UNIVERSITÉ DE YAOUNDÉ
|
fa
I OAUN
|
IVERSITY OF YAOUNDE I
|
****** ÉCOLE NATIONALE
SUPÉRIEURE POLYTECHNIQUE ****** DÉPARTEMENT DES
GÉNIES INDUSTRIEL ET MÉCANIQUE
|
|
****** NATIONAL ADVANCED SCHOOL
OF ENGINEERING ****** DEPARTMENT OF INDUSTRIAL AND MECHANICAL
ENGINEERING
|
MISE SUR PIED D'UNE UNITÉ INDUSTRIELLE
DE
TRANSFORMATION DES CÉRÉALES
POUR
L'OBTENTION DE LA FARINE : PROJET
INDUSTRIEL
DU GROUPE SEEDS OF AFRICA(SOA).
Mémoire de fin d'études/Master of
engineering
Présenté et soutenu par :
PONDI JOSEPH
En vue de l'obtention du :
Diplôme d'Ingénieur de Conception en Génie
Mécanique.
Sous la direction de :
Dr. TCHOTANG Théodore
Devant le Jury Composé de :
? Président : Pr. OUMAROU HAMANDJODA,
Maitre de conférences, ENSP, UY1
? Examinateur : M. DJOMI ROLLAND, Assistant,
ENSP, UY1
? Rapporteur : Dr. TCHOTANG THEODORE,
Chargé de Cours, ENSP, UY1 ? Invité : M.
TATSINDA FOUTSOP BERTRAND, Promoteur du Groupe SOA
Année académique 2015-2016
et soutenu par : PONDI
JOSEPH
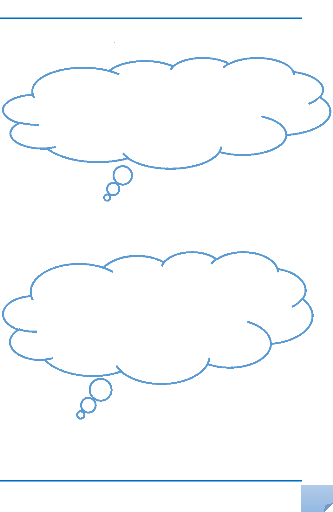
Mise sur pied d'une unité industrielle de transformation
des céréales pour l'obtention de la farine : projet industriel du
Groupe SOA
DéDICACES
A l'Eternel Dieu, Tout puissant mon
créateur et mon sauveur, mon gui6e
suprême, source 6e force, 6e sagesse,
d'intelligence et de grâce.
A mes très chers parents, M. et Mme
PONDI, en reconnaissance 6e tous les
efforts consentis.
Mémoire de fin d'études pour l'obtention du
diplôme d'Ingénieur de Conception en Génie
Mécanique, rédigé et soutenu par : PONDI
JOSEPH
i
Mise sur pied d'une unité industrielle de transformation
des céréales pour l'obtention de la
farine : projet industriel
du Groupe SOA
REMERCIEMENTS
c
e travail n'aurait pas pu aboutir sans l'apport de divers
moyens matériels et compétences humaines. C'est l'occasion pour
nous d'exprimer humblement et sincèrement notre profonde gratitude
à toutes ces personnes ayant contribué à la
réussite de notre projet de fin d'études. A cet effet, nous
tenons sincèrement à remercier :
. Pr. OUMAROU HAMANDJODA, pour avoir
accepté de présider notre jury ;
. Dr. TCHOTANG Théodore pour le suivi de
ce travail et la disponibilité dont il a fait
preuve à notre égard, sa compréhension et
ses suggestions de très haute qualité;
. M. DJOMI Rolland, pour avoir accepté
d'examiner ce mémoire ;
. M. TATSINDA FOUTSOP BERTRAND mon encadreur
professionnel et promoteur
du projet SOA pour ses conseils, sa patience et son encouragement
permanent;
. Pr. AWONO ONANA le Directeur de l'ENSPY ;
. Pr. NGABIRENG CLAUDE MARIE le Directeur
Adjoint chargé des études de
l'ENSPY ;
. Pr. MEVA'A Lucien, chef de Département
des Génies Industriel et Mécanique, qui a
accepté de signer ma lettre de mise en stage me donnant
ainsi l'autorisation de
commencer mon travail ;
. M. TIMBA Marc-Stéphane autre promoteur
du Groupe SOA ;
. Le Directeur Général du groupe Beltex Sarl :
M.MAHMOUDOU HAMAN-DJODA ;
pour m'avoir permis de travailler dans les locaux de son
entreprise;
. M. MAZOU MOUSTAPHA et Mme MINKOS
SUZANE employés du groupe
Beltex Sarl pour leur accueil;
. mon oncle PONDY RAYMOND, pour le soin qu'il a
pris pour ma formation à
polytechnique ;
. M. et Mme GOUATER pour leurs
conseils et soutiens multiples ;
. Mes frères et soeurs
pour leurs encouragements et assistances ;
. Mon Cousin PONDY JOSEPH pour son soutien et
encouragement ;
. Mon oncle BAMSECK Emmanuel pour son soutien
;
. Mon amie NGO KAMEN Phalone pour son
encouragement et son assistance ;
. Les Ingénieurs, MBIDA Yves, SINGHA Emmanuel,
KONDE Julienne, NJIKI
Valdèze, KAMNANG Franklin, TAMO Arnaud,
pour leurs conseils et soutiens ;
. Mes soeurs en Christ particulières : OLIVADE
KAMENI, MICHELLE MAKOU et
GAELLE CHIME pour leur assistance ;
. Mes camarades et amis de la promotion 2016 pour leur
convivialité;
. Finalement, je tiens à exprimer ma profonde
reconnaissance envers mes amis et
frères
du Groupe chrétien de l'ENSPY qui m'ont inlassablement
encouragé tout au long de ce
travail, et à tous ceux qui de près ou de loin ont
contribué à la réalisation de ce travail.

ii
Mémoire de fin d'études pour l'obtention du
diplôme d'Ingénieur de Conception en Génie
Mécanique, rédigé et soutenu par : PONDI
JOSEPH
Mise sur pied d'une unité industrielle de transformation
des céréales pour l'obtention de la
farine : projet industriel
du Groupe SOA
GLOSSAIRE
Sigles et abréviations
Tableau 1 : sigles et
abréviations
Sigles et abréviations Signification
ACDIC
|
Association Citoyenne de Défense des Intérêts
Collectifs
|
AFNOR
|
Agence Française de Normalisation
|
AMDEC
|
Analyse des Modes de Défaillance, de leurs Effets et de
leurs Criticités
|
AN
|
Application Numérique
|
CEEAC
|
Communauté Economique des Etats de l'Afrique Centrale
|
CEMAC
|
Communauté Economique et Monétaire de l'Afrique
Centrale
|
EME
|
Elément du Milieu Extérieur
|
ENSPY
|
Ecole Nationale Supérieure Polytechnique de
Yaoundé
|
EPC
|
Equipement de Protection Collective
|
EPI
|
Equipement de Protection Individuelle
|
FAST
|
Functional Analysis System Technique
|
FC
|
Fonction de Contrainte
|
FCFA
|
Franc de la Communauté Financière Africaine
|
FP
|
Fonction Principale
|
FS
|
Fonction de Service
|
GM
|
Génie Mécanique
|
ha
|
Hectare
|
HR
|
Humidité Relative
|
INS
|
Institut National de la Statistique
|
IRAD
|
Institut de Recherche Agronomique pour le Développement
|
kg
|
Kilogramme
|
OMC
|
Organisation Mondiale du Commerce
|
OMS
|
Organisation Mondiale de la Santé
|
PDI
|
Protein Dispersability Index
|
PG
|
Poste de Gardiennage
|
PPP
|
Partenariat Public-Privé
|
PT
|
Poste de Transformation
|
SOA
|
Seeds Of Africa
|
t
|
Tonne
|
UB
|
Unité Brabender
|
UCD
|
Unité Chopin Dubois
|
VAN
|
Valeur Actuelle Nette
|

iii
Mémoire de fin d'études pour l'obtention du
diplôme d'Ingénieur de Conception en Génie
Mécanique, rédigé et soutenu par : PONDI
JOSEPH
Mise sur pied d'une unité industrielle de transformation
des céréales pour l'obtention de la
farine : projet industriel
du Groupe SOA
Symboles techniques
Tableau 2 : symboles techniques
Symboles Significations Unités
????
|
Puissance appelée
|
kVA
|
????
|
Surface d'évolution
|
m2
|
????
|
Surface totale
|
m2
|
????
|
Surface de gravitation
|
m2
|
????
|
Surface au sol
|
m2
|
????
|
Effort statique
|
daN
|
???? ??
|
Effort dynamique
|
daN
|
????
|
Capacité horaire
|
t/h
|
????
|
Courant d'emploi
|
A
|
????
|
Puissance apparente
|
kW
|
????
|
Puissance du réchauffeur
|
kW
|
????
|
Puissance utile
|
kW
|
????
|
Débit de mouture
|
t/h
|
????????
|
Débit de claquage
|
t/h
|
????????
|
Débit de convertissage
|
t/h
|
????????
|
Débit de décorticage
|
t/h
|
????????
|
Débit de nettoyage
|
t/h
|
????
|
Débit d'air du ventilateur
|
??3/h
|
??????
|
Volume d'air humide
|
m3
|
????
|
Vitesse de déplacement des céréales
|
m/s
|
????
|
Humidité finale
|
/
|
????
|
Humidité initiale
|
/
|
????
|
Chaleur latente de vaporisation de l'eau
|
kJ/kg
|
????????
|
Largeur minimale
|
mm
|
??????
|
Mais d'air humide
|
kg
|
??????
|
Masse d'air sec
|
kg
|
????
|
Masse d'eau
|
kg
|
????
|
Masse finale
|
kg
|
????
|
Masse sèche
|
kg
|
????????
|
Taux de claquage
|
/
|
????????
|
Taux de convertissage
|
/
|
????????
|
Taux de décorticage
|
/
|
????????????
|
Taux d'impuretés
|
/
|

iv
Mémoire de fin d'études pour l'obtention du
diplôme d'Ingénieur de Conception en Génie
Mécanique, rédigé et soutenu par : PONDI
JOSEPH
Mise sur pied d'une unité industrielle de transformation
des céréales pour l'obtention de la
farine : projet industriel
du Groupe SOA
Symboles Significations Unités
???
|
Masse d'eau évaporée
|
kg
|
D
|
Diamètre
|
mm
|
Ks
|
Facteur de simultanéité
|
/
|
Ku
|
Facteur d'utilisation
|
/
|
P
|
Puissance
|
kW
|
S
|
Surface
|
m2
|
T
|
Température
|
°C
|
T
|
Temps
|
Seconde
|
X
|
Taux d'humidité
|
/
|
??
|
Masse volumique
|
kg/m3
|

v
Mémoire de fin d'études pour l'obtention du
diplôme d'Ingénieur de Conception en Génie
Mécanique, rédigé et soutenu par : PONDI
JOSEPH
Mise sur pied d'une unité industrielle de transformation
des céréales pour l'obtention de la
farine : projet industriel
du Groupe SOA
RéSUMé
L
e groupe Seeds Of Africa envisage la construction d'un
complexe agro-industriel, constitué d'une chaine de transformation et de
conditionnement des céréales (maïs, blé, sorgho et
soja) dans la localité de Santchou d'une capacité maximale de
6t/h. L'objectif de notre étude était de mettre sur pied une
méthodologie scientifique nous permettant de suivre les
différentes étapes de la conception de ladite de chaine de
transformation ; afin de permettre à l'unité d'atteindre
dès sa mise en service, les objectifs de production et d'en assurer la
pérennité.
La méthodologie utilisée passe par l'analyse des
techniques et des technologies de transformation des céréales en
farine, le dimensionnement des équipements principaux et annexes de la
chaine dans le but de faire de meilleurs choix auprès des fournisseurs,
la proposition d'un plan de maintenance préventive pour les
équipements critiques. Nous avons utilisé comme outils : la
méthode de V.CAUDILL qui donne les étapes
à suivre pour la mise sur pied d'une nouvelle unité de
transformation ; l'analyse fonctionnelle pour la conception de
la chaine de transformation ; le diagramme de Pareto pour le
choix des équipements auprès des fournisseurs, l'abaque
de Noiret pour le choix des équipements critiques d'une chaine
afin de mettre un accent particulier sur leur maintenance.
Nous avons par la suite calculé la puissance d'appel de
l'usine et avons fait le choix du transformateur adéquat, nous avons
également calculé la surface minimale de l'implantation de
l'usine de transformation.
Notre travail s'est achevé par une analyse
financière du projet et nous sommes arrivés à un
coût d'investissement qui s'élève à 325 177
065FCFA et une valeur actuelle nette de 1 090 634 349FCFA
après 5 ans et la présentation des
recommandations pour aider les promoteurs à prendre des
décisions.
Mots clés : chaine de
transformation, dimensionnement, céréales, farine.

vi
Mémoire de fin d'études pour l'obtention du
diplôme d'Ingénieur de Conception en Génie
Mécanique, rédigé et soutenu par : PONDI
JOSEPH
Mise sur pied d'une unité industrielle de transformation
des céréales pour l'obtention de la
farine : projet industriel
du Groupe SOA
ABSTRACT
s
eeds Of Africa group considers the construction of an
agro-industrial complex made up of cereals (maize, wheat, sorghum and soya)
transformation and conditioning chains in the locality of Santchou with a
maximum capacity of 6 t/h. The objective of our study was to set up a
scientific methodology enabling us to follow the various stages of the design
of the transformation chain in order to allow the unit to meet the production
targets from its start and to ensure its sustainability.
The methodology used consists of the analysis of techniques
and technologies used in the transformation of cereals into flour, the
dimensioning of principal and secondary equipment in order to choose suppliers
close to the plant, the proposal of a preventive maintenance plan for the
critical equipment. The tools used were: the V.CAUDILL method
which gives the steps to be followed for the setting-up of a new transformation
unit; functional analysis for the transformation chains
design; the Pareto's diagram for the choice of the equipment
suppliers, and the abacus of Noiret for the choice of critical
chains equipment in order to place a particular stress on their maintenance.
We thereafter calculated the factory's power demand, made the
choice of the adequate transformer, and calculated the minimal surface area of
the factory's transformation plant. Our work then was completed by a financial
analysis of the project and we obtained an investment cost of about 325
177 065 FCFA, with a net value of 1 090 634 349 FCFA
after 5 years as well as the presentation of recommendations to help
the promoters make decisions.
Keys Word: transformation chains,
dimensioning, cereals, flour.

vii
Mémoire de fin d'études pour l'obtention du
diplôme d'Ingénieur de Conception en Génie
Mécanique, rédigé et soutenu par : PONDI
JOSEPH
Mise sur pied d'une unité industrielle de transformation
des céréales pour l'obtention de la
farine : projet industriel
du Groupe SOA
LiSTES DES FigURES
Figure 1 : Organigramme de SOA 4
Figure 2 : Evolution de l'importation des
céréales au Cameroun 7
Figure 3 : Diagramme de mouture du maïs [14] 10
Figure 4 : Diagramme de mouture du blé 11
Figure 5 : Diagramme de mouture du soja 12
Figure 6 : Diagramme de mouture du sorgho[19] 13
Figure 7 : Diagramme de synthèse sur la mouture des
céréales 14
Figure 8 : Méthode de détermination des
proximités et des flux 27
Figure 10 : Diagramme bête à corne 34
Figure 11 : Diagramme pieuvre 36
Figure 12 : Structure d'un diagramme FAST [24]. 37
Figure 13 :FAST_FP 38
Figure 14 :FAST_FC1 38
Figure 15 :FAST_F 39
Figure 16 :FAST_FC3 39
Figure 17 : FAST_FC4 39
Figure 18 :FAST_FC5 40
Figure 19 : FAST_FC6 40
Figure 20 :FAST_FC7 40
Figure 21 : Evolution de l'air lors d'une opération de
séchage convectif [8]: 42
Figure 22 : Modèle d'étude pour le calcul des
rouleaux 50
Figure 23 : diagramme de Pareto des critères de choix
de la moissonneuse-batteuse 55
Figure 24 : Diagramme de Pareto des critères de choix
du nettoyeur-séparateur 58
Figure 25 : Modèle fonctionnel d'une installation
électrique [27]. 60
Figure 26 : Plan de masse 68
Figure 27 : Schéma synoptique de la chaine de
transformation 79
Figure 28 : Module d'entrée des paramètres 90
Figure 29 : Module « résultat » 91
Figure 30 : Analyse de la production en prenant une seule
céréale 92
Figure 31 : Combinaison de deux céréales 92
Figure 32 : Combinaison de la mouture de trois
céréales. 93
Figure 33 : Courbe comparative des différentes
combinaisons 93
Figure 34 : Schéma de principe de la chaîne de
conditionnement 99
Figure 35 : Schéma de principe séchoir solaire
99
Figure 36 : Schéma de principe unité de
nettoyage 100
101
Figure 37 : Schéma de principe séchoir à
air chaud à convection forcée 101
Figure 38 : Zone de matière première 102
Figure 52 : Choix du transformateur 103
Figure 53 : Diagramme de l'air humide 106
Figure 54 : Synoptique 3D des équipements de la chaine
118

viii
Mémoire de fin d'études pour l'obtention du
diplôme d'Ingénieur de Conception en Génie
Mécanique, rédigé et soutenu par : PONDI
JOSEPH
Mise sur pied d'une unité industrielle de transformation
des céréales pour l'obtention de la
farine : projet industriel
du Groupe SOA
LISTE DES TABLEAUX
Tableau 1 : sigles et abréviations iii
Tableau 2 : symboles techniques iv
Tableau 3 : Cultures et cycle de maturation 5
Tableau 4 : Offre et demande de maïs au Cameroun [3]
7
Tableau 5 : Importation du maïs par an au Cameroun [3]
7
Tableau 6 : Importation des produits de la minoterie [4] 8
Tableau 7 : Comparaison entre les différentes
technologies de séchage [4] 15
Tableau 8 : Tableau comparatif entre les modes de
séchage artificiel [18] 16
Tableau 9 : Comparaison entre les différentes
technologies d'égrenage [7] 17
Tableau 10 : Etude comparative des différentes
technologies de décorticage [17] 17
Tableau 11 : Etude comparative des technologies de broyage
18
Tableau 12 : Etude comparative entre les différents
nettoyeurs de céréales [17] 19
Tableau 13 : Comparaison entre les différents types de
convoyeurs [23] 20
Tableau 14 : Synthèse sur les technologies retenues
21
Tableau 15 : Méthode de mise sur pied d'une nouvelle
unité de production [17] 22
Tableau 16 : Facteur influençant l'ingénierie du
projet [18] 23
Tableau 17 : Tableau de comparaison des techniques d'analyse.
25
Tableau 18 : Technique de choix des équipements
critiques 28
Tableau 19 : Age des équipements 29
Tableau 20 : Indépendance des équipements 29
Tableau 21 : Intervalle des coûts des équipements
30
Tableau 22 : Complexité et accessibilité des
équipements 30
Tableau 23 : Robustesse et précision des
équipements 30
Tableau 24 : Origine des équipements 30
Tableau 25 : Type d'utilisation des machines 31
Tableau 26 : Impacts sur les produits 31
Tableau 27 : Délais d'attente d'un équipement
défaillant 31
Tableau 28 : Récapitulatif de l'étude de la
détermination des équipements critiques 31
Tableau 29 : Résumé technique 33
Tableau 33 : Verbalisation du besoin 34
Tableau 31 : Calcul des pourcentages de
préférence de chaque critère 54
Tableau 32 : Pondération des critères pour
l'égreneuse de maïs 55
Tableau 33 : Tableau de notation des critères de la
moissonneuse-batteuse de maïs 56
Tableau 34 : Notation des moissonneuses proposées par
les fournisseurs 57
Tableau 35 : Caractéristiques de la moissonneuse de
maïs 57
Tableau 36 : Calcul des pourcentages de
préférence des critères du nettoyeur -séparateur
58
Tableau 37 : pondération des critères pour le
nettoyeur-séparateur 59
Tableau 38 : Tableau de notation des critères pour le
nettoyeur-séparateur 59
Tableau 39 : Notation des nettoyeurs -séparateurs 59
Tableau 40 : Caractéristiques du nettoyeur
séparateur 60
Tableau 41 : Evaluation de la puissance installée 61
Tableau 42 : Bilan des puissances de l'usine 62
Tableau 43 : Caractéristiques du transformateur 63

ix
Mémoire de fin d'études pour l'obtention du
diplôme d'Ingénieur de Conception en Génie
Mécanique, rédigé et soutenu par : PONDI
JOSEPH
Mise sur pied d'une unité industrielle de transformation
des céréales pour l'obtention de la
farine : projet industriel
du Groupe SOA
Tableau 44 : Bilan de calcul des surfaces de l'usine. 64
Tableau 45 : Données pour l'implantation de l'usine
65
Tableau 46 : Définition des secteurs d'activité
66
Tableau 47 : Détermination des proximités et des
flux 66
Tableau 48 : Détermination des équipements
critiques par l'abaque de Noiret 83
Tableau 49 : Coûts des équipements 85
Tableau 50 : Récapitulatif sur les charges
prévisionnelles annuelles 87
Tableau 53 : Ventes annuelles prévisionnelles 88
Tableau 54: Tableau récapitulatif pour le calcul des
cash-flows 89
Tableau 51 : Diamètre recommandé pour les
rouleaux. 103
Tableau 52 : Coefficient de participation FP 103
Tableau 53 : Choix du facteur K 103
Tableau 54: Ecartement maximal pour les stations
supérieures et inférieures 104
Tableau 55 : Coefficient de frottement interne f des produits
et des parties tournantes 104
Tableau 56 : Vitesse maximale conseillée 104
Tableau 57 : Coefficient d'utilisation 104
Tableau 58 : Coefficient lié à l'environnement
105
Tableau 59 : Coefficient de choc Fd 105
Tableau 60 : Coefficient de vitesse Fv 105
Tableau 61 : Diamètre recommandé des tambours
105
Tableau 62 : Exemple de fiche de maintenance préventive
des équipements critiques 107
Tableau 63 : Caractéristiques du blutoir 108
Tableau 64 : Caractéristiques du compresseur 109
Tableau 65 : Caractéristiques du ventilateur 109
Tableau 66 : Machine d'emballage 109
Tableau 67 : Caractéristiques de la table
densimétrique 109
Tableau 68 : Caractéristiques du trieur
alvéolaire 109
Tableau 73 : Caractéristiques du pré-nettoyeur
110
Tableau 70 : Caractéristiques du convoyeur à vis
110
Tableau 71 : Caractéristiques du surpresseur 110
Tableau 72 : Caractéristiques convoyeur à bande
110
Tableau 73 : Caractéristiques du torréfacteur
110
Tableau 74 : Caractéristiques du broyeur 111
Tableau 75 : Charges salariales du personnel de l'usine 117

x
Mémoire de fin d'études pour l'obtention du
diplôme d'Ingénieur de Conception en Génie
Mécanique, rédigé et soutenu par : PONDI
JOSEPH
Mise sur pied d'une unité industrielle de transformation
des céréales pour l'obtention de la
farine : projet industriel
du Groupe SOA
SOMMAIRE
DéDICACES I
REMERCIEMENTS II
GLOSSAIRE III
Sigles et abréviations iii
Symboles techniques iv
RéSUMé. VI
ABSTRACT VII
LISTES DES FIgURES VIII
LISTE DES TABLEAUX IX
SOMMAIRE XI
I.
|
CONTEXTE ET PROBLéMATIQUE
|
2
|
|
I.1 Contexte
|
3
|
|
I.1.1
|
Présentation du groupe SOA
|
3
|
|
I.1.2
|
Missions et visions de SOA
|
4
|
|
I.1.3
|
Stratégie de SOA
|
4
|
|
I.1.4
|
Le modèle d'entreprise
|
5
|
|
I.1.5
|
SOA : les leviers du succès
|
6
|
|
I.1.6
|
Implantation
|
6
|
|
I.2 Problématique
|
6
|
II. CONCEPTS DE BASE POUR LA MISE SUR PIED ET DU SUIVI
D'UNE UNITé DE
TRANSFORMATION INDUSTRIELLE. 9
II.1 Généralités sur les farines de
céréales 10
II.1.1 Généralités sur les farines de
maïs 10
II.1.2 Généralités sur la farine de
blé 10
II.1.3 Généralités sur la farine de soja
11
II.1.4 Généralités sur la farine de sorgho
12
II.1.5 Synthèse sur les techniques d'obtention des farines
de céréales 13
II.2 Généralités sur les technologies
d'obtention des farines de céréales 14
II.2.1 Technologies de séchage 14
II.2.2 Technologie d'égrenage 16
II.2.3 Technologie de décorticage 17
II.2.4 Technologies de broyage 18

xi
Mémoire de fin d'études pour l'obtention du
diplôme d'Ingénieur de Conception en Génie
Mécanique, rédigé et soutenu par : PONDI
JOSEPH
Mise sur pied d'une unité industrielle de transformation
des céréales pour l'obtention de la
farine : projet industriel
du Groupe SOA
II.2.5 Unité de nettoyage 19
II.2.6 Choix du type de convoyeur 20
II.2.7 Synthèse sur les technologies retenues 20
II.3 Procédure de mise sur pied d'une unité de
transformation industrielle 21
II.4 Présentation de la méthode de V.CAUDILL 22
II.4.1 Technologie des équipements 22
II.4.2 Conception en équipe de ligne 22
II.4.3 Ingénierie du projet 23
II.5 Elaboration d'une technique d'analyse pour le choix des
machines 24
II.6 Démarche à suivre pour la conception de
l'implantation d'une unité de transformation
industrielle 26
II.6.1 Elaboration d'une méthode pour le choix des
équipements critiques 27
II.6.2 Choix de la méthode pour la maintenance
préventive 27
II.6.3 Description et utilisation de l'abaque de Noiret 28
III. ETUDE DE RéALISATION ET D'IMPLANTATION DU
PROJET INDUSTRIEL. 32
Description : 32
III.1 Conception en équipe de ligne 33
III.1.1 Cahier de charge technique 33
III.1.2 Analyse fonctionnelle 34
III.1.3 Analyse fonctionnelle du besoin 35
III.1.4 Analyse fonctionnelle technique. 37
III.2 Ingénierie du projet 41
III.2.1 Enjeux d'une démarche de conception et de
dimensionnement. 41
III.2.2 Dimensionnement des équipements. 41
III.2.3 Dimensionnement des équipements de mouture. 45
III.2.4 Dimensionnement de l'unité de nettoyage 48
III.3 Dimensionnement des équipements annexes 49
III.3.1 Dimensionnement des convoyeurs à bande 49
III.3.2 Caractéristiques de la bande 50
III.3.3 Conduite de transport pneumatique 53
III.4 Choix des machines auprès des fournisseurs 54
III.4.1 Mise en oeuvre de la méthode de Pareto pour le
choix des machines. 54
III.5 Dimensionnement de l'installation électrique de
l'usine 60
III.5.1 Structure fonctionnelle d'une installation
électrique 60

xii
Mémoire de fin d'études pour l'obtention du
diplôme d'Ingénieur de Conception en Génie
Mécanique, rédigé et soutenu par : PONDI
JOSEPH
Mise sur pied d'une unité industrielle de transformation
des céréales pour l'obtention de la
farine : projet industriel
du Groupe SOA
III.5.2 Evaluation des bilans de puissance de l'usine et choix du
transformateur 61
III.6 Dimensionnement de la surface minimale de l'usine 63
III.6.1 Evaluation de la surface au sol Ss des
équipements 63
III.6.2 Evaluation de la surface de gravitation Sg
63
III.6.3 Evaluation de la surface d'évolution Se
64
III.6.4 Etude de l'implantation optimale de la chaine 65
III.6.5 Schéma d'implantation et schéma synoptique
de l'usine. 67
IV. MOYENS DE MAITRISE ET ANALYSE FINANCIèRE DU PROJET
INDUSTRIEL 81
IV.1 Mise en oeuvre de l'abaque de Noiret pour le choix des
équipements critiques 82
IV.1.1 Cas pratique du broyeur 82
IV.1.2 Récapitulatif 82
IV.2 Analyse financière et rentabilité
économique 83
IV.2.1 Définitions 84
IV.2.2 Coût des équipements. 85
IV.2.3 Coût d'investissement du projet 86
IV.2.4 Charges prévisionnelles annuelles 86
IV.2.5 Estimation des ventes annuelles 88
IV.2.6 Calcul de la VAN 89
IV.3 Présentation du progiciel d'aide au dimensionnement.
89
IV.3.1 Environnement de programmation 90
IV.3.2 Présentation des différents modules. 90
IV.3.3 Analyse des résultats : guide pour la prise de
décision. 91
CONCLUSION GéNéRALE ET PERSPECTIVES
94
V. BIBLIOGRAPHIE. 95
Annexe1 : photos de certains équipements de la chaine de
production. 97
annexe2 : Schéma de principe des unités de la
chaine de transformation 98
Annexe3 : abaques et tableaux d'aide au dimensionnement 102
Annexe4 : fiche de maintenance préventive 107
Annexe6 : Caractéristiques des équipements de la
chaine de production et charges salariales
108

xiii
Mémoire de fin d'études pour l'obtention du
diplôme d'Ingénieur de Conception en Génie
Mécanique, rédigé et soutenu par : PONDI
JOSEPH
Mise sur pied d'une unité industrielle de transformation
des céréales pour l'obtention de la
farine : projet industriel
du Groupe SOA
INTRODUCTION fi~RaI.~
La production industrielle demeure l'une des
préoccupations majeures du Cameroun qui se veut émergent à
l'horizon 2035 ; mais la nutrition, parmi, tous les besoins des ménages
est considéré comme le plus important et le plus
impérieux, le Cameroun entend donc renforcer son secteur agricole et
agro-industriel qui jusqu'à présent présente des
énormes manquements ; les statistiques nous indiquent par exemple que
l'indice de consommation du maïs au Cameroun est d'environ
51kg/Habitant/an [1] ; ce qui crée un déficit de plus 120 000
tonnes de maïs par an ; le maïs est d'une importance capitale, dans
l'alimentation humaine, l'alimentation animale (fabrication de la provende), la
fabrication des boissons (les entreprises brassicoles), et autres
agro-industries ; il convient également de noter que deux Camerounais
sur trois consomment le maïs sur toutes ses formes.
Dans tout le Cameroun, il est difficile de trouver plus de 15
producteurs qui possèdent plus 100 hectares de maïs ; c'est alors
la raison pour laquelle le Groupe SOA entend mettre sur pied des vastes
plantations de maïs de plus de 500 hectares et une unité de
transformation de cette culture ,laquelle unité transformera aussi le
blé, le sorgho et le soja ; c'est ce qui justifie le thème qui
nous a été confié : « mise sur pied d'une
unité industrielle de transformation de céréales pour
l'obtention de la farine » il s'agira donc pour nous d'atteindre
les objectifs qui nous ont été prescrits, pour participer
à la pérennité de la future entreprise ; pour atteindre
ces objectifs, notre travail sera articulé de la manière suivante
:
2s. Le chapitre premier nous permet de présenter
exhaustivement le contexte dans lequel s'inscrit notre projet et la
problématique ainsi soulevée ;
2s. Le second chapitre quant à lui, focalisé sur
des études théoriques va nous permettre de mieux comprendre les
notions importantes et les travaux antécédents ;
2s. Le chapitre3, l'essentiel de notre contribution, porte sur
l'étude de réalisation de d'implantation du projet industriel ;
nous faisons l'analyse fonctionnelle de la chaine de transformation, ensuite le
dimensionnement des équipements principaux et annexes de la chaine, le
choix des machines auprès des fournisseurs, le dimensionnement de la
partie électrique et de la surface minimale de l'usine ;
2s. Le quatrième chapitre est réservé aux
moyens de maitrise du projet industriel et à l'analyse
financière, ainsi qu'à la mise sur pied d'une application d'aide
au dimensionnement.

