II.2.2.2. Préparations des renforts
D'après les rouleaux des tissus de fibres de verre et
de carbone (Figure II.2) on coupe deux surfaces larges pour
l'extraction des plis de nos stratifiés, ensuite :
(1) On mesure avec une règle 40/40 cm du tissu de fibre
de verre et celle de carbone.
(2) On découpe 8 couches des deux fibres (Carbone/Verre)
en utilisant un ciseau.
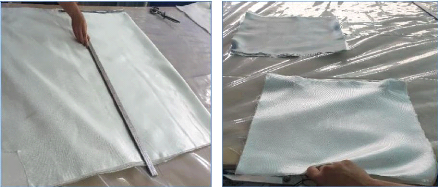
1 2
Figure II.5 : Préparation
des renforts (Etape de découpage)
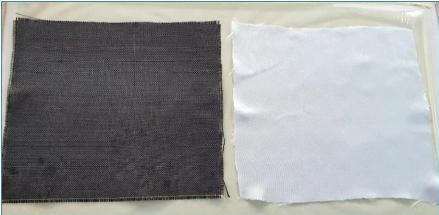
Figure II.6 : Tissus des Fibres
de carbone et de verre (taffetas)
II.2.3. La matrice
Les matériaux composites à matrice
polymère sont de plus en plus utilisés en aéronautique
à cause de leur faible masse. C'est un mélange homogène de
résine (EPOCAST 50-A1) et de durcisseur (HARDENER 946 US) qui se
présente comme un agent de
CHAPITRE II Procédés
d'élaboration et caractérisation des matériaux
composites
28 | P a g e
réticulation[4]. Ces ratios sont
basés sur les normes spécifiées par le fabricant, qui
nécessite un mélange de 100 grammes de résine pour 15
grammes de durcisseur. Figure II.7.
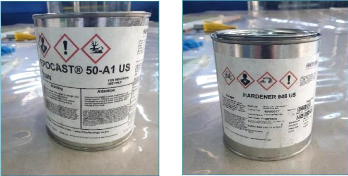
A B
Figure II.7 : A. Résine
EPOCAST 50-A1. B. Durcisseur (HARDENER 946)
II.2.3.1. Caractéristiques de la résine
Est une résine thermodurcissable utilisé pour la
stratification à cause de sa facilité à être
manipulée. Et peut être utilisé dans la fabrication ou la
réparation de structures composites aéronautiques. Les produits
sont conformes à la norme BMS 8-201.
Des détails supplémentaires sur cette
résine sont mentionnés dans la fiche technique fournie par le
fournisseur (Tableau II.3)
Tableau II.3 :
Caractéristiques des Epocast 50-A1/946
Caractéristiques
|
Valeurs
|
Densité g/cm3
|
2
|
Coefficient de dilatation thermique 10k
|
35
|
Résistance en compression MP
|
140
|
Module d'élasticité en compression
MP
|
11000-11500
|
Résistance en flexion MP
|
110
|
II.2.3.2. Préparation de la matrice
La quantité de résine nécessaire par
mètre carré de tissu a été calculée à
partir des normes imposées par le constructeur (Airbus) qui impose
375g de résine pour 1 m2 de
tissu (pour une seule couche).
· CHAPITRE II Procédés
d'élaboration et caractérisation des matériaux
composites
Calcule de la masse de résine et durcisseur de nos
plaques composites : La surface d'une couche de fibre (Sf) est de :
Sf=400mm*400mm=160000mm2 On a un stratifié de 8 couches donc
la surface totale St est de : St=8*160000=1280000mm2 La
quantité de résine plus durcisseur a appliqué M sera :

1m2 375g
1.28m2 M
M= 480g
29 | P a g e
Donc la masse totale pour imprégner 8 couches de
40/40cm est 480grammes (en epocast + durcisseur) donc par un petit calcul on
trouve la masse de durcisseur et d'Epocast qu'on doit mélanger.
480 X 15
100
= 72 g en durcisseur
480 - 72 = 408 g d'epocast
· Dans notre cas on a deux plaques
élaborées donc on a consommé le double de cette
résine.
Finalement on suivra les étapes suivantes pour
l'utilisation de la résine.
1. On pèsera la bonne quantité de la résine
Epocast (408 grammes)
2. On ajoute la quantité nécessaire du durcisseur
72 g
3. Après un mélange à peu près de
3 min on voit que la couleur de notre résine est homogène, Donc
notre matrice est prête à utiliser.
