V.2.Modélisation des temps d'attentes suite à
un évènement non souhaité
(ENS).
V.2.1. définition et traitements des
évènements non souhaités (ENS).
Les systèmes de décision des entreprises sont
plongés dans un environnement qui génère de plus en plus
d'événements. Une des principales tâches des
systèmes de décision consiste donc à les prendre en charge
de façon efficace les « évènements non
souhaités », c'est à dire lorsqu'ils gênent le
fonctionnement normal du système industriel. C'est dans ce cas que
l'amélioration de la réactivité est primordiale. Les
Évènements Non Souhaités doivent donc
être caractérisés afin que le système de
décision puisse rapidement les identifier et mettre en oeuvre le
traitement adéquat.
V.2.1.1. Définition.
Un évènement non souhaité est
définie comme étant toute information qui contredit une
prévision faite aussi bien sur le système opérant que sur
l'évolution des objectifs élaborés à partir de la
prévision de l'évolution de l'environnement [004].
En d'autres termes les ENS sont des
événements dont l'occurrence n'est pas planifiée, qui sont
susceptibles de gêner le déroulement d'opérations de
production et dans certains cas, de remettre en cause l'objectif même de
production.
Modelisation du temps de reaction d'un systeme industriel :
Application aux centrales thermiques d'OYOMABANG I et II .
V.2.1.2. Catégories
d'Évènements Non Souhaités (ENS).
Les principales catégories d'ENS reconnues en
gestion de production sont recensées par la
figure 29.
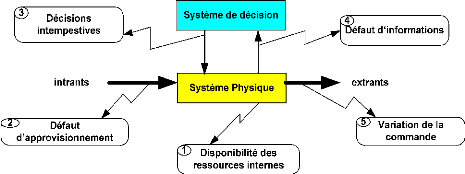
Figure 29 : Les principales catégories d'ENS en
gestion de production et en maintenance
1) Les ENS générées par le
système opérant sont parfois appelées "ENS internes".
Elles sont principalement engendrées par les aléas de
disponibilité et de fiabilité des ressources (hommes ou machines)
du système opérant. On trouve dans cette catégorie les
erreurs humaines, l'absentéisme, les pannes machines, les casses
d'outils, etc.
2) Les aléas liés aux fournisseurs et
sous-traitants se transforment en ENS sur les intrants qui se traduisent par
des défauts d'approvisionnement du système de production.
Généralement, ces ENS sont générées par des
retards de livraison ou la présence de non- conformités dans les
matières, pièces ou composants livrés.
3) Les aléas de fonctionnement du système de
décision créent des ENS que l'on peut qualifier de
décisions intempestives. Elles résultent
généralement de solutions élaborées à la
hâte ou sans prendre en compte certaines contraintes ou encore sans
considération pour les conséquences qu'elles entraînent sur
les autres activités de l'entreprise. C'est le cas, par exemple, de la
décision du service commercial de proposer des délais de
livraison excessivement courts pour enlever un marché au mépris
de la capacité réelle de production du système
opérant.
4) Les aléas de fonctionnement du système
d'information produisent des ENS dans les transmissions de données. En
découlent des défauts d'informations qui se traduisent soit par
un manque total (l'information ne parvient pas à son destinataire), soit
par une
Modelisation du temps de reaction d'un systeme industriel :
Application aux centrales thermiques d'OYOMABANG I et II .
insuffisance (l'information est incomplète ou
erronée). Concrètement, on trouve dans cette catégorie les
perturbations générées par des défaillances
humaines (oubli de transmission d'informations, erreurs de transcription de
données, etc.) ou techniques (panne du matériel support de la
communication, etc.).
5) Les aléas liés aux clients
génèrent des ENS sur les extrants. Leur origine est une variation
de la demande des clients qui porte principalement sur la quantité ou
les délais de livraison des produits. Dans cette catégorie d'ENS,
sont classées, par exemple, les augmentations ou baisses soudaines du
niveau des commandes dues à une variation de l'environnement ou à
un effet de mode (le succès imprévu d'un produit aboutit à
une incapacité du système à le produire dans les
délais annoncés, etc.).
Les ENS qui entrent dans les quatre dernières
catégories sont parfois appelées "ENS externes" parce qu'elles
sont générées par l'environnement du système
opérant.