80
Mémoire de fin d'études pour l'obtention du
diplôme d'Ingénieur de Conception en Génie
Mécanique, rédigé et soutenu par : PONDI
JOSEPH
Mise sur pied d'une unité industrielle de transformation
des céréales pour l'obtention de la farine : projet industriel du
Groupe SOA
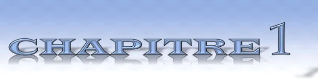
CONTEXTE ET PROBLéMATIQUE
Description :
Le but de cette partie est de présenter la
société d'accueil de notre stage et le contexte
d'élaboration de notre problématique, les enjeux et les objectifs
à atteindre. Pour cela nous commencerons par la présentation du
groupe Seeds Of Africa (SOA) ; ses objectifs, ses visions et ses
stratégies ; nous finirons par poser la problématique puis la
présentation des objectifs à atteindre.

2
Mémoire de fin d'études pour l'obtention du
diplôme d'Ingénieur de Conception en Génie
Mécanique, rédigé et soutenu par : PONDI
JOSEPH
Mise sur pied d'une unité industrielle de transformation
des céréales pour l'obtention de la
farine : projet industriel
du Groupe SOA
I.1 Contexte
I.1.1 Présentation du groupe SOA
Le projet agroindustriel SEEDS OF AFRICA (SOA) a pour
promoteurs deux opérateurs économiques camerounais :
M.TATSINDA FOUTSOP BERTRAND et TIMBA MARC STEPHANE.
Il a pour objectif principal, la construction d'un complexe
agroindustriel constitué d'une unité de recherche (laboratoire),
de magasins de stockage, d'une chaîne de transformation et
conditionnement des produits des plantations de SOA. Ces actions sont
engagées depuis début 2016 à SANTCHOU dans le
département de la MENOUA, région de l'ouest Cameroun. SEEDS OF
AFRICA a pour objectif à moyen terme (10 à 15 ans) de :
- Figurer parmi les entreprises agroindustrielles du top de la
CEEAC ;
- Réaliser un chiffre d'affaires à dix chiffres (en
dizaines).
- Contribuer au développement de l'économie, de
l'emploi qualifié et des technologies agro-industrielles avancées
au Cameroun dans l'ensemble de la CEEAC.
L'organigramme futur du complexe industriel sera constitué
comme suit :
y' Un conseil de surveillance ;
y' Un directeur général ;
y' Un directeur d'usine ;
y' Un secrétaire ;
y' Un cabinet juridique ;
y' Un conseil technique ;
y' Un conseil financier, fiscal, comptabilité ;
y' Des responsables de plantation.
De manière plus détaillée l'organigramme se
présente comme nous l'indique la figure suivante :

3
Mémoire de fin d'études pour l'obtention du
diplôme d'Ingénieur de Conception en Génie
Mécanique, rédigé et soutenu par : PONDI
JOSEPH
Mise sur pied d'une unité industrielle de transformation
des céréales pour l'obtention de la
farine : projet industriel
du Groupe SOA
|
|
|
|
|
|
|
|
|
|
|
|
|
|
|
|
|
|
|
|
|
|
|
|
|
Secrétaire
|
|
|
|
|
|
|
|
|
|
|
|
|
|
|
|
|
Directeur d'usine
|
|
|
|
|

Cabinet juridique
Expert juridique
IRAD: conseil technique
Partenaire technique
Conseil financier.
plantain et banane
|
|
|
|
|
|
|
|
|
|
|
|
|
|
|
Conseil de surveillance
|
|
|
|
|
|
|
|
|
|
|
|
Directeur général
|
|
|
|
|
BTS
|
|
BTS
|
|
BTS
|
|
|
|
|
|
|
|
BTS
|
|
|
|
|
|
|
Figure 1 : Organigramme de SOA
Responsable plantation
Responsable
plantation maïs
Responsable
plantation avocat
Responsable
plantation cacao
Responsable
palmier à huile
Chef plantation
Contremaitre
Chef plantation BTS
Chef plantation
Chef plantation
Chef plantation
Contremaitre
Contremaitre
Contremaitre
Contremaitre
Ouvriers
Ouvriers
Ouvriers
Ouvriers
Ouvriers
I.1.2 Missions et visions de SOA
Le projet SOA, consiste à créer à moyen
terme (15 ans), quarante mille (40 000) hectares (ha) de plantations au
Cameroun ; entre 2016 et 2020 SOA plantera 5 000 ha au moins de plantations
dans des terroirs camerounais rigoureusement sélectionnés. Dans
sa phase pilote, SOA entend développer 3 500 ha au moins de plantations
de : cacao, avocat, maïs, et palmier à huile. Les produits de ces
plantations seront transformés sur place en biens manufacturés
finis ou semi-finis destinés soit à la grande consommation sur le
marchés local, soit à l'exportation vers le marché sous
régional (CEMAC) et ensuite des niches précisément
ciblées au plan international. Dans cette phase pilote, le marché
camerounais est la principale cible de SOA. Des études sont cependant en
cours pour évaluer la profitabilité des autres marchés
internationaux en zone CEEAC. SOA entend accompagner sa croissance par le
financement et la promotion d'actions de développement
socioéconomiques durable dans les terroirs et auprès des
populations riveraines de ses installations.
I.1.3 Stratégie de SOA
Pour peser dans le marché très compétitif
de la production et de la transformation des cultures de rente, SOA a
opté pour une stratégie d'agriculture extensive ou intensive.
Cette stratégie est déclinée comme suit :
? Phase A : Entrée dans la filière

4
Mémoire de fin d'études pour l'obtention du
diplôme d'Ingénieur de Conception en Génie
Mécanique, rédigé et soutenu par : PONDI
JOSEPH
Mise sur pied d'une unité industrielle de transformation
des céréales pour l'obtention de la
farine : projet industriel
du Groupe SOA
- Location à long terme avec option d'achat de
plusieurs centaines d'hectares de terres culturales dans les terroirs,
auprès de particuliers et de communautés coutumières.
- Signature de partenariats avec des collectivités
territoriales décentralisées, dans le but d'acquérir
d'anciennes exploitations agro-industrielles en concession, soit sous forme de
partenariat public-privé (PPP), soit dans le cadre de la politique de
développement d'agropoles mise en oeuvre par le gouvernement
camerounais.
- Création d'archipels de petites exploitations autour
des pôles SOA dans le but de générer des réseaux de
plantation.
? Phase B : Positionnement
- Investissements prioritaires dans les cultures
multi-récoltes/an (le maïs), de manière à se
ménager des revenus conséquents dès les premières
années d'exploitation, ainsi qu'un pouvoir de négociation fort
face aux partenaires financiers et institutionnels (banques, autres
opérateurs de services de financement, organismes nationaux et
internationaux de développement de l'agriculture) ;
- Création de plantations dédiées aux
cultures de rente (cacao, palmier à huile, avocat, riz,
bananes-plantains, Etc.) sur plusieurs milliers d'hectares.
- Création de pôles d'excellence dans les
installations de SOA au bénéfice des riverains et des populations
locales ou autres : aide au financement des économats,
équipements marchands, gares routières, écoles primaires
et secondaires, cités agricoles, centres de formation aux techniques et
technologies agricoles.
I.1.4 Le modèle d'entreprise
Le modèle d'entreprise de SOA, sera entièrement
opérationnel dans les cinq prochaines années (2017 ; 2018 ; 2019
; 2020 ; 2021). Au cours de ces cinq années, SOA développera 2500
ha environ de cacaoyer, palmier à huile, avocatier, riz et maïs.
Toutes ces cultures sont des variétés camerounaises
développées par l'IRAD, toutefois, SOA envisage également
de tester avant de cultiver le cacao MERCEDES, une variété
ivoirienne réputée pour sa résistance aux parasites et son
fort taux de rendement (3.5 t/ha). SOA envisage aussi la transformation du
blé, du sorgho et du soja. Le tableau3 suivant présente le cycle
de maturation de certains de ces produits.
Tableau 3 : Cultures et cycle de
maturation
Cultures Durée du cycle de maturation
(mois)
Cacao IRAD
|
18-24
|
Cacao Mercedes
|
18-24
|
Palmier à huile
|
36
|
Avocat
|
36
|
Maïs
|
03
|
Banane-plantain
|
10-11
|

5
Mémoire de fin d'études pour l'obtention du
diplôme d'Ingénieur de Conception en Génie
Mécanique, rédigé et soutenu par : PONDI
JOSEPH
Mise sur pied d'une unité industrielle de transformation
des céréales pour l'obtention de la
farine : projet industriel
du Groupe SOA
Au vu de l'ancienne usine de la SODERIM abandonnée, SOA
se propose de rénover ses installations afin de lancer au plus vite la
transformation des produits des plantations (maïs). La fonction du
complexe sera de renforcer la valeur ajoutée de SOA par la
transformation locale de ses céréales selon des
procédés industriels respectant des standards internationaux.
Elle est indéniablement un atout supplémentaire pour être
compétitive dans les marchés cibles à l'international.
I.1.5 SOA : les leviers du succès
La réussite planifiée de SOA tient
également à la qualité de l'environnement dans lequel il
va opérer. Cet environnement plus que favorable tient à
l'engouement du maire de SANTCHOU pour le projet de SOA. Ce dernier a
réussi dès les premiers contacts à convaincre les
promoteurs de SOA que la mairie de SANTCHOU les accompagnerait dans cet
important investissement profitable à tous points de vue aux
populations. Il convient également de relever l'impact de la route
bitumée Melong-Dschang qui garantit au projet l'écoulement facile
et rapide de ses produits bruts ou transformés vers les grands centres
commerciaux et ports du Cameroun, ainsi que vers les grandes
agglomérations des pays de la CEEAC.
I.1.6 Implantation
Compte-tenu du choix des cultures opérées par
SOA, après de nombreuses investigations et descentes dans divers
terroirs, SANTCHOU s'est imposée comme le bassin de production le mieux
adapté au projet de SOA. Ce bassin propose de nombreux avantages[20]
:
. Totale adéquation avec toutes les cultures ;
. Excellente pluviométrie ;
. Multiplicité de petits cours d'eau ;
. Relief adapté à des cultures de natures diverses
;
. Vastes étendues de terres culturales permettant
l'agriculture extensive ;
. Tradition de la pratique de l'agriculture par des populations
vaillantes et dynamiques ;
. Intérêt de la mairie, des chefferies
traditionnelles et autorités administratives pour le
projet de SOA.
I.2 Problématique
Plusieurs journaux camerounais affirment que [2] : le Cameroun
n'est ni en autosuffisance alimentaire ni en sécurité
alimentaire. Produire en quantité suffisante demeure un objectif pour le
Cameroun. La production des produits et des farines
céréalières ne répond pas toujours à la
demande nationale. Selon l'OMC [3](l'organisation mondiale du commerce) les
produits agricoles importés par le Cameroun en 2013 sont chiffrés
à plus de 1458 milliards de FCFA, et ce chiffre croit au fil des
années, la figure suivante nous indique par exemple les statistiques sur
l'évolution des importations des céréales sur 12 ans.

6
Mémoire de fin d'études pour l'obtention du
diplôme d'Ingénieur de Conception en Génie
Mécanique, rédigé et soutenu par : PONDI
JOSEPH
Mise sur pied d'une unité industrielle de transformation
des céréales pour l'obtention de la
farine : projet industriel
du Groupe SOA
400000
350000 300000 250000 200000 150000 100000 50000
|
|
0

1 2 3 4 5 6 7 8 9 10 11 12
année importation (en tonnes)
Figure 2 : Evolution de l'importation des
céréales au Cameroun
Partant, nous constatons que le Cameroun importe
énormément les céréales ce qui n'est pas avantageux
pour un pays qui se veut émergent à l'horizon 2035 ; Si nous
prenons par exemple le cas simple du maïs, les statistiques de
l'Association Citoyenne de Défense des Intérêts Collectifs
(ACDIC), nous indiquent que: deux Camerounais sur trois consomment le maïs
; l'indice de consommation du maïs au Cameroun est d'environ
51kg/Habitant/an. Les tableaux suivants montrent le gap entre la demande et la
production de maïs et les importations du maïs au Cameroun.
Tableau 4 : Offre et demande de maïs au Cameroun
[3]
Années Offre : production (tonne) Demande (tonne)
Déficit (tonne)
2007
|
1
|
143
|
000
|
1
|
180
|
000
|
37 000
|
2008
|
1
|
170
|
000
|
1
|
230
|
000
|
60 000
|
2009
|
1
|
380
|
000
|
1
|
500
|
000
|
120 000
|
2013
|
1
|
800
|
000
|
2
|
000
|
000
|
200 000
|
2014
|
1
|
600
|
000
|
2
|
000
|
000
|
400 000
|
Tableau 5 : Importation du maïs par an au
Cameroun [3]
Années Importations (tonnes)
2004
|
2016
|
2005
|
12 782
|
2006
|
4
|
082
|
2007
|
1
|
637
|
2008
|
3
|
404
|
2009
|
22 662
|
2010
|
14 751
|
2011
|
4
|
706
|
2012
|
5
|
314
|

7
Mémoire de fin d'études pour l'obtention du
diplôme d'Ingénieur de Conception en Génie
Mécanique, rédigé et soutenu par : PONDI
JOSEPH
Mise sur pied d'une unité industrielle de transformation
des céréales pour l'obtention de la
farine : projet industriel
du Groupe SOA
En observant les tableaux 4 et 5 nous constatons que sur la
céréale seule qu'est le maïs, le Cameroun rencontre
d'énormes difficultés sur le plan de la satisfaction de la
demande. S'il y a donc déficit au niveau des céréales, il
y en aura forcément au niveau de la farine des céréales ;
l'institut national de la statistique nous donne les importations du Cameroun
des produits de la minoterie pendant 4 années ;
Tableau 6 : Importation des produits de la minoterie
[4]
Années
|
2007
|
2008
|
2009
|
2010
|
Importations (t)
|
95 066
|
91 936
|
103 012
|
109 141
|
Au vu de toutes ces statistiques, nous constatons donc
effectivement que le Cameroun n'est ni en sécurité ni en
autosuffisance alimentaire. C'est dans cette lancée que le gouvernement
camerounais dans le cadre de référence de l'action
gouvernementale pour la période 2010-2020, en vue de l'émergence
à l'horizon 2035, a mis sur pied un certains nombres de
stratégies ; principalement dans son document de stratégie pour
la croissance et l'emploi dans la section industries et services en son
point 219 : « les agro-industries constituent un
débouché important pour la production agricole et un puissant
facteur d'intensification des activités et de transformation du monde
rural. Dans une approche par filière privilégiant le
développement de la chaîne des valeurs, le Gouvernement entend
négocier et mettre en place systématiquement des plans de
développement des industries de transformation des produits du terroir
(farines locales, sucre, huile de palme, banane plantain, maïs, cacao,
coton, etc...) » [6] .C'est donc dans ce même ordre d'idée
que le Groupe SEEDS OF AFRICA s'est donné pour mission de faciliter ces
actions et d'accompagner l'Etat dans sa vision afin d'assurer aux citoyens
camerounais une autosuffisance et une sécurité alimentaire
à long terme; d'où la nécessité de mettre sur pied
une unité industrielle de transformation des céréales
principalement le maïs, le blé, le sorgho et le soja pour
l'obtention de la farine, du gritz, de la semoule et d'autres produits
dérivés destinés à satisfaire la consommation
humaine, les entreprises brassicoles, les provenderies etc. d'où le
thème à nous confié par SOA : « mise sur pied
d'une unité industrielle de transformation des céréales
(maïs, blé, sorgho et soja) pour l'obtention de la farine
»
Notre travail sera donc circonscrit de la manière suivante
:
v Présenter les techniques de productions des farines de
céréales ;
v Présenter les technologies utilisées pour la
production des céréales ;
v Proposer une procédure de mise sur pied d'une
unité industrielle de transformation des céréales ;
v Faire une implantation optimale de la chaine de production
;
v Faire une étude financière du projet.

8
Mémoire de fin d'études pour l'obtention du
diplôme d'Ingénieur de Conception en Génie
Mécanique, rédigé et soutenu par : PONDI
JOSEPH
Mise sur pied d'une unité industrielle de
transformation des céréales pour l'obtention de la
farine :
projet industriel du Groupe SOA
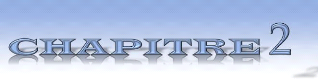
CONCEPTS DE BASE POUR LA MISE
SUR PIED ET DU SUIvI D'UNE UNITé DE
TRANSFORMATION INDUSTRIELLE.
Description :
Dans ce chapitre nous présenterons, des concepts
inhérents à la réalisation de notre projet.
L'intérêt sera porté sur la présentation des
produits moulus et des farines obtenues, aux processus d'obtention des farines
issues de ces céréales, aux différentes technologies de
mouture des céréales, aux outils d'aide au dimensionnement ,
à la conception et au choix des machines industrielles et de mise sur
pied des unités de production et de transformation industrielle.

9
Mémoire de fin d'études pour l'obtention du
diplôme d'Ingénieur de Conception en Génie
Mécanique, rédigé et soutenu par : PONDI
JOSEPH
Mise sur pied d'une unité industrielle de
transformation des céréales pour l'obtention de la
farine :
projet industriel du Groupe SOA
II.1 Généralités sur les farines
de céréales
II.1.1 Généralités sur les farines
de maïs
II.1.1.1 Processus de transformation du maïs en
farine.
La mouture du maïs est précédée d'une
série d'opérations importantes et indispensables Ces
étapes sont résumées dans le diagramme suivant
(fig.3) :
[1] :
Grains humides
Grains humides propres
Grains bruts
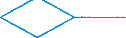
Récolte
Farine
OUI
Pré-nettoyage
NON
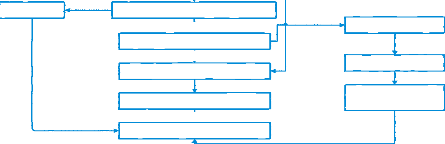
Gritz
Décorticage+ séparation
Séchage
son 12 à 15%du brut
Germes+paille
Grains secs
Dégermage
Nettoyage
complète?
Tamisage
germe
Farine fine 38 à 40%du brut
conditionnement
Figure 3 : Diagramme de mouture du maïs [14]
Dépourvus de germe 80 à 85 %du brut
Mouture
Extraction
Tourteaux de
II.1.2 Généralités sur la farine
de blé
La transformation du blé en farine suit les
principales étapes présentées dans la figure ci-dessous
:

10
Mémoire de fin d'études pour l'obtention du
diplôme d'Ingénieur de Conception en Génie
Mécanique, rédigé et soutenu par : PONDI
JOSEPH
Mise sur pied d'une unité industrielle de
transformation des céréales pour l'obtention de la
farine :
projet industriel du Groupe SOA

97-98 %des grains bruts
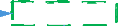
Semoule
97-98 %des grains bruts
Blé non purifié
Conditionnement
Grains humidifiés
Nettoyage
10-15%de farine,60%de semoule
Mouillage
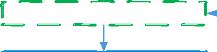
Farine de blé
Broyage
Ensachage
55-60%des grains bruts
Claquage
60 %des grains bruts
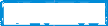
Convertissage
Figure 4 : Diagramme de mouture du blé
Tamisage ou blutage
Farine fine 10-15%des grains bruts
II.1.3 Généralités sur la farine
de soja
L'ordre de ces étapes lors de la production de la
farine de soja est donné par le diagramme suivant[16][2 :

11
Mémoire de fin d'études pour l'obtention du
diplôme d'Ingénieur de Conception en Génie
Mécanique, rédigé et soutenu par : PONDI
JOSEPH
Mise sur pied d'une unité industrielle de
transformation des céréales pour l'obtention de la
farine :
projet industriel du Groupe SOA
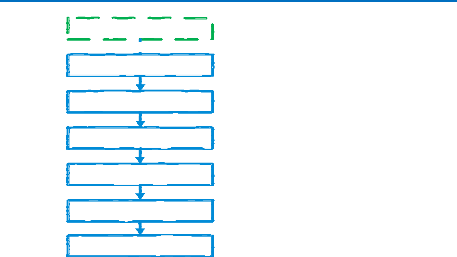
Réception des grains de soja
grains bruts
Triage-tamisage
97-98%des grains bruts
Grains grillés et disgestibles
60-65 %des grains bruts
Figure 5 : Diagramme de mouture du soja
Dépélliculage
70-80 %des grains bruts
Torréfaction
Mouture
Tamisage
II.1.4 Généralités sur la farine
de sorgho
Pour produire la farine de sorgho les étapes suivantes
sont indispensables :
V' Le nettoyage : élimination
des impuretés (sable, paille, pierres) ;
V' Décorticage :
élimination des enveloppes du grain (son) et une partie du germe ;
V' Séparation :
séparation son et grains décortiqués ;
V' Mouture : Broyage des grains ;
V' Pesage et conditionnement : mise en
sacs des produits, soudure des sacs en plastique
ou coutures des sacs en papier.
Conditionnement
Le diagramme suivant donne l'ordre dans lequel doit se faire ces
opérations :

12
Mémoire de fin d'études pour l'obtention du
diplôme d'Ingénieur de Conception en Génie
Mécanique, rédigé et soutenu par : PONDI
JOSEPH
Mise sur pied d'une unité industrielle de
transformation des céréales pour l'obtention de la
farine :
projet industriel du Groupe SOA
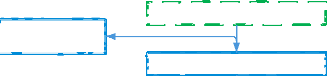
Impuretes (autres grains,
pailles , sables etc)
Grains bruts
Nettoyage
Grains propres
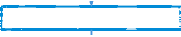
Mouture
Farine fine 60-65 %du brut
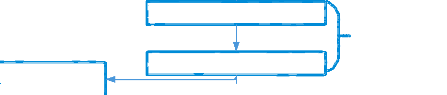
80-82%du brut
Son(12 à 15 %des grains
bruts)
Souvent en une étape
préalable)
Décorticage(Hydratation
Separation

Ensachage + conditionnement
Figure 6 : Diagramme de mouture du sorgho[19]
II.1.5 Synthèse sur les techniques d'obtention
des farines de céréales
En sommes, pour produire la farine de céréales,
particulièrement celles qui nous intéressent dans ce projet
à savoir : le maïs, le sorgho, le blé et le soja ; et
étant donné que la majorité de ces céréales
nous seront fournies en grains secs, les opérations primordiales et
indispensables sont les suivantes :
- Le nettoyage des grains secs :
opérations qui consistent à éliminer les impuretés
de tout ordre ;
- Le décorticage ou le
dépélliculage selon la céréale ;
- La mouture et le tamisage pour l'obtention de
la farine et enfin le conditionnement.
Mais selon les céréales d'autres opérations
supplémentaires sont nécessaires telles que :
- Le mouillage ou l'hydratation
: qui consiste à ajouter une certaine teneur en eau aux grains
;
- La torréfaction pour le cas du soja
particulièrement est une opération qui permet de griller le soja
par un torréfacteur pour le rendre digestible ;
- Le claquage et le convertissage
pour transformer la semoule de blé en farine ;
Le diagramme suivant nous donne un aperçu
général sur le procédé d'obtention de la farine
à base du maïs, du blé, du sorgho et du soja.

13
Mémoire de fin d'études pour l'obtention du
diplôme d'Ingénieur de Conception en Génie
Mécanique, rédigé et soutenu par : PONDI
JOSEPH
Mise sur pied d'une unité industrielle de
transformation des céréales pour l'obtention de la
farine :
projet industriel du Groupe SOA
Grains de maïs prets pour le séchage
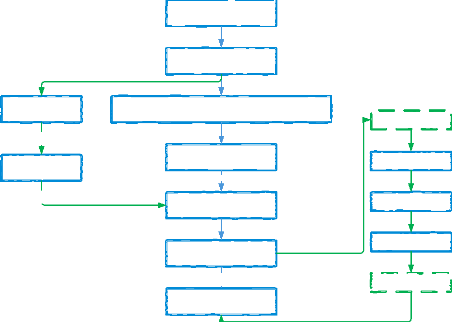
Grains de maïs secs (15%teneur en eau)
Grains de maïs bruts
Grains de céréales propres
Pré-nettoyage
Grains décortiqués
Séchage
(maïs+ sorgho)
Nettoyage
Hydratation + conditionnement (obligatoire
pour
le blé, sans importance pour le soja
Tamisage ou blutage
Dépélliculage
Soja dépélliculé
Soja torréfié
Semoule de blé
Claquage
Convertissage
Tamisage
Torréfaction
Decorticage+ séparation
conditionnement
Mouture
Figure 7 : Diagramme de synthèse sur la mouture des
céréales
II.2 Généralités sur les
technologies d'obtention des farines de céréales
Farine de céréales
Ensachage +
Farine de blé
II.2.1 Technologies de séchage
Dans l'industrie agroalimentaire, le séchage est
considéré en tant que procédé particulier qui
intervient dans la fabrication de nombreux produits finis ou
intermédiaires. L'opération de séchage a pour objectif de
réduire considérablement, voire complètement l'eau
présente dans un corps initialement humide.
Le séchage du maïs peut s'opérer de trois
façons principales : Ces méthodes peuvent aussi être
combinées. Le choix sera dicté par la nature du produit à
sécher (maïs en épis ou maïs en grains). Les
principales caractéristiques de ces méthodes sont
résumées au tableau suivant :

14
Mémoire de fin d'études pour l'obtention du
diplôme d'Ingénieur de Conception en Génie
Mécanique, rédigé et soutenu par : PONDI
JOSEPH
Mise sur pied d'une unité industrielle de
transformation des céréales pour l'obtention de la
farine :
projet industriel du Groupe SOA
Tableau 7 : Comparaison entre les différentes
technologies de séchage [4]

Séchage naturel
Séchage artificiel
Convection Convection forcée
Au soleil solaire libre Air
ambiant
Air chauffé
Débit de séchage
|
Très faible
|
Moyen
|
Faible
|
Moyen
|
Elevé
|
Investissement
|
Très faible
|
Moyen
|
Faible
|
Moyen
|
Elevé
|
Qualification du personnel
|
Faible
|
Moyenne
|
Moyenne
|
Moyenne
|
Parfois élevée
|
Main-d'oeuvre
|
Nombreuse
|
Raisonnable
|
Nombreuse
|
Peu
nombreuse
|
Peu
nombreuse
|
Exigences techniques
|
Minimes
|
Modérées
|
Peu élevées
|
Elevées
|
Elevées
|
Assujettissement au climat
|
Total
|
Important
|
Nul
|
Faible
|
Nul
|
Assujettissement à un combustible
|
Nul
|
Nul
|
Total
|
Nul
|
Total
|
Assujettissement à une source
extérieure
|
Nul
|
Total
|
Nul
|
Total
|
Total
|
Contrôle du
séchage
|
Nul
|
Modéré
|
Faible
|
Elevé
|
Elevé
|
Sensibilité aux
dégradations (graines)
|
Modéré
|
Faible
|
Elevée
|
Faible
|
Faible
|
Protection contre
l'infestation par
les insectes ou des microbes
|
Faible
|
Modéré
|
Modéré
|
Modéré
|
Elevée
|
|
Il ressort de notre tableau comparatif que nous allons
adopter un séchage artificiel pour des raisons
de productivité agricole et de disponibilité de la main-d'oeuvre
en milieu rural. Dans la littérature les modes principaux de
séchage artificiel sont les suivants : convection, conduction,
rayonnement et lyophilisation.

