IV.5- SUGGESTIONS
La qualité des briques produites à PROMOBAT peut
être améliorée par l'installation d'un broyeur en
début de chaîne de production. Cela limitera les fentes de
séchage et pourra permettre le cas échéant l'utilisation
de chamotte (casses sur cuit) comme dégraissant. Ceci nous donne
l'organigramme de production suivant :
Argile d'ETOA (Brut de carrière)

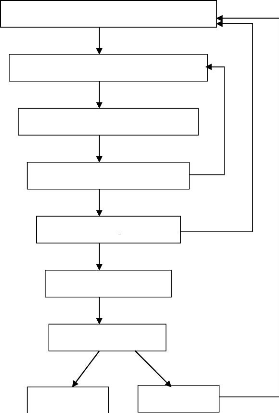
Expédition
Mélangeur mouilleur
Broyeur à cylindre
Sortie four et tris
Chambre à vide
Extrudeuse
Séchage
Cuisson
Casses
46
Figure 12 : Organigramme de production
proposé à PROMOBAT
PROMOBAT gagnerait également en augmentant l'espace de
séchage. Cela pourra permettre entre autre le stockage d`une
quantité plus importante de briques sèches, le maintien d'un
travail constant au niveau de la fabrication, et une limitation de
l'utilisation du séchoir électrique. En effet, l'espace de
séchage actuel permet le stockage de 40.000 à 50.000 briques
(10,5x15x30cm ). Pour une production moyenne de 6000 briques par jour, il faut
environ une semaine pour remplir l'espace de séchage et de stockage. Si
entre temps les cuissons ne sont pas faites, la fabrication est
paralysée à cause de la non disponibilité d'espace
à sécher et à stocker les produits façonnés.
D'autre part, lorsque la demande est forte et que PROMOBAT se trouve
obligée de réaliser deux à trois cuissons par semaine, les
briques sèches disponibles sont parfois insuffisantes. Si au contraire
PROMOBAT augmente l'espace de séchage de façon à pouvoir
sécher et stocker 100.000 à 200.000 briques à la fois,
elle pourra se passer de l'utilisation du séchoir électrique dont
la consommation énergétique est assez significative.
En effet, le temps moyen de séchage naturel d'une
brique (environ 10 jours) et la vitesse de façonnage de 6000 briques par
jour pourront être suffisant pour alimenter les deux fours en briques
sèches pour des cuissons de 10 à 20000 briques par semaine, ce
qui représente à peu près la capacité de production
actuelle de PROMOBAT.
L'énergie pour le séchage naturel étant
gratuite, le séchoir électrique ne serait alors utilisé
qu'en cas de nécessité (demande de briques de format non
disponible, conditions climatiques très défavorables,
augmentation de la production suite à la construction de nouveaux
fours...).
Pour ce qui est de la cuisson, l'une des astuces qui pourrait
rendre le processus efficient serait de s'assurer que toutes les briques
entrant dans le four sont totalement sèches. Ainsi, on ne gaspillera pas
de combustible pour achever un processus qui aurait pu être fait
naturellement [38]. Ceci anéantirait d'autre part le risque de casse
dû à l'élévation de la pression de vapeur d'eau dans
les pores des produits lorsqu'ils sont enfournés humides.
Concernant le combustible bois, il serait
bénéfique pour PROMOBAT lors des achats de rechercher les
matériaux les plus massifs et de les entreposer à l'abri des
pluies : en effet, le bois massif sec montre des propriétés
calorifiques plus élevées que le bois humide [39].
47
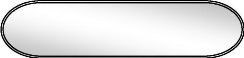
CONCLUSION
48
Il ressort de ce travail que les propriétés
céramiques de nos différents produits de cuisson (masse volumique
apparente, la résistance à la flexion, la perte au feu et le
retrait linéaire de cuisson) croissent avec l'évolution de la
température pendant que le pourcentage d'absorption d'eau
décroît.
Nous avons également observé que les ajouts de
dégraissants diminuent les propriétés mécaniques de
l'argile d'Etoa, malgré le fait qu'ils améliorent son aptitude au
séchage. Les résultats de résistance à la flexion
de nos échantillons cuits à basse température (850 -
1050°C) sont relativement faibles par rapport aux normes Françaises
(7Mpa pour les briques normales) [5] ; Cependant, étant donné la
difficulté et le coût énergétique qu'une entreprise
supporterait en cuisant ses briques à haute température (
1100°C ), il serait sans doute plus sensé, si l'on veut
améliorer les propriétés mécaniques des produits de
cuisson, de rechercher plutôt une matière première fusible,
qui pourrait développer des propriétés optimums autour de
950°C. Malheureusement, dans la pratique, cette hypothèse est le
plus souvent écartée à cause du coût
économique du transport quand le gisement et l'usine sont assez
distants.
L'insensibilité de l'argile de Nkolbisson entre 850 et
1100°C (retrait linéaire et perte de masse qui croissent de 0
à 1,49% et 4,64 à 6,58% respectivement) laisse envisager la
possibilité de son utilisation dans l'industrie des réfractaires
alumino-silicatés.
En somme, PROMOBAT devrait prendre un certain nombre de
disposition pour pouvoir pallier aux casses.
Au niveau de la fabrication, l'installation d'un broyeur en
début de chaîne contribuerait beaucoup à diminuer les
fentes de séchage. PROMOBAT devrait également veiller à ce
que les produits se sèchent sans brutalité et s'assurer au moment
de leur enfournement que le processus de séchage est terminé.
Pour ce qui est de la cuisson, un équipement en capteur de
température pourra alléger la tâche des cuiseurs tout en
leur permettant de rechercher le cycle de cuisson optimum.
Il serait enfin bénéfique pour PROMOBAT
d'effectuer des tests tels que la résistance à la flexion et le
taux d'absorption d'eau sur un échantillonnage de brique
prélevé après chaque cuisson. Cela pourra leur permettre
de s'assurer au moins de la constance de la qualité de leurs
produits.
Les analyses chimiques et minéralogiques de nos
échantillons pourraient rendre plus aisé l'interprétation
des résultats.
49
[1]

