«Etudes technico-économiques sur la plate-forme
gazéifieur : de l'étude de la ressource à l'utilisation du
gaz dans un moteur pour la production d'électricité»
MÉMOIRE POUR L'OBTENTION DU MASTER
D'INGÉNIERIE DE L'EAU ET DE L'ENVIRONNEMENT.
OPTION :ENERGIE
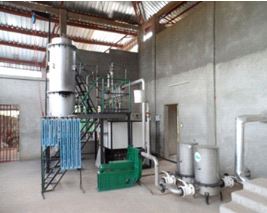
Présenté et soutenu publiquement le 18 Octobre
2013 par
AristideDEJEAN
Travaux dirigés par : Dr. François
PINTA, Enseignant-Chercheur Cirad/2iE
Bruno PECHINE, Chef de projet EDF
Jury d'évaluation:
Président : Dr.Daniel YAMEGUEU
Membres et correcteurs : Dr. Sayon SIDIBE
Dr. François PINTA
M. Justin BASSOLEPromotion [2012/2013]
Dédicace
A Dieu tout puissant, ma force et mon
réconfort ;
A mes parents DEJEAN Philippe et
Edwige ;
A mes frères et soeurs Firmin, Natacha, Esther
et Séni ;
A Alice Agnissey, tu es ma muse !
REMERCIEMENTS
Je tiens à remercier le Directeur du centre
Songhaï Fr.NZAMUDJO Godfreypour m'avoir accueilli durant ces 6 mois de
stage et m'avoir appris le sens de l'investissement de soi ;
Je tiens aussi à remercierMonsieur Bruno PECHINE ET
ERIC NANTEAU de EDF pour leurs appui durant tout le mémoire et la
formation sur l'instrumentation qui m'a été très utile;
Je remercie tout particulièrement le Directeur du
laboratoire LBEB, Dr. Joël BLIN pour m'avoir accueilli pour mon
mémoire ;
Je remercie tout particulièrement le Dr.
François PINTA et Dr. Sayon SIDIBE pour leurs conseils avisés,
leur encadrement et appui tant sur le plan professionnel que
personnel;
Je remercie Monsieur Justin LEKOTO, responsable du
département Enr pour son encadrement et ses conseils
avisés ;
Mes remerciements envers tous les employés des
sections de Songhaï Centre en particulier, M. Marius, M. Constantin, M.
Félicien, M. Lucien ;
A mes compères du département Enr JerryAyosso,
Romain Agbokamey, Hénoch Gnanga, Alvine Medem, Hadi et
Sylvianne ;et les voisins d'en face de la section champignon Juste et
Marcelle je vous envoie mes sincères remerciements pour l'accueil et
l'aide, et les fous rires durant ces six mois d'aventure ;
Je tiens à remercier tous les élèves
fermiers de songhaï Centre pour leur aide et disponibilité ;
A tous mes collègues de la promotion 2011 Master 2iE
Energie, en particulier, Jaliilou Zakané mon ingénieur
Jathropha,Koucoï Gabin ;Koffi Stéphane et ONDO Nang ;
Je remercie les membres du jury d'avoir accepté de
juger ce travail.
RESUME
La gazéification est une des voies prometteuses de la
valorisation de la biomasse. L'Afrique en général et surtout la
région sub-saharienne en particulier dispose d'un grand potentiel pour
développer cette technologie. Mais il est nécessaire de maitriser
l'ensemble de la chaine des valeurs de ce système
énergétique : itinéraire technique, organisationnel
et économique afin de lui permettre de prendre son essor.
Cette étude fait ressortir l'impact de certains
facteurs ; à savoir la matière première en
particulier son conditionnement et sa flexibilité en termes d'essences,
le coût d'investissement et le taux de couverture journalière sur
le coût de l'électricité fourni. Nos travaux ont
montréque ce coût peut varier de 217 FCFA/kWh à 78 FCFA/kWh
si on va de 25% à 75% de taux de couverture journalière en termes
de temps de fonctionnement, quand la plateforme de gazéification
fonctionne à une charge élevée de 91,6%, en utilisant
comme matière premièrele bois de plantations d'Acacia
auriculiformis de deux (2) ans d'âge.
Dans l'optique d'appliquer ce système dans un
environnement ruralet le rendre attractif, en particulier au niveau du concept
`'ville rurale verte de Songhaï'', nous avons procéder à une
étude technico-économique de l'unité pilote de
Songhaï Centre Porto Novo.Pour ce faire,nous avons installé une
instrumentation de base afin d'étudier les paramètres en
fonctionnement de la plateforme,diagnostiquer les pannes et les
équipements sensibles, et procéder à des recommandations
pour la gestion efficiente de l'unité actuelle et des unités
futures.
Mots clés : Gazéification,moteur,
électrification rurale, ressource, coût de
l'électricité.
ABSTRACT
The gasification is one of the promising ways of the
valorization of the biomass.Africa in general and especially the sub-Saharan
area in particular has a great potential to develop this technology but it is
necessary to mastered all the process of the values chains of this energetic
system: technical organizational and economic itinerary, in other to increase
his development.
This study emphasizes the impact of some factors like the raw
material in particular its conditioning and its flexibility in terms of species
involved, the capital cost and the daily cover rate onthe cost of
electricity.
Thus, This cost can vary from 217 FCFA/kWh to 78 FCFA/kWh if
the dailycover rate vary from25% to 50% at high load of 91,6% with wood as raw
material which is coming from two year old Acacia auriculiformis plantation.
In other to install such a system in a rural environment and
to make it competitive, in particular at the level of the Songhaï `' green
rural city ''concept, we carry out a technical and economic study of the pilot
unit of Songhaï Centre Porto-Novo.Thus, to do this study we installed a
basic instrumentation in other to study the parameters under operation of the
platform, to diagnose the breakdowns and sensitive equipment and also to
deliver recommendations for an efficient management of the current and
futuregasification unit.
Key words:Gasification, engine, rural electrification, raw
material, cost of electricity.
LISTE DES ABBREVIATIONS
2iE : Institut International
d'ingénierie de l'Eau et de l'Environnement
ADEME: Agence De l'Environnement et de la
Maitrise de l'Energie de France
CIRAD : Centre de coopération
International en Recherche Agronomique pour
Développement
BRF : Bois Raméal
Fragmenté
CCREHD : Centre Commun de Recherche
Energie et Habitat Durable
EPI : Equipement de protection
Individuel
EDF R&D : Electricité De
FranceRecherche & Développement
ESF : Electricien Sans Frontière
(ONG)
LBEB : Laboratoire Biomasse Energie et
Biocarburant
LEC : Levelized Electricity Cost
ONG : Organisation non
gouvernementale
PCI : Pouvoir Calorifique
Inférieur
SYNGAS : Synthetic Gaz
Table des matières
Dédicace
ii
REMERCIEMENTS
iii
RESUME
iv
ABSTRACT
iv
LISTE DES ABBREVIATIONS
v
LISTES DES TABLEAUX
viii
LISTES DES FIGURES
ix
I. INTRODUCTION
1
1. Contexte et problématique
1
2. Objectifs et méthodologie
2
II. ETUDE BIBLIOGRAPHIQUE
3
1. La gazéification : Etat de
l'art
3
1.1. Principe de la gazéification
3
1.2. Les réactions chimiques de la
gazéification
3
1.3. Nature des gaz produits
5
1.4. Les différents
procédés de gazéification
6
1.4.1. Le procédé à lit
fixe
6
1.4.2. Les procédés à
lits étagés
7
1.4.3. Comparatif des différents
procédés
7
1.5. Applications de la
gazéification
8
1.5.1. La production directe de la
chaleur
8
1.5.2. La production
d'électricité
9
2. Application de la
gazéification : production d'électricité dans les
pays en développement
10
2.1. Introduction
10
2.2. La ressource
11
2.3. Filtration
13
2.3.1. La séparation des particules
ou poussières
14
2.3.2. Elimination des goudrons
15
2.3.3. L'élimination des alcalins
15
2.4. Moteur
16
3. Retour globale d'expérience
villageoise en Afrique et en Asie
17
3.1. Projet 1 : Production
d'électricité dans le village MELANI, province Cape Est en
Afrique du Sud
17
3.2. Projet de gazéification de
l'exploitation agricole de thé au Muzizi en Uganda
18
3.3. Projets d'électrification dans
la province de Battambang au Cambodge
20
3.4. Projet d'électrification rurale
village d'hosahalli et Hanumanthanagara, Inde
21
III. MATERIEL ET METHODES
23
1. Description de la plateforme de
gazéification
23
2. Protocoles expérimentaux
25
2.1. La ressource en biomasse
25
2.1.2. Détermination du PCI du
bois
26
2.2. Test de performance du
gazéifieur
26
2.2.1. Préparation du
Matériel
27
2.2.2. Tests de performance
28
2.2.4. Recommandations
30
IV. RESULTATS ET DISCUSSION
30
1. Présentation des tests
réalisés
30
2. Analyses et interprétations
33
3. Perspectives d'amélioration des
tests
34
V. ANALYSE TECHNICO-ECONOMIQUE DE LA
PLATEFORME GAZEIFIEUR
35
1.1. Etude de la ressource disponible
35
1.1.1. Ressources bois : Acacia
auriculiformis et d'Eucalyptus senegalensis
35
1.1.2. Ressources : coques de noix de
coco et noix de palmes
38
1.2. Comparaison de la ressource pour
BRF et le gazéifieur
40
1.2.1. Méthodologie d'application des
BRF
40
1.2.2. Matières premières du
BRF à Songhaï
41
2. Analyse technico-économique
41
2.1. Analyse technico-économique de
la plateforme gazeifieur
41
2.1.1. Etat de la plateforme gazeifieur
41
2.1.2. Scénarios
technico-économiques
42
2.2. Analyses et recommandations
44
VI. CONCLUSION ET PERSPECTIVES
48
VII. BIBLIOGRAPHIE
49
ANNEXES
51
LISTES DES TABLEAUX
Tableau 1 : Composition moyenne du gaz en
fonction du type de procédé [2]
3
Tableau 2 : Comparatif des différents
procédés de gazéification, (source Rapport ADEME/Cirad
forêt)
7
Tableau
3 : Puissance escomptable, ADEME 2001
8
Tableau 4 : Comparatif des
procédés de gazéification (ADEME,2001)
8
Tableau 5 : Propriété de
biomasse et procédé de gazéification adapté
12
Tableau 6 : Diffèrent type de biomasse
et leur application électrique par gazéification
13
Tableau 7 : Qualité des gaz
nécessaire pour la production d'électricité et la
synthèse d'éthanol (n.l. : non limité) ,source
Observer
14
Tableau 8 : Taux de réduction des
différents systèmes d'épuration (ADEME)
16
Tableau 9 : Conditions de fonctionnement du
gazéïfieur du village de Melani
18
Tableau 10 : Caractéristiques du projet
de gazéification
20
Tableau 11 : Caractéristiques des
plateformes d'Hosahalli et Hanumanthanagara
22
Tableau 12 : Problèmes
rencontrés dans les opérations de fonctionnement et de
maintenance du gazeifieur d'Hosahalli
22
Tableau 13 : Spécifications des
équipements de la plateforme
25
Tableau 14 : Humidité moyen du bois
d'acacia auriculiformis du Centre Songhaï
26
Tableau 15 : Résultats d'analyse des
taux d'humidité et PCI de 2 échantillons d'Acacia auriculiformis
dans un lot préparé pour alimenter le gazéifieur (en mai
2013)
26
Tableau 16 : Equipements pour
expérimentation
27
Tableau 17 : Bilan avec le bois
31
Tableau 18 : Bilan avec les coques de noix de
coco
32
Tableau 19 : Scénarii pour l'estimation
de la ressource, source T. Buchholz
37
Tableau 20 : Estimation de la surface à
cultivée en fonction de la charge
37
Tableau 21 : Cout à l'hectare d'acacia
auriculiformis
37
Tableau 22 : Cout de la matière/tonnes
à 31% et 75 % de charge
38
Tableau 23 : Estimation de la consommation des
coques de noix de coco
39
Tableau 24 : Tableau représentant les
jours de non-fonctionnement et leurs causes
42
Tableau 25 : Etudes
technico-économiques de la plateforme
44
LISTES DES FIGURES
Figure 1 : Processus de gazéification
,[1]
3
Figure 2: Gazogène à contre-courant
(a gauche) et a co-courant (à droite)
6
Figure 3 : Equipements du gazogène
23
Figure 4 Bois d'acacia auriculiformis
découpé et séché
25
Figure 5 : Consommation spécifique avec
du bois suivant les charges simuler de 31% et 75%
33
Figure 6 : Consommation spécifique avec
des coques de noix de coco sur 75% de charge
33
Figure 7 : Bois d'acacia auriculiformis
récupéré pour application agricole : tuteurage
(à gauche), séché pour le gazeifieur (à droite) sur
Songhaï site Porto-Novo
36
Figure 8 : Cycle de la ressource bois
36
Figure 9 : Coques de noix de coco (à
gauche) et coque de noix palmiste (à droite) en séchage
naturel
38
Figure 10 : Estimation de la quantité
de coque en fonction de la quantité de noix de coco
38
Figure
11 : Plateforme BRF (à gauche), parcelle recouverte de BRF
(à droite)
40
Figure 12 : Plage de couverture sur les mois
de Mars à Aout 2013
41
Figure 13 : Coût comparé de
l'électricité du réseau et du gazeifieur
45
Figure 14 : Variation du LEC Gazeifieur en
fonction du Taux de couverture journalière
46
INTRODUCTION
Les limites de la technologie se font clairement ressentir
quand tous les contours ne sont pas bien étudiés. Il faudrait
avant toute installation faire alors une étude de faisabilité qui
montre l'intérêt d'installer cette forme d'énergie
renouvelable qu'une autre afin que cela ait un réel impact social et
économique. L'étude ci-après s'inscrit dans ce cadre.
1. Contexte et problématique
Le Centre Songhaï est une Organisation Non
Gouvernementale (ONG) créée en 1985 qui prône le
développement de l'Afrique sur la base de la promotionde
l'agriculture,l'élevage et la pisciculture à travers un
modèle de développementdécentralisé Il y a 4
centres au Bénin et 5 au Nigéria et le PNUD veut que Songhaï
développe leur centre dans 13 autres pays en Afrique. Songhaï est
devenu un centre d'excellence pour son système intégré
depuis 2008 (production agricole - transformation et commercialisation
associé à la formation et à la recherche
appliquée). Songhaï développe une gamme
d'activitésassez diversifiées qui touchent principalement trois
secteurs de développement àsavoir les secteurs primaires
(production végétale, production animale et
pisciculture),secondaires (agro-industrie,mécanique-fabrication) et
tertiaires (commercialisation,marketing). Basé sur le principe de
synergie, (interaction entre trois pôles :
agriculture-élevage-pisciculture), le système
intégré de production de ce centrerecycle et valorise tous
lessous-produits et déchets biologiques générés par
ses diverses activités.
Depuis 2008, une coopération technique est
engagée entre EDF R&D, ESF (Electricien Sans Frontières) et
le Centre Songhaï de Porto Novo pour la mise en place d'un Parc
Technologique Energies Renouvelables Décentralisées.
Ce parc technologique a pour objectif de promouvoir la
production d'énergie renouvelable à partir de biomasse pour
l'alimentation en électricité des centres Songhaï, des
agriculteurs et des villages sous le concept de « ville rurale
verte » qui est défini comme un système ou les villes
arriveraient à s'auto-suffire et implanter les infrastructures pour leur
développement et enfin de dégager des biens et services qui
doperaient leur économie en se basant sur l'agriculture.
Pour cela une plate-forme d'expérimentation est mise en
place avec le soutien d'EDF R&D ,d'ESF et avec l'appui financier de l'ONUDI
pour la partie gazéification de la biomasse.La plateforme va permettre
de maîtriser les moyens de production d'énergie biomasse,
d'optimiser leur fonctionnement pour une rentabilité et de
définir les formations pour l'exploitation et la maintenance de ces
installations.
Après avoir démarré par le biogaz,
présent à Songhaï depuis 1991, la plate-forme s'est
élargie en 2011 par la production d'électricité à
partir de biocarburant de jatropha et en 2012 par la gazéification de
biomasse solide. La plateforme expérimentale Energies Renouvelables
Décentralisées su Centre de Porto Novo comporte à ce
jour :
§ Une section dédiée à la bio
digestion comportant huit (8) digesteurs de 20m3 et un
générateur à biogaz de 22 kVA injecté au
réseau ;
§ Une section biocarburant disposant de deux groupes
adaptés de kit de bicarburation (huile de Jatropha/Diesel),
§ Une Centrale de production d'électricité
par gazéification de biomasse solide d'une capacité de production
électrique de 40 kVA dont les équipements seront décrit
dans le corps de ce rapport
L'étude ci-après proposedoit contribuer à
la réalisation d'études technico-économiques sur la
production d'électricité à partir d'un gazéifieur
indien. Les travaux ont été réalisés dans le
cadre d'une collaboration du Centre Songhaï, EDF R&D et le
Laboratoire Biomasse Energie et Biocarburant (LBEB) du 2iE de Ouagadougou.
2. Objectifs et méthodologie
L'objectif final de l'étude est d'établir un
bilan technico-économique de l'utilisation des déchets solides /
bois fragmenté et sous-produits agricoles dans un gazéifieur qui
fonctionnerait dans les conditions de production d'électricité
pour un village.
L'étude s'est déroulée selon les
étapes suivantes :
Ø Etude bibliographique sur la production
d'électricité à partir de gazéifieur dans les pays
en développement avec une synthèse par domaine : ressource
en biomasse, procédés de gazéification, filtration du
syngaz, type de moteur et retour d'expérience globale villageoise en
Asie et Afrique.
Ø Etude de la ressource disponible entre une
utilisation BRF (paillage des sols) et une utilisation pour la
gazéification : classification de la ressource par usage : cas
d'application sur Songhaï.
Ø Instrumentation d'un gazéifieur indien +
moteur syngaz de 40 kVA et réalisation de tests de performance et
d'endurance pour différents types de ressources biomasse disponible sur
le centre : rédaction de programme d'essai détaillé
sur différents points de fonctionnement et différents types de
déchets.
Ø Réalisation d'un bilan
technico-économique de la production d'électricité
à partir de gazéifieur au niveau du centre Songhaï de Porto
Novo et guide des points de suivi pour l'exploitation de ce typed'unité
de production d'électricité par gazéification.
II. ETUDE
BIBLIOGRAPHIQUE
1.
La gazéification : Etat de l'art
1.1. Principe de la gazéification
La « gazéification » désigne une
transformation thermochimique consistant à décomposer par la
chaleur un solide combustible carboné (charbon, biomasse)
hétérogène en présence d'un réactif gazeux
(gaz carbonique, vapeur d'eau puis oxygène/air) dans le but d'obtenir un
mélange gazeux combustible. La réaction de gazéification
se passe dans des conditions de température très
élevées (plus de 1000°C). Le gaz de synthèse obtenu,
appelé « le syngas » (pour « synthetic gas »).