15
Mémoire de fin d'études pour l'obtention du
diplôme d'Ingénieur de Conception en Génie
Mécanique, rédigé et soutenu par : PONDI
JOSEPH
Mise sur pied d'une unité industrielle de
transformation des céréales pour l'obtention de la
farine :
projet industriel du Groupe SOA
Tableau 8 : Tableau comparatif entre les modes de
séchage artificiel [18]
Mode de séchage
|
|
Avantages Inconvénients Exemple
Utilisation
|
|
|
|
Convection
|
Séchage à contre- courant
|
Diminution rapide de la température
|
Sécheurs à tambour rotatif
|
- Industrie
chimique
- Produits non collant
- Produit en poudre
|
|
|
- Grains,
céréales ;
|
|
- Séchage de
précision
- Température
élevée
|
Contact avec les parois du sécheur et faible
quantité
|
Sécheur à tambour rotatif
|
Produits minéraux
supportant des très hautes températures
|
|
Textiles, papiers,
matières plastiques
|
Rayonnement
|
- Produit à
épaisseur très faible
- Propre
- Facile à
réguler
|
Couteux
|
Sécheurs à infra rouge
|
Produits alimentaires,
produits minéraux (engrais,
pigments...),
|
|
Produits alimentaires, produits minéraux (engrais,
pigments...), produits organiques, lessives.
|
Lyophilisation
|
Conservation de la qualité des produits
|
- Très
couteux
- Procédé complexe
|
|
Produits alimentaires, jus de fruit, plasma sanguin,...
|
|
Il en résulte que de tous les modes de séchage
artificiel, celui le plus approprié est le séchage par
convection à air chaud.
II.2.2 Technologie d'égrenage
Lorsqu'on compare deux méthodes d'égrenage, il
faut tenir compte de toutes les opérations annexes [4]. Certaines
machines assurent la totalité de ces opérations, d'autres une
partie seulement ; d'autres enfin n'effectuent que l'égrenage. Il faut
donc tenir compte, dans toute étude comparative, des coûts
entrainés par les opérations annexes suivantes :

16
Mémoire de fin d'études pour l'obtention du
diplôme d'Ingénieur de Conception en Génie
Mécanique, rédigé et soutenu par : PONDI
JOSEPH
Mise sur pied d'une unité industrielle de
transformation des céréales pour l'obtention de la
farine :
projet industriel du Groupe SOA
- Dépouillage ;
- Nettoyage ;
- Criblage ;
- Ensachage ou emballage, le cas échéant.
Le tableau suivant nous permettra donc de résumer les
critères de choix de la technologie d'égrenage et de faire un
choix sur la technologie adéquate pour notre projet.
Tableau 9 : Comparaison entre les différentes
technologies d'égrenage [7]
Débit
Coût
Taux d'écrasement
Dépouillage
Rendement
Faible (pour les petites productions)
Faible
Elevé
N'intègre pas le dépouillage
Faible
Egreneuses électriques
|
Elevé (pour les
productions industrielles)
|
Elevé
|
Faible de l'ordre de 2
|
%
|
Intègre souvent le dépouillage
|
Elevé
|
|
Egreneuses à pédale
Moyenne
Moyen
Moyen
N'intègre pas le dépouillage
Faible
Egreneuses manuelles
Il ressort donc de notre tableau que : les
égreneuses électriques sont les mieux
adaptées pour notre projet. Mais compte tenu du fait que nous avons
associé l'opération d'égrenage et de récolte, nous
allons utiliser une moissonneuse-batteuse.
II.2.3 Technologie de décorticage
On distingue 03 types de décortiqueuses utilisables
dans la littérature pour les céréales et les grains.
Tableau 10 : Etude comparative des
différentes technologies de décorticage [17]
Avantages Inconvénients Domaine
Technologie
d'utilisation utilisée
|
Décortiqueuse à abrasion
|
- Très bon
rendement
- Pureté
|
- Approprié
pour les graines
|
Produits ayant un taux d'humidité
|
Abrasion
|
|
excellente
|
sphériques
|
inférieur à
|
|
|
- Peu
couteux
|
- Présence des
impuretés
|
13% (maïs,
riz, froment,
|
|
|
- Simple
d'utilisation
|
- Uniquement
pour les grains durs
|
millet, orge...)
|
|
|

17
Mémoire de fin d'études pour l'obtention du
diplôme d'Ingénieur de Conception en Génie
Mécanique, rédigé et soutenu par : PONDI
JOSEPH
Mise sur pied d'une unité industrielle de
transformation des céréales pour l'obtention de la
farine :
projet industriel du Groupe SOA
Avantages Inconvénients Domaine
Technologie
d'utilisation utilisée
|
Décortiqueuse à friction
|
- Bon
rendement (environ 80
|
- Risque de
contamination du produit
|
Maïs, riz,
fonio...
|
- Friction et
cisaillement
|
|
%)
|
|
|
|
|
- Possibilité
de traiter les grains
humides
|
|
|
|
Décortiqueuse
|
- Grains
|
- Forme
|
Farine de
|
Ecrasement
|
à impact (à
|
dense
|
arrondie
|
céréales
|
|
ailettes, à
marteau, à
cylindre)
|
- Bon
rendement
(80%)
|
uniquement
coque très durs
|
(maïs,
sorgho, mil, riz,...)
|
|
|
Au sortir de notre étude comparative, nous constatons que
les décortiqueuses à abrasion seront les
meilleurs pour le décorticage de nos céréales.
II.2.4 Technologies de broyage
Nous distinguons 02 grands types de broyeurs selon l'orientation
de l'axe [22] :
- Les broyeurs verticaux
v Billes
v Galets - Horizontaux
v Presse à rouleaux
v Boulets ou barres
Mais pour résumer nous allons les classer par mode de
broyage.
Tableau 11 : Etude comparative des technologies de
broyage
Avantages Inconvénients Domaine
Technologie
d'utilisation utilisée
|
Broyeur
|
- Pas de
|
- Echauffement
|
- Produits
|
Percussion ou
|
à bille ou
|
contamination
|
important
|
miniers
|
choc
|
à boulets
|
par l'air ambiant
|
- Changement
fréquent des billes
|
- minéralurgie
|
|
|
- Finesse des
produits
|
- Vitesse à surveiller
|
|
|

18
Mémoire de fin d'études pour l'obtention du
diplôme d'Ingénieur de Conception en Génie
Mécanique, rédigé et soutenu par : PONDI
JOSEPH
Mise sur pied d'une unité industrielle de transformation
des céréales pour l'obtention de la
farine : projet industriel
du Groupe SOA
Broyeur à
marteau
|
Ecrasement des grains ayant une forte teneur en eau
|
mauvais rendement
|
Céréales
|
Ecrasement
|
Broyeur à
mortier
|
- finesse du
produit
|
- risque de
contamination
du produit
|
Céréales
|
Abrasion ou
attrition
|
Broyeur à disque
|
Bien adapté pour le broyage humide du maïs
|
Consommation élevée
d'énergie par rapport aux autres broyeurs
|
Céréales,
principalement maïs
|
Cisaillement
|
Broyeur à
cylindre
|
Possibilité de fixer la granulométrie
|
Convient seulement à très grande échelle
industrielle
|
Céréales
|
- Ecrasement et attrition
- écrasement et cisaillement
|
Il ressort de notre étude que le broyeur
à cylindre est le mieux adapté pour la mouture de
nos céréales.
II.2.5 Unité de nettoyage
Dans la littérature on rencontre 04 principaux types de
nettoyeurs de grains de céréales : le
nettoyeur-séparateur, le trieur alvéolaire, le trieur optique
et la table densimétrique. Le tableau suivant
nous permet de mener une étude comparative et d'en choisir celui qui
convient à notre projet.
Tableau 12 : Etude comparative entre les
différents nettoyeurs de céréales [17]
Avantages Inconvénients Champ d'action
Technologie
|
Nettoyeur- séparateur
|
- C'est le nettoyeur le plus poussé pour les
céréales
- Débit très intéressant
|
- Un seul type
de graine propre à la fois
-
|
- Epaisseur,
largeur,
volume et poids
|
- Grille
|
Trieur alvéolaire
|
Sépare les grains de tailles presque similaires
|
- Trie mais ne
nettoie pas
- Débit faible
|
- Longueur
|
- Alvéoles
|
Trieur optique
|
Précision de
triage
|
Montant de l'investissement important et adapté pour
être sur une chaine de
|
- Couleur ;
forme
|
- Ejection
|

19
Mémoire de fin d'études pour l'obtention du
diplôme d'Ingénieur de Conception en Génie
Mécanique, rédigé et soutenu par : PONDI
JOSEPH
Mise sur pied d'une unité industrielle de transformation
des céréales pour l'obtention de la
farine : projet industriel
du Groupe SOA
|
|
trie avec d'autres équipements
|
|
|
Table
densimétrique
|
Précision de
triage
|
Montant de l'investissement important
|
- Densité
|
- Coussin
d'air vibration
|
Il ressort de notre tableau que nous allons utiliser un
nettoyeur -séparateur. II.2.6 Choix du type de
convoyeur
Pour faire le choix du convoyeur, nous nous focaliserons sur les
caractéristiques du produit à convoyer et l'étude
comparative dans le tableau ci-dessous nous permet d'en choisir un pour notre
projet.
Tableau 13 : Comparaison entre les différents
types de convoyeurs [23]
Types de Granulométrie Forme Longueur Inclinaison
Pouvoir Fluidité
convoyeur du produit des du du abrasif du
produits convoyeur convoyeur des produit
produits
|
Convoyeur à bande
|
|
G+
|
R+I
|
F+G+M
|
F+M+G
|
A+B+C+D
|
T
|
Convoyeur à courroie crantée
|
|
M
|
R
|
F+M
|
F
|
B
|
M
|
convoyeur à chaine
|
|
M
|
R
|
F+M
|
F
|
B
|
M
|
Convoyeur à
pas de pèlerin
|
|
M
|
R
|
F+M
|
F
|
B
|
M
|
Convoyeur à rouleaux
|
|
G+M
|
R
|
F+M
|
F
|
B
|
M
|
Convoyeur à vis sans fin
|
|
F
|
R+I
|
F+M
|
M
|
A+B+C
|
T
|
Convoyeur pneumatique
|
|
F
|
R+I
|
M
|
F
|
|
T
|
II.2.7 Synthèse sur les technologies
retenues
Le tableau suivant nous donne le récapitulatif des
technologies retenues en fonction de chaque opération de notre
unité de mouture des céréales.

20
Mémoire de fin d'études pour l'obtention du
diplôme d'Ingénieur de Conception en Génie
Mécanique, rédigé et soutenu par : PONDI
JOSEPH
Mise sur pied d'une unité industrielle de transformation
des céréales pour l'obtention de la
farine : projet industriel
du Groupe SOA
Tableau 14 : Synthèse sur les technologies
retenues
Opération
|
Equipement
|
Récolte - dépouillage du
maïs
|
Moissonneuse batteuse
|
Séchage
|
Sécheur par convection
|
Nettoyage
|
Nettoyeur- séparateur
|
Stockage des céréales
|
Silos de stockage
|
Hydratation
|
Mouilleur
|
Décorticage
|
Décortiqueuse à abrasion
|
Mouture
|
Broyeurs à cylindre
|
Claquage- convertissage
|
Claqueur, convertisseur (broyeurs à cylindre lisse)
|
Torréfaction de soja
|
Torréfacteur
|
Tamisage ou blutage
|
Tamiseur vibrant ou blutoir
|
Ensachage
|
Thermo soudeuse
|
Convoyage des graines et épis de
maïs
|
Convoyeurs à bande
|
Convoyage des produits moulus
|
Convoyeurs à vis
|
Convoyage des graines
|
Convoyage pneumatique le cas échéant
|
II.3 Procédure de mise sur pied d'une
unité de transformation industrielle
Les étapes de mise en service d'une nouvelle
unité de production ne sont pas standard, elles varient d'une entreprise
à une autre en fonction de plusieurs critères tels que :
- Les fonctions à réaliser ;
- Les limites de fournitures ;
- Les exigences de maintenance à respecter ;
- Les performances à garantir ;
- Les exigences de qualités à respecter ;
- Les caractéristiques techniques ;
- Les critères de validation ;
- Documentation à fournir ;
- Etc.
Les procédures de mise en place d'une nouvelle
unité de production sont nombreuses dans la littérature.
Plusieurs auteurs ont écrit sur ces procédures ; et dans le
tableau ci-dessous, nous faisons une étude comparative des principales
méthodes afin de choisir celle qui convient dans notre étude.

21
Mémoire de fin d'études pour l'obtention du
diplôme d'Ingénieur de Conception en Génie
Mécanique, rédigé et soutenu par : PONDI
JOSEPH
Mise sur pied d'une unité industrielle de transformation
des céréales pour l'obtention de la
farine : projet industriel
du Groupe SOA
Tableau 15 : Méthode de mise sur pied d'une
nouvelle unité de production [17]
Méthodes Avantages
Inconvénients
PIGNAULT ET SOHIER
- Projet en cours de réalisation
Uniquement pour les projets en phase initiale
V.CAUDILL
|
- prend en compte les projets en cours
- projet en phase initiale
- économique (ne nécessite pas un travail d'expert,
ni de consultant externe)
|
Collecte des données assez vaste
|
MAROULIS ET
SARAVACOS
Projet en cours de réalisation
Nécessité d'une équipe pluridisciplinaire
La procédure qui sied le mieux à notre contexte
est celle proposée par V.CAUDILL. Elle se décline en 5
étapes :
II.4 Présentation de la méthode de
V.CAUDILL
II.4.1 Technologie des équipements
La technologie est dans la tradition grecque, «
l'inventaire des procédures qui caractérisent les savoirs
et savoir-faire qui échappent aux déductions spéculatives,
mais reposent sur des connaissances expérimentales. »
ainsi, il sera question ici de décrire les processus mis sur
pied au sein de la nouvelle unité. La description devra non seulement
reposer sur les caractéristiques techniques des différentes
parties de l'unité mais également sur le fonctionnement de
l'unité complète.
II.4.2 Conception en équipe de ligne
Il sera question ici de donner des informations sur
La configuration de la ligne : nous devons montrer par des
calculs quelle sera l'implantation des machines au sein de l'usine.
Les besoins de production : il s'agira ici de présenter
la cadence de production c'est-à-dire la quantité de
céréales qui doit être moulue par une unité de temps
que nous aurons choisi.
Justifications économiques : il sera question de faire
une étude financière du projet et justifier si les moyens
disponibles nous permettrons de réaliser les objectifs de production.
Ergonomie et le degré d'automatisation : c'est
l'étude des conditions de travail et des relations entre l'homme et la
machine. Il sera donc question de montrer le taux

22
Mémoire de fin d'études pour l'obtention du
diplôme d'Ingénieur de Conception en Génie
Mécanique, rédigé et soutenu par : PONDI
JOSEPH
Mise sur pied d'une unité industrielle de transformation
des céréales pour l'obtention de la
farine : projet industriel
du Groupe SOA
d'implication de l'homme dans le travail. Montrer
également si les machines seront automatisées ou non, quelle sera
l'implication de l'homme à chaque secteur d'activité.
II.4.3 Ingénierie du projet
Dans cette phase du projet, il sera question de faire
l'étude de dimensionnement des différents équipements en
fonction des objectifs visés par la hiérarchie ; ce sera ici le
lieu de faire les dessins et les mises en plan pour la fabrication des
machines, de proposer des solutions pour le transfert des produits d'une
machine à une autre, de dimensionner l'énergie nécessaire
à l'installation des équipements, de penser à la
construction des lieux d'installation de la nouvelle unité.
Ici nous devons tenir compte de plusieurs facteurs clé
tels que résumé dans le tableau suivant : Tableau 16
: Facteur influençant l'ingénierie du projet
[18]
Domaine Paramètre Questions
Conditions d'exploitation
|
Qualité
|
- Risques de qualité ?
- Risques pour le produit ?
- Faisabilité des contrôles ?
|
Main d'oeuvre
|
- Nombre de poste de
travail ?
- Charge de travail des opérateurs ?
|
Consommation d'énergie
|
-
|
Conditions de travail
|
Sécurité
|
- Circulation du personnel ?
- Risques individuels ?
- Hygiène ?
- Risque d'incendie ?
|
Ambiance physique
|
- Nuisance sonore ?
- Pollution, toxicité ?
- Propreté ?
|
Charge de travail
|
- Facilité de maintenance ?
- Contrainte de
mémorisation ?
|
Relation de travail et organisation
|
Rapport avec l'environnement
|
- Atteinte à la protection de
l'environnement ?
|
Rapport entre services
|
- Relation avec le service
qualité ?
- Relation avec le service général ?
- Relation avec la production ?
|

23
Mémoire de fin d'études pour l'obtention du
diplôme d'Ingénieur de Conception en Génie
Mécanique, rédigé et soutenu par : PONDI
JOSEPH
Mise sur pied d'une unité industrielle de transformation
des céréales pour l'obtention de la
farine : projet industriel
du Groupe SOA
Evolution après mise en place
|
Evolution de l'usine
|
- Equipements qui
s'intègrent dans l'usine ?
- Problème à terme ?
|
Evolution des technologies
|
- Durée d'amortissement
compatible avec
l'apparition des nouvelles technologies ?
|
Evolutions produits et marché
|
- Adaptabilité à un
accroissement de la demande ?
|
Evolution de la législation
|
- Evolution en matière de
sécurité et travail ?
|
II.4.3.1 Construction
Au cours de cette phase, il sera question de la fabrication
des équipements et autres éléments dimensionnés au
cours de la phase d'ingénierie. Au cours de cette phase, des
vérifications, des tests et des corrections devront être faits sur
les équipements.
II.4.3.2 Mise en route
Cette phase sera le clou de notre installation de
l'entreprise. Ici, il faudra faire des tests complets sur toute l'unité,
s'assurer d'une installation optimale des équipements, mettre des
procédures de suivi de la production, des procédures de suivi des
équipements, de gestion des ressources humaines et bien d'autres
encore.
II.5 Elaboration d'une technique d'analyse pour le
choix des machines
La commande d'une machine de production ou de transformation
industrielle exige une certaine analyse, car la machine doit assurer la
performance souhaitée par le producteur ; pour cela il est judicieux
d'utiliser un outil d'analyse pour le choix d'une machine ; les outils les plus
utilisés dans ce domaine sont [5] :
- Le diagramme « causes-effet » ;
Ce diagramme est une représentation graphique
ordonnée permettant de visualiser l'ensemble des causes ayant une
influence sur un effet constaté ou un phénomène ;
- Histogramme de coûts par fonction ;
L'établissement des coûts par fonction sert
notamment à :
· Déterminer si le coût de chaque fonction est
en rapport avec leur importance relative dans le produit étudié
;

24
Mémoire de fin d'études pour l'obtention du
diplôme d'Ingénieur de Conception en Génie
Mécanique, rédigé et soutenu par : PONDI
JOSEPH
Mise sur pied d'une unité industrielle de
transformation des céréales pour l'obtention de la
farine :
projet industriel du Groupe SOA
· Hiérarchiser les fonctions et à orienter
l'action « analyse de la valeur », en permettant de faire porter les
efforts de réduction de coûts prioritairement sur les fonctions et
coûts qui offrent les fortes possibilités de gain.
- Le diagramme de Pareto ;
Il permet de :
· Distinguer dans un ensemble de facteurs ceux qui sont les
plus importants ;
· D'effectuer des choix ;
· D'établir des priorités ;
Le tableau suivant résume quelques avantages et
inconvénients de ces trois méthodes : Tableau 17 :
Tableau de comparaison des techniques d'analyse.
Méthode Avantages Inconvénients
« causes-effet »
|
Pas besoin de connaitre
toutes les performances techniques de la machine
|
Connaitre obligatoire les
effets dus à l'utilisation de la machine.
|
Coût par fonction
|
Orientation précise et bonne analyse de la valeur.
|
Détermine le coût par rapport à
l'importance
|
Pareto
|
Bien adapter pour effectuer les choix
Etablit les priorités
|
Considère principalement les facteurs importants
|
Il ressort de notre tableau que le diagramme de
Pareto est le mieux adapté pour notre cas, car il est plus
apte à effectuer les choix.
Méthodologie
- Etablir la liste de données par valeur
décroissante ;
- Quantifier chacune de ces données ;
- Effectuer la somme des valeurs obtenues ;
- Calculer pour chaque valeur le pourcentage ;
- Effectuer le cumulé des puissances obtenues ;
- Représenter le graphique des pourcentages ;
Cette démarche permet de prendre en compte les
opportunités du marché, l'évolution de l'environnement et
les techniques possibles. Elle est caractérisée par :
- Une identification des critères de choix ;
- Un classement de ces critères de choix ;
- La détermination du poids de chaque critère en
fonction de la somme pondérée établit
dans la matrice de préférence ;
- La détermination de la note de chaque critère
;
- La détermination de la note générale de
chaque fournisseur ;

25
Mémoire de fin d'études pour l'obtention du
diplôme d'Ingénieur de Conception en Génie
Mécanique, rédigé et soutenu par : PONDI
JOSEPH
Mise sur pied d'une unité industrielle de transformation
des céréales pour l'obtention de la
farine : projet industriel
du Groupe SOA
- Le choix de la machine chez les fournisseurs ;
II.6 Démarche à suivre pour la conception
de l'implantation d'une unité de transformation industrielle
Pour atteindre les objectifs de production en respectant aussi
bien les règles de production, les règles de
sécurité que les règles d'hygiène et de
salubrité, il faudrait pouvoir trouver une disposition optimale des
différents équipements de l'unité. Ainsi, nous allons
suivre la démarche suivante :
a- Recueil des données caractérisant l'entreprise
Au cours de cette étape, il sera question de définir :
Les clients, les fournisseurs, les produits, la
qualité, organisation et les conditions de travail, organisation
possible pour la production,
Les plans de construction (nombres de bâtiments)
possibilité d'extension de l'unité, les moyens de transport
disponibles, les plans de situation, etc.
Le type de transformation, les méthodes de
transformation (pression, déformation...), les locaux d'entretien,
etc.
Les stockages des produits finis, de la matière
première, des produits dangereux, etc.
L'accès sur le site, les voies de circulation, aires
de chargement et de déchargement, les aires de service (lavage, ateliers
de première intervention...).
b- Définition des secteurs d'activité
Le terme secteur d'activité peut désigner selon la
taille du projet, un atelier, le travail sur une machine, ou encore un espace
fonctionnel :
Secteurs à risque liés à la circulation des
véhicules, des engins et des personnes (chargement des produits finis,
déchargement des matières premières,...) ;
Secteurs à risque avec des nuisances liées aux
ambiances physiques et chimiques (zone propre pour produits finis, secteurs
d'emballage...) ; Autres secteurs sans flux de matières (bureaux,
laverie,...) ;
Secteurs avec des flux de matières ;
Secteurs à risques pour les produits ;
c- Détermination des proximités et des flux
Cette étape consiste à déterminer les
besoins de proximité ou d'éloignement entre secteurs en
s'appuyant sur des estimations collectées.
Le choix des degrés de proximité
/d'éloignement, est effectué en fonction des exigences de
production, de qualité de produits et de vie au travail, des besoins de
communication et en s'appuyant sur des critères concourant à la
prévention des risques et à l'amélioration des

26
Mémoire de fin d'études pour l'obtention du
diplôme d'Ingénieur de Conception en Génie
Mécanique, rédigé et soutenu par : PONDI
JOSEPH
Mise sur pied d'une unité industrielle de transformation
des céréales pour l'obtention de la
farine : projet industriel
du Groupe SOA
conditions de travail. La figure suivante illustre mieux une
méthode de détermination des proximités et des flux.
|
|
|
|
|
|
quantitatives)
|
|
défavorables
|
avec risques professionnels
|
|
|
|
|
|
|
|
|
|
|
|
professionnels
|
|
|
|
Définition des proximités ou
liaisons fonctionnelles entre les secteurs de production
(informations qualitatives) Définition des
flux matières/ produits entre les secteurs
(informations Définition des secteurs à
risques : secteurs avec circulation, flux,
avec ambiances physiques
Figure 8 : Méthode de détermination des
proximités et des flux
Au travers de cette figure, nous constatons que nous pouvons
faire une implantation basée soit sur les proximités, soit sur
les flux de matières, soit sur les deux. Un tableau de proximité
sera alors établi : il aura en abscisse et en ordonnée les
secteurs d'activité.
Calcul des besoins
en surface des
secteurs
- implantation basée sur les
proximités - implantation basée sur les flux de
matière - implantation basée sur les proximités
et les flux de matières tenant compte des secteurs
Implantation finale mixte basée sur les
proximités et les flux matières tenant compte
des secteurs à risques
d- Diagramme d'implantation
Il s'agit de donner une représentation
schématique du tableau proximité/éloignement. Pour cela,
il faudra disposer les différents secteurs d'activités en
fonction des proximités ou des éloignements tel
qu'élaboré dans le tableau de proximité.
e- Schéma d'implantation
Il est obtenu en prenant en compte les informations contenues
sur le schéma fonctionnel et les surfaces nécessaires par
secteurs d'activités.
II.6.1 Elaboration d'une méthode pour le choix
des équipements critiques
II.6.2 Choix de la méthode pour la maintenance
préventive
La mise en oeuvre d'une politique de maintenance
préventive nécessite l'identification des équipements
critiques et qui doivent donc être traités en priorité.
Deux types de méthodes s'offrent alors :
- La méthode prédictive : méthode qui essaie
de prévoir les pannes, même si elles ne sont pas encore produites
(on se projette dans les probabilités futures). La méthode de
l'AMDEC machine est indiquée dans ce cas.
- La méthode d'analyse à postériori qui
produit des résultats émis à partir des données
historiées. L'abaque de NOIRET et le diagramme de PARETO.