REFERENCES BIBLIOGRAPHIQUES
A. BOUQUILLON (2001)- Histoire des céramiques,
Matériaux et processus céramiques, Hermes Sciences, Paris,
47-72.
[2] D.RHODE (1986)- Terres et glaçures, DESSAIN
et TOLRA , Paris, 22- 31.
[3] P.BOCH (2001)- Composés céramiques,
Matériaux et processus céramiques, Hermes Science, Paris,
19- 46.
[4] E. KRAUSE (1973)- Principes et techniques de cuisson et
de construction de fours céramiques. Septima, Paris.
[5] J. SIGG (1991)- Les produits de terre cuites,
Septima, Paris.
[6] International Labour Office (1986)- Small-Scale
Brickmaking, Technology series, Geneva.
[7] C.A. JOUENNE (1984)- Traité de céramique
et matériaux, Septima, Paris.
[8] E. KRAUSE (1977)- Le séchage en céramique,
principes et techniques, Septima, Paris.
[9] G. ALIPRANDI (1979)- Matériaux
réfractaires et céramiques technique, Septima, Paris.
[10] E. LAMBERCY (1993)- Les matières
céramiques et leur transformation par le feu, Granit 1. Des
dossiers argiles.
[11] W.E. WORRALL (1986)- Clays and ceramic raw materials,
Second edition, Elsevier Applied Science Publishers, London and New York.
[12] A.K. CHAKRABORTY, K. GHOSHD (1978)- Reexamination of the
kaolinite- mullite reaction series, J. Am. Ceram. Soc.,61[3-4], 170-13.
[13] NGON NGON (2001)- Prospection et caractérisation
macroscopique des argiles alluviales pour l'industrie céramique à
Etoa, Actes 1ère conférence GCA, 123-128.
[14] E. KAMSEU (2002)- Projet de dimensionnement des
briques cuites: étude de la relation dimension des moules - retrait -
dimension des produits, MIPROMALO/PROG. CER et BTC.
[15] H. CHAMAYOU, J.P. LEGROS (1989)- Les bases physiques,
chimiques et minéralogiques de la science du sol, Presse
universitaire de France.
[16] A. DEMOLON, D. LEROUX (1952)- Guide pour l'étude
expérimentale du sol. 2e édition,
Gauthier-Villars - Paris.
50
[17] ENSP YAOUNDE (1999)- Analyse granulométrique
d'un sol fin, Travaux pratiques de géotechniques.
[18] LCPC (1970)- Analyse granulométrique par
sédimentométrie, Dunod, Paris.
[19] J. KARSTEN (2001)- additifs pour l'industrie des tuiles
et des brique, Industrie céramique et verrière - N°
970, 268 - 271.
[20] J. KARSTEN (2000)- Additive in the brick and tile
industry, NOVOKERAM, 25-39.
[21] M. VOUILLEMET (2001)- Maîtriser les produits
grâce à la modélisation des comportements des
mélanges, Industrie céramique et verrière , 964[11],
686 - 689.
[22] Dictionnaire Larousse de poche (1987).
