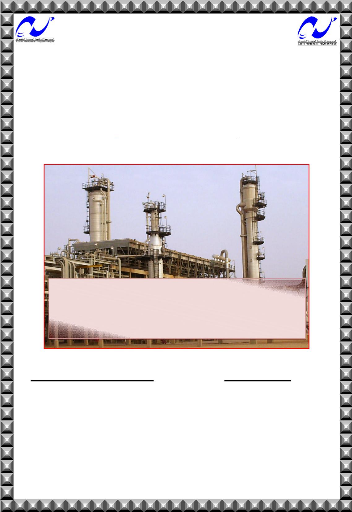
République Algérienne Démocratique et
Populaire
Ministère de L'Enseignement Supérieur et
de
La Recherche Scientifique Ecole Nationale
Supérieure Polytechnique Département Génie
Chimique
Thème: Simulation d'un train de traitement
de gaz à l'aide des outils HYSYS et PRO
II
Proposé et dirigé par: Etudié
par:
Mr E.H.BENYOUSSEF Mr A.GOURI
Mr A.LAMECHE Mr K.LEMLOUMA
PROMOTION JUIN 2009
A mes très chers parents qui ont toujours
été là pour moi, et qui m'ont donné un magnifique
modèle de labeur et de persévérance. J'espère
qu'ils trouvent dans ce travail toute ma reconnaissance et tout mon
amour.
A mesfrères et mes soeurs Sans oublier ma
fiancée A toute mafamille
A tous mes amis
Je dédie ce mémoire
A mes parents pour leur aide et leur amour A
mesfrères et ma soeur A Ayoub, Maroua et Hichem A toute ma
famille A tous mes amis Je dédie ce modeste
travail.
Kamel LEMLOUMA
Remerciement
Cette étude a été réalisée
au sein de la structure GTFT (centre de production de gaz naturel à
Illizi), sous la direction du Professeur .E-H. BENYOUSSEF et de Monsieur
A.LAMECHE (Chef service process à GTFT).
Nous tenons à témoigner notre profonde
reconnaissance à Messieurs E-
H.BENYOUSSEF et Mr.A.LAMECHE, pour nous avoir confiés
ce sujet ; mais aussi pour les encouragements, conseils précieux, et les
orientations qu'ils nous ont prodigués sans lesquels ce travail n'aurait
pas pu aboutir. Qu'ils trouvent ici l'expression de notre profonde
gratitude.
Nous tenons à exprimer notre profonde gratitude à
Madame F.SOUAHI Maitre de conférences, de nous avoir fait l'honneur
d'accepter la présidence du jury.
Ainsi que Madame A.MEFTI Maitre de conférences à
ENP, Monsieur A.SLATNIA Professeur à ENP,
Trouvez l'expression de nos vifs remerciements pour avoir
accepter d'être membre de notre jury.
Nos remerciements au personnel du groupement TFT pour leur aide
et leur compréhension.
Simulation d'un train de traitement de gaz à
l'aide des outils PRO II et HYSYS Résumé:
Ce travail porte sur la simulation d'un procédé
de traitement de gaz utilisant un turborxpander pour la
récupérations des liquides du gaz naturel .la comparaison des
résultats obtenus par les deux simulateurs ,l'influence de la
déplétion du gisement sur le process de l'usine, la
nécessité d'installer une nouvelle unité de Boosting pour
revenir aux conditions optimales de fonctionnement .vérifier , par le
biais de simulation, si les modifications apportées au process
après l'intégration du Boosting sont justifiées par le
projet.
Mots clés: Simulation, gisement,
déplétion, turboexpander, Boosting.
Simulation of a gas treatment plant with simulators PRO
II and HYSYS Summry
This work talk about a simulation of a gas treatment plant
witch used a turboexpander for liquids recovery from Natural gas Comparison of
results obtained with simulators, the effect of fall pressure of raw gas on the
plant's process .installation of a booster compressor to back on optimal
conditions .check with simulation if the introduced modifications after booster
compressor installation are justified.
Key words: Simulation, raw gas, fall pressure,
turboexpander, booster compressor.
Glossaire
Boosting : unité de compression de gaz
lors de son dépletion au niveau du gisement . Cold box :
ou boite froide, c'est un ensemble de deux
échangeurs de chaleur placés en parllele dont le but est de
refroidir le gaz.
Joule-thomson : une vanne qui fait une
détente de type isenthalpique.
Sécheurs : équipement
destinés à purifier le gaz de l'eau à l'aide des tamis
moléculaires. Slug catcher: séprateur primaire
ou le gaz brut provenant des puits subit une séparation triphasique
(gaz, condensate, et eau).
Turboexpander : une turbine d'expansion à
travers laquelle le gaz subit une détente Isentropique.
Liste des abréviations
XV : slug catcher ou séparateur
primaire.
E2 : échangeur de chaleur (rebouilleur ou
condenseur).
TIC : régulateur de
température.
PFD : diagramme de circulation de
fluides.
V4 : ballon séparateur (ballon de flash,
ballon de reflux).
T6/T2 : tour de traitement (colonne de
distillation, tamis moléculaire). PV : vanne de
régulation de pression.
C8 : un compresseur ou un détendeur
SOMMAIRE
Introduction 1 Chapitre I: Généralités
sur le traitement et le fractionnement du gaz à
Condensât 3
I.1. Généralités 4
I.2. Séparation des condensats 7
I.3. Opérations de purification .8
I.3.1. Absorption par un solvant ..9
I.3.2. Perméation gazeuse 10
I.4. Déshydratation .10
I.4.1. Déshydratation par adsorption ..11
I.5. Le transfert thermique ..12
I.6. Fractionnement des condensats 13
I.6.1. Fractionnement par réfrigération 14
I.7. Description des procédés de traitement de gaz
16
I.7.1. Le procédé PRICHARD 16
I.7.2. Le procédé HUDSON 17
Chapitre II : Présentation du champ du Gaz GTFT 23
II.1.Situation géographique 24
II.2.Développement et capacité du champ .25
II.2.1.Roche mère et genèse des hydrocarbures
.25
II.2.2.Description du réservoir 25
II.2.3. Historique de production 26
Chapitre III : Description du procédé du traitement
du Gaz GTFT 31
III.1. Description générale de l'usine de
traitement de Gaz GTFT 32
III.1.1. Section de refroidissement et séparation primaire
..33
III.1.2. Section de déshydratation ...35
III.1.3. Section de refroidissement et de détente 36
III.1.4. Section de fractionnement ..37
III.2. Description de la section Boosting 39
III.2.1. Rappel thermodynamique sur la compression 39
Chapitre IV : Simulation 42
IV.1. Présentation des simulateurs PRO II et HYSYS
..43
IV.1.1. Définitions ..43
IV.1.2. Modèle thermodynamique .43
IV.1.3. Les simulateurs HYSYS et PRO II 44
IV.2. Choix du modèle thermodynamique .47
IV.2.1. Utilisation du facteur de compressibilité 47
IV.2.2. Utilisation des équations d'état ..47
IV.2.3. Etendue d'utilisation des équations d'état
50
IV.2.4. Recommandations des modèles .51
VI.2.5. Choix d'un modèle thermodynamique 52
IV.3. La simulation d'un train de traitement de gaz GTFT 55
IV.3.1. Le cas design ..55
IV.3.2. Le cas actuel 57
IV.3.3. La baisse de pression (sans Boosting) 60
IV.4. Simulation d'un train de traitement de gaz avec
l'intégration de
Boosting ..62
IV.4.1. Le reflux du stabilisateur 63
IV.4.2. L'échangeur E2-1208 ...65
IV.4.3. La boucle d'huile du rebouilleur E4-1402 67
IV.5. Etude technico économique du projet Boosting 70
IV.5.1. Les critères de choix d'un investissement ..70
IV.5.2. Etude de la rentabilité du projet Boosting
...70
Conclusion .75
Références bibliographiques 77
Annexes .78
Liste des figures
Figure 1 : Traitement du gaz naturel [2] .5
Figure 2: Chemins thermodynamiques des procédés
dans l'enveloppe des
phases [3] .....6
Figure 3 : Séparateur horizontal 7
Figure 4 : Séparateur vertical .8
Figure 5 : Schéma de principe d'une opération de
traitement par absorption......9
Figure 6 : Peméation gazeuse schéma de principe [4]
10
Figure 7 : Procédé de déshydratation par
adsorption ....11
Figure 8 : Schéma fonctionnel d'un échangeur de
chaleur [6] .13
Figure 9 : Fractionnement par réfrigération 14
Figure 10 : Réfrigération par détente
isenthalpique [7] .15
Figure 11 : Réfrigération par turbine d'expansion
[7] 15
Figure 12 : Schéma simplifié du
procédé PRICHARD ..17
Figure 13: Schéma simplifié du
procédé HUDSON ..18
Figure 14 : Le diagramme enthalpie -entropie (détente
isenthalpique) .19
Figure 15: le diagramme enthalpie -entropie (détente
isentropique) .20
Figure 16 : Température en fin de détente .22
Figure 17 : Situation géographique du GTFT 24
Figure 18 : Coupe de réservoir 25
Figure 19 : La production de gaz sec du champ GTFT [11] .26
Figure 20: La production en G P L du champ GTFT [11] .27
Figure 21 : La production en Condensat du champ GTFT [11] 27
Figure 22: Schéma bloc de l'usine GTFT ..33
Figure 23 : L'enveloppe des phases sortie E2-1002/1003
|
34
|
Figure 25 : Schéma bloc de la section Boosting
|
39
|
Figure 26: Courbe de performance typique pour un compresseur
|
41
|
Figure 27 : Structure générale d'unsimulateur
|
44
|
Figure 28 : L'interface du simulateur HYSYS
|
.46
|
Figure 29: Le choix du modèle thermodynamique
|
53
|
Figure 30 : Impact de la baisse de pression sur la production du
gaz sec
|
..60
|
Figure 31 : Impact de la baisse de pression sur la production du
GPL
|
..61
|
Figure 32 : Impact de la baisse de pression sur la production du
condensat......
|
61
|
Figure 33: L'influence de la baisse de pression sur le taux de
récupération en GPL .62
Figure 34 : L'emplacement de l'échangeur E2-1208
|
.66
|
Figure 35 : La modification apportée à la boucle
d'huile
|
.69
|
Figure 36 : Rentabilité d'un investissement
|
72
|
Liste des tableaux
Tableau 1 : la distribution des puits sur les trunklines 28
Tableau 2 : Comparaison des propriétés physiques de
PROII et HYSYS .45
Tableau 3 : Comparaison des propriétés critiques
dans HYSYS et PRO II......46
Tableau 4 : Les modèles recommandés dans un
simulateur 52
Tableau 5: Le domaine d'application de PR et SRK8 54
Tableau 6 : Comparaison des quantités produites (cas
design) ..56
Tableau 7 : Spécifications des produits pour le cas design
56
Tableau 8 : Les paramètres de marche usine (cas actuel)
..58
Tableau 9 : Les quantités produites pour le cas actuel
...58
Tableau 10 : Les spécifications des produits (cas actuel)
...59
Tableau 11 : L'alimentation du stabilisateur pour le
scénario 2012 ..64
Tableau 12 :L'alimentation du stabilisateur pour le
scénario 2015 64
Tableau 13 :Les températures à l'entée et
à la sortie du E2-1207 ..65
Tableau 14 : La température du condensat sortie E2-1208
66
Tableau 15 : La quantité liquide du deethaniseur T6-1401
avec la baisse de
pression 67
Tableau 16 : La quantité de chaleur échangée
dans le rebouilleur E4-1402.....68 Tableau 17 : Prix des équipements du
Boosting 73
Introduction
Devant les enjeux économiques et la flambée des
prix du pétrole et les nouvelles recommandations pour la
réduction des rejets de gaz à l'atmosphère, cause
principale du réchauffement de la terre, le gaz naturel se positionne
comme étant une source d'énergie alternative et relativement
propre.
Ces qualités le positionne pour jouer un rôle
énergétiquement croissant dans le développement
économique, l'importance des réserves et les avantages qu'il
présente sur le plan environnemental favorisent son utilisation,
notamment dans des secteurs à forte valeur ajoutée : industries
de précision, production d'électricité et
pétrochimie.
Les coûts techniques de production, de traitement et
surtout de transport du gaz naturel restent toutefois élevés et
représentent un handicap de taille, Cette difficulté est d'autant
plus réelle que la plus grande part des réserves de gaz naturel
est située en mer ou dans des zones difficiles.
Le traitement du gaz naturel consiste à séparer
au moins partiellement certains des constituants présents à la
sortie des puits tels que l'eau, les gaz acides et les hydrocarbures lourds
pour amener le gaz à des spécifications de transport ou à
des spécifications commerciales, Les spécifications à
respecter pour les gaz traité sont liées soit aux conditions de
transport, soit aux conditions d'utilisation.
La répartition de ces traitements entre les lieux de
production et de livraison résulte de considérations
économiques, Il est généralement préférable
de ne réaliser sur le site de production que les traitements qui rendent
le gaz transportable.
Compte tenu des différences entre les
spécifications de transport et les spécifications commerciales,
un traitement complémentaire peut être requis avant que le gaz ne
soit expédié dans le réseau de distribution, Ainsi, le
traitement réalisé pour obtenir les spécifications de
transport peut être accompagné d'un fractionnement, dans le but
d'obtenir une fraction liquide comprenant les GPL (propane, butane), il
apparaît avantageux de valoriser cette fraction liquide
séparément ,dans certains cas particuliers, une séparation
d'azote peut être nécessaire et une récupération
d'hélium est envisageable, si le gaz naturel en contient.
SONATRACH, TOTAL et REPSOL viennent de mettre
en production le champ de gaz naturel de Tin Fouye
Tabankort (TFT), situé dans le sud-est de l'Algérie,
à environ 1300 k m d'Alger, Ce champ est exploité conjointement
par les trois partenaires qui sont liés par un contrat de partage de
production signé en janvier 1996 pour une durée de vingt ans
à compter du démarrage de la production.
Vu la nature du gaz brut du gisement du champ GTFT (Gaz
humide), le traitement se fait comme suit:
- La séparation des fractions liquides
éventuellement contenues dans l'effluent des puits (fraction liquide
d'hydrocarbures, eau libre).
- La récupération du GPL (Gaz Pétrole
Liquéfié), contenue dans la fraction vapeur, issue de la
séparation primaire
Le gisement de gaz GTFT connaît depuis quelques
années une déplétion de la pression du gisement suivi
d'une variation de la composition de l'effluent, qui se manifeste par la baisse
de la production et du taux de récupération GPL, Afin de palier
à ce problème, GTFT a lancé un projet pour la
réalisation d'une section Boosting afin d'augmenter la pression à
l'entrée des trains.
Dans le cadre de notre projet de fin d'études, nous
nous sommes intéressés à la simulation du train de
traitement du champ gazier GTFT sans et avec intégration de la section
Boosting à l'aide des outils de simulations PRO!! et
HYSYS, Cela nous a permis d'une part de nous initier aux logiciels de
simulations et d'autre part, de développer nos connaissances dans le
domaine des procédés gaziers.
Notre objectif est de :
- Observer et analyser l'influence de la baisse de la
pression et la variation de la composition du gaz brut à
l'entrée des trains sur la qualité et les quantités des
produits expédiés (taux de récupération des
liquides).
- Intégrer une section Boosting dans le
procédé et atteindre par simulation les résultats induits
par cette modification.
- Comparer les résultats obtenus par les deux
simulateurs.
Chapitre I:
Généralités sur le traitement et
le
fractionnement du gaz à condensât
I.1.Généralités
Au cours d'un procédé de traitement de gaz
naturel. certains composants des gaz naturels doivent être extraits soit
pour des raisons imposées par les étapes ultérieures de
traitement ou de transport, soit pour se conformer à des
spécifications commerciales, il peut être nécessaire
d'éliminer au moins partiellement :
> l'hydrogène sulfuré H2S toxique et corrosif
;
> le dioxyde de carbone CO2, corrosif et de valeur thermique
nulle ;
> le mercure, corrosif dans certains cas ;
> l'eau, conduisant à la formation des hydrates;
> les hydrocarbures lourds, condensant dans les réseaux
de transport;
> l'azote, de valeur thermique nulle.
C'est la raison pour laquelle des opérations de
séparation, de déshydratation et de fractionnement des condensats
sont envisagées dans le but est de fournir un produit conforme aux
exigences,la figure 1 illustre les différentes étapes
nécessaires au traitement du gaz naturel afin de récupérer
les hydrocarbures lourds (condensat), et la fraction GPL (propane et butane)
[1].
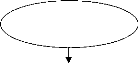
Gaz et liquides des puits
Sulfures
Désacidification
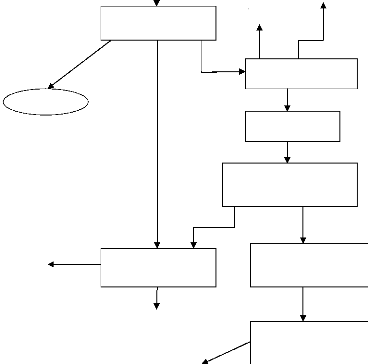
Condensats
GPL
Compression du gaz résiduel
Gaz d'entrée
Eau libre
CO2
Traitement du gaz
Déshydratation
Récupération des hydrocarbures
Traitement des hydrocarbures
Récupération d'hélium
Gaz commercial

