Une configuration typique d'un train de laminage à
chaud est exposée dans la figure (2) composé de 4 caisses
d'ébauche (R1, R4) et 6 caisses de finition (F1, F4), ou sont
indiquées les réductions typiques de caisses.
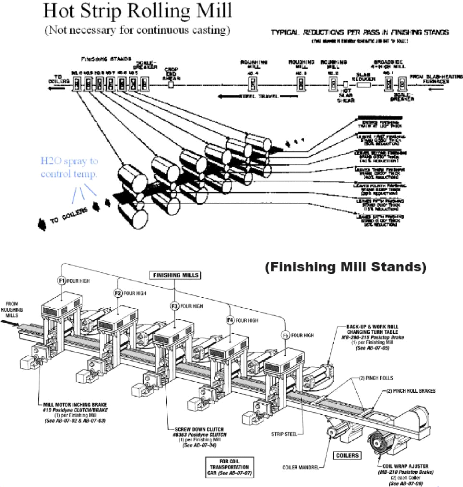
Figure I.2.1 Fabrication, formation et
traitement de l'acier.
Les ensembles fondamentaux d'un laminoir sont :
> Une ou plusieurs cages de laminage ; > Le moteur ;
> Le réducteur ;
> La cage à pignon ;
> Le volant ;
Toute l'installation est placée sur une fondation
commune.
Cage de laminage : bâti en fonte ou en
acier coulé comportant quatre colonne disposées
de
façon à recevoir les cylindres de laminoirs dans un même
plan vertical. L'écartement
des cylindres est réglable grâce à des
dispositifs à vis (figure I.2.2) [5].
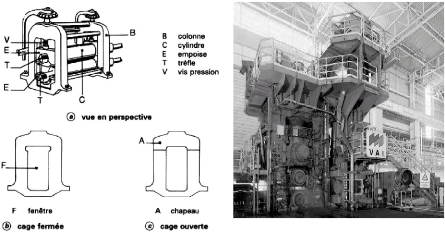
Figure I.2.2 Cage de laminage.
Les cages peuvent être réparties en cinq groupes
suivant le nombre et la disposition des cylindres (duos, trios, quarto,
à cylindres multiples et universelles). La figure I.2.3
représente les différents types de cages.
Les cages duos comptent deux cylindres à sens de rotation
constant, dont les axes sont placés horizontalement. (Figure
I.2.3.a).
Dans les cages trios (trois cylindres) chaque cylindre tourne
toujours dans le même sens ; les cylindres sont disposés dans le
plan vertical (figure I.2.3.b).
Les cages quarto comportent quatre cylindres placés
l'un au-dessus de l'autre dans le plan verticale. Les deux petits cylindres
sont les cylindres de travail, alors que les deux autre, plus grands, forment
l'appui ; ils reçoivent la pression développée pendant
l'opération et réduisent la flexion des cylindres de travail.
(Figure I.2.3.f).
Les cages universelles sont employées pour le laminage
des larges plats, des tôles et des brames. Dans ces cages, le
métal est réduit par les cylindres horizontaux et verticaux.
(Figure I.2.3.h).
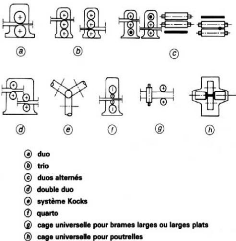
Figure I.2.3 Types de cages.
Les éléments de base du processus de laminage
sont les cylindres qui, à leur tour, sont utilisés dans des
opérations effectuées tant à chaud qu'à froid
fabriqués avec des matériaux ferreux (acier) et aussi avec des
alliages non ferreux [1] .ils représentent aussi un important
investissement dans le coût de la fabrication. Ainsi, prolonger la vie
utile des cylindres de travail à une importance immédiate tant
pour l'opérateur du train de laminage que pour le fabricant du
cylindre.
I.3 LES CYLINDRES DE LAMINAGE À CHAUD 1.3.1
DEFINITION
Les cylindres de laminage sont les outils essentiels de ce
procédé de mise en forme; ils sont soumis à de fortes
sollicitations cycliques tant mécaniques que thermiques. L'optimisation
de leur durée de vie est donc particulièrement cruciale car leur
détérioration influe de manière pénalisante sur la
qualité de surface des produits ainsi que sur les arrêts des
installations industrielles. Dans un souci multiple d'augmenter la
durabilité des outils, la qualité des produits et de
réduire les coûts, il est nécessaire de contribuer à
la maîtrise de ces dégradations et en particulier à celle
de l'usure.
I.3.2 MATERIAUX UTILISEES DANS LA FABRICATION DES
CYLINDRES DE TRAVAIL
Pour que ces cylindres réunissent les conditions de
qualité exigées en vue d'obtenir des tolérances
dimensionnelles du produit laminé très étroites et une
finition superficielle plus parfaite, et d'augmenter la productivité du
train de laminage, il est nécessaire d'améliorer la
résistance des cylindres dans les actions de service. Il s'agit alors
d'obtenir une plus grande qualité du produit laminé, uns plus
grande productivité, avec un plus petit nombre de changements des
cylindres dans le train pendant le service, ce qui permet d'obtenir finalement
un faible coût de production.