Ce syngas peut être potentiellement
utilisé :
· comme source de production de chaleur ;
· comme source de production d'électricité;
· comme source de production d'hydrogène, de
méthanol et de méthane par traitement chimique ;
· comme source de production de carburant de synthèse
par le procédé Fischer-Tropsch
1.2. Les réactions chimiques de la
gazéification
La gazéification consiste en une transformation
thermique d'un solide combustible (charbon, bois etc..) en présence
d'un composé gazeux appelé agents gazéifiant
(O2,air,CO2, vapeur d'eau) .Il est possible aussi
d'utiliser un mélange de plusieurs agents gazéifiant afin
d'obtenir du gaz avec des propriétés particulières. Par
exemple, la gazéification à l'oxygène produit un gaz dont
le pouvoir calorifique est nettement supérieur à celui d'un gaz
où l'agent gazéifiant est l'air. Le but de cette transformation
est généralement de convertir le solide en un mélange
gazeux combustible.
Pour parvenir à la production du syngas, plusieurs
réactions préalables sont nécessaires. L'ensemble de ce
processus est appelé gazéification. Il nécessite, à
partir d'une matière organique, d'obtenir au préalable dans le
réacteur de la vapeur d'eau (H2O), du carbone (C) et de
produire une chaleur suffisante pour la réaction finale de
gazéification. Quatre étapes successives, fortement
couplées, sont nécessaires, la troisième produisant la
chaleur requise par les trois autres. Les étapes sont décrites
brièvement ci-après :
Ø 1ère étape :
séchage de la matière pour produire de la vapeur
d'eau
Cette étape se déroule à des
températures comprises entre 100°C et 160°C. Sous l'effet de
la chaleur, l'eau contenue dans la matière organique s'évapore.
Le combustible carboné résultant est sec et de différentes
natures (charbon, biomasse, etc.). Dans le cas de produits non
homogènes, une phase préalable (tri, broyage) est
nécessaire avant d'introduire cet intrant dans le gazéifieur.
Ø 2e étape : pyrolyse de la
biomasse pour obtenir du coke (résidus de carbone) et des gaz de
pyrolyse
Cette étape sans oxygène (anaérobie) se
déroule à des températures situées entre 120°C
et 600°C. Elle est dite « auto thermique »
car elle ne produit ni ne consomme d'énergie. En augmentant
progressivement la température en l'absence d'oxygène, la
matière séchée se décompose et les atomes de
carbone s'associent entre eux. Il se forme alors :
· du carbone réducteur presque pur (coke ou
résidus de carbone) ;
· un mélange de gaz oxydants condensables et
non-condensables composés majoritairement de monoxyde de carbone (CO) et
d'hydrocarbures (CH4) ;
· des goudrons et des matières volatiles condensables
issues de vapeurs de composés organiques (acides acétiques,
aldéhydes).
Autrement dit les principes de la pyrolyse à savoir la
cinétique de pyrolyse, la répartition gaz/solide formée
ainsi que les composantes chimiques des produits résultant
dépendent fortement de nombreux paramètres ou la
température, la vitesse de montée en température, la
granulométrie et la nature du combustible sont les grandeurs les plus
influentes.
Ø 3e étape : oxydation des
gaz de pyrolyse pour générer une chaleur suffisante à la
gazéification
Cette étape se déroule en présence
d'oxygène à des températures comprises entre 1200°C
et 1500°C. Les matières volatiles issues de la pyrolyse s'oxydent.
Cette combustion dégage la chaleur nécessaire aux deux
étapes précédentes et à l'étape suivante de
la gazéification. Elle nécessite un fort apport en
oxygène.
Ø 4e étape : la
réduction ou « gazéification » du
carbone pour produire le syngas
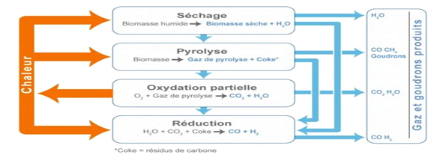
Cette étape se déroule à des
températures comprises entre 800 °C et 1200°C.Enl'absence
d'oxygène, le coke obtenu lors de la phase de pyrolyse réduit la
vapeur d'eau et le gaz carbonique obtenus dans l'étape
précédente respectivement en hydrogène et en oxyde de
carbone pour former du syngas, combustible composé en proportions
variables du Monoxyde de carbone (CO) et du Dihydrogène (H2)
, du Méthane (CH4).
Figure 1 : Processus de
gazéification,[1]
Les mécanismes de la gazéification
définies ci-dessus couplés aux phénomènes de
transferts thermiques et massiques mis en jeux sans oublier les
propriétés du combustible(granulométrie, densité,
porosité etc..) sont des facteurs qui vont conditionner la technologie
des réacteurs adaptés à chaque procédé de
gazéification de la biomasse.
1.3. Nature des gaz produits
Lors de la gazéification la partie organique du
combustible est transformée principalement en monoxyde de carbone (CO)
et en dihydrogène (H2) et dans des proportions plus faibles
en méthane CH4.Selon le type de réacteur mais surtout
de d'agent gazéifiant la somme H2 +CO varie dans de fortes
proportions et peut représenter par exemple jusqu'à 80% dans le
gaz de synthèse obtenus par gazéification à
l'oxygène.
Ces gaz contiennent aussi divers gaz inertes : vapeur d'eau
(H2O) , azote (N2) et dioxyde de carbone
(CO2), en proportion variable en fonction des procédés
et de la matière première ; ainsi de divers composés
à l'état de traces, dont les proportions sont directement
liées à la nature du combustible tels que le Chlorure
d'hydrogène (HCl) ,Fluorure d'hydrogène (HF), Ammoniac
(NH3), Cyanure d'hydrogène (HCN), les métaux lourds
volatils à basses températures, etc...(Cirad
forêt,2001)[ 2 ]
Enfin une part plus ou moins importante de composés
hydrocarbonés, les goudrons résultant de la pyrolyse, peuvent
être présents dans le gaz ceci en fonction du type de
réacteurs utilisés et primordialement de la nature de la
matière première.
Le pouvoir calorifique inférieur (PCI) du gaz et sa
composition est fonction de :
v la nature du combustible,
v la nature et la proportion de l'agent gazéifiant
L'utilisation de l'air comme agent gazéifiant tend
à faire baisser le PCI du gaz, du fait de la forte proportion d'azote
dans le gaz. Le PCI du gaz obtenue varie de 3 à 6 MJ/Nm3.
Dans le cas où l'agent gazéifiant est de la
vapeur d'eau, on peut obtenir un gaz à forte teneur en hydrogène.
Le PCI d'un tel gaz peut varier de 10 à 15
MJ/Nm3.(Gai et Al,2012)[ 3 ]
v et évidemment du type de réacteur.
Ce PCI peut être exprimé grâce à la
formule suivante :
PCI (MJ/m3) = 0,126 * CO (%) + 0,108*
H2 (%) + 0,358* CH4 (%)
Le tableau ci-dessous illustre la nature du PCI
dépendamment des facteurs précités :
Gazéification à l'air
|
Lit Fixe co-courant
|
Lit fixe contre-courant
|
Lit fluidisé circulant
|
Humidité biomasse
|
% mh1
|
6-20
|
n.d
|
13-20
|
Particules
|
mg/Nm3
|
100 - 8 000
|
100 - 3 000
|
8 000 - 100 000
|
Goudrons
|
mg/Nm3
|
10 - 6 000
|
10000 - 150000
|
2 000 - 30 000
|
PCI du gaz
|
MJ/Nm3
|
4,0 - 5,6
|
3,7 - 5,1
|
3,6 - 5,9
|
H2
|
% vol
|
15 - 21
|
10 - 14
|
15 - 22
|
CO
|
% vol
|
10 - 22
|
15 - 20
|
13 - 15
|
CO2
|
% vol
|
11 - 13
|
8 - 10
|
13 - 15
|
CH4
|
% vol
|
1 - 5
|
2 - 3
|
2 - 4
|
Cn Hm
|
% vol
|
0,5 - 2
|
n.d
|
0,1 - 1,2
|
N2
|
% vol
|
différence
|
différence
|
différence
|
Tableau 1 : Composition moyenne du gaz en
fonction du type de procédé [2]
1.4. Les différents procédés de
gazéification
Le choix d'un type de procédé est guidé par
la taille de l'installation, le solide combustible carboné
utilisé, l'usage du gaz produit et la maturité des technologies.
Il existe plusieurs procédés de gazéification
(Procédis, 2004[4]).
1.4.1. Le procédé à
lit fixe
Il peut être soit à co-courant soit à
contre-courant 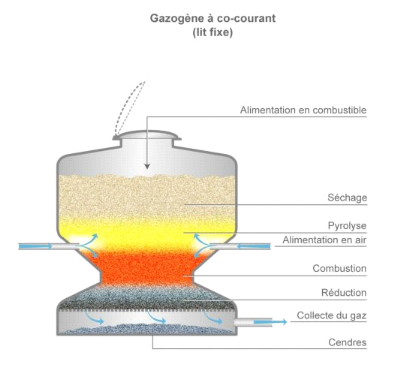
Figure 2: Gazogène à contre-courant (a
gauche) et a co-courant (à droite)
§ À co-courant (downdraft)
Les différentes étapes de la réaction de
gazéification sont successivement réalisées de haut en bas
dans le réacteur. La matière organique est d'abord introduite
à son sommet. De l'air est injecté à mi-hauteur pour
amorcer la combustion et fournir de la chaleur à l'ensemble du
réacteur. L'augmentation progressive de la température permet
d'obtenir les différentes réactions entrainant les gaz produits
vers la zone la plus chaude du réacteur. Le syngas est
récupéré au niveau du socle du réacteur du
gazogène. Il en résulte alors une faible concentration en
goudrons beaucoup plus faible que pour les procédés a
contre-courant.la conversion thermo chimique est alors plus aboutit. Ce type de
gazeifieur est utilisés exclusivement pour de la biomasse relativement
sec (15% d'humidité),ce qui est notre cas au niveau du Centre
Songhaï.
§ À contre-courant (Updraft)
L'air est injecté à la base du réacteur
et le syngas est récupéré sous son sommet, au-dessus de la
zone de pyrolyse et présente de ce fait une teneur en goudron importante
mais est faiblement chargé en particules. Le combustible solide est
quant à lui complètement converti en gaz et en goudron. Les
procédés à contre-courant peuvent être
utilisés pour des combustibles solides très humides (% H 60%)
et sont relativement peu sensibles à la taille de la matière
première. Ce type de gazeifieur rencontre des difficultés pour le
traitement des goudrons des gaz produits d'où l'intérêt de
ne pas l'utiliser pour la production d'électricité
(encrassement et corrosion des installations) mais plutôt
privilégier une valorisation thermique. Ce procédé doit
assurer une dégradation complète des goudrons.
1.4.2. Les procédés à
lits étagés
Le principe des gazéifieurs étagés est
assez proche du celui des gazéifieurs à co-courant, mais
contrairement à ce dernier, les deux étapes de pyrolyse et de
gazéification sont réalisés dans des réacteurs
différents. Le premier réacteur est destiné à la
pyrolyse de la biomasse fraichement introduite. Le combustible y est
séché puis pyrolysé à température
contrôlée. Le charbon et les gaz de pyrolyse alimentent un second
réacteur. Dans ce second réacteur, les gaz de pyrolyse subissent
une oxydation où un apport en oxygène permet leur combustion. Les
gaz chauds obtenus réagissent avec le lit de charbon pour produire les
gaz combustibles. Ce type de réacteur a l'avantage de permettre une
conduite indépendante des phases de pyrolyse et de gazéification.
Ce procédé permet de réduire considérablement le
taux de goudrons dans le gaz produit à la fin du procédé.
En effet, les gaz issus de la pyrolyse dans le premier étage sont
thermiquement craqués et oxydés dans le second
étage.(Floriane Mermoud, 2006) [5]
1.4.3. Comparatif des différents
procédés
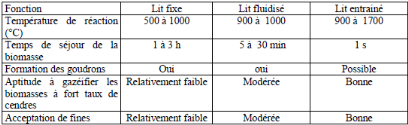
Tableau 2 : Comparatif des différents
procédés de gazéification, (source Rapport ADEME/Cirad
forêt)
Tableau 3 : Puissance
escomptable, ADEME 2001
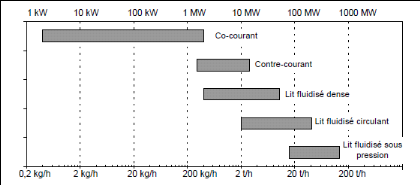
Le
tableau 2 compare les éléments caractéristiques de la
réaction de gazéification des différents
procédés. Cela met en évidence que la différence la
plus significative concerne le temps de séjour du solide dans le
réacteur avec ses conséquences sur la flexibilité du
procédé vis-à-vis de la nature de la biomasse. Le temps de
séjour de la phase gazeuse est toujours faible, entre un (1) et quelques
secondes pour l'ensemble des procédés(Cirad
forêt,2001)[2].La figure 3 ci-dessous représente
les différentes puissances escomptables en fonctions des
procédés.
Le tableau 4 ci-dessous nous donne les avantages et
inconvénients inhérents à chaque procédé.
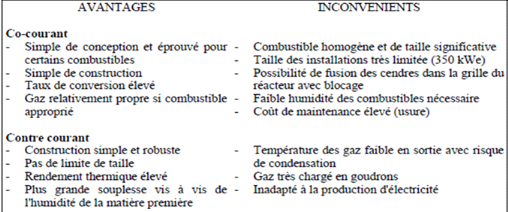
Tableau 4 : Comparatif des procédés
de gazéification (ADEME,2001)
1.5. Applications de la
gazéification
Le gaz de synthèse issu de la gazéification
peut être valorisé de manière différente.
Nous avons principalement :
1.5.1. La production directe de la
chaleur
La gazéification peut être le plus souvent
utilisée pour la production de chaleur grâce à la
combustion directe du gaz produit dans un foyer ou une chaudière. La
chaleur produite par le gazéifieur sert pour les chauffages domestiques
ou collectifs, la transformation agroalimentaire (séchage, cuisson), les
transformations industrielles qui requièrent la chaleur.
Les rendements obtenus par la production directe de chaleur
varient souvent entre 70% et 95%. Cela peut s'expliquer par le fait qu'il n'est
pas nécessaire de refroidir le gaz ou de condenser les goudrons avant
utilisation. Les technologies dans le domaine de la production de chaleur sont
conceptuellement simples, facile à optimiser, conviennent à la
plupart des biomasses et sont parfaitement maitrisées. En plus,
l'investissement pour la réalisation de gazéifieurs à
production directe de chaleur est relativement abordable. On trouve
également ces gazéifieurs à différents
échelles selon les besoins de l'application. La puissance thermique de
ces gazéifieurs varie souvent entre quelques kilowatts à
plusieurs mégawatts. (Kabore D., 2012)[6]
1.5.2. La production
d'électricité
L'utilisation de la gazéification dans la production
d'électricité, ce qui est notre cas ici, est plus récente
que la production directe de chaleur. Cette technologie est toujours en pleine
évolution, même si elle est assez bien maitrisée.
Le principe de la production d'électricité
consiste à convertir ce gaz dans un moteur à combustion interne
ou une turbine à gaz, couplé à un alternateur. Ce dernier
composant se charge de convertir l'énergie contenue dans le gaz en
électricité.
Une pile à combustible haute température (de
type SOFC ou MCFC par exemple) peut également être utilisée
à la place d'un moteur à combustion interne, mais cette option
technologique est encore au stade de recherche/développement.
L'utilisation du gaz de synthèse pour la production
d'électricité présente une contrainte majeure étant
la cause de beaucoup d'échec. Il s'agit de l'épuration du gaz
produit par la gazéification avant son utilisation sur les machines
produisant l'électricité.
L'objectif de l'épuration du gaz est de réduire
la teneur en goudrons et en poussières pour atteindre un teneur de moins
de 10 mg/Nm3 de gaz pour l'utilisation dans un moteur à
combustion interne.
Pour atteindre cet objectif, les moyens suivants peuvent
être employés:
§ L'utilisation d'un séparateur de particules ou
cyclone pour l'élimination des poussières dans le gaz juste
à la sortie du réacteur.
§ Le refroidissement du gaz se fait
généralement à l'intérieur d'échangeurs de
chaleur utilisant l'eau comme liquide de refroidissement. Le refroidissement du
gaz entraine la condensation d'une part importante des goudrons et de la vapeur
d'eau.
§ L'élimination catalytique à haute
température des goudrons dans un réacteur secondaire placé
en aval du gazéifieur.
Le concept de cogénération permet
d'améliorer, le rendement énergétique global des
installations de gazéification a été
amélioré. La chaleur est récupérée durant
les opérations de traitement de gaz et au niveau des moteurs thermiques
grâce à des échangeurs de chaleur. Cette chaleur est
généralement utilisée pour le chauffage ou le
séchage.[6]
Conformément à notre sujet d'étude nos
travaux portent sur la production d'électricité dans les pays en
développement en Afrique et en Asie avec un focus sur la ressource, les
moyens de filtration du gaz et un retour d'expérience villageoise.
2.
Application de la gazéification : production
d'électricité dans les pays en développement
Introduction
Le manque de source énergétique et l'absence
d'électrification surtout dans le secteur énergétique
aggravent la pauvreté des pays en développement. Les technologies
de développement durable et renouvelable peuvent être
considérées comme des outils efficaces pour pallier à ce
manque. Plus de 80% des personnes qui n'ont pas accès à
l'électricité sont localisées en Asie du sud et en Afrique
sub-saharienne (World Energy Outlook,2004)
L'électrification peut augmenter de façon significative
le niveau de vie de l'homme en améliorant l'accès à la
santé, à l'éducation, le bien-être et le
développement technologique et de facto contribuer au dynamisme
économique. Les études notamment ceux de F.s Jvadi et
Al.,2012[7]ont montrer que les énergies renouvelables sont le
meilleur choix particulièrement dans les sites isolés mais cela
nécessiterais qu'on étudie tous les aspects techniques et
économiques relatif à l'environnement comme l'on souligner
Matthew Owen et Al,2012[8],et Ralph E. H. Sims,2003 et
Al[9].
La gazéification, outil des énergies
renouvelables, dans les pays en développement est en train de connaitre
une forte vulgarisation qui est suscité par l'intérêt de
plus en plus prononcé pour les énergies alternatives,
principalement la biomasse énergie.
En Afrique, la plupart des gazéifieurs sont
situés en Afrique du Sud, pionnière dans la technologie
(Classement SFA pacific[2]), où les carburants
synthétiques et les produits chimiques sont produis à partir du
charbon depuis 1955. Mais d'autres pays africain comme l'Uganda, le Ghana ont
déjà amorcé les possibilités d'utilisé ces
unités de gazéification principalement pour la production
d'électricité en site isolé.
En Asie, les installations de gazéification se situent
principalement en Inde, en Chine, au Japon ,au Cambodge, ou en Malaisie. Les
pays d'Asie comme la Chine constituent le marché le plus important en
termes de capacité installée et de marché potentiel.
L'ensemble des pays tropicaux en somme représentent une zone de
développement importante qui devrait émerger très
rapidement dans les années à venir dans ce procédé.
Les études menées par Roland
Siemeons,2000[10],ou par Anil K. Rajvanshi,1986[11]
ou encore de Dasappa,2011[12] sur le potentiel et la
faisabilité des projets de gazeïfication dépendamment de la
ressource et de l'environnement local ;comme le précise
Buchholz et Da silva,2010[13]ou Y.S. Mohammedet
Al,2012[14]dans leurs expérimentations.