Liquéfaction

Gaz naturel liquéfié (GNL)
Figure 1 : Traitement du gaz naturel [2].
Etant donne que la majorité des
procédés de traitement de gaz naturel sont conçues
pour éliminer d'abord les hydrocarbures lourds (C5+),
et pour récupérer le GPL, ce dernier nécessite un
contrôle de point de rosée (afin d'éviter la formation
d'une phase liquide lors du transport) ; de ce fait, il
s'avère indispensable de savoir positi onner les conditions
opératoires du gaz brut dans l'enveloppe des phases.
La figure 2 montre le comportement de phase d'un gaz
naturel comme une fonction de T-P, chaque refroidissement en
dehors de la zone de condensation rétrograde (zone ou les
hydrocarb ures lourds présentent un comportement non
intuitive) ; engendre une apparition d'une phase liquide [3],
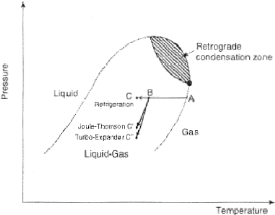
Figure 2: Chemins thermodynamiques des
procédés dans l'enveloppe des phases [3].
Dans le traitement de gaz naturel, et selon les
conditions thermodynamiques de l'effluent issu du gisement (température,
pression, composition, débit...,),on fait appel aux opérations de
séparation ,de purifications et de fractionnement dans le but d'avoir
des produits finis (gaz sec ,condensat et GPL),qui répondent aux
spécifications.
Un aperçu sur ces opérations est
présenté dans ce qui suit.
I.2. Séparation des condensats
Dans une première étape, la phase liquide est
séparée à une pression proche de la pression en tête
de puits ,elle contient alors, sous haute pression, une proportion importante
d'éthane et des hydrocarbures légers dissouts et doit être
stabilisée et cela, en réduisant sa pression, Cette
opération permet de produire, d'une part du gaz supplémentaire et
d'autre part une phase liquide, La tension de vapeur finale du liquide est
très importante car elle conditionne la sécurité au cours
du stockage et du transport ainsi que les pertes éventuelles [1].
Le choix du séparateur gaz-liquide dépend de
l'application envisagée ; toutefois, un séparateur gaz -liquide
doit avoir généralement les éléments suivants :
> une zone de séparation primaire afin de donner un
mouvement centrifuge au fluide renforçant l'effet de la gravité
;
> une zone de décantation avec un temps de
séjour suffisant pour séparer les gouttes de phase liquide ;
> un dévésiculeur à la sortie du gaz pour
piéger les plus petites gouttelettes ;
> des équipements de régulation et de
sécurité (régulations de pression, de température,
de niveau, etc, ,).
Les figures suivantes illustrent les trois principaux types de
séparateurs :
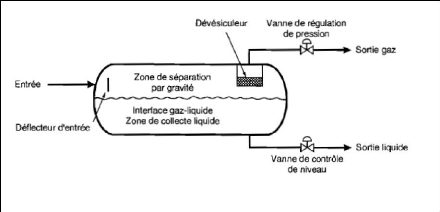
Figure 3 : Séparateur horizontal.
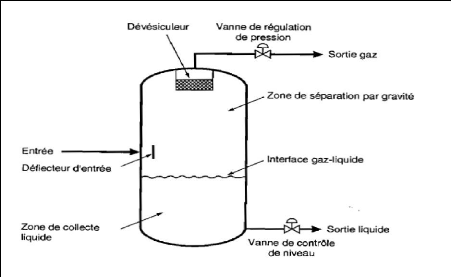
Figure 4 : Séparateur vertical.
I.3.Opérations de purification
L'ajustement requis de la teneur en eau, et en hydrocarbures
lourds, est réalisé par des opérations de traitement, qui
permettent de purifier le gaz naturel en séparant les constituants
à éliminer du gaz traité.
Ces opérations font appel à des
procédés de séparation divers : absorption par solvant,
adsorption, fractionnement, par réfrigération, perméation
gazeuse.
Il est à noter qu'en dehors de la perméation
gazeuse, les procédés de séparation utilisés sont
tous basés sur le principe d'un changement de phases: le constituant
à séparer est transféré sélectivement de la
phase gazeuse à une phase liquide ou solide [1].
Dans le cas de la perméation gazeuse, la séparation
est basée sur la différence entre les vitesses de passage des
constituants à séparer à travers une membrane
sélective.
I.3.1. Absorption par un solvant
Le principe de base de l'absorption par solvant est
représenté sur la figure suivante :
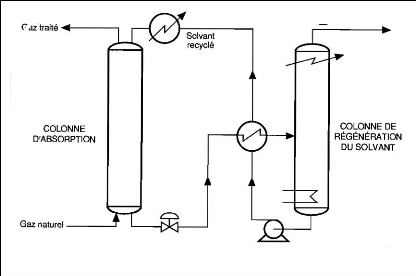
Figure 5 : Schéma de principe d'une
opération de traitement par absorption.
Le gaz à traiter est mis en contact à
contre-courant avec un solvant sélectif dans une colonne à
plateaux ou à garnissage.
Si le solvant qui arrive en tête est pur, il est
possible, en jouant sur le taux de solvant et le nombre de plateaux ou la
hauteur de garnissage dans la colonne, d'obtenir en sortie la teneur en
impuretés correspondant à la spécification imposée,
Le solvant sortant de la colonne d'absorption, est envoyé à une
colonne de régénération par distillation.
Après régénération le solvant est
recyclé ,il passe par un échangeur de chaleur, destiné
à une température proche du domaine de température dans
lequel opère la colonne d'absorption, tout en chauffant la solution de
fond de colonne, Avant d'être renvoyé à la colonne
d'absorption, une étape de réfrigération
complémentaire dans un échangeur est nécessaire.
La pureté du solvant recyclé est essentielle, En
effet, la concentration en impureté du gaz traité ne peut
être inférieure à celle qui est imposée par
l'équilibre avec la phase solvant recyclée.
I.3.2. Perméation gazeuse
Le schéma de principe d'une opération de
séparation par peméation gazeuse est représenté sur
la figure ci-dessous :
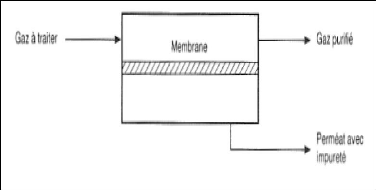
Figure 6 : Peméation gazeuse schéma de
principe [4].
Pour que la séparation soit efficace, la membrane doit
être très perméable vis-à-vis de l'impureté
à séparer, qui passe à travers la membrane sous l'effet de
la pression et très peu perméable vis-à-vis du
méthane.
Les procédés de séparation par membranes
mettent en jeu des surfaces de membranes élevées, qui s'expriment
généralement en milliers de mètres carrées [1].
I.4. Déshydratation
La présence d'eau entraîne différents
problèmes pour l'exploitation : suivant les conditions de
température et de pression qui règnent dans une installation, la
vapeur d'eau peut se condenser et provoquer la formation d'hydrates, se
solidifier ou favoriser la corrosion si le gaz contient des composants
acides.
Pour éviter ces problèmes, il est nécessaire
de réduire la teneur en eau du gaz naturel au moyen de techniques de
traitement appropriées.
La purification du gaz naturel est réalisée par
différents types de procédés :
> absorption; > adsorption; > perméation
gazeuse.
Parmi ces procédés de déshydratation, c'est
l'adsorption qui est la plus couramment utilisée.
I.4.1. Déshydratation par adsorption
Le schéma de principe d'une opération de
déshydratation par adsorption en lit fixe est représenté
sur la figure ci-après, Le procédé fonctionne d'une
manière alternée et périodique.
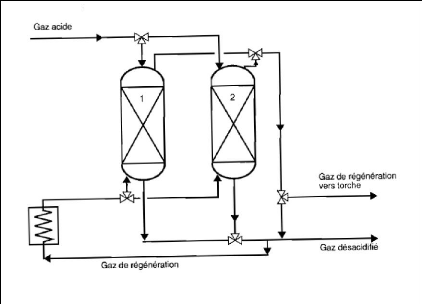
Figure 7 : Procédé de
déshydratation par adsorption.
Au cours de l'étape d'adsorption. le gaz traité est
envoyé sue le lit d'adsorbant qui fixe l'eau .lorsque le lit est
saturé. du gaz chaud est envoyé pour
régénérer l'adsorbant,
Après régénération et avant
l'étape d'adsorption, le lit doit être refroidi, ceci est
réalisé en envoyant du gaz froid, après
réchauffage, ce même gaz peut servir à effectuer la
régénération [1].
Pour un adsorbant soit efficace, il doit présenter les
caractéristiques suivantes :
> capacité d'adsorption à l'équilibre
importante ;
> adsorption réversible permettant de
régénérer l'adsorbant ;
> cinétique d'adsorption rapide ;
> faible perte de charge;
> pas d'effet de dilatation de volume avec la
température et la saturation. I.5. Le transfert
thermique
L'élaboration des produits commerciaux dans l'industrie
pétrolière est caractérisée par une série
d'opération décrites dans le schéma de fabrication ,les
unités de séparation, telles que distillation ,extraction par
solvant et cristallisation, nécessitent des quantités importantes
d'énergie calorifique pour obtenir le gradient de température qui
permettra le fractionnement ,et cela de même pour les unités
mettant en jeu des réactions de transformations ,telles que le craquage
ou la synthèse , C'est pourquoi, on s'attache à réduire au
maximum ce poste, en réalisant un circuit de récupération
de chaleur entre l'alimentation froide et les effluents chauds de
l'installation, L'équipement de récupération est
constitué par des appareils tubulaires d'échange de chaleur.
On distingue généralement trois classes
d'appareils, correspondant à des fonctions très
spécifiques :
-Les échangeurs et réfrigérants
dans lesquels ne se produit aucun changement de phase, la
désignation « échangeurs » est réservée
aux appareils ou le transfert entre fluides chaud et froid correspond
effectivement à une récupération de chaleur, alors que le
terme « réfrigérant » s'applique aux appareils ou l'on
refroidit l'effluent par un fluide auxiliaire ;
-Les condenseurs qui permettent la
condensation et le refroidissement d'un effluent vapeur en tête de
colonne, soit à l'aide d'un fluide froid, soit à l'aide d'un
fluide auxiliaire (eau, air, produit frigorigène ...) ;
-Les rebouilleurs qui assurent une vaporisation
partielle des produits des fonds de tours grâce à la circulation
d'un effluent chaud, ou d'un fluide auxiliaire [5].
Dans tous ces appareils la surface de transfert est
matérialisée par des tubes dont les divers arrangements
permettent de résoudre avec satisfaction les nombreux problèmes
de récupération de chaleur rencontrés dans l'industrie.
Le schéma fonctionnel d'un échangeur de chaleur
classique est généralement défini comme suit:
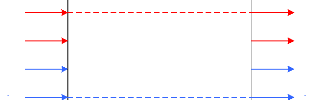
QmC TCE
QmF
TFE
ECHANGEUR : PARAMÈTRES K et S
QmC TCS
QmF
TFS
Figure 8 : Schéma fonctionnel d'un
échangeur de chaleur [6] .
Les indices C, F, E et S étant respectivement relatifs
aux paramètres Chaud, Froid, Entrée et Sortie, Les
paramètres de l'échangeur sont ici son coefficient
d'échange global K et sa surface d'échange
S.
I.6. Fractionnement des condensats
Lorsque le gaz contient une fraction importante
d'hydrocarbures autres que le méthane et l'éthane (gaz à
condensat ou gaz associé), la séparation d'au moins une partie de
ces hydrocarbures apparait nécessaire pour éviter la formation
d'une phase liquide au cours du transport.
Cette opération est en général
réalisée par abaissement de température avec formation
d'une phase liquide ; elle peut être également effectuée
par une opération d'absorption ou d'adsorption.
I.6.1. Fractionnement par réfrigération
La figure 9 montre le schéma de principe d'un
procédé de fractionnement par réfrigération ,ce
schéma correspond au cas d'un gaz préalablement
déshydraté ,afin d'éviter tout risque de formation
d'hydrates par réfrigération ,le gaz sortant du séparateur
haute pression est refroidi par un échange de chaleur avec le gaz
traité ,suivi d'une étape de réfrigération
réalisée soit au moyen d'un cycle de réfrigération
externe ,soit par détente.
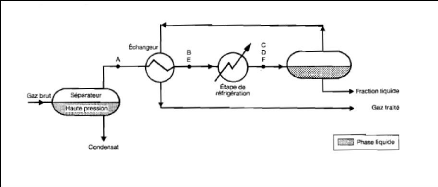
Figure 9 : Fractionnement par
réfrigération. I.6.1.1. La détente
isenthalpique
La réfrigération par détente
isenthalpique à travers une vanne représente le
procédé le plus simple ,c'est aussi un procédé
relativement inefficace, car pour une même pression, elle conduit
à une température nettement plus élevée, et c'est
la raison pour laquelle le travail de détente étant
dégradé en chaleur ,l'abaissement de la température obtenu
par détente isenthalpique est qualifiée d'effet Joule-Thomson,Le
schéma de principe d'une unité de traitement mettant en oeuvre
une détente isenthalpique est donné par la figure suivante :
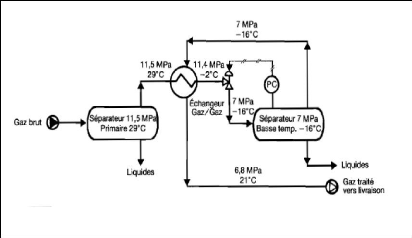
Figure 10 : Réfrigération par
détente isenthalpique [7].
Le pré refroidissement du gaz par échange avec le
gaz traité, joue un rôle essentiel pour atteindre des
températures relativement basses.
I.6.1.2. La détente isentropique
Un procédé de traitement de gaz à travers
une turbine est schématisé sur la figure ci-après :
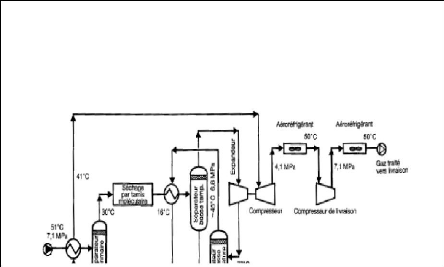
Figure 11 : Réfrigération par turbine
d'expansion [7].
La détente à travers une turbine qui se
rapproche d'une détente isentropique est beaucoup plus efficace, Elle
est surtout utilisée lorsqu'une séparation poussée des
hydrocarbures autres que les fractions C2-, est
recherchée.
Le procédé fonctionnant à basse
température, nécessite un séchage poussé du gaz par
tamis moléculaire et éventuellement une décarbonatation,
pour éviter la cristallisation du dioxyde de carbone.
La turbine de détente entraine en général un
compresseur, pour recomprimer partiellement le gaz détendu.
L'utilisation d'un cycle de réfrigération externe
permet d'abaisser la température du gaz à traiter sans
réduire la pression, aux pertes de charge près.
La réfrigération est réalisée par
vaporisation à une pression relativement basse d'un fluide
frigorigène ; celui-ci est le plus souvent le propane ou parfois, un
fluide halogéné de type `fréon', le fluide
frigorigène vaporisé est comprimé, condensé sous
pression en transférant la chaleur de condensation à un fluide de
refroidissement (eau ou air), et enfin recyclé après
détente à travers une vanne.
Enfin ; les contraintes liées à l'environnement
et la nécessité de réduire les couts, notamment en cas de
production en zone difficile, rendent nécessaire toutefois le recours
à des procédés innovants, Ils dérivent pour une
large part de procédés plus anciens, mais peuvent conduire
à des réductions importantes de couts d'investissement et
d'exploitation,
I.7. Description des procédés de
traitement de gaz
Parmi les différents procédés de traitement
de gaz, nous allons citer deux procédés : le
procédé PRICHARD et le procédé HUDSON.
I.7.1. Le procédé PRICHARD
Connue aussi sous le nom de réfrigération
mécanique, c'est le plus simple et le plus direct procédé
pour la récupération des liquides, il est muni d'une boucle de
réfrigération externe comme le montre la figure 12, utilisant
généralement le propane comme fluide frigorifique avec un
compresseur (centrifuge ou réciproque), pour ramener les frigories du
basse vers haute pression opératoire, L'échangeur gaz-gaz dans la
figure 23 représente une étape préparatoire pour la
réfrigération [3].
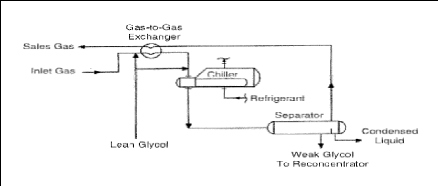
Figure 12 : Schéma simplifié du
procédé PRICHARD.
Le chemin thermodynamique suivi par le gaz dans ce type de
procédé est représenté par la ligne ABC dans la
figure 2, avec AB : l'échangeur gaz-gaz ; BC : la
réfrigération,
Une étape de déshydratation ou une injection
d'inhibiteur d'hydrates est prévue dans le cas de présence d'eau
de process pour éviter la formation d'hydrates lors de la
réfrigération.
I.7.2. Le procédé HUDSON
Le procédé qui prédomine la
récupération de GPL est bien le procédé de
turboexpander (figure 13);ce procédé utilise la pression du gaz
brut pour produire les frigories par une détente à travers une
turbine d'expansion, Puisque cette détente est presque isentropique, la
baisse en température du gaz est plus importante que dans le cas d'une
vanne Joule-Thomson (détente isenthalpique),il est important de noter
que la détente de l'expander fourni un travail considérable ,ce
dernier set utilisé dans une étape ultérieure (par un
compresseur centrifuge),pour comprimer le gaz résiduel du process [3]
.
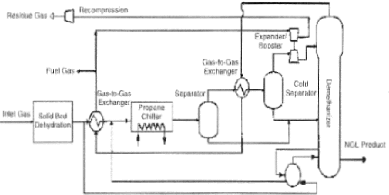
Figure 13: Schéma simplifié du
procédé HUDSON.
Une vanne J-T est installée en parallèle avec le
turboexpander, et cela pour chasser le sur flux du gaz dans l'expander ou bien
lorsque l'expander est hors service [8].
Un aperçu sur les deux types de détentes
(isenthalpique et isentropique), pour voir la différence.
I.7.2.1. Principes thermodynamiques de la vanne
Joule-Thomson
L'équation ÄH = W + QE
appliquée à une vanne montre que :
W = 0 pas de travail et frottement négligé,
QE = 0 pas d'échange de chaleur, conditions adiabatiques
(vanne calorifugée)
Sur le diagramme H,S dans la figure 14, la droite horizontale
allant du point P1 , t1 à P2, t2 représente la détente
isenthalpique, L'enthalpie H1 à l'entrée est égale
à l'enthalpie H2 à la sortie
H1 = H2 ÄH = 0
(I.1)
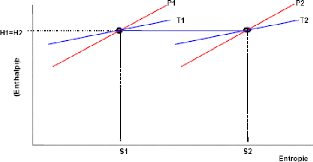

Figure 14 : Le diagramme enthalpie -entropie
(détente isenthalpique).
I.7.2.1.1. Procédure de calcul de la
température en fin de Détente
a) Sans condensation
Les graphes de AP = f (AT) [8].
b) Avec condensation:
La procédure pour déterminer la température
de sortie T2 est la suivante : - Calculer H1 à P1, T1
- Estimer T2,
Compositions du liquide et vapeur
- Calculer H2=Hv+Hl
- si ?1 = ?2, ?2 estimée est la
température en fin de détente, - H1 ~H2, refaire une
autre estimation de T2 [9].
I.7.2.2. Principes thermodynamiques du
turbo-expander
Un turbo-expander est une machine dynamique, à travers
laquelle l'effluent de gaz subit une détente isentropique, Cette
détente s'accompagne d'une production de froid dont l'énergie est
égale au travail mécanique obtenu, Soit une turbine
détendant un fluide de pression P1, et
température T1 enthalpie H1 à l'entrée
jusqu'aux conditions de sortie P2 , T2 , H2 ,Dans une évolution
isentropique le trajet vertical représenté sur le diagramme H-S
de la figure 15 correspond à une récupération
d'énergie mécanique maximale.
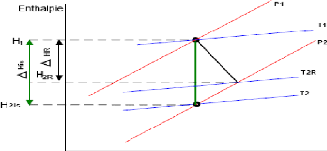

