3-1-4-1- Description de la ligne de production du "float
glass"
> Préparation de la composition
Ce système concerne les matières
premières déjà traitées, il est
équipés d'installations de levage, pesage et mélange.
L'extraction des poussières est située à l'endroit
où la poussière est habituellement produite. Des balances
électroniques avec différentes échelles sont
adaptées en fonction des quantités nécessaires de
matières premières, de calcin de l'usine ou extérieur.
L'atelier de composition est prévu pour fonctionner 24 heures sur 24.
Il est cependant dimensionné pour produire la
quantité de batch nécessaire en 16 heures, afin de permettre les
opérations de maintenance. Des alimentations séparées
seront prévues pour (a) le sable, (b) la soude, (c) la dolomie et le
calcaire pour empêcher que les matières premières ne se
contaminent entre elles.
Les matières premières seront stockées
dans les silos de l'atelier de composition et des installations de stockage qui
sont prévus pour une capacité de fonctionnement de 72 heures
minimum avec un stockage complémentaire au sol d'un mois pour la soude,
le sulfate et les autres matériaux.
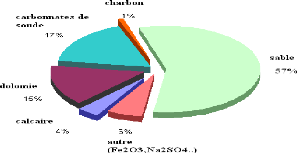
Figure 10. Dosage en matière première pour le verre
plat. > Traitement de sable
Ce poste en option peut être nécessaire en
fonction des caractéristiques réelles des matières
premières disponibles dans l'usine. Il comprendrait différentes
fonctions comme le broyage, le traitement, le séchage, la
séparation magnétique et l'homogénéisation du
sable. Dans tous les cas, l'installation de traitement de sable doit être
définie après analyse du sable et des matières
premières disponibles pour le projet.
> Le four de fusion
Construit en briques réfractaires, un four type
contient jusqu'à 2000 tonnes de verre fondu à 1550°C. La
température est contrôlée en permanence. Un des
systèmes les plus employés à ce jour est le
pyromètre. Exemple d'installation La fusion du verre pour la ligne
« float » sera assurée par un four à
régénérateurs à brûleurs transversaux. Le
verre fondu est affiné et homogénéisé. Le verre est
ensuite conditionné à température contrôlée
avant d'arriver au bain d'étain.
Pour assurer un bon fonctionnement, le four est
équipé de dispositifs automatiques de mesure, enregistrement et
régulation de pression et de niveau de verre, d'un système de
minuterie et d'inversion automatique de flamme, d'instruments de mesure,
enregistrement et régulation de température en différents
endroits du four et d'un dispositif de régulation de pression de gaz
naturel. Les fumées sont évacuées par tirage naturel par
une cheminée. Pour protéger l'environnement, les fumées
passeront par un équipement de dépollution à tirage
forcé conçu en fonction de la réglementation locale.
> Bain d'étain
Le processus de formage consiste à étirer ou
à comprimer mécaniquement la pâte de verre tout en la
solidifiant par refroidissement contrôlé.
En absence de toute contrainte extérieure, le verre
s'étalerait en formant sur l'étain liquide un ruban
d'épaisseur naturelle de 6,88 mm. Le verre, à une
température de 1100°C, se déverse
régulièrement sur l'étain en fusion grâce à
un système de régulation de débit appelé tweel. La
densité spécifique du verre lui permet de flotter sur
l'étain d'où la terminologie "float" couramment employé
pour décrire le procédé. Le verre et l'étain ne
réagissent pas entre eux et restent séparés, leur
résistance mutuelle à l'échelle moléculaire rendant
le verre parfaitement lisse.
Le bain est un système étanche avec une
atmosphère contrôlée composée d'azote et
d'hydrogène. Il se compose d'une structure en acier, d'une enveloppe
métallique supérieure, d'une enveloppe métallique
inférieure protégée de l'étain par des
réfractaires spéciaux et de systèmes de contrôle de
la température du ruban de verre et du formage. Le bain mesure environ
60 m de long sur 8m de large avec une vitesse de défilement pouvant
atteindre jusqu'à 25 m/min. Le bain contient près de 200 tonnes
d'étain pur, fondu à une température moyenne de 800 °
C.
Les dimensions du ruban de verre sont obtenues par
l'intermédiaire de forces de traction ou de compression
effectuées par des machines appelées top rolls, situées
sur chaque côté du bain.
Un programme de contrôle détermine les
réglages optimaux du process. L'épaisseur du verre peut varier de
0,55 à 25 mm.