Nous allons nous pencher donc dans ce document sur les
applications électriques en faisant un résumé sur les
projets de gazéification en procédant à une
synthèse par domaine : la ressource, la pyrolyse, la filtration, le
moteur et un retour d'expérience globale villageoise en Asie et
Afrique.
2.1. La ressource
Les projets de gazéification pour qu'ils soient
économiquement viable en Afrique ou en Asie ont fait ressortir comme
par ailleurs la nécessité de se pencher sur la matière
première du procédé afin de produire un gaz de
synthèse à haut rendement. Selon
Dasappa,2011[12]le potentiel estimé de puissance pour
la gazéification en Afrique sub-saharienne, en utilisant 30% de
résidus agro-industriel de et 10% de résidus bois de
l'agroforesterie s'élève respectivement à 5000 MW et
10000 MW.
Les principales ressources envisagées proviennent donc
des produits ou sous-produits de l'agroforesterie ou des résidus
agricoles ou des process de transformation.
La biomasse pouvant entrer dans le processus de
gazéification doit respecter les conditions physiques comme la
granulométrie, la masse volumique ; l'humidité (% H 15% sur
brute) ,un bon PCI, et de bonnes propriétés thermiques.
Les projets comme par exemple celui du village Melani en
Afrique du Sud[15] étudié par
Ntshengedzeni S. Mamphweli et Edson L. Meyer en 2009 ont
définis que la plupart des bois énergie sec tel que les essences
Acacia auriculiformis, Eucalyptus, Pinus
patula,Pinusellioti ,Pinus canariensis ou le bois de
cyprès en morceau bien découpé, en copeaux ou les
sciures avec une densité (au-delà de 200 kg/m3) sont
adaptés comme combustible. Les coques de noix de coco
mélangées avec des coques noix de palmes ont
montré aussi leur grande potentialité dans ce genre
d'installation tant qu'ils sont découpés à la taille
adéquate et mélangés dans de bonne proportion pour avoir
la densité adéquate pour limiter la production de goudrons et de
particules. Par contre en Uganda les ressources utilisées
étudié par Wilson B. Musinguzi et
Al.,2012[16]sont l'Eucalyptus grandis
en particulier et au Vanuatu selon Barry
Fischer et Attilio Pigneri,2010[17]c'est le Leucaena
Leucocephala.
La différence entre les essences montre que la
ressource dépend fortement de l'environnement et de
l'intérêt économique de la biomasse.
Ainsi au Cambodge qui est un grand producteur de riz par
exemple (7 Millions de tonnes en 2009, selon UNIDO), ils ont vulgarisé
la gazéification à base de résidus rizicoles comme la
balle de riz qui a un grand potentiel
énergétique et dispose d'autres biomasses comme le
bois, les coques de noix de palme, les rafles de maïs, la bagasse, les
coques d'anacarde selon les études de Rogier van
Mansvelt,2011[18],et Orkide Akgün et Jyrki
Luukkanen,2011 [19].
Le tableau 3 ci-dessous récence les
propriétés de quelques type de biomasse et les traitements
opérés avant gazéification(Anil K.
Rajvanshi,1986)[11] et les observations faites à l'issu de la
conversion.
Fuel
|
Treatment, bulk density, moisture (m.c.)
|
Tar produced g/m3
|
Ash content %
|
Gasifier
|
Experience
|
Alfalfa straw
|
Cubed, 298 kg/m3
m.c. = 7.9%
|
2.33
|
6
|
downdraft
|
No slagging, some bridging
|
Bean straw
|
Cubed,
440 kg/m3 m.c. = 13%
|
1.97
|
10.2
|
downdraft
|
Severe slag formation
|
Barley straw (75% straw; 25% corn fodder and 6% orza binder
|
Cubed, 299 kg/m3
m.c. = 4%
|
0
|
10.3
|
downdraft
|
Slag formation
|
Coconut shell
|
Crushed(1-4 cm),435kg/m3
m.c. = 11.8%
|
3
|
0.8
|
downdraft
|
Excellent fuel. No slag formation
|
Coconut husks
|
Pieces 2-5 cm, 65kg/m3
|
Insignificant tar coconut
|
3.4
|
downdraft
|
Slag on grate but no operational problem
|
Corn cobs
|
304 kg/m,3m.c. = 11%
|
7.24
|
1.5
|
downdraft
|
Excellent fuel. No slagging
|
Corn fodder
|
Cubed, 390 kg/m3
m.c. = 11.9%
|
1.43
|
6.1
|
downdraft
|
Severe slagging and bridging
|
Cotton stalks
|
Cubed, 259 kg/m3
m.c. = 20.6%
|
5
|
17.2
|
downdraft
|
Severe slag formation
|
Peach pits
|
Sundried, 474 kg/m3
m.c. = 10.9%
|
1.1
|
0.9
|
downdraft
|
Excellent fuel. No slagging
|
Peat
|
Briquettes,555 kg/m3
m.c. = 13%
|
-
|
-
|
downdraft
|
Severe slagging
|
Prune pits
|
Air dried, 514 kg/m3
m.c. = 8.2%
|
0
|
0.5
|
downdraft
|
Excellent fuel
|
Rice hulls
|
Pelleted, 679 kg/m3
m.c. = 8.6%
|
4.32
|
14.9
|
downdraft
|
Severe slagging
|
Safflower
|
Cubed, 203 kg/m3
m.c. = 8.9%
|
0.88
|
6.0
|
downdraft
|
Minor slag formation
|
Sugarcane
|
Cut 2-5 cms, 52 kg/m3
|
Insignificant
|
1.6
|
downdraft
|
Slag on hearthring. Bridging
|
Walnut shell
|
Cracked, 337 kg/m3
m.c. = 8%
|
6.24
|
1.1
|
downdraft
|
Excellent fuel. No slagging
|
Walnut shell
|
Pelleted.
|
14.5
|
1.0
|
downdraft
|
Good fuel
|
Wheat straw
|
Cubed, 395 kg/m3
m.c. = 9.6%
|
-
|
9.3
|
downdraft
|
Severe,slagging bridging. Irregular gas production
|
Wheat straw and corn stalks
|
Cubed (50% mix),
199 kg/m3
m.c. = 15%
|
0
|
7.4
|
downdraft
|
Slagging
|
Wood blocks
|
5 cm cube, 256 kg/m3
m.c. = 5.4%
|
3.24
|
0.2
|
downdraft
|
Excellent fuel
|
Wood chips
|
166 kg/m3
m.c. = 10.8%
|
6.24
|
6.26
|
downdraft
|
Severe bridging and slagging.
|
Tableau 5 : Propriété de biomasse
et procédé de gazéification adapté
La figure 5 ci-dessous indique les potentiels de quelques
ressources de référence pour la production
d'électricité par gazéification exposé
parS.M. Shafie et al, 2012[20].
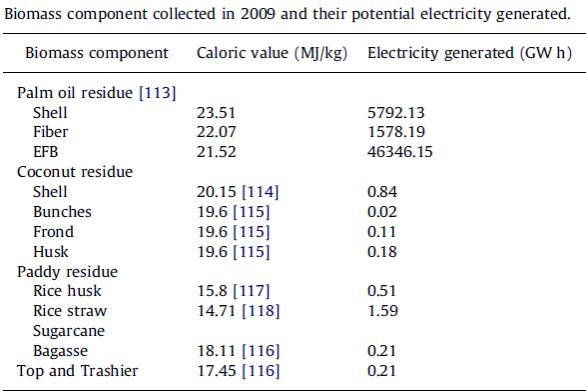
Tableau 6 : Diffèrent type de biomasse et
leur application électrique par gazéification
Ø Préparation de la ressource
La biomasse en entrée doit être sèche
(humidité inférieure à 20%) et calibrée (maximum 5
à 15 cm de côté selon la puissance de l'installation) pour
le bois par exemple. Pour un gazéïfieur fonctionnant au bois il
faut éviter d'incorporer trop d'écorce du bois, du sable ou tout
autre matériau contenant de la silice qui peuvent bloquer le
fonctionnement de l'installation.
La biomasse est calibrée à la bonne dimension
(presse ou broyeur selon le type d'installation), stockée et
séchée grâce à l'énergie thermique produite
par cogénération avant d'être introduite dans le
gazéifieur. Le séchage est ainsi accéléré
par rapport à un séchage à l'air libre: quelques jours
à une semaine peuvent suffire dépendamment du type de
biomasse.
Des études ont montré notamment au Cambodge
l'intérêt économique de ces ressources afin de remplacer
les combustibles conventionnels(Cirad forêt,2001)[2].
La ressource étant un grand point de notre travail, il va
y être étudié l'Acacia auriculiformis et les coques de noix
de coco et de noix de palme comme principales matières
premières.
2.2. Filtration
Le gaz chargé d'élément gênant
(poussière, goudrons, alcalins, cendres etc..), produit doit subir tout
un processus de filtration et d'épuration du gaz avant d'être
valoriser énergiquement.
Le tableau 5 ci-dessous donne les valeurs des teneurs admises par
diverses techniques de valorisation du gaz de gazéification par rapport
aux principaux polluants(Cirad forêt,2001) [2].
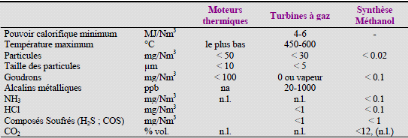
Tableau 7 : Qualité des gaz
nécessaire pour la production d'électricité et la
synthèse d'éthanol (n.l. : non limité) ,source
Observer
Dans la littérature et nous appuyant sur les documents
techniques de la plateforme gazéïfieur du centre songhaï de
Porto Novo nous pouvons définir les process d'épuration
suivants:
2.2.1. La séparation des particules
ou poussières
Les particules proviennent pour la grande majorité de fine
de charbon et pour une faible part des cendres. Leur concentration qui
s'exprime en mg/Nm3 dépend pour beaucoup de la nature de la
matière première et du procédé de
gazéification. La concentration est comprise entre 100
mg/Nm3et 100 g/Nm3.
Le dépoussiérage des gaz se fait de
différentes façons. Le plus simple consiste à utiliser des
dispositifs classiques (cyclone, filtres à marche, laveurs,..) en sortie
du réacteur afin de séparer la phase solide de la phase gazeuse.
Cette opération ne peut se faire qu'à des températures
relativement basses ce qui nécessite le refroidissement du gaz en amont
avec la problématique de la condensation des goudrons et la perte
d'énergie des gaz, notamment pour les applications en cycle
combiné.
D'autres techniques comme la filtration à chaud
viennent pallier à ce manquement mais cette technologie est toujours
à l'étape de recherche et développement. Cette technique
consiste à utiliser des filtres à chandelle conçu en
céramique réfractaire pouvant supporter des températures
élevée de l'ordre de 800 à 900°C.Le rendement de ces
filtres sont extrêmement élevé supérieur à
99%.Mais leur utilisation imposerait des coûts supplémentaires et
a ce stade s'ajoute le souci de fiabilité pour un fonctionnement de
longue durée.
Une autre option est d'utiliser les filtres métalliques
produits à partir de poudre d'acierinoxydablequi ont été
testés et ont montré de bonnes performances.
2.2.2. Elimination des goudrons
Les goudrons contenus dans les gaz de gazéification
sont encore très mal définis dans la littérature. La
concentration en goudron est fortement variable en fonction du
procédé retenu, de la matière première, de la
disposition des entrées de l'agent gazéifiant, des valeurs allant
de 10 mg/Nm3 à 150 mg/Nm3 sont
généralement admises.
Plusieurs méthodes d'épuration sont utilisés
ou en cours de développement basés sur les
procédés suivants :
Ø Le traitement thermique :
Décomposition des goudrons à haute température
(>1000°C) par simple craquage.
Ø Le traitement catalytique : La
décomposition des goudrons est réalisée par l'action
simultanée de la température (800 °C) et d'un catalyseur
solide. Les tests ont montrés des performances pouvant aller
jusqu'à 99%. Cette solution pose un problème de coût par
suite de désactivation assez rapide par encrassement et
contamination.
Ø Le lavage humide : De l'eau
pulvérisée est mise en contact avec le gaz et assure la
condensation des goudrons, c'est le cas de Songhaï. Les goudrons sont
récupérés dans de l'eau de lavage en sortie de la chambre
de lavage. Si ces derniers sont réputés éprouvés,
les problèmes rencontrés notamment sur les petites installations,
montrent que l'efficacité de cette solution n'est pas aussi
évidente et que de nombreux problèmes subsistent. Ils sont en
particulier dus à la présence d'aérosol dans les gaz.
Les filtres électrostatiques en serait un bonne alternative (test du
CIRAD sur les fumées de pyrolyse).Un système classique comprend
une étape de refroidissement du gaz suivie d'un pulvérisateur
haute performance qui favorise le contact entre particules et gouttelettes et
qui , en augmentant leur taille va favoriser leur récupération.
La dernière étape est constituée d'une tour qui permet de
réduire la vitesse des gaz et d'augmenter le temps de séjour des
gaz pour rééquilibrer le système. Un niveau
inférieur à 20 mg/Nm3 de goudrons et 10
mg/Nm3 de poussière est réalisable par ce type de
procédé. La production d'eau polluée peut être
importante et son traitement, obligatoire, occasionner un coût
prohibif.
Ø La condensation forcée : Le
gaz traverse un échangeur convectif assurant la condensation des
goudrons (sans contact direct) et la récupération
d'énergie thermique. Ce procédé est en cours de recherche
et développement au niveau du CIRAD.
2.2.3. L'élimination des
alcalins
Les métaux alcalins sont responsables de corrosion sur
les pales des turbines provoquant une altération du surfaçage. Il
est communément admis que leur élimination est obligatoire mais
pas dans le cas de Songhaï, même s'il n'y a cependant pas eu
d'essais sur des nouveaux alliages développés et utilisé
en surfaçage. La température maximum qui est admise pour la
condensation de ces produits est d'environ 600°C.Ils sont potentiellement
récupérables avec les particules sur les filtres hautes
température.
Le tableau 8 suivant rassemble les caractéristiques
d'utilisation des différents systèmes d'épuration ainsi
que le taux de réduction envisageable (Source HASLER).
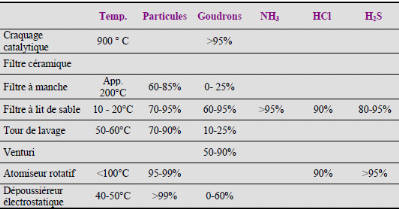
Tableau 8 : Taux de réduction des
différents systèmes d'épuration (ADEME)
2.3. Moteur
Selon F.Mermoud,2006[5]la principale application
de la gazéification concerne la cogénération
d'électricité et de chaleur grâce à un couplage avec
un moteur à gaz ou une turbine à gaz.
2.3.1. Moteur à gaz (MAG)
Il s'agit d'un moteur à allumage commandé
fonctionnant à l'origine avec de l'essence ou du gaz naturel. Il doit
donc être modifié pour pouvoir recevoir le gaz pauvre issu de la
gazéification, dont le pouvoir calorifique est dix fois plus faible que
celui de l'essence ou du gaz naturel. De plus, le gaz de synthèse est
très dilué et ne nécessite pas les mêmes rapports
stoechiométriques avec l'air.
Les rendements électriques rapportés sur
différentes installations de gazéification couplées
à un moteur à gaz sont compris entre 15 et 25% ;
à noter que le rendement de ce type de moteurs est de 30
à 40% avec du gaz naturel.
Les moteurs de type "dualfuel", qui
acceptent comme combustible un mélange de diesel et d'un autre
carburant, permettent également de valoriser le gaz de synthèse.
Cette alternative est intéressante car le diesel vient suppléer
aux éventuelles carences de qualité du gaz de synthèse.
Environ 80% de l'énergie qui serait consommée par un
diésel de même puissance est fournie par le gaz de
gazéification.
Les équipements de couplage au réseau sont
maintenant fournis en standard et peuvent être conteneurisés. Ils
comprennent, entre autres, un régulateur de tension, un contrôleur
de facteur de charge pour les générateurs synchrones (ADEME
2001).
2.3.2. Turbine à gaz (TAG)
Une turbine à gaz est constituée d'un
compresseur (pour amener l'air à haute pression), d'une chambre de
combustion à haute pression (dans laquelle la combustion du
mélange produit desfumées à haute température) et
enfin d'une turbine qui entraîne un générateur.
L'alimentation en combustible se fait sous pression (10-20bar) dans la chambre
de combustion.
Les TAG, qui fonctionnent habituellement au gaz naturel,
acceptent une grande variété de gaz combustible, dont le gaz de
synthèse. Le rendement électrique d'une TAG varie entre
25 et30% mais il chute rapidement hors des conditions de
fonctionnement optimales en termes de puissance et de qualité du gaz
combustible.
Le choix entre moteur à gaz et turbine à gaz
à la sortie d'une installation de gazéification
estessentiellement guidé par la taille (puissance installée) de
l'installation. La puissance des moteurs est très variable (de
100 kWe à quelques MWe) alors que les turbines ont en
général une puissance supérieure à 5 MWe, et
nécessitent un gaz combustible sous haute pression. Les moteurs sont en
règle générale moins exigeants que les turbines sur la
qualité du gaz (PCI supérieur à 4 MJ/Nm3).
La turbine à gaz peut être associée
à une turbine à vapeur dans un cycle combiné de type IGCC
("Integrated Gasification Combined Cycle"). Le gaz de synthèse
est d'abord brûlé dans la turbine à gaz. Les fumées
détendues sont ensuite conduites vers un échangeur qui permet de
produire de la vapeur pour alimenter la turbine à vapeur. Le surplus
d'électricité produit par la turbine à vapeur permet de
maximiser le rendement électrique. A notre connaissance aujourd'hui, la
seule installation de ce type à avoir accumulé plusieurs milliers
d'heures de fonctionnement est celle de Värnamo en Suède (avec un
rendement électrique de 35%).
3.
Retour globale d'expérience villageoise en Afrique et en Asie
Les expériences villageoises sont de plus en plus
vulgarisées pour l'électrification des milieux isolés qui
rentre dans la politique de dynamisme économique des pays en
développement.
Des études ont été suivies avec grand
intérêt en Asie et en Afrique ,nous citerons
quelques projets avec les principaux détails des procédés
utilisés.
3.1. Projet 1 :
Production d'électricité dans le village MELANI, province Cape
Est en Afrique du Sud
Ntshengedzeni S. Mamphweli et Edson L. Meyer en
2009[15]on reportéqueEskom et l'université de Fort Hare
ont piloté ce projet de gazéification de la biomasse en
utilisant le système SJBG ( System Johansson Biomass gasifier ).Le SJBG
a été installé dans le village de Melani situé dans
la province du Cap Est en Afrique du Sud, afin d'effectuer une étude
sur la viabilité et l'accessibilité de l'électrification
par la gazéification de la biomasse en Afrique du Sud. Une étude
des besoins du village composé de 2800 habitants, ont été
réalisées avant l'installation effective de la centrale.
L'étude fait ressortir le besoin de fournir une
électricité à bas prix à des commerces comprenant
des champs, des élevages de poulet de chair ; des industries de
fabrication de fenêtres et portes, les ateliers de couture, des
boulangeries etc...