V.2.1.3. Évènement Non
Souhaité flou
Qu'elles soient exogènes ou qu'elles soient
endogènes, les ENS peuvent avoir un caractère « flou ».
C'est le cas par exemple, de celles engendrées par les commandes clients
(annulation d'une commande, arrivée d'une commande urgente,
etc.)[004]. En effet, les prévisions de ventes au
début d'une année nécessite d'intégrer des
commandes en cours de négociation. Ce type de commande engendre des
bouleversements. De ce fait, ces commandes doivent pouvoir être
modélisées de façon à pouvoir en tirer le
caractère « sûre ». Il est cependant difficile de
répondre objectivement par « oui ou non » à la question
« La commande est elle sûre ? » et ceci tout simplement parce
que la commande d'un client est incertaine. Elle ne peut donc pas être
modélisée par la logique booléenne au risque de nous
écarter de la réalité. On fait appel pour ce type de
problème à la logique floue qui permet de définir une
fonction d'appartenance permettant de mieux le rapprocher de la
réalité.
En conclusion, qu'elles soient internes, externes et/ou floues,
les ENS ont toutes un impact sur le système opérant.
Modelisation du temps de reaction d'un systeme industriel :
Application aux centrales thermiques d'OYOMABANG I et II .
V.2.1.4. classification des
évènements non souhaités
Du point de vue de la réactivité du
système industriel, l'objectif est d'identifier rapidement les ENS et de
mettre en oeuvre le traitement adéquat. La complexité de ce
traitement est essentiellement fonction de l'importance de l'impact des ENS sur
le fonctionnement du système opérant.
En conduite de système industriel, les ENS se classent en
trois catégories :
> ENS faiblement perturbantes si elles ne
contraignent pas le système de décision à remettre en
cause le plan de production ; les objectifs assignés au système
opérant peuvent être remplis grâce à un traitement
des ENS qui ne prend en compte que le groupe d'opérations
perturbées et les ressources associées ;
> ENS moyennement perturbantes si elles
impliquent le calcul d'un nouveau plan de production sans générer
de conséquences sur les extrants ; ces ENS peuvent être
absorbées par le système opérant sans effet
détectable sur les sorties du système de production ; les
objectifs de coût, qualité et délais sont respectés
;
> ENS fortement perturbantes si,
malgré l'élaboration d'un nouveau plan de production, elles ont
des conséquences sur les extrants du système opérant ; les
objectifs de coût, de qualité et particulièrement de
délais ne peuvent plus être respectés.
V.2.1.5. Traitement des
évènements non souhaités
La survie des entreprises dépend de leur
faculté à faire face aux fluctuations de leur contexte
économique, technologique, social voire politique. C'est pourquoi, dans
un premier temps, il est indispensable de réduire le nombre d'ENS
qu'elles auront à affronter. Ce sont des actions stratégiques
à long terme, de nature préventive, qui permettent de mettre en
place des moyens susceptibles d'éviter l'occurrence de certains ENS. Par
exemple, pour le cas des fournisseurs et sous-traitants, il peut être
bénéfique pour l'entreprise de mettre en place des relations
étroites de partenariat. Elle peut ainsi obtenir la garantie de la
régularité et de la qualité de la fourniture
nécessaire à l'entreprise. En ce qui concerne les clients, elle
peut disposer d'un organe de veille qui lui permet de surveiller les signes
d'évolution de la demande. Les moyens déployés pour
limiter les ENS liés aux systèmes de production peuvent consister
en la formation des hommes, le développement d'une maintenance
préventive, etc.
Modelisation du temps de reaction d'un systeme industriel :
Application aux centrales thermiques d'OYOMABANG I et II .
Toutes les mesures ainsi mises en place ne peuvent
empêcher l'apparition de certains ENS tels que: ceux qui sont liés
à des informations manquantes, erronées ou mal exploitées,
ceux qui surviennent au cours de la réalisation des tâches comme
la casse d'un outil ou la panne inopinée d'une machine, etc.
Il est donc indispensable de mettre en place des moyens
palliatifs qui permettent d'assurer l'efficacité de la
réactivité du système pour prendre en charge ces ENS. Une
grande partie de celle-ci est détectée au niveau du
système opérant et peuvent donc être rapidement prises en
charge par le niveau de décision le plus proche de celui-ci.
