1.1.1.1. Controlled-expansion pistons
Controlled-expansion pistons are pistons with struts that
control thermal expansion. They are installed in gray cast iron crankcases. The
main target of controlled-expansion piston designs, and many inventions in this
field, was and still is to reduce the relatively large differences in thermal
expansion between the gray cast iron crankcase and the aluminium piston
We distinguish in this category the Autothermic pistons,
slotted at the transition from the piston crown to the skirt, at the height of
the oil ring groove. They are characterized by their particularly quiet running
behaviour.
The unalloyed steel struts cast in between the skirt and the
piston pin boss, together with the light alloy that surrounds them, form
control elements. They reduce the thermal expansion of the skirt in the
direction that is critical for the
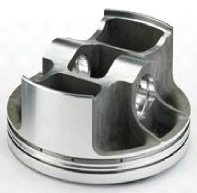
Fig.1.2: BOX-type piston
guiding of the piston in the cylinder.
1.1.1.2. Box-type pistons:
Compared with controlled-expansion pistons, this piston type
is characterized by its reduced mass, optimized support, and box-like, often
slightly oval skirt design. The box-type piston is compatible with both
aluminium and grey cast iron crankcases. With a flexible skirt design, the
difference in thermal expansion between the gray cast iron crank case and the
aluminium piston can be compensated very well in the elastic range. If the box
width is different on the thrust and antithrust sides, the piston is referred
to as an asymmetrical duct piston. Box-type pistons are cast or forged.
1.1.1.3. Forged aluminum pistons:
In engines with very high power densities--such as highly
loaded
turbocharged gasoline engines--cast pistons reach their
limits. Forged pistons are a particularly good fit for this area of
application; Figure 1.15. Their strength advantage in the temperature range of
up to about 250°C improves the load carrying capacity for lateral forces,
and increases the load carrying
8
Chapter 1: Overview on engine's piston
capacity of the pin bore and the fracture toughness. Forged
pistons are therefore especially well suited for high-speed concepts and
turbocharged engines. Because of the high ductility of the forged material,
they also react more tolerantly peak pressures that can arise if an engine is
operated very close to the knock limit. This allows lower ring land widths,
among other things, and therefore lower compression heights. Since the
manufacturing process is very stable, the forged pistons can be designed to the
limit in order to minimize component weight.
1.1.2. Pistons for diesel engines 1.1.2.1. Ring
carrier pistons
Ring carrier pistons; have been in use since 1931. The first
and at times even the second piston ring are guided in a ring carrier that is
securely joined to the piston material by metallic bonding.
The ring carrier is made of an austenitic cast iron with a
similar coefficient of thermal expansion to that of the piston material. The
material is particularly resistant to frictional and impact wear. The top ring
groove, which is the most vulnerable, and the piston ring inserted in it are
thereby effectively protected against excessive wear. This is particularly
advantageous at high operating temperatures and pressures, which are
particularly prevalent in diesel engines.
|
|
Fig 1.3: Ring carrier piston
|
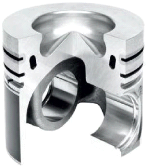
Fig.1.4: Ring carrier piston with cooling gallery
1.1.2.2. Cooling gallery pistons
The cooling gap inside the piston head is generally used to
optimize heat extraction. The high-speed collision of the engine oil on the
gallery surfaces improves the heat transfer capacity due to the impact caused
by the movement inside the cylinder. The heat flux removed by the cooling
gallery can reach 60% to 70% of the total heat transmitted to the piston by the
combustion gases, thereby effectively reducing the thermal loading of the
piston. When the engine is running, the cooling oil is injected from the oil
jet nozzle into the gallery through the inlet hole, flows in the
circumferential direction and exits the gallery through the exit hole, the
cooling oil does not fill the piston galley, the cooling oil exits the gallery
at high speed under the inertia of the movement
However, the structure of the cooling gallery limits to some
extent the resistance of the piston. With the steady increase in the maximum
pressure inside the diesel engine there is also the prolonged exposure of the
engine oil to higher temperatures in the piston cooling gallery which causes a
degradation of the characteristics of the lubricant which will not only affect
the piston but all engine components and carbon build-up, thereby reducing
cooling efficiency and resulting in overheating.
9
Chapter 1: Overview on engine's piston
1.1.2.3. Optimized monobloc steel
pistons:
This piston type is a single-piece forged steel piston that is
greatly weight optimized. With a small compression height (to less than 50% of
the cylinder diameter) and machining above the pin boss spacing (internal), the
piston mass, including the piston pin, almost corresponds to the mass of a
comparable aluminium piston with piston pin. In order to improve the piston
cooling, the outer cooling cavity is closed off by two cover plate halves. The
MONOTHERM® piston is used in passenger car and commercial
vehicle engines with peak cylinder pressures of up to 20 MPa.
1.1.2.4. Composite pistons
|
|
Fig.1.5: Optimized monobloc steel
piston
|
The composite piston enables the incorporation of cooling
cavities and the combination of the properties of various materials in one
piston. The performance range of four-stroke engines with composite pistons
extends from 500 to 30,000 kW, with up to 20 cylinders. Areas of application
include genets, main ship drives and auxiliary ship drives, and heavy
construction and railroad vehicles.
Here are many variants of composite pistons. Common to them
all is a design consisting of two main constituents: the piston crown with the
ring belt (upper part of piston) and the piston skirt with the piston pin boss
(piston skirt). The two parts are screwed together with appropriate threaded
fasteners
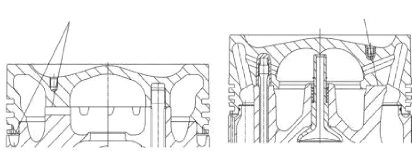
With two contact surfaces With one contact
surfaces
Fig. 1.6: Upper part of piston cooled by gallery (left) and
by orifice (right)
The upper part of the piston is made of forged steel, while
the piston skirt can be made from three distinct materials:
- Piston skirt made of forged aluminium-base
alloy, forged aluminium skirts, are suitable for low and medium peak
cylinder pressures, exhibit a low mass, and are easy to machine.
- Piston skirt made of nodular cast iron, Key
features of a composite piston with nodular cast iron piston skirt, Figure 1.6,
are low cold piston clearance and the resulting low secondary piston motion as
well as high seizure resistance.
10
Chapter 1: Overview on engine's piston
The casting process, in contrast to forged steel, allows for
undercuts and therefore a lighter design Superior to 200 bar. Compared with
pistons with aluminum skirts, however, the mass is increased as a result of the
higher material density.
- Piston skirt made of forged steel provides
ultrahigh component strength and, related to the process, a material with
extremely few defects. They are suitable for ultrahigh stresses greater than 24
MPa. Similar to pistons with nodular cast iron piston skirts, they provide the
advantage of low cold piston clearance, resulting in low secondary piston
motion.
1.2. Different forms of wear
Metal surfaces which are subjected to solid or fluid friction
in the presence or absence of a lubricant may be affected by wear patterns
which may range from regular, controllable wear (normal wear) to sudden
deterioration causing the failure of the mechanism.
Surface deterioration is an isolated or simultaneous
phenomenon classified into four basic forms: adhesive, abrasive, corrosive and
fatigue.
|