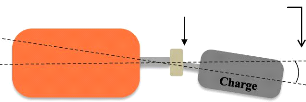
D > 0 mm et Äö > 0 °
Moteur
Fig.I.17. Désalignement combiné.
[S. Kouidri et K. Ghris]
I.6.6. Flexion du rotor
Deux paliers du même arbre d'une machine : les axes des
deux paliers d'un même corps de machine ne sont pas concentriques. Cette
anomalie peut être la conséquence d'un défaut de montage
d'un palier, mais également d'un mauvais calage des pattes de fixation
ou d'une déformation de chassis (par exemple, sous l'effet de
contraintes thermiques), qui se traduit par une flexion de l'arbre du rotor.
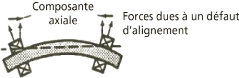
Fig.I.18. Flexion d'arbre due à un défaut
d'alignement ou de concentricité des paliers.
[29]
Ill y a 3 modes élastiques d'un rotor flexible
:

Analyse Vibratoire des Machines sur un Banc d'Essai - Cas
d'un Disque Tournant - 21
Fig.I.19. Modes élastiques d'un rotor flexible.
[25] I.6.7. Défaut de déséquilibre
(balourd)
Le balourd est le résultat d'un ensemble de forces
engendrées par les écarts existant entre les centres de
gravité des différents éléments constituant le
rotor et son axe de rotation. Cette force centrifuge, issue de ces
défauts de « non-concentricité » ou d'ajustage, est
proportionnelle à la masse de matière qui crée ce
déséquilibre et au carré de la vitesse. Elle
génère des efforts tournants qui vont agir sur les
différents éléments constitutifs du rotor, les ancrages de
la machine et les paliers jusqu'à entraîner leur
dégradation. Le défaut de balourd
Chapitre I Principaux Défauts de la Machine
Asynchrone, Causes et Conséquences
Analyse Vibratoire des Machines sur un Banc d'Essai - Cas
d'un Disque Tournant - 22
Chapitre I Principaux Défauts de la Machine
Asynchrone, Causes et Conséquences
Chapitre I Principaux Défauts de la Machine
Asynchrone, Causes et Conséquences
est l'une des principales causes de réduction de la
durée de vie des équipements et il constitue l'un des principaux
risques pour la sécurité. C'est pour cette raison sans doute
qu'il fait l'objet de normes importantes, tant pour son évaluation que
pour sa correction. Ainsi, pour une classe d'équilibrage donnée,
comparer l'amplitude de la vibration induite à des seuils fixes dans des
normes ou à des spécifications de constructeurs, permettra de
statuer sur le caractère acceptable ou non du déséquilibre
et sur la nécessité de procéder ou non à un
équilibrage suivant une procédure bien définie.
Le balourd, déséquilibre massique, peut provenir
de défauts d'usinage, d'assemblage et de montage, mais aussi :
- D'une altération mécanique (perte d'ailette,
érosion ou encrassement...),
- D'une altération thermique ou d'une
déformation suite à des dilatations différentes des
matériaux constituant le rotor ou encore à des différences
de température localisées (balourd thermique).[29]
I.6.7.1. Les paramètres de
déséquilibre
Les paramètres ci-dessous est paramètres de
déséquilibrage :
"M" - Masse du rotor
"m" - Masse du balourd
"C" - Centre de masse
"e" - Déplacement du centre de la masse
"r" - Distance entre le centre du rotor et C.G
du la masse "m" de balourd
"F" - Force due au déséquilibre
"U" - Déséquilibre du rotor
"N" - Vitesse du rotor (RPM)
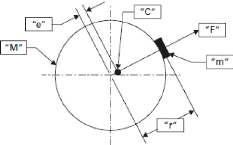
Fig.I.20. Déséquilibre du rotor.
[26]
Analyse Vibratoire des Machines sur un Banc d'Essai - Cas
d'un Disque Tournant - 23
Et nous avons :
I.6.7.2. Déséquilibre et
vitesse
De nombreuses personnes pensent que le
déséquilibre s'aggrave avec l'augmentation de la vitesse. Nous
savons que ce n'est pas le cas. Ce graphique montre que le balourd est une
constante - c'est une propriété de masse du rotor.
