6 REALISATION
6.1 Lecture de
l'existant
Le flux réception :
Avant la réception des marchandises, à la suite
d'une commande du responsable approvisionnement, le fournisseur contacte la
réception par mail afin d'obtenir un rendez-vous.
La réception, grâce à OAPF, outil d'aide
à la planification donne le jour de rendez-vous ainsi que le
créneau horaire au fournisseur.
Le jour de la réception :
Le transporteur se présente à l'accueil avec son
bon de livraison, l'accueil vérifie alors le numéro de commande
et l'heure de rendez-vous grâce à l'outil OAPF et indique alors
que le camion est arrivé.
Dès que le camion peut être pris en charge, la
réception indique dans OAPF le quia du déchargement, dans la
mesure du possible toujours au plus près là ou la marchandise
sera stockée.
L'accueil demande alors au chauffeur de se mettre au
numéro de quai attribué, le camion se présente au quai en
respectant le protocole de sécurité, ce dernier est alors pris en
charge par le magasinier.
Le 1er magasinier :
Décharge le camion avec le bon de déchargement
à l'aide du chariot adapté aux produits après avoir
récupérer les clefs du chauffeur et renseigne les supports de
manutention.
Le 2nd magasinier :
Contrôle qualitativement et quantitativement en
contrepouvoir avec le bon de réception et son scanner.
Il déclare alors les manquants et la casse
éventuelle.
Le magasinier réalise alors un rapprochement entre les
documents fournisseurs et les documents de la commande initiale, si
écart celui-ci effectuera un second contrôle.
Il pose une étiquette LPN (LogisticPalettNumber) pour
identifier les palettes.
La marchandise reste dans la zone de réception et
devient alors disponible pour l'équipe rangement appelée 2RP.
Le flux rangement :
Les magasiniers sont pilotés par WMS pour effectuer en
fonction des départs camion :
- Le rangement des palettes contrôlées par la
réception.
- Le réappro picking dans les zones de
préparation.
- La préparation des palettes homogènes pour
l'expédition.
Le rangement
Le magasinier est dirigé sur une zone de
réception, il scanne l'étiquette de la palette et est ensuite
dirigé vers une adresse de rangement la plus proche possible du
picking.
Les zones de rangement sont approvisionnées avec :
- Des chariots de type 5 dans toutes les allées,
picking en bas et stock en hauteur.
- Des chariots tri-directionnels pour les allées
étroites. Concernant les cuisines et meubles de salle de bain picking en
hauteur et stock en bas.
Le logiciel WMS calcule les emplacements de stockage
disponible selon plusieurs critères, tels qu'être dans la
même allée que le picking en tenant compte de la hauteur, volume
et poids de la palette. Le WMS optimise et densifie le stockage.
Réapprovisionnement du picking :
Le magasinier est dirigé par WMS pour alimenter les
pickings.
Le réapprovisionnement se fait alors par ordre de
priorité selon le besoin de la préparation de commande qui est
tiré par le plan de transport.
Préparation des palettes homogènes :
Le magasinier va chercher sa palette homogène
grâce à l'indication de WMS, il dépose alors la palette
dans la zone correspondante en bipant l'emplacement.
L'imprimante édite une étiquette à coller
sur la palette homogène qui précise le magasin, le type de flux,
le code du préparateur ainsi que la date d'expédition.
Il précise ensuite le flux sur la palette, en collant
les scotchs utilisés dans tous les entrepôts Leroy Merlin :
- Bleu libre-service LS
- Rouge emporté marchandise EM
- Blanc commande client CS
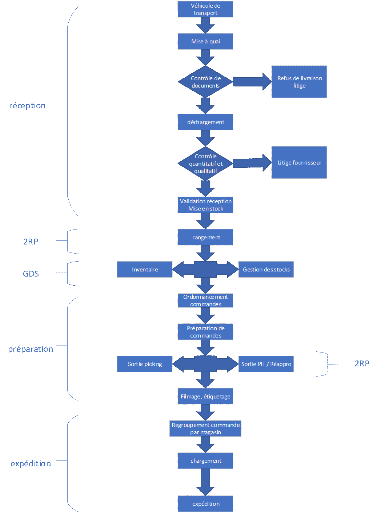
Ordinogramme d'enchainements d'activités au sein de
l'entrepôt de Leroy Merlin Dourges :
Nous pouvons donc constater que la réception a comme
client interne l'équipe 2RP.