27
Mémoire de fin d'études pour l'obtention du
diplôme d'Ingénieur de Conception en Génie
Mécanique, rédigé et soutenu par : PONDI
JOSEPH
Mise sur pied d'une unité industrielle de transformation
des céréales pour l'obtention de la
farine : projet industriel
du Groupe SOA
Les équipements étant neufs à leur
arrivée dans l'usine, il serait difficile d'implémenter
facilement la méthode AMDEC, dans laquelle il nous sera difficile
d'évaluer la fréquence des pannes. Ce qui nous empêche
d'évaluer l'indice de criticité.
Le diagramme de Pareto lui, permet de positionner les
équipements critiques (selon un critère défini)
d'après une répartition de type 80/20 : 20 % des
équipements produisent 80% des pannes. Les équipements sont
classés selon un ordre décroissant par rapport au critère.
Mais pour que cette méthode soit efficace, il est indispensable d'avoir
un historique couvrant au moins une année de maintenance.
L'abaque de Noiret quant à lui fournit des
recommandations quant à la pertinence ou non d'une politique de
maintenance préventive sur un équipement de production. C'est un
outil de calcul scientifique qui permet d'orienter le choix de la politique de
maintenance en fonction :
- Des caractéristiques de l'équipement ; - De son
utilisation ;
Le résultat en est une recommandation offrant trois
options possibles :
- Préventif recommandé ; - Préventif
possible ;
- Préventif non nécessaire.
Pour mieux effectuer notre choix nous allons résumer
ces trois techniques d'analyse dans le tableau suivant :
Tableau 18 : Technique de choix des
équipements critiques
Méthode Avantages Inconvénients
Pareto
Noiret
AMDEC
Positionnement des
équipements critiques
Pas besoin des fiches d'historique
On peut prévoir l'apparition prochaine d'une panne
Avoir un historique des pannes sur au moins un an
Détecte uniquement les équipements critiques
Evaluation de la fréquence d'apparition des pannes
Il en résulte de notre tableau comparatif que
l'abaque de Noiret est le plus approprié pour
notre cas et nous apportera des résultats satisfaisants avec le moins de
contraintes.
II.6.3 Description et utilisation de l'abaque de
Noiret
L'abaque de Noiret est basé sur les critères
suivants[22] :
a- L'âge de l'équipement ;
b- Son interdépendance : dans quelle mesure est-il vital
pour la production ;
c- Son coût d'achat ;
d- Sa complexité et son accessibilité ;

28
Mémoire de fin d'études pour l'obtention du
diplôme d'Ingénieur de Conception en Génie
Mécanique, rédigé et soutenu par : PONDI
JOSEPH
Mise sur pied d'une unité industrielle de transformation
des céréales pour l'obtention de la
farine : projet industriel
du Groupe SOA
e- Sa robustesse et sa précision ;
f- Son origine : France ou étranger ;
g- Son utilisation dans le temps ;
h- Les conséquences de ses défaillances sur les
produits ;
i- Les délais de production qui lui sont liés ;
Chaque critère se décline en plusieurs options qui
chacune correspond à un certain nombre de points. Les points ainsi
obtenus sont additionnés.
Remarque : un seul choix est possible par
critère ; il faut donc prendre celui qui est le plus
représentatif de l'équipement.
a- Age de l'équipement
Tableau 19 : Age des
équipements
Age (ans )
20 19 18 17 16 15 14 13 12 11 10 9 8 7 6 5 4 3 2 1
0
58
54
86
38
42
46
50
30
26
62
66
34
22
74
78
82
70
90
18
14
10
Poi nts
Formule de calcul : points = 90 - âge * 4 b-
Interdépendance
Tableau 20 : Indépendance des
équipements
Critères Points
Matériel essentiel et marche en
continu
|
70
|
Matériel essentiel et marche en semi
continu
|
60
|
Matériel essentiel et marche en
discontinu
|
50
|
Matériel sans tampon aval ou amont
|
40
|
Matériel semi indépendant
|
30
|
Matériel indépendant
|
20
|
Matériel double (ou plus)
|
10
|
Il faudra justifier si notre machine sera utilisée en
continue ou de manière discontinue et surtout l'impact de l'absence de
celle-ci.
c- Coût

29
Mémoire de fin d'études pour l'obtention du
diplôme d'Ingénieur de Conception en Génie
Mécanique, rédigé et soutenu par : PONDI
JOSEPH
Mise sur pied d'une unité industrielle de transformation
des céréales pour l'obtention de la
farine : projet industriel
du Groupe SOA
Tableau 21 : Intervalle des coûts des
équipements
Critère en euro Points
Moins de 3000
|
5
|
[3000 à 15000[
|
15
|
[15000 à 30000[
|
25
|
[30000 à 45000[
|
35
|
[45000 à 150000 [
|
45
|
150 000 ou plus
|
55
|
Il faut estimer l'intervalle dans lequel se trouve le prix
d'achat de notre équipement.
d- Complexité et accessibilité
Tableau 22 : Complexité et
accessibilité des équipements
Critère Points
Matériel peu complexe et accessible
|
5
|
Matériel très complexe et
accessible
|
25
|
Matériel peu complexe et
inaccessible
|
25
|
Matériel très complexe et
inaccessible
|
45
|
|
e- Robustesse et sa précision
Tableau 23 : Robustesse et précision des
équipements
Critère Points
Robuste
|
5
|
Courant
|
10
|
Robuste et de précision
|
15
|
Peu robuste (délicat)
|
20
|
Travail en surcharge
|
25
|
Délicat et de précision
|
30
|
|
f- Origine
Tableau 24 : Origine des
équipements
Critère Points
Français de grande série
|
20
|
Français de petite série
|
40
|
Etranger avec SAV en France
|
50
|
Etranger sans SAV en France
|
70
|
Etranger sans service technique
|
90
|

30
Mémoire de fin d'études pour l'obtention du
diplôme d'Ingénieur de Conception en Génie
Mécanique, rédigé et soutenu par : PONDI
JOSEPH
Mise sur pied d'une unité industrielle de transformation
des céréales pour l'obtention de la
farine : projet industriel
du Groupe SOA
g- Utilisation ;
Tableau 25 : Type d'utilisation des
machines
Critère Points
Marche à 1 poste de travail
|
75
|
Marche à 2 postes de travail
|
175
|
Marches à 3 postes de travail
|
250
|
|
h- Perte de produits (conséquences sur les produits en
cas de défaillance de la machine) Tableau 26 : Impacts sur
les produits
Critère Points
Produits vendables
|
10
|
Produits à reprendre
|
35
|
Produits perdus
|
55
|
|
i- Délais
Tableau 27 : Délais d'attente d'un
équipement défaillant
Critère Points
Délais libre (constitution de stock)
|
25
|
Délai serré
|
100
|
Délai impératif (risque de
pénalités de retard)
|
150
|
Délai impératif (risque de
pénalités de perte de client)
|
225
|
|
j- Détermination des équipements critiques
Tableau 28 : Récapitulatif de l'étude
de la détermination des équipements critiques
Domaine Recommandation
0 à 510
|
Préventif non nécessaire
|
511 à 559
|
Préventif possible
|
559 à 910
|
Préventif recommandé
|

31
Mémoire de fin d'études pour l'obtention du
diplôme d'Ingénieur de Conception en Génie
Mécanique, rédigé et soutenu par : PONDI
JOSEPH
Mise sur pied d'une unité industrielle de transformation
des céréales pour l'obtention de la
farine : projet industriel
du Groupe SOA
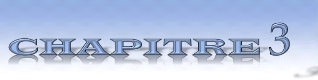
etude de réalisation et
d'implantation
DU PROJET INDUSTRIEl.
Description :
Le but de ce chapitre est mettre en oeuvre la
méthodologie de conception et d'installation des nouvelles unités
de transformation industrielle ; nous allons succinctement faire l'analyse
fonctionnelle de la chaine de transformation, dimensionner les
équipements principaux et annexes de la chaine de transformation, faire
le choix des machines auprès des fournisseurs, dimensionner la partie
électrique et la surface minimale de l'usine.
32
Mémoire de fin d'études pour l'obtention du
diplôme d'Ingénieur de Conception en Génie
Mécanique, rédigé et soutenu par : PONDI
JOSEPH
Mise sur pied d'une unité industrielle de transformation
des céréales pour l'obtention de la
farine : projet industriel
du Groupe SOA
III.1 Conception en équipe de ligne
III.1.1 Cahier de charge technique
· Le maïs
L'usine aura à sa disposition 500 ha de maïs par
an soit environ 4000 tonnes de maïs en épis par an qui devront
être transformées. Les produits issus de cette transformation
doivent être : la farine de maïs, la semoule.
· Le blé
Le blé sera livré en grains secs dans l'usine,
le blé principalement utilisé sera le blé dur d'une
quantité maximale de 4000 tonnes par an.
· Le sorgho et le soja
Le sorgho et le soja utilisés seront ceux produits par
nos agriculteurs et qu'on peut rencontrer sur nos marchés, les semences
sont produites par l'IRAD, à leur arrivée dans l'usine elles
seront toutes en graines de céréales et sèches. Les
quantités maximales du sorgho et du soja seront respectivement de 4000
tonnes par an et 1250 tonnes par an
· Destination des produits à la sortie de l'usine
Les produits à la sortie de l'usine seront des farines
qui serviront à alimenter les provenderies, les entreprises brassicoles,
les usines alimentaires pour aliments de nourrissons et enfants, pour
compléments alimentaires, etc.....
Tableau 29 : Résumé
technique
Produits Etat d'arrivée à Quantité
annuelle Etat du produit à la
l'usine sortie
|
Maïs
|
Grains humides
|
4000 t
|
- Farine fine
- Semoule ;
- Gritz ;
|
Blé
|
Grains secs
|
= 4000??
|
- Farine fine ;
- Semoule ;
|
sorgho
|
Grains secs
|
= 4000??
|
- Farine fine ;
- Semoule ;
|
Soja
|
Grains secs
|
1250 t
|
- Farine fine ;
|

33
Mémoire de fin d'études pour l'obtention du
diplôme d'Ingénieur de Conception en Génie
Mécanique, rédigé et soutenu par : PONDI
JOSEPH
Mise sur pied d'une unité industrielle de transformation
des céréales pour l'obtention de la
farine : projet industriel
du Groupe SOA
III.1.2 Analyse fonctionnelle
III.1.2.1 Analyse du besoin
Ø Qu'est-ce que le besoin ? [6]
Définition AFNOR : « Un besoin est
un désir (ou une nécessité) éprouvé par
l'utilisateur d'un système »
Classification du besoin : On recense deux
formes principales de besoin : exprimé et latent (pouvant être
détecté ou suscité). Quoi qu'il en soit, chaque besoin
doit pouvoir être formulé.
Ø Verbalisation du besoin : Diagramme bête à
corne
La méthode de l'Analyse du Besoin s'appuie sur deux
hypothèses :
Hypothèse 1 : La satisfaction du besoin
est réalisée par l'utilisation du produit à concevoir.
Hypothèse 2 : Le besoin est satisfait par le changement
d'état d'une matière d'oeuvre.
Pour cela, il faut se poser trois (03) questions (... et y
répondre !) : Tableau 30 : Verbalisation du
besoin
Questions
|
Réponses
|
« À qui le produit rend-il service
? »
|
Au groupe SOA
|
« Sur quoi le produit agit-il ? »
|
Sur les céréales (maïs, blé,
sorgho et soja)
|
« Dans quel but ? » (pour quoi faire
?)
|
Pour produire la farine de céréales
|
|
D'où le diagramme « bêtes à cornes
» suivant :
Produire la farine de céréales
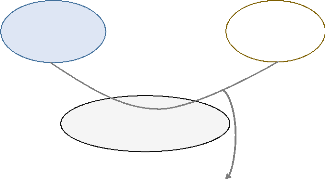
Groupe SOA
Usine de
transformation
Céréales
Figure 9 : Diagramme bête à corne

34
Mémoire de fin d'études pour l'obtention du
diplôme d'Ingénieur de Conception en Génie
Mécanique, rédigé et soutenu par : PONDI
JOSEPH
Mise sur pied d'une unité industrielle de
transformation des céréales pour l'obtention de la
farine :
projet industriel du Groupe SOA
A partir de ce diagramme, on formule le besoin comme suit :
L'usine à concevoir rendra service au groupe SOA
pour l'aider à produire la farine à base des
céréales.
Ayant donc définit clairement le besoin, l'on
procède à l'analyse fonctionnelle de ce besoin.
III.1.3 Analyse fonctionnelle du besoin
L'Analyse Fonctionnelle du Besoin tout comme l'Analyse du Besoin
est fondée sur des hypothèses.
Ø Hypothèses [6]
Hypothèse 1 : Le besoin est satisfait
par l'utilisation d'un produit.
Hypothèse 2 : Le produit est un
générateur de services (ou « prestations client »).
L'Analyse Fonctionnelle du Besoin ou Analyse Fonctionnelle
extérieure est appelée ainsi car elle va permettre de traduire le
besoin par des fonctions à réaliser : les Fonctions de
Service.
Ø Identification des fonctions de service : Diagramme
Pieuvre.
Le diagramme Pieuvre est un outil qui nous permet d'identifier
les différentes fonctions de service de notre produit. Rappelons que
:
· Les relations du produit avec son milieu extérieur
sont représentées par des traits.
· Chaque trait correspond à une Fonction de Service
(F.S.)
· Chaque trait doit relier le produit à un
Élément du Milieu Extérieur (EME) ou bien relier plusieurs
EME en passant par le produit.
Nota : Un E.M.E. doit pouvoir être
défini de façon objective pour tous les protagonistes de
l'étude. Si on ne peut pas définir entièrement un
élément par des critères objectifs, alors cet
élément n'est pas un élément du milieu
extérieur.

35
Mémoire de fin d'études pour l'obtention du
diplôme d'Ingénieur de Conception en Génie
Mécanique, rédigé et soutenu par : PONDI
JOSEPH
Mise sur pied d'une unité industrielle de transformation
des céréales pour l'obtention de la
farine : projet industriel
du Groupe SOA
On obtient alors le diagramme suivant :
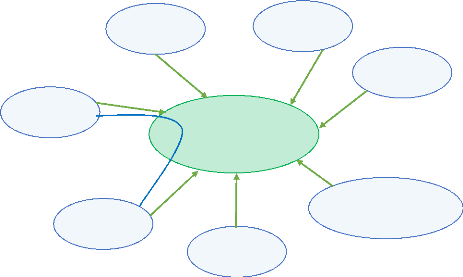
Réseau ENEO
Normes de sécurité
F FC3
Normes de qualité
Céréales
FC1
FC4
Usine de
transformation
FC5
FP
Farine de céréales
FC7
FC6
Normes
environnementales
Milieu ambiant
Figure 10 : Diagramme pieuvre
Légende :
FP : transformer les céréales en
farine.
FC1 : recevoir les céréales.
F :s'adapter au réseau
électrique
FC3 : satisfaire les normes d'exigence de
sécurité.
FC4 : satisfaire les normes d'exigence de
qualité.
FC5 : satisfaire les normes
environnementales.
FC6 : s'adapter au milieu ambiant.
FC7 : contenir les farines de
céréales.
Les Fonctions de service étant identifiées, nous
réalisons ensuite l'analyse fonctionnelle technique.

36
Mémoire de fin d'études pour l'obtention du
diplôme d'Ingénieur de Conception en Génie
Mécanique, rédigé et soutenu par : PONDI
JOSEPH
Mise sur pied d'une unité industrielle de transformation
des céréales pour l'obtention de la
farine : projet industriel
du Groupe SOA
III.1.4 Analyse fonctionnelle technique.
Elle permet de faire la transition entre l'Analyse
Fonctionnelle du Besoin (qui reste étrangère aux
préoccupations d'ordre technologiques) et la conception
détaillée, qui entre de plain-pied dans les considérations
technologiques.
L'Analyse Fonctionnelle Technique aussi appelée Analyse
Fonctionnelle interne est réalisée en utilisant le diagramme
FAST. Cette méthode ordonne et décompose logiquement les
fonctions identifiées pour aboutir aux solutions techniques de
réalisation. Son principe est résumé par le diagramme
ci-contre :
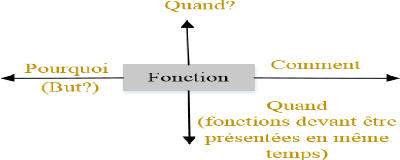
Figure 11 : Structure d'un diagramme FAST [24].
On obtient donc les diagrammes suivants (fig.16 à
fig.21) sur lesquels les éléments en vert correspondent aux
solutions technologiques c'est-à-dire les technologies les mieux
adaptées à la fonction technique ici ce sont les cases autre que
celles en bleu. Les fonctions techniques sont les fonctions qui permettent de
réaliser les fonctions de service susmentionnées par un moyen
technique ; c'est ce moyen technique que nous appelons solution
technologique. C'est parmi la large gamme des solutions technologiques
que nous allons choisir quelques-unes, celles qui sont parfaitement
adaptées à notre contexte, les dimensionner, et faire le choix
adéquat auprès des fournisseurs.

37
Mémoire de fin d'études pour l'obtention du
diplôme d'Ingénieur de Conception en Génie
Mécanique, rédigé et soutenu par : PONDI
JOSEPH
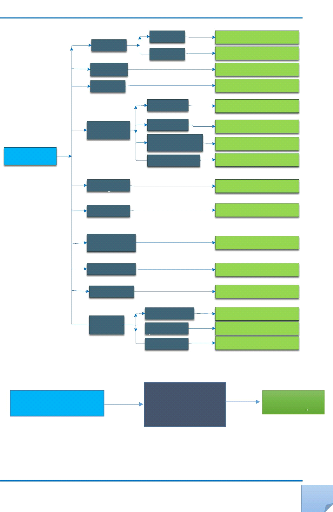
Mise sur pied d'une unité industrielle de transformation
des céréales pour l'obtention de la farine : projet industriel du
Groupe SOA
Récolteuse,
dépouilleuse ,
égreneuse,
dépouilleuse
|
Moissonneuse, égreneuse
motorisée,
dépouilleuse
|
Pré-nettoyeur, nettoyeur,
|
Sécheur solaire, sécheur
infra
rouge,
|
|
Trieur magnétique,
séparateur
de metaux.
|
|
Nettoyeur-séparateur,
épierreur
|
Trieur optique
|
Table densimétrique,
nettoyeur
séparateur, calibreur
|
Séparer le son
Hydrater le blé
céréales d un
Conditionner
les produits
finaux
Déplacer les
poste à un autre
Transporter les
produits moulus
de la graine
Moudre les
céréales
Peser les produits
finaux
Emballer les
produits finaux
Etiqueter les
produits finaux
Figure 12 :FAST_FP
FC1 : recevoir les
céréales
Prévoir les enceintes
pour la réception et
le
stockage des céréales
Figure 13 :FAST_FC1
Mémoire de fin d'études pour l'obtention du
diplôme d'Ingénieur de Conception en Génie
Mécanique, rédigé et soutenu par : PONDI
JOSEPH
FP: transformer les
céréales en farine
Enlever les
impuretés dans
les céréales
Déshydrater
le maïs
Nettoyer le
maïs
Recolter le
maïs
Enlever les
grains impurs
Enlever les grains de
couleur différente
Enlever les
matières minérales
Dépouiller le
maïs
Enlever les
metaux
Egrener le
maïs
Dégermeuse,
décortiqueuse,broyeur
Mouilleur, hydrateur.
convoyeur à bande,
convoyeur
pneumatique
Broyeur à cylindre, broyeur
à
disque, décortiqueuse,
Convoyeur à vis, convoyeur
pneumatique
Balance, péseuse
Machine d emballage, doseur
Machine de vérification,
étiqueteuse
Trémie, silos de
stockage
38

Laboratoire
Mise sur pied d'une unité industrielle de transformation
des céréales pour l'obtention de la
farine : projet industriel
du Groupe SOA
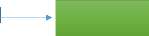
Adapter tous les
équipements
électriques en
toute
sécurité
Relais,
contacteur.
F :s'adapter au réseau
électrique

Transformateur
Fournir à l'usine la
puissance nécessaire.
Figure 14 :FAST_F
Protéger les opérateurs contre les risques
d'électrocution
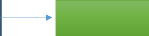
Isolants, EPI, EPC.
FC3 : satisfaire les
exigences de sécurité

Arrêt d'urgence
Protéger les opérateurs contre les accidents, les
blessures...
Figure 15 :FAST_FC3
FC4: satisfaire les
exigences de qualité
Analyser les produits

Utiliser les sacs thermo soudés
Bien emballer les produits.
Figure 16 : FAST_FC4

39
Mémoire de fin d'études pour l'obtention du
diplôme d'Ingénieur de Conception en Génie
Mécanique, rédigé et soutenu par : PONDI
JOSEPH
Mise sur pied d'une unité industrielle de transformation
des céréales pour l'obtention de la
farine : projet industriel
du Groupe SOA
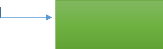
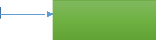
Réduire la dispersion des fumées et des gaz
d'échappement et leur concentration au sol
Système de collecte des fumées
Eviter de laisser
trainer les produits au
sol
Bac de stockage de déchets
FC5: satisfaire les normes
environnementales.
FC7: s'adapter au milieu
ambiant.
Figure 17 :FAST_FC5
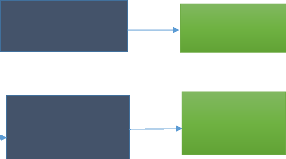
Résister aux vents
Les machines
doivent être
encastrées au
sol
Permettre la mouture
quelle que soit la
saison
Construire l'usine
dans une enceinte
couverte de
tôle.
Figure 18 : FAST_FC6

Stocker la farine après mouture
Silo de stockage
FC7: contenir les farines
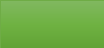
Salle de stockage
Stocker la farine
après ensachage
Figure 19 :FAST_FC7

40
Mémoire de fin d'études pour l'obtention du
diplôme d'Ingénieur de Conception en Génie
Mécanique, rédigé et soutenu par : PONDI
JOSEPH
Mise sur pied d'une unité industrielle de transformation
des céréales pour l'obtention de la
farine : projet industriel
du Groupe SOA
III.2 Ingénierie du projet
III.2.1 Enjeux d'une démarche de conception et
de dimensionnement.
Une démarche de conception a pour but de
réaliser un produit qui répond à un besoin exprimé
par un utilisateur. Cela consiste à concevoir, innover, créer et
réaliser un produit à partir d'un besoin à satisfaire. Le
produit envisagé peut être entièrement nouveau ou
être l'amélioration d'un produit existant [24].
Dans notre cas, nous n'avons pas une chaine de transformation
existante. Nous sommes donc dans le cas d'un produit inexistant.
III.2.2 Dimensionnement des équipements.
III.2.2.1 Dimensionnement du séchoir
Notre maïs sera séché en grains. Nous
rappelons que dans la partie technologique nous avons choisi un séchoir
à convection forcée à air chaud. Il sera donc question
pour nous dans cette partie de trouver les caractéristiques optimales de
ce séchoir adapté à notre projet.
. Les éléments sur lesquels nous allons nous
appesantir sur le dimensionnement de notre séchoir sont : le ventilateur
; le réchauffeur ; l'enceinte de séchage. Les données de
base dont nous disposons sont les suivantes :
- L'humidité relative du maïs (c'est-à-dire
à la récolte) h?? = 0.35
- L'humidité relative finale du maïs (après le
séchage) h?? = 0.15
- Températures de l'air de séchage sont : T?? =
25°C ;T1 = 50°C [7]
- Humidité relative de l'air de séchage :HR =
50%
- Taux d'humidité du maïs : Le taux
d'humidité du maïs est donné sur la base sèche,
c'est-
à-dire en prenant le rapport entre la teneur en eau que
contient le corps à sécher et ce
même corps à l'état de siccité
lorsqu'il a été débarrassé de toute son
humidité.
h?? - h??
X = h??
|
0.35 - 0.15
=
??.35
|
? 57%
|
X: le taux d'humidité
h??: humidité initiale du maïs
h??: humidité ??inale du maïs
asséché

41
Mémoire de fin d'études pour l'obtention du
diplôme d'Ingénieur de Conception en Génie
Mécanique, rédigé et soutenu par : PONDI
JOSEPH
Mise sur pied d'une unité industrielle de transformation
des céréales pour l'obtention de la
farine : projet industriel
du Groupe SOA
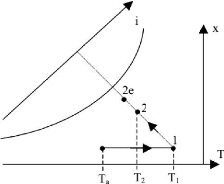
Figure 20 : Evolution de l'air lors d'une opération de
séchage convectif [8]:
Il ressort de ce diagramme que : l'air sort de l'enceinte de
séchage au point 2, il sortirait au point 2e si
l'équilibre avec le produit était atteint.
Dimensionnement du ventilateur
Les éléments à prendre en compte lors du
dimensionnement du ventilateur pour faire le choix auprès des
fournisseurs sont principalement : le débit d'air et la puissance du
moteur ;
- Puissance du moteur :
Soit ?? la quantité de maïs à sécher
par heure ; et ??? la masse d'eau évaporée lors de
l'opération de séchage ; ???? et ???? respectivement la masse
d'eau et la masse sèche ; on a :
?? 1.5
???? =
|
=
1 + h??
|
1 + 0.35 1.2 ??
|
???? = h?? * ???? = 0.15 * 1.2 = 0.18 ??
La masse du maïs obtenue après séchage est
donc : ???? = ???? + ???? = 1.38 ?? la masse d'eau évaporée sera
alors : ??? = ?? - ???? = 1.5 - 1.38 = 0.12 ??
La puissance minimale à fournir pour évaporer cette
quantité d'eau en une heure est alors :
??? * ????
?? = [7]
??
??? *????
??= ??
|
??.????*????????*????????
= = ????.?????? Nous prenons alors : ????????
|
?? = ????????
- Débit d'air
Le diagramme de l'air humide en annexe3 nous donne :
42
Mémoire de fin d'études pour l'obtention du
diplôme d'Ingénieur de Conception en Génie
Mécanique, rédigé et soutenu par : PONDI
JOSEPH
Mise sur pied d'une unité industrielle de transformation
des céréales pour l'obtention de la
farine : projet industriel
du Groupe SOA
- Pour le point A : ??a = 9.84g/kg et ja =
50.22kJ/kg
- Pour le point 1 : ??1 = 9.84g/kg et j1 = 75.81kJ/kg ,??h1 =
25.1°C
Si l'échange de chaleur et de matière
air/produit était parfait, l'air sortirait saturé après
avoir subi un refroidissement adiabatique, nous en déduisons les
caractéristiques de sorties idéales pour le point 2 : ??2
= ??h2 = 25.1°C, ????2 = 100% et ??2
= 20,13g/kg
L?? 120
La masse minimale d'air sec à utiliser est donc : mas = =
11662kg
??2-??1 0.02013-0.00984
Soit une masse d'air humide à l'entrée est de :
mah = (1 + ??a)mas = (1 + 0.00984) * 11662 11777 kg Et un volume
d'air humide
correspondant de : ??ah =
|
????h
????h
|
11777
=
1.177
|
10006m3
|
Le débit d'air du ventilateur ???? est donc : ?? ?? =
????h
?? = 10006
1 = 10006m3/h
???? = 10006m3/h
Dimensionnement du réchauffeur
Le facteur qui nous intéresse sur le réchauffeur
est sa puissance ; le calcul de la puissance du réchauffeur est simple :
il faut 1.25 kJ pour réchauffer 1m3 d'air de 1°C. Soit
une puissance nécessaire de 17 kW pour réchauffer 10 000 m3
/h de 5°C. Le fuel fournit 35000 kJ/l ; le gaz naturel fournit 46000
kJ/kg. La puissance du réchauffeur est donnée par :
???? = ????(??1-????)1.25
3600 = 10006*25*1.25
3600 = 86.86???? Nous allons prendre :
???? = ????????
Choix du réchauffeur
L'énergie la plus pratique à utiliser est le gaz
; d'un pouvoir calorifique presqu'identique à celui du gasoil, deux fois
plus important que celui de la biomasse ; le gaz présente l'avantage
suivant : l'air issu de la chambre de combustion peut être
mélangé avec l'air sous forme de température alors que la
combustion de gasoil ou de biomasse nécessite l'utilisation d'organe
d'interface (échangeurs) pour céder l'énergie des gaz de
combustion à l'air de séchage. Nous retenons donc comme
réchauffeur le gaz naturel.
Calcul de la quantité de gaz nécessaire par
jour.
Étant donné que notre séchoir doit
fonctionner pendant huit heures par jour, la quantité d'énergie
nécessaire quotidienne sera de :
?? = ????. t = 87 * 8 * 3600 = 2 505 600 kJ ; La quantité
de gaz sera donc : q?? = w
46000 = 2 505 600
46000 = 54.5 kg soit alors une quantité annuelle
de :

43
Mémoire de fin d'études pour l'obtention du
diplôme d'Ingénieur de Conception en Génie
Mécanique, rédigé et soutenu par : PONDI
JOSEPH
Mise sur pied d'une unité industrielle de transformation
des céréales pour l'obtention de la
farine : projet industriel
du Groupe SOA
???? = ???? ??????????
Nous avons également pensé qu'en période
d'étiage nous pouvons utiliser l'énergie solaire pour
sécher notre maïs.
Dimensionnement de la surface du capteur solaire ;
Pour calculer la surface du capteur solaire, nous nous basons sur
l'hypothèse suivante [24]: un débit d'air de 100m3/h
par m2 de capteur couvert permet d'évaporer en moyenne 1 kg
d'eau par m2 par jour, sous des conditions moyennes d'ensoleillement
et de température.
100*???
Soit S la surface du capteur : ?? = 24 *
Q??
100*120
A.N : ?? = 24 * 10006
|
= 28.78 nous allons donc prendre un capteur de surface :
|
??= ???? ????
- volume de l'enceinte de séchage
Le volume du séchoir est donné par la formule : ??
= ??*????
??*???? [25]
GI: la quantité de produit introduite dans le sechoir en
t/h ??: La durée du séchage en heures ;
??: ???? ??é????é de remplissage de l'enceinte de
séchage;
????: ???? Masse volumique moyenne du matériau en
????/m3
1-h?? = 1.5 1-0.15
On a : ????=m = 3??/h
1-X 1-0.57
Le matériau de notre enceinte de séchage sera
l'acier de masse volumique moyenne ???? = 7800????/m3
??= 0.4
On a fixé le temps de séchage ?? = 1 h
1*3
Le volume du séchoir sera donc : ?? = 0.4*7.8
|
= 0.97m3
|
??= ??. ????????
Description de l'installation
La zone de séchage sera composée de deux circuits
:
1. un circuit de gaz avec les éléments suivants
:
? un détendeur à pression variable ;
? un manomètre de visualisation de la pression
réglée par le détendeur (nécessaire au pilotage du
séchoir)

44
Mémoire de fin d'études pour l'obtention du
diplôme d'Ingénieur de Conception en Génie
Mécanique, rédigé et soutenu par : PONDI
JOSEPH
Mise sur pied d'une unité industrielle de transformation
des céréales pour l'obtention de la
farine : projet industriel
du Groupe SOA
? un robinet de sécurité piloté par une
sonde thermocouple, un thermostat de détection de température,
anormalement haute dans le séchoir et un relais indicateur de la
présence d'alimentation électrique pour le ventilateur ;
? un bruleur avec gicleur intégré ;
La sonde thermocouple à interrupteur, en combinaison
avec le robinet fonctionne de la manière suivante : l'opérateur
exerce une pression sur la manette du robinet en position ouverte après
allumage du bruleur, le thermocouple chauffé par le brûleur,
génère un micro courant dans un solénoïde
intégré au robinet. Au bout de 15 secondes, la pression sur la
manette peut être relâchée, le brûleur reste
allumé (le clapet du solénoïde reste en position «
ouvert »). Dès que la flamme s'éteint, le micro courant
n'est plus.
2. Un circuit électrique basse tension. Sur une prise
220V monophasée, se branche une alimentation non stabilisée
(transformateur) reliée à un relais « normalement ouvert
» : lorsque le relais est alimenté électriquement (coupure
électrique), le contact est ouvert, c'est à dire que le circuit
constitué est interrompu. Le relais est le premier de trois composants
montés en série sur le circuit. Le deuxième est le
thermostat, qui s'ouvre lorsque la température dans le séchoir
s'élève au-delà de 50°C. le troisième est
l'interrupteur de la sonde thermocouple, qui lui aussi est ouvert lorsque le
brûleur est éteint ou s'ouvre lorsque le brûleur
s'éteint.
Le schéma de principe de ce séchoir ainsi que son
circuit de sécurité sont mis en annexe2.
III.2.3 Dimensionnement des équipements de
mouture.
III.2.3.1 Broyeur
Nous rappelons que dans la partie technologique nous avons
opté pour un broyeur cylindres. Il s'agit d'une
enceinte dans laquelle se frottent deux cylindres l'un contre l'autre, et les
céréales sont alors écrasées en passant entre ces
deux cylindres, les produits les plus fins sont alors blutés et
conditionnés tandis que les autres sont encore renvoyés dans la
chambre de broyage. Pour le dimensionnement en vue du choix de ces broyeurs
auprès des fournisseurs, nous nous intéresserons aux indicateurs
de performance les plus significatifs qui sont : le taux d'extraction de la
farine et le débit de broyage. Il en sera ainsi de tous les
équipements de mouture.
- Taux d'extraction de la farine
(Tb)
Le taux d'extraction est la quantité de farine qui est
extraite par le meunier lors de la mouture de 100 kg de céréales.
Il est donné par la formule :
quantité de farine obtenue
Tb =
quantité de farine obtenue+quantité de
produits non transformés
Il varie en fonction des céréales, souvent de
l'ordre 65 à 75% nous allons donc le prendre à la valeur maximale
pour limiter les pertes.