Figure 15: le diagramme enthalpie -entropie
(détente isentropique)
Dans la réalité et compte tenu des imperfections
des machines réelles, la détente du gaz s'accompagne d'une
augmentation de l'entropie qui se traduit par le segment oblique, Cela a pour
conséquence :
- Une température de sortie T2R plus élevée
que T2is dû au réchauffement du gaz par les
frottements,
- Une chute d'enthalpie AHr inférieure à AHis en
résumé :
AHis = W is (I.2)
AHis = W R (I.3)
L'évolution d'un gaz parfait dans une machine parfaite est
donnée par :
PVK = Constante
K = CP / CV = CP / (CP -- R/M
) (I.4)
La température T2is en fin de détente isentropique
est donnée par la relation :
T2is = T1 (P2/P1)(K --
1)/K (I.5)
Elle dépend :
- du taux de détente P2/P1
- De la température initiale T1
- De la nature du gaz caractérisé par son
coefficient K, Pour un gaz fardait
A llis = CP (T2is --
T1)
Soit : Allis = W is = K/K --
1 * R T1 / M [(P2/P1) (K --
1)/K -- 1 ] (I.6)
Le rendement isentropique est défini comme :

P= pression
V = débit volumique
K= Coefficient isentropique
R= gaz constante
M= poids moléculaire
CP, CV = chaleurs massiques
I.7.2.2.1. Procédure de calcul de la
température en fin de Détente
Les conditions d'entrée sont généralement
connues :
Q = débit de gaz
P1 = pression d'entrée
T1 = température d'entrée
Les conditions de sortie : Seule la pression de sortie turbine
est connue car elle est imposée par le process.
P2 = pression de sortie
- Calculer l'enthalpie H1 et l'entropie S1 aux conditions
d'entrée
P1, T1, La température T2 est calculée par
itération
- Fixer trois températures de sortie T', T", T"' à
la pression de
Sortie P2, à chaque température et P2, calculer les
conditions d'équilibre de l'effluent sortant de l'expander et
déterminer son enthalpie (H) et son entropie (S)
- Pour une application au gaz naturel déterminer la
Température isentropique T2 du méthane sur le diagramme de
Mollier obtenue par une détente à partir de T1, P1 à P2 A
partir du graphe dans la figure 16 déterminer la température
isentropique T2is qui correspond à S1 et à
T2IS lire
AH isentropique, Appliquer le rendement donné par le
constructeur pour calculer AHr (différence d'enthalpie
réelle).
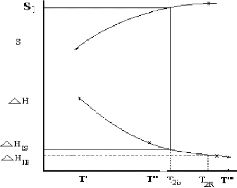
Figure 16 : Température en fin de
détente.
ÄHisxhis =
ÄHR en Appliquant AHR lire la
température T2R (réelle) correspondante : - Dans les
conditions réelles P2 et T2R, refaire le calcul de flash pour
déterminer les compositions des liquides et vapeurs.
- Calculer le travail produit et la puissance réelle
[8].
Chapitre II :
Présentation du champ du Gaz
GTFT
II.1.Situation géographique
Le périmètre Tin Fouyé Tabankort (TFT)
couvre 1200 km dans la région du Tinrhert dans le Sahara
algérien, dans la wilaya d'Illizi, Il est situé le long de la
route nationale N3, à environ 1350 km au sud-est d'Alger, 380 km au
sud-est d'Hassi Messaoud, et environ 200 km à l'ouest d'In
Aménas, dans la commune de Bordj Omar Driss elle-même
située à une centaine de kilomètres à l'ouest du
périmètre, Cette zone est déjà
développée pour l'exploitation des hydrocarbures, avec notamment
le gisement de gaz de TFT, un réservoir de gaz présent dans des
formations de grès ordoviciens, en production depuis avril 1999.
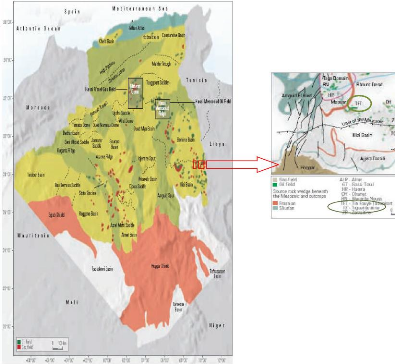
Figure 17 : Situation géographique du
GTFT.
II.2. Développement et capacité du champ:
II.2.1.Roche mère et genèse des hydrocarbures
:
Les argiles du silurien constituent la roche mère,
source génératrice des hydrocarbures à l'échelle de
toute la plate forme saharienne, Cette source est représentée par
les argiles noires, très riches en matière organique.
Dans le gisement de gaz TFT, la roche mère,
représenter par les argiles du silurien, qui a génère les
hydrocarbures de l'ordovicien, Elle joue aussi le rôle de roche
couverture dont l'épaisseur varie de 170m à 200m.
II.2.2.Description du réservoir:
Le gisement de Tin Fouye Tabankourt fait partie d'un
anticlinorium complexe d'extension régionale, comportant des structures
alignées le long d'accidents majeurs, Le réservoir est recoupe
par des failles d'orientation diverses qui délimitent des compartiments
d'orientation subméridienne, Les rejets des accidents majeurs sont
importants, Ces failles sont généralement sub-verticales, de type
normal et parfois inverse, Les formations rencontrées vont du
PRECAMBRIEN au CRETACE avec le réservoir ORDOVICIEN, très
fissuré et très hétérogènes, dont la
couverture est assuré par une couche argileuse d'environ 2000m de
puissance [10].
Le gisement de gaz TFT est un gisement avec un gas humide
très riche en condensât,
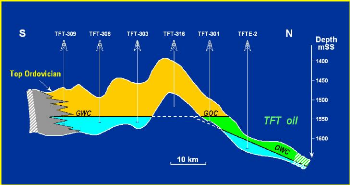
Figure 18 : Coupe de réservoir.
II.2.3. Historique de production:
La production a démarré au rythme de 5
millions de m3 /j de gaz humide et devrait
atteindre d'ici quelques semaines le débit nominal de 20 millions de
m3/j, soit environ 7 milliards de m3 par an, Ce gaz humide est
séparé en gaz sec, GPL et condensats dans l'usine d'extraction du
champ, qui comprend deux trains de traitement identiques construits par Brown
& Root avec la participation de plusieurs sociétés de service
algériennes, Les condensats et les GPL sont ensuite transportés
séparément jusqu'à la côte au rythme de
respectivement 2800 T/jour et 2600 T/jour, Le gaz naturel sec est quant
à lui expédié dans le réseau de transport
SONATRACH.
Les figures suivantes montrent l'évolution de
productions du champ GTFT ; en gaz sec, GPL et condensât
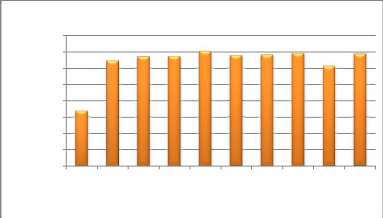
Gaz sec (10^9 N mA3)
4,00
8,00
0,00
7,00
6,00
5,00
3,00
2,00
1,00
1999 2000
Production annuelle Gaz sec
2001 2002 2003 2004 2005 2006 2007
Années
2008
Figure 19 : La production de gaz sec du champ GTFT
[11].
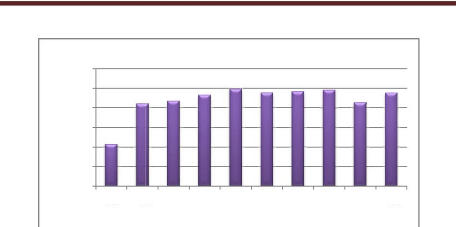
2008
2001 2002 2003 2004 2005 2006 2007
Années
1999 2000
Production annuelle GPL
12,00
10,00
GPL (10^5 T)
8,00
6,00
4,00
2,00
0,00
Figure 20: La production en G P L du champ GTFT
[11].
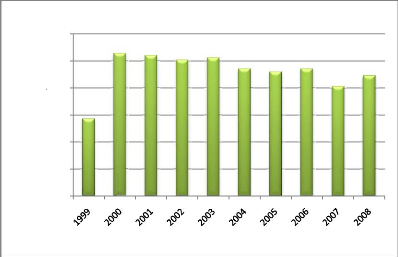
condensat (10^5 T)
12,00
10,00
4,00
0,00
8,00
6,00
2,00
Production annuelle condensat
Années
Figure 21 : La production en Condensat du champ GTFT
[11].
Le groupement TFT produit actuellement environ 19
,2 MNm3 / J de gaz export (sec) du le gisement de
TFT, au moyen de 80 puits (sur un total de 86 puits, dont certains sont
temporairement suspendus ou abandonnés), Les fluides produits sont pris
en charge dans le réseau de collecte du champ, connecté au moyen
de manifolds vers six canalisations de
collecte principales (trunklines), la répartition des
puits sur les collecteurs est donnée par tableau suivant :
Tableau 1 : la distribution des puits sur les trunklines
[12].
Trunklines
|
Nombre de puits
|
Collecteur TL 1
|
14
|
Collecteur TL 2
|
16
|
Collecteur TL 3
|
12
|
Collecteur TL 4
|
15
|
Collecteur TL 6
|
11
|
Collecteur TL 7
|
17
|
Ces trunklines aboutissent au manifold d'entrée de
l'installation de traitement de GTFT, et le flux de production subit une
première séparation dans un slug-catcher (séparateur de
phases), Il entre ensuite dans deux unités de traitement fonctionnant en
parallèle, dans lesquelles le condensât (fractions C5+) et le GPL
(fractions C3-C4) sont séparés du flux de gaz, Le gaz est
déshydraté puis comprimé au moyen de compresseurs
entraînés par des turbines à gaz, puis il est envoyé
vers le réseau commercial dans le pipeline GR1, exploitée par
SONATRACH, Le condensât stabilisé et le GPL subissent un stockage
intermédiaire, respectivement dans deux cuves à condensât
et trois sphères à GPL, d'où ils sont pompés dans
des pipelines de SONATRACH (respectivement vers les installations de Mederba
pour le condensât, et vers la conduite LR1 pour le GPL).
Plus le gisement mûrit, plus la pression du
réservoir, et donc également la pression de production à
l'entrée de l'installation, diminuent, réduisant ainsi
graduellement le flux de production, Pour remédier à cette perte
de pression, et ainsi permettre à l'installation de traitement de
fonctionner dans des conditions de rendement optimales, GTFT prévoit de
construire des installations de boosting (compression du gaz brut) à
l'entrée de l'usine, Ces installations se composeront de deux lignes
parallèles de compresseurs, entraînés par des turbines
à gaz, qui maintiendront le flux de production dans la ligne de
traitement, Le projet de Boosting a été prévu dès
les phases initiales de conception des installations; en conséquence,
une aire technique a été prévue dans l'emprise actuelle
des installations pour les nouvelles installations, Les modifications de
procédé dans les installations de TFT
occasionnées par les nouvelles installations de
Boosting, seront mineures et principalement liées au fonctionnement des
turbines et des compresseurs de Boosting en amont des lignes de traitement.
Afin de maintenir le flux de production alors que la pression
du réservoir chute, GTFT a également besoin de forer des puits
supplémentaires sur le gisement de TFT, Le nombre total des puits sur le
périmètre devrait passer de 80 actuellement à une centaine
- bien que le nombre de puits futurs et leurs dates de forage seront
évalués et finalisés sur une base annuelle
(développement de la zone est du champ, appel d'offre de la sismique en
cours), Les forages sur le champ de TFT ont été
réalisés par ENAFOR dans la phase deux, la société
de forage nationale algérienne, Ils sont réalisés au moyen
d'un appareil de forage, opérant typiquement un à deux mois par
point de forage, Sur le champ de TFT, les forages sont uniquement
réalisés en utilisant des boues à base d'eau - ce qui
permet de décharger les déblais de forage sur site dans une
fosse, qui, une fois sèche, est remblayée sous la plateforme
finale du puits, Les autres rejets environnementaux associés au forage
sont principalement liés à la consommation de carburant des
générateurs et des moteurs de la plateforme de forage, et au
torchage d'hydrocarbures pendant les essais de puits, Ceci peut
également arriver sur des puits existants lors de phases
ultérieures de reconditionnement (workover) et de maintenance du
puits.
Enfin, GTFT envisage de poursuivre l'exploration du
périmètre de TFT, afin de découvrir d'éventuels
prolongements du gisement non encore développés par les
installations existantes, Les opérations d'exploration sismique seraient
réalisées le long de lignes prédéfinies, sur
lesquelles des vibrations sont générées en surface
à l'aide de vibreurs montés sur des camions, Les vibrations
envoyées dans le sol sont renvoyées par les formations
géologiques en profondeur puis enregistrées à leur retour
à la surface, Ceci permet une caractérisation de la structure et
de la nature des formations en se basant sur l'interprétation des
signaux enregistrés, Les campagnes d'acquisition sismique sont des
opérations temporaires, d'une durée inférieure à un
an (selon la surface couverte), En l'absence d'informations précises
aujourd'hui disponibles sur les campagnes sismiques à venir, cette EIE
se limite à fournir des informations génériques sur les
opérations sismiques dans le désert du Sahara et sur leur impact
environnemental [12].
Le personnel du groupement TFT et ses sous-traitants sont
hébergés dans une base de vie principale, les équipes de
forage résidant dans une base spécifique à l'ouest du
périmètre.
Chapitre III:
Description du procédé du traitement
du
Gaz GTFT
Puisque ce sont les qui constituent l'origine du gaz du champ
TFT, et pour permettre son exploitation de manière efficace,
l'emplacement de chaque puits est tel qu'il permet une production maximale
à un cout réduit ; pour cela, plusieurs puits peuvent être
reliés à un même manifold desservant une des conduites
d'amenée, Cette disposition permet de récupérer le gaz de
différentes zones et de l'expédié à une
installation de la manière la moins couteuse et la plus souple [13].
A la sortie des puits, dans le cas d'un gaz associé ou
à condensat, le gaz naturel se trouve en présence d'une phase
liquide, Dans certaines circonstances, cette phase liquide peut être
transportée en même temps que le gaz, en milieu bi phasique
,Néanmoins, elle est nécessairement séparée
à un stade ultérieur, le gaz devant encore subir des
opérations de traitement complémentaires avant d'être
expédié, pour l'usine du GTFT (qui comporte deux trains de
traitement identiques), on distingue :
> Section de refroidissement et séparation primaire,
> Section de déshydratation,
> Section de refroidissement et de détente,
> Section de fractionnement
Un schéma détaillé pour la circulation des
fluides est presenté dans le PFD (voir annexe A.1).
Gazsecversexpedition