Il a été relevé durant le fonctionnement
des soucis socio-environnementaux venant de la part de la population, sur la
technologie de gazéification de résidus de scierie comme moyens
de gestion durable des déchets. Le SJBG a été
utilisé pour valoriser l'excès de biomasse afin de fournir de
l'électricité à bas prix afin de dynamiser
l'économie de la communauté locale et les divers initiatives de
développement.
L'étude technico-économique a fait ressortir une
capacité de consommation de 300 Nm3/h de
biomasse à installer afin d'alimenter le village.
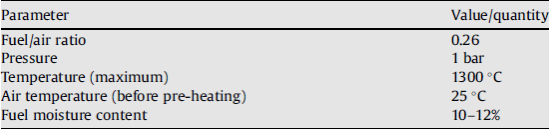
Le tableau ci-dessous représente les conditions de
fonctionnement du gazeifieur
Tableau 9 : Conditions de fonctionnement du
gazéïfieur du village de Melani
3.2. Projet de
gazéification de l'exploitation agricole de thé au Muzizi en
Uganda
[21]L'étude reportée par T.
Buchholz et T. Volk,2007 décrit l'exploitation agricole de Muzizi
isolée du réseau qui à des besoins d'énergie
électrique et thermique pour le séchage du thé à
une température de 80°C.Une étude de faisabilité de
l'ensemble du système de gazéification a été
réalisée en 2005 suivi d'une installation effective en mai 2006,
l'usine commençant sa production à partir d'Août 2006.
La ressource en combustible provient d'une plantation de 99
hectares d'Eucalyptus. Ce bois nécessitant un séchage externe
pendant 6 mois afin d'atteindre un taux d'humidité de 15%.
Le générateur du gazéïfieur fourni une
puissance de 200 kW net d'électricité. Le système
installé comprend :
o Un gazeifieur à co-courant de marque ANKUR, avec un
réacteur de 400 kWth avec un système automatisé
pour le chargement du bois, et de collecte des cendres et des charbons.
o Un cyclone séparant le gaz chaud et les cendres
o Une unité de refroidissement et de lavage à
l'eau
o Deux unités de filtres mis en parallèle pour des
soucis de maintenance
o Un souffleur pour assurer une bonne circulation du syngas
o Un moteur à gaz Cummins India de 250 kW couplé
à une génératrice Stanford
o Des systèmes de cogénération pour
récupérer la chaleur sur les points chauds du système
Ø Démarrage du
système :
Le démarrage se fait grâce à un groupe de
30 kW afin de fournir les éléments critiques du système
(pompes, souffleur, système d'alimentation de bois et les unités
de contrôle).Ce démarrage se fait en sept minutes quand le
système est froid mais peut durer moins si le système est chaud.
L'alimentation des charges est en triphasée.
Ø Consommation de la ressource
Le système consomme1,6 tonne de bois sec par
MWh produit. Le taux de conversion est de l'ordre de
15% en considérant une capacité
énergétique du bois à 5 Mwh/tonne
d'Eucalyptus. L'électricité annuelle produite
s'élève à 381 MWh/an.
Le gazéïfieur ne fonctionne pas pendant une (1)
journée en semaine pour des soucis de maintenance. La moyenne de
production s'élève à 87 kW, soit un taux de
43,5% de charge, ce qui est loin de la capacité de 200
kW. Le taux de récupération du système de
cogénération est de 80%.
Le bois est fourni par des plantations durables est payé
à juste prix afin que les planteurs soient encouragés à
fournir la centrale continuellement. Il faudrait pour un fonctionnement
à temps partiel (50%) et un rendement électrique de 15% et des
champs à 5t/ha/an de rendement, une ressource bois de 1,9
ha/kW. Le meilleur scénario pour des champs à grand
rendement (15t/ha/an) et un rendement électrique de
24%, serait une consommation 0,3ha/kW.
Cela nécessiterait alors pour fournir 200
kW à temps partiel (50%) et pour 24% de rendement
électrique une plantation de 60 hectares.
Ø Effets économique, social et
environnemental
Une étude à montrer que le coût de
l'électricité est égal à
0,159Euros/kWh. Les coûts d'installation
s'élèveraient quant à elles à 1505
Euros/kW installés. En estimant une durée de vie
actuelle à treize (13) ans, les coûts sont repartis comme
suite : capital 43%, coût de fonctionnement (ressource et
maintenance) 29%, charge fixe 28%. Le système est alors
économiquement viable comparer au prix de l'électricité du
réseau 0,18 Euros/kWh.
Le temps de retour sur investissement en fonction de tous ces
paramètres est de 9,5 ans pour un taux de
rentabilité interne de 6%.Une projection pour un
gazéïfieur de 150 kW qui remplace un
générateur conventionnel au diésel (0,238Euros/kWh avec
0.231 Euros uniquement pour le diésel),le temps de retour sur
investissement est de 4,5 ans avec un taux de
rentabilité interne de 18%.
Pour que le système soit viable il faut une bonne
gestion des ressources et promouvoir le dynamisme économique autour de
la centrale en s'assurant de créer des opportunités de
création d'emploi et de commerces de bien et de services. En outre la
production doit toujours suivre la consommation pour rendre le système
efficace.
Le traitement de l'eau de lavage par vidange qui contient des
cendres et du charbon, se fait environ une fois(1)/mois et servirait à
la fertilisation des champs, et le charbon récupérer pour bruler
dans des chaudières.
Le gazéïfieur génère une petite
quantité de soufre, et le CO2 émis est recyclé
par les plantations durables, ce qui en fait un système à un
bilan Co2 nul. Le système remplaçant à peu
près 120 000 litres de diésel/an on
économiserait environs 314 tonnes/an de
CO2.
3.3. Projets
d'électrification dans la province de Battambang au Cambodge
Ø La centrale de gazéification
installée par SME Cambodge pour une industrie de riz afin valoriser la
balle de riz :
Présentation de l'installation
Le projet de gazéification bien qu'aillant dynamiser
l'économie local par les commerces qui sont alimenter, ont par ailleurs
dégagées des soucis concernant et la valorisation des goudrons
et l'eau usée sortant du process car l'un peut avoir un effet
cancérigène et l'autre contient des phénols qui sont
connus comme germicides tuant les bactéries du sol et pouvant avoir un
impact sur l'environnement.
Les cendres issus des process ne trouve pas aussi une bonne
valorisation alors qu'ils peuvent être utilisés dans des
industries de pneu ,d'aciérie, de cimenterie comme additif au
ciment, la construction pour la fabrication des briques, ou encore des
industries de silicium pour la fabrication les plaquettes amorphes, les cendres
peuvent être valoriser dans les plantations et augmenter les
rendements.(Source SME Cambodge)
Le tableau 10 ci-dessous présente les
caractéristiques de la plateforme.
Paramètres du système
|
Quantité de Diesel avant
gazéification
|
8 400 litres/mois
|
Coût du diésel avant
gazéification
|
5 628 US$/mois
|
Capacité du gazeifieur
|
200 kW
|
Taux de remplacement du diesel
|
77%
|
Quantité de Diesel après
gazéification
|
1932 litres/mois
|
Coût du diésel après
gazéification
|
2 128 US$ /mois
|
Diésel économisé
|
6468 litres/mois
|
Coût du diésel
économisé
|
3 500 US$/mois
|
Quantité de balle de riz
utilisée
|
48 tonnes/mois
|
Temps de retour sur investissement
|
2 ans
|
Tableau 10 : Caractéristiques du projet de
gazéification
Ø Projet de gazéification dans le village
de Anlong Ta Mei,Battambang,
cambodge
[22]Depuis 2005 dans la province de
Battambang, d'après une étude de Hitofumi Abe et
Al. en 2007,une coopérative a installé un
gazéïfieur de 9 kW avec le soutien de l'Agence
Canadienne pour le développement Internationale. Ce gazeifieur fournit
de l'électricité pendant (6) six heures/jour
à 70 foyers. Ce plateforme de gazéification est fourni
en ressource par du bois de Leucaena contenant
12% d'humidité pour une consommation de 1,26
kg/h/Wh ; venant de forêts aménagées qui sont
prêt à être abattu à l'âge de 10
à 12 mois avec un rendement de 8,2t/ha/an, et
acheté aux membres de la coopérative au prix de 20
dollar/tonne de bois sec. Le prix de revient de
l'électricité est de 300 dollar/MWh produit ce
qui est beaucoup moins cher par rapport au 700-900 dollar/MWh
de l'opérateur local d'électricité.
3.4. Projet
d'électrification rurale village d'hosahalli et Hanumanthanagara,
Inde
Une étude technico-économique menée par N.
H. Ravindranath et Al[23]en 2004sur le retour
d'expérience dans les villages d'hosahalli et de Hanumanthanagara ont
fait ressortir les performances et l'impact observés sur
l'électrification décentralisée par gazéification
de la biomasse.
Ces projets menés depuis 1988 ont été
planifiés et installés en suivant les étapes
suivantes :
o Etape 1 : Des meetings ont été
organisés avec les communautés locales des deux villages afin de
leur expliquer la technologie, le but, les responsabilités, les
avantages ainsi que le besoin qu'ils soient parties prenantes des projets
o Etape 2 : D'un commun accord les communautés
locales ont accepté de participer et d'aider à la création
de forêts aménagées pour la fourniture en ressource des
gazéifieurs (respectivement en 1988 et 1996 pour le village d'Hosahalli
et Hanumanthanagara)
o Etape 3 : Les plateformes de gazéification ont
été installées dans le village de hosahalli en 1988 et en
1996 dans le village de Hanumanthanagara, et les différentes charges
installées progressivement.
o Etape 4 : Des jeunes des deux communautés ont
été formés afin d'être à même de
gérer les plateformes et d'intervenir sur les activités de
maintenances mineures.
o Etape 5 : Les subventions pour l'installation des
plateformes ont été acquises
o Etape 6 : Des comités villageoises gèrent
les plateformes, prennent les décisions relatifs au fonctionnement,
protègent et renouvellent les forêts et garantissent les
payements des différents charges des plateformes
Le tableau 11 ci-dessous présente les différentes
caractéristiques des installations en 2004 :
Description
|
Hosahalli
|
Hanumanthanagara
|
Année d'installation
|
1988
|
1996
|
Nombre de foyers
|
35
|
58
|
Population
|
218
|
319
|
Surface des plantations pour le gazeifieur
(ha)
|
4
|
8
|
Capacité installée (kWe)
|
20
|
Charges (kWe) :
-Eclairage
-Pompe eau potable
-Moulin
-Pompe d'irrigation
Total
|
4
2,6
5,6
18,5
30,7
|
4
2,6
5,6
25,5
37,7
|
Tableau 11 : Caractéristiques des
plateformes d'Hosahalli et Hanumanthanagara
Le fonctionnement des plateformes nécessite en moyenne
entre 1,27 et 1,6 kg/kWh de bois dépendamment du choix de fonctionnement
( gaz ou dual-fuel),et amené à une réduction de 85% de
dépendance au diésel montrant l'efficacité des
systèmes. Les essences utilisées sont l'acacia
auriculiformis (13%), l'Eucalyptus (58%), Dalbergia
Sisso (7%),et le Casia Siamea (22%) avec un rendement de 6t/ha/an
en matière sèche.
Le tableau 12 ci-dessous relèves les divers
problèmes rencontrés pendant le fonctionnement et les
maintenances sur une période de six ans.
Tableau 12
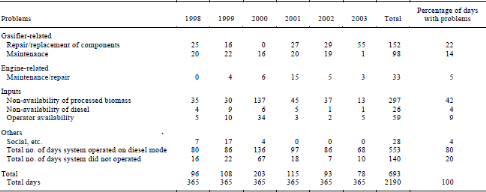
: Problèmes rencontrés dans les
opérations de fonctionnement et de maintenance du gazeifieur
d'Hosahalli
Selon Ravindranath et Al les études d'impacts
environnementales ont montré que la création de forêts
comportant plusieurs espèces a conduit à la conservation du sol
et de l`eau dans des terres sujet à la dégradation. cela a
contribué au développement de la biodiversité dans les
terres comme l'ont démontré l'expérience d'hosahalli. La
biomasse a produit peu de cendre comparée au charbon et sa combustion
amenée à une émission de soufre négligeable.
III. MATERIEL ET METHODES
1. Description de la plateforme de
gazéification
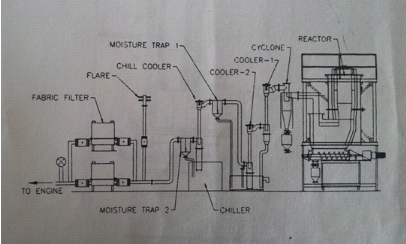
Figure 3 :
Equipements du gazogène
Le gazéifieur est de type co-courant, de conception et
fabrication indienne de La firme ONV BIO et de l'Institut des sciences de
Bangalore, les auxiliaires et leurs caractéristiques sont définis
dans le tableau 13. Le syngaz est utilisé par un moteur à
syngaz CUMMINSIndecouplé à une génératrice Stanford
d'une capacité de 40 kVA. Il est adapté pour les conversions
thermochimiques de biomasse solide de types bois énergie, coques de noix
de coco et de noix de palme. Les spécifications des équipements
sont détaillées dans le tableau 13 ci-dessous :
Ref/N°
|
Equipements
|
Spécification
|
Quantité
|
A
|
Traitement biomasse
|
1
|
Scie circulaire
|
50 kg/h, P=1,48 kW
|
1
|
2
|
Séchoir
|
Capacité de 40 kg/isolation en céramique
|
1
|
Souffleur d'air chaud
|
P= 1,48 kW
|
1
|
Conduite d'air chaud
|
Revêtement en aluminium
|
20 mètres
|
B
|
Système de gazéification
|
1
|
Réacteur avec revêtement en brique pourvu d'air
nozzles
|
Co-courant
|
1
|
2
|
Couverture du réacteur
|
|
1
|
3
|
Convoyeur-Extracteur de résidus
|
P= 0,4kW
|
1
|
4
|
Collecteur de charbon
|
Capacité de stockage 1heure
|
1
|
5
|
Valves de fermeture pneumatique
|
100 mm
|
2
|
6
|
Cyclone avec valves pneumatiques
|
75 mm
|
1
|
7
|
Collecteur de poussière
|
Capacité 8h
Valve de 75 mm
|
1
|
8
|
Manomètre de mesure de pression
|
Sur la chaîne de mesure du gaz
|
02 (Entrée/Sortie)
|
9
|
Refroidisseur à eau
|
150 mm
|
01
|
10
|
Unité de séparation de gaz
|
|
01
|
11
|
Epurateur à eau et tuyauterie
|
|
01
|
12
|
Unité de séparation de gaz
|
|
01
|
13
|
Epurateur d'eau réfrigéré et tuyauterie
|
|
01
|
14
|
Unité de séparation d'eau
|
|
01
|
15
|
Piège d'humidité
|
|
01
|
16
|
Souffleur
|
|
01
|
17
|
Moniteur d'oxygène
|
|
01
|
18
|
Filtre en tissu
|
|
01
|
C
|
Système de traitement d'eau
de lavage
|
1
|
Réservoir de floculation avec agitateur &
collecteur de déchets
|
|
01
|
2
|
Réservoir de mélange d'alun avec
agitateur
|
|
01
|
3
|
Réservoir de mélange
poly-électrolyte avec agitateur
|
|
01
|
4
|
Trémie pour charbon actif
|
|
01
|
5
|
Collecteur de déchets
|
|
01
|
6
|
Réservoir d'eau
réfrigérée
|
|
01
|
7
|
Pompe de dosage chimique
|
|
01
|
8
|
Tour de refroidissement
|
|
01
|
D
|
Accessoires
|
1
|
Pompe de lavage et de refroidissement direct
|
Débit 8m3/hr
H=40 m ;P=2,2kW
|
2 pompes
(principal/secours)
|
2
|
Tour de refroidissement
|
Delta T=5°c P=1,1kW.
|
1
|
3
|
Chiller
|
P = 2,6 kW
|
|
4
|
Pompe du chiller
|
T°=8°C débit 4m3/h, H= 40 m P=
1,1kW
|
2 pompes (principal/secours)
|
5
|
Pompe du tank de floculation
|
Débit 5m3/h hauteur 20 m P=1,1kW
|
2 pompes (principal/secours)
|
6
|
Pompe psf
|
Débit 5m3/h hauteur 30 m ,P=1,1kW
|
2 pompes (principal/secours)
|
7
|
Pompe de dosage (poly électrolyte)
|
Débit 1m3/h hauteur 20 m, P=1,1kW
|
01
|
8
|
Pompe pour eau d'appoint
|
Débit 6m3/h hauteur 30 m P=1,1kW
|
2 pompes (principal/secours)
|
9
|
Pompes du refroidisseur principal
|
Débit 8m3/h hauteur 20 m P= 1,5kW
|
2 pompes (principal/secours)
|
10
|
Souffleur de gaz
|
Débit 350 m3/h hauteur 500 mm P=1.5kW
|
1
|
11
|
Valves du cyclone
|
Pneumatique,
|
02
|
12
|
Valves extraction de cendre
|
Pneumatique
|
02
|
13
|
Extracteur de cendre
|
Moteur de 1.5 CV
|
01
|
14
|
Unité de refroidissement d'eau
|
|
01
|
15
|
Isolation de l'épurateur du chiller
|
30 mm d'isolant
|
----
|
16
|
Capteurs de température
|
Thermocouple type K
|
04
|
17
|
Structure
|
Plateforme gazeifieur
|
----
|
18
|
Tableau de commande
|
|
1
|
Tableau 13 : Spécifications des
équipements de la plateforme
Dans la suite de cette étude nous appellerons
auxiliaires les équipements dont le gazeifieur a besoin pour fonctionner
en permanence qui sont les suivantes : le chiller et sa pompe ;les
pompes des refroidisseurs directs ; le souffleur de gaz, le ventilo de la
tour de refroidissement et sa pompe dont la somme en puissance installée
équivaut à 14kW.
Les équipements de l'eau de lavage sont indiqués
au niveau C du tableau.
2. Protocolesexpérimentaux
2.1. La ressource en
biomasse
Le process de gazéification à co-courant faisant
appel à l'utilisation du bois (Acacia auriculiformis ou
Eucalyptus Senegalensis) ou des coques de coco et des coques de noix
de palmes, il s'avère important de préparer une quantité
suffisante de matière pour la durée des tests tout en sachant que
la capacité maximale de conversion est de 35 kg/heure de matière,
valeur qui peut varier selon la charge.
Il est important de s'assurer de l'humidité (<=
15%), dela granulométrie (3cm x3 cmx 3 cm pour le bois) de la ressource
avant de peser et de charger la matière dans le réacteur du
gazeifieur car cela est un facteur important du process. Avant tout aussi
s'assurer de la non présence de sable ou matière
métallique dans la ressource.
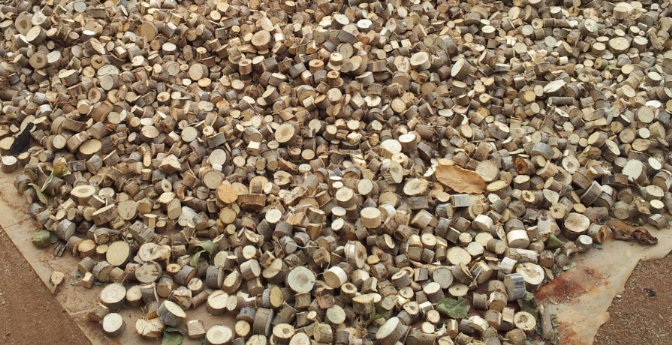
Figure
4Bois d'acacia auriculiformis découpé et
séché
2.1.1. Analyse du taux d'humidité moyen
L'humidité de la biomasse est un des facteurs
importants à déterminer avant son utilisation dans un gazeifieur.