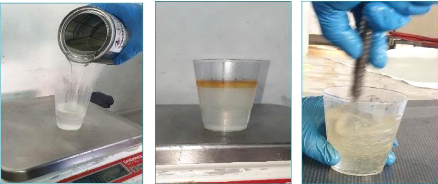
1
2
3
Figure II.8 : Etapes de
préparation de la matrice Epocast 50-A1
CHAPITRE II Procédés
d'élaboration et caractérisation des matériaux
composites
30 | P a g e
II.2.4. Tissu d'arrachage
Sont des tissus antiadhésifs présentent
plusieurs avantages lorsqu'ils sont utilisés sous vide. Ce tissu est
connu pour la finition de surface qu'il confère aux pièces des
composites, il permet aussi d'absorber la quantité de résine
surplus et il évite également l'adhésion de
l'échantillon à tous les tissus lors de la dissociation (lors du
démoulage).
II.2.5. Feutre de drainage
Son rôle est d'absorber la quantité de
résine supplémentaire aussi et de la piéger pour qu'il n'y
ait pas de débordement, et aussi il assure la bonne répartition
de l'aspiration de l'air dans le système sous vide. Il est connu aussi
sous le nom (de la ouate).
|
|
Figure II.9 : Tissu
d'arrachage
|
|
|
Figure II.10 : Feutre de
drainage
|
Tableau II.4 :
Caractéristiques du feutre de drainage
Caractéristiques
|
Valeurs
|
Matière
|
Fibres 100% polyester
|
Couleur
|
Blanc
|
Epaisseur (mm2)
|
4
|
Poids nominal (g/m2)
|
150
|
Température d'utilisation (?)
|
205
|
Température de fusion (?)
|
250
|
II.3. Procédure de
fabrication
La réalisation des éprouvettes stratifiés
carbone/époxy, verre/époxy de huit plis est faite par un moulage
sous vide en ajoutant la résine sur la surface des fibres et
l'étaler en utilisant la raclette comme vous montre en détails
dans les étapes et les figures jointes suivantes :
CHAPITRE II Procédés
d'élaboration et caractérisation des matériaux
composites
En premier lieu, après le malaxage de la
résine et le durcisseur en respectant le taux de pourcentage 100/15, en
étale une couche d'imprégnation sur le film inférieur
utilisé pour l'étanchéité et sur la
1ère couche des renforts.
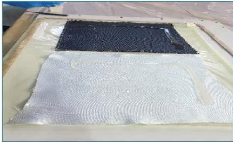
Figure II.11 :
Imprégnation de résine sur les 1ères couches de
fibres
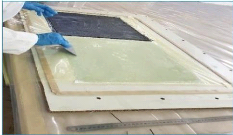
En deuxième étape on dépose les
couches des tissus sur la 1ère couche de renfort, de la
même façon que la première on étale une autre couche
de résine sur ces plis et en pose un autre pli, cette opération
est répétée jusqu'au huitième couches, ce sont tous
de même orientation (0.90°)
Figure II.12 : Imprégnation
de résine de 8 couches successives
Troisièmement, on pose directement le tissu
d'arrachage qu'est découpé selon les mêmes dimensions de
nos renforts. Et faire rentrer les deux tuyaux de la pompe sur les
côtés pour effectuer par la suite l'opération d'aspiration
de l'air.
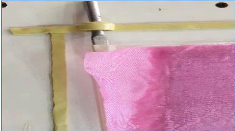
Figure II.13 : Dépôt
du tissu d'arrachage
31 | P a g e
CHAPITRE II Procédés
d'élaboration et caractérisation des matériaux
composites
32 | P a g e
Ensuite, on pose le tissu d'absorption (de drainage)
qu'est découpé de même dimensions qui couvre toute surface
du moule limité par le mastic d'étanchéité, en le
plaçant ainsi sur les tuyaux de la pompe à vide avant la
fermeture de notre système.
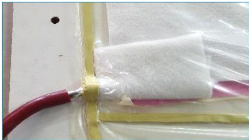
Figure II.14 : Dépôt
de tissu de drainage
Finalement on utilise un film plastique pour la
fermeture, d'où le but de son utilisation est
l'étanchéité l'ensemble de système et
réaliser la dépression par le système de création
de vide utilisé et coller ses extrémités avec le mastic
d'étanchéité pour éviter tout risque de fuite.
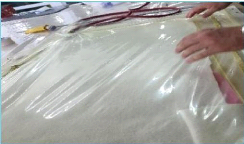
Figure II.15 : Dépôt
de film plastique pour fermeture du système
|