Des résistances électriques, regroupées
en zones de chauffage, permettent une régulation fine de la
température du verre qui est progressivement réduite, lorsque le
verre a atteint les caractéristiques dimensionnelles
désirées. Le ruban est alors parfaitement plat et ses faces sont
parallèles.
A ce stade, les revêtements réflectifs, Low-E,
pour contrôle solaire, autonettoyants ou photovoltaïque peuvent
être déposés en utilisant le système de
dépôts chimiques en phase vapeur par pyrolyse. Le verre est
ensuite prêt à être refroidi.
> Étenderie :
Pour relâcher les contraintes physiques, le ruban est
soumis à un traitement thermique dans un long four de recuisson
appelé étenderie. Les températures sont étroitement
contrôlées dans le sens longitudinal et transversal du ruban.
L'étenderie sert à recuire et à refroidir
le verre. L'étenderie fermée est en construction
métallique, elle refroidit le verre par rayonnement et le recuit selon
les exigences de la spécification de production. Après recuisson,
le verre est refroidi rapidement de manière contrôlée par
un refroidissement adapté et un système de chauffage.
Le verre sera transporté dans l'étenderie sur un
convoyeur à rouleaux dont l'écartement permet le supportage du
ruban en toute sécurité. La commande est transmise
mécaniquement aux rouleaux par le système d'entraînement.
Un système d'entraînement de secours doit être disponible
pour prendre le relais en cas de panne électrique ou mécanique du
système de commande. Tous les rouleaux sont démontables pendant
le fonctionnement. Pour assurer un fonctionnement non-stop des rouleaux, une
commande de secours basse vitesse (pony) doit aussi être
intégrée au système de commande de l'étenderie de
même que le dispositif pour faire fonctionner l'entraînement
à la main.
> La découpe
Le ruban de verre ainsi produit est refroidi à l'air
libre, puis est contrôlé de manière permanente
(épaisseur, qualité optique, défauts, etc.), coupé
en plateaux de superficie standard et « débordé »
automatiquement (enlèvement des bords). Les plaques ainsi produites sont
placées verticalement sur des chevalets, grâce à des
releveuses à ventouses.
> Le lavage :
Après la découpe, les plaques de verre sont
généralement lavées afin d'éliminer les
impuretés organiques et inorganiques qui sont éventuellement
présentes à la surface. Les substances organiques se
déposent sur le verre par contact avec les différentes parties de
la chaîne de production (par exemple avec les ventouses en caoutchouc
utilisées pour leur déplacement). Ces substances altèrent
les propriétés de surface du verre en particulier la
mouillabilité.
> Le stockage :
La phase de stockage est la plus délicate de la
«vie» d'un float. Les différentes plaques de verre sont
séparées à l'aide de poudres intercalaires (ex. leucite)
puis emballées et laissées en attente avant la commercialisation.
Dans la majorité des cas les magasins ne sont pas pourvus d'un
système de contrôle de la température et de
l'humidité relative. Ainsi les verres sont soumis à des cycles de
condensation évaporation qui provoquent une détérioration
des deux plaques adjacentes sur les hydroxydes formés à partir de
Na+ et Ca2+). Parfois l'altération est très
importante car le rapport surface de verre/solution altérante est
élevée des piqûres se forment.
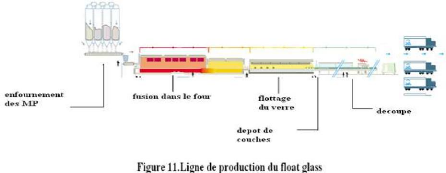
Description de l'unité MFG :
Mediterranean float glass , filiale du groupe CEVITAL
conçue pour la fabrication du verre plat, installée à
Larbaa à 30 km de Blida sur une surface de 10 hectares avec une ligne de
longueur de 630 m et une largeur de 39 m .375 travailleurs dont 95 cadres
veillent sur le bon déroulement de travail dans l'unité afin
d'assurer la production journalière de 600 t/j .
La première feuille du verre a vu le jour le
22/08/2007, depuis MFG maintient sa position de premier fournisseur du verre
plat en Algérie avec une réalisation dépassent 104% De
l'objectif visé, en laps de 3 mois, MFG a triplé ses exportation
en Europe avec 12220tonnes, contre 4428 tonnes au début 2008.
MFG adopte une système QHSE ce qui lui a permis
d'être certifiée en iso9001 version 2000, iso 14001et dans le
référentiel OHSAS18001, cela lui permet d'être
compétitive sur le marché international.
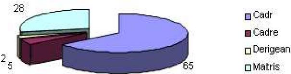
Figure13.Distribution de personnel formé en niveau MFG
|