[23] J. RIGAUD (1978)- La céramique de A à
Z, Septima, Paris.
[24] N F P18-554 (1979)- Mesures des masses volumiques,
porosités, coefficient d'absorption et teneur en eau des gravillons et
cailloux., AFNOR.
[25] N F P61-503 (1982)- Carreaux et dalles
céramiques - Détermination de la résistance à la
flexion., AFNOR.
[26] Handbook of Chemistry and Physics ,55TH ,
Edition 1974- 1975 CRC PRESS, E-106- E107.
[27] J.P BONNET, J.M GAILLARD (2001)- Céramique
silicatées, Matériaux et processus céramiques, Hermes
Science , Paris, 113- 140.
[28] A ELIMBI ,D NJOPWOUO , P PIALY, R WANDJI (2001)-
Propriétés des produits de cuisson de deux argiles
kaolinitiques de l'ouest Cameroun, Sil. Ind., 66 [11-12],121- 125.
[29] Y TSUZUKI , K NAGASAWA (1969)- Transitional stage to
the 980°C exotherm of kaolin minerals, Clays Sciences Japan,
3,8-102.
[30] J LEMAITRE, A.J LEONARD,B DELMON (1977)- The sequence
of phases in the 900- 1050°C tranformation of metakaolinite, Proc.
Int. Clay Conf. ,60 [1-2] 37-43
[31] B.A. SABRAH, H. El - DIDAMONY, M. M. El.- RABIECHI
(1989)- Ceramic studies of the clay / Rice composition and physical
properties of high dam lake sediments, Tile & Brick Int. Vol.12
N°1, 16-19.
[32] ] A. A. KHALIL, E. M. HAMAD, I. MOHAMED (1996)-
Effect of firing temperature on the phase composition and physical
properties of high dam lake sediments, Tile & Brick Int. 12 [1],
12-19.
[33] K. PIMPAKA, M WILHELM, W. WRUSS (2000)- A new Approach
to the production of bricks made of 100% fly ash, Tile & Brick Int, 16
[6], 428-433.
51
[34] V.T.L BOGAHAWATTA , A. B POOLE (1991)- Estimation of
the optimum firing condition for kaolinic clay bodies, Br Ceram Trans. J.
90, 52-96.
[35] C. MELO et al. (2001)- Effcet of fluxes on the fired
properties between 950 - 1050°C of some cameroonian clays. Actes
1ère conférence GCA, 57-69.
[36] T ROUXEL (2001)- Propriétés
mécaniques, Matériaux et processus céramiques, Hermes
Science, Paris, 19-74.
[37] W KURZ , J.P MERCIER , G ZAMBELLI (1991)- Introduction
à la science des matériaux, Presse polytechnique et
universitaire Romande.
[38] J.P.M Pavoy MBE, B.A, MICT (1979)- Brick making in
developing countries, Building research establishment, Garston, Waford.
[39] C. MELO, S. MONGET (2001)- Brick firing in a
Down-Draught wood fired kiln. Actes 1ère conference GCA, 49-56.
52
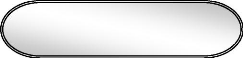
ANNEXES
53
CALCUL D'ERREURS
a) Limite de liquidité