De ce fait des échantillons de bois d'acacia auriculiformis ont
été prélevés dans le plantation parcelle
témoin de de 0.35 hectares de Songhaï Porto-Novo.
Des analyses ont été effectuées en vue de
déterminer le taux d'humiditéde la biomasse au laboratoire
Songhaï et du LBEB du 2iE.Le protocole utilisé pour
l'échantillonnage de la biomasse en rondin est défini dans
`'GIRARD P., 1992''.
N° de lot
|
Taux d'humidité moyen sur masse brute
%
|
1
|
41,2
|
2
|
36,4
|
Tableau 14 :
Humidité moyen du bois d'acacia auriculiformis du Centre
Songhaï
2.1.2. Détermination du PCI du
bois
Des échantillons de bois d'acacia auriculiformis ont
été prélevés dans un lot de prêt pour
alimenter le gazéifieur et transmis au laboratoire du LBEB au 2iE pour
la détermination du PCI selon les normes en vigueur.
Des échantillons de bois d'acacia auriculiformis ont
été transmis au laboratoire du LBEB pour détermination du
taux d'humidité et du PCI . Les résultats sont
présentés ci-après :
N° Echantillon
|
Taux d'humidité sur masse brute %
|
PCS brut (j/g)
|
PCI brut (j/g)
|
1
|
4,5
|
19 663
|
18 338
|
2
|
4,1
|
18 858
|
17 534
|
Moyenne
|
4,3
|
19 260
|
17 940
|
Tableau 15 :
Résultats d'analyse des taux d'humidité et PCI de 2
échantillons d'Acacia auriculiformis dans un lot préparé
pour alimenter le gazéifieur (en mai 2013)
2.2. Test de performance du
gazéifieur
Le protocole ci-aprèsva définir la
méthodologie adopter pour les tests de performance avec un combustible
bien défini pour le gazeifieur, chaque série étant
constitué de trois (3) tests représentatifs sur une
période de 4h ou 5 h continue ou qui peuvent
être répartie en deux séances de 2h00 ou
2h30 le matin et l'après-midi. Les paramètres suivant
seront relevés pour servir à l'analyse de performance :
§ la consommation de bois par heure (avec mesure
intermédiaire chaque 15 min) et suivant la charge (kg/h/%charge),
§ les relevés de production d'énergie des
différentes charges (kWh),
§ les temps de fonctionnement
(démarrage/arrêt)
§ les températures (chiller (groupe de
condensation),gaz sortie réacteur ,séchoir, eau de lavage de
gaz).
2.2.1.
Préparation du Matériel
Afin de réaliser les essais et relever les données
il est important de recenser et préparer le matériel afin
d'éviter les erreurs de manipulations.
Un cahier de manipulation est rempli pour toutes les
interventions et expérimentations sur la plateforme de
gazéification.
Un canevas (modèle) de tableau est utilisé pour
noter les tableaux ; les paramètres relevés et est ensuite
mis sous forme d'un fichier Excel, pour stockage numérique et
traitement.
2.2.1.1. Matériel
Les équipements suivants ont été
utilisés : cf. tableau 16. Avant tout essai le matériel
adéquat doit être rassemblé afin de se donner les moyens
d'atteindre les objectifs de tests de performance
Désignation
|
Caractéristiques
|
Commentaires
|
Compteurs triphasés
|
LJ électronique CE 9016 ; Nombre 3, mesure de
l'énergie active et réactive
|
Pour chaque charge BRF, auxiliaires et usine de recyclage
|
Transformateur de courant
|
Six (6) de 50/5 et 3 de 100/5
|
Vérifier l'installation et multiplier l'énergie
par le rapport des TC
|
Balance calibrée
|
Marque Diamond, calibrée à 150 kg, Incertitude
+/- 0,5 kg
|
Afin de peser la masse du combustible ajoutée
|
Une montre
|
Cadran numérique
|
Déterminer le temps de l'expérience
|
Thermocouple portable type K
|
Chauvin Arnoux Physics Line classe A
|
Relevé de la température de l'eau de lavage
|
Une pince ampéremétrique
|
Chauvin Arnoux 600v/400A
|
Mesures Température, courant, tension
|
Afficheur de température
|
Incertitude +/- 2 °C
|
Déterminer le temps de séjour du combustible dans
le séchoir
|
Station météorologique
|
Marque Davis Vantage Pro2 Integrated Sensor Suite
|
Relevés conditions météorologiques de
l'expérimentation
|
EPI
|
Une blouse, des gants et des lunettes
|
protection pour chaque opérateur
|
Une fiche de relevé daté
|
Fiche papier et Excel
|
Faire le compte rendu de l'expérimentation
|
Tableau 16 :
Equipements pour expérimentation
2.2.2. Tests de
performance
L'objectif est de relever les paramètres de
fonctionnement pouvant intervenir dans l'analyse de performance du
gazéifieur. Il s'agit de faire un bilan l'énergie produite en
fonction du kilogramme de combustible consommé afin de ressortir le prix
du kWh.
Tout en respectant les procédures de démarrage
et d'arrêt et en laissant au moins 15 min au process pour se stabiliser,
il faudra pendant un essai relever les points suivants :
Ø Les charges alimentées (% de charge) : ici
nous les tests qui seront réalisables sont les charges des auxiliaires
de la plateforme constitués de nombreux moteurs électriques (14
kW installés) et des moteurs électriques du broyeur à
végétaux BRF (19 kW installés).
Ø Les conditions météorologiques
d'essai : Température et humidité
Ø La quantité de bois ajouté jusqu'à
remplir le réacteur avant et après fonctionnement et les
quantités ajoutées durant le fonctionnement (chaque 30 min, en
kg)
Ø L'heure d'allumage du gazéifieur et l'heure de
l'allumage du bruleur (nombre d'heures et minutes)
Ø L'heure de démarrage de la
génératrice (nombre d'heures)
Ø Les variations d'appel de courant avec la pince
ampérométrique (Ampère)
Ø La variation de température de l'eau de lavage
chaque 15 min (°C)
Ø Les variations de température du séchoir
(chaque 15 min)
Ø Les remarques et observations : relever tout
facteur ou incidents
Le générateur ayant une puissance de 40
kVA avec un Cos phi = 0.8 équivalent à 32 kW en
pointe, plusieurs configurations ont
ététestés :
1. Alimentation des auxiliaires plateformes de
gazéification (Pinst= 14 kW) avec un taux de charge moyen
de ces équipements de 70%(10 kW)
2. Alimentation des auxiliaires plateformes de
gazéification (Pinst= 14 kW) + Broyeur végétaux
pour BRF (Pinst= 19 kW) = avec un taux de charge moyen de ces
équipements de 72,3% (24kW)
La ressource utilisée est essentiellement du bois mais
les coques de coco et de noix de palmes ont été utilisées
selon la disponibilité.
Les tests ont été réalisés pour
chaque charge dépendamment de la disponibilité des charges et la
de l'état de fonction de la plateforme.
Expressions des calculs et
résultats
L'énergie produite et les consommations de bois par
kWh seront déterminées par les calculs suivants :
(1)

L'expression des résultats finaux seront la moyenne
des calculs de chaque test.
2.2.3. Analyse économique
L'analyse économique adopte le plus souvent les
techniques de marge brute d'autofinancement basées sur l'approche
d'analyse du coût de cycle de vie. Dans cette étude, l'analyse du
coût sera effectuée en utilisant les couts fixes, et les couts
variables qui sont le cout moyen du combustible, les coûts
d'opération et de maintenance.
Le coût d'opération et de maintenance doit
inclure par exemple pour le générateur le coût de tous les
consommables tels que l'huile de graissage, les filtres d'huile et les
garnitures utilisés pendant l'entretien et la distribution
électrique ; pour le gazeifieur par exemple on inclura le
coût de l'eau de lavage, du carburant pour l'amorçage, du charbon
de bois pour les premiers chargements. Les paramètres du site doivent
être considérés à savoir le coût de la
main-d'oeuvre qui devra inclure le salaire mensuel des opérateurs, et
Concernant le coût de la biomasse (ici le bois ou les coques de noix de
coco), on fera une estimation en se basant sur l'expérience Songhaï
et les fournisseurs locaux externes.
Le coût de l'électricité (en FCFA/KWh) qui
sera le point de chute de cette analyse sera estimé en utilisant les
coûts variables, puisque le système peut fonctionner à
différente charge. Le coût par KWh de l'électricité
est calculé en prenant les couts d'investissement ; le productible
en énergie, les couts relatifs à la matière
première, et les coûts d'opération et de maintenance
réellement utilisé à différentes charges sur le
système de production d'électricité.
Etant donné que la plateforme dépend du
réseau au démarrage, il sera estimé le coût de la
consommation à facturer. Le prix sera déduit à partir de
la méthode du LEC (Levelized Elecricity Cost) par la formule
suivante :

Ka= 
Avec : I= investissement nette
Ka= facteur d'actualisation
Kmaint = coef de maintenance (1%) ,n= temps d'analyse
économiquei= Taux d'actualisation (8%) , Ea :
Productible en énergie (Ea= nbre d'heure*nbre de
jr*Pinst)
Il faudra en outre y ajouter le facteur de charge d'usine qui
sera déterminé en priorité car étant l'un des
facteurs principaux de contribution au coût de
l'électricité.
Nous allons faire cette analyse en nous basant sur trois (3)
scénarios de fonctionnement :
.
§ Le scénario N°1 est l'analyse en estimant la
charge à 75% (P= 24kW)et le taux de couverture journalier à 25%
(6 heures/jour) qui est le cas réalisable.
§ le scénario numéro N° 2 est le cas
probable où on fonctionnait uniquement en alimentant à 75% (P=
24kW)de charge avec un taux de couverture de 50 % (12 h/jour) qui est le cas
optimiste.
§ Un dernier scénario N°3 , à un taux de
couverture de 75% (18h/jour) sera évalué pour servir de cas
très optimiste.
2.2.4.
Recommandations
Les résultats des tests obtenus doivent être
réitérer au moins trois (3) fois afin d'avoir une
représentativité.
Il est important avant tout test de s'assurer :
o D'avoir lus tous les documents inhérents au
fonctionnement du gazéifieur,
o De se procurer des EPI pour la sécurité
o De vérifier les rapports de conversion des
transformateurs de courant pour avoir les relevés compteurs
(Rapport*index).
o De relever tout facteur ou incident durant la manipulation
pouvant influencer les résultats.
IV. RESULTATS ET
DISCUSSION
1. Présentation des
tests réalisés
Les tests d'analyse d'humidité et les tests de
performances on donner les données suivantes :
Ø Test d'humidité et du
PCI
Le taux d'humidité moyen, avec le protocole BFT (Bois
et Foret Tropical),sur masse brute est de 36 %pour le premier lot et de 52 %
pour le deuxième lot caractérisé.
Ø Tests de performance
Les tests ont été réalisés en
utilisant les compteurs d'énergie (présenté en Annexe 2)
mais un problème d'incohérence entre les valeurs mesurées
et la capacité maximale de l'installation a conduit à se baser
sur un autre indicateur, la production d'électricité a
été alors évaluée en faisant un calcul de
puissance se basant sur l'intensité lue sur l'afficheur du groupe
électrogène durant chaque test, la valeur moyenne a
été évaluée par l'opérateur de
l'expérimentation sur les données observées sur
l'afficheur du groupe (résultats ci-dessous).
% charge
|
N°Essai/Date
|
Nombre d'heure
|
Pmoy
(kW)
|
Quantité de bois consommée
(Kg)
|
Consommation spécifique (Kg/kWh)
|
Energie
Produite au cours du test (kWh)
|
Observations
|
31%
(10kW)
|
1 (24/08/13)
|
2h00
|
10
|
57
|
2,85
|
20
|
Néant
|
2(06/06/13)
|
2h00
|
10
|
52
|
2,6
|
20
|
Néant
|
3(07/06/13)
|
2h00
|
10
|
60
|
3
|
20
|
Néant
|
75%
(24kW)
|
1 (16/06/13)
|
2h00
|
24
|
54
|
1,13
|
48
|
3 arrêts du Brf de 5 min chacune
|
2(17/06/13)
|
2h30
|
24
|
79
|
1,32
|
60
|
2arrêts du Brf de 5 min chacune
|
3(18/06/13)
|
2h30
|
24
|
82
|
1,37
|
60
|
3 arrêts du Brf de 5 min chacune
|
4(04/07/13)
|
5h00
|
24
|
175
|
1,46
|
120
|
Néant
|
5(08/07/13)
|
5h00
|
24
|
155,5
|
1,30
|
120
|
Néant
|
6(09/07/13)
|
4h00
|
24
|
145
|
1,51
|
96
|
Néant
|
Tableau 17 : Bilan
avec le bois
% Charge
|
N° Essai/date
|
Nombre d'heure
|
Pmoy
(kW)
|
Consommation coque
|
Quantité de coques consommée
Kg/kWh
|
Energie
Produite durant le test (kWh)
|
T° cyclone
|
Observations
|
75%
(24kW)
|
1 (12/07/13)
|
02h00
|
24
|
63
|
1,31
|
48
|
211°C+/- 10°C
|
Quantité moindre de particule fine,
|
2(20/08/13)
|
02h00
|
24
|
55,5
|
1,16
|
48
|
160<T°<200°C
+/- 10°C
|
Quantité moindre de particule fine,
|
3(26/09/13)
|
02h00
|
24
|
60
|
1,25
|
48
|
180<T°<220°C
+/- 10°C
|
Quantité moindre de particule fine,
|
Tableau 18 : Bilan avec
les coques de noix de coco2. Analyses et
interprétations
Les expérimentations ont fait ressortir que plus la
charge augmente plus la consommation spécifique de bois diminue.
Les essais longs durés (4 ou 5h) sur les auxiliaires
(31%) n'ont pas été possibles du fait des contraintes de terrain
et de la priorité de la gestion de la ressource, même si les
résultats obtenus sont assez satisfaisants sur les plages horaires
testées.
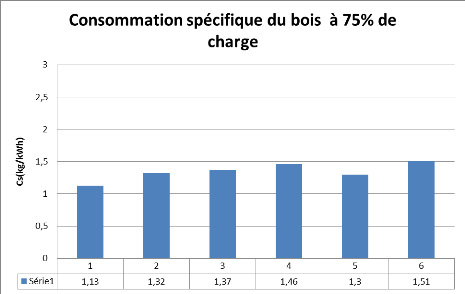
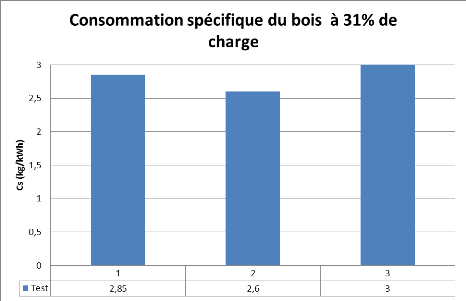
Figure 5 :
Consommation spécifique avec du bois suivant les charges simuler de 31%
et 75%
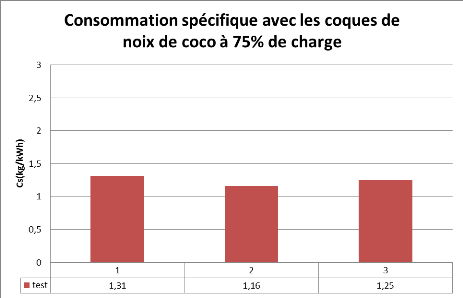
Figure 6 :
Consommation spécifique avec des coques de noix de coco sur 75%de
charge
Le combustible utilisé pour chaque test a
été sélectionné dans un lot qui a subi le
même parcours de conditionnement et qui respecte les exigences de type,
de granulométrie et d'humidité. Les mesures de débit de
biomasse ont été réalisées chaque 15 min de
fonctionnement en laissant 15 min au process au préalable pour
être stable avant de débuter les prises de mesures.
On observe sur la figure 5 que pour une charge (75%) les
consommations spécifiques sont entre 1,13 et 1,46
kg/kWh pour le bois ,et sur la figure 6pour les coques de noix de coco
de1,16 à 1,31 kg/kWhindépendamment du nombre
d'heure de test qui allait jusqu'à 2h30 pour les test 1,2 et 3 ; et
5 heures pour les test 4,5 et 6.
La consommation spécifique est alors relativement
stable et basse.Les mêmes mesures à 31% de charge
montre une consommation ente 2,6 et 3 kg/kWh sur 2 heures pour
chaque test.
La différence enregistrée au niveau de
l'énergie surtout sur les 75% de charge relève
du fait que le BRF n'est pas un process continu et les mesures de consommation
fluctuent et dépendent de la matière à broyer et de
l'habilité de l'opérateur.
Le process de conversion s'est déroulé dans des
conditions optimales de fonctionnements tout au long de l'essai depuis
l'obtention du gaz jusqu'à l'arrêt du système aussi bien
avec le bois que les coques de noix de coco.
Les températures au niveau du cyclone montrent une
stabilité du process en fonctionnement entre 150 et
230°C.
La température récupérée en
cogénération atteint les 100 à 120 °C dans le
séchoir au bout de 15 min de fonctionnement, ce qui nous permet de la
valoriser le séchage final de la matière première et
d'abaisser l'humidité de 30% à 15 % en trois heures.
La variation de l'eau de lavage entre 0,7 et 1 au bout d'une
heure indique que l'on peut se délester des moteurs de la tour de
refroidissement pendant quelques minutes et libérer de la puissance pour
démarrer éventuellement des charges assez gourmandes en courant
comme celles de l'usine de recyclage de plastique.
A partir de cette expérimentation nous avons pouvons
estimer les quantités de combustible, notamment le bois ou les coques
de noix de coco à ajouter à intervalle régulier en
fonctionnement.
3. Perspectives
d'amélioration des tests
Ces tests pourraient être plus précis et complet
si l'on y ajoutait une instrumentation afin de suivre l'évolution des
paramètres de fonctionnement. Les équipements cités
ci-dessous seront plus adaptés pour des tests longes durées (5
à 7 heures continues) pouvant aider dans l'étude des performances
plus précises du système en générale et du moteur
à gaz en particulier :
Ø 1 thermocouple pour la température de
fumée
Ø 1 thermocouple pour la température ambiante
Ø 1 Pt1000 pour la température de sortie du gaz a
la sortie du réacteur
Ø 1 Pt100 pour la température du gaz à
l'entrée du groupe élec
Ø Un capteur de pression à l'entrée du gaz
coté groupe électrogène
Ø Une centrale d'acquisition de données afin
d'avoir plus de précisions et de données sur les
résultats
Ces outils devraient aider pour suivre la courbe de charge du
gazéifieur, et les paramètres critiques en fonctionnement pour
des analyses d'endurance et de performance afin réaliser une
étude plus complète surtout côté moteur afin
étudier et déterminer conditions optimales de fonctionnement.
La nature des charges testées au-delà des 31%
même s'il respecte les contraintes de terrain n'est pas stable pour
réaliser des tests de précision .De ce fait il faudrait penser
à trouver si possible un process plus stable et continue faisant des
appels de puissance stable.