Les cylindres conventionnels ne peuvent pas satisfaire de nos
jours toutes ces exigences, particulièrement avec les conditions de
travail de plus en plus sévères. Les cylindres de travail doivent
être fabriqués avec un matériau dur et résistant,
capable de supporter la pression de contact due à la force de laminage,
les fortes gradients thermiques
cycliquement répétés et, en même
temps les cylindres doivent aussi posséder une haute résistance a
l'usure, dans le but de maintenir la qualité superficielle du produit
laminé et augmenter la productivité du train.
Les cylindres en fonte douce sont coulés dans des
moules de sable employés au dégrossissage a chaud de l'acier. Les
cylindres en fonte dure, coulés dans des coquilles, sont largement
employés dans des trains a tôles et dans et dans les cages de
finissage des trains profilés et a fils.
Les premiers essais des cylindres en acier rapide dans les
trains a bandes laminées a chaud sont très récents, ils
commencent a la fin des années 80 au Japon et au débit des
années 90 en Europe[1][15].
Dans la production des cylindres de laminage a chaud des
premières caisses finisseuses des trains a bande laminée a chaud,
les cylindres en acier rapide suscitent un intérêt en constante
croissance puisqu'ils permettent d'atteindre un meilleur rendement que les
cylindres en fonte a haute teneur en chrome [4].
La principale vertu des cylindres d'acier rapide est son
excellent comportement mécanique a des très hautes
températures, ajoutant a cela son supérieur résistance a
l'usure et a la fissuration thermique, favorisé par le haut pourcentage
de carbone (1.5 - 2.5 o/o) et des éléments
d'alliage, comme V, Nb, Cr, Mo et W, qui forment des carbures durs et
stables[4].
Le carbone est l'élément essentiel pour durcir
l'acier. Role des éléments d'alliage :
Les éléments carburigènes tels que le
chrome, le molybdène, le tungstène et le vanadium, ajouté
séparément ou conjointement a l'acier au carbone, ont des
influences communes sur le comportement de cet acier [16].
v' Vanadium;
Il est utilisé essentiellement comme
élément générateur de carbures. C'est un
élément
d'alliage important dans les aciers rapides pour
l'obtention d'une bonne dureté a chaud et
d'une bonne
résistance a l'usure en raison de la présence de particules
très durs de carbure
de vanadium. Le vanadium est rarement utilisé seul dans
les aciers à outils, mais la plupart du temps en association avec le
chrome, le molybdène et le tungstène [16].
v' Chrome;
Cet élément est utilisé dans la plupart
des aciers à outils (cylindre de laminage), en qualité allant de
0.5 à 17 o/o. cet élément joue un rôle
essentiel dans l'augmentation de la trempabilité. Il entraîne
également une très forte réduction de l'oxydation à
haute température, ainsi, l'addition de plus de 10
o/o de chrome entraîne une augmentation
substantielle de la résistance à la corrosion [16].
v' Tungstène ;
Il a été l'un des éléments
d'alliage les plus employés dans le domaine des aciers à outils
en raison de son pouvoir carburigène très important. Certains
aciers rapides contiennent jusqu'à 22 o/o de
tungstène. Plus la teneur en tungstène est élevée,
plus la température de fusion de l'alliage est augmentée. Les
aciers à outils au tungstène sont peu sensible à la
décarburation mais ont une résistance au choc thermique assez
faible [16].
v' Molybdène ;
Dans les cylindres de laminage, cet élément a
un comportement analogue à celui du tungstène. Les aciers au
molybdène présentent, par rapport aux aciers au tungstène,
un certain nombre d'avantages et d'inconvénients :
· Avantages ;
Meilleur ductilité et densité plus faible ;
Mise en solution plus facile des carbures de molybdènes
:
· Inconvénients ;
Plus grande sensibilité à la décarburation
et au phénomène d'oxydation catastrophique entre 1000 et 1100
°C [16].
D'une manière générale, les aciers pour
travail à chaud doivent avoir une résistance à la
déformation convenable, donc des caractéristiques
mécaniques à chaud et une résistance à l'usure
élevées sans que le ténacité, indispensable pour
limiter les risques de fissuration rapide, soit trop sacrifiée, ainsi
qu'une bonne tenue aux différences de température en cours de
travail, causes de chocs thermiques. Ces aciers doivent avoir également
une résistance à la déformation suffisante lors des
traitements thermiques. La plupart des aciers que nous étudions ici
étant assez alliés, et contenant du chrome en particulier, ont
une trempabilité élevée et répondent bien à
cette exigence. Une bonne usinabilité est également
recherchée.
Ces aciers sont répartis d'après la norme NF
A35-590 en cinq groupes :
> les aciers résistant aux chocs thermiques ;
> les aciers résistant à l'usure aux
températures élevées ; > les aciers résistant
aux très hautes températures;
> les aciers résistant à certaines corrosions
[16].