WL = × 1 00
P P
h - s
P Tare
s -
ln(WL) = ln(Ph - Ps) - ln (Ps - Tare)
dWL =
|
d P P
( )
h S
- d P Tare
( S - )
-
|
WL ( P P
h S
-
|
(PS- Tare)
|
ÄWL = WL
ÄPh
Ph-PS
Ph-PS
Ph-PS
+ ÄPS + ÄPS +
ÄTare ÄPh Tare

Ph = ÄPs = ÄTare = ÄP
ÄWL = WL
|
3 ÄP
|
+ ÄP
|
P P
h S
-
|
|
|
|
P Tare
S -
|
Exemple de calcul:
WL = 40,08; Ph = 32,97g ; Tare = 1,25g ; Ps = 18,82g ; ÄP =
0,01g
ÄWL = 40,08 [ 3 2 1,

97-1
82-1
3 × 0,0 125 + 8 0,0 125 0 6
WL = 0,6 WL = 40,8 #177;0,6 b) Limite de
plasticité
ÄP
Wp
3 ÄP +
Ph-Ps

ÄWP = Ph--Ps
×1 00.
Ps-Tare
Ps-Tare
3 0,0 1
× 0,0 1
Exemple de calcul : ÄWP = 26,4 + = 0,49


9 ,67 7 ,9 1
- 7 ,9 1 1 ,25
-
WP = 26,4 #177; 0,5
c) Indice deplasticitéeIPp = WL---
WPdI P dW L dW P Ä I P Ä W
L Ä W P
ln IP = ln (WL - WP) = - = -pIPpW
W
L - P pWL-WP p IPpW W
L - P pWL-WPp
ÄIPp =IPp (L
Ä W L Ä W P
+ P )
54
W W
L - P W W
- pExemple de calcul: ÄIP = 14,4
40,06 6+ #177;0,499
=(40,08 - 26,4440,08 -26,40,44
IP = 14,4 #177; 0,4
d) Retrait linéaire
R = × 1 00
L L
o -
Lo
ln R = ln (Lo - L) -ln(Lo) + ln100
dL0 dL0 dL
R Lo- L L0 Lo-L Lo-L
L0
d( L o - L) dL0
dR = -
=
dR [ ] [ ]dL
1 1 1
= - dL 0 +
R L L L
o - 0 L L
ÄR
R
|
1 1
Lo - L L0
|
ÄL0
|
+
|
1
L0-L
|
ÄL
|
|
|
|
|
|
|
0 -
Exemple de calcul : ÄL0 = ÄL = 0,05cm ; L0 =
6,55cm ; L = 6,30cm ; R=3,81%
1
1
1
ÄR = 3,81
× 0,05+
0,05
×
6,5 5
6,5 5 -6,3 0
6,5 5 -6,3 0
R = 3,8 #177; 0,4% e) Perte au feu PF =
100
m m
0 ×
-
m0
Ln(PF) = ln (m0 - m) - ln(m0) + ln100
dPF
PF m0- m m0 m0- m m0- m
m0
d(m 0 - m)
dm 0 = dm0 dm
dm0
- -
dPF PF
|
[ 1 1 -
m0- m m0
|
] [ ]dm
1
dm 0 +
m m
0 -
|
1 1
1
ÄP F =
+ m0
Äm0
Äm
-
m 0- m m0
PF
m
Exemple de calcul: Äm0 = Äm = 0,1g m0 = 84,4 m =
76,9 PF = 8,9
ÄPF = 8,91
|
|
1
|
|
|
|
1
|
×
|
0, 1 +
|
|
1
|
|
|
|
×
|
0, 1
|
|
84,4 -7 6
|
,
|
9
|
|
84,4
|
|
84,4 -76
|
,
|
9
|
|
|
|
|
|
|
|
|
|
|
|
|
|
|
|
|
|
PF = 8,9 #177; 0,2%
f) Pourcentage d'absorption d'eau
ab = × 1 00
Ma Ms lnab = ln (Ma - Ms) - lnMs + ln100
-
Ms
Ä ab = ÄMa +
ÄMs + ÄMs or
ÄMa = ÄMS = ÄM
55
ab Ma- Ms Ma- Ms Ms
Äab = ab ( Ms )
2Ä M Ä M
+
Ma Ms
-
Exemple de calcul : Ms = 10,4932g Ma = 12,6957g M'a =
6,6325g
ab = 20,9897 ÄM = #177; 0,0001g
0, 0001 2
× 0, 0001
Äab = 20,9897 (1 2, 6957-1 0, 4932+ 1
0, 4932 0, 0021
ab = 20,989 #177; 0,002%
g) Masse volumique apparente
ñ = Ma-

s ñe = lnñ = lnMs -
ln(Ma - M'a) + lnñe
M
a
dñ = dMs dMa dMa
+ +0 car ñe = cste
ñ Ms Ma
-Ma Ma-Ma
dñ = dMs dMa +
dMa or, ÄM'a = 2ÄMa = 2ÄMs
= 2ÄM
D'où
ñ
M
s
M
a
-
M'
a
M a-Ma
ñ = ñ ( 1 + 3
Ms Ma-Ma
Exemple de calcul : ñ = 1,7306
Äñ = 1,7306 3 )
(1 0, 4932+ 1 2, 6957-6, 6325 <0, 0001=0, 0004
ñ = 1,7306 #177; 0,0004g/cm3
h) Résistance à la flexion
ä
3 FL 2 bh2
lnä = lnF + lnL - ln - 2lnh + ln 23
d ä = Ä F
+ÄL db 2dh

h
äF Lb
b
Ää = ä ( Ä F L Ä
2
h )
h
+ + Ä Ä +
F L b Exemple de calcul
ÄF = 5N Äb = Äh = ÄL = 0,002mm F = 922N
ä = 7,40Mpa h = 16,80mm
5 0,0 1 0,0 1 0,02
Ää = 7,40 + + + =0,052
56
922 55 3 6,40 1 6, 80 ä = 7,40 #177; 0,05 Mpa
|