A cela on pourrait éventuellement ajouter une ligne
d'échantillonnage afin de mesurer la composition du syngaz et la teneur
mesurée en poussières et goudrons, et calculer les taux de
conversion et le rendement énergétique du gazeifieur.
V. ANALYSE TECHNICO-ECONOMIQUE DE LA
PLATEFORME GAZEIFIEUR
1. Etude de la ressource
L'étude de la ressource est un des paramètres
des plus importants dans l'installation d'un système de
gazéification. L'estimation de son coût et la logistique à
mettre en place pour s'assurer d'un approvisionnement durable et renouvelable,
en continue est déterminant dans l'estimation du prix du KWh juste et
compétitif par rapport à des sources alternatives
d'électricité.
« L'utilisation du bois comme source d'énergie ne
peut être considérée comme renouvelable et participant
pleinement au développement durable que si les rejets émis sont
faibles et maîtrisés. À l'heure actuelle, toutes les
installations satisfont aux normes de rejets en vigueur, mais il est maintenant
nécessaire d'aller plus loin et d'atteindre des performances thermiques
et environnementales proches de celles obtenues avec les combustibles fossiles
»(Wikipédia)[24]
Une étude de la ressource disponible : le bois
majoritairement, et les coques de noix de coco et des coques de noix de
palmes pour une utilisation pour la gazéification va être faite.
Une étude entre l'utilisation gazeifieuret une utilisation BRF (Bois
raméal fragmenté, paillage des sols) sera aussi faite en
procédant à une classification de la ressource par usage :
cas d'application sur Songhaï.
1.1. Etude de la ressource disponible
Le gazeifieur du Centre Songhaï est adapté pour
l'utilisation de la biomasse suivante : tout type de bois énergie
en particulier les essences d'Acacia auriculiformis et
d'Eucalyptus Sengalensis, lescoques de noix de coco, les coques de
noix de palmetraité ayant une granulométrie
Longueur*largeur*hauteur de 3cm*3cm*3cm et une densité de 250kg/m3
et une humidité de moins de 15%.
Au niveau du centre on dispose d'une surface de 0,35 à 0,5
hectares situé à Songhaï Est réservée pour les
plantations de bois avec les essences mélangés d'Acacia
auriculiformis et quelques pieds d'Eucalyptus.Le reste des essences de
l'agroforesterie n'étant pas adapté pour une utilisation, le
reste des résidus est privilégié pour le BRF (Bois
raméal fragmenté).
1.1.1. Ressources bois : Acacia auriculiformis et
d'Eucalyptus senegalensis
Il a été procédé en 2011 à la
mise en terre d'essences d'Acacia auriculiformis en majorité et
de quelques pieds d'Eucalyptus Senegalensis sur une surface de 0,35 ha
avec une extension sur d'autres parcelles (0,15 ha) plus jeunes de quelques
mois (3 mois, février 2013), pour les besoins du
gazéïfieur.
Le rendement sur cette surface est égale 3060
plants/0.35ha actuellement en prenant une perte de 10% soit 9000 plants/ha,
perte qui pourrait progresser jusqu'à 30% ou 50% en fonction des
besoins en bois réclamer par les autres sections à savoir
l'agroforesterie, le jardin, les champignons etc.

Figure 7 :Bois
d'acacia auriculiformis récupéré pour application
agricole : tuteurage (à gauche), séché pour le
gazeifieur (à droite) sur Songhaï site Porto-Novo
La plateforme a été mise en service en Mai
2012, le combustible utilisé était du bois acheté à
des producteurs locaux dont la provenance n'est pas certifié, et il est
quantifié et facturé à raison de 40 000 FCFA
à 45 000 FCFA le véhicule de convoyage (Bâchée)
qui correspond environs à entre 1 et 1,5 tonnes de bois.
L'abattage des plants de la plantation Songhaï se fait
dans le même modèle de gestion que les plantations durables
d'abord avec une première portion composée du tiers de la surface
totale qui a été mis en séchage naturel. Il sera à
chaque fois procédé à un reboisement de la partie abattue
avant de migrer vers la portion suivante du champ.
Les plants arrivent à maturité au bout de 12 mois
à 18 mois dépendamment du diamètre désirée.
Le cycle de coupe et de stockage et traitement pour les plants est de 3
mois. Il sera à chaque fois procédé à une analyse
de l'humidité du bois suivit des étapes définies dans le
cycle ci-dessous :
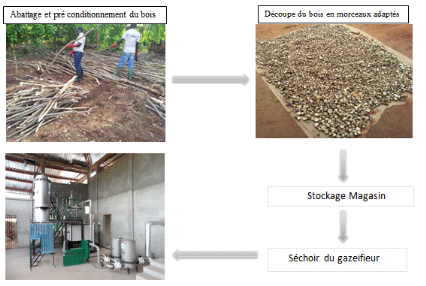
Figure 8 : Cycle de
la ressource bois
La production de bois sec/an/ha si nous nous referont à
l'étude de T.Buchholz et al,2012[25]pourrait
être estimé à travers des scénarii. Pour un taux de
50% de charge et une productivité en bois sec faible de 5t/an/ha un
gazeifieur fonctionnant avec un générateur à 100% de
syngaz pour un rendement électrique entre 10% et 20% requerra 1
à 2 ha/kW.
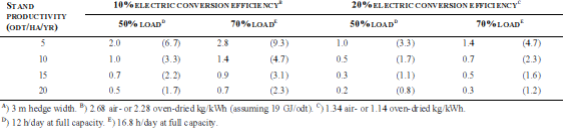
Le tableau ci-dessous présente divers scénario de
50 % et 70% de charge et une productivité de 5 à 20 t/ha/an.
Tableau 19 :
Scénarii pour l'estimation de la ressource, source T.
Buchholz
En nous basant sur ces scénarii nous pouvons nous en
rapprocher à 20% de rendement électrique et selon les charges
testés dans le tableau suivant :
Rendement électrique
|
Rendement Tonnes de bois sec /ha/an
estimé
|
% charge
|
Surface estimée (ha)
|
20 %
|
15 t/an/ha
|
31%
|
8,51
|
20%
|
15t/an/ha
|
50%
|
10,8
|
20%
|
15t/an/ha
|
75%
|
23,56
|
Tableau 20 : Estimation
de la surface à cultivée en fonction de la charge
Il faut préciser que ces estimations ont été
faites en tenant compte des temps de fonctionnement à pleine
capacité sur des plages optimales de 12h/jour à 16,8 h/jour.
Ø Prix de la ressource bois
L'agroforesterie a défini le coût pour les
plantations de l'hectare d'acacia auriculiformis en prenant en compte les
paramètres suivants :
Désignation
|
Nombre
|
Prix
|
Total
|
Plant
|
10 000
|
50 FCFA
|
500 000 FCFA
|
Piquetage, repiquage
|
1 fois
|
50 000 FCFA
|
50 000 FCFA
|
Sarclage
|
6 fois
|
1500 FCFA
|
9 000 FCFA
|
Arrosages
|
20 litres/jour/2 semaines
|
1687,98 FCFA*
|
1687,98 FCFA
|
560 687,98 FCFA
|
Tableau 21 : Cout
à l'hectare d'acacia auriculiformis
*tarif SONEB : 2em tranche (453 Fcfa), TVA (18%), compteur
(calibre 60,1323 fcfa)
Cout de la matière par tonne de bois sec en estimant
les moyennes de consommations :
%charge
|
Taux de couverture journalière
|
Consommation Tonnes bois sec/an
|
Prix de la matière/tonnes (FCFA)
|
Cout/an
(FCFA)
|
31%
|
25%
|
43,99
|
37 379,18*1
|
1 644 310
|
45 000*2
|
1 979 550
|
75%
|
25%
|
68,39
|
37 379,18*1
|
2 556 362
|
45 000*2
|
3 077 550
|
Tableau 22 : Cout de la
matière/tonnes à 31% et 75 %de charge
*1 Cout Agro foresterie Songhaï
*2 Cout fournisseurs extérieurs
1.1.2. Ressources : coques de noix de coco et noix de
palmes
Le gazeifieur de Songhaï centre est conçu pour
utiliser des coques de noix de coco(Cocos nucifera L.) et de noix de
palmes(Elaeis guineensis Jacq.) ayant une granulométrie par
pièce de 2 à 5 cm et 250 kg/m3 en densité.
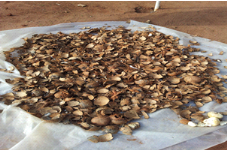
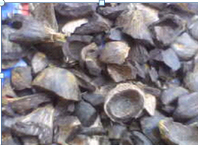
Figure 9 : Coques de
noix de coco (à gauche) et coque de noix palmiste (à droite) en
séchage naturel
[26](Rousset P.2008) Le cocotier est une plante
pérenne dont la production s'étale surtoute l'année. Sa
densité de plantation dépend des conditions climatiques et de la
variété (grand ou nain).La récolte est manuelle. Elle
s'effectue tous les mois, voire tous lesdeux mois.
Le schéma ci-dessous fait ressortir l'estimation de
quantité de coque sur 1000 noix de coco :
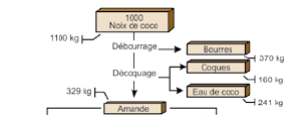
Figure 10 : Estimation
de la quantité de coque en fonction de la quantité de noix de
coco
Le palmier à huile quantà luiaussi est une
espèce pérenne. Sa période d'incubation(germination,
prepépinière et pépinière) est de 12 à 15
mois. Il commenceà produire à partir du trentième mois
après avoir été planté. Il atteint
samaturité productive (soit de 25 à 30 t/ha/an) à
l'âge de huit ans. Cetteproductivité est maintenue jusqu'à
sa 16ème année, ensuite il commence àdécliner
jusqu'à la fin de sa vie utile, suivant le matériel
végétal utilisé et lesconditions pédo-climatiques
de la zone de culture.La récolte est manuelle. Elle a lieu tout au long
de l'année et lesarbres sont visités tous les 10 jours afin de
recueillir des régimes à bonnematurité.Il s'agit de plus
ou moins 12 régimes par an. Chacun d'entre euxest composée de
1000 à 3000 fruits. Le fruit est ovale, d'une taille de 5 cmet d'un
poids de 10g. Il est composé d'un noyau (8%) et d'un
mésocarpe(92%). Compte tenu du pouvoir calorifique de la noix (9104
kcal/kg) de sa coque, c'est un produit idéal pour la
gazéification.
Le Bénin en général et la région de
l'Ouémé en particulier sont de grand producteur de noix de coco
et de noix de palmes. La valorisation est faite dans le domaine de la
cosmétique, l'agro-alimentaire comme c'est le cas de Songhaï sur la
fabrication de jus, de biscuits etc..,la production d'huile de palme
raffinée ou non.
Il faut préciser qu'il n'a pas vraiment un marché
déclaré de la matière première. Les prix recueillis
sur marché au Bénin ont donné une variation suivant les
saisons de 50 à 200 FCFA pour la noix de coco et un
prix de 60 à 100 FCFA pour le kilogramme de noix de
palme.
Les prix résidus de la matière première
n'est pas vraiment fixe puisque non systématiquement valorisés.
Malgré tout, les prix retrouvés chez certains
professionnels(www.Espaceagro.com)[27], des industries, et des
commerces locaux nous permettent de faire une estimation du prix variant
entre20 FCFA et 30 FCFA le kilogramme de coques.
Le système pour s'accorder un peu plus de souplesse dans
la gestion de la ressource pourrait fonctionner à temps partielle
suivant la disponibilité des coques.
La consommation en charge sur une annéeà 25% de
couverture par exemple,avec les coques de noix de coco nous donne les
paramètres suivants :
%Charge
|
Couverture journalière
|
Consommation kg/kWh
|
Consommation à l'année t/an
|
Coût de la matière/an
|
75%
|
25%
|
1,24
|
46,42
|
928 400 FCFA
|
Tableau 23 :
Estimation de la consommation des coques de noix de coco
La gestion de la ressource étant déterminant on
pourrait s'appuyer sur les données ombrothèrmiques (annexe 3)
observées sur la ville de Cotonou et que l'on peut étendre au
département de l'Ouémé pour permettre de gérer
l'utilisation de la ressource et alimenter la plateforme en continue.
Dépendamment des saisons, par exemple en période
de saison pluvieuse (Mars à juillet et septembre à octobre) on
pourrait stocker assez de bois et le laisser sécher et utiliser plus les
coques de noix de coco et de palmes et en saison sèche (Janvier à
Mars, Novembre à Décembre) on utilisera le bois et on stocke les
coques de noix de coco ou de palmes. Cette méthode aura non seulement
l'intérêt d'impacter sur le coût du kilowattheure
d'électricité et la gestion optimale de la ressource. Il faut
préciser que pour de futur expansion ou installation on pourrait
disposer de plus de quatre cents hectares (400 ha) disponible sur les sites
annexes tels que Savalou et Parakou afin d'y instaurer des plantations
durables.
1.2. Comparaison de la ressource pour BRF et le
gazéifieur
Le BRF est le résultat du broyage de branches vertes (pas
de bois mort et sec) d'un diamètre de 10 à 12 cm maximum issues
des feuillus. Les conifères sont toutefois tolérés en
mélange (20 %). Il s'agit d'un amendement organique de choix qui va
nourrir les habitants du sol et ainsi reconstituer ce dernier afin d'y cultiver
des plantes alimentaires ou non.
Les pays africains bien nantis dans le domaine forestier
peuvent être lesfournisseurs primaires de BRF pour les pays ou
régions dépourvus de forêts. Cecipermettrait à frais
réduits d'utiliser les ressources forestières non
utilisées dans lesrégions limitrophes de celles qui en ont besoin
pour amorcer le cycle dereconstitution des sols tant agricoles que forestiers.
Les régions les mieux nantiessont celles du sud du
Sénégal, la ceinture littorale entre Dakar et Saint-Louis,
demême que les régions de l'ouest et du sud du Bénin.
Plusieurs autres pays africains ont des ressources qui peuvent servir un
commerce relativement important qui seraitavant tout inter-régional,
mais également international; la ressource étant
abondantelocalement et de haute qualité. Cecipermettrait d'amorcer la
formation de véritables sols, sans quoi il sera impossible
dereconstituer la fertilité tant agricole que forestière.Le moyen
maintenant connu, qui a fait ses preuves en Afrique comme enAmérique, et
dont le Canada est à l'origine, a été retenu par les
participants à laconsultation de l'ICRAF (International Centre of
Research in Agroforestry (Nairobi, Kenya)en octobre 97, et ce sont les bois
raméaux fragmentés (BRF)[28].
Leur utilisation selon une technologie relativement simple a
permis demultiplier lesrendements de cultures vivrières en
améliorant l'environnement et laqualité de la vie dans les
milieux où ils furent mis à l'essai, et Songhaï en est un
exemple de réussite.
L'intérêt de l'étude sommaire à
Songhaï est d'arriver à valoriser les résidus venant de
l'exploitation des plantations du gazeifieur et éventuellement de
classifier les résidus des essences agro-forestières non
utilisées vers ce type de valorisation.
1.2.1.
Méthodologie d'application des BRF
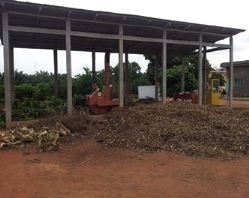
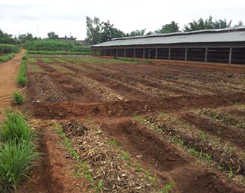
[29](Lemieux G.et al,2003)Les BRF sont
constitués de trois parties, les branches, les rameaux et les feuilles
et ils sont riches en sucres, protéines, celluloses et lignines. Tous
ces éléments jouent un rôle très précis dans
la formation et le maintien d'un sol fertile. Ce n'est pas le cas des
écorces, du bois de tronc, des sciures, des copeaux de rabotage ou de
tout autre résidu d'origine industrielle, etc. La méthodologie
d'application est expliquée en annexe 5.
Figure 11 : Plateforme BRF (à gauche),
parcelle recouverte de BRF (à droite)
1.2.2.
Matières premières du BRF à Songhaï
Outre les essences Acacia auriculiformis et Eucalyptus
sengalensis produit au niveau de songhaï servant pour le gazeifieur et
dont les branches issues de l'abattage peuvent être une matière
première du BRF, le reste de la biomasse principalement les
résidus de l'agroforesterie est transformé en BRF. Nous parlons
par exemple des quelques essences ci- après : Moringa
oleifera, Persea americana, Manguifera indica, Eucalyptus citriodora,
Terminalia mentalis,Azadirachta indica,Newbouldia laevis etc...
2. Analyse
technico-économique
2.1. Analyse
technico-économique de la plateforme gazeifieur
2.1.1. Etat de la
plateforme gazeifieur
Une analyse de la plateforme relevée sur 6 mois a permis
d'établir un graphe des plages de fonctionnement couvertes (figure 12)
et les pannes qui ont empêché l'exploitation efficiente
relevé dans le tableau 24.
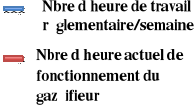
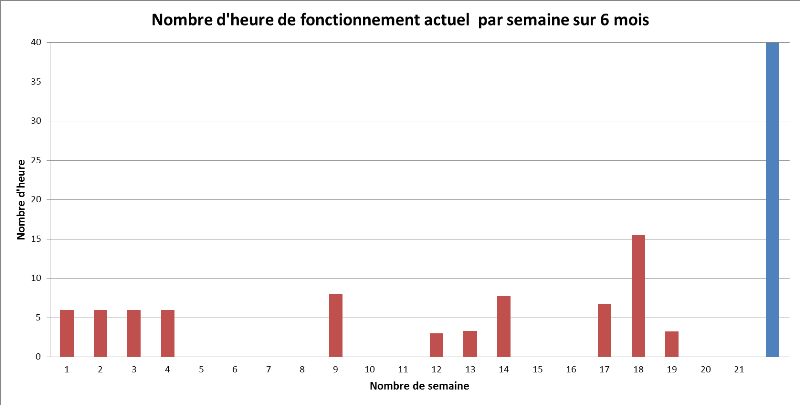
Figure 12 : Plage de
couverture sur les mois de Mars à Aout 2013
Causes des problèmes
|
Mars
|
Avril
|
Mai
|
juin
|
Juillet
|
Août
|
Pourcentage de jours avec des
problèmes
|
Gazeifieur (réacteur et auxiliaires)
|
3
|
5
|
7
|
7
|
9
|
2
|
30%
|
Générateur
(Maintenance et réparation)
|
0
|
0
|
0
|
0
|
3
|
10
|
11,82%
|
Ressources (biomasse et personnel)
|
7
|
4
|
5
|
1
|
2
|
5
|
21,82%
|
Autres (charges,organisationetc..)
|
5
|
6
|
4
|
16
|
5
|
4
|
36,36%
|
Total/184 jours
|
15
|
15
|
16
|
24
|
19
|
21
|
59,78%
|
Tableau 24 : Tableau
représentant les jours de non-fonctionnement et leurs causes
Ces résultats montrent que la plupart du temps c'est
les charges (BRF, usine de recyclage)qui sont en défaut ou le
gazogène qui présente des problèmes à savoir les
problème de goudron qui bouchent les systèmes de refroidissement
et le moteur, suivit de près par la biomasse à savoir sa
disponibilité et son conditionnement. Outre ces cas, la plateforme
étant plus utile pour la démonstration, ceci amène
à un problème d'organisation qui ne permet pas d'assurer la
continuité de fonctionnement. Ceci fait ressortir les facteurs pouvant
influencer sur la gestion de la plateforme de gazéification.