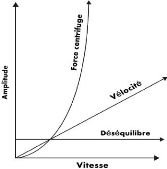
Fig.I.21. Le déséquilibre, la
vélocité de vibration et la force centrifuge en fonction
de
la vitesse de rotation [26]
Le déséquilibre est une propriété du
rotor et ne change pas avec la vitesse de rotation. La vélocité
de vibration change en rapport direct avec la vitesse de rotation.
La force centrifuge change en fonction de (RPM)2.
Si un rotor avec un balourd "nul" est utilisé à
n'importe quelle vitesse, il n'y aura pas de vibrations ni de forces sur les
paliers. Il ne s'agit bien sûr que d'une situation théorique. Si
un poids d'une masse de 1 gramme est ajouté au rotor à un rayon
de 100 mm, lorsqu'il tourne, il y aura des vibrations et des forces d'appui qui
changeront avec la vitesse, mais le déséquilibre est fixé
à 100 g.mm - à moins que nous tournions assez vite pour que le
poids s'approche de la vitesse de la lumière, auquel cas il deviendrait
plus court et plus massif - mais c'est un autre problème.
I.6.7.3. Sources du
déséquilibre
La plupart des fabricants de moteurs électriques
standardisent l'équilibrage de leurs éléments rotatifs
avec la totalité de la rainure de clavette remplie d'une demi-clavette.
C'est-à-
Analyse Vibratoire des Machines sur un Banc d'Essai - Cas
d'un Disque Tournant - 24
dire que l'arbre est totalement rempli. Les fabricants
d'accouplements pratiquent les mêmes procédures lorsqu'ils
équilibrent leurs accouplements. Lors de l'assemblage de ces deux
éléments, une clavette en L ou en T doit être
utilisée pour maintenir l'équilibre d'origine. La figure I.22
montre certaine des sources les plus courantes de déséquilibre
associées à l'installation d'un accouplement. Chacune de ces
conditions peut entraîner une défaillance prématurée
dans les roulements, des accouplements ou des joints.[27]
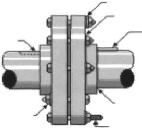
Rondelle supplémentaire
Rondelle manquante/ absente
Matériel clé
Manquant de matériel clé
Moyeu desserré sur l'arbre
Boulon en arrière
Boulon trop long
Fig.I.22. Sources de déséquilibre
[27] I.6.7.4. Déséquilibrage
statique
Imaginons un rotor parfaitement en équilibre. Ajoutons
en un endroit de ce rotor une masse M. Le rotor
présentera un déséquilibre. Même à
l'arrêt, le rotor reviendra à une position d'équilibre. Il
s'agit d'un déséquilibrage statique. Dès que le rotor sera
en rotation, la masse M exercera une force radiale
proportionnelle à la vitesse de rotation selon la relation
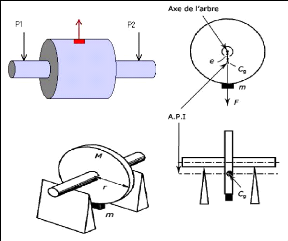
Force centrifuge
??
Chapitre I Principaux Défauts de la Machine
Asynchrone, Causes et Conséquences
Analyse Vibratoire des Machines sur un Banc d'Essai - Cas
d'un Disque Tournant - 25
Chapitre I Principaux Défauts de la Machine
Asynchrone, Causes et Conséquences
Analyse Vibratoire des Machines sur un Banc d'Essai - Cas
d'un Disque Tournant - 26
Fig.I.23. Déséquilibrage statique.
[31] [28]
On mesure l'amplitude de l'accélération du
signal vibratoire au point P1 et P2. Au point
P1, l'amplitude vibratoire sera maximale lorsque la masse sera en haut du
rotor. Elle sera minimale lorsqu'elle sera en bas du rotor, et ainsi de suite,
à chaque tour du rotor. Il se passe la même chose au point P2. On
voit que les efforts exercés sont en phase. Le signal
vibratoire a donc une période de 1 tour. Pour trouver la
fréquence de ce signal, il faut répondre à la question
suivante :
Combien de fois ce signal sera-t-il au maximum en 1 seconde ?
Si on tourne à 1500 tours / minute, le signal sera
à son maximum 1500 fois par minute. La fréquence du signal sera
:
N
|