Figure 22: Schéma bloc de l'usine GTFT.
Condensât versstockage
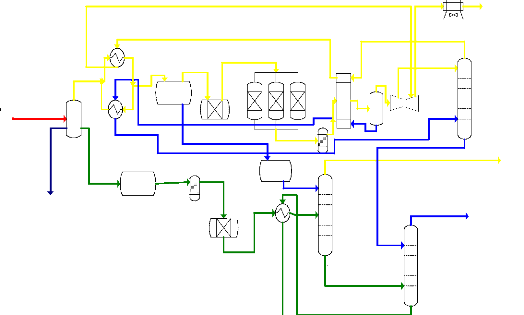
Gazhumide 65bar , 50°C
Eau
SlugCatcher
E2-1003
E2-1002
V4-1204
29°C
V4-1004
E-34
V4-1205
E2-1207
Sécheurs ClodBox
P-55
Stabiliseur
63bar
-19°C
Debutaniseur
20bar -63°C
GPLversstockage
Deethaniseur
Fuel Gaz
III.1.1. Section de refroidissement et séparation
primaire :
Le réseau de gaz brut transporte le gaz saturé
sortant du séparateur de condensat (Slug-catcher) vers les deux trains
de traitement oil il passe à travers des échangeurs E2-1002,E2-
1003,le séparateur V4-1004, et filtres F2-1005 A/B destinés
à séparé le condensat et l'eau du gaz.
L'objet du slug-catcher XV-0701 est de récupérer
les bouchons de condensat et d'eau qui se forment dans les conduites et de
séparer le gaz des liquides. pour permettre au deux courants
d'alimentation de rentrer dans l'unité ,l'un étant un courant
léger de gaz saturé et l'autre un courant plus lourd de condensat
,cette disposition assure une meilleure stabilité et efficacité
de l'alimentation des zones de traitement de gaz et de condensat de
l'unité, L'eau issue du slug-catcher est envoyé vers le ballon de
dégazage de l'eau de process V4-1601 [13].
III.1.1.1. Refroidissement :
Le gaz brut est refroidi lorsqu'il passe du côté
tube de l'échangeur de gaz brut /gaz résiduel E2-1002, Le gaz de
sortie est maintenu à 23° C par TIC-1032 qui contrôle le
courant froid du gaz résiduel (qui est du cold box) côté
calandre de l'échangeur, Les hydrates se forment à 18,14°C,
Ne pas régler la température du gaz de sortie à une valeur
trop proche de cette température,une partie du courant du gaz brut passe
du côté tube de l'échangeur de gaz brut/ liquide E2-1003
où il est refroidit par le courant liquide froid (alimentation issue du
cold box) du côté calandre, La figure 23 illustre le comportement
de l'enveloppe des phases à la sortie des échangeurs
E2-1002/1003.
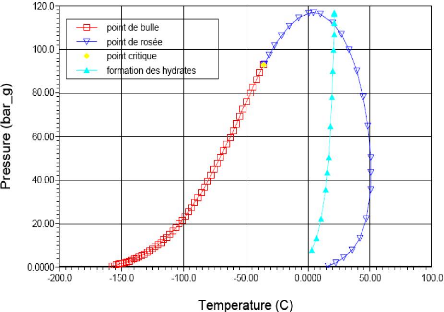
Figure 23 : L'enveloppe des phases sortie
E2-1002/1003.
III.1.1.2. Séparation primaire :
Après le refroidissement du gaz dans le
côté tube des échangeurs, il s'achemine vers le sommet du
séparateur d'alimentation des sécheurs V4-1004, L'eau s'accumule
au fond du séparateur puis drainé vers le ballon de
dégazage eau du process, V4-1601, Le condensat
récupéré après passage par des chicanes dans le
séparateur et envoyé vers le séparateur primaire de
condensat V4-1205, Le gaz brut passe à travers des filtres F2-1005AB en
sortant du V4-1004 afin de récupérer les particules liquides
entraînées, puis vers les sécheurs (T2 - 1101 ABC).
III.1.2. Section de déshydratation :
III.1.2.1. L'adsorption :
L'objet du système d'adsorption de gaz est
d'éliminer l'eau présente dans le courant du gaz de process afin
d'empêcher la formation d'hydrates dans la section froide du process,
ainsi d'éviter la contamination du produit par l'eau, L'eau est
adsorbée au niveau des tamis moléculaires dans chaque
adsorbeur.
Le système de régénération permet
d'éliminer l'eau des tamis moléculaire saturés à la
suite de la phase d'adsorption, Ceci est réalisé en
réchauffant par un courant de gaz sec à 246° C en le faisant
passer dans les réchauffeurs de gaz de régénération
E2-1104 /E2- 2104, le gaz passe du coté tubes des échangeurs pour
être réchauffé par un fluide caloporteur qui passe du
coté calandre, Le gaz sec réchauffé est ensuite
envoyé en contre courant dans l'adsorbeur horizontal.
Au fur et à mesure que le lit de tamis
moléculaire réchauffé, l'eau est vaporisée et
évacuée de l'adsorbeur par le courant de gaz chaud.
III.1.2.2. La régénération :
Le système de régénération permet
d'éliminer l'eau des tamis moléculaires saturés, Le gaz de
régénération est soutiré du courant de gaz sec
à la sortie des adsorbeurs, Le gaz est comprimé à 68 bars;
Pression suffisante pour faire passer le gaz de
régénération à travers le circuit de
régénération et le renvoyer à l'entrée,
Après compression le gaz est réchauffé dans un
échangeur afin d'obtenir la température requise pour vaporiser
l'eau dans les tamis saturés.
Le gaz de régénération chaud
s'écoule à contre-courant dans l'adsorbeur afin de
réchauffer le lit d'adsorption du bas vers le haut, Une fois sortie de
l'adsorbeur, le gaz est refroidi dans un autre échangeur et
envoyé vers un séparateur qui élimine la plus grande
partie
de l'eau présente dans le gaz, Le gaz est ensuite
renvoyé au collecteur de gaz brut tandis que l'eau accumulée au
fond du séparateur se dirige vers le ballon de dégazage d'eau de
process.
III.1.3. Section de refroidissement et de détente:
III.1.3.1. Le refroidissement :
A cette étape du process, le condensât et l'eau
ont été éliminés du courant de gaz et il faut
réduire la température et la pression pour que les C3
et les gaz plus lourds puissent être séparés des
C2 et les gaz plus légers.
Le gaz chaud sec traverse deux échangeurs à
plaques à ailettes en Aluminium dans lesquelles il est refroidi par un
courant de gaz froid en provenance de déethaniseur et un courant de
liquide froid en provenance du séparateur d'entrées de
l'expandeur, Le gaz ainsi refroidi passe ensuite dans le séparateur
d'entrée de l'expandeur dans lequel le liquide condensé est
séparé du gaz.
III.1.3.2. La détente:
Le turbo-expandeur permet d'utiliser l'énergie du gaz
par détente, réduisant ainsi la pression et la température
en vue de faciliter la séparation des hydrocarbures légers,
L'énergie provenant de la détente de gaz sur les lames de
l'expandeur est ensuite utilisé pour entraîner le compresseur qui
augmente la pression des fractions légères dans une phase du
procédé d'expédition.
Le gaz froid sec en provenance de E4-1301/1302 entre dans le
séparateur d'entrée de l'expandeur V3-1303 où les
hydrocarbures liquides s'accumulent et sont évacués sous
contrôle de niveau pour former un courant de liquide froid vers E4-1302,
Le gaz traverse un tamis anti-entraînement au sommet du séparateur
et à l'entrée du turbo-expandeur C8-1304, ou le by-pass de
l'expandeur, La vanne PV -1338-A est une vanne de détente Joule -Thomson
située sur la ligne de by-pass qui permet l'expansion du gaz lorsque
l'expandeur est arrêté.
Pour l'enveloppe des phases (à la sortie de l'expander
C8-1304), la courbe de rosée est déplacée , grâce au
détente isentropique, en réduisant la zone du mélange
liquide-vapeur ,ce qui est traduit par une récupération d'une
phase liquide plus importante,(figure 24)
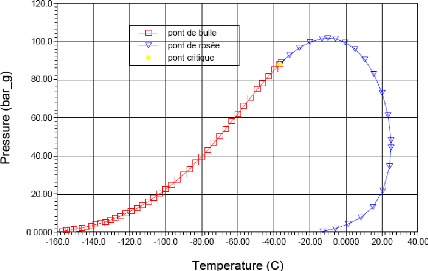
Figure 24 : L'enveloppe des phases sortie expander
C8-1304.
Le compresseur C8-1304 est relié à l'expandeur
et entraîné par l'énergie libérée par la
détente du gaz sur les lames de l'expandeur est utilisé pour
comprimé les fractions légères avant l'expédition,
L'expandeur / compresseur construit par Mafi-Trench est un ensemble sur Skid
muni de dispositif de contrôle et d'un système d'huile de
lubrification et d'étanchéité.
III.1.4. Section de fractionnement :
Elle comporte également trois colonnes de fractionnement,
le déethaniseur, la colonne de stabilisation, et le
débutaniseur.
III.1.4.1. Le déethaniseur :
Le déethaniseur T6-1401 est une colonne conçue pour
séparer l'éthane et les fractions gazeuse plus
légères du propane et des fractions plus lourdes,
Le déethaniseur est la première colonne dans la
section du process froid, C'est à ce point du process que les
hydrocarbures légers tels que l'éthane et le méthane sont
séparés du propane et des hydrocarbures plus lourds, La colonne
est équipée de plateaux et de garnitures pour assurer une
séparation maximale permettant aux hydrocarbures lourds de descendre
pour s'accumuler au fond de la colonne tandis que les hydrocarbures
légers sont vaporisés et
barbotent dans le liquide vers le sommet, La garniture et le
Tamis anti-entraînement au sommet de la colonne extraient les
gouttelettes de liquide de la vapeur et contribuent à empêcher
l'entraînement de liquide plus lourds par la vapeur, Le liquide
accumulé sur le plateau inférieur s'écoule vers le
rebouilleur qui produit de la vapeur chaude :Celle-ci est renvoyée
à la colonne pour séparation, Le propane et les produits lourds
sont soutirés du fond de la colonne par l'intermédiaire d'une
vanne de contrôle de niveau.
III.1.4.2. Le stabilisateur :
Pendant la séparation du courant d'alimentation
liquide, Les hydrocarbures légers se vaporisent par détente et le
courant d'alimentation devient bi phasique, Ce courant est stabilisé en
le faisant passer dans la colonne de stabilisation dont laquelle les fractions
légères sont extraites sous forme de vapeur, et les
C3+ et restent en phase liquide, Le courant liquide monophasique
résultant est donc plus stable et plus facile à contrôler
en vue de son épuration ultérieure.
Le liquide d'entrée est réchauffé dans
l'échangeur d'alimentation de la colonne de stabilisation E2-1207 avant
d'entrer dans la colonne de stabilisation T4-1202, Le courant d'alimentation
réchauffé entre au sommet de la section inférieure tandis
qu'un courant d'alimentation plus froid en provenance du séparateur
primaire sur condensât produits V4- 1205 entre au sommet de la section
supérieure, Le rebouilleur E2-1203 fournit la chaleur nécessaire
pour entraîner les gaz légers au sommet de la colonne d'où
ils sont envoyés au réseau de gaz combustible sous contrôle
de pression de la colonne, Le liquide qui s'accumule au fond de la colonne
forme l'alimentation du Splitter dont le débit est contrôlé
par contrôle de niveau du fond de la colonne.
III.1.4.3. Le débutaniseur :
Le débutaniseur T6-1501, est une colonne conçue
pour séparer le propane et les fractions légères du butane
des fractions plus lourdes, Il constitue la dernière étape du
procédé de production de GPL pur où il reçoit deux
alimentations, l'une froide provenant du fond du déethaniseur et l'autre
chaude provenant du fond du stabilisateur.
Les utilités : air instruments, eau industrielle, azote et
une section fuel gaz. III.2. Description de la section
Boosting
Etant donne que la pression du gisement diminue, Le
rôle principal du Boosting c'est d'augmenter la pression du gaz venant du
slug cacher (séparateur primaire) à l'aide d'un compresseur, pour
revenir aux conditions de fonctionnement normal des trains, Un s
chéma bloc et une partie concerne la compression sont
représentés ci dessous [14]
- (voir annexe A,2);
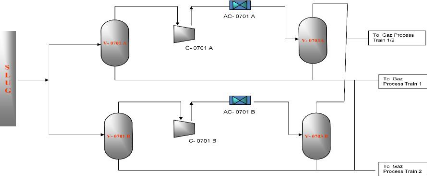
Figure 25 : Schéma bloc de la section
Boosting.
III.2.1. Rappel thermodynamique sur la compression
Le rôle d'un compresseur est d'augmenter
l'énergie de pression d'un gaz (comme pour une pompe pour un
liquide) ; l'énergie consommée est d'autant plus
élevée que le rendement du compresseur est faible.
Pour le compresseur, le rendement isentropique ne
permet pas de déterminer l'accroissement de
température de refoulement du aux imperfections, il est
nécessaire d'utiliser une autre référence que l'on appel
rendement polytropique.
?=Wp/Wi (III.1)
Avec : Wp : travail polytropique du compresseur
;
Wi : travail indiqué en bout d'arbre.
III.2.1.1. Détermination de la
température polytropique en fin de compression
Au lieu de l'exposant isentropique K, on utilise un exposant n
plus grand appelé exposant polytropique.
(n_1)
n
(k-1)
= (III.2)
(k.çp)
Soit : Tp = T1
(1,1,21)1('
(III.3)
Avec : K'=
(n-1)
n
,,, _ (K.çp) * (R.T1)
r(p2)(K_1)(K.çp
) - 1i
(III.4)
W v P -- (K_1) M L'.P1
Cependant,il y a quelques considérations à
prendre en compte pour le bon fonctionnement du compresseur afin
d'évietr d'endommager le compreseur,c'est la raison pour laquelle ,on
fait appel aux courbes de performance pour détérminer les
conditions critiques (vitesse critique ,zone de pompage ...),la plus commode de
ces courbes est illustrée dans la figure suivante [8] ;
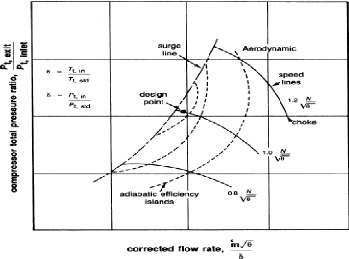
Figure 26: Courbe de performance typique pour un
compresseur.
La nouvelle section Boosting installée au niveau du GTFT
comporte les équipements suivants :
· Un ballon d'aspiration V-701 ;
· Un compresseur C-701 ;
· Aéroréfregirant AC-701 ;
· Ballon de refoulement V-703 ;
· Une vanne Joule-Thomson.
Le gaz issu du slug cacher est envoyé au V-701 ou
l'eau et les hydrocarbures sont récupérés du gaz ,le
compresseur centrifuge C-701 est conçu pour refouler à 80 (bar_
g); sous les conditions d'aspiration suivantes (pression minimale : 35(bar_g) ;
pression maximale : 52 (bar_g) , le refroidissement du gaz comprimé est
assuré par l'aéroréfrégirant AC-701 jusqu'à
50 °C ; le liquide formé au cours de refroidissement est
récupéré dans le séparateur V-703,et la pression du
gaz à l'entrée des trains est maintenue à 66 (bar_g) par
la nouvelle vanne Joule-Thomson ,et cela pour un fonctionnement normal de
l'usine [14],
ChapitreIV:
Simulation
IV.1. Présentation des simulateurs PRO II et
HYSYS
IV.1.1. Définitions
La simulation est définie comme étant la
représentation d'un phénomène physique à l'aide de
modèles mathématiques simples permettant de décrire son
comportement ,autrement dit, la simulation permet de représenter les
différents phénomènes : transfert de matière et de
chaleur, se dans les différentes opérations unitaires par
modèles thermodynamiques, qui traduisent leur comportement par
l'intermédiaire de résolution des équations
analytiques.
IV.1.2. Modèle thermodynamique?
Le modèle thermodynamique est composé par une
série d'équations développées dans l'objectif de
décrire le comportement d'un système en évolution
(opération unitaire : séparation de phases, fractionnement de
composants, compression, détente, échange de chaleur ...etc,),ce
sont des équations de conservation de masse, d'énergie et de
quantités de mouvement,ces équations peuvent être
algébrique ou différentielles.
Le développement de l'informatique dans le domaine de
simulation nous permet de résoudre le problème de calcul manuel
long, en utilisant comme outil les logiciels de simulation.
Le simulateur peut être utilisé lors de la
conception d'un procédé industriel afin de :
v' Etablir les bilans de matière et d'énergie ;
v' Dimensionner les équipements de ce
procédé ;
Ou bien dans le suivi des procédés
déjà existants afin de :
v' Réajuster les paramètres de fonctionnement
dans le cas de changement de composition
de l'alimentation ou les conditions de fonctionnement d'un
certain équipement ; v' Déterminer les performances des
équipements.
La structure générale du simulateur est la
suivante :
Banque de données des
propriétés physiques
Modèles thermodynamiques
Solution