En général, les travaux effectués sur le
traitement des ENS se concentrent uniquement sur les ENS internes ayant pour
origine les machines de productions. En fonction du plus haut niveau d'impact
de la perturbation, le traitement visera alors à trouver une nouvelle
planification et/ou un nouvel ordonnancement qui soit aussi proche que possible
de ce qui était initialement prévu et appliqué jusque
là, pour atteindre les mêmes objectifs initiaux. Dans ce contexte
plusieurs résolutions sont proposées. Nous citerons quelques unes
:
> Une approche par modification de la planification qui
consiste en des ajustements successifs du planning initial, à partir de
modifications locales et limités des plans de charge des ressources
impliquées ;
> La méthode AHP (Analytic Hierarchy process), qui
est une approche multicritères permettant, lorsqu'on est face à
l'impossibilité de réaliser une tache sur une machine
initialement prévue, de déterminer la « meilleure
»machine pouvant la remplacer. Cette approche intègre
différente indicatrice propre à chaque machine candidate, selon
les critères temps, cout et fiabilité.
> Une approche par séquence de groupe de taches
permutables qui consiste à rechercher un ensemble d'ordonnancement
admissible prédictif.
Lorsque l'ENS est d'origine externe le plus souvent, les
objectifs de production sont remis en cause, et par ricochet la planification
initiale. Le traitement va donc consister à définir de nouveaux
objectifs et donc une nouvelle planification.
Modelisation du temps de reaction d'un systeme industriel :
Application aux centrales thermiques d'OYOMABANG I et II
v.2.2.modélisation du processus.
V.2.2.1) Traitement périodique (ENS sans
arrêt de production).
Lorsqu'un problème technique se pose (appareil
défectueux, panne de machine, incident d'exploitation, etc.),
constaté soit par l'exploitant de la salle de commande, soit lors de la
ronde des exploitants, une demande d'intervention (D.I) est remplie par le chef
de quart et transmise à son supérieur, le chef de service
exploitation, pour validation. Si celui-ci valide la D.I, il la transmet au
chef service maintenance. Ce dernier évalue la gravité du
problème et planifie l'intervention en fonction du degré de
gravité de l'ENS (immédiatement si l'ENS peut interrompre la
production, quelques jours après, ou une semaine après si ce
n'est pas le cas). Ce dernier émet alors le l'ordre de travail, (OT)
correspondant, et la transmet à la section correspondante
(mécanique ou électrique) pour la formation d'une équipe
de travail et l'intervention. L'équipe formée, doit
élaborer une JSA (Job safety Analysis), qui décrit les
étapes de travail, les risques courus, et les précautions
à prendre. Le chef d'équipe présente donc tous les
documents relatif à l'intervention (DI, OT, JSA) au chef de quart qui
les vérifie et initie le permet de travail pour le faire valider par le
chef de la centrale. Ensuite, le chef de la centrale vérifie tous les
documents et signe le permit de travail (PT). Ce n'est qu'après cette
signature que l'équipe de maintenance peut intervenir sur un
équipement. Apres le travail, les maintenanciers signalent le chef de
quart qui clôture le Permet de travail.
N.B: il est à noter pour les
raison de célérité, la signature du permit de travail
à été délégué par le CC. Les chefs
services et le coordonnateur HSE peuvent alors signer le permit de travail.
V.2.2.2) traitement évènementiel
(incident : ENS avec arrêt de production). Lorsqu'un
problème technique se pose lors de la production
d'électricité (lorsque les groupes sont en marchent),
constaté par l'exploitant de la salle de commande, une demande
d'intervention (D.I) est remplie par le chef de quart après avoir mis
hors service l'équipement concerné (consignation). Ce dernier
informe immédiatement : le chef service d'exploitation, le chef de la
centrale, le chef service maintenance, le Grid dispach et essaye de
repérer l'origine du problème. Fait appel aux personnes en
astreintes, pour intervention immédiate tout en respectant toutes les
mesures de sécurités au travail. Le chef de quart est tenu de
rédiger un rapport d'incident qu'il va transmettre à la
hiérarchie.