2.1.2.
Scénarios technico-économiques
Les éléments ci-après ont
été pris en compte dans l'estimation économique :
v cout OM : 3 % de cout d'investissement (inclus les
couts du charbon de bois, du fuel pour l'amorçage, de l'eau de lavage)
et ceci pour chaque scénario ;
v Cout personnel : deux opérateurs
qualifiés plus un opérateur non qualifié :
290 000 FCFA/mois, dans un souci de simplification des calculs on
considère quel que soit le taux de couverture le personnel sera
mobilisé en permanence, ce qui est spécifique au cas de
Songhaï et peut être revue en fonction des besoins et condition de
fonctionnement ;
v valeur d'actualisation en vigueur dans l'espace UEMOA de
8%.
v Matière première produit à
songhaï, car Songhaï est un centre agro-industriel et est a
même de se fournir par ses propre plantations ;
v Coût de la facture d'électricité
calculé sur la base de la facturation de la SBEE de 111 FCFA/KWh, qui
correspond au tarif appliqué aux abonnements professionnels.
L'estimation de la facturation a été faite en prenant un temps
de consommation d'heure/jour 30 minutes pour le démarrage et 30 minutes
pour l'arrêt ;
v Le productible en énergie est estimé sur 5
jours de fonctionnement par semaine sur toute l'année multiplié
par le taux de charge ;
Les hypothèses suivantes caractérisent le
système et sont communes à tous les scénarii :
Paramètres techniques du système :
§ Puissance installé 32 kW,
§ demande interne auxiliaires 10kW,
§ Taux de charge : 75 %
§ rendement de conversion : 20 %
§ source demande auxiliaire réseau nationale
§ temps de dépréciation : 10 ans
§ Moyenne de consommation ressource bois :1,37
kg/kWh
§ Moyenne consommation ressource coque de bois de
coco : 1,24 kg/kWh
§ Taux d'humidité de la biomasse : Entre 15
et 20 %
§ Température des fumées par
cogénération au niveau du séchoir à biomasse :
120°C
Paramètres financiers du système :
§ Coût capital investissement :
60 156 000 FCFA
§ Coût par kW installé
:1 671 000 FCFA/kW
§ Coût d'opération et de maintenance :1
804 680 FCFA
§ Cout personnel/an :
3 480 000 FCFA
§ Coût électricité facturé par
la SBEE : 328 512 FCFA
§ Coût matière première bois:51,2
FCFA/kWh
§ Coût matière première Coques:
24,8 FCFA/kWh
§ Coût traitement déchets : Non
évalué
Paramètres d'étude
technico-économique
|
Scénario
|
1(6h/jr)
|
2(12h/jr)
|
3(18h/jr)
|
Moyenne temps journalier d'utilisation
|
25 %
|
50 %
|
75%
|
Energie productible (kWh)
|
49 920
|
99 940
|
149 760
|
Consommation ressource bois (t/an)
|
68
|
139
|
205
|
Coût matière première (Bois)
FCFA/an*3
|
2 556 377
|
5 117 875
|
7 669 299
|
Coût matière première (coques de
noix de coco) FCFA/an
|
1 238 016
|
2 478 512
|
3 714 048
|
Investissement Total
(Bois)
|
68 325 569
|
70 887 067,29
|
73 438 492
|
Investissement Total
(coques de noix de coco)
|
67 007 208
|
68 247 704
|
69 483 240
|
TRI avec le bois (an)
|
14,1
|
6,8
|
4,5
|
TRI avec coques (an)
|
13,8
|
6,5
|
4,3
|
Prix élec FCFA/kWh
(Bois)
|
217
|
112
|
78
|
Prix élec FCFA/kWh
(coques de noix de coco)
|
213
|
108
|
74
|
Tableau 25 : Etudes
technico-économiques de la plateforme
2.2. Analyseset
recommandations
L'étude technico-économique de la plateforme
gazeifieur nous permet de dégager les trois scénarios de base qui
font ressortir l'influence nette du taux de couverture journalier et du taux de
charge sur le cout de l'électricité, outre celle des coûts
d'investissement et coût d'opération et de maintenance.
Les différents scénarios nous permettent de
dégager un coût et le dégagement de
bénéfices à partir de 50% de couverture
journalière. Le cout de la matière et son conditionnement comme
décris dans l'étude de la ressource influence clairement.
On observe que le coût de l'électricité
avec le bois comme combustible, peut alors chuter de 217 FCFA/kWh
à 78 FCFA/kWh,quand on monte de 25% à 75% de couverture
journalière à 75% taux de charge, ce qui devient attractif et
largement inférieur au prix du réseau qui est de 111
FCFA/kWh.
Le prix de l'électricité ne varie pas trop avec
l'utilisation des coques de noix de coco et est entre 213 et
74FCFA/kWhpour une variation de 25%à 75 % de couverture
journalière. Par contre elles présentent l'avantage de ne pas
nécessiter ni trop le temps et de moyenspour le conditionnement.
Les résultats nous amènent à conclure
qu'à partir de 50 % de couverture la plateforme pourrait commencer
à dégager des bénéfices et rendre la technologie
attractive et dégager des bénéfices à 75% de taux
de couverture.
Au-delà des pannes des équipements de la
plateforme sur le gazeifieur et les auxiliaires qui paralysent le
fonctionnement, le système fourni de l'électricité
à des charges qui ne sont pas très fiables et qui subissent trop
de pannes ou dépendent de la programmation des activités
inhérents à ces sections, ce qui amène à des
périodes creuses pouvant s'étaler sur des semaines ou le
gazeifieur ne fonctionne pas. Il faudrait dans ce cas multiplier les charges
autour de la plateforme ou penser à l'injecter sur le réseau
interne du centre.
La non-disponibilité de la biomasse bien conditionner
fait partie des facteurs qui réduisent l'efficacité de la
plateforme.Ce facteur est vraiment déterminant car il influe sur le prix
de l'électricité.
Les problèmes et leurs causes relevés sur les six
mois d'étudesont signalés dans le tableau 24,et cela montre que
la technologie n'est pas bien maitrisée. Les équipements dont
certains critiques pour la valorisation électrique étant
régulièrement en pannes rendent le systèmedifficilement
rentable sauf dans des conditions de fonctionnement optimales.
Une étude comparée des retours d'expérience
et de notre système font ressortir les points suivants :
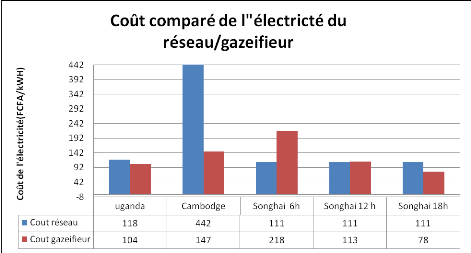
Figure 13 :Coût
comparé de l'électricité du réseau et du
gazeifieur
La figure 13 montre qu'on est généralement toujours
généralement en deca du coût de l'électricité
du réseau, sauf dans les cas où on n'a pas un bon taux de
couverture journalière comme dans le scénario N°1 de
Songhaï. La figure 14 suivante montre la variation du coûtce qui
montre la fluctuation du coût dépendamment du taux de couverture
de 4 à 75%.
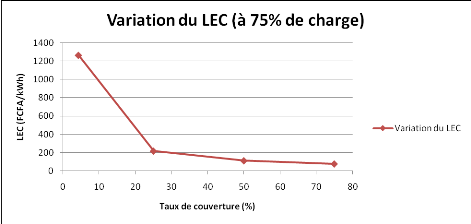
Figure 14 : Variation
du LEC Gazeifieur en fonction du Taux de couverture
journalière
Cette variation est observé sur la plupart des
systèmes basé sur la gazéification, nous pouvons prendre
par exemple le cas de la plateforme dans le village de Anlong Ta Mei Battambang
disposant d'un gazéifieur de 9 kW on arrive à diviser le prix
par trois (3) quand il fonctionne avec un taux de charge et de couverture
élevé. A 25% de taux de couverture à Songhaï on reste
perdant et le TRI passe au double qu'à 50% de charge alors que quand on
estime un temps de dépréciation sur dix (10 ans), on a tout
intérêt à augmenter ce taux de couverture.
Le coût d'investissement aura une grande influence car
le montant dépensé regroupe tous les frais liés au
transport et à l'ingénierie du point de fabrication (Inde)
à l'installation (Porto Novo),on pourrait réduire fortement cet
impact en se fournissant dans un rayon restreint mais on est limité par
le manque de fournisseur. On remarque par exemple que dans la
littérature sur de telle puissance on trouve des coûts de 1000
à 1500 Dollar/kW installé alors que sur la plateforme
Songhaï on est à 2000 dollar/kW installé (investissement
pour le gazeifieur de 80 milles dollar et 40milles dollars pour le
bâtiment pris en compte).
Dans le cas de Songhaï Porto-Novo il faudrait envisager,
afin de réduire les couts d'exploitation et réduire les
périodes liés à des pannes autres que le gazogène,
une valorisation thermique du syngaz vers l'usine de production de jus ou vers
d'autres des postes de consommation relocaliser vers Songhaï-Est.
Concernant des projets éventuelsd'installation de
gazéifieur sur d'autres sites Songhaï qui disposent soit de grande
de surface pour les plantations comme Parakou,Savalou ( au moins 400 ha) ou de
matière première ( balles de riz) comme kewindji par exempleil
faudrait s'assurer de la flexibilité de la technologie surtout en termes
de ressources en se fournissant avec d'autres types de biomasse comme les
coques de noix de coco ou les coques de noix de palmes qui sont à notre
avis pas assez exploités compte tenu de l'abondance noté dans
l'environnement béninois.Dans ces cas on devrait s'orienter vers
d'autres fournisseurs avec des technologies (gazéifieurou
bi-étagés par exemple) de traitement du syngas
(intérêt du traitement catalytique de la biomasse) plus efficace
et n'étant pas assujettie à des pannes fréquentes venant
des auxiliaires ou du gazogène lui-même ; ou
privilégier les générateurs `'Dual Fuel'' pour
suppléer au carence de la gazéification comme dans le cas du
retour d'expérience au Cambodge ou on arrive à avoir une
installation performante pour un taux de remplacement du diésel de
77%.
Dans de futur cadre d'étude technico-économique
il faudrait en plus prendre en compte le calcul de la Limite de Distance
Economique (EDL :Economic Distance Limit) qui est déterminé
en faisant une analyse comparée du coût de cycle de vie du
système et celui de l'extension du réseau.On pourrait en outre
s'appuyer dans le cadre de futurs projets de gazéification sur les
étapes suivit sur les expériences validées
d'électrification rurale des villages Hosahalli et Hanumanthanagara afin
de mieux cerner les tenants et les aboutissants surtoutdans un contexte aussi
délicat que l'Afrique de l'Ouest.
Le coût affecté au traitement des déchets
est nulle car nous avons pu remarquer que bien que disposant d'un
système de traitement de l'eau de lavage, il n'a pas été
procédé à son utilisation, le centre
préférant la valoriser pour la fertilisation des champs.
La cendre, le goudron et les particules fines recueillies ont
étéutilisées pour le compostage. La sciure issue du
conditionnement du bois est utilisée comme matière
première pour la production des champignons. Il faudrait
néanmoins procéder à une étude pour montrer
l'impact de l'application de ces types de valorisation en particulier l'aspect
environnemental pour l'eau de lavage et surtout économique sur le reste
des déchets car cela pourrait devenir non négligeable
dépendamment de la puissance installée sur de futur
plateforme.
CONCLUSION ET
PERSPECTIVES
L'étude menée sur la plateforme
gazéifieur du Centre Songhaï fait ressortir une similarité
envers d'autres projets de gazéification. Cela nous a permis de faire
une étude technico-économique en nous basant sur des
scénarii avec des taux de plage de fonctionnement variable afin de
savoir comment optimiser la gestion d'une telle plateforme. Le contexte
d'étude assez particulier de Songhaï nous avons pu effectuer des
expérimentations et des calculs économiques qui sont assez
satisfaisants mêmes si on peut s'avancer vers une étude plus
longue sur le point technique par des tests de longues durés
appuyés d'une instrumentation poussée pour déterminer les
impacts du fonctionnement sur le temps sur ce type d'installation.
Il est clair d'après notre
étudetechnico-économique, qu'on se trouve en présence
d'une plateforme de démonstration dont le but actuel n'est pas forcement
d'arriver à se suppléer totalement au réseau mais
plutôt cerner les aspects techniques, économiques, sociaux et
environnementaux à prendre ne compte pour l'installation de
système de production décentralisé efficient et
compétitif.
Le cout de l`électricité de la plateforme
Songhaï qui varie de 217 FCFA/kWh à 78 FCFA/kWh
quand on passe de 25% à 75% de taux de couverture de fonctionnement
journalière relève l'importance de faire fonctionner la
plateforme au-delà des 50% pour dégager des
bénéfices nettes, ce qui pourrait être
éventuellement confirmé par des tests d'endurances appuyer par
une instrumentation poussée.
L'étude de la ressource est un impératif quel
que soit le système à installer car il en va de la fourniture
d'une l'électricité stable et continue et compétitif.
Nous avons pu faire ressortir que ce coût dépend forcement des
charges et qu'il faut dans le cas d'un gazéifieur prévoir
d'instaurer des plantations durables bien avant l'installation de la plateforme
elle-même ou s'assurer d'un approvisionnement continue et flexible selon
la matière afin de rendre cette énergie propre et moins couteuse.
Nous avons aussi pu faire ressortir que le taux de
60 % de temps de non fonctionnement et le taux de charge ,
qu'il faudrait s'assurer d'avoir des équipements assez efficaces et pas
trop complexes à gérer et dont la maintenance qui doit être
aisé. Cela alors pourrait ne pas causer trop d'arrêt de
fonctionnement de la plateforme car il faut relever que l'intérêt
d'installer ce genre de technologie est qu'il soit gérable par un
opérateur formé et pas forcément qualifié au
départ.
Cette étude nous permis donc de relever les points
clés à prendre en compte afin de rendre cette technologie
adaptable au concept `'ville rurale verte'' à savoir :
Ø la matière première depuis la mise en
terre jusqu'à son conditionnement (découpe,séchage
etc...),
Ø le coût d'investissement et le choix de
technologie ;
Ø le taux de couverture journalière et le taux
de charge ;
Ø la valorisation des déchets issus du
process.
Cela pourrait aider stimuler l'électrification rurale
et un développement durable par la biomasse énergie et faire
chuter les barrièressur la technologie de gazéification de la
biomasse.
BIBLIOGRAPHIE
[1]Fondation d'entreprise Alcen pour la
connaissance des énergies, 2011
[2] CIRAD-Forêt,2001, Observatoire des
énergies renouvelables, Pyrolyse et gazéification dela
biomasse pour la production d'électricité, rapport
ADEME.
[3] Gai, Chao et Dong, Yuping.
2012Experimental study on non-woody biomass gasification in a
downdraft gasifier.Jinan 250061 : s.n.
[4]Procédis ,2004Pyrolyse -
Gazéification de déchets solides.
[5] Floriane, Mermoud.,
2006,Gazéification de charbon de bois à la vapeur d'eau :de la
particule isolée au lit fixe continu, thèse INPT
2006,CIRADMontpellier : s.n.,
[6]Dimitri Kabore ;
2012 ,Mémoire de fin d'étude, 2ie Master 2
énergie.
[7] F.S. Javadi et al., 2012,Global policy of
rural electrification, Elsevier
[8]Matthew Owen et Al ;2012, Can there be energy
policy in Sub-Saharan Africa without biomass?; Elsevier.
[9] Ralph E.H.SIMS et al.2003 ; Biomass and
ressources, Elsevier.
[10] V.Siemons,2000,''Identifying a Role For
Biomass Gasification in Rural Electrification in Developing Countries: The
economic Perspective.'';Elsevier.
[11] Anil K.Rajvanshi,1986, `'Biomass
Gasification'',Chapter (No. 4) in book «Alternative Energy in
Agriculture», Vol. II, Ed. D. Yogi Goswami,CRC Press, , p. 83-102.
[12] Dasappa ;2011,S. Potential of biomass
energy for electricity generation in sub-Saharan Africa. Energy Sustain
Dev;15(3):203-13.
[13] Buchholz and Da Silva,2010, «Potential
of Distributed Wood-based Biopower Systems Serving Basic Electricity Needs in
Rural Uganda.», , Elsevier
.[14] Y.S. Mohammed et Al, 2012,An overview of
agricultural biomass for decentralized rural energy in Ghana,,Elsevier.
[15]Ntshengedzeni S. Mamphweli et Edson L.
Meyer ,2009; Implementation of the biomass gasification project for
community empowerment at Melani village, Eastern Cape, South Africa;.
[16]B. Musinguzi et Al ;2012 , Thermal
characterization of Uganda's Acacia hockii, Combretum molle, Eucalyptus grandis
and Terminaliaglaucescens for gasification,
[17]Barry Fischer et Attilio Pigneri ;2010 ,
Potential for electrification from biomass gasification in Vanuatu.
[18]Rogier van Mansvelt;2011 ,IFC Gasifier
Study.
[19]Orkide Akgün et Jyrki
Luukkanen,2011;Extension of rice husk gasification technology for
electricity generation in Cambodia, Energy Procedia.
[20] S.M. Shafie et al ;2012 , A review on
electricity generation based on biomass residue in Malaysia.
[21]T. Buchholz and T. Volk,2007 ,
«Technology and assessment report for a 200 kW gasifier producing
electricity in Uganda», State University of New York, Syracuse, NY.
[22]Hitofumi Abe et al.;2007 ,Potential for
rural electrification based on biomass gasification in Cambodia, Elsevier.
[23]N. H. Ravindranath et Al ;2004, Sustainable
biomass power for rural India: Case study of biomass gasifier for village
electrification, IISc Bangalore.
[24]
http://fr.wikipedia.org/wiki/Bois_énergie
consulté le 25 Février 2003.
[25] T.Buchholz et al; 2012, Electricity from
wood-fired gasification in Uganda-a 250 and 10 kW case study.
[26]Rousset P,2008, Guide technique pour une
utilisation énergétique des huiles végétales.
[27]
www.espaceagro.com
consulté le 19 Mars 2013
[28]Groupe de Coordination sur les Bois
RaméauxUniversité Laval, Québec, Canada
[29]Gilles Lemieux et al ;2003,La
technologie pédogénétique du BoisRaméal
Fragmenté (BRF), une ressourcenaturelle qui contribue à
l'établissementet au maintien de la fertilité des sols
auSénégal et au Bénin».