Optimisation

Etude économique
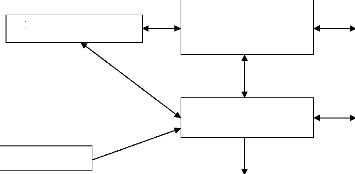
Modèles numériques
Données
Modèles des
opérations Unitaires
Interface d'utilisation
Figure 27 : Structure générale d'un
simulateur.
Les simulateurs existants tels que Aspen Plus, ChemCAD, HYSYS,
PRO II sont les plus vendus et qui deviennent de plus en plus indispensables
pour concevoir de nouvelles
unités et pour optimiser les procédés
industriels qui fonctionnent parfois loin de leur optimum [15].
Cela dit, les simulateurs HYSYS et PROII sont les plus
performants simulateurs utilisés dans l'industrie
pétrolière.
IV.1.3. Les simulateurs HYSYS et PRO II :
L'utilisation des simulateurs HYSYS et PROII se fait de la
façon suivante :
v' L'utilisateur doit spécifier les constituants du gaz,
du liquide ou du mélange; v' Il choisit un modèle thermodynamique
;
v' Il doit établir le schéma du
procédé (PFD) ;
v' Il doit aussi spécifier les paramètres
nécessaires pour le calcul de chaque opération unitaire ;
v' Le simulateur résout le schéma de
procédé ;
v' Le simulateur peut aussi dimensionner quelques
équipements.
Et pour la réalisation de celle-ci, HYSYS et PRO II
contiennent :
1' Une bibliothèque de modèle de calcul des
propriétés physiques et thermodynamique des corps purs et des
mélanges, couplée à une banque de données de corps
purs ;
v' Une bibliothèque de module standard de simulation des
opérations unitaires les plus couramment présentés dans un
procédé de fabrication;
1' Une bibliothèque de modules de méthodes
numériques algébriques ;
1' Une bibliothèque de modules de génération
de diagnostiques.
Étant donné que PRO II (Simulation Sciences Inc,)
et HYSYS (Hyprotech) ne sont pas délivrés par le même
fournisseur ; il est important de citer la légère
différence dans les bibliothèques des propriétés
physiques des corps purs, ainsi que les corrélations utilisées
pour le calcul des propriétés critiques des constituants purs.
A titre indicatif, le tableau 2 représente une
comparaison entre les deux bibliothèques pour quelques constituants purs
:
Tableau 2 : comparaison des propriétés
physiques de PRO II et HYSYS [16].
|
Poids moléculaire (kg/mol)
|
Masse volumique (kg/m3)
|
T ébullition (°C)
|
|
HYSYS
|
PRO II
|
HYSYS
|
PRO II
|
HYSYS
|
H2O
|
18,02
|
18,02
|
997,46
|
997,99
|
100
|
100
|
N2
|
28,01
|
28,01
|
807,96
|
806,37
|
-195,81
|
-195,8
|
CO2
|
44,01
|
44,01
|
816,43
|
825,34
|
-78,48
|
-78,55
|
C1
|
16,04
|
16,04
|
299,7
|
299,39
|
-161,49
|
-161,52
|
|
30,07
|
30,07
|
355,04
|
355,68
|
-88,6
|
-88,6
|
C3
|
44,1
|
44,1
|
505,79
|
506,68
|
-42,04
|
-42,1
|
nC4
|
58,12
|
58,12
|
584,34
|
583,22
|
-0,5
|
-0,5
|
|
Le tableau ci-dessous, illustre les propriétés
critiques (température et pression critiques);
ainsi que le facteur acentrique w; calculés à
partir des données (poids moléculaire et masse volumique dans cet
exemple) :
Tableau 3 : Comparaison des propriétés
critiques dans HYSYS et PRO II [16].
|
Tc (°C)
|
Pc (bar)
|
Facteur acentrique
|
|
HYSYS
|
PRO II
|
HYSYS
|
PRO II
|
HYSYS
|
H2O
|
373,98
|
374,15
|
220,55
|
221,2
|
0,3449
|
0,344
|
N2
|
-146,95
|
-146,96
|
34
|
33,94
|
0,0377
|
0,04
|
CO2
|
31,06
|
30,95
|
73,83
|
73,7
|
0,2236
|
0,2389
|
C1
|
-82,59
|
-82,45
|
45,99
|
46,41
|
0,0115
|
0,0115
|
|
32,17
|
32,28
|
48,72
|
48,84
|
0,0995
|
0,0986
|
C3
|
96,68
|
96,75
|
42,48
|
42,57
|
0,1523
|
0,1524
|
nC4
|
151,97
|
152,05
|
37,96
|
37,97
|
0,2002
|
0,201
|
|
L'utilisateur peut fonctionner le simulateur en mode
stationnaire (steady state) ou en mode dynamique (dynamic).
Les simulateurs ont été conçus pour
permettre le traitement d'une vaste gamme de problèmes allant des
séparateurs bi et tri phasiques simples jusqu'à la distillation
et la transformation chimique.
A titre d'exemple, l'interface du simulateur HYSYS pour la
production du propylène glycol est la suivante :
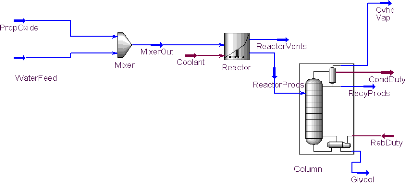
Figure 28 : L'interface du simulateur
HYSYS.
IV.2. Choix du modèle thermodynamique
Pour décrire le comportement des fluides réels
durant une chaine de transformations; nous faisons appel soit au facteur de
compressibilité, soit aux équations d'états [17].
IV.2.1. Utilisation du facteur de
compressibilité
Les différences de comportement entre un fluide
réel et un gaz parfait peuvent être mises en évidence en
suivant l'évolution du rapport du volume du fluide réel V
à celui du gaz parfait ??? en fonction des conditions
de pression et de température dans lesquelles se trouve le fluide .
Ce rapport noté Z set appelé facteur de
compressibilité.
?
? = (IV.1)
???
V Volume molaire du fluide réel
??? Volume molaire du gaz parfait
On sait que le volume d'un gaz parfait est donné par la
relation:
??
??? = (IV.2)
?
En conséquence:
??
? =
??
Soit :
?? = ???
Cette loi peut être qualifiée de loi des gaz
réels ,le facteur de compressibilité apparaissant comme
coefficient de correction à la loi des gaz parfaits ,quand le facteur de
compressibilité prend la valeur 1son comportement est identique à
celui du gaz parfait et cela intervient quand le fluide est un gaz à
très basse pression[17].
IV.2.2. Utilisation des équations d'état
:
Une autre voie permettant de résoudre le même type
de problème tout en étant plus adaptée aux calculs
numériques sur ordinateur s'est beaucoup développée, il
s'agit de l'utilisation des équations d'état.
IV.2.2.1. Equation de Van der Waals (1872) :
Les équations d'état ont pour objet de
représenter le comportement des fluides réels à l'aide
d'une expression mathématique ?(?, ? , ?) = 0 .
La plus ancienne est celle de Van der Waals (1872) qui modifie
la loi des gaz parfaits en y Introduisant deux termes correctifs :
-la pression du gaz parfait est réduite pour tenir compte
des forces de cohésion intermoléculaires existant dans les gaz
réels, celles-ci freinent les molécules qui créent en
conséquence une pression plus faible, le facteur correctif correspondant
appelé pression de cohésion est pris égal à
?/? ?, a étant une constante dépondant de la
nature du gaz et V étant le volume du gaz [1].
?????é?? = ? ??????????- ?/?2
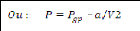
(IV.3)
(IV.4)
-le volume du gaz parfait est augmenté d'un facteur b qui
tient du volume propre des molécules du gaz réel dépend de
la nature du gaz et est appelé covolume.
L'équation d'état des gaz parfaits écrite
pour une mole de gaz
?????? = ??
Devient en conséquence
??+ ? ???(?-?)=??
|
Equation d'état de Van der Waals
|
|
IV.2.2.2. Equation de Redlich-Kwong(1949)
A partir de la fin du 19émée siècle et
jusqu'à l'époque actuelle de nombreuses équations
d'état sont apparues pour mieux représenter le comportement des
fluides réels : Clausius (1880), Berthelot(1900), Benedict-Webb-Rubins
(1940),Redlich-Kwong ,etc, cette dérniere, l'équation
d'état de Redlich-Kwong est apparue en 1949 et possède une forme
assez voisine de celle de l'équation de Van der Waals[1] .
Équation d'état de Redlich-Kwong:
|
|
|
Cette équation empirique a connu depuis son origine,
plusieurs centaines de modifications qui visent à la rendre plus
performante, les formes les plus récentes (Soave Redlich Kwong, peng
Robinson) sont très utilisées dans tous les programmes de calcul
des propriétés thermodynamiques des fluides.
Dans le cas d'un corps pur, les paramètres a et b peuvent
être à partir de ses conditions critiques Tc et Pc.
???
? = 0.0867 ? = 0.4278
??
|
?? ?? ?.?
|
|
|
????
a et b étant déterminés, l'équation
d'état permet également de calculer ??= le
??
facteur de compressibilité critique ,la valeur obtenue
??= 1/3 est trop élevée par rapport à
celles fournies par l'expérience qui sont comprises le plus souvent
entre 0,27 et 0,29 ,ce décalage montre que le comportement des fluides
réels est assez mal représenté par cette équation
d'état au voisinage du point critique.
L'utilisation de l'équation d'état est rendue plus
agréable en procédant à des changements de variables.
??
En introduisant le facteur de compressibilité ?
= l'équation d'état de Redlich Kwong est
??
?
? =
????
transformée en une équation du troisième
degré en Z que l'on présente souvent de la manière
suivante[1].
(IV.6)
Dans cette équation A et B sont des constantes qui
dépendent de la nature du corps et des conditions opératoires.
? =
? 0.0867
=
?? ????
?
? = ? ? = 0.6542
?.? ????.?? ?? ?.????
IV.2.2.3. Équation de Peng-Robinson (1976)
Cette équation diffère de l'équation de
Redlich-Kwong par l'introduction d'une fonction a(T) qui dépend
du facteur acentrique.
Elle a été introduite en vue d'améliorer
les résultats obtenus par l'équation de Soave (1972), notamment
en ce qui concerne le calcul des densités en phase liquide, sans
modifier le nombre de paramètres [1]:
(IV.7)
R
P = T
V--b
|
a(T)
V(V+b)+b(V--b)
|
|
Les termes a(T) et b sont définis par
les relations suivantes :
R2V
a = 0.45724 - a(TR)
PC
a(TR) = [1 + m (1 --1/TR
)]2
m = 0.37464 + 1.52260) --
0.269920)2
PC
b = 0.0778 RTC
Ces équations sont très largement utilisées
dans les modèles de simulation, en production et traitement de gaz
naturel [1] .
IV.2.3. Etendue d'utilisation des équations
d'état
L'intérêt des équations d'état ne
réside pas uniquement dans leurs capacité à fournir les
propriétés de volume des fluides, Elles constituent en fait un
outil de base à partir duquel on peut déterminer :
-les volumes ou les masses volumiques des phases vapeur et
liquide, la représentation correcte du volume de la phase liquide est un
des progrès apporté par les nouvelles équations type SRK
ou PR.
-les tensions de vapeur
-les équilibres liquide - vapeur par
l'intermédiaire des coefficients de fugacité -l'enthalpie des
fluides réels à partir des l'enthalpie du même fluide
considéré comme gaz parfait
-l'entropie par la même approche
Il n'existe pas actuellement une équation
d'état capable de donner des résultats excellents pour toutes ces
propriétés et pour tous les fluides ,une bonne précision
peut toutefois être espéré quand on se trouve dans le
domaine de meilleure validité d'une équation proposée
[3].
IV.2.4. Recommandations des modèles
L'utilisateur peut choisir, selon la composition du
mélange et les conditions de température et de pression, entre
une équation d'état (PR, SRK, Lee Kesler ...,), un modèle
d'activité (NRTL, UNIQUAC, Van Laar, Wilson...,,), un modèle de
Chao-Seeder
Ou un modèle de pression de vapeur, dans le tableau
suivant quelques modèles sont présentés pour l'utilisation
d'un tel modèle [15].
Tableau 4 : Les modèles recommandés dans
un simulateur [15].
Type de système
|
Modèle recommandé
|
Distillation atmosphérique (Topping)
|
PR
|
Déshydratation TEG
|
PR
|
Eau dure
|
PR, Sour PR
|
Cryogénie et traitement des gaz
|
PR, PRSV
|
Séparation de l'air
|
PR, PRSV
|
Colonnes sous vide
|
PR, PR Option, GS (<10 mmHg)
|
Système à H2 élevé
|
PR, ZJ ou GS
|
Système réservoir
|
PR, PR Options
|
Vapeur d'eau
|
Stream package, CS ou GS
|
Systèmes chimiques
|
Modèles d'activité, PRSV
|
Inhibition d'hydrate
|
PR
|
Alkylation à HF
|
PRSV, NRTL
|
Déshydratations au TEG avec aromatiques
|
PR, Amine
|
Systèmes HC ou la solubilité de l'eau est
importante
|
Kabadi Danner
|
|
IV.2.5. Choix d'un modèle thermodynamique
Les modèles thermodynamiques ont fait l'objet de nombreux
travaux en vue d'accroitre leurs précisions et d'étendre leurs
domaines d'utilisation.
Le choix d'un modèle thermodynamique est
délicat car il doit aboutir à une méthode relativement
validée dans les conditions du procédé (conditions
opératoires, nature des fluides étudiés...).
La figure ci-après constitue une première
approche de base pour le choix du modèle thermodynamique, qui doit
être complétée et nourrie par l'expérience
industrielle propre à chaque projet [17].
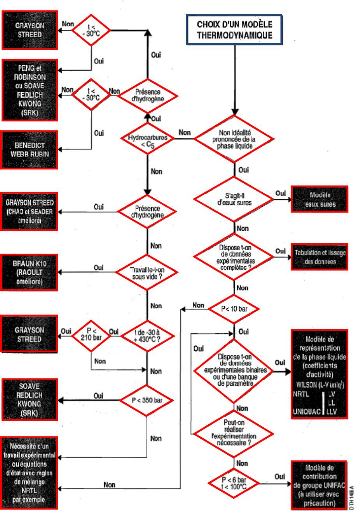
Figure 29: Le choix du modèle thermodynamique
[17].
Noter que les modèles thermodynamiques les plus
utilisés dans le domaine de traitement de gaz naturel sont Soave Redlich
Kwong (SRK) et l'équation de Peng Robinson (PR), parce que le domaine
d'application de ces équations d'état (en terme de pression et de
température), est compatible avec le cas de l'usine GTFT (pression
entrée trains P=65(barg), température au niveau du
séparateur primaire slug catcher T=44 °C).
Le tableau suivant montre le domaine d'application des deux
équations d'état : Tableau 5: Le domaine d'application de
PR et SRK [15].
Modèle thermodynamique
|
Température °C
|
Pression (bar)
|
PR
|
|
> -271
|
<
|
1000
|
SRK
|
>
|
-143
|
<
|
350
|
|
IV.3. La simulation d'un train de traitement de gaz
GTFT:
La procédure suivie pour la simulation, consiste
à faire en première étape une simulation comparative du
procédé de traitement par les deux simulateurs PRO II et HYSYS
(le reste de simulation est fait par HYSYS).
Ensuite, nous basculons vers la simulation d'un cas réel
qui correspond à une journée de fonctionnement choisie
arbitrairement.
Une fois la simulation du cas réel est validée, et
en intégrant la nouvelle section de Boosting, nous vérifions les
modifications qui résultent de cette intégration.
IV.3.1. Le cas design
L'usine du GTFT a été conçue pour avoir une
expédition de 18000 KNm3/j en gaz sec, les
spécifications sur les produits sont les suivantes :
Gaz sec:
Humidité : 50 ppmv max
Température : 60 °C
Pression : 71 barg max dans le pipeline
GPL:
- : 3,0 mol% max
C5+ : 0,4mol % max
Récupération GPL : >75,1 mol
% Condensat :
TVR : 10 pisa max
Récupération C5+ : > 98,07 mol %
Pression : 31 barg max dans le pipeline
Une comparaison entre la simulation par HYSYS et les
résultats obtenus par PRO II (simulation faite par KBR, bureau
d'engineering américaine) ; va nous permettre de caller notre simulation
avec le design; et cela en se mettant dans les mêmes conditions
opératoires du design (pression, température, débit et
composition), ainsi que le même modèle thermodynamique
utilisé par KBR pour la simulation: Soave Redlich Kwong (SRK), (voir
tableau 5), Les tableaux suivants montrent les produits finis en termes de
quantité et de qualité (modèle thermodynamique: SRK)
Tableau 6 : Comparaison des quantités produites
(cas design).
Quantités produites
|
HYSYS
|
PRO II
|
Erreur relative %
|
Gaz sec (KNm3/j)
|
8956
|
8968
|
0,13
|
GPL(T/j)
|
1277
|
1279
|
0,15
|
Condensat(T/j)
|
1424
|
1411
|
0,92
|
|
Tableau 7 : Spécifications des produits pour le
cas design,
Spécifications
|
HYSYS
|
PRO II
|
Humidité % mol (gaz sec)
|
2,85E-005
|
3,07 E -003
|
- % mol (GPL)
|
2,57
|
2,53
|
C5+% mol (GPL)
|
0,26
|
0,33
|
Taux de récupération GPL
% mol
|
75,66
|
75 ,75
|
TVR (condensat) psia
|
8,69
|
8,34
|
|
Nous remarquons que les produits sont on
spécifications (% - GPL< 3, %C5+ GPL <0,4 et
TVR du condensat < 10 psia ) , et l'erreur relative sur les quantités
des trois produits est inferieur à 1 % .
La différence que donne le simulateur HYSYS par rapport
au PRO II est expliquée par:
la différence entre les bases de données
(propriétés physiques et chimiques des corps purs), pour les deux
simulateurs (un exemple sur les propriétés physiques de quelques
corps purs est illustré dans les tableaux 2 et 3).
IV.3.2. Le cas actuel
Dans le but de valider la simulation avec la marche actuelle
de l'usine, cette simulation est envisagée en comparant les
résultats des quantités produites avec le bilan journalier du 26
février 2009 (voir annexe A,3); les paramètres opératoires
sont retenus des prélèvements des opérateurs pour la
journée concernée.
Noter que le modèle thermodynamique utilisé
pour le reste de la simulation est Peng Robinson (PR),puisque le domaine
d'application de cette équation est bien adéquat avec le cas du
train de traitement GTFT (voir tableau 5) ;en plus ,les améliorations
apportées par Hyprotech à cette équation d'état lui
permettre d'être très fiable pour une variété de
système sur un large domaine de conditions ,elle résout
rigoureusement tous les systèmes composés d'une seule phase ,bi
phasique ou tri phasique avec haut degré d'efficacité et de
précision.
Ci-dessous les paramètres de marche du train 1, ainsi que
les quantités produites en gaz sec, GPL et Condensat issus de la
simulation comparés avec la marche usine.
Tableau 8 : Les paramètres de marche usine (cas
actuel).
Paramètres de marche
|
Cas simulation
|
Marche usine
|
Erreur relative %
|
Température °C sortie E2-1002/1003
Coté tubes
|
23,18
|
23 ,29
|
0,47
|
Température °C
sortie E4-1301/1302
|
-19,00
|
-18,75
|
1,33
|
Température °C
sortie Expandeur
|
-63,18
|
-62,75
|
0,68
|
Pression (bar_g) sortie Expandeur
|
19,52
|
19,30
|
1,13
|
Température (°C)
fond Déethaniseur
|
84,74
|
83,25
|
1,78
|
Température (°C)
fond Debutaniseur
|
203,00
|
202,00
|
0,49
|
Température (°C)
fond Stabilisateur
|
161,64
|
160,25
|
0,86
|
|
Tableau 9 : Les quantités produites pour le cas
actuel.
Quantités produites
|
Cas simulation
|
Marche usine
|
Erreur relative %
|
Gaz sec (KNm3/j)
|
19041
|
19041
|
0,00
|
GPL(T/j)
|
2724
|
2724
|
0,00
|
Condensat(T/j)
|
2498
|
2447
|
2,08
|
|
Tableau 10 : Les spécifications des produits
(cas actuel).
,
Spécifications
|
Cas simulation
|
Marche usine
|
Humidité (gaz sec) ppm
|
4,33
|
6,00
|
- (% mol) GPL
|
1 ,25
|
1,87
|
C5+ (% mol) GPL
|
0,19
|
0,14
|
Taux de récupération GPL (%
mol)
|
76,87
|
76,39
|
Taux de récupération
C5+ (% mol)
|
98,26
|
98,55
|
TVR (condensat) psia
|
8,69
|
8,30
|
|
La simulation est callée avec la marche usine pour les
paramètres opératoires, les spécifications des produits
sont toujours respectées (% - GPL< 3, %C5+ GPL
<0,4 et TVR du condensat < 10 psia), et l'erreur relative pour les
quantités produites en gaz sec et en GPL est inférieure à
1%, tandis que l'erreur relative pour la quantité du condensat est de
l'ordre de 2,08%, cette différence acceptable en quantités serait
due éventuellement aux pertes.
IV.3.3. La baisse de pression (sans Boosting):
Sachant que le gisement va connaitre une
déplétion (à raison de 5 à 6 barg par an à
partir de 2010) ; et si le projet de Boosting est repoussé, une
simulation pour la baisse de
production.
pression s'avère nécessaire afin de voir
son impact sur la
Pour des conditions opératoires de l'alimentation
de la journée traitée précédemment
; les résultats de la baisse de pression sont les suivants
:
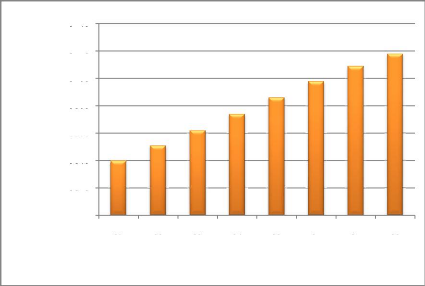
production gaz sec ( KNm3/j )
19140
19120
19100
19080
19060
19040
19020
19000
67 66 65 64 63 62
Pression entrée usine (barg)
61 60
Figure 30 : Impact de la baisse de pression sur la
production du gaz sec.
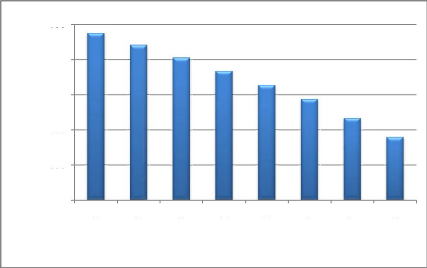
production GPL ( T/J )
2750
2700
2650
2600
2550
2500
67 66
Pression entrée usine (barg)
65 64 63 62 61
60
Figure 31 : Impact de la baisse de pression sur la
production du GPL.
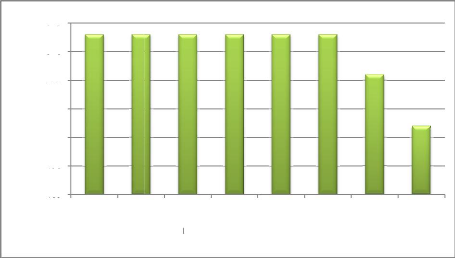
Production condensat ( T/J)
2515
2510
2505
2500
2495
2490
2485
67 66 65 64 63 62
Pression entée usine (barg)
61 60
Figure 32 : Impact de la baisse de pression sur la
production du condensat.
Nous remarquons que la production du GPL est touchée
considérablement par la baisse de pression au profit de la production en
gaz sec, tandis que la production du condensat ne subit de variations que pour
des basses pressions (61 barg et 60 barg) ; pour cela il est nécessaire
de voir l'influence de la baisse de pression sur le taux de
récupération de GPL (en considérant toujours que la
température du gisement est de 44 °C).
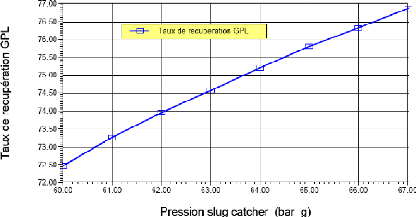
Figure 33: L'influence de la baisse de pression sur le
taux de récupération en GPL.
De la figure précédente, nous constatons que si
l'usine fonctionnera à 61(barg), le taux de récupération
de GPL diminue de 1,93 % par rapport aux conditions de design, ce qui fait une
perte de production de 64,8 (T/j), en GPL, L'équivalent de 32400
$/J.
A partir de ces résultats, la nécessité
d'installer une section Boosting s'avère nécessaire : projet
étude et réalisation par TR (Bureau
d'engineering espagnole).
IV.4. Simulation d'un train de traitement de gaz avec
l'intégration de Boosting
L'intérêt de la section Boosting c'est de
revenir aux conditions de design (pression entrée trains 65 barg) ;afin
de permettre un bon fonctionnement des trains et une stabilisation de taux de
récupération pour le GPL.
Le bureau d'engineering TR a proposé, au cours se son
étude de Boosting, certaines DMI (Demande Modification Installation)
(voir annexe A,4), et des raccordements d'équipements dans le but
d'assurer une bonne marche pour les trains ,et cela après
l'intégration du Boosting entre autre :
· Réalisation d'une modification pour l'appoint de
reflux issu du V4-1205 vers le stabilisateur, du ballon V4-1204 ;
· Installation de l'échangeur E2-1208, pour
refroidir le condensat vers les bacs de stockage ;
· Une DMI concernant la boucle d'huile dans le rebouilleur
du déethaniseur E4-1402, suite à l'arrivée importante du
liquide du ballon V4-1303 vers le déethaniseur. Ces trois modifications
vont être vérifiées par le biais du simulateur HYSYS.
IV.4.1. Le reflux du stabilisateur :
Pour décrire le comportement du stabilisateur T4-1202,
il est nécessaire de voir le comportement de son alimentation avec la
baisse de pression, sachant que le stabilisateur est alimenté par 2
courants :
v' Un courant liquide issu du slug catcher qui passe par le
ballon séparateur V4-1204;
v' Un courant liquide issu du ballon V4-1205, ce dernier est
alimenté par le ballon V4- 1004.
Pour l'étude de reflux vers le stabilisateur, deux
scénarios seront présentés :
· Un scénario 2012 (pression de slug catcher: 63-51
barg) ;
· Un scénario 2015 (pression de slug catcher: 50-35
barg).
En travaillant avec une température du slug catcher: 50
°C, un débit de gaz brut de
17956 (kgmol /h) (par train), et en attribuant à chaque
scénario la composition correspondante.
IV.4.1.1. Scénario 2012
Le tableau suivant montre l'évolution de l'alimentation
de la colonne de stabilisation avec la baisse de pression :
Tableau 11 : L'alimentation du stabilisateur pour le
scénario 2012.
Pression au slug catcher (bar_g)
|
63
|
61
|
59
|
57
|
55
|
53
|
51
|
Quantité liquide issu du
V4-1205 (kg/h)
|
8093
|
8591
|
9091
|
9590
|
10091
|
10593
|
11100
|
Quantité liquide issu du
V4-1204 (kg/h)
|
37909
|
37415
|
36920
|
36423
|
35921
|
35413
|
34895
|
|
En baissant en pression de 63 à 51 barg ; la
quantité liquide issue du slug catcher diminue (moins de condensation
des lourds avec des pressions basses ),ce manque en liquide qui va se
présenter au niveau du ballon V4-1204, va être compensé en
premier lieu par une augmentation de reflux issu du ballon V4-1205, et une
augmentation du quantité liquide au niveau du ballon V3-1303,qui sera
présenté dans la modification de la boucle d'huile.
IV.4.1.2. Scénario 2015
Le comportement de l'alimentation du stabilisateur de condensat
pour ce scénario est présenté par le tableau ci-dessous
:
Tableau 12 :L'alimentation du stabilisateur pour le
scénario 2015.
Pression au slug catcher (bar_g)
|
50
|
47
|
44
|
41
|
38
|
35
|
Quantité liquide issu du V4-1205
(kg/h)
|
11152
|
11244
|
11426
|
11728
|
12168
|
12764
|
Quantité liquide issu du V4-1204
(kg/h)
|
34799
|
34448
|
33996
|
33435
|
32756
|
31951
|
|
De même, pour le scénario 2015, la diminution du
liquide dans le ballon V4-1204 au cours de la baisse de pression au slug
catcher de 50 à 35 barg est traduit par l'augmentation du reflux dans le
ballon V4-1205.
Nous constatons donc que la baisse de pression au niveau du
slug catcher engendre une augmentation de reflux de la colonne de
stabilisation, contrairement aux résultats du bureau d'engineering.
IV.4.2. L'échangeur E2-1208 :
Etant donné que le condensat (produit fini), doit
être stocké à une température de 48°C, il est
nécessaire de voir la variation de la température du condensat
vers stockage à la sortie de l'échangeur E2-1207,pour cela, en
prenant la température au niveau du slug catcher de 50 °C, avec une
baisse de pression de 63 à 51 (barg) , les résultats sont
présentés dans le tableau suivant :
Tableau 13 : Les températures à
l'entée et à la sortie du E2-1207.
Pression du slug catcher (barg)
|
63
|
61
|
59
|
57
|
55
|
53
|
51
|
Température entrée E2-1207
(°C)
|
44,07
|
44,51
|
44,93
|
45,33
|
45,72
|
46,08
|
46,43
|
Température condensat à
stocker sortie E2-1207 (°C)
|
50,91
|
51,18
|
51,44
|
51,78
|
52,03
|
52,261
|
52,48
|
|
Nous remarquons qu'avec la baisse de pression, la
température du condensat qui arrive à l'échangeur E2-1207
provenant du ballon V4-1204 est de plus en plus élevée, ce qui
conduit à une consommation moindre de calories pour maintenir la
température du condensat vers la colonne de stabilisation T4-1202
à 47°C ,et c'est la raison pour laquelle la température du
condensat à stocker sera supérieure à 48°C.
D'où la proposition d'installer un nouveau
échangeur E2- 1208 en série avec
l'échangeur E2- 1207, (dont l'alimentation en frigories
du gaz provenant du E4 -1301(voir l'annexe A, 4) , pour
refroidir le condensat vers st ockage à moins de
48°C(figure 34),