Modelisation du temps de reaction d'un systeme industriel :
Application aux centrales thermiques d'OYOMABANG I et II .
Après chaque incident, il est prévu une
root causes Analysis: qui est une réunion qui regroupe
tous les acteurs qui entrent en jeu dans le processus de traitement pour faire
une évaluation profonde des causes de l'incident afin d'en tirer les
résolutions pouvant ainsi permettre de prévenir ce genre
d'incident dans le futur.
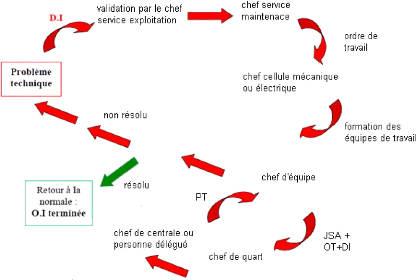
Figure 30 : modélisation du processus de
traitement
V.2.3. modélisation de la dynamique de
traitement des ENS.
Comme nous l'avons mentionné au paragraphe ci-dessus,
le processus de traitement comporte 3 niveaux dans le cas le plus
défavorable et 5 sous-processus. Pour définir les
paramètres de notre modèle, nous avons fait un recensement des
ENS qui ne nécessite pas un arrêt de production et des incidences
pendant la période allant de janvier à juin 2010. Ces
résultats sont consignés dans les tableaux qui suivent :
Modelisation du temps de reaction d'un systeme industriel :
Application aux centrales thermiques d'OYOMABANG I et II .
date
|
installation
|
Description de la tache
|
Début
|
fin
|
Temps
|
05/01/10
|
GRP 203
|
Nettoyage de radiateur
|
08/01/10 à
|
08/01/10 à
|
06H00
|
|
|
|
8H00
|
14H00
|
|
08/01/10
|
GRP 102
|
Étanchéité des Fuites d'eau pipe circuit
|
08/01/10 à
|
08/01/10 à
|
06H50
|
|
|
préchauffé
|
8H00
|
14H50
|
|
18/01/10
|
GRP 102
|
Etanchéité fuite de fuel et resserrage de
|
18/01/10 à
|
13/01/10 à
|
05H30
|
|
|
canalisation fuel
|
8H00
|
13H30
|
|
19/01/10
|
GRP 101
|
Remplacement des pipes hautes pressions
|
19/01/10 à
|
19/01/10 à
|
03H30
|
|
|
cylindre B7
|
8H00
|
11H30
|
|
20/01/10
|
GRP 102
|
Inspection et recherche fuite d'eau et vapeur,
|
20/01/10 à
|
20/01/10 à
|
03H00
|
|
|
poste de visite arbres à cames, resserrages
visserie canalisation retour fuel cylindriques
|
8H00
|
11H00
|
|
25/01/10
|
GRP 102 et
|
Révision des équipements des culasses
|
25/01/10 à
|
25/01/10 à
|
05H00
|
|
GRP 208
|
|
8H00
|
13H00
|
|
23/02/10
|
Pompe HFO
|
nettoyage des filtres pompe dépotage HFO
|
23/02/10
|
24/0/10
|
06H00
|
|
dépotage
|
colmate.
|
8H00-
|
08H00-
|
|
|
|
|
11H00
|
11H00
|
|
01/03/10
|
Porterelle
|
refixer porte local dépotage cassé
|
01/03/10
|
01/03/10
|
06H00
|
|
dépotage
|
|
09H00
|
15H00
|
|
11/03/10
|
Pompe effluent
|
Révision de la pompe effluente.