ANNEXES
Annexe 1 : Résultat de l'analyse du
taux d'humidité moyen du bois d'acacia auriculiformis de Songhaï
Porto-Novo
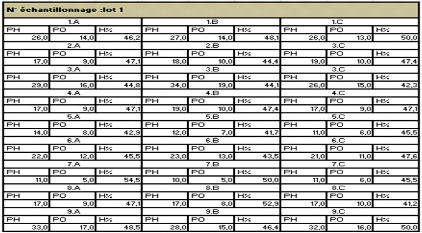
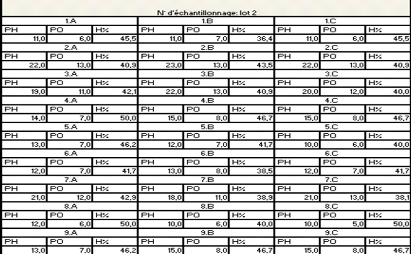
Légende : PH : poids humide
PO :poids sec %H : pourcentage humidité
Annexes 2Résultats de tests
réalisés avec les compteurs avec le bois et les coques de noix
de coco.
Bilan avec les coques de noix de coco
|
% Charge
|
N° Essai
|
Heure Démarrage groupe
|
Heure arrêt groupe
|
Nombre d'heure
|
Quantité de coques consommée
Kg/kWh
|
Energie
Produite (kWh)
|
Courant d'appel
(A)
|
?T° eau de lavage
(°C)
|
T° séchoir
(°C)
|
Observations
|
75%
|
1 (12/07/13)
|
15h40
|
17h40
|
02h00
|
0,42
|
150
|
Min 37
Max 45
|
1
|
120°C
15min
|
Quantité presque infime de particule fine,
T° Cyclone 211°C
|
2 (20/08/13)
|
10h00
|
11h30
|
02h00
|
0,39
|
140
|
Min 38
Max 42
|
0,8
|
120 °C en 10 min
|
T° du cyclone 160 <T°< 200°C
|
3 (26/09/13)
|
15h30
|
17h30
|
02h00
|
0,35
|
170
|
Min 37
Max 45
|
1
|
120°C en 10 min
|
T° du cyclone 180 <T°< 220°C
|
BILAN AVEC LE BOIS
|
% charge
|
N°Essai
|
Nombre d'heure
|
Pmoy
(kW)
|
Quantité de bois consommée
(Kg)
|
Consommation spécifique (Kg/kWh)
|
Energie
enregistrée (kWh)
|
Courant d'appel
(A)
|
?T° eau de lavage
(°C)
|
T° cyclone
|
Observations
|
31%
|
1 (24/08/13)
|
2h00
|
10
|
|
2,85
|
20
|
Min : 19
Max : 20
|
0,8
|
150°C+/- 10°C
|
néant
|
2(06/06/13)
|
2h00
|
10
|
|
2,6
|
20
|
Min : 18
Max : 20
|
1
|
110°C +/- 10°C
|
néant
|
3(07/06/13)
|
2h00
|
10
|
|
3
|
20
|
Min : 18
Max:20
|
1,4
|
137°C+/- 10°C
|
néant
|
75%
|
1 (16/06/13)
|
2h00
|
|
|
0,67
|
80
|
Min : 35
Max: 40
|
0.7
|
150°C+/- 10°C
|
3 arrêts du Brf de 5 min chacune
|
2(17/06/13)
|
2h30
|
|
|
0.60
|
130
|
Min : 36
Max : 41
|
1
|
200°C+/- 10°C
|
2 arrêts Brf de 5 min
|
3(18/06/13)
|
2h30
|
|
|
0,4
|
200
|
Min : 37
Max:45
|
0 ,7
|
236°C+/- 10°C
|
3 arrêt Brf de 5 min chacune
|
4(04/07/13)
|
5h00
|
|
|
0,53
|
330
|
Min : 36
Max:41
|
0,8
|
220°C+/- 10°C
|
néant
|
5(08/07/13)
|
5h00
|
|
|
0,55
|
280
|
Min : 36
Max:44
|
0,7
|
210°C+/- 10°C
|
néant
|
6(09/07/13)
|
4h00
|
|
|
0,60
|
240
|
Min : 37
Max:45
|
1
|
226°C+/- 10°C
|
néant
|
Annexe3 :Courbe ombrothermique et courbe
de température mensuelle moyenne (mesure sur Source Département
géographie Université Abomey-Calavi,Bénin
2012)
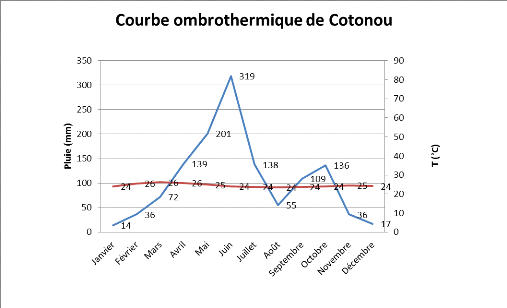
Annexes 4 : Gestion de la plateforme de
gazéification
1. Chargement du système
a. Chargement du charbon de bois
Après s'être assuré que le système
d'extraction de cendre à la base est boulonné correctement au
réacteur, et la vis du convoyeur est à l'arrêt, on peut
charger le réacteur avec le charbon de bois sec, de
préférence jusqu'au-dessus d'un (1) mètre au-dessus du
niveau des orifices d'air. Le charbon de bois doit être
découpé en petit morceaux mesurant 15 x 15 x 15
millimètres et chargé suivi de plus grand de 30 x 30 x 30
millimètres. Il faut s''assurer qu'aucun élément
étranger comme des pierres ou du sable n'est chargé avec le
charbon de bois.
b. Chargement de la biomasse
La gamme de la biomasse qui peut être employée
dans le gazéïfieur est les essences de différentes de
bois, noix de palmes et coques de noix de coco etc., dont la densité est
au-dessus de 300 - 350 kg/m3.
La biomasse doit une granulométrie de 30x 30 x 30mm,
et avoir la teneur en humidité maximum de 12-15%.De plus petites
pièces pourraient égalementêtre utilisé (25 x 10 x
10 millimètres), mais la quantité est limitée un maximum
de 50% du mélangeau total pendant chaque étape du chargement.
Le premier chargement générateur gaz exige du
réacteur d'être complètement chargé avec le
charbon de bois sec (100 - 120 kilogrammes),cependant, les chargements
suivants n'exigent pas le chargement frais du charbon de bois.
2. Procédure de
démarrage et d'arrêt
a. Procédure de démarrage
v Etape 1 : démarrage du gazéifieur
o 1.1 Démarrer le chiller et fixer la
température de consigne à 10°C,
o 1.2 Ouvrir après le couvercle du
réacteur,
o 1.3 Allumer le convoyeur de cendre du
réacteur (évacuation de 1,5kg durant les 30 secondes de
fonctionnement préconisé),
o 1.4 Préparer la torche (sans
allumer) qui servira pour l'allumage du gazéifieur et ensuite pour
l'ignition de la flamme de la torchère,
o 1.5 Ouvrir partiellement la vanne du
bruleur et fermer la vanne d'entrée des filtres,
o 1.6 Allumer le Chilled water pump et le
direct Cooler pump (main ou standby selon le choix de mise en marche),
o 1.7 Remplir le réacteur de
combustible,
o 1.8 Ouvrir les 3 orifices d'entrée
d'air : buses d'air (air Nozzles),
o 1.9 Allumer la torche et le placer au
niveau des buses d'air jusqu'à observer le combustible bruler dans le
réacteur,
o 1.10 Attendre 5 min environ la
production du syngaz et mettre le feu au niveau de la torchère. En cas
de non production de syngaz se référer à la section
défaut de fonctionnement en annexe,
o 1.11 Faire bruler le gaz pendant 10
à 15 min pour les démarrages de routine,
o 1.12 Alimenter en biomasse le
réacteur dans un intervalle de temps régulier selon la charge,
o 1.13 Faire fonctionner le gazeifieur en
brulant le gaz produit pendant 2 heures au premier démarrage
après maintenance du réacteur pour s'assurer une bonne
qualité du gaz pour le moteur.
NB : Si le précédent démarrage date
de moins de 2 jours ignorer alors les étapes 1.4 et
1.9.
Avant tout démarrage faire le test de fuite
avec l'équipement approprié.(cf manuel constructeur)
v Etape 2 : Démarrage du
générateur
o 2.1Après s'être assurer de la
qualité du gaz(cf manuel constructeur), et du bon fonctionnement du
process, démarrer le souffleur du bruleur et fermer sa vanne,
o 2.2 Ouvrir les vannes d'entrées et de
sorties des filtres,
o 2.3 Vérifier l'arrivée du gaz au
niveau du by-pass et refermer,
o 2.4 Tourner la clé de démarrage
moteur et faire varier la vanne du by-pass pour démarrer et le refermer
quand le générateur prend,
o 2.5 Allumer la pompe du séchoir
(capacité 280 kg de bois humide à 30% pendant 3 heures pour
atteindre 15% d'humidité) et faire varier la valve de température
pour obtenir 100°C,
o 2.6 Sur le tableau électrique basculer
l'alimentation de la plateforme du réseau (situation de
démarrage) vers le groupe électrogène à syngaz en
actionnant l'inverseur,
b. Procédure d'arrêt
v Partie 1 : Arrêt du
gazéifieur
o Arrêter le ventilateur d'aspiration du syngaz
o remplir le réacteur de combustible adéquat
o fermer les orifices d'air
Si le générateur est en fonctionnement
alors :
1- Arrêter les charges connectées
2- Basculer l'inverseur du groupe vers le réseau
3- Fermer la vanne d'entrée des filtres et ouvrir la
torchère et initier la flamme
v Partie 2 : arrêt de
gazéifieur
o Garder les vannes d'entrée et de sortie des filtres
fermées
o Attendre la fumée à la sortie du haut du
réacteur
o Arrêter les pompes et tous les équipements depuis
le tableau de commande
o Remplir le haut du réacteur d'eau dans la zone
prévu à cet effet et le refermer afin d'éviter les
entrées d'air
o Arrêter le tableau de commande
o Attendre 5 min et refermer la vanne du bruleur
c. Gestion du
système
Le fonctionnement normal du gazeifieur peut être
assuré et vérifier par :
· une inspection visuelle de la zone de pyrolyse au niveau
des orifices de prise d'air qui doit présenter une couleur vive
· Un flux continu de la biomasse dans le
réacteur : ce point est déterminant pour un avoir un gaz de
bonne qualité
· Une bonne pression observée au niveau des
manomètres : vérifier les chutes et les montées de
pression qui peut être due à une accumulation de cendre au niveau
du réacteur empêche le flux normal du gaz qui peut être
régler en faisant fonctionner l'extracteur de cendre
· Un rechargement en combustible à interval
régulier du réacteur selonle type de biomasse et le régime
de fonctionnement
Annexes 5 :
Procédure de maintenance de quelques équipements de la
plateforme
a) Maintenance du Cyclone, scrubber 1 et 2 et de
l'extracteur
Il a été défini qu'en cas de pression
élever au niveau du réacteur, du cooler 1 et 2 du scrubber, du
cyclone et des filtres il faut procéder à l'extraction de cendre
au niveau du réacteur.
La méthode est de :
§ démonter les deux trémies du réacteur
pour les nettoyer
§ ouvrir la partie de l'extracteur de cendre pour extraire
le surplus accumulé.
b) Vidange du réacteur
La maintenance consiste à vider le réacteur en
extrayant tous les résidus du précédent
démarrage : charbon, bois, coques de coco ou de noix de palme, et
cendre. Cette maintenance est à faire une fois que la chute pression au
niveau du réacteur dépasse et se maintient à 150 mm. Il
sera procédé à la récupération du charbon,
et du bois coques de coco ou de noix de palme pour une utilisation
ultérieure. La méthode est la suivante :
§ attendre une journée après le
précédent fonctionnement du gazéifieur afin que celui se
refroidisse
§ ouvrir le bas du réacteur
§ s'équiper des équipements de
sécurité : gants, cache nez, lunettes et blouse
§ extraire à l'aide d'une tige en fer le bois coques
de coco ou de noix de palme et le charbon du réacteur sur des plaques en
métal
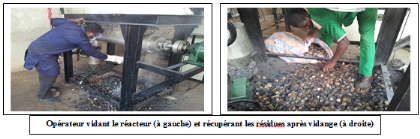
§ Après avoir éteint le reste de flamme dans
le charbon, séparer et récupérer les résidus
(cendres, bois et charbon de bois),
§ Refermer le bas du réacteur et procéder au
remplissage,
§ Peser entre 120 et 150 kg de charbon de
bois et remplir le réacteur jusqu'à atteindre ai moins un (1)
mètres au-dessus des orifices d'air,
§ Ajouter du bois sec jusqu'à remplir
complètement le réacteur en laissant 30 cm de marge.
c) Nettoyage et remise en état du souffleur et des
filtres
Afin de limiter l'encrassement des filtres et rendre le gaz
plus propre, il faut procéder au nettoyage du souffleur
accompagné du remplacement des filtres.
La méthode pour remplacer les filtres consiste
à :
§ enlever la partie supérieure du filtre
§ ouvrir et enlever les sacs de filtration usagés et
les lavés;
§ procédé au remplacement par des filtres
déjà nettoyés issus de la précédente
maintenance
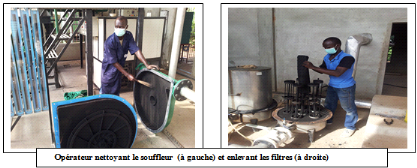
§ refermer hermétiquement la partie
supérieure
§ d) Maintenance des cooler
Les variations intempestives de pression observées au
niveau des manomètres des cooler nous indiquent la possibilité
d'un encrassement qu'il faut vérifié et nettoyé.
La procédure standard est de démonter les
équipements en question et enlever le goudron accumulé sur les
injecteurs d'eau des cooler et dans la tuyauterie à l'aide d'une brosse
métallique et ensuite de procéder à un rinçage
à l'eau avant de les replacer.
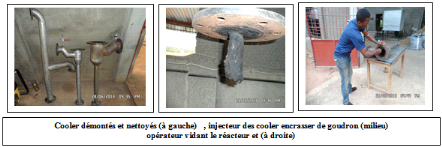
e) Maintenance du chiller et de l'eau de refroidissement
extérieure
La maintenance de ces équipements se fera chaque 150
heures de fonctionnement. Pour le chiller, l'état d'encrassement peut
s'observer en fonctionnement au niveau du flotteur dont le niveau
dépasse la marque inferieure autoriser.
Pour faire la maintenance du chiller il faut :
§ selon l'état d'encrassement ouvrir le tank, enlever
le goudron en suspension avec une écumoire, ensuite nettoyer les parois
et vider totalement l'eau sale,
§ renouveler de l'eau de lavage à partir d'un
appoint d'eau en respectant le niveau du flotteur,
§ Mettre en marche et vérifier s'il atteint la
température de consigne.
Concernant l'eau de refroidissement extérieure
après 60 heures de fonctionnement il faut
procéder à son renouvellement suivant les étapes
suivantes :
§ Chercher un tuyau assez long pour arriver au BRF et une
motopompe accompagné des élastiques pour assurer
l'étanchéité,
§ Vider le bac et s'assurer de nettoyer le fond,
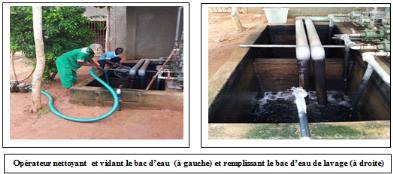
§ Remplir à nouveau le bac à partir d'un
appoint d'eau.
Annexes 6 :
Point sur la sécurité
La plateforme de gazéification est une plateforme de
conversion thermochimique, dans ce sens elle doit respecter certaines mesures
de sécurité.
Equipements de
protection individuels
Chaque opérateur doit avant toutes interventions que ce
soit pour le fonctionnement (démarrage, arrêt) ou la maintenance
s'équipé d'équipement de protection individuel.
L'opérateur doit au minimum avoir à sa disposition les
éléments ci-après :
§ Une blouse
§ Des gants isolants adaptés
§ Des lunettes de protection adaptée
§ Un Casque anti bruit
§ Un cache nez
Equipements de
protections collectifs
La plateforme doit pour le bien des personnes et des biens
s'équiper des équipements de protections collectives. Le Centre
étant aussi un lieu de visite, la plateforme doit être
balisé afin de délimité et restreindre l'accès
à certains espaces sensibles comme par exemple la salle du groupe, tous
les points chauds (le réacteur, le cyclone, le séchoir
etc...).
Les équipements ci-dessous constituent une liste
d'équipements minimum à installer :
§ Des panneaux expliquant la sécurité et les
démarche à suivre en cas de problèmes :
électrocution, asphyxie, brulure, etc..
§ Des affiches signalétiques des différents
éléments sur lesquels faire attention : chaleur,
électricité etc..
§ Des extincteurs accessibles et adaptés
Affiches signalétiques
|
Localisation
|
· Incendie
· Matières inflammables
· Travaux Points Chauds

|
· Réacteur
· Cyclone
· Bruleur
· Séchoir
· Moteur
|
· Electrique

|
· Tableau générale
· Moteur
· Disjoncteur générale
· Réseaux de câble
|
· Thermique

|
· Réacteur
· Cyclone
· Bruleur
· Séchoir
· groupe
|
· Chutes
 

|
· Réacteur
· Salle du groupe
|
· Chimique

|
· Réacteur
· Réseaux de tuyauterie de syngas
|
· Manutention Mécanique et
Manuelle

|
· Réacteur
|
· Autres

|
|
· Explosion

|
· Réacteur
· Réseaux de tuyauterie de syngas
|
· Anoxie

Locaux Accès libre
Locaux Accès Réglementé
|
· Réacteur
· Réseaux de tuyauterie de syngas
|
· Bruit

|
Plateforme gazeifieur
|
Annexes 6 : Méthodologie d'application
du BRF
Ø Les essences forestières
Comme elles sont les atouts majeurs en produisant les rameaux
nécessaires à fragmentation pour en donner des BRF, elles doivent
être disponibles à proximité oubien être
implantées comme partie intégrante au programme dans des terres
choisiesà cet effet, Songhaï Centre et les sites annexes comme
Parakou et Savalou en particulier disposent quant à elle d'une surface
de plus quatre Cents (400) hectares avec une assez bonne proportion
destinée à l'agroforesterie qui regorge d'essence
variée.
Ø La fragmentation-broyage
Les rameaux, une fois prélevés, doivent
être fragmentés ou broyés selon lesmodes
utiliséspour que la dimension des particules ne dépasse pas 10
à 12 cm.Ainsi réduites, ces particules de rameaux sont faciles
à manipuler et leurincorporation au sol est mieux répartie.
Les mécanismes pédogénétiques sont
ainsirapidement amorcés par les micro-organismes qui en sont les uniques
responsables.La fragmentation est plus facile si elle est faite à l'aide
d'appareils conçus à ceteffet, mais elle peut être faite
manuellement à l'aide de machettes, même si le travailest
fastidieux.
Ø L'incorporation au sol
L'épandage des BRF sur les champs peut être fait
à la main, si lesparcelles sont de petites dimensions (de 10 à 20
m²). Pour des champs de plusgrandes superficies, le motoculteur peut
s'avérer un outil utile et efficace.On doit incorporer les BRF au sol
quand ils sont frais ou séchés, évitant
ainsitoutesdégradations par moisissures ou bactéries, afin de
favoriser le contact avec lesol pour amorcer tous les mécanismes de
régénération.
Les BRF doivent être incorporés aux premiers 10
cm du sol. Quant auxquantités, ellespeuvent varier selon
l'intensité des carences, la texture du sol etl'efficacité des
différentes essences forestières ou mélange d'essences.
Les volumespeuvent varier de 150 à 200 m3/ha.
|