45
Mémoire de fin d'études pour l'obtention du
diplôme d'Ingénieur de Conception en Génie
Mécanique, rédigé et soutenu par : PONDI
JOSEPH
Mise sur pied d'une unité industrielle de transformation
des céréales pour l'obtention de la
farine : projet industriel
du Groupe SOA
Tb=0.75
Qb =
temps de mouture
- Débit de mouture (Qb): c'est la
quantité de produits pouvant être transformés par heure
par le
broyeur.il est déterminé
par la formule suivante :
quantité de produits moulus
13500
Qb = 12 * 4 * 6 * 8 ? 6t/h
Qb = 6t/h
III.2.3.2 Claqueur et convertisseur
Les claqueurs : ce sont les broyeurs
équipés de cylindres lisses tournant en sens inverse l'un de
l'autre, qui ont pour rôle la réduction des semoules issues du
broyage.
- Taux de claquage (Tc/a): c'est la
quantité de farine obtenue lors de la mouture de 100 kg de semoule ; il
est déterminé par :
quantité de farine obtenue
Valeur beaucoup plus liée au constructeur, elle de
l'ordre :
Tcla = 98%
- quantité de blé temps de claquage
Débit de claquage : c'est la quantité de
produit pouvant être claquée par heure ; il est
déterminé par :
quantité de semoules claqués
Qcla = temps de claquage =b
1.75
Qcla = 1. 4t/h
Les convertisseurs quant à eux sont
toujours placés à la fin de la chaine de mouture ils sont
constitués de série de cylindres lisses tournant en sens inverse
les uns des autres ils permettent la mouture des produits issus du claquage
pour l'obtention des produis plus fins.
- quantité de farine obtenue
Taux de convertissage (acon) :c'est la
quantité de farine obtenue lors de la mouture de 100 kg de produits. Il
est déterminé par :
acon =
quantité de farine obtenue +quantité non
convertie
Pour les mêmes raisons que pour le claquage, nous allons
prendre :
Icon = 98%

46
Mémoire de fin d'études pour l'obtention du
diplôme d'Ingénieur de Conception en Génie
Mécanique, rédigé et soutenu par : PONDI
JOSEPH
Mise sur pied d'une unité industrielle de
transformation des céréales pour l'obtention de la
farine :
projet industriel du Groupe SOA
- Débit de convertissage : c'est la quantité de
produit pouvant être converti en une heure ; il est
déterminé par :
quantité de produits convertisQuantité de
blé
_
Qcon = temps de convertissage -- ~b temps de
convertissage
La quantité de blé qui est claquée est
presque égale à la quantité convertie car ces deux
opérations sont successives et très similaires ; pour plus de
fiabilité, nous allons donc prendre : Qcon = Qcla d'où
:
Qcon = 1.4t/h
III.2.3.3 Décortiqueuse et
torréfacteur
La décortiqueuse que nous avons retenue dans la partie
technologique est la décortiqueuse à abrasion
pour son bon rendement et sa pureté excellente ; les
indicateurs de performance qui vont nous intéresser sont : le taux de
décorticage, et le débit de décorticage ou le
rendement.
- Taux de décorticage : c'est le ratio entre la
quantité de produit décortiqué et la quantité non
décortiquée il est déterminé par :
Tdec =
|
masse de produits decortiqués
masse de produits decortiqués + masse restante
[9]
|
|
Valeur principalement dépendante du constructeur elle est
de l'ordre de :
Tdec = 90%
- Rendement ou débit de décorticage ; c'est la
quantité de produits décortiqués sur le temps mis pour les
décortiquer il est déterminé par :
quantité decortiquée 13500
Qdec == 12 * 4 * 48 = 6t/h temps de de??orti??age
Qdec = 6t/h
Le torréfacteur sera utilisé
uniquement pour le soja ; il permet de griller le soja afin de le rendre
digestible ; les indicateurs qui nous intéressent sont : la
capacité horaire, la capacité technique et le taux
d'extraction.
- La capacité horaire détermine la quantité
de soja traité par l'équipement en une heure ; il est
déterminé par la formule :
Ms
Ch =T s
{
Ms: quantité traitée Ts :
durée de torre f action Ch: capacité horaire

47
Mémoire de fin d'études pour l'obtention du
diplôme d'Ingénieur de Conception en Génie
Mécanique, rédigé et soutenu par : PONDI
JOSEPH
Mise sur pied d'une unité industrielle de
transformation des céréales pour l'obtention de la
farine :
projet industriel du Groupe SOA
1250
Ch = 12 * 4 * 48 =0.6t/h
Ch = 0.6t/h
- Capacité technique : c'est la quantité de soja
pouvant être traitée par la machine en un an sans
défaillance elle est déterminée par la formule :
K=Ch*N*m*n
Ch: capacité horaire de la machine
N: nombre de jour de travail dans le mois {m: nombre de mois
de travail n: nombre d'heure de travail par jour
K = 0.6 * 24 * 12 * 8 = 1382.4t/an Nous allons prendre
:
- Taux d'extraction : c'est le rapport entre la quantité
de de grains torréfiés et la quantité initiale il se
détermine par la formule suivante :
T=Mt* 100
Mt: quantité de grains torre f iés
{ML: quantité initiale T: taux d'extraction
C'est un indicateur principalement lié aux constructeurs
il est de l'ordre de :
T=98%
III.2.4 Dimensionnement de l'unité de
nettoyage
Nous rappelons que les principales impuretés souvent
présentes dans les céréales sont : les impuretés
métalliques, les graines étrangères, les matières
minérales agglomérées ; pour faire le choix de
l'unité de nettoyage nous devons donc tenir compte de ces 3 types
d'impuretés. C'est la raison pour laquelle notre unité sera
constituée de :
- Un trieur magnétique pour éliminer les
impuretés métalliques ;
- Nettoyeur - séparateur pour éliminer les
impuretés et les graines étrangères
- Un épierreur pour éliminer les matières
minérales agglomérées.
Son schéma de fonctionnement se trouve en annexe2.
Les indices de performance qui vont nous guider dans le choix de
l'unité de nettoyage sont :
- Le débit de nettoyage : c'est la quantité de
céréales que peut traiter l'unité de nettoyage par heure
il déterminé par la formule :

48
Mémoire de fin d'études pour l'obtention du
diplôme d'Ingénieur de Conception en Génie
Mécanique, rédigé et soutenu par : PONDI
JOSEPH
Mise sur pied d'une unité industrielle de
transformation des céréales pour l'obtention de la
farine :
projet industriel du Groupe SOA
quantité nettoyée
Qnet =
temps de nettoyage
13500
Qnet = 12 * 4 * 48 ? 6t/h
Qnet = 6t/h
- Taux d'impuretés à éliminer : c'est le
pourcentage d'impureté présente dans les céréales
et qui doit être éliminé par l'unité de nettoyage il
est déterminé par :
quantité d'impurtes
En général les céréales
présentent un taux d'impuretés de l'ordre de 3% pour les raisons
de sécurité nous allons choisir un taux d'impureté un peu
supérieur à cette valeur :
~impur = 5%
NB : dans cette partie, la durée de travail que nous
avons considérée est celle édictée par l'article 80
du code du travail camerounais qui limite 48 heures de travail par semaine pour
une entreprise agricole soit 8 heures de travail par jour [10].
III.3 Dimensionnement des équipements
annexes
III.3.1 Dimensionnement des convoyeurs à
bande
Etant donné que nous prévoyons de temps
à autre un changement du convoyeur d'un poste vers un autre, nous allons
dimensionner nos convoyeurs de telle manière qu'ils puissent supporter
la charge maximale quels que soient les postes dans lesquels nous les
placerons. Nous disposons des données techniques suivantes :
- Masse volumique : 0.45t/m3 [6]
- Granulométrie :
- Abrasion : faible ;
- Angle d'éboulement : 30°
- Production journalière des épis de maïs
14t
- Débit de transport souhaité : l, =
2t/h
Caractéristiques de l'installation :
- Variation de la hauteur H = 2m
(élévation)
- Pente : = 20%
- Conditions d'exploitation : normales ;
- Utilisation : 8h par jours
- Bande ayant une catégorie de résistance
égale à 200N/mm, et une valeur qode 8.9 kg/m. Vitesse et
largeur de la bande transporteuse

49
Mémoire de fin d'études pour l'obtention du
diplôme d'Ingénieur de Conception en Génie
Mécanique, rédigé et soutenu par : PONDI
JOSEPH
Mise sur pied d'une unité industrielle de transformation
des céréales pour l'obtention de la
farine : projet industriel
du Groupe SOA
III.3.2 Caractéristiques de la bande
Les caractéristiques physiques du produit à
manutentionner (ici les grains de céréales) sont les
éléments déterminants pour le calcul de la vitesse de la
bande. Une granulométrie, une abrasivité ou une masse volumique
plus importantes nécessitent de réduire la vitesse de la bande
transporteuse, au vu des caractéristiques du produit (produit faiblement
abrasif, granulométrie moyenne, masse volumique de : 0.5
à 1t/m3) la vitesse maximale et la largeur maximale
recommandées sont :
????????: 3??/??
???????? = 800????
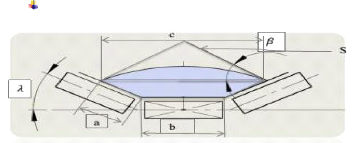
Détermination de l'angle d'inclinaison des rouleaux
Figure 21 : Modèle d'étude pour le calcul des
rouleaux
Hypothèses de base : a = 306 mm /3
= 300 ; b = 388???? ; ?? = 2 * ?? * cos(A) + b
Il s'agit de déterminer A qui permettra un meilleur
transport du produit et au débit proposé dans le cahier de charge
; pour cela l'aire S est donnée par :
[2 * ??* cos(A) + b) * 2 * sin (/3)]
?? = + (?? * cos(A) + b) * ?? * sin (A)
4
En remplaçant avec les données numériques on
trouve :
?? = 0.25 * [0.612 * cos(A) + 0.388] + [0.306 cos(A) + 0.388]
* 0.306 * sin (A) étant donné que cette équation est
difficile à résoudre nous allons choisir A l'abaque placé
en annexe3.
A = 300 Peut minimiser la surface s ; nous prenons
donc :
A = 300
Choix des rouleaux
Dans le tableau58 (annexe3) pour une bande de 800 mm de
largeur, on peut choisir des rouleaux de 89 mm de diamètre.
???? = 89????
50
Mémoire de fin d'études pour l'obtention du
diplôme d'Ingénieur de Conception en Génie
Mécanique, rédigé et soutenu par : PONDI
JOSEPH
Mise sur pied d'une unité industrielle de transformation
des céréales pour l'obtention de la
farine : projet industriel
du Groupe SOA
On peut maintenant chercher à déterminer l'effort
qui s'exerce sur les rouleaux porteurs et celui qui s'exerce sur les rouleaux
du brin inférieur. En supposant qu'on peut utiliser une bande ayant une
catégorie de résistance égale à 200 N/mm, et une
valeur q?? de 8.9kg/m.
C?? = a0 * (q?? + 3.6 * ??
* 0.981)[daN]
Pour les rouleaux porteurs, l'effort statique sera donné
par la relation ci-dessous :
l
2
C?? = 1.2 * (8.9 +
|
3.6 * 3
* 0.981)
|
C?? = 10.7 daN
L'effort dynamique sera donné par la relation ci-dessous
:
C??1 = C??* F?? * F??* F?? [daN]
C??1 = 10.7 * 1 * 1.7 * 0.9
C??1 = 16.5 daN
Où : F??; F??; F?? désignent respectivement les
coefficients d'utilisation ; les coefficients de choc ; coefficient lié
à l'environnement ; ces valeurs sont choisies dans les tableaux62,
63,64. qui sont placés en annexe3;
L'effort sur le rouleau central d'une station porteuse est obtenu
de la manière suivante :
C??= C??1 * F??
C?? = 16.5 * 0.65 = 10.75 daN
Pour les rouleaux inférieurs l'effort statique sera
donné par la relation ci-dessous :
C?? = a?? * q??*0.981[daN]
C?? = 3 * 8.9 * 0.981 = 26.2 daN
L'effort dynamique sera donné par la relation ci-dessous
:
C??1 = C??* F?? * F* F?? [daN]
C??1 = 26.2 * 1 * 1.1 * 1.05 = 30.3 daN
|
F: e??t d??nné ??a?? le ta??lea?? q??i ??e??a ??i?? en
annexe
Puissance du moteur
Pour déterminer la puissance du moteur nous disposons des
données suivantes :
· D=89mm diamètre du rouleau

51
Mémoire de fin d'études pour l'obtention du
diplôme d'Ingénieur de Conception en Génie
Mécanique, rédigé et soutenu par : PONDI
JOSEPH
1.5
9.1
q1 =
q2 =
q3 =
Mise sur pied d'une unité industrielle de transformation
des céréales pour l'obtention de la
farine : projet industriel
du Groupe SOA
· f=0.017 coefficient de frottement interne du produit
et coefficient de frottement des parties tournantes (tableau en annexe)
· ???? = 4 coefficient de résistance
fixe (tableau en annexe)
· q?? = 8.9 ????/?? (en utilisant une bande de
résistance de 200N/mm)
· ????= 1 coefficient de résistance
passive en fonction de la température (tableau en annexe)
q1 =
q2 =
Déterminons d'abord les valeurs suivantes que nous nommons
: q1; q2; q2 poids des parties tournantes
des stations superieures
e??arte??ent des stations superieures
poids des parties tournantes des stations
inférieures
e??arte??ent des stations inferieures
????
q3 =
3.6 * V
10.4
= 6.95????/??
3 = 3.03????/??
2
3.6 * 3 = 0.19 ????/??
L'effort tangentiel total F?? est le résultat
de la somme algébrique des efforts tangentiels F?? et
F?? correspondant aux sections supérieures et
inférieures de la bande, à savoir :
F??= F??+ F?? [da??]
F?? = [L * ???? * f * ????(q?? + q1 +
q3) + H * (q3 + q??)] * 0.981[da??]
F?? = [L * ???? * f * ????(q?? + q2) - H * (q??)]
* 0.981[da??]
F?? = [16 * 4 * 0.0175 * 1(8.9 + 6.75 + 0.19) + 2 * (8.9 +
0.19)] *
|
0.981[da??]
|
F?? =
|
35.25da??
|
|
|
|
|
F?? =
|
[16 * 4 * 0.0175
|
* 1(8.9 + 3.03) - 2 * (8.9)]
|
* 0.981[da??]
|
|
|
F?? =
|
-4.35da??
|
|
|
|
|
|
|
|
|
|
|
F ?? =
|
35.25 - 4.35 =
|
30.9da??
|
|
|
|
|
En considérant un rendement mécanique moyen de
l'ordre de ?? = 0.8 ; la puissance P du moteur sera donnée par
:

52
Mémoire de fin d'études pour l'obtention du
diplôme d'Ingénieur de Conception en Génie
Mécanique, rédigé et soutenu par : PONDI
JOSEPH
Mise sur pied d'une unité industrielle de
transformation des céréales pour l'obtention de la
farine :
projet industriel du Groupe SOA
???? * ??
??=
??
30.9 * 3 * 10
??=
= 1158.75??
0.8
Conclusion : la puissance utile est de ?? = 1158.75??
nous installons de puissance P=2kW
??= 2????
Choix du diamètre des tambours
Le tableau67 qui est mis en annexe3 nous permet de choisir
les diamètres des tambours moteur et de renvoi en fonction de la largeur
de la bande ; étant donné que nous avons une bande transporteuse
de largeur 800 mm nous choisissons pour :
- Tambour moteur : ?? = 500mm
- Tambour de renvoi : ?? = 315mm
III.3.3 Conduite de transport pneumatique
Données techniques de base :
- masse volumique maximale des farines de céréales
: ???? =0.82t/m3
- masse volumique maximale des graines de céréales
: ???? =0.77t/m3
- débit de production des graines de
céréales : ???? =6t/h
- vitesse de déplacement des grains de
céréales : ?? ?? = 5m/??
Calcul du diamètre de la canalisation de
transport dans le cas des céréales :
Soit Q le débit de déplacement des
graines de céréales dans la canalisation de transport
On a :
Q = ???? = ????. ?? = ????. ??????
?? On trouve alors ?? = J 4*????
????*????*??*3600
????
??= J
|
4*6 = 22.45 mm Nous prendrons alors un diamètre
de :
5*0.77*3.14*3600
|
|
?? = 30 mm
Le matériau couramment utilisé pour les
canalisations est l'acier inoxydable.

53
Mémoire de fin d'études pour l'obtention du
diplôme d'Ingénieur de Conception en Génie
Mécanique, rédigé et soutenu par : PONDI
JOSEPH
Mise sur pied d'une unité industrielle de
transformation des céréales pour l'obtention de la
farine :
projet industriel du Groupe SOA
III.4 Choix des machines auprès des
fournisseurs
III.4.1 Mise en oeuvre de la méthode de Pareto
pour le choix des machines.
III.4.1.1 Application sur la moissonneuse- batteuse de
maïs III.4.1.1.1 Identification des critères de choix
· Coût ;
· Puissance ;
· Dimensions ;
· Poids ;
· Rangées de travail ;
· Largeur de travail ;
· Consommation de carburant ;
· Hauteur de chargement ;
· Productivité ;
III.4.1.1.2 Classement des critères de choix
Après avoir déterminé les
différents critères de choix nous allons suivre à la
lettre la méthodologie définie plus haut ; nous pouvons alors
quantifier ces critères de choix et nous obtenons le tableau suivant
:
Tableau 31 : Calcul des pourcentages de
préférence de chaque critère
critères de choix degré de préférence
pourcentage cumul pourcentage
coût
|
95
|
95
|
50%
|
puissance
|
72
|
167
|
87%
|
consommation
|
10
|
177
|
93%
|
productivité
|
4
|
181
|
95%
|
rangées de travail
|
2
|
183
|
96%
|
largeur de travail
|
2
|
185
|
97%
|
encombrement;
|
1
|
186
|
97%
|
écartement des rangs
|
1
|
187
|
98%
|
plage de travail
|
1
|
188
|
98%
|
poids
|
1
|
189
|
99%
|
hauteur de chargement
|
1
|
190
|
99%
|
vitesse normale
|
1
|
191
|
100%
|

54
Mémoire de fin d'études pour l'obtention du
diplôme d'Ingénieur de Conception en Génie
Mécanique, rédigé et soutenu par : PONDI
JOSEPH
Mise sur pied d'une unité industrielle de transformation
des céréales pour l'obtention de la
farine : projet industriel
du Groupe SOA
100 90 80 70 60 50 40 30 20 10
0
|
|
|
120% 100% 80% 60% 40% 20% 0%
|
|
|
|
|
|
|
|
|
|
dégré de préference cumul pourcentage
|
|
|
Figure 22 : diagramme de Pareto des critères de choix de
la moissonneuse-batteuse III.4.1.1.3 Détermination du poids
de chaque critère
Il ressort donc de notre diagramme que les critères sont
classés par ordre de préférence de la manière
suivante :
1. coût (C) ;
2. la puissance totale (PT) ;
3. consommation (Con) ;
4. productivité (Pr) ;
5. rangées de travail(R) ;
6. largeur de travail (L) ;
7. encombrement(E) ;
8. poids (P) ;
9. hauteur de chargement (II) ;
10. vitesse nominale (V) ;
Ces critères nous permettent d'établir la matrice
de préférence à partir de laquelle on obtient le poids
(P1) pour chaque critère ;
Tableau 32 : Pondération des critères
pour l'égreneuse de maïs
Caractéristiques C ??T
Con ??r R L E P H V
Poids
(P1)
|
C
|
|
|
|
|
|
|
|
|
|
|
|
|
|
|
|
|
|
|
|
|
|
10
|
|
1
|
|
1
|
|
1
|
|
1
|
|
1
|
|
1
|
|
1
|
|
1
|
|
1
|
|
1
|
|
|
|
|
|
|
|
|
|
|
|
|
|
|
|
|
|
|
|
|
|
|
|
|
|
|
|
|
|
|
|
|
|
|
|
|
|
|
|
|
|
|
|
|
|

55
Mémoire de fin d'études pour l'obtention du
diplôme d'Ingénieur de Conception en Génie
Mécanique, rédigé et soutenu par : PONDI
JOSEPH
Mise sur pied d'une unité industrielle de transformation
des céréales pour l'obtention de la
farine : projet industriel
du Groupe SOA
Caractéristiques C PT Con
Pr R L E P H V Poids
(P??)
|
PT
|
|
1
|
1
|
1
|
1
|
1
|
1
|
1
|
1
|
1
|
9
|
Con
|
|
|
1
|
1
|
1
|
1
|
1
|
1
|
1
|
1
|
8
|
Pr
|
|
|
|
1
|
1
|
1
|
1
|
1
|
1
|
1
|
7
|
R
|
|
|
|
|
1
|
1
|
1
|
1
|
1
|
1
|
6
|
L
|
|
|
|
|
|
1
|
1
|
1
|
1
|
1
|
5
|
E
|
|
|
|
|
|
|
1
|
1
|
1
|
1
|
4
|
P
|
|
|
|
|
|
|
|
1
|
1
|
1
|
3
|
H
|
|
|
|
|
|
|
|
|
1
|
1
|
2
|
V
|
|
|
|
|
|
|
|
|
|
1
|
1
|
III.4.1.1.4 Détermination de la note (????) de
chaque critère
La détermination de la note de chaque critère se
fera sur une échelle de 3 car l'analyse multicritère
prévoit de noter entre 1 et 3.
Tableau 33 : Tableau de notation des critères
de la moissonneuse-batteuse de maïs
Critères notes 3 2 1
Coût (FCFA)
|
= 10 000 000
|
10000000 -
30000000
|
= 30 000 000
|
Puissance(KW)
|
75-100
|
100-120
|
= 120
|
Consommation l/hm2
|
12-30
|
30-40
|
= 40
|
Productivité
|
= 0.7
|
0.5-0.7
|
0.3-0.5
|
Rangées de travail
|
6-7
|
4-5
|
< 4
|
Largeur de travail (mm)
|
2000-3500
|
1000-2000
|
= 2000
|
Encombrement (m3)
|
4*3*3-6*4*3
|
6*4*3-8*5*4
|
= 9 * 7 * 5
|
Poids (kg)
|
3 000 -5 000
|
5000-6000
|
> 6 000
|
Hauteur (mm)
|
400-800
|
300-400
|
<300
|
Vitesse (tr/min)
|
2000-3000
|
1000-2000
|
< 1000
|
La note générale d'une machine est donnée
par :
N = ? ???? * ????[26]
Cette formule de la somme pondérée des notes de
chaque critère permet de faire le choix de la machine. En effet des
notes (????) attribuées aux critères que nous offre chaque
fabricant, nous

56
Mémoire de fin d'études pour l'obtention du
diplôme d'Ingénieur de Conception en Génie
Mécanique, rédigé et soutenu par : PONDI
JOSEPH
Mise sur pied d'une unité industrielle de transformation
des céréales pour l'obtention de la farine : projet industriel du
Groupe SOA
pouvons donc dégager à partir de la formule de la
note générale d'une machine. Une moyenne de chaque machine chez
les fournisseurs.
Tableau 34 : Notation des moissonneuses
proposées par les fournisseurs
|
|
|
|
|
|
F3
|
|
|
|
|
fournisseur
|
|
F1 F2
|
|
|
F4
|
|
|
|
|
|
|
|
|
Critère
|
|
|
|
|
|
|
|
|
|
|
|
|
|
|
|
Coût
|
1
|
1
|
3
|
3
|
Puissance
|
1
|
1
|
3
|
3
|
Consommation
|
1
|
1
|
3
|
2
|
Productivité
|
2
|
3
|
2
|
3
|
Rangée de travail
|
2
|
3
|
1
|
1
|
Largeur de travail
|
1
|
1
|
1
|
1
|
Encombrement
|
1
|
1
|
3
|
3
|
Poids
|
1
|
1
|
3
|
1
|
hauteur
|
1
|
3
|
1
|
3
|
Vitesse
|
2
|
3
|
2
|
3
|
Note finale
|
69
|
87
|
131
|
129
|
Pour notre projet nous choisissons donc l'égreneuse du
fournisseur F3 car elle a la meilleure note et nous estimons qu'elle a le
meilleur rapport qualité/prix et ayant les caractéristiques
ci-dessous :
Tableau 35 : Caractéristiques de la
moissonneuse de maïs
C(FCFA) PT(KW Con
Pr(hm2/ R L(mm
E(m3) P(kg H(mm V(tr/min
) (l/ha h) ) ) ) )
)
|
|
|
6 000 000
|
83
|
20
|
0.5
|
3
|
1860
|
5.9*2*
3.1
|
3600
|
2000
|
2 400
|
F
3
|
|
|
|
III.4.1.2 Cas du nettoyeur séparateur
III.4.1.2.1 Identification des critères de
choix
· La puissance
(PT)
· Le poids (P)
· Le coût (C)
· L'encombrement (E)
· Débit de nettoyage horaire
(QH)
· Taux de nettoyage (T)

57
Mémoire de fin d'études pour l'obtention du
diplôme d'Ingénieur de Conception en Génie
Mécanique, rédigé et soutenu par : PONDI
JOSEPH
Mise sur pied d'une unité industrielle de transformation
des céréales pour l'obtention de la
farine : projet industriel
du Groupe SOA
III.4.1.2.2 Classement des critères de choix
Après avoir identifié les critères de choix
nous allons les classer suivant la méthodologie précédente
; nous obtenons alors le tableau suivant :
Tableau 36 : Calcul des pourcentages de
préférence des critères du nettoyeur
-séparateur
critère de choix degré de préférence
Cumul cumul de pourcentage
coût
|
98
|
98
|
48%
|
puissance
|
84
|
182
|
88%
|
débit de nettoyage
|
10
|
192
|
93%
|
taux de nettoyage
|
5
|
197
|
96%
|
encombrement
|
3
|
200
|
97%
|
tournez vitesse
|
2
|
202
|
98%
|
gravité
|
1
|
203
|
99%
|
filtre d'angle
|
1
|
204
|
99%
|
taille du tamis
|
1
|
205
|
100%
|
poids
|
1
|
206
|
100%
|
total
|
206
|
|
|
120
|
|
120%
|
|
dégre de preference
|
100 80 60 40 20
0
|
|
100% 80% 60% 40% 20% 0%
|
cumul de pourcentage
|
|
|
|
|
|
|
|
critère de choix
dégré de préférence cumul de
pourcentage
Figure 23 : Diagramme de Pareto des critères de choix du
nettoyeur-séparateur III.4.1.2.3 Détermination du
poids de chaque critère
D'après notre diagramme de Pareto, les critères de
choix seront classés par ordre de préférence de la
manière suivante :
1. Le coût (C)
2. La puissance (PT)
3. Débit de nettoyage horaire
(QH)
4. Taux de nettoyage (T)