|
16/03/10
|
16/03/10
|
06H00
|
|
|
|
9H00
|
15H00
|
|
17/03/10
|
Vanne
|
Traitement de la Vanne d'appoint d'eau
|
17/03/10
|
17/03/10
|
02H00
|
|
d'appoint d'eau
|
|
8H00
|
10H00
|
|
24/03/10
|
Pompe
|
Dépose et entretient de la pompe
|
24/03/10
|
24/03/10
|
02H00
|
|
d'appoint
|
|
8H00
|
10H00
|
|
31/03/10
|
Bac de rétention
|
Déboucher la canalisation permettant
|
31/03/10
|
31/03/10
|
03H10
|
|
|
l'écoulement
|
8H00
|
11H10
|
|
08/04/10
|
SEPHF (2)
|
Remplacement des masselottes
|
08/04/10
|
08/04/10
|
02H00
|
|
|
|
8H00
|
10H00
|
|
|
Tableau 4 : traitement des ENS sans interruption de
production
Sources : cahier de programmation et consignations des
travaux mécaniques
date
|
installation
|
Description et causes probables de l'incident
|
Actions menées
|
Début
|
fin
|
Temps
|
18//01/10
|
GRP101
|
Raccord de fixation pipe d'alimentation pompe d'injection
N° B7 dévissé, provoqué probablement suite aux
multiples vibrations.
|
Information de la hiérarchie, établissement
d'une DI, ronde autour du groupe et fixation des raccords de fixation pipe
d'alimentation.
|
20H26min
|
20H48min
|
22min
|
01/02/2010
|
GRP103
|
Importante fuite de combustible au niveau du pipe principal
combustible banc A cylindre A9.les vis de fixation du distributeur de fioul se
seraient desserrées suite probablement aux vibrations.
|
Balisage et consignation du groupe, Information de la
hiérarchie, appel du chef cellule mécanique pour intervention,
intervention effective dans 30min,
|
17H43min
|
20H30
|
2H47 min
|
25/02/10
|
GRP 101
|
Fumée abondante et la présence des flammes au
niveau des turbos compresseurs du groupe. Les causes probables sont, la
projection de combustible sur le turbo et les parties chaudes du groupe
provoquant ainsi des flammes suite à une rupture des vis de fixation du
pipe d'alimentation en combustible du banc B
|
Arrêt d'urgence du groupe, prompte réaction dans
l salle des machines des exploitants et des main tenanciers extincteurs en
mains pour éteindre le feu, arrêt des modules du groupe,
information de la hiérarchie, balisage de la zone et début de
nettoyage du groupe et du sol au provalent, interventions immédiate de
la maintenance mécanique et électrique.
|
16H01min
|
19H01
|
03H00
|
01/03/10
|
GRP 101
|
Arrêt automatique du groupe par déviation d'un
cylindre, causes probables, disfonctionnement du connecteur de sonde du
cylindre B1 qui transmettait de mauvaises valeurs au superviseur.
|
Information de la hiérarchie, appel de du chef cellule
mécanique pou intervention, intervention des exploitant et des
mécaniciens.
|
19H00
|
20H01
|
1H01
|
|
Tableau 5 : traitement des
incidences
Sources : rapports d'incidences.
Modelisation du temps de reaction d'un systeme industriel :
Application aux centrales thermiques d'OYOMABANG I et II .
A partir des tableaux précédent, nous constatons
que :
Les ENS détectés lors du fonctionnement sans
interruption de la production sont traité le lendemain. Et quand il y a
pas d'ENS ce sont les travaux de maintenance planifiés tels que les
visite après un certains nombres d'heures de marche, le nettoyage et
l'entretient de certains équipements. Nous pouvons alors définir
les paramètres de notre modélisation comme suit :
> Unité de temps : minutes
> Date de référence : nous allons prendre
06H00 qui est l'heure de prise de service du 1er quart de la journée qui
travaillera pour préparer la période de pointe. Cette date sera
considérée comme origine de temps : to
> Nous supposons que la date d'occurrence de l'ENS est la
6ème heure après l'heure de référence,
soit 360 minutes : U0.0= 360. Donc à 12 heures. (c'est
une variable qui dépend des ENS, cette valeur est arbitraire et
n'influence aucunement le résultat).
> Les périodes des niveaux sont les suivantes :
ü Après constatation de l'ENS, l'exploitant (chef
de quart) a 5 minutes pour remplir la DI, la transmettre au chef service
exploitation et informer le Grid dispach et le chef de la centrale.
Parallèlement, les équipes d'interventions disposent du
même temps pour remplir la fiche d'évaluation des risques et
transmettre les documents du chantier au chef de quart pour validation du
permit de travail. P0 = 5.
ü Le chef de service exploitation quant à lui a
10 minutes pour vérifier l'effectivité de l'ENS, mesure la
gravité, la valide et la transmet au chef service maintenance.