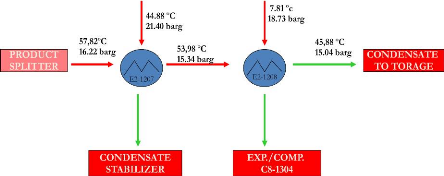
Figure 34 : L'emplacement de l'échangeur
E2-1208,
Le tableau suivant montre l'évolution de la
température du condensat à stocker à la sortie
due l'échangeur E2- 1208
Tableau 14 : La température du condensat so rtie
E2 -1208.
Pression du slug catcher (bar_g)
|
63
|
61
|
59
|
57
|
55
|
53
|
51
|
Température condensat à stocker
sortie E2-1208 (°C)
|
44,97
|
45,21
|
45,43
|
45,73
|
45,93
|
46,12
|
46,30
|
|
A travers ces résultats, l'échangeur
E2 condensât vers stockage à moins de
48°C .
- 1208 répond aux exigences en refroidissant
le
IV.4.3. La boucle d'huile du rebouilleur E4-1402 :
La boucle d'huile représente la circulation du fluide
caloporteur qui est utilisé à différentes étapes du
process par les rebouilleurs des colonnes E2-1203 ; E2-1402 et E2- 1502, ainsi
que l'échangeur E2-1104 (boucle de régénération)
(voir l'annexe A,5).
L'huile (Therminol 66), subit un chauffage au des
récupérateurs de chaleur H4-5201A/B jusqu'à 290°C,
cette quantité (700 m3/h pour un train) sera partagée
en trois :
· Une quantité de 335m3 /h passe dans
l'échangeur de régénération E2-1104 ;
· Une quantité de 65 m3/h, passe dans le
rebouilleur du stabilisateur E2-1203 ;
· Une quantité de 300 m3/h, passe d'abord
par le rebouilleur du débutaniseur E2-1502, puis
54 m3/h qui passe par le rebouilleur du deethaniseur
E2-1402.
Pour l'étude de la boucle d'huile, le scénario
2012 est envisagé, dont la pression du slug catcher varie de 63
jusqu'à 51 barg, et une température de 50 °C ; et cela en
travaillant avec un débit de gaz brut de 17956 kg mol/h (par train), et
une composition qui correspond à ce scénario.
Le tableau ci-dessous illustre le comportement de l'alimentation
liquide du deethaniseur T6-1401 avec la baisse de pression :
Tableau 15 : La quantité liquide du
deethaniseur T6-1401 avec la baisse de pression.
Pression Slug Catch (barg)
|
|
|
|
|
|
|
|
|
63
|
61
|
59
|
57
|
55
|
53
|
51
|
Quantité liquide vers
deethaniseur
|
|
|
|
|
|
|
|
|
73382
|
73876
|
74038
|
74521
|
74813
|
74975
|
75277
|
T6-1401(kg/h)
|
|
|
|
|
|
|
|
|
La baisse de pression du gaz à l'entrée du slug
cacher ,de 63 à 51 barg ,entrainera une augmentation de la
quantité liquide provenant du ballon de flash V3-1303 (voir tableau 15),
qui représente l'alimentation liquide pour le déethaniseur
T6-1401, cet excès en liquide exige un apport de chaleur plus important
que la quantité de chaleur maximale fournie par le rebouilleur du
deethaniseur E2-1402 dans la feuille de données (datasheet) de cet
échangeur (voir l'annexe A.6).
Un tableau comparatif de la quantité de chaleur
échangée dans le rebouilleur E4-1402 pour ce scénario
comparée avec la quantité de chaleur du rebouilleur E4-1402
donnée par la feuille de données est présenté
ci-dessous :
Tableau 16 : La quantité de chaleur
échangée dans le rebouilleur E4-1402.
comparaison des quantités de
chaleur
|
|
|
|
échangées
|
Feuille de
|
Simulation
|
|
(109cal/h)
|
données
|
design
|
2012
|
E2-1402/2404
|
4,75
|
4,30
|
|
|
|
Ce tableau montre la nécessité de faire un
apport supplémentaire de chaleur pour le rebouilleur du
déethaniseur E4-1402, par le biais d'un by pass au niveau du collecteur
principal, et cela pour augmenter la température d'huile à
l'entrée du rebouilleur E4-1402 (Figure 35).
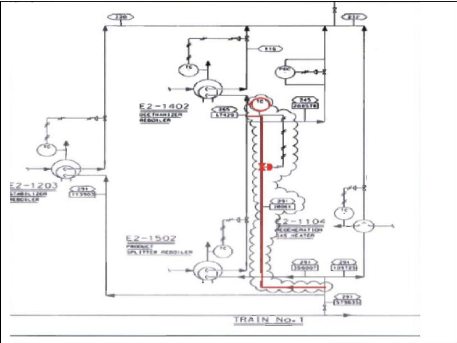
Figure 35 : La modification apportée à
la boucle d'huile.
IV.5. Etude technico économique du projet
Boosting
Le développement à grande échelle d'un
tel projet doit avant tout obéir à certaines règles,
notamment la rentabilité économique présente et future,
L'étude technico-économique deviendra obligatoire pour juger
d'une part, de l'utilité d'un tel investissement et d'autre part, de sa
rentabilité économique vis-à-vis d'autres solutions [18],
Il est nécessaire d'effectuer une analyse économique convaincante
selon les méthodes les plus pertinentes, la présentation de
certaines définitions et formules financières seront d'une
utilité certaine.
IV.5.1. Les critères de choix d'un
investissement
Financièrement, un projet d'investissement se
présente comme une opération qui, en contrepartie de
dépenses immédiates, procure des avantages futurs,
Les critères de choix d'investissements les plus souvent
rencontrés sont :
· D'abord et avant tout la valeur actuelle nette (VAN) qui
mesure la création de valeur engendrée par l'investissement.
· Le taux de rentabilité interne (TIR) qui mesure le
taux de rentabilité actuariel de l'investissement.
IV.5.1.1. La valeur actuelle nette (VAN)
La valeur actuelle nette d'un projet d'investissement est
égale à la différence entre la valeur actuelle des
rentrées nettes de trésoreries associées au projet et la
dépense initiale du projet, l'actualisation étant faite à
un taux (a) choisi en relation avec le taux minimum de rentabilité. La
détermination de la VAN d'un investissement appelle les étapes
suivantes [19]:
1. Fixer le capital investi (I)
n
R
2. Faire la somme des cash-flows actualisés nets ( )
i
i
?= +
1 a
i 1
3. Fixer le taux d'actualisation (a)
On a :
n R
B 0 VAN I
( ) = = -- + (IV.8)
0 ?= + i
( ) i
1 a
i 1
i= 1,n n étant la durée de vie du projet
a : taux d'actualisation ; Ri : recettes.
Tout projet d'investissement ayant une valeur actuelle nette
positive est rentable [19], Le choix entre plusieurs variantes rentables d'un
même projet, se portera normalement, à dimension et durée
identiques des variantes, sur celle dont la valeur actuelle nette est la plus
élevée.
IV.5.1.2. Le taux interne de rentabilité (TIR :
r)
Le taux interne de rendement d'un projet d'investissement est
le taux r pour lequel la valeur actuelle des rentrées nettes de
trésoreries associées au projet est égale à la
dépense initiale d'investissement [18][19]; ce taux interne de rendement
peut être calculé à partir de l'équation suivante
:
n R D
i - i
Si. B I
= -- + =
0 = ( ) i
1 + a
i 1
Rj : recettes
Dj : dépenses
a : taux d'actualisation I0 : investissement initial.
|
0 (IV.9)
|
I0
|
?
|
n
??
i 1
|
n
? ? ?
( ) ?
1 1
R D
-- a ?
i i = R * ?
(IV.10)
( ) i
1 + a a
? ?
|
Comme a= r, l'équation (VI.10) devient :
I -- +
( ) ? n
0 ? 1 1 r (IV.11)
R r
Si, n tend vers le long terme( n -* oo) ,
l'équation (1,8) devient :
R
r ? (IV.13)
I0
Avec R : recettes nettes
J0 : investissement initial
Le caractère rentable ou non rentable d'un projet
dépend, dans le cas où ce critère est retenu, de la
position relative du taux interne de rendement du projet et du taux minimum de
rentabilité exigé pour cet investissement [19], Entre plusieurs
variantes comparables (même durée de vie) et rentables d'un
même projet d'investissement, la variante retenue sera celle dont le taux
interne de rendement est le plus élevé [19].
Si a<r, le bénéfice est positif, ce qui donne un
investissement rentable.
Si a>r, le bénéfice est négatif, ce qui
donne un investissement non rentable, comme le montre la figure suivante :
B VAN > 0 VAN < 0