58
Mémoire de fin d'études pour l'obtention du
diplôme d'Ingénieur de Conception en Génie
Mécanique, rédigé et soutenu par : PONDI
JOSEPH
Mise sur pied d'une unité industrielle de transformation
des céréales pour l'obtention de la
farine : projet industriel
du Groupe SOA
5. L'encombrement (E)
6. Le poids (P)
Ces critères nous permettent d'établir la
matrice de préférence à partir de laquelle on obtient le
poids (P1) pour chaque critère ;
Tableau 37 : pondération des critères
pour le nettoyeur-séparateur
Caractéristiques C PT QH T E P Poids
(Pi)
C
|
1
|
1
|
1
|
1
|
1
|
1
|
6
|
PT
|
|
1
|
1
|
1
|
1
|
1
|
5
|
QH
|
|
|
1
|
1
|
1
|
1
|
4
|
T
|
|
|
|
1
|
1
|
1
|
3
|
E
|
|
|
|
|
1
|
1
|
2
|
P
|
|
|
|
|
|
1
|
1
|
III.4.1.2.4 Détermination de la note (ni) de
chaque critère
La détermination de la note de chaque critère se
fera comme précédemment sur une échelle de 3 car l'analyse
multicritère prévoit de noter entre 1 et 3.
Tableau 38 : Tableau de notation des critères
pour le nettoyeur-séparateur
Critères notes 3 2 1
Coût (FCFA)
|
500 000-1000 000
|
1000 000-2 000 000
|
2 000 000-3 000 000
|
Puissance(kW)
|
3-5
|
5-7
|
>_ 7
|
Débit (kg/h)
|
4000-6000
|
2000-4000
|
1000-2000
|
Encombrement (m3)
|
2.3**1.1*2.4-
3.2*1.7*3.5
|
3.2*1.7*3.5-
3.9*1.9*4
|
3.9*1.9*4-5*2*6
|
Taux de nettoyage (%)
|
98.5-99
|
98-98.5
|
97.5-98
|
Poids (kg)
|
300-600
|
600-900
|
>_ 900
|
Tableau 39 : Notation des nettoyeurs
-séparateurs
fournisseur Critère
|
F1
|
F2
|
F3 F4 F5 F6 F7 F8
|
C
|
1
|
3
|
1
|
1
|
1
|
1
|
1
|
1
|
PT
|
1
|
3
|
1
|
3
|
1
|
3
|
3
|
3
|
QH
|
2
|
2
|
3
|
3
|
3
|
3
|
3
|
3
|
E
|
2
|
3
|
1
|
3
|
2
|
3
|
3
|
3
|
TN
|
1
|
3
|
1
|
1
|
1
|
1
|
1
|
1
|
P
|
3
|
3
|
3
|
3
|
1
|
3
|
3
|
1
|
Total des notes
|
30
|
59
|
37
|
47
|
32
|
47
|
47
|
45
|

59
Mémoire de fin d'études pour l'obtention du
diplôme d'Ingénieur de Conception en Génie
Mécanique, rédigé et soutenu par : PONDI
JOSEPH
Mise sur pied d'une unité industrielle de transformation
des céréales pour l'obtention de la farine : projet industriel du
Groupe SOA
Pour notre projet nous choisissons donc le nettoyeur du
fournisseur F2 car il a la meilleure note et nous estimons qu'il a le meilleur
rapport qualité/prix et ayant les caractéristiques ci-dessous
:
Tableau 40 : Caractéristiques du nettoyeur
séparateur
C(FCFA) PT(kW) Q??(kg/h) E
(m3) T5 P (kg)
(%)
F2
|
1000 900
|
4.1
|
3000
|
2.3*1.1*2.4
|
99
|
510
|
NB : Pour ne pas surcharger le document nous n'allons pas
rédiger la même procédure pour tous les équipements
dans cette partie ; pour les autres équipements nous allons juste faire
apparaitre les tableaux contenant les caractéristiques de leurs
critères de choix ; et ces tableaux sont placés en annexe6.
III.5 Dimensionnement de l'installation
électrique de l'usine
III.5.1 Structure fonctionnelle d'une installation
électrique
Les règles à observer dans la conception des
installations électriques basse tension sont définies par des
normes (exemple NFC 15-100) tous les équipements de force motrice sont
construits sur le modèle fonctionnel suivant [30] :
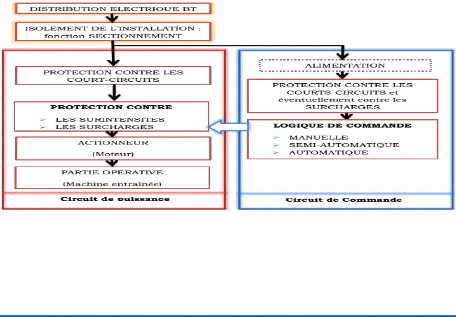
Figure 24 : Modèle fonctionnel d'une installation
électrique [30]
60
Mémoire de fin d'études pour l'obtention du
diplôme d'Ingénieur de Conception en Génie
Mécanique, rédigé et soutenu par : PONDI
JOSEPH
Mise sur pied d'une unité industrielle de transformation
des céréales pour l'obtention de la
farine : projet industriel
du Groupe SOA
III.5.2 Evaluation des bilans de puissance de l'usine
et choix du transformateur
III.5.2.1 Calcul de la puissance installée
La puissance installée est obtenue par une somme
arithmétique sur la liste des récepteurs installés. En
tenant en compte des prises de courant sur lesquels peuvent être
raccordés les récepteurs mobiles, et les luminaires pour
l'éclairage. La puissance supplémentaire active Pa/sup
puissance active assignée à ceci prise à 20 %,
conduit à une puissance installée globale comme dans le tableau
suivant :
Tableau 41 : Evaluation de la puissance
installée
Eléments de l'installation Expression
|
|
|
|
|
|
|
|
Récepteurs
|
|
|
|
?????? = ? ????
|
|
|
Prises de courant + autres suppléments Puissance
installée globale
|
|
????/?????? = ??,???? * ??????
|
|
|
???? = ??,?? * ??????
|
|
|
|
|
|
|
|
|
|
|
|
|
|
|
|
III.5.2.2 Calcul de la puissance
utilisée
La puissance installée est supérieure à
la puissance réellement utilisée. Pour connaître cette
dernière il faut appliquer aux puissances des récepteurs ou
groupes de récepteurs des coefficients tenant compte de leur
fonctionnement :
· facteur d'utilisation maximale (ku =
1) qui correspond à la fraction de la puissance totale du
récepteur utilisée.
· facteur de simultanéité (ks
=1) qui tient compte du fait que des groupes de récepteurs ne
fonctionnent pas forcément simultanément.
La somme des diverses puissances affectées des
coefficients précédents donne la puissance utilisée Pu
(kW), qui est une partie de la puissance installée.
????(????) = ? ???? * ?? ?? * ????
III.5.2.3 Calcul de la puissance appelée
Une sommation arithmétique donne un ordre de grandeur
suffisant compte tenu:
· des approximations déjà faites (valeurs
statistiques et facteurs d'utilisation)
·

???? (??????) =
?????(????) * ???? * ???? ? . ??????( Ø)
des valeurs faibles et voisines des angles correspondant aux
cosØ.

61
Mémoire de fin d'études pour l'obtention du
diplôme d'Ingénieur de Conception en Génie
Mécanique, rédigé et soutenu par : PONDI
JOSEPH
Mise sur pied d'une unité industrielle de transformation
des céréales pour l'obtention de la
farine : projet industriel
du Groupe SOA
En général, le rendement ? est de
80% et les cos (0) des différents
récepteurs sont tous égaux à 0.85, le calcul de la
puissance appelée conduit à :

Sa (kVA)
=1Pi(kW)*Ku*Ks
0,80* 0,85
Compte tenu de la diversité des appareils
électriques dont dispose l'usine, le bilan des puissances sera
recensé dans le tableau ci-après :
Tableau 42 : Bilan des puissances de
l'usine
appareils
|
nombre
|
Pa(KW) Pi =
1.2Pa
|
Ku
|
Ks
|
Pu
|
Sa(KVA)
|
pré-nettoyeur
|
1
|
0,75
|
0,9
|
0,85
|
0,9
|
0,69
|
1,01
|
trieur alvéolaire
|
2
|
1,1
|
2,64
|
0,85
|
0,9
|
2,02
|
2,97
|
table
densimétrique
|
2
|
8,5
|
20,4
|
0,85
|
0,9
|
15,61
|
22,95
|
machine d'emballage
|
1
|
2,7
|
3,24
|
0,85
|
0,9
|
2,48
|
3,65
|
broyeur
|
1
|
82
|
98,4
|
0,85
|
0,9
|
75,28
|
110,70
|
décortiqueuse
|
1
|
4
|
4,8
|
0,85
|
0,9
|
3,67
|
5,40
|
blutoir
|
1
|
1,5
|
1,8
|
0,85
|
0,9
|
1,38
|
2,03
|
ensacheuse
|
1
|
2,7
|
3,24
|
0,85
|
0,9
|
2,48
|
3,65
|
torréfacteur
|
1
|
1,1
|
1,32
|
0,85
|
0,9
|
1,01
|
1,49
|
compresseur
|
4
|
5
|
24
|
0,85
|
0,9
|
18,36
|
27,00
|
surpresseur
|
4
|
1,1
|
5,28
|
0,85
|
0,9
|
4,04
|
5,94
|
convoyeur à bande
|
4
|
2
|
9,6
|
0,85
|
0,9
|
7,34
|
10,80
|
ventilateur
|
1
|
80
|
96
|
0,85
|
0,9
|
73,44
|
108,00
|
convoyeur à vis
|
1
|
3
|
3,6
|
0,85
|
0,9
|
2,75
|
4,05
|
Nettoyeur-séparateur
|
1
|
4,1
|
4,92
|
0,85
|
0,9
|
3,76
|
5,54
|
total
|
|
|
|
|
|
|
315,16
|
La puissance apparente étant donc de 315.16 KVA, et
étant donné qu'il y a des pertes de charge souvent de l'ordre de
30% alors nous choisissons un transformateur normalisé de telle sorte
que : 0.7X = 315.16
X étant la puissance active du transformateur
On trouve alors X=450.23 nous choisissons la valeur
normalisée directement supérieure : 630 KVA qui
satisfera aussi les extensions futures. (Annexe3).
III.5.2.4 Détermination du courant maximal
d'emploi(IE)
Au niveau des circuits terminaux, c'est le courant qui correspond
à la puissance apparente des récepteurs ; au niveau des circuits
de distribution, c'est le courant correspondant

62
Mémoire de fin d'études pour l'obtention du
diplôme d'Ingénieur de Conception en Génie
Mécanique, rédigé et soutenu par : PONDI
JOSEPH
Mise sur pied d'une unité industrielle de transformation
des céréales pour l'obtention de la
farine : projet industriel
du Groupe SOA
à la puissance d'utilisation, laquelle tient compte des
coefficients de simultanéité et d'utilisation. Il se
détermine de la manière suivante :
???? = ??'Ev3 D'où
'E =
|
????
??v3
|
315.16*1000
A.N 'E= 380*v3
|
= 479.4A
|
'E = 479.4A
Notre transformateur aura donc les caractéristiques
suivantes : Tableau 43 : Caractéristiques du
transformateur

630
479.4
0.8
50HZ
Primaire
15KV
Secondaire
380V/220V
Puissance active (KVA)
Intensité maximale(A)
Distribution Fréquence Cos
Ø
La bobine du secondaire sera couplée en étoile
pour permettre l'alimentation des moteurs à 380 V et les prises de
courant à 220V ;
III.6 Dimensionnement de la surface minimale de
l'usine
L'évaluation de la surface minimale d'une implantation
d'atelier est un processus qui se fait suivant une démarche bien
méticuleuse ; l'étude est restreinte ici à la
détermination de la juste surface de la salle de production où
sont disposées les machines. Les surfaces relatives aux bureaux ; aux
magasins de stockage des matières premières et de produits finis
ne sont pas prises en compte ici. Le principe repose sur trois étapes
dont le but est d'évaluer les déférentes surfaces qui
constituent la salle des machines.
III.6.1 Evaluation de la surface au sol ???? des
équipements
La surface au sol des équipements représente la
surface exclusivement occupée sur le sol par les équipements.
C'est la surface propre dans le plan du sol des équipements qui y sont
installés. Son expression est la suivante :
???? = L
· * ??
·
L
· * ??
· : est
l'encombrement de l'équipement i ; L
· et
??
· étant respectivement sa longueur et sa
largeur maximales.
III.6.2 Evaluation de la surface de gravitation
????
La surface de gravitation représente la surface
utilisée autour du poste de travail par l'ouvrier et par les
matières premières approvisionnées. Sa formulation
mathématique est la suivante :
???? = ???? * N

63
Mémoire de fin d'études pour l'obtention du
diplôme d'Ingénieur de Conception en Génie
Mécanique, rédigé et soutenu par : PONDI
JOSEPH
Mise sur pied d'une unité industrielle de transformation
des céréales pour l'obtention de la
farine : projet industriel
du Groupe SOA
???? : La surface au sol des équipements
précédemment évaluée ; N: Le nombre de
côtés d'accès à la machine ;
III.6.3 Evaluation de la surface d'évolution
S??
La surface d'évolution représente la surface qu'il
est nécessaire de réserver entre les postes de travail pour les
déplacements et les manutentions ; elle est donnée par :
???? = (???? + ????) * K
Avec K un facteur qui tient compte du moyen de manutention
utilisé dans l'usine ; le tableau58 qui renseigne sur le choix du
facteur K placé en annexe3.
Le tableau suivant donne le bilan du calcul de toutes les
surfaces susmentionnées de notre usine :
Tableau 44 : Bilan de calcul des surfaces de
l'usine.
appareils
|
nombre
|
Longueur
|
largeur
|
N
|
K
|
Ss
|
Sg
|
Se
|
trieur alvéolaire
|
2
|
1,9
|
0,6
|
4
|
0,5
|
2,28
|
9,12
|
5,70
|
table densimétrique
|
2
|
0,53
|
0,53
|
4
|
0,5
|
0,562
|
2,2472
|
1,40
|
pré-nettoyeur
|
1
|
1,095
|
0,88
|
4
|
0,5
|
0,964
|
3,8544
|
2,41
|
nettoyeur
|
2
|
2,3
|
1,1
|
4
|
0,5
|
5,06
|
20,24
|
12,65
|
broyeur
|
1
|
12
|
8
|
4
|
0,7
|
96
|
384
|
336,00
|
décortiqueuse
|
1
|
1,2
|
0,85
|
4
|
0,7
|
1,02
|
4,08
|
3,57
|
torréfacteur
|
1
|
2,3
|
1,3
|
4
|
0,6
|
2,99
|
11,96
|
8,97
|
convoyeur à vis
|
1
|
4,5
|
1,5
|
4
|
0,4
|
6,75
|
27
|
13,50
|
ensacheuse
|
1
|
4,1
|
1,05
|
4
|
0,5
|
4,305
|
17,22
|
10,76
|
convoyeur à bande
|
4
|
16
|
0,8
|
4
|
0,4
|
51,2
|
204,8
|
102,40
|
enceinte de séchage
|
1
|
14
|
10
|
4
|
0,6
|
140
|
560
|
420,00
|
surpresseur
|
4
|
6,3
|
2,4
|
4
|
0,3
|
60,48
|
241,92
|
90,72
|
compresseur
|
4
|
6,3
|
2,4
|
4
|
0,3
|
60,48
|
241,92
|
90,72
|
total
|
|
|
|
|
|
432,1
|
1728,36
|
1098,81
|
La surface minimale totale d'implantation ??t de
l'usine est obtenue par une somme arithmétique des surfaces
calculées ci-dessus. On a :
??t = ???? + ????+ ????
??t = 432.1 + 1728.36 + 1098.81 ? 3259.27
??t = 3259.27??2

64
Mémoire de fin d'études pour l'obtention du
diplôme d'Ingénieur de Conception en Génie
Mécanique, rédigé et soutenu par : PONDI
JOSEPH
Mise sur pied d'une unité industrielle de transformation
des céréales pour l'obtention de la
farine : projet industriel
du Groupe SOA
III.6.4 Etude de l'implantation optimale de la
chaine
Dans cette partie nous allons suivre la méthodologie
décrite au chapitre précédent.
a- Recueil des données
Ce tableau nous permet de recenser toutes les informations dont
nous avons besoin pour installer l'unité. Il nous faudra des
informations bien élaborées et détaillées.
Tableau 45 : Données pour l'implantation de
l'usine
Objectifs Données
récupérer
Organisation et conditions de travail
|
- Horaire : 8H/24 ;
- Débit de transformation : ? 6??/h
|
Organisation possible pour la production
|
|
Hygiène alimentaire
|
La majorité des équipements seront
nettoyés facilement.
|
Projet de construction
|
- Extension de l'usine
|
Plan de situation
|
Zone rurale
|
Voie d'accès au site
|
Voie routière
|
Transformation
|
Physico-chimique
|
Matière
|
Nature : alimentaire Etat d'origine : solide
|
Transformation par :
|
Broyage filtrage
|
Types de stockage
|
Silos
|
Stockage produits finis
|
Sac de 25 kg
Sac de 50 kg et autres
|
Vestiaires et sanitaires
|
Blocs vestiaires Blocs sanitaires Toilettes
|
Lieux d'accueil
|
Bureau
Local pour réunion
|
Ressources en eau
|
Réseau CDE
Pompe et tanks de stockage
|
Electricité
|
Réseau ENEO
Groupe électrogène
|
|
b- Définition des secteurs d'activités

65
Mémoire de fin d'études pour l'obtention du
diplôme d'Ingénieur de Conception en Génie
Mécanique, rédigé et soutenu par : PONDI
JOSEPH
Mise sur pied d'une unité industrielle de transformation
des céréales pour l'obtention de la
farine : projet industriel
du Groupe SOA
Tableau 46 : Définition des secteurs
d'activité
Différents secteurs d'activité
Exemple
Secteurs à risques liés à la
circulation des véhicules et personnes
|
Entrée, sortie personnel
Zone de déchargement des
matières premières
Zone de chargement des produits finis
|
Secteurs à risques avec des nuisances
liées aux ambiances physiques et chimiques
|
Zone de broyage
Zone de torréfaction de soja
|
Autres secteurs sans flux de matière
|
Bureaux Vestiaires Bloc sanitaire
|
Secteurs avec flux de matières
|
Zone de nettoyage Zone de décorticage Zone
d'égrenage Zone de séchage
|
secteurs à risques pour les produits
|
Zones de broyage Zone de nettoyage Zone d'empaquetage
|
c- Détermination des proximités de flux
Tableau 47 : Détermination des
proximités et des flux
|
Entrée sortie personnel
|
Zone de déchargement des matières
premières
|
Zone de chargement des produits finis
|
Zone de broyage
|
Zone de torréfaction
|
Bureau
|
Vestiaires
|
Zone de nettoyage
|
Zone de décorticage
|
Zone de séchage
|
Zone d' empaquetage
|
Entrée sortie personnel
|
|
ET
|
ET
|
ET
|
|
PT
|
PT
|
|
|
|
|
Zone de déchargement des matières
premières
|
|
|
|
|
|
|
|
|
PTT
|
PTT
|
|
Zone de
chargement des produits finis
|
|
|
|
|
|
|
|
|
ET
|
ET
|
|
Zone de broyage
|
|
|
|
|
|
|
|
|
PTT
|
|
|

66
Mémoire de fin d'études pour l'obtention du
diplôme d'Ingénieur de Conception en Génie
Mécanique, rédigé et soutenu par : PONDI
JOSEPH
Mise sur pied d'une unité industrielle de transformation
des céréales pour l'obtention de la
farine : projet industriel
du Groupe SOA
|
Entrée sortie personnel
|
Zone de déchargement des matières
premières
|
Zone de chargement des produits finis
|
Zone de broyage
|
Zone de torréfaction
|
Bureau
|
Vestiaires
|
Zone de nettoyage
|
Zone de décorticage
|
Zone de séchage
|
Zone d' empaquetage
|
Zone de torréfaction
|
|
|
|
|
|
EI
|
|
|
|
|
|
Bureau
|
|
|
|
|
|
|
|
|
|
EI
|
|
Vestiaires
|
|
|
|
|
|
|
|
|
|
EI
|
|
Zone de nettoyage
|
|
|
|
|
|
|
|
|
|
|
|
Zone de décorticage
|
|
|
|
|
|
|
|
|
|
|
|
Zone de séchage
|
|
|
|
|
|
|
|
|
|
|
|
Zone
d'empaquetage
|
|
|
|
|
|
|
|
|
|
|
|
EI : éloignement important ; PI : proximité
importante ; ETI : éloignement très important ; PTI :
proximité très importante ;
Ce tableau nous permet de déterminer les postes de
travail qui peuvent être côte à côte afin de gagner en
espace et en temps lors de l'installation ; il nous permet également de
juger et voir comment disposer les entrées, les sorties et même
les bureaux avec l'homme comme facteur d'influence afin de garantir une
sécurité optimale.
III.6.5 Schéma d'implantation et schéma
synoptique de l'usine.
III.6.5.1 Schéma d'implantation
Grâce au tableau précédent, nous parvenons
à sortir la disposition et la délimitation des zones dans le
complexe ; les zones seront délimitées comme nous l'indique la
figure29.

67
Mémoire de fin d'études pour l'obtention du
diplôme d'Ingénieur de Conception en Génie
Mécanique, rédigé et soutenu par : PONDI
JOSEPH
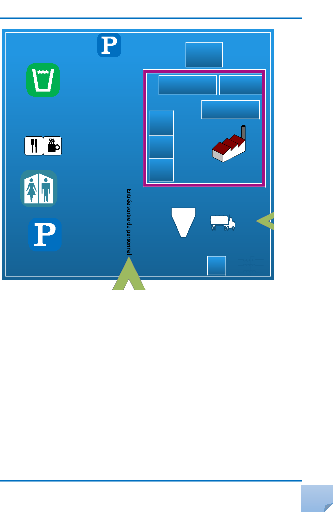
Mise sur pied d'une unité industrielle de transformation
des céréales pour l'obtention de la farine : projet industriel du
Groupe SOA
Station d'eau potable
Deuxième parking
|
|
|
|
|
|
|
|
|
|
|
|
|
|
Bureau
|
|
|
|
|
Bureau des
|
|
|
|
|
|
cadres
|
|
Stockage de produits
Stockage
|
Zone d emballage et
de contrôle
Zone de transformation
PG
produits finis
PT
Entrée
d entretiens
Bureau
Salle de
repos
Figure 25 : Plan de masse
Vestiaire et toilettes
Parking
camions
III.6.5.2 Schéma synoptique de
l'usine
Ayant obtenu au paragraphe précèdent notre
schéma d'implantation qui nous permet de voir comment le complexe sera
structuré, il est important pour nous de faire le schéma
synoptique pour illustrer comment les équipements seront liés
entre eux et comment se déroulera de façon technologique la
production de la farine. L'illustration est donc faite sur la figure suivante
:
Mémoire de fin d'études pour l'obtention du
diplôme d'Ingénieur de Conception en Génie
Mécanique, rédigé et soutenu par : PONDI
JOSEPH
68
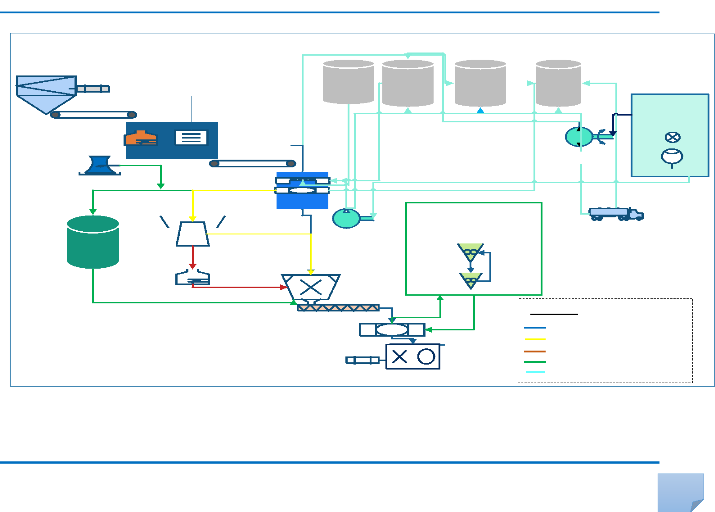
Mise sur pied d'une unité industrielle de transformation
des céréales pour l'obtention de la farine : projet industriel du
Groupe SOA
Pre-nettoyeur
Synoptique de la chaine de transformation
Hydrateur
Silo repos
du blé
Zone de
séchage
Torréfacteur
Unité de
Decortiqueuse
Convoyeur
à bande
nettoyage
Broyeur
Compresseur
Silo de
stockage
maïs grain
Convoyeur à vis
Blutoir
Stockage
de blé
Zone de claquage et
de convertissage
Machine
d'emballage
Stockage
sorgho
Légende :
Stockage
soja
Circuit principal
Circuit secondaire1 (maïs, sorgho)
Circuit secondaire2 (soja)
Circuit secondaire3 (blé)
Circuit soufflage (transport)
Surpresseur
Chambre
compresseur
Figure 26 : Schéma synoptique de la chaine de
transformation
Mémoire de fin d'études pour l'obtention du
diplôme d'Ingénieur de Conception en Génie
Mécanique, rédigé et soutenu par : PONDI
JOSEPH
79
Mise sur pied d'une unité industrielle de transformation
des céréales pour l'obtention de la
farine : projet industriel
du Groupe SOA
III.6.5.3 Description de la chaine de
transformation
Le maïs arrive à l'usine en grains, ces grains
sont introduits dans le pré-nettoyeur pour assurer un séchage
efficace ; ensuite ils sont introduits dans la zone de séchage où
ils sont séchés ; les grains de maïs sont donc introduits
dans l'unité de nettoyage pour un nettoyage complet ; ensuite ils sont
dirigés dans la décortiqueuse ou directement dans le broyeur en
fonction du type de farine que nous voulons obtenir ; (soit la farine
complète ou dégermée) ils peuvent également
être dirigés dans un silo de stockage ; après le broyage la
farine est convoyée à l'aide d'un convoyeur à vis vers un
blutoir où elle est tamisée ;les produits obtenus peuvent alors
être emballés à l'aide de la machine d'emballage et
conditionnés.
Les autres produits quant à eux arrivent à
l'usine en grains de céréales déjà secs, ils sont
alors introduits dans leurs silos respectifs, le sorgho suit le même
processus que le maïs, le soja est d'abord torréfié pour
être digestible avant d'être broyé ensuite il suit le
même processus tel que décrit précédemment sur les
autres céréales ; le blé quant à lui après
nettoyage est hydraté à l'aide de l'hydrateur, conditionné
et mis en repos dans un silo déjà aménagé (silo du
repos du blé) après un temps de repos, il sera dirigé vers
le broyeur pour être moulu, ensuite la farine obtenue est
transportée à l'aide du convoyeur à vis, vers le blutoir ,
la farine sera alors blutée ; la farine fine sera dirigée vers la
machine d'emballage ; et prêt pour l'emballage et le conditionnement ;
quant à la farine moins fine, elles sera dirigée vers la zone de
claquage et de convertissage où elle sera encore moulue ; ensuite
renvoyée vers le blutoir pour être tamisée ensuite
emballée et prête pour le conditionnement ; voilà donc de
façon sommaire le fonctionnement technologique de notre chaine de
transformation du maïs, blé, sorgho et soja. Nous avons fait les
schémas de principe de certaines unités notamment l'unité
de nettoyage et de séchage pour faciliter la compréhension de
cette chaine de transformation et aussi la chaine de conditionnement; ces
schémas sont mis en annexe2.