Parallèlement, les chefs de cellules mécaniques et
électricités ont également le même temps pour former
les équipes de travail quand ils ont reçu l'ordre d'intervention
du chef service de maintenance : P1= 10.
ü Le chef service maintenance lui a 15 minutes pour
valider les suggestions de solutions proposées, planifier
l'intervention, donner l'ordre d'intervention (permis de travail), et
désigner les cellules impliquées pour la résolution du
problème : P2= 15.
> Nous allons initialiser la période de
référence de toutes les périodes à la date de
référence to ainsi, on a :
X0=X1=X2=0.
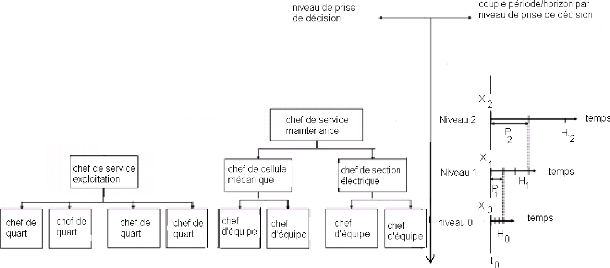
Figure 31 : couple horizon/période par niveau de
prise de décision.
Modelisation du temps de reaction d'un systeme industriel :
Application aux centrales thermiques d'OYOMABANG I et II .
V.2. 4.évaluation du temps de
réaction.
D'après la classification des ENS par ordre de
gravité, il est important de signaler que, compte tenu de notre
processus de traitement, certains ENS trouverons d'embler leur solution
après leur examens par les exploitants et d'autres ayant une
gravité un peu plus grande trouverons leur solutions après
l'examen du chef de service maintenance et/ou avec l'apport du chef de la
centrale. Dans la suite nous allons présenter le temps mis pour le
traitement dans chaque étape et par niveau de prise de décision.
Nous avons la modélisation suivante :
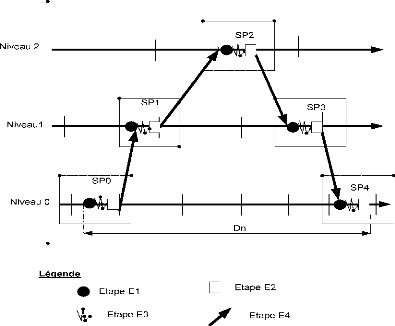
Il est à noter que :
Ce sont les exploitants qui interviennent dans le
sous-processus 0, le chef service exploitation dans le sous-processus 1, le
chef service maintenance dans le sous-processus 2, les chefs de cellules dans
le sous-processus 3 et les équipes de maintenances dans le
sous-processus 4.
|
: Etape E1
|
|
: Etape E3
|
: Etape E4
|
|
: Etape E2
|
Sous-processus 0 (SPo)
|
constatation de l'ENS. Cette étape peut
prendre 1 minute
|
c'est le temps qui s'écoule entre la fin de la
rédaction et le la transmission de la DI ; c'est le temps d'attente.
|
rédaction de la DI par le chef de quart cela peut prendre
3 minutes
|
c'est la transmission de la DI chez le chef d'exploitation cela
peut prendre 2 minutes.
|
Sous-processus1 (SP1)
|
prise en compte de la DI par le chef service exploitation.
Cette étape peut prendre 2 minutes
|
C'est le temps qui s'écoule entre la fin de
l'examination de l'ENS par le chef service exploitation et sa transmission chez
le chef service maintenance : c'est le temps d'attente
|
c'est l'étape ou le chef d'exploitation examine la
gravité de l'ENS et son impact sur la production. Cela peut 5
minutes.
|
c'est la transmission de la DI chez le chef service maintenance
cela peut prendre 2 minutes.
|
Sous-processus2(SP2)
|
prise en compte de la DI par le chef service maintenance, cela
peut prendre 2 minutes
|
c'est le temps qui s'écoule entre la fin de traitement
de la DI et la transmission du PT et de la DI correspondante aux chefs de
cellules : c'est le temps d'attente
|
validation des propositions de solutions proposées pour
la résolution de la DI, planification de l'intervention, et choix des
cellules qui doivent intervenir. cela peut prendre 10 minutes.