L'équipe 2RP doit attendre que le bordereau de 2eme
réception soit effectué avant de ranger les palettes dans les
zones appropriées, si possible au plus près du picking.
Concernant l'équipe 2RP, celle-ci a 2 clients internes
:
- Le secteur préparation, au fur et à mesure de
l'avancement de la préparation, les pickings se vident, c'est alors que
l'équipe 2RP entre en jeux et réapprovisionne les pickings pour
que la préparation ne mette pas les contenants en attente et ou en non
servi.
- Le secteur expédition, car l'équipe 2RP
prépare les palettes homogènes (PH) et les dépose dans les
zones de largage ou directement dans la zone de TIR en fonction de
l'affrètement.
Afin de comprendre les déplacements des caristes, j'ai
donc réalisé un diagramme représentant les flux de
réception vers les zones de stockage.
L'entrepôt se compose de 5 zones de réception.
La cellule H, la plus grande zone de réception, la ou
les camions sont déchargés et ou les palettes sont posées
en zone H1, H2 et H3.
Les zones H4 et H5 sont réservées pour le
déchargement des conteneurs 20' ou 40' vrac.
Les palettes posées en H seront stockées en aile
droite dans les cellules I, J, K, L. Cela concerne les produits issus des
rayons luminaire, sanitaire et rangement cuisine.
La cellule L a la particularité d'être une
cellule en allée étroite.
La cellule D, stocke des produits de grandes longueurs tels
que plans de travail, crédence, dressing, caisson armoire, plinthes,
grande façades/ joues.
Les cellules B et C stocke des produits du monde menuiserie,
tels que porte d'intérieur ou extérieur, fenêtre, baie
vitrée et autres consommables. On y retrouve dans la cellule B des
longueurs tels que des tablettes, panneaux et dalles OSB.
La cellule A est la jumelle de la cellule L avec ses
allées étroites, mais celle-ci a la particularité d'avoir
une équipe de préparation dans la moitié de ses
allées.
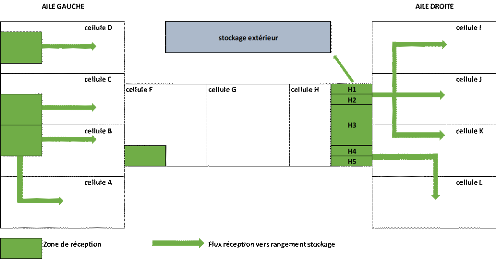
Puis j'ai été amené à
réaliser un diagramme de cause à effets afin d'identifier les
différentes causes d'encombrement de la zone H.
J'ai eu recours à un brainstorming avec chaque membre
de l'équipe (caristes), pour rechercher ces causes en les classifiant
selon les 5M :
- Main-d'oeuvre (caristes)
- Matière (palettes à ranger)
- Méthode de préparation (rangement ou
réappro)
- Matériel (Chariot élévateur)
- Milieu (zones de roulage)
A partir de ces résultats nous avons
décidé d'agir sur les items tels que le reconditionnement, la
typologie de marchandise à ranger, le réappro (paramétrage
des pickings) et le nombre de palettes à ranger.
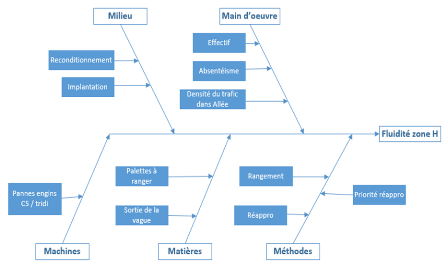
|