80
Mémoire de fin d'études pour l'obtention du
diplôme d'Ingénieur de Conception en Génie
Mécanique, rédigé et soutenu par : PONDI
JOSEPH
Mise sur pied d'une unité industrielle de transformation
des céréales pour l'obtention de la
farine : projet industriel
du Groupe SOA
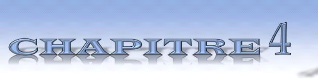
MOYENS DE MAITRISE ET ANALYSE
FINANCIèRE DU PROJET INDUSTRIEL
Description :
Il est question dans ce chapitre de détecter les
équipements critiques et de faire un plan de maintenance
préventive desdits équipements, de faire une brève analyse
des déchets de notre usine, de mettre sur pied une application d'aide au
dimensionnement, et enfin faire une analyse financière du projet : cette
analyse financière consistera à évaluer l'investissement
initial, puis faire une étude prévisionnelle des ventes afin de
ressortir le cash-flow pour obtenir la VAN afin de pouvoir monter aux
investisseurs si le projet est fiable.
81
Mémoire de fin d'études pour l'obtention du
diplôme d'Ingénieur de Conception en
Génie
Mécanique, rédigé et soutenu par :
PONDI JOSEPH
Mise sur pied d'une unité industrielle de transformation
des céréales pour l'obtention de la
farine : projet industriel
du Groupe SOA
IV.1 Mise en oeuvre de l'abaque de Noiret pour le choix
des équipements critiques
Face aux contraintes d'exploitation (personnel de maintenance
limité, temps disponible pour la maintenance, besoin de
disponibilité de l'installation, ...), mais également des
contraintes de temps et d'informations, il est nécessaire de mettre en
évidence les équipements critiques pour l'installation afin de
concentrer l'effort de maintenance préventive sur ces
équipements. Le choix des équipements critiques nous permettra
d'investir notre temps dans la partie de la chaîne.
Pour mettre donc en oeuvre l'abaque de Noiret
présenté au chapitre2, nous allons faire la mise en oeuvre pour
un seul équipement et nous allons dresser un tableau
récapitulatif pour les autres équipements.
IV.1.1 Cas pratique du broyeur
- Age : la machine vient tout juste
d'être fabriquée donc on lui donnera 0 an soit :
points = 90 - âge * 4 = 90 points
- Interdépendance : le broyeur
fonctionnera en plein temps ; car si le broyeur ne fonctionne pas le produit
final ne peut pas être obtenu : il sera donc classé dans «
matériel essentiel et marche continue » soit 70
points.
- Coût : son prix d'achat se situe dans
la catégorie [15000-30000[. Soit 25 points.
- Complexité et accessibilité :
la machine est très grande mais l'accès aux différentes
parties est assez évidente, nous la classerons donc dans «
matériel peu complexe et accessible » soit 5 points.
- Robustesse et précision : machine
très robuste et avec précision nous la classons donc dans :
« robuste et de précision » soit 15 points.
- Origine : elle est fabriquée en
chine ; donc catégorie « étranger sans service technique
» soit 90 points.
- Utilisation : le broyeur est unique et
utilisé uniquement pour une chaine ; soit 75 points. - Pertes de
produits : si la machine s'arrête les produits peuvent
être repris et même
perdus pour assurer la sécurité nous supposons
que les produits seront perdus
soit : « produits perdus » 55 points
- Délais : les produits issus des
broyeurs sont conditionnés et vendus certains sont stockés ; donc
« délais impératif (risque de pénalités de
retard » soit 150 points
Nous avons au total 575 points ; ce qui nous permet de
conclure qu'une maintenance préventive est nécessaire pour cet
équipement.
IV.1.2 Récapitulatif
En appliquant la procédure précédente
à tous les autres équipements nous obtenons le tableau suivant
:

82
Mémoire de fin d'études pour l'obtention du
diplôme d'Ingénieur de Conception en
Génie
Mécanique, rédigé et soutenu par :
PONDI JOSEPH
Mise sur pied d'une unité industrielle de transformation
des céréales pour l'obtention de la
farine : projet industriel
du Groupe SOA
Tableau 48 : Détermination des
équipements critiques par l'abaque de Noiret
Machines critères
Age équipement
|
Egreneuse
90
|
Nettoyeur - séparateu r
90
|
Décortique use
90
|
Torréfacteur
90
|
Machine d'emballag e
90
|
Interdépendance
|
70
|
60
|
20
|
70
|
70
|
Coût
|
5
|
5
|
5
|
5
|
15
|
Complexité et
accessibilité
|
5
|
5
|
5
|
5
|
5
|
Robustesse et
précision
|
10
|
10
|
10
|
10
|
10
|
Origine
|
90
|
90
|
90
|
90
|
90
|
Utilisation
|
75
|
175
|
75
|
75
|
75
|
Perte de produits
|
35
|
35
|
35
|
55
|
35
|
Délais
|
100
|
150
|
25
|
150
|
225
|
Total
|
480
|
520
|
355
|
550
|
615
|
Machines critères
|
Sécheur à
infra rouge
|
Convoyeu r à bande
|
Compresse ur
|
Ventilateur
|
Convoyeur à vis
|
Age équipement
|
90
|
90
|
90
|
90
|
90
|
Interdépendance
|
70
|
70
|
70
|
70
|
70
|
Coût
|
5
|
5
|
5
|
5
|
5
|
Complexité et
accessibilité
|
5
|
5
|
5
|
5
|
5
|
Robustesse et
précision
|
10
|
10
|
10
|
10
|
10
|
Origine
|
90
|
90
|
90
|
90
|
90
|
Utilisation
|
75
|
75
|
75
|
75
|
75
|
Perte de produits
|
35
|
10
|
10
|
10
|
55
|
Délais
|
100
|
25
|
25
|
100
|
225
|
Total
|
480
|
380
|
380
|
455
|
625
|
Il ressort de notre étude que les équipements
critiques sont : le broyeur, le torréfacteur, la machine
d'emballage et le convoyeur à vis ; leurs plans de maintenance
sont mis en annexe4.
IV.2 Analyse financière et rentabilité
économique
Il est question dans cette section d'effectuer l'analyse
économique et financière du projet. Ceci consistera à
évaluer l'investissement initial, le temps nécessaire pour le
retour à l'investissement. Nous allons commencer par quelques
définitions portant sur l'évaluation des projets
d'investissement.

83
Mémoire de fin d'études pour l'obtention du
diplôme d'Ingénieur de Conception en
Génie
Mécanique, rédigé et soutenu par :
PONDI JOSEPH
Mise sur pied d'une unité industrielle de transformation
des céréales pour l'obtention de la
farine : projet industriel
du Groupe SOA
IV.2.1 Définitions
IV.2.1.1 Investissement
On appelle investissement, l'engagement d'un capital dans une
opération dont on attend des gains futurs étalés dans le
temps. Un investissement est acceptable lorsque les gains actuels attendus sont
supérieurs au capital à investir.
IV.2.1.2 Capital à investir
C'est la dépense que doit supporter l'entreprise pour
réaliser le projet. Il comprend entre autres :
- Le prix d'achat hors taxe (ou coût de fabrication) ;
- Les frais accessoires (frais de transport, d'installation) ; -
La TVA non récupérable ;
- L'augmentation du besoin en fonds de roulement.
IV.2.1.3 Durée de vie du projet
Il est important de connaitre la durée d'exploitation d'un
projet afin d'évaluer les gains attendus. Si la durée de vie du
projet est difficile à prévoir, on lui substitue une durée
d'amortissement. Dans le cas présent la durée de vie de notre
projet est de 5 ans.
IV.2.1.4 Notion de cash-flow
De tout investissement, une entreprise attend :
- Soit des rentrées d'argent (recettes-dépenses)
;
- Soit des économies sur les coûts d'exploitation
;
Ces différentes attentes sont désignées par
le terme cash-flow.
cash - flow = économies réalisées
imputables au projet IV.2.1.5 Critère d'évaluation du
projet industriel
Evaluer un projet d'investissement revient à comparer le
capital à investir Io à l'ensemble des
cash-flowsC1, C2, ..., Cn. Cette
comparaison implique l'évaluation du capital investi et des cash-flows
à la même date.
Pour évaluer la rentabilité de notre projet, nous
avons choisi d'utiliser la valeur actuelle nette et le délai de
récupération.
? La valeur actuelle nette
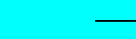
n
VAN= -Io+
? Fi
(1 + r)i
1
La valeur actuelle nette est la différence entre les
cash-flows actualisés à la date 0 et le capital investi.

84
Mémoire de fin d'études pour l'obtention du
diplôme d'Ingénieur de Conception en
Génie
Mécanique, rédigé et soutenu par :
PONDI JOSEPH
Mise sur pied d'une unité industrielle de transformation
des céréales pour l'obtention de la
farine : projet industriel
du Groupe SOA
· r : taux d'investissement ;
· Io : capital investi ;
· Fi: cash - f lows;
· n : durée de vie du projet.
? Délai de récupération
Le délai de récupération DR du capital
investi est le temps au bout duquel le montant cumulé des cash-flows
actualisés est égal au capital investi.
??°°
DR = ???? [32]
· Io: investissement initial.
· FM : flux monétaire annuel du projet.
IV.2.2 Coût des équipements.
Les différents coûts sont répertoriés
dans le tableau suivant : Tableau 49 : Coûts des
équipements
Equipements Quantité Prix unitaire Prix
total
|
moissonneuse-batteuse
|
1
|
6 000 000
|
6 000 000
|
pre-nettoyeur
|
1
|
2 000 000
|
2 000 000
|
table densimétrique
|
2
|
2 000 000
|
4 000 000
|
trieur alvéolaire
|
2
|
20 000 000
|
40 000 000
|
nettoyeur - séparateur
|
2
|
1 000 900
|
2 001 800
|
blutoir
|
1
|
1 500 000
|
1 500 000
|
broyeur
|
1
|
30 000 000
|
30 000 000
|
décortiqueuse
|
1
|
2 500 000
|
2 500 000
|
torréfacteur
|
3
|
1 057 565
|
3 172 695
|
machine d'emballage
|
1
|
5 600 250
|
5 600 250
|
convoyeur à bande
|
4
|
2 500 000
|
10 000 000
|
ventilateur
|
1
|
1 499 500
|
1 499 500
|
compresseur
|
4
|
220 350
|
881 400
|
surpresseur
|
4
|
500 000
|
2 000 000
|
convoyeur à vis
|
2
|
1 000 000
|
2 000 000
|
silos de stockage
|
4
|
3 000 000
|
12 000 000
|
transformateur
|
1
|
25 000 000
|
25 000 000
|
C equip pro net
|
|
|
150 155 645
|

85
Mémoire de fin d'études pour l'obtention du
diplôme d'Ingénieur de Conception en
Génie
Mécanique, rédigé et soutenu par :
PONDI JOSEPH
Mise sur pied d'une unité industrielle de transformation
des céréales pour l'obtention de la
farine : projet industriel
du Groupe SOA
Nous allons majorer la somme des coûts estimés
des équipements et des opérations nécessaires à
l'obtention de la totalité des pièces de 20% pour prévoir
des éventuels surcoûts et les frais d'importation et de
logistique. A cet effet, nous trouvons donc un coût des
équipements de :
Cequip pro = Cequip pro net + 0.2 * Cequip pro net = 180
186 774 FCFA
IV.2.3 Coût d'investissement du projet
C'est le montant global nécessaire pour réaliser
le projet ; c'est le résultat de la somme des coûts des autres
travaux qui doivent être mis sur pied pour la réalisation du
projet ; qui sont entre autre [12] :
2s. Coût des services généraux et stockages
(11)
11 = 0.4 * Cequip pro net = 60 062 258 FCFA
2s. Frais d'études et d'ingénierie (12)
12 = 0.12(11 + Cequip pro net) = 25 226 148.4 FCFA
2s. Frais de contracteur (13)
13 = 0.05(11 + Cequip pro net) = 10
510 895.2 FCFA
2s. Dotations sur les imprévus(14)
|
|
|
|
|
|
14 = 0.2 * (Cequip pro net + 11
|
+ 12
|
+ 13)
|
=
|
49
|
190 989.3 FCFA
|
Cinv =Cequip pro + 11 + 12
|
+ 13
|
+ 14
|
=
|
325
|
177 065 FCFA
|

1o = 325 177 065 FCFA
Notons que les coûts relatifs à l'achat du
terrain et à la construction locale de l'usine n'ont pas
été pris en compte ici : ces deux éléments
bâtiments et terrains seront octroyés au Groupe par l'Etat du
Cameroun SOA.
IV.2.4 Charges prévisionnelles annuelles 2s.
Charges électriques.
Nous aurons un transformateur de 630 kVA et un cosinus phi de
0.8, et l'usine dans les normes fonctionnera 8h par jour et 6 jours par semaine
; la consommation moyenne en énergie par an sera donc de l'ordre de :
1161216 KWh ; étant donné qu'en moyenne tension Eneo facture le
prix du kWh à 70 FCFA pendant les heures de pointe et 55 FCFA en dehors,
la facturation annuelle sera de : 81 285 120 FCFA.

86
Mémoire de fin d'études pour l'obtention du
diplôme d'Ingénieur de Conception en
Génie
Mécanique, rédigé et soutenu par :
PONDI JOSEPH
Mise sur pied d'une unité industrielle de transformation
des céréales pour l'obtention de la farine : projet industriel du
Groupe SOA
? Achat et implantations des champs de céréales.
Nous aurons besoin par an de maximum 4000 t de blé ; ce
qui est équivalent à une dépense de 838 400 000
FCFA.
Pour ce qui est du sorgho ; nous aurons également besoin
de maximum 4000 t de sorgho par an ce qui revient à dépenser :
432 300 000 FCFA.
Nous aurons 1250 t de soja ce qui est équivalent à
312 500 000 FCFA.
Pour ce qui est du maïs nous aurons besoin de 500 ha de
maïs par an, un hectare de maïs revient à 268 925 FCFA ce qui
est équivalent à une dépense annuelle sur le maïs de
: 134 462 500 FCFA.
L'implantation des champs et l'achat des céréales
revient donc à coût annuel de :
1 717 662 500 FCFA.
Le tableau ci-dessous résume les charges
prévisionnelles annuelles pendant la durée de vie de notre
projet.
Tableau 50 : Récapitulatif sur les charges
prévisionnelles annuelles
Année 1 Année 2 Année 3 Année
4 Année 5
charges du
personnel
|
9 750 000
|
10 237 500
|
41 429 375
|
43 500 844
|
45 675 886
|
charges d'électricité
|
0
|
300 000
|
81 285 120
|
81 285 120
|
81 285 120
|
achat
combustible de séchage
|
0
|
0
|
8 161 920
|
8 161 920
|
8 161 920
|
achat
carburant
pour la moisson
|
0
|
0
|
6 000 000
|
6 000 000
|
6 000 000
|
achat des
céréales
|
0
|
|
2 583 200 000
|
2 583 200 000
|
2 583 200 000
|
charges sociales
|
1 755 000
|
1 842 750
|
7 457 288
|
7 830 152
|
8 221 659
|
amortissement
|
0
|
0
|
25 870 097
|
25 870 097
|
25 870 097
|
charges d'eau
|
0
|
200 000
|
1 000 000
|
1 000 000
|
1 000 000
|
autres charges
|
0
|
300 000
|
2 000 000
|
2 000 000
|
2 500 000
|
total
|
11 505 000
|
12 880 250
|
2 756 403 800
|
2 758 848 133
|
2 761 914 682
|

87
Mémoire de fin d'études pour l'obtention du
diplôme d'Ingénieur de Conception en
Génie
Mécanique, rédigé et soutenu par :
PONDI JOSEPH
Mise sur pied d'une unité industrielle de transformation
des céréales pour l'obtention de la
farine : projet industriel
du Groupe SOA
IV.2.5 Estimation des ventes annuelles
100 kg de maïs produisent en moyenne 38 kg de farine fine
; les autres céréales : blé, sorgho et soja produisent en
moyenne 65 % de farine par rapport aux grains bruts ; ce qui signifie qu'en une
année nous aurons en moyenne : 1 520 000 kg de farine de maïs, 2
600 000 kg de farine de blé et de sorgho, 812 500 kg de farine de
soja.
Les farines de maïs, de blé, de sorgho et de soja
ont un prix moyen de 500 FCFA le kilogramme sur le marché local.
Ainsi sur les 5 années de notre étude, nous aurons
deux phases :
- La phase d'implantation de la chaine qui fera deux ans ; - Et
la phase d'exploitation ;
NB : nous avons supposé 10 % de pertes de produits.
Tableau 53 : Ventes annuelles
prévisionnelles
Année 1 Année 2 Année 3 Année
4 Année 5
Farine de maïs produite (kg)
|
0
|
0
|
1 368 000
|
1 368 000
|
1 368 000
|
Farine de soja produite (kg)
|
0
|
0
|
731 250
|
731 250
|
731 250
|
Farine de
sorgho produite (kg)
|
0
|
0
|
2 340 000
|
2 340 000
|
2 340 000
|
Farine de blé
produite (kg)
|
0
|
0
|
2 340 000
|
2 340 000
|
2 340 000
|
Prix farine de maïs
produite(FCFA)
|
0
|
0
|
752 400 000
|
752 400 000
|
752 400 000
|
Prix farine de
soja produite (FCFA)
|
0
|
0
|
365 625 000
|
365 625 000
|
365 625 000
|
Prix farine de sorgho produite (FCFA)
|
0
|
0
|
1 170 000 000
|
1 170 000 000
|
1 170 000 000
|
Prix farine de
blé produite (FCFA)
|
0
|
0
|
1 170 000 000
|
1 170 000 000
|
1 170 000 000
|
Total vente
(FCFA)
|
0
|
0
|
3 458 025 000
|
3 458 025 000
|
3 458 025 000
|

88
Mémoire de fin d'études pour l'obtention du
diplôme d'Ingénieur de Conception en
Génie
Mécanique, rédigé et soutenu par :
PONDI JOSEPH
Mise sur pied d'une unité industrielle de transformation
des céréales pour l'obtention de la
farine : projet industriel
du Groupe SOA
IV.2.6 Calcul de la VAN
Le cash-flow représente l'ensemble des flux de
liquidités générés par les activités d'une
société. C'est tout simplement la différence entre le
revenu et les dépenses d'exploitation, à laquelle sont
retranchées les différentes taxes pour l'impôt sur
les sociétés (I.S) :
Ø Calcul du résultat net avant impôt ;
resultat net avant impôt = vente previsionnelle -
charge - amortissement resutat avec impôt = résultat net avant
impôt(1 - taux IS)
Ø Cash-flow
cash flow = résultat net avant impôt +
amortissement
Ø Cash-flow actualisé : cette méthode
estime la valeur de rendement futur l'entreprise sur la base du cash-flow
disponible après impôts.
cash flow actualisé = (1 + r)-n * cash flow
Notre étude se fera sur les premières années de
production :
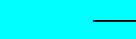
VAN= -Io+
?' (1 + r)n 1
n
Avec n= nombre d'années ; et r= taux d'actualisation qui
est de 10 %
Tableau 54: Tableau récapitulatif pour le
calcul des cash-flows
Année 1 Année 2 Année 3 Année
4 Année 5
l0
|
325 177 065
|
325 177 065
|
325 177 065
|
325 177 065
|
325 177 065
|
cash-flow
|
-11 505 000
|
-12 880 250
|
701621200
|
699176867
|
696 110 318
|
cash-flow actualisé
|
-10459090,91
|
-10644834,71
|
527138392,2
|
477547207,8
|
432229739,6
|
VAN = -325 177 065 + 141581141414=1 090 634 349
FCFA
VAN = 1 090 634 349 FCFA Après 5 ans
.La VAN étant positive, le projet peut
être retenu sachant qu'il permettra aux investisseurs de revenir sur
leurs capitaux.
IV.3 Présentation du progiciel d'aide au
dimensionnement.
Nous avons mis sur pied un progiciel d'aide au
dimensionnement, c'est une application qui a pour but de d'aider les promoteurs
dans la prise de décision, d'aider les ingénieurs dans le
dimensionnent ou le redimensionnement des équipements de la chaine au
cas où le débit de production est modifié.

89
Mémoire de fin d'études pour l'obtention du
diplôme d'Ingénieur de Conception en
Génie
Mécanique, rédigé et soutenu par :
PONDI JOSEPH
Mise sur pied d'une unité industrielle de transformation
des céréales pour l'obtention de la
farine : projet industriel
du Groupe SOA
IV.3.1 Environnement de programmation
Java est une technologie développée par Sun
Microsoft : (la technologie). Elle correspond à plusieurs produits et
spécifications de logiciels qui ensemble, constituent un système
pour développer et déployer des applications. Java est
utilisée dans une grande variété de plates-formes depuis
les systèmes embarqués et les téléphones mobiles
jusqu'aux serveurs, les applications d'entreprise, les superordinateurs et dans
une moindre mesure pour les interfaces graphiques comme les applets Java du
Web.
Depuis des années, Sun Microsoft appelle java la «
technologie Java » dans son ensemble. En pratique, beaucoup de
programmeurs utilisent le mot « Java » pour désigner le
langage de programmation, tandis que la plate-forme d'exécution est
appelée « JRE » (Java Runtime Environment d'exécution
Java) et le système de compilation : « JDK » (Java Development
Kit) plutôt que « compilateur Java ». Java est sous licence GNU
GPL depuis novembre 2006.
IV.3.2 Présentation des différents
modules.
IV.3.2.1 Interface d'entrée des
paramètres.
Lors du lancement de l'application il apparaît une page
d'accueil qui se présente comme la figure 36 cette page nous permet
d'entrer les paramètres de production c'est-à-dire les
débits annuels de production en fonction des céréales.
88
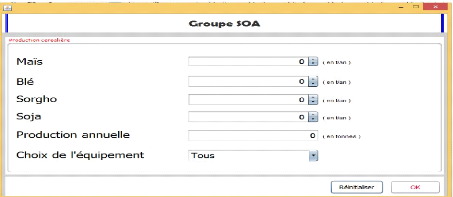
Figure 27 : Module d'entrée des paramètres
IV.3.2.2 Interface de présentation des
résultats.
Lorsqu'on clique sur le bouton «
ok» du module d'entrée, il apparait une
fenêtre comment l'indique la figure32 qui nous renseigne sur les
caractéristiques de tous les équipements de la chaine de
transformation, le coût d'investissement, la puissance appelée, la
surface minimale, ainsi que les quantités de farines produites, nous
avons également la possibilité de sauvegarder les
résultats à l'aide du bouton « sauvegarder
»
90
Mémoire de fin d'études pour l'obtention du
diplôme d'Ingénieur de Conception en
Génie
Mécanique, rédigé et soutenu par :
PONDI JOSEPH
Mise sur pied d'une unité industrielle de transformation
des céréales pour l'obtention de la
farine : projet industriel
du Groupe SOA
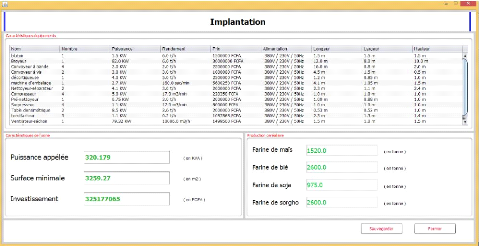
Figure 28 : Module « résultat »
IV.3.3 Analyse des résultats : guide pour la
prise de décision.
Nous avons fait varier les débits en fonction des
céréales en faisant la combinaison entre les
céréales ; ceci dans le but de faire connaitre aux promoteurs les
combinaisons des céréales les plus rentables et le débit
minimal que nous leur suggérons de moudre par an.
Il convient donc de noter que :
? Les courbes obtenues sont des droites dont la pente est
positive, ce qui signifie naturellement que l'augmentation de la production
annuelle pour chaque céréale augmente le rendement de
l'unité mais ce rendement n'est pas le même pour toutes les
combinaisons. Si nous faisons la mouture d'une seule céréale par
an (fig.34), la céréale la plus rentable est le
sorgho ; et la deuxième est le maïs : mais nous suggérons
aux promoteurs de mettre plutôt l'accent sur le maïs à cause
de l'écologie de la zone, mais aussi à cause de la
diversité et de la densité de celui-ci.
Légende :
(1) : Sorgho ;
(2) : Maïs ;
(3) : Soja
(4) : Blé

91
Mémoire de fin d'études pour l'obtention du
diplôme d'Ingénieur de Conception en
Génie
Mécanique, rédigé et soutenu par :
PONDI JOSEPH
Mise sur pied d'une unité industrielle de transformation
des céréales pour l'obtention de la
farine : projet industriel
du Groupe SOA

Légende :
(1) sorgho
(2) Maïs
(3) Soja
(4) Blé
Figure 29 : Analyse de la production en prenant une seule
céréale
? Si nous faisons la mouture de la combinaison de deux
céréales par an, la combinaison la plus rentable est la
combinaison sorgho+ maïs ; (fig. 35)
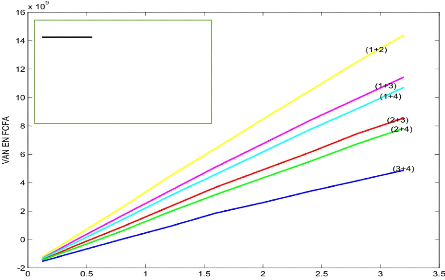
Légende :
(1+2) sorgho+ maïs (2+4) maïs + blé (1+3) sorgho
+ soja (3+4) soja+ blé (1+4) sorgho+ blé
(2+3) maïs+ soja
Figure 30 : Combinaison de deux céréales

92
Mémoire de fin d'études pour l'obtention du
diplôme d'Ingénieur de Conception en
Génie
Mécanique, rédigé et soutenu par :
PONDI JOSEPH
Mise sur pied d'une unité industrielle de transformation
des céréales pour l'obtention de la
farine : projet industriel
du Groupe SOA
? Si nous faisons la mouture de la combinaison de trois de ces
céréales, la combinaison la plus rentable est la combinaison
sorgho + maïs + soja (fig.36)
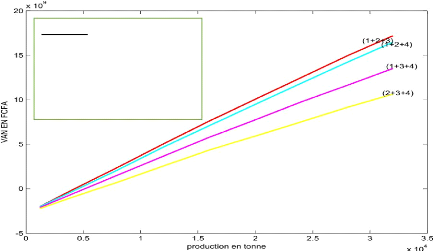
Légende :
(1+2+3) sorgho + maïs+ soja (1+2+4) sorgho + maïs+
blé (1+3+4) sorgho + soja + blé (2+3+4) maïs+ soja+
blé
Figure 31 : Combinaison de la mouture de trois
céréales.
? De toutes ces combinaisons, la plus rentable est la mouture
des quatre céréales (fig.37) ; ces
résultats nous permettent donc de suggérer aux promoteurs de
privilégier la mouture des quatre céréales, laquelle devra
être minimum de 5000 t de céréales par an.
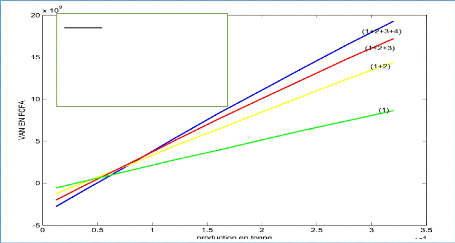
Légende :
(1+2+3+4) sorgho+ maïs + soja + blé
(1+2+3) sorgho + maïs+ soja
(1+2) sorgho+ maïs
(1) sorgho
Figure 32 : Courbe comparative des différentes
combinaisons

93
Mémoire de fin d'études pour l'obtention du
diplôme d'Ingénieur de Conception en
Génie
Mécanique, rédigé et soutenu par :
PONDI JOSEPH
Mise sur pied d'une unité industrielle de transformation
des céréales pour l'obtention de la
farine : projet industriel
du Groupe SOA
CONCLUSION géNéRALE ET PERSPECTIVES
Le présent travail consistait à mettre sur pied
une unité industrielle de transformation des céréales
(maïs, blé, sorgho et soja) pour l'obtention de la farine, projet
du groupe Seeds Of Africa. Notre démarche tout au long de ce travail a
porté sur :
· L'étude des techniques et des technologies de
production de farine à base du maïs, du blé, du sorgho et du
soja.
· L'étude des méthodologies de mise sur
pied des unités industrielles et nous avons retenu la
méthodologie de V.CAUDILL ;
· La conception et le dimensionnement de la chaine de
transformation ; nous avons commencé par faire l'analyse fonctionnelle
de ladite chaine, ensuite le dimensionnement des équipements annexes et
principaux de la chaine de production et le choix des machines auprès
des fournisseurs.
· Le dimensionnement de la partie électrique et
la surface minimale de l'usine.
Une analyse financière a été faite
incorporant les investissements en équipements de production et de
l'installation électrique ; les coûts relatifs au terrain et au
bâtiment local de l'usine n'étant pas pris en compte ici. Nous
sommes arrivés à un investissement de 325 177 065
FCFA.
Une étude de rentabilité a aussi
été faite, reposant sur les charges d'exploitation (consommation
en énergie électrique, rémunération des
opérateurs, achat des céréales, achat des combustibles
pour le séchage) ; et les ventes sur la période
d'évaluation. Nous avons trouvé une VAN positive après 5
ans qui est de : 1 090 634 349 FCFA . Nous pouvons encourager
les investisseurs sur ce projet car il une VAN positive c'est-à-dire
qu'il sera rentable dès la cinquième année à savoir
la troisième année de transformation des quatre
céréales. Les perspectives que nous ouvre un tel travail sont les
suivantes :
y' Mise en place d'une politique de maintenance de tous les
équipements de la chaine de transformation ;
y' Etendre l'utilisation du progiciel pour des débits
supérieurs à 60000t/an ;
y' Mettre sur pied des études d'automatisation, des
circuits pneumatiques, électroniques etc.
y' mettre sur pied une équipe de contrôle des
travaux ;
y' mettre sur pied un processus d'amélioration continue
conformément à l'esprit des
normes ISO 9000(version 2000) et particulièrement du
management par les processus ; y' signer les partenariats avec les meuneries
nationales et/ou internationales pour la
formation du personnel.