|
c'est la rédaction de l'ordre de travail et la
transmission aux chefs de cellules concernées. Cela peut prendre 4
minutes.
|
Sous-processus3(SP3)
|
réception des DI et PT validé par le chef
service maintenance par les chefs de cellules. Cela peut prendre 1 minute
|
temps qui s'écoule entre la formation des
équipes de travail et la mise en leur possession des DI et PT : c'est le
temps d'attentes.
|
Formations des équipes de travail pour l'intervention par
les chefs de cellules. Cela peut prendre 5 minutes
|
transmission des DI et PT aux équipes d'intervention. Cela
peut prendre 3 minutes.
|
Sous-processus4(SP4)
|
réception DI et des PT par les chefs
d'équipes et remplissage de la fiche d'analyse des
risques. Cela peut prendre 2 minutes.
|
temps d'observation du comportement de la
structure réhabilitée : c'est le temps
d'attente.
|
Validation des documents d'intervention par le chef de quart
et intervention. La durée de cette étape dépend de la
gravité de l'ENS. Ici nous allons prendre 3 heures soit 180 minutes.
|
|
Tableau 6 : acti vités dans les sous-processus
en traitement périodique.
Modelisation du temps de reaction d'un systeme industriel :
Application aux centrales thermiques d'OYOMABANG I et II .
Nous pouvons donc résumer les temps des différentes
étapes dans le tableau qui suit :
Sous-processus(i)
|
Durée E1 (di, 1)
|
Durée E3 (di, 3)
|
Durée E4 (di, 4)
|
0
|
1
|
3
|
2
|
1
|
2
|
5
|
2
|
2
|
2
|
10
|
4
|
3
|
1
|
5
|
3
|
4
|
2
|
180
|
|
Tableau 7 : temps d'activite dans les sous-processus
en traitement
periodique.
Comme le temps de réaction du système est la
différence du temps de sortie et du temps d'entrée que nous
connaissons déjà, nous allons donc déterminer le temps de
sortie du système Sn.
U0=360
système
|
paramètre définissant le système
|
sous-processus
|
Xm (0)
|
période Pm
|
Durée di, 1
|
Durée di, 3
|
Durée di, 4
|
SPO
|
0
|
5
|
1
|
3
|
2
|
SP1
|
0
|
10
|
2
|
5
|
2
|
SP2
|
0
|
15
|
2
|
10
|
4
|
SP3
|
0
|
10
|
1
|
5
|
3
|
SP4
|
0
|
5
|
2
|
180
|
|
Tableau 8 : Paramètres du
système
sous-processus i
|
Entrée Ui
|
|
attente di, 2
|
|
synchronisation Ki, n
|
sortie SPI
|
|
SPO
|
|
360
|
|
4
|
73
|
|
370
|
SP1
|
|
370
|
|
8
|
38
|
|
387
|
SP2
|
|
387
|
|
1
|
26
|
|
404
|
SP3
|
|
404
|
|
5
|
41
|
|
418
|
SP4
|
|
418
|
|
0
|
84
|
|
600
|
Tableau 9 : Données initiales
calculées
Modelisation du temps de reaction d'un systeme industriel :
Application aux centrales thermiques d'OYOMABANG I et II .
Pour le calcul des données, nous procédons de la
manière suivante :
Les périodes de synchronisation Ki, n en appliquant la
formule suivante : iki,n=A. si 3 A. e IN
Ut(n)+di,i_xm(o)=APin
/U1 (n)+clio. --Xm(0))
(V-1)
ki,n=E1 +1 sinon
Pm
Après avoir calculé
ki,1 nous calculons alors la sortie du
sous-processus Si(n) de la manière suivante :
Si(n) = Xm(0) + ki,1 X
Pm + ? l=3clij (V-2)C'est à partir de la
que nous pouvons alors calculer les temps d'attente du sous processus ainsi
qu'il suit :
c11,2 = Si(n) -- (Ui(n) + ? jEti,3,41 di,i)
(V-3)
Nous pouvons donc calculer toutes les données du tableau
précédent quant on sait que la sortie du sous-processus n est
l'entrée du sous-processus n+1.
Modelisation du temps de reaction d'un systeme industriel :
Application aux centrales thermiques d'OYOMABANG I et II .
|