Projet Retenu
Projet rejeté
r
Figure 36 : Rentabilité d'un
investissement.
IV.5.2. Etude de la rentabilité du projet
Boosting
Les prix des équipements ainsi que le cout total de
l'unité Boosting sont présentés dans le tableau ci-dessous
:
Tableau 17 : Prix des équipements du
Boosting.
NB: 1 $ = 72,00 DZD
|
Valeurs en DZD
|
Valeurs en $
|
Compresseur
|
80000000,00
|
1110000,00
|
Pièces détachées
|
90000000,00
|
1250000,00
|
Nouvelle vanne J-T
|
50000000,00
|
694000,00
|
Tuyauterie
|
1100000000,00
|
15278000,00
|
Ballons,1208,aero
|
100000000,00
|
1388000,00
|
Total
|
1420000000,00
|
19720000,00
|
Donc, l'investissement initial I0 du projet Boosting est
évalué à 19720000,00 $. IV.5.2.1. Calcul de la
VAN
Pour calculer les cash-flows, il faut évaluer les recettes
Ri , la durée de vie du projet i et le taux d'actualisation a.
Recettes Ri
Le gain en production après la mise en service du
Boosting est localisé dans la production du GPL, car son taux de
récupération va être 78% (au lieu de 77% actuellement), ce
qui est traduit par un gain de 32 T/J en GPL.
Sur un an nous avons : 32*365=11680 T/an. Avec le prix de 500 $
/T de GPL, la recette Ri est :
· Ri =11680* 500 =5840000 $/an,
· i = 10 ans (la durée du vie du projet)
· a = 10 % (taux d'actualisation estimé), La VAN est
calculé par la relation VI, 8:
VAN = 2795782 > 0 d'où la rentabilité du
projet.
IV.5.2.2. Calcul du TIR
Le taux interne de rendement peut être calculé
à partir de la relation VI, 13 (car la durée de vie est
relativement longue):
TIR = 3 %
Avec : R = Ri*10 = 5840000*10 =58400000 $. I0 = 19720000 $.
Finalement, l'investissement mobilise très souvent
d'importants moyens financiers, Cette situation implique qu'un investissement
ne peut se réaliser sans étude préalable entraînant
des hypothèses et des choix, Du point de vue financier, un
investissement englobe toute dépense qui générera des
revenus, ou réalisera des économies, sur les périodes plus
ou moins longues, et qui est capable d'assurer sa remboursabilité,
Aussi, réaliser un investissement ne se limite pas seulement à
mobiliser les moyens financiers nécessaires à l'achat des
équipements et autres moyens, mais englobe également, la
mobilisation de moyens financiers supplémentaires, en particulier pour
l'exploitation du projet.
Conclusion
Enfin, le gaz naturel occupe une position très importante
dans l'ensemble des énergies fossiles, vu la facilité de son
exploitation et son large domaine d'utilisation.
Nous avons vu aussi que le traitement du gaz naturel
notamment le gaz humide se focalise sur la valorisation de la fraction liquide
(GPL et Condensat), et cela en utilisant des outils de fractionnement par
réfrigération tels que la boucle de réfrigération
extérieure (le cas du procédé PRICHARD), ou bien
l'utilisation d'une turbine d'expansion appelée turboexpander (le cas du
procédé HUDSON).
Ces outils sont caractérisés par un taux de
récupération de GPL (qui est saturé dans le gaz brut),
très important. C'est ce qui était remarqué à
travers l'exemple du centre de production GTFT qui utilise le turboexpander
afin d'avoir une récupération en GPL plus que 75%.
L'épineux problème qui affronte les exploitants
au niveau du GTFT c'est la déplétion du gisement, cette
dernière se manifeste sur la production de façon
générale, plus particulièrement sur la
récupération du GPL, pour palier à ce problème,
GTFT a lancé un projet d'une nouvelle section de Boosting (une section
placée en amont de chaque train), afin d'assurer le bon fonctionnement
des trains et une récupération optimale du GPL.
Durant cette étude, nous avons appris à
manipuler avec des outils de simulation récents tels que PRO II et
HYSYS, pour éviter le problème de calcul manuel long, notamment
la résolution des bilans de matière et de chaleur, et cela pour
un large domaine de paramètres opératoires entre autre :
· Le cas design (où nous avons pu comparer les
résultats obtenus par les deux simulateurs), pour voir l'ordre de
grandeur que donne HYSYS par rapport au PRO II ;
· Le cas réel, qui correspond à une
journée de fonctionnement choisie arbitrairement afin de caller la
simulation de HYSYS avec la marche usine ;
· Une simulation, toujours avec HYSYS, a
été envisagée cette fois ci pour voir l'impact de la
déplétion de gisement sur la production et sur le taux de
récupération de GPL et cela si le projet Boosting a
été repoussé.
Le bureau d'engineering chargé de l'étude et de
la construction du Boosting a proposé, au cours de son étude, des
modifications a apportées au projet telles que : une modification
concernant le reflux du stabilisateur, une autre pour la boucle du fluide
caloporteur et la dernière qui consiste à ajouter un nouveau
échangeur pour refroidir le condensat à stocker (ces
modifications ont été vérifiées par le biais de la
simulation avec HYSYS).
Finalement, il faut noter que les modifications
apportées par le bureau d'engineering à l'usine GTFT après
la mise en service du Boosting sont justifiées (l'échangeur
E2-1208 et la boucle d'huile), à l'exception de celle de reflux du
stabilisateur T6-1202.
Cette étude mérite d'être poursuivie pour une
plus grande affinité de simulation concernant, par exemple, un bilan
énergétique détaillé pour la boucle du fluide
caloporteur.
Références bibliographiques
1- A.POJEY, B.DURAND, C.JAFFRET, S, JULLIAN, M.VALLAIS.Le gaz
naturel production traitement transport .pp :253-310.Ed Technip Paris 1994.
2- J.KIDNAY, R.PARRISH. Fundamantals of natural gas processing,
pp :165-203. Ed CRC Taylor and Francis , 2006.
3-S.MOKHATAB, A.POE, G.SPEIGHT. Handbook of natural gas
transmission and processing. pp : 365-372. Ed GPG Gulf Publications.2006.
4- M.MEYER, G.RENESME, Les procédés de
séparation par prméation gazeuse à travers des membranes
polymères organiques, Recueil des communications du
18ème congrès du gaz .pp :3-54, Montpelier, 1991.
5- P.WUITHIER. Le pétrole raffinage et génie
chimique, Tome 2. 2ème édition, publications de
l'institut français du pétrole ,Ed Technip , Paris 1974.
6-
www.wikipédia.com
7- ATG, Le traitement du gaz naturel sur gisement, Association
technique de l'industrie du gaz en France .p :112.1988.
8- GPSA. Engineering data book, Vol.2, section:
19,21.10ème édition .Ed Gas processors association.1987.
9- Gas Conditionning and processing,
10- GTFT, Département Gisement. Hassi Messoud 2009.
11- GTFT, Département Exploitation (XP) , service process
2009.
12- GTFT, Département Engineering et Production (EP),
service puits 2009.
13- Manuel opératoire d'exploitation usine GTFT.
14- Manuel opératoire d'exploitation (section Boosting
),Révision n° :5 ,Mars 2009.
15- N.REBAI. Simulation des procédés ,initiation
au simulateur HYSYS,IAP (école de Boumerdès ,2008.
16-Initiation aux simulateurs HYSYS et PRO II, JGC, 2004.
17- Introduction à l'utilisation des modèles
thermodynamiques .ENSPM formation industrie .IFP training 2006.
18- B.Bouzidi et al, "Analyse micro économique des
systèmes énergétiques - Station de
pompage, " ICPEW, Tlemcen, Algérie 2004.
19- M. Boubaker, Mathématiques Financières,
Edition ENAG, 1997.
Annexe A
A .1 Diagramme de circulation de fluides PFD
(sans Boosting)
A.2 Diagramme de circulation de fluides PFD (avec
Boosting)
A.3 Bilan journalier du 26 fevrier 2009
A .4 Modifications apportées par le
bureau d'engineering après l'integration du Boosting
A.5 La boucle du fluide caloporteur
A.6 La feuille de données (datasheet) du
rebouilleur du déethaniseur E4-1402
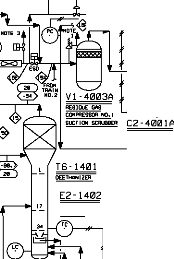
I0-0Jd-Z80
NORMALLY NO FLOW
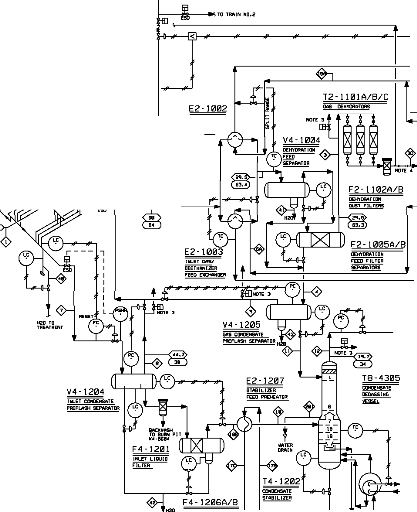
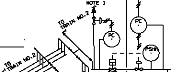
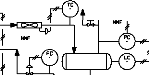
PS NOTE 1
----4111-SE0114;R.'B'
ESD
RESIDUE GAS
TO PIPELINE
GAS TO 140. SIEVE REGENERATION
( 082-UF0.06
XV-0701
SLUG CATCHER
SOY
C8-1304
, EXPANDER/COMPRESSOR
V3-1303
EXPANDER
FEED SEPARATOR
ES FROM
MTE1/-Ireft-S TO
AC-1305
EXPANDER/
COMPRESSOR AFTERCOOLER
ESD
S--11114 COMPRESSOR FROM
R
:7.'8'
VAPORIZATION PUMPS (THIS SHEET)
GAS FROM MOL SIEVE 2 REGENERATION
I OM-UFO.06 >
E4-1301
COLO GAS/
GAS EXCHANGER
TO FUEL GAS SYSTEM OW-UFO.85
AC-1503
PRODUCT SPLITTER NOTE 3 $7-OVERHEAD
CONDENSER
D4 PS NOTE 1
18.1
151
NOTE 3 -v
RESIDUE GAS COMPRESSOR
INLET GAS/ RESIDUE GAS EXCHANGER
RESIDUE GAS COOLER 77.8
· NOTE 2
IHI
NOTE
4.
E4-1302
COLO GAS/ LIQUID EXCHANGER
DEETHANIZER REBOILER
AC-1506
CONDENSATE PRODUCT COOLER
Ay
T6-1501
PRODUCT
SPLITTER
·
V4-1504
PRODUCT SPLITTER 1,0VERHEAD
ACCUMULATOR
P1-1505A/B
1-1( PRODUCT SPLITTER REFLUX
PUMPS
-06.-16 · · E2-1502
FROM
TRAIN NO.2
li
13 18
29
31 =`
,
4-1---INS NOTE
1
EMS pIQ a ',NOTE 1

TO
TRAIN NO.2
a S Y AP
E2-1507
PRODUCT s-
SPLITTER PREHEATER
(RESET)
PRODUCT

TO FUEL GAS SYSTEM
SPLITTER REBOILER
<MD
ROM
TRAIN NO.2

WELL FLUIDS FROM MANIFOLDS
3
4
5

SCALE
EYN 06/25/96
m REISSUE FOR DESIGN
NO. I RELEASED FOR
A(PRELIMINARY
BY DATE DRAWN BY DATE
.114 / / LAC 12.08-94
APPO
REFERENCES
RS RS
B (APPROVED FOR DESIGNIFEE01 / / CHECKED BY
DATE
REVISED AFD SAF 04/21/94
REV. 11
DRAWING NO.
082-PFD-01
SONATRACH
NO.
|
DATE
|
REVISIONS
|
BY
|
CHKD
|
1
|
/ / ISSUE FOR CONSTRUCTION
|
|
|
18
|
81/01/84 AS BUILT
|
JANV.2004
|
MB
|
ML
|
11
|
01/01/05 AS BUILT
|
JANV. 2005
|
ML
|
ML
|
|
|
|
|
|
|
|
D
|
ISSUE FOR CONTRACT
|
JNI
|
09/01/94
|
PACKAGE ·
|
|
|
|
|
|
|
|
E
|
ISSUE FOR REVIEW
|
OBK
|
01/13/96
|
030-100 · S4
|
|
|
|
|
|
|
|
F
|
ISSUE FOR APPROVAL
|
OBK
|
05185/96
|
COST/SCNED-AREA
|
|
|
|
|
|
|
|
0
|
ISSUE FOR DESIGN
|
SAF
|
06/16/95
|
|
6
z1
87
I
88
410119W
DATE
Brown &Root
TFT GAS FIELD DEVELOPMENT PROJECT
PROCESS FLOW DIAGRAM LPG RECOVERY PLANT' BASE
CASE
CONTRACT NO. OWNER N.
KF-2058
APPROVED BY DATE
- -
APPROVED BY
S2-4302 (CLOSE/OPEN)
CONDENSATE VD S2-4301A/B
OFF-SPEC TANK CONDENSATE PRODUCT
STORAGE TANKS
E2-1203
STABILIZER REBOILER
P1-4104A/B

(RESET)
V6-4102A/B V6-4101
LPG OFF-SPEC LPG ON-SPEC STORAGE
SPHERE
.STORAGE SPHERES
P1-4201A/B/C
FLELIaLKLIK__>
INLET LIOUI0 COALESCERS

NOTES.
I. TO FLARE.
2. CONNECTIONS FOR FUTURE INLET GAS
COMPRESSOR.
3. OEPRESSURING VALVES.
4. SPACE FOR FUTURE MERCURY TRAP.
|
LPG RERUN PUMPS
|
|
NC
|
P1-4103A/B/C LPG BOOSTER PUMPS
|
LPG PIPELINE PUMPS
|
LPG VAPORIZATION PUMPS
|
NAIF
|
|
|
|
|
CONDENSATE TO PIPELINE
· I
|
P1-4401A/B/C LEGEND
CONDENSATE PRODUCT <:::: TEMPERATURE
'C
PIPELINE PUMPS O PRESSURE
BANG
-04--404TO .4001A/B
COMPRESSOR DISCHARGE (THIS SHEET)
h=!
P3-4105A/B
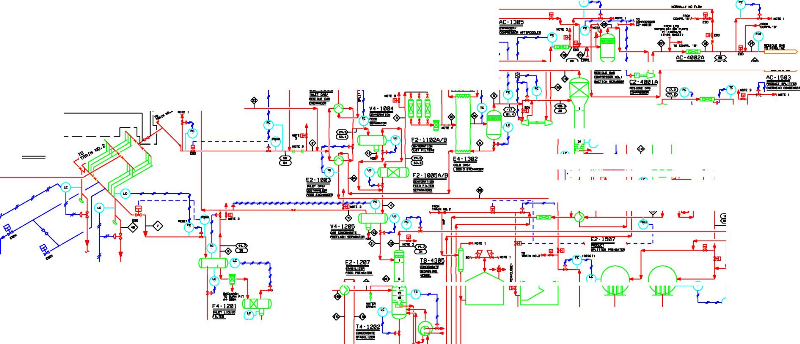

21110-03d-Z80
'MN vN 0100111
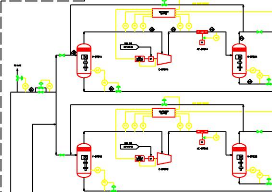
_AL L

v
1
2
3
4
5
BOOSTING PROJECT
ELMO'
01.#0 ·0
TO aw
---]
PlIOCESSINO
MEIN 112
PMC01103
00 MM. 1 oa I NU MO
M
POUR INFORMATION
PC
0 TRAIN 10.2
:1

4'
0TE 3 ·
031

T6-1501
|
tr:r
|
-- "c V4-1504
'COT SR I TTEN
0000117 001100131
|

T6-140I mommmn
E2-1402
CIEEMMIZEN MOILER
7C
OM MON 10. SIEVE
0000/01011
.__OGNEM

C8-1304
111101010/CON1011 ·011
SLUG CATCHER XV-0701
710.17701
V3-1303
E IMMIEN
§ IIEP01001
|
|
P1-1505A/B
-0-1 INIM110 ,LITTER POLON TWOS
|

4'
AC-1506
CONLIDOWE
mmarmtun
-4%
E2-1502
IPL1770111113101LEN
E1-11.ZEU
WATER FILTER TRAIN 2

ILIMBO WATER FILTER IBALN1
100 TO 7711A 071
V4-1204
INL11 00001071
01011.00 1000701
%D
·
70 1110. ORS MIEN
--A:3E5E3(Z>
001
TWAIN ME

re
S2-4302 0700000 0, ·IIPEC
70111
0.000,011
S2-430IA/B
0110000 MMWT 01011N0 TRAMS
V6-4102A/B LPO 10 ·11PEC ITOMCI
MINIS
111E1E71
V6-4101
LPO ON ·IPEC INONME ,NN
70 72 ·00111/11 CO101E11107 01100/LIE ITNIS
EMT/
RATE I
E2-1203 mamma mom'
V3-1602
MIEN PLAIN TAM
|
WarM
B-M17-,1-'1C",. ·-7-.1-t-'--7LB-MWM-
W.MM I
4 MM
ULL:Mr ·T[1101 .1
0...-0 M,.M M.-0 L....,31. :=...0.
WM . 1.M.
,11.-1,.111::m
[I41!, 1 0.-0 49...11
M_ML...ILAII-,E_:- ·_,..rtil.AA
III#44#41 ·41
· · 111 lid hill
|
|
PROCESS FLOW DIAGRAM LPG RECOVERY PLANT' BASE
CASE
|
|
--114.
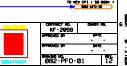
LRAM
.(=> Tewoonse .c 1=`,1 mom erne
NOTES.
I. TO FLARE.
2. COOSECTIONS FOR FUTURE INLET GAS
comemssoR.
3. CEPRESSURINO VALVES.
4.
111 L
SPACE FOR FUTURE PIERCURT TRAP.
PI -4I04A/B
T.P61111101101111--
Fe
P1-4401A/B/C CONODOWE 010111CT PIPELINE
PLOWS
47-Z1-4201A/B/C
PI-4103A/B/C eumms
LPG Cl!! 112ol
Jmos Nr
---11
P3-4I05A/B
<0.-1F4-1206A/B mm
mAtuamo
COPLEICERS
LTD 1001107101
P UMPS
CONCIE100 TO P110.110
GTFT RAPPORT JOURNALIER du: 26/02/2009
GAZ
PRODUCTION GAZ BRUT
|
22 407,312
|
103Sm3
|
PRODUCTION GAZ SEC
|
20 415,743
|
103Sm3
|
CONSOMMATION
|
329,393
|
103Sm3
|
TORCHAGE
|
0,000
|
103Sm3
|
INJECTION GPL
|
0,000
|
103Sm3
|
EXPEDITION VOLUME
|
20 086,351
|
103Sm3
|
EXPEDITION ENERGIE
|
774 700,000
|
106btu
|
HUMIDITE
|
6,26
|
PPMV
|
P.C.S.
|
9 719
|
kcal/Sm3
|
|
00H 00
|
24H 00
|
RELEVE COMPTEUR LOCAL
|
2 871 358
|
2 890 399
|
CONDENSAT
STOCK INITIAL ON-SPECS
|
2 522,065
|
t
|
STOCK INITIAL OFF-SPECS
|
687,311
|
t
|
PRODUCTION
|
2 447,662
|
t
|
STOCK FINAL ON-SPECS
|
2 677,176
|
t
|
STOCK FINAL OFF-SPECS
|
636,206
|
t
|
EXPEDITION MASSE
|
2 343,656
|
t
|
EXPEDITION VOLUME
|
3 378,000
|
Sm3
|
DENSITE
|
0,6938
|
|
T.V.R.
|
8,30
|
psi
|
P C S
|
52 356
|
kcal/m3
|
Richesse de condensat en gaz sec
|
120
|
g/Sm3
|
Couleur
|
|
Saybolt
|
|
00H 00
|
24H 00
|
RELEVE AU COMPTEUR LOCAL
|
2 640 828
|
2 644 206
|
G.P.L.
STOCK INITIAL
|
154,230
|
t
|
STOCK FINAL
|
149,532
|
t
|
GPL RETRAITE
|
-
|
t
|
GPL REINJECTE
|
0,000
|
t
|
PRODUCTION
|
2 724,337
|
t
|
EXPEDITION MASSE
|
2 729,035
|
t
|
EXPEDITION VOLUME
|
5 101,000
|
Sm3
|
Teneur -
|
1,89
|
%mol
|
Teneur C5+
|
0,14
|
%mol
|
Densité
|
0,535
|
|
P C S
|
25 271
|
kcal/m3
|
Richesse de GPL en gaz sec
|
133
|
g/Sm3
|
|
00H 00
|
24H 00
|
RELEVE AU COMPTEUR LOCAL
|
3 575 211
|
3 580 312
|
|
|
|
NOMMIN NO FLOW
|
|
vuo
|
4-1--#177;-4°--PnLEP'
.. &OPPRESSOR
|
1
|
GM 70 OCR IMO REGREW=
|
|
1--EM -40810
mow we
|
|
=wow/
|
|
|
vulvrees
|
|
TO PI
|
.1
OISCMACE
|
|
r r r
,r,
|
, , ,
|
CI
|
|
|
--0-1
t
|
.4. AM.
|
|
·
|
m cam -s · '
|
|
|
r r r
|
('--'1
|
IMEIWE'44..
|
|
f
|
K. AAA
ROME MS COMER 4L10 11110 GAS MIN
|
|
&CJORTISIMI IRMI
|
|
|
|
|
|
|
el
|
|
|
.
|
1'
'P
|
|
VI-4003A
|
|
|
|
IRS ROM MR
|
|
|
|
|
SUM= SOURER
|
MM. PIPER
|
MS
mg.,
|
|
|
Li
|
calgalg
RESOLE GM COMPRESSOR
|
mgoom oompeop
el
1114
|
|
moo. Goomum=
|
|
MS EIGIMMIM
|
114
|
"
|
|
|
|
4)
|
|
|
|
|
· ·
l- ,1
|
"le
|
I I I /j lj lj
|
|
|
.1 -- --111.
|
|
,
|
|
XV-0701
|
|
|
|
|
P.7
|
|
W-1004
110MORPOR
|
|
41111
|
|
|
' DEMIPMER
INH-422
17 EIEEPPRER
.-
|
|
_
-
--E4=
|
|
1
|
0
ilit
|
«n.'
|
|
|
|
6
|
.P
|
|
|
1
|
... ../.......
|
|
|
|
Is-Ism
|
|
PROWL" SELMER
........,..
|
SLIM GATOR
|
<>
|
SELMER
|
11
|
|
|
..
|
|
ourr FILTERB
|
|
|
.-..
|
I;,
0 1
MIL MUM
FRM MMUS I
o 611
|
|
' -O.K.
:
|
|
|
w_taxt %lag
|
|
|
elAniAte
|
40
|
|
la --
|
|
|
|
|
|
MU GM/ --
|
|
|
il I-C)
|
|
|
|
.40 0 .1
|
. a
GPM MEMVII.
|
|
|
|
to coss-a
|
E2-1
|
|
|
orr
|
|
la
|
1
I
|
|
....
|
Rom romt SEPARPORO
|
|
|
|
|
DEERIEMOIR
ROO
IMUJO601 ·
|
PROMPT MILER
|
|
|
|
|
|
fil
|
|
|
0....anill=ke
|
|
*
|
I1- · · ·-- ·"-
|
Y
|
|
|
|
|
|
|
|
|
|
|
|
|
.....,_
|
|
|
|
|
1'
111.1141'
|
|
|
|
|
I
|
11111,97
|
|
112-1002
|
PRERAM
SEPARAMII
|
ELMER MOMS
|
MIMI PROEM
|
I
|
MO M WARM
1.10110 FROM MP COMIES11011 MAIII
|
|
|
0
|
|
P.
|
.
|
|
I
'
IIRMI .1 PO-2=-En
|
|
I
|
0..
....,
|
|
I
|
|
|
|
i
|
|
|
|
|
r_li
|
|
|
|
|
|
|
|
|
I 0M-PRI-OS >
4411
MEM 4I)
|
|
-
|
|
|
|
|
|
· .
|
|
|
|
|
|
ill
|
|
|
|
|
I:
|
|
|
|
|
|
|
AO
|
|
|
|
|
MC
|
|
|
|
|
|
|
|
|
|
|
|
|
|
|
|
|
|
|
|
PEA
|
_..
|
-..-.5.t
(.....1
|
|
|
|
|
|
=RAGE
|
'EN
|
|
lingaMP
|
W-41°I _
|
|
NI
|
|
|
|
a
|
|
IN
|
|
|
E2-1203
|
|
|
|
|
|
|
|
|
|
P1-420IMIA
|
P21-41064/11
|
|
|
|
LPG
|
MIMS
|
1!116alite
|
|
|
|
|
|
|
LPG MOSIER
|
|
RAPS
|
|
|
|
|
|
|
10 RPEUX
|
|
|
|
|
|
|
|
16/02/06
|
|
|
REVEW MERE INDICA1 ED
|
|
|
pa
|
GROUPEMENT TFT TFT -- PHASE 2 BOOSTING
PROJECT
|
|
|
T6/10/07
|
DewWHERE INDICATED
|
|
|
14/06/07
|
APPROVED FOR CONSTRUCTOR
|
t
|
i
|
g
|
11
|
Wil
|
MIP
vi
|
UTILITY FLOW DIAGRAM FUEL GAS SYSTEM
|
|
|
24/433/07
|
ISSUED FOR DESIGN
|
|
|
|
|
M
|
|
|
01/12/06
|
ISSUED BY SIM
|
|
|
|
|
Mil
|
|
p.)., 64,3
c.d. 082-PFD-01
|
Soo.
ESC
|
Rev. .
G
|
|
|
DATE
|
DESCRIPTOR
|
|
|
|
|
CUB PREMED
IT
|
|
|