94
Mémoire de fin d'études pour l'obtention du
diplôme d'Ingénieur de Conception en
Génie
Mécanique, rédigé et soutenu par :
PONDI JOSEPH
Mise sur pied d'une unité industrielle de transformation
des céréales pour l'obtention de la
farine : projet industriel
du Groupe SOA
BIBlIOgRAPHIE
Articles dans les revues et périodiques
[1] Abdou Maïga, (2012), production et transformation du
maïs, 31P.
[2] Laurent Guerreiro(2014), Toulouse, sélection du soja
: les défis à relever, 23p.
Cours et livres
[3] A. Bhalla(1990), production de farine de maïs à
petite échelle, bureau international du travail, génève,
132p.
[4] André Chévalier(2004), guide du dessinateur
industriel, Hachette technique,paris,338p.
[5] Ruth Charrondiere(2015), base de données sur la
densité-version 2.0, FAO, Rome, 25p.
[6]F.AUDRY(2010), analyse fonctionnelle : guide pour le
professeur, académie de versaille, 19p.
[7]Yves Jannot(2011), thermique solaire, 81p.
[8]A.Singbo, Ahouansou(2010), évaluation des performances
techniques de deux torréfacteurs d'amande de karité, 9p.
[9] Njandeu Monique(2014), cours de droit du travail et des
affaires, ENSPY. [10]Jean Nganou(2016),cours de gestion et maitrise des
coûts d'un projet, 82p. [11] Azzaro-Pantel, calcul des investissements,
33p.
[12]Emmanuel Ngnikam(2016), cours de gestion et traitement des
dechets,27p.
Rapports
[13]DSCE(2010) pour l'emploi, cadre de reference de l'action
gouvernementale pour la periode 2010-2020, 174p.
[14]agridoc, «fabrication de farine à base de
maïs,» 7p.
[15]13guide pratique de l'accueil des écoles primaires
chez les professionnels de la filière
céréalière(2014), Eloviva developpement durable,
100p.
[16] Banque Nationale de developpement agricole agricole),
«fiche technique soja version 1.0,» p. 1.
[17] mise au point de pains composites à base de
mélanges de farines de sorgho-blé et analyse texturale(1998) p.
9.
[18] dossier d'information pour les PME d'Afrique sur la
transformation agroalimentarie,» céréales-farine,
sémoule, brisure, p. 18.
[19] CHOPIN, «etude du conditionnement du blé
dur,» [Quality control for grains and flours], p. 5.

95
Mémoire de fin d'études pour l'obtention du
diplôme d'Ingénieur de Conception en
Génie
Mécanique, rédigé et soutenu par :
PONDI JOSEPH
Mise sur pied d'une unité industrielle de transformation
des céréales pour l'obtention de la
farine : projet industriel
du Groupe SOA
[20] Bertrand Tatsinda et Stephane Timba, (2016), description
du projet SOA, definitive resume for Santchou, 21p.
Thèses et mémoires
[21] Clément DEBITON(2010),Identification des
critères du grain de blé favorables à la production de
bioétanol par l'étude d'un ensemble de cultivars et par l'analyse
protéomique de lignées isogéniques waxy.Thèse de
doctorat, université blaise pascal;France,276p.
[22] Yves Mbida (2015), mise sur pied d'une unité
industrielle de transformation des fêves de cacao, mémoire de fin
d'étude, UY1, ENSP, Cameroun,128p.
[23] Meli Tedon, conception,diemensionnement et étude de
réalisation d'un convoyeur pour rafle de noix de palmes. Mémoire
de fin d'études, UY1, ENSP, Cameroun, 106p.
[24] Singha Emmanuel (2015), conception d'un poste de chargement
automatisé pour camion citerne, mémoire de fin d'étude,
UY1, ENSP, Cameroun, 128p.
[25] Diagne Mame Abdoiu(2003), conception d'un séchoir
à cylindre rotatif pour les produits granulés à base de
céréales, mémoire de fin d'étude, Ecole
polytechnique de Thises, Senegal, 79p.
[26] BWEKAM Crépin,(2014)étude de
faisabilité et mise sur pied d'un outil d'aide au dimensionnement d'une
usine de production de sachet plastique biodégradable dans la zone de
bonaberi ; memoire de fin d'étude,UY1,ENSP,Cameroun 129p.
[27] ISAAC DJAMEN(2014), etude de faisabilité,
dimensionnement et implantation d'une usine de transformation de
tôles.mémoire de fin d'étude université de
YaoundéI,Cameroun, 88p.
[28] F. Chemin(2002), évaluation des risques sanitaires
dans les études d'impact des industries agroalimentaires memoire de fin
d'étude, école Nationale de la santé publique ,France,
77p.
Sites internet
[29]
http://www.journalducameroun.com,[En
ligne] [consulté en Juin 2016].
[30]
http://www.camenews.com/le-cameroun-gros-importateur-des
produit, [En ligne] [consulté en Mai 2016].
[31]ACDIC, «
http://www.acdic.net,» [En
ligne] [consulté en Juin 2016].
[32]Institut National de la Statistique [en ligne]
[consulté en Juin 2016] disponible sur le site «
www.statistics-cameroon.org,»
.
ANNEXES

96
Mémoire de fin d'études pour l'obtention du
diplôme d'Ingénieur de Conception en
Génie
Mécanique, rédigé et soutenu par :
PONDI JOSEPH
Mise sur pied d'une unité industrielle de transformation
des céréales pour l'obtention de la
farine : projet industriel
du Groupe SOA
Annexe1 : photos de certains équipements de la
chaine de production.

97
Mémoire de fin d'études pour l'obtention du
diplôme d'Ingénieur de Conception en
Génie
Mécanique, rédigé et soutenu par :
PONDI JOSEPH
Mise sur pied d'une unité industrielle de transformation
des céréales pour l'obtention de la
farine : projet industriel
du Groupe SOA
annexe2 : Schéma de principe des unités de
la chaine de transformation
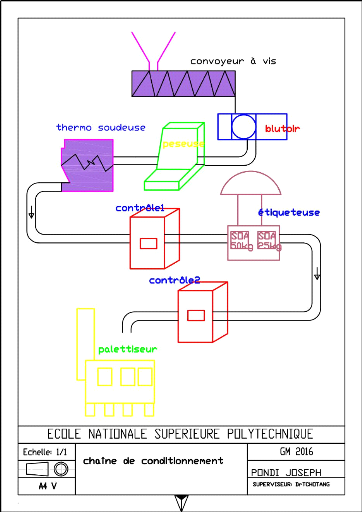

98
Mémoire de fin d'études pour l'obtention du
diplôme d'Ingénieur de Conception en
Génie
Mécanique, rédigé et soutenu par :
PONDI JOSEPH
Mise sur pied d'une unité industrielle de transformation
des céréales pour l'obtention de la
farine : projet industriel
du Groupe SOA
Figure 33 : Schéma de principe de la chaîne de
conditionnement
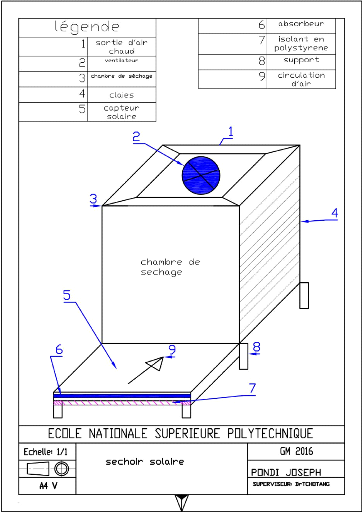
Figure 34 : Schéma de principe séchoir solaire

99
Mémoire de fin d'études pour l'obtention du
diplôme d'Ingénieur de Conception en
Génie
Mécanique, rédigé et soutenu par :
PONDI JOSEPH
Mise sur pied d'une unité industrielle de transformation
des céréales pour l'obtention de la
farine : projet industriel
du Groupe SOA
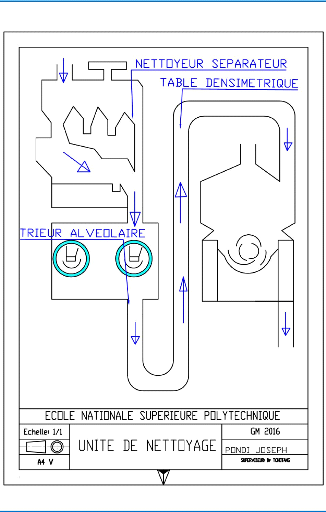
Figure 35 : Schéma de principe unité de
nettoyage
100
Mémoire de fin d'études pour l'obtention du
diplôme d'Ingénieur de Conception en
Génie
Mécanique, rédigé et soutenu par :
PONDI JOSEPH
Mise sur pied d'une unité industrielle de transformation
des céréales pour l'obtention de la
farine : projet industriel
du Groupe SOA
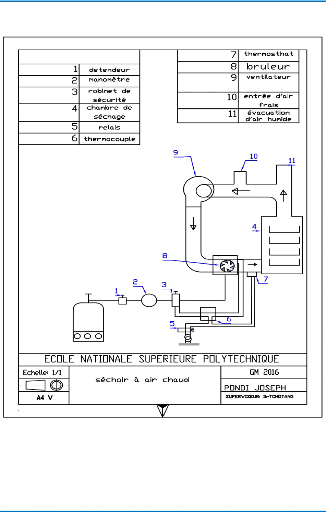
Figure 36 : Schéma de principe séchoir à air
chaud à convection forcée
101
Mémoire de fin d'études pour l'obtention du
diplôme d'Ingénieur de Conception en
Génie
Mécanique, rédigé et soutenu par :
PONDI JOSEPH
Mise sur pied d'une unité industrielle de transformation
des céréales pour l'obtention de la
farine : projet industriel
du Groupe SOA
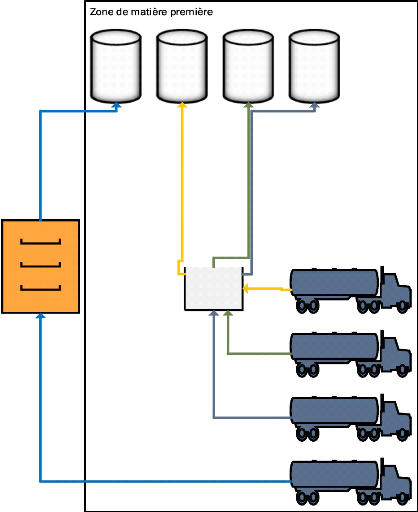
Unité de séchage
Silo maïs
grain
Silo soja
Trémie réceptrice
Silo sorgho Silo blé
Transport sorgho
Transport soja
Transport blé
Transport maïs
Figure 37 : Zone de matière première
Annexe3 : abaques et tableaux d'aide au
dimensionnement
102
Mémoire de fin d'études pour l'obtention du
diplôme d'Ingénieur de Conception en
Génie
Mécanique, rédigé et soutenu par :
PONDI JOSEPH
103
Mise sur pied d'une unité industrielle de transformation
des céréales pour l'obtention de la
farine : projet industriel
du Groupe SOA
Tableau 51 : Diamètre recommandé pour
les rouleaux.
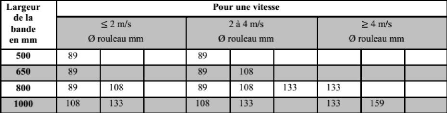
Tableau 52 : Coefficient de participation
FP

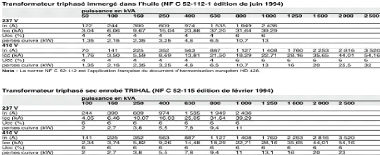
Figure 38 : Choix du transformateur Tableau 53 :
Choix du facteur K
Pont Balancelles Convoyeurs Manutention Transpalette Chariot
roulant manuelle élévateur
0,10 0,20 0, 3 à 0,4 0, 5 0,75 à 1 2
à 3
Mémoire de fin d'études pour l'obtention du
diplôme d'Ingénieur de Conception en
Génie
Mécanique, rédigé et soutenu par :
PONDI JOSEPH
Mise sur pied d'une unité industrielle de transformation
des céréales pour l'obtention de la
farine : projet industriel du Groupe SOA
Tableau 54: Ecartement maximal pour les stations
supérieures et inférieures
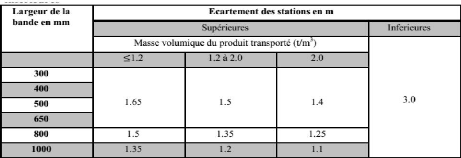
Tableau 55 : Coefficient de frottement interne f des
produits et des parties tournantes
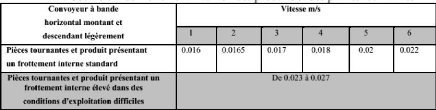
Tableau 56 : Vitesse maximale
conseillée
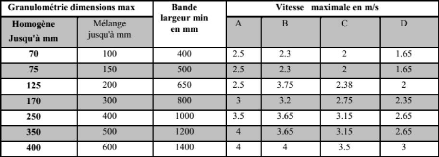
Tableau 57 : Coefficient
d'utilisation

104
Mémoire de fin d'études pour l'obtention du
diplôme d'Ingénieur de Conception en
Génie
Mécanique, rédigé et soutenu par :
PONDI JOSEPH
Mise sur pied d'une unité industrielle de transformation
des céréales pour l'obtention de la
farine : projet industriel
du Groupe SOA
Tableau 58 : Coefficient lié à
l'environnement

Tableau 59 : Coefficient de choc Fd
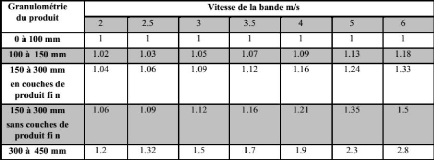
Tableau 60 : Coefficient de vitesse
????
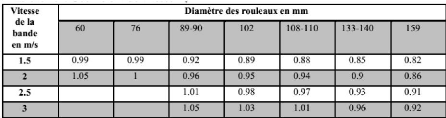
Tableau 61 : Diamètre recommandé des
tambours
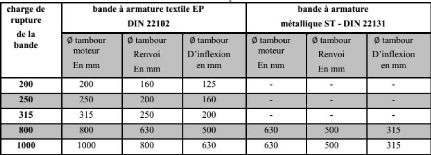
105
Mémoire de fin d'études pour l'obtention du
diplôme d'Ingénieur de Conception en
Génie
Mécanique, rédigé et soutenu par :
PONDI JOSEPH
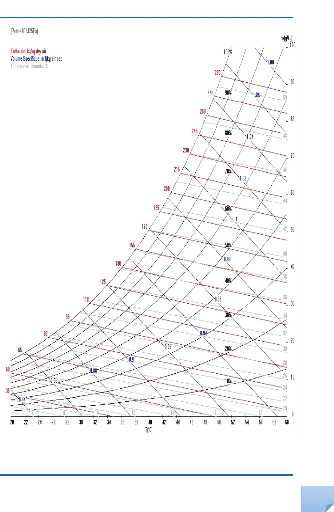
Mise sur pied d'une unité industrielle de transformation
des céréales pour l'obtention de la farine : projet industriel du
Groupe SOA
Figure 39 : Diagramme de l'air humide
Mémoire de fin d'études pour l'obtention du
diplôme d'Ingénieur de Conception en Génie
Mécanique, rédigé et soutenu par : PONDI
JOSEPH
106
Mise sur pied d'une unité industrielle de transformation
des céréales pour l'obtention de la
farine : projet industriel
du Groupe SOA
Annexe4 : fiche de maintenance préventive
Tableau 62 : Exemple de fiche de maintenance
préventive des équipements critiques
|
Maintenance préventive
|
Standard de contrôle et d'entretien
|
Système : unité de broyage
|
Sous- systèmes : moteur et vis sans fin
|
Conditions préalables de sécurité :
|
1- Seules les personnes habilitées sont
autorisées
|
2- Utilisation des chiffons et lampe torche le cas
échéant
|
3- Respect des conditions de qualité,
sécurité et hygiène de l'environnement
|
4- Port des E.P.I obligatoire
|
|
N°
|
Emplacem ent
|
Opération à effec- tuer
|
Outils
|
Critère
|
Fréquence
|
Durée
|
Operateu r
|
I1
|
Vis sans
fin
|
I11
|
Contrôle de fonctionne ment
|
Automat
e pc :
lancer le
démarrag
e du moteur
|
Rotation de la vis lors du démarrage du moteur
|
Hebdomad aire
|
1min
|
Personn
e en charge de l'automa
te sur PC ; mécanici en
|
I12
|
Nettoyage
|
Chiffon
|
Pas de produit
entassé au tour de la vis
|
Hebdomad aire
|
2min
|
Mécanic ien
|
I2
|
Moteur
|
I21
|
Contrôler
l'état du carter
|
Visuel
|
Pas de fissure
|
Une fois
par mois
|
1min
|
Mécanic ien
|
I22
|
Contrôle la températur
e du moteur
|
Thermo laser
|
T (°C) <=35°C
|
Une fois
par
semaine
|
2min
|
Mécanic ien
|
I23
|
Contrôle
de l'état des roulement s
|
Manuel
|
Pas de roulement cassé ;
|
Une fois
par
trimestre
|
5min
|
Mécanic ien
|

107
Mémoire de fin d'études pour l'obtention du
diplôme d'Ingénieur de Conception en
Génie
Mécanique, rédigé et soutenu par :
PONDI JOSEPH
Mise sur pied d'une unité industrielle de transformation
des céréales pour l'obtention de la
farine : projet industriel
du Groupe SOA
|
|
I24
|
Contrôle de fonctionne ment
|
Automat e sur PC
|
Voyant allumé
lorsque le silo est fermé
|
Journalier
|
1min
|
Electrici en,
|
I25
|
Contrôle niveau d'huile
|
Visuel
|
Ouvrir le bouchon de niveau ; s'il n'y a pas sortie d'huile,
remplissez jusqu'à ce qu'il y ait des fuites (huile 90)
|
Une fois
par mois
|
10 min
|
mécanici en
|
I26
|
Graissage des
roulement
s et des paliers
|
Graisse (multi
EP2) + pinceau
|
Graisse couvre
totalement le
roulement et le palier
|
Une fois
par mois
|
5 min
|
Mécanic ien
|
I27
|
Vidange d'huile
dans le réducteur
|
clé mal
de 5
|
Enlever les huiles mauvaises dans le réducteur (dès
que l'odeur n'est pas celle du départ)
|
Une fois
par an
|
5min
|
Mécanic ien
|
Annexe6 : Caractéristiques des équipements
de la chaine de production et charges salariales
Tableau 63 : Caractéristiques du
blutoir

108
Mémoire de fin d'études pour l'obtention du
diplôme d'Ingénieur de Conception en
Génie
Mécanique, rédigé et soutenu par :
PONDI JOSEPH
Mise sur pied d'une unité industrielle de transformation
des céréales pour l'obtention de la
farine : projet industriel
du Groupe SOA
Tableau 64 : Caractéristiques du
compresseur

Tableau 65 : Caractéristiques du
ventilateur
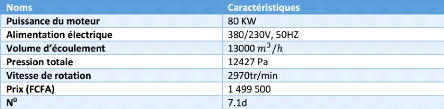
Tableau 66 : Machine d'emballage
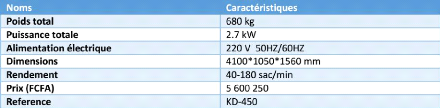
Tableau 67 : Caractéristiques de la table
densimétrique

Tableau 68 : Caractéristiques du trieur
alvéolaire

109
Mémoire de fin d'études pour l'obtention du
diplôme d'Ingénieur de Conception en
Génie
Mécanique, rédigé et soutenu par :
PONDI JOSEPH
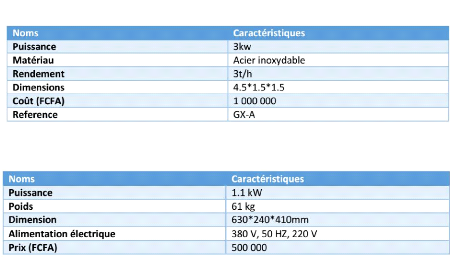
Tableau 70 : Caractéristiques du convoyeur
à vis
Tableau 71 : Caractéristiques du
surpresseur
Tableau 72 : Caractéristiques convoyeur
à bande
Mise sur pied d'une unité industrielle de transformation
des céréales pour l'obtention de la
farine : projet industriel
du Groupe SOA
Tableau 69 : Caractéristiques du
pré-nettoyeur

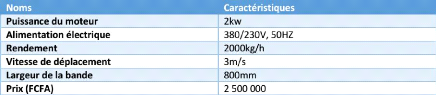
Tableau 73 : Caractéristiques du
torréfacteur
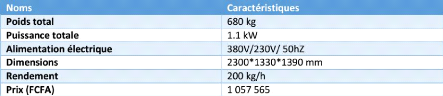
110
Mémoire de fin d'études pour l'obtention du
diplôme d'Ingénieur de Conception en
Génie
Mécanique, rédigé et soutenu par :
PONDI JOSEPH
Mise sur pied d'une unité industrielle de transformation
des céréales pour l'obtention de la
farine : projet industriel
du Groupe SOA
Tableau 74 : Caractéristiques du
broyeur
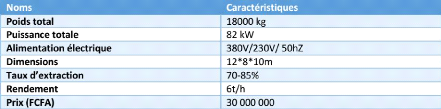
111
Mémoire de fin d'études pour l'obtention du
diplôme d'Ingénieur de Conception en
Génie
Mécanique, rédigé et soutenu par :
PONDI JOSEPH
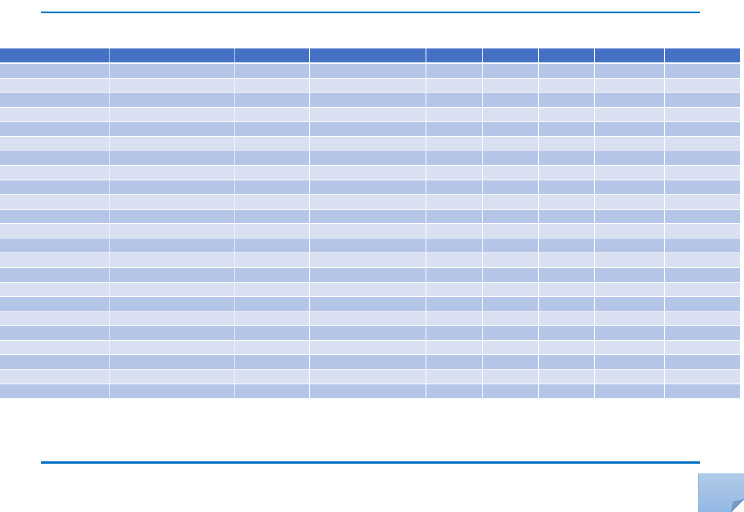
Mise sur pied d'une unité industrielle de transformation
des céréales pour l'obtention de la farine : projet industriel du
Groupe SOA
Tableau 75 : Charges salariales du personnel de
l'usine
nombre de responsables
|
base
|
salaire mensuel
|
année1
|
année2
|
année3
|
année 4
|
année5
|
1
|
13
|
300 000
|
3900000
|
4095000
|
4299750
|
4 514 737,50
|
4740474,375
|
1
|
13
|
250 000
|
3250000
|
3412500
|
3583125
|
3762281,25
|
3950395,313
|
1
|
13
|
200 000
|
2600000
|
2730000
|
2866500
|
3009825
|
3160316,25
|
2
|
13
|
100 000
|
0
|
0
|
2600000
|
2 730 000,00
|
2 866 500,00
|
1
|
13
|
100 000
|
0
|
0
|
1300000
|
1 365 000,00
|
1 433 250,00
|
1
|
13
|
100 000
|
0
|
0
|
1300000
|
1 365 000,00
|
1 433 250,00
|
1
|
13
|
100 000
|
0
|
0
|
1300000
|
1 365 000,00
|
1 433 250,00
|
1
|
13
|
100 000
|
0
|
0
|
1300000
|
1 365 000,00
|
1 433 250,00
|
1
|
13
|
100 000
|
0
|
0
|
1300000
|
1 365 000,00
|
1 433 250,00
|
1
|
13
|
100 000
|
0
|
0
|
1300000
|
1 365 000,00
|
1 433 250,00
|
1
|
13
|
100 000
|
0
|
0
|
1300000
|
1 365 000,00
|
1 433 250,00
|
1
|
13
|
100 000
|
0
|
0
|
1300000
|
1 365 000,00
|
1 433 250,00
|
1
|
13
|
100 000
|
0
|
0
|
1300000
|
1 365 000,00
|
1 433 250,00
|
4
|
13
|
100 000
|
0
|
0
|
5200000
|
5 460 000,00
|
5 733 000,00
|
1
|
13
|
100 000
|
0
|
0
|
1300000
|
1 365 000,00
|
1 433 250,00
|
1
|
13
|
100 000
|
0
|
0
|
1300000
|
1 365 000,00
|
1 433 250,00
|
1
|
13
|
100 000
|
0
|
0
|
1300000
|
1 365 000,00
|
1 433 250,00
|
1
|
13
|
100 000
|
0
|
0
|
1300000
|
1 365 000,00
|
1 433 250,00
|
2
|
13
|
60 000
|
0
|
0
|
1560000
|
1 638 000,00
|
1 719 900,00
|
4
|
13
|
60 000
|
0
|
0
|
3120000
|
3 276 000,00
|
3 439 800,00
|
1
|
13
|
100 000
|
0
|
0
|
1300000
|
1 365 000,00
|
1 433 250,00
|
|
|
|
9750000
|
10237500
|
41429375
|
43500843,75
|
45675885,94
|
|
|
|
1755000
|
1842750
|
7457287,5
|
7 830 151,88
|
8 221 659,47
|
Mémoire de fin d'études pour l'obtention du
diplôme d'Ingénieur de Conception en Génie
Mécanique, rédigé et soutenu par : PONDI
JOSEPH
postes
directeur d'usine
directeur d'usine adjoint
secrétaire comptable
moissonneuse-batteuse
pré-nettoyeur
table densimétrique
trieur alvéolaire
nettoyeur -séparateur
blutoir
broyeur
décortiqueuse
torréfacteur
machine d'emballage
convoyeur à bande
ventilateur
compresseur
surpresseur
convoyeur à vis
femme de ménage
ouvrier de manutention
silos de stockage
charges totales
charges sociales
117
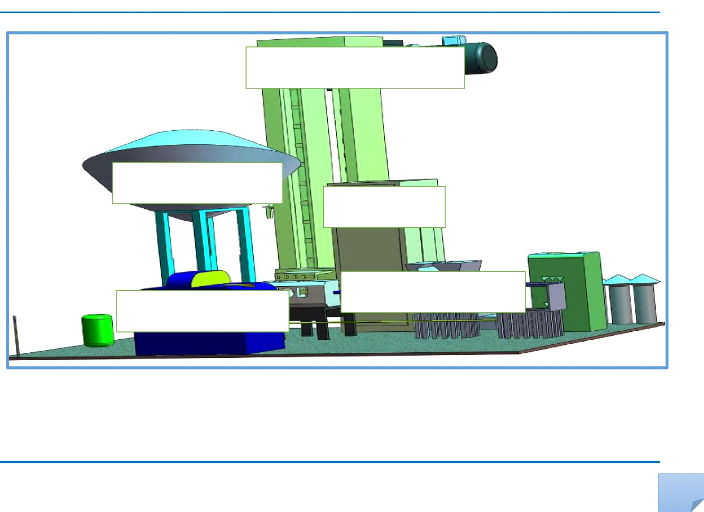
Mise sur pied d'une unité industrielle de transformation
des céréales pour l'obtention de la farine : projet industriel du
Groupe SOA
Zone de torréfaction
Zone de nettoyage
Approvisionnement en matière
première
Zone de séchage
Zone de mouture et de décorticage
Figure 54 : Synoptique 3D des équipements de la chaine
Mémoire de fin d'études pour l'obtention du
diplôme d'Ingénieur de Conception en Génie
Mécanique, rédigé et soutenu par : PONDI
JOSEPH
118
Mise sur pied d'une unité industrielle de transformation
des céréales pour l'obtention de la
farine : projet industriel
du Groupe SOA

118
Mémoire de fin d'études pour l'obtention du
diplôme d'Ingénieur de Conception en Génie
Mécanique, rédigé et soutenu par : PONDI
JOSEPH