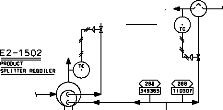

A
F
K
B
C
E
6
J
H
zo-aJn-zeo
'ON ONIAVUO
LL
N2S
TO FLARE
1 A 1
V4-5203
)
HEATING OIL EXPANSION VESSEL
S2-5206 P5-5207
3, y 3,

HEATING OIL STORAGE TANK
HEATING OIL TRANSFER PUMP
019>
Immo
MISC. HOT OIL EOUIPIENT DRAINS
P1-5204A/B/C
·
HEATING OIL CIRCULATION PUMPS
) · 2
/
2
2
7E7)--
V4-5208 P1-5209
1 TO TURBINES
HOT OIL
HEATING OIL DRAIN PULP
DRAIN TANK
-- '<TIT>
--< 113
A,/ a
z
C-191."
· < 245
12935511
3
3
H2-5202
245>
E2 --1402
GAS FIRED HOT OIL HEATER (NOTE 11
293551
E2-2402 045>
MUMMZER REBOILER
FUEL GAS SUPPLY
<245>
1 55824H
DEETHANIZER REBOILER
55824
I
-$1
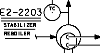

S-1110
/_-11 · C
·
E2-1203 (zee>
STABILIZER 1=51--
REBOILER
<288
E2 --2104


4
4
E2 --1104
REGENERATION GAS HEATER

TURBINE EXHAUST
REGENERATION GAS HEATER
#a
H4-5201A WASTE HEAT HOT OIL HEATER
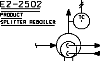
411) EtIM
411, 1=1
0

5
5
<288>
TIT>
07-15386901


41I) IEEE
53869
TURBINE EXHAUST
TRAIN No.1
TRAIN No.2
H4-5201B WASTE HEAT HOT OIL HEATER
NOTES:
LEGEND:
r-----1 FLOW Ck0/h1
<--> TEMPERATURE I ·C1
1.HEATER RATED FOR REGENERATION OF TWO TRAINS
SIMULTANEOUSLY.
6
zm
81
z
4,3 m- oo o
10
CONTRACT MI
K F -2 05 8
OWNER NEL
NO.
DATE
REVISIONS
BY
CHKO
APPO
REFERENCES
NO.
RELEASED FOR
BY
GATE
DRAWN BY DATE JIM 03-02-94
~NMI
SONAT RACH
TFT GAS FIELD DEVELOPMENT PROJECT
ISSUE FOR CONSTRUCTION
EYN
/ /
A
PRELIMINARY
/
AS BUILT JANV. 21104
MB
01/01/04
SR
10
ML
B
APP. FOR DESIGN (FEED 1)
DBK
05/05194
".. · ,,M0 I
CHECKED BY DATE
DATE
APPROVED BY
AS BUILT JAM.20916
FL
01/01/06
IT
11
ML
onvvi
C
ISSUE FOR CONTRACT
JM
a ) N
7 0
PACKAGE NO. 030- lee. S4
DBK DBK
ISSUE FOR REVIEW
01/13195
UTILITY FLOW DIAGRAM HOT OIL SYSTEM
APPROVED BY
DATE
E
ISSUE FOR APPROVAL
05/05195
Brown &Root
COST/SCHED-AREA
ISSUE FOR DESIGN
SAF
06/19/95
06/25/96
0
REISSUE FOR DESIGN
EYN
DRAWING --02
REV.
11
SCALE
/ /
e.=
· ritiSILW'STS
|
Brown
& Root
and Chemicals
Petroleum.
|
JOB NO. PURCHASE
SPECIFICATION REVISION PAGE
|
BF-4749 ITEM NO. E2-1402 1 2402
|
|
ORDER
NO_ 1
|
NO.
1
|
NO. 4749-100-117-4-P-88
|
|
100-0 3- P-117-004
|
SHELL- AND- TUBE HEAT EXCHANGER DATA SHEET METRIC
UNITS
|
DATE SEPTEMBER 27, 1996
|
OF
|
2 BY V M PATEL
|
|
|
a'
4"--" g ·-RFI* t4 Fig"- '
712'-gP A 2Ni:in 24; · 477.P; V 42 71 t4 2A 22tig
g:
CI VI
|
APPLICABLE TO Q INQUIRY 3 PURCHASE Q AS BUILT
|
|
SERVICE OF DNIT DEETHANIZER REBOILER
MANUFACTURER FABSCO
|
|
CUSTOMER SONATRACH LOCATION TIN FM/YE TABANKORT ALGERIA
|
|
SIZE 787.4 mm / 13203 mm X 5490 m TYPE EKG (3)
CkI, HORM 0 VERT CONNECTED IN ONE PARALLEL ONE SERIES
|
|
SURF/UNIT 0 GROSS ( EFF. 201.9 m' SHELLSrUN/T
ONE SURF/SHELL GROSS 3 EFF. 201,9 41-0
|
|
PERFORMANCE OF ONE UNIT
|
|
F L LNG ALLOCATION
|
SHELL SIDE
|
TUBE SIDE
|
|
FL ui 0 NAme
|
GE ETHANIZER BOTTOMS
|
Nor OIL
|
|
FLU to 04JANTITy, TOTAL, kiln,
|
120,494 {21
|
55.824
|
|
VAPOR 0 NraUT)
|
-
|
5851
|
|
|
|
LIQUID
|
120,09
|
81 944
|
55.624
|
55.824
|
|
STEAM
|
|
|
|
|
|
WATER
|
|
|
|
|
|
HONCONOENSABLES
|
|
|
|
|
|
Tad.PERATuRE 0N/bun. .c
|
713.
|
82
|
245
|
113.3
|
|
DENSITY LN, kalm.
|
447.71
|
451 9 /4747
|
733
|
855
|
|
VISCOSITY LN, cP
|
0.0118/
|
0.072410.0111
|
0.830
|
4.00
|
|
MOLECULAR WEIGHT, VAPOR
|
|
47.7
|
|
|
|
MOLECULAR WEIGHT, NONcoNDENSABLE
|
|
|
|
|
|
SPECIFIC HEAT CAPACITY LN, kr...2A; 'C
|
0.783/
|
0.802/0.574
|
0 843
|
0.533
|
|
THERMAL CONDUCTIVITY LN kin Vp.- m 'C
|
0.0824 .1
|
0.0803 / 0.0231
|
0.114 AVG
|
0,114 AVG.
|
|
LATENT HEAT. kcallkg 431 *C
|
|
|
|
|
|
|
|
|
INLET PRESSURE, e411(1)
|
19.86
|
|
|
VELOCIM m/s
|
|
|
|
PRESSURE DROP, ALLOW/CA LC.. bra'
|
1 NEGL
|
0.890 1 0.134
|
|
FOULING RESISTANCE (MIN). mr" ·-C-Nksal
|
0.0304
|
0.0004
|
|
HEAT EXCHANGED 4.323,C0O x 1.1 k..all'h lin,
(CORRECTED' 79.8 'C
|
|
TRANSFER RATE, kcagh- m'-"C SERVICE 2115 .8 CLEAN 14-czLT-
.-C
|
|
CONSTRUCTION CF ONE SHELL
|
SKETCH (BuNaL / NOME ORIE'NTADDN)
|
|
|
SHELLSIOE
|
TUBESIDE
|
_
|
|
DESIGN PRESSURE. bar(o)
|
32
|
10
|
DESIGN TEMPERATURE/ MOW, 'C
|
110 I · 5
|
330 1 $
|
NO. OF PASSES PER SHELL
|
KETTLE
|
SIX
|
CORROSION ALLOWANCE, mm
|
1.5
|
i,5
|
CONNECTIONS w_E A-1%i D RATING
|
IN NPS
|
Br Jr 3006 RF
|
5' / 3030 SF
|
OUT NPS
|
113- VAP, 8' UR/303F RF
|
EF Jr 303( RF
|
INTERM. NPS
|
3000 RF
|
3000 RF
|
TUBE NO. 297 11 ] 00 19.05 mm 1-1-11C1( 3 MIN AVG.
211 mm
|
LENGTH 54190 m PITCH 25.4 mm
|
|
TUBE TYPE BARE MATERIAL SA 214 0 WLD Q
smi.s
|
· p · . 30' · .. · C. m
, Kr t iv
|
|
|
SHELL COVER MATERIAL SA-316-70 GI INTECi.
REMOV.
|
|
|
CHANNEL COVER MATERIAL
SA-510-70
|
|
|
|
|
PROTECTION 0 YES NO
% Cur: 0 cZs:L.---o AREA ;SPACING:Gfc
1575
|
mm
|
|
|
nun
|
|
|
|
|
|
· C
|
|
pv. INLET NOZZLE BUNDLE ENTRANCE BUNDLE
EXIT TUBES
|
|
GASKETS: SH ELLSIPE (1) TUBE SIDE (1) FLOATING HEAD
|
|
CODE ASME AGmE SECT. Vitt 41V,1 STAMP 3 YES NO
riArh. BOARD REG. (I YES 0 NO TEMA CLASS:
|
FI
|
WEIGHTS' DRY FILLER WITH WATER BUNDLE
|
kg
|
INSULATION 3 YES Q NO THICKNESS 301100 rnm
INSULATION SUPPORTS R EQUIRED 3 SHELLS:DE. 3 TUEESIDE
|
|
PAINT REOUIRED Ct SHELL5IDE 0 TustESIDE spECrFICATION OF
-4I 749-000-020-G-1943-021
|
|
REMARKS (11 304 SS SPIRAL WOUND (2) STRAGIAT LINE VAPORIZATION
(3) WITH WEIR
|
|
(4) SADDLES ARE TO BE FIREPROOFED (5)
TWO UNITS ARE R EOLIREO
|
|
|
|
|
|
Annexe B
Manuel d'utilisation de HYSYS
Démarrage du HYSYS
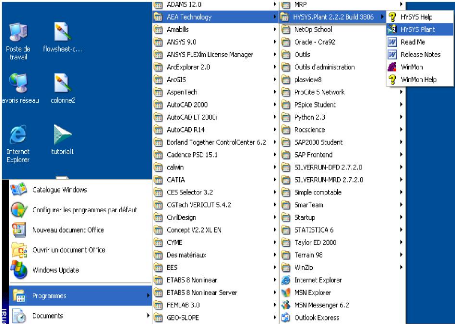
Choix du système d'unités

Création du « FluidPackage
»
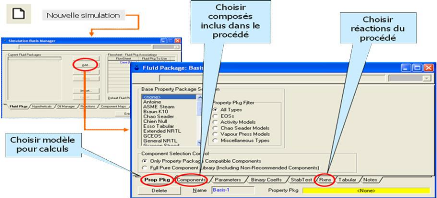
Choix des composés du
procédé
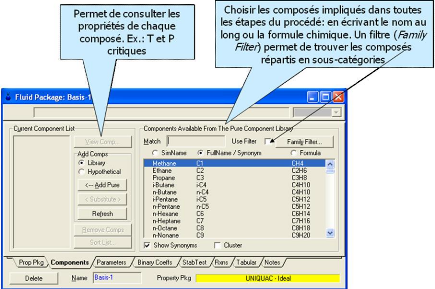
Construction des réactions du
procédé
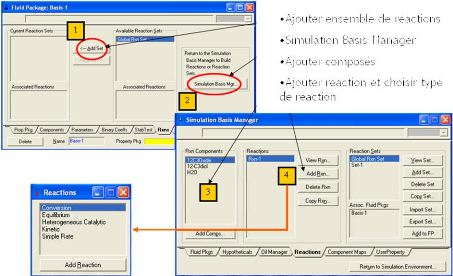
Construction des réactions du
procédé (2)
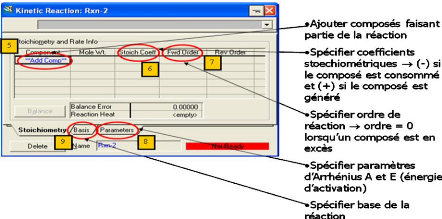
Types d'environnement HYSYS et barres
d'outils
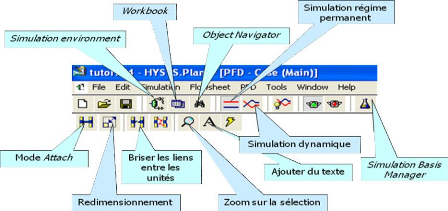
Construction du schéma de
procédé
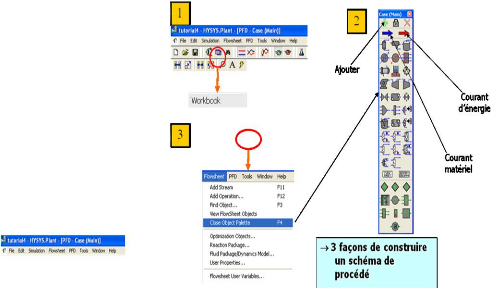
Courants et unités
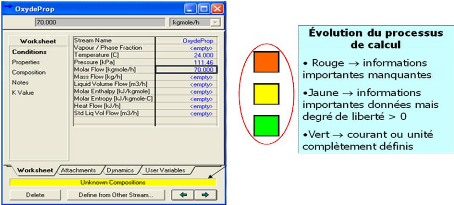
Installation d'unités
d'opération
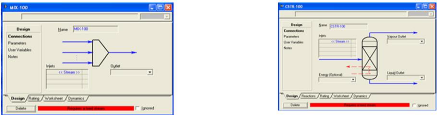
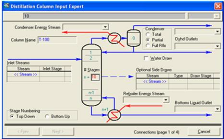
Workbook
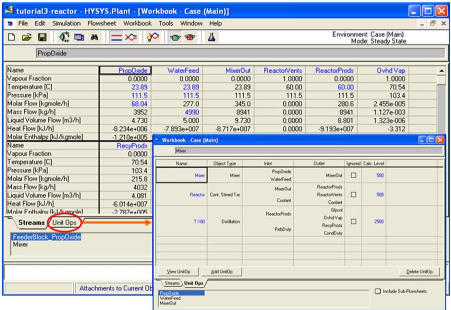
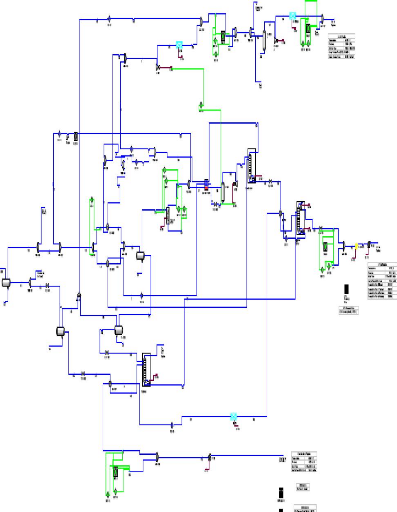
ro "
L.R. MAW MEM
i11